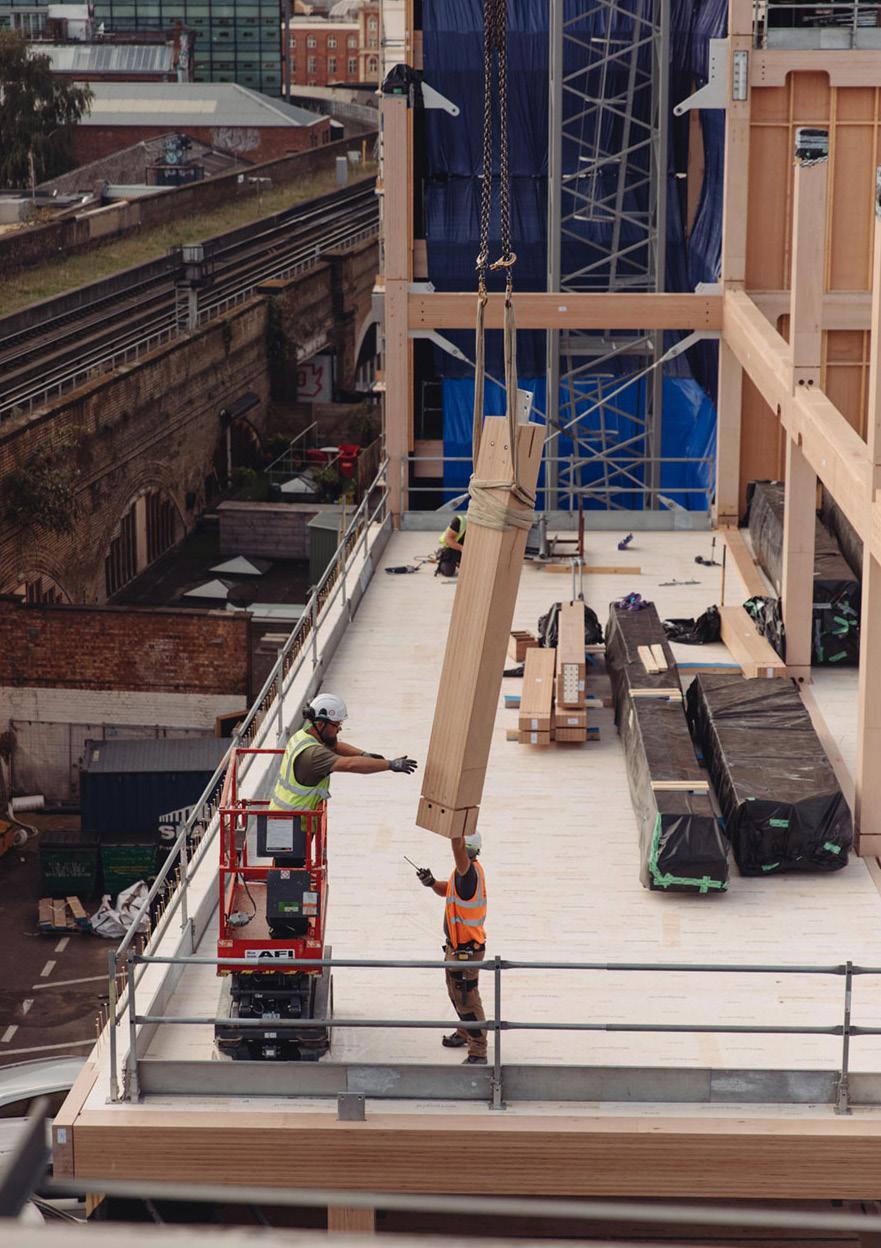
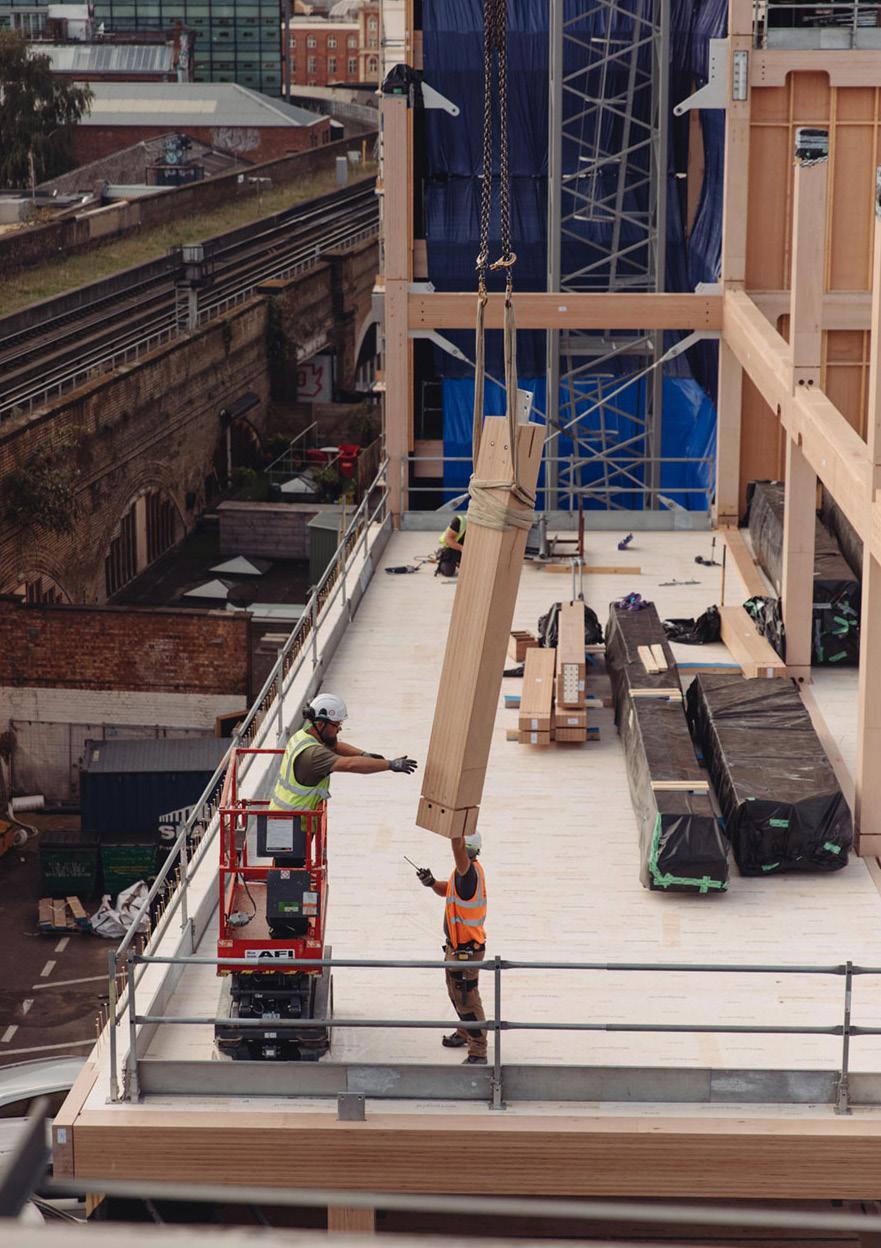
LOW CARBON SOLUTIONS TO SUPPORT SUSTAINABLE INDUSTRIAL GROWTH
The world faces a climate emergency. We are at tipping point, and it is imperative that we make the right choices now.
Currently accounting for 15% of the building stock in the UK, industrial and commercial buildings are a a rapidly growing sector of construction.
Unlike residential property, commercial and industrial buildings typically cover a large surface area and incur a substantial Carbon footprint both in the embedded carbon of the construction process and building materials and the energy they take to operate. However, this presents the opportunity for significant carbon capture from a single building, offering businesses a way to meet their ESG targets and reduce their Scope 3 emissions.
As a practice we work to dismantle the perceived barriers facing the wide spread adoption of more sustainable building choices, providing guidance on how building in mass-timber can improve the speed, efficiency and economy of a construction project. The replicable elements
of an engineered timber system cuts down on production and building time, leading to lower costs overall and a higher assurance in the timely completion of a building. In use, mass-timber makes for higher performing buildings, reducing running costs and operational carbon.
From the users perspective, timber buildings offer the added value of biophilic design; living and working in a wooden building has been proven to increase both the mental and physical health of its users.
This document showcases the advantages of using mass timber for industrial and commercial buildings. Using our HQ for Vitsoe, designed and delivered in mass timber; our design for a range of concepts for Stora Enso using their standard products range, and a comparative cost vs carbon study of industrial buildings in the USA, to demonstrate this.
In this document we use the term ‘industrial’ to encompass buildings of different uses; logistics, manufacture, data centres, showrooms, agricultural buildings.
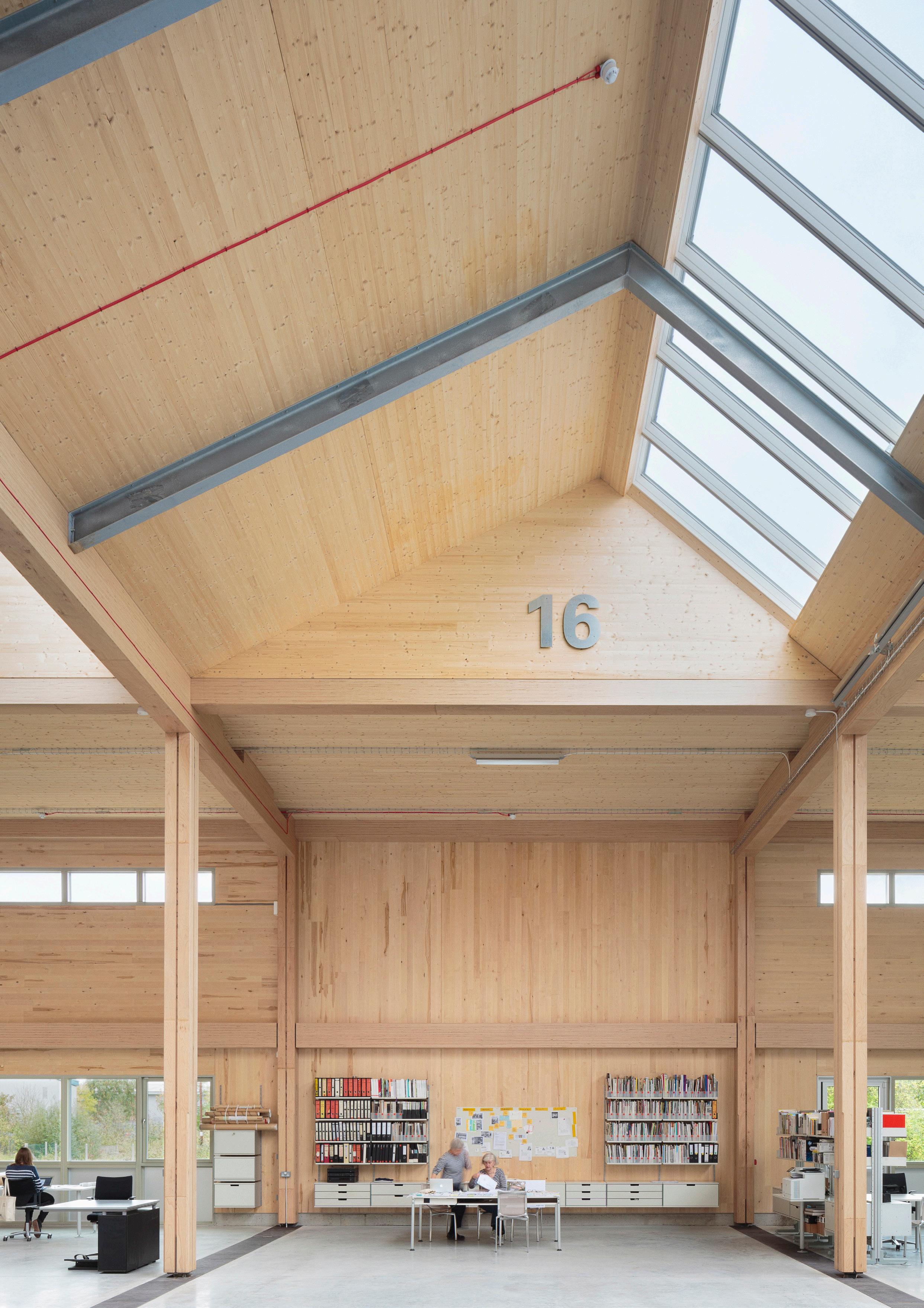
1. VITSOE
1.1 PROJECT SUMMARY
Component based system: designed for extension and re-use
Erected in just 23 days, our beautiful and functional manufacturing facility designed with Vitsoe is the first LVL structure to be built in the UK.
Using less material than glulam, the beam depths of LVL are comparable to steel, and operationally advantageous.
The fully replicable pre-fabricated system means the structure of eighteen 7.5m bays can be simply extended from its current size for additional floor area.
The structure is also highly efficient in its operation by prioritising bio-based materials and passive methods of climate management and daylighting.
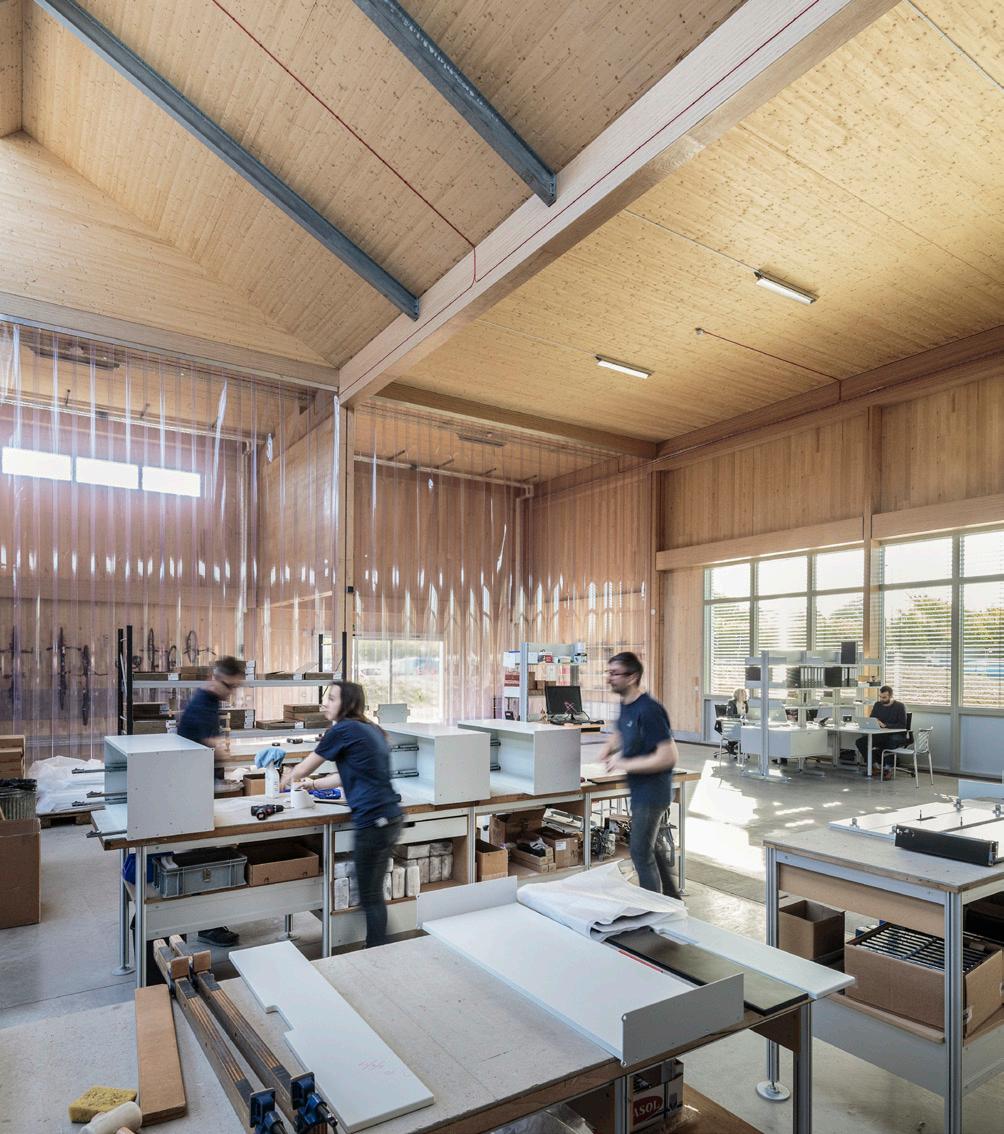
LOCATION
Leamington Spa, UK
PROJECT SECTOR
Manufacturing / Workplace
PROJECT VALUE
£5.75 million
COMPLETION DATE
October 2017
GIA
3,675 m 2

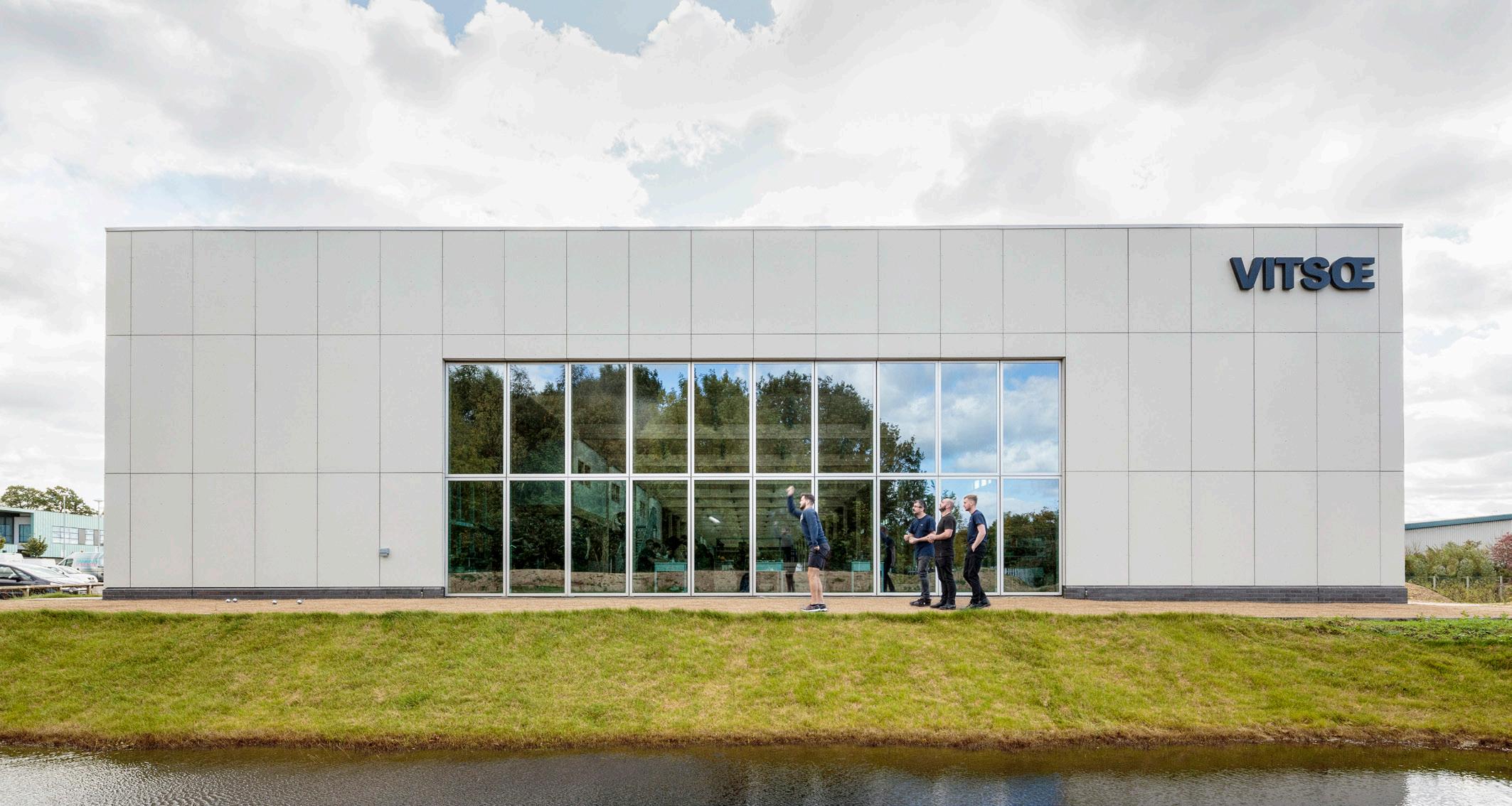
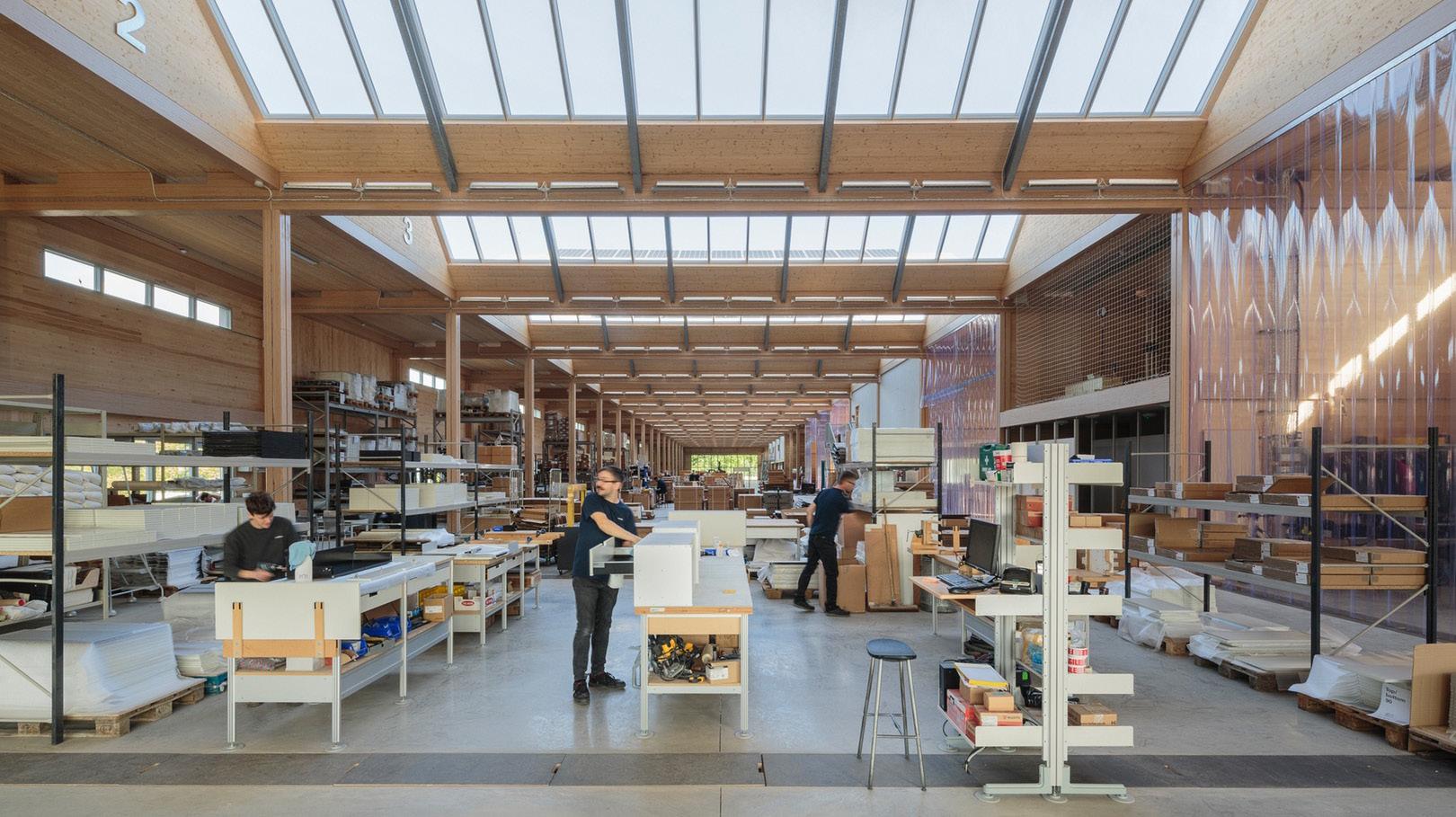

2. STORA ENSO CONCEPTS
2.1 PROJECT SUMMARY
Eight cost competitive building concepts in timber.
We have developed a set of eight building systems using existing Stora Enso products to meet a range of uses.
These concepts were developed to demonstrate the versatility of timber to meet industrial building requirements, from a premium facility to a warehouse space.
These designs are cost effective, flexible and modular. The building system encompasses manufacture and assembly (DfMA) and has been designed with disassembly and reassembly in mind; which in turn improves the functionality and profitability of the building throughout its life.
Designing in mass-timber has both environmental and social advantages; these buildings yield 30% less embodied carbon as compared to the EU benchmark, and all timber components used are sourced from sustainable, managed forests. Wooden buildings have also been linked to the increased well-being and productivity of their occupants.
The following pages summarise these eight concepts; showcasing three in detail.
LOCATION Europe
PROJECT SECTOR
Manufacturing / Workplace
PROJECT VALUE Varies COMPLETION DATE
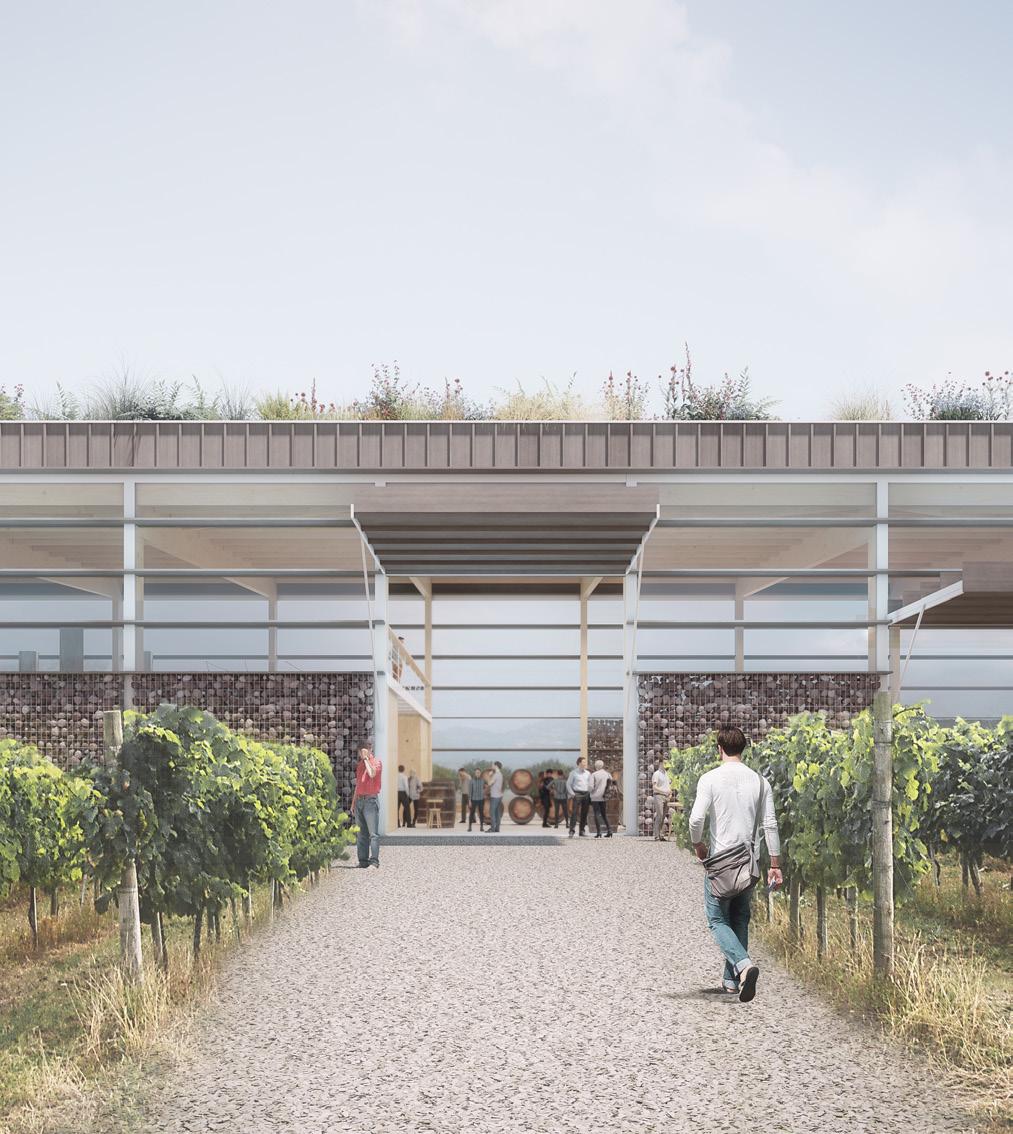

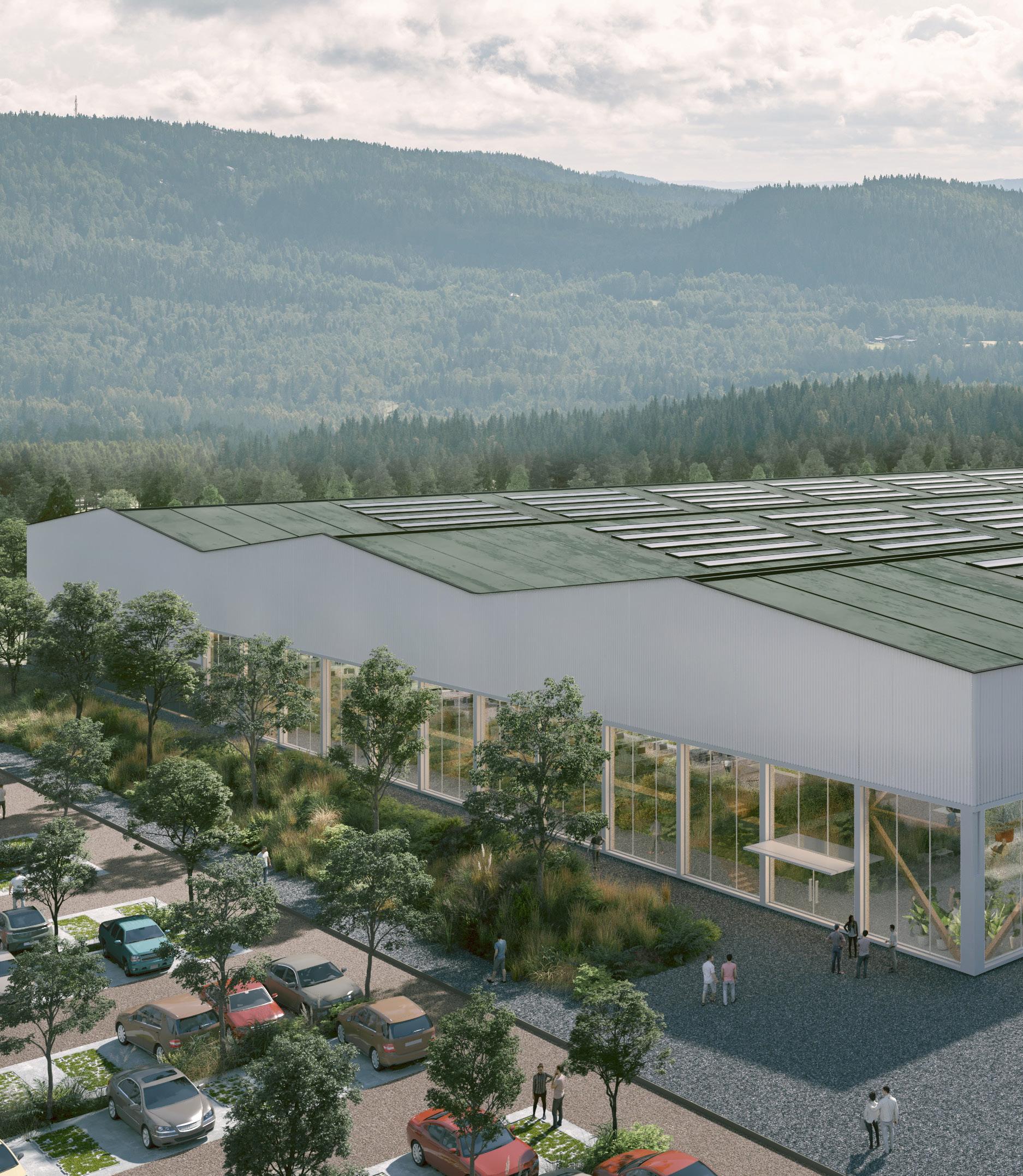
2.2 BUILDING CONCEPTS
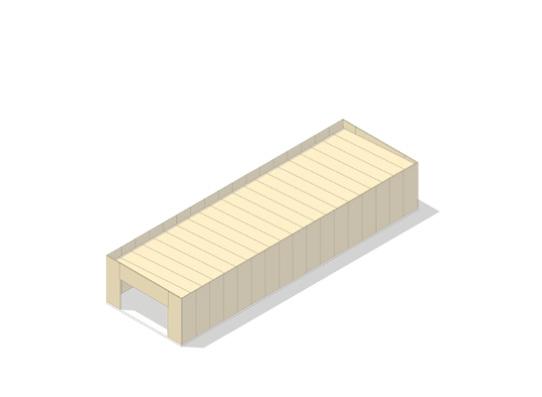
CLT WITH RIB ROOF
Span target: 16 m
Range: from 12 m - 18 m
Intended for small scale workshops and storage facilities where the atmosphere and aesthetic of the interior is a design priority; the working areas can be easily integrated with sales and visitors’ areas.
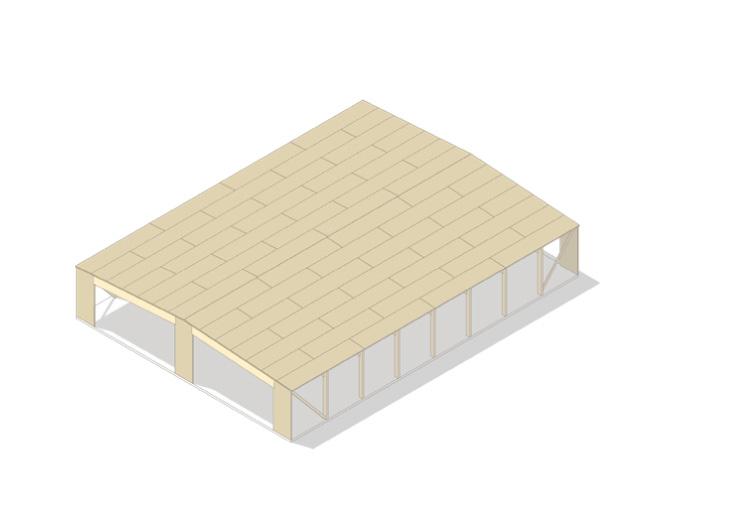
BEAM AND COLUMN (18 M)
Span target: 18 m
Range: from 16 m - 20 m
Ideal for lightweight structures with a heavy roof, designed with mass timber, green roofs or high snow fall in mind.
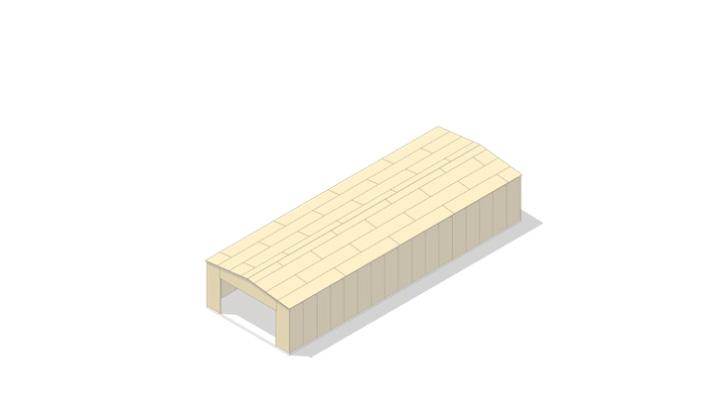
CLT BOX
Span target: 18 m
Range: from 14 m - 20 m
High quality indoor spaces integrating showrooms and other sales functions alongside warehouse and manufacturing processes.
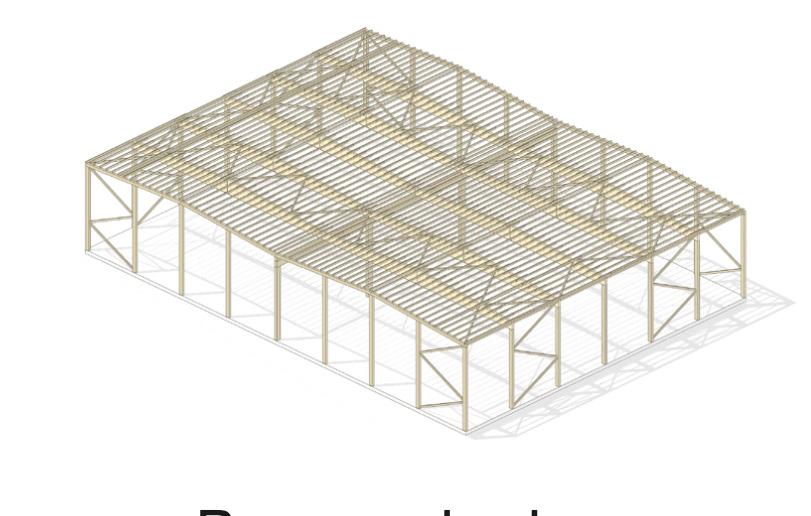
BEAM AND COLUMN (24 M)
Span target: 24 m
Range: from 18 m - 26 m
For medium to large warehouses with low to medium roof loads, such as those in moderately snowy areas.
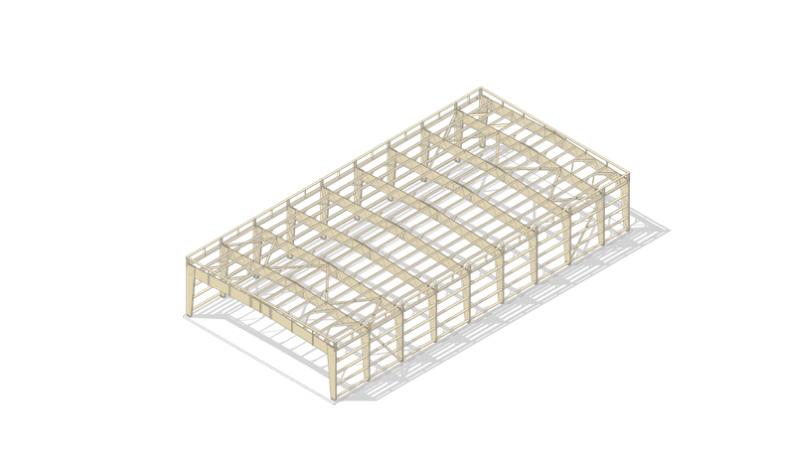
TWO-PIN PORTAL FRAME
Span target: 20 and 27 m
Range: from 18 m - 30 m
A materially effective solution for lightweight structures. These semi-flat roofs have no need for additional lateral bracing due to the portal frame structure

BEAM AND COLUMN (36 M)
Span target: 36 m
Range: from 14 m - 36 m
Built for medium to large warehouses with large spans, this structure uses a wood-steel hybrid main beam to support light to medium loads.
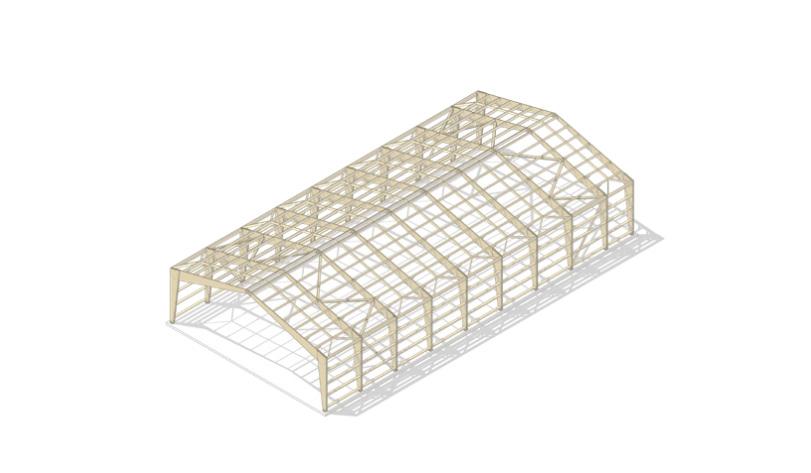
THREE-PIN PORTAL FRAME
Span target: 20 and 28 m
Range: from 18 m - 30 m
The most lightweight and materially efficient solution for pitched roofs. No need for additional lateral bracing due to the portal frame.

TWO STOREY WAREHOUSE
Span target: 16 m roof, 11 m floors
Range: from 12 m - 24 m
A timber frame designed for medium to large warehouses spanning two floors, or projects with a mezzanine handling medium to light loads.
2.3 BEAM AND COLUMN (18M)
This typical modular post and beam solution is highly flexible, and can be easily expanded to meet changing size requirements.
This structure can be used with any type of envelope; suitable for high roof loads, the design is optimised for semi-flat and green roofs.
Only the beams require special transport, cutting cost and build time.
The treatment of the timber ensures 30 minutes of fire resistance, meaning no additional protection measures are required and they can be exposed.
CLT roof on main beams to avoid secondary structures

Span:18m
Internal spine: 12m spacing
Spacing:from 6m
CLT roof for diaphragm action
Lateral stabilisation with CLT and/or diagonals
2.4 BEAM AND COLUMN (36 M)
This solution is similar to those shown above, modified to meet the standard of 36 m spans for logistics buildings in the UK.
This is a hybrid solution that utilises the best qualities of wood and steel in combination. This optimises material use and performance, and can be adapted for any type of envelope.
Roof stiffening with timber diagonals and long modular spans maximises the flexibility and functionality of the structure.
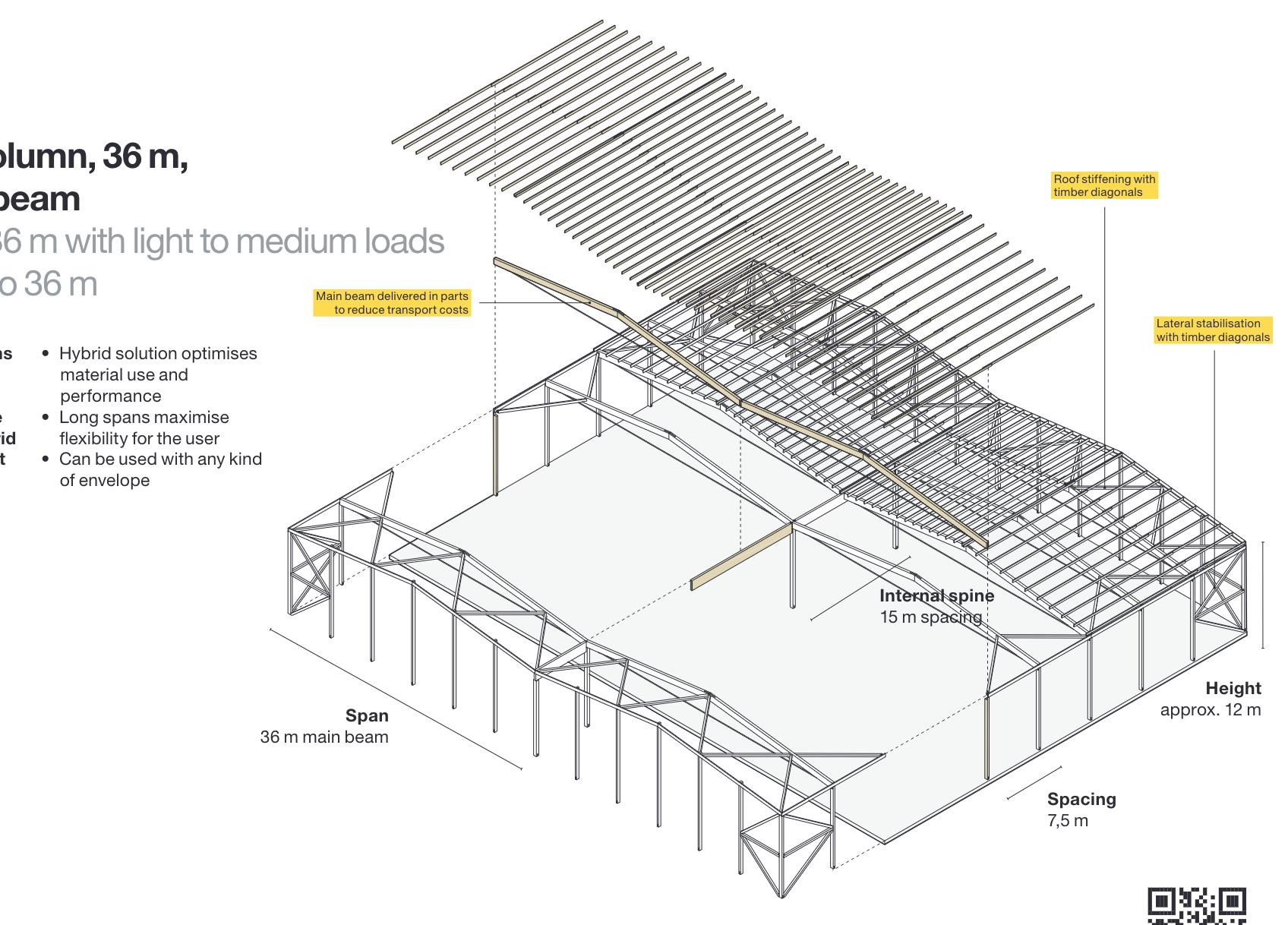
Main beam delivered in parts to reduce transport costs
Roof stiffening with timber diagonals
Lateral stabilisation with timber diagonals
Span:36mmainbeam
Spacing:7.5m
2.5 TWO STOREY WAREHOUSE
This structure utilises both ground and upper floor CLT slabs, and can be flanked in any kind of envelope.
This design boasts all the benefits of a premium timber building in a two-storey facility. Separate floors provide different uses and the middle floors are built to accommodate high loads.
Fire resistance is resolved without any additional protection, whilst maintaining the aesthetic integrity and biophilic benefits of exposed timber in the interior. intermediateSpan:11mfloor
Designed with LVL connections

Lateral stabilisation with timber or diagonals
CLT for upper floor slabs
Spacing:5.4m
Height:
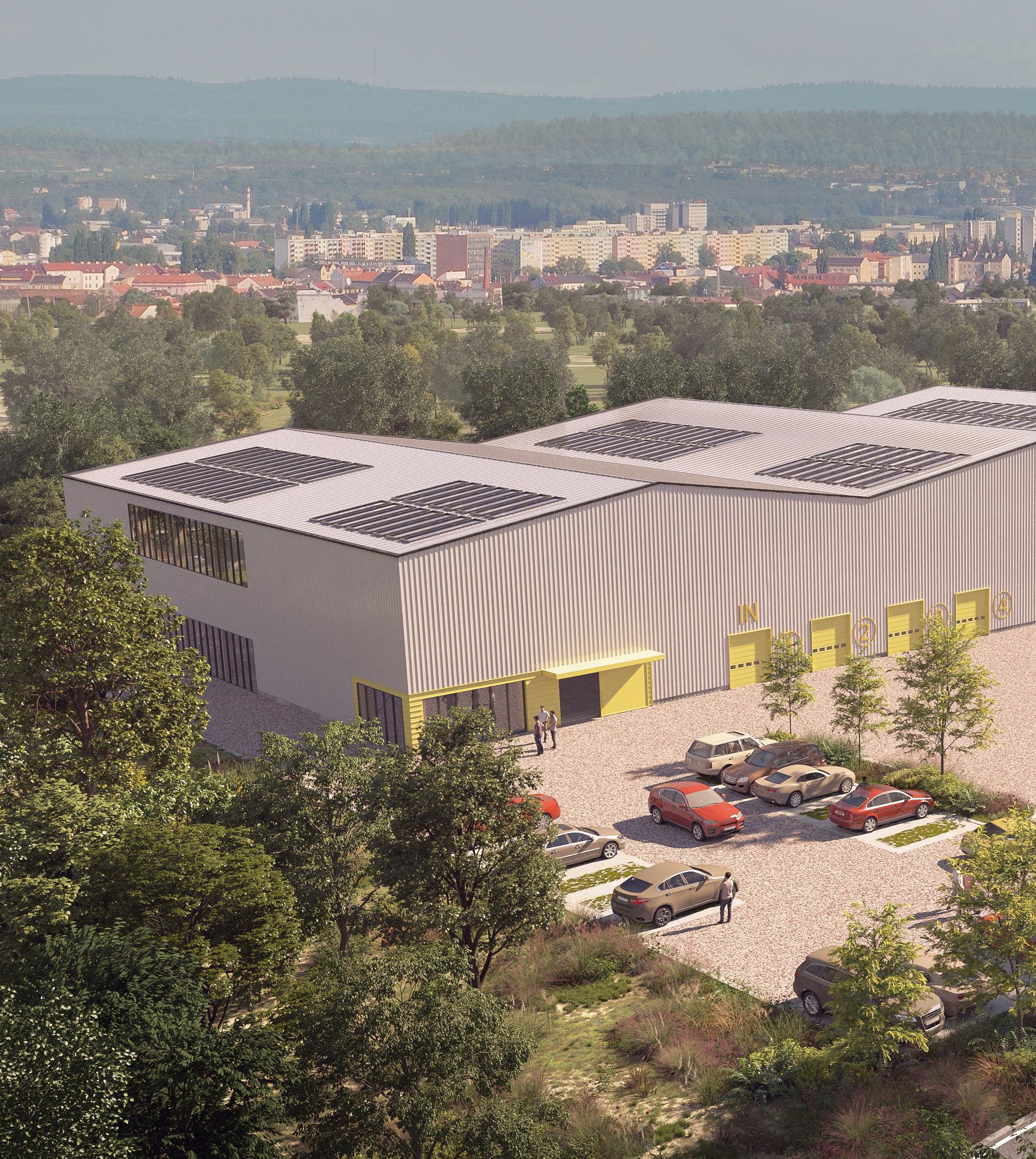

3. MASS TIMBER UTAH
3.1 PROJECT SUMMARY
A cost-carbon benefits study that challenges the barriers facing the wide spread adoption of timber based design
This study was prepared for a client in Salt Lake City, Utah, an area seeing significant growth in industrial buildings. In this region the typical construction methodology is ‘tiltup’; steel frame with heavy concrete walls, cast on the ground. This process is carbon intensive and does not meet the current standards of sustainability.
This study identifies a stepped approach of three systems, which are configured to suit different budget points, with an entry point at only a 5% premium and an expected 45% reduction in net carbon. This has been achieved through the close examination and subsequent optimisation of the aforementioned systems, to meet the functional requirements identified with developers, structural engineers and contractors with expertise in the field.
The streamlined construction process of timber reduces build time and cost, and the carbon sequestration of the timber frame offers the added benefit of carbon credits.
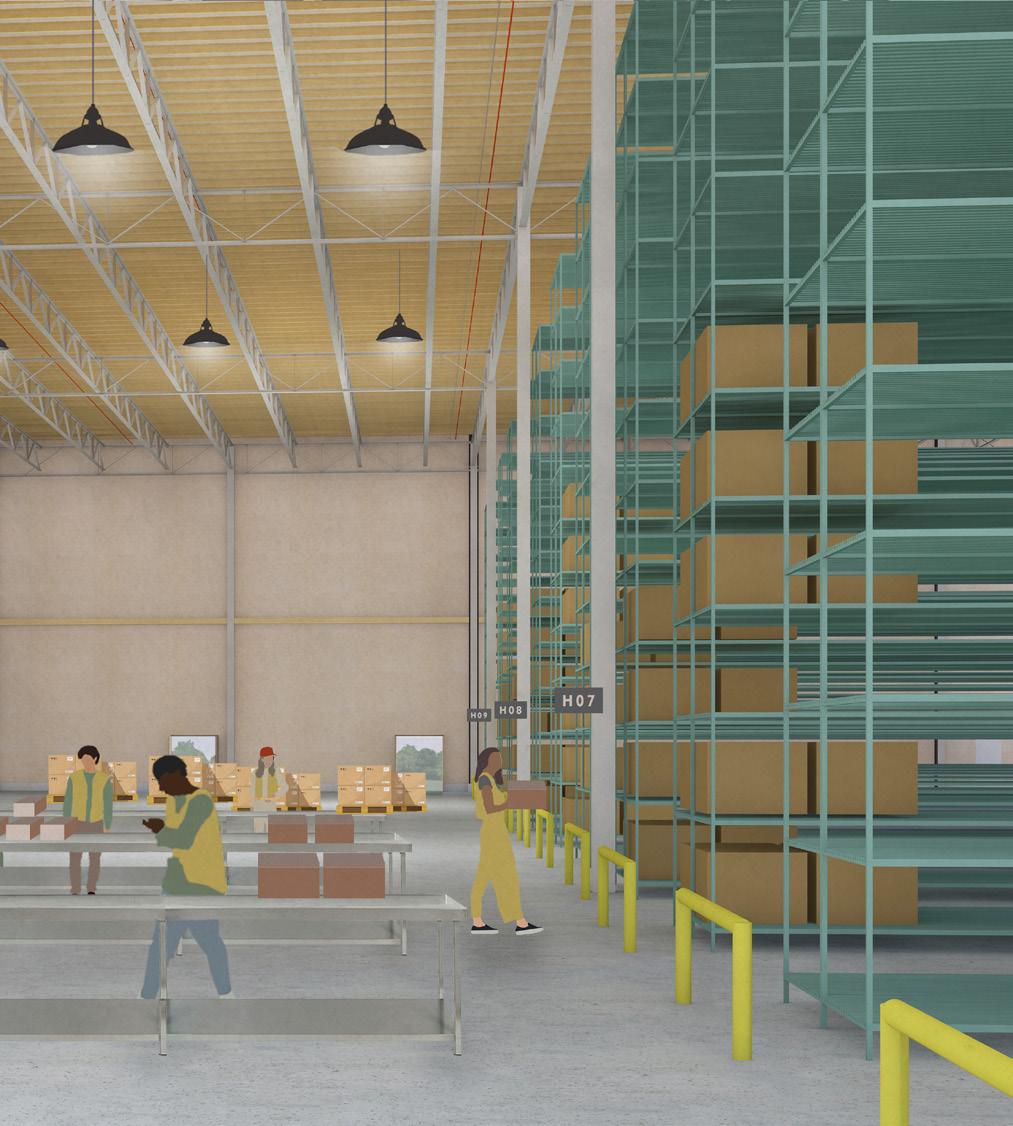
LOCATION
Utah, USA
PROJECT SECTOR
Manufacturing / Workplace
PROJECT VALUE
Varies
COMPLETION DATE
Ongoing
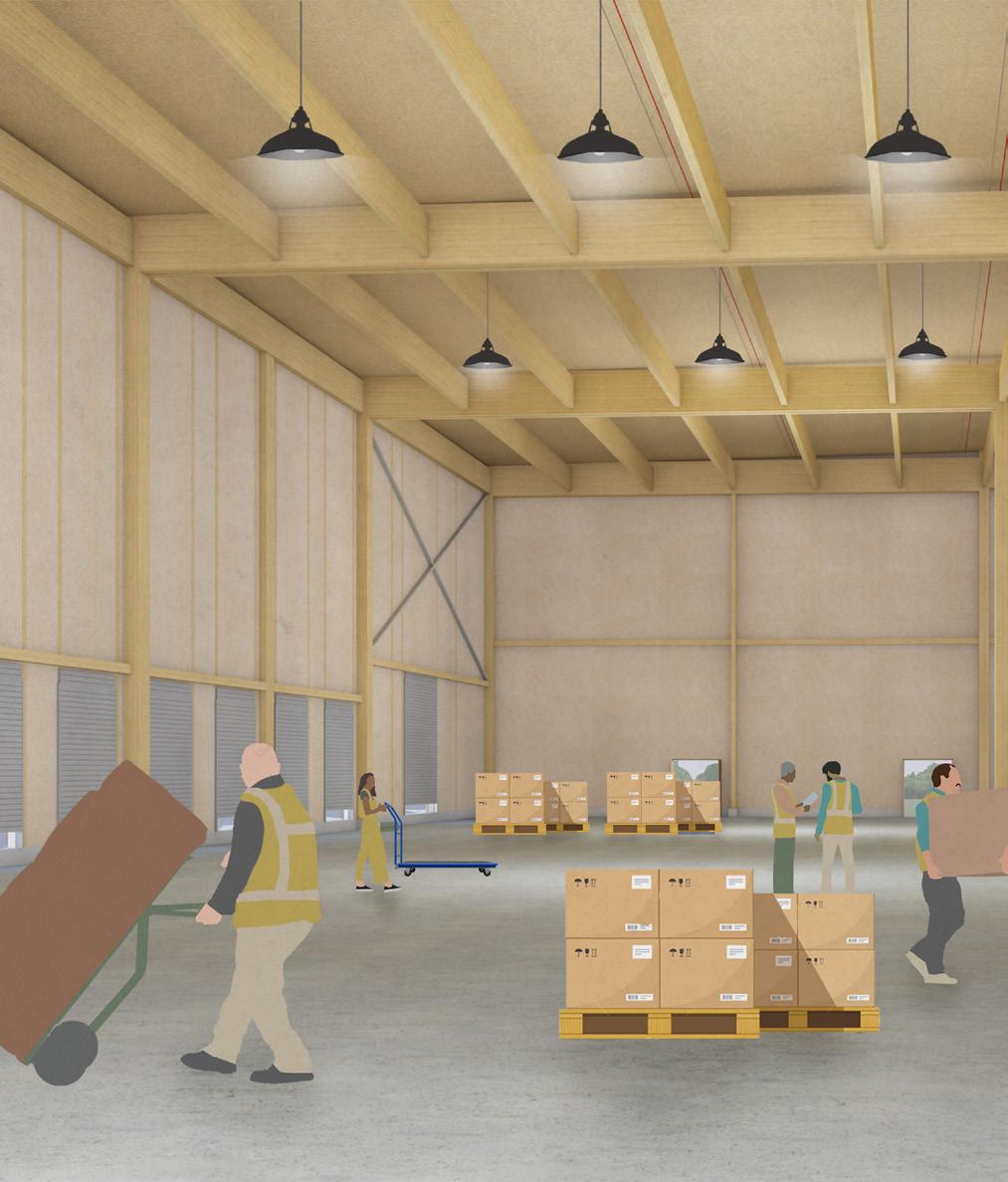

3.2 TILT PLUS
An optimised version of the traditional industrial building model, this system introduces biogenic carbon benefits at small premium from the current, tilt-wall model.
Retaining its steel frame, the interior follows a format that meets current market requirements, maintaining the standard 17 - 18 m bays.
The CLT panels used for the walls are prefabricated, providing the option of waterproofed and pre-clad siteready delivery. Once on site, the timber panelised roof system is integrated with the bar joists and installed in large pieces, drastically cutting built time.
Large areas of exposed timber benefit the internal spaces, contributing to biogenic carbon store and the well-being and productivity of occupants.
3.3 TIMBER PLUS
This materially-efficient design uses 11.2 to 12 m high spans of CLT to meet current sizing standards for racking modules and access routes for distribution warehouses.
Clear height standards can be met using slightly reduced speed bays of 11.4 m to suit the larger 18 m span.
Two options are available for the roof, steel deck or MMP panels, to suit different price points, biogenic carbon targets and the exposed timber finish of the interior.
The structure is adaptable; alternative truss types can be used for structures with more aesthetic requirements such as showrooms.
Roofing
Steel profiled deck
Mass ply panel deck (MPP)
Glulam joists
Glulam girders
Glulam columns and girts CLT wall panels
3.4 TIMBER MAX
Timber Max offers a sustainable, alternative building system for sites that require longer structural spans of up to 18.2 m
This system offers the same benefits as Timber Plus, using the same connections and building methodology with larger girder and joist components to accommodate the extra length of the spans.
A slightly reduced maximum clear height of 11.3 m is driven by the size of these components. There is the added option of using alternate timber hybrid girders, such as a queen post truss, to improve the aesthetic qualities of the spans.
3.5 COMPARATIVE OVERVIEW
Designing using timber systems offers a significant reduction in the carbon burden of a building, with very little uplift in the overall cost as compared to conventional warehouse design.
This can be achieved by introducing more timber based elements into the design, which can be done without any compromise to the internal layout and functional requirements of the building.
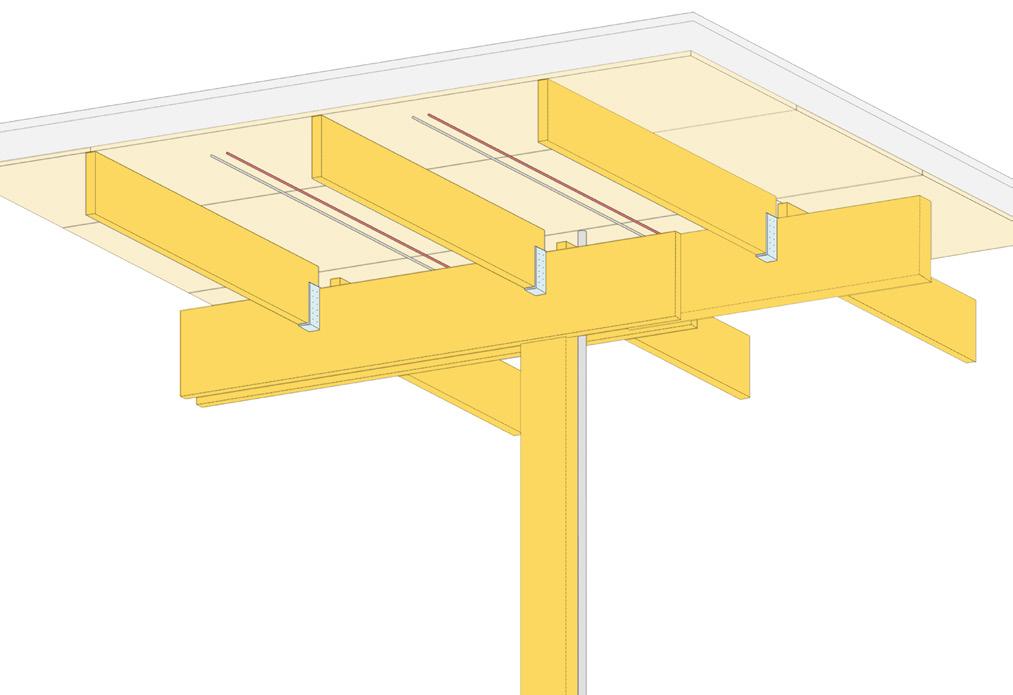