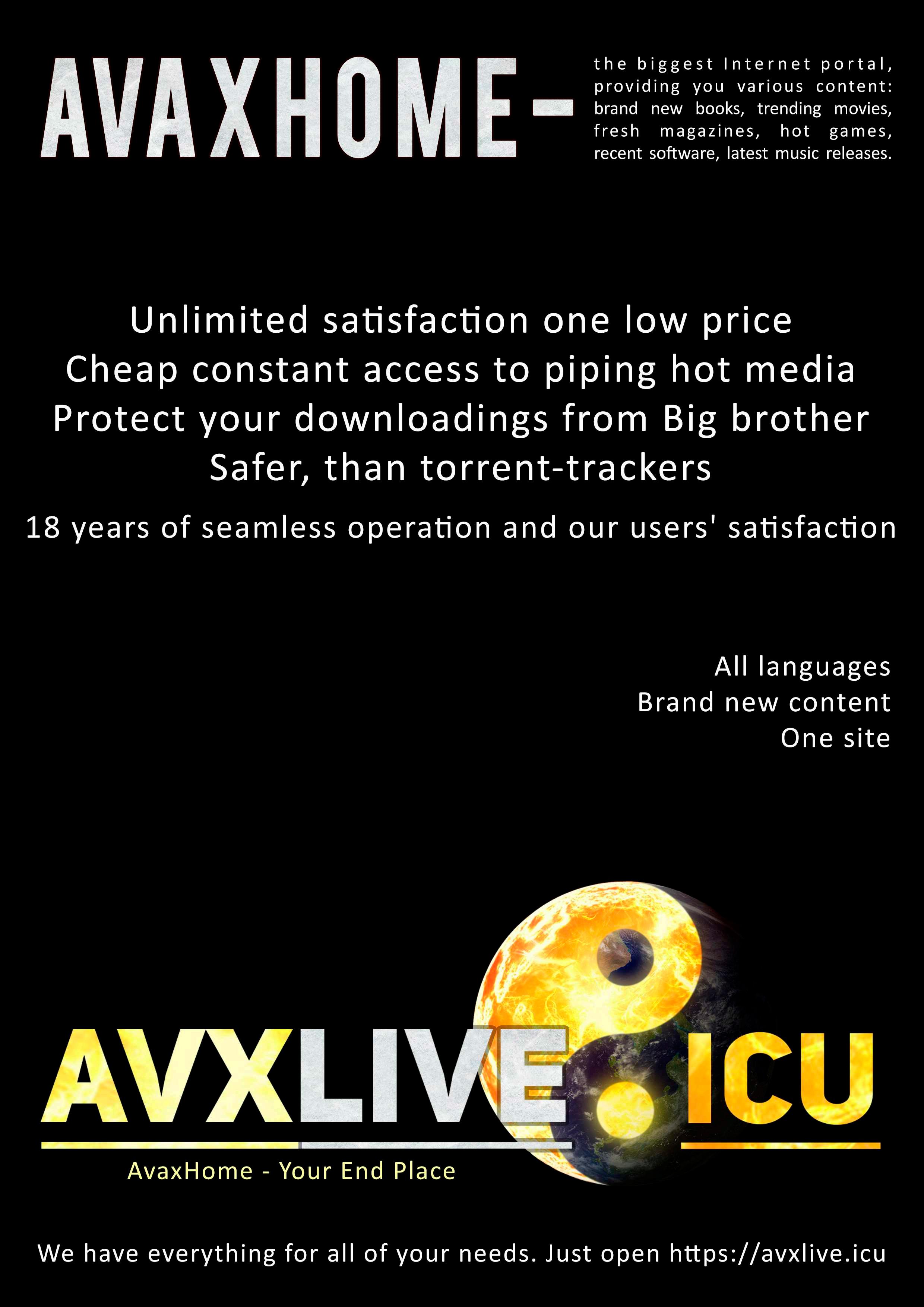
6 minute read
DENIM ENCORE TOTE
Skill Level: Beginner
SUPPLIES • One pair L or XL non-stretch denim jeans
Advertisement
• 1⁄2 yard each of coordinating lining & lightweight fusible interfacing
• Two 1"-wide 18"-long leather straps
• All-purpose thread
• Size 100/16 denim needle
• Removable fabric marker
• Rotary cutting system
• Removable fabric marker
• Four rivets & attachment tool
• Denim presser foot (optional)
tip Choose an old pair of non-stretch jeans from your wardrobe for the project or purchase used denim at a local thrift store, garage sale or clothing swap.
PREPARE Prewash and dry the jeans.
Position the jeans on a flat work surface. Remove each pant leg just below the crotch, and then trim away the hems. Trim away the outer leg seam and inseam (1). two 4"×111⁄2" rectangles for the center panels. Designate the side-panel darker-wash sides as the right side and the center-panel lighter-wash sides as the right side.
From the lining and interfacing, cut two 111⁄2"×121⁄4" rectangles.
Fuse the interfacing to the lining rectangles following the manufacturer’s instructions. Designate one long edge of each lining-rectangle as the upper edge.
CONSTRUCT Use 1⁄2" seam allowances unless otherwise noted.
Install a denim needle and foot onto the machine. Position one side panel and center panel with right sides together along one long edge; pin, and then stitch. Press the seam allowances toward the center panel, and then press open.
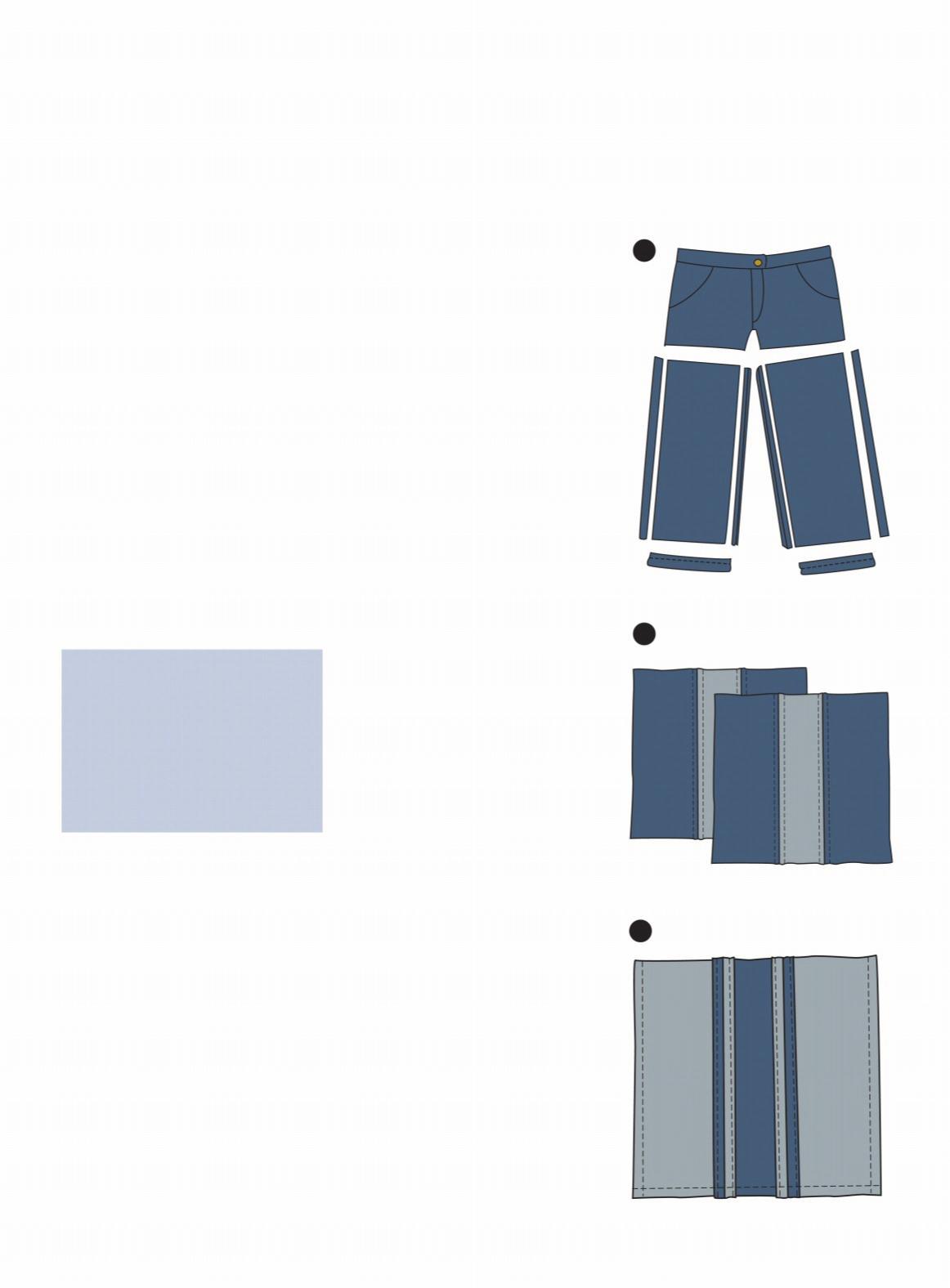
Repeat to attach another side panel to the opposite center-panel long edge.
Select a 3mm stitch length. Topstitch 1⁄4" to either side of each seamline (2). Designate as the front panel and one long edge as the upper edge.
Repeat to construct the back panel.
Cut and square the pant legs into four separate panels using a rotary cutting system.
From the panels, cut four 5"×111⁄2" rectangles for the side panels and Position the front and back panel with right sides together, aligning the seamlines; pin. Stitch the sides and lower edges, leaving the upper edge open (3). 1
2
3
Repeat to stitch the lining rectangles, leaving a 5"-long opening along the lower edge for turning. To reinforce the seams, backstitch over each side and lower edge at the cut edge.
Position the tote wrong side up on a flat work surface. Mark a 11⁄2" square at each lower corner using a removable fabric marker. Trim away each square. To create box corners, flatten one tote corner with right sides together, matching the side and lower seams; pin, and then stitch. Repeat to box the lining corners.
Press the tote exterior and lining seams allowances open. Turn the tote exterior right side out.
Insert the tote exterior into the lining with right sides together, aligning the seamlines and upper edge; pin. Stitch the upper edge.
UPCYCLE OPTIONS
The basic tote is a great starting place for customization. Use the same basic steps to create a pieced tote (such a great way to upcycle odd scraps!). Keep finished seams intact as design details and lengthen the strap for an easy-to-wear crossbody bag. Increase the size for a messenger-style bag with unique pieced elements featuring the upcycled fabric wrong side.
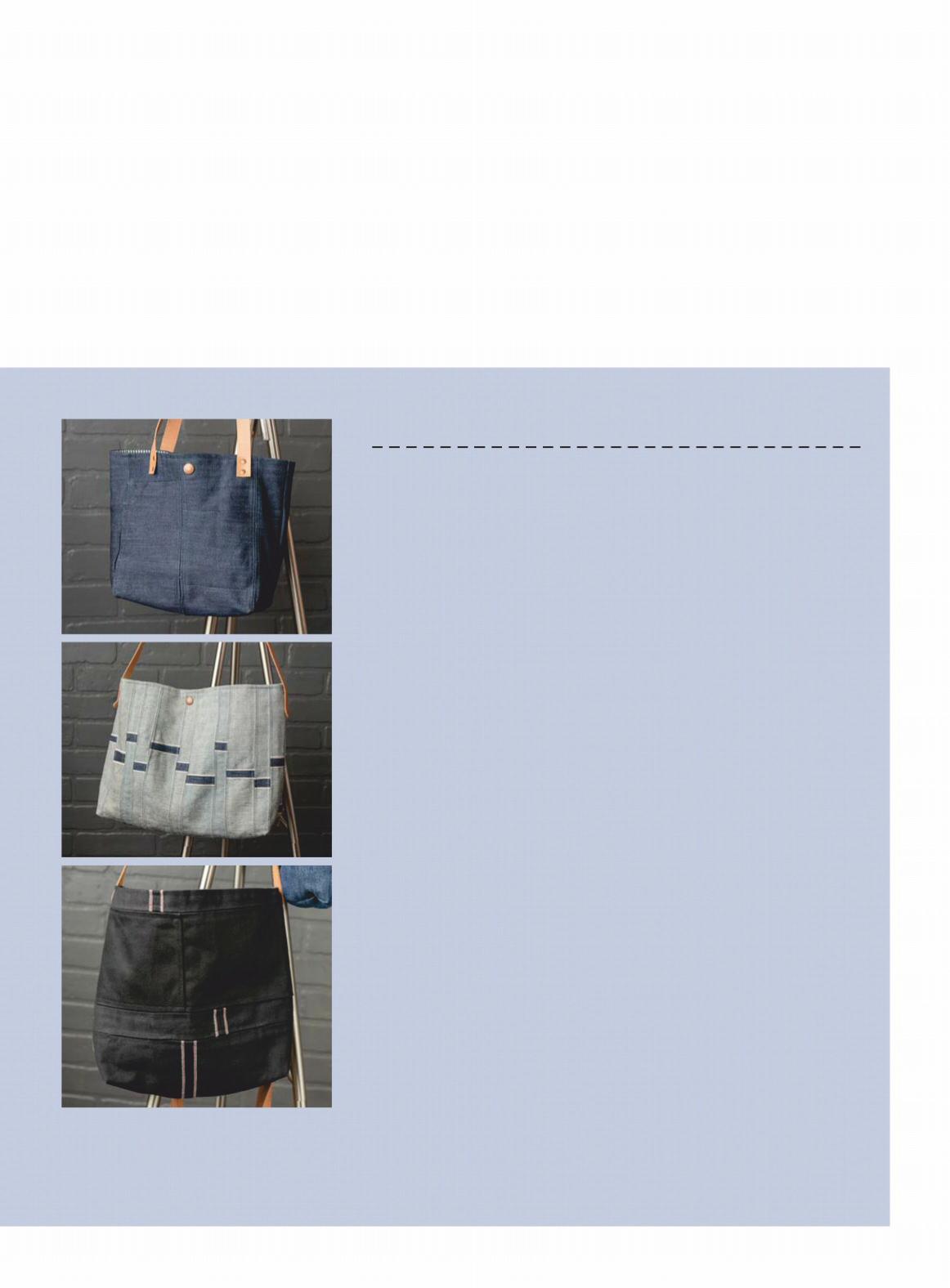
RE-SOURCING FABRIC Try reaching out to clothing and textile companies based in your hometown or region to see how you can put their scraps and extra fabric to work. Detroit Denim, known for creating high-quality denim goods within the city of Detroit, is a company known for helping makers in their community. Scraps are often made available to those looking to work with them, and their studio doors are regularly open to teach others how to sew everything from aprons to reusable market totes — because being a part of the Detroit maker community is at the core of their philosophy.
OCTOBER/NOVEMBER 2019 a garment and use it often, it is inevitable that it will eventually begin to show wear and tear. Whether this wear is aesthetic, structural, or both, mending clothes serves many purposes,” said Detroit Denim co-owner Brenna Lane. “First, it keeps the garment out of the trash heap, which is a win for the environment. Secondly, repairing saves us money by reducing our need to purchase new garments.
“Finally, repairing our clothes adds to their character and charm. We live our lives in our clothes — they serve so many purposes beyond simply protecting our bodies. We develop meaningful attachments to our clothes. Clothing that has been repaired has even more emotional cache for the wearer. We hope that by encouraging our customers to mend their garments, they will have longer, more meaningful relationships with their clothes, and that this idea of having a meaningful relationship with your things will carry into other aspects of their lives.”
Turn the tote right side out through the lining opening. Insert the lining into the tote exterior with wrong sides together; press. Topstitch the tote exterior 1⁄4" from the upper edge; press. Hand stitch the lining opening closed.
Mark 2" to either side of the tote front upper-edge center and 1" below the upper edge.
Center a mark on one strap 3⁄4" above each short end. Using a rivet, attach one strap short end to each tote-front mark following the manufacturer’s instructions.
Repeat to attach the remaining strap to the tote back.

tip Use the excess denim and pockets for other upcycling projects.
BUILDING COMMUNITY THROUGH BAGS
Over the course of two warm, sunny summer days in Detroit in August 2018, local fiber and textile enthusiasts gathered in a renovated 1940s U.S. Post Office building to learn how to screenprint tote bags, try their hands at embroidery, dye fabric with natural materials and turn denim scraps into one-of-a-kind totes for the first-annual Textile Takeover at POST Detroit. The event was hosted by POST owners Clare Fox and Wayne Maki as a celebration of their locallysourced storefront, which also doubles as a maker and education space, thanks to weekly DIY workshops hosted by area makers, artists and teachers. With a natural dye garden situated within the front corner of the property, talented makers willing to show off their talents and a community eager to learn, a weekend dedicated to all-things textile seemed like the perfect thing to do.
“We invited more than 40 textile and fibers artists to dye, knit, print and weave in the vacant lots across the street from POST," said Fox. “The turnout was amazing; this will definitely become an annual event for our little neighborhood. It was all very Detroit: no permits, no funding, minimal planning, but all for the love of work, creation and fun.”
Elizabeth Royal of Mend Detroit brought local makers together during Textile Takeover for a community-based creation project. Known for her workshops teaching visible mending and stitching, she sees the mending and upcycling community movement as an exciting way to bring makers of all backgrounds together.
“I find that the mending community is super inclusive and has a low barrier to entry. All you need is a needle and thread, and you're good to go,” Royal said. “Sure, you can go buy Sashiko needles and thread at a specialty store and mend your jeans that way, but I've had people in my mending workshops make beautiful, serviceable repairs with a basic needle and thread. And mending is something that happens across cultures — you'll find examples of it almost everywhere in the world.”