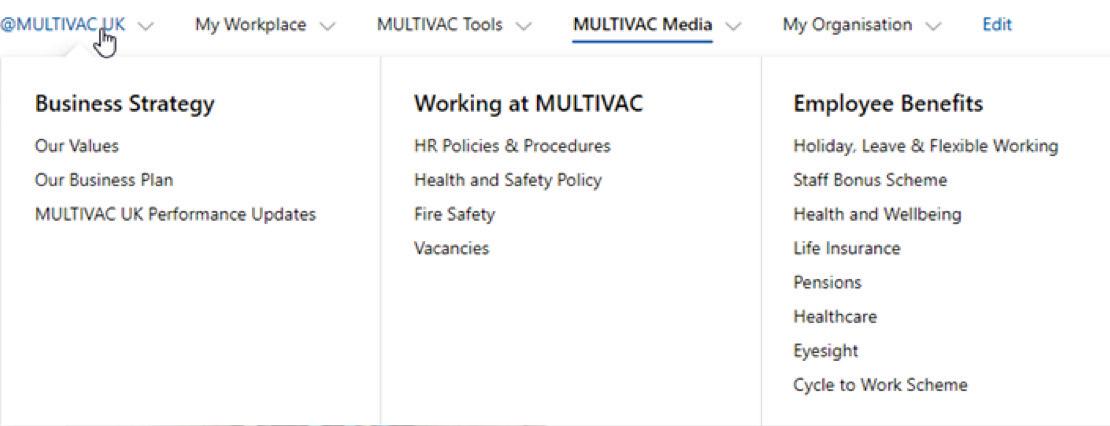
8 minute read
Introducing... Ask HR
We want to make it as simple and easy as we can for you to find out information that you need about HR policies and process and to enable you to do so quickly and efficiently. We know that if you have a question or a query that’s urgent for you, you’re looking for a quick answer or advice.
As a small team we have a broad range of issues that we need to work on and like everyone we ’ re always busy so making sure that you receive what you need in a timely way can at times be challenging. We know that we can improve how quickly we deal with your queries but to do so we ’ll need to change our current approach.
Advertisement
From 1st June we will be launching a new support model aimed at providing you faster and more efficient ways to find what you need
Find
Most of the questions that you have regarding benefits, policies and procedure can be found on the revamped intranet on our new sharepoint page which can be located here or by using the Multivac UK navigation and clicking on HR Policies & Procedures.
We encourage you to start by visiting the intranet as it’ s likely that 90% of what you need to know will be here.
Ask HR
If however you can ’t locate what you ’ re looking for or you have a one off query, then you can email our new inbox call Ask HR. We ask that you use this central inbox rather than email the team individually as it means that we can track and monitor incoming queries more efficiently and therefore provide a better service to you. It also means that anyone of the team can deal with your query so avoiding significant delays.
Things that you might want to send to Ask HR could include:
• Holiday queries • HR Hub queries and guidance • Leave and absence queries • Pay/Payslip/Payroll queries • Working from home queries • Benefits queries (pension, BUPA etc.) • General HR queries
We ’d also encourage you to talk to your manager as they should be able to help you with many of the above.
We will aim to deal with all queries to the inbox within 72 hours and in most situations 48 hours.
Escalate
From time to time you may raise a question that needs to be escalated to a senior member of the team who will handle it and respond directly to you.
Rio Neesom: HR Admin
Find
Is the information you’re looking for on the Intranet or HR Hub?
If you can’t find the answer, email the HR team via AskHR@multivac.co.uk where you will receive a response within 48 hours.
If the answer can’t be provided by AskHR, it will be escalated to the HR Business Partner, or HR Director who will respond directly to you.
Ask HR
Escalate
Morrisons International Seafoods
New Line 1 - R575MF with I211 and MUUK’s first Thom and Carsoe Crate Loader
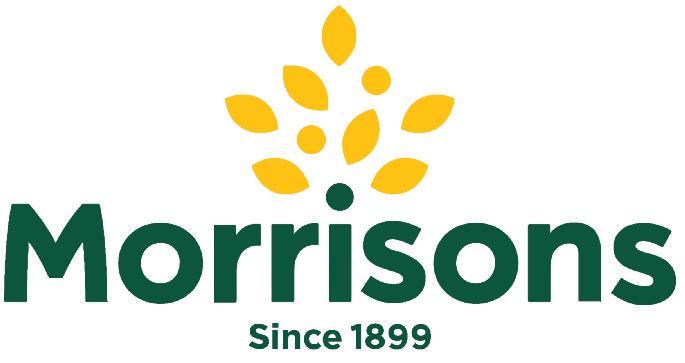
International Seafoods, owned by Morrisons, have two factories based on the Europac Industrial estate just off the A180 four miles from Grimsby. They are commonly known in Multivac as Pegasus Way and Lakeside.
These sites are Morrisons ‘ primary seafood operations (there is a third facility in Cornwall, Falfish). The Pegasus way operation is their primary retail processing facility for fish and Lakeside is their further processing and retail packing operation for seafood.
International Seafoods pack their finished products into Bale Arm Crates, ready for delivery to their stores around the UK.
Bale arm crates now form an important and integral part of the supply chain. These crates offer safe transport of products, are continually reused and offer a more environmentally friendly method of product transport, when compared the pervious SRP (Shelf Ready Packaging) cardboard boxes.
Like many of our customers Morrisons face the challenges of rising employment costs, the availability of workers and limited floor space. This drives a need to increase output from the same production footprint and reduce where possible the number of people needed.
In January 2022 we delivered and commissioned a new Multifresh packing line. The customer ’ s ROI (Return On Investment) justification for this investment was based on increasing output from 80 to 120 packs per minute and to operate with only one a single operator at the end of line instead of the normal three.
A four track, three row format and ten cycles a minute is a fairly standard application for a R575 MF Thermoformer.
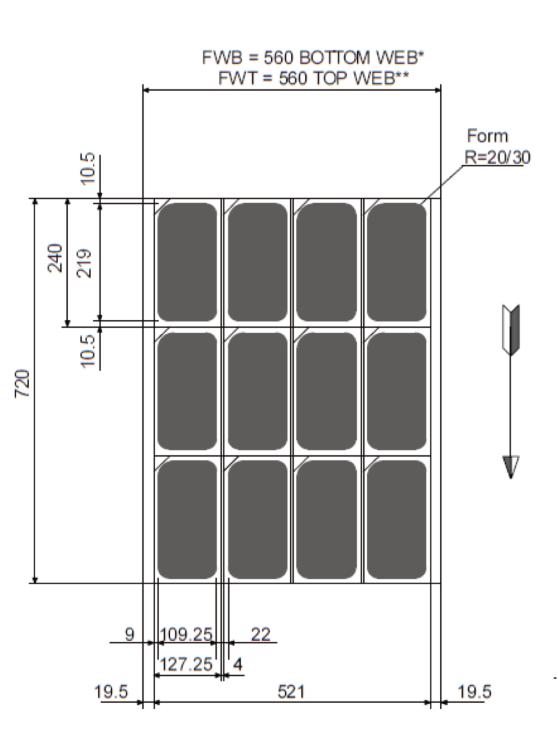
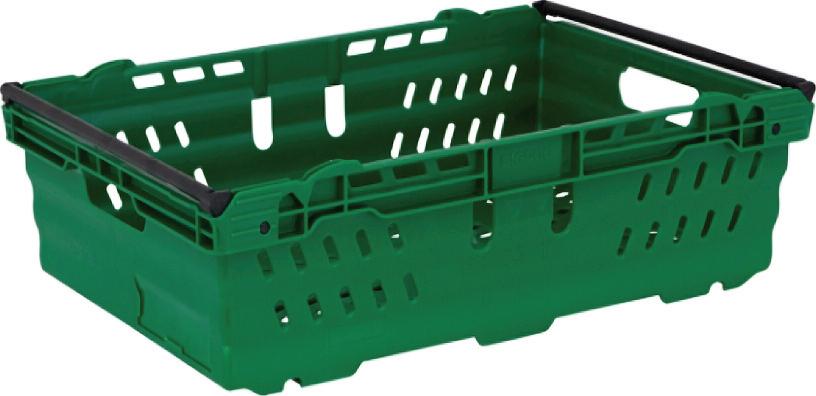


However, getting eight finished packs in a single bale arm crate, at 15 crates a minute isn ’t. The traditional solution of robots picking and placing would normally require a three robot cell solution, significant floor space and make the project financially unjustifiable due to the cost of the robots.
It would have been easy to say it can ’t be done and that there isn ’t a viable solution available.
However, it’ s in situation like this that Multivac UK excels. Bring together the experiences and knowledge of Sales, Project and Product Management and the strong relationships we have with our 3rd party OEM partners. This process produced a simple crate loading solution, with only minor tweaks to existing equipment designs and enable us to offer a very cost effective solution, from proven technology (limiting the risk to Multivac), in our offer.
The end result was a satisfied customer (we fulfilled the brief) and a new standard solution that can be replicated on other lines and at other customers.
Ian Wells: Key Account Manager
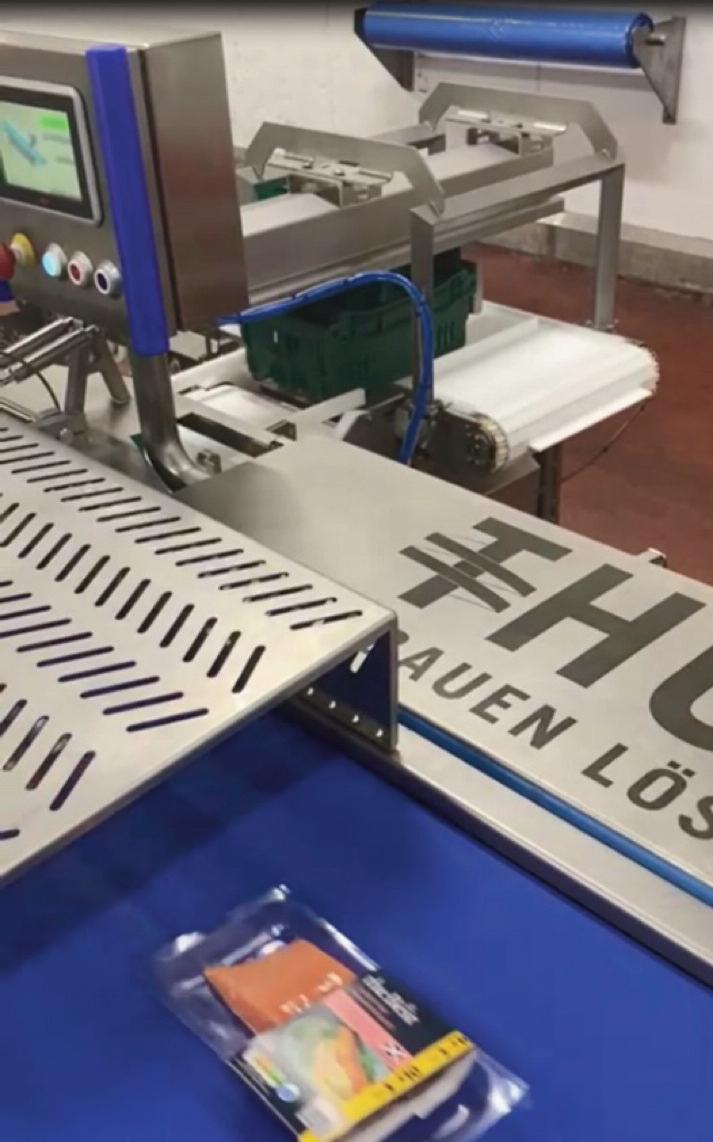
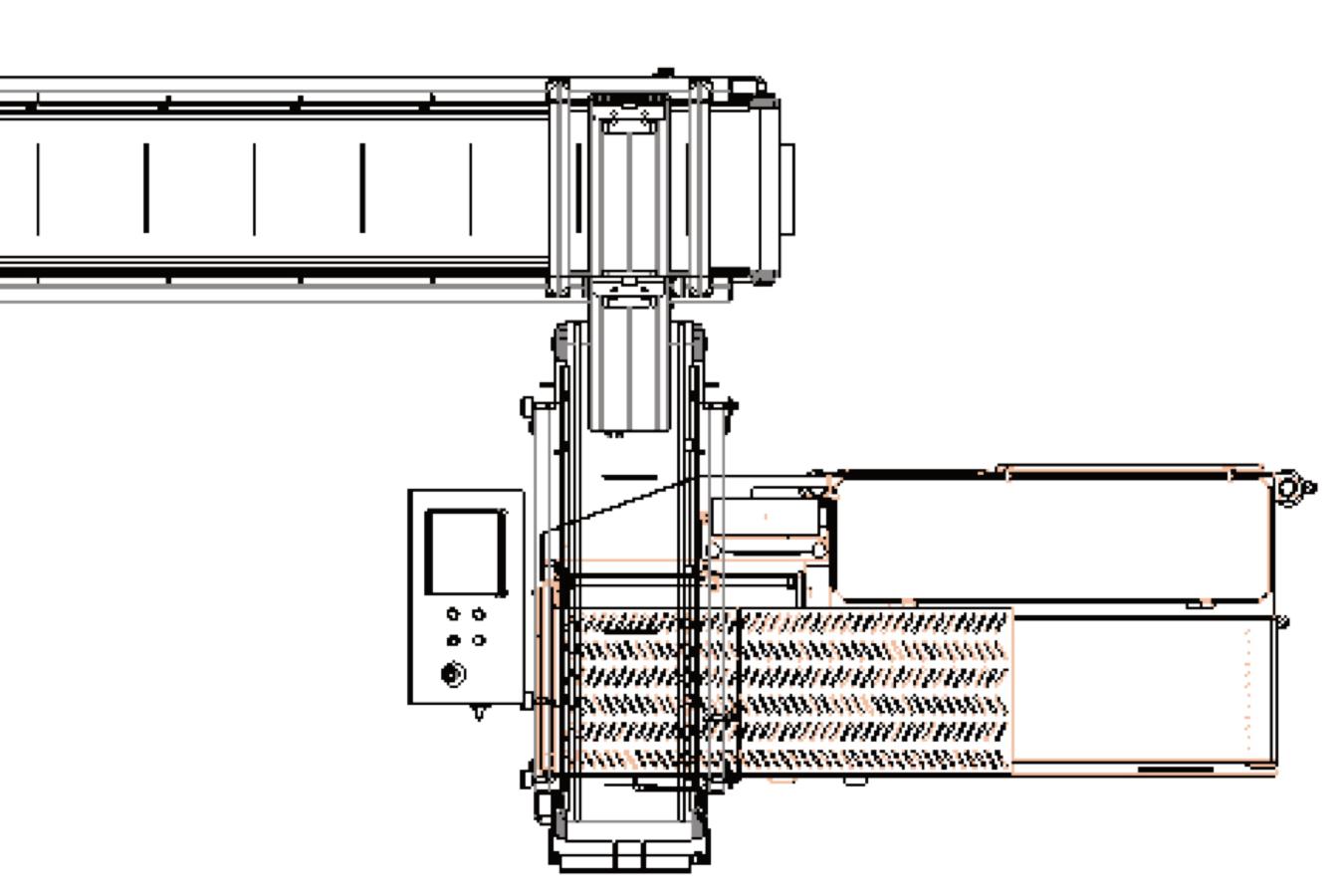
First complete line order for Fritsch
A major force in the UK Addo Foods have multiple sites across the UK including Poole, Nottingham, Spalding and Market Drayton. Addo’s Market Drayton site is responsible for the manufacture of some 312 million products per year!
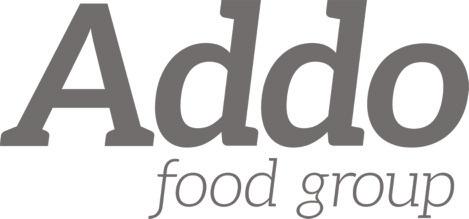
Founded some 200 years ago in 1786 by Richard Wall, todays modern Market Drayton site is responsible for manufacturing suppling some of the nations favourite products including pies and sausage rolls under own label and supermarket branding.
Multivac UK have enjoyed a long-term relationship with Addo Foods and have previously supplied number of standalone vacuum packing machines for is pie filling products and more recently a new high speed tray sealing line complete with Multihead Weigher for its Sausage Roll products.
With such a high output of core products Addo employ high levels of manufacturing automation making it difficult to accommodate and develop new products that do not readily lend themselves to their current manufacturing plant.
Not so with the Fritsch Varioflex M700 unit, a compact versatile unit taking up just 5900mm x 1360mm x 1600mm of floor space. the Varioflex is a portable line that can be configured for low / medium level production of products including sausage rolls, D Shape Pasties, slices and Pin Wheel products
Addo Foods have ambition to produce a range of pinwheel products both sweet and savoury and following successful virtual trails amidst the Covid pandemic and taking advantage of Fritsch unrivalled “World of Bakery ” facility, Multivac UK were able to demonstrate the Varioflex M700 was the right machine for them.
A collaborative decision to proceed headed up by Neil Parry Site Director, Mick Haslem - Engineering Manager and Elain Bell – Product Development it was plain to see that high quality consistent products could be produced and replicated on what is in essence a portable make up line.
The Fritsch Varioflex is designed to accept reels of pre laminated pastry typically 600mm wide and wound on to what the industry commonly refers to as spools. These spools are manually transferred to the Fritsch Varioflex M700 line where they are passed through a calibrating head designed to regulate the thickness of the sheet typically from between 0.1mm –4.2mm depending on the product to be manufactured.
A longitudinal Guillotine will then cut the now regulated pastry sheet, remove any scrap ahead of a filling unit that will coat the pastry with a sweet or savoury filling. Once coated a spreading bar system ensures an even filling coating is applied to the entire pastry sheet. In this instance the Varioflex is fitted with a coiling unit which is in essence a driven motorised cone that rotates at a set angle to the main conveyor. As the coated sheet passes the coiling unit the sheet is wound in such a way to produce a roll that captures the filling layers, not that
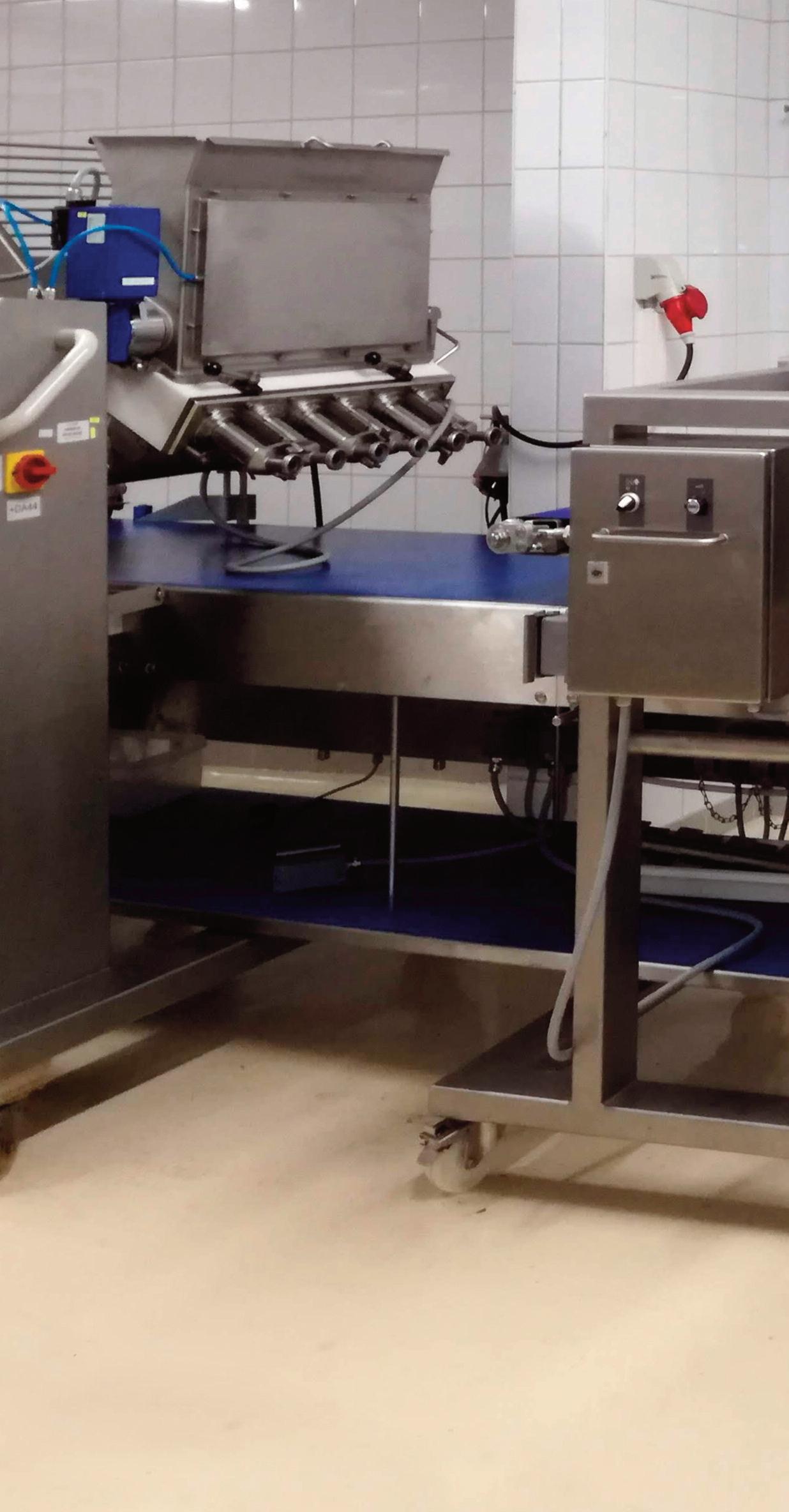
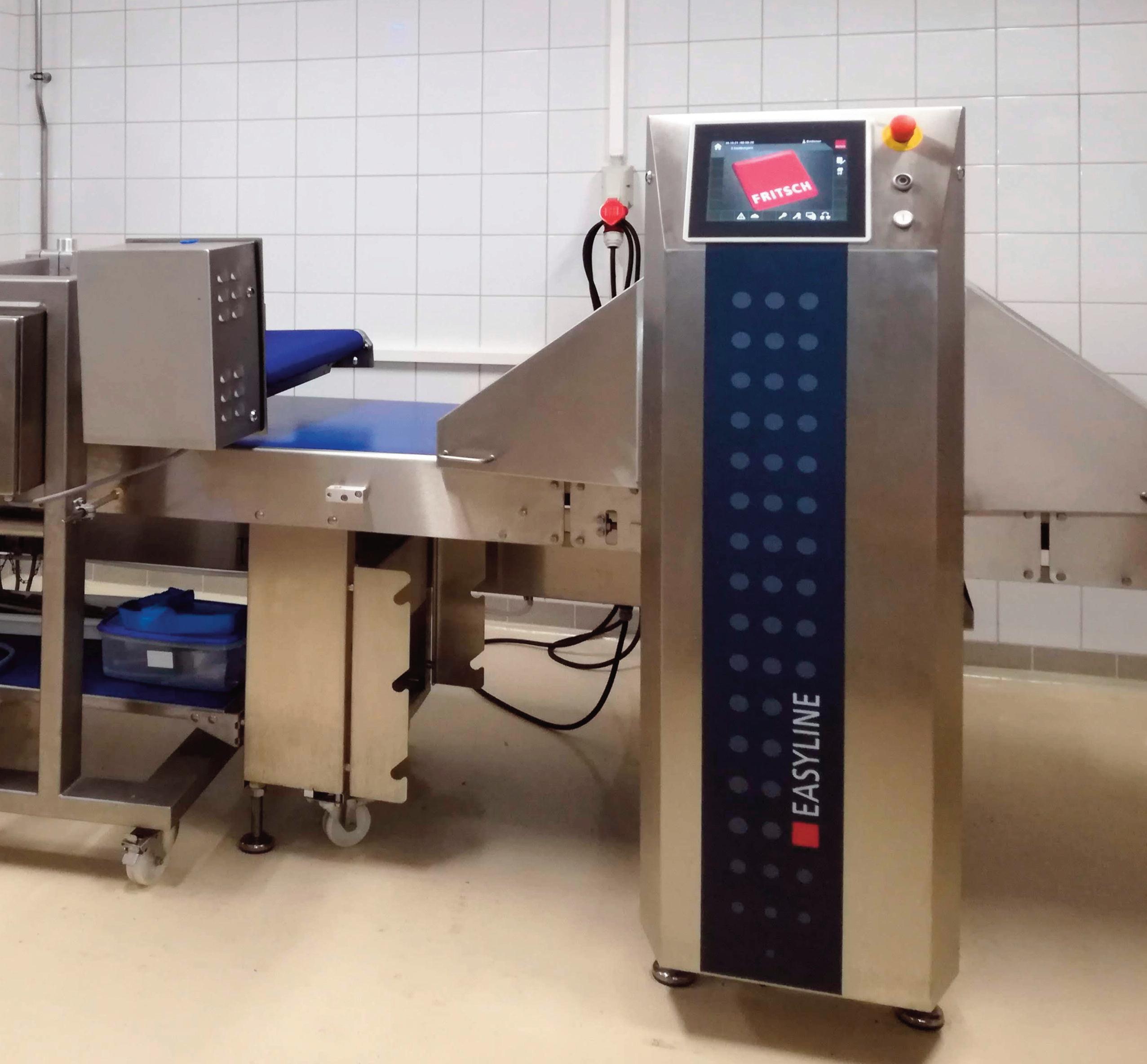
indifferent to a Swiss roll a product we all know and love. Finally, once the desired “ pin wheel” diameter has been produced a guillotine that runs across the width of the conveyor cuts the coiled product into individual pieces ready for baking.
Addo had several reasons for purchasing the Varioflex M700 from Multivac , the primary reason being the units versatility and its ability to be quickly and effortlessly changed to manufacture different products such as slices or D shaped pasties with relatively low financial outlay, Addo also recognised that not only is the Fritsch line of the highest quality but Multivac UK has a recognised and proven track record when it comes to unrivalled aftersales care and support, important in fast moving business like Addo.
With the line due to be delivered into Market Drayton shorty the Varioflex M700 marks the beginning a new era of product development for Addo ’ s business, exciting times lie ahead and we at Multivac are privileged to be considered as Addo ’ s preferred partner, should be honoured to be invited to come along for the ride.
Steve Owens: Regional Sales Manager
Multivac Slicing has a new cutting edge...
