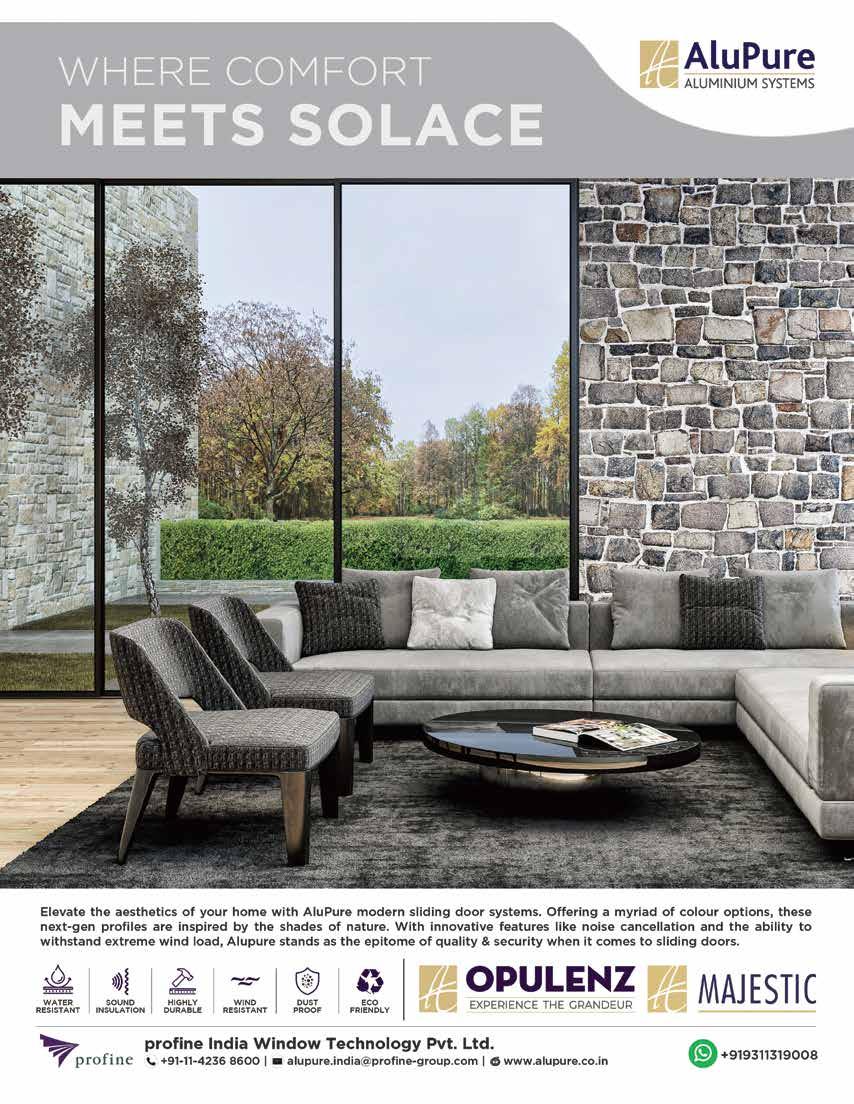
9 minute read
Challenges in Building Fully Curved Unitised Panel
combined. The rates for cycling and the minimum number of movement cycles depend upon the type of movement required. Whilst ASTM E2307 clearly states the criteria for the movement cycling, it is not uncommon to see listings where movement has been evaluated in accordance with ASTM E1399/E1399M-97(2017) - Standard Test Method for Cyclic Movement and Measuring the Minimum and Maximum Joint Widths of Architectural Joint Systems - a cyclic movement test standard for linear joints - not a perimeter fire barrier construction: two very different things.
Checking if these tests have been third-party certified by an accredited organisation that conforms to strict ISO requirements is an important step for specifiers to ensure confidence in the performance and consistency of the products. Gaining certification is not easy. It is a tough and lengthy process, usually involving reviewing product test data against appropriate standards and requirements, as well as submitting product samples for analysis and as comparative samples. Maintaining certification is even more arduous with ongoing surveillance activities including unannounced factory visits and random audits. If any significant changes are observed, certification is withdrawn, and re-testing is required.
Advertisement
Manufacturers of these products may also carry out their own accelerated age testing to further determine the robustness of their products.
The Significance of the ‘Spandrel Zone’ Both EN 1364-4 and ASTM E2307 are tests of the façade system. Accordingly, it is essential that the complete tested and certified solution, including protection materials for the critical spandrel zone in the case of aluminium framed façades, is fully understood and detailed at the time of project design and specification. The perimeter fire seal, spandrel insulation, and any additional perimeter fire barrier boards for protecting the spandrel panel, mullions and transoms all function together to deliver performance and cannot be used interchangeably or substituted without repeating the full curtain wall façade set of tests.
Fit for Function Curtain walls are an attractive and functional façade option, but sufficient regard must be given to ensuring the passive fire protection measures are appropriate to avoid any risk of compromising the property protection and life safety strategies. Specifying perimeter fire seals that have been engineered and third-party tested and certified to ensure their performance reflects their intended use as part of a constantly moving curtain wall façade, is a safe specification strategy for containing fire and smoke and providing peace of mind that they will protect properly for the lifetime of the building.
For more information and guidance on passive fire protection, visit www.siderise. com
For more details, contact: Siderise India Pvt. Ltd, Apeejay Business Centre, Cabin 10, 1st Floor, Apeejay Express, Plot 87, Sector 17, Navi Mumbai, Maharashtra 400703, India; T: +91 998 700 4611; siderisein@siderise.com; www.siderise.in
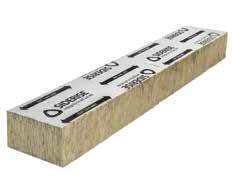
The pre-compression enhances the integrity criterion when the foil delaminates releasing the compression and allowing the lamella core to expand laterally SREENIVAS NARAYANAN
Technical & Compliance Director – India, MEI + AP,
Siderise Insulation

ABOUT THE AUTHOR
Sreenivas is the Technical and Compliance Director for India, the Middle East, and Asia Pacific at Siderise Group. He is an avid advocate of advancing fire safety to build safe buildings by getting it right the first time round.
Siderise has 50 years’ experience in the passive fire protection industry and three fundamental principles underpin their activity: Insight, Ingenuity, and Integrity. Siderise is the only passive fire protection products manufacturer offering a complete factory-engineered solution for spandrel protection comprising perimeter fire seals and perimeter fire barriers. They place technical, accredited and third partycertified product performance at the very heart of their passive fire protection solutions. Siderise believes that if buildings are to be designed and built with integrity, optimising fire safety in facades and curtain wall structures should start at the concept and design stages.
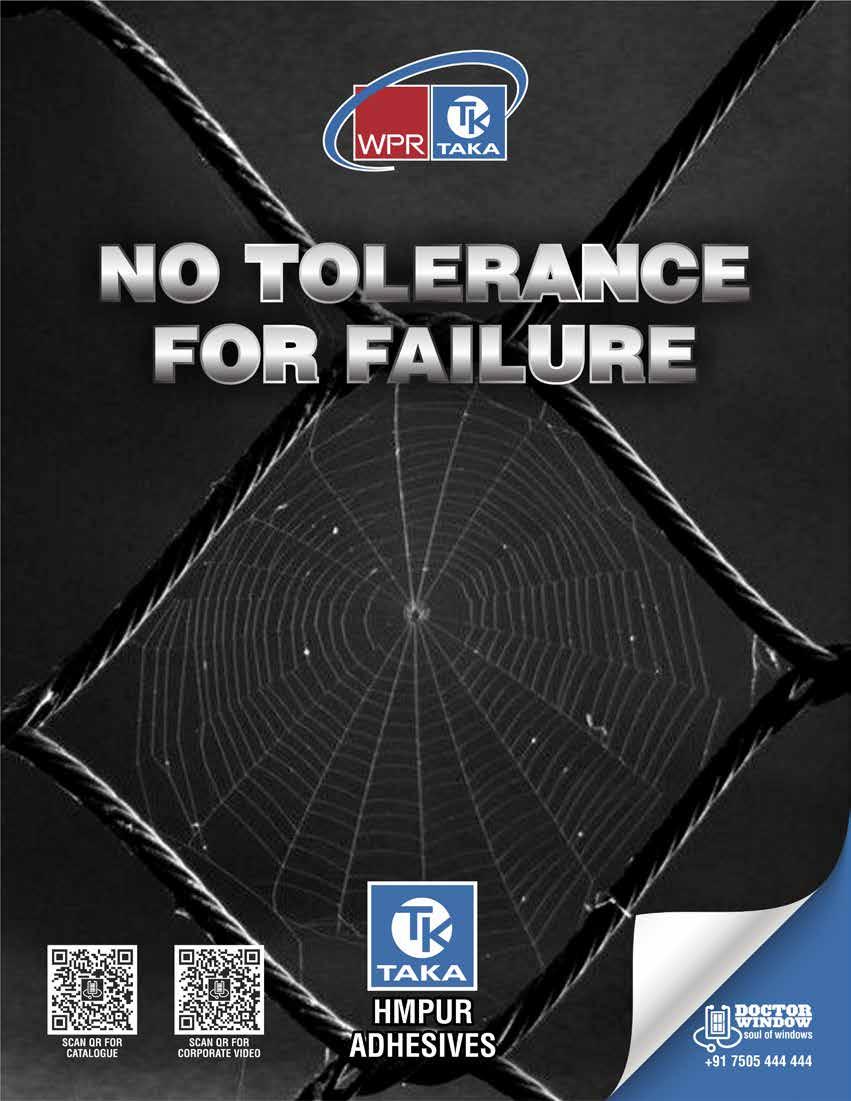
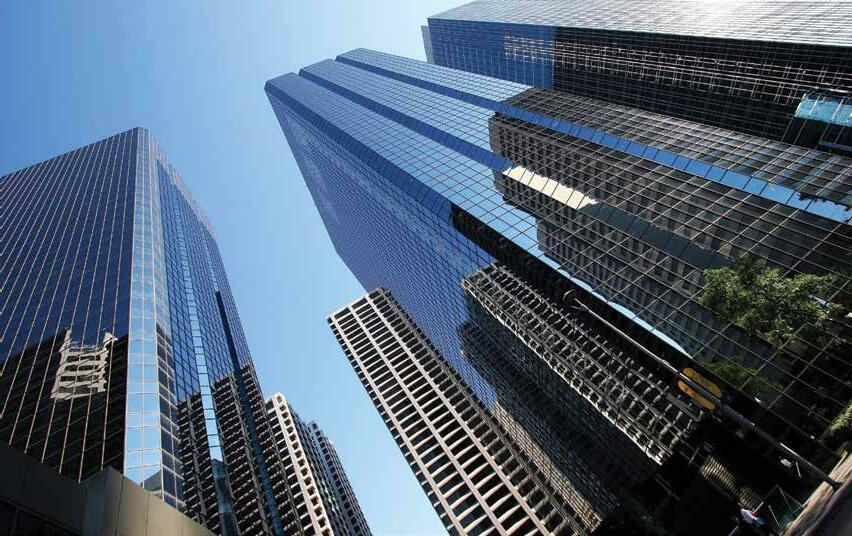
The point of this article is to show the intricacy of planning a DGUcurve façade with and work with this assignment practically speaking for plans which face these kinds of difficulties just as fill in as broad information for those doing additionally investigate in this theme.
The point of this exploration was to see if the current unitised curtain wall systems’ techniques can be utilised for DGU-curve façade and, assuming this is the case, is to make understand exterior project workers and architects about the process involved in planning a DGU-curved unitised curtain wall system.
The examination procedure comprised of having three sub-fields of exploration: DGU unitised frameworks investigation, design examination, and material examination. This situation would, on a fundamental level, imply that curve DGU glass, straight and turned or single-bended, and bent transoms would need to be utilized. Objective is to analysis need to be done on initial stage, what exactly project needs? Therefore, the design development phase focused on the design of a unitised system for the “floor-based twisted extruder” using double-curved insulating glass, straight or single-curved transoms and single curved mullions. The use of
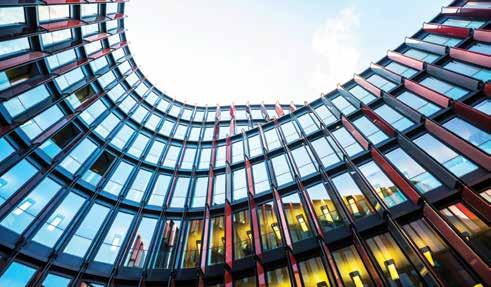
non-twisted profiles led to several rotations or deviations in the cross joint (where four units meet) as well as to varying angles between the glass unit and the load-bearing curtain wall profiles.
Questions to be asked before going manufacturing curved unitised panels:
1. can the current unitised component-based curtain wall systems’ strategies be used for DGU curved facades?
2. what is theoretically possible with bent glass and aluminium framing for non-orthogonal buildings now or in the near future and what would be the most practical type of unit to develop?
3. how do the particularities of curtain wall unitised systems interact with the double curved glass and framing possibilities?
Design Flow chart (images 1 to 4)
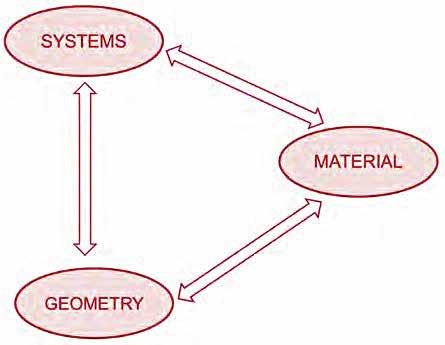
Image 1: Overall flow chart

PHASE 1 TO PHASE 5 = P1 TO P5
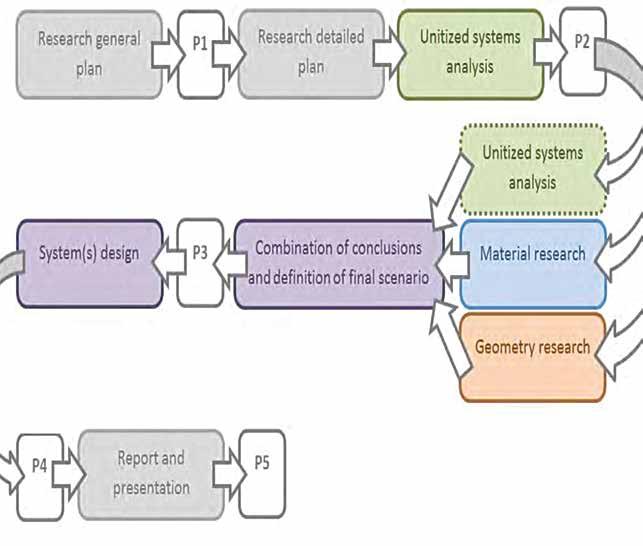
Image 3: Design flow chart according to the geometry and loads
Bending Efficiency oF Aluminium & Shape

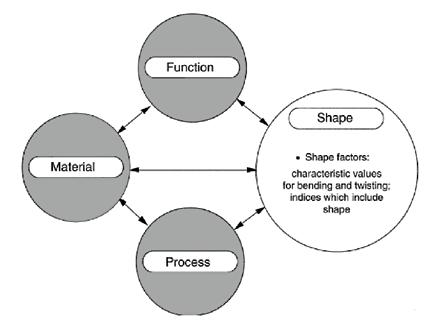
In axial tension, the area of the crosssection is important but its shape is not: all sections with the same area will carry the same load. Not so in bending: beams with hollow-box or I-sections are better than solid sections of the same cross-sectional area. Torsion too has its ‘best’ shapes: circular tubes, for instance, are better than either solid sections or I-sections. To deal with this, we define a shape factor which measures, for each mode of loading, the efficiency of a shaped section.
6061-T6 aluminium is tempered and notorious for not bending easily. From a bending perspective, it’s always best to bend these parts in an annealed state and then temper them to the correct condition. That’s the ideal, anyway, but the reality is that many parts arrive at the press brake in a less than ideal state. Alas, it’s the life of a press brake operator.
T6 aluminium is precipitation-hardened, which is a form of artificial aging that causes particles within the metal to be spread evenly throughout the grain structure of the metal. Once the particles become dispersed, they hinder any further dislocation of the grain, thereby strengthening the metal.
To create these precipitates, the aluminium is heated using a solution treatment at high temperatures and at a prescribed time, then quenched for rapid cooling. This type of hardening typically is performed in an inertatmosphere vacuum at temperatures between 900 and 1,150 degrees F. The process can take up to four hours to complete, depending on the characteristics of the material.
When bending aluminium , know that the smaller your inside bend radius, the larger the chance that cracking will occur in the part. Also know that, for the best results and fewer cracks on the outside of the bend, the bend line should go across or diagonal to the material grain when and where possible.
Ideally, part designers should know that when it comes to aluminium grades, 3003 and 5052 will bend, 6061 will not. This is generalising, of course, as there are ways to form 6061. The aluminium series’ ability to bend tends to decrease as you move down the list of tempers, from annealed to T4 and T6. Bending these tempered alloys is not impossible, but it is very difficult and will most likely require large bend radii to avoid cracking on the outside of the bend. If you’re not careful, you can completely fracture the bend line.
Heating Aluminium While bending of 6061-T6 aluminium, eliminate cracking by having a large radius relative to the material thickness. And sometimes we have performed a three-step bend — a 2-degree bend in front of the bend centerline, a 2-degree bend from behind the bend, and then an 86-degree bend in the center.
Looking at heating the part, which involves heating the part with an oxyacetylene torch in the following manner:
1. Detune the acetylene torch and coat the area to be bent with soot
2. Turn back the O2 and set your rosebud tip to an ordinary flame
3. Heat the part uniformly until the black soot goes away
This should anneal the 6061-T6 (or other “T”) into a T-0 material. This makes the aluminium about as bendable as it can get.
Note that aluminium does not change colour when heated, so getting burned becomes a real concern. Also, as aluminium comes from the mill, it develops a coating, aluminium oxide, as it cools. This surface condition is left alone by the mill because it’s a natural coating that protects the aluminium from the elements during transport and storage.
While protective, this coating creates another problem for anyone who is self-annealing the material: Aluminium oxide melts at a higher temperature than the encased aluminium . You must use extreme caution, as the aluminium will melt from the inside out. You can blow a hole in the material before you see any visible sign that any melting is occurring.
A generic temperature for forming is around 500 degrees F. Know that if you heat materials enough to bend them, you can change the temper of the base material, in which case you will need to retemper it.
Glass Bending Process
Warm Bending Process The existing warm bending processes directly after the extrusion process can be divided into two groups. The first group influences the material flow of the extrusion material during the extrusion process, which can be achieved using three process variations. The first one influences the material flow in the deformation zone using a forming pocket, the second one influences the material flow before the deformation zone using an eccentric positioned mandrel and the third one influences the material flow after the deformation zone by varying the length and/or form of the bearing surface. Extrusion using a die recess is applied if the continuous extrusion process is desired. This method reduces the dead time between each extrusion cycle, since the puller can work continuously too. Another advantage of using a die recess is that the geometry of the die recess can be modified to make some corrections in the material flow. Influencing the material flow intentionally to make a bent profile