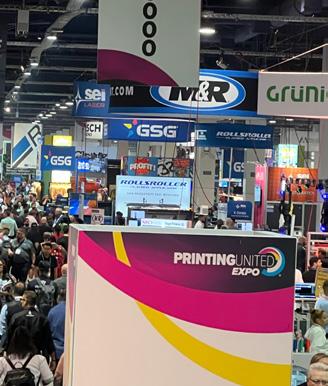
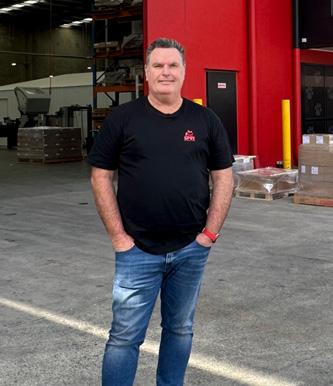
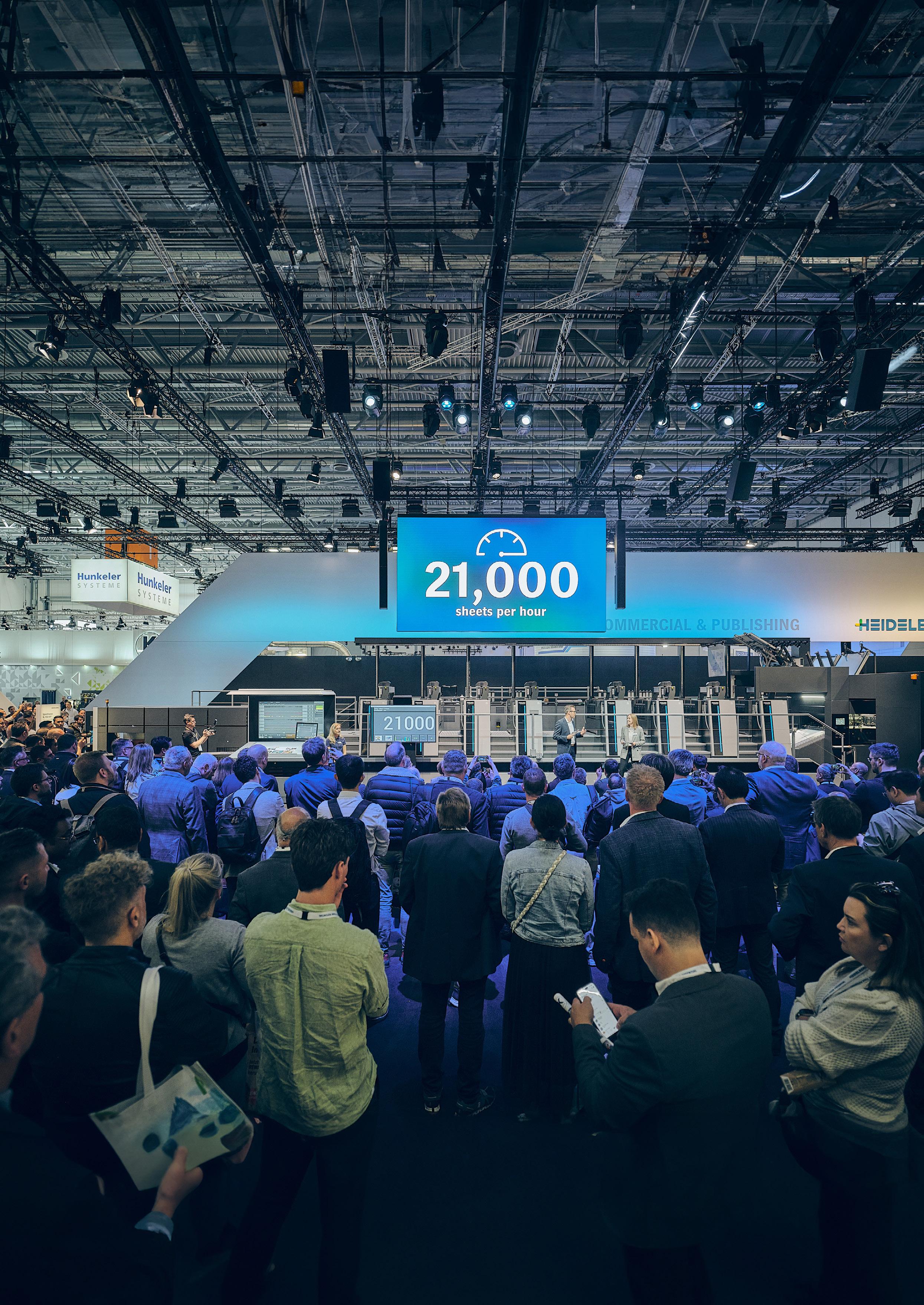
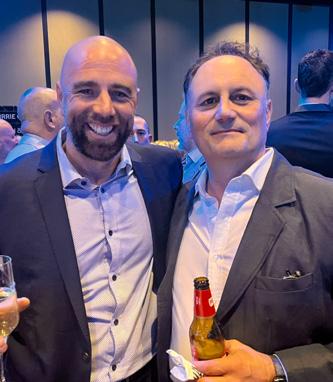
6-12 Update
A news round-up from the world of print
14-15 Currie Group National Sign & Graphics Awards
The industry celebrated excellence at this gala awards dinner
16-17 Star Business: Spot Productions
MD Simon Carmody tells all about what makes his business tick
18-20 Cover Story: drupa highlights from Heidelberg
Heidelberg unveiled numerous innovations at this year’s drupa under the theme ‘Unfold Your Potential’
22 Case Study
UPP buys Koenig & Bauer Rapida 76
24 Case Study
Zünd cutter worth the wait for Blueprint Digital
26 Case Study
Grafico celebrates 10 years on The Block, boosted by Canon Colorado’s UVgel Printing Technology
What a whirlwind two months it has been. We’re only just taking a moment to breathe, let it all sink in and reflect on what we’ve experienced.
In just this period alone, we’ve attended the FPLMA Conference in Melbourne, Printing United expo in Las Vegas, and Labelexpo Americas expo in Chicago –and that’s not including all the other recent and local awards and social gatherings.
If that doesn’t satiate your thirst for learning about the latest products, visit Sprinter and watch the videos we took of the machines in action.
This issue also features a Star Business profile of Spot Productions, and several case studies of how print service providers benefitted from their press investments.
United Printing & Packaging discusses why it decided to invest in a Koenig & Bauer Rapida 76, while Blueprint Digital details how its purchase of a Zünd G3 3XL-3200 led to the company providing the best service to its industry customers.
40 Comment: Charles Watson Employees on jury service − employer obligations
41 Comment: Mick Rowan
AI and smart workflows herald a technology-driven future
42 ProPrint Diary
Keep up to date with the latest industry events
Editor Claire Hibbit, chibbit@intermedia.com.au
Editor Hafizah Osman, hosman@intermedia.com.au
Design and Production Manager Sarah Vella, svella@intermedia.com.au
Managing Director James Wells, james@intermedia.com.au
Subscriptions (02) 9660 2113, subscriptions@intermedia.com.au
Printed by Hero Print Alexandria, NSW, 2015
Mailed by D&D Mailing Services Wetherill Park, NSW, 2164
It’s clear that the printing and packaging space has plenty going on – and it’s thriving! We got to feast our eyes on so many new innovations and technologies, learnt about the latest trends and caught up with our international friends.
This issue of ProPrint brings you our in-depth review of Printing United. Read all about the latest in trends, equipment and solutions.
In addition, Grafico tells us more about how its Canon Colorado UVgel Printing Technology creates detailed prints on The Block
There’s also a socials gallery from the recent 2024 Currie Group National Sign & Graphics Awards.
And if you’re keen on finding out more about what happened at the FPLMA Conference and at Labelexpo Americas, have a read of ProPack.pro to benefit from the world of packaging.
The Acuity Ultra R2 is a modular system with scalable architecture, meaning it can grow and change as your business evolves.
Multi-roll capability maximises productivity for smaller jobs
Auto media thickness and position measurement
Our Acuity Range is known for its excellent high quality, productivity and reliability on a massive industrial scale. Engineered with the operator in mind, LED configurations work in harmony with specialist inks to support the printing of exceptional near-photographic interior graphics and the high speed printing of banners and PVC signage.
With a throughput of over 600 m² per hour, the machine has the potential to produce huge volumes of work when printing on three rolls simultaneously, as well as printing superwide format graphics up to five metres in width.
The Acuity Ultra R2 is equipped with a media detector mounted on the carriage. This is used to determine the position and thickness of the media.
To discover more, scan below:
Victoria-based Complete Colour and Adams Print have merged, bringing together two well-established brands.
However, both brands will be kept intact, with Complete Colour operating from its purpose-built 3,500 square-metre facility in Cheltenham, Melbourne and Adams Print operating from its Geelong site.
Together with the announcement of the merger, Adams Print also mentioned that co-owner Robert Soutar will retire, while his brother Shane Soutar will remain as managing director.
“I am excited to bring the rich legacy of the Adams Print brand into Complete Colour, a company renowned for its industry-leading environmental credentials and commitment to quality. Over the past 25 years, my brother Robert and I have been proud custodians of our 130-yearold company, building a reputation for excellence and integrity,” Shane said.
“With Robert now retiring, we are confident that this transition will further elevate our brand within the trusted and environmentally conscious Complete Colour family. This merger represents not only a continuation but an enhancement of the values and standards our clients have come to expect from Adams Print.”
Complete Colour is a privately owned printing business that provides services to corporate, government and general commercial businesses. It is also a standard-bearer of environmentally credentialed printing.
PacPrint 2025, which is set to take place at the Sydney Showgrounds from 20-23 May 2025, has revealed its new board of directors.
Kirsten Taylor, known for her leadership at Taylor’d Press, has been appointed as the chair of the board. Co-hosts Visual Connections and the Visual Media Association said Taylor brings a wealth of experience and a fresh perspective to the role, promising to drive innovation and ensure the event continues to meet the evolving needs of the industry.
Joining Taylor on the board are industry veterans who collectively represent the diverse spectrum of the print, sign, and graphics sectors.
Some of the services of the 30-year-old company include digital and offset printed products, including variable data and mailing, warehousing, distribution and electronic media. The business is run by partners Tim Michaelides and Geoff Lawyer.
Adams Print is a highly awarded business, respected for providing innovative print solutions with a rich 130-year history. It has earned over 30 gold medals, three prestigious Judges Awards, and two Heidelberg ‘Excellence in Craft’ accolades at the National Print Awards over the past 20 years.
The companies decided on the merger as they both share a laser focus on service, quality, value, innovation and trust, which they say are well-aligned to further build personal relationships with clients and partners, communities and regions across Australia.
Complete Colour managing director
They include Jonny Rumney from Celmac, Priscilla Dickason of Epson, Kevin Pidgeon of Lithocraft, Andrea Trumble of Pozitive and Sharon Dowsey of Spicers. The co-hosts said their extensive
Tim Michaelides said, “Now we get to combine the best of two highperformance businesses for the benefit of our loyal existing clients together with future prospective clients, who can expect to receive the trusted and innovative print and communication services we are both known to deliver”.
Complete Colour director Geoff Lawyer said, “We are thrilled to join Adams Print, a prestigious company that has consistently operated at an exceptional level, playing a crucial role in Victorian communities and beyond since the Gold Rush era. The outstanding craftsmanship and expertise they have cultivated over the decades perfectly complement the environmental innovations and sustainable practices that Complete Colour has pioneered for the past 32 years. This synergy fills us with immense excitement, energy and optimism for the future of our business together”.
experience in the industry will be crucial in curating an event that showcases the best the industry has to offer.
“I feel privileged to become chair of the PacPrint25 board. I am grateful to be working with some very talented members of our industry, who share a passion for collaboration across our diverse sector,” Taylor said.
“Sharing the knowledge from our Board members, who are exhibitors to customers and have long-standing industry experience should bring together a fantastic show.”
Despite being a few months away, excitement around PacPrint 2025 is already building, with many of the industry’s leading suppliers already confirmed and others eager to secure their spots.
As preparations continue, the board, along with the event organisers, say they are committed to delivering “an unparalleled experience that will leave a lasting impact on all attendees”.
CO-LOCATED
Easy Signs has hit the big time in the US by featuring in an article on the front page of the New York Times after being impacted by 400 per cent import tariffs.
The New York Times article focused on the challenges American-based businesses have with tariffs being placed on products from China such as aluminium components used in signage that began under President Trump in 2018, and may not be resolved regardless of who wins the American election later this year.
The New York Times article commenced with a direct reference to the growth of the Easy Signs business.
“Were it not for the trade war between the world’s two largest economies, Easy Signs would now be hiring dozens of workers at its factory in Allentown, Pennsylvania. It would be readying plans to build a second plant somewhere out West — Salt Lake City was a contender — that would generate another 100 jobs,” the article stated.
“Its cloth signs are displayed on aluminium stands made in China. Those products are now subject to a series of tariffs reaching as high as 365 per cent under a policy set in motion by former President Donald J. Trump and continued by the Biden administration in the name of protecting American industry from Chinese government subsidies.
“The costs of imported components could increase further, should Mr. Trump win November’s presidential election and follow through on his threat to add a tariff of 60 per cent or more on all Chinese goods, and 10 per cent to all imports.
Ball & Doggett has acquired Queenslandbased signage distributor, Sign Essentials, as of 1 October.
Part of the OVOL Japan Pulp & Paper Group of companies, Ball & Doggett is a leading Australian distributor of printable materials and consumables.
Established in 1991, Sign Essentials is a privately owned and operated family business, based in Geebung, Queensland, specialising in the distribution of a wide range of sign, display and digital products
“That’s definitely a scary concept,” said Andy Fryer, co-founder of Easy Signs.“The whole feasibility goes out the window.”
In an exclusive interview with ProPrint, Fryer provided further insights into the tariff difficulties and how the article came about.
“We had been running into huge challenges with tariffs being applied on imported aluminium products such as pull-up banner stands, media wall frames and gazebos adding up to 370 per cent of the value of the aluminium. This forced us to redirect containers that had arrived to the US from China, all the way to Australia,” said Fryer.
“We have been working with a law firm that is experienced with tariff issues trying to work out how to navigate the situation. During this we reconnected with one of our contacts who heads up the economic development team in Pennsylvania who was across this issue and the impact it was having on other businesses.
“He was contacted by the New York Times about a story being put together to discuss the negative impact of tariffs impacting businesses and jobs in the
including hardware, media, servicing and parts.
Ball & Doggett said this acquisition further solidifies its commitment to the
US. He recommended us as a worthwhile business for the reporter to talk to, so he reached out and set up a conversation with Adam and I online.
“After the conversation he asked if he could come to our factory to see first-hand the types of jobs we were creating along with a photographer. In the article he references talking to two dozen American manufacturers, so it appears he thought our story was worthwhile as we were the feature throughout including a couple of quotes and lots of photos and detail about our operation.
“We sell the same hardware in Australia, however with our free trade agreement with China we only pay 10 per cent GST when importing. In comparison when the same components are imported to the US, we are hit with the 25 per cent China tariff – which is known as the 25 per cent China Tax that President Trump implemented while in office. He has since stated that he will increase this 25 per cent to 60 per cent if he is re-elected.”
In addition to the China Tax, Easy Signs has also been hit with an additional antidumping tariff in place for aluminium imports into the US from 15 countries.
sign, display and digital market.
Ball & Doggett CEO Luke Wilkinson said, “We are delighted to welcome Sign Essentials into the Ball & Doggett Group, a company that aligns with our core values and commitment to the sign, display and digital market”.
Sign Essentials general manager Sean Strange said, “This is an exciting next step in the Sign Essentials journey. Ball & Doggett has the resources and infrastructure to take the business forward, which will ultimately provide greater value to customers, suppliers and staff… we are excited about what the future holds”.
Sign Essentials will continue to operate independently in Queensland from its Geebung site.
Are you looking to partner with an Australian company with a large workforce to complement your business?
With expansive operations, warehousing, logistics and labour force capability across metro and regional NSW, we provide high quality manufacturing, printing, assembly and other service solutions to Government and private sector.
By partnering with CSI, your organisation empowers people and contributes to safer communities for everyone. We specialise in import replacement work, supporting Australian businesses to keep manufacturing onshore.
Speak to our team today to find out more.
This document contains statements related to our current and future operations and is subject to change without notice. All diagrams, drawings, products, machinery, and any other types of images in this document are for display purposes only.
Compliance to AS/NZS ISO 9001:2015 Quality Management Certification, applies to select Business Units. While the information in this document has been presented with all due care, the Department of Communities and Justice does not guarantee or warrant, and accepts no legal liability whatsoever arising from or connected to, the accuracy, reliability, currency or completeness of any material contained in this document. Enquiries relating to this document should be directed to csi@dcj.nsw.gov.au or 02 4582 2420.
For further information
Call 02 4582 2420
Email csi@dcj.nsw.gov.au
Visit csi.nsw.gov.au
Fireworks Digital Signage Solutions, which was based at Loganholme in Queensland, has merged with Brisbanebased Signright and are now operating under the entity of Signright Australia.
The merger is expected to bring their combined clientele base added capabilities and print solutions.
With over 30 years of experience in illuminated signage and lettering, wide format digital print, POS and digital signage, Fireworks Digital Signage Solutions has designed, manufactured and installed specialist signage and retail graphics.
However, five months ago, a devastating fire tore through the Loganholme facility, causing a total loss.
It was a challenging period, but with sheer determination and the unwavering support of its clients, the business kept moving – its team worked from various sign suppliers’ workshops to ensure projects continued without a hitch.
Having gone through the ordeal and
Signright Australia will now operate from Cannon Hill in Brisbane, with Tim Best, Steve Boyd and Kerry-Anne Boyd all becoming co-owners of the combined entity.
“Five months ago, a spark in our warehouse led to an all-consuming fire that swept through our Loganholme facility, causing a total loss,” Signright Australia co-owner and former Fireworks Digital business development manager
we’ve navigated both a complete rebuild and solutions for our clients. Your support has kept us going and has meant the world to us. From the ashes, opportunity is born.
“We crunched the numbers and after reviewing all of our options, chose to embark on a new adventure.
“Now, we’re thrilled to announce a powerful new chapter in our story: we have merged with a Brisbane-based
Victoria-based POS Visual Solutions is growing and evolving alongside advancements in printing technology with the investment of an HP Latex 2700W printer through SMARTECH Business Systems.
POS Visual Solutions said goodbye to its HP Latex 1500, which it had for nearly seven years, to make way for the new HP Latex 2700W printer.
“[We said] goodbye to a great workhorse! For nearly seven years, our HP Latex 1500 has been an amazing, eco-friendly printer that has delivered time and time again for us and our valued customers. However, it’s time for an upgrade. We now look forward to our new HP Latex 2700W… [taking] us to another level of printing speed and quality,” POS Visual Solutions said.
POS Visual Solutions has been a longstanding partner of SMARTECH and HP Latex – its first install was an HP Latex 260 just over 15 years ago.
Spicers Australia has increased the costs of several of its products, with affected portfolios including Commercial Print and Digital Print, Visual Communications, and Narrow Web/Roll Label. The new pricing model takes effect as of 1 October.
Within the Commercial Print and Digital Print portfolio, prices of self-adhesive sheets will go up four per cent, while carbonless sheets and rolls will cost five per cent more and speciality papers will cost six per cent more.
In the Visual Communications portfolio, roll media and finishing prices will increase between three to six per cent, banner pricing will increase between six to 11 per cent, rigid products will increase between five to 10 per cent, and all other products in this category will increase between three to six per cent.
As for the Narrow Web/Roll Label category, all products will see a four per cent price hike.
In a statement to customers, Spicers Australia said, “As you are likely aware, our highly competitive industry continues
“Just over
Today, we are thrilled to announce the next chapter in our journey together as we support POS Visual Solutions in acquiring the latest innovation: the HP Latex 2700W printer. This state-of-the-art equipment represents not just an upgrade but a leap forward in printing technology, offering unparalleled quality, efficiency, and sustainability,” a representative from SMARTECH told ProPrint
The HP Latex 2700W is engineered to deliver vibrant colours with high precision, while its eco-friendly features ensure a reduced environmental footprint. With faster speeds, smarter technology, and enhanced reliability, this printer empowers businesses to expand their capabilities and explore new markets.
“Reflecting on a remarkable journey of growth and partnership, it has been over 15 years since I had the pleasure of selling an HP Latex 260 printer to a valued customer, POS Visual Solutions,” SMARTECH Business Systems sales representative Nick Papamihail said.
“Over the years, we’ve worked together, evolving through various advancements in technology, and I’ve witnessed the incredible progress my customer has made. We are excited to continue our journey of growth with POS Visual Solutions, embracing the future with technology that truly makes a difference.”
to present challenges for all involved. Unfortunately, Spicers is not exempt from these difficulties, and we are experiencing ongoing upward pressure on our supply pricing.
“The price adjustments listed reflect direct increases in material costs from our manufacturers, largely due to rising shipping expenses, energy costs, input costs, and inflation, particularly from our European suppliers. While these
increases are not exclusive to Europe, the majority do originate from this region, and we find ourselves in the position of having to pass these costs on to our customers.
“As we have done in the past, Spicers remains committed to mitigating the impact of these increases wherever possible to ensure a sustainable and reliable supply option for your business.”
Redefine Commercial Printing Standards and elevate production with Next-Gen High-Speed Inkjet
PRODUCTIVITY
•High productivity
•560mm paper width
•High machine uptime
QUALITY
•New Inkjet 1200dpi PHs
•New saturated ink SC2
•Enhanced image quality
USABILITY
• Energy-efficient drying
•Easy operation
•Offset-coated papers
AGILITY
•Optimised integration
•Precision paper sensing
•Complete New Platform
The print and visual communications industry recently came together to enjoy the ‘night of nights’ at the 2024 Currie Group National Sign & Graphics Awards.
More than 300 industry identities recently gathered at Doltone House, overlooking Sydney’s Hyde Park, to celebrate the achievement of excellence in the sign, display and graphics industry at the 2024 Currie Group National Sign & Graphics Awards Gala Presentation Dinner.
The event, which was hosted by the Australian Sign & Graphics Association (ASGA), is one of the pinnacles of achievement in the Australian industry.
The gala dinner presentation was the culmination of the industry’s awards, while enjoying a glamorous night of fine dining and catching up with industry colleagues and friends.
The industry took the chance to relax, enjoy, and let their hair down. Here are some photos from the evening.
Having seen massive growth in recent years, Simon Carmody recently invested in several new machines to deliver on quality products for Spot Productions’ clients.
Expansion is the name of the game, and keeping up with technological advancements in printing to support its full-service business is what’s driving Simon Carmody’s agenda at Spot Productions. Even though the company is Brisbanebased, it services a local, national and international clientele, encompassing many applications of services including offset, short-run digital and wide-format printing.
Carmody, who is the managing director of Spot Productions, said his new investments include a Screen 8900N II E CTP, two wide-format machines from Fujifilm – a Mimaki UJV55-320 LED-UV inkjet printer and a Fujifilm Acuity Prime 20 LED UV flatbed printer – and a new Ryobi eight-colour press that was installed following a fire at the factory in November last year. There’s no stopping Carmody as he’s already looking to add a 2.5m Fujifilm Acuity Hybrid to the mix to print on rolls and rigid boards.
Spot Productions is certainly going through a wave of growth, but it emerged from humble beginnings – Carmody’s father Peter and his business partner Mark Jackson started the boutique business, which was then named Spot the Printer, in 2001.
books.
Carmody started off his career in print at News Limited as an apprentice. He then joined the late Tom Lusch at Platypus Print Packaging and worked there for about nine years in the ‘90s. Soon after, Carmody joined Spot the Printer in 2007, and that same year renamed the business to Spot Productions and moved it to where it is currently located in Pinkenba.
“In my early days, I had experience on the printing floor as well as working as foreman and a production manager. I then transitioned into sales and enjoyed dealing with clients. I also learnt so much from my time at Platypus Print Packaging and still keep in touch with them today,” he said.
“When I joined the business, there was only about 10 staff and when we moved to this site, we increased our team size to 18 people. Over the journey, we now have over 90 staff.”
The presses that the company own have also changed significantly. In the initial days, it only housed a few A3-sized presses but that has now expanded to include
A2- and A1-sized presses, all of which are multicoloured and perfecting presses.
“It has certainly been a big jump for Spot Productions. We’ve been on this site for 17 years and I have seen the business grow and evolve throughout my entire journey. At Spot Productions we keep up with technology as much as our budget can afford; this has been an integral part of the process,” Carmody said.
“Offset sits around 70 per cent of Spot Productions’ turnover. Cut sheet, digital and wide format makes up the remaining 30 per cent. Business in these areas is continually growing for us – at present the only area we haven’t got any appetite to expand into is packaging.”
At the forefront of technology
According to Carmody, Spot Productions was the first to bring LED printing into
Australia with the install of a Ryobi. Since then, it has added another eight-colour machine and upgraded its facility with more offset, digital and wide-format machines.
“We’re certainly at the forefront of technology with our offset offerings. Recently, over the last four months, we’ve added some Fujifilm wide format gear and are in the process of finalising a proposal with Fujifilm for the Acuity as well,” Carmody said.
“We’ve had a pre-existing relationship with Fujifilm through the purchase of some cutsheet Iridesse machines, so that partnership’s really strong – and we wanted to strengthen it further.”
“We also had to buy a new plate setter from Fujifilm because we couldn’t keep up with the demand of work. We can do up to 100 plates an hour now, which is incredible because prior to the investment we were only outputting 30 plates an hour.”
“Since the installation of our new Mimaki UJV55-320 and Fujifilm Acuity Prime 20 from Fujifilm, our speed to market and quality has increased multi-fold. Our staff are happy to run the machines as well, as they’re easier to use and are seamless to operate. They’re just the right fit for our business.”
Spot Productions got a change-up in machines again at the end of 2023, when unfortunately, a fire caused damage to the existing Ryobi 10-colour press.
“The fire happened on the back of the best four months I’ve ever had in our business – we had just added a Ryobi eight-colour A1 in July to sit alongside the 10-colour Ryobi. Then, in November, an electrical malfunction between the perfecting units resulted in a fire. The damage was assessed and agreed upon that the fault was caused just by accident, and we were best off getting a new machine,” Carmody recalled.
“That’s easier said than done. We were lucky because Cyber was installing a Ryobi eight-colour press in Malaysia. We knew that client well, so after some discussions,
it was agreed that this machine would be installed at Spot Productions instead, as this was crucial for the security of our business.
“This machine was up and running in five months. In the interim, Cyber and Ryobi had a four-colour press available, which they installed within four weeks. This machine and my other two Ryobi presses ran for 24 hours a day until we got the new eight-colour up and running.”
At the back of drupa, a Spot Productions tradesman also visited China to check out some finishing equipment for highspeed die cutting and PUR binding.
“We’re not going to jump into that just yet but we need to understand what this may look like for our business in the future. We enjoy a very close relationship with our finishing suppliers in Queensland and they are a great extension of our business. But in this environment, we can’t afford to not have a Plan B if they decide to shut down or merge with another printer or supplier. So, to be safe, we’ve got to future-proof our business,” Carmody mentioned.
Carmody is not only investing in the best of the best in equipment. He’s also investing in the people of Spot Productions.
In mid-2023, Carmody took to importing labour and hired staff from overseas as the manufacturing industry faced a shortage of skilled workers.
At that time, Spot Productions was approved by the Department of Foreign Affairs and Trade to have skilled labour imported. So Carmody brought into Australia international staff – personnel from the Philippines, Malaysia, and South Africa – to service roles within wide format printing, offset printing and internal estimating in customer service within Spot Productions.
But since then, Carmody said finding local talent has become a lot easier.
“Unemployment and immigration numbers are now increasing, so we now attract about 15 applicants for a job ad instead of the minimal prior. In addition, there’s plenty of consolidation happening in the Queensland print market and that has resulted in people looking for jobs,” he said.
“Retention of staff has also been easier to maintain. There’s a lot more stability in the industry and I expect this to get stronger over the next year or two. We continue to source labour from New Zealand, Philippines and South Africa, and that has been tremendous for Spot Productions.”
Spot Productions’ future is bright, with Carmody saying that the company is moving on the trajectory that he has planned for.
“We’re at the size now where we’re quite a substantial player in the Australian market. Larger organisations look forward to using Spot Productions for their offerings. We’re certainly positioned nicely to be a tier two printer, and that’s where we are excelling,” he added.
“We’ve also expanded our premises and moved into our new facilities across the road – it has taken us about three years to do this. Adding more machinery, adding more power, and having the right workflow and production has taken us a fair while, but this is now completed and we’re seeing the right results.
“We’re now in about 6000 square metres of space and can expand it further if we do wish to, but we’re settled for the next three to four years. We’ve found that the output of the business and our turnover has increased tremendously, and our available space to get more work done has increased as well. We’ve got plenty to look forward to at Spot Productions.”
Heidelberg unveiled numerous innovations at this year’s drupa under the theme ‘Unfold Your Potential,’ focusing on optimising businesses to maximise potential using the latest technologies and services.
drupa 2024, held in Düsseldorf from May 28 to June 7 this year, marked its first on-site event in eight years since 2016. The 11-day event attracted exhibitors from 1,643 companies across 52 countries and saw a turnout of 170,000 visitors. The Heidelberg booth in Hall 1 was a hub of activity, with many visitors attending daily presentations focused on commercial, packaging, and label printing.
Heidelberg’s focus at drupa was on four key messages based on market megatrends and promoting solutions through innovation, including:
• Competitiveness: Productivity increased by up to 20 per cent,
significantly reducing print shop costs.
• Skills shortage: Reduced staffing needs in print production, through autonomous printing and cluster production.
• Sustainability: New technologies that save energy and reduce raw material consumption.
• Digitalisation: Integration of the entire production process within the printing industry.
The printing industry faces four significant challenges: increased cost pressures, a shortage of skilled workers, and rising demands for sustainability and digitalisation. To address these megatrends, Heidelberg unveiled numerous innovations at drupa under the
theme ‘Unfold Your Potential’ focusing on optimising businesses to maximise potential using the latest technologies and services. Innovations such as the new generation Speedmaster XL 106 enable Heidelberg to support customers with a holistic concept that achieves up to 20 per cent higher productivity compared to previous solutions.
How can the printing businesses enhance production efficiency?
With rising cost pressures, print shops need to invest in productivity, efficiency, and new business areas to stay competitive. Heidelberg understands the value drivers of its customers in the commercial and packaging printing industries and develops
The Speedmaster XL 106 demonstration at drupa emphasised reducing manual tasks from 20,000 to just 400 per day
optimal products to adapt to market changes. For example, innovations like the new generation Speedmaster XL 106, with a printing speed of up to 21,000 sheets per hour, AI-assisted systems, and enhanced push to stop functionality, make industrial offset printing more competitive. Heidelberg also displayed new innovations for the packaging printing industry at drupa, such as the Boardmaster, setting new productivity standards with up to 90 per cent machine utilisation and a top printing speed of 600 metres per minute. Compared to previous generations, this machine concept dramatically reduces the total cost of ownership for industrial packaging production.
“With rising cost pressures, print shops need to invest in productivity, efficiency, and new business areas to stay competitive. Heidelberg understands the value drivers of its customers in the commercial and packaging printing industries and develops optimal products to adapt to market changes.”
How do print shops address skills shortage?
The printing industry is increasingly facing a severe shortage of labour and skilled workers. In response, Heidelberg offers automated product and process solutions and provides training for print shop staff. In commercial printing, fully automated plate to unit plate logistics on the Speedmaster XL 106 and the new robotics solutions for postpress operations are two examples of this. The new-generation Speedmaster XL 106 also supports cluster production, whereby a single operator controls an entire machine park. Heidelberg plans to enable autonomous
printing for standardised packaging applications and will continue to support complex printing jobs with navigated user guidance.
How can the printing industry produce sustainably and economically?
Sustainability is a global megatrend and a significant challenge for the industry. Modern print shops aim for sustainability by reducing energy and resource consumption. Print products are also changing, though moving away from plastic and toward more paper.
Heidelberg offers sustainable print solutions that help save energy and raw materials. Comparing the 1990 Speedmaster with the current version shows up to a 40 per cent reduction in
energy consumption per 1,000 sheets.
At drupa, Heidelberg announced the latest generation presses could produce up to 21,000 sheets per hour, further reducing per-sheet energy consumption. Moreover, the use of artificial intelligence and new auxiliary systems reduces paper waste, saving even more resources.
How does digitalisation benefit the printing industry?
Digitalisation in the printing industry enables the integration of the entire production process, from receiving digital customer orders to preparing print data, planning and executing print jobs, delivering printed products for postpress, shipping, and billing. At drupa, Heidelberg showcased end-to-end autonomous printing for commercial and packaging customers. The introduction of a new customer portal elevates digitalization to the next level, enhancing press management, including capacity management, maintenance, and servicing.
“The printing industry is increasingly facing a severe shortage of labour and skilled workers. In response, Heidelberg offers automated product and process solutions and provides training for print shop staff.”
Eighty per cent of print shops consider maintaining competitiveness their greatest challenge, while 70 per cent are concerned about labour market issues. Addressing increased cost pressures and labour shortages, the demonstration of the Speedmaster XL 106 at drupa emphasised reducing manual tasks from 20,000 to just 400 per day. In commercial printing, the elimination of 98 per cent of manual
Heidelberg’s focus at drupa was on four key messages based on market megatrends, promoting solutions through innovation
interventions from production data to finished brochures in the value chain is achieved compared to non-push to stop production. In packaging printing, the numerous innovations in the Speedmaster XL 106 enhance overall productivity by up to 20 per cent, while simultaneously reducing labour, paper waste, and energy consumption. This results in lower costs per print sheet, becoming a critical competitive factor for print shops. In partnership with POLAR and MK Masterwork, Heidelberg addresses the most pressing challenges facing industrial printers, including cost pressure, skills shortages, sustainability, and digitalisation.
Additionally, the new highly automated Peak Performance generation of the Stahlfolder TH 82-P folding machine restores a 1:1 performance ratio between pressroom and postpress operation. This means that the new Stahlfolder TH 82-P can handle the full output of the new generation Speedmaster XL 106 at the postpress stage. The new Stahlfolder TH 82-P generation offers approximately a 15 per cent net output increase without increasing the machine speed. Moreover, the new collaborative robot system, StackStar C, reduces staff burden by automatically stacking products in the postpress section.
The StackStar C is mobile and can be easily moved between different machines. Operating collaboratively, it features an innovative safety concept that eliminates the need for safety fences, allowing staff and the robot system to work together safely. Additionally, quality control processes can be conducted during production without stopping the robot. By linking two StackStar C units, production capacity can be doubled, with various stacking patterns and pallet sizes intuitively selectable from the control terminal.
“Enhanced automation and process efficiency enable our commercial printing customers to increase productivity while reducing resource usage. This way, we help them further enhance their competitiveness for the future,” said Dr. Frank Schaum, who is in charge of the print segment at Heidelberg.
Heidelberg also offers digitalisation solutions that elevate automation to a new level using the Prinect workflow system. For instance, Prinect provides additional data to many assistance systems and operates using artificial intelligence. Many new and enhanced digitalisation features, such as Intellistart 3, reduce operations at
the Press Center by about 70 per cent, while the improved Color Assistant Pro system achieves fully automatic ink presetting, preventing operational errors. This reduces makeready times by up to four minutes and cuts paper waste by 100–150 sheets per job. Combined with the inline Prinect Inpress Control measurement system and automated delivery logistics, inline waste is eliminated. This provides waste-free stacks for post-press operations, enhancing overall process efficiency.
“Heidelberg displayed new innovations for the packaging printing industry at drupa, such as the Boardmaster, setting new productivity standards with up to 90 per cent machine utilisation and a top printing speed of 600 metres per minute.”
The need to reduce operator workload whilst achieving higher output with fewer staff, and lower costs is required. This is achieved with advanced automation technology, digital workflow integration, and intelligent operator assistance systems. As maximising existing potential becomes increasingly important, digital integration and automation make production more economical than ever. Heidelberg recognised these needs at drupa with innovation and technology to suit the industry moving forward.
UPP’s decision to invest in the Koenig & Bauer press was significantly influenced by the level of local service and support as well as the advanced technologies and customised options on the new Rapida 76.
After a successful career of over 17 years with a large labels and folding carton organisation, Said Khoury identified an opportunity and purchased the 30-year-old United Printing & Packaging (UPP) business in February 2014.
Within 12 months of buying the business, Khoury’s hard work saw sales double and within five years, the company relocated from Arndell Park to specific premises at Smithfield in Western Sydney.
UPP now focuses on delivering a high level of service to folding carton customers in the pharmaceutical, animal health, cosmetic and FMCG markets.
“There is nothing in the folding carton workflow that we can’t offer in house –from prototyping, CAD cutting, die lines, CTP as well as flatbed die cutters and a multifunctional gluing line for straight line, crash lock and fancy glues,” Khoury said.
After two years of research, Khoury had “very honest and transparent conversations” with former Koenig & Bauer managing director Dave Lewis and service manager Graham Harris who has since been appointed to replace Lewis as MD.
“We left no questions unasked to ensure we got exactly what we wanted,” Khoury said.
“With the coating unit, we wanted the UV gloss to be glossier, the matte to be flatter and spot gloss to be more prominent; and after sending samples to Germany, they came back with specific anilox rollers that would help us achieve this result.
“While we offer no minimum order quantity, the additional productivity and efficiency from the Rapida 76 and its ability to run at 16000 sheets an hour means we can tap into medium to high volume work where we could not compete previously.
“The technology on the press was important, but we chose Koenig & Bauer because of the service and support we receive from local engineers based here on the ground in Sydney including John Studley from electrical who has been with the business for 16 years and David Spinks from mechanical who has been with the business for seven years.
“We then decided the Koenig & Bauer Rapida 76 was the right press for us as it allows us to deliver folding carton work with precision and consistency which is paramount for our premium and boutique clients.”
“The Rapida 76 offers several additional custom features for our needs including Interdeck UV drying, which can be interchanged on every print unit, as well as two dryers on the delivery. The flexibility of having every print unit that is Interdeckready means we can change our printing configurations depending on the job and the substrate as well as the colour sequence.
“This allows us to print on specialty substrates and achieve complex specifications for our clients with multiple finishes in the one pass up to 0.8mm thickness.”
Harris said UPP was reassured by having remote support from Germany, unlimited local support as well as continuous software upgrades.
“All of our presses are connected to a 24/7 help line, allowing our customers to connect directly with the service team in Germany in the unlikely event of a breakdown. In 80 per cent of cases, faults can be diagnosed or fixed before a technician is required,” Harris said.
“We have been doing this since 1995, so it is very mature technology. We monitor different alerts and, in some cases, we can contact the customer before they know there is something wrong.”
Preparations for the arrival of the Rapida 76 took place several months before the installation in July this year.
A concrete slab within the premises was prepared with 12 three-metre piers installed as well as 600mm of reinforced steel –meeting the Koenig & Bauer specifications.
“I decided not to make any short cuts,” Khoury said. “While the epoxy was curing on the slab, we installed stainless steel plumbing through the ceiling as well as a six-head cooling unit. We also had preformed trenches in the slab for the eight thick cables to power the Interdeck drying between each print unit for both aesthetics and safety.”
Harris said the installation went very smoothly based on the prior preparations that Khoury had made.
“Said chose Koenig & Bauer based on our reputation for service and support. He was perfectly prepared based on our agreed plans and as a result, this was one of the best installations we have ever done –it’s always a nice and efficient installation process when our customers are organised as Said was, makes the install so much easier,” Harris mentioned.
“We have invested a lot on research and development as well as new design and features on our machines including the new Rapida 76. Koenig & Bauer now manufactures all components including its own UV dryers without having to rely on OEMs or third parties. Keeping electronic components compatible across the entire range of presses from the 76 to the 105/106/145 and 164 size presses reduces the number of spare parts, which also streamlines our service and support.”
The Rapida 106 X maximizes every second for the highest productivity. Industry-leading technology ensures the fastest throughput. Print at up to 22,000 sheets per hour. Plate and substrate logistics, parallel makeready processes and digital services are among the benefits which help you always surpass your goals.
See the Rapida 106 X in action: rapida106x.koenig-bauer.com/en
Koenig & Bauer (AU)
Rayne Simpson
+61(03) 9548 7277
rayne.simpson@koenig-bauer.com.au
The decision to invest in the Zünd G3 3XL-3200 was a deliberate decision by Blueprint Digital to provide the best service to its industry customers.
After waiting 15 months to receive his Zünd flatbed cutter, soft signage and fabric specialist trade printer Marty West from Blueprint Digital in Sydney has significantly increased his productivity and capacity overnight.
West first placed an order for his Zünd G3 3XL-3200 in April 2023. Financial challenges experienced by Zünd’s reseller Starleaton at the time, meant the cutter that should have taken three months to arrive took almost 18 months to finally be installed – but it was worth the wait.
“We bought the Zünd, because we believe it is the best cutter in the industry, and it is now finally here,” West said.
“The Zünd is multifunctional and modular, and has the ability to not just cut our main print products – soft signage and fabrics –but can be upgraded with other tools to help us work with a whole range of different print products. By investing in a Zünd, we are future proofing our business as we move into additional print markets.
“We recently invested in the Durst P5 TEX iSub dye sublimation printer which is the best direct-to-fabric printer in the industry, so we also wanted to replicate this with the Zünd when it came to the cutter by purchasing the biggest and fastest in the industry. We now have the top of the range printer and cutter – and they perfectly complement each other.
Starleaton’s decision to enter voluntary administration earlier this year further delayed the already-late Zünd cutter ordered by Blueprint Digital, but just weeks later, Zünd Switzerland made the decision to create its own subsidiary
and appoint Dale Hawkins as the managing director of the business.
“When Dale took on the role at Zünd Australia in March, he was able to work something out with Zünd so that we could get our machine. Since then, the installation process was very smooth,” West said.
The decision to invest in high-end equipment was a deliberate decision by Blueprint Digital to provide the best service to its industry customers.
“We are a wholesale trade printer,” West said. “With our expansion into new machinery, we are able to increase our capacity. With the Durst and Zünd, we can print a lot more – we can cut faster and turn jobs around much more efficiently.”
Hawkins said he was very pleased to see the arrival of the Zünd G3 3XL-3200 at Blueprint Digital.
“We are very pleased to finally install the Zünd at Blueprint Digital after almost 18 months. The order was originally placed by Zünd’s reseller at the time and they did not supply the product due to financial challenges,” Hawkins said.
“As soon as we created the new subsidiary – Zünd Australia – we were motivated to find a solution for Marty and his team. But we also knew we needed to earn that trust after the journey that he went on with the former Zünd reseller. It was clear to us that Marty was determined to purchase a Zünd even though he went through the issues relating to the delay and delivery.
“The order was re-signed with Zünd Australia in April 2024 and we are very
pleased that his cutter has now been installed and is fully operational.
“Zünd cutting tables are modular and this will provide Marty’s soft signage and textiles business with options to add or retrofit tools and other accessories at a later stage. The Zünd digital cutter allows them to load a printed textile roll onto the unwinder and have the signage cut out automatically as Blueprint Digital’s system includes material transport system providing continuous cutting until the whole roll is complete.”
The Zünd G3 3XL-3200 at Blueprint Digital has been fitted with a driven rotary tool for textile cutting. The Z50 decagonal or 10-sided cutting blade is specifically designed to avoid getting caught in the textile weave. Blueprint’s Zünd also includes the central driven unwinder system that provides a smooth feed for textiles minimising creases and stretching that can happen with other unwinding approaches.
Zünd Australia is a wholly owned subsidiary of Zünd Switzerland and commenced business in March this year with Hawkins at the helm of the new organisation.
“The Zünd Australia team in place includes some of the best technical people in the digital cutting, application and system automation,” Hawkins said.
“Since we commenced operation, we have been servicing existing Zünd customers –some of which have been in the market for over two decades. Over the last few months, we have also provided existing customers with additional accessories and consumables, and installed several new Zünd digital cutters.
“We moved into our new Melbourne premises last month at Keys Road in Cheltenham and we will have a purposebuilt, 150 square metre showroom operational from October featuring two operating machines – one G3 1800 x 2500 model and the S3 model with an extension table.
“This showroom will be available for customers to experience in-house training and the building will also include the offices for Zünd Australia.”
Grafico’s decision to adopt the Canon Colorado printer was driven by the need for reliable colour consistency and production efficiency.
Grafico, the renowned design and printing company, is celebrating its 20th anniversary with a major milestone: its return as official wallpaper product sponsor for Channel 9’s hit TV show, The Block
Having first opened its doors in 2004 from founder Damian Corney’s home and his grandmother’s garage, Grafico has since grown into a leading provider of custom print solutions, including vehicle wraps, custom wallpapers, tiles, and signage. The company’s participation in The Block over the last decade has cemented its reputation for innovation and quality across Australia and beyond.
The Block 2024: Grafico’s role and new innovations
For the latest season of The Block, set in picturesque Phillip Island, Victoria, Grafico has once again taken the spotlight.
Grafico provides contestants with a dedicated budget to utilise its unique offerings, particularly its custom print wallpapers.
“We love being involved with The Block,” said Corney. “It’s a thrilling and high-stress environment, but the impact we can make on each space is immensely rewarding. Our products save time, add interest, and help contestants achieve that ‘wow’ factor that judges and viewers love.”
This season, contestants continue to have access to Grafico’s innovative range of wallpapers, custom art prints, and tiles.
A key factor in delivering these highquality products is the Canon Colorado printer.
“Switching to the Canon Colorado has been a game-changer for us,” said Corney. “The UVgel technology offers superior colour consistency, ensuring that every print, whether produced today or in six months, looks exactly as intended. This level of consistency is crucial,
especially when our designs are used across multiple projects.”
Grafico’s decision to adopt the Canon Colorado printer was driven by the need for reliable colour consistency and production efficiency – qualities that are essential for high-profile projects like The Block.
“Before the Canon Colorado, we faced significant challenges with our previous latex printer, including colour inconsistency and frequent breakdowns,” explained Corney.
“These issues led to high rework costs and frustrated customers. The Colorado’s robust performance, combined with its
unique matte and gloss printing capabilities, has enabled us to explore new creative possibilities while ensuring high-quality results.”
Even in the high-stress environment of The Block, where construction dust and constant handling are common, the prints remain vivid and scratch-resistant. The printer also ensures dimensional stability, so there are no issues with prints bowing or stretching. Moreover, the durability of the UVgel inks means our wallpapers can endure the wear and tear on The Block sets without needing to be replaced.
Grafico’s growth and future directions
Grafico’s involvement in The Block has significantly boosted its brand recognition, not only in Australia but internationally.
The company’s online store, which launched just before the COVID-19 pandemic, has grown to become a key part of its business. Fans of The Block can easily purchase the exact designs featured on the show, shipped directly to their doors, whether in Australia, New Zealand and the rest of the world.
Looking ahead, Grafico plans to expand its online presence and continue developing large-scale projects, particularly in the hospitality sector. Recent successful projects, such as custom wallpapers for hotels, have demonstrated Grafico’s capability to handle extensive orders with precision and reliability, thanks to the Colorado.
Steven Badger, head of sales and professional services at Canon Production Printing Australia said, “We are thrilled to partner with a high-profile business like Grafico and see the impressive results of our Canon Colorado printer come to life in stunning wall coverings on The Block
“Grafico’s use of the Colorado printer on The Block highlights the key strengths of UVgel technology: dimensional stability, repeatability, and durability.”
From product launches to education and networking opportunities to mass sales on the show floor, this year’s expo in Las Vegas delivered in a big way.
Printing United, produced annually by Printing United Alliance, recently took place in Las Vegas with continued reports of record sales on the show floor. This year’s show drew 24,969 registered attendees, 800 exhibitors, and industry thought leaders from 115 countries, offering a blend of product launches, live demonstrations, immersive education sessions, and high-powered networking opportunities.
The three-day expo was reported to be a great success for exhibitors who showcased their newest technology. With more square feet of technology being shown than in 2023, the expo delivered for exhibitors and attendees alike at this year’s event.
“With the many concurrent events taking place, as well as 2024 being a ‘drupa year’, we were really pleased with the crowds, but even more so, with the impressive volume of equipment running live on the show floor and, not surprisingly as a result, the sales being reported,” Printing United Alliance events and exhibitions president Mark J. Subers said.
Exhibitor sentiment was at an all-time high at this year’s expo. Here are some of the highlights:
BlueCrest announced its partnership with Ricoh at the tradeshow. BlueCrest provides comprehensive data-through-
delivery technology solutions, changing how business is done within the postal and parcel industries.
BlueCrest mail inserters offer high-speed, accurate, and user-friendly solutions that ensure integrity by automating the mail production process, minimising the potential for errors and reducing labour costs typically associated with manual tasks and adjustments that can also slowdown workflows.
The first phase of this collaboration will add BlueCrest’s range of high-speed, highvolume inserters and sorters to Ricoh’s production print portfolio in the US, giving users more ways to automate their mail production workflows and expand their
market reach with high-quality direct mail and communication materials.
In parallel, Ricoh and BlueCrest will integrate the technology platforms through software integrations to co-innovate with customers to deliver operational savings, scalability, automation and flexibility.
Canon has added its FLXflow technology to the Arizona 1300 series, which brings new productivity and performance features to the flatbed printer series. The company made this announcement at Printing United.
Previously known as FLOW technology, the new FLXflow offers not only the original ‘hold’ functionality, which helps to hold media down on the flatbed table, but also the new optional ‘float’ and ‘instant switch’ functionalities to improve media handling.
This allows Arizona users to benefit from enhanced productivity, print quality and application versatility thanks to FLXflow, a range of print modes, ease of use, workflow optimisation and UV-LED curing technology.
Catering to growing mid-volume operations, the Arizona 1300 FLXflow supports a wide variety of substrates and applications. This enables large format graphics printers and other print service providers (PSPs) to offer customers a wide range of applications for the retail, interior décor, packaging, and industrial market segments more efficiently.
Arizona 1300 FLXflow customers can also take advantage of the Advanced Image Layout Controls, which allow last-minute adjustments at the printer, giving additional flexibility when positioning substrates on the table and reducing waste of expensive materials. Productivity is further enhanced by service support tools
such as PRISMAservice, which provides predictive maintenance and facilitates authorised remote assistance by qualified service technicians to increase uptime.
Customers of the current Arizona 1300 series with FLOW technology can upgrade their printer to the latest version with FLXflow technology, including the optional Float and Instant Switch functionalities.
Upgrades also include features like the Advanced Image Layout Controls. They can also add PRISMA XL Suite workflow software to provide a preview function, which allows users to see what the final product will look like before it’s printed while allowing them to make any necessary adjustments.
Available with the Arizona 1300 FLXflow is PRISMAelevate XL, which enables layered printing up to a height of 4 mm to help customers create stand-out, tactile artwork for elevated print applications that enhance and expand their product offering.
It enables customers to explore new applications, such as high-value, textured, permanent signage, product decoration, awards, décor materials and package prototyping, as well as applications for the visually impaired. As LED-UV printers, the series also consumes at least 15 per cent less energy compared with its UV-halide predecessors, and offers power-saving features such as first-time-right printing and instant-on functionality.
Its inks are UL GREENGUARD Gold certified, which ensures prints are safe for use in sensitive environments such as hospitals, schools and other public places.
Newly-appointed Vanguard sales manager John Bryson introduced Australians to the new Harpeth print-to-cut finishing system for Vanguard machines.
Visitors to the Durst and Vanguard booth saw the new Harpeth automated printto-cut system comprised of the flagship Vanguard VK3220T-HS UV-LED flatbed printer accompanied by the in-line transport system partnered a digital cutter from Colex.
The Harpeth finishing system was named after the Harpeth River located near Nashville, Tennessee in the US.
According to Bryson the ability to automate the workflow will reduce cost and reduce media handling times for greater productivity.
“In today’s competitive landscape, efficiency is the key to success in any print business,” Bryson said.
“This Vanguard VK3220T-HS on show is configured with the auto-offloader, so it picks up the sheet and drags it off the automated table onto the Colex cutter. This Colex cutter does square cuts, detail cuts, and so on.
“The Vanguard VK3220T-HS is loaded with 15 print heads, resulting in highspeed production of a minute per board on each side. Print heads are arranged in a fashion that they print the same colour, in the same lay, in both directions.”
The Vanguard VK3220T-HS is a 3.2m by 2m machine with up to three rows of printheads. Its print speeds can reach over 353m2 per hour.
Utilising 4 picolitre drop size Kyocera printheads and a high-speed magnetic drive, there’s no compromise on speed to achieve remarkable quality. With the ability to add channels for additional speed or application potential after installation, the VK3220T-HS can grow alongside business possibilities.
Currie Group business unit manager –sign and display, Paul Whitehead, was one of the first people to experience the new EFI VUTEk M3 hybrid printer unveiled at Printing United.
The VUTEk M3h is a 3.2m hybrid flatbed/ roll-fed LED printer designed for print providers looking to make the move to higher-volume, production-level printing.
It is designed for print providers looking to make the move to higher-volume, production-level printing to reduce costs, increase margins, turn jobs faster, and differentiate their offerings with new
substrates and/or applications at a lower cost.
Whitehead said the press is a “very exciting addition” to the Currie Group sign and display portfolio, and that the VUTEk M3h is well suited to the local market.
“It is perfect for the Australia and New Zealand market. It is a mid-range unit with features such as 40 boards an hour and a new inkset. Come talk to us to learn more about it,” he said.
EFI also exhibited the VUTEk Q3h XP printer at its booth. This high-speed hybrid flatbed/ roll-fed LED printer aims to offer exceptional imaging quality, flexible production-level throughput, and advanced media handling and automation options, making it a perfect solution for businesses looking to address current labour challenges and costreduction initiatives.
Several of EFI’s preferred partners also exhibited EFI wide format printers in their booths, including the new EFI Pro 16h+ hybrid LED printer and EFI Pro 30f+ flatbed LED printer, which aim to deliver high-quality imaging at production-level speeds and even more printing capabilities – all with a low total cost of ownership (TCO).
The EFI Pro+ printers, feature new high-performance EFI ProGraphics+ Series LEDcurable inks, raising the bar for entry-level, wide-format production-level printing.
The Epson SureColor S9160, which the company recently launched at Printing United in Las Vegas, will be making its way to A/NZ in mid-2025.
The machine, known as the SureColor S9170 in the US, is the first in the next generation of Epson’s SureColor S-Series eco-solvent printers.
Replacing the flagship SureColor S80600 and SureColor S80660L models, the new 64-inch SureColor S9160 aims to deliver exceptional image quality, an expanded colour gamut, productivity and a compact, user-friendly design.
The SureColor S9160 is equipped with Epson’s latest user-replaceable 2.64-inch PrecisionCore MicroTFP printhead, and features an integrated temperature sensor, nozzle verification technology and nozzle replacement.
These advancements ensure reliable image quality and consistent colour output while significantly boosting productivity.
The SureColor S9160 utilises an advanced 11-colour ink set, including red, orange and an all-new green, as well as opaque white ink, which can be used on clear or dark substrates to add versatility and enhance colour.
This expanded ink set delivers a broad colour gamut and enables vibrant and accurate prints on a variety of media types, including vinyl, canvas, film, wallpaper and other roll media up to 1626 mm.
“The SureColor S-Series printers have built the standard for quality in the signage market over the years, renowned for their reliability, exceptional colour gamut, colour consistency and accuracy,” Epson Australia professional print solutions product manager Shuhei Sato said.
“The new SureColor S9160 builds on these strengths, integrating the latest imaging technologies to elevate performance to the next level. The SureColor S9160 is a complete solution for businesses looking to achieve the highest quality standards in signage printing.”
Shaun Holdom from Fujifilm demonstrated the Acuity Prime Hybrid machine during the Printing United exhibition in Las Vegas.
The Acuity Prime Hybrid was launched last year at the Fespa exhibition in Munich. Modelled on the highly successful Acuity Prime, the machine brings additional versatility due to its ability to handle rigid and flexible media.
When used as a flatbed machine, the Acuity Prime Hybrid can print on substrates up to 2m in width. It can simultaneously print on up to four pieces
of rigid media and features registration pins for exact edge-to-edge printing.
The Acuity Prime Hybrid can produce a print at production quality starting from 92 square metres per hour. It also features front and back handling tables to support all media types while facilitating easy media positioning.
The roll-fed configuration can be loaded with two rolls each up to 0.9m wide, and its GreenGuard Gold certified ink makes it suitable for wallpaper production – as well as an extensive range of other applications.
The Acuity Prime Hybrid is suited to a wide range of media, including Dibond, foamboard, acrylic, polyester and more.
Klieverik
Klieverik showcased the latest model from its Vertex series – the Vertex-1850T –at Printing United.
The Vertex series has been designed as an affordable, entry level machine for efficient single piece transfer printing, but the calender is also capable of roll-toroll printing. Some of its features include an oil-based drum, robust build, compact design and ease of operation.
In addition, it has a new shaft bearing construction and a fully functional compact operating touch screen, with maintenanced instructions displayed when due. The machine is optimised for ease of operation and is suitable for all kind of PES textiles.
Ball & Doggett supplies Klieverik in the local region.
Konica Minolta
Konica Minolta showcased a number of devices to demonstrate how it is strengthening and expanding the business of commercial and industrial printing. It had several of its presses on display, including:
The AccurioPress C14010s: The development teams at Konica Minolta have made some new enhancements to further build upon the company’s ‘flagship’ high-volume, toner-based production press, the AccurioPress C14000. The updated press features a fifth station for white toner. Other upgrades include new hardware and firmware, and the addition of new accessories and features. This includes the new IQ-601 for the latest in one-touch colour management, as well as the IM-104/IM-105 to hone in on variable media attributes, ensuring the engine can quickly and easily adjust for the media being fed into the
system. These features and more will all be available with the new C14010s model.
The AccurioWide 250: A versatile printer with superior image quality and high productivity for both outdoor and indoor job applications, increasing opportunities for customers to grow their business. This printer is equipped with UV LED lamps that allow users to print on a wider range of media, while simultaneously saving energy, time and cost. The 4-colour plus white ink configuration creates even more possibilities for printing on transparent material for backlit applications or for printing white as a spot colour. The 6-colour ink configuration offers a larger colour gamut, enabling the capability to print those hard-to-hit colours.
The AccurioLabel 230: This is a digital toner press that meets the growing market needs for shorter runs and more customisation, and provides substantial operational benefits for those looking to bring label production in-house. Printing speeds of 77 ft/min assure that short-run
label production is done quickly and on-time. The simple user interface and integrated software packages allow any user to quickly learn and operate the press, unlike the skilled labour set required for traditional flexographic presses.
The PKG-1300 full colour packaging printer and AccurioShine 3600 together with iFoil One option were also on display.
Mimaki
Mimaki took the wraps off four new products at Printing United. The first was the CJV200 series, a roll-to-roll print and cut MFP with eco-solvent ink. The CJV200 is equipped with a single print head of ‘330 Engine’ in the flagship printer, enabling even inexperienced operators to produce printed products beautifully, quickly, and easily.
The CJV200 is also equipped with a variety of drafting modes to suit various printing applications, and can output 17.0 m2/h in
the practical drafting mode, which is one of the highest productivity rates for an entry-level printer, contributing to reliable print output even during busy periods.
The next is the JFX200-1213EX mid-sized flatbed UV inkjet printer. The JFX2001213EX offers a new table size of 1,270 x 1,300 mm, compatible with international A0 standards. This makes it ideal for producing poster-sized sign graphics.
One of its standout features is its ability to print braille and pictorial signs at double the speed of conventional printers, setting a new benchmark for productivity.
The third machine that was launched is the TxF300-1600, a 3.2m-wide roll-to-roll inkjet printer that can output both direct sublimation printing and sublimation transfer printing for large format soft sign applications and home and textile markets.
The new TxF300-1600 delivers a 30 per cent increase in custom T-shirt print productivity compared to its predecessor. Certified safe and eco-friendly with the ECO-PASSPORT certification, Mimaki’s DTF ink meets the rigorous standards required for OEKO-TEX certification, making it a sustainable textile printing choice.
The last of the new machines that was launched at the expo is the TS3303200DS DTF (Direct-To-Film) printer.
As the trend for fabric signage continues to grow in commercial and exhibition settings, the TS330-3200DS hybrid printer supports both direct-to-fabric and sublimation transfer printing on media up to 3.2m wide, catering to the expanding demand for large-format interior fabrics.
All of these products will be commercially available in Australia later this year.
Currie Group demonstrated the Canon Colorado M-series working in conjunction with Italian finishing specialist Neolt Factory for the first time at Printing United.
Currie Group announced the partnership with Neolt Factory during the Visual Impact exhibition in Brisbane. The partnership includes the exclusive supply of a range of Neolt Factory loading, unloading and finishing systems for the Canon Colorado M-series printer range.
These include ‘jumbo roll in – jumbo roll out’ systems which increase the capacity for long run lengths of products like wallpaper without need for operator intervention, and jumbo roll-to-cut solutions which allow rolls to be converted automatically straight off the printer.
Paul Whitehead, Currie Group business unit manager – sign and display, said the Neolt Factory finishing will deliver huge advantages, particularly for businesses doing large runs of wallpapers or similar products, or multiple smaller runs of wallpapers or trimmings that require post-production finishing.
“The benefits of automation are well established. Higher productivity is an obvious advantage, but importantly this can be achieved more profitably and while maximising the value of your staff resources, by removing touchpoints in the production process and making the entire, end-to-end process simpler and more streamlined,” he said.
“The Neolt systems will allow Canon Colorado M-series users to lift their productivity with no additional labour requirement, by fully utilising the automated features of the printers and enabling longer, unattended production runs as well as in-line converting.
“This is a particular advantage for businesses in markets like Australia and New Zealand where qualified staff are in short supply, and wages running at a premium.”
Under the new agreement, Currie Group is the exclusive agent for the Neolt Factory product suite across Australia and New Zealand, where the company also supplies the Canon Colorado and Canon Arizona printer ranges.
Rollem took to Printing United to showcase its Insignia 7H (Hybrid) die cutter, one of the models from its Insignia 7 Series. This new class of larger format die-cutting machine creates a distinct space in the print finishing market for
sheetfed, short-long run label, packaging and mail applications.
The Insignia 7H houses two cutting drums. The H model dual magnetic Insignia systems offer the ability to utilise a single cutting tool, or a paired set of dies when looking to produce packaging products or other scored work.
When running a single cutting die, a ‘blank’ lower jacket is wrapped around the lower cylinder and acts as the cutting surface for the upper die. This setup allows for cost savings on tooling when producing straight die cut product and/or die cut/kiss cut decal work.
If producing boxes or the like, a paired set of dies allow for zero make ready from machine operators as well as enables embossing and/or debossing of substrates in a single pass.
This twin drum can also just be used as a single counting drum. The machine also has an inline stripping system on it, which means users get a finished product out the end. It also takes only minutes to set up compared to large flatbed cutters, which can take a couple of hours.
The tooling for this type of machine is a flexible plate that is held on through high power magnetic drums, and it means that make-ready for the operator is in minutes and maintenance is minimal.
Insignia machines weigh between two and five tonnes depending on size of machine (die cutting section only). These machines are built strong with thick solid side-frames measuring between 38mm to 64mm to house the cylinder section and support the cutting station.
Rollem is available from Graph-Pak in the local region.
Pozitive Sign & Graphic Supplies showed Aussie attendees at Printing United in Las Vegas the latest innovations from swissQprint, Summa, Valiani, and DGI.
Industry leaders from around the globe gathered at Printing United 2024 in Las Vegas, where the latest advancements in print technology were on display. Among the attendees was Warren Davey from Pozitive Sign & Graphic Supplies, supporting key brands like swissQprint, Summa, Valiani, and DGI.
At the swissQprint stand, the Kudu UV LED flatbed printer continued to draw attention. Having already made an impact in Australia, with installations at Allprint Graphics, Mezographic, and Briner Signs, the Kudu showcased its versatility and precision.
With a 3.2m x 2m flatbed and swissQprint’s patented tip-switch vacuum system, the Kudu handles a wide variety of substrates – from silver foil to rigid materials. Its ability to run 24/7 while delivering up to 304m² per hour, without sacrificing quality, positions it as the ideal printer for businesses looking to enhance their production capabilities.
Warren’s involvement at the swissQprint stand allowed him to engage with
Australian printers, sharing insights on how the Kudu could elevate their production workflows. swissQprint’s presence in Australia continues to grow, and the Kudu remains a key player in helping businesses achieve new levels of efficiency and creativity.
Over at the Summa booth, the F Series flatbed cutters reinforced their position as an essential tool for high-performance digital finishing. Known for their ability to handle diverse materials with speed and precision, Summa’s cutters are designed to meet the demands of a wide range of applications.
Warren highlighted how the F Series’ seamless transitions between substrates make it invaluable for businesses working with everything from decals to packaging and signage. Summa’s ability to enhance productivity while maintaining accuracy makes it a top choice for Australian companies looking for flexible finishing solutions.
In addition to swissQprint and Summa, Valiani showcased its flatbed cutting systems, known for precision cutting
in industries like packaging and fine arts. Valiani’s systems offer Australian businesses opportunities to expand their product lines while maintaining high standards of detail and quality.
DGI, a leader in textile printing solutions, demonstrated the growing potential of digital textile printing with applications across fashion, home décor, and soft signage. Their presence highlighted the rapid evolution of this sector and the opportunities it presents for businesses looking to diversify into new markets.
For Warren, attending Printing United was about more than seeing the latest products – it was about exploring new applications that can benefit Australian businesses. The technologies on display from swissQprint, Summa, Valiani, and DGI showcase how far the industry has come and where it is heading.
This time, what happens in Vegas doesn’t stay in Vegas – Warren’s insights are set to make a Pozitive impact back home, helping Australian businesses stay ahead of the curve.
The prototype of the new DigiTech TruFire LT/X3 was on display at Printing United and was very popular with local printers attending the American exhibition.
Celmac has introduced Australian printers to the DigiTech TruFire LT/X3 flatbed UV printer at Printing United in Las Vegas – the successor to the LT/X2 machine shown during Visual Impact in Brisbane.
A prototype of the new DigiTech TruFire LT/X3 was on display at Printing United in Las Vegas, and according to Celmac sales manager, Jonny Rumney, it was very popular with local printers attending the American exhibition.
“The LT/X3 features 18 heads in three rows of six, compared to the LT/X2 that has 12 heads across two rows of six. The LT/X3 is 30 per cent faster overall, and this makes a huge difference particularly for customers looking at a two-pass solution, as the quality is substantially improved. A fullsized board is capable of being printed in 20 seconds,” Rumney said.
“The DigiTech TruFire LT/X3 was received very well during Printing United and was a real eye-opener for the people that made the journey to the exhibition seeing it printing and cutting in both two-pass and three-pass modes, in real-time.”
This next-generation LT/X3 from DigiTech gave the Australian visitors the opportunity to engage with the US development team and see first-hand the unique design elements that has led to its success across North America, and more importantly the further automation it has planned in the new year.
“At the show, several American users of DigiTech equipment consistently commented about the reliability of the machines. One of the printers – Steve Parrott from Parrott Productions in El Paso, Texas – only experienced his first fault with the machine after three and a half years and 325,000 square metres leading up to the exhibition in Las Vegas,” Rumney said.
“Being a small shop, we continuously look for that edge where we can reduce labour while increasing throughput,” Parrott said.
“Everything is moving to full automation and DigiTech is leading the way. Everything it has done has been top notch.”
To emphasise the reliability of these American-made workhorses, Rumney confirmed with ProPrint that DigiTech printers are not reliant on overseas suppliers. With this manufacturing advantage, DigiTech remained resilient during the uncertain COVID period, and was able to consistently supply spare parts, which was reassuring for printers making important purchasing decisions.
Celmac began conversations to represent the DigiTech brand in the local market over five years ago.
“We started our due diligence into the DigiTech brand in 2019 and then COVID delayed our official launch into Australia,” Rumney said.
“Earlier this year, we commissioned the LT/X2 at SS Signs in Brisbane and held an open house event to demonstrate the machine during Visual Impact. SS Signs operates its DigiTech LT/X2 at its factory
The LT/X3 features 18 heads in three rows of six, compared to the LT/X2 that has 12 heads across two rows of six
in Cleveland, east of Brisbane, with an Aristo six-metre cutter. Owner Steve Lambourne said it’s the best decision he has made, and it’s materially transforming the business.”
Also demonstrated at Printing United was full pallet-to-pallet or pallet-tocutter automation without any human intervention, which will be available for Australian customers next year. The full automation features unique operation to perform double sided printing without any operator involved.
Celmac also supplies INX, Jessup, Kala and Onyx to the local market.
Click on the QR code to view a video of Celmac managing director Wayne McIntyre discussing the DigiTech LT/X3 at Printing United.
Click on the QR code to view a demonstration of the DigiTech full pallet-to-pallet concept, also launched at Printing United.
A large number of local printers and suppliers travelled to Printing United in Las Vegas this year to experience ‘American Drupa’ and see the latest technologies on display.
Printing United recently took place in Las Vegas, bringing together the printing industry to experience the latest in equipment, solutions, and trends. More than 800 exhibitors and almost 25,000 people from around
the world unveiled their latest solutions spanning market segments in apparel decoration; commercial and publishing; functional/industrial; graphic installation; graphics/wide format; in-plant; labels and packaging; mailing, shipping, and
fulfillment; and promotional products. There was plenty of technologies to see, trends to hear about, and peers to meet and catch up with. Here are some familiar faces that our team met at the event.
Employers should be proactive in understanding their jury service-related obligations to prevent disruptions to business operations and to avoid significant legal consequences.
Properly
and manageable situation
Employees performing jury service don’t arise that often. However, when it does, the effects on employees and employers can be confusing. A recent NSW Local Court decision highlights the legal obligations employers have to their employees who are selected to sit on a jury panel, and that if not managed appropriately by employers they can have significant legal consequences.
In the case before the NSW Local Court, an employer was found guilty of threatening an employee who took Court recommended time off while performing jury duty. Over the course of an eight-week murder trial before the Supreme Court, the juror had been rostered to work three out of every four weekends by their employer.
However, the judge advised the jurors they should take weekends off so they may ‘rest and process’ due to the facts of the case.
Despite letters from the judge stating the juror was to rest on the weekends, the employer contacted the employee to say she had breached company policy by failing to fulfil her working hours. Then, after returning to work, the employee was advised they would be subject to an
upcoming disciplinary hearing, at which they would face either a warning or termination.
The Court was having none of that, and the Sherriff’s Office pursued the employer who was found guilty on charges of threatening an employee called for jury service with dismissal or an alteration to their employment.
The Magistrate said the threats undermined the Jury Act, and labelled the conduct of the employer ‘inexcusable’. Sentencing will occur in November, where the punishment for such threats to employees who are called up for jury service can include fines of up to $22,000 and potentially imprisonment of up to 12 months.
Aside from the obligations under the Jury Act or equivalent, the Fair Work Act also details various other employer related obligations.
Under the Fair Work Act an employer is required to pay permanent full-time or part-time employees for the first 10 days of jury service. Employers are entitled to require employees provide evidence of their jury service requirements, and
any evidence of receiving payment for performing jury service.
Noting that not all Courts make payments to jurors, if the employee does receive such payments the employer has an obligation to provide make-up pay, being the difference between the Court payment and the employees base pay for the ordinary hours of work.
Any attendance allowance paid by the Court (i.e. bus fare) to the juror should not be considered as a substitute for the employee’s salary or wages.
Of particular relevance to small businesses, an employer can provide an employee with a detailed letter stating reasons why it will be difficult to operate if the employee is empanelled.
It is recommended that such a letter be provided by the employee to the Court for its consideration as early as possible prior to the employee attending on their summons date, as once they are empanelled, they cannot generally be excused.
However, even if they are excused on that particular occasion, they may nevertheless be called up again in the future.
Additionally, employers cannot require an employee to use personal or annual leave when performing jury duty, and cannot require an employee to work extra hours to make up for any time lost as a result of jury service.
Further, and as the decision evidences, an employer does not want to find itself on the wrong side of the Jury Act and or the Fair Work Act, by acting to dismiss, injure or alter any employee’s position for performing jury service.
Employers should be proactive in understanding their jury service-related obligations to prevent disruptions to business operations and to avoid significant legal consequences in both a Court and the Fair Work Commission. Properly handled, employees on jury service can be a temporary and manageable situation.
Charles Watson GM – IR, Policy and Governance Visual Media Association
This article is of a general nature and guidance only and does not constitute legal advice.
DThe future of print is already materialising through aggressive investment as well as research and development by global market leaders.
uring drupa 2024, the printing industry got an exhilarating preview of its tech-driven future on the showroom floors. Immersive displays and live robotics demonstrations provided a tantalising glimpse of the highly automated, AI-powered print manufacturing operations that leading players are aggressively bringing to life.
Major exhibitors like Heidelberg, Komori, HP, Canon and Bobst captured attendees’ imaginations with their visions of intelligent, self-optimising production lines seamlessly integrating the digital and physical worlds. Legacy offset and digital press manufacturers were joined by bold innovators showcasing flexible new approaches integrating conventional and digital technologies.
However, the true showstoppers were the robotics zones simulating the future lights-out automated factory. Automated guided vehicles zipped across floors transporting materials to manufacturing cells, while industrial robotics choreographed a brilliant dance of speed and precision, rapidly executing tasks like loading, unloading, quality inspection and finishing work.
These demonstrations were a wake-up call that the future of print is already materialising through aggressive investment as well as research and development by global market leaders. This reality presents an amazing opportunity for printers in Australia and New Zealand to secure decisive competitive advantages. Those bold enough to strategically invest in automation, AI and connected smart workflow solutions can position themselves as pioneering industry leaders. However, achieving that vision requires careful planning and patience, not a haphazard plunge that risks operational disruption. Conducting comprehensive audits to pinpoint optimisation opportunities through intelligent automation is a crucial first step. Identifying bottlenecks, quality issues, and inefficiencies allows targeting the right processes to transform.
Partnering with knowledgeable systems integrators is vital for ensuring new hardware and software seamlessly integrate with existing infrastructure. Their expertise in complex IT requirements like workflow redesigns, systems mapping, and new standard operating procedures (SOPs) is invaluable. Getting it right maximises the technology’s impact.
Perhaps most importantly, print leaders must champion organisational change through comprehensive staffing and training initiatives. Empowering employees to adapt to new technology-driven roles and responsibilities may be the biggest key to long-term success. Incremental rollouts with continual skills development allow for a smooth transition.
From a sales and marketing perspective, implementing advanced automation represents a powerful differentiator for attracting new business. Companies should showcase their innovation leadership through high-impact campaigns highlighting transformative capabilities like:
• Dramatically faster turnaround times
• Mass customisation/versioning possibilities
• Reduced human errors and waste
• Cost efficiencies from lights-out production
• Sustainable practices and material sourcing
Building this reputation requires a multifaceted effort, including compelling case studies, videos, print samples, and thought leadership content demonstrating the advanced capabilities in action. Ensure the sales team is empowered as “technology evangelists” who can vividly articulate the value proposition and convey mastery through interactive technology demos.
While upfront investment costs may give some sticker shock, it brings long-term competitive and supply chain agility payoffs. As demands intensify for quick turnarounds, on-demand product personalisation, seamless omnichannel experiences, sustainable sourcing and end to end supply chain connectivity, printers with fully automated and AI-driven operations can capitalise on new opportunities. Digitally transformed print businesses will have the adaptable, lightsout production flexibility required to seamlessly pivot to evolving market needs and customer requirements. They’ll be optimised for rapid innovation cycles, unencumbered by legacy constraints, while traditional competitors get left further behind.
At drupa, the global printing industry got a brilliant sneak peek at its future digital renaissance already unfolding in Düsseldorf’s sprawling halls. For printers in Australia and New Zealand, the time is now to decide their fate. Be bold. Be a fearless market disruptor by strategically automating production, integrating artificial intelligence and fortifying connected smart workflows. Reap the incredible rewards of unleashing manufacturing’s next great revolution.
Otherwise, you risk becoming obsolete by watching from the sidelines as nimbler, tech-driven competitors sprint ahead unchallenged to dominate the market’s most lucrative new opportunities. The future favours the bold; printing’s revival won’t wait. Evolve with an applied technology vision or become extinct – the choice is yours.
Mick Rowan has spent the past decade building printIQ into one of the most recognised software brands in the printing industry, and with over four decades of experience, Mick truly has ink in his veins.
Hosting an event? Send an email to the editor Claire Hibbit chibbit@intermedia.com.au with the details
• Near total coverage of roller requirements for the graphic arts sector
• Wide range of rollers for printing and packaging, laminating, gluing, transport and nip
• Specialised services for non-standard applications
• In-house expertise to help you achieve your production goals
Imagination Graphics is your trusted partner in digital printing, graphic design, A2 posters and CTP (Computer to Plate). We support most press CTP sizes.
CMYK 1 side on 170gsm art starting from
A2 x 100 $230
A2 x 500 $310
A2 x 1000 $410
A2 x 2000 $725
CTP (computer to plate)
A3
$20 A2
$40 A1 ........................... $55
Please call to discuss pricing on large volume plate production.
*Plus GST and delivery. Prices based on C.O.D.
02 9560 6511 | 33-35 Sydney Street, Marrickville NSW 2204 quotes@imaginationgraphics.com.au | www.imaginationgraphics.com.au/trade
This is a rare opportunity to purchase a unique business with a strong customer base and substantial growth potential within the fast-paced outdoor advertising industry.
Since the company’s inception in 1997, we have always strived to provide a unique product supported by our reliable and prompt sales service.
• ADCOAT Graphic Solutions has developed a range of specialised coatings that we supply and/or apply as liquid laminates on a variety of substrates and inks used in the outdoor media industry.
• We have an in-house coating room where we can laminate large-format banners of virtually any size.
• All our coating systems are locally manufactured here in Sydney under our designed formulations.
• Our customer base is built on a long-standing repeat business model for both our coating service and product sales. We supply to local government departments, infrastructure units, and small and large print companies.
For all inquiries and further information on this unique opportunity, please contact Paul Elliott at 0412 383 240 or email paul@adcoatgraphicsolutions.com.au
– BOPP –SupaGloss, SupaMatt, Antiscuff, Soft Touch, Rough Touch, UniGloss, UniMatt, Premium Digital in Gloss, Matt, Soft Touch, Antiscuff. Sizes – 220mm – 710mm width
– PET –Gloss, Matt – 42mic, 75 mic, 80 mic, 125 mic & 250 mic Size - 315mm – 1550mm width
– PSA (Cold Film)Gloss, Matt, Texture (sand), Monomeric, Polymeric, AntiGraffiti. Sizes - 500mm – 1530mm
– Foils –Gold, Rose Gold, 24K Gold, Silver, Bronze, Pink, Black, Green, Red, Blue, Clear, White. Size – 320mm width
– Backing Film –500 to 1580mm width
JTS Engineering servicing the industry for all machinery and engineering requirements, has partnered with Longer Machine Industrial Co Ltd to supply a specialised range of paper guillotines systems featuring high speed, precision and safety.
Contact us anytime for all service and guillotine requirements
JTS Engineering Services Pty Ltd
Jim Strounis, Owner
Mobile: 0433 100 243 Email: jim@jtsengineering com.au Scott Mohammed, Service & Account Manager
Mobile: 0431 887 501 Email: scottm@jtsengineering com.au
Unit 5, 80-82 Seville Street, Fairfield, NSW, 2165 Web: jtsengineering.com.au
Volunteer or Sponsor help us
Come and see the extensive expansion and renovations.
Need a venue for a function? Talk to us we can help. Visit https://www.printingmuseum.org.au/
Revolutionise Your Bookbinding with Our State-of-the-Art Hard Case Solutions.
Print Logistics is proud to offer cutting-edge, hard case binding technology that delivers a new level of durability and sophistication. Our innovative process involves expert casing of the hardcover, resulting in a final product that exceeds the competition in both robustness and elegance.
Elevate your publications, specialty books, and projects to new heights with our superior hard case binding solutions, perfect for customers who refuse to compromise on quality.
• Fast turnaround times
• Competitive trade-only pricing
• Privileged communication
• Family owned and run
• Variety of customisation options to meet your specific needs
“We’ve relied on Print Logistics for years and couldn’t be happier with their service. Their professionalism, precision, and dedication to confidentiality make them invaluable partners. We highly recommend Print Logistics for exceptional printing and binding services.” Principle Design
Print is perception and we treat it accordingly.
Contact Us Today
Phone: 1300 659 029
Email: contactus@printlogistics.com.au
Visit: www.printlogistics.com.au
CCS Packaging has taken their business up to the next level of high-value-added shorter to long run packaging printing. Their RMGT 970ST-7+C+LD is powering the Sydney company into a new segment of the print market. Utilising seven colours to achieve the many colour variants required for high quality packaging printing, the new RMGT 970 is built on the rich heritage of the 920 and 1060 series. It combines the small footprint, ease of use, low running cost, superior quality and high productivity of the 920 series with the advanced features, skeleton transfer system and heavy-duty packaging construction of the 1060 series. CCS has built its reputation over 37 years in the demanding media business and is now applying their considerable expertise to service the cosmetic, health and wellness packaging segments. With enhanced productivity and finishing capabilities, CCS capitalises on decades of production experience to offer their customers high quality packaging with short lead times. CCS is expanding the mindsets of customers by deploying JIT (just-in-time) operations to reduce business cost and waste.