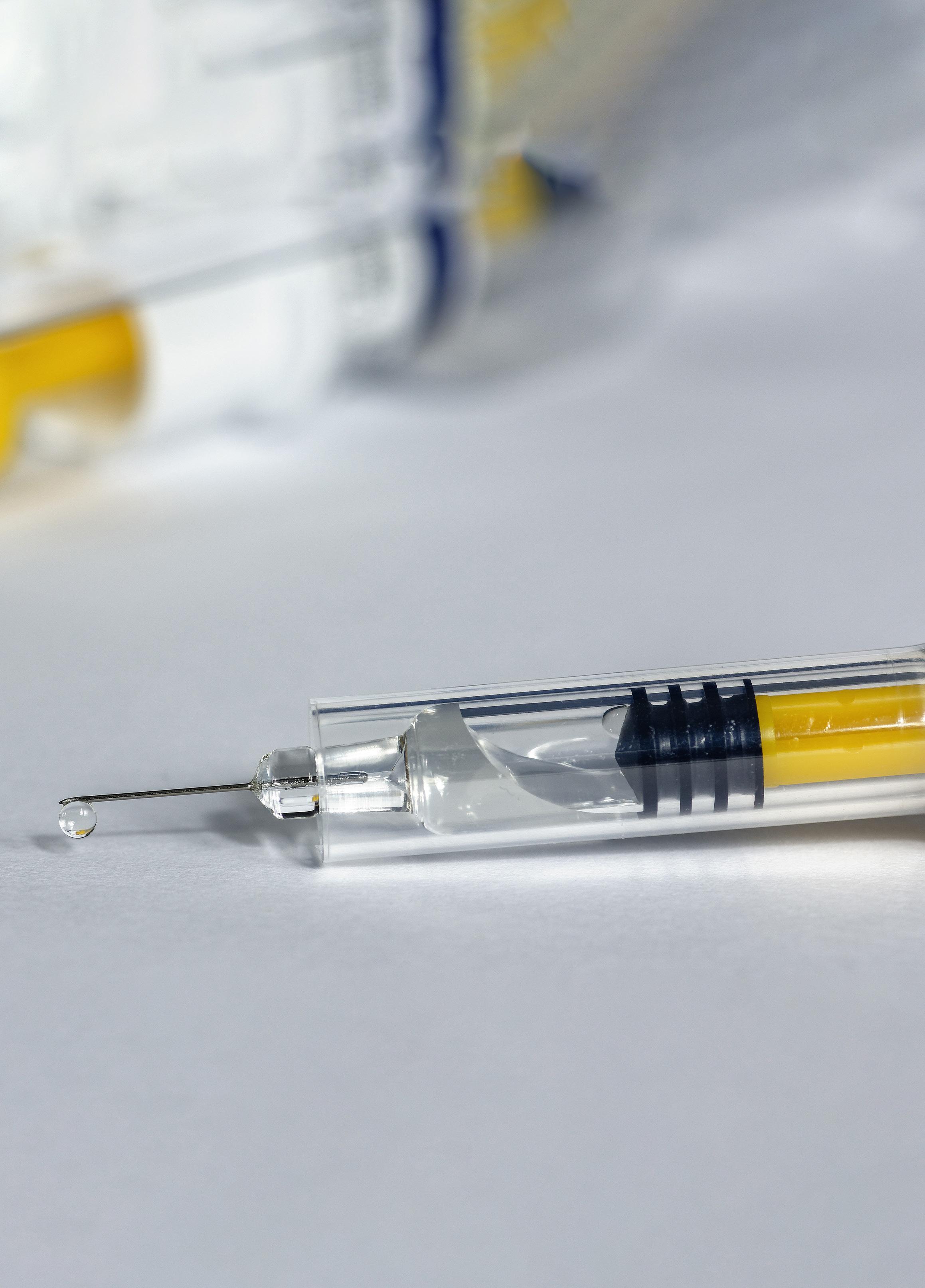
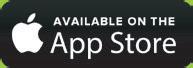
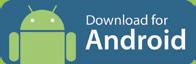
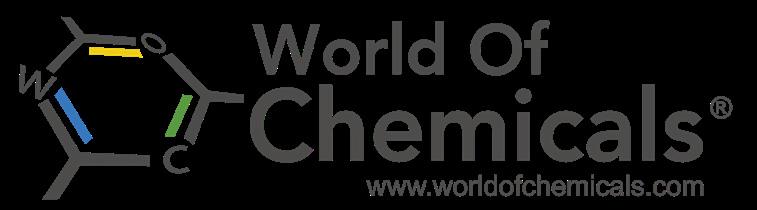
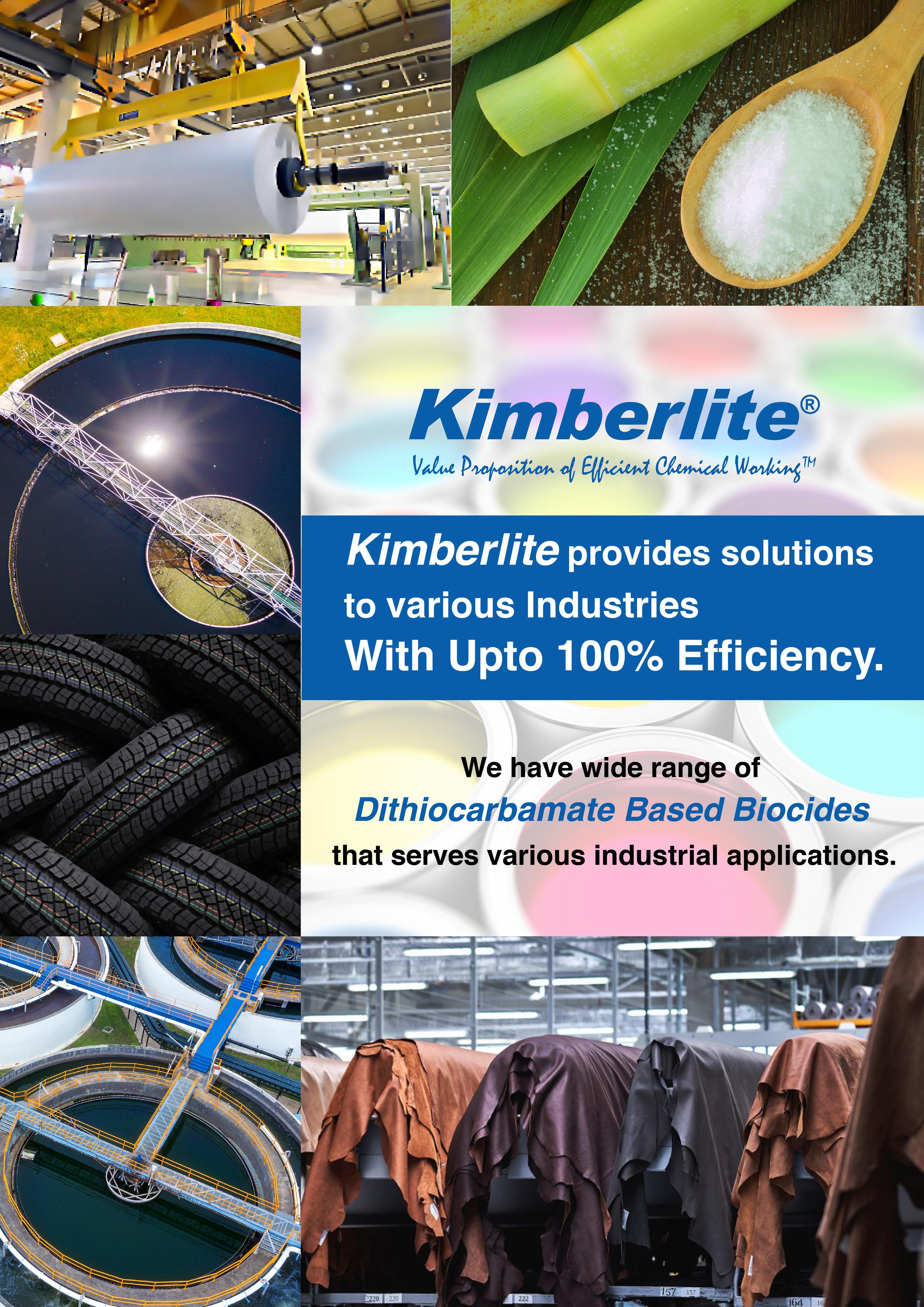
Presently countries and organizations are learning to cope up with the challenges that the COVID 19 pandemic threw up in front of them. Among all the challenges, the main concern was the uncertainty surrounding the global and Indian supply chains of the pharmaceutical industry. The other major issue was research and viability of medicines and vaccines to keep citizens safe from the pandemic outbreak.
With the circumstances in the last few years, the pharmaceutical industry is undergoing a rapid and fundamental transformation. We need to now ‘Reimagine the Pharmaceutical Industry,’ in view of the changing global market dynamics and economic challenges.
Today, Pharma companies are faced with the growing scale of operations and need to be focused on staying agile and resilient due to the disruption, led by fluctuating market demands and diverse customer needs.
Considering the continuing COVID 19 pandemic and growing cases of newer diseases such as Monkeypox, bird flu or the Swine flu across the world, the learnings of the pharma industry from the pandemic times, will definitely help in the long run.
The pandemic crisis pushed the pharma industry to seriously establish risk management systems and even provide for any upcoming future risks. Also the supply chain structures are undergoing a change in their operations. Moreover, rather than being dependent on global logistics and pharma ingredients supply from China, Indian pharma industry needs to enhance their sourcing and transportation globally.
The most important development in current times is the expanding pharmacovigilance market. Often, medicines and vaccines behave in different ways in patients, hence information and accurate data will be key in improving quality and research of healthcare products. Moreover, continuous digital transformation will help in reducing R&D costs, increasing efficiency, refining multiple processes and even support with ease of operations.
For this month, we explore how India has become a vaccine research and manufacturing hub over the years. The country’s potential in vaccine manufacturing was well displayed over the last two years, where Indian vaccines on coronavirus has been reaching the world and has saved millions of lives many times over. This has not just proven India’s mettle in medical research but has also made it the most sought-after vaccine manufacturing destination in the world.
The rise of e-commerce and access to new technologies has accelerated counterfeiting and other forms of illicit trade. That makes fighting counterfeit medical products an ever-more urgent priority for pharma companies both in terms of patient safety and brand reputation.
Yann Ischi
Director, New Channels and Partnerships, SICPA
Within the Volkswagen Group, we have a clear strategy for how we want to put battery-electric vehicles into series production across our brands and in many different market segments. However, a major qualification for success in the volume market is more powerful battery concepts. In Volkswagen Group R&D we are focusing on close cooperation, not only with industrial partners but also with the smart minds of the scientific community.
Dr Ulrich Eichhorn
Head, Group R&D, Volkswagen AG.
India is a very important market for polyurethanes and has a wonderful potential for growth. When leaders of the industry from all over the world get together under one roof, it leads to better production and faster growth of the industry
R C Bhargava
Former CEO and current Chairman, Maruti Suzuki.
Indian Solar Manufacturers Association (ISMA) members have expressed positive sentiments as manufacturing and Make in India initiative gathered momentum. The phenomenal growth opportunity of Renewal Energy is unparalleled in the world today, looking at current and future energy consumption in India over the next 2-3 decades. All stakeholders have immense opportunities especially those who make and develop products in India.
K N SubramaniamCEO, Moserbear Solar Ltd and Treasurer, Indian Solar Manufacturers Association (ISMA)
BENGALURU/NEW
DELHI, INDIA: Hero Electric, India’s largest electric two-wheeler company, said it has delivered the first batch out of 1000 electric scooters to the delivery partners of Shadowfax Technologies, India’s crowdsourced third-party logistics platform for last-mile delivery.
In a strategic partnership with Hero Electric, Shadowfax plans to convert 75 percent of its fleet to EVs by 2025, where Hero Electric’s two-wheeler EVs will be utilised by Shadowfax’s delivery partners to ensure sustainability in last-mile logistics. As part of its ‘No Emission’ mission, Hero Electric is forging multiple B2B partnerships in the delivery segment as it fronts the shift from combustion engine vehicles to EVs. With the government promoting sustainable mobility projects, the improving infrastructure is propelling a faster shift of B2B fleets to electric in the delivery segment.
Piyush Prasad, business head, Hero Electric and Praharsh Chandra, co-founder and COO, Shadowfax, attended the delivery ceremony in Bengaluru, Karnataka.
“We are delighted with our association with Shadowfax. The last-mile delivery segment is growing at an unprecedented pace, with more businesses switching towards a sustainable EV ecosystem to reach their company goals. This partnership will ensure a carbon-free fleet in the logistics market while catering to consumer needs and minimising emissions. Policymakers across central and state governments continue
to encourage this shift as more businesses opt for cleaner solutions to reach their consumers. At Hero, we strive to provide 360-degree solutions to our B2B customers through our strong network presence across India,” said Sohinder Gill, CEO, Hero Electric.
“With 1.2 lac+ monthly transacting partners delivering over 10 lac orders every day, Shadowfax has been actively looking at green mobility solutions. Focusing on enabling sustainable deliveries, we have partnered with Hero Electric and received the first batch of 100 e-scooters for our delivery partners, the first step in our journey of reducing carbon emissions. Over the next few months, we will deploy 1000 e-scooters to ensure that most of our delivery vehicles’ fleet are EVs. We look forward to a long-standing partnership with Hero Electric as we jointly make positive changes for the betterment of our customers and the planet,” said Chandra.
With several unicorns and e-commerce giants on its client list, Shadowfax caters to customers across 900+ cities and 8000+ pin codes to ensure timely deliveries. Hero Electric, going strong with its vision to transform mobility, recently inaugurated its new dealership in Lucknow and also rolled out electric scooters from Mahindra’s Pithampur facility. Aiming to convert 65 percent of sales from the B2B segment in the next few years, Hero Electric has been steering forward in its endeavour to provide seamless delivery experiences to its consumers and maximise traction towards the EV transition in India.
unveiled the indigenously developed lithium-ion battery cell and will begin mass production of the cell - NMC 2170, from its Chennai-based Gigafactory by 2023.
The company has become the only Indian electric vehicle company selected by the government under its ambitious Rs 80,000 crore cell PLI scheme, receiving the maximum capacity of 20 GWh for its bid in March.
Ola’s Battery Innovation Center (BIC) is all set to become operational from August and it is expected to be “the cornerstone for core cell tech development and battery innovation out of India for the world,” the company said.
INDIA: Ola Electric said it signed an agreement under the Government of India’s production-linked incentive (PLI) scheme to manufacture advanced cells in the country. It recently
“Today, 90 percent of global capacity for cell manufacturing is in China, and to reverse this import dependency locally manufactured cell technology is key. The ACC PLI scheme will be instrumental in making India self-reliant and localizing the most critical aspects of the EV value chain. At Ola, our roadmap to develop cell technology and manufacturing is vigorously progressing; making us a stronger vertically integrated mobility company across - products, mobility services and tech,” said Bhavish Aggarwal, CEO and founder, Ola.
DELHI, INDIA: The government is considering setting up an exploratory mining centre in Sikar district of Rajasthan where over 14,000 tonnes of uranium ore deposits have been discovered.
In a written reply in Lok Sabha, Minister of State in the Prime Minister’s Office Jitendra Singh said pre-project activities required for obtaining statutory clearances have been initiated by Uranium Corporation of India Limited (UCIL), reported PTI.
As a part of this, the state government of Rajasthan has issued Letter of Intent (LOI) for granting of mining lease to UCIL, he said. According to the information shared by the minister, the Atomic Minerals Directorate for Exploration and Research (AMD) found 8,813 tonnes of uranium oxide deposits in Rohil in Sikar district, 1,086 tonnes in Rohil west, 3,570 tonnes in Jahaz and 1,002 tonnes in Geratiyon ki Dhani.
At Umra in Udaipur district, the AMD had found uranium oxide deposits to the tune of 1,160 tonnes. The total uranium ore deposits
found in Rajasthan are 15,631 tonnes 14,471 tonnes in Sikar district and 1,160 tonnes in Udaipur, Singh said, adding that these deposits have been classified as “small deposits”.
“Mining technology and economics are important criteria which decide the exploitation and extraction status of a deposit like other mineral deposits,” Singh said.
Across the country, the AMD, a constituent unit of the Department of Atomic Energy (DAE), has established a total of 3,82,675 tonnes in situ U3O8 in 47 uranium deposits in Andhra Pradesh, Telangana, Jharkhand, Meghalaya, Rajasthan, Karnataka, Chhattisgarh, Uttar Pradesh, Uttarakhand, Himachal Pradesh and Maharashtra.
Presently, the deposits at Jaduguda, Narwapahar, Bagjata, Bhatin, Banduhurang, Turamdih and Mohuldih in Jharkhand and Tummalapalle in Andhra Pradesh are under exploitation by UCIL, Singh said.
INEOS Styrolution announced it has agreed to sell its entire shareholding interest in INEOS Styrolution India to Shiva Performance Materials, part of the Shiva Group. Shiva Performance Materials will acquire INEOS Styrolution’s 61.19 percent equity interest in INEOS Styrolution India.
The transaction triggers a mandatory tender offer (MTO). Shiva Performance Materials has businesses in specialty chemicals for pharmaceuticals, agrochemicals and other intermediates.
“The business continues in Shiva Performance Materials’ experienced hands, serving the existing customer base and seeking future growth potential to enhance the company’s current position in the Indian market,” said Steve Harrington, CEO, INEOS Styrolution.
DAHEJ, INDIA: BASF said it has completed the installation and start-up of a state-of-the-art acrylic dispersions production line in Dahej, India, serving the coatings, construction, adhesives and paper industries for the South Asian markets. BASF began production of polymer dispersions in Dahej, India in October 2014, and this additional production line will almost double its capacity. BASF is one of the leading producers and suppliers of acrylics and butadienecontaining dispersions in the Asia Pacific region.
“As a global supplier for polymer dispersions, we are committed to ensuring the supply of high-quality products, supporting our customers’ expansion plans. The South Asian market is one of the fast-growing sub-regions within the Asia Pacific region. Our customers are looking for global partners like BASF, who can bring innovation and expertise
with its extensive footprint to help them differentiate in their markets,” said Milind Joshi, director, Dispersions South Asia, BASF.
The new production line complements the existing setup and allows the production of new dispersions technologies under Styronal® PLUS 7918, Styronal® ES series, Basonal® FCB, Acronal® EDGE, Acronal® PLUS, and next-generation Acronal® ECO product ranges.
“In construction polymers and architectural coatings, our innovations continue to deliver increased functionality including sustainability features, as well as durability improvement, driving premiumization of the industry. For instance, our DURA-COLOR binders for exterior coatings enable formulations of exterior paints with outstanding dirt pick-up resistance and color retention. In paper coatings for example, we continue to drive improved cost-in-use solutions. Styronal® PLUS 7918 is our high-strength product that allows a substantial reduction of binder usage,” said Bir Darbar Mehta, senior vice president of Dispersions Asia Pacific, BASF.
“Dispersions is an important business for us in India, and this project reflects our commitment to the Indian market and our customers in the country,” said Narayan Krishnamohan, managing director, BASF India Limited and head of BASF Group Companies in India.
The site in Dahej, Gujarat is an integrated hub for polyurethane manufacturing which houses production facilities for polymer dispersions as well as care chemicals. BASF also produces dispersions in Mangalore, a production site in the southern part of India.
NEWDELHI, INDIA: DCM Shriram Ltd and ReNew Power, India’s major renewable energy company, announced signing of two captive power agreements (CPAs) that will see 50 MW of renewable energy supplied from ReNew’s two upcoming projects in Bhavnagar, Gujarat, to DCM Shriram’s chlor-alkali manufacturing facility in Bharuch district, Gujarat.
The 50-MW hybrid project, which, overall, has ~100 MW of wind and solar generation capacity at its backend, is expected to generate ~250 million units of renewable energy every year exclusively for the DCM Shriram’s Bharuch facility.
ReNew will be setting up the two hybrid projects with a total investment of ~ ?8 billion through an equity partnership of ~ ?630 million by DCM Shriram Ltd. The combined transaction is one of the largest corporate renewable power supply deals in India under an OpEx (operating expenses) with a captive model.
“We as a group are committed to improving our energy footprint and this is a step in that direction. We are happy to collaborate with ReNew Power in our journey towards renewable energy for our ChlorAlkali manufacturing facility at Bharuch, Gujarat,” said Ajay Shriram, chairman and sr. managing director, DCM Shriram Ltd.
“With a long-term commitment towards ESG, the Captive Power Agreements for green energy have been signed for 25 years and will mitigate ~2,25,000 tCO2e (carbon emissions) annually,” said Shriram.
“We are proud to partner with DCM Shriram, which is showing leadership is moving to cleaner sources of energy and in addressing broader climate issues, as well as in supporting India’s ambitious climate goals. We are confident that more such responsible corporates will move to renewables, as it not only shows a focus on sustainability concerns that are critical but also reflects that green energy is increasingly costeffective for businesses,” said Sumant Sinha, founder, chairman, and CEO of ReNew Power.
INDIA: Merck announced the opening of its first microbiology application and training (MAT) lab in Jigani, Bengaluru, offering facilities and technical expertise to support the India life science community on microbial quality control capability development.
With an investment of €200,000, the MAT Centre spans an area size of 1,100 sqft. The testing services offered in the lab includes sterility testing, rapid bioburden testing, pyrogen Testing, advance Membrane filtration and other pharma QC microbiology applications. The MAT Lab includes a vibrant space for certified training, application support, feasibilities studies and method development for Pharma and Biopharma industries.
“According to IBEF, the Indian biotechnology industry was valued at $70.2 billion in 2020 and is expected to reach $150 billion by 2025. Merck’s MAT lab will be a space for pharma and biopharma companies to collaborate and enhance their capability in microbiology analysis,” said Veena Panicker, head, BioMonitoring, Merck Life Science in India.
“Merck is a global leader with proven track record in technical expertise, training, method development and feasibility trials. Partnering with our
customers, we can support them in product demonstrations, hands-on training, formal bioprocessing educational courses and experiments, as well as apply best practices and new approaches to develop, optimize and scale-up processes and simplify global technology transfer,” added Panicker.
“In the global pharmaceuticals sector, India is a significant and rising player. India is the world’s largest supplier of generic medications, accounting for 20 percent of the worldwide supply by volume and supplying about 60 percent of the global vaccination demand,” said Sreenath NS, country speaker, Merck India and managing director, Merck Life Science.
“The newly launched MAT lab is a space that enables pharmaceutical and biopharmaceutical manufacturers to work side-by-side with our global microbiology and application experts to solve critical process developments and production challenges,” said Sreenath.
The lab offers customizable solutions and services that help pharmaceutical and biopharma companies as well as regulatory to improve their processes from drug discovery, development to manufacturing.
BANGALORE, INDIA: The Karnataka Government recently signed memorandum of understanding (MoUs) with the Malaysia-based Petronas Hydrogen and Continental Automotive Components (India) for a total investment of Rs 32,000 crore in the presence of chief minister Basavaraj Bommai. The CM assured the two companies of all cooperation and urged the companies to implement the projects within the time frame.
Petronas has committed to invest Rs 31,200 crore to set up a renewable energy plant in Mangaluru. This project will add about 3000 jobs. Continental Automotive will invest about Rs 1000 crore in an R&D centre which is expected to add about 6000 jobs. The company is engaged in automotive software development and mobility technology development. The proposed investment is towards the expansion of its technical center India.
The state government had, recently, signed an MoU with ReNew Power Company at Davos for an investment of Rs 50,000 crore in the renewable energy sector. The state has also signed an MoU with ACME Cleantech Solutions for setting up hydrogen and ammonia production plants in Mangaluru with an associated solar power unit at an investment of Rs 52,000 crore.
The state government is also working on a green hydrogen policy to further strengthen its position in the renewable energy sector.
AHMEDABAD, INDIA: Meghmani Finechem Limited (MFL) announced the successful commissioning of chlorinated polyvinyl chloride resin (CPVC Resin) plant at Dahej in Gujarat. The newlycommissioned facility with a production capacity of 30,000 tonnes per annum (TPA) is the largest of its kind in India. CPVC resin demand is around 1,40,000 tonnes per annum (TPA) in the country and it is expected to grow by around 13 percent CAGR over the next five years. Approximately 95 percent of the CPVC resin demand of India is met through imports. MFL’s entry into this product is in line with the central government’s initiative of Aatmanirbhar Bharat and Make in India. This will reduce the dependence of CPVC resin consumer on imports thereby helping the country save its foreign exchange reserves.
CPVC resin is used in manufacturing CPVC pipes and fittings. CPVC pipe has high heat resistance and chemical resistance properties. Considering its features, CPVC is widely used for domestic (households) and industrial purposes.
CPVC resin is a high value product. Considering the current prices of CPVC resin, MFL expects asset turnover ratio to be above 2.0x, which will improve the company’s absolute EBITDA and will end up providing higher ROCE (Return on Capital Employed), ultimately creating value for the shareholders.
“I would like to congratulate our project team for commissioning the plant within the estimated capex limit. Production of CPVC resin has started and it is under approval process with various customers. We estimate that it will take around 3 months’ time for approval and stabilisation process. We expect that volume of CPVC resin should pick from Q3FY22 onwards and should reach optimum capacity utilisation by Q1FY24,” said Maulik Patel, chairman & managing director, MFL.
“With this plant, we are moving in the direction of being a multiproduct company and this will increase revenue contribution from the Derivative and Specialty Chemical segment. Also, this will further strengthen our fully integrated complex, as part of the raw material for CPVC resin will be available within the plant itself,” added Patel.
LONDON, UK/CHENNAI, INDIA: Manali Petrochemicals Limited (MPL), part of the AM International group, announced the execution of the long-form agreement with UK-based Econic Technologies. Last year, the companies entered a Memorandum of Understanding (MoU) to introduce more environment-friendly, CO2containing polyols into the global $28 billion global polyols market.
The signing of the long-form sets the stage for the initiation of the MPL-Econic partnership. It will comprise a two-year demo scale-up at the 1,300 ltr reactor at the MPL plant 1. The following three years will be spent on industrial scale-up of the technology of MPL’s 12,000+ reactors and commercialisation of CO2-containing polyols by the company.
In the initial phase, the MPL and Econic teams will collaborate on the design of retrofit equipment required, engineering, procurement and construction of retrofit, demo plant commissioning and operation. In the industrial scale phase, the companies will work together to prepare for front-end engineering design provision, FEED and EPC work, industrial plant commissioning and operation.
“Science and innovation will play a key role in ensuring that our manufacturing plants implement eco-friendly and cost-efficient technology. MPL’s partnership with Econic Technologies brings significant R&D-led improvements to the production process. Alongside delivering a greener product to our customers, it reaffirms our ESG commitment towards a carbon neutral planet,” said Ashwin Muthiah, chairman, MPL and founder-chairman, AM International Holdings.
The MPL-Econic partnership, a one-of-its-kind in India, offers
excellent upside across MPL’s business value chain. Econic’s patented catalyst and process technology incorporates waste CO2 as a feedstock to manufacture polyols. In an increasingly eco-conscientious world, the green polyols strategy will also lend a competitive edge to the company’s prospects in the $28 billion global polyols market.
“We appreciate this next development in our partnership with MPL and the opportunity to work with them as a pioneering licensee of Econic’s technology in one of the world’s biggest and fastest growing geographies. It’s an exciting time to be implementing solutions that meet consumer demand for more sustainable products made using waste CO2,” said Keith Wiggins, CEO, Econic Technologies.
“At MPL, we are continuously introducing sustainable technologies in our operations. Through this, we envision just not financial saving but serving our customers with eco-friendly solutions. The collaboration with Econic will add further impetus to our efforts to build a cleaner future by using alternate energy resources,” said Muthukrishnan Ravi, MD, Manali Petrochemicals and CEO, Petrochemicals, AM International Holdings.
Polyols are the building block for polyurethanes. They are used to produce flexible and rigid foams, elastomers, adhesives, sealants and coating, which find application across a wide range of necessary everyday products, from mattresses and automotive interiors, building insulation and refrigeration to sports and footwear, protective coatings and industrial products. Econic’s unique catalyst technology incorporates tailored amounts of CO2 into polyols to meet the exact requirements for material properties, such as strength, water resistance, flexibility and processability. Thus, the polyurethanes made with catalyst technology will be customised to suit MPL’s wide range of customer requirements.
SOUTH KOREA/DETROIT, US: LG Chem and General Motors Co announced a binding agreement for the supply of Cathode Active Material (CAM) from LG Chem to GM. The supply agreement will help GM meet its fast-growing EV production needs. GM and LG Chem will also explore the localization of a CAM production facility in North America by the end of 2025.
Through the long-term supply arrangement, LG Chem plans to supply more than 950,000 tons of CAM to GM beginning the second half of 2022 through 2030, enough for approximately 5 million units of EV production.
The CAM secured by GM will be used by Ultium Cells LLC, a joint venture between GM and LG Energy Solution, at its battery cell plants in Warren, Ohio, Spring Hill, Tennessee and Lansing, Michigan. CAM is a key battery material consisting of components like processed nickel, lithium and other materials representing about 40 percent of the cost of a battery cell.
“This agreement builds on GM’s commitment to create a strong, sustainable battery raw material supply chain to support our fastgrowing EV production needs,” said Jeff Morrison, GM vice president, Global Purchasing and Supply Chain. “LG Chem has demonstrated
technical expertise, high-quality and mass production capabilities of cathode active materials over the last decade. At the same time, this agreement demonstrates GM’s commitment to strong supplier relationships, and compliments our many other recent EV supply chain announcements.”
“Importantly, GM now has contractual commitments secured with strategic partners for all battery raw material to support our goal of 1 million units of EV capacity by the end of 2025,” added Morrison.
The cathode materials that LG Chem plans to supply are NCMA (nickel, cobalt, manganese and aluminium) cathode materials for EVs built on GM’s Ultium Platform. NCMA cathode material is a product that combines LG Chem’s best material technology and is characterized by its excellent sta-bility and output. Aluminum was applied to the material technology to strengthen stability while de-creasing the amount of cobalt used in GM’s previous generation of batteries by 70 percent.
“Based upon a close collaboration with customers, LG Chem will further strengthen its position as a global leader in the market by producing the world’s best cathode materials,” said Shin Hak Cheol, CEO, LG Chem.
Established in 1998, TotalEnergies Egypt operates about 7 percent of service stations in Egypt. The contemplated partnership between TotalEnergies, a leading global multi-energy company, and ADNOC Distribution, the UAE’s largest fuel retail distributor, includes a portfolio comprising 240 fuel retail stations, as well as wholesale fuel activities, an aviation fuel business and lubricants sales. The acquisition is expected to complete in Q1 2023.
‘’TotalEnergies is pleased to join forces with ADNOC Distribution in Egypt. The rich experience of an experienced fuel distributor in the GCC region will bring a significant added value to TotalEnergies Marketing Egypt. We look forward to collaborating with ADNOC Distribution in a combined growth strategy,” said Thierry Pflimlin, president, marketing & services at TotalEnergies.
CAIRO, EGYPT: The partnership between TotalEnergies and ADNOC has been further strengthened following the signing by ADNOC Distribution of an agreement to acquire a 50 percent stake in TotalEnergies Marketing Egypt LLC for a consideration of approximately $200 million.
This new transaction follows the signing of the strategic partnership agreement signed by TotalEnergies and ADNOC on the occasion of the state visit in Paris of Sheikh, Mohamed bin Zayed Al Nahyan, president of the United Arab Emirates.
“TotalEnergies Egypt is a well-established business with a solid track record of operational excellence and in-depth knowledge of the Egyptian fuel and retail sector. This move aligns with our vision to establish ADNOC Distribution as a regional leader in the fuel distribution sector. We look forward to providing the best possible service to customers in Egypt, and working with TotalEnergies to accelerate our international expansion in Egypt and beyond,” said Bader Saeed Al Lamki, CEO, ADNOC Distribution.
SAUDI ARABIA: The Saudi Arabian Oil Company
Aramco announced it has agreed to purchase US-based Valvoline Global Products (VGP) business for $2.65 billion. Within the equity purchase other factors will be included as in motor oils, transmission fluids, coolants and other automotive maintenance products.
Valvoline Global Products is a leading worldwide independent producer and distributor of premium branded automotive, commercial and industrial lubricants, and automotive chemicals.
Aramco will benefit from VGP’s manufacturing & distribution network and global brand recognition. The acquisition will complement Aramco’s line of premium branded lubricant products, optimize its global base oils production capabilities and expand its own activities.
“Valvoline’s global products business fits perfectly with Aramco’s growth strategy for lubricants as it will leverage our global base oils production, contribute to our R&D capabilities and strengthen our existing relationships with OEMs. Valvoline’s brand strength and global recognition will continue to be developed and extended under Aramco’s stewardship,” said Mohammed Al Qahtani, Aramco senior vice president, downstream.
Following the transaction, Valvoline will focus on its retail services business and extend its preventive auto maintenance service model to EV owners, and fleets as the car parc evolves.
“The sale of global products represents the successful outcome of our strategy to unlock the full, long-term value of our strong but differentiated retail services and global products businesses,” said Sam Mitchell, Valvoline CEO. “We are pleased that our global products team will have a strategic new home with Aramco to further grow the business while developing the brand into a global lubricants leader.”
YONGIN-SI, GYEONGGI-DO, SOUTH KOREA: Samsung SDI said it will construct its second battery production facility in Seremban, Malaysia. Samsung SDI Energy Malaysia (SDIEM) will start mass-production of PRiMX 21700 cylindrical batteries (21mm X 70 mm) in 2024 and they will invest 1.7 trillion won in phase-by-phase process until 2025. The battery production from plant 2 will be used in various applications ranging from electrical tools, micro-mobility to electric vehicles.
The groundbreaking ceremony of plant 2 at SDIEM was attended by Samsung SDI’s president and CEO Yoonho Choi, the Menteri Besar of Negeri Sembilan, Dato’ Seri Haji Aminuddin bin Harun, state legislatures of Negeri Sembilan, ambassador of the Korea to Malaysia, Lee Chi-beom, and many representatives from SDIEM’s partner companies, including POSCO Chemical, W-SCOPE and Iljin Materials.
“Today’s groundbreaking ceremony will serve as a starting point for realizing our vision to become a Global Top Tier Company by 2030. The successful completion and early stabilization of plant 2, we will make SDIEM the center of global battery industry. With support from the Malaysian state government and partner companies, we will be able to realize the vision much faster,” said Choi.
“Investments from high-impact industries, such as Samsung SDIEM
are integral to our vision of driving robust economic growth in Malaysia and Negeri Sembilan, which is outlined in our Malaysia Vision Valley 2.0 plan. Samsung SDIEM’s investment to be the pioneer in electric vehicle (EV) battery cell manufacturing in Seremban will continue to create jobs for the youth and spur more opportunities for local businesses,” said Negeri Sembilan Menteri Besar.
LONDON, UK: Iberdrola and bp announced that they will form a strategic collaboration aiming to help accelerate the energy transition. The companies will significantly expand fast EV public charging infrastructure to support the adoption of electric vehicles, as well as develop large scale green hydrogen production hubs in Spain, Portugal and the UK. bp and Iberdrola aim to finalise both joint venture agreements by end 2022.
“With this agreement, we continue advancing in the decarbonization and energy self-sufficiency through the electrification of two key sectors of our economy, transport and industry. The scale of this challenge requires alliances between companies such as Iberdrola and bp, which have the technology and knowledge necessary to help accelerate Europe’s industrial development,” said chairman, Iberdrola, Ignacio Galan.
“Creating the lower carbon energy solutions that our customers want and need requires the integration of different technologies, capabilities and forms of energy. We can deliver this faster and at scale when we work in partnership with others,” said Bernard Looney, CEO, bp.
Iberdrola and bp plan to form a joint venture that intends to invest up to €1 billion to roll-out a network of up to 11,000 rapid and ultra-fast EV public charge points across Spain and Portugal, significantly expanding access to charging for consumer and fleet customers thus accelerating electric mobility.
The plan includes installing and operating an initial 5,000 fast charge points by 2025, and up to a total of 11,000 by 2030, including bp and Iberdrola’s existing and future fast charging hubs. The companies are also looking at options to jointly serve EV customers in the UK.
Iberdrola offers comprehensive mobility services to cover the needs of electric vehicle users: residential, business and public charging, including solutions for urban and heavy transport (electrification of buses and trucks).
Iberdrola leads the public charging infrastructure in Spain and Portugal with more than 2,500 points in operation and others under development, with renewable energy to decarbonize transport end-toend.
bp aims to rapidly expand its EV charge points globally and continues to invest in rapid and ultra-fast charging. Customers already have access to its European network of over 10,000 charge points, mainly in UK and Germany.
bp expects to use some of its extensive and conveniently located network of 1,300 retail sites in Spain and Portugal as locations for charging hubs for the joint venture. EV drivers would be able to charge in safe locations with access to additional convenience services.
The companies also plan to form a joint venture for large-scale integrated green hydrogen production in Spain, Portugal and the UK as well as production of derivatives such as green ammonia, and methanol, that can be potentially exported into Nothern Europe. This strategic collaboration will combine Iberdrola’s world-class track record in renewables development and its global customer base, with bp’s experience in gas processing, trading and its global customer portfolio.
The companies aim to jointly develop advantaged hydrogen production hubs in Spain, Portugal and UK, with total capacity of up to 600ktpa, integrated with new renewable power. The green hydrogen project at bp’s Castellon refinery will be part of the agreement. The two companies, together with the Instituto Tecnologico de la Energía, have submitted the Castellon project to the Spanish government’s hydrogen value chain PERTE call.
Likewise, Iberdrola and bp´s industrial hydrogen projects under development, as well as new projects, will be part of the agreement. Based on this collaboration in Spain, Portugal and UK, Iberdrola and bp intend to explore potential future opportunities for green hydrogen production in other geographies.
IBERDROLA, BP TO DEVELOP EV CHARGING NETWORK AND GREEN HYDROGEN PROJECTSIberdrola, bp will develop in Spain, Portugal and UK large scale production of green hydrogen, open to other geographies, aiming for up to 600ktpa production capacity.
FRANKFURT, GERMANY: INEOS and SINOPEC have signed three back-to-back deals worth a combined value of $7 billion. These landmark agreements are expected to generate a combined turnover of around $10 billion from 7 million tonnes of capacity. The three agreements will significantly reshape INEOS’ petrochemicals production and technology in China.
Each transaction is currently anticipated to complete before the end of the year and will be financed through a combination of internal cash resources and external financing.
Firstly, INEOS has agreed to acquire a 50 percent stake in Shanghai SECCO Petrochemical Company Limited (SECCO), a subsidiary of China Petroleum & Chemical Corporation (SINOPEC). SECCO currently has a production capacity of 4.2 million tonnes of petrochemicals - including ethylene, propylene, polyethylene, polypropylene, styrene, polystyrene, acrylonitrile, butadiene, benzene and toluene. It is a 200-hectare facility, located inside the Shanghai Chemical Industry Park.
Secondly, INEOS has agreed to establish a new 50:50 joint venture with SINOPEC with the intent to build production capacity of up to 1.2 million tonnes of ABS, to meet rapidly growing demand in China. The 600ktpa ABS plant in Ningbo, which is currently under construction by INEOS Styrolution and is planned to be operational by the end of 2023, will become part of the joint venture.
INEOS and SINOPEC also plan to work together on two additional 300ktpa ABS plants, which will also be built by the joint venture based on INEOS’ world-leading Terluran® ABS technology. One of these
300kt plants will be located in Tianjin, the location of the third unit is yet to be decided.
The third agreement will see INEOS and SINOPEC also establish a 50:50 joint venture to build a new 500ktpa HDPE plant in Tianjin. In addition to the Tianjin plant INEOS and SINOPEC shall build at least two additional 500ktpa HDPE plants in the future to produce INEOS pipe grade under license. The Tianjin plant is expected to be onstream by the end of 2023.
INEOS already has joint ventures in operation with SINOPEC following the acquisition of the Acetyls and Aromatics business from BP in January 2021, and both companies know each other well through two decades of commercial interfaces at various levels. They see a natural fit to working more closely in the future. Through this close relationship SINOPEC gains access to some of the best downstream technology in the world from INEOS and INEOS achieves a substantial presence in China, the fastest growing market in the world.
“These agreements significantly reshape INEOS’ petrochemical production and technology in China. We are pleased to make these major investments with SINOPEC in areas that provide the best growth opportunities for both companies. Both parties recognise the potential for closer collaboration across a number of other areas as we look ahead,” said Jim Ratcliffe, chairman and CEO INEOS.
China is a key growth region for INEOS and the agreements significantly extend its petrochemicals business with a focus on products where it has some of the leading proprietary technologies.
SAO PAULO, BRAZIL/DORTMUND, GERMANY: Unigel said it installed the first industrial scale green hydrogen plant in Brazil.
The company, which is one of the largest chemical companies in Latin America and the largest manufacturer of nitrogen fertilizers in Brazil, invests a total of $120 million in the development of the production site for green hydrogen. Unigel relies on the world-leading technology of thyssenkrupp nucera.
The plant will starts its production planned for late 2023. At this moment, Unigel’s integrated green hydrogen and green ammonia plant is expected to be the largest in the world. In the first phase of the project, Unigel installs three 20 MW standard electrolyzers from thyssenkrupp nucera, adding up to a total capacity of 60 MW.
The company plans to quadruple its production of green hydrogen in the years following the inauguration by expanding the electrolyzer plant to a multi-hundred MW facility, which will produce approximately 40,000 tons of green hydrogen. The new factory is expected to employ more than 500 people, so that the chemical company also gives an important impulse for the whole region.
“Throughout our nearly 60-year history, we have always been attentive to technological innovations and have invested to meet industrial and agribusiness demands. With this project, Unigel takes the first step towards the decarbonization of several sectors, contributing substantially to combating climate change on the planet,” said Henri Slezynger, chairman, board of directors and founder of Unigel.
“This project is the first of its kind in Brazil and reinforces the
pioneering spirit of Unigel to produce green molecules on an industrial scale. As Brazil is one of the world-leading countries in terms of installed renewable energy, we are pleased to enter this partnership to make green hydrogen an affordable energy vector already today,” said Dr. Werner Ponikwar, CEO, thyssenkrupp nucera. “Only through largescale production with robust, reliable and cost-effective technologies at competitive renewable power prices green hydrogen will become market-ready with widespread use.”
Located in the Camacari Industrial Complex (BA), the new plant will have an initial production capacity of 10,000 tons/year of green hydrogen and 60,000 tons/year of green ammonia. The products will be offered to customers who aim to decarbonize their production chains eg. the steel industry, oil refining, and e-fuels. Green ammonia will also be used in the value chain of Unigel, as it is a raw material in the manufacturing of fertilizers and acrylics.
“Given the potential of Brazil in the generation of wind and solar energy, we believe that the country has a great opportunity to be a reference for the world in green hydrogen, a solution that brings versatility to transform renewable energy into raw materials and zero carbon fuels,” said Roberto Noronha Santos, CEO, Unigel.
“Brazil’s energy mix already has a very high share of renewables. Around three quarters of the energy used in electrolysis of the project comes from renewable sources. This makes Unigel and thyssenkrupp nucera first movers on an industrial scale in one of the most important markets in South America.”
UNIGEL TO INSTALL FIRST INDUSTRIAL-SCALE GREEN HYDROGEN SITE IN BRAZILUnigel has installed the first industrial scale green hydrogen plant at Camacari Industrial Complex, Brazil (in picture), investing a total of $120 million for the site development. Unigel installs three 20 MW standard electrolyzers from thyssenkrupp nucera, adding upto a total capacity of 60 MW.
GERMANY: Bayer, Bunge and Chevron USA Inc, subsidiary of Chevron Corporation, said they have agreed for Bayer’s acquisition of a 65 percent majority ownership of the winter oilseed producer CoverCress Inc (CCI). The remaining 35 percent of CCI will continue ownership under Bunge and Chevron.
CCI, Bayer, Bunge and Chevron aim to provide corn and soybean growers another revenue outlet by providing desirable fuel product and high-protein meal for animal feed.
CCI will continue to operate as an independent entity. It has developed CoverCress™, a unique crop whose grain is a lower carbon, low-input source for fuel and feed. Oil extracted from CoverCress™ grain can be made into renewable diesel with Bunge’s expertise in oilseed processing and Chevron’s proficiency in fuels manufacturing.
“CoverCress is exciting because it has the potential to become an important source for biofuel production as a new harvested rotational crop, while giving growers an innovative option to continue effective stewardship of their land and improve soil quality by acting as a cover crop,” said Rodrigo Santos, member, board of management of Bayer AG and president, crop science division.
“As a global leader in crop science, we are committed to decarbonizing agriculture and helping farmers around the world become more sustainable through game-changing products and solutions that can impact climate change,” he added.
“Since our founding in 2013 we have actively sought - and benefited
from scientific, operational, and financial support from our academic and strategic partners. The progress we have made in converting pennycress into our novel, lower carbon intensity oilseed technology, CoverCress™, would have been much slower without this critical support,” said Mike DeCamp, CEO and president of CCI. “Our longstanding strategic partnership with Bayer and our more recent strategic partnerships with Bunge, and Chevron have provided us with access to expertise and capital that positions CCI very well for future success.”
“Connecting the full value chain - from seed development to end consumer - is an important step to bringing this crop to market at scale. We look forward to helping meet the growing demand for renewable fuels with this next generation lower carbon feedstock,” said Greg Heckman, Bunge’s CEO.
North America will soon gain access to cash crop that provides the benefits of a cover crop as well as being harvestable for use as a renewable fuel feedstock.
“Chevron is seeking to create innovative renewable fuel feedstocks by collaborating with America’s farmers. We are excited to work with Bayer and Bunge to accelerate the adoption of CoverCress™, which will ultimately be used to help supply the US transportation system with lower lifecycle carbon intensity fuels,” said Mark Nelson, Chevron’s executive vice president for Downstream & Chemicals.
Developed by converting field pennycress through breeding and gene editing tools, CoverCress™ has the potential to decrease nitrogen loss, help store carbon in the soil and improve soil health.
US: Dow and Nexus Circular announced that they have signed a detailed letter of intent (LOI) for Dow to secure the production output of a newly constructed advanced recycling facility in Dallas, Texas. The new facility will process and convert over 26,000 MTs annually of previously non-recycled plastic into circular feedstock that will be delivered back to Dow as a raw material to create new, recycled plastics for food-contact, health, hygiene and fitness applications.
The LOI builds on Dow and Nexus Circular’s initial joint effort as the chosen advanced recycler for the Hefty® EnergyBag® program, launched in collaboration between Dow, Reynolds Consumer Products and others, to collect hard-to-recycle plastics at residential curbside to convert them into valued resources.
Nexus Circular is a commercial leader in advanced recycling that uses a proprietary process and pyrolysis (high temperature decomposition) technology to transform waste plastics into high-quality circular feedstocks its partners use in the production of circular polymers. Nexus Circular has optimized the technology to create a highly efficient, economic, commercial and scalable system for delivering cost-effective, high quality and environmentally friendly circular products for its partners and customers.
In 2020, Nexus Circular was named a grant recipient of Dow’s Business Impact Fund for the development of pre-processing to incorporate post-consumer, hard-to-recycle plastics collected through the Hefty® EnergyBag® program in Cobb County, GA.
This current expansion of the Dow-Nexus collaboration into Dallas, among other locations, will result in the further collection and conversion of landfill-bound plastics into plastic products that will be used in consumer applications, in order to help close the used plastics loop. The program builds on the impact of the Hefty® EnergyBag® which has diverted over 1,800 tons of hard-to-recycle plastics from landfills to date.
“Expanding our past, scaled success with Nexus to drive production of high-quality circular feedstocks, the new facility in Dallas marks an important step in meeting unmet market demand for circular plastics in Texas and other markets,” said Manav Lahoti, global sustainability director for Hydrocarbons, Dow. “We now have an even greater opportunity to close the loop on Dow’s materials through the delivery of Nexus’ circular products back to our plants, further accelerating progress toward our 2030 goal to enable 1 million metric tons of plastic to be collected, reused or recycled.”
“We are excited for the next phase of our growing partnership with Dow to build on our joint efforts to extend the life of used plastics. With this meaningful LOI, we’ll be better positioned to collect and convert more landfill-bound waste plastics into new materials using advanced recycling in markets worldwide,” said Clint Thompson, chief commercial officer, Nexus Circular.
US: ADM announced it has elected ex-Corteva CEO Jim Collins to the board of directors. Collins was CEO and Corteva Agriscience board member from 2019 to 2021.
Corteva Inc had announced that James (Jim) Collins Jr will retire from Corteva, effective 31 December 2021, after more than 37 years with the company. He served in a variety of leadership positions in the agriculture business at Corteva’s predecessors, DowDuPont and DuPont, prior to 2019.
“Our Board’s deep and diverse experience and leadership have been critical as we’ve transformed ADM into a global leader meeting growing needs in food security, health and well-being, and sustainability,” said chairman and CEO Juan Luciano.
“Jim brings to ADM a wealth of expertise in innovation and global agriculture, and a keen understanding of how to support farmers as we work together to improve the sustainability of our agriculture and nutrition value chains. His experience leading a global Fortune 200 company will make him a valuable partner as we continue to build a better ADM and align our portfolio to meet needs in growing global trend areas,’ added Luciano.
Care Company and Herc Holdings. He is also a senior advisor at New Mountain Capital. He most recently served as CEO of Platform Specialty Products Corporation, a leading global specialty chemicals company, from 2016 to 2019.
Prior to that, Sachdev led Sigma-Aldrich Corporation, a leading S&P 500 global life sciences and technology company, as its president and CEO from 2010 until 2015, when it was acquired by Merck KGaA. He previously held executive positions at Meritor Inc, a global supplier of automotive systems and components, and Cummins Inc, a global engine and power systems manufacturer.
GLEN
MILLS, US: Axalta Coating Systems Ltd announced that Robert Bryant will step down as president and chief executive officer to pursue other opportunities, effective 31 August. He will also step down as a member of the board of directors at such time. Rakesh Sachdev, an independent director and former chief executive officer of Platform Specialty Products Corporation (now renamed Element Solutions Inc) and Sigma-Aldrich Corporation, will assume the role of interim chief executive officer at that time. The board has initiated a comprehensive search process to identify a new CEO.
Sachdev has served as an independent director of Axalta since August 2020. He is currently chairman of the board of Regal Rexnord Corporation and serves as a board member of Edgewell Personal
“Our board remains committed to continuing the acceleration of Axalta’s performance and unlocking long-term value for our shareholders and enhanced opportunities for our employees. With more than three decades of experience in the management of public and private chemical, life sciences and industrial businesses, Rakesh is a proven leader and the right choice to serve as Axalta’s interim CEO. The board has tremendous confidence in Axalta’s leadership team and is focused on ensuring the team’s continuity during this transition,” said Bill Cook, Axalta’s board chair.
“Axalta is an industry leader with clear priorities and paths to achieve secular growth and market share gains by leveraging our technology platforms and continuing to launch new and innovative products. During this transitionary period, I look forward to partnering with Axalta’s deep bench of senior leaders to drive further growth as endmarkets normalize over time and to execute flawlessly on our strategy to significantly enhance value for all our stakeholders,” said Sachdev.
MUMBAI, INDIA: Merck India announced it has appointed Pratima Reddy as the managing director for Merck Specialities Pvt Ltd, the healthcare business of Merck KGaA, Darmstadt in India. Reddy is the first woman CEO for Merck Healthcare in India and successor to Anandram Narasimhan, transitioning into a regional role at APAC.
Reddy was the regional franchise leader (RFL) of the Cardiovascular, Metabolism and Endocrinology (CM&E) franchise in APAC before taking over as MD of India Operations, the company said.
Reddy has an extensive experience for over 17 years, with nine years in the pharmaceutical Industry. She had significant roles with both the national and global teams since joining Merck in October 2013. In addition, she headed the Oncology unit in the country.
“Today, more than ever, we need to realize and fulfil our responsibility to improve the overall healthcare ecosystem by working towards providing advanced medical care to patients.” said Reddy.
Currently, Ahmed is based at the IMCD offices in Cairo, Egypt and will be reporting to Manuel Baumann, managing director, IMCD Middle East & Global Director Construction.
“IMCD Egypt has seen rapid growth through its purely organic journey from a true green field start. Over the last two years, we were able to broaden our business from the initial Pharma focus into Coatings & Construction, Home Care I&I, Beauty & Personal Care as well as Food & Nutrition and Advanced Materials. All these business units excel despite the challenging supply chain realities, thanks to our local expertise and we are therefore investing further,” said Baumann.
“Ahmed has a strong track record in specialty chemicals, a deep knowledge on the market’s trends and an understanding of the importance of innovation and sustainable solutions, we strive to offer to our partners,” he added.
ROTTERDAM, THE NETHERLANDS: IMCD Egypt, part of
IMCD Group, said it has appointed Ahmed Nousser as the new managing director, effective 1 August. The new MD of IMCD Egypt will have to fill-in many gaps, among them focusing on leading the company’s constant strategic growth through knowledge and blending it with new and existing principals.
Keeping with the M&A opportunities needs to be explored, navigating towards commercial excellence, talent development and making the business excel towards digitization and furthermore.
“I am honoured and excited about the opportunity to lead IMCD Egypt and looking forward to the continual improvement, sustainable growth and success. With the solid foundation of IMCD Egypt and the highly motivated teams, I am looking forward to growing further the opportunity pipeline across all industries and make IMCD Egypt a leading specialty chemical distributor, further strengthening our existing relations and to make Egypt attractive to new partners,” said Nousser.
From 2010 to 2013, Twitchell was executive vice president and chief financial officer of Landmark Aviation, a private equity-backed fixed base operator for the aviation industry. Prior to 2010, she was Vice President and Treasurer of LyondellBasell Industries/Lyondell Chemical Company. Twitchell has also held senior management positions in the aluminum and cement manufacturing industries.
Boss is currently on the board of directors of Cooper-Standard, Wabash National and Libbey Inc. Most recently, he was president and CEO of Momentive Performance Materials, a specialty chemicals and materials business from 2014 until 2020. Prior to Momentive, he was president of Honeywell Safety Products from 2012 to 2014.
announced the appointment of Karen Twitchell and John (Jack) Boss to the board of directors effective 2 August. Concurrently, Calumet announced that Robert (Bob) Funk has elected to retire from the board of directors.
Twitchell was chair of the board of Trecora Resources, a petrochemical and specialty wax manufacturer, until the sale of the company in June. In addition, she serves on the board of Kraton Corp and HMTX Industries. Previously she served on KMG Chemicals’ board.
He held various managerial roles within Honeywell’s Specialty Materials and Chemicals businesses from 2003 through 2014. Prior to Honeywell, he served as VP at Great Lakes Chemical Corporation. He also has experience at International Specialty Products, Allied Signal Corporation and Dresser Industries.
“We are delighted to add Karen and Jack as independent directors. Their addition will add strength and depth to the board. Their skills, values and experiences will be tremendously helpful as they are aligned with our stated strategic objectives of standing up two best of breed businesses and de-levering Calumet’s balance sheet,” said Steve Mawer, executive chairman.
US: RPM International Inc announced the appointment of general (retired) Ellen Pawlikowski to its board of directors, effective 18 July. Currently, she serves on the board of defense contractor, Raytheon Technologies, ranked 58 on the 2022 Fortune 500 list. Pawlikowski is a retired four-star general of the US Air Force and is an independent consultant, providing expertise to industry and academia on strategic planning, program management, logistics and R&D.
Pawlikowski commanded five times as a general officer and served as the program director and program executive officer for several multibillion-dollar weapon system acquisitions. In her last assignment with the Air Force, she served as commander, Air Force materiel command at Wright-Patterson Air Force Base, Ohio. She will stand for election by the stockholders at the 2022 annual meeting.
“Ellen is a remarkable leader with a distinguished background in management, logistics and strategic planning. Her unique perspective will be a considerable asset for RPM’s growth and continued value for our stakeholders,” said Frank Sullivan, RPM chairman and CEO.
“Since the acquisition of Whawon in 2019, South Korea has proven to have high growth potential for IMCD. We continue the integration process and diversification of the business into more market segments,” commented Andreas Igerl, Asia president of IMCD.
“Henri’s valuable knowledge and understanding of the Korean market, from both a manufacturer and distributor point-of-view, is key to leading the team to the next level of growth.”
“I’m excited to join IMCD as I always have a positive impression of IMCD since our previous interaction in Roquette,” remarked Kwon. “I would like to deliver my heartfelt thanks to Won, who founded and has grown the Korean business, which helped us open our ambition in the area. I will continue to build on the great foundation that the team has set and uncover more growth opportunities.”
ROTTERDAM, THE NETHERLANDS: IMCD announced the appointment of Henri Kwon as managing director of IMCD Korea, effective 1 August. With 30 years of experience in management roles in several speciality chemicals and ingredient companies, Kwon will be responsible for continuing the growth trajectory of IMCD Korea.
Kwon will lead strategic growth ambitions by focusing on expanding new and existing suppliers, driving commercial excellence, exploring opportunities for M&As, developing talents, and further advancing the business’s digitalisation. Upon Kwon’s appointment, Whawon’s founder, Young-Hee Won, will begin his transition into retirement.
With a background in Food Science & Technology, Kwon started his career as an account manager at Doosan Group. He has since progressed to multiple commercial roles with local and regional appointments, having lived in China for seven years. Before joining IMCD, Kwon spent 20 years with Roquette, with his last role as Korea’s country head and head of distribution for Asia.
IMCD Korea and Whawon, an IMCD company, provide sales, marketing and formulation expertise to customers and suppliers in pharmaceuticals, personal care, coatings, food, nutrition and other speciality industrial markets. Its office is based in Seoul, and the pharmaceuticals’ in-house analytical lab provides testing, reliable quality control and assurance throughout customers’ product development cycle.
WATERFORD, US: Momentive Performance Materials (Momentive) named Bob Bush as its new chief financial officer, effective 7 July. Prior to Momentive, he held several financial leadership positions at ITT Corporation and at GE. Having begun his Momentive journey in 2013, he has held several finance leadership roles in FP&A, global operations, business finance, and most recently served as vice president & treasurer.
“Bob has been an instrumental part of Momentive’s Finance organization for the last several years and we are excited to have him continue to lead us on our journey and drive profitable growth as our new CFO,” said Momentive president and CEO Sam Conzone.
Bush has responsibility for all areas of Finance within Momentive, including Financial Planning & Analysis (FP&A), Treasury, Global Tax and Controllership, as well as Finance Shared Services and Information Technology.
Vaidya comes to Cosmo Speciality Chemicals with over 30 years of experience in sales & marketing, business development and strategic planning. He has in depth understanding of textile dyes and chemicals industry and would capitalize his expertise to drive sales for the speciality chemicals business.
“With more than three decades long career in the textile industry, Sunil has knowledge and expertise across various domains of sales, development, and strategic planning. I am delighted to welcome Sunil as part of Cosmo’s Team and confident that his addition would be instrumental in accelerating sales and powering growth for our speciality chemicals business in the textiles industry and beyond,” said Pankaj Poddar, Group CEO, Cosmo First Ltd.
NEWDELHI, INDIA: Cosmo Speciality Chemicals, subsidiary of Cosmo First Ltd, announced it has appointed Sunil Vaidya as head sales, textile division. In his new role, Vaidya will be responsible for driving sales and development for Cosmo Speciality Chemicals nationally. He will report to Anil Gaikwad, business head, Cosmo Speciality Chemicals.
“Within a few years, Cosmo Speciality Chemicals – Textile division has launched multiple products and built credibility across industry which can be witnessed by its phenomenal growth. I am thankful that the leadership has entrusted me with the responsibility of driving growth via sales for speciality chemicals business across markets. I look forward to leveraging expertise and R&D capabilities of the team to help unlock new market opportunities,” said Vaidya.
“We are excited to have Bollywood’s superstar Ajay Devgn as part of our IIL family. IIL believes in bringing in the right technology within the reach of every small and marginal farmer. Ajay Devgn has established himself as one of the India’s most popular and versatile actors with fierce performances and resonates well with our products. With IIL entering the next phase of growth, we are sure that his popularity, along with the credibility of our products, will help us to increase the penetration of our communication in our existing markets as well as newer markets,” said Rajesh Aggarwal, managing director, Insecticides (India) Ltd.
recently that it has appointed actor Ajay Devgn as their brand ambassador. Devgn, who has a mass appeal among the rural audience, will spread the message of judicious use of agrochemicals besides communicating about their products and boosting farmer awareness in India to the grassroots level.
“I am looking forward to working with Insecticides (India) Ltd. I am pleased to be associated with a company that works to improve the lives of farmers by their innovative products. IIL is a well-known crop protection and nutrition brand founded on the principles of quality, integrity, and commitment to Indian agriculture. Given the strong culture of invention and the ongoing need to adapt to shifting preferences, there was a lot of common ground. I’m equally excited about our journey together,” said Devgn.
Multilayer packaging based on polyethylene terephthalate (PET) can have a bright and sustainable future. This is the message of the strategic partnership of four leading technology companies, whose closed-loop recycling model is sparking new discussions on the role PET-based multilayer will play in tomorrow’s packaging industry.
The European Green Deal requires all packaging to be reusable or recyclable by 2030 – a regulation that is perceived as particularly challenging for multilayer packaging, since its layers first need to be separated before entering recycling streams. However, that perception could be about to change.
Sulayr, a recycling company operating in Europe, has successfully commercialized a multilayer recycling process that achieves ‘closed-loop’ status and enables PET to be reused with virtually zero waste. With this, a circular economy practice for PET containing packaging materials already exists, but this process can be improved and become more practical and effective, if the whole value chain works together with the target to make the separation of the layers easier.
Industrial adhesives specialist BASF, packaging machinery OEM Bobst and films expert Evertis are supporting Sulayr in this endeavour. Together, the companies form a strategic partnership combining expertise from across the entire packaging value chain. Their collaborative contributions are key to the success of this impressive recycling process, and its potential for adoption at a bigger scale.
At the core of the process is a multilayer film produced by Evertis, comprising PET and polyethylene (PE) layers, laminated with a BASF’ Epotal® water-based adhesive and processed with a Bobst coater. Multilayer films are used for various packaging materials; after use, the waste is delivered to sorting facilities. Sulayr can use the so-called waste as raw material, ensuring a closed-loop. The company separates the multilayers and makes the PET available for re-use, with recycled PET delivered to Evertis and other film producers who then restart the cycle.
This is seen as an important step towards universal recycling of PET, enabling its continued use in a Green Deal-compliant packaging economy. The process can apply to post-consumer and post-industrial waste – meaning it has enormous potential to transform the entire PET-based packaging use model.
Sulayr has been able to separate different types of multilayers since 2009, but the speed and cost-effectiveness of the process depends on the debonding of the films.
“Our technologies enable us to delaminate most types of PET-containing multilayers and bring the recycled PET back to the industry. However, we see a difference in the trays coming from the post-use phase to our facility.
With BASF’s water-based Epotal® adhesives for example, our separation process is simplified, because the adhesive allows a quick and easy separation with a high quality of the recyclates which is not the case with solvent-based adhesives for example. We are sure that a streamlined process can help scale up the recyclability of PET-based multilayers, giving the packaging industry a new way to meet its sustainability challenges,” said Miguel Ángel Arena, CEO of Sulayr.
One way to optimize the recycling process is to produce all PET/PE trays under specific conditions that facilitate easy separation. This is an area in which the partners are collaborating: before bringing a new laminate to market, Evertis for example, qualifies it to be recyclable in Sulayr’s process, ensuring its layers can be separated easily.
The four partners emphasize that collaboration, as well as cutting-edge technology, is key to the success of the process.
“This collaboration can be game-changing for the future of flexible packaging. It demonstrates that a circular economy for PET-based packaging is commercially possible – if we all work together. When it comes to recycling and debonding on multilayers we see good results with our water-based adhesives which can be key in this process, and we are confident that we can improve this process even further. At BASF, we are working on special adhesives that enable even easier separation under certain conditions. The more we do to demonstrate the viability of the process, the quicker it can become standard for all lamination adhesives – which would take the recycling of multilayers to the next level,” commented Thomas Peter Schiele, vice president, Adhesives, Fiber Bonding and Paper Coating Chemicals at BASF.
“This cooperation is a best practice for the packaging industry and significant for the future of multilayer packaging materials. The requirements of the Green Deal compel us all to do everything within our power to scale up the sustainability of our products, and to implement systemic changes to future-proof our industry. I am proud of the contribution this project makes to that goal,” said Rui Silva, chief product and innovation officer at Evertis.
Sulayr and its collaboration partners also hope to change industry perceptions on a wider basis. Multilayers based on PET are necessary for many industrial uses, but were not thought of as a sustainable solution – until now. This best-practice process could change the conversations about PET, waste, and sustainability that are taking place within value chain leaders and packaging associations, such as Petcore and CEFLEX.
“We want to move forward, collaboratively as one industry, towards a sustainable future for all forms of flexible packaging. As a manufacturer of printing and converting machinery, we have a duty to contribute to a future-proof, recyclable solution,” said Sara Alexander, marketing and communication manager, Flexible Packaging at Bobst. “We have done so by developing our equipment platform in terms of the most suited coating technology, process agility and speed with water-based adhesives to meet the project’s scope. Now, thanks to all the partners’ contribution, we have an opportunity to secure that future for PET-based multilayer laminates.”
By collaborating and optimizing further with our respective technologies, solutions and expertise, we can close the loop on packaging material recycling and create a more circular economy for packaging that begins and reoccurs with end-of-life products.
In the packaging sector, isododecane and similar substances are a challenge for thermoplastic elastomers (TPEs). If a material has not been specifically developed for use in the field of cosmetics, there is a risk that modifications such as swelling or degradation of the material may occur. This particularly affects products that are based on waterresistant formulations. With High Resistance TPE for Cosmetics, KRAIBURG TPE is introducing a product development that reliably meets standard requirements over the long term.
For manufacturers, the requirements that cosmetic products have to meet are high, as product reliability has to be ensured at all times. But visual and haptic qualities, which have a direct influence on purchasing decisions, are also vitally important. Along with these criteria, mechanical properties also play a crucial role for processors.
High Resistance TPE for Cosmetics has enabled KRAIBURG TPE to expand its portfolio to include a compound series that withstands contact with particularly demanding ingredients, including isododecane. So the TPE manufacturer from Waldkraiburg, Germany, is now able to provide further solutions for the beauty market, including applications such as waterproof mascara, pipette lids, lip gloss applicators and cosmetics packaging.
This new response for beauty applications is based on an established product from the company. COPEC® was developed to meet the requirements for high resistance to sebum oils. Due to its velvety surface, it also meets the demand for high-quality haptics in the field of consumer electronics.
“We are now presenting our new materials solutions, High Resistance TPEs for Cosmetics, which for the first time make it possible to elegantly satisfy the high standards set by the cosmetics industry. Prospective clients will also benefit from the broad range of processing options available with the materials. This new product series is enabling us to meet customers’ current wishes and to open up new applications,” said Dr. Jan Bothe, product development scientist at KRAIBURG TPE.
High Resistance TPE for Cosmetics is available with hardness grades of 65, 75 and 85 Shore A and can be customized in many ways due
to its opaque color. In addition, the new compounds have good processing properties in injection molding and allow adhesion to selected plastics.
The materials also meet the standards of the cosmetics industry in accordance with US FDA CFR 21 and Regulation (EC) No. 10/2011 and comply with REACH, RoHS, California Proposition 65 as well as Mercosur No. 39/19. The TPEs are free of animal ingredients, so that they can be used throughout the cosmetics market. This is another product from KRAIBURG TPE that is suitable for inprocess recycling. High Resistance TPE for Cosmetics is now available worldwide.
SABIC introduced BLUEHERO™, an expanding ecosystem of materials, solutions, expertise and programs aimed to help accelerate the world’s energy transition to electric power and support meeting global goals on climate change. The company’s starting point with BLUEHERO is support of the automotive industry’s mission to create better, safer and more efficient electric vehicles (EVs), with an emphasis on improving structural battery components with unique flame retardant materials and solution development expertise.
The automotive industry is leading the charge in moving toward new, more sustainable mobility systems. This includes a major shift towards battery powered EVs, which can convert over 77 percent of electricity into movement compared to only 12 to 30 percent for vehicles with internal combustion engines. In addition to this high performance, EVs also emit no tailpipe pollutants and are typically responsible for significantly fewer greenhouse gas emissions during operation – enabling important contributions to meeting global goals on climate change.
“With our strategic BLUEHERO initiative, we have vigorously committed to invest in, develop and deliver material solutions that can support the transition to electric power, drive down emissions and help address climate change,” said Abdulrahman Al-Fageeh, SABIC’s executive vice president for Petrochemicals.
“Our decision to initially focus on automotive reflects the urgency of making progress in that space and the strengths we already have with established materials and capabilities that can allow us to support the shift to electric vehicles and contribute to a low carbon future. With BLUEHERO, aligned with our purpose of delivering ‘Chemistry that Matters™’ and shaping a more sustainable future, we are bolstering our position to develop and deliver impactful solutions that the industry requires to collectively and heroically move us ever closer to a clean air economy.”
SABIC provides cost-effective and technologically advanced thermoplastics – which can offer significant advantages over conventional materials (metals) – to help the automotive industry further enhance the performance of EVs. For example, using plastics in EV battery, electrical and charging components can deliver multiple benefits: reduced weight and system complexity, extended driving range, expanded design freedom, streamlined manufacturability, recyclability, and enhanced thermal management and occupant safety.
The new BLUEHERO electrification initiative also leverages specific knowledge and expertise around large part molding, compression molding, advanced injection molding and polymer flame interaction to help support customers with solutions that can meet critical requirements and enable efficient production.
The company expects to strengthen and expand its thermoplastic offering to help enable electrification with the elevated focus and new investments that will become available under BLUEHERO.
“Transitioning from vehicles based on internal combustion engines to electric propulsion is not a simple, linear process,” said Abdullah Al-Otaibi, general manager, ETP & Market Solutions, SABIC. “In fact, a successful shift will require a willingness to forgo many traditional materials and deep-rooted design, engineering and manufacturing methods. Through the BLUEHERO initiative, our team is following a holistic systems engineering approach in their work with the industry – enabling customers to optimize EV battery systems more efficiently using thermoplastics.”
An integral element of SABIC’s BLUEHERO ecosystem is its
global team of engineers, research fellows and scientists. This team is harnessing its established and growing expertise in design, testing and data generation for EV batteries and related applications to problem solve and overcome current limitations. As part of its work, the team collaborates with customers, development partners and others across the value chain, from OEMs and tiers to tooling suppliers and testing agencies.
With promising opportunities for the world to employ electric technologies, SABIC anticipates expanding the focus and scope of its BLUEHERO initiative to help support efforts in additional sectors. Those could potentially include energy storage, charging infrastructure, other modes of transport and industrial and consumer equipment.
The world is rapidly changing, and in all manners of the term. Rising temperatures, unprecedented weather systems, and its after-effects on collective health, economy, and ecology are all standing proofs of this change. This has been a result of accelerated industrialisation, urbanisation and modernisation over the past 150 years, which was required in the first place to meet the growing demands of a growing population the world over.
India, with its 1.3 billion people is also one of the fastest growing economies of the world. We are heavily dependent on coal for power generation, but how we use it, combined with the diesel usage for captive generation push up the carbon intensity of India’s power sector. A further increase in population will create more demand for energy, anticipating a rise in emissions from India. We are in need of a deep decarbonisation strategy, or a process of reducing carbon emissions into the atmosphere. While the world at large aims to limit the global warming to below 2°C above pre-industrialised level, we have to make significant reductions in our contribution to global emissions.
The Indian government is committed to increase its renewable, non-fossil energy capacity, reduce the intensity of its carbon emissions, as it is on its way to reach its net-zero target by 2070. Its announcements made in this direction signify the way the country sees itself play a role in global climate action, demonstrating that acting on climate is the path to development, and that it is the only way to attain and continue on a path of resilient, inclusive, and sustainable growth.
In Glasgow COP26 summit, Indian government announced reducing its carbon emission intensity by 45 percent (compared to 2005) by 2030 from earlier commitment of 33 percent, also India stated its commitment to meet 50 percent of its energy requirement from non-fossil sources by 2030.
As a nation, we have set our targets to reaching nonfossil fuel capacity on more accessible sources such as solar and wind power, having increased our investments in solar photovoltaics, giving incentives to renewable manufacturing hubs, and new policies for Biofuels. These actions combine measures for the short-, medium-, and long-term steps towards net-zero, strengthening India’s mandate to transition to a low-carbon economy.
For an entire economy to make its emissions commitments come true, it is industry that needs to step forward in full participation. Companies across the board have echoed the sustainability and decarbonisation intent and have made it a part of their goals to take the lead on this front. With the current policy environment, coupled with India’s accelerated growth over the past few decades, the onus is on us collectively to take steps towards decarbonisation.
The key lies in striking a balance between decarbonisation of key contributing sectors, along with meeting the increased demand for energy and electrification. However, the road ahead is strewn with challenges such as unaffordable electric supply, inefficient operations, theft, all leading to a financial crisis.
The bigger challenge is also in seeking alternative energy sources that can be quickly, efficiently, reliably, and affordably replace existing mechanisms. On the other hand, fuel-efficiency standards for industries, as well as vehicles, are essential to limit emissions.
The government’s “Perform, Achieve and Trade” scheme includes 11 energy-intensive sectors, and is targeted to bring efficiency standards in these industries close to global best practice levels over the next couple of decades. Some measures towards material efficiency include increased recycling, weight reduction in consumer products, increased fabrication yields, increased recycling rates, and resource efficiency in energy-intensive materials.
Track record over the past few years has been impressive and reflecting positively on the country’s ability to deliver on its promises. The industry at large plays a key role in climate protection as an enabler of progress in many other sectors. The industry at large is contributing in their way, in taking the country towards its goals, by leaps and bounds.
Evonik’s Climate and Sustainability strategy for the 2020s is geared to reducing its greenhouse emissions. The objective is a climate-friendly
optimisation of internal production processes, as well as an expansion of the product portfolio with particular sustainability benefits. The company is also deeply aware that sustainability is now a huge part of what consumers demand, therefore making sustainable applications a strategic part of its agenda.
Water is an essential process resource, whether for cooling, processing or in steam generation – and Evonik has been in the process of creating customised prevention plans for the sites the world over to avoid water stress in the long term, whilst actively collaborating with stakeholders to find and respond to newer opportunities in hyper-local scenarios.
The inauguration of the Zero Liquid Discharge Plant at our Dombivli (Maharashtra, India) site is evident of how we accept responsibility for our businesses, our employees, the environment and the society.
Supporting India’s transition to net-zero is akin to supporting global climate change mitigation. India’s journey can also serve as a template for other developing and emerging countries to approach and finance sustainability and decarbonisation efforts, while supporting economic growth. While the challenges for India are immense, they are not insurmountable. A streamlined roadmap, a conducive policy environment, and sustained efforts by businesses can take India ahead on its path to deep decarbonisation.
Source: Vinod Paremal, Regional President and MD, Evonik, India SubcontinentGiven the increasing environmental concerns combined with their high cost of implementation, Paper Mills in India are constantly looking for green alternatives. Currently some of the speciality bio-chemicals help appropriately in this space by minimizing the consumption of certain hard chemicals, thereby minimizing cost and load on the effluent.
After successfully implementing solutions in the textiles processing industry, Proklean Technologies Pvt Ltd introduced the range of speciality bio-chemicals for the pulp & paper industry. While the chemical industry has made significant progress with speciality chemicals to improve processes, new-age products based on probiotics technology has broken new grounds by contributing to sustainability in pulp & paper processing without any compromise on cost or performance.
Newer range of speciality bio-chemicals for the pulp & paper industry help in reducing the use of cooking, bleaching and delignification chemicals, cuts down the generation of sulphides/mercaptans at cooking, Overall, this results in lower emissions even while enhancing the profitability while reducing the carbon foot print of paper mills.
Some of the key features of the speciality bio-chemicals is that this is a revolutionary technology/product for application in the pulp & paper industry. it reduces consumption of bleaching chemicals up to 30 percent while also reducing odour in the mill and the final paper and eventually reduces cost by minimizing the use of chemicals. While applying the technology or shifting towards use of the new products, no change is required in the operations and process conditions. It can be applied at a broad pH and temperature range.
The non-enzyme-based product is also non-toxic, readily biodegradable, can be stored at ambient temperatures up to 500 C, has a one-year shelf life and on the whole, it reduces the effluent load.
Key features of the technology
ProCharta is the first of its kind of technology to work in different process segments of the pulp & paper industry. It effectively works by reducing or eliminating the chemicals such as bleaching chemicals, sodium hypochlorite, biocides and surfactants at various process stages.
All these products when used in the process works in two ways: a. The probiotic microbes play an important role in odour reduction, metal sequestration & sulphide removal. It populates in the anaerobic conditions of the mill and competitively exclude the bad anaerobic microbes responsible for biofilm & slime formation. It eventually suppresses the volatile fatty acids & sulphides, which are produced by these odour causing bacteria.
b. The bio-dispersant plays an important role in reducing the surface tension across the process water. It helps in penetrating inside the hidden machine parts & break the biofilms & slime deposits. It helps also in dissolving the pith, pitch & stickies deposits on the machine & wire parts. Thus, number of breakages of paper come down and the boil out programs also come down.
a. Capable of producing organic acids responsible to kill the pathogenic growth in the stagnant water bodies
b. Excrete anti-adhesion molecules (Exo polysaccharides) that changes the surface hydrophobicity
c. Prevents the growth of unwanted microorganisms/pathogens on all the contact surface
d. Prepares a productive good surface for incoming good bacteria
Controls volatile fatty acid formation
a. Can penetrate & wet the hidden parts of the machine & the chests
b. Destroys the existing biofilm by releasing the biosurfactants
Very low in the toxicity & high in the biodegradability
b. The optimum buffered conditions help in getting the maximum effectiveness of bleach chemicals at lower concentration
a. The organic acids can form peracids at the alkaline conditions of the ODL
b. The peracids are formed in situ in the unbleached pulp of ODL stage and works effectively in breaking down the carry over lignin particles
c. This effectively lowers down the active consumption chemicals in the ODL stage
a. Proven to consume the inorganic & organic sulfur compounds
b. Effective in oxidizing H2S & other sulfides into the nontoxic sulphur compounds
c. Improves the oxidative conditions (ORP) of the water
Inhibits microbiologically influenced corrosions (MIC)
a. Organic acids produced by the Probiotic microbes work as a source of bio sequestering agents2.
b. Effectively mask the metal ions such as Fe, Mn, Cu
a. The organic acids help in buffering the system specifically for the pulp bleaching stages such as Do, EoP & D
Formulations developed for application at the Cooking stage are essentially biodegradable bio-surfactants which are free of anthraquinone. The surfactant character enables better penetration of cooking liquor which helps in dissolving lignin and other derivatives. This results in lowering the kappa number without degradation of fiber, thereby improving yield and reducing rejects while reducing AA.
The various products developed under the ProCharta range are successfully utilized at various large mills in India. For instance, the Prowhite is used for delignification and bleaching enhancer at Virgin mills; ProCook in cooking enhancer cum odour controller for Virgin Pulp Mills; ProKlear for slime control program; ProSolve+ for odour control for recycled kraft paper mills; ProBleach as bleaching booster for Recycle Paper; ProSC for stickies controller for Recycled Mills; ProPC as pitch controller for Virgin Mills; and ProRB as reductive bleaching booster for Recycle Paper.
ProKlean’s extensive research & studies around probiotics and biosurfactant has led to the development of the wide range of products umbrella ProCharta. It is a green gateway for paper industry by reducing or eliminating their hazardous chemicals & environmental concerns and providing an efficient utilization of water resources available in the mill.
ProCharta provides a sustainable & biodegradable option for entire paper industry to improve its environment footprints & produce a good quality paper in a natural way. It is an attempt to push the paper industry towards cleaner & greener processes by improving their water conditions & hence environment. ProKlean facilitates mills to reduce climate change impact, enter into green certifications, & reduce carbon footprints.
Probiotics are known for their good effects not only for the well-being of human beings but also for the environment wherever pathogens are the issue. Water is always one of the important elements on the earth and any attempt towards making it more acceptable & recyclable will be an effort towards making the mother earth greener & cleaner. ProCharta is a promising solution for paper industry to make it a better place to work.
All the products are REACH & FDA compliant and are used in commercial operations across many large paper mills in India.
The pandemic and war have triggered a supply chain transformation around the world. The imposition of sanctions and further political developments in Europe are impacting the industry on various fronts.
-Affected region accounts for nearly 15-20 percent of packaging board exports from Europe. Sanctions are driving these volumes to North American and West European markets, where demand has been high so far, and markets are slowly loosening
-To some extent production of pulp is getting impacted in Europe with restricted supply of wood logs from the affected region
b. War is impacting the energy situation globally leading to disruptions and inflationary pressures on the economy both on supply and demand sides
c. Shipping: Shipping continues to be a challenge globally, albeit some relief of reduced congestion in North American and other major hub ports. Though the overall freight index has softened, it is specific to transpacific routes and freight rates in other lanes continue to be impacting global trade in paper and paperboards
d. Covid pandemic is still not over and recent developments of strict lockdown in some Asian cities has impacted global trade of Paper and Boards. Lower domestic demand in an Asian major has provided additional opportunities for exports - impacting prices in Asia and Middle East. With resurgence of Covid cases in a few cities in some Asian majors, beginning July, there is a fear of stricter lockdowns being re-imposed, further distorting demand and supply situation
All above may keep the global prices of pulp, energy and chemicals high, beside supply chain disturbances. The high input cost scenario for paper manufacturing companies may not reverse anytime soon.
Global trends in paperboard and specialty papers segment.
Sustainability in packaging is the mega trend and consumer concern for environment and climate change, emerging sustainability regulations with increasing frequency, varying regulatory focus across the countries at times even within the country across states/provinces are the micro trends shaping the paper & board industry. Customers are exhibiting distinct willingness to experiment with different packaging substrates and paper/board stands to gain.
We are also witnessing structural changes in global packaging boards trade, trends of broadening supply base and a tendency to add more vendors is on the rise. This is expected to change the place of packaging board consumption, opening new opportunities. We also see a trend of on-shoring converted product buying - reducing dependence on deep sea suppliers.
Paperboard and specialty papers potential in Asia Pacific & India.
Asia Pacific region is one of the fastest growing regions in terms of paper and board demand, driven by strong domestic consumption and export competitiveness. Besides growth in demand, this region has a
few of the world’s large and contemporary P&B capacities. The shift away from plastic substrate based packaging to sustainable sources like paper and paperboards will further provide a fillip to the industry. In India we see clear growth opportunities for carton boards, food service boards, liquid packaging boards and moulded fibre products. Among the speciality products we believe that decor papers will grow rapidly aided by the governmental thrust on improving housing and infrastructure in the country. During last couple of years, there is also a considerable amount of investment by wood product-based industry, in capacity expansion and contemporary technology which augurs well for growth of the decorative laminate base papers.
Enhancing local production to reduce paper imports in India.
Imports are not very significant in case of paper boards, uncoated papers and import dependent segment has been coated 1/s and 2/s papers and there is a clear opportunity to set up capacities for these grades. Another import dependent segment has been Decor papers where local Indian mills have share of less than 30 percent and ITC has decided to invest in this segment to participate in the fast-growing laminating industry. The key enabler to attract more capital in to manufacturing of paper and paper board is to ensure secure supply of fiber. This can happen through enabling policy innovation by the government in favour of long tenure lease of land for private sector plantation of pulp wood on degraded forests.
Digital technology to support paperboard, specialty papers segment.
The pulp & paper industry is one of the largest industrial sectors in the world. Over the past two decades, it has experienced considerable change, from process and equipment technological advancements, stringent environmental regulations, rising energy and labor costs, to sustainability targets becoming a key business imperative.
By embracing digital technologies which connect disparate systems and unify data residing in different sources coupled with application of various digital tools and techniques such as artificial intelligence/ machine learning (AI/ML), several companies in our industry continue to unearth insights and address complex operational challenges, which were once regarded as difficult if not impossible.
Over the decades, we at ITC PSPD have always been early adopters of transformative philosophies in the industry. In the recent past, several projects using Digital levers such as IoT, Advanced Analytics and Image Analytics have been successfully completed addressing key business areas wherein significant potential for Strategic Cost Management, Product Superiority and performance on Sustainability metrics were identified. The results have been very encouraging and we were able to expand our margin by 230 basis points over the last two years.
In addition, many mills have extended their digital footprint to domains beyond manufacturing targeting supply chain efficiency improvements and seamless inter-connectedness with customers and suppliers to ensure superior service levels. Ultimately, the goal of these digital transformations is to make the pulp and paper industry more sustainable and to globally competitive.
Global trends impacting paperboard, specialty papers manufacturers.
But while this technology is solving business challenges and driving growth, it is important to recognize the fact that it is also highlighting a digital skills gap across industry and emphasising the need for existing workforces to be upskilled.
Insight into the company’s national and international business.
We have built our international business over last 2 decades and we enjoy a wide geographical market spread to more than 50 countries. Europe and Middle East are our big markets. Through consistent product quality & performance, stability in supply chain we have developed niche businesses in each of the regions we operate. ITCPSPD is on the forefront of developing plastic alternative products and plans to grow in these products globally.
R&D efforts for paperboards and specialty papers segment.
We are uniquely focussed in our industry on R&D. We have two tier structure for driving innovation at divisional level as well as at corporate level. We leverage ITC’s R&D strength through collaboration with Life Sciences and Technology vertical. Our innovation starts from sourcing sustainable and certified fiber from small, marginal and medium farmers.
These farmers are grouped together under the ITC umbrella to follow FSC guidelines meeting the triple bottom line targets while suppling sustainable wood. We have pioneered developing plastic substitution products in packaging of soaps, oily greasy foods, aqueous frozen foods, ice creams and dispensing beverages. Our Filo, Omega and Indo series of products enjoy high market reputation, share and we continue to expand the product range.
Improving sustainability for paperboards and specialty papers.
Sustainability has been one of our cornerstones long before it became a buzz word. Environmental friendliness is in built in all our operations from procurement, processes, products to end of life disposal and beyond.
Certifications like FSC, CII Greenco, WWF, GFTN, Book Chain Project, Life Cycle Analysis etc. drive our sustainability metrics.
We also continue to lead the industry in specific water and energy consumption by inducting contemporary technologies.
Recycling aspects for the paperboards and specialty papers segment.
The key gap that lies today is the critical information given in a simple manner to the consumer about the packaging that the brand has used. One of the ways in which this can be achieved is in evolving a star rating system similar to that of the Bureau of Electrical Energy star rating system.
Another approach can be certification systems like that of the CII Greenco which certify the entire manufacturing unit and the
packaging substrate thus produced can be from such Platinum or Gold rated units.
Thirdly carbon neutral products are gaining traction across industries and paper industry is well placed to develop this category for conscious customers who look to enhance their brand salience with sustainable product offerings.
Government regulations to support paperboard, specialty papers.
The EPR rules is a step in the right direction. This may increase work load and costs in the initial phase but is a sound move by the Government. Such regulations will force the brands to re-think their packaging design not only from aesthetics and cost point of view but also from end of life disposal and environmental impact view point.
The PWM and EPR are also driving paper manufacturers to come up with innovative paper based alternatives to single use plastics and in this area too ITC PSPD is leading the industry.
Also among the challenges faced by paperboard, specialty papers manufacturers, raw material security is the key concern for the industry in India. Other than that, the rising energy costs, depreciating Indian currency are the new headwinds impacting the competitiveness of the industry.
Opportunities for chemical manufacturers in paperboard, specialty papers segment.
Market dynamics in Indian paperboard and specialty paper industry are rapidly changing. Industry needs de-risking its input supply chain. High growth trajectory offers large enough volumes to attract investment to manufacture inputs such as performance, sizing, coating and other chemicals in the country.
Currently, performance chemicals are imported in bulk, repacked, labelled for distribution or imported inputs are processed at the final stage of preparation. Thus, there is hardly any real manufacturing taking place in absence of sufficient volumes.
With changing scenario, industry needs new innovative products to meet challenges arising out of:
a) strict environment regulations
b) need for lower fresh water demand and less load on ETP
c) fiber shortage that will compel usage of higher ratio of recycled fiber whose quality is going down owing to recycling same fiber multiple times
d) high energy cost
Changing macro economy in the paper and printing industry.
Compounding the damage from the COVID-19 pandemic, the Russian invasion of Ukraine has magnified the slowdown in the global economy, which is entering what could become a protracted period of feeble growth and elevated inflation.
As per the World Bank’s latest Global Economic Prospects report, this raises the risk of stagflation, with potentially harmful consequences for middle- and low-income economies alike. Global growth is expected to slump from 5.7 percent in 2021 to 2.9 percent in 2022— significantly lower than 4.1 percent that was anticipated in January.
It is expected to hover around that pace over 2023-24, as the war in Ukraine disrupts activity, investment, and trade in the near
term, pent-up demand fades, and fiscal and monetary policy accommodation is withdrawn. As a result of the damage from the pandemic and the war, the level of per capita income in developing economies this year will be nearly 5 percent below its pre-pandemic trend as per World Bank statement.
Taking in account the Indian sector, it is said that the Paper consumption in India is projected to grow by 6-7 percent per annum in the next five years so as to reach 30 million tonne by FY2026-27 making it the fastest growing paper market in the world.
According to A S Mehta, president of the Indian Paper Manufacturers Association (IPMA) - Paper industry in the country has undergone a transformation of sorts in the last few years.
The industry has gone up the sustainability curve and has become far more technologically advanced. In the last five to seven years, an amount of over Rs 25,000 crore has been invested in new efficient capacities and induction of clean and green technologies.
Trends and opportunities for the Indian printing industry.
Printing and Print– Packaging industry in India is growing; people are taking keen interest in this key industry now. There are more than 36 printing institutes; some of them provide post-graduate education. Every year, more than 3500 new printing engineering graduates join the industry, while many more get on-the-spot training in print shops. Printing, especially Packaging printing, is now a major industry. It is said that since 1989, the growth of the Printing coupled with Packaging Printing industry is over 14 percent.
Over the decades, we have witnessed many transformations; from the early age of a block printing letterpress. Today we celebrate printing electronics and 3-D Printing; a most exciting and revolutionary technology mankind has witnessed in the printing industry.
Due to digitization, there are bound to be many changes in the next decade. With industry 4.0 revolution, one can produce anything without any infrastructures. Printing is not untouched, there are many companies which do not own any printing press but are in the business of print. Change is the only constant and with industry 4.0 revolution, printing is going to change the way we think of printing henceforth.
Some print decline as we substitute electronic methods. This is to be expected as technologies clash and certain printed products lose out to more effective approaches. But new printed products will evolve to fill the void because printing technology is constantly evolving. Packaging, functional printing, printed electronics, web to print, 3D printing and green/sustainable printing are opening up new sectors for printers.
The concept of printing in the enterprise has undergone a major paradigm shift in the last few years. One of the major reason behind this is rapid growth in the area of printing technology. This has created a scenario where printers have evolved much beyond the basic printing function.
The increased innovation in technology has led to many industries being overhauled, with the printing industry being no exception to this. Naturally, this has led to a variety of trends affecting the niche over the past few years; while some have been around for a while, some are only beginning to start.
Some of the recent trends, and area of new specialization in printing and packaging are: greater demand for security, increased personalization, increased digitization, internet of things, minimalism in design, cutbacks & acquisitions, printing on-thego and improved sustainability, 3-D Printing, printed electronics, smart packaging and print-as-a-service etc.
Opportunities for the Indian pulp & paper industry.
Paper prices continue to rise with no noticeable improvements. Most of the paper majors in India say that the reason for these moves is the continued increase in the cost of gas, chemical raw materials and logistics services.
According to IPMA, the continuing coal shortage and nonavailability of adequate railway rakes, paper mills in India are finding it extremely hard to source adequate and uninterrupted thermal coal supplies for their captive power plants.
In yet another development in anti-dumping duties, the directorate general of trade remedies (DGTR) recommended the Ministry of Finance (MOF) to impose anti-dumping duty on decor paper being imported from China, for five years. The moot question is: are we qualitatively and quantitatively ready to stop all imports? Who is calculating, who is behind the planning?
R&D and innovation in printing industry.
There is no Research & Development department or institution in India. All the development are being practiced by the printers inhouse on their own without any form of support. The automation of society and technological breakthroughs have had a substantial impact on the workplace environment, and the print industry isn’t left behind. Enterprises, especially in the manufacturing segment, are now jumping on the bandwagon by creating a workflow, which falls in line with the future of printing.
A prominent move that’s happening in the printing industry is the adoption of Intelligent Workplace Services (IWS). This change will reduce the complications of on-premise printing management as all the print jobs gets submitted to a virtual print server and ensures elimination of on-premises servers reducing the maintenance & improving efficiency.
The Indian manufacturing industry is adopting 3D printing technology at an early stage to capture a significant market share through rapid prototyping. Another benefit is that one can postpone the physical production and associated costs with it. Some of the latest innovation where printing industry is working these days includes, Printed Electronics, Smart Packaging and Sustainable Printing etc.
Improving international trade in global markets.
During these days of fast development and technological revolutions, I feel that networking between printers of different neighbouring countries is essential. With 250,000 printing companies, India is the leading country of the world, but more than 87 percent out of these are Micro or Small. Networking is the key for the survival of Micro and Small printers of the country. Micro and small printers of India can cooperate with the printers of these countries for the supply of services and material to 3rd world countries.
On the other hand the printers of India can also be benefited if some material or services are available at lower prices in these countries. It is necessary to develop bilateral relations between the printers of these countries for the overall development and growth of the Indian Printing and Packaging industry.
The commercial printing market is fragmented due to the presence of many players. Due to reasons such as overcapacity of firms and pricing pressures, the market appears to be extremely competitive in nature. With networking production, not only your cost of production will drop, but you will be able to bid for larger orders which are beyond your capacity. It will also avoid additional capital investment.
The print industry has been conscientiously pursuing green printing techniques and there has been a real push in recent years to look at more sustainable printing techniques. While there is a drive for digital innovation, it’s a fact that for many businesses it’s not possible to just stop printing and go completely paperless.
Printing green is always a paradox or, as some people call it, is an oxymoron. But the fact is that it is not a question of whether printing is green or not, the question is how green it can get and that is where the adoption is going to be critical. Now a days industry has already started green practices, printing with green plates and ink are common now.
Opportunity for raw material manufacturers.
India has the largest printing companies in the world, making it a massive market for the consumables and machinery, including pulp and paper, chemicals etc. Since printing in India is growing therefore the need for consumable is bound to grow therefore there are endless opportunities.
Today, India is fast becoming one of the major print producer and manufacturer of printed paper products for the world markets. The quality standards have improved dramatically and immense production capacities have been created. Some printers have won recognition by winning prizes at international competition for excellence in printing.
The current annual turnover of printing industry (except packaging printing) is estimated to be around Rs 1.I0 lakh crores. The turnover of packaging printing including labels is more than Rs 1.5 lakh crores. Thus combining both the worth of Indian printing market is more than Rs 2.60 lakh crores.
Challenges faced by the Indian printing industry.
The Indian Printing and Packaging industry, during past couple of years has noticed many ups and downs, for instance, Government’s ‘Not to Print Calendars and Dairies’; ‘unnecessary increase in the prices of raw material especially paper’; ‘Lock-Down due to second wave of pandemic’; ‘decreasing demands of printing’ and increase in the GST rates etc.
More than physical impact, COVID influenced the Indian printers very hard economically. Printers, especially commercial printers and micro and small printers suffered the maximum due to the long lockdown.
To save the commercial printing industry we urgently need at
least three vaccines: an affordable vaccine for the coronavirus; a government vaccine to boost the balance sheets of small & micro print firms; and a macro-economic vaccine. Though we all are confident that none of the three are provided or will be available in near future. At the same time since almost all the machinery used is imported from other countries, my sincere demand is that there may not be any import duty on the machinery/products not manufactured in India.
It is very well known to all that the prices of our printed products are governed by the customers. One has to supply at the price quoted by the customer, otherwise someone else will get that order. It is the true status of our business today. In these circumstances, it is seen that the printer, knowingly or unknowingly, start charging the rates lower than his cost of production, for not losing the customer.
Selling below the cost will lead to closer of the establishment one day. At the same time there is a need to produce at the lowest possible cost, else someone will do it and that will be the death nail for your establishment. Selling below the cost is foolishness and at the same time production at minimum possible rates is our necessity.
WPCF supporting members to improve global effectiveness.
The objective of the WPCF is to form one single global platform for the printing and related industries in order to promote business opportunities and the image of the print. The WPCF facilitates the exchange of information on economic and other relevant business indicators, sharing best practices on environmental issues, and providing intelligence to support business opportunities for its members.
The purpose of WPCF is to promote the development and prosperity of the printing, graphic arts, communication and allied industries in all regions of the world. To improve the management of these industries with a view to their continuing and increasing prosperity. The World Print & Communication Forum recognises the need to promote print, to co-operate internationally in order to address common emerging challenges and pressing issues in different countries, such as technological development and environmental and sustainability issues.
In a world of globalized economy and growing interdependence, the printing industry is challenged by the constant development of new technologies and media that is accelerating the transformation of traditional print markets. In order to promote print and the prosperity of the printing industries worldwide there is an increasing need for printing, packaging and graphic communication industries to share information and to be aware of emerging trends.
The WPCF’s main purpose is to act as a platform whereby printers and their suppliers are able to discuss and share best practices on a regular basis. Among other things, the WPCF is engaged to stage the World Print & Communication Congresses and smaller, ad-hoc conferences which facilitate co-operation and the exchange of information between users and suppliers of technology and services in the related sectors.
Dr. Bob Maughon, Executive Vice President, Sustainability, Technology &
and
& Sustainability Officer, SABIC talks
regarding the need
The COVID-19 pandemic has resulted in a surge in demand for plastic, primarily driven by the manufacturing of personal protective equipment (PPE), masks, syringes and other healthcare accessories, along with increased needs for packaging. A majority of these are made of polymers such as polyurethane (PU), polypropylene (PP), polyethylene (PE), polycarbonate (PC), and composites/blends where SABIC has a leading position.
While this is indeed an opportunity for the plastics industry, we see it as an important indicator on the need to promote a focus on the end-of-use for plastics, with clear solutions needed for mechanical recycling, advanced recycling, bio-based polymers, and services like design for recycling and closed loop solutions. Our priority has been to continue to invest in research to develop safe and sustainable solutions that can deliver against these needs.
So, our focus has shifted to drive environmental sustainability into the plastic value chain through revolutionary recycling technology. We have processes that can break down mixed plastic products to serve as feedstock for making high-performance resins. This is reflected in our TRUCIRCLE™ portfolio and services provide customers with highly sustainable solutions.
Measures needed to make plastic more sustainable, environment friendly.
Our vision for the future is that plastic should never end up in the environment, landfill or in our oceans and instead, is reused and recycled into new products. This vision requires a total transformation of the value chain. We have been working with our downstream and upstream partners to reinvent and pioneer our way towards a circular economy for the good of people and the planet.
Our TRUCIRCLE™ portfolio and services play a significant part in achieving our vision and closing the loop on used plastic. We believe that our cutting-edge innovation towards building a circular economy will be able to help in future-proofing India’s growth journey. With the country phasing out single-use-plastic (SUP) from 1 July, we are supporting the nation in developing more sustainable solutions.
Our TRUCIRCLE™ portfolio and services play a significant part in achieving our vision and closing the loop on used plastic. We believe that our cutting-edge innovation towards building a circular economy will be able to help in future-proofing India’s growth journey.
Streamlining use of pyrolysis oil globally.
In Europe, we worked on a marquee technology wherein we produced circular polymers through feedstock recycling of low quality, used mixed plastic that would otherwise be discarded in landfills. Using the process called pyrolysis, plastic is heated at an extremely elevated temperature in an oxygen-free environment, producing pyrolysis oil, which is further refined and upgraded for use as feedstock. This produces polymers that have identical properties to virgin-based polymers, allowing plastics to be recycled repeatedly with no loss of properties or characteristics.
The finished circular products are then supplied to our customers for a variety of applications, including certified food standard packaging, personal and home care products and healthcare - to name just a few. Our circular products, for example, have been used in the production of seven million ice cream tubs for Unilever’s Magnum™ brand, which is also sold in India.
To scale up supply of certified circular products, SABIC and Plastic Energy are building a new plant in the Netherlands to convert endof-use plastics into recycled oils to create virgin polymers. This process can be leveraged in India as well. We can support Indian companies with our technology to help them purify oil made from plastic waste to create a cleaner pyrolysis oil devoid of additives like chloride, and collaborate on how to integrate these materials into petrochemical assets.
SABIC can also play a strategic role in helping companies with their marketing strategy for such products. The goal is to further develop the technology to enable an even wider range of used plastics that can be converted into this circular feedstock, improving the cost and scalability of the technology.
Impact of Russia-Ukraine war on petrochemicals industry and ways to deal with the crisis.
The petrochemicals sector by nature is cyclical, and the crisis is Ukraine has led to high oil price volatility which impacts the industry, given its linkages. For our sector, the key is to focus not only on exploring product and process innovation but also to focus on energy transition and exploring renewable feedstock, where there is significant opportunity in India. As an organization committed to our partners, we will help them utilize these feedstocks to make them more suitable for the entire petrochemical value chain by making usable plastics out of them.
Global trends in the alternate energy space and organization goals.
Through reducing emissions and product impacts, we strengthen our business while supporting a sustainable future. Last year, we made a public commitment to reduce our Scope 1 and 2 GHG emissions by 20 percent vs our 2018 baseline and to target carbon neutrality within our assets by 2050. The pledge is a statement of intent and a marker that will henceforth orient all our efforts to combat the most pressing issue of our time: climate change.
To operationalize this pledge and drive us toward our carbon neutrality ambitions, the Energy Efficiency and Carbon Management (EECM) body, together with representatives from all Strategic Business Units (SBUs) and Corporate Sustainability, developed SABIC’s Carbon Neutrality Roadmap.
Sustainability & technology future growth while achieving net zero targets.
We have an ongoing strategic roadmap to ensure that we not only embrace the potential of new technology but also update ourselves in terms of sustainability benchmark going beyond our targets.
For example, last year, we continued our low-carbon journey by exploring various applications for ammonia outside of fertilizers and chemical intermediaries and expanding into power generation, shipping fuel and acting as a hydrogen carrier.
We are also exploring opportunities in both blue and green ammonia production using carbon capture, and sustainable electricity, water, and air to reduce the carbon footprint in existing affiliates. Producing green ammonia via green hydrogen derived from water electrolysis is becoming more cost-effective and will eventually compete with conventional ammonia production using non-renewable fossil fuels and blue ammonia derived from blue hydrogen (via carbon capture).
We have also strengthened our internal governance through the creation of two additional new structures aimed at meeting regulation, setting targets, and increasing disclosure. The first structure is our Energy Efficiency and Carbon Management (EECM) body, which oversees the Carbon Neutrality Roadmap and contributes to the overall roadmap for SABIC’s energy-efficiency portfolio.
The second structure, our ESG Reporting Steering Committee, which includes representation by senior managers across SABIC, and is sponsored by our CFO (Tim Leveille) and myself as CTO/CSO. This committee sets general ESG reporting strategy, which includes consideration of climate risk, goals, metrics, and disclosure.
Insight into company’s R&D and innovation division.
The Corporate Technology and Innovation (T&I) comprises over 1,660 full-time employees working on various research projects at 20 centers around the world. Our research centers focus on delivering differentiated and sustainable product and application solutions and sustainable cost-advantaged process innovation to meet the needs of our customers and the value chain over the near-, mid- and long-term horizon.
The goal is to meet needs of a sophisticated marketplace through smarter product design and functionality, and greater sustainability. We are committed to understanding our customers’ industries and challenges and translating these insights into solutions that address their needs. Our network of global research and technology centers gives us a unique environment to deliver on this commitment.
We believe that innovation adds an economic edge and helps our business build a sustainable future. And we pursue innovation through the lens of sustainability. Our 2025 strategy focuses on driving sustainability, technology, and innovation to create value that is greater than the sum of individual parts.
Ways in which the company has an edge over industry peers.
The first and foremost is our alignment with the government’s goals for sustainable development. We also have our global sustainability strategy, and we integrate our global technologies, expertise and activities to support the Government’s growth aspirations, helping in future-proofing the economy and industries.
Secondly, we see sustainability as an ongoing journey that requires continuous learning, adaptation, and improvement of our basic business processes and our response to the priorities of our diverse stakeholders. That is why we invest in innovation and are committed to bringing breakthrough solutions to the market, with examples like our partnership on e-cracking with Linde and BASF and our TRUCIRCLE™ portfolio of circular solutions.
Three, we embrace collaboration as a key element of success. We are a member of the World Plastics Council and the Alliance to End Plastic Waste (AEPW), and a partner of The Ocean Clean-Up.
A breakthrough in helping mitigate marine plastic pollution is our partnership with Malaysia-based plastic recycling company HHI, to create the first certified circular polymers produced through the advanced recycling of recovered mixed and used ocean-bound plastic.
The certified circular polyolefins from ocean-bound plastic, from SABIC’s TRUCIRCLE™ portfolio of circular solutions, can be used by our customers to develop new circular products, and we are engaged in collaborations across the value chain to enable this.
Challenges faced in incorporating sustainability at an organizational level.
Sustainability is deeply ingrained at our organizational level, and we are committed to achieving our goals. What is important is to have a clearly articulated roadmap and securing the buy-in of our employees and partners.
In fact, we have identified five primary pathways to decarbonization: Reliability, Energy Efficiency, and Improvements; Renewable Energy; Electrification; Carbon Capture; and Green/Blue Hydrogen. These five pathways, along with our ongoing focus on circular and renewable feedstock, will drive our efforts in the years and decades to come.
And we also continuously evaluate our achievements. In our earlier articulations of our climate ambitions, we set out intensity-based targets and mandated reductions in our greenhouse gas emission intensity (along with reductions in energy intensity, water intensity, and material loss intensity) by 2025 from a 2010 baseline. However, evolving understandings and expectations of climate change action in the corporate landscape has prompted us to re-evaluate the targets.
We have now set a goal of a 20 percent reduction in absolute greenhouse emissions (Scope 1 and 2) by 2030 to support SABIC’s Carbon Neutrality commitment. While we will continue to report our progress on both intensity-based and absolute reduction targets through 2025, these new absolute reduction targets will be our primary focus after 2025.
Vision for the technology & innovation center in Bengaluru, India.
We have invested more than $100 million in our SABIC Technology Center in Bengaluru (STC-B), which is focused on research and development. The center plays a critical role supporting our SHPP, SANCO, and SABIC PetChem technology needs – with broad capabilities including catalysis, organic chemistry, process, product and application development application, process engineering, life cycle assessments (LCA), among others. We also validate designs, build prototypes, conduct tests, and offer predictive engineering support.
For instance, we work with automotive OEMs to design lighter and more fuel-efficient cars without compromising on safety. The technology center in India focuses on leveraging India’s domestic research capabilities. It employs about 300 scientists, engineers and designers. It further develops innovative and cutting-edge solutions to some of the biggest challenges faced by our society and industry today. The center is well integrated with other SABIC research centers globally and works in collaboration with cross-regional teams. With sustainability and innovation at the core of everything at SABIC, STC-B plays a key role in the region and globally.
Dow has signed a Memorandum of Understanding (MoU) with China’s leading food and beverage group, Want-Want, to drive zero-solvent emissions and develop a circular economy for flexible packaging. This agreement aims to deepen value-chain partner collaborations with customized adhesives solutions to address the needs of the industry for more sustainable packaging choices.
Solvent emissions are a source of pollution and contribute to greenhouse gas emissions. Enabled by Dow’s water-based and solventless adhesives technologies, Want-Want is dedicated to using environmentally-friendly laminating adhesives for all its flexible packaging while exploring opportunities to adopt recyclable packaging across more products under its portfolio.
“Investing in sustainability is an ongoing process; this significant step with Want-Want can help both parties optimize our sustainability roadmaps in the long run,” said Bambang Candra, Asia Pacific commercial vice president, Dow Packaging & Specialty Plastics. “We will continue to drive innovative solutions and support more partners in achieving their sustainability goals.”
“Adhesives is an important sector that can help reduce emissions and enable a circular economy. Not only are we advancing
sustainable packaging on a larger scale, but we are also exploring benefits such as efficiency optimization and energy savings, supporting customers in reducing carbon footprint during production and transportation processes,” said Jayne Wong, global adhesives business director, Dow Packaging & Specialty Plastics. The signing of the MoU agreement aligns with Dow’s sustainability goals for carbon neutrality by 2050, as well as supports WantWant’s sustainability goals to achieve carbon neutrality and adopt recyclable packaging for all products.
“In order to tackle climate change and create long-term value, we have an important part to play as one of China’s largest food and beverage companies to establish an environmentally-friendly value chain – that inspires and encourages our consumers to make positive changes for the planet,” said Yongmei Cao, general manager of operations, Want-Want Group. “Solving sustainability challenges is not a one-man nor a one-organization job, but also falls on the shoulders of all stakeholders. Not only are we thrilled to advance further in this journey with Dow, but we are also encouraged by the reality that we can offer our customers’ favorite products that are enveloped by Dow’s sustainable packaging innovation.”
Grupa Azoty SA is the first company in Poland to introduce a line of biodegradable and compostable polymer granules to the market.
The new line under the envifill® brand is based on the technology developed by Grupa Azoty to obtain thermoplastic starch, which is made of bio-renewable and compostable materials and does not contain plasticizers.
Envifill® products are dedicated to processing in the extrusion blow molding technology, injection molding and other technologies, including 3D printing technology.
The products of the envifill® line are intended for processing by extrusion and injection methods, using conventional equipment for processing plastics, which is their undoubted advantage. The products created with the use of these technologies include: films, packaging, pots, elements of devices that are consumable or require frequent replacement, elements of tableware, packaging for cosmetics. Products made of envifill® injectionmolded granules are characterized by unique surface aesthetics and relatively low processing shrinkage, ie. size reduction.
For example, films made of envifill® granules have high strength and flexibility, a velvety texture, semi-transparency with a milky shade and a characteristic smell. They can be welded using traditional LDPE polyethylene foil welders. Envifill® granulate films can be used for the production of shopping bags, garbage bags, especially bio-waste, agro films and unit packaging. It is possible to obtain from envifill® granules both thin films, less than 15 μm, but also thicker films with very high strength.
The thermoplastic starch on the basis of which the envifill® line was created is distinguished primarily by the fact that it can be used as a stand-alone polymer in some applications and as a base or additive to polymer, biodegradable or compostable compositions. And so, on the basis of thermoplastic starch - in addition to polymer granules
- Grupa Azoty has also developed an ecological hot-melt adhesive that can be used as a binder for wood-based and cellulose products, which was confirmed during customer tests. The glue does not contain formaldehyde or toxic additives.
“I have no doubts that the introduction of a new line to our offer is a revolution on the domestic market of granules, it is also our next technology that meets the requirements of the European Green Deal. We are observing an increase in interest in biodegradable plastics among customers - this is a market with great potential; hence we are probably taking further steps towards the development of this business area. The envifill® line is our response to the trends related to the development of applications of biodegradable and compostable thermoplastics. What is key, the share of bio-renewable ingredients in the granules of the new line can reach up to 100 percent, and the resulting compositions do not contain plasticizers,” said Tomasz Hinc, President of the Management Board, Grupa Azoty SA.
“Since we launched a thermoplastic starch production line a year ago, we regularly receive an increasing number of inquiries about our product. The envifill® brand products are made of vegetable, biodegradable and compostable ingredients. Their decomposition in soil or compost takes place in the presence of wet organisms, only to CO2, H2O and biomass, without leaving microplastics. As a standard, these granules are biodegradable and compostable in accordance with the EN 13432 standard, within no more than 180 days in home composters and no longer than 90 days in industrial composters. Thanks to our advanced technological facilities, we are able to adjust the time of product degradation depending on the expectations and needs of the client,” said Dr. Grzegorz Kądzielawski, Vice President of the Management Board, Grupa Azoty SA.
Harmful fungi cause enormous agricultural losses. Conventional techniques for combating them involve the use of poisonous fungicides. Researchers at Karlsruhe Institute of Technology (KIT), working with partners from Germany, France, and Switzerland on the DialogProTec project, have developed environmentally safe alternatives that trick the pathogens’ chemical communication with plants. Now that the research has been completed, the new technology is ready for use.
First, the leaves turn brown, then the entire grapevine dies. A fungal infection called esca is a threat to wine production in Europe and causes millions in damage to winemakers every year. “This disease has been known in Southern Europe since the Middle Ages, but it never played a major role,” said Dr. Alexandra Wolf from KIT’s Botanical Institute, which coordinates the DialogProTec project. “But because of climate change, the fungus is now encountering many plants weakened by climate stress.”
Conventional plant protection usually involves the use of poisonous fungicides to fight fungal diseases like esca. In DialogProTec, the researchers have developed a completely new approach that works without any environmentally hazardous toxins. “In nature, organisms interact using chemical signals. We’ve been able to identify some of the signals between the host and the pathogen, and to manipulate them,” said Wolf, who adds that this “biohack” is precise and effective and has a minimal ecological footprint. To develop the new methods, the KIT-led project founded an interdisciplinary research network including specialists in botany, fungal genetics, microsystem technology, organic chemistry, and agricultural sciences. The network used about 20,000 fungus strains from the collection at the Institute of Biotechnology and Drug Research (IBFW) in Kaiserslautern and about 6,000 plant species from KIT.
The researchers didn’t need to work with entire plants and fungi
to identify and exploit the right signals. Instead, they worked with individual cells. A microfluidics chip jointly developed with KIT’s Institute of Microstructure Technology served as the basis for a miniature ecosystem. “We placed plant and fungi cells on chips a few square centimeters in size so that they can’t come into physical contact but can interact chemically via a microfluidic current,” said Christian Metzger from the Botanical Institute at KIT. “To make this interaction visible, we equipped the genetic material in the plant cells with a gene switch and a fluorescence gene. Whenever a chemical signal activates the immune system, we can measure the green fluorescence.” The gene switches are from wild grapevines, in which the researchers had previously detected an especially active immune response.
During their investigations, the researchers first decoded the chemical communication between fungus and plant that accompanies a fungal attack. One of the things they identified was signal substances that the fungus uses to suppress the plant’s immune response. “They’re part of a chemical interaction shaped by a long evolutionary process and are produced as soon as the fungus detects specific stress signals from the plant,” explains Professor Peter Nick, who heads the project and the Botanical Institute. The team then identified molecules that could be used to reactivate the immune response. “When we use them for plant protection, the plants can often ward off the fungus. You can think of it as a vaccination for plants,” said Nick.
DialogProTec’s innovative technology is already on its way into practical use and is soon to be tested in the field. In addition to their work on an alternative to fungicides, the project team has also developed new approaches to promoting plant growth or fighting weeds, where signal substances could also replace poisonous herbicides in the future.
To help advance their commitment of achieving 100% packaging that can be recycled, repurposed, or reused, McCormick is joining with packaging and plastics industry leader, Berry Global. The collaboration leverages Berry’s expertise and access to mechanically recycled polyethylene terephthalate (rPET). The new McCormick Assorted and Neon Food Color bottles are made from 100 percent post-consumer recycled (PCR) plastic and will begin appearing on shelves across North America this month.
Partnering for the greater good McCormick and Berry have both set 2025 sustainable packaging goals and science-based emissions reduction targets aligned with limiting global temperature rise to 1.5°C in support of the global goal of net-zero emissions by 2050. By shifting to a bottle made from 100 percent PCR plastic, McCormick is increasing the circularity of its packaging while reducing associated carbon dioxide (CO2) emissions.
“Deadlines for achieving sustainability goals are fast approaching, and brands want partners who can provide effective, impactful
ways to reach those commitments quickly. Berry’s sustainability expertise, coupled with access to recycled content, provides the ability to commercialize sustainable packaging solutions with a lower carbon footprint,” said Robert Flores, vice president of Sustainability at Berry Global.
A lifecycle assessment estimates McCormick will realize a reduction of 86.8 metric tons of CO2 emissions with the new PCR bottle in comparison to the same bottle made from virgin material. This amounts to a 59 percent reduction in CO2 emissions, which is equivalent to Greenhouse gas emissions from 18.7 gasolinepowered passenger vehicles driven in a year CO2 emissions from 201 barrels of oil consumed Carbon sequestered by 103 acres of US forest in one year.
“By collaborating with key suppliers like Berry, we gain access to valuable recycled content. This 100 percent PCR bottle furthers our journey towards our emission reduction goal through packaging,” said Michael Okoroafor, chief sustainability officer, McCormick.
Rigid Packaging (ARP) is now offering samples of spirits bottles made of recyclable polyethylene terephthalate (PET) that meet the newly approved US Tax and Trade Bureau (TTB) sizes. Amcor’s new offering was developed to provide customers with the freedom and flexibility to explore new markets while gauging consumer interest.
The six new ARP bottles were developed to maximize ease of use in customer production and shipping. Each newly designed bottle subscribes to an axiom of similarity, maintaining a common set of dimensions — including height, depth, width, diameters, and shared geometry — with existing ARP stock options. This development initiative by APR’s world-class engineering team is the first product line family in the marketplace to align sizing across bottles with different capacity.
“Amcor created these new sizes to help provide flexibility for brands,” said Jonathan Jarman, Amcor marketing manager for Spirits & Wine. “New sizes create new opportunities, and through these new bottles, we are offering our customers a smooth, seamless transition to these newly approved sizes with the freedom to introduce these containers without additional investment in parts or equipment.”
“At Amcor, our engineers have an insatiable appetite to explore, capture insights, experiment and stay ahead of market trends
to benefit the customers we serve,” said Terry Patcheak, VP of research & development and advanced engineering at ARP. “When the TTB approved these expanded size options, we worked quickly to ensure our customers had early access to samples of these new sizes to help them gain a competitive advantage.”
With a commitment to develop all its packaging to be recyclable, compostable, or reusable by 2025, ARP is always innovating to improve the sustainability advantages of its products. In addition to manufacturing these bottles that are fully recyclable, these containers also deliver the lowest carbon footprint versus other packaging types. In fact, the manufacturing of PET containers produces far less – up to 77 percent fewer – greenhouse gasses than glass bottles. Plus, PET packaging is 80 to 90 percent lighter than glass bottles of the same size range -- fewer raw materials needed in production leads to less fuel used in transportation.
“A change in the TTB sizes offers a unique opportunity to our customers. This includes design assistance and creating moulds to suit a customer’s brand identity,” added Jarman. “By offering these sizes, we can help our customers differentiate, compete in the crowded marketplace, allow craft distillers to standout on crowded shelves, and ultimately determine how they can drive profits.”
Innovia Films is launching RayoForm™
EUP60, a white BOPP film for in-mould labelling (IML). Produced in Europe at one of its production facilities, EUP60 is a very high opacity, high yield product, having a density as low as 0.55 g/cm3. Combined with its specially formulated and printable matte surface, EUP60 is engineered to give outstanding high-speed sheet feeding and adhesion for both UV and oxidative inks.
EUP60 is designed with special features that make it suitable for any shape container or lid without risk of distortion to the container or lid. This film is perfect for use on small-to-medium size, thin or thick wall PP or PE containers, providing a tactile ‘soft-touch’ finish after moulding. It also means a finished, polyolefin mono-material container can be produced, making the final pack fully recyclable, and meeting the Plastic Recyclers Europe packaging design recommendations.
“As well as the technical performance of EUP60, we can produce reels for the customer that are longer than anything else in the marketplace. More linear metres in a reel leads to less changeovers and improved printing efficiency, with printing speeds of up to 14,000 sheets per hour being realised. This applies to either rollto-roll or roll-to-sheet conversion processes and customers can choose either horizontal or large diameter vertical reel packing, depending on their requirements,” explained Alasdair McEwen, product manager, labels.
The large diameter rolls that Innovia can supply, means less roll changes and higher efficiencies for converters as well as a dramatic reduction in packaging waste. “Our 5-layer film technology allows us to produce this film with the optimum combination of yield, opacity, whiteness and printability, ensuring excellent off-press ink adhesion with either traditional or UV offset inks,” added McEwen.
Vaccination
has been one of most important links in medical science towards preventing life threatening diseases. India’s tryst with vaccines began in the 1800s when smallpox vaccines were imported from Great Britain.
From being a country, which had to wait for years to procure vaccines from abroad for some of the most life-threatening diseases like smallpox, hepatitis B and polio; the country and its medical research has today reached its pinnacle and is called the ‘Pharmacy of the World’.
The Indian vaccine market which was valued at Rs 95 billion in 2020 is now expected to grow at a CAGR of 18 percent to reach a value of approximately Rs 256.5 billion by 2026, according to Expert Market Research report.
The country’s potential in vaccine manufacturing was well displayed over the last two years, where Indian vaccines on coronavirus has been reaching the world and has saved millions of lives many times over.
This has not just proven India’s mettle in medical research but has also made it the most sought-after vaccine manufacturing destination in the world.
While medical research across the world was eliminating lifethreatening diseases, India, around a century back, was struggling to get access to vaccines on time. For instance, smallpox which was eliminated in North America and Europe by 1953, took until 1975 to eradicate in several Asian countries including India. Polio eradication journey too was a long one. However, India played a pioneer-leader in polio research — epidemiology, vaccine-prevention, and manufacturing of Oral Polio Vaccine (OPV) and Injectible Polio Vaccine (IPV), noted T. Jacob John and M. Vipin Vashishta in Indian Journal of Medical Research (IJMR).
Several vaccine institutes came up in different parts of the country including the Central Research Institute, in Kasauli, Himachal Pradesh and Pasteur Institute of India (CII) in Coonoor among others which enabled the manufacturing of several vaccines including diphtheria, pertussis, tetanus, tuberculosis and many more in India, by 1940. However, over the decades, several public research institutes were closed down making way for private research companies to come to the fore.
In 2010, India became the last country in the world to introduce second dose of measles vaccine in the national immunization programme. The potential of Indian vaccine manufactures was put on the test when the need for vaccine against Novel H1N1:2009, also known as the swine flu, instigated a pandemic alert. Indian vaccine manufacturers including Serum Institute of India (SII), Zydus Cadila, Bharat Biotech and Panacea Biotech came up to the task and developed pandemic flu vaccine in a short period of time.
With passing years, the Indian vaccine industry is credited to several other vaccines including bivalent oral cholera vaccine, meningitis-A vaccine, indigenous rotavirus vaccine, typhoid conjugate vaccine and indigenous Japanese encephalitis (JE) vaccine which were developed either by Indian manufacturers or in collaboration with international partners.
By 2019, the Indian government scaled up efforts to promote the HPV vaccine for girls to prevent cervical cancer, which is the second largest killer among cancers in women. While the efforts began in 2008, the government began providing a newer version of the vaccine in 2018. Recently, in July 2022, the Drugs Controller General of India (DGCI) recently approved the market authorization of the indigenously made vaccine, Cervavac, by SII which according to the company is India’s first quadrivalent HPV vaccination.
The COVID-19 pandemic, has put the Indian vaccine industry on the global map where several vaccines were manufactured in India. MoS Health, Bharati Pravin Pawar, announced that as of July 2022, India has supplied 23.9 crore COVID-19 vaccine doses to 101 countries, and UN entities in the form of a grant, commercial export, or through the COVID-19 Vaccines Global Access (COVAX) program.
In addition, with over 200 crore doses administered to its citizens, India has long surpassed the entire Europe where the vaccination numbers stand at about 130 crore. During the pandemic, India developed not one but multiple vaccines for Covid-19 including Covishield, manufactured by the Serum Institute of India (SII), Covaxin, manufactured by Bharat Biotech and Corbevax, manufactured by Biological E.
As the world still fights the COVID pandemic, the hunt for new vaccines is far from over. The country’s first home-grown mRNA Covid-19 vaccine, GEMCOVAC-19, developed at Pune’s Gennova Biopharmaceuticals has got a restricted emergency use nod for the 18-and-above age group. The technology uses genetically engineered mRNA to instruct cells to make the S-protein found on the surface of the Covid-19 virus.
India’s central drug authority is also gearing up towards inoculating children. Serum Institute’s Covovax has been granted emergency use authorisation for vaccinating children aged 7 to 11 years. Biological E’s intramuscular vaccine Corbevax is currently being used to vaccine children aged 12 to 14 years, while those in the 15-18 age group are being administered Bharat Biotech’s Covaxin.
Not just humans, but the Centre also launched nation’s first animal vaccine, Ancovax, a COVID-19 vaccine for animals like dogs, lions, leopards, mice and rabbits. It contains an inactivated SARS-CoV-2 (Delta) antigen capable of neutralizing both Delta and Omicron variants. Developed by the Indian Council of Agricultural ResearchNational Research Centre on Equines (ICAR-NRCE), this vaccine is one of the six vaccines indigenously produced by the institute.
Now, with the advent of Monkeypox in India, the National Institute of Virology (NIV) under the Indian Council of Medical Research (ICMR), has isolated the monkeypox virus from the clinical specimen of a patient and has invited Indian vaccine manufacturers for the development of indigenous vaccines for monkeypox. This could pave a new path for the industry’s growth.
To substantial the exponential growth the industry expects in the future, many vaccine manufacturers are expanding their operations to meet the growing demand and spread their presence across the globe.
Hyderabad-based vaccine maker, Biological E, announced its plans to invest more than Rs 1,800 crore in its facilities in Genome Valley. This will Increase Hyderabad’s vaccine manufacturing capacity by more than 50 percent to 14 billion doses, the highest for any region in the world. Hyderabad currently accounts for one-third of global vaccine production with a capacity of about 9 billion doses per annum. The move also aims at positioning the city as the ‘vaccine capital of the world’.
“This investment would be focused on manufacturing of Janssen Covid vaccine, MR vaccine, PCVA vaccine, Typhoid vaccine, Covid vaccine, Tetanus Toxide Ampoules, IPV vaccine, and Pertussis vaccine, biological APIs, and formulations,” said Mahima Datla, Managing Director, Biological E.
Serum Institute of India (SII) is also mulling over setting up a manufacturing plant in Africa as it looks to expand globally. The company is expected to invest over USD 300 million for setting up the manufacturing facility. “It’s never been a better time to be a vaccine manufacturer. I’m looking at expanding our manufacturing across the globe,” SII CEO Adar Poonawalla said at the World Economic Forum in Davos.
Bharat Biotech, has also partnered with BIOFABRI, a Spanish biopharmaceutical company, to join forces to develop, manufacture and market a new tuberculosis vaccine in more than 70 countries in Southeast Asia and sub-Saharan Africa. “TB infects more than 20 percent of the global population is the second leading cause of deaths from infectious disease after COVID-19. We are proud to announce this partnership with BioFabri, where MTBVAC can become a global TB vaccine,” said Dr. Krishna Ella, Chairman and Managing Director Bharat Biotech.
There are several factors which has made India a favourable destination for vaccine manufacturing. For instance, the introduction of the Universal Immunization Program (UIP) which is aimed at raising immunization coverage against treatable diseases in the country has boosted the need for vaccines in the domestic market. Also, advanced technology, manufacturing capability and cold chain storage facilities have aided to the growth of the industry. Furthermore, rising number of private vaccine companies in India which offers world class vaccines at low cost has also transformed the Indian vaccine market. All this has in-turn transformed India into a global manufacturing hub for vaccines so as to cater not just the domestic demand but also the global demand. Some of reasons that make India a global manufacturing hub include: Cost Efficiency in Vaccine Manufacturing: India’s low cost of production, research and development has made the country a cost-efficient destination for vaccines as well as pharmaceutical manufacturing. As per reports in investindia.gov, producing pharmaceuticals in India is 33 percent less costly than western markets.
Generic Drug Industry: India is the world’s largest generic drug provider. According to Expert Market Research, India represents about 60 percent of the total vaccines supplied to UNICE, 40 percent of generic drug demand in the US and 25 percent of all medicine in the UK. This is because of low cost of manufacturing and clinical trials in India.
Anti-China Sentiment: While India has already proven itself to be a major manufacturer in the global market, the current geo-political scenario has also given rise to a ubiquitous anti-China sentiment across the world. Hence, while many industries are shifting their base from China, their reliance on India is increasing. Banking on this sentiment, the “Make-in-India” and “Make-for-World” strategy, has proven positive to Indian vaccine manufactures in the current times.
Thus, today several Indian vaccine manufactures are fast becoming the vaccine manufacturing power houses of the world. The country needs to stride ahead from this point, grab the opportunities in offer and soar high in the global vaccine manufacturing industry.
The increase in healthcare budgets and rise in the number of surgical procedures propel global surgical gloves market growth, finds a recent analysis on global surgical gloves growth opportunities. Implementing strict regulatory norms favoring surgical gloves across regions further inflates their demand.
Due to this, the market for global surgical gloves is expected to reach $3.43 billion by 2026 from $2.24 billion in 2021, a boost at a compound annual growth rate (CAGR) of 8.9 percent, according to a report. The market will also be driven by the increased adoption of eco-friendly and biodegradable products.
“As consumers become more environment-conscious and governments impose stringent laws against single-use plastic, the demand for environment-friendly biodegradable gloves is expected to increase,” said Anjan Kumar Roy, chemicals, materials & nutrition industry analyst at Frost & Sullivan.
“This encourages manufacturers to focus on sourcing sustainable alternatives that can improve the recyclability of surgical gloves.”
“Since powdered latex can cause serious allergic reactions, businesses are switching to synthetic gloves. This trend will strengthen the synthetic gloves segment, which is expected to occupy 58.3 percent of the market by 2026,” Roy added.
The increasing demand for surgical gloves due to rising healthcare spending and strict regulations across different regions — the rest of the world (RoW), North America, and Europe — presents the following growth prospects for market participants:
• Manufacturers must focus on increasing investments in eco-friendly initiatives and source sustainable raw materials for enhanced product acceptance.
• Surgical glove manufacturers (primarily brand owners) should diversify their supplier base to mitigate supply-chain and price risks.
• In response to customer expectations of enhanced comfort, sensitivity, and elasticity, companies should invest in new technologies or new products with features similar to latex gloves but without the inherent risk of allergies.
The surgical gloves market is fiercely competitive and dominated by global players like Ansell, Cardinal Health, Mölnlycke Health Care, Semperit AG Holding and Medline Industries Ltd. Stringent regulatory norms and an expected increase in the demand for surgical gloves in the coming years opens up potential M&A opportunities for larger manufacturers to remain viable in this highly competitive space.
The Asia-Pacific mining chemicals market was estimated to be $1,549.65 million in 2017. The market is expected to register a CAGR of 4.72 percent during 2018 to 2023 (the forecast period). China is expected to lead the market, followed by India. By the function segment, floatation chemicals are expected to possess high share in the market.
Specialty chemicals are used in almost all the steps in the mining process. The mining industry has witnessed shifts in its production techniques, from tunneling to open pit mining, which has made it possible to mine ores of declining grades and decrease the overall costs. In addition, specialty chemicals are also used in the later stages of production chain, like smelting, refining, manufacturing and commodity trading.
Collectors dominated the flotation chemicals segment in 2017, while dispersants are expected to register the fastest growth through 2023. However, certain factors, such as logistics and transportation costs of flotation chemicals and stringent regulatory policies, are expected to adversely affect the profitability margins of the players in the market.
China holds the majority share of the Asia-Pacific mining chemical industry. The Chinese mining industry has more than 10,000 mines, the majority share is held by the state. It is world’s largest producer of gold, coal and other earth minerals. Moreover, it is also a leading consumer of mining products. In addition to the existing wastewater treatment plants, there are ongoing advances, such as expansion of existing wastewater sewage treatment plants and establishment of new sewage treatment plants. Mining chemicals are largely used in the mining industry for recovering minerals from the slurry, separation of impurities, purification of certain minerals and many other applications.
April 2017: BASF to increase prices for flocculants for the mining industry worldwide.
March 2017: Dow launched Sustainable Natural Solution to address mine-impacted water.
Major Players in the Asia-Pacific mining chemicals market are BASF SE, The Dow Chemical Company, Cytec Solvay Group and Clariant, amongst others.
The rising demand for alkyd resins in coatings and paints is likely to drive the growth of the global coatings raw materials market. Raw materials, in the form of specific chemical elements that are incorporated into paints and coatings, are an extremely complicated and important subset of the wider specialty chemicals sector. They can be used in paint and coating formulations, as well as multi-component coating systems, throughout the production process, according to a report for the forecast period 2021 to 2031.
Expanding construction and automotive sector expansion, rapid industrialization across the globe, and increased raw material consumption to produce protective coatings are all anticipated to bode well for the global coatings raw materials market. Raw ingredients can improve the weathering qualities of protective coatings dramatically. In addition to that, the presence of a wide range of coating polymers,
increased printing ink output, and a rising number of technical advancements are all expected to increase demand for coating raw materials. The use of these basic ingredients in printing inks enhances gloss, improves the smoothness, and scratch resistance of the ink.
To enhance their market share and extend their geographic reach, industry participants are entering into acquisitions, mergers, agreements, joint ventures and partnerships. Businesses are also concentrating on boosting customer knowledge of the uncertainty around the substances used, while complying with international regulatory norms. Some of the noted players that are operational in the global coatings raw materials market are Momentive Performance Materials Inc, Eastman Chemical Co, Akzo Nobel NV, PPG Industries Inc, Evonik Industries AG, Arkema SA and Dow Inc.
Below-mentioned market trends and opportunities mark the global coatings raw materials market:
The growing demand for alkyd resins in paints and coatings is likely to propel the global coatings raw materials market forward, while market expansion can be hampered by factors such as changing crude oil prices. The advent of innovative application techniques, together with rising demand for high-performance fluorine resin-based coatings, is further likely to offer enormous potential for development of the global coatings raw materials market in the forecast period.
Flexibility in crude oil prices, as well as growing public awareness about environmental concerns, are predicted to function as market
restrictions for the expansion of coatings raw materials in the forecasted period. Stringent VOC restrictions will be one of the main and most significant impediment to the market’s expansion.
Due to fast industrialization, an expanding automotive industry, a developing construction sector, as well as the presence of several market participants in the area, Asia-Pacific is likely to dominate the global coatings raw materials market. In Asia Pacific China is a major market for coatings raw materials.
Asia Pacific has been experiencing rapid expansion and is likely to provide market players with huge commercial prospects. The rising demand for coatings raw materials in the construction sector is one of the primary reasons driving growth in Asia Pacific.
Organosilicon polymers composites are organometallic compounds that contain the carbon-silicon bond. Generally, the organosilicon compounds are like ordinary organic compounds and display similar characteristics: flammable, colorless, stable to air and hydrophobic. For instance, silicone is a polymeric organosilicon compound that is thermally stable and chemically inert. The polysiloxane polymer compound has more than one organic group connected with a silicon atom which helps to offer better thermal oxidation stability, electrical properties and weather resistance.
The organosilicon polymers (polysiloxane) market is projected to register a CAGR of around 4.28 percent to reach $2,201.24 million by the end of 2028, as per a recent report.
The prominent factor favoring the growth of the organosilicon polymers (polysiloxane) market is the demand from application in the construction sector and from the growing automotive industry, which is opting for cleaner and greener material sources owing to the stringent regulations on emission, especially from the US, EU countries, China, India and other Southeast Asian countries. They are also used extensively in the application of coatings for protective and industrial purposes. These compounds are also extensively used as fire retardants in various materials.
Silicone compounds are extensively used in the automotive industry.
The need for greener and eco-friendly materials in the automotive and transportation sector is expected to create major traction for the market demand. The regulations towards eco-friendly materials and awareness of environmental pollution are expected to gain major traction for the organosilicon polymers (polysiloxane) market in the coming years. Additionally, the production and sales increase of passenger cars, especially of the small passenger cars such as subcompacts, microcars, and superminis, are significantly high end account for over 33 percent of total vehicles sold in 2019. According to the Center for Automotive Research, the demand is expected to reach over 32 million vehicles by the end of 2021.
Additionally, synthetic organosilicon polymers can be modified with the help of organic fillers, which are obtained from the waste of plants. These types of organosilicon polymers are generally used in the electronics and semiconductor industries. The application field of silicone compounds includes the thermal protection systems in which silicone rubber composites are used, which helps to increase the flame retardancy of the electrical cables. It also helps with the production of white light by colorimetric and photometric conversions in lightemitting diode (LED) packages coupled with various applications in marine antifouling surfaces. Silicone composites provide elastic technical materials using the correct fillers, and these composites can be used to produce materials with high-performance properties.
However, the tensile strength, hardness, and tear strength properties are very poor in silicone rubber, making them less reliable to produce high-quality products. Contrarily, factors such as technology development, product innovation, and the expansion of the automotive and construction industry in emerging economic regions such as the Middle East and Africa, and Latin America are estimated to create new demands and growth opportunities for the manufacturers in the organosilicon polymers (polysiloxane) market.
The indefinite halt of world travel has radically changed the market demand and disrupted the global supply chains. The pandemic has affected and continues to impact the various industry verticals; while food and medicine-related industrial sectors continue to gain high demand and priority, other verticals such as transportation, construction, electronics, automotive, oil & gas have suffered from low sales and demand. Some countries, however, have opened their borders, the market demand is still less than the pre-pandemic levels. As the global economy starts to recover, companies have started with continuous R&D and are making impacts studies on their supply chains – from their sourcing and workforce to its supply chain suppleness.
The chemical industry helps to produce over 96 percent of manufactured goods globally each year. This industry is responsible for manufacturing over 70,000 diverse products out of its raw materials, which have their application in the agriculture, food, healthcare, transportation, consumer goods and building & construction sectors. The demand for chemicals isa direct function of the demand created by the customers. Although the chemical industry has been affected negatively in some sectors such as automotive and construction, it has benefitted in other sectors such as medical equipment and packaged food.
Moreover, the companies are working aggressively toward safeguarding the health and wellbeing of their employees while also supporting government goals of maintaining critical business activities in power generation, food production, and healthcare.
There are numerous fiscal and monetary policies that governments across the globe implicate to mitigate the impact of COVID-19 on the industrial sector while providing some relief to its consumers. According to the United Nations, the global economy is expected to decline by about 3 percent or more instead of recording a 2.5 percent growth which is projected by the World Economic Situation and Prospects report 2020.
The key raw materials used in the production of organosilicon polymers (polysiloxane) include carbon and silicone. Some of the key suppliers are Dow, Wacker Chemie AG, Shin-Etsu Chemical Co Ltd, Elkem ASA and KCC Corporation, among many others. The distribution channel in this market comprises of distributors, wholesalers and e-commerce merchants.
The organosilicon polymers (polysiloxane) market has been segmented on the basis of product type, application and region.
By product type, the organosilicon polymers (polysiloxane) market has been segmented into silicone oil, silicone rubber, silicone resin, and silicone emulsion. The silicone rubber segment accounted for the largest market share in 2020 due to its wide use in the automotive sector. It is aimed to reduce the carbon footprint from various parts. Based on the application, the organosilicon polymers (polysiloxane) market has been categorized into coatings, elastomers, foams,
adhesives & sealants and others. Among these, the coatings segment emerged as the fastest-growing segment.
According to the product type segment, the market is expected to gain major traction from the silicone rubber segment. However, the silicone oil segment is expected to be the fastest-growing segment due to its application in the construction, electronics, and marine industry.
The organosilicon polymers (polysiloxane) market has been studied across Asia-Pacific, North America, Europe, Latin America, and the Middle East & Africa. Asia-Pacific accounted for more than 40 percent of the organosilicon polymers (polysiloxane) market share in 2020. The players majorly operating in the Asia-Pacific region are embracing numerous business strategies, including R&D, expansions, new product launches, joint ventures, acquisitions and agreements to fortify their presence in the market.
The market growth in Europe can be attributed to the stringent emission control regulations in Western Europe and the increasing automotive and construction in the region.
The US has one of the largest automotive markets. According to the US Department of Commerce, International Trade Administration (ITA), in 2020, the light vehicle sales were over 22 million units 2020. Additionally, the growing demand for silicone oil in the construction sector is expected to increase the demand for organosilicon polymers (polysiloxane) market in the coming years.
The rapidly growing pharmaceuticals market coupled with rise in generics production is driving the market growth for pharmaceutical excipients. However, the increasing regulatory stringency regarding the approval of drugs and excipients, along with the cost and time-intensive drug development process, are expected to restrain the growth of this market. The pharmaceutical excipients market is projected to reach $11.5 billion by 2027 from $8.6 billion in 2022, at a CAGR of 5.9 percent during the forecast period.
The COVID-19 pandemic had a significant impact on the pharma industry. Lockdowns imposed in the wake of the outbreak disrupted the supply of raw materials from manufacturing hubs such as India and China. This slowed drug development and manufacturing, severely impacting companies that relied heavily on outsourcing.
The entire pharmaceutical ecosystem was disrupted initially. Moreover, regulatory authorities also had to reframe and construct new laws to ensure maximum patient safety after drug consumption. The end of the lockdowns saw the pharma industry gaining momentum, especially given the demand for drugs such as hydroxychloroquine and Remdesivir, which showed positive results against COVID-19. The increasing demand for these drugs drove revenue growth for some companies. Thus, the mass production of drugs has positively influenced the demand for pharmaceutical excipients products.
According to industry experts, generic erosion is expected to result in significant revenue and volume losses for the branded drugs industry. This will enable the entry of cheaper generic counterparts into the market, which will boost the volume of drugs sold. The growing affordability and increasing healthcare expenditure in emerging economies will also drive the sales volume of generics in the forecast period. This is considered as a positive indicator of the growth of the pharmaceutical excipients market.
According to the California Biomedical Research Association (CBRA), it takes 12 years for a drug to travel from the research lab to the patient, including 1–6 years for toxicology studies alone. Moreover, late-stage failures in the drug development process also impact the time and cost associated with drug development. Although excipient and drug production has seen significant advances in recent years, the requirement for high capital investments is expected to hamper market growth during the forecast period
The development of excipients capable of multiple functions is considered a novel solution to counter the high time and cost requirements for bringing a drug to the market, a process that may take, on average, 10–12 years.
Multifunctional excipients enhance the drug manufacturing process and improve flowability, compressibility, bioavailability and particle size distribution. It thus produces lucrative growth opportunities.
A large part of the pharmaceutical excipient manufacturing process is outsourced to smaller manufacturers in low-cost countries. This leads to low control over the excipient manufacturing process and quality, thereby increasing the need for process transparency in the entire supply chain. However, achieving immediate streamlining and
maximum transparency in supply chain activities poses a challenge for drug manufacturers and excipient manufacturers.
Based on product, the pharmaceutical excipients market is segmented into organic chemicals, inorganic chemicals and other chemicals. The organic chemicals segment will continue to dominate the market during the forecast period. The large share of this segment can be attributed to the use of these chemicals in most pharmaceutical formulations.
The market is segmented into five major regions — North America, Europe, the Asia Pacific, Latin America and the Middle East & Africa. In 2021, Europe accounted for the largest share of the market. The large share of this region can be attributed to the presence of many pharmaceutical giants with large production capacities leading to high consumption of excipients. The growing emphasis on superior pharmaceutical products, generics, and biosimilars has also led to the increasing demand for novel excipients, which, in turn, is expected to drive market growth.
Some of the key market players in the global pharmaceuticals market are Ashland Global Holdings Inc (US), International Flavors &
Fragrances Inc (US), BASF SE (Germany), Evonik Industries AG (Germany), Roquette Freres (France), Associated British Foods Plc (UK), Archer Daniels Midland Company (US), Lubrizol Corporation (US), Innophos Holdings (US), Kerry Group Plc (Ireland), Wacker Chemie AG (Germany), Air Liquide (France), Dow Chemicals (US), Colorcon (US), DMV-Fonterra Excipients (Germany), JRS Pharma GmbH (Germany), Meggle GmbH & Co Kg (Germany), Finar Limited (India), Fuji Chemical Industries Co Ltd (Japan), Merck KGaA (Germany), Captisol (US), Ideal Cures Pvt Ltd (India), Corel Pharma Chem (India), Biogrund GmbH (Germany), Nitika Pharmaceutical Specialties Pvt Ltd (India), among others.
Growing demand for high-performance and function-specific chemicals across the end-use industries such as oil & gas, pulp & paper, personal care and cosmetics is expected to be one of the prime market growth factors. Specialty chemicals are also referred to as performance chemicals or effect chemicals. Some popular examples include essential oils, gelatin, castor oil and collagen. These chemicals are referred to as specialties as they are produced in lesser volumes and cater only to a few applications unlike the rest of the fine and commodity chemicals (according to the European Chemical Industry Council (Cefic).
The global specialty chemicals market size was valued at $586.5 billion in 2020 and is expected to grow at a compound annual growth rate (CAGR) of 4.3 percent from 2020 to 2028.
Innovation and R&D are some of the key growth prospects as the market is majorly consumer-driven. Manufacturers’ focus on providing innovative and custom-made product offerings for target applications and catering to the demand of specific customers has driven research and development investment and thus, driven the development of innovative specialty chemicals and expanded the market product portfolio.
Concerns regarding the harmful effects of conventional chemicals on the environment and humans have prompted the demand for user-friendly and environment-friendly specialty chemicals. Therefore, several players’ focus has shifted towards the development and marketing of specialty chemicals in order to edge out from the conventional fine and commodity chemical manufacturers.
However, the technicalities associated with their small-scale production, especially for those produced via bio-refineries such as collagen pose significant challenges to the industry. Further, the competition from more economical conventional counterparts of specialty chemicals adds to the industry challenge.
The rising adoption of rechargeable, miniaturized, and sustainable electronic components have created a significant demand for products that can foster enhanced performance with lesser maintenance. This factor has led to considerable growth in the demand for specialty chemicals from the electrical and electronics end-use.
The automotive industry is expected to remain a lucratively growing segment with high demand for adhesives, lubricants, paints, and coatings for weight reduction and cost-saving end-uses. Growing awareness and rising adoption of a healthy lifestyle among consumers has driven the product demand for pharmaceuticals and nutraceuticals end-use. Increasing disposable income is significantly driving consumer focus towards personal care and this is likely to augment the product demand in personal care and cosmetics end-use.
The industrial and institutional cleaners segment accounted for the largest market revenue share of 9.8 percent in 2020 and is projected to witness a growth rate of 4.6 percent from 2020 to 2028. The CASE segment which includes, coatings, adhesives, sealants, and elastomers emerged as a lucrative segment accounting for a value share of 4.9 percent in 2020. Numerous technological advancements and product innovations have led to the performance enhancement of such products and have boosted the growth of the specialty chemicals market in the past years.
Construction chemicals are expected to emerge as one of the prominent product segments with significant growth projections between 2020 and 2027. The demand for products such as specialized water-proofing compounds, repair and renovation compounds, joint fillers, and tile fixing adhesives is considerable in the construction and building industry.
Infrastructural growth in emerging economies such as India, China and Brazil has contributed to segment growth. This demand is not restricted to the developing nations of the Asia Pacific and South America. The US Department of Commerce has stated that the value of construction put in place in the US was more than $1,369 billion in January 2020, which signifies the immense demand for specialty construction chemicals in North America.
The rapid expansion of refining capacity and shale oil & gas drilling activities in the past few years has boosted the consumption of products in the oil and gas end-use industry. This is further driven by the considerable growth in oil refinery throughput across the geographies. According to the BP Statistical Review of World Energy report of 2019, the refining throughput in countries such as China, Colombia, and Vietnam grew by 6.7 percent, 7.6 percent and 85 percent per annum respectively.
Asia Pacific accounted for a revenue share of 46.8 percent in 2020 in the market for specialty chemicals. The prominence of China as one of the top manufacturing hubs for most industries such as pharmaceuticals and nutraceuticals, personal care and cosmetics, automotive, and electrical and electronics has resulted in the emergence of the Asia Pacific region as one of the fast-growing markets for specialty chemicals. Further, the growing diversification and industrialization
in economies such as Singapore, Malaysia, Thailand and India are expected to generate lucrative opportunities in the market for specialty chemicals.
Europe is expected to be one of the stable markets for the product. According to the European Chemical Industry Council (Cefic), more than 27.0 percent of the total chemical sales in the EU were represented by specialty chemicals in FY 2018. It is one of the largest exporting sectors of the region, holding around one-third of the total chemical exports in 2018. The Middle East and Africa are expected to be one of the top markets for oilfield chemicals owing to the prominence of oil and gas companies in the Middle East countries. Rapid growth in the construction activities of GCC, Oman, Qatar and UAE is going to benefit the market for specialty construction chemicals.
The rapid outbreak of the COVID-19 (Corona Virus) pandemic that accelerated its rate of spread by the end of February 2020 across the countries such as China, Italy, Iran, France, and Germany dreadfully is expected to develop a severe economic downturn in FY 2020, which is likely to affect the market in all regions.
Positioning in high-growth countries such as China, strategic alliances, intensive R&D for sustainable, efficient product development and adoption of new technologies are some of the prominent operational strategies among the market participants. Further, R&D for bio-based specialty chemicals has gained significant momentum over the past few years owing to changing end-user perceptions and favoring regulatory mandates.
The product manufacturers tend to be members of associations such as the British Association for Chemical Specialties (BACS), Society of Chemical Manufacturers and Affiliates (SOCMA), Chemical Industries Association (CIA), and the Northeast of England Process Industry Cluster (NEPIC) in order to stay updated with the industry trends and drive the market for specialty chemicals, collectively.
The manufacturers are focusing on capacity expansion and technological advancement of manufacturing facilities in order to gain traction and increase their market competency. In addition, manufacturers are maintaining long-term supply agreements with raw material suppliers or end-users to ensure stability.
Some of the prominent players in the specialty chemicals market include - Solvay AG, Evonik Industries AG, Clariant AG, Akzo Nobel NV, BASF SE, Kemira Oyj, LANXESS AG, Croda International Plc, Huntsman International LLC, The Lubrizol Corporation, Albemarle Corporation, to name a few.
Source: Grand View ResearchZero Valent Iron is a special kind of zero valent metal applied as a reductant for sequestering several types of contaminants from soil and groundwater. Variation of chemical properties and physical properties for different forms of ZVI results in its various applications and efficiency. As per a recent study, demand of Zero Valent Iron (ZVI) is estimated to grow with a growth rate of 5.0 to 6.0 percent during the forecast period of 2021 to 2031.
What are the driving factors for Zero Valent Iron?
Growing contaminants in ground water increasing water pollution impacting ecology and human health as well. This is due to increase of industrial waste disposal, domestic waste disposals and many others in landfills and in open spaces in several countries. Spillage of hazards such as, organic compounds, heavy metals, pathogens etc. from these waste are impacting the environment to a significant extent.
From this soil, groundwater and other water bodies are getting contaminated. Zero valent metals are being used to decontaminate these hazardous and toxic substances from soil, ground water and from waste water. Zero valent iron is expected to remain a key metal for soil and groundwater remediation over the forecast period.
Rising demand for groundwater and soil remediation, waste water treatment, is boosting the consumption rate for the product. Further increase in soil contaminants owing to rising landfills and waste disposals are anticipated to boost the demand in the coming years.
Groundwater, Wastewater Treatment are expected to boost consumption
Growing waste water all over the globe owing to industrial waste stream disposal with less treatments, domestic waste disposal in water bodies are expected to boost the demand in the coming years as ZVI are used in water treatment. With the growing spillage from landfills and open disposal of waste, groundwater are continuously getting polluted with contaminants like heavy metals, organic compounds and pathogens and many others.
This is expected to boost the demand of zero valent metals in the coming years as it is used in removing of contaminants from groundwater and wastewater. With the growing field of nanotechnology, production of nanoparticles are in the commercialization phase, which is anticipated to boost the industry of ZVI in the coming years, as nanoparticles utilization increases application’s efficiency to a substantial extent.
Demand from growing groundwater remediation in US and Canada are expected to boost the demand of Zero Valent Iron during the forecast period. Significant rise
in waste disposal in landfills are increasing ground water contamination along with soil contamination. This is anticipated to benefit the market of zero valent iron in the coming years.
Growing in wastewater treatment in both the countries are also bolstering the consumption rate. Further the growing investment in research and development is also boosting the efficiency to treat contaminated ground water and waste water, especially investment in nanotechnology for the synthesis of enhanced zero valent metals nanoparticles.
Moreover strong presence of key manufacturers in US and Canada maintains the supply volume for the product, with their marketing strategy, ZVI is further expected to gain traction in the North American market.
Significant rise in the waste disposals in Asian countries like ASEAN, India, China and others are contaminating the surroundings. Further waste are not disposed in a properly constructed landfills in several countries of Asia Pacific. These factors are anticipated to bolster the growth of the industry of zero valent iron during the forecast period.
Growing remediation of waste water, soil, groundwater contaminants are estimated to contribute considerably for the consumption of zero valent metals over the coming assessment period. Increase in governments initiatives for water treatments in Asia Pacific region are also expected to benefit the market in the coming years.
Some of the key manufacturers and suppliers of Zero Valent Iron are: American Elements, GMA Industries, NANOIRON sro, Hongwu International Group Ltd, RemQuest, SAGWELL, Reade International Corp, Peerless Metal Powder & Abrasives Company, Redox Tech LLC, CERES Corporation, Envirotecnics, Geo-Cleanse International Inc and many others.
Key market participants are maximizing their utilization rate to meet the increasing demand from the end use industries. These players are also focusing on providing services for groundwater treatment and soil remediation to increase their preference order which is expected to benefit the company to increase their annual turnover.
Key players are also focusing on introducing automation to their manufacturing process by merging 5G tech, IoT, AI, machine learning into their production processes. This is anticipated to benefit the company for sustainable development and it will help to decrease human error in the production technology.
Source: Persistence Market ResearchTo address the industrial air pollution issue, Worldofchemicals and Chemical Today Magazine along with Dürr India Pvt Ltd as its Knowledge Partner, conducted a technology update and knowledge sharing webinar on 8 July.
Industrial air pollution has become a cause of major concern with the alarming increase in the carbon emissions and the deteriorating health of the planet. Industrialization has led to the growth of global economies and overall progress of humankind. However, on the flip side, industrialization has had an alarming impact on the environment due to the huge amounts of air pollutants that is released by industries.
According to the World Health Organization (WHO), each year air pollution is responsible for nearly seven million deaths around the globe. Nine out of ten human beings currently breathe air that exceeds the WHO’s guideline limits for pollutants, with those living in low- and middle-income countries suffering the most.
Taking matters into hand, the United Nations has recognized air pollution as a pressing sustainability concern and out if its 17 Sustainable Development Goals (SDG), several goals are aimed at reducing air pollution.
Several industries across the globe are adopting sustainable and environment-friendly technologies to curb the emission of hazardous air pollutants. Hence, Exhaust Air Pollution technologies play an important role in achieving the global mission of clean air.
In a country like India, where high level of pollution is already chocking several states, addressing air pollution- especially industrial air pollution concerns, is all the more necessary. Playing its part in curbing air pollution, chemical manufacturers too are looking to adopt proper emission control technologies. Moreover, the clean air standards, regulatory, legal and compliance requirements are making the chemical industry consider further
technology enhancement and take responsibility at a much larger level.
However, it is easy said than done. Many manufacturers- big and small, are still in the dilemma over choosing from a myriad of solutions available in the market, deciding between being environment-friendly and pocket friendly, and being tangled in numerous myths and misinformation.
Acknowledging the need to create more awareness and understand how exhaust air pollution technology has evolved, Worldofchemicals and Chemical Today Magazine conducted a technology update/ knowledge sharing session with chemical manufacturers along with Dürr India Pvt Ltd as our ‘Knowledge Partner’.
Dürr is a global leader in clean technologies and has implemented exhaust air pollution technologies across the chemical industry be it oil & gas, petrochemicals, chemicals, fertilizers, pharmaceuticals, printing & coating, plastics, carbon fiber, composites and rubber industry.
The company offers a comprehensive range of Exhaust Air Pollution Control Systems that remove all traces of these pollutants from exhaust air. Dürr’s state of the art exhaust air pollution control technologies provides environmental solution to customers around the world.
Dürr’s Oxi.X RE/ Oxi.X DF/ Sorpt.X CA/ are the most efficient technologies which are able to destruct/control volatile organic compounds generated across industries and to keep the exhaust gas emission levels within the limit. These technologies dispose the exhaust gases efficiently with reduction in energy consumption, operating expenditure and guarantee high reliable process.
The webinar delved into the latest trends in Clean Technology Systems, Environmental Solution for Industry emissions and Solvent Recovery System. The experts delved into the different technology solutions available in the market, explained the need for companies
to have a customised solution for each company that can be the best fit for individual processes and also pointed out the common issues that most companies face while incorporating air pollution control systems.
and every industry produces hazardous air pollutants, VOCs, hydrocarbons etc, which cannot be discharged in environment directly as every government has specific emission norms defined for each industry. However, to keep the emissions under control, emission control technologies play a very important role. Various emission control technologies are available in the market like the Regenerative Thermal Oxidizers which regenerates the energy present in the stream and provides 98-99.3% VOC destruction efficiency and 95-97% thermal efficiency.
Most emissions from petrochemical and chemical industry are in the area of VOCs, CO and HAPs which can be addressed with technologies like RTO, DFTO which will help to destruct, control or recover the solvents so that the free air can be exhausted into the atmosphere. Emissions can also be in the form of:
NOx which can be addressed with Selective Catalytic Reduction Systems or Selective Non-Catalytic Reduction.
Particulate can be dealt with Dry Electrostatic Precipitators
SO2 Acid Gases can be dealt with Spray Dryer Absorbers or wet scrubbers
H2S can be addressed with non-regenerative Carbon Adsorption and Acid Mists can be handled with Wet Electrostatic Precipitators
For any environmental issues pertaining to this industry, there are effective solutions to each problem. Dürr’s portfolio includes Oxi.X ( for Oxidizers), Sorpt.X (for Solvent Recovery system), Part.X (for Particulates) and Catalytics (For Catalytic Oxidizers).
The selection of each and every technology depends on the pollutants and type of hydrocarbons being used, the capacity of the streams that needs to be treated and the amount of the VOC load present in the steam.
Every industry and every company need a different solution and we as a solution provider, work with the customer the understand their process and their problem to come up with the best fit solution so as to help the company meet the emission standards and limits defined by the Central Pollution Control Board (CPCB) and State Pollution Control Boards (SPCB).
Solvent Recovery System (Sorpt.X) is a non-restrictive technology which is used to remove VOCs from low to medium concentration gas streams. Sorpt.X is generally used which a stringent outlet concentration which must be made as per the exhaust guidelines prescribed by the central and the state pollution control boards.
Durr supplies this proprietary Regenerative Carbon Adsorption System for high efficiency removal, recovery and purification of solvents from process exhaust air streams. This technology gives direct benefit to the customers’ OPEX requirement. This technology can be used in chemicals, petrochemicals and coating process, rubber and pharmaceutical industry.
The Sorpt.X is designed as per consumers’ specific requirement with size ranging from 1000 cfm to 780,000 cfm. It can handle an array of solvents including Alkanes, Aromatics, Esters, Ethers, Alcohols, Ketones and Halogenated Solvents. The solvents which are recovered are- N-Methylpyrrolidone, Toluene, Methylene chloride, Trichloroethylene, Alcohols, Ketones and almost all types of hydrocarbons. More than 1000 systems have been installed by Durr in over 20 countries.
With Sorpt.X we are able to recover more than 99 percent of all solvents for reuse. We can also remove VOCs and HAPs from process emissions to meet or exceed regulatory requirements. Use of Sorpt.X can increase profitability by reducing solvent expense. It has a wide range of airflows and solvent loadings, and is suitable of wide variety of solvent types.
Seeing the global trends, Worldofchemicals and Chemical Today magazine is organising the virtual conference - Pharma Connext: Formulating for the Future on August 12th, 2022 with an aim to explore the opportunities in Pharma Research and Innovation in APIs & Formulations in India.
BY DEBARATI DASThe last two years have proven the world’s immense dependence on medical science and pharmaceutical research. While COVID-19 pandemic created a global havoc and shows no sign of disappearing any time sooner, the medical fraternity is additionally rattled with the advent of monkeypox. The rise and disappearance of new viruses is nothing new. The rate at which new medicines and vaccines can be developed to combat these medical emergencies is all that matters.
According to data published by the GOI’s Department of Pharmaceuticals in its Annual Report 2020-2021, the Indian pharmaceutical industry is the world’s 3rd largest by volume and 14th largest in terms of value. Additionally, India is also the 3rd largest market for APIs globally. The country aces in the departments of generic drugs, OTC Medicines and API/Bulk Drugs, Vaccines, Contract Research & Manufacturing, Biosimilars & Biologics.
India has been a global leader in the supply of diphtheria, pertussis and tetanus (DPT), Bacillus Calmette–Guérin (BCG) and Measles vaccines. Over the last two years, India has also shown its competence in manufacturing vaccines to combat coronavirus and has also supplied 23.9 crore COVID-19 vaccine doses to 101 countries. India accounts for 60 percent of global vaccine production, contributing 40 to 70 percent of the WHO demand for DPT and BCG vaccines, and 90 percent of the WHO demand for the measles vaccine.
All these numbers only point at the competence of India in the area of pharmaceutical research. To understand the opportunities, challenges and dynamics of the pharmaceuticals industry, Worldofchemicals and Chemical Today Magazine have organised a virtual conference - Pharma Connext: Formulating For Future, on August 12, 2022 which will highlight the ways in which the pharmaceutical industry needs to evolve to be future ready to combat diseases, epidemics, pandemics and rising life-threatening ailments. The virtual conference, will have the stalwarts from the industry from Novartis, Evonik, Cadila Pharmaceuticals Ltd and Dr. Reddy’s Laboratories discussing every aspect of the Pharma Industry.
With a targeted focus on the fast-growing pharmaceutical research eco-space in India, the conference will have a variety of topics including Business Strategy in Pharma R&D, Changing Outlook of Clinical Research & Trials for Vaccines, Role of Lipids in delivery of mRNA and Modelling & Simulation in Clinical Research.
Pharma manufacturers and professionals joining the Pharma Connext virtual conference will surely get an insight into the dynamics of the pharmaceuticals industry in India and be a part of the promising growth segment.
As one of the largest-volume industrial chemical processes today, hydroformylation converts olefins, H2 and CO into aldehydes and related products more than 10 million tons annually.
Although Au exhibits good ability towards olefins activation, H2 dissociation and CO bonding, it is conventionally considered inactive for hydroformylation due to its intrinsic inertness.
Now, a research team led by profs. Wang Hui and Sun Yuhan from the Shanghai Advanced Research Institute (SARI) of the Chinese Academy of Sciences designed a zeoliteencaged Au single-atom catalyst with Au1-OSiOX motifs, which shows remarkable catalytic activity and selectivity towards propene hydroformylation. The study was published in Chem Catalysis in July.
Preliminary performance evaluation of impregnated Au on zeolite demonstrates that sub-nanometer Au clusters exhibit higher activity than nanoparticles in hydroformylation.
Inspired by this, the confinement effect of
zeolite is utilized to regulate the particle size of Au. Nanoparticles/sub-nanoclusters and atomically dispersed Au species within zeolite can be unambiguously observed through highangle annular dark-field scanning transmission electron microscopy (HAADF-STEM).
The Au1@S-1 catalyst shows a total 3,794 μmol butyraldehyde and noticeable stability after five cycles, which is about one order of magnitude more active than Au nanoparticles and is even comparable to Rh-based catalysts.
Detailed characterizations and theoretical calculations indicate that the isolated Au atoms within the zeolite matrix are stabilized via oxygen bridge bonds. The formed Au1O-SiOX motifs render maximum active site density and high structural stability, which are identified as the real active sites for efficient hydroformylation.
This work makes conventionally inactive Au efficient alternative for hydroformylation by reasonably tailoring the size, contact structure and electronic environment of active metals on specific reactions.
Generating
Solar-powered synthesis gas could recycle carbon dioxide into fuels and useful chemicals, an international team of researchers has shown. This way, producing synthesis gas, a precursor of a variety of fuels and chemicals, will no longer require natural gas, coal or biomass.
“If we can generate syngas from carbon dioxide utilizing only solar energy, we can use this as a precursor for methanol and other chemicals and fuels. This will significantly reduce overall CO2 emissions,” said Zetian Mi, professor of electrical and computer engineering at the University of Michigan, who led the study published in the Proceedings of the National Academy of Science. Composed mainly of hydrogen and carbon monoxide with a little methane, syngas is commonly derived from fossil fuels with the help of electricity. In addition, toxic chemicals are often added to make the process more efficient.
“Our new process is actually pretty simple, but it’s exciting because it’s not toxic, it’s sustainable and it’s very cost effective,” said Roksana Rashid, first author of the study, who performed the experiments as a doctoral student in electrical and computer engineering at McGill University in Canada.
To create a process that uses only solar energy, Mi’s group overcame the difficulty of splitting carbon dioxide molecules,
which are among the most stable in the universe. For this, they peppered a forest of semiconductor nanowires with nanoparticles. Those nanoparticles, made of gold coated with chromium oxide, attracted the carbon dioxide molecules and bent them, weakening the bonds between the carbon and oxygen.
The gallium nitride nanowires used the light energy to free electrons and the positively charged spaces they leave behind, known as holes. The holes split water molecules, separating the protons (hydrogen) from the oxygen. Then, at the metal catalysts, the electrons split the carbon dioxide, producing carbon monoxide and sometimes drawing in the free hydrogen to make methane. Processes are under development to separate the oxygen from the other gases.
“Our technology sheds light on how to build distributed syngas production from air, water and sunlight,” said Baowen Zhou, co-corresponding author of the study with Mi and a former postdoctoral research fellow in Mi’s lab at McGill University and U-M.
By changing the ratio of gold to chromium oxide in the nanoparticles, Mi’s team was able to control the relative amounts of hydrogen and carbon monoxide produced in the reaction. This is important because the ratio of hydrogen to carbon monoxide affects how easy it is to produce a type of fuel or chemical.
“What is surprising is the synergy between gold and chromium oxide to make the CO2 reduction to syngas efficient and tunable. That was not possible with a single metal catalyst,” Mi said. “This opens up many exciting opportunities that were not previously considered.”
Mi’s tunable syngas setup uses standard industrial manufacturing processes, and is scalable. While Rashid used distilled water in this experiment, seawater and other electrolyte solutions are also expected to work, and Mi has used them in related water-splitting studies.
“The semiconductor we use as the light absorber is based on silicon and gallium nitride, which are the most commonly produced semiconductors, and we use very little material for the gallium nitride. Each nanowire is about one micrometer in thickness,” Mi said.
Mi’s next goal is to increase the efficiency of the device, which currently stands at 0.89 percent. When 10 percent of the light energy is converted to chemical energy, he hopes that the technology could see the technology be adopted for renewable energy, similar to solar cells.
Researchers from the University of Tsukuba and collaborating partners experimentally measured hydrogenation of metaladsorbed formate. This development will facilitate practical conversion of carbon dioxide pollutant into methanol fuel.
Carbon dioxide pollution continues to change the global climate. Researchers know how to pinpoint such pollution, even on a regional and near-real-time basis, as highlighted this year in Science Advances in April. As part of a solution to carbon dioxide pollution, many studies focus on how to convert this pollutant into a fuel, such as methanol. Copper-based catalysts are a tool for such conversions.
Understanding the corresponding step-by-step chemistry is essential for optimizing conversion of carbon dioxide pollutant into methanol fuel. However, the details of this chemistry remain unclear; experiments are needed to test hypotheses that are currently based on computer simulations.
Now, in a study recently published in Journal of the American Chemical Society researchers from the University of Tsukuba and collaborating partners have experimentally measured hydrogenation of copper-adsorbed formate. This study will help researchers optimize critical steps in the aforementioned pollutantto-fuel process, and thus accelerate methanol production.
“Hydrogenation of carbon dioxide into methanol is a potential key technology for producing fuel and chemical feedstocks, but optimizing the reaction remains difficult,” explained Dr. Kotaro Takeyasu, senior author. “That’s because it’s difficult to experimentally detect chemical intermediates in the step-by-step reaction mechanism.”
Infrared reflection absorption spectroscopy and temperatureprogrammed desorption were critical to obtaining two main findings. First, at a temperature of 200 Kelvin, exposure to atomic hydrogen corresponded to hydrogenation of adsorbed formate. The exact chemical nature of the product isn’t yet clear. It was also found that, at a temperature of 250 Kelvin, the hydrogenated formate decomposed back into adsorbed formate or gaseous formaldehyde, in a 96:4 ratio.
“On the basis of our experimental and computational work, the activation energy of the hydrogenation of adsorbed formate is approximately 121 kilojoules per mole,” stated Takeyasu. “Our results are consistent with reported results of methanol synthesis studies.”
Copper-zinc alloys are particularly common in this line of work. The research group is currently investigating how the activation energies reported in the present study compare with particularly useful catalytic alloys, which also require experimental and computational investigations.
The results of this study will help researchers optimize methanol production from carbon dioxide. Such work will help convert an atmospheric pollutant into fuel for vehicles, and chemical feedstocks for industry. It provides a means of adding value to carbon dioxide, which is commonly considered to be waste. By optimizing the hydrogenation reaction described here, researchers might have a new tool for making maximum use of limited resources.
Pharmaceutical production is ridded by the lack the agility, flexibility, and robustness in batch production technology and is responsible for high amounts of waste. Alternative manufacturing platforms are needed to overcome present and future environmental and economic challenges in the pharmaceutical industry. Olivia Morales Gonzalez has investigated new process platforms, namely reactive extraction with ionic liquids, polymeric nanoreactors, and novel process windows.
Gonzalez carried out life cycle assessments and technoeconomic evaluations to identify hot spots in these process concepts before their industrial implementation, and suggested several optimizations.
Firstly, Gonzalez assessed novel process windows by looking at the life cycle assessment of the production of vitamin D3. Novel process windows are a new way of process design to boost micro process technology for the production of highadded value fine chemicals using harsh conditions (eg. high temperature and pressure). This vitamin was chosen for the research because it is a very common and necessary nutrient produced and consumed worldwide.
Moreover, the novel process windows were benchmarked against multiple batch processes. The vitamin D3 is produced continuously in microreactors (ie. microflow) and combines UV photoirradiation and high pressure and high temperature (photo irradiation- high pressure and temperature) processing. Then, continuous crystallization purifies the product.
The processes were modeled with ASPEN Plus process simulation software using foreground data from the experimental continuous setup, and background data from different patents. The environmental impact of the continuous process is mainly due to use of acetonitrile and methyl tertiary-butyl ether (t-BME), which are both solvents.
In comparison with the batch processes, the continuous process offers a significant reduction in terms of environmental impact. Even considering the high recycling rates (95 percent) of solvent in batch scenarios, the impact is at least double. Moreover, it is necessary to recycle them without any additional purification steps.
Next, Gonzalez conducted a techno-economic evaluation of the production of Cross-Linked Enzyme nano-Aggregates (c-CLEnA) at the laboratory scale. These are bowl-shaped polymeric vesicles were used as supports, with the advantage of high activity retention and ease of recycling.
The support represents a large fraction of the cost in the case of enzymatic processes. Thus, Gonzalez assessed the production to find hot spots that could be optimized. The estimated cost per 0.5 ml of CalBloaded c-CLEnA is €139, and this is mainly driven by the capital expenditures (costs related to purchasing fixed assets such as equipment). This cost was benchmarked against traditional cross-linked supports, whose production is simpler compared with c-CLEnA, but more leakage results. Gonzalez found that c-CLEnA needs to be recycled around 20 times to obtain any sort of economic benefit. Finally, process changes were discussed regarding the impact on the production cost.
Finally, the concept of the Functional Solvent Factory (FSF) is introduced as well as solubility, which is its main KPI. A case study (for the synthesis of benzyl azide) assessed the combined use of reactive extraction with ionic liquids. This case study was based on literature due to the low technology readiness level (TRL) of this concept. Two models for the FSF were created using ASPEN Plus software. Then, the concept was benchmarked against two other process alternatives, state-of-the-art (batch) and solvent-less (continuous). A life cycle assessment was conducted to compare and identify hot spots. Hot spots are the processes and activities in the life cycle that have a large contribution
to the total environmental impact. Identifying them helps in the decision making process of designing optimal production processes.
Results show that the environmental impact of both FSF cases is larger than the benchmark cases. In particular, the solvent-less case resulted in the lowest environmental impact. Despite the results, the research focus was on collecting the data needed for further stages of development, and for other solvent factories.
To bring this platform to market, it is necessary to optimize the use of ionic liquids, low amounts of solvent usage, low processing temperatures, high recyclability, and avoid contamination of the ionic liquids. Gonzalez concludes that these performance indicators will influence future developments of this platform. Gonzalez also addressed the uncertainties of the previous case study, particularly the FSF scenarios. Applying a life cycle assessment at early stages of development is more challenging compared with noncommercialized technologies. Many uncertainties arise from the missing or inaccurate data, temporal and spatial variability, and inaccuracy of the models among other factors.
To address these uncertainties, stochastic parameters with probability distributions instead of fixed values and propagation of the sampling were conducted using Monte Carlo simulations. Then the overlap area approach was used to assess the results of these comparative LCAs. This created a different result compared to the determinist LCA, as the similarity in both cases is higher in comparison to previous results. Moreover, it highlighted the need to address the correct use of ionic liquids.
Skoltech researchers, along with colleagues at Moscow State University, have installed charge storage mechanisms for NiBTA, a newly discovered material that could lead to advanced batteries with high charge rates. Their work has been published in the journal Chemical Science.
Quick-charge batteries are needed for a variety of applications, including electric vehicles, for which owners are acutely at risk of untimely discharge of cars on the road. However, the anode materials of modern batteries are either not suitable for reliable operation under fast charging conditions, or they provide low energy consumption. This motivates scientists to look for new materials that have increased capacity and can work safely at high charge rates.
Recently, researchers have presented NiBTA, a new promising anode material, which is a coordination polymer based on nickel and tetraaminobenzene. However, it remained unclear how NiBTA is charged and discharged in batteries. Different
scientific groups have proposed vastly different mechanisms, mainly because the data were too ambiguous to draw firm conclusions. In the new work, scientists at Skoltech combined cuttingedge techniques to gain insight into the behavior of NiBTA in lithium, sodium and potassium batteries.
“The beauty of this work is that it brings together a variety of techniques, both experimental and theoretical,” said Roman Kapaev, the first author of the work. “This helped to get reliable results, since each method allows you to see only part of the picture. Among other things, we used X-ray diffraction and Raman spectroscopy in operando modes, which made it possible to follow in detail the structural changes inside the batteries. We are the first to take such a rigorous approach to this class of compounds. This work sheds light on the electrochemistry of coordination polymers, which could be useful for a variety of applications.”
Ateam of chemists at RIKEN has created a manganese and cobalt oxide electrocatalyst that represents an important step forward in the affordable production of cleaner hydrogen fuels.
Hydrogen can be made using electricity that induces a chemical reaction to split water into its constituent elements: oxygen and hydrogen. “One of the biggest hurdles in generating industrialscale hydrogen has been finding a suitable catalyst for the oxygen evolution reaction at one of the electrodes of this production system,” explained Ailong Li, who co-led the study at the RIKEN Center for Sustainable Resource Science.
‘Green hydrogen’ is made using renewable sunlight or wind energy to generate the electricity that splits water. It could hugely reduce global carbon dioxide emissions if it replaced fossil fuels at industrial scales, said Shuang Kong, who co-led the study. And when hydrogen is then combusted to produce energy, it reverts to water again, making it a truly pollution-free fuel.
While some electrocatalysts already exist that meet both conditions of stability and activity, they all suffer from one drawback—they contain one of the scarcest elements on Earth: iridium.
Then in a 2019 study, Li and his co-workers discovered that manganese oxide showed excellent stability in acid for catalyzing the oxygen evolution reaction. Now, they have shown that, by incorporating manganese into cobalt oxide—another electrocatalyst—to produce a mixed oxide, it is possible to increase
the lifespan of the electrocatalyst in strong acid by a factor of about 100 without sacrificing activity. This takes the lifetimes of iridiumfree electrocatalysts from just days or weeks to longer than two months.
Li was thrilled when he first saw the electrocatalyst in action. “Our electrocatalyst was very active,” said Li. “Even before we made the measurements, it was a beautiful sight to see it generate a cascade of bubbles.”
The manganese imparts stability to the electrocatalyst, while the cobalt gives the oxide its high activity. Kong describes manganese as “nature’s catalyst for water oxidation.” The team found that the optimal mixture was two atoms of cobalt to every one of manganese. Importantly, both manganese and cobalt are vastly more abundant than iridium: the global annual production of manganese is more than 60,000 times greater than that of iridium and it is the fifth most common metal in the Earth’s crust.
There is still room for improvement in the catalyst’s lifespan. While the activation barrier of the mixed oxide rivals that of iridium oxides, iridium catalysts can last for decades before needing to be replaced. But Li is encouraged by the advance. “In the long run, we believe that this is a huge step toward creating a sustainable hydrogen economy,” he said.
Hydrogen, he added, is also an important industrial chemical that is used to produce ammonia, a key component of fertilizers. The current industrial process for manufacturing ammonia is highly energy intensive and uses fossil fuels: it accounts for nearly 2 percent of the global emissions of carbon dioxide. Green ammonia produced from green hydrogen could help to slash these emissions.
An early inspiration, said Kong, was a 2004 speech by Nobel laureate Richard Smalley, in which Smalley describes a future in which trillions of watts (terawatts) of renewable energy is generated to drive industry instead of burning fossil fuels.
Looking forward, Li sees lots of ways to enhance their electrocatalyst and produce green hydrogen more efficiently. “There are so many avenues we can pursue to advance this technique,” he said. “In addition to improving the electrocatalyst, we can also enhance the water-splitting membrane that is sometimes used.”
Li pointed out that when you’re dealing that terawatt-scale hydrogen production, even a small rise in efficiency can yield great gains. “Just a 1 percent increase in efficiency across today’s large scale-industry could save 88 billion kilowatt hours per year and reduce carbon dioxide emissions by 34 million tons.”
For years, consumers and businesses have been anticipating the availability of 5G technology. Well, 5G is here and it’s quickly revolutionizing the agribusiness industry.
Connected cows, precision farming, autonomous vehicles, predictive crop monitoring—the use cases are rapidly emerging for opportunities to improve efficiency and production, with cash flow effects that are very promising. 5G brings higher data capacity, lower latency, greater device density, and, with that, opportunities to leverage analytics, artificial intelligence and machine learning as never before.
Consider the magnitude of change societies experienced when 3G and 4G technologies entered the market. Smart phones may now seem an obvious innovation to emerge from those technologies, but few could have imagined the seismic impact of all-new business models introduced by brands like Uber and Airbnb. Similarly, 5G holds the promise of shaking up the agribusiness industry with entirely new ways of doing business.
Take dairy farming, for example, where 5G is connecting cows to the cloud and enabling revolutionary new levels of automation, resulting in greater efficiency and higher production. A British agricultural technology research center uses 5G-connected collars on cows to monitor diet, rest, milk production and movement. With 5G, continuous data monitoring and real-time intelligence are making it possible to act on fluctuations that may indicate critical events, such as cows going into labor. Other possibilities include allowing cows to choose when they are milked in a “self-milk” station. This leads to greater dairy production as the cows aren’t constrained by human schedules.
Of course, 5G enables farmers to link more than cows. Connected workers can use wearables and augmented reality technology to tap into geo-located agronomy data and visually pinpoint where to plant, what to plant and how much to plant. Connected farm vehicles equipped with telematics can automatically manage where and for how long they operate to optimize fuel consumption and fertilizer supply.
With 5G-enabled solutions like these, farmers will be able to produce more food with fewer resources to meet the demands of growing populations. They’ll be able to use real-time insights into crops and agribusiness to make predictive and proactive farming and operational decisions. Simply put, the increased use of automation and improved precision farming that 5G enables will help farmers work smarter, not harder—and get much more in return.
For instance, a drone helps to identify pestilence, deploys targeted crop protection and then communicates with other drones so they can learn from each other is revolutionary.
Increasing yield without increasing labor or land Precision farming alone does not require 5G. However, 5G enables all the devices used in precision farming technology to communicate and work together. This spurs a virtuous cycle of insights leading to prediction, preventive interventions and more insight.
Think of it this way: A drone that identifies pestilence is interesting. A drone that identifies pestilence and then intervenes with targeted crop protection is compelling. A drone that identifies pestilence, deploys targeted crop protection and then communicates with other drones so they can learn from each other is revolutionary.
We are entering a world of interoperable systems that will demand networks capable of handling intense device density growth and the ability to share large volumes of data. Imagine, for example, the benefits gained if that same intervening drone could also utilize soil probes, intelligent bug traps, weather analysis and the ability to share that data with other farmers.
Agribusiness is a capital-intensive industry. Farmers must keep a lot of assets on the books while managing cash flow that surges during seasonal harvests, when livestock are sold at market or assets are otherwise liquidated. Whatever the scenario, costs are steady and revenue is variable. Moving from a CAPEX to an OPEX model can alleviate this disparity and improve cash flow.
For example, farmers often purchase harvesting equipment so they can be assured it will be available when needed, rather than use a temporary, less reliable lease arrangement. Farm equipment retailers are unable to just sell services because of the uncertainty in available labor in markets that become tight during harvest.
One way to shift from an equipment ownership to service-based fee structure could be autonomous machines that reduce the need for human labor. Imagine a world in which farmers may take advantage of renting self-driving combines to reduce their harvest time and potentially avoid losses due to adverse weather that could arise during a longer harvest time. Imagine, furthermore, that farmers could rent 10 of these combines and execute a large harvest in one day of perfect weather, as opposed to over several days and weeks, when wind, bugs, rot or snow could devastate yield. 5G could play a key role in enabling
that autonomy to move farming from CAPEX to OPEX as the reliance on human labor is reduced.
The fact is all these industry innovations are only made possible by having access to a 5G network. But the cost of building out 5G infrastructure remains a significant challenge in many rural areas. Some private carriers are hesitant to invest in expanding 5G more broadly in less populated areas due to lower device density, which could limit profitability.
However, the situation may start to change. In the United States, Congress has allocated $65 billion in the Infrastructure Investment and Jobs Act to promote broadband deployment in underserved areas. Furthermore, the National Telecommunications and Information Administration has started receiving applications for rural communities to request access to broadband.
As this infrastructure is built out over the coming months and years, those in the agribusiness industry should start now to understand how 5G can produce more food without expanding labor and land inputs, while at the same time loosening the asset-rich, cash-poor constraints of a seasonal business.
No one can predict the full extent of the new business services that will be enabled as 5G and subsequent technologies continue to evolve. But we are confident that players in the agribusiness sector can begin realizing valuable gains today in terms of improved efficiency and production, and a reduction in resources across the value chain. Beyond that, the possibilities are endless.
Authors:
Andres Centeno is Senior Manager, Digital Industrial Workforce; Priscila De Pinho is Managing Director, Global Agrochemicals Lead; and Matthew Ritchie is Managing Director, Global Agriculture Lead, at Accenture.
The metals and mining industry has recovered quite sharply after the pandemic-led slowdown, as a result of price surges for iron ore, copper, and steel, (and especially driven by electric vehicle sales), lithium, cobalt, and nickel. Consequently, metals and mining companies are looking closely into improving operational efficiency and assuring production to maximize profitability.
Metals and mining organizations have typically been stragglers in fully embracing digitalization when compared to comparable industries. While some metals and mining operators have embraced the notion that significant benefits can be achieved through a digitalization shift, many operations have been reluctant to set out and execute against a digital strategy.
That is changing and even accelerating as early mining projects have qualified and endorsed the digitalization opportunities. Given that key challenges in metals mining are costly downtime, lost production
tonnage, cost versus rewards funding allocation, and safety risks, the following are proven digitalization areas for value creation in metals and mining:
• Throughput Improvement 10 - 20 percent
• Yield
• Emission
2 - 5 percent
15 – 30 percent
• Injury Reductions 5 - 12 percent
Consistent with other manufacturing, the primary area to achieve the earliest and most profitable digitalization wins come in asset performance management (APM), particularly in increasing asset utilization by preventing breakdowns and reducing extensive equipment service and repair. AspenTech addresses asset reliability, availability, and utilization with prescriptive and predictive maintenance in its Aspen Mtell® software application.
The early digitalization movers in metals and mining recognize and support prescriptive and predictive maintenance which eloquently addresses equipment breakdowns and the subsequent delays, repairs, and production losses. In the past such asset failures appear to have been largely taken for granted and accepted as part of the mining business.
An increasing awareness leads plant operators to believe they can do better to start to understand the early warning signals, especially on low-level support systems on assets allowing early action to avoid a full breakdown. They can also understand when and how a failure will happen and have sufficient time to plan an orderly, risk-reduced, and safe shutdown and service/repair plans that reduce unplanned downtime, mitigate lost tonnage, and prevent safety issues.
Aspen Mtell provides early warnings of equipment degradation weeks and months ahead of an imminent failure giving metals and mining staff more opportunity to mitigate the negative impact of sudden unexpected issues, to better identify bottlenecks, improve troubleshooting, carry appropriate stock spares, and schedule appropriate maintenance.
Consider, for example, a site that receives an early warning of impending bearing failure with 60 days lead time before the anticipated event. Prescriptive maintenance enables early action by the facility to avert a major catastrophe, saving an estimated $400K in avoided production losses and much lower maintenance costs. By implementing the solution, they also avoided unplanned downtime and reduced the likelihood of a mishap occurring at the site.
Which predictive and prescriptive maintenance solution is the right choice? Following are important selection criteria:
• Low-touch. Does the solution work easily and simply with your current staff with what they know now without them learning new skills or requiring technical and data science expertise?
• Early Detection. How far in advance does the solution alert of degradation that if unattended will lead to a failure causing equipment breakdown?
• High Accuracy. Does the solution provide measured, precise failure pattern recognition so operators can act on predictions with confidence, or are they just model estimates with copious false alerts?
• Scalability. How quickly can the solution adapt to diverse types of assets rotating, static, mechanical, and process from a single asset to a whole enterprise? If the operating mode changes, can you adjust automatically or do have to call in the experts? Does it drag-ndrop a solution from one asset to another without expert attention?
Aspen Mtell is the solution that ticks all the boxes. Powered by machine learning executing precise pattern recognition of normal, abnormal,
and precise degradation events, Aspen Mtell is a gamechanger for metals and mining, and other industries. See how metals and mining companies are deriving value by applying the Aspen Mtell prescriptive maintenance solution to equipment throughout the value chain.
Monitored cutter motors to schedule planned maintenance.
Savings: $300K USD per year
Forecast degradation to optimize scheduled maintenance for truck engines.
Savings: 10% lower maintenance spend
Identified gearbox oil imbalance in advance of failure occurring.
Savings: $1M USD per failure
Early, less-intrusive action saved major breakdown, saving production.
Potential savings: $500K USD
20 days lead time gives to order spares and plan maintenance. Repair times reduced: 30%
Detects wear pattern on pumps and applies to other pumps … scalability.
Potential savings: $2.5M USD per year
The metals and mining industry is at a maturity level to fully embrace today’s digital optimization technologies. Leaders in metals and mining will build a strategy to accelerate digital transformation realizing that a first execution in prescriptive maintenance will quickly bring results that improve performance of existing capital assets by eliminating unplanned downtime.
Aspen Mtell performs prescriptive maintenance by forecasting degradation and equipment failures, alerting staff well in advance of when a failure could occur, identifying potential causes and the scope of any failure, and providing advice on the corrective action to avoid or mitigate the impending failure. The impact to your operations: increased operational efficiency resulting in improved energy efficiency, reduced emissions, and higher return on assets.
Global trends making a difference for chemical manufacturers.
The pandemic exposed the depth of challenges that manufacturers globally are facing. At the same time, we have seen the global demand for chemical products grow, and with that growth comes new business challenges including rising input costs, supply chain disruption and skilled worker shortages. Chemical manufacturers must also operate within a complex regulatory environment and are under pressure to improve sustainability and drive better productivity from ageing infrastructure.
Digital solutions and innovations are already having a significant impact on many areas of the chemical industry—making supply chains more efficient, increasing productivity, improving sustainability, and driving innovation.
Digital technologies have opened the door to new ways to merge operational technology (OT) and information technology (IT). By using real-time data that is available to all personnel, chemical manufacturers can optimise plant operations.
Another focus area is energy. It is expensive, and you want to use it as little as possible without negatively impacting your operations. This also plays well if you have an energy management program or broader sustainability efforts. Either way, using technology to help save energy equates to reduced operating costs and a more efficient plant.
Arvind Kakru, Director, Sales, Rockwell Automation India delves into the ways in which digital technologies have opened the door to new ways to merge operational technology (OT) and information technology (IT). With real-time data, chemical manufacturers can optimise plant operations, manufacturing and be in sync with the global competition. He also opens up on the right approach that manufacturers should take for transforming their set up into a connected plant.
Chemical manufacturers can also benefit from consulting, implementation, and managed services, from assessing digital readiness and building a business case, to implementing and integrating technologies.
We are seeing more and more companies using advanced analytics to deliver business impact from the substantial amounts of unstructured data coming from their production facilities. Augmented Reality and Virtual Reality, digital twins, artificial intelligence and improved cyber security for OT systems are other technologies that are already available and will be commonplace in the future.
Automation, IIOT, software development in Asia Pacific & India.
Building a connected plant is a great start and platform for digital transformation. This is beneficial for all manufacturing industries, but more so for process heavy industries like pharma, chemicals and oil & gas. Some of the industry challenges that it can help solve include technological-led innovations and meeting regulations, whether they are statutory, quality, compliance, or manufacturing standards-related.
Environmental, social and governance (ESG) factors have an enormous impact on how businesses are perceived.
Digitally connected operations - units or locations - can deliver significant benefits in this critical area. Supply chain disruptions are another key challenge that can be addressed.
A few of the key opportunities for these industries would be to reduce safety, security, and compliance risks, maximise asset utilisation, improve maintenance and support, and improve operational flexibility. Though all of these are global trends, they are equally applicable to India and the Asia-Pacific region.
Potential for automation, IIOT and software in chemical industry.
Most chemical producers are eager to deploy a connected plant, but the question is where to begin. A modern automation process control system, intelligent motor control, and information systems create the foundation of seamless connectivity and real-time information sharing.
They allow chemical producers to take advantage of other information-enabled technologies such as process and maintenance analytics, integrated power control with connectivity to intelligent electrical devices, smart instruments etc. Consequently, analytics can further increase asset performance.
Organisations can use Artificial Intelligence for lifecycle analysis impact while connected operations can deliver the best impact by using IIoT, OEE, remote monitoring, track and trace extending to warehousing and coordination. Within the chemical industry, the segments that benefit the most from deploying digital technologies would be supply chain, manufacturing, research and development, workforce, quality and marketing. The larger sustainability benefits are extremely high in these organisations.
Adoption of automation, IIOT to support sustainability strategy.
Everyone, recognizes the importance of reducing carbon emissions. As individuals make lifestyle changes for the good of the environment, they expect industry to do the same. When it comes to facilitating sustainability as a core business driver, capitalizing on the latest development in automation and digital enables innovative approaches that weren’t previously possible.
By deploying automated digital technologies, companies can improve efficiency and reduce consumption across three key areas:
• Energy: industrial energy management software and service to reduce consumption
• Water: smart water applications to improve quality and efficiency in water-intensive industries
• Waste: Waste Management and recycling solutions and partnerships to enable the circular economy.
Government and industry to ensure proper growth of automation, IIOT solutions segment.
The good news is that there is already a tremendous focus from government and industry in place, and it has grown significantly in the past few years. However, one area that still needs work is around upskilling the workforce. That could be developed by industry collaboration with universities, public-private partnerships and governments rolling-out incentives to drive training.
Recently, the Indian manufacturing industry has seen increasing quality-related issues, which are impacting its reputation as a high quality and reliable supplier. Digital transformation and automation can eliminate or reduce production faults. A Production Linked Incentive (PLI) scheme for the chemical industry would be a great boost for domestic production and cut our dependence on costly imports. There could be incentives for companies to adopt these new technologies too.
Company: Shell plc
Date Posted: 08-Aug-2022
Country: INDIA City: Bengaluru
Company: Dow Inc.
Date Posted: 08-Aug-2022
Country: UNITED STATES City: Freeport, TX
Chemical Process Engineer Company: F. Hoffmann-La Roche Ltd
Date Posted: 08-Aug-2022
Country: UNITED STATES City: Branchburg, NJ
Company: Saudi Arabian Oil Company
Date Posted: 06-Aug-2022
Country: SAUDI ARABIA
City: Dhahran
Company: BASF SE
Date Posted: 06-Aug-2022
Country: UNITED STATES City: Huntsville, AL
Associate Chemist Company: Eli Lilly and Company Limited
Date Posted: 06-Aug-2022
Country: UNITED STATES City: Indianapolis, IN
Research Assistant Company: Reliance Industries Limited
Date Posted: 05-Aug-2022
Country: INDIA City: Jamnagar
Process Technology Engineer Company: Axalta Coating Systems
Date Posted: 05-Aug-2022
Country: UNITED STATES City: High Point, NC
Principal Chemical Engineer Company: Eastman Chemical Company
Date Posted: 05-Aug-2022
Country: UNITED STATES City: Longview, TX
Job Description: Develop significant depth and breadth of knowledge regarding polyols and competitive products, develop familiarity with associated process technology. Develop significant depth and breadth of knowledge regarding the actions and chemical properties of polyols at the molecular level and its impact on product properties (foam and non-foam applications). Assess customer needs and work closely with Process technologist and Product team to develop and support new business opportunities. Fill-the-pipeline-, and/or step-out R&D activities.
Job Description: Oversee daily operation of the assigned pilot or mini-plant unit, providing input and support for operating technologists. Partner with experts to perform plant/product troubleshooting. Prepare for and leads pilot plant trials for the assigned unit with teams of R&D campaign stakeholders including preliminary reviews, data interpretation, and final reporting. Apply the Scientific Method in the planning and execution of experimental plans and problem solving.
Job Description: Assess existing processes and equipment; identify and implements to reduce cost / labor hours and increase operator safety. Assist in designing and implementing new equipment and tools to improve manufacturing efficiencies, reduce ergonomic stress and improve quality. Update, create and sustain standard operating procedures. Work together with scientists as part of a project team in the development and/or implementation of new processes and equipment.
Job Description: Address and tackle constraints identified in Aramco assets the system through Solomon benchmarking analysis and input from other organizations and stakeholders. Review Downstream facility debottlenecks and recommend mitigation measures. Identify and propose valuedriven opportunities to enhance overall profitability on individual asset as well as regional levels. Evaluate growth project proposals and JV offtake arrangements.
Job Description: Support Process Engineering Team, Slurry preparations and Coating operations. In addition, support operations in day-to-day production troubleshooting as needed, and Process Optimization, as well as lead various Continuous Improvement projects at site to improve overall productivity, improve quality, reducing process losses and scrap reduction.
Job Description: Design – in collaboration with colleagues in Medicinal Chemistry, Computational Chemistry and Molecular Pharmacology – new molecules to address hypotheses and issues in portfolio projects. Design and implement multi-step synthetic routes towards targeted compounds. Independently set up and complete a variety of organic chemistry reactions, including those with air sensitive and hygroscopic reagents.
Job Description: Carry out assigned technical jobs of conducting experiments and upkeep of equipment/ units laboratory/pilot plant and record data with diligence. Set up reactor assemblies /experimental set ups to carry out tests/experiments. Carry out preparation/synthesis of samples in lab scale.
Job Description: Optimize manufacturing processes for Axalta by generating improvement ideas, designing, and performing experiments to support implementation on a plant scale. Lead process development and commissioning for capital projects. Collaborate with R&D and Alignment Chemists to support scale up of finish product and intermediate products. Participate in a forum to support and/or troubleshoot plant process and quality issues.
Job Description: Conduct technical experiments (lab and pilot scale). Lead and participate on multidisciplinary teams. Develop hands-on and in-depth technical expertise. Install, operate, maintain, and trouble-shoot scale-up equipment. Resolve production issues with colleagues. Work in a fast paced, results-oriented team environment to assist in developing new technologies.
Website: http://www.worldofchemicals.com/chemical-jobs.html
BASF launches PuriCycle®, a new line of advanced highperformance products for the purification of most complex waste plastics pyrolysis feeds. The PuriCycle portfolio includes novel catalysts and adsorbents developed to selectively remove or convert a wide range of impurities in pyrolysis oils and enable downstream processing of circular plastics streams. PuriCycle can help customers meet industry compositional compliance standards, benefit from high efficiency purification and upgrading solutions, and increase their flexibility in the chemical recycling process of plastics.
Contact: BASF SE
Carl-Bosch-Str. 38. 67056 Ludwigshafen. Germany
Tel: +49 621 60-0
Email: Kerstin.Hoffmann@basf.com Web: www.basf.com
Symrise is repositioning its multifunctional skin care emollient SymClariol® (decylene glycol) to better focus on the ingredient’s strengths. So far, the ingredient belonged to the product protection portfolio. The company is now relaunching it under the category of skin protection/hygiene. With SymClariol®, Symrise is offering an emollient with antimicrobial properties that protects the skin from scalp to toe. Among other functions, the ingredient supports dandruff control concepts. SymClariol® can go into foot care products, too, as it prevents odors and comes with protective properties.
Contact: Symrise AG Mühlenfeldstraße 1 37603 Holzminden, Germany
Tel. +49 5531 90 0
Email: bernhard.kott@symrise.com Web: www.symrise.com
Clariant has launched its first universal polymeric dispersing agent for high quality pigment preparations that can incorporate organic and inorganic pigments and can be used for all types of water-based paint systems. In addition, waterborne pigment preparations with Dispersogen Flex 100 can also be compatible with solvent-borne base paint systems. The new, universal solution gives pigment paste producers, and paint producers who also produce pigment pastes, an innovative, multifunctional and easy to use additive. Dispersogen Flex 100 is a fully universal product which is low VOC, label free and carries Clariant’s EcoTain label. It is available in paints and coatings markets globally.
Contact: Clariant International Ltd Rothausstrasse 61 CH 4132 Muttenz 1 Switzerland
Tel: +41 61 469 5111 Email: stefanie.nehlsen@clariant.com Web: www.clariant.com
Master Bond EP17TF is a one part epoxy with a paste consistency, that can be readily dispensed evenly and uniformly. It has a moderately high glass transition temperature and a wide service temperature range. Designed to compensate for thermal mismatches, this compound resists impact, vibration, shock and rigorous thermal cycling. EP17TF is a reliable electrical insulator which maintains its properties, even at higher temperatures. The system has good toughness, exhibits superior strength properties, bonding well to similar and dissimilar substrates such as metal, ceramics, plastics and composites. EP17TF withstands many chemicals, including acids, bases, fuels, oils and many solvents.
Contact: Master Bond Inc 154 Hobart Street Hackensack, NJ 07601 USA
Tel: +1-201-614-5859
Web: www.masterbond.com
The HD gas filter from WITT for installation in pipework provides reliable protection against fine contaminants and condensates in the gas supply. The filter inserts made of stainless steel is ideal for applications with hydrogen, but can also be used for oxygen (up to 50 bar) and other technical gases (up to 300 bar). The HD gas filter reliably traps even the finest dirt particles, thus cleaning the gas and ensuring the optimum functioning and protection of sensitive processes downstream at all times. The HD gas filter is simply installed in the existing gas line and is immediately ready for operation. Filter cartridges can be quickly changed in-line, saving the user time and money.
The industrial supply chain is constantly evolving, and the need for flexibility in manufacturing is growing. Maximizing production efficiencies is essential to staying ahead of the demand and competition. The ROSS PDDM Planetary Dual Disperser is a robust mixer that offers unmatched shear intensity and rapid dispersion of dry powders into viscous batches. With this system, solid additions can be made quickly and efficiently, thanks to two stainless steel High Viscosity “HV” stirrer blades and two high-speed shafts with saw-tooth dispersers. When equipped with removable disperser shafts the PDDM can be used as a regular double planetary mixer for processing even more viscous applications.
Contact: WITT-Gasetechnik GmbH & Co KG Salinger Feld 4-8, 58454 Witten Germany
Tel: +49 (0)2302 8901-0 Email: witt@wittgas.com Web: www.wittgas.com
Contact: Charles Ross & Son Company 710 Old Willets Path Hauppauge, New York 11788, USA
Tel: 631 234 0500 Email: mail@mixers.com Web: www.mixers.com
Analytical Instruments introduced the SPECTROMAXx LMX10 ARC/SPARK OES analyzer for fast, accurate, advanced elemental analysis in metal producing and fabricating plants, and iron and non-ferrous foundries. The LMX10 is the newest version. SPECTROMAXx delivers outstanding repeatability, reproducibility, and reliability in material control analyses from incoming materials to inprocess testing to final quality inspections — adding certainty to critical supply chains. SPECTROMAXx users obtain ultrafast information on changing process conditions while achieving drastically reduced cost of ownership with lower consumables.
Contact: SPECTRO Analytical Instruments GmbH Boschstr. 10 47533 Kleve, Germany
Tel: +49 2821 8 92-0 Email: spectro.info@ametek.com Web: www.spectro.com
Vacuum introduces new multi-stage Roots pumps ACP 90, which are designed for oil- and particle free applications in the pressure range between atmosphere up to 3x10-2 hPa. These vacuum pumps meet the requirements where clean and dry vacuum is needed like drying, sterilization, coating as well as semiconductor and R&D applications. With their unique design, these pumps are robust and can withstand frequent pump downs. Highly valuable materials render the pumps more resistant to light corrosive gases. ACP 90 is ideal when pumping large amount of condensable gases like in drying applications, high humidity environments or large insulating volume pumping.
Contact: Pfeiffer Vacuum GmbH Berliner Strasse 43 35614 Asslar/Germany
Tel: +49 6441 802-0 Email: info@pfeiffer-vacuum.de Web: www.pfeiffer-vacuum.com
Bacteria, viruses and fungal spores are everywhere and must be reliably killed for sensitive processes in the pharmaceutical and food industries or biotechnology. A residue-free disinfectant such as hydrogen peroxide (H?O?) is ideal for this purpose. To ensure that this works reliably in practice, Burkert Fluid Control Systems has developed a scalable system for chemical disinfection with a compressed air-operated dual-substance nozzle that ensures homogeneous and fine aerosol formation with minimal chemical and energy input and thus meets the highest disinfection standards. The system is individually adjustable, very flexible and suitable for a wide range of applications such as the sterilization of packaging, HEPA filters or for room disinfection.
CIRCOR International Inc announced a new member of the Houttuin 200 series, the 249.TT. This new twin-screw pump is compliant with API 676, is designed to accommodate today’s shaft-sealing solutions, and is optimized for modern production technologies. In combination with the best cost design, it is ideal for oil & gas applications as well as for any process and transport duties in chemical, non-hygienic food & beverage, marine and other segments. In transfer and unloading applications, the need is speed and flexibility. The Houttuin 249.TT is a non-contacting screw pump, able to pump nearly all types of fluids and fluid mixtures – from light condensate over water to highly viscous chemicals or emulsions. The pump is self-priming, dry run capable and comes with very low NPSH requirements.
Contact: Christian Burkert GmbH & Co. KG
Christian-Burkert-Strasse 13 - 17 74653 Ingelfingen, Germany
Tel: +49 7940 10 0
Email: info@burkert.com Web: www.burkert.com
Contact: CIRCOR International, Inc 30 Corporate Drive Suite 200, Burlington, MA 01803 United States
Tel: +1 781-270-1200
Email: products@circor.com Web: www.circor.com
During the industrial manufacture of various products in the food and luxury food sectors as well as in the chemical industry grinding and classifying are both important process steps. The finer the product has to be, the more energy is required to achieve it and it cannot be achieved with standard impact milling technology. Furthermore, the demand to narrow the particle size distribution means that a certain proportion of coarse or fine product has to be separated after grinding. A smart solution has been developed by NETZSCH: by expanding the well-known LabCompact system especially for such tasks and designed the new LabPilot system. In addition to a facelift that not only brought visual changes, but also further advantages in terms of user-friendliness, easy cleaning, maintenance and includes additional grinding technologies.
Valmet is extending its versatile butterfly valve product range with Neles™ Q-Disc™, a new high-performance feature to help flow balancing in control valve applications. The launch complements the offering of the modular Neles™ Neldisc™ and Jamesbury™ Wafer-Sphere™ butterfly valve platform that was introduced to the market in June 2021. The modular butterfly valve range was developed to help customers solve problems in complex process conditions. Q-Disc™ is specifically designed for control applications. One of its key benefits is that it helps to avoid oversized actuators for control valve packages, and thus provides a solution that is more cost and energy efficient.
Contact:
Erich NETZSCH GmbH & Co. Holding KG
Gebrüder-NETZSCH-Straße 19 95100 Selb, Germany
Tel: +49 9287 75-0
Email: info@netzsch.com Web: www.netzsch.com
Contact: Valmet Keilasatama 5 / PO Box 11 FI-02150 Espoo, Finland
Tel. +358 (0)10 672 0000
Email: kaisa.voutilainen@valmet.com Web: www.valmet.com