
32 minute read
Takeuchi Mini Diggers Big Hit with Kellys Point Hire Customers
TAKEUCHI MINI DIGGERS A BIG HIT WITH KELLYS POINT CUSTOMERSHIRE
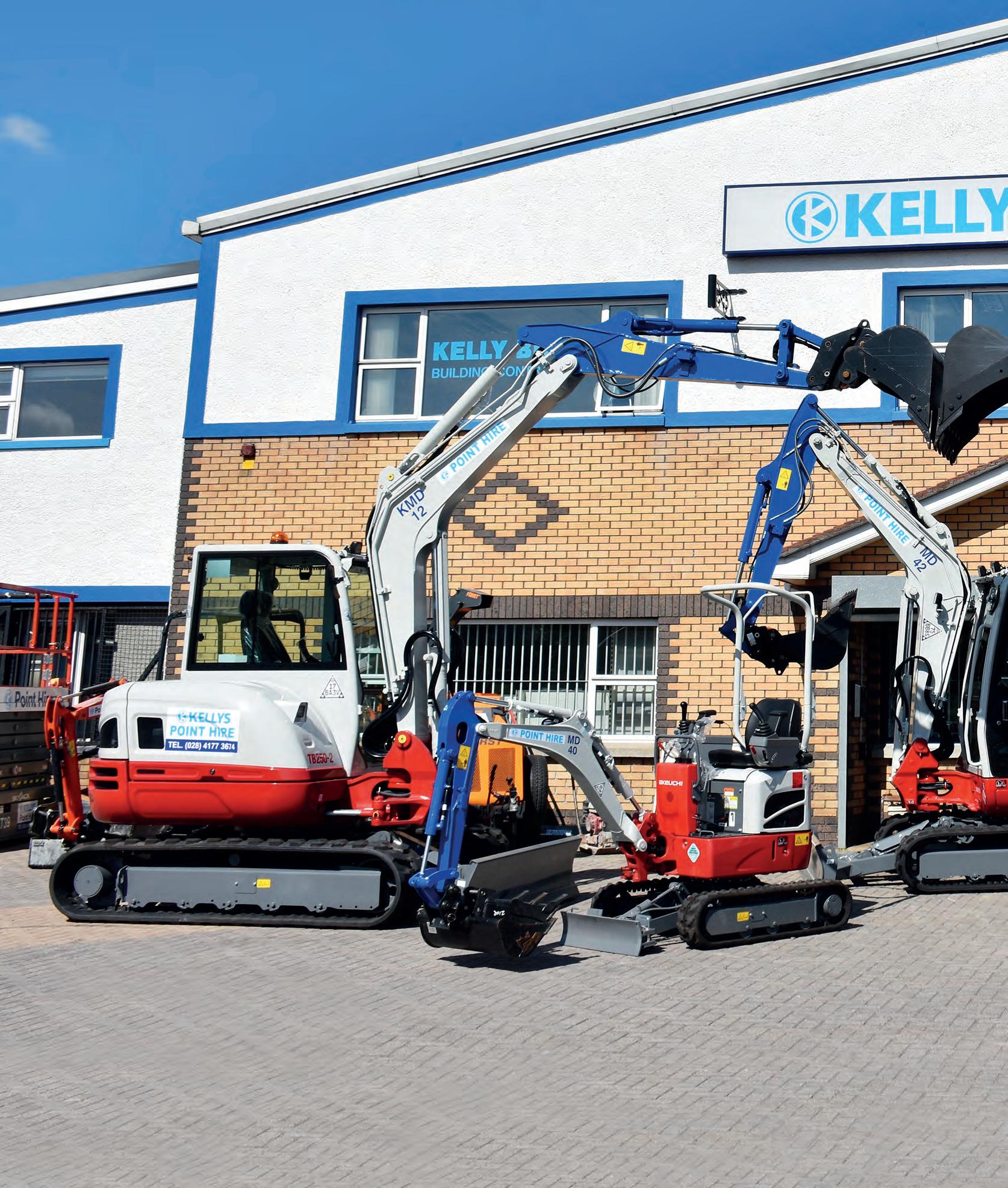

Having once been a Takeuchi dealer themselves some 25 years ago, Warrenpoint based Kellys Point Hire has continued investing in the brand through Alan Milne Tractors; it is a relationship that has grown over the past two decades, as Plant & Civil Engineer’s David Stokes reports.
The company, founded some 30 years ago by the late Leonard Kelly and today headed up by his son Gary, has recently invested in 18 new compact Takeuchi mini excavators, bringing the total Takeuchi’s in their hire fleet to more than 30 machines. “The Takeuchi brand has been tried and tested over the years and it is what our customers want,” says Gary. “The excavators have served us very well; they are low maintenance machines, their residual value is second to none, which is important to hire companies like ourselves, and they are operator friendly.” The new batch of Takeuchi machines range from one tonne up to nine tonne; some are replacing older models, but most are additional to the fleet. “These machines are top of their class, industry leading pieces of kit with modern technology and superior comfort. We are constantly endeavouring to provide the highest quality hire equipment to our customer base, and this latest round of investment is a move to ensure that the quality of our equipment is second to none.” Adds Ross Milne: “We have been dealing with Kellys Point Hire for a very long time. It is an excellent, well run company and we are delighted its customers continue to favour Takeuchi mini diggers.” And says Sales Manager Maurice McCrea, who has a long standing relationship with Kellys Point Hire: “This latest order includes four 9 tonne machines, and a mix of four, five and six tonne diggers, together with a couple of micros, so it is a substantial investment for the company.” Indeed, as Gary Kelly tells us, investment over the years has been pivotal to the company’s success in the hire sector. “To stay ahead in this business, you have to be investing not every couple
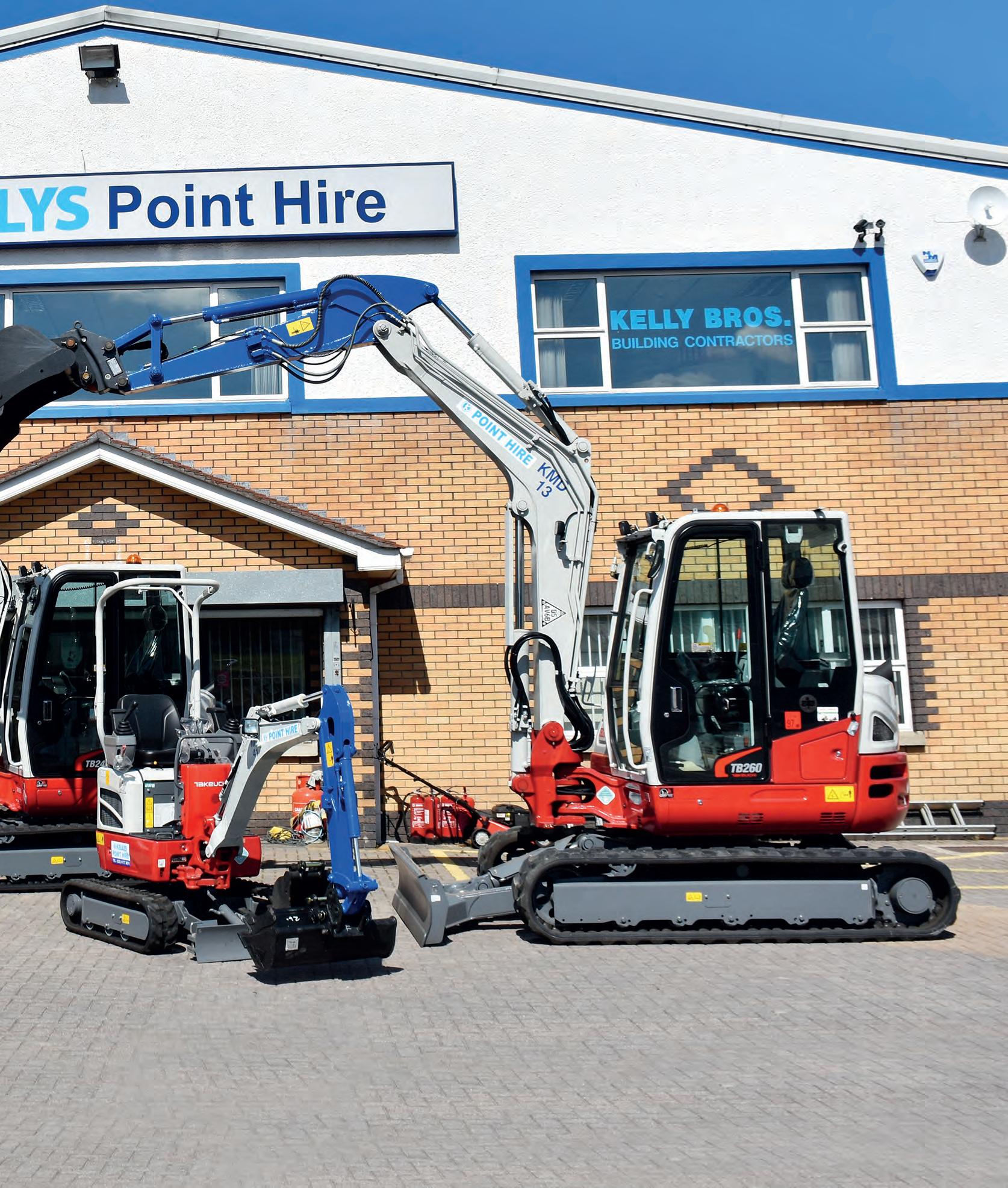
of years but every couple of months because our customers deserve to have the very best plant and equipment available; indeed, it is what they have come to expect and appreciate from us. “There is a huge difference between using older machinery on site and using fresh new machines. Not only is the safety and reliability of the machines vastly improved, but also the speed and efficiency of the work, and, of course, comfort for the workers.”
Service & Support
Kellys Point Hire provides large and small equipment and machinery not just to the local area, but regularly delivering to clients as far away as Dublin and Belfast for larger scale construction projects. It has its own workshops where its team of trained mechanics regularly service and maintain all its plant and equipment before it goes out on hire. Says Gary: “Our customer base is a loyal and a growing one and our main aim is to provide the highest levels of service and support to them, making sure we can always meet their needs, on either short or long term hire contracts.” Being located just a short drive away from the Newry by-pass and the main Belfast to Dublin motorway is a bonus. “We are only a few miles away from the motorway network, so we have easy access to supply and service our customers whether they are in the north or south of the country.”
Impressive Features
The new Takeuchi mini diggers in Kellys Point Hire’s fleet deliver excellent performance and provide an impressive list of standard features in a very compact design – from the one tonne TB210R which has a retractable undercarriage, foldable ROPS, and minimal tail swing enabling it to work in the most confined spaces to the four tonne TB240 which despite its compactness provides exceptional power and performance; its cab is spacious and well appointed ensuring operator comfort and efficiency and not surprisingly is a favourite with housebuilders and landscapers with excellent tool carrier versatility. Also in Kellys Point Hire’s latest order are a couple of five tonne TB250 machines which offer even greater operating capacity. With excellent breakout force, reach and lifting capacity, these machines work well above expectations in the 5-tonne weight class. Popular, too, with hire customers is the six tonne TB260, with its larger than average operator cab, spacious and well appointed ensuring maximum operator comfort and efficiency for all day excavating. For those needing something even bigger, Kellys Point Hire’s new additions include some nine tonne TB290 machines, a proven powerful excavator designed for major groundworks and earthmoving.
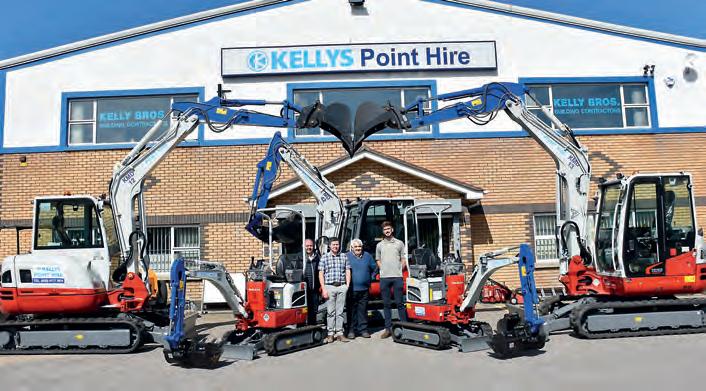
Gary Kelly, Ronan Kelly, Maurice McCrea and Ross Milne.
Good Choice
“We serve a very broad customer base, so we need to have a good choice of machine to offer, and we have that with the Takeuchi brand,” says Gary. “They are all powerful, efficient and reliable, which is what our customers like. “When my father Leonard started the company he already had a lot of experience in the industry and had an eye for a good machine which is why he introduced the Takeuchi to the business and we haven’t looked back since.” On the company’s long relationship with Alan Milne Tractors, he adds: “We have been dealing with their sales manager Maurice for many years, and with Alan, of course, and that has continued with Ross who joined the business just a couple of years ago; it all works very well for us – and for our hire customers.”

LIEBHERR LAUNCHES ITS TOTALLY REDESIGNED TA230 ARTICULATED DUMP TRUCK
The latest addition to German manufacturing giant Liebherr’s Generation 8 portfolio is the all new TA230 articulated dump truck.
The TA230 is not a new model number and is probably the only thing carried over from the company’s first foray into the ADT market over eight years ago. The first model unfortunately suffered from a number of technical issues with Liebherr withdrawing the model and subsequent 40t version soon after. The following years saw the company invest heavily in developing a replacement for the original TA230, the prototypes of which were launched to the press at the end of 2019. Launched to the World via a digital event, units have quickly been dispatched to dealers recently with field follow demonstration models coming to the UK for staff evaluation, quickly followed by the first customer units heading off to Scotland and Wales. The new TA230 has been redesigned from the ground up to give class leading figures in almost every sector. Sitting on new front and rear chassis frames, the truck rides on tried and tested ZF heavy-duty axles which give it one of the best ground clearances in its class. Matched to an 8-speed automatic powershift transmission, the driveline is designed to keep the truck moving under all conditions thanks to actively controlled inter-axle diff locks and automatic traction control. Stopping the loaded truck is taken care of with a combination of hydraulic multi-disc brakes on all axles along with an engine brake and hydrodynamic retarder which will bring the truck to almost a dead stop. Four-point suspension to all three axles provide a smooth ride over almost every surface The TA230 has been fitted with a totally new engine from Liebherr in the shape of a 12 litre, 6-cylinder D956 which delivers 360hp and has been set at a 7-degree angle under the steeply sloping bonnet. This has been done for two reasons, to aid in forward visibility but also allows the rear of the engine to connect into the ZF transmission. The large bonnet lifts electrically to reveal the engine and both cooling packs which can swing out for maintenance and cleaning. A sturdy fold-down step provides access to the engine compartment from the front of the machine. The engine aftertreatment pack is located to the rear of the cab and is made up of an SCR and DOC catalytic convertor both of which require minimum maintenance.
New Cab Layout
The Liebherr’s totally new cab design has been well thought out from the ease of access thanks to wide non-slip steps and well-placed grab rails to the large, glazed door. The UK machines will come with a heated and cooled air suspended premium seat option as standard adding to the comfortable ride. The fully adjustable seat and steering column allow for the operator to get a comfortable position with the view out of the cab claimed to be best in class thanks to the large area of glazing, the sloping bonnet, and the large, well placed mirrors. The mirrors are also heated and electrically operated so the driver doesn’t have to leave the seat to adjust them to suit his or her seat position. The overall finish to the cab is to an excellent standard with Liebherr’s new 9-inch full colour touch screen, a built-in cool box and a number of handy storage compartments along with easy-to-use controls giving a simple and clean working environment. Outside the cab and right around the machine LED lighting has been included in the UK package including the ‘guide you home’ step lighting activated by a button on the handrail.
High Spec
The body has been redesigned from the previous model dropping in capacity to 18.1m3 bringing it in-line with other 30t class trucks and giving a payload of 28 tonnes. The UK models will be brought in with both the body heating and tailgate options as standard giving the truck one of the highest specifications on the market. The quoted tip time to raise the body to its full 70-degree maximum is just 12 seconds whilst lowering is completed in an impressive 8 seconds. Cylinder damping provides a smooth end to the tip and lower cycle but can be turned off if sticky material is being carried with the body hard-stopping on the tip cycle to remove any stuck material. The operator is warned in the cab both visually and audibly should the body not be lowered to the chassis and pull away speed is limited automatically until the skip is totally lowered.
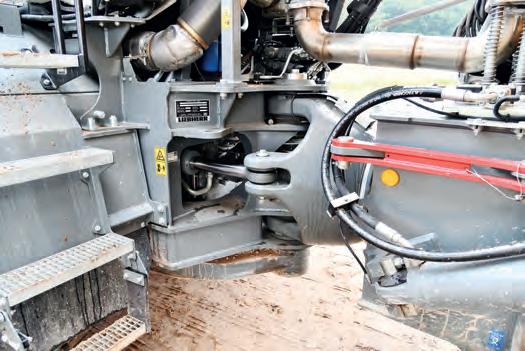

The truck had been taken to Mansfield Sand’s Two Oaks Quarry where the Liebherr demonstration team was carrying out product evaluation with the sales and aftersales teams. Loaded by a new 36 tonne class R934 excavator, the truck was filled in just sixpasses and was then taken around a short route to show off its stability, climbing ability and speed across the ground. When it comes to getting the truck from the loading area to the tip, the Liebherr’s top speed of 57km/h exceeds anything the competition has making it that little bit more productive over a shift. Fully loaded the truck’s hill climbing ability looked very impressive with the gearbox dropping down quickly to keep the truck heading forward as it hit the slope. Michael Atkinson is Liebherr GB’s Product Specialist for the range and was extremely upbeat about the new truck: “Liebherr has invested significantly in the development of the new TA230to ensure it can compete with the current market leaders in performance, build quality and reliability. The dedicated testing track at the Kirchdorf factory has seen the pre-production trucks spend thousands of hours under fully loaded conditions going through some very strenuous testing regimes before the factory were happy to let the machine out into the public eye. “We have decided to bring the truck to the UK market with a high standard specification to make it appeal to both large and small fleet operators. Early indications have shown us that the design of the truck is right and that the build quality is comparable if not better than many of our competitors and we are looking forward to getting the first examples out in full working conditions very soon.”

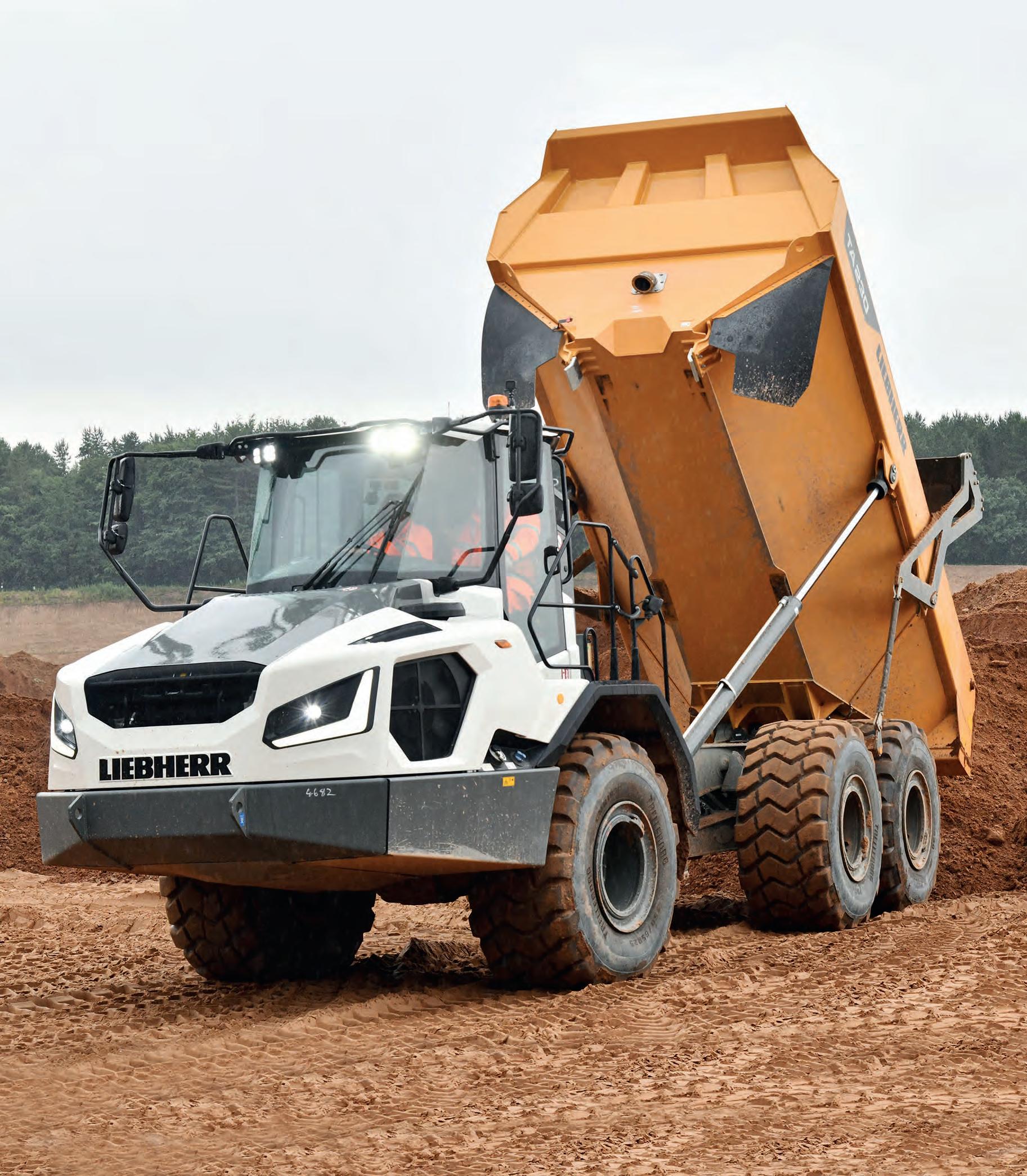
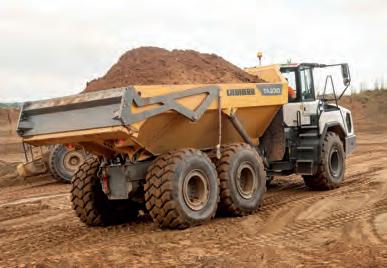

TEREX WASHING SYSTEMS HOST VIRTUAL SHOWCASE LIVE FROM COUNTY CORK
Terex Washing Systems hosted a highly successful ‘Virtual End to End Washing Solution Showcase’, which was broadcast live from a Keohane Readymix site in County Cork.
The event showcased a recently installed full turnkey solution for washing and classifying to produce specification sand and aggregate for Keohane Readymix. A team of washing experts explained the different pieces of equipment that came together to form the bespoke plant and outlined how combined, this washing system is proving to be a success for the customer. Keohane Readymix, founded in 1979 by Paddy Keohane, is now a third-generation company serving a broad customer base throughout Ireland with a range of concrete products, sand and aggregates. The washing solution is situated at their site at Brinny, Co. Cork, which feeds sand and gravel product to other Keohane Readymix sites in the region. Viewers were taken on a journey from the start of the design process, which was determining the nature of the material to be processed. Johnston Patterson, Applications Manager for Terex Washing Systems explained, “The material is a natural sand and gravel deposit which, while fairly free flowing, can get sticky and has some clay through it, as well as some organics, sticks and roots. The feed material is 60/40 sand to gravel and predominantly minus 150mm, but it can be up to 300-400mm. The typical % passing 63micron is around 10%.” To get started with the process of designing the new plant, Keohane Readymix provided a sample of their material and instructed the team on what products they would like to make from it. This material was analysed in a Terex Washing Systems lab and from this, the team were able to propose a bespoke plant that would meet their needs. Viewers were then taken through the operational site, learning about key features of each piece of equipment that make up the full plant - including an H30 Feed Hopper, AggreSand 206, AggreScrub 150, a Deep Cone Thickener, a Floc Dosing Unit, a Central Control Panel and stockpiling conveyors. Viewers also saw how the plant uniquely features a freshwater tank buried beneath the machine in order to reduce its overall footprint. This in depth look at the inner workings of the entire washplant allowed viewers to see the years of experience that have gone into the engineering of Terex Washing
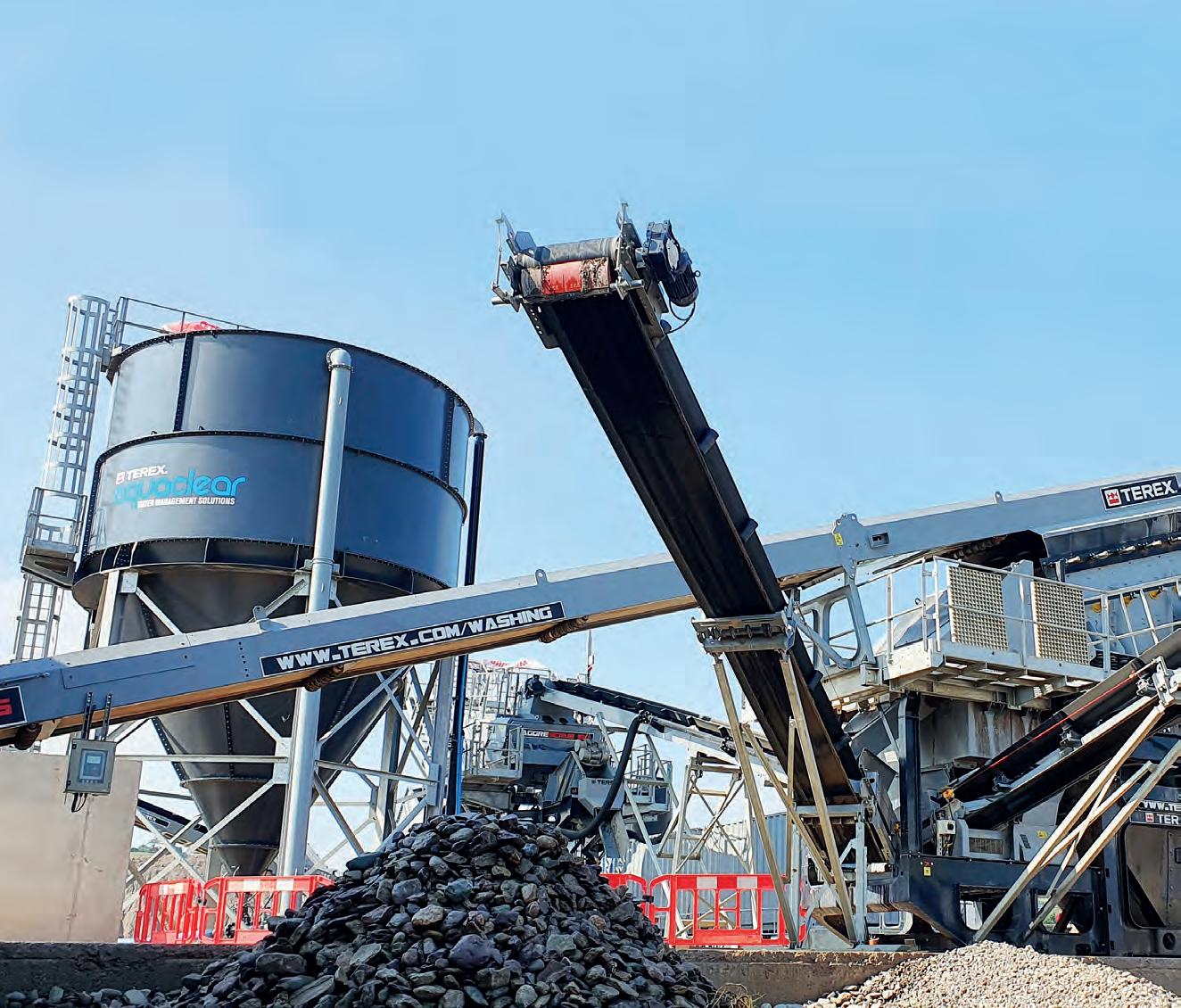

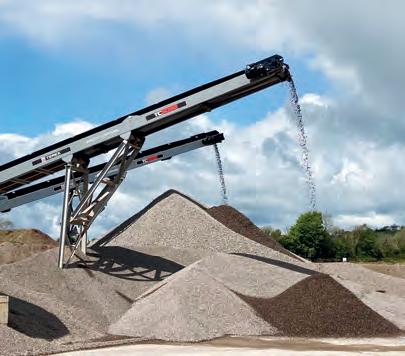
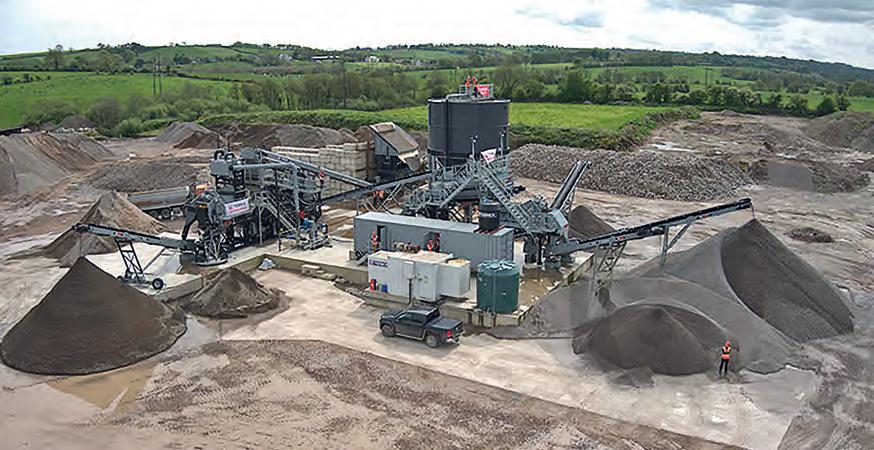
Systems. All aspects including the design, manufacturing and installation of the system were covered by Terex Washing Systems, which allowed for a truly integrated system. Barry McMenamin, Business Line Director at Terex Washing Systems explains, “Our team worked with the Keohane business in assessing the application and designing the plant that specifically suits their needs. They also helped to design the civil concrete works that the plant is seated on, a very unique and innovative feature here is the fact that the fresh water tank is beneath the machine, within the plinth itself, demonstrating the extent to which this plant is tailored to the requests from the customer.” Viewers also heard directly from Gavin Twohig, Operations Manager of Keohane Readmix, on how the plant is performing. Speaking of his experience of the plant, Gavin said, “We’ve been very happy with the output of the plant. We had decided to put in a log washer system because of the cleanliness of the material. With the log washer on site it’s doing an excellent job and the chips are very clean”.
Q&A Session
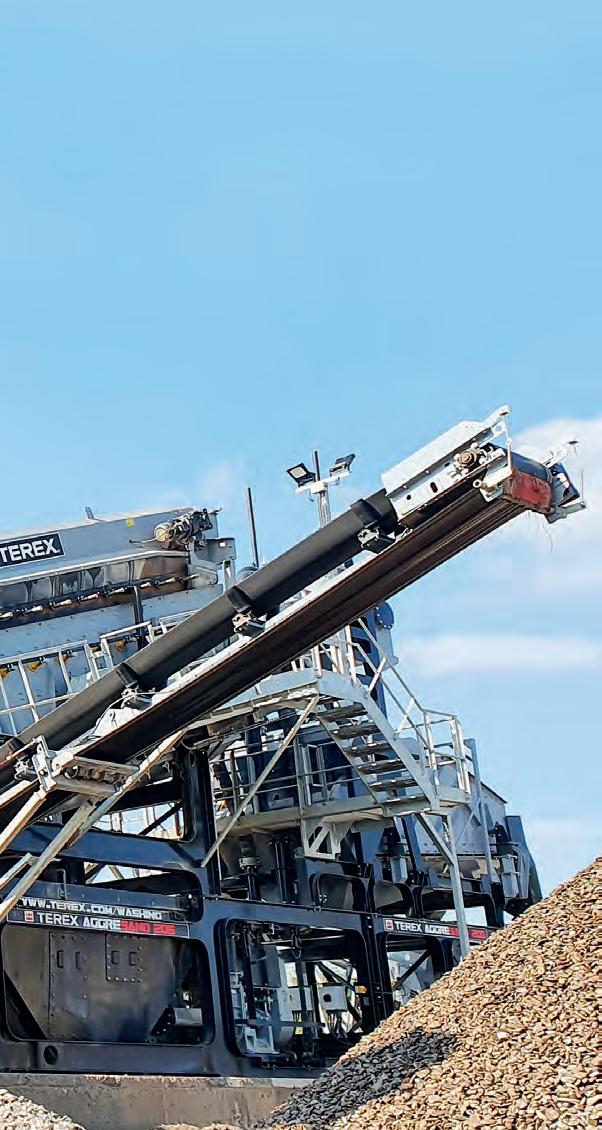
Following the showcase, those watching online were able to take part in a question and answer session with the washing experts on site. Questions ranged from queries about levels of accessibility for maintenance to more specific water management inquiries. Attendees were also able to ask about the potential for a Filter Press on a site where water is limited (similar to the situation at Keohane’s Brinny site) as well as ask about how a plant could be tailored for their site. The digital format of this live event enabled Terex Washing Systems to bring one of their modular washing systems into the homes and workplaces of hundreds of attendees in a single day.
Huge Success
Barry McMenamin explains, “In today’s world, where our customers are not able to be with us in person, we wanted to provide a ‘walk around’ of this operational site in the real world; explain the features of the equipment and show it in operation. We believe this is the best way to give our customers a complete understanding of how we can provide an end-to-end solution that is tailored to their needs. The live event was a huge success - to be able to showcase a system that we’re massively proud of to such a large audience has been fantastic. “No such installation or project would be complete without investment from a customer, and we are glad that Keohanes chose Terex Washing Systems as a partner for this project. We’d like to extend our appreciation to all at Keohane Readymix for enabling us to showcase their plant to the world, live from their site.”
Learn More
If you’d like to learn more about Terex Washing Systems or any of the machines featured in the End to End Washing Solutions Live Showcase please contact Martin Loughran at Martin.Loughran@terex.com or visit www.terex.com/washing. For more information on Keohanes Readymix visit www.keohanereadymix.com

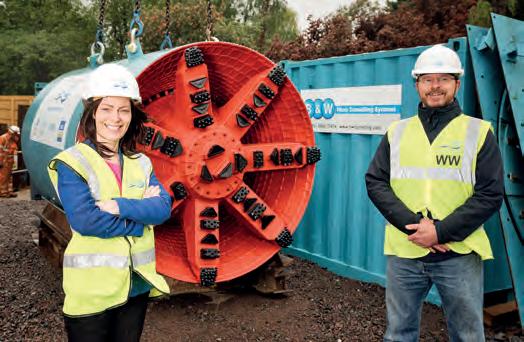
Infrastructure Minister Nichola Mallon Infrastructure Minister Nichola Mallon and NI Water’s Mark Sefton mark the arrival of the Tunnel Boring Machine. Pictured here (L-R), are Sean O’Connor Atkins, Paul McSparran BSG Infrastructure Minister Nichola Mallon and NI Water’s Mark Sefton.
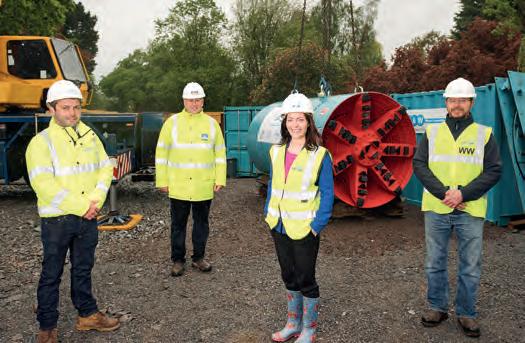
Major Tunnelling Machine Arrives at £8m Flood Alleviation Project
A “friendly giant” Tunnel Boring Machine (TBM) over 10 feet in length has arrived in Belfast, for use on a major £8million Flood Alleviation Project; BSG Civil Engineering are the main contractor for this project, with Atkins providing design and Project Management Support.
The work is to upgrade the sewerage infrastructure and substantially reduce the risk of out-of-sewer flooding in the Marguerite Park area of South Belfast, and pave the way for future works in the Sicily Park area. Work on Phase one of this major infrastructure project is underway within the grounds of Musgrave Park& Musgrave Park Hospital, and the overall project will take up to two years to complete. The machine will help reduce disruption within Musgrave Park/ Musgrave Park Hospital and Malone College by tunnelling around 800m of the new sewer underground. It will also tunnel under the main Belfast to Dublin Railway line, avoiding the need for any closures. The tunnelled sections of sewer will be up to 8m below ground level, the equivalent height of 2 double decker buses. Mark Sefton, NI Water Project Manager, said: “The machine will remove approximately 4000 tonnes of soil, equivalent to 250 full lorry loads of earth from below the ground, while users of the park and hospital will be unaware of what is happening below their feet! Tunnelling will also significantly reduce excavation works, and avoid the use of 21,000 tonnes of new stone fill, saving around 24,000 litres of fuel in transportation.” The overall project involves constructing over 1.3km of new large diameter sewer from the ‘Grovelands’ area of Musgrave Park, through the park grounds, Musgrave Park Hospital and Malone College, crossing under the railway line and through an area of private land into Diamond Gardens/Marguerite Park and Donegal Park.
Operators Urged to Fit Safety Devices Following Shocking Findings from the HSA
Brigade Electronics is urging operators to improve safety practices following the shocking findings of a recent report by Ireland’s Health and Safety Authority (HSA) into work related deaths involving vehicles.
A review of work-related deaths over the past 10 years found that of the 490 reported, a disproportionate amount - 44%, involved vehicles. The Agricultural sector was attributed as being the highest contributor to the numbers, followed by Transportation and Storage, Construction and Wholesale and Retail Trade. According to the report, the most common type of fatal incident involved vehicles striking people on foot or on bicycles. A previous report from the HSA’s Transport and Storage sector also lists reversing and slow speed manoeuvres as one of the most associated causes of vehicle related deaths and injuries. Incidents which, Brigade Electronics say, could be prevented with the fitment of vehicles safety devices such as; camera monitor systems, sensors and reversing and warning alarms. Ireland based Vehicle Safety Specialist, Chris Ewing from Brigade said: “The size and weight of commercial vehicles and machinery often create deadly blind spots around a vehicle, which is where most incidents occur. “We recommend operators invest in a range of both passive and active systems. While passive systems, such as mirrors and cameras, assist drivers by enabling them to see objects in a vehicle’s blind spot, active systems, including sensor alerts and reversing alarms, ensure that both drivers and pedestrians receive an immediate, audible warning that a danger is present.” Over the past 10 years, the UK has seen the introduction of vehicle safety standards and legislations such as FORS (Freight Operator Recognition Scheme), CLOCS (Construction Logistics and Community Safety) and more recently London’s Direct Vision Standard, put in place to reduce the number of incidents involving vehicles, workers and vulnerable road users. All require the fitment of various safety systems including cameras, nearside sensors and reversing alarms to comply. Could a similar standard be a potential solution in reducing the number of vehicle related deaths in Ireland? Says Chris Ewing: “Our vision at Brigade is that no more lives should be lost in collisions with commercial vehicles and mobile machinery. We have been at the forefront of the vehicle safety market since 1976 when we introduced the first ever reversing alarm into the market and we continue to campaign for improved vehicle safety practices around the world. The Health and Safety Authority in Ireland has been championing Vehicle Safety in the Workplace for many years, a cause which we fully support.”
WEL-TECH LIMITED SEES STEADY GROWTH AFTER A CHALLENGING YEAR

Despite the challenges thrown up by the Covid-19 pandemic, Wel-Tech Limited, which supplies Topcon’s range of measurement, monitoring and control equipment, and RDS Technology’s onboard vehicle weighing systems, is reporting another year of steady progress.
The company, headed up by Gavin Weldon, took over the RDS Technology distributorship for Northern Ireland from David McCollum just two years ago. Up until then, through his Weldon Agri business, he had been offering Topcon systems for a number of years, covering the North East Counties and Northern Ireland, providing sales, service and support to the agricultural industry. Still supported by David in a consultative role, Gavin has been expanding the business into the construction, quarrying and industrial sectors with quite some success from Wel-Tech’s offices in Newry in County Down and Ardee in County Louth. “It has been challenging not being able to attend shows and exhibitions because of the social distancing restrictions up until now, but we have successfully worked our way around that in getting our products out into the marketplace,” says Gavin, “and this year we have seen a steady increase in business across a range of sectors. “We have experienced a big surge, for example, in onboard weighting systems for loading shovels and forklifts, and we have recently completed some major contracts, including others for quarries, stone yards at builders merchants and even garden centres.”
Popular Systems

One of the most popular systems is the LOADMASTER a50, a highly accurate, on- board weighing system for loaders that helps increase loading efficiency, cutting vehicle movements on site, increasing safety and ensuring trucks are correctly loaded first time. It uses a 7” colour-resistive touch screen display and additional physical keys providing a modern and ergonomic operator interface. Suitable for use with up to 10 different attachments, e.g. buckets or forks, the system can be retrofitted onto wheeled, telescopic and tractor type loaders. It offers the input of a target weight from which it indicates the remaining load required. It also has a last bucket tip-off function that allows the adjustment of the final bucket load to the exact amount required. Another is the LOADMASTER 100, designed for the fastest loading environment. It uses a CAN-based system to enable wheel loaders with precise weighing for improved productivity. It is built to compensate for uneven, sloped ground and restricted loading areas to reduce cycle times and maximise tons-perhour performance. Loading correctly the first time reduces the need for return trips, which means greater efficiency and reduced machine and tyre wear. The Loadmaster 100, which also uses a 7” colour-resistive touchscreen display, is suitable for use with up to 10 different

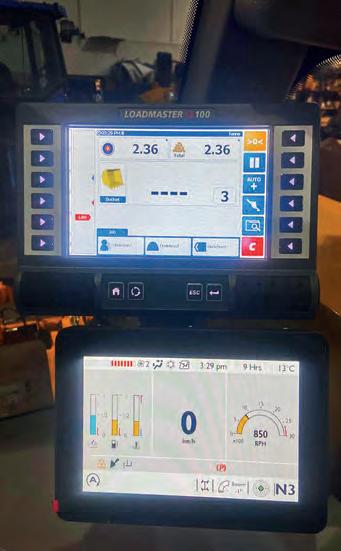
attachments, e.g., buckets or forks, and can be retrofitted onto wheeled, telescopic and tractor type loaders. The system continually measures hydraulic pressure using up to four sensors to compensate for changes in pressure to provide accurate weighing.
Online Software
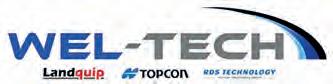
Online platforms, too, are increasingly popular, such as RDS Technology’s iSOSYNC software, which allows the rapid transfer of job information from a central computer to the loader or excavator and the resultant load information sent back to a PC on completion. The system can be one or two-way and is designed to operate fully automatically and without changing the loading routine for the mobile operator. Job instructions are sent direct to the loader operator. After each vehicle is loaded and the ‘clear’ button pressed to reset the instrument, the loading record is transmitted back to the central computer and can be logged into the load management software. Its use improves safety, eliminating unnecessary vehicle and personnel movements, measures tons per hour performance, identifies site bottlenecks by tracking entry and exit times, provides an immediate record of load data for invoicing and stock control, ensures clear and concise instructions sent to loader operator upon arrival minimising error and with fast data transfer speeds, it enables operators to load more trucks per shift.
Topcon Sitelink
Also available from Wel-Tech is Topcon’s Sitelink3D, which provides remote access and support for your machines. It brings you connectivity and control with views of project crews and their exact positions, activities, files in use, and a myriad of other functions. A simple key stroke lets users interact with any machine connected to the system; office managers have full access to equipment status, project productivity, and other tools to effectively “manage” remotely. All the while, operators at the site complete assigned tasks as well as send and receive files and messages so project data is updated in real time. With uninterrupted communication from the cab of your machines to any web browser, it provides equipment monitoring, remote support assistance, file transfer and messaging for any jobsite using your PC, tablet or mobile device. Hooking up Sitelink to any machine is easy, whether using a single in-cab controller or a simple add-on to your software back at the office. Just enter crew members, assign them to machines, assign the machines to the job – and start increasing your productivity right away.
WEL-TECH PLANT LTD
21 Shinn Road, Newry BT34 1PE +353 (86) 395 7258 | +44 739 363 4192 weltechrds@gmail.com
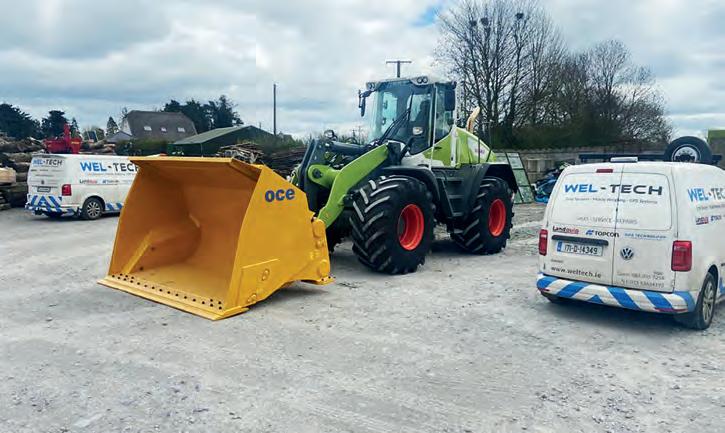
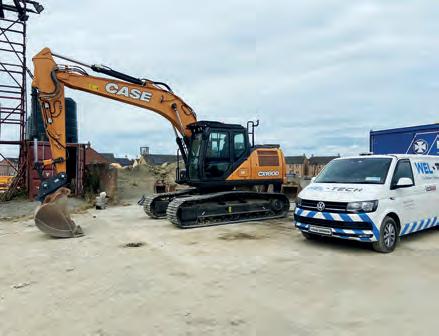
news
Metso Outotec keeps the customer in the center with a new marketing approach
The Covid-19 pandemic has changed the way we all interact with each other and we recognize that our customers are looking for safer and more diverse ways to engage with us. As a result, Metso Outotec is announcing a new marketing approach aimed at closer engagement with the company’s customers and stakeholders.
Metso Outotec will be moving towards a more marketspecific and multi-channel approach to its customer engagement strategy. To build stronger and more sustainable customer relationships, this strategy will focus on: • Having local representation either through our sales
organization or our distribution partners • An increased focus on regional
Metso Outotec branded events, in partnership with distributors where applicable • Increasing the ways that customers can engage with us digitally whether it is via our websites, through webinars, or via online tools and events that help customers explore problems and solutions As a result of this redefined strategy, combined with an even sharper focus on safety and sustainability, Metso Outotec has decided not to attend both MINExpo 2021 and Bauma Munich 2022. Despite its withdrawal from exhibiting at these two tradeshows, it will ensure that some commercial representation will be present, focused on targeted meetings and relationship-building. These will take place in the form of physical, digital, and hybrid events. Where it has physical events, it aims to minimize as much as possible travel and ensure a safe environment where it can avoid having large crowds of people. Metso Outotec has not ruled out future participation at these or other large tradeshows, instead, it will allow customers’ behaviours and preferences to drive its ongoing marketing strategy development. Currently, it is still planned for Metso Outotec’s McCloskey brand to be featured at Bauma. Physical interaction and faceto-face engagement will remain a key component of the Metso Outotec strategy. The goal is to augment that with the increasing possibilities that new technologies bring, allowing for greater efficiency, sustainability, and personalization. “Our goal is to be closer to our customers and to provide them with the tailored content that they need in the formats that will best suit them,” says Lilli Nykänen, VP, Marketing. A flexible and adaptive approach is being taken for this across Metso Outotec products and services, as well as across the industries that we serve. “Over the past year, the company has explored many digital-first marketing initiatives including the launch of the Liveroom virtual showroom and the Packed with Performance webinar series. These have been met with great enthusiasm from our diverse customer base and are things we will continue to build on moving forward.”
Safety First as JCB Site Dumper Crowned Hire Product of The Year
The safety benefits of JCB’s smallest site dumper have been honoured with a national award from the rental sector; the JCB 1T-2 site dumper has been crowned Hire Industry Product of the Year at the Hire Awards of Excellence 2021.
The award has been presented to JCB and Travis Perkins, which has purchased 200 of the machines complete with a host of safety innovations designed and developed by the two companies. Organised by Hire Association Europe and Event Hire Association (HAE EHA), the winners were announced at a virtual awards ceremony. JCB General Manager – National Accounts, Paul Williams, said: “We are delighted that our joint efforts to take safety to the highest possible level has been recognised by one of the top awards in the rental sector.” Travis Perkins Tool Hire Fleet Director, Yas Swindell said: “We are pleased that our joint venture has been recognised in such prestigious national awards; it proves that working together to
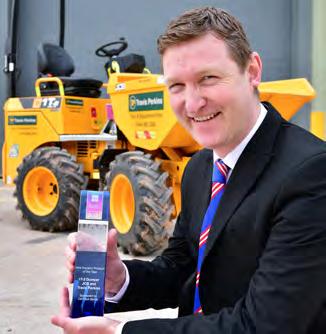
UK National Accounts Sales General Manager Paul Williams pictured with the Hire Industry Product of the Year for the development of the JCB 1T-2 site dumper.
continuously improve safety has tangible benefits to our customers.” The EU Stage V compliant 1.0-tonne site dumpers were supplied to Travis Perkins by dealer Watling JCB and are equipped with a drive inhibit system, preventing travel unless the seatbelt is in use and an initial movement alarm, that provides an audible warning before forward or reverse travel commences. Another key feature of the machines is the Smart Safety pack which includes an intelligent tilt warning system using proven technology from JCB’s marketleading Loadall telescopic handler range. It is designed to sound an alarm when the skip is raised with the dumper sitting on dangerously uneven ground. It also shows the operator when they are driving the dumper on uneven ground that could pose a risk of overturning. The final safety development to catch the judges’ attention was the option to specify the machine with a wider track for additional stability. This uses an increase in wheel offset to raise the width of the machine from 850mm to 988mm, still allowing access through a standard one metre doorway. The increased track boosts machine stability, further increasing safety on rougher site conditions.

Helping businesses thrive again.
Release working capital from assets, such as machinery, stock and customer invoices.
closecommercialfinance.ie
in profile YANMAR BRAND ‘TICKS ALL THE BOXES’ FOR HAVEN HIRE CUSTOMERS
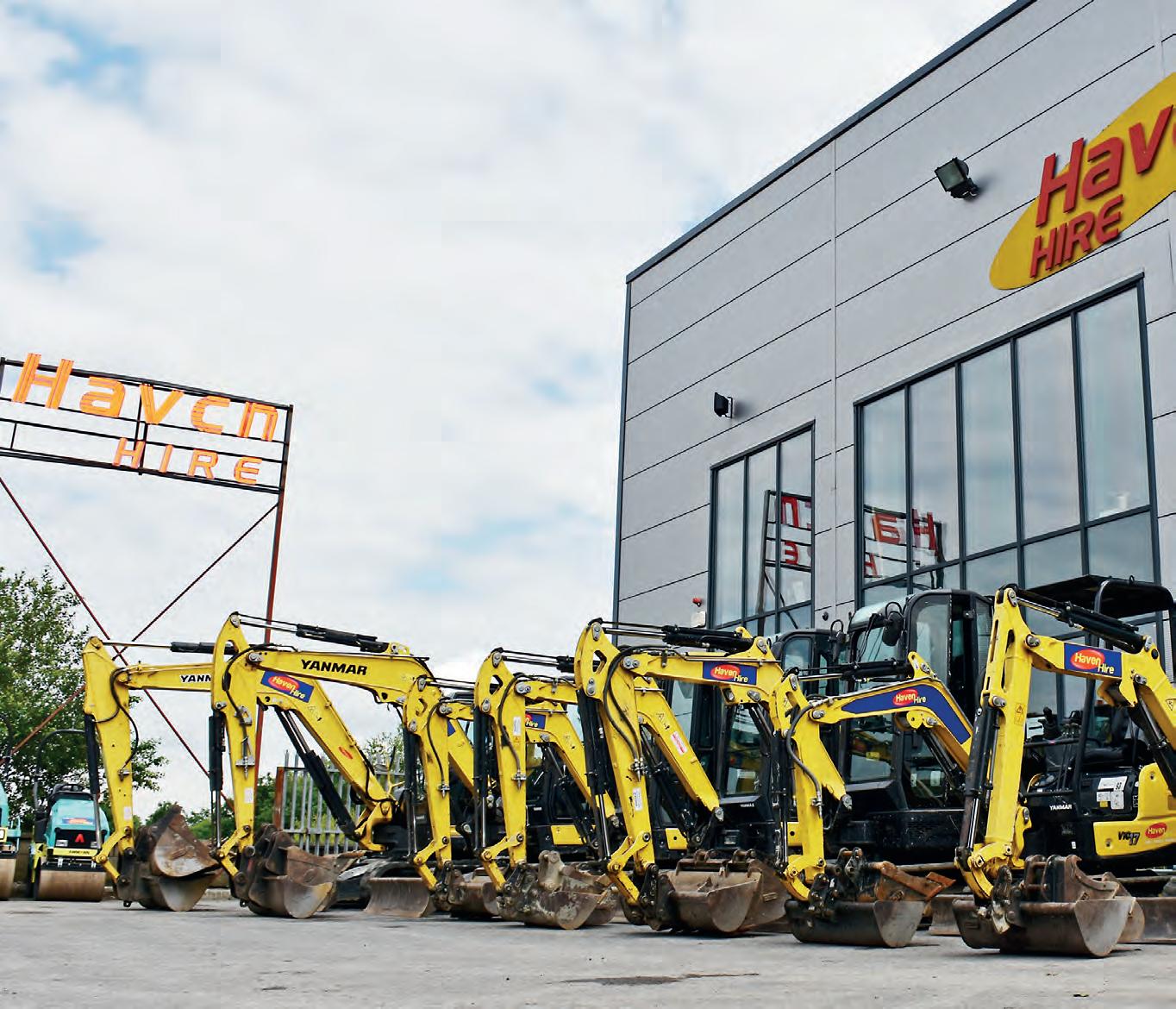
To say Haven Hire and its customers are big fans of the Yanmar brand would be something of an understatement; the Kildare based company has in excess of 60 Yanmar excavators, and continues to add more, as Plant & Civil Engineer’s David Stokes has been finding out.
The company’s relationship with Yanmar and dealers Crumlin Plant Sales stretches back over two decades, and remains as solid as ever. Comments Managing Director Audrey Kilgallon: “As a company we try to remain brand loyal on our equipment. Our purchases are based on reliability over price, and the Yanmar as a brand has always ticked all the boxes.” The business was initially established in1986 by Audrey’s father Eamonn Kilgallon, a fitter by trade, who saw an opening in the market for plant hire and sales of construction plant. He quickly established a reputation under the umbrella of Haven

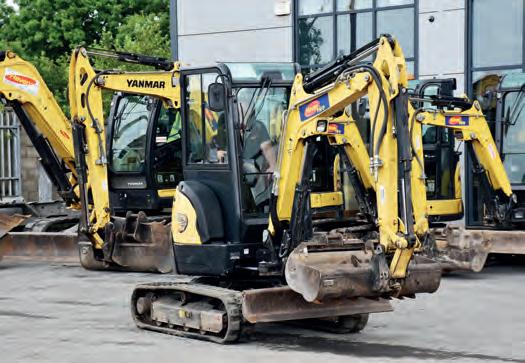
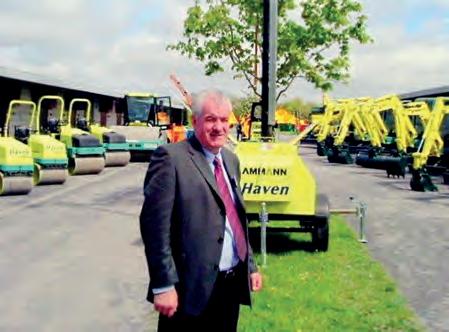
Eamonn Kilgallon.
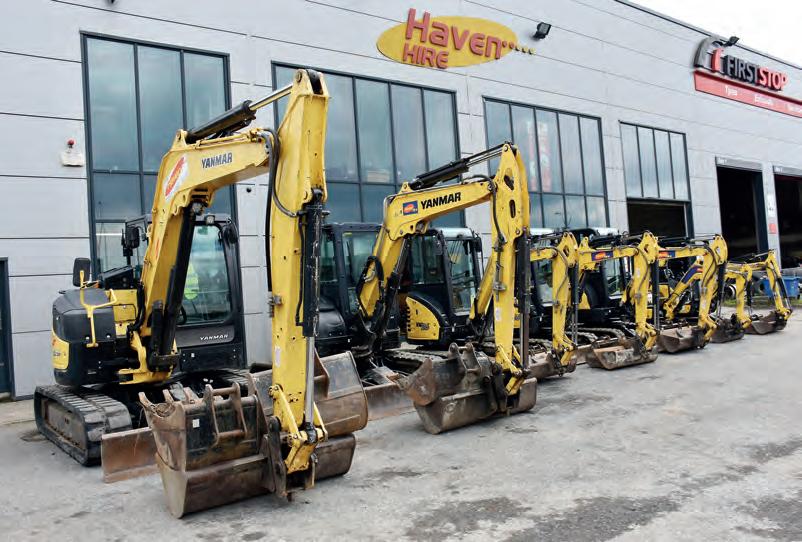

Engineering and in 1993 the Kilgallons seized an opportunity when they bought Celbridge Hire and amalgamated the two companies to form Haven Hire. It has since expanded into Maynooth and Naas. “We have great team of experienced depot managers who have a wealth of knowledge of the industry and are all focused on customer service,” says Audrey, whose clients range from domestic users to major civil engineers and building contractors. “Our professional, skilled technicians and staff follow the highest standards to ensure that all the equipment we supply is right for the job and in excellent condition.”
Hand-On Approach

Haven Hire’s hands-on approach to the business has certainly kept it in close contact with its large customer base. “Constant customer focus and our large and diverse product range are key to our continued success. Hire is very much about the process, ensuring that the quality of each hire is like the first hire and that each customer has a positive experience every time they hire from us.” Which brings us to Yanmar and Crumlin Plant Sales: “We have been dealing with Keith and Matt Willis and the team at Crumlin Plant for the past 20 years and enjoy an excellent relationship; the support and service we get from them is second to none,” says Audrey. And adds Matt Willis: “It is always a pleasure to deal with Haven Hire and we hope we can continue building on that relationship for many years to come. It is quite clear that their hire customers like the Yanmar brand and this year so far they have taken a number of new machines from us. We are having to continually re-stock and pre-order to cope with growing demand which has exceeded all our expectations since the beginning of 2021.”
New to the Fleet
Machines going to Haven Hire this year already include some SV15VT machines; with a powerful engine and a double gear pump hydraulic system, these compact excavators offer impressive performance and are perfect for job sites where space is limited. Innovative design and a light transport weight makes the SV15VT easy to move between sites. Also on Haven Hire’s buy list this year was the Yanmar five tonne ViO57, a zero tail machine that offers exceptional stability and durability, together with greater safety and operator comfort. Joining the fleet, too, was some eight tonne zero tail swingViO80s that offers the performance of a larger machine along with the benefits of a compact excavator. Particularly suited for work in urban areas, it can easily operate along walls and in confined spaces where other machines in its weight class cannot go, yet still provides all-day comfort for operators.
Award Winning
“Our hire customers love the Yanmar brand; the excavators are robust, reliable and operator friendly. Currently, our fleet of Yanmar machines extend from 0.8 tonnes up to 10 tonnes. We are always adding new models and replacing older ones,” says Audrey, whose company is a past recipient of an Outstanding Dealership Award from Yanmar.
