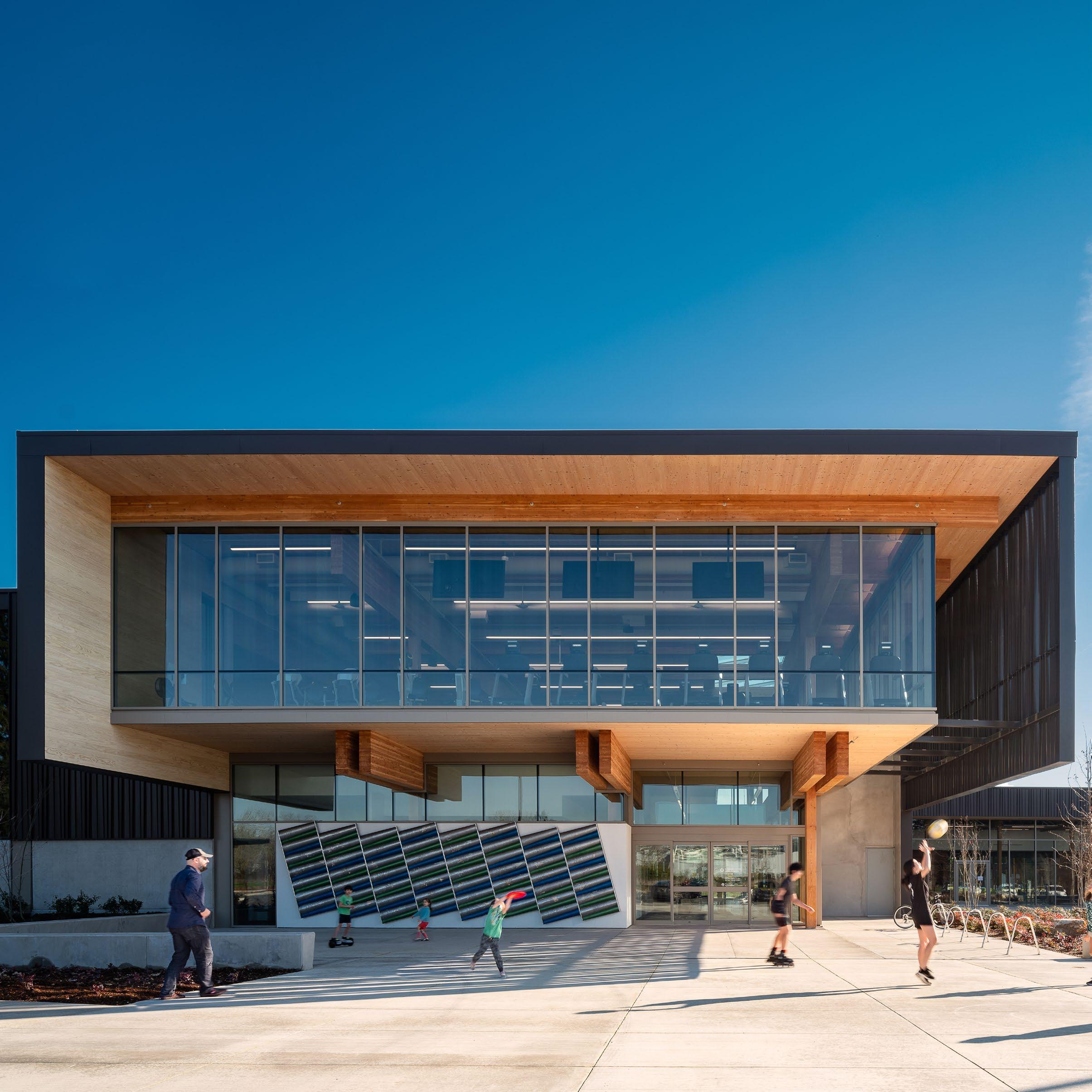
HOLISTIC MASS TIMBER SYSTEMS
FROM START TO FINISH
MISSION
TO ACCELERATE THE MAINSTREAM ADOPTION OF MASS TIMBER TO BENEFIT THE PLANET AND ITS PEOPLE.
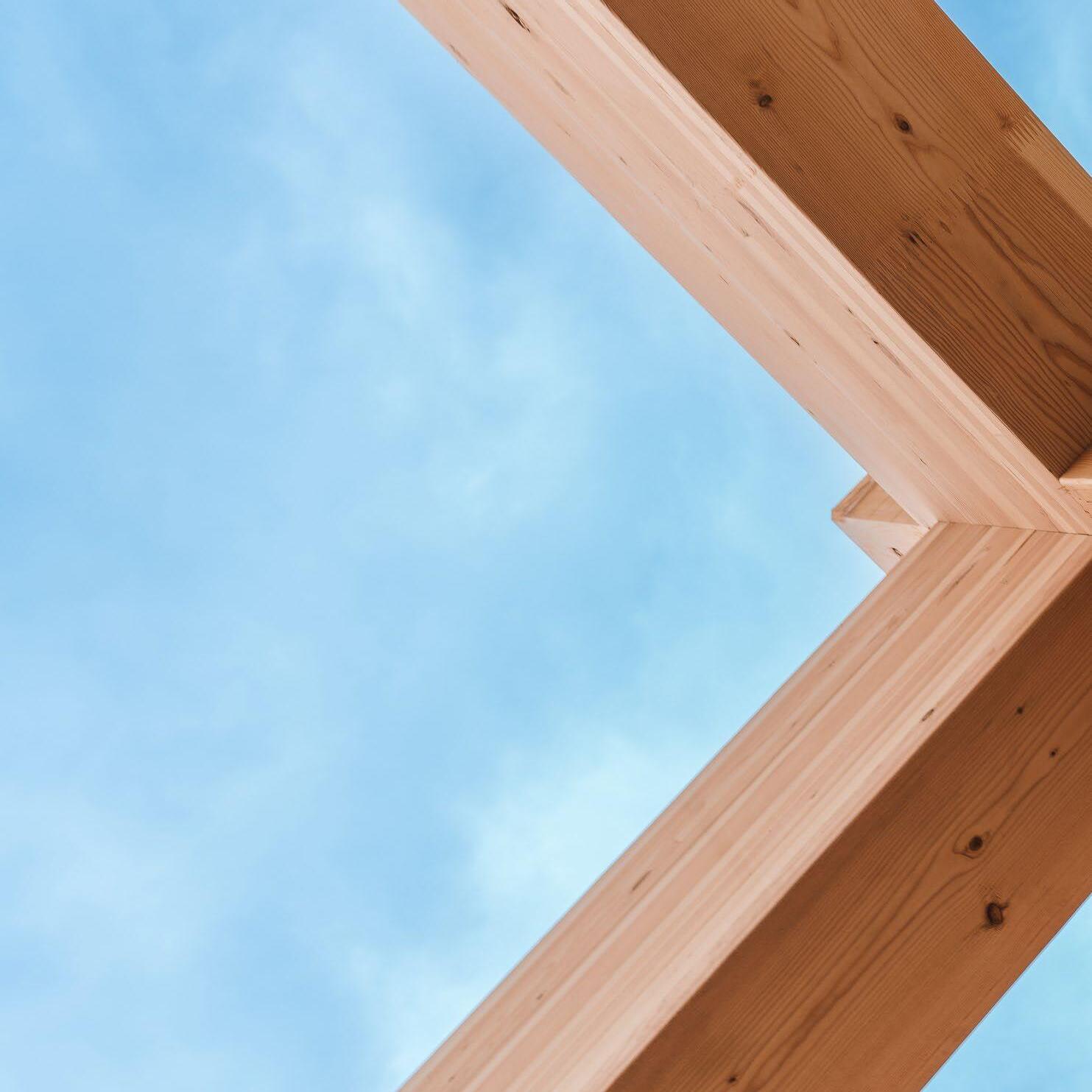
Since 2017, Timberlab has delivered over 60 mass timber projects across the U.S.
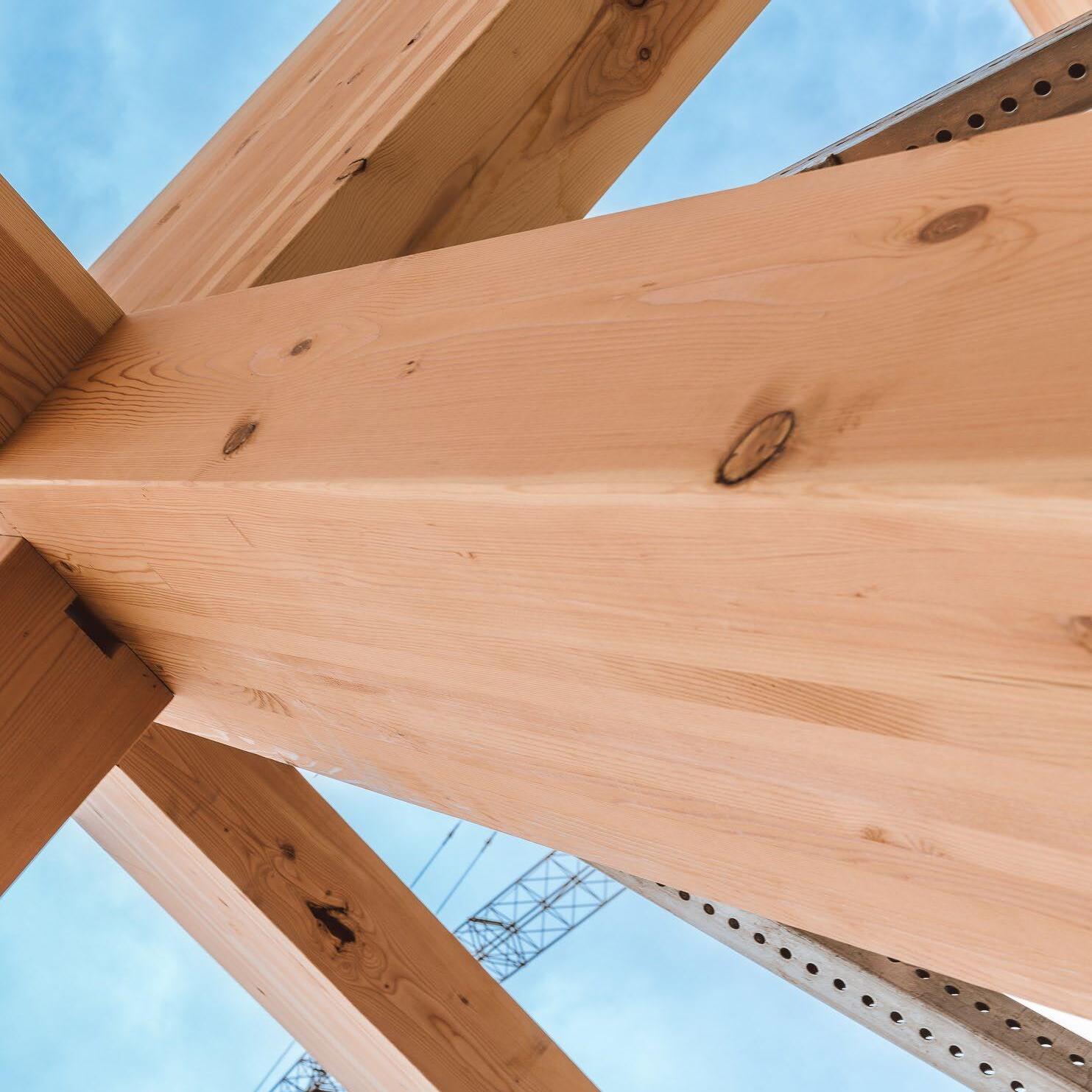
FROM START TO FINISH
MISSION
Since 2017, Timberlab has delivered over 60 mass timber projects across the U.S.
Timberlab’s mission is to advance the mainstream adoption of mass timber construction to benefit the planet and its people. Our team of dedicated innovators has delivered cutting-edge mass timber projects across the U.S. As a vertically integrated organization, we offer a wide array of mass timber services to ensure a project is successful at every step, from material production, to fabrication, to on-site assembly and installation. We are passionate about optimizing timber’s natural strength and durability to build a sustainable, low-carbon future.
Originally Swinerton Mass Timber, Timberlab was launched in 2021 to meet the growing demands of the sustainable construction sector. As a team of architects, engineers, and builders, we see every project from multiple vantage points, providing solutions that result in beautiful mass timber structures. With 5 mass timber facilities across the United States, our team is at the forefront of this new building methodology and is on track to be the leading full-service provider of mass timber.
MASS TIMBER SERVICES
• MANUFACTURING • PRECONSTRUCTION • TIMBER ENGINEERING • DIGITAL CONSTRUCTION
• CUSTOM FABRICATION
• INSTALLATION
Take your project to new heights with mass timber—a smart, resilient, and renewable alternative to concrete and steel construction.
Secure occupancy and long-term leases with speed. Prefabricated timber buildings significantly reduce construction time so you can get your next building on the market faster.
Providing a better end-user experience pays dividends. Natural materials improve health and wellness, increase productivity, and reduce stress.
Increase density while minimizing environmental impact. Timber offsets emissions associated with energy-intensive construction and stores carbon in the structure.
With prefabrication, much of the “construction” process takes place off-site in controlled environments. This allows material to be shipped and installed upon arrival. The result is a more efficient process with less waste.
Our Portland, Oregon facility provides custom fabrication services for glulam, with state-of-the-art CNC machining, finishing, and connection hardware installation to provide a holistic kit of parts.
Timberlab's CLT manufacturing plant in Millersburg, Oregon will serve the U.S. market with high-quality CLT panels. The manufacturing facility will be highly automated and climate controlled, ensuring a consistent product. This facility will lead North American CLT manufacturing both with the volume of production and process control to ensure the highest level of quality is achieved. The facility is on a rail spur, enabling rail transport of products across the country, resulting in lower shipping costs and reduced embodied carbon related to transportation emissions.
In operation since 1962 (acquired by Timberlab in 2024), the Drain and Swisshome facilities produce the highest quality of custom glulam in the country. Utilizing Douglas Fir, Southern Yellow Pine, and Alaskan Yellow Cedar, these operations have an annual capacity of 20 million board feet.
Our Greenville, South Carolina facility provides custom fabrication services for glulam, with state-of-the-art CNC machining, hand fabrication, and connection hardware installation. The Greenville facility fabricates material from our Oregon manufacturing facilities and other manufacturers. The Greenville facility is near a rail spur, able to receive manufactured products by rail transport and deliver fully fabricated products by rail closer to your project site.
Timberlab’s service-oriented Preconstruction and Timber Engineering teams are here to support structural engineers and project teams with constructability-driven design. We engage as a partner, seeking first to understand the specific needs of the team and then proposing services that we believe will add significant value by reducing cost, accelerating schedule, or increasing the viability of unprecedented innovation.
Our Digital Construction team evolves a mass timber design into fabrication-level information used to prefabricate a kit-of-parts off-site. With deep expertise in the digital construction process, we translate intricate designs into precise fabrication instructions, unlocking new levels of efficiency, accuracy, and customization. We bridge the gap between architectural vision and physical structure, ensuring that every timber component is precisely crafted to fit seamlessly in the construction process.
Timberlab reviews the superstructure for cost, procurement strategy, fabrication, and constructability, offering solutions for efficient design.
When engineering a complete timber frame, or a more limited scope of timber connections, our timber engineering team works directly with the design team and collaborates internally with our estimators, digital construction engineers, CNC operators, and superintendents to arrive at the best solution.
We produce drawings and calculations for installation of mass timber systems. Our understanding of the construction process and timber systems allow us to produce efficient installation sequences.
Linking the design to construction, we build a model to millimeter precision that accounts for manufacturing and installation tolerances for the timber and other materials with which the timber interacts. This process raises awareness of complex construction interactions in preparation for the fabrication of timber components, such as opposing structural elements with varying tolerances, architectural finishes, devices and equipment, and installation requirements.
To harness the full prefabrication potential of mass timber, we seek to integrate all penetrations for mechanical, electrical, plumbing, and fire sprinkler systems, and work with trade partners to ensure their information is integrated into our model. Why? Because a CNC machine can do in one minute what it would take a carpenter 1 hour to do on-site, without the safety risk.
Timberlab currently provides some of the best quality glulam in the U.S. construction market. With facilities based in the heart of Oregon’s timber basket, our operations ensure that your projects are using the highest-grade material in the country.
In 2024, our team launched manufacturing operations with ambitions to grow the market supply and support regional timber economies. Offering multiple species types, we produce glulam that meets the most stringent performance and aesthetic standards— making them ideal for a wide range of structural and architectural applications.
TIMBER SPECIES AVAILABLE:
Learn more about our full range of glulam products at: Timberlab.com/products/glulam
Smart decisions before we arrive on site result in a smooth, efficient installation process. Our installation team brings projects to life through collaboration with architects, engineers, and other building specialists by providing construction schedules, managing budgets, and ensuring job site safety.
Timberlab is proud to be born from Swinerton Builders, a renowned general contractor with an impressive legacy of over 130 years in the construction industry. As a result of this strong foundation, we bring a wealth of experience and expertise to our timber installation projects. Being one of the early adopters of mass timber as a building material, Timberlab has been at the forefront of the industry’s evolution. Our extensive experience with mass timber construction allows us to deliver projects on schedule while never compromising on quality and safety.
Hillsboro, OR
First Tech Credit Union, a five-story 156,000-squarefoot office headquarters in Hillsboro, Oregon, was our team’s first mass timber project—delivered by Swinerton Builders—and for a while, it was the largest mass timber building in America. The building’s design prioritizes natural light while also providing ample open space to benefit health and well-being.
Portland, ME
Serving as the hub for the university’s Portland Campus, the brand new, three-story Career and Student Success Center provides space for students, faculty, employers, and the community. The 42,000-squarefoot building is a hybrid steel and timber structure, of which 17,000 square feet is mass timber.
Milwaukee, WI
At 284 feet, Ascent lives up to its name. The 25-story luxury apartment building is the world’s tallest hybrid mass timber structure, with 19 stories and 273,000 square feet of mass timber providing 260 residential units to the Milwaukee market. Timberlab was brought on as the trade partner, managing the procurement and delivery of the building’s mass timber.
Portland, OR
The centerpiece of the PDX Terminal Core Redevelopment is a stunning, 400,000-square-foot timber roof that highlights the region’s innovation in mass timber. Comprised of approximately 3.3 million board feet Douglas Fir, the roof features over 400 80-foot glulam arches and mass plywood panels for the roof diaphragm and skylight curbs.
Wilmington, NC
Live Oak Bank Building 4 accommodates 400 employees in a four-story, 64,000-square-foot addition to its rapidly growing corporate campus. Aside from the steel envelope, the vast majority of the Live Oak Bank project utilizes a mass timber structural system and features regionally-sourced Southern Yellow Pine.
Seattle, WA
This 275,000-square-foot mixed-use project spans five stories, with 158,000 square feet of mass timber office and lab-ready space. The mass timber system has a lighter footprint than other structural alternatives; a Life Cycle Assessment of the embodied carbon in the timber will be performed to understand its impact compared to more conventional construction types.
LET’S BUILD A MORE SUSTAINABLE FUTURE