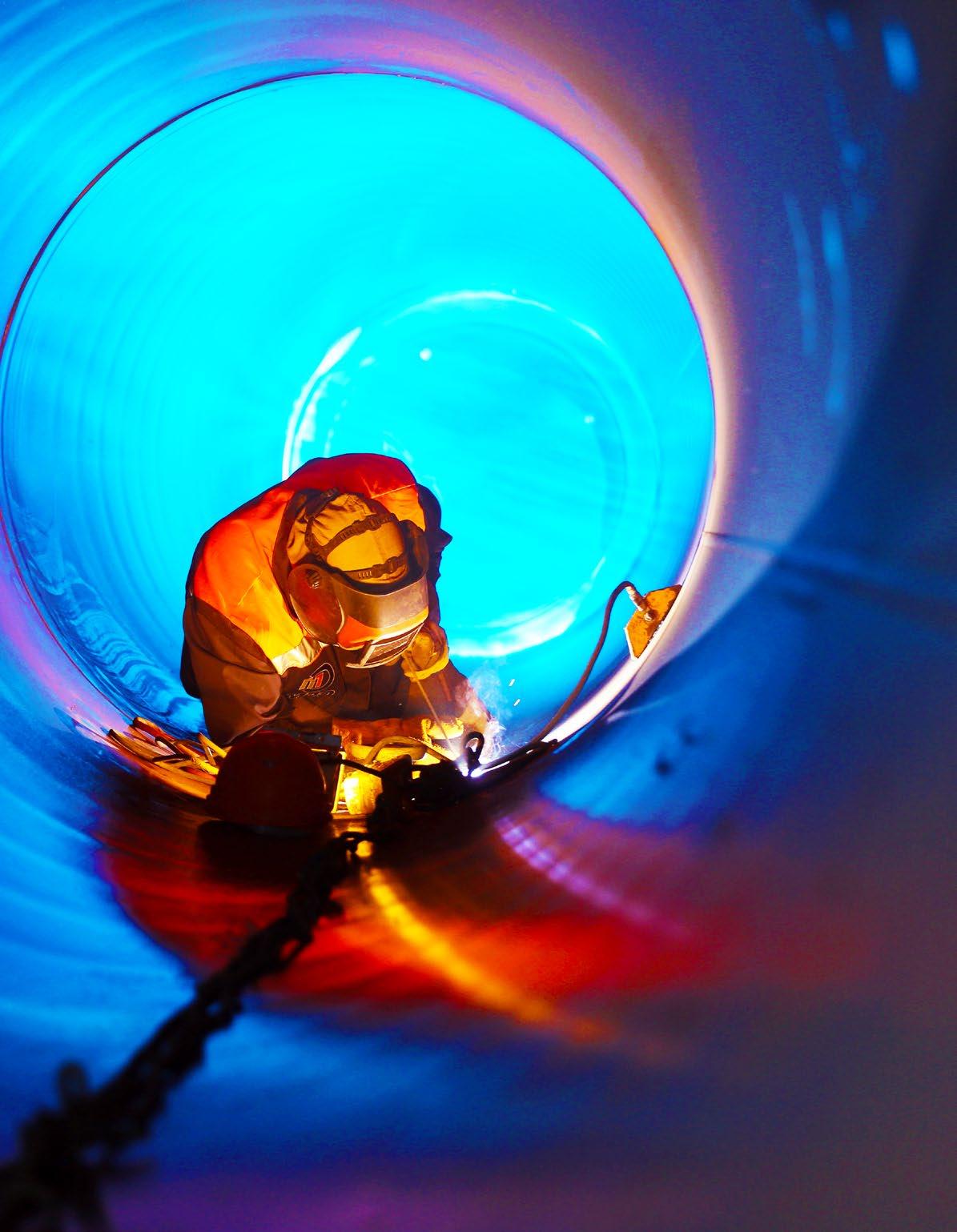
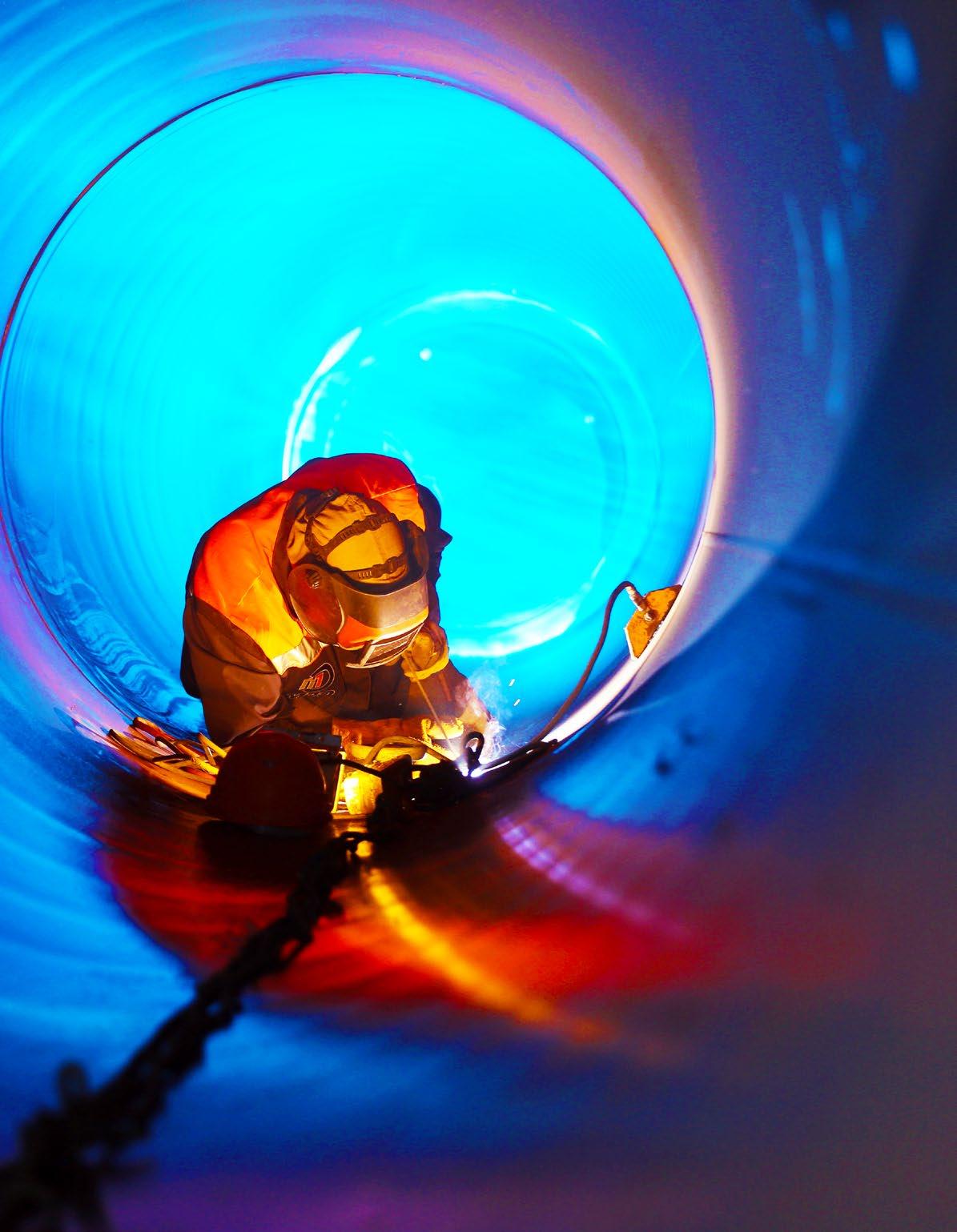
2019 Year In Review
Welcome to Weld Australia’s 2019 Year In Review – a look at our achievements, projects and programs over the last 12 months. 2019 has been a highly successful year for Weld Australia in many ways. It really is an exciting time to be a Weld Australia member. We are committed to using our extensive experience, combined with an innovative new approach, to achieve our core mission—promoting the interests of our members within the field of welding, not just in Australia, but across the globe.
9 Advanced Welder Training Centres Funded
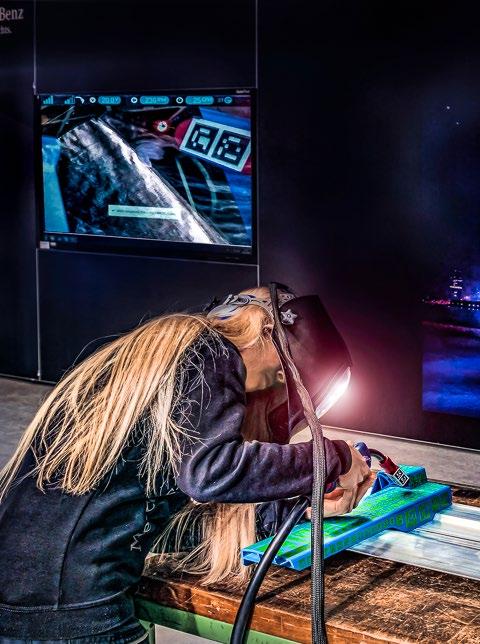
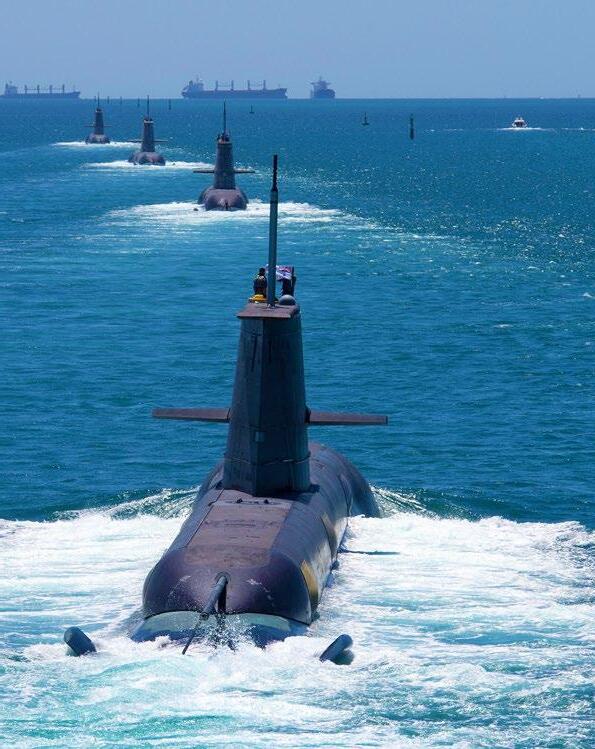
24 Member Events
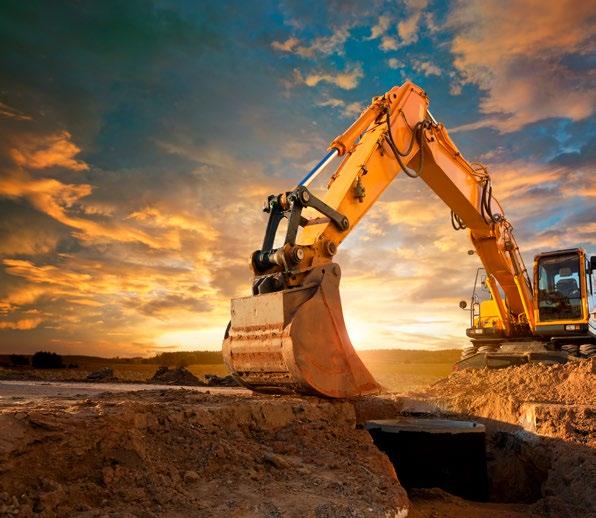
18 Presentations at Industry Events
12 State Division Committee Meetings
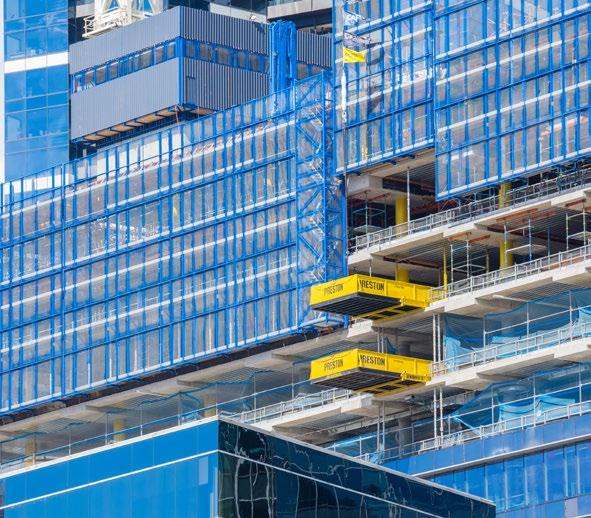
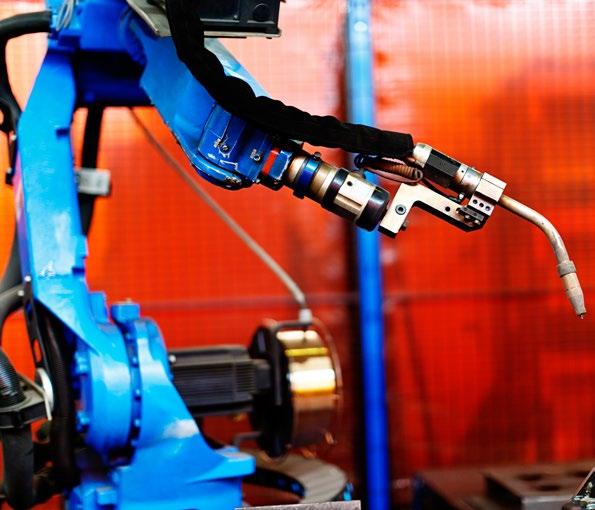
74 Hotline Queries Resolved
2019: Member Events
Weld Australia is committed to ensuring that the Australian welding industry remains both locally and globally competitive. Engaging the welding community at a local level plays a key role in upholding this commitment. With the help of state committees, Weld Australia regularly holds member events, from site visits and technical presentations, through to networking opportunities. Weld Australia state committees act as our voice in their local community, and provide us with information on what we can do to help in their local area. If you would like to join your state’s committee in 2020, contact membership@weldaustralia.com.au.
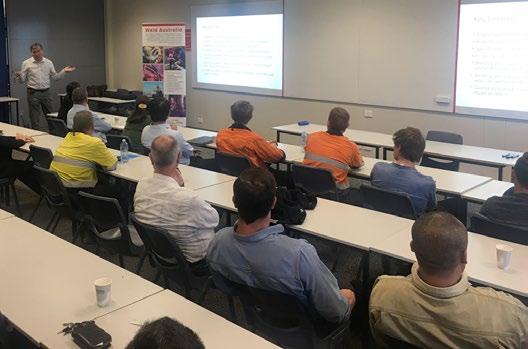
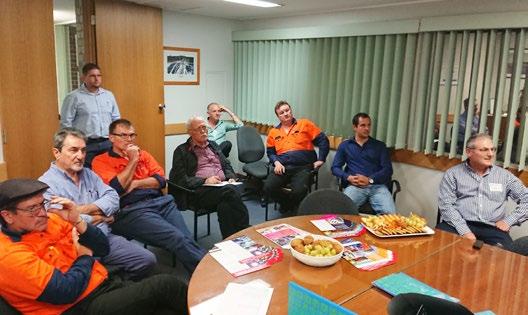
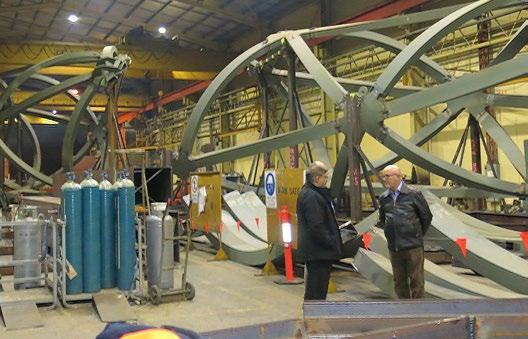
Technical Presentation, Melbourne, March
Weld Australia facilitated a technical presentation by Robert Wiseman (Business Development - Education, Lincoln Electric) on the King Street Bridge Failure. In 1962, Melbourne’s newly completed King Street Bridge suffered major fractures in several of the main fabricated steel beams, causing the bridge to sag some 300mm. Fortunately, total collapse was avoided. A Royal Commission examined the failure in great depth. Robert Wiseman took attendees through the fascinating story of how a major steel bridge project went wrong, the findings of the Royal Commission, and how the learnings from this major failure are still highly relevant today.
Augmented Reality Welding Simulator Roadshow, Queensland, April
In late April, Geoff Crittenden (CEO, Weld Australia) and Michael Pitt (National Business Manager, Weld Australia) undertook an augmented reality welding simulator roadshow. Held at Maxcon Industries in Ipswich and HiVue in Toowoomba, Geoff and Michael gave detailed presentations and demonstrated the advanced training capabilities of the welding simulator. Welding apprentices learn and understand welding procedures and techniques through a more interactive training method, gaining hands-on experience in a controlled, safe, interactive environment that captures the imagination.
S&L Steel Site Tour, Sydney, June
In June, the New South Wales Division hosted a site tour and presentation at S&L Steel. The event proved very popular and was very well received by all in attendance. S&L Steel is currently involved in the fabrication and welding of a very unique bridge—it features curves, rather than the usual straight lines. This shop-floor visit offered an invaluable opportunity for attendees to see how work on the project is progressing. Attendees also had the opportunity to tour S&L Steel’s facilities, which include two 60 tonne overhead cranes. Plus, with over 6,000m2 of open yard space, S&L Steel can accommodate a number of large projects simultaneously.
S&L Steel is currently fabricating a very unique bridge featuring curves, rather than the usual straight lines.
Robert Wiseman (Business Development - Education, Lincoln Electric) presents to Weld Australia members.
Some of the attendees at Maxcon Industries in Ipswich during the augmented reality welding simulator roadshow.
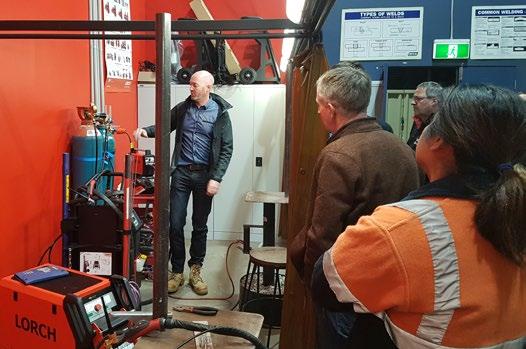
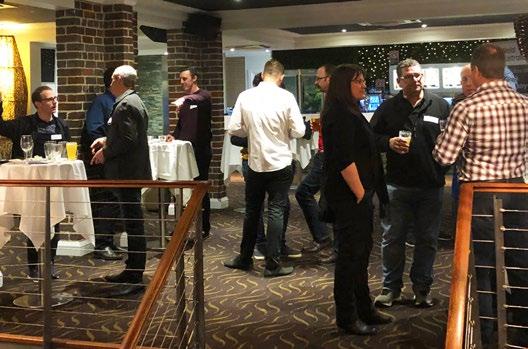
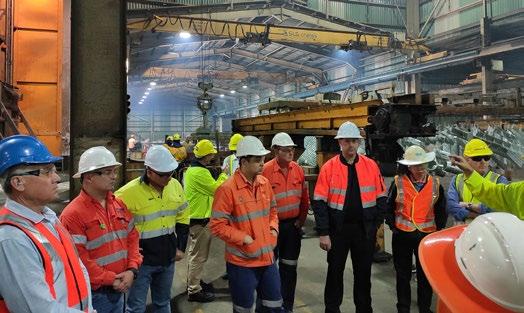
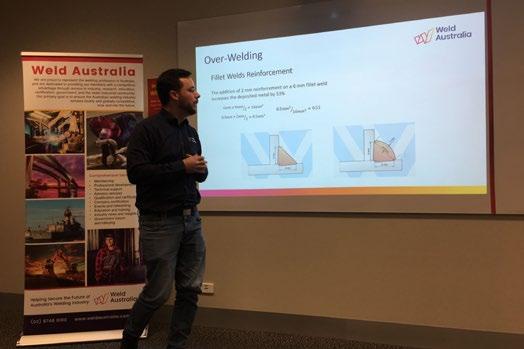
Technical Event & AWS Site Tour, Adelaide, June
Dr Rahim Kurji (Lead Engineer, Australian Welding Solutions) gave a presentation on The Effect of Shielding Gas Composition on Welding Performance. The selection of gas mix significantly impacts the quality of the weld, so it is crucial to have an understanding of gas choice, in order to deliver a quality weld at a lower cost. Dr Kurji gave attendees a sound understanding of the science behind gas selection, and explained why the gas mix is an essential variable in a welding procedure. Dr Kurji also demonstrated a range of gas mixes. Attendees then had the opportunity to tour the Australian Welding Solutions facilities.
Networking Event, Wollongong, July
In July, Weld Australia facilitated a very well-attended networking event for members at the North Wollongong Hotel. The networking event proved to be a great opportunity to meet up-and-coming welding engineers from all around Australia, as well as Weld Australia team members and Directors. Attendees had the opportunity to discuss industry issues and challenges in a relaxed, informal setting. This networking evening coincided with the final module of Weld Australia’s International Welding Engineer (IWE) and Technologist (IWT) course, which was held on campus at the University of Wollongong.
Valmont Coatings Site Tour, Queensland, August
The Queensland Division recently held a technical event that brought together experts from the Galvanizers Association of Australia and Valmont Coatings to present a detailed analysis and review of various aspects of the galvanizing process. Attendees gained valuable insights into the effects of various materials on galvanizing, and what the industry offers. Attendees were also treated to a tour of the Valmont Coatings facilities in Carole Park. Valmont Coatings is a leading provider of hot-dip galvanizing and protective coating services for a variety of metal products, bolstering their durability, lifespan and aesthetic value.
Technical Presentation, Melbourne, October
Weld Australia’s Victoria Division hosted a technical event on The Cost and Economics of Welding. Victor Blain (Senior Welding Engineer, Weld Australia) took attendees through the basic principles required to identify and manage the costs of production in order to reduce expenses and ensure quality. In an industry that is continually competing with lower cost countries, this was a must attend event. Victor covered a range of factors that are essential in cost effective quoting, including how to calculate the cost of welding by the weight of deposited weld metal, labour costs, and how to optimise the welding process to save money.
Weld Australia members at the Wollongong networking event.
Victor Blain (Senior Welding Engineer, Weld Australia).
Weld Australia members tour Valmont Coatings.
Weld Australia members tour the Australian Welding Solutions facilities in Adelaide.
2019: Industry Events
Weld Australia was involved in various industry events this year, with Geoff Crittenden (CEO, Weld Australia) and Michael Pitt (National Manager Education and Training, Weld Australia) delivering keynote presentations and participating in expert panel discussions on numerous occasions. Just some of the industry events in which Weld Australia was involved include National Manufacturing Week, BAE Systems Australia’s Factory of the Future and AIMEX. In addition, Weld Australia facilitated the National Manufacturing Summit in June. With over 100 delegates and more than 20 keynote speakers and panelists, the Summit addressed two crucial constraints faced by the manufacturing sector: energy insecurity and fragmented skills and training.
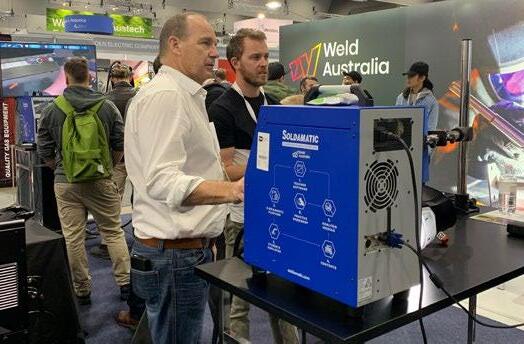
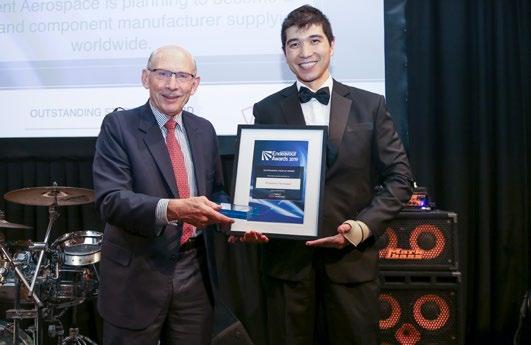
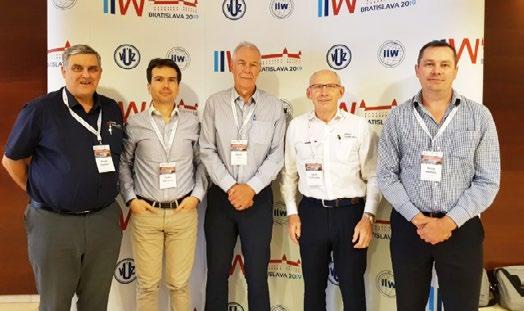
National Manufacturing Week, Melbourne, May
National Manufacturing Week (NMW) is one of Australia’s largest gatherings of manufacturing decisionmakers. Welding, heat-treating, joining and associated products and technologies were featured on the exhibition floor in the Welding Technology Product Zone. Weld Australia impressed delegates with interactive, hands-on demonstrations of the Soldamatic augmented reality welding simulator. It proved to be extremely popular with the crowds; there were people lining up to try their hand at this innovative advanced welding training technology and learn more about the myriad benefits it has to offer.
Endeavour Awards, Melbourne, May
The 16th annual Endeavour Awards saw leaders from the Australian manufacturing industry celebrate their success at the Arts Centre Melbourne in May. The Endeavour Awards are presented annually by Manufacturers’ Monthly, supported by National Manufacturing Week. Recognised as the premier awards program within the manufacturing industry, the evening is a chance to celebrate the many successes within Australian manufacturing. Weld Australia was proud to sponsor the Outstanding Startup Award, which was won by Persistent Aerospace, a Western Australia manufacturer of military specification drones.
72nd IIW Annual Assembly and International Conference 2019, Bratislava, July
Representatives from Weld Australia attended various Commissions at the 72nd IIW Annual Assembly and International Conference, to ensure continued access to state-of-the-art knowledge in a variety of areas, including safety, education, materials, NDT, design, and fatigue. Bruce Cannon (Principal Welding Engineer, Weld Australia) and Geoff Crittenden (CEO, Weld Australia) participated in Commission VIII – Health and Safety, engaged in important discussions related to the safety of welding fumes. Geoff Crittenden also gave a presentation to Commission XIV – Education and Training.
Michael Pitt demonstrates the Soldamatic welding simulator.
L To R: Geoff Crittenden presents the Outstanding Start-up Award to Syed Shah on behalf of Persistent Aerospace.
Weld Australia representatives at the IIW Conference.
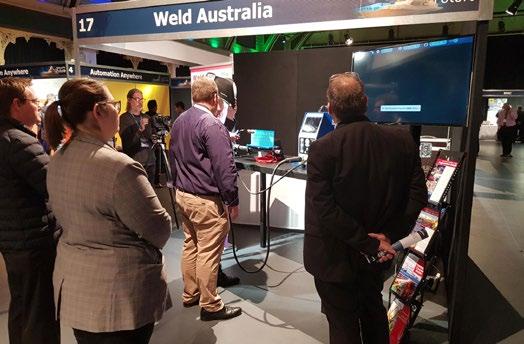

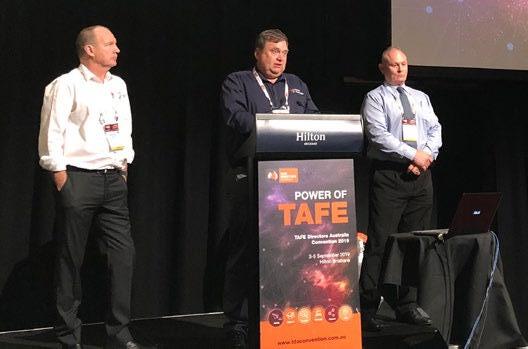
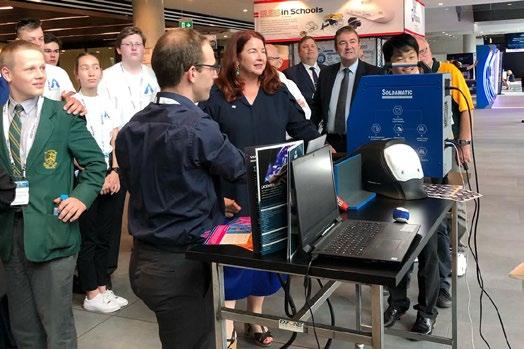
BAE Systems Australia’s ‘Factory of the Future’, Melbourne, July
Hosted by BAE Systems Australia’s shipbuilding business, ASC Shipbuilding, the ‘Factory of the Future’ was held in Melbourne. It featured some of Australia’s most exciting innovators and creators of Industry 4.0 solutions. The event was attended by more than 250 people from the defence, supply-chain, government and technology sectors, who were able to play with and witness first-hand local innovations. Weld Australia was invited by BAE Systems to showcase the Soldamatic augmented reality welding simulator, and demonstrate how it can help train the welders of the future.
AIMEX, Sydney, August
AIMEX is the largest free-to-attend conference for the mining sector. The program concentrated on three key themes: Future Sector, focused on lifting industry standards; Future Workforce, which highlighted future skills; and Future Governance, which considered the effects of the shift towards a low carbon economy and energy consumption. Geoff Crittenden (CEO, Weld Australia) was invited to participate in a panel discussion: Tomorrow’s Workforce—Enabling and Cultivating Our Future Miners. He also presented on the topic of using advanced welder training technology to reduce costs and increase outputs in the mining industry.
TAFE Directors Australia (TDA) Convention, Brisbane, September
In September, Weld Australia attended the TDA Convention. The theme of the convention was The Power of TAFE—a celebration of the role TAFEs play in vocational education for the benefit of citizens and supporting economic wellbeing and building communities. Michael Pitt (National Business Development Manager, Weld Australia), Brian Rungie (National Manager Strategic Partnerships, Weld Australia) and Garry Hargreaves (Corporate Solutions Manager Commercial, SkillsTech TAFE Queensland) facilitated a workshop on the Soldamatic augmented reality welding simulators.
PACIFIC 2019, Sydney, October
Weld Australia exhibited at PACIFIC 2019 - the biennial Pacific International Maritime Exposition. The event provided a showcase for the commercial maritime and naval defence industries to promote their capabilities to decision-makers from around the world. It was strongly supported by the Royal Australian Navy, Sydney Harbour Foreshore Authority, Defence Science and Technology, the Department of Industry, Innovation and Science, the Department of Infrastructure, Regional Development and Cities and the New South Wales Government. The Royal Australian Navy invited Navy Chiefs and senior leaders from 35 countries to attend.
AIMEX Panel Tomorrow’sWorkforce—EnablingandCultivating Our Future Miners
L to R: Michael Pitt, Brian Rungie and Garry Hargreaves.
Weld Australia’s stand at the Factory of the Future event.
Minister for Defence Industry the Hon. Melissa Price MP inspects Weld Australia’s welding simulators at PACIFIC 2019.
2019: National Manufacturing Summit
The 2019 National Manufacturing Summit was held at The Australian Synchrotron in Melbourne in August. With the theme Skills for the Future , the critical constraint of workforce capability and availability formed the basis of discussions throughout the Summit. Now in its third year, the Summit brought together thought leaders in the manufacturing sector to discuss the sector’s prospects, and identify policy measures designed to support industry growth and sustainability.
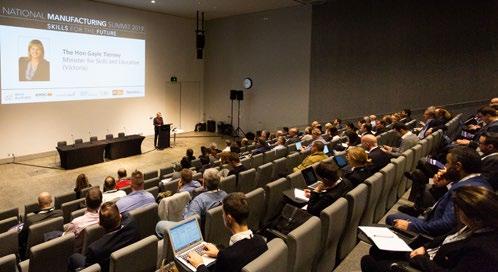
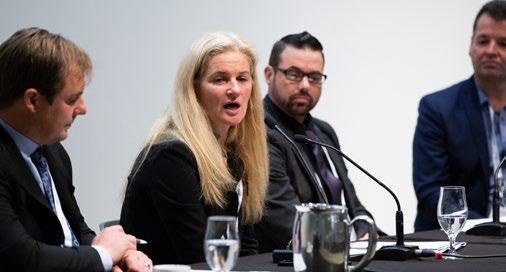
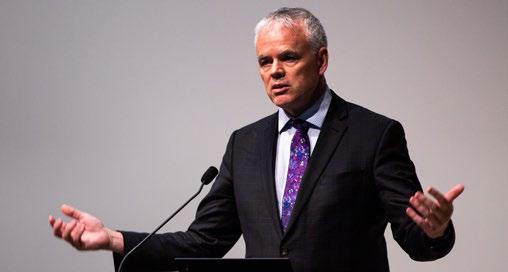
Top: Minister for Training and Skills, and Higher Education, the Hon
Middle: Skills for a High-Tech Manufacturing Future Panel. L to R: Chris Brugeaud (CEO, SSS Manufacturing), Justine Evesson (Advisor, Skills and Apprenticeships), Stuart Birkin (Education Manager: Engineering, Manufacturing and Automotive, Federation TAFE) and Michael Sharpe (Director, AMGC).
Bottom: Dr Jim Stanford (Economist and Director, Centre for Future Work at the Australia Institute).
Minister for Training and Skills, and Higher Education, the Hon Gayle Tierney MP, focused on manufacturing workforce capability and availability, and touched on how the Victorian Government is investing in more places through TAFEs and training organisations in areas that meet the skills needs of Victorian industries and priority workforces.
Professor Michelle Gee (Director, Sir Lawrence Wackett Centre) spoke in detail about how universities and industry can work more closely together. “I think that the formula for universities and industry to really be effective in the way they work together to support each other is, firstly, to support the growth of industry and, secondly to support the business that is universities— the development of people and capability. It is about working together in an immersive way.”
Federal Shadow Minister for Employment and Industry, the Hon Brendan O’Connor MP focused on both the challenges and opportunities facing manufacturing. “There is no doubt in my mind that a strong, diverse, agile manufacturing sector is critical to Australia’s future. To ensure this is the case, we need to address the skills crisis facing this country, by developing an appropriately skilled workforce to drive us into the new era of manufacturing.”
Nick Howie (Training Solutions Manager, Naval Shipbuilding College) provided delegates with an overview of the Naval Shipbuilding College’s mission: to ensure a suitably skilled and qualified Australian workforce will be available – at the right time – to meet the needs of industry.
Dr Jim Stanford (Economist and Director, Centre for Future Work) spoke about the potential of valueadded manufacturing in Australia (tied into the current momentum around lithium and lithium based products), in the context of Australia’s history.
The program also featured several highly informative and engaging panels: Unlocking the Power of Collaboration, Skills for a High-Tech Manufacturing Future, and The Future of Skills and Diversity—Beyond Ticking the Box.
Gayle Tierney MP addresses delegates.
2019: Training & Certification
Several major Weld Australia training and certification projects continued throughout 2019. The Australian Welder Certification Register (AWCR) and WeldQ platform continued to grow. Over 625 users registered on WeldQ this year, taking the total number of users (including the initial bulk upload) up to 9,829.
Welder qualifications also increased, with Weld Australia issuing over 100 ISO 9606-1 Qualification testing of welders — Fusion welding welder qualifications in 2019. Plus, Weld Australia held 28 online examinations for AS 1796 Certification of welders and welding supervisors, with 108 applicants sitting these exams.
Weld Australia continued the development of the International Welding Specialist (IWS) Blended Learning

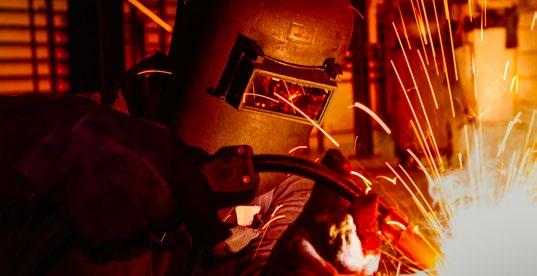
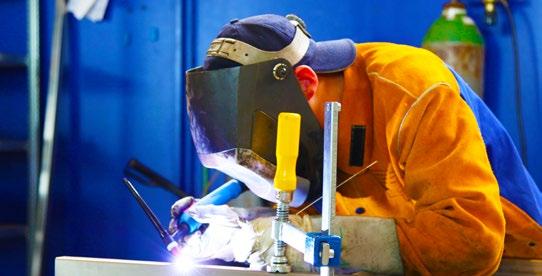
Course in 2019. This project involved the application of distance learning to the course content, which will reduce the face-to-face component of the course to approximately two weeks.
Weld Australia again conduct the International Welding Engineer (IWE) and International Welding Technologist (IWT) Course at the University of Wollongong. Successful completion of the course saw 16 graduates obtain the globally recognised qualifications.
Finally, Weld Australia facilitated a number of specialised industry workshops, such as the Pipeline Repair, Hot Tapping and In-Service Welding Workshop in Perth in August. All workshops received very positive feedback from attendees.
or peruse the 2020
Calendar on page 52.
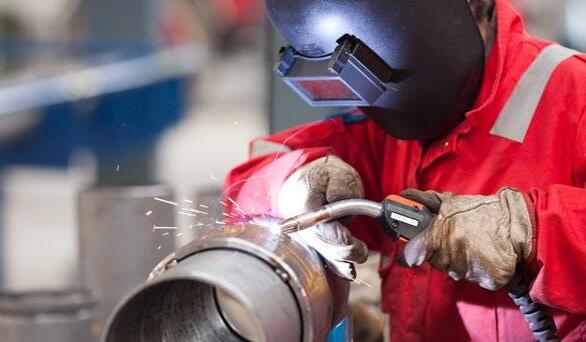
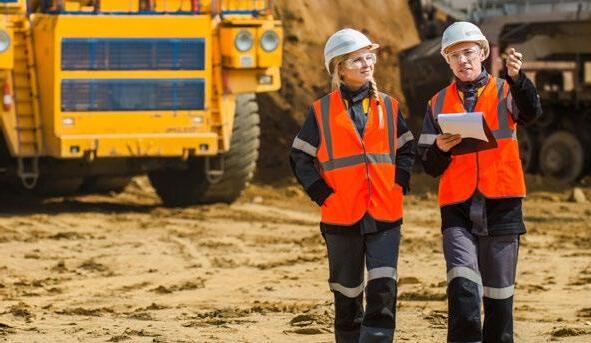
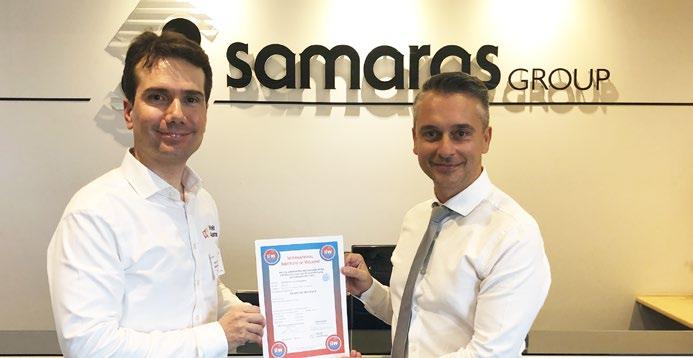
L to R: Paolo Corronca (Qualification and Certification Manager, Weld Australia), presents George Samaras (Executive, Samaras Group) with ISO 3834 certification.
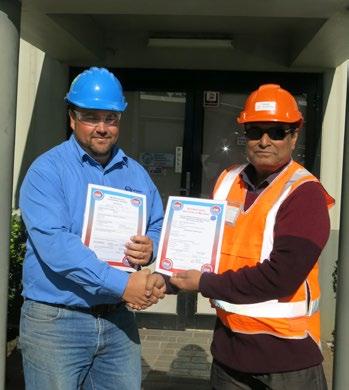
L to R: Craig Robinson (Manager, M&S Fabrications) and Sasanka Sinha (Senior Welding Engineer, Weld Australia).
2019: Weld Australia Company Certifications
Weld Australia would like to congratulate all companies who were awarded certification in 2019. These members include Samaras Group, Master Steel, M&S Fabrications, NWEC, TEi Services, Fabinox, Callidus Welding Solution, JC Butko, Macfab, Frontline Manufacturing, Alfabs, BendWorx SteelPro, Downer EDI Rail - Maryborough, AWI Steel, and Williams Metal Fabrications all of which achieved certification to AS/NZS ISO 3834 Qualityrequirementsforfusionweldingofmetallicmaterials .
Samaras Group
Samaras Group was the first South Australian structural steel fabricator to be awarded certification to IIW MCS ISO 3834:2. Founded by the Samaras family in 1974, Samaras Group has grown into one of Australia’s largest privately owned multi-disciplinary heavy engineering and construction services providers with a solid reputation for innovation, service, quality and an ongoing commitment to safety.
Operating from a huge 75,000m2 manufacturing facility in Gillman, South Australia, Samaras has a national workforce of over 220 highly experienced tradesmen and construction professionals. Samaras specialises in the largest and most complex projects the industry has to offer. Just some of their recent projects include the Adelaide
Convention Centre, Chadstone Shopping Centre, the Torren to Torrens Rail Bridge and both the Melbourne and Sydney Airports.
Master Steel
Master Steel was awarded certification to IIW MCS ISO 3834:3. Master Steel was founded in 1993 on the Gold Coast by an engineertradesman duo, with their 2,400m2 workshop built by one of the business’ founding members.
In recent years, Master Steel acquired the help of mechanical engineer Gabriel Dio in the role of managing director. The company has moved towards niche technical fabrication, recruiting a certified welding supervisor to control quality. Master Steel now provides fabrication and manufacturing services, and assembly of complex steel components for the
construction, commercial, heavy and public sectors. From structural steel to test bed machinery – no project is too complex. Their services include: weld traceability and compliance; manufacturer’s data reports; nondestructive testing; post-weld heat treatment; and documentation control.
M&S Fabrications
Awarded certification to IIW MCS ISO 3834:2. M&S Fabrications was established in 1995 by Managing Director, Greg Martin. Over the past 25 years, M&S Fabrications has become a highly respected steelwork fabrication business, undertaking projects in the industrial, commercial and mining fields. Just some of their major clients include John Holland, Thiess, McDermott’s, Roads and Maritime Services, Caterpillar Global Mining, Seymour
Whyte, Daracon, Lendlease, Fulton Hogan, Abergeldie and Freyssinet. With over a quarter of a century worth of experience delivering the highest level of product specification and finish, M&S can cater for a wide range of disciplines, including: metal engineering, light to heavy fabrications, structural steel, mining equipment and associated maintenance and repair, bridgework, handrail manufacture and most methodologies for installation.
NWEC
New World Engineering and Construction (NWEC) was awarded certification to IIW MCS ISO 3834:2. NWEC is a leading Australian steel fabrication, painting, installation, construction management and welding resource supply company with over 35 years of experience, headquartered in Sydney. Their multi-disciplinary engineering construction service provides turnkey solutions for structural, mechanical and piping requirements, as well as tank design, construction and maintenance.
Their expertise also includes metal section bending and rolling, as well as both on-site and offsite painting. Their proven track record and experience within the industry solidifies their position as an organisation providing first class services to the petrochemical, rail, road, oil and gas, mining, industrial, power generation and heavy industry sectors across Australia, New Zealand and the Asia Pacific.
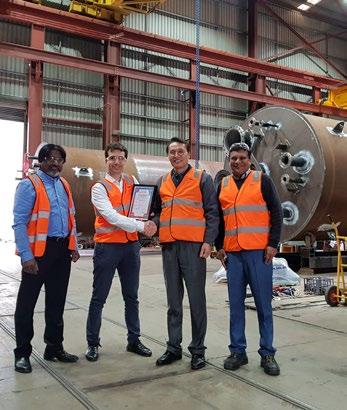
TEi Services
TEi Services was certified to IIW MCS ISO 3834:2. Headquartered in a 5,500m2 manufacturing facility in Townsville, North Queensland, TEi Services is a locally and privately owned engineering and construction company. Since their incorporation in 1968, TEi has built success from a diverse range of engineered solutions, from architectural structural projects through to industrial warehouses, complex mechanical agriculture and transport assets, mining infrastructure and mineral processing equipment.
TEi has an extensive international client base (particularly in the supply of ball and SAG mill trommels) and a strong domestic presence in industrial construction associated with the resources industry. TEi values long-term partnerships and provides quality and value-added services to all of its clients. They are known for their unquestioned commitment to quality products.
Fabinox
Fabinox is a Sydney-based company that provides full service fabrication and installation of structure steel, process piping, architectural and laser cutting. The layout of Fabinox’s workshops have been carefully designed to allow for ultimate efficiency in workflow, from run-ofthe mill high tonnage projects to small, unique jobs. With over 700 jobs successfully completed every year, Fabinox’s commitment to
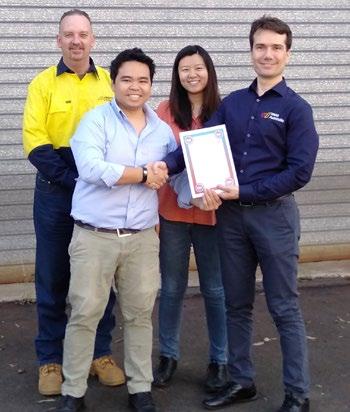
safety, high quality and integrity is the cornerstone of their business.
With a list of clients that features some of the most high-profile firms in Australia, it comes as no surprise that Fabinox has been involved in some of Australia’s most recognisable projects, from the Barangaroo development, the T1 International Airport and Hawkesbury Race Tower in Sydney, through to current work at Crown Casino in Sydney.
Callidus Welding Solutions
Callidus Welding Solutions (CWS) is dedicated to providing world-class engineering solutions tailored to client-specific erosion and corrosion challenges. CWS was awarded certification to IIW MCS ISO 3834:2
Left: TEi Services is presented with their certification. Terry Eaton (Production Manager, TEi) Geoff Crittenden (CEO, Weld Australia), Adam Packer (Business Development Manager, TEi).
Middle: Master Steel is presented with their certification. David Walsh (Welding Coordinator, Master Steel), Gabriel Dio (Managing Director, Master Steel), Bianca Dio (Secretary, Master steel) and Paolo Corronca (Qualification and Certification Manager, Weld Australia).
Right: NWEC is presented with their certification. Imma Kathir (Business Director, NWEC), Paolo Corronca (Qualification and Certification Manager, Weld Australia), Jae Lee (Managing Director, NWEC), and Bushan Salunke (Quality Assurance and Control Manager, NWEC).
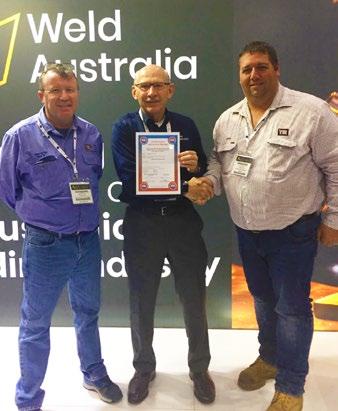
in June of 2019. The company’s main 3,400m2 workshops are based in Wangara, Perth.
With nearly 20 years of experience, CWS specialises in repair and fabrication of non-ferrous equipment. Conventional techniques are augmented by the latest robotic welding, thermal spray and nitriding technologies in order to ensure that clients are offered the best possible solutions.
JC Butko Engineering
Established in 1975, JC Butko Engineering has grown to be the largest steel fabricator in the Albury Wodonga region, with a workforce in excess of 150. JC Butko is highly regarded in the wine and food processing industry, as well as servicing heavy industries such as mining, water treatment, pulp and paper, petrochemical, and road and rail infrastructure.
JC Butko has in-house capability to concept design, 3D model, certify, fabricate and install projects ranging from large structural steel, tanks, bridges, pressure vessels, heat exchangers, hoppers, and pressure piping systems, through to conveyor
Top (Left and Right): Callidus Welding Solutions is a world class company delivering engineering solutions tailored to client specific erosion and corrosion challenges. Their highly trained team provides significant experience in the joining, rebuilding and overlay of corrosion and wear-resistant alloys for the mineral process, power generation, marine and mining industries. Images courtesy of Callidus Welding Solutions.
Bottom: Williams Metal Fabrications can undertake on-site welding, repairs and maintenance—both on land and in the water—via their tough aluminium commercial workboat (which is provided with a certified operator). The 6.2m vessel can accommodate scaffolding, generators and welders, and their licensed coxswain is able to perform inspections, repairs and installation from the water.
systems, food and materials handling. With a total fabrication area in excess of 7,000m2, split across three factories to ensure full segregation of materials, they also offer water jet cutting, CNC machining, and CINC pressing capabilities to 6m and 630 tonnes. JC Butko Engineering also offers complete project management solutions onsite incorporating Site management, design, OH&S Management, Compounds, Mobile workshops, mobile plant and access equipment, offices and amenities.
Macfab
Macfab Engineering was established in Albury in 1996 by Wayne and Michelle Clarke, and specialises in the manufacture of a diverse range of road, rail and general fabrications, in their 3,350m2 factory that is well equipped to manufacture structural, stainless and mild steel, as well as aluminium and sheet metal.
In recent years, Macfab has enhanced their production capacity by commissioning a Peddinghaus drill line, Peddinghaus plasma plate cutter and a Daito multihead cutting, coping and drilling machine. Given their location on the
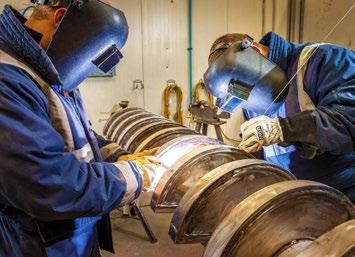
Victoria-New South Wales border, Macfab transports and installs their fabrications across a wide geographic footprint that includes anywhere in New South Wales and Victoria. Macfab Engineering has a team of approximately 85 people, including qualified engineers, project coordinators, quality inspectors, tradespeople and apprentices.
Frontline Manufacturing
Founded in Brisbane in 1996 as a toolmaking operation, Frontline Manufacturing now supports a true one stop-shop specialising in medium to large component manufacture. With a dedicated team of engineers and skilled operators, Frontline delivers superior fabrication services. Frontline currently runs two state-of-the-art Panasonic Robotic Welding cells for repetitive component welding. Their services include laser cutting and high definition plasma cutting, CNC Folding, CNC machining and turning, and welding. Frontline can supply metal products, from a simple plate to a fully integrated assembled product, ranging from 5kg to 15 tonne. Their strength is within heavy industry, such as the mining and defence sectors.
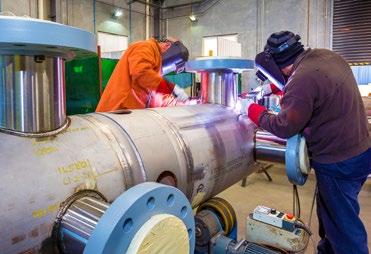
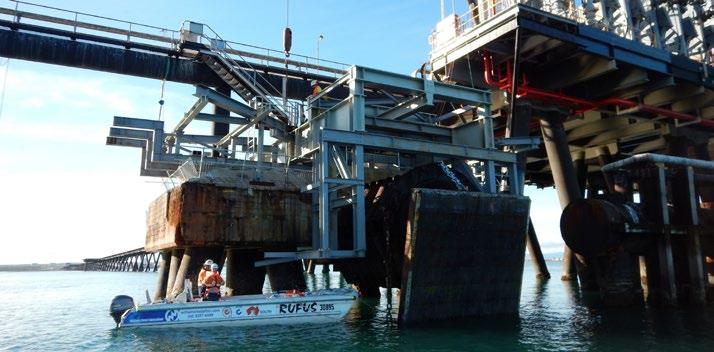
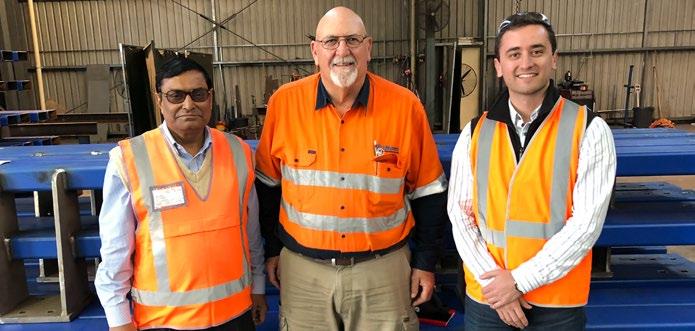
Alfabs Group of Companies
Alfabs Engineering is a wellestablished heavy engineering company that boasts experience and diversity through many different business units across the mining infrastructure, energy and construction sectors in New South Wales and Queensland. Their business units include construction, maintenance and repairs, engineering and fabrication, protective coating, mining and mining equipment, equipment hire, and transport and logistics.
Alfabs Engineering fabrication business unit is based in Kurri Kurri New South Wales. Their 3,000m² workshop comprises of 1 x 30 tonne, 3 x 15 tonne (all with a height of 7.2m under the hook), as well as 9 x 1 tonne wall jigs, and 2 x 5 tonne portal cranes. Alfabs also has a beamline, clipper, robotic welder and 5 acres of storage. The workshop size enables the use of mobile cranes to supplement lifting capabilities. Alfabs Engineering has fabricated structures that exceed 150 tonne sections.
BendWorx-SteelPro
Bendworx-Steelpro is one of Australia’s leading steel specialists. Based in Brisbane, they provide expert steel forming services and pipe and steel casing products to light and heavy industries, both nation-wide and internationally. Their ISO 9001 and ISO 3834 certified workshop manufactures quality-assured pipe and steel casings and has been an integral part of some of Australia’s largest infrastructure projects, such as the
RiverWalk rebuild, Kingsford Smith Drive upgrade, and Albion Park Rail bypass. Their precision bending and forming capabilities extend to mild and stainless steels, boiler plate, quenched and tempered wear plate and aluminium up to 10,200mm in length. When it comes to rolling, Bendworx-Steelpro delivers cylinders, cones, bucket skins, frames, merchant bar, structural and hollow sections, and much more.
Downer EDI Rail - Maryborough
Downer has over 100 years’ rail experience providing end-to-end, innovative transport solutions. They are a leading provider of rollingstock asset management services in Australia, with expertise in delivering whole-of-life asset management support to their customers.
Their capability spans all sectors, from rollingstock to infrastructure, and every project phase, from design and manufacture to throughlife-support, fleet maintenance, operations and comprehensive overhaul of assets. Downer sets industry best practice with forwardlooking technology solutions like their TrainDNA data analytics platform to deliver safe, efficient and reliable services for the public transport sector.
AWI Steel
AWI Steel was established by Director Paul Mirabito in 1992. Using Tekla modelling software, the AWI Steel team can efficiently estimate, 3D model, fabricate, deliver, install and certify just about any type of fabrication project. Their workshop offers a CNC beam line, detailed
welding, corrosion protection and customised finishes. AWI Steel also offers quite a unique service: virtual 3D walk-throughs of construction plans. These can help detect and eliminate clashes early-on to prevent costly delays and rework.
Williams Metal Fabrications
Williams Metal Fabrications manufactures reliable and innovative solutions for high-end infrastructure projects. Their business and people strive to stretch the boundaries of what can be achieved, no matter what a project or client requires.
Based in South Australia and familyowned and operated, their team some of the most experienced people in the industry, from boilermakers and welders through to riggers. Williams Metal Fabrications provides turn-key solutions, from 3D site scanning and point cloud, steel detailing and fabrication in our workshop all the way through to installation, onsite labour hire, maintenance, and even boat and crane truck hire.
They can even carry out on-site welding, repairs and maintenance— both on land and in the water—via their tough aluminium commercial workboat (which is provided with a certified operator). The 6.2m vessel can accommodate scaffolding, generators and welders, and their licensed coxswain is able to perform inspections, repairs and installation from the water.
Further Information
For further information about certification according to AS/NZS ISO 3834 Qualityrequirements forfusionweldingofmetallic materials, please contact: Paolo Corronca (Qualification & Certification Manager, Weld Australia) on p.corronca@ weldaustraliacom.com.au.
Left: (L to R): Sasanka Sinha (Senior Welding Engineer, Weld Australia), Keith Quinn (Quality and OHSE Manager, JC Butko) and Mehdi Tajfar (Welding Engineer, Weld Australia).
2019: Advanced Welder Training Centres
In 2018-2019, Weld Australia secured over $5 million in Government funding for the establishment of nine Advanced Welder Training Centres (AWTCs), located at: TAFE SA Regency Campus in Adelaide, South Australia; Tasmanian Minerals, Manufacturing and Energy Council in South Burnie, Tasmania; TAFE Queensland at SkillsTech Acacia Ridge in Brisbane, Caboolture, Townsville and Cairns; Box Hill TAFE in Melbourne, Victoria; Bendigo Kangan Institute in Victoria; and Federation University Australia in Ballarat, Victoria. The AWTCs will use augmented reality welding simulators to upskill qualified welders and train transitionary workers to international welding certification standard AS/NZS ISO 9606-1 Qualificationtestingofwelders-Fusionwelding .
TAFE SA Regency Campus, Adelaide
South Australia’s first AWTC opened for business at TAFE SA’s Regency Campus in late March 2019. This AWTC will help ensure local welders are ready to meet the huge demand that will be created by the naval shipbuilding program. Minister for Education, the Hon John Gardner MP and Minister for Industry and Skills, the Hon David Pisoni MP were both on-hand at the official opening ceremony. Minister Pisoni said the state-of-the-art equipment will provide a valuable training platform to supply skilled workers to the Osborne naval shipyard when the program commences next year.
“There are enormous naval shipbuilding opportunities on the horizon that are heading to South Australia and the Marshall Liberal Government is ensuring that we provide the right resources to fill these jobs through appropriate skills and training. Welding techniques required for shipbuilding are of a higher quality standard than regular welding techniques and these simulators will allow students to practice their technique until they consistently meet the quality standard,” said Pisoni.
Minister Gardner was excited to see TAFE SA students
being skilled in areas that lead to jobs. “This new Advanced Welder Training Centre offers an incredible training opportunity for TAFE SA students to learn using the most advanced welding simulators currently available. These simulators are another example of TAFE SA utilising the latest technology in an educational environment to prepare students with the skills and knowledge for long and successful careers.”
Regency TAFE also completed all ‘Train the Trainer’ courses and is using the simulator technology in the delivery of courses within the MEM05 Metal and Engineering Training Package. These courses include Certificates I, II, III and IV in Engineering, among others. Regency TAFE is also investigating the use of the Soldamatic augmented reality welding simulators in other trades that feature welding.
Federation University TAFE, Ballarart
In May 2019, Weld Australia secured $650,000 of State Government funding to help establish an AWTC at Federation University TAFE in Ballarat. This funding will be used to establish a state-of-the-art augmented reality welder training lab, featuring six Soldamatic simulators. A skills shortage in welding across western
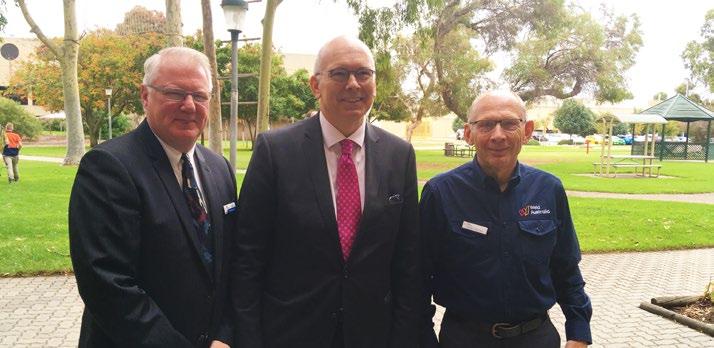
Right (L to R): The launch of the AWTC at TAFE SA Regency Campus. Bill Docalovich (Program Director, Naval Shipbuilding College), Minister for Industry and Skills the Hon David Pisoni MP, and Geoff Crittenden (CEO, Weld Australia).
Victoria prompted Federation University TAFE to instigate the new project to attract more welding students and improve the skills of existing welders.
“These augmented reality welders are like a standard welder but instead of touching the stick to metal, you touch it to plastic which contains a sensor. As a student you get feedback through the hand-piece whether you are close enough or travelling at the right speed,” said Bill Mundy (Workforce and Business Development Manager, Federation University TAFE). “It allows them to practice, repeatedly, in a very safe environment and build muscle memory before they actually go in to a real welding environment.”
Tasmanian Minerals, Manufacturing and Energy Council Centre of Excellence, South Burnie
The Tasmanian Minerals, Manufacturing and Energy Council (TMEC) Centre of Excellence in South Burnie facilitated a range of training programs throughout the year. In May, eight TasTAFE metals teachers were trained in specialised welding techniques thanks to a partnership between TMEC, TasTAFE and Weld Australia. In June, ten participants completed a 15-day, intensive training course in welding and small tool skills at TMEC. Delivered via RDA Tasmania funding as part of the Regional Employment Trail Scheme (RETS), the course led to internships with Tasmanian manufacturers for eight of the participants.
In August, TMEC delivered two weeks of welder training at Mountain Heights High School in Queenstown—Tasmania’s most remote school. This was the first metals program completed in the school within the last four years. The training comprised both the use of Soldamatic augmented reality welding simulators, and real-world welding skills in a class room environment for a total of 80 students.
Box Hill TAFE, Melbourne
Box Hill TAFE in Melbourne also completed its first pilot training program utilising the new simulators and the brand new curriculum, training and testing five welders according to AS/NZS ISO 9606-1. The pilot was very well received by all in attendance. Box Hill TAFE is also integrating the augmented reality
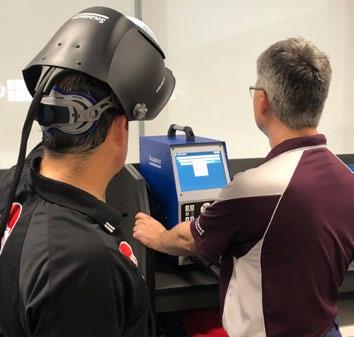
technology into their apprentice and pre-apprentice programs to enhance learning, increase efficiency, reduce risk and consumable costs.
Kangan Institute, Bendigo
Bendigo TAFE held the official launch of their AWTC in February. Minister for Training and Skills, and Higher Education, Gayle Tierney announced more than $2.3 million of funding through the Regional and Specialists Training Fund for Bendigo TAFE to deliver courses in welding, plumbing, horticulture and disability to meet the needs of the local community and industry. Some of this funding will be directed towards the establishment of an AWTC. Minister Tierney gave an extremely positive speech on how important welding is to the community. The Kangan Institute is working towards AWTC accreditation, having had their welding staff complete the ‘Train the Trainer’ program on the Soldamatic augmented reality welding simulators, and now preparing to embark on the ISO 9606-1 component.
TAFE Queensland at SkillsTech Acacia Ridge in Brisbane, Caboolture, Townsville and Cairns
SkillsTech in Brisbane completed all of its training and the set-up of its AWTC, before holding its first pilot program, training five welders according to AS/NZS ISO 9606-1. SkillsTech is working closely with major industries in its region to deliver training solutions through ISO 9606 and the augmented reality technology. SkillsTech also plans to incorporate their technology into welding training in their apprenticeship programs and other government subsidised courses. As such, SkillsTech has recently commenced a campaign to market ISO 9606 and their new facility.
The North Queensland AWTC is currently located in Townsville, as part of the government funded Manufacturing Hub in that region. This AWTC will eventually settle in Cairns. There has been a lot of interest in ISO 9606 in the North Queensland region, and the AWTC will be focusing on delivering training to service that need. The Caboolture AWTC is set to be located in the Caboolture TAFE Campus. This AWTC will employ a mixed mode delivery, offering programs on campus as well as delivering programs in the workplace.
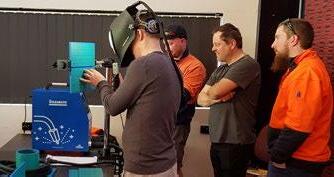
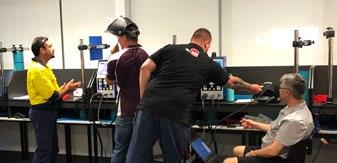
All these courses were very well received by all in attendance, with the AWTCs going on to complete training in AS/NZS
Far Left: ‘Train the Trainer’ at TAFE Queensland, SkillsTech at Acacia Ridge in Brisbane.
Top Left: ‘Train the Trainer’ at the Tasmanian Minerals, Manufacturing and Energy Council (TMEC) Centre of Excellence in South Burnie.
Bottom Left: ‘Train the Trainer’ at Kangan Institute in Bendigo.
ISO 9606-1.
2019: The Changing Face of Australian Standards
Australian Standards are dynamic documents, with changes constantly made to reflect progresses in science, technology and systems. To ensure their relevancy, Standards come under periodic review, with amendments and revised editions published. Activity within the standards arena in Australia has been busy throughout 2019. A number of standards across a range of areas have been revised and others are in the process of being updated or replaced by relevant ISO standards.
Pressure Equipment
Revision of AS/NZS 3992 Pressure equipment—Welding and brazing qualification was completed late in 2018, and a pubic review draft was released in July 2019. With public review closing in September 2019, the comments received during this period have now been resolved.
A ballot draft will now be prepared by Standards Australia for review and ballot by Committee ME-001. Publication of the revised edition of the standard is likely to occur in Autumn 2020.
During 2019, Weld Australia assisted with the revision of AS/NZS 3788 Pressure equipment—In‑service inspection. The draft has been completed on schedule, and will now be prepared for submission to Standards Australia.
Steel Structures
During 2019, Committee BD-001 worked on preparation of public review drafts for the revision of two of its Standards: AS/NZS 5131 Structural steelwork—Fabrication and erection; and AS 4100 Steel structures
With the public review drafts being released in June, comments received have now been resolved. Due to technical changes made during the resolution of comments received, updated drafts will be released for a second round of public comment.
Welding of Structures
The revision of AS 2214 Certification of welding supervisors—Structural steel welding was completed by Committee WD-003 during 2019. It was published as AS/NZS 2214 in November.
The draft amendment to correct an error within AS/NZS 2980 Qualification of welders for fusion welding of steels—Additional requirements for Australia and New Zealand was released for public comment in July. The public comments received are currently being resolved. Publication of the amendment is likely to occur in Autumn 2020.
The preparation of a public review draft of the revision of AS/NZS 1554.2 Structural steel welding—Part 2: Stud welding (steel studs to steel) is well advanced with the release for public review now due in early 2020. As previously indicated, the draft has taken cognisance of the relevant ISO standards, and to this end, ISO 13918 is being adopted for stud materials providing for the use of stainless steel studs and studs for wear applications.
During 2019, Committee WD-003 also adopted the latest revision of ISO 3834-5 Quality requirements for fusion welding of metallic materials—Part 5: Documents with which it is necessary to conform to claim conformity to the quality requirements of ISO 3834 2, ISO 3834 3 or ISO 3834 4 to replace
the aged AS/NZS ISO 3834.5. Committee WD-003 also adopted ISO/TR 3834-6 Quality requirements for fusion welding of metallic materials—Part 6: Guidelines on implementing ISO 3834 as AS/NZS ISO 3834.6 to assist users of the ISO 3834 series of standards.
Non-Destructive Testing
Committee MT-007 has advised that due to the age of Australia’s nondestructive testing (NDT) standards and lack of resources to revise these standards, the equivalent ISO standards have been reviewed and will be considered for adoption as AS/NZS ISO standards.
The NDT processes affected include magnetic particle, liquid penetrant, eddy current and ultrasonic thickness testing, with public review drafts open for comment until December 2019. Consideration on the replacement of AS 2207 Non‑destructive testing— Ultrasonic testing of fusion welded joints in carbon and low alloy steels by its ISO equivalent has been deferred at this point in time.
ISO Adoptions
During 2019, a number of ISO standards relevant to welding were adopted, enabling a number of aged Australian standards to be updated. These include ISO 9017 Destructive tests on welds in metallic materials— Fracture test as AS/NZS 2205.4.1, and ISO 17639 Destructive tests on welds in metallic materials— Macroscopic and microscopic
examination of welds as AS/NZS 2205.5.1.
In addition, ISO 17637 was adopted as AS/NZS ISO 17637 Non‑destructive testing of welds— Visual testing of fusion welded joints, and ISO 5817 was adopted as AS/NZS ISO 5817 Welding— Fusion‑welded joints in steel, nickel, titanium and their alloys (beam welding excluded) – Quality levels for imperfections
Separate to these adoptions, ISO 3821 is being adopted as AS/NZS 1335 Gas welding equipment—Rubber hoses for welding, cutting and allied processes, with public comment closing in November 2019.
Register
ISO Update
ISO TC44/SC10 has commenced the revision of the ISO 3834 series of standards, primarily to take cognisance of changes to ISO 9001 Quality Assurance and the recently published ISO 14731 Welding coordination—Tasks and responsibilities. Similarly, ISO TC44/ SC11 has commenced the revision of ISO 9606-1 Qualification testing of welders—Fusion welding—Part 1: Steels with the intention of combining all 5 parts into the one standard. This will simplify the ongoing maintenance and review requirements for the standards as parts 2 to 5 of ISO 9606-1 in need of revision. Australia is participating in the revision process on both subcommittees.
Separate to the standards review, Standards Australia hosted the ISO TC44 meeting in Sydney in September, providing a unique opportunity for Australian standards committee members across a range of disciplines to meet with the relevant world experts across a range of welding related matters.
2020
The coming year will be just as busy in terms of revisions and updates, with many of the proposed changes expected to be finalised and published in 2020. Australia will also continue to support the revisions to ISO standards relevant to Australia. Weld Australia members will be kept informed through regular updates in Australian Welding magazine.
the AWCR Today
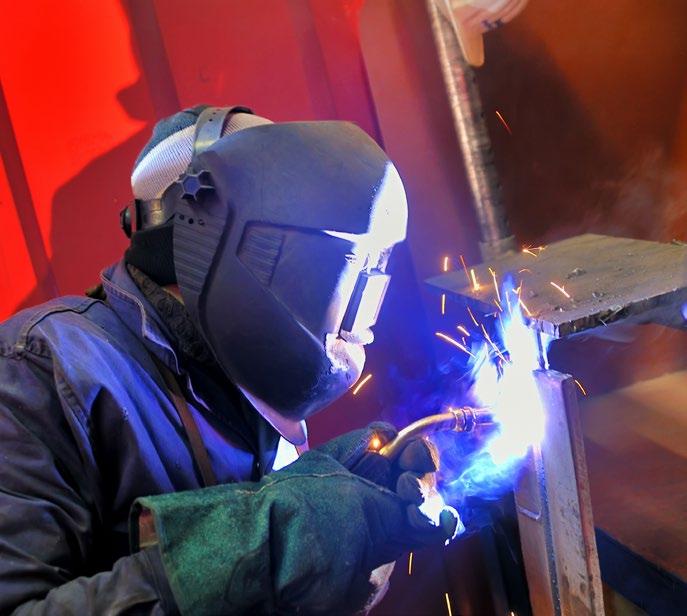
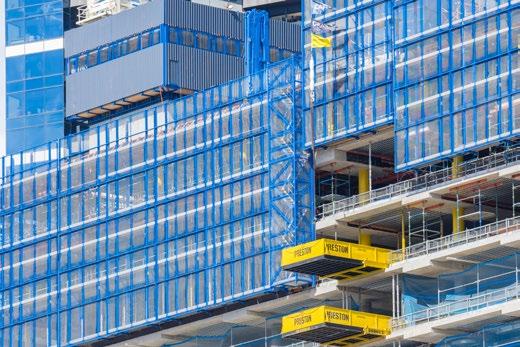
How to Register
2019: Weld Australia Industry Group Activities
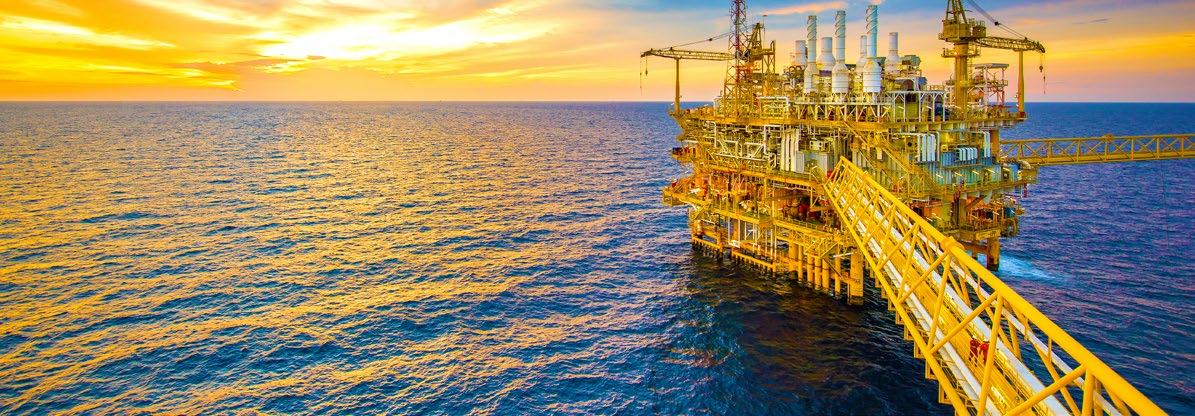
Weld Australia’s Industry Groups provide a forum for technology transfer and research and development, linking members with industry and research organisations. Weld Australia works with Industry Group members to ensure they remain diverse and resilient in the ever-changing and increasingly challenging global markets. Industry Group members engineer innovative solutions that enhance safety, manage risk, reduce cost, and optimise operating efficiency.
Defence Industry Group
This year has been exceptionally busy for the Defence Industry Group. As a result of the Groups’ activities, Weld Australia signed a Memorandum of Understanding (MoU) with both BAE in relation to support for the Hunter Class Frigates; and the Naval Shipbuilding College to develop a national shipbuilding welding education and training competency framework.
Partnering with BAE and the Indigenous Defence and Infrastructure Consortium, Weld Australia developed a proposal to establish Indigenous Welding Schools focused on training disadvantaged individuals in line with ISO 9606-1 for entry into the defence industry. The scheme is awaiting funding.
Weld Australia also helped design and implement a custom augmented reality welding template, tailored to the welding skills required for Thales’ next generation Hawkei protected vehicles. The Hawkei vehicles feature complex welding processes, not previously used by Thales welders. With the funding of an AWTC in Bendigo (that now utilises these custom augmented reality welding templates), Thales’ welders will be quickly and efficiently trained to the requisite global Standard.
In July, as result of discussions
during the Industry Group meetings, Geoff Crittenden (Chief Executive Officer, Weld Australia) visited two BAE Systems shipyards in Glasgow, Scotland: Govan Shipyard, and Scotstoun Shipyard. It is here that BAE Systems is building the eight Type 26 Frigates ordered by the Royal Navy. The ‘First of Class’ HMS Glasgow is under fabrication, due for completion in 2023. The purpose of the visit was to observe the production of the HMS Glasgow, in order to understand BAE System’s process for welder training. BAE has a comprehensive training program tailored BAE’s needs and the requirements of the shipyards. The lessons learnt during the trip will be essential in establishing Australia’s own Frigate shipyard in South Australia.
In August, Weld Australia participated in the PACIFIC 2019 International Maritime Exposition in Sydney. Weld Australia’s exhibition stand proved popular, with visits from Assistant Minister for Vocational Education, Training and Apprenticeships the Hon Steve Irons, as well as the Minister for Defence Industry the Hon Melissa Prince. Both Minister Irons and Minister Prince tried their hand at the augmented reality simulator. Minister Irons was extremely positive about Weld Australia’s participation in the future of welding—particularly in relation to the Government’s
continuous Naval Shipbuilding Program—and acknowledged how important it is to increase the quality and number of skilled welders in Australia.
The major Defence Industry Group meeting took place in November at Thales Australia in Bendigo. Attendees toured Thales’ facilities, where the Hawkei protected vehicles are being manufactured for the Department of Defence. Attendees also enjoyed highly informative presentations from Murray Brown (Operations Manager, Thales Bendigo), Cameron Baker (Director, Victorian Skills Commission), Neil Fitzpatrick (Manager Global Supply Chain and Australian Industry Capability, Rheinmetall), Stephen Harvey (Defence Business Adviser, Centre for Defence Industry Capability), Chris Coates (LHD Chief Engineer, BAE), and Geoff Crittenden (CEO, Weld Australia).
Several key issues were discussed, including welder safety, practical application of augmented reality training, welder qualifications, welding standards, robotic welding in armoured vehicle production, the impact of welding skill shortages on defence projects, and indigenous participation in defence.
During the meeting, key projects for 2020 were agreed upon. The
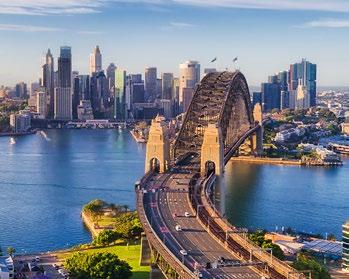
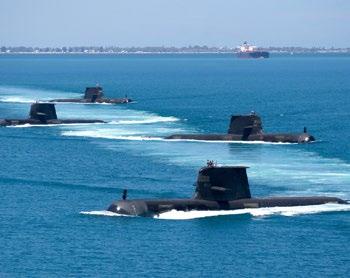
Defence Industry Group will establish a working group to collaborate on identifying appropriate welding and fabrication companies to participate in a common supply chain. Several of the defence prime contractors expressed interest in joining the working group, including Austal, BAE, Rheinmetall and Thales.
In addition to this major undertaking, the Defence Industry Group will investigate the use of cobots for welding applications in confined spaces, which is particularly applicable to shipbuilding.
Given these exciting developments, it is little wonder that some of the nation’s largest defence industry prime contractors, such as BAE, Navantia and Rheinmetall have pledged their support for the Group in 2020.
Road and Rail Industry Group
The Road and Rail Industry Group met in July in Melbourne. Hosted by VicRoads, the meeting was attended by representatives from Roads and Maritime Services (New South Wales), VicRoads (Victoria), Transport and Main Roads (Queensland), Main Roads (Western Australia), and Weld Australia. The two major projects that progressed in 2019 were the Austroads Steel Fabrication Specification (ASFS), and the Austroads Stainless Steel Fabrication Specification. Collaborative work on the development of the ASFS was completed, and forwarded to the Austroads publication department. This represents a significant milestone for the Group. The ASFS is currently under review by Austroads. The Austroads Stainless Steel
Specification will set out the minimum requirements for the preparation, welding, inspection and testing, and final acceptance of stainless structures and components which must be fabricated in accordance with the technical specifications. The objective of this Specification is to provide rules for the welding of a wide range of stainless steel fabrications, including statically and dynamically loaded welds.
Power Technology Industry Group
The Australian Power Technology Industry Group met at ALS in Newcastle in June, and again at CS Energy in Brisbane in October. A major focus of the first meeting was Maintenance and Outages: Managing Welding Quality. Several presentations were provided, including: Quality Assurance: Failures and Success by Wayne Hill, (Operations Support, Energy Australia NSW); Management of Welding and Quality by Doug Harman (Quality Assurance Controller and Responsible Welding Coordinator, Synergy); Welding and Quality Coordination by Mehdi Tajfar (Welding Engineer, Weld Australia); and Third Party Inspection for Overseas Procurement by Helena Zhu (Inspection Engineer, HRL).
Following the presentations, a discussion around strategies to improve industry-wide welding quality issues ensued. As a result, Weld Australia has requested feedback from all attendees on what should be specified for welder products, especially for safety critical plant such as HEP, turbines and generators. Based on this feedback,
To become a Weld Australia Industry Group member contact us via membership@ weldaustralia.com.au or +61 2 8748 0100.
Weld Australia will then generate a Technical Guidance Note.
The second focus of the meeting was The Importance of Process Safety. Several members provided an overview of process safety at their organisation, including Bob Hazard (Asset Engineering Specialist Integrity, CS Energy), and Dr Stuart Mann (Principal Engineer, AGL Energy). Barbara Lucas (Principal Consultant, Nuffield Group) presented on the topic Process Safety Lessons Learned from Major Hazard Industries, while Dr Nan Xu (Senior Metallurgist, ALS Global provided a case study on quality assurance and documentation of weld repairs.
In October, the Group also facilitated a seminar on the topic From Baseload to Flexible Operations With growing renewable generation, higher penetration of variable and intermittent generation and other market forces, coal plants designed for baseload operation are increasingly looking to operate in flexible modes. This event provided an overview of the current Australian National Electricity Market, as well as the drivers for flexible operations. These issues will be illustrated with overseas experiences and case studies in similar flexible operations.
Representatives from local power stations also discussed methodologies considered for cycling and low load operations. Life management of cycling plant components under combined loading will be covered, together with challenges and successes achieved under low load.
2019: What Weld Australia Members Have to Say
Weld Australia Member Testimonials
Weld Australia’s members are made up of individual welding professionals, as well as companies of all sizes. In fact, Weld Australia members are involved in almost every facet of Australian industry and make a significant contribution to the nation’s economy. We recently spoke with a number of our members, eliciting their feedback on our activities, services and membership benefits. This is what they had to say.
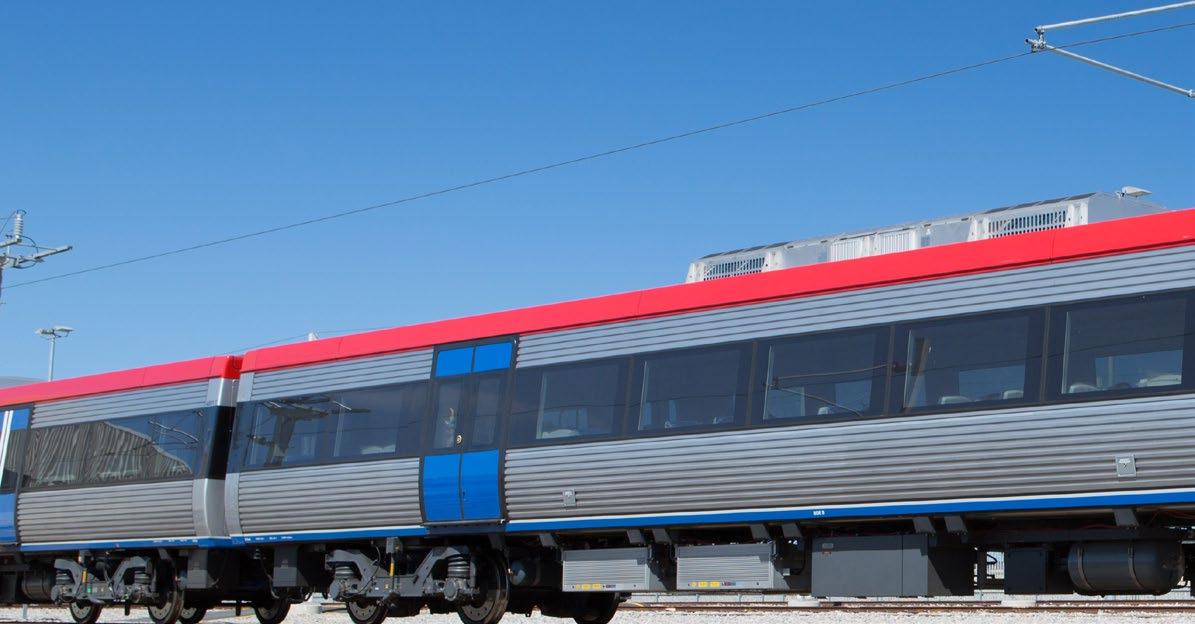
Bill Mundy, Sales Manager, Federation University Australia
“Federation University determined that there was a need to provide highlevel skills for welders in the local region, particularly with infrastructure maintenance and construction, export work, and defence industry projects continuing to grow. There was a sense within the business that we needed to determine: what higher qualifications for welding look like; how to support local industry; and how to ensure welders have the skills needed for the jobs of the future. We recognised the need for better skilled and more stringent control of welding and welding techniques across the manufacturing sectors in our local region.”
“We came across the new welder qualifications developed by Weld Australia and the Victorian Skills Commissioner, and expressed an interested in delivering those qualifications. That put us in contact with Weld Australia, who was at the forefront of developing those qualifications.”
“Our interactions with Weld Australia can only be described as excellent. Quite frankly, I cannot fault the level of support that has come from Weld Australia. We have built a partnership with Weld Australia, rather than a relationship of supplier and client.”
“Moving forward, we will harness
the support of Weld Australia to muster industry in our local region. Weld Australia is in a position to help us educate our regional manufacturers on the importance of what we’ve done, the investment we’ve made, and benefits it will bring to local industries. Weld Australia’s industry support and connections will be pivotal in our future industry engagement.”
“Weld Australia is benefitting the Australian industry as a whole via a number of aspects. They are driving an agenda which is designed purely and simply around delivering a better quality product to an end consumer, regardless of who that end consumer might be—defence, manufacturing, construction. Through better qualified welders, we will deliver a better quality product.”
“Weld Australia is also delivering much better quality training outcomes in the welding space. This includes everything from a Certificate III in Engineering—where ISO qualification is now embedded in the apprenticeship program—to support for teachers so they have an additional bow to their arrow in terms of the skills they can deliver.”
“In terms of broader strategy benefit, Weld Australia is helping to lift Australia’s game in relation to the products delivered on the world
stage. If we want to be a country known for our manufacturing quality, we need to deliver internationalstandard products. Whether defence equipment—or any product at all really—we need quality products, delivered by quality welders, who have undertaken quality training, delivered by quality teachers. It’s a differentiating strategy that allows Australia to compete on a world stage.”
“There is a symbiotic relationship between the work Weld Australia does and the training we want to do. If we work together, there is a greater chance of success in lifting Australia’s quality aspirations, and achieving better product outcomes across the country.”
Ali Enayati, Project Manager, Bombardier Transportation in Australia
“Bombardier Transportation Australia undertakes a significant amount of welding for Melbourne’s Trams and Vlocity Trains at its Dandenong site. Part of our agreement with our customer is for the train and tram car bodies to be welded locally and be compliant with AS/NZS 1554.6 Structural steel welding or EN 15085 Railway applications Welding of railway vehicles and components.”
“In order to ensure compliance,
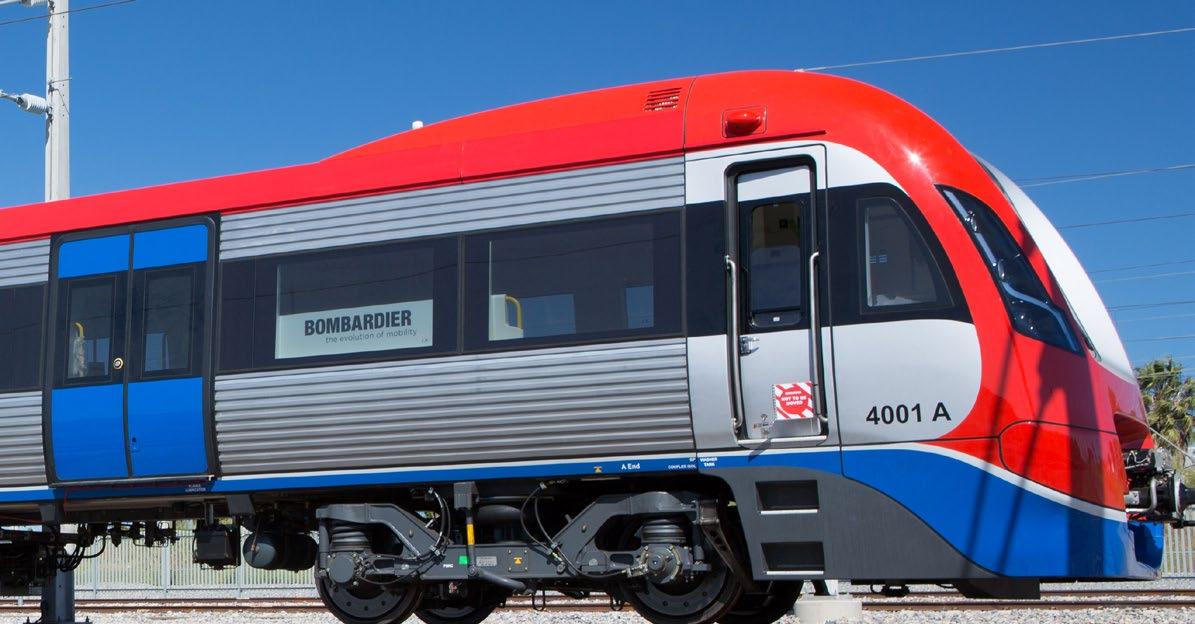
we need to follow all the Standard requirements. Weld Australia has supported Bombardier to develop and establish a welding school at our Dandenong site. In addition, Weld Australia provided us with a range of technical support in becoming the first rail company in Australia to achieve International Railway Welding Certification.”
“The Welding Training Centre at Bombardier’s Dandenong site in Victoria is now an accredited facility for securing and growing local welding capabilities and for delivering industry-recognised certifications to staff, external suppliers, and industry partners in Australia. This certification demonstrates our local capabilities and competitiveness in the Australian fabrication and manufacturing sector. It is key for Bombardier in Australia to uphold Standards and lead the way in quality rollingstock manufacturing. Investing in skills and capabilities is the best way we can support and grow a sustainable rail industry in Australia.”
“Over the years, Certification EN 15085 has become the Standard for railway manufacture and repair worldwide. This certification enables the Dandenong site in Australia to manufacture carbodies to the latest European Standards. Bombardier offers welding courses for internal
and external candidates and our Dandenong facility has trained and qualified over 40 welders in addition to several key supply partners.”
“During the certification process, I was the head of supplier quality assurance at Bombardier Transportation in Australia. In this capacity, I worked with several different certified local bodies and consultants.”
“Given Bombardier’s longterm presence in the Australian market and unique local welding capabilities, we have developed local expertise and specialty in welding. In terms of engagement, we have
been particularly happy with the service and quality provided by Weld Australia.”
“We appreciate their efficient processes and systems while working with us. All the inputs and changes requested were implemented in a timely manner.
Weld Australia has a team of experts with local connection across rail, construction and manufacturing.”
Jason Elias, Managing Director, Precision Metal Group
“Precision Metal Group joined Weld Australia because it was governing body responsible for certifying companies within the welding and
Weld Australia Membership Types
• Individual Membership: Individual membership is open to apprentices, tradesmen, inspectors, supervisors, technologists, engineers, academics and others with an interest in welding.
• Corporate Membership: Corporate membership is open to all companies associated with welding or related activities.
• Industry Groups Membership: Industry Groups identify and meet the critical welding needs of key Australian markets, such as mining, power, construction, defence, and oil and gas.
• Free Apprentice Membership: As part of our ongoing commitment to nurturing the next generation of skilled welders in Australia, Weld Australia is pleased to offer apprentice welders free membership.
• Free TAFE Membership: Weld Australia is proud to support, and encourage development of, Australian TAFEs and their teachers, which is why we are pleased to offer free membership to both.
Image credit: Bombardier Transportation.
fabrication arena, in addition to its strong history and large footprint within the broader marketplace.”
“We utilised the services of Weld Australia in gaining our certification to AS/NZS ISO 3834 Quality requirements for fusion welding of metallic materials. Overall, this was a very educating journey, from better welding practices through to upskilling within the Australian market to contend with international work. It was not so much of an auditing process—it was more of an educational process to get us ready for certification.”
“One of the major benefits of becoming certified to ISO 3834 is that the certification has opened many doors for us in terms of new work, particularly projects commissioned by the Australian Defence Force. The certification process itself helps streamline your processes, and improve your productivity and efficiency, and therefore bottom line. Plus, it helps your entire workforce better understand it’s role within the broader industrial sector.”
“We also use some of Weld Australia’s other services from timeto-time. We work with Weld Australia for welder qualifications, and have own training school that has been certified by, and is supervised by, Weld Australia.”
Matthew Ellis, Special Projects Manager, Frontline Manufacturing
“Frontline Manufacturing was asked to meet several different requirements by Rheinmetall. In order to do so, we looked for a company that could help us throughout the whole AS/NZS ISO 3834 Quality requirements for fusion welding of metallic materials certification process. Weld Australia was suggested as the peak industry body that we should be working with on certifications.”
“Once we decided that we wanted to leverage Weld Australia’s expertise in this area, we decided to join Weld Australia as a corporate member—to support the industry. The support and advice we received throughout the certification process was exceptional. We made a few
mistakes internally along the way on how we went about the process. We found that Weld Australia was really good in communicating the requirements to us and supporting us in terms of getting through the process. Their team was very open, honest, and encouraging through all the new and difficult requirements.”
“Paolo Corronca (Senior Welding Engineer) was one of my main points of contact. He was outstanding in his communications with me. Paolo has been very accommodating and quite a good business relationship has ensued as a result.”
“We are also utilising Weld Australia for training at the moment. We have two staff currently completing advanced training in Wollongong, and another in Brisbane. One is undertaking the International Welding Supervisor course, and the other is completing the International Welding Engineer course.”
“Now that Frontline Manufacturing is certified, I’m sure that we will find we need help with new opportunities as they arise. In doing so, we are now in
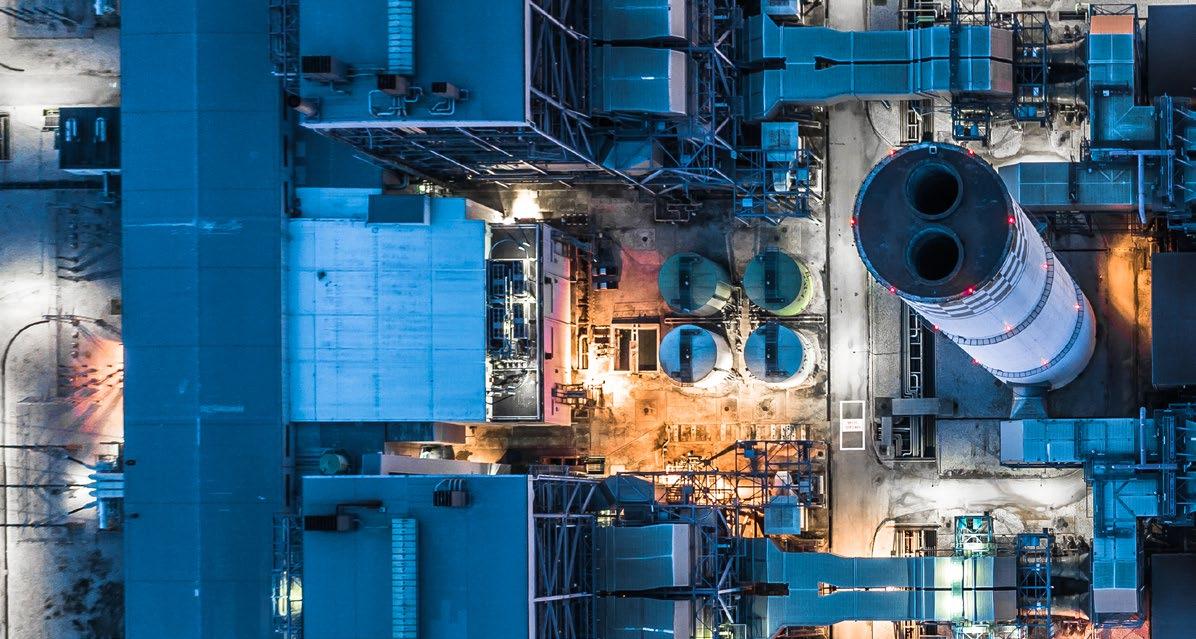
a position to draw on the significant resources offered by Weld Australia.”
Adam Packer, Business Development Manager, TEi Services
“TEi Services decided to join Weld Australia because they are the peak industry body and a great advocate for industry. Weld Australia really does advocate the importance of Australian manufacturing and keeping the industry on-shore, particularly with the defence primes that TEi is targeting.”
“We recently used Weld Australia’s technical hotline service, which was a great experience. The hotline helped us to overcome a problem that we were having some difficulty with. The problem actually turned out to be quite simple—we were just misinterpreting the Standard. Weld Australia’s technical experts certainly have sound knowledge of how to interpret Australian and International Standards.”
“We also used Weld Australia’s auditing service to obtain our certification to AS/NZS ISO 3834.2
Quality requirements for fusion welding of metallic materials. The certification process itself was very rewarding. While our systems and processes were generally in line with the Standard’s requirements, going through the desktop and site audits with Weld Australia helped us to identify areas for improvement, to raise our practices to the next level, and close some gaps that we identified. It has set us on a pathway to readiness for global supply chain opportunities.”
“The Australian welding industry has always been focused on Australian Standards when it comes compliance. Now we have to shift mindset to global Standards and acceptance so that Australian manufacturers can access global supply chains. Weld Australia is advising and training industry on how to do exactly this. We currently have personnel undertaking the training in ISO 9606 Qualification testing of welders Fusion welding, and in the International Institute of Welding (IIW) International Welding Specialist (IWS) training programs.”
Kent Wyllie, General Manager, Tasmanian Minerals, Manufacturing and Energy Council
“We first got involved with Weld Australia as a result of the need to establish an Advanced Welding Training Centre. Collaborating with Weld Australia, we were able to attain the appropriate equipment and define the curriculum, which played a vital role in the development and implementation of the Centre.”
“We’ve found Weld Australia to be very approachable at all levels, and have certainly appreciated their ongoing support and willingness to think ‘outside the box’ to find solutions as problems arise.”
“Weld Australia plays a pivotal role in promoting welding in general, and raising awareness around the need for welder training to incorporate new forms of advanced teaching methods, tailored to the needs of business and industry. As the national industry body, Weld Australia is able to give the sector one common voice to achieve results that are positive for all businesses.”

Join Weld Australia Today
Weld Australia membership is an investment in the success of your career or the success of your business. We will help you increase your income, decrease your costs and give you a competitive advantage over companies or people who are not Weld Australia members.
A Weld Australia membership delivers:
• Community and networking opportunities
• Widespread credibility
• Visibility within the industrial sector
• Career opportunities and professional development
• Industry insights and knowledge sharing
• Expert help and technical advice
• Collective power
To join Weld Australia:
• Visit: weldaustralia.com.au
• Email: membership@weldaustralia.com.au
• Call: +61 (0)2 8748 0100