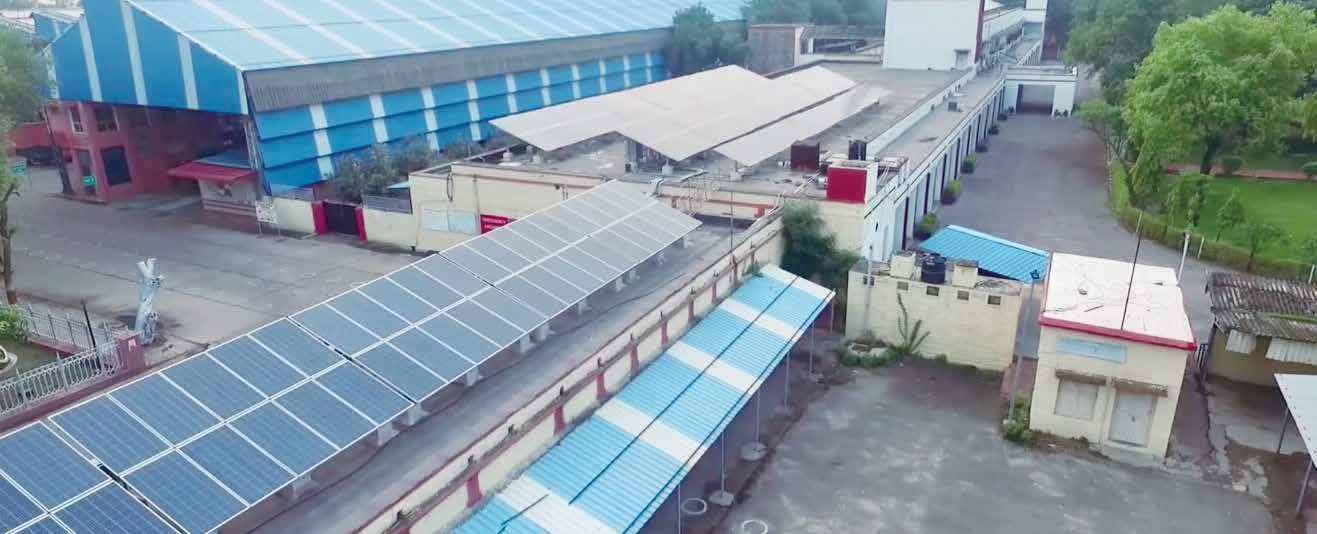
4 minute read
WAGON REPAIR SHOP KOTA, RJ
Gold wAGOn repAIr shOp kOTA, rAjAsThAn
About the workshop
Advertisement
Wagon Repair Workshop, (WRS) Kota was established in November 1957. The workshop was set up for undertaking the periodic overhauling (POH) of Tank wagons with an initial capacity of 250 FWU per month. The workshop capacity has since been augmented & developed and over a period of time and now the workshop has an outturn of 500 wagons per month. This workshop has been the pioneer in overhauling LPG wagon and is only workshop over Indian railway to maintain BTPGLN wagons. WRSKota workshop is IMS certified with IMS certification consisting of IMS (ISO 9001, ISO 14001, ISO 45001 & ISO 50001), ISO 3834 certification for Welding and 5S for workplace Management.
Wagon Repair Shop, Kota is the only organization on West Central Railways to achieve GreenCo Gold Rating. The entire process of getting this recognition made us more aware towards achieving a more environmentally sustainable unit and work systems. Team WRS is thankful to the entire team of CII for their constant encouragement, support and guidance for this wonderful learning experience. manish Kumar Gupta, Chief Workshop Manager
Key Achievements
1. 30% energy substitution and carbon foot print saving by 576 MT per annum has been ensured by using 500 KWp renewable solar power plant.
2. 3. 100% provision of LED lights replacing conventional lights. Natural illumination increased by proving transparent sheets at roof top on shop floors.
4.
5. Introduction of Lock Bolting system in place of traditional riveting method Conventional EOTs replace with VVVF drive operated EOT and provision of energy saver in all welding plant. 6.
7.
8.
9.
100% recycle / Reuse of packing material. The benefit of this is reduction in waste generation and prevention of resources. 100% ETP treated water is used in gardening and wagon process. STP treated water used for Hydraulic testing, steam cleaning and gardening. Implementation of Digital tools such as E-office, HRMS, IMMS thereby reducing use of paper to a great extent. 100% recycling of entire scrap generated. 10. DA consumption was 88% in 2017-18 and it is decreased to 36% in 2020-21 by using CNG System and Plasma Arc Cutting process and reduce Carbon foot print by 264 TCO2e.
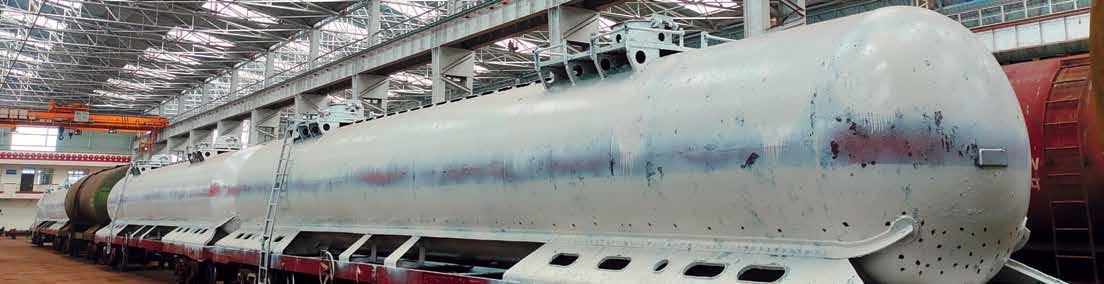
Innovation
environmental friendly Cleaning of Cartridge taper roller Bearing
Cleaning of CTRB (Cartridge Taper Roller Bearing) was earlier done manually through kerosene. Now with a new CTRB cleaning plant this activity is now been automated. Cleaning is now done with the help of environmental friendly chemicals. The other advantages of this are: y High degree of cleanliness compared to manual cleaning. y Saving of kerosene Approx 42000 KL per annum equivalent to 110 TCO2e. y Less land contamination as no oil spillage. y Treatment facility of water through in built ETP.


Energy Efficiency
y Use of Plasma cutting machines in place of conventional Oxy cutting. y 100% Replacement of LED light fittings in place of conventional light fittings and BLDC fans provided in place of conventional fans. y Natural illumination has been increased by provided transparent sheet at roof top of shops. y All screw compressors have been replaced with energy efficient reciprocating type Air Compressors. y Conventional EOTs have been replaced with VVVF drive operated EOTs. y 100% Provision of energy savers in all welding plants. y Riveting work replaced with Huck bolting. y Provision of Automatic Power factor controller at substation y 500 KWp solar power plant has been installed which meets 30% of total Electrical Energy demand.
Green Supply Chain
y Motivated the local vendors for environment prevention by vendor awareness program and vendor recognisation program. y Use of Integrated Material Management System for real time information availability of regular stock, y Implemented Used Depot Module to make sure that issue and receipt of material is real time, transparent and paperless. y Consumption of raw / consumable material decreased due to recycling of reclaimed material. y Motivated the outstation vendors mostly operating from Eastern part of india for clubbed supply and use of environment friendly vehicles.
Waste management
y Waste oil release from ETP/CTRB/other process used as alternative fuel for firing furnace in Smithy Shop. y Disposal of released grease for lubrication of railway tracks y Segregation and selling of ferrous & non ferrous waste before their auction through store department. y Sewage / effluent treated water reused in workshop in processes and gardening.

Water Conservation
y One Rain Water Harvesting System having annual water harvesting potential of approx 4975 KL and rain water harvesting work for all shop / sheds under construction after this WRS will meet 96% of total potential (i.e. 65341 KL) y Strictly maintaining Zero discharge policy. y STP water is used for hydraulic testing of tank wagons and
ETP water is being used for plantation and roof leakage testing of covered wagons. y 100 KL water tank made for recycling of spilled water at the time of Hydraulic testing of BTPGLN / BTPN wagons. y Water metering arrangement have been ensured on all end user points by providing 23 new water meters at various locations for close monitoring. y One in-built ETP is there in CTRB cleaning plant aimed at reduction of fresh water consumption
Contact: mr. manish Kumar Gupta, Chief Workshop Manager New Railway Colony, Railway Station Area, Kota - 324002, RAJASTHAN Phone: 9001017450 | Email: cwmkota@gmail.com
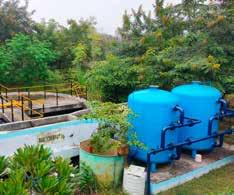
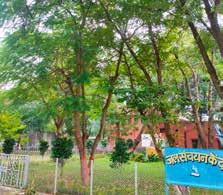