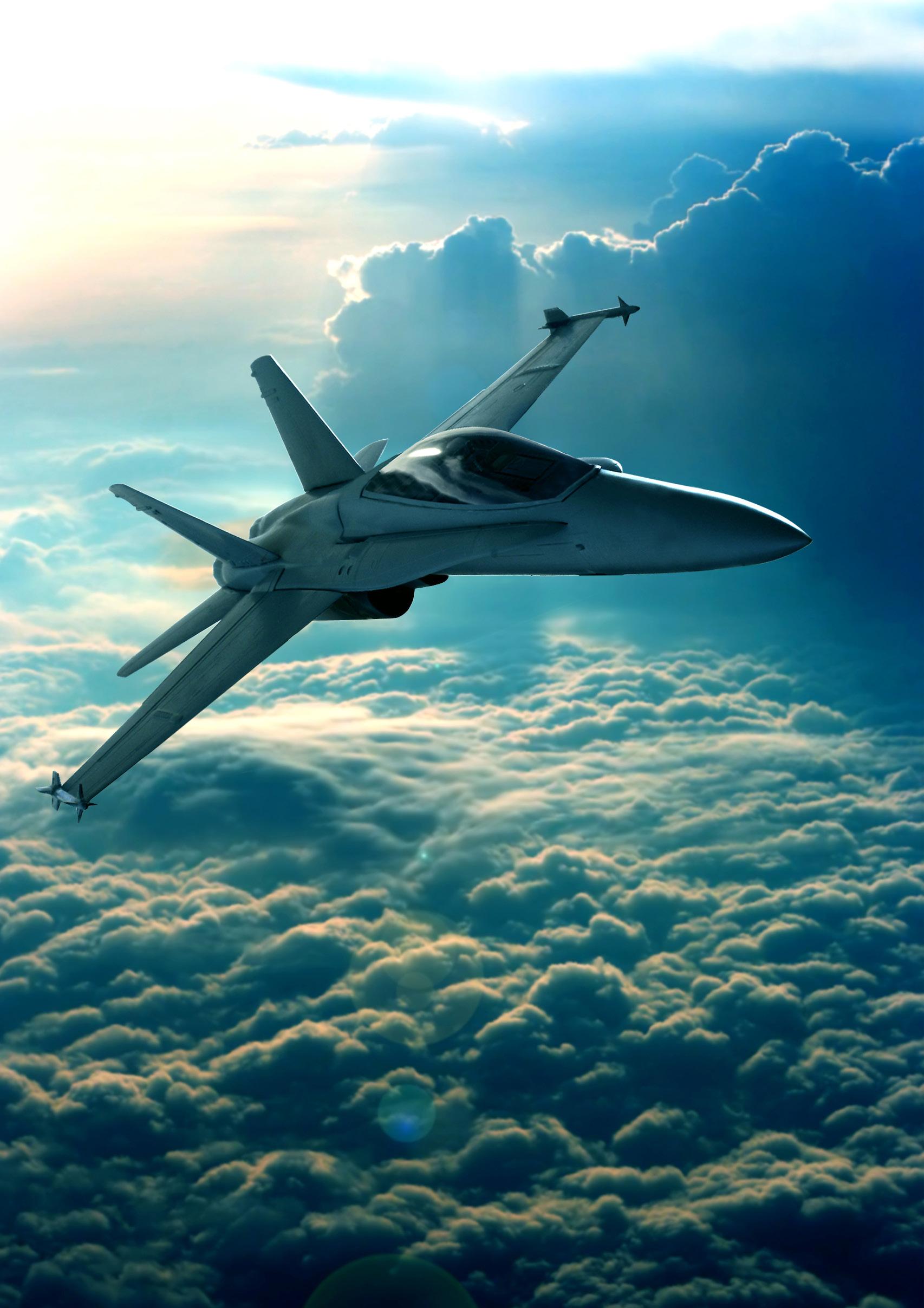
5 minute read
ELECTROLUBE
Join The Eco Revolution in Coating Technology - Bio-based Conformal Coatings
Electrolube, a brand of MacDermid Alpha Electronics Solutions, is among the world’s foremost experts in the formulation and application of conformal coatings designed to meet international approvals (including European and American military specifications). Conformal coatings are thin, protective polymeric coatings, that are applied to protect the metal surfaces of printed circuit boards from corrosion, condensation, dielectric breakdowns and mitigate against tin whisker formation and conductive metal particles.They are designed to cover and protect solder joints, the leads of electronic components, exposed traces, and other metallised areas, ultimately extending the working life of the PCB. Electrolube’s extensive range of coatings include acrylics, silicones, polyurethanes, hybrid chemistries and more recently, the company has introduced a brand new bio-based range of environmentally friendly coatings.
After significant research and development, Electrolube has developed a viable and sustainable alternative to materials derived from petrochemicals and has introduced a new bio-coating to market that is completely solvent-free, a global first for the industry. The electro-chemicals manufacturer has launched the first 2K UV coating, UVCLX, which incorporates 75% bio-organic content from renewable sources and meets the needs of both manufacturers and consumers, essentially based on ethics, performance and process. The use of solvents has become more restricted, and consumers are increasingly becoming aware of the ‘waste’ of these processes in the form of the energy required to remove the solvents, as well as the impact of their release on the environment.
UVCLX, UV Cure Coating Xtra, is a bio-based conformal coating that is completely unique to the industry and provides the highest levels of protection whilst maintaining a rapid processing time. Applied via a selective coating machine, UVCLX exceeds traditional UV Cure Coatings, by being touch dry after just a short exposure to LED-365nm UV light. Full cure is guaranteed in less than 24 hours by virtue of the secondary chemical cure mechanism, which ensures that even shadowed areas are fully cured in a matter of hours.
UV curing uses intense ultraviolet light to set off a chemical reaction within the coating in order to cure almost immediately in areas exposed to the UV radiation. With traditional UV Cure materials, the rapid nature of the primary UV cure, as well
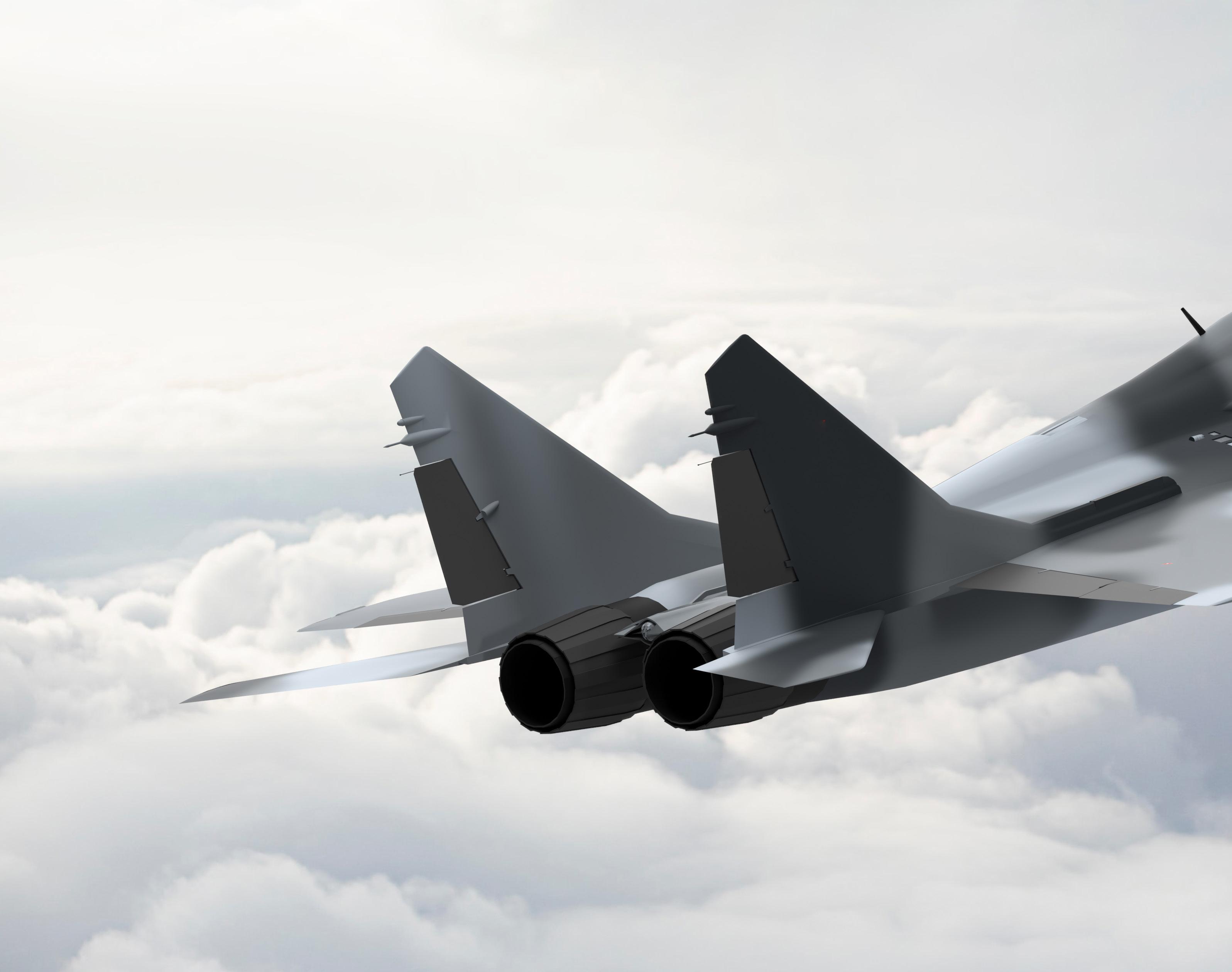
as the polymerisation process itself, tends to cause significant amounts of shrinkage, which creates a lot of stress in the coating that is commonly alleviated by stress-cracking during thermal cycling. In addition, the materials must also contain a secondary curing mechanism to ensure material beneath components, or otherwise shadowed from UV radiation by taller components, cross-links and develops hardness and other critical properties. This is commonly a moisture cure, and can take weeks, months or even years to complete, due to the fact that the outside of the material is partly cured from exposure to UV radiation and moisture must permeate through this membrane, and CO2 gas produced during this curing process must permeate back out through the same membrane.
Due to the 3D nature of most assemblies there will nearly always be areas that remain unexposed to the UV radiation and therefore a secondary cure mechanism is unavoidable. There are formulations available that use heat, although the cure times are relatively long and the temperatures are quite high, which places additional thermal fatigue on the assembly and detracts from the main benefit of UV curable materials, fast-cure times with relatively low energy inputs.
The benefit of a 2K UV curable material like UVCLX is that once the 2 components are mixed, the reaction will proceed to completion in less than 24 hours in these shadowed areas that are not exposed to UV radiation. The additional cure nature of the reaction ensures significantly less shrinkage and less stress, resulting in more flexible coatings that can better survive thermal shock. UVCLX performs in stark comparison to traditional UV Cure Coatings and enables a greatly reduced level of work in progress.
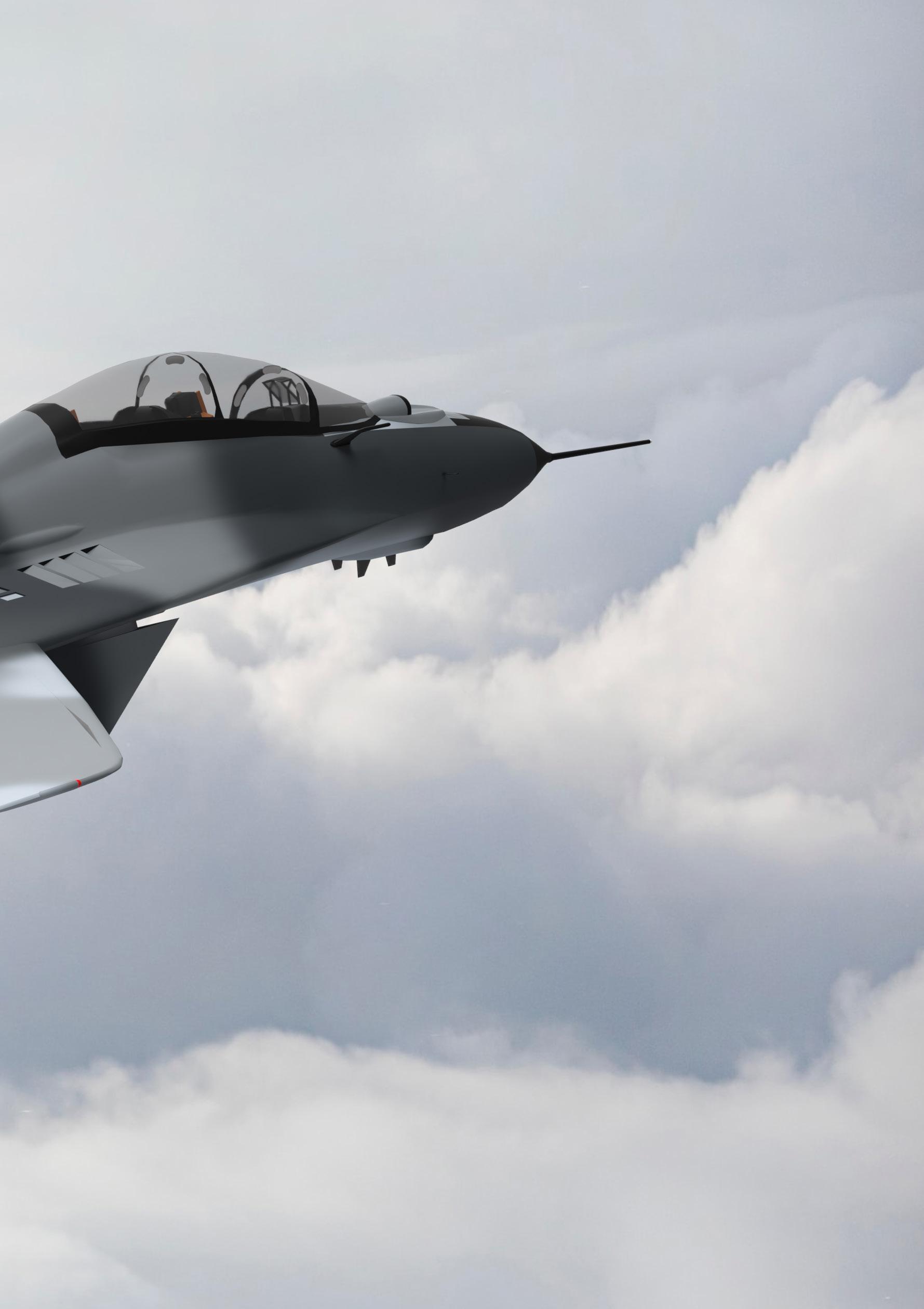
UVCLX is optimally applied at between 200-350µm and achieves excellent edge coverage even over sharp components. It provides unrivalled protection, even during temperature cycling and thermal shock, vastly out-performing other UV coatings on the market even in the most hostile environments. Due to its hydrophobic nature, UVCLX offers exceptional protection against moisture, salt mist and even full immersion for short periods. This immersion period can be extended by applying the coating more thickly. Camouflaging components and PCB tracks for more sensitive designs, UVCLX is a highly versatile coating that can be deployed wherever a coating is needed and is ideal for automotive and EV applications. The most astonishing benefit observed during the development of UVCLX was the improvement in terms of performance that were achieved. The bio-based polymers showed improved condensation resistance, thermal stability, flexibility, and adhesion than many petrochemical derived polymers that were developed. More or less every single ingredient in a typical formulation can be formulated from either completely bio-based or a high degree of biocontaining raw materials, with the current exception of flame retardants. The bio-coating has both performance and top environmental credentials to match, making it a win-win solution.
“The highest level of performance with full cure guaranteed in 24 hours.”
Bio-based coatings really come into their own whenever thermal shock cycling and condensation resistance are the two main failure mechanisms.
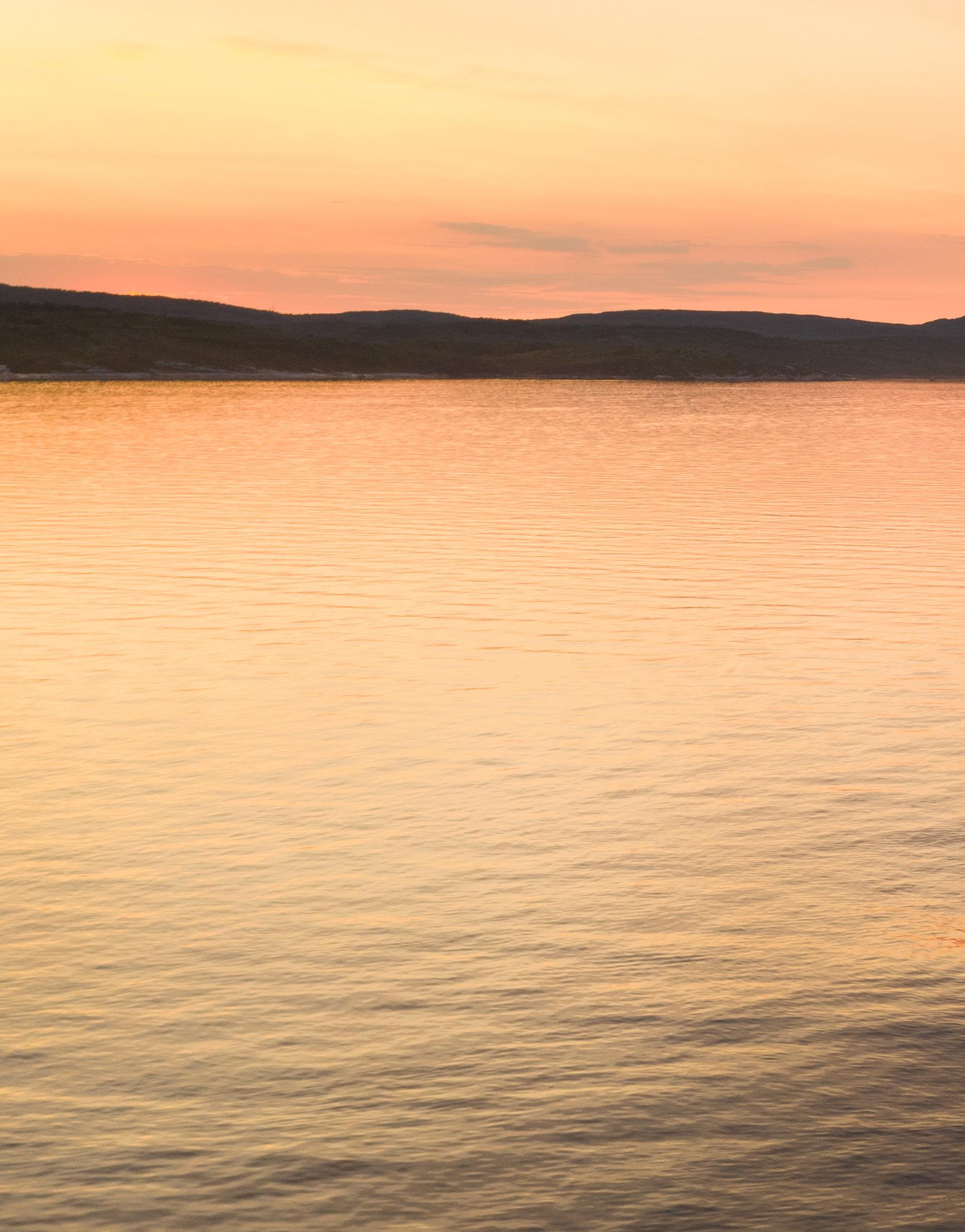
As for testing the bio-based coating, much of the development work focussed on doing a lot of work in harsh environments testing and demonstrating improved condensation resistance due to the combined improvements of thickness and coverage provided by the material, further to the usual automotive requirements of thermal shock and max continuous operating temperatures with long term thermal humid ageing,
The industry can expect more high-performance, bio-based coating solutions from Electrolube. Having proven what UVCLX can do in terms of the environmental and performance benefits, the company aims to introduce new bio-based materials in all new product developments.

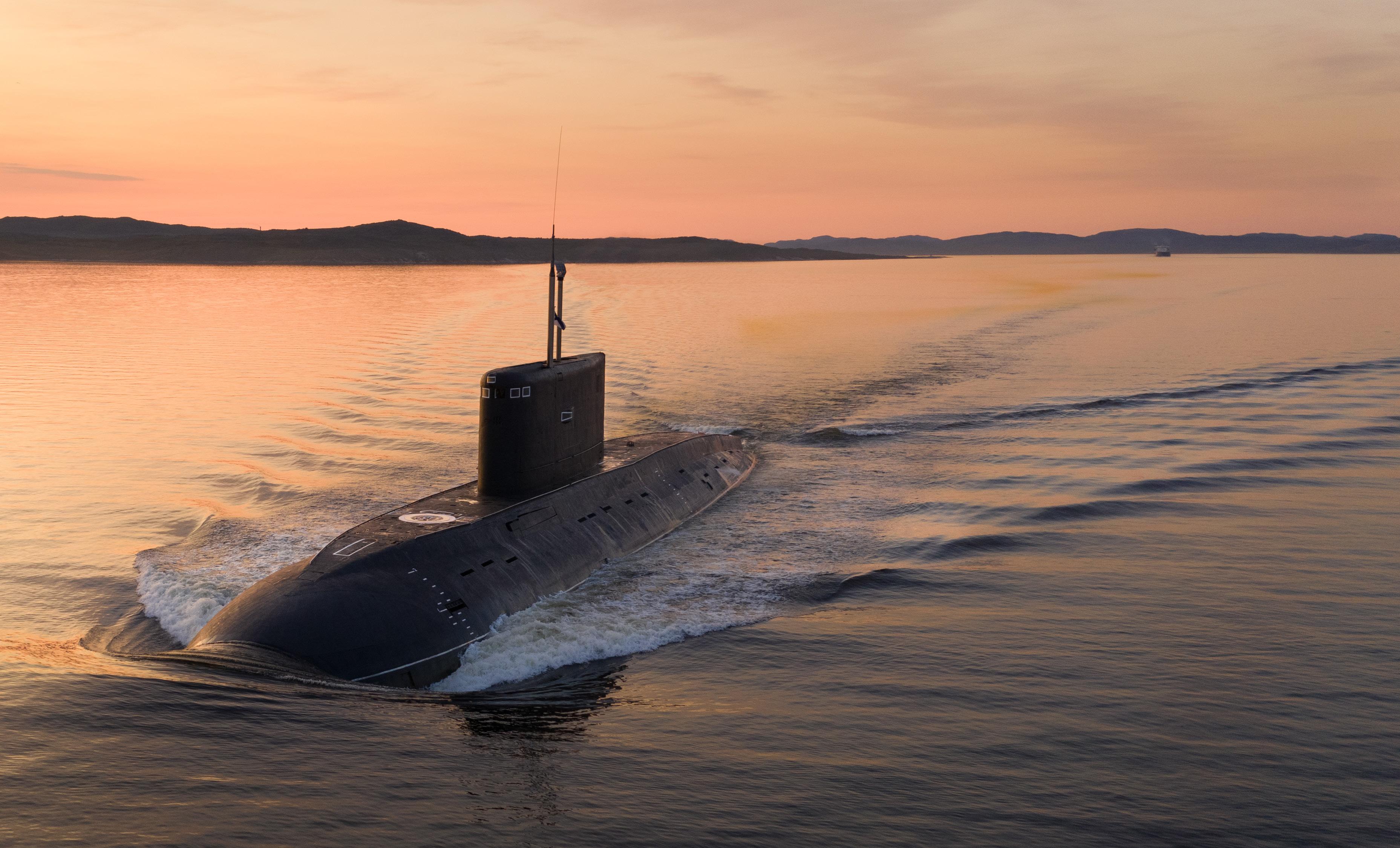