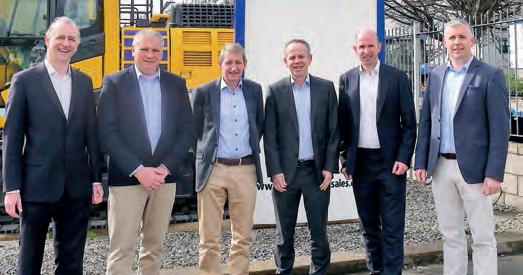
26 minute read
Superfan Purchases First JCB 56Z-2 in Northern Ireland
news
McHale Plant Sales Announces New Board and Management Appointments
Construction equipment specialists, McHale Plant Sales – distributors in Ireland of Komatsu, Komatsu Forest, Metso Outotec, Merlo and Terex Ecotec equipment – has announced a number of senior board and management appointments.
Chairman Michael McHale says the move “will resource the organisation at senior level, reinforce capacity across our various and diversified fields of operation, enable us to capitalise on future growth opportunities that may present, and strengthen the service we give to our customers”. All of significant importance in terms of their expected contribution to the company’s current and future requirements, four of the appointments are at director level and a further three are to senior management positions. Four appointments are made to the Board of Directors: Kevin Nugent is appointed to the position of Finance Director and Liam Foley to the position of Commercial Director. Denis McGrath is appointed to the
McHale Plant Sales chairman, Michael McHale (centre right) and managing director, Tim Shanahan (centre left) pictured with four senior staff members whose appointments to the Board of Directors of the company are announced. They are (left to right) Liam Foley (Commercial Director), Denis McGrath (Sales Director), Anthony Ryan (Aftersales Director) and Kevin Nugent (Finance Director).
position of Sales Director and Anthony Ryan to the position of Aftersales Director. Kevin Nugent previously held the post of Financial Controller for many years and now takes up the position of Finance Director. Liam Foley moves to the new and more broadly focused position of Commercial Director. In his new position as Sales Director, Denis McGrath succeeds the late John O’Brien, a legendary and admired figure within the industry whose recent death was marked by tributes paid by colleagues across the sector. His appointment as Sales Director recognises, in part, his long service to the company which he joined as an apprentice, graduating over recent years to frontline sales and general management. The appointment of Anthony Ryan to the position of Aftersales Director is one that gives a voice at board level to all facets of after-sales management. In particular, it recognises the increasing importance that McHale Plant Sales attaches to the broad issue of customer care, one to which Anthony will bring his extensive experience in aftersales management. Other appointments from within the company’s ranks sees Pat Shanahan promoted to the new position of Sales Manager, Keith Carey to the new position of Parts Manager and the promotion of Niall Culligan to the new position of Service Manager. Comments Michael McHale: “Through these new appointments, an extra strong foundation has been put in place on which the company can plan for future growth and expansion. Drawn from within the company’s own ranks, a team has been appointed that will plan and manage the company’s affairs into the future, all with the experience, product knowledge and market awareness needed to meet the demands of current and future trade, to deliver on the priorities of those we represent, and to satisfy the expectations of our customers.”
JCB Superfan Purchases The First JCB 56Z-2 In Northern Ireland
A landfill and quarrying company has bought the first Stage V JCB 56Z-2 models in Northern Ireland.
Supplied by dealer Dennison JCB, the new midi excavator has been purchased by Belfast-based Macwill Services. Owner Chris McLaughlin, a self-confessed JCB superfan who hosts his own YouTube channel – The JCB Club - chose the brand new machine for civil engineering duties and essential environmental projects within Macwill Services’ Belfast landfill site and family farm estate. “We have bought, hired and used many different manufacturers of construction equipment over the years but to me there’s something about JCB which makes them special compared to all the others. I always choose JCB when it comes to buying new machinery as they make fantastically engineered machines and are a company with true British pedigree. Just as important to me is that JCB has a fantastic dealership network that supports my business and treats every phone call as essential. It’s what I call great back up! “As far as the JCB 56Z-2 is concerned we liked the ‘built for purpose’ robust and strong design of the machine. The cab for the operator is so modern and comfortable and the engine access is well thought out for easy service access. All the drivers love the speed and accuracy of the hydraulics and the super bright LED lights let you work safely into the night. We opted for steel tracks this time as opposed to rubber and the extra stability and pushing power that the steel tracks give is very noticeable. We’re very, very pleased with just how much power this JCB digger punches,” said Christopher who has one of the largest collections of JCB memorabilia and collectibles in the world. The new JCB Stage V 56Z-2 is powered by a 1.7-litre, turbocharged three-cylinder common-rail Perkins diesel engine, delivering 34kW (45.6hp). Part of the ‘Dash 2’ range of midi excavators is it equipped with a Diesel Oxidation Catalyst (DOC) and a Diesel Particulate Filter (DPF), there is no requirement for a Diesel Exhaust Fluid (DEF) such as AdBlue. Macwill Services was established in 1987 and operates a number of JCB machines within its landfill and quarrying fleet from modern day machines to rare JCB classics. The fleet comprises a JCB Hydradig, JCB Fastrac, JCB Loadall telescopic handler, JCB backhoe loaders, JCB mini excavators and classic machines including a 1985 JCB 805B Turbo crawler excavator and JCB 3DMK111 Powertrain backhoe loader.

news
New JCB Store Set to Revolutionise Machine Purchasing
JCB has launched an innovative new online platform which will transform the way customers can buy the manufacturer’s equipment - https://machinestore.jcb.com/
The new JCB Store is an online machine marketplace which allows customers to search for JCB plant and equipment within one centralised platform and view all machines available to them from their local dealer. The new system offers four times as many machines for online order than was previously possible and the site will display exact machines specifications and dealer specific pricing – giving the customer all necessary information to make a purchasing decision. JCB started to sell machines online for the first time in its history in May 2020 to support businesses with their plant requirements during the first Covid-19 lockdown. A select range of compact equipment was available for direct delivery. The brand new JCB Store offers a wider range of machines, greater insight and added flexibility to provide an even more enhanced customer experience. The machines available to purchase via JCB Store include: JCB’s full mini excavator, site dumper, vibratory tandem roller and JCB Access ranges along with a selection of JCB light equipment. JCB UK and Ireland Sales Director Steve Smith said: “Online ordering of JCB equipment has proved to be extremely popular. The JCB Store marks a significant evolution of the concept with more machines, more options, and more insight available. We have invested heavily in creating a high-quality platform tailored to the needs of an evolving market and a new generation of customers. “It capitalises on the support and expertise of our unrivalled dealer network and gives customers all the information they need in one centralised platform. It will transform the way our customers order JCB machines and makes access to our range of equipment simpler than ever.”
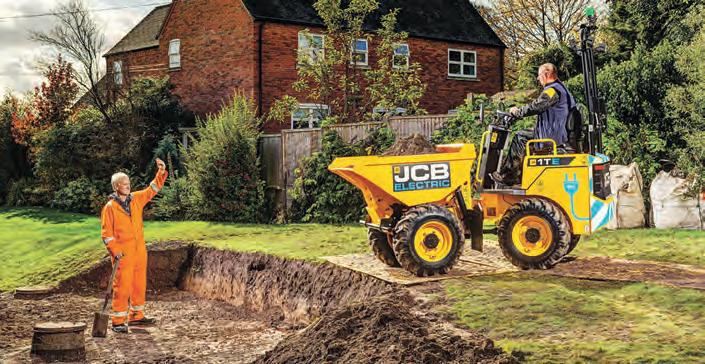
BRIAN JAMES TRAILERS DIGGER PLANT PERFECT FOR BUSINESS REQUIREMENTS
Brian James Trailers innovative Digger Plant range provides a modern, advanced and compliant transport solution for many tracked excavators and plant machines such as chippers and shredders. With obvious appeal to larger organisations the ideas pioneered in the Digger Plant also translate to medium and small size fleets interested in efficiency and safety.
Being a part of the Brian James Trailers portfolio, Digger Plant embodies a low and flexible design for optimal distribution of weight and stable towing performance.
DEALERS
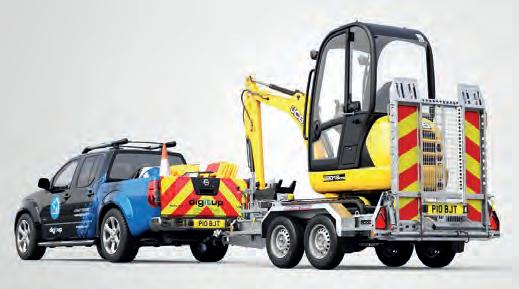
The new Brian James Digger Plant is available to order from your local Brian James Authorised Retailer now. In Northern Ireland, Eakin Brothers, Co. Londonderry and Trailertek (NI) Limited, Co. Armagh. The Republic of Ireland dealers include AD Test Centre Limited Co. Kilkenny, Barrett Trailers Co. Limerick, BG Motors Co. Kerry, Blue Print Autos Co. Roscommon, DH Farm Machinery Co. Galway, Heneghan Plant Hire Ltd Co. Mayo, Noblewood Co. Cork, SME Group Co. Meath and Trailerstuff (KER Group) Co. Donegal.
DIGGER PLANT
FROM BRIAN JAMES TRAILERS
available to order now

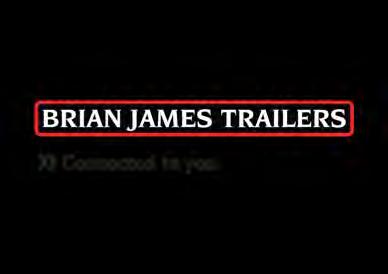
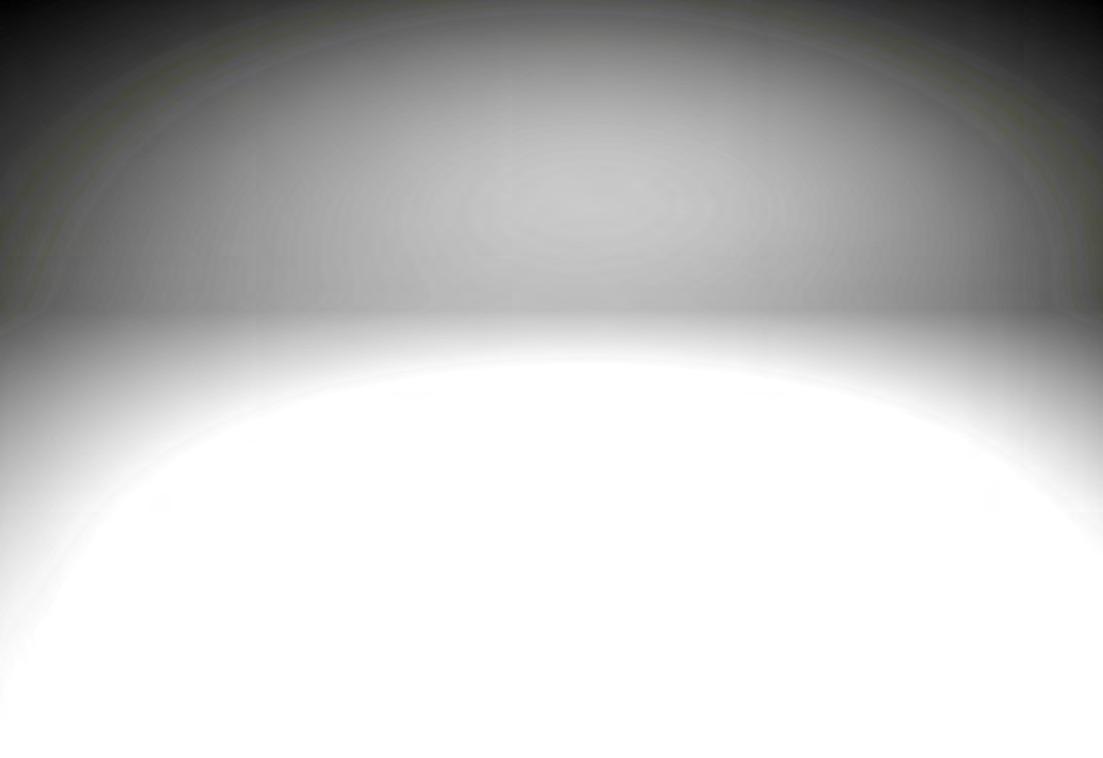
news Edge Innovate Win Second Queen’s Award For International Trade
EDGE Innovate has been honoured with a prestigious Queen’s Award for Enterprise. It now joins an elite group of companies to have won multiple Queen’s Awards having won their first Queen’s Award in 2019.
EDGE Innovate was recognised for its excellence in International Trade and is one of only seven companies to achieve two Queen’s Awards for Enterprise in 2022. Employing 170 people directly, the family owned company was set up in 2008. It develops, manufactures, markets and exports sophisticated technologies for shredding, stacking, screening and sorting of primary and secondary raw materials in production processes and recycling. The company currently exports 94.4% of their products outside the United Kingdom from its 187,000ft² manufacturing facility within Co. Tyrone. The family run brand has developed a strong presence throughout overseas markets such as North America, Australia, and Middle East. “The team at EDGE Innovate are absolutely delighted to win the Queen’s Award for Enterprise. This award is recognition of the hard work and resilience of all our stakeholders over the last three years, especially during the time of the pandemic,” said Darragh Cullen, EDGE Innovate Managing Director. “With staff suffering from covid, isolating and with enforced lockdown, it has been an extremely challenging period. I want to thank our entire team for their help during this time. We have worked together as a tight knit unit, focusing on delivering for our customers. To our suppliers who have been faced with their own difficulties, thank you for your support. To our customers who have had to deal with long delivery times and increased costs, thank you very much for your patience. “EDGE is a growing organisation and working closely with all our stakeholders in the context of mutual respect and teamwork has allowed this growth to continue over the last three years. Continual growth during the pandemic is remarkable and a testament to who we all are and how we conduct ourselves. We accept this award as recognition of that success.” Now in its 56th year, the Queen’s Awards for Enterprise are the most prestigious business awards in the country, recognising and celebrating business excellence across the UK. EDGE Innovate has demonstrated outstanding success in its respective field of international trade. It has been an exceptionally hard few years for businesses and this achievement is testament to the resilience of the entire EDGE Innovate business network has shown through these unprecedented times. EDGE Innovate currently export both its material handling and recycling equipment to almost 70 unique countries via a 50strong distributor network. The company has experienced exceptional growth with exports rising from 85% in 2016 to 94.4% in 2020. Given the growth trajectory, the company has successfully completed the construction of a new 37,500ft² facility to house a new paint shop and stores facilities. This expansion has resulted in a 30% increase in production capacity. EDGE Innovate also have plans to start construction on a new Customer Welcome Centre to house its ever-expanding sales, marketing and aftersales departments. The new, improved, larger manufacturing facilities and office space will enable EDGE Innovate to increase its production capacity and allow for the introduction of new production lines for the latest product innovations in an efficient manner, with the aim of increasing EDGE Innovate’s sales volume and exporting figures even further.
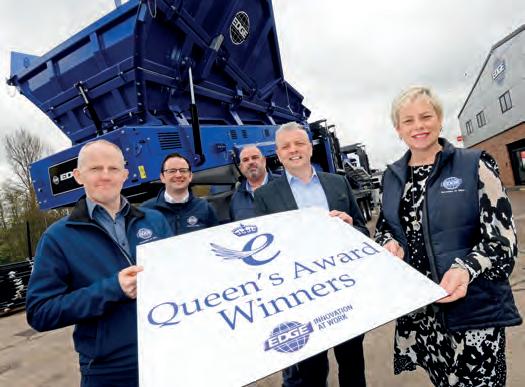
EDGE Innovate staff after their Queen's Award wwin was announced.
First Merlo Cingo Models Arrive in Ireland
Merlo distributors in Ireland, McHale Plant Sales, has received first deliveries at their Rathcoole centre of the new Cingo, a wholly new addition to the Merlo range which McHale claims is ‘tailor-made for the small contractor and rental market’.
Described by their sales director, Denis McGrath as ‘a hugely innovative range of tracked carriers’, Cingo is designed for small-scale construction, agricultural, landscaping and utilities contractors whose needs can be met by a transportable and versatile trailer-size machine. Four types of machine make up the wide range available, all with rapid coupling devices allow numerous different attachments to be used. With capacities from 400 kg up to 1200 kg, the compact and easy-to-handle Cingo is made for working in tight spaces, along narrow passages and through smaller than normal doorways. Helping is its and its skid-steer and counter-rotational tracks. With easy-to-use hydraulic controls and hydrostatic transmission – and a stepon, stand-on operator platform – the Cingo has a low centre of gravity that ensures maximum stability on slopes, with tracks that apply less ground pressure and provide greater adherence on uneven and irregular terrain. Versatile and hugely functional, the multitasking Cingo is equipped to tackle a myriad of uses that include conventional transporting and loading of materials. Beyond that, excavating, transport, concrete mixing, tipper and self-loading dumper uses in construction; maintenance of green spaces and landscaping functions; road and forestry cleaning and snow clearing; and agricultural and animal care functions are cited amongst its many applications.
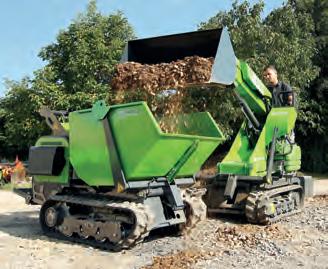
HIDROMEK’S FUEL EFFICIENCY AND DEALER SUPPORT WINS OVER ARC QUARRIES
A combination of exceptional fuel efficiency and a high level of dealer support mean the team at ARC Quarries Limited based at Macosquin in County Londonderry have had no regrets in switching to the Hidromek brand.
The quarry operators have two Hidromek 390 LC excavators and a 640 wheeled loader and when we visited the site they were busy feeding a couple of Tesab 800 jaw crushers. “We work the machines maybe up to 12 hours a day,” says ARC Quarries’ co-director Ryan Caldwell, “and so far they haven’t let us down. They have exceeded our expectations, especially on fuel economy.” Adds Ryan: “Our Hidromek 640 loading shovel, for example, operates for long periods each day and uses around 17 litres of fuel an hour, while other brands we have used in the past took 33 litres an hour doing the same work. That represents a significant cost saving to us.” He particularly appreciates the fact that the Hidromeks come with a three year/ 6000 hour warranty which gives him extra peace of mind, and he was full of praise for Maghera based AJ Armstrong, who are Hidromek dealers for Northern Ireland and Donegal. The company was formed in 2005 by Andrew Armstrong mainly offering a servicing and repair service for JCB farm equipment and excavators. Since then the business has grown and developed into selling a range of quality used machines and three years ago took on the sales and servicing of the Turkish built Hidromek brand. AJ Armstrong has its own fleet of five service vans on the road and also has a parts specialist and service manager. “I couldn’t speak too highly of Andrew and his team. The service and support we have had from them is exceptional,” says Ryan. “If we ever need assistance, and it has been a rare occasion, they respond within the hour, which is essential as our operation cannot afford any unnecessary downtime.
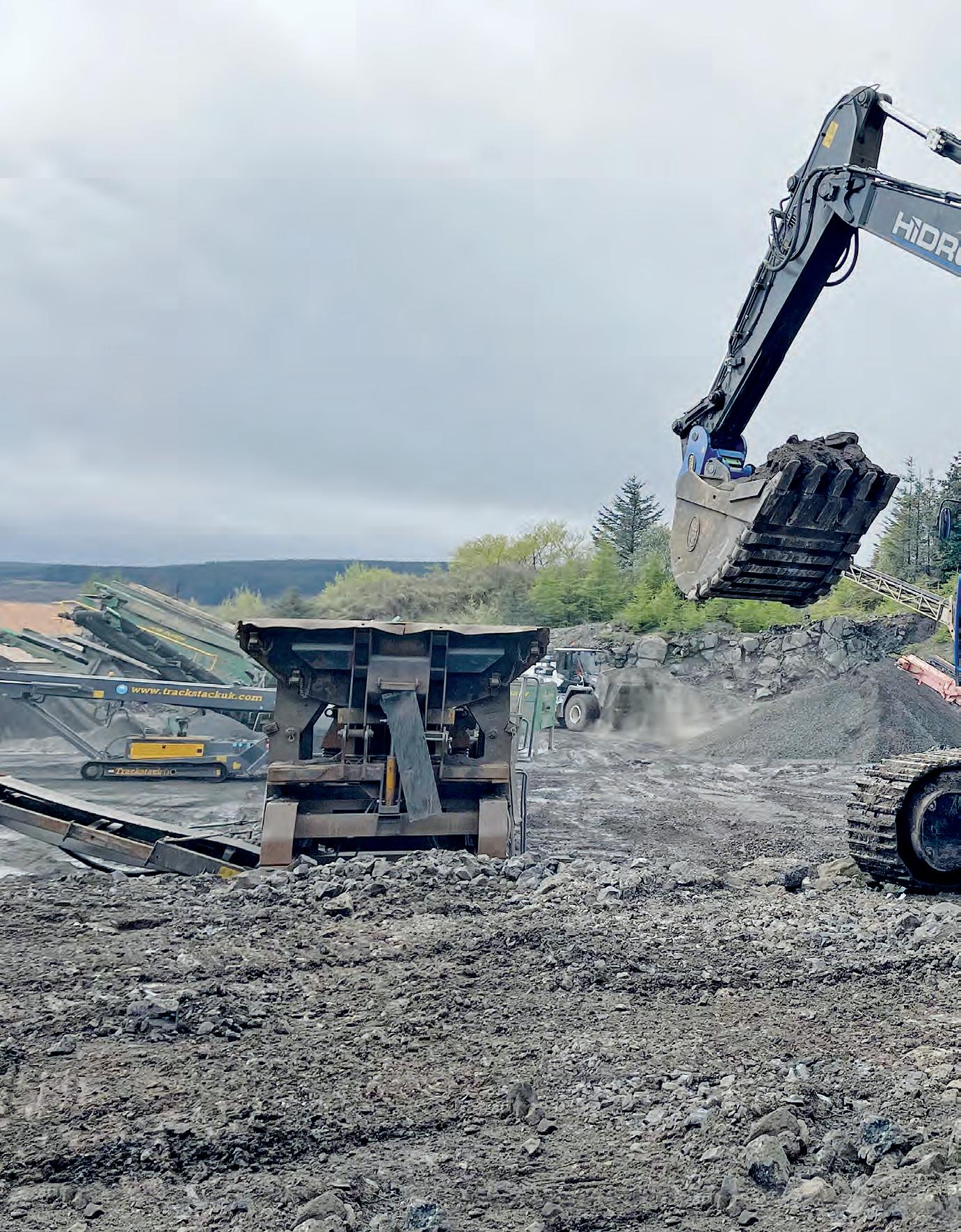
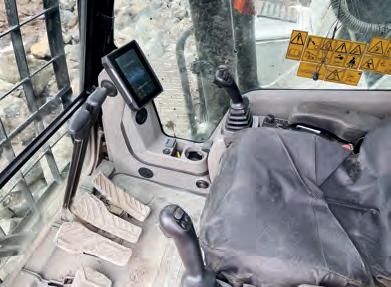

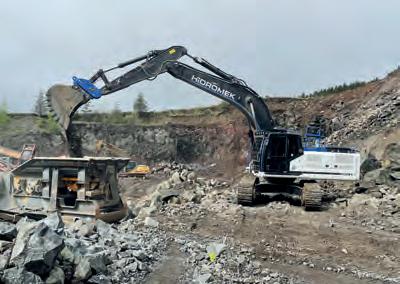
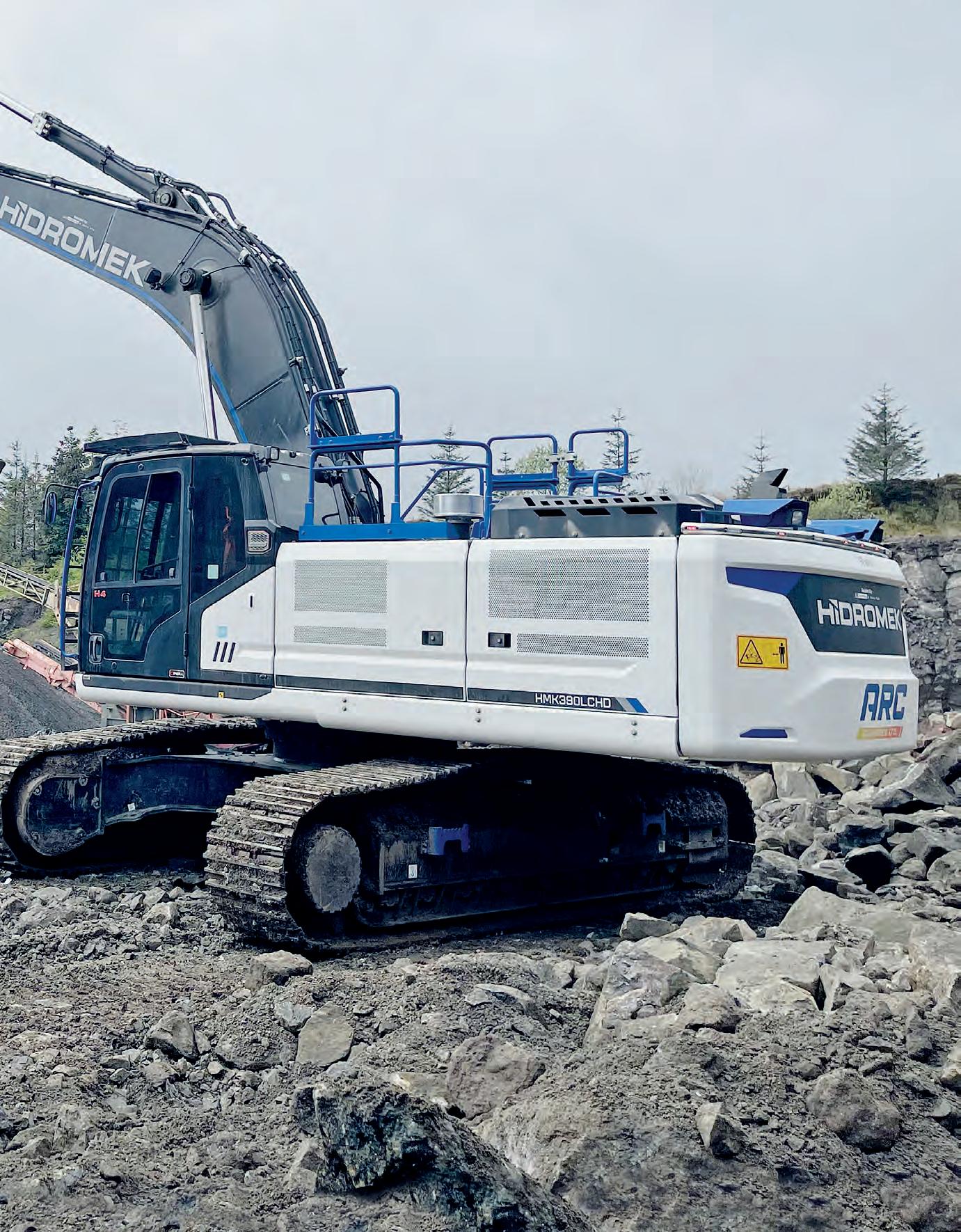
VIDEO STORY
HMK 390 LC EXCAVATOR SCAN THE QR CODE TO WATCH THE VIDEO.
“Up until we switched to Hidromeks we ran a couple of different branded excavators and shovels, and we have no regrets.” It was just last year when ARC Quarries invested in a Hidromek 640 loading shovel and a HMK 390LC excavator, and several months ago acquired a second 390, which is one of the biggest in the range at 42 tonnes OPERATORS IMPRESSED
“We were very pleased with how the Hidromek 640 wheel loader was performing, so we had little hesitation in acquiring a 390 excavator, adding a second 390 a couple of months later,” says Ryan. The 390 machines are well built with quality components, are reliable and are very stable at work. Our operators love them. They tell us they are easy to handle, perform very well and have a comfortable cab. “Like we discovered with the 640 loading shovel, we also find the Hidromek 390s are using about 16 to 18 litres per hour while some other excavators we ran were burning 30 litres per hour which again represents a significant saving, especially as fuel costs are continuing to increase.” As Ryan mentioned, the Hidromek 390LC features all top-quality components including an Isuzu engine, Kawasaki hydraulic pumps, Nabtesco Japanese slew motor and final drives. It is a big step up in comparison to the earlier 370LC model in the Hidromek range, featuring as it does much smoother and sharper lines and a brand new upgraded, restyled cab that offers an excellent working environment for the operator. This latest generation model also benefits from a relocated switchboard, remodelled travel pedals and levers, high capacity air-conditioning and high-resolution LED backlight colour LCD display.


CONTINUED
Other features enhancing the operator’s comfort is the new versatile and fully adjustable seat designed to enable him to work without stress and fatigue for longer hours. The joystick console and seat can move independently so the operator can easily adjust it to the most suitable position for his body structure. The cab is supported by 6 silicon viscose mounts that dampen the effects of noise, shock and vibrations regardless of working conditions of the machine. There’s plenty of storage space, too, for the operator’s bits and pieces, including a cooled storage room, glass holder and a variety of storage pockets. INNOVATIVE CONTROL SYSTEM
The 390LCHD is fitted with Hidromek’s Opera Control System, an easy to use interface that facilitates communication between the operator and the machine. The operator can easily switch between menus in Opera, change settings, such as hydraulic flow, and check the status of the machine, including pressure, temperature and engine load. The information and warnings on the instrument panel are always easy to see and control, thanks to the positioning of the Opera interface. Other features of the system include automatic powerboost switch-on switch-off, automatic electric power-off and automatic powershift to improve performance. HMK 640 WHEEL LOADER
The heavy duty HMK 640 wheel loader, meanwhile, boasts a 26.3 tons operating weight and a 4.2 m³ bucket capacity, and with its Mercedes engine having 324 hp and 1600 Nm torque, it offers a high loading capacity in a short cycle time. The operator enjoys a panoramic view from the well sound proofed cab, with a rear view camera and heated rearview mirrors. The working environment is further enhanced by the provision of a fully automatic air conditioning system, together with other features including a heated seat with air suspension and which can be adjusted to suit the operator’s preferences. A large, touch sensitive, digital LCD display gives the operator full control over essential machine information, while a dual speaker AM/FM radio with USB input can make the working day even more enjoyable – and access to the cab is made safe and easy thanks to well designed and positioned steps and handles. As with the HMK390s, the wheel loader also features the Opera control system that brings together vital information and functions required during the operation of machine. Meanwhile, a TIPSHIFT function makes it possible to change the direction quickly by pressing a single key without using the gear lever when the machine is moving forward or backward while loading or unloading. This increases productivity and ensures safe operation without the loss of steering control. Not surprisingly, the 640 wheel loader has won international design awards such as Reddot Award, German Design Award, Good Design and Automotive Brand Contest, and like the 390 excavators, it is completely at home at ARC Quarries.
VIDEO STORY
HIDROMEK HMK 640 WHEEL LOADER SCAN THE QR CODE TO WATCH THE VIDEO.
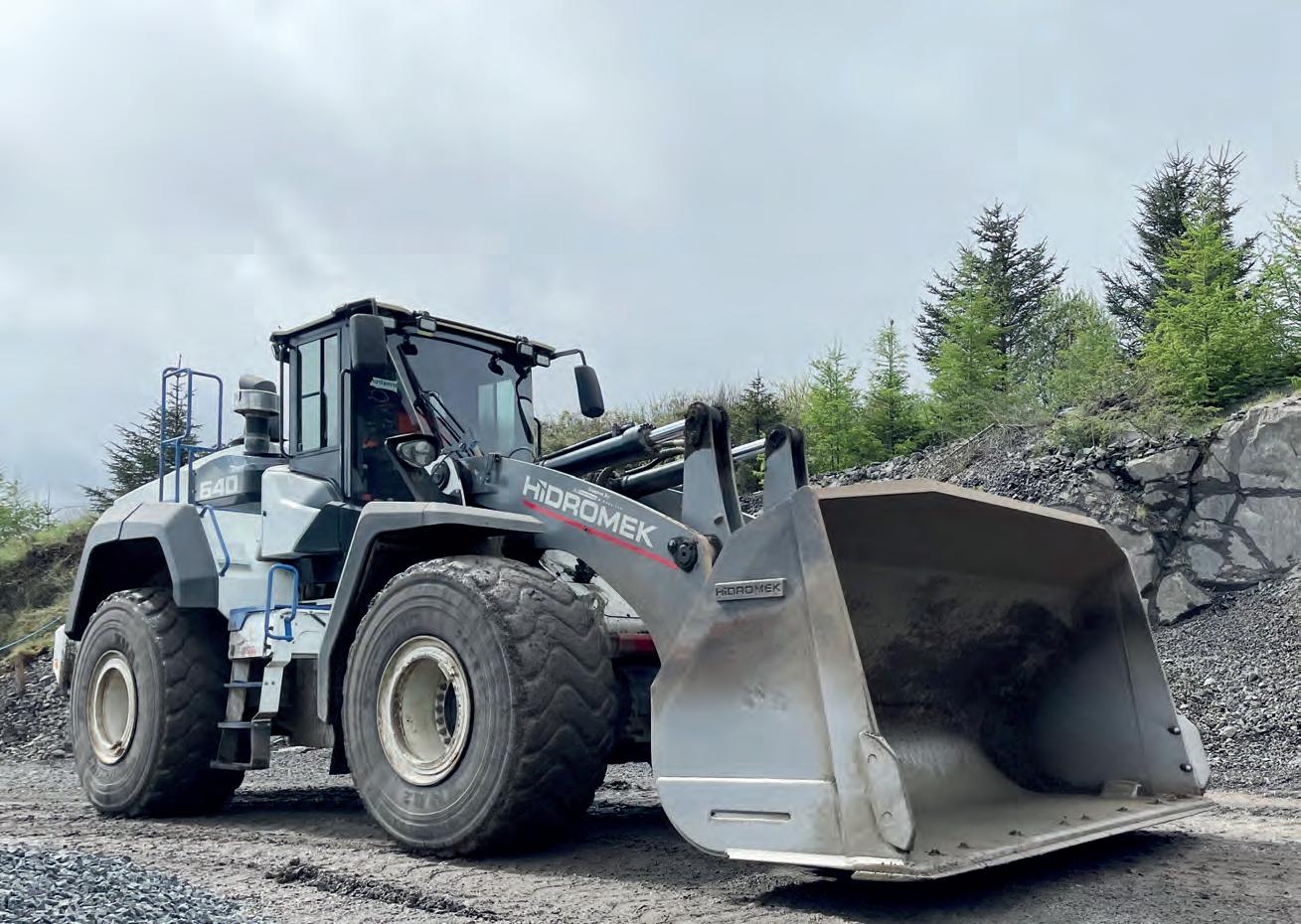
news Engcon Launches Third Generation Tiltrotator
engcon will launch its third product generation in 2022. To meet future demands, the new tiltrotator system is taking progressive steps towards sustainability, applying smart technology to reduce energy consumption and is adapted ready for the electrification of excavators.
The integrated and user-adapted system builds on engcon’s successful concept – an increased profitability with flexibility that provides greater comfort and safety for the end user. The third generation tiltrotator system was presented for the first time at the Norwegian trade fair Vei og Anlegg in May and production will begin in the second half of 2022. The technology is based on a newly developed type of valve in combination with a smart software that collaborates with the excavator’s load-sensing hydraulic system. This optimises both the tiltrotator’s functions and the excavator’s excavator movements, which leads to smoother digging with higher precision. At the same time, the excavator’s wear and need for maintenance also decreases. “Our new tiltrotator system shows that engcon is at the forefront of innovative solutions that drive the development forward to reduce dependence on fossil fuels and thus the climate impact of excavators,” says Stig Engström, founder and owner of engcon and the leader of the company’s product development. With an app, the third generation tiltrotator system also enables a higher degree of individual customisation in the form of improved possibilities for, amongst other things, connected remote diagnostics and mobile support. In addition to the energy-efficient technology, the new series EC-Oil, the automatic quick hitch system can easily and smoothly connect the tiltrotator and hydraulic gear automatically, without the driver having to leave the cab. For full compatibility with today’s modern excavator systems, engcon also builds in a newly developed tilt and rotation sensor as standard in this third generation product. The sensors contain one of the market’s first “absolute” sensors and have a Plug & Play solution for both integrated and third-party machine control systems. “The third generation will be our premium offering where the excavator operator gets the very latest technology as standard, while at the same time they get an energyoptimised excavator that becomes even smoother to drive,” Engström comments.
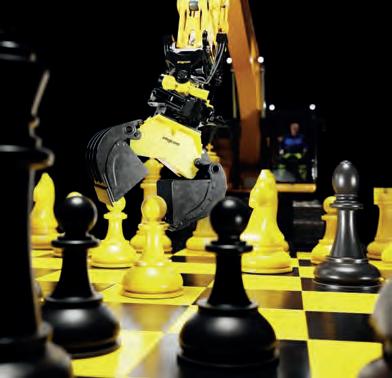
Successful 2022 European Dealer Conference for Doosan
Under the theme of UNITE 2022, Doosan held the company’s European Dealer Conference in Barcelona recently; the company normally organises these meetings every two years and the last one was held in Lisbon in February 2020.
The event had an audience of 182 attendees, 134 of which were Doosan European dealers from 22 countries. Among the attendees were members of the Hyundai Doosan Infracore executive team from Korea, as well as managers from various areas of the company. Seunghyun Oh, CEO of Hyundai Doosan Infracore, opened the day with a keynote speech about Hyundai Doosan Infracore globally. He spoke about the company’s achievements, product portfolio, proven product quality, opportunities and new technologies for the future. He also described the global market outlook and the strategic direction of the company. He confirmed the record market share in Doosan’s markets including wheel loaders and crawler excavators, with record sales in 2021and reminded the audience of the great development capacity at Doosan, with the launch of 20 new machines last year and the multiple international awards won by various Doosan models.
Dealer Awards
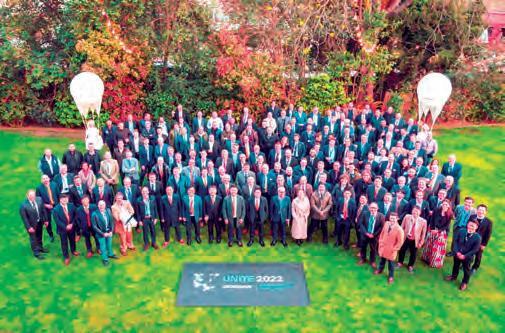
Some of the dealers attending made presentations about their trajectory and growth, sharing their experiences with the rest of the audience. This was followed by a panel discussion, break-out working sessions, a gala dinner and team-building entertainment activities. Under the UNITE 2022 theme, the presentations at the Doosan conference showed the participants that they were all united by their passion for construction equipment, the Doosan brand, the best product - innovative and competitive, and that they also shared the success and recognition of customer satisfaction with the brand and service, which together resulted in ever stronger and more united dealers. The conference also emphasised the company’s slogan, ‘Powered by Innovation‘, defining innovation as one of the pillars of the company, including its vision as a world leader in infrastructure solutions. The event also confirmed health, safety and the environment as the number one management priority. On a final note, in lieu of corporate gifts for attendees, Doosan decided instead to make a donation to Médecins Sans Frontières/Doctors Without Borders (MSF), the international medical humanitarian organisation. As we all know one country where the help of MSF is much needed now is Ukraine and teams from the organisation are working hard to deliver emergency medical aid to people still in Ukraine, as well as those now seeking safety in neighbouring countries
Metso Outotec develops new electric Lokotrack range
In response to the growing demand for sustainable solutions, Metso Outotec is conducting a programme to develop a new, complete range of electrically driven track-mounted crushers and screens.
The new Lokotrack range will be built on a unique platform that Metso Outotec has been developing since 2020 with a total R&D investment of €20 million. The development work will take place primarily at Metso Outotec’s technology center in Tampere, Finland. The platform concept has now been developed, and Metso Outotec is currently entering the design phase of the first new products. The new Lokotrack range will be transformational for the whole aggregates industry of mobile crushing and screening. This will also significantly contribute to Metso Outotec’s Planet Positive strategy and its commitment to reach the 1.5 C climate target. “The next generation Lokotrack range will address the needs of our crushing and screening customers by providing new easy-to-use diesel-electric equipment,” comments Renaud Lapointe, Senior Vice President at Metso Outotec’s Aggregates business area. “The possibility to run track-mounted machines from an integrated genset or to connect to an external power source lowers operational costs and allows access to renewable energy for our customers,” he continues. The new unique platform will enable a faster and more agile way to develop products and reduce the number of components. “Using one common architecture throughout the range allows scalable solutions that can be seamlessly combined and adapted for different applications and capacities. Harmonised design together with advanced digital solutions enables our global service network to support the customers throughout the entire equipment lifecycle,” says Jarmo Vuorenpää, Director, New Lokotrack Offering, Aggregates business area at Metso Outotec. The concept of track-mounted crushers and screens was developed in Finland in 1985 to minimise the cost and energy use. Lokotrack has made it possible to provide on-site mobility close to the processed raw materials lowering transport and hauling costs and emissions. During the last 35 years the concept has grown significantly with thousands of units manufactured and sold globally every year.

PLANT & CIVIL
Find us on Facebook
Plant & Civil Engineer
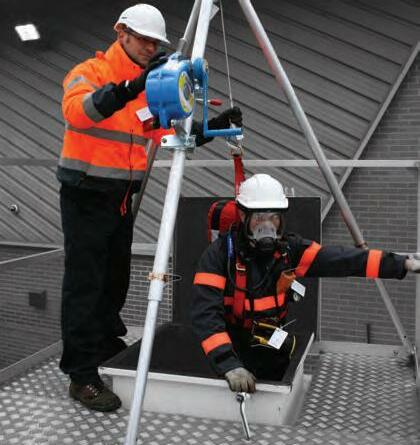

CONFINED SPACE SAFETY Reliable & industry-leading safety equipment for use in hazardous environments, major shutdowns and working at height
SURVEY EQUIPMENT A wide range of quality survey products offering precision technology for use in the surveying, civil engineering & construction industries ENVIRONMENTAL MONITORING Test & measurement equipment from leading manufacturers offer the perfect tool for monitoring the environment
THINK SAFE. WORK SAFE. BE SAFE.
Groundforce Safety is Ireland’s
leading supplier of safety, survey and environmental monitoring equipment. Our extensive rental fleet is maintained in specialist workshops and delivered by trained driver technicians.
www.vpgroundforce-safety.ie
SERVICES OFFERED: RENTAL, SALES SERVICE, TRAINING & SAFETY & RESCUE
Contact:
Lisburn 0800 783 2055
Mountmellick 1890 882 364
Groundforce Safety
TEREX FINLAY ANNOUNCES COMPANY REBRAND CELEBRATING THEIR “STRONG HERITAGE, STRONG FUTURE”
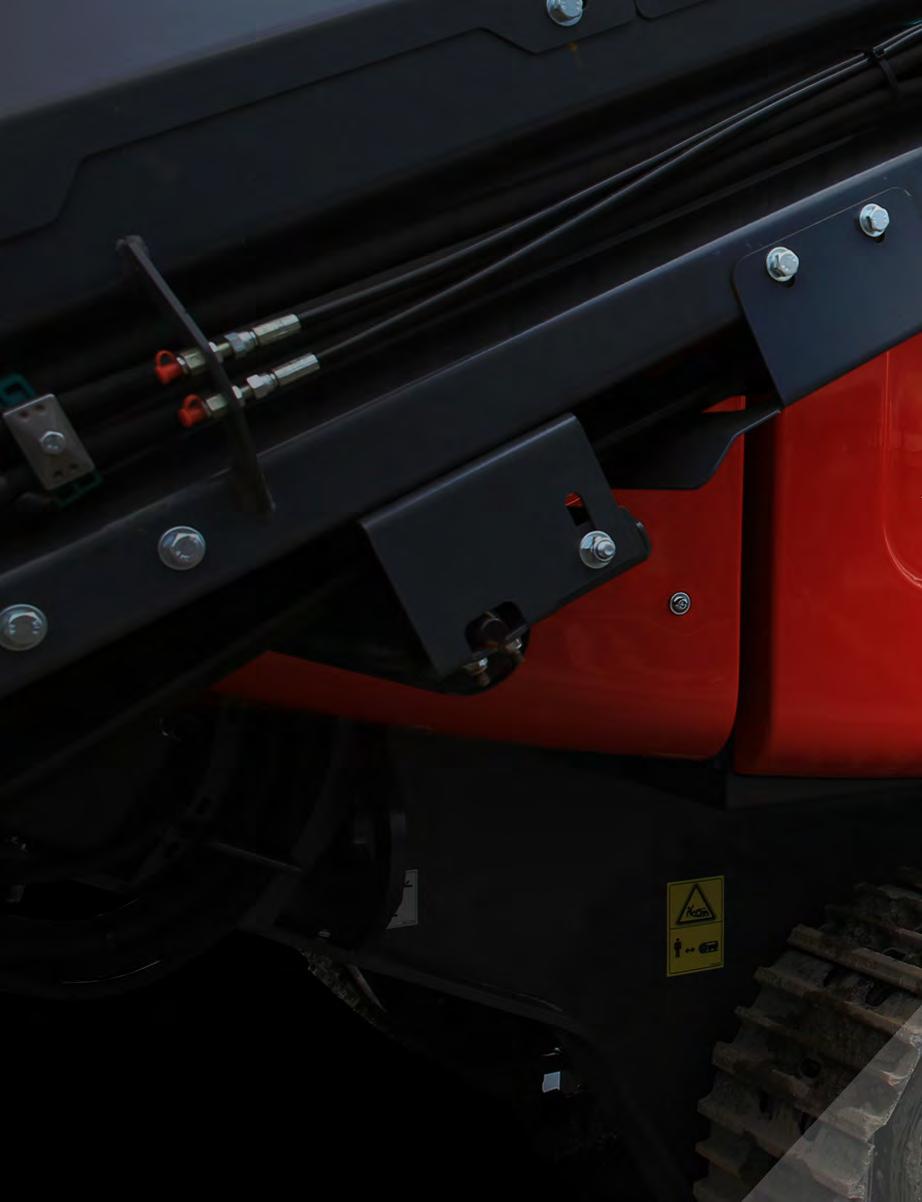
Northern Ireland based Terex Finlay has announced a rebrand of the business to update and refresh its image based on its traditional core values and future strategies.
The business is to rebrand globally as ‘Finlay’ to include a new logo, slogan and a new house style for its marketing collateral. Global Business Line Director, Matt Dickson explained that the rebrand is part of an on-going drive for improvement, growth and innovation across the business. “Our founder, John Finlay pioneered the concept of mobile screening equipment and his name has been iconic in the industry with a reputation built upon reliability and performance for over 65 years. In the past decade we have implemented an aggressive growth strategy focused on the delivery of the most comprehensive range of tracked equipment on the market today
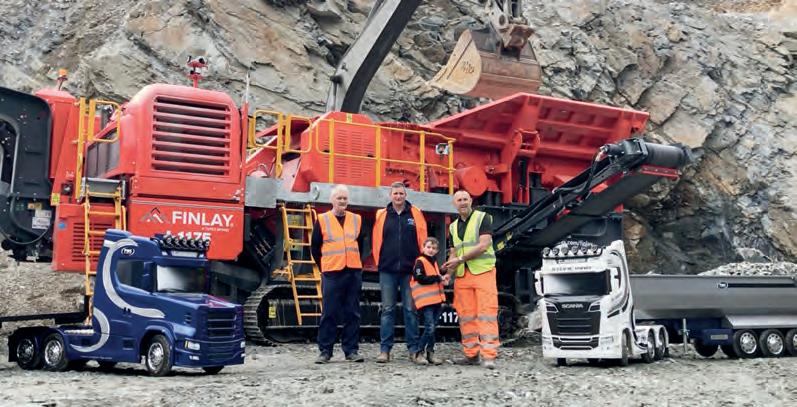
P Woods and Sons Ltd take delivery of the first Finlay branded machine in Ireland.
along with the infrastructure to support the machines globally. “Our product offering will forever evolve and expand to meet the needs of our customers. We already offer an extensive array of machines powered by hybrid technology and in the coming years we will further develop hybrid and electric powered equipment through our product road map based on the ‘voice of customer’ feedback that we have received.” Matt adds: “Aftersales service support and the deployment of digitalisation solutions to support this is key to ensure we remain at the top of our
FINLAY
A TEREX BRAND STRONG HERITAGE, STRONG FUTURE
industry. Through extensive market research with our dealers, partners and customers, we realised the importance of developing our brand identity to reflect our history, success and status in the global market for tomorrow’s customer. Adopting the new Finlay logo, offers a fresh and modern approach, yet familiar with our extensive history. “The new slogan ‘Strong Heritage, Strong Future’ reflects on the strength and depth of our heritage, which encompasses the attributes in our products such as innovation, performance and reliability, complimented by the service and support associated with our dealer network. The strength within the future of the brand, advocates our future strategies across product and geographical development, operational improvements and support services.’’ Commented Neil McIlwaine, Business Development and Marketing Director: “The rebrand will include a full suite of internal and external marketing material, refreshed social media and digital channels, integrated into a modernised and refreshed website. “The new identity has been purposefully designed to be adaptable across both traditional, and new digital communication platforms. We are well placed for the future, focused on continuing our growth and strengthening our brand. “Our bold, new identity is a visual signifier of our position as one of the world’s leading crushing, screening and conveying manufacturers and we are excited to deploy our products and services for the years ahead,”

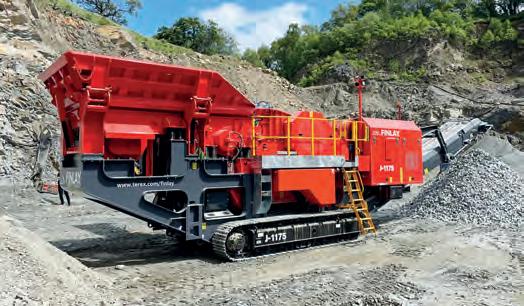
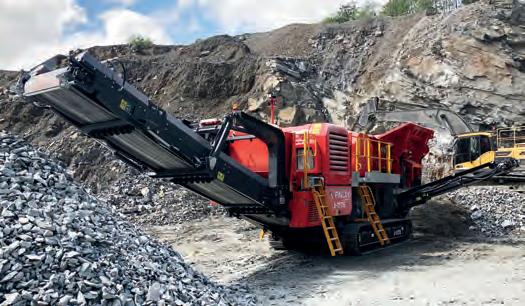