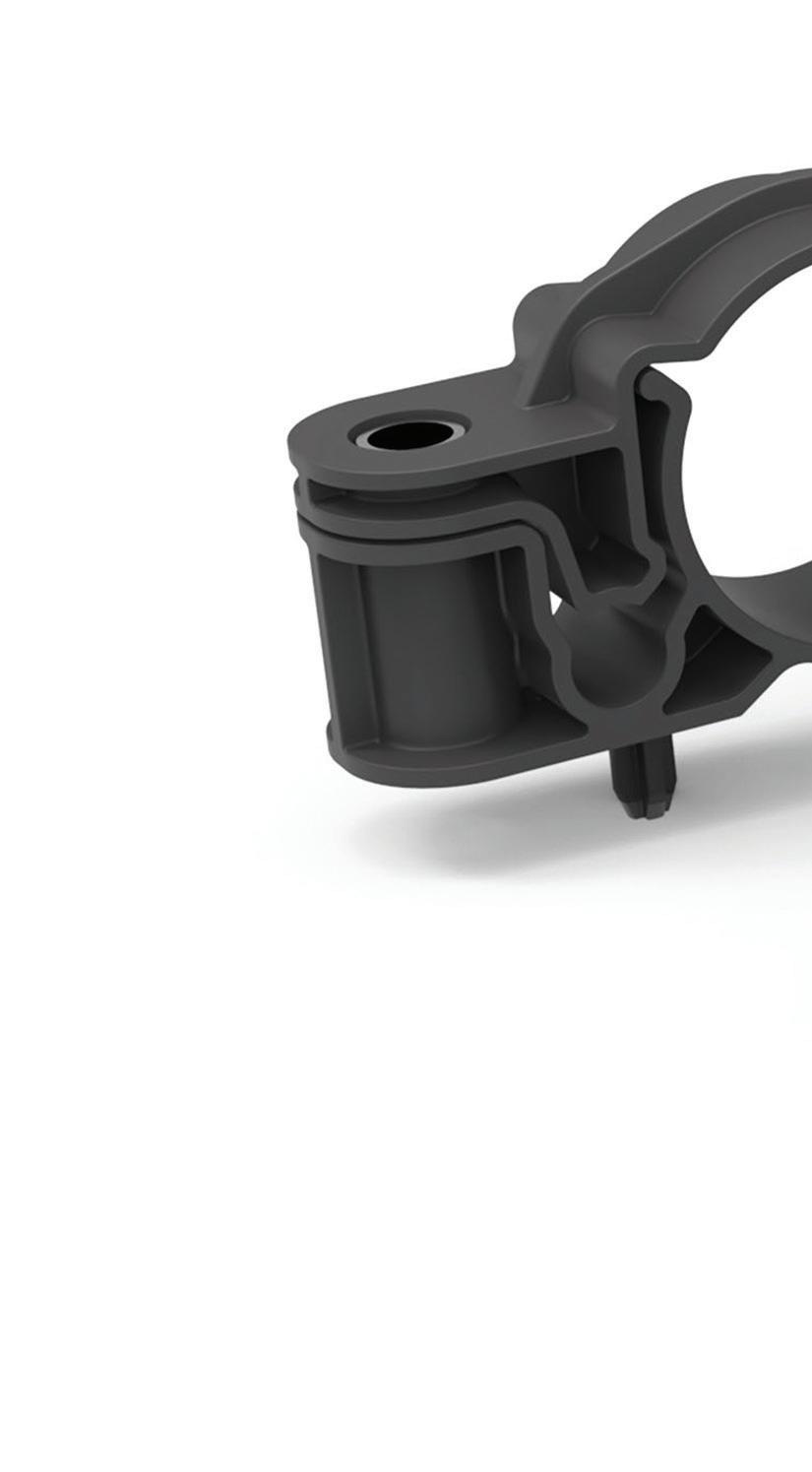
4 minute read
MATERIALS
How is lightweighting affecting fastener materials and designs?
Chris Kanaan, Sales Manager, ARaymond
As fastener manufacturing advances, the
lightweighting of fastener designs is also evolving. This is when a fastener is made lighter than typical, usually by replacing steel with other materials, such as aluminum.
However, joining lightweight materials can present challenges like different panel thicknesses, tolerances, retention requirements, corrosion — and the need to reduce the complexity of fastening interfaces. New fastener designs must meet performance and reliability standards, so developing mechanically and chemically compatible solutions are essential.
This trend in lightweighting is primarily driven by market demands. This is especially true in the automotive sector, given the growth of electric vehicles (EVs). The efficiency of EVs relies heavily on lighter-weight parts. This is also a requirement of the aerospace sector and several electronics manufacturers.
Material matters Structural integrity and durability are critical when developing lightweight fasteners for any industry. Any new component design must include design and validation processes to ensure it performs as intended in any given application. This can be easier said than done.
Materials performance can vary depending on an application and the environmental conditions, so choosing wisely is a must. Material costs are also a consideration with lightweight compounds. Currently, several manufacturers are moving away from heavier steel as a material for fasteners and toward other materials, including: • Aluminum • Carbon fiber • Multi-material assemblies • Nylon • Plastic • Titanium
These options typically let engineers shed weight from a manufactured fastener without shedding strength or reliability. In fact, many of these materials offer the same strength as a fastener made with heavier metals.
Multi-material assemblies can also lower production costs. This is primarily thanks to new technologies and manufacturing processes.
Assembly advances So, how can manufacturers lower the assembly costs of lightweight fasteners? One way is through the advancements in 3D printing. Another way is through the recent advances in plastics and multi-material assemblies.
3D printing – Also known as additive manufacturing, 3D printing builds a three-dimensional object from a CAD or a digital 3D model. One benefit is that it’s possible to print almost any design since there are no limitations on bends
and cuts. This makes this technology a worthy consideration for fastener designs compared to injection molding.
It’s particularly ideal for prototyping ideas and for fasteners with unique shapes and materials. However, given today’s advances in 3D printing, if you can think it, you can print it.
Plastics and material assemblies –Multi-material assemblies typically combine mild steels and rubbers/plastics, with the same functional properties as high-strength steels, but at a lower total cost of ownership. They also offer an overall reduction in mass, which is key for lightweight fasteners.
While it’s best to avoid bolting or screwing directly into nylons or plastics, overmolding provides greater design possibilities. Overmolding is an injectionmolding process where one material is molded onto a second one. It lets engineers use nylon material with an overmolded compression limiter, installed directly into the customer’s end item.
In this case, end users retain the high functional product requirements but gain critical cost and weight savings from their overall assembly.
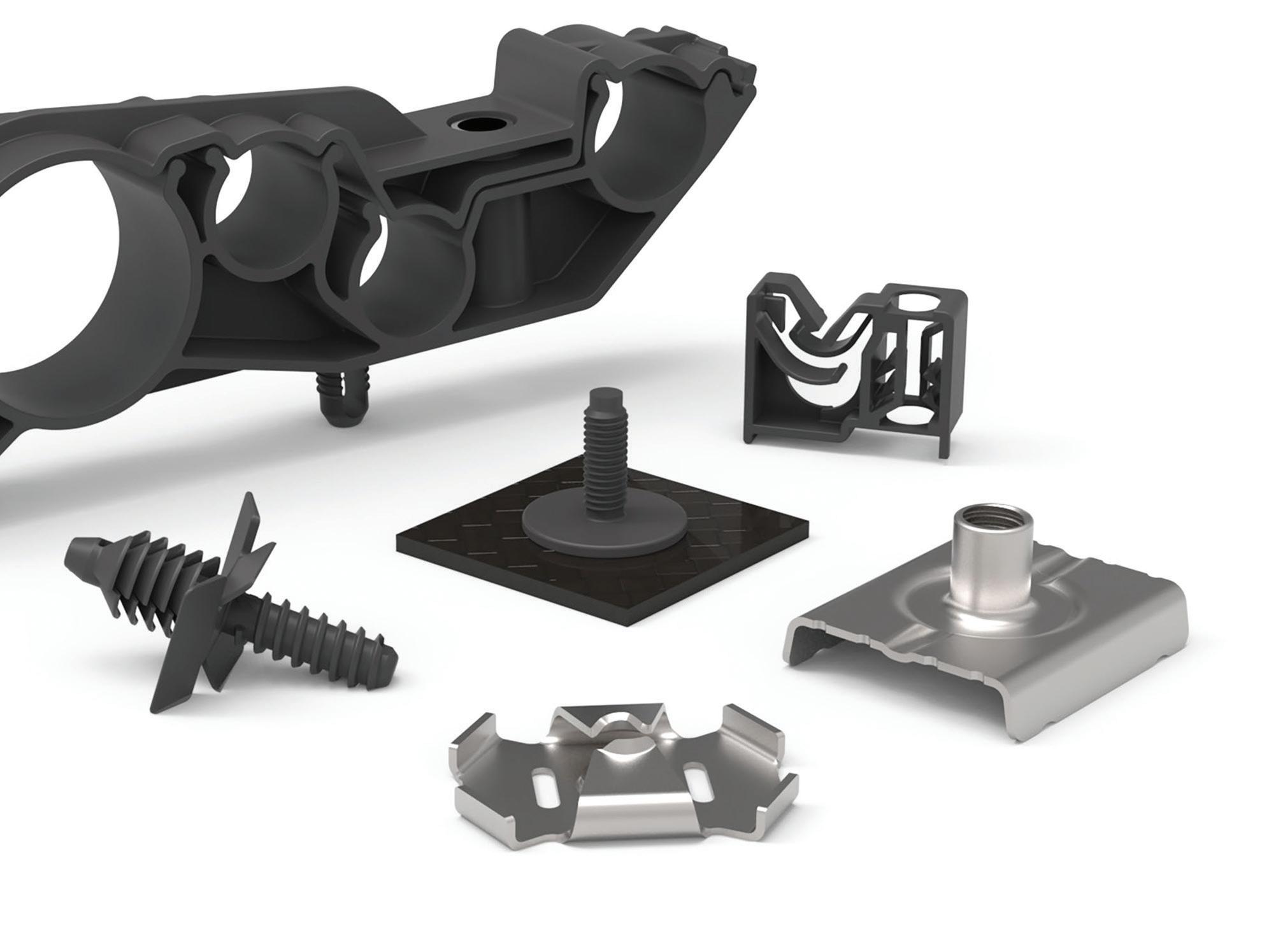
Automotive implications The fast-growing electric-vehicle market is providing an opportunity to upscale current production capabilities to support lightweighting in several EV applications, including structural connections, power connections, and thermal and moisture
A few examples of lightweight automotive parts. They’re made with alternative materials to reduce weight by up to 50%. These fasteners from ARaymond can adapt to a range of panel thicknesses, enabling a load distribution that prevents damage to the parts.

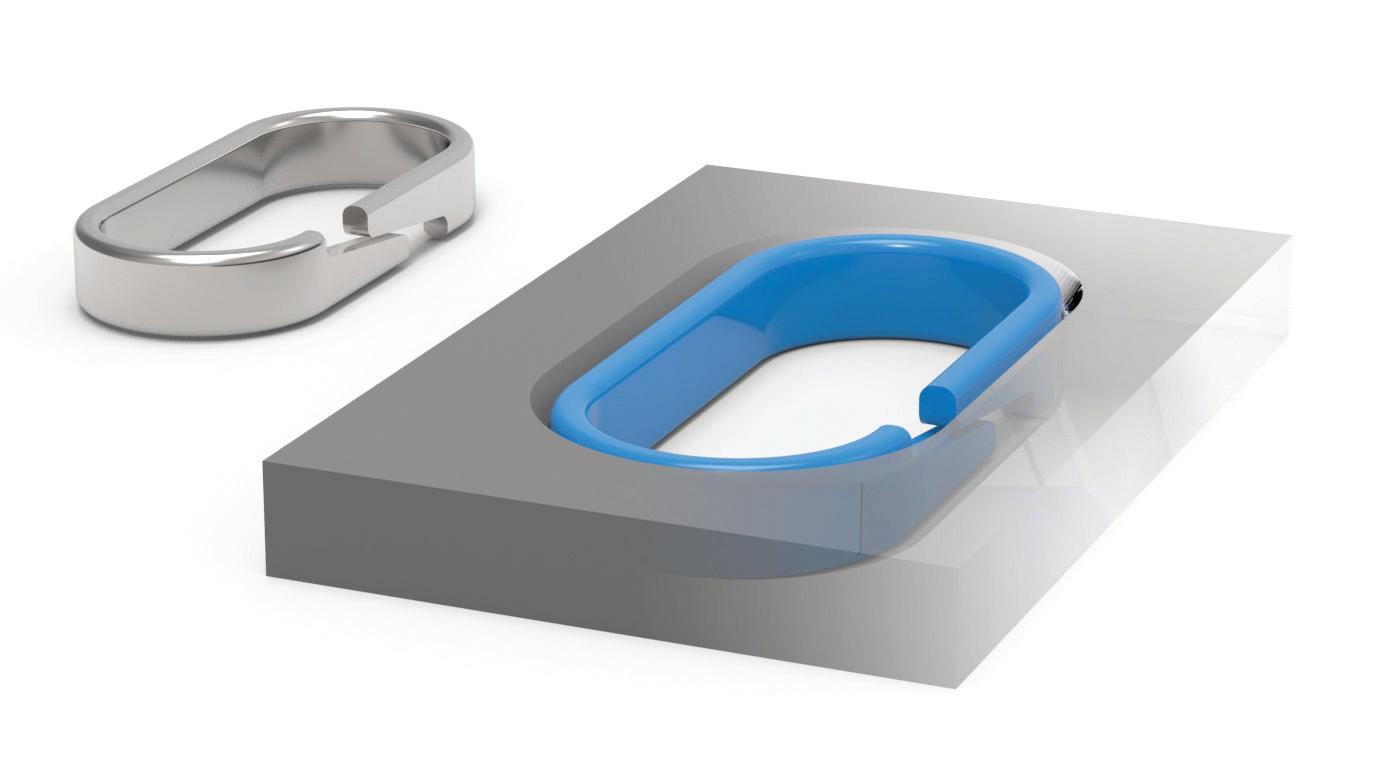
Go design.
Emerson’s expertise in plastic joining and fluid control make complex medical devices more compact and easier to manufacture.
Learn more at Emerson.com/Medical
materials
An overmolded compression limiter, which prevents creeping, for plastics and composite materials.
sealing.
Lightweight fasteners are rapidly replacing heavy metal joints and aiding in key EV areas of concern, such as water sealing and battery-pack optimization. There’s a safety aspect to these lightweight fasteners, too, such as the importance of securing the battery-pack lids.
Additionally, materials in EVs must have significantly higher heat capacities for potential thermal issues. For example, higher safety requirements for durability and flammability must be met, particularly for plastic or other resin-based materials.
Lightweight fasteners might come with a higher price tag than conventional, off-the-shelf parts, but for a good reason. And when the total cost of ownership is considered, the lightweight choice typically provides a greater long-term value.
New fastener designs also require communication and collaboration between OEMs and their supply base to best develop new standards and product lines for future success.
No matter the industry, the trend is clear: Lightweighting is a must-have tool for engineers as they develop fasteners that meet industry and assembly demands. Lightweighting is providing a key feature as manufacturers reinvent fasteners for changing market conditions.