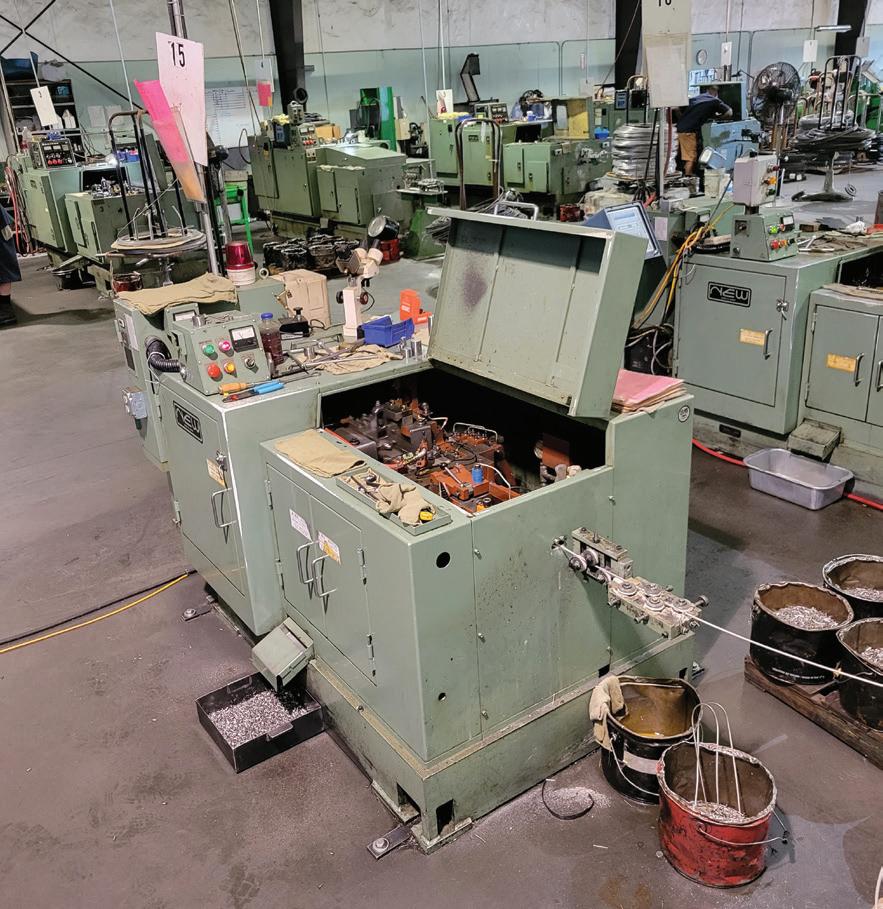
2 minute read
MANUFACTURING: Cold Forming
cold forming
What is cold-form manufacturing?
Article courtesy of RISCO, Inc.
Cold heading or cold forming is a method that
has been used for well over 100 years. The technology has come a long way since its origin but, essentially, still involves taking a piece of metal and forging it into a specific shape — without adding heat.
Cold forming has become a high-speed process that lets manufacturers produce large amounts of metal-based components in a fast, consistent manner.
For fastener manufacturing, cold forming is a quick and efficient method for producing standard and customized parts, including those with complex shapes. Compared to machining methods, cold-formed components are structurally stronger and more durable, offering products without compromising the natural grain flow of the material by forming as opposed to cutting. This also provides a smoother surface finish.
The material is never cut (it’s formed), so speed in manufacturing and material strength are two major coldforming advantages. This type of fastener manufacturing
A cold-header machine, which is used to form metal parts and fasteners. is ideal for high-volume requirements, providing costeffective results for larger orders.
Forming, as opposed to cutting, greatly reduces the amount of scrap metal, which saves costs. In fact, cold forming is capable of producing up to 70,000 pieces within an eight-hour shift.
The machine The most common type of cold header is a one-die, twoblow style. As the name suggests, these machines use one die to form the body of the fastener and two blows to forge the head of the fastener.
The first blow, or upset/cone blow, is the initial progression used to create the proper geometry of the part. It loads the blank into the die while starting the head forming. This process also forms the body of the part.
The second blow is known as the finishing one, which puts the drive (such as a Hex, 6-lobe, Philips, etc.) in the fastener and completes the initial process of cold forming a fastener. For more complex parts, some coldforming machines have several dies and blows, such as 2-die/3blow, 2-die/4-blow, or 3-die/3-blow — all the way up to six or more dies.
After the fastener is cold-headed, secondary operations are often used to complete the part, depending on the requirements. These operations include trimming, thread rolling, slotting, grinding, heat treating, plating, and others.
One thing to consider is that because parts are produced in such a high volume, there can sometimes be fluctuations for certain dimensions. It’s worth asking your manufacturer what tolerances they can hold. The tolerance is the acceptable amount of dimensional variation that will still allow the part to function properly.
Cold-form manufacturing is typically not recommended for low-volume, high-tolerance requirements.
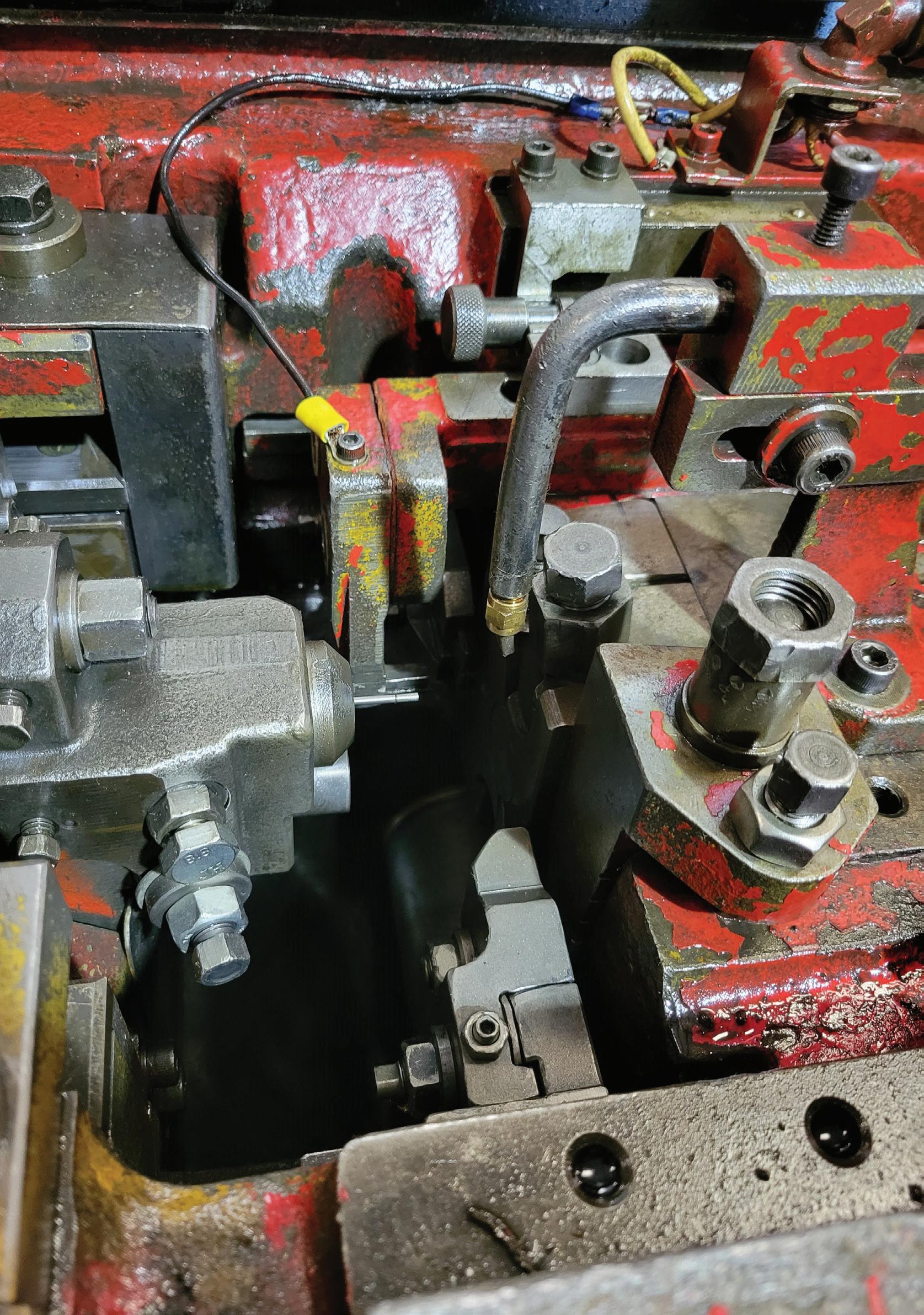
Manufacturer capabilities
Choosing a manufacturer that meets your requirements is essential to ensuring production to spec, product reliability, and on-time delivery. When it comes to cold-formed fasteners, here are a few considerations to discuss before placing an order.
• Manufacturer’s experience and certifications • Quality-assurance processes • Material availability • Typical lead times • Machine capabilities and tolerances • Samples (ask if there’s a first article or part sample available before production)
This is one of the most common types of cold-header machines — the one-die, twoblow style.

The making of fasteners: Progression of a hex head with a washer.
From start to finish: The manufacturing of a Phillips pan-head screw.
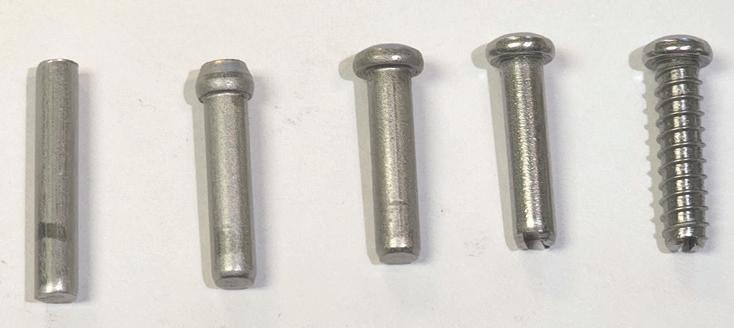