
6 minute read
SIEMENS
The Supply Chain Crunch: A Temporary Trend or Transformation Driver?
Oren Manor
Director of Business Development, Siemens Digital Industries Software
LISTEN TO PODCAST
Supply chain challenges:
Of all the manufacturing stages in any electronic product’s production, components are the part that takes the longest to manufacture - which is why we have such a bottleneck now.
Increasing manufacturing capacity for semiconductors takes several years - it is almost impossible to close the gap.
Electrification is on the rise, creating even larger demands - IoT, EV, + additional verticals.
Long-lead items - previously large inventories were considered inefficient and expensive. For specific items, manufacturers would “keep them in a drawer”. Therefore manufacturers preferred not to have large inventories. Now all components are long-lead items.. manufacturers need to have large inventories to ensure delivery.
Component shortages are here to stay. COVID-19 hasn’t gone away yet, we’re still seeing lockdowns, and the global supply chain is impossible to predict.
Electronics manufacturers need to be more agile and adjust to global manufacturing.
Three things manufacturers need to do in order to become more agile:
1.
Left-shift - make decisions about components much earlier in the process. Alternative components need to be considered early in the process (left-shift), and also - based on component availability in different locations.
Simulation - Early DFM on different components, ensuring that component geometry is accurate with VPL, making sure that these components can be used in the planned manufacturing process (pick and place, testing..).
Digitalization - Even with all the proper planning, you may come across component shortages later on in the process. Digitalization provides the agility to make adjustments quickly while not compromising on quality.
2.
3.
https://www.linkedin.com/in/orenmanor/
Thoughtful Design for Component Shortages
Susan Kayesar
PCBflow Product Manager,Siemens Digital Industries Software
How are current supply chain pressures affecting PCB design? How are PCB designers coping with these challenges? How is this affecting their workflows?
Component availability is an issue that PCB designer never had to deal with - now it’s something that they have to take into account when planning their design.
Meeting budget and NPI timeline requirements is more challenging.
LISTEN TO PODCAST
1.
“Thoughtful” design - components are becoming a larger factor when planning the PCB
Looking for tools that can help make more informed decisions about components
Are the components even available? What are the alternatives? Can I plan one design to fit several alternatives?
Lead times Minimum order quantities Obsolete/out of stock
2.
https://www.linkedin.com/in/susan-kayesar-1a641010/
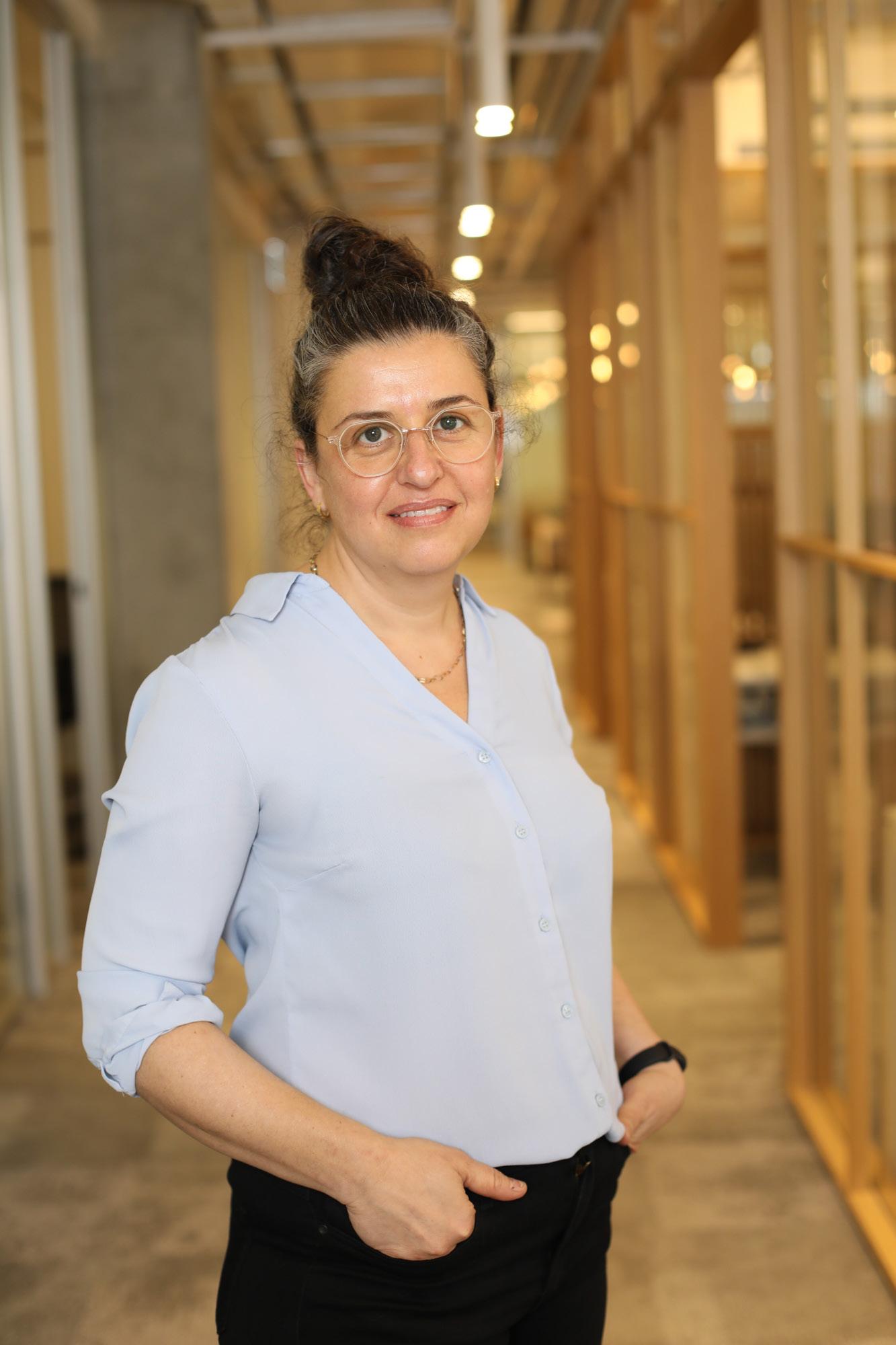
Supply Chain Challenges During New Product Introduction
Mark Laing
Business Development Manager at Siemens Digital Industries Software
LISTEN TO PODCAST
Component Sourcing:
In the previous podcast, we discussed how component shortages are affecting the PCB design process - creating more “thoughtful” designs.
Alternative Parts and AVL management:
Need to expand the number of vendors How do you manage them? Functional/physical equivalency Dynamic management - bi-directional communication to qualify parts Communication challenge - large impact on efficiency and time-to-market. Changes in lead times make it difficult to decide which products should be manufactured. Storage - need to plan storage for longer periods - JIT/lean manufacturing is more challenging
Take advantage of solutions that can be flexible with searching for parts through on-line portals. Not just looking 1:1 based on the manufacturer part number but also looking for equivalent parts that are functional and fit. The functional part is usually easier than the fit. Being able to run a check of the part against the board is the only reliable way to be sure that it will fit on the footprint of the board.
In higher mix environments, being able to be more flexible with production schedules is key. So for the NPI area, being as efficient as possible is creating all the necessary manufacturing collateral is important. This means relying on as much common data as possible, particularly in the area of part libraries. It is not possible to be managing multiple libraries across all the different machines when a streamlined flow is necessary to achieve quick turnaround as schedules change.
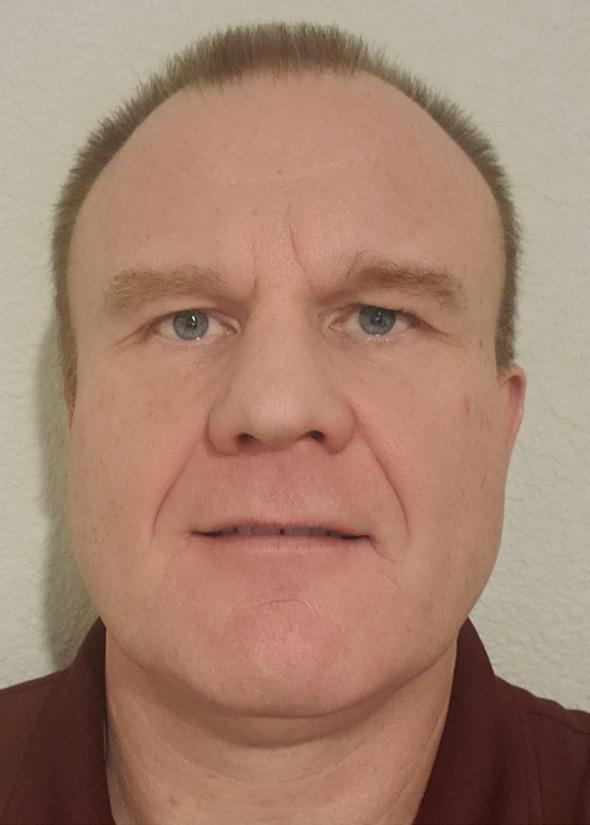
1.
2.
3.
How can manufacturers cope with these challenges?
https://www.linkedin.com/in/mark-laing-aab4bb1/
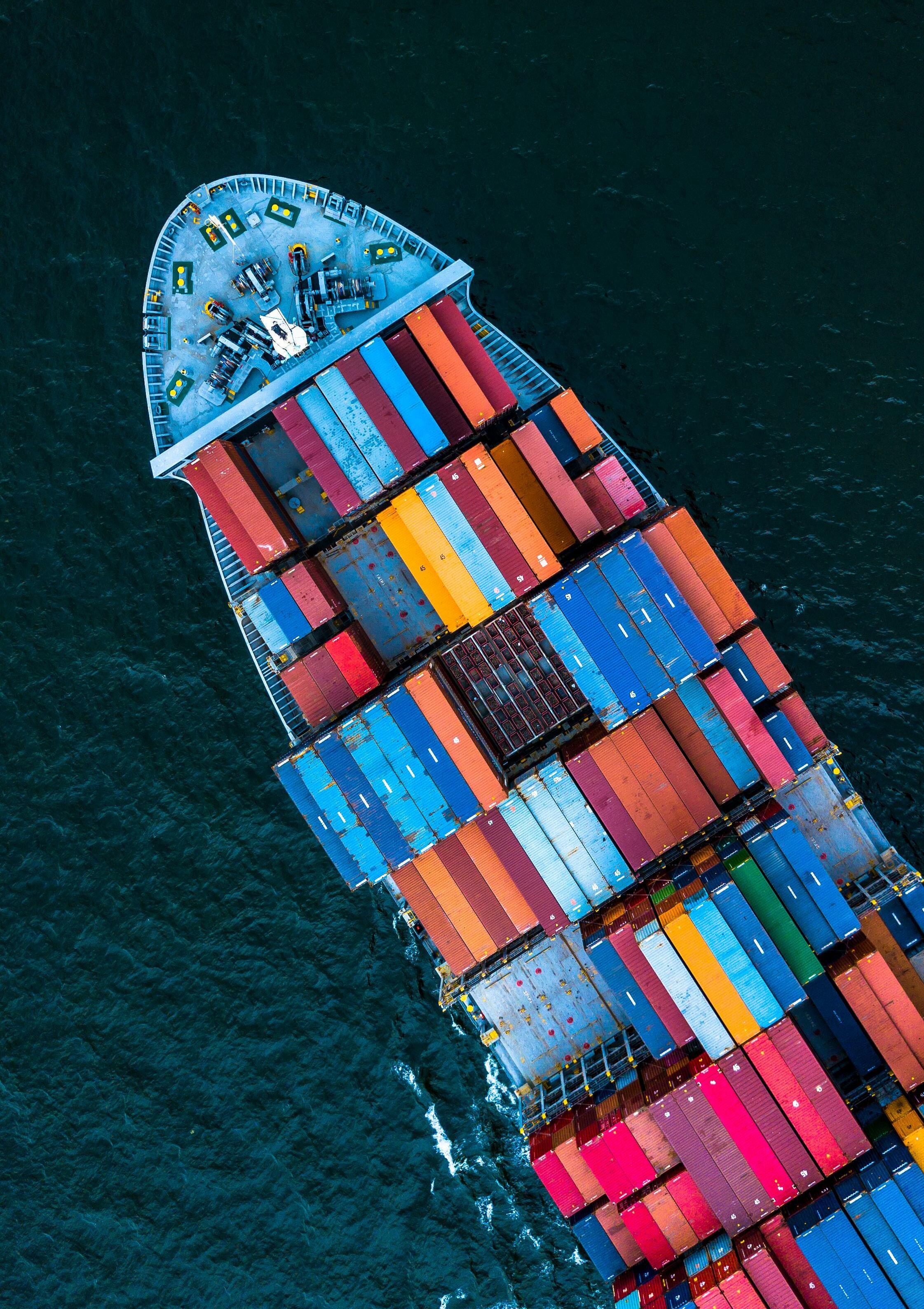
Component Shortages on the Shop Floor
Zac Elliott
Technical Marketing Engineer, Siemens Digital Industries Software
LISTEN TO PODCAST
How are current component shortages affecting electronics manufacturers?
What are manufacturers doing to procure components in such challenging times? Are there risks in getting components from third-party distributors? How are manufacturers mitigating that?
In the worst case if a component is no longer available or the lead times are too long to supply planned production, board designs are being changed to alternate components, and of course there is a lot of work involved in creating a new revision of a product. But there are still a lot of components out on the market, so people are getting really creative to find the components they need.
We see a lot of manufacturers who in the past typically only purchased components directly from the manufacturer or through certified suppliers. This way, they have all the confidence and certificates that they are getting genuine, authentic components. But with lead times like they are on many ICs, manufacturers are starting to loosen their controls and purchase from other distribution channels, like third-party distributors. Yes there is more risk than procuring components directly from the manufacturer. Apart from all of the opportunities for some bad actor to slip counterfeit components in the mix or perhaps pass off forged documentation, there are many opportunities for simple mistakes in the handling of these materials that have sometimes already been sold and then purchased and resold by a distributor. To mitigate the extra risk, manufacturers are doing extra inspection on components from third-party distributors.
Most of this is manual work on a sampling of the components. Someone doublechecks the documentation and some of the components are sent to a lab for destructive inspection and testing.
This type of additional inspection is absolutely necessary, but it still leaves some gaps as it is a manual method based on sampling. New methods are being developed now to use AI image processing to inspect 100% of all components being assembled in the line.https://www.linkedin.com/in/zac-elliott/
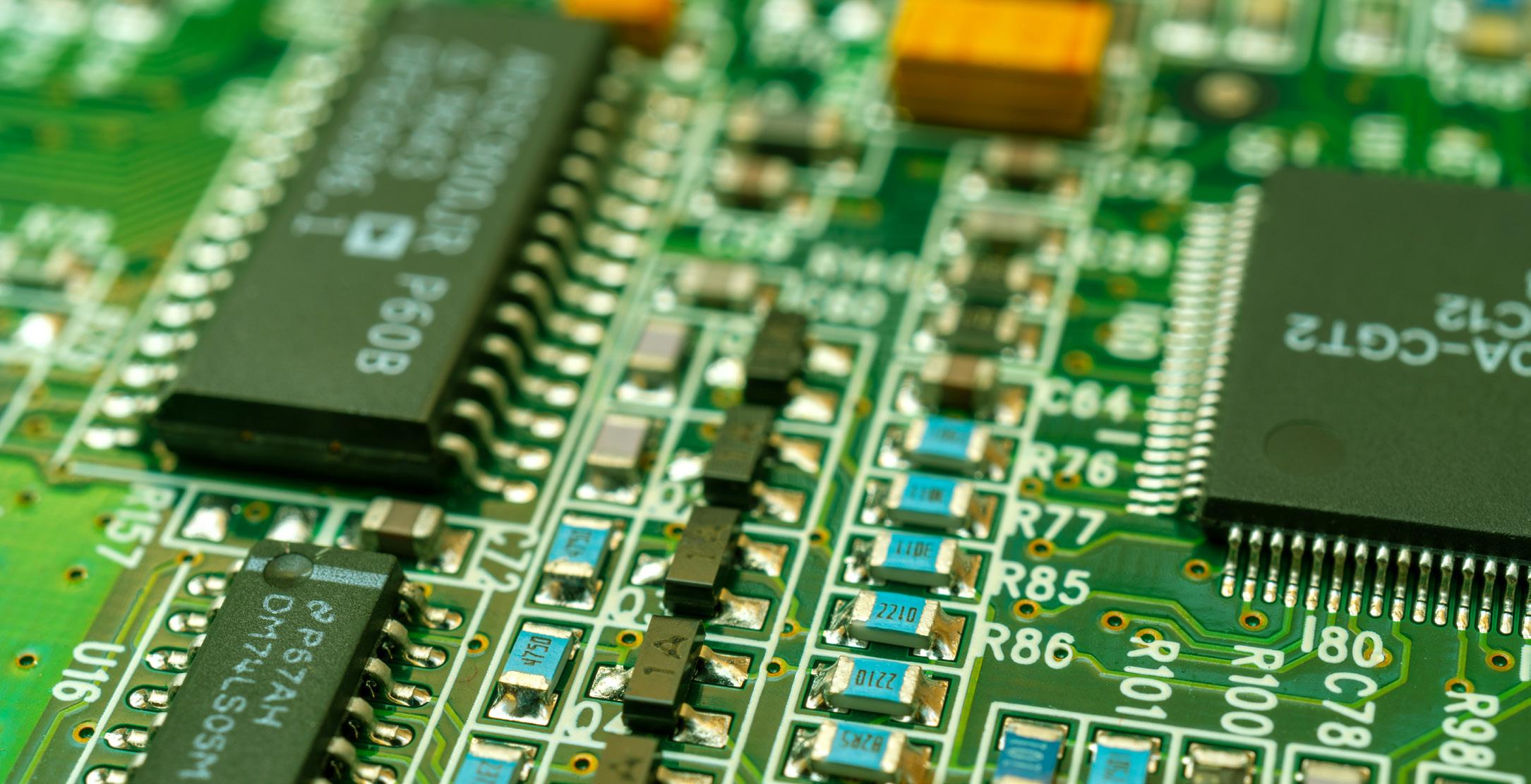
Does this environment create challenges with actual assembly? There are several logistical challenges with component shortages:
How can manufacturers overcome these challenges?
Handling an increase in new product introduction processes to support new product revisions for replacement parts. Scheduling based on inventory availability – handling deliveries coming in the future or building out whatever they can based on current inventory. Managing a growing inventory.
Closed-loop manufacturing is key to handle increased new product introduction. CLM ties together ERP-MES-PLM to support efficiently running many different revisions of a product. Beyond efficiency, CLM is key to maintaining quality in this environment.
Automated production scheduling capabilities are key to managing the production schedule based on inventory availability. You need to be able to dynamically adjust the production schedule to account for deliveries coming in the future, so delaying certain orders because the parts are coming soon. You can also decide to split an order and just consume the available on hand inventory.
