
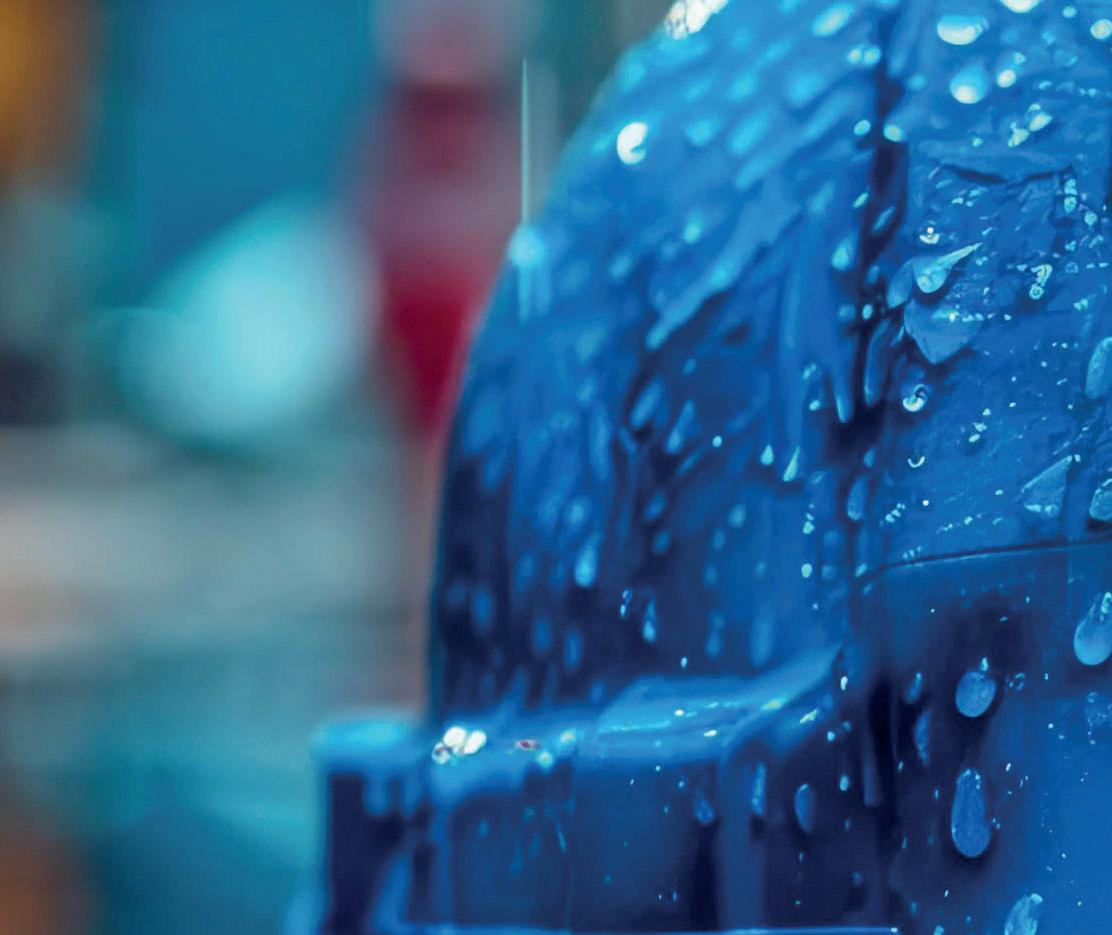
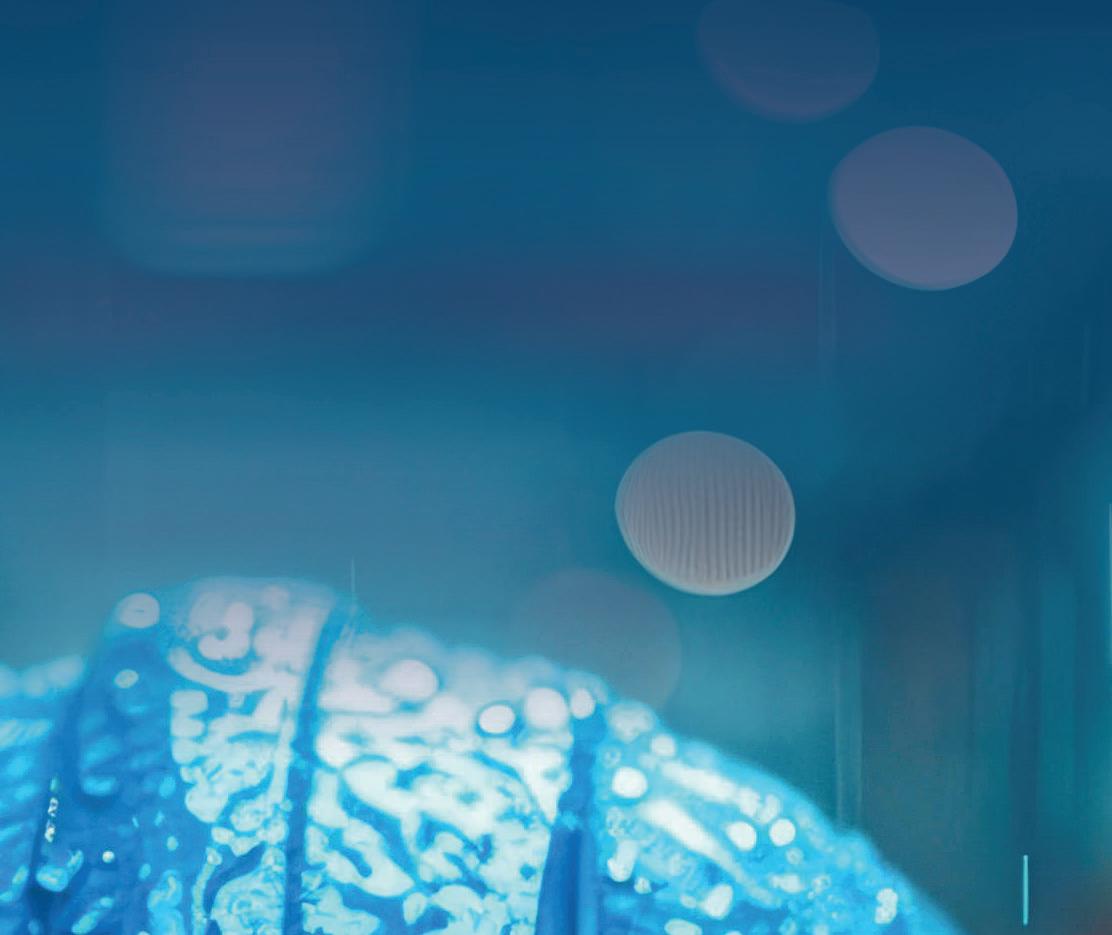
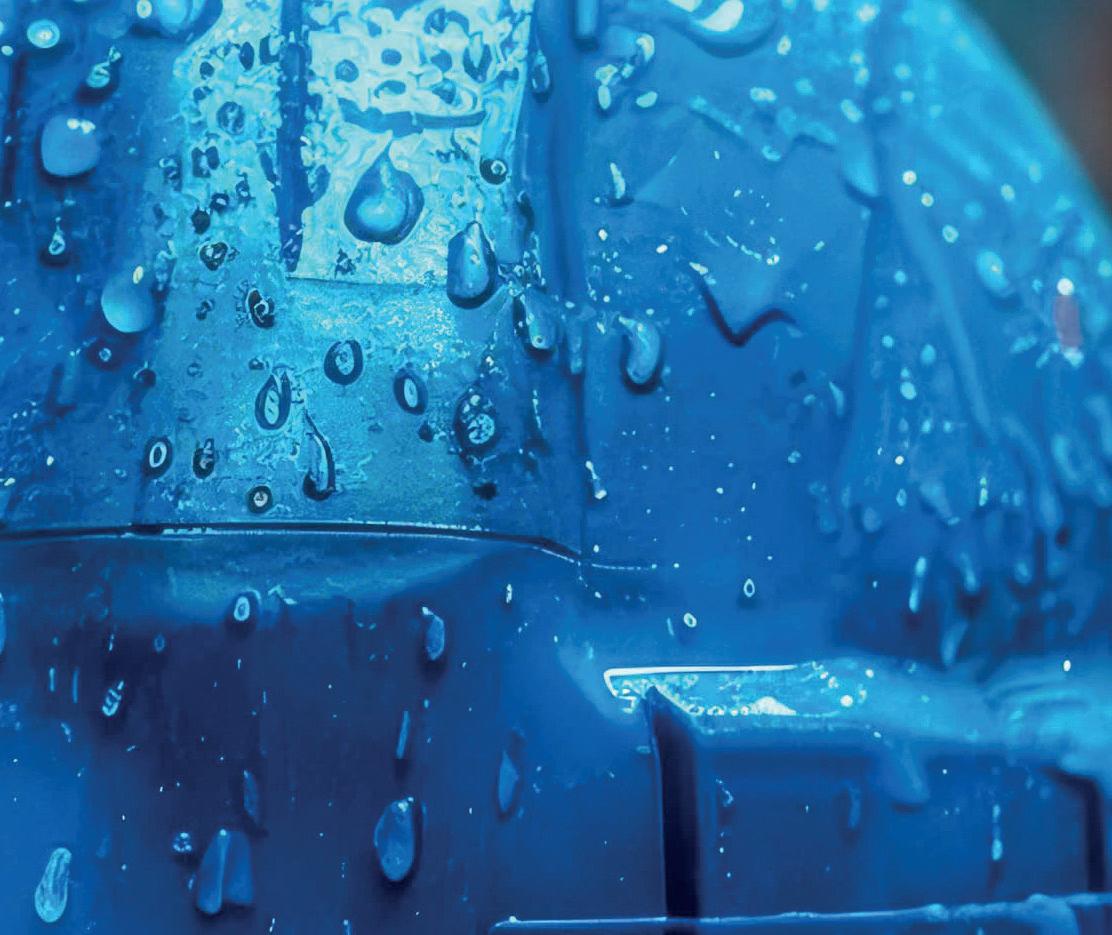

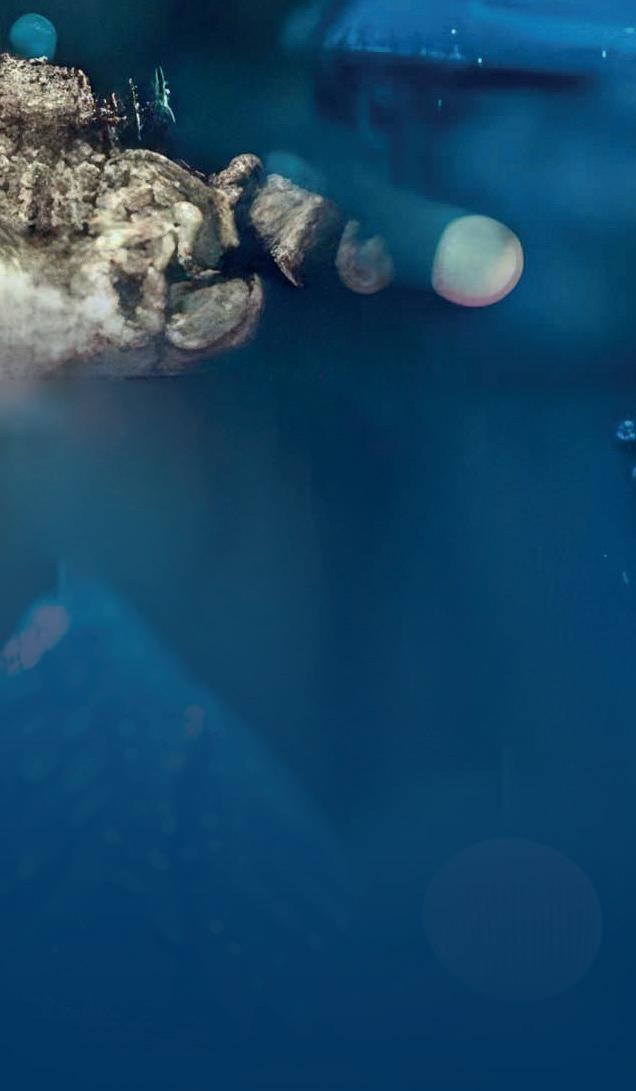
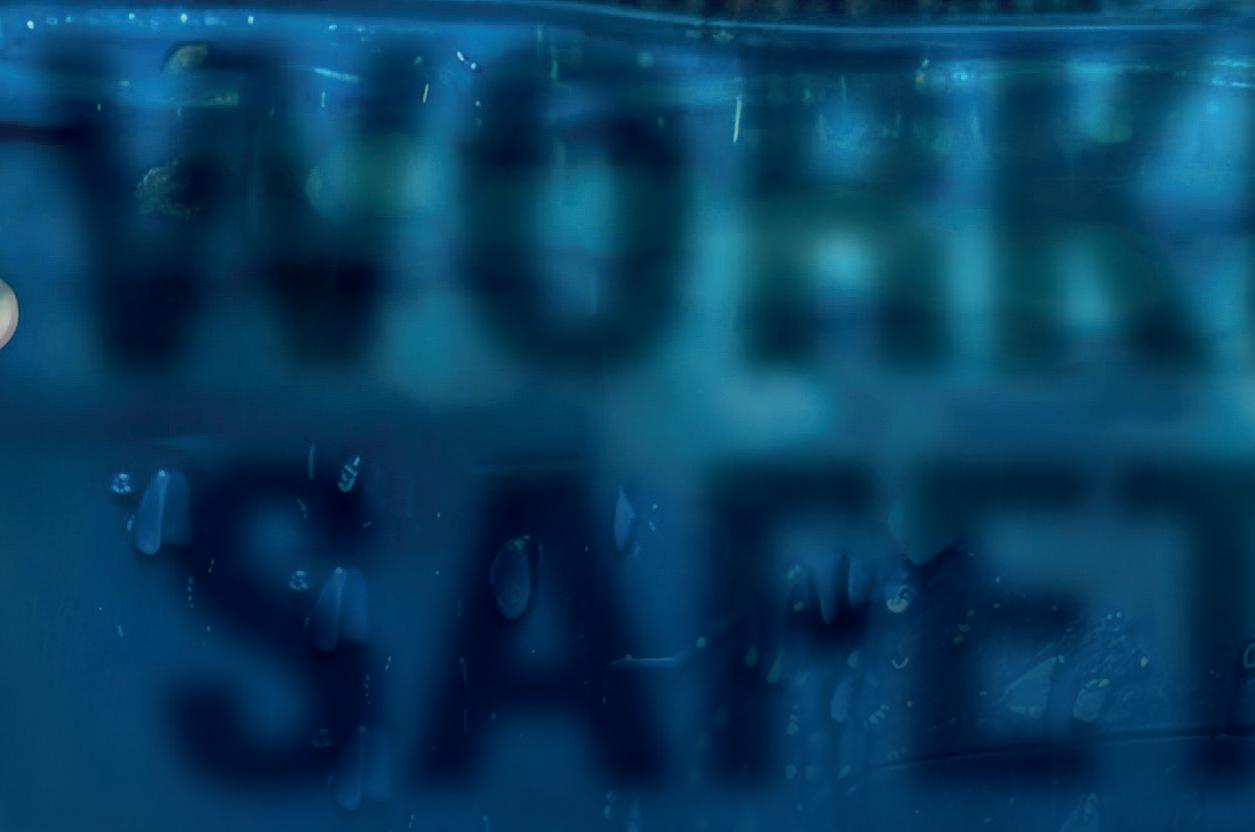
The rapid technological growth that has altered today’s wire and cable manufacturing landscape calls for new measures of understanding and implementation. Share your expertise at INTERWIRE 25 in one of the following areas:
• AI and Industry 4.0
• Material Advancements
• Market Trends & Economic Factors
• Safety & Standards Compliance
• Sustainability & Environmental Impact
• Product Development
• Production Efficiency
• Quality Management
• System Security
• Workforce Training
• Professional Development
Submit your abstract here: bit.ly/WAIabstracts
Accepted authors receive one year WAI membership & conference registration.
ABSTRACTS DUE: OCTOBER 31, 2024
NOTICE OF ACCEPTANCE: NOVEMBER 7, 2024
MANUSCRIPTS DUE: FEBRUARY 13, 2025
Conference: May 13 - 15, 2025
Georgia World Congress Center Atlanta • Georgia • USA
This feature presents a range of perspectives about safety, a perennial industry issue, with a focus on violations. Much of the content comes from OSHA records that outline just how many potential hazards can exist even before one factors in the human nature potential for “a bad day.” Countering that is one manufacturer’s signature approach to making safety a company-wide commitment and an update on an AI-based program to proactively warn of potentially unsafe behavior and a common-sense perspective from a supplier of used equipment. There’s also a column that calls for an increase in the size of OSHA fines, authored, appropriately enough, by AI.
In an April 2024 safety poll by Vector Solutions (VS), The State of Industrial Worker Safety and Wellbeing, respondents cited many concerns, some listed below. For more about VS, which offers “impactful technology solutions ... (to) the world’s most critical industries,” go to www.vectorsolutions.com. Of editorial note, for all the concerns, the last “finding” underscores a real-world “x” factor.
• 35% Have been exposed to harmful chemicals and 42% to extreme temperatures at work.
• 20% Of workers feel that the risks of their job extend beyond what they signed up for, and those in maintenance were 120% more likely than average to say this.
• 75% Have been asked to work extended hours.
• 39% Report that the equipment they use at work is outdated.
• 26% Say that the equipment they use at work isn’t properly maintained.
• 20% Workers report that their company doesn’t see safety as a top priority, and those in electrical maintenance were 235% more likely than average to say this.
• 83% Feel that their company’s safety protocols feel like check boxes rather than genuine commitments to employee well-being.
• 43% Report that there has been a safety incident in the past 12 months. And of those, five is the average number of incidents reported in the past 12 months.
• Of those who had incidents in the past 12 months, 88% say that at least some ... could have been prevented through improved safety measures – with 27% saying that all incidents could have been prevented this way.
• 81% Of workers believe that safety issues are a stain on their company’s reputation.
• 23% Have noticed a hazard but didn’t report it.
• 58% Of workers believe that additional training would improve their workplace safety.
• 100% Say that safety training is essential for fostering a safe workplace.
• An encouraging 81% of workers attest that their training instills in them a stronger commitment to remain with the company, while 57% say that safety issues make more seasoned workers leave, underscoring the profound impact of training on employee retention and loyalty.
• Safety is the second most important matter for industrial workers, with pay being cited as the only thing that outranks it.
Some of the findings in a recent report from the Travelers that assessed 1.2 million worker compensation claims will not come as a surprise, but the overall findings confirm just how important safety is.
The report—which considered injures that resulted in claims of more than $250,000—cited the top five causes of injuries to be: overexertion (29%); slips, trips and falls (23%); being struck by an object (12%); motor vehicle accidents (5%); and caught-in or caught-between hazards (5%). The types of injuries that led to the most lost days were dislocations (142), fractures (92), inflammation (85), strains and sprains (54) and contusions (30). If one is looking for good news, it may be that for lost work days, manufacturing was listed as coming in fifth, with 67 days. It follows construction (103 days), transportation (83 days), services (72 days) and wholesale (71 days).
heading comes: Fall Protection - General Requirements (1926.501)—which has led OSHA’s top 10 list for 14 years in a row—as well as Ladders (1926.1053), Fall Protection – Training Requirements (1926.503) and Scaffolding (1926.451).
Coming in second is a category that may seem unlikely: poor housekeeping. This concerns exit routes blocked by containers, machinery or garbage, and can include uncleaned material or chemical spills and clutter that can result in slips, trips and falls. It also includes “distracted workers” with cellphones.
A recent article in Safety & Health Magazine provided a list of seven common workplace hazards, citing a National Safety Council (NSC) report that Working At Height represents the single most dangerous threat. Under that
Coming in third is a widely used industry resource: forklifts. Per NSC experts, operators should always wear a seat belt and never speed or engage in horseplay as forklifts have a tendency to swing out and pose a real threat to pedestrians. Other categories include hand hazards, fourth, while electricity, fifth, included electrical cables with damaged insulation or exposed bare wires; damaged electrical outlets or outlets with covers missing; blocked electrical panels; and “daisy chaining” multiple extension cords. Coming in sixth was confined spaces, and seventh was transportation accidents.
Fatal work injuries are rare in the wire and cable industry, but worker injuries are not. Per its last annual report (Nov. 9, 2023), the U.S. Bureau of Labor Statistics said that private industry employers had 2.8 million nonfatal workplace injuries and illnesses in 2022, up 7.5% from 2021. Below are summaries of four OSHA wire industry incidents, followed by a runnning list of citations/fines that were assessed for a range of wire and cable operations from 2023 and 2024.
An employee tending to a wire stranding machine saw that finished steel wire coming out from the machine had a rough surface and was crooked. When he tried to clean the moving wire with a sponge his gloved hand was caught by the wire and pulled between the forming heads where the stranded wire was compressed. His little and ring fingers were hurt, with the tips of both amputated. He was treated without hospitalization.
Employees were exposed to molten metal sparks while operating the resistance welding machines. The employer had not provided adequate personal protective equipment to include gloves, arm guards and/or fire rated clothing to employees operating the resistance welders. An employee suffered skin burns from exposure to flying metal sparks.
A 23-year-old machine operator, was operating a welding unit. The employee placed his hand on an exposed belt, resulting in a partial amputation of the distal phalanx of the right index finger. The employee was treated without hospitalization.
An assistant refiner was exposed to copper fume (as Cu) at an 8-hour time weighted average concentration of 0.41 milligrams per cubic meter of air while tapping and working a furnace during the casting phase. The level was 4.1 times the permissible exposure limit of 0.1 milligrams per cubic meter of air averaged over an 8-hour period.
(section continued)
You are invited to share your knowledge of today’s wire and cable manufacturing landscape with delegates at the 2025 Wire & Cable Conference in Krakow, Poland. Your participation should provide an in-depth view of the manufacturing advances in wire and cable research, operations, or production. Ferrous and nonferrous topics are welcome. Choose from the following topics or suggest one of your own.
conference: 14 OCTOBER 2025
ABSTRACTS DUE: MARCH 31, 2025
• Product Development
• AI and Industry 4.0
• System Security
• Workforce Training
• Production Efficiency
• Material Advancements
• Quality Management
• Professional Development
• Market Trends & Economic Factors
• Safety & Standards Compliance
• Sustainability & Environmental Impact
NOTICE OF ACCEPTANCE: MAY 21, 2025
MANUSCRIPTS DUE: SEPTEMBER 1, 2025
SUBMIT YOUR ABSTRACT:
ORGANIZED BY: bit.ly/WAIabstracts