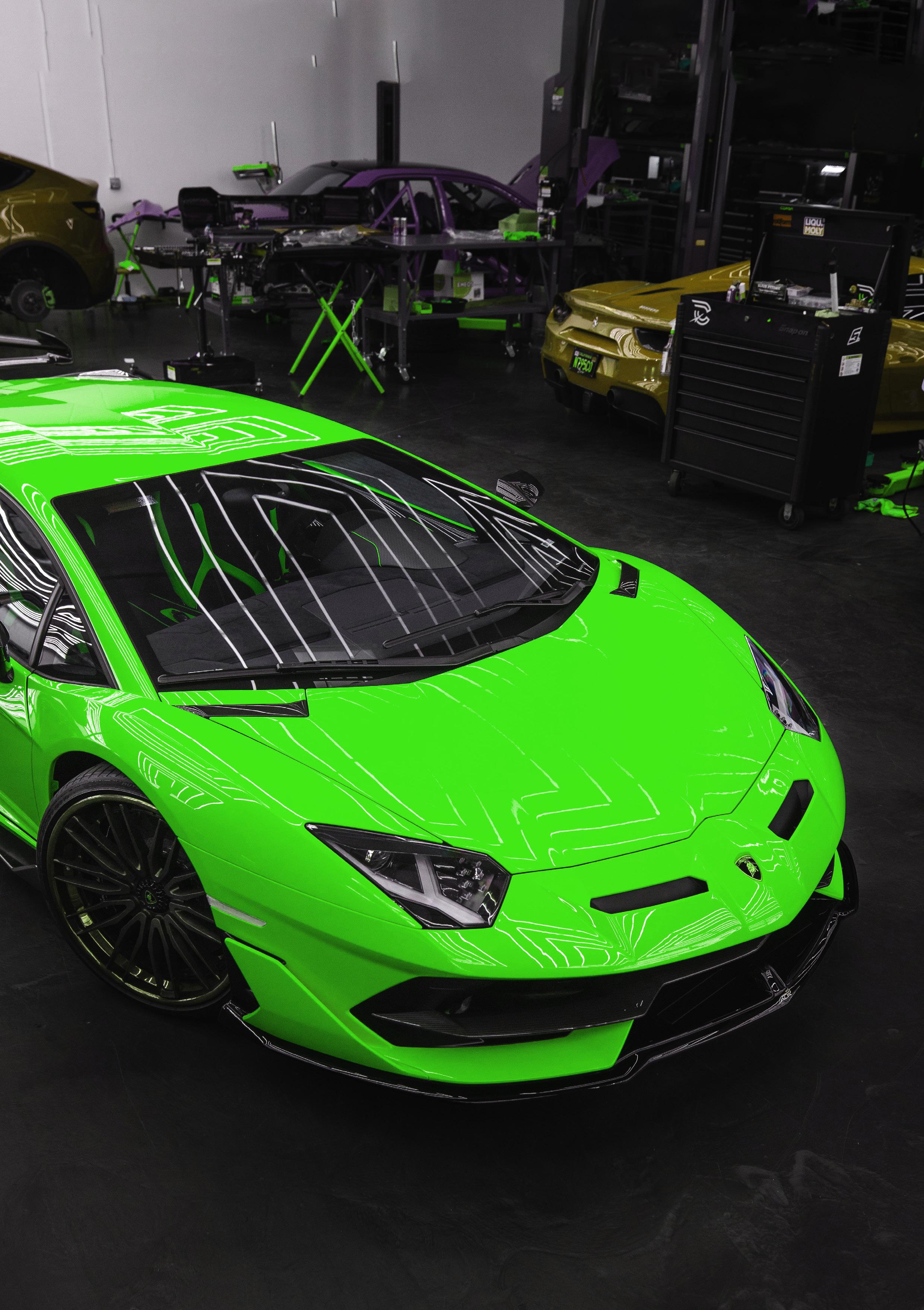
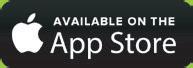

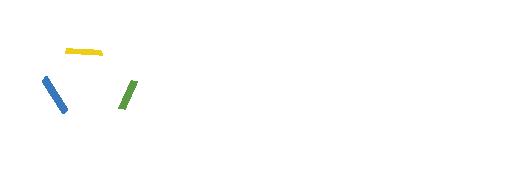
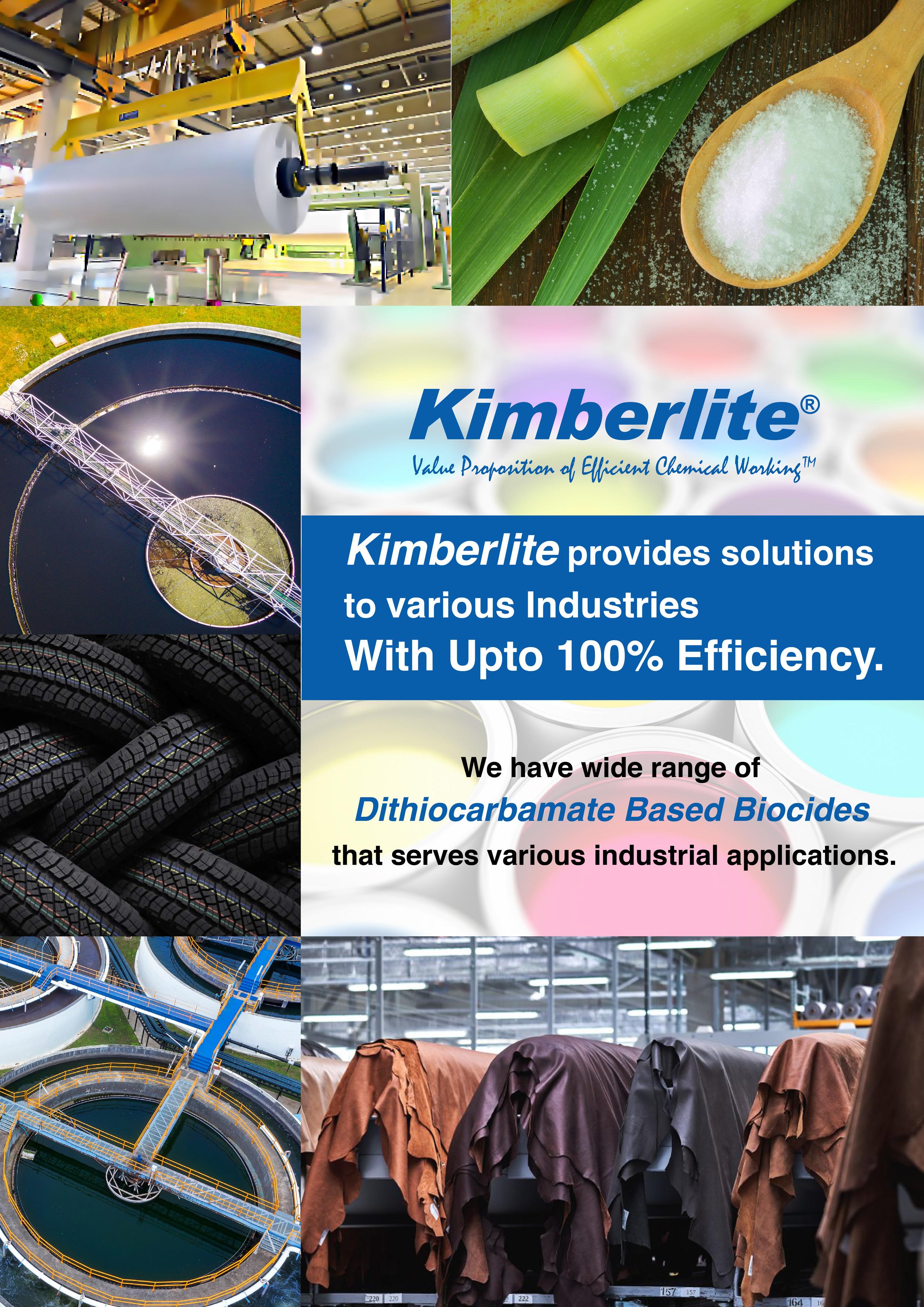
The automotive industry is one of the major sectors providing growth opportunity for the chemical industry. Presently, the sector is going through a transformation moving towards e-mobility.
The changing dynamics of the powertrain technology, lithium-ion battery requirements, demand for lightweight materials, sustainable coatings all provide tremendous opportunity for the chemical industry. The chemical raw materials needs will go up 2x times and give room for all round innovation and collaboration.
Also, there is increasing use of water-borne technologies in the automotive coatings market. This has to an extent helped reduce the VOC and air emission levels. As many countries are implementing stricter paints & coatings usage regulations, the adoption of water-borne technologies as an environment-friendly solution is sure to gain prominence.
Further, the use of digital technologies is enriching the automotive coatings solutions for the industry. It helps to improve the efficiency, effectiveness and give a glimpse into the real-time look & feel of the paint. Using artificial intelligence and 3D virtual technology the customer preferences, color and texture designs can help in increasing personalization and the overall customer satisfaction.
Other than the coatings, the paints application process too is undergoing reinvention to make it more sustainable.
Last month on 7 June, we celebrated the World Food Safety Day with the focus on - ‘Safer food, better health.’ The theme lays emphasis on the fact that food safety is of utmost importance for people. This can help in creating higher immunity for citizens and even effectively combat outbreak of diseases at a global level. With food security and demand being a priority for many countries, the agricultural industry and agrochemicals too are being considered in a big way.
Various research and innovation efforts are being directed towards agricultural productivity and eco-friendly solutions. Tremendous research is going on in the area of seeds and traits, natural, biobased, sustainable - herbicides, crop protection products and digital farming solutions. In terms of sustainability, even the agriculture industry is looking for solutions that reduce the impact on the environment. They are looking at solutions that reduce greenhouse gas emissions and CO2 emissions from the soil & diesel use.
Moreover, to enhance the availability of food and establish proper food safety systems, there is a need for a global legal and regulatory framework. When adopted by stakeholders across the agriculture and food value chain, it can create a sustainable food production and transport system to provide access to healthy foods for nations in need across the globe.
The rise of e-commerce and access to new technologies has accelerated counterfeiting and other forms of illicit trade. That makes fighting counterfeit medical products an ever-more urgent priority for pharma companies both in terms of patient safety and brand reputation.
Yann Ischi
Director, New Channels and Partnerships, SICPA
Within the Volkswagen Group, we have a clear strategy for how we want to put battery-electric vehicles into series production across our brands and in many different market segments. However, a major qualification for success in the volume market is more powerful battery concepts. In Volkswagen Group R&D we are focusing on close cooperation, not only with industrial partners but also with the smart minds of the scientific community.
Dr Ulrich Eichhorn
Head, Group R&D, Volkswagen AG.
India is a very important market for polyurethanes and has a wonderful potential for growth. When leaders of the industry from all over the world get together under one roof, it leads to better production and faster growth of the industry
R C Bhargava
Former CEO and current Chairman, Maruti Suzuki.
Indian Solar Manufacturers Association (ISMA) members have expressed positive sentiments as manufacturing and Make in India initiative gathered momentum. The phenomenal growth opportunity of Renewal Energy is unparalleled in the world today, looking at current and future energy consumption in India over the next 2-3 decades. All stakeholders have immense opportunities especially those who make and develop products in India.
K N SubramaniamCEO, Moserbear Solar Ltd and Treasurer, Indian Solar Manufacturers Association (ISMA)
NEW DELHI/ MUMBAI, INDIA: Industry body India Hydrogen Alliance (IH2A) has proposed a 25/25 National Green Hydrogen Hub Development Plan for creation of 25 National Green Hydrogen Projects and Five National H2 Hubs by 2025. The plan seeks to develop first-generation green hydrogen projects, with public finance support of $360 million over next three years; create a National Hydrogen Development Corporation and public-private hydrogen taskforce. The 25/25 Green Hydrogen Hub Development Plan was submitted by IH2A to NITI Aayog and Ministry of New and Renewable Energy, Government of India.
IH2A’s 25/25 National Green Hydrogen Hub Development Plan focusses on create scalable green hydrogen projects and hubs that can grow to gigawatt-scale projects in three years. The plan recommendations are:
1) India should build at least 25 scalable green hydrogen projects, aggregating to 150 MW installed electrolyser capacity by 2025, designated first-generation ‘national green hydrogen projects’ – 12 industrial de-carbonisation projects in chemicals, refinery, steel industries; three heavy-duty transport projects, three H2-blending in CGD projects and seven distributed waste-to-H2 municipal projects.
2) Five National Green Hydrogen Hubs in Gujarat, Karnataka, Maharashtra, Kerala and Andhra Pradesh; clustering the 25 Green Hydrogen projects, where multi-sectoral demand for green hydrogen can be produced and used, without building expensive new infrastructure in next three years. This includes:
Ankleshwar-Vadodara in Gujarat as National Green Chemicals and Ammonia Fertilizer Hub with 40 MW electrolyser plant, producing 8000 tonnes Green H2 per annum for chemical and fertilizer units; to reduce 8 Mmt of CO2 in the hub within a decade.
Bellary-Nellore (Karnataka-Andhra Pradesh) as National Green Steel and Chemicals Corridor with 30 MW electrolyser plant, producing 5000 tonnes Green H2 per annum for steel and chemical plants in the corridor, to reduce 5 Mmt of CO2 within a decade.
Pune-Mumbai (Maharashtra) as National Green Steel and Transport Hub with 30 MW electrolyser capacity plant, producing 5000 tonnes Green H2 per annum, to reduce 5 Mmt of CO2 within a decade.
Kochi (Kerala) as National Green Refinery and Transport Hub with a 30 MW electrolyser capacity plant, producing 5000 tonnes Green H2 per annum, to reduce 5 Mmt of CO2 within a decade.
Vishakhapatnam (Andhra Pradesh) as National Green Refinery and Transport Hub with a 20 MW electrolyser plant, producing 4000 tonnes Green H2/ annum, to reduce 4 Mmt of CO2 within a decade.
3) Public finance support of $360 million over next three years from Government of India for capital expenditure on electrolysers, balanceof-plant (BoP) equipment; and a green hydrogen price support of
$2 per kg of H2 in first-generation green hydrogen projects. Public funding is important for inducing early-stage green hydrogen demand and supporting first-generation projects that create public project development experience which can be applied to the next generation of scaled-up projects, after 2025.
4) Formation of Green Hydrogen Project Development Consortia by Industry Champions, in partnership with State Governments and preparation of State Green Hydrogen Policies to create the Green Hydrogen Hubs.
“This is a blueprint of how the green hydrogen economy can be developed over the next three years in India. The estimated $360 mn public finance support in project development will help India quickly commercialize green hydrogen projects at scale in the region. Government support for hydrogen project development contributes to further investment from both global green climate investors and the private sector,” said Jill Evanko, chief executive and president, Chart Industries, and founding member, IH2A.
“The next few years will be critical for rapidly developing expertise and developing end to end green hydrogen ecosystem. While individual industrial groups can execute some aspects of green hydrogen projects at scale, developing a national hydrogen end-to-end ecosystem – from renewable power, electrolysis, storage, logistics, and consumption will require collaboration across the industry as well as in the form of stronger public-private partnerships. The 25/25 Green H2 Hub Development Plan lays out a roadmap for this to be achieved,” said Sanjay Mashruwala, Reliance and IH2A member.
“The 25/25 Plan shows a pathway for India to leverage green hydrogen for industrial decarbonisation in hard-to-abate sectors. Industrial majors must collaborate and co-build the green hydrogen economy through national hubs, as has been demonstrated in the plan. This goes beyond individual actions for green hydrogen commercialisation and longer-term net-zero action plans announced by companies. We will lead by example in the steel and cement sector, by helping build these national hubs,” said Prabodha Acharya, chief sustainability officer, JSW Group and IH2A member.
“The 25/25 plan addresses immediate project development priorities by providing a pathway to first 150 MW that will help India learn, improve, collaborate and build scalable GW-scale green hydrogen projects in the 2025-30 period. It benefits government and industry decision makers so that they can commercialize green hydrogen in a focussed, costeffective manner. The proposed public spends are a fraction of what other economies are spending,” said Amrit Singh Deo, senior managing director, FTI Consulting, and IH2A secretariat lead.
The 25/25 Green Hydrogen Hub Development Plan has been proactively prepared by India Hydrogen Alliance (IH2A) to accelerate hydrogen commercialisation.
INDIA HYDROGEN ALLIANCE TO PLAN FOR GREEN HYDROGEN PROJECTS, HUBS
Oil India Ltd, India’s second-largest oil & gas explorer and a Govt of India Enterprise, said it has signed an initial agreement with Homi Hydrogen Pvt Ltd to work together in the green hydrogen value chain. The memorandum of understanding (MoU) signed with Homi Hydrogen is “to boost India’s efforts towards energy transition for achieving net-zero by 2070 and support development of indigenous technology and manufacturing under Atmanirbhar Bharat in the field of hydrogen and green energy technology,” the company said in a statement.
Homi Hydrogen Pvt Ltd is having exclusive license for electrolyser
technologies and is promoted by Greenstat Hydrogen India Pvt Ltd, H2ePower Pvt Ltd and Bluebasic Ama Engg Pvt Ltd.
“Oil India and Homi Hydrogen plan to work together to establish a framework that can enable the parties to study, structure and agree on a possible long-term partnership, which could include manufacturing and packaging of electrolysers in India and become an integral part of the Green Hydrogen value chain,” the company said.
The collaboration will provide impetus toward a hydrogen economy in the country, the mentioned the company.
ASANSOL, INDIA: Great Eastern Energy Corporation Ltd (GEECL), the fully integrated, pioneering Indian Coal Bed Methane (CBM) Company, announced that it has executed an amendment to its Petroleum Mining Lease (PML) and will now progress with its shale exploration program.
The GAIL pipeline installation offers the company an ability to deliver additional future production volumes to new customers and markets and, coupled with the increasing demand for natural gas both in India and globally and the Shale program, all provide support for the overall growth strategy.
“We are thrilled to achieve this significant milestone by executing an amendment to our PML and will now commence our Shale program.
Given the large potential Shale Gas resource in our Raniganj (South) block of up to 6.63 TCF of original gas in place, it provides an exciting and excellent growth opportunity for the company. We will now make plans for the initial core wells in the Shale program and, based on the results obtained, we will then progress to a development plan to drill pilot production wells,” said Prashant Modi, managing director & CEO, Great Eastern.
“Our QHSE and CSR policies along with our commitment to sustainable practices all help us provide an alternative and cleaner source of energy to our customers that improves the air quality of the region and contributes towards the reduction of greenhouse gas emissions. This will help us secure an ongoing competitive advantage in the longer term,” said Modi.
MUMBAI, INDIA: Bayer announced the signing of a Memorandum of Understanding (MoU) in India with ADM, a partnership to enhance sustainable value offerings to soybean farmers in the Latur, Osmanabad & Beed districts of Maharashtra and expand further to Karnataka, subsequently.
In India, ADM’s principal business is processing of oilseeds into edible oils, animal feeds and feed ingredients and human nutrition ingredients. ADM has a large network of farmers in Maharashtra and Karnataka, through Krishi Vikas Kendras’ (KVK) network of 50+ crop-development and procurement centers. The centers are staffed by agronomists who offer local farmers training in best agricultural practices, as well as procurement services. ADM’s Sustainability Program creates opportunities for small landholding farmers to get training in socioeconomic and environmental sustainability principles and third-party audits, through the European organization, ProTerra Foundation.
Bayer aims to reach twenty-five thousand soybean farmers in ADM’s network in the first year. During the period, Bayer will provide a specialized schedule of crop management prepared in consultation with ADM and agricultural universities for all the crops in the working area as and when required. It will also develop a crop protection package for all crops of soybean & pulses by providing legally permitted, nonhazardous crop protection chemicals as allowed under sustainable crop production principles.
ADM will provide Bayer with details regarding the partner farmers & area of operations. Bayer will follow a Seed to Market approach with the inclusion of sustainability elements such as complete package promotion of seed treatment, pesticides, and agronomic advisory along with Integrated Pest Management (IPM) practices. It will also demonstrate good agricultural practices on demo plots & conduct field
visits for extending practical experience to farmers. The MoU will be valid for a period of three years.
“In contrast to cereal production, India is far from self-sufficient in edible oil production, importing nearly 60 percent of its domestic edible oil requirement. Increasing the yield of soybean cultivation sustainably is essential to reduce import dependency and increase the income for soybean farmers to increase the attractiveness of the crop. We are thankful to ADM for their willingness to be a part of creating a holistic ecosystem that will help improve smallholder farmer incomes by sustainably enhancing their soybean yield through the right market linkages and helping India achieve self-sufficiency,” said SimonThorsten Wiebusch, country divisional head, Crop Science Division, Bayer for India, Bangladesh & Sri Lanka.
“This partnership is aimed at training the farmers to adapt responsible agricultural practices and progressively enhance the level of compliance to sustainable standards of agricultural production. Together, Bayer and ADM are making a tangible, positive impact at the field level by partnering with farmers to not only focus on environmental security, but also on food security,” said Amrendra Mishra, MD Oilseeds country manager India.
Regular training will be provided to the ADM cluster agronomist team in soybean markets on complete crop cultivation practices such as nutrition & pesticide schedules, BayG.A.P and Proterra principle (train the trainer) training. ADM will help Bayer put in place an input supply mechanism for their member farmers. It will further ensure that the partner farmers are using the crop protection inputs as per expert recommendations of the Bayer team. Seed Treatment training will also be provided through Bayer Roller Mixer machines at the sowing time following all safety protocols.
INDIA: Vinati Organics Limited said that it will expand the ATBS (2-acrylamido-2-methylpropane sulfonic acid) capacity from 40000 MT to 60000 MT, given the strong demand outlook. It will invest Rs. 300 crores for the expansion, to be funded by internal accruals and expects it to get commissioned by December 2023, the company said in a BSE filing.
Additionally the company mentioned that the capital expenditure in Veeral Organics Pvt Ltd (fully owned subsidiary of Vinati Organics Limited) is under progress. The total capex is approximately Rs. 280 crores and the products include 2000 MT of mequinol (MEHQ) & Guaiacol and 30000 MT of Iso Amylene. These products are used in polymerization inhibitors, flavours, fragrances, pharmaceuticals and pesticides. The commissioning is expected by September 2023.
NEW DELHI, INDIA: Cairn Oil & Gas, India’s largest private oil & gas exploration and production company, said it has signed a contract with Baker Hughes, an energy technology company, to harness geothermal energy from its repurposed oil & gas wells. On successful execution, the contract will help Cairn Oil & Gas co-produce up to 2.4 MW of electricity along with oil & gas and offset 17,000 tons of greenhouse gas per annum. This contract follows Cairn Oil & Gas’s recently announced ESG roadmap where it committed to becoming a net-zero company by 2050.
Based on preliminary studies, hydrocarbon wells in and around the Raageshwari Deep Gas field (Barmer Basin, Rajasthan) have been identified for the production of geothermal energy. The contract between Cairn Oil & Gas and Baker Hughes will be executed through phases that include studying the feasibility and potential for the generation of geothermal energy by repurposing producing or exploratory hydrocarbon (oil and gas) wells, designing the concept of the project, a pilot project to test the concept and, subsequently, execute the full-scale project. The first step of conducting the feasibility study of the project is set to be completed in four months from the start of the project. The feasibility study stage will include geoscience data integration and interpretation, the study of the geothermal potential of the area, mandatory field visits to assess surface facilities, the development of a thorough review report etc.
“At Cairn, we are firmly committed to fulfilling India’s domestic energy demand while also encouraging sustainability in practices. Our association with Baker Hughes brings the best of technology to contribute to India’s green energy basket. Across the world, there is a drive to promote geothermal energy production from dying oil fields and at Cairn, we are committed to bringing the best of global practices to India and aid our country’s journey towards energy aatmanirbharta,” said Prachur Sah, deputy CEO, Cairn Oil & Gas.
“With Baker Hughes’ and Cairn Vedanta’s strong relationship, we are excited to work with Cairn on their journey towards net-zero by 2050. We will jointly conduct a feasibility study for re-purposing existing oil and gas wells drilled in high-temperature formations to generate geothermal energy. As India looks for cleaner and more sustainable energy sources, we are confident that Baker Hughes’ technology can play a significant role in supporting Cairn Oil & Gas to drive a more sustainable energy future,” said Neeraj Sethi, country director, India & Bangladesh, Baker Hughes.
This agreement for geothermal energy exploration with Baker Hughes follows the ESG roadmap announced by Cairn Oil & Gas in February this year. Cairn Oil & Gas also recently announced the initiation of the process to convert its Mangala pipeline into a fully solar-operated pipeline. These innovations, among other initiatives, are helping the company venture deeper into the sphere of renewable energy and remain committed to the country’s net-zero targets.
MUMBAI, INDIA: Dwarikesh Sugar Industries Ltd has announced
the commissioning of its 175 KL per day (KLPD) distillery at its Dwarikesh-Dham (Faridpur) unit in Bareilly district.
“The plant will use cane juice syrup and ‘B’ heavy molasses as feedstock for producing ethanol. The commissioning is within the scheduled time and is in line with the lofty traditions of ‘on-time’ commissioning of all its plants. The setting up of the distillery is an important milestone in the annals of Dwarikesh Sugar as the company’s distillery capacity now stands enhanced at 337.5 KL per day. It will result in recalibration of its revenue stream. While ethanol production will be doubled, sugar
production will be moderated,” said Vijay Banka, managing director, Dwarikesh Sugar Industries Ltd.
“The distillery is based on cutting edge technology which will result in Zero liquid discharge. The plant will be fully compliant of rigorous pollution emission norms, thus strengthening the company’s ecological relevance. Following commissioning of this distillery, the company has taken a decisive step towards environment protection and the National goal of 20 percent ethanol mixing by 2025,” said Banka.
Dwarikesh Sugar Industries is engaged in the business of manufacture and sale of sugar co-generation of power and industrial alcohol.
MUMBAI, INDIA: thyssenkrupp nucera announced that it will grant the license and supply proprietary equipment to the expansion plans of the caustic soda (NaOH) plant for Kutch Chemical Industries in Padana, Gujarat, India. The company plans its completion and commissioning of the plant for 2023. The company statement reports that the contract size is in the lower double-digit million-euro range.
The current plant is operating since 2020 and consists of five electrolyzers with thyssenkrupp nucera’s proprietary BM Single Element technology. With this expansion, the capacity will be more than doubled to an additional 670 metric tons per day NaOH (100 percent).
With this investment, Kutch Chemical Industries intends to strengthen its market position and meet the growing demand for basic chemicals in the region and growing internal demand as well. Caustic soda is essential for a large number of end products, like detergents, soaps and disinfection, as well as used to process raw aluminium for example.
“thyssenkrupp nucera together with its long-lasting partner thyssenkrupp Industrial Solutions India is an expert for system integration of holistic chlorine electrolysis plants catering to each project’s individual needs. With this second project for Kutch Chemical Industries, we are very proud to continue a successful business partnership and support our client on their growth path,” said Denis Krude, CEO, thyssenkrupp nucera.
thyssenkrupp nucera’s scope in the chlorine electrolysis business includes the supply and services around engineering, supply of all major plant equipment, supervision of the erection and commissioning activities, training of the operating personnel as well as holistic 360-degree service solutions for the entire lifecycle of a plant. Kutch Chemical Industries Ltd belongs to the Goyal Group of Industries and is highly experienced in the processes of Chlorination, Nitration, Sulphonation and Dye Intermediate products.
DELHI, INDIA: HPCL has intended to expand its refining capacity from 8.5 mmpta to 15 mmpta under Visakh Refinery Modernization Project (VRMP). To facilitate the new units, for a reliable grid power supply at 220kV level, HPCL has intended to evacuate 220kV power supply from the nearest grid pooling substation at Kalapaka. PTC was involved in this project since conceptualization, carrying-out the feasibility study, detailed engineering and estimation, package designing, bid process management and subsequently for providing project management advisory services to HPCL.
PTC along with its consortium partner, WAPCOS have jointly taken-up
Project Management Consultant works, and is involved in supervision of survey works, detailed engineering, drawing review and approvals, inspection of equipment/material and issuing dispatch clearances, supervision and certification of work execution incl. electrical and civil works, testing and commissioning activities etc.
“PTC has enhanced the Engineering and Project Management Consulting portfolio. Expertise of more than 23 years in Power sector of the company can be leveraged with similar ongoing and potential assignments,” said PTC India chairman Dr. Rajib Mishra.
INDIA: RA Chemicals Pvt Ltd recently announced that it plans to start production of calcium zinc stabilizers, calcium organics, modified processing aids and other specialty aids in phase 1 of its operational strategy. The planned capacity for these products will be about 45,000 MTPA, with manufacturing at its plant in Ahmedabad by its subsidiary Foxcon Elements Pvt Ltd.
All the products will be marketed under the brand name of ‘STABICON.’ The company has already started sampling of the products and
commercial production will start from 15 July.
The Ahmedabad, Gujarat-based company also plans to appoint distributors across geographies for selling these products. The company has branches in Vadodara, Surat in India and Nairobi in Kenya, Africa. Further, it plans to achieve Rs.100 billion turnover by 2025 via its core distribution business of supplying innovative high performance products for plastics, rubber, engineering plastics, cosmetics, paints & coatings, printing inks, flavour & fragrances and lubricants.
PUNE, INDIA: Rockwell Automation, Inc inaugurated its new Software Development Centre (SDC) in Hinjewadi, Pune. The site enhances Rockwell Automation’s global research and development capacity and will develop smart manufacturing software to help both local and global customers on their digital transformation journeys.
Nearly one-third of Rockwell Automation’s global software and control production operations management workforce is based in India. The Pune SDC has already employed people across roles like product management, software architecture and engineering and plans to hire many more as demand grows. The SDC will give employees a chance to work in a challenging product development space with an opportunity to share and learn from teams and customers across the globe.
“We are proud to inaugurate the Software Development Centre in India. It is a world-class facility for building and developing software products catering to both local and global market needs. It is a testament to India’s strength in digitalization and a great example of a global company investing in the country and participating in the ‘Make in India’ national program,” said Martin Dittmer, director of software engineering, software and control, Rockwell Automation.
“India is an important market for Rockwell Automation, and we aim to keep growing in the software development space. The new SDC in Pune will help us enhance our research and development capacity and to develop software products in line with global standards. We plan to further build our capability by leveraging India’s highly skilled software talent to grow our local teams. The investment in our new SDC shows our faith in India’s growth story and its digitalization and smart manufacturing policy initiatives,” said Dilip Sawhney, managing director, Rockwell Automation India.
Key members of Rockwell Automation’s global leadership team attended the inauguration ceremony of the SDC including Dittmer; Wes Mukai, chief engineering officer, software and control; and Martin Petrick, business manager, manufacturing executing systems. The local India leadership team was represented by Sawhney, India MD. Rockwell Automation has been growing its footprint in India across areas such as engineering, commercial, supply chain and its software and technology capabilities. It has more than doubled its workforce in India since 2015.
Materials announced a partnership with Toyota Motor North America to create a battery ecosystem across their lineup of electrified vehicles that encompasses all steps for full circularity. Redwood is creating a closed-loop supply chain for electric vehicles that extends well beyond recycling to encompass collection, refurbishment and remanufacturing of large-scale sources of anode and cathode battery materials. The goal is to create a fully closed loop to drive down the environmental and economic costs of electric vehicles.
Toyota paved the way for clean transportation with the introduction of the Toyota Prius hybrid electric vehicle more than 20 years ago. The first wave of battery-electric vehicles retiring from roads today, ready for recycling, are predominantly Prius vehicles. Toyota remains committed not only to selling millions more electrified vehicles this decade but to ensuring their vehicles’ circularity into the future.
Together, Toyota and Redwood will create a truly closed-loop solution for batteries. Initially, the focus will be on testing and recycling Toyota batteries, creating end-of-life pathways for the original hybrid electric vehicles. The companies will then expand into other areas including battery health screening and data management, remanufacturing and battery material supply throughout North America.
Work will be focused at Redwood’s ~175-acre Northern Nevada Battery Materials Campus, located adjacent to the world’s oldest and largest electric vehicle market, California, where the first wave of Priuses and soon, electric vehicles, are retiring from roads. As Redwood plans for our additional operations, we will be located in the region near Toyota’s recently announced North American battery plant and many of our other partners on the East Coast, further localizing our process and increasing the sustainability of batteries.
Redwood is driving down the environmental footprint and cost of lithium-ion batteries by offering large-scale sources of domestic anode and cathode materials produced from recycled batteries. Today, the company receives more than ~6 GWh of end-of-life batteries annually for recycling, which are then refined and remanufactured into critical battery materials. It is ramping production of anode and cathode components in the US to 100 GWh annually by 2025, enough to produce more than one million electric vehicles a year and then scaling to 500 GWh, enough for five million EVs annually, by 2030.
Together, Toyota and Redwood will work to seamlessly incorporate battery recycling through domestic battery materials manufacturing into Toyota’s battery production strategy. Both companies plan to drive down the environmental footprint and cost of transportation will continue to accelerate the adoption and access to electric vehicles.
IRVING, US: ExxonMobil, Shell, CNOOC and Guangdong Provincial Development & Reform Commission have signed a memorandum of understanding to evaluate the potential for a world-scale carbon capture and storage project to reduce greenhouse gas emissions at the Dayawan Petrochemical Industrial Park in Huizhou, Guangdong Province, China. In addition to assessing the commercial opportunity for carbon capture and storage in one of China’s largest industrial areas, the companies will also evaluate the carbon policy systems in China and propose policies for consideration that would support the deployment of carbon capture and storage in Dayawan Petrochemical Industrial Park.
Initial assessments of the project indicate the potential to capture up to 10 million metric tons of CO2 per year from Dayawan’s industrial sector, supporting China’s ambition of carbon neutrality by 2060. The project could also serve as a model for the chemical industry as one of the first petrochemical projects to be decarbonized.
“Collaboration with government and industry is an important part of
unlocking future carbon capture and storage opportunities, with the potential for large-scale reductions of emissions from vital sectors of the global economy,” said Dan Ammann, president of ExxonMobil Low Carbon Solutions. “Well-designed government policies will help accelerate the broad deployment of lower-emissions technologies in support of society’s net-zero ambitions.”
While renewable technologies are important to help reach society’s net-zero objectives, carbon capture and storage is a safe, proven and consistent technology that can enable some of the highestemitting sectors such as manufacturing, power generation, refining, petrochemical, steel, and cement industries to reduce their emissions. The prospect of bringing together public and private entities to utilize carbon capture and storage collectively to reduce industrial emissions offers tremendous opportunity.
ExxonMobil is also pursuing strategic investments in biofuels and hydrogen to bring those lower-emissions energy technologies to scale for hard-to-decarbonize sectors of the global economy.
LEVERKUSEN, GERMANY: Covestro, South Korean petrochemical company SK geo centric and Neste are cooperating to enable the production of a major polyurethane raw material based on renewable raw materials via mass balance. The cooperation will see Neste provide SK geo centric with renewable Neste RETM, an ISCC certified feedstock for polymers and chemicals made from 100 percent renewable raw materials such as waste and residue oil and fats.
SK geo centric will process this feedstock into benzene at the company’s facilities in South Korea and supply it to Covestro to use as raw material for methylene diphenyl diisocyanate (MDI) at its site in Shanghai, China. MDI is a key raw material for the manufacture of rigid polyurethane foam, which is a well-proven insulating material for buildings and used in the cold chain helping to save CO2 emissions and reduce energy consumption during its product life.
The cooperation marks the start of possible future collaborations between the three companies, aiming at replacing fossil feedstocks by more sustainable ones in the production of polymers and chemicals in the APAC region and beyond.
“With renewable solutions available, we are now entering the phase of scaling up their usage in the chemical industry,” said Mercedes Alonso, executive vice president, renewable polymers and chemicals at Neste. “This will be crucial in replacing the vast amounts of fossil resources the industry is currently depending on. To make this ramp-up a success, we’ll need to establish collaborations along the value chain – and this one between three sustainability-minded partners is a prime example of how the industry can do just that.”
Replacing the common crude oil-based fossil feedstock with Neste RE provides a significant reduction in greenhouse gas (GHG) emissions, thereby improving the carbon footprint of the polyurethane raw materials produced by Covestro and of downstream industries. Neste RE is produced with renewable raw materials such as waste and residue oils and fats.
“I am much pleased that through this collaboration we continue to ramp up the market for sustainable alternative materials. This enables us to supply our customers in Asia-Pacific with more sustainable MDI based on mass-balanced raw materials,” said Sucheta Govil, chief commercial officer of Covestro. “Using such materials is attractive because it will also help them achieve their climate goals. Another core benefit of this line of products is that it is a technical drop-in solution that our customers can use immediately without a major changeover in their plants.”
“We are delighted to ship and export our first renewable Benzene produced with 100 percent renewable Neste RE feedstock,” said Woohyuk-Choi, vice president of SK geo centric’s Aromatic Business Unit. “SK geo centric will actively work with Covestro and Neste as we mark the first collaboration of this kind in the Asia-Pacific region.”
Under the strategy of “Green for Better Life”, SK geo centric announced its ambitious target to become “Net-Zero” before 2050. To fulfill its responsibility, the company will drive its business transformation by expanding its high-quality renewable products portfolio. SK geo centric will respond to increasing global demands in the market by leveraging the strong synergies between collaboration partners.
KASSEL, GERMANY: K+S has signed a letter of intent with the Swedish company Cinis Fertilizer on future cooperation in the synthetic production of potassium sulfate (SOP). Under the planned agreement, K+S intends to supply Cinis Fertilizer with its entire potassium chloride (MOP) requirements. In return, K+S could purchase up to 600,000 tonnes of potassium sulfate (SOP) per year from Cinis.
Cinis Fertilizer is planning the synthetic production of potassium sulfate in the so-called Glaserite process at several production sites in Scandinavia. In addition to potassium chloride supplied by K+S, the company will use residues from battery, pulp, and paper production as raw material and renewable energy. Sodium chloride (salt) is also
generated as a by-product in the production of potassium sulfate.
“The agreement fits perfectly with our new corporate strategy, which includes the expansion of our core business through cooperation,” said
K+S chairman, board of executive directors Dr. Burkhard Lohr. As a result, K+S will secure additional quantities of the specialty fertilizer potassium sulfate. K+S will therefore be in an even better position to supply its customers as well as to acquire new customers.
K+S and Cinis Fertilizer intend to convert the letter of intent now reached into a binding contract for both sides in the short term and thus establish a long-term business relationship.
SNAITH, UK: Croda International Plc announced that it has entered into a cooperative agreement with the US government in which the government will provide up to $75 million to expand the company’s US manufacturing capacity of ingredients for lipid systems used in novel therapeutic drugs, such as mRNA vaccines. In line with the company’s strategy to ‘Empower Biologics Delivery,’ Croda will also invest up to $58 million, bringing the total project investment to up to $133 million.
The investment will be used to establish a new lipid facility as part of a new multi-purpose cGMP site in Lamar, Pennsylvania. Construction is expected to start later this year, with the new capacity anticipated in 2025. The investment supports expansion of the portfolio of patient health care solutions offered by Croda, by creating a third manufacturing site for lipid systems, alongside Croda’s existing Alabaster, Alabama, US (Avanti) and Leek, UK capabilities.
The cooperative agreement is a joint award from the Biomedical Advanced Research and Development Authority (BARDA), part of Office of the Assistant Secretary for Preparedness and Response within the US Department of Health and Human Services and the US Department of Defense’s Joint Program Executive Office for Chemical, Biological, Radiological and Nuclear Defense (JPEO-CBRND) in partnership with the Army Contracting Command’s Joint COVID Response Division (ACC JCRD). The new facility is part of a programme to expand the US industrial base supporting critical vaccine and therapeutic manufacturing activities. The facility at Lamar will support US preparedness for future health emergencies, by ensuring enough capacity is available in the US to produce the necessary components for vaccine manufacture.
Croda’s Pharma business is a leading partner in the development of delivery systems for biologics. Croda’s platforms enable the next generation of vaccines and therapeutics. Through acquisition of Avanti Polar Lipids in 2020, Croda was the first company to supply clinical and commercial quantities of critical lipid systems to support the rollout of COVID-19 vaccines globally.
Lipid systems offer significant potential as the delivery system for a wide range of nucleic acid applications, including novel mRNA-based therapeutics, such as flu vaccines and cancer treatments. Given the scale of the current clinical development pipeline, the market for lipid systems is expected to grow significantly over the next ten years.
“We are grateful to the US government for its support of Croda. The delivery technology based on lipid systems offers significant potential for the safe and efficient delivery of next generation vaccines and therapeutic drugs.
As a result of this investment, Croda will be able to expand its capabilities to develop and manufacture ingredients in support of this important technology. This will help ensure that the US is well prepared for future health emergencies and equipped to offer advanced treatments for some of the most prevalent illnesses in the world today,” said Daniele Piergentili, president, Croda Life Sciences.
“The US government is pleased to be a part of these Industrial Base Expansion efforts to expand production of raw materials for mRNA vaccines,” said Nicole Kilgore, deputy joint program executive officer for Chemical, Biological, Radiological and Nuclear (CBRN) Defense.
AUSTRALIA: Australia’s Lynas Rare Earths has signed a $120 million follow-on contract with the US Department of Defense to build a commercial heavy rare earths separation facility in Texas, the firm said. Lynas is the world’s largest processor of rare earths outside China, and the contract with its US subsidiary builds on ‘Phase 1’ funding for a facility announced in July 2020, reported Reuters.
The project, for which the Pentagon provided initial funding, is expected to be built in an industrial area on the Texas Gulf Coast and be operational in financial year 2025, the company said.
Lynas intends to combine the heavy rare earth separation plant with a light rare earth separation facility, which is half-funded by the Defense Production Act office of the US Department of Defense.
The plant would be the first outside China that is able to separate heavy rare earths, chief executive Amanda Lacaze told Reuters in an interview. “And that’s why this is such an important step,” she said after the news.
Lynas mines rare earths in Western Australia and ships the material to
Malaysia in southeast Asia, where it produces rare earth oxides.
The company’s goal to boost output by 50 percent by 2025 would not be sufficient to meet rising demand, Lacaze said, however. “The rapid growth in the market, particularly over the last 12 months, tells us that we need to accelerate that plan,” she said of the target the company set itself in 2019.
After supplies were disrupted by the COVID-19 pandemic, interest from Western nations, Japan, the European Union and others has grown as they recognised the risk of relying on China as their sole source of supplies.
“The issue here is not whether it’s Chinese or non-Chinese ... it’s simply that a singular supply chain is problematic, particularly in an area where you’ve got rapid growth and you’ve got a material which is critical for success,” Lacaze said.
“We are certainly highly engaged with governments who are concerned about supply chain security, and we’ll continue to do so.”
ESPOO,
FINLAND: From June 2022 onwards, Marr Contracting (The Men From Marr’s) has been using renewable diesel (also known as HVO100) from Neste in their heavy lift luffing tower crane fleet in Australia. This is an important step towards the business’ journey to net-zero carbon emissions and supports Marr in its commitment to reduce carbon emissions and impact on the environment as part of their 2021 Social Value Strategy. The switch to Neste-produced 100 percent renewable diesel comes after significant consultation with Marr clients and leaders within Australia’s construction industry on the best solution for transitioning away from fossil fuels. After investigating alternative power sources and taking the time to understand the issues associated with currently available options, Marr’s R&D team scoured the world for the best solution.
“We’ve looked at the alternatives and believe this is the most sustainable fuel currently available for the work that we are doing. That’s because it allows us to transition away from fossil diesel and maintain the speed, power and reliability of our cranes to drive productivity and
cost-efficiencies on the projects we are working on – while at the same time helping our clients achieve their sustainability goals,” said Marr’s managing director, Simon Marr.
“Renewable diesel from Neste is a more sustainable alternative to fossil diesel, helping its users reduce greenhouse gas emissions by up to 90 percent when emissions over the fuel’s life cycle are compared with fossil diesel. With renewable diesel from Neste, Marr will reduce its climate emissions significantly in an instant by just changing the fuel,’’ said Peter Zonneveld, vice president sales, Europe and APAC, Renewable Road Transportation at Neste. “We are committed to supporting our customers to reduce their greenhouse gas emissions by at least 20 million tons annually by 2030.”
Renewable diesel from Neste is produced from 100 percent renewable raw materials. Neste’s renewable diesel is a drop-in fuel, fully compatible with all diesel engines, not requiring any modifications to the existing vehicles or fuel distribution infrastructures.
THE WOODLANDS, US/BINZHOU, CHINA: Indorama Ventures
Public Company Limited (IVL) said it has signed a license agreement with Shandong Binhua New Material Co Ltd, (Binhua), a subsidiary of Befar Group, a leading petroleum and chemical enterprise in China, to build, own and operate a propylene oxide (PO), t-Butanol (TBA) and t-Butyl methyl ether (MTBE) co-production unit.
Featuring the world’s only MTBE ‘single-step’ reaction technology, IVL’s proprietary innovation, the project is part of the ‘C3 and C4’ comprehensive utilization project in Shandong, China.
“On completion, this project will be able to produce 600,000 tons of propylene, 800,000 tons of butane isomerization, 150,000 tons of synthetic ammonia, 240,000 tons of propylene oxide and 742,000 tons of MTBE per year.
With the lowest operational cost of all other propylene oxide technologies and close to 50 consecutive years of successful and safe operation, the license with IVL was selected because of its superiority, unique features,
and competitiveness,” said Liu Hongan, vice president of Befar Group and general manager of Shandong Binhua New Material Co Ltd.
Under the contract, IVL will provide a design package, technology, operational know-how and training to enable the construction and operation of a PO co-production with MTBE and TBA units for Binhua. The plant is part of a larger complex comprising propane dehydrogenation to propylene, butane isomerization, synthetic ammonia, and other installations.
“IVL is honored to be providing this important technology license, enabling the monetization of Binhua’s raw materials in Shandong Province with a world-class and cost-effective plant. Our technology uses 130 US patents and more than four decades of continuous development. This allows IVL to provide both the license, and owner/ operator knowledge to deliver the quality and effective solutions a project of this scale requires,” said Alastair Port, executive president, Integrated Oxides and Derivatives (IOD), IVL.
TOKYO, JAPAN: Tosoh SMD Inc, a wholly owned subsidiary of Tosoh Corporation headquartered in Ohio, US, announced the decision to expand its sputtering target manufacturing facilities. The company will approximately double its capacity, with an investment of 10 billion yen which started in July 2021 to be completed by July 2025.
Demand for Tosoh’s sputtering targets is expected to continue increasing well into the future. Sputtering targets are managed under Tosoh Corporation’s advanced materials operations and are used as thinfilm deposition materials in the electronics field. Applications include semiconductors, flat panel displays and solar cells.
In July 2021, Tosoh began to increase its capacity to meet the shortage of thin-film deposition materials in the semiconductor market. It subsequently saw a potential growth in demand that exceeded previous expectations. The company decided to expand its production facilities, not only in response to customer needs, but also to establish a manufacturing base that can maintain a stable supply. By implementing this capacity increase, the Tosoh Group will continue to respond to rapidly growing demand, as well as strengthen the profitability of its advanced materials operations.
HOUSTON, US: 1PointFive, a subsidiary of Occidental Petroleum Corporation’s Oxy Low Carbon Ventures LLC (OLCV) business, and Manulife Investment Management announced that OLCV and Manulife entered into a lease agreement for approximately 27,000 acres of timberland in Western Louisiana. The agreement provides 1PointFive with access to subsurface pore space and surface rights to develop and operate a carbon sequestration hub, with access to permanently store industrial carbon emissions. Two Class VI injection permits, required by the EPA for geologic sequestration, have already been filed for the site. The lease agreement is a pivotal step in 1PointFive’s strategic vision to develop carbon capture and sequestration hubs, some of which are expected to be anchored by Direct Air Capture (DAC) facilities.
Manulife Investment Management’s acreage offers excellent storage capacity within proximity to point source industrial emitters, who would otherwise emit carbon dioxide to the atmosphere. 1PointFive would also like to recognize New Dawn Energy, which is a Manulife land lease partner, and has been cooperative and supportive of the project.
“We are excited to join with Manulife and lease the acreage to develop a hub that will provide sequestration infrastructure and services for industrial emitters and 1PointFive’s future DAC facilities,” said Dr. Doug Conquest, vice president, OLCV. “This agreement strengthens our CCUS position and advances commercial-scale decarbonization solutions in line with Oxy’s net-zero goals.”
“We understand the importance our forests and underlying land play as a natural climate solution in decarbonization,” said Eduardo Hernandez, managing director and global head of Timberland Operations at Manulife Investment Management. “We focus on sustainably managing our forests for climate-positive and nature-positive impact, and we are excited to find additional opportunities to continue this work for clients.”
1PointFive and Manulife Investment Management are also exploring other locations and projects throughout the region and country with the potential to add additional acreage for carbon removal and sequestration. 1PointFive adheres to US Environmental Protection Agency (EPA) standards for monitoring, reporting and verifying (MRV)
the amount, safety and permanence of CO2 stored through secure geologic sequestration. The company and its affiliates hold three EPAapproved MRV plans for geologic sequestration. 1PointFive will apply this expertise toward the safe design and operation of the project.
Manulife Investment Management manages approximately 6 million acres of timberland across the United States, Canada, New Zealand, Australia, Brazil, and Chile. It also oversees approximately 400,000 acres of prime farmland in major agricultural regions of the United States and in Canada, Chile, and Australia.
NORWAY: Equinor has initiated a safe shutdown of the Gudrun, Oseberg South and Oseberg East fields after members of the Norwegian Organisation of Managers and Executives (Lederne) trade union went on strike from midnight.
The background for the strike is that the members of Lederne in a referendum voted against the mediator’s proposal during the wage negotiations for offshore personnel between the labour organisations and the employers’ organisation, the Norwegian Oil and Gas Association (Norog).
Total production from Gudrun, Oseberg South and Oseberg East is around 89,000 barrels of oil equivalent (boe) per day, of which 27,500 boe per day is natural gas.
A further extension of the strike has been notified for the Heidrun, Kristin and Aasta Hansteen fields, taking effect from the night before Wednesday 6 July. To Equinor this means that the above-mentioned installations will perform a controlled shutdown of production, including the Tyrihans field, which is tied to the Kristin platform.
Total production from Heidrun, Kristin/Tyrihans and Aasta Hansteen is around 333,000 boe per day, of which 264,000 boe per day is natural gas. A further escalation has been announced from 9 July at Sleipner, Gullfaks A and Gullfaks C. Consequences of this escalation is not yet clear.
AMSTERDAM, NETHERLANDS: AkzoNobel has announced that Gregoire Poux-Guillaume will become the company’s new chief executive officer (CEO) as of 1 November. He will succeed Thierry Vanlancker, who has been CEO and member of the management board since 2017, and whose term of office is coming to an end.
Poux-Guillaume (52), a French national, has a distinguished track record of building successful, profitable businesses in challenging environments, accelerating business growth and improving margins. Previous roles include CEO of Sulzer, CEO of GE Grid Solutions (previously Alstom Grid) and senior managing director of CVC Capital Partners.
“Gregoire Poux-Guillaume is an experienced business leader with a track record of delivering above market growth and building strong teams. We’re happy and confident to have found the best match for AkzoNobel to continue our position as a frontrunner in our industry,” said Nils Smedegaard Andersen, chair, AkzoNobel’s supervisory board.
“I’m honored to have been selected by AkzoNobel’s Supervisory Board to lead the company through its next stage of development. AkzoNobel is a leader in innovative and sustainable products and solutions; a truly global company with a proud heritage. I look forward to meeting my new colleagues and together building on the progress that has been achieved over the last few years,” said Poux-Guillaume.
The appointment of Gregoire Poux-Guillaume to AkzoNobel’s Board of Management will be on the agenda of an extraordinary general meeting to be scheduled in September this year.
INDIA: Effective 1 July, Namitesh Roy Choudhury assumes the role of vice chairman and managing director of LANXESS India Pvt Ltd. He also take on the responsibility of region head for India. In this new role, he will represent the businesses of LANXESS India to the global organization and will report to Dr. Anno Borkowsky, member of the board of management and head of all the four regions, globally.
Roy Choudhury has been the executive director since 1 October 2021 and vice president, Industrial & Environmental Affairs for LANXESS India since 2007. He moved to the LANXESS India organization in 2004 after the carve out from Bayer as the head of production, technology, safety & environment (PTSE) and capital investment.
“On behalf of the entire board of management, I would like to thank Namitesh Roy Choudhury for his excellent work to date and wish him every success in his new tasks,” said Borkowsky.
PUNE, INDIA: Air Products announced that it has appointed Sushila Mani as managing director of Prodair Air Products India Pvt Ltd. In this role. Mani will lead Air Products’ world-class Engineering, Procurement and Construction (EPC) centers in Pune and Vadodara, India. Mani joins Air Products following her role as senior director, operations for Worley India where she managed an office of over 600 employees and had full Profit & Loss (P&L) responsibility.
Prior to that Mani led Project Management at BASF Chemicals India with accountability for project and construction management, construction safety and quality for all capital investment projects executed in Southeast Asia.
Mani also spent 14 years at ThyssenKrupp Industrial Solutions, serving as general manager, Projects/Project Director, and general manager, Strategic Business Development.
“I am very pleased that Sushila has joined Air Products. We are excited to have Sushila join our organisation and are confident her strong leadership will build on the successes we already have and enable new opportunities for our EPC organisation to support India’s energy and sustainability growth strategy well into the future,” said Air Products’ chief operating officer Dr. Samir Serhan.
OSLO, NORWAY: As a consequence of Statkraft’s updated strategy and increased ambition within green hydrogen and related businesses, Birgitte Ringstad Vartdal has decided to step down from Yara International ASA board of directors, in order to avoid any potential conflicts of interest with Yara, effective as of 1 July.
Vartdal had joined Yara International ASA board of directors in May 2020. She is the executive vice president, European Wind and Solar at Statkraft. She is responsible for developing wind and solar in Europe, project delivery, procurement and new business development for the company.
(55) will be responsible for the BYK and ECKART divisions as well as the central functions Key Account Management, Innovation Management, Environment, Health & Safety, ALTANA Excellence, and Procurement. Until 2020, Boinowitz held various management positions at Evonik. At the beginning of 2021, he moved to the ALTANA Group where he became president of the BYK division.
“Tammo Boinowitz is not only ideally suited professionally but has already proven his expertise as well as his value-oriented leadership style within the ALTANA Group,” said Martin Babilas, chairman, management board, ALTANA AG. “We are looking forward to working with Tammo Boinowitz on the ALTANA Management Board and already wish him great success and joy in his future position. Together, we will continue ALTANA’s story of sustainable profitable growth.”
Dr. Tammo Boinowitz
WESEL, GERMANY: ALTANA AG has announced a change in the composition of its Management Board. Dr. Christoph Schlunken will retire at the end of this year and hand over his board responsibilities to Dr. Tammo Boinowitz as of January 1, 2023. Boinowitz is president of ALTANA’s largest division, BYK, and for the time being will continue to hold this position in parallel.
In his new role as ALTANA management board member, Boinowitz
Schlunken (60) joined the ALTANA Group in 2001 as managing director of ELANTAS GmbH, having held various sales and marketing positions at the former Bakelite AG since 1994. In 2005, he took over as president of the ECKART division. As part of the rotation of all four division presidents, Schlunken became head of BYK in November 2012. In 2014, he was appointed to ALTANA’s management board.
As of January 1, 2023, the management board of ALTANA AG will thus consist of Martin Babilas (Chairman), Dr. Tammo Boinowitz, and Stefan Genten.
OSRAM, a global leader in optical solutions, and trinamiX GmbH, a wholly owned subsidiary of BASF SE and pioneer of new biometric technologies, developed a demonstration system that shows face authentication from behind an OLED screen with the ultra-high security performance required for mobile payments. The demonstrator is first showcased in San Jose, US.
ams OSRAM and trinamiX are working together to provide smartphone manufacturers with a highly secure and convenient user authentication system that will be available later this year. The core of the full solution are trinamiX’s certified face authentication software and a dedicated projector by ams OSRAM. Based on this innovative combination, the solution is able to perform behind smartphone displays while enabling for a small technical footprint and a cost-efficient integration.
More recently, trinamiX Face Authentication has proven to reliably reject advanced fraud attacks by means of a novel liveness check based on skin detection. The solution was certified in compliance with the world’s
leading mobile payment standards of Android™ Biometric Class 3, the IIFAA Biometric Face Security Test Requirement and FIDO Alliance.
‘trinamiX’s solution has been tested exhaustively against spoofing attempts. Even when attackers used ultra-realistic masks, the spoofing was detected and access reliably rejected. We present mobile phone manufacturers with a solution that fulfills top security requirements for mobile payments while being easy to integrate into their devices,” said Matthias Gloor, Senior Product Manager of ams OSRAM.
The companies’ first demonstration system leverages ams OSRAM’s dot-flood infrared projector and trinamiX’s unique hardware/software setup – both allowing for a highly secure and convenient performance, also when integrated behind OLED displays. ‘ams OSRAM’s optimized projector is the perfect match for our solution,’ said Stefan Metz, Head of Smartphone Business Asia at trinamiX. ‘The combination of our unique hardware and algorithms rapidly produce reliable face authentication results to create an extremely smooth experience for smartphone users. We are happy to finally present this next-generation solution to customers.’
On the road to alternative energy generation Covestro is developing innovative PUR resins for use in wind turbine rotor blades at its new Wind Technology Center. A win-win-win situation for Covestro, customers and the environment.
“The development of these resins is very important to us. After all, it contributes to the expansion of alternative energies and strengthens our strategic orientation to sustainably reduce the CO2 footprint and take even more steps towards climate neutrality,” explained Klaus Franken, Head of Application Development Wind and Pultrusion at Covestro. “To be competitive, the wind industry faces the constant challenge of reducing the Levelized Cost of Electricity. We can help here by enabling our customers to produce rotor blades faster and thus more cost-effectively. At the same time, higher energy yield through optimized blade properties and longer service life also play a role.”
One goal of the Wind Technology Center is to develop robust materials that combine the properties important for rotor blades, such as
strength, stiffness and temperature resistance. Existing products are continuously optimized and completely new formulations are developed and tested. Another goal: application technology development in close cooperation with customers. “Here we can simulate our customers’ manufacturing processes and show how our PUR resins help them to realize both their rotor blade designs and the manufacturing process in the best possible way,” said Franken.
Covestro attaches great importance to optimally tailoring its products to the needs of its customers. That is why a number of cooperative ventures with European and Asian wind turbine manufacturers are already in place. The focus here is on constructing and testing prototypes.
The high-tech center is located in Leverkusen and was completed and put into operation at the beginning of this year. It comprises two interconnected units: a laboratory area for chemical development and an Upscaling Plant. The latter is home to processing technology and application development.
The center offers clear advantages: “Chemical development and application technology can work hand in hand here. On top of that, the physical proximity makes it easier to exchange information directly and quickly. We use identical resources and the same infrastructure and quickly obtain a comprehensive depiction of the process. This helps us to pursue our goals in a results-oriented manner and without losing knowledge, and enables us to offer new, innovative solutions to our customers,” explained Technical Center Manager Frank Grimberg. “Process and plant safety, explosion protection, machine safety and, of course, occupational safety are always in the spotlight here,” explained
Tobias Wollersheim, who as Project Management was responsible for planning and implementing the investment.
Another positive aspect: with the innovative technology center, Covestro is increasing its attractiveness as an employer. Indeed, wind technology offers a wide range of new, interesting fields of work that arouse curiosity and offer diversity. Covestro has taken on a newly qualified chemical technician from its own training program to operate the machines. He is being intensively trained in the processes and machine technology. This much is clear: Things are moving in the area of wind energy.
Devan is looking to launch novel technologies for the home textiles market. The first innovation Devan is bringing to the world is a range of bio-based and biodegradable microcapsules. With increased sustainability and circularity requirements in Europe and beyond, Devan is pushing the limits further of its encapsulation methods, also in terms of wash durability. The capsules are biodegradable and hence no harm for risk of microplastics. The new R-Vital NTL range includes evergreen Aloe Vera, waste-material based avocado seed oil (very high hydration abilities!) and Vitamine E.
Devan, as part of the Pulcra Chemicals Group, co-launches the new Pulcra TEC-SU, a new biobased C0 DWR. This hydrophobic agent has a bio-content above 60 percent and contains no APEO or formaldehyde. It keeps performing very good after multiple washings.
The Devan bio-based thermoregulation range, like Tones of Cool Bio which is already several years on the market, is having a positive effect on carbon footprint. The company is now expanding its cooling range with a specific foam-solution. In the home textile industry new (bio) foam types are introduced the last 1,5 years to comply with the EU GreenDeal and circularity / recycling requirements. A good enough reason for Devan to develop a foam-specific cooling system. After all, research shows that our bedroom interiors get warmer every year, partly due to better insulation but also due to global warming. On top of that the company’s thermoregulation solutions can save energy and water during application: low curing solutions are available next to cooling products to that can be applied, using less water.
Nouryon introduces Expancel® HP92 microspheres, a new innovation that is breaking boundaries for thermoplastic microsphere fillers in high-pressure manufacturing processes for the automotive industry. Lightweight materials are in high demand from automotive manufacturers to meet increasingly strict emission regulations and strong consumer interest in fuel-efficient vehicles that do not compromise on performance or passenger comfort.
“The ability to produce lightweight solutions for our key markets presents tremendous growth opportunities for Nouryon as our customers increasingly focus on implementing more sustainable solutions,” said Johan Landfors, Executive Vice President and President of Technology Solutions and Europe at Nouryon. “Our customers in the transportation industry are looking for innovations that address several technical requirements in one product and we are proud to support them with a solution that not only improves fuel efficiency, enhances acoustics and seals for harsh weather conditions but also supports the reduction of carbon dioxide emissions.”
Expancel® microspheres consist of a polymer shell that encapsulates a gas. When heated, the gas expands allowing the microspheres to be
used as a lightweight filler and blowing agent to make end products lighter and obtain different surface effects. They also reduce costs and environmental impacts by requiring less raw material and reducing weight.
“When used in underbody coatings and sealants, Expancel® HP92 microspheres allow our customers in the automotive industry to use high-pressure application processes on surfaces with up to four times better volume recovery to its original shape after pressurization compared to an older grade of thermoplastic microsphere,” said Sylvia Winkel Pettersson, Vice President Engineered Polymers at Nouryon. “Our technology is aimed at combining and optimizing the pressure resistance associated with glass microsphere grades with the light weight of thermoplastic microspheres fillers in one refined solution.”
Expancel® HP92 microspheres are currently produced in Stockvik, Sweden, with production expected in Green Bay, Wisconsin, US in early 2023, and will be available globally through the Nouryon distribution network. Expancel® microspheres have been produced for more than 40 years and are sold in more than 80 countries.
has joined forces with Heinz, Tesco and Berry in an innovative recycling trial in the UK designed to close the loop on soft plastic food packaging. Flexible plastic packaging collected from Tesco stores has been used to produce certified circular polypropylene (PP) from SABIC’s TRUCIRCLE™ portfolio for microwavable Heinz Beanz Snap Pots, made from 39 percent recycled soft plastic. The transformation of the industry towards a circular economy requires unprecedented innovation and intensive collaboration across the value chain. The latest achievement is yet another example of the company’s commitment to accelerate the change and ensure that plastic products are designed, produced, used and recycled more sustainably. Consumers are encouraged to return soft plastic packaging to collection points set up at Tesco stores. A portion of this collected plastic packaging is converted into recycled oils, called TACOIL, through a thermal anaerobic conversion process. SABIC uses the oil to produce certified circular polypropylene of the same quality as virgin
SABIC
resin. With these polymer pellets, Berry Global, a leading supplier of innovative packaging solutions, then manufactures the new Beanz Snap Pots and sends them to Heinz for filling with Beanz and delivery to Tesco. Once emptied, the pots and sleeves can be returned to kerbside collection points.
The collaboration aligns with SABIC’s TRUCIRCLE program and the company’s commitment to drive the transformation of the plastic packaging economy towards circularity. “We are happy to reaffirm our role as a provider of unique circular solutions,” said Lada Kurelec, General Manager PP, PET, PS, PVC, PU & Elastomers Businesses for Petrochemicals at SABIC. “Next to the material know-how, we have brought value chain partners together and provided crucial elements such as support with certification processes or life-cycle assessment calculations, all while helping to prevent valuable used plastics from being lost to landfill or incineration.”
The Snap Pots recycling trial is part of Heinz’s global pledge aimed at making 100% of its packaging recyclable, reusable or compostable by 2025. Jojo de Noronha, President Northern Europe at Heinz, said, “We’re proud to have teamed up with experts in the field of advanced recycling and sustainable packaging to bring this important innovation to our customers. Our hope is that this prompts an industrywide look at what more can be done to address the lack of soft plastics being recycled in the UK, and we can, as a collective, get better when it comes to developing new packaging solutions that are both good for both our consumers and for our planet.”
“This is a prime example of an innovative advancement in circular packaging design made possible by collaboration across the entire value chain. This type of circular approach helps capture and reuse plastics that currently go unrecycled to keep materials in use and out of our oceans and landfills,” said Jean-Marc Galvez, President of Berry Global’s Consumer Packaging International Division.
To date flexible packaging has been difficult to recycle, and until 2020 just 6% of soft plastic packaging was being recycled in the UK. Tesco started collecting soft plastic in all its large stores in 2021 to help plug this recycling gap in the UK. The Heinz and Tesco project with certified circular polymer from SABIC is considered a breakthrough with the potential of a real game changer. James Bull, Tesco’s Head of Packaging, said: “This innovative collaboration is one of the ways that soft plastic returned to stores by our customers will be recycled into new food-grade packaging. After doing everything we can to remove and reduce plastic, we want to develop circular recycling solutions so that used packaging can be recycled back into packaging again.”
The new Heinz Beanz microwavable pots are made with 39% of certified circular SABIC® PP homopolymer suitable for injection molded or thermoformed food packaging products.
The material meets the requirements of food-contact safety regulations and is a true drop-in solution to replace virgin PP in this thin-wall application without compromising processability or mechanical performance. The recycled content in the Snap Pots is validated by mass balance according to the International Sustainability & Carbon Certification (ISCC) PLUS program.
SABIC’s certified circular polymers form part of the company’s TRUCIRCLE portfolio and services for circular solutions. The offering also includes design for recyclability, mechanically recycled products, certified renewable polymers from bio-based feedstock and closed loop initiatives to recycle plastic back into high quality applications and help prevent valuable used plastics from becoming waste.
1. Collect – Post-consumer soft plastic packaging which would otherwise be incinerated or taken to landfill is collected at Tesco stores nationwide
2. Convert – The collected packaging is then converted using a thermal anaerobic conversion process into an optimal oil feedstock
3. Transform – SABIC takes the recycled oil and uses it as alternative feedstock in the production process to manufacture virgin, food-contact approved polymer pellets
4. Create - On site at its ISCC-certified manufacturing sites, sustainable packaging specialist Berry Global then applies its thermoforming capabilities to mould the food-contact approved polymer pellets made with 39% recycled plastics based on a mass-balance approach into new, post-consumer recyclable Snap Pots
5. Recycle - Finally, the completed Snap Pots are sent to Heinz to be filled with Beanz and delivered back to Tesco stores. Once used, the pots can be recycled as part of kerbside collections
Leading chemical manufacturer BASF SE points out to Chemical Today magazine, the opportunities that the recent global adversities offer to various industries and ways in which chemical manufacturers across the globe should grab these opportunities to build a more sustainable, reliable and future-ready industry.
Impact of Russia-Ukraine war on the chemical industry.
Russia and Ukraine are important suppliers of energy and agricultural raw materials and of metals. The expected impact of the war and the sanctions imposed by the West against Russia have already caused commodity prices to rise massively. Higher uncertainty among consumers, companies and in the financial markets is added to this.
Higher prices for energy, agricultural products, food and other consumer goods will weaken real purchasing power worldwide. Europe will be hit harder than other regions because of its high direct dependence on Russian energy imports. In addition, supply difficulties are increasing in some of our customer industries. Supplies from Ukraine play an important role for some European auto manufacturers in particular. Most external scenarios assume a discount of at least one percentage point in global growth.
It cannot be ruled out that the very high energy and raw material prices, especially in Europe, could have a negative impact on growth in the global economy, industry and chemical production. It is also an open question how the pandemic and thus the economy in China will continue to develop. However, we continue to feel strong demand in
our markets. A reliable assessment of the further course of events is not possible at present though. Mobility sector and opportunities for chemical manufacturers.
The automotive industry is in the middle of a major transformation, in all circles around the transformation of the drivetrain technology and the move from internal combustion engines to electrified mobility. We assume in our models that, by 2030, roughly 30 percent of all cars produced worldwide will be either fully electric or a plug-in hybrid version. As you can see, this share will increase significantly, even beyond 2030. The electrification of the powertrain will be the dominant trend in this industry.
It’s particularly relevant to BASF because automotive is one of our key customer industries and 20 percent of the group sales today are connected to the automotive industry through our direct business with OEMs, but also through a lot of tier suppliers and our aftermarket businesses. So, this is a very significant industry for us. Of course, if this industry is in the middle of such a big transformation, we are in a particularly advantageous position to benefit from our strengths in this industry during this transformation.
The transformation of the powertrain from internal combustion engine to battery-driven provides a significant upside for a chemical supplier like BASF, because the chemical content per car is going to increase significantly. We assume that the chemical content, as we define it, per car is going up by a factor of 2.5 when you switch from a model internal combustion engine car to a fully electrified vehicle. Of course, the majority of this additional value comes from the powertrain technology, or through the battery. Hence, it has been, for quite some years, a strategic focus for us to capture growth opportunities in this transformation.
This, of course, relates to a very, very strong growth in the market for cathode active materials. We predict that over the next years, until 2030, we will see annual growth rates of north of 20 percent per year. The market size for cathode active materials will reach 4.2 million tons by 2030. This corresponds roughly to a market value at predictable metal prices of roughly 100 billion euros. Just to put this into perspective for you: That is the entire market size of today’s polypropylene market.
Agriculture industry trends and opportunities for chemical manufacturers.
There has never been a more challenging time in agriculture. But there has also never been a time of greater opportunity. By 2050, farmers will have to feed an estimated 9.7 billion people, requiring an increase in productivity of 50 percent. At the same time, agriculture is facing challenges driven by climate change, limitations in arable land and new demands for transparency and healthy, sustainable, and affordable food. Despite these challenges, we want to grasp opportunities that come with them. and believe in finding the right balance for success – for farmers, for agriculture and for future generations.
We are convinced that we can deliver solutions to increase productivity and resource efficiency while minimizing the impact of agriculture on the environment. We see the following trends in agriculture:
Innovation: We offer innovative solutions that enable agricultural productivity, environmental protection and value to society. We have an unprecedented innovation pipeline and continue to innovate across our pipeline of seeds and traits, seed treatment, biological and chemical crop protection, as well as digital farming solutions. We will launch major pipeline projects across all business areas over the next decade.
The value of the innovation pipeline is strong, with an estimated peak sales potential of more than €7.5 billion. In 2021, it spent about €900 million in R&D in the Agricultural Solutions segment, representing around 11 percent of the segment’s sales. In 2022, BASF will continue to invest in research and development of agricultural innovations at a high level.
To give one example, wheat farmers need to increase their yield by 1.7 percent annually for the next 20 years to meet the needs of a growing global population. We contribute to this with our innovations that optimize agricultural outcomes and sustainability. One of them is IdeltisTM hybrid wheat with value-added traits, such as increased yield, quality, and disease and insect resistance, that address specific local needs and conditions. Ideltis hybrid wheat will be launched in the second half of the decade.
Digitalization: We are committed to a digital future in agriculture and therefore continue to invest in it. Digitalization is one of the
key differentiators of our business strategy. We are advancing our digital technologies together with other innovations across the whole portfolio. This combination allows farmers to achieve better yield on existing arable land, while supporting biodiversity preservation.
For example, to control weeds with precision inputs, we developed the Smart Spraying solution together with Bosch, that combines xarvio®’s agronomic intelligence with Bosch’s high-tech camera sensor technology and software. The technology offers real-time, automated pre- and post-emergence weed identification and management. Smart Spraying reduces the risk of weed resistance by using specifically developed herbicide formulations and optimized rates, ensuring that herbicide is applied only where and when needed. Through spot application, it can reduce herbicide volume use by up to 70 percent, depending on prevailing field conditions and weed pressure.
Sustainability: We embed sustainability criteria in everything we do – making sure that we are able to balance environmental protection, value for society and business performance via the fulfillment of our sustainability commitments.
One example of these commitments is our support for farmers to become more carbon efficient and resilient to volatile weather conditions. We therefore deliver solutions that increase yield, make farm management more effective, and decrease environmental impact.
These include:
• Nitrogen management products such as Vibelsol® and Vizura® that reduce greenhouse gas emissions
• Crop protection products such as the herbicide Kixor® that enable farmers to grow crops without plowing, reducing CO2 emissions from the soil and diesel use
• New crop varieties such as InVigor® canola seeds providing higher yield stability especially under more severe weather conditions
• Biological inoculants and innovative digital solutions
Besides this, to continuously steer our product portfolio towards even more sustainable solutions, we apply the Sustainable Solution Steering method, which is unique in the industry and third-party audited, in the early stages of research and development. Company’s future business dynamics in Asia Pacific region.
In order to achieve our global targets for growth (growth exceeding that of the global chemical market), we have prioritized the fastest growing geographical market – China, and the fastest growing sector in the chemical industry – battery materials for electromobility.
China is the major growth driver for global chemical production: Two thirds of growth will come from Greater China by 2030.
• We forecast that global chemical production will continue to grow above GDP – at an attractive rate of around 3.3 percent per year between 2020 and 2030. Already today, Greater China accounts for around half of global chemical production. Global growth in chemical production until 2030 will be dominated by Greater China, which will account for more than two thirds of the total growth during this period.
• The automotive industry is in a transformational stage towards battery-driven mobility. Not only are customer preferences changing, but the entire ecosystem is evolving rapidly. For BASF, electromobility is the single largest growth opportunity in the chemical space.
• The chemical content per car is higher in a Battery Electric Vehicle (BEV) compared to an Internal Combustion Engine (ICE), with cathode active materials (CAM) as the single largest growth opportunity.
• Global market forecasts project a CAGR of 21 percent for CAM, culminating in a market volume of 4,200 kt of CAM by 2030. This equals a market value of €100 billion by 2030.
• As a leading supplier for CAM, we are convinced that our technology, expertise and products will be key to enable this transformation.
Digitalization is an essential element of our corporate strategy. With innovative, digital solutions, we increase customer loyalty and create added value for our customers. In addition, we increase the effectiveness and efficiency of our divisions, in production, in the supply chain as well as in service and research units.
In its production plants, BASF uses, for example, predictive maintenance to detect and predict deviations from desired operating states at an early stage. This allows maintenance demands to be identified at an early stage and maintenance activities to be better planned. In this way, we increase reliability and transparency and avoid unexpected downtimes.
With the supercomputer Quriosity, much more complex models are possible in research and development, in which significantly more parameters can be varied. This can not only result in substantially reduced development times, but also previously unknown relationships can be recognized and used to advance completely new research approaches.
At BASF’s Agricultural Solutions division, we develop digital tools that help farmers to optimize sustainable crop production. This is how we support farmers in balancing growing their business while reducing their environmental footprint. For example, xarvio® FIELD MANAGER provides real-time analysis of disease and pest pressures and provides optimal timing for crop protection as well as nutrient applications. Furthermore, it offers field-zone specific nutrition and crop protection application maps based on real-time satellite and drone data.
Digitalization is also the central enabler for BASF’s aim to achieve net zero CO2 emissions by 2050. Our digital solution and methodology for calculating the product carbon footprint of BASF’s products creates opportunities worldwide by providing our customers with tailor-made sustainable offers.
Insights into company’s R&D and innovation in Asia Pacific.
BASF has been continuously expanding its research and development footprint in Asia Pacific to drive innovation by integrating customer and market needs at an early stage. BASF operates two Innovation Campuses in Shanghai, China, and Mumbai, India.
The Innovation Campus Shanghai, located at the BASF Shanghai Pudong Innovation Park, was inaugurated in 2012, and expanded in 2015 and 2019. In April 2021, BASF broke ground for the third phase of its Innovation Campus Shanghai. The expansion includes an additional R&D building and one R&D workshop building. Upon its completion, the total investment of BASF into its Innovation Campus Shanghai will sum up to around €280 million.
The Innovation Campus Mumbai, with complementary research focusing on crop protection and specialty chemicals, is an important pillar of BASF’s growing R&D network in Asia Pacific. It includes state-of-the-art laboratories for chemical synthesis, application and process development, as well as analytics. In 2021, BASF inaugurated a new facility in analytics for reverse phase purification of molecules at Innovation Campus Mumbai and further strengthened its research pipeline, particularly in crop protection.
We implement our corporate purpose – We create chemistry for a sustainable future – by systematically incorporating sustainability into our strategy, our business, and into our assessment, steering and compensation systems. We secure our long-term success with products, solutions and technologies that create value added for the environment, society and the economy.
We also want to live up to our responsibility for climate protection. One way we do this is with our products, which enable our customers to lower CO2 emissions. But that is not all: We also become more efficient in our production and energy use, we will increase our use of renewable energies and we will accelerate the development and deployment of new CO2-free processes for the production of chemicals.
The company also provides to customers innovative solutions based on their demands. These can stem from many sources eg. regulations, quality standards, resource availability or technological changes. BASF contributes to our customer success by creating innovative high-quality value-adding products to changing customer demands.
UPM Raflatac is the first company in the world to invest in Ocean Bound Plastics (OBP) waste as label raw material in their new Ocean Action labels. The Ocean Action labels are made from ocean bound plastic using mass balance approach. Ocean bound plastic is abandoned plastic waste recovered from areas up to 50km inland from waterways, defined as “at risk of ending up in the ocean” by OBPCert. The new innovative label material is made possible by close collaboration with multiple partners in the product’s value chain.
The world desperately needs more sustainable and commercially viable ways to recycle post-consumer plastic. The United Nations has recognized the need to recycle more post-consumer plastic and launched a new plastic pollution treaty in 2021. OBPCert has estimated that ocean bound plastic generates 80 percent of plastic marine litter. Today, only around 10 percent of plastic waste globally gets recycled, while the rest ends up at landfills, in incineration, and leakage to nature or oceans. One solution to this problem lies in creating markets for products made from ocean bound plastic.
”The new innovative Ocean Action label material is the latest step in our beyond fossils journey. It does not only help prevent the plastic waste from ending up in the oceans but also offers brand owners the possibility to meet their recycled content targets for packaging. The Ocean Action label material is an easy-to-use drop-in solution created especially for food and cosmetics end-uses as it has exactly the same performance as the current fossil-based labels,” said Eliisa Laurikainen, business development manager from UPM Raflatac.
The Ocean Action label material is available as White and Clear Top Coated PP films with RP37, RF37, and RP74 adhesives and PET 23 PCR and glassine liners. These label materials are a perfect fit for fastmoving consumer goods (FMCG), such as household goods, personal care, packaged foods, and beverages.
To make Ocean Action label a commercially successful product, UPM Raflatac has collaborated closely with multiple partners in the value chain. The collaboration is necessary to make circular economy a
reality. At first stage HHI, a Malaysian-based plastic recycling company collects and sorts the ocean bound plastic waste with its partners. HHI has Ocean Bound Plastics certification under Zero Plastic Oceans program that ensures the responsible sourcing, proper collection and management of the ocean bound plastic waste.
After collecting and sorting the ocean bound plastic waste, HHI uses chemical recycling to convert the waste into pyrolysis oil. The pyrolysis oil is then used by SABIC to create high-quality PP plastic granulates.
“We are proud to offer our customers another more sustainable choice through the advanced recycling of used plastic that could otherwise end up in our oceans and rivers. These labels containing ocean bound plastic connect with our TRUCIRCLE™ program of circular solutions designed to help reduce plastic waste, mitigate fossil depletion and protect our planet,” said Lada Kurelec, general manager PP, PET, PS, PVC, PU & Elastomers Businesses for Petrochemicals at SABIC.
After SABIC, the plastic granulates are used in the process in which the film manufacturer Taghleef Industries produces the label film that is used to produce the final label material by UPM Raflatac.
“We are proud to be part of this initiative that represents a further step towards a more circular economy, thanks to an efficient reuse of valuable material, and is a responsible effort to preserve our environment, especially for younger generations,” said Simone Baldin, business unit manager – Labels Europe, Taghleef Industries.
The plastic waste used in the value chain of making Ocean Action label material is certified under the Zero Plastics Oceans program, and the final label material under ISCC PLUS. The label material is produced using sustainable recycled feedstock, replacing the equivalent amount of virgin fossil resources used in the production process, using a mass balance approach, accounting for the amount of sustainable resources. These verify that the Ocean Action label material is traceable and sustainably sourced.
will roll out the new mono-material pouches, which are “designed to be recyclable”, on two of its biggest brands. The shift for the Gourmet Mon Petit and Felix Soup ranges builds on Purina’s promise to introduce reusable or recyclable packaging by 2025. These robust pouches can withstand heating and sterilization processes, replacing the non-recyclable, multi-layer alternatives of the past
Purina is pushing forward in its plan to make pet care packaging easier to recycle, launching its first full pouch ranges “designed to be recyclable” this year. Gourmet, the European super-premium wet cat food, will debut the cutting-edge new mono-material packaging with the relaunch of its Mon Petit range, building on a successful yearlong pilot study under the Felix brand in the Netherlands. This new packaging will be introduced in more than 20 countries across Europe, including the UK, Ireland, Belgium and Italy and will be available in stores from mid-May.
This relaunch marks an important step in Purina’s path towards 100 percent reusable or recyclable packaging by 2025. This journey will continue in early 2023 with the introduction of packaging that is “designed to be recyclable” for the Felix Soup range. Felix is the EU leader in wet cat food.
The new pouches address a long-standing challenge for manufacturers – how to provide consumers with simpler plastic structures that are easier to recycle without compromising on product taste, quality and safety.
The improved packaging is made of Polypropylene (PP), which allows the pet food pouches to be designed to be recyclable, whilst being resistant to high temperatures and offering robust protection for their contents.
The pouches will be sold in a cardboard box which itself is recyclable. This box will contain 6 pouches with 3 different flavours. As well as reducing the complexity of packaging, Purina is also exploring innovations including new paper-based materials and piloting reusable packaging systems where customers can bring their own containers to fill with dry petfood.
“The new mono material pouches are another great example of our commitment to using simpler packaging, making recycling easier for pet owners. These new pouches demonstrate progress and can now be recycled at larger supermarkets in the UK and at kerbside in Ireland,” said Sokhna Gueye, head of packaging Nestle UK&I. “Simplification of our pouch structures will also enable this type of packaging to be part of flexible packaging household recycling collection, which has been announced by the government to be introduced by March 2027. We look forward to rolling out mono material pouches across the rest of our UK pet portfolio in the coming years.”
“We are proud to be playing our part in creating a world where pets and people can thrive, and initiatives like this support our goal of offering solutions that are better for pets, and the planet,” said Jeff Hamilton, Europe chief executive officer Nestle Purina. “This innovation is a significant step forward in our drive to deliver recyclable or reusable packaging on all of our products by 2025. As one of the world’s leading pet care and pet nutrition providers, Purina aims to help create richer lives for pets and the people who love them. This vision extends to the world in which we all live, and Purina is working hard to reduce the environmental footprint of the materials we use.”
Leading sustainable packaging manufacturer Coveris has launched a range of recyclable, reduced plastic pouches for Iceland’s grated cheese, supporting the retailer’s commitment to become the UK’s first plastic neutral supermarket.
Moving from a former mixed, nylon laminate to a new fully recyclable polyethylene (PE) monolaminate, Coveris’ innovative MonoFlexBE pouches use 1g less of plastic per pack to deliver an easy to recycle solution, with a significant plastic weight saving. Matching current shelf-life and delivering like-for-like functional performance, the packs also support the retailer’s food waste reduction commitments, as well as Coveris’ own vision for NO WASTE.
Available across 250g packs of Iceland’s grated mature and mild cheddar, and grated mozzarella, the new lightweight pouches offer a total plastic weight saving of around 7 tonnes per annum, whilst 41 tonnes of plastic are now easily recyclable nationally through retailer
front of store plastic film collections, including Iceland’s instore plastic collection and recycling service available in over 150 Food Warehouse stores.
“Our journey to plastic free will be supported by great work like this, which helps us all reduce plastic and ensure the plastic we do use is easily recyclable,” said Stuart Lendrum, head of packaging, Quality and Food Safety at Iceland.
“We’re really proud to have supported Iceland with the launch of the new recyclable, reduced plastic packs. Delivering major sustainable benefits in line with Iceland’s plastic-neutral commitments as well as our own plastic and food waste reduction targets, the packs deliver real sustainable innovation with no downsides to freshness or performance for a technically challenging, extended shelf-life product,” added Mark Robinson, Coveris’ UK Flexibles technical director.
Solvay has introduced Mirasoft® SL L60 and Mirasoft® SL A60 - two new high-performance biosurfactants that enable the development of sustainable beauty care products. Based on rapeseed oil and sugar with low environmental and carbon footprint, these glycolipid biosurfactants are suitable for a broad range of applications in beauty care such as shampoos, conditioners, shower gels, face washes and creams.
Mirasoft® SL L60 and Mirasoft® SL A60 are 100 percent biobased and biodegradable surfactants manufactured through a cost-efficient fermentation process, targeting a broad range of applications in hair and skin care.
The new Mirasoft® range aligns with Solvay’s most recent growth platform on “Renewable materials and biotechnology,” which aims to meet the growing demand for sustainable solutions by increasing the share of renewable carbon in Solvay’s product offering and developing new business opportunities enabled by biotechnology and product endof-life management.
“This product launch underlines both our commitment to surfactants technology and our long-term vision for the future,” commented Jean-
Guy Le Helloco, global vice president, home and personal care at Solvay. “We focus on future technology shifts to enable our customers to reach their sustainability goals.”
“With the potential of a net neutral carbon footprint in the near future, biosurfactants represent a step-change technology in the eco-design of next-generation beauty care products. The eco-profile of Mirasoft® SL L60 and Mirasoft® SL A60 is truly a breakthrough compared to conventional, fossil fuel-based surfactants,” said Galder Cristobal, research & innovation director, Home & Personal Care at Solvay.
Mirasoft® SL L60 and Mirasoft® SL A60 are designed to provide the same performance as synthetic ingredients without harmful environmental effects. Readily biodegradable and 100 percent biobased, they follow green chemistry processes and fully reflect Solvay’s commitment to sustainability and the creation of a circular, regenerative economy.
In line with Solvay One Planet roadmap, designed to preserve resources and contribute to safer, cleaner and more sustainable products, Solvay’s Beauty for the Planet initiative aims to accelerate the transformation of sustainable beauty ideas into concrete actions, provide beauty for consumers and maintain beauty for the planet.
While Circular Economy is turning mainstream, many types of packaging are still difficult to be recycled, for instance, multimaterial flexible packaging that consists of inseparable layers of different material. Main reason of using multi-material is the function to protect product inside with material in each layer guarding different type of components like oxygen or water. SCGC sees the importance of material design to be recyclable for easier path to circulate resource in our economy. SCGC GREEN POLYMER™’s latest development is now advancing our Mono-Material packaging solution to “High Barrier” level in order to serve the sustainable flexible packaging better.
After more than three years of research, testing, and value-chain collaboration, our coating technology, “BWO1501G”, is approved by “RecyClass”, world’s renowned certified body, as the First barrier coating agent in ASEAN that is compatible with the PE flexible recycling stream. The plastic generated by the recycling process can be used in high quality applications, such as PE blown films, up to 25 percent concentration.
SCGC’s Mono Directional Oriented of polyethylene (MDOPE) film coupled with a thin barrier coating delivers good oxygen transmission
rate (OTR, at 23 °C, 0% RH) at lower than 10 cc/m2/day and water vapor transmission rate (WVTR, 38°C, 90 percent RH) at below 10 g/ m2/day. As a result, this high barrier coated MDOPE film can be applied as printing layer and can replace BOPA (Nylon) and BOPET films for Mono-Material packaging in various applications, such as Personal and Homecare Products, Frozen and Chilled Food, and Dried Food.
Using high barrier coated MDOPE film, the overall structure of MonoMaterial packaging is more than 90 percent PE, passing FDA and EU testing on migration test, while maintaining performance in existing printing and lamination process. Beside ability to recycle, this sample can reduce 22 percent carbon footprint compared to Multi-Material packaging.
This SCGC GREEN POLYMER™ Mono-Material solution is a huge step to make single type of material to perform high level protection to prevent deterioration currently provided by multi-material packaging leading us to design for a better world.
Scientists use spent coffee grounds and tea leaf residue to successfully manufacture hydrogen peroxide, a chemical with much industrial utility.
Hydrogen peroxide (H2O2) is an important chemical, with a wide variety of applications. However, the current method used to manufacture H2O2 is expensive and generates a considerable amount of waste, making it an unsustainable approach. In this study, a group of researchers from Japan produced H2O2 from waste coffee grounds and tea leaves, and then demonstrated its industrial use. Their novel method proved to be simple, cost-effective, and most importantly, sustainable.
Coffee and tea are two of the most popular beverages around the world. The extensive consumption of these drinks produces large amounts of coffee grounds and tea leaves, which are typically discarded as waste. These unused biomass resources, however, have the potential to produce several useful chemicals. Tea and coffee contain a group of compounds called polyphenols, which can produce hydrogen peroxide (H2O2).
H2O2 has a lot of industrial value; this chemical plays a critical role in the oxidation of several compounds. The oxidation process is typically catalyzed by an enzyme called P450 peroxygenase, but it can’t occur unless H2O2 is present. These oxidation reactions are used to produce many chemicals of note. Now, H2O2 is currently produced through an unsustainable method called the anthraquinone process, which is not only energy-intensive but also produces a lot of waste, highlighting the need for a greener, environmentally friendly alternative. While there are other methods which use enzymes or light to produce H2O2, these are expensive because they require catalysts and additional reagents.
Keeping these issues in mind, a group of scientists from Japan including associate professor Toshiki Furuya and Hideaki Kawana from Tokyo University of Science, and Dr. Yuki Honda from Nara Women’s University, Japan have found an alternative way to produce H2O2. Their product comes from an unlikely source the leftovers of brewed
tea and coffee, called spent coffee grounds (SCG) or tea leaf residue (TLR)!
“Given their polyphenol content, we predicted that SCG and TLR could be used to produce hydrogen peroxide,” said. Furuya. Proving their prediction to be true, their study published in ACS Omega in June details their successful production of H2O2 using these underutilized biomass resources.
The team’s production method involved adding coffee grounds and tea leaves to a sodium phosphate buffer, then incubating this solution while shaking it. In the presence of the buffer, SCG and TLR interacted with molecular oxygen to produce H2O2.
The team also explored the scope of using this H2O2 to synthesize other chemicals of industrial importance. The newly-synthesized H2O2 aided in the production of Russig’s blue. Moreover, in the presence of peroxygenase (an enzyme that catalyzes an oxidation reaction using H2O2), TLR- and SCG-derived H2O2 was allowed to react with a molecule called styrene to produce styrene oxide which has several applications in medicine and another useful compound, phenylacetaldehyde.
These results prove that the team’s new approach of using SCG and TLR to produce H2O2 proved to be simple, cost-effective, and environmentally friendly, compared to the traditional anthraquinone process. Hailing these promising results, Furuya said, “Our method can be used to produce hydrogen peroxide from materials that would otherwise have been discarded. This could further result in new ways to synthesize industrial chemicals like styrene oxide, opening up new applications for these unused biomass resources.”
These findings thus open up a new way towards the sustainable production of H2O2, from the most unexpected sources: tea and coffee waste!
Every time we buy a car, we delve a lot on the colour. Should we go for matte or metallic finish? Would it be blue, black, white or one of those neon colours which are so trendy these days? While we choose from an array of gorgeous, vibrant colours, it probably never crosses our mind that these colours have a huge role to play in the global warming quotient of the planet.
The coating process in automotives, is one of the most energy-intensive processes as it emits a large number of volatile organic compounds (VOC), hazardous air pollutants (HAPS) and CO2.
Infact, the automotive coating processes adds way more to the environmental burden compared to other stages of vehicle manufacturing. It won’t be wrong to say that, although not in the form of thick black industrial pollution, the spray of colours has been emitting harmful chemicals into the air while painting the automotives. It is now of utmost importance to make the coating industry greener with sustainable colour formulations and application process.
The industry has been trying to bring in a balance for decades between meeting the customers’ demand for latest and the trendiest colours while making the automotive coating less polluting and harmful for the environment and the workers. Many companies are also trying to reduce fossil fuel dependence for making colour schemes more sustainable.
“By reducing our use of fossil raw materials, we can conserve natural resources and lower CO2 emissions at the same time. To achieve this, we are increasingly relying on sustainability innovations in our supplier network.
Innovative paints based on renewable raw materials are an important step in this direction,” said Joachim Post, member of the Board of Management of BMW AG, responsible for Purchasing and Supplier Network.
However, making coatings process sustainable is twice as challenging as the adhesives, the paints and the process of applying coatings all contribute to emissions.
The good news though is that coating manufacturers are working towards making sustainable coatings solution. Efforts are also being made to reduce this impact through legislation, resulting in the introduction of new coating formulations and application technologies. Moreover, with rising level of awareness, consumers are becoming environmentally conscious and are making informed choices to buy sustainable products. This gives an additional boost to the manufacturers to make sustainable products. Hence, there is a rise in the sale of green vehicles and practices.
Here are some ways in which the automotive coating industry is trying to reducing air emissions.
One of the primary ways to address the issue of sustainability in the coatings industry is to have paints with lower HAPs and VOCs. The two major types of coatings used today are waterborne and solvent borne coatings.
Solvent borne coatings are more popular as it is more durable and holds up better against humidity. It also spreads out thicker making it easier to cover the imperfections below. However, it is not a very environment friendly option. Waterborne paints, on the other hand, comprise of 80 percent water, making it a much safer paint option because it has a much lower emission of VOCs than solvent borne paint.
Many manufacturers are adopting waterborne solvents not just because they are better for the environment but also because they are much easier to blend, minimizes waste, and make cars aesthetically better.
It is during the painting process when the harmful chemicals from the paint are emitted into the air. However, not just the environment, this exposure to solvents and harmful chemicals poses great risks to workers in the industry leading to occupational asthma, headaches, and other lung issues are among the health problems workers. Although personal protective equipment (PPE) and trainings for proper application help reduce worker exposure to HAPs and VOCs in the auto industry, it is not yet enough.
Unfortunately, while solvents cannot be eliminated completely from paints, waterborne solvents which has lesser amounts of VOCs has way less environment impact that other paints. Powder coatings and UV cured coatings are also seen as environment friendly alternatives to solvent borne coatings.
The industry is making further innovations for eco-friendly alternatives so as to make paints completely safe for the environment.
Recently, BMW teamed up with BASF’s biomass balance approach and chose CathoGuard® 800 ReSource e-coat and the iGloss® matt ReSource clearcoat as its coating solutions. These coatings have been tested to be more sustainable versions as it enables CO2 avoidance of around 40% per coating layer. According to the company, this will reduce the amount of CO2 emitted in the plants by more than 15,000 metric tons by 2030.
“As the largest provider of chemical products to the automotive industry, we are aware of our responsibility to support our customers with innovative, eco-efficient solutions. The biomass balance approach allows us to make our coatings solutions even more sustainable while retaining the same quality. We are delighted that the BMW Group has chosen to play a pioneering role in the automotive industry and that our products play a key part in helping it achieve its ambitious sustainability goals,” said Dr. Markus Kamieth, member, board of executive directors of BASF SE.
In BASF’s biomass balance approach, renewable raw materials like bio-based naphtha and biomethane from organic waste are used as raw materials when manufacturing primary chemical products and are fed into the production Verbund. The proportion of bio-based raw materials is then arithmetically assigned to certain sales products according to a certified method. This use of renewable raw materials also significantly reduces the dependence on fossil resources.
Sustainability in automotive coating is becoming a very crucial aspect. Many major automotive giants are making a conscious decision to incorporate sustainable coating solutions. For this, major automotives are joining hands with coating experts.
Recently, AkzoNobel partnered McLaren’s racing team as its Sustainability Partner to introduce a more integrated approach for its high-performance coatings.
“Our shared focus on outstanding performance and pioneering innovation will help to propel us both forward and add a new dimension to our formula for success,” said Patrick Bourguignon, director of AkzoNobel’s Automotive and Specialty Coatings business.
“We’re looking forward to taking a more integrated approach to development that will see AkzoNobel support us on our mission to become a more sustainable team,” said Matt Dennington, director of partnerships at McLaren Racing.
The Sherwin-Williams Company also has joined hands with Gross & Perthun GmbH, a Germany based developer, manufacturer, and distributor of coatings primarily for the heavy equipment and transportation industries.
“This high-quality business brings us innovative waterborne and solvent liquid coatings technology and technical team focused on delivering innovative and value-added solutions,” said John Morikis, chairman and CEO, Sherwin-Williams.
Although several innovations are being made for sustainable coating solutions in the automotive industry, there is a lot more work to be done to reduce the overall air emissions and move the industry in the right direction. Better coating solutions are being tried and tested everyday so as the industry can finally contribute to make this world a better place with its colours sans the emissions.
a global leader in nutrition that powers many of the world’s top food, beverage, health and wellness brands, released its outlook on the global human microbiome market, which is expected to balloon to nearly $9.1 billion by 2026. The findings, based on research from ADM’s proprietary Outside VoiceSM consumer insights platform, highlight the consumer trends shaping the fastgrowing market for solutions that include prebiotics, probiotics, and increasingly, postbiotics. This deep dive into the microbiome segment builds on the release of ADM’s 2022 Global Consumer Trends report, which showcased the eight areas of focus for food, beverage, health and wellness, and animal nutrition brands this year. Made up of trillions of unique microorganisms, the human gut microbiome’s link to wellness is increasingly understood by consumers.
“There is a growing body of scientific evidence that links the gut microbiome to key aspects of health and well-being. Nutrition is one of the most effective tools at our disposal in supporting healthy microbiome function. ADM’s research is bringing new discoveries and insights to the fore – demonstrating the potential positive impacts of dietary microbiome support on aspects of health and well-being. By combining clinical research with investments in realworld applications, such as our partnerships with innovators like Nourished and Brightseed, ADM empowers its customers with the knowledge and solutions to meet consumer needs,” according to Mark Lotsch, president, Global Health & Wellness, ADM.
The path forward for nutrition solutions and dietary supplements that support the microbiome and help consumers meet their wellness needs relies on product innovation for new market segments, more personalized assessment tools and science-backed products.
The top five trends shaping the sector this year include:
Growing consumer awareness of the gut-brain connection and the link between microbiome function with mood and cognition
In partnership with FMCG Gurus, ADM’s Outside VoiceSM research found that more than half (58 percent) of global consumers are aware of the potential benefits that bacteria of the digestive tract may have on aspects of health and well-being. With growing awareness of the connection between mind and body, consumers are paying more attention to the impact their food, beverage and supplement choices may have on their well-being. In fact, 53 percent of consumers state that products designed to support brain health are appealing. Emerging research supports this connection: according to a study from the University of Oxford, BioKult’s multispecies probiotic supplement have shown that the product can support mood along with other related aspects of cognitive health.
Personalized nutrition solutions designed to support everyday performance for Olympians and Weekend Warriors alike
Consumers are adopting a more holistic view of their diet and lifestyle
choices, with gut health at the center. The microbiome has become the new frontier for the next generation of personalized nutrition, with growing evidence of links to sleep hygiene, overall mental wellbeing, immune function and more. Protein bars and ready-to-drink shakes are household staples for all active lifestyles—soon they will be tailored to support each individual’s specific activity and lifestyle needs.
Consumers are using test-kits to benchmark the make-up of their microbiome as the personalized nutrition phenomenon gains hold
Personalized assessment solutions are helping consumers learn more about their bodies, including analyses of their individual gut microbiomes – and these services are fast becoming mainstream. New technology in the field is equipping consumers with testing kits to benchmark the make-up of their microbiomes, and consumers are using this information to try new diet and lifestyle habits. More than half (59 percent) of global consumers find the idea of nutritionfocused genetic testing appealing, and of those, 64 percent would be willing to use this technology, according to data from FMCG Gurus.
Consumers increasingly believe the benefits of probiotics extend beyond the gut, and research is beginning to uncover the role of the skin microbiome and how probiotics may support skin health in both oral and topical applications. But in a crowded skincare market, consumers are looking for solutions that back up their claims. ADM has a rapidly growing number of clinical trials researching the role of the gut microbiome in skin health to inform its development of probiotic formulations that provide adjuvant support for the skin.
Consumer interest in immune health will be a top priority today and in the future
With the ongoing COVID-19 pandemic converging with a resurgent cold and flu season earlier this year, support for immune function remains top of mind among consumers. Research shows 75 percent of global consumers say they will make greater attempts to stay healthier, and 65 percent are more conscious of their immune health due to COVID-195. What’s more, 66 percent of global supplement consumers are seeking out supplements formulated to support immune function. While the pandemic has amplified conversations around immune health, the trend is likely to continue as consumers carry new nutritional routines into their new normal.
Together, these emerging developments in the field of biotic solutions supporting the microbiome, combined with growing mainstream consumer interest, have created a market with high growth potential. ADM’s team of researchers, nutrition scientists and regulatory experts, in concert with its innovative partners, puts the leading global food solution provider in a position to help shape the future of nutrition with the microbiome at its core.
This year’s theme for World Food Safety Day (June 7) - ‘Safer food, better health’, underlines the need for continuous efforts toward keeping food safe that is accessible to people from all walks of life. The theme emphasizes the golden rule of “Safety First”, which has a direct connection to ensuring food safety and security that aids in ensuring health and wellness but also influences a nation’s economic prosperity and sustainable development. It recognizes the growing concerns about foodborne illness and draws attention to the need for sustained action to detect and manage food-borne risks and calls for a more pre-emptive approach to ensure food security for all. Continuous monitoring for food safety hazards and food-borne diseases is one of the important ways to guarantee food security as it can reduce spoilage and losses during supply chain transit and decrease the incidence of food-borne diseases.
The US Center for Disease Control and Prevention (CDC) defines a food-borne disease (FBD) outbreak as “two or more illnesses/diseases caused by the same microorganism such as virus, fungi or bacteria, which occurs after consumption of the same food.” These outbreaks often affect populations of all ages while placing a significant economic burden on the government and industry as it results in product recalls and the need for significant source tracing. Federal agencies across the globe have laid down policies and guidelines for ensuring food safety throughout the supply chain. However, statistics still show that foodborne illness outbreaks are an ongoing concern. WHO highlights that food-borne diseases affect at least 1 in 10 people worldwide. The US FDA reported 585 food recalls in 2019, 495 in 2020 and 427 in 2021. The CDC and Singapore Food Agency (SFA) reports have resulted in product recalls ranging from onions to drinking water due to pathogenic contamination. Africa and Southeast Asia have the highest food-borne disease burden, with around 150 to 200 million cases accounted for annually.
These incidences show the global nature of food safety risks and the need for preventive action to ensure safe food that can meet the required nutritional demands of all age groups, leading to a healthier population. A key aspect of ensuring food safety is to continuously track and monitor potential contamination routes throughout the value chain and devise preventive strategies. Existing techniques and tools for contaminant tracking and detection are often time-consuming and are not widely adopted globally due to a
lack of infrastructure, cost, availability, or awareness. This poses a problem when food products are one of the most exported/imported commodities.
Technological developments in contaminant indicating materials, bio- and nano-sensors, imaging techniques, and molecular assays can overcome the challenges of existing techniques. The global transition to the digitalization era has led to the adoption of IoT, AI and data analysis tools for predicting possible contamination and facilitating timely action. The development of miniaturized, handheld, and remote monitoring devices for monitoring and detecting microbes, allergens, and other contaminants can ensure food safety.
Convergence of digital technologies with analytical and diagnostic tools and sensors can ensure rapid detection through real-time monitoring and efficient prediction, while the integration of spectral techniques and imaging tools, such as hyperspectral imaging or Terahertz sensing can improve physical and microbial contaminant detection. These technologies can provide quantitative and qualitative detection and be adopted by all stakeholders, including food producers, manufacturing and processing, and retail units for better food safety management. There is a need for multisectoral collaboration to design, implement, educate and follow up on food safety programs for a healthier today and tomorrow. At present, despite the presence of international food safety standards, country-specific and regional standards and guidelines often take precedence. While these ensure the safety of imported and locally sold food products, it can make global trade and exports a laborious undertaking.
A global legal framework with support measures for all stakeholders in the agriculture and food value chain can help in establishing global food safety systems that comply with international safety standards. It can also create a sustainable food production and transport system for providing better access to safer and healthier foods to endconsumers across geographies. However, this is not an easy task, and a collaborative approach between policymakers, industries, and consumers across nations and geographies is needed to ensure that current food chains are transformed sustainably to provide food safety and security for all to pave the way for a healthier tomorrow.
Author: Aarthi Janakiraman is Research Director, TechVision at Frost & Sullivan.The Indonesia adhesives and sealants market is estimated to witness a healthy growth, at an estimated CAGR of greater than 7 percent, over the forecast period of 2022 to 2027. Due to the COVID-19 outbreak, nationwide lockdown around the globe, disruption in manufacturing activities and supply chains, production halts have negatively impacted the market in 2020. However, the conditions started recovering in 2021. Presently the market has now reached pre-pandemic levels, thereby restoring the growth trajectory of the market studied during the forecast period.
• Increasing demand form packaging industry is expected to drive the market during the forecast period.
• Over-reliance on import of raw materials is likely to hinder the market’s growth.
• Growing popularity of bio-based adhesives is likely to create opportunities for the market’s growth in the future.
• By end-user industry, the paper, board, and packaging segment dominated the market.
• Water-borne acrylic adhesives are considered as an environmentally friendly and economically feasible substitute to solvent-based adhesives. The major advantage of water-borne adhesives is the absence of volatile organic compounds.
• The properties of the acrylics include durability, color retention, quick-drying, environmentally friendly, impact-resistant, etc. Acrylics are majorly used on exterior and interior surfaces, such as on frames, doors, wall surfaces, trim, etc.
• Acrylics can be applied to areas, such as primed metals, direct to metal applications, wood, and masonry surfaces. Acrylics are also used directly to metal or as a topcoat for many colors and gloss levels.
• The application of the acrylics includes bonding wood, paper, wall panel bonding, sealing (grouts), textiles bonding, paper stamps, leather tile envelopes, labels, etc. Acrylics are used by various end-user industries, such as buildings and construction, woodworking and joinery, paper, board, packaging, etc.
• Furthermore, acrylics are majorly used by paper, board, and packaging industries. Packaging industry dominates the demand for acrylic adhesives with numerous applications in products, such as tapes, labels, cases and cartons.
• Factors, such as e-commerce, online food deliveries, and innovation and development in the packaging industry has been driving the growth of the packaging industry in the country.
• Adhesives and sealants have been extensively used in the building and construction industry owing to their characteristics and physical properties. These properties include good adhesion and elasticity, cohesion, high cohesive strength, flexibility, the high elastic modulus of the substrate, resistance from thermal expansion, and environmental resistance from UV light, corrosion, saltwater, rain, and other weathering conditions.
• They have a myriad of applications. They are used in heating, ventilation, air conditioning (HVAC), concrete, joint cement, manufactured housing, resilient flooring, roofing, wall covering, prefinish panels, drywall lamination, joints in exterior walls, spandrels, repair of larger cracks, the perimeter of doors and fixed window frames, etc.
• Indonesia’s construction industry, is already worth 10 percent of the country’s massive GDP, is estimated to grow into one of the largest in the world in the coming decade.
• One of the major projects include, the construction of new Indonesian capital on Borneo Island named Nusantara, to replace Jakarta, 40 percent of which is estimated to be submerged by 2050. Moreover, the construction of new capital from the ground up is estimated to cost $32.4 billion.
• In April 2021, PT Jababeka Morotai, a subsidiary of Jababeka Group, has collaborated with the OISCA International College Foundation (OISCA International) for developing Morotai Special Economic Zone (KEK). Under this collaboration a World War II monument and supporting facilities are to be constructed in KEK, North Maluku Province, Indonesia.
• Indonesia also plans to develop $1 billion worth 900 MW hydropower project in Kayan River in the North Kalimantan (Kaltara) province. The project stands at EPC stage with startup date planned for 2022. Post completion of the construction, the project is expected to get commissioned in 2025.
• All the aforementioned factors, in turn, are expected to boost the demand for adhesives and sealants in the country during the forecast period.
The Indonesia adhesives and sealants market is a consolidated market with many healthy competitions in the market. The major companies (not in any particular order) include 3M, HB Fuller Company, Arkema Group, Sika AG and PT Henkel Indonesien, among others.
In Feburary 2022, Ashland Global Holdings Inc announced it has completed the previously announced sale of its Performance Adhesives business to Arkema in an all-cash transaction valued at approximately $1.65 billion. This will enhance adhesive segment of Bostik in Indonesia.
In April 2021, 3M announced its latest addition to a new class of silicone adhesives that balances strength, flexibility and comfort, the 2484 3M Single Coated Medical Film Tape with Hi-Tack Silicone Adhesive on Liner.
Sodium silicate has numerous uses, such as textile processing and metal cleaning, dairy equipment, floors, bottles, automobiles and floors. Sodium silicates are incorporated within synthetic detergent compositions to minimize corrosion and alkali attack. Without the use of sodium silicate, detergent compositions would be corrosive to zinc, aluminum, and other metal alloys in washers. Synthetic detergent composition silicate may also glaze the surface of fine china and porcelain decorations. Therefore, a rise in demand from the soap and detergent industry is projected to bolster the expansion of the liquid sodium silicate market size over the coming years, mentioned a report forecast 2020 to 2030.
Steady Growth of major End-user Industries such as Adhesives and Construction to Boost Sales: Sodium silicate is an excellent bonding agent for sealing fiberboard boxes, as it has the ability to firmly hold together the flaps in less time. A wide range of advantages of liquid sodium silicates include suitable viscosity, good setting properties, high strength, easy wetting of the surfaces to be held together, and controlled penetration.
It is primarily used as an adhesive, due to its ability to change from a liquid state to a semi-solid state as required, without excess water consumption. Liquid sodium silicate used in the binders of cement and increases the cement’s heat and temperature resistance. It also increases the waterproofing ability of the cement. The liquid sodium silicate market will witness a rise in demand from adhesive and construction industries.
Decrease in Groundwater Reserves Increasing Sales in Water Treatment Industry: Liquid sodium silicate’s semi-solid colloidal solutions, which act as coagulants, can be used for treating waste and raw water. Liquid sodium silicate increases the rate of floc formation, as well as floc density, size and stability. It also has the ability to act as a coagulant at low temperatures, therefore acting as an efficient filter aid. Unlike other waste water treatments, liquid sodium silicate does not require phosphate or zinc.
It forms a microscopic film, on the inside of the waste water treatment pipe, which acts as a corrosion inhibitor that prevents the leaching of lead solders. High pH level of liquid sodium silicate is used as an advantage in water treatment systems. Added in proper amounts, it can raise the system’s pH to the alkaline range to lower lead levels in municipal water treatment facilities. It can also help contain high amounts of manganese or iron to eliminate red-water staining.
High PH of Liquid Sodium Silicate Can be hazardous to Human and Aquatic Life: The pH of liquid sodium silicates ranges from 11.2 to 12.7, which makes it irritable to mucous membranes, the skin and eyes. If it comes in contact with the eyes, it can lead to pain, irritation, and conceal burns, which might also result in blindness.
The psychological effects of the contact of liquid sodium silicate on the eyes depends on the alkalinity of the silicate causing irritation due to chemical burns. Inhaling mists or the musty odour of it can lead to moderate effects such as cough, pain, and choking. Sodium silicate is not stable in aquatic systems, but is acutely toxic to aquatic life. It has exhibited low to medium toxicity to aquatic organisms and low toxicity to terrestrial organisms.
High pH levels of liquid sodium silicate could therefore hamper the growth of the liquid sodium silicate market.
Tier-1 players account for around 35-40 percent of the global liquid sodium silicate market share, which is estimated to be consolidated in nature. Key participants in the global liquid sodium silicate market are PQ Corporation, OxyChem Corporation, WR Grace & Company, PPG Industries Inc, BASF SE, Evonik Industries AG, Glassven CA, Kiran Global Chem Limited, Nippon Chemical Industrial Co Ltd, Comfia Industries Pvt Ltd and others. To gain a competitive advantage in this landscape, market participants are investing more in R&D activities so as to launch new products.
The COVID-19 pandemic has resulted in lockdowns, travel restrictions, and huge decreases in industrial activities across the world. As far as the global liquid sodium silicate market is concerned, it is projected to experience a sharp decline in all applications except detergents & cleaning compounds, in the year 2020-2021.
The global liquid sodium silicate market is estimated to witness substantial growth, owing to increasing use in the detergent & soap industry, where liquid sodium silicates are used with synthetic detergent compositions to minimize alkali attacks and control corrosion. East Asia is anticipated to account for around two-fifth of the global liquid sodium silicate market share in 2020. The detergents & cleaning compounds segment is estimated to hold more than onethird of the market share, and is projected to dominate the market over the forecast period.
The market size for paints & coatings is projected to grow from $184 billion in 2021 to $212 billion in 2026, at a CAGR of 2.9 percent. The key factor driving the growth of the market includes the increasing demand from end-use industries. The residential sector, by end-use industry in APAC region is expecting a boom in the forecasted period and will lead to an increase in the demand for paints & coatings.
According to recent updates by the IMF (International Monetary Fund), there will be a recession as bad as the global economic crisis of 2008 or worse in 2020. The IMF has warned of a total output loss of $9 trillion of the world economy between 2020 and 2021. The extent of the economic damage still depends on how the virus spreads in Europe, the US, and other major economies.
• According to economists, the Chinese economy is likely to be hit further by reduced global demand for its products due to the effect of the outbreak on economies around the world. As the pandemic escalates, the growth rate will fall sharply against the backdrop of volatile markets and growing credit stress.
• Initial data from China suggests that its economy has been hit far harder than projected, although a tentative stabilization has begun. In Europe and the US, increasing restrictions on travel & transportation and prolonged lockdown will lead to a demand collapse that is expected to recover a little in the second quarter before significant recovery begins later in the year.
• Central banks have swung into action and are undertaking some combinations of sharply reduced policy rates, resumed assets purchase, and liquidity injections. Fiscal authorities have generally lagged but begun to loosen their purse strings. It is expected that larger and more targeted spending to the most affected groups is forthcoming.
• Restrictions on movement in Europe and the US are putting a severe dent on economic activity. India and Southeast Asian countries are also facing major disruption in their economies.
New rules and regulations such as the Eco-product Certification Scheme (ECS) are set by the European Commission and other Federal government agencies. These regulations ensure a green and sustainable environment with minimum or zero harmful VOC emissions. Also, the regulations on lead control in household and Paints & Coatings were implemented in 2016, after the Quality Council of India (QCI), Pollution Control Board Authorities, and the National Referral Centre for Lead Projects in India (NRCLPI) strongly recommended to the Government of India (GOI) to fix lead content below 90 ppm for all decorative and household paints. These regulations encourage Paints & Coatings manufacturers to invest in bio-based raw materials within paints & coatings, making the Paints & Coatings more eco-friendly. In addition, government regulations in the US and Western Europe, especially concerning air pollution, will continue to drive the adoption of new, low-polluting coating technologies.
There is more time required for drying and curing of waterborne coatings than that of the solventborne coatings. In addition, waterborne coatings have excellent flow properties that change with humidity, affecting the coating application. During high humidity, water does not easily evaporate, resulting in poor cure and a decrease in performance. Waterborne coatings are also sensitive to freezing conditions. Many waterborne coatings are not usable after freezing.
Opportunities: Increasing applications of fluoropolymers in the building & construction industry
In the building & construction industry, fluoropolymers such as polyvinylidene difluoride (PVDF) are used in both industrial as well as architectural coatings. PVDF is used especially in architectural applications, where both excellent appearance and substrate protection have to be maintained for a long period. PVDF is the most preferred fluoropolymer since it has enough solvency in ester and ketone solvents and the same can be formulated into solvent dispersion coatings.
With the increasing number of regulatory policies adopted by various governments, paints & coatings producers have to constantly improve their processes to comply with the new policies. Products that fail to meet the legal
requirements are not allowed in the countries that have strict environmental regulations, especially in Western Europe and North America.
Unfortunately, some legislators continue to limit emission values based only on the concentration of VOC in the exhaust gasses. This can lead to approval for high mass emissions from processes which require high airflows as against low mass emissions, which need only very low airflows. The concentration approach also ignores the reduced atmospheric emissions when low-VOC coatings are used.
Residential end-use industry segment accounted for the largest share in 2020
Residential end-use industry is the largest sector for the market. Paints & coatings are widely used in residential construction to reduce the shrinkage and cracks in the concrete and to improve its aesthetic quality and workability. Economic growth and higher incomes in the last few years have resulted in the construction of several new houses and remodeling of old ones. Architectural paints and coatings for residential construction include new paint and repainting. These coatings mainly include architectural and functional products, such as paints, stains, lacquers, primers, and cleaners. Architectural paints and coatings are used in both interior and exterior applications in the residential sector. Repainting is associated with giving a new look to an old or worn-out interior and exterior of a construction.
APAC is projected to be the fastest-growing market during the forecast period. The region comprises countries with different levels of economic development. The growth in the region is mainly attributed to the use of Paints & Coatings in different end-use industries such as architectural (residential and non-residential), and industrial.
The market size for global piperidine market is projected to grow from $64 million in 2022 to $86 million by 2027, at a CAGR of 5.9 percent from 2022 to 2027. The growth of the piperidine market is attributed to their high demand as solvents, base and catalyst in pharmaceutical, agrochemical and others industries.
99 percent purity segment to be largest type of piperidine
Piperidine with 99 percent purity and above is the purest form of piperidine available. The pharmaceutical end-use industry is boosting the demand for piperidine with 99 percent purity. Some piperidine derivatives, namely, N-Methyl, N-Benzyl piperidone derivatives, are extremely useful and versatile API intermediates in organic synthesis.
Agrochemicals refer to the chemical products used in the agriculture field. They are comprised of pesticides, fertilizers, and other plant-growth hormones used in agriculture. The demand for agrochemical products is driven by the increasing global population and requirements to fulfill the increasing demand for food from limited croplands available.
Emerging economies in the region are expected to experience significant demand for piperidine because of the growing pharmaceutical and agrochemical industries. In addition to this, the growing population in these countries represents a strong customer base. According to the World Bank, Asia Pacific is the world’s fastest-growing region in terms of population and economic growth. Factors such as the ready availability of raw materials and workforce, along with sophisticated technologies and innovations, have driven the economy in Asia Pacific.
The piperidine market comprises major manufacturers, Jubilant Ingrevia Limited (India), Vertellus (US), KOEI Chemical Co Ltd (Japan) and BASF (Germany). among others.
The global polycarbonate sheets market size was valued at $1.5 billion in 2021, and is projected to reach $2.6 billion by 2031, registering a CAGR of 5.7 percent from 2022 to 2031. Polycarbonate sheets are transparent thermoplastic sheets. These are highly tough in nature with moistureabsorbing as well as flame-retardant, chemical resistant, and impact-resistant properties. Polycarbonate sheets are used in numerous applications such as window glazing, medical equipment, food processing, skylights, and roofs. Further, these sheets are used in various industries such as automotive, building & construction, and electrical & electronics. Their properties such as high strength, optical clarity, thermal stability, and exceptional dimensional stability make them material of choice in production of electric components, riot shields, headlamp lenses, vandal-proof glazing, baby-feeding bottles, and safety helmets.
Demand for polycarbonate sheets is expected to increase in the future, owing to rise in demand for product roofing systems. In addition, growth in the automotive industry is expected to boost the market growth. There is increased use of polycarbonate sheets for producing headlamps, mirrors, and vehicle body parts globally. However, negative environmental impacts of polycarbonate sheets hamper the steady growth of the market. Nonetheless, growth of the agriculture industry, along with rise in demand from the sector is anticipated to create lucrative opportunities for the polycarbonate sheets market growth.
The global polycarbonate sheets market is segmented on the basis of type, end-use industry, and region. By type, the market is classified into solid, multiwall, corrugated, and others. By end use-industry, the market is categorized into building & construction, electrical & electronics, automotive & transportation, aerospace & defense, packaging, and others. Region wise, the market is analyzed across North America, Europe, Asia-Pacific, and LAMEA. Region wise, Asia-Pacific holds the highest global polycarbonate sheets market share, owing to surge in demand for these sheets in commercial applications in the region.
The key players profiled in the report include Covestro AG; Emco Industrial Plastics; Exolon Group; Jiaxing Innovo Industries Co Ltd; PALRAM INDUSTRIES LTD; Polyvalley Technology Co Ltd; SABIC; Spolytech; TEIJIN LIMITED; and UVplastic Material Technology Co Ltd. Other players in the value chain of the polycarbonate sheets market include Suzhou Omay Optical Materials Co Ltd, Gallina, Spartech, Koscon Industrial SA, ISIK Plastik, Safplast Company, Brett Martin Ltd and others.
These companies compete for the share of the market through product launch, joint venture, partnership, and expansion of the production capabilities to meet the future demand for the polycarbonate sheets market during the forecast period.
For instance, in 2021, Seraphin Group, the parent company of Exolon, acquired Covestro’s European polycarbonate sheets business, which comprises manufacturing units in Belgium and Italy, central management operations, and sales support in Europe. This acquisition has strengthened its polycarbonate sheet business.
Asia- Pacific occupies the largest part of the polycarbonate sheets market. The market growth in the region is driven by growth in end-use industries. In addition, rise in demand
from construction and electronics industries is anticipated to propel the market growth in the coming years.
The multiwall segment dominated the global polycarbonate sheets market, in terms of revenue, in 2021, owing to its properties such as high impact strength, high clarity, and lightweight. Besides, it is widely used in applications such as canopies, displays, conservatories, roof lights, signage, vertical glazing, swimming pool roofs, insulation, walkways, and others.
The electrical & electronics segment held the highest global polycarbonate sheets market size, in 2021, owing to growth of the electronics industry along with growing inclination towards smart homes and smart offices environment in the region. Polycarbonate sheets are a promising material for building sensor components, LCD pieces, switching relays, laptops, mobile phones, cables, CDs, and DVDs, owing to its lightweight and high impact properties.
The COVID-19 pandemic negatively impacted the overall polycarbonate sheets market and supply chain. Issues regarding supply and demand for raw materials, owing to lockdowns and stringent government laws hindered production, thereby negatively impacting production facilities globally. Moreover, the pandemic negatively impacted building & construction, automotive, and electrical & electronics sectors which are the major endusers of polycarbonate sheets. However, with the COVID-19 vaccination campaign globally and as the economies are getting stable, there is growth in the demand from enduse industries, which in turn is anticipated to augment the demand for polycarbonate sheets in coming years.
Source: Allied Market ResearchRussian specialty chemicals market is a major contributor to the economy for the chemical sector within this region.
The government continuously works in order to upgrade the country’s chemical market. The production of chemicals in the country in 2020 increased by 6.7 percent compared to the previous year. The Russian government plans to invest up to $285 million to develop the national specialty chemicals industry in the country. The country imported fine and specialty chemicals worth nearly $7.4 billion in the year 2019.
The Russian specialty chemicals market is still in the developing stage as compared to other chemical segments like the commodity chemicals market. The country has limited technology for the production of specialty chemicals. Russia majorly imports various specialty chemicals. This trend has, however, changed over the years. Various MNCs have entered the Russian specialty chemicals market. These companies have set up their sales operation or manufacturing operation sites in the country. The domestic players on the other hand largely depend on the production of commodity chemicals which require minimal processing. Neohim is associated with the production and development of specialty chemicals for various leading industries. The company attention to the introduction of its products at plants, providing services on the scientific and technical aspects of the client’s production. It is one of the members of the Expert-Ecology-Neohim Group of Companies. Banmark is a Finnish company and is operating in the Russian chemical market since 2004. The company provides the most advanced methods for solving complex problems in the paper and pulp industry based on modern technologies. Neohim and Banmark have been strategic partners for more than ten years. Neohim produces chemicals in the country using European raw materials following the quality standards provided by Banmark.
The pharmaceutical industry, which involves the production, development, and marketing of medicines is actively expanding in Russia. The Russian pharmaceutical industry is expected to grow by 147 percent during 2017 and 2030. The industry was dependent on import trade which was valued at around $13.8 billion in 2019. One of the driving forces for the pharmaceutical industry is the evolution of online retail for over-the-counter medication. Physical stores are not permitted to sell these drugs. Due to the COVID-19 pandemic, laws legalizing the sales of OTC drugs were adopted in Russia. The Russian pharmaceutical industry was valued at $4.32 billion in the year 2020.
Pfizer is one of the leading pharmaceutical companies, founded in New York. The medicines and vaccines manufactured by Pfizer help people fight various diseases. Through global resources and innovation, the company improves the health and well-being of people at every stage of life. Pfizer produces pharmaceuticals and vaccines along with various world-renowned vitamins. The employees of Pfizer work in developing and developed countries to prevent and treat today’s most serious diseases. Pfizer now operates in more than 50 countries.
Pfizer opened its first production site in Russia in 1992. The company’s diversified product portfolio includes biological small molecule drugs and vaccines for humans. Pfizer also produces products for healthy nutrition and a range of overthe-counter drugs around the world. Presently, more than 100 products manufactured by Pfizer are registered in the Russian Federation. The drugs produced by Pfizer are used for the treatment of diseases of the musculoskeletal system, cardiovascular system, urological drugs, and antibiotics, among many others. The latest scientific developments have changed the paradigm of the treatment of socially significant diseases. Pfizer has significantly contributed to the development of Russian innovations in the field of medicine. The company has been involved in the modernization of the pharmaceutical industry. The treatments offered by Pfizer have improved the quality of medical care, increased life expectancy, and have improved health and quality of life.
During the COVID-19 pandemic, vaccination continues to be critically important. The pandemic has caused a decline in the number of children receiving routine immunizations. This reduction could lead to an increase in illness and death from preventable diseases. WHO has urged countries to ensure the continuation of essential immunization and health services. Pfizer has also developed the vaccine for COVID-19. Russia
has registered two vaccines for domestic use. Pfizer was seeking approval for the new COVID-19 vaccine developed in Russia.
BIOCAD is one of Russia’s leading innovative biotechnology companies, combining a world-class research and development center. The company has ultra-modern pharmaceutical and biotechnological manufacturing facilities. BIOCAD exports the medicines it produces to 24 countries. The company has an excellent preclinical and clinical research infrastructure compliant with international standards. BIOCAD is one of the world’s leading full-cycle drug development and manufacturing company. They are involved in the discovery of a new molecule and genetic engineering to large-scale commercial production as well as marketing support. The medicines produced by BIOCAD are used to treat complex health conditions including rare genetic anomalies. These medicines are also used in the treatment of cancer, autoimmune diseases, and orphan diseases.
The Russian specialty chemicals market is expected to witness excellent growth in the coming years. Rhodia is expected to maintain its lead in the country’s specialty chemicals segment with a 23% market share. The rise in end-user applications in the automotive, oil, gas, and construction sectors has increased the demand for specialty chemicals in Russia. Presently, nearly 50 percent of the demand for specialty chemicals is met through imports. The Russian manufacturers usually export raw materials to the developed nations. They in turn import the high-value specialty chemicals, causing profit margin erosion. The government, has, therefore, targeting the reduction of imports of specialty chemicals to 12 percent. To meet the demand, the country is developing domestic production for complex secondary chemical formulation.
Source: Chemical Market ForecastClean air is a basic human right. However, ironically, the idea of ‘clean air’ might soon become a surreal concept. Today, every human is constantly exposed to toxic air and this exposure which has been seeping into our system for decades is now starting to show its side effects. Exposure to toxic air is one of the prime reasons which has led to a spike in various health issues including cardiovascular and respiratory diseases, lung and other cancers, strokes, type-2 diabetes, and other illnesses in this generation.
Among various type of air pollution, industrial air pollution is among the major culprits behind climate change. The United Nations Sustainable Development Goals too has put a huge emphasis on curbing air pollutions. Out if its 17 goals, several goals focus on air pollution. For instance,
Goal 3: Good Health and Well-Being: Focuses on reducing mortality rates by decreasing hazardous chemicals in air, water and soil.
Goal 9: Industry, Innovation and Infrastructure: Targets to upgrade infrastructure and retrofit industries to make them sustainable, with increased resource-use efficiency and greater adoption of clean and environmentally sound technologies and industrial processes.
Goal 11: Sustainable Cities and Communities: Emphasises on the reduction in adverse per capita environmental impact of cities by 2030, by paying special attention to air quality.
Goal 12: Responsible Consumption and Production: Aims to achieve environmentally sound management of chemicals and all wastes throughout their lifecycle and significantly reduce their release to air, water and soil in order to minimize their adverse impacts on human health and the environment.
Most countries have imposed stringent rules on industries to
minimize air pollution. Yet, most chemical companies today are struggling with the global demand to be sustainable and curb the amount to air pollution that their plants release.
This quest for carbon neutrality can be a reality if you have the right technology in place. Technologies that reduce air pollution can have significant benefits on health, productivity, and overall welfare while potentially giving the world a path to reduce carbon emissions and meet targets to slow climate change.
Understanding this need gap, worldofchemicals.com and Chemical Today magazine along with technology partner, Dürr, has organised a virtual conference on July 8th, focusing on Exhaust Air Pollution Control Systems.
Dürr offers a comprehensive range of Exhaust Air Pollution Control Systems that remove all traces of these pollutants from exhaust air. The company’s state of the art exhaust air pollution control technologies provides environmental solution to customers around the world.
Dürr’s Oxi.X RE/ Oxi.X DF/ Sorpt.X CA/ are the most efficient technologies which are able to destruct/control volatile organic compounds generated across industries and to keep the exhaust gas emission levels within the limit. These technologies dispose the exhaust gases efficiently with reduction in energy consumption, operating expenditure and guarantee high reliable process.
Our panellist will delve into the latest trends in Clean Technology Systems, Environmental Solution for Industry emissions and Solvent Recovery System. The virtual conference will be of great importance for companies who are struggling to make their operations sustainable and for those who want to improve their carbon neutrality with better technologies to curb exhaust air pollution.
Our world is facing severe climate change issues due to industrial pollution, environment pollution, unmanaged waste disposal and many such pollutants. The planet is becoming a dumping yard of toxic waste released into ocean, fumes of hazardous gases released from factories and millions of tonnes of plastics left buried in the soil. With every inch of this world being covered with some kind of pollution, climate change is threating the survival of this planet.
The oil, petrochemical and refinery industry, which forms one of the core industries that rule the global economy, is considered to be part of the sector contributing to the climate change issues. However, most companies are taking notice of the concerns and are looking at implementing new and sustainable ways of operating as the need of the hour. Hence, the Oil & Gas, Petrochemicals and Refining Industry is undergoing a 360-degree transformation to be in sync with the UN sustainable development goals. Giving an added thrust to this transformation, the industry is witnessing demand for renewable sources of energy rather than dependence only on fossil fuels. Further, the industry is considering environmentfriendly and sustainable alternatives that will improve the move towards net zero, reduction in carbon
footprint and even minimize the harmful effects of climate change.
However, while many major companies are investing heavily into R&D for the right technology and making their operations sustainable, many companies are still dwindling over where to start and the right pathway to attain sustainability.
Understanding these concerns, the knowledge gap, the need to collaborate, share industry know-how and peep into the future regarding how the segments will pan out moving forward in India, Worldofchemicals and Chemical Today, took the initiative to organize the OPR Summit 2022: Future of Oil, Petrochem and Refinery Industry. The virtual conference, which was held on June 17th, had an illustrious group of panellists from some of the top petrochemical and refining companies in the world.
Over all, the oil, petrochemical and refinery industries are gearing up towards bringing in sustainability, recyclability and clean energy in the future. The virtual conference was attended by over 200 people from all across India who went back with ideas to take their organizations onto the part of becoming more sustainable and circular.
The industry has a twin dilemma - we need more energy but we should emit less carbon. On one hand we have the GPD growth, population expansion and urbanization and on the other hand we need to have energy for all while addressing the climate change and air pollution situation. It is a very difficult challenge to address. This has resulted in net zero promises by most companies across the world.
While most companies have committed to net zero by 2050, India has committed to net zero by 2070. For a country like India, it is essential to make sure that every citizen has access to the right type of energy at all times. Hence, in the next 20 years, India needs to lay the foundation for a long term, seamless strategies to achieve net zero.
There are three-fold challenges in this transition to net zero:
Technological challenge: We have not yet commercialized technologies which are required to achieve net zero like carbon capture, sequestration, carbon-di oxide removal etc.
Financial Challenge: The world needs $9.2 trillion per year to meet the climate change goals. However, the current global energy sector spent is only $ 5.7 trillion per annum. Hence, there is a big leap in funding required.
Socio Economic challenge: This is the most important challenge as there is a need for a ‘just’ transition so that the citizens of India will not be put into too much of burden. In the fossil fuel sector in India, we employ a workforce of more than 2.6 million people which manifests the need for an orderly transition.
There are a lot of changes happening in the global industry towards sustainability: for eg: electric vehicles, digitization etc. The Indian industry needs to be in sync with the changes and transformation happening globally.
Worldofchemicals and Chemical Today Magazine organized the OPR Summit 2022 virtual conference on 17th June. The conference gave a national & international perspective, discussed ongoing projects and opportunities in the Oil, Petrochemicals and Refinery Industry in India.
Oil is a key factor in our energy basket. With the rise in electrical vehicles, ethanol blending etc, we will be having surplus oil in the future which should be used judiciously in the petrochemical production The Indian Chemical industry is poised to reach $300 billion by 2025 driven by rising demand in the end-user segments for specialty chemicals and petrochemicals segment.
India is one of the largest global Chemical Markets, sixth in the world and fourth in Asia with respect to global sales of chemicals. India accounts for 2.5 percent of the world’s global chemical sales.
Petrochemicals are the fastest growing sector in oil industry demand. The global olefin market is set to see capacity additions of over 15 million tonnes in 2022 which will have global ethylene operating rates plunging down to 84 percent. Ethylene capacity additions of 41 million tonnes is expected between 2022 to 2026 out of which 50 percent will come in from northeast Asia (primarily China).
India has only 11 crackers whereas China is five times bigger than us with 56 crackers. In
the refinery segment, India has a capacity of 5.32 million barrels per day as against China’s 16 mn BPD. In ethylene and propylene segment, there is a huge demand supply gap likely to happen from 2025 to 2040.
Currently, we are hugely import dependent in petrochemicals and out of the 20 imported petrochemical products in 2020, we are importing almost 50 percent of our PVC, methanol, acetic acid, polycarbonate demand.
However, the bright side is that the PE market will see major growth in Packaging, Consumer Durables, Infrastructure and Agriculture sectors. The packaging industry alone accounts for 48 percent of the total polymer consumption in India with a growth rate of 15 percent and the pandemic saw an exponential growth in this sector.
Worldofchemicals and Chemical Today Magazine organized the OPR Summit 2022 virtual conference on 17th June. The conference gave a national & international perspective, discussed ongoing projects and opportunities in the Oil, Petrochemicals and Refinery Industry in India.
Plastic is a miraculous material. It has applications right from packaging to medical applications. But the major problem is of plastic pollution and the global awareness about plastic pollution and its impact on the ecosystem continues to grow. Businesses are facing growing pressures from regulators and NGOs on how to deal with plastics. SABIC also believes that plastics should not end up as waste. It should be used again and again.
We all see plastic waste all around us. Our aim is to convert these products into useful products. We need to prevent plastics from leaking into the environment and for plastics which have already leaked into the environment, we need to bring them back and put them into use.
SABIC has been successful in converting waste plastic material to useful packaging solutions. Many multinational companies are buying these recycled plastics as it is becoming a regulation in the Europe to incorporate at least 25% of the recyclable or renewable content in the products. This gives a huge opportunity for this kind of technologies to be adopted in India and make a difference.
In advanced recycling of plastics, we can convert mixed plastic waste into pyrolysis oilwhich has the composition similar to fossil feedstock- and feed it back into the cracker to make materials which are as good as virgin material.
Currently, a portion of pyrolysis oil is mixed with fossil fuel and fed into steam cracker. However, the vision is that as the technology gets enhanced, we aim to increase the portion of pyrolysis oil into the fossil feedstock to make a polymer. We are also collecting mixed plastics from ocean and river and converting them into pyrolysis oil and finally making virgin quality products.
SABIC is also working towards capturing CO2 from industries and converting them into useful products like urea and methanol.
Worldofchemicals and Chemical Today Magazine organized the OPR Summit 2022 virtual conference on 17th June. The conference gave a national & international perspective, discussed ongoing projects and opportunities in the Oil, Petrochemicals and Refinery Industry in India.
Thecrude oil price fluctuations have put a strain on the margin of the industry. Along with this the environmental impact, advent of EVs and renewables have had an impact on the refinery industry.
As per Energy demand projections, Oil & Gas is expected to maintain its largest share in the energy mix till 2045, however, oil demand is expected to reach plateau by 2035 and renewable energy growth will pick up momentum after 2025. Because of this, the Refiners are forced to explore high margin chemicals production. There is a dire need to increase the petrochemical yield. Most refineries are exploring the latest trend of COTC (Crude to Chemical) technology which will be adopted widely as it gives higher yield of chemicals per barrel of crude.
The Crude to Chemical technology can give up to 80 percent petrochemical yield and is being successfully implemented in many refineries in China currently.
Once we achieve this, our path to go beyond COTC would be to achieve a One Pot Configuration- where there will be one reactor which will have integrated reaction, stripping and regeneration and will take crude to make the petrochemical. This will lead to an increased light olefins yield (>30 percent) &
reduced coke yield. HPCL has developed its patented HP-COAT process which will have just one unit that will directly take the crude and produce 40 percent of the petrochemicals yield.
The future trends will also be towards Carbon Neutral Refinery with new technologies and novel materials can capture CO2 from Refinery emissions. There is also a lot of excitement around CO2 valorisation to fuel and chemicals, Green Hydrogen technology through water splitting using renewable energy etc.
Refining also needs to undergo transformation. Traditional refineries use crude oil and uses power to produce conventional chemicals and fuels. Down the line in the future, we are all talking about low caron refineries, feedstock will come from pyrolysis or biomass. Gas and water can be used to produce hydrogen and we can have e-fuels which will define the future of low carbon refineries.
Worldofchemicals and Chemical Today Magazine organized the OPR Summit 2022 virtual conference on 17th June. The conference gave a national & international perspective, discussed ongoing projects and opportunities in the Oil, Petrochemicals and Refinery Industry in India.
Flare system is common to all facilities in hydrocarbon sector- upstream or downstream; and everybody’s endeavour is to reduce the flaring to bare minimum and reach Zero flaring. However, zero flaring is a misnomer as we can only minimize flaring and bring it to almost zero levels.
There are 3 sectors of flaring- Routine flaring, Safety flaring and Non-routine flaring. However, the key point here is that if you want to reduce flaring, you have to measure it properly. As you can’t control something that you cannot measure. Most companies specify a flare meter which starts from the purge gas and which they want to capture the peak flaring. However, there is no meter in the world which will have such high turndown. The best way to measure purge gas is by rotameters and peak loads can be measured with an ultrasonic flare gas meter.
Another important aspect is the OSD requirements for the spacing between the
flares and other facilities. We generally refer to OSD 118 standards which manifests on putting up a sterile area of 90-meter radius. It is a very paradoxical requirement as many refineries may not have this sterile area as it is difficult to maintain. There are also other limitations for maintaining this sterile area in every facility.
Lastly, there is a debate on whether to release a poisonous gas like H2S or burn it -converting it into SO2, which is also very toxic. Yet another paradoxical situation where there is no safer way out.
Worldofchemicals and Chemical Today Magazine organized the OPR Summit 2022 virtual conference on 17th June. The conference gave a national & international perspective, discussed ongoing projects and opportunities in the Oil, Petrochemicals and Refinery Industry in India.
Methane, the main component of natural gas, shale gas and flammable ice, is a clean and inexpensive chemical feedstock with abundant reserves. Nevertheless, the high C-H band energy and low polarizability of a methane molecule inhibit the utilization of methane.
Recently, a research team led by prof. LIU Zhongmin and prof. ZHU Wenliang from the Dalian Institute of Chemical Physics (DICP) of the Chinese Academy of Sciences (CAS) developed a novel route to directly transform CH3Cl to acetic acid through a carbonylation reaction using acidic zeolites as the catalyst.
The study was published in Angewandte Chemie International Edition in May.
The researchers used pyridine-treated MOR as catalysts to achieve high acetic acid and methyl acetate selectivity. They found that the coupling of CH3Cl with CO and H2O occurred over acidic
zeolites especially one-dimensional with 8-member ring (8 MR) or 10-member ring (10 MR).
In particular, the selectivity of acetic acid and methyl acetate reached 99.3 percent over pyridine-treated MOR under the optimized conditions, which was superior to that of Rh/AC under CH3I-free conditions. The Bronsted acid sites in 8 MR were proven to be the main active site for chloromethane carbonylation.
Moreover, with multiple characterizations, the researchers proposed the reaction mechanism which included the chemical adsorption of CH3Cl, the formation of acetyl groups, and the hydrolysis of acetyl groups.
“Our study may present potential in the efficient and practical transformation of methane into oxygenates in the future,” said Wenliang.
They are also generally toxic to humans. Catalytic oxidation of organic pollutants in water, without electrochemistry, addition of electron-accepting oxidant chemicals, or photochemistry, has not been sustainably demonstrated to date, McCurry said. Until now.
With platinum, the process speeds up. For a while, McCurry and his team of researchers used platinum to oxidize different pharmaceuticals as a matter of experimentation.
“We knew we could oxidize certain things, but we didn’t have a clear application in mind for this catalyst,” McCurry said. Ultimately, their hope was to find an impactful application for their work. Eventually, after a year of experimenting, the idea came to him while riding his bike home from Stanford’s campus. “What if we could use platinum in water treatment to oxidize contaminants?” he said. “It would happen essentially for free, and because the oxygen is already in the water, it’s the closest you could get to a chemical-free oxidation.”
As wastewater treatment for potable – drinkable – reuse becomes a more viable and popular option to address water shortages, the question of what harmful byproducts might form in treatment and how to address them looms large. One group of these chemicals, aldehydes, are known to stubbornly persist through treatment. Toxic to humans, aldehydes will be at the top of the list of regulated byproducts in forthcoming reuse regulations, University of Southern California (USC) researchers believe, and require sustainable methodology to be removed from our drinking water.
In research published in Environmental Science & Technology, USC Viterbi School of Engineering researchers introduce platinum to help clean even the most stubborn toxins from wastewater. Platinum, the same metal used in catalytic converters to clean up air pollutants in car exhaust, can serve as a catalyst, said Dan McCurry, assistant professor in civil and environmental engineering, speeding up oxidation to transform once-toxic aldehydes into harmless carboxylic acids.
When wastewater is recycled, McCurry said, the resulting water is “very pure, but not 100 percent pure. There’s still a tiny amount of organic carbon detectable and these carbon atoms could be attached to molecules that are very toxic or completely innocent.”
A study conducted by UC Berkeley researcher David Sedlak revealed that “one-third to one half” of these molecules are present in the form of aldehydes, McCurry said. Aldehydes are chemical compounds characterized by a carbon atom that shares a double bond with an oxygen atom, a single bond with a hydrogen atom, and a single bond with another atom or group of atoms.
The breakthrough, McCurry said, is not as relevant for most existing water reuse plants, as many of them favor “indirect potable reuse.” This is where, after all the water treatment and recycling processes are complete, water is pumped back into the ground—so they are essentially creating new groundwater. “Once they are in the ground, it’s likely some microbe will eat the aldehydes and the water will be cleaned that way,” he said.
“But more and more people are talking about direct potable reuse,” he said, “where we are talking about a closed water loop where water goes from the wastewater treatment plant to the reuse plant and then either to a drinking water plant or directly into the distribution system into homes and businesses.”
In these cases, aldehydes could potentially reach consumers, McCurry said. While they are currently unregulated, McCurry suspects that the presence of aldehydes in recycled wastewater will soon attract regulatory attention.
The team did a preliminary experiment using platinum in batch reactors on a few gallons of water. The experiments were successful, but McCurry said for this to catch on at a mass production level, additional research would need to be done regarding how long the catalyst remains active. The team is looking into how to potentially regenerate the catalyst, as well. McCurry said it will also be important to test the system with dirtier water, which can foul up the catalyst and make it less effective.
The process, for which the team has a patent pending, will look to be more sustainable than alternative methods which might require introduction of additional chemicals and energy, McCurry said.
An international research collaboration between Kobe University and Inner Mongolia Medical University has developed a simple, low cost and comparatively environmentally friendly method of synthesizing diphenylmethanol derivatives using alumina from China. Diphenylmethanol derivatives are used as raw materials in the manufacture of perfumes and pharmaceuticals, among others. The researchers discovered that alumina can be repeatedly reused for this reaction if it is washed with water and dried between usages. This recycling reduces both the need for more alumina and the amount of waste produced, lowering synthesis costs and the impact on the environment. As global environmental awareness continues to increase, the researchers hope that this new method of chemical synthesis will contribute towards realizing a carbon neutral society and achieving the SDGs.
This discovery was made by an international research group, which included associate professor TSUDA Akihiko of Kobe University Graduate School of Science (who is also a visiting professor at Inner Mongolia Medical University) and researchers from Inner Mongolia Medical University, including professor CHAOLU Eerdun (who obtained their PhD. from Kobe University’s Graduate School of Science) and lecturer LIANG Fengying.
A patent application for this method was filed in China in April 2021, with a priority claim application made in September of the same year. Subsequently, the results of this research were published online in the academic journal ‘ChemistryOpen’ in May.
China is the world’s biggest producer of alumina, producing 77.48 million tons in 2021 (source: JOGMEC Mineral Resources Information). Various useful functions of alumina have been discovered; it is recyclable and it can be used as a catalyst, an adsorbent and for organic synthesis.
The researchers successfully produced high yields of diphenylmethanol derivatives via a simple process. This involved reacting two generic organic solvents together (chloroform and a methyl-substituted benzene) with inexpensive aluminium chloride serving as the catalyst. The product of this reaction was then treated with alumina containing water.
This process does not require high-cost specialist equipment nor chemicals; the alumina can be repeatedly reused simply by washing it with water and then drying it, making it a simple, safe and low cost catalyst for organic synthesis. Scientific methods using new chemical reactions that are low energy/ have a low environmental impact will greatly contribute towards achieving carbon neutrality and the SDGs.
Alumina (Al2O3) is an aluminium oxide mainly used as a raw material for the production of aluminium. However, it is also utilized as a catalyst in the field of organic synthetic chemistry. Alumina is also used to adsorb impurities in the organic synthesis field and as a stationary phase substance in chromatography. However, issues such as its high cost as a raw material and the large amount of non-burnable waste it generates means that there is a trend towards replacing it with substitutes. Under these circumstances, professor Tsuda led a research group at Inner Mongolia University (China) that succeeded in developing a new, sustainable method of organic synthesis using alumina, which China produces in great quantities.
Professor Tsuda has been conducting international joint research with Inner Mongolia Medical University since 2017. He has been engaged in the joint development of pharmaceuticals, polymers and functional materials using the natural resources (such as metallic minerals and plants) found in the Inner Mongolia Autonomous Region.
The goal of the research is to greatly expand this reaction’s range of applications to develop a more general synthesis method that can be used to produce various useful chemicals.
Amidst rising global environmental awareness, it is hoped that the new chemical reaction developed in this study will become a novel method of synthesizing chemical products which will contribute towards recycling efforts, carbon neutrality and the SDGs. It is predicted to bring about fresh innovation in the organic synthesis and organic chemical industries. It is hoped that continued development of this method through the international research collaboration with China, the world’s number one producer of alumina, will result in highly practical large-scale implementation.
RIKEN chemists have demonstrated a powerful way of designing molecules to satisfy predefined specifications by using it to create six fluorescent compounds. This method, which combines machine learning and quantum chemistry, promises to save chemists a lot of time making and testing compounds in the lab. The conventional approach to molecular design is to start with a molecule that has properties close to the desired ones and then to try to improve on it through trial and error. This can be a time-consuming and hit-and-miss affair, as there is no guarantee that the final molecule is the best one.
Chemists have long wanted to reverse the situation so that they start with desired properties and then search all possible molecules for one that fits the bill. But a limitation has been that data only exists for a tiny fraction of all molecules.
Now, Masato Sumita of the RIKEN Center for Advanced Intelligence Project and his co-workers have demonstrated a new strategy that makes it possible to search the universe of molecules without having to make each compound individually. They used a de novo molecule generator, which employs machine learning to suggest a molecule based on the desired properties. A simulator that performs quantum chemical calculations was then used to
predict the molecule’s properties. The cycle was repeated up to a specified computational time.
To demonstrate the power of this approach, the team used their method to search for molecules that give off fluorescent light at wavelengths visible to the human eye. After five days of number crunching, the computer came up with more than 3,600 candidate molecules. The team picked eight of them to synthesize and found that six of them were fluorescent—including one compound that had never been reported before.
“This is the first time a de novo molecule generator combined with quantum-chemistry calculations has been used to discover fluorescent molecules,” said Sumita. “I was very surprised at the high success rate of the method—75 percent of the eight candidate molecules fluoresced when we made them in the lab.”
The search for a fluorescent molecule was a rigorous test for the method since, unlike simpler molecular properties such as light absorption, fluorescence is a multi-step process, making it tough to predict from molecular structure. Sumita and his team now intend to apply their method to other chemical properties and to try to use it to optimize more than one property simultaneously.
Researchers have published a paper describing, for the first time, the use of ketones as alkyl cross-coupling synthons.
For Xin-Yang Lv and Dr. Roman Abrams, researchers in prof. Martin’s group at the Institute for Chemical Research of Catalonia (ICIQ), keeping up with scientific literature is a source of inspiration for the development of new synthetic methodologies. Taking a recent publication one step further, the scientists in Prof. Martín’s group have devised a new strategy that facilitates the creation of organic molecules of pharmacological interest. The method has been published in the open-access journal Nature Communications.
The strategy developed by the Martin group makes ketones available to chemists to be used as alkyl cross-coupling synthons.
“This method provides an enormous flexibility to chemists and pharmacists in the synthesis of organic molecules, by moving beyond the classical reactivity of ketones and towards the use of this abundant class of compound as cross-coupling partners,”
explained prof. Ruben Martin, leader of a research group at ICIQ and ICREA professor.
The originality of the work lies in the use of ketone derived dihydroquinazolines as radical precursors. The researchers have used a dual catalytic approach, using nickel and a photoredox catalyst to generate and trap radical intermediates for the ensuing cross-coupling, forming a new C-C bond in a selective and controlled manner. Being able to use widely abundant and easily preparable ketones as cross-coupling handles, together with the mild reaction conditions, is key to the potential widespread use of this new strategy. The authors provide examples of the use of this methodology in the presence of other synthetic handles in the paper.
“The method stands out for its great scope and wide application for the synthesis of organic molecules. It is a new approach for the construction of architectures of great interest for medicinal and pharmaceutical chemistry,” said prof. Martin.
study resolves a debate on the best combination of metals to catalytically clean NOx from vehicle emissions.
Smog-producing chemicals could be almost eliminated from the tailpipes of diesel cars and vans, using a new exhaust catalyst concept developed at KAUST. After systematically studying multiple catalyst compositions, the research team identified the ideal atomic recipe to catalytically remove NOx from vehicle emissions. The findings resolve an ongoing debate over additive atoms in the catalyst mix.
Recent developments in high-efficiency engine design, alongside tightening vehicle emission regulations, demand improved engine exhaust catalysts. Current-generation NOx catalysts for small diesel engines perform optimally above 200 degrees Celsius. Catalysts that operate at lower temperatures are now required. Such catalysts need to quickly remove NOx after a cold start and partner with new low-temperature combustion engines.
To develop a new generation of improved NOx catalyst, automotive emissions control company Umicore partnered with a KAUST
Catalysis Center research team, led by Javier Ruiz-Martínez, to optimize the catalyst design.
“We investigated materials that are based on manganese due to their good performance and low cost,” Ruiz-Martínez explains.
Manganese-based NOx catalysts have typically used cerium as a dopant, even though there was no consensus on cerium’s role in NOx removal. “The best way to develop new catalysts is by first
understanding how those materials work,” Ruiz-Martínez says. So, the team produced a series of catalysts, incorporating varying amounts of cerium, to settle the debate.
The team first established methods to produce each catalyst with a homogenous nanostructure to enable a comparison between them. “After making sure that the catalyst materials were as we designed, we looked for correlations between catalytic activity and the amount of cerium and manganese,” Ruiz-Martínez says.
After accounting for differences in catalyst surface area, the team showed that the presence of cerium lowered the catalytic activity of the manganese atoms.
In previous studies where cerium had appeared to boost catalytic NOx removal, cerium’s apparent positive effect disappeared once the team had factored in its impact on catalyst surface area. However, the cerium did have one benefit: suppressing an undesired side-reaction producing N2O. As N2O formation likely requires the participation of two neighboring manganese sites, the addition of cerium may dilute the number of surface manganese sites and so suppress the reaction.
“Our findings show that the design of more active catalyst materials requires the maximization of manganese atoms on the catalyst surface and that these manganese atoms be atomically spaced to avoid N2O formation,” Ruiz-Martínez says. “We are now designing catalysts exposing manganese atomically dispersed on the surface, and the results are extremely promising.”
Encouraged by the early benefits realized from Industry 4.0 solutions in operational efficiency on the shop floor and service efficiency with smarter products, companies are now going beyond their pilot implementation for digital manufacturing.
Trends indicate that in the smart manufacturing space, early investors in Industry 4.0 initiatives are now striving for the next level of gains with global deployment of use cases and scaling of solutions by implementing an increasing number of use cases on the Internet of Things (IoT) platform framework.
While the business benefits and Return on Investments (ROI) from Industry 4.0 solutions is well understood by business leaders, it is important to note that decision making is typically very decentralized at a plant level. This makes it necessary to articulate and document the business benefits for a successful global implementation. Infosys is helping its clients navigate their Industry 4.0 journey by overcoming the challenges for global deployment of solutions to realize large scale benefits.
A five dimensional approach to overcome industry 4.0 implementation challenges
The challenges we typically encounter during the implementation of a comprehensive solution across production lines and plants, and the approach we take to overcome them, are:
A three-tier reference architecture for a seamless IT-OT integration: Given the disparate systems that typically exist across different manufacturing plants, it becomes challenging to implement a solution that takes into consideration the Information Technology (IT) - Operational Technology (OT) integration in a seamless manner right from “sensors to insight”. In other words, how can one transform the manufacturing environment such that the information in the systems residing on the shop floor can flow in real time to the systems in the enterprise allowing business leaders a view into what’s happening on the production side at any point of time?
Infosys has defined a three-tier reference architecture for such implementations of Industry 4.0 solutions, and the same has been implemented across multiple industry verticals. The reference architecture comprises:
• Edge layer with sensors, gateway and edge analytics component
• Shop floor/plant-level IoT platform for driving visibility at shop floor, machine and production line levels
• Enterprise-level IoT platform for driving correlation of data and sharing insights on production parameters across plants
This reference architecture acts as a template that can be taken to multiple plants/sites for faster implementation of Industry 4.0 use cases.
A framework to gather the right data from shop floor machines/equipment: In a brown-field setup, the legacy equipment on the shop floor rarely has the necessary capacity to transmit all the data that it generates. This leads to a lack of information on the current equipment/production line efficiency and the Overall Equipment Effectiveness (OEE), making it challenging to identify and thereby address problem areas. This is a common issue we encounter at multiple implementations. Infosys has designed a gateway framework software that helps with:
• Equipment interface challenges by supporting standard industrial protocols for getting data from shop-floor equipment and sensors to the plant level and from thereon to the enterprise level using a router or gateway. We have also partnered with machine Original Equipment Manufacturers (OEMs) to bring in data from their industrial controller to the gateway device used for transmitting data
• Challenges around data volume by using the right kind of filtering and pre-processing of data on the edge layer so that only necessary event-related data is pushed to the next layer for analytics
• Latency and turn-around time by providing accurate insight to shop-floor personnel by doing analytics on the edge and passing the insight/events to handheld devices leveraging near-field communication protocols.
Reducing long lead time in global deployment of uses cases/solution: Seamless and faster deployment of solutions across plants with minimal or no disruption to manufacturing operations is a key ask from every plant manager. The deployment of solutions has broadly two dimensions:
• Helping plants prepare for the implementation by providing them with a detailed implementation plan and enabling them with the pre-requisites, and
• Having the right toolkit that will help during the deployment phase
Infosys has devised a comprehensive deployment toolkit for adoption of Industry 4.0 solutions across plants. The toolkit consists of implementation readiness checklist, elaborate implementation/ configuration document, reference framework, tools/accelerators, reference user training material etc. These tools help in faster and seamless deployment of solution in a plant or production line.
A global machine tools company needed to modernize its factories across multiple locations to improve operational efficiency & move to paperless digitized process for various personas in their plant. Infosys IoT solution captures real-time production data from factory floor equipment and systems providing digitized process and journey maps for personas like specialists and operators. This led to an increase in the overall line effectiveness by 20 percent, reduction in manual paperwork by 90 percent and zero enterprise data duplication.
A leading global food manufacturer did not have visibility of realtime ingredients and batch operating parameters and the energy consumption for their process was not optimal. Infosys solution for real-time batch parameter trend and deviation analysis along with
alerts to address specific production line operational issues helped improve visibility of batch operations and reduced manual errors by 60 percent. The solution also led to reduction in energy consumption in packaging area.
Lowering deployment cost: Given the scale of deployment of Industry 4.0 solutions across production lines, geographies and plants, new pricing models “Plant as a service” and “Machine connectivity as a service” are gaining adoption. These pricing models provide clear visibility to the customer on the cost involved in global implementation of use cases and how economies of scale can be leveraged to drive lower implementation cost.
The Infosys pricing model takes into consideration the plant floor landscape, support and interface available for collecting equipment data, instrumentation involved for getting use case-centric data, connectivity, availability of manufacturing process data, etc. The complexities involved in the implementation of a use case is a function of these critical parameters.
Focusing on user experience: The expectation of the shop floor personnel has changed over time, from a user experience perspective. This has led to newer ways of approaching the user experience dimension during the solution development process. One critical aspect is Design Thinking-based problem definition along with Agile development. End user feedback is factored in at every step of the solution design and development.
With the adoption of the above approach, in our experience, we were able to bring down the deployment cost by close to 60 percent on an average by bringing in more and more capabilities to the platform framework in addition to reducing the deployment time to weeks rather than months.
Given the potential benefits and efficiency gains through the implementation of digital manufacturing solutions, it becomes imperative to provide the necessary governance to these initiatives so that any intervention or course correction can be done in a timely manner to make it a success.
Authors: Ramchandra Kulkarni is Associate Vice President, Head of Sales, Engineering Services, Europe and Raman Kartik Iyer is Director, IoT Practice, both at Infosys.
The EU Green Deal, which calls for net-zero greenhouse gas (GHG) emissions by 2050, will affect businesses across the board—but it will have a tremendous impact on Europe’s chemical industry as it brings both significant challenges and huge opportunities.
To better understand this impact, Accenture and NexantECA, an energy and chemicals advisory company, conducted a comprehensive, plant-by-plant assessment of 236 chemical plants in Europe. This analysis determined that in order to reach net zero by 2050, the chemical industry will need to cut annual GHG emissions by 186 million tons over the next three decades.
“This in-depth research helps build a picture of key considerations for European chemical companies as they prepare for our sector’s biggest transformation in its history,” said Marco Mensink, Cefic Director General.
By comparison, the industry has already reduced annual emissions by 171 million tons since 1990 according to the European Environment Agency (EEA). That’s good news, but capacity declines and plant shutdowns were a key driver of those reductions, as the EU share of total global chemical production fell considerably during roughly this same period. Thus, the industry has harvested much of the “lowhanging fruit” in reducing GHG emissions—and what remains will be more difficult.
Getting there will also be expensive, and involve
Companies will need to make large investments in new core equipment and the design, construction and modification of large numbers of facilities.
As companies retrofit, improve or rebuild plants, they will see months of halted production, leading to significant losses in profits.
The industry will need to change traditional production processes and adopt new technologies—some of which are still in development.
New plants will need to be built in new locations to be closer to renewable energy sources, biomass materials or GHG-capture facilities.
The research found that altogether, achieving the 2050 Green Deal goals will require an investment in the €1 trillion range from the chemical industry. That in turn means that the industry will need to fill in a substantial funding gap, compared to current capital spending, and increase capital investments by more than €12 billion a year over the next three decades. (See Figure 1)
Not all of the required changes will be under the chemical industry’s direct control. For example, the extensive modification and building of plants will require equipment manufacturers and the engineering, procurement and construction industries to expand their capacity significantly. And governments and businesses will need to address the social impact of the industry’s pursuit of net-zero goals, as plant downtime and closings affect employment and communities.
Access to the renewable energy needed for a net-zero industry will also be a challenge, as it will require an estimated additional 3.2 PWh of renewable energy—about five times the renewable energy generated in the EU today. Much of this will depend on the efforts of utilities and governments, but chemical companies will need to work closely with them, because the economic feasibility of increased renewable energy capacity depends on demand from plants, and plant electrification using non-renewable energy will not result in the needed reductions in GHG emissions.
Meeting the Green Deal’s goals will be expensive for the chemical industry. But there is more than compliance at stake, and chemical companies should weigh the costs of change against the monumental benefits of making that change. Most industries will be affected by the EU Green Deal, as well as the growing consumer sentiment that favors environmentally friendly products. Those realities have prompted companies in a variety of industries to make public commitments to sustainability—and they will need to change many of the offerings they bring to market to meet these commitments. And chemical products will be a big part of the solution for these customer industries.
Going forward, chemical companies that focus on net-zero innovations and produce new materials that are lighter, more sustainable and made with processes that result in lower GHG emissions will find expanding markets for their offerings, in Europe and elsewhere. As European chemical companies reshape themselves for the Green Deal, they are likely to gain a head start in the race to bring carbon-neutral,
sustainable and circular economy-related solutions to market, giving them a competitive advantage in global markets. Ultimately, the chemical industry can play a critical enabling role in the success of the EU Green Deal by helping companies across industries reach their net-zero goals—and at the same time, position itself to prosper and grow in a more sustainable future.
Authors: From Accenture: Michael Ulbrich, Managing Director, Global Chemicals Sustainabil ity Lead, Dr Eike Christian Eschenroder, Senior Manager, Strategy, Chemicals, and Dr Bernd Elser, Managing Director, Global Chemicals Lead and Europe Lead for Chemicals and Natural Resources.
From NexantECA: Mais Haddadin Finn, Principal, Global Sustainability Lead, Dr Nuno Faísca, Sector Leader, Head of Technology Evaluation and Management, and Richard Sleep, President.
Company: Shell plc
Date Posted: 04-Jul-2022
Country: NETHERLANDS City: Assen
Company: Akzo Nobel N.V.
Date Posted: 15-Jun-2022
Country: UNITED STATES City: Reading, PA
Process Chemist Company: Eastman Chemical Company
Date Posted: 04-Jul-2022
Country: UNITED STATES City: Kingsport, TN
Company: MMomentive Performance Materials Inc.
Date Posted: 01-Jul-2022
Country: UNITED STATES City: Waterford, NY
Development Chemist II Company: PPG Industries, Inc.
Date Posted: 01-Jul-2022
Country: UNITED STATES City: Milford, OH
Pharmaceutical Chemist III, Formulation Company: Catalent Pharma Solutions
Date Posted: 01-Jul-2022
Country: UNITED STATES City: San Diego, CA
Quality Engineer Company: Exxon Mobil Corporation
Date Posted: 30-Jun-2022
Country: INDIA City: Bengaluru
Senior/Lead Research Engineer Company: Dow Inc.
Date Posted: 30-Jun-2022
Country: UNITED STATES City: Midland, MI
Company: Boehringer Ingelheim GmbH
Date Posted: 30-Jun-2022
Country:Boehringer Ingelheim GmbH City: Biberach, GERMANY
Job Description: Provide independent chemistry expertise to maintain/improve drilling fluid design, completion, and workover fluids; cementing and through the entire Global Well Delivery Program (GWDP) lifecycle (including Dutch specific requirements on plug and abandonment). Provide technical assurance (TA2) on cement and/or drilling fluids. Provide timely input to regulatory chemical approval processes. Understand legislative requirements.
Job Description: Understand the purpose of formulation components and reformulate to solve straightforward customer (internal/external) problems with minimal supervision. Manage the assigned LWR /projects, including timeline and planning, on a weekly timescale. Provide data-driven insights to support diagnostics and resolution of issues in manufacturing, application, and formulation. Summarize test data in the form of spreadsheets, reports, and presentation; draws conclusions.
Job Description: Contribute to safety programs in the lab and manufacturing area. Analyze existing processes and recommend actions to improve safety, reduce costs and maximize production. Develop and improve lab scale models of existing manufacturing processes. Identify key processes variables and acceptable operating ranges for assigned manufacturing area
Job Description: Drive process cycle time reduction and process improvements beyond weekly time horizon. Create additional capacity on existing assets. Track metrics to discover areas of improvement and monitor progress. Asses and maintain compliance with safety and quality standards.
Job Description: Ensure adherence to all applicable environmental, health and safety regulations, standards, and policies to help eliminate health hazards to prevent work stoppage and time loss due to accidents. Work closely with the color, manufacturing, and product development teams to ensure the initial product scale up is successful. Perform and document generally standardized, routine chemical and physical test of finished goods and compare the results with established standards and customer requirements.
Job Description: Conduct and/or supervise the execution of formulation studies for oral drug candidates in the form of a solution, suspension, tablet, capsule, or amorphous intermediate. Develop strategic experimental plans and timelines. Collaborate with other departments to oversee scale-up and manufacture for clinical manufacturing projects with minimal supervision. Review manufacturing batch records with minimal supervision.
Job Description: Develop and execute Quality Surveillance plans, programs, procedures and tools to manage Procurement Quality across multiple project(s). Provide Quality discipline input to the Project Organization Plan and manage staffing of Quality Source Inspection personnel. Prepare and maintain Project Quality Plan, Surveillance Programs, quality procedures and tools and ensure their successful implementation across the project. Interface and coordinate work activities between Quality and other Project disciplines.
Job Description: Lead introduction of new products from laboratory scale to manufacturing. Interface with Research and Development, Technical and Sales Service, Supply Chain, Marketing, and Manufacturing to successfully transfer new products to plant scale. Design, perform experiments, and analyze data at laboratory scale (glassware) and pilot scale (steel vessels) to assist with new product scale up and troubleshoot manufacturing issues.
Job Description: In compliance with regulatory requirements and with Boehringer Ingelheim standards assume responsibility for supply chain assessments and for supplier qualification. Compile and update qualification files for our suppliers. Author and negotiate quality assurance agreements with external partners. Plan supplier audits, and supervise corrective and preventative action resulting from audits and inspections.
Website: http://www.worldofchemicals.com/chemical-jobs.html
Textile Effects has released PHOBOTEX® R-ACE, a breakthrough PFC-free and formaldehyde-free durable water repellent (DWR) that makes it possible for mills and brands to deliver high-performance outdoor and extreme sports apparel and everyday wear while meeting stringent environmental standards and optimizing production flow. PHOBOTEX® R-ACE delivers excellent water repellence on all types of fibers. Textiles remain breathable, retain their soft handle and continue to look good and perform well through repeated laundering and drying. It also meets new bluesign® restrictions on 2-Butanone oxime in chemical products, which will come into effect in June 2022.
Contact: Huntsman International (India) Pvt Ltd
BU: Advanced Materials Division Hiranandani Business Park, Lighthall ‘B’ Wing, Saki Vihar Road, Chandivali, Andheri (East), Mumbai - 400 072.
Tel: +91-22-42875100
Email: Contact_India@huntsman.com Web: https://www.huntsman.com/about/ textile-effects
BASF has extended its series of Licity® anode binders for Liion battery manufacturing. The second-generation styrenebutadiene rubber (SBR) binder Licity® 2698 X F facilitates the use of silicon contents exceeding 20 percent. In addition to the established properties of the Licity® product family, this binder enables higher capacity, increased number of charge/discharge cycles and reduced charging times. Additionally, Licity® 2698 X F can be manufactured according to the biomass balance approach.
Contact: BASF SE 67056 Ludwigshafen, Germany
Tel: +49 621 60-0
Email: marie.schuetz@basf.com Web: www.basf.com
Clariant offers a natural-derived, readily biodegradable opacifier to support personal care formulators in minimizing the impact of shampoos, conditioners, handwashes and other rinse-off shower and bath products on marine and river life. New Plantasens OP 95 is a microplastic-free option which delivers powerful opacifying performance even at low concentrations, for a creamy white appearance with luxurious, caring consumer appeal for shampoos and liquid soaps. Plantasens OP 95 offers formulators an easy-to-use, sulfate-free drop-in solution for opacifying and also suited to the regulatory initiatives as ban on microplastics take shape. It is possible to reach ideal viscosity without adding rheological agents, which means less formulation complexity.
Contact: Clariant International Ltd Rothausstrasse 61 4132 Muttenz 1 Switzerland
Tel: +41 61 469 6742
Web: www.clariant.com
NYLEO® is the new brand for DOMO’s Performance Fibers product line, bringing together a compelling combination of well-established performance fibers and groundbreaking new solutions. Based on nylon 66, NYLEO® is used in numerous applications in the textile, flooring, flock and abrasive markets. NYLEO® merges a rich heritage in the nylon 66-based fiber market with a new focus on innovation with three pioneering products: NYLEO® PROTECT with improved flame retardancy, NYLEO® 4EARTH® with enhanced biodegradability, and NYLEO® SAFE with bacteriostatic properties.
Contact: DOMO Caproleuna GmbH
Am Haupttor, Bau 3101 06237 Leuna, Germany
Tel: +49 3461 43-2200 Email: Francoise.Jirgens@domo.org
Web: https://www.domochemicals.com
One advantage of working with an OEM like ROSS is the unique ability to completely engineer and customize a product from the ground up. That was the case with this customdesigned Mixing/Melting and Holding Tank System used to produce highly potent and reactive materials at 350°F and up to 10 psig internal pressure. The system includes a pressure-rated sealed enclosure with an operator-friendly safety glovebox and two mixers each equipped with a two-wing anchor agitator, Teflon scrapers and jacketed 6-gallon vessel. One functions as a mixer/melter connected to a vacuum powder loading system; the other functions as a holding tank which gravity feeds the finished product to a downstream coating machine. A specially designed elevator system enables the mixers to be lowered to a maintenance position and raised to an operating height which allows for gravity feed from the melter to the holding tank.
Sulzer launches the latest addition to the SALOMIX agitator family, the SSF150. SALOMIX offers excellent performance in all industrial segments. The new size will be used mainly in large pulp mills, and typical applications will be storage towers, pulpers and bleaching towers. SSF150 strengthens Sulzer’s position as the leading full-line equipment supplier to the pulp, paper, and board industry. SALOMIX SSF side-mounted geardriven agitators are used for mixing and agitating process liquids in demanding industrial applications. The agitators ensure a homogenous mixing result, high process reliability and efficiency, low operating costs and low environmental stress. They are also suitable for customers in the chemical process industry.
Roots pumps from Pfeiffer Vacuum’s OktaLine are ideal for use in processes in potentially explosive environments or for evacuating explosive gases. Designed in accordance with the ATEX Directive (2014/34/EU1 and/or 1999/92/EC) with pressure surge resistance of PN 16, they meet the very highest explosion protection requirements. Zone entrainment of explosive gases is ruled out as a result. Potential applications range from the chemical, biotechnology and pharmaceutical industries to industrial applications such as vacuum furnaces or heat treatment. All pumps are suitable for temperature class T3. Installation is possible without flame arresters. All pumps can be used at ambient temperatures ranging from -20 °C to + 40 °C.
For many years, the semiconductor industry has been successfully using diaphragm valves from the GEMU CleanStar series all over the world. It offers the advantages of the design and the multitude of possible applications due to the sophisticated graduation of actuator sizes 1 to 3. Now, the valve specialist is expanding its GEMU CleanStar family with actuator size 4, and thus setting standards in terms of footprint and flow. The semiconductor industry’s requirements of valve designs are constantly growing. The new combination allows large media quantities to be transported and ultra pure valve designs to be used even at the supply and distribution level of semiconductor production.
Contact: HMD Kontro Sealless Pumps Marshall Road
Hampden Park Industrial Estate Eastbourne, East Sussex, BN22 9AN, UK
Tel: +44 (0)1323 452 000 Email: info@hmdkontro.com Web: https://hmdkontro.com
Contact: Sulzer Management Ltd Neuwiesenstrasse 15 8401 Winterthur Switzerland
Tel: +41 52 262 30 00 Web: www.sulzer.com
Contact: Pfeiffer Vacuum GmbH Berliner Strasse 43 35614 Asslar/Germany
Tel: +49 6441 802-0 Email: info@pfeiffer-vacuum.de Web: www.pfeiffer-vacuum.com
Contact: GEMU Gebruder Muller Apparatebau GmbH & Co. KG Fritz-Muller-Strasse 6-8, 74653 Ingelfingen-Criesbach Phone: +49-79 40 - 123 0 Email: info@gemue.de Web: www.gemu-group.com
The innovative Rotork CK range of modular electric valve actuators has been extended to include a new part-turn variant, known as the CKQ. The entire range has a modular design that provides flexibility and high degrees of configurability, enabling a fast order turnaround and quick delivery. CK actuators provide flow control in non-hazardous locations and are especially suited for diverse applications in the water and power markets. This new part-turn variant is especially well suited for harsh and demanding environments. Continuous mechanical valve position indication is provided (even without power) and the CKQ provides up to 60 starts per hour at a rate up to 1 start every 6 seconds. All options within the CK range provide oil bath lubrication for extended life, mounting in any orientation and motor-independent handwheel operation available. The modular structure of actuators in the CK range means a wide variety of options and features are available.
Contact: Rotork Plc
Brassmill Lane Bath, BA1 3JQ, UK Tel: +44 1225 733200 Web: www.rotork.com
Sensirion is the first company in the world to successfully launch its mass flow controllers for catalog distribution. The sensor manufacturer is expanding its product range with two additional mass flow controllers from the successful SFC5500 series and four new mass flow meters in the SFM5500 series. The new mass flow controllers and meters are ideally suited for analytical, medical and industrial applications. The high-performance mass flow controllers and meters are calibrated for multiple gases and come with push-in fittings, which can be easily swapped out by the user from the list of compatible parts. Thanks to the ultrawide range, each device can cover several of the flow ranges found in conventional devices. The new range allows to build radical mass flow controllers and meters with best-in-class performance and excellent reliability.
Contact: Sensirion AG
Laubisruetistrasse 50 8712 Stäfa, Switzerland Tel: +41 44 306 40 00
Email: info@sensirion.com Web: https://sensirion.com
Yokogawa Electric Corporation announces the release of the OpreX™ Vortex Flowmeter VY Series. These flowmeters comply with major explosion-proof standards (IECEx, ATEX, FM, FMc) and are SIL2 certified. The new product series, which is part of the OpreX Field Instruments family, will be released first in Southeast Asia, Oceania, India, the Middle East, and South America, excluding Brazil. When used in combination with specialized software, the OpreX Vortex Flowmeter VY Series supports remote maintenance functions that enable planned and efficient condition-based maintenance. It can handle a wider range of fluid types, temperatures, and pressures. The new series has been developed with the aim of supporting the implementation of digital transformation (DX) in large plants in the form of efficient and planned condition-based maintenance.
Contact: Yokogawa Electric Corporation 4-9-8 Myojin-cho, Hachioji-shi, Tokyo 192-8566, Japan Web: www.yokogawa.com
With the recent expansion, the CSI range of chemical and industrial service pumps to ISO standards, now numbers 29 different models, with additional hydraulics and a wider variation in the inlet and outlet sizes allowing for much increased operational options. Continuing the Modularity benefits of the CSI, including Versatility, Reliability, Efficiency, Safety, Serviceability and Availability, the range is now available in 13 x Frame 1 and 16 x Frame 2 sizes, allowing for a wider range of flow rates. Meeting the ISO dimensional and construction standards 2858 and 15783 the expansion of the CSI range means that we continue to offer a world-class chemical pumping solution for the ISO markets.
Contact: HMD Kontro Sealless Pumps Marshall Road
Hampden Park Industrial Estate
Eastbourne, East Sussex, BN22 9AN, UK
Tel: +44 (0)1323 452 000 Email: info@hmdkontro.com Web: https://hmdkontro.com