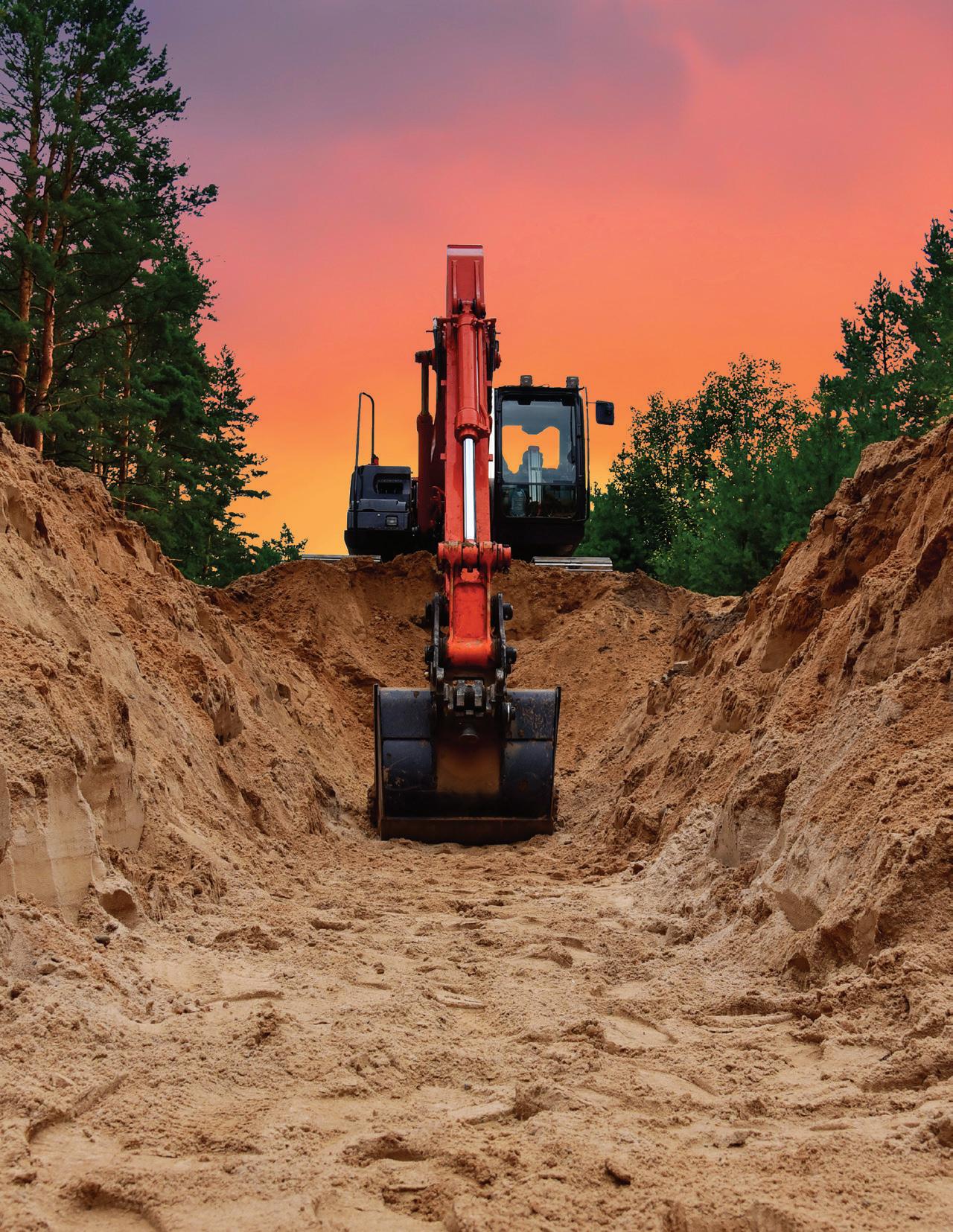



As VPPPA approaches its 39th year this September, we’re reminded that our Association, much like our profession, has evolved to meet the needs of workplace safety and health. Our understanding of how the interplay of technology, processes, and even culture, affect continuous safety improvement has grown to help usher in what some (especially VPP sites) might call the “enlightened age” of workplace safety.
As Chairperson of VPPPA’s Board of Directors, I’m fortunate to have the opportunity to work alongside dedicated volunteer leaders representing the very best of our industry. Each member of our board recognizes the role that they play in helping VPPPA advance health and safety excellence. That’s why, when the board convened in Charlotte last October to begin laying the groundwork for VPPPA’s next strategic plan, our diverse group of safety professionals began with this simple question:
What is VPPPA’s mission?
Or, to put it another way, has VPPPA’s mission—the what, how, and why that defines VPPPA—evolved with the times?
After much (occasionally spirited) discussion, the consensus was this: VPPPA’s core mission is still the same as it was at that first meeting back in September of 1985, and indeed, the same as the Voluntary Protection Programs themselves—to save lives. However, the Association has grown and evolved to represent a broader audience beyond VPP sites— an audience of companies and sites, suppliers and safety professionals, united behind a singular concept:
Advancing health and safety excellence through collaboration, mentorship, and education to raise the standard for a safe and healthy workplace.
And thus, VPPPA’s new mission statement was born.
It’s a statement that recognizes the origin of the VPP and the Association while helping define what we do, how we accomplish it, and, most importantly, our continuing goal.
We are better together!
—Terry Schulte, Chairman—National VPPPA Board of Directors
VPPPA’s core mission is still the same as it was at that first meeting back in September of 1985 and, indeed, the same as the Voluntary Protection Programs themselves— to save lives.
While the safety industry is still a male-dominated industry, the number of women is increasing each year. It’s important to identify and communicate the issues that women face. In each issue of the Leader, we will be including an article from a prominent woman working in the safety and health industry. If you, or someone you know, would like to write for this column, please contact VPPPA at communications@ vpppa.org
Leah Beckworth, CSP, STSC, MS, UCOR Industrial Safety Manager Stephanie Miller, CSP, CIH, STS, MS, UCOR Safety Systems Integration ManagerHi, we are Leah and Steph. A long time ago, unbeknownst to each other, we went to the same college a couple years apart. We both even studied in the same Occupational Safety and Health Department, and both held the position of lead graduate assistant. Upon graduation, Leah moved to Washington State to work. After several years she moved to Tennessee. Right around then Steph graduated and what do you know—she moved to Washington State to work. A couple moves later Steph also landed in Tennessee. As the tale goes, Steph went to work where Leah once worked, but had since left. It’s a great company called UCOR. So great in fact, that Leah’s husband worked there. Steph and he worked together. Leah and Steph knew of each other and their common school and work lineages, but still the two had never met. As time progressed Leah missed UCOR and returned. So, finally in January of 2019, Leah and Steph met. The rest is history, and the story has a happy ending. We became best friends, and so are our kids. Leah has two little boys. Steph has two little girls— ages 6, 6, 5, and 3.
In life, we are blessed to support each other as both coworkers and moms. It’s quite fun, really. At 3:00 p.m.
we may be in a work meeting talking about industrial hygiene sampling, by 6:00 p.m. we are at the ball fields cheering on our kiddos, and certainly by 7:00 p.m. we are playing post game freeze tag, where Steph will inevitably wipe out while dodging Leah’s oldest, who is quite fast.
Life is crazy and wild, and we navigate it together as members of the same tribe. As working moms, we balance a lot, and because of that skill set, we are unquantifiable
worlds even collide. Tuck a kiddo into bed, log onto the computer to review a report, throw a load of towels in the dryer, and do all of this while mentally preparing for a big meeting in the morning. Creative problem solving is a mom’s specialty. This can take on many forms both at home and at work. At home we must figure out how to create “crazy pants day” at 9 pm because the school sent out a late-in-the-day email about this “fun event
in value. We dialogue about being working moms often and recently sat down together and brainstormed our top 10 list that working moms are prone to offer an organization. However, before we go into our list (which is in no particular order) we want to make it clear that we do not negate the value of working dads or others in various stages of life; we simply are not writing from their perspective today.
Working moms can prioritize and reprioritize as needs arise while never letting anything drop. We do this at home. We do this at work. Sometimes the two
for the kids.” Hand us a hot glue gun, yarn, scissors, and we will scavenge for other random household items to create crazy pants the likes of which Amazon has never seen. At work, creative problem solving may manifest as thinking outside the box about how to create or implement a new idea. Or when someone says it “can’t be done,” creative problem-solving finds three alternative ways to overcome the hurdle. Failure is not an option. As moms, we will move heaven and earth to not fail our
As working moms, we balance a lot, and because of that skill set, we are unquantifiable in value.
children. This becomes part of the DNA of motherhood. It infiltrates into work as well. Give a mom a deliverable that seems near impossible and in lightning speed she will assemble a team, create a plan, and deliver the results before the deadline. She will do all this and remember to send cookies to school for the 36th school party of the year.
Moms are communicators. We have to be so our kids remember to pick up their socks, brush their teeth, wash their hands, and not forget their coats. The same skillset applies to work. Communication is key to success. Communication is the art of strategically understanding what you want to convey, how you will convey it, ensuring it was well received and if needed, inspiring others into action. After all, if you can make a 3-year-old eat cucumbers and peppers, you can do anything.
Let’s face it—our kids can be little puzzles and so can our team members. When it comes to figuring them out, moms have superpowers. A mom’s skillset helps her put the pieces together to optimize the team. She easily discerns what each team member is good at, what motivates them, what type of support is needed for their success, and what their unique attributes bring to the table.
As moms, our primary parental responsibility is to guide our tiny humans, so they blossom into independent contributors to society. We do this by exposing them to
new opportunities and experiences. They may even struggle at first, but we provide them the support, tools, and knowledge to persevere. And once they do, we celebrate their success. We bring this to our employees as well when we see opportunities for growth, they may not see in themselves. We see them through it. We arm them with tools. We cheer them on. We celebrate their successes. Admittedly, once one becomes a mom, it can be hard to turn it off. Mothering forever will be a part of a woman’s identity after having children. We bring this nurturing trait to work with our routine checkins on our team’s wellbeing and the occasional homecooked goodies. It makes our work family feel like well, family. Managing the business of day-to-day morning routines, sports games, dance practices, work schedules, school events, and birthday parties demands a well-organized plan of attack. We stay three steps ahead. We prepare meals in advance, pack duffle bags of sports gear and favorite stuffed animals to stay ahead, and we identify who is responsible for each leg of transportation. In the workplace, we seamlessly plan the work and work the plan while maintaining the flexibility necessary to adjust at a moment’s notice. If coordination and logistics were a superpower, we would have it.
Whether we experience a sudden change in the baseball game schedule or
a tot that wants to test out their negotiation skills, moms must be quick to adjust and evaluate all courses of action to identify the best path forward. In milliseconds, she can assess the adjustments that must be made to the carpool or identify where to draw the line on the size of the afterdinner treat. She takes a quick and balanced approach to charting a winning path forward for all involved; a skill that translates well in the workplace to balancing what is good for the company as a whole and what is good for the individuals and work groups she supports. For our tenth and final item on the list, working moms are results oriented. Whether at home or at work, they understand the importance of the bottomline outcomes for critical items—Did we coordinate all the necessary pieces to get the school project done on time? Did we find a way to motivate all the youngsters to willingly participate in the fun activity we have been planning for weeks? Did the work crew accomplish its goal of seamlessly rolling out a newly developed program to the company?
Moms know that a solid communications plan, paired with a robust execution strategy, is a recipe to achieve any goal.
To sum it up, with the mothering tendencies that cross over into the workplace, working mothers can not only make their teammates feel cared for and valued, but they can elevate the performance of individuals and the collective. The diversity of thought and skill they bring is a desirable compliment to their occupational aptitude. We end this column with a final thought on partnership. We couldn’t be the moms or workers we are without a robust support network. This includes family members, friends, the community, and our work families. Historically, working moms have not always had an easy journey. Some felt they had to choose between their kids and their job. A little employer support and flexibility goes a long way in aiding moms like us to be our best selves, which ultimately pays dividends on what we can accomplish with our teams at work and at home. We are thankful that companies like ours recognize the need for flexibility and partner with us to ensure our success. After all, in the end, we won’t let anyone down—a mom never does!
With the mothering tendencies that cross over into the workplace, working mothers can not only make their teammates feel cared for and valued, but they can elevate the performance of individuals and the collective.
MEASURES AIM TO REVERSE THE RISE OF TRENCH-RELATED FATALITIES
Through the end of November 2022, 35 workers had fallen victim to deadly trench collapses—more than double the number in all of 2021.
Every one of these tragedies could have been prevented had employers complied with Occupational Safety and Health Administration standards. There simply is no excuse for ignoring safety requirements to prevent trench collapses and cave-ins, and leaving families, friends, and co-workers to grieve when the solutions are so well-understood.
In a matter of seconds, workers can be crushed and buried under thousands of pounds of soil and rocks in an unsafe trench. The alarming increase in the
controlled when employers act responsibly, train employees and follow federal standards.
In keeping with our National Emphasis Program on trenching and excavation, from January 1 through December 2, 2022, OSHA compliance officers conducted 1,975 inspections nationwide where they stopped at, and inspected, excavation sites during their daily duties. During this time, approximately 1,500 citations were issued for violations of OSHA’s trenching and excavation standards. States that operate their own Occupational Safety and Health plan have similar emphasis programs in place.
These actions place additional emphasis on how agency officials evaluate penalties for trenching- and
In the past six months, OSHA has conducted nearly 600 compliance assistance activities involving trenching, reaching about two million people. Compliance assistance specialists and safety and health officers have spoken at various events nationwide, sharing information on trenching and excavation hazards to contractors, builders, excavators, and workers, as well as fire departments and academies, and public utilities. We have and will continue to conduct outreach programs, including safety summits, in all of our 10 regions to ensure any employer who wants assistance gets it. The stakes are too important. OSHA is calling on all employers engaged in trenching
number of workers needlessly dying and suffering serious injuries in trenching incidents must be stopped.
Recent incidents in Texas and Indiana highlight the dangers of trenching. On Nov. 17, 2022, a worker in Anna, Texas, installing new sewer lines was fatally injured after a portion of a 30-foot-deep excavation collapsed. On Nov. 28, 2022, a 22-year-old working with a team to move water and sewer lines in Clarksville, Indiana, was trapped when a trench collapsed. Though rescued, the worker later died at the hospital.
Workers do not have to suffer serious and fatal injuries when performing trenching and excavation operations. Trenching hazards can be
excavation-related incidents, including criminal referrals for federal or state prosecution to hold employers and others accountable when their actions or inactions kill workers or put their lives at risk.
To help the agency stay informed about trenching hazards, 30 OSHA compliance officers and enforcement staff participated in a training program in December 2022 in Crosby, Texas, at the International Union of Operating Engineers (IUOE) National Training Fund training center. During this course, OSHA learned from IUOE instructors about the hazards that they experience during trenching and excavation activities.
and excavation activities to act immediately and maintain efforts to ensure required protections are fully in place every single time their employees step down into or work near a trench.
We urge workers to contact their local OSHA or state plan office, or call 800-321-OSHA, if their employer requires working in or beside trenches that are not sloped, shored, or shielded and are five or more feet in depth, or if you are reading this article and know of or see worksites performing unsafe trenching activities.
OSHA stands ready to assist any employer who needs help with complying with our trenching and excavation requirements
OSHA is calling on all employers engaged in trenching and excavation activities to act immediately and maintain efforts to ensure required protections are fully in place every single time their employees step down into or work near a trench.
U.S. Department of Labor
July 14, 2022
Alarming rise in trench-related fatalities spurs U.S. Department of Labor to announce enhanced nationwide enforcement, additional oversight
WASHINGTON—In 2022’s first six months, 22 workers have fallen victim to the deadly hazards present in trenching and excavation work— surpassing 15 in all of 2021—and prompting the U.S. Department of Labor’s Occupational Safety and Health Administration to launch enhanced enforcement initiatives to protect workers from known industry hazards.
To stress the dangers of disregarding federal workplace safety requirements for trenching and excavation work, OSHA enforcement staff will consider every available tool at the agency’s disposal. These actions will place additional emphasis on how agency officials evaluate penalties for trenching and excavation related incidents, including criminal referrals for federal or state prosecution to hold employers and others accountable when their actions or inactions kill workers or put their lives at risk.
In keeping with its National Emphasis Program for excavations, OSHA compliance officers will perform more than 1,000 trench inspections nationwide where they may stop by, and inspect, any excavation site during their daily duties.
“The Occupational Safety and Health Administration is calling on all employers engaged in trenching and excavation activities to act immediately to ensure that required protections are fully in place every single time their employees step down into or work near a trench,” said Assistant Secretary for Occupational Safety and Health Doug Parker. “In a matter of seconds, workers can be crushed and buried under thousands of pounds of soil and rocks in an unsafe trench. The alarming increase in the number of workers needlessly dying and
suffering serious injuries in trenching incidents must be stopped.”
“Every one of these tragedies could have been prevented had employers complied with OSHA standards,” Parker continued. “There simply is no excuse for ignoring safety requirements to prevent trench collapses and cave-ins, and leaving families, friends and co-workers to grieve when the solutions are so well-understood.”
A recent incident in central Texas highlights the dangers of trenching and an impetus for OSHA’s action. On June 28, 2022, two workers, aged 20 and 39, suffered fatal injuries in Jarrell, Texas, when the unprotected trench more than 20 feet deep collapsed upon them as they worked. Trench shields, which could have saved their lives, sat unused beside the excavation.
Trenching and excavation operations require protective systems and inspections before workers can enter. When employers fail to install trench protection systems or properly inspect the trench, workers are exposed to serious hazards, including risk of being buried under thousands of pounds of soil. By some estimates, a cubic yard of soil can weigh as much as 3,000 pounds, equal to that of a compact car.
States that operate their own Occupational Safety and Health plan have similar emphasis programs in place, and OSHA also encourages those states to consider additional measures, including criminal referrals for federal or state prosecution for trenching-related incidents.
Trenching standards require protective systems on trenches deeper than 5 feet and soil and other materials kept at least 2 feet from the edge of a trench. Additionally, trenches must be inspected by a knowledgeable person, be free of standing
water and atmospheric hazards and have a safe means of entering and exiting prior to allowing a worker to enter.
“OSHA stands ready to assist any employer who needs help to comply with our trenching and excavation requirements,” Parker added. “We will conduct outreach programs, including safety summits, in all of our 10 regions to help ensure any employer who wants assistance gets it. The stakes are too important.”
OSHA’s On-Site Consultation Program, a free and confidential health and safety consulting program for small- and mediumsized businesses, will assist employers in developing strategic approaches for addressing trench-related illnesses and injuries in workplaces.
The agency also urges workers to contact their local OSHA or state plan office, or call 800-321-OSHA, if their employer requires working in or beside trenches that are not sloped, shored, or shielded and are five or more feet in depth.
OSHA’s trenching and excavation webpage provides additional information on trenching hazards and solutions, including a safety video Learn more about OSHA.
Media Contacts:
Mandy McClure, 202-693-4675, mcclure.amanda.c@dol.gov
Denisha Braxton, 202-693-5061, braxton.denisha.l@dol.gov
Release Number: 22-1491-NAT
U.S. Department of Labor news materials are accessible at http://www.dol.gov. The department’s Reasonable Accommodation Resource Center converts departmental information and documents into alternative formats, which include Braille and large print. For alternative format requests, please contact the department at (202) 693-7828 (voice) or (800) 877-8339 (federal relay).
22 workers have perished in the first half of 2022BY JOE TANTARELLI
Originally published in the 2018 Spring Leader
My accident—we’ll call it that for lack of a better term— happened in June 1983. I was 26 years old. Maybe you can relate to me at 26: my Sundays usually bled into my Mondays and getting to bed at 2:30 a.m. only to leave for work at 5:30 a.m. was perfectly normal. That morning, I allowed myself a 20-minute nap as I rode in the passenger seat of the tractortrailer rig that hauled our excavator to the job site.
I had been in the excavating business for seven years, five of which as the operator-foreman on the basement crew. When I first started in the business, my safety orientation was straight to the point, I was told:
We hustle here, all day, every day. If you’re not a hustler then go home now because there’s no way we can find the time to waste on you.
1. Hurry up and get the pipe buried in the trench before it buries you.
2. The longer the trench is open, the more chance it’s going to cave in.
3. If the trench caves in but doesn’t kill you right away, just hang tight because there’s going to be a second cave-in. And that second collapse is going to be more catastrophic than the first one—it will be the one that takes you out.
In the seven years since receiving that less than 10-minute overview, I had learned a lot. In fact, I was even responsible for training other people on my job sites. On this particular site, I was working with two 17-year-old laborers— both inexperienced and with their own reasons for being
there—but learning the trade was not their priority.
In order to save money, the customer decided they would have their plumber supply the 4-inch pipe for the job. My boss gave them the approval to do so on the condition that the pipe was delivered to the job site before we got there. But when we arrived that morning, the pipe wasn’t there and I was livid.
I jumped into the pipe truck and sped over to the site office trailer to tell the foreman that we were leaving to go to another job that was actually ready for us because they obviously weren’t. The foreman managed to calm me down and assured me the pipe was on its way and would be ready when I needed it.
Against my better judgment, I went back to the site and began work. I let the laborers install the 6-inch pipe we brought while I dug the trench for the 4-inch pipe that wasn’t there yet. Two hours passed as I sat with my open ditch waiting for the pipe that was on the way. In order to turn a profit, we needed to complete two basements a day. I went into a tailspin thinking about how in two hours I should have had all of the pipe in the ground and backfilled, which would have completed threequarters of that basement. I knew if I wasn’t making money for the company, I wouldn’t be around much longer, so my urgency to get that pipe in the ground was high.
The plumber finally delivered the pipe. My patience was already low, I didn’t have time for on-the-job training and my laborers were taking what seemed like forever to make a decision on something. I intervened and asked what they needed. They said they wanted to put a bend on the pipe. I knew from experience that they didn’t need a bend but I had no time
left to argue with them. I ran and got the only 4-inch schedule 40 bend I had on the truck and some PVC glue to affix it to the fitting. They were fumbling trying to get the fitting on and I knew that if the glue set, they would end up losing it. I had no room for error so I yelled for them to get out of the way, jumped into the trench, put a little more glue on the outside of the pipe and inside the fitting and slammed that pipe into the fitting. Just as I was about to scold them on how easy it was, I noticed movement out of the corner of my eye.
A 25–30 feet long section of the trench wall was moving a little bit. A collapse was imminent. I knew that I needed to get to the very end of the trench because its configuration there causes an arch effect and provides a safe cocoon in the event of a trench failure. Just as I was about to turn and run I realized that both laborers were down in the trench with me and they had no idea what was about to happen.
If a 6 feet long, 4 feet wide, 8 feet deep section of a trench collapses, it can send 10 tons of soil crashing down on a person. Knowing that all three of us were in harm’s way, every second mattered. I shoved both boys to safety against one end of the trench but I was unable to make it to the same area so I turned to run to another safe spot. I thought I would get away with it because I had done it so many times before without any negative repercussions. But this time I didn’t make it out—I was right at the tail end of the trench collapse and I was buried up to my armpits.
Luckily, I’d succeeded in pushing the boys to safety and they came running down to help me. Right then, my 10-minute safety overview from when I first started in the business hit me.
“If the trench caves in but doesn’t kill you right away, just hang tight because there’s going to be a second cave-in. And that second collapse is going to be more catastrophic than the first one—it will be the one that takes you out.”
I was in and out of consciousness, but I remember pleading with myself to stay awake. I knew that if I passed out again I would die because those young boys did not know how to help me. Every time I inhaled, the dirt got tighter around my chest. The only shovel we had was buried in the trench, so one of the laborers, who was 6 feet 6 inches tall and 300 pounds, grabbed my wrists with the intention of pulling me out by my arms. I knew that with the weight of a car on top of me, that action would have ripped me apart. I yelled for him to stop and explained how they should carefully dig me out with their hands instead. They did and as soon as I could move my legs I was scrambling to get out.
We didn’t have 911 service or cell phones back then, so my ambulance was a 1978 Chevy Pickup. I was in and out of consciousness the whole ride to the hospital. But whenever I was conscious, I was self-diagnosing my injuries. I determined that I probably had a broken rib or two and I’d be home by dinner.
When we got to the hospital I managed to take two or three steps towards the emergency room and the next thing I remember is my toes dragging across the parking lot. I woke up again to a nurse taking my blood pressure. “He’s 60 over 40,” I heard her say to the other nurse. I went back to self-diagnosing. I knew that my blood pressure wasn’t supposed to be 60/40, so my initial diagnosis must have been a bit off and I probably wasn’t going to be home for dinner.
Here’s the part of the story I can’t tell first-hand because I had learned about it later: by the time the attending physician made it into the emergency room that day, I had flatlined. My self-diagnosed broken rib was actually internal bleeding that required surgery and my left kidney had to be removed in order to get me stabilized. Over the next 48 hours, I only remember the last 30 minutes of every four-hour interval because that was when the morphine wore off. I was completely out for the first three and a half hours and then I was in excruciating pain for that last 30 minutes until they gave me my next shot of morphine at the four-hour mark.
Aside from the physical consequences that include three bulging discs near my sciatic nerve, the results of which I can only describe as feeling like you’re walking on the sharp end of a sword instead of a leg, it’s the emotional consequences that are the worst. You could set a clock to when I wake up screaming from recurring nightmares, but they are nothing compared to the emotional damages this accident caused my family. Every time I left for work, they feared I was never coming back. If I was 10 minutes late walking through the door, the house was in hysterics.
For years, after I went back to work, I spent every safety training class searching for the answer to how my accident
happened. I was the last person this should have happened to—I was considered one of the safest operators in town. I was competent in my job. I had trained a lot of workers in safety. As the operatorforeman, my job was to stand up top and watch for signs of a trench failure. I knew the risks. So why did this happen to me?
It wasn’t until I had taken some human factors training that it clicked for me. Your state of mind can greatly impact your critical decisions. I knew the hazards but I wasn’t in tune with how complacency and other states of mind can impact safety. I had a happy ending to what could have been a tragic story, but if I’d known how to
prevent the errors caused by my mental state, this incident could have been avoided.
You may never get caught in a trench collapse, but the tasks of your job and the risks you face at home or while driving can still cause serious physical injuries and leave lasting emotional effects on you and the ones you love. My accident could have been prevented and so can your future accidents. Because protecting people through engineering solutions is a basic requirement, but how can they be protected against their own state of mind?
If there’s one lesson I took from this and want to share with you it’s this: learn more about human factors training—it could save your life.
• Keeps extension ladders from slipping on slick surfaces such as composite decking
• Unique design of foam creates tiny suction cups that grip the surface, even when wet
• Light weight for easy use, weighs less than 6 pounds
• Works on smooth surfaces, plastic, wood, concrete, etc., even when wet
• Prevents marring and scratches to deck caused by ladder feet
• Attaches to the bottom ladder rung, with adjustable strap, for easy movement of ladder along wall
• Fits most extension ladders, up to 21” wide
• Replaceable self-adhesive foam pad
* https://www.cdc.gov/niosh/ nioshtic-2/20034690.html
888-456-3372
• www.softknees.com
• info@softknees.com
Patent US 10,240,392 B1
Joe Tantarelli teaches people about human factors as a Safety Consultant with SafeStart. In his 40 years in heavy equipment construction, he went from laborer to operator to manager. Joe was a training specialist for over eight years which provided a natural transition for him to become a speaker and implementation specialist.June is Trench Safety month!
Through the end of November 2022, 35 workers had fallen victim to deadly trench collapses—more than double the number in all of 2021. –OSHA
5,190 fatal work injuries occurred in the United States in 2021 according to the BLS.
In the past six months, OSHA has conducted nearly 600 compliance assistance activities involving trenching, reaching about two million people.
From January 1 through December 2, 2022, OSHA compliance officers conducted
1,975 inspections nationwide where they stopped at, and inspected, excavation sites during their daily duties. Approximately
1,500 citations were issued for violations.
There were 130 fatalities recorded in trenching and excavation operations between 2011 and 2016. The private construction industry accounted for 80%, or 104, of those fatalities.
NEVER enter a trench unless it is properly inspected!
As an OHS attorney and safety professional for over 30 years, I deal in disaster: over 400 fatal workplace accidents to date. Many of these have involved trenching and excavation (T&E), which is no surprise since it is one of the “Fatal Four” causes of construction fatalities. According to the Bureau of Labor Statistics, between 2011–2016, there were 130 deaths attributable to T&E activities. The private construction industry accounted for 80 percent of these, and while 38 percent occurred at industrial premises, an equal number were at private residences, and 20 percent in street or highway settings. Notably, public sector employees are not covered by federal OSHA (state plan states and state agencies in the federal OSHA states of NJ, NY, IL, and CT do cover these state and municipal workers), so the fatalities attributable to public sector activities in trenches are likely underreported.
While in law school, T&E meant “Trusts and Estates.” In my practice, it
signifies “Trenching and Excavations”—the cause of so many preventable injuries and deaths. The root causes of these tragedies generally come down to three factors: short cuts, improper delegation of authority to those who lack power, and the absence
The root causes of [trenching and excavation] tragedies generally come down to three factors: short cuts, improper delegation of authority to those who lack power, and the absence of effective training.
of effective training. In the aftermath of these tragedies, clients often claim that the event was idiosyncratic, unforeseeable. That’s really not true, although these are among the “affirmative defenses” that I have argued over the years in mitigation of OSHA allegations.
Let’s explore the intricacies of T&E safety law and performance failures.
be told to stay in the shallow end, yet in my experience, OSHA often has photos showing that they strayed into the deeper areas during the course of their work—justifying a citation.
hazardous, or dangerous to employees, and who has authorization to take prompt corrective measures to eliminate them.” This element of control is key, and the competent person will be viewed as an agent of management by OSHA, and their negligent actions will be imputed to the company to enhance the negligence classification. They may also become the target of criminal action if a case turns deadly.
The first causal factor is the short cut. Employers may justify that the workers “will only be in the trench for a few minutes” or they may argue that it is difficult or “infeasible” to place a trench box into an excavation that already contains utility pipes or where they will be installed. They may argue that the type of soil “looks stable” (usually without performing any tests)—inevitably OSHA will disagree, after the fact, with their soil classification and OSHA will perform the tests.
To be sure, there are times when installing a trench box may not be feasible, but those are extremely limited. Moreover, there are alternative methods of supporting the ground during trench entry, including shoring using boards, or benching the area. Some employers also argue that if a trench varies in depth, perhaps from four to seven feet across its length, but the workers are “directed” to stay in the shallow end, they can avoid using support systems. OSHA will usually measure the depth from multiple points, and once it is five feet or deeper (or in very unstable soil), support will be required. Workers may
The second cause that I often encounter is lack of a truly competent person to oversee the controls and to direct the workforce. More often than not, the competent person is an hourly worker, often bilingual, who has no authority to hire, fire, or direct the workforce. Some do have the necessary OSHA training, but the effectiveness may be questionable. After conducting training for one contractor who had received a willful OSHA T&E citation, and covering the competent person requirements, when I asked for questions, the first one was, “When will this company hire someone competent?”
OSHA issued a revised Compliance Directive on its construction excavation standard, 29 CFR Part 1926, Subpart P, in July 2021. See CPL 02-00-165. The 53-page Compliance Directive details OSHA protocol for examining training, safety equipment, review of excavation protection programs, documenting employee exposure, and interviewing them. With respect to competent person requirements, OSHA stresses that the designated person must be “capable of identifying existing and predictable hazards in the surroundings, or working conditions which are unsanitary,
The third fatal flaw at trenching operations is poor or absent training. What does OSHA require for effective training on the hazards of trenching and excavation? To begin with, the training needs to be in a language and vocabulary that the workers will understand. I have been that trainer who shows up, only to find out that half the class does not speak English (and I do not speak Spanish). I have had showdowns with clients because I refused to certify that training was provided if the person could not understand what I was communicating. A citation for lack of training can result in a civil penalty of up to $145,000, but falsification of training records can net you a criminal sentence in federal prison. To the trainers reading this, just say NO to demands to sign off on training that you know was not effective. It isn’t worth it, and the consequences of poor training can be deadly and hard to deal with personally, if you know that inadequate training was a factor. It is also important for those who use temporary workers
from a staffing agency, a union hiring hall, or subcontractors to perform their trenching and excavation activities to ensure that they also have the mandatory training, and that it is documented. Too often, either due to assumptions or lack of communication, the general contractor (GC) believes that the laborers provided have the requisite training and puts them to work immediately. In one such case, after the temporary laborer was killed in a trench, neither their direct employer nor the GC had any training records—in fact the GC’s safety officer left the scene, wiped his computer files, and was never seen again. Both the labor agency and the GC got cited in the fatality, but the GC bore the heavier burden as the entity in control of the worksite. It is also important to remember that if OSHA issues a willful citation in conjunction with a fatality, this can be reviewed for criminal referral to the U.S. Department of Justice (or the Attorney General, in a state plan state). What needs to be covered in T&E training, besides ensuring that the training is delivered in the right language and vocabulary (and also taking into account the literacy levels of workers if written materials will be used)? Ideally, after training is delivered, the participants will be able to:
1. Understand excavation risk factors
2. Identify excavation and trenching hazards
3. Recognize employer requirements for excavation safety
4. Understand the role of a competent person for excavation
5. Describe trench protective systems and other excavation hazard controls
6. Apply best practices for excavation safety
7. Understand the challenges of trench rescue operations.
Since 2018, OSHA has had a National Emphasis Program (NEP) on Trenching and Excavation that both federal OSHA and the state plan states must follow. See CPL 02-00-161. The original OSHA NEP on trenching started in 1985—clearly this is an old and pervasive safety issue, and more progress is needed. Under the current NEP, if an inspector drives by an open trench and is able, they are supposed to check and see if the ground is supported, if a ladder is available for safe access and egress, confirm that spoil piles are not situated where they can fall into the trench, and consider nearby traffic and vibration of heavy equipment (in addition to soil classification) when considering the potential for collapse.
OSHA says that employees exposed to potential cave-ins must be protected before the trench reaches “imminent danger of collapse” and OSHA believes there is a potential for collapse in virtually all excavations. OSHA will shoot video, take soil samples (from two different locations) and trench measurements, and otherwise document worksite conditions through sketches and photographs. They will also interview workers to determine their training levels and who is in control of the worksite.
OSHA can expand the scope of the inspection beyond T&E if there are other violations or hazards in plain view or if workers raise concerns during private interviews.
The bottom line is that trench hazards are pervasive and wellknown, yet workers continue
to be injured or killed during excavation activities. In just seconds, workers faced with a trench collapse can be buried in thousands of pounds of soil. The basics are simple: ensure a safe
way to enter and exit the trench, provide cave-in protection, keep materials away from the edges of the excavation, watch for water and environmental hazards, and ensure that the competent person inspects the trench before allowing workers to enter. Prevention can avoid deadly situations and the need for a T&E attorney.
To the trainers reading this, just say NO to demands to sign off on training that you know was not effective.
n July 14, 2022, OSHA issued a national news release (see pages 12–13) to make the country aware of an “alarming rise in trench-related fatalities,” and to announce it was launching enhanced enforcement initiatives to protect workers from known industry hazards.” While the greatest risk of trenching activities is clearly to employees who enter the trench, there is also a significant risk to personnel who must access the top surface of the ground at the edge of the trench, including OSHA inspectors (“CSHOs”). That is the focus of this article.
According to the OSHA Compliance Directive for the Excavation Standard (“the Excavations Directive”),1 “OSHA believes there is a potential for a cave-in or collapse in virtually all excavations.”
If there is a potential for a cave-in or collapse in virtually all excavations, that strongly suggests there is a potential for the adjacent ground to collapse into the trench and take anyone standing on that ground into the trench.2 The measures implemented for the “protection of employees in excavations” against caveins/collapses pursuant to §§ 1926.651 and 1926.652 should also protect someone on the adjacent surface from that type of event.3 In other words, when the Certified Safety & Health Official (CSHO) is gathering information about the trenching activity at the site—the qualifications of the individual designated as the competent person for excavations, what soils are present, what soil testing was performed, how long the excavation has been open, what protective system has been implemented, dimensions of the
trench, purpose of the trench— the CSHO is not only looking out for the employees at the site but also the CSHO’s well-being. Since a CSHO is not familiar with the conditions at a trench site and does not know whether appropriate protective systems have been installed, maintained, and adjusted as necessary in light of any significant changes in conditions, OSHA has established a simple rule for its CSHOs: “Never enter a trench excavation, regardless of depth.” OSHA relies on training and the application of other safety measures to protect CSHOs from the substantial remaining risks.
An obvious and significant hazard for a CSHO required to access the top surface of the ground at the edge of the trench is the fall hazard but that is not even mentioned in the Excavations Directive and it was not an oversight. A June 24, 2002 OSHA Letter of Interpretation4 clarifies this issue and reads as follows:
This is in response to your letter . . . requesting an interpretation of fall protection requirements when working around trenches. Specifically, you ask if fall protection is required around vertical walled trenches that have a depth 6 feet or greater; if there are any exceptions to fall protection around trenches implied or stated; and whether a controlled access zone be used in lieu of fall protection.
29 CFR 1926.501(b)(7) provides:
(i) Each employee at the edge of an excavation 6 feet (1.8 m) or more in depth shall be protected from falling by guardrail systems, fences, or barricades when the excavations are not readily seen because of plant growth or other visual barrier; *
(ii) Each employee at the edge of a well, pit, shaft, and similar excavation 6 feet (1.8m) or more in depth shall be protected from falling by guardrail systems, fences, barricades, or covers.
Under these provisions, if the trench is not readily visible because of plant growth or other visual barrier, fall protection is required.2 Thus, unless the trench you are describing is obscured from view, there is no requirement for fall protection to be provided.5
*Note also that §1926.651(f) of the Excavations standard requires that:
when mobile equipment is operated adjacent to an excavation, or when such equipment is required to approach the edge of an excavation, and the operator does not have a clear and direct view of the edge of the excavation [where a CSHO might be standing], a warning system shall be utilized such as barricades, hand or mechanical signals, or stop logs. If possible, the grade should be away from the excavation.
It is unclear why OSHA concluded its CSHOs should take the same approach rather than taking the opportunity to be a role model for enhanced safety, even if the trench is only four feet deep, the fall protection threshold for the soft-headed employees in general industry. If CSHOs are not required to use fall protection in these situations, the safest approach for the CSHOs would be for OSHA to tell them to stay away from the edge of the trench. Unfortunately, given the current technology generally available to CSHOs, and the on-site tasks required of CSHOs, that approach simply will not work.
While the greatest risk of trenching activities is clearly to employees who enter the trench, there is also a significant risk to personnel who must access the top surface of the ground at the edge of the trench, including OSHA inspectors.
The Excavations Directive requires CSHOs to obtain various measurements (including “the depth, width, and length of the excavation in several locations), soil samples from different locations (and levels if there is stratification) of the trench, and photographs of the trench. In carrying out that assignment, the Excavations Directive indicates that the equipment available to the CSHO may include a “Small Unmanned Aerial System (SUAS)” (portable drone):
Note: If a Small Unmanned Aircraft System (SUAS) is available, SUAS videos and photos can often provide a good view of the site and document the working conditions. Procedures from current SUAS policy guidance shall be followed at all times.
If the SUAS is not available, or cannot perform all these functions, or the CSHO cannot employ it effectively, or the Solicitor’s Office cannot validate calibration and accuracy of measuring devices, then CSHOs are apparently left to the methods of ancient times. The Excavations Directive states:
Ways to obtain measurements while minimizing exposure to potential excavationrelated hazards:
(1) Count rungs of a ladder which may be present in the excavation and then calculate the total length or height based on the distance between the rungs.
(2) Use reference objects with known dimensions such as wood, a concrete vault, etc., to assist in estimating the depth and width.
(3) Measure the height of an employee who was observed/photographed in the excavation (with employees’ permission).
(4) Use an engineering rod (trench rod) horizontally with an eyebolt attached at the end, a string threaded through the eyebolt and a plumb bob attached to the string. . . . The telescoping rod should be placed on the ground. The plumb bob should touch the ground at the bottom of the excavation and the string should be taut. Tape or hold the string tight to the trench rod to ensure that the length of the string remains unchanged. Remove the trench rod from the excavation and measure the length of the string from the eyebolt to the end of the plumb bob with a measuring tape. Document and take a photo of the measurement.
Arguably, a stiff fishing rod and reel with a plumb bob would be more practical than approach number 4, above. Approach number 2 appears to have limited practicality. Getting an employee’s permission to take a photograph of the employee for potential use in an enforcement action does not seem promising. A recent case demonstrated the problem with approach number 1, above.
Section 1926.652(a)(1) provides that “each employee in an excavation shall be protected from cave-ins by an adequate protective system . . . except when . . . excavations are less than 5 feet (1.52m) in depth and examination of the ground by a competent person provides no indication of a potential cavein.” In Secretary v. A-1 Sewer and Water Contractors, Inc.,6 there was a factual dispute as to whether the depth of the trench was at least five feet. The CSHO relied on a ladder rung count of rungs with known spacing; the employer successfully argued that the ladder was angled against the wall of the trench rather than vertical, the angle was unknown and, therefore,
OSHA had not carried its burden of proof. Taking judicial notice of the “Pythagorean Theories [sic],” the administrative law judge (“ALJ”) assigned to the case vacated the citation.
In critiquing the CSHO’s selected approach for determining the depth of the trench, the ALJ’s opinion inadvertently highlighted the hazards faced by the CSHO:
It was not impossible or impractical for the CSHO to have had the ladder and measuring rod be placed directly vertical to the excavation wall to obtain the depth measurement. It would have taken the CSHO little time and effort to ensure the vertical placement of the ladder and measuring rod when taking his measurements. In this case, where the issue boils down to “approximately” seven inches from having the regulation apply or not apply (from 4 ft. 11 inches to approximately 5 ft. 6 inches as set forth in the Citation), being thorough and complete in the correct placement of the measuring rod and ladder would have not placed the measurements of Complainant into question.
In addition, the CSHO testified he was trained and had used in the past a method which would been better to use in this case to obtain accurate measurements when entry into a trench is not feasible. He referred to that method as a “fish tape” method. This method is where fish tape is put on the top of a measuring rod and then dropped into the trench to obtain measurements. Tr. 50–51. This certainly would have avoided the geometry principle invoked by Respondent to invalidate the method and measurement taken by the CSHO in this case.
In short, the opinion seems to imply that a CSHO, presumably
with a good faith concern about the possibility of a trench cavein/collapse, is expected to either:
(1) Walk to the top edge of the trench with a trench pole in one hand (assuming no spoils pile or other material or equipment blocks the way), pull the ladder into a vertical position against the trench wall, place the trench pole into a vertical position against the trench wall, ensure both the ladder and trench pole are vertical in the x and y axes (which may require balancing the ladder on one leg), ensure neither the ladder nor the trench pole is sitting on a large mound or in a deep divot that would distort the measurement, and note and memorize the measurement (assuming a second CSHO is not there to take a photograph, which might increase the risk of a cave-in/collapse); OR
(2) Get down on the ground near the top edge of the trench to place the horizontal trench rod flat on the ground (removing any materials or equipment that might be in the way), extend the rod far enough out to allow the line to clear the entire wall of the trench (which, in other situations, may be (albeit inadequately) benched or sloped), and do whatever is necessary to be sure the plumb bob has reached the floor of the true floor of the trench rather than either a large mound, a divot, etc.
It is unclear how this would be accomplished in a situation such as that presented in Secretary v. Conie Construction7 where “the Secretary demonstrated that in order to comply with the standard [1926.652], the top of the excavation would have to have been 28 feet wide, instead of the 20 to 22 feet it actually was, to have been sloped ¾ to 1.”
If safe measurement was not enough of a challenge, the CSHO is also directed to look for evidence of fissures, seeping water, soil stratification and soil disturbance8, and obtain soil samples:
[T]he CSHO should collect at least two soil samples from different locations. The number of soil samples taken is a matter of judgement based on observed conditions and the size of the project. If the project is so large that more than one crew is working in separate locations, samples should be taken in each area where employees are working.
If examination of the excavation side walls reveals visible soil stratification (i.e., the presence of different layers of soil), then the CSHO should attempt to obtain samples from each layer. In most cases, stratification should be recognizable because of color differences in the layers. The CSHO should avoid mixing soils from different strata, which should be left intact for lab analysis or other means used to determine classification.
Sampling from a spoils pile is much easier and safer but could make it challenging to establish those samples are representative of actual conditions in the trench wall or represent the various stratified layers.
Clearly, excavation is an activity with elevated hazards. I would have preferred to see OSHA announce a more comprehensive approach to this issue that combined enforcement and outreach, not only to the excavation contractors and general contractors but also to the purchasers of excavation services (including homeowners and insurance companies), and to the government agencies that establish the required depth for burying utility lines. In addition, it appears that OSHA could do more to protect the safety of its CSHOs conducting excavation inspections.
This article is not intended to and does not provide legal advice. It represents only the personal views of its author regarding the control of excavation hazards and does not necessarily represent the view of VPPPA or the law firm of Keller & Heckman LLP or any of its clients.
1 OSHA Directive Number: CPL 02-00-165, Compliance Directive for the Excavation Standard, 29 CFR 1926, Subpart P, Effective Date: 7/1/21. https://www.osha.gov/sites/default/files/enforcement/directives/CPL_02-00-165.pdf
2 See Trench Cave In Oregon OSHA compliance officer caught cave in on tape https://www.youtube.com/ watch?app=desktop&v=uLs1_8yohb8
3 In addition, § 1926.501(a)(2) provides: The employer shall determine if the walking/working surfaces on which its employees are to work have the strength and structural integrity to support employees safely. Employees shall be allowed to work on those surfaces only when the surfaces have the requisite strength and structural integrity. where the term “walking/working surface” means: any surface, whether horizontal or vertical on which an employee walks or works, including, but not limited to, floors, roofs, ramps, bridges, runways, formwork and concrete reinforcing steel but not including ladders, vehicles, or trailers, on which employees must be located in order to perform their job duties.
4 https://www.osha.gov/laws-regs/standardinterpretations/2002-06-24-2
5 Apparently, at least in the United States, this situation is viewed by OSHA as comparable to the unprotected edge of a commuter railway platform although the exposure to fall hazards at the trench site is likely to be more hazardous, taking into account length of exposure, frequency of exposure, distance to the unprotected edge, vertical drop and surrounding distractions and noise.
6 OSHRC Docket No.: 21-0562. https://www.oshrc.gov/assets/1/18/A-1_Decision_and_Order-after_trial_-_PBA_ (final)_(002).pdf?12149
7 OSHRC Docket No. 92-0264. https://www.oshrc.gov/assets/1/6/92-0264.pdf?3727
8 In Secretary v. Scafar Contracting, Inc., OSHRC Docket No. 97-0960, the ALJ held that soil would be considered “disturbed” where it had been dug up 100 years earlier to install a sewer line. https://www.oshrc.gov/ assets/1/6/97-09601.pdf?3445
It appears that OSHA could do more to protect the safety of its CSHOs conducting excavation inspections.
The Bureau of Labor Statistics reports that 5,190 fatal work injuries occurred in the United States in 2021—that means an American died every 101 minutes from a work-related injury. This represents an 8.9 percent increase from 4,764 reported in 2020.
These starling statistics include an average of 20 fatalities each year that are attributed to inadequately planned and/or performed excavation and trenching activities. The consistent implementation of a welldesigned safety management system (SMS) coupled with a robust safety culture are key to preventing excavation and trenching accidents.
Management should clearly establish safety culture expectations to foster a psychologically safe environment in which workers are expected and encouraged to identify concerns during planning, work performance, and closeout phases. Management has the ultimate responsibility to ensure that resources necessary to safely accomplish the work are available. In addition, management should reinforce the importance of robust conduct of operations that yields unwavering compliance with company procedures and work controls, regulations, and standards.
While the following basic SMS functions are vital to safe excavation and trenching activities, they can be applied to any industry and type of work being performed.
• Define the Scope of Work: All members of the planning and work performance teams should have a clear understanding of the work to be performed and the expected outcomes.
• Analyze Hazards: Existing and predictable hazards such as the potential for cave-ins, falls, being struck by equipment, tools, or materials, contacting dangerous utilities, or being exposed to toxic substances or hazardous atmospheric conditions must be considered. Aids such as drawings, maps, historical documents, and soil analysis are required to adequately identify hazards.
• Develop and Implement Controls: The hierarchy of hazard controls should be implemented when developing measures to protect the workforce, members of the public, and the environment. Highquality training which includes confirmation of proficiency, should be considered when identifying administrative controls. Installation of protective systems such as trench boxes when required; complaint means of safe ingress and egress within 25 feet of workers; setbacks for spoil piles and heavy equipment; and physical barriers to prevent accidental entry into the excavation must be considered when developing and implementing safety controls. Given that quick expert assistance is critical to the success of an emergency response, a comprehensive response plan must be in place.
• Perform Work: Work teams must always proceed in a manner that consistently conforms with company policies, procedures, and work controls—every task, every activity, every time. A heightened sense of situational awareness and the use of critical thinking skills are required from every team member for high-risk operations such as excavation and trenching.
• Feedback: All members of the work team must be empowered to raise concerns and stop or pause work if a changed or previously unidentified condition is encountered. Feedback during and after work completion from team members is required to understand what went right and what should be improved.
Excavation and trenching teams require an OSHA competent person, a diverse team of subject matter experts (SMEs), and highly trained and skilled workers to be successful.
OSHA defines a competent person as being, “one who is capable of identifying existing and predictable hazards in the surroundings or working conditions which are unsanitary, hazardous, or dangerous to employees and who has authorization to take prompt corrective measures to eliminate them” [29 CFR 1926.32(f)]. A competent person must demonstrate understanding of excavation regulations [29 CFR 1926.650 and 1926.651], be able to classify soil types, be familiar with the installation and use of protective systems [29 CFR 1926.652], and perform inspections of the excavation/ trench work area. The competent person acts as the official authority who authorizes and suspends excavation/trench work activities.
Access to subject matter experts representing disciplines such as industrial or construction safety, industrial hygiene, construction/heavy equipment, hoisting and rigging, electrical safety, and fall prevention and protection is required to ensure safety during excavation and trenching activities.
Equipment operators must be trained to operate the specific equipment to be used. Training should include hands-on, field-based activities to verify proficiency of operational capabilities, understanding of load charts, inspection requirements, hoisting and rigging operations, the recognition of struck-by hazards, work zone safety, and the impact of field/ environmental conditions.
Heavy equipment spotters should be trained to recognize potential struck-by hazards and be able to demonstrate proper use of signaling and three-way communication.
All workers both inside and outside of the excavation/trench and emergency responders should be trained to recognize and respond to changing conditions and potential hazards.
Excavation and trenching operations are inherently dangerous and require an advanced degree of planning and preparation. Don’t start an excavation/trenching operation if you don’t have:
• A well-defined and clearly understood scope of work
• An adequate hazardous analysis that identifies both existing and predictable hazards
• Trained workers with critical thinking skills; access to subject matter experts; and an OSHA competent person
• Resources to implement physical controls such as work zone barriers and protective shoring and shielding systems; the proper personal protective equipment; and an established emergency response plan
• A safety culture where all team members are empowered and capable of voicing concerns.
It is equally important to be prepared to stop work if a changed condition occurs.
As the Department of Energy Oak Ridge Environmental Management lead environmental cleanup contractor, United Cleanup Oak Ridge LLC (UCOR) has worked for more than a decade to demolish, cleanup, and dispose of waste associated with some of the most hazardous nuclear facilities in the DOE Complex. Under a shared governance leadership model, UCOR’s 2,200 member highly skilled workforce has accomplished first-of-a-kind environmental restoration projects and stands mission ready to accomplish future DOE milestones.
Contributors:
• Jay Hocutt, CSP, SGE, CWD, UCOR Construction Heavy Equipment Program Manager
• Dustin Hanuhorst, CSP, Construction Heavy Equipment Subject Matter Expert
• Lynn Trout, UCOR Heritage Center Safety and Health Operations Manager
• Ryan Cannday, CSP, UCOR Heritage Center Deputy Safety and Health Operations Manager
• Christian Barnhill, UCOR Safety Specialist
hether you’re working indoors in a poorly lit warehouse, or outdoors in hot sweltering conditions, the safety glass market has evolved to the point where there are now specific lenses tailored to suit specific needs—this includes prescription lens requirements as well.
If you haven’t taken a look at the safety glass market recently, you may be surprised at how much has changed as
Winnovations from R&D labs now allow leading manufacturers to develop lenses for a wide range of specific uses including those who work outdoors in excavation jobs as well as in the trenches. Perhaps one of the biggest advancements that impact those specific jobs are new lens technologies that prevent fogging and scratches and adapt to varying light conditions. For those who work in trenches, hazards can stem from an array of situations including glasses that fog in hot steamy days, to flying debris from
excavators that can lead to scratched lenses. At the same time, varying light conditions can impact workers as they shift into different positions during trench work.
Today, technology like PLATINUM, from Bollé Safety, feature an anti-fog, anti-scratch coating designed to eliminate fogging and scratching. This gives workers one less thing to worry about while they are on the job site. The coating is applied permanently through a dipping process on both sides of the lens and, at Bollé, is now available in more than 60 percent of all SKUs offered.
Beyond fog and scratch prevention, the industry has also evolved to the point that ‘use specific’ lenses are now available. With indoor and outdoor needs, workers are battling glares and shadowing that come from working in varying light conditions, which those working in trenches often encounter.
Technology, like CSP, (Comfort, Sense, Perception), also from Bollé Safety, delivers filtering advancements designed
to go beyond protection to enhance vision and performance.
Workers in widely different environments, from factories with LED lighting to outdoor UV rays, can be exposed to a variety of hazards throughout the day. High-risk activities like welding, mining, trench work, electrical, and drilling require visual precision while protecting eye health. Working in low light, LED lighting, or full sunlight requires safety glasses designed to reduce eye strain and filter UV rays.
CSP lenses ensure optimal comfort and exceptional visual definition, no matter the situation. The innovative technology shields the eyes while boosting the senses, increasing the precision of tasks and movements.
Protective eyewear is an important PPE that must be compatible and adaptable to changing conditions and circumstances that workers face, and tinted lenses now come in a wide range of colors designed for ultimate performance enhancement. Lenses, including some with
polarization, are designed for a full range of outdoor uses.
For example, Copper and Copper Flash colored polycarbonate lenses protect the eyes of hard-working employees such as forklift truck operators, drivers, and night workers, who operate in factories with LED lighting.
For outdoor activities, including in marine and drilling environments, or long-distance drivers, Silver Flash, Cobalt Flash and Fire Flash lenses ensure protection in full sunshine.
For those in low light conditions, Quartz lenses improve the depth perception and contrast by increasing visual acuity. Bronze tints enhance vision in low luminosity, including in mines, electrical and outdoor work.
By absorbing over 75 percent of blue light, visual contrast is improved for better accuracy and safety.
Those who primarily work outdoors, including those working in trenches and doing excavation work, may choose dark-colored Polarized lenses, which improve visual comfort, contrast, and depth, while reducing strain are a recommended option as they allow for infallible protection for a range of outdoor activities like rig drilling. A total UV blocker, such as Onyx lenses filter 99.99 percent of UVA and UVB rays, ideal for construction and building industries.
If you haven’t taken a look at the safety eyeglass market recently, you may be in for a pleasant surprise.
The VPPPA Safety Star of the Quarter is a program to honor and recognize an employee’s achievements in safety performance and professionalism. Thank you to all our VPPPA Safety Stars and VPPPA members for their continued contributions to the safety and health community. Safety Stars of the Quarter will be featured on our website, social media, Leader magazine, On the Level e-newsletter, and receive a certificate.
Jeremy Presnal
Shermco Industries
Senior Vice President, EHS & Workforce Development
Irving, Texas (Region VI)
To learn more about Jeremy, or to submit someone to be considered as a Safety Star, please visit our website: https://www.vpppa.org/ membership/safety-star/. You can also email membership@vpppa.org.
LinkedIn: VPPPA, Inc.
Facebook @VPPPA
Twitter: @VPPPA
Instagram: @VPPPA_Inc
Save the date! VPPPA and the Safe + Sound Campaign will host a free webinar on trench safety essentials in June in observance of Trench Safety Month. The webinar will be presented as part of the Partner Seminar Series for OSHA’s Safe + Sound campaign, a national initiative aimed at promoting awareness and understanding of workplace safety and health programs.
• Cost: Free
• When: June 21, 2023, from 1:00–2:30 p.m. ET
• Registration: vpppa.org/webinars
“The cost of injury prevention is far less than the cost of an injury.”
For many of us, a large portion of our day is spent at work; in fact, the average person will spend 90,000 hours at work over a lifetime. It’s safe to say your job can make a huge impact on your quality of life. And that is why I can’t stress enough the importance of workplace safety.
Each person who leaves their home should come back to their home in good health. Have you ever imagined that your loved one will never return home? Or you get a call that he/she is in the hospital due to some incident that occurred? These thoughts give us goosebumps. This is why it is important to create a safe working environment.
VPPPA values our members and their participation in, and support of, our safety and health management community. Our goal is to provide our members with the education, resources, and tools to help prevent worksite injuries and fatalities; and have you return home in the same or better condition than when you left.
Keeping that in mind, we are working on new benefits every day to assist with that goal. Please make sure to update your contact information and renew your membership to ensure the continuation of your membership benefits. You don’t want to miss out on:
• Educational resources to help safety professionals raise the standard for a safe and healthy workplace through professional development, innovation and sharing of best practices among sites and companies engaged in world-class EHS&S practices.
° FREE webinars, live and recorded
° Access to the new VPPPA eLearning Toolbox (Learning Management System)
° Mentoring partnership program
• Discounted rates on exclusive VPPPA events and other associated training and networking opportunities.
° VPPPA’s Safety+ Symposium in Orlando, Florida, September 17–20, 2023
° 2023 Regional conferences and events
• Free publications, including the Leader Magazine—our award-winning quarterly magazine, “On the Level” monthly e-newsletter, and access to the weekly, award-winning VPPPA blog
• Discounted access to our new VPP electronic self-evaluation platform
• Connecting with other members through our Member Directory
• Access to VPPPA Awards and 4 annual Scholarships for members and their families.
The cost of injury prevention is far less than the cost of an injury. A safe and healthy workplace attracts and retains quality employees; it’s an asset to a community, operates more efficiently, and enjoys a healthy bottom line. Both the business and the workers thrive in a safe, healthy, respectful, and caring environment. Please feel free to contact us at membership@vpppa.org if you have any questions.
Is your worksite looking to strengthen its EHS&S program in 2023? VPPPA and AuditSoft’s valuable evaluation and improvement tool, VPP Online, can help.
VPP Online is a year-round continuous improvement self-assessment tool that will allow you to collaborate with teams across your site and company to identify potential improvement areas and regularly monitor your site or company’s progress on critical improvement initiatives and, more importantly, identify real-time strategies to address each issue.
If you are interested in a 30-minute demo, please contact Pete Spence at Peter.Spence@AuditSoft.co
For more information visit vpppa.org/vpp-online, contact Heidi Hill at 703-761-6511, or email hhill@vpppa.org
The Labor Summits are monthly 30-minute webinars showcasing a diverse mix of speakers and topics designed to engage workers, both represented and nonrepresented, to jointly and collectively discuss workplace safety. Labor summits last 30 minutes to minimize impacts to work schedules and are available as recordings the same day. Topics range from women in the workforce to building a safety culture within your workplace, new workplace hazards, worker trainer programs, and more. Learn more at www.vpppa.org/webinars
Many VPPPA Regions are hosting events in the coming year. Make sure to visit www.vpppa.org/ regional-events for the most up-todate information on regional events.
www.vpppa.org
Chairperson
Terry Schulte, NuStar Energy
Vice Chairperson
Dan Lazorcak, Honeywell Secretary
Bill Linneweh, CSP, Hendrickson International Treasurer
Sean Horne, Valero
Director from a Site With a Collective Bargaining Unit
Jack Griffith, Central Plateau Cleanup Company
Director from a Site Without a Collective Bargaining Agent
Vacant
Director from a DOE-VPP Site
Michelle Keever, United Cleanup Oak Ridge (UCOR)
Director from a VPP Contractor/ Construction Site
Brad Gibson, S&B Engineers and Constructors
Director-at-Large
Tim Belitz, Honeywell
Director-at-Large
Daniel Charles, Brandenburg Industrial Service Company
Director-at-Large
Andy Foster, Central Plateau Cleanup Company
Director-at-Large
Shelly Ettel, Amentum
Director-at-Large
Saprena Lyons, Fluor Idaho
Director-at-Large
Christina Ross, Morton Salt
Editor
Kerri Usher, VPPPA, Inc.
Associate Editor
Ariana Hanaity, VPPPA, Inc.
The Leader (ISSN 1081-261X) is published quarterly for VPPPA members. The Leader delivers articles from members for members, safety and health best practices, developments in the field of occupational safety and health, association activities, educational and networking opportunities and the latest VPP approvals.
Ideas and opinions expressed within the Leader represent the independent views of the authors.
Postmaster >> Please send address changes to:
VPPPA, Inc. • 7600 Leesburg Pike, East Building, Suite 100 • Falls Church, VA 22043-2004
VPPPA, Inc., the premier global safety and health organization, is a nonprofit 501(c)(3) charitable organization that promotes advances in worker safety and health excellence through best practices and cooperative efforts among workers, employers, the government and communities.
VPPPA contacts
Chris Williams Executive Director cwilliams@vpppa.org
Sara A. Taylor, CMP Director of Operations staylor@vpppa.org
Heidi Hill Partnership Manager hhill@vpppa.org
To reach the VPPPA National Office, call (703) 761-1146 or visit www.vpppa.org. To reach a particular staff member, please refer to the contact information below.
Lisa Silber Senior Event Sales & Advertising Coordinator lsilber@vpppa.org
Ariana Hanaity Communications Coordinator ahanaity@vpppa.org
Sierra Johnson Senior Education Coordinator sjohnson@vpppa.org
Son Nguyen Membership & Outreach Manager snguyen@vpppa.org
Bryan Knight UX Web Services Programmer bknight@vpppa.org
“My favorite thing was sharing best practices with other companies.” – 2022 attendee “Vast amounts of safety information. Great networking event!” – 2022 attendee
September 17–20, 2023
Orlando World Center Marriott