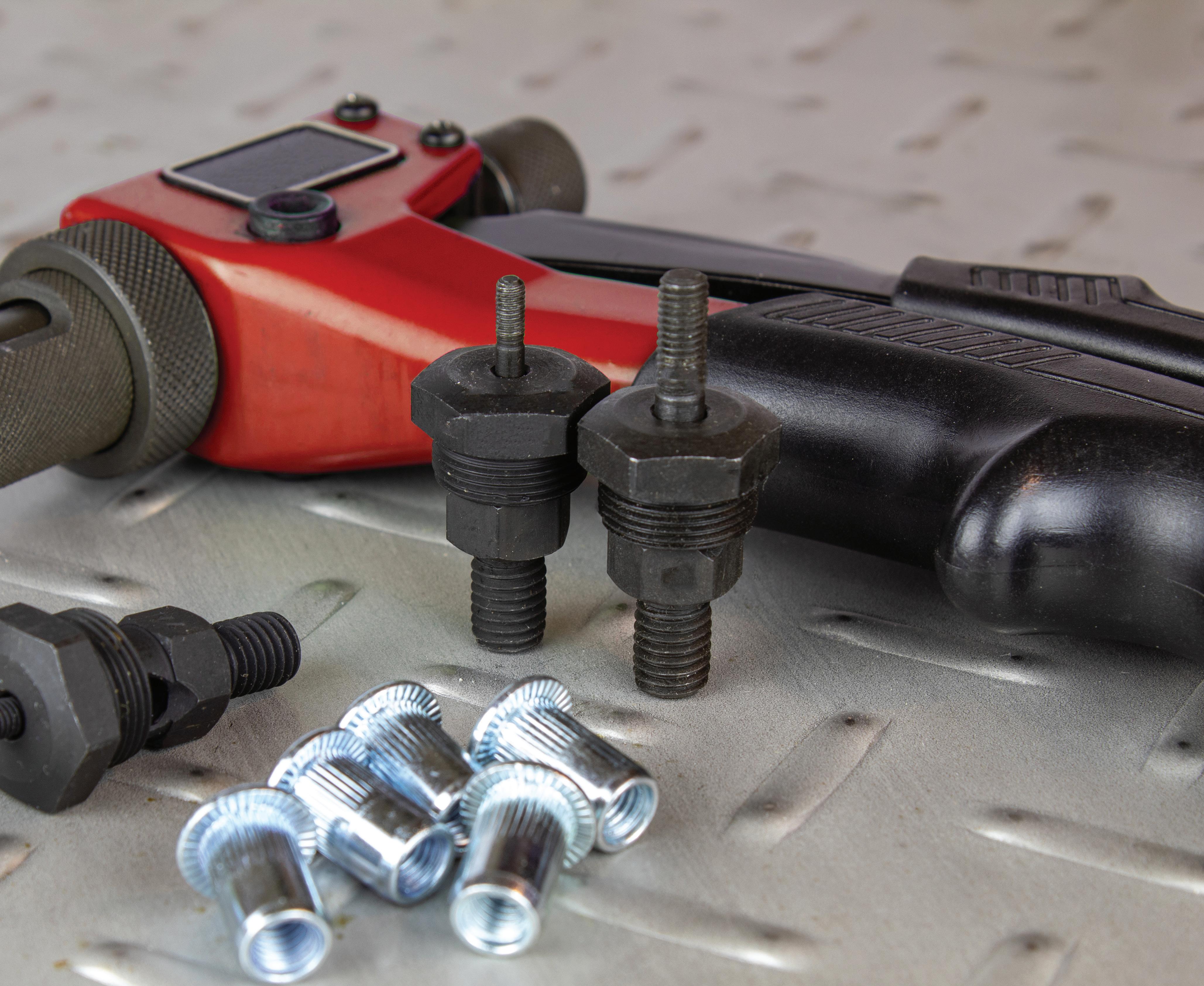
4 minute read
RIVETS
How to best choose and install rivet nuts?
Rosa E Hearn, CFS, Product Manager
Proferred Rivets Brighton-Best International
Since the original rivet nut was invented in 1936 to attach de-icers to aircraft wings, this versatile fastener has found new uses in several industries. Developed by BF Goodrich, these components were initially sold under the trademark name RIVNUT, but today you’ll find several brands in various shapes and sizes as a type of blind fastener.
Rivet nuts are unique, internally threaded fasteners anchored from only one side of a workpiece or application. Like a blind rivet, they’re installed from the front of a workpiece and are ideal for use when there’s limited or no access to the backside.
Rivet nuts are tough, versatile, and dependable. They reduce or eliminate the use of loose hardware, typically reducing assembly costs. They’re commonly used in aerospace, automotive, electronic, HVAC, appliance manufacturing, and any other industry using thin materials.
Proper installation Did you know that a socket-head cap screw is required to install a rivet nut? This is called the mandrel. It was created to provide loadbearing threads in thin sheet materials that are too thin for a tapped thread. Rivet nuts add strength to thinner materials, making them an excellent choice for manufacturers focused on lighter-weight applications.
Most rivet-nut tools come standard with two or three socket screws. The standard sizes are 3/8, 5/16, and M8. For non-standard sizes (1/4-20, 1/4-28, M6, M10, etc.), the purchase of a separate mandrel is necessary.
Too often, the socket-head cap screw (mandrel) is not given the attention it deserves to ensure proper rivet-nut installation. A correctly sized mandrel must extend beyond the face of the anvil — far enough to allow at least one thread of the mandrel to protrude past the end of the insert.
If the cap screw has damaged threads, installation problems can and will occur. Damaged threads prevent the mating part from fastening correctly, leading to costly rework or scrapped parts. To prevent this from occurring, ensure the cap screw occupies all the rivet nut’s threads. This will help ensure the internal threads avoid distortion or uneven compression when the rivet nut is cinched to a workpiece.
Rivet-nut setting tools use an alloy socket-head cap screw. This prevents wear on the threads of the tool since they’re stressed repeatedly during the pulling of the part. Typically, the longer the screw (within reason), the better the performance because the forces are spread across more threads.
If the threads are repeatedly damaged, it’s possible that a worn (softer) bolt is the problem. A well-worn bolt typically leads to the first few threads getting marred, which ruins the nut — and, therefore, the screw.
Rivet-nut tool guidelines recommend using a high-quality socket-head cap screw (mandrel) that’s the correct length for the application.
Condition of the mandrel For most tools, the mandrel is a standard ASTM A574 socket-head cap screw. The threads should be clean and lightly lubricated to ensure a proper and smooth installation. It also extends the life of the mandrel. If unwaxed, the installers should apply oil to the cap screw end before use.
The condition of the tool will affect the pull-up force required for ideal rivet-nut installation. Keep the tool properly maintained, ensuring the head thrust bearing is lubricated.
Quality counts
The advantages of using high-quality rivet nuts:
• Provide a strong thread in thin materials that cannot be tapped • Can be installed from one side of the workpiece, known as a “blind application” • Can be installed in many kinds of materials, including steel, plastic, and fiberglass • Ideal for use when easy disassembly and reassembly of products are necessary • Once installed, additional components with threaded fasteners can be attached
rivets
Types of rivet nuts Ribbed or splined rivet nuts provide extra torque strength over standard rivet nuts with no spline. This is thanks to their knurled expansion surface. The splined body provides increased torque-to-turn resistance.
When installing the knurled part of the fastener, it bulges out and clamps the parent material on the blind side, offering excellent resistance to vibration and spinning. This is why knurled body “nutserts” are commonly used in the automotive industry with trucks and trailers — or with anything that might need a firm fix.
Overall, when choosing rivet nuts, the hardness of the material matters. Rivet nuts must be annealed to create a soft crimp. Rivet nuts, which are internally threaded fasteners, are also known as rivnuts, nutserts, threaded rivet nuts, blind rivets, and blind inserts.

How to install a rivet nut?
Several types of rivet-nut installation tools are available. Regardless of the tool, the process is the same:
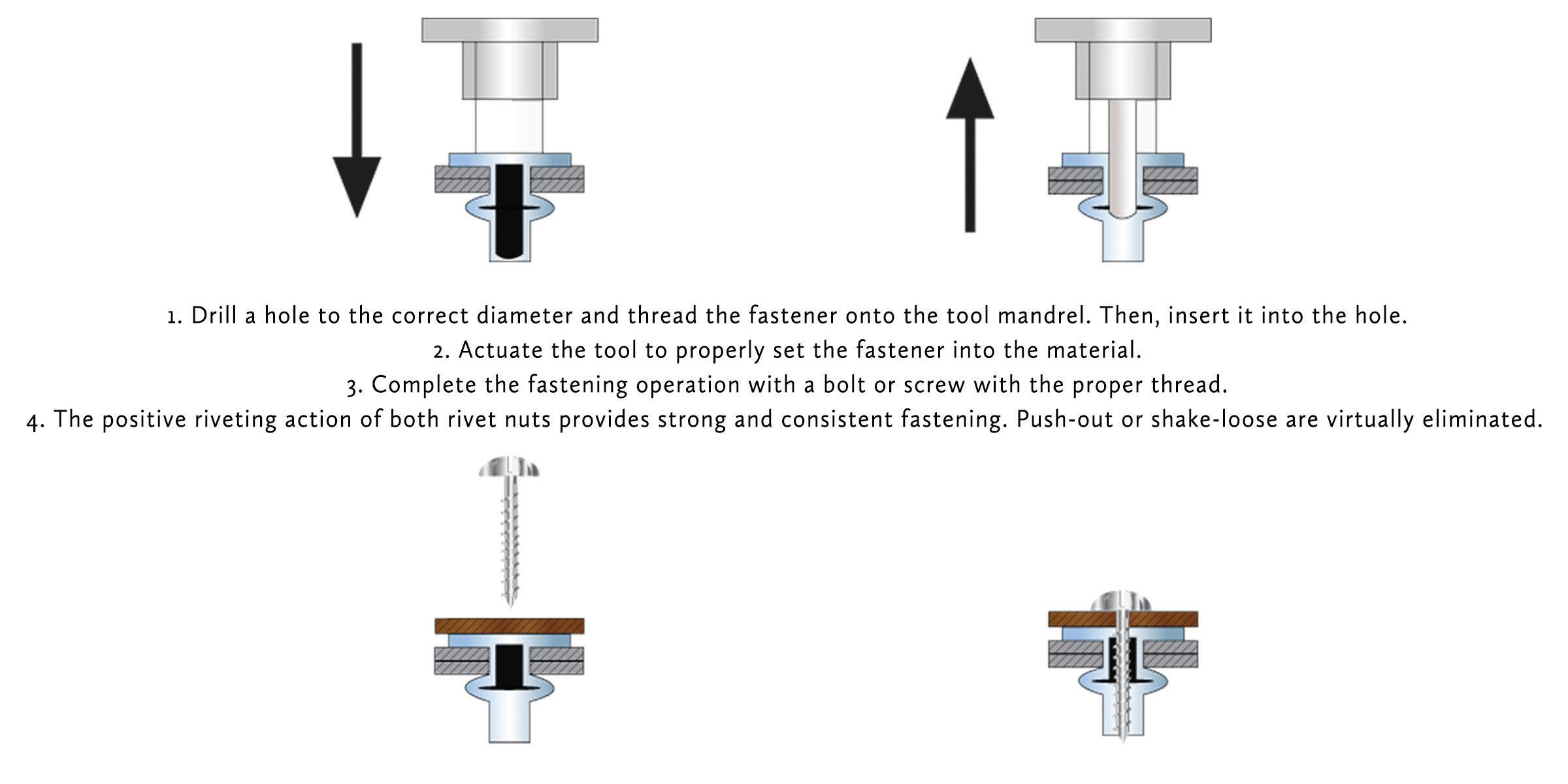