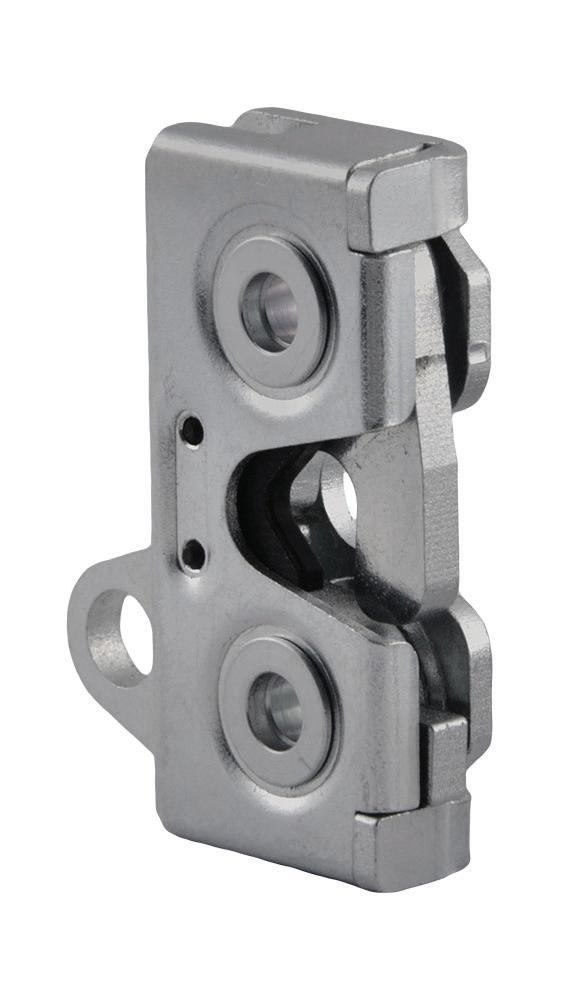
5 minute read
HARDWARE
How advances in latches and hinges are enhancing user experiences
Steve Spatig, General Manager, Electronic Access Solutions, Southco & James Stroud, Manager of Product Management, Southco
Recent changes in end-user application requirements have been driving new developments in latch and hinge technology — two common devices, often seamlessly integrated into applications. New features and capabilities are providing more options that optimize the end-user experience.
Latches range in complexity depending on the application zone, security requirement, ease of use, and other ergonomic factors. From simple cam locks securing an access panel to compression latches that create a clamping force between two surfaces, conventional latches fit several applications. Modern electronic access solutions (EAS) combine electronic locks with electronic credentials, such as RFID cards or smartphone-based access, ensuring more secure and convenient latching with remote-access control and monitoring.
Door hinges offer a similar range of function-based options. Fixed-position detent hinges hold open doors at pre-determined angles, eliminating the cost and labor of additional components. Counterbalanced positioning hinges provide lift and freedom of design for positioning panels or screens.
Regardless of choice, design engineers are focused on innovation and greater functionality for today’s latches and hinges.
The latest latching tech Demand is strong for all major categories of latching systems — cam or rotary, compression, push-to-close, draw, and sliding latches. One significant trend is the use of certain latches outside their typical applications.
For example, the rotary latch is a simple yet durable device that’s the go-to mechanism for car and truck door handles. This Hidden solutions feature sleek push-to-close operation with a space-saving design that facilitates interior door mounting. This is Southco’s R4 Rotary Latch solution.
use case has been extended to secure panels, such as doors on ATMs or self-service kiosks in restaurants and convenience stores. Access to these kiosks is restricted to technicians and personnel refilling cash and printout materials (in the case of ATMs).
Rotary latches provide a more secure solution than push-to-close latches and can be actuated with a physical key. They can incorporate electronic actuation and be controlled and monitored electronically in applications where a higher level of security or remote actuation is necessary.
Electronic access solutions (EAS), such as electronic locking and access control devices, are increasingly used in commercial vehicles such as delivery vans and utility trucks, as well as offhighway construction, agricultural, and mining equipment. EAS can be connected to an existing network to track equipment access.

Constant torque positioning hinges, such as Southco’s E6 Series, provide reliable positioning with consistent operating efforts, eliminating secondary support components to hold doors or panels in position.
Additionally, rotary latches are now used in industrial applications, such as exterior panels on rail cars. In such high-vibration applications, some manufacturers are enhancing the latch with rubber bumpers to protect against vibration-generated wear and tear and deliver longer lifecycle performance.
Other more sophisticated latching systems are also in demand in atypical applications, such as on and offroad all-terrain vehicles (ATVs) and utility task vehicles (UTVs). These vehicles are designed for rugged environments, but users are requesting greater interior amenities and design features similar to those in high-end automobiles. As a result, ATV and UTV manufacturers are upgrading door and storage compartment latches to provide a higher-end touch-point experience. This includes push-to-close or “slam” latches that shut with a single push on the door. A physical and audible “click” when closed assures a user the panel is secure, so the vehicle is safe to operate off-road.
Another development is the growth of the electric vehicle (EV) market, which is leading to new challenges for electronic locks, which are standard devices in these cars.
A fundamental engineering task for EV manufacturers is power management and maximizing the efficient use of the vehicle’s battery. Electronic latching suppliers are developing extremely lowpower mechanisms to minimize the power requirement of these devices and offering self-powered battery-operated solutions.
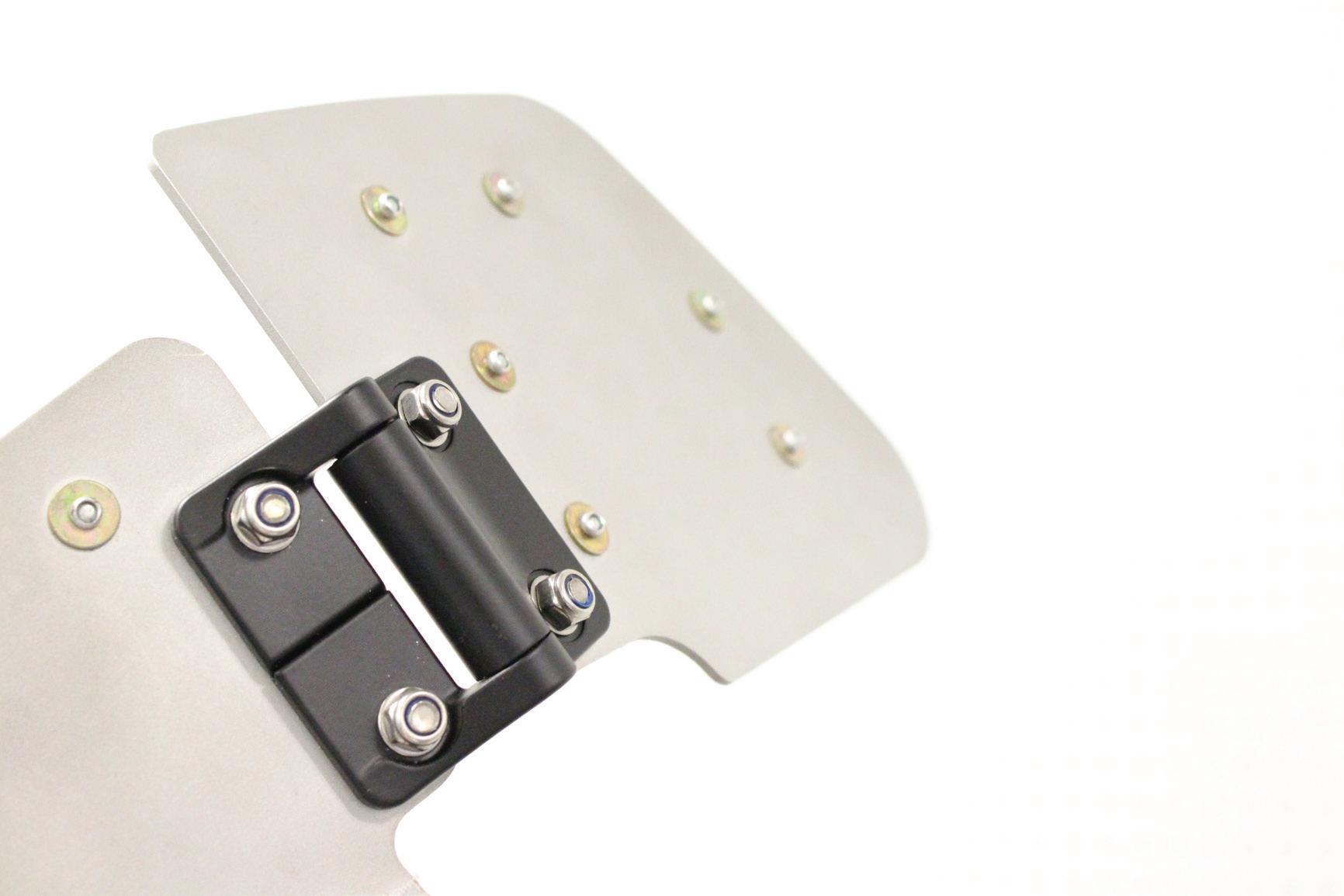
New hinge positioning control Hinge technology has become more sophisticated, with features incorporating
hardware
higher-quality experiences for users. The fastest-growing types of hinges are those with constant torque technology. With this kind of positioning hinge technology, designers can define and adjust the operating effort required to move or position doors, display screens, safety shields, and lights — or virtually any mounted component that’s opened, closed, and moved.
Hinges with integrated constant torque enable single-handed adjustment of connected monitors. Constant torque hinges use engineered friction to provide a specific resistance against motion. For instance, they enable the positioning of a cab operator’s screen at any angle with a simple adjustment. The screen must maintain that angle until re-positioned, even when the vehicle is in motion.
These same hinges are also useful in a vehicle’s center console. So, instead of using one hand to hold the console door open (while searching for an item), it’s possible to unlatch and pull it open, where it remains until closed.
Manufacturers have also advanced the hidden hinge, particularly for use on the exterior of enclosures and vehicles. Hidden hinges, which can also incorporate constant torque technology, are easily installed on the back side of a door or panel and fit flush with the fixed portion of the vehicle or enclosure.
These hinges offer two advantages: security and design. Security is enhanced because thieves and vandals can less quickly identify potential pry points, given the hidden hinge points. Hidden hinges also let industrial designers create sleeker, more streamlined designs, elevating the appearance of public enclosures and enhancing a vehicle’s visual appeal.
Access hardware manufacturers are continuing to innovate their product portfolios, incorporating new technologies, functionality, and materials to enhance the touch point experience of users. Through ongoing consultation, collaboration, and engineering, expect even more innovations in the future.
Hardware trends
Market dynamics are continually impacting the development of latch and hinge technology and the delivery of products to multiple industries. One ongoing trend is the global supply-chain disruptions caused by the pandemic, which is still making it difficult for OEMs to obtain latches and hinges without high costs or delivery delays.
This includes automotive, aerospace, railway, RV, and construction manufacturers. Few markets, if any, have been spared.
Suppliers and customers can expect delays with latching systems that use electronics and require microprocessors. There are also material shortages, such as plastics and steel, because supply plants were mostly idle during Covid. Production restarts are still lagging.
The result is that suppliers are strengthening and diversifying their manufacturing footprints and material supply chains to meet demands more effectively. Many companies are collaborating more closely with customers and, for example, supplying alternatives when a specific model or type of latch or hinge is in short supply.
It’s ideal to work with an innovative manufacturer or supplier that can offer options and expertise.