
Farra Engineering Becomes New Zealand’s First Company
Certified to EN 15085
Page 42
Q&A with a Weld Australia
Member: Harrison Field, AOK Metal
Page 38
Women
22
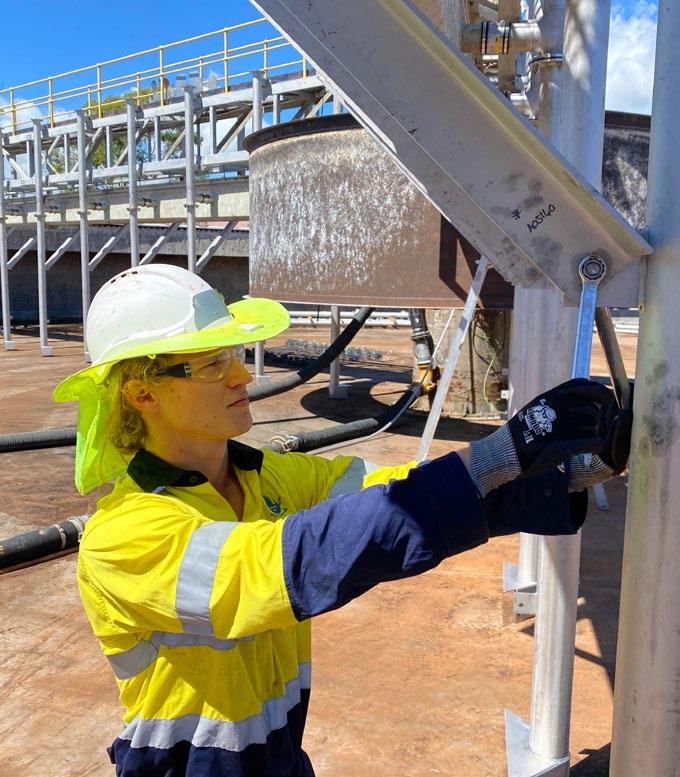
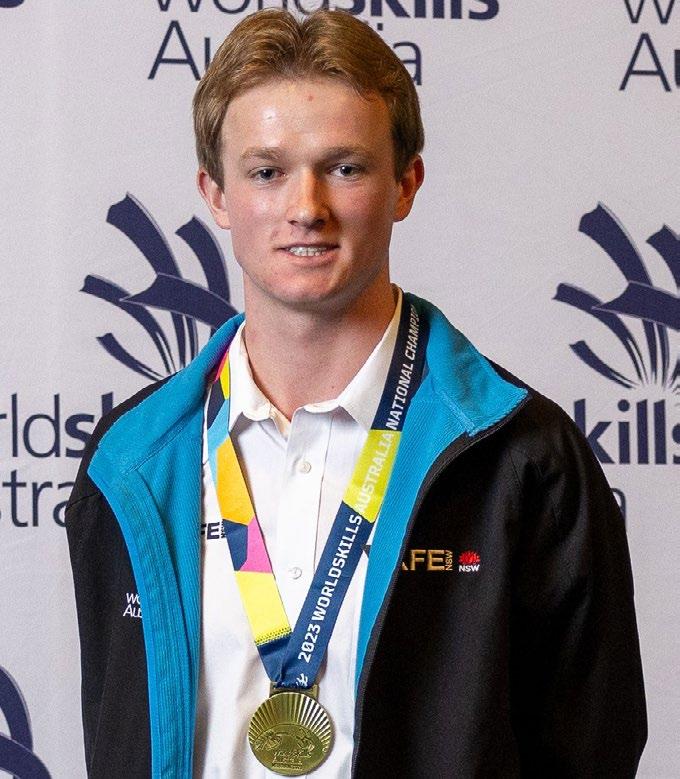
38
Farra Engineering Becomes New Zealand’s First Company
Certified to EN 15085
Page 42
Q&A with a Weld Australia
Member: Harrison Field, AOK Metal
Page 38
Women
22
38
National Office PO Box 197 Macquarie Park BC NSW 1670 1800 189 900 office@weldaustralia.com.au weldaustralia.com.au
Chief Executive Officer
Geoff Crittenden 1800 189 900 g.crittenden@weldaustralia.com.au
ENGINEERING
Victor Blain, General Manager Engineering 0409 823 991 v.blain@weldaustralia.com.au
TRAINING
Guy Brooks, General Manager Training Operations 0488 743 322 g.brooks@weldaustralia.com.au
MARKETING
Michelle Bignold, Executive General Manager, Sales & Marketing 0437 106 726 m.bignold@weldaustralia.com.au
MEMBERSHIP
David Choudry, Membership Manager 0417 878 104 d.choudry@weldaustralia.com.au
QUALIFICATION & CERTIFICATION
Deniz Yalniz, Executive General Manager, Technical Services 0487 487 170 d.yalniz@weldaustralia.com.au
Subscription to Australian Welding is a Weld Australia member benefit included in annual membership fees. All rights reserved. No part of this publication may be reproduced or copied in any form without the written permission of Weld Australia. Weld Australia and its agents are not responsible for statements or opinions expressed by contributors in this publication, which are not necessarily those of Weld Australia. Publication of any advertisement does not constitute endorsement by Weld Australia of any product, nor warrant its suitability.
As we step into the new year, I’m excited to share that Weld Australia has a host of plans and activities lined up. It’s going to be a year full of opportunities for growth, learning, and community engagement. We’re committed to making this an impactful and positive year for all our members.
Our program of events is already taking shape. We’ve already hosted two very successful Industry Drinks Nights: one in Melbourne sponsored by Cigweld; and one in Sydney sponsored by TAFE NSW. These events were a great opportunity to network with local industry colleagues.
In collaboration with the Australia Institute’s Centre for Future Work, we will again host the National Manufacturing Summit. The Summit
will be held at the Amora Hotel in Brisbane on 31 July and 1 August 2024.
Building on the momentum of the 2023 National Manufacturing Summit, which focused on the Renewable Energy: Challenges and Opportunities, the 2024 Summit embarks on an ambitious journey with its theme: Pathways to Success…Making the Renewable Energy Revolution a Reality (See page 14 for further details.)
Planning is underway for the 2024 Welding Excellence Awards. Five awards ceremonies will be held across the country throughout October and November, to acknowledge the incredible calibre of work achieved by members over the past 12 months. Our state committees are also putting together a calendar of local events and technical events for the year.
Our training department will continue to go from strength to strength, with exciting major projects underway.
Last year, we launched our MEM Resources Project, with the resources officially already adopted by some TAFEs. Weld Australia also won the excellence in manufacturing skills development award at the 2023 Endeavour Awards
This year, Weld Australia will focus on the implementation of the Resources by more TAFEs and RTOs nationally, ensuring that welders receive the same high quality standard of training, regardless of whether they’re in Karratha or Kalgoorlie, Toowoomba or Traralgon. To this end, we’re having an official launch and networking lunch in Sydney on Tuesday 7 May. Be sure to register now or see page 59 for further details
We’ve also launched a new training course: Welding Inspector - AS 1796 Certificate 11. Recently introduced to AS 1796, this qualification builds upon the foundation knowledge expected of a Welding Supervisor with a distinct emphasis on inspection activities related to pressure equipment. The first course kicks off on 15 July.
In 2023, we expanded our certification services, adding AS/NZS 9001, AS/NZS ISO 14001 and AS/NZS ISO 45001 to our offering. We’ve recently added the IIW International Welding Practitioner (IWP) qualification. The IIW IWP qualification is awarded to professionals who have demonstrated a thorough understanding of welding technology and its applications.
We’re also undergoing the final stages of JAS-ANZ certification for AS/NZS ISO 3834 and expect this to be finalised some time this year.
Weld Australia’s Industry Groups provide a forum for technology transfer and research and development, linking members with industry and research organisations. In the year ahead, we will continue to foster industry connections. We will continue to grow our Industry Groups, particularly the newly established Defence, Advanced Manufacturing and Renewable Energy Industry Groups.
Weld Australia is set to undertake two projects designed to improve the productivity of Australia’s welding and fabrication industry.
Our first project will involve the measurement of welder productivity as defined by the number of onarc hours per welder per shift.
According to member reports, the average on-arc time for a welder in Australia is approximately two hours. However, in countries such as Germany and the United States (which have equivalent Workplace Health and Safety standards to Australia), industry works on an average of five hours on-arc per welder per day. This is obviously a marked difference.
Simplistically, if Australia could increase its productivity to internationally competitive rates, we could effectively double the welding capacity of our industry. This would go a long way to solving the issue of labour shortages and capacity constraints.
Weld Australia will undertake in-depth research into Australia’s welding practices and productivity, and compare this to the situation in Germany and the United States. We will then review possible solutions, such as leveraging Trades Assistants to complete tasks like grinding, set up and cleaning, or using robots and cobots.
The second project Weld Australia is working on is a productivity based training scheme. Under this program, Weld Australia would help fabrication businesses conduct their own staff training. We would provide advanced learning resources, train their trainer, accredit their training facility, and then certify welders according to ISO 9606 or AS/ NZS ISO 1554. Fabrication companies would be able to quickly qualify production welders able to successfully undertake fillet welds, rather than waiting three years or more for a Certificate III or IV trained welder. Weld Australia is currently seeking grant funding, which would enable us to implement the project at little to no cost for members.
Australian businesses, communities, First Nations, and workers stand to benefit significantly from the energy transition—so long as our governments prioritise local content requirements in the drive to decarbonise our economy and transition to net zero.
Local content legislation must specify that 60% of all fabricated steel used in our renewable energy projects is manufactured in Australia by local welders.
The Federal Government’s Capacity Investment Scheme presents a critical opportunity to bolster local economic participation in the renewable energy transition. The Scheme, a federal initiative that complements state efforts, aims to expedite dispatchable renewable energy and storage, supporting the federal target of 82% renewable energy by 2030.
The Scheme provides a national framework to encourage new investment in renewable capacity, such as wind and solar, as well as clean dispatchable capacity, such as battery storage.
When it was first announced in December 2022, the Federal Government estimated that the Scheme would drive approximately $10 billion worth of investment in renewables.
The Scheme’s expansion in November 2023 promises a substantial increase in clean energy investment.
The expansion will encompass a new revenue underwriting scheme that the Hon Chris Bowen, Minister for Climate Change and Energy, hopes will unlock $40 billion in private
investment, adding another 32 gigawatts of capacity on top of the 28 gigawatts of clean energy already in the National Electricity Market.
While the expansion of the Scheme and billions in private investment are obviously welcome, it is essential that local and First Nations content requirements are incorporated into Capacity Investment Scheme tenders. This will fortify domestic clean energy supply chains, boost investor confidence, and cultivate a skilled workforce for the energy transition, positioning Australia as a global renewable energy leader.
Australian businesses have long advocated for specific, measurable local content requirements in government contracts.
Even the recent House of Representatives committee report into manufacturing in Australia - Sovereign, Smart, Sustainable recommended stated that: “All levels of government have potential to drive developments in advanced manufacturing by targeted procurement of Australian products.”
The report continues, recommending that: “In partnership with the states and territories, the government should identify further steps it could take to increase locally manufactured content in renewable energy infrastructure and equipment installations, and other areas where governments are major customers.”1
However, tangible examples of local content procurement policies are yet to materialise in Australia.
Globally, since 2008, more than 140 local content requirement programs have been employed in a variety of sectors from automotive to extractive industries2. However, policymakers have focused heavily on wind and solar power in recent years to foster economic and technological development. Prominent cases where solar or wind energy local content requirement have been introduced include the US, India, China, Brazil, Indonesia, South Africa, and Turkey.
In the United States, the Inflation Reduction Act requires that all structural steel in new products is manufactured in the US. In addition, the minimum percentage of domestic
content for manufactured products in solar, battery, and wind installations (including the labour costs required to make them) must be 40% for projects on which construction starts by the end of 2024, 45% for projects starting construction in 2025, 50% in 2026 and 55% thereafter.3
In India, the government implemented the ‘Make in India’ initiative in July 2019. Under this program, solar cells and modules must be manufactured domestically, and wind projects must be comprised of 80% local content. Another driver is the $5 billion scheme known as the PM Kusum program to develop decentralised, small-scale solar for agricultural consumers. The program components focused on solar water pumps mandate the use of domestically manufactured cells, modules and balance-of-system parts.4
In addition, India has a national certification program requiring that any manufacturer wanting to sell turbines in the country must have quality certification for its devices together with a local assembly unit and an operations and maintenance (O&M) team. This is done to ensure
that only quality equipment is installed domestically.5
The main competition for Australian wind tower manufacturers are overseas suppliers from Vietnam, China and Indonesia. The issue is that the quality of imported wind towers is appalling. They do not adhere to Australian Standards. Local fabricators comply to internationally recognised Australian Standards and are certified by the relevant Australian authority.
In this way, Government and private clients can ensure the quality and safety of projects. Imported steelwork, which does not meet these requirements, is often of inferior quality and may not meet the Australian safety requirements.
These quality and safety issues will only be exacerbated by increased global demand in the race to net zero. The whole world is looking to transition to renewable energy. Countries like Scotland, New Zealand and Sweden are all investing in wind power. Not only will increased global demand likely reduce the quality of
“ It is essential that local and First Nations content requirements are incorporated into Capacity Investment Scheme tenders. This will fortify domestic clean energy supply chains, boost investor confidence, and cultivate a skilled workforce for the energy transition, positioning Australia as a global renewable energy leader.”
wind towers manufactured overseas, it will also increase scarcity of supply. There are already global supply chain issues—imagine how these will be magnified.
Local manufacturers like Keppel Prince Engineering and Crisp Bros. & Hayward cannot win jobs on their doorstep when governments and multi-national companies place a premium on price over and above quality and safety.
The Federal Government must commit to building sovereign manufacturing capability for renewable energy projects by legislating local content policy. Local content legislation must specify that 60% of all fabricated steel used in our renewable energy projects is manufactured in Australia by local welders. This local content legislation must be drafted in conjunction with industry to eliminate the loopholes
that so often arise in these types of policies.
This will create a capacity mechanism that generates a clear, long-term signal for investment by private equity and local manufacturers. The Federal Government must also mandate that all wind towers are constructed, erected and inspected according to Australian Standards.
Local welding and manufacturing companies will then be assured of the security of sufficient orders to enable them to invest in the necessary workforce, plant and equipment to deliver high quality, cost effective renewable energy assets. With long-term demand a reality, local manufacturers—like Oxycut who are world leaders in building wind tower anchors—will have the confidence to improve production efficiencies and global competitiveness.
Unless industry and governments
come together now to formulate a plan of attack, when the time comes to manufacture the assets needed for our clean energy transition, there will be no fabrication facilities, no skilled workforce, and no regulatory frameworks in place. There will be no sovereign manufacturing capability. Specifying local welding companies in the Federal Government’s Capacity Investment Scheme tenders is imperative.
Refrences
1. https://parlinfo.aph.gov.au/ parlInfo/download/committees/ reportrep/RB000196/toc_pdf/ Sovereign,smart,sustainable.pdf
2. https://www.sciencedirect.com/science/ article/abs/pii/S1364032122007146
3. https://www.shearman.com/en/ perspectives/2023/05/inflation-reductionact--new-guidance-on-domestic-contentbonus-credits
4. https://www.sciencedirect.com/science/ article/pii/S2211467X2030122X
5. https://www.sciencedirect.com/science/ article/pii/S2211467X2030122X
The NSW Government recently unveiled a $275 million allocation in grants as part of the Net Zero Manufacturing Initiative, aimed at cementing NSW as the premier destination for the development and production of clean technology.
According to the NSW Government, the initiative will reshape the state’s economy, ensure that NSW manufacturing plays a pivotal role in this transformative journey, and yield local and stable employment opportunities throughout the state, fostering the diversification of regional economies.
The allocation of funds will be guided by the NSW Decarbonisation Innovation 2023 Study, a blueprint published by the Office of Chief Scientist and Engineer to identify key opportunity areas. These include future energy systems and storage, transportation, the built environment, biomanufacturing, power fuels including hydrogen, and agricultural technologies.
For more information and to apply, visit: energy.nsw.gov.au
Austal Australia has been awarded a contract extension for the construction of two additional Evolved Cape-class Patrol Boats for the Royal Australian Navy. The $157 million contract follows the announcement made in November 2023 by the Commonwealth and brings the total number of Evolved Cape-class Patrol Boats being delivered to the Navy to ten.
Austal CEO, Paddy Gregg, said, “These additional Evolved Capes, designed and constructed by Austal in Henderson, Western Australia, are helping us to retain and build our sovereign, naval shipbuilding workforce and continue to engage supply chain partners from across Australia.”
The Evolved Cape-class Patrol Boats feature larger amenities to accommodate up to 32 people, improved quality of life systems and advanced sustainment intelligence systems that enhance the Navy’s ability to fight and win at sea. The patrol boats are used for a wide variety of missions and play a critical role in Australia’s national security, as a high-performing, reliable and effective maritime asset.
GFG Alliance has signed an agreement with the South Australian Government to explore opportunities for the supply of hydrogen from its 250MW electrolyser in Whyalla to support the transformation to green iron and steel.
GFG Alliance executive chairman Sanjeev Gupta said, “Being a key offtaker for the supply of green hydrogen from the world’s largest electrolyser being built in Whyalla is a real privilege for GFG. This step is vital in our plans to produce premium green iron and steel in Whyalla, and a huge boost to Australia’s determination to lead the world in decarbonisation.”
GFG has also entered into a memorandum of understanding with global energy company Santos for potential long term natural gas supply to its Whyalla operations. This is in addition to a recent grant of $63.2 million from the Federal Government’s Powering the Regions Fund to support the purchase and installation of an electric arc furnace and a $50 million grant committed by the South Australian Government pending approval for use towards the EAF.
Rio Tinto has signed Australia’s largest renewable power purchase agreement (PPA) to date to supply its Gladstone operations in Queensland, agreeing to buy a majority of electricity from Windlab’s planned 1.4GW Bungaban wind energy project.
The agreement, which follows the announcement last month of PPA for the Upper Calliope solar farm in Queensland, will make Rio Tinto the biggest industrial buyer of renewable power in Australia and is another major step in the work to repower the company’s Gladstone production assets of Boyne aluminium smelter, Yarwun alumina refinery and Queensland alumina refinery.
Under the new PPA with Windlab, Rio Tinto will buy 80% of all power generated from Bungaban wind energy project over 25 years. The remaining 20% of the project’s generated electricity will supply Australia’s National Electricity Market, delivering clean electricity to homes and businesses.
With Incat leading the world in the transition to zero-emission ferries, more people than ever before want to be a part of this ship building revolution. Incat has welcomed 15 new apprentices, including the highest intake of female apprentices in the company’s history.
Incat Chairman Robert Clifford said it’s great to have the new apprentices on board. “It has never been a more exciting time to join the company. We are currently building the largest battery electric zero emission ship in the world, and we are also well advanced with our discussions for the next build as well,” Clifford said. “We had a record number of applications for this apprenticeship intake at almost three times the amount for the same period last year. This shows that people want to be a part of our plans to revolutionise the industry by delivering more zero emission ships more efficiently than anyone else.”
This intake of apprentices will undertake a Certificate III in Welding and Fabrication. Incat is the largest single site employer of trainees and apprentices in Tasmania.
The Productivity Commission has unveiled a report shedding light on Australia’s productivity decline, with labour productivity experiencing a sharp downturn in the 2022-23 period.
Despite a record-breaking surge in hours worked, economic output failed to match the same level of increase.
Titled the Annual Productivity Bulletin 2024, the report offers comprehensive insights into the factors driving Australia’s productivity slump during the specified timeframe.
According to Deputy Chair of the Productivity Commission Alex Robson, “We now have a clearer understanding of what’s behind Australia’s productivity slump. Sharp increases in working hours have seen productivity decline, but this makes policies to boost productivity even more important.”
Labour productivity plummeted by 3.7%, significantly below the long-term average growth rate of 1.3%. This decline was propelled by a staggering 6.9% surge in hours worked by Australians, marking the highest annual increase in history.
Building on the momentum of the 2023 National Manufacturing Summit, which focused on the Renewable Energy: Challenges and Opportunities, the 2024 Summit embarks on an ambitious journey with its theme: Pathways to Success…Making the Renewable Energy Revolution a Reality
The 2024 Summit will delve into the practical aspects of manufacturing within the renewable energy sector, highlighting the essential components that will drive Australia’s transition to a sustainable future.
The Australian Government’s commitment to reducing emissions by 43% by 2030 and achieving net zero by 2050, as outlined in the Climate Change Act 2022, sets the stage for a transformative era in renewable energy. With an anticipated growth in renewable energy generation from 64GW to over 218GW by 2050, the manufacturing sector is at the forefront of this change, presented with unparalleled opportunities and significant challenges.
The Summit will see a diverse group of industry stakeholders assemble on 31 July and 1 August 2024. The Summit gathers leading representatives from all the major stakeholders in Australia’s manufacturing sector—business, unions, universities, the financial sector, suppliers, and government—to discuss the sector’s prospects, and identify promising, pragmatic policy measures designed to support an industrial turnaround.
Registration details will be announced shortly—be sure to keep an eye out!
The 2024 National Manufacturing Summit will be held at the Amora Hotel in Brisbane
Book your stay at the Amora Hotel during the Summit and enjoy an unparalleled 15% discount off the best available rate at the time of booking. This discount will apply from July 30 to August 2. This special offer is designed exclusively for our delegates, ensuring your experience is not just memorable, but also more affordable.
Rate URL: https://reservations.travelclick. com/113954?RatePlanId=8550782
Access Code: WELD24
Weld Australia’s National Manufacturing Summit is one of the most prestigious events on the manufacturing industry calendar. Sponsors are essential to the success of the Summit; without you, we would be unable to facilitate our industry-leading program.
With a diverse range of members from across Australia, we offer curated sponsorship packages that give you unparalleled access to your ideal customer base. Not only will you enjoy superior brand exposure opportunities, you can rest assured that your marketing is reaching an engaged group of industry professionals.
On top of the chance to market your brand in front of industry decision-makers, you will also be reinvesting in the welding and fabrication industry—giving back to the industry that makes your business so successful.
To tailor a sponsorship package, or for further information, contact Michelle Bignold (Executive General Manager, Sales & Marketing, Weld Australia) on +61 437 106 726.
DOWNLOAD A COPY OF THE SPONSORSHIP PROSPECTUS >>>
Welding is a potentially dangerous process, with many hazards and risks to people’s health. These risks are compounded by the fact that welding is undertaken across a wide range of locations and situations, from workshops and field work, through to confined spaces, underground mine sites, and more.
Hazards in each of these situations will be different, and require different controls to keep welders and others in close proximity safe. It is critical to manage these risks and hazards so that people working in the welding industry are kept safe and return home at the end of each day without injury.
To this end, Weld Australia has developed and released two free online welder safety training courses.
Weld Australia has developed two comprehensive online welder safety training courses – one course aimed at welders, and the second aimed at welding engineers and supervisors. These courses are now online and freely available to the public.
The objective of these courses is to improve safety awareness, knowledge and outcomes across the welding industry.
The courses cover a broad range of subject material across welding processes. They provide details of hazards that may be encountered and how to manage them in the workplace. The hierarchy of controls are discussed, with a particular focus on engineering controls and the correct use of PPE.
The courses also reinforce procedures that should be used, such as correct set up and use of equipment and the correct handling of gas cylinders and welding machines. Assessment and certification for course participants is also available.
The courses can be accessed via the Weld Australia website or directly via: https://weldtraining.online
To start the courses, all you need is an account for Weld Australia’s online training platform. If you don’t already have an account, you can quickly and easily create one via the link in the top right-hand corner of the platform’s homepage.
Enhance Staff Inductions
Incorporating the welding safety courses into your induction process for new hires ensures all employees start with a solid foundation in safety practices. It helps set a companywide safety standard from day one.
Regular Employee Refreshers
The courses can be used as part of an ongoing training program to keep employees up to date with the latest safety techniques. Regular refreshers help maintain safety awareness, reducing risk of accidents.
Compliance with Regulations
By leveraging the courses, organisations can help ensure compliance with safety laws and regulations. This helps avoid legal issues and fines and, more importantly, creates a safer working environment.
Reduce Accidents and Insurance
Educating employees on safety can reduce workplace accidents, leading to lower workers’ compensation claims and insurance costs. A welltrained workforce is less likely to engage in unsafe practices.
Improve Your Knowledge
By undertaking these courses, you can gain essential knowledge on how to protect yourself from hazards like burns and harmful fumes. Learning about PPE and emergency procedures can be life-saving.
Improve Your Employability
Looking to start or advance a career in welding? Completing the courses demonstrates to employers that you are serious about your profession and committed to safety working, making you stand out in the job market.
Support for Hobbyists
If you’re a hobbyist welder (or know someone who is), safety education is just as important. Free courses can provide you with the knowledge to safely enjoy welding at home, protecting yourself, your family, and your property.
By educating yourself, you contribute to a culture of safety within the welding community. Sharing knowledge with peers, and practicing safe welding can influence others to prioritise safety, reducing welding-related accidents.
FURTHER INFORMATION
Questions? Queries? Contact Andrew Davies (Manager, Technical Industry Networks) on a.davies@weldaustralia.com.au or 0438 428 966.
Tuesday 9 April | 11am – 12 noon (AEST) | Online via Zoom
Learn more about the courses, including how and why they were developed, the content they cover, and how and why you can use the free courses in your business or career.
Safe Work Australia recently announced that Work Health and Safety Ministers have agreed to an immediate reduction in the workplace exposure standard for welding fumes, from an 8-hour time weighted average (TWA) of 5 mg/m3 to 1 mg/m3.
As the exposure standard for welding fumes has been reduced, all necessary controls must be implemented to meet this higher standard.
Based on the hierarchy of controls, the following actions are recommended:
1. At-source fume control is recommended to maximise the level of fume captured and controlled as it is generated. Suitable methods include local exhaust ventilation (LEV) such as a hooded fume extractor and/or on-gun fume extraction. Captured fume should be filtered and exhausted to atmosphere, preferably outside the workshop.
2. Welders also require personal respiratory protection, particularly where the welder’s head is likely to be in or near the weld
plume. For example, the use of Powered Air Purifying Respirators (PAPRs) offer an excellent measure of protection in most welding situations. Externally air-fed helmets may be preferable or be required in some situations, such as confined spaces where oxygen monitoring is required.
3. Good overall ventilation throughout the workshop to protect the general workforce.
If in doubt, specialist advice should be sought from an occupational hygienist and fume exposure monitoring undertaken.
The change to the workplace exposure standard for welding fumes becomes mandatory once implemented in the WHS/OHS laws in the Commonwealth, states and territories. All states and territories have already implemented this new exposure limit.
Under the model WHS laws, persons conducting a business or undertaking (PCBU) – like an employer – must eliminate or minimise the risks to worker health and safety so far as is
In recent years, the welding industry has become increasingly aware of the hazards posed by metal fume produced during the welding process.
This fume, comprising of microscopic particles of hot metal and gases, poses serious risks when inhaled by welders.
In March 2017, the International Agency for Research on Cancer (IARC) reclassified welding fume from Group 2B Possibly Carcinogenic to Humans to Group 1 Carcinogenic to Humans. Their assessment was subsequently published in IARC’s Monograph 118 in July 2018.
IARC through Monograph 118 stated that there is evidence for welding fumes causing lung cancer and limited evidence causing renal cell cancer. Ultraviolet radiation from welding was also evaluated and similarly classified as Group 1 Carcinogenic to Humans in Monograph 118.
reasonably practicable, including those associated with chemical exposure.
A PCBU must also ensure that workers are not exposed to any airborne contaminant above the concentration listed in the Workplace exposure standards (WES) for airborne contaminants (WES list). Welding fumes are a complex mix of hazardous chemicals. Some individual components of welding fumes also have their own WES.
In addition to ensuring workers’ exposure to total welding fumes is below the WES, PCBUs must ensure workers’ exposure to individual welding fume components is below those respective WES also.
Monitoring must be carried out when employers are unsure if a relevant exposure standard is being exceeded, or where there may be
a risk to health. Health monitoring may also be required if workers are exposed to certain substances specified by the WHS Regulations that are likely to cause them harm.
The model Code of Practice: welding processes provides guidance to help manage the risks associated with welding, including exposure to welding fumes.
According to Safe Work Australia, there are four things PCBUs can do to help protect workers from exposure to welding fumes:
1. Identify the hazardous components in welding fumes at your workplace. This can come from air monitoring data or from the safety data sheets for the welding rods, if available. Arrange for air monitoring if you
are uncertain which components are produced and whether the relevant WES would be exceeded.
2. Assess the risk of welding fumes at your workplace. This includes consideration of the processes and work environment, observing the nature of work and consulting with workers about work activities that may lead to fume exposure, as well as reviewing incident reports.
3. Review the control measures you have in place to eliminate or minimise your workers’ exposure to welding fumes.
4. Talk to your workers and any health and safety representatives (HSRs) about the reduced WES, how it might impact your workplace, including changes to control measures and any training your workers might need.
Fume Minimisation Guidelines: Welding, Cutting, Brazing and Soldering, which includes all the information required to help protect workers from the hazards associated with welding fumes. This has been revised in line with the changes, and a new edition is now available.
Technical Note 7: Health and Safety in Welding, which gives guidance on health and safety practices in welding, cutting, allied processes and metal spraying.
Established by Weld Australia in early 2019, the Welding Safety Council provides a forum for industry and legislative safety authorities to discuss issues and work collaboratively to identify solutions. By drawing together key government stakeholders, statutory bodies and industry into a single independent body focused on eradicating welding related injury, the Australian welding industry continues to take a significant steps forward in protecting both the general public and welders.
Weld Australia is currently developing two comprehensive online welder safety training courses. One course is tailored for welders, while the other is aimed at welding engineers and supervisors. These courses cover a raft of activities across a range of welding processes, welding fume safety, and welding in confined spaces, at heights, or in hot and humid conditions. These courses are are now freely available via https://weldtraining.online
Hanlon Industries is a premier steel and construction partner, delivering quality steel manufacturing and solutions-driven project and site management for a broad range of clients across Australia.
The company was founded in Geelong in 2000 as a specialist steel fabrication business. Since then, Tom Hanlon and his team have grown the company’s facilities and reach across Australia. Throughout its success, Hanlon Industries has stayed true to its core of supporting professional development and training the next generation of industry practitioners.
The company was recently certified to AS/NZ ISO 3834.2, which will help attract new opportunities in the competitive national manufacturing sector.
For over 20 years, Hanlon Industries have delivered quality steel manufacturing solutions to clients across Australia in a safe working environment. Experienced tradespeople and professionals operate across steel fabrication and infrastructure, with a core focus on servicing communities, employees and customers.
This opens the door for Hanlon Industries to work with clients on road, rail, aviation and commercial development projects. Personnel operate out of four workshops and fabrication facilities in Geelong, Victoria; Alexandria in New South Wales; Narangba in Queensland; and Malaga in Western Australia.
These facilities offer advanced manufacturing capabilities including the Voortman beamline, and cranes able to support up to 25 tonnes. Trades staff are encouraged to share their best ideas and collaboratively work towards common goals in line with the company’s values of safety, respect, relationships, wellbeing, culture and innovation. Bringing these values to life requires a team of
dedicated and focussed professionals who are trained in the latest industry processes.
As such, Hanlon Industries understands the value of prioritising continuous improvement and staff development. This has become essential in the increasingly competitive global manufacturing space.
A business-as-usual approach may not afford the same opportunities as it once did. As such, Australian companies are taking matters into their own hands to ensure their teams are well-trained and certified, which translates into a solid pipeline of projects.
As part of the pursuit towards constant professional development, Hanlon Industries was recently certified to AS/NZS ISO 3834.2.
Tom Hanlon, International Welding Specialist and Director at Hanlon Industries, said professional development, including certification,
has helped the company in its mission of always striving to be better.
“Our motivation for becoming certified is continuing best practice within our company and being on the forefront of industry progress.”
The certification journey requires companies to take a deeper look at their operations and make appropriate changes. It prompts senior welding practitioners to analyse the entire lifecycle of a project—from the initial stages like design to the welding process and final inspection—to understand the aspects affecting the quality of a weld. Achieving certification is a detailed and complex process but, according to Tom, the rewards are worth it.
“It requires a high level of commitment from the organisation, across all levels, to commit to the process, make the required changes, achieve and maintain certification.”
“I’d suggest that anyone looking to embark on the certification process first conducts a gap analysis then set clear timeframes and milestones which are to be communicated across the company,” Tom said.
Hanlon Industries is open for business, and the internationally-
recognised AS/NZS ISO 3834.2 certification strengthens existing client relationships, while opening doors for new opportunities in existing markets.
“We are now part of an exclusive pool of fabricators that are certified to complete state and road projects ensuring we meet the requisite certifications required to complete these projects,” said Tom.
“Being independently audited gives clients assurance that we are working to best practice and ensuring regulatory compliance on our client’s projects.”
“Weld Australia were fantastic to work with. They were extremely thorough, knowledgeable and are certainly setting the bar for best practice in the industry. Whenever we have encountered welding challenges in the past, we have been able to collaborate with Weld Australia to find the best solution,” Tom said.
Weld Australia’s guidance helped the company identify challenges in its current operations and develop its resilience for the future.
“The certification process led our business to close small gaps in systems and processes, which has given us confidence in our existing processes and put us in a really strong position to continue to power forward.”
For likeminded companies who are seeking to certify to AS/NZS 3834.2, Hanlon offered some sound advice: “I cannot stress enough, that this process requires buy-in from all levels of your organisation, so clear and upfront communication early on is vital so that everyone understands the goal posts.”
Australian Manufacturing Week organiser AMTIL wants AMW 2024 to be more than an exhibition, it wants the show to be the centrepiece of a week-long celebration of manufacturing in Australia. Australia’s premier manufacturing technology trade show, Australian Manufacturing Week is a dynamic event that brings together professionals, companies and experts from many industries related to manufacturing, engineering and technology.
“We are very pleased to have the support of the NSW Government as the Major Sponsor for AMW 2024. Government support is important in delivering the message to our industry that manufacturing is important and that the support mechanisms are there to assist,” said Shane Infanti, CEO of AMTIL.
“On the back of the overwhelming success of AMW 2022 in Sydney, we have returned to Darling Harbour, Sydney for April 2024 and we’re excited to be delivering another strong show.”
The numbers from the Melbourne AMW 2023 show are something of which AMTIL is particularly proud, as 15,914 attendees visited 348 exhibitors in the biggest exhibition space in Australia. AMW 2024 is expected to deliver the same if not better.
“We will again be running the Future Solutions Speaker Program on the floor of the show. Themed towards opportunities and managing change, the speaker program is once again
free for visitors to attend,” said Kim Banks, AMTIL’s Head of Events. “Our plans for AMW 2024 include expansion of our Welding and Air Technology Zone and Robotics and Automation Zone. This will round out the event in representing the manufacturing technology sectors in Australia.”
A reminder of the seven distinct zones at AMW 2024, each showcasing the highlights of the different active sectors in Australian manufacturing.
The AUSTECH Machine Tool Zone is targeted at the metalworking, machine tool and ancillary market. AUSTECH covers advanced manufacturing products and processes including:
• CNC machinery, lathes, mills
• Contract manufacturing and precision machining
• Cutting tools, tooling and tool holding
• Forming and fabricating machines
• Plasma, laser, waterjet and ultrasonic machines
• Ancillary equipment suppliers.
The Additive Manufacturing Zone will showcase the most advanced additive technologies and techniques including: stereolithography, selective laser sintering, material extrusion, sheet lamination, binder jetting, cold spray-processing, material jetting, directed-energy deposition, powderbed fusion, VAT photo-polymerisation and wire-arc manufacturing.
The Australian Manufacturers Pavilion showcases the capabilities of Australia’s precision engineering and advanced manufacturing. It includes some of Australia’s more accomplished component manufacturers, precision engineering firms, toolmakers, advanced manufacturers, and general engineering companies.
The Manufacturing Solutions Zone exhibits solutions to the most common manufacturing challenges — from materials handling and warehousing to integrated manufacturing and safety. Equipment from materials handling and logistics, safety products, through to the latest software for streamlining manufacturing operations, as well
as specialist services including law, finance, skills, training, and recruitment are all here.
The Robotics and Automation Zone at AMW 2024 will feature the latest state-of-the-art equipment and processes for the optimisation of manufacturing operations. Robots are practical technologies, with artificially intelligent software ‘brains’, created and designed by engineers to refine, manufacture, and move Australian manufacturing ahead. The robots of today are liberating human workers from an ever-growing array of repetitive and dangerous tasks. There will be industrial robotics, robots, automated solutions, instrumentation control systems, measurement, pneumatics, IOT, Industry 4.0 and digitalisation.
The Weld and Air Solutions Zone will highlight advanced welding processes and offers interactive experiences that demonstrate developments and applications. Welding is used in creating more than half of all products manufactured in Australia and of course is critical in metal fabrication and manufacturing.
The Plastics Technology Zone is a hands-on opportunity to see and feel the latest in plastics machinery, mould-making technologies, recycling materials, and many processes in plastics manufacturing. Plastic technology is a specialisation which includes the study of diverse types of chemicals that exhibit plasticity and ways plastics can be used.
The AMW Future Solutions Speaker Program rolls out through the week, a free Conference within AMW2024, covering major topics within the manufacturing industry.
Just some of the exciting presentations will include:
• Dr Robert Acres, Commercial Technical Consultant at ANSTO on the topic Sovereign capability for Australian Manufacturers
• David Chuter, Executive DirectorIndustry Growth at Department of Industry, Science and Resources on the topic Australian SME commercialisation and growth opportunities
• Allan Aaron, Defence Industry
Advisor at Office of Defence Industry Support, Capability Acquisition and Sustainment Group, Department of Defenceon the topic Defence Industry Support
• Sharon Robertson, Chief Executive Officer at Manufacturing Industry Skills Alliance on the topic Addressing the challenges of the changing manufacturing workforce
• Bruce McLean, Chief Engineer – Sydney Manufacturing Hub at The University of Sydney on the topic Growth and Change of Advanced Manufacturing Technology
This editorial was supplied as part of a paid sponsorship package.
AWM2024
When: 17-19 April 2024
Where: Sydney ICC Darling Harbour australianmanufacturingweek.com.au
Can you describe your job?
I am a boilermaker welder at Jayben Group on the north west coast of Tasmania. I have been here for just over 12 months and during that time my responsibilities have been in the manufacturing sector. My role revolves around the production of civil and mining products, catering to a diverse range of industries.
One of the significant aspects of my job entails capitalising on defence fabrication opportunities, where precision and durability are paramount. Working with a wide range of materials mainly carbon steel and aluminium, I am tasked with fabricating structures that adhere to stringent quality standards.
Considering the demanding requirements inherent in defence projects, Jayben has invested in my professional development, enabling me to complete certifications such as the IWI-B (International Welding Inspector - Basic) and commence training for AS 2214 (Structural Steel Supervisor).
These certifications not only enhance my ability but also compliment our commitment to delivering excellency in defence fabrication projects.
Cheynae Bramich is a boilermaker at Jayben Group in Tasmania. A boilermaker by trade, Cheynae recently gained her International Welding Inspector - Basic (IWI-B) qualification and has started training for AS 2214 Structural Steel Supervisor. Cheynae answered some questions about her career in welding.
What inspired you to chose a career in welding?
Going through school, not really knowing what I wanted to do as a career I studied childcare as many of my friends and fellow students chose to, courses were readily available and the need for child carers in industry was high. I enjoyed my studies however I found working with children challenging. So I began looking for new opportunities and signed up to a local job agency.
One day I receive a phone call and was asked if I’d be interested in a short course in welding. I was available, so I agreed to try something new. I arrived at a very small, local workshop eager to learn all about welding. I thoroughly enjoyed my short course in welding and I was pulled aside by the gentleman running it to say that I should pursue a career in welding!
The industry was booming on the north west coast of Tasmania and in a matter of weeks I scored a trial in a boiler making/heavy metal fabrication workshop in Somerset. I applied for the first apprenticeship I saw advertised. I was called for an interview and once that process was completed, I was offered an apprenticeship! One could say it
“
By entering a typically male dominated workforce, we are challenging stereotypes. We are able to inspire others to pursue careers based on our interests and abilities rather than social expectations.”
was a snowball effect that led me to my apprenticeship in heavy metal fabrication. And one that I was not expecting. The process of being able to join two pieces of metal together has always intrigued me as I remember Dad when I was a child welding in the shed at home. Also my older brother successfully pursued a career in welding and the metal fabrication industry as soon as he left high school, and I thought to myself, “If he can do it, so can I!”
Why do you think women should consider a career in welding?
I think women should consider a career in welding for a few different reasons. Firstly boilermakers are in high demand across different industries such as construction, manufacturing and automotive.
Welding offers a wide range of career paths including fabrication, inspection, supervision and management roles, engineering and so much more!
Welding and fabricating is a hands on job, yes. But it enables you to problem solve and allows you to develop valuable technical skills and contribute to projects that require precision and creativity.
And lastly women should consider a career in welding because, by entering a typically male dominated workforce, we are challenging stereotypes. We are able to inspire others to pursue careers based on our interests and abilities rather than social expectations.
Do you have any advice for women considering a career in welding?
Seriously, wear your PPE and follow safety protocols. They are in place for a reason and everyone wants to get home to their family safely at the end of each shift. Build self confidence, believe in yourself and your abilities, and don’t let stereotypes and gender biases deter you from your work.
Be strong, and resilient and persevere through any setbacks or difficulties you may encounter along the way. Seek mentorship and network with a range of people in the welding industry. By building these connections it opens you up to more opportunities for career advancement and support.
And lastly, don’t be afraid to advocate for yourself, speak up if you encounter any discrimination because of your gender. Remember you deserve to be treated with respect and fairness in your workplace.
Have you found working in a traditionally male dominated industry difficult? If so, how have you overcome any challenges? Yes, I’m not going to lie here. Working in a male dominated industry was tough for me during my apprenticeship.
It was in my second year that I fell pregnant with my son. During that time I was subjected to a lot of harsh judgement about what I should and shouldn’t be doing regarding my personal health and safety. I was shunned by many men in the workplace, and I was subjected to workplace harassment and bullying behaviours to some degree.
But despite the negativity that I was receiving, I remained strong in my own beliefs that what I was doing (by continuing my work and my apprenticeship) was the best thing for me and my baby. When times got tough I reached out to family and friends for guidance and support. Over the next decade, I learnt that overcoming these challenges and many like them require a combination of personal strength, resilience, and determination to succeed professionally.
What is the most interesting project you’ve worked on? Why? Among all the projects I’ve undertaken, none captures my fascination quite like our defence
project. Its attraction lies not only in its significance but also in the intricacies it presents.
One of the most captivating aspects is the challenge of weld procedure qualifications, particularly when it comes to PWHT of aluminium—a material known for its sensitivity to temperature variations. Navigating aluminium welding while adhering to stringent standards demands attention to detail and precision.
Furthermore, being entrusted with the role of a welding inspector adds another layer of complexity, as I must ensure compliance with relevant standards while maintaining the integrity and quality of our work.
The dynamic nature of this project, coupled with the technical challenges it presents, makes it an endlessly intriguing opportunity that pushes the boundaries of my expertise and fuels my passion for excellence in fabrication.
Who has inspired you professionally and why?
I’d like to make mention of my brother, who successfully completed his apprenticeship as a boilermaker welder and has continued to work in the industry ever since. Without him I would never have pictured myself following this amazing career path. Or known that this trade was even a possibility for me.
His ability to fabricate and weld heavy machinery to the level in which he does, has given me insights into what it means to be a skilled tradesman. Initially, it was his passion for welding that inspired me to give it a go in the first instance and I am grateful that I did.
Not to mention the countless kind men (and women) who taught and supported me throughout my career. Without encouragement and guidance from fellow work mates, TAFE teachers and people within industry, I would not be achieving what I am today. It’s the passion and potential that I see in other people which continues to inspire me to do what I enjoy.
What do you believe is the biggest challenge for the welding industry at the moment?
There is a massive skilled labour shortage. As it is an aging workforce, experienced workers retire and fewer younger people are entering the field.
I believe that a lack of understanding about the welding trade and its career paths prevents young people from applying themselves and considering it as a potential career. Additionally, promoting diversity and inclusion within the welding profession can and will help mitigate the shortage of skilled workers.
What about the biggest opportunity?
One significant opportunity in welding
is the growing demand for skilled welders across various industries. As infrastructure projects, construction, manufacturing and other sectors continue to expand, there is a continuous need for qualified welders to fabricate, repair and maintain metal structures and components. This demand creates ample job opportunities and the potential for career advancement for individuals with welding skills and expertise.
Additionally, advancement in welding technology and techniques open doors for innovation and specialisation within the fields, presenting further opportunities for growth and development.
The landscape of pipe spool welding is undergoing a significant transformation, spurred by advancements in automation technology. This shift addresses the inherent challenges within the industry, including labour shortages and the increasing demand for repeatable quality. This technical overview delves into the evolution and future of pipe spool welding automation, highlighting the PerfectPass-iQ development as a case study in innovation.
Complete automation in preparation is still impossible due to the complex, imperfect nature of spool components. Since weld preparations are imperfect, robots must adapt to these variations. This is compounded by labour shortages, which translates into more inexperienced welders and higher turnover.
Spool automation once had a low adoption rate. Since the goal was to increase productivity, companies preferred the safety and flexibility of doing things the same old way: manually. Most just hired more workers for bigger projects, while a few examined the ROI calculations, decided to become pioneers and invest in automation.
Today, automation is becoming a must to increase weld quality, not just productivity. And the labour shortage is a direct cause. Even India is starting to make the shift to fulfill projects that specifically require robotic welding.
This push to automate brings a new challenge. Past automation required
a good welder to operate the robots because they weren’t intelligent. To remove human error, new robots need to weld autonomously and they need welding intelligence that adjusts the welding parameters to compensate for the imperfections of the spool preparations.
That’s why Tecnar developed the PerfectPass-iQ system for its Rotoweld welding robot. It’s a leap forward in welding automation technology since it uses advanced image analysis to adjust welding parameters in real time.
Its vision system analyses the weld in real time by measuring such things as the gap, high-low, penetration during the root pass, arc position and length, misalignment, out-of- round and tacks.
It then adjusts all the welding parameters to optimise the penetration, arc position relative to the puddle, arc length, stick -out, leftright tracking, weaving and more. Now, the operator only needs to press start. The robot will make perfect welds every time and provide a detailed analysis and an alert if anything was out of range.
The operator only needs to be there to operate the robot. PerfectPass-iQ manages the quality of the weld.
Make sure your next robot’s design makes set-up quick and easy since the highest arc-on-time will maximise productivity. Most importantly, make sure it has the highest welding intelligence so that human error doesn’t impact the weld quality.
This editorial was supplied as part of a paid sponsorship package.
Collaboration, trust and reliability are the three key ingredients for Munster Services’ success. From humble beginnings, the company has grown into a construction, engineering, and maintenance company focussed on operational excellence. Today, over 115 staff are united in delivering projects for Queensland. Strengthening the next generation of fabricators and securing Australia’s onshore manufacturing capabilities remain a key focus for Munster into the future. Apprentices are learning the ropes, while existing employees are developing their skills to take on a new suite of projects. In recognition of their commitment to the sector, Munster received Weld Australia’s 2023 Company of the Year Award—Fabrication for Queensland and the Northern Territory.
Munster Services was a bold idea born in the back of a Holden Rodeo. Eric Guthrie, who was living in Ireland before relocating to Australia in 2008, was the pioneer who saw an opportunity to support the local government and utilities sectors. He established the Queensland company, which began conducting maintenance works on water and wastewater treatment plants.
Guthrie remains at the helm of Munster—bringing over 24 years’ experience working in the local and international construction sector—cementing him as a leader when overseeing quality projects and commercial growth. Today, the company employs over 115 people from 21 nationalities.
Stuart Ackerman (Health, Safety, Environment and Quality Manager at Munster) said the company can attribute much of its success to Guthrie’s vision.
“Eric has strategically driven the growth and service capabilities of Munster, while developing long term business relationships with our valued clients. Eric is a passionate and commercially minded business owner who oversees and strategically directs the Group’s ongoing expansion into emerging markets,” Stuart said.
Today, the company is proud to deliver turnkey engineering, fabrication, construction, maintenance and refurbishment solutions. However, the local community and delivering for the Australian economy remain at the core of Munster’s business.
Forty-two per cent of Munster’s local distributors are small-medium sized enterprises, while Queensland companies make up 76 per cent of all suppliers. Queensland businesses attract 81 per cent of the company’s spend, which ultimately reinvests
Photos
nearly $19 million back into the local economy.
This grassroots approach to business has opened a window of loyal customers. Some of the company’s clients include Queensland Urban Utilities, Unitywater, City of Gold Coast, Utiltia, Downer, Ventia, John Holland and Veolia.
Munster’s senior leadership team drives an agenda of continuous improvement to quality, safety and environmental management initiatives. Welding personnel help to sustain and develop long-term strategic partnerships, community engagement objectives, and collaboration.
“We have a mechanical and electrical refurbishment division, a projects division, a fabrication division and a maintenance labour hire division,” Stuart said.
Munster’s
deliver
across the infrastructure, water, utilities, wastewater, food processing, industrial and building sectors.
Munster works cooperatively with clients from local, state, and federal governments; local jobs programs; and not-for-profits to drive change and make a meaningful contribution. “We believe if everyone does a little the difference it make can be a lot,” Ackerman said.
Australia’s manufacturing sector is no stranger to turbulent times, which were exacerbated by the COVID-19 pandemic. The alreadystretched sector was in the grips of a labour shortage, a habit of offshore manufacturing, and a limited pipeline of future-ready workers. At the same time, Queensland was experiencing some of the worst floods recorded in history. Approximately $2 billion damage was recorded to homes and businesses across the state.
Munster swung into action by redesigning workflows and operating hours to service the community and prevent further damage. This action plan would not be possible without Munster’s continued investment in staff and training.
The company has grown two-and-ahalf times the number of personnel in the past three years alone.
“With low unemployment rates nationally and the reality that the skill sets of our trade team are all on the Priority Skills List and in national shortage, Munster’s capacity to grow the team has been reliant on training the next generation of mechanical fitter, boilermakers, electricians and plumbers.”
Apprentice programs are one way in which Munster is securing Australia’s future. The company has been crucial in the establishment of over 45 trade apprentice programs through TAFE Queensland. This provides fresh opportunities for apprentices and trade-qualified personnel to upskill into a higher level or second trade qualification, like a Certificate IV in Engineering.
Munster has also started an additional 29 trainee programs focussing on supervision, safety and project management. Together, this has supported a pipeline of career-ready practitioners and the upskilling of six existing trade personnel to better fulfill diverse roles within the business.
“We have many second chances working for us. People who needed a life pathway change, an employment change, a retraining opportunity, we have even taken in ex-service people who were injured while serving their country and were rehabilitated and entered into a private workforce.”
“The secret to our success is simply two things, our people and
relationships,” Colin McDonnell (Operations Manager) said.
The company is also steadfast in their commitment of delivering Australian products made by Australians. “We demonstrated our local investment in 2020 when we brought offshore manufacturing back to Queensland for one of our key clients, manufacturing equipment used on treatment plants, equipment previously made in Europe and Asia.” Munster’s ‘Buy Local’ commitment was recognised by being awarded the Putting Queenslanders First award by the Department of Energy and Public Works.
These awards celebrate companies who supply products and services to the Queensland Government, and contribute to the life and economy across the state.
“Not only do we follow a ‘Buy Local’ approach, financially reinvesting in the local economy through our procurement policy, we also reinvest in local communities through training, support and employment opportunities,” McDonnell said.
Munster is proud to offer its clients a diverse range of customised and in-house fabrication services. From design and manufacturing to onsite installation and breakdown services, Munster stands by their high-quality approach to metal fabrication. Personnel constantly have their
work rigorously inspected by their team leaders, and independent third party organisations, like the National Association of Testing Authorities. The team is qualified to AS 3992, Pressure equipment—Welding and brazing qualification and AS 1554 Structural steel welding.
According to Eric Guthrie (Managing Director), “At Munster, it is critical that our team are trained and equipped, ready for a highly variable work environments in water and wastewater networks across the south east Queensland region.”
In the past year alone, Munster’s fabrication team employed 24 fulltime boilermakers and apprentices, which contributed over $9 million in wages to the local economy. This team recently executed their largest fabrication project.
Personnel were tasked with the installation of a series of counterweights, and a bespoke lifting frame and gantry for the Sunwater Coolmunda Dam under a project working alongside Abergeldie Complex Infrastructure. The multi million dollar project needed tight alignment between design and sitebased urban environments to ensure its success.
“While quality is always of the highest priorities, the remote nature of the work combined with the sheer scale of fabrication, including 14 tonne counterweights and a bidirectional gantry system, necessitated intensive
quality assurance at each step of the journey,” McDonnell said.
To bring these projects to life, Munster relies on an exceptional team matched with world-class facilities.
“Munster expanded its boilermaking from a complimentary activity to a standalone business element when we opened our new purpose built facility in 2020.”
“Further accomplishments of late have included the return of manufacturing to Queensland with the fabrication of inlet screens for wastewater treatment plants with ongoing works supporting local and national wastewater outcomes,” Stuart said.
Munster’s facilities are poised to grow in 2024, with plans to triple the company’s fabrication floor area.
“We are exploring technological changes and process developments which will ensure we are at the forefront of the industry including review of lean processes, quality assurance, energy efficient welders and green energy technologies to support low carbon outcomes.”
“By fostering and culturing good relationships and looking at the next 10 years, not 10 weeks, we have built a business that has grown year on year since 2008. To maintain these good relationships, we need good people. They go hand in hand,” Guthrie said.
The Weld Australia awards are the premiere event for celebrating the best in the welding and fabrication industry.
Munster Services received the 2023 Company of the Year Award—Fabrication for Queensland and the Northern Territory. The award recognises Munster’s contributions to the local economy and fabrication sector.
Weld Australia’s CEO Geoff Crittenden said the awards celebrate businesses and individuals committed to the pursuit of innovative, sustainable solutions that minimise risk and maximise project outcomes.
“The 2023 Welding Excellence Awards shine a light on the remarkable talents of welders and fabricators right across Queensland and the Northern Territory.”
“Weld Australia is thrilled to celebrate both businesses and individuals who are making waves in welding through their dedication to quality, safety and innovation,” Crittenden said.
The BlueVenom XF353 has been designed and engineered in Australia to provide a MIG Inverter solution with modular adaptability. With a large intuitive digital display the XF353 can perform simple MIG welding tasks, using Wire Feed Speed (WFS) and Voltage (V) controls at the touch of a button.
The XF353 can seamlessly connect to the All-New 4R-Rover™ digital remote wirefeed system (sold separately) - a compact 300mm plug n’ play, 4 Roll geared wire drive unit with an 8m lead with low mount handle that you can setup where you need it.
The BlueVenom XF353 is also a single and double pulse work horse! Simply plug in the hand-held PulseMate™ (sold separately) into the XF353 machine or 4R-Rover™ and start getting TIG like looking welds through our simple yet intuitive SimplePulse™ MIG system.
The XF353 has made Synergic Plate Thickness control even easier. The intuitive unit will work out the settings you need for different metal types based on Plate Thickness (mm) settings – no more guessing which synergic settings to use.
And finally for additional scalability, the XF353 can run a direct connect Push-Pull MIG Gun without additional wiring, a Spool Gun, and a TIG Torch to give you the perfect welding setup.
The all new BlueVenom XF353 is a beast - a complete Industrial grade MIG welding system that can tame the toughest welding tasks!
In light of recent legislative changes addressing welding fume exposure, many organisations have asked for clarification on the measures they should take to meet the new regulations. To set the stage - the new workplace exposure standard dictates that the average airborne concentration of welding fume inhaled by a worker over an eight-hour working day, across a five-day working week, must not exceed 1 milligram of welding fume per cubic meter of air. This standard is applicable to both welders and individuals working near welders.
The new regulations are tough, in fact Australia’s law is one of the toughest mandated in the world. The achievement of the low exposure concentration level is not a simple solution.
Fume exposure needs to be assessed at each work location to understand the magnitude of welding fume produced. Only then can a range of solutions be put in place to address the requirements.
There is no one, magic fix-all solution, for all situations. Some of the control solutions to address the protection of the workers* from welding fume (*the welding operator and people working
in the area around the welders who are exposed to the welding fumes) are listed below.
1. PAPR welding helmets designed to protect the individual welding operator and other PPE such as P2 and P3 disposable respirators
2. At source fume extraction, including welding fume MIG guns and TIG torches connected to fume extraction networks or portable fume extractors
3. Hooded capture Local Extraction Ventilation (LEV) fixed or wheeled
4. Work area air flow ventilation
5. Base metal preparation to reduce harmful elements, such as rust, dirt, paint, galvanised and other coatings that contribute to higher generated welding fume
6. MIG and flux cored welding wires that can be shown to reduce welding fume, please check with your welding wire supplier for low fume, filler metal options
7. Welding shielding gases that can be shown to reduce welding fumes.
A lot of work has been undertaken by the world’s major gas companies, BOC/Linde, Air Liquide and major welding research organisations and institutes. The research has focused on providing MIG and FCAW shielding gases with lower oxidising levels by keeping oxidising gas components (carbon dioxide and oxygen) to minimum levels. Some serious reductions in generated fume level (~20 - 30%+) can be achieved by using certain shielding gas mixtures without sacrificing penetration and operator appeal.
Fume exposure needs to be assessed at each work location. Only then can a range of solutions be put in place to address the new requirements.
The European standard EN 12941 outlines the criteria for a comprehensive powered air filtration apparatus that incorporates a face helmet or visor. EN 12941 does not establish a separate categorisation for particle filters (P); instead, the particle filter is an integral component of the overall system classification. The standard defines three performance classes (TH1, TH2, and TH3), each with designated numerical values indicating the level of performance (inward leakage) and the tensile strength of breathing tubes and couplings within each class. TH1 has a maximum allowable inward leakage of 10%, TH2 permits a maximum of 2%, and TH3 allows for a maximum of 0.2% inward leakage.
Various studies, including internal testing by ESAB, outline that PAPR systems are the most effective (93%99.5%) when compared to on-gun fume extraction (85%-95%) and hooded capture Local Extraction Ventilation (LEV) fixed or wheeled (60%-67%). Hooded capture LEV proves less effective when the welding joint/pool moves away from the LEV capture point and is very much dependant on the distance
from the weldment to the extractor nozzle. LEV’s are especially good at collecting fumes from concentrated areas such as over welding fixtures and jigs.
Highlighting product distinctions, it’s crucial to note that certain PAPR systems may outperform others, with factors like EN 12941 TH3 certification and the presence of a P3 filter differentiating them.
The ESAB Sentinel A60 Air PAPR System is one of a limited number of PAPR helmets on the Australian market that holds both EN 12941 TH3 and AS/NZS 1716 certifications, coupled with a P3 filter.
Moreover, the EN12941 certificate reveals compatibility of older ESAB Air helmets, including the Sentinel A50 Air, with the new EPR-X1 blower unit. This means existing ESAB Sentinel A50 Air owners can attain compliance with the standard by purchasing only the blower unit (EPR-X1), which is EN12941 TH3 certified.
In summary, achieving optimal protection involves a combination of engineering controls such as on-
gun fume extraction and hooded capture LEV, work area air flow ventilation, base metal preparation, fume reducing welding wires, and low oxidisation potential shielding gases, along with personal protective equipment.
It’s important to note that a standalone PAPR unit might not be enough to meet the new minimum regulations on its own. Employers are encouraged to ensure comprehensive protection for both welders and other personnel in the work area.
By utilising the above mentioned controls (4,5, 6 and 7) plus a fume MIG gun with an extraction unit in the work area, alongside a PAPR system like the Sentinel PAPR Kit, will ensure the best possible protection factor for welding operators and people working in the general welding area.
This article was supplied as part of a paid advertising package.
For further information, visit: cigweld.com.au or email
technical@cigweld.com.au
In the race towards manufacturing efficiency and the growing shortage of qualified welders, integrating a robotic welding system isn’t just an option; it’s an imperative.
Integrating a robotic welding system requires a strategic approach, starting with finding the right robotic welding specialist systems integrator. Their expertise will shape the success of your automation journey, ensuring alignment with your goals, your daily tasks, and future visions.
Defining a system that’s not only precise but also scalable is key. It’s about anticipating tomorrow’s challenges today and investing wisely. With technology advancing at lightning speed, and Australian government incentives awaiting those ready to embrace automation, there’s no time to waste. Use this opportunity to future-proof your business or risk being left further behind.
Selecting a recognised robotic welding integrator for your application is paramount to the success of your project. Begin by identifying integrators with proven local tech support and experience and expertise in your specific sector, before requesting a complimentary audit to assess their suitability for your needs.
An integrator’s capabilities can be evaluated by examining similar systems they’ve implemented. Their ability to provide local servicing and parts is often overlooked but is crucial for maintaining your system, whilst also proactively enhancing future performance.
Communication is key - The integrator must be aware of your expectations, productivity targets, accuracy standards, and future visions. Estimating your available space, resources, budget, and automation skills gap, will ensure clarity throughout the process, and avoid limitations of your new production system.
By carefully selecting the right robotic welding integrator that
suits your needs, you will set the foundation for a successful and enduring partnership in automation implementation.
Finding a targeted welding system that is both precise and scalable for your future production volumes is paramount for long-term success in manufacturing. Scalability anticipates and accommodates growth without the need for frequent system upgrades or replacements.
By investing in a scalable automation solution, manufacturers can optimise productivity, maintain competitiveness, and future-proof their operations against evolving market demands.
Robotic welding systems are considered a productive solution capable of scaling up your capabilities, which is one of the most targeted grant funding expectations. Your integrator should have access to specialists who can source applicable grants, before composing and submitting your application.
The implementation timeframe of a new robotic welding system holds significant importance in minimising disruptions to the production process. Constructing a well-planned timeline is essential to ensure the efficient setup of the new system while considering various factors such as available resources, cash flow constraints, ongoing projects, and production backlogs. It’s crucial to anticipate potential challenges and allocate sufficient time and resources accordingly to mitigate any impact on operations.
Additionally, budget and timing allowances must be allocated for the fabrication of future jigs and accessories, ensuring seamless integration with the new system. Upon completion of delivery, installation, and testing phases, the training component becomes paramount. Comprehensive training programs must be implemented to equip all staff with the necessary skills to operate the system proficiently.
By carefully orchestrating each stage of the implementation process within a structured timeline, businesses can minimise impacts, and seamlessly transition to the new integration system without any surprises.
Integrating robotic automation into your manufacturing business requires experienced planning and execution across three key steps. Finding a suitable integrator, defining the system parameters, and managing the implementation timeline are vital for success.
This article was supplied as part of a paid advertising package.
RA are integration experts and have provided over 3,500 installations across ANZ over the last 36 years, making them well-equipped to guide businesses through this process.
Their high-level tech support and preventative maintenance packages are available to limit production down-time and maximise productivity.
RA’s welding division utilises robotic experts, welding engineers and a solutions team with exclusive access to one of the worlds largest industrial robotic welding libraries from Yaskawa Motoman.
They can provide complete packages fully tailored to your requirements, using system components all from a single source for seamless compatibility during the integration process.
By partnering with RA, businesses can confidently navigate the complexities of automation, optimising productivity, and future-proofing operations.
For information, visit: roboticautomation.com.au
Harrison Field completed his apprenticeship and Certificate III Engineering Fabrication Trade in 2022. He is currently employed by A-OK Metal Fabrication in Bathurst. Known for his exceptional welding skills, Harrison has a genuine passion for the craft. His talent and hard work have not gone unnoticed, having won gold at the 2023 WorldSkills Australia competition for Welding, as well as winning Weld Australia’s 2023 Young Tradesperson of the Year Award for New South Wales and the ACT.
Growing up, Harrison had a natural urge to create things and could always be found making ad-hoc sculptures and structures with whatever materials he could get his hands on. So, when Harrison left school at the end of year 10 to begin his training as a metal fabricator, his friends and family knew it would be a great fit and one that he’d thrive in.
Having taken out the gold medal at the 2023 WorldSkills Australia competition for welding, Harrison is now focussed on continuing to build experience and hone his skills
ahead of the World Skills international competition in Lyon, France this year.
“I’ve never been overseas before, so it’s exciting to be travelling for the first time while doing what I love. I just love welding – making stuff and seeing the finished product is a reward in itself, but this award has shown me that hard work pays off,” said Harrison.
When not training under his mentor, Harrison can be found racing his car around the track or on the soccer pitch – two sports in which he’s
achieved significant successes. Harrison hopes his competitive mindset and focus, along with his ability to learn from mistakes and remain calm during the heat of competition, will help him give his best performance while in Lyon.
“One of my favourite parts of the WorldSkills journey has been getting to meet new people within the industry and see the little differences in how they tackle the same problems. It’s been really rewarding to share how I do things too.”
“ I just love welding – making stuff and seeing the finished product is a reward in itself, but this award has shown me that hard work pays off.”
Can you describe your job?
I am part of the team at AOK Metal Fabrication in Bathurst. AOK provide welding and manufacturing services, both private and commercial to the local and surrounding communities.
AOK has worked on many large and varied projects including the ramp and stair rails for the new Parramata Aquatic Centre, a large structural shed in Sydney and stainless steel fit outs for multiple KFC franchises in New South Wales. AOK has multiple aquatic centre projects in the near future. AOK weld and fabricate stainless steel, aluminium and mild steel for any custom project.
What inspired you to choose a career in welding?
During my childhood and school years, I enjoyed designing and making things with a variety of materials. I have a passion for car racing and would compete in Hillclimbs and Super Sprints on Mt Panorama. I became interested in metal and the fabrication of roll cages and other parts for the car, so my dad contacted a local welding company about doing some work experience during my school holidays. I really enjoyed welding and being able to make something from scratch. I was offered an apprenticeship and when I was old enough, I began my career in welding.
What do you enjoy most about your job and welding?
I really enjoy starting a job with either the drawings or the sheets of materials and building a product that is functional, while making sure the finer details of the project are perfect. I take pride in my work and ensure the welds are neat, there are no blemishes on the project, and it is symmetrical.
Why do you think young people should consider a welding career?
Welding and Fabrication is a great career choice for young school leavers. Learning the skills and having the creative freedom to be able to transform raw materials into an amazing project is so rewarding.
Do you have any advice for people considering a career in welding?
I would say to anyone considering a career in welding to give it a go. If you enjoy designing and construction, you could just find your forever career. If you love what you do, going to work and striving to be the best you can be is easy and fun.
What is the most interesting project you’ve worked on?
AOK has been involved in some interesting and challenging projects. The Parramata Aquatic Centre was one of these projects. This project was not dissimilar to other work
What are your top 3 ‘bucket list’ items?
• Watch the Indy 500 and Daytona 500 live
• Travel America
• Complete an ultra marathon
If you could be famous, what would you want it to be for? I would be a famous sports star
If you could meet anyone, who would it be? Nedd Brockman
What is your top tip for welding excellence?
Preparation is everything
we have completed, but the scale of the project was immense. It was rewarding to be involved in such a large project, with so many trades bringing the project together.
One of my most enjoyable projects was manufacturing a roll cage for a race car, complete with an air jack system. The technicality and engineering of the project was rewarding and challenging.
Who has inspired you professionally?
My mum and dad have always supported and inspired me to succeed. They have shown me what it means to have a strong work ethic and to be dedicated and proud of what I do. I have been mentored by the best. Nathan Kelly, Adam Klower, Brendan Swift, Mitchell Thurn and Craig Simpson have always encouraged, motivated and supported me and I wouldn’t be where I am today without them.
What do you believe is the biggest challenge for the welding industry?
One of the biggest challenges in any manufacturing industry today is the lack of workers and tradespeople. Even with the advances in technology, tradespeople will always be essential to complete manufacturing projects.
Thousands of Queenslanders study their engineering apprenticeship each year with TAFE Queensland, but less go on to enhance their career with post-trade training at one of Australia’s top training providers
While completing an apprenticeship is a tremendous achievement, in the ever-changing engineering industry it is just the beginning.
Post-trade training can usually be completed around work hours and allows experienced industry members to enhance their skills and broaden their scope of work and career opportunities. As engineering and other industries across Queensland
change in coming years, a broader range of digital skills will be required of industry workers including Computer Aided Design (CAD) and CNC programming.
TAFE Queensland offers a range of post-trade training options aligned to these skills, including the Certificate III in Manufacturing Technology – CAD (MSA30208) which is available under the Queensland and Australian Governments’ Fee-Free TAFE initiative at no cost to eligible Queenslanders.
This course is delivered online with optional on-campus tutoring available with expert TAFE Queensland
“ Engineering is such a wide-ranging industry and an apprenticeship is just the beginning, and TAFE Queensland has so many post-trade courses on offer to enhance your career.”
teachers, and gives students specialist knowledge in CAD which can be used to greatly diversify the employment opportunities available to them.
Business Manager of Engineering Training at TAFE Queensland’s flagship Acacia Ridge campus, Kevin Roos, says the course is a perfect upskill opportunity for engineering workers looking to enhance their career with a post-trade qualification.
“Gaining skills in CAD will drastically broaden the scope of work and the businesses that you can work in as an engineer, with many businesses prioritising workers who can run projects from start to finish,” Roos said.
“This course builds on the skills taught across an apprenticeship and develops skills from interpreting technical drawings into producing basic technical drawings and 3D models,” he said.
Another popular post-trade course in the engineering industry is the Introduction to CNC - CNC Operations (NONAC03098) which provides students with an understanding of basic coding and enables them to apply principles to a variety of different models and machines.
This one month course would be suitable to engineering professionals looking to gain a basic understanding of CNC so they can hit the ground running in a new role which requires on the job CNC learning and development.
For engineering professionals looking to transition away from working on the tools, a Certificate IV in Engineering Drafting (MEM40422) will deliver the skills required to become a technical officer or draftsperson in the industry. This course is delivered online with optional oncampus practical training available for students who prefer to learn in a physical classroom setting.
The next step in an engineering career available at TAFE Queensland is the Diploma of Engineering –Technical (MEM50222), which advances students’ skills in mathematics, materials science, quality assurance, engineering drawing and computing, and management and maintenance strategies.
The online course, available in a self-directed delivery mode or with on-campus practical training at TAFE Queensland’s Acacia Ridge campus, requires approximately 15 hours per week from students and takes one to two years to complete.
Also available is the Advanced Diploma of Engineering (MEM60122), which requires a similar commitment from students to the Diploma of Engineering – Technical.
Offered by TAFE Queensland online with additional on-campus practical training, this course provides students with detailed drafting and design
skills, and teaches them higher level engineering concepts where strong foundations in mathematics and physics can help transition students into professional careers.
Students will also develop their knowledge of engineering processes and principles, project management, quality systems, and team building. Completion of the advanced Diploma of Engineering can provide credits for further tertiary studies in engineering.
Roos says that with so many upskill opportunities in the engineering industry at TAFE Queensland, industry members are spoilt for choice.
“Engineering is such a wide-ranging industry and an apprenticeship is just the beginning, and TAFE Queensland has so many post-trade courses on offer to enhance your career,” Roos said.
“There are options for workers at all stages of their career and all corners of the industry, and TAFE Queensland’s industry expert teachers are passionate about passing on the skills to enhance careers.”
“For those interested themselves in passing on their trade skills to the next generation, the Certificate IV in Training and Assessment (TAE40122) is available for eligible Queenslanders under the Fee-Free TAFE initiative and will qualify them to become a teacher at TAFE Queensland,” he said.
This article was supplied as part of a paid advertising package.
For more information about post-trade engineering training at TAFE Queensland contact Client.Solutions@tafeqld.edu.au or call 1300 308 233 to define your greatness today.
At the dawn of the Otago Gold Rush in the 1860s, Joseph and Janet Farra became pioneers in elevating New Zealand’s local engineering capabilities. Still owned by the founding families, the team at Farra Engineering continue to grow their legacy, delivering access machines, maintenance, repairs, overhail and contract manufacturing for OEMs. Farra recently became New Zealand’s first company to certify to EN 15085, which will further advance their operations in a market of international manufacturing opportunities.
The Otago Gold Rush of the 1860s brought a wave of aspiring settlers to Dunedin, New Zealand’s first city in the lower South Island. Among them were the founders of Farra, who sought their fortune in the gold fields.
During the late 1800s three engineering companies, Farra Bros, Dunedin Engineering and Otago Iron Rolling Mills merged to become Farra Engineering. Each company brought its expertise in fabrication works, such as railway wagons, ships, and machinery for local factories and mining operations.
Under one roof, Farra Engineering flourished, weathering challenges like two world wars, the Great Depression of the 1930s, and even a global pandemic. Throughout its history, the company has achieved notable milestones, including engineering massive gantry cranes for ports and power stations in the 1960s, manufacturing the first access machines in the 1980s, and recently building the largest linkage building maintenance unit in the southern hemisphere—possibly the largest in the world.
Today, Farra operates across three areas of expertise. These include access machines maintenance,
repairs and overhaul, and contract manufacturing. The company has strong capabilities in:
• engineering design
• sheetmetal
• stainless and heavy fabrication
• machining
• powder coating and finishing
• laser and plate profiling
Ben Wild is Farra’s Production Operations Manager, who said the company’s long-standing history in engineering makes it the perfect place to push the boundaries of applied innovation.
“We take pride in being New Zealand’s best manufacturing engineers. Home to the broadest range of proven engineering capabilities that you will find under one roof in the country.”
One hundred and sixty years on, the descendants of those founding families remain the major shareholders of Farra Engineering.
As globalisation shifts manufacturing offshore, Farra remains on course delivering high-value engineering and sub-assemblies for customers in Australia and New Zealand.
“ We made the conscious choice to take a ‘quality first’ approach to contract manufacturing. This required significant investment in time, people, process, equipment, certification and ultimately our quality system.”
While Farra’s products and services have changed, its core value of quality assurance remains.
The company’s Quality Management System means all project objectives are clearly communicated and tracked to ensure satisfaction among internal and external stakeholders.
“We made the conscious choice to take a ‘quality first’ approach to contract manufacturing. This required significant investment in time, people, process, equipment, certification and ultimately our quality system,” Wild said.
Farra delivers contract manufacturing capabilities including design, machining, sheetmetal, fabrication, and powder coating. Together, this supports a comprehensive suite of manufacturing capabilities in New Zealand. The company’s manufactured products can be seen in light rail and public transport; telecommunications and electronics; government and commercial infrastructure environments; the aerospace industry; and in appliances found around the world.
To bring these products to life, Farra is home to some of the largest machinery in the country. “Continuous improvement whether it be process or machines is essential to stay head on the curve,” said Wild.
“Our most recent machine purchase is a 2022 FL4020 Phoenix 10kw Fibre Laser with an automated materials tower enabling us to cut 30mm stainless and mild steel, 25mm aluminium, 12mm copper and 15mm brass up to 4m by 2m.”
“Our laser is powered by a nitrogen generator. Generating our own energy has been another positive step towards more control over our supply chain and sustainable manufacturing practices.”
Staff also operate a powdercoating workshop equipped with the Rolls Royce of suites, including an integrated overhead track system, an automated conveyor line up to 2m long, high batch oven, and chromefree pre-treatment tanks. It means staff can deliver bigger jobs of up to 8m.
“It’s this huge breadth of equipment and associated capability across all of Farra that enables us to achieve the things that others can’t. We have a huge versatility of operations. When you have 130 staff across a specialist sheetmetal shop, an expansive stainless and heavy fabrication shop, as well as the largest and most proven machining shop in the country, we have things pretty well covered,” said Wild.
“Personnel in the machining shop operate a selection of CNC turning, CNC vertical and horizontal borers, multipallet HMC’s includes our DMG Mori multi-pallet (work bench) horizontal machining centre.”
“Every year Farra manufactures hundreds of thousands of parts and sub-assemblies supporting New Zealand and Australia’s industries.
We are the engineering name behind some of Australasia’s biggest brands,” Wild said.
Farra takes the time to think about the procedures designed to meet quality standards on some of their more difficult welding projects.
“We have always had a focus on weld procedures in pockets of the business,” said Andrew Bryant (Quality Manager and Welding Coordinator). “Now we are better at it being a core focus across the business as a whole.”
“Our sheetmetal and light fabrication team has worked on train subassembly spot welding—meeting the American Welding Society’s C1.1 standard—and carrying out daily production tests, including tensile pull tests and macros.”
“We provide a number of industries with weld procedure support including energy and heavy industry,” said Bryant.
Farra was a partner in the Tekapo
A Intake Gate project, which was designed to protect one of the country’s most vulnerable power stations from earthquake risks. The site, which provides power to 100,000 homes, is New Zealand’s only power station surrounded by water.
Farra was successful in their weld of the main shaft housing the intake gate, which is 22m deep and weighs 50 tonnes. They welded dissimilar materials, carbon steel to 316SS and 630SS to 316SS using a flux core arc welding procedure.
“As a direct result of all the good work that had already been done including our ISO weld procedures, planning mapping, repair procedures, staff training and support structures we were motivated to continue our quality improvement journey into Australasian rail manufacturing,” Wild said.
Farra Engineering recently became the first New Zealand Company certified to EN 15085 Railway applications—welding of railway vehicles and components.
EN 15085 seeks to coordinate the requirements for welding materials during the manufacture and maintenance of railway vehicles. In November 2023, the Australian Government published the National Rail Procurement and Manufacturing Strategy. It seeks to grow a sustainable rail manufacturing sector, increase productivity, international competitiveness and industry participation.
“Localisation and standardisation of the rail manufacturing in Australasia and further afield will be great for rail manufacturers like us, and it’s assumed that New Zealand will be included in this plan.”
“We hope EN 15085 sets us up well to participate in this as a key supplier as well as serve Alstom well with their current needs,” Wild said.
The strategy will work in partnership with Australian states and territories to support an onshore manufacturing capability, and the development of high-quality, low-emissions passenger and freight trains.
“Many rail projects are demanding
this standard now. We feel wellpositioned to take on even more rail work than we are doing now.”
“Acquiring EN 15085 is a pat on our back that we have demonstrated we can and we will, and we have,” Wild said.
As an International Institute of Welding (IIW) Authorised Nominated Body, Weld Australia is the ideal partner for companies seeking to certify to EN 15085.
Weld Australia’s audit and assessment teams ensure companies are well-equipped to succeed in their certification journey.
Wild said the certification process was seamless but urged likeminded companies not to be complacent.
“Have your house in order first. It’s not enough just to do a few pretty parts, it goes beyond that. Weld
“
Every year Farra manufactures hundreds of thousands of parts and sub-assemblies supporting New Zealand and Australia’s industries. We are the engineering name behind some of Australasia’s biggest brands.”
procedures, certifications, the way your team work and communicate, the way you capture information, inspections, NCRs, logistics… it’s the whole package.”
“Have a plan for the work that you want to get and make sure it’s in line with your company’s business strategy. Work closely with a regulatory body,” he said.
Weld Australia’s team of experts collaborate with members to examine and improve existing processes and bring them into line with Australian and international standards.
“The significance is in future opportunities and recognition, for our clients it’s reassurance and proof. Proof of Farra’s continuous investment in plant, process, quality and people; that we are accredited to international standards; and that Farra’s tailor quality system to meet client’s need and challenges,” Wild said.
For further information about Farra Engineering and their capabilities, visit: farra.co.nz
First Nations communities are gaining first-hand knowledge of welding and fabrication through a joint venture program. Indigee Metals supports young Aboriginal and Torres Strait Islanders to learn valuable skills and make their mark in the sector. This is a gamechanger for Indigenous communities to travel to the city and gain practical knowledge in a trade.
In recognition of their work, Indigee Metals recently won Weld Australia’s 2023 Indigenous Company of the Year Award for NSW and ACT. The award supports the company’s skills program, and provides increased confidence to continue their work bridging the gaps between Australian communities.
Indigee Metals is a majority Indigenous owned company operating as a joint venture between the JNC Group and Precision Metal Group (PMG).
The company works in underserviced regional areas across Australia, where it develops young Indigenous professionals and services their local communities. Staff are also tasked with increasing awareness and sharing a better understanding of Australia’s Indigenous culture, while sparking new opportunities in the welding and fabrication sector. The partnership between the two companies was founded in 2021.
JNC Group is an Indigenous company holding a diverse capability and portfolio of works delivered across remote and regional Australia. Meanwhile, PMG’s innovation and passion for the sector allows it to
deliver quality for high-level Australian Government projects.
Jason Elias (CEO at PMG) said the idea came together in a meeting between likeminded professionals. “They wanted a more fabrication side to their business, and we wanted to participate in more indigenous programs. And with all the certifications we had, and the proven track record of indigenous participation that JNC had—it just came relatively easy.”
Indigee Metals operates across a variety of industries, including: automotive, construction and engineering, defence, manufacturing, mining, rail, steel, water, energy and oil and gas.
The group has a proven track record of delivering complex projects that meet tight deadlines across remote, national and international clients. This is backed by coveted standards like ISO 3834, DIN 2303, and EN 15085. Together, it places Indigee Metals as one of the premier employers and supporters of Aboriginal and Torres Strait Islander groups in the welding and fabrication sector.
According to the 2021 Census, 52 per cent of Indigenous Australians aged 15–64 had employment. In ‘very remote’ areas, the employment rate drops to 32 per cent.
Indigee Metals seeks to bridge these gaps as a Supply Nation registered manufacturing company. Since 2009, Supply Nation has promoted and shaped the Indigenous and Torres Strait Islander business sector. As a member services organisation, Supply Nation facilitates connections between Indigenous businesses members’ procurement departments.
Professional development and upskilling opportunities are central to Indigee Metals’ mission to excel and thrive at delivering complex projects in remote and regional Australia. The team places exceptional customer experience at the core of their works, while supporting local businesses.
A 2016 analysis by House of Representatives Standing Committee on Indigenous Affairs found the most common occupations for Aboriginal and Torres Strait Islander peoples aged 15–64 were technicians and trade workers.
Local employment opportunities and Indigenous business pathways with TAFEs and registered training organisations are one way in which local apprentices and practitioners gain valuable insights.
Indigee Metals offers a student exchange program, which hosts regional students in the city. The program means young people have the opportunity to put their passion to the test before leaving school, by opening fresh opportunities to learn and experience a trade in a supportive environment.
Students can take their knowledge back to their community and work towards future employment opportunities. It also serves as a boost to the sector’s pipeline of future-ready personnel.
Indigee Metals has a strong portfolio working across a variety of projects. However, delivery of defence security is the company’s bread and butter. Working across nationwide capabilities and extending to global reach, Indigee Metals provides tailored solutions for the military and navy sectors. Projects include onsite machining and welding projects to meet the demands of a sovereign defence program.
In the maritime sector, Indigee
For further information about Indigee Metals and their capabilities, visit: indigeemetals.com
Metals works on-site to deliver machining and welding solutions, including maintenance on dry docks and slip ways.
The company’s fabrication works are certified to meet Australian and international standards. The collaboration and unique skillsets of the JNC Group and PMG means personnel are well-placed to meet the challenges of their clients.
Jason said Indigee Metals hopes to bolster its ties with Indigenous programs and people within the regions and cities across the nation to continue their agenda.
“It’s the collaboration of two proven companies to deliver proven track records with the Indigenous participation factor in place.”
“
It’s the collaboration of two proven companies to deliver proven track records with the indigenous participation factor in place.”
Two Navy veterans are behind one of Australia’s fastest-growing manufacturing companies. Allship Engineering has navigated some of the most unchartered waters in the welding and fabrication sector to secure a solid pipeline of local clients, including the Royal Australian Navy. The company’s staff are focused on professional development and training to ensure they remain competitive at the top of their field. As such, Allship was recently certified to AS/NZS ISO 3834 Qualityrequirementsforfusion weldingofmetallicmaterials . The certification means Allship is prepared to take on larger contracts with unmatched skill and confidence.
Serving your country is one of the greatest honours thousands of Australians have embraced. However, adjusting to life after service can be a complex path to navigate.
For Christopher Demos and Andrew Neaves, there was an appetite to give back to the community by helping Australia’s sovereign defence capabilities.
In 2016, the pair founded the mechanical fitting and rigging company, Allship Engineering. Since then, the company has become a major supplier for the Royal Australian Navy. The team also manufactures and supplies parts for BAE Systems Australia, Naval Ship Management and Luerssen Australia. Over 45 employees help Allship to deliver sheet metal parts, insulation,
pipe welding, structural welding, laser cutting, heat shield manufacturing, isolations risk management and a range of other niche services when required.
Australian veterans make up 35 per cent of the Allship workforce. The company is a proud member of the Veteran Employment Program (VEP), which seeks to help businesses fill a diverse skill set. Over 6,000 veterans transition from the Australian Defence Force each year. Through the VEP, veterans have access to a suite of post-service employment opportunities.
Andrew Neaves, Managing Director at Allship, said the company’s team is central to its success. “This focus on people and training, allows us to maintain our experienced workforce
as they have security and opportunity within the company.”
Approximately 20% of Allship’s workforce are apprentices, while 90% of their workforce are full-time employees.
Allship operates a workshop facility in Tempe, Sydney and in Henderson, Perth. “The Tempe facility is 400m2 with multiple welding bays, machine shop and storage bays.”
“The Henderson facility is 4,000m2 with an overhead crane, multiple workshops separated for material hygiene, 1500x3000 bed laser cutter, machine shop, industrial textiles sewing workshop, 16 tonne forklift, rolling, pressing and other sheet
metal equipment,” Neaves said. The facilities are well-positioned to provide machining of steel services, and manufacturing of components for the upgrade and repair of shipbuilding works.
“In our Henderson facility, we have our Automated Orbital Pipe Welding machine that we are still developing procedures for and hope to have fully coded by mid-2024,” Neaves said.
This advanced manufacturing capability will help Allship to produce pipelines with larger and ticker diameters, which can resist immense pressure. Employees are trained as Authorised Isolation Officers, which enhances quality and safety across all parts of the supply chain.
In addition, Allship sources and procures materials and products in an ethical and sustainable way. The company boasts a dedicated health, safety, environment and quality team, who are committed to fulfilling ongoing training and development.Maintaining a high morale is a key priority for Neaves, who said the company offers flexible working conditions.
“Both the New South Wales and Western Australia branches of Allship operate a four day working week, enabling a greater work/life balance for our staff.”
Allship recently certified to AS/NZS ISO 3834. The certification is essential for companies who are
seeking to maximise their profitability and improve the quality of their welding.
Neaves said the certification process came naturally, after a period holding DNV workshop approval, which is specific to marine work. “We found we were missing the opportunity to tender some fabrication work as ISO 3834 was the requirement.” “In addition, already holding ISO 9001, 14001 and 45001, we felt it wasn’t a huge leap to get to ISO 3834,” he said.
As such, Allship’s two facilities have recently become certified. This enhances interoperability and standardises the company’s workflow across its two sites.
For Allship, Neaves believes the benefits of certification have already come to light. “We have been able to firm ourselves as a preferred supplier to a major defence prime. We have also upskilled several employees to their IWS and CSWIP 3.1,” he said.
The certification process prompts senior company staff to take a whole-of-organisation approach. Weld Australia’s team of auditors and assessors take the time to collaborate with companies and improve operations.
Neaves said the process was confronting and “a big leap for the company in some of our welding processes and procedures”. However, he encouraged companies who are in a similar boat to become certified.
“Be prepared for a long process as it is not easy.”
“I would recommend aligning your entire management system to include ISO 3834, as it won’t operate as a satellite entity to ISO 9001 or other quality standards. Integration is the only way to make it work,” he said.
As technology continues to pick up speed at an unprecedented pace, the welding and fabrication industry is not immune to the pressure to innovate to meet the demand to supply key components (such as pipes and tanks) to build the world’s infrastructure.
According to Infrastructure Australia’s third annual Infrastructure Market Capacity Report, released in December 2023, “investment in both regional areas and the energy sector is expected to grow to between three and four times its current level, with cross-sectoral demand placing ongoing pressure on market capacity”.
Labour is a key issue “with a shortage of 229,000 full-time infrastructure workers predicted as of October 2023”, compounded by the fact that “local materials cannot meet demand, particularly in steel and quarry products”. However, the report states there is “an opportunity to increase domestic capacity and markets through low-emission construction materials”.
The good news is that within the traditional industry of welding, by deploying software and automation to a process that is performed manually, there is a solution to the current labour challenges, with the added value of enhanced safety for the welders. From the bottom line, automation has streamlined processes, enhancing efficiency, and improving overall productivity in welding operations. As an example, Novarc’s collaborative welding technology, the Spool Welding Robot (SWR)™ is not only providing a solution to the labour gap, but is
also providing a collaborative solution (where the human welder works with the robot). This allows more precision, safer welds, enhanced productivity and a cleaner, greener process.
Welding is a core process in most greenhouse gas intensive industries in Australia including oil and gas, and mining. Unfortunately, there are significant environmental impact concerns:
• Welding fumes emit carbon dioxide, carbon monoxide, and ozone, the main drivers of global warming and climate change.
• Welding releases metal pollutants to the air such as vaporised heavy metals and oxides from the molten puddle.
• Welding processes take a large amount of energy during every weld, imposing a significant burden on the energy system.
From an environmental perspective, these concerns are being brought to the forefront as Australia has a 2030 emissions target of a 43% reduction below 2005 levels, and an ambitious target to achieve net zero emissions by 2050.
From a health and safety perspective, there are heightened concerns about welders. Safe Work Australia recently announced that Work Health and Safety Ministers have agreed to an immediate reduction in the workplace exposure standard for welding fumes, from an 8-hour time weighted average (TWA) of 5 mg/m3 to 1 mg/m3. As the exposure standard for welding fumes has been reduced, all necessary controls now must be implemented to meet this higher standard.
Automation presents a solution to not only improve productivity and therefore decrease greenhouse gas emissions, but also positively impact the health and safety of welders.
Novarc’s full stack customised automation solution significantly reduces welding duration, delivering lower airborne fumes, energy consumption, and metal waste for the fabrication phase. Welding metal waste control is critical for minimising overexploitation of natural resources.
Novarc’s automation technology has reduced welding and active arc time. This improvement also reduces energy consumption and environmental impact. Minimising the active arc time means less airborne emissions and fumes that pose a risk to the welder; and less energy consumption from external power sources. Manual welding has no control on arc time and is significantly
slower, where automation technology can reduce welding operator hours and active arc time. Other mechanized welding machines do not have the flexibility of Novarc’s robotic system for lowering the arc-time needed for completing the joining. Novarc’s system consumes 20% to 30% less energy than manual welding because of precise control of the on-time of arc. There is also a minimum of a five time reduction in CO2 emission. Similar ratios apply to metal fumes and hazardous airborne materials.
Novarc’s automation system reduces human exposure to dangerous welding fumes such as manganese, hexavalent and chromium. This will help fabrication shops that need to meet the new fume exposure requirements. This is achieved by having the welding operator work several meters away from the welding arc (they don’t have to have their head physically in the direct welding fumes). Conventional manual welders work closer to the arc, and fumes enter their
breathing zones. Novarc’s welding technology allows the operators to work remotely from the arc, and with the use of proper ventilation, most fumes can be eliminated.
Automation in welding involves the use of robotic systems to perform tasks traditionally carried out by human welders. When it comes to pipe welding, a primary safety goal is to keep welders away from the arc whenever necessary and the best way to do this is with the use of a cobot (collaborative robot), Novarc’s Spool Welding Robot (SWR) is an example of this. This robot was designed with the welder’s safety and longevity in mind. Robotic welding systems are designed to handle repetitive, hazardous, or difficult tasks, offering precision and speed that may surpass human capabilities.
For welders, the SWR offers the following benefits:
• Reduction in welder fatigue
• Reduction in exposure to health
hazards such as flashing by arc, UV light, carcinogenic fumes and excessive heat
• Reduction in release of ambient fumes
• Reduction of defect rates and waste
For the environment, the SWR provides the following benefits:
• Reduced welding and active arc time
• Less airborne emissions and less energy consumption from external power sources
• Precise control of final weld shape eliminates wasting metal during welding
• Elimination of extra work for grinding the excessive weld bead (an indirect energy saving in addition to the natural resourcesaving); and,
• Less requirement for post weld NDT - another indirect advantage for saving power and avoiding exposure to X-ray
Weld Australia offers a ‘Hotline’ service to all Corporate Members. The purpose of the Hotline is not to provide a solution, but to advise the enquirer on practical next steps. For further advice, Weld Australia’s highly experienced welding consultants can speak to you over the phone or visit your site in person. If you have a Hotline query, complete our online form: weldaustralia.com.au/hotline
A member recently contacted Weld Australia for advice regarding the wearing religious headwear whilst welding. The two forms of headwear in question were the Islamic headscarf or hijab, and the turban. Weld Australia advised as follows.
Hijab
Wearing a well-fitting hijab in a metal working environment would place the wearer in a safer position than other workers with long hair as the hair is fully covered and not exposed to rotating machinery. If exposed to hot work, the only issue here is the flammability aspects of the material from which the hijab is made.
There are a variety of materials and style of hijab worn in Australia, with a lightweight flowing chiffon quite common because of its attractive appearance. It is made of a mix of cotton, silks and synthetics which potentially would be highly flammable. In Saudi Arabia, the hijabs are often made from viscose which is a cellulosic fibre similar to cotton but potentially finer therefore more flammable.
“Flowing hijabs” would be problematic in any metal working environment due to the risk of loose material being caught in machinery. There is also similar issue with some of our young (usually male) employees who like to leave their (flammable) undergarments hanging
out over their trousers whilst welding or grinding.
If the hijab is tight fitting around the face and head and is made from cotton, it is still potentially problematic but keeping in mind that welders wear cotton caps and cotton balaclavas, it would be no worse.
Wearing a welder’s balaclava over the hijab would offer a good measure of protection, especially if the balaclava has been treated to be flame resistant or is made of leather. Additionally, hijabs made from flame resistant materials are also commercially available.
As with all general advice regarding clothing suitable for welding, hijabs manufactured from synthetics such as nylon or polyester should never be worn whilst welding (including under a balaclava or other welding attire) as should spatter penetrate the balaclava, these synthetic materials can melt and adhere to the skin inflicting a nasty burn on the wearer.
This Hotline update covers a specific query encountered during the last few months. Whilst accuracy in welding is critical, it is impossible to report in detail the full circumstances of the query. As such, Weld Australia recommends that further technical advice is sought in relation to specific, individual circumstances.
Turbans are often made from various cotton materials, some very light weight. The lighter the fibre, the more flammable it is. In addition, its wrapping style could lead to entrapped spatter with the risk of smouldering and bursting into flame depending on material flammability. Wearing a turban with a welding helmet is also problematic and there would need to be a discussion with the wearer about alternative headwear options. A discreet discussion with the turban wearer may elicit this.
Some people wear their turban as a fashion statement and in that case wearing proper welding attire whilst working would not present a problem as the turban can be removed. For many turban wearing people though, the wearing of a turban is a religious issue and a discussion will usually confirm that the hair must be covered (and left uncut) at all times. In this case, a suitable (flame resistant) cap or balaclava could be a viable option for them to maintain their hair covering whilst working and welding.
In summary, for wearers of religious headwear, there are likely to be mutually acceptable options that enables the employer to meet their WHS safety obligations whilst enabling the wearer to satisfy their religious and/or cultural obligations when welding or performing hot work.
Weld Australia has a range of safety resources available that cover effective use of personal protective equipment and more. These resources include:
Fume Minimisation Guidelines: Welding, Cutting, Brazing and Soldering, which includes all the information required to help protect workers from the hazards associated with welding fumes. This has been revised in line with the changes, and a new edition is now available for free download.
Technical Note 7: Health and Safety in Welding gives guidance on health and safety practices in welding, cutting and allied processes such as brazing, soldering, pre- and post-weld material treatments and metal spraying.
Visit the Weld Australia website to download your free technical resources.
Australian Standards are living documents. They reflect progresses in science, technology and systems To maintain their relevancy, all Standards are periodically reviewed, with amendments and revised editions published. The last few months have seen several developments, including ongoing reviews into Standards related to welding safety and consumables, pressure equipment, bridges and steel structures.
The revision of AS/NZS 3788 Pressure equipment—In-service inspection is progressing well. Public comments received have been resolved and the draft is being balloted by committee ME-001.
Committee WD-002 has reviewed and updated most aged standards for welding consumables. The Committee has commenced the revision of AS 2576 Welding consumables for build-up and wear resistance. Good progress is being made.
The revision of AS 1674 welding safety series is well advanced. The initial drafting of AS 1674.1 Safety in Welding and allied processes—Part 1 Fire precautions has been completed and public review is scheduled to commence in March. The standard is used extensively in industry to establish fire preventative measures whilst welding in locations not necessarily designed for hot work.
Separate to this project, Committee EL-019 commenced the revision of the sister standard AS 1674.2 Safety in Welding and allied processes—Part 2 Electrical in August 2023. Work is progressing.
Associated with these projects is the revision of AS 2812 Welding, brazing and cutting of metals — Glossary of terms by Committee WD-003. Public comments received have resolved and the draft is being prepared for committee ballot.
The amendment to AS/NZS 5100.6 Bridge design — Part 6: Steels and composite construction is well advanced and following a period of public comment, comments have been resolved. The draft amendment has been balloted and is being prepare for final approvals and publication.
The revision aligns the requirements of the standard with the latest revision of AS 4100 Steel structures, AS/ NZS 5131 Structural steelwork — Fabrication and erection, and the New Zealand steel structures design standard NZS 3404.1. The revision will resolve known conflicts and anomalies via an amendment.
Standards Australia commenced a major revision of AS 4100 Steel structures in May 2023. Committee BD-001 is managing the project. Cognisance will be taken on the relevant amendments to AS/NZS 5100.6.
WD-003’s project to revise
AS/NZS 2214 Certification of welding supervisors —Structural steel welding is well underway. The project will see the standard split into parts and renamed. The existing standard has become Part 1 and has been revised to accommodate welding inspection, similar to the latest revision of AS 1796. The draft opened for public comment on 21 February 2024 and closes on 24 April 2024.
Part 2 covers bolting supervisors and inspectors, and has been drafted with the assistance of members of BD-001 and ME-029. As previously advised, the long term intention is to add additional parts to cover the qualification of key personnel relevant to AS/NZS 5131. The draft opened for public comment on 21/02/2024 and closes on 24 April 2024.
Committee BD-023 is currently revising AS/NZS 1594 Hot-rolled steel flat products. Formerly managed by Committee MT-001, this standard primarily relates to grades of steel used in hot rolled coil product form but also relates to lighter gauge plate manufactured from hot rolled coil for structural purposes. The draft is being prepared for public comment.
ISO Update
ISO TC44/SC10 has completed the revision of ISO 3834 Quality requirements for fusion welding of metallic materials series of standards primarily taking cognisance of changes to ISO 9001 Quality management systems — Requirements and the 2019 edition of
ISO 14731 Welding coordination — Tasks and responsibilities
Parts 1 to 5 inclusive have been published and adopted by Standards Australia as direct text adoptions. Revision of Part 6 of ISO 3834 is now well advanced and is currently undergoing FDIS ballot. Consideration for adoption in Australia will commence after finalisation by ISO.
TC44/SC10 has also been revising ISO 17660 Welding — Welding of reinforcing steel. This edition is planned to combine the two existing parts into a single document. Work is ongoing.
Similarly, ISO TC44/SC11 has been revising ISO 9606-1 Qualification testing of welders—Fusion welding— Part 1: Steels to combine all 5 parts into the one standard. This will simplify the ongoing maintenance and review requirements for the standards currently published as Parts 2 to 5 of ISO 9606-1. Comments received from the CD draft and ballot are currently being resolved.
Weld Australia’s Industry Groups provide a forum for technology transfer and research and development, linking members with industry and research organisations. Weld Australia works with Technology Network members to ensure they remain diverse and resilient in the ever-changing and increasingly challenging global markets.
A special meeting of the Welding Safety Council was held on 29 January 2024 to discuss the recent changes to the Weld Fume Workplace Exposure Limit from 5mg/m3 to 1mg/m3.
This change will require a more stringent approach to the implementation of controls during the welding process to achieve the requirements of the new limit. In particular the hierarchy of controls needs to be considered when implementing these controls. In particular the following needs to be considered:
• At source fume extraction
• Good general workplace and workshop ventilation
• Powered Air Purifying Respirators (PAPR)
Weld Australia has developed two comprehensive online training courses designed to improve safety outcomes across the country.
One course is tailored for welders, while the other is aimed at welding engineers and supervisors. These courses are now available via the Weld Australia website or via: https://weldtraining.online
The next meeting of the Welding Safety Council will be held on 9 April 2024.
The Defence Industry Group met on 7 December 2023. There were three key discussions and presentations.
Ashley Bell (BAE Systems) provided an overview of BAE Systems operations at Osborne in South Australia. Geoff Crittenden gave an update on Weld Australia’s activities.
Jason Elias (CEO, Precision Metal Group) led an open discussion on local Australian manufacturing in the defence industry, focused on issues and challenges.
The discussions highlighted that one
of the major challenges currently facing the defence industry is that of skilled labour, especially the shortage of qualified welders and engineers with a good foundation in hands-on manufacturing.
The next meeting will be held on 10 April 2024.
The next meeting of the Advanced Manufacturing Industry network is scheduled for 3 April 2024 and will focused on cobotic welding. It will be co-hosted by the Australian Cobotic Centre.
The following meeting is scheduled for May 2024 and will focus on additive manufacturing.
The next meeting of the Renewable Energy Industry Group is currently being planned and will be held in June 2024.
The next meeting of the Boiler Industry Group will be held on 19 and 20 June 2024 at Loy Yang B Power Station in Victoria. The Process Safety Group will meet on 3 April 2024.
For further information or to join one of our Industry Groups, contact: Andrew Davies (Manager Technical Industry Networks) on a.davies@weldaustralia.com.au or 0438 428 966.
Occupational health and safety is designed to help organisations reduce workplace injuries, illnesses and fatalities, as well as to promote and protect the physical and mental health of workers.
AS/NZS ISO 45001 provides a framework for organisations to establish, implement, and maintain an Occupational Health and Safety (OH&S) management system. Introduced in 2018, the leadership-lead approach of AS/NZS ISO 45001 means that it meets moral, legal, ethical and industry-best practice when it comes to an employers’ duty of care over staff.
The main objectives of ISO 45001 are:
• Identify and Control Hazards: By assessing risks and opportunities, organizations can proactively address potential OH&S issues.
• Reduce Workplace Accidents and Diseases: Through systematic policies, processes, and practices.
• Establish Operational Controls: To manage OH&S risks and their potential impacts.
• Evaluate OH&S Performance: And seek continuous improvement.
• Engage and Ensure Participation of Workers: And ensure their consultation in decision-making processes.
• Meet Legal and Regulatory Requirements: Ensuring compliance with current regulations related to occupational health and safety.
AS/NZS ISO 45001 certification shares principles with a range of other essential standards within the welding, fabrication and manufacturing space.
This certification offers numerous benefits. It not only helps reduce the incidence of accidents and health-related absences but also demonstrates your commitment to the safety of your workforce. This proactive approach to health and safety can enhance a firm’s reputation, boost employee morale, decrease insurance premiums, and help ensure compliance with legal and regulatory requirements.
Weld Australia is a highly respected and independent third-party, and is proud to be the International Institute of Welding (IIW) Authorised Nominated Body for Company Certification. Our certification process ensures a rigorous audit system is in place, confirming your business as a leader in the competitive fabrication industry.
When Weld Australia conducts your certification audits and assessment, you have access to our highly qualified team of experts. All our assessors are:
• Qualified and experienced in quality system auditing
• Welding industry experts, with extensive experience
• Certified in Integrated Management System (IMS) Certifications
• Experts in quality management systems, auditing principles and AS/NZS ISO 19011 Guidelines for auditing management systems
For more information, visit our website.
Starts 8 April
An AS1796 Welding certificate is by far the most well known and requested welder certification nationally. It is used in both structural and pressure equipment Standards. The course is delivered online over 15 sessions, live via Zoom. Participants can ask questions, in real time, of our experienced welding technology trainer.
Starts 27 May
This face-to-face training runs over a 1-week block at our Wollongong office. The first 4 days consist of theory and practical training, with the final day a practical exam. The theory exam will be scheduled online the following week. The IWI-B course is a globally recognised IIW qualification that covers general knowledge of welding and inspection.
Starts 20 May
This face-to-face training runs over a 1-week block at our Wollongong office. The first 4 days consist of theory and practical training, with the final day a practical exam. The theory exam will be scheduled online the following week. The IWI-B course is a globally recognised IIW qualification that covers general knowledge of welding and inspection.
& AS2214
Starts 8 July
A Welding Supervisor qualification expands your career horizons enormously. Both AS 2214 and AS 1796 Certificate 10 meet the requirements outlined in AS/NZS 1554.1 to supervise the welding of structural steel. Similarly, AS 1796 Certificate 10 meets the requirement for a welding supervisor under AS 1210 for pressure vessels.
Starts 20 May
This course provides advanced knowledge of welding and inspection, including NDT, mechanical and visual inspection, acceptance criteria, identification of weld imperfections and more. The training runs over 8 days at our Wollongong office. The first 7days consist of theory and practical training, with the final day a practical exam.
WELDING INSPECTOR - AS1796 CERTIFICATE 11
Starts 15 July
The Certificate 11 is an Australian Welding Inspection qualification recently introduced to AS1796, this qualification builds upon the foundation knowledge expected of a Welding Supervisor with a distinct emphasis on inspection activities related to pressure equipment, as well as the documentation associated with this role.
Weld Australia designed and created a suite of resources for delivery of the 12 welding and fabrication units of competency in the Manufacturing and Engineering (MEM) Training Package. These Resources have been praised by industry and won the 2023 Excellence in Manufacturing Skills Development Award at the 2023 Endeavour Awards.
Weld Australia designed and created a suite of resources for delivery of the 12 welding and fabrication units of competency in the Manufacturing and Engineering (MEM) Training Package.
According to Geoff Crittenden (CEO, Weld Australia), “Our resources help simplify the learning process for students, teachers and training institutes and—most importantly— place the student at centre of the learning process.”
“Weld Australia believes that a national industry, which has a national learning package, needs national learning resources. Whether you’re an apprentice in Kalgoorlie, Ultimo or Davenport, you should have access to the same, high-quality training. Our goal is to help ensure that highquality welder learning is consistent across the country.”
Weld Australia formed a national consortium of TAFEs to work on the
project. Over the last two years, the consortium has collaborated with us to develop the most engaging, up-todate resources possible.
Weld Australia’s MEM Resources have been built with students, teachers and training organisations in mind. It reimagines the learning process with its user-friendly interface, diversified delivery methods, and audited and accurate material. The new MEM resources are completely online and accessible via phone, mobile device or computer. This allows students to access learning at the time, place and pace that suits them best.
Members of the consortium piloted use of the resources, and some TAFEs have already permanently adopted them.
South Metropolitan TAFE in Fremantle, Western Australia was the first training organisation to
facilitate an official pilot. The feedback received from students and lecturers alike was extremely positive.
According to Jonathon Maile (Executive Director – Engineering, Transport and Defence, South Metropolitan TAFE), “The resources have been terrific, not only for our team here at South Metro TAFE, but we’ve also upheld these and shared these with some external customers as well. So from a quality perspective, the resources have been tremendous.”
“Being able to link in with Weld Australia and other TAFEs, improved training outcomes—there is a better consistency from a technical perspective Australia-wide. It has improved our focus on digitisation and e-learning, and the increased the flexibility of how we deliver. We’re able to utilise these training resources in class to support lecturers. If apprentices miss classes, they can access the resources and catch up a lot more quickly than trying to reschedule another block later on.”
Brenda Micale (General Manager, Training Services at South Metropolitan TAFE) agreed. “The resources have improved our delivery across the fabrication area quite significantly. We’ve had some really great feedback from our industry partners too.”
“On our own, we could have developed an adequate suite of materials for the qualification. Through the national collaboration, we got a much higher quality resources. On a TAFE budget, we
never could have got all the bells and whistles—the videos, the eLearning— it’s just financially out of our reach.”
“It’s great when I go out to Rockingham, the Thornley and Naval Base campuses where fabrication is taught and you can see apprentices engaging with the technology. They’re able to download it onto their mobile phones, they can play the videos, its interactive.”
The online platform that houses all the MEM resources is called Weldpool. Weldpool is Weld Australia’s purpose-designed Moodle platform that integrates easily with your own Moodle, or a blackboard website. The purpose of Weldpool is to provide a simple user interface where student can find the resources they need as quickly as possible.
The new MEM resources are completely online and accessible via phone, mobile device or computer. This allows students to access learning at the time, place and pace that suits them best. In one of our units, you can expect:
• Theory presentations
• Practical demonstrations
• Written resources, including student and safety notes complete with hot tips, QR codes
to access videos, and review questions
• Online review quizzes, which are fuelled by a bank of multiple choice, short answer and interactive questions.
• Anywhere, any time. The new resources are completely online and accessible via mobile device (like phones and tablets) or computer. This allows students to access learning at the time, place and pace that suits them best.
• Easy to use. The platform on which all the resources are hosted features a simple, easy to navigate user interface where students can find what they need as quickly as possible.
• Better use of on-campus time. With a comprehensive suite of resources at their fingertips, students can focus on developing their practical skills while oncampus, rather than reading through theory.
• Unlimited access. Students have unlimited access to all resources, throughout their entire period of enrolment in the unit. This means students can go back and revise material if they need to.
• Multiple delivery methods. There are multiple delivery methods available, including lock step, workplace delivery, institutional delivery, self-paced learning and distance learning. Every option is covered, for a flexible solution.
• Avenues to provide regular feedback. Teachers can submit feedback which will be reviewed by Weld Australia’s team of experts and incorporated into the relevant resources as quickly as possible.
• Save time. With a comprehensive suite of resources at their fingertips, teachers slash preparation and administration. Leaving more time to devote to students or reducing overall working hours.
• Peace of mind. Teachers can rest assured that all units of competency are covered in full by the up-to-date suite of resources. Students will be fully prepared to pass exams and enter the workforce.
• Cost savings. Organisations save costs on both the development and maintenance of resources. Resources will be reviewed annually and updated in line with latest technology and training packages.
• Standardised. Training organisations can rest assured that all their teaching material is consistent across all their campuses, regardless of the staff involved.
• Audited and accurate. All resources are fully mapped to the units of competency and independently audited by a team of experts. All resources have been vetted by a consortium of TAFEs nationally.
• Easily integrated. The online platform that houses all the MEM resources is called Weldpool. Weldpool is a purpose-designed Moodle platform that integrates easily with your own Moodle, or a blackboard website.
TUESDAY MAY 7TH
12PM SESSION LAUNCH
12:45PM - 2:30PM NETWORKING LUNCH
SOFITEL SYDNEY WENTWORTH
BRISBANE ROOM
101 PHILLIP STREET SYDNEY NSW