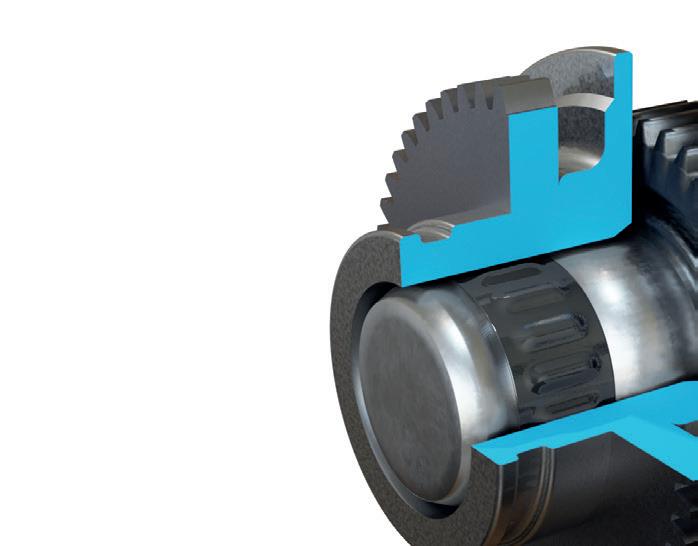
11 minute read
A TAILOR-MADE INLINE SLIP CLUTCH
Engineers working at robotic companies all commonly use torque overload protection devices, slip clutches or torque limiters to prevent damage during accidental collisions between robots and other moving machines and keep actuators and speed reduction units safe. A RENCOL® Tolerance Ring can fulfill this need at a fraction of the space and weight of traditional torque limiters.
A RENCOL® Tolerance Ring, which uses spring force and friction as its operating principle, installs coaxially into a drive assembly instead of being installed in series with an assembly. It has wave features which provide a radial force that acts as the spring force to provide friction between components. The peaks of the tolerance ring’s waves embed into the ID of the mating outer housing or gear, and the ID of the tolerance ring acts as the slip surface at the interface with the inner shaft.
The RENCOL® Tolerance Ring fixes two driven components together, transferring torque during normal operation. If a torque threshold is exceeded, the tolerance ring allows the components to slip relative to each other, limiting the torque and protecting the system from damage.
All our RENCOL® Tolerance Rings are custom designed and manufactured for specific customers and can provide torque overload protection ranging from 0.15 Nm to 2100 Nm torque slip thresholds. These are the components that are currently being used in some high-performing robots that are recognized around the world.
Space and weight saving
Fits coaxially with existing components and eliminates the need for a bulky and heavy subsystem
Tailored for your specific torque requirements
Designed to slip at the specific torque slip threshold while still fitting your mating hardware dimensions and sizes
Consistent and repeatable
Provides repeatable performance over multiple torque slip cycles capacitors onto a relatively thick metal substrate, usually aluminum or copper. The trick to making this sandwich work is the use of a mechanically rigid dielectric layer which e ciently transfers the heat om the copper PCB to the metal layer.
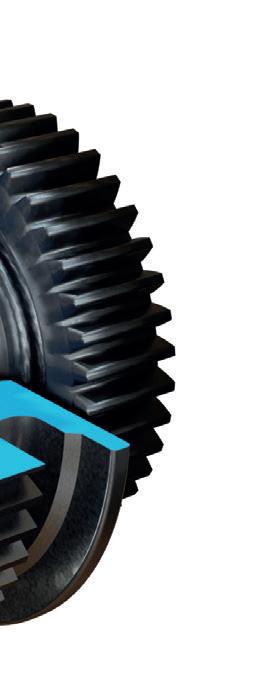
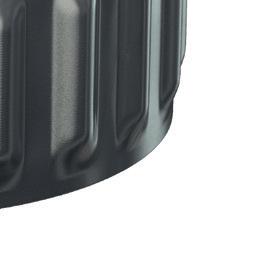
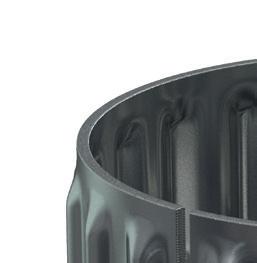
The RENCOL® Tolerance Rings guarantee immediate slip for the drive system and eliminate downtime since there is no need to reset anything after a torque slip event.

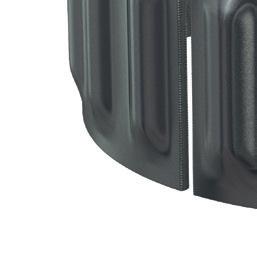

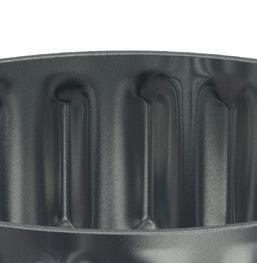
Prior to the development of this heat management technology, manufacturers used a separate step to bond a traditional non heat-conducting PCB to the metal substrate. That approach is more time consuming and not as e cient at transferring heat.
A specific example of how effective such a thermal sandwich can be comes om the PMD laboratory. During one of the many thermal performance tests PMD conducts to certi its amplifier designs, our new N-Series ION Digital Drive, which has a heat sink interface area of about 10 cm2, recorded a temperature drop of only7 deg C om the bottom surface of the abovediagrammed thermal stack to the operating surface of the MOSFET. What makes this remarkable is that these measurements were taken while the amplifier was outputting nearly 2 KWs of power continuously.
Altogether this important new packaging technology has helped accelerate the power density of motion control amplifiers, allowing newer generations of motor and actuator amplifiers to achieve drive output densities of 100W per cc3 and higher.
Step motor machining inaccuracies |
Why can't I y an egg on this motor?
To finish up our discussion of advancements in motion controllers that impact small motor operation, we will look at two control techniques, one for Brushless DC motors and one for step motors that improve e ciency, and therefore reduce heat generation in the motor. For motors that may be implanted in the patient are operated by hand, cool operation is vital.
The first technique to improve e ciency we will look at is FOC (Field Oriented Control) and its close cousin sinusoidal commutation. Both of these techniques apply to Brushless DC motor control and allow these motors to operate more e ciently with more of the commanded voltage creating usable torque.
The traditional approach toward commutating Brushless DC motors is called trapezoidal or six-step commutation. This method relies on Hall sensors which provide a new commutation vector every 60 degrees, which corresponds to six discrete locations per electrical cycle.
In an ideal world, however, the commutation vector would be kept exactly 90 deg om the rotor's N-S (north south) vector at all times. The fact that instead, Hall-based controllers receive a new update only every 60 degrees, means the drive vector will be off by up to 30 degrees, and therefore ine cient. The effective torque output of the motor is reduced in a cyclic pattern by up to 13%. Averaged over a complete rotation the average loss of e ciency is 5%.

Bring on the closed loop stepper
The second control technique we will spotlight applies to step motors. This new type of control technique is called closed loop stepper, also sometimes called stepper servo. What makes closed loop stepper powerful is that it can use a standard step motor yet extract more effective torque out of it, particularly over the full range of operating speeds. How does closed loop stepper work? Closed loop step motor operation is different in three key ways om traditional open loop step motor operation. The first is that it requires an encoder to be attached to the step motor, one with a fairly high resolution. For standard 1.8 degree step motors you will want an encoder with no less than 2,500 counts per mechanical rotation.
The second difference is that closed loop stepper operates the motor like a two-phase Brushless DC motor and commutates the phase angle using the actual encoder position. The third difference is that rather than being constant, the height and sign of the current waveform are continuously adjusted based on the output of a position PID (Proportional, Integral, Derivative) loop.
This means closed loop stepper drives the step motor with just enough power to get the job done. Open loop step systems must drive the motor at a power level to handle the worst-case profile and load scenario. The result is that closed loop stepper can drive the motor with much less heat generated.
Small step motors benefit particularly om the closed loop stepper control method. Since the encoder determines the position, small variations in the teeth spacing which would otherwise result in bumps and wiggles of the motion, are handled ‘invisibly’ by the servo, which increases or decreases the applied torque to compensate.
This is similar to the experience that many users have had with regular DC Brush or Brushless DC motors. A welltuned servo can do a remarkable job of masking small problems with the motor bearing, the gear head, and even the load itself. This is in fact the basis of most machine monitoring observers, and the related art and science of machine failure prediction.
By looking at how the PID’s servo error and servo error integral buildup change over time, a lot can be learned about the health of the downstream mechanical components, even if the motor is staying within its servo accuracy target spec and functioning acceptably. Machine failure prediction is a fascinating subject area which is receiving more and more attention and which we will look at in a future article.
Architecture, architecture, architecture
Let’s look at two approaches to achieving a motion controller function. In one, motors and sensors are located at the target machine while the motion controller and amplifier are located remotely, perhaps in a rack, or perhaps in the form of a motion control board mounted in an industrial computer
The second shows everything hosted locally - the motor, the sensors, and the entire motion controller. When hosted locally, the motion controller can take the form of cable connected modules, an application specific control board built from PCB-mounted modules, or an application specific control board built from an assemblage of ICs.
As it turns out, just as 'smaller is better' for an increasing number of applications when it comes to the motor and amplifier size, 'closer is better' when building machines that use motion control particularly those that integrate analog sensors such as sin/cos encoders.
The reason boils down to two simple principles: shorter signal runs mean cleaner more accurate signals, and shorter signal runs means the servo loop can run faster while still maintaining safe phase margins. Both of these factors have a major impact on motion performance, but in particular on positioning accuracy. While some machine applications will not see big performance improvements from shorter signal runs, systems with smaller motors, and systems utilizing newer generations of encoders such as sin/cos encoders striving for ultrahigh accuracy measured in nanometers or even picometers will. Similarly, for spindles that need to maintain high position or velocity control accuracy, fast servo loops and clean sensor signals can make a big difference.
Embedded we stand
The above principle of 'closer is better' explains a slow but distinct trend toward embedded motion control solutions versus remotely mounted solutions. This trend is most noticeable for smaller machines, but can be observed even for larger machines such as those commonly used with semiconductor capital equipment, laboratory equipment, and packaging equipment.
While there may not be a big motion performance gain with embedded control in these 'bigger' applications, a single PCB-based embedded motion solution located right at the machine makes the final solution more compact relative to a machine with a control setup that uses cable bundles emerging from the machine connecting to a remote mounted control rack or industrial computer.
Cost-wise, embedded control can be cheaper than module or board based control but this is volume dependent. If the local PCB is designed at the IC level the upfront design effort is usually greater, but if there is enough volume this will be amortized over the larger number of machines and the per system cost may well be lower.
There is a new motion control device however that is easing the barrier to building application specific embedded control boards. Known variously as an intelligent amplifier, programmable amplifier, or motion control module, these PCB-mountable devices greatly simplify the task of creating a custom control board.
This is because these devices do all the heavy lifting associated with the machine control function. They can run user application code, generate motion profiles, handle servo positioning, and drive the motor with an on-board amplifier. These devices also offer multiple interfaces, typically serial, CAN, and Ethernet. Most importantly they are small, often measuring just 3-5 cms on a side.
For the design engineer building an application specific motion control board using these plug-andplay devices, the task is more one of interconnecting then of actual circuit design. Whereas a full blown motion board designed from ICs would typically require a 10+ layer PCB and serious digital and analog design skills, a board made with these plug-and-play motion control modules is typically a 2 or at most 4 layer board, and the design task focuses on selecting connectors and specifying the board's form factor.
While not new, PCB-mounted motion control modules have shrunk dramatically in size and increased dramatically in power output over the last ten years. They are very much a product of the type of electronic advancements discussed earlier. Owing to their tremendous convenience we can safely say that these devices are here to stay and will continue to shrink in size and expand in capability in the future. RR
TOOL-LESS ADJUSTMENT COMPONENTS
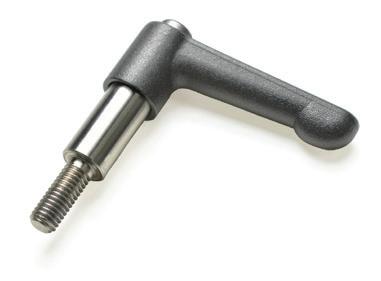
• Adjustable handles and knobs replace standard hardware and can be used to torque components without tools.

• Levers can be used with Ruland shaft collars for quick installation and adjustment.
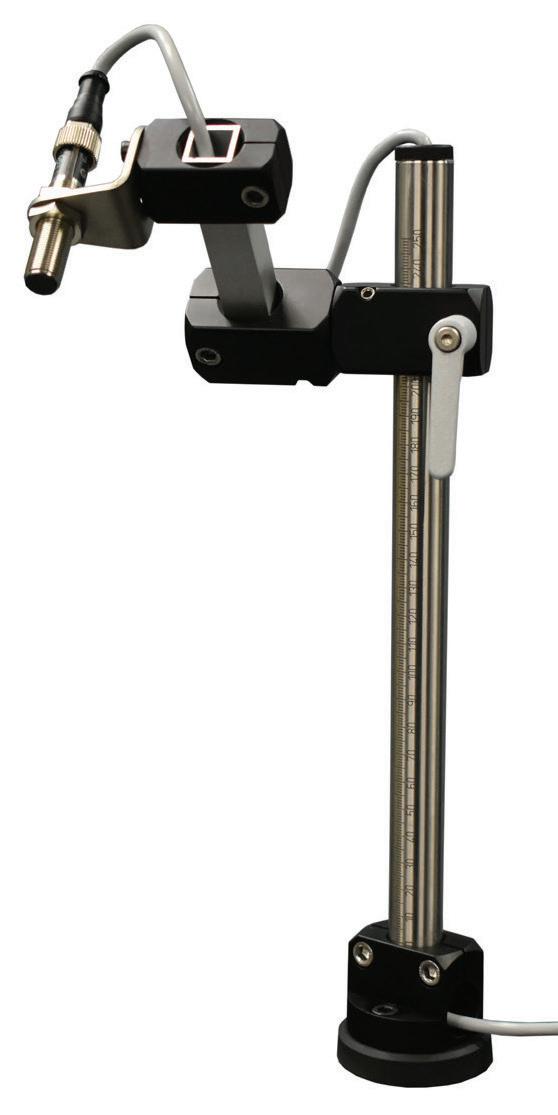
All products available directly on RULAND.COM
Precision Couplings
• Beam couplings accommodate light weights and high misalignment.
• Zero-backlash jaw couplings for vibration dampening and a variety of performance options.

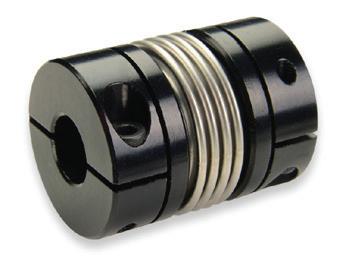
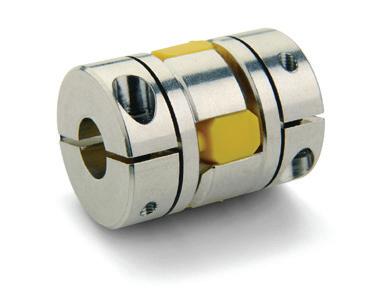
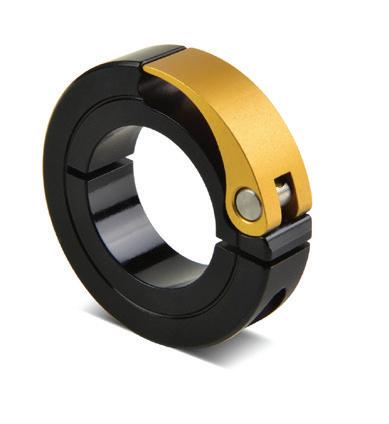

• Bellows couplings for high size to torque ratio.
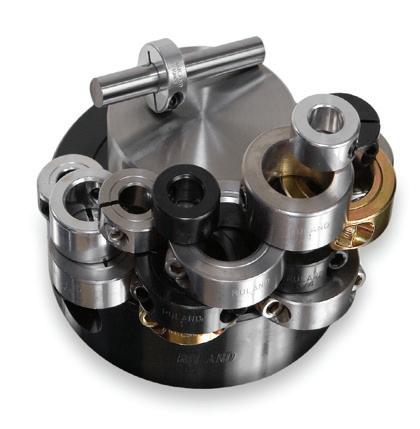
Ruland Manufacturing is proud to support the FIRST Robotics Competition as a Gold Supplier of precision shaft collars & couplings.
Shaft Collars
• Thousands of size and style options.
• Proprietary manufacturing processes ensure superior fit and finish.
• 8 material options.
Vibration Isolating Components
• Rubber bumpers are ideal as end stops or mounting feet.
• Vibration isolation mounts can be sandwiched between components to dampen shock loads.
• Both types can have studs or tapped holes.
Modular Mounting Systems
• Assorted components allow you to build small assemblies for mounting sensors, conveyor rails, machine guards, and more.
• Optional pre-designed kits make it easier to select the right system for your application.
Quick Clamping Collars
• No tools required to install, remove, and adjust.
• Best suited for systems that require frequent adjustments.
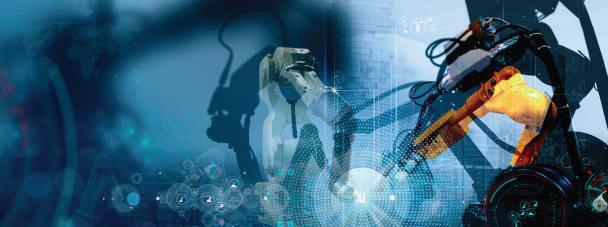
Robotics
Robotics
Canon U.S.A., Inc.
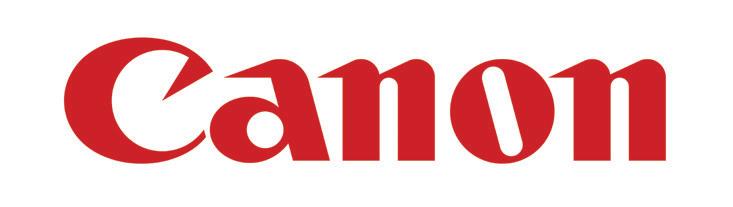
DC brushless Servo Motors
Today’s increasing demands of automation and robotics in various industries, engineers are challenged to design unique and innovative machines to differentiate from their competitors. Within motion control systems, flexible integration, space saving, and light weight are the key requirements to design a successful mechanism.
Canon’s new high torque density, compact and lightweight DC brushless servo motors are superior to enhance innovative design. Our custom capabilities engage optimizing your next innovative designs.

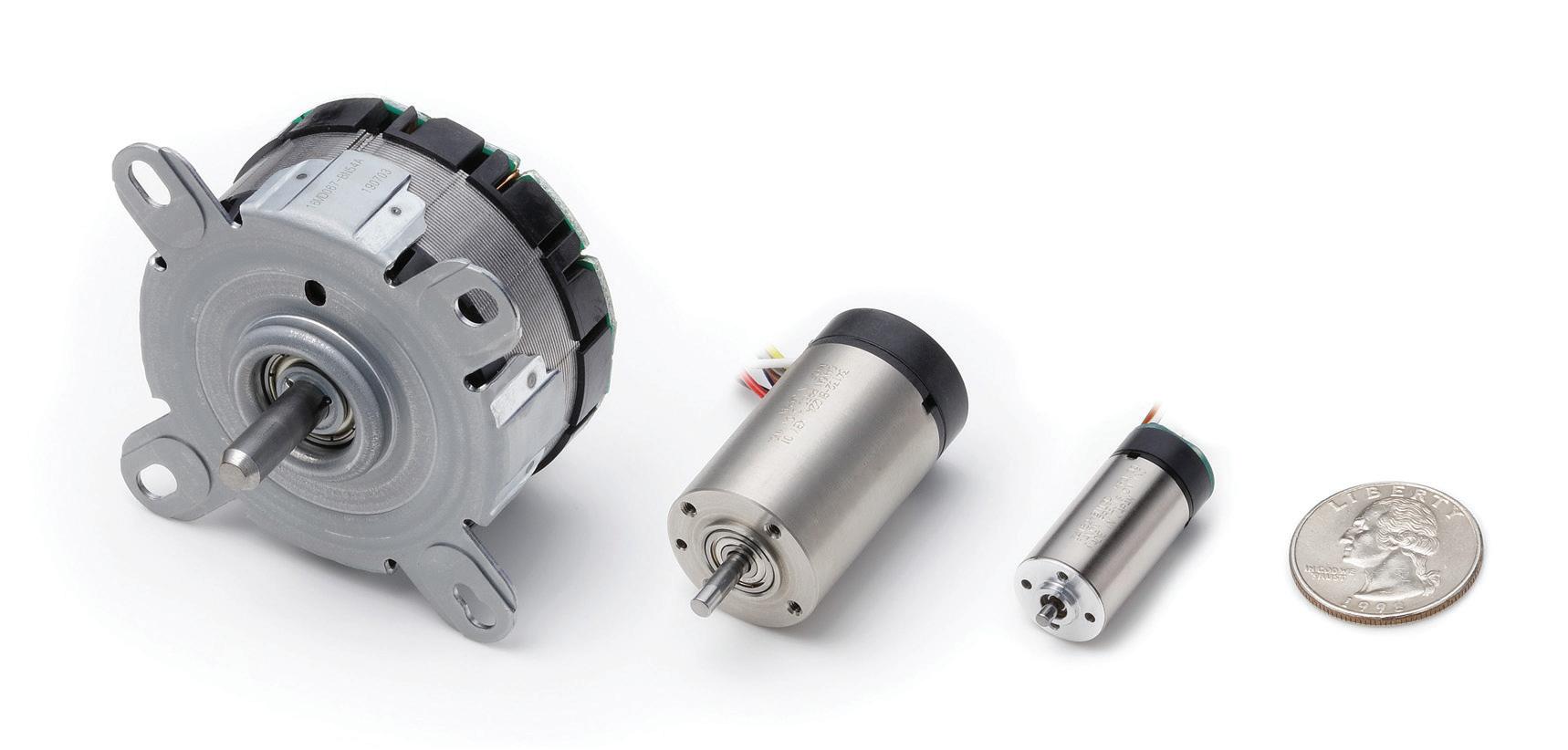
We are committed in proving technological advantages for your success.
CGI Inc.
Advanced Products for Robotics and Automation
At CGI we serve a wide array of industries including medical, robotics, aerospace, defense, semiconductor, industrial automation, motion control, and many others. Our core business is manufacturing precision motion control solutions.
CGI’s diverse customer base and wide range of applications have earned us a reputation for quality, reliability, and flexibility. One of the distinct competitive advantages we are able to provide our customers is an engineering team that is knowledgeable and easy to work with. CGI is certified to ISO9001 and ISO13485 quality management systems. In addition, we are FDA and AS9100 compliant. Our unique quality control environment is weaved into the fabric of our manufacturing facility. We work daily with customers who demand both precision and rapid turnarounds.
Canon U.S.A., Inc Motion Control Products 3300 North First Street San Jose, CA, 95134
408-468-2320 www.usa.canon.com
CGI Inc.
3400 Arrowhead Drive Carson City, NV 89706
Toll Free: 1.800.568.4327
Ph: 1.775.882.3422
Fx: 1.775.882.9599
WWW.CGIMOTION.COM
SHA Rotary Actuator with Integrated Servo Drive
The SHA-IDT Series is a family of compact actuators that deliver high torque with exceptional accuracy and repeatability. These hollow shaft servo actuators feature Harmonic Drive® precision strain wave gears combined with a brushless servomotor, a brake, two magnetic absolute encoders and an integrated servo drive with CANopen® communication. This revolutionary product eliminates the need for an external drive and greatly simplifies cabling yet delivers high-positional accuracy and torsional stiffness in a compact housing.
www.Harmonicdrive.net
Robotics
Lin Engineering
https://www.harmonicdrive.net/products/rotary-actuators/integrated-actuators/sha-integrat ed-with-servo-drive
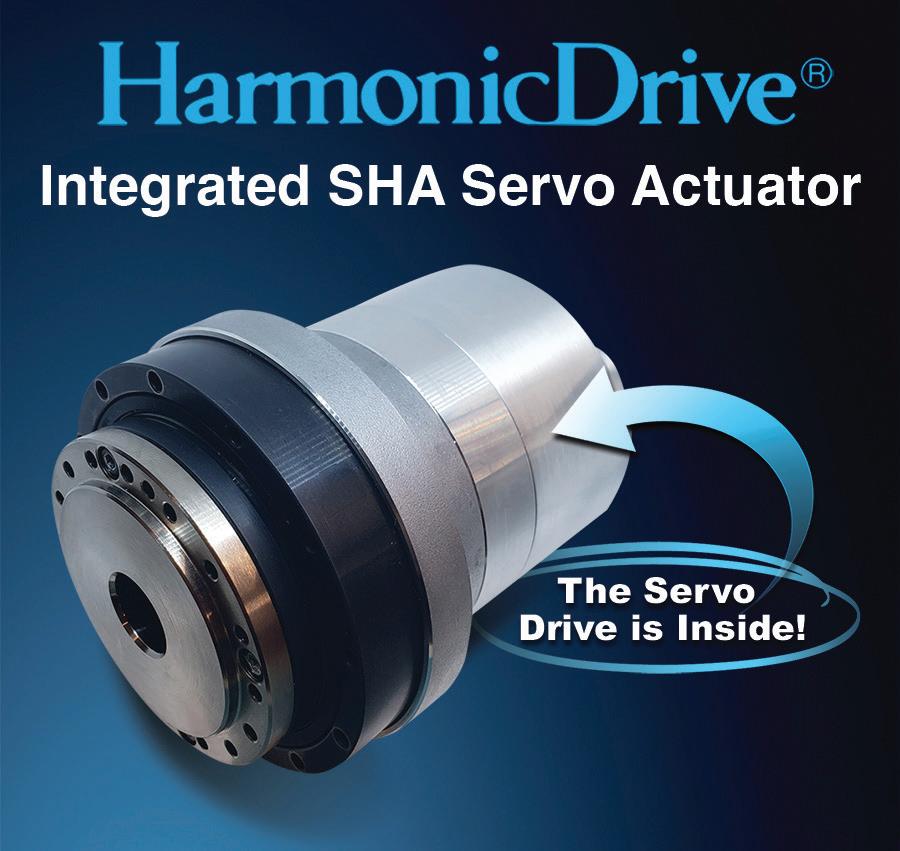
Here at Lin Engineering, we find solutions to your problems by focusing on three basic elements: Find, Optimize, and Integrate. There are such a vast number of products on the market that just narrowing the options can be difficult. Our engineers will help you find the motor you need. The motor may then be optimized for your application by changing the winding, magnets, bearings, and more. We work with your team throughout this process to configure the motor to your application so it can be seamlessly integrated within your product or assembly.
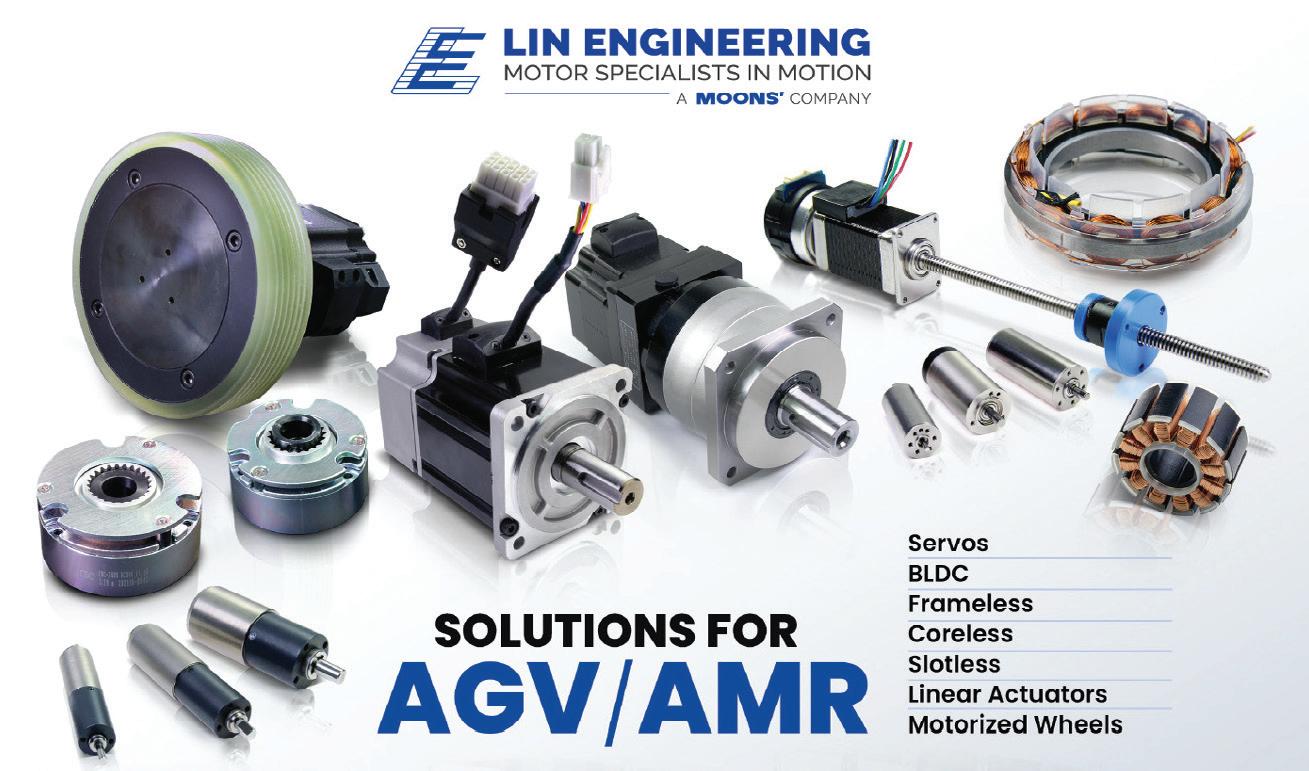

Contact info: Lin Engineering 16245 Vineyard Blvd. Morgan Hill, CA 95037 https://www.linengineering.com/ 1.408.919.0200
Robotics
Robotics
New England Wire Technologies
Advancing innovation for over 100 years
Why accept a standard product for your custom application?
NEWT is committed to being the premier manufacturer of choice for customers requiring specialty wire, cable and extruded tubing to meet existing and emerging worldwide markets. Our custom products and solutions are not only engineered to the exacting specifications of our customers, but designed to perform under the harsh conditions of today’s advanced manufacturing processes. Cables we specialize in are LITZ, multi-conductor cables, hybrid configurations, coaxial, twin axial, miniature and micro-miniature coaxial cables, ultra flexible, high flex life, low/high temperature cables, braids, and a variety of proprietary cable designs. Contact us today and let us help you dream beyond today’s technology and achieve the impossible.
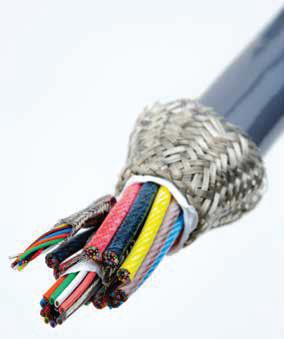