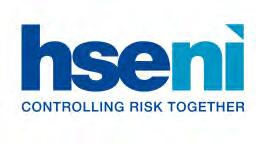
18 minute read
HSENI Safety Alert: Mast Climbing Work Platforms
HSENI have issued a safety alert on mast climbing work platforms. The alert is intended to tell industry, employers, duty holders and workers that use Mast Climbing Work Platforms (MCWPs) that a serious technical fault has been identified by the Health and Safety Executive (HSE) in Great Britain.
Mast climbing work platforms (MCWPs) are used widely across construction projects. These can be used in other industries for access and to maintain large plant. Platforms could fall from height where mechanical faults in drive units go undetected. If not rectified quickly, the fault could cause serious injury, or even death. The safety alert has information and advice on what to do if you supply, install, use, inspect, service, maintain or examine MCWPs for use at work. HSE has discovered that some MCWPs, which rely on two independent motor drive units per mast as the means to prevent the platform falling with overspeed, are not fitted with suitable and sufficient controls to manage this risk. This means work platforms could fall from height where mechanical faults in drive units go undetected. If not rectified quickly, the fault could cause serious injury, or even death. Failures in drive units can be such that neither the centrifugal brakes (intended to limit the speed of descent) nor the automatic brakes (intended to engage when powered travel is stopped) within the drive units are able to have an effect. Malfunctions in drive units which endangers proper function are foreseeable and unless a means of detection of such malfunctions is provided there is a risk of platforms falling with overspeed.
Immediate action required
You are advised immediately to check that the necessary control measures are in place for all MCWP in use or available for use at a work. If the control measures are not in place, you need to withdraw the MCWPs from use until those responsible for supply, installation, use, inspection, servicing, maintenance and for thorough examination of MCWPs ensure that: - there is the means to identify a loss of mechanical integrity in each drive
unit where this is the system to prevent falling with overspeed - each individual drive unit is fitted with a mechanical device, eg centrifugal brake, that automatically prevents the work platform descending at excessive speed - damage to drive units due to platforms being powered onto buffers/base frames is prevented - platforms and associated equipment are not damaged by physical overloading - thorough examinations, inspections and tests, and visual and functional checks are appropriately planned and carried out. Detect malfunctions in each drive unit which endanger proper function: Where two or more drive units are installed as the system to prevent falling with overspeed, you should ensure that: - there is the means to detect malfunctions in each drive unit that could indicate a loss of mechanical integrity which results in a differential in the current demand between each drive unit, exceeding 25% of the full load current - detection is in accordance with the manufacturer’s instructions, eg it initiates a stop command and generates audio-visual alarms - the means of detection is functionally tested in accordance with the relevant technical standard or the manufacturer’s instructions. Prevent falling with overspeed: Where two or more drive units are installed, you should ensure that each individual drive unit is fitted with a mechanical device, eg a centrifugal brake, that automatically prevents the work platform exceeding 0.4 m/s descent speed. Prevent failure of the automatic brakes you should: - ensure operators are competent and conform to the manufacturer’s
instructions for emergency lowering of the platform, eg to prevent overheating - check brakes for wear and assess them against discard criteria in accordance with manufacturer’s instructions - carry out functional checks of the individual automatic brake on each of the paired drive units in accordance with the manufacturer’s instructions. Prevent damage to drive units caused by contact with buffers or base frames due to the platform being powered down onto them, you should: - ensure limit switches are appropriately positioned such that the lowest level that stopping is initiated by a terminal switch is achieved before contact with the buffers (and before contact with the final limit switch) - Include functional tests of limit switches in checks and maintenance inspections. Prevent damage due to physical overloading you should: - clearly and indelibly affix to the platform the safe working load for configuration of the platform - include functional testing of the overload warning device(s), if fitted, in maintenance inspections Prevent failure due to defects or deterioration being undetected, as part of your risk management and control arrangements, you should: - review your risk assessment with a focus on periodicity of inspections and thorough examinations and tests, with reference to national regulations and the manufacturer’s manual - ensure periodic inspections, measurements and checks include those items listed by the manufacturer in their maintenance and service schedule - ensure checks and inspections are undertaken only by those competent to do so. Or you need to take equally effective measures required to comply with Regulation 4 of the Provision and Use of Work Equipment Regulations 1998.
PLANT & CIVIL
HSE action
Where MCWPs are found in use or available for use without suitable controls to manage the risk set out above HSE enforcement action will be taken in line with enforcement policy and procedures.
FOLLOW US ON
PLANT & CIVIL
CONSTRUCTION, QUARRY & RECYCLING MAGAZINE AWARDS2022 SAVE THE DATE THURSDAY 24th NOVEMBER 2022

CROWNE PLAZA, SHAW’S BRIDGE, BELFAST. www.plantandcivilengineer.com
news Steelwrist extends quick coupler and tiltrotator range
Steelwrist’s new range of SQ50 quick couplers and tiltrotators is targeted toward 7-13 ton excavators; the SQ is a high performing fully automatic oil connection technology, used in quick couplers and tiltrotators on excavators to connect hydraulic work tools.
Outstanding flow characteristics and competitive building height and weight are significant advantages of SQ50 which meets the specifications of the Open-S standard for fully automatic quick couplers. The SQ50 will be phased in on X12 and X14 tiltrotators which means that future S-type quick couplers and tiltrotators will be upgradeable to SQ-type. S50 and SQ50 quick couplers are steel casted and have the Steelwrist Front Pin Lock safety solution. Front Pin Lock is a mechanical lock of the front shaft which significantly limits the risk of an unintended drop of work tools. The X12 and X14 tiltrotators are redesigned with a new top and attachment coupler in order to make it possible to upgrade from S50 to SQ50 at a later stage, even if the customer did not include SQ in the initial order. The new generation X12 and X14 tiltrotators will start to ship out during the third quarter 2022. SQ on the top side (upper coupler) of the tiltrotator for rapid change between tiltrotator and other work tools, and SQ on the bottom side (attachment coupler) of the tiltrotator will allow for rapid change between hydraulic work tools. By using SQ, tiltrotator work tools can be made less expensive as the rotation function is included in the tiltrotator. “With the introduction of SQ50 fully automatic quick couplers and tiltrotators, we will change the game in the growing 10 ton excavator segment with flow capacities of 120 litres per minute with low back pressure. This allows for efficient use of high flow work tools also for mid-size excavators,” says Stefan Stockhaus, CEO of Steelwrist AB. With the introduction of SQ50 the Qplus technology has been updated to allow for even higher flows, adding another 20 percent to flow capacity which allows users to run also the high flow requiring work tools on mid size excavators. With the introduction of SQ50 Steelwrist will during 2022 also introduce a new Absolute Rotation Sensor in order to give higher accuracy to Machine Control Systems. Together with Steelwrist Autotilt this allows for even higher productivity. All Steelwrist SQ products follow the global Open-S industry standard for fully automatic couplers for excavators. This means that the SQ system is designed to be able to connect to other brands following the Open-S standard.
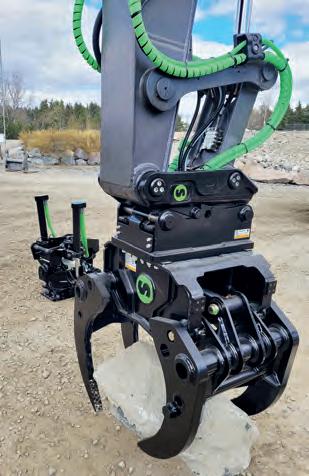
MyMecalac Connected Services telematics now available for site dumpers
Mecalac Construction Equipment UK has announced the international roll-out of state-of-the-art telematics connectivity across its site dumper portfolio. The latest models can now be equipped with MyMecalac Connected Services, either as an option from the factory or as a retrofit kit.
Helping operators to minimise downtime and optimise productivity through real-time equipment data, MyMecalac Connected Services telematics provides a smart solution to enable remote fleet management. From insight into fuel consumption and productivity, to service reminders, maintenance alerts, remote diagnostics and geofencing capability, the innovative solution keeps fleets running at full speed and full efficiency. Comprising an in-depth web portal and handy mobile app, the service solves a number of industry pain points. It spotlights machines in need of immediate care and allows technicians to stay one step ahead of potential breakdowns. Mark Royse, Head of Sales at Mecalac Construction Equipment UK, commented: “MyMecalac Connected Services provides owners and operators with an incredibly powerful tool to manage their machines. Rolling out the state-of-the-art solution across our site dumper portfolios will help construction professionals to further increase equipment uptime and maximise productivity.” Alongside telematics capability, MyMecalac Connected Services also includes a startup digicode unit. Effectively an immobiliser keypad, the device requires operators to enter a specific code before starting the engine. With the ability to assign a specific code to each user, change codes at and time and programme expiration parameters, the digicode provides complete control of machine access. Royse added: “With equipment security paramount, especially for hire fleets, the inclusion of our start-up digicode system ensures complete peace-of-mind. At Mecalac, we are streamlining the ownership experience and bringing game-changing technology to our world-leading site dumpers.”

PLANT & CIVIL
CONSTRUCTION, QUARRY & RECYCLING MAGAZINE AWARDS2022 SAVE THE DATE THURSDAY 24th NOVEMBER 2022

CROWNE PLAZA, SHAW’S BRIDGE, BELFAST. www.plantandcivilengineer.com
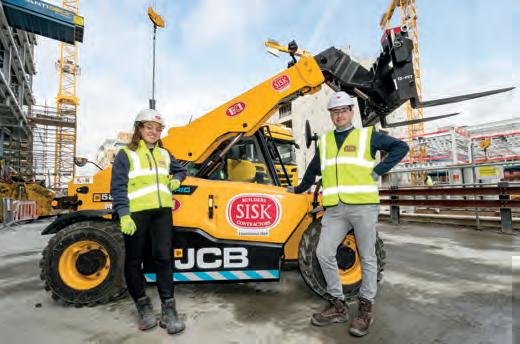
Engineer Megan Duffy and Ian O’Connor, Energy Manager, both John Sisk & Son. Ian O’Connor and Jim Worth from John Sisk & Son with Denis Murray, MD ECI JCB.
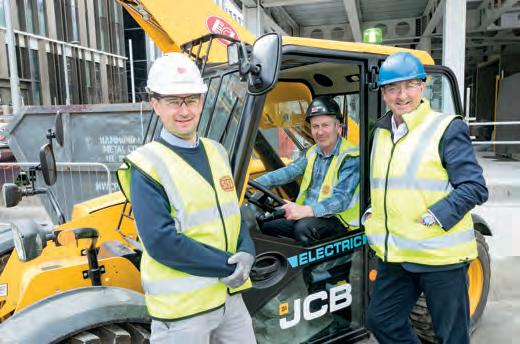
Sisk and JCB driving change with Ireland’s first electric telehandler
John Sisk & Son has become the first construction and engineering firm in Ireland to invest in an electric telehandler. The JCB 525-60E electric telehandler is 100 percent electric, zero emissions piece of plant machinery. This is a significant step in the Sisk sustainability journey, as they aim to achieve Carbon Neutrality by 2030.
With no diesel engine this new electric JCB telehandler offers near silent operations on site combined with health benefits of zero emissions and significantly reducing energy costs. It also has considerably lower operating costs compared to a conventional telehandler in terms of its maintenance requirements. The JCB 525-60E electric telehandler model has two electric motors – one for driveline, the other for lifting operations – powered by a 96-volt lithium-ion battery. The hydraulic system is completely new and also features ‘smart regeneration’ with power recovered during boom lowering and retraction fed back into the battery. JCB state this new innovative telehandler, charged by 24kWh battery, powers a full day on a single charge. Ian O’Connor, Energy Manager, John Sisk & Son said: “We are very excited to receive this next generation JCB electric telehandler, the first of its kind in the country. By the end of Quarter 1 this year, Sisk will have invested almost €2m in our Plant renewal and expansion programme. Each investment includes a weighting to carbon output as part of our investment criteria. With the inception of our 2030 Sustainability Roadmap in 2021, Sisk has a clear vision aligned with United Nations (UN) Sustainable Development Goals. This investment is a major milestone towards achieving our goal to be carbon neutral by 2030 while supporting clients and the wider community in achieving their own goals.” Denis Murray MD ECI JCB comments: “It is fantastic to see Ireland’s leading provider of construction services embrace this pioneering technology as it continues its impressive sustainability journey. We are proud to support John Sisk & Son and to see our first electric Loadall in Ireland working on high profile projects in Dublin City Centre.” Paul Mabey JCB Electric Technology Sales Manager: “JCB is the world market leader for telescopic handlers and the introduction of the JCB 525-60E Loadall means equipment electrification can now spread further into the general construction and industrial sectors. Designed to deliver the same performance as the conventional diesel-powered machine, the 525-60E enables zero-emissions operation when working inside buildings, in underground construction and maintenance work or in urban areas with stringent emissions regulations and low emissions zones. It is proving extremely popular with those organisations striving to be at the forefront of reducing the carbon footprint of the industry.
R&D Spending in Construction Rises to New Record
R&D spending in the construction sector surged 18% last year to a new record high despite ongoing pandemic disruption, according to the latest ONS data analysed by innovation funding specialist Catax.
The ONS recently published its Q4 2021 statistics for R&D spending, completing the fullyear picture. R&D spending is important to the UK economy because it creates skilled jobs and helps UK firms compete for revenue and foreign investment in globalised markets, particularly where new technology is concerned. The construction industry spent £471m on R&D in 2021, up from £399m invested in 2020. The increase came despite continued supply chain disruption caused by Covid19. The quarterly total rose to £121m in Q4, also a record high. R&D spending has continued to grow despite the pandemic, and was £121m higher during 2021 than its pre-pandemic total of £350m recorded in 2019. The construction sector’s performance was significantly better than the performance of UK industry as a whole. Total R&D spending by UK businesses rose 5.6% to £42bn last year. By comparison, GDP in 2021 was up 7.4%% on an annual basis according to the ONS2. The ONS R&D spending statistics don’t factor inflation, which was running at an annual 5.4% in December last year3. Mark Tighe, CEO of R&D tax relief consultancy Catax, comments: “Construction might have ground to a halt in the early days of the pandemic but the sector’s R&D spending has kept motoring. This is a very positive sign, particularly against the backdrop of big strides being made in innovation as the industry builds an eco future for housing and building. The UK is all about the race to net zero now and construction has a huge role to play.”
Auger Torque launch Cone Crusher Bucket
Manufacturer and global provider of earthmoving attachments Auger Torque have added a Cone Crusher Bucket to their product portfolio.
Promising to save the user time, money and hassle, Auger Torque have developed the Cone Crusher Bucket – engineered to work with excavators (2.5T to 8T), skidsteers, backhoes and telehandlers. It provides a simple, efficient, and costeffective way to reprocess and/or recycle small volume construction rubble and debris into useable aggregate. With an output of 5T-10T per hour (depending on your material), the cone crusher bucket, saves on transport costs of removing onsite waste, material costs of importing hardcore to site, and minimal site traffic, delays and hassle. From general clay construction brick, light concrete walling blocks, hollow concrete ‘breeze blocks’, concrete pavers, asphalt and more, the Auger Torque Cone Crusher Bucket can crush to an output produced material size of up to 70mm. Ideal for use in applications including foundation laying, track and yard surfacing, landscaping, roadways or using as a base layer below poured concrete or filling a disposal skip most efficiently.
Key Features
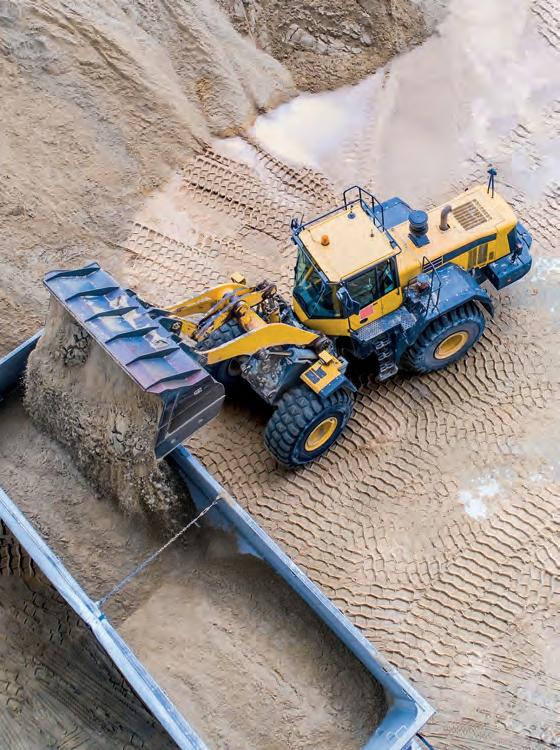
• Easy to use and compact for small working sites - compatible with excavator, backhoe skidsteer, telehandler • Bucket mouth for effective scooping and sorting • Seven-sided rotating cone inside a cylindrical drum • Grinding faces made in steel and tungsten carbide • Built around a series 3.5 sub gearbox • Auger Torque’s industry leading warranty Matt Hencher, Global Engineering Manager says: “The cone crusher bucket is a great product to add to our portfolio, perfect for construction, agriculture, farming, estates and so on. It removes the hassle factor of arranging skips to take rubble away and waiting for hardcore to be delivered. “With sales already in UK and Europe, and 60,000 views of our video on Tik Tok, we’re really excited for the opportunities this product presents across all our locations.”

RFID detection system
ZoneSafe uses Radio Frequency Identifi cation (RFID) technology to create detection zones around vehicles and mobile plant.
Vehicle-mounted antennas detect RFID tags which can be worn by workers, or placed on objects or property. When a ZoneSafe tag enters a detection zone, the vehicle operator receives a visual and audible alert. A vibrating tag also warns the detected worker of an approaching vehicle. ZoneSafe RFID technology does not require line-of-sight and tags will be detected regardless of obstructions, blind spots, adverse weather or poor visibility.
01322 420300 brigade-electronics.com
THE SUSTAINABLE EVOLUTION OF BUILDING MACHINERY
If you work in the construction industry, building machinery might be commonplace in your everyday life. So why not take this opportunity to explore the evolution of building machinery?
Here, we will explore the origins of advanced building equipment, specifically the cherry picker and the crane. This will consider the sustainable changes made recently, using expert commentary to explore the sector today. First and foremost, cherry pickers are invaluable on a construction site. Otherwise known as ariel lifts, these allow professionals to access those areas those hard-to-reach areas. It doesn’t matter which site you enter, you will probably see a worker or two utilising a cherry picker. But where do they come from? Cherry pickers have a fruitful history. Invented by Jay Eitel in 1944, these machines were originally invented to make picking cherries hassle-free. It must have been tiresome to manually move the ladder between fruit trees, after all. So these weren’t originally intended for use in the construction industry, believe us or not. Eitel’s cherry pickers have been useful in many industries. Advancements in telecommunications, for example, have been propelled by its invention. This is no doubt due to the fact that professionals can install telephone cables with ease from a mobile vehicle. The list goes on, ranging from the cleaning and film industries to the fire and emergency services. Today, a cherry picker will look and operate a lot differently from its predecessor. Not only has the appearance and ability of these machines improved, but the motor functions have also evolved to meet consumer demands. To achieve net zero by 2050, sustainability is at the forefront of UK development. Niftylift, a leading provider of cherry pickers, has invested in the distribution of hybrid aerial platforms. These combine diesel and electric motors, lowering the negative effects of carbon emissions. Nick Higgins, Chief Operating Officer of Niftylift, comments: “The hybrid cherry pickers are extremely popular with our customers. The low emissions make them ideal for use on restricted sites, in low emission zones, specialist applications and indoor work and will increase service levels and flexibility to our customers across the entire UK.” Overall, cherry pickers have come a long way since their relatively recent creation. The future looks bright for this piece of machinery as experts continue to improve and adapt their design. What do you think the next generation of cherry pickers will look like? CRANES
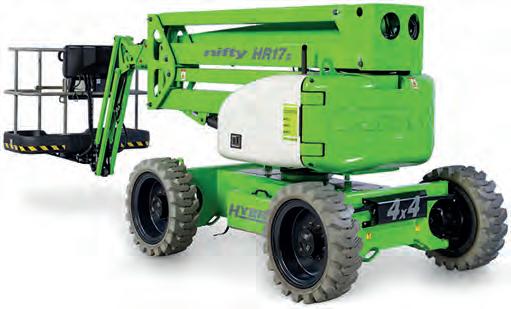
Cranes are also an important piece of building machinery. The origins of this piece of machinery are even more exciting than the cherry picker if we do say so ourselves. Historians have found instances of the crane being used as early as the sixth century BC. In Ancient Greece, cranes were used to build the stone structures we still admire today, such as the Parthenon. The inventions were also used in popular plays, such as Euripides’ Medea. But enough about ancient history – what does the crane look like now? Fast forward two thousand years and cranes are just as much of an integral part of any construction site. Today, they’re a regular feature in city skylines, helping to build skyscrapers. Similar to cherry pickers, cranes have also adapted to suit consumer demands for a sustainable nation. Liebherr, for example, has distributed electric cranes. These cranes do not emit any carbon into an already fragile environment, paving the way towards a carbonneutral company. In recent months, Liebherr’s cranes have started working on HS2, a high-speed rail network between London and Wigan. Ainscough Crane Hire has also decided to replace diesel and other natural fuels with hydronated vegetable oil (HVO). This will reduce their carbon emissions by 90 per cent. Peter Gibbs, CEO of this company, comments: “Our move to HVO fuel is not just a breakthrough moment for the domestic crane hire market – it’s a global first too. Our fuel usage is the most significant aspect of our carbon footprint, accounting for the vast majority of the business’ carbon emissions. By achieving this 95 per cent reduction and undertaking offsetting we have been able to make sure our company will be a carbon-neutral business within the first months of 2022.” Cherry pickers and cranes may have changed for the better, but the innovations don’t stop there. On any construction site, there will be multiple pieces of machinery that have interesting histories and are sure to have innovative futures. Which piece of equipment do you think will change with the environment in mind?
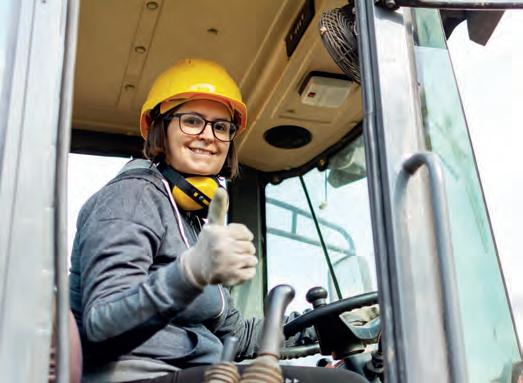