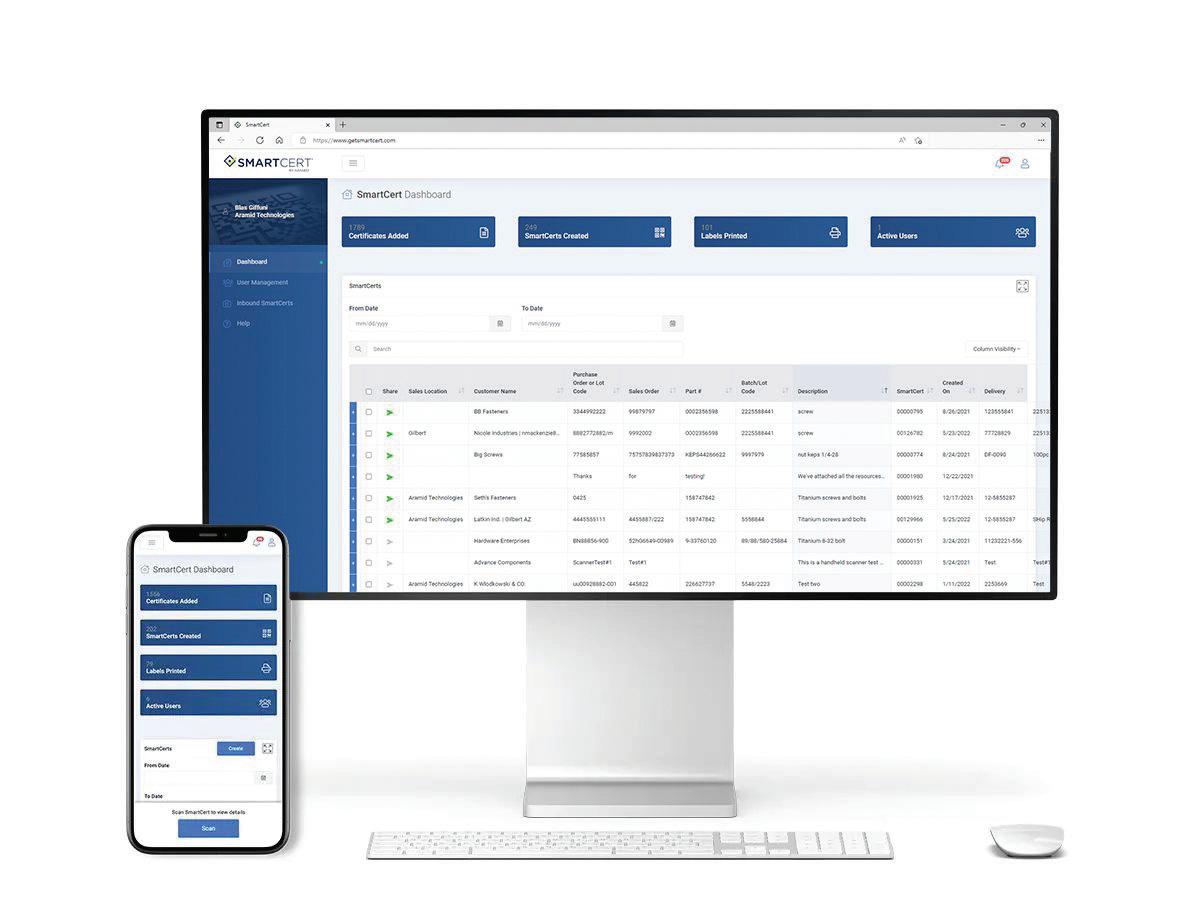
4 minute read
SUPPLY CHAIN
Supply chain issues: How much is lost paperwork costing your company? Lonni Kieffer Marketing & Customer Success, SmartCert
For hundreds of years, paper documentation has been used to deliver critical information, from receipts and prescriptions to certifications. This medium has faded from daily use.
The digital era is here. Email, software, and automated systems are commonplace. However, in the fastener industry, several organizations have yet to fully integrate digital processes or eliminate physical paperwork.
The problem is paper costs supply chains thousands of dollars, not counting the price of paper, ink, and printing, which undoubtedly adds to these expenses. Supply chains are most affected by paper documentation when this antiquated system fails.
Paper results in a lack of visibility, traceability, and efficiency. There’s a chance important documents could get lost, misplaced, or damaged. These risks are not as negligible as one might think. The disadvantages of losing vital records in the supply chain are vast and showcase why digitization is the ideal way forward. Physical paperwork leads to: • Increased risk of errors due to unreadable or missing documents • Time wasted filing and organizing paper documentation (keeping employees from other essential tasks) • An inability to quickly share documents between departments or remote parties • Challenges in quick accessibility, particularly if products are recalled or fail • Risks of delays in manufacturing or shipping
There’s also a negative environmental impact as paper copies are printed and eventually discarded. In fact, an average American office worker goes through as many as 10,000 sheets of paper each year.
Here are a few common scenarios that further outline the problem: 1. A distributor handles $30M of products yearly and scraps $180k because of related certification problems. The issue? The paperwork got lost, and the products could not be shipped due to the lack of certification required for compliance.
The certification process for fasteners — the inbound and outbound exchange of quality certifications – has changed little for many organizations, which still rely on paperwork. But paper results in a lack of traceability and efficiency. Fortunately, digital options are available.
For example, SmartCert automates the transfer of required documentation between companies, replacing paper and printing costs to reduce missing documents and promote sustainability.
2. A customer has installation problems and thinks they might have the incorrect inserts. The supplier must first find and review the certification. In the meantime, the parts are quarantined, with several employees affected. Instead of getting the job done, they’re spending time tracking down the paperwork and dealing with the stalled implementation.
When the supplier finally locates the correct documentation, it’s clear the inserts were provided by a different manufacturer and require a different installation process. Four employees spent a couple of hours each addressing this issue, costing the company in the hundreds.
3. A distributor sells parts to a customer but accidentally includes the wrong documentation. As a result, it’s necessary to quarantine the parts and send replacements. The new parts also include incorrect paperwork, leading the distributor to recommend an alternate source. This customer is now potentially lost for good.
In this case, the cost for the distributor includes: • Labor of $1,500 • Red shipping and two lost sales for $120 + $2,400 + $2,500 = $4,920 • The loss of a customer at $66,000 ARR Time is money. According to a recent Gartner study, it takes an average of 25 hours for lost documents to be recreated. This results in wasted time and money for a company.
Another report estimates that the average business spends $8,000 on paper and another $8,500 on filing and storage. This process also requires a dedicated file manager to ensure the organization of these documents, which can cost another $30,000 or more per year in labor.

Reducing lost paperwork Many organizations still rely on legacy procedures. Some lack department time or insight to update these processes or fear investing in new technology. Awareness is key. Tracking the actual cost of paper and the risks involved can help supply chain organizations decide to change.
Going digital is not as challenging as it might sound. Ideally, the software or automated processes selected should allow your company to easily store, access, and edit certifications for your products in the cloud.
Additionally, the technology should: • Establish the origin and complete history of a product as it travels through your supply chain • Create a centralized repository for documents that are accessible to your teams The consequences of antiquated processes There are three costly ways companies lose money with paper certifications.
1. Organizations lose 20 to 30% of revenue annually due to inefficient processes. 2. Approximately 40% of workers spend a quarter of their week on repetitive tasks. 3. Up to 40% of on-the-clock time is wasted searching for missing paperwork.
Advanced companies want to work with other well-run organizations. Adopting an automated solution gives team members the tools necessary to spend less time worrying about paperwork and more time improving the business.
• Share a unique QR code or email for each product to let any user in the chain access relevant and up-to-date certifications • Search active and archived certifications • Update certifications even if a product is already in transit, sitting on a warehouse shelf, or in use
Digital documentation creates a traceable supply chain in which all actors in a distribution life cycle can review a product’s history and legitimacy. As a result, your organization can significantly reduce the risk of counterfeit or defective products making their way to your customers.