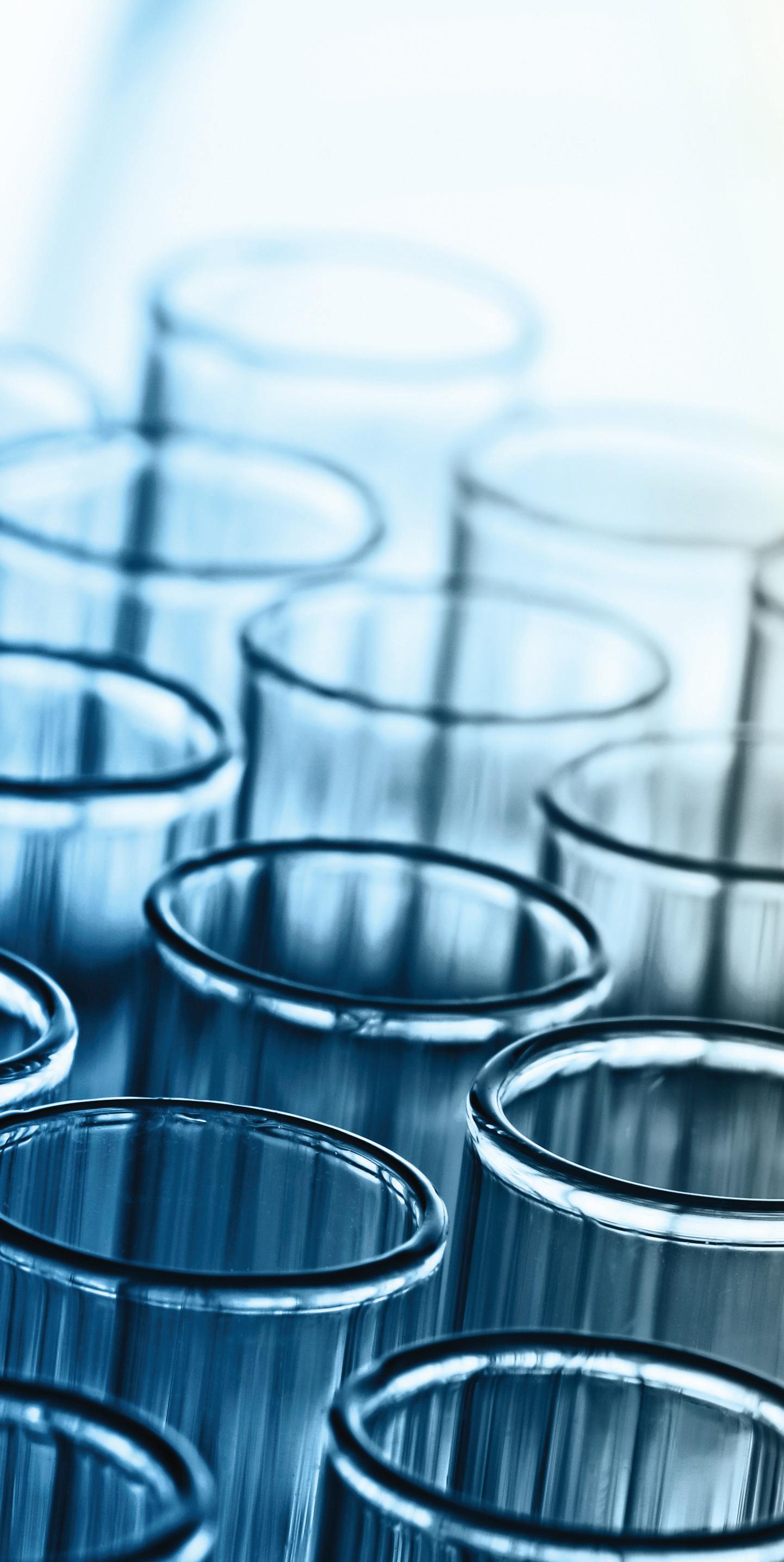
5 minute read
ADHESIVES: Formulations
FORMULATIONS
What projects require custom adhesive formulations and why?
Article courtesy of Gluespec
Some products, regardless of how big or small, require custom-formulated adhesives. Although formulations vary depending on technicality, the objective is a reliable and costeffective end product that complies with a company’s quality, design, and manufacturing goals.
Scenarios calling for custom adhesives Purchasing an off-the-shelf adhesive as a component for an assembly or mechanical project is a common step in the design process — but sometimes it’s simply not possible.
There are a few reasons why an adhesive with the ideal combination of qualities might not exist for a specific assembly. In such cases, a custom formulation is necessary. This is particularly true in heavy industries where stringent manufacturing requirements and performance are essential.
The following are a few examples where customization is worth considering to ensure reliable manufacturing.
No adhesive matches the project’s needs. If your design specifications call for a specific level of bonding and no off-theshelf adhesive can meet the requirements, your whole production schedule might be in jeopardy. This is common when dealing with precision engineering in aerospace, transit, or defense projects. If no adhesive provides reliable results, it’s time to consider custom formulation.
An off-the-shelf formula is discontinued. What happens when you’ve found an adhesive that works, but it’s removed from production? In such cases, keeping the assembly line moving can be challenging, and it’s time to reach out to a lab that can formulate a new high-quality epoxy, urethane, silicone, or another adhesive type.
It’s possible the custom replacement won’t only match the performance possible with the old formula but also improve upon it.
Existing adhesives fail to comply with regulations. As governmental agencies tighten the restrictions around which chemicals are deemed safe, it’s not uncommon for older substances to be banned. An integral ingredient in your company’s products might be listed for non-compliance. As with discontinued formulations, it’s important to find a lab that can create a custom formulation to replace the lost chemical.
The new formulation must deliver the same performance or better while also complying with the law in question.
Types of adhesives (according to Adhesives.org) Between off-the-shelf options and new formulations, acquiring an adhesive that fits just about any description or requirement is possible. To better understand why certain products require custom adhesive formulations, it’s necessary to delve into the types of adhesives and what they’re used for.
An adhesive is a non-metallic binder that acts via adhesion and cohesion. The classification of adhesives depends on their:
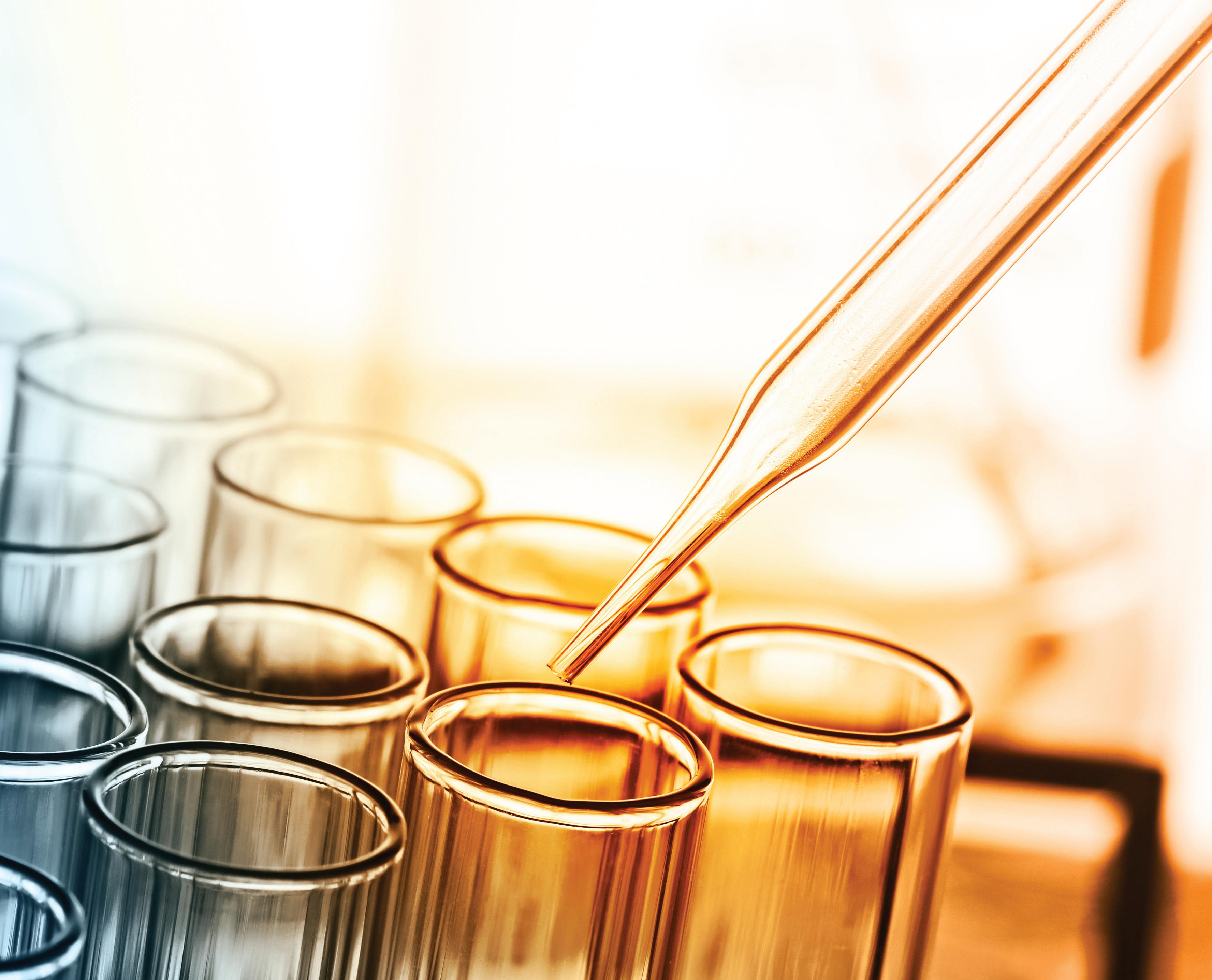
• Form (paste, liquid, etc.) • Chemistry (polyimides, epoxies, etc.) • Type (hot melt, contact, etc.) • Load-carrying capability (structural or non-structural) Structural adhesives are strong, known as load bearing, and are useful for engineering applications. Consisting of epoxies, cyanoacrylates, and some acrylic adhesives, these products can undergo shock, vibration, and other destructive agents and remain bonded.
Pressure-sensitive adhesives are typically purchased as tapes or labels and do not solidify to form a solid material. Bonds are formed by bringing the adhesive film in contact with the substrate and applying pressure. Pressure-sensitive adhesives are typically used to temporarily hold objects in place during assembly.
Thermosetting structural adhesives are typically available in two-part forms and are mixed carefully within a limited time window. They usually have a “pot
When deciding on an adhesive for an application, manufacturers consider the tensile and shear strength, dimensional stability, temperature resistance, and compatibility of materials.
| AdobeStock
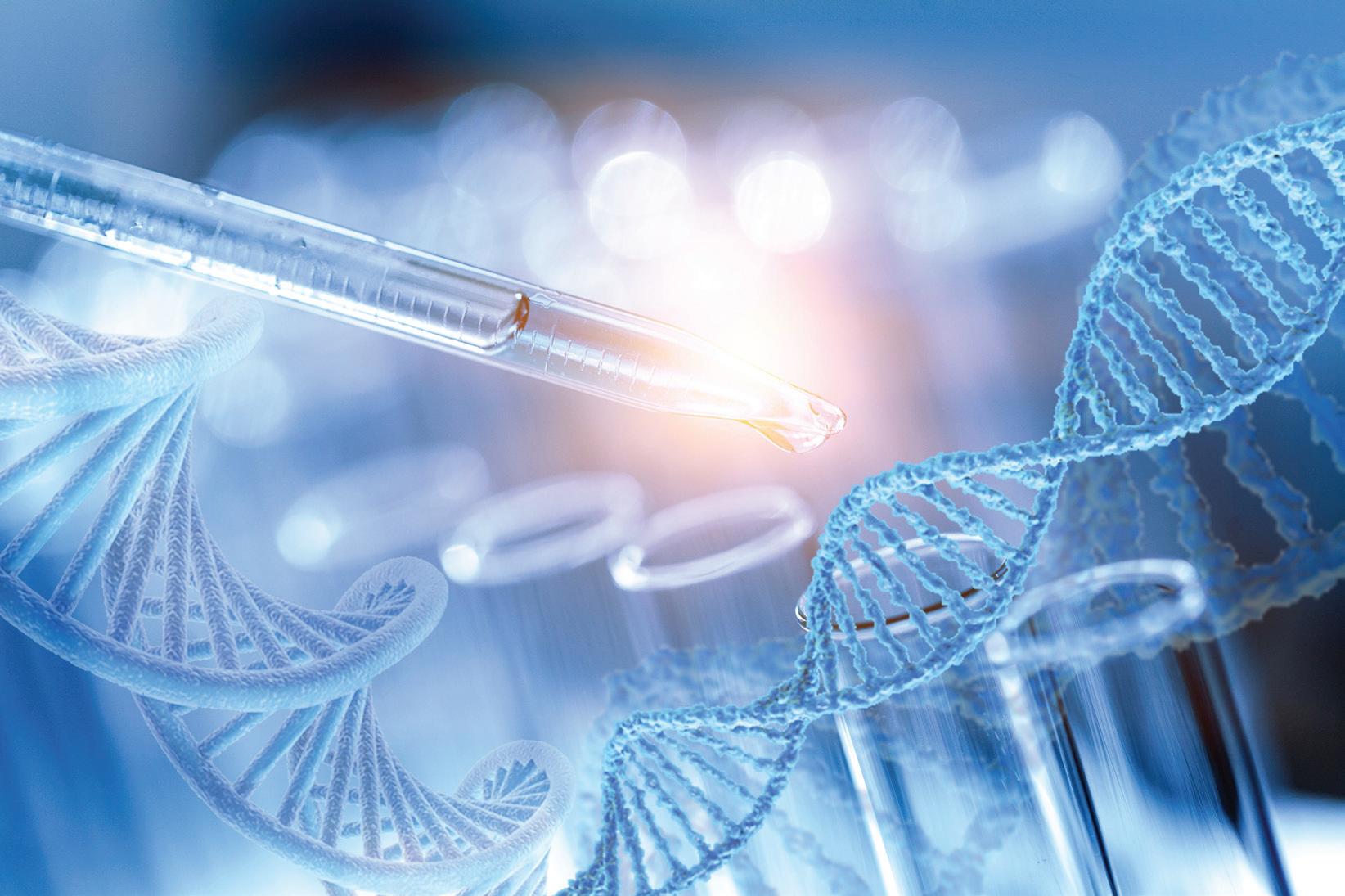
FORMULATIONS
life,” which is the amount of time the adhesive is workable once mixed and able to make a satisfactory bond.
Reactive versus non-reactive Reactive adhesives can be characterized by the formation of permanent bonds between substrates that create resistance against chemicals, moisture, and heat (think structural adhesives). Typically, a reactive adhesive is made of a monomer (resin) and an initiator. Due to the chemical bond, reactive adhesives have long-term durability and high bond strength.
When choosing an adhesive, it’s essential to consider what the product will need to endure. For example, reactive adhesives cure to form a material, as opposed to solvent or hot-melt adhesives. This means reactive adhesives are more durable against the effects of extreme temperature and general environmental resistance.
Epoxies are one of the most used structural adhesives due to their range of forms, high-tensile strength, dimensional stability, and ability to adhere to several materials. They can be room-temperature or heat-cured (depending on the additives). Advances in additives and formulation have made epoxies more resistant to chemicals.
A reactive two-part adhesive works as follows: base resin + hardener/curing agent → plastic or rubber
It transforms into a thermoset polymer via a cross-linking process. For a reactive one-part adhesive, UV light, heat, or moisture is required (it’s a pre-mixed, two-part adhesive, but the reaction requires light, heat, or moisture to begin). Other reactive adhesives include acrylic, silicone, urethane, and cyanoacrylate (super glue).
Non-reactive adhesives do not have a permanent chemical bond, but bond through a physical change. Examples include polyvinyl acetate, construction adhesive, hot glue, and contact adhesive.
An emulsion adhesive works as follows: adhesive + evaporative solvent → solvent evaporates
As the solvent evaporates, it leaves the adhesive behind. Natural versus synthetics Another categorization of the many forms of adhesives is if they’re natural or synthetic. Historically, adhesives were made of naturally occurring components, but now it’s common to find a combination of natural and synthetic compounds.
Natural adhesives are made from natural materials, like animal and plant matter, and occasionally, minerals. Animal-based adhesives are made from albumin, beeswax, casein, and gelatin. Plant-based adhesives are made from components like dextrin, natural resins (gum arabic, balsam), oils, waxes, soybean protein, and starch. Mineral-based adhesives come from components of amber, paraffin, silicates, and sulfur.
While these types of adhesives are generally affordable to manufacture and are still used for wood, paper, film, and foil materials, most adhesives employed today belong to the newer synthetics category. Synthetic adhesives are developed from human-made polymers.
Although more costly than natural adhesives, synthetic alternatives are customizable and feature greater bond strengths.
To learn more, visit https://tinyurl.com/GlueSpec
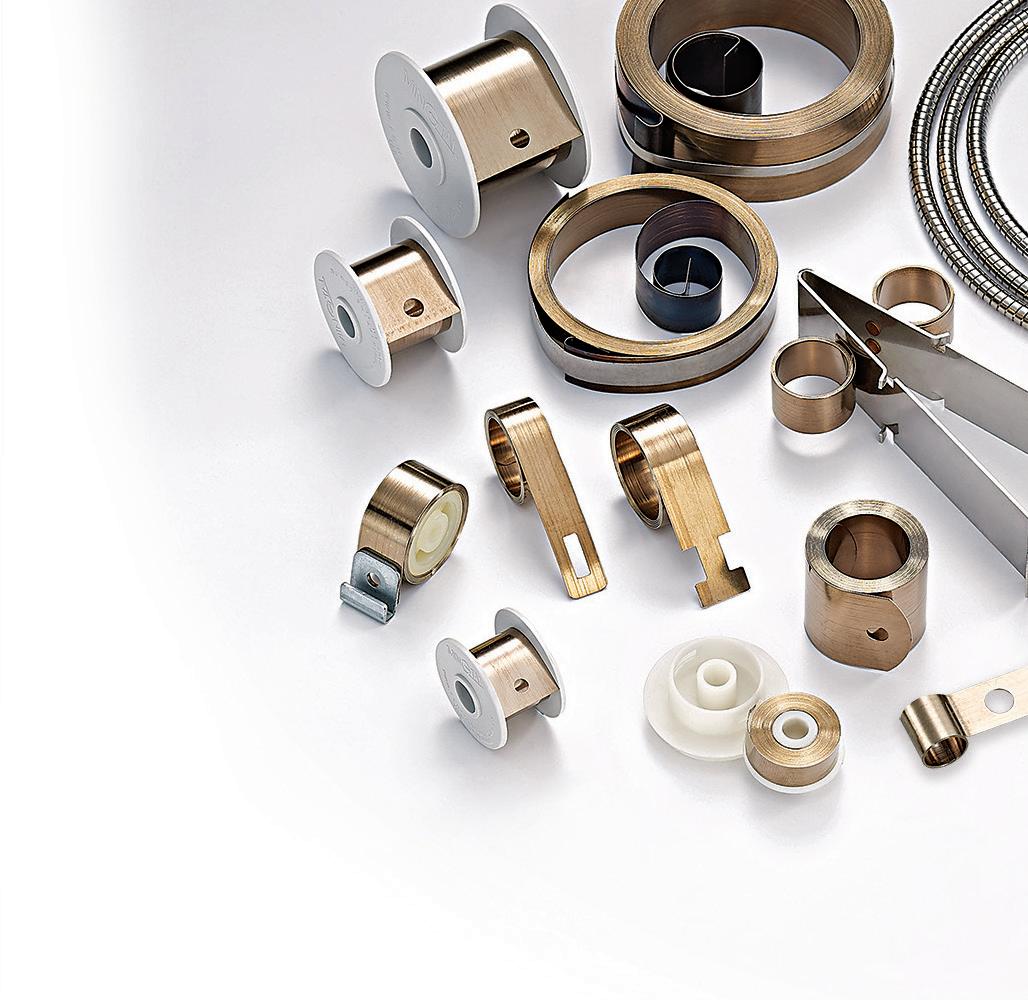

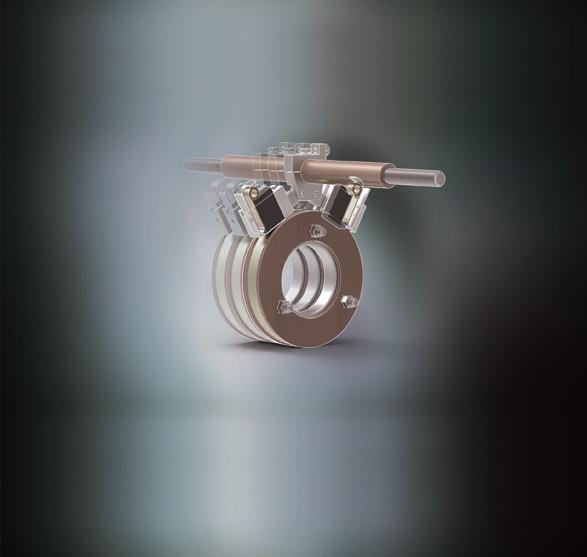