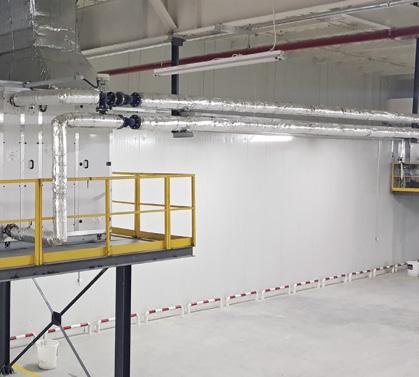
11 minute read
saNitaryWarE
controlling the initial sanitaryware drying process, an increasingly critical stage given the constant development of special and complex pieces. In many factories the majority of production is now spagless, but there are also areas set aside for traditional and high-pressure casting. In spagless casting, water is evacuated from the moulds by means of compressed air and exits in either liquid or gaseous form. In reality it consists not just of saturated air but also of entrained microparticles of ceramic slip. To prevent the water vapour from propagating through the interior space and causing an uncontrolled increase in relative humidity, it must be collected in the vicinity of the moulds by a distributed and well-balanced extraction system. A system like this will only work if it is used in conjunction with the casting shop’s central air conditioning system, not least because it is not possible to extract air from a room without an adequate inflow of the same volume. So while the water vapour is evacuated from the casting benches, the air handling units introduce treated and filtered external air with a lower absolute humidity than the internal air, while keeping the thermodynamic parameters of the process constant. The extraction speeds and pressure control are determined by two different factors: control of the relative humidity values in the casting shop area and vapour formation near the casting benches. During demoulding, the operator manually presses a button located close to the casting bench to activate the localised extraction process and introduce the same volume of external air via the air handling unit.
In the case of Kohler, the extracted air was channelled into la produzione e alle specifiche termo igrometriche richieste. Si presta inoltre al controllo della prima essiccazione dei sanitari, momento sempre più critico vista la continua ricerca di pezzi particolari e sofisticati. In molte fabbriche la maggior parte della produzione è ormai di tipo spagless, ma vi sono anche sale riservate al colaggio tradizionale e in alta pressione. Nel colaggio spagless, l’acqua viene fatta evacuare dagli stampi attraverso l’aria compressa ed esce sia in forma liquida, sia gassosa. Si tratta, in realtà, non solo di aria satura, ma anche di micro-particelle di slip ceramico che migrano con essa. Per evitare che il vapore acqueo si propaghi nell’ambiente, facendo aumentare in modo incontrollato l’umidità relativa, è necessario prelevarlo in prossimità degli stampi stessi con un’aspirazione distribuita e ben bilanciata. Un sistema come questo funziona solo se viene abbinato al condizionamento centralizzato della sala, anche per il fatto che non è possibile estrarre aria da un ambiente senza un’adeguata immissione della stessa quantità. Così, mentre il vapore acqueo viene evacuato dai banchi, le unità di trattamento introducono aria esterna trattata, filtrata e con una umidità assoluta più bassa di quella interna, mantenendo costanti i parametri termodinamici del processo. Il controllo della velocità e della pressione delle estrazioni obbedisce a due logiche distinte: la prima riguarda la regolazione dei valori di umidità relativa nella sala, mentre la seconda è connessa alla formazione di vapore in prossimità dei banchi. Nel momento in cui avviene la sformatura, l’operatore preme un tasto posto vicino al banco che attiva la procedura di estrazione localizzata, unita all’inserimento della stessa quantità di aria esterna dell’unità di trattamento.
Advertisement
Nel caso Kohler, le estrazioni puntuali sono state convoglia-
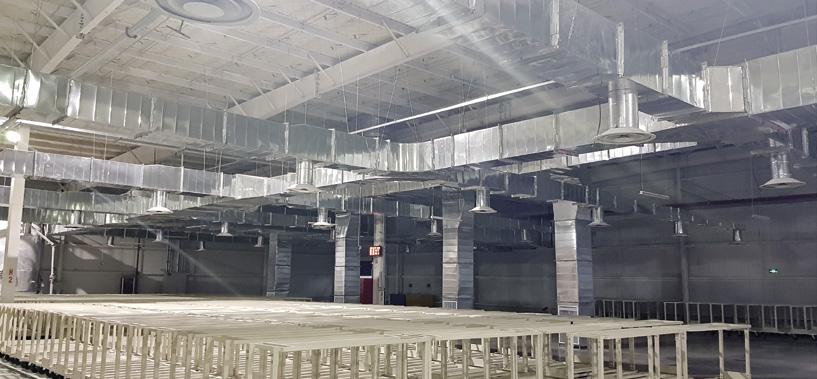
Spot extraction while awaiting assembly of the casting benches Aspirazioni puntuali in attesa di montaggio dei banchi di colaggio
one or a maximum of two channels per room connected to an inverter-driven axial fan with suction pressure feedback. According to the project design, each individual extraction unit is managed by a servocontrolled gate valve which opens when the extraction request button is pressed. The air handling units are all supplied with heat from a superheated water circuit, which ensures perfect temperature control and rapid return to internal conditions during the saturated air intake phase. Each machine can automatically partition the recirculated air (i.e. drawn from inside the room) and introduce drier air from outside, depending on changes in climatic conditions. The machines also operate in free-cooling mode, which means that during the transition from the night-time temperature (during mould recovery) to the daily set point, external air is introduced for rapid cooling and quick set point recovery. The air is introduced via a system of galvanised ducts that extends uniformly throughout the room. A series of diffusers that can be adjusted in terms of both flow direction and flow rate moves the air and pushes it as far as the floor, but at a speed that does not create problems for the freshly demoulded parts. Finally, a high-pressure humidification system allows high and constant set points to be maintained regardless of the external conditions. The humidity is generated in the form of a mist and immediately put back into circulation by the air leaving the diffusers. In each room there is also a storage area, where the cars with the day’s output remain for a certain period of time until they are ready to safely undergo the first part of the contraction process and lose up to 3-4% of their moisture content in a safe and controlled manner.
❱ Traditional casting procedure
In traditional casting shops the moulds are reused, which means that the quantity of water accumulated during the day’s casting operations has to evaporate overnight. The system gradually increases the temperature to 40°C or higher, and this, together with a lower relative humidity (45%) and an airflow directed at the moulds themselves (excluding the cast pieces), allows the mould to return to its initial morning pre-casting weight. The system also continuously filters out ceramic dust from the air (up to 12 times per hour), ensuring a healthier and cleaner workplace for all employees. ✕ te in uno o massimo due canali per sala e connesse ad un ventilatore assiale pilotato da inverter, con retroazione sulla pressione di aspirazione. Il progetto prevede che ogni singola aspirazione sia gestita da serranda servo comandata che si apre quando viene premuto il pulsante di richiesta aspirazione. Le unità di trattamento aria sono tutte termicamente alimentate da un circuito di acqua surriscaldata: questo garantisce un perfetto controllo della temperatura e un ripristino veloce delle condizioni interne durante la fase di aspirazione dell’aria satura. Ciascuna macchina può parzializzare automaticamente l’aria ricircolata (quindi ripresa da interno sala) per far entrare aria esterna più secca, a seconda del fluttuare delle condizioni climatiche. Le macchine lavorano anche in free-cooling: nel passaggio dalla temperatura notturna (durante il recupero degli stampi) al set point giornaliero viene immessa aria esterna per un raffreddamento rapido e un ripristino veloce del set. L’aria viene introdotta attraverso una rete di canali zincati che va a coprire omogeneamente l’intera sala; una serie di diffusori regolabili, sia nella direzione del flusso che nella portata, muove l’aria spingendola fino a terra, ma sempre con una velocità tale da non causare problemi ai pezzi appena sformati. Infine, un sistema di umidificazione in alta pressione permette di mantenere set point elevati e costanti indipendentemente dalle condizioni esterne: l’umidità è generata sotto forma di nebbiolina e subito messa in ricircolo dall’aria in uscita dai diffusori. In ciascuna sala vi è poi un’area dedicata allo stoccaggio, dove i carri con la produzione giornaliera rimangono per un certo periodo affinché possano affrontare la prima parte della contrazione in sicurezza e arrivare a perdere fino al 3-4% della loro umidità in modo controllato e sicuro.
❱ Come si procede nel colaggio tradizionale
Nelle sale adibite al colaggio tradizionale è previsto il recupero degli stampi, vale a dire che la quantità di acqua accumulata durante la colata del giorno deve essere fatta evaporare durante la notte. Le temperature che il sistema incrementa progressivamente fino a raggiungere i 40°C e oltre, unite ad un’umidità relativa più bassa (45%) e ad un flusso d’aria indirizzato sugli stampi stessi (esclusi i pezzi colati), permettono allo stampo di ritornare al peso iniziale del mattino, quello precedente al colaggio. Va inoltre considerato che il sistema filtra continuamente l’aria dalle polveri ceramiche (anche fino a 12 volte all’ora), garantendo un ambiente più sano e pulito a tutti gli operatori. ✕
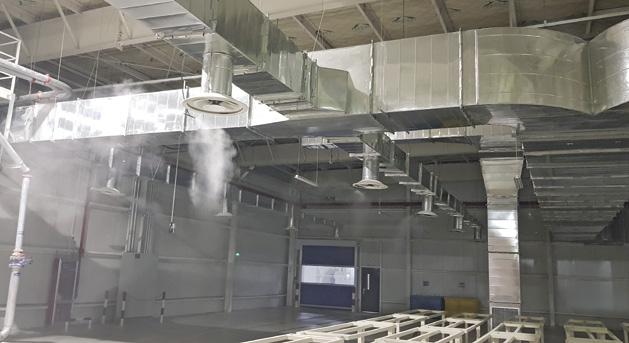

Sanitaryware, the automatic smart inspection solution Sanitari, la scelta automatica “intelligente”
Sacmi Sanitaryware (Imola, Italy)
As part of its journey towards increasingly digitalised smart factories, the ceramic sanitaryware industry requires advanced quality control departments capable of identifying, controlling, classifying and tracking pieces in a precise, objective and repeatable manner. To meet this need, Sacmi has developed a new solution for fully automatic inspection of fired pieces capable of eliminating all variability in terms of response and ensuring far greater precision than even the most experienced and expert human eye. As well as saving time, SACMI D3 Qualitrack ensures the highest levels of efficiency in the management of sorting operations.
❱ How it works
SACMI D3 Qualitrack combines an HD camera system and sophisticated analysis and control software with an anthropomorphic robot that completely eliminates the need for manual piece handling operations The aim of the system is to inspect a product according to a set of instructions, also known as “recipes”, developed offline specifically for the individual products. In the first stage, the system acquires 2D images to check for surface defects, then uses 3D images to check the dimensions and search for deformations. This phase is entirely managed by the robot and is followed Nel suo percorso verso l’implementazione di smart factory sempre più digitalizzate, l’industria del sanitario in ceramica deve poter contare su reparti dedicati al controllo qualità altrettanto evoluti, capaci di identificare, controllare, classificare e tracciare i pezzi in maniera precisa, oggettiva e ripetibile. Per rispondere a questa esigenza, Sacmi ha sviluppato una nuova soluzione per l’ispezione totalmente automatica dei pezzi cotti che, rispetto all’ispezione fatta anche dall’occhio umano più esperto, consente di eliminare ogni tipo di variabilità nella risposta. È SACMI D3 Qualitrack, che, oltre a far risparmiare tempo, garantisce il massimo livello di efficienza nella gestione delle operazioni di scelta.
❱ Come funziona
SACMI D3 Qualitrack associa un sistema di acquisizione con telecamere HD, un sofisticato software di gestione, analisi ed elaborazione dati, e l’utilizzo di un robot antropomorfo che elimina completamente le operazioni manuali di movimentazione dei pezzi. Obiettivo del sistema di visione è di ispezionare un prodotto sulla base di un insieme di istruzioni, dette anche “ricette”, sviluppate off line e dedicate ai singoli prodotti da esaminare. Nella prima fase, il sistema acquisisce immagini 2D per la verifica di eventuali difetti superficiali nel pezzo, successivamente acquisisce immagini 3D per i controlli dimensionali e la verifi-

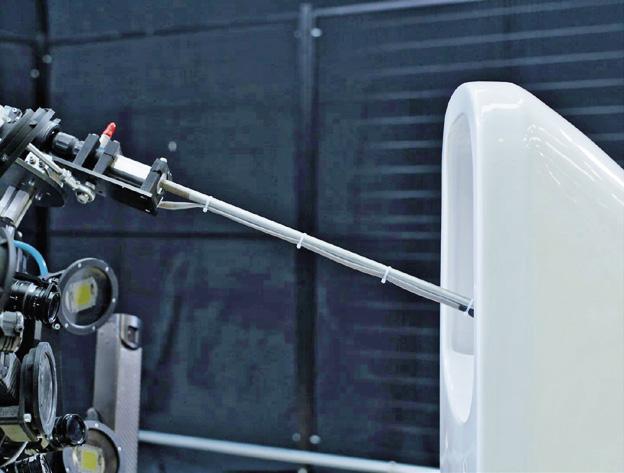
by software analysis, during which the platform checks for any ca di presenza di eventuali de- ni, eventuali difetti superficiali). potential deviation of the parameters from the pre-set recipe, formazioni. Ad ogni pezzo viene così assegenerating an inspection report via an intuitive user-friendly A questa fase, gestita intera- gnata una vera e propria ideninterface. Each report can also be viewed remotely from any mente dal robot, segue l’analisi tità digitale che, associata al device connected to the company network, software, du- codice a barre, consente una smartphone, PC or tablet. rante la qua- classificazione oggettiva del Along with the automation and total repeat- le la piatta- prodotto e la possibilità di agiability of the operations, the main strength forma verifi- re in retroazione sul processo in of Qualitrack is its ability to generate re- ca ogni po- modo più rapido ed efficace. al-time data on all key quality parameters ENDLESS INNOVATION SINCE 1919 tenziale sco(size, deformation, surface defects). This al- stamento dei Oggettivizzare e storicizzare i lows each piece to be assigned a digital parametri dati è il grande vantaggio delidentity, which together with the bar code allows for objective dalla ricetta preimpostata, ge- la proposta, che Sacmi offre inclassification of the product and the possibility of making ad- nerando un report di ispezione sieme ad una personalizzaziojustments to the process more quickly and effectively. tramite intuitiva interfaccia user ne completa delle movimentafriendly. Ogni report è visiona- zioni sia a monte sia a valle del The biggest advantage of this solution is its ability to obtain bile anche da remoto, da qual- sistema. Con Qualitrack, Sacand store objective data, as well as the option of complete- siasi dispositivo connesso alla mi muove un altro passo verso ly customising the handling operations both upstream and rete aziendale, smartphone, pc la “fabbrica a luci spente” nel downstream of the system. o tablet. Oltre all’automazione mondo Sanitaryware. La prosWith Qualitrack, Sacmi takes another step towards “lights-out delle operazioni e alla loro to- sima sfida è l’ulteriore automamanufacturing” in the sanitaryware industry. The next chal- tale ripetibilità, il punto di for- zione di alcuni controlli, quali lo lenge is to further automate some of the checks, such as cool- za di Qualitrack è la capacità di sfilo e la prova del vuoto, e la ing cracks and vacuum testing, and to extend Qualitrack to generare dati in tempo reale su possibile estensione del Qualithe upstream stages of casting and finishing. tutti i parametri di qualità rile- track alle fasi a monte, ossia il ✕ vanti (dimensione, deformazio- colaggio e la finitura. ✕

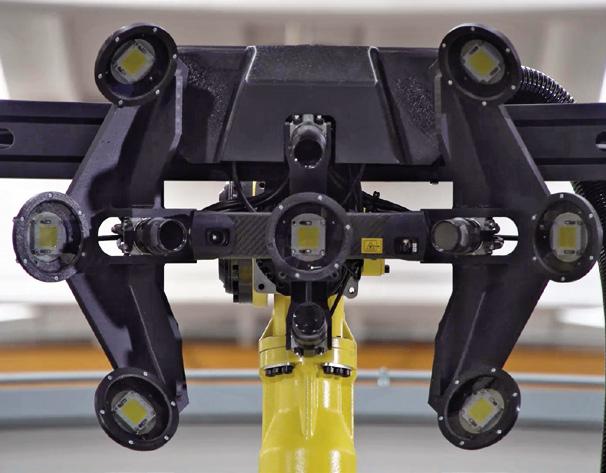
