
24 minute read
Looking Forward to Vertikal Days Show
GET READY FOR VERTIKAL DAYS…
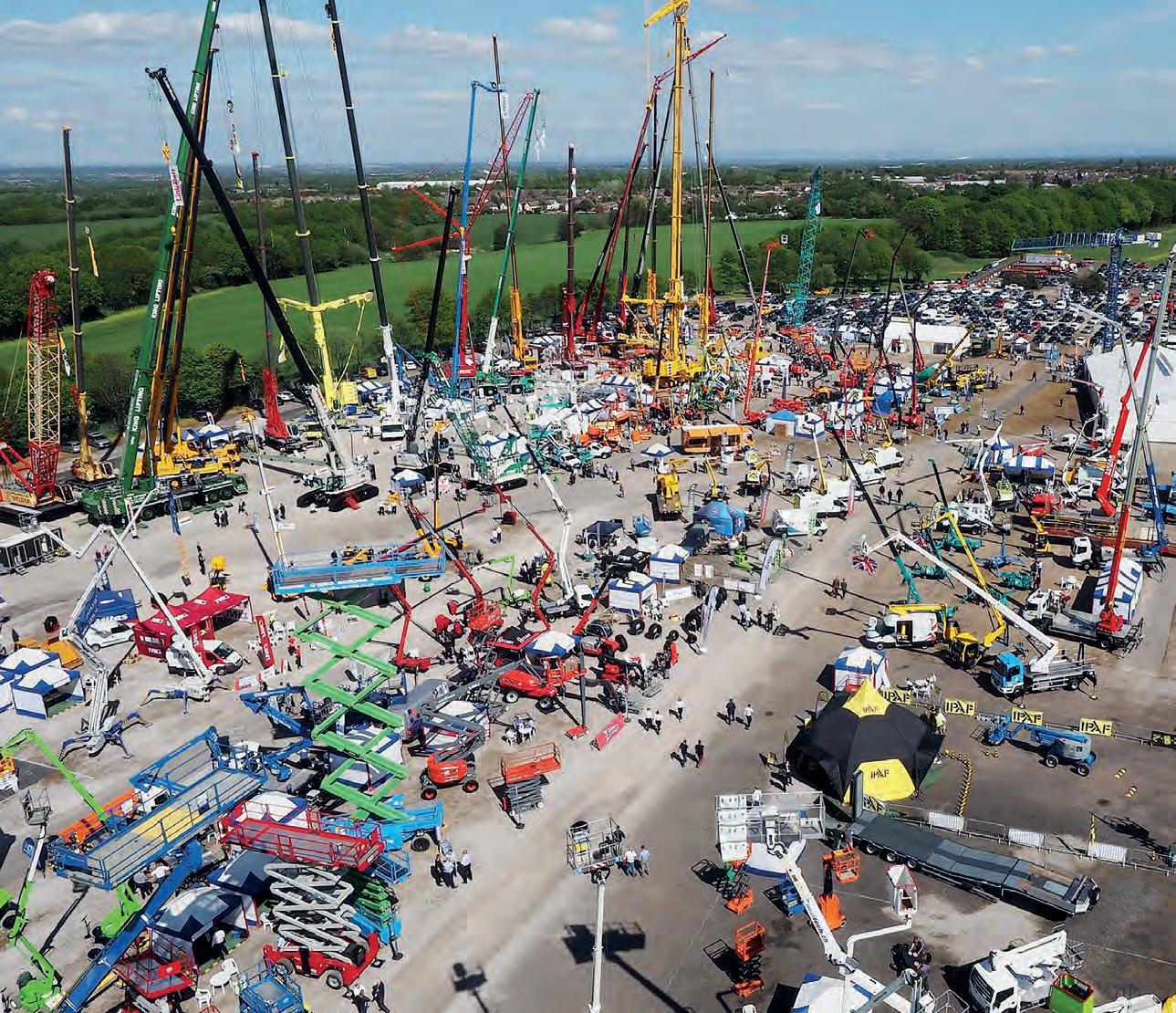
After what will be 28 long months since the last Vertikal Days event, there is a very positive vibe in the air from the UK crane, access and telehandler fraternity looking forward to catching up in late September at our new venue, the East of England Arena & Showground in Peterborough.
Taking place on September 22nd and 23rdVertikal Days will be one of the first events in the UK since it ‘lockdowned’ in March 2020. It will also be the first outing for a host of new products, with visitors treated to a good number of World, European and UK ‘firsts’ from the crane, access platform and telehandler manufacturers, plus an abundance of new ancillary products and services in the Marketplace. The show is the largest event in Europe dedicated solely to the lifting and working at height industry, and a perfect opportunity for rental companies, utilities, major contractors, and a plethora of end users who visit the show to see and hear about the latest developments on hand and ‘in the iron’. Staying true to its roots, visitors will also benefit from everything being complimentary, from parking and entry, through to refreshments and catering.
Marketplace Pavilion
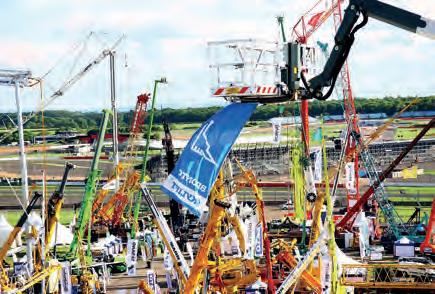
Located centrally within the showground, the Marketplace Pavilion is almost a show within a show, andwill include an even more comprehensive mix of companies displaying the very latest in ancillary products and services related to cranes, access equipment and telehandlers, such as safety equipment, software, innovative components, rigging solutions, training suppliers, financial solutions and electronics. It will also feature the main café serving complimentary tea, coffee and soft drinks all day – a great place to network or simply sit for 10 minutes to
digest not only the pastries, but the host of equipment and services on offer.
Lifting Equipment
Making its world premiere is the 150 tonne Liebherr LTM 1150-5.3 All Terrain crane, which is set to replace the manufacturer’s popular 130 tonne LTM 1130-5.1. while Kranlyft will have the new all electric Maeda MC285CB-3 spider crane alongside a range of other Maeda cranes, including compact mini crawler. This will also be the first chance to see the new six tonne Klaas K1100 RHX truck mounted aluminium crane and the heavy duty Uplifter GW1125 glass handler. Jekko distributor JT Cranes will have the recently launched lithium-ion powered five tonne SPX650 spider crane on show, as well as its600kg MPK06 battery powered mini pick & carry crane/glass handler. For Spierings it is the first opportunity to demonstrate its new zero-emission eLift self-erecting mobile tower cranes in the form of the seven tonne SK597-AT4 and 10 tonne SK1265-AT6. Kobelco will have its latest 100 tonne Stage V compliant CKE900G-3 lattice boom crawler crane on its stand, while also being the first outing for its new Used Cranes Services.
Powered access
Genie is another company with a host of new models to show, including the 14ft GS-1432m and 19ft GS-1932m micro scissor lifts launched last month, along with other E-Drive models. Dingli could well take the award for most new products on show, with both diesel and electric versions of its new telescopic and articulated boom lift range, as well as its new high reach Rough Terrain and narrow aisle scissor lifts. Haulotte will be another stand brimming over with new technology, with its all new HS18E-Pro electric Rough Terrain Pulseo scissor lift and 46ft all electric Sigma16 Pro articulated boom lift. Snorkel will launch its new lithium-ion battery powered scissor lifts, in the form of the 27ft S2755RTE and 39ft S3970BE Rough Terrain scissor lifts, as well as the battery powered SL30RTE Speed Level. Niftylift will have the first chance to show its new 50ft HR17 while demonstrating its latest technology. Italian spider lift company CMC will display a number of new spider lifts including the fully hydraulic S18F, the heavy duty 22 metre S22HD and 23 metre S23. This will also be the first show for Access Platform Sales (APS)since it took on the distribution of the LGMG range of scissors and booms, which it will show alongside a number of Hinowa spider lifts, including the 33 metre 33.17. It will also unveil the new Boss PA-lift push around scissor lift which is set to replace the current BoSS models. Platform Basket distributor Promax will have the all new 25ft tracked RR9/200 Road Rail self-propelled articulated boom alongside a 20 metre hybrid Spider 20.95 and a 33 metre Spider 33.15. Avant UK will have Leguan’s newly redesigned 13.5 metre 135 Neo and 19 metre 190 spider lifts, while new subsidiary Almac Atlantic will have two world first outings on its stand - the 18 metre B1890 from its new Spider boom range and the ML 3.0 FX MultiLoader tracked carrier, as well as the 43ft Jibbi U-1570 which features a Multitel Pagliero boom on Almac tracked chassis. The Imer line up of scissor and spider lifts will include its new 15 metre IM R 15 DA lithium-ion spider lift, the first model in its range to feature a dual sigma type riser. Versalift will unveil the all new VTA-135 pick-up mounted lift, on a Toyota Hilux and Isuzu D-Max chassis, alongside its type approved VTL-135 van mount and a new hybrid model. CPL /Klubb will look to rival it with its KT range of 3.5 tonne van mounts and new 13.1 metre Palfinger P130A on an Isuzu D-Max 4x4 pick-up truck. More European debuts can be found on the GSR stand with its 21 metre B210PXJ on a 3.5 tonne Mercedes Sprinter chassis, a 22 metre B220TJ telescopic that now features a jib and its newly updated PX/PXE range. At the opposite end of the spectrum the latest developments in mast climbers and hoists can be found on the Alimak and Mace Geda stands and CLM will show its Maber product line.
Telehandlers
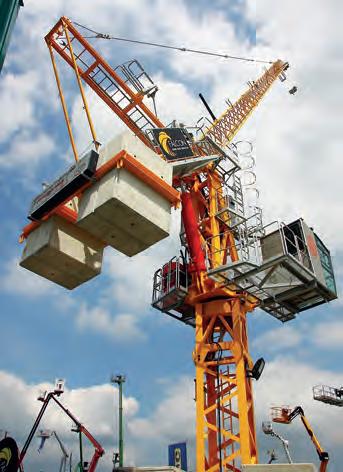
World firsts from JCB include its all new fully electric 2.5 tonne/six metre 525-60E compact telehandlers as well as the 5.5 tonne/20.5 metre 555-210R 360 degree model. Snorkel will also have its 626 electric telehandler on show, while Magni will debut its six tonne/10 metre TH 6.10 fixed frame telehandler announced at the start of the year. GGR will highlight its increasingly popular Faresin Full Electric compact telehandler and might just have news on a larger electric model from the Italian manufacturer.
SHOW INFORMATION
Venue: East of England Arena and Events Centre, Peterborough, PE2 6XE UK
DATES/TIMES
Wednesday 22nd September - 10am to5.30pm ; Thursday 23rd September - 10am to 4pm To check out the full exhibitor list visit: www.vertikaldays.net
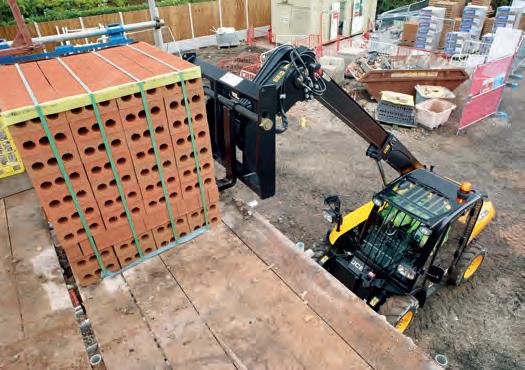
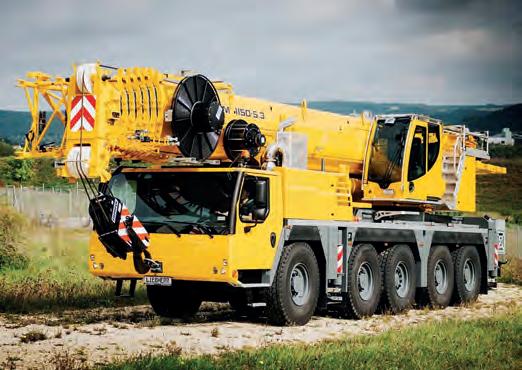
South West College Students Awarded CITB NI Inaugural Bursary For Built Environment
Students from South West College have been awarded the Construction Industry Training Board NI (CITB NI) inaugural bursary award aimed at encouraging school leavers to consider a career in construction and undertake a third level Built Environment related qualification.
Twelve first year, full time students from across Northern Ireland, were awarded £1000 towards the cost of their training. South West College students Callum Snow, Emer Condon and Padraic Rodgers, who are studying Civil Engineering Foundation Degree were the recipients of the CITB NI bursary. To qualify applicants must have applied to study a third level Built Environment related qualification at Level 4 or above with a Northern Ireland training provider. Following the completion of an application form, applicants were entered into a draw for one of the 12 awards. The bursary scheme 2021 will open to applicants from 9th August, terms and conditions apply. With such varied and wideranging opportunities, a career in construction is challenging, exciting and rewarding. From the design, construction and maintenance of buildings and
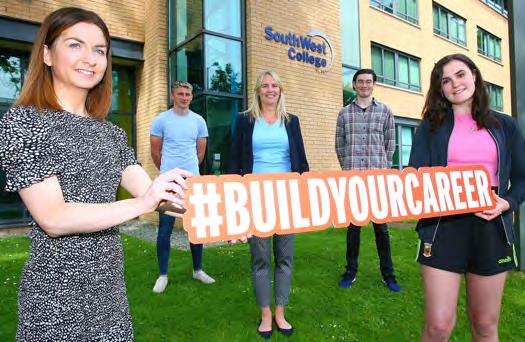
Celebrating receiving the inaugural CITB NI bursary for built environment at South West College Omagh were, from, left: Danielle McKelvey (Deputy Head of School for Natural and Built Environment), student Padraic Rodgers, Amanda Stevenson (CITB NI), students Callum Snow and Emer Condon.
infrastructure projects such as bridges, roads, tunnels, waterways, etc. Construction boasts a variety of careers including skilled trades, IT, marketing, project management, design and much more. New emerging digital technologies are rapidly changing the Built Environment landscape. With Building Information Modelling, Drone usage and Augmented Reality/ Virtual Reality, Computer Aided Design (CAD) and even nanotechnology on the rise, companies are actively seeking to recruit people with these skills. Congratulating the students awarded the inaugural Built Environment Bursary Award, CITB NI Chief Executive, Barry Neilson said: “This is fantastic support for undergraduates who have completed their first year. We hope that this support helps students on their built environment career journey. The bursary will reopen for applicants on 9th August 2021 and the process is simple. All applicants need to do is visit our website, ensure they meet the criteria set out in the terms and conditions, fill in and submit the application form. We wish everyone applying this year the very best of luck.” William Young, Project Officer for Civil Engineering Curriculum Development Programme at South West College, said: “The Built Environment Bursary Award is a fantastic initiative from CITB NI and we’re delighted that three of our students are the inaugural recipients. It is a fantastic boost for the students themselves, for South West College as a training provider in this area, and for local industry. Callum, Emer and Padraic are all talented, hard working students. “This financial support eases a lot of pressure and allows them to focus on their studies and their future, which is of enormous benefit to them. We look forward to continuing to train and support them, and we hope to work with CITB NI again in the future and to see more South West College students benefit from these bursaries.” Applications for the Built Environment Bursary will be available from 9th August 2021. Download the application form and terms and conditions from www.citbni.org.uk. Follow CITB NI on Facebook, twitter and Instagram #BuildYourCareer.
Speedy Invests £10m in Core Kit As Demand For Four-Hour Delivery Grows
Construction equipment and services provider Speedy has invested £10 million in new products for its four-hour guaranteed delivery promise, to meet rising customer demand for quick site deliveries.
The investment adds 25,000 new assets to the company’s most popular 350 products made available through the service. It will boost the availability of equipment from lighting towers to power tools and materials handling kit from the firm’s network of 200 service centres across the UK and Ireland. The hire provider has fulfilled 13,000 fourhour deliveries in the last 12 months, which represents a 30% year-on-year increase for the service from customers. Through the service, Speedy guarantees equipment to be delivered within four hours to anywhere in the UK and Ireland when ordered before 3pm, or customers receive a week’s free hire. The £10 million investment follows the £27 million invested in new kit since September last year, as the business responded to increases in customer activity. A significant percentage of this was in sustainable products, including increased investment in more sustainable battery powered equipment aligned with its strategy to reduce the carbon output of its hire fleet through investment in solar, hybrid, electric and hydrogen technology. Dan Evans, Chief Operating Officer at Speedy, said: “The growing demand for our four-hour delivery promise reflects the value it’s providing our customers, helping them to be more productive and complete projects on time by giving them quick access to essential site equipment. “This latest investment boosts the availability of our top products throughout the UK. It provides our customers with the re-assurance that we can support them to get the job done on time, so that they can avoid costly delays to the projects they are working on.” Speedy became the first hire firm to promise same-day delivery on tools and equipment in May 2018 by launching Capital Commitment through a trial for construction contractors operating in London, Set up by a team led by London and South East Regional Director Dan Rice, the scheme was enhanced to a four-hour UK-wide delivery promise in January 2020, with the company expanding the available range from 52 to 350 products in September last year. Dan Rice said: “What started as a trial in London has developed into a major nationwide operation which is now core to our unique service promise to customers. Continual investment in new products and digital infrastructure has been essential to achieving this, digitising the hire journey for the benefit of our customers. We look forward to continue building on this success to help businesses across the UK to deliver their projects safely and efficiently.”
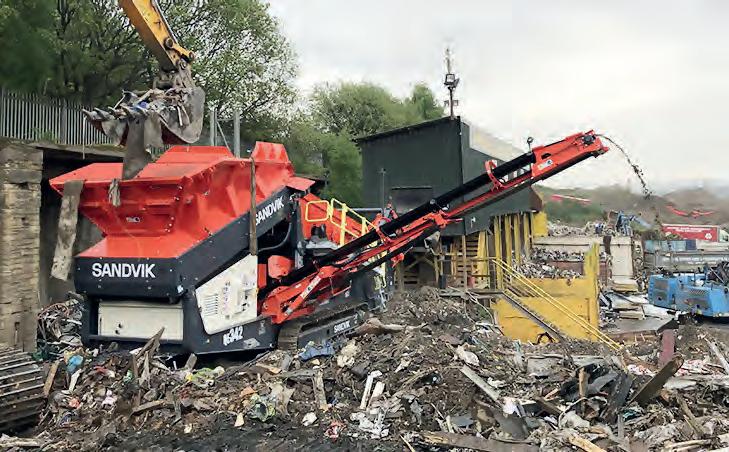
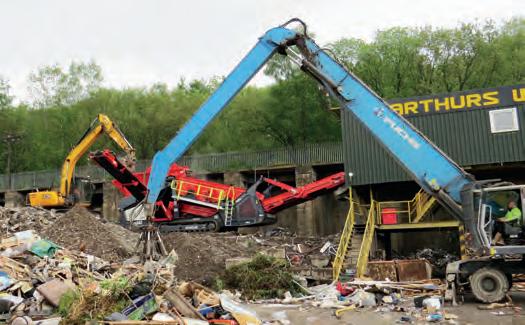
ARTHUR’S SKIPS EXPANDS THEIR FLEET WITH A SANDVIK QE342 MOBILE SCALPER
Arthur’s Skips have been a loyal customer of Sandvik for a number of years. They have recently invested in the latest mobile scalper for their recycling operation due to the reliability and back-up provided.
Arthur’s Skips was established in 1994 by Arthur Hartley and his son, James. They began trading with just two vehicles and eight skips. The business has since grown over the years and they have relocated to a large 13 acre site, where they now operate 30 trucks servicing over 2,000 skips and containers in Sheffield and the surrounding areas, employing 70 members of staff. With a £2m investment in aggregate production, the company now offers a complete waste management service as well as supplying recycled aggregates to its customers. This expansion has put them alongside the fastest growing recycling companies in the country. Sustainability is an integral part of Sandvik’s business. We are committed to using engineering and innovation to make the shift towards more sustainable business and drive to a more circular economy. Manufacturing equipment which will help our customers achieve their sustainability targets and add value to their operation, as well as society as a whole, is high on our agenda. This ties in well with Arthur’s Skips and their mission to improve waste handling and the recycling processes they operate. Arthur’s Waste Management and recycling services offer complete recycling and waste management solutions to the construction and demolition sector. They provide onsite and offsite segregation for all recycling and waste materials, which they say are recycling in excess of 95% of most waste – the alternative to landfill. “With Site Waste Management Plans and annual increases in landfill tax, sustainable waste management is not just an environmental improvement, but a financial one” says James Hartley, Managing Director.
Expanding Fleet
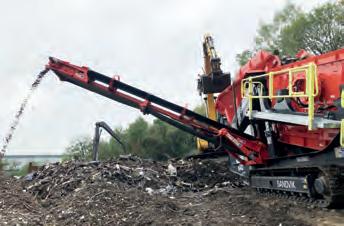
Needing to invest in a new scalper due to increasing demand, they turned to Sandvik once again. They have been operating two Sandvik QE341 scalpers for the past 5 years and have been happy with both the product and aftermarket support provided, which James comments as “far superior in terms of build quality and reliability”. They decided to purchase a new QE342, the successor to the QE341, which was upgraded to include a number of additional features for ease of operation, safety and performance. As operational user friendliness is vital for enhanced use, the QE342’s electrical control system incorporates several features to improve both the operational effectiveness and machine safety. The simple, easy to use system features a key switch, a mode selector switch (set-up, operation & tracking) and one global plant button to commence sequential automatic start-up & automatic shut-down of the plant whilst in operating mode. A large visual display is also provided to enable to operator to view engine & plant status. Prestart warnings on all plant functions, ensure that safety, as well as ease of operation, is paramount at all times.
Versatility & Durability
With its wear resistant rigid hopper and steel apron feeder, it has been purpose designed to accommodate many tough and difficult to screen applications. It is versatile with a choice of screen media and is compatible for 2-way or 3-way split configurations, as well as having the ability to interchange side conveyors. The screen-box jack up facility allows easy access to the bottom deck for maintenance and screen media changes. The QE342 comes fitted with the latest generation fuel efficient engine for maximum performance and cost efficiency. Its extended hydraulic fluid change intervals from 2,000 to 4,000 hours also contributes to a reduced cost of ownership. The new QE342 fits in right at home at Arthur’s working at their waste transfer station, which was established in 1996. It is dealing with a variety of construction and demolition waste and pre-screening prior to being fed into a picking station. The fines as well as the waste are processed further. James says “this process enables us to capture good minerals that are located in C&D waste and makes the waste easier to sort through by hand to get it into the correct recycling waste stream”. The QE342 also comes fitted with Sandvik My Fleet as standard to help optimize utilization and performance. This technology will help Arthur’s Skips with their maintenance and servicing schedule reducing downtime, as well as facilitating remote operator support. When asked about the level of service and support received from Sandvik, James Arthur comments: “Sandvik service is very good and they are always willing to talk you through faults over the phone which is unique. 9 times out of 10 any issues can be sorted over the phone without the need to send a technician to site costing time and money.”
MFC’S NEW MERLO ROTO 50.26 S-PLUS EXCELS IN VERSATILITY & EFFICIENCY
From multi-national firms to private clients and from local authorities to historical buildings, M. Fitzgibbon Contractors (MFC) has built a formidable reputation for completing a string of high class projects down through the years across Ireland’s Mid West.
From developing business parks to roads infrastructure and water mains systems, MFC has found its niche fulfilling a broad spread of Irish civil engineering contracts, employing directly all civil engineering and construction staff – which gives them total control over the quality of work, the cost and the completion of projects. Based at Ennis in County Clare, the company runs a substantial fleet of plant and machinery, including excavators, dump trucks and tippers, and invested in its first Merlo Roto just a couple of years ago; since then, it has had three, such has been the positive impact the brand has made. Its latest acquisition, a replacement for an earlier model, is a Merlo Roto 50:26 S-Plus, supplied by McHale Plant Sales, and it is living up to the company’s high expectations. “Our previous Merlo had a 30m reach, but we find this new 26m machine just that bit more agile, manoeuvrable and versatile around the site,” says Michael Fitzgibbon. “It is easier for the operator to handle and manage.” Up until the arrival of Merlo machines on site, the company generally employed cranes to do the lifting at height work, but says Michael: “The Merlo Roto 50:26-S-Plus is a very stable machine and can easily accomplish tasks previously done with a crane, plus it also acts as an effective teleporter.” The new machine is currently being utilised on a busy social housing site at Ennis where 40 homes are being built on behalf of Clare County Council. “There is a lot of activity on the site, so good all round visibility from the cab is essential, and the new Merlo Roto doesn’t disappoint. It is actually better than the model it has replaced. The operators love the cab; it is well designed and set out, is comfortable and has a lot of built in safety features,” adds Michael. “The current driver was always used to operating a different brand of machine over the years, and the switch to Merlo has been a very positive experience for him.” Michael also pointed out that dealing with McHale Plant Sales made the investment process straightforward, and he adds that the aftersales service and support has been excellent. “Any issues we have are quickly sorted out, which means we don’t have any unnecessary downtime.”
Top-of-the-Range
Taking a closer look at the Merlo Roto 50:26-Plus: with a 360 degree operation thanks to the rotating turret, which offers a greater range of action compared to a fixed telescopic handler, this model represents the top of the range. It has a high level of standard equipment, including Grammer warmed seat, roof wiper, sunshade, LED light on cab, lights on boom, and towing hook. The large 10.1” colour display shows all the machine’s operating information. The screens are navigated using the wheel control positioned on the armrest, which can be used to configure the machine’s settings, like adjustment of the maximum movement speeds and geometric limitation of the work areas. From the driver’s seat the operator can activate the cab’s tilting via a dedicated button. The longitudinal inclination reaches 20°, allowing you to easily monitor the movements of the load when working at a height, while intelligent hydropneumatic suspensions on the axles, give great frame levelling control (12% lateral and 4% front inclination). The lower part of the cab is connected using Silent blocks to drastically reduce noise and vibrations. Operational comfort is further improved by the tac-lock system, which allows the tools to be hydraulically clamped with no need to leave the driver’s seat.
Stability & Safety
The standard ASCS automatic load management system, which is equipped with a high definition digital display for viewing the operational and safety parameters, guarantees maximum performance without altering the machine’s stability. The S-Plus ROTO model is equipped with an active suspension system designed to compensate for sloping terrain, thereby allowing the materials to be lifted in complete safety. It is also a very stable machine, as Michael pointed out. Its stabilisers are structured to facilitate rapid and safe deployment that can be adjusted based on the operational conditions of the site. The exclusive design of
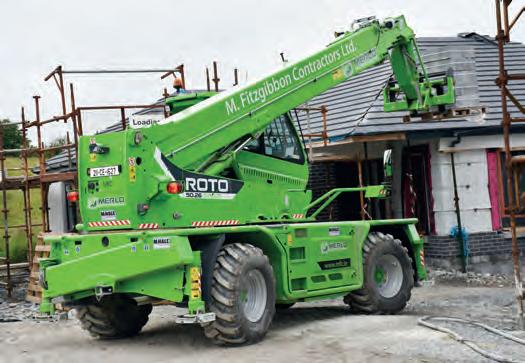
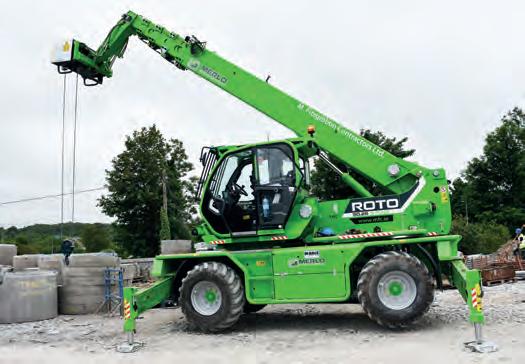
the telescopic stabilisers guarantees the stabilisation from the totally retracted position to maximum extension, managed independently for each of the stabilisers. The load diagram automatically adjusts based on the position and consequent stabilisation area. Its Load Sensing and Flow Sharing hydraulic circuit allows for multiple simultaneous boom movements and rapid turret rotation, without compromising the accuracy of the movements themselves, for precision load positioning. Moreover, the hydrostatic transmission guarantees millimetric precision during machine movements. The innovative multi-function armrest, made with automotive-style materials, is extremely intuitive to use, and is equipped with automatic systems for positioning the stabilisers. The ROTO model can even be manoeuvred effectively by less experienced operators. The active suspensions of the front and rear axles make road travel more comfortable and safe even on rough terrain, and ensure perfect levelling of the machine during lifting.
The machine is powered by a 125 kW - 170 hp engine and combined with its exclusive Hydrostatic transmission with “Eco Power Drive” electronic management system, it is extremely fuel efficient.
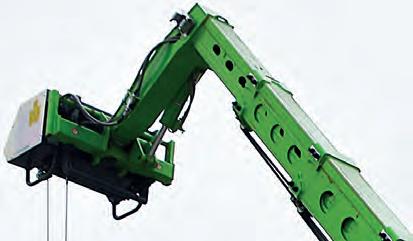
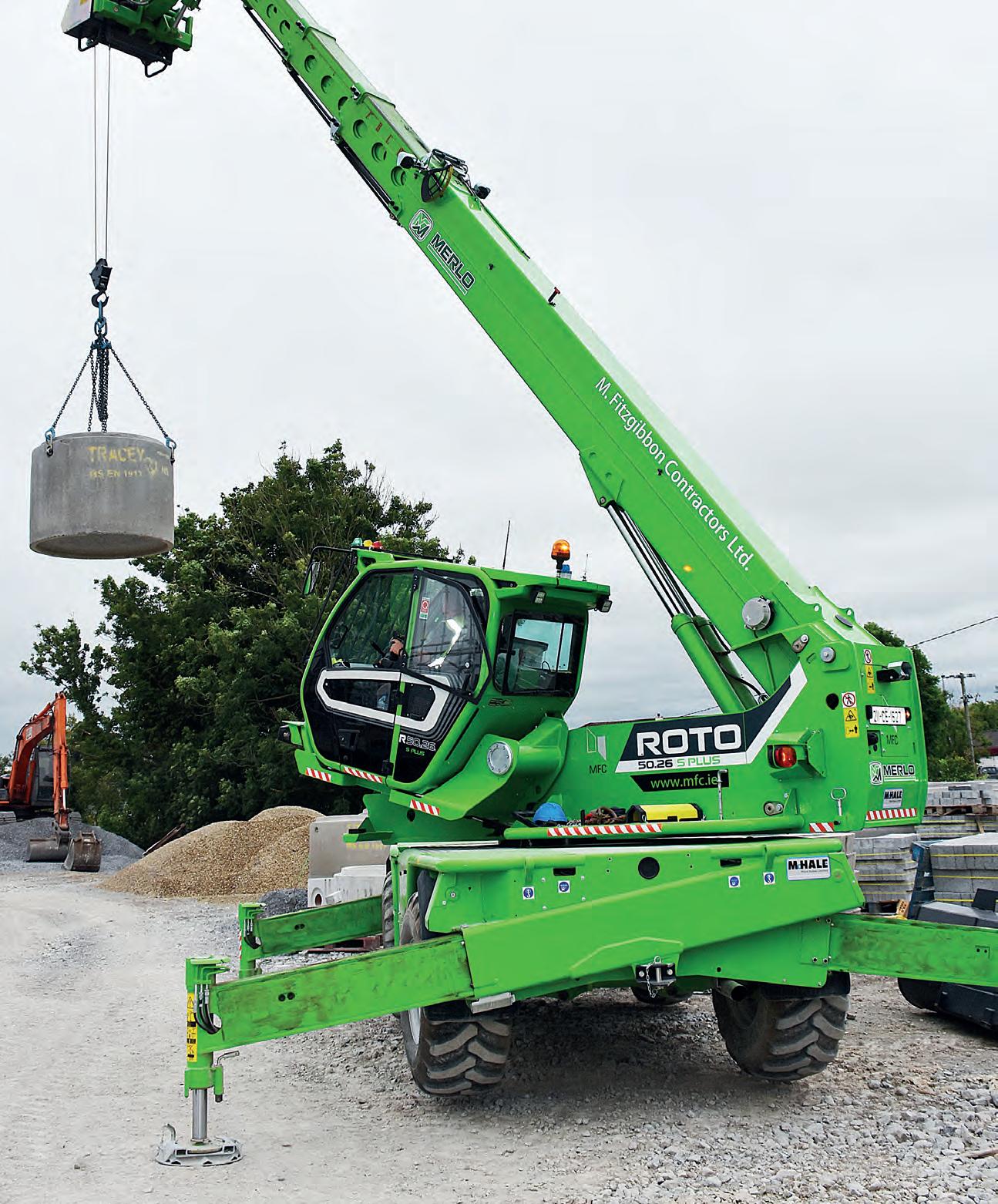
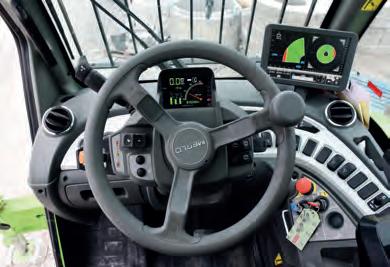
news Merlo Launches New ‘More Powerful, More Versatile’ Telehandler
Construction contractors will be high on the list of targets when a new, more powerful, more versatile Merlo Turbofarmer model TF35.11 TT-145 telehandler makes its appearance on the Irish market early next year.
Included for the first time are hydraulicallypowered stabilisers or ‘outriggers’ that extend its versatility in construction and other applications by increasing stability for those working on aerial building repairs or conducting overhead maintenance on high vehicles. An additional feature will be its ability to carry a work basket for servicing overhead lights, conducting inspections in high and inaccessible areas, and when carrying out overhead maintenance on tall buildings, roof structures and high-rise machinery. Distributed by McHale Plant Sales of Birdhill and Rathcoole, the new unit is equipped with a more muscular105 kW/143 hp engine with a road speed of 40 km/h, it has a lifting capacity of up to 3,500 kg to a maximum height of 11 metres, and the power to tow up to 24 tons weight. Commenting, McHale Plant Sales general manager, Denis McGrath said: “By virtue of its capacity to handle a broad range of attachments such as forks, bucket, crane hoist and aerial work baskets – and stabilised to ensure maximum stability when using an aerial work platform – the new TF35.11 TT-145 unit combines the functionality of a conventional load carrier and bulk materials handler with those of an aerial work station when carrying out buildings maintenance works with personnel at height.” Described by him as ‘quite a beast’, its much more powerful engine at 143hp is said by McGrath to “contrast favourably with a standard construction machine in the 75-105hp range”. Amongst its numerous features are load sensing and stability control functions that enable operators to guard against the risk of frontal tipping when fully loaded. Others include precise and powerful hydraulics with load sensing and flow sharing technology, telescopic boom sideshift for precise load positioning, and EPD transmission that, Merlo claims, can reduce fuel consumption by up to 18 percent. Its optional features include one that regulates and delivers a constant flow of oil to implements.
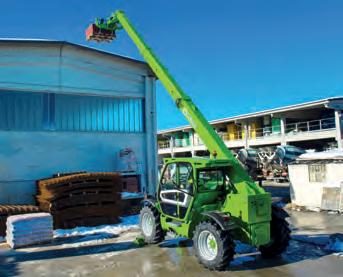
Specialist Police Unit to target Construction Plant & Agricultural Machinery theft
The theft of equipment from construction sites and farms has a significant impact on the businesses targeted from both the loss and replacement of the equipment taken, in addition to the cost of temporarily reduced activity and downtime within these sectors.
The launch of the Construction Equipment Association (CEA) owned Official CESAR Scheme (www.cesarscheme.org) back in 2007, has had a major impact on criminality across both sectors, driving down theft significantly for machinery brands that have adopted the Scheme. Now, with the launch of a new Police Unit, CESAR will have an ally in its fight against this type of crime. The newly established dedicated Agricultural and Construction Equipment (ACE) specialist police unit will be managed and operated within Opal, which is the national intelligence unit focused on serious organised acquisitive crime (SOAC) across the UK. The ‘foundation’ launch of ACE took place in April 2021, where
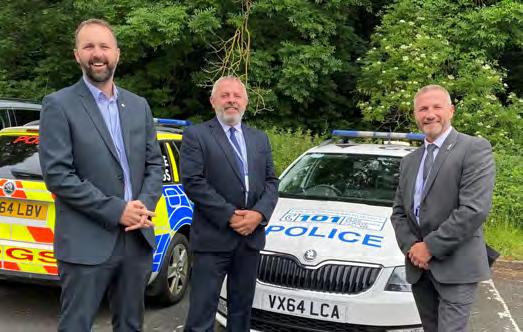
(L-R) Det Sgt Tom Grundey, DSU Neil Austin and DI Ernie Locke.
the new unit was introduced to police forces nationwide, key partners and collaborating trade associations. The key message was that cross-industry cooperation is crucial for the success of the new unit. The ACE team is here to support the wider problem solving approach through partnership – ‘prevention is better than the cure’. Opal was established in April 2019 under the governance of DCC Amanda Blakeman, the national police lead for acquisitive crime. The unit has ten intelligence staff, including intelligence analysts and researchers, alongside police officers, under the day-to-day lead of Detective Superintendent Neil Austin. The unit will focus on the offences committed by organised crime groups which are part of a series and involve cross border offending. By developing proactive working relationships with law enforcement, partner and business agencies the ACE Unit will work to reduce the theft of stolen plant and agricultural equipment and maximise the recovery of stolen equipment, both nationally and internationally. Officers from ACE will work to develop, collate and co-ordinate intelligence from a variety of sources to identify and disrupt organised criminality and target those involved in these thefts, also identify any current and emerging crime trends and threats. The reason ACE was established on the back of Opal is because the unit already has a foothold nationally and intelligence can be shared between the forces. The ACE national intelligence hub team will work closely with the industry, developing positive working relationships to support and promote schemes such as CESAR to prevent theft and maximise the recovery of stolen equipment. Rob Oliver, Chief Executive of the CEA, is looking forward to a strong working relationship between ACE, the CEA and the wider construction industry. “Stakeholders through the industry have been keenly awaiting this initiative to come to fruition, so it is great that it is now in operation with the partnership with Opal. We will be engaging with companies and organisations, such as CITS (Combined Industry Theft Solutions), to support the work of ACE in what is an evolving criminal threat”.