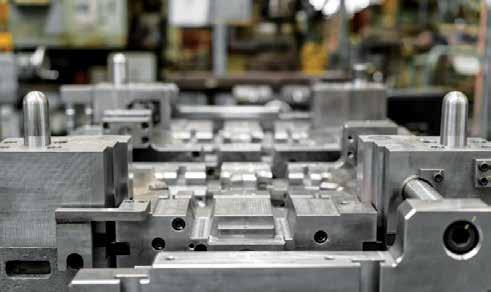
15 minute read
Why Should We Consider Building Movement When Specifying Perimeter Fire Seals for Curtain Wall Façades?
View from high pressure aluminium die casting setup
Advertisement
Almost all companies with high technology and high brand recognition have started to produce their handle arms from aluminium
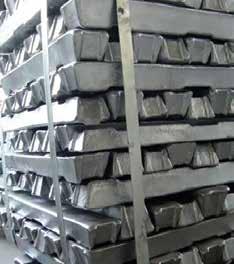
In the last century, in addition to the contributions of chemistry to our lives, the changes in the world markets after the Covid changed both the preferences of the producers and the preferences of the consumers. This change of preference causes people to question traditional value judgments in their minds, rather than seeking only material benefits.
This change will only enable companies that can sense this change to survive. This applies not only to companies that manufacture accessories but also to window manufacturers that use them. It should be competitive by focusing on quality and correct accessories in the face of increasing costs falling on window manufacturers and conscious consumers. For this, we will first need to change our traditional value judgments, question the wrongs here by putting a shark in our brain, and find the right alternatives and bid deals
When we say value judgments, explaining this with a few examples will make the subject more understandable. Today, almost every house has a car or motorcycle. These cars stay outdoors for years. Are they rusting? never! If that were the case, wouldn’t all cars have to be made of stainless steel? Here is what we need to immediately throw a shark in our brains and question, so why do we think it is right to use stainless espagnolettes in our windows? What a big mistake, right? Moreover, these espagnolettes are not directly exposed to external factors, and even the sun does not touch the surface of most of them. Using stainless espagnolettes was a simple solution when metal was cheap and technology was not developed and it played into the hands of China, which has the most stainless steel reserves in the world. Today, when we consider nationalism in the preferences of the consumer who is aware of this issue, and the policies developed to

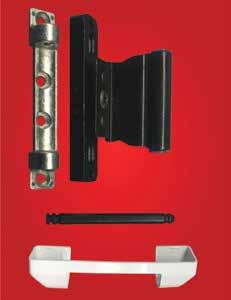
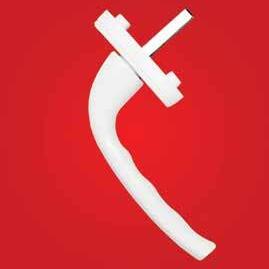
New generation adjustable hinge set with cataphoresis coating
Composite window handle made of aluminum casted arm, high-tech plastic base and glass fiber reinforced gear system
use national resources correctly are also supported by the states. Now, instead of stainless steel in espagnolettes, steels developed against corrosion with surface treatments will be used. Yes, we all know that the standard galvanizing process is not enough. However, advanced chemical technology product lacquers are coated on top of this, and advanced corrosion resistance is gained. Even the e-coat (cataphoresis) coating technology used in the automotive industry has started to be used in the coating of window accessories. This change, which started in the world’s leading and quality companies, has started to spread rapidly. The beautiful thing is that even the leading companies in the Indian market are now starting to use their preferences in this direction. I am really happy to observe this.
In addition, as a result of increased metal prices and imbalances in some metal prices in the process after Covid, there is a very rapid transformation from zinc to aluminium in the accessories sector. Almost all companies with high technology and high brand recognition have started to produce their arms from aluminium.
Of course, these transformations require high investments and knowledge. In this change process, not only the conversion from zamak (zamak is a family of alloys with a base metal of zinc and alloying elements of aluminium, magnesium, and copper) to aluminium but also from zamak to plastic has gained a significant acceleration. Of course, the plastics mentioned here are high-tech, reinforced with new generation additives. Glass fibre reinforced, carbon fibre reinforced, ceramic filled and even aramid filled plastics got involved and presented a picture that gave better results than metal.
As I mentioned above, the increased metal prices after the covid increased the efforts of the countries to be selfsufficient and made recycling important. Even consumers have come to attach importance to the fact that the products they buy are recyclable or eco-friendly.
However, my feeling is that this change will not be limited to this. We should not be surprised if we see plastic window espagnolettes designed for this, containing high technology, very soon. BERK SECKIN
Founder and CEO,
DOCTORWINDOW

ABOUT THE AUTHOR Berk Seckin, Founder and CEO of DOCTORWINDOW has vast experience and rich global exposure of 27 years in Doors & Windows industry. Before India, he worked as a senior manager in companies operating in the door and window industry in many countries such as Turkey, Ukraine and Libya. He has extensive experience in all stages from profile extrusion to window assembly.
DOCTORWINDOW was founded in 2019. The company has brought a single roof solution to the industry, highlighted the importance of product diversity and played a major role in the development of the sector in digital media. The big manufacturers in the window industry call DOCTORWINDOW a “GAME CHANGER” as a result of its success in a short time. DOCTORWINDOW carries out its studies to present the search for new solutions to the Indian market by using its relations in the international arena.
What is the Importance of Window Sills?
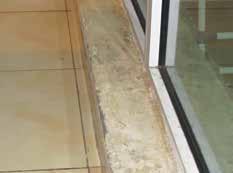
Sill window - The Indian way
Window sills are an integral part of any building’s structure. The building envelope is the outside part and has to face many weather conditions or the fury of nature. We protect the outer skin by having different kinds of claddings; for example, stone cladding, marble cladding, etc. In some areas, we fix tiles or wooden cladding or go for special plastering, so that the area of the outer structure looks presentable and is protected against the weather condition.
But in India, that window sill area is completely neglected. Outer walls by default are vertical. So when the rainwater hits the wall, it will flow down. But the window sill area, where usually the windows are fitted in the centre, has a 2 to 4-inch horizontal plain area. So eventually in this area the rainwater and dust may also collect. If a mason does not make the slope towards the outer wall, the water will collect towards the window. In monsoon, there are chances of water leakage and the water will enter inside the house.
What are the options to consider?
Option 1: You can have a stone cladding at the sill area but even then care should be taken that there is one inch of overlap so that the water flowing out from the window sill is actually going down and not hitting back to the outer surface of the wall.
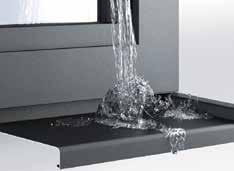
Stone cladding at the sill area
Option 2: This is widely used in Europe where the window sills are made out of aluminium. You can choose colour options to match it with the colour of the window. You could go in from lighter shades to darker shades to match the outer walls.
The rainwater hitting the glasses will drain down on the window sill. As the window sill will have a slope angle of 5 to 8 degrees, the water will completely drain out. If the window sill is around 50 mm in front of the building, then the rainwater will drop down hitting the surface of the building. This will ensure there is complete water tightness. So in the monsoon when the water comes through the glass, it will immediately drain out.
At the sides where the Aluminium sill is attached to the wall, end caps are connected. This will assure complete water tightness and it provides the perfect connection to the wall. MARIO SCHMIDT
Managing Director,
Lingel Windows and Doors Technologies Pvt Ltd


ABOUT THE AUTHOR
Mario Schmidt has been the Managing Director of Lingel Windows and Doors Technologies since 2006. He is also the Company Director of Fensterbau Lingel Germany gmbh. With his immense knowledge in Mechanical Science he has been able to add more value to the company’s innovation plan and has helped launch various new products. Mr. Mario Schmidt is the President of the uPVC Windows and Doors Manufacturers Association (UWDMA). He is a voracious reader and an orator who can speak on various topics related to the industry.
Why should We Consider Building Movement When Specifying Perimeter Fire Seals for Curtain Wall Façades?
Curtain walled buildings may require bespoke perimeter fire seal solutions to manage varying depths between the façade and floor slab As more and more sky-high multi-occupancy buildings emerge across India’s densely populated megacities, it is not only crucial that curtain wall façades are designed and constructed to withstand constant movement but that the passive fire protection measures incorporated within can accommodate this movement.
With clean lines, sleek glass surfaces and technological glazing innovations, curtain walls offer an ultra-modern aesthetic, floor-to-floor natural daylight and excellent weatherproofing. Unlike more traditional wall constructions, curtain walls are not part of the building’s supporting structure. They are a non-loadbearing and self-supporting vertical enclosure or envelope that separates and protects the internal environment from the external climatic conditions. This makes them highly susceptible to movement caused by wind and rain loads, seismic sway, occupancy loads on the floor slab and thermal loads that cause the structure to expand and distort. Whilst various calculations and computer modelling can help designers to better understand the range of potential movement and work needed to mitigate it, it cannot be designed out completely.
Consequently, curtain walled buildings are commonly built with a gap between the edge of the floor slab and the façade itself to allow for both vertical and lateral deflection. This is known as the movement gap or the expansion joint and the designed perimeter gap can vary considerably in void size. For instance, this can be wider in certain cases such as where buildings are built in locations with high movement risk (e.g. frequent seismic activity) or include more dynamic, complex design elements (e.g. curved elevations). Whilst vital for allowing free movement without damage to the structure, this gap can present a huge challenge when it comes to ensuring passive fire protection.
Perimeter Fire Seals Unprotected and improperly protected movement gaps can provide a clear path for flames, smoke, and hot gases to be drawn upwards due to the chimney effect, enabling the fire to spread floor to floor. To inhibit this, perimeter fire seals— also referred to as firestops— must be installed at each floor level to maintain the integrity of the compartment floor slab right up to the internal surface of the curtain wall and achieve compartmentation.
However, as the gap width is in constant flux, it is important that the specified solution not only achieves the required fire resistance, but that it can maintain a tight seal whilst withstanding constant inward and outward movement for the lifetime of the building. If the perimeter seal does not adequately recover from the compression cycles, then gaps could form between the curtain wall façade system and the structure, allowing the fire to spread through the building envelope and putting people’s lives and property at risk.
It is thus recommended that curtain wall perimeter fire seals provide a 7.5% or greater movement capability
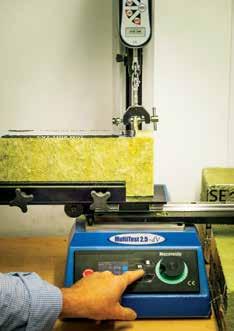
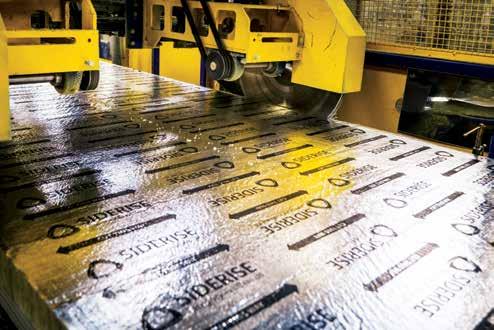
Perimeter fire seals for curtain wall systems must be engineered to deal with both inward and outward movement for the lifetime of the building.
at the movement joint, allowing both compression and flex. To do this, they must be installed under compression. The Association for Specialist Fire Protection (ASFP) stresses the importance of this in its Red Book- Firestopping: Linear Joint Seals, Penetration Seals & Cavity Barriers (4th Edition):
“The effectiveness of the fire stop will depend on the ability of the curtain walling/cladding system to maintain the compression fit for the duration of the required fire resistance period. Unless the system is installed pre-compressed and can move to maintain compression, premature failure of the fire-stopping may occur.”
Therefore, careful consideration needs to be given to how well a firestopping product can withstand these compressive forces over time, whilst retaining its ability to recover/flex.
Form and Fit There are several perimeter fire seal options on the market, and their suitability for curtain wall applications is dependent on the compressibility of the product, and how well it can recover to allow for flex. Traditional approaches required installers to cut and compress noncombustible insulation material (also known as safing) onsite and seal it with a sprayed-on wet compound. They are often referred to as ‘wet systems’ and must be applied in dry conditions to prevent washout. Once the compound is applied, the only way to verify if the right compression has been achieved is through destructive testing. This type of system also typically uses standard rock wool insulation with horizontal fibres. Whilst this makes the product stable, this orientation also makes them difficult to repeatedly compress without resulting in a breakdown of the bonding between the fibres. If this happens, the product will not recover and flex in line with the façade movement, resulting in gaps and distortions forming and causing the compartmentation to fail.
However, innovative single-part ‘dry systems’ have been developed that use vertical fibre orientation. They are engineered through a unique manufacturing process that involves cutting a special formulation stone wool slabs into sections and rotating the sections 90 degrees to vertically orient the fibres. These sections are then laterally compressed using an automated factory process to remove any gaps between the sections and assist in uniformity of product density. While the inline compression is being applied, foil facings are simultaneously heat fused to retain the ‘pre-compression’. This aluminium foil also provides weather protection without the need for wet seals. They are then further compressed by 10% when they are installed, wrinkling the foil, and making it very easy to confirm if they have been installed correctly.
Accounting for Movement in Test Standards As with any fire protection product, it is vital that curtain wall perimeter fire seals are tested to standards that accurately reflect how they will be used and the conditions they will be subjected to. This ensures that their fire resistance performance is truly accurate. Consequently, EN 1364-4 and ASTM E2307, the most commonly used fire test standards for perimeter fire seals in curtain wall constructions include provision for movement.
The EN 13830 product standard for curtain walling stipulates fire resistance testing in accordance with EN 1364-4 and durability and cycling in accordance with ETAG 026 (now superseded by EAD 350141-00-1106). EN 1364-4: 2014 – Fire resistance tests for non-load bearing elements (Curtain walling – part configuration) is the European standard for curtain wall perimeter fire seals. It is a part configuration test that applies to both Type A - fire rated, and Type B – non fire rated, curtain wall systems. Non fire rated façades are typically made from aluminium and therefore when being tested, the critical spandrel zone requires protection to enable it to survive for the duration of the test.
As the test construction is representative of curtain wall construction, the perimeter fire seal will be subjected to movement caused by deflection of both the floor slab and the curtain wall façade due to the thermal load of the fire. However, EN 1364-4 also includes provision for long-term façade movement by referring to the European Technical Approval Guidelines 026-3, which is now superseded by European Assessment Document (EAD) 35014100-1106. This is a harmonised technical specification for linear joint and gap seals developed by the European Organisation for Technical Assessment (EOTA) for cases where a product is not fully covered by harmonised European standards. EADs are the basis for issuing European Technical Assessments (ETAs). EAD 3501141-00-1106 requires that the perimeter seal is subjected to a minimum of 500 cycles between the minimum and maximum joint width, to simulate wind sway, seismic activity and thermal load at a rate designated by the test applicant. After this cycling, the construction is left to stabilise for 24 hours and cannot be altered before testing. The pre-cycled perimeter seal and curtain wall system is then exposed to furnace testing of over 1000°C at 20Pa positive pressure as per the EN 1364-4:2014 test standard.
If manufacturers are voluntarily applying a CE Mark, it is imperative to understand if they have been tested in accordance with EAD 350141-00-1106 as it is only in these cases that true movement testing has been applied.
EN 1364-4 has also been the recommended test standard by the Association for Specialist Fire Protection (ASFP) since 2014, as per their Advisory Note 7 -
“The ASFP recommends that horizontal linear gap seals used in association with curtain walls are only tested to BS EN 1364-4 and that test evidence obtained using BS EN 1366-4 cannot be used to support that end-use application”
It is important to note that EN 1366-4 is a static test whereby the specimen is sandwiched between two concrete floor slabs. As such, it cannot be used to support curtain walling applications. The same is also true for the older BS 476-20 test standard.
ASTM E2307-20 ‘Standard Test Method for Determining Fire Resistance of Perimeter Fire Barriers’ is the American test standard for curtain wall firestops. This is widely referred to in regulations in the USA, UAE, and various regions in the wider Middle East and Asia Pacific. It is designed to measure the performance of the perimeter fire seal only, assessing its ability to “maintain a seal to prevent fire spread during the deflection and deformation of the exterior wall assembly and floor assembly during the fire test.” It uses intermediate scale multi-storey apparatus to expose the perimeter joint to fire, both from the room where the fire started, and the exterior as the fire plume exits the room of fire origin through a window opening.
Like EN 1364-4, it also includes provisions for pre-cycling, or ‘cold’ movement of the test specimen before the test begins, covering thermal load, wind sway, seismic movement, and all these
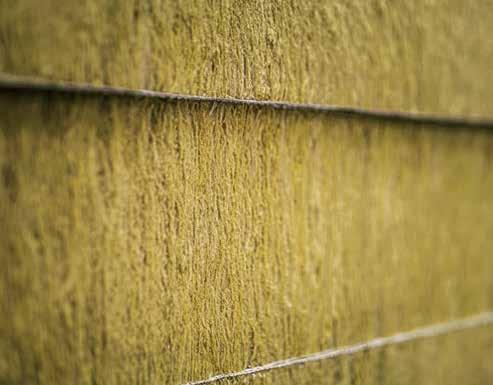
The unique characteristics of lamella allow the perimeter fire seal to flex and recover without degrading when accommodating dynamic movement in curtain wall façades