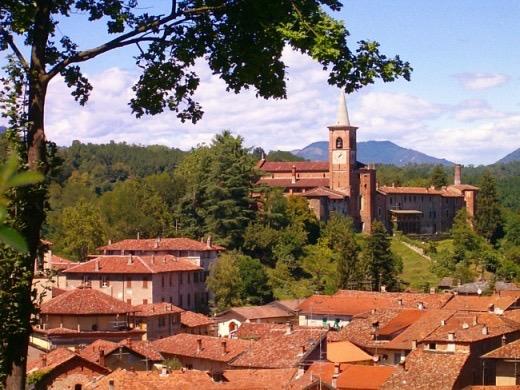
23 minute read
Near Varese, late ‘70s Vicino a Varese, fine anni ‘70
These were the years of the beginning of the use of the anti-reflection treatment also for prescription lenses, following the wave of the sales of a famous leading company which launched it, so that this additional step in the production cycle became almost obbligatory. At that time, building a “prescription lens” was the result of a technology known from the production of glass lenses, by using adapted to the new organic material machinery. At that time it was known as CR39® sold by the brand of the inventor of the base mixture, the PPG. A nickname which nowadays remains inextricably linked even to similar materials, from other manufacturers with other brands, but with the same refractive index.
The acronym CR39 came from Columbia Research 39 and was significant of research number 39 for “a transparent material, resistant
Advertisement
Erano gli anni degli inizi della diffusione, anche per le lenti di prescrizione, del trattamento antiriflesso, sull’onda delle vendite di una famosa Azienda leader che lo lanciò, tanto che questo passo addizionale del ciclo produttivo divenne quasi obbligatorio.

A quei tempi il costruire una “lente di ricetta” era frutto di una tecnologia nota dalla produzione delle lenti di vetro, con macchinari adattati al nuovo materiale organic0. A quei tempi era noto come CR39® dal marchio dell’inventore della miscela di base, la PPG, nomignolo che a tutt’oggi resta indissolubilmente legato impropriamente anche a materiali simili, di altri produttori con altre marche, ma con lo stesso indice di rifrazione).
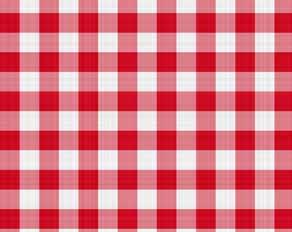
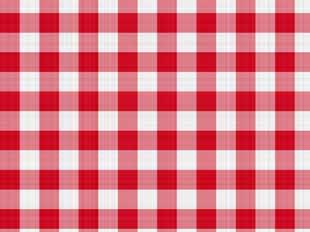
L’acronimo CR39 proveniva da Columbia Research 39 ed era significativo della ricerca numero 39 per un materiale trasparente, resistente ad urti to shocks, solvents and oils such as to be able to constitute an inspection stub for the passages of Avio petrol in military jets which often complained of dangerous interruptions of fluid vein due to accelerations during combats”. The prescription lenses production procedure was at that time not only known, but relatively simple; however, the addition of a process step, where the units of measurement involved passed “from tenths to nanometres”, undoubtedly introduced a real novelty and caused a need for modernization of knowledge and systems. And, as if that weren’t enough, the step included acquiring new generation machinery that, compared to those in use before, they looked like a microtome instead of a knife. There was talk of “vacuum deposition of a thin film formed by a multilayer sandwich of e a solventi e olii tale da poter costituire un tronchetto di ispezione dei passaggi della benzina Avio nei jet militari che spesso lamentavano pericolose interruzioni della vena fluida a causa delle accelerazioni durante i duelli aerei. indices where an extinction is produced inside by a multiple reflection of waves out of phase by 180° ... in order to extinguish in effectively the reflection generated by the surfaces of the lens”. Scientifically clear and concise definition but to make the guts tremble even to the most prepared optics expert. However, the matter was also known in the 1930s for treatments on glass ophthalmic lenses, where a spray of magnesium fluoride was enough to have a decent extinction of the reflection but with a horrendous purplish effect, or in slightly more sophisticated worlds fine optics where we worked with glued lens packets or, raising the bar, in the construction of lenses for telescopes and here we played with deposition in the liquid state or with sequential vacuum deposition in modest voids generated with multiple venturi pumps through flows with recycled truck oil fumes. Well here you had to open your brain to very different concepts. Luckily there was a vacuum system manufacturer with a technician who, in addition to providing a service, became my friend and this luck allowed me to go beyond a normal installation of the necessary equipment in our company. The deposition process had a duration including: waiting to reach the necessary vacuum of about 20 minutes, the process time to finish the evaporations of a few minutes and, finally, that of returning to atmospheric pressure. Thanks to these pauses of waiting, Gabriele (that was his name), between one explanation and another of the technology, became a friend and a precious teacher who I duzione di micro-grumoli durante l’evaporazione, originati da spari (i cosiddetti sputi) di materiale production” we carried out a series of tests and everything seemed to go in the right direction. The lenses were inspected visually, sometimes with the help of a magnifying glass in search of any defects originating from the process that had been added, for which we operated on new lenses, pre-inspected and judged perfect QC before the added procedural phase . In particular, it was feared that two phenomena could possibly intervene.

Lino Barbieri, consultant and great expert of ophthalmic lenses, has worked in national and international companies all over the world, in B2I, B2B, B2C. He currently works with L.O. V. oftalmica (Varese, Italy) as a technical/commercial consultant. Affable, curious and ironic, Lino helps us to better understand themes and problems related to the world of lenses.
Il processo della ricettazione era allora non solo noto, ma relativamente semplice; l’aggiunta però di un passo di processo, dove le unità di misura in gioco passavano dai decimi ai nanometri, costituiva indubbiamente una vera novità ed una necessità di modernizzazione delle conoscenze e degli impianti.
E, come se non bastasse, il passo comprendeva il dotarsi di macchinari di nuova generazione che stavano a quelli in uso come un coltello sta a un microtomo.
Si parlava di “deposizione sotto vuoto di film sottile formato da un sandwich multistrato di materiali a indici di rifrazione alternativamente alti e bassi ove all’interno si producesse una estinzione per una riflessione multipla di onde fuori fase di 180° … allo scopo di estinguere in modo efficace il riflesso generato dalle superfici della lente”. Definizione scientificamente chiara e concisa ma da far tremare le budella anche al più preparato esperto di ottica.
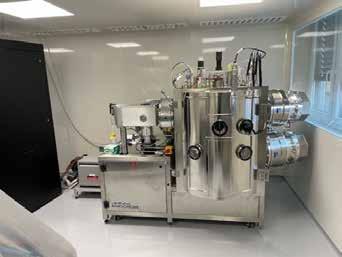
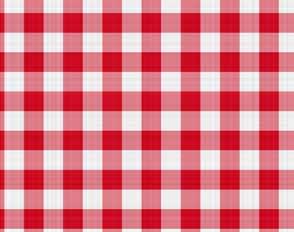


La faccenda era comunque nota anche negli anni ’30 per i trattamenti su lenti oftalmiche di vetro, dove bastava uno spruzzino di fluoruro di magnesio per avere una decente estinzione del riflesso ma con un orrendo effetto violaceo, oppure in mondi un po’ più sofisticati dell’ottica fine dove si operava con pacchetti di lenti incollate oppure, alzando il tiro, nella costruzione delle lenti per i telescopi e qui si giocava con deposizioni di vuoto sequenziali in vuoti modesti generati con pompe a venturi multipli mediante flussi con vapori di olio di camion riciclati. Ebbene qui si dovette aprire il cervello a concetti ben diversi.
Per fortuna ci fu un fabbricante di impianti per vuoto con un tecnico che, oltre a fornire un servizio, mi divenne amico e questa fortuna mi permise di andare oltre ad una normale installazione degli equipaggiamenti necessari nella nostra Azienda.
Il processo di deposizione aveva una durata comprendente: l’attesa di raggiungere il vuoto necessario di circa 20 minuti, il tempo di processo per terminare le evaporazioni di pochissimi minuti e, in coda, quello di tornare a pressione atmosferica. Grazie a queste pause di attesa, Gabriele (questo era il suo nome), tra una spiegazione e l’altra della tecnologia, divenne un amico ed un docente prezioso che ricordo volentieri anche per un avvenimento piuttosto comico che racconto volentieri. Finita l’installazione, le prove e le dovute correzioni, prima di “mettere in produzione” operammo una serie di test e tutto sembrava andare per il giusto verso. Le lenti si ispezionavano a vista, con l’aiuto talvolta di una lente di ingrandimento alla ricerca di eventuali difetti originati dal processo che era stato aggiunto, per cui si operava su lenti nuove, pre-ispezionate e giudicate perfette CQ prima della fase processuale aggiunta. In particolare, si temeva potessero eventualmente intervenire due fenomeni.
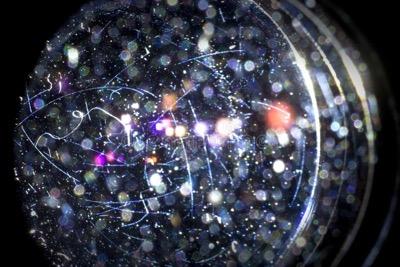
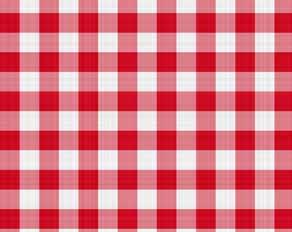
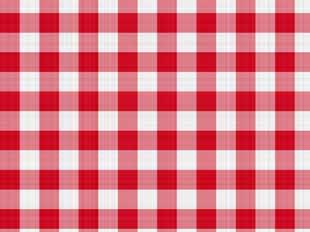

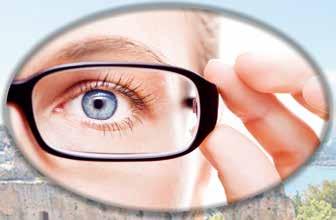
The first, that a sporadic production of microclumps occurred during evaporation, originating from shots (so-called spits) of evaporating material. Phenomenon which, with some molecules coagulated with others in forming the single layers, in supposedly uniform growth, would instead have generated some visible local non-uniformities. Pic. 3
The second, the cracking of some layers due to reciprocal tension due to the different expansion coefficient of the materials themselves which, by depositing one on the other and cooling down, at the border between one and the other, find themselves shrinking differently.
It should also be taken into account that this happens in a sequence of differently rigid layers because they are made up of various inorganic materials, more or less hard and of unequal thickness from each other and all of them resting on one side of a lens which is made of an organic material, soft and elastic and expandable by heat. Let me give you an example: a wall built on rammed earth, without foundations, of layers of bricks, then of stones, adding a few centimeters of cooked clay, then a little gravel mixed with a little cement and finally a final layer of bricks. Undoubtedly a nice mechanical instability!
But in the end all was well, perfect lenses, eliminated the white reflection of 4% per surface, the classic of lenses produced without antireflection coating, a beautiful greenish residue, perfectly centered on 530 nM in the measure of 1.2% per surface ...everybody was ready for the final toast ... except that I was, as I am even now, a “puzzler” by nature and I wanted to look under the microscope at the surface where we had noticed some specks, as if there was dust under the coating. It might actually have gotten dust on the lenses during the process. In fact, the filtering and evaporante. Fenomeno che, con qualche molecola coagulata con altre nel formare i singoli strati, in crescita supposta uniforme, avrebbe invece generato alcune disuniformità locali visibili. Il secondo, la rottura a crepe di alcuni strati dovuta alla tensione reciproca per il diverso coefficiente di dilatazione dei materiali stessi che, depositandosi uno sull’altro e raffreddandosi, alla frontiera tra uno e l’altro si trovano a restringersi differentemente. Occorre tener conto, inoltre, che ciò succede in una sequenza di strati differentemente rigidi perché costituiti da vari materiali inorganici, più o meno duri e di disuguale spessore uno dall’altro e tutti quanti appoggiati su una faccia di una lente che è di un materiale organico, morbido ed elastico ed espandibile al calore. Vi faccio un esempio: un muro costruito su terra battuta, senza fondazioni, di strati di mattoni, poi di sassi, aggiungendo qualche centimetro di argilla cotta, poi un po’ di ghiaietto impastato con poco cemento e per finire un ultimo strato di mattoni. Indubbiamente una bella instabilità meccanica!

Ma alla fine tutto bene, lenti perfette, eliminato il riflesso bianco del 4% per superficie classico delle lenti prodotte senza coating antiriflesso, un bellissimo residuo verdolino, perfettamente centrato sui 530 nM nella misura di 1.2% per superficie … tutti pronti al brindisi finale … eccetto che io ero, come sono anche ora, un “rompino” di natura e volli guardare al microscopio la superficie dove avevamo notato qualche puntinatura, come se ci fosse polvere sotto il coating. Avrebbe potuto in effetti essersi infiltrata durante il processo del- conditioning equipment had not yet been started up at that moment, waiting for the “go/no go” at the end of our tests la polvere sulle lenti. Infatti, le apparecchiature di filtraggio e di condizionamento non erano state a quel momento ancora avviate, attendendo il “go/ no go” alla fine dei test.
You should know that all vacuum evaporation machinery works in a class 100 clean room, much cleaner than an operating room. I wanted to understand the nature of that dirt, whether it had come from the pre-wash water or from the ambient air, which was of considerable importance to me. Gabriele, now sure of the process, snorted and put a cigarette in his mouth, throwing the pack at me. We went down the hall for a cup of coffee while waiting for the instrument to be set up with our tray of lenses to inspect. With the door of the refreshment room open onto the courtyard in a splendid spring day, he said to me, speaking the Lombard language: “Va là, amis, vedarèt che’l va tut ben” (Don’t worry, my friend, you will see that everything will be fine…).
A quarter of an hour later the lenses were under a microscope objective and I saw what I never wanted to see … a series of very fine parallel cracks, a typical case of a multiple fracture of surfaces by thermal tension which is opened and the subsequent cooling then closes it so that it is not visible to the naked eye but generates fogging due to diffraction of the invisible but efficient miniprisms of the fractures.
Horror and terror, with Gabriele openly declaring that this was only possible after years of using a lens. Me ranting at him saying that we had carried out the deposition at a too high temperature (actually we were talking about 80 degrees instead of 70). Gabriele who replied that if you don’t operate at 80 degrees the coating jumps off etc. etc. The evening came and the following morning, with a fresh mind, we resumed our investigation.
The first thing proposed, suggested by Gabriele, was to pre-inspect the lenses under a microscope, followed by my laughter which was the reaction to being convinced that my laboratory had a very high standard of process. But since I gave in to the credibility of his age, which also made wisdom and experience. Basically it was a matter of discovering “only” how, when, where and why the fractures were generated … On the final inspection of the new lenses with the naked eye nothing was visible, no cracks.
Dovete sapere che tutto il macchinario di evaporazione sotto vuoto lavora in una camera pulita classe 100, molto più pulita di una sala operatoria. Io volevo rendermi conto della natura di questo sporco, se fosse arrivato dall’acqua dei prelavaggi o dall’aria ambiente, cosa che per me aveva un’importanza notevole. Gabriele, ormai sicuro del processo, sbuffò e si mise una sigaretta in bocca, gettandomi il pacchetto. Andammo per un caffè in fondo al corridoio in attesa che lo strumento venisse approntato col nostro vassoio di lenti da ispezionare.
Con la porta della saletta ristoro aperta sul cortile di una splendida giornata di primavera mi disse “Va là, amis, vedarèt che’l va tut ben”.
Un quarto d’ora dopo le lenti erano sotto l’obiettivo di un microscopio e vidi quello che non avrei mai voluto vedere … una serie di crepature parallele finissime, tipico caso di una frattura multipla di superfici da tensione termica che viene aperta e il successivo raffreddamento la richiude poi in modo che non è visibile ad occhio nudo ma genera un appannamento dovuto a diffrazione degli invisibili ma efficienti miniprismi delle fratture. Orrore e terrore, con Gabriele che dichiarava apertamente che ciò non era possibile se non dopo anni di uso della lente.
Io che gli sbraitavo contro affermando che avevamo eseguito la deposizione a temperatura troppo elevata (si parlava in realtà di 80 gradi invece di 70).
Gabriele che replicava che se non si opera a 80 gradi il coating salta via ecc. ecc.
Si fece sera ed il mattino seguente, a mente fresca, riprendemmo l’indagine.
La prima cosa proposta, suggerita da Gabriele, fu di pre ispezionare le lenti al microscopio, seguita da una mia risata che era la reazione all’essere convinto che il mio laboratorio aveva uno standard di processo altissimo.
Ma cedetti alla credibilità della sua età, che faceva anche saggezza ed esperienza. In fondo si trattava di scoprire “solo” come, quando, dove e perché si generassero le fratture …
All’ispezione finale delle lenti nuove ad occhio
Under the microscope, same result. The honor of my laboratory was safe. We proceeded step by step through the process, which required a preliminary washing with water, ultrasonic cleaners, rinsing and dipping in demineralised water to avoid limescale dust and drying in hot air, all in an automatic system.
At the end of this, inspection with dry lenses after which the result was that the CR 39 lenses already showed cracks in that phase!!!
Panic… At this point I had a doubt and I took 4 pairs of “standard” lenses, those produced by polymerization of both sides without mechanical machining of the inner side and I passed them through the same process until the end of the washing. Surprise: the lenses were perfect, a few small comet-tail scratches, outside the 40 mm optical zone, in 2 or 3 of the 8 lenses and nothing more. Defects from scratched but unrelated molds.
What had happened? Indeed, what was happening in the process that we had been carrying out for several years, that nobody complained about?
Some explanation is in order.
For the experts or almost experts and for the old in nudo nulla era visibile, niente crepe. Al microscopio, stesso risultato. L’onore del mio laboratorio era salvo.
Procedemmo a passi lungo il processo, che richiedeva un lavaggio preliminare con acqua, detergenti in ultrasuoni, risciacqui e tuffo in acqua demineralizzata per evitare polverine di calcare ed asciugamento in aria calda, il tutto in un impianto automatico.
Alla fine di ciò, ispezione a lenti asciutte dopodiché il risultato fu che le lenti in CR 39 mostravano già in quella fase le crepe!!!
Panico … the trade I remind them that the first anti-reflection coatings were deposited on the bare lens, without a pre-treatment of a hardening resin on the surfaces to protect them from wear scratches and also providing a more elastic intermediate layer that cushioned the stresses.
A questo punto mi venne un dubbio e presi 4 coppie di lenti “di serie”, quelle prodotte per polimerizzazione di ambo le facce senza lavorazioni meccaniche del lato interno e le passai allo stesso processo sino alla fine del lavaggio.
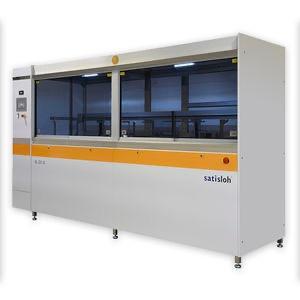
Sorpresa: le lenti erano perfette, qualche piccolo graffietto a coda di cometa, al di fuori dei 40 mm di zona ottica, in 2 o 3 lenti delle 8 e nulla più. Difetti da stampi graffiati ma non attinenti.
Cosa era successo? Anzi, cosa succedeva nel processo che eseguivamo da vari anni, di cui nessuno si lamentava? Qualche spiegazione è di dovere.
First point to note: at the end of the recipe back surface manufacturing process there was no need or benefit of ultrasonic cleaning. The prescription lenses, once processed and after cleaning at the end of the polishing in aluminum oxide and rinsing with a shower, were inspected for surface defects and possibly re-polished for a few tens of seconds.
Once free from defects, they were detached from the fixing block on the front surface, rinsed and dried again, then, their power measured, placed in a bag with pant (the classic scratch-proof protective paper) and shipped.
Second point to note: no one had ever cared about an examination under a microscope. Combining the first point with the abovementioned second point it was possible to derive a sensible reason for the defect and it was clearly demonstrated that a series of parallel scratches, due to the rubbing of aluminum oxide granules, which is a powder similar to talcum powder which is suspended in a liquid , was always present on the surface of the lenses especially if the pressures of the polishers, the polishing time and the granulometry of the oxide were not correct. But since the lens was washed without the aid of an ultrasound system which acts through the micro-cavitation of the water bubbles, the humid residue of the aluminum oxide was crushed into the micro-scratches and stuck in a row of granules along these scratches. of oxide which, once dried, no one could see and these scratches did not appear for years, occasionally making themselves visible in some areas but not to the naked eye but they did exist.
A good anti-reflection coating also makes everything more visible due to greater transparency, so here’s where a donkey fell, a friend fell and the two happily resumed their journey after taking appropriate measures!
Gabriele, if you were still here among us we would laugh together about our adventure, when we combined your experience and my exaggerated
Per gli esperti o quasi esperti e per i vecchi del mestiere ricordo che i primi coating antiriflesso venivano depositati sulla lente nuda, senza un pre trattamento di una resina indurente sulla superficie per preservarla dai graffi di usura e fornendo anche uno strato intermedio più elastico che ammortizzasse gli stress.
Primo punto da annotare: alla fine del processo di lavorazione della superficie posteriore delle ricette non esisteva bisogno o vantaggio di un lavaggio ad ultrasuoni.
Le lenti di ricetta una volta lavorate e dopo una pulitura alla fine della lucidatura in ossido di alluminio e un risciacquo con una doccetta venivano ispezionate per difetti di superficie ed eventualmente rilucidate per qualche decina di secondi. Una volta esenti da difetti, venivano staccate dal blocchetto di fissaggio sulla superficie anteriore, ancora sciacquate ed asciugate, indi, misurato il loro potere, messe in una bustina con mutanda (quella classica cartina antigraffio di protezione) e spedite.
Secondo punto da annotare: di un esame al microscopio nessuno si era mai curato.
Unendo il primo punto al predetto secondo punto si poté derivare una ragione sensata del difetto e si dimostrò chiaramente che una serie di graffi paralleli, dovuti allo strofinio dei granuli di ossido di alluminio, che è una polverina simile al borotalco che è sospeso in un liquido, era sempre presente sulla superficie delle lenti soprattutto se le pressioni delle lucidatrici, il tempo di lucidature e la granulometria dell’ossido non erano corretti.
Ma essendo la lente lavata senza l’ausilio di un impianto ad ultrasuoni che agisce tramite la microcavitazione delle bolle d’acqua, il residuo umido dell’ossido di alluminio veniva spappolato nei micrograffi e lungo questi graffi si incastrava in una fila di granuli di ossido che, una volta asciugato, nessuno più poteva vedere e questi graffi non si manifestavano per anni, rendendosi visibili occasionalmente in alcune zone ma non ad occhio nudo ma peraltro esistevano.
Un buon coating antiriflesso inoltre rende tutto più visibile per la maggior trasparenza, ecco quindi dove cascò un asino, fece cascare un amico e i due ripresero il cammino in allegria dopo aver preso opportuni provvedimenti!
Gabriele, se tu fossi qui ancora tra noi rideremmo perfectionism to set up the first and (I say) the best coating plant.
To this first experience we added, the following year, an intermediate treatment between lens processing and AR coating, by interposing a hardening lacquer developed in Japan by our Company, consequently launching on the market a unique lens and for years never surpassed in quality, on the pouch and on the advertisement featured a strawberry with two halves, one scratched and one undamaged, and the name of the coating that became famous: UTMC, Ultra Tough Multi Coat.
Thank you Gabriele, even if only with my memory.
Read me again, coming back soon … simply yours assieme dell’avventura, quando unimmo la tua esperienza ed il mio esagerato perfezionismo a mettere in piedi il primo e (io dico) il migliore impianto di coating.
A questa prima esperienza aggiungemmo, l’anno seguente, un trattamento intermedio tra Lavorazione della lente e AR coating, interponendo una laccatura di indurimento sviluppata in Giappone dalla nostra Azienda, lanciando sul mercato una lente unica e per anni mai superata in qualità; sulla bustina e sulle réclame campeggiava una fragola con due metà, una graffiata ed una indenne ed il nome del coating che divenne famoso: UTMC, Ultra Tough Multi Coat.
Grazie Gabriele, anche se solo col mio ricordo.
A rileggerci, torno presto… semplicemente vostro.
Alcon has partnered with Plastic Bank, a Canadian company whose mission is to clean up the world’s oceans and waterways of plastic. Alcon and Plastic Bank have devised an environmental offset program that involves removing one ton of plastic from the oceans for every ton of plastic Alcon uses in the production of PRECISION1™ and DAILIES TOTAL1™ contact lenses and blisters.
The initiative involves more than 90 countries.
Alcon ha stretto una partnership con Plastic Bank, società canadese la cui missione è ripulire dalla plastica gli oceani e i corsi d’acqua del mondo. Alcon e Plastic Bank hanno ideato un programma di compensazione ambientale che prevede la rimozione di una tonnellata di plastica negli oceani per ogni tonnellata di plastica che Alcon impiega nella produzione delle lenti a contatto e dei blister PRECISION1™ e DAILIES TOTAL1™.
L’iniziativa coinvolge più di 90 Paesi.
Marcolin and Harley-Davidson have extended their worldwide eyewear licence agreement until 31 December 2027. The new agreement will now also include Performance and Protective sunglasses, designed to be worn by motorcyclists. The partnership was established in 2013 following Marcolin’s acquisition of Viva International.
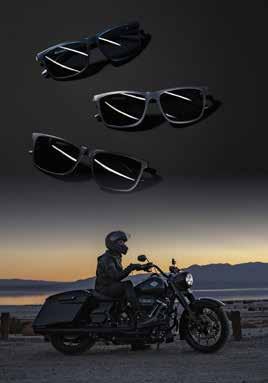
To respond to the needs of today’s children, Centro Style has announced a partnership with Optikid, the optical centre in Rome known to be one of the most authoritative on the subject of children on the national scene.
From the sharing of reciprocal experience and professionalism, new Active Frames models will be created, as well as awareness and communication projects for both the optical market and families.
Centro Style’s Research & Development team will be joined by Francesca Benedetti of Optikid who, in addition to the creation of new products, will contribute her experience to the development of branding projects.
Per rispondere alle esigenze dei bambini di oggi, Centro Style ha annunciato una partnership con Optikid, il centro ottico di Roma noto per essere uno dei più autorevoli sul tema bambino nel panorama nazionale.
Dalla condivisione delle reciproche esperienze e professionalità, nasceranno nuovi modelli Active Frames oltre a progetti di sensibilizzazione e di comunicazione sia per il mercato dell’ottica che per le famiglie.
Il team di Ricerca&Sviluppo di Centro Style verrà affiancato da Francesca Benedetti di Optikid che, oltre alla realizzazione di nuovi prodotti, contribuirà, con la sua esperienza, allo sviluppo di progetti di branding.
Marcolin e Harley-Davidson hanno esteso l’accordo mondiale di licenza eyewear fino al 31 dicembre 2027. Il nuovo accordo comprenderà ora anche gli occhiali da sole Performance e Protective, progettati per essere indossati dai motociclisti. La partnership era nata nel 2013 in seguito all’acquisizione di Viva International da parte di Marcolin.
The Horace in Cadillac frame, a signature piece in the Centena Collection by Kirk & Kirk, has been nominated for the Men’s Frame of The Year at the Love Eyewear Awards which take place at 100% Optical at Excel, London in February. This model is hand-crafted in France from 10mm acrylic so, despite the chunky appearance, weighs virtually nothing and is extremely comfortable to wear.
La montatura Horace in Cadillac, pezzo forte della collezione Centena di Kirk & Kirk, è stata nominata montatura maschile dell’anno ai Love Eyewear Awards che si terranno a febbraio presso 100% Optical all’Excel di Londra. Questo modello è realizzato a mano in Francia in acrilico da 10 mm e, nonostante l’aspetto massiccio, non pesa praticamente nulla ed è estremamente comodo da indossare.
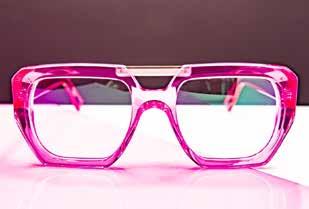
Fielmann Group has acquired 100 per cent of the share capital in the retail, wholesale and manufacturing activities of MFI Group, a leading optical and acoustic company in northern Spain.
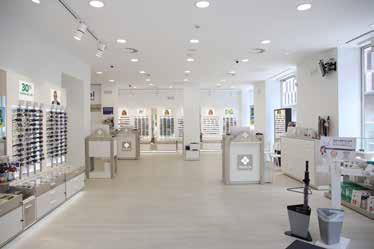
MFI Group operates three business divisions: with 19 retail shops and one online shop, Medical Óptica Audición is the market leader in the Basque Country and one of the leading suppliers of optical and acoustic products in northern Spain. The company also runs its own workshop for processing optical surfaces and lenses and the production of personal protective equipment (PPE). MFI had revenues of €35 million in 2021 and employed 285 employees.
Fielmann Group ha acquisito il 100% del capitale azionario nelle attività di vendita al dettaglio, all’ingrosso e di produzione di MFI Group, azienda leader nel settore ottico e acustico nel nord della Spagna.
MFI Group gestisce tre divisioni aziendali: con 19 negozi al dettaglio e un negozio online, Medical Óptica Audición è leader di mercato nei Paesi Baschi e uno dei principali fornitori di prodotti ottici e acustici della Spagna settentrionale. L’azienda gestisce anche un proprio laboratorio di lavorazione di superfici e lenti ottiche e la produzione di dispositivi di protezione individuale (DPI). MFI nel 2021 ha avuto ricavi per €35 milioni e impiegato 285 dipendenti.
The De Rigo Group and Twinset S.p.A., owner of the homonymous Italian brand of women’s clothing active in the contemporary luxury sector, announced a worldwide license agreement for the design, production and distribution of Twinset Milano-branded optical frames and sunglasses. The first collection designed will be available from March 2023, by way of the De Rigo distribution network and Twinset Milano boutiques.

Il Gruppo De Rigo e Twinset S.p.A., società titolare dell’omonimo marchio italiano di abbigliamento femminile attivo nel settore del lusso contemporaneo, hanno annunciato un accordo di licenza mondiale per il design, la produzione e la distribuzione di montature da vista e occhiali da sole a marchio Twinset Milano
La prima collezione sarà disponibile a partire da marzo 2023 attraverso la rete distributiva di De Rigo e presso le boutique Twinset Milano.
Alessio Puleo, in Marcolin since 2021, is the new Group Marketing Director of the Group.

Reporting directly to CEO & General Manager Fabrizio Curci, Alessio will be in charge of the Group Brand Management and Trade Marketing & Training areas and of Marketing Analysis activities.
He will lead the development of the Marketing department to accelerate the growth of the brand portfolio globally in line with the Group’s guidelines and strategies.
Alessio Puleo, in Marcolin dal 2021, è il nuovo Group Marketing Director del Gruppo.
A diretto riporto del CEO & General Manager Fabrizio Curci, Alessio sarà responsabile delle aree di Group Brand Management e Trade Marketing & Training e delle attività di Marketing Analysis.
Guiderà lo sviluppo del dipartimento Marketing, per accelerare la crescita del portafoglio marchi a livello globale in coerenza con le linee guida e le strategie del Gruppo.
Since the beginning of the year Daniela Poletti has become Head of Marketing at Rodenstock Italia, reporting directly to General Manager Massimo Barberis. Poletti has an important seniority in the industry: after a degree in Political Science and a series of master’s degrees, in 1996 she started working in the Italian market at Hydron Biocompatibles. In 2002 she joined CooperVision and at the end of 2013 moved to Optocoop Italia-Oxo, bringing her expertise to the retail world.
Da inizio anno Daniela Poletti è Head of Marketing di Rodenstock Italia, a riporto diretto del General Manager Massimo Barberis. Poletti ha una seniority importante nel settore: dopo la laurea in Scienze Politiche e una serie di master, nel 1996 comincia a occuparsi di questi temi per il mercato italiano in Hydron Biocompatibles,. Nel 2002 entra in CooperVision e a fine 2013 passa in Optocoop Italia-Oxo, portando le sue competenze anche nel mondo del retail.

Schalcon (a company of the Omisan Group), closes 2022 brilliantly with a 30% increase in sales compared to 2021. Thanks to major commercial and image investments, Schalcon is now an Italian centre of excellence for contact lenses and ocular well-being, a reference point for opticians and optometrists. The company is expanding its sales force with new single-handed agents, particularly in the regions of Northeast Italy, Lazio and Rome.
Schalcon (azienda del Gruppo Omisan), chiude brillantemente il 2022 con un +30% delle vendite rispetto al 2021. Grazie ad importanti investimenti commerciali e di immagine, Schalcon è oggi un polo di eccellenza italiano per la contattologia e il benessere oculare, punto di riferimento per ottici e optometristi. L’azienda sta ampliando la sua forza vendita con nuovi agenti monomandatari, in particolare nelle regioni del Nord Est Italia, nel Lazio e nella città di Roma.
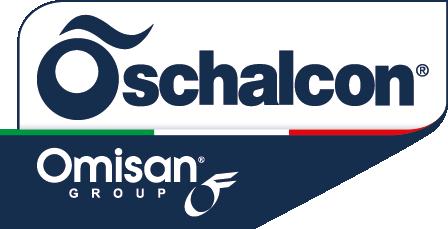
Italy-based Franco Sordelli has entered into a distribution agreement with the Belgian eyewear company DMB managed by Patrick Deforche aiming at distributing the SNOB Milano collections to opticians across The Netherlands in addition to Belgium. A long-running partnership today expanding furthermore as DMB is distributing SNOB Milano in Belgium since 2016.
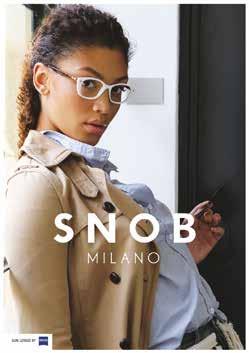
L’azienda italiana Franco Sordelli ha stipulato un accordo di distribuzione con l’azienda belga di occhiali DMB, gestita da Patrick Deforche, per distribuire le collezioni SNOB Milano agli ottici dei Paesi Bassi oltre che del Belgio. Una partnership di lunga data che oggi si espande ulteriormente, visto che DMB distribuisce SNOB Milano in Belgio dal 2016.
Two brands with a strong Italian identity and a commitment to high-end design have joined forces: Retrosuperfuture has announced its latest licensing partnership with the iconic Italian sportswear brand Briko The new Briko eyewear collection takes into account not only high-level technical performance, but also the extension of sport into the everyday lifestyle.
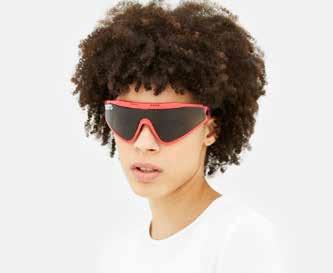
Due marchi con una forte identità italiana e l’impegno per un design di alto livello hanno unito le forze: Retrosuperfuture ha annunciato la sua ultima partnership di licenza con l’iconico marchio italiano di abbigliamento sportivo Briko La nuova collezione di occhiali Briko tiene conto non solo delle prestazioni tecniche di alto livello, ma anche dell’estensione dello sport allo stile di vita quotidiano.
Another record year for the Zeiss Group in all group segments. Sales grew by 16 % to EUR 8.8 billion (previous year: EUR 7.5 billion) in the fiscal year 2021/22.
The Vision Care division recorded growth in all countries, in particular due to ZEISS-branded lenses, innovative technologies and optical centre instrumentation, closing with sales of EUR 1.39 billion.
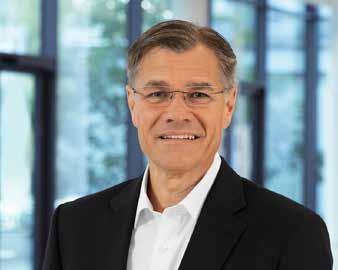
Un altro anno record per il Gruppo Zeiss in tutti i segmenti del gruppo. Il fatturato è cresciuto del 16%, raggiungendo gli 8,8 miliardi di euro (anno precedente: 7,5 miliardi di euro) nell’anno fiscale 2021/22.
La divisione Vision Care ha registrato una crescita in tutti i Paesi, in particolare grazie alle lenti a marchio ZEISS, alle tecnologie innovative e alla strumentazione per il centro ottico, chiudendo con un fatturato di 1,39 miliardi di euro.
Advertisers
Publisher
Edizioni Ariminum Srl
Via Negroli 51/A - 20133 Milano Italy www.vedere.it – welcome@vedere.it
Tel.+39/02.73.00.91 r.a.
Publishing Director
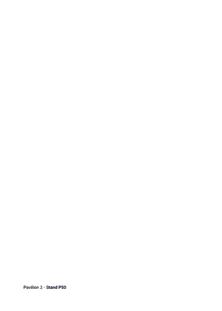
Isabella Morpurgo – isabellamorpurgo@vedere.it
Advertising
Gloria Della Ciana – marketing@vedere.it
Adv/Editorial Coordination
Rita Ferraro – ritaferraro@vedere.it
Editorial Staff
Manlio Valli – communication@vedere.it
Layout
Enrico Alvarez – graphic@vedere.it
• The journal publishes articles and releases from individual authors or firms. Publishing this material does not involve the journal’s opinion or liability.
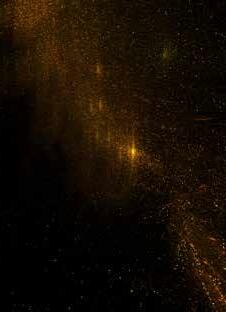
Autorizzazione Tribunale di Milano del 23-03-1991 N. 221
Associata a A.N.E.S. Associazione
Editoria Periodica Specializzata
• Reproduction without written express authorization of the publisher is prohibited.