
6 minute read
Member Feature: ADRAD - Thriving in the winds of change
THRIVING IN THE WINDS OF CHANGE
ADRAD has been manufacturing radiators in Australia since 1985
In the 35 plus years that have passed since they first opened their doors, the team at ADRAD have successfully navigated the winds of change on numerous occasions. Today, ADRAD is still a proudly Australian owned family company specialising in the manufacture, importation and distribution of quality radiators, automotive air-conditioning parts, other heat exchange products, plus a growing range of automotive service and replacement parts. “Our range of radiators available in copper, brass, aluminium and steel is the most extensive in Australia and New Zealand,” ADRAD Business Development Manager for Aluminium Performance Products, Darren Duncan, said. “The quality of our range and our commitment to the highest levels of service continues to raise the industry benchmark. “Our products are diverse and meet the needs of automobiles, light trucks and commercial vehicles, heavy on-highway vehicles and heavy off-highway vehicles; but my passion lies in our customised aluminium products for racing and performance vehicles.” In May this year, Darren will celebrate 20 years of working in the radiator industry, and 38 years in the automotive industry. “I’ve seen the industry evolve significantly during that time. Still, the one constant has been the value of maintaining a range of quality products that match the shifting range of popular applications,” he said. When the ADRAD leadership team needed someone with experience to develop their range of aluminium performance products, Darren took the opportunity. “It quickly became a passion of mine, and to this day, I still get a buzz when I work with customers to develop a bespoke heat transfer solution,” Darren states. During his time managing ADRAD’s aluminium performance division, Darren has witnessed massive change and innovation. ADRAD’s founder, Gary Washington, and the company’s talented manufacturing team have invested in significant upgrades to enhance their design and manufacturing capabilities. “In the last five years, we’ve seen the evolution of aluminium radiator configurations advance at an ever-increasing rate,” Darren explained. The significant increases in engine performance have been the driving force behind this new era of innovation in the range of aluminium products for racing and performance vehicles. “Five or six years ago, a streetcar with 500 horsepower under the hood was considered a beast,” Darren described. “But today, more and more cars are pushing out in excess of 1000 ponies at the rear wheels, and more horsepower means more heat, and this has driven innovation across our entire range.” It is a challenge to develop new products to help tame these high-performance thoroughbreds. “Back in the day when all we had was the old copper and brass radiators, the only way to keep performance engines cool was to keep adding rows of tubes which made them thicker and thicker and thicker,” Darren explained. “But these days, there’s not much room in modern engine bays. That, along with the increasing trend towards LS and Barra engine swaps, means that the space between the engine and the radiator support panel is at a premium and as a result, building thicker radiators is no longer an option in most applications.” Armed with these insights, ADRAD’s design team focused on innovating within the core and experimenting with fin profiling and design. From the outside, any radiator core looks pretty simple; it just consists of water tubes and cooling fins. But in reality, selecting the right combination
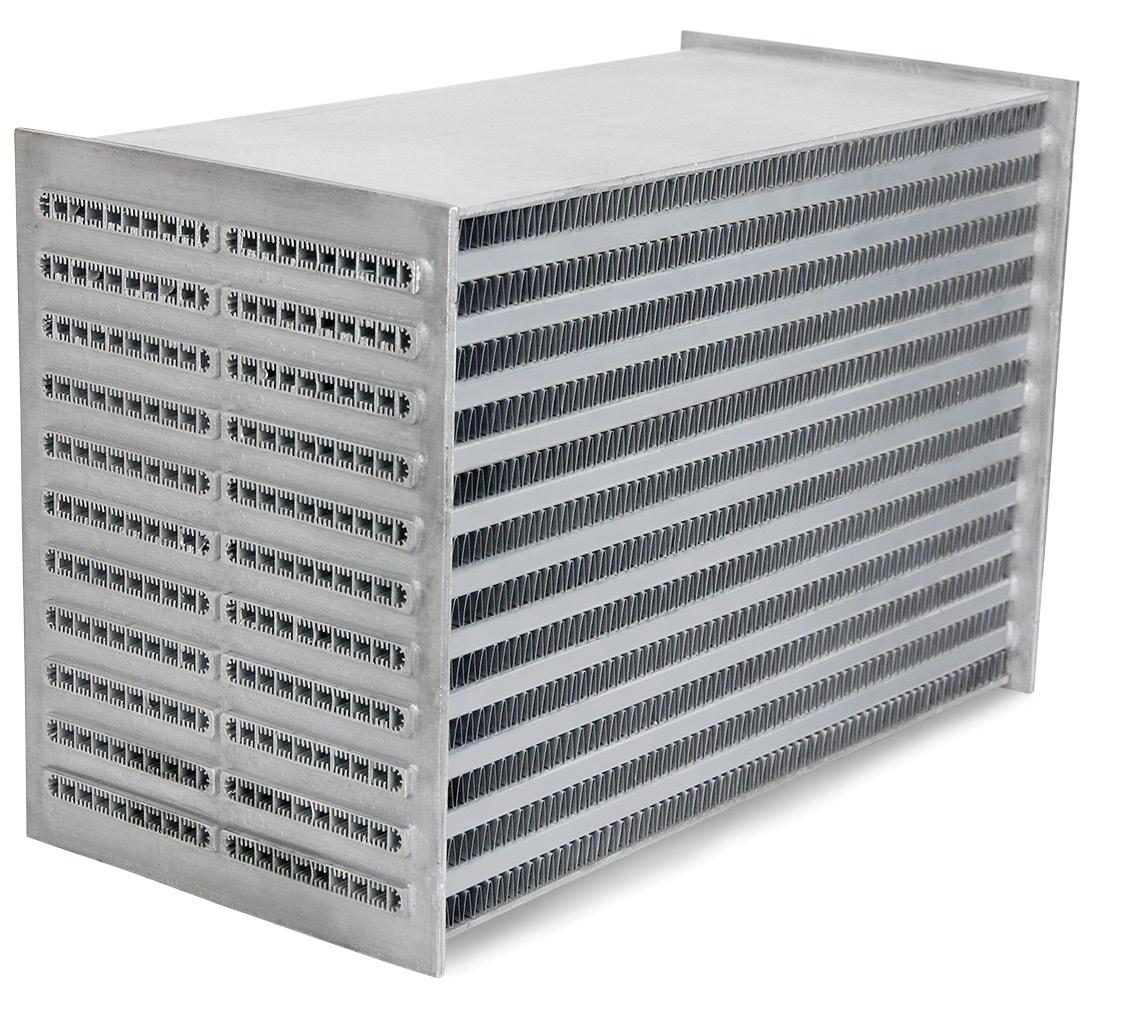
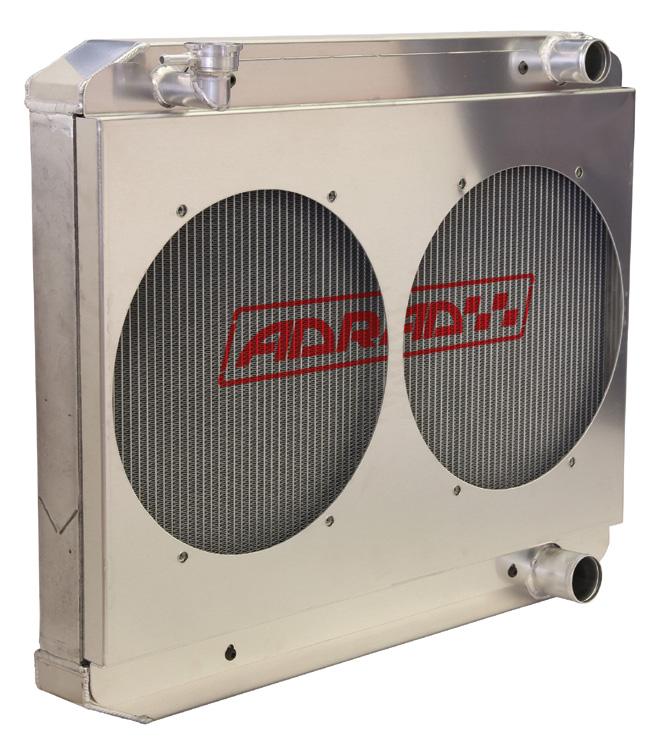
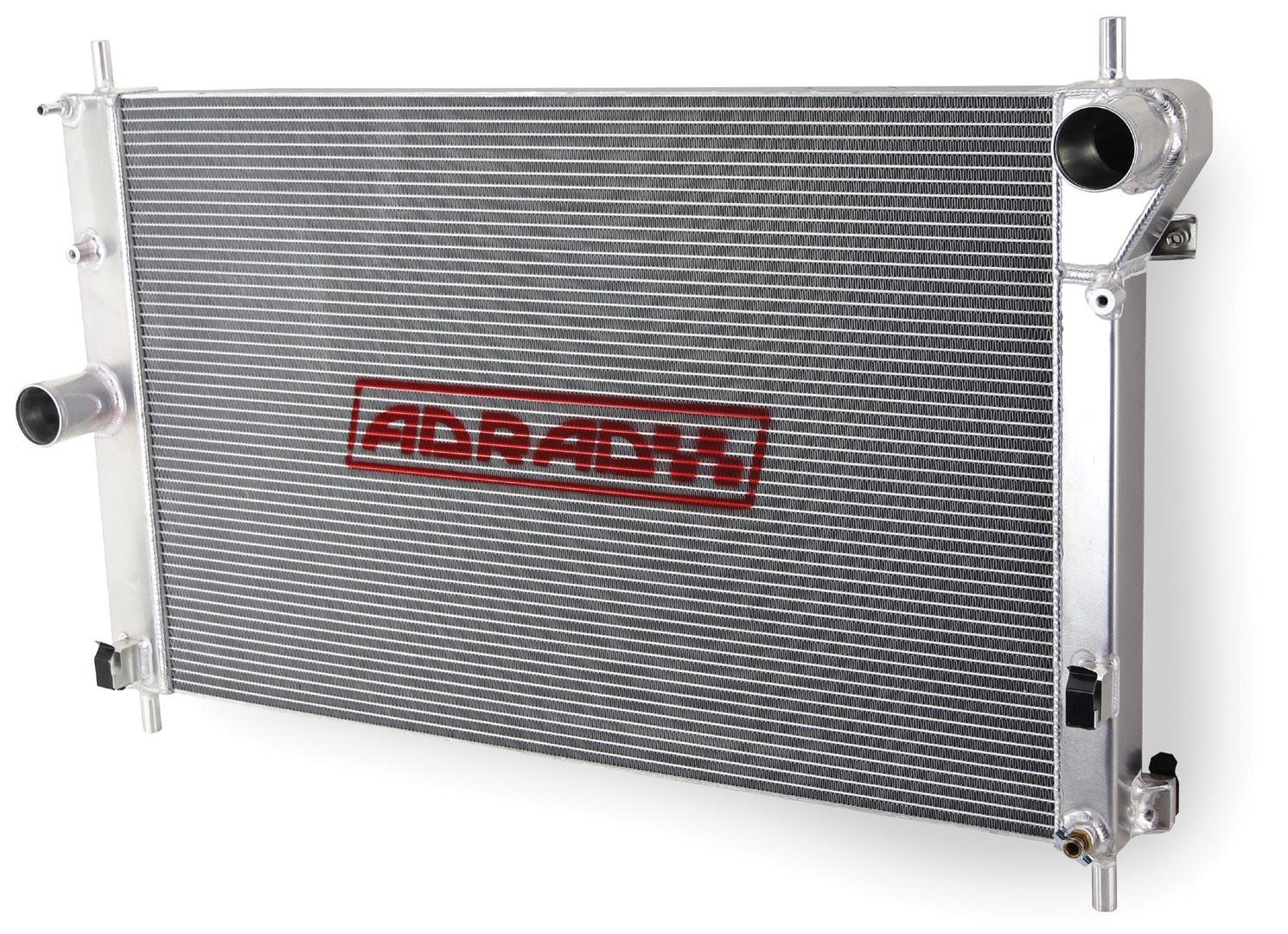
of these two components is a highly specialised and technical process. “We’ve got a number of different tube sizes and profiles available,” Darren explained. “We can build a radiator using tube diameters ranging from 16 millimetres to 73 millimetres. Then, depending on the application, we can marry these with low profile fin height.” ADRAD has invested heavily in fin technology. Its unique, low-profile design allows them to increase the total number of tubes in the radiator and increase the rows of fins, the combination of which increases thermal efficiency. Helping customers select the right combination of tube diameter and fin profile is where ADRAD’s technical knowledge really adds value and proves its expertise. “We have a series of questions that we ask all customers before we start the design process,” Darren said. “It’s critical to understand what set up the vehicle is running and how it will be used before we even start engaging with our design team.” Obviously, a car that will be towing for long distances will require a very different radiator configuration to a drift car, just like a track car’s radiator will run very different specifications to a dedicated burnout car. “We ask questions like what water pump are they are running, because if we’re going to be increasing the capacity of the radiator, it’s critical that we match the water flow rate,” Darren explained. “In addition, we also need to confirm what the fan set-up our customer is planning to run so we can ensure there’s adequate airflow to the radiator.” A large part of Darren’s job is to help educate customers and debunk the widespread belief that simply installing a larger radiator will increase thermal efficiency. He goes to great lengths to ensure they understand how all the components in their cooling system must work together to deliver the thermal exchange required to match their specific performance application. “In most cases, if we simply installed a larger capacity radiator without making any other changes, the coolant flow inside the radiator slows significantly, resulting in what we call laminar flow,” Darren said. Laminar flow becomes evident when the coolant makes a smooth passage through the radiator. While it sounds ideal, a radiator experiencing laminar flow has reduced thermal exchange efficiency. “To ensure optimal thermal exchange, we want the water to be churning and tubulating as it flows through the radiator tubes,” Darren explained. “This maximises the contact of the water to the inside wall of the water tube, in turn, dissipating the heat to the tube, then through to the fin and out to the atmosphere. “That’s why it’s important to match the right radiator configuration with the right water speed or tube velocity.” Many of ADRAD’s aluminium performance radiators also feature a hemmed fin design. During the fin manufacturing process at their facility in South Australia, the fin material is folded back over onto itself to increase rigidity and reduce the potential for damage. This adds additional strength and helps keep the fin profile intact, helping to maintain optimal performance over the life of the radiator. In the more recent past, and possibly as a side effect of the COVID-19 pandemic, Darren has observed that the market has moved away from cheaper, imported products, particularly in the performance market. “The cost of building a modified engine can cost from a few thousand dollars to several tens of thousands and many consider a quality radiator, that has been designed and manufactured to suit their specific requirements, as an insurance policy that will protect their investment,” Darren said. “ADRAD is committed to innovation, customer education and to providing excellence in service and delivery of product through our extensive network of warehouses throughout Australia and New Zealand and that’s what sets us apart from the competition,” he added. To find out more about ADRAD, visit www.adrad.com.au
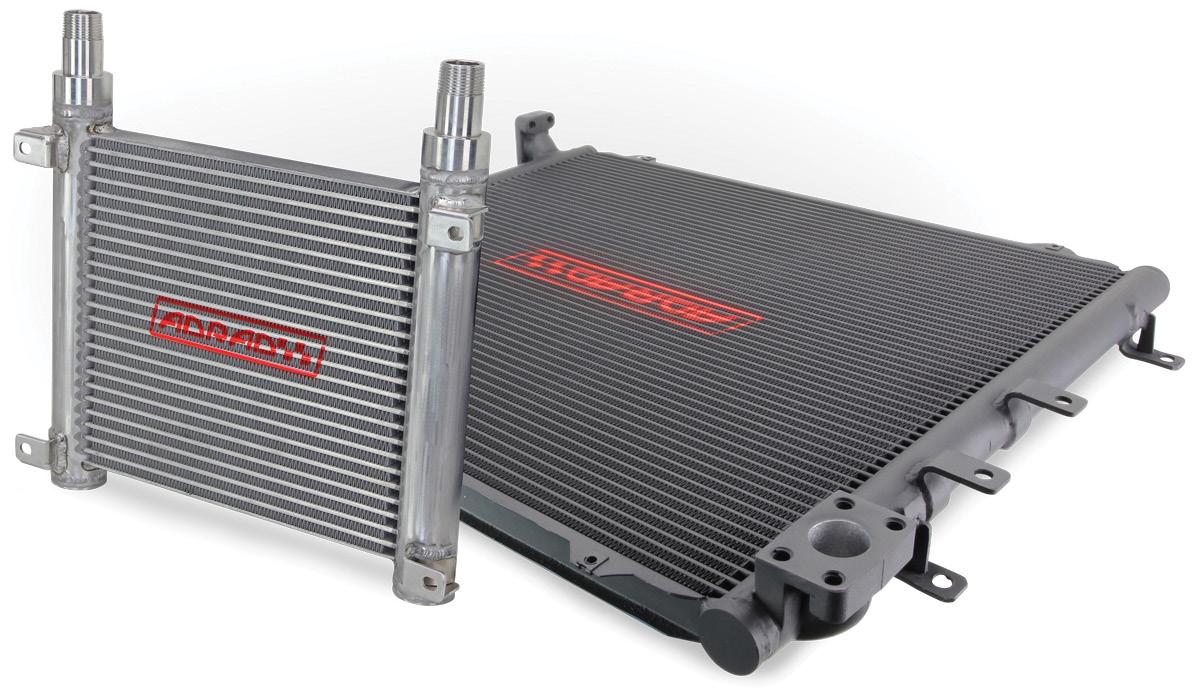