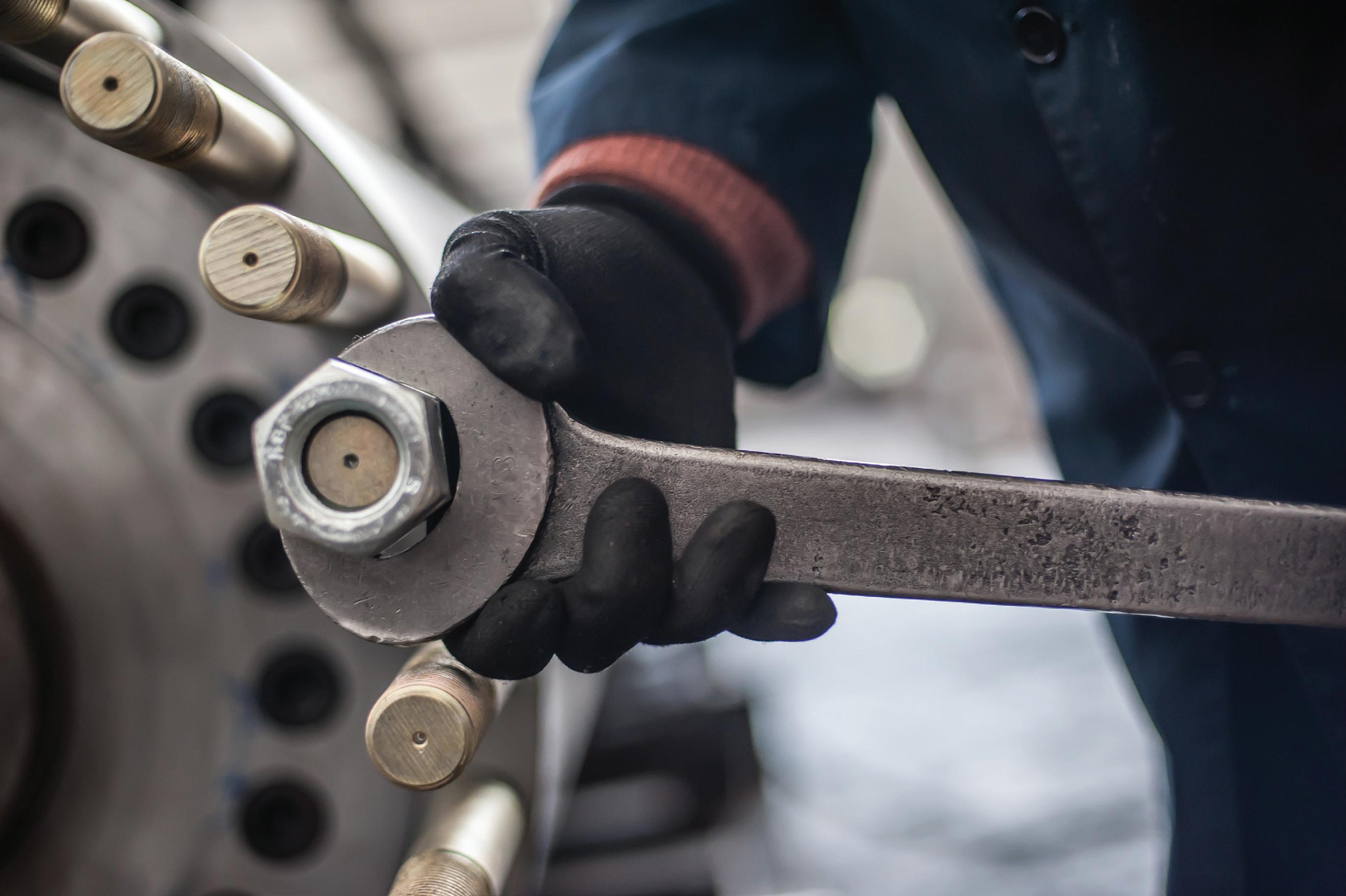
4 minute read
BOLTS
When does an application warrant the use of a bolt instead of a screw?
Screws and bolts are the most commonly used mechanical fasteners. Although similar and sometimes referred to interchangeably, screws and bolts offer unique features and are ideal for different applications.
A screw is an externally threaded fastener, typically used to assemble objects with threads. A bolt, on the other hand, is used to assemble unthreaded objects and usually with the use of a nut. Unlike some screws, bolts are not self-tapping and are only partially threaded. A self-tapping fastener is one that can tap its own hole as it is driven into the material.
Screws (if self-tapping) are designed to be installed in a pre-drilled or pilot hole, or (if self-drilling) can tap their own hole during installation — thanks to a sharp, drill-bit point and full threading. Most significantly, screws do not use a nut to retain the assembly. For this reason, they’re shorter than the width of the fastened part and do not protrude through to the other side. It’s the friction at the threads, which is the force that keeps the parts securely fastened.
The most common type of bolt is the hex bolt. It has a hexagonally shaped head, providing a flat surface for tools to apply torque during fastening.
Bolts are slightly different in the way they fasten an assembly. The hole for a bolt is untapped. Instead, the bolt is pushed through the hole and fastened using a nut at the back of the assembled part. Therefore, a bolt is longer than the width of this part and protrudes for the nut to screw onto the other side.
The unthreaded portion of the bolt remains unseen and in the assembled part. It’s what provides an advantage over most screws. Typically, bolts are selected for an application because they add strength, making the assembled parts more resistant to shear forces when compared to fully threaded screws. Compared to screws, they offer far more holding power.
A washer is also often used with a bolt and nut to spread the load over a larger surface area, thereby reducing stress and wear and tear that might otherwise loosen the bolt over time.
Bolts are installed or removed using a handheld or pneumatic wrench (screws, of course, use a screwdriver or drill bit). The benefit of a pneumatic wrench is that it provides more torque than a handheld tool, which makes the task easier.

Banking on bolts Generally, screws are used when basic or medium-holding power is required, such as for sheet metal, plywood, drywall, pressboard, deck planks, etc. The reliability of screws is moderate.
Bolts are the go-to choice for heavyduty applications and are a reliable choice for use with concrete, beams, and studs. This is because the nut and bolt assembly creates a high clamping force, keeping two parts fastened under compression.
When a load is placed solely on a bolt, it’s limited to the amount that it can handle before failing. However, when a bolt is tightened against the material of the part to be fastened, it distributes the force throughout the part. This means the bolt only holds a portion of the load — which is important with heavy applications, otherwise, the bolt might fail.
Essentially, the threads of the nut work with those of the bolt to apply force to either side of the fastened material. This tension, or compression force, is referred to as the bolt preload. Preload is important because a properly installed bolt assembly can withstand a much heavier load without the risk of fastener failure.
There are a few ways to ensure bolt preload. For example, there are preload-indicating washers that spin until a certain amount of load is applied to them. When the washer stops spinning, the preload has been met. There are also direct tension indicating washers, which have tiny, raised bumps that flatten when the preload has been achieved
Torque is also significant. A quality torque wrench can also indicate the optimal torque, which should typically be in close range to the ideal preload.
Getting the grade Much like any fastener, bolts and nuts are available in a variety of sizes, types, and material options. Steel bolts are the most common. The ideal choice will depend on the application. First assess the type of material to be joined, its thickness, and the weight and strength requirements.
Bolt grade markings, which typically appear on the head of the bolt, should
Bolts are graded according to their strength, using two numbers separated by a point, that are stamped onto the bolt head. The first number before the point is the ultimate tensile strength (UTS) in MPa, divided by 100. The second number is the ratio of yield strength to the UTS. Common classes are 5.8, 8.8, and 10.9. For example, a grade 8.8 bolt has a UTS, the load at which it would fail, of 800 MPa and will yield at 80% of this value (640 MPa).
be referred to and serve to indicate the minimum acceptable standard of mechanical properties or performance that the fastener must meet. Higher grades offer greater mechanical strength.
For commonly used ASTM and SAE steel grades, there are grade identification tables for the commonly used grades (ASTM and SAE), which specify the minimum acceptable values of proof, tensile, and yield strength, etc.
In summary, bolts are used for fastening unthreaded parts whereas screws are used for threaded parts. Bolts provide a much greater holding strength and are preferred for use in high, loadbearing applications. However, this also means bolts typically cost more and require a nut (and usually a washer) for secure fastening.