
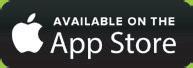
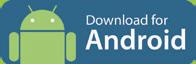
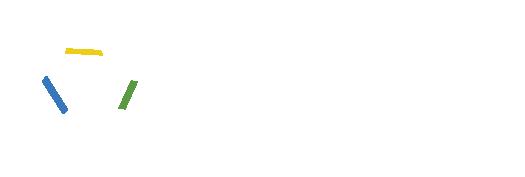
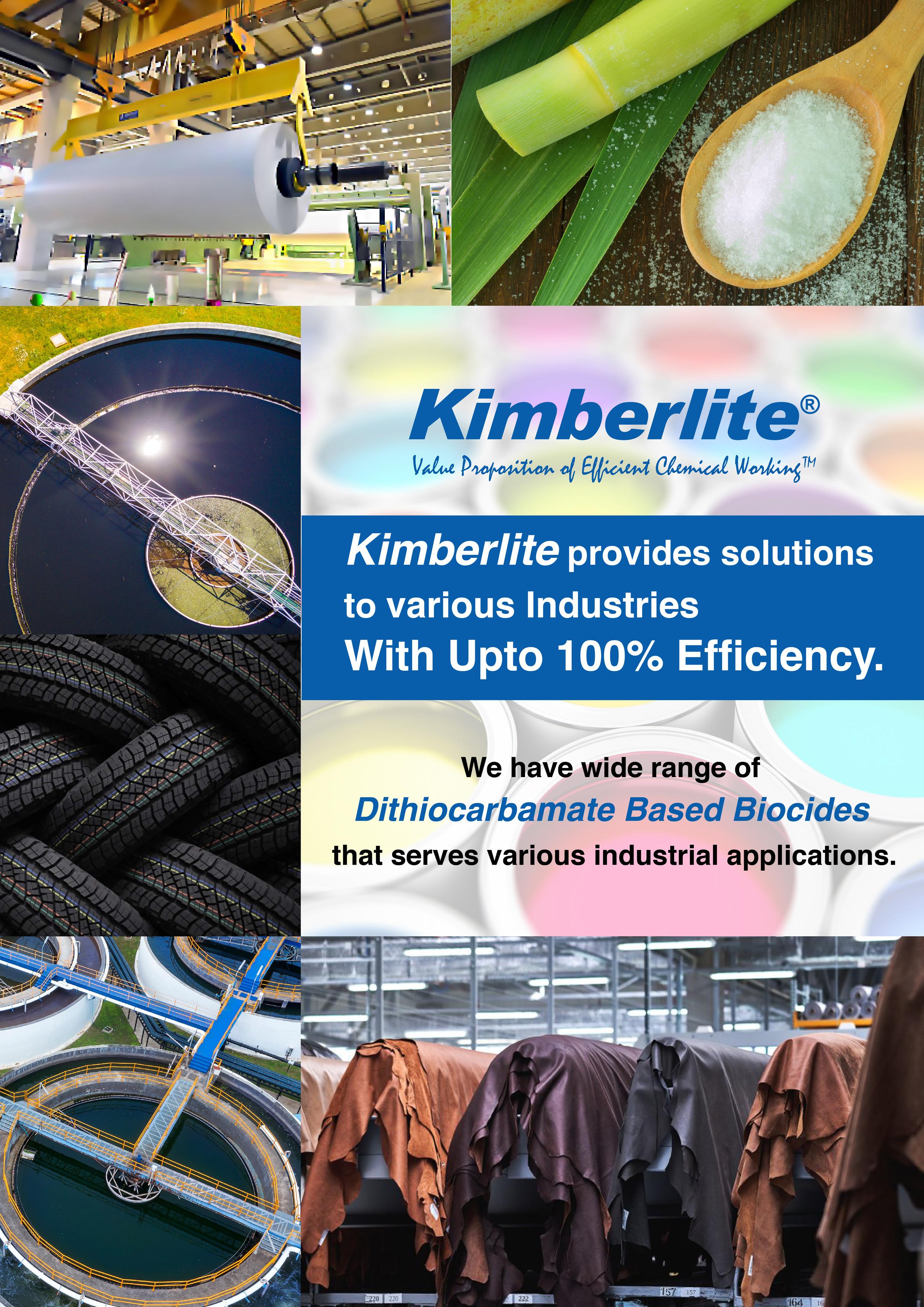
In recent years, India has spent the highest foreign currency for the import of items such as - Mineral fuels including oil, coal, natural gas; Gems, precious metals; Organic chemicals; Animal/vegetable fats, oils, waxes; Iron, steel; Inorganic chemicals; Paint, printing ink and allied products; Agrochemicals; Dyes and dyes intermediates; and Plastics raw materials. These products are imported from various regions such as Asia Pacific, Middle East, US, Europe among others. And they are essential to fulfill various consumer demands in the country. Further, some of the finished goods are exported to different global regions.
But most important for international trade to happen is that proper means of logistics, supply chain, transportation are in place for the long haul. Also, it needs to be taken into account that the chemicals transported have complex characteristics. They can be in the solid, liquid, gaseous form and can further be classified as hazardous or non-hazardous. Herein, the risk associated with the storage & warehousing, transfer and distribution have also to be noted during chemicals in movement.
The global chemical logistics market is expected to grow from $251.94 billion in 2021 to $271.73 billion in 2022 at a compound annual growth rate (CAGR) of 7.9 percent, while it is expected to reach $317.17 billion in 2026 at a CAGR of 3.9 percent as per a report from ResearchAndMarkets.
Considering the modes of transportation in the chemical industry, US and Europe majorly use inland waterways and railways while Asia Pacific, South East Asia markets dominantly use roadways - trucking means for transportation.
At present, the chemical Industry is evaluating their logistics & supply chain network and modes of transportation in order to decarbonize the chemical supply chain. These companies are also devising new green logistics solutions to further reduce greenhouse gas (GHG) emissions. Further, efforts are on to adopt and scale up use of low-emission fuels and energy efficient vehicles for transportation. Organisations are working with their suppliers and logistics providers to achieve climate-neutrality targets and move towards a circular economy.
That is not all. Companies are also assessing digitalisation as a means of achieving sustainability goals. Digital technology is used for handling end-to-end shipping and logistics management, providing solutions for planning, booking and executing shipments, while sorting out issues such as rate discovery, booking shipments, and container tracking, credit solutions etc, across geographies. This is also an effective measure to ensure proper safety, compliance and international trade regulations for transportation of chemicals across various ports and countries.
For suggestions or feedback write to editorial@worldofchemicals.com
© 2022 worldofchemicals.com
Cover Image Source : freepik.com
The rise of e-commerce and access to new technologies has accelerated counterfeiting and other forms of illicit trade. That makes fighting counterfeit medical products an ever-more urgent priority for pharma companies both in terms of patient safety and brand reputation.
Yann
IschiDirector, New Channels and Partnerships, SICPA
Within the Volkswagen Group, we have a clear strategy for how we want to put battery-electric vehicles into series production across our brands and in many different market segments. However, a major qualification for success in the volume market is more powerful battery concepts. In Volkswagen Group R&D we are focusing on close cooperation, not only with industrial partners but also with the smart minds of the scientific community.
Dr Ulrich Eichhorn
Head, Group R&D, Volkswagen AG.
India is a very important market for polyurethanes and has a wonderful potential for growth. When leaders of the industry from all over the world get together under one roof, it leads to better production and faster growth of the industry
R C BhargavaFormer CEO and current Chairman, Maruti Suzuki.
Indian Solar Manufacturers Association (ISMA) members have expressed positive sentiments as manufacturing and Make in India initiative gathered momentum. The phenomenal growth opportunity of Renewal Energy is unparalleled in the world today, looking at current and future energy consumption in India over the next 2-3 decades. All stakeholders have immense opportunities especially those who make and develop products in India.
K N SubramaniamCEO, Moserbear Solar Ltd and Treasurer, Indian Solar Manufacturers Association (ISMA)
ROTTERDAM, NETHERLANDS/ MUMBAI, INDIA:
LyondellBasell and Shakti Plastic Industries (plastic scrap recycler and waste collection company), have signed a Memorandum of Understanding (MoU) to form a joint venture to build and operate a fully automated, mechanical recycling plant in India.
The plant is intended to process rigid packaging post-consumer waste and produce 50.000 tonnes of recycled polyethylene (PE) and polypropylene (PP) per year.
LyondellBasell will market the recycled products produced by this joint venture adding volume to its Circulen Recover range of existing PE and PP materials to help meet increasing demand by converters and brand owners in India for recycled polymer materials.
“The proposed joint venture will allow us to address the issue of plastic waste in the second most populated country in the world and expand our circular polymer product offering to India,” said Yvonne van der Laan, LyondellBasell executive vice president, circular and low carbon solutions.
“Together with LyondellBasell, we will be on the forefront in India taking significant steps to recycle rigid plastic waste which supports the government initiative to reuse recycled plastic in packaging applications,” said Rahul V. Podaar, managing director of Shakti Plastic Industries.
NEW DELHI, INDIA: Asian Paints has approved the setting up of a manufacturing facility for Vinyl Acetate Ethylene Emulsion (VAE) and Vinyl Acetate Monomer (VAM) in India for a proposed investment of approximately Rs 2,100 crore over a period of three years.
The installed capacity would be manufacturing 100,000 tons per annum for VAM and 150,000 tons per annum for VAE.
Speaking about the manufacturer in India, VAM and VAE would provide substantial sustainable cost efficiencies, substituting
company’s dependence on imports and would be used for the its internal consumption.
The statement also said the plan is subject to entering into definitive agreements, including technology license agreement from the USbased Kellogg Brown & Root, for manufacturing VAM and VAE and obtaining the necessary regulatory and other approvals.
VAE is considered to be the emulsion of the future, and the key constituent for manufacturing environment friendly paints.
MUTTENZ, SWITZERLAND / MUMBAI, INDIA: Dorf Ketal announced it will acquire Clariant’s North American (NORAM) Land Oil business, a provider of chemical technologies and services to the North American oil & gas industry.
Clariant’s NORAM Land Oil business, which posted 2021 revenues of $113 million, represents an exciting growth opportunity for Dorf Ketal and the transaction is expected to be finalizes by the first quarter of 2023.
Once completed, the acquisition will include all the assets of Clariant’s NORAM Land Oil business, including a team of 170 employees in North America, a technology portfolio of more than 40 patent families, and manufacturing units located in Bakersfield, California; Midland, Texas; and Black Hills, Texas producing more than 2,000 formulations for drilling, production and stimulation.
“This acquisition will bring additional strategic assets, innovative new technology, talented people, and strong customer relationships into Dorf Ketal,” said Sudhir Menon, chairman, Dorf Ketal Chemicals India Pvt Ltd.
“Upon completion, it will enable our continued growth in North America – a significant and growing market for energy services, further
aligning with our global focus and commitment to providing innovative services throughout the energy sector.”
“The divestment of the North American Land Oil business is another logical step in repositioning Clariant’s portfolio towards true specialty chemicals and in our sustainability transformation journey. With its strong reputation as a supplier of premium oilfield chemical products and services, its geographical presence, and its solid customer relationships, Dorf Ketal is the right owner for the combined business, for our employees, customers, and other stakeholders,” said Conrad Keijzer, CEO, Clariant.
From a mere $30 million turnover in oilfield chemical business in 2018-19 to almost $275 million turnover business. Ramp up in such a short period of time with organic growth supported by research driven pathbreaking products and inorganic growth by acquiring businesses, Dorf Ketel has become the largest oilfield chemicals and service company in Asia, mentioned Dorf Ketel.
Dorf has been competing with global conglomerates such as Baker Hughes, ChampionX and has grown the business exponentially in just 3 years, said the company. Ernst & Young India advised Dorf Ketal on this transaction.
agrochemical innovator customer, post 3 years of successful supply under our Exclusive / Contract Manufacturing business model.
The renewal is as per the clause of automatic renewal every year, post completion of the original contract duration of 3 years, agreed upon by the Parties in the long-term agreement signed 3 years ago.
These two products were developed by Aether initially under the CRAMS (Contract Research and Manufacturing Services) business model and were subsequently transferred to the Exclusive / Contract Manufacturing business model by the customer.
“The renewal of this contract is a significant achievement for us and further strengthens our relationship with this global innovator agrochemical company. This renewal will also make a substantial contribution to our Exclusive/Contract Manufacturing business model revenues in the current fiscal year itself,” said Aman Desai, promoter, and whole-time director of Aether Industries.
TEL AVIV, ISRAEL / MUMBAI, INDIA: ICL announced the launch of ICLeaf, a diagnostics tool, which will provide farmers with 10 different elements in a leaf sample and then deliver accurate, real-time feedback and a recommendation regarding nutrient use.
The process begins with the collection of leaves from the targeted crop, which are then analysed using unique technology. Within three days results are available using ICLeaf tool, and it is more sustainable than traditional testing, stated ICL. The new took will allow farmers to make quick and data-driven decisions, based on the measurements, and enable them to take multiple samples each year and make immediate, in-season improvements.
ICLeaf is complementary to Crop Advisor, an optimized data-based crop nutrition plan, which provides customized fertilizer recommendations, based on type of crop, location, and environmental conditions.
“As a company focused on creating impactful solutions for humanity’s sustainability challenges in the global food, agriculture and industrial markets, we are proud to introduce our new and advanced Israeli technology, which will help farmers gain greater visibility into their fields and maximize yields,” said Elad Aharonson, president of Growing Solutions for ICL.
“This unique specialty service will assist farmers in planning for optimum nutrient management, by timely identifying deficiencies and enabling them to use the right products at the right time to improve yields and increase sales,” added Aharonson.
ICLeaf is currently available for grape, cotton, banana, tomato, and pomegranate crops in India, with other crops being added. The diagnostics tool was created at the Center for Fertilization and Plant Nutrition (CFPN), which was founded through a partnership between ICL and the Volcani Institute (Agricultural Research Organization ARO) a research arm of the Israeli Ministry of Agriculture and leads.
The digital technology suite – including the ICLeaf and Crop Advisor solutions, among others – was developed by Agmatix, an ICL owned digital ag startup, which can drive the agronomic innovation cycle from research and experimental data. The Agmatix platform can read and interpret thousands of the different data points commonly used across the agricultural industry to help scientists, agronomists and farmers make actionable decisions.
OSAKA, JAPAN/BENGALURU, INDIA: Air Water, the Japanbased industrial gas company, said it will grow its business in India by constructing a new industrial liquefied gas manufacturing plant in Chennai, Tamil Nadu, in Southern India.
Built by Air Water’s subsidiary Air Water India Pvt Limited (Air Water India), the new plant will increase the supply of liquefied oxygen (Lox), liquified nitrogen, liquefied argon, and other gas and fill cylinders with them for shipments.
The plant will have a production capacity of liquefied oxygen 5,100N m3/h of LOx, 1,600N m3/h of liquefied nitrogen and 200N m3/h of liquefied argon.This process will satiate the increasing demand of
industrial gases driven by India’s crude steel production industry, of which the Indian government intends to increase production to 300 million tonnes by 2030.
Air Water is expected to invest about ¥4 billion (US$26.7 million) in the project. It plans to break ground in October 2023 and open the facility in October 2024.With an eye on sustainability, Air water India plans to reduce carbon dioxide (CO2) emissions by 35 percent and using renewable energy to generate 40 percent of the power that the plant is expected to use every year.
The company is working to expand the network of an industrial gas supply infrastructure, essentially production, filling, and transportation.
WOKING, UK/ NEW DELHI, INDIA: Linde announced it has expanded its existing long-term agreement for supply of Industrial Gases with Jindal Stainless Limited (JSL).New Air separation Unit, at the Kalinganagar Industrial Estate in Odisha, East India is expected to start-up in first half of 2024 and will be an additional supply source for local merchant market.
“We are proud to develop our partnership with JSL as it embarks on
a significant expansion of its stainless-steel production facility at Kalinganagar,” said Moloy Banerjee, president of ASEAN & South Asia, Linde.
“By building additional capacity to support JSL’s growth, we will increase Linde’s own network density in one of India’s most important industrial regions,” Banerjee added.
MUSCAT, OMAN: Oman plans to produce a million tons of green hydrogen by 2030 and has set up a state-owned company as part of its plan to achieve net-zero carbon emissions by 2050.Hydrogen Oman, better known as Hydrom, will be a subsidiary of Oman’s stateowned Energy Development Oman.
Oman has earmarked two blocks in the southern port city of Duqm and another four blocks in Salalah to be tendered for the development of green hydrogen projects.On November 6, Hydrom will open a first public bid round to award the first land blocks by 2023 to meet its production target.
Hydrom will oversee the development and construction of the projects, while working closely with the Oman’s Public Authority for Special Economic Zones and Free Zones to set up infrastructure such as roads, power lines and other installations.
“Oil and gas, electricity, industry and transportation, as well as the construction field — all of these sectors are interconnected,” said Minister of Energy and Minerals Salim Al Aufi.The main goal shared by the sectors is to work towards the achievement of Oman’s net-zero target by 2050, he said.
Hydrogen comes in various forms, including blue, green and grey hydrogen. Blue and grey are derived from natural gas while green is produced using renewable sources.“It is our responsibility to look at the international markets, the local markets and understand what the demands are,” said Hydrom’s acting executive director Firas AlAbdawani.
The new partnerships could accelerate the decrease of limestone residues released into the sea, building upon the action plan announced in September to invest in new technical solutions at the site.
Apart from IPSIIS, Solvay is also working with German-based Ferro Duo, specialized in recycling industrial materials, to use the inert solids from soda ash manufacturing as components of fertilizers to enrich soils where precious elements like calcium, sulfur, potassium, magnesium, and iron are found. Solvay’s Rosignano plant has been producing soda ash for over a century and is mainly used for the production of glass and sodium bicarbonate.
“We are excited to work with IPSIIS and Ferro Duo to develop the capabilities to create a circular economy for our soda ash production in Rosignano,” said Philippe Kehren, president of Solvay’s Soda Ash & Derivatives division.
“The IPSIIS process enables the recycling of secondary products to produce lower carbon footprint materials.
IPSIIS and Ferro Duo have the potential to transform limestone residues into re-usable products for construction and agriculture sectors to improve environmental footprint of all Solvay manufacturing sites. Solvay and Belgium-based IPSIIS, who manufacture environmentally friendly, non-flammable, lightweight and geo-sourced insulating mineral foams, are testing the use of soda ash manufacturing residues to produce specialized construction products.
Partnering with Solvay in this circular economy program is key for IPSIIS’s development and fits totally with our company vision and daily commitment,” said Gilles Bocabarteille, IPSIIS board member and managing director.
“ Ferro Duo is excited to be working with Solvay on this ambitious sustainability project and propose a new value-creating application for limestone residues from the Rosignano plant,” said Pietro Squilla, managing director of Ferro Duo.
TOKYO, JAPAN/ TEXAS, US: Zeon Corporation has signed a Memorandum of Understanding (MOU) with Shell Eastern Petroleum (Pte) Ltd for the supply of bio-based butadiene to be used in the production solution styrene butadiene rubber (SSBR).
The agreement, signed by subsidiary Zeon Chemicals Singapore, is part of the group’s carbon-neutrality ambitions and its shift to sustainable raw materials for circular economy, Zeon said.Zeon is also in the process of obtaining international certification for biomass-derived
raw materials, including S-SBR made from sustainable butadiene as a certified product.
Shell has also entered into an agreement with Asahi Kasei concerning the production of ‘circular’ SBBR in Singapore, under a deal announced last November.Zeon is working to realize carbon neutrality by transforming its “MONOZUKURI” as a strategy under its MediumTerm Business Plan launched in FY2021.Under the arrangement, Shell will convert scrap plastics into pyrolysis oil at its site in Bukom and feed it to a naphtha cracker to produce butadiene feedstock.
SEOUL, SOUTH KOREA: Lotte Chemical collaborated with Samsung Electronics Logitech to expand the packaging materials by recycling waste vinyl made of polyethylene.
Lotte Chemical said it would collect waste vinyl used by Samsung Electronics Logitech for packaging to produce high-quality packaging materials and supply them back to the logistics company.
They would recycle waste packaging materials at a logistics centre in Suwon on a trial basis and expand cooperation to other areas and increase recycling items.
Lotte Chemical makes stretch films for packaging through a technology that turns discarded plastic into an initial form of pellets through the process of selecting, pulverizing, and cleaning.
Physical recycling uses post-consumer recycled (PCR) materials by grinding collected polyethylene terephthalate (PET) bottles and other materials into little pieces. Chemical recycling, which breaks down and returns plastic to its pure, raw material form to address the explosive growth of plastic waste and disposal problems.
The accumulation of plastic waste has become a serious global problem. South Korea nurtures the white biotechnology industry that focuses on the creation and distribution of biodegradable bioplastics.
With an aim to produce recycled bioplastics by 2030, the company in 2022 launched the pilot production of chemically recycled PET as part of efforts to convert its PET production plant into an outpost for chemical recycling that breaks down and returns plastic to its pure, raw material form.
TOKYO, JAPAN: Idemitsu Kosan announced to invest in Vecco, which promotes the vanadium business in Queensland, Australia.
Vecco is proceeding with a vanadium mine and electrolyte plant project (project name: Debella Project, hereinafter “Debella PJ”) in Queensland will produce electrolytes for redox flow batteries using vanadium.
This project will build a value chain of local production for local consumption, mining vanadium, refining it to vanadium pentoxide, and producing vanadium electrolyte, stabilizing the supply, and creating demand for vanadium in geopolitically stable Australia.
Under the energy plan announced by the Queensland government, the state aims to raise the renewable energy ratio to 80% by 2035 (21% as of 2022), the development of renewable energy sources, the development of power grids, and power storage facilities that are responsible for adjusting supply and demand.
For power storage facilities in particular, the introduction of large-scale redox flow batteries that utilize vanadium produced in the state, added the company.
TEXAS / NEW CASTLE, US: Electroninks and FUJIFILM Imaging Colorants announced a manufacturing (OEM) agreement and selected Electroninks’ metal complex silver inks for the manufacture of proprietary metal complex conductive inks for the customers worldwide at Fujifilm’s New Castle, Delaware plant.
“Electroninks customers can feel confident in Fujifilm’s experience and capabilities to produce our metal-complex particle-free silver products inks at scale, with the ultimate in quality assurance,” said Melbs LeMieux, co-founder and president of Electroninks.
“This relationship positions us well to accommodate our continued growth and to meet the expanding demands of our customers through a proven, world-class global electronics manufacturing supply chain,” added LeMieux.
Electroninks’ products are based on its proprietary particle-free conductive metal inks which provides cost-effective, highly-stable
and reliable solutions for applications in semiconductor packaging, consumer electronics, and medical devices.
FUJIFILM Imaging Colorants is a manufacturing centre in the FUJIFILM Ink Solutions Group, an experienced inkjet ink and dispersions partner to equipment manufacturers, integrators and ink formulators.
The ISO 9001 certified Delaware facility specializes in the manufacture of inkjet inks and pigment dispersions and is experienced in contract manufacturing of complex ink chemistry.
“Fujifilm is proud to partner with an innovator like Electroninks. Our dedicated expert teams have been working in close collaboration on technology transfer and scale-up of lab formulations to deliver precision manufactured, quality assured inks,” said Melissa Toledo, general manager at FUJIFILM Imaging Colorants.
GERMANY: BASF SE said it has appointed Dirk Elvermann as the new chief financial officer (CFO), effective October and will succeed Hans-Ulrich Engel.
Engel will step down after the annual shareholder’s meeting next year, to be replaced by Dirk Elvermann, who has led BASF’s corporate finance division since 2019.“I am convinced that Dirk Elvermann with his broad experience and leadership skills will be an excellent addition to BASF’s Board of Executive Directors,” said Kurt Bock, chairman of the supervisory board of BASF SE.
On the other hand, Martin Brudermueller’s terms as chief executive was extended until the end of the 2024.
“I am pleased that Martin Brudermüller will continue to lead the company with prudence and determination in these difficult times,” said Kurt Bock, Chairman of the Supervisory Board of BASF SE.Dirk Elvermann has been with the company since 2003 and has been leading the Corporate Finance division since 2019.
NEW DELHI, INDIA: Gas Authority of India (GAIL) Limited said it has appointed Sandeep Kumar Gupta as Chairman and Managing Director (C&MD) GAIL effective from October.
Gupta, who replaced Manoj Jain, has a wide experience of over 34 years in the oil and gas industry. Before joining GAIL, Gupta was working with Indian Oil Corporation (IOC) since 2019 and handled F&A, Treasury, Pricing, International Trade, Optimization, Information Systems, Corporate Affairs, Legal, Risk management.
After joining the position of C&MD GAIL, he addressed the employees of the Company and recognized the balanced business portfolio of the company built over time and overall contribution to development of natural gas sector in the country.
Paints, India’s leading paints company and part of $22 billion JSW Group, has introduced Vogue range of finishes that offers curated wall-effects to enhance décor at home. The company extends its “Think Beautiful” promise to Vogue by offering luxurious effects to create fashionable walls for the modern, cosmopolitan Indian consumer. Vogue is inspired by the latest trends in fashion and culture to bring alive walls at home.
Vogue encourages imagination and creativity in creating effects for walls that bring out luxury, style & uniqueness. To kick-start the imagination, Vogue has introduced 8 exclusive wall effects. They are inspired by elements of nature and culture. Bandhej captures the aesthetic beauty of one of the oldest Indian techniques of fabric pattern. On the other hand, the Ikat effect captures the blurry yet charming technique of colouring fabric permeating luxury across the living space.
While the Blaze effect embodies passion & confidence, the Stacks effect infuses a classic, relaxed look that
creates a lovely accent on the wall. If one is a fan of pastels and loves the serene look, then Horizon brings forth that feeling.
The Thatches effect gives a country-style décor look. It is rustic, timeless and feels homely. While Thatches helps connect one with their roots, the Orbital effect takes one on an adventurous journey into space. Continuing with love for astronomy, the Meteor effect is meticulously designed to replicate the mesmerising beauty of a meteoroid shower.
“Vogue by JSW Paints is a designer collection of luxurious visual effects for walls. We are delighted to bring forth a curated collection of fashionable effects, inspired by India, Nature and Space. These aim to unleash your imagination and delightfully decorate homes with rich visual effects and textures,” said A S Sundaresan, Joint MD & CEO, JSW Paints.
Vogue is available in a wide range of metallic and nonmetallic colours to transform the walls of every Indian home.
Dow launched the world’s first recyclable silicone self-sealing tire solution. The solution has been successfully utilized in Bridgestone’s newly released B-SEALS, a recyclable tire sealant technology. With its new SiLASTIC™ SST-2650 Self-sealing Silicone, Dow is meeting self-sealing tire manufacturers’ demands for high performance and sustainability, while providing drivers and passengers with a lighter-weight, safer, and more durable solution.
“Dow is dedicated to leveraging its long-standing expertise in materials science to improve manufacturer and customer experiences in mobility – and this includes the emerging technology of self-sealing tires, which provide enhanced safety, convenience, and weightefficiency,” said Jeroen Bello, Global Marketing Director for Mobility and Transportation, Dow Consumer Solutions.
“With a growing consumer and enterprise awareness of environmental protection, especially among customers of premium brands, we saw the demand for a more sustainable, higher-performing solution. Through our collaboration with Bridgestone, Dow has developed a new selfsealing silicone and successfully applied it to B-SEALS. Embracing the
philosophy of Seek Together ™ and our commitment to sustainability, Dow is looking forward to working with more innovative partners to explore further possibilities of self-sealing tire solutions.”
With growing demands for material circularity and sustainability in the global automotive industry, self-sealing tires are becoming a new solution which enable lighter-weight vehicles. The new silicone sealant technology is designed to form a self-sealing layer on the inner surface of a tire. It provides outstanding sealing performance following puncture, allowing driving long distances without loss of tire pressure. The sustainability attributes of conventional self-sealing tires is severely limited, resulting in non-recyclable tires, causing extra burden and inhibiting industrial sustainable development. In addition, the complex high temperature application process and need for extensive laser cleaning of the tire surface prior to coating increase energy consumption and environmental impact during production.
As a global leader in silicone technology, Dow leveraged its material expertise to develop SiLASTIC™ Self-sealing Silicone, which provides customers with a lighter-weight, safer, and more durable solution.
Unlike most of the conventional sealants on the market, SiLASTIC™ Self-sealing Silicone sealants can be separated from tires at the end of life, enabling further recyclability of both tires and silicone. Meanwhile, it also removes the need for spare tires, thus reducing vehicle weight, improving vehicle range and fuel efficiency, and enabling more design freedom. With Dow’s innovative technology, SiLASTIC™ Self-sealing Silicone is leading the industry’s transition to a more sustainable future.
Benefitting from the unique advantages of silicone materials, only a thin layer of silicone sealant is required to achieve puncture resistance,
long-term stability and airtightness. Through Dow’s exclusive material technology, the sealant’s processability is enhanced with reduced cycle time and less processing costs. Tires using SiLASTIC™ Selfsealing Silicone sealants can be easily and quickly manufactured with standard equipment at room temperature without precleaning and pre-compounding.
With SiLASTIC™ Self-sealing Silicone, Dow continues to showcase its commitment to meeting the needs for low-carbon mobility through cutting-edge materials science technologies, and close collaboration with partners. Dow has implemented a companywide commitment to reduce its net annual carbon emissions. By 2030, Dow will reduce its net annual carbon emissions by 5 million metric tons versus its 2020 baseline, a 15 percent reduction. By 2050, Dow intends to achieve carbon neutrality (Scopes 1+2+3 plus product benefits).
ground-breaking Appretan® NTR range based on 30 percent renewable raw material can now be applied to impart barrier properties to selected types of food packaging.
Consumers are increasingly frowning upon being served their favorite street foods or fast foods in polystyrene or plastic based boxes and wrappings. Paper-based packaging can offer a much more sustainable alternative if they are not lined with a plastic film which can make them unsuitable for recycling and composting. The solution is to carefully select paper coatings and barriers solutions which are fit for purpose and that are designed to make food packaging both safe for food contact and more recyclable.
Archroma is well known for its innovations and sustainable solution systems aimed at helping packaging & paper manufacturers to optimize productivity and/or create value in their markets. Just a few months ago the company launched Cartaseal® VWAF, a PFC-free and ammonia-free* barrier for odorless paper-based food packaging, as well as in 2019, a ground-breaking binder, Appretan® NTR, made with 30 percent active content based on natural, renewable raw materials, designed for use in nonwoven articles such as tea bags and coffee filters.
In line with the principles of “The Archroma Way to a Sustainable World: Safe, efficient, enhanced, it’s our nature”, the paper & packaging R&D experts of Archroma decided to explore the properties of Appretan® NTR for paperbased packaging applications.
They investigated a new specific application aimed at providing a more sustainable barrier option for general food packaging used with a short contact time, such as burger or sandwich paper wraps.
The Appretan® NTR range is made with over 30 percent renewable raw material component, allowing the reduced use of fossil fuel based resources without compromising on the needed performance of water, oil and grease resistance. It is a more sustainably responsible option for packaging manufacturers and food retailers willing to help tackle the impacts of our food consumption habits.
The Appretan® NTR range is therefore at the core of NATURE BITES, a barrier system just launched by Archroma. In this new system, Appretan® NTR can be combined with Cartacoat® primers suitable for food contact that will seal the paper surface for further increased performance.
“Consumers are increasingly questioning how products are made, and expecting them to be harmless for themselves and their loved ones, and the planet,” commented Andy Bell, Head of Competence Center Paper Chemicals, who added, “That is why it is critical that major food and beverage brands and retailers have a close look at their packaging supplier, and ensure that they work only with leaders in sustainable innovations such as Archroma. Appretan® NTR and the NATURE BITES system illustrate once again the commitment of Archroma to drive sustainable innovation in everything we do. Because it’s our nature.”
is engaged in research into microorganisms that provide cereal crops with atmospheric nitrogen and thus promote their growth. Plants need nutrients such as nitrogen in order to grow. To meet this essential need, farmers currently use large quantities of synthetic fertilizers. However, these impact the environment and the climate. Evonik is working on an alternative: The new development is a unique combination of bacteria and bio-based additives that has the potential to significantly reduce the use of synthetic nitrogen fertilizers.
“Our new solution can help farmers safeguard crop yields with less fertilizer in the future,” said Jan Wolter, who heads the Farm to Form area at Creavis, Evonik’s strategic innovation unit and business incubator. The European Union’s goal is a 20 percent reduction in the use of fertilizers by 2030.
Evonik’s new development belongs to the class of microbial biostimulants. These stimulate natural processes in soil and plants, improve nutrient uptake, and promote growth. Like conventional leaf fertilizers, Evonik’s biostimulants are sprayed onto the upper side of foliage. From there, they reach the underside, where there are small pores known as stomata. Through these, the nitrogen-fixing bacteria penetrate the leaf, where they can act as biostimulants.
Within the leaf, the bacteria are protected from environmental factors such as rain and UV radiation and act as natural nutrient providers. “In extreme weather periods, the protection offered by the inside of the leaf is important for the efficacy of biostimulants,” explained Wolter.
To make sure the bacterial agents reach the right site in the plant, a biodegradable spreader from Evonik’s BREAK-THRU® product range is used. In combination with SIPERNAT® silica, this increases the lifetime and storage stability of the microorganisms. “We are benefiting from our expertise in microbiology, agriscience, and chemical formulation because the bacteria’s specific ability to provide nitrogen to the plants can only be used efficiently in combination with these Evonik aids,” said Wolter.
An initial greenhouse trial with wheat and corn showed a promising reduction of up to 50 percent in the use of nitrogen fertilizers. Wolter’s team is now conducting field trials in various environmental conditions to verify the results obtained in the greenhouse. In addition, the team is working on the optimum formulation of bacteria and additives, in this case spreaders and carriers. Evonik expects to launch the first biostimulant formulations commercially between 2025 and 2027. “Our innovation has the potential to become a stepping stone to the future of agriculture. It could greatly reduce the use of nitrogen fertilizers without reducing crop yields,” said Wolter.
In conventional agriculture, crops mainly obtain the essential nitrogen nutrients from synthetic fertilizers. Worldwide, 113.7 million metric tons of fertilizer were used in 2020/2021. However, production generates more CO2 than product: 1.2 metric tons of CO2 per metric ton of fertilizer. Furthermore, intensive fertilization contaminates the soil and groundwater and generates laughing gas, a greenhouse gas that adversely affects the climate.
The European Commission wants to counteract this with its Farm to Fork Strategy and is aiming to greatly reduce the amounts used by 2030: The goal is to reduce agricultural use of mineral fertilizers by 20 percent and pesticides by 50 percent. These goals, together with rising fertilizer prices, are increasing pressure on the agricultural sector to find new and more sustainable ways of producing food.
At the same time, the new EU Fertilising Products Regulation of July 16, 2022, is giving Evonik’s R&D tailwind: In this regulation, for the first time, the European Commission provides biostimulants with a uniform legal basis as a new class of crop protection products. That paves the way for EU-wide commercialization. The European Biostimulants Industry Council estimates that the market for biostimulants is growing by between 10 and 12 percent a year.
Plant biostimulants are additives such as microorganisms, algae extracts, and amino acids. Unlike fertilizers, they have an extremely low nutrient content. Biostimulants do not contaminate plants or the environment. They stimulate natural processes in soil and plants and promote growth by improving nutrient uptake and protecting plants against abiotic stress factors such as drought and frost.
Sukano, a global specialist in the development and production of additive and color masterbatches and compounds for polyesters, biopolymers, and specialty resins and Emery Oleochemicals, a leading global manufacturer of natural–based chemicals made predominantly from natural oils and fats, announced the launch of their jointly developed PET Antifogging compound for direct food contact PET packaging.
Two years of intensive testing and simulations of end use applications of the end use in real life scenarios in both research and development laboratories resulted in this new antifogging compound. It is formulated to be used at 100 percent in cold applications to prevent fogging in packaging surfaces.
The products are designed for all kinds of Coex –films (rigid & oriented) having Sukano’s co polyester – compound in one cap –layer of a film extrusion line A/B structure and PET as core –layer.
The resulting product performance is so robust that even after orientation in several different ratios, the antifogging function remains active and integral, and the film remains transparent.
Fogging, or the undesired formation of small water droplets on the surface of films, is a common problem when packing moisture –containing products such as fruits, vegetables, or meat in a tight container. When the water condenses on the surface, it often forms droplets due to the lower surface tension of plastic materials. These
droplets ‘fog’ the film and hinder a clear view into the Packaging. This not only makes packed food look less fresh and less attractive, but sensitive applications can even be damaged or have their shelf life reduced due to the presence of water droplets.
Antifogging agents solve these issues by inhibiting the formation of water droplets through a homogeneous, transparent water layer. However, the PET food packaging industry is longing for an antifog performance in the form of a compound that can be used in their packaging materials to replace the painful existing coating process.
Antifog coatings are well known and in use, but have the downside of adding another operational step to filmmaking. And typical solutionbased coatings are inactivated when the surface is washed. As an internal additive in plastics, antifog additives work on in the nonpolar polymer, and the low glass transition temperature.
However, polyolefins have limitations in recyclability and gas barrier performance. PET, on the other hand is a well recyclable packaging material with good barrier performance. and transparency. However, the current antifog additives on the market do not work in PET. Due to the polymer polarity, coupled with the glass transition temperature. Until today’s announcement, the industry had to make do with the limitations faced by polyester packaging structures.
It is an extensive understanding of polyesters, molecule design and packaging processes that worked as the foundation for this new antifog compound for polyester packaging applications.
Partnership driven by specialized companies to overcome the challenge
Antifogging agents are already common products in the portfolio of Emery Oleochemicals ‘GreenPolymer Additives business. ‘’ However, additives that work well in flexible vinyl meat wrap films or polyolefin films do not necessarily work well in PET,” said Dr. Annika Heinrich, Technical Development Manager ata Production site in Loxstedt, Germany. “Polarity, Crystallinity and other physical or chemical characteristics of the base polymers are too different, and the additive molecule design needs to take that into consideration.”’
At a very early stage, we understood that to be successful in producing effective antifogging agents for PET we must find a strong masterbatch specialist partner,” added Dr. Christian Mueller, Global Technical Market manager by Emery Oleo Chemicals ‘Green Polymer additives, and Sukano is one of the most renowned companies when it comes to developing Functional additive masterbatches and compounds. Sukano’s significant experience creating state-of-the-art masterbatches and compounds for PET applications made them an ideal fit for this joint development project.”
The key overall benefits of this new internal antifogging agent compound for PET are transparency, durability, and homogenous effect associated with easy handling, since no additional machinery investment is required to make it work. Beyond this, customers will be able to minimize any material wastage. “Internally added antifogging agents are known to create processing issues in PET such as a strong viscosity drop of the polymer melt. Clouding of the final article is another obstacle,” stated Christian Schanzer, Global product manager of antifogging additives compounds at Sukano.
That’s why Emery Oleochemicals and Sukano decided to bring together their unique specializations into a collaboration to overcome the challenge.
“Emery globally masters the development and production of LOXIOL antifogging agents. Our partnership combined a specialist in designing internal antifogging agents’ molecules with Sukano’s expertise in masterbatches and compound applications and processing of polyesters to make it possible to incorporate such long desired functionality directly into the plastics material in the compounding step,” reinforced Michael Kirch, Global Head of Research and Development at Sukano.
The compound additive was tested in PET lidding films applications, PET clam shells and thermoformed lids and trays. The final parts were then shredded, ground, washed and submitted to additional heating Conditions, simulating the critical recycling steps of a PET tray dedicated recycling stream according to the PETCORE TCEP protocol.
As responsible companies, the very natural step to evaluate the influence of such innovative technology in the PET tray recycling stream is in the core of the design principles of both companies. The Tests reflected consumer habits and local countries demands, such as extracting or not the lidding film when the packaging is disposed of.
It is with great satisfaction that we confirm the launch of this longawaited technology for the PET industry.
Technically speaking, paper is a thin sheet material produced by mechanically or chemically processing cellulose fibers derived from wood, rags, grasses, or other vegetable sources in water, which is then drained through fine mesh leaving the fiber evenly distributed on the surface, followed by pressing and drying.
The word paper comes from papyrus, a reedy plant that used to grow abundantly along the Nile River in Egypt. Centuries ago, ancient Egyptians removed the fibrous layers from the stem of this plant and cemented them together to create a durable woven writing material also known as papyrus. Examples of papyrus manuscripts have survived to the present.
The papermaking process developed in East Asia, probably China, at least as early as 105 CE, by the Han court eunuch Cai Lun, although the earliest archaeological fragments of paper derived from the 2nd century BCE in China.
By the early seventh century, paper and its production had been introduced into Japan. From here, it spread to Central Asia by 750.
Paper did not make its way into Europe until about 1150, but it spread throughout the continent over the next few centuries. Rags were the chief source of paper fibres until the introduction of papermaking machinery in the early nineteenth century when it became possible to obtain papermaking fibers from wood.
When paper was originally invented, it was made in the form of single sheets by hand. Till 1970s paper making was an art, not science. In the present day, almost all of it is made on large machines—some of whom make 10-metre-wide reels effortlessly, while running at 2,000 meters per minute, and are capable of producing up to 600,000 tons of paper a year. The modern pulp and paper industry is global, with China leading its production, followed by the United States. Today it is considered to be complete science with both Chemistry and Physics including lot of technology in it.
First things first: paper is versatile. You can print or write on it, use it for packaging or as wallpapers, decorate things with it, or simply use it for cleaning. Other uses include laminated worktops, filter papers, currency papers, security papers, and a wide range of industrial and construction processes.
Paper is an indispensable part of everyday life. Beyond its use as the basic material for written and printed communication, paper in its various forms is used for hundreds of other purposes, including packaging, wrapping, insulating, and towelling.
Over the centuries, paper has been made from various materials such as cotton, wheat/ rice straw, sugar cane waste, flax, bamboo, wood, linen rags, sabai grass, banana stem and hemp. Regardless of the source, you need fiber to make paper. Today fiber comes mainly from two sources — wood and recycled paper products.
With the advancement in technology, we have replaced paper in many of our educational and official work. However, nothing beats the satisfaction of smelling a new book, the emotions enclosed in a heartfelt letter, and well, the roll of toilet paper in our daily lives! Hence, paper is still very much a necessity in various forms.
Now that we’ve established that paper is versatile, are you wondering what types does it exist in? Well, here are various types of paper that make it such an indispensable part of our lives:
● Writing & Printing Papers
● Recycled Papers
● Tracing Papers
● Gloss and Matt Coated Papers and Board
● Packaging Boards
● Kraft Papers and Boards
● Tissue Papers
● Copier Papers
● Photo Papers
● Business Stationery Papers
● Tobacco Papers
● Carton Liner Papers
● Parchment Papers
● Newsprint Papers
● Waxed Papers
● Inkjet Papers
● Cup Stock Paper & Boards
● Religious Printing Papers
● Wax Match Tissues
● Food Grade Papers
● Acid-Free Papers
● Filter Papers
● Litmus Papers
● Artist’s Papers
● Manilla Papers
● Banana Papers
● Sandpapers
● Wall Papers
● Blotting Papers
● Wrapping Papers
● Pharma Print Papers
● Straw Papers
● Candy Stick Papers
● Carbonless Papers
● Insulating Papers and Decorative Papers
Can we say that various grades and varieties of Papers/Boards manufactured across the globe are made without help of Chemistry or Physics? Paper making starts with chemistry and ends with chemistry and also some physics. Chemicals play a major role in imparting requisite properties to Paper/ Paper Board/Speciality Papers.
The paper production process consists of several stages. In the first stage, the fragmentation and purification of the pulp take place, which may be of primary origin (wood) or secondary (wastepaper). The main source of cellulose fibers is wood obtained in sawmills under several forms, eg, as logs, wood chips or sawdust.
In the next stage, the fibrous material undergoes further processing, where it is converted into pulp, which is next processed into paper. The production of pulp can be held by mechanical or chemical methods.
In the chemical pulping process, alkali (e.g., sodium hydroxide in the form of a lye or caustic soda) is usually used to remove the lignin that binds the fibers.
The use of defoamers at every stage of paper production is also crucial. Defoaming substances are used in the manufacturing process of all types of paper products. Foam is created by mixing gases with cellulose pulp and is retained in it due to the presence of surfactants. Products from the PCC Group’s offer can be successfully used for the removal of foam produced in the next stages of paper production.
These include EO / PO block copolymers (ROKAmer) and a series of alkoxylated fatty alcohols (ROKAnol LP). Their high effectiveness in the elimination of foam and in the prevention of its formation enables an improvement in the efficiency of subsequent technological steps.
Chemical pulping processes mainly consist of the use of various chemical reagents as well as heat to soften the lignin. As a result, it is dissolved and then mechanically refined to separate the fibers. In practice, two different chemical pulping processes are used.
The first of these is the kraft pulping process, also known as a sulphate process. Currently, it is the dominant technology – about 80 percent of the world production of pulp is processed using this method. Kraft pulping has become the most used method due to several factors. Sulphate processed fibers have better durability compared to those obtained because of other available technologies. In addition, it can be used for all types of wood, and the process itself allows effective recovery of the chemical raw materials used.
The kraft process consists of combining wood chips with white liquor (it is an aqueous solution of sodium hydroxide and sodium sulphide). Under conditions of elevated pressure and temperature, this solution dissolves lignin, releasing cellulosic fibers. After completing the digestion reaction, a black liquor and cellulose pulp is obtained.
The liquor contains dissolved organic substances that are recovered and can be used in the chemical process again. Lignin is removed from the mass in the process of oxygen delignification (in the presence of oxygen and sodium hydroxide). The material obtained in this way is bleached to achieve appropriate performance, such as strength, brightness and purity of the final product.
The second process of chemical digestion is the sulphite process. It consists of using an aqueous solution of sulphur dioxide in the presence of alkalis (e.g. calcium, magnesium, sodium and ammonium). The products obtained in this process are lighter and easier to whiten, however, they have much lower strength compared to the more frequently used sulphate pulping.
The sulphite process also requires careful selection of wood raw material – this method is intolerant, for example for pine wood. The sulphite process compared to kraft pulping is more efficient, produces less unpleasant gases and also allows to obtain a very light pulp, which is easily leached. Unfortunately, due to the lower fiber quality, higher energy consumption and low recoverability of the chemical raw materials used in the process, sulphite technology has been replaced by the kraft process.
Mechanical pulping provides a very high yield of pulp from wood. The main processes used on an industrial scale is the process of stone groundwood pulping (SGW), the thermomechanical pulping (TMP) and chemo thermomechanical pulping (CTMP) process.
Groundwood pulp is obtained in the process of abrading wood on the stone at atmospheric pressure. The wood (from which the bark has been previously removed) is pulped using stone and then washed with water. The prepared mass is dried in hydro cyclones, from where it is transported to the compactor. In the next stage, dense wood mass is transported to the vat and the circulating water (filtrate) is recycled back to the pulp mill.
During the production of pulp from processed wood, resinous substances are released, which easily agglomerate and create sediment on the grinder or internal walls of the pipelines. They often cause fouling of the surface of the stone, which worsens its abrasive properties. In order to remove these so-called “resin problems” various chemical agents are used. The most commonly used agent for this purpose are dispersants, which are designed to disperse deposits which are formed, facilitating their subsequent removal.
The products of the ROKAcet and ROKAfenol series are excellent dispersants dedicated to the pulp and paper industry. In addition to their dispersing capabilities, these products can act as cleaning agents, emulsifiers, and anti-electrostatic agents. ROKAfenols are perfect for the emulsification and stain removal processes of paper pulp and cellulose. While ROKAcet R40W is a product with a softening property that can be used in the textile, leather and paper industry.
The improvement of the SGW method is the thermomechanical pulping (TMP). In the TMP process, wood chips are initially washed to remove sand, stones and other hard impurities, then heated by steam under increased pressure, and further pulped in a disc mill. In the next stage, the mass is transported to the vat, where straightening and elimination of deformation of the fibers takes place.
Finally, it is directed to the storage tank. In order to reduce the number of harmful resins formed in the TMP process, similar chemicals are used as in the SGW process. The mass created in this way is most often used for the production of newsprint.
The CTMP process combines the TMP process together with the chemical impregnation of chips. In the first phase, they are washed and sieved and then impregnated. Depending on the type of wood, appropriate chemical solutions are used. Sodium sulphate is usually used for softwood, while alkaline peroxides are usually selected for hardwood.
After the impregnation process is complete, the chips are heated and mixed with water, which loosens the lignin bonds and releases the fibers. The CTMP process allows to obtain clean pulp with sufficient strength and appropriate optical properties. CTMP is mainly used for the production of fibrous components of paper pulp, which can be used for the production of printing and hygiene papers.
The next stage of pulp processing is de-inking combined with mechanical removal of impurities. In the production of paper, the most important parameter is the colour (the whiteness – in the case of printing paper). For this reason, the recycled paper must be thoroughly cleaned of the printing ink. The basic condition for its removal is the release of paint particles from the fibers and keeping them in a dispersed state.
The finely divided ink particles are then separated from the fiber suspension. This is usually done on the basis of differences in physical properties of materials, such as specific weight of undesirable substances in comparison with fibers and water. Due to the fact that larger impurities, such as metal parts (staples), stones and sand, are already removed at the defibering stage, flotation processes are very often used in relation to fine impurities.
A frequent additional process is bleaching and is used in products requiring high purity, where yellowing is not desirable (e.g. papers for writing and printing). Sodium hypochlorite is a very popular substance used for bleaching. It can also be used for the production of carboxymethyl cellulose (CMC) from sawdust. Sodium hydroxide solution and chloroacetic acid (MCAA) are also used in this process. Bleaching involves the use of appropriate chemicals that are added directly to the dispersant to increase the whiteness of the mass.
The type of fibers used, and the desired final properties of the product have a great influence on the degree of pulp bleaching. The masses containing high-density materials are difficult to bleach and require high doses of chemicals. Sewage from bleaching installations before recycling requires several chemical agents that are intended to reduce their foaming, corrosiveness or reduce the ability to form scale.
The PCC Group’s products, such as ROKAmers, are perfect for use in processes where the foaming of sewage and technological waters occurs. ROKAmer products are block copolymers of ethylene oxide and propylene. These products reduce the surface tension between liquid and air, at the same time improving the “drainage” of foam, which in effect causes its reduction.
After the dissolving, flotation and bleaching processes, the finished cellulose pulp is processed into paper pulp, which is then used for the production of paper. This process involves several stages:
1. mixing of the cellulose pulp, 2. formation of pulp dispersion in water, 3. refining,
4. introduction of the necessary additions.
Additives are used to produce paper products with special properties (so-called special papers) or to improve the paper process. The most popular additions are:
1. resins and waxes for hydrophilization, 2. fillers, such as e.g. clays, talc and silica, 3. inorganic and organic dyes, 4. inorganic compounds improving the structure, density, brightness and quality of printing (e.g. titanium dioxide, calcium sulphate and zinc sulphide),
5. e) emulsifiers and cleaning agents. The PCC Group offers ROKAcet product series that can perform both functions. Thanks to their structure, they can also be used in the paper industry as lowfoaming and softening agents.
During the final stage, the mass is processed into a paper product using special machines. After the process is completed, the paper is rolled to protect it from damage and dirt. The PE-paper laminate is the most commonly used for packaging of the paper. Such packaging provides good protection against mechanical damage, dust and moisture.
The great advantage of this type of packaging is also that it is completely recyclable.
There are about 3000 or so different types of chemicals which can be used in papermaking, in practice only about 200 individual chemicals are typically used, each satisfying a specific need.
Conclusion:
Making of paper and its allied products involve numerous chemicals which are highlighted in this paper. Now only few players are involved in making such functional and speciality chemicals. Restriction on use of single use plastic and other plastic products has huge potential for the growth of paper industry as well as chemicals used in paper making.
Several Corporates and R & D Organisations are working on usage of Green Chemistry for better sustainability of nature and reduction of usage of hazardous and toxic chemicals in pulp and paper production. So Indian MSME industries or any start-ups should come forward and set up chemical plants in the vicinity of paper industries for win-win situation.
Gouri Shankar Patnaik is General Manager (QA & TS) and Sunil Kumar Pradhan is Assistant Director (PAPRI), both at J K Paper Mills.
impacting biopharma, pharma,
manufacturers.
Since the genesis of pandemic, Governments have stepped up spend and investments in the Healthcare sector. Pandemic has led to significant geo-economic and geopolitical shifts, with government driving selfsufficiency agenda and industries recalibrating their business models. Improving access to medicines, achieving equitable and sustainable healthcare with ramping up health expenditures and serving an ageing population in advanced economies are the areas of focus.
Biopharma, Life Sciences and Pharma all shone during the pandemic that made investing in them a promising opportunity. Developing vaccines and drugs that saved millions of lives all over the world helped soar publicly traded stocks.
There was significant collaboration across the sector. The pandemic brought everyone together. Large life science organisations researched together to bring out life-saving vaccines and drugs, hoping to pursue innovations together. Digitisation has spiralled growth across all sectors, healthcare management and patient engagement are better and getting more seamless because of this digital transformation.
There is better scope for real world data which gives an exclusive insight into rare, complicated diseases that open up opportunities for informed treatment. The sector is definitely evolving, and opportunities opened up during the pandemic. These trends will continue to drive the three sectors in the coming years.
Global trends in biopharma, pharma and life science segment.
We expect a see change in the Biotech landscape in India and globally. Over the past few years, significant investments and advancements are visible both in traditional and novel modalities. We see more number of biosimilars getting approved for use globally. There are many companies working on novel modalities like, Cell & Gene Therapy, ADC (Antibody-drug Conjugates), HP-API (high-potency API), viral vector, and mRNA (Messenger Ribonucleic acid)).
For COVID vaccines, under development protein sub unit, viral vector, and nucleic acid based vaccines are the top modalities being explored by companies and molecules are at different stages of development.
We also anticipate the manufacturing landscape transforming in the Biotech space over the next 5 years. Efforts towards making Biosimilars / Mabs more affordable in order to be competitive globally and widen the market opportunity and is in line with the vision Government has for Healthcare and Pharma Industry.
The focus has been on improving the yield of the products, driving down cost of manufacturing, improving efficiency of the products using continuous processing, manufacturing units moving from multi use to single use technologies and many more.
Life Sciences has shown a legacy of growth with a digital first approach. Long term strategic digital objectives are the focus of life sciences going forward and will also require greater commitment to enterprise agility.
There is scope for better investments, with increased focus on medicine accessibility, pricing of drugs, environmental sustainability, diversity, inclusivity amongst others. The entire healthcare sector has become more patient-centric and digital technologies are being adopted at a breakneck speed to develop therapies and improve the quality of life.
Potential of biopharma, pharma and life science in Asia Pacific and India.
Asia Pacific is not homogeneous. While developments in the healthcare sector of course get duplicated here at the same time as with the rest of the world, but the diverse markets, demographics, regulations and disease profiles make it an interesting region to look into healthcare aspects differently.
New developments in this sector are 3D printing, artificial intelligence and blockchain – all of which are transformative technologies. The countries in this region are some of the most densely populated countries in the world. And hence the strategy for this region must be positive health management that looks at preventive rather than treatment as the goal.
Another point to reiterate from the previous questions is patient centricity. Wearable technologies and validated health applications are increasingly helpful in bettering the accessibility towards good health. The Indian government is doing a lot in terms of regulations and standards and cloud-based hospital applications that help the government streamline data to analyse health indicators. Mobile healthcare is another segment that aims to better healthcare management.
The way forward is digital adoption and collaboration. Clinical innovation and research will always pave the way for growth in an ecosystem that has all parties – stakeholders, manufacturers, academia, governments, non-profits and patients can all work together to invest in a sound healthcare system.
Digital technology, automation in biopharma, pharma and life science segment in India.
India has been amongst the world leaders in accelerating and adopting digital transformation in healthcare, that included bolstering policies, regulations and innovation. The Ministry of Health and Family Welfare of India (MoHFW) steered the country on the path of telemedicine which has been a breakthrough. It is a remarkable step towards wholesome healthcare in our country.
It looks into aspects of medical practitioners and patient relationships, care, informed consent, emergency referral services, medical records, health education, counselling amongst many others. This along with proper medical diagnosis, treatment and incidental processes are a step in the right direction in an age of social distancing. Virtual consultation took off in India in a big way, thanks to a fast-developing digital infrastructure in the country.
The government’s efforts towards digitisation with its Digital Health Program will help to promote e-health standards and best practices. There are lot of other digital initiatives being carried out by the government. For example, e-shushrut and e-hospital, e-sanjeevani are some of the steps being taken for patients to connect with them better, provide them with better records to help in sound diagnosis, and provide comprehensive tele-consultations.
From a manufacturing perspective, improving efficiency, yield, pressure for cost reduction, and needs from regulators are driving adoption of pharma 4.0.
Learnings of the pandemic for biopharma and pharma research.
The biggest scientific breakthrough in the 21st century would probably have to be the development of the COVID vaccine at a record time. The logistics of developing, manufacturing and dispensing vaccine to such a large population was a herculean challenge. The choke points were at various levels.
The entire value chain collaborated to overcome hurdles and delivered. In spite of the pandemic, our scientists and experts worked closely with vaccine manufacturers on process development. Supply of required raw materials was a major challenge for vaccine manufacturing operations. Expected turn-around time was much lower than the production schedule. As a social responsibility, we preferentially prioritized supplies to COVID vaccine manufacturers.
Rising to the occasion, the regulators also expedited the pathway of emergency use authorization. With all these practises in place, the industry is well poised to handle future emergencies.
This approach along with Digitalization and Collaborative approach between firms is going to be the way forward, in shortening the cycle of drug development and commercialization.
Insight into BioProcess business and roadmap for the future.
The BioProcess business strives to be the 1st choice & premium partner for biopharma companies in India by being the Preferred partner through technical and regulatory consultancy.
The business offers a diverse range of products to biotechnology and pharmaceutical companies that enables customers to develop large and small molecule drugs safely, effectively and cost-efficiently. Our solutions include filtration, cell culture, single-use, chromatography’ virus reduction and purification products.
The M Lab™ Collaboration Centre in Bengaluru, is managed by a team of expert, scientists & engineers with Global expertise which helps create a difference to the Life Science industry in India. Skill development has been one of the major focus areas for M Lab™. Our M Lab™ Collaboration Centre also acts as a platform to engage with customers to solve challenges in the pharmaceutical and biopharmaceutical industry.
We have a manufacturing facility in Peenya Bangalore, where we manufacture custom engineered equipment and prefilters for the Biopharma industry. Our Validation Services lab in India supports customers in their filter validation studies and regulatory documentations. Our warehouse at Patalganga is well connected to all key pharma hubs in the country and proximity to port facilitates rapid and cost efficient movement of goods. The DC caters to the needs of markets across APAC and South Africa.
Our team of cross functional team members are located across India, closer to our customers, to support them achieve their business goals.
India is a very important market for Merck. Our goal is to invest in using path breaking technologies to simplify treatment and make it accessible to all those in need, in collaboration with drugs manufacturers across India and scale up to make treatments and therapies available to all.
Research & development and innovation at MLab.
M Lab™ Collaboration Centre is managed by a team of expert, scientists & engineers with Global expertise which helps create a difference to the Life Science industry in India.
Managed by an experienced team of engineers and scientists, our M Lab™ Collaboration Centers allows one to explore technical solutions, test applications, assess technologies and optimize your process.
• Support customers who are unable to have high quality labs to support in their development process
• To give a feel and demo of infrastructure to Greenfield projects and Startups / Emerging Biotech Accounts
• Give a hands-on experience to customers through planned and customized trainings
• Pilot lab for non-classified trouble shooting and process development trials to customers
• Digital and advanced tools for remote troubleshooting and demonstration
We continue to invest in our M Lab™ Collaboration Center, to bring in novel and innovative technologies that helps accelerate drug development programs. We also plan to partner and mentor earlystage Biotech companies by bringing in our technologies, knowledge and expertise.
Development of COVID vaccine was the biggest scientific breakthrough in recent times. There were challenges because of the changing nature of the variants that posed serious and unknown threats to the lives of people. The mutant variants and their high infectivity were throwing everyone off-guard.
Merck’s Collaboration Labs in India and APAC rose to the challenge and stepped up their capabilities to support vaccine manufacturers in various ways. Some of the ways that the organisation helped was by technical consultation for process developments, regulatory services for risk mitigation, patient safety and approvals, expanding our facilities and supplying in the midst of severe global disruption to facilitate the early launch of vaccines for immunization.
Improving sustainability parameters in the company.
At Merck, we believe that we can harness science and technology to help tackle many global challenges such as climate change, resource scarcity and unequal access to health. Always guided by a robust set of values, we approach all our actions and decisions with a sense of responsibility. Sustainability has been vital to us for many generations.
As a sustainable enterprise, we seek to balance environmental, social and governance aspects – for us as a business, for our stakeholders and for society at large.
We want to create long-term added value for society, which is why we have defined three goals within our sustainability strategy:
• In 2030, we will achieve human progress for more than one billion people through sustainable science and technology.
• By 2030, we will integrate sustainability into all our value chains.
• By 2040, we will achieve climate neutrality and reduce our resource consumption.
In order to reach our sustainability goals, we are concentrating on seven focus areas in which we are pursuing numerous initiatives and projects, measuring our progress along the way. This ensures that we successfully implement our sustainability strategy and that sustainability becomes a success factor across all our business sectors.
Government regulations and global standards to support growth of the industry.
Regulatory affairs in the pharma industry has a crucial role to play in all phases of drug development, drug approval, and marketing, in compliance with the norms, regulations, and guidelines. Stricter government regulations ensures quality and patient safety and it builds the confidence of consumers on Biopharma and Pharma products.
At the moment, we see a large gap in regulatory capacity and expertise between emerging and developed countries. Harmonization of regulatory requirements/regulations or different elements of regulatory affairs will allow manufactures to explore different markets.
Potential of testing and training in biopharma, pharma, life sciences in India.
Over the last few decades, Indian pharma industry has strengthened its expertise in manufacturing and supplying quality generic drugs to address the growing need for affordable health care around the world. Both the government and industries in India have an aspirational growth outlook and we see the industry in India focusing on complex Biologics and other emerging novel modalities. According to an E&Y report, India is the third-largest global manufacturer of drugs, but it ranks 14th in terms of value.
The need of the hour is to further step up the R&D ecosystem in India, which establishes Indian Pharma industry not only in the generics space but also in Biologics. There is a huge potential to establish the country as the global innovation hub of the future. This would need significant investments in skill development, more investments in R&D, collaborations between Industry and academia and funding from the government and private parties.
Collaborative steps between the academia and industry can facilitate a better ecosystem in the country. The Indian Ministry of Science and Technology has created research ecosystems through its biotech parks and incubators. These kinds of facilities will enable opportunities to our younger generations to thrive in STEM education and learning cutting edge technologies that are most relevant.
We need to spur innovation and entrepreneurship amongst the younger minds and help them develop products to solve real life problems. We need a strong research system that encourages independent thinking, bold ideas and a new generation scientists and world leaders.
Borealis, a leading provider of advanced and sustainable polyolefin solutions and a European front-runner in polyolefins recycling, and Tupperware®, a leading global consumer products company selling sustainable kitchen and lifestyle products, have teamed up to extend the Tupperware ECO+ product line to include a coffee to go cup made using renewable feedstock from the Bornewables portfolio of premium circular polyolefins.
Based on the proprietary Borstar® Nucleation Technology, Bornewables™ RG466MO is a sustainable polypropylene (PP) random copolymer with organoleptic properties. Using this grade enables Tupperware to further reduce the carbon footprint of its ECO+ product line. By helping extend the range of more sustainable materials used to produce Tupperware products, this partnership represents the EverMinds™ spirit of advancing plastics circularity.
Strategic partners in circularity
Tupperware has long used the PP random copolymer BorPure™ RG466MO in production. Because RG466MO is based on the proprietary Borstar® Nucleation Technology, it offers faster cycle times and lower processing temperatures in the production process. It boasts excellent organoleptic properties. Its outstanding stiffness/ toughness balance enables the production of durable and robust items like the ECO+ coffee to go cup, which is now composed of 100% Bornewables™ RG466MO. Drinks can be safely stored and transported while maintaining temperature and taste in the reusable
and attractive Coffee to go cup, which itself is fully recyclable at end of life.
Like all Bornewables grades, the commercially available Bornewables™ RG466MO is made using renewable feedstocks derived solely from waste and residue streams. ISCC PLUS certification according to the mass balance model ensures that sustainable content can be tracked and verified along the entire supply chain. Overall, the use of Bornewables compared to conventional fossil-based feedstocks results in significant carbon footprint reductions in the end product.
“The ECO+ Coffee to go cup, brings together the core components of our cascade model for plastics circularity: Reuse rather than single-use. Use of renewable rather than fossil-based feedstock,” explained Peter Voortmans, Borealis Global Commercial Director Consumer Products. “And at end of life, we recycle the Coffee to go cup rather than throwing away a valuable material resource. This is a prime example of how we are working with our partners to re-invent essentials for more sustainable living.”
“Extending our ECO+ product line to include more products manufactured with renewable feedstock shows our commitment to reducing waste at every step of the product life cycle,” said Sophie Wolters, Vice President of Product & Category Management at Tupperware. “As pioneers of reuse, we are glad to find partners like Borealis who share our conviction that there is no time to waste in achieving greater sustainability. We will continue to drive innovation and development of the next generation of sustainable materials.”
The Durethan-brand polyamide 6 compounds from LANXESS are not only cost-effective alternatives to polyamide-66based compounds but are also much more climate-friendly. This is according to calculations performed by the specialty chemicals company based on its own data and on figures published by a range of institutions including various associations of the plastics industry.
“With 3.66 metric tons of CO2 equivalents emitted per metric ton of material produced, the carbon footprint of our polyamide 6 base resin is much more than 40 percent lower than the current published European industry average for polyamide 66,” said Dr. Guenter Margraf, Head of Sustainability and Product Management in High Performance Materials. “The carbon footprint of our polyamide 6 compounds is therefore also correspondingly smaller, which is why they are the perfect substitute for polyamide 66.”
The carbon footprint of the polyamide 6 compounds from LANXESS can be reduced even further by producing them not from conventional glass fibers, but from the resource-conserving Eco glass fibers developed by the company. Industrial glass waste is used in their production, which reduces the consumption of raw materials and energy and avoids waste.
“The carbon footprint of our Eco glass fibers is around twothirds smaller than that of conventional glass fibers,” said Margraf. LANXESS offers the corresponding compounds that are mass-balanced in accordance with ISCC Plus (“International Sustainability and Carbon Certification”) under the brand name Durethan ECO. They contain up to 60 percent by weight
of recycled fiber. Mass balancing helps to determine the share of sustainable material in the compound and to indicate it in a transparent manner for processors.
Under the name HiAnt, LANXESS offers a range of services designed to support customers in the transition from polyamide 66 to polyamide 6. These services range from joint concept development for the design of components and material optimisation through to cutting-edge methods in computeraided engineering (CAE) for predicting component properties.
“The right choice of material and a weight-optimised component design – for example, making walls less thick where they are subjected to lower loads and optimally positioning reinforcing ribs – can help to tangibly reduce the carbon footprint of a component still further,” said Margraf.
The extent to which the carbon footprint can be reduced is demonstrated by the cover for an on-board battery charger installed in an all-electric compact vehicle made by a German carmaker. It consists of Durethan BKV50H3.0, which is highly reinforced with 50 percent by weight of short glass fibers.
According to Margraf, “Compared with a component solution made from a polyamide 66 compound containing the same amount of glass fiber, the carbon footprint can be reduced by 36 percent. The use of a BKV50 type with Eco glass-fiber reinforcement could potentially have reduced the carbon footprint by as much as 46 percent.”
Eastman, maker of Naia™ Renew sustainable fibers and yarns, announced its collaboration with Patagonia® to offer a limited run of T-shirts made with Naia™ Renew ES — Eastman’s latest fiber offering made with increased recycled content — for the outdoor apparel retailer’s Workwear line.
Named for its enhanced sustainability, Naia™ Renew ES is made with 60% recycled content. Unlike other cellulosebased yarns and fibers, this option requires fewer virgin materials to make an environmentally friendly product. Naia™ Renew ES is made from a combination of molecularly recycled waste material (40 percent), recycled cellulose (20 percent) and renewable wood pulp (40 percent).
The 20 percent recycled cellulose comes from waste materials, textiles waste and non-forest-derived cellulose waste. This innovation is made possible through Eastman’s continuous efforts to collaborate with eco-conscious partners throughout the value chain. For example, the Naia™ team has partnered with GP Cellulose, a pulp supplier with a focus on sustainability, to integrate renewable forest fibers and nonforest fiber solutions into its feedstock.
The remaining 40 percent recycled content comes from Eastman’s cutting-edge molecular recycling technology that breaks down hard-to-recycle waste materials like plastic packaging and old carpet into fundamental building blocks to produce the acetic acid used to make cellulose acetate yarn
and fiber. This process not only produces fewer greenhouse gas emissions but also diverts waste materials from landfills, incinerators and other undesirable end-of-life destinations, finding new value for pre- and postconsumer waste that is not suitable for recycling by traditional means.
“Patagonia has always been a company that chooses its fibers carefully and responsibly,” said Ruth Farrell, Eastman textiles general manager. “The collaboration we’ve enjoyed with Patagonia has been instrumental in developing materials that appeal to its customers — environmentally conscientious people who work and play hard. Patagonia customers want garments that reflect who they are and what they care about without compromise on comfort and quality.”
Patagonia’s Workwear line is a Fair Trade line of apparel made for people who work hard daily to make the planet a better place to live, perform and produce. It features durable, low-impact fibers with a lower carbon footprint.
“Now more than ever, people want to know how and where our clothes are made, paying particular attention to what they’re made from,“ Farrell said. “Naia™ Renew ES is our answer to the overconsumption of raw materials, a growing plastic waste problem, and rising greenhouse gases caused by deforestation. It’s a future-focused fiber made with the next generations in mind — one that doesn’t compromise on the quality of the garment or the health of our planet.”
SCG Chemicals or SCGC has partnered with Colgate-Palmolive (Thailand) Limited to launch packaging of personal care products made from High Quality Odorless PCR Resin under the brand SCGC GREEN POLYMER™.
Palmolive shower cream is the first product line to have packaging made from this High Quality Odorless PCR Resin, with plans to introduce it to other product lines in the future. For the first time, Colgate and SCGC collaborated to use PCR plastic for personal care product packaging that focuses heavily on the product’s fragrance and keeps unwanted odors from interfering with the fragrance contained within the packaging.
The solution addresses customers’ needs in the South Pacific market that continue to place a high value on quality and sustainability which has been commercialised since June 2022. The approach helps minimise waste and promote household used plastic recycling, following circular economy principle, while lowering greenhouse gas emissions, a sustainable way of addressing the global warming crisis.
Colgate-Palmolive is committed to achieving sustainable changes in both society and the environment, with the goal of reimaging a healthier future for all people and our planet. The partnership with SCGC reinforces Colgate’s sustainability strategy, which aims to use at least 25 percent PCR in all plastic packaging and reduce the use of virgin resins by a third by 2025, as well as to achieve net zero greenhouse gas emissions by 2040. The solution has been firstly introduced to the Palmolive shower cream product, launched on the market since June. This heralds the increase of recycled plastic in personal care packaging in the South Pacific.
Tanawong Areeratchakul, President of SCG Chemicals or SCGC said, “SCGC is moving towards “Chemicals Business
for Sustainability” and conducts business in line with ESG (Environmental, Social, and Governance) to innovative green polymer materials based on the principles of the circular economy.
Its application can now be expanded to personal care products that require special attention to fragrance, such as body and hair care products. SCGC has developed High Quality Odorless PCR under brand “SCGC GREEN POLYMER™” and cooperates with Teamplas Chemical Co Ltd, a leading plastic recycler in Thailand, by recycling well-sorted and cleaned post-consumer plastic within Thailand.
It uses deodorising technology prior to molding them into packaging, making them free of unwanted odors. Furthermore, packaging traceability is available for verifying the origin of recycled plastics certified by the Global Recycled Standard (GRS). The manufacturing of PCR plastic requires less energy than conventional plastic, contributing to a 70 percent reduction in greenhouse gas emissions.”
The High Quality Odorless PCR is one of the eco-friendly solutions under the brand “SCGC GREEN POLYMER™” which comprises eco-friendly polymer solutions encompassing four areas:
• REDUCE – reducing resource consumption and increasing resource efficiency
• RECYCLABLE – design for recyclability;
• RECYCLE – implement recycling; and
• RENEWABLE – developing environmentally friendly bio compostable compound and bioplastics made from renewable resources.
new MAM
Neste, Borealis and MAM collaboratively announce the launch of its first climate-neutral soother. The new MAM Original Pure soother is composed of renewably-sourced polypropylene (PP) from the Bornewables™ portfolio of circular polyolefins, manufactured with Neste RE™ produced entirely from renewable raw materials.
The packaging of MAM Original Pure soother, which also functions as a steriliser box, is also made using the Bornewables. This development is an excellent example of how eco-efficient design and the use of circular polyolefins can substantially reduce the carbon footprint of a product while at the same time guaranteeing its safety and superior product quality.
In their efforts to decarbonise and reach their sustainability targets, many industry sectors are seeking safe and cost-efficient alternatives for plastics made using fossil-based feedstock. Grades in the Borealis Bornewables portfolio are often the ideal replacement solution.
Using renewable Neste RE feedstock consisting of renewable propane which is derived for this collaboration solely from vegetable oil origin waste and residue streams, the Bornewables are produced according to the mass balance model which enables circular polyolefins to be tracked, traced, and verified throughout the entire value chain. Neste supplies Neste RE feedstock to Borealis for dehydrogenation. It is first converted to renewable propylene, then to renewable polypropylene (PP) at Borealis’ ISCC PLUS certified production facilities in Belgium.
“In line with our EverMinds™ initiatives to work with partners along the value chain to accelerate action on circularity, we strive to offer innovative and circular material solutions that help our partners and customers attain their own ambitious climate and sustainability targets – with this we re-invent essentials for sustainable living,” said Peter Voortmans, Global Commercial Director Consumer Products at Borealis. “The collaboration with Neste and MAM is a prime example of how upstream and downstream partners can come together to accelerate plastics circularity.”
“The MAM Original Pure soothers show how renewable feedstock such as Neste RE has become a viable alternative to conventional fossil feedstock even in sensitive applications,” said Maria Carcole, Head of Brand Owner Management from Renewable Polymers and Chemicals business unit at Neste. “We are happy to contribute to new products with significantly reduced greenhouse gas emissions while helping maintain product safety and performance at the highest level.”
“After nearly a decade of intensive research and as a next milestone in our sustainability efforts, we are now very proud to launch our MAM Original Pure soother range made of renewably-sourced raw materials. A new product range is made for the healthy growth of babies and contributes to sustainable development that secures the future of our planet,” said Peter Rohrig, CEO and Founder of MAM.
Employing mono-material compositions for packaging is an effective way to improve recyclability. Also the PP mono-material barrier packaging suitable for retort sterilization delivers superior recyclability for a more eco-friendly
Toppan, a global leader in communication, security, packaging, decor materials, and electronics solutions, has added to its comprehensive range of GL BARRIER1 brand products centered on transparent barrier films by developing new polypropylene (PP) mono-material barrier packaging with outstanding heat and water resistance, making it suitable for retort sterilisation.
The new packaging takes advantage of GL BARRIER’s vapor deposition and coating technologies to provide the heat and water resistance needed for retort sterilisation, something that has proved challenging with conventional PP films. This means that packaging with mono-material compositions for enhanced recyclability can now be used for retort foods. In addition, the absence of metal in the packaging enables microwave heating and the use of metal detectors to check for foreign objects.
This adds further to the lineup of GL BARRIER products that meet growing demand for mono-material solutions, particularly in Europe and North America. Toppan will supply ALL PP packaging to food manufacturers and customers in a wide range of other industries. Samples will be available globally from spring 2023, with sales targeted for launch within the same year.
The key concept for Toppan’s MediumTerm Plan, which was published in May last year, is Digital & Sustainable Transformation. One of the priorities identified is responding to global demand for sustainable packaging and accelerating the establishment of a network enabling local production for local consumption.
Efforts to circulate resources from packaging waste are underway in the EU, with a target to make all packaging reusable or
recyclable by 2030. Employing mono-material compositions for packaging is an effective way to improve recyclability, and there is demand for barrier films and packaging for PP-based monomaterial packages. By developing ALL PP mono-material barrier packaging with the superior heat and water resistance needed for retorting, Toppan has made it possible to shift to mono-material structures for retort food packaging.
Features of ALL PP mono-material packaging
・PP mono-material composition for enhanced recyclability
Toppan has achieved excellent recyclability by switching to a PPbased mono-material composition.
・Suitable for retort sterilisation
Vapor deposition and coating technologies accumulated in the development and manufacture of GL BARRIER products have been leveraged to create a PP film that delivers barrier performance as well as water and heat resistance that have previously been difficult to achieve. Combining PP barrier film with advanced coating know-how has enabled barrier packaging with a mono-material composition that takes advantage of PP’s heat resistance.
・CO2 emissions reduced by switching from aluminum foil
CO emissions during manufacture can be reduced by approximately 26%2 if the new PP-based mono-material packaging is adopted as an alternative to conventional multimaterial packaging that uses aluminum foil.
Toppan plans to expand sales of this and other mono-material packaging products as it works to contribute to a sustainable global society.
Global supply chains have seen unprecedented disruption, and container freight rates are at record highs. COVID-19 led to a boom in US containerized consumer goods demand, causing congestion, and reducing effective container logistics capacity. Global container shipping rates have, on average, increased to four to five times their 2019 levels while some spot markets have seen even higher rates.
Shippers have struggled to locate capacity, with acute shortages of vessel space, container boxes, chassis, warehouse space, intermodal capacity, and labor. Shippers that managed to find access to the constrained capacity have experienced record low reliability both at sea and on land. Average container schedule delays have doubled globally, and increased by six times on the Far East and North America
trade from two days in the first quarter 2020 to 12 days in the last quarter of 2021.
Global demand growth is moderate; the challenges are caused by a North American import demand boom
COVID-19 caused substantial fluctuations in containerized goods demand that upset the global containerized logistics supply. Restrictions and shutdowns imposed by most countries early in the pandemic decreased container trade and demand. Demand recovered in Q3 2020 across the globe, particularly in North America that saw import volumes jump an average of approximately 20 percent throughout 2021 when compared to 2019. By comparison, global import volumes have grown around 3 percent when compared to 2019.
When China went into lockdown at the beginning of 2020, export volume slumped. Retailers feared a global recession and cut back orders. Ocean carriers responded by cancelling sailings and idling vessels to match the logistics supply with demand. This measure allowed ocean carriers to protect rates from crashing, but it failed to reposition empty containers back to Asia effectively. Once China’s factories restarted, demand for containerized goods recovered by Q3 2020. Container box shortages at export locations increased rates as shippers scrambled to secure access to the limited boxes.
Lockdowns in North America saw a strong rebound in consumer demand and ocean carriers captured this surge in demand by shifting
vessels and container equipment to the Transpacific and Transatlantic trade lanes. Allocated container vessel capacity on the Transpacific trade lane—Far East and North America—increased by 31 percent between January 2020 and December 2021, which is more than three times the growth of the next largest East-West trade lane by capacity, Far East and Europe. Idle capacity, and smaller North-South trade lanes, contributed to vessel and equipment capacity being diverted to North American import-related trade.
As imports from Asia poured into North American ports, cargo operations started to slow down at container terminals. By September 2020, the hinterland intermodal subsystems, particularly in the US West Coast, became overwhelmed and failed to keep cargo moving out of the congested terminals.
by
Slowdowns in Los Angeles and Long Beach began to radiate across the industry and other short-term shocks such as the Suez Canal blockage in March 2021, and closure of Yantian in May 2021 and Ningbo in August 2021 due to COVID-19 outbreaks, exacerbated the situation.
By December 2021, congestion had removed around 16 percent of global container ship sailing capacity when compared to September 2020. Ocean freight rates climbed higher in all major trade lanes as shippers continued to show willingness to pay premium rates to secure capacity, especially for containers carrying high-value goods.
It is almost impossible to predict exactly when supply chains will normalize. Efforts are being put in place to remedy the situation, however, massive uncertainty remains.
To help shippers navigate the path towards normalization, we have developed four possible scenarios of rate outcomes. The scenarios were developed by considering drivers of container demand and containerized logistics capacity that form the basis of the current industry and market dynamics.
Container demand is driven by end consumer spending on goods, shippers’ desire to continue stocking inventory, and an economic reopening that may shift spend back to services.
The container demand surge seen in North America is tied to consumers’ spend on goods. COVID19 lockdowns shifted the share of US personal expenditure on goods from 31 percent to 35 percent. Between September 2019 and September 2021, goods spending increased and remains 14 percent higher than the prepandemic trend.
In the wake of the pandemic, governments provided stimulus payments to mitigate the impact of the economic shutdown, allowing consumers’ spending power to remain in place while almost all service-industry associated activities were heavily restricted. Overall spending has increased, with US consumer spend on services only 2 percent below the prepandemic trend. Full economic reopening may spur spend towards services leading to prepandemic levels of spend and demand for goods.
Containerized logistics capacity can be defined as the volume capable of being processed and transported by the system at any time. This capacity is dependent on hinterland logistics and equipment availability, ocean capacity and equipment availability, and labor availability. The lack of effective capacity—caused by congestion across the supply chain—is the biggest driver of the current spike in rates.
The recovery of port and hinterland logistics capacity from current congestion will depend on landside operators working together. The unexpected surge of US container imports after Q3 2020 overwhelmed the system. While part of the congestion came from lower labor availability, our analysis suggests that slower trucking equipment turnover—including tractors and chassis—is the main factor driving the current congestion.
Trucking plays an important role in container hand-offs. Fixing trucking and improving equipment turnover requires a respite from the continuing volume surge and a relaxation of the pinch-points that delay trucking. This cannot be achieved if warehouses continue to be at full capacity, empty storage at terminals is congested, and shippers are not receiving and releasing equipment as quickly as possible.
Several interventions could mitigate current congestion and improve containerized logistics capacity. Regulators are extending ports’ working hours and number of shifts, adjusting stacking height regulations, and prompting shippers to commit to moving containers out of terminals at a faster pace. Railroads are improving dwell times at ports, and incentivizing shippers to use weekend in-gates. These interventions will help stakeholders re-establish the coordination needed to get the value chain moving again.
Supply will also increase as ocean carriers invest their record profits to order new vessels, with around 5.5 million TEUs of new capacity expected by the end of 2024. Availability of container boxes has already increased, and an additional 4 to 5 million new containers are expected in the coming year.
The pandemic has amplified labor shortage across all economic sectors, leading to lower capacity across containerized logistics. Logistics employers are responding with increased wages which could attract workers back to the sector. This, combined with the acceleration of automation projects at warehouses and ports, should help the industry become more resilient in times of labor shortage.
Trends in container demand and logistics capacity inform four scenarios—each with different implications as to how long the supply/ demand imbalance will last.
In this scenario, logistics capacity recovery begins in Q1 2022 with full quick recovery possible by Q3 2022. Three things must occur for this early recovery: 1) demand slows down and pent-up or unexpected demand shocks must not materialize to overwhelm supply chains; 2) logistics operators utilize the drop in demand to execute coordinated efforts to clear container inventories; 3) no further external disruptions interrupt operations (such as COVID-19-related terminal shutdowns, weather impacts, or labor challenges).
Rates are expected to remain elevated throughout the 2022 contracting season and decline rapidly after Q3 2022 when competition between the ocean liners picks back up. Ocean tender and spot rates could come down close to prepandemic levels by Q3 2022 (Exhibit 6).
In this scenario, containerized logistics capacity recovery is expected by Q1 2024. Three things would occur for this scenario to materialize: 1) interventions from regulators and operators have only marginal success; 2) container trade volumes continue to demonstrate modest growth and some pent-up demand from underperforming commodity sectors materializes (notably auto parts); 3) containerized logistics operations are interrupted by minor, short-term disruptions from weather and/or labor challenges.
Freight rates on both the ocean and hinterland side are expected to remain elevated until normalization is robust. Ocean shipping rates will remain elevated through the contracting season of 2022 and 2023. Similarly, railroads will maintain current rate levels to keep operating ratios low while trucking and drayage rates may witness a slight decline. While ocean rates will come down, ocean carriers will better match capacity with demand, and shipping spot rates could stabilize at around 50 percent higher than prepandemic levels after Q1 2024.
All four scenarios assume disruption to last at least another five to six months. Regardless of which scenario occurs, shippers can take steps to improve supply-chain resilience right now.
Shippers are operating in a world where disruptions have become regular occurrences. Averaging across industries, businesses can expect supply-chain disruptions lasting a month or longer to occur every 3.7 years, and the most severe events can take a major financial toll.
In the short term, shippers can look for creative alternatives and adjust contracting to continue moving goods.
There is space available on container ships, but at high spot prices asked for by forwarders and ocean carriers. Some shippers could decide that it is better to defer or cancel shipments, especially when moving lowervalue goods. This may lead to lost business in some sectors. But there are opportunities to be creative with supply routes.
For instance, some shippers have found Canadian ports (eg, Prince Rupert) to be less congested than those in Southern California and still provide rail services into the US Mid-West. Other shippers are using all-water services to East Coast ports, where congestion is less severe. As another alternative, some shippers have shifted away from inland point intermodal container movements, towards transloads in the immediate port vicinity.
Some larger shippers have made the move to chartering their own vessels. These efforts have primarily focused on general cargo ships as there are no cellular container ships available for charter beyond those already in use by the ocean carriers. Shippers looking to charter their own vessels need to find other ship types which, while not designed specifically for container carriage, can carry between 500 and 1,000 containers.
Multi-purpose ships or open-hatch bulk carriers, previously used for breakbulk, can be used. But this does not remove the fundamental challenge of finding available ports. Even with a chartered vessel, shippers need to find a US port that can unload it. A ship chartered by a large US retailer recently waited for 25 days outside Los Angeles, before giving up and unloading in Portland.
Some shippers have managed to use smaller second-tier ports that are not on the major container trade routes. For example, the port of Everett outside Seattle is usually used for moving parts for Boeing. It has now received several special container charters. Dedicated charters can offer emergency help, but this is unlikely to be a long-term solution.
The other challenge facing shippers now is how to contract for volumes in 2022 and 2023. Ocean carriers are offering contracts, but at considerably higher rates than in previous years, and often proposing these higher rates for several years on a take-or-pay basis. The future rate environment is uncertain. In some scenarios, rates could normalize by end of Q3 2022. In other scenarios, rates could remain high until 2023 or even beyond that.
One potential solution is a mixed approach, hedging the risk. Shippers could contract some volumes now and potentially for the next two years, while leaving some to contract in the usual April-May 2022 rate season. They could also leave some volumes to secure on the spot market. The right mix of contracted and spot will be different for each shipper. To find the right balance, shippers should consider the value of goods in the container, substitute products, and the business trade-offs between high rates and supply-chain interruptions.
Shippers may also want to sign firmer contracts with forwarders or ocean carriers. Historically, agreements in container shipping have been called “contracts”, but they were not enforceable. They are rate agreements, not firm contracts. These rate agreements indicated minimum quantities shippers commit to move, but typically were not enforced by the ocean carriers with no punishment for not meeting commitments. In many cases, over 10 percent of cargo booked on a ship was not honored, with no penalties for the shippers who had booked space and failed to use it.
This flexibility suited shippers well in the last ten years, but it came at a cost, and that cost is that ocean carriers typically do not guarantee space. Consequently, bookings with ocean carriers are subject to space being available, or container equipment being available, and the rates exclude surcharges. Ocean carriers have been honoring only the minimum level of these rate agreement volumes.
There has been a shift toward enforceable contracts, in which shippers make firm take-or-pay commitments of volumes, and in return ocean carriers and forwarders give commitments that capacity will be available. These contracts could help stabilize the industry over the longer term and reduce the uncertainty in the industry which has not been positive for either ocean carriers or shippers.
In the medium term, shippers could shift their supply chains or rethink product design
In the short term, manufacturers may have little option when it comes to changing their current suppliers and existing manufacturing footprint, but in the medium term they could cultivate alternative suppliers. Some successful strategies could evaluate near-shoring options, or use suppliers in India and South America that reduce exposure to the main Transpacific trade lane.
Manufacturers can also rethink product design, particularly to limit highly customizable components that are complex to source. Assessing products and redesigning packaging is often a quick win and can help to improve efficiency in container space utilization.
Shippers can also re-evaluate their overall supply-chain design and strategy. The last 12 months have reminded shippers that relying on just-in-time supply from container shipping can be risky. Companies may need to increase inventories and safety buffers, both at departure and at arrival ports. This adds costs to the supply chain, which may lead to broader redesigns in product sourcing and manufacturing.
David Dierker is expert in McKinsey’s Zurich office, Ezra Greenberg is a partner in the Stamford office, Steve Saxon is a partner in the Shenzhen office and Tewodros Tiruneh is an expert in the Waltham office.
unveiled its third annual outlook on the global consumer trends that will shape the food, beverage and animal nutrition industries and drive market growth in the years ahead.
Dissecting the intersection of health and well-being, sustainability and food security, ADM has identified eight spaces that detail consumers’ evolving behaviors, attitudes and aspirations. The eight areas serve as anchor points to inspire innovation, ushering in a new wave of products and services for 2023.
“Often interconnected, these key themes are permeating throughout consumers’ choices, demands and expectations of brands,” said Brad Schwan, vice president of marketing for ADM.
“The desire for a healthy mind, body and soul, as well as the global community and planet, is manifesting in proactive and decisive conscientious consumption across categories. As consumers look to prioritize what is most important to them, they want nutrition brands to do the same. Companies that can nimbly evolve alongside consumers are poised for success in the coming year and beyond.”
Below are the eight global consumer trends identified by ADM that are powering purposeful design and ingenuity for human, animal and pet nutrition and throughout supply chains.
More than half (52 percent) of global consumers now consider themselves flexitarians, incorporating both animal-based and plantbased or other alternative proteins into their diet1. Within that 52 percent, nearly two-thirds are defining their eating style as “trying to use more plant-based foods,” leading to more demand for expanded protein options1.
As technology natives Gen Z and Gen Alpha grow up, acceptance of applying scientific advancements to make our food will continue to become more commonplace, and practices like cellular agriculture, precision fermentation, hybrid products, and those with insect-based protein, are likely to flourish.
Emotional, mental, physical, even spiritual health are increasingly seen by consumers as being intertwined, and as important as each other. Consumers are adopting a synergistic approach and making intentional and mindful choices about how they eat and spend their time to address energy levels, disease prevention and overall mood and feeling. Globally, 79 percent of consumers believe that supporting their mental health has a positive effect on their overall health and wellness1. Plus, 48 percent of global consumers plan to address their mental well-being over the next year, making the issue among their top concerns after immune function, digestive and heart health2.
What works for one person’s wellness may not be ideal for another’s. A “one size fits all” strategy for health and eating has fallen away in favor of tailored, “better for me” approaches. In fact, 63 percent of global consumers say they are interested in food and drink products that are customized to meet their individual nutritional needs3. On top of that, 55 percent of global consumers say they are willing to spend more on functional foods that can support their health goals1. Additionally, these personalized solutions would ideally integrate into one’s lifestyle and take taste and culture preferences into consideration.
From soil to table, consumers want to know where their food comes from, who made it and precisely what ingredients are included. They want to know how the product was produced and if the conditions of its production were humane. Some headway has been made in garnering
consumer trust, with research showing that 42 percent of global consumers have become more trusting of environmental claims made by products and brands in the last two years4.
This need for transparency is borne not only from food safety concerns but also from a desire for connection with the food and the communities that grow or make it. As such, consumers are looking to support companies they perceive as honest and authentic and that utilize technology like QR codes or blockchain to allow the traceability of products and ingredients to their origins.
Globally, 49 percent of consumers claim to have changed their diet in the last two years to lead a more environmentally friendly lifestyle4. They’re also demanding a higher standard from the companies they purchase from regarding their environmentally conscious practices. Consumers are greatly focusing on reducing their own food waste4, and they will expect the same from the brands they support. Consumers want proof of environmental rebuilding and restoration, as well.
Using their voices and their purchasing power, consumers are demanding that companies practice fair and humane treatment of the people and animals involved in every aspect of production. Almost 30 percent of global consumers have actively boycotted a product or brand because of its ethical credentials, and 40 percent seek out brands that guarantee farmers have been treated in an ethical manner4.
Ensuring workers’ and farmers’ livelihoods, employing inclusivity and diversity methods throughout the organization, and keeping products affordable and accessible to the end user are all important considerations to modern consumers when making purchasing decisions.
For many, pets are part of the family, and their nutritional and emotional needs are being treated on par with their owners. In light of this, many pet parents require that their pets’ food be made from the same ingredients as their own. Plus, as consumers pay increased attention to the well-being of their pets, branded health ingredients are highly sought-after, with more than 60 percent of global cat and dog owners saying that branded health ingredients for their pets are important5.
This increasing personification of pets is leading to a holistic approach to pet care, with mental well-being, gut health, exercise and diet considerations all being made in conjunction with one another.
Increasingly, global consumers are getting more adventurous with their food, as 74 percent express a desire to try new flavors from around the world and 63 percent report they like to be experimental when cooking6. While seeking out new and interesting flavor profiles, eaters also want to engage with fun and playful brands as part of the experience. If those brands can encourage participation through co-creation and virtual experiences, loyalty can be won with the sense of community it creates and the entertainment it provides.
From health and wellness for both people and their pets, to environmental considerations and elevated consumption occasions, these eight trend spaces present opportunities for innovative forwardthinking companies to meet the evolving needs of consumers today. ADM is at the forefront of each of these areas, supporting brands in creating novel offerings as a leading full-service supplier coupled with a deep pantry of ingredients and solutions, a global team of trend spotters, technical experts, scientists and more.
In Asia-Pacific, investments in building and infrastructure improvement projects have increased. The region is viewed as an attractive destination for specialty chemical makers. Increasing R&D for eco-friendly chemicals is also expected to give a profitable potential for the market.
Asia-Pacific Specialty Chemicals Market size is growing at a good pace over the last few years and is expected to grow at a CAGR of 5.81 percent from 2023 to 2030. In Asia-Pacific, investments in building and infrastructure improvement projects have increased. As a result, Asia-Pacific is viewed as an attractive destination for specialty chemical makers, promoting the market growth.
Specialty chemicals are chemical compounds that have a variety of effects and are used in a variety of industries to make items like coatings, ink for printing, sealants, cleaners, fragrances, explosives, additives corrosion and photographic films.
Agrichemicals, adhesives, colors, materials for cleaning purposes, construction chemicals, industrial gases, cosmetic additives, flavors,
food additives, elastomers, perfumes and lubricants are examples of specialty chemicals. These compounds have long been regarded as some of the most appealing product areas in the agriculture, aerospace, automobile, cosmetics, food and chemical industries.
Urbanization and industrialization, along with increasing disposable income and standard of living in developing countries, have raised the demand for specialty chemical residential housing projects. This, in turn, is likely to propel market expansion over the forecast period. The need for these items is predicted to increase depending on the specifics of the application. Stringent government regulation, as well as the usage of environmentally friendly chemicals, is assisting the market’s growth.
Nevertheless, fluctuating raw material prices, as well as severe regulations and standards in different countries, are some of the primary factors that may hamper the market growth. Furthermore, increasing R&D work for the creation of eco-friendly as well as cost-effective chemicals is expected to give a profitable potential for the market to grow. In Asia-Pacific, investments in building and infrastructure improvement projects have increased.
As a result, Asia-Pacific is viewed as an attractive destination for specialty chemical makers, promoting the market growth. The primary trend in the APAC specialty chemicals industry is the relocation of production to APAC.
As a result, Asia-Pacific is viewed as an attractive destination for specialty chemical makers, promoting the market growth. The primary trend in the APAC specialty chemicals industry is the relocation of production to APAC.
Various corporations are transferring their manufacturing base to APAC due to severe environmental standards in other regions, mainly Europe and North America. Furthermore, high labor costs and declining profit margins are encouraging firms in the European and North American sectors to relocate to APAC, which is a low-cost area.
Asia-Pacific Specialty Chemicals Market: Segmentation Analysis
The Asia-Pacific Specialty Chemicals Market is segmented on the basis of Type, Function, And Geography.
• Agrochemicals
• Advanced Ceramics
• Construction Chemicals
• Water Treatment Chemicals
• Others
Based on Type - The market is segmented into Agrochemicals, Advanced Ceramics, Construction Chemicals, Water Treatment Chemicals, and Others. Agrochemicals are estimated to account for the most share in the market.
The increasing population, coupled with higher food demand, is raising the demand for Agrochemicals for increased crop growth and safety, supporting the specialized chemicals market’s expansion. Furthermore, increased farmer awareness of the usage of Agrochemicals in farming drives the market growth.
As urbanization and industrialization expand, farmland decreases, leading to an increase in the need for Agrochemicals to boost crop yield per acre of land, hence propelling the market of the Asia-Pacific Specialty Chemicals Market over the projected period. Construction chemicals are predicted to expand the fastest during the forecast period. This can be linked to the region’s vast population’s growing domestic need for commercial and residential buildings.
• Pharmaceutical Ingredients
• Specialty Coatings
• Separation Membranes
• Demulsifies
• Antioxidants
• Others
Based on Function - The market is segmented into Pharmaceutical Ingredients, Specialty Coatings, Separation Membranes, Demulsifies, Antioxidants, and Others. Pharmaceutical Ingredients held the highest proportion of the Asia-Pacific Specialty Chemicals Market, and this is expected to continue during the projection period. This is due to the many applications in the pharmaceutical business, such as the production of medications for cardiovascular disorders, skin problems and Hughes syndrome.
These are essentially active chemicals used in pharmaceutical goods. They are created in massive reactors in various manufacturing sites from basic chemical components. After the base or chemical compound is treated, it becomes an intermediate, which is then converted into a medicinal ingredient.
• China
• India
• Japan
• Rest of Asia Pacific
On the basis of Geography - The Asia-Pacific Specialty Chemicals Market is segmented into China, India, Japan, and the Rest of APAC. So far, China has dominated the APAC Specialty Chemicals Market. This might be ascribed to the country’s enormous population driving up domestic consumption of commercial and residential buildings. Furthermore, the abundance of raw materials and low labor costs are fueling the country’s market expansion.
During the forecast period, India is anticipated to be the fastest expanding APAC Specialty Chemicals Market. The country’s highest growth is linked to the country’s expanding urbanization trend, rising expendable cash, and high desire for improved aesthetics in domestic constructions. Automobile, architecture, personal care, F&B, and electronics are all industries that use specialty chemicals.
Some of the major players in the market include BASF SE, DowDuPont Inc, Eastman Chemical Company, Ashland Global Holdings Inc, China Petroleum & Chemical Corporation, Evonik Industries AG, Mitsui Chemicals Inc, LOTTE Fine Chemical, AkzoNobel NV, Mitsubishi Chemical Corporation.
• May 2022 – Vinmar Group, a leading chemicals and polymers manufacturer, has paid an undisclosed price for the acquisition
of Engineering & Chemical (India) Pvt Ltd, which is a Mumbaibased firm specializing in the import and distribution of specialty chemicals.
• May 2022 – Azelis, a prominent global innovative services company in the specialty chemicals & food ingredients industries, has announced a deal to purchase the distribution assets of Chemo India and Unipharm Laboratories. Both companies are well-known local distributors of specialty chemicals and components in India for the L&MWF, CASE and pharmaceutical markets.
Theglobal dimethyl carbonate market is expected to be worth $512.5 million in 2022, representing a 5.6 percent year-on-year increase. DMC sales are predicted to rise at a 5.8 percent CAGR, reaching $954.1 million by 2032. The massive rise in the manufacturing of lithium-ion batteries is predicted to increase dimethyl carbonate utilization during the evaluation period.
Market growth of Dimethyl Carbonate is primarily driven by the following key factors:
• DMC is in great supply as a battery electrolyte in the manufacture of lithium-ion batteries. The significant quantity of lithium-ion battery fabrication is expected to drive dimethyl carbonate revenues.
• Excess supply of polycarbonate-based materials is also anticipated to increase DMC sales in the following decade.
• Increasing adoption for DMC as a battery electrolyte in lithiumion battery manufacturing, elevated lithium-ion battery production volume.
• The compound is employed as a solvent in the manufacturing of paints & coatings for traffic paints, architectural elements, and floor paints, which is expected to stimulate consumption. Increasing R&D efforts will enhance effectiveness in green DMC synthesis to promote market growth.
Carbon is a plentiful element that is required in the manufacture of fuels and polymers. Because of carbon’s non-toxic characteristics, dimethyl carbonate traders have been compelled to convert carbon dioxide (CO2) into chemical precursors such as dimethyl carbonate (DMC).
This trend is anticipated to continue, as conventional ways such as phosgenation have drawbacks such as the use of deadly poisonous and corrosive phosgene gas and the creation of large amounts of inorganic salts.
As a consequence, dimethyl carbonate market participants are intensifying their R&D efforts in order to boost effectiveness in green chemistry. Automakers are implementing procedures that involve the decisive synthesis of dimethyl carbonate from CO2 and methanol to enhance the productivity of green chemistry. Because methanol serves as a less expensive raw material, green synthesis of DMC is gaining popularity as a cost-effective procedure.
global dimethyl carbonate market in 2021. The clamor for dimethyl carbonate in the Asia Pacific region is anticipated to rise throughout the forecast period due to a significant increase in the utilization of polycarbonates.
Because of the rise in consumption of dimethyl carbonate in various industrial applications such as cleaning agents, paints and coatings, pesticide residues, sealants, and lithium-ion batteries throughout the region, the dimethyl carbonate market in the Asia Pacific is anticipated to expand at an enticing rate over the forecast period.
The Asia-Pacific region accounted for a considerable proportion of the
The region’s dimethyl carbonate market is led by India, China, South Korea, and Japan. The China dimethyl carbonate market is projected to increase by 6.4 percent year on year in 2022. Total dimethyl carbonate revenues in East Asia are likely to account for approximately 42 percent of global DMC volume.
Asia Pacific is expected to offer the largest opportunity
In China, Thailand, Japan, and Taiwan, dimethyl carbonate is predominantly utilized in the manufacturing of polycarbonates, whereas in India, it is largely employed in the pharmaceutical, paints & coatings, and agrochemical businesses to produce multiple products such as medicines, paints and pesticides.
Market expansion will be fueled by increasing developments by key manufacturers
To increase their market existence, key players in the global dimethyl carbonate market are establishing manufacturing units. Further participants are establishing industrial facilities in China, India, and ASEAN countries in order to cut overall production costs and improve operating margins.
Due to a rise in consumption of the electrolyte in the production of lithium-ion batteries as especially in comparison to other industrial applications, prominent brands are also concentrating on manufacturing battery-grade methyl carbonate rather than industrialgrade.
Growing production of polycarbonate-based materials is also expected to benefit sales of DMC in the forthcoming years. Higher plastic and battery production in China and the US will fuel sales in the market. The global consumption of dimethyl carbonate is estimated to represent around 4-5 percent of the overall methylating agent market.
Demand for methyl carbonate has witnessed year-over-year growth of 5.1 percent and 5.5 percent between 2017 and 2021. Significant production volume of polycarbonate had bolstered the consumption
of dimethyl carbonate in the past, as the compound is used as an intermediate for commercial manufacturing of polycarbonate. However, sales of dimethyl carbonate are anticipated to growth at a 5.8 percent CAGR over the period. Growth can be attributed to growing demand for DMC as a battery electrolyte in the production of lithiumion batteries. High production volume of lithium-ion batteries is expected to fuel sales of dimethyl carbonate.
Further, increasing production of paints and coatings is expected to propel demand as the compound is used as a solvent for the production of paints and coatings for traffic paints, architectural components, and floor paints.
How Is growing demand for polycarbonate bolstering sales of dimethyl carbonate?
Polycarbonates find a wide range of applications including safety helmets, roofing, and glazing, bulletproof glass, compact disc, electronic items, data storage, and 3D printing. This is expected to create significant demand for polycarbonate, owing to growth in the building and construction and electronics sectors.
Dimethyl carbonate is used as an intermediate for the production of polycarbonate. Increasing demand for polycarbonate-based materials is estimated to bolster the consumption of dimethyl carbonate over the forecast period.
Further, polycarbonate sheets are used in the automotive industry, farming applications, hardware gadgets, electronic items, and others. Growing demand for polycarbonate sheets is also expected to propel the growth in the dimethyl carbonate market.
The automotive industry is witnessing high demand for electric vehicle across various countries. Lithium-ion batteries are used as the power source in electric vehicles. Demand for electric vehicles is expected to increase significantly in the forthcoming years, which, in turn, will drive sales of dimethyl carbonate.
Dimethyl carbonate is significantly used as an electrolyte solvent in lithium-ion batteries. This organic compound is one of the most promising electrolyte solvents owing to its low viscosity and high solvation properties.
Growing production of electric vehicles is anticipated to create opportunities for growth for dimethyl carbonate manufacturers over the assessment period owing to an uptick in the usage of lithium-ion batteries in these vehicles.
Increasing demand for lithium-ion batteries will boost sales of dimethyl carbonate. The US is the second-largest manufacturer of plastics and polycarbonate-based products. Owing to significant production volume, the country is expected to remain a prominent consumer of dimethyl carbonate. The country is estimated to account for about 89 percent of the overall North America dimethyl carbonate market share over the forecast period.
Further, increasing production of electric vehicles in the US has also led to the production of lithium-ion batteries. This is estimated to propel sales of dimethyl carbonate in the forthcoming years.
Expansion of the paints & coating sector in China will spur demand for dimethyl carbonate. In 2022, the China dimethyl carbonate market is expected to grow by 6.4 percent year-on-year. Across East Asia, total sales of dimethyl carbonate are expected to account for about 42 percent of the global DMC volume.
China is expected to account for about four-fifths of the global lithium-ion battery production and is a top manufacturer of polycarbonate-based products. Further significant growth in battery production, paints and coatings, and polycarbonate materials manufacturing are expected to boost the consumption of dimethyl carbonate in the country.
What factors are boosting demand for batterygrade dimethyl carbonate?
Rising adoption of battery-grade dimethyl carbonate in the automotive sector will fuel growth. Increasing production of electric vehicles is propelling the demand for lithium-ion batteries. Battery-grade dimethyl carbonate is used as an electrolyte solvent for lithium batteries.
Despite the high dimethyl carbonate manufacturing capability, only few companies can produce high-purity battery-grade DMC due to substantial separation and purification barriers. Considering the rapid development of the energy sector and storage, demand for battery-grade dimethyl carbonate will increase.
Battery grade of methyl carbonate is estimated to witness a growth rate of 6.7 percent over the forecast period. Further, the supply of industrial-grade DMC is expected to be more than its demand, whereas, battery-grade DMC is expected to face a supply restraint in owing to higher demand and relatively less production.
Sales of dimethyl carbonate for polycarbonate synthesis will remain high. Sales in the polycarbonate synthesis segment are estimated to grow by 5.5 percent year-over-year in 2022. The demand in the battery electrolyte segment is expected to increase 6.2 percent between 2021 and 2022, giving the combined dimethyl carbonate market year-over-year growth of 5.6 percent in 2021.
DMC is expected to be consumed for the production of polycarbonate-based materials. However, the battery electrolyte segment is anticipated to witness a significant gain in the market share.
Key players in the global dimethyl carbonate market are setting up manufacturing units to boost their market presence. Further players are setting up manufacturing facilities in China, India and ASEAN countries to minimize the overall production expenditure and propel operating margins.
Leading players are also focusing on manufacturing battery-grade methyl carbonate instead industrial-grade owing to an increase in the demand for the electrolyte in the production of lithium-ion batteries as compared to other industrial applications. Source: Future Market Insights
The India Water Treatment Chemicals Market size was valued at $2,045.08 million in 2020 and the market is projected to register a CAGR of over 6 percent in terms of revenue during the forecast period of 2021 to 2027.
The market was negatively impacted by COVID-19 in 2020. Owing to the pandemic scenario, various end-user industry such as petrochemical had cut their throughput production during the lockdown, considering the decline in the demand.
For example, Indian Oil Corporation Ltd, with the production capacity of 5 million barrels per day of crude oil, had cut its crude oil processing by about 30 to 40 percent and shut its Panipat cracker located at Haryana of India as of march end 2020, thus led to a decrease in the
production of wastewater from these end-user industries, which in turn negatively impacts the market demand for water treatment chemicals within the country.
Over the short term, the increasing demand from the chemical manufacturing industry is expected to drive the market’s growth. However, the toxicity of water treatment chemicals is restraining the demand for water treatment chemicals in the country.
Among the applications, power generation sector accounts for the largest market share and is likely to dominate the market during the forecast period. Among the product types, corrosion and scale inhibitors segment is dominating the market.
The increasing investments in sewage treatment plants in the country is to provide a major growth opportunity to the market studied.
Water treatment chemicals are widely used in the various enduser industry such as chemicals (including petrochemicals), power generation and others. These end-user industries generate wastewater from their facilities as a byproduct, which needs to be treated before reuse or disposing of, considering the longer shelf life of the equipment and government regulations to protect the environment. Some of the water treatment chemicals include corrosion inhibitors, biocides, flocculants and others.
The India water treatment chemicals market is segmented by product type and end-user industry. By product type, the market is segmented into Biocides and Disinfectants, Coagulants and Flocculants, Corrosion and Scale Inhibitors, Defoamers and Defoaming Agents, pH Adjusters and Softeners, and Other Product Types.
the market is segmented into Power Generation, Oil & Gas, Chemical Manufacturing, Mining and Mineral Processing, Municipal, Food and Beverage, Pulp & Paper and other end-user industries.
• Corrosion inhibitors are general-purpose chemicals applied to counter the corrosion caused in boilers. Corrosion occurs due to the reaction of oxygen with metallic parts in a boiler, which forms oxides. Corrosion affects the metallic part of the boiler and thereby increases the cost of energy and maintenance. It acts by forming a thin layer of barrier over the exposed parts of the boiler from the water.
• Several types of corrosion inhibitors are used in water boilers, including - condensate line corrosion inhibitor, diethyl hydroxylamine, polyamine, morpholine, cyclohexylamine, and carbon dioxide corrosion inhibitor.
• These inhibitors are also used in cooling water treatment, to ensure metal protection and prevent metal loss, which may lead to critical system failures in recirculating water piping, process cooling equipment, and heat exchangers.
• The scale is a precipitate formed on the surface of water treatment towers, as a result of precipitation of soluble solids that become insoluble as temperature increases. This, in turn, causes metallic corrosion that affects the functioning and maintenance of the cooling water towers. This deposition increases corrosion rates, causing loss of production, restricting water flow, and interfering with heat transfer.
• In the boiler water treatment, if untreated water is used in the boiler, it brings with it a number of soluble salts. These remain soluble in cold water, but with the rise in temperature inside the boiler, salts become insoluble. Carbonates and bicarbonates are formed from calcium and magnesium chemicals dissolved in water.
• Water boilers, heat exchangers, cooling systems are the key equipment of the chemical industry. According to the India Brand Equity Foundation (IBEF), the Indian chemicals industry was valued at $178 billion in 2019 and is expected to reach $304 billion by 2025, registering a CAGR of 9.3 percent. The demand for chemicals is expected to expand by 9 percent per year by 2025, thus led to increase in the demand for corrosion and scale inhibitors, which in turn expected to stimulates the demand for the water treatment chemicals market within in the country.
• In the first half of FY2020, India has produced about 5.81 million tons of major chemicals and the production volume of major chemicals was accounted for about 11.58 million tons in FY2019, with a growth rate of about 4.6 percent compared to the previous year, thereby enhanced the demand for the water chemicals market in the country.
• Therefore, the aforementioned factors are expected to show significant impact on the market in the coming years.
• India’s power sector consists of conventional sources, ‘such as coal, hydro, and nuclear power’ to non-conventional sources, such as wind, solar, and agriculture and domestic waste.
• Water in the power generation industry is used in steam production for spinning turbines, humidifying airflow into gas turbines, the inter-cooling air in gas-turbine plants, and various other applications.
• The electric power generation industry is one of the major sources of industrial wastewater. Their wastewater contains significant levels of toxic metal impurities, such as lead, mercury, arsenic, chromium and cadmium, among others. These impurities can cause significant damage to the environment, if not treated properly. Therefore, the electric power generation industry needs water treatment chemicals.
• The electricity generation in India was amounted to about 1,613 terawatt hour (TWh) in 2019, with a decline rate of about 0.31 percent compared to the previous year, thus led to a decrease in the production of waste water at the electric generation facility, which in turn negatively impacts the market demand for water treatment chemicals in India.
• Electricity demand in the country is expected to grow in the coming years, owing to growing industrialization, urbanization, and population.
• Therefore, the aforementioned factors are expected to show significant impact on the market in the coming years.
The Indian water treatment chemicals market is partially fragmented, with no player in the market accounting for a significant share of the market. Key players in the market studied include Thermax Limited, Ion Exchange, Chemtex Specialty Limited, SicagenChem and Ecolab (Nalco), among others.
The global pharmaceutical chemicals market size accounted at $104 billion in 2020 and is predicted to reach $197.4 billion by the end of 2030, representing impressive CAGR of 6.9 percent during the forecast period 2021 to 2030. Increasing demand for advanced drugs and rise in demand for the active pharmaceutical chemicals are major growth driver of pharmaceutical chemicals market.
Emerging applications of the pharmaceutical chemicals are projected to generate lucrative growth opportunities for the major players operating in the global pharmaceutical chemicals market. Development of new pharmaceutical drugs, coupled with evolving markets are major trends observed in the global pharmaceutical chemical market. This trend is
expected to continue and will boost growth of the target market in the near future.
Increasing healthcare expenditure in emerging markets is influencing the worldwide business strategies of pharmaceutical chemical market owing to high profitability. The attention of these emerging markets is favoring towards health concerns affecting individuals owing to which they are focusing on increasing investment and launching advanced products across the globe.
The manufacturing costs of pharmaceutical drugs can be reduced by innovations, hence the key players operating in the target industries are constantly increasing healthcare expenditure. Further, major companies in the global industry are collaborating in order to have a competitive edge in the global market.
Crucial factors accountable for market growth are:
• Increasing demand for advanced drugs
• Growing geriatric population
• Rise in demand for the active pharmaceutical chemicals
• Development of the neurological drugs
• Easy availability of healthcare insurances
• Government support for research and development activities
• Advantages offered by pharmaceutical chemicals
Significant Market Trends: Basic building blocks segment reported foremost market stake in 2020
Basic building blocks segment recorded the prime market share in the global pharmaceutical chemicals market by product in 2020. The advanced intermediates product segment is predictable to rise at a noteworthy CAGR during the forecast time-frame.
On the basis of the application segments the global market is segregated into gastrointestinal diseases, infectious diseases, musculoskeletal diseases, oncology, respiratory diseases, diabetes, neurology, metabolic system, cardiovascular, other. The cardiovascular application segment is expected to dominate in terms of revenue over the forecast time frame.
The growth is attributed to the increasing use of pharmaceutical chemicals for the treatment of blood vessels and heart diseases across the globe. Increasing prevalence of heart diseases is primarily responsible for the greater market share of cardiovascular in the application segment of the pharmaceutical chemicals market. Oncology segment will expand at a significant CAGR during the forecast time-frame.
On the basis of the application segments the global market is segregated into gastrointestinal diseases, infectious diseases, musculoskeletal diseases, oncology, respiratory diseases, diabetes, neurology, metabolic system, cardiovascular, other. The cardiovascular application segment is expected to dominate in terms of revenue over the forecast time frame.
The growth is attributed to the increasing use of pharmaceutical chemicals for the treatment of blood vessels and heart diseases across the globe. Increasing prevalence of heart diseases is primarily responsible for the greater market share of cardiovascular in the application segment of the pharmaceutical chemicals market. Oncology segment will expand at a significant CAGR during the forecast time-frame.
Geographically, pharmaceutical chemicals market is conquered by North America owing to favorable government mandates for the production of the pharmaceutical chemicals, coupled with increasing research and development activities for production of pharmaceutical chemicals in the countries of this region, especially in the United States.
Asia-Pacific is expected to register the fast growth rate, on account of increasing API production and growing investment in research and development sector by key market players in the region. Also, increasing prevalence of chronic diseases is anticipated to drive growth of the target industry in the countries of Asia Pacific region.
Further, increasing population in the Asian countries is responsible for the high demand for pharmaceutical chemicals in the region. Latin America and the African and Middle Eastern region will display noticeable growth over the forecast period.
The cosmetic pigments and dyes market is expected to be growing at a growth rate of 7.55 percent in the forecast period of 2021 to 2028.
This rise in cosmetic pigments and dyes market value can be attributed to the various factors such as increased focus of the product manufacturers on product innovations, surging demand for beauty and personal care products especially in the developing economies, strong presence of innovative home care products, growing popularity of e-commerce platforms especially in the developing economies and increasing personal disposable income.
From the name itself, it is clear that cosmetic pigments and dyes are the chemical additives that are added to the cosmetic products. Color plays an important role in the marketing of a cosmetic product and the major aim behind the application of cosmetic pigments and dyes in cosmetic products is to impart color into them.
Rising modernization and globalization are the major factors fostering the growth of the market. Growing shift in consumer
buying trends, rise in the research and development activities and surge in the usage of cosmetic dyes in toiletries, skin care, and hair care products across the globe are some other indirect market growth determinants.
Consumer interest in environment-friendly and sustainably produced ingredients and growing penetration of e-commerce platforms pigments will also create lucrative and remunerative market growth opportunities in the long run.
On the flip side, fluctuations in the prices of raw materials will pose a major challenge to the growth of market in the long run. Maintaining the quality of cosmetic pigments for mass-market products, rise in regulations on certain color additives that are harmful to skin will further derail the market growth rate. Also, high cost of natural or organic cosmetic products and intense pricing pressure among the vendors and disruptions in the supply chain will yet again hamper the market growth rate.
The cosmetic pigments and dyes market is segmented on the basis of elemental composition, type, technology and application.
• Based on elemental composition, the cosmetic pigments and dyes market is segmented into inorganic pigments, organic pigments, oil soluble colors and water soluble colors.
• On the basis of type, the cosmetic pigments and dyes market is segmented into dyes and pigments.
• Based on technology, the cosmetic pigments and dyes market is segmented into pigment dispersion and surface treatments.
• The application segment for cosmetic pigments and dyes market includes facial makeup, eye makeup, lip products, nail products, hair color products, special effect and special purchase products and others.
Egypt and UAE in Middle East and Africa region dominate the cosmetic pigments and dyes market and will continue to excel its trend of dominance during the forecast period owing to the improving lifestyles, growing income and demand for facial makeup products in the countries.
The major players in the cosmetic pigments and dyes market are Dayglo Color Corp, Eckart GmbH, Sandream Specialties., Geotech, Kolortek Co Ltd, LANXESS, LI Pigments, Merck KGaA, Miyoshi Kasei Inc, Nihon Koken Kogyo Co Ltd, Sun Chemical, Sudarshan Chemical Industries Ltd, Toshiki Pigment Co Ltd, Toyal Europe and Venator Materials PLC, among others.
Source: Data Bridge Market ResearchSoap & detergent market size is expected to reach nearly $245.83 billion in the forecast period 2022 to 2027 with the CAGR of 8.83 percent.
A detergent is an organic compound or mixture of compounds used as a vacuuming agent. A soap is a washing agent that is composed of one or more salts of oily acids. Detergents are normally used in products for personal hygiene, dishwashing, clean washing as well as laundry. They are also recycled as ingredients in antiseptic agents, laundering solutions, greasing oils and gasoline.
Introduction of innovative new products in the soap and detergent is the major factor contributing toward the global soap and detergent market growth. The mandate for effective and anti-allergic cleaning products are increasing rapidly, which boost the growth in the global soap and detergent market. Some of the major key players are incessantly focusing on innovative product development to furnish the unmet needs of their consumers.
Anti-allergy soaps and natural ingredients inclosing detergents are heavily adopted by consumers with delicate skin. The household soaps segment is expected to witness 3.5 percent significant growth because of the increasing population and rising disposable income in developing regions. The rising influence of modern lifestyle has prominent soaps from luxury to essential product.
The soap and detergent industries are one of the most regulated of all and in addition to the regulation of its products, it is subject to several requirements that aim at reducing the release of chemical substances into the environment during the process of manufacturing. Such requirements generally include limitations on the quantity of a substance, which can be released to the environment.
Soaps and detergents are dynamic necessities as consumer goods and most widely used by the enormous population. The rising penetration of washing machines in the emergent countries is expected to drive the market growth. The large mass of demand for washing machines is from the urban cities and rural areas, which turns to sustainable consumption of powder and liquid detergents required for washing clothes.
The Asia Pacific region is expected to grow at a 3.5 percent of CAGR during the forecast period. The increasing population of the region tied with rapid urbanization in countries such as India, China and Indonesia are they key drivers for the emergent demand for the soaps and detergents. The stable penetration of the washing machines in this region has enlarged the potential growth in the global soap and detergent market.
The increasing development in the textile and apparel industry in the Asia Pacific region is projected to boost the growth Global Soap and Detergent Market. Growing textile market is projected to provide a huge demand for the soaps and detergent products over the forecast period.
Key market players in the global soap and detergent market are Colgate Palmolive, Johnson & Johnson, Chicco, Procter & Gamble, Unilever, LUX, Sebapharma, Pigeon, Galderma Laboratories, Burt’s Bees, Himalaya, PZ Cussons, Weleda, Mustela, Walch, Safeguard, Dettol and OLAY. Source: Maximize
The Chemical Industry is one of the most important industries in the world. With a chemical supply chain that spans from chemical manufacturing to chemical distribution, it is essential for this industry to run a tight ship. However, with many stakeholders involvedincluding chemical consumers-there are several challenges on the way to keeping operations running smoothly.
In a world where 96 percent of all manufactured goods depend on chemicals in one way or another, there are ample opportunities for chemical companies to grow. Transportation and Logistics in Chemical Industry plays an important role to keep the demand and supply in balance.
According to Precedence Research, the global chemical logistics market size was estimated at $265.2 billion in 2021 and is expected to become $377.35 billion by 2030, registering a growth at a CAGR of 4 percent from 2021 to 2030.
Chemical manufacturers striving to secure a larger share in the marketplace, have created an extremely competitive battleground.
Growing industry trends like protectionist trade policies, tariff wars, transportation and industry consolidation are also pushing businesses to adopt new ways to stand out. As these trends pervade the blooming chemical industry, many businesses are remodelling to adapt for profitability and scale down risk. Safety remains a high priority while sustainability has increasingly become a focus in the logistics business.
On the other hand, Logistics management is a complex process which involves a network of planning, manufacturing and supply, storage and distribution and transportation/shipping. For this, digitisation of the entire supply chain is playing a pragmatic role in ensuring safe transport, real time tracking and on time deliveries across the globe.
Supply chains for chemical have evolved and adopted new digital technologies in the past few decades. Artificial intelligence (AI) is no exception to this trend, with chemical companies turning to AI tools for several segments including chemical management, risk assessment, and more. The overall goal of a logistics enterprise is to optimise the operation and bring the best out of the complex structure.
For chemical companies, their supply chains play a crucial role in their business transformation. Whether be the need to support continuous production lines with effective storage solutions; increase margins with supply chain cost-efficiencies; improve safety and compliance or gain customer loyalty with greater visibility and on-time deliveries- supply chain partners have to add value at every stage.
E-commerce, liberalisation of trade agreement, investments in transportation infrastructure, improved methods of international communication, and advancement in transportation technology, among other factors which have opened new market opportunities and broader avenues for partnership and collaboration. To create a balance between supply and demand, digital technologies, better policies, less complex process should be used to bridge the gap.
Understanding the need for the chemical industry logistics to be at par with the evolving market dynamics, Worldofchemicals and
Chemical Today Magazine is organising a virtual conference on Chemical Logistics on November 11th, 2022, titledChemicals in Transit 2022: Management of Logistics & Supply Chain.
The event will have eminent speakers who will be speaking on topics including handling issues - global supply chain disruptions & unpredictable demand fluctuations (as a chemical prospective), setting up hubs and proper warehouse & storage facilities and digitalization in logistics.
The discussions will give an in-depth insight into the problems and challenges that the industry faces, understand the complex nature of logistics business and know the solutions one should adapt to provide flawless end-to end supply chain services to chemical companies.
Lignocellulosic biomass is the most abundant feedstock in production of bio-based fuels and materials. Enzyme “cocktail” is considered as a powerful tool to allocate diverse specific activities in one matrix.
Recently, researchers led by prof. QI Wei from the Guangzhou Institute of Energy Conversion of the Chinese Academy of Sciences have reported an efficient cellulase “cocktail” produced by co-cultivation of several Penicillium strains with lytic polysaccharide monooxygenases (LPMOs) producing strains, which achieves excellent hydrolysis yield of pretreated poplar materials.
“Fermentation of fungal consortium is an effective approach to improve the yield of enzymes and coordinate the proportion of enzyme system through the synergistic effect of mutual benefit and symbiosis among multiple strains,” said Prof. QI, corresponding author of the study.
The researchers investigated co-fermentation of four kinds of Penicillium strains with Thermoascus aurantiacus and Neurospora crassa by mixture design methodology.
Taking the commercial cellulase as benchmark, they conducted comparative analysis of the enzyme components, activities
and the strains transcriptome. They found that the enzyme “cocktail” from Penicillium consortium presented superior expression on diverse Glycoside Hydrolases (GHs), Glycosyl Transferases (GTs), Polysaccharide Lyases (PLs) and other auxiliary enzymes, accelerating the chemical bonds breaking of hemicellulose and cellulose fractions.
In order to improve synergistic enzyme actions, the researchers also developed a new formulation by blending fermented enzyme cocktail with commercial cellulase in an appropriate proportion. The pretreated poplar was hydrolyzed to release glucose at an yield of 88%, with an increase of 32% compared to using commercial cellulase alone.
“The proposed fungal consortium and enzyme formulation have good potent to be applied in industry as a green and powerful tool, which can enhance lignocellulose biodegradation and consequently reduce enzyme cost. It is important for sustainable development of agriculture and forest wastes biorefinery, as well as the production of biofuels and materials,” said Prof. QI.
Medicaladhesives with high adhesion, low toxicity, and capable of decomposing in the body can contribute greatly in the development of minimally invasive surgery and organ transplants. Adhesives based on natural proteins have high biocompatibility but insufficient adhesive strength while synthetic polymer adhesives have greater adhesion but do not decompose well in the body.
A joint research team led by professor Myungeun Seo and professor Haeshin Lee from the KAIST Department of Chemistry developed a bio-friendly adhesive from biocompatible polymers using tannic acid, the source of astringency in wine.
The research team focused on tannic acid, a natural polyphenolic product. When tannic acid is mixed with hydrophilic polymers, they form coacervates, or small droplets of jelly-like fluids that sink. If the polymers used are biocompatible, the mixture can be applied as a medical adhesive with low toxicity. However, coacervates are fundamentally fluid-like and cannot withstand large forces, which limits their adhesive capabilities. Thus, while research to utilise it as an adhesive has been actively discussed, a biodegradable material exhibiting strong adhesion due to its high shear strength has not yet been developed.
The research team figured out a way to enhance adhesion by mixing two biocompatible FDA-approved polymers, polyethylene glycol (PEG) and polylactic acid (PLA). While PEG, which is used widely in eyedrops and cream, is hydrophilic, PLA, a well-known bioplastic derived from lactic acid, is insoluble in water. The team combined the two into a block copolymer, which forms hydrophilic PLA aggregates in water with PEG blocks surrounding them. A coacervate created by mixing the micelles and tannic acid would
behave like a solid due to the hard PLA components, and show an elastic modulus improved by a thousand times compared to PEG, enabling it to withstand much greater force as an adhesive.
Furthermore, the research team observed that the material’s mechanical properties can be improved by over a hundred times through a heating and cooling process that is used to heat-treat metals. They also discovered that this is due to the enforced interactions between micelle and tannic acid arrays.
The research team used the fact that the material shows minimal irritation to the skin and decomposes well in the body to demonstrate its possible application as an adhesive for hair transplantation through an animal experiment. Lee, who has pioneered various application fields including medical adhesives, hemostatic agents, and browning shampoo, focused on the adhesive capacities and low toxicity of polyphenols like tannic acid, and now looks forward to it improving the limitations of current hair transplant methods, which still involve follicle transfer and are difficult to be repeated multiple times.
This research was conducted by first co-authors Dr. Jongmin Park (currently a senior researcher at the Korea Research Institute of Chemical Technology) from Seo’s team and Dr. Eunsook Park from Lee’s team in the KAIST Department of Chemistry, and through joint research with the teams led by Professor Hyungjun Kim from the KAIST Department of Chemistry and professor Siyoung Choi from the Department of Chemical and Biomolecular Engineering. The research was published online on August 22 in the international journal Au (JACS Au) under the title Biodegradable Block Copolymer-Tannic Acid Glue.
NUS chemists have developed a new strategy to generate therapeutically relevant C-glycosides and S-glycosides through a catalyst- and transition metal-free approach under visible light illumination at ambient temperature.
Glycosides play an indispensable role in diverse physiological functions and are found in a wide variety of natural products and synthetic compounds. C-glycosides are an important class of glycosides, which consist of a sugar-containing unit joined to an organic moiety or another sugar-containing compound, through a carbon-carbon (C–C) bond. They possess a myriad of biological activities and are structurally diverse. One convenient way to construct such products involves the direct union of a glycosyl precursor (donor) with a carbon-based reagent.
However, the scope of C-glycosides that can be accessed using currently reported methods is severely limited. This owes to the lack of practical glycosyl donors available to facilitate mild C–C coupling. A general class of bench-stable glycosyl precursors that can be readily synthesised and isolable on large scale, and yet sufficiently reactive to undergo expeditious and stereoselective cross-coupling at ambient conditions is highly desirable but elusive.
A research team led by assistant professor KOH Ming Joo, from the Department of Chemistry, National University of Singapore has devised robust procedures to synthesise solid
heteroaryl glycosyl sulfones on multi-gram scale. The team discovered that these bench-stable sulfones are also redoxactive. By using visible (blue) light illumination and a Hantzsch ester-base complex, the researchers are able to activate the sulfones to produce chemically reactive glycosyl radicals.
These radicals react readily with various electrophiles (see Figure 1). With this method, they are able to obtain a wider range of valuable C-alkyl, C-alkenyl, C-alkynyl, C-heteroaryl and S-linked glycosides in an efficient and highly selective manner. The researchers also used ultraviolet/visible absorption spectroscopic and radical clock studies to gain insights into the mechanism of these transformations.
“This catalyst- and transition metal-free method effectively overcomes previous limitations in scope, scalability and glycosyl donor instability,” said Koh.
“We expect this general class of glycosyl precursors and their newly discovered reactivity under visible light illumination to find extensive utility in various carbohydrate synthetic applications, enhancing efforts towards the discovery of new sugar-based therapeutics and our understanding of biological processes,” added Koh.
The research team plans to work with companies to utilise these findings for the synthesis of sugar-derived compounds.
team demonstrated that ultrathin polymer-based ordered membranes that can effectively remove salt from seawater and brine and can provide a promising alternative to existing water desalination systems.
“Water desalination membranes should simultaneously exhibit high water flux and high salt rejection,” said Yu Han, who led the study. Carbon nanomaterials, such as carbon nanotubes and graphene, are expected to meet these requirements because of their unique surface chemistry and propensity to stack into channels with diameters smaller than one nanometer. Yet, channel alignment and stacking difficulties make their large-scale use in membranes challenging.
“One way to address these limitations is through two-dimensional porous carbonaceous membranes with regular and uniformly distributed subnanometer-sized molecular transport channels,” said first author Jie Shen, a postdoc in Han’s group. However, these membranes are typically synthesised in solution, which promotes the random growth of a disordered three-dimensional structure with poorly defined micropores.
KAUST professors Yu Han, Vincent Tung and Ingo Pinnau and former KAUST scientist Lance Li have developed a method that helps control the growth of two-dimensional conjugated polymer frameworks into ultrathin carbon films using chemical vapor deposition.
The researchers deposited the monomer triethynylbenzene on atomically flat single-crystalline copper substrates in the presence
of an organic base that acts as a catalyst. Triethynylbenzene bears three reactive groups that serve as anchor points for additional monomers. These groups show a 120-degree angle with respect to each other, generating organised arrays of well-defined cyclic structures that stack into subnanometer-sized rhombic hydrophobic channels.
The membrane displayed excellent water desalination performance in forward and reverse osmosis configurations, surpassing those containing advanced materials such as carbon nanotubes and graphene. It also showed strong rejection for divalent ions, as well as small charged and neutral molecules.
The researchers discovered that the water molecules formed a three-dimensional network inside the membrane instead of moving through the membrane along vertical triangular channels as one-dimensional chains. This explains the fast water transport through the membrane. “This unexpected result revealed that the seemingly discrete vertical channels are actually interconnected by short horizontal channels that can be easily overlooked in the projected structural model,” Han said.
The team is now working on improving the antifouling property, mechanical strength and long-term chemical stability of the membrane for future practical applications. They are also finetuning its surface-charge properties and channel sizes. “Our ultimate goal is to provide a versatile multifunctional platform that meets the needs of various applications, such as ion sieving, single-molecule sensing and neural interfaces,” said Han.
Hokkaido University material chemist Shinya Furukawa and his team recently developed a new catalyst—a substance that acts as a guide to chemical reactions and as such can open up otherwise inaccessible reaction pathways—that allows them to use carbon dioxide to turn propane into propylene instead of the more commonly used oxygen.
In their Nature Communications paper they not only demonstrated that the catalyst was highly efficient, very selective and stable under high temperatures, its use also had the side effect of turning carbon dioxide into carbon monoxide, which is a useful resource for the production of many bulk chemicals.
The researchers achieved this feat by building on their previous studies on catalyst design, but this time chose a unique new way: Using an alloy of platinum and tin on a ceria support as the base, they replaced a fraction of these atoms with the metals cobalt, nickel, indium and gallium. Each of these elements was chosen for a specific purpose: Platinum-tin alloys had already been known as good catalysts for the reaction, but including nickel and cobalt increased both the catalyst’s ability to activate carbon dioxide and its selectivity to the desired reaction.
Hokkaido University researchers find a new way of producing the industrially important propylene that is more energy efficient than existing approaches—and in the process turns carbon dioxide into another usable resource. Their pioneering catalyst design thus contributes to the carbon neutralisation of the petrochemical industry.
Propylene is a gas used to make a large variety of packaging and containers and is considered to be the second most important starting product in petrochemical engineering. However, its production from propane is currently very energy-intensive. In addition, the process accumulates unwanted side products that need to be purged by burning regularly. It is therefore very desirable to find another approach to the production of this valuable molecule that is more efficient, produces fewer side products, and still uses materials that are stable at high temperatures.
On the other hand, inserting indium and gallium was beneficial for the catalyst’s temperature stability. Finally, the ceria support made carbon dioxide capture and catalyst purging easier. The research team also confirmed that the catalyst can be regenerated and reused without a loss of performance.
Furukawa explained the significance of this result thus: “This work not only demonstrates the outstanding performance of our catalyst, but it also opens up a new window of catalyst design concepts based on our technique. The new catalyst outperforms our previous Pt-Co-In catalyst by a large margin. These insights will contribute to the carbon neutralisation of the industrial production of small petrochemicals.”
Ateamof researchers led by Meenesh Singh at University of Illinois Chicago has discovered a way to convert 100% of carbon dioxide captured from industrial exhaust into ethylene, a key building block for plastic products.
Their findings are published in Cell Reports Physical Science.
While researchers have been exploring the possibility of converting carbon dioxide to ethylene for more than a decade, the UIC team’s approach is the first to achieve nearly 100 percent utilisation of carbon dioxide to produce hydrocarbons. Their system uses electrolysis to transform captured carbon dioxide gas into high purity ethylene, with other carbon-based fuels and oxygen as byproducts.
The process can convert up to 6 metric tons of carbon dioxide into 1 metric ton of ethylene, recycling almost all carbon dioxide captured. Because the system runs on electricity, the use of renewable energy can make the process carbon negative.
According to Singh, his team’s approach surpasses the net-zero carbon goal of other carbon capture and conversion technologies by actually reducing the total carbon dioxide output from industry. “It’s a net negative,” he said. “For every 1 ton of ethylene produced, you’re taking 6 tons of CO2 from point sources that otherwise would be released to the atmosphere.”
Previous attempts at converting carbon dioxide into ethylene have relied on reactors that produce ethylene within the source carbon dioxide emission stream. In these cases, as little as 10 percent of CO2 emissions typically converts to ethylene. The ethylene must later be separated from the carbon dioxide in an energy-intensive process often involving fossil fuels.
In UIC’s approach, an electric current is passed through a cell, half of which is filled with captured carbon dioxide, the other half with a water-based solution. An electrified catalyst draws charged hydrogen atoms from the water molecules into the other half of the unit separated by a membrane, where they combine with charged carbon atoms from the carbon dioxide molecules to form ethylene.
Among manufactured chemicals worldwide, ethylene ranks third for carbon emissions after ammonia and cement. Ethylene is used not only to create plastic products for the packaging, agricultural
and automotive industries, but also to produce chemicals used in antifreeze, medical sterilisers and vinyl siding for houses.
Ethylene is usually made in a process called steam cracking that requires enormous amounts of heat. Cracking generates about 1.5 metric tons of carbon emissions per ton of ethylene created. On average, manufacturers produce around 160 million tons of ethylene each year, which results in more than 260 million tons of carbon dioxide emissions worldwide.
In addition to ethylene, the UIC scientists were able to produce other carbon-rich products useful to industry with their electrolysis approach. They also achieved a very high solar energy conversion efficiency, converting 10 percent of energy from the solar panels directly to carbon product output. This is well above the state-ofthe-art standard of 2 percent. For all the ethylene they produced, the solar energy conversion efficiency was around 4 percent, approximately the same rate as photosynthesis.
New technology developed at the University of Waterloo could make a significant difference in the fight against climate change by affordably converting harmful carbon dioxide (CO2) into fuels and other valuable chemicals on an industrial scale.
Outlined in a study published in the journal Nature Energy, the system yields 10 times more carbon monoxide (CO) – which can be used to make ethanol, methane and other desirable substances – than existing, small-scale technologies now limited to testing in laboratories.
Its individual cells can also be stacked to form reactors of any size, making the technology a customisable, economically viable solution that could be installed right on site, for example, at factories with CO2 emissions.
“This is a critical bridge to connect CO2 lab technology to industrial applications,” said Dr. Zhongwei Chen, a chemical engineering professor at Waterloo. “Without it, it is very difficult for materials-based technologies to be used commercially because they are just too expensive.”
The system features devices known as electrolysers that convert CO2, a major greenhouse gas produced by burning fossil fuels, into CO using water and electricity.
Electrolysers developed by the researchers have new electrodes and a new kind of liquid-based electrolyte, which is saturated with
CO2 and flowed through the devices for conversion into CO via an electrochemical reaction.
Their electrolysers are essentially 10-centimetre by 10-centimetre cells, many times larger than existing devices, that can be stacked and configured in reactors of any size.
“This is a completely new model for a CO2 reactor,” said Chen, the Canada Research Chair in Advanced Materials for Clean Energy. “It makes the whole process economically viable for industrialisation and can be customised to meet specific requirements.”
The researchers envision on-site reactors at coal-fired power plants and factories, perhaps the size of a house or more, that would be directly fed CO2 emissions, further reducing costs by eliminating the need to capture and collect CO2 first.
They are also developing plans to power the reactors with on-site renewable energy sources such as solar panels, contributing to the environmental benefits.
“I’m excited by the potential of this technology,” said Chen. “If we really want to make a difference by reducing emissions, we have to concentrate on reducing costs to make it affordable.”
Chen’s collaborators at Waterloo included postdoctoral fellow Dr. Guobin Wen and chemical engineering professors Dr. Aiping Yu and Dr. Jeff Gostick. Several researchers at the South China Normal University also contributed.
In the age of globalization and international trade, effectively managing transportation and logistics is vital to the health of the economy and society in general. As events surrounding the COVID-19 pandemic illustrate, logistical disruptions can have catastrophic impacts on both business-to-business operations and consumer behavior. In today’s interconnected digitized world, logistics and supply chain strategies are perhaps more important than ever—and more complex. Before the pandemic, the average consumer didn’t think much about how the products they used or foods they ate were transported— they just took it for granted that everything they wanted was already available. Now, “supply chain” is common vernacular and stories of
disruption dominate news cycles as capacity shortages, rising transport costs, and the acceleration of online commerce continue to pose challenges.
The overall goal of a logistics enterprise is optimized operations at all times—a tall order that is easier said than done. Even during times of more stability, logistics management is a complex discipline, involving a network of moving parts and systems ranging from logistics planning, to manufacturing and supply, storage and distribution and transportation/shipping.
Organizations rely on logistics optimization models to help them reduce overall costs while satisfying capacity constraints and meeting demand through effective procurement, production, storage, distribution, and transportation. And the more information involved in the logistics equation, the better. More information, however, also means more complex models that require exponential increases in computing power. Today’s logistics providers are facing complexities that push the limits of their technologies. At scale, these problems are challenging to solve with only classical computing technologies.
Supply chain and logistics professionals have been stretched thin over the past several years. An increasing amount of uncertainty—from labor shortages, to extreme weather, to pandemic-fueled changes in supply and demand—has increased logistics complexity exponentially.
The solution to this complexity requires a broader perspective. Silo-
based, function-based, or even enterprise-wide optimizations no longer provide the cure for supply chain and logistics challenges. Instead, businesses need supply chain optimizations that account for the full complexity of the entire ecosystem. They need quantum logistics. But accounting for the complexity of an ecosystem so vast requires a level of real-time coordination among partners, governments, and shippers that current optimization solutions—using classical computing—cannot fully provide.
The maturation and development of quantum computing, however, could change this equation significantly. If individual transportation providers, regulators, and customers can better share insights and collaborate to optimize operational decisions, quantum computers could deliver seamless service and provide better overall outcomes for the entire supply chain—and for humanity.
Although quantum computing technologies are still in a nascent state, they show promise in solving global logistics optimization models. Doing so with practically significant accuracy will require still-tocome, advanced, error-corrected quantum computers with very large numbers of qubits. However, even not-so-distant small computational gains could translate to cost savings and improved customer service in the near term.
In transportation and logistics, as in other industries, pairing quantum computing capabilities with classical computers could help organizations address a number of critical logistics challenges. Here three potential use cases can be:
1. Last mile delivery: Improve last mile delivery with quantum-enabled optimization models.
2. Disruption management: Improve decision-making and recovery times with faster, more accurate simulations.
3. Sustainable maritime routing: Reduce inefficiencies and port congestion with more accurate optimization techniques.
1. Quantum algorithms for last mile delivery? Game-changing potential.
By supporting global routing optimization and more frequent reoptimization, quantum computers could help significantly reduce doorto-door freight transportation costs and boost customer satisfaction. IBM worked with a commercial vehicle manufacturer to show how a mix of classical and quantum computing could optimize delivery to 1,200 locations in New York City. Using a route-based approach, the team factored in the need for 30-minute delivery time windows, while recognizing truck capacity constraints— all while reducing the total cost of delivery.
2. Quantum-enabled disruption management can put uncertainty on notice.
Classical systems are mainly rule-based, consisting of manual and ad hoc processes. Siloed and sequential, they provide limited insight for supporting flawless recovery decisions.
Quantum computing could support better decision-making by simulating more disruption scenarios and quantifying their impact on various parts of the network. Quantum computers performing risk and impact analysis may be able to reduce the number of “what if” simulation scenarios necessary, helping improve recovery times, lower costs, and lessen operational and customer service impacts. In addition, quantum machine learning may enable more precise classification and prediction of disruption events.
3. Quantum computing could help sustainable maritime routing make a quantum leap.
With contingencies that include large fleets and uncertainties such as weather and demand fluctuations, many optimization challenges in shipping operations can’t be precisely solved exactly using classical computers.
ExxonMobil is exploring how blending classical and quantum computing techniques might solve big, complex, pressing global challenges as it ships liquefied natural gas (LNG). Teams at IBM Research and ExxonMobil Corporate Strategy Research have collaborated to model maritime inventory routing on quantum devices, analyzing the strengths and trade-offs of different strategies for vehicle and inventory routing, and laying the foundation for constructing practical solutions for their operations.
Organizations in the transportation and logistics arena could be among those with the most to gain from quantum computing’s groundbreaking capabilities. An organization’s path from initial investigation of quantum computing to actual readiness for implementation can span a few years.
A wait-and-see approach could mean the difference between being disrupted and being the disruptor. That’s why it’s important to begin building quantum readiness sooner rather than later.
Because the learning curve for quantum computing is steep and quantum computing skills are scarce, much of the expertise may need to be developed in house. Identify and upskill both technical and business talent inside your organization in forming your quantum computing team. Build capabilities around this technology that align with your organization’s objectives and constraints.
Identify the most critical and compelling use cases
Highlight the ways your organization could not only benefit from quantum computing but also be threatened by it. Look at the three use cases we discussed and examine other potential uses for your particular organization. Once you’ve identified use cases, you can then estimate the time pressure to act.
Translate your use cases into proofs of concept, providing the opportunity to explore quantum computing and learn how it fits into your strategies
Partner with quantum computing experts to develop prototypes. Obtain access to the quantum computing hardware and software platforms you’ll need. Experiment with quantum computing code in a scalable fashion so that when quantum computers are ready, so is your code.
Identify the steps in your workflows that might benefit from Quantum Advantage. Understand how quantum and classical workflows and dataflows can intersect. Learn how quantum and classical computing can be combined to leverage each
other. And employ design thinking to help you examine your endto-end processes so you can make the most of quantum computing’s potential.
Process Safety Engineer
Company : LyondellBasell Industries
Date Posted : 07-Nov-2022
Country : UNITED STATES City : Edison, NJ
Process Development Engineer (m/f/d) Company: BASF SE
Date Posted: 07-Nov-2022
Country: GERMANY City: Ludwigshafen
Senior Analytical Chemist Company: W.R. Grace & Co
Date Posted: 07-Nov-2022
Country: UNITED STATES City: South Haven, MI
Advanced Scientist
Company: Momentive Performance Materials Inc.
Date Posted: 27-Oct-2022
Country: INDIA City: Bengaluru
Sr. Scientist - Dispersion
Company: Axalta Coating Systems
Date Posted: 27-Oct-2022
Country: UNITED STATES City: Philadelphia, PA
Job Description : Accountable for personal safety, the safety of fellow employees and contractors, and for promoting a safe work environment. Perform Process Hazard Analysis. Maintain compliance with OSHA PSM, EPA-RMP, and New Jersey TCPA regulations. Maintain Process Safety Information including P&ID’s, Relief Valve Design Basis documentation, and Building and Facility Siting evaluations.
Job Description : Control, document and evaluate progress in the project and coordinate the transfer of results to the pilot plant, production and other units. Approach innovative research topics with enthusiasm and thus contribute to the further development of field of work. With the help of responsible way of working, ensure compliance with work, safety and environmental protection regulations. With a great deal of commitment, build up a network within research as well as with production, technology, engineering and marketing.
Job Description : Responsible for method development, method transfer and method validation in a GMP environment. Experience developing LC and GC methods for in-process controls and final product analysis is essential. Ability to bring innovative analytical techniques into our projects. Comfortable learning new technologies whenever needed to support a project. Possess excellent interpersonal communication skills both with team members on site, colleagues and customers.
Job Description: EH&S: Learn & adhere to safe work practices in lab; Exhibit & promote pro-active safe behaviors in lab activities. Responsible for design, synthesis and development of novel silicone-based polymers, oligomers or silane materials for varied applications. Work inclusively in close collaboration with BU’s/global stakeholders across multiple functions. Work collaboratively in a team setting & work with project leaders to execute project plans for timely positive progress – Technical problem-solving aptitude is required.
Job Description : Develop new or improved dispersions, including formulation, stability/durability testing, and pigment selection for automotive, performance and industrial coatings. Apply statistically designed experiments and six sigma methods to conduct research and validate results. Supervise technician(s), organize work flow, including setting and meeting key deadlines. Participate in creation of best practice processes for dispersion testing and qualification.
Quality Control Lab Chemist I Company: Sanofi S.A. Date Posted: 27-Oct-2022
Country: UNITED STATES City: Chattanooga, TN
Quality Control Lab Chemist Company: LyondellBasell Industries Date Posted: 18-Oct-2022
Country: UNITED STATES City: Channelview, TX
Chemical Process Engineer Company: PPG Industries, Inc.
Date Posted: 18-Oct-2022
Country: UNITED STATES City: Circleville, OH
Senior Analytical Chemist Company: Pfizer Inc
Date Posted: 18-Oct-2022
Country: SINGAPORE City: Singapor
Job Description : Conduct and document routine compendial (NF/USP/BP/EP/JP/ACS) and noncompendial raw material testing, in cGMP environment to support manufacturing. Able to seek additional tasks or non-routine functions and accomplish them according to written procedures in compliance with cGMP with general supervision. Overcome minor conflicts with priorities. Consult supervisor with major conflicts of priorities. Work with manager to conduct laboratory investigations related to raw material testing.
Job Description: Assist with recommendations and setting direction for lab HSE, methods, procedures, techniques and technical guidance for Quality Lab through guidance of senior chemist and lab specialist. Work with senior chemists, lab technicians and lab specialists in understanding of laboratory systems, methods, troubleshooting for technical assurance. Develop ability to challenge the status quo in lab practices and methods to provide better response and data to the supporting units and business teams.
Job Description : Monitor the quality of and continuously improves manufacturing methods from raw material receipt to customer delivery to ensure all customer requirements are met. Own the proper operation of reactor systems to ensure compliance with established safety standards, customer requirements and IATF 16949 standards. Lead the scale-up of new products and assures quality systems are in place for process changes to existing products.
Job Description : Perform chemical analysis using analytical instrumentation such as but not limited to UPLC, HPLC, FTIR and GC using existing methods or with modification where required. Set up test methods in the lab as per procedures. Write and maintain accurate, complete and timely data in electronic laboratory notebooks as per good documentation and good laboratory practice. Analyse and interpret test data.
Website: http://www.worldofchemicals.com/chemical-jobs.html
Styrolution has introduced the first bio-attributed Terluran® ABS solutions. Terluran is INEOS Styrolution’s standard ABS consisting of acrylonitrile, butadiene and styrene monomer. The company’s new Terluran® ECO grades are based on renewable feedstock and can be used as a replacement for conventional feedstock for all three components in ABS (acrylonitrile, butadiene and styrene monomer). This approach allows to maximise the renewable feedstock in the material while minimising the CO2 footprint. Terluran is the material of choice for a broad range of applications in various industries including automotive, household, electronics, construction and toys, sports & leisure.
Contact: INEOS Styrolution Europe GmbH Mainzer Landstrabe 50 60325 Frankfurt am Main, Germany Tel: +49 69 509550 1200 Web: www.ineos-styrolution.com
For more than 40 years, Seppic has offered well-known vaccine adjuvants for Animal Health: the MONTANIDE ™ range. These adjuvants are mainly dedicated to the injection and mucosal route. Now Seppic adds to its offer an adjuvant specially designed for oral vaccination, a safe and effective alternative for many species, especially for fish. MONTANIDE™ GR 01 contains a matrix which traps the antigen. Thus, the antigen is protected from the gastric environment until its liberation in the intestine where it can interact with immune cells. MONTANIDE™ GR 01 can be easily used to formulate veterinary oral vaccines by emulsification with aqueous antigens.
Contact: Seppic SA Paris La Defense 50 boulevard National CS 90020 92257 La Garenne Colombes Cedex France
Tel: +33 (0)1 42 91 40 00 Web: www.seppic.com
Allnex has launched its latest product, the CRYLCOAT® 2406-2, designed to meet the customers’ needs for an industrial outdoor grade that can be cured by both TGIC and HAA - all while maintaining a good balance of performance. The ability to be cured by both TGIC and HAA demonstrates our innovative approach in bringing new and unique products to the market. The benefits of the CRYLCOAT 2406-2 are it has excellent matting efficiency, good flow and appearance, outstanding mechanical properties and good weathering for outdoor industrial application.
Contact: Allnex Management GmbH
The Squaire 13, Am Flughafen 60549
Frankfurt am Main, Germany
Tel: (69) 6435710-20
Email: business@allnex.com Web: https://allnex.com
Cortec® Corporation announced its new, improved MCI®2040 High Performance Vertical/Overhead Repair Mortar. This is yet another component of Cortec’s High Performance Repair System (HPRS®), which helps concrete repairs last longer by inhibiting corrosion and reducing the risk of the insidious ring-anode effect. With MCI®-2040, Cortec® has extended the protective qualities of MCI®-2041 (horizontal repair mortar) to vertical and overhead surfaces. MCI®-2040 is a single-component, fast-setting, high-strength, cementbased repair mortar that is enhanced with Migrating Corrosion Inhibitors (MCI®). MCI®-2040 offers corrosion protection to reinforcing metals both in the patch and in the surrounding areas. Once applied and hardened, MCI®-2040 provides a high level of adhesion and durability, as well as resistance to water and carbonation attack.
Contact: Cortec® Corporation
4119 White Bear Parkway St. Paul, MN 55110, USA
Tel: 651-429-1100
Email: productinfo@cortecvci.com Web: www.cortecvci.com
GEMU launched its 567 eSyDrive motorised control valve which is designed for aseptic applications and is based on a unique sealing concept –plug diaphragm technology (the PD design). The design has been developed by GEMÜ in order to unite the advantages of diaphragm valves with globe valves. The valve’s geometry allows for a hermetic separation of the actuator from the media flow and a high level of control accuracy. It enables quantities of 2 l/h right up to 63,000 l/h to be safely controlled.
Contact: GEMU Gebruder Muller Apparatebau GmbH & Co. KG
Fritz-Muller-Strabe 6-8 74653 Ingelfingen-Criesbach, Germany Tel: +49-79 40 - 123 0 Email: info@gemue.de Web: www.gemu-group.com
introduced the new Type 855BP Miniature Back Pressure Regulator, a compact relief valve that provides economical, high performance pressure relief with an adjustable set point. Its typical application is to provide protection against over pressurisation in the downstream portion of a pneumatic system. The Type 855BP will handle a 250 psi (17.5 bar) maximum system pressure and offers five setpoint pressure ranges from 0-5 psi (0-0.4 bar), up to 0-100 psi (0-7 bar).
Contact: ControlAir 8 Columbia Drive Amherst, New Hampshire 03031, USA Tel: (603) 886-9400 Email: sales@controlair.com Web: www.controlair.com
TDK Corporation introduced the compact, rugged B58620F3800B768 AFA pressure transmitter for screw mounting for a wide range of industrial applications. It is designed for a pressure range of 1 bar to 11 bar and temperatures from -20 °C to +125 °C. The piezoresistive pressure transmitter is based on MEMS technology with a robust stainless steel pressure port. It is suitable for pressure measurement of non-freezing media such as fuel, diluted acids or contaminated air.
Contact: TDK Corporation 2-5-1 Nihonbashi, Chuo-ku, Tokyo, 103-6128, Japan Tel: 81-3-6778-1000 Web: www.tdk.com
Sensor Solutions introduced a new line of Hazardous Location LVDTs (Linear Variable Differential Transformers) that operate safely and accurately in hazardous and explosive environments with the presence of flammable or ignitable gases and liquids such as those found in refining and petrochemical plants, pipelines, and oil and storage tanks. The sensors are ideal for pipeline and LNG storage tank structuring monitoring and real-time position sensing of different valves in oil and gas fields, chemical process plants, gas turbines and oil refinery platforms and rigs.
Contact: NewTek Sensor Solutions
7300 US Route 130 North, Bld # 7 Pennsauken, NJ 08110-1541 USA Tel: +1 (856) 406-6877
Email: sales@newteksensors.com Web: www.newteksensors.com
WITT launched MG 2000-ME ERC+ electronic gas mixer for applications needing high flow rates of gas mixtures, such as steel production or the chemical industry. Precisely and reliably, the device generates high-quality gas mixtures of two technical gases, even when the flow rate is fluctuating. The system is controlled either remotely via Ethernet or analog output, or directly on the unit via an intuitive touchscreen.
Contact: WITT-Gasetechnik GmbH & Co KG Salinger Feld 4-8 58454 Witten, Germany Tel: +49 (0)2302 8901- 0 Web: www.wittgas.com
Yokogawa Electric Corporation has introduced OpreXTM Magnetic Flowmeter CA Series. The products in this new series are all capacitance-type magnetic flowmeters that are capable of measuring the flow of conductive fluids through a measurement tube without the fluids coming into contact with the device’s electrodes. The main application areas include chemicals, paper and pulp, mining, food and beverages, water and sewerage etc.
Contact: Yokogawa Electric Corporation 9-32, Nakacho 2-chome, Musashino-shi, Tokyo 180-8750, Japan Web: www.yokogawa.com
Picarro Inc has introduced the first comprehensive solution for monitoring ambient levels of Ethylene Oxide (EtO or EO) at community monitoring stations and industrial fencelines. With this system, air quality networks, medical sterilisation facilities, and petrochemical plants will be able to monitor and quantify low, ambient levels of EtO for months. The system enables the detection of EtO down to levels previously unmeasurable by unreliable and suspect canister-based methods and legacy technologies.
Metrohm Process Analytics launched the new 2060 The NIR Analyzer. The process analyzer is the perfect solution for inline process monitoring of multiple parameters at the same time. The 2060 The NIR Analyzer can measure up to five sampling points hundreds of meters away and it is available in four different configurations to target multiple applications and industries. The 2060 The NIR-Ex Analyzer and 2060 The NIRREx Analyzer can be safely operated in potentially explosive atmosphere.
Contact: Picarro Inc. 3105 Patrick Henry Dr. Santa Clara, CA 95054, USA Tel: +1 408 962 3900 Email: info@picarro.com Web: www.picarro.com
Contact: Metrohm AG Ionenstrasse 9100 Herisau, Switzerland Tel: +41 71 353 8585 Email: info@metrohm.com Web: www.metrohm.com