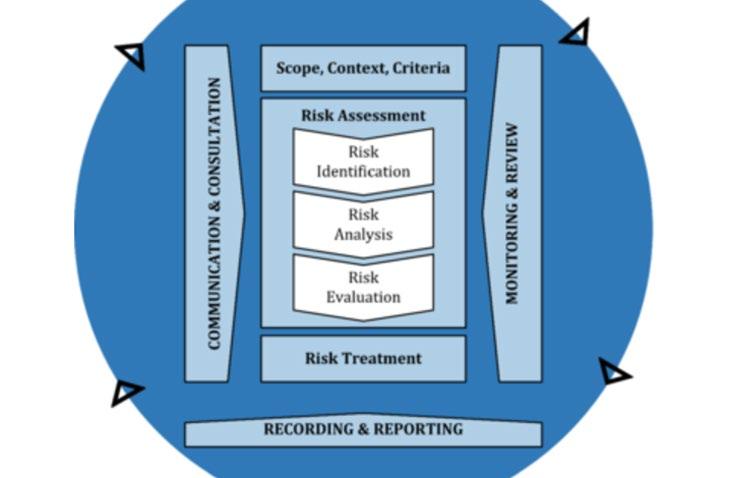
4 minute read
Figure 41: Risk Management Process (ISO 31000, 2018
Figure 41: Risk Management Process (ISO 31000, 2018)
8.1.2 Roles and Responsibilities
Risk Manager: Develop a general risk management process for the organization; Establish the level of risk the company are willing to take and figure out the proper contingency level; plan and distribute the risk budget; conduct policy and compliance audits; develop response measures; compile risk reports.
Risk Analyst: Perform risk analysis and evaluation through qualitative and quantitative methods; analyze root causes of risks to assist the development of
response measures.
Project Manager: Authorize the implementation of risk response plans; assist the risk manager by coordinating team members to take corresponding actions for risks; make decisions on the priority of risks; review risk reports.
Design Manager: Minimize design risks, ensure the structural stability and compliance of the design.
Site Engineer & Site Manager: Minimize construction risks on site, especially from the perspective of quality.
Site Foreman: Minimize risks caused by improper handling of materials or improper operation of equipment; identify and report potential safety hazards to site manager or project manager.
WHS Manager: manage site inspections; organize WHS trainings; hold regular safety meetings.
Contract Administrator & Procurement Manager: Manage contractual risks and procurement risks; ensure smooth cooperation with suppliers and subcontractors.
8.1.3 Risk Management Budget and Timing
According to previous cost management section, a total budget of 382.8 million is assigned for the risk management, which accounts for 15% of the cost baseline. It is a ratio higher than the average construction contingency (5-10%) because the Sydney Metro is an extremely largescale infrastructure project which will last for many years. And a large share of the total risk budget is expected to be allocatedto work packages in the planning and the construction phases as they are the stages in which most risks happen. In the section of Quantitative Risk Analysis, the method used for determining the contingency for each risk will be discussed in detail.
In fact, the risk management is carried on throughout the entire project life cycle. However, the frequency of different departments or management roles of reviewing risks and taking responsive actions can be different. Please refer to the risk monitoring and controlling section and future documents for more information.
8.2 Risk Identification
Basically, risk identification entails a set of processes to ensure that the list of identified risks is comprehensive, and it is necessary to understand what source of the risk is before risk identification and that could be the root reason causing the risk. This RMP will conduct risk identification by going through a series of qualitative method such as Checklist, Failure Mode, Effect Analysis (FMEA), Ishikawa (fishbone method). In this process, risk manager, project manager and integrated project team are asked to identify project risks in their area of responsibility.
8.2.1 Tools and Techniques Applied
• Failure Mode and Effect Analysis (FMEA)
According to Juran (2018), Failure Mode, Effect Analysis gives insight into the reliability of systems by looking at the components and their comparative reliabilities. In this RMP of Sydney Metro, FEMA as a systematic method is to identify possible failures that pose the risk for a process, product, and service of different project work packages.
As a tool, FEMA is one of the most effective low-risk techniques for predicting risks and identifying the most cost-effective solutions for preventing problems. Furthermore, the analysis is a bottom-up approach, working from the components to the whole system, which assists manager to recognise and track risk items of each activity. It is important to document and assess all changes that occur which affect quality and reliability. There is a FEMA template applied for risk identification (shown in Appendix D).
A sample Failure Mode and Effect Analysis form for identifying risk applied in Sydney Metro project is shown below:
System: Underground services of rail corridor Subsystem (Components): Underground electrical cable and drainage, sewer pipe Drawing No:1 FEMA No: 1 Rev No: 1
General Description Description Failure Mode Cause of Failure
Electrical cables, sewer pipes, drainage Contact with underground utilities and damage the pipe and cable Inappropriate excavation and digging Pipe burst with continuous flowing, and water floods the channel under the corridor Leakage of low or high voltage electricity causes fatality by electrocution
FAILURE MODES AND EFFECT
ANALYSIS(FEMA)
Hazard Cause/Effect
Sheet: One Of: One Prepared by: Site Engineer Date: 08/03/19 Reviewed by: Safety Supervisor Date: 08/03/19 Approved by: Safety Manager Date: 08/03/19
Corrective Action
Effect of Failure on Subsystem/System Probability of Occurrence Severity of Occurrence Possible Controlling Measure and Remarks
0.04 Critical ▪ First refer engagement and drawing as per site excavation plan ▪ Seek information about the underground utilities and check for the same before excavation ▪ Use hand digging initially till underground facility located if drawings not available
Resolution
Get fully site investigation and avoid influence zone
151