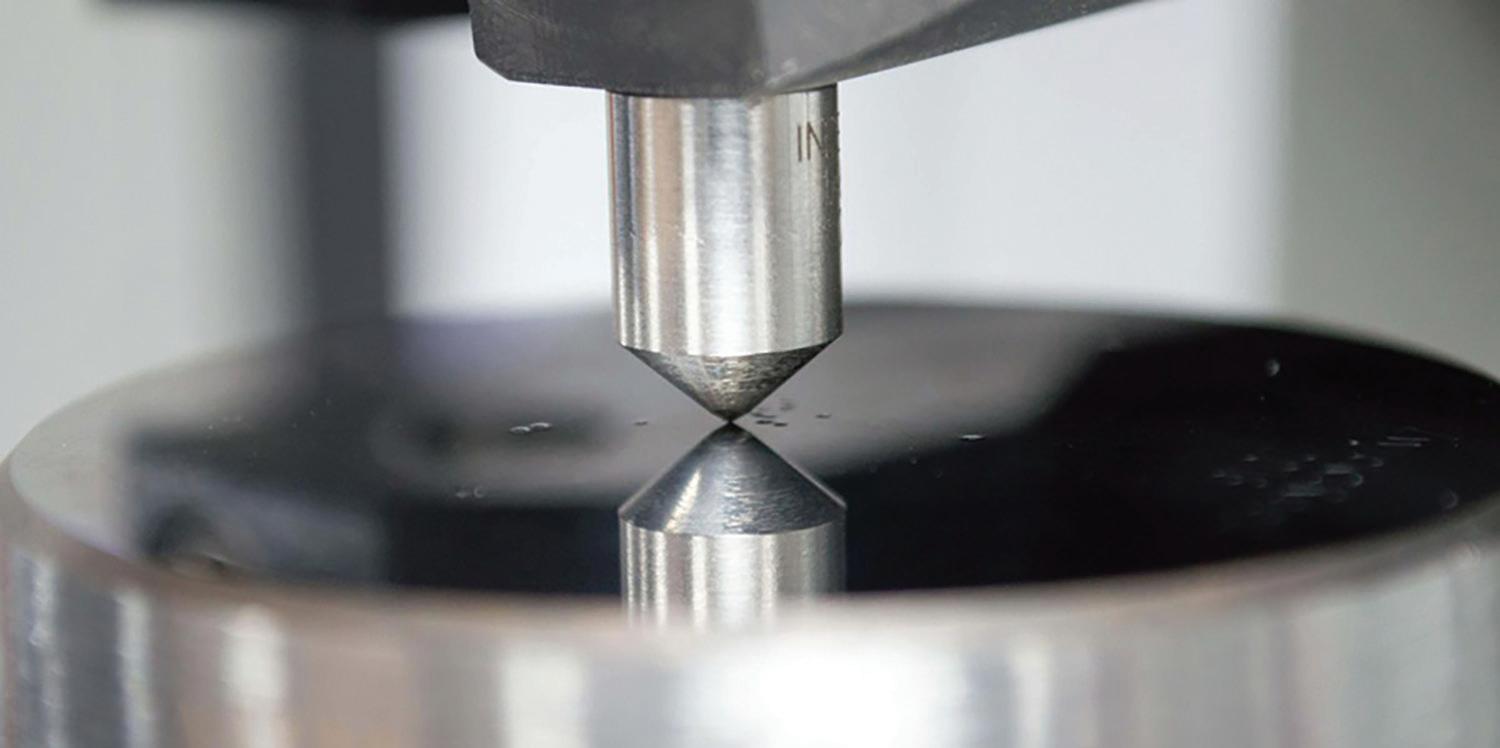
3 minute read
TESTING
Why should you test the fasteners you sell?
Rob LaPointe
President & CEO, AIM Testing Laboratory
Hardness testing is one of the most common and informative fastener tests.
Fastener testing is integral to making or distributing a product with proven performance and reliability for its intended job. While not all fasteners require testing, it’s a good business strategy to understand the performance and quality of the products you sell. Let’s explore three main reasons for fastener testing.
The most important reason to test fasteners is that it’s required by the drawing or manufacturing specification. Most fasteners made to specific standards — such as ASTM A574 or ISO 898-1, grade 12.9 — have specific performance requirements such as chemistry, hardness, ultimate tensile, and yield tensile. Many products have additional requirements, including shear strength, proof load, and microstructure.
These tests and others are often required, with the results provided to a customer upon sale. Typically, the manufacturer is responsible for testing, performing it at an in-house accredited laboratory, or submitting the work to an accredited third-party testing lab.
After testing, the seller is given certified test reports showing the product tested with identifying information such as the part description, heat number, lot number, manufacturing specification, testing specifications, acceptance criteria, and test results.
Each report should be serialized and traceable by the laboratory and declared with a global conformance or nonconformance statement. To obtain a global conformance statement, all test results pertaining to the order must be conforming. If there are mixed conforming and nonconforming results, the test report should have a global non-conformance statement and give attention to the specific non-conforming results.
The second most important reason to provide fastener testing to customers (even if testing is not required) is to position your business as a provider of quality and reliable products. Providing certified test results, or at least making them available on request, means that you stand behind your products — and can provide proof of your assertions.
Additionally, this is an excellent profit strategy. There are enormous and often unaccounted-for costs when recalling or replacing faulty fasteners. Most profits are lost when a customer returns a product because it fails to perform. The fastener must be scrapped or reworked and then replaced.
In such cases, your company not only loses money on the cost of goods but also on the labor of servicing the replacement part, additional vendor costs, and administration and shipping costs. And then... there’s your reputation to account for.
Several of these expenses are not ascribed to a particular product replacement and show up in the profit and loss statement under general operation. Typically, a more detailed accounting indicates the financial penalty of shipping a faulty product.
It’s far less costly to submit fasteners for testing, gaining the assurance they’ll perform as anticipated before they’re sold. This also provides recourse should a customer experience a problem with the product. You’ll have the evidence and supporting documentation that the fastener meets or exceeds the advertised performance.
The third most important reason to test the fasteners you sell is to understand the process and product as you manufacture or perform secondary processing. In-process testing can provide insights into making gains in efficiency and eliminating waste from manufacturing. It can also help you catch mistakes before they are incorporated into a product.
It’s inefficient to find out that a product fails to perform as expected after completing the manufacturing or secondary processing of a product. Finding mistakes at this stage often requires undoing a process, fixing the issue, and then redoing the process. A significant amount of time and money is lost by not first testing and proving the process from start to finish.
There are many more reasons to test fasteners and fully understand the products you’re selling, but these three are critical to a successful business. The fastener industry is interfaced with many different sectors, such as aerospace and automotive, where a reliable product delivered on time is critical. It’s worth the effort and expense to ensure that your industry contribution is received without issues, complaints, or concerns.
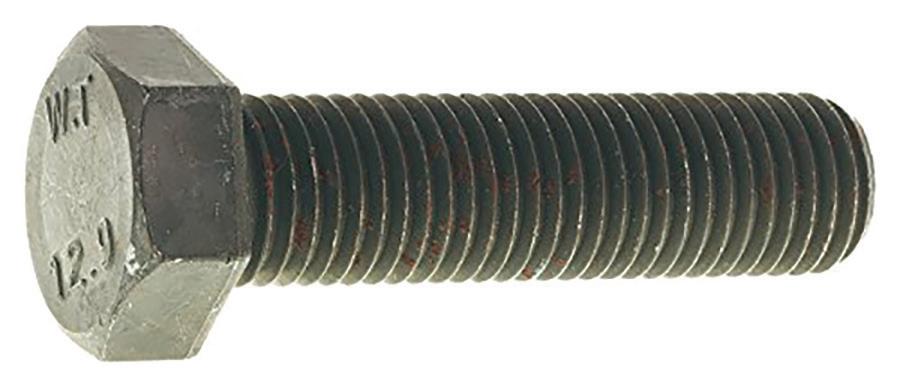
The most important reason to test fasteners is that it’s required by the drawing or manufacturing specification. An ISO 898-1, Class 12.9 hex cap screw is shown here.
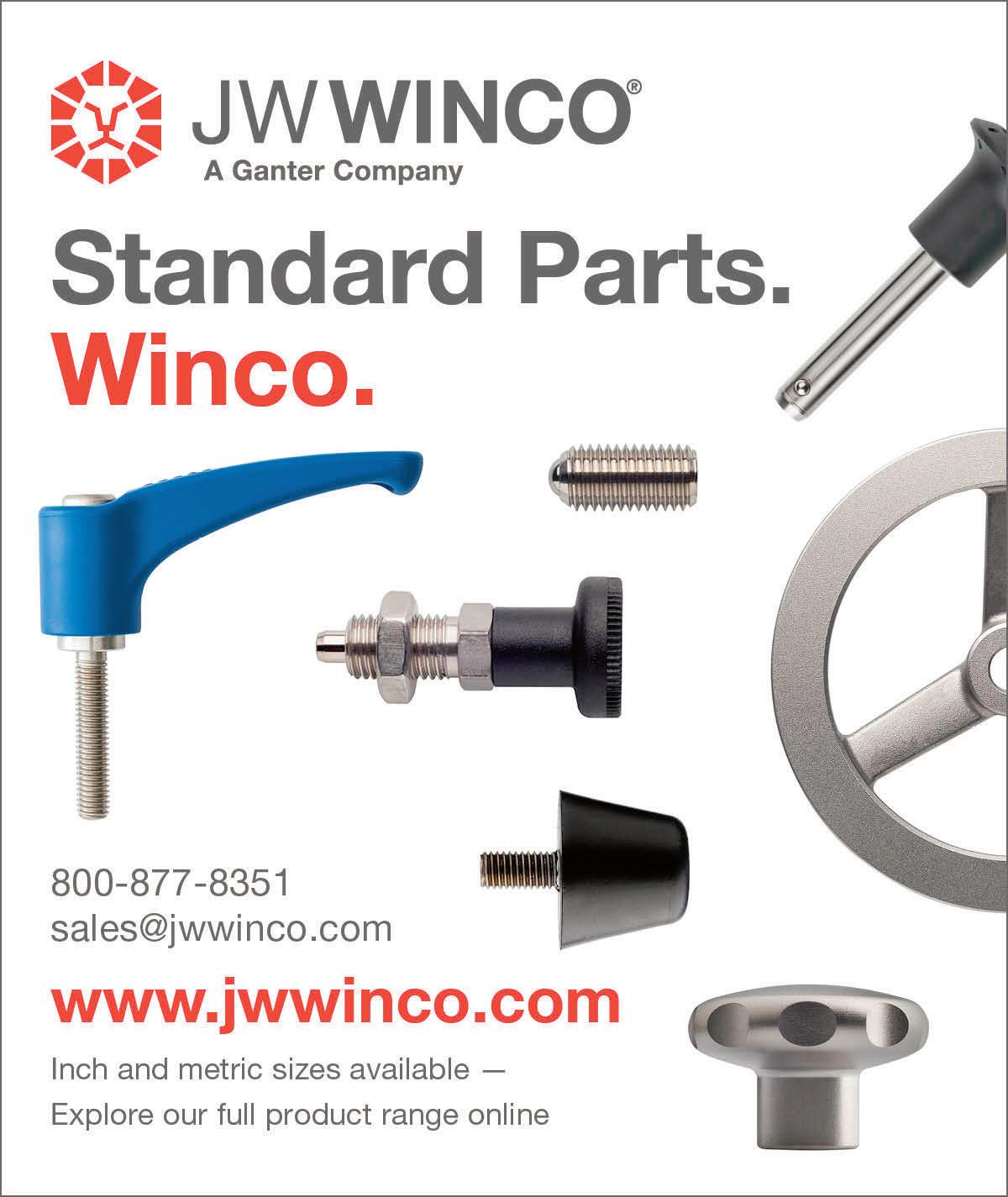