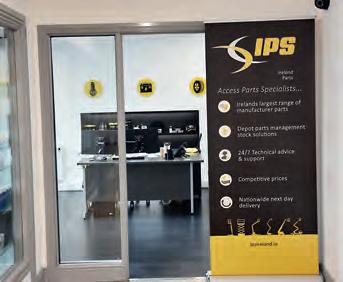
18 minute read
IPS Ireland Plays its Part Keeping Customers Well Serviced
IPS IRELAND YOUR ACCESS PLATFORM PARTS SPECIALISTS
Despite all the challenges of the global pandemic and economic uncertainties thrown up over the past year because of Brexit issues, it has been quite a positive period of growth for IPS Ireland, one of our leading suppliers of Access Platform & Material Handling Parts.
Based in Dundalk, the company now operates out of new and expanded premises, including offices and stores, and has also invested in recruiting new staff members to take the business forward in the years ahead. Since it was established just a few years ago, IPS Ireland has built up a well respected reputation for providing practical, convenient parts solutions to help keep customers’ rental fleets and access platforms working safely and efficiently as they should. In terms of availability, IPS Ireland’s extensive warehouse stocks over 10,000 manufacturer parts from all the leading manufacturers such as Genie, Hinowa, Niftylift, Snorkel, Manitou, JLG, BoSS and many others. “The range of parts, batteries and accessories, covering all Access Platform & Material Handling equipment, includes those for scissor lifts, telescopic boom lifts, articulated boom lifts, vertical mast boom lifts, tracked spider lifts, push-around lifts and material lifts,” says Business Development Manager Trevor Lambe. “And because we enjoy a close working relationship with leading manufacturers and suppliers means we can guarantee short delivery times with the most competitive prices in the market. Downtime on your equipment will be minimal if you buy from us. Whatever part you need, whenever you need – if we haven’t got it we will source it for you.” Anticipating potential parts availability issues ahead of Brexit, IPS Ireland took the decision to bring in extra stock, a move that was greatly welcomed by its ever growing customer base across the island of Ireland - and recognising the difficulties and challenges brought about by the Covid19 pandemic, the company also increased its stocks of hand sanitizers, protective face masks and other safety products.
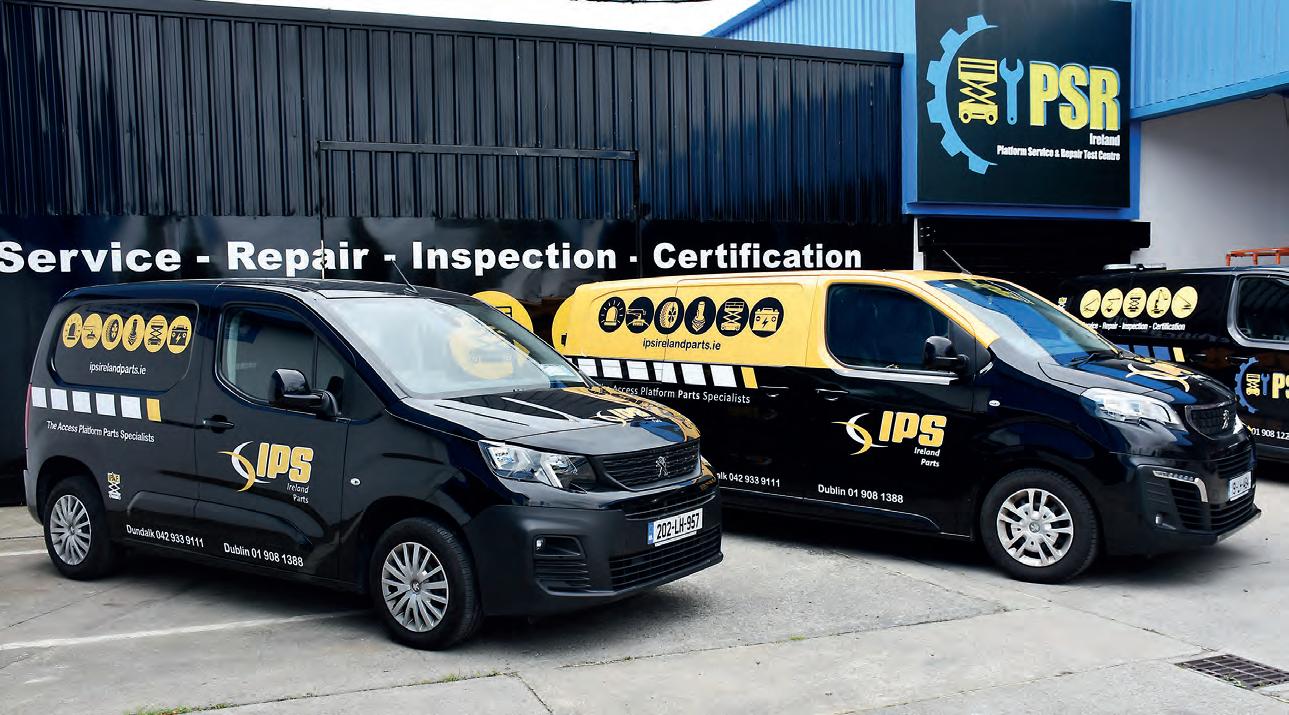
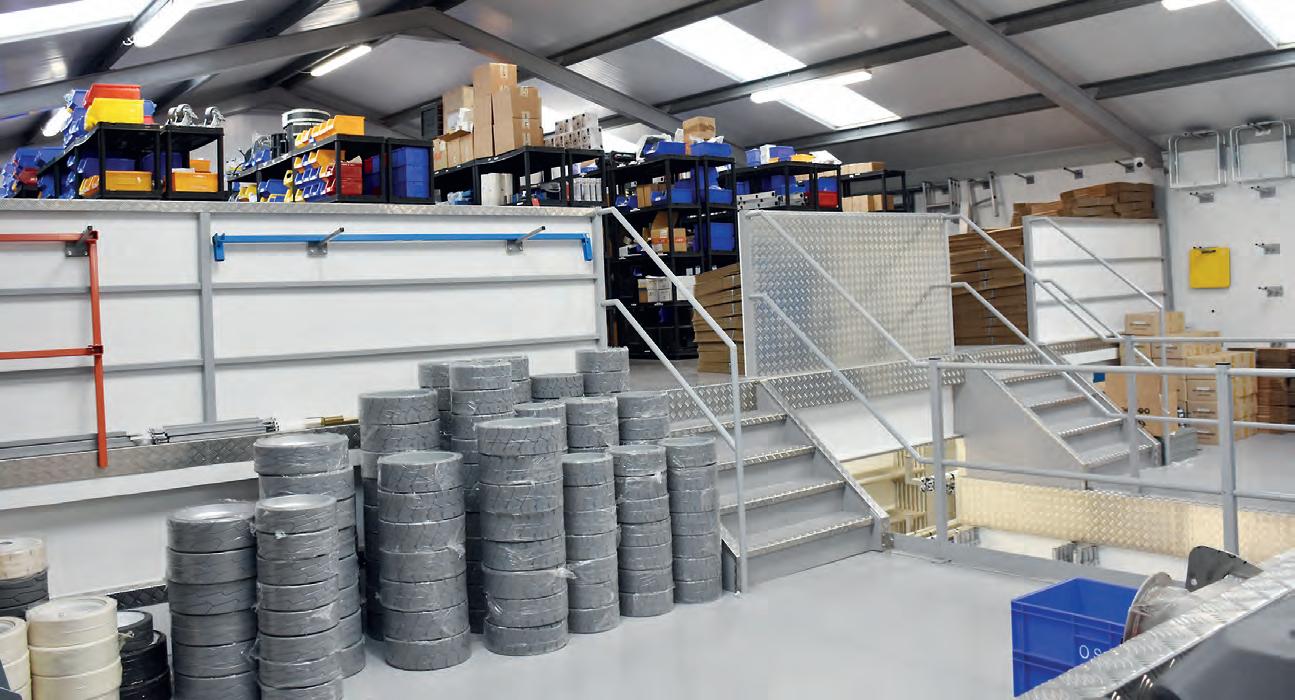
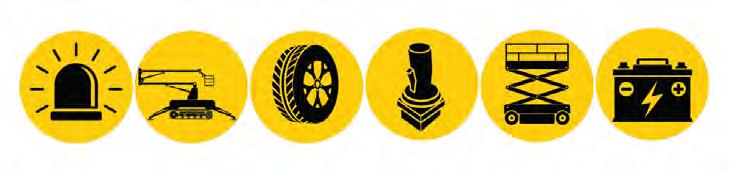
Customer Loyalty
“It is all about providing a comprehensive, all embracing service for our customers, who have like all of us been facing some unprecedented times, and that’s what we have built our success on,” says Trevor. “Our customers have been loyal to us, and we remain committed and loyal to them, come what may.” His colleague, Gary Power, has also been out on the road managing core accounts and ensuring customers’ needs are quickly met. He visits hire outlets and other customers’ workshops to keep them fully stocked with fast moving parts and accessories, with free next day deliveries. “We recognise that customers cannot afford the luxury of unnecessary downtime simply because they can’t source a part, so we make sure their own workshops are fully replenished on a regular basis,” says Gary. Customers can also pre-book their parts order, subject to availability, for a delivery time that suits them or schedule a regular visit to ensure their parts stock is topped up at all times.
Continued Investment
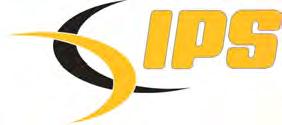
As we mentioned earlier, investment is also a key to IPS Ireland’s success. Apart from expanding its offices and warehouse facilities, it has also put several new parts delivery vans on the road in recent times. “Having the additional vehicles on the road gives us extra scope us to further develop IPS as a whole, and most of all will enable us to provide an even better service to our customers.” Last year, the company also launched a brand newly designed customer friendly website at www.ipsirelandparts.ie The site features a streamlined, modern minimal design with improved functionality. “Our primary goal during the redesign process was to create a more valuable, user-centric and responsive resource across all platforms and devices. “Specifically, we wanted to focus on making it easier for our users to learn and locate valuable information about our services for their particular application or industry not only at their desk but on mobile devices. The website is adapted to any device so our customers can easily log-on when on the go via mobile or tablet. Finding what you want is only a click away.”
Service & Support
IPS Ireland's sister company PSR Ireland based in Dundalk offer Service - Repair - Inspection & Certification of Access Platform & Material Handling Equipment throught the island of Ireland. Their highly experienced engineers are familiar with all major makes and models of powered access platforms & lifting equipment including Hinowa, Genie, Skyjack, JLG, Snorkel, Haulotte, Niftylift, Manitou, Boss, Ommelift and many more. As a member of the International Powered Access Federation (IPAF) which promotes the safe and effective use of powered access equipment worldwide, IPS Ireland also has access to a range of services, benefits and special offers which improves knowledge as a service provider and ensures customers are getting the safest service available. IPS Ireland entered into the world of parts back in 2012 operating from a small stock room with very few parts on the shelf. Today, with a huge range of readily available quality parts at competitive prices, 24/7 technical advice and with highly experienced staff from backgrounds in plant and access equipment, confidently offering customers peace of mind, IPS Ireland can clearly look forward to many more years of well deserved success.
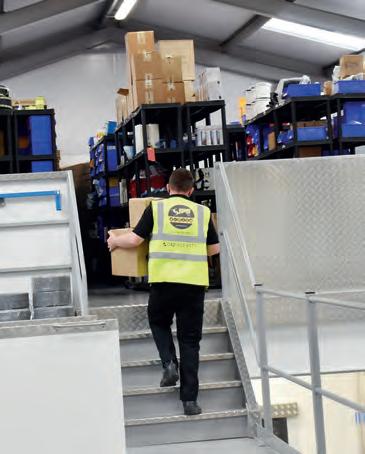
Ireland
CONTRACTORS COMPLETE £12.2 MILLION GRAND OPERA HOUSE RESTORATION
The £12.2 million restoration and development of the Grand Opera House in Belfast has been completed; it was delivered by specialist construction firm, Tracey Brothers Ltd, and more than 60 sub-contractors.
The restoration project, which is supported by The National Lottery Heritage Fund, Department for Communities, Arts Council of Northern Ireland, Foyle Foundation, Garfield Weston Foundation and The Wolfson Foundation, has seen the auditorium’s paintings and decorative and ornate plasterwork painstakingly restored and conserved, as well as new seating, carpets, curtains and drapes installed. The design of the foyer and public spaces has been totally reimagined, with a new bar installed in the restored 1980 glass extension overhanging Great Victoria Street, as well as beautifully refurbished stalls and circle bars. As part of the project, the Theatre’s technical infrastructure has been upgraded and a permanent heritage exhibition installed telling the fascinating story of the Theatre’s 125year history. Facilities for those customers with access needs have also been greatly enhanced throughout. Commented Colin Loughran, Chairman of the Grand Opera House Trust: “The ambitious restoration project has delivered fantastic results and we are hugely confident that it will ensure the Theatre remains on the world stage as a centre for theatre-going and as a Belfast visitor and tourist attraction. We would like to thank our funding partners for their unwavering support which has helped to secure the Theatre for generations to come.” Welcoming the project completion, Paul Mullan, Director, Northern Ireland, The National Lottery Heritage Fund said: “The work to conserve the building’s unique architectural features and paintings has been undertaken by local conservationists and tradespeople, which emphasises the value that heritage brings to the economy, people and wider community.”
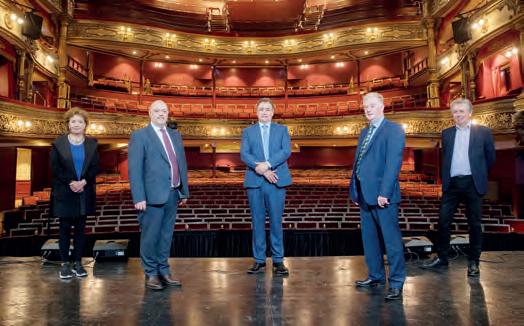
Pictured at the unveiling of the results of the restoration project are (L-R): RoisÍn McDonough, Chief Executive. Arts Council of Northern Ireland, Ian Wilson, Chief Executive, Grand Opera House; John Tracey, Director of Tracey Brothers; Colin Loughran, Chairman Grand Opera House Trust and Paul Mullan, Director, Northern Ireland, National Lottery Heritage Fund.
Unusual Project
John Tracey, Director of Tracey Brothers, said: “The project was unusual as it was made up of two separate sites. The focus of the work was the extensive restoration of the 1895 listed building and the installation of state-of-the-art sound and lighting systems to meet modern-day theatregoer expectations. Alongside this was the reimagination of the 2006 extension to make it more sympathetic to the Matcham building, complete with a stunning helical staircase, enhanced bar and hospitality facilities, and the installation of new interpretative spaces telling the story of the Grand Opera House. “Tracey Brothers are delighted to have been involved in the project and the quality of the final result is testament to all involved. We hope that the Grand Opera House continues, not only as a source of great entertainment for young and old alike, but also as a landmark Belfast venue to visit for many years to come.” As well as Tracey Brothers as main contractor, the project team included architects Consarc Design Group, interior design by Sundara Design, project management WH Stephens, special theatre consultants Charcoalblue, M&E by Semple & McKillop, and structural engineering by Albert Fry Associates. The Grand Opera House was designed by the leading Victorian theatre architect Frank Matcham and opened on 23 December 1895. Many of the world’s leading actors, singers, dancers and entertainers have appeared on its stage, including Charlie Chaplin, Sarah Bernhardt, Laurence Olivier, Vera Lynn, Luciano Pavarotti, Darcey Bussell and Laurel and Hardy.

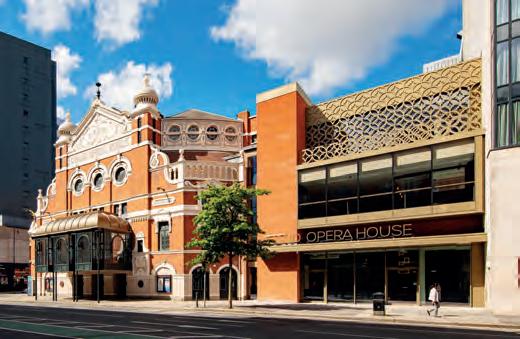
MANITOU DEALERS GET UP CLOSE & PERSONAL WITH NEW MRT RANGES
Having launched no less than 25 new construction machines during its BUILD THE FUTURE virtual online event which was broadcast worldwide earlier this year, Manitou recently invited the Press and UK & Ireland dealers to see the VISION and VISION+ MRT telehandler ranges up close at a special demonstration.
During the day at Stoneleigh Park in Warwickshire, we were able to get an overview of the new ranges, plus the opportunity for a machine walk round, as well as demonstrations and test drives. A number of special training days for dealers were also arranged. Manitou say that by modernising the design and ergonomics of the newly renamed model, it is now able to offer a single cab across all the models in the range, thus providing excellent visibility to users whatever the model. Having the same cab also means having an equivalent control station on all models, making them quicker to get to grips with.” Two new machines, the MRT 1645 and MRT 1845, have been added to the VISION range. With 500 kg (1,100 lbs) of additional load capacity compared to their predecessors, these two products offer a lifting height of 16 metres (52’5”) and 18 metres (59’1”) respectively for a load of 4.5 tons (9,900 lbs). They are also equipped with a new Stage V engine, producing power of 75 hp and 116 hp respectively. The VISION range offers a wide selection of 14 models with heights ranging from 16 metres (52’5”) to 25 metres (82’), for a load capacity of up to 4.5 tons (9,900 lbs). The VISION+ range features 12 new models, including the MRT 2260, MRT 2660, MRT 3570 (also available in an electronic suspension version), MRT 2570 and MRT 3060, most of which were made available to inspect on the day The manufacturer says there is growing demand from customers wanting machines that offer higher performance on construction sites and say that this high-capacity range meets those expectations perfectly with a very high level of equipment.
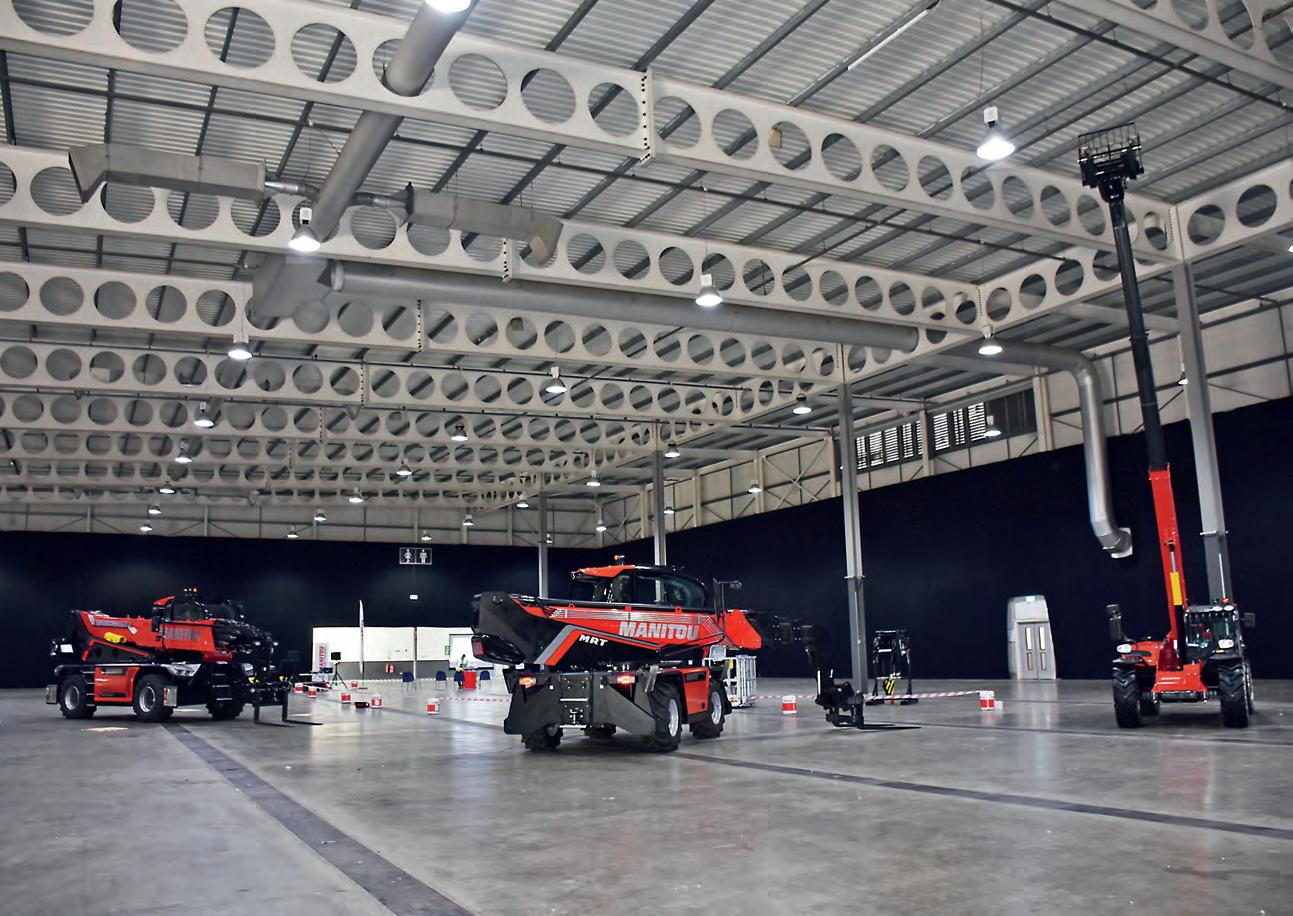


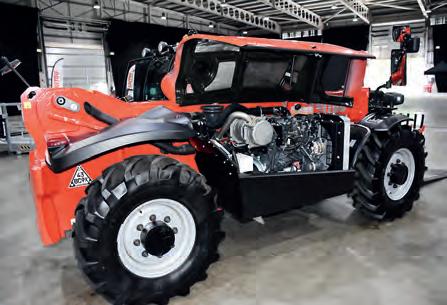

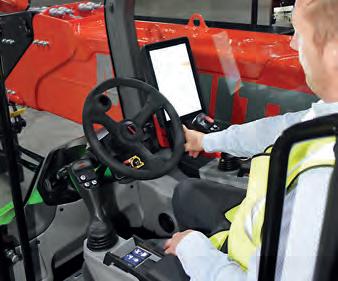
With models offering a lifting height of 22 metres (72’9”) to 35 metres (114’8”) and a much improved capacity of up to 7 tons (15,400 lbs), this range is ideal for the installation of structural steelwork, renovation of buildings and even demolition. These two ranges are connected as standard in order to optimise maintenance, increase the machine’s operating hours and therefore reduce the total cost of ownership for the user. The VISION and VISION+ ranges are now available worldwide and will be delivered to the dealer network, to rentals and to key accounts by September 2021.
Safety
In order to give operators complete visibility, a pack of five LED headlamps ensures full lighting all around the machine, plus two boom head worklights for excellent visibility during loading operations at height. A rear camera that sends images to the cab allows the machine to be manoeuvred in complete confidence. Four accesses built into the chassis, on the left and right, and at the front and rear of the machine, now enable the operator to climb into and out of the machine regardless of which way the cab is rotated. For an optimum experience, the group is reaffirming its intention to offer increasingly comfortable working conditions with evolving cab ergonomics. The brand-new 8” vertical touchscreen on the VISION range, which comes in a 12.1” XXL version on the VISION+ range, is a real human-machine interface that prides itself on being able to rival anything in the automotive sector. The VISION and VISION+ ranges also feature hydrostatic transmission offering greater driving flexibility and giving the operator a maximum speed of 40 km/h, for the Vision Plus, and 25kph for the Vision. The latest addition to the VISION+ range, the MRT 3570 allows the operator to carry out handling operations up to 35 metres (114’8”), the greatest height available from Manitou. For increased visibility at this height, the group’s R&D and marketing teams have introduced a new electric seat that tilts by up to 18° to easily monitor deployment of the boom. Manitou Group will also be offering a full electric extension to the VISION+ range by the end of the year, as well as a hybrid version combining a smaller engine with a lithiumion battery. Many models will be available, enabling 100% electric use where work sites and regulatory constraints call for it.
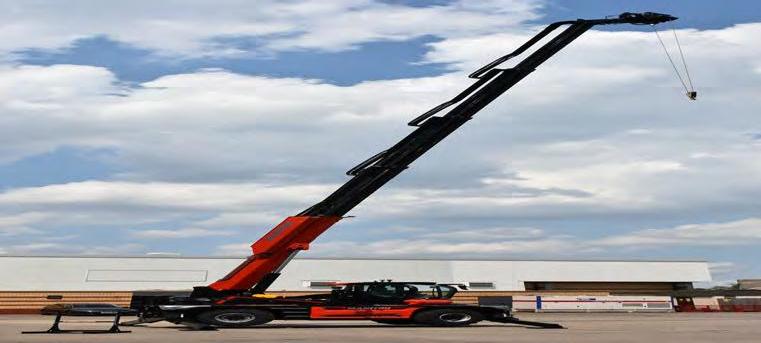
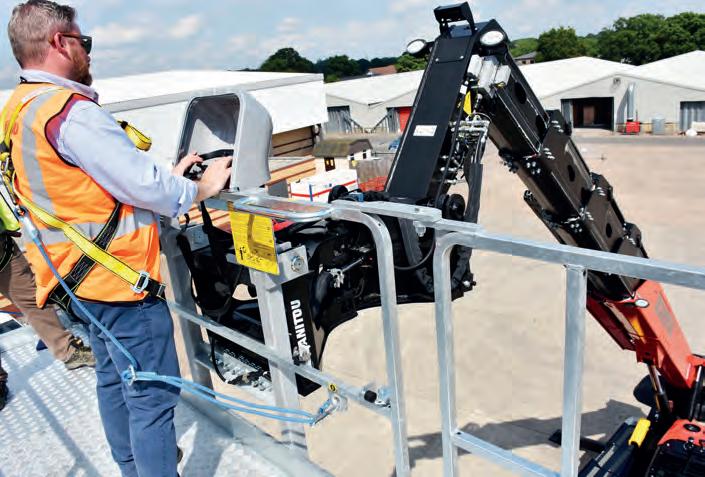

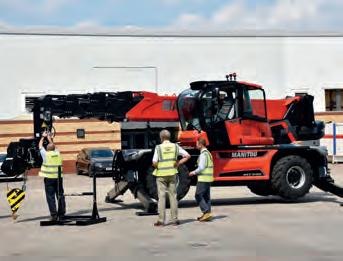
test drive GETTING UP CLOSE TO JCB’S STAGE V BACKHOE LOADERS
JCB has simplified its worldbeating backhoe loader line-up, to make it easier for customers to specify the right machine for their application, reports Dan Gilkes for Plant & Civil Engineer.
The range now includes the 3CX Eco, the 3CX Plus and the 3CX Pro. The 4CX is offered in Plus and Pro models, while the 5CX is available solely in Pro specification. JCB also still offers the 4CX Polemaster and the 5CX Wastemaster specials. All get new name graphics, while you’ll easily spot Pro models, as they now come with black wheels. For EU Stage V emissions regulations, the 3CX Eco uses JCB’s 430 3.0-litre engine, producing 55kW (74hp). Already offered in last year’s 750,000th Special Edition model, the 55kW powerplant does without Selective Catalytic Reduction, so requires no AdBlue exhaust additive. It drives through a choice of four-speed Synchroshuttle or Powershift transmissions. The 3CX Plus can be had with JCB’s 448 4.8-litre engine delivering an 81kW (109hp) rating, that comes as standard with the Powershift box. The Powershift transmission also gets TorqueLock as standard, reducing fuel consumption while roading. The 3CX Pro comes with the 81kW engine and a six-speed Autoshift transmission, again with TorqueLock. This EcoRoad transmission is said to cut travel times and reduce fuel use by up to 15% when driving between sites. The 4CX Plus has the 72kW engine and a choice of four-speed synchroshuttle or Powershift transmissions, while the 4CX Pro and 5CX Pro get the 81kW engine and the six-speed Autoshift box. All of the machines benefit from an Auto Stop system that will shut down the engine when the machine has not been used for a pre-set time to save fuel. The operator can vary the time through the in-cab monitor.
Advanced automation


JCB has offered a variety of automated features on its backhoe loaders for a few years, but the Pro models bring the whole collection together, to really deliver a new level of assistance to the operator, boosting productivity and reducing effort. The systems on offer include Auto Drive, which allows the operator to set an engine speed that is automatically maintained when roading.
There is also Auto 2WD, which drops from 4WD to 2WD as travel speed increases, reducing tyre wear and fuel use.
For those models with the optional
Advanced Easy Control (AEC) seatmounted servo levers, Auto Seat
Select automatically changes the lever controls as the seat is rotated between front loader and rear backhoe use.
Where AEC is fitted you can also now have Auto Stabilisers, that not only extend and retract with one touch, but that will automatically level the machine on uneven ground before working the backhoe. AEC machines also benefit from an isolator lever, similar to that found on excavators, to lock and unlock the seat controls.
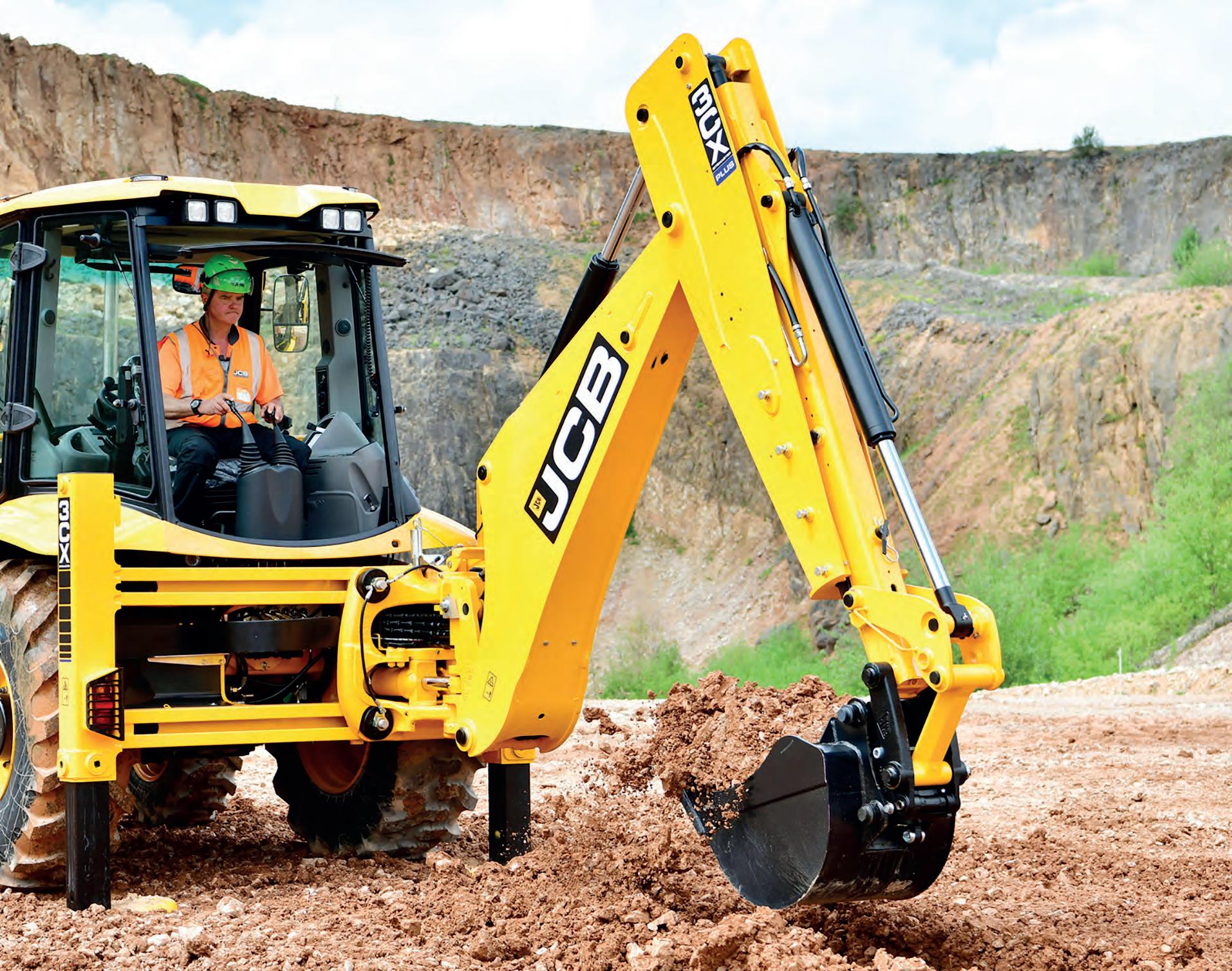
All of the new backhoe loaders come with Auto Smooth Ride System (SRS) boom suspension as standard, along with return-to-dig, rear light guards, front bumpers, shovel clam ram guards and high-flow auxiliary pipework.
Operator’s cab
JCB’s CommandPlus cab has been updated, both internally and outside. There is a new roof cap, that incorporates LED flashing beacons in each corner. This removes the need for the operator to climb up each day to secure a flashing beacon on the roof before starting work. You can specify up to 10 LED working lights and there are larger rear-view mirrors, to provide all-round visibility, while bolt-on yellow grab handles make it easier to enter or exit. Inside, the cab looks smart, with darker grey material in the lower half and lighter grey above. There’s an upgraded seat, with the option of seat heating and air suspension, while a headrest is now standard on AEC models, or optional on manual lever machines. All models have a new steering wheel, providing a better view of the updated front display screen, while the side display now gets a 7” monitor to allow more information to be shown. Operators can even access ‘How To’ videos on the side screen, for key functions if required. Equally welcome are additional secure storage, with a lockable compartment next to the radio. That’s a factory-fit radio now too, with Bluetooth compatibility for smartphone use that can be controlled through the rotary switch on the side console. Heating and ventilation controls have been moved to the cab’s B-pillar, for easier use whichever way the seat is facing.
Conclusion

Updating and improving such a mature product range must be quite a task for JCB’s engineers. Daunting too, given the massive share of the global market that the company enjoys. Yet, by simplifying the range and making standard much of the equipment that customers might have added to tailor a machine to their needs, JCB has certainly made it easier for buyers to choose exactly which model they need. In the UK, the backhoe loader might not be quite as important as it once was, with other machine types taking over the digging and lifting duties on site. However, globally, the backhoe remains a big seller and a massively important model for JCB in many countries. This update should keep those customers coming back for more.
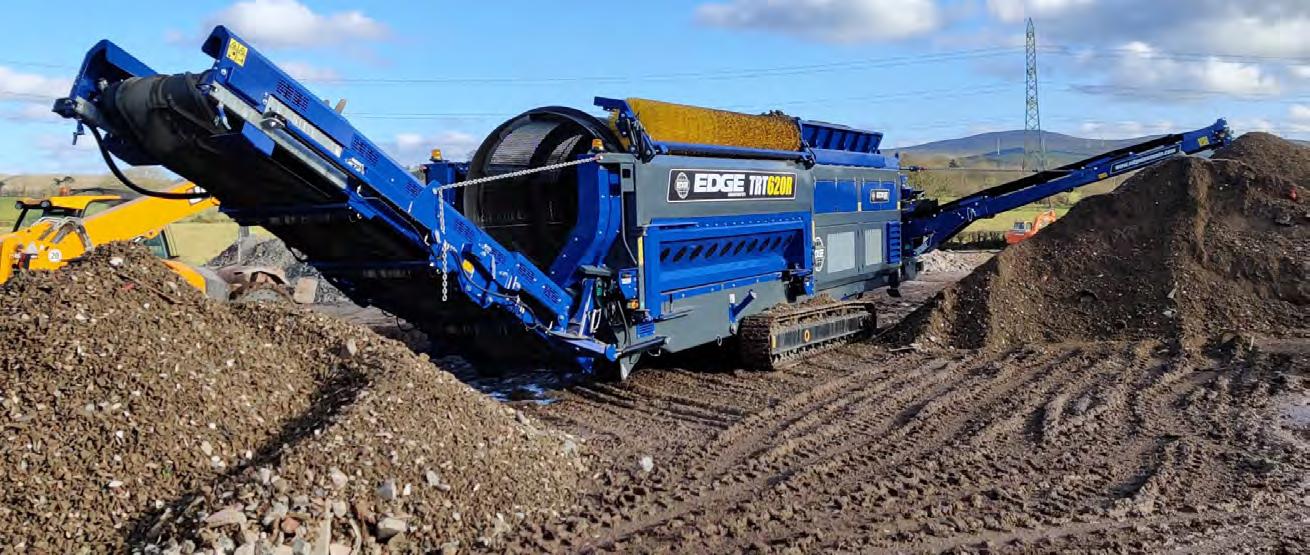
EDGE INTRODUCE NEW ADDITION TO TROMMEL SERIES

The EDGE TRT620R tracked trommel has been designed for maximum productivity and superior screening efficiency.
A heavy-duty construction design and high maneuverability ensures it is the perfect screening solution for a wide range of applications including, compost, mulch, soil, biomass or construction and demolition waste. The EDGE TRT620R has a unique feature of a remote operated, 180° radial fines conveyor which has been combined with the ability to track, screen and stack material simultaneously. This functionality allows for enhanced production capacities, reduced material handling and the ability to create large radial or windrow stockpiles. The positioning of the radial fines conveyor whether at 0° or 180° allows the TRT620R to have the same small footprint of a side conveyor trommel format but with a much superior product separation and reduced material contamination. Designed to accept several other trommel manufacturers drums, the EDGE TRT620R enables operators to take full advantage of their existing drum stock as well as loaned drums from other operators and drums from equipment hire outlets. A quick and simple drum exchange procedure is facilitated via an innovative sliding feeder design and double sided 180° swinging drum doors allowing the screening drum to be exchanged in a matter of minutes. With superior stockpiling ability, efficient screening, intelligent load management and quick drum exchange; the EDGE TRT620R offers all the expected benefits of 620 class trommel and more.
AT A GLANCE
• Intelligent operating system ensures maximum up-time. • 180° Radial Fines Conveyor fitted as standard for improved stockpiling. • Innovate feeder design and drum swinging doors allows for quick drum exchange procedure. • Punch plate drum is compatible with
Doppstadt, Pronar, Neuenhauser and Terex Ecotec models. • 2m (6’9”) x 5.5m (18’) long drum provides a screening area of 30m² (35.8yds²).
