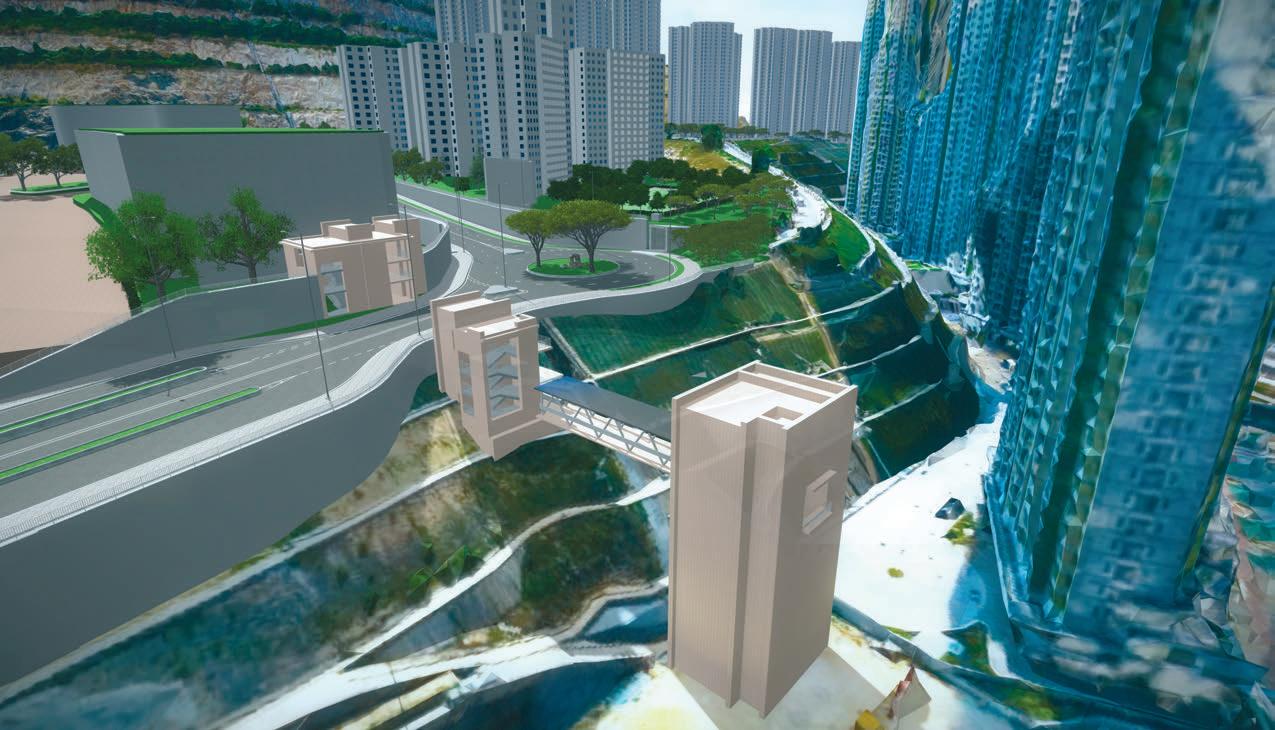
4 minute read
Making the grade
AECOM used reality modelling to help transform the dangerous terrain of a Hong Kong quarry into a commercial and residential development for 25,000 people
To support the surge in eco- road improvement works, pedestrian quarry’s terrain was steep, sloping, and nomic development and pop- connectivity facilities, underground util- immense. Additionally, using manual ulation, Hong Kong has ities, and housing estates. The company photography to monitor progress would invested in numerous large- turned to BIM and reality modelling put surveyors at risk, capture only a porscale infrastructure works technology from Bentley Systems to opti- tion of the area, and take 40 days to comand new building structures. mise planning and construction efficien- plete, missing the required 30-day
For more than 50 years, Anderson Road cy, streamline workflows, facilitate stake- reporting deadline. Quarry supplied aggregate, asphalt, holder communication, and meet client To overcome the challenges of the site’s stone, and concrete for construction pro- reporting requirements. topography within the client’s 30-day grams in Hong Kong. Now a vacated site, Hong Kong’s Civil Engineering and ‘‘ Traditional survey methods for the reporting timeframe, AECOM decided to use reality modelling to best moniDevelopment Department (CEDD) has initiated a USD 40-hectare quarry site would have been tor the site’s progress. Using drone photogram1 billion project to develop inaccurate and inefficient because the quarry’s metry, the team captured the quarry in response to the acute housing shortage, terrain was steep, sloping, and immense 3,000 photos monthly and used ContextCapture to genthe result of rapid population growth. The quarry site offers 40 hectares of ’’ erate a reality mesh of the entire site for an accurate visualisation of the construction proland to construct approximately 9,400 Safe and accurate site monitoring gress within one day. The 3D precise and private and subsidised housing flats to As part of the project, AECOM was real-textured reality mesh provided the accommodate a planned population of required to report to the client about the team with an efficient and comprehen25,000 people. construction progress on a monthly sive platform to oversee site progress and
AECOM was retained as the engineer- basis. Traditional survey methods for the eliminated the need to have on-site staff ing consultant for sustainable infrastruc- 40-hectare quarry site would have been perform the survey, avoiding potential ture design, including site formation, inaccurate and inefficient because the hazards and improving safety.
Reality modelling meets 4D Construction management ContextCapture contractor, the client, and the Beyond creating visualisations, AECOM With different disciplines and drone public for a holistic project understood that reality modelling pro- required for the site and infraphotogrammetry of the quarry approach. vides a comprehensive record of a site’s structure development, it was generated accurate The technology enabled current conditions that can be utilised in necessary to have accurate col- reality meshes of the AECOM to work closer with the future. Leveraging Bentley BIM laboration and information 40-hectare site the contractors for more effimethodology and reality modelling capa- sharing among the team and cient supervision and allowed bilities, AECOM partnered with Earth with stakeholders. the building contractors to anticipate Solutions to implement a Site Data The mass quantity of project data was and solve problems in advance. Management Solution (SDMS), using managed and analysed in ProjectWise; The use of reality meshes provided ContextCapture as the foundation. that information was attached to reality more precise and accurate site monitor-
This innovative construction manage- meshes in SDMS and on-site building ing through detailed visualisations, ment solution extended the function of contractors and team members accessed enhancing client decision making and reality meshes from visualisations to the data through their mobile devices. facilitating citizen understanding of the more informative uses to achieve a full This set-up enabled any conflicts construction progress. 4D BIM methodology approach. The ability to add information, such as key ‘‘ The ability to add information, such as key “By creating synergy between our expertise in project management and the construction dates, images, and BIM renderings, to spe- construction dates, images, and BIM further utilisation of reality modelling and BIM, we succific points in the reality renderings, to specific points in the reality cessfully increased producmeshes optimised planning and construction. meshes optimised planning and construction tivity and safety,” said Ivan H.K. Tsang, vice president at By automatically overlaying models, the SDMS highlights locations or changes in height to regarding site boundary and foundation ’’ AECOM Asia. Future smart city visualise works in progress and cut and works to be identified and resolved Anderson Road Quarry will serve as the fill volumes for easy interface of earth- prior to construction for more careful fundamental model to develop other works balance, all in the same platform. planning. communities in Hong Kong that, when
The use of reality modelling for topo- The enhanced information mobility combined, will gradually form the smart graphic surveys and photo recordings enabled fast, temporary traffic diversion city of Hong Kong. saved a total of 55 resource-days per arrangements and minimised impact to Although the model was populated month and using the SDMS for automat- travelling citizens. Integrating LumenRT with facility data for this specific project, ing and processing data saved over 200 to simulate construction progress and it can be integrated with other data resource-days. produce animated visualisations helped sources for uses in other cases, ranging
The combined solution streamlined communicate progress to the public adja- from energy efficiency and environmenworkflows and improved communica- cent to the site. tal sustainability analyses to generating tion among the team and with stake- Having an effective, integrated con- master plans for future facility, transporholders, minimising rework and signifi- struction management solution opti- tation, utilities, and security plans. cantly reducing project costs. mised collaboration among AECOM, the ■ bentley.com
