
3 minute read
SEALS
How to choose an O-ring for your application
Kim Keating, Director of Customer Success ZAGO Manufacturing Co.
Sealing screws with O-rings engineered onto each fastener.
An O-ring is a circular-shaped seal or gasket that’s made from an assortment of materials depending upon the application and the environment it will be used in. Sometimes called a packing or toric joint (because of its shape), it’s used to seal two working surfaces. O-rings are essential for protecting industrial machinery, electronic equipment, and a system’s inner components from wear and tear, including the detrimental effects of contaminants, seepage, or leakage.
Rubber O-rings are commonly used as they’re available in rigid and flexible materials with different strengths and tolerances. In the case of a sealing fastener, the rubber O-ring is engineered under the head of the screw or face of the nut or washer. Sealing fasteners provide a unique ability to protect conventional machinery and complex equipment with high-tech properties — thanks, to the inclusion of an O-ring.
Once torqued, the O-ring squeezes outward to form an unbreakable 360-degree seal that prevents gases and liquids from entering or exiting equipment operating in hazardous, treacherous, and/or pressured environments. The undercut groove ensures that the O-ring will not break or crack once installed, and the metalto-metal contact prolongs the life of the O-ring, which is not compromised under pressure.
With its impervious, unbreakable O-ring seal, the sealing fastener has the added benefit of protecting the environment from harmful contaminants. This can include disinfectants, oil, gas, humidity, dust, moisture, saltwater, or any debris or chemicals that can damage or destroy equipment. At the same time, it prevents equipment leakage of contaminants (i.e., acid leakage from lithium batteries) into the environment.
Equipment applications include hydraulic cylinders, water flow pumps, vacuums, and pneumatic medical devices such as pneumatic respirators.
Material choices Choosing the ideal material for an O-ring is important to ensure reliability and longevity. This choice should be based on the application, including its exposure to contaminants, temperature range(s), and required standards.
For example, military-grade sealing O-rings that meet the requirements of the Military Standard MS3212/MS3213/
NASM 82496 and that are pressuretested to 1500 psi are available. This is also true of FDA-approved O-rings.
Below are six types of O-ring materials that work in various applications.
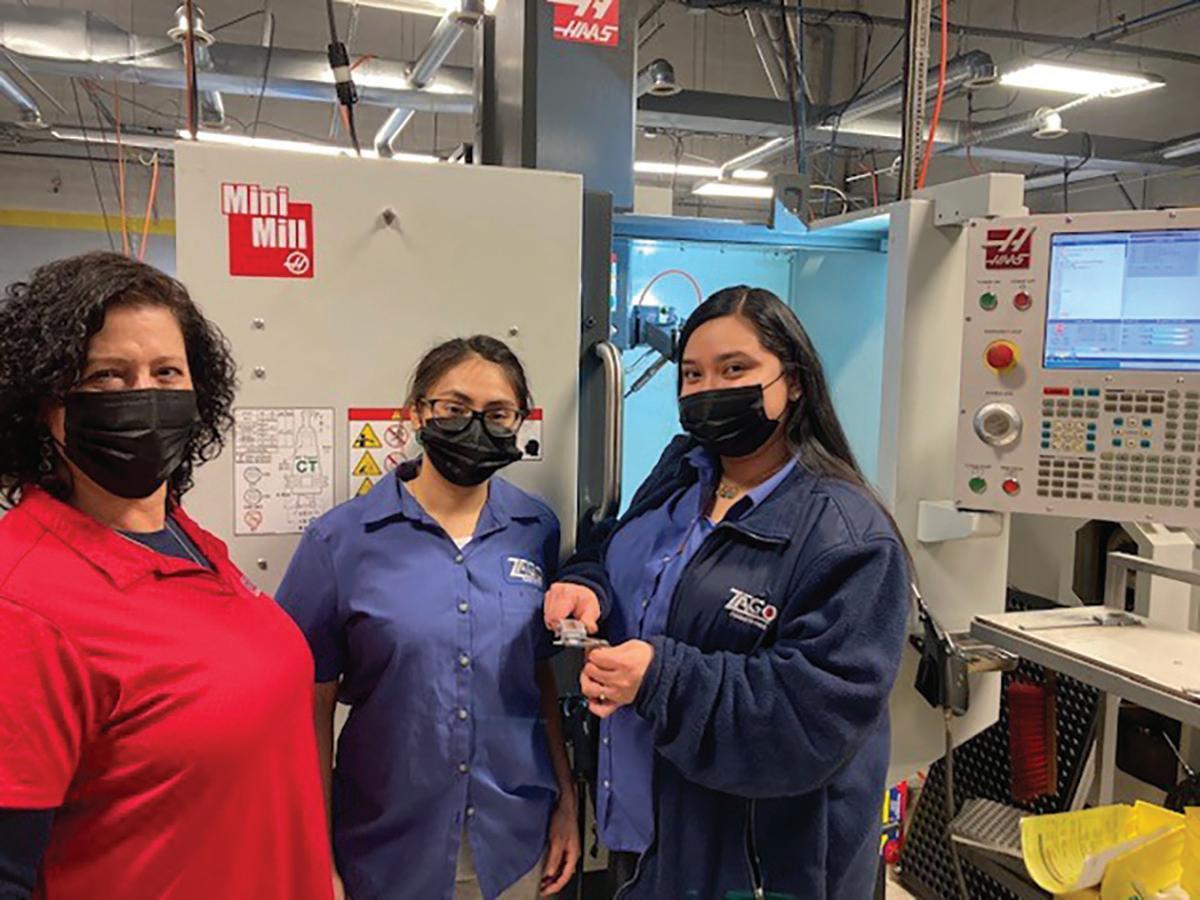
1. Silicone – an inert synthetic compound that’s available in a variety of forms (including rubber). Silicone is highly flexible and tolerates extreme temperatures without becoming brittle if exposed to cold. Silicone O-rings are used in several industries (such as aerospace, automotive, and electronics). This material is not recommended for dynamic seals because it lacks optimal solvent and oil resistance.
Temperature range: -80° to 400° F | -62° to 204° C Shelf life: Unlimited
2. Buna-N – also known as Nitrile and NBR rubber, is one of the most costeffective and widely used elastomers. It offers a versatile resistance to water, saltwater, petroleum-based substances, hydraulic fuels, and alcohols. However, Buna-N is unsuitable for strong acids, weathering, and sunlight. It’s typically used in marine and offshore equipment applications.
Temperature range: -40° to 225° F | -40° to 107° C Shelf life: 15 years
3. Fluorosilicone – a variation of silicone rubber that maintains high-temperature stability and durable mechanical properties. O-rings offer excellent fuel, oil, and solvent resistance and are commonly used in the automotive, aerospace, and military industries.
Temperature range: -67° to 350° F | -55° to 177° C Shelf life: Unlimited 4. Fluorocarbon – active surfactants offering high chemical and thermal stability. Fluorocarbon O-rings can withstand high temperatures, harsh chemicals, greases, and fuels. They’re ideal for sealing aircraft engines and equipment in the automotive, transportation, and chemical industries.
DuPont trademarked the wellknown Viton brand — a fluoropolymer elastomer and synthetic rubber compound that’s reliable in harsh environments.
Temperature range: -20° to 400° F | -29° to 204° C Shelf life: Unlimited
5. EPDM – a synthetic rubber made of ethylene, propylene, and diene monomers. EPDM O-rings are extremely durable, providing outstanding ozone, heat, steam, and chemical resistance. They’re typically used to seal outdoor equipment, including weather and water-resistant applications and appliances.
Temperature range: -65° to 225° F | -54° to 107° C Shelf life: Unlimited
The ZAGO team inspecting parts after manufacturing.
6. Chloroprene – a synthetic rubber better known by its trade name, Neoprene. This material has strong chemical stability and can be used over a wide temperature range. Neoprene O-rings are excellent at resisting ammonia, freon, oil, oxygen, as well as ozone and sunlight. They’re used in the automotive, HVAC, and refrigeration industries.
Temperature range: -40° to 225° F | -40° to 107° C Shelf life: 15 years