Heartwood Apartments
MASS TIMBER HOUSING STRUCTURE | SEATTLE, WA
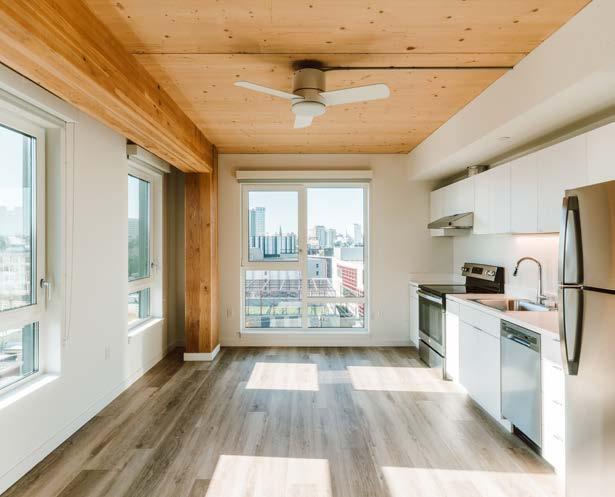
Heartwood—the first mid-rise, middle-income mass timber housing structure in the United States—is setting a new precedent for mass timber construction. In addition to being the first mass timber building of its height and tier of affordability in the United States, Heartwood also boasts several other important achievements:
- First US mass timber building permitted as-of-right under the 2021 International Building Codes New Tall Wood Building Type IV-C
- First US all-timber 2-hour fire-rated beam-to-column-to-panel connection
- First tall wood building permitted by the City of Seattle
- Tallest mass timber building in the State of Washington
- Tied for the tallest all wood building on the west coast
Heartwood’s design by atelierjones, mass timber by Timberlab, engineering by DCI, and general contracting by Swinerton strictly adhered to the new codes for Type IV-C construction, making the project a landmark for the design-build team and for mass timber construction in the United States. Heartwood offers a new typology for residential projects validating mass timber as a replicable option for mid-rise housing development.
Project Introduction
Enabling Mass Timber Construction
Designing by the Book
Building Heartwood
Results/Impact
Heartwood is a 70,000-square-foot, eight-story mass timber building in the dense urban core of Seattle, Washington. The project is owned by Community Roots Housing (CRH), one of Seattle’s biggest champions of affordable and middle-income housing. As a nonprofit, CRH actively manages nearly 50 properties that provide affordable and middle-income residences for over 2,000 people in central Seattle.
CRH recognized that the middle-income housing market in the city’s expensive urban core was also deeply underserved- with the average median rent in the area north of $2,300 per month - and so they sought to partner with developer Skipstone to address this need. Heartwood was designed to serve CRH’s mission of helping everyone put down roots and thrive—including teachers, public safety workers, nonprofit workers, and others whose income is between 60 to 100% of the Average Median Income (AMI).
With Heartwood’s grand opening in 2023, 126 new workforce housing apartments will be available for rent to help address Seattle’s housing crisis. The building uses cross-laminated timber (CLT) with exposed glulam columns and beams throughout the 113 studio and 13 one-bedroom units ranging from roughly 300 to 500 square feet, and features a 2,800-square-foot outdoor courtyard, bike parking, retail, laundry, and multiple bike storage rooms.
Seattle finds itself with a “missing middle” on two fronts: building height and affordability. Due to previous building codes, the city’s building heights tend to cluster either in five-story buildings over two-story podiums—for seven stories total—or true high-rises of twelve stories or more, and little in between. The city also faces an urgent need to create middle-income housing which has not been met through traditional tax credit financing or market forces. Heartwood was designed to address both challenges:
1.
2.
Helping densify the urban landscape and maximize lot size and zoning through a mid-rise building between six and ten stories.
Adding middle-income housing for healthcare workers, teachers, nonprofit employees, and other households earning between 60-100% of the Annual Median Income (AMI), and yielding higher returns for investors without requiring public subsidies.
Heartwood implements the updates to the 2021 IBC, which enable the construction of three new types of Type IV buildings—Type IV-A, IV-B, and IV-C— and which allow for a greater height of mass timber or noncombustible structures. The codes also define specific exposure levels of mass timber elements within those buildings and provide additional fire-resistance ratings (FRR). All Type IV buildings are based on the previous Heavy Timber construction type (now called Type IV-HT).
Type IV-A allows for fully encapsulated structures of up to 270 ft (18 stories) and a 3-hour FRR for columns, and 2-hour FRR for beams and floors. Type IV-B currently allows for partially encapsulated structures of up to 180 ft (12 stories) and a 2-hour FRR, though as of Summer 2023 there is an amendment under review to allow for full exposure of mass timber elements.
Type IV-C allows for fully exposed mass timber structures of up to 85 feet (8 stories) with a 2-hour FRR.
Type IV-C construction is similar to Type IV-HT in the allowable height of 85 feet, but is greater in the number of allowable stories, with Type IV-C allowed eight stories and Type IV-HT allowed six. The difference in allowable stories stems from the overall greater fire-resistance rating of two hours for Type IV-C compared to the typical 1-hour FRR for Heavy Timber.
In 2021, principal Susan Jones of atelierjones set out to build the first mass timber housing project in the United States using the newly adopted 2021 Tall Wood Building codes. Jones was instrumental in authoring the codes, helping them gain adoption into the 2021 IBC, and emphasizing the value of an additional floor of units as part of the codes. Early in the process her team wrote and won a United States Forest Service Wood Innovations Grant which kicked off the study of a new 8 story building in Seattle.
With the newly adopted Type IV-C construction type, developers can build eight stories of apartments (as opposed to the typical five-over-two model) at a maximum height of 85 feet, without a concrete podium, and include the additional benefit of a fully-exposed, beautiful, natural mass timber structure.
Heartwood was designed to follow the 2021 IBC exactly, showcasing the viability of building an eight-story housing project using mass timber. By following the prescriptive code provisions for Type IV-C construction, the design-build team was able to acquire permits without a single variance request. Swinerton, atelierjones, DCI, and Timberlab worked closely with the jurisdiction to clarify any areas of the code where the intent was not clear in order to ensure that the codes were as straightforward as possible and reflected in the building’s design.
Jeremy Wilkening, Vice President of Real Estate Development for Community Roots Housing says,
“The structural review and the review process for a CLT building was a challenge, but we got through it by hiring the experts—Swinerton [and Timberlab] have extensive experience in mass timber and Susan Jones is the premiere expert architect in the city of Seattle on CLT projects.”
With support from a $250,000 U.S. Forest Service Wood Innovations Grant, the project team was able to validate the financial viability of Type IV-C multifamily housing in a light-wood, 5-over-2 structure, and an 8-story, fully mass timber structure. The grant funded mockups of two designs—built in parallel—with unit layouts designed around an optimal structural framing plan. The study generated real cost and schedule data to support the comparison between light-wood and mass timber structures.
Developer A. P. Hurd of Skipstone remarks,
“One of the things that made such a big difference on this project was having access to the Wood Innovation Grant. Not every project would ever need this grant. However, it gave us a clear understanding of what we could achieve on Heartwood and provided a blueprint for others to replicate workforce housing units in their cities - and out of beautiful mass timber elements.”
A primary test of Heartwood’s viability was achieving as-of-right status, where project design and permitting occur in parallel, without the imposition of special conditions or discretionary approval from a local zoning commission. Heartwood was the first building in the US to be permitted “as-of-right” under the 2021 IBC codes for Type IV-C construction.
The design-build team set an aggressive goal to submit the building permit in six months and receive the Master Use Permit (MUP) 12 months—typically an 18-month process. Obtaining as-of-right status greatly accelerated both the design and land use entitlement, since these processes could occur in parallel, rather than sequentially. The City of Seattle approved the land use and MUP on December 4, 2020—under the 12-month goal. Achieving as-of right-status:
• Correct zoning requirements = No land use variations or exceptions filed
• Height and square footage did not exceed zone’s structural limitations = no design review was required
• Fire rating?
Heartwood is the first mass timber workforce housing project ever to be built with or without public subsidies. CRH and Skipstone explored several options for developing financially responsible housing without relying on public funds, and settled on a pro forma that offers investors an advantageous return, in an Opportunity Zone that provides tax advantages, all while maintaining workforce housing status.
CRH secured a precise GMP and financing at an opportune moment for interest rates in Fall 2020, maximizing yearly net returns on the original project budget. Financing also enabled Swinerton and Timberlab to create the mass timber deposits needed to break ground on time in Spring 2021 for a more efficient construction start.
Due to the highly collaborative nature of Heartwood its inception, several processes were able to run in parallel to optimize efficiency in the schedule. As the designbuild team completed the design drawings, the land use process occurred in tandem. In addition, the project was soon permit-ready very soon after the design was complete, which enabled the project to be financed and commenced in an efficient way.
When considering the aesthetics of Heartwood, Design Principal Susan Jones of atelierjones says, “With mass timber, we have an opportunity to decide what kind of cities we want to have. Heartwood is emblematic of the cities of the future. I imagine people living in these beautiful, habitable, carbonsequestering structures. We want every resident to have that access and connection to nature—to see and smell the elements of the forests from the comfort of their tight, urban lifestyle.”
The unit layout was designed around an optimal structural framing plan, where demising walls align with the beams and columns. To showcase as much of the beautiful, biophilic mass timber as possible, the design hides or encases nearly all mechanical elements. Each unit features exposed CLT ceilings with minimal soffits for ventilation and sprinklers, and one bay of exposed glulam columns and beams. Strong BIM coordination between atelierjones, Timberlab, and Swinerton refined the building’s design to maximize visibility of the mass timber.
Situated on a 23,000-square-foot former surface parking lot, Heartwood required complex site logistics to maintain a clean, quiet construction site in a dense urban neighborhood. The project was able to achieve 86 feet of building height due to the installation benefits of mass timber—such as the lightness of the structure compared with foundation—whereas a standard concrete and structure would not have been achieved given the site’s constraints: size, location at the end of a block, historic trees, and city restrictions.
William Silva, Director of Preconstruction at Swinerton Builders, says,
“The Heartwood building site is an exemplary example of the benefits of mass timber construction. We were able to erect this structure quickly, efficiently, and quietly—all with a minimal crew. Had we taken a traditional approach on this site, we would have had three times the workforce, and it would have taken 20 percent longer than what we were able to achieve through mass timber.”
Swinerton and Timberlab were able to work around logistics constraints in the following ways:
• Prefabrication of CLT panels streamlined the delivery process despite limited and narrow street access, minimizing the number of trucks needing to access the site.
• Mass timber made installation quieter, minimizing disruptions to neighbors— some in an apartment building 12 feet from the site. Pre-drilled holes and prefabricated mass timber panels require much less machinery to install, thereby reducing noise.
• Timberlab manufactured beams of 8’6” (rather than the typical 10’) in order to conform with Seattle’s curfew on oversize load delivery. The shorter beam length could be delivered during working hours.
• Highly coordinated logistics were required to pick up and set down CLT panels while avoiding power lines on two sides of the site. CLT panels were picked in bundles, placed on the deck, unbundled, and then spread where needed. The process reduced risk to pedestrians and public vehicles from a single pick, made it easier for workers to unwrap and inspect pieces on a stable deck, and allowed for easy relocation of the panels. This process will become the standard method, increasing efficiency in materials inspection and delivery, particularly on tight sites.
• The site featured several 3 historic trees which required preservation. Mass timber elements could be maneuvered more easily around these trees than traditional construction materials or equipment.
Type IV-C buildings require a 2-hour fire rating for the primary structural frame. This includes the glulam columns and beams, CLT panels, and all glulam connections. In an effort to minimize the amount of greenhouse gas-emitting concrete and steel, the Heartwood project team worked with DCI Engineers to create a fully wood-to-wood assembly to connect the beams, columns, and CLT panels. The impact of these assemblies were even greater than the team anticipated, saving the financial and environmental costs of steel as well as the time associated with the procurement, fabrication, and installation.
The beam-to-column connection is a mortise-andtenon joint fabricated on Timberlab’s Biesse computer numerical control machine to 1/8” tolerances. During the design phase, Timberlab fabricated and built a full-scale mock-up of the connection to validate that the detail submitted for permit was machinable and constructible. The mock-up offered the team the opportunity to refine the tolerances of the connection and provided cost certainty in the design.
Key to the development of this all-wood connection is Adam Jongeward of DCI Engineers, who describes the innovation as follows:
“The connection…really sets [this project] apart. We started with the idea that steel is expensive to fabricate and install. Steel is also hard to fire rate, especially in a two-hour application. Stripping out all the steel elements was really important to us on Heartwood. We ended up with a mortise and tenon joint, a design that goes back hundreds of years. We wanted to modernize this connection in the speed at which it could be fabricated and constructed on-site. Utilizing the intumescent fire tape on the joint allowed for a clean, all-wood aesthetic while still upholding that two-hour fire rating”
To increase fire resistance, the top of columns and the ends of beams are routed to receive an intumescent fire tape that provides floor-to-floor fire separation at the joint. Partnering with Tenmat, Timberlab tested the intumescent tape to ensure it would meet the fire protection requirements of construction. Results validated that the fire tape is a clean and high-quality approach to fireproofing that avoids labor-intensive and often messy field application of fire caulking and sealants.
Mass timber significantly reduces carbon sequestration values by allowing for a disassembly process that reuses more materials than steel and concrete structures. By eliminating steel connectors, reducing the number of bolts and bolt holes, and utilizing layers of slip sheet and gypcrete for sound attenuation on top of the CLT in place of the traditional composite concrete slab, the project can be more easily disassembled at the end of its life cycle, reducing wood fiber waste, and allowing for immediate reuse of the CLT.
Swinerton and CRH did not compromise on reducing Heartwood’s environmental impact amidst affordability. The building features a high-performing (stick built fiber cement) exterior, an R49 roof, triple glazed windows, continuous insulation under the slab-on grade, Energy-star rated appliances, and a domestic hot water system
Timberlab, Swinerton, and atelierjones have delivered a replicable, proof of concept for a Type IV-C building under the 2021 IBC. Community Roots Housing’s Heartwood Apartment Building begins to address Seattle’s “missing middle”—both in building height and affordability—and brings a beautiful design with natural materials into reach for middle-income urban residents.
• Received Master Use Permit in 12 months due to as-of-right status;
• >6 month reduction in time needed to obtain entitlements and building permits
• Design maximized unit numbers and visibility of mass timber throughout in Type IV-C construction;
• Private funding with a significant pro forma for investors;
• Boosted cost efficiency for CRH in maintenance, staffing efficiencies, and additional storage/amenities;
• Innovation in fire resistance ratings, including an all-wood connection for columns and beams;
• 4-Star Green Built Certified
Early involvement and collaboration from all parties contributed to Heartwood’s success and accelerated delivery.
Owner | Community Roots Housing
Developer | SkipStone
Development Manager and Owner’s Representative | DA LI
General Contractor | Swinerton
Architect | atelierjones, LLC
Mass Timber Trade Partner and Fabricator | Timberlab
Glulam Supplier | DR Johnson
CLT Supplier | Kalesnikoff
Mass Plywood Panel Supplier (stairs) | Freres
Structural and Civil Engineer | DCI Engineers
Electrical | Bergelectric
Fire and Envelope | WJE
Mechanical and Plumbing | HV Engineering