

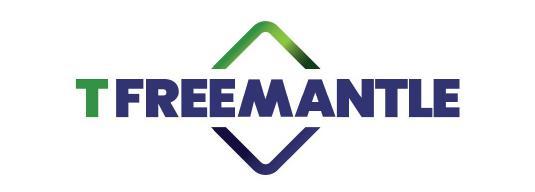
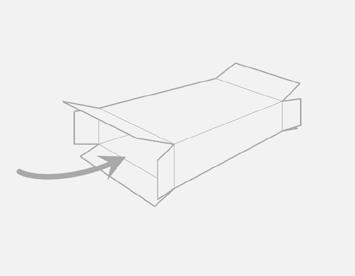
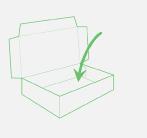
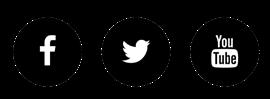


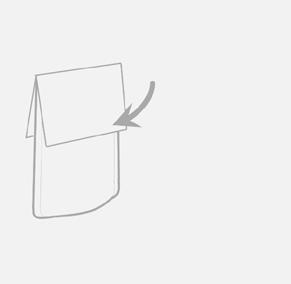

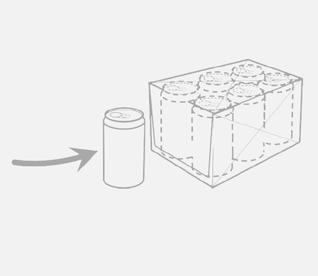
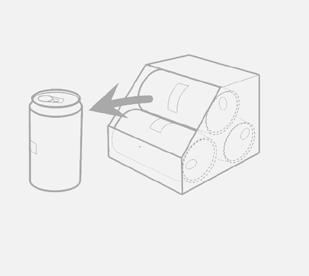
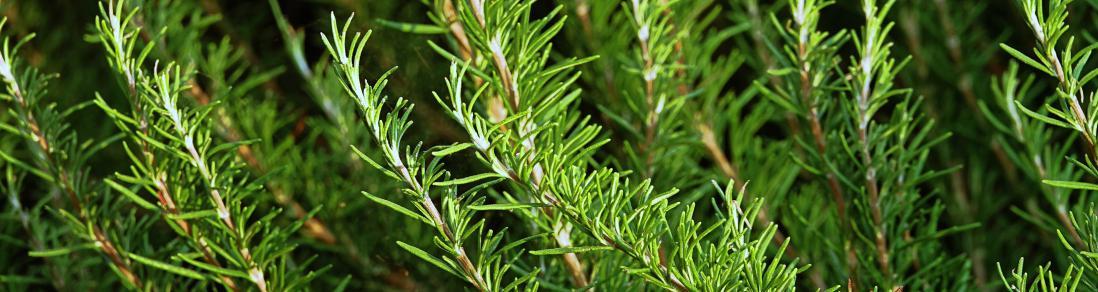

The new rosemary-based range is designed for diverse food-based applications and responds to consumer demand for more natural ingredients
Syensqo is launching Riza, a 100% plant-based range of antioxidants and flavors derived from rosemary. The launch of this range follows Syensqo’s majority share acquisition of Moroccan rosemary extraction company Azerys, which took place in July 2024.
Rosemary extract accounts for more than a third of total natural preservatives used in food, which has increased significantly in recent years, due to growing demand for natural ingredients driving food manufacturers to reformulate their recipes.
“The Riza range aims to help food manufacturers eliminate artificial preservatives by providing them with a natural alternative,” says Christophe Cartier, Syensqo’s Aroma Market Director. “With the natural benefits of rosemary extract antioxidants, we can create tailor-made solutions for our customers’ needs.”
“Azerys’ capabilities & extraction knowledge, combined with Syensqo’s innovation power, provides our customers with the expertise required to meet their natural expectations” says Moulay-Rachid Cherkaoui, CEO of Azerys.
Based on ethically-sourced wild rosemary harvested in Morocco’s Atlas mountains, the large variety of endemic species ensures that the Riza range contains no pesticides or heavy metals, and provides a reliable supply. As an antioxidant, rosemary helps to preserve omega-3 fatty acids - such as DHA – for longer, in addition to stabilization of flavor and color properties, and maintenance of product quality and shelf life.
The range can be used in diverse applications including meat, bakery, instant meals, oil and fat-based food products, as well as pet foods or feed ingredients – swine, poultry, fish – and beverages. Solutions covering pure rosemary and mixed blends, are available as a powder or liquid, and contain different carnosic acid contents.
Syensqo will showcase its new Riza range at Fi Europe 2024 in Frankfurt, Germany from 19-21 November (Hall 3.1 Booth #K20) and will also present the conference “‘Rosemary: The Key to Extending Product Shelf Life, Demonstrated with Oils.”
Learn more at www.syensqo.com
EDITORIAL:
AKP Public Relations
Easyfairs UK Ltd
Hale Events
Hygiena
Koelnmesse PTE Ltd
PPMA Group of Associations
PHD Marketing
Trane Technologies International Ltd
ADVERTISEMENT SALES:
KIMBERLEY READ (Advertisement Sales Manager) JOANNE MURPHY
AMANDA WALMSLEY EVELYN WOOLSTON
RACHEL RILEY - Designer
WALTONS PUBLICATIONS LTD
46 HENEAGE ROAD, GRIMSBY N.E. LINCOLNSHIRE DN32 9ES
Kimberley Read at: kimberley@ foodanddrinknetwork-uk.co.uk or Joanne Murphy at: joanne@foodanddrinknetwork-uk.co.uk
foodanddrinknetwork.co.uk
True Sports Hydration is revolutionising the way athletes and fitness enthusiasts stay ahead of their hydration needs with the first intracellular hydration drink.
Combining ultra-pure water with essential electrolytes, it provides proactive hydration, ensuring rapid cellular absorption to enhance endurance and recovery—all without added sugar or salt. With Gemma Burke at the forefront, True Sports Hydration is setting a new standard in sports science, helping athletes stay ahead of the game with optimal performance and well-being. To find out more visit https://sportshyeu.com/
Leading UK distributor ACI Group Ltd (‘ACI Group’) has announced its partnership with DolCas Biotech LLC (‘DolCas Biotech’) to distribute its range of clinically researched nutraceutical ingredients in the UK market.
The collaboration strengthens ACI Group’s functional ingredient portfolio at a crucial time. According to intelligence firm Grand View Research, the global nutraceuticals market is expected to grow at a compound annual growth rate (CAGR) of 8.4% from 2024 to 2030, driven by increasing consumer focus on proactive health management.
DolCas Biotech, established in 2006, is a branded ingredients firm, specializing in the development, global positioning and commercialization of clinically researched ingredients. Part of a larger contract research and development organization (CDMO), DolCas Group, their range of science-driven actives address key health areas such as gut function, women’s health, healthy ageing, brain & mood health, and cardiovascular health. Vertically aligned, DolCas’ broader reach supports market strategy options for its customers and partners that easily move their premium ingredients from standalone actives to full formulations and finished product formats.
Bluewater appoints Niklas Ivarsson President Commercial Division (Horeca) at Bluewater
Bluewater USA Inc, a wholly-owned member of Sweden’s Bluewater Group, a global innovator in water and beverage solutions, is excited to announce the appointment of Niklas Ivarsson as President, Commercial Division HoReCa North America.
With a 20-year track record in global sales and marketing in the food and beverage and manufacturing industries, Ivarsson will play a pivotal role in relaunching Bluewater Brand business-to-business operations in the North American market.
Karsten Smet, CEO of ACI Group, commented: “This partnership with DolCas Biotech opens doors for our customers to create truly differentiated products that command attention. In today’s competitive market, brands and their formulators need ingredients that not only work in a targeted way to address critical health priorities but substantiates those claims. DolCas Biotech’s clinically proven range, with focus on superior bioavailability and potency, supports the development of innovative formulations that meet consumer demands for efficacy and ease of use. We look forward to supplying these ingredients to our health and nutrition customers across the UK and helping to usher in the next generation of nutraceutical solutions.”
The partnership brings several key products to the UK market, including Curcugenâ, Morikolâ, BergacynFFâ, NitrateBurstâ, Fortiquinâ, and MMP50â. These ingredients enable the creation of advanced nutraceutical products with attention-grabbing features and benefits.
For instance, the high potency of Morikol and NitrateBurst enables brands to offer collagen and phytonitrate supplements in convenient tablet or capsule forms, rather than the traditional powders requiring 5-20g daily doses.
For more information on ACI Group or its activities, please visit acigroup.biz/
Niklas Ivarsson brings broad-spectrum experience in sales and, marketing, and branding roles, with over a decade dedicated to building sales strategies at the territory, regional, and national levels in North America. His previous leadership role as Chief Commercial Officer at Gruppo Cimbali SpA showcased his ability to drive business turnarounds and international expansion. Ivarsson’s extensive background includes influential positions at Waring Commercial, Matfer Bourgeat USA, FETCO, and F. Gaviña and Sons, Inc.
“Now is a key time for Bluewater as we prepare to launch the company’s unique Café Station into the North American coffee industry,” said Ivarsson. “I’m stoked to join such an innovative company and be part of this historic moment to shape the foodservice and coffee industry’s view of the way they use water.”
Ivarsson added that in contributing to its growth in this dynamic American market, the Bluewater focus will very much be on delivering service excellence and exceptional value to its partners and trade and consumer customers. He noted that the Bluewater Café Station “is a truly revolutionary commercial integrated water purification and mineralization system innovated to enable professional qualityminded baristas to bring flavors of coffee to new levels of perfection.”
With an educational background in industrial electronics, Ivarsson possesses a diverse skill set in sales management, new business development, customer service, and product education. His hands-on leadership style and integrity have consistently resulted in profitable sales growth for companies of all sizes.
Bluewater founder and CEO Bengt Rittri said the Bluewater Brand is poised to enhance its presence in North America under Ivarsson’s leadership, aligning with a strategic plan to strengthen operational activities and integrate its brand portfolio from coast to coast. “The upcoming launch of Bluewater’s innovative offerings for the hospitality industry, including our unique Café Station, underscores the company’s commitment to sustainability and quality in the beverage industry,” Mr. Rittri said.
Sapling Spirits has appointed Mark Cornell as a Chairman, bringing his extensive leadership experience from the global wine and spirits industry to the team.
Mark’s career highlights include serving as CEO of Krug Champagne (2002), President and CEO of Moët Hennessy USA (2006), and CEO of ATG Entertainment (2016). He most recently joined Sapling as non-executive Chairman in September 2024. A graduate of the prestigious IMD Lausanne with an MBA, Mark has over 11 years of experience in the wine and spirits sector, with a deep understanding of both brand-building and distribution, particularly in the US and Asian markets. His decision to join Sapling reflects his alignment with the company’s sustainable approach to spirits innovation.
On his decision to join Sapling, Mark stated, “As a challenger brand within the super-premium spirits segment, with first-class product quality and with a clear commitment to sustainability, Sapling is extremely well positioned to appeal to the trade and consumers alike, globally. At the same time, Sapling should bring a smile to many faces for all sorts of reasons. Cheers
Leading glass packaging company, Croxsons, has recently teamed up with the Society of Independent Brewers (SIBA) to support their Indie Beer campaign, an initiative designed to promote and protect the UK’s independent brewing community.
As part of this collaboration, Croxsons, a SIBA Gold Member, will supply bespoke Indie Beer-branded crowns (crown corks) that help breweries show their support for the campaign and highlight their status as independent producers of high-quality, handcrafted beer.
To make the campaign accessible to as many breweries as possible, SIBA is providing a 50% subsidy on the first 500,000 crowns, encouraging breweries to proudly display their support for the movement.
The Indie Beer campaign seeks to make the Indie Beer mark a trusted symbol for consumers seeking quality craft and cask beer, brewed passionately by independent brewers. With support from key industry groups the Campaign for Real Ale (CAMRA), the Independent Family Brewers of Britain (IFBB) and the British Institute of Innkeeping (BII), the campaign advocates for independent brewers and encourages a deeper connection between brewers and beer lovers.
“SIBA is delighted to be working with Croxsons to provide new Indie Beer crowns for breweries to signify themselves as a part of the campaign and a genuine independent brewer,” said Neil Walker, head of comms & marketing. “By working together, independent brewers and suppliers can help consumers make a more informed choice, ensuring they’re buying beer handmade by real people who truly care about the quality and flavour of the beer they produce.”
Commenting on the campaign, Croxsons’ CEO, Tim Croxson, added: “By using Croxsons’ Indie Beer crowns, breweries can proudly showcase their commitment to quality and their independent status, helping consumers make conscious choices that support local businesses, protect pubs and contribute to a more sustainable beer industry.”
For more information on the Indie Beer campaign, visit https://www.indiebeer.uk/
For more information on Croxsons’ Indie Beer crowns, visit https://www.croxsons.com/our-products/siba/
everyone!” Sapling Spirits, known for its commitment to sustainability, welcomes Mark’s strategic vision and leadership as the company continues to champion environmental responsibility within the drinks industry. His appointment will support Sapling’s mission to create high-quality, environmentally conscious products that resonate with today’s conscious consumers.
https://saplingspirits.com/
Food manufacturers urged to act fast ahead of new food waste legislation
Food manufacturers across the UK are being encouraged to act fast and get prepared, before stringent new food waste legislation comes into effect early next year.*
Applicable to all businesses that generate food waste on site,** the new rules state that all commercial food waste (be that preparation waste, offcuts, spoiled produce or plate scrapings) should be separated at source, stored and collected for recycling by a reputable service provider. Any business that fails to adhere will be liable to significant penalties.
Richard Poskitt, head of supply chain/commercial at ReFood, the UK’s leading food waste recycler, believes that the move is a significant step forward. He says: “Every year, food manufacturers in the UK throw away a huge volume of food waste, contributing to a national mountain exceeding 10.5 million tonnes. When left to rot in the ground, food waste releases greenhouse gases considered 21 times more damaging to the environment than CO2. For this reason alone, mandating a ban is simply common sense.” While businesses may be concerned about the cost and disruption of embracing food waste recycling services, Poskitt explains that working with a proven supplier can make the whole process quick, simple and seamless. What’s more, it can significantly improve your sustainability credentials alongside. ReFood’s unique ‘bin swap’ service sees full bins exchanged with clean, sanitised, replacements. This means that bins can be hygienically used indoors, enabling staff to separate at source with no disruption to service.
For more information about ReFood, visit www.refood.co.uk, or call 0800 011 3214 and speak to the team about your requirements.
* Non-household municipal premises will be required to make arrangements for separate food waste collections and present the waste in accordance with legislation by 31 March 2025.
** Micro-firms will have extra time to bring in new requirements for dry recyclable waste streams (excluding film) and food waste – they must comply by 31 March 2027.
Our new name represents a renewed commitment to strategic thinking and client success.
Whether you’re a long-time client or meeting us for the first time, we’d like to share our journey as Think B2B Marketing.
Ten years ago, our founder, Joanna Stephenson, led the Marketing and Innovation division at one of the world’s largest packaging companies. Frustrated by agencies that didn’t understand the print and packaging industries’ intricacies, especially globally, Joanna saw an opportunity. PHD Marketing was born, dedicated to providing communications services tailored to the sector.
From there, we expanded rapidly, building strong relationships with clients who appreciate our in-depth industry knowledge. This expertise allows us to suggest targeted marketing strategies that more generalised agencies often overlook. Over the years, we’ve grown into a full-service partner, offering solutions that span industries, including life sciences and technology. Our commitment, grit, and proactive team have built our reputation, and now we’re entering a new chapter of growth.
Our rebrand reflects our commitment to strategic, industryspecific marketing. Many of our clients, having worked with high-profile agencies in London or New York, value our pragmatic, no-nonsense approach. Instead of flashy offices, we offer a team of experienced professionals—copywriters, digital experts, graphic designers, and web developers— focused on your success. In today’s world, where cost control and ROI are critical, our thoughtful, results-driven marketing stands out.
While Think B2B Marketing may be a new name, we continue offering the same high-quality services you knew from PHD Marketing. We specialise in the print, packaging, life sciences, manufacturing and technology sectors, helping companies of all sizes find their voice and connect with customers.
Joanna Stephenson, Managing Director, said:
“It’s easy to look at agency rebrands and think ‘so what?’ but for us, the switch from PHD Marketing to Think B2B Marketing is a graduation. We’ve scaled enormously and we’re ready for the next phase of our growth journey, while staying true to the core values and approach that have made us such a force in the industry over the last decade. A lot of agencies claim to be ‘like an extension of their clients’ teams’, but we’re a business that walks that walk; we don’t get lost in flashy slide decks and gimmicks. We stay laser-focused on delivering tangible results and real ROI.”
Our services include:
• Strategic marketing planning
• Content creation and management
• Digital marketing and social media
• Web design and SEO
• Public relations and media outreach
• Media planning and advertising
• Event planning and execution
Ready to elevate your marketing? Visit our website at www.thinkb2bmarketing.com to learn more.
Let’s get started!
The root causes of batch rejections and RTMs can start from the beginning of the manufacturing process and are a constant risk until the batch is satisfactorily delivered. By working together, we can eliminate these risks.
Every batch rejection is the consequence of a quality failure, either in raw materials, processes or in the accuracy of packaging/coding and therefore, every such costly event is totally avoidable.
Easily capture results for seamless data integration and analysis through direct connectivity with peripherals.
An article By Roy Green, Harford Control Ltd. November 2024
From 11th to 15th November, businesses and organisations worldwide will celebrate World Quality Week, an annual event that raises awareness about the importance of quality management. This year’s theme, “Quality: From Compliance to Performance,” emphasises the need for organisations to go beyond mere regulatory adherence and focus on driving outstanding performance. Quality principles are the key to navigating challenges, achieving long-term success and improving overall efficiency.
Quality issues: still a persistent challenge
Despite advancements, quality-related issues continue to pose significant challenges. Factors such as product recalls, contamination, labelling and packaging errors, together with inconsistent product quality, can severely undermine the effectiveness of the whole organisation.
Both Tesco and Waitrose have announced product recalls since the start of October this year. Tesco recalled its Tesco Finest 6 All Butter Pastry Mince Pies after it was found that the product might contain pieces of dried glue from the packaging. This contaminant made the pies unsafe to eat. Waitrose issued recalls for its Easy to Cook Scottish Salmon En
Croute and Easy to Cook Salmon and Sweet Potato Curry, due to a failure to declare certain allergens on the packaging. The products contained milk, mustard, soya, and wheat (gluten), which were not listed on the label, posing a significant health risk to those with allergies or intolerances.
These recalls resulted in significant wastage, added substantial costs to the bottom line, and damaged brand reputation, whilst also negatively impacting the environment. Consistently high quality is never by coincidence, but is the consequence of disciplined due diligence at every step of the production process, from goods in to the retailer. It is relentless. No sooner has one production batch finished, than another begins. Product changeovers are particularly challenging, especially where the
manufacturer has a large product portfolio and many short batch runs.
Cross-contamination poses significant risks to food quality and safety. It can facilitate the transfer of harmful pathogens, such as Salmonella, E. coli, and Listeria, from one food product to another. Additionally, if the same production line is used to process allergen-free products immediately after handling nuts or other allergenic foods, without thorough cleaning, the risk of cross-contamination, of course, increases
dramatically. This not only jeopardises consumer health and, more specifically, the risk of severe allergic reactions, plus the inevitable damage to the brand.
A recent incident underscores this danger: thousands of sandwiches, wraps, and salads containing a specific variety of salad leaves were recalled after the UK Health Security Agency (UKHSA) linked them to an E. coli outbreak that hospitalised at least 86 people.
To mitigate such risks, food factories must implement better raw materials and inprocess quality control checks to track and trace ingredients and conduct quality checks on individual and grouped materials. Early detection of cross-contamination can prevent compromised products from progressing down the production line.
Harford offers Materials and Process Quality Solutions to empower manufacturers to ensure consistent quality from raw materials to finished goods, focusing on achieving excellence, ‘right first time, every time’. With end-to-end traceability, 5 Whys and Fishbone Diagrams, it becomes easier to identify the root causes of quality issues, ensuring consistently high quality throughout production.
Whilst implementing robust quality control measures is essential for preventing contamination, the methods used for recording data can also significantly impact overall quality management effectiveness.
Paper recording is another major contributor to quality issues, as it slows processes and lacks real-time visibility of production processes. Without instant, actionable data, businesses struggle to achieve a “Right First Time” approach. Paper-based systems can also very quickly become out of date.
One of our brewery clients faced this challenge—they were using paper recording and couldn’t identify the root cause of downtime in real time. They sought solutions to reduce paper recording, improve quality consistency, and gain real-time visibility of performance metrics.
Harford installed a fully paperless system at their facility. As a result, all quality checks became instantly visible and traceable, allowing operators and shift managers to work efficiently in a paperless environment. Management also benefits from real-time data visibility on schedule adherence, production performance, quality, efficiency and instant traceability. Live ‘Short Interval Control’ screens above production lines provide instant updates on key performance indicators and improvement opportunities, enhancing operational efficiency and data accuracy.
The longer a factory operates without quality issues or ‘near misses’, the higher the risk of encountering them. Quality issues are necessarily complex and require a holistic approach to enhance production quality effectively. Once quality and compliance challenges are resolved, each factory can focus on improving performance.
Today, the Harford Quality Solution is unquestionably the most comprehensive and advanced system available to manufacturers. Harford quality solutions combine decades of experience with continuous improvement, heavily influenced by user input from FMCG, food and beverage, pharmaceutical, cosmetics and chemical manufacturers.
When you’re ready to minimise risks and enhance your quality control, we are ready to listen. Please contact us at info@harfordcontrol.com or call us on +44 (0)1225 764461.
The PPMA Show, the UK’s leading event for processing and packaging machinery, including industrial automation and machine vision systems, has once again been acclaimed as a great success. Established more than 35 years ago, the renowned exhibition welcomed thousands of visitors over the course of its three-days at the NEC Birmingham. The event offered visitors the opportunity to experience a complete production line from start-to-finish.
The exhibition hall was busy from the moment the doors opened until the show finished, providing a perfect platform for visitors to observe the latest cutting-edge technologies and solutions, exciting live demonstrations and product launches, as well as top up their knowledge with hours of free expert seminars.
This year’s show was made extra special by the well-known broadcaster, entrepreneur and writer, Gregg Wallace - who spent a day at the show as he went ‘Inside the Exhibition’ - interviewing exhibitors to gain their insight. These recordings will be available soon online.
The PPMA Show, which is owned and organised by Automate UK, gave visitors the chance to see how the of state-of-the-art solutions on display could improve the efficiency of their own businesses, giving them key competitive advantages over their competitors.
The show boasted an impressive line-up of more than 350 exhibitors – including over 100 new exhibitors. These companies showcased their cutting-edge solutions spanning the full spectrum of the manufacturing industry, including: pharmaceuticals, food, beverages, building materials, pet care, microbrewers and distillers.
Informing their decision-making before investing, visitors held face-to-face conversations with exhibiting experts, gaining guidance on the suitability and benefits the various innovative solutions can bring to their businesses.
Exhibitors included many well-known companies in the sector, such as: Packaging Automation, PFM, Holmach, Keymac, Omori, Wipotec, Somic, Markem-Imaje, Ilapak, Bizerba, Ulma, Beckhoff, Schur Star Systems, Ilpra, Sidel, and JBT Proseal.
Scott McKenna, Chief Operating Officer at Automate UK said:
“The PPMA Show has consistently been the premier destination in the UK for exploring technology across the entire processing and packaging industry. Our main challenge as organisers is to ensure the exhibition evolves and stays relevant to the highcalibre visitors we are proud to attract each year.
“This year, we can confidently say, we exceeded our own expectations, with an outstanding turnout of attendees eager to invest in the remarkable range of innovative technologies showcased at the event.”
One of the many attractions of the show were the expert presentations at the seminar theatres. These talks delivered updates on both the latest industry insights and trends. They were crafted to be thought-provoking in a way that would encourage visitors to reflect on how they could apply their seminar learnings in their own businesses.
This year’s inspiring keynote speakers were Jessica Sansom from Huel and Stefan Casey from Nestlé. Jessica’s presentation focused on the manifestations of climate changes and how to rise to the challenge and adapt to a new normal. Stefan shared some of his knowledge on the digital transformation of FMCG industry, including challenges and opportunities in packaging across the whole value chain.
One visitor to the show, Callum Reader, of Marco Ltd, said:
“It was great to be back at the PPMA Show for the first time in about four years. There was such a wide range of innovative and inspiring machinery to see. I would recommend this event to anybody in the food industry; it has so many different and fantastic solutions to learn about as well as providing a great opportunity to catch up with all the latest developments in the industry.”
Another visitor, Tom White from DaceCrown, said: “This year’s event was busier than in the past, offering a wealth of innovative solutions to explore. It was also great to see the net zero and eco-friendly initiatives present in a substantial number of showcased products.”
New for this year, Automate UK debuted a free PPMA Show app, packed with features such as a function to retrieve exhibitor information via QR codes, detailed seminar information, and a floorplan to navigate around the show. All of which improved visitors’ exhibition experience. In addition to the app, other innovations included a live demonstration theatre and show tours, plus a networking reception for visitors and exhibitors.
The PPMA Total Show will return to the NEC next year, promising to be bigger and better than before. The event will bring together suppliers and end users, making it easier for visitors to discover the latest cutting-edge solutions for their businesses. Attendees can once again look forward to a diverse range of innovative exhibits, thrilling demonstrations, inspiring seminars, and plenty of networking opportunities, all designed to enhance the visitor experience.
For more information, please visit: ppmashow.co.uk
Sustainability and innovation are driving the agenda at Food ingredients Europe, which returns to Frankfurt from 19-21 November 2024.
With just a few weeks to go until Fi Europe opens its doors at Messe Frankfurt, the event is gearing up to welcome over 25,000 visitors from 135 countries. The Startup Challenge, Fi Innovation Awards, Fi Conference and Future of Nutrition Summit are some of the highlights that will make this a must-attend event for food professionals looking to get to grips with the latest trends and developments in ingredients.
Yannick Verry, Brand Director of Fi Europe & Americas says:
“We’re really looking forward to Fi Europe 2024. The event has been growing and evolving with the needs of the F&B ingredients industry and this year we have some great additions alongside our tried and trusted favourites.”
More than 1500 exhibitors are confirmed for the main show arena, which will be populated by offerings spanning the full F&B ingredients spectrum and will be zoned for easy navigation. There will be more than 25 country pavilions, connecting visitors with exhibitors from Denmark, France, USA, Germany, Japan, Poland, Spain and more; dedicated areas for health ingredients, natural ingredients and organic ingredients; a startup pavilion showcasing up-and-coming innovators; and a newly expanded Food Technologies & Solutions zone for those seeking practical and innovative ways to optimise their supply chains and future-proof their operations, from R&D to delivery.
NEW! Pet Food Suppliers’ Hub
Meeting demand for a dedicated pet food platform within Fi Europe, this year will see the launch of the Pet Food Suppliers’ Hub. This new area will showcase ingredients and technologies that can support the pet food industry in developing nutritious, safe and innovative products. Companies of all sizes will participate, from major F&B suppliers such as Cargill, Brenntag or Barentz to specialist players in the petfood sector such as IQI or Agronutris.
“Pet food manufacturers are challenged with finding new ways of tapping into the pet humanisation trend and are looking to the ingredient industry to power their innovation. Fi Europe has a strong track record of facilitating business partnerships that deliver successful products and the new Pet Food Suppliers’ Hub will create a vibrant forum for exchanging ideas, inspiring innovation and forging new relationships,” says Verry.
The entire event is designed around inspiring, enabling and celebrating innovation, through features like the New Product Zone, curated by Innova Market Insights, and Innovation Tours led by NutriMarketing guides. All visitor passes include free access to the Innovation Hub, which will host presentations and discussions on trends, innovations and opportunities throughout the three days.
Recognising the crucial role that startups play in driving innovation, Fi Europe will once again stage the Startup Challenge, now in its ninth year. More than an awards programme, the Challenge is a platform for advancing potentially transformational solutions from young companies.
This year’s Challenge will feature four exciting categories, including the new Most Innovative Foodtech Solution plus a special Jurys Choice award for the Most Innovative Sustainable Solution. Finalists will pitch their ideas to a live audience in the Innovation Hub on 19 November and winners will be announced during the show.
“Startups are defining and designing the innovative food ingredients of tomorrow, but often lack the scale and funds to bring their solutions to market. Connecting with the right partners is therefore a fundamental part of any startup’s journey, and the Fi Europe Startup Challenge is the ideal place to do so,” says Verry.
The Fi Innovation Awards will also return this year, with nine accolades for the taking, including four new categories that capture the cutting-edge trends shaping the future of food. These are: Dairy Alternative Innovation, Food Manufacturing, Pet Food Innovation, and Future Foodtech Innovation. The programme will culminate in a glittering ceremony on the evening of 19 November, when the winners are announced. Entry to the Innovation Awards is included in the VIP pass.
Content is king
Fi Europe’s comprehensive content programme is always a major draw and this year is no exception. Free access to the two-day Fi Europe Conference (19-20 November) is included with all visitor passes. Expert-led sessions will focus on four topical themes: health and wellbeing; plant-based and alternative proteins; reformulation; and tech-led ingredient innovation. The Future of Nutrition Summit, accessible with a delegate pass, is another opportunity to ingest cutting-edge
content. It takes place at the Mövenpick Hotel Frankfurt City on 18 November, the day before Fi Europe opens its doors. Here, industry leaders and visionaries will give presentations and lead discussions on future trends and developments in health and nutrition.
Sustainability a core theme
Sustainability will be a key thread running throughout Fi Europe 2024. At the Fi Conference and Future of Nutrition Summit, thought leaders will discuss sustainable development and supply chain transparency; the Fi Innovation Awards and Startup Challenge will raise the profile of pioneering sustainability-led solutions, and the exhibition floor will offer a hub for buyers and suppliers to engage in dialogue around sustainable ingredient sourcing.
The event’s sustainability partner, Solidaridad, will be present, sharing its expertise on addressing sustainability issues in supply chains, with the aim of empowering brands to source ingredients ethically and sustainably while meeting calls for enhanced supply chain transparency.
“Our partnership with international civil society organisation Solidaridad is part of our ongoing commitment to sustainability,” says Verry. “Through the event’s features and content we will highlight sustainable sourcing, transparency, regulatory compliance and more.”
With data-driven matchmaking and The Women’s Networking Breakfast also back this year, Fi Europe offers unrivalled networking opportunities. To help attendees plan their days, book meetings and optimise their time, the user-friendly Fi Europe event platform is available online now.
For more information and to register your attendance, please visit the Fi Europe website at https://www.figlobal.com/europe/en/home.html
Wein@BrauBeviale What fits together ferments together“.
A single slogan for the combined package: The trade fair organisers’ clear aim is to raise the profile of products and services for wine production and attract more visitors from the wine sector to BrauBeviale. The wine industry has had a defined focus at BrauBeviale since 2023. This year, from 26th to 28th November in Nuremberg, the offer for the wine industry will be further expanded.
53 per cent of exhibitors will have specific solutions for the wine industry as part of their exhibition and product portfolio. In addition to process technology for the production of wine, sparkling wine and spirits with destemmers, preparation tanks, fermenters, fermentation and storage tanks and filtration technologies, exhibitors at BrauBeviale 2024 will also offer a complete infrastructure equipment overview including pumps, valves and pipework. Furthermore, winemakers can gather detailed information from manufacturers of bottles and containers and learn the latest EU requirements related to bottling and containers. The range of products and services in the wine sector will be rounded off by the integration of the special wine show in Hall 4A. This special show will feature additional suppliers who focus specifically on the wine industry.
From wine experts for wine experts
BrauBeviale is coordinating this thematic focus in close cooperation with a team of experts – wine mentoring, so to speak.
This guarantees direct insight into the latest developments in the industry: the German Winegrowers’ Association (DWV) will be there as a technical advisor, as well as experts from the German Wine Institute (DWI), Geisenheim University, the Bavarian State Institute for Viticulture and Horticulture and the HBLA Klosterneuburg in Austria. (Highschool and Austrian Federal Office of Viticulture and Pomology)
A broad programme of lectures will also be offered. The lectures will take place on all three days in Hall 4A. Some examples of the subjects to be covered:
• Non-alcoholic wines from the cellar to the bottle: Focus on production technology, with Dr Matthias Schmitt, Hochschule Geisenheim University, among others
• Challenges and opportunities of climate change in wine production, with Franz G. Rosner, HBLA Austria, Klosterneuburg
• What will the wine of the future taste like? Target group preferences for wine marketing in the next generation, with Steffen Schindler, German Wine Institute
In addition to cellar technology, sustainability and quality assurance, other main topics will cover marketing and sales issues and offer some fascinating insights into comparative scenarios between beer and wine. The lecture programme will be available in the event planner on the BrauBeviale website from the end of September.
Information for winegrowers – in a compact trade fair format The lecture programme will be complemented by a wine tasting zone featuring wines from the MUNDUS VINI wine competition organised by Meininger Verlag.
Overall, it is clear that the wine experts are happy to use this platform for dialogue, especially as it is easily accessible for winegrowers from Germany, Austria and other Central and Eastern European countries. “With the focus on Wine@ BrauBeviale, we are opening up a convenient information platform for visitors from the wine sector,” explains Cornelia Ebner, who is responsible for wine in the BrauBeviale team. “We see the potential for both sides: exhibitors can address an additional target group at BrauBeviale and visitors from wine-growing regions can compare the individual technologies required. They will see for themselves that the BrauBeviale portfolio extends far beyond just bottling machines.” Winegrowers will find all the information they need for a successful visit to the show on the landing page www.braubeviale.com/wine which was specifically designed for visitors from the wine industry.
Cornelia Ebner
Revitalise your business with top suppliers, new trends, and fresh ideas.
If you’re in food & drink retail, or hospitality, then save the dates for these two essential 2025 trade shows, both brought to you by Hale Events.
The Source is a must-attend event for anyone with an interest in high-quality products, profitable catering, and creative hospitality solutions. Bringing together the latest in food and drink, services, equipment, and industry insights, from around 200 exhibitors, The Source offers something for every retail or hospitality business. In collaboration with regional food group Taste of the West, the show will feature the latest flavours and ideas for your business.
For over 40 years, Expowest Cornwall has been the go-to event for those in the hospitality, catering, food, and drink industries. Whether you run a small café or a large-scale operation, this show offers the perfect chance to prepare for the year ahead with two days packed full of inspiration and opportunity.
Both The Source and Expowest Cornwall cater to a wide range of businesses including pubs, hotels, restaurants, cafés, delis, farm shops, holiday parks, tourist attractions, and supermarkets. These events are essential for anyone serious about making connections, discovering new products and innovation, and understanding the latest trends shaping the local and regional market, offering the perfect opportunity to set your business up for success in the year ahead.
Register now for free trade entry!
Register for free entry at thesourcetradeshow.co.uk and expowestcornwall.co.uk or call 01934 733456.
If you’re interested in a stand, please call 01934 733433 or email stands@hale-events.com.
Packaging Innovations & Empack 2025 returns to the NEC Birmingham on 12 & 13 February, offering key decisionmakers from across the packaging industry a unique platform to explore the latest innovations in Food Service, Label & Print, and the newly launched Smart Packaging Zone.
Packaging Innovations & Empack 2025 is now open for registrations, with the event poised to be its largest yet. Taking place on 12 & 13 February 2025 at Halls 3 & 3a, NEC Birmingham, the UK’s flagship packaging exhibition will once again connect the entire packaging supply chain, offering a unique platform for businesses to showcase the latest innovations, services, and sustainable solutions.
Exhibitors will have the chance to engage with a rich pool of prospects, with stands typically generating an impressive average of 86 leads. Attendees will include representatives from top brands and sectors such as food & beverage, FMCG, pharmaceuticals, beauty & personal care, and e-commerce, all seeking advancements in primary and secondary packaging. Leading companies like Autajon Packaging, Simply Cartons, FlexPET BV, Coveris UK, and AstroNova® will present their latest innovations to leading UK brands like Asda, Unilever, Nestlé, Procter & Gamble, and many others that place their trust in the annual showcase.
“It’s a fantastic show. A lot of our work is done online, so it’s a great opportunity to get to meet and talk with people and see what innovations are out there,” said Jon Wells, Sustainable Packaging Manager at ASDA.
“The reason I attend this show is to find new opportunities and see the latest innovations happening around the world,” said Muhammad Usman Zafar, Senior Procurement Manager –Global Packaging at PZ Cussons. “It provides a great way to understand where the world is heading, where suppliers focus, and whether it aligns with customer needs. Being in the FMCG industry, we are closely connected with consumers, but it’s also important to ensure that the upper or secondary industries think along the same lines.”
One of the key highlights of Packaging Innovations 2025 is the introduction of the Smart Packaging Zone, where the future of packaging will be on full display. Featuring NFC chips, RFID tags, and augmented reality (AR) solutions, this new zone is designed to showcase the potential of interactive packaging, offering customers and brands a futuristic, immersive experience.
The event also brings back its ever-popular Foodservice Packaging Zone, which is expected to attract key figures from the UK’s top retailers and food-to-go outlets, while the Label & Print Zone will be a hub for those looking to streamline their production processes, connecting labelling, corrugated packaging suppliers, and print finishing with decision-makers from brands like Unilever and Marks & Spencer. The Contract Pack & Fulfilment Zone, held in partnership with the BCMPA, is not to be missed for businesses looking to outsource packing and fulfilment services. This area, held in collaboration with the BCMPA, is the only event in the UK dedicated to outsourced packing, co-packing, and fulfilment services.
“There are very few opportunities where you can gather almost the entire sector in one place, and Packaging Innovations is truly that opportunity for anyone interested in packaging,” said Margaret Bates, Head of the UK pEPR Scheme Administrator. “This is the place to catch up with people, learn about the latest innovations, discover current trends, and even learn about future plans. You can see not only what’s currently on the shelves but also what will be on the shelves and what influences those behaviours.”
In addition to these focus zones, Empack Birmingham will be a key draw for those working with packaging machinery, robotics, and automation technology. This event area will bring suppliers and manufacturers together to present coding, marking, filling, palletising, and warehouse automation innovations. Brands like Amazon and Tesco are expected to attend, looking for solutions to increase productivity, enhance safety, and improve traceability in their supply chains.
Naomi Stewart, Marketing Manager at Easyfairs, said: “This event is where groundbreaking ideas come to life. We’re proud to connect stakeholders from across the supply chain, giving them direct access to the latest packaging technology and sustainable solutions. The synergy and collaboration that emerge from these interactions often lead to transformative advancements in the industry.
We look forward to showcasing innovative solutions that will shape the future of packaging and drive progress across various sectors.”
Will Mercer, BU Paper R&D Director at Coveris, highlighted its importance: “This show brings together the entire supply chain under one roof. It’s an unparalleled opportunity to showcase our innovations and see what the rest of the industry is doing.”
“I think it’s a great mix of inspiration just from walking around and seeing what people are exhibiting, and also a bit of challenge and insight—food for thought—from dipping into some presentations,” said Lisa Meade, Head of Structural Packaging at Kingfisher. “It’s also a great opportunity to catch up with people I may not have seen for a while and to connect with others in the industry. I can see what’s happening, meet new people, discover new packaging innovations, and hopefully start planning for future-proofing and similar initiatives.”
Register your attendance at Packaging Innovations & Empack 2025 now and be part of the future of packaging!
Don’t miss your chance to connect with industry leaders, discover cutting-edge technologies, and explore over 460 suppliers displaying the latest sustainable and interactive packaging trends.
In just a few months’ time, Cologne will become the central hub of the global sweets and snacks industry from 2 to 5 February 2025. ProSweets Cologne, the ultimate event and content platform for the supplier industry, is introducing a brand-new trade fair concept next year. With independent theme worlds that present trends and innovative solutions from the production, materials and raw materials sections as well as many new event formats, a next-level trade fair experience awaits the visitors.
The best of ProSweets Cologne and ISM
In the scope of the “Sweet Week”, ProSweets Cologne and ISM, the world’s biggest trade fair for sweets and snacks, are moving even closer together in 2025. In order to strengthen the synergies of the two trade fairs, the Lab5 by ISM is going to be located in Hall 10.1, directly next to Entrance East. The Lab5 by ISM offers room for the latest trends, start-ups, scale-ups and small handicraft businesses. Thanks to the spatial and thematic proximity to the Lab5 by ISM, ProSweets Cologne offers ideal conditions for effective networking between the manufacturers of sweets and snacks and the suppliers of raw materials and ingredients, packaging as well as machines and plants. In addition, the innovations in the stated segments will be centrally bundled for the producers and suppliers and new business opportunities created.
Matchmaking, networking, digitalisation and AI under focus
In addition to impressive product ideas, ProSweets Cologne 2025 offers a diversified event programme: Practice-oriented lectures, exciting discussions and exclusive tastings will take place on the Expert Stage and on the new Sweet Week - Talks & Tasting Stage.
A special highlight is the Sweet Week Production Summit from 1:30 to 5:00 p.m. on 3 February on the Sweet Week Talks & Tastings Stage, that is being organised for the first time and which brings production managers, CEOs and owners of the production companies exhibiting at ISM together with the supplier industry (exhibitors of ProSweets Cologne) in a targeted manner. First-class examples of best practice on the implementation of AI tools for a
cost-efficient and future-proof production will be showcased here. Three-minute pitch sessions of the supplier industry by ProSweets Cologne exhibitors will additionally be held here followed by a matchmaking forum in the Networking Area to promote concrete solutions and business relations.
ProSweets Cologne is once again offering Guided Tours in 2025 organised by its partners, DLG e.V. and Sweets Global Network e.V.. The DLG Guided Tours whisk the participants off on a journey through the world of sweet and snackable ingredients, where the focus lies on revolutionary ingredients and new taste experiences. The SG Guided Tours invite the most important decision-makers of ISM to join them - a perfect opportunity to meet business partners directly on-site. And the legendary ProSweets Cologne Party, where one can establish new contacts while enjoying music and drinks in a relaxed atmosphere, is also taking place on the Sweet Week Talks & Tasting Stage on 3 February, from 6:00 p.m. on.
The DLG Careers Day is also celebrating its premiere in 2025 on 2 February. Here, students and young professionals have the opportunity to network with leading supplier companies from the sweets and snacks industry and gain valuable insights into their future career. The Careers Day offers lectures, company pitches and the exclusive opportunity to have application documents checked on-site.
ProSweets Cologne 2025 offers a diversified programme and practical solutions for all of your business challenges - register now: https://www.prosweets.com/lp/ prosweets-cologne-for-your-business?utm_ source=advertorial&utm_medium=kooperation&utm_ campaign=foodanddrinknetwork_UK_
At Cross+Morse we aim to fulfil all industry demands, from the simplest to the highest level of precision required. Our objective is to offer a complete solution - not just products - to your power transmission challenges.
Cross+Morse are known in the industry as pioneers in quality standards, which is why we take our quality control processes very seriously. Quality assurance is central to our organisation with controls encompassing all aspects of design, manufacture, logistics and customer service. We are ISO 9001:2015 accredited and have been for over 30 years.
At Cross+Morse we have continuously invested in top of the range measuring equipment: Co-ordinate Measuring Machine (CMM), digital tri-bore gauges and micrometers which are constantly calibrated to comply with ISO standards. Our stringent inspection process guarantees that when manufacturing each operation is thoroughly inspected by either a highly trained shop-floor staff supervisor or an inspector, ensuring that manufacturing is only allowed to continue when each phase has been approved. Our hardening treatment is checked using either our Rockwell or Vickers hardness testing machines.
We review our quality procedures continuously to provide up-to-date mechanisms for ensuring conformity to the quality system; different audits are carried out on all activities in the company throughout each year.
freewheels, roller ramp clutches, combined sprag and bearing units and many more.
Cross+Morse is the largest authorised distributor and stockist for American transmission products manufactured by RegalRexnord (formerly EPT) in the United Kingdom. The range includes Sealmaster®, Browning®, Jaure®, Kop-Flex®, McGill® and Morse®.
We pride ourselves in offering a complete range of overload protection devices ranging from the simplest to the most accurate and precise overload clutch: Sheargard range of overload clutches, wedge pin type, available as a chain coupling and the option of low inertia rubber elastic couplings for higher speed drives. The Crossgard range, ball detent type, comes in 3 versions and also available with roller chain and low inertia rubber coupling option. The Safegard CS series, ball/roller detent type, comes in 2 two basic types (standard or mini) and also available as shaft couplings. Series CZ and CN zero backlash Safegard clutches for responsive overload protection, available in both basic and shaft coupling types.
Inverted tooth chain: including the standard SC type from 3/16” to 2” pitch and HV type from 3/8” to 2” pitch; as well as conveyor chains up to 12” width in centre or outside guide construction. We manufacture standard and special sprockets in-house for a complete drive solution.
We offer a wide stock range of flexible shaft couplings to accommodate different types of misalignment: Jaw couplings, elastomeric couplings, roller and Delrin® chain couplings, gear couplings GFA & GFAS, polymer gear couplings, Morflex elastomeric disc couplings and Crossflex disc couplings.
Our Crossbore® rework service includes reboring, keywaying and setscrewing of standard sprockets, pulleys and gears in a dedicated production area with specialised CNC machines for a rapid response. Induction hardening of teeth is also offered in-house.
Shaft clamping elements for precision transmission of torque with no backlash: a complete range from stock. Three ranges of locking devices available in corrosion resistant stainless steel.
Our range of Freewheel clutches for overrunning, indexing and backstopping applications; including sprag clutches, industrial ratchet
For further information contact:
Telephone: +44 (0) 121 360 0155 Email: sales@crossmorse.com or visit www.crossmorse.com
Bespoke vs customised
As the experts in hygienic furniture design, Teknomek are well-equipped to find a customised or bespoke solution for your unique work requirements. Which Teknomek service you require will depend on the changes needed. If you want a small alteration to the dimensions of an existing product, then this will be a customised solution. If you need an entirely new design, our bespoke service is on-hand to help.
Teknomek’s leading service levels means that your approved designs can be with you in as little as three weeks.
Creating a sterile environment starts
sterile environment people
with up to 15 operatives being able to progress through the station in one minute (depending on the hygiene station used).
with up to 15 operatives being able to progress through the station in one minute (depending on the hygiene station used).
with up to 15 operatives being able to progress through the station in one minute (depending on the hygiene station used).
Hygienic furniture and equipment specialist, Teknomek, has launched a brand new product especially for organisations that utilise a large number of tote bins.
fundamental aspect of the the food sector in order audit-ready and compliant with regulations. To prevent crossenhance this should before
Sanitisation is a fundamental aspect of the hygiene process for the food sector in order remain audit-ready and compliant with hygiene regulations. To prevent crosscontamination and enhance workplace safety, this hygienic focus should begin with staff before they enter the workplace environment.
reduce
environment aspect of the sector in order compliant with crossstations maintain hygienic
with up to 15 operatives being able to progress through the station in one minute (depending on the hygiene station used).
Providing hygienic furniture and equipment for every stage of the changing room process, our innovative designs speed up the changing room flow and increase clean down efficiency. We break down some of our key hygienic design aspects below:
The Teknomek automatic tote bin washer removes the need for manual handling and cleaning whilst ensuring each bin is sanitised to an exceptional level.
The automatic tote bin washer is designed to clean 200 litre and 300 litre bins efficiently using a 15 kW pump and rotating spray arms. It uses just 4-5 litres of water per bin and offers four wash programmes. Whilst the tote bins are loaded and unloaded from the 304-grade stainless steel washing unit by hand, the machine does the rest: removing the chance of human error in the cleaning process.
Sanitisation is a fundamental aspect of the hygiene process for the food sector in order to remain audit-ready and compliant with hygiene regulations. To prevent crosscontamination and enhance workplace safety, this hygienic focus should begin with staff before they enter the workplace environment.
Apron washers and motorised boot washers are also available to suit your cleaning environment.
Designed for hygiene-conscious industries, the boot washer can remove debris from the soles and sides of both high and low boots for the highest level of hygiene.
We use seamless welding techniques, such as electrochemical weld cleaning, to create smooth joins that eliminate crevices where dirt, bacteria and contaminants can accumulate.
range of hygiene stations to help maintain hygienic various
enforcing strict hygiene protocols, employers can reduce risk of external contaminants entering zones where hygiene imperative. As solution to this, now offer a range of hygiene stations boot washers to help maintain hygienic standards across various environments.
By enforcing strict hygiene protocols, employers can reduce the risk of external contaminants entering zones where hygiene is imperative. As a solution to this, we now offer a range of hygiene stations and boot washers to help maintain hygienic standards across various environments.
Apron washers and motorised boot washers are also available to suit your cleaning environment. Designed for hygiene-conscious industries, the boot washer can remove debris from the soles and sides of both high and low boots for the highest level of hygiene.
The hygiene stations also offer a tool-free, quick and easy-to-remove brush system for effortless cleaning between shifts and maintenance. Spare brushes are also available to purchase from our website for use during the washing process.
cross-contamination via processes
Where possible, we have removed unnecessary flat surfaces where organisms can accumulate in favour for sloped tops. This small change to our cabinets, lockers and wash troughs makes a big difference in the fight against bacteria.
Preventing cross-contamination via staff cleaning processes
Apron washers and motorised boot washers are also available to suit your cleaning environment. Designed for hygiene-conscious industries, the boot washer can remove debris from the soles and sides of both high and low boots for the highest level of hygiene.
Michelle Locke is product and marketing manager at Teknomek:
“We have launched this new product in direct response to a customer enquiry,” Michelle explains. “A leading manufacturer in the food sector approached us because they were looking for an effective solution for washing a large quantity of tote bins. They wanted to avoid significant manual handling but needed reassurance that each bin was properly cleaned to their exacting hygiene standards.”
Apron washers and motorised boot washers are also available to suit your cleaning environment. Designed for hygiene-conscious industries, the boot washer can remove debris from the soles and sides of both high and low boots for the highest level of hygiene.
“Seeing that Teknomek offered a pneumatic washing frame, they asked us if we could find a solution to their problem and our automatic tote bin washer is the result. We quickly realised that this is a product that will be of value to many of our customers.”
The hygiene stations also offer a tool-free, quick and easy-to-remove brush system for effortless cleaning between shifts and maintenance. Spare brushes are also available to purchase from our website for use during the washing process.
The hygiene stations also offer a tool-free, quick and easy-to-remove brush system for effortless cleaning between shifts and maintenance. Spare brushes are also available to purchase from our website for use during the washing process.
The hygiene stations also offer a tool-free, quick and easy-to-remove brush system for effortless cleaning between shifts and maintenance. Spare brushes are also available to purchase from our website for use during the washing process.
cross-contamination
range of hygiene stations provide an intuitive one step process to the changing room flow by combining hand sanitisation sole washing in one tidy package. With poorly washed hands and unclean footwear being two of the major sources of cross-contamination in the food industry, this automated equipment removes the possibility of human error and ensures that each staff member is suitably sanitised before proceeding through the turnstile to the next station.
hygiene stations provide an process to the changing combining hand sanitisation one tidy package. With hands and unclean of the major sources of cross-contamination in the food automated equipment possibility of human error and staff member is suitably proceeding through the station.
The majority of our furniture, equipment and accessories are made from 304L-grade stainless steel with the option to upgrade to 316L on request. This ensures that our products can withstand stringent hygiene processes with high chemical and corrosion resistance.
Our range of hygiene stations provide an intuitive one step process to the changing room flow by combining hand sanitisation and sole washing in one tidy package. With poorly washed hands and unclean footwear being two of the major sources of cross-contamination in the food industry, this automated equipment removes the possibility of human error and ensures that each staff member is suitably sanitised before proceeding through the turnstile to the next station.
The sanitisation process is a crucial aspect of hygienic environments, but it is not just restricted to the cleaning process of the equipment, the staff can easily cause cross-contamination and the spread of bacteria without a focus on hygiene culture. The use of our hygienic equipment, such as our hygiene stations and boot washers, maintains an emphasis on hygiene and reduces the chance of human error or staff negligence via the implementation of an automated process.
equipment, employers cannot staff members are equally sanitised. These stations time-efficient solution
cross-contamination via provide an changing sanitisation package. With unclean sources of equipment error and is suitably through the employers cannot are equally stations solution
The automatic tote bin washer cleans up to 30 bins per hour and the powerful pump and rotating spray arms, with stainlesssteel nozzles, blast away debris in just a few minutes. The washer has been created to be user-friendly, with a touch screen control and four programmable cycles of between two and ten minutes. It’s also designed with sustainability in mind. It has a 350-litre recycled water tank and its prewash cycle prevents foam formation which saves water and energy, whilst also delivering faster and better cleaning.
The sanitisation process is a crucial aspect of hygienic environments, but it is not just restricted to the cleaning process of the equipment, staff can easily cause cross-contamination and the spread of bacteria without a focus on hygiene culture. The use of our hygienic equipment, such as our hygiene stations and boot washers, maintains an emphasis on hygiene and reduces the chance of human error or staff negligence via the implementation of an automated process.
Without this equipment, employers cannot certain that all staff members are equally effectively sanitised. These stations create a hygienic, time-efficient solution
The sanitisation process is a crucial aspect of hygienic environments, but it is not just restricted to the cleaning process of the equipment, the staff can easily cause cross-contamination and the spread of bacteria without a focus on hygiene culture. The use of our hygienic equipment, such as our hygiene stations and boot washers, maintains an emphasis on hygiene and reduces the chance of human error or staff negligence via the implementation of an automated process.
Call now on +44 (0)1603 788 833, visit teknomek.co.uk or email mail@teknomek.co.uk
Without this equipment, employers cannot be certain that all staff members are equally and effectively sanitised. These stations create a hygienic, time-efficient solution
Want to know how our hygienic equipment can speed up your hygiene flows?
“One of our priorities as a business is to help our customers to be audit ready, every day, and that means paying close attention to every detail,” continues Michelle Locke. equipment is hard to access it is harder to clean. So, as well as cleaning tote bins efficiently, the automatic washer has been designed to allow for the machine itself to be easily cleaned. Made from 304-grade stainless steel, the washer can itself withstand robust cleaning methods to ensure it actively contributes to risk management within any hygienic environment.”
The sanitisation process is a crucial aspect of hygienic environments, but it is not just restricted to the cleaning process of the equipment, the staff can easily cause cross-contamination and the spread of bacteria without a focus on hygiene culture. The use of our hygienic equipment, such as our hygiene stations and boot washers, maintains an emphasis on hygiene and reduces the chance of human error or staff negligence via the implementation of an automated process.
Want to know how our hygienic equipment can speed up your hygiene flows?
Want to know how our hygienic equipment can speed up your hygiene flows?
Please call our Teknomexperts on +44(0)1603 788 833
Want to know how our hygienic equipment can speed up your hygiene flows?
Please call our Teknomexperts on +44(0)1603 788 833
Please call our Teknomexperts on +44(0)1603 788 833
For more information about the Teknomek automatic tote bin washer, please call the customer services team on +(0)1603 788 833 or visit Automatic tote bin washer | Teknomek UK.
Please call our Teknomexperts on +44(0)1603 788 833
< Carl Knight, Managing Director
With the two types often being confused, Carl Knight, managing director of heat transfer specialist Fulton Limited, discusses the differences between shell type fired steam boilers and steam generators.
The objectives of a steam raising plant are simple: to release the energy in the input fuel as efficiently as possible; to transfer the released energy to the water and raise steam by the most efficient method possible; separating the steam from the water ready for export to the plant, where the steam energy (heat) can be transferred to the process.
Steam generators operate with low water content, pumping water into a continuously wound steel tube (coil) where steam and water are produced. These coils are housed in an insulated jacket with a burner typically firing from the top
Due to their design, steam generators cannot produce steam when the burner is off and are not suitable for fluctuating steam loads. However, they can quickly reach operational pressure from a cold start, although a purging cycle before firing can delay steam availability.
In contrast, shell-type steam boilers, like Fulton’s VSRT, are constructed as pressure vessels with a larger water volume that can generate flash steam even when the burner is off. This design allows them to respond
effectively to varying steam demands, making them more versatile despite longer cold start times. Additionally, they achieve rapid burner firing without the need for a water purging cycle.
Steam generators face challenges in matching burner output with steam requirements, often leading to excess feedwater that must be recirculated. This can possibly increase maintenance costs arising from premature pump failure which, due to their complex nature, require skilled technical support. Conversely, steam boilers utilise multistage centrifugal pumps that are far easier to maintain.
To ensure dryer steam from generators, an advanced steam separator is used to remove excess water, which is often sent to drain. High total dissolved solids (TDS) in separated water can lead to additional costs if disposal is necessary. Ineffective separation may allow TDS water droplets into the steam system, impacting process efficiency. A critical issue for generators is that phase changes from water to steam occur over the same coil length, where hard mineral deposits accumulate and potentially overheat/block the coils. Stringent water treatment and evacuation are essential to prevent costly coil replacements.
Shell type boilers also require TDS control; managing TDS through automated blowdown systems that prevent high TDS building in the boiler and entering the steam system. While feedwater quality control is crucial for both systems, it is less stringent for boilers due to their robust design and versatility,
with their simpler control systems allowing for quicker easier repairs.
Provided shell type boilers are maintained properly, minimum life expectancy is 15 to 20 years, with Fulton regularly servicing and maintaining boilers that have been operating for 25 years or more.
In summary, while both steam generators and shell-type boilers serve similar purposes in energy production through steam, their designs cater to different operational needs. Steam generators excel in quick startups and compactness but struggle with variable loads and require careful management of feedwater quality. Shell boilers offer greater flexibility in handling fluctuating demands due to their larger water volume and robust construction but do have marginally longer startup times. Understanding these differences is crucial for selecting the appropriate system based on specific operational or process requirements.
For further information on the VSRT, call Fulton on 0117 972 3322, email sales@fulton.co.uk or visit www.fulton.co.uk.
Our class-leading range of fuel-fired and electric steam boilers and portfolio of aftercare solutions can help with your decarbonisation strategy and put your company on the Road to Net Zero.
As a complete solutions provider, Fulton can provide your food processing facility with:
· fuel-fired and electric steam boilers
· off-grid and point-of-use solutions
· ancillary plant / engineered systems
· steam surveys
· project management
· water treatment contracts
· accredited / certified training
· installation / commissioning / upgrades
· repair / service / maintenance programmes
For further information scan the QR code, visit www.fulton.co.uk, email sales@fulton.co.uk or call the office on +44 (0)117 972 3322.
Employing Eriez powerful magnetic separators for ferrous contaminants and metal detectors for both ferrous and non-ferrous metals ensures your product is free of dangerous tramp metals. Regardless of your process and material, Eriez offers a solution for gravity, conveyed, pneumatic or liquid line flows.
Below are several factors to consider when choosing a magnetic separator for your food application.
Temperature: Permanent magnetic materials lose strength when exposed to elevated temperatures. Some losses are reversible, so that when the temperature is returned to normal, the magnetic strength returns. Depending on the specific material, permanent magnets heated beyond certain temperatures may also suffer irreversible loss—a reduction in strength that cannot be recovered by cooling. When specifying a magnet application, it is important to note the ambient as well as any clean-in-place (CIP) temperatures to ensure a proper magnet design suitable for long-term separation performance.
Flow characteristics: Many products exhibit different flow characteristics when damp or moist. Are there large chunks that may plug an opening or gap in the separator? Will the product flow freely through the selected magnetic separator? For example, brown sugar with any significant moisture content will not flow between the tubes in a grate magnet assembly, although they may be positioned only 1 inch apart.
Process issues: How will the material be presented to the separator? Is the material metered or do you need to handle surge flow? Can the system be stopped for cleaning or is a selfcleaning magnet required? Is access available for cleaning? Is there ferrous material in the area that may create a hazard for magnet handling? How much contamination is to be removed? And finally, what level of product purity is required?
ERIEZ_BEstDefence_HalfPgAd_F&DN_4_24.qxp_Layout 1 3/22/24 5:13 PM Page 1
Flow rate: Magnetic separators perform best when the contamination is presented to the surface of the separator. It is best to select a magnetic separator configuration that provides for a thin “burden depth” or thickness of the material layer over or under the magnet to ensure the magnet will havethe best opportunity to capture the ferrous contamination.
Understanding these considerations will help select the appropriate equipment to ensure your process is free of metal contamination.
Eriez offers a wide range of magnetic separators to get metal out
Hygiena®, a leader in food safety and quality control solutions, is proud to announce the launch of its latest innovation within the SureTrend® platform: the Sampling Plan Module. Designed to address key challenges faced by food safety professionals, the new module offers a streamlined, efficient approach to sampling management that enhances traceability, simplifies data management and improves collaboration.
Traditional sampling processes are often plagued by inefficiencies and challenges, including manual data entry, fragmented communication and difficulties in maintaining regulatory compliance. The new Sampling Plan Module was developed to tackle these issues directly, ensuring a smoother, more reliable approach to sampling management.
“We understand the difficulties food safety teams face when managing complex sampling plans across different product lines and facilities,” said Mark Carter, Sr. Global Software Product Manager at Hygiena. “Our new Sampling Plan Module automates many of the manual tasks and provides real-time updates, enabling teams to focus on what truly matters: ensuring the safety and quality of their products.”
Key Features of the Sampling Plan Module
Efficient Sampling Plan Creation and Management: Customizable templates allow users to quickly set up sampling plans, with automated scheduling and notifications to ensure timely execution. Real-time updates enable teams to adapt swiftly to changing requirements.
Enhanced Traceability and Compliance: The module offers centralized tracking and documentation of sampling activities, complete with unique sample IDs and timestamp records, simplifying audit preparations and ensuring compliance.
Seamless Collaboration: Automatic notifications and alerts keep stakeholders informed, while easy sharing of sampling plans and results ensures effective coordination with external labs and team members.
Data-Driven Insights for Continuous Improvement: The module’s analytical capabilities convert raw sampling data into actionable insights, helping teams identify areas for optimization and track key performance metrics.
For companies without the resources to implement a full-scale Laboratory Information Management System (LIMS), the Sampling Plan Module provides a light version of LIMS functionality, offering efficient data management without the complexity and cost. The module acts as a unified platform, consolidating information and automating workflows to streamline the sampling process.
For more information about the Sampling Plan Module or to schedule a personalized demo, please visit https://www.hygiena.com/news/new-suretrendsampling-plan-module-transforming-food-safetysampling-processes
T. Freemantle’s Automatic Beverage Multipack Machine has played a pivotal role in Belvoir Farm’s move into canning, which has seen the soft drinks manufacturer invest £2m in a state-of-the-art canning line at its Leicestershire on-farm factory. Thanks to the machine’s unrivalled ability to carton virtually any can size into any multipack configuration, the fast and flexible system has enabled Belvoir to embark on an innovation drive that has sent sales of its canned drinks on an upwards trajectory.
The popularity of the canned RTD (Ready To Drink) format has surged in recent years, on the back of changes in market culture and the rise of conscious consumerism. Light and convenient, cans are perfect for outdoor occasions, which have become a way of life since the pandemic. They are also one of the most sustainable forms of packaging as they can be recycled time and time again.
Whilst the canned RTD market is dominated by alcoholic offerings, there is huge demand for more sophisticated soft options, such as mocktails and botanical sodas. Premium soft drink producer Belvoir Farm had been servicing this market with a range of cans produced by a co-packer. However, by 2022, the company recognised it needed to bring can production in-house to fully capitalise on the canned RTD opportunity.
“Our canned portfolio was growing at such a pace that we needed to invest in in-house production. Up until that point, we hadn’t truly committed to the category,” says Martin Reynolds, head of engineering & project leader at Belvoir.
Belvoir wanted to roll out a number of new lines in canned format to drive the growth of its brand. It had plans to launch its RTD mocktails in 250ml cans alongside a new range of light soft drinks in 330ml slim cans and botanicals in 150ml cans. It also wanted to move into the multipack space, with fridge-friendly four packs (4 x 330ml slim cans) and six-packs (6 x 150ml mixer cans).
“We started looking at equipment for the canning line and when it came to the cartoning machine, the same name kept cropping up in conversation: T. Freemantle,” recalls Martin.
Belvoir invited T. Freemantle to its facility to discuss whether the packaging machinery manufacturer could meet its brief for a format-flexible cartoning machine that could be delivered within a six month timeframe.
“T. Freemantle confirmed everything we were hoping to hear - that their machine could handle all of the can formats we were hoping to run as well as those we might want to introduce in the future, such as 10 or 24 can multipacks for export markets,” says Martin.
“We did look at other machinery manufacturers but they couldn’t compete on timeframe, price, format flexibility, fast and simple cleandown or parts/service availability. We were quoted lead times of up to 12 months and the quotes were much higher as they said they would need to build bespoke systems to accommodate the different formats we wanted to run. T. Freemantle were very confident that a six month lead time from order to delivery was possible,” he adds.
At this stage in the project, Belvoir hadn’t quite finalised what form the multipacks would take. Therefore, it tapped into T. Freemantle’s design studio service, which marries engineering expertise with
knowledge of pack styles, materials, glues etc to come up with a design that would be line-compatible, practical and aesthetically appealing.
“Initially we were thinking we wanted an open-sided pack, but T. Freemantle’s advice was that a FEC (Fully Enclosed Carton) would be more viable. They gave us a good steer on what cartonboard would be suitable and pointed us in the direction of Graphic Packaging for designing and printing the cartons. They also recommended a really good glue supplier,” says Martin.
Belvoir placed its order in January and - true to its word - T. Freemantle installed the Automatic Beverage Multipack Machine six months later.
“Time was of the essence as we had already closed the contract with our co-packer so there was massive pressure on the factory to get can production moving again,” recalls Martin.
To ensure the project was delivered within the timescales, T. Freemantle took the unusual step of carrying out the FAT (Factory Acceptance Testing) as part of the installation - demonstrating not only its commitment to the customer but also complete confidence in its technology.
“T. Freemantle were fully aware of the importance of starting can production on the specified date and they pulled out all the stops to make that happen,” says Martin.
High speed packing of beverage cans into smaller cartons is an application that few engineering firms have mastered. It is possible to run four-packs on a machine designed for producing 12 or 24 can multipacks from thicker corrugated board, but the line speeds tend to be unfeasibly slow, which is why many beverage manufacturers resort to hand-packing smaller cartons.
T. Freemantle has come at this challenge from a different angle, drawing on its expertise in high speed food production lines. Instead of wrapping a blank around a collation of cans and then gluing it, the Automatic Beverage Multipack Machine uses pre-glued cartons, which are picked one at a time from a magazine holder, erected and presented to the can collation. This continuous motion process speeds up the cartoning process considerably.
T. Freemantle’s can collation solution is another unique design feature that sets the Automatic Beverage Multipack Machine apart from the competition and supports high speed performance. An infeed gate system facilitates the efficient release of cans into the machine, where they are guided into a diamond shape that is maintained along the length of the machine until they have been deposited in the open cartons.
“The diamond formation makes it much easier to insert the cans into the cartons than if they were presented square on. It also reduces the risk of snagging on the edges of the
cartons,” explains Simon Holt, head of sales (UK & Ireland) at T. Freemantle.
The company’s engineers have also put a lot of thought into the safe passage of cans through the machine - a particular challenge for taller cans and larger collations. The cans are supported throughout the insertion process to ensure can stability is maintained. They have also focused on keeping downtime for cleaning and changeovers to a minimum; can size changeover is simple and easy to perform with no change parts - format changeovers can be executed in as little as 15 minutes.
All of these features combine to make the Automatic Beverage Multipack Machine the fastest flexible can cartoning solution on the market today. Belvoir’s minimum line speed requirement - set by the filler - was 12,500 cans per hour, which equates to 50 cartons per minute. Martin reports that the line “easily and consistently” runs at 55 cartons per minute and could potentially reach 70 cartons per minute.
Having this capacity will allow the producer to ramp up its output to keep pace with demand.
In the first six months of operation (June to December 2023), Belvoir produced 1.5 million cans - more than a year’s worth of production under the co-packer arrangement.
“When the figures were presented to our executive board they were really impressed,” says Martin.
For 2025, Belvoir is targeting between five and ten million cans, produced across several canning campaigns.
“As our canning line currently shares some equipment with our bottling line, we don’t can all the time. We plan a two or three week ‘canning campaign’, usually every other month, based on forecasts,” explains Martin.
The entire project was structured with short term sales targets and a long term goal of achieving payback within five years. To this end, in 2025, the company will invest £2m in new pasteurising and palletising equipment to allow the canning line to run independently, thereby further increasing capacity.
As to whether the project is delivering on its objectives Martin says: “It’s early days, but already we have secured new distribution for our RTD canned launches and are seeing growth from export markets, in particular the US, Australia, Canada, Japan and China. The flexibility afforded by the Automatic Beverage Multipack Machine is invaluable in helping us to adapt to market demands, whether that is producing an extra 10,000 cans or a 10-can pack for a US retailer.”
Lucy Bosten, Head of Marketing and Communications at Carlton Packaging, explores matching packaging to its purpose and finding your place in a changing sector
Where does inspiration for the next big thing in packaging come from? Get a room full of packaging designers together, and they may struggle to agree. The industry is a hotbed of innovation, with new technologies and trends emerging every year that can influence packaging for years to come.
Sustainability has been one of the most prominent recent trends influencing packaging design. From choosing recyclable or biodegradable substrate materials, to designing out waste using the latest technology, converters across the sector are increasingly prioritising more eco-conscious designs that help brands stand out and shrink their carbon footprints.
However, whether or not these features are always correctly matched to what consumers want from their packaging is a difficult question. With the growing complexity of designing packaging, converters need to understand what their customers and consumers actually want – and achieving this is not always easy.
This issue was an omnipresent topic of discussion at last year’s Packaging Innovations event, which saw thought leaders and experts from across the packaging sector come together to discover the trends and challenges shaping the industry’s future. Among those in attendance was Lucy Bosten, Head of Marketing and Communications at Carlton Packaging, a global designer and manufacturer of smarter packaging materials and processes, who took home one of the coveted Future Trailblazers Awards. Speaking to Easyfairs ahead of Packaging Innovations & Empack 2025, which will be held at NEC Birmingham on February 12 & 13, her enthusiasm for helping customers find the packaging that works for them and consumers alike was obvious. Bosten has clearly found her sweet spot in the sector – designing packaging tailored for the end user experience.
“When I receive my perfume, I’m not going to expect just a brown box,” explained Bosten. “I want some messaging in there. Over the years, I think sustainability has impacted how parcels are packaged. People have taken less care with it because they emphasise being green. It gets to the point where the excuse is, ‘Well, we’re green, so that’s why it’s broken when it arrived.’ It might be a paper bag that didn’t arrive in the best condition, but hey, we’re sustainable.
“However, things have matured since then, and now people are focusing on bringing back quality and research and development. It’s about ensuring that you can still use sustainable products while delivering the correct message and keeping the brand intact. Regardless of the brand— whether you’re sending out garden furniture, perfumes,
or meat—there’s always a level of branding or consumer interest involved. What we consistently find with our clients, whether they’re at the bottom end of the spectrum, like pound shops that pack as much as they can into a box, or high-end stores like Harrods and Harvey Nichols, is that the branding message and desire remain constant. The biggest point for any business is their brand and encouraging returning business.
“While the perception of a brand might look great with certain packaging, it can result in more board or material waste. I remember someone proposing a recycled tear strip that would be great for the market but would cost an additional 20 pence per board. Everyone thought it was a good idea until they realised the cost would be passed on to the customer. Most customers aren’t that concerned about a plastic tear strip if it can be recycled correctly.”
Carlton Packaging meets this by designing for consumer requirements first and foremost before sending its designs to a manufacturer to print, cut, and send it back. However, its work is backed up by extensive research to discover the innovations that people actually want.
This methodology has been fundamental to building a consumer-led approach to design. The company conducts mystery shopping before engaging with brands to learn how they package their products and talks to them to discover what they consider the most important parts of their delivery process. If their priority is product safety during the delivery, more recyclable materials like cardboard may not offer sufficient protection. However, ongoing innovations in sustainability mean there are a multitude of other ways that packaging’s environmental impact can be reduced.
“We do a lot of research on what’s happening in the market, working with manufacturers to innovate,” said Bosten. “We explore options like adding more recycled content, creating closed-loop systems, or providing returnable packaging. Taking these ideas to brands is where our strongest selling point lies.”
To support its research, Carlton Packaging recently launched its InsightLoop portal that enables customers to leave feedback on packaging, regardless of what the product is. This provides added value for businesses because, instead of customers venting about negative packaging experiences on social media, they can provide feedback through the portal. What’s more, their feedback helps ensure that future packaging can be designed with consumer expectations in mind.
Consumers can provide feedback by scanning a QR code, sending their comments directly to the relevant person responsible for the packaging or the marketing team. As a result, the company can start developing solutions. For example, if a brand is receiving negative feedback about plastic mailers from eco-conscious consumers, Carlton Packaging can suggest actions such as switching to paper mailers instead. Alternatively, if negative feedback is received about paper mailers arriving damaged and intelligence suggests their consumers are not as concerned about the environment, the business could recommend adding messaging to the plastic bag about how to recycle it instead.
“To me, this feedback system is one of the biggest research tools because we’re all consumers and love to give feedback,” said Bosten. “When we get something we don’t like, especially across different age ranges—from Gen Z to Baby Boomers—we tend to voice our opinions on social media. With this platform, consumers can provide feedback in one place, allowing the relevant team to receive real-time information. This way, feedback doesn’t just sit with a social media manager who might not pass it on to the right people. Instead, it reaches those who are passionate about handling and acting on that information.”
It’s commonly said packaging has a problem attracting new talent, as the industry can struggle to make itself look like an appealing option for potential new recruits. With an aging highly skilled workforce, invaluable knowledge and expertise are leaving the sector each year. Overcoming this problem and preventing further brain drain will require packaging to focus on promoting how fulfilling a career it can be.
“If you had told me 10 years ago that I would be in packaging and selling boxes, I would have said, ‘No way, that’s not for me’,” said Bosten. “It’s not something you wake up wanting to do at 22. I started at Carlton as a junior marketer and initially thought, ‘What am I going to market? Cardboard boxes?’ But over time, as we saw developments and possibilities, I realised the potential.”
Marketing the benefits of a career in packaging has not always been a huge focus for the industry, pushed for by a few distributors and manufacturers over the last few years. But by investing in education and awareness-raising activities, and shouting out about the exciting developments being made, businesses have the opportunity to attract new talent, opening the door to the next generation of packaging innovators.
Packaging Innovations 2025 is an ideal showcase of the best that the packaging industry has to offer. With a packed programme covering the latest trends and technologies, the event is a standout date in the packaging calendar for professionals looking to get ahead of emerging challenges and opportunities. What’s more, events like the annual Future Trailblazers Awards are spotlighting the innovative, forwardthinking individuals who are shaping the industry’s future, celebrating the passion, innovation, and fresh perspectives that they bring.
With nominations open for entries now, Packaging Innovations & Empack 2025 looks set to be the ideal place to promote packaging as a thriving industry and enhance its appeal for the next generation of professionals.
“Packaging has taken me all over the world—I’ve been to Packaging Innovations in Paris, and I’m heading to Chicago next month,” Bosten added. “I’ve travelled across the UK, Europe, Amsterdam, and Dublin. You wouldn’t believe it, but packaging is everywhere, and there are opportunities.
“I had a conversation with a recruiter the other day who asked, “Why would someone want to get involved in packaging?” I said that’s a great question because nothing is the same every day. Everything’s new. Brands are constantly evolving. Especially when you’re young and want to get into packaging, design, or marketing, you might not think of sending your CV to a packaging company because you aim for fashion or mechanical design. But actually, I probably have more day-to-day relationships with consumers than many of my friends in marketing agencies. I travel the country more than many people working in high-end brands.
“We get to experience the best of both worlds—working with great big brands and different brands all the time and working for a business that is continuously evolving. So, for me, it’s just something I would definitely recommend considering.”
Don’t miss out on your chance to nominate someone for the 2025 Future Trailblazers Awards. If you or someone you know is significantly impacting the packaging industry, from design to sustainability, submitting a nomination could you gain recognition as one of the industry’s brightest talents.
When it comes to innovative packaging solutions, the relationship between Myco and National Flexible is a prime example of what can be achieved through trust, collaboration, and expertise. Myco has always been at the forefront of the plant-based revolution, delivering products that are not only delicious but also sustainable. With the rising demand for their Hooba mince, Myco needed a packaging solution that would reflect the quality and innovation of their product. Naturally, they turned to National Flexible, a partner they have trusted for years.
A pioneering company, dedicated to revolutionizing plant-based nutrition through an emphasis on taste, texture, and environmental sustainability, Myco’s ethos centres on creating delicious, satisfying food that mirrors the flavours and textures of traditional meat products while prioritizing the health of our planet. By leveraging innovative food science and sustainable practices, Myco Foods aims to provide high-quality, eco-friendly alternatives that delight the palate and support a more sustainable future.
Our relationship with Myco has been built on a foundation of reliability, creativity, and a deep understanding of their brand ethos. When Myco approached us for a solution to showcase their Hooba mince, we were super excited to take on the challenge.
Hooba mince, like all Myco’s products, is a symbol of the future of food—sustainable, plant-based, and full of flavour. The packaging needed to not only protect the product but also convey its premium quality and appeal to environmentally conscious consumers. Myco was looking for a unique and eye-catching pouch that would stand out on the shelves, effectively communicate the brand’s message, and maintain the freshness of the mince.
Our team of experts immediately got to work, bringing our wealth of experience in flexible packaging to the table. The goal was to create a patterned lacquer pouch that was not only functional but also showed off the visually striking design.
Our solution was a custom-designed patterned lacquer pouch that perfectly aligned with Myco’s brand identity. The pouch features a distinctive colourful pattern that really catches the eye, making it easy for consumers to spot Hooba mince among the many products on the shelf. The lacquer finish adds a touch of elegance, while also providing additional protection to ensure the product’s freshness.
The process of creating this pouch was a collaborative effort. Myco’s team provided insights into their brand and customer base, while National Flexible’s experts focused on the technical aspects of the design and production. We worked closely with Myco to ensure that every detail was perfect, from the material selection to the final print.
The result is a packaging solution that not only meets but exceeds Myco’s expectations. The patterned lacquer pouch is not just a protective container; it’s a reflection of Myco’s commitment to quality and sustainability. The pouch’s unique design helps the Hooba mince stand out, making it easier for consumers to choose a
product that aligns with their values.
The success of this project is a testament to the strong relationship between Myco and National Flexible. Our ability to understand Myco’s needs and deliver a solution that perfectly aligns with their brand is why they continue to trust us with their packaging requirements.
At National Flexible, we pride ourselves on our ability to provide bespoke packaging solutions that meet the unique needs of each client. The project with Myco is just one example of how we bring our expertise to the table, ensuring that our clients can showcase their products in the best possible light.
As Myco continues to grow and innovate in the plant-based food sector, we look forward to many more years of collaboration, providing them with packaging solutions that help them succeed in a competitive market.
The patterned lacquer pouch for Hooba mince is more than just packaging—it’s a symbol of the partnership between Myco and National Flexible. Together, we have created a product that not only protects and preserves but also elevates the brand, helping Myco to continue its mission of providing sustainable, plant-based food to the world.
National Flexible is proud to be a trusted partner of Myco, and we are excited to see what the future holds for our collaboration.
For help with your project, call our team 01274 685566 or email marketing@nationalflexible.net
In today’s rapidly evolving manufacturing landscape, businesses often face the need to reassess their equipment to stay competitive. Whether it’s due to the closure of a production site, to create space for new machinery, or changing production demands, selling your food and beverage machines can be a strategic move. Unused or depreciating equipment represents untapped capital that could be reinvested into new production opportunities.
By auctioning your surplus equipment, whether just a few machines or an entire production site or line, you not only maximize your returns but also contribute to a more sustainable industry by reusing machinery. You can maintain your focus on optimizing production and meeting your business goals, while the auction platform handles every aspect of the sales process. From listing and marketing to finalizing the sale, the auctioneer ensures a smooth and efficient transaction, allowing you to unlock the value of your unused equipment without diverting attention from your core operations.
Auctioning by Industrial Auctions offers several advantages. “The shortage of qualified personnel in the food industry presents significant challenges for food producers and traders. We aim to alleviate this burden by taking the entire sales process off their hands. Additionally, we have a large international database, which allows us to reach a wide network of professionals within the industry, effectively connecting supply and demand”, explains the CEO of Industrial Auctions.
“We are always committed to making each auction a success. The hard work pays off when we see the satisfaction on everyone’s faces at the end. Working closely with a committed team not only makes the process more enjoyable but also drives us to achieve even greater results.”
Want to buy or sell your company assets? Visit the website now by scanning the QR code: https://www.Industrial-Auctions.com/ sell-your-food-beverage-assets/
At Waltons Digital Media, we blend creativity with technology to elevate your brand online. Our comprehensive services include tailored digital marketing strategies, visually stunning web design and development, engaging content creation, and impactful graphic design. We focus on delivering solutions that drive engagement, enhance visibility, and ensure your brand stands out in a crowded digital landscape. With a commitment to quality and innovation, we partner with you every step of the way to bring your vision to life and achieve lasting success in the digital world. Let’s create something extraordinary together, turning your ideas into powerful digital experiences that resonate with your audience and leave a lasting impact.
At Walton’s Digital Media, we create content that grabs attention and builds lasting connections with your audience.
At Walton’s Digital Media, we offer expert Marketing Consultancy services to provide strategic direction and hands-on guidance.
Sameh Metawea BA (Hons) Corporate Account Manager
At Walton’s Digital Media we craft powerful, results-driven digital and marketing strategies tailored to your business.
Walton’s Digital Media offers expert Communication and PR services, from crafting compelling messages to managing crises effectively.
At Walton’s Digital Media, we specialise in Graphic Design & Branding services that enhance and strengthen your brand.
At Walton’s Digital Media, we design custom, mobile-responsive websites that are visually stunning on any device.
26 – 28 November 2024 Nuremberg, Germany
Free entry to BrauBeviale 2024 voucher code BB24UK
Discover state-of-the-art solutions for the production of beer, wine, spirits and more at BrauBeviale in Nuremberg. Expand your network and discuss current topics. Be there when industry leaders set the course for tomorrow! Experience the variety of the beverage industry!
Secure your ticket now and join the community of the industry!