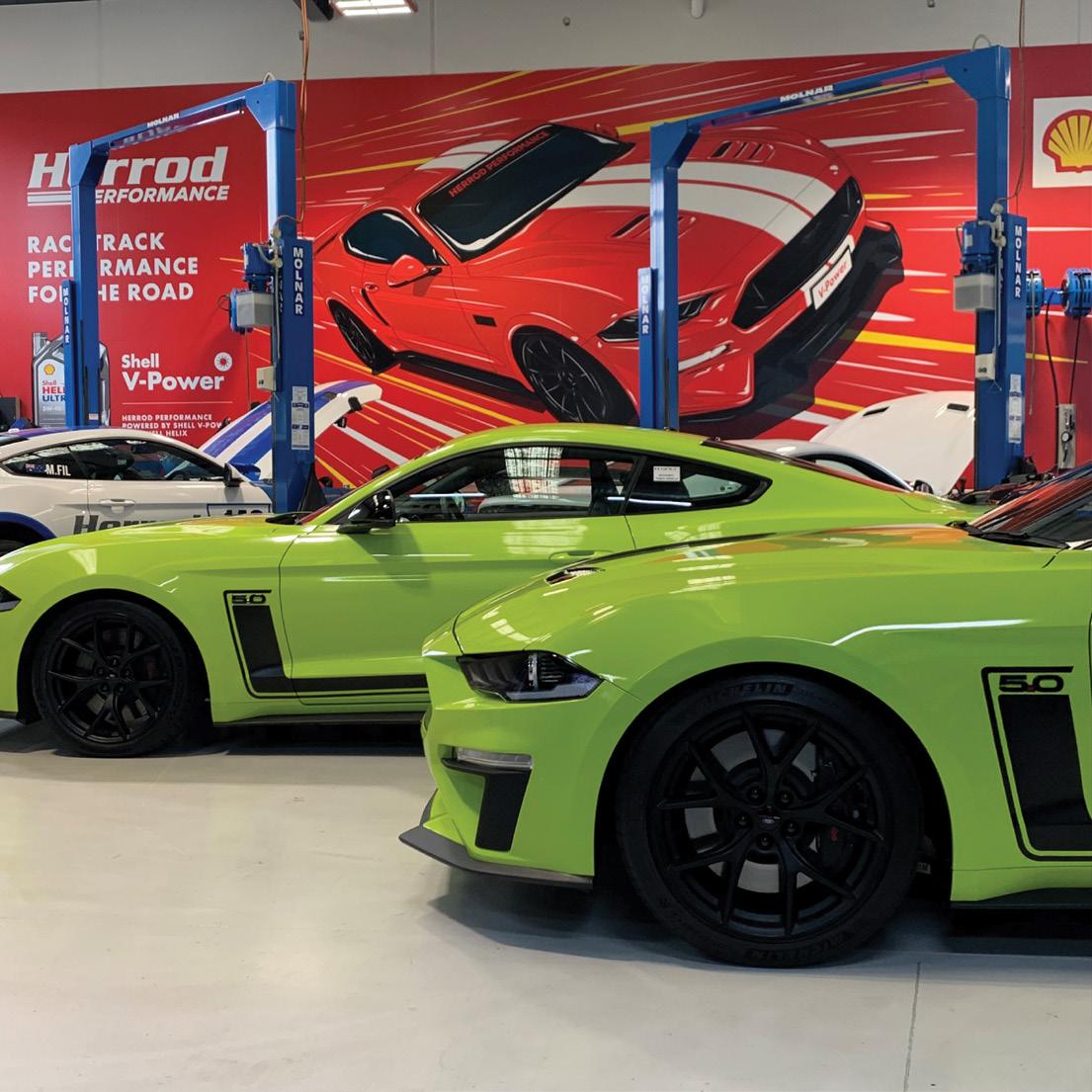
3 minute read
Product R&D: Transformed by Milwaukee
TRANSFORMED BY MILWAUKEE
Rob Herrod reflects on just how far workshop tools have come since the ‘70s
With a career spanning over four decades, Rob Herrod, the man behind the legendary Herrod Performance, has witnessed countless advancements in the automotive industry. He has also witnessed the evolution of automotive tools as workshops have transformed since his early days as an apprentice mechanic, to now, managing his world-renowned Ford Performance specialist workshop. In 1975, Herrod began his career as a mechanic aged 15. He initially participated in work experience with his father, then left school to embark on an apprenticeship. He recalled the tools that he worked with at this time were limited to “normal spanners and bits and pieces.” “There was nothing really…of what we have now in the way of tools… We had to make do with what we could find,” Herrod said. “If we never had a tool, we had to make a tool. The only thing we had back in 1975, and earlier when I was a kid, was an air gun.” Herrod recounted the first game-changer in his father’s workshop was the purchase of an electric gun for removing wheel nuts. But that came with its own set of challenges – namely, hoses and cords. “It was a nuisance. The cord would break. The cord would twist. And it would always break down and play up,” Herrod said. The move to a cordless workshop has been a blessing for Herrod who said that cordless tools have without a doubt revolutionised the automotive industry. “I have had other cordless tools in the past. And I was not particularly happy with (those tools). They were always breaking down or something,” Herrod said. He says his switch to Milwaukee cordless products has changed that, significantly improving efficiencies for his team. “We’ve probably reduced, maybe an hour of build on each car by using a Milwaukee cordless tool,” Herrod said. One of Herrod’s biggest challenges during his early days was lighting. Fortunately, that’s a problem of the past. “If I go back to 1975… the grief we used to go through! We used to have a handheld light, with a little cage around it that you put a normal light bulb in… And you’d hang that under the car with the electric lead running somewhere,” he said. Herrod recalled, not only the blinding glare of these makeshift lights, but just how often they would fall and break. “Then you’d have to go hunting for a globe, and you’d run out of globes. And you’d do this all day long, every day,” Herrod said.
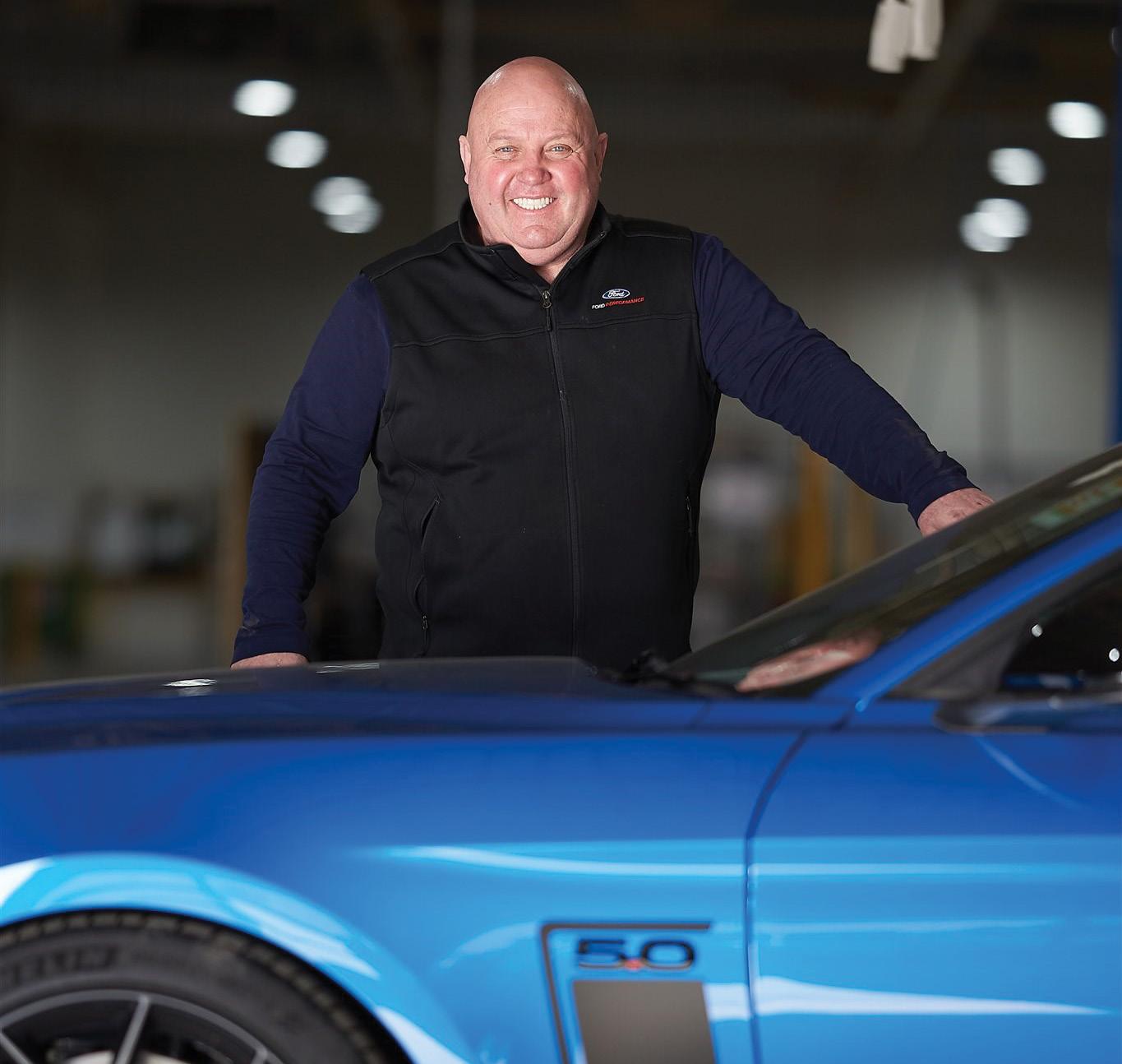
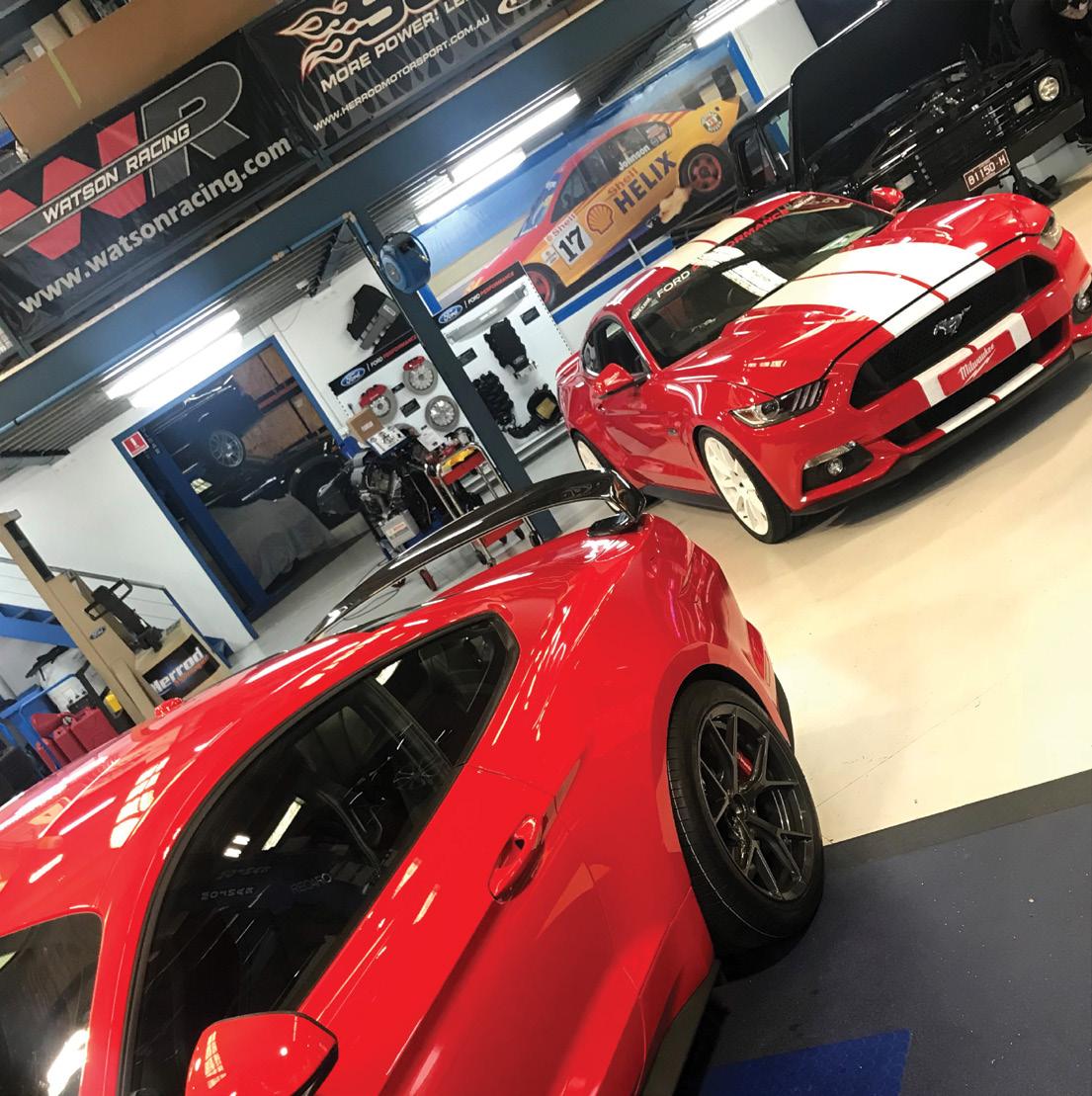
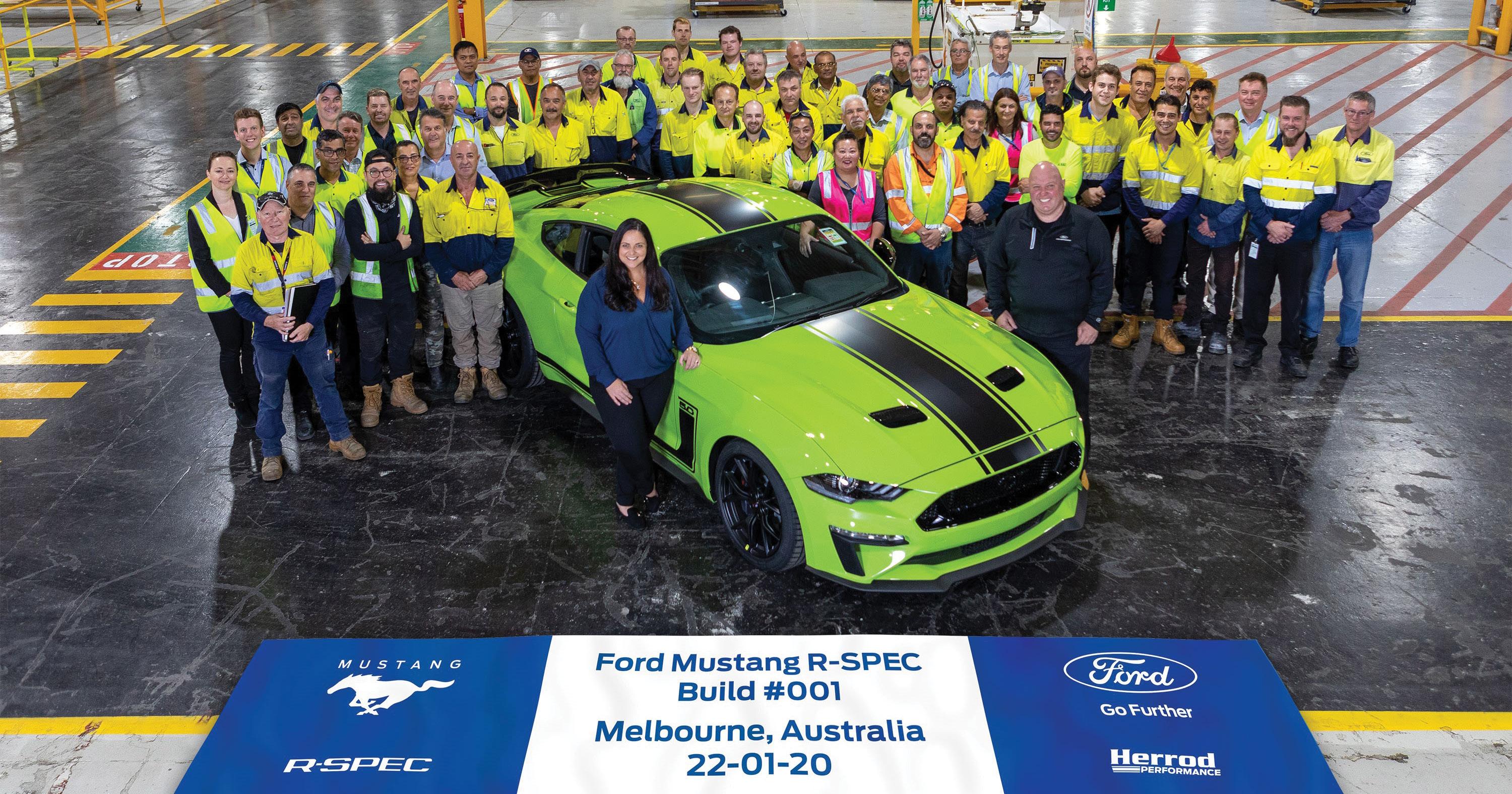
“Now with Milwaukee tools, this never happens. Never. The under hood lights, the lighting systems – all that has just revolutionised the industry.” During the past three to four years Herrod has trusted the Milwaukee range to support his workshop’s greatest projects. Over that time Herrod estimates that they have built, in-house, around 300 supercharged Mustangs, including the Scott McLaughlin Limited Edition Mustang, the Dick Johnson Limited Edition Mustang, and the special edition Ford Mustang R-SPEC. When building the R-SPEC, Herrod and his team heavily used Milwaukee routers, cordless ratchets and cordless guns. These tools were used along a Ford production line, which to Herrod, demonstrates the quality of these products. “When we’re doing a build of a car, we’ll have certain guns and certain tools set up… we just reach for the one, the right one and ‘bing-boombam’ and it’s done,” Herrod said. “No matter what (Milwaukee) bring out—it’s above and beyond.” “I keep saying to all my guys that work for me ‘you guys have got it so good. You do not understand how good you got it!’ “I know. I’ve been. I’ve seen. I started when everything was nowhere... to where it is now, and it’s like, ‘wow’.” For more from Milwaukee Tool, visit www.milwaukeetool.com.au
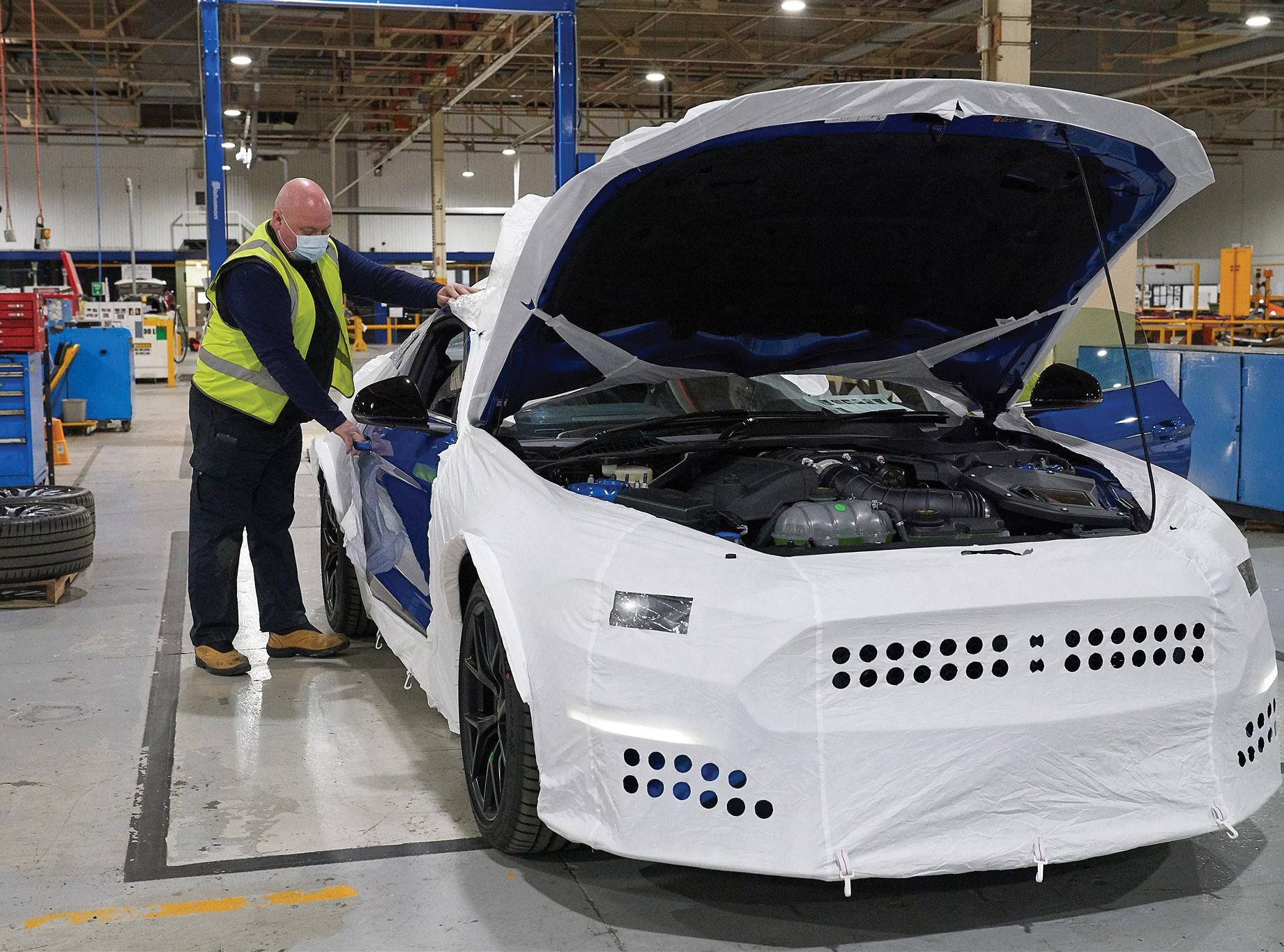
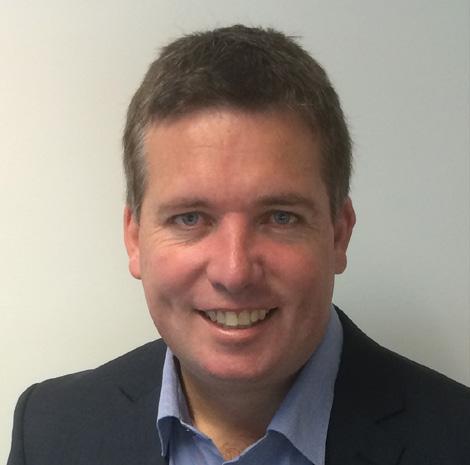
Australian Automotive Aftermarket Magazine Publisher, Cameron McLachlan, takes a look at the products driving the automotive aftermarket. cameron@aaaa.com.au
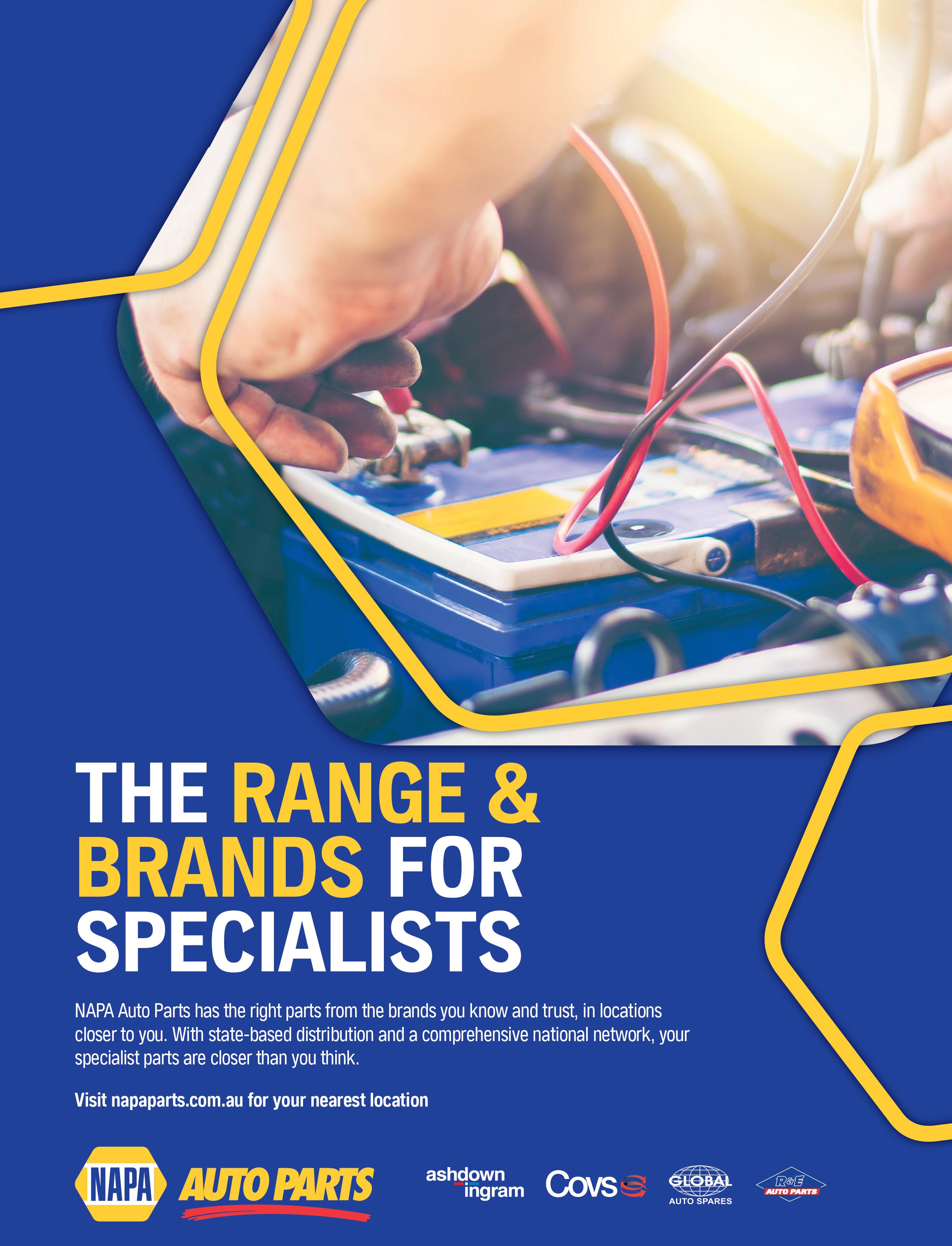
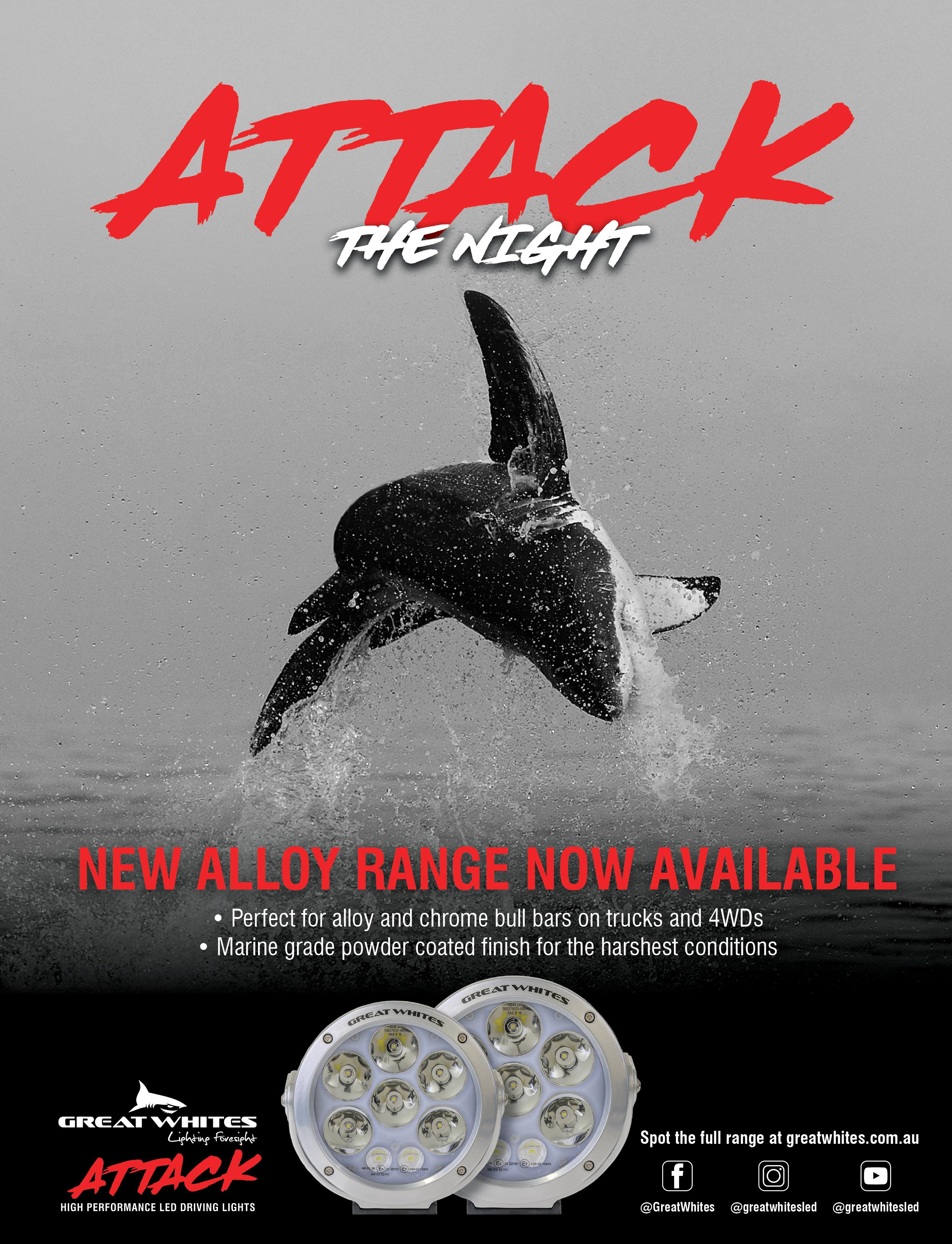