
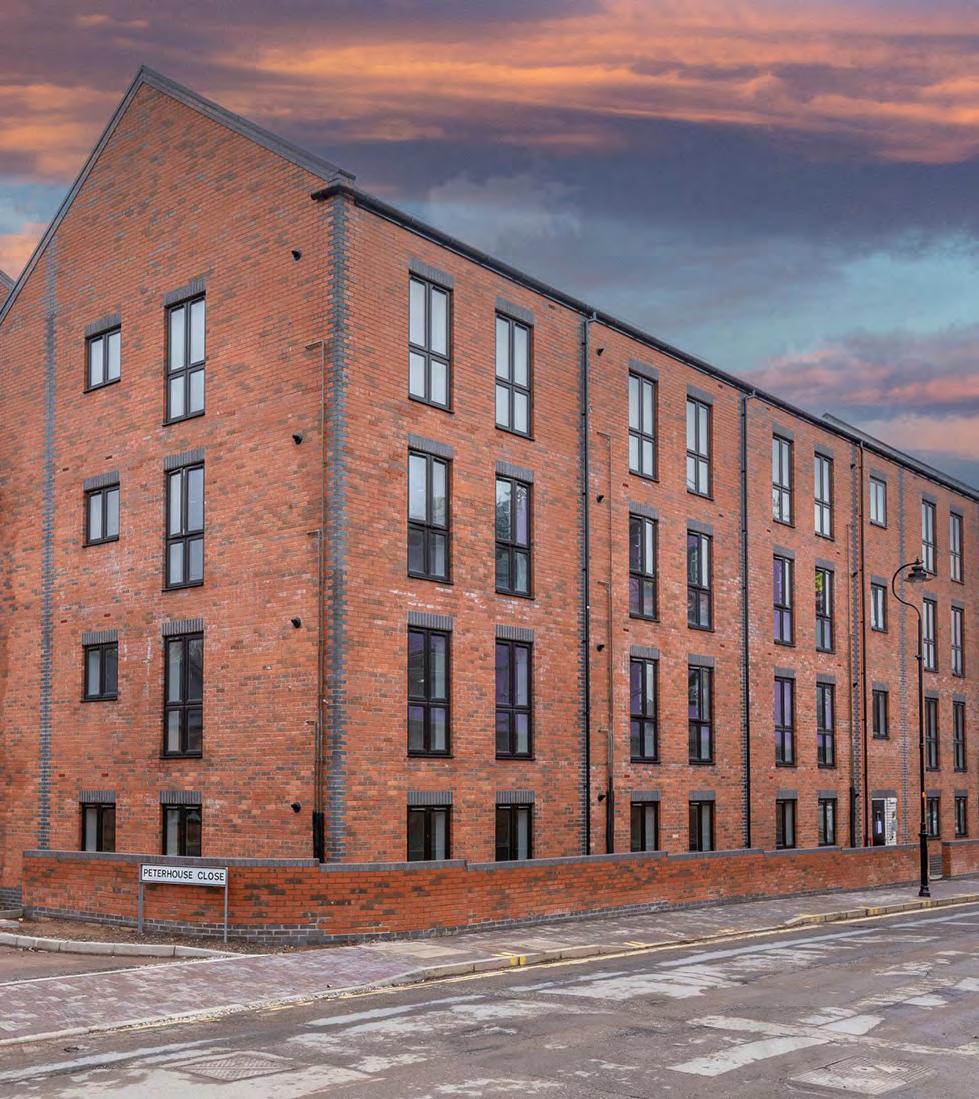
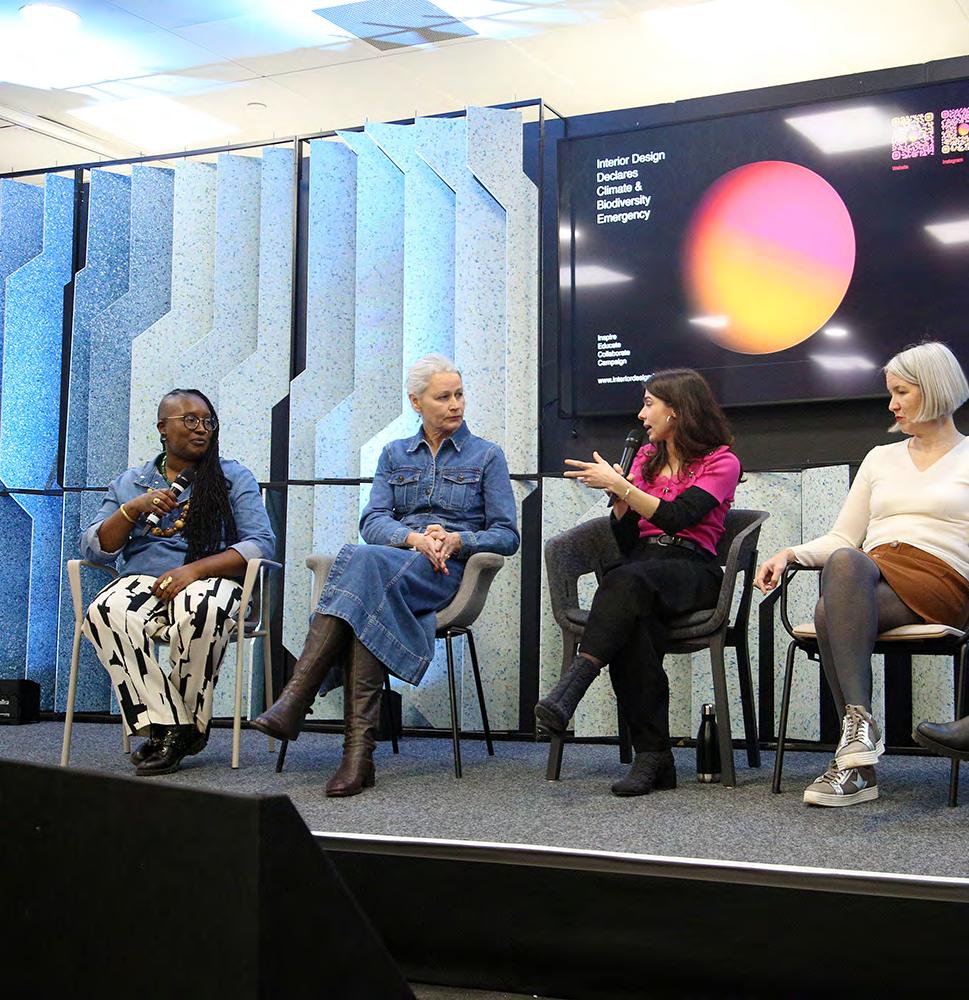
GIS Expands Lightweight Hoist Range
Causeway Technologies Promotes Paul Devlin to CEO as Phil Brown Transitions to Executive Chariman
CP&A Encourages Structural, Civil Engineers to Consider Crane Industry
CU Later, 2024: Why It’s Time To Leave Plastic Pipes In The Past
Ideal Heating Commercial Announces 10-Year Warranty on Evomax 2 Boiler
One of the Midlands’ fastest growing developers of affordable housing and extra care schemes has signed a deal to deliver a new service designed to unlock tens of thousands of acres of land for development. Keon Homes, which recently announced it is building out the stalled £35m Phase 3 Port Loop development in Birmingham, has joined forces with niche residential development consultancy Foster, Green+Brown (FG+B) to launch ‘Brownfield Reborn’.
The two companies have a strong track record in this arena and will partner with clients to provide a free in-depth assessment of a site, covering a range of technical considerations, historic land uses, land designations and high-level planning overviews.
This will then be used to outline the most appropriate uses, whether that is for residential purposes through much-needed affordable homes, care homes, retirement schemes, open market housing or repurposing for commercial use.
Importantly, the service will also give firms and individuals the opportunity to request the potential value for their sites – all of this delivered in just four weeks from the first point of contact.
Richard Williams, Managing Director of Keon Homes, commented: “‘Brownfield First’ has long been the mantra of political parties, however, we all know it is not as easy as just inserting it into a manifesto.
“There tends to be heavy reclamation costs to get the land fit for purpose, owners tend to sit on sites as they don’t understand the true value of them and developers often prefer the easier routes of grey or indeed green belt.
“Well, this could all be about to change with the introduction of our tailored service that helps landowners maximise their brownfield opportunity. “
He continued: “Brownfield Reborn will clearly show you what your land is worth if it was released for much-needed development, providing not only an honest valuation but also
the softer benefit of knowing you are helping play a role in solving some of the biggest issues facing society today.
“Our tried and tested system has already supported tens of landowners to understand the value of their land and secure a lasting legacy for their families and wider communities.”
Since a soft launch of the initiative in December, Keon Homes has been inundated with requests for a valuation, highlighting the demand for support to help landowners understand the true value of their brownfield sites.
For further information, please visit www.keonhomes.co.uk or email andy@fgandb.co.uk
GIS AG, a leading global manufacturer of electric chain hoists, is expanding its LPL lightweight series.
Building on the success of the LPML250 which was designed for D8 applications, the LPL series is now also suitable for D8+ and C1 installations.
The LPML250 is the lightest hoist in its class with a weight of just 12kg and a capacity of 500kg in D8. The LPL500 weighs 23kg yet has a maximum lifting capacity of 1,000kg, while the LPL1000 offers a 2,000kg capacity and weighs only 46kg.
Designed for the entertainment industry, the LPL range is part of GIS’s popular LP chain hoist series. LPL motors were initially intended for D8 category applications in mobile use, such as concerts and open-air events, where riggers prefer the lightest possible motors. This expansion means they are now also suitable for D8+ scenarios – holding loads without secondary securing – and C1 applications for holding and moving loads above people. This makes them also ideal for fixed applications in theatres and concert venues.
“Since its launch in 2020, our LPL range has quickly gained a reputation for combining outstanding performance with very low product weight,” said Ivan Muri, CEO of GIS AG. With this expansion, these advantages can be utilised in many more areas.”
LPL electric motors feature chains with a larger cross-section, providing increased load capacity while maintaining their compact design and low weight. They are among the lightest entertainment hoists in the world.
“LPL chain hoists offer exceptional performance for the entertainment industry, with one of the best ratios of dead weight to load capacity,” added Ivan. “With chain hoists typically used in groups, the increased load capacity means that fewer suspension
points are required for the load and consequently fewer chain hoists need to be installed. In other cases, it enables the rigger to use a smaller chain hoist which, in addition to the lower weight, also brings price advantages.”
Reliable and durable, the LPL series come with a three-year warranty and an IP65 protection rating as standard. Operation is quiet and efficient thanks to the three-step drive system with helical gearing. GIS uses a polygonal design for ease of maintenance, and the hoists are also available as a kit with a flight case and controller.
GIS is headquartered in Switzerland, with additional facilities in North America, Germany and the UK. It has manufactured and supplied more than half a million hoists worldwide.
GIS will officially launch the enhanced LPL range at Prolight + Sound, the leading international trade fair for audio and visual technologies used in the live entertainment industry. Celebrating its 30th anniversary this year, Prolight + Sound takes place in the Messe Frankfurt, 8th-11th April. Visit GIS in Hall 12 at booth E65.
gis-ag.ch/en
Construction insurance tailored to you.
Gallagher offers the strength and positioning of a global insurance group, combined with the personalised care and attention of a local UK broker. With a rich history dating back to 1927, we believe we have the expertise and experience to meet your construction insurance needs.
CONNECT WITH A
For further information, please scan the QR code.
Causeway Technologies is delighted to announce that Chief Operating Officer Paul Devlin, has been promoted to Chief Executive Officer.
Paul will take over the CEO role from Causeway’s Founder Phil Brown, who becomes Executive Chairman. Phil’s new role will see him supporting Paul and the leadership team as they execute Causeway’s vision and strategy, with a particular focus on CausewayOne, an industry-first cloud platform that will see Causeway achieve its founding vision for a fully digitalised and connected construction industry.
Paul said “It is with huge pride that I become a first-time CEO. I am committed to working with the team to continue to grow this phenomenal company. As COO, I have seen first hand – and share – the passion that has driven Causeway’s success for more than a quarter of a century.”
Welcoming Paul’s appointment, Phil Brown said “I am delighted that Paul has accepted the challenge to lead Causeway. His track record speaks to building great teams that serve customers globally, bringing scale-up knowledge to Causeway as we enter the next chapter of our story. The passion and belief that I have for this business burns brightly and I want to use my new role to get even closer to the companies and people that are going to drive the digital revolution that is coming in the industry we serve.”
Paul continued “Phil has been the driving force behind the remarkable success story that is Causeway Technologies and it is a great honour to be handed the baton by him. We will be working very closely in the future as I build on the impressive work that he has spearheaded.”
In his new role, Paul will head the executive senior leadership and guide the day-day operations of a workforce of more than 500 employees addressing the needs of over 3,000 customers worldwide.
Causeway’s software solutions serve over 200 local authorities, 600 engineering consultants, and more than 1,000 contractors, making it the UK’s largest software provider for construction
and infrastructure companies and their supply chains.
From design to build, operation and maintenance, Causeway delivers integrated, cloudbased software that streamline business processes across teams bringing clarity and efficiency to construction, supply chain management, and infrastructure operations.
Providing an insight into his vision for the business, Paul stated that Causeway sits in a prime position to lead the digitalisation of the construction industry and broader built environment.
“Ultimately my vision is to see Causeway at the forefront of innovation that is changing construction and maintenance for the better. A company that is admired and trusted for leading digital transformation and an aspirational employer that positively impacts the lives of people who work here.”
“Causeway has 25 years in the market delivering targeted software solutions that have delivered significant impact for our customers. Today billions of commerce flows through our systems. We have access to unprecedented data about the construction process in the UK and the latest technology innovations have brought Causeway to a position where it can bring all of this together in one connected ecosystem.”
At the top of Paul’s agenda will be accelerated growth fuelled by the roll out of CausewayOne, including a significant investment in Data and AI as well as building on the unique culture of the company.
By Chris Mansfield – QUALICOAT Chair
QUALICOAT UK & Ireland are proud to be partnering the FIT Show at the end of April, one of the most prestigious events in the trade Window, Door, and Glazing Industry. It is an excellent opportunity for the QUALICOAT Membership to connect with the leading innovators and experts, share ideas, and stay at the forefront of industry trends. The FIT Show offers a platform to showcase cutting-edge technologies and discuss sustainable practices, all of which are essential to shaping the future of the sector. It’s a true privilege to be part of an event that brings together so many like-minded professionals with a shared passion for advancing the Industry.
Partnering the FIT Show allows QUALICOAT to engage with the vibrant community of manufacturers, suppliers, and designers, all working towards excellence in their fields. The wealth of knowledge and experience on display is unmatched and it is inspiring to see so many dedicated individuals pushing the boundaries of what is possible. Whether it’s through hands-on demonstrations or insightful seminars, the show is an invaluable resource for anyone looking to stay ahead in the dynamic world of window and door design. We look forward to making the most of this incredible event and forging new connections that will help drive both personal and industry-wide growth.
Located on stand T76 the team at QUALICOAT offer a drop-in centre for any generic questions about architectural
powder coatings, this may be about maintenance, repair, life expectancy and of course the importance of getting the highest quality of coatings to ensure aluminium door and window systems offer an extensive life expectancy. We look forward to answering all your questions.
Specification is as simple as stating ‘to the QUALICOAT specification’ on orders for powder coated aluminium or fabricated products, where installations are located in harsher environments, such as near to coastal waters, request the involvement of a specialist coater at the early design stages of any installation. All QUALICOAT UK & Ireland members are available to offer advice and can be found on the Association website at qualicoatuki.org
Small and medium sized construction firms are boosting their financial resilience through the increasing use of personal guarantee backed loans and invoice financing. This is based on the latest analysis from Purbeck Insurance Services – the UK’s only provider of personal guarantee insurance.
63% more SME construction firms applied for personal guarantee backed finance in 2024 compared to the previous year. This is where the owner/director puts their personal assets up as security for the loan and uses insurance to mitigate that risk.
1 in 4 uses Invoice Finance
There was also a notable rise in construction firms using invoice finance in Q4 2024 – 24% of applications were for this type of financing compared to 7% in Q4 2023. Invoice finance is when the lender uses unpaid invoices as collateral for funding, giving construction firms a percentage of the value of those invoices. It is often used as a fast solution when other lending products fail to offer the amount of funding needed.
Just under half (49%) of the SME construction firms taking on a new loan, were doing so to provide working capital for the business. This is
considerably higher than other business sectors where, on average 34% of loans are used for this reason.
Todd Davison, MD of Purbeck
Personal Guarantee Insurance said: “Small to medium sized construction industry firms are facing increasing costs following the Budget in October 2024 and concerns have been raised about the impact of changes to Business Property Relief on the many family businesses in construction.
However, it is evident that finances are already under immense pressure given the number of loans being taken for working capital and the rise in those using invoice finance as a fast route to funding. With promises of a building boom, it is vital that firms take positive steps to improve their financial resilience so that they can stay the course. One way is to use insurance to mitigate some of the risks associated with personal guarantee backed loans. By using this tool, an increasing number of SME construction firms are gaining access to the finance they need without exposing themselves to additional risk.”
www.purbeckinsurance.co.uk
Indoor air quality and ventilation manufacturing specialist Nuaire has had its MRXBOX Hybrid Cooling Systems installed into the new Berkeley Oval Village mixed use development in central London.
103 MRXBOX Hybrid Cooling Systems with Nuaire ducting are being installed into one bedroom apartments at Oval Village in an area called the Zone, which are available on a shared ownership basis. Compact in size, they are being installed within each apartment’s utility cupboards.
The MRXBOX Hybrid Cooling System, which is a cooling extension for the MRXBOX Mechanical Ventilation with Heat Recovery (MVHR) range, combines the heat-exchanger coolth recovery of an MVHR system with the cooling effect provided by a DX coil. A wallmounted room temperature sensor senses indoor temperatures and activates the cooling module automatically when necessary.
The MRXBOX Hybrid Cooling System has been designed specifically to address the issue of overheating in problem areas of developments, where specific apartments or groups of apartments cannot be naturally ventilated and where site wide cooling technologies are not an option. The MRXBOX Hybrid Cooling System significantly lowers the temperature of the fresh-air supply for occupant comfort, and enables compliance with Building Regulations Part O which addresses overheating mitigation requirements in new build properties.
Whilst passive ventilation solutions, such as opening windows, are prioritised under Approved Document O,
there are instances when this is neither desirable, nor practical; this could be due to safety considerations, external noise and/or pollution. Located in the heart of London, Oval Village has these issues to contend with, plus higher temperatures than in other parts of the UK as a result of the Urban Heat Island effect.
The MRXBOX Hybrid Cooling System was selected by the consultant on the Oval Village development following an assessment of the acoustics, air quality and overheating. For apartments that would not meet the noise criteria, natural ventilation was not an option and an alternative solution had to be found in the form of mechanical ventilation. Cooling technologies for individual apartments impacted by overheating where looked at. While split systems with fan-coils are a tried and tested option, they weren’t universally suited to all apartments in the development. Such cooling systems come at a premium price and, furthermore, are relatively energy hungry so residents have to have the means to pay to run them. With a number of the apartments at Oval Village allocated as affordable housing, the cost of cooling for the home owner was an important consideration.
The Nuaire MRXBOX Hybrid Cooling Systems were welcomed by the consultant as a means of achieving compliance with Part O without the energy cost of a full cooling system that occupants have to pay for. As well as creating a simple solution to overheating in summer months, the units provide a high standard of indoor air quality year round via high-efficiency MVHR.
To find out more about Nuaire’s Hybrid Cooling System go to www.nuaire.co.uk/product-list-page/ mrxbox-hybrid-cooling-system
Casper, Phillips & Associates Inc. (CP&A) is reaching out to trainee and experienced structural engineers who might not have considered what the crane industry has to offer. Cranes typically require structural engineers to ensure the structure is robust enough for its service class; mechanical engineers to design the power transmission systems; and electrical engineers for controls and power. There is some overlap between disciplines. For example, mechanical engineers can be educated on both control theory and strength of materials.
Richard Phillips, mechanical engineer at CP&A, said: “There is a lot of potential in this industry for structural engineers. Cranes are complex structures and require a lot of interesting analysis.”
Their peers in mechanical engineering realize that, with good reason. Automated cranes are essentially giant robots and robotics is a hot topic in mechanical engineering. The kinetic architecture sector also requires mechanical engineers to keep stadium roofs and drawbridges moving, but the crane industry gets its fair share of this professional talent.
Think about the engineering required to put a floating crane system to work that can lift 3,500 metric tons — that’s just shy of eight million pounds. Container cranes are as prominent on many coastal city skylines as buildings and bridges, yet they often go unnoticed.
CP&A offers a wide variety of services, including specification, design, manufacturing review, modification, and accident investigation. Thusly, it is well placed to observe the scarcity of structural engineers, a specialty within civil engineering.
“There is high competition for structural engineers,” said Phillips. “But the crane industry shouldn’t be overlooked. Cranes can be located in hurricane zones and high seismic zones; this means you get to practice and develop both of these skills. Cranes are often built at a manufacturing plant then transported to the installation site. For container cranes, they are often shipped on vessels in potentially rough seas. Analyzing a structure that is traveling across an ocean is not something every engineer gets to do.”
Phillips has highlighted engineers aspiring to work on, or already working with, bridges as being especially suited to raising their aspirations. After all, a crane boom acts as a bridge for the trolley to travel across to pick up the container from the vessel and take it to where it needs to go. Even for overhead cranes, the industry refers to part of the structure as the ‘bridge’. The trolley runs back and forth on the bridge, while it picks up and places loads.
Like bridges, crane engineering can take people places. Phillips said: “There is a lot of opportunity for travel in the crane industry. Cranes are located all around the world and as world-class engineers, our services are in demand globally. We currently have ongoing projects in Washington, California, Massachusetts, Delaware, New York, and Georgia. We also have projects in Indonesia, Canada, Germany, and Argentina. There is a consistent need for new ship-to-shore cranes, even as vessel sizes increase. The cranes need to be taller and have larger cantilevers.”
There are synergies between cranes and stadiums too — and there are a lot more cranes being built than retractable stadium roofs. Mobile stadium roofs require a rail system, and the specialist to calculate loads associated with motion of large structures. This may include the inertial effects of accelerating and decelerating. This infrastructure has a lot of motion cycles, so fatigue analysis starts to come into focus. These motion systems need to integrate with other types of engineers, such as mechanical and electrical.
The wider scope for engineering excellence within cranes must be seen to be believed, as the lack of civil engineers seems to bear out. CP&A has been utilizing nonlinear time history analysis (NLTHA) for research and engineering projects since 1991. Its crane base anti-seismic isolation system (BASIS), for ship-to-shore gantry cranes at the quayside, is built on NLTHA and can protect the crane main structure from damage even in contingency level earthquakes.
Phillips said: “These are very useful analysis tools to evaluate non-building structures that do not behave like buildings. Crane structures are unique, and the typical structural codes were not written with cranes in mind. This can result in interesting clauses applying that require application of advanced analysis techniques, such as non-linear time history. The genesis of the BASIS system was based on our experience with the seismic upgrade of Boeing Everett; after studying the problem we discovered friction dampers were the best solution.
“When you use dampers of any kind, this will create a non-linear response so typical seismic design procedures, such as a response spectrum based on the soil class and periods of vibration, are not always appropriate. This is where non-linear time history comes into play. These are called performance based design procedures.”
Global Lifting Awareness Day will shine a spotlight on education more intently than ever with its sixth staging later this year.
Powered by the Lifting Equipment Engineers Association (LEEA) and supporting
organizations, it is now a widely celebrated day where manufacturers, suppliers, and end users are among those that share material that promotes safe and high-quality load lifting. Social media posts, videos, articles, and in-person activity will again be bound together by the hashtag, #GLAD2025.
Phillips said: “I think most people see cranes as something necessary to build important structures, but the focus stays on the end product and not the process to get there. The GLAD movement gives us a chance to help showcase what makes the crane industry so interesting. And we have much to build on. The entry level hires we’ve brought on board are as well prepared as any generation, and they take to our mentoring system. It’s just difficult to find the right engineers.
“From the outside looking in, it appears that the other industries are doing a better job at attracting students. Anecdotally, we aren’t seeing as many
civil engineering graduates who focused on structures. Computer science and AI [artificial intelligence] are generating a lot of interest. Environmental and water resources management are both sub-disciplines under the civil engineering umbrella that tend to be attracting more students.”
If any trainee or experienced structural engineers are convinced, prepare to learn one’s crane vocabulary — and the rest will follow. While the design of cranes may have some unique characteristics and goals, the laws of physics don’t change. The fundamental approach to designing a structure will be more similar to other industries than it is different.
“The pinnacle of each engineer’s career is very personal, and each engineer will have a unique experience,” said Phillips. “Most engineers take great pride in handing over a custom crane design to a client. For me, that has been the biggest source of accomplishment and a very real symbol of the impact we make as engineers.
“Sometimes I have to take a minute and let it really sink in what I am designing. AI and computers are great at refining solutions to problems that have been previously solved. When you design a custom crane you are solving a new problem that potentially hasn’t been solved before. Computer programs are great at doing the routine busy work for us so that we can spend more of our budget on the cutting edge. Most projects are unique when we get involved.” www.casperphillips.com
By Andrew Surtees,
In 2024, an estimated 220 million tonnes of plastic waste was generated globally – equivalent to 28kg per person. Of that waste, approximately a third (69.5 million tonnes) was mismanaged, ending up in the natural environment.Meanwhile, the global plastic pipe industry continues to expand at an exponential rate and is projected to reach a staggering $147.2 billion by 2030 due to growing demand in the construction industry.
The impacts of the plastics industry are clear to see, with increasing amounts of plastic waste causing harm to the environment and our health. Yet the use of plastic pipes in construction, medical devices, and other industries continues to increase year-on-year. In fact, the plastics lifecycle is set to contribute as much as 19% of global greenhouse gas emissions by 2040, with the construction sector consuming 20% of all plastics and 70% of all polyvinyl chloride (PVC) produced around the world.
Plastic pipes, especially those made from PVC, are a major contributor to microplastic pollution, releasing harmful chemicals into our water systems. Ingesting microplastics has already been linked to serious health concerns, and is known to impact the lungs, gut and brain function. Studies show that the average person unknowingly consumes up to 211,000 microplastic particles annually, primarily through drinking water.
With PVC pipes being the most used type of plastic pipe, they are a common feature in homes and everyday environments, including office buildings and hospitals.
Known to release dangerous chemicals such as phthalates and dioxins, this is a serious cause for concern.
Copper pipes are naturally antimicrobial, resistant to corrosion and do not release
harmful substances into drinking water, posing a safer option for residential and nonresidential buildings.
In addition to the health risks, plastic pipes pose serious fire safety concerns. Plastics are highly combustible and can spread quickly in a fire, with the smoke produced containing hazardous chemicals such as carbon monoxide, which can be inhaled and absorbed through the skin.
The release of these toxic substances during a fire makes plastic pipes particularly dangerous in residential and commercial buildings, as they can worsen fire conditions and increase the risk of long-term health problems.
On the other hand, copper has a high melting point of 1,085°C – higher than the temperature of most building fires – making it a safer, fireresistant option for built environments.
Used for centuries in plumbing, copper has proven sustainability credentials and continues to outperform plastic in terms of durability and longevity. Nearly 80% of all copper ever mined is still in use today, and opting for 1 ton of recycled copper results in 65% fewer CO2 emissions compared to using virgin materials – a testament to its sustainability and minimal environmental impact.
With plastic pipe production expected to continue to increase globally in 2025, this alarming fact highlights the urgent need for change in the materials we use for plumbing and construction. Copper is not only a safer alternative to plastic, but its recyclability plays a key role in reducing waste and carbon emissions, and CuSP is dedicated to driving this change forward to create a more sustainable future.
As we face growing environmental, health and fire safety risks from plastic pipes, it’s clear that we need to leave plastic behind and embrace safer, more sustainable alternatives like copper. With its durability, recyclability, and minimal environmental impact, copper offers a responsible choice for the future of construction and plumbing. CuSP is committed to driving this change and building a safer and greener environment. Let’s work together to transition away from plastic and create a better future for our construction industries.
To find out more about the risks of plastic pipes in construction, please click here:
Serving as a Board Director for the Council for Aluminium in Building (CAB) offers a unique opportunity to play a pivotal role in shaping the future of the Aluminium Fenestration Industry. The Board provides a platform to influence strategic decisions that directly impact the growth of aluminium fenestration, innovation, and sustainability practices.
By becoming a director, a CAB member has the chance to collaborate with key stakeholders, including manufacturers, fabricators, contractors, and architects, to ensure the Industry remains at the forefront of advancements in technology and environmental responsibility. Active involvement in CAB helps the Association address challenges such as promoting circular economies, driving sustainability through aluminium recycling, and championing industry standards that enhance the quality and reputation of CAB Members across the UK & Ireland.
Along with the opportunity to shape policy, serving on the CAB board positions its directors as leaders within the Industry. The Board offers unparalleled networking opportunities and access to insights about market trends, legislative changes, and emerging technologies. It also contributes to the professional development as members are involved in high-level discussions that refine strategic thinking and leadership. Representing CAB as a Board Director allows members to amplify their organisation’s voice and advocate for its
interests, while simultaneously contributing to the broader development of a resilient and sustainable industry. This role is not only an investment in the industry’s future but also an opportunity to leave a meaningful legacy.
As the Association grows, additional board members are needed to best represent the interests of its members across the aluminium supply chain. This year we are delighted to welcome to the Board two additional directors who offer both skills and valuable insights into the ever evolving supply chain.
Sam Nuckey is the Managing Director of Window Ware, a leading distributor of innovative fenestration hardware, tool and consumable solutions. With a keen eye for commercial detail and a passion for quality and excellence to build strong partnerships and businesses, she has been instrumental in driving the company’s success. Under her leadership, Window Ware continues to set new standards to partner with and support businesses in the aluminium sector. She brings to the CAB Board over eighteen years of fenestration industry experience and twenty-six years in senior commercial and financial roles and is dedicated to delivering exceptional products and services to meet the evolving needs of the aluminium sector.
Rhodri John, Commercial Director of AluFoldDirect brings to the CAB board over 24 years of experience in the aluminium fenestration industry, AluFoldDirect is one of the UK’s leading aluminium glazing specialist. He leads the project sales and commercial teams, overseeing the delivery of highquality and bespoke glazing solutions for residential and commercial projects across the country. Rhodri is responsible for new business development, key account management, and glazing systems that aims to identify and secure new opportunities, build and maintain strong relationships with clients and partners, and ensure customer satisfaction and loyalty. Collaborating at the same time with AluFold Direct’s technical and operational teams, providing strategic input and feedback on product development, innovation, and quality standards.
The appointments bring the CAB board up to ten members which, together with Nigel Headford our Chief Executive, is driving CAB through a growth phase over the next few years. 2025 brings a busy programme of events and training opportunities to its membership.
More information about CAB’s 2025 training webinars and events is available through the CAB website. Should you wish to learn more about the use of Aluminium used in Construction, please contact CAB, join the Association and be recognised as being involved in supporting your Industry and helping to shape its future.
More information on our website at c-a-b.org.uk
UK ventilation manufacturer Domus Ventilation is proud to announce that its industry leading ventilation ducting will now be manufactured primarily from recycled plastic.
The company already uses 100% recycalate on its rectangular ducting and over 95% of its fittings use 100% High Impact Polystyrene (HIPS) which comes from post-consumer recycled plastic. As part of the Genuit group, which has committed to have 62% of its ducting source material come from
recycled plastics by 2025 where at all feasible, Domus Ventilation has now progressed to manufacturing its entire ducting range primarily from recycled plastic. This will make Domus Ventilation ducting one of the lowest carbon choices on the market, without any detrimental impact on the quality of the product that Domus ducting is renowned for.
Click here to read the full article >
• Freshwave is partnering with Electracom Projects to deliver 4G mobile signal to the 50-storey development
• An innovative commercial model sees landlord areas covered and occupiers also able to opt in to connecting to the in-building system
• 8 Bishopsgate is the UK’s tallest BREEAM Outstanding building
Connectivity infrastructure-as-a-service provider Freshwave, working with real estate technology specialists Electracom Projects, has brought 4G connectivity from all four mobile network operators (MNOs) to 8 Bishopsgate. 8 Bishopsgate is the latest flagship City of London development of Mitsubishi Estate London and Stanhope PLC. The 50-storey tower offers more than 900,000 sq ft of space, 500,000+ sq ft of which is for offices. It’s also the UK’s tallest BREEAM (Building Research Establishment Environmental Assessment Method) Outstanding building.
Freshwave designed and deployed a 4G distributed antenna system (DAS) to provide assured connectivity for everyone in the building, no matter which mobile network they use. Freshwave are supporting the system via an ongoing managed service. As well as delivering mobile coverage for the landlord areas, occupiers can also connect to the service thanks to an innovative commercial model agreed between 8 Bishopsgate, Freshwave and Electracom. Sixteen occupiers have already opted into the service.
Modern building materials often block mobile signal from entering from outdoors, making an in-building system essential to support the ubiquitous mobile connectivity people expect today. The DAS connects securely into the MNOs’ networks, guaranteeing the quality of service.
Brendan Hourihane, Senior Director at Freshwave, said: “We’re delighted to have delivered connectivity from all four operators to this spectacular building through our valued partners at Electracom Projects. Mobile signal is essential for modern life now, whether it’s for dealmaking in the office or keeping in touch with loved ones, so it’s a must in high-quality buildings such as 8 Bishopsgate to give the best experience.”
Nick Seaton, Director at Electracom Projects, said: “8 Bishopsgate is a smart building and the advanced technology it contains will be of great benefit to both its staff and occupiers. A mobile app allows people to do everything, from accessing the building itself to booking rooms and event spaces, so we knew we needed reliable mobile signal. We’re proud to be working on this prestigious project for Stanhope and happy to partner with Freshwave on mobile connectivity.”
Dan Ward, Senior Development Director at Stanhope, said: “We’re committed to providing a superlative experience for our occupiers across every facet of 8 Bishopsgate, from the physical surroundings to the amenities they enjoy. Seamless mobile provision is an important part of our exceptional technology offer.”
8 Bishopsgate has 75,000 sq ft dedicated to amenity space, which is 10% of the building. This includes a restaurant, café, 7,600 sq ft communal terrace, events space and The Lookout viewing gallery on floor 50, which members of the public can also book viewing tickets for free of charge. The building is designed by award-winning architects WilkinsonEyre.
Evomax 2, the UK’s number one selling commercial wall-mounted boiler from Ideal Heating Commercial, is now available with a 10-year warranty.
As with all Ideal Heating Commercial condensing boilers, Evomax 2 is designed specifically for the UK market, and produced in a state of the art manufacturing plant in Hull which has seen considerable investment over recent years. “Ideal Heating Commercial is one of the few true British manufacturers left in the heating industry” states Andy Forrest, National Sales Manager – Ideal Heating Commercial “and we consider the 10-year warranty we have introduced on Evomax 2 to reflect both our confidence in this market leading commercial boiler and our commitment to British manufacturing.”
The new warranty covers 10-year parts and labour when Evomax 2 is installed on an Ideal Heating pipework header kit with plate heat exchanger, and commissioned by Ideal Heating Commercial. Commissioning is provided as a free service and not only saves installers time and money, but ensures that the boiler is operating correctly before it is put into service. An Enhanced Appliance and Primary System Check, which is chargeable at £250 per boiler, is also required under the terms and conditions of the 10year warranty.
The new 10-year warranty does not affect the existing 5-year warranty proposition, which will continue to be available with free commissioning.
The Evomax 2 is not only Ideal Heating Commercial’s best selling boiler, but the best selling wall mounted boiler in the UK. Its popularity is attributed to its reliability and performance, as well as its flexibility, and quick and easy installation.
Highly efficient, Evomax 2 has up to 99.6% full load efficiency and up to 110% part load efficiency, can operate at up to 30° Δ T, and boasts a high turndown of 5:1. NOx <40mg/kWh (Class 6) is achieved for all Evomax 2 natural gas boilers, for low emissions. It is available with outputs from 30-150kW, which can be increased to 900kW using six Evomax 2 boilers in cascade.
When using Evomax 2 in cascade, Ideal Heating Commercial has made this process even easier through the provision of low height and standard frame and header kits to suit all plantrooms, along with an online cascade configurator tool to make choosing what you need straightforward. Building
an Evomax 2 cascade system is also fast: a threeboiler cascade can be built in under 90 minutes, as demonstrated in Ideal Heating Commercial’s video.
Evomax 2 is available with a range of accessories, including hydraulic separation, all with market-leading availability, all designed and manufactured in the UK.
Ideal Heating Commercial delivers commercial heating solutions that are at the forefront of technology and developed in line with the latest market trends and legislation.
With under a week to go to until the Business Design Centre opens its doors to architects and designers from across the globe to explore the latest in surface materials, the Surface Design Show is thrilled to announce its exceptional speaker’s program for the 2025 edition of the show. Featuring a diverse range of topics and discussions with the leading industry experts. Join us to hear from the likes of Grant Gibson, Kate WatsonSmyth and Morgan Lewis.
The programme will be held on the Main Stage sponsored and designed by Procédés Chénel, consisting of 15 presentations from over 40 speakers, including architects, designers, manufactures and journalists. The main stage will once again return to the gallery level, featuring furniture supplied by Surface Matter. The 2025 theme, Creative Conscience will be present throughout the speakers’ programme, with topics giving key insight into future of materials for the built environment, focusing on sustainability, technological advancement, and the human experience.
Next door to the main stage will be the Designer Hubs, where guests can network, relax and reflect on the inspiring talks heard at the show. The space is designed in conjunction with Surface Matter and The Collective and features a stunning chandelier made from salvaged CD cases from Spark & Bell.
Opening night will kick off at 18:30 with the hot topic of AI in the debate A True Companion? The Power of AI in A&D. The panel will dive into the potential of AI as a design tool along with its applications, challenges and ethical implications. Leading the discussion will be well known editor of Design Insider, Alys Byran, joined by panelists: Professor Des Fagen – Head of Architecture at Lancaster School of Architecture, Mariangela Iodice – BIM Coordinator at Make, Zuzana Phillips –Creative Director at Accanto Interiors, and Christos Passos – Director at Zaha Hadid.
Material Passports (11:40-12:20) is an exploration into the concept of them and their role in supporting sustainability and ethical sourcing. Moderated by Harsha Kotak, CoFounder of the Sustainable Design Collective, the session will discuss how companies are leveraging technology to track and trace materials, ensuring
transparency of the supply chain. Participants include Asif Din – Director of Regenerative Design for Perkins and Will, Anja Schellenbauer – Associate Director of John Robertson Architects, Joanna Knight – Co-Founder of the Sustainable Design Collective, Carmen Wocher – Material Researcher for TP Bennett and Ana Rita Martins –Sustainability Lead for MCM.
Unlock the depths of material innovation with The Futures Lab and their talk; Firing Up the Future (12:30 –13:10). Join Colin Macgadie, Founder of ForEveryday.Life and chair of Future Lab, as he introduces ‘Fire Walk with Me’ – a provocation from Studio Thus That on harnessing ‘fire’ for bio-regional material innovation.
Navigate trends with Kate Watson Smyth, Founder of MadAboutTheHouse and her talk on Trends: Should You or Shouldn’t You? (13:30 – 14:15), Kate will give an insight into the consistently evolving world of interior design trends and share her expertise on distinguishing between fleeting fads and enduring styles.
Hear about building a sustainable future with Deepthi Ravi – Sustainability Coordinator at PLP Architects, Astrid Hugo – Regional Design
Resilience Leader (Europe) for Gensler, Marco
Franchi – CEO of Franchi and Morgan Lewis –CEO of Material Index. Partners in Circularity:
Building a Sustainable Future Together (14.3015.20) will discuss how to drive circularity and sustainability within different parts of the industry. The talk will spotlight retrofitting, working with existing structures, strategies for adaptive reuse and examining the successes within circular design.
For those in the hospitality industry, don’t miss The Future of Surface Design in Hospitality (15:30 – 16:15), the panel will cover topics of emerging materials, luxury and understanding the future customer. It will consist of speakers from a range of companies including Zaha Hadid, Conran and Partners, Muza Lab and Hotel Designs.
Legends Live (16.30-17:00) will be retuning for its fourth year, with different hosts over two different sessions. The first of which will be led by Sophie Harper – Editor of Hotel Designs, who will engage with three designers that have
impacted her professional journey. These intimate conversations will provide an insight into the guests’ design philosophies, portfolios and future aspirations, a must see for anyone looking to grow within the industry.
Don’t miss this year’s Surface Design Awards ceremony which will take place on the 5th of February from 18:00 – 20:00 on the main stage.
Day two (6th February) will open with Designing with Stone – The Original Sustainable Material (10:3011:15) where you can hear from Matt Robb of Stone Federation, Tim Gledstone of Squire & Partners, Venessa Brady OBE and Roisin Lafferty Founder and Creative Director about their views on natural stone and its potential for creating sustainable interiors.
Following that will be a discussion regarding the role of the built environment in shaping our wellbeing, including a closer look at the science of wellness design, designing for diverse needs and how technology can facilitate this. The panel will feature representatives from all parts of industry including but not limited to; sustainability, architecture, workplace design and commercial design. Designing for Wellness: A Holistic Approach (11:30 – 12:15).
Legends Live (12:30-13:15) is back for its second session with a discussion between Elspeth Pridham of The Insider and Simon Goff, Founder of the innovative rug brand FLOOR_STORY. They will dive into Simon’s
entrepreneurial journey, highlighting his dedication to sustainable manufacture, collaborating with designers, and the product itself.
One not to miss for those invested in sustainability is The Power of Biophilic Design and Sustainable Sourcing. With Vanessa Champion, Founder of the Journal of Biophilic Design hosting, it promises to be packed with insights into sustainable sourcing, realworld examples and reducing your businesses carbon footprint.
Join Adẹ̀kọ́ & Co, Kevin Haley Designs and Space Magazine for a panel on Weaving Narratives into Space (14:30 – 15:15). The discussion will explore the intersection of design, culture and community with key points including using materials to tell a story, the role of design to evoke emotion and designing in response to local and social context.
Finally, there will be a Case Study Session on What Makes an Excellent Residential Interior? (15:30-16:15) Where attendees can join the BIID for an informal discussion that will refer to two different residential projects to discuss some of the ways designers can create unique residential spaces.
To read the full speakers programme, please click on the link below; Main Stage Programme | Surface Design Show 2025 | 4-6 February
www.surfacedesignshow.com
In modern agriculture, the need for robust and adaptable construction materials is more critical than ever. As farms expand and diversify, the demand for versatile building solutions grows, leading to innovative approaches in infrastructure development. The use of stackable concrete blocks in agricultural applications has emerged as a highly effective option.
In the rapidly changing landscape of agriculture, ensuring that your infrastructure is both robust and flexible is crucial. This is where stackable concrete blocks come into play, offering a solution that meets these demands head-on. These blocks are not only versatile but also durable and easy to install, making them a popular choice among farmers looking to enhance their agricultural settings. Moreover, betonblock.com has become a valuable resource for those interested in exploring this innovative building material further.
Stackable concrete blocks explained
Stackable concrete blocks are prefabricated building materials designed to interlock easily, creating strong and stable structures. These blocks are widely used across various construction sectors due to their ease of use and adaptability. Their applications range from simple landscaping projects to more complex constructions like retaining walls and storage facilities. The primary benefits of these blocks include their durability, ease of installation, and reusability, which make them particularly suitable for agricultural environments where conditions can be harsh and demanding.
The blocks’ ability to be reused or reconfigured with minimal effort is a significant advantage in agricultural settings. Farmers can quickly assemble or dismantle structures as needed without requiring specialized equipment or skilled labor. This flexibility not only reduces construction time but also minimizes costs associated with traditional building methods. With these benefits in mind, it’s no surprise that stackable concrete blocks are becoming a favored choice for enhancing agricultural infrastructure.
Agricultural uses of stackable concrete blocks In agriculture, stackable concrete blocks offer numerous practical applications that can help streamline operations and increase efficiency. For instance, they are ideal for constructing retaining walls that prevent soil erosion on sloped terrains— an essential feature for maintaining fertile land. Additionally, these blocks can be used to build secure storage facilities for grains and produce, ensuring protection from pests and weather-related damage.
Another critical application is creating barriers for livestock enclosures, which must be sturdy enough to withstand pressure from animals while remaining safe and secure. Real-world examples demonstrate the success of these applications; numerous farms have reported improved productivity and operational efficiency by incorporating stackable concrete block structures into their operations.
For farmers seeking cost-effective construction solutions, stackable concrete blocks present a compelling option. They allow for significant savings on labor and materials due to their straightforward installation process and longlasting nature. Additionally, because these blocks can be disassembled and reused multiple times, they contribute to sustainable farming practices by minimizing waste.
The environmental benefits extend beyond waste reduction; using locally sourced materials for block production reduces the carbon footprint associated with transportation. Furthermore, by choosing recyclable materials in their manufacturing process, Betonblock forms contribute to more sustainable building practices in agriculture.
When selecting stackable concrete blocks for agricultural use, it’s crucial to consider the technical specifications provided by manufacturers like betonblock.com. These details ensure that you choose the right type of block suited for your specific needs, whether you’re constructing a small barrier or a large storage facility.
Key factors to consider include the block’s weightbearing capacity, weather resistance properties, and interlocking capabilities. Understanding these specifications helps in planning efficient designs that maximize both functionality and safety on your farm.
Stackable concrete blocks hold great potential for enhancing agricultural infrastructure through their versatility and durability. They offer farmers innovative solutions that meet the growing demands of modern agriculture while promoting sustainable practices.
betonblock.com info@betonblock.com
Sovereign Sports offer more than 40 years’ experience in tennis court construction, installation and maintenance, assisting clients across the South East of England. The family run business is dedicated to delivering complete customer satisfaction, and are happy to assist in all associated services, like floodlighting, fencing and resurfacing. Call today for more information and a no-cost quote.
Website: www.sovereign-sports.co.uk :: Telephone: 01634 684 235
MTS Cleansing Services offer a wide range of domestic, commercial and industrial waste management services throughout the UK. Find out more by visiting their website.
Website: www.mtscleansing.co.uk :: Telephone: 01634 250326
BSE 3D is a team of building services engineering consultants with offices in London, Sussex and Ireland. Dealing with everything from mechanical and electrical engineering through to HVAC system design, and so much more, the company has a team of dedicated professionals with years of industry experience.
Website: www.bse3d.com :: Telephone: 0207 193 7146
Our Mission is to continue leading the construction site broadband market by empowering clients whilst on-site. Whether that be for site offices, sales centres or new homes, our temporary connectivity platform enables site professionals to work more effectively, saving time and money for every project.
Website: tardis4g.uk :: Telephone: 01708774420
If you’re looking for a specialist repair or restoration for your home’s original box sash windows, call Sash Window Experts today for a free estimate. With over 25 years’ experience and a passion for preserving beautiful architectural period features, our expert craftsmen can remedy any cosmetic, structural and operational problems, leaving you to enjoy your home as you should.
Website: sashwindowexperts.com :: Telephone: 01403 602701
Never settle for a broken garage door. Thanks to the team at Wessex Garage Doors, you can replace or repair it instead! With a wide range of models, styles and finishes to choose between, the team make maintaining, repairing or installing garage doors a breeze, utilising their substantial skills and years of experience. Find out more through the website.
Website: www.wessexgaragedoors.co.uk :: Telephone: 01737 309 103
We offer the installation of specialist bespoke sliding doors, bi-folding doors, glass roof structures, windows and frameless glass balustrades. We manufacture and design innovative, frameless glazing systems. We also work closely with established manufacturers, offering both UK and Offshore designed systems, with lead times as quick as one week on specific items.
Website: www.1stfoldingslidingdoors.co.uk :: Telephone: 020 8997 2448
Rolec EV offers high quality home electric vehicle charging points from £100 and has a huge range of commercial EV charging options. It’s EV Ready home charger offers mode 2 charging and doubles up as a 13amp outdoor home maintenance socket.
Website: www.rolecserv.com :: Telephone: 01205 724754