
6 minute read
RINGS
Article courtesy of Rotor Clip
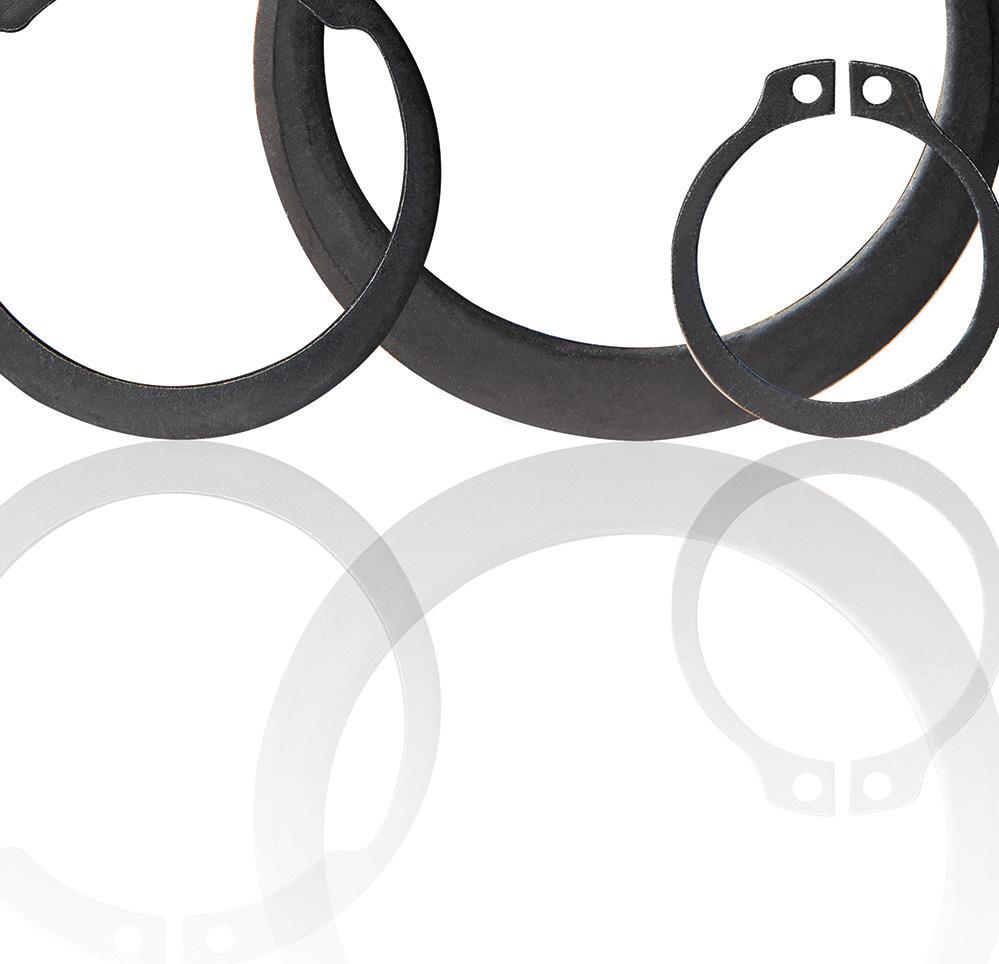
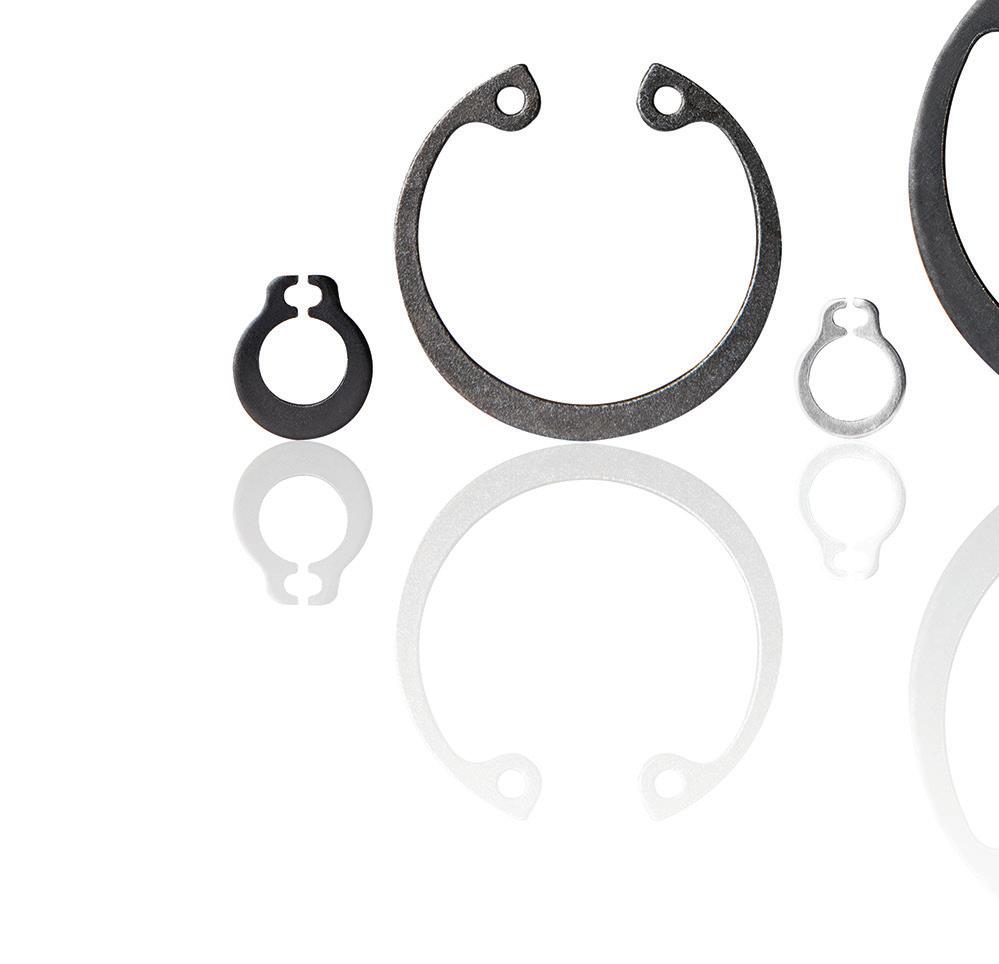
What are the technical factors to consider before choosing retaining rings for an assembly?
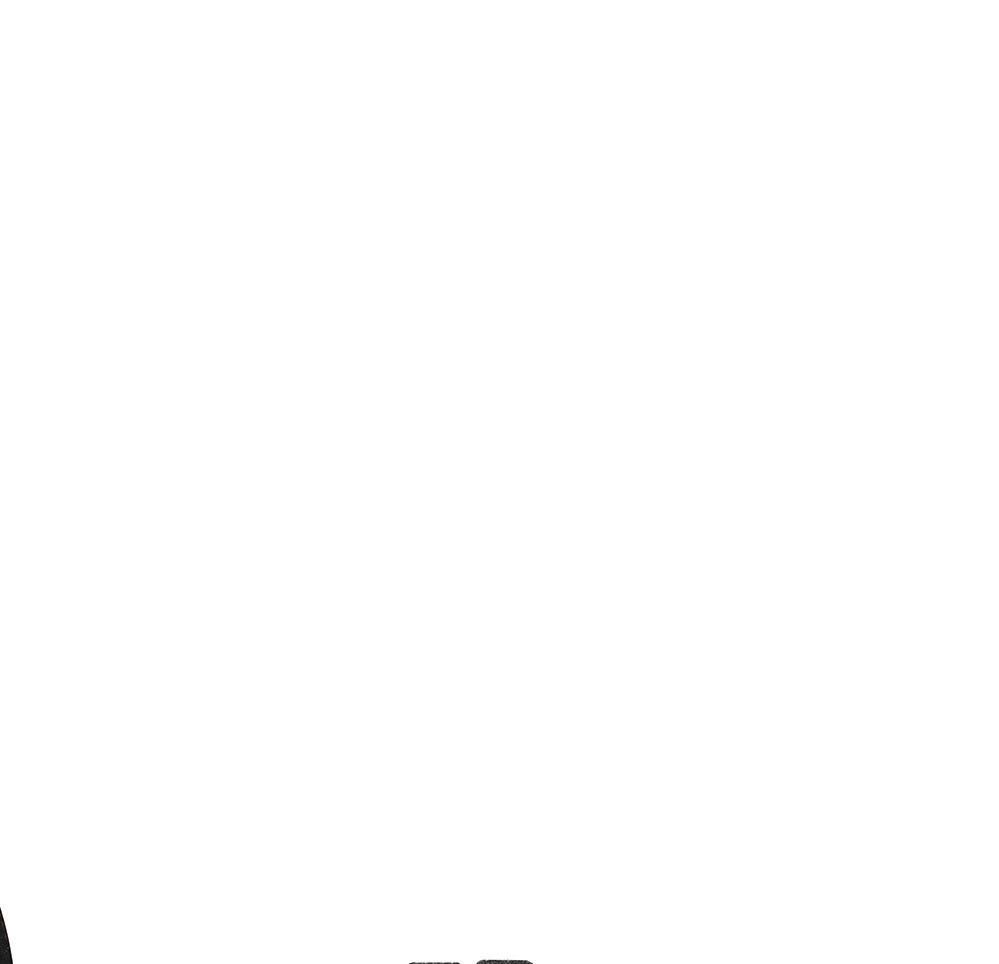
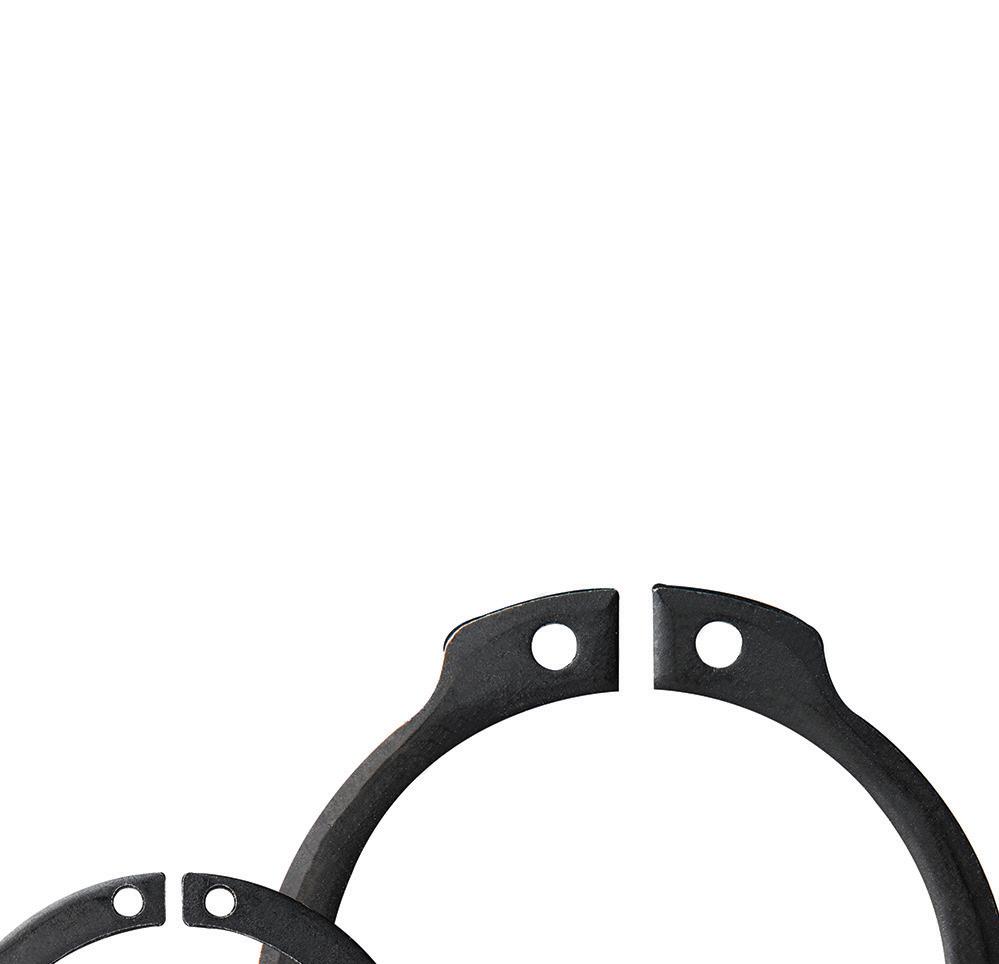
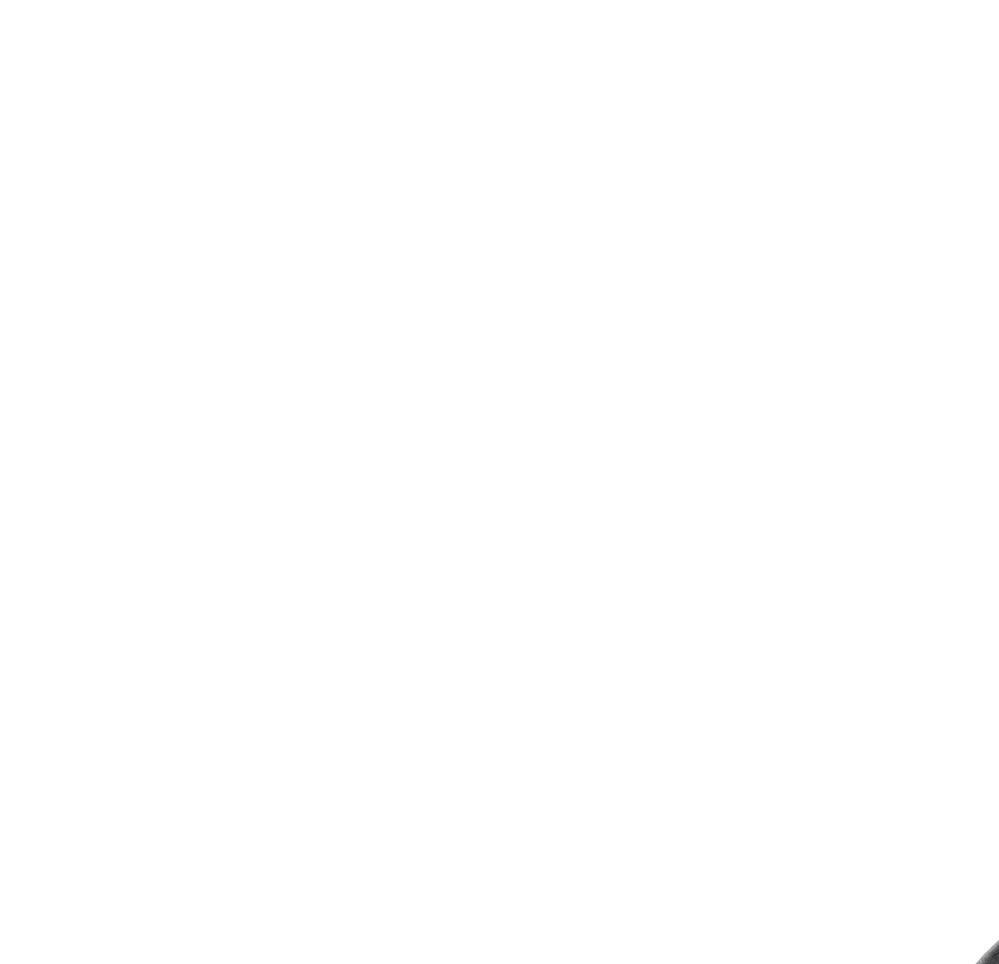

Much like a screw requires a correctly tapped hole, retaining rings need properly cut grooves for high-quality performance. Both grooved walls should be parallel and perpendicular to the axis of the shaft or housing. It’s challenging to develop economical designs that reduce weight, size, raw materials, labor, and costs. Retaining rings hold components in place while accomplishing these goals.
Retaining rings are metal fasteners that secure components or assemblies onto a shaft or in a housing or bore. Essentially, these devices keep parts in place using a compact design that requires fewer machining operations than other fastening techniques.
Like most fasteners, retaining rings can range in size (from 1 mm to 1 m in diameter) and are available in di erent combinations of size, shape, style, and material. However, knowing which ring is ideal for an application will contribute to the overall e ectiveness and economy of the design.
Here are some factors to consider before choosing a retaining ring for an assembly.
Groove depth and preparation Retaining rings are installed into a groove on a shaft or bore and, therefore, should fi t the specifi c grooves to perform as designed. The grooved walls should be parallel to one another, yet perpendicular to the axis of the shaft or housing.
When a load is applied, it creates a lever action against the loaded, grooved wall. Under extreme loads, this can lead to a defl ection of the ring and, ultimately, failure. Failure is far more likely to occur if the incorrect ring is used for the application.
Standard or inverted lugs Before settling on a retaining ring style,
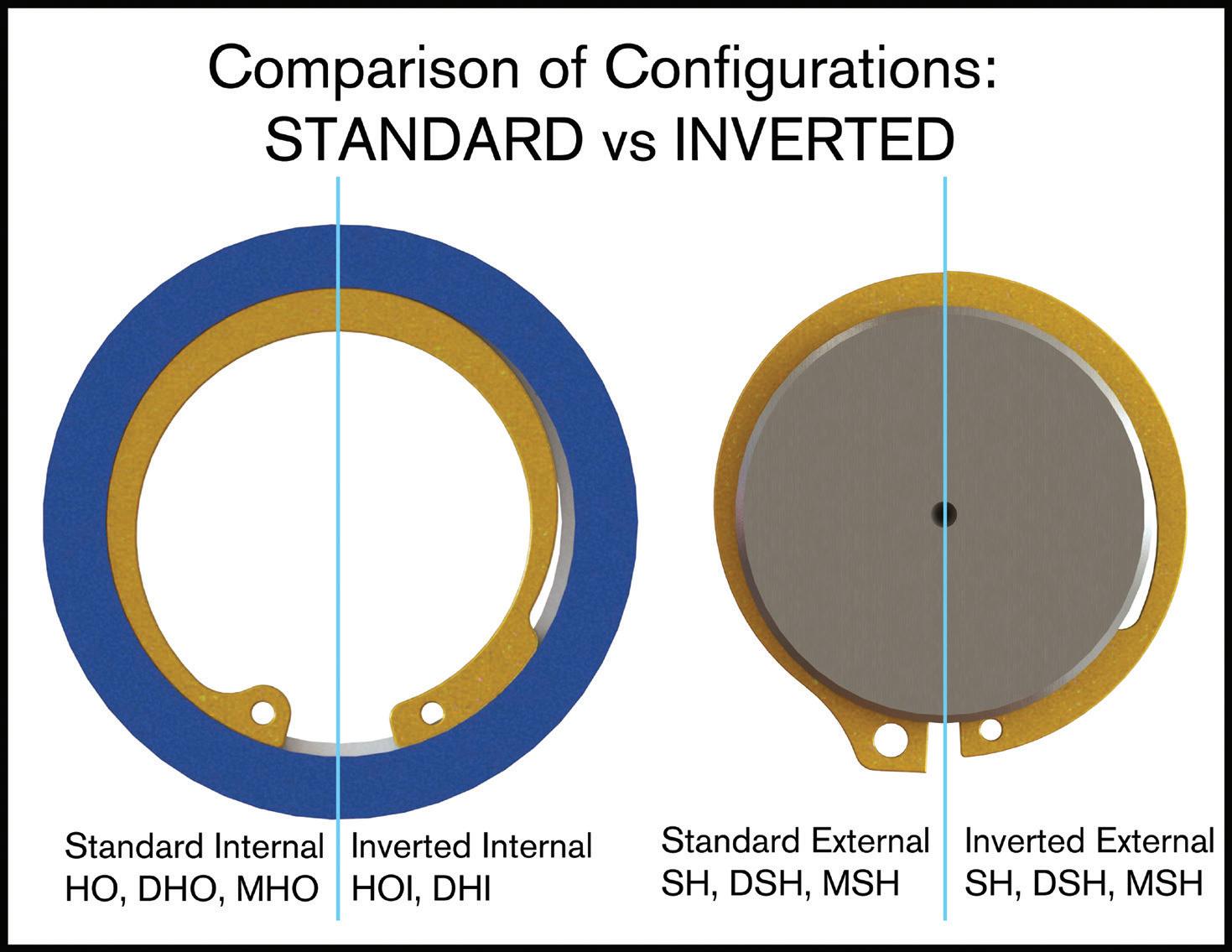
Inverted retaining ring designs mean the lugs do not stick out from the shaft, allowing for greater clearance.
Beveled retaining rings o er the cost-saving benefi ts of conventional rings with an added advantage: they compensate for accumulated tolerances or wear in the retained parts and provide rigid endplay take-up in the assembly. it’s important to assess the demands of the application. For example, if the loading conditions of an application call for maximum groove engagement, standard retaining rings are generally an ideal choice.
However, if the force or load of an application is not a critical factor, preference should be given to inverted rings — and particularly when lug protrusion might cause an interference challenge. The lug is the part that protrudes from the ring, often containing lug holes, which are used for installation and removal. Since they protrude, the lugs can get in the way.
But this is no problem for inverted lugs as they allow for greater clearance. Inverted ring designs are also often used in low-load capacity applications where aesthetics or compatibility are the main criteria. Otherwise, these two styles are interchangeable as far as the groove dimension is concerned.
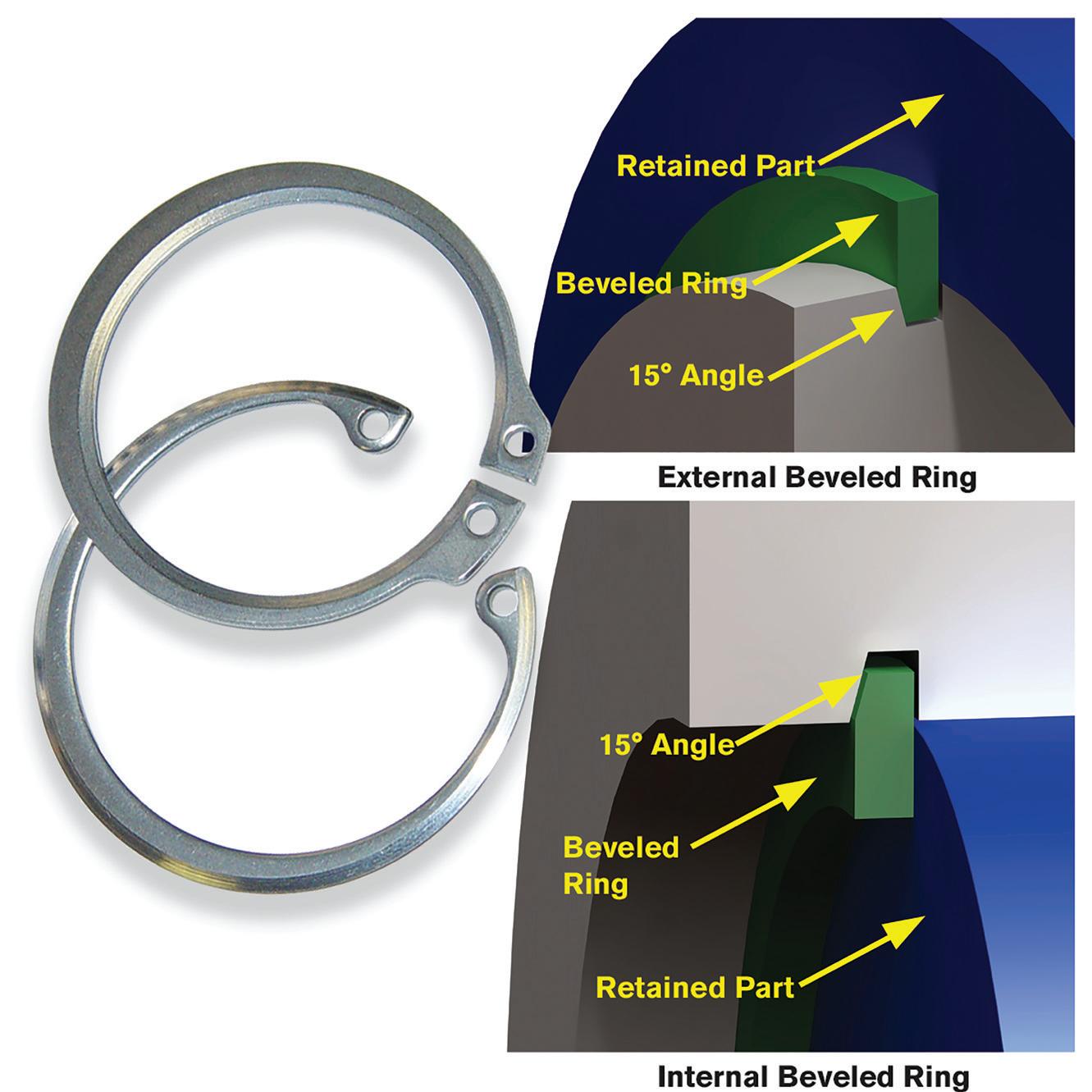
Basic versus heavy-duty To ensure reliability in applications with signifi cant loads, a reinforced retaining ring will typically outperform a nonheavy type. This is because of the larger section, lug shape, and thickness of the
RINGS
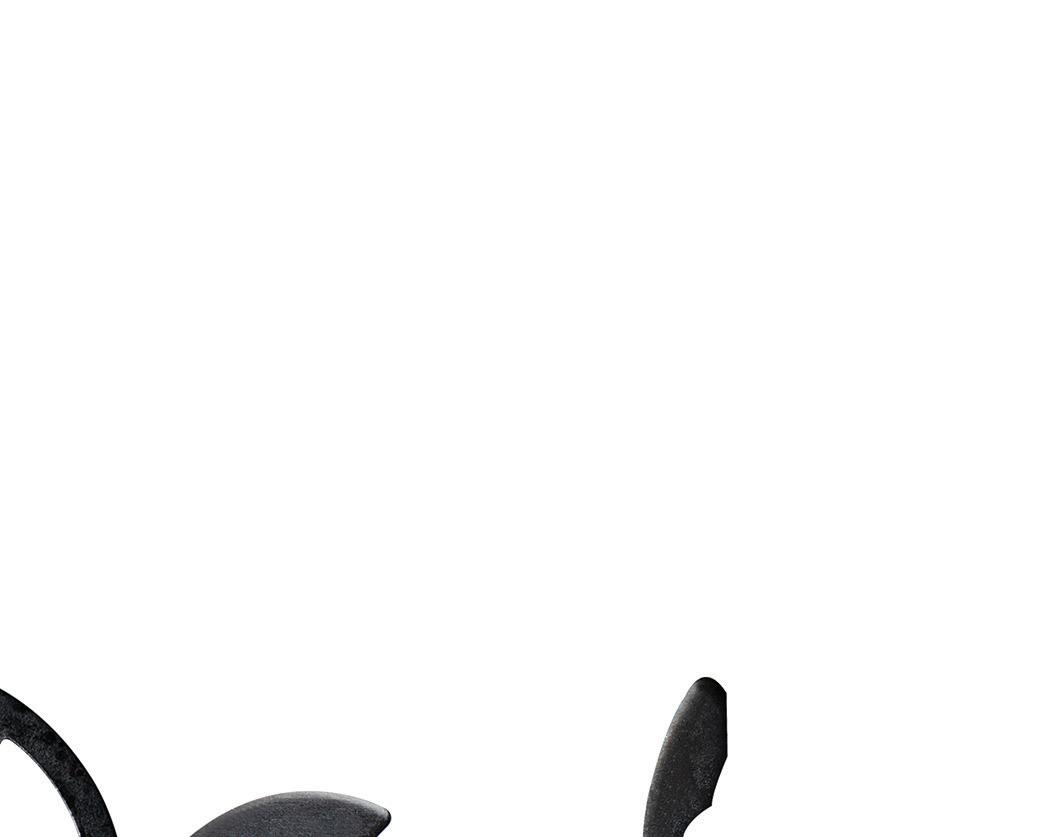

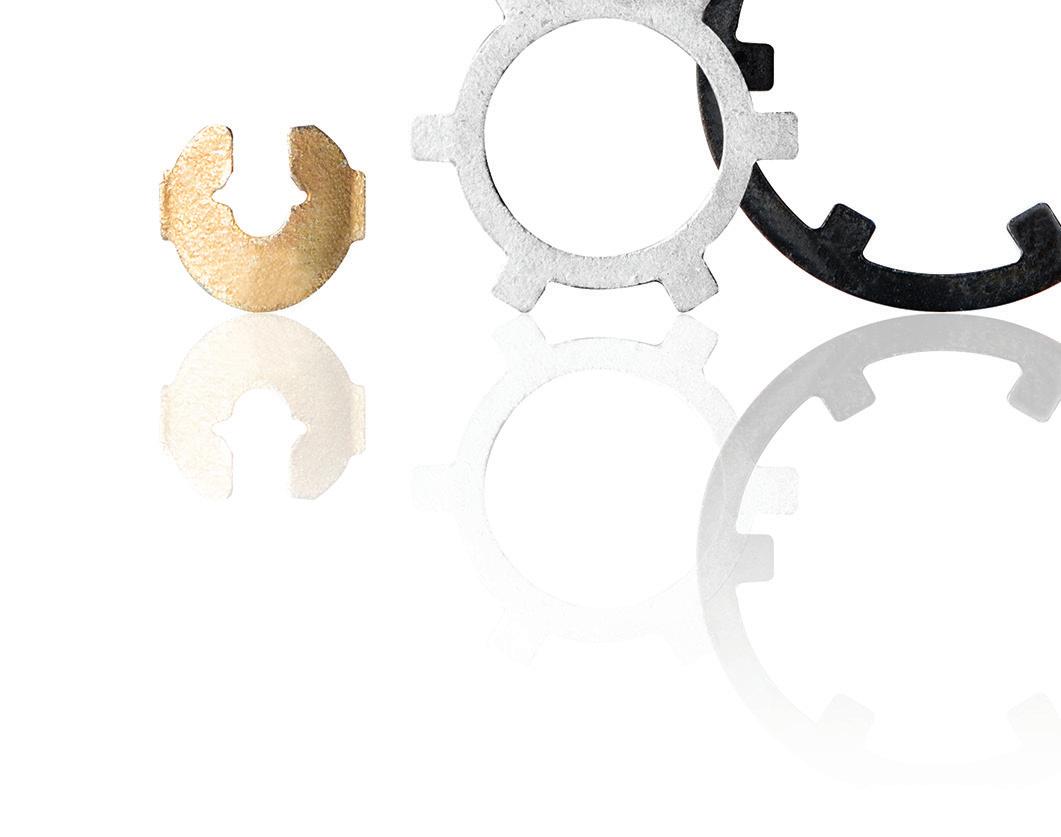
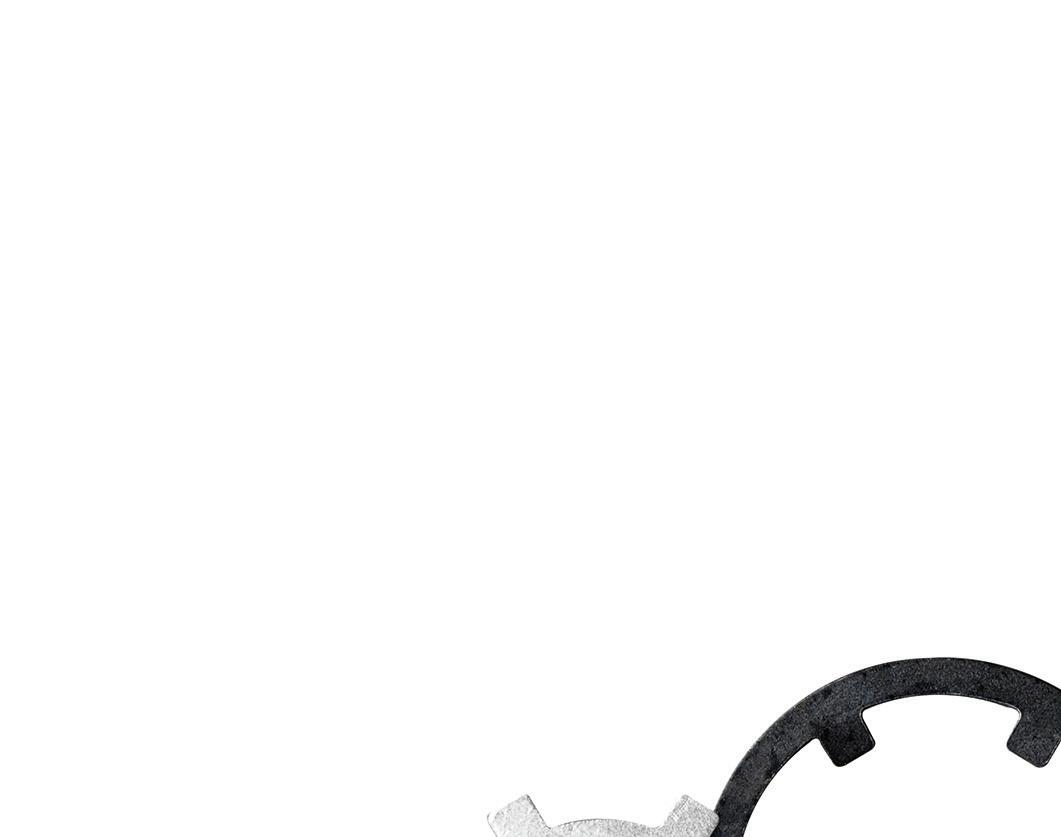
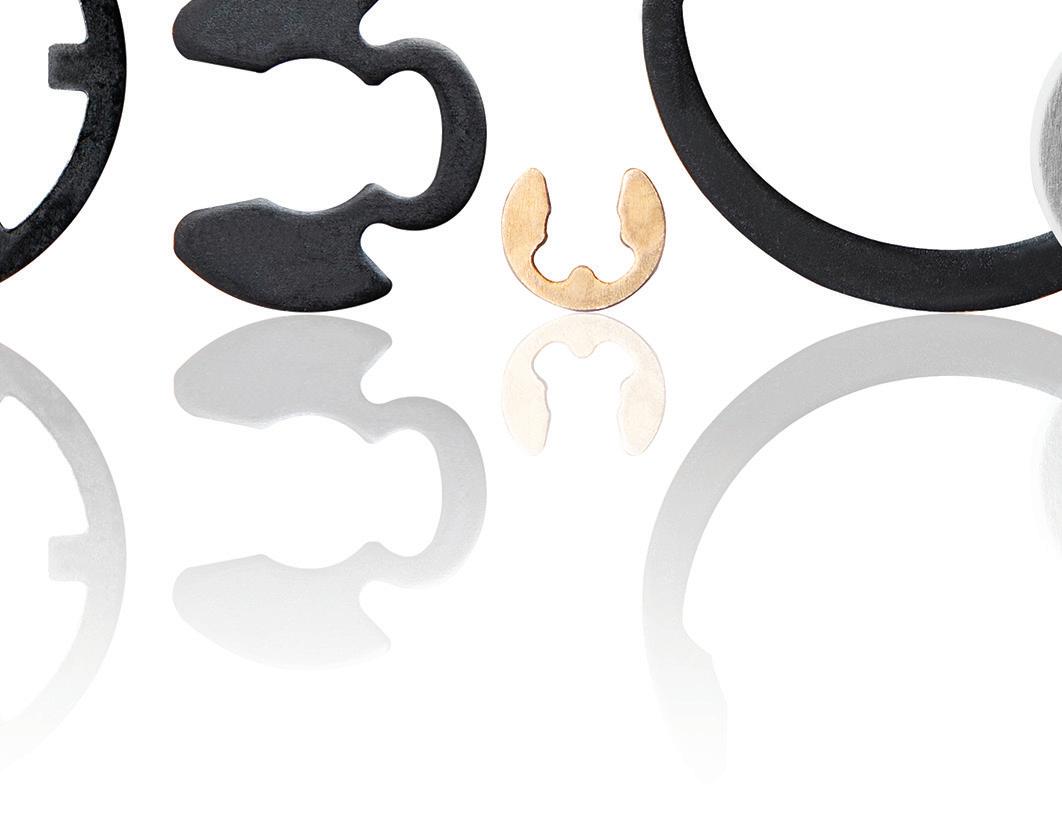

Self-locking or push-on retaining rings o er easy installation and security in one solution. They’re suitable for devices with shaft or housing diameters of one inch or less that require low thrust loads. reinforced ring, which is better able to remedy instances of fatigue failure.
For radially installed retaining rings, where space is at a premium and loads are small, a crescent C-ring is usually the best choice.
E-clips are a kind of shaft-mounted retaining ring, which are ideal for use with higher loads as they o er a larger abutment area for retaining. Reinforced E-rings function best in applications characterized by high vibration, or with RPM and cyclic loads.
Bowed and beveled retaining rings Retaining rings can o er multiple advantages, depending on the type. They can be used to compensate for
any accumulated tolerances or wear in an assembly and can exert pressure between and against retained parts.
Bowed rings, for instance, can fl atten under specifi ed loads and will return to their original height when the application’s load is decreased and removed. When the ring is fl at, it exerts a counter-load much like a spring, o ering endplay take-up and producing a compressive force that reduces chatter and vibration.
In many assemblies, dimensional tolerances in ring thickness, groove location, or the overall length of the components being retained add up to a degree of clearance — or endplay — between the abutting surfaces of the ring and retained part. The endplay can sometimes be eliminated by shims, washers, or similar components by “selective assembly” in which the parts (with plus or minus tolerances) are carefully matched to provide the desired tight fi t.
In high-speed production, however, such alternatives can be prohibitively costly. In such cases, manufacturers have benefi tted from substituting beveled retaining rings, which o er unique spring characteristics. The 15-degree bevel on the grooved side of the ring acts as a wedge between the grooved wall
and the retained part, which then locks securely. This is unlike the bowed ring, which may deflect while under the load.
Although bowed rings offer greater endplay take-up than beveled retainers, beveled rings offer rigid endplay takeup and should be considered where cyclic loads occur. An additional consideration: high rotational speeds do not work well with beveled circlips.
Applications without grooves Self-locking rings are used on shafts or within bores without grooves and have a flat rim that supports moderate static loads. Its prongs or teeth resist any counterpressure by digging lightly into the shaft.
These single-use rings can only be installed in one direction and are destroyed upon removal. An external grip ring can move in either direction and its position can be adjusted after installation. This style is more suitable for applications where components may have to be disassembled for repair or maintenance.
Whatever the requirement, there is a retaining ring to meet it. When choosing the ideal component, consider the application’s requirements, including its force or load, the frequency with which the rings will be installed or removed, and the installation method.
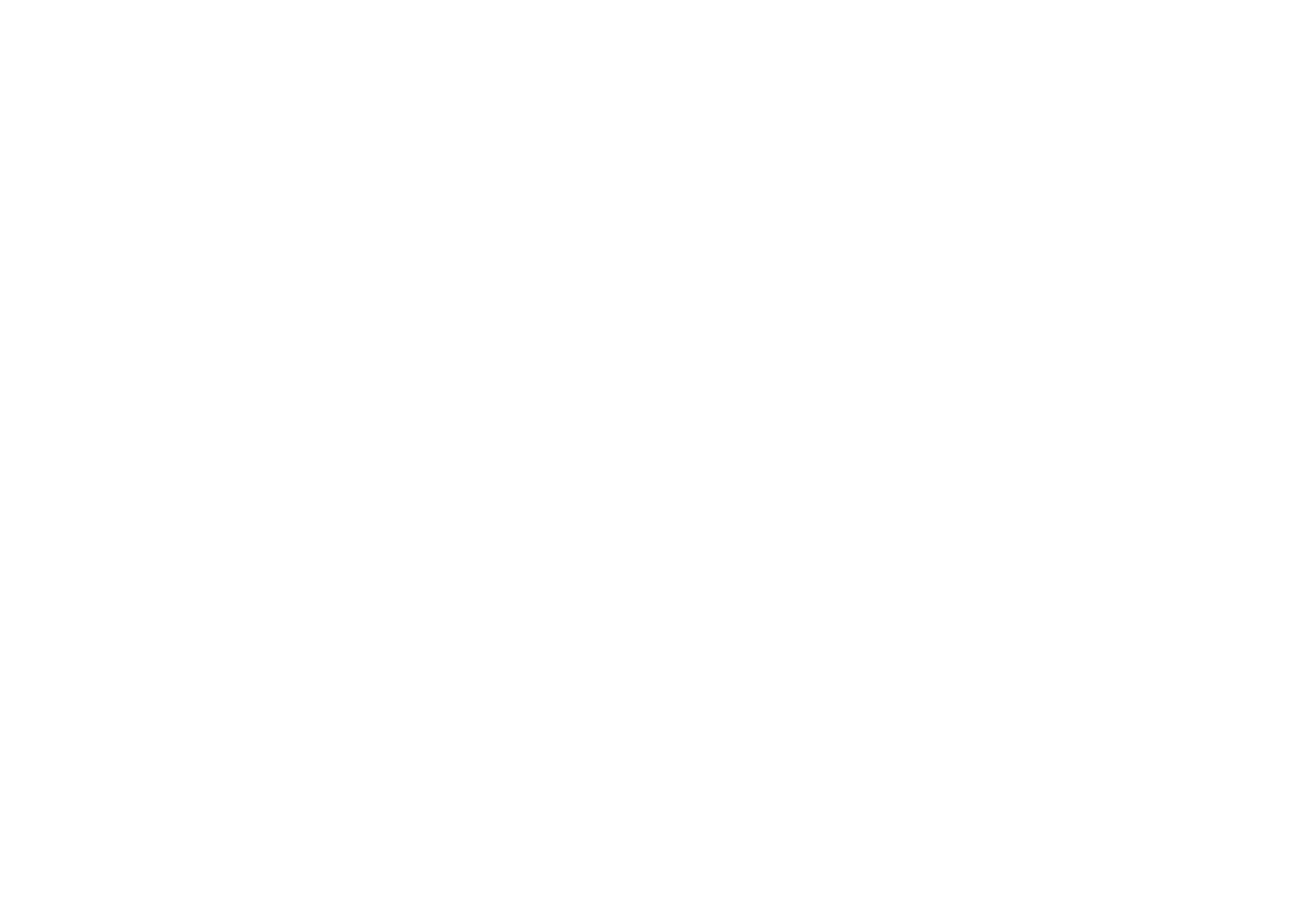
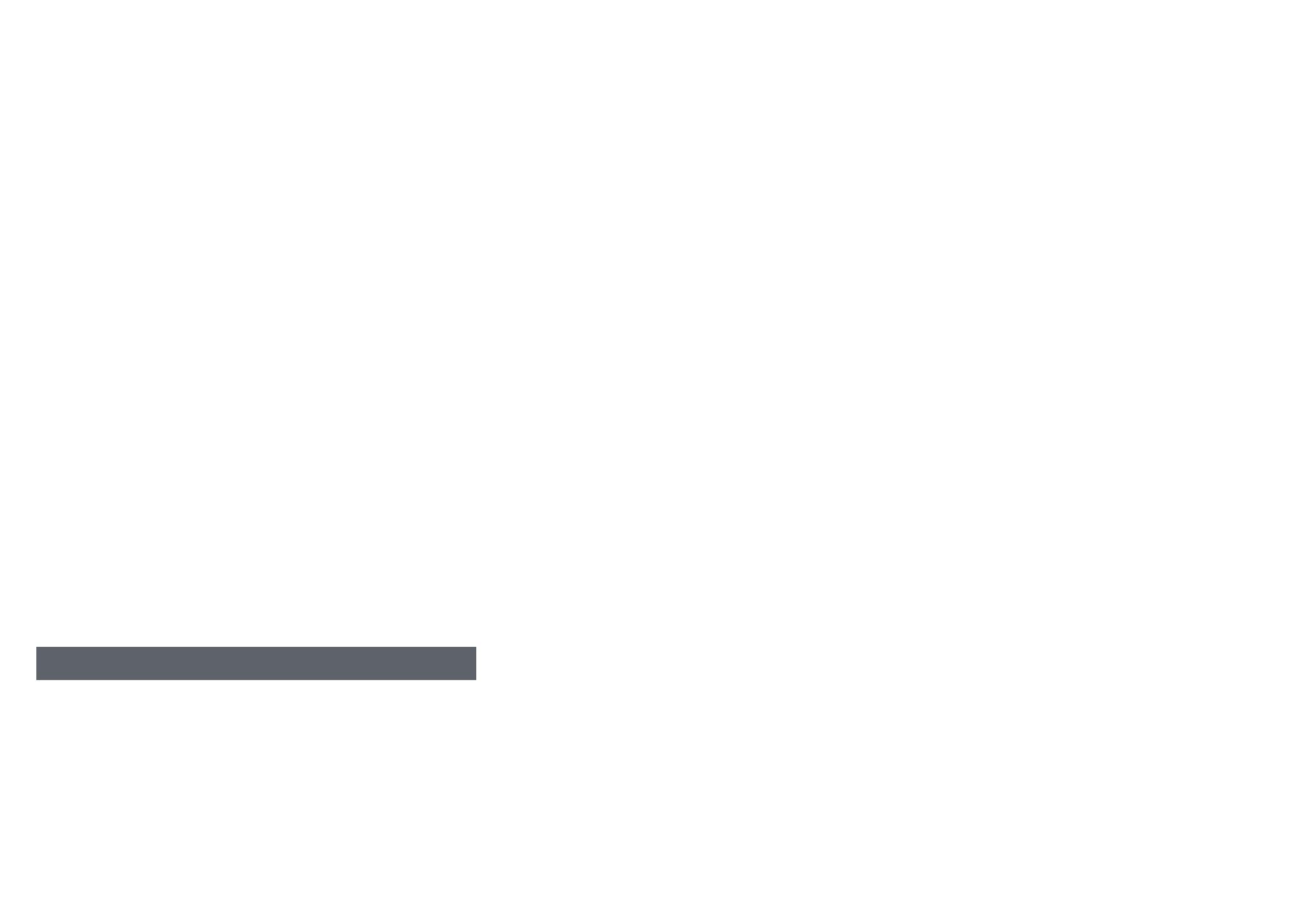
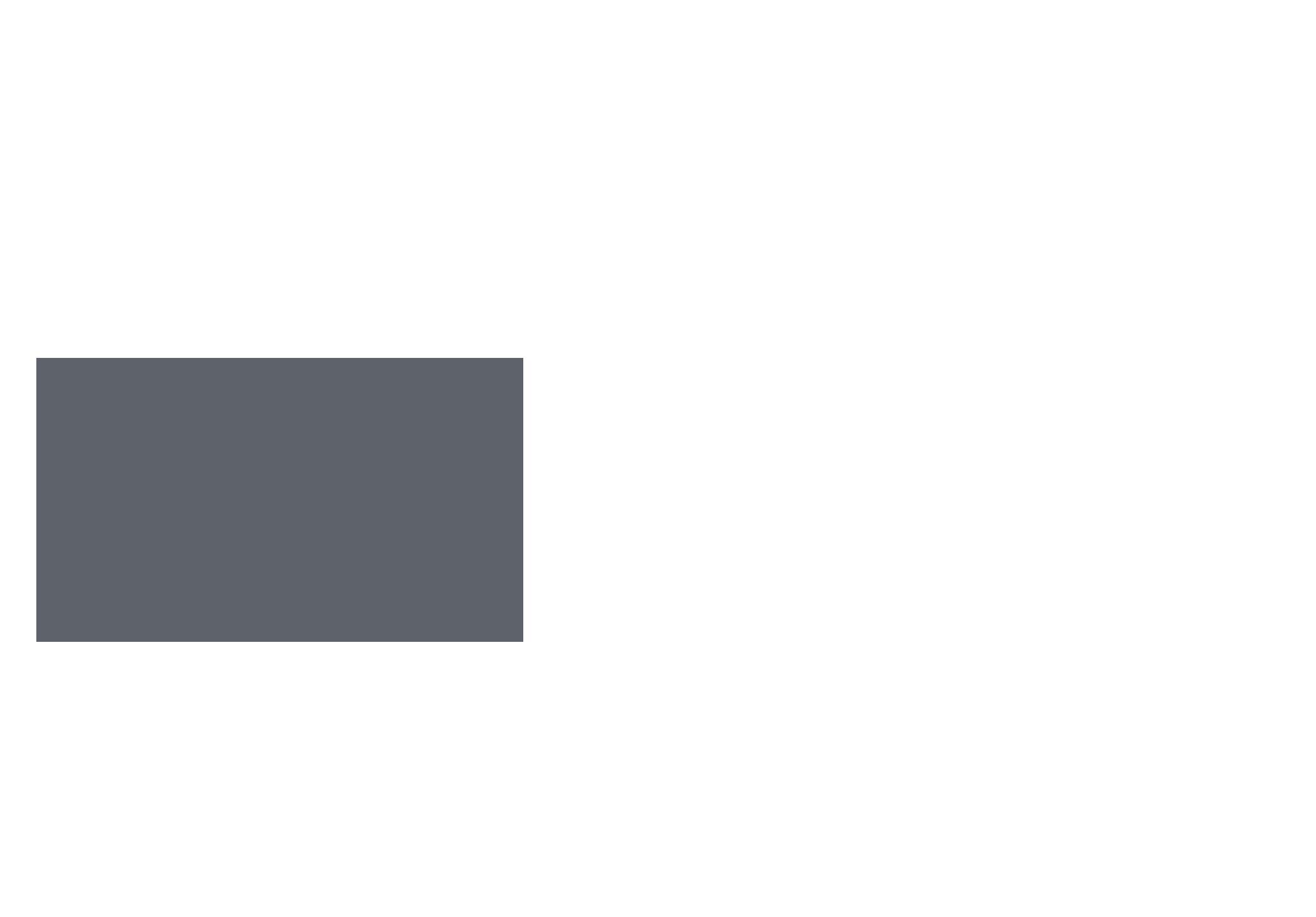
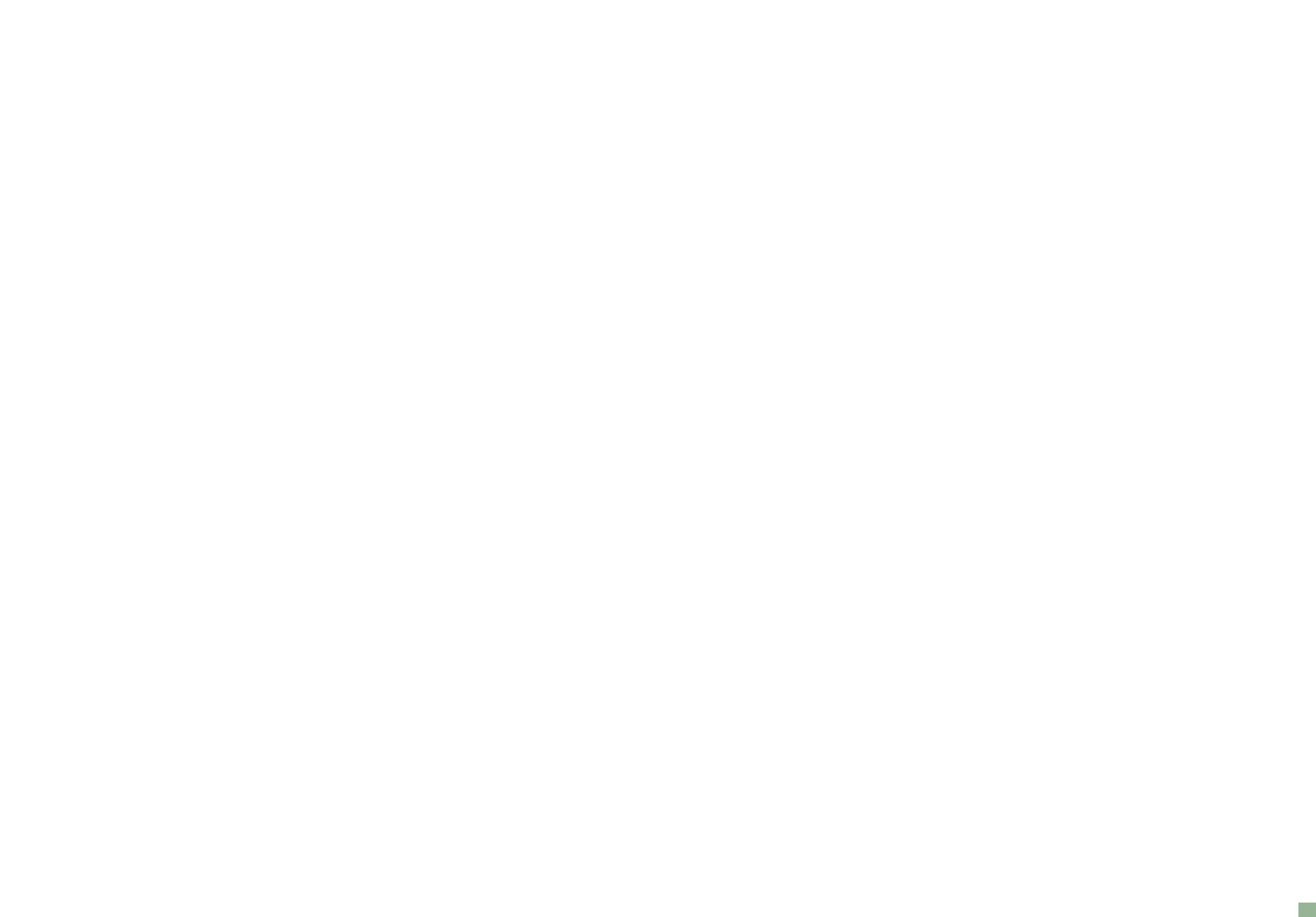
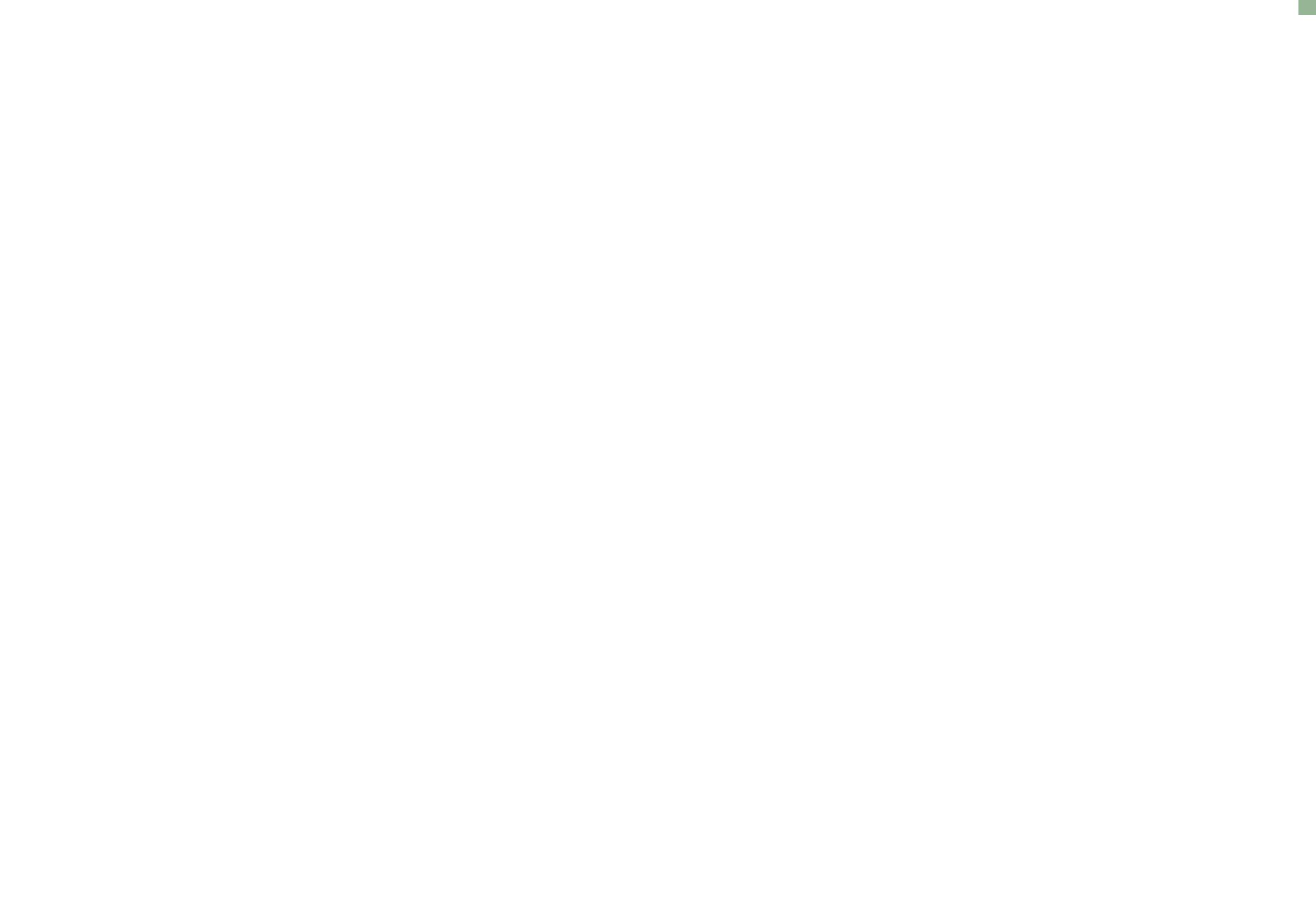
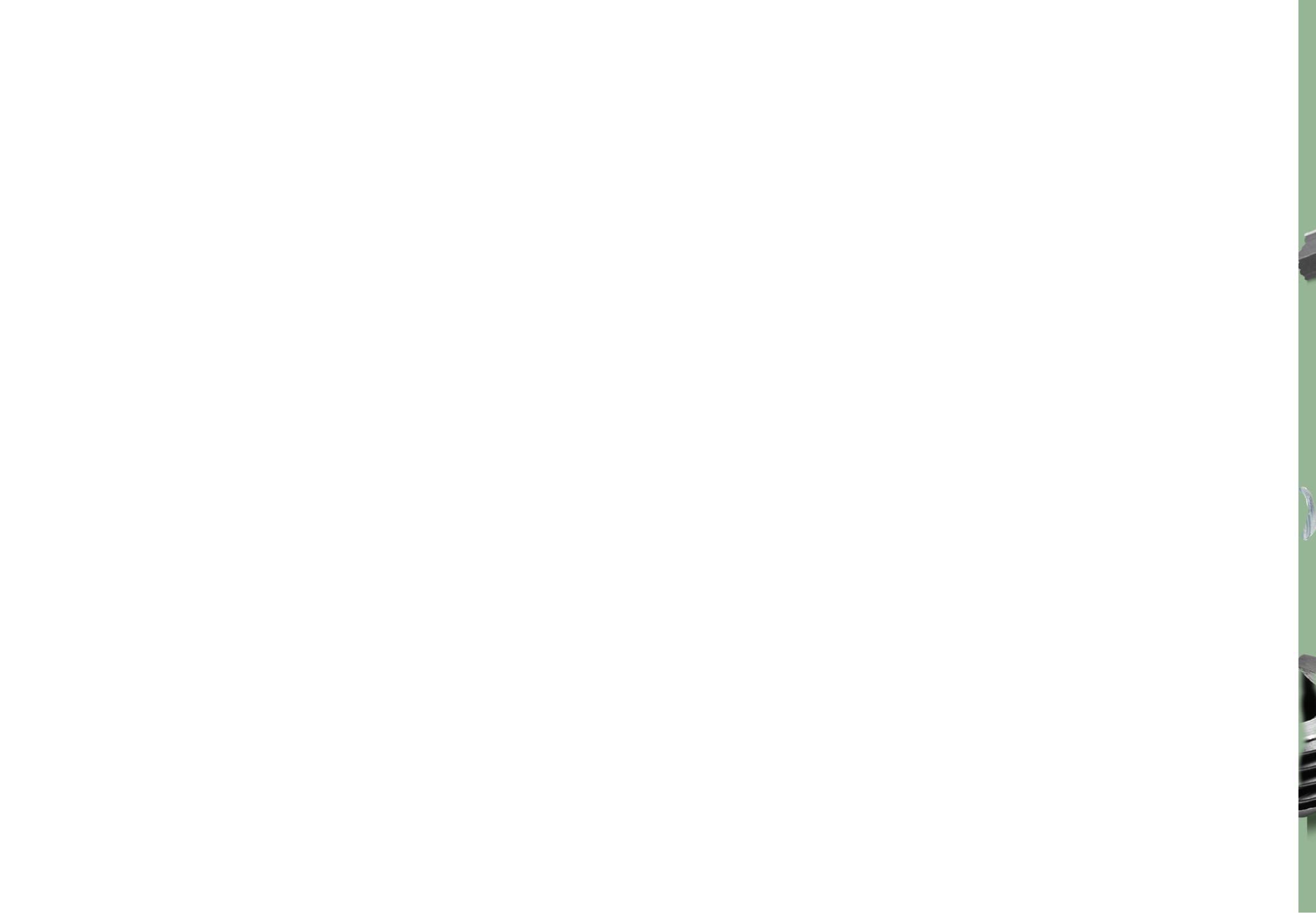
HEX SOCKET SET SCREWS
SOCKET, FLAT & BUTTON HEAD CAP SCREWS
SQUARE HEAD SET SCREWS
SHOULDER BOLTS
HEX & TORX KEYS
ZINC PLATED SOCKETS
S SPECIALS, STANDARDS & SECONDARIES
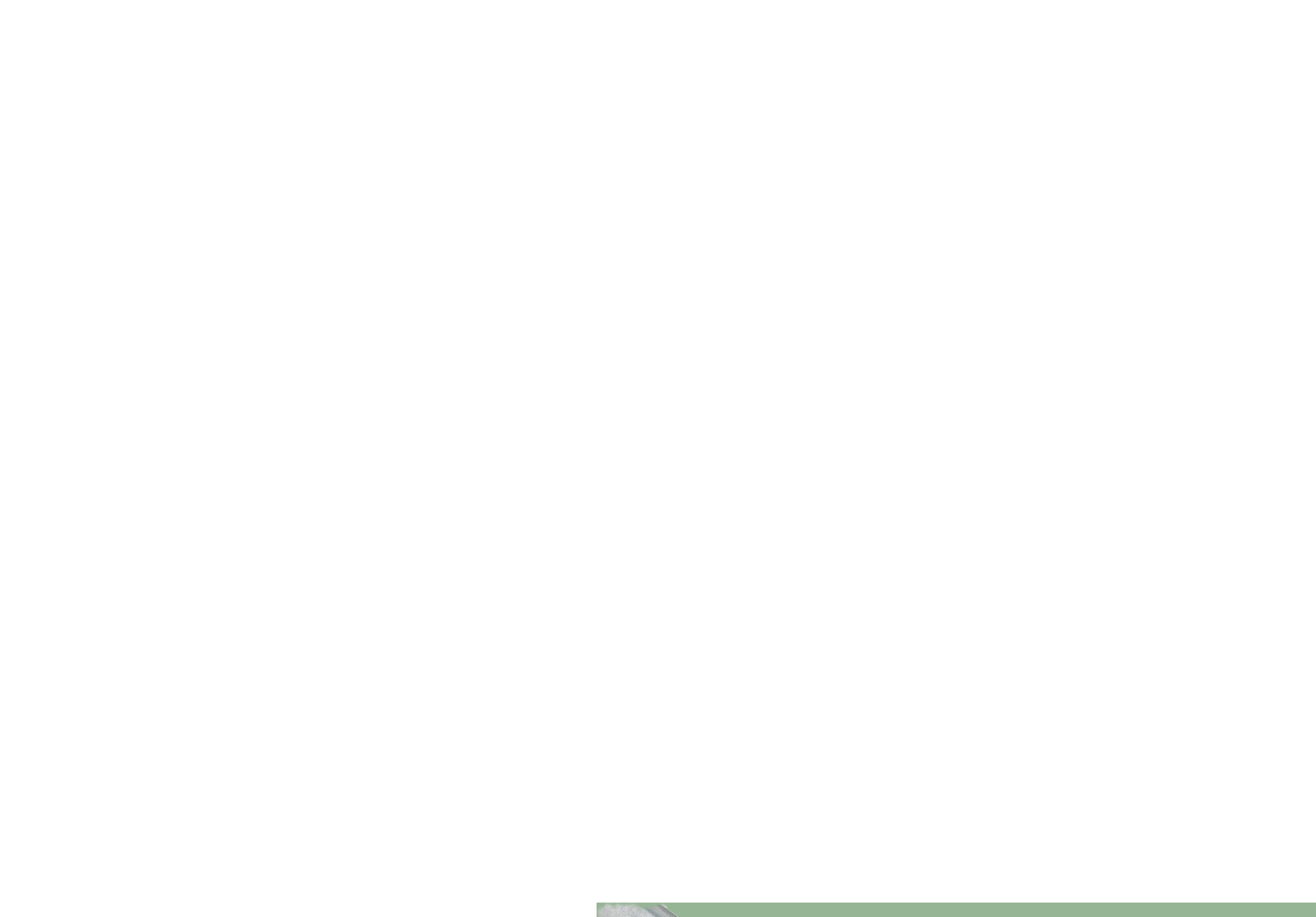

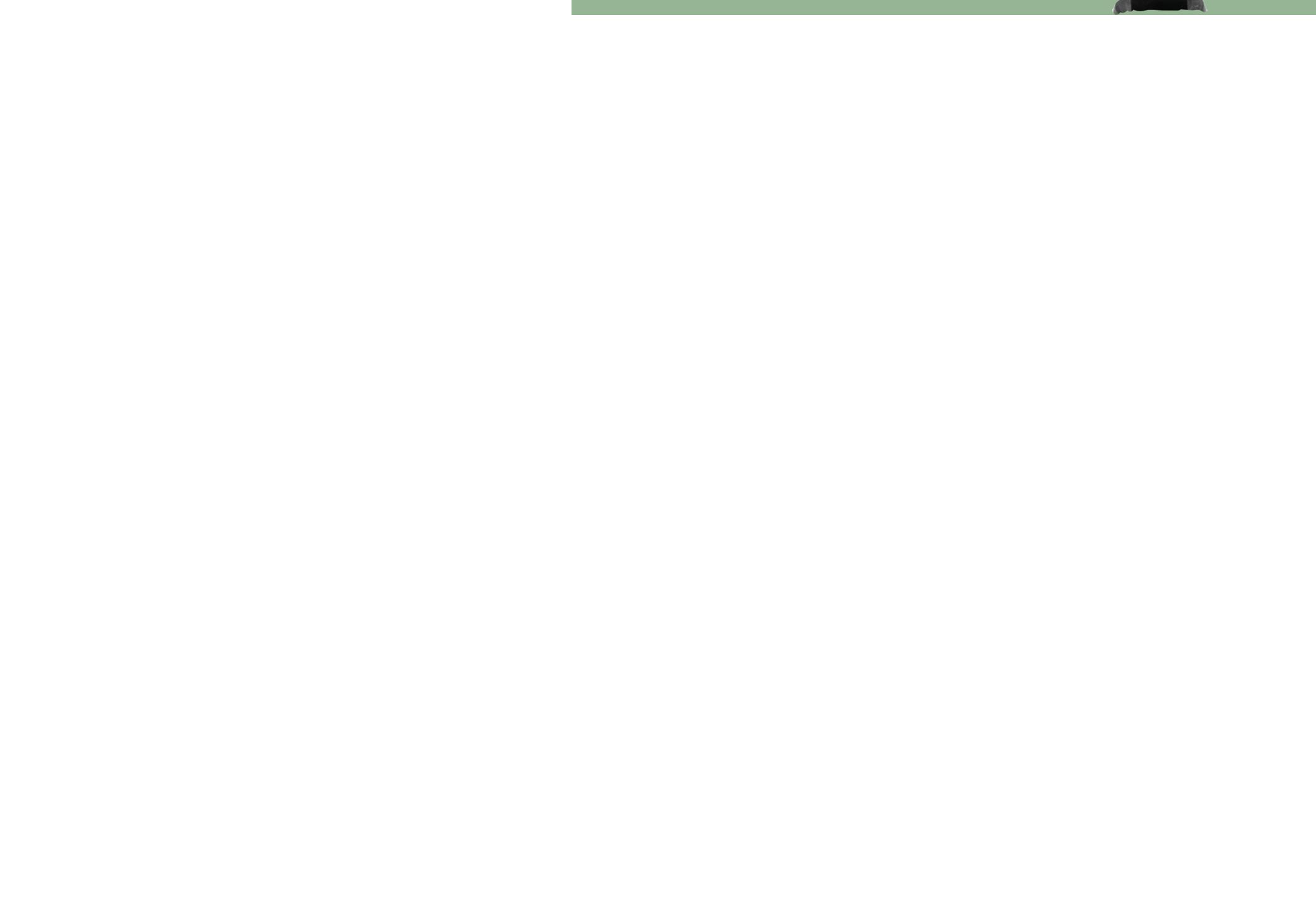
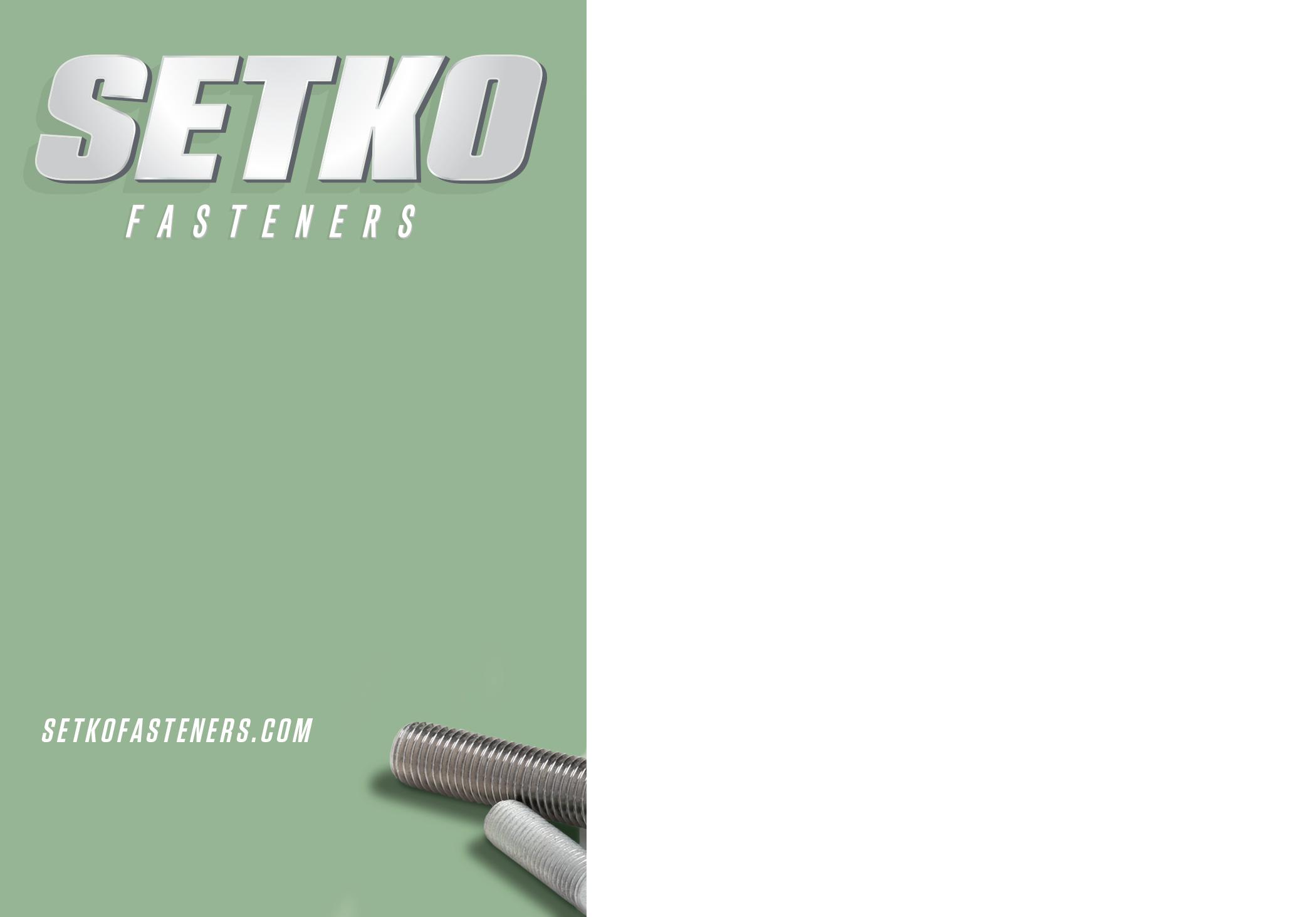
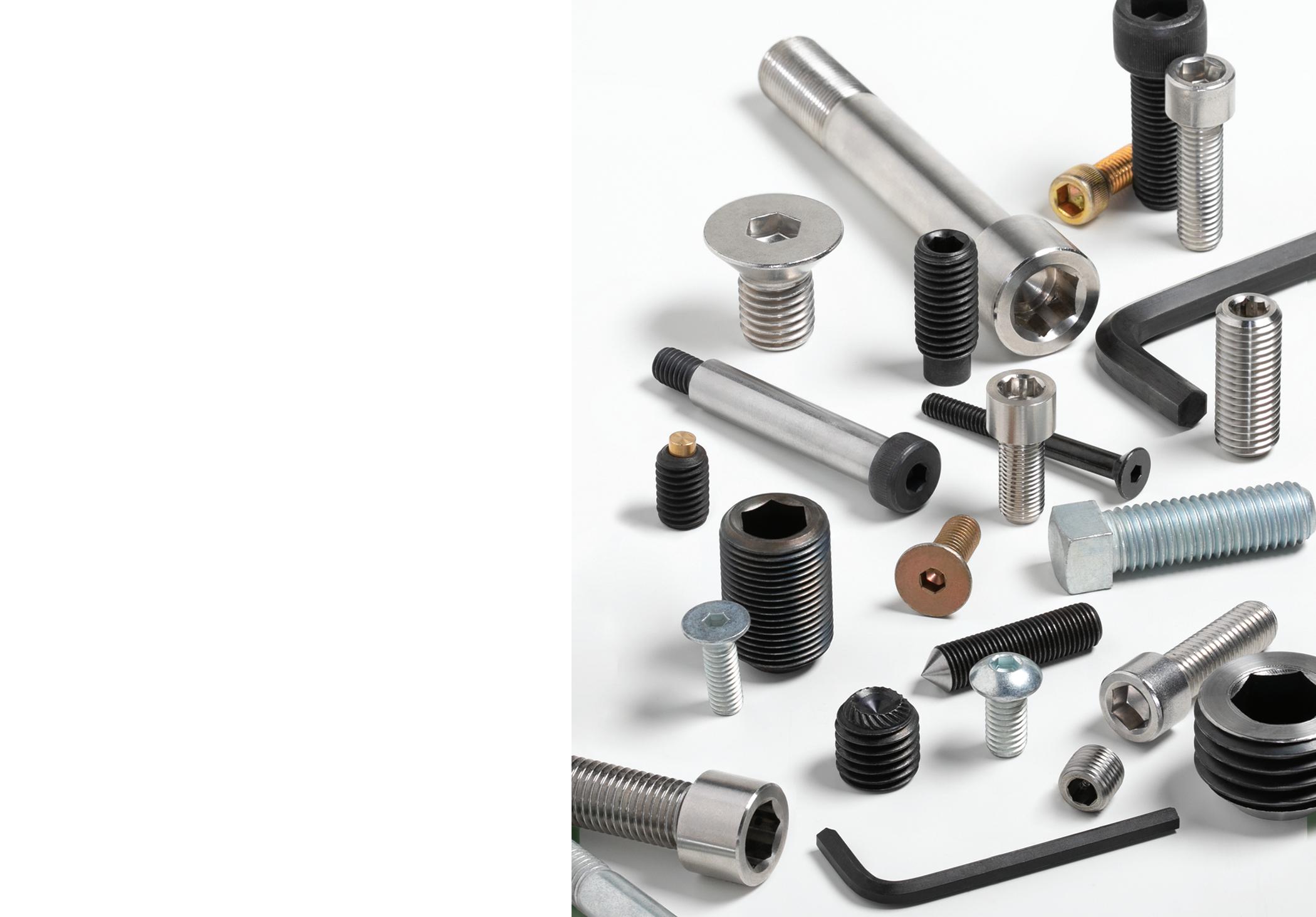
300 North Klick St., Hampshire, IL 60140