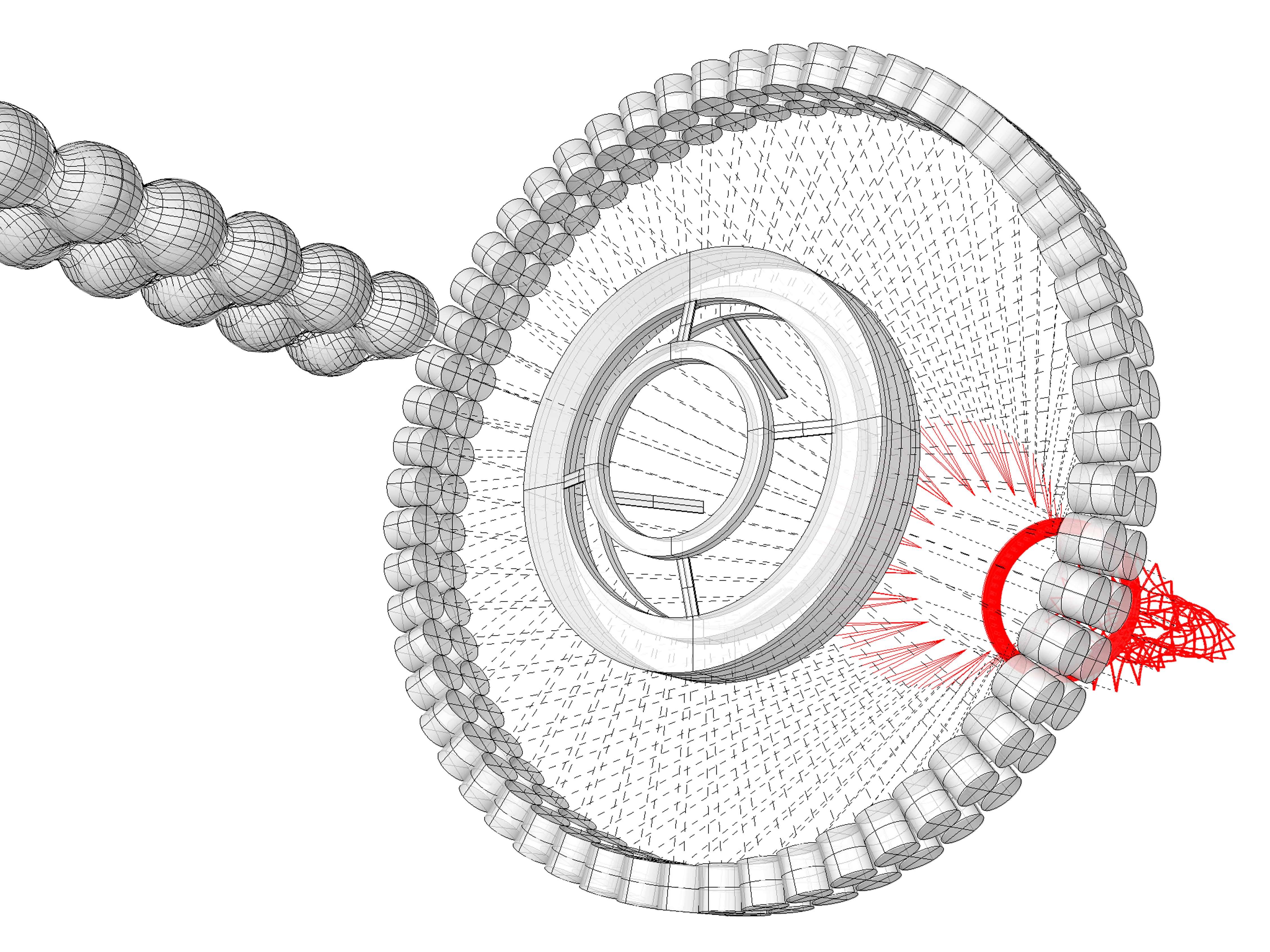
ARCHITECTURAL ASSOCIATION SCHOOL OF ARCHITECTURE
GRADUATE SCHOOL PROGRAMMES
COVERSHEET FOR
PROGRAMME: Emergent Technologies and Design
TERM: Summer 2008
STUDENT NAME: Evan Greenberg
THESIS TITLE: Thermoplastic Radial Pulbraiding for a Fiber Composite Structure
SUBMISSION DATE: 10-Oct-08
DECLARATION:
“I certify that this piece of work is entirely my/our own and that any quotation or paraphrase from the published or unpublished work of others is duly acknowledged.”
Signature of Student:
Part I: Introduction
Chapter 1 Aim, Scope and Hypothesis
1.01 Aim and Scope
1.02 Hypothesis
Chapter 2 Larger Research Context
Chapter 3 Context
3.01 Research Precedents
3.02 Architectural Context
3.03 Fabrication Context: Traditional Techniques
Chapter 4 Research Methodology
4.01 Material | Tooling | Structure
Part II: Material
Chapter 5 Natural Fiber Composites
Chapter 6 Synthetic Fiber Composites
6.01 Glass Fibers
6.02 Stiffening Matrices
Part III: Tooling
Chapter 7 Fiber Composite Fabrication Techniques
7.01 Braiding
7.02 Industrial Braiding
7.03 Pultrusion
7.04 Pulbraiding
7.05 Large-Scale Precedents
7.06 Comparative Analysis of Manufacturing Possibilites
Chapter 8 Generating a Mandrel Geometry
8.01 Form-Active Tension Systems
8.02 Balloon Configurations
8.03 Pneu-Cable Net Configurations
Chapter 9 The Machine
Part IV: Structure
Chapter 10 Mechanical Testing of Pultruded Rods
Chapter 11 Case Studies and Design Experiments
11.01 Introduction
11.02 Case Study: Aberfeldy Footbridge
11.03 Design Experiment: Hong Kong Pencil Tower
11.04 Design Experiment: Patagonia Footbridge
11.05 Case Study: Baraut/Gambardella Footbridge
11.06 Patagonia Footbridge Revisited: Comparative Analysis
Part V: A Synthesized Fabrication Technique
Chapter 12 Conclusions
Part VI: References
Chapter 13 Glossary
Chapter 14 Acknowledgements and Credits
14.01 Acknowledgements
14.02 Image Credits
14.03 Bibliography
Part VII: Appendices
Chapter 15 Appendix A
15.01 Stiffening Experiments
15.02 Out-of-Surface Action
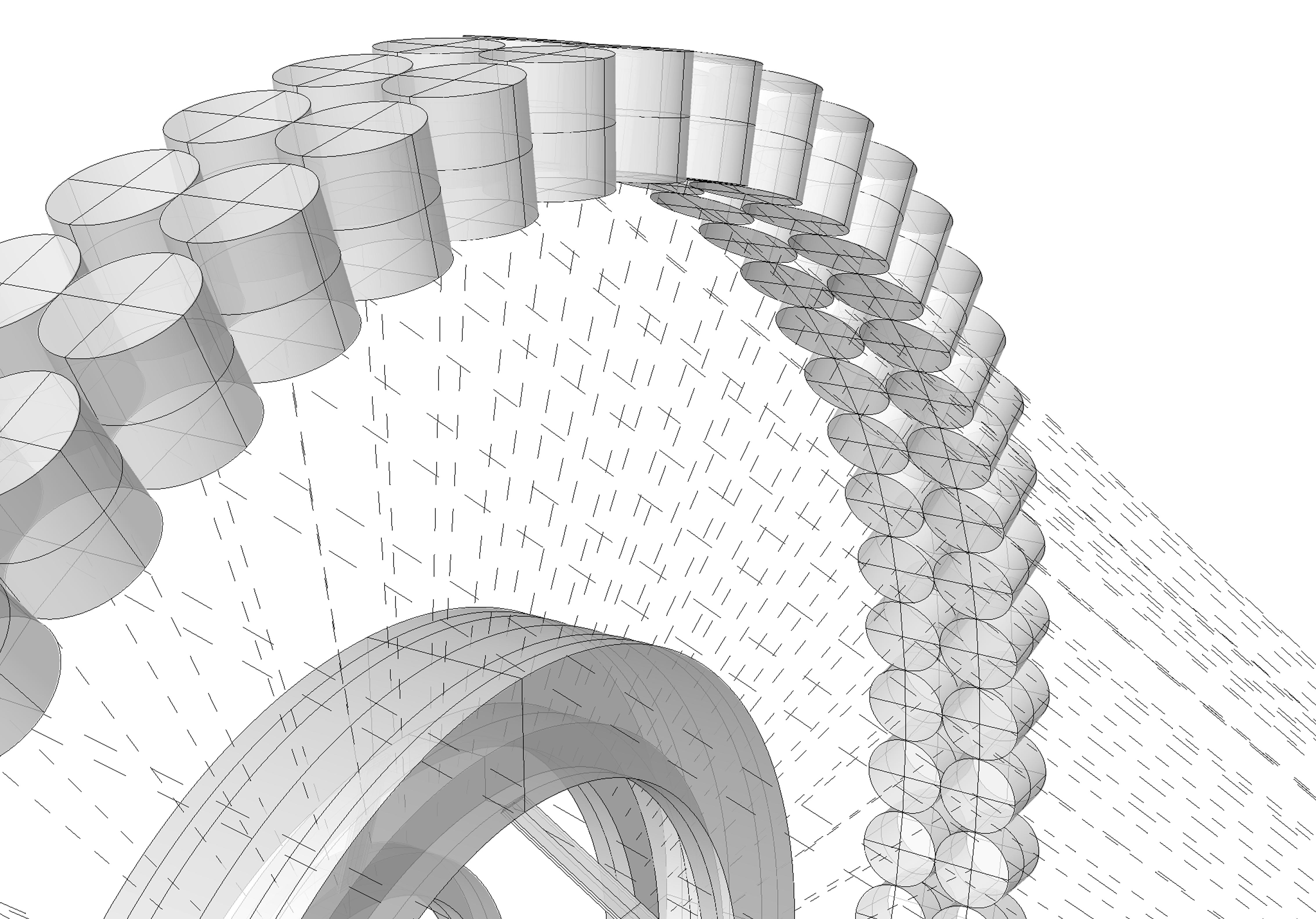
INTRODUCTION
This research aims to investigate a novel fabrication technique for the design and construction of a pulbraided glass fiber composite structure in a resin matrix. The need for a new technique is situated within three lines of context – speculative research, current fabrication and construction processes, and built work. By analyzing the Carbon Tower by Peter Testa as well as the dissertation Adaptive Growth of Fiber Composite Structures by Christina Doumpioti - two projects that employ fiber composites in the design of architectural structures - this body of research can build upon these references while reacting to potential in fabrication and construction unrecognized or previously neglected. In exploring three traditional fabrication processes in concrete, timber, and steel, it is possible to situate the necessity for a novel technique that reacts to problem areas in the most common fabrication and construction practices in architecture. Finally, the Korkeasaari Viewing Tower in Helsinki, Finland is considered as a built project of modest scale in which an experimental form is constructed in a traditional manner, unsuccessfully achieving platforms, joints, and openings in its structure.
By examining these three contextual cases and their problematic conditions, the basis is provided for a novel fabrication technique, specifically for the design of a fiber composite structure. In all cases, the material employed, the tool used to process that material, and the subsequent structures realized are three separate stages of construction. Doumpioti explores the adaptation of a fiber composite material system, but speculates on a form mold geometry designed off-site and a structure craned in place without considering viable connectivity to the existing site conditions. Concrete mix design is an expensive iterative process; constructing with concrete requires the design and construction of wooden formwork, only to be removed and discarded after pouring and curing is completed. Timber construction requires vast knowledge of mechanical jointing and wood joinery skills along with the processing of a natural material difficult to control in a factory. Steel construction also requires extensive knowledge and skill of connections. All three techniques, which are based in and continue to work within the practices of industrialization, involve material fabrication in factories but construction elsewhere. The Korkeasaari Zoo Tower, constructed of wood members attempts to achieve viable platform, opening, and connection conditions while creating interesting views to the outside, but falls victim to an inefficient and ineffective design and construction process.
With this context comes the basis for the necessity of a novel fabrication technique. By understanding current fiber composite fabrication techniques used in other industries, the technological groundwork can be laid for their adaptation, and ultimately the invention of a novel technique. Because design and construction currently follows traditional and commonplace practices, it is necessary to investigate current techniques, and thus the potential for a novel fabrication technique that combines material, tooling, and structure into one cohesive design and on-site construction process of a fiber composite structure.
MATERIAL
Braided fiber composite structures are designed through a bottom-up process. Synthetic fiber composites follow the logic of fiber organization in natural systems. The biological model utilizes relatively weak individual fibers, but organizes them into a specific material organization in which certain advantageous performative qualities emerge. These include a high strength to weight ratio, redundancy leading to adaptive response, and load-specific fiber path design. The emergence of these capabilities has a direct causal relationship on the morphology of the individual. Trees are made up of a sophisticated fiber path hierarchy, where fiber orientation and organization create an extremely strong structural material. These fibers possess the ability to organize in order to overcome adverse local conditions, such as in phototropism. When the orientation of a tree branch is not in line with the sun, fibers will reorient themselves to allow the branch to change its path of growth and lignify to create tension or compression wood. The morphological effects of this adaptive growth are clearly seen in sections of this wood, as well as in its global form.
TOOLING
The construction method investigated in this body of research is thermoplastic radial pulbraiding. The basis for this proposed technique is 3D radial overbraiding, which when applied to fiber composite structures, is an industrial fabrication process used predominantly in the aerospace industry in highintensity, high-impact applications such as jet engines and rocket launchers. The strength, stiffness, and lightweight characteristics of synthetic fiber composites have been exploited in architectural construction for many years, however large-scale structures have not been explored. In addition, current tooling processes do not take full advantage of the material’s structural capacity. The flexibility in local braid angles, fiber volume, fiber path, and local braid thickness are advantages which are present in 3D radial overbraiding, but until now have only been exploited in other disciplines.
The aerospace industry has been able to benefit from these principles of emergence in the
fabrication process; it is now possible for architecture to benefit from these advantages as well. By understanding the recent history of the adaptation and application of industrial manufacturing techniques, this dissertation aims to propose a new fabrication technique - thermoplastic radial pulbraiding - that can successfully be employed to construct a fiber composite structure.
STRUCTURE
In biology, material is structure. Plants and trees are made up of fibers organized in an optimal configuration so that the minimal amount of material is used to generate the maximum efficient results. In intelligent organization, simple materials perform to a high structural degree. Although the tool of adaptive growth - as employed in a biological model - is not simulated in this work, the fabrication process investigated and proposed is in a similar vein; thermoplastic radial pulbraiding is a tool that can provide desired effects such as buckling stiffness as a structural performative requirement, and platforms, openings, and density changes as programmatic requirements, through the design and organization of a simple material.
NOVEL FABRICATION: EMERGENT TECHNOLOGIES AND DESIGN
Situated within its architectural context, a novel fabrication technique is explored to synthesize material, tooling, and structure, so that each process component is dependent on one another, thus resulting in an architectural artifact where material is structure as a direct result of its tooling. This exploration into emergent technologies and design is threefold, and present in each part of the synthesized process. Firsly, the material proposal is based in biology; by referencing both logics and processes found in biology, this research draws upon the paradigm where material properties and organization have a direct causal relationship to performance. Secondly, the adaptation of existing tooling in the aerospace industry for architecture is pushing the current fabrication paradigm in which architects currently work. By advancing architecture’s design and fabrication tools, huge potential can be discovered. Finally, the way in which multiple parameters are negotiated within the proposed fabrication technique, resulting in effective structural and programmatic performance, follows in the conceptual framework of emergent technologies and design. With the coherence of material becoming structure through an adapted tooling process, new fabrication technologies are discovered and applied.
HYPOTHESIS
Traditional manufacturing and construction processes for architectural applications are often disjointed, disconnected, and disorganized. While architects employ high-tech design tools - and at times manufacturing tools - construction is often carried out through means grounded in 100-year-old technology. Even contemporary fiber composite manufacturing processes fail to incorporate tooling within material design in the realization of structures.
By combining these traditionally separate processes into one coherent method, a new paradigm in construction can emerge. Through the investigation of thermoplastic radial pulbraiding, a pulbraided glass fiber structure can exist where material, tooling, and structure are fully synthesized. Design input, which regulates the quantity of fibers and resin necessary in the composite matrix, as well as the required fiber density and braid angles directly affect a composite at the material level. The material input directly affects the machining process, and outputs an artifact where the material is the structure. In doing so, required local and global buckling stiffness and programmatic and spatial elements such as entry, platform, porosity, and ground connection are negotiated between material and construction within the fabrication process.
CHAPTER 1 - AIM, SCOPE AND HYPOTHESIS
FUTURE APPLICATIONS OF FIBER COMPOSITES AND THEIR FABRICATION
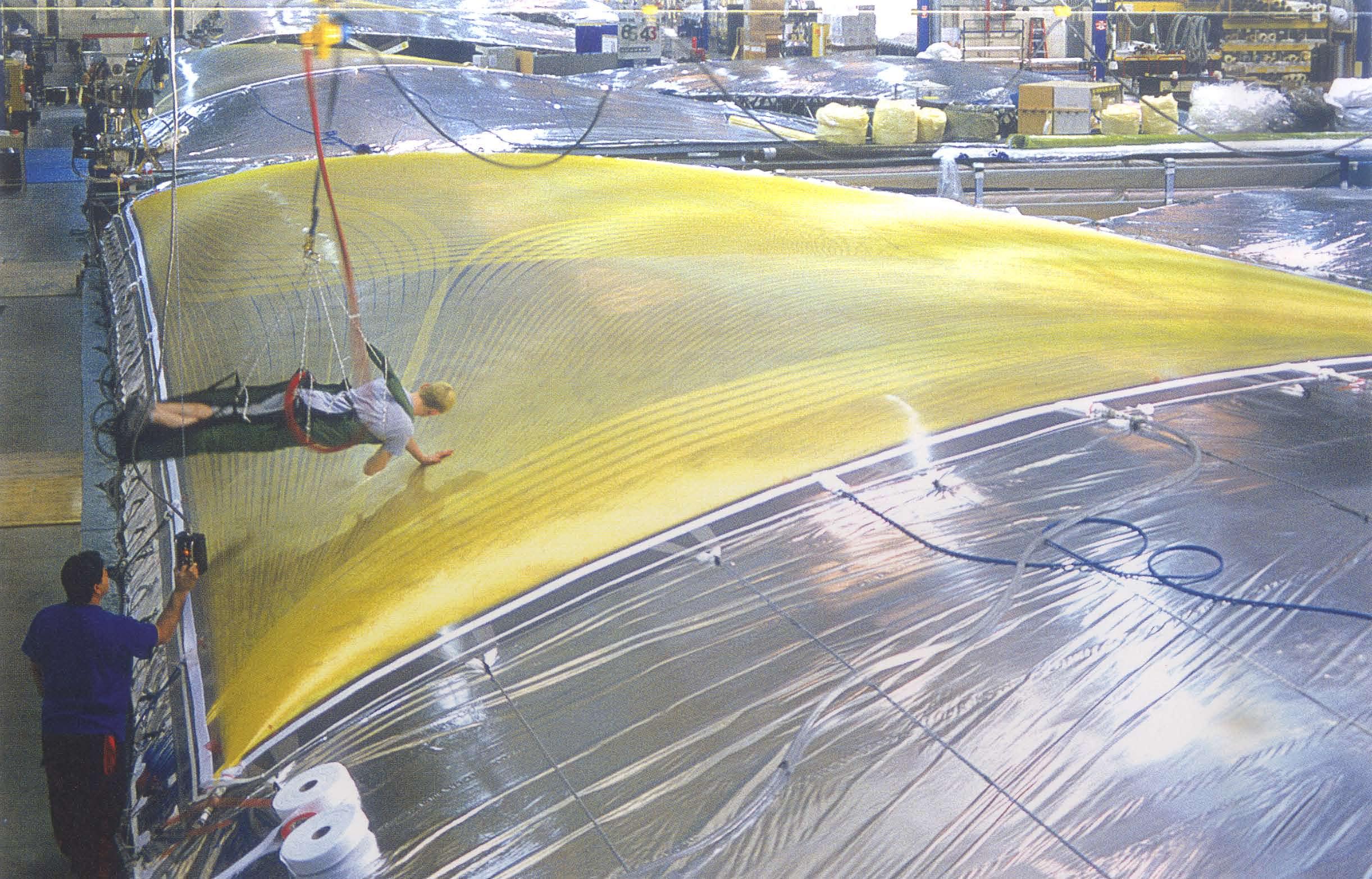
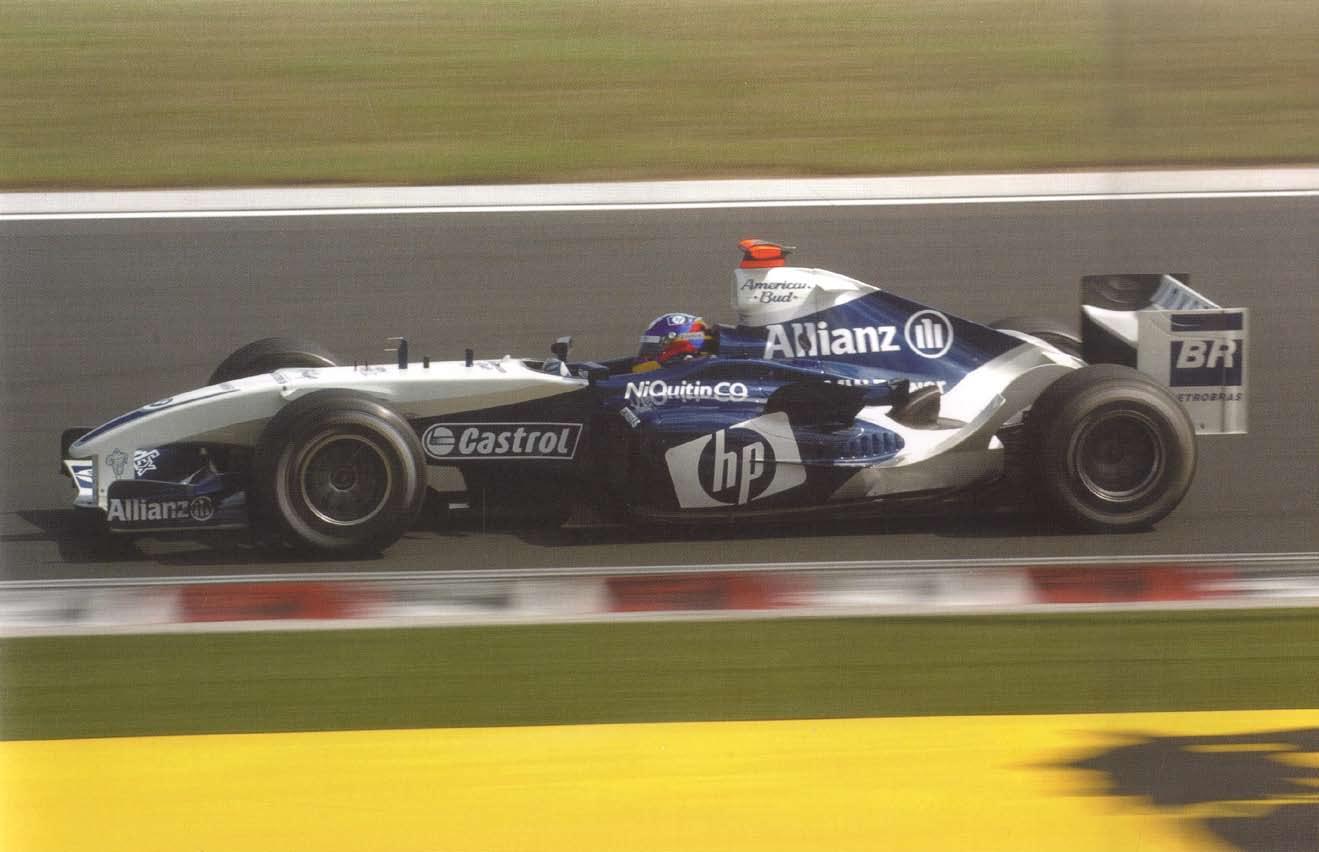
While this work references traditional construction techniques, it is important to situate it within current fiber composite applications. Three areas in particular must be noted in order to understand the larger scope of research in which this work is based - scale, material choice, and design application.
Braiding is a widely used material technique at extremely small scales. Medical equipment as well as electrical equipment are often braided because of the material system’s resistance to torsional forces. However, this dissertation attempts to connect the manufacture of this material system at a larger scale. The fabrication of the new AirBus airplanes (Figure 02) highlights the use of composite materials at larger scales; the AirBus is still fabricated piece-by-piece however, where a system of composite parts are adhered to each other. The continuity of material, as well as structural and spatial effects created by braiding is an area of research that can be explored further with the exploration of a novel large-scale fabrication technique.
While the scope of this dissertation is limited to glass fiber composites, the material technique investigated is not limited to only one material. Technically, any fibrous material can be applied, assuming the strands are commingled with a resin fiber. Depending on application, high-performance fibers or natural fibers could potentially be explored as material options. It would also be possible to explore different resin choices depending on application.
Fiber composites have been researched and used in construction since the 1950’s. For many years, it has been mentioned that fiber composites have the ability to bridge the gap between material and structure. Up until now, however, there have only been advancements in this area of research in extremely specific applications. Fiber composites are being used in the design and fabrication of weapons, automobiles (Figure 01), and sports equipment. Rarely, fiber composites are applied to small bridges. However in most of these cases, component-based fabrication is employed, and parts are connected through either chemical bonding or mechanical joints (Figure 03). This research aims to explore a novel fabrication technique synthesizing material, tooling, and structure into one coherent process; just as this research is reacting to both traditional fabrication techniques as well as current fiber composite applications, further research can build upon the possibilities of a new technique on different design applications.
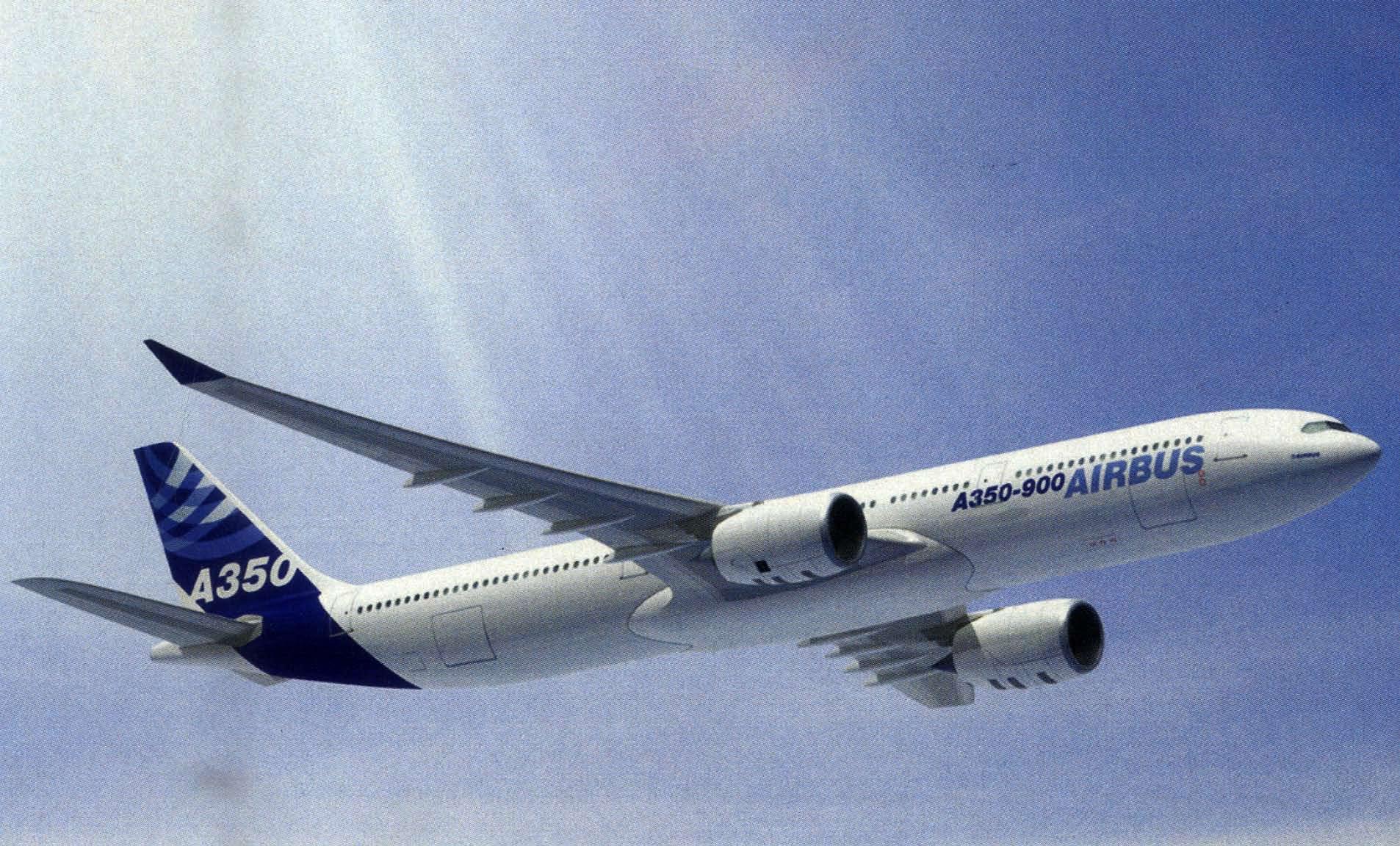
PETER TESTA, CARBON TOWER, 2005
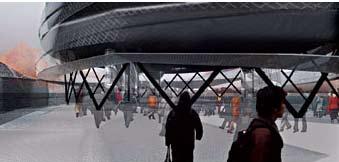
In his Carbon Tower design, Peter Testa implements a carbon fiber composite structure to a large-scale tower by means of weaving and pultrusion methods. The main structure of the tower is comprised of woven pultruded elements (Figure 01 and Figure 02) formed continually, as they rise up the building, by twenty-four robots. A shell, providing the functions of a facade, is constructed of continuously wound fiber bands one foot wide and one inch thick (Figure 02, Figure 03). Floor plates are created by horizontally-crossed bands branching from the braided pultruded structure that act as a framework into which woven strands tie (Figure 03). While Testa succeeds in designing a building where fibers are continuous regardless of geometry and where joints are eliminated, he fails to address two major points in architectural design. The goal of this work is to achieve multiple building system interconnectivity (McQuaid, 2005); Testa proposes large robots which act as fiber tows carrying strands of carbon fiber up the tower. While this speculation acts as reference for this dissertation, there is no investigation into this fabrication process. There can be no evaluation of the proposition because no manufacturing processes - past or current - are explored to provide a viable basis. Furthermore, the two fiber systems - pultruded rods and braided fibers - are not interconnected, thus acting as a counterpoint to the desired interconnectivity of systems.
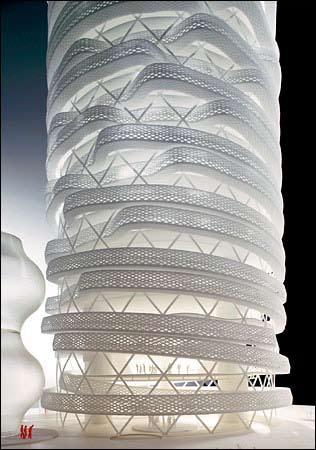
CHRISTINA DOUMPIOTI, ADAPTIVE GROWTH OF FIBER COMPOSITE STRUCTURES, 2008
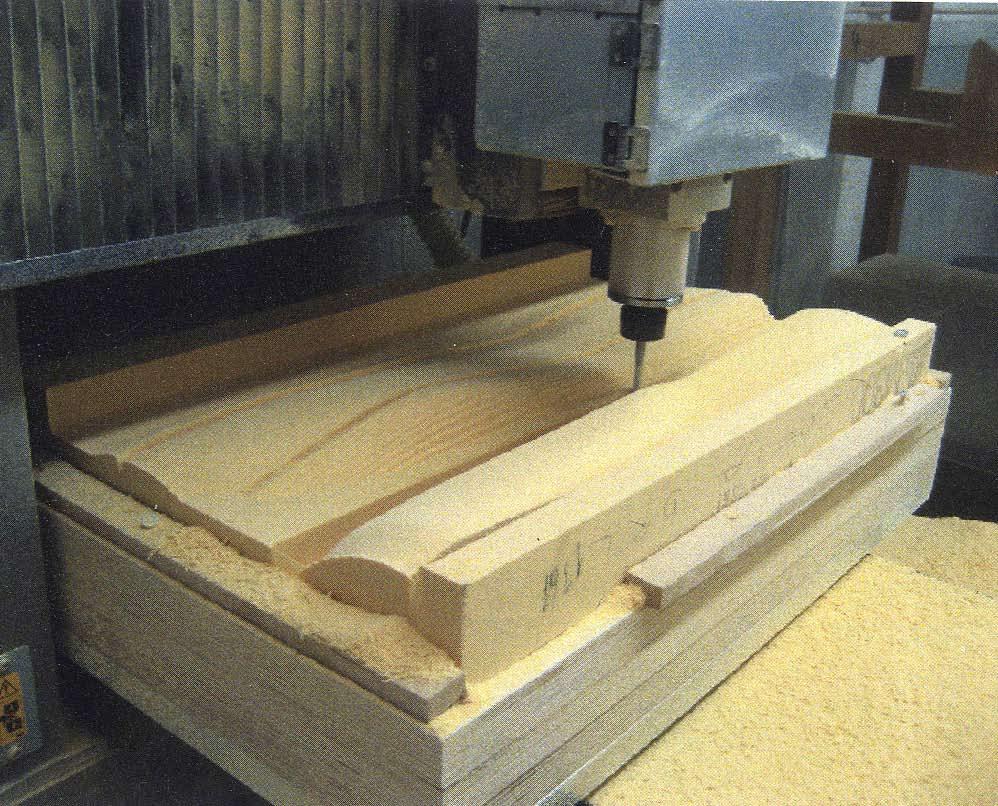
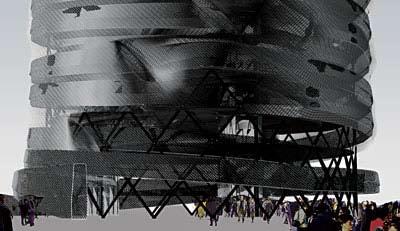
In this Master of Architecture dissertation project undertaken in the Emergent Technologies and Design Program at the Architectural Association School of Architecture, Christina Doumpioti proposes the design of a ten meter span bridge in a courtyard behind the Architectural Association in central London (Figure 04). The methodology executed is one of shape-finding and fiber path-finding, in which a bridge can be manufactured using glass fiber composites through a tow-steering system (Doumpioti, 2008). The project succeeds in developing a structure that responds both to structural loading conditions as well as microclimatic environmental issues. Numerous biological processes in relation to fibrous composites are referenced, and a successful adaptive growth process is used to achieve the aim of the dissertation. In addition, a productive and successful fiber placement strategy is employed where stress analyses derive individual path distribution as well as laminate types and order. However, there some issues which are not addressed fully in relation to manufacturing and construction. Firstly, this project aims to fabricate the bridge by building up fiber laminates over a pre-designed mold geometry (Figure 05). This mold is designed by the definition of multiple points on a surface. The ten meter bridge is constructed off-site in this way and then transported to the site where it is lifted into place by a crane (Doumpioti, 2008). This work aims to propose a fabrication technique that eliminates this segmented process, allowing for fully synthesized on-site fabrication, and eliminating the necessity for transportation of a large structure. While Doumpioti’s work makes breakthroughs in the performance of a new material, construction of the bridge is similar to that of traditional materials, where material is fabricated in a factory and then assembled on site. Secondly, the edge condition of fiber laminates poses a performative problem. While Doumpioti addresses this issue by suggesting numerous fabrication measures (connection points are in locations with the least stress, additional resin is applied to edges), they contradict her proposals for connection to the existing site. Doumpioti explains that, similar to spider webs, fibers can continue through the edge and into the adjacent buildings, as drawn in Figure 06. However, she does not address how additional resin application can affect this solution.

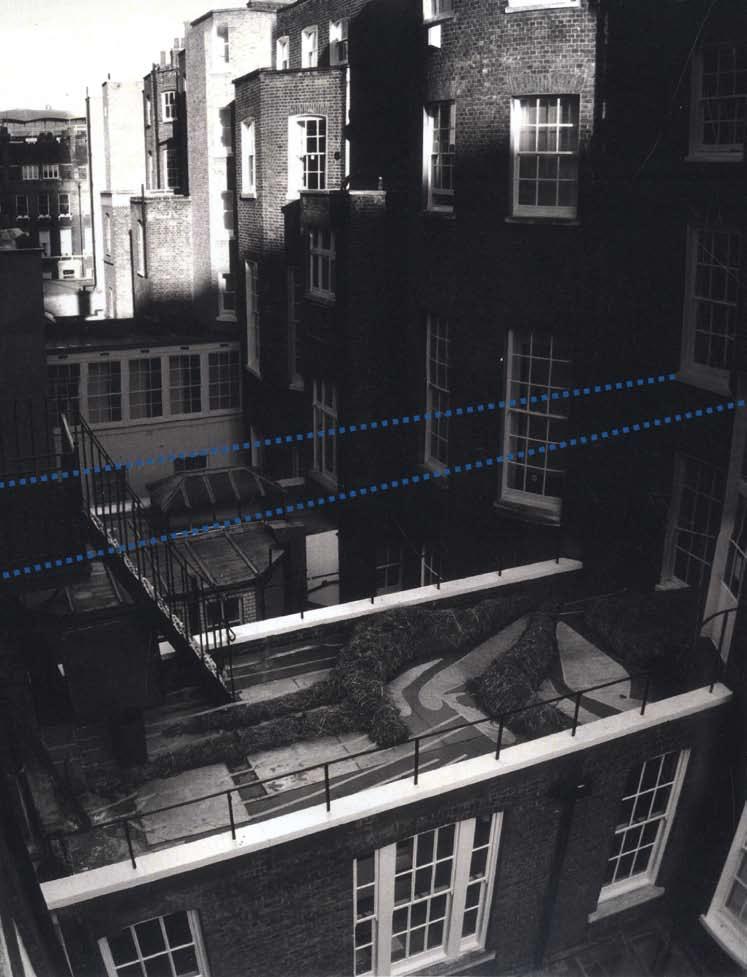
CHAPTER 3 - CONTEXT
.0 RESEARCH PRECEDENTS
VILLE HARA, THE BUBBLE, KORKEASSAARI ZOO LOOKOUT TOWER, HELSINKI, FINLAND, 2003
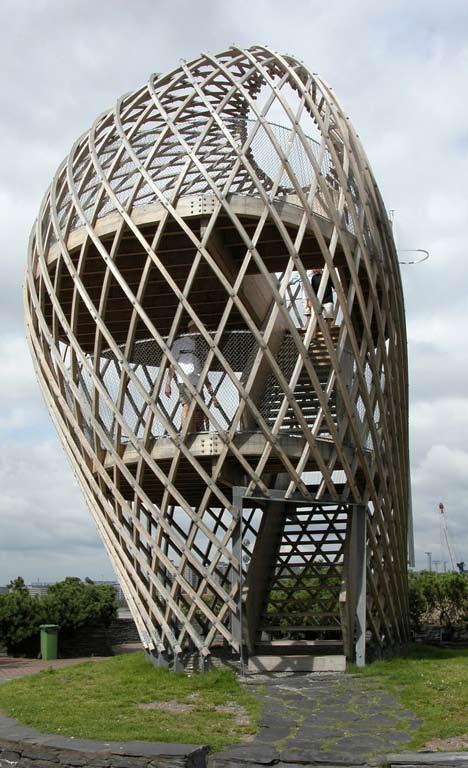
The Bubble (Figure 07), designed by architecture student Ville Hara for a competition entry for a Lookout Tower at the Korkeassaari Zoo in Helsinki, Finland is a ten meter high viewing tower built of laminated timber battens. The gridshell construction consists of seventy-two timber battens that were pre-manufactured, bent into seven different curvatures (Figure 08) and steamed into their final positions on site. Each batten is interconnected through a series of bolt connections through a steel nailplate (Figure 10) - over six hundred joints in total (Davey, 2003). Two solid wood platforms create a threestory tower, where each platform is supported by steel edge beams at the perimeter and a steel truss supporting the center of each platform. This beam then ties into the edge beams, and load is transferred to the wood batten shell structure. The tower meets the ground on a series of pin joints, which sit on a hidden reinforced concrete foundation buried underground. These pin joints are specially designed and fabricated using steel. The timber is treated only with linseed oil (Davey, 2003), which penetrates the wood making it resistant to dents and scratches. The entrance into the tower is a simple rectangularly cut, steel-framed opening (Figure 11), similar to traditional door frames. Finally, a chain-link fence, as shown in Figure 09, is installed at the perimeter of each platform to function as a railing system.
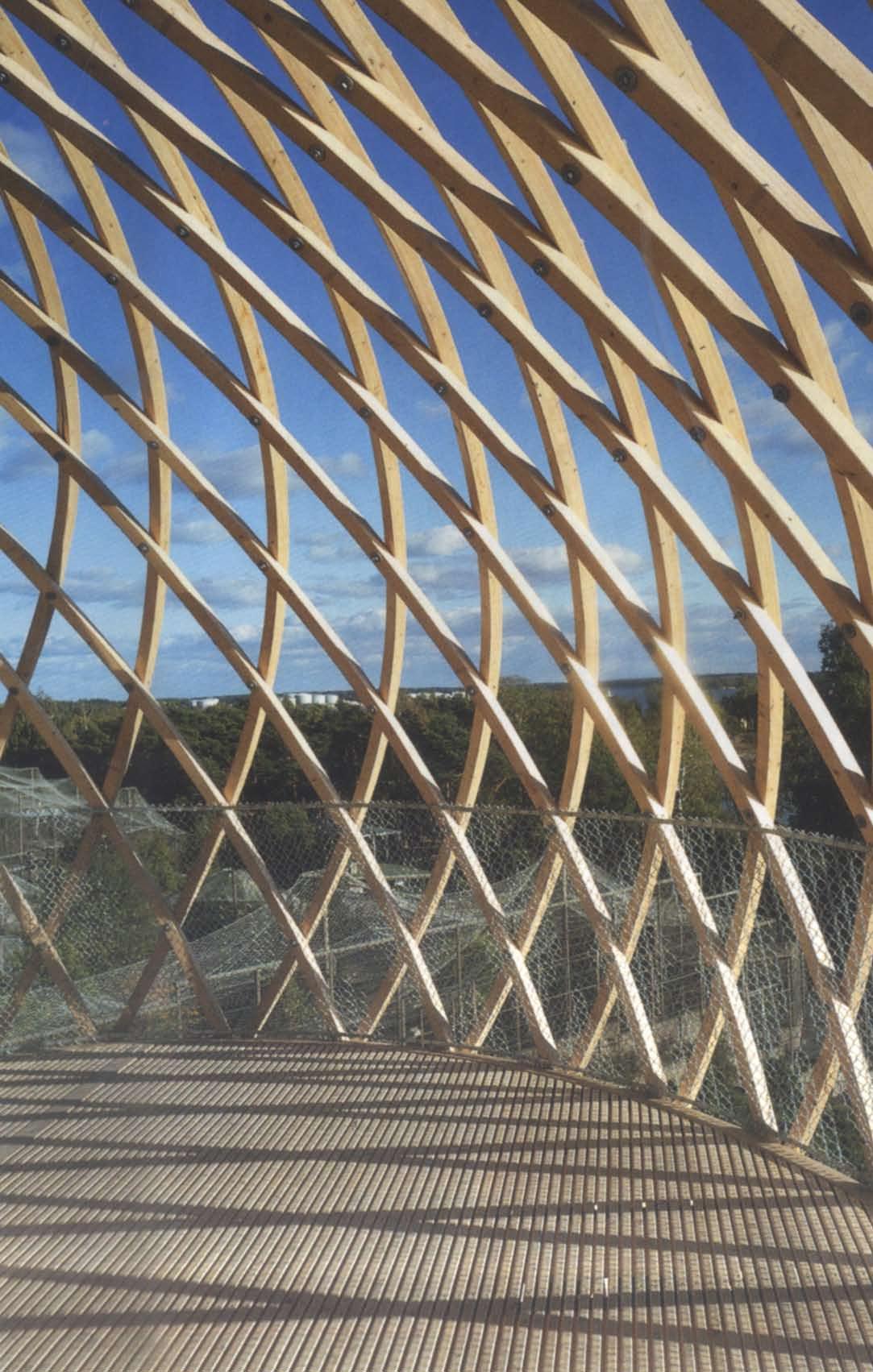
THE DESIGN PROBLEM
This viewing tower design has many problematic issues, and poses an interesting design problem. Construction issues play a major role in the inefficiency of the design process, with its many specific joints and connections. Although limiting batten geometry to only seven specific curves is an intelligent measure, the necessity of steaming each specific batten into proper shape leads to a great deal of error to take place on site. Furthermore, the inclusion of disguised steel beams gives the delicate wood batten system a heavy feeling, and is structurally dishonest. While a chain-link fence plays a vital role of functioning as a safety railing, material choice and execution are read somewhat as an afterthought, similar to the rectangularly cut, steel-framed door opening. There is a lack of integration of different material treatments and systems throughout, leading to a design process which reads as poorly articulated and a construction process poorly executed.
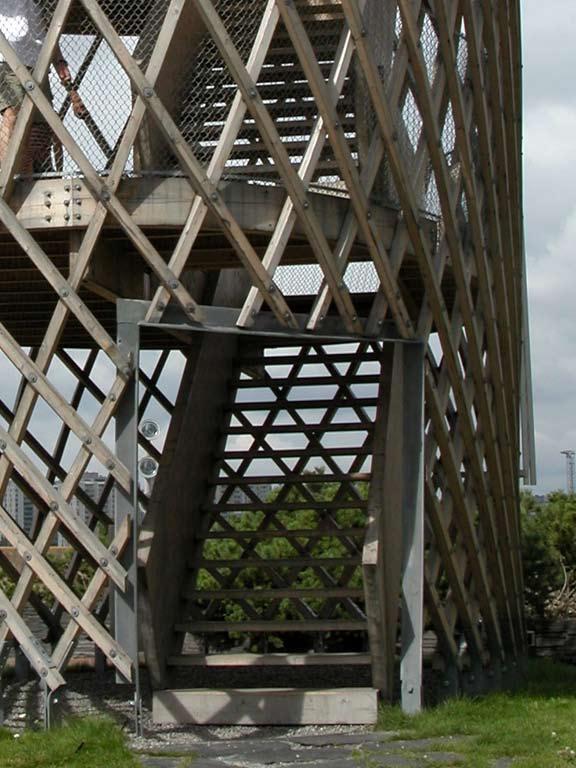
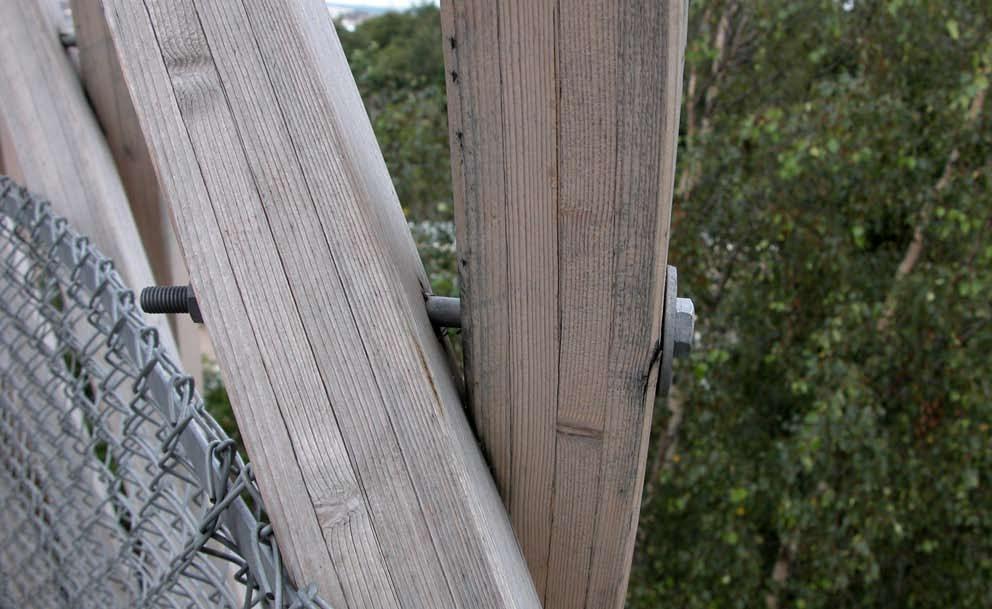
This dissertation aims primarily to address these design and construction issues, taking The Bubble as a contextual case study to drive the possibilities delivered by a fabrication process where material, tooling, and structure are synthesized.
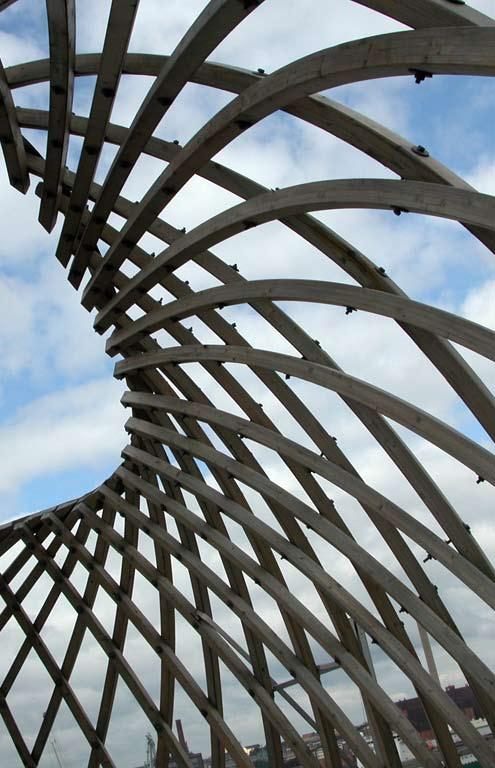
MATERIAL FABRICATION VS MATERIAL PERFORMANCE
This dissertation aims to propose a novel fabrication technique capable of producing an effective and performative pulbraided glass fiber composite structure. In order to understand the advantages of this novel technique, as well as to address any specific limitations, it is necessary to investigate other techniques currently used in architecture as a point of comparison. This research expands upon the design of a structure driven by its structural performative capacities as it relates to the fabrication process; it is not necessary to include in its scope the performative capacities of other material systems, but only the process in which they are fabricated, both materially and on the scale of a structure - here defined as “material fabrication.”
Three materials - concrete, timber, and steel - are widely used in the architecture industry, and therefore research into the quality of their performance is unnecessary and omitted from the scope of this dissertation. The way in which these materials are fabricated, in relation to the fabrication of a fullscale structure, however, is important to investigate in order to situate the proposal of a novel fabrication technique. Therefore, it is solely the way in which concrete, timber, and steel are fabricated materially which will be investigated in the following chapter. CHAPTER 3 -
CONSTRUCTING WITH CONCRETE
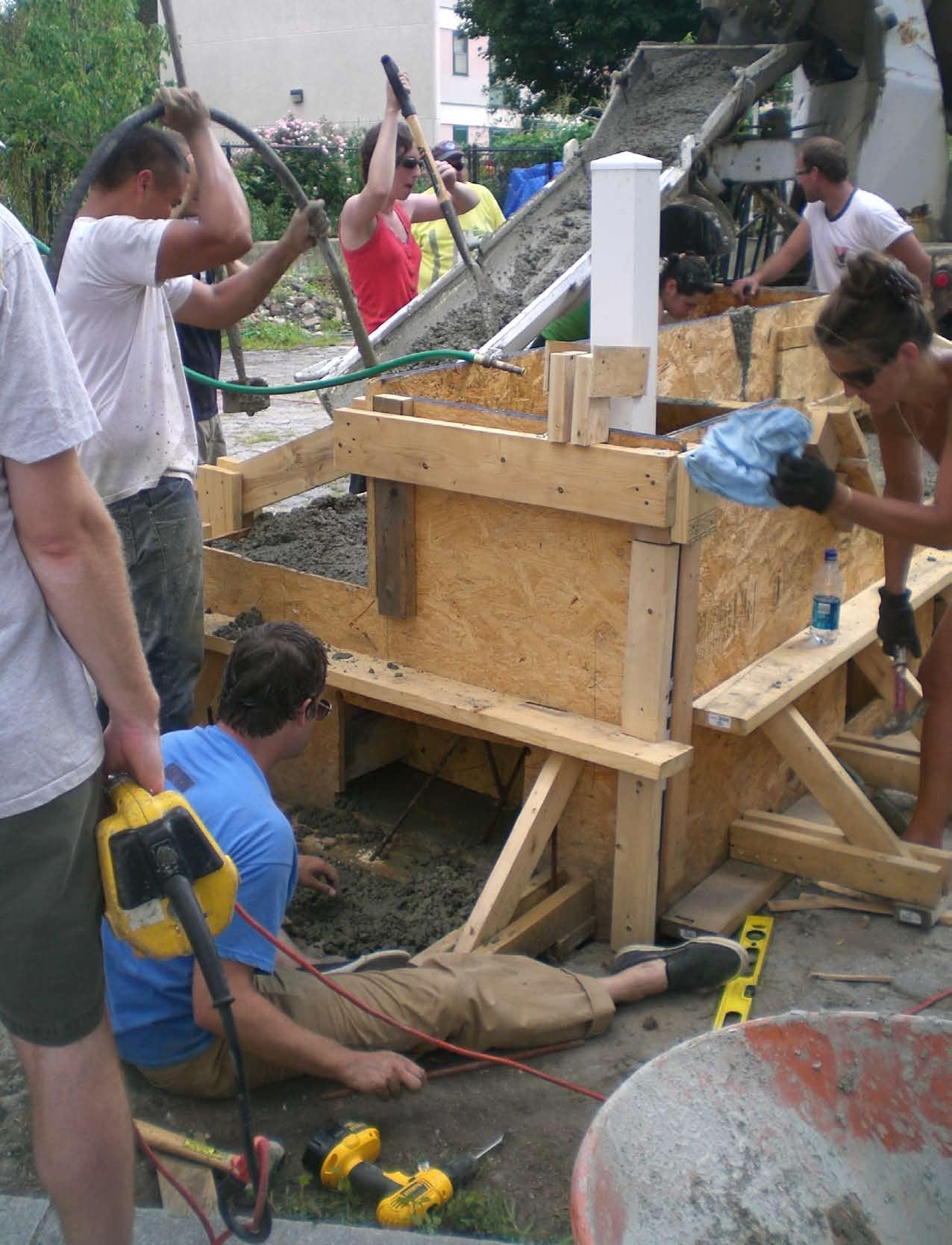
Concrete is an extraordinarily advantageous material for building construction. Concrete - a mixture of cement, fine aggregate, coarse aggregate, and water (Figure 12) - has high compressive strength and can be used as a composite material along with reinforcing steel bars or high-performance fibers to achieve high tensile strength. However, the design of an effective concrete mix, along with the physical process of making and curing the concrete can be extremely expensive and time-consuming, resulting in an inefficient process.
THOUSANDS OF COMBINATIONS
Concrete mixing - the proportioning of each of concrete’s components - is a non-exact process driven by a trial-and-error procedure; most are changed after simply seeing the product, and adjustments are made accordingly. This adjustment is extremely helpful in that the initial mix designed does not need to perfect (Day, 1995), yet only give an understanding of how the mix will perform. Thus, the adaptability of concrete is an advantage of the material.
However, there are enormous amounts of material that can be chosen for inclusion into the concrete mix. Cements vary from a standard makeup to high early strength or low heat emitting makeups (Day, 1995). Aggregates, both fine and coarse, differ greatly in their size, surface texture, and strength - all factors affecting overall performance of concrete. A standard rule of mixture design is to use aggregates that are readily and locally available (Day, 1995); while these may be suitable, their characteristics will undoubtedly affect the cement to water ratio necessary to create the proper concrete mixture. While there are only four major ingredients to designing a concrete, each has numerous variations that could cause great expense in the design of an effective concrete.
MIXING AND TESTING CONCRETE
As mentioned, a concrete mixture can easily be amended to match performance requirements. However, a great deal of trial mixing and testing is necessary to come to a conclusion on performance of the material. Often concrete poses problems of durability, directly caused by mixture content, permeability, shrinkage, and heat generation (Day, 1995). Each of these problem areas must be addressed within the mix, and then tested to evaluate performance. Generally, the entire process of trial testing must be carried out for every aggregate type and ratio desired (Day, 1995). In order to test strength, four to six casts are made for each mixture and tested in compression and tension at intervals of two, three, seven, twentyeight, and fifty-six days (Day, 1995). The flexibility of concrete mixture control is advantageous, however this is a process that may not yield positive results overcoming its expense.
EXTERNAL FACTORS
In addition to complications and the expense of mixing concrete, there are a number of external factors which pose potential problems and inefficiencies in implementing concrete as a structural material. Firstly, while mixing can be tested and changed infinitely, and even simulated by computational processes (Day, 1995), problems can occur when the concrete mix is physically made. A poorly mixed concrete, which does not have evenly distributed aggregate or contains air pockets (due to the lack of sufficient vibration during the pouring process) decreases the concrete’s overall strength.
Secondly, poor formwork can greatly impact concrete’s performance. The framing of plywood formwork for concrete must be an exact process, where any imperfections will be reflected in the final form and performance of the concrete itself. Figure 13 shows the extreme complexity of concrete formwork.
CONCLUSION
While concrete is a widely used material and has specific structural advantages, there are many problem areas uncovered in this section that must be considered. The amount of time and labor involved in designing and testing a proper concrete mix, and then using it to build in the correct way can be an extremely inefficient process. The recursive process used to find a proper mix has great potential in finding an efficient and effective structural material. In addition, the computational simulation of this process can, in fact, speed it up. However, even if these problem areas are overcome, the external factors affecting concrete construction are too great to overcome, and therefore prove the technique to be problematic.
CHAPTER 3 - CONTEXT
.0 FABRICATION CONTEXT: TRADITIONAL TECHNIQUES
Figure 12, diagram, describing the components in a concrete mix.COMPLICATIONS IN WOOD FABRICATION
Timber construction is hundreds of years old and still widely used today. While the processing of wood for structural means has advanced widely, many of the same traditional jointing techniques are still employed. Wood is readily available as a natural resource; while this can be seen as advantageous, it also poses problems of material discontinuity.
There are many factors in material discontinuity that complicate the wood fabrication process. Grain angle, the existence of knots, wood density, ring width, and moisture content all affect not only wood quality, but also wood processing. Wood density is one property that has a great influence on machining. As wood density increases, the blade of the cutting machine will dull quicker. While this seems to be an intuitive relationship, it is important to note the cyclical process that will affect wood quality (Dinwoodie, 2000). The performance of a quality wood may be high based on internal materiality, but may worsen during the fabrication process.
Moisture content is a factor affecting fabrication directly due to internal fibrous makeup. Because wood is a natural material, it is composed of fibers which make up its cell walls. These fibers have a great deal of elasticity. While moisture content in wood is high, elasticity is also high. This may cause cutting problems at the outset, but more importantly can cause the sawn wood to shrink after drying (Dinwoodie, 2000), and thus may cause a change in performance.
BUILDING-SCALE FABRICATION
There are many techniques to employ when building with wood. However, two in particular are discussed, in order to situate this work in the architectural context which is driving - The Bubble in Helsinki, Finland. Because this architectural artifact uses timber battens laminated and then steam-bent, these are the two techniques upon which this research will expand.
STEAM BENDING AND LAMINATING
Steam bending is a popular fabrication technique used to produce curved members. The Bubble consists of seven different steam-bent sections to create the desired global form. While steam bending is an interesting way to develop curvature from a somewhat rigid material, there are many factors which need consideration. Steam bending softens the lignin in wood, rendering it less stiff, and enabling it to be bent around a form. While this seems like a straightforward process, there are many constraints. Firstly, the wood being bent must be constrained until stiffened, lengthening the process. Secondly, the deformation achieved is mechanically irreversible. Only over long periods of time will the wood begin to retain its initial shape; this in turn may cause serious performative problems. Finally, only certain species of wood can be steam-bent (and only within a certain radial dimension) without cracking (Dinwoodie, 2000). Finally, the dimension of the material desired is constrained to its geometric viability when bent. Laminating is another wood fabrication technique used for The Bubble. Laminating is often used when a material is relatively thin in one dimension in comparison to its excessive length. In laminating timber, thin strips of wood are glued together to form a larger section. This technique may provide additional strength while keeping sectional dimensions to a minimum. However, similar to steam bending, laminating requires that glued sections be clamped together until completely dry. Because the length of wood members are limited by natural reasons - the useable length of a tree - long laminated members must be jointed, creating the possibility for more complications (Dinwoodie, 2000).
JOINTING
While joining occurs within laminated members, it also occurs between all wood members. Wood connections are either through wood joints or mechanical joints. The former requires incredible knowledge of wood types and joint types, and the understanding of which joints can be used not only for the kind of wood involved, but also of its application and desired performance (Figure 14). Mechanical joints too require knowledge and skill, but also include the addition of another material - traditionally steel. As seen in The Bubble project, steel mechanical joints do not always comply with the geometry in place, and can cause local stresses which decrease performance. In addition to this, the physical labor involved is often extremely costly in terms of material parts and time needed.
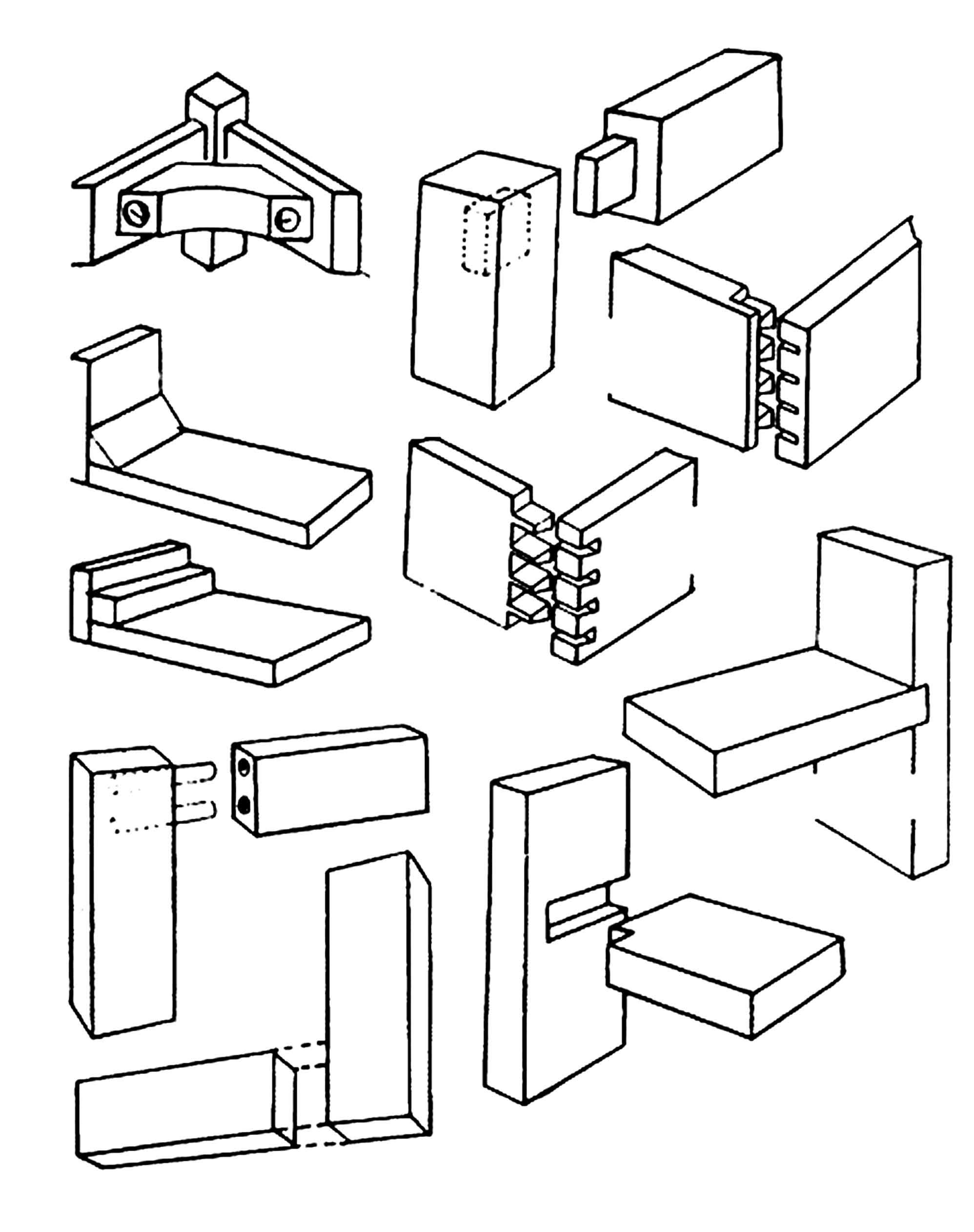
CONCLUSION
Although wood, and knowledge of how to work with wood, is widely available, its natural makeup provides an extreme amount of variability in machining, and ultimately in performance. In addition, the necessity for joints in wood construction poses issues of time and labor. Both of these areas provide the potential for a great margin of error, both of which cannot always be controlled, and therefore do not provide efficient material fabrication.
Figure 14, diagram, describing many of the variations in wood joinery. Each joint has specific advantages and disadvantages and must be chosen according to wood quality and joint performance. (modified diagram from Selecting Case Goods - Wood. Wood joinery methods. Online. 2006-2007.) glued and screwed corner block triangular corner blockSTEEL FABRICATION
Steel is fabricated in a highly industrialized manner, making the manufacture and use of the material extremely cost-effective and efficient. Due to steel’s isotropic material organization, it is easy to fabricate steel in all different shapes and sizes. All of these shapes are fabricated on a roller (Figure 15), where large textured wheels roll out iron ore that has been heated to 2200° F. While creating desired shapes, rolling also increases the strength of the steel (Shuster, 1997). While steel fabrication has been widely mastered and automated, there is an area which needs to be addressed as one that affects production. This factor is the plasticity of steel. Plasticity is the deformation of a material past its ability to return to its initial configuration. During fabrication of steel members, time, temperature, steel’s elastic limit, and the elongation of the material must be considered in order to avoid material plasticity. If the plastic limit of steel is reached during fabrication, its performance will greatly change (Shuster, 1997).
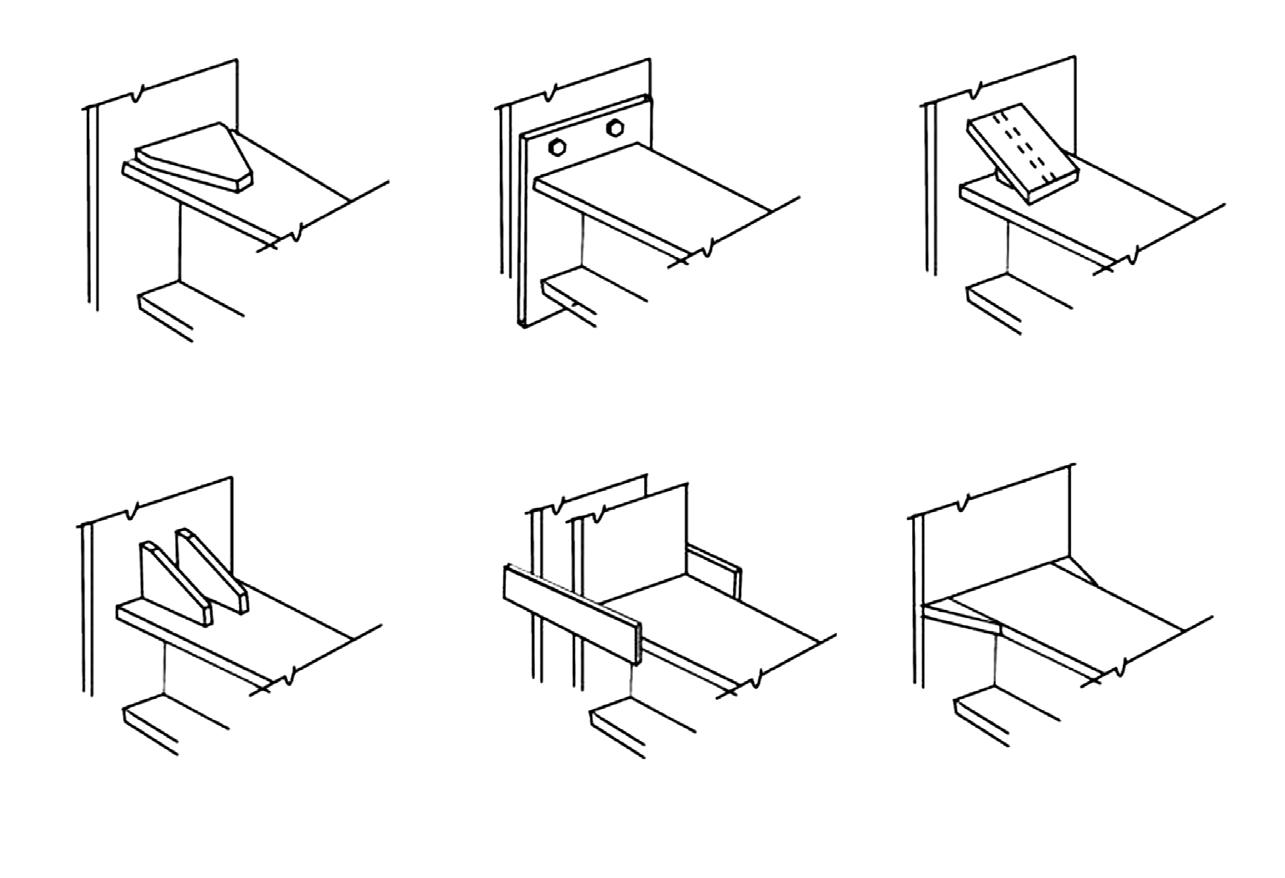
NUMEROUS POSSIBILITIES WITH EASE
As mentioned, many different steel shapes are possible, and only changing the design and configuration of the roller is necessary to generate these differences. In addition, steel can technically be fabricated to a limitless dimension. Because the material is man-made, and is not constrained by natural limits of length or width, steel can be produced as large as transport will allow. Traditionally, steel is transported by rail, and therefore does not pose a limit to size (Shuster, 1997).
BUILDING-SCALE FABRICATION - PARTS AND LABOR
While the fabrication of the material for construction is relatively simple and does not require a great deal of time and skill, on-site fabrication of a steel structure is very much the opposite. Steel structures must be fabricated by hand, usually requiring two to three skilled laborers per connection of members. Each laborer requires a series of hand tools to ensure alignment between members as well as alignment of bolt or rivet holes (Shuster, 1997). This manual labor covers three widely used fabrication techniques - welding, bolting, and riveting. Welding involves the material bonding of two steel members, thus eliminating the need for angles, plates, or any type of connections (Shuster, 1997). Bolting involves two workers tying two steel members together through a threaded bolt mechanical connection. While bolting allows for pre-cut holes in steel members in the factory and thus minimizes labor on-site while eliminating cracking that may occur through welding, the added weight and sheer number of parts necessary makes it an inefficient process (Shuster, 1997). Riveting is another jointing technique using a compressed air gun, where rivets are driven through steel while eliminating any connections that need to be screwed together. While riveting does create strong connections without any parts that may come loose, it does require the labor of three workers and on-site puncturing of rivet holes. The small tolerances allowed in riveting render the technique quite expensive. Figure 16 describes the many variations in connection types and techniques.
CONCLUSION
The emergence of steel as the standard material used in the fabrication of most structures is evidence of the usefulness of the material by way of its manufacturing process. However, constructing with the material does not offer the same benefits. The amount of manual labor necessary to fabricate a structure using steel is great, as is the skill and knowledge necessary to carry it out. The number of parts necessary for connection may create inefficiencies in construction, especially when dangerous conditions are considered. In order to construct large-scale structures, cranes are necessary, and workers must work at very high altitudes to make connections. It is said to take three quarters of a worker’s strength just to stand in place at approximately 60m in the air (Shuster, 1997); when skilled labor is added to these conditions, the margin for error will surely increase.
CHAPTER 3 - CONTEXT
.0 FABRICATION CONTEXT: TRADITIONAL TECHNIQUES
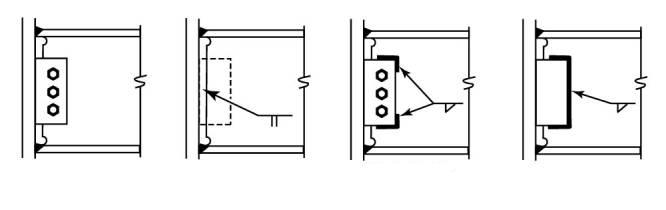
PROVIDING THE CONTEXTUAL BASIS FOR A NOVEL TECHNIQUE
By understanding the complexity and complications involved in processing concrete, timber, and steel, as well as the problematic areas in constructing with each material, it is now possible to situate both the need and benefits of a novel fabrication process. By providing this context, the synthesis of a thermoplastic radial pulbraiding fabrication process can now be understood within a specific context.
TRADITIONAL VS NOVEL FABRICATION: CONCLUSION
Each fabrication technique explored in this dissertation - both traditional and novel - involves a series of designed steps necessary to carry out a process. Concrete fabrication involves an iterative proportioning of the correct types of ingredients and the knowledge and manpower required to construct on site; timber fabrication requires this same on-site knowledge in order to effectively join members while continuing to consider the actual processing which affects these decisions; steel fabrication, while highly automated, requires strict control of temperatures and material elasticity while involving, similar to other techniques, a serious knowledge of mechanical jointing options. Finally, thermoplastic radial pulbraiding involves machine setup as well as careful design of the ratio of glass to resin fibers in a commingled matrix.
The three traditional fabrication techniques explored in the previous chapter uncover the great deal of complexity involved in their use in construction. Thermoplastic radial pulbraiding, in comparison, does have certain process requirements but allows for their greater control. The proposed synthesized process gives the designer control over design, fabrication, and construction while eliminating both fabrication and construction complications.
Although the comparative analysis of concrete, timber, and steel fabrication uncover the disadvantages, or problematic issues necessary for consideration in the fabrication process, it also provides strong groundwork to investigate critically the new fabrication method proposed. While this comparison does provide a strong basis for the need for and the benefits from thermopastic radial pulbraiding, the investigation of traditional techniques necessitates the consideration of any possible constraints and limitations.
CHAPTER 3 - CONTEXT
fibers polymers
fiber & polymer morphology
design of composite structures
material design design criterion
structure design
manufacturing processes
simulation & analysis
mechanical & physical properties
fibers polymers
simulation & analysis
fiber & polymer morphology
structure design
manufacturing processes (tooling)
A NEW PARADIGM IN DESIGN AND CONSTRUCTION
mechanical & physical properties
material design design criterion
design and fabrication of composite structures
The investigation into three traditional fabrication techniques undertaken in this chapter clearly exposes potential problems in their design and construction. However, a shift to a new material is not enough to address these issues. While fiber composite structures do provide specific benefits relative to traditional materials along with an advantageous design process (Figure 01), a novel fabrication technique can further these benefits by synthesizing material, tooling, and structure into one coherent fabrication technique. Figure 02 describes this new paradigm of design and fabrication.
CHAPTER
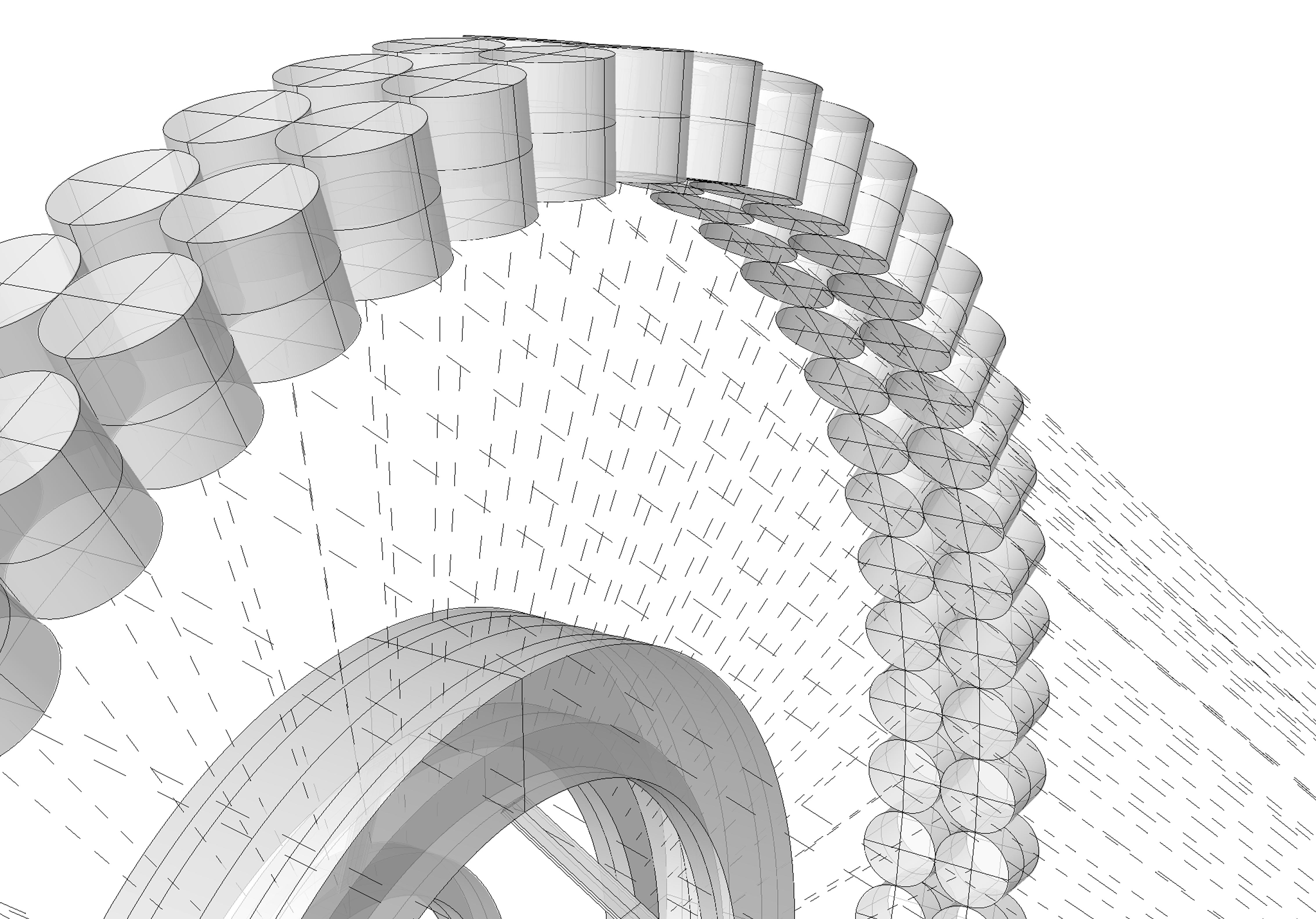
STRENGTH IN ORGANIZATION
Four fibers in nature - cellulose, chitin, collagen, and silk - carry almost all loads in nature. However, fibers alone are generally weak, and it is their organization within a composite matrix that gives them strength. Bone, as shown in Figure 01, for example, is composed of the natural fiber collagen in a mineralized matrix (Jeronimidis, 2004). Cellulose fibers in trees (Figure 02) are bonded within a lignin matrix (Dinwoodie, 2000). The combination of optimal organization of fibers in addition to their rigidification in a matrix create complex and strong natural systems.

Fiber organization in nature is reliant on three major factors: hierarchy, anisotropy, and prestressing. Hierarchical development in biology leads to redundancy. In classical engineering, redundancy is looked at as a negative characteristic, described as the “opposite of efficiency.” Traditionally, structures are designed with minimal use of material, simple organization, and component standardization (Weinstock, 2006). However, redundancy is an essential principle in biology, allowing for a complex material organization that accepts local disruptions (Hensel, et al., 2004), and therefore adapts for global equilibrium by providing multiple path-load vectors (Elices, 2000). Natural fibrous composites implement hierarchies (Figure 03) to achieve efficient use of material, a complex yet adaptive structural organization, and highly specific, particularly arranged components.
FIBER DIRECTIONALITY
Anisotropy, a characteristic in which a material exhibits different behavior when measured in different directions, is of utmost importantance in natural fiber composites. Fibers are inherently anisotropic, because the molecules that comprise each fiber are oriented with a fiber direction and therefore provide an extremely high level of optimization as compared to isotropic materials when considering the direction of applied loads. Fibers optimize their mechanical behavior due to this anisotropy, are oriented parallel to applied stresses, and therefore read as a map of stresses on a biological structural system. This optimization then can be described in that “biology produces a large number of patterns of load-bearing fiber architectures, each a specific answer to a specific set of mechanical conditions and requirements (Jeronimidis, 2004, p. 92).”
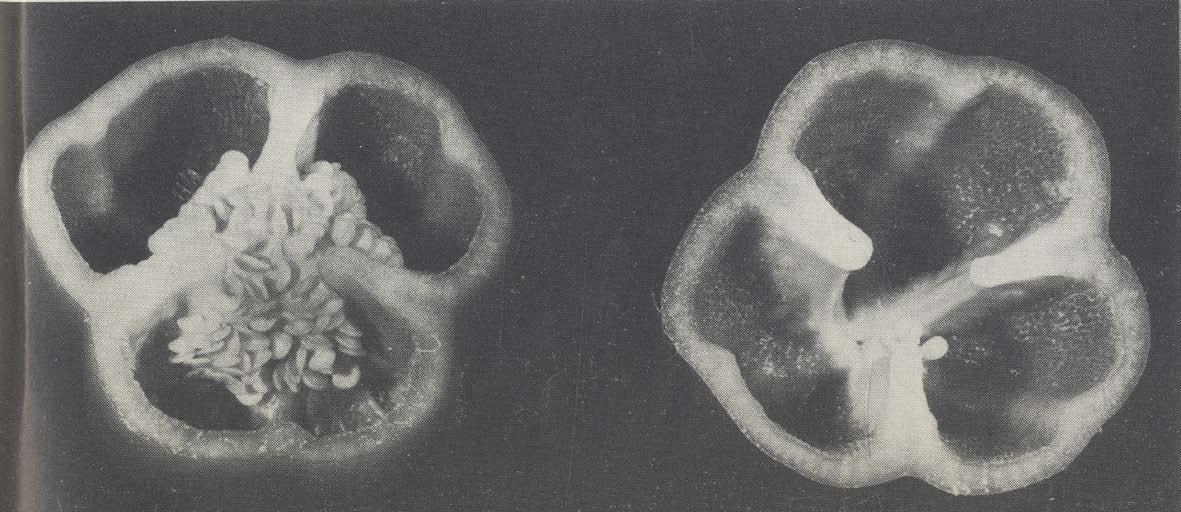
Although fiber directionality allows for efficient load transfer, fibers in biology are always working in tension, and do not provide a good deal of compressive strength (Jeronimidis, 2004). In order to achieve these tensile properties and thus reduce compressive loads, fibers are pre-stressed, either organizationally or through fluid pressure (Jeronimidis, 2006). Trees execute the pre-stressing of their fibers through internal organization, by which new cellulose cells are bonded to old dry lignin cells. This “cross-linked” fiber network pre-stresses the fibers into tension and provides lateral stiffness to counteract buckling (Elices, 2000). Pre-stressing by using internal fluid pressure occurs in almost all natural biological systems. All animal cells and organs, fruits and vegetables are made up of fibers prestressed by internal fluid pressure. Cells are stressed and in turn gain compressive strength. While some of these fibrous systems remain flexible, as in the pig’s colon shown in Figure 04, some systems rigidify (Figure 05).
EFFICIENCY AND EFFECTIVENESS
The organization of natural fibers provides strength in natural systems, but their existence within a composite matrix provides a functional bond that transfers stress between fibers while laterally stabilizing them, thus affording considerable shear resistance (Dinwoodie, 2000). It is important to note that this rigidifying material, or natural “resin,” does not provide compressive strength. In fact, fibrous composite materials are quite brittle (Elices, 2000). However, with its highly optimized and adaptive growth, biology possesses the ability to organize and stress fibrous material to work efficiently and effectively.
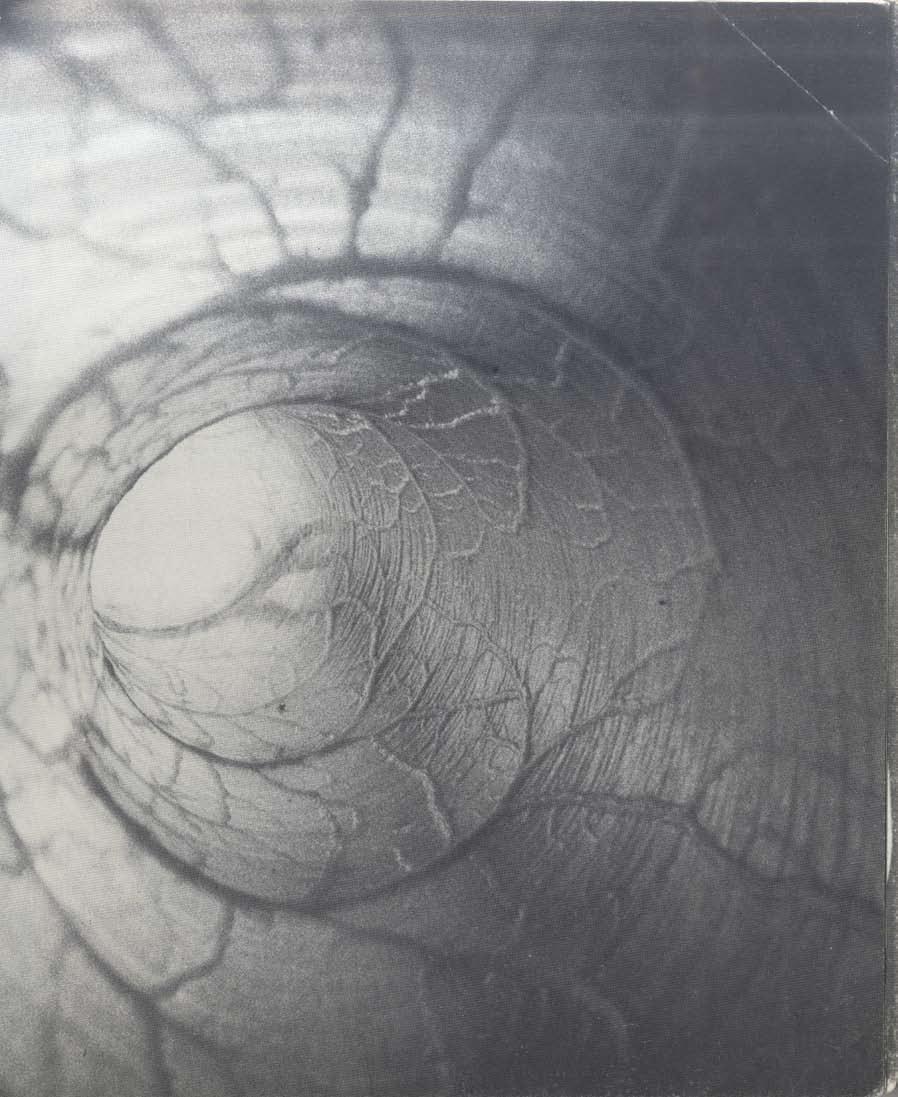
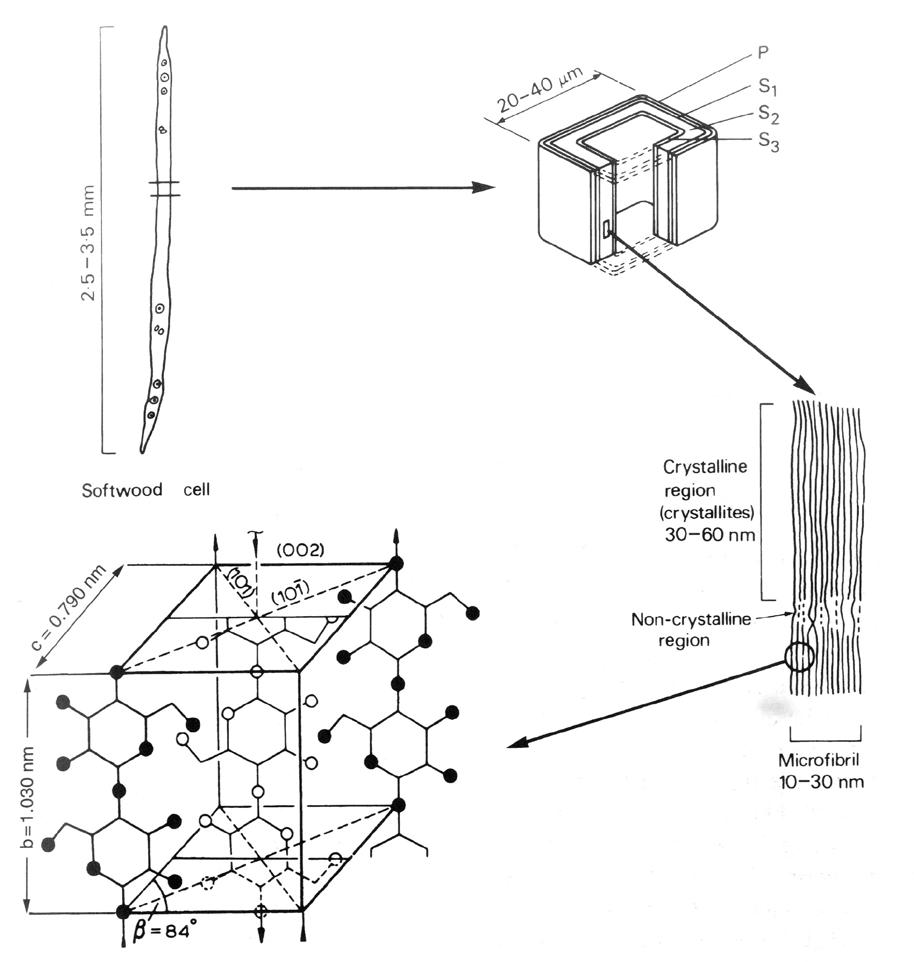
CHAPTER 5 - NATURAL FIBER COMPOSITES
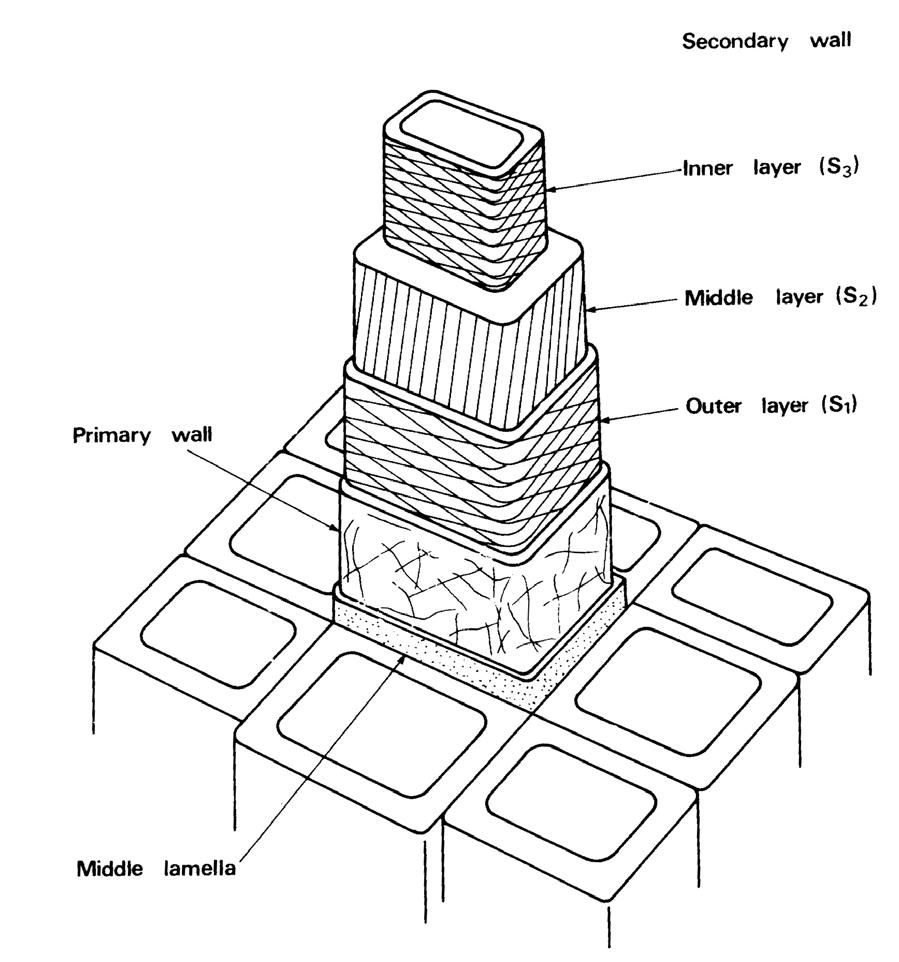
HIGH MODULUS FIBERS (glass, graphite, aramid, ceramic, steel, etc.)
HIGH-TENACITY FIBERS (tire cord, ropes) TEXTILE FIBERS (acrylics, cotton, nylon, olefin, polyester,
Apparel
USE OF SYNTHETIC FIBER COMPOSITES
Man-made fiber composites are extremely advantageous material systems designed from the logic taken from natural fibrous structures. Advantages of fiber composite materials include high specific stiffness and strength, low density, light weight, controllable anisotropy, low maintenance, and an excellent corrosion resistance (Beukers & Van Hinte, 2005). Fiber composites are material systems combining fibers (glass, carbon, etc.) with a stiffening matrix, most often a resin. Composites are used in all major industries, including aerospace, ground transport, civil engineering, and sports (Beukers & Van Hinte, 2005). Composites allow for limitless shapeability and provide a cheaper solution to manufacturing complex shapes, in comparison to steel and other structural materials (Beukers & Van Hinte, 2005).
MANUFACTURING PROCESS OF GLASS FIBERS
Glass fibers were first spun in the 1930’s, and have generally been used for the construction of boat hulls, circuit boards, insulation and fiber optics. (McQuaid, 2005). Glass fibers used in highend applications are manufactured through the marble melt process, where molten glass is melted and formed into two to three centimeter diameter glass marbles, which are then remelted and extruded through a platinum alloy die, typically three to twenty micrometers in diameter. Although standard glass fiber, or E-glass, is not as strong or as stiff as carbon fiber or other advanced fibers, glass fiber does provide exceptional hardness, transparency, stability, strength, and stiffness (Figure 01) (Wallenberger, et al., n.d.).
PARAMETERS AFFECTING THE PROPERTIES OF GLASS FIBERS
Although the tensile strength of glass fiber increases as the amount of alkali oxides in the glass decreases (Wallenberger, et al., n.d.), they are, just like natural fibers, weak in compression. Because of this, their inclusion within a resin matrix stiffens the fibers and allows for the transfer of loads through them. However, there are certain variables that can be attributed to fiber strength. These include orientation of fibers, fibers of uniform strength, discontinuous fibers, and interfacial conditions. Because glass fibers are anisotropic, directionality of each fiber can be designed to properly distribute load parallel to each fiber. Misoriented fibers can greatly weaken the structural properties of the composite (Agarwal & Broutman, 2006). In addition, glass fibers that are mishandled can lose considerable strength. By rubbing together, fibers can become damaged, and therefore are often treated with a sizing, or a coating that prevents abrasion between fibers (Wallenberger, et al., n.d.). The resin matrix also takes on part of the responsibility for this protection. Finally, fiber strength is dependent on fiber length. Generally, longer fibers have a greater chance to become damaged (Agarwal & Broutman, 2006), and are therefore usually less strong. However, if handled properly, the endless length of fibers in composites can provide huge design potential, especially when compared to steel. Fibers take deformation five to ten times higher than steel (Jeronimidis, 2006), have a higher specific strength, and a lower density (Figure 02) (Beukers & Van Hinte, 2005). In addition, composites provide a greater price to performance ratio, as “it won’t take long before deeper thinking in metal will cost more money than it saves (Beukers & Van Hinte, 2005, p. 59).”
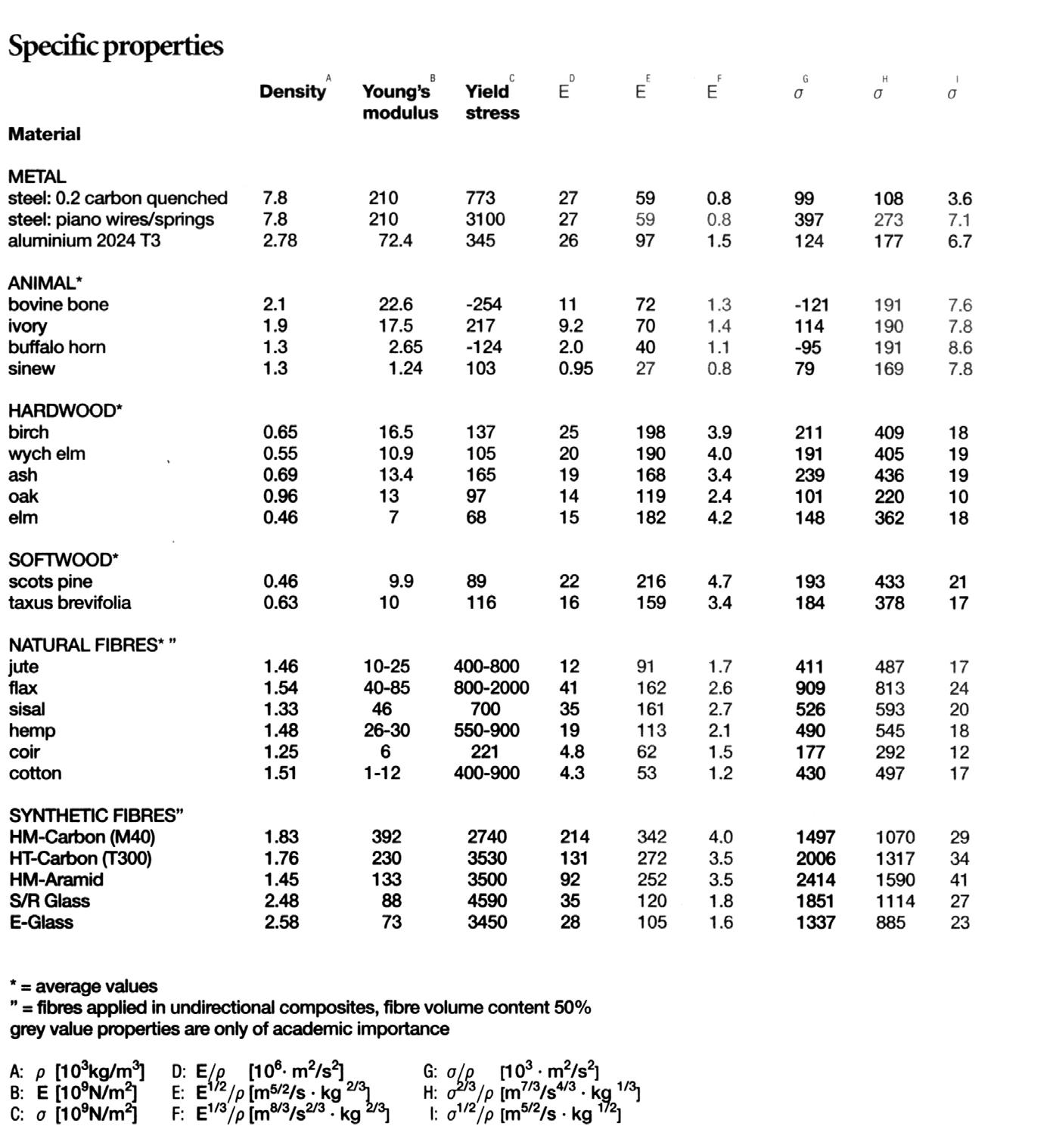
CHAPTER 6 - SYNTHETIC FIBER COMPOSITES .0 GLASS FIBERS
Figure 03, chart, describing the maximum temperature at which resins are effective. Past these temperatures, thermosets tend to burn, while thermoplastics will begin to melt.
STIFFENING MATRICES
Fiber composites are composed of fibrous material bonded together by a matrix, which plays the functional role of transferring loads between fibers. The matrix material can be almost any material, so long as it can exist as both a liquid and a solid. In most fiber composites, two types of resin matrices are employed - thermoset resins and thermoplastic resins (Aird, 1996).
THERMOSET RESINS
Thermoset resins are stiffening resins that cure permanently. They work within a thermoset system; both a resin and a catalyst are necessary, and bond together through a chemical reaction which both uses and produces heat. Most thermosets are versatile and easily worked, and often cure at room temperature (Aird, 1996). Polyester resin is the most common thermoset, and with glass fiber, led to the post-war boom of increased construction of glass fiber composite boats. This industrial event led to the cost-effectiveness and availability of both polyester resins and glass fiber. Polyesters can cure at an adjustable rate; by altering the amount of catalyst added to the mixture, the resin’s hardening rate can be controlled. Although polyesters are abundantly available and easy to use, when used with glass fiber, they produce a low strength material (Aird, 1996). Additionally, they do not form suitable material when combined with advanced fibers such as carbon fiber and kevlar (Aird, 1996). Epoxy resins, on the other hand, yield high-strength materials when combined with glass fiber, and perform considerably better at higher temperatures (Aird, 1996). Figure 03 shows the maximum temperatures at which thermoset and thermoplastic resins perform effectively.
THERMOPLASTIC RESINS
Thermoplastic resins are stiffening resins that have the ability to be remelted; they soften when heated and harden when cooled (Campbell, 2004). This property can be highly effective for applications where form must be easily reworked. Examples of thermopastic resins include polypropylene, polyethylene, and polyvinyl chloride (PVC).
PRE-PREG AND COMMINGLED FIBERS
Fibers can either be dry or pre-impregnated. While dry fibers are cheaper and have a longer shelf life, pre-preg fibers are of a higher quality and minimize resin waste from over-application (Campbell, 2004).
A new technology is being introduced where fibers are no longer pre-impregnated, but are composed into strands with resin fibers. These commingled fibers are as flexible as pre-preg fibers, but allow for the exact design of reinforcing fiber-to-resin ratio. This is extremely advantageous in the reduction of waste resin, which does not provide any strength. One disadvantage of commingled fibers, however, is that the mechanical properties of the reinforcing fibers are lower than pre-preg fibers (Mallick, 1997). However, this may be due to its evaluation based on fiber volume employed. In order to take advantage of the potentials of commingled fibers while maintaining effective performance, fiber volume may have to increase.
HEAT AND FIRE RESISTANCE
Fiber composites in architectural applications provide a difficult problem in relation to heat and fire resistance. Although, as noted in Figure 03, certain resins can withstand relatively high temperatures, it is the behavior of the resin at these maximum temperatures that is troubling. Because thermosets cannot change back to liquid after curing, they do not soften at high temperatures, but only burn. In contrast, thermoplastic resins will soften rather than burn. While the softening of a fiber composite structure could allow for greater egress time, it is important to note the repercussions of using such a material for architectural applications.
CHAPTER
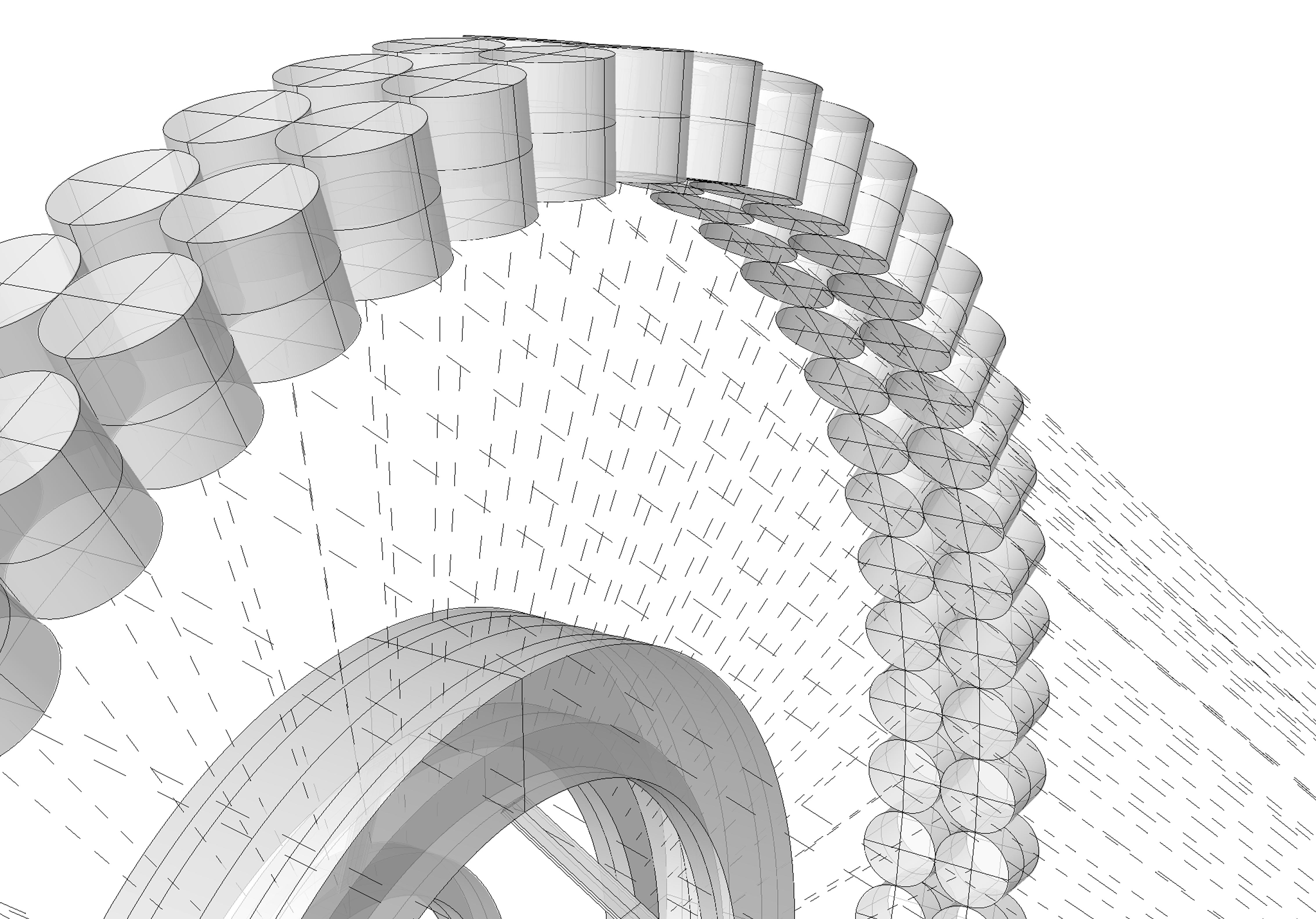
Figure 04, chart, describing the performative relationship between braided fiber composites with different braid angles. These charts show how fibers perform at both room temperature and at 350° Fahrenheit under tensile, compressive, and shear stresses. While fibers braided at 45° angles do not perform as well in tension and compression, they perform superior to other angle braids when loaded under shear stresses.
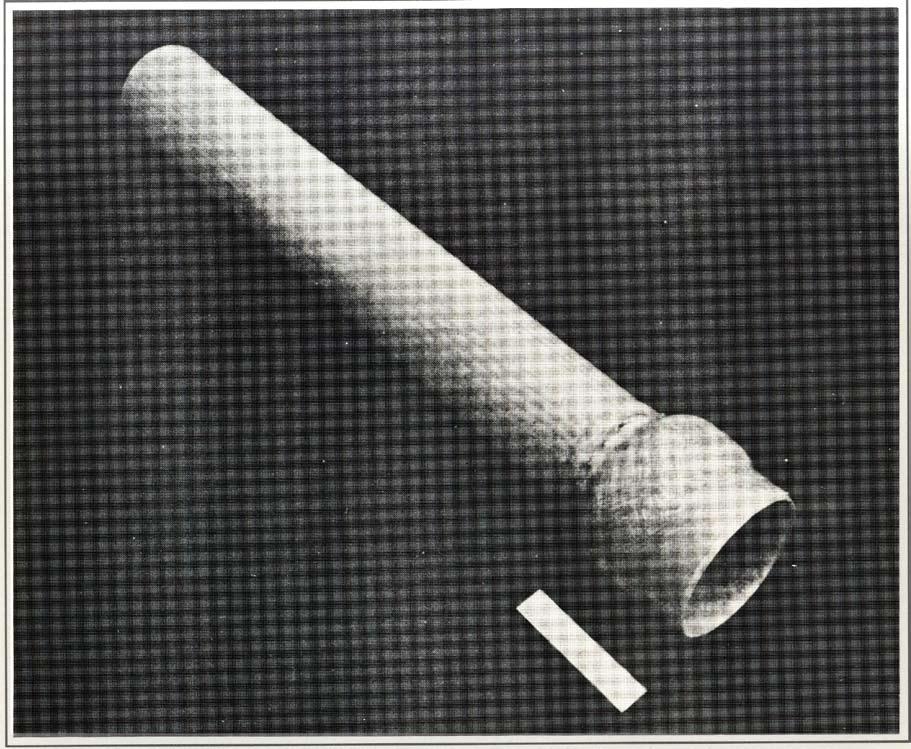
(redrawn from Dr. Frank Ko, Dr. Christopher M. Pastore, and Andrew A. Head, Atkins and Pearce Handbook on Industrial Braiding, 1989)
BRAIDING - USES AND ADVANTAGES
Braiding is a textile technique where individual elements meet at oblique angles, in an overunder-over fashion (Figures 01 and 02). Traditionally, braiding is used for plaiting hair or creating baskets and sturdy straps. Braids are also quite flexible and are often fabricated as tubes, because they mold easily over various forms (McQuaid, 2005).
In addition to textile applications, braiding is used in the airplane industry for the fabrication of engines and propellers (Figure 03). Rather than thin braided sleeves, however, the aerospace industry uses three-dimensional braiding as well as three-dimensional overbraiding in the manufacture of these products. Three-dimensional braids allow for high impact resistance due to the ability to control fiber thickness as well as flexibility of fiber orientation and varying cross-section (Rudd, 1997). These two characteristics of three dimensional braiding technology provide huge potential to architecture, where fabrication of a 3D tubular braid can include spatial qualities (Figure 02) such as transparency of structure and connection between interior and exterior space (Garcia, 2006). Braiding is an efficient material technique in taking tension and compression loads because all fibers are interlocked at regular intervals, allowing even distribution of applied loads as well as high global elasticity (Garcia, 2006). This load distribution can also be attributed to the redundancy of the braided system (see Chapter 5 for a description of redundancy), where the existence of more fibers than necessary braid together to transfer loads if other areas of the system do not perform.
THE PREFERED TECHNIQUE
When compared to other textile techniques, braiding is a preferable one for the purposes of architectural design and construction. Unidirectional composites, while strong in the direction of fiber orientation, are weak when stressed perpendicular to fiber directionality. Because of the interlocking nature of a braid, these stresses can be distributed equally. Braiding also has a lower fiber volume when compared to filament winding applications, allowing for a cheaper, lighter structure (Freger, 2004). Although laminated woven composites can be organized bidirectionally to perform well under stresses in multiple directions, they are weak at terminating ends and tend to delaminate.
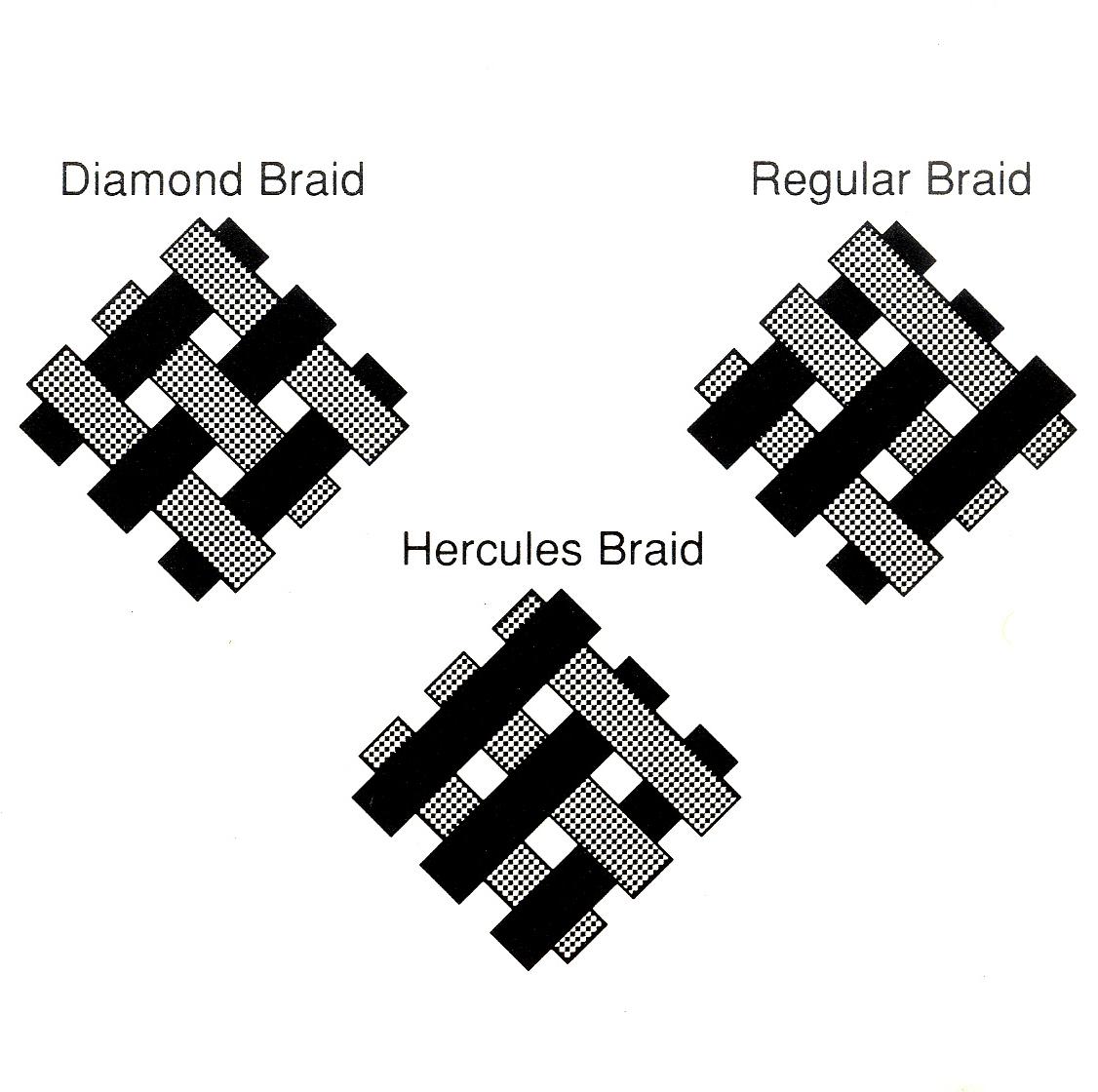
A major advantage of braided composite structures is the ability to control fiber directionality locally and fiber angle globally. As shown in Figure 04, braids are most often used in applications where shear stresses are high, at an optimum braid angle of forty-five degrees. However, this angle does not provide sufficient tensile and compressive strength for unidirectional loads parallel to a tube, due to the nonparallel fiber paths being stressed (Ko, Pastore, and Head, 1989). Therefore, the flexibility of a braid is advantageous in that it will allow for the specific design of fiber directionality and
CHAPTER 7 - FIBER COMPOSITE FABRICATION TECHNIQUES
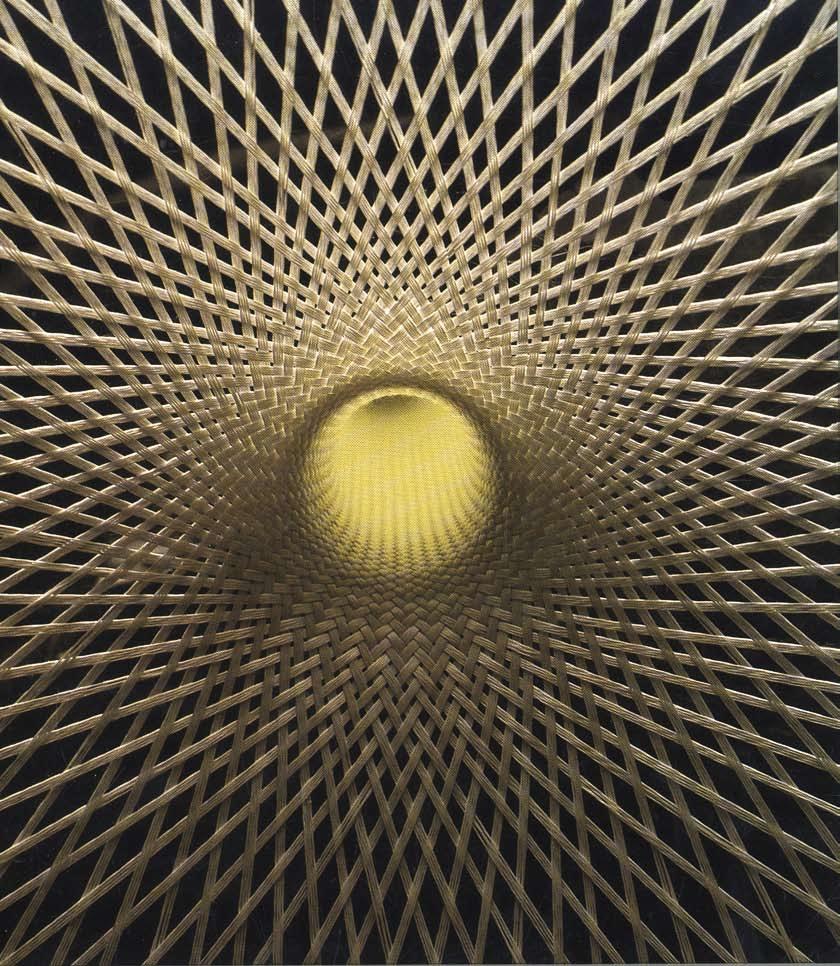
BRAIDING HIERARCHIES
Pulbraiding on a CNC radial overbraider creates possibilities of complex fiber organization with simple members. Braiding occurs on two different scales; individual fibers are commingled through braiding to design a specific fiber-resin makeup of strands, and these strands are then braided before the pultrusion process.
Braiding to form fiber strands can create a strong internal fiber organization, giving strength to pultruded members. Strand braiding can help evenly distribute loads between fibers in a matrix, both resisting buckling as well as possibly reducing the amount of resin needed to properly bond and transfer loads between fibers. By braiding these strands, of which have already been braided, the equal distribution of loads and buckling resistance is strengthened further. In addition, greater possibilities arise in the differentiation of braid angle, node-to-node length, and pultruded rod radius, due to the hierarchical structural system’s ability to transfer load to other working members.
Through these hierarchical organizations (Figure 05), fibrous material is composed and fabricated to form a coherent structure. The input of material directly affects its machining, and subsequently the form and performance of the final structure.
Figure 05, diagram, showing two braid hierarchies present in the fibrous material made possible by using a pulbraiding fabrication technique. A radial overbraider allows for the formation of both braided strands (left) and braided fibers to be pultruded (right).INDUSTRIAL BRAIDING MACHINES
Industrial braiding (Figure 06) has been given the greatest attention and advancement in the aerospace industry, due mainly to the wall thicknesses achieved in three-dimensional tubular braiding and their impact resistance (Rudd, 1997). 3D tubular braiding takes place on a radial overbraider (Figure 07, following page), which braids individual tow lines of fiber over a mandrel. Each tow line, carrying a specified number of fibers, is individually controlled by a Computer Numerically Controlled (CNC) system, where direction, speed, and rotation angle can be individually designed to achieve optimal braiding patterns. This advancement in industrial three-dimensional radial overbraiding was achieved in 2000, by A&P Technology. The braider, called Mantis, allows for fully automated control over each braiding parameter as well as mandrel position. By altering these two sets of variables, any braiding pattern, indeterminate of necessary fiber volume or mandrel geometry, can be achieved. In addition to these important advantages in the manufacturing process, the ability to control all aspects of braiding allows for mechanical properties identical to laminate construction, while located within a single fiber layer. By allowing independent control of each braiding tow line, necessary thicknesses and braid angles can provide structural performance while decreasing the possibility of interlaminar failure. When braided structures do fail, the failure occurs within a braid (Braley and Dingeldein, n.d.). However, due to the inherent robustness of braided structures, this failure does not cause an immediate structural concern. The current large-scale braider available (Mantis) has the capability of braiding a structure over a mandrel just larger than eight feet (254 cm) in diameter and up to fifteen feet (457.2 cm) in length (Braley and Dingeldein, n.d.). However, the size of the braider is only dependent on the construction time necessary to build one. The technology is readily available and theoretically, economy is the driving factor in the fabrication of larger machines1. One scale constraint that must be mentioned, regardless of technical possibilities is that of prebraiding. Prebraiding is a material phenomenon where single raw fibers begin to braid themselves due to their continuous long length. When large-scale construction is employed, prebraiding is a length limitation to consider2. However, the ability to cure a structure as it is being constructed is a possible way to overcome this phenomenon.
1 In conversation with Guido Grave, Managing Director of August Herzog Maschinenfabrik, Oldenberg, Germany. Via e-mail, 23 April 2008.
2 In conversation with Dr.-Ing. Markus Milwich, Head of Composites/Braiding, ITV Denkendorf. University of Reading, 6 August, 2008.
CHAPTER 7 - FIBER COMPOSITE FABRICATION TECHNIQUES
.0 INDUSTRIAL BRAIDING
B = number of bobbins
T = number of threads
Vm = mandrel velocity
M° = angle of mandrel
parameters affecting the size of a CNC radial overbraiding machine. The number of bobbins (B), number of threads (T), mandrel velocity (Vm), and mandrel angle (M°) all contrribute to the vast array of possible braided geometries.
CHAPTER 7 - FIBER COMPOSITE FABRICATION TECHNIQUES .0 INDUSTRIAL BRAIDING
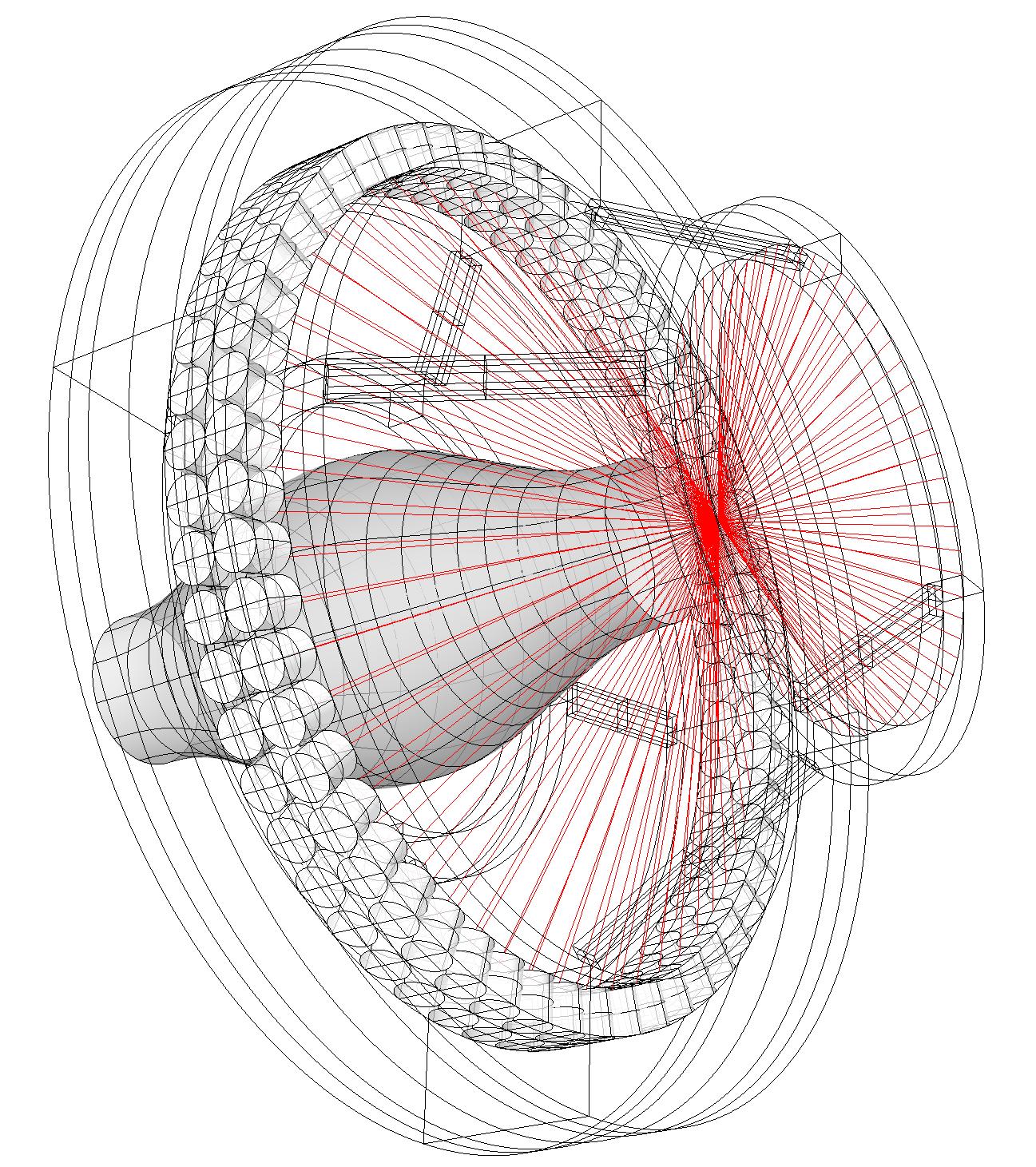
PULTRUSION TECHNOLOGY
Pultrusion is a method of rigidifying synthetic fibers by pulling them through a die and resin bath. Parallel fiber strands are rigidified as they come through a die and materialize as tubular geometries with the ability to conform to variable sections (Figure 08). There are limits to profile section, in that standard pultruded members have circular or rectangular sections. Pultrusion is used typically in electronics applications as well as for fishing rods, tent poles, and ladders. Parallel fiber pultruded members are low in stiffness and therefore are subject to bending when stressed in compression along the parallel axis of the fibers (Starr, 2000). To overcome this mechanical property, pultruded members can be pulwound, where layers of parallel fibers are combined with layers of helically wound fibers. This dual-axis fiber orientation creates a member with high stiffness and high torsion resistance (Zhongshan Pulwell Composites Co, 2008). In relation to internal fiber organization, pultrusion is an advantageous technology which keeps fiber strands untwisted when included in a matrix. By preventing twisting, the axial strength and stiffness of fibers are uncompromised (Freger, 2004).
CHAPTER 7 - FIBER COMPOSITE FABRICATION TECHNIQUES
TECHNICAL PLANT STEM, ITV DENKENDORF
ITV Denkendorf is a materials science research and composite manufacturing company focusing on biomimetic engineering of fiber composite structures. One area of research currently being explored is in the development of a technical plant stem. By using the giant reed as a biological reference, engineers are studying the plant’s complex structure and decreasing lignification which contribute to a gradually decreasing stiffness between fibers and its matrix. This physical makeup leads to high vibration damping, a performative aspect which can be exploited for numerous applications (Milwich, et al., 2008).
By modifying the resin within the matrix, a synthetic technical plant stem can be achieved (Figure 10). This is done through a differentiated resin application; rather than applying either a standard resin which is quite weak, or resin with the addition of stiffening nano-particles which is very expensive, the high-strength resin is applied to only the interface between fibers and a standard resin (Figure 11). This variegated matrix provides effective bending stiffness and an increase in vibration damping as compared to other fiber composite matrices (Milwich, et al., 2008).
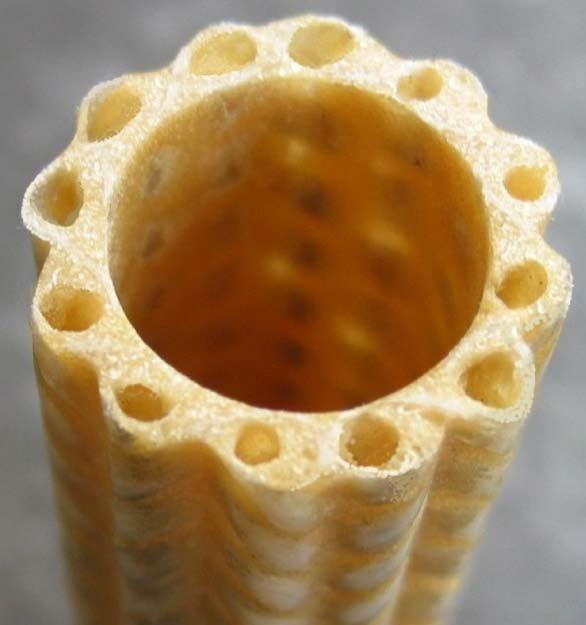
PULBRAIDING
By combining the braiding process within the pultrusion process, the desired composite can be fabricated on one machine. The ITV pulbraider (Figure 09) collects yarns through a braider, combining unidirectional and spiral-wound fibers, and sends them through a heated die. The fibers are pulled through this die and then rolled out and saw-cut to their necessary lengths (Milwich, et al., 2008). The combination of unidirectional and spiral-wound fibers contribute to the high torsional and high bending stiffness of the structure. These properties, along with the necessary morphology of the technical plant stem - variable solids and voids - are possible due to the pulbraiding process. The end product results in a cost-efficient, high damping, lightweight structure suitable for tensile, compressive, bending, and torsional loads in the architecture, aerospace, and sports equipment industries (Milwich, et al., 2008).
Although this technique is specific to the scale (less than 20 mm) and material used here, the availability of ITV’s pulbraiding machine gives possibility to many other hybrid manufacturing machinery and techniques.

CHAPTER 7 - FIBER COMPOSITE FABRICATION TECHNIQUES
.0 PULBRAIDING
Figure 11, diagram, describing three matrix options: fibers in a regular, weak matrix (left), fibers in a high-strength matrix (center), and fibers with high-strength resin at fiber perimeters (right). (redrawn from M. Milwich. Plant Stems as Role Models for Composite Fibers. 2008. Figure 09, ITV Pulbraider. ITV Denkendorf has developed a pulbraiding machine where fibers are braided then pultruded all in one seamless process. Figure 10, Technical plant stem. ITV Denkendorf has developed technical plant stem based on the the giant reed as a biological model, and produced it on a pulbraiding machine.LARGE-SCALE CONSTRUCTION
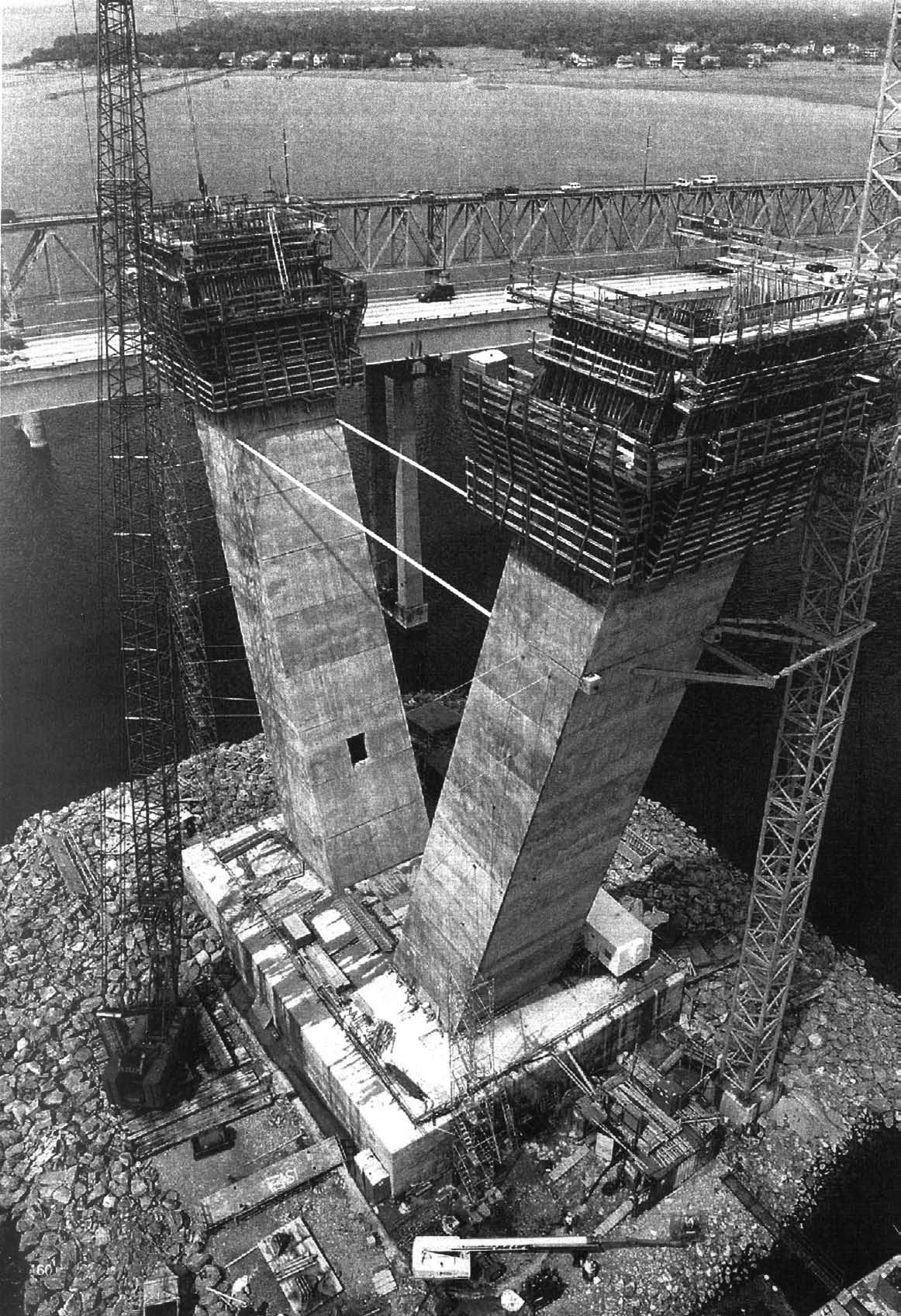
While the scope of this dissertation includes only the construction of a fiber composite structure, it is valuable to reference a large-scale construction technique external to this to draw comparisons in the viability of a novel technique. So even though concrete construction is viewed as potentially problematic (see section 3.03), slipform casting is a commonly accepted and widely used concrete fabrication technique which can provide a basis for the feasability of a novel technique.
Concrete structures span many different scales, and demand ever-evolving fabrication techniques. Formwork is necessary to contain concrete as it is poured and molded. At smaller scales, workers can build this formwork using plywood and standard hand tools. However, as structures increase in size, different methods are necessary.
SLIPFORM CASTING
Slipform casting (Figure 12) is a concrete casting method used in large-scale, on-site vertical construction. This method is particularly advantageous in situations where space is limited and the construction footprint is constrained. The slipform method also allows for rapid production and minimal interaction by builders (Weijenberg, 2004-2005).
Slipform casting involves a small section of formwork which is built for a specific casting geometry, and along with a minimal scaffolding platform, is moved up along the vertical structure as the concrete is being poured, through a series of hydraulic jacks; one section of concrete is poured into the cast and cured, allowing the same formwork to be lifted up and continue the process section by section. The formwork used per section can also be altered to meet specifically designed sectional requirements and can change path in order to meet geometric requirements as well (Weijenberg, 2004-2005).
VERTICAL FABRICATION
The implementation of slipform casting as a large-scale vertical fabrication technique provides an interesting precedent for the pulbraiding technique proposed in this dissertation. Although concrete construction poses clear problems as described in section 3.03, slipform casting can be advantageous in on-site, constrained instances, while still allowing for control over global and local geometric changes. The wide acceptance of slipform casting in construction (Figure 13) proves that a similar setup, although applied to pulbraiding a large-scale fiber composite structure, could allow for a new fabrication technology to emerge.
CHAPTER 7 - FIBER COMPOSITE FABRICATION TECHNIQUES .05 LARGE-SCALE PRECEDENTS
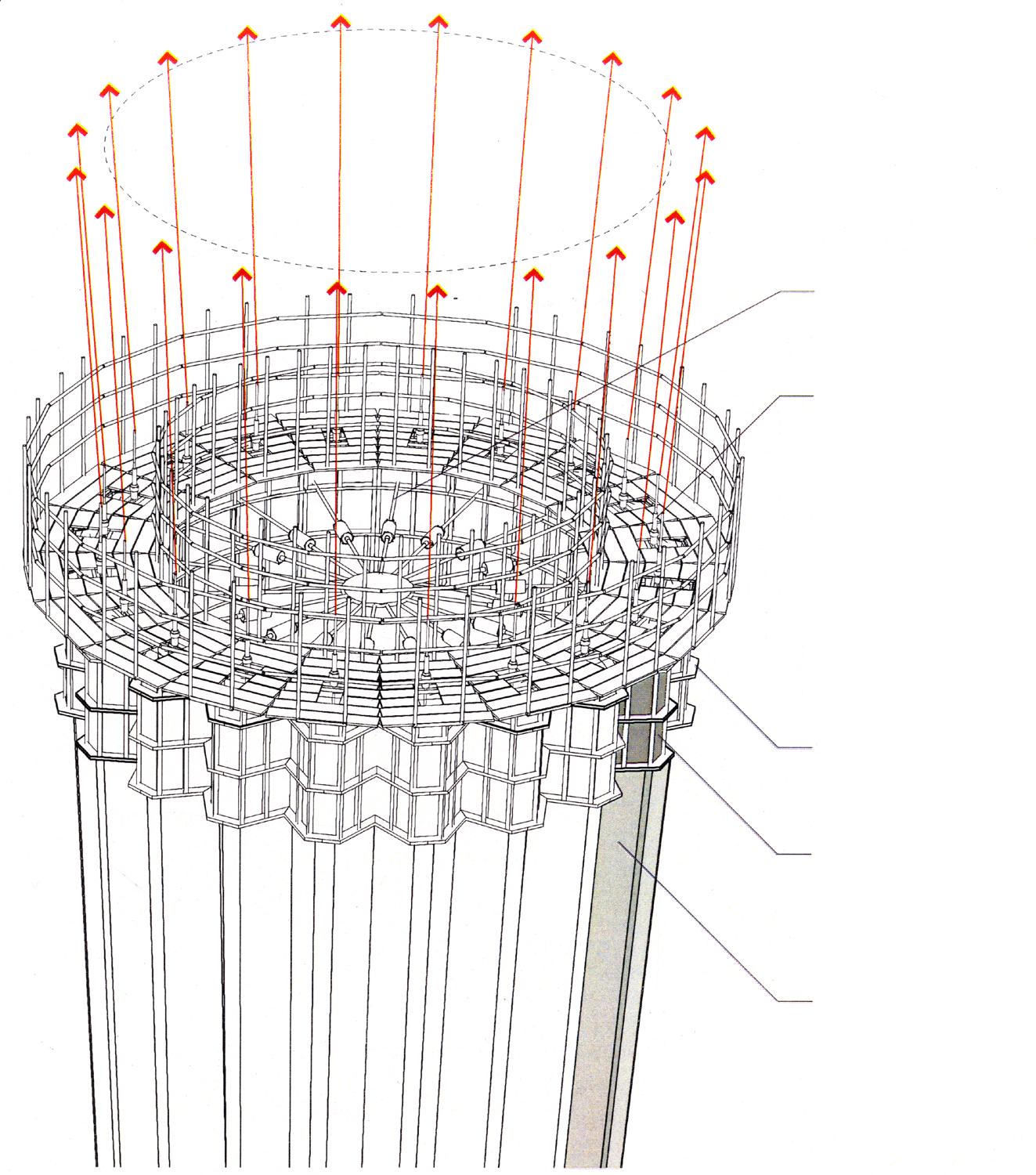
dry fibers pultrusion through thermoset resin bath
braiding mechanical joint
dry fibers pultrusion through thermoplastic resin bath
braiding tack-welding
dry fibers braiding and pultrusion through thermoplastic resin bath
rigid joint
A NOVEL FABRICATION METHOD
Traditional construction techniques have been developed over thousands of years based on component systems. Timber members are glued or joined just as steel members are bolted or welded together. Fabricating concrete requires a long and expensive process of mixing, testing, and remixing. Even fiber composites are currently constructed either over a seperately designed formwork geometry or in separate pieces. These methods are somewhat antiquated; the technology available in order to build faster and more efficiently is not being used. By exploring the potential of manufacturing capabilities within industries outside of architecture, a new paradigm in building construction can begin. Textile machines for industrial applications can provide this new potential when considering the use of continuous fibers in the design of a composite structure.
BRAIDING, PULTRUSION AND CHOOSING THE CORRECT FIBER MATRIX
pre-preg or commingled fibers (w/ thermopastic resin)
braiding and pultrusion through heated die
rigid joint
When considering braiding and pultrusion as applied manufacturing techniques, a fiber matrix must be taken into account. Firstly, in designing a large-scale structure, post-application of a stiffening agent would require more time, as well as numerous safety precautions - scaffolding, harnessing, and a huge amount of workers. In the attempt to design an all-encompassing on-site construction process, pultrusion is a preferable application option (see section 7.03). However, if pultruded rods are to be braided, there will be issues of interconnectivity. If thermoset resins are to be used in this instance, an external joint is necessary (Figure 14). Although this is possible with pultruded members, it could pose a complicated construction process, and is not taking full advantage of the continuous fiber potential of composite materials.
Thermoplastics offer interesting possibilities when combined with braiding and pultrusion. Three processes are available in which fibers, when combined with a thermoplastic resin, can create a composite structure (Figure 15). Firstly, pultruded rods can be braided, heated and then “tack-welded,” as described in Figure 16. Because thermoplastic resins can be remelted, combining the two rods would result in a single rigid joint. While this is a viable option, it poses the same construction problems as connecting thermoset rods would relative to safety precautions and time issues. Secondly, dry fibers can be braided then pultruded using a CNC radial overbraiding machine (Figure 17). Technically, it is possible to alter a braiding machine to include a resin bath and pultrusion dies. However, this option calls for extreme care in handling the resin.
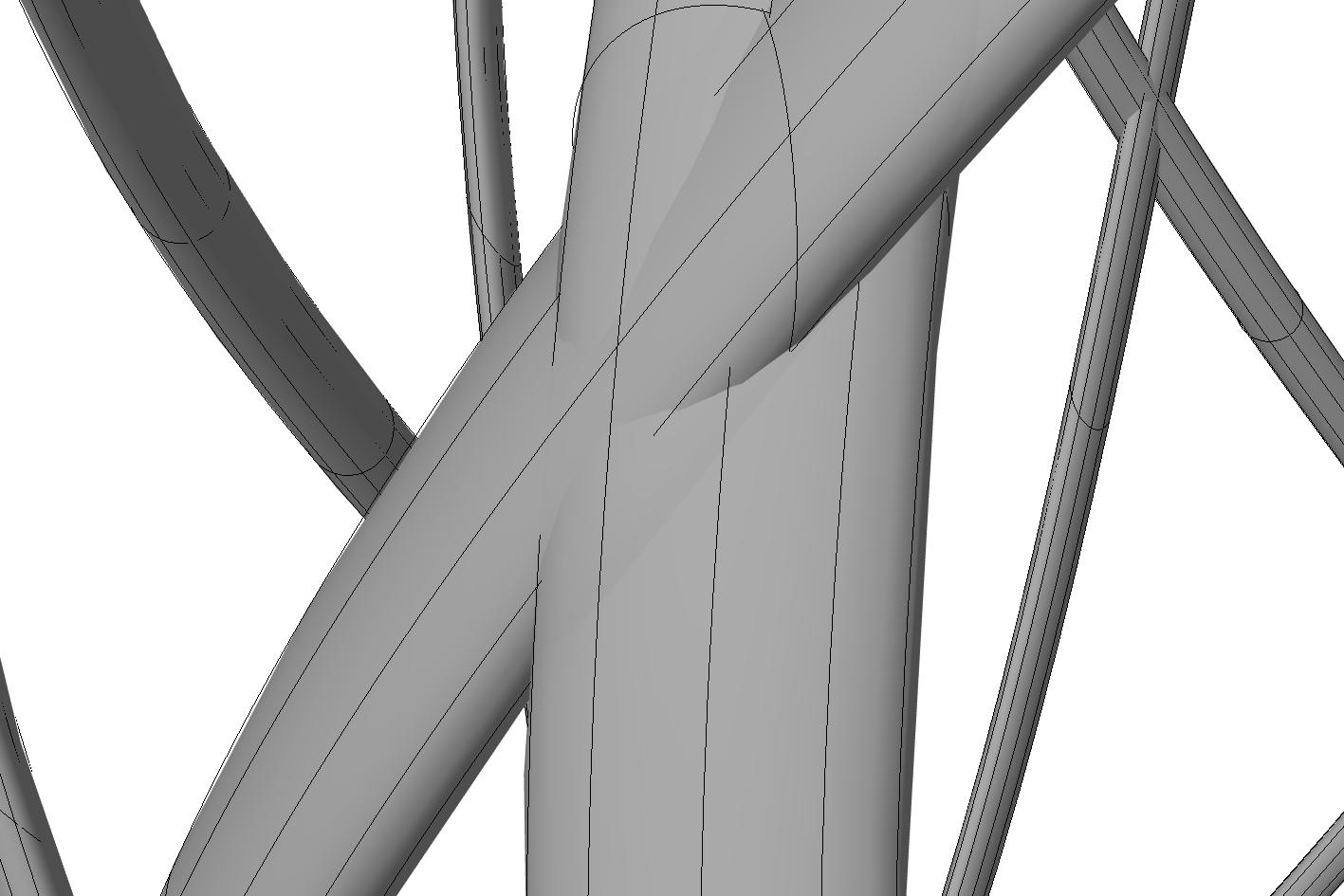
THERMOPLASTIC RADIAL PULBRAIDING
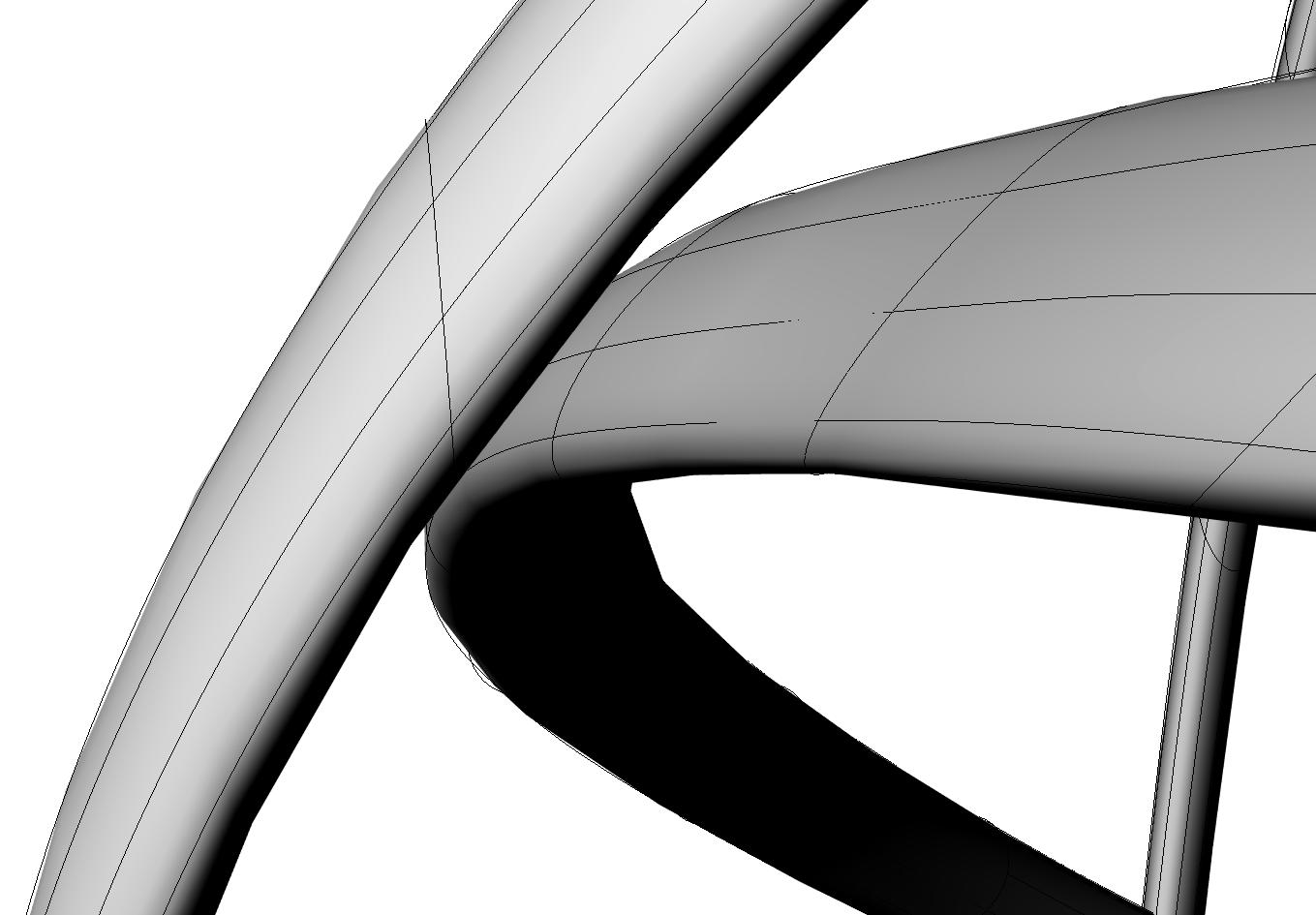
Finally, an option exists where fibers, which are either pre-impregnated or commingled, are braided and then heated by a heat source built into the braider. This would allow for maximum efficiency in amount of resin used, as well as eliminate all precautions when handling liquid resins. Furthermore, if commingled fibers are used, the polymer fibers, along with reinforcing fibers, can be spooled on the braider, and complete control of all fiber volumes can be controlled computer-numerically to follow the design specifications. This then creates a direct dependent link between material design and structure, via the tooling process.
CHAPTER 7 - FIBER COMPOSITE FABRICATION TECHNIQUES
7.06 COMPARATIVE ANALYSIS OF MANUFACTURING POSSIBILITIES
ON-SITE ADAPTABILITY
As described in section 7.02, it is necessary to include a mandrel geometry of which to braid over in the radial overbraiding process. In order to further advance the notion of a synthesized fabrication technique, a form-found pneu-cable net mandrel geometry is proposed to allow for the generation of a lightweight, adaptable, and constructed-on-site formwork. This lightweight formwork can be overbraided, and then deflated and reused for other construction purposes.
PHYSICAL FORM-FINDING
Physical form-finding is a physical process where a material configuration self-organizes due to the implementation of external stresses. Cable structures as well as fabric membranes are often used as structural systems, however because they are activated under tension, they cannot be described through simple mathematics like compression structures. Therefore, the form-finding method is necessary. The form-finding method effectuates what Frei Otto and his team at the Institute for Lightweight Structures call the “Lightweight Principle,” where the minimum amount of material is used while maximizing stability and strength (Lewis, 2003). Form-active tension systems are fine examples of tension systems following Otto’s Lightweight Principle.
Form-active tension systems are non-rigid material systems shaped and secured by fixed ends that redirect, through tension, external forces by simple normal stresses. The resulting systems are self-supporting. When form-active tension systems are working properly, they are in full tension with no appearance of creases, folds, or wrinkles. At this stage, the self-organizing system is working fully in tension, and transmitting load optimally for that specific material configuration. This synthesis of form generation and material organization is crucial for proper structural performance, and deviation from the found form could decrease functionality, and therefore require additional mechanisms for compensation (Engel, 1997).
A HYBRID FORM-ACTIVE TENSION SYSTEM
Of four possible form-active tension systems, shown in Figure 01, this project will reference two - cable structures and pneumatic structures - as well as achieve a hybridized system. Cable systems, and more specifically, cable-net structures (Figure 03), when loaded, are sagging systems (Engel, 1997), and due to their fibrous nature must be stabilized to prevent deformation against vibration, asymmetrical loads, and other environmental conditions (Engel, 1997). There are numerous methods of stiffening tension cables under tensile stress.
Pneumatic structures (Figure 02) use forces acting centrifugally in the direction of pressure equalization, and therefore the direction of the membrane, to equally distribute tensile stresses through a surface (Engel, 1997). The scope of this dissertation does not involve pneu behavior, but only the implementation of pneumatic structures as a device to pre-stress a cable-net form-active tension system.
This hybrid system uses tensile forces to generate form, and through self-organization of the material system, an optimal structural functionality.
CHAPTER 8 - GENERATING A MANDREL GEOMETRY
8.01 FORM-ACTIVE TENSION SYSTEMS
Figure 02, pneumatic stress diagram, describing the behavior of a pneu under tensile stress and the transfer of those loads across a surface. (redrawn from Heino Engel, Structure Systems. 1997. Basic shape of membrane spherical plane Figure 03, diagram, describing a cable net in tension, supported by four anchor points. (redrawn from Heino Engel, Structure Systems. 1997)PNEU-CABLE NET EXPERIMENT PRECEDENTS
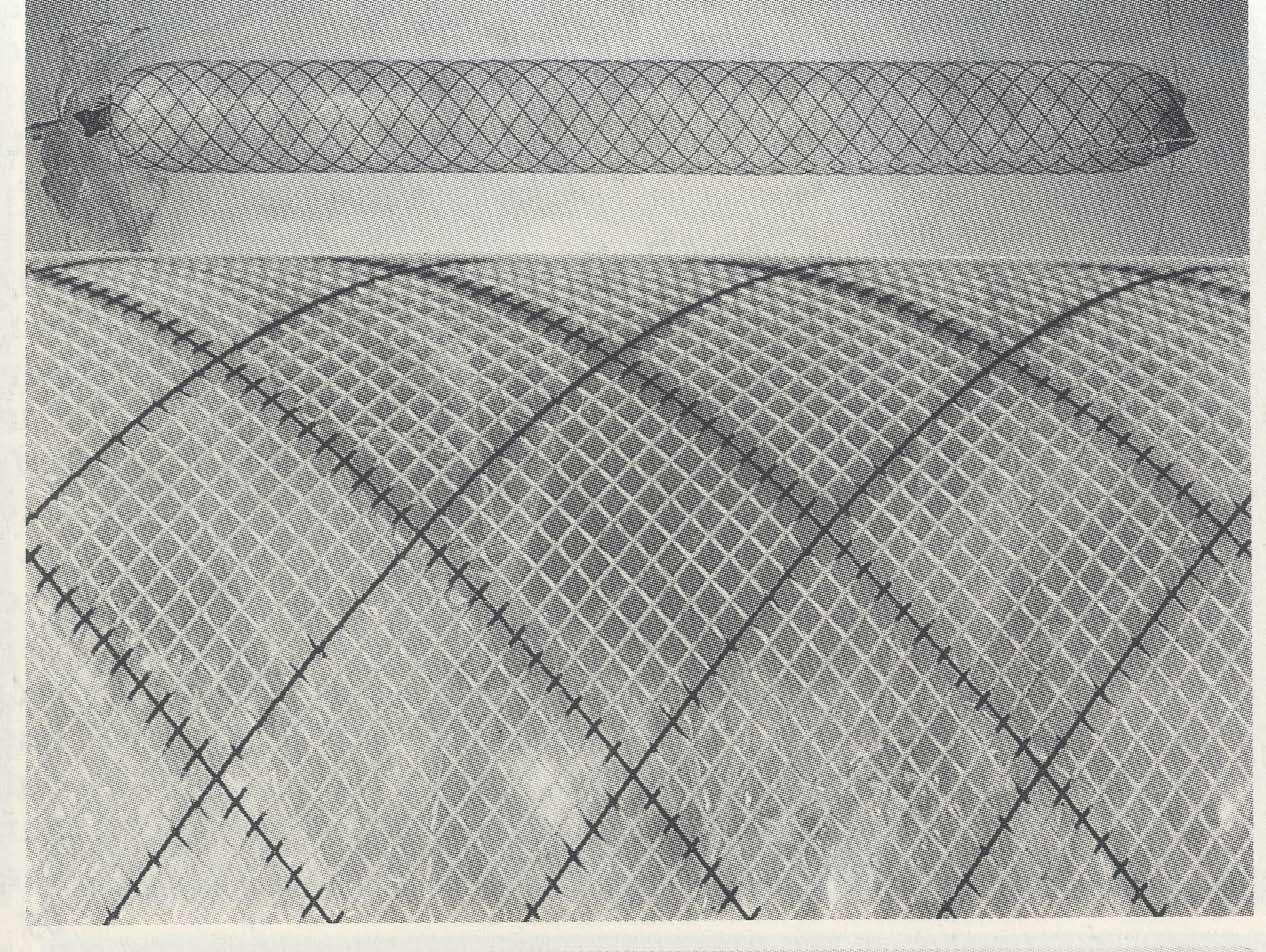
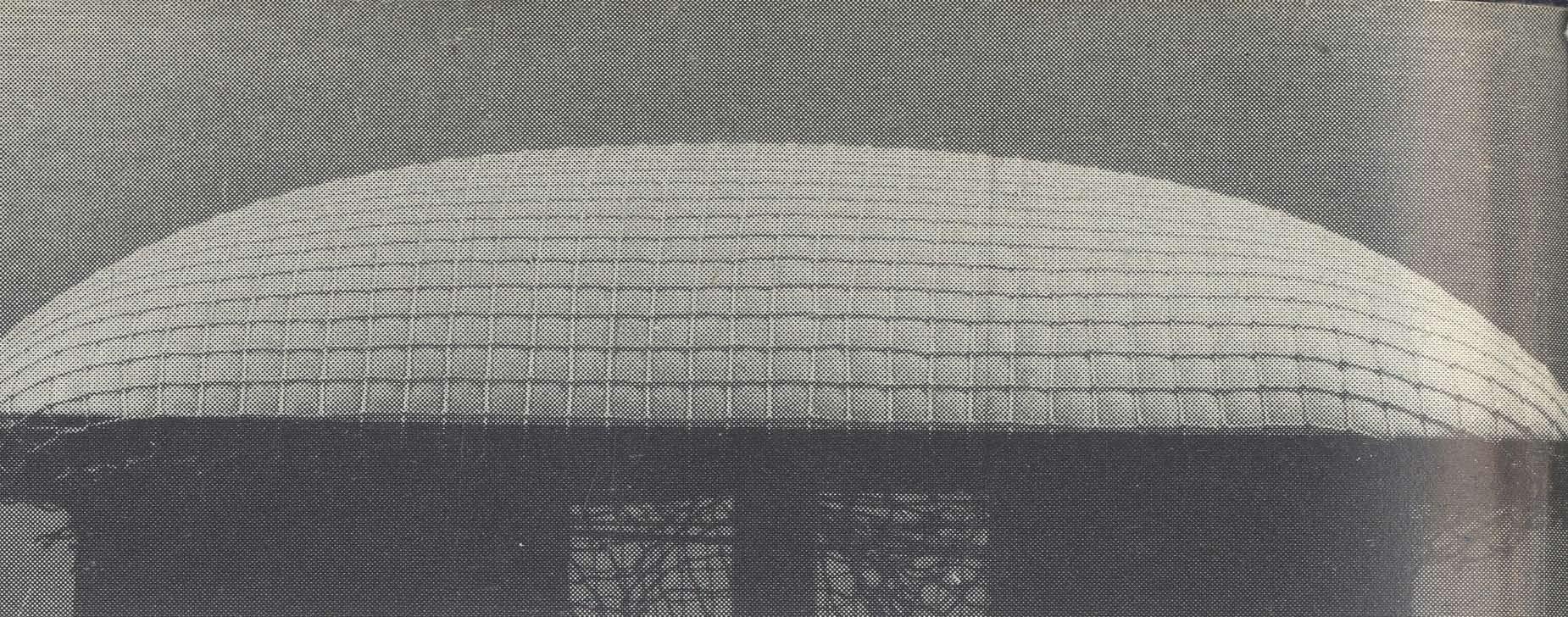
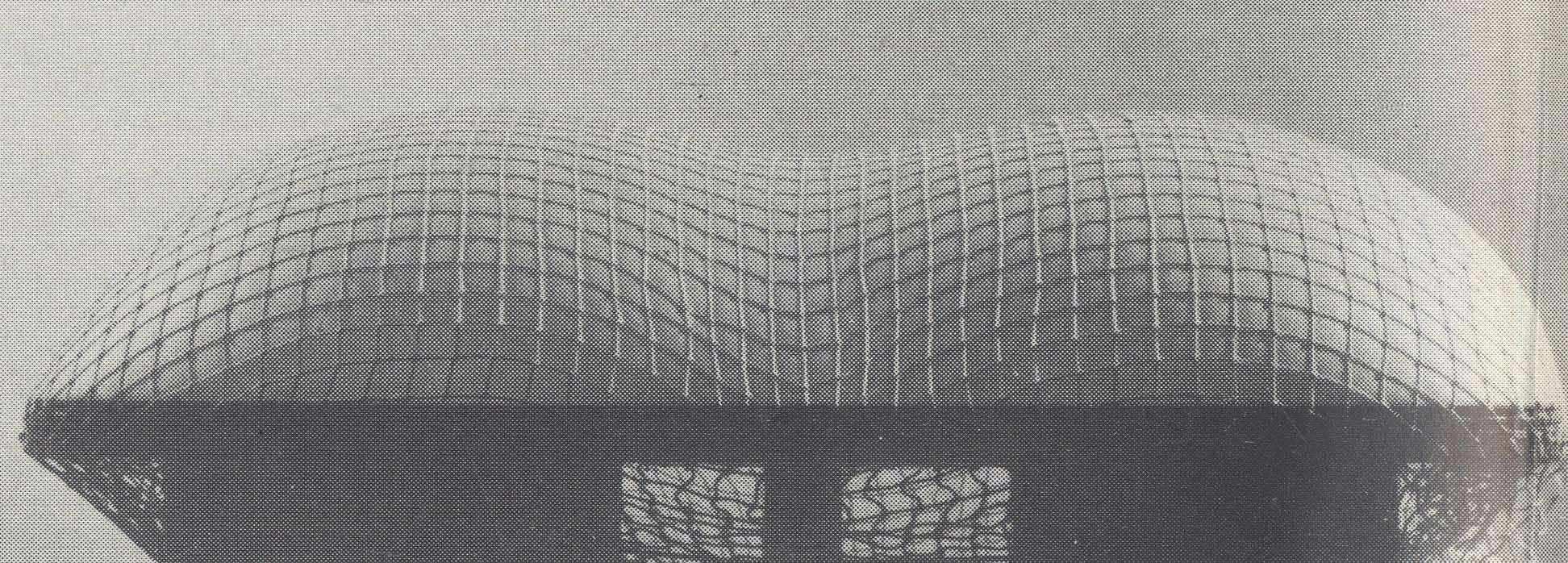
Frei Otto and his team at the Institute for Lightweight Structures in Stuttgart, Germany performed numerous experiments with pneu-cable net material systems (Figures 04 to 09). These experiments were undertaken in order to observe the interaction between the pneu membrane and the cable net, as well as to observe the variety of forms that these systems can achieve. Net-supported pneumatic structures can be used to transmit tension forces from membrane to net, creating many different formal consequences. Figure 04 and Figure 05 describe investigations into tubular pneus and how different mesh configurations affect deformation of the material system when under load (Gass, 1990). Figures 06, 07, and 08 describe experiments where varying net tension affects the form of the pneu being inflated. The Institute for Lightweight Structures also experimented with meshes of extremely high tension as compared to tension n the pneu membrane (Figure 09).
THE POTENTIAL OF A MATERIAL SYSTEM
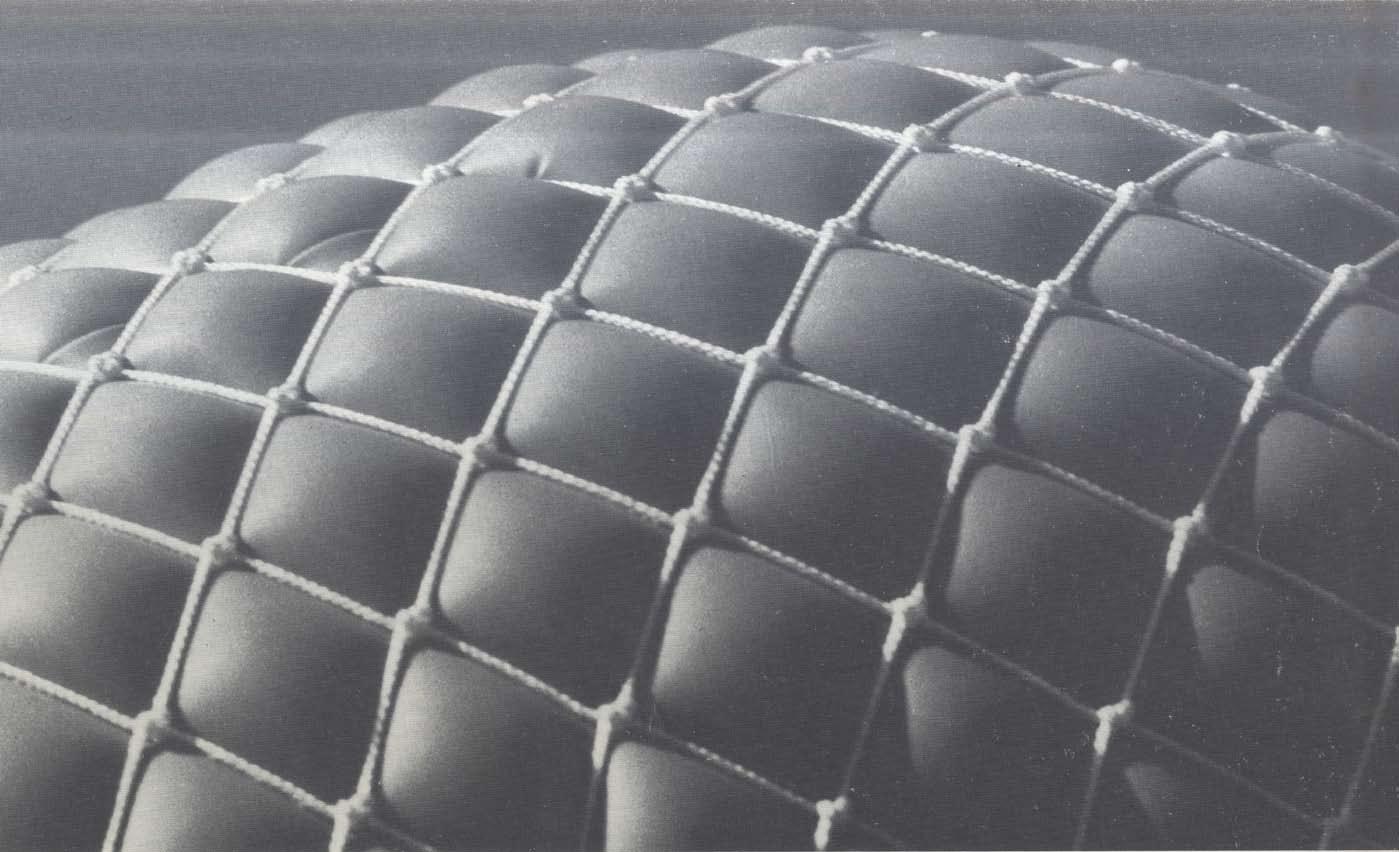
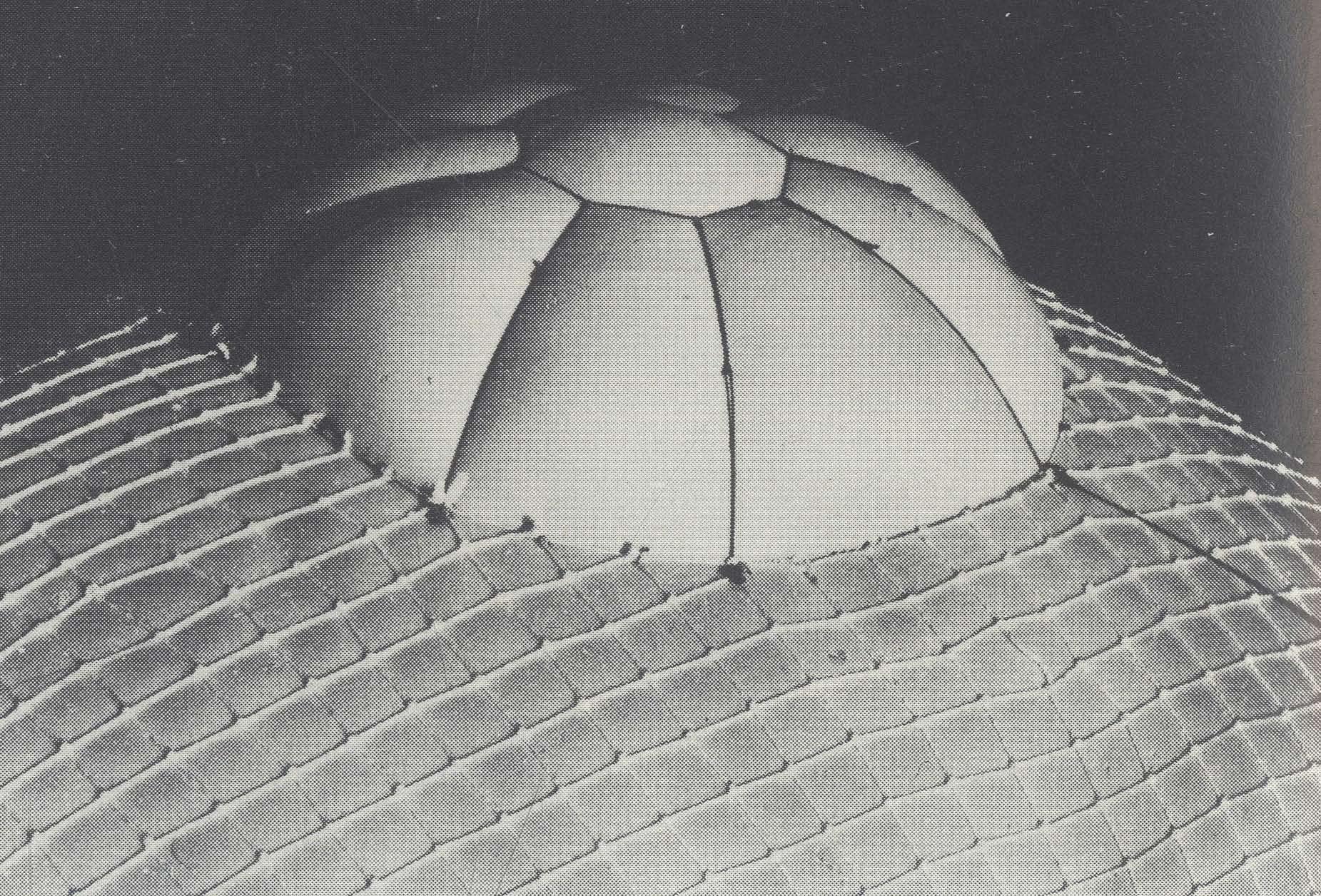
These experiments uncover a huge amount of potential in pneu-cable net material systems. By altering specific net parameters, changes in form can be achieved. Many of these experiments include a condition of structural loading as well, and begin to describe behavior under these conditions. However, these investigations are only observed for morphological changes, and are not considered for their structural performative capacity. One of the aims of this section is to advance the research started at the Institute for Lightweight Structures, and both uncover and exploit the inherent advantages in specific configurations of pneu-cable net form-active tension systems.
SCALE OF EXPERIMENTATION
It must be noted that the following pneu-cable net experiments are only “desktop” experiments - that is to say, data collected can only be used for the specific scale of the material system investigated. However, the geometric observations made can be understood as conceptually relevant. Although the material tested will act differently at different scales, if the experiments are to be scaled up, the same concepts will apply. Behavior of the material may change, but the system components remain, and therefore their concepts still apply.
CHAPTER 8 - GENERATING A MANDREL GEOMETRY .0 BALLOON CONFIGURATIONS
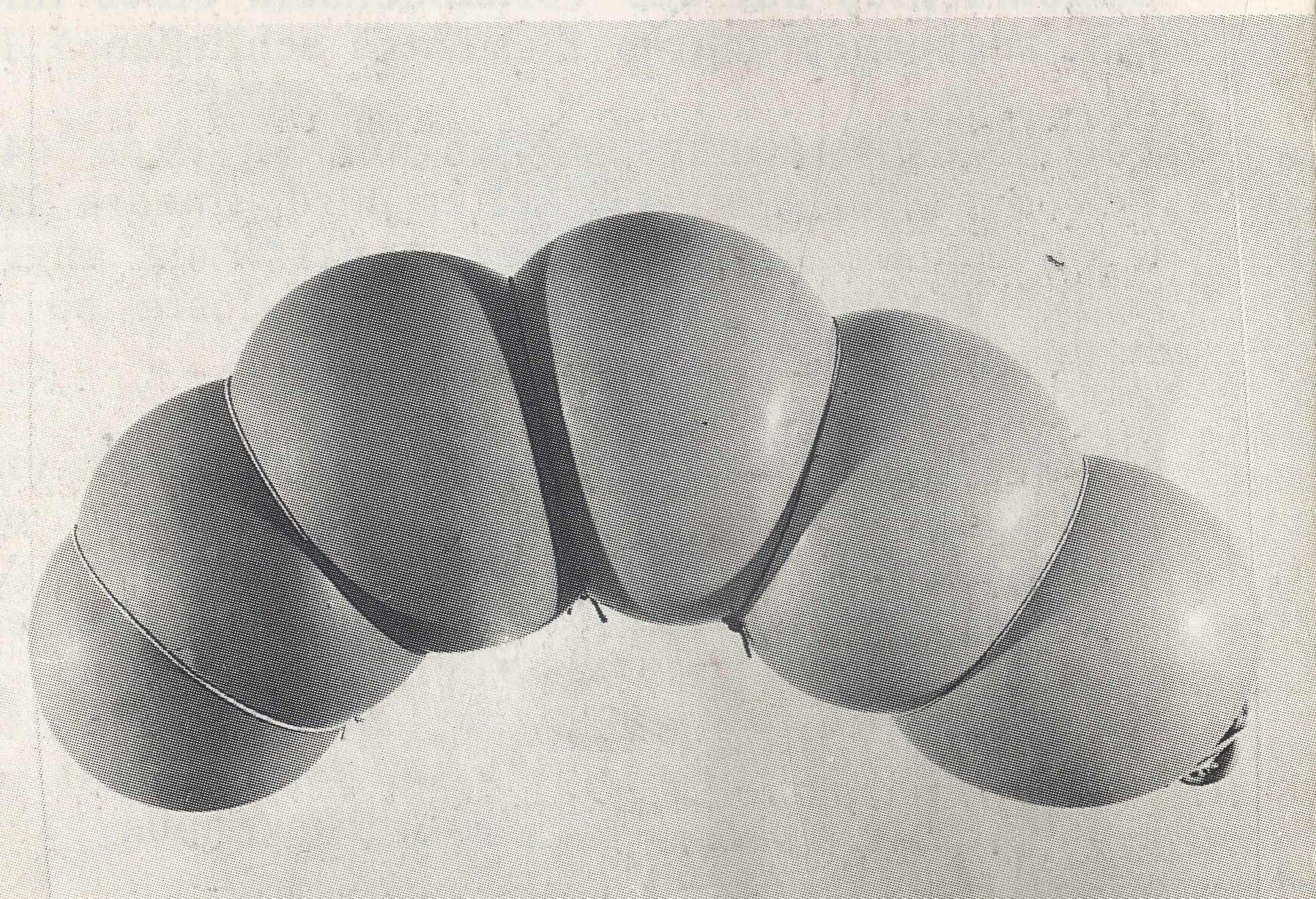
POSSIBILITIES IN FORM
This experiment aims to achieve and understand various configurations possible by employing a pneu-cable net hybrid form-active tension system. The experiment utilizes braided nylon fishnet stockings and balloons, along with cable clips to connect nets to one another.
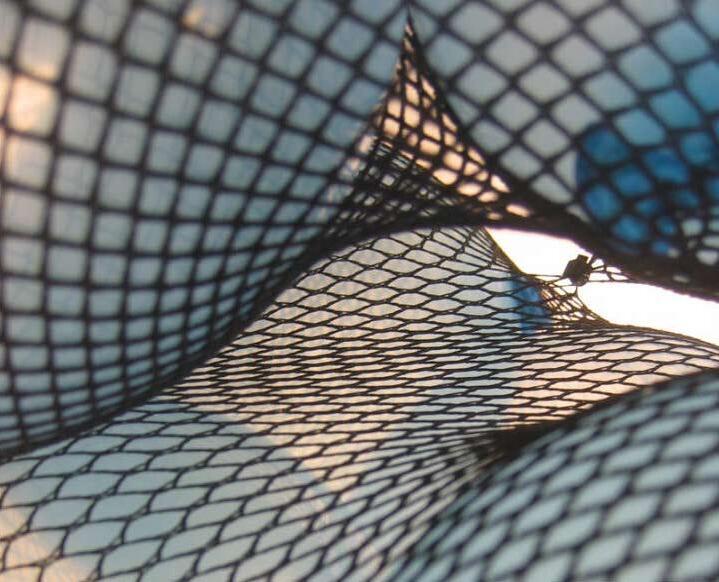
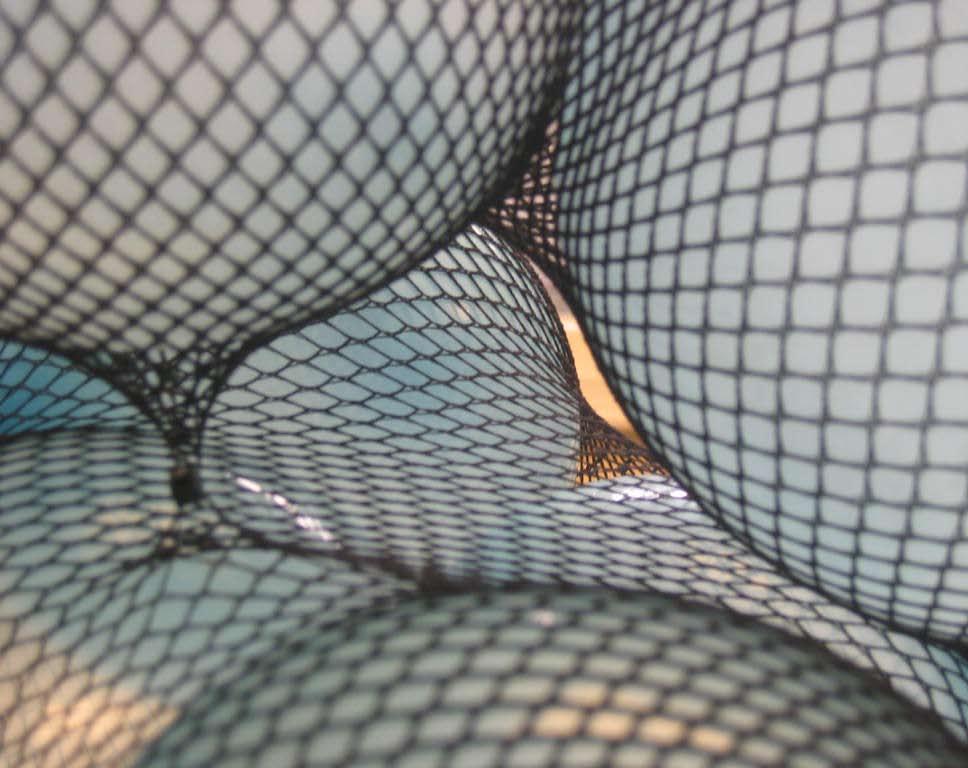
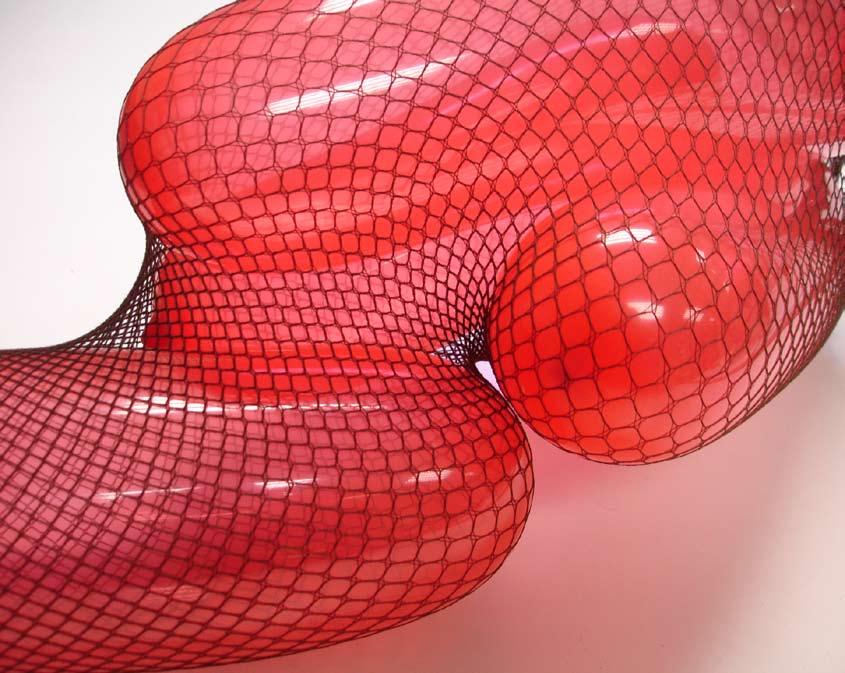
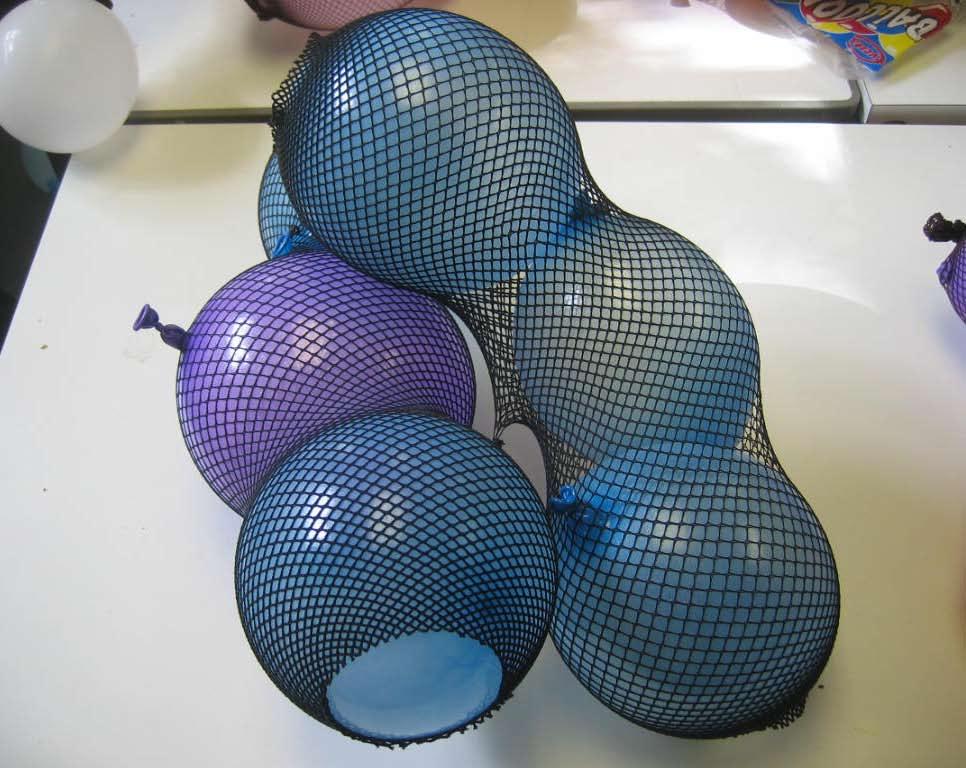
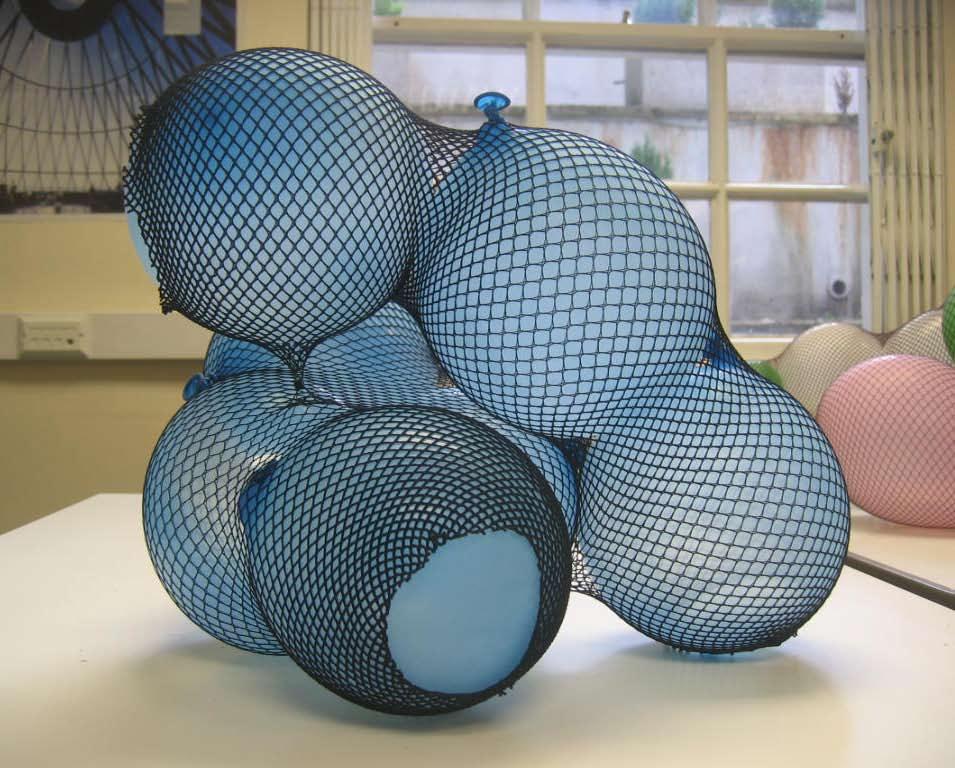
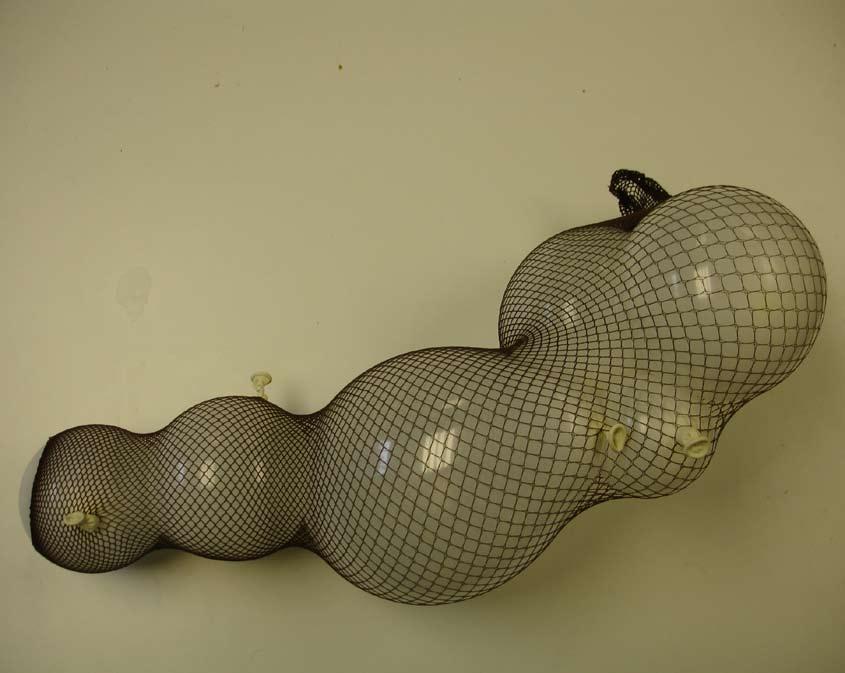
Figure 10 displays the start of the experiment, where a single balloon is inflated inside a cablenet. From this, the number and size of balloons inflated is varied, randomly, to observe the effects of resolution change on the cable net (Figure 11). Although larger balloons stretch the net to a greater degree, creating larger areas of anticlastic geometry, synclastic surfaces form between all pneus and do not provide any resistance to compressive load (simple finger poking). By inflating tubular pneus as opposed to spherical pneus, as shown in Figure 12, large synclastic surfaces approaching flatness are generated. Complex and interesting anticlastic surfaces are created as well, and although a majority of the surface is synclastic, anticlastic geometries pose problems of stability, as seen in the previous model. In addition, tubular pneus are difficult to control, since scale in one direction is so much greater than the other two. By connecting nets at different locations (Figures 13-15), various configurations emerge. Pneunets begin to twist on themselves and each other, creating spatial configurations (Figure 16). Connection points create stiffened peaks, as seen in Figure 17, and although this brings local stability, it fails to solve this problem globally. By layering the nets, as shown in Figure 18, a more stable system is achieved overall. However, distortion of the pneus must be noted as a possible cause of stabilization.
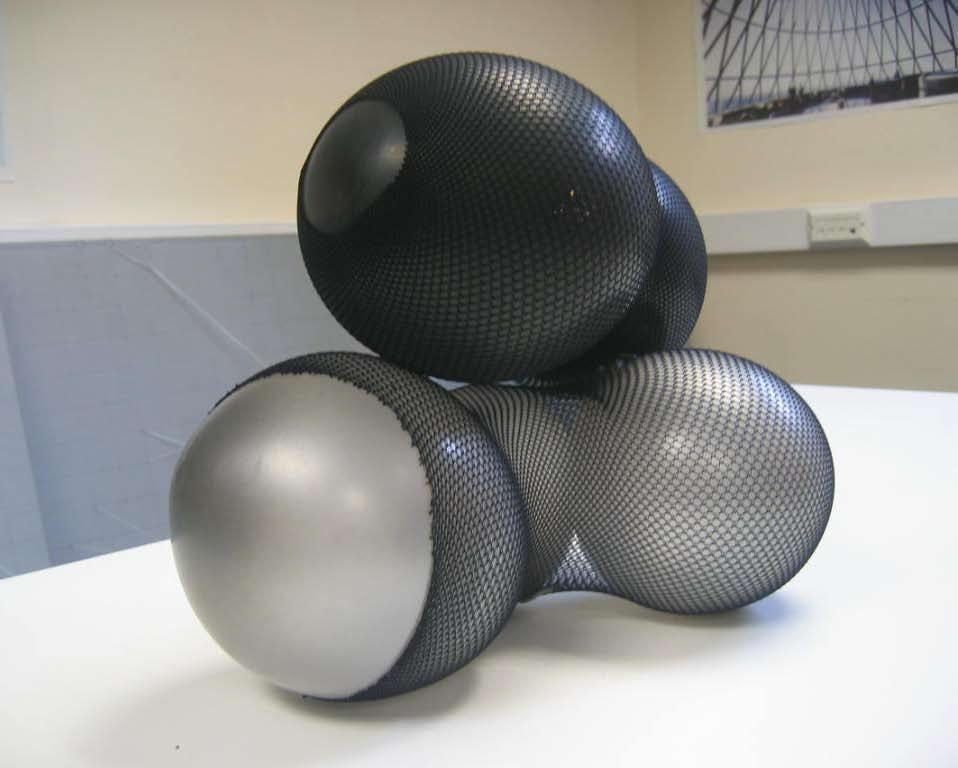
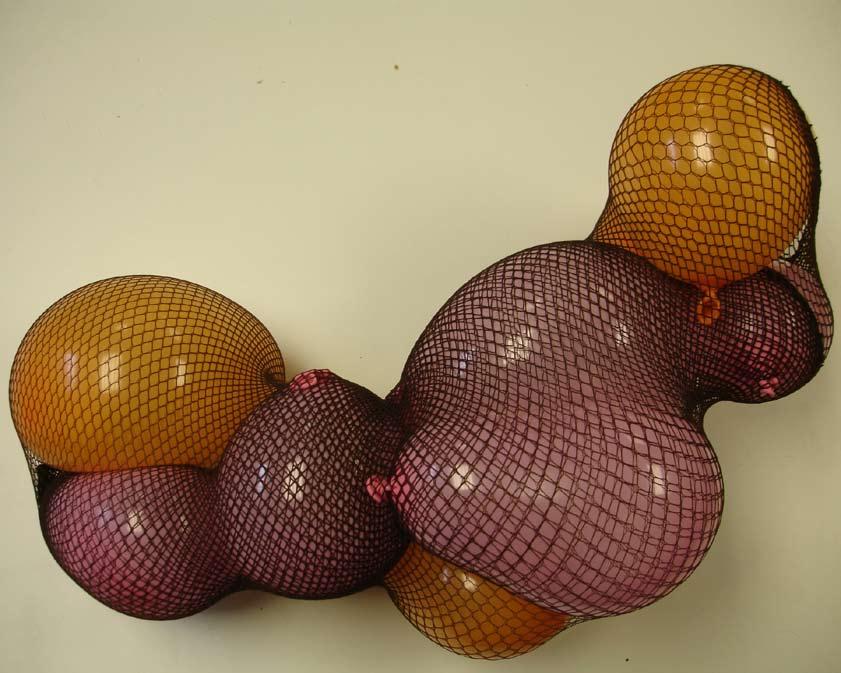
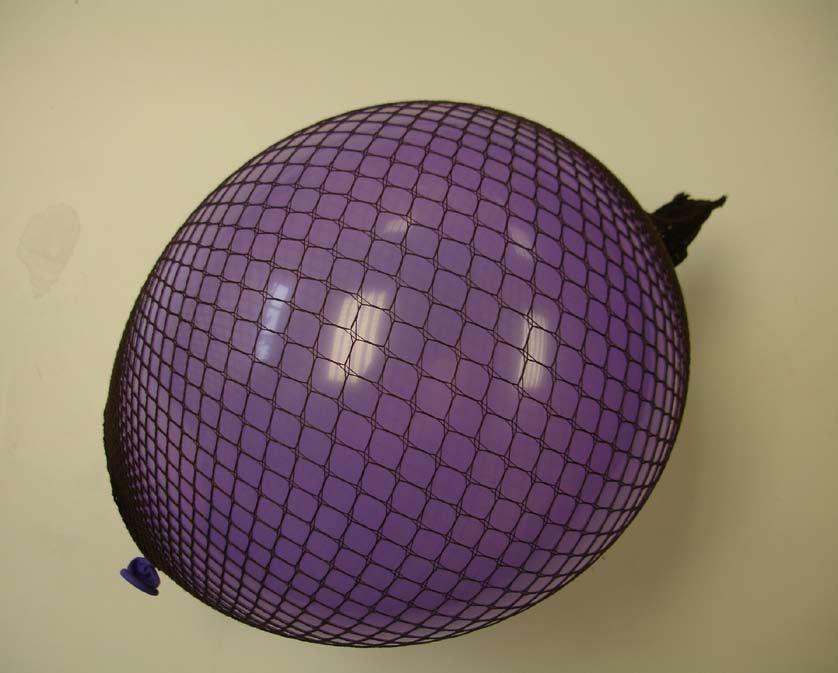
height = 20cm > 30cm diameter = 10cm/15cm [oval] pressure = 10psi
height = 20cm > 26cm diameter = 10cm pressure = 10psi
height = 20cm > 25cm
connection to base location of pneu connection between nets
height = 20cm > 25cm diameter = 10cm pressure = 10psi
height = 20cm > 27cm diameter = 10cm pressure = 10psi
height = 20cm > 32cm diameter = 10cm/15cm [oval] pressure = 10psi
height = 20cm > 27cm diameter = 10cm pressure = 10psi
height = 20cm > 30cm diameter = 10cm/15cm [oval] pressure = 10psi
height = 20cm > 30cm diameter = 10cm/15cm [oval] pressure = 10psi
height = 20cm > 30cm diameter = 10cm/15cm [oval] pressure = 10psi
CONFIGURATIONS FOR STABILITY
This experiment aims to stabilize the cable net internally, exploring pneu and net configurations (Figures 20 and 22) to find resistance to compressive load through tensioning the system. The experiment uses braided nylon fishnet stockings, twenty centimeters in length, balloons, cable clips, and an MDF wood base. Clothespins are used to secure the ends of each balloon so that numerous configurations can be achieved quickly. Each model is attached to the MDF base through a cable tie and string, with the configuration of the connections acting as one variable parameter in the system. Other parameters include interconnectivity of the nets and location of the pneus, as drawn in Figures 19 and 21. One parameter kept constant is air pressure within each balloon, set to ten psi (pressure/sq. inch), or the amount of air pressure necessary to achieve a near-spherical pneu. The nylon stocking is doubly layered, in order to achieve a greater global stability. It is found that as the number of connections, either to the base or to another net is increased, global stability increases slightly (Figures 24 and 25). However, these connections increase local stiffness greatly. It is noted that synclastic surfaces lack stiffness due to outof-surface action (Figure 23), and although attempts to eliminate these surfaces take place, each attempt creates other synclastic surfaces prone to out-of-surface action.
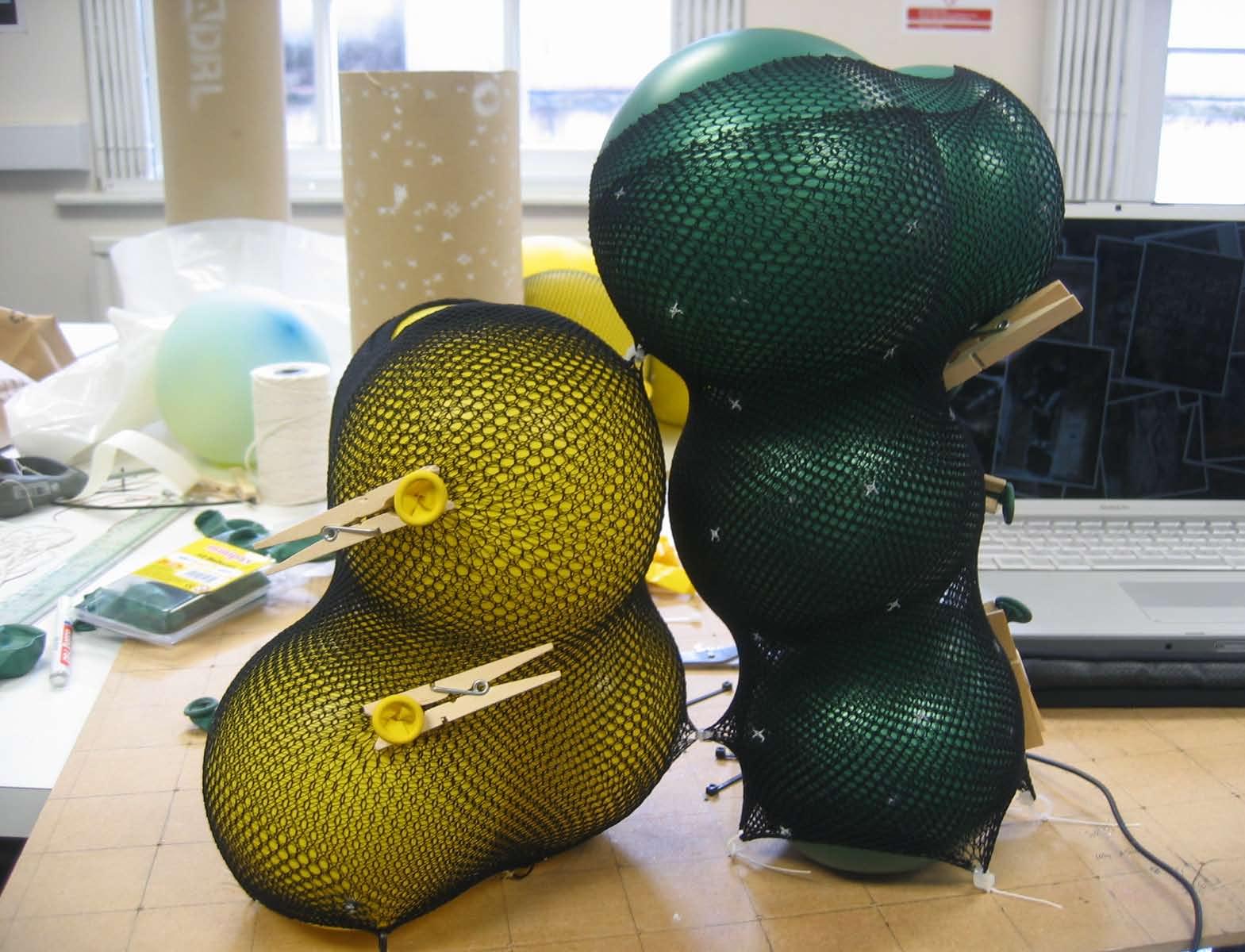
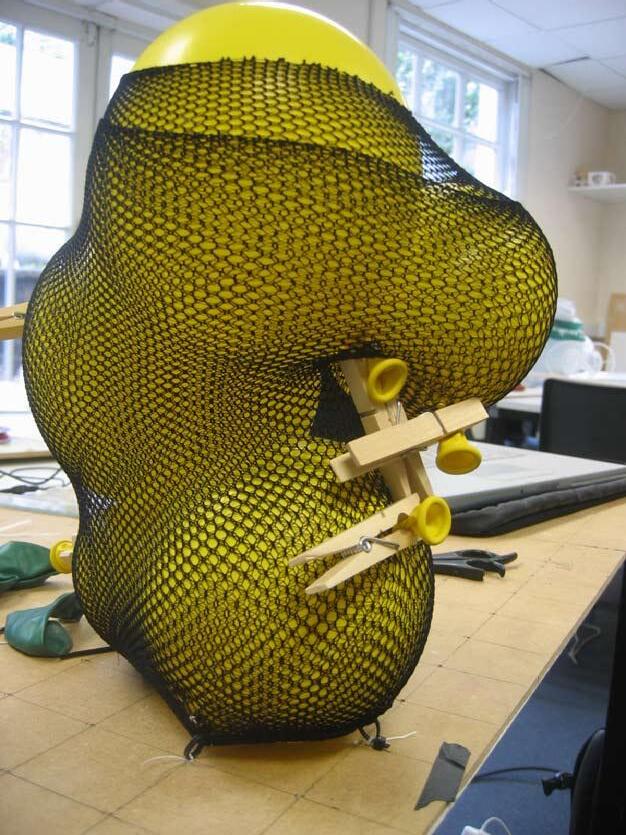
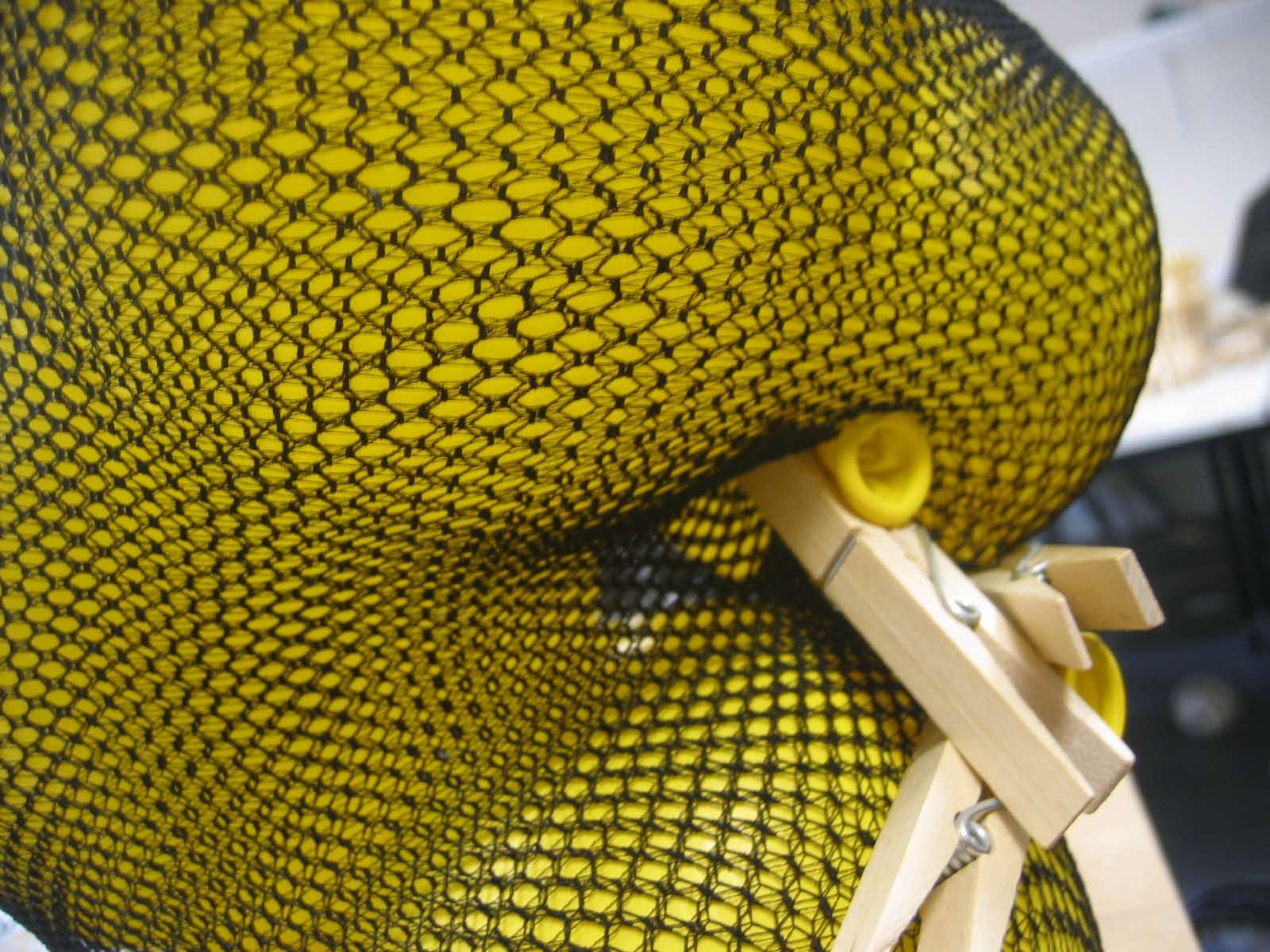
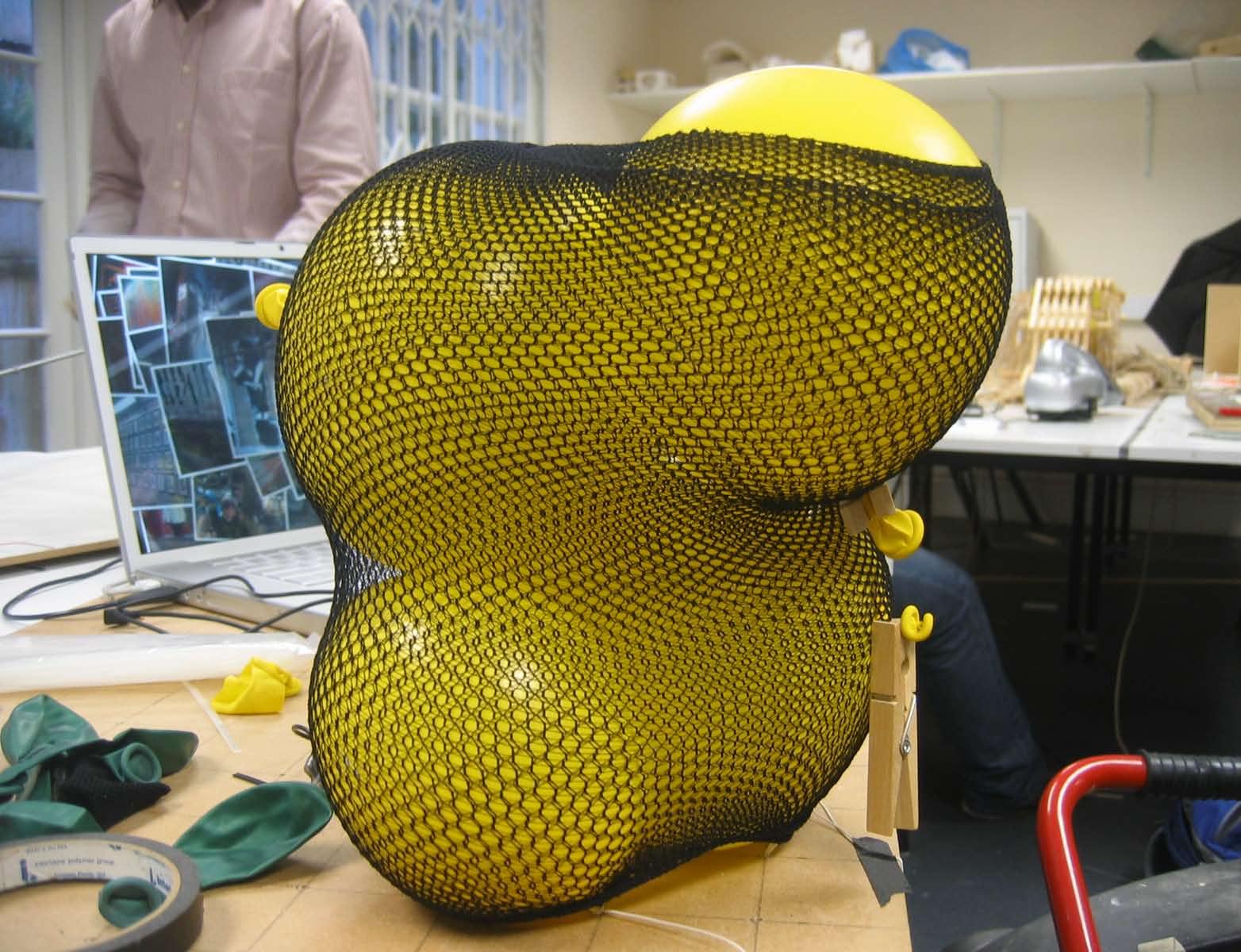
height = 20cm > 31cm diameter = 10cm/15cm [oval] pressure = 10psi
CHAPTER 8 - GENERATING A MANDREL GEOMETRY .0 PNEU-CABLE NET CONFIGURATIONS
Figure 19, diagram, describing net and pneu configuration (diameter 10 cm). Figure 20, model, showing the outcome of the setup of Figure Figure 21, diagram, describing net and pneu configuration (diameter 10 cm). Figure 22, model, showing the outcome of the setup of Figure Figure 23, diagram, describing areas of transition between anticlastic and synclastic geometry where out-of-surface action occursconnection to base location of pneu connection between nets
height = 20cm > 31cm diameter = 10cm/15cm [oval] pressure = 10psi
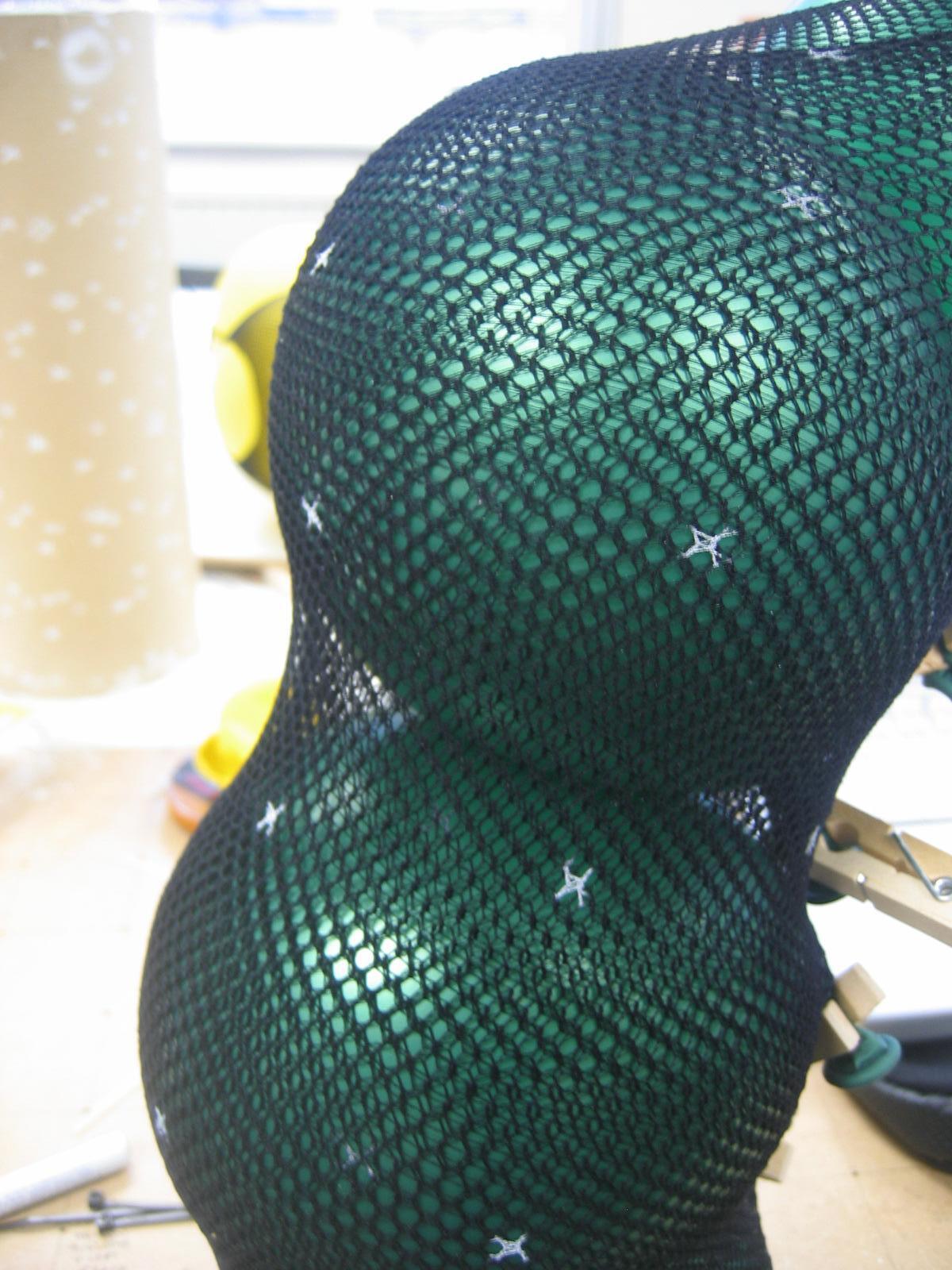
OUT-OF-SURFACE ACTION
Complexity in the configuration increases by the addition of multiple connection points. In addition, a pneu is added external to the nets (Figure 26) to observe any changes in stiffness. As observed in earlier experiments and setups, local stiffness is achieved in the form of arches (Figure 27) and peaks (Figure 28). Although the balloon depicted in Figure 27 does achieve a greater amount of global stiffness, the configuration continues to suffer from out-of-surface action (see Glossary), described in Figure 29. Out-of-surface action is occurring in this setup due to the force vectors in the net material when under compressive stress. The force vector takes the path along the synclastic surface, and wants to continue along that vector to the synclastic surface below. Because the surface geometry changes at the peak of the anticlastic surface, however, a weak spot occurs at this interface. The thinness of the net material can be attributed to this problem; the lack of continuous material to transfer the force vector through the net or the lack of an additional force to alter the direction of the existing force vector need to be addressed in order to solve out-of-surface action that is experienced at these junctions.
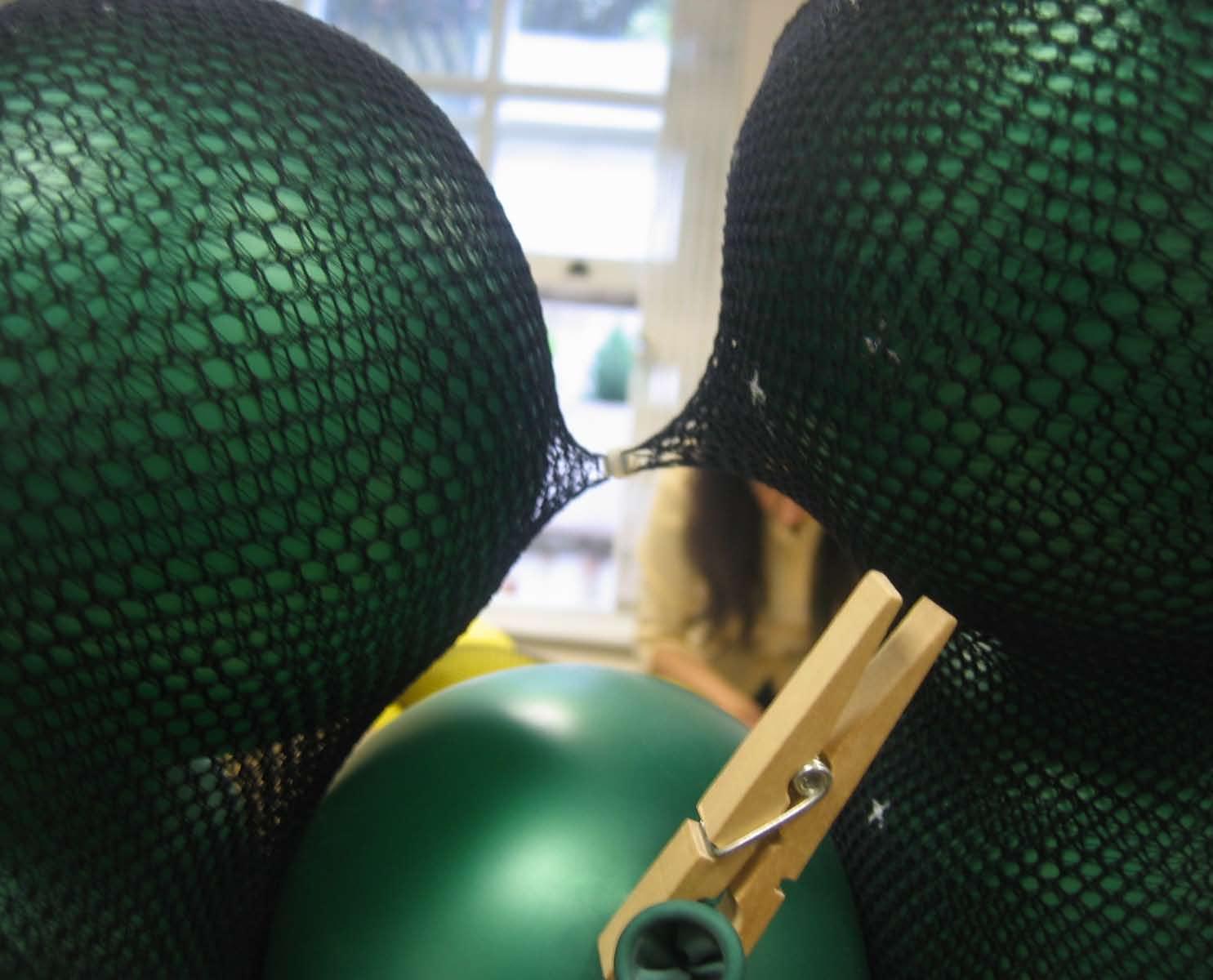
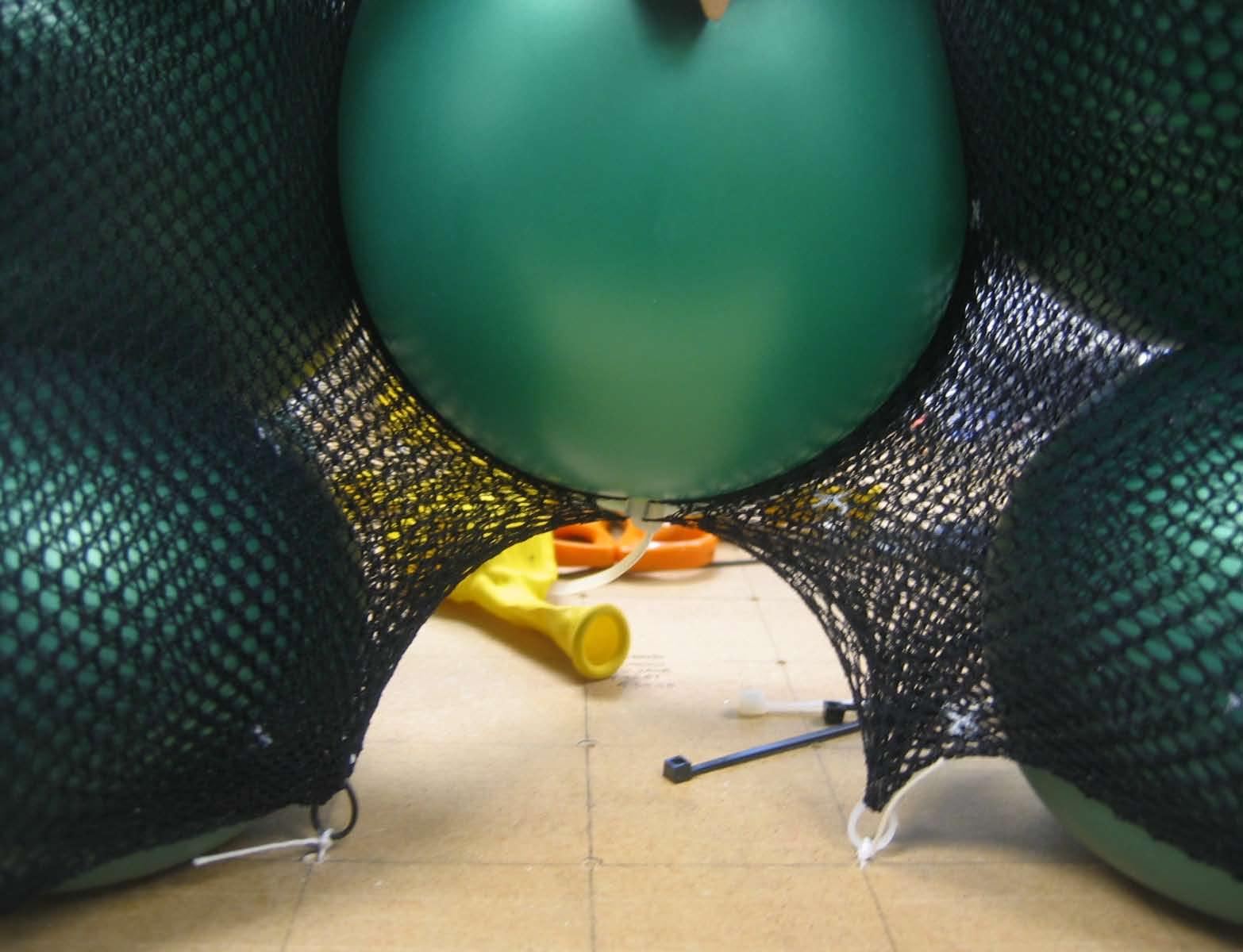
For an in-depth exploration into solving out-of-surface action, see section 15.02 (Appendix A).
CHAPTER 8 - GENERATING A MANDREL GEOMETRY .0 PNEU-CABLE NET CONFIGURATIONS
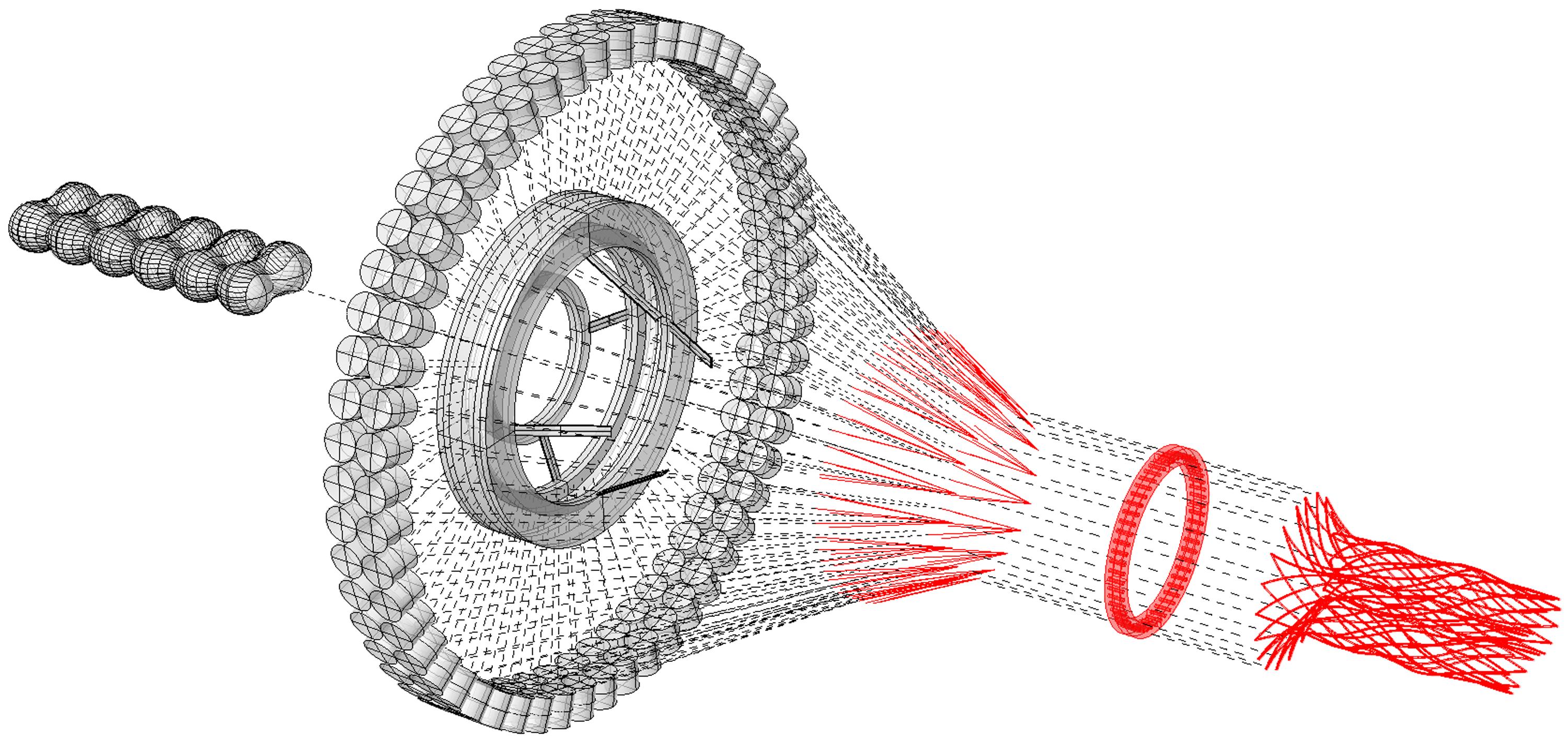
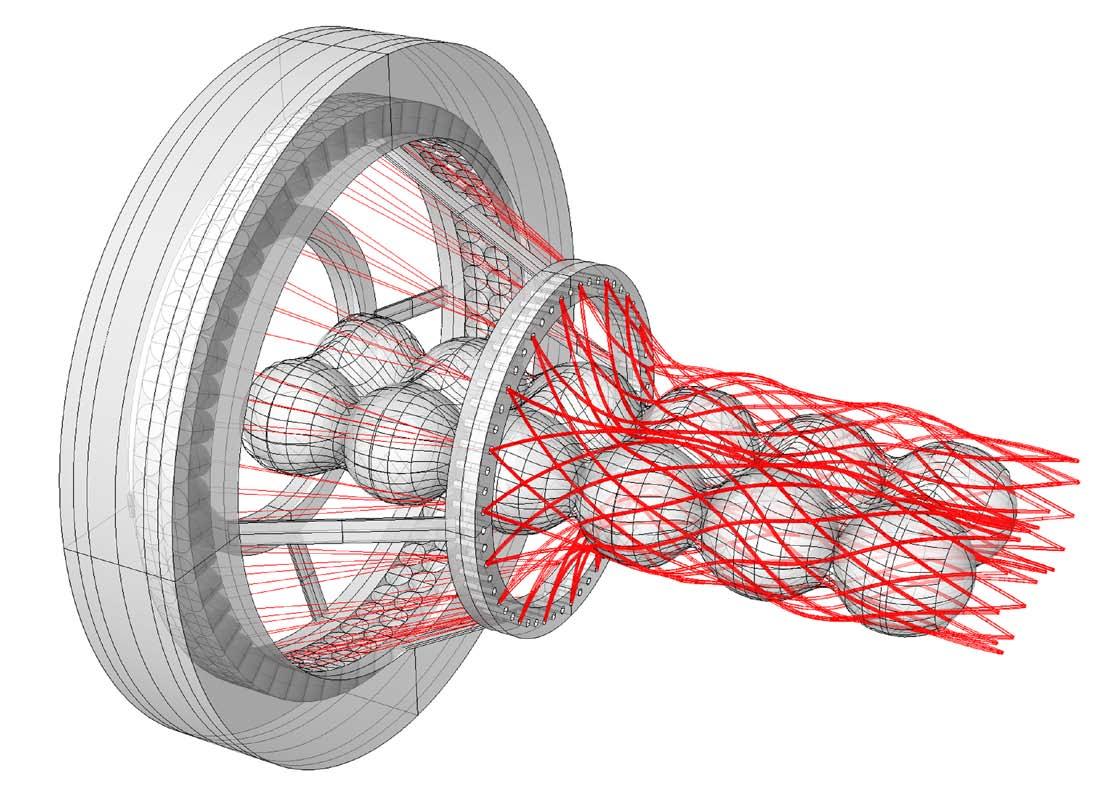
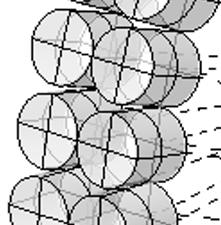
pneu-cable net mandrel geometry commingled fibers
braider moves up vertically as it rotates
pneu-cable net mandrel geometry
braider moves up vertically as it rotates
TWO METHODS OF IN-SITU CONSTRUCTION
flexible thermoplastic matrix structure
commingled fibers
flexible thermoplastic matrix structure
cured fiber composite structure
braider moves up vertically as it rotates pneu-cable net mandrel geometry commingled fibers
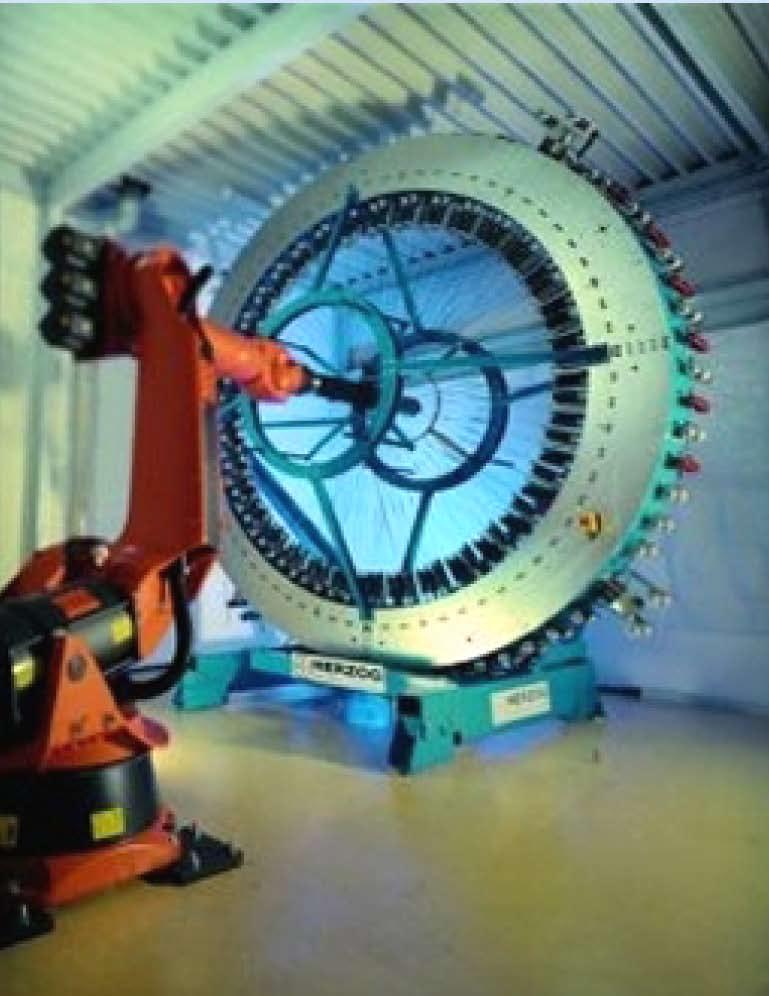
flexible thermoplastic matrix structure
cured fiber composite structure
Now that the thermoplastic radial pulbraiding machine has been defined and described, the fabrication process can now be explained. Firstly, two ways of construction must be considered. The first construction process can be considered similar to current 3D radial overbraiding techniques, where a robot arm (Figure 31) moves the braider over the mandrel geometry. A second method can be considered where the machine is temporarily supported while the first section of structure is pulbraided and cured, and then used as the structure for the machine itself. Figure 32 diagrams the process carried out by the thermoplastic radial pulbraider; once a certain section of the structure is cured, this can then bear the weight of the braider as it continues its vertical path of fabrication. This second method creates an interesting speculation on how to keep the fabrication technique fully internailized, and begins to talk to an in-situ construction within a constrained site. By eliminating the need for a robotic arm controlling the process, the machine setup becomes smaller and more manageable where space is lacking.
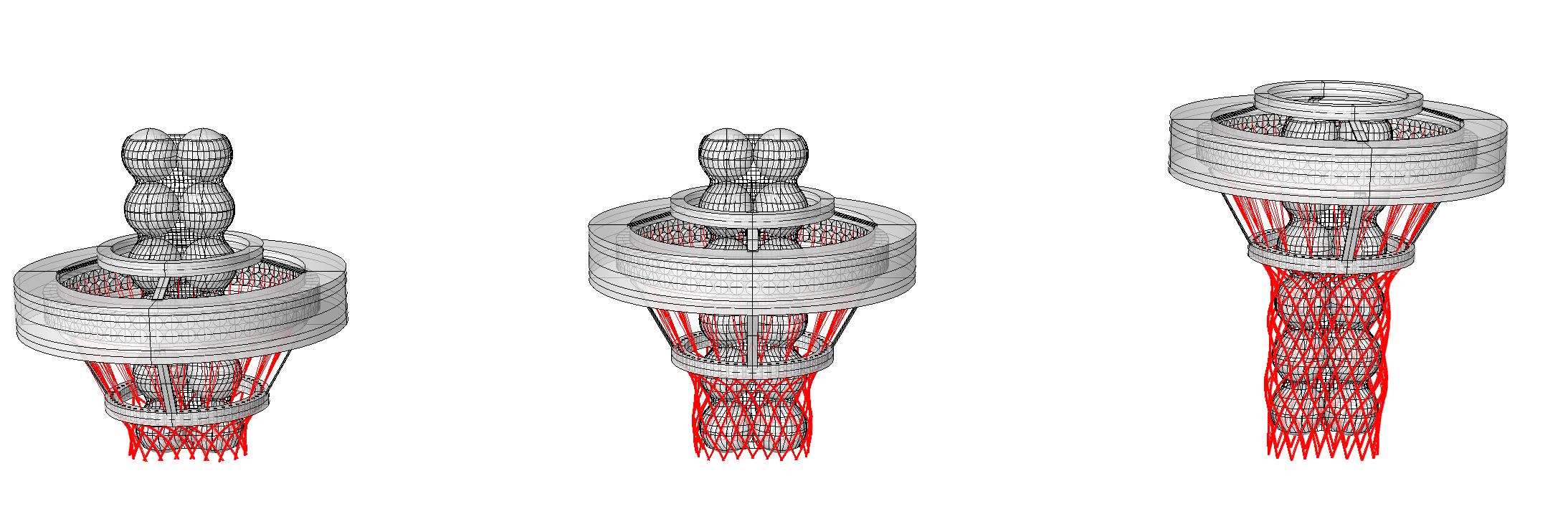
FABRICATION DIAGRAM
As mentioned, Figure 32 diagrams the thermoplastic radial pulbraiding process. The braider rotates, braiding fibers based on required angle and density while moving along the mandrel pneu-cable net mandrel geometry. The pulbraided commingled fibers are at first pliable. As the braider moves up continuing the braiding process, the previously pulbraided structure cures in place. The mandrel can then be removed, leaving just the pulbraided structure behind.
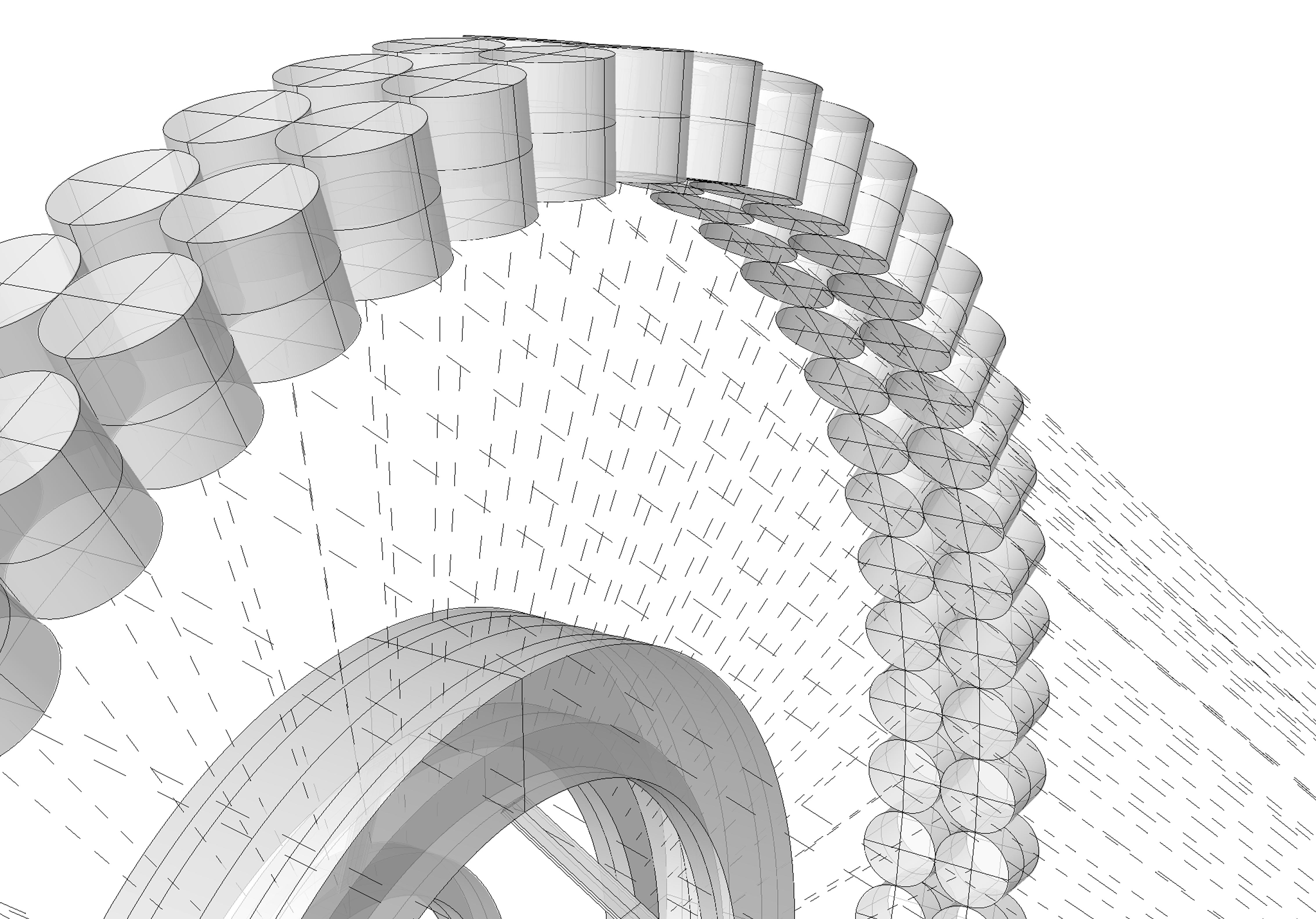
TESTING A SINGLE PULTRUDED ROD
Pultruded glass fiber rods, of parallel strand organization are tested in this experiment to both observe the stress and stiffness of the material. The experiment is set up using a framework constructed of MDF and 10mm aluminum rods, with a sheet of MDF free to slide at the top of the model. The setup dimensions are 400mm by 300mm at the base, and 1050mm high, in order to account for 1000m long glass fiber rods. This initial experiment aims to test a singular rod’s behavior when displaced a dimension of 50mm, 100mm, and 200mm. Three points on each rod tested are plotted and their displacement in space while under compression is recorded.
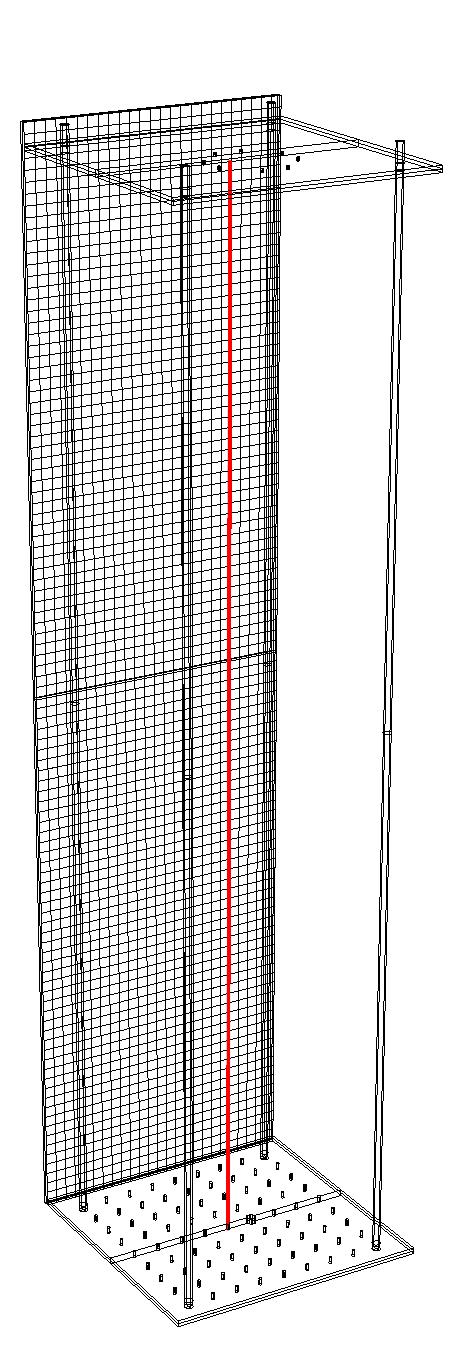
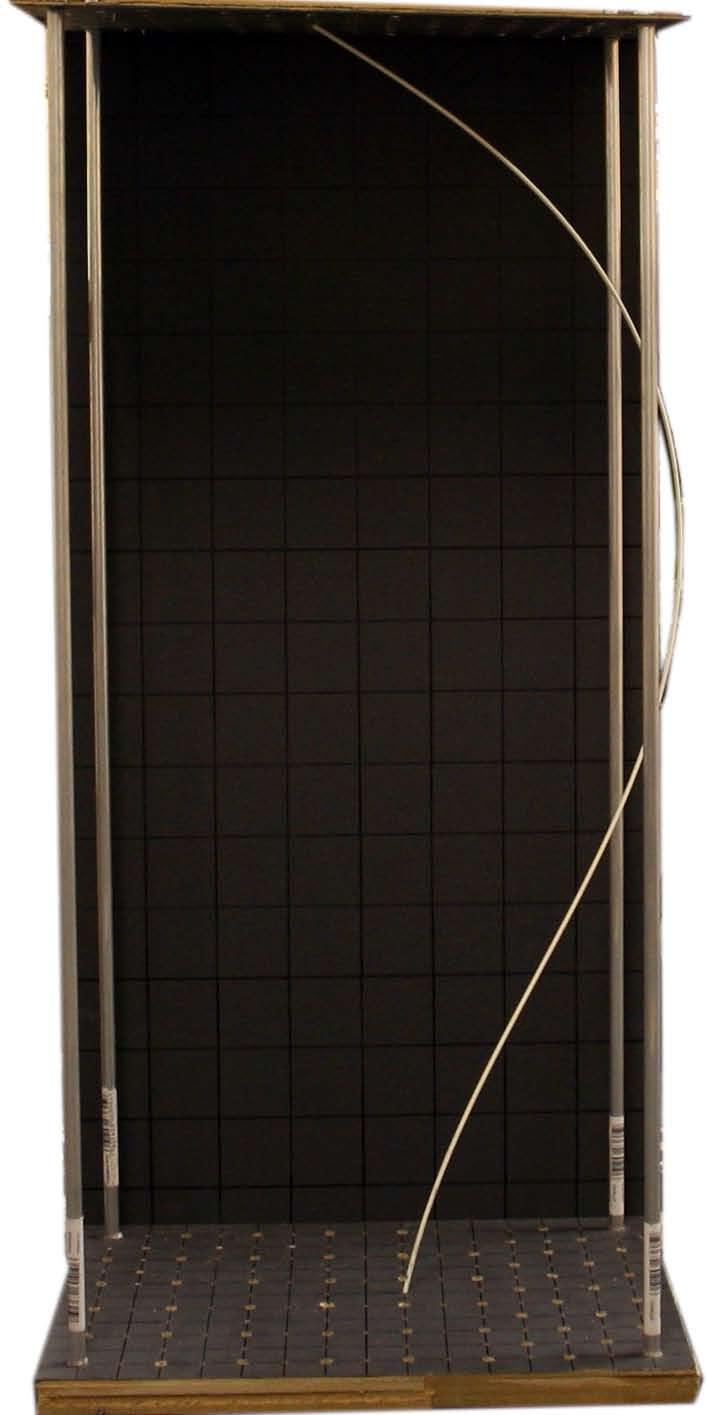
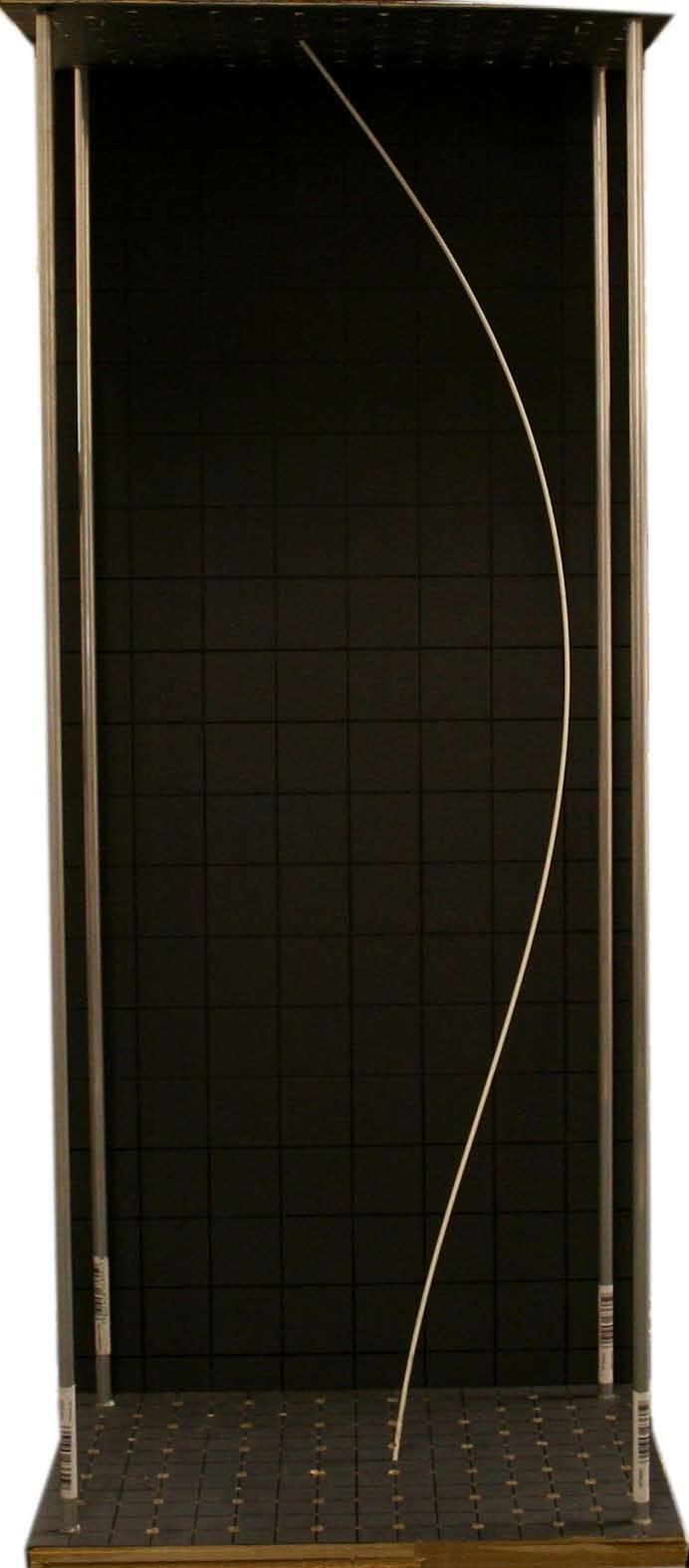
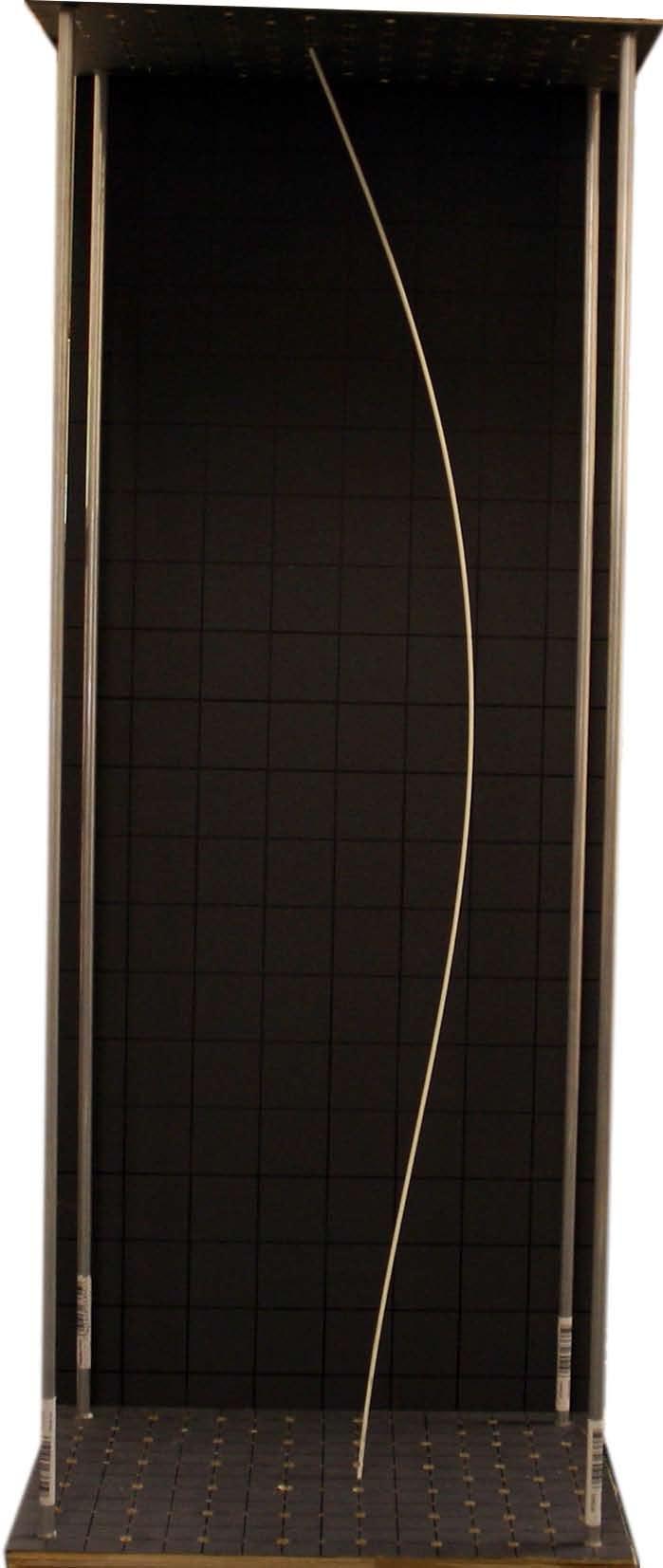
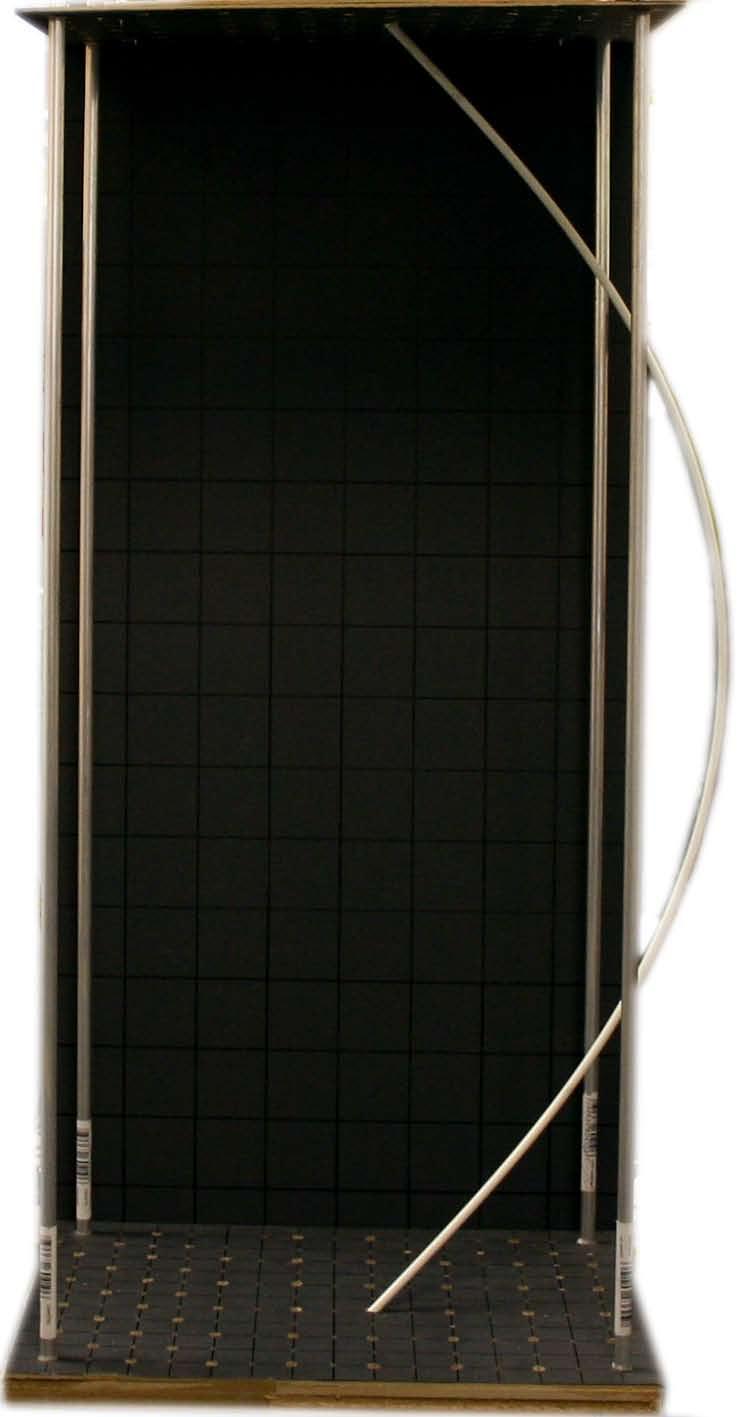
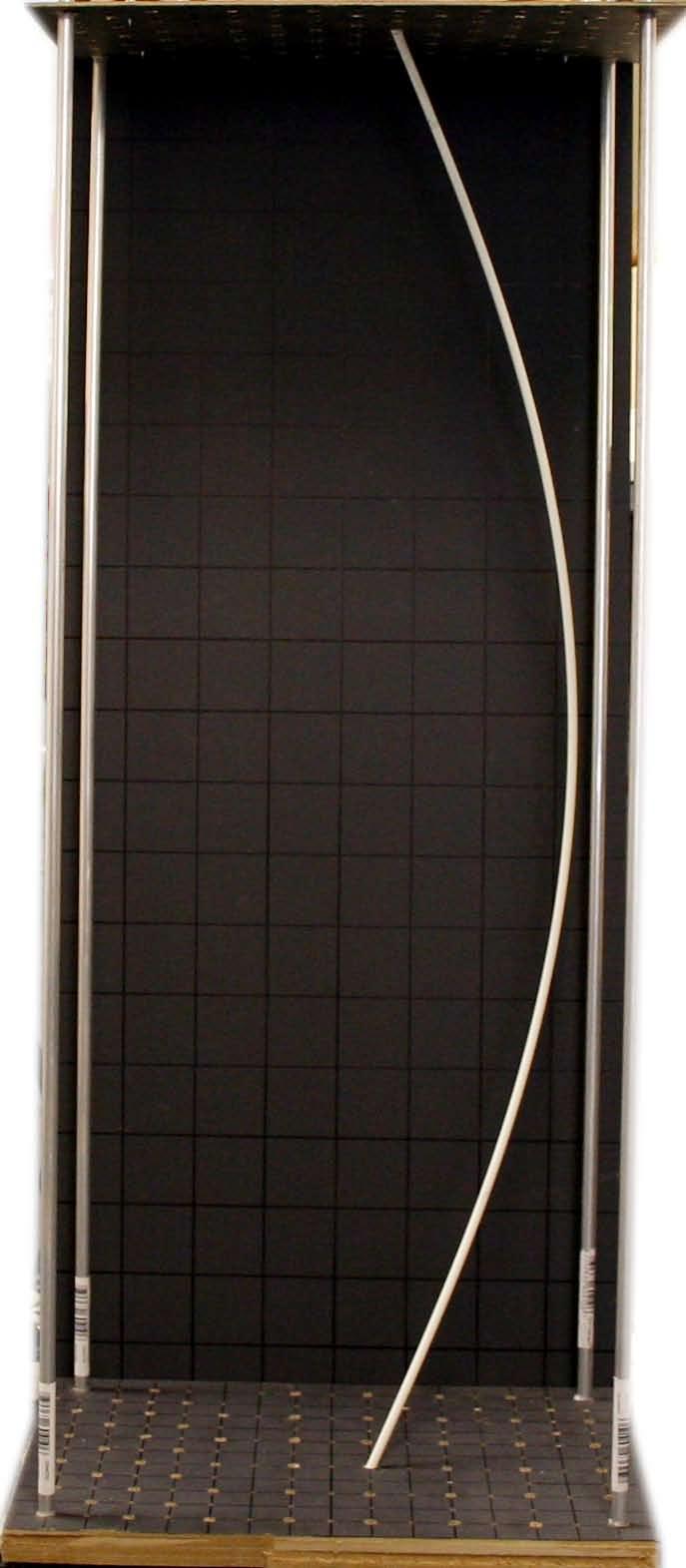
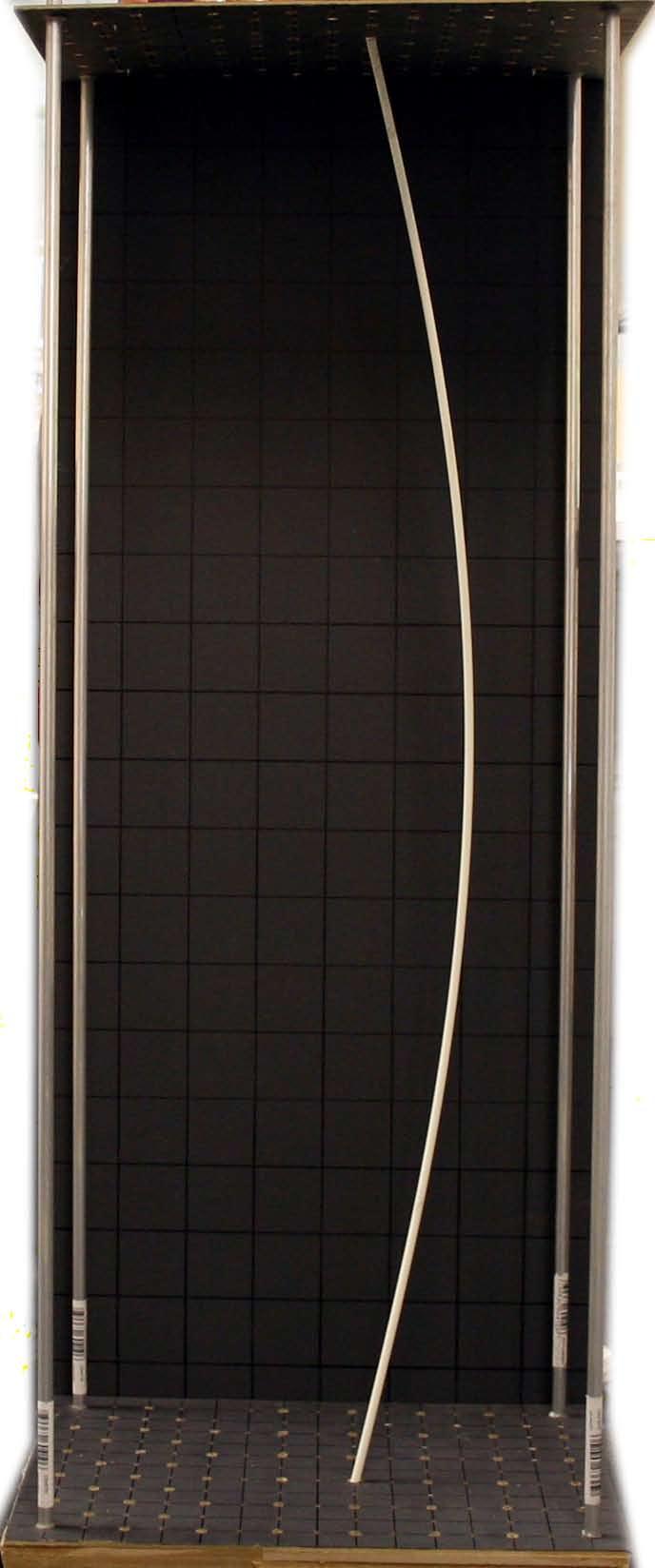
EXPERIMENTAL PARAMETERS
The parameters of this setup are rod length (L), rod radius (r), vertical displacement of the rod when under compression (Vd), as well as the change in vertical (z) and horizontal (x) position of each of the three points (point75 at 750mm, point50 at 500mm, and point25 at 250mm) located on the rod. Figure 01 diagrams the aforementioned setup.
HYPOTHESIS
It is hypothesized that as the radius of the pultruded rod increases, there is a lesser change in point values from their initial locations. This, therefore, states that the stress necessary to displace a rod of n mm increases as the radius of the rod increases. Figure 02 describes the results of the physical experiment testing this hypothesis.
CHAPTER 10 - MECHANICAL TESTING OF PULTRUDED RODS
MATHEMATICAL EXPRESSION OF PHYSICAL BEHAVIOR
By observing the displacement of three points in both the X and Z directions in the experimental setup, a graph is drawn to find a curve to represent the behavior of a 1.5mm radius pultruded glass fiber rod (Figure 03). By using the these points located at 750mm, 500mm, and 250mm along a 1000mm rod, in addition to the point at the top of the rod, a cubic equation can be written to describe each of these curves.
f[point75_X] = .005d³-.164d²+2.22d
f[point75_Z] = 2.348d³-43.934d²+162.092d+75
f[point50_X] = -.054d²+2.327d
f[point50_Z] = -.828d³+10.129d²-31.442d+50
f[point25_X] = .007d³-.252d²+3.1283d
f[point25_Z] = .015d³-.364d²+.119d +25; where d = displacement of the rod (mm)
By establishing the equation of the curve each point takes when being compressed, the behavior of a 1.5mm radius rod can be understood mathematically. This information can be used to predict the behavior of the material under any measurement of displacement.
FINDING STRESS
By understanding the behavior of a rod of this radius, a further equation can be written to understand the force needed to act on a rod of any radius to behave in a similar fashion. In this instance, the length of the rod (1000mm) is constant, and only the radius of the rod affects the force necessary to cause the same behavior in rods of different radii. Thus, it can be understood that the stress is directly related to the square of the radius of the rod:
S = F/πr²;
where S = stress, F - applied force, r = radius
In Figure 04, the relationship of stress to radius of the glass fiber pultruded rod is graphed, and a curve is found to represent this data.
Figure 07, graph, showing the relationship between the radius of a pultruded glass fiber rod and its bending stiffness. The resulting curve describes the increase of stiffness at a fourth power rate as radius increases.
BUCKLING STIFFNESS
When understanding the behavior of rods under compressive load, it is important to look at two major instances: short, fat struts, and long, thing struts. The former instance tends to fail by shearing or crushing, while long thing members fail by buckling (Figure 05). Buckling was first analyzed by Euler, who identified three buckling cases - both ends pin-jointed; both ends fixed in both position and direction; and one end fixed, one end pin-jointed. Each of these cases can be evaluated based on a specific mathematical equation, as shown in Figure 06.
FINDING BUCKLING STIFFNESS
In addition to stress, the buckling stiffness of the material can also be expressed as a function of both rod radius and length. Assuming that rod length stays equal between experiments (1000mm), and by knowing the elasticity of the material (Young’s Modulus (E)), an equation can be written to describe the buckling stiffness of the specific pultruded glass fiber rod tested:
Pb = π²EI/L² ;
where Pb = bending stiffness, E = Young’s modulus, I = second moment of area (for a circular section, I = πr4/4 where r =radius),
L = length
In these experiments, the glass fiber rod tested is 65% glass fiber oriented unidirectionally and parallel to the grain of the rod. This proportion, along with the intrinsic properties of the fibers used, yields an average E-value of 23,500 mPa (megaPascals). Figure 07 describes the relationship between radius of the pultruded rod and its bending stiffness. It is found that as the radius of the rod increases, its bending stiffness increases to the fourth power.
Determining buckling stiffness dependent on rod length will yield a similar relationship. However, stiffness is a square function of rod length. That is to say, the buckling stiffness of a rod will increase at a second power rate as the length of a pultruded rod increases, assuming radius remains equal (1.5mm).
Figure 08 describes this relationship.
CHAPTER 10 - MECHANICAL TESTING OF PULTRUDED RODS
TESTING A GROUP OF COUPLED RODS
A subsequent experiment aims to understand the behavior of multiple glass fiber pultruded rods under a similar loading condition. Four sets of coupled 1.5mm radius rods are arranged in a square configuration, with each pair of rods spaced 100mm away from on another (Figure 09). The rods are then displaced 50mm, 100mm, and 200mm, while three points on each rod are observed for changes in x and z grid positions. It is found that each paired rod behaves in the exact same manner as its partner, and therefore the points at 750mm, 500mm, and 250mm in height measured on each rod can be applied to each rod in a pair (Figure 11). Furthermore, each pair of rods deforms similarly, however always bends at a 45-degree angle away from the center of the square configuration (Figure 10).

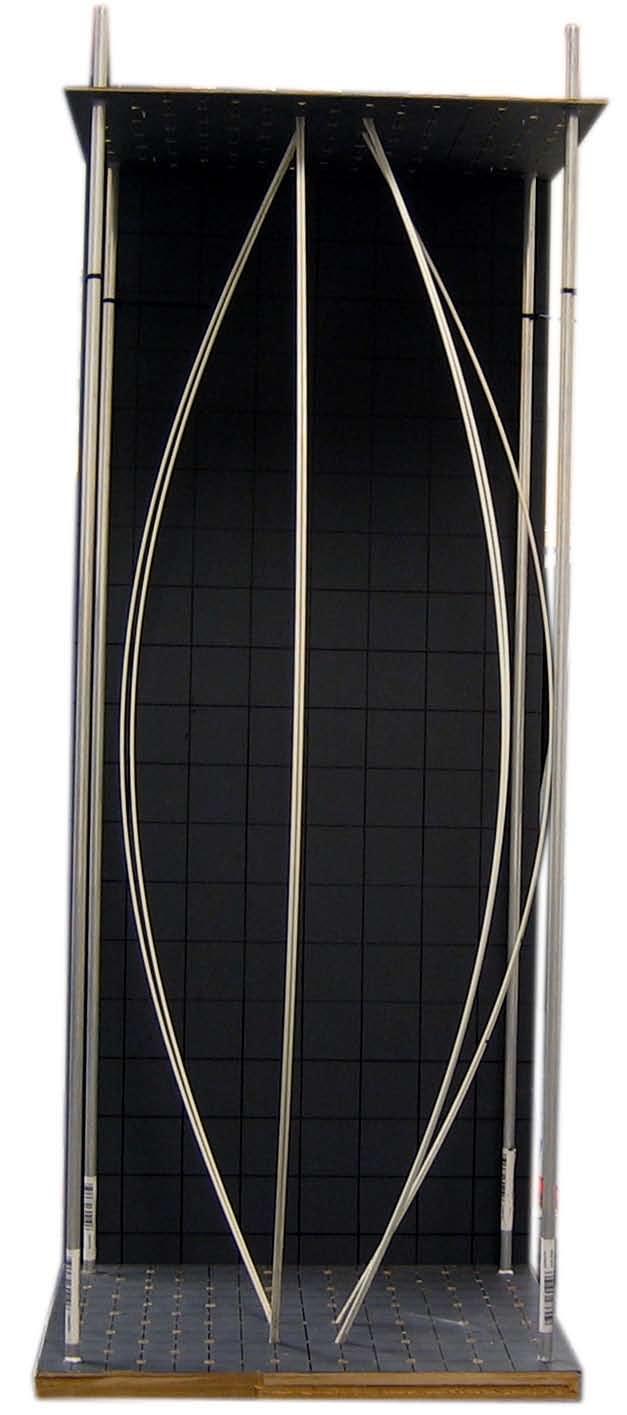
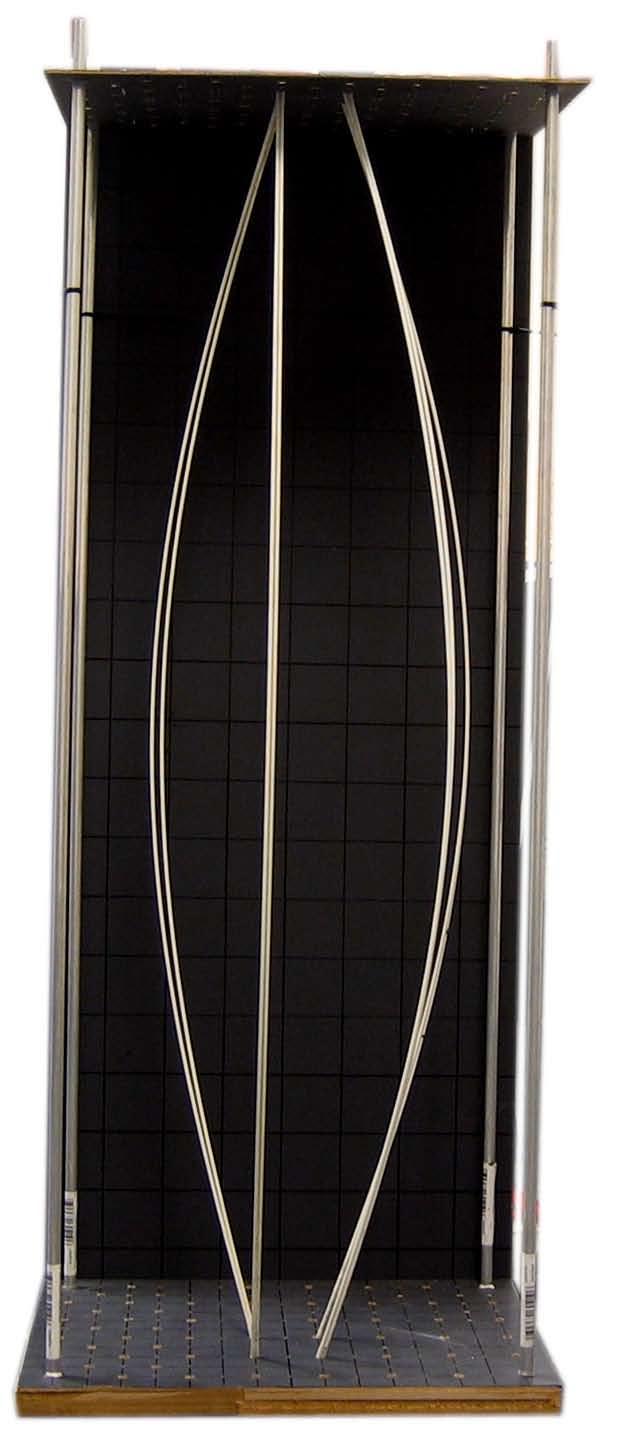
COMPARING BRAIDED RODS
It should be noted that this experimental setup was designed to lead into a similar experiment in which the pultruded rods were to be braided. However, after several attempts to braid these somewhat rigid rods, it was found that the task would be better suited in a digital environment.
CHAPTER
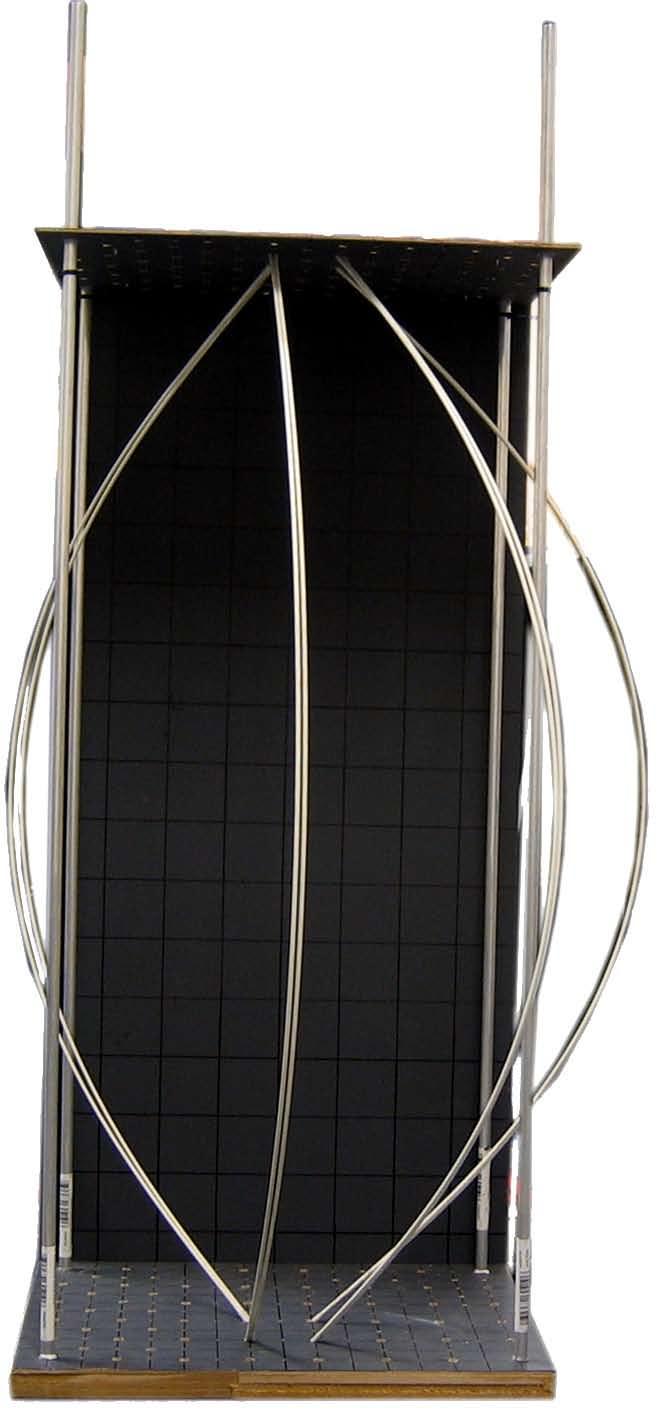
MATHEMATICAL EXPRESSION OF PHYSICAL BEHAVIOR
Because the rods behave similarly, one equation for each of the points for displacement in both the x and z directions can be expressed by the following equations:
f[point75_X] = -.002d³+.036d²+1.098d
f[point75_Z] = -.001d³+.044d²-.967d+75
f[point50_X] = .003d³-.089d²+2.215d
f[point50_Z] = -.196d³+.784d²-1.464d+50
f[point25_X] = -.002d³-.0015d²+1.502d
f[point25_Z] = .099d³-2.47d²+9.047d+25;
where d = displacement of the rod (cm)
COMPARISON OF STRESSES
By establishing the equation of the curve (Figure 12) each point takes when being compressed, the behavior of a pair of 1.5mm radius rods can be understood mathematically. Furthermore, this experiment allows the behavior of a group of rods to be observed and understood. A single rod still has a radius of 1.5mm, and the stress in this rod can now be solved:
S = F/πr²
S = 50/π×1.5²
S = 22.22
What is important to note, however, is that although 8 rods are tested in this setup, the stress in each paired rod is the same as in an individually tested rod. Because the rods are not mechanically connected in any way, there is no transfer of stress between them.
CHAPTER 10 - MECHANICAL TESTING OF PULTRUDED RODS
FABRICATION DRIVEN BY MATERIAL POTENTIAL
It is important to look at an architectural example employing fiber composites as its main structure. The Aberfeldy Footbridge in Aberfeldy, Scotland is a fully composite bridge which is extremely lightweight and performs structurally. While the aim of the endeavor - designing and constructing a bridge capable of being built on site with ordinary farm machinery - is met, there is a huge missed opportunity in the use of fiber composites. Why are fiber composites - materials which can be manufactured to react to specific loading conditions, eliminate mechanical joints, and achieve required programmatic conditions - used in construction in the same manner as if they were steel or wood members? This case study highlights the performative possibilities of a new material, while uncovering the neglect of constructing an architectural artifact without bearing in mind its connection to material and tooling.
Additionally, two subsequent design experiments will investigate two different typologies - a tower and a footbridge - at similar scales to the Aberfeldy Footbridge in order to reveal the potential advantages, and critical shortcomings of a fiber composite structure designed for and fabricated by a proposed novel fabrication technique - thermoplastic radial pulbraiding. The first case study, a “pencil tower” in Hong Kong, addresses the issue of site constraint due to high urban density, and is evaluated based on structural performance, and ultimately the abilitiy for a fabrication technique to produce desired structural effects. The second case study, in contrast, investigates the construction of a fiber composite footbridge on a remote site, and is evaluated based on programmatic requirements and the manufacturing possibilities available to achieve them. Furthering this investigation, a comparative analysis of spatial and structural performance is investigated between the Patagonia footbridge and a similar footbridge proposed by Guillem Baraut and Mattia Gambardella.
While both experiments design for structural and programmatic performance, respectively, they must be understood in the context of their fabrication process - meaning their performance is only viable if fabrication is possible.
CHAPTER 11 - CASE STUDIES AND DESIGN EXPERIMENTS
ABERFELDY FOOTBRIDGE, WOLFSON BRIDGE RESEARCH UNIT AT THE UNIVERSITY OF DUNDEE WITH MAUNSELL ENGINEERING, ABERFELDY, SCOTLAND, 1990
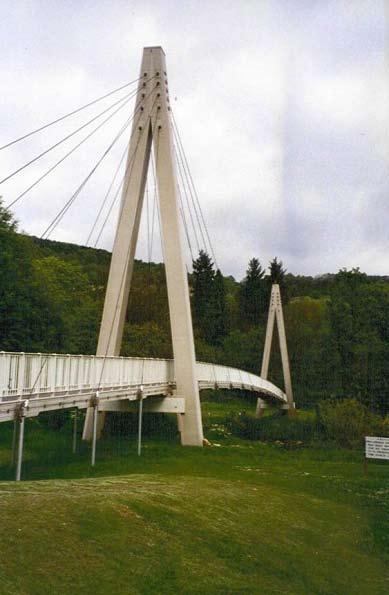
The Aberfeldy Footbridge is a fully fiber composite pedestrian bridge spanning 63m across the River Tay (Figure 01). The bridge synthesizes both glass fiber and aramid fiber reinforced plastics into a lightweight, easily assembled structure. One of the first fully composite structures to be designed and built, the Aberfeldy Footbridge presented an interesting design problem based on its construction logic. Because composite structures are not commonly used in bridge design, the new production processpultrusion - and new material properties of fiber composites led to a new design process for the engineers. The decision to use fiber composite materials was one of pure practicality; using traditional materials would require the use of equipment too heavy to use on site, and construction was limited to the use of machinery found in an agricultural environment (Harvey, 1993).
The pultruded glass fiber bridge deck, along with the aramid fiber ropes supporting them are highly advantageous in their anisotropic properties. However, this created a limited number of load paths possible, and ultimately minimized the formal possibilities. In addition, due to the cost of pultrusion dies, standard cross-sections had to be used; circular and square sections are most common. Although this may seem like a limitation, the potential of these somewhat standard shapes to create interesting geometries while bearing significant load is extremely interesting. With this restriction, however, the cost of the bridge is comparable to a similar bridge built using lightweight steel, but extremely lighter. In fact, a similar steel bridge would not be able to be built on site and by unskilled laborers, whom in this case, were the same students that designed the bridge (Harvey, 1993).
The bridge deck and supporting cables, along with two 18m high glass fiber composite pylons weigh 14.5 tonnes. However, because each component in the system is so lightweight, no site cranage was necessary to build the bridge. The repercussions of this component construction, though, were that there were a great deal of connections; parapet rail to post and post to deck connections are abundant, and “clearly...required a precise sequence of assembly (Harvey, 1993, p. 230).” These connections create high risk of cutting fibers, reducing the strength of the composite.
Not all joints are purely mechanical, however. In some cases, mechanical joints were used to clamp down adhesive bonds between composite components. The biggest problem area with this adhesive construction was that all parts of the assembly needed to be dry before and during the curing process in order for a proper bond to cure (Harvey, 1993).
NEW MATERIAL, TRADITIONAL CONSTRUCTION
Although the component-based system brings problematic issues for the construction process, the use of a composite material, and the different composites used dependent on type of structure necessary, provides great insight into the possibilities and advantages to constructing with fiber composites.
From a pragmatic viewpoint, it can be said that the traditional use of new materials - that is to say, the way in which these composite materials are put together is similar to that of steel - is somewhat advantageous. Construction drawings were documented in the same fashion that they would for any project, thus creating a coherent transition into the new building material for the contractors. As stated earlier in this section, the design of the bridge was driven purely by on-site constraints, and therefore the lightweight nature of the composite material was the driving factor in the decision to use it.
That being said, this case study clearly describes the problems with current fabrication techniques. Fiber composites afford the possibility of connecting material and structure, yet the Aberfeldy Footbridge does not draw this link, but only perpetuates the shortcomings of traditional construction. If fiber composites have the potential to advance the fabrication techniques in which they are produced, why is this crucial point so commonly neglected?
The following design experiments aim to investigate this problem, and explore the possibilities given by a novel fabrication technique.
PENCIL TOWERS IN HONG KONG
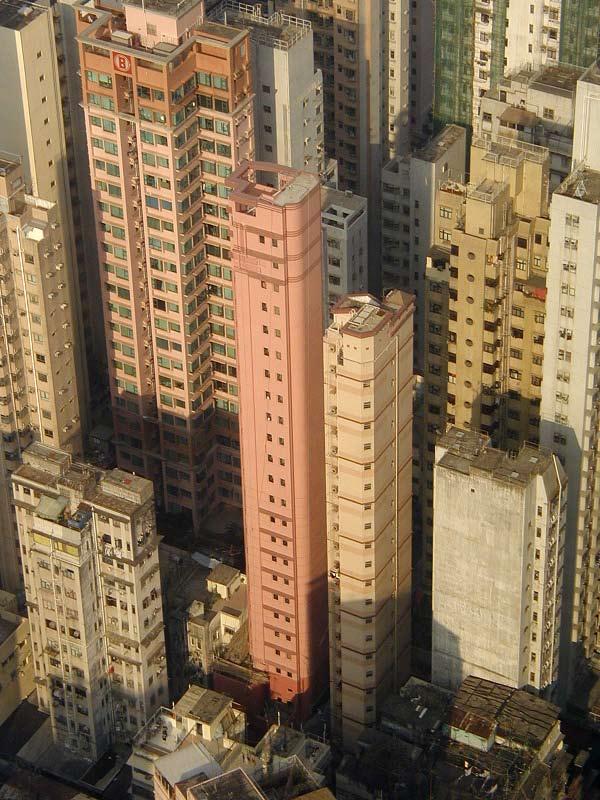
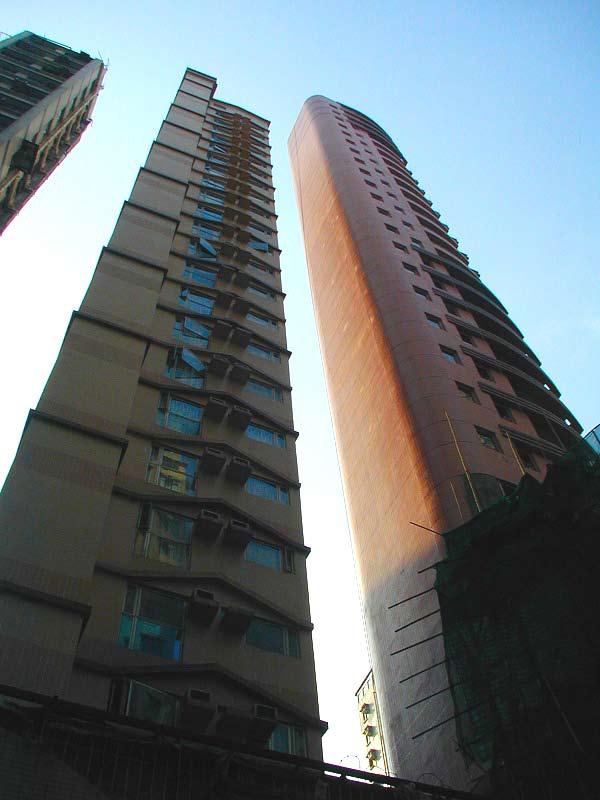
Hong Kong is an incredibly dense city with limited space to build. Pencil towers - extremely slender tower-like apartment buildings, as seen in Figures 02 and 03 - began to be constructed in the 1980s to take advantage of the height allowed for development while adhering to the extremely small footprint available. In some cases, the footprint of a pencil tower can be as small as one apartment big - only 16 square meters in area. Despite their small footprint, pencil towers can be as tall as 30 stories (Leubkeman, n.d.).
FORM MADE POSSIBLE BY MATERIAL CHOICES
To allow for this typology to exist, careful design using reinforced concrete is necessary. Although windloads can create a structural concern for these tall and slender buildings, the reinforced concrete employed provides sufficient stability for the building to perform structurally. One important question to investigate, therefore, is if a braided fiber composite material can perform structurally in the given context.
TESTING A TYPOLOGY
The pencil tower is a suitable case study to test this dissertation’s proposed fabrication technique due to its strictly defined scale and site constraints. The ratio of footprint to height creates a defined size limitation, while the density of the context in which the typology is situated provides a suitable site for which the proposed technique is advantageous.
This design experiment will be evaluated on the structure’s buckling stiffness. A pencil tower is to be designed based on the specific architectural typology, and driven by its structural performance. In addition to the global structural condition, it will be imperative to explore the possibilities in platform conditions of the structure.
Although this design experiment seeks to find an effective structural design to bear applied loads, what is important to understand is the possibility of fabricating a differentiated structure. By exploring variability in a pulbraided structure, this design experiment aims to show the potential of a novel technique.
CHAPTER 11 - CASE STUDIES AND DESIGN EXPERIMENTS
.0 DESIGN EXPERIMENT: HONG KONG PENCIL TOWER
Figure 02, photograph, showing a pencil tower in Hong Kong. The high density of the city and scarcity of available plots of land to build on have led to this typology phenomenon. Figure 03, photograph, showing a series of pencil towers in Hong Kong. While the area of the footprint of a pencil tower differs between structures, the extreme difference in scale between footprint and height are the signature characteristic of these towers.GENERATING THE BRAID CONFIGURATION
In order to investigate the pencil tower typology as a design experiment for a pulbraided structure, an appropriate braid must be generated. To properly generate this form, the previous pneu-cable net experiments are referenced. Therefore, because this tower is a vertical construction, double pneus must be employed. A mandrel geometry of paired pneus within a tensioned cable-net is generated with pneus of a radius of 1.6 meters each, giving an approximate floor area of 16 square meters - the minimum floor area for a typical Hong Kong pencil tower. The paired pneus are proliferated to a height of 10 stories, in order to simplify the analysis of the structure, totalling a height of 32 meters. After modeling the pneu geometry, a design method, negotiating between scripting and digital modeling, is used to create a cable net surface geometry, plot points of varying densities on the surface, and braid through those points (Figure 04).
LIMITING SCOPE: UNIFORM DENSITY
Because this experiment is focusing solely on structural performance, a uniform point density is used. While varying densities have been generated as a test of the modeling tool, only a surface point density of 10 (10 point rings of 10 points each) will be used in order to simplify the experiment, and focus its scope on structural performance. It is important to note that a different braid density will result in a different geometry and different density of fibers; however, this design experiment will experiment with the degree of differentiation of rod diameters as well as the performance of platforms.
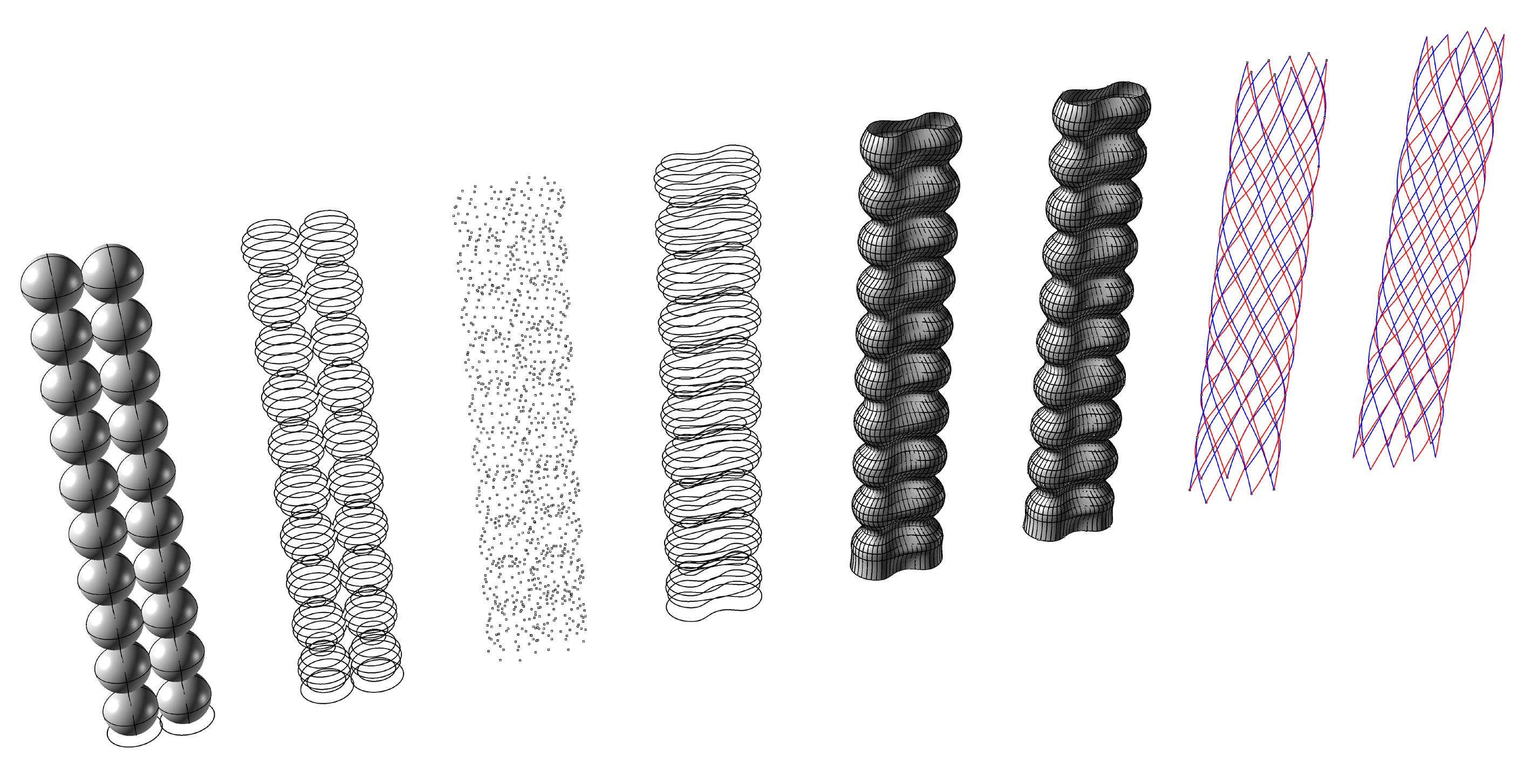
CHAPTER 11 - CASE STUDIES AND DESIGN EXPERIMENTS
.0 DESIGN EXPERIMENT: HONG KONG PENCIL TOWER
Figure 04, photograph, showing a series of pencil towers in Hong Kong. While the area of the footprint of a pencil tower differs between structures, the extreme difference in scale between footprint and height are the signature characteristic of these towers.STRUCTURAL PERFORMANCE AS A DESIGN PARAMETER
While strength of the material is an important parameter in the design of the tower, it is its buckling stiffness that will contribute as the major structural driver in the structure’s design. While buckling will cause structural failure, and thus discontinue all transfer of loads through the member that has buckled, it is important to understand the parameters that will affect the buckling stiffness of the system. Redundancy will exist due to the inherent characteristics of the braided structure’s equal distribution of loads; if one member fails, the system may adapt for this failure. However it is crucial to understand the behavior of the system in order to design for these situations. The two parameters contributing to buckling stiffness in pultruded rods of circular section are rod radius and length. Because the system is braided, however, rod length must be understood as the length of a member between nodes. Figure 05 diagrams this relationship.
LOCAL CURVATURE
While designing for the global buckling stiffness of the structure is imperative, it is important to note two local parameters that will affect this global performance. The initial curvature of a rod between nodes will affect the stiffness of the structure. The greater the initial curvature of a rod, the greater its deflection under a buckling load. In addition, the direction of the applied load in relation to a single rod will affect its performance. As the angle of the rod at its point of loading deviates from 90° (or from a vertical position), the greater the rod’s deflection. Figure 06 describes these two local parameters, and how a curved rod behaves when a vertical load is applied.
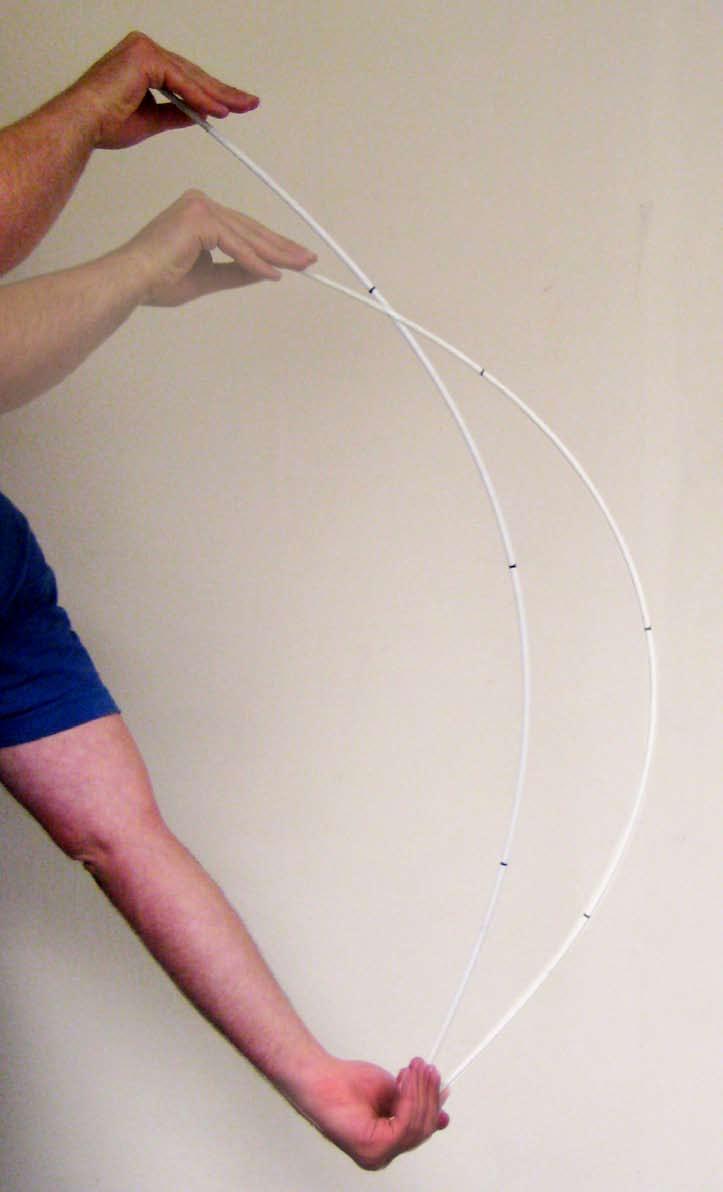
CHAPTER 11 - CASE STUDIES AND DESIGN EXPERIMENTS
.0 DESIGN EXPERIMENT: HONG KONG PENCIL TOWER
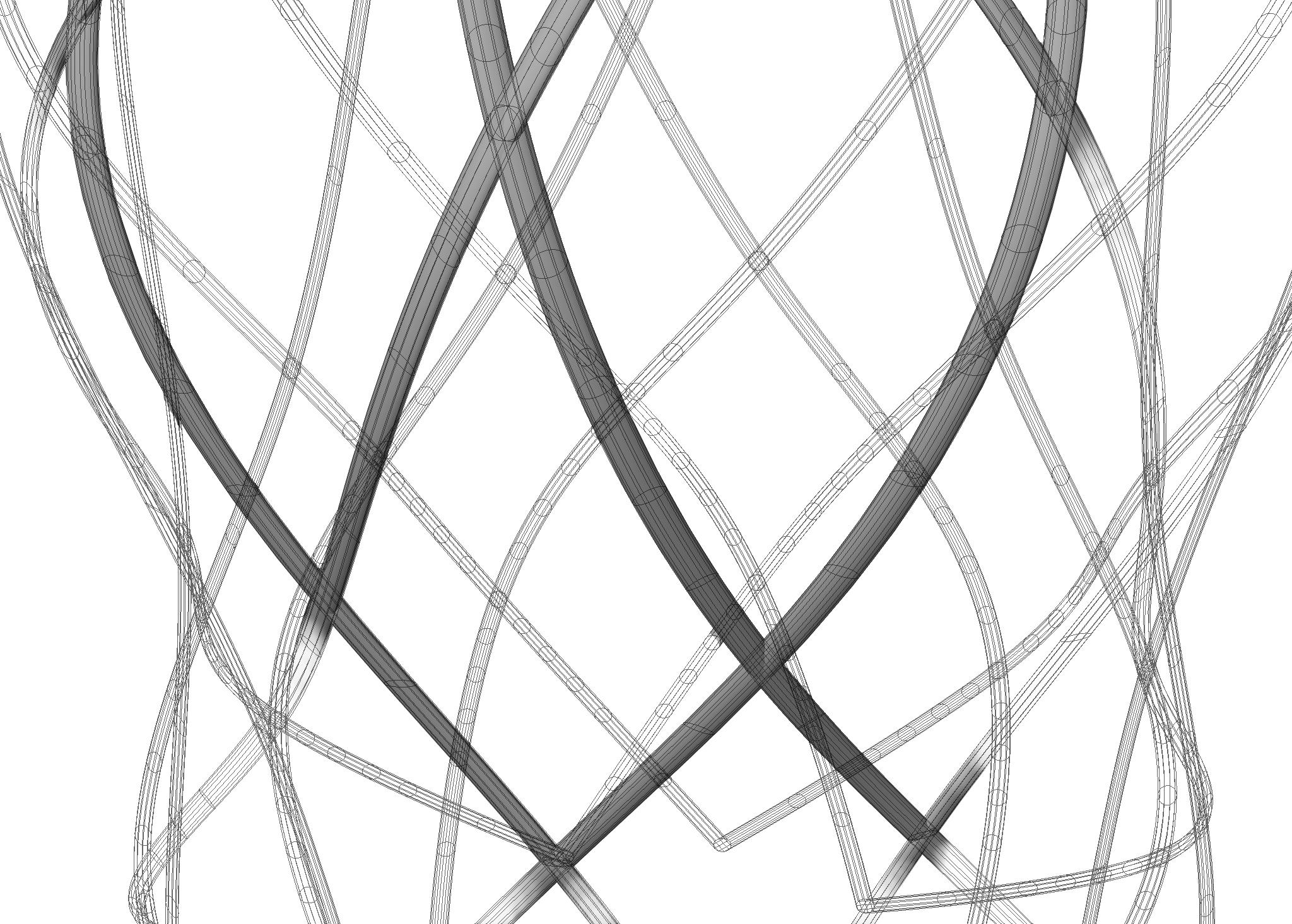
THREE SCALES OF BUCKLING
Within the realm of buckling, it is important to note the buckling which may occur on three different scales; globally, locally, and materially (Figure 07). The structural system as a whole has a buckling stiffness which will prevent bending globally. It is hypothesized that by braiding rigid rods, a “spread bundling” effect will occur; rather than adding a tension ring to support the center of the structure against buckling failure, the braiding system will interlock each individual rod and prevent this failure from occurring. The spread bundling effect decreases the deformation of the rods due to their increased stiffness (Figure 08).
On the local level, the length of rod from one node to its adjacent node can be studied and tested as an individual rod prone to buckling. The behavior of each rod, based on global geometry, will create a differentiated rod diameter across the entire structural braid. Finally, there can be buckling which occurs at the scale of the individual fiber, often referred to as “microbuckling.” Because each glass fiber is in itself acting as a long, thin rod, it can be subjected to buckling failure. Although its inclusion within a matrix attempts to prevent against this by transferring load between fibers and through fiber organization on the whole, microbuckling is another failure mode of which to take note.
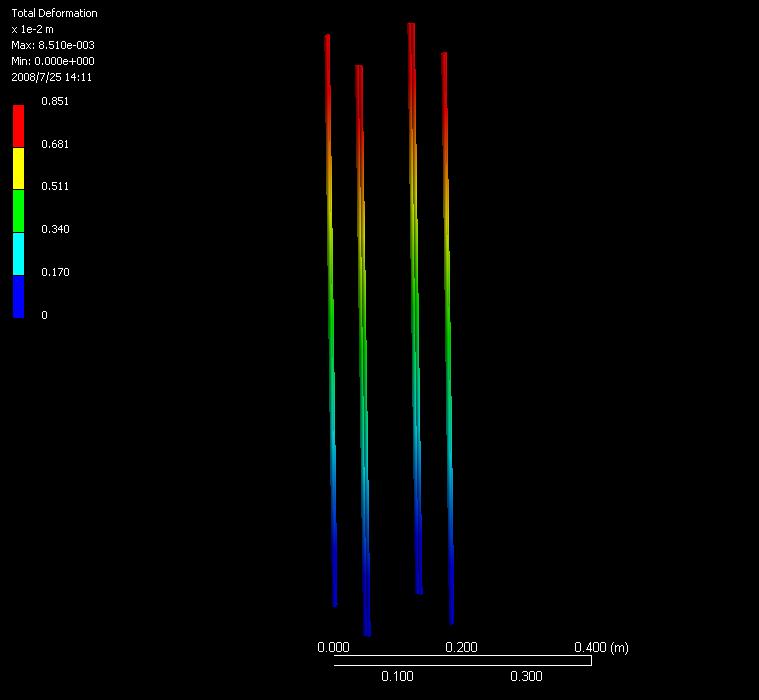
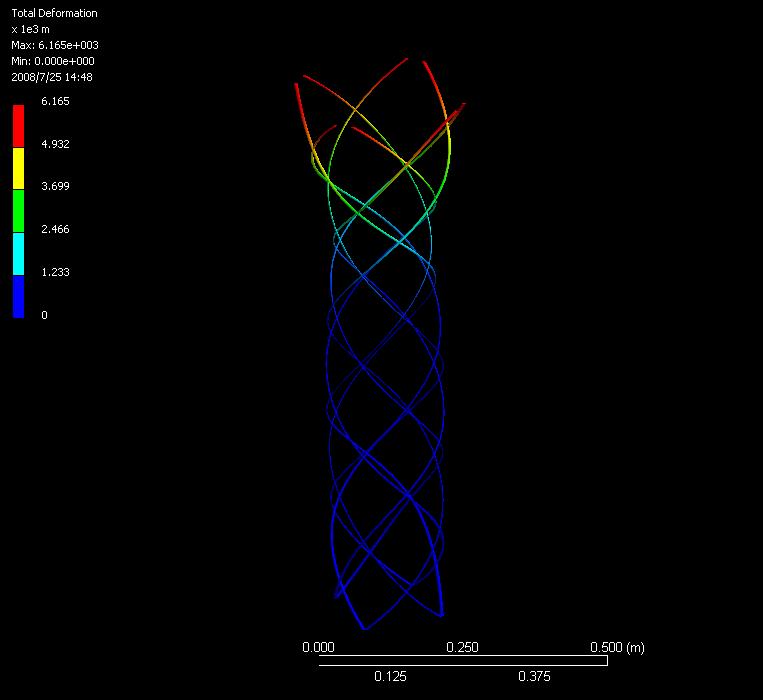
CHAPTER 11 - CASE STUDIES AND DESIGN EXPERIMENTS
.0 DESIGN EXPERIMENT: HONG KONG PENCIL TOWER
Figure 08, model, showing a Finite Element Analysis model of four coupled rods (left) and eight braided rods (right) under compressive load. This analysis shows decreased deformation in a braided configuration.BUCKLING ANALYSIS
In order to test the structural performance that informs the design of a pulbraided fiber pencil tower, a buckling analysis is necessary. Buckling of a long, slender rod, as defined by Euler in Chapter 10, must be considered due to the intrinsic material properties of pultruded rods. However, the structure cannot be viewed simply as whether or not it buckles. Buckling, in general terms, is not desired. However, when a structure buckles, it may still find a configuration in which it is in equilibrium and may still transfer loads effectively (however not necessarily efficiently). Therefore, a static analysis will not provide completely useful results.
EIGEN BUCKLING
A static analysis, as discussed, yields the deformation of a structure at a specific loading condition; this may or may not describe a structure’s failure, because the tested load may not be its critical load. An Eigen buckling analysis, however, will test the critical load a structure can bear, and describe for which loading conditions exist equilibrium configurations.
The structure’s load-bearing capabilities are described as a multiplier by which the loading condition differs from the critical load in a specific configuration.
These configurations (Eigen modes or eigenvalues), are the different configurations in which a rod will buckle as a load is consecutively applied to a structure, surpassing the critical load (Shames & Dym, 1985). Figure 09 describes the first three modes of Eigen buckling. The first mode of buckling, which is the configuration taken under the smallest applied critical load, is often called the “Euler Load,” and takes the shape of Euler’s first buckling case (Shames & Dym, 1985).
In this case study, buckling stiffness will be driven by the performance of the structure under this first eigenvalue at its critical load. However, subsequent eigenvalues will be investigated in order to understand the changes in morphology of the structure under bearable critical loads.
CHAPTER 11 - CASE STUDIES AND DESIGN EXPERIMENTS
.0 DESIGN EXPERIMENT: HONG KONG PENCIL TOWER
PLATFORMS PROVIDING STIFFNESS
When considering the structural performance of a pulbraided pencil tower, it is obvious to understand how the structure behaves with platforms or floors. While providing the necessary programmatic function, these floors also provide lateral stiffness to the overall structure (Figure 11). The fabrication of these floors is an important aspect of the technique proposed and will be explored later in this section.
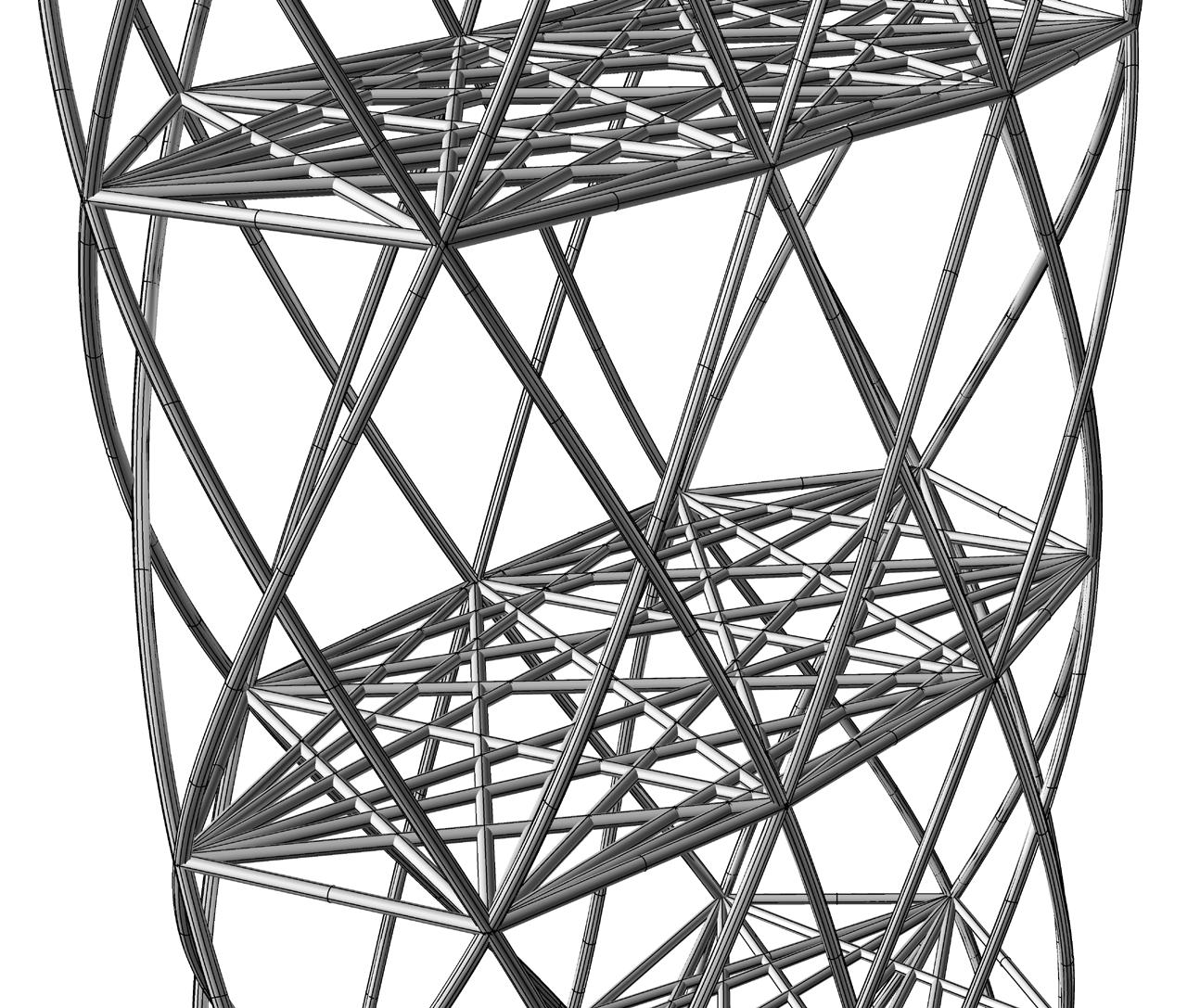
To begin investigating the structural behavior of a tower, it is assumed that the platforms are made up of a series of fibers (as mentioned, the method in which they are fabricated will not be discussed at this moment). Fibers are used to continue with the intention of generating a fully pulbraided fiber composite structure.
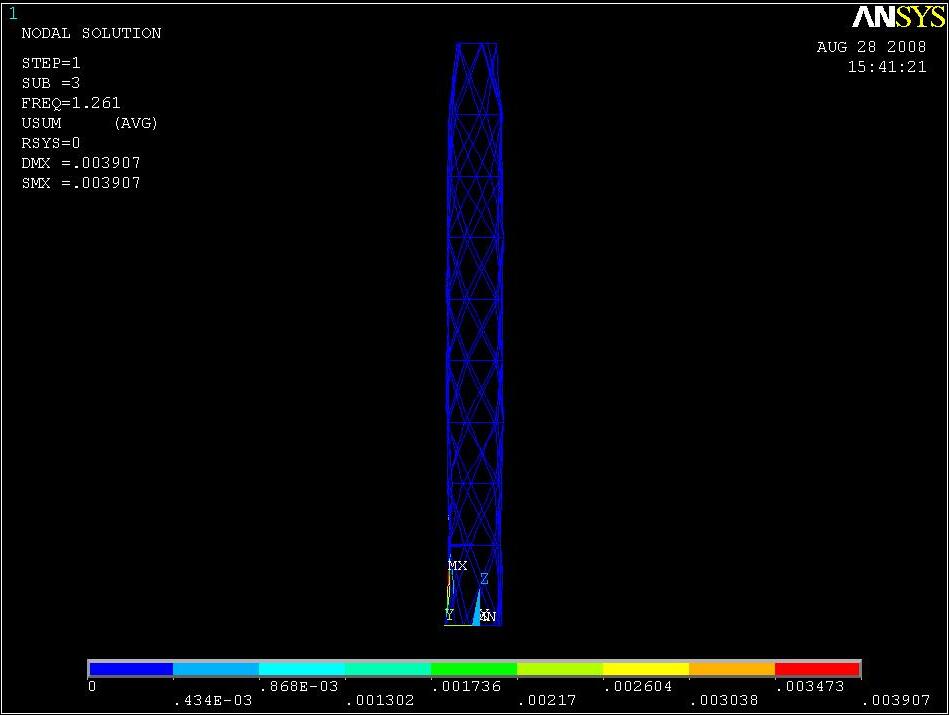
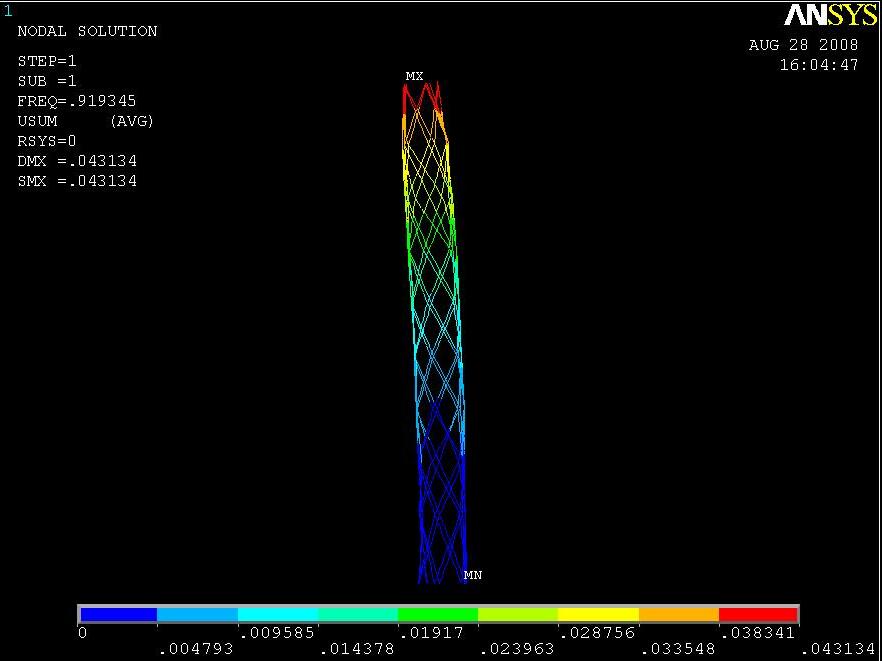
The subsequent investigation, therefore, is based on a platform generated from connecting each braid node point to each other, except where these lines would cross outside the boundary of the structure itself. Figure 10 describes this platform design.
CHAPTER 11 - CASE STUDIES AND DESIGN EXPERIMENTS
.0 DESIGN EXPERIMENT: HONG KONG PENCIL TOWER
Figure 11, diagrams, showing a braided structure with and without internal platfrom supports. From these Finite Element analyses, it is clear that internal platforms give lateral global stiffness to the structure. Figure 10, diagram, showing the floor plate design used in this experiment. All nodes are connected to each other strengthening connection points while creating a network of interconnected lines.FINDING THE EIGEN BUCKLING SOLUTION
In order to analyze the structure in relation to buckling stiffness, the eigen multiplier must be set at 1. When this is met, the analysis will yield the critical load at which the structure will buckle. To begin this analysis, a braided structure is loaded with gravity, as well as an applied load of 500N distributed across each platform (Figure 12). Through a series of iterations varying the uniform diameter of the pulbraided rods, the structure is evaluated through a static analysis (Figure 13) in order to provide elastic deformation for Eigen Buckling analysis. When the Eigen multiplier is near 1, the first three eigenmodes are observed (Figure 14, following page) and a differentiated structure can be designed.
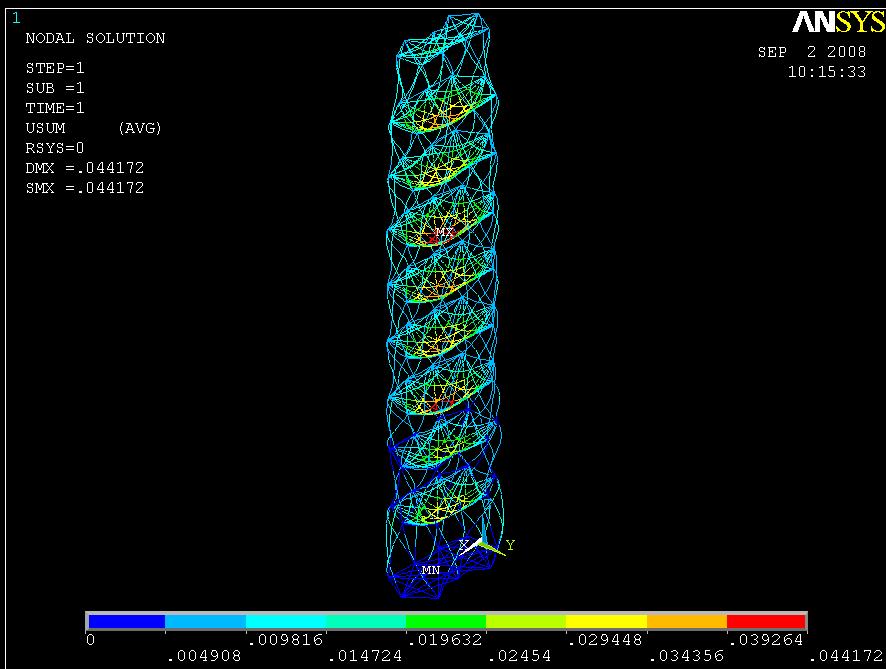
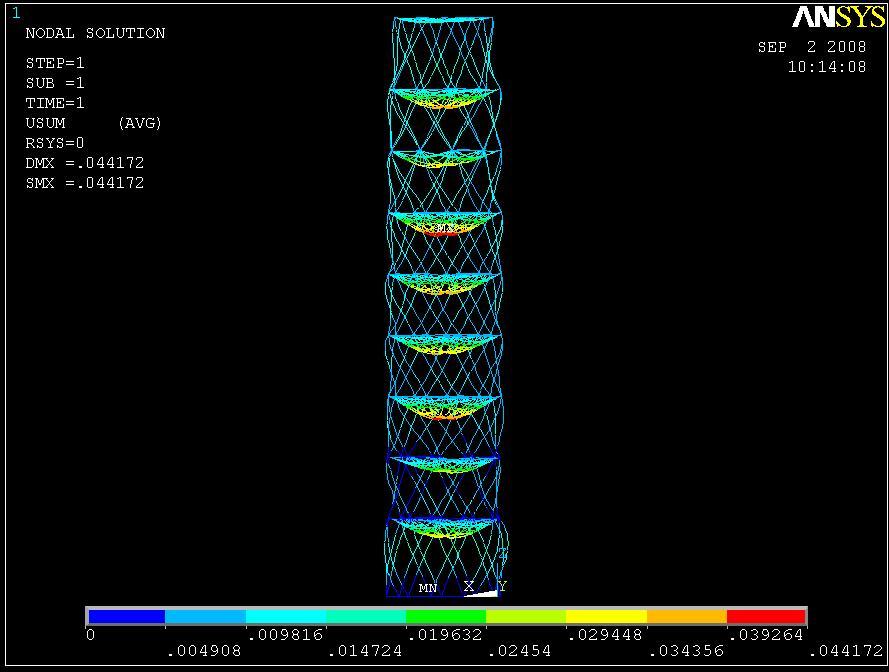
CHAPTER 11 - CASE STUDIES AND DESIGN EXPERIMENTS
.0 DESIGN EXPERIMENT: HONG KONG PENCIL TOWER
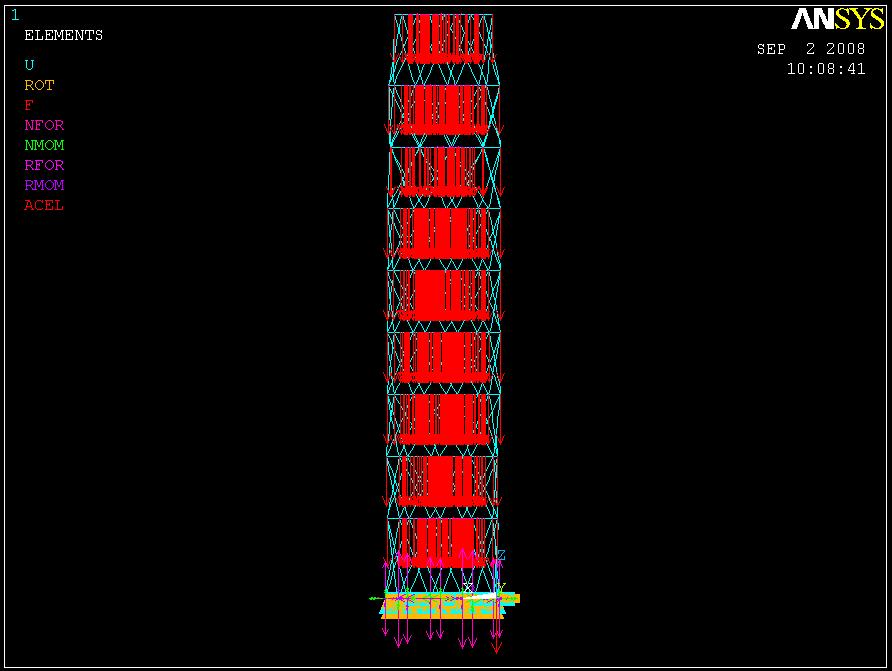
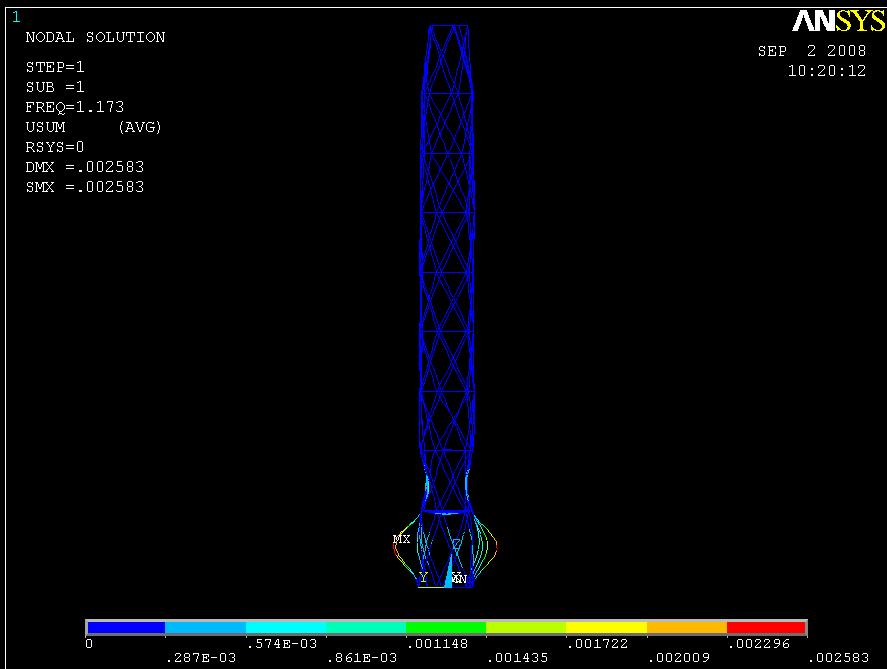
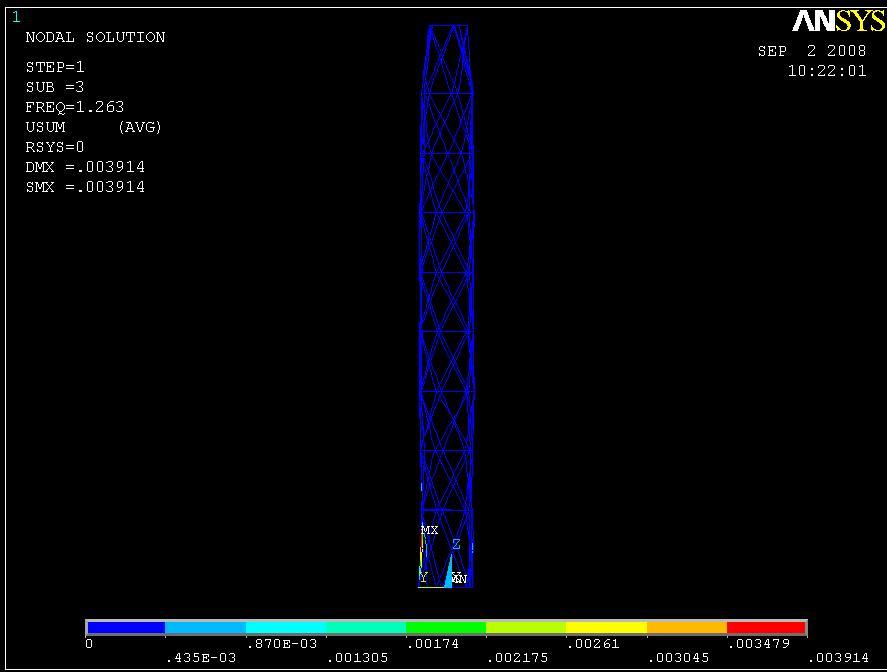
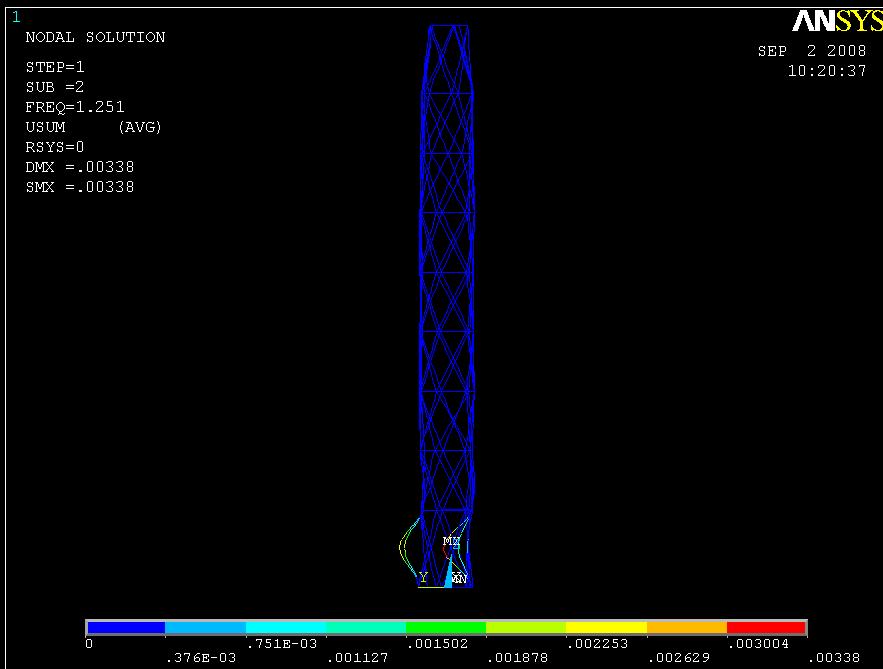
DIFFERENTIATED STRUCTURE
Figure 15 shows the deflection of a differentiated pulbraided structure under the specified loading conditions. Radii are varied to limit deflection of platforms to under 21.3mm, or 1/300th of the width of the platform (6.4m). The resulting effective structure has a rod radius of 50mm at the structure’s base, and tapers to 35mm at the top. Each platform has a rod thickness of 30mm at its outer edges, while growing to 40mm at the center to bear applied load causing deflection. Figure 16 describes this differentiation.
FABRICATION POSSIBILITIES
It is important to note that this design experiment is not intended to investigate the process of solving an optimized structural solution for a specific loading problem; rather, the effective structural solution proposed is necessary to achieve in order to investigate the possibilities in fabricating this solution. In other words, this experiment allows for the questioning of the potentials and limitations of thermoplastic radial pulbraiding. It is possible, then, to fabricate the vertical structure, with varying crosssections as found in this experiment based on the previous research undertaken in this work. However, there are two local conditions that must be considered further when understanding which fabrication possibilities exist. These local conditions to be explored are the fabrication of platforms, as well as the inclusion of a service core.
CHAPTER 11 - CASE STUDIES AND DESIGN EXPERIMENTS
.0 DESIGN EXPERIMENT: HONG KONG PENCIL TOWER
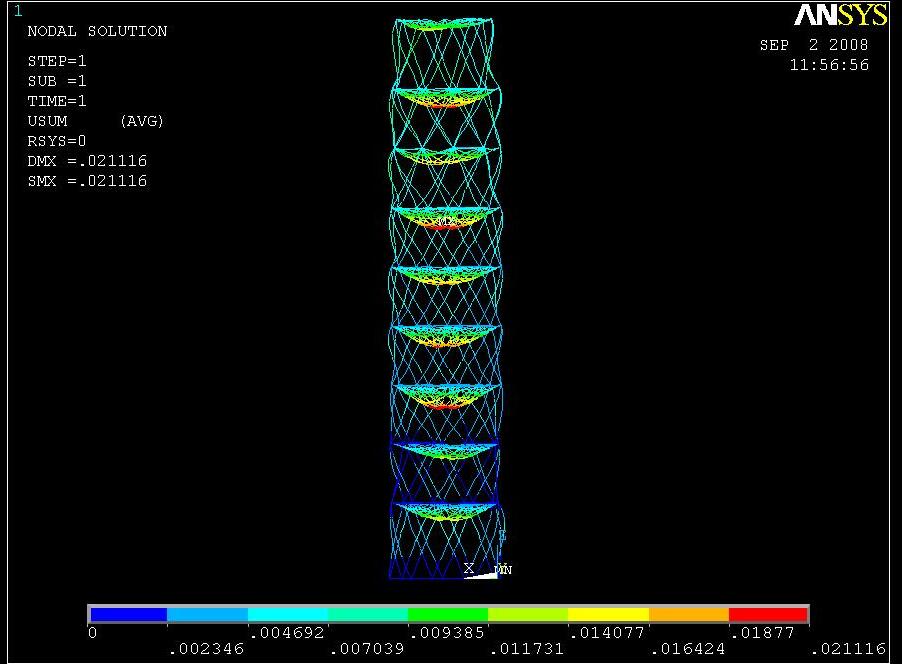
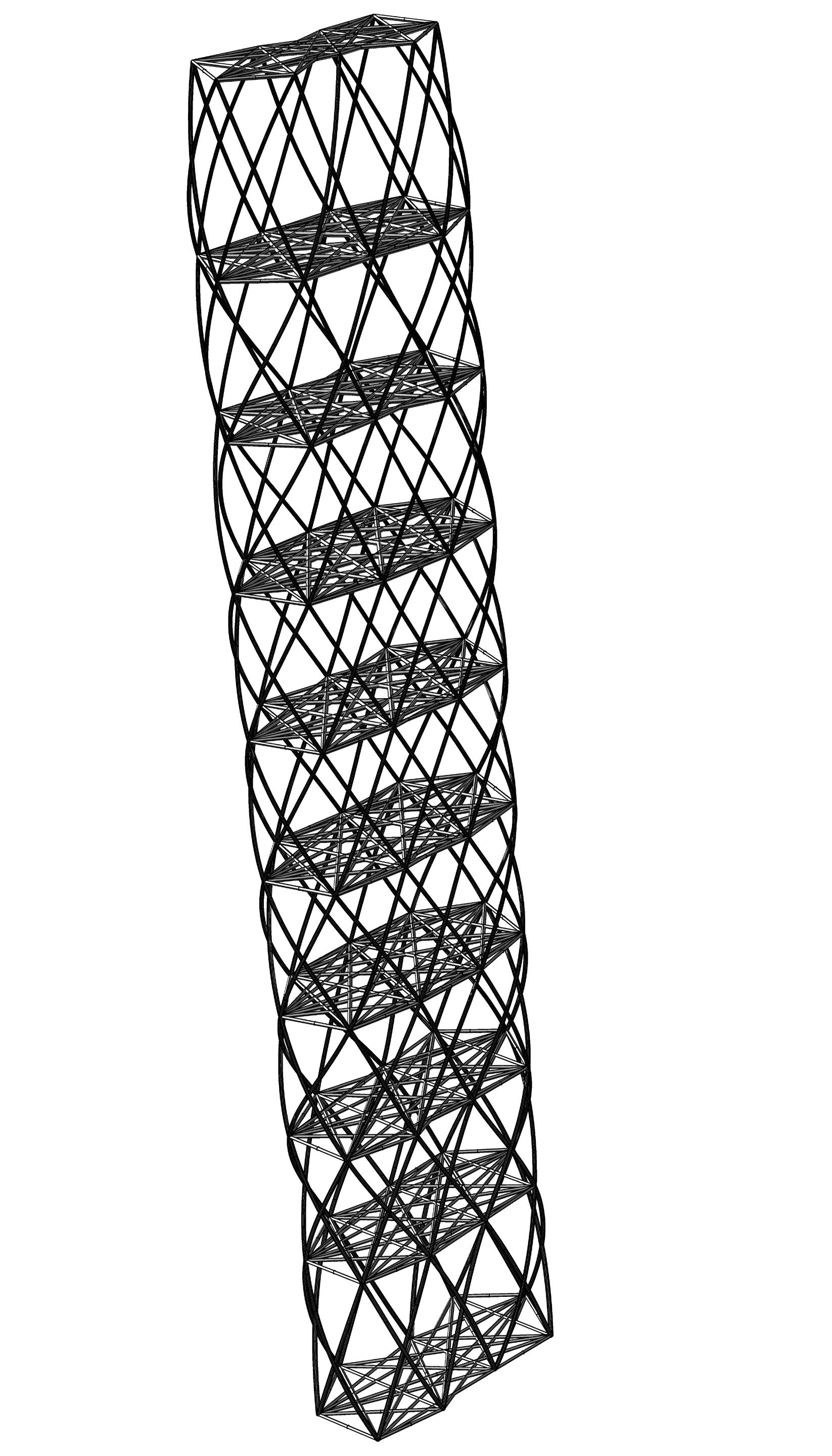
CHOOSING A TOWER CORE
In order to correctly investigate the design of a tower, the critical characteristic of the typologythe circulation core - must be considered. Figure 18 describes the three core options of a tower. Because thermoplastic radial overbraiding takes place around a mandrel geometry, the only viable option for the design of a core is one that is exterior to the main volume of the tower. An additional pneu-cable net configuration (Figure 17) is then added to the existing confguration in order to create a pulbraided tower with a core. The density of the core is increased to a ring density of 20 points, each containing 20 points of their own. This increase in density creates a tighter braid and therefore a small interior gap between core and tower. The resulting tower is shown in Figure 19.
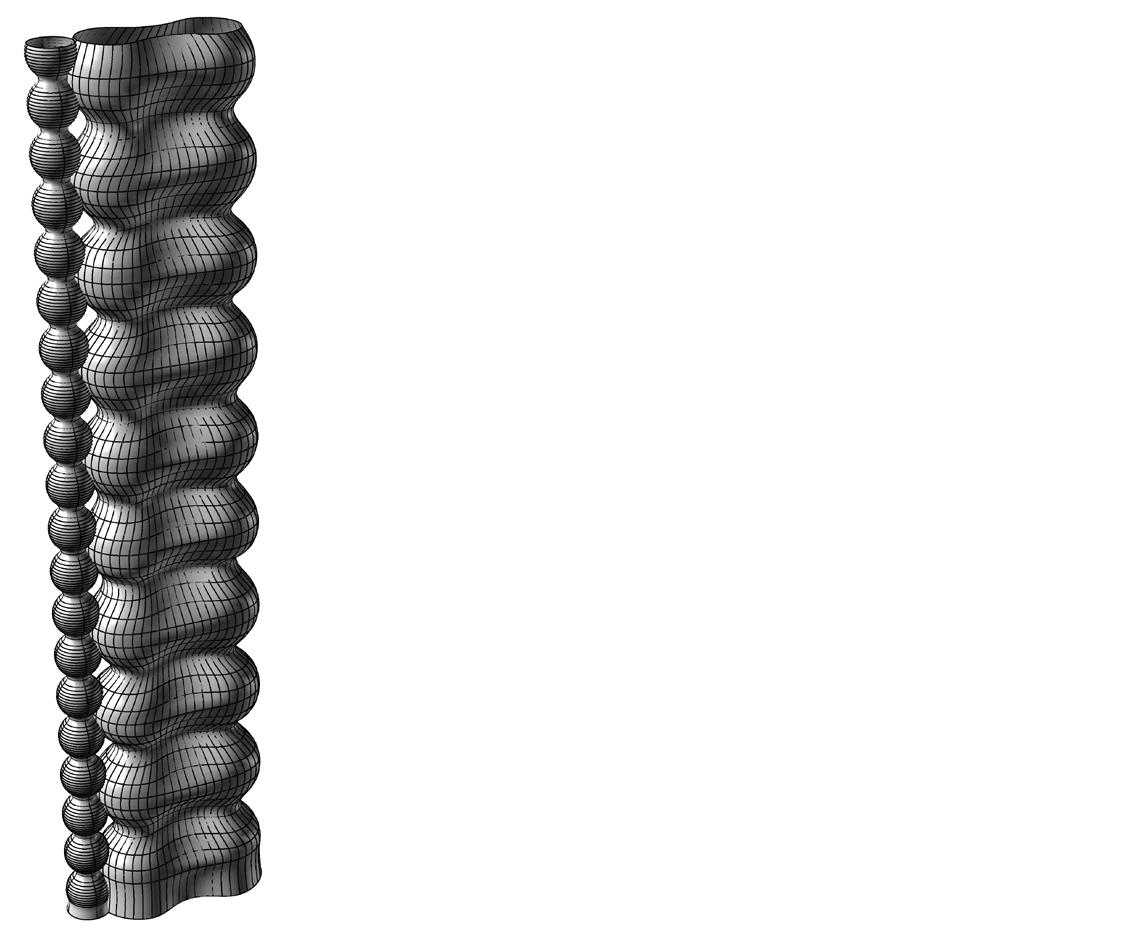
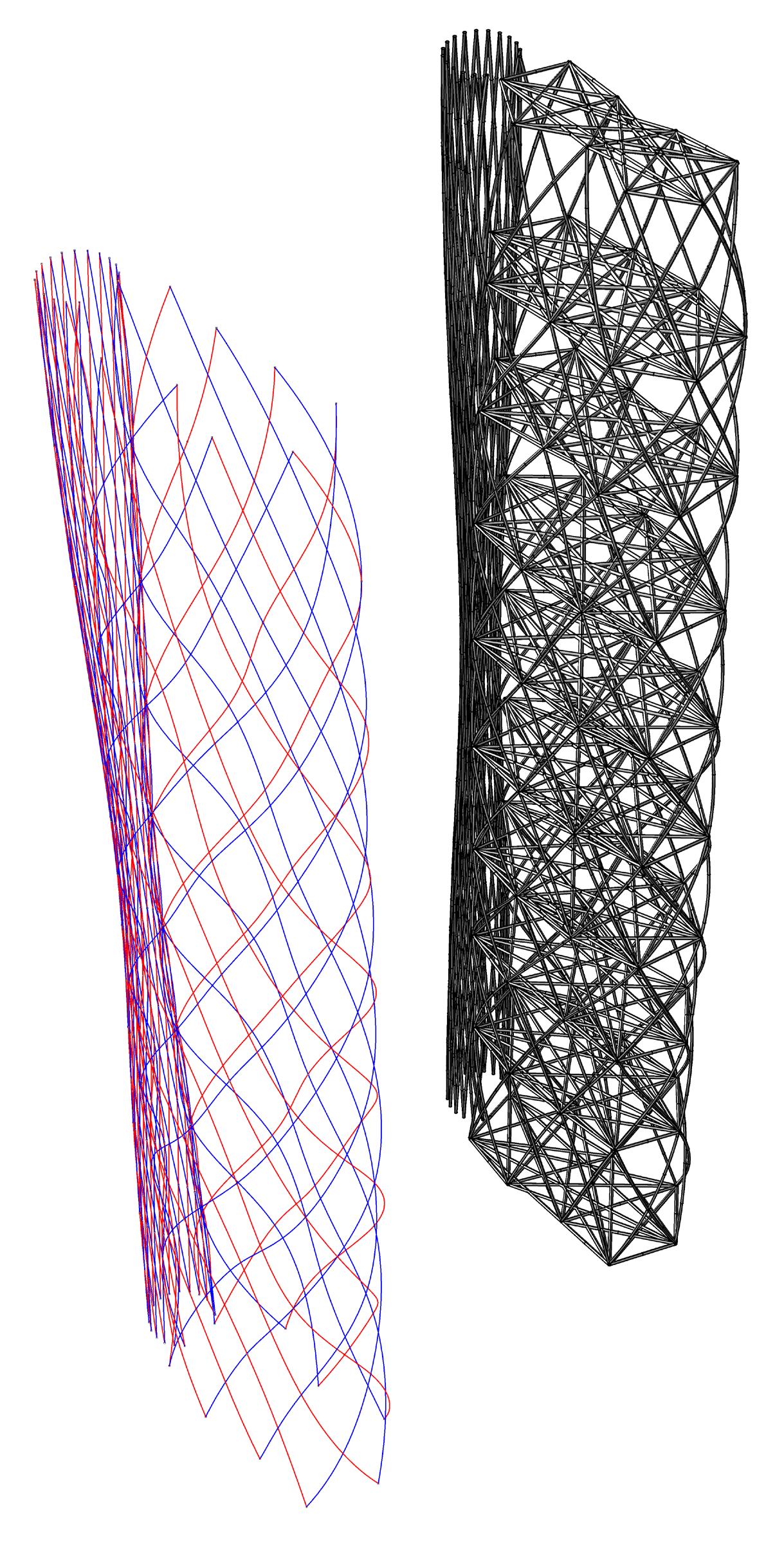
CHAPTER 11 - CASE STUDIES AND DESIGN EXPERIMENTS
.0 DESIGN EXPERIMENT: HONG KONG PENCIL TOWER
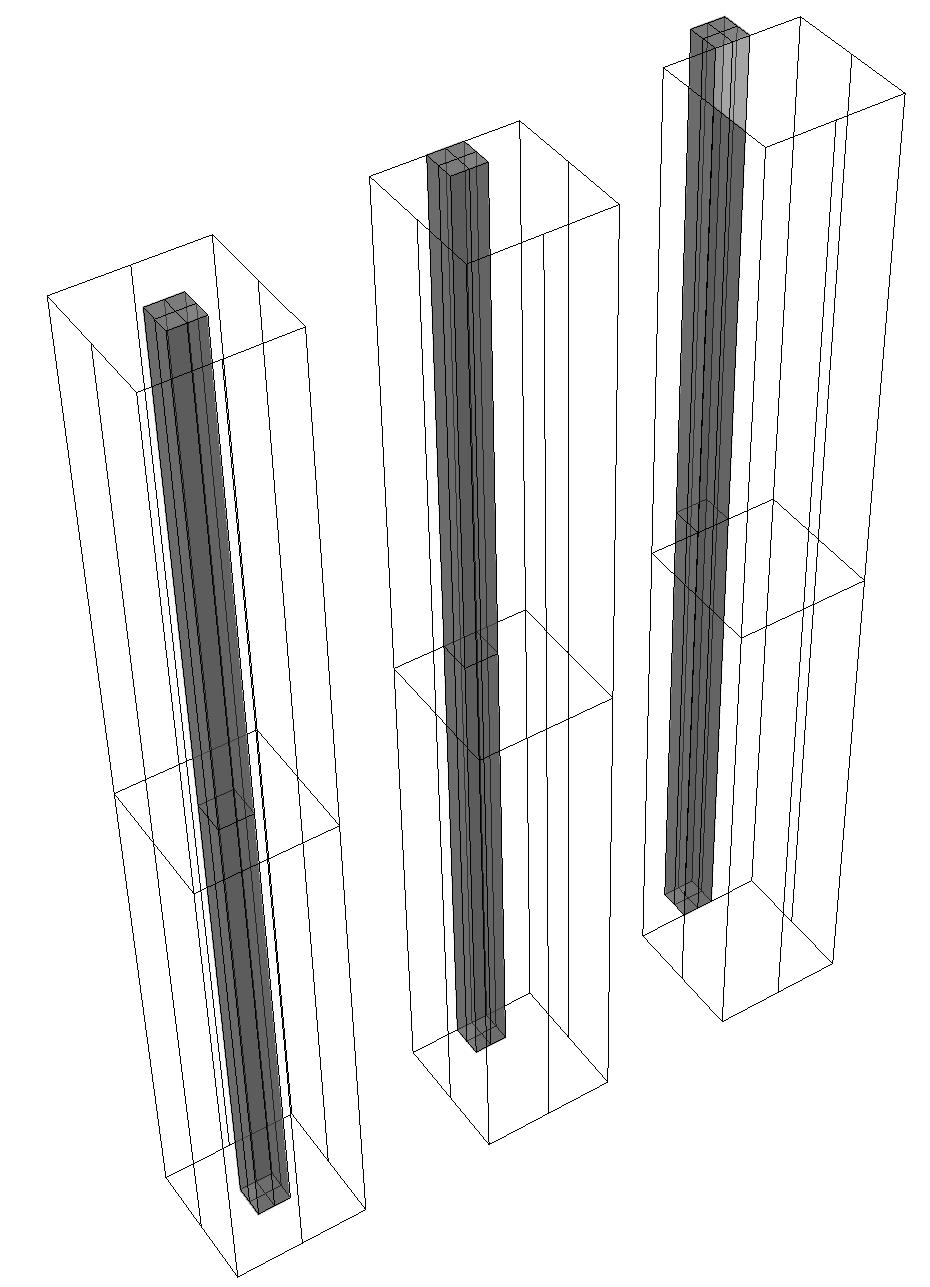
CONSTRUCTING PLATFORMS
The construction of each platform in a tower (Figure 20) is a local condition that needs to be considered. However, the fabrication of platform as an inclusive part of the thermoplastic radial pullbraiding process poses a technical constraint. Because the process requires an internal mandrel to braid around, geometry is limited to a shell-type structure. For this reason, as mentioned, a tower core must be present outside of the main tower geometry. Therefore, it must be noted that this process limitation exists.
ADVANTAGES OF A THERMOPLASTIC RESIN MATRIX
Although floors cannot be constructed using the mandrel geometry generation researched in this work, the composite matrix characteristics allow for the investigation of an alternative platform construction. Because the pulbraided rods are made up of thermoplastic resin fibers, which allow for remelting or softening of the resin, an option exists where platforms can be generated outside of the main fabrication process, hoisted up through the center of the structure, and then tack-welded onto the structure. While this does not provide a synthesized solution to the main hypothesis of this dissertation’s argument, it is a possible solution that keeps with the material proposed.
Even still, there are a number of problematic issues associated with this type of construction. Although the pulbraided structure can act as a supporting structure when lifting platforms up through the tower’s center, tack-welding lies outside of the synthesized process in which this work is investigating. Furthermore, the structural envelope fabricated must be structured to perform effectively under selfweight, without the stiffness supplied by internal platforms. This structural problem can lead to an overstructured solution, thus working counterintuitively to the optimization allowed by the fabrication technique. Finally, the labor involved in tack-welding platforms requires a great deal of skill and safety measurements to be employed, which counteracts the main argument of this dissertation.
FURTHER INVESTIGATION
While the synthesized fabrication of platform is not possible due to process constraints, it opens the possibilty for further investigation into the generation of a mandrel geometry. For example, is it possible to inflate and deflate pneus consecutively so that the pulbraided envelope is fabricated around a pneu-cable net, which is then deflated to allow for the pulbraiding of a platform? The pneu-cable net mandrel can then move up to the next level and the process can continue (Figure 21). This speculation allows for the advancement of a fabrication technique aiming to synthesize completely material, tooling, and structure.
A NOTE ON IN-SITU CONSTRUCTION
While it is viable to speculate on the ability for the thermoplastic radial pulbraiding technique to be used in a constrained site, it is important to discuss some limitations that may affect the reality of this construction. First, the size of the braider is large relative to the size of the structure produced. The “Mantis” megabraider discussed in section 7.02 runs in a 120 foot (36.57m) cell, while outputting a smaller structure. Although the actual braider is not this large, the scale of the workspace necessary to ensure setup is indicative of the space needed to construct with this proposed technique. Therefore, the limited site in which pencil towers are built may not be ideal for this kind of construction. However, it is possible to speculate on a new urban environment generated using thermoplastic radial pulbraiding; that is to say, while the technique may not be ideal for an extremely constrained site, in-situ construction is still possible.
CHAPTER 11 - CASE STUDIES AND DESIGN EXPERIMENTS
.0 DESIGN EXPERIMENT: HONG KONG PENCIL TOWER
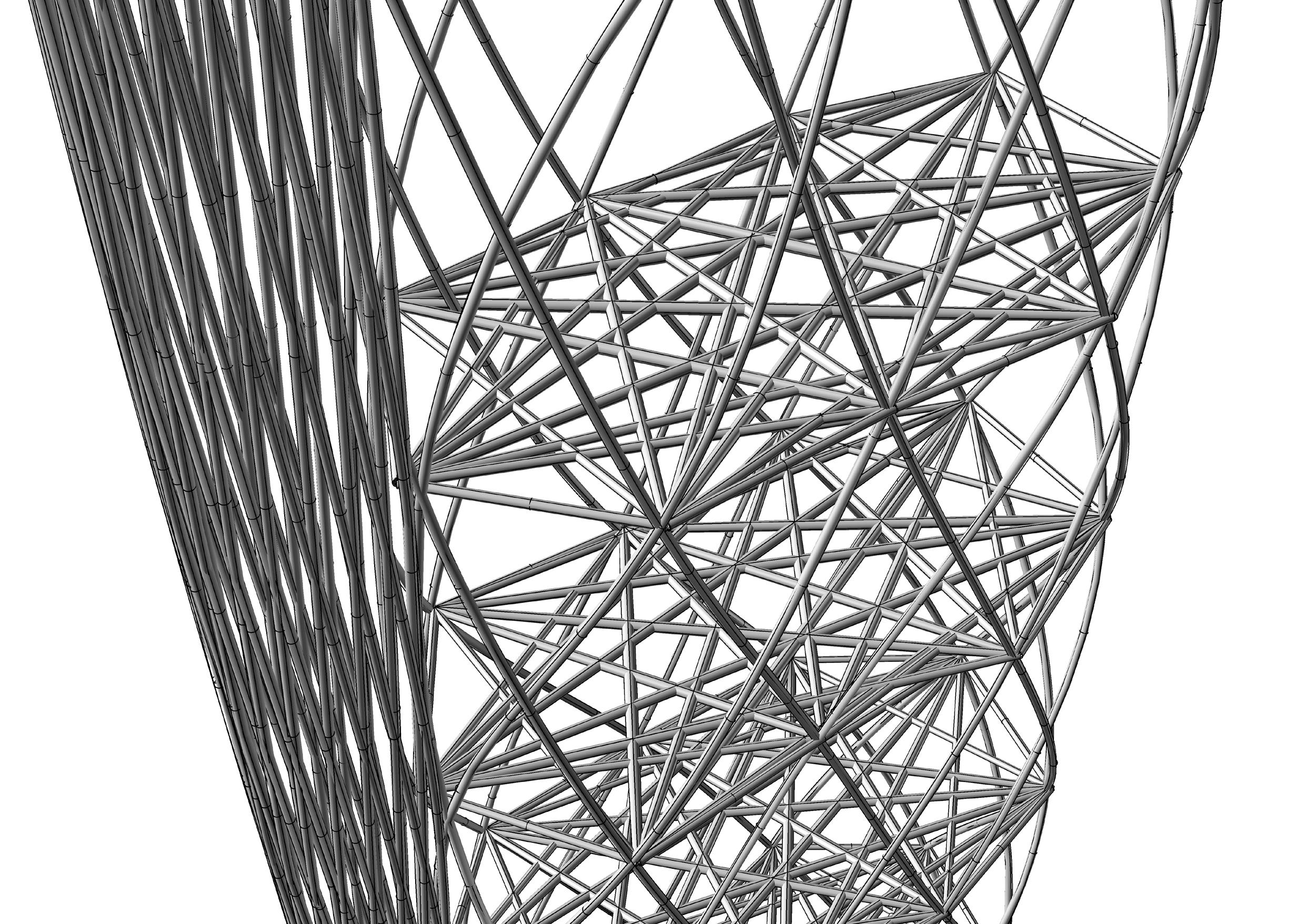
PROPOSAL FOR A FOOTBRIDGE IN PATAGONIA
A proposal for a footbridge in Patagonia (Figures 22 and 23) was undertaken by a group of students (Renata Elizondo, Mehran Gharleghi, Evan Greenberg, Tommy Johnson, Elina Pavlea, Amin Sadeghy, and Gennaro Senatore) in the Emergent Technologies and Design Program at the AA School of Architecture aimed to achieve a bridge design where form, structure, and program were fully integrated. A tensile cable system was used to structure the bridge, anchoring it to the ground, while wood members organized in a helical pattern stiffened the system, formed a walking path, and created changing views as the user walks through the bridge (Figure 24).
While the form-found bridge is evocative of an all-encompassing structural material system, the construction method is unresolved; a traditional scaffolding system was proposed to be constructed to allow for fabrication of the footbridge over a river. Also, each member was to be individually tied to the structural cables, creating a time-intensive and extremely dangerous process.

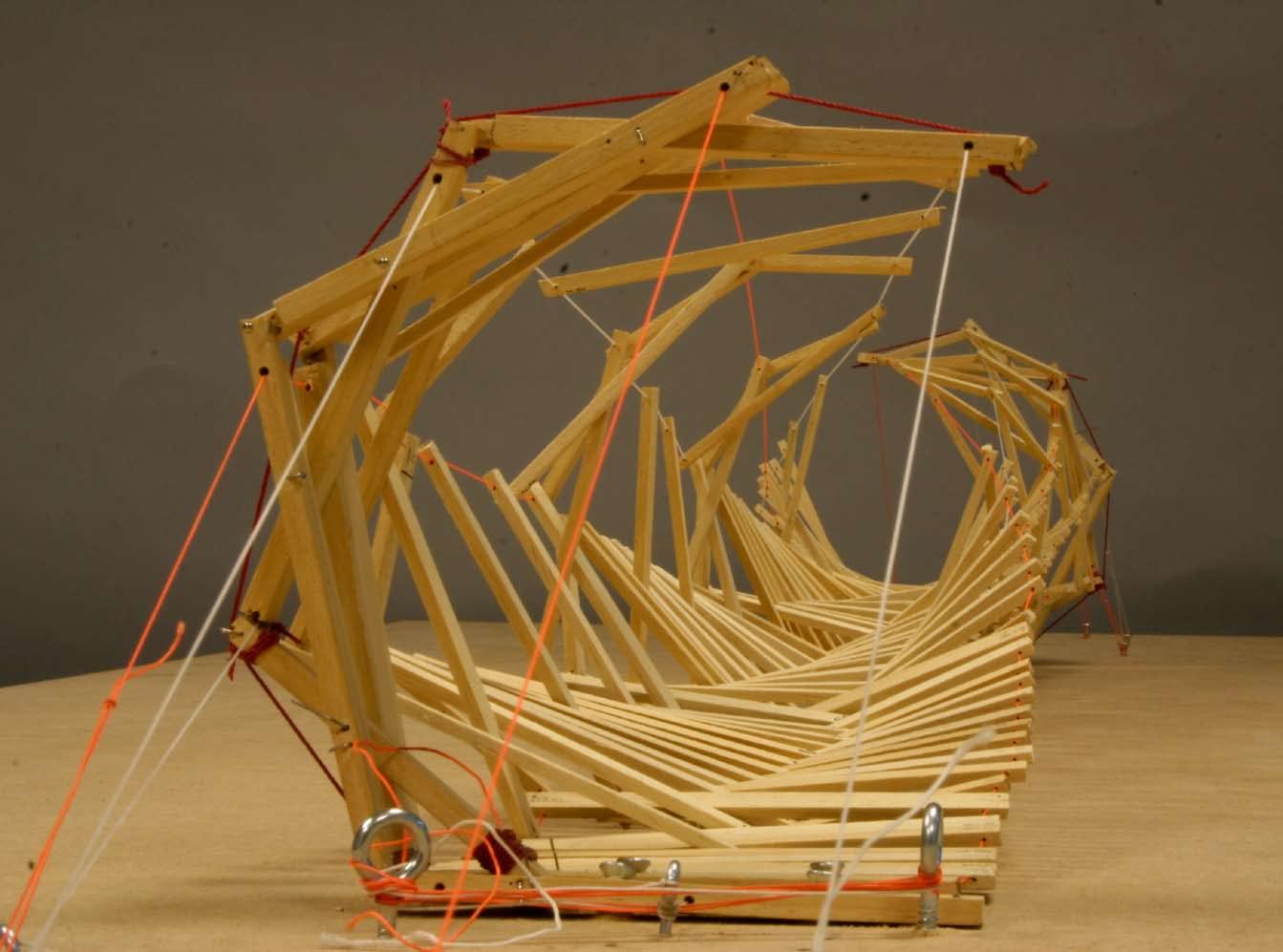
IMPLEMENTING A SYNTHESIZED FABRICATION TECHNIQUE
The proposed footbridge provides an interesting case study for which to apply the pulbraiding technique discovered in this dissertation. Fiber volume and braid angle are two parameters which can be changed in order to achieve the same spatial characteristics spoken to by the varied density of wood members. Although this bridge is a horizontal construction, the logic of the integrated system achieved can be tested using a fiber composite fabrication technique.
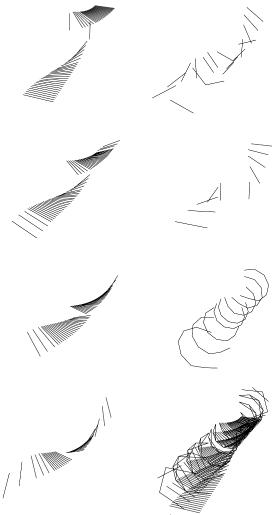
HI-TECH FABRICATION, LOW-TECH SITE
In addition, the remote site - Chilean Patagonia - provides a productive context to test this fabrication technique. Although the materials and machinery proposed are of high technology, the actual process in which the machine goes through is an extremely low-tech concept. Braiding is an extremely old textile technique, used prior to the industrialization of material construction processes. Therefore, the structure’s design, driven by the simplicity of the fabrication concept, is viable in a low-tech environment.
While the fabrication process responds to the global morphological conditions, such as the need for a footpath and varied view, there is an important local condition to consider. The way in which the footbridge meets the ground is essential to investigate in this case study, and the viability of an integrated connection to the existing ground condition must be considered.
CHAPTER 11 - CASE STUDIES AND DESIGN EXPERIMENTS
.0 DESIGN EXPERIMENT: PATAGONIA FOOTBRIDGE
COMPUTATION AND MODELING
An interactive process combining scripting and digital modeling is employed to develop an accurate geometric model to simulate the fabrication process understand form. Building off of pneucable net physical experiments from Chapter 8, a base geometry of same-sized spheres are created, and configured based on user input of bridge length, height above the ground, and clear height inside the bridge through a small script. The bridge proposal investigated in this case study is 12m long, 1m above the ground at its midpoint, and 2m in clear height at its highest point. The spheres are then decomposed into a point field in order to create two interpolated curves for which to sweep the base curve. A surface, simulating the cable net geometry formed by pneu inflation is generated and points are then distributed on the surface. This case study aims to address fiber density and pattern parameters; therefore a script used to distribute surface points can be altered to change the density of points in both the U and V directions of the surface. Distribution of points in each direction can be controlled as well. Figure 25 shows an array of braided configurations generated through this modeling method.
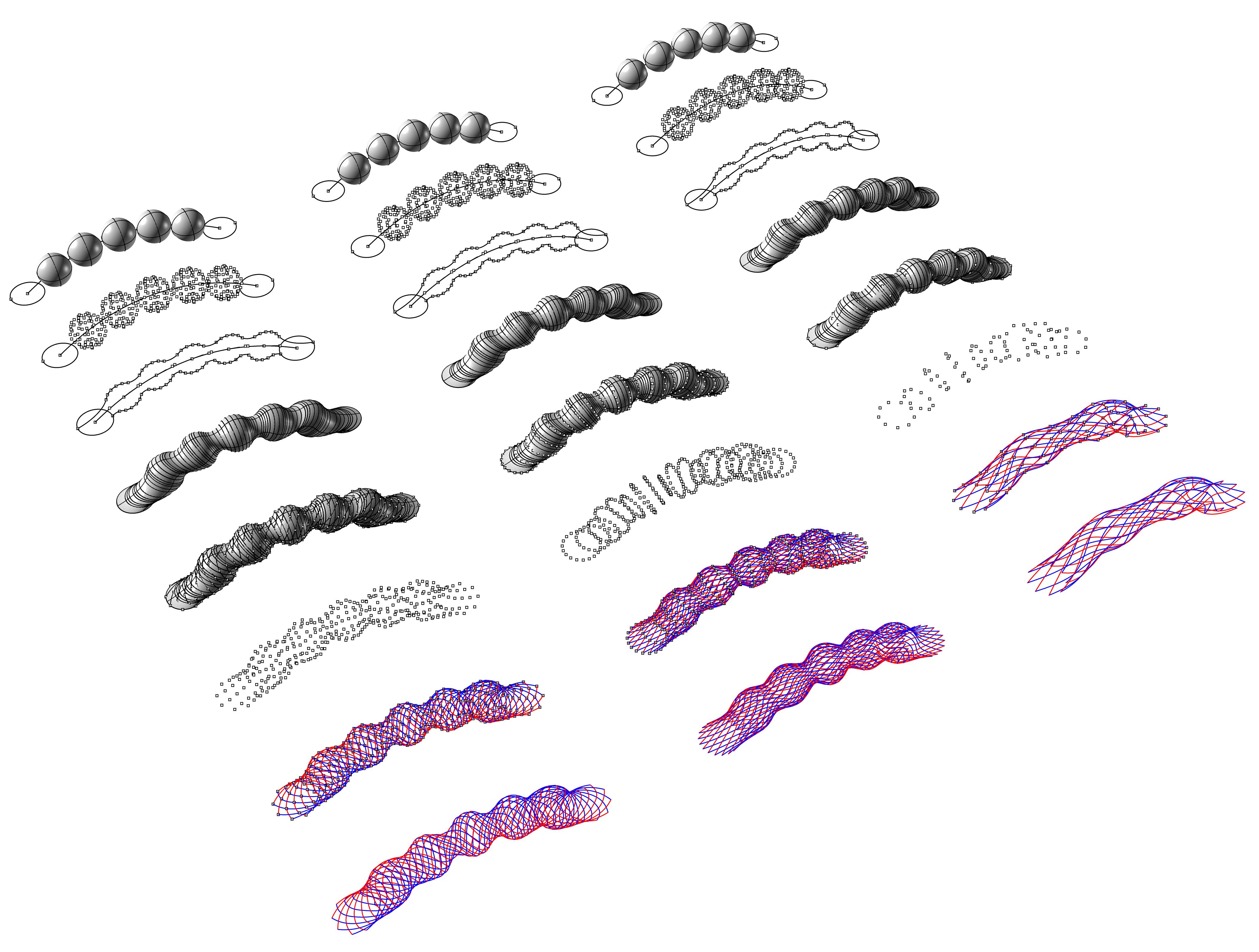
CHAPTER 11 - CASE STUDIES AND DESIGN EXPERIMENTS
.0 DESIGN EXPERIMENT: PATAGONIA FOOTBRIDGE
VARIATIONS IN CONFIGURATIONS
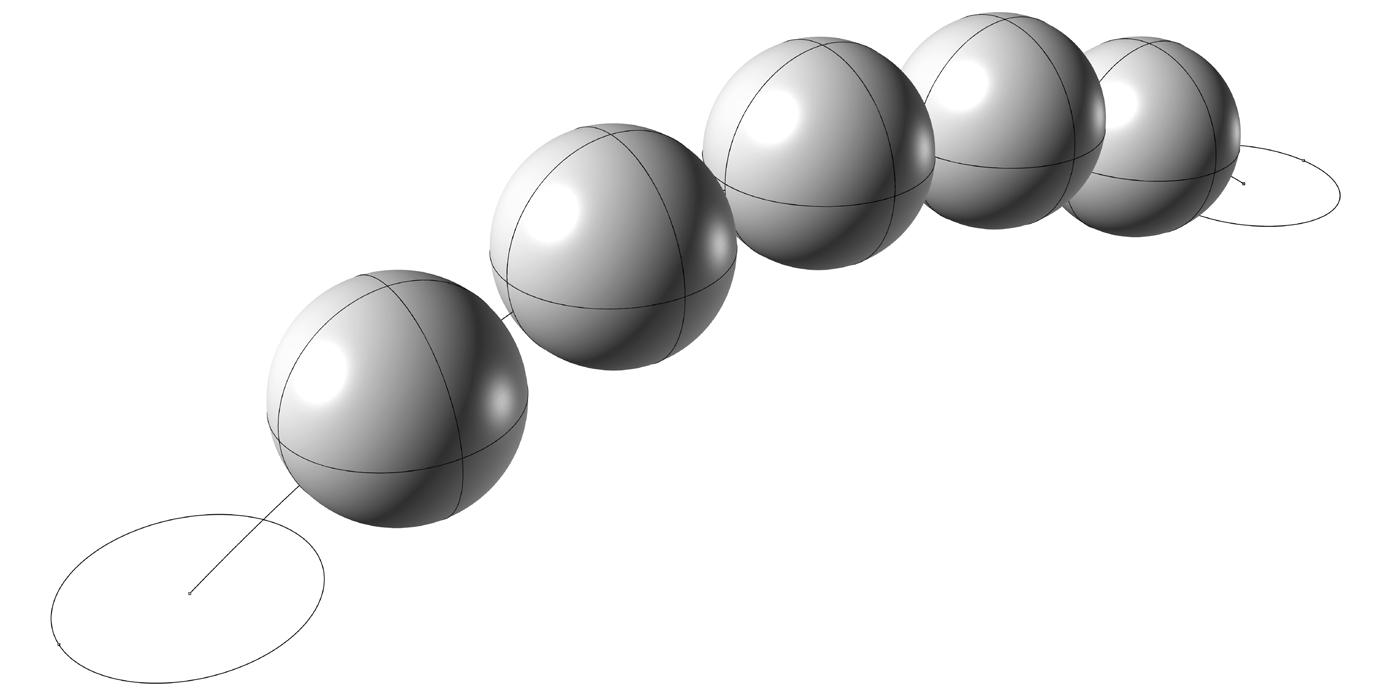
By automating the configuration of pneus as well as the density of points on the surface to braid through, a varied series of computational models can be developed relatively quickly. While the pneucable net configuration for this particular case study (shown in Figure 26) remains constant, the braiding pattern may change (Figure 27) based on the walking path necessary, as well as variations in visibility at specific points.
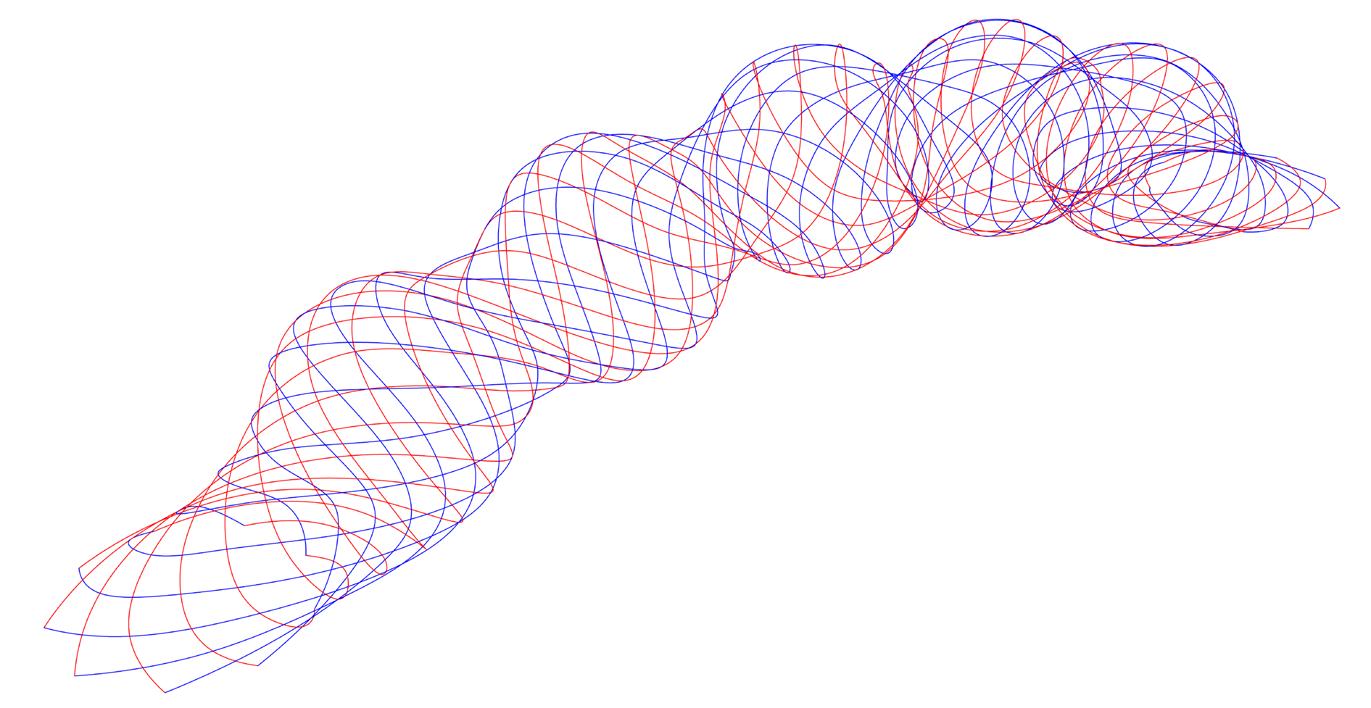
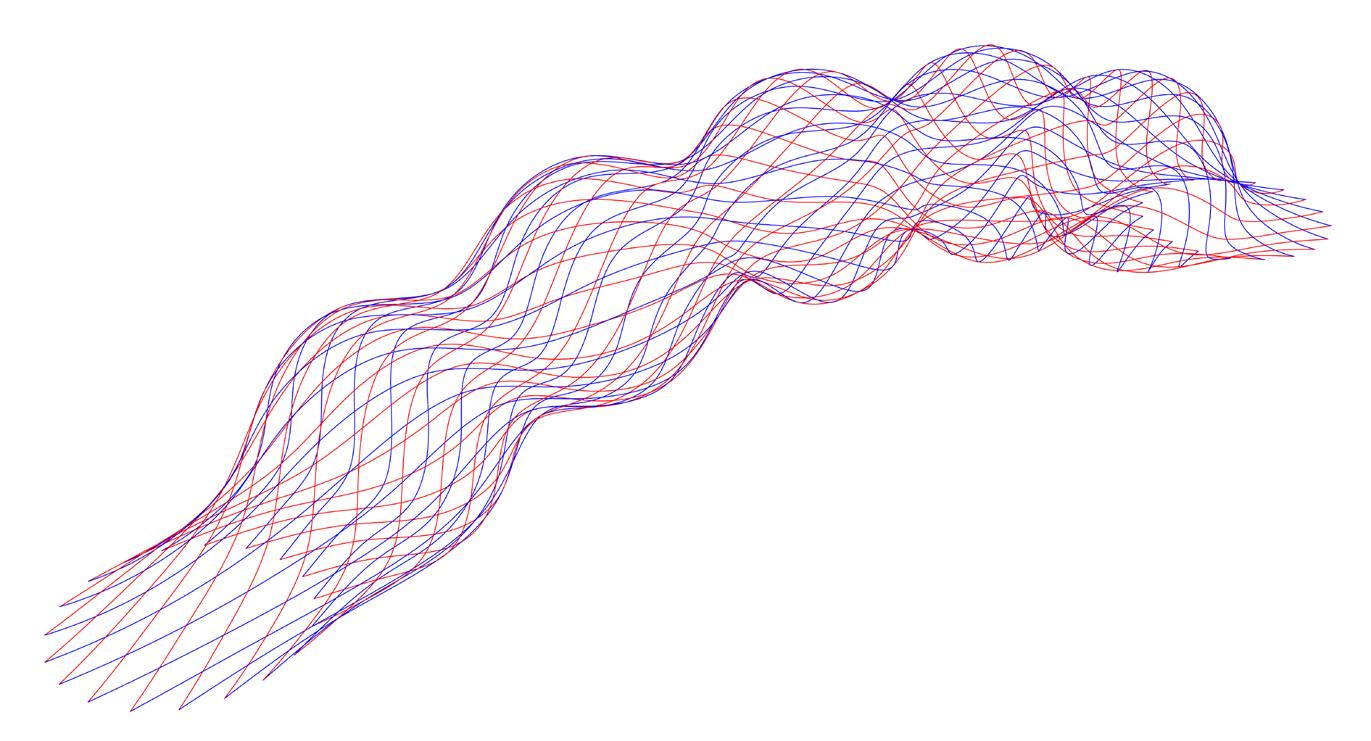
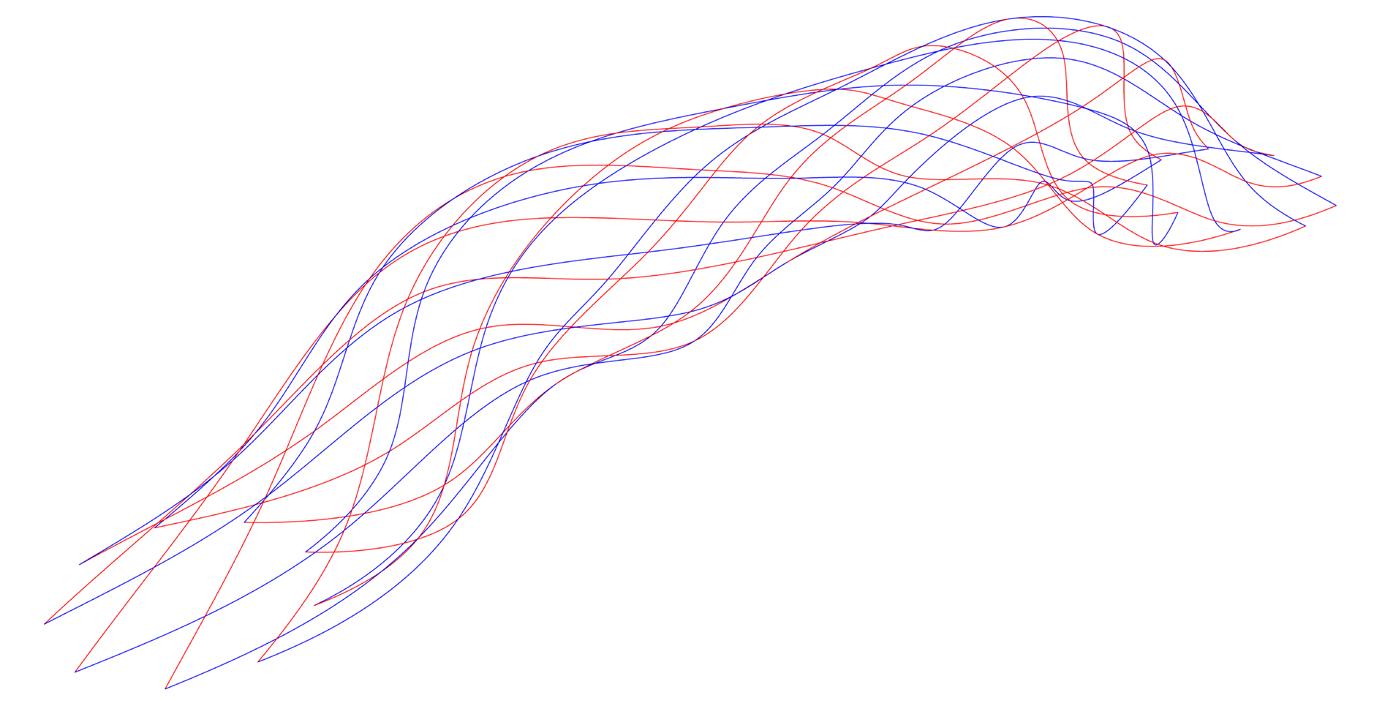
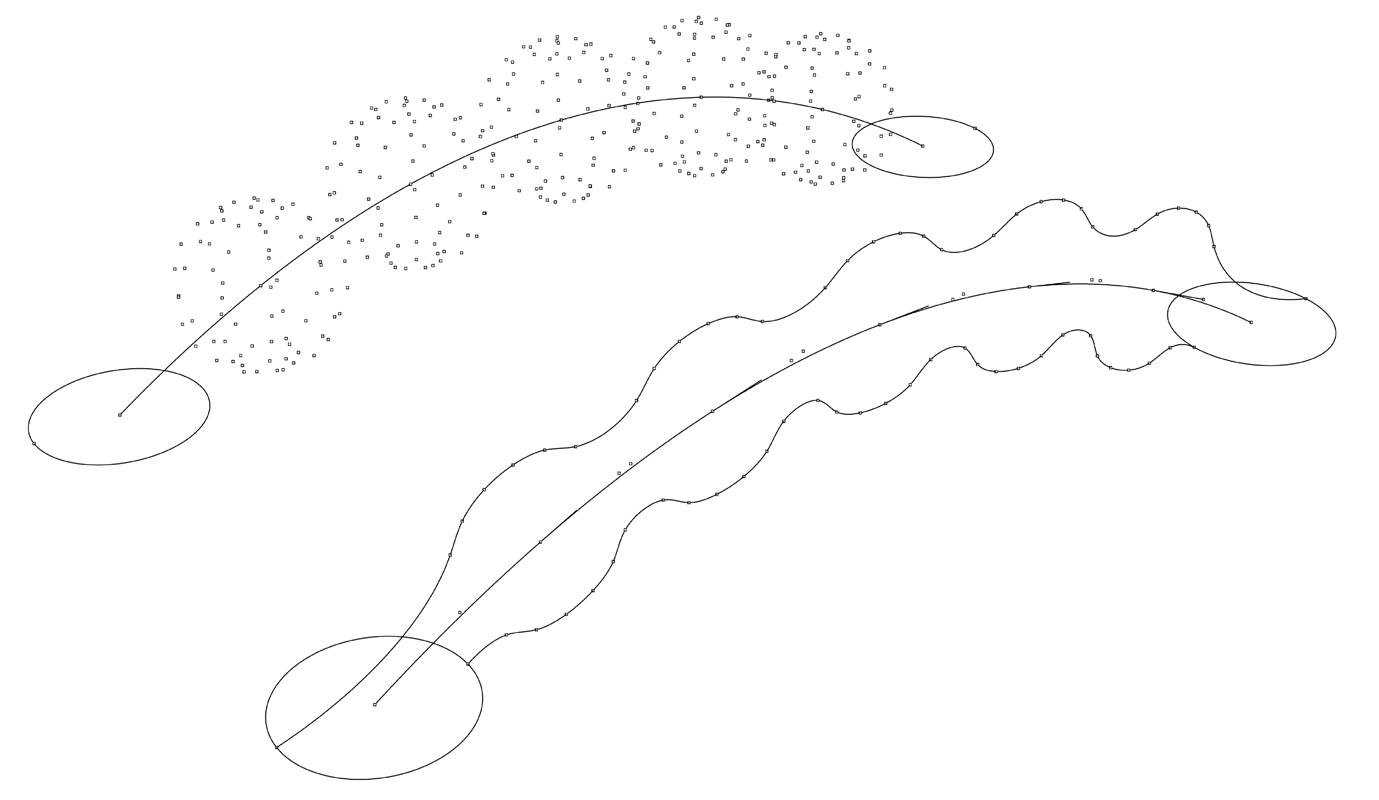
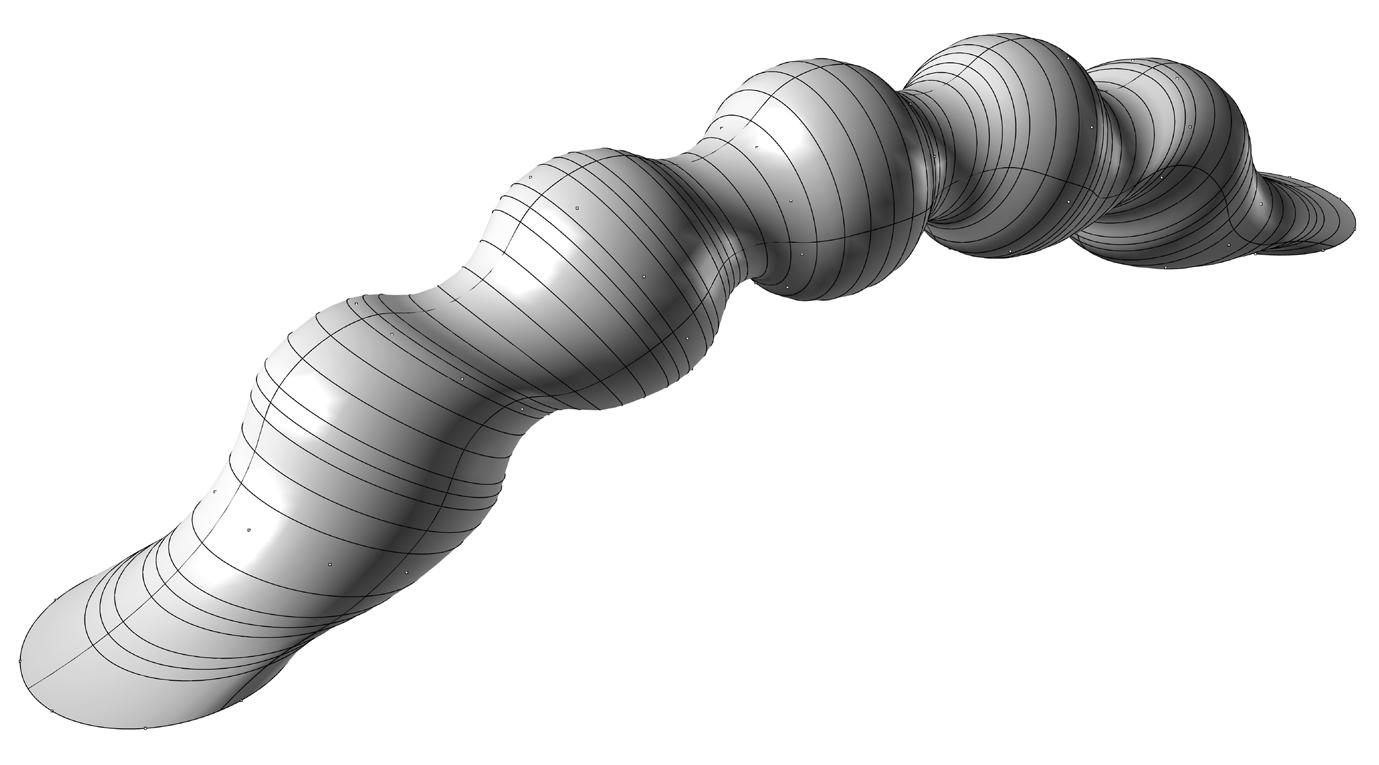
HYPOTHESIS
By controlling the fiber density of a fiber composite footbridge, a fully integrated path and structural system can be designed using the proposed thermoplastic pulbraiding fabrication technique. It is believed that this design method and fabrication technique can effectively be used to achieve the integration and control of fiber density of the proposed Patagonia footbridge.
CHAPTER 11 - CASE STUDIES AND DESIGN EXPERIMENTS
.0 DESIGN EXPERIMENT: PATAGONIA FOOTBRIDGE
DENSITY AFFECTS FORM - RELATIONSHIP TO THE MANDREL GEOMETRY
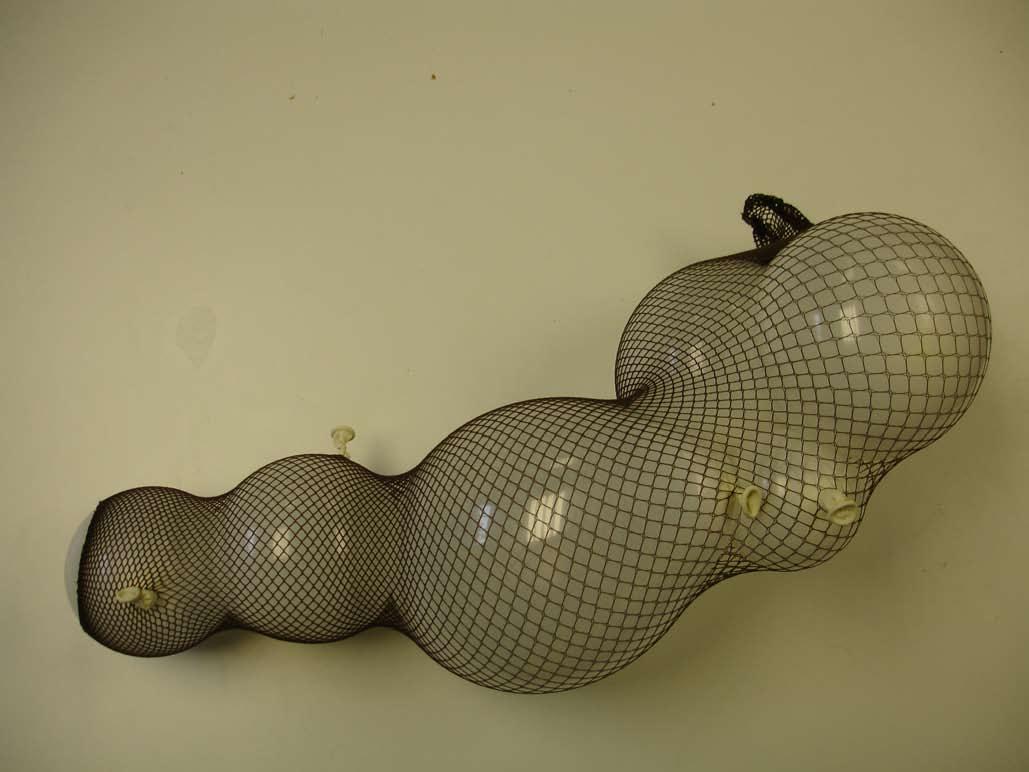
Point density accounts for two major changes in the configuration of the bridge. Because point density governs the number of nodes on the surface through which braiding occurs, the higher the density of points that exists, the “tighter” the braid; the braider will cross strands more often, and at smaller intervals, thus creating a form more directly resembling that of the mandrel geometry. If there are less braiding nodes, the braid will be looser. Figure 28 describes a braid with a surface point density of 10 - where there are 10 rings of 10 points each - uniformly spaced on the surface. Figure 29, in contrast, shows a braid configuration with a uniformly spaced surface point density of 20, resulting in a tighter, more defined global geometry.
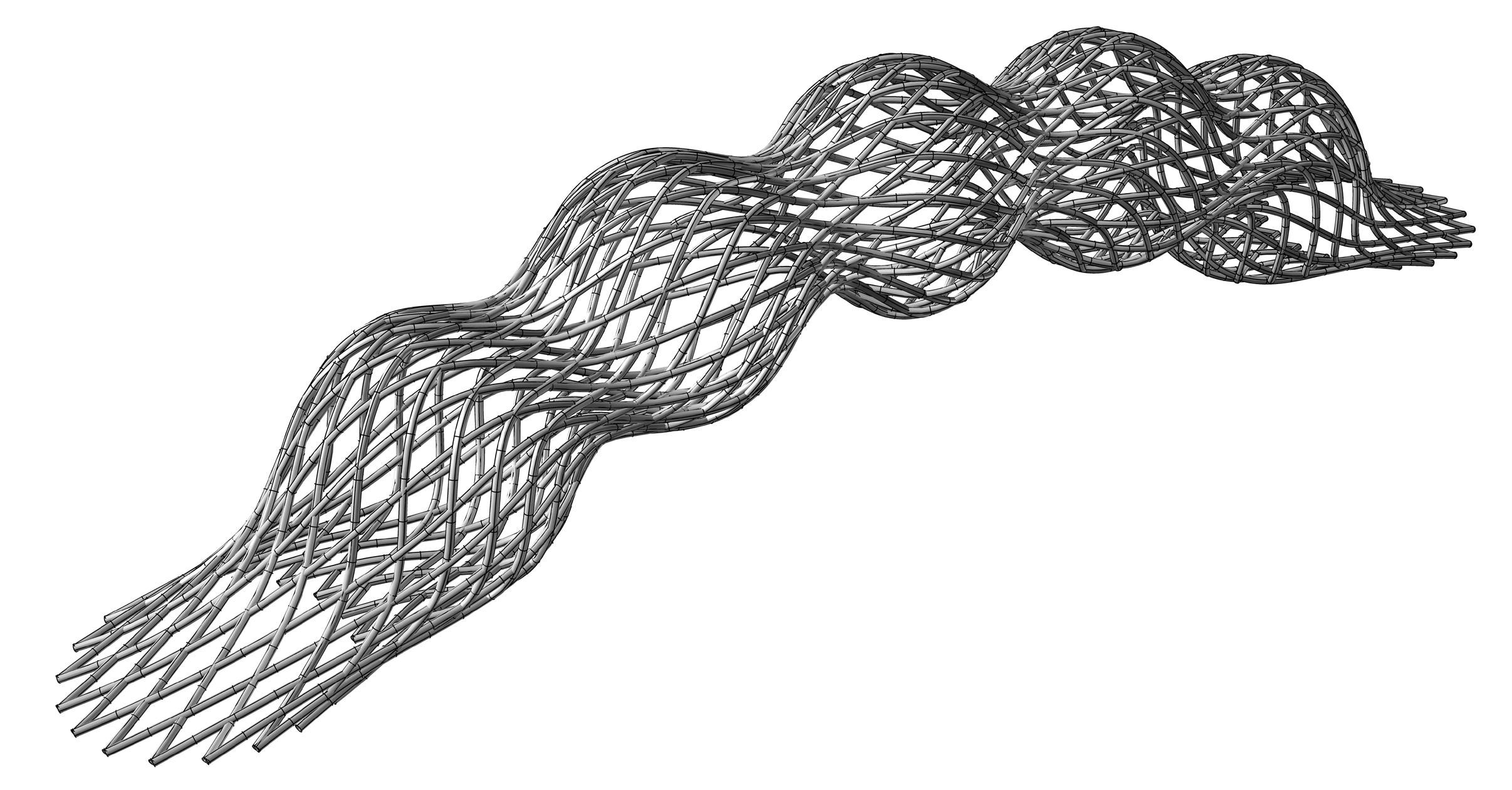
This is an important point in the discussion of the fabrication of a footbridge. The mandrel geometry, and fiber paths around it, have a direct causal relationship to form. The spherical pneumatic formwork proposed in this dissertation is the most important global morphological factor for the pulbraided structure (Figure 29a). While density will affect how closely the structure resembles the spherical nature of the formwork, the resulting form will always be a result of the mandrel geometry generated. However, as mentioned, density of points and therefore braid nodes will determine how close this resemblance is taken.
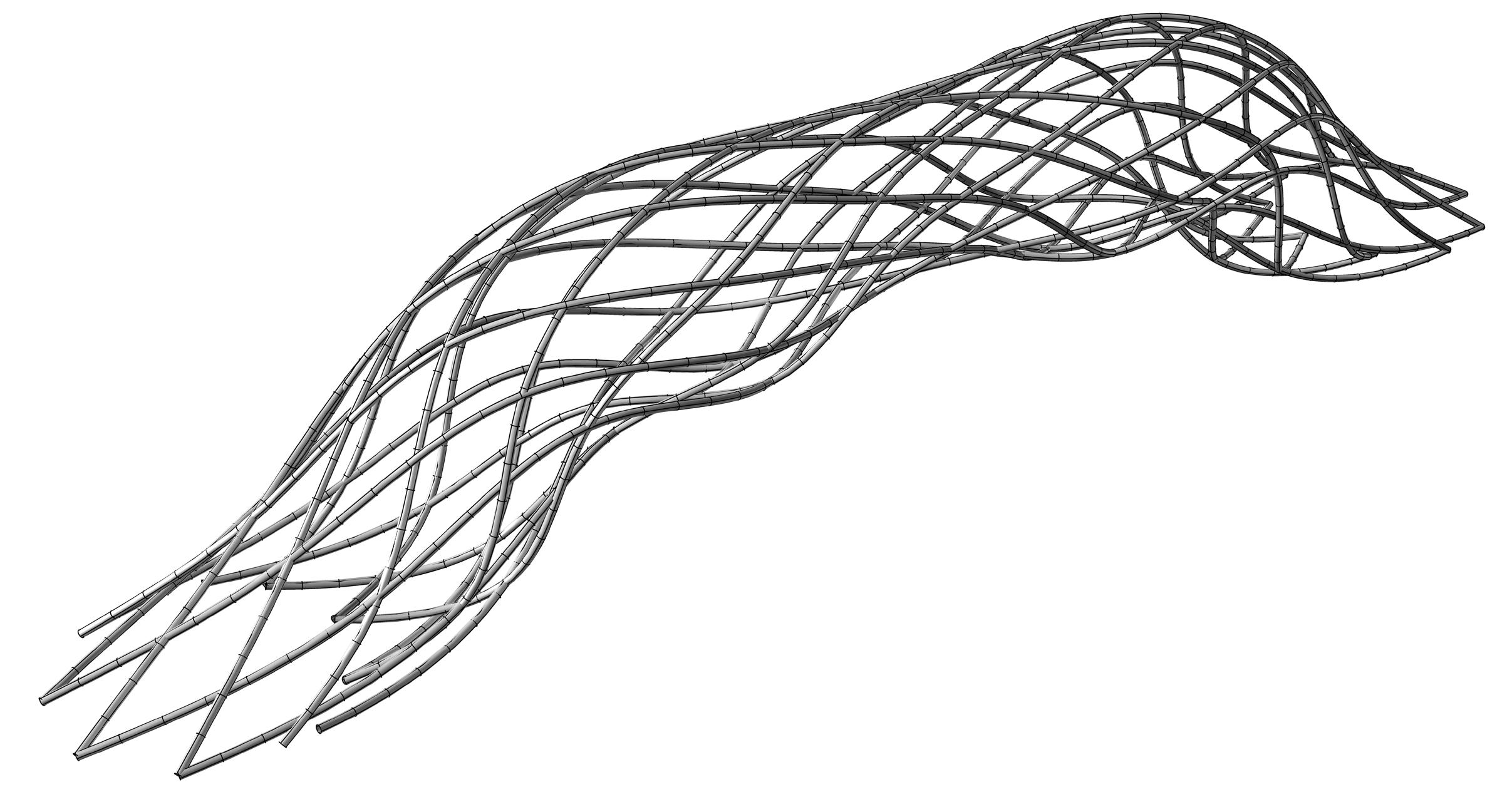
POINT DENSITY AND A WALKING PATH
While point density will affect the global morphology as discussed, it also affects the distribution of fibers. Both examples shown in Figures 28 and 29 describe uniformly spaced point nodes, thus resulting in a uniform braid pattern. However, by altering the spacing of these points, local morphological changes can occur, therefore allowing for the creation of an integrated walking path.
Again, it is important to be aware that mandrel geometry once again will affect the local walking path. The spherical nature of the pneus creates a non-perfect arch; however, the compliance of a walking path to building restrictions is not considered in this design experiment. By noting this phenomenon, it becomes a design consideration for further investigation.
CHAPTER 11 - CASE STUDIES AND DESIGN EXPERIMENTS .0 DESIGN EXPERIMENT: PATAGONIA FOOTBRIDGE
EXPLORING A WALKING PATH
By experimenting with varying point densities within each ring distributed on the surface, nonuniform braiding patterns emerge. Figure 30 describes a braid pattern with a V-direction (longitudinal) surface point density of 10. However, each ring has a redistribution of points where 20 points are spread evenly across its bottom half, and 10 points across its top. This differentiation in point density, driven by a simple computational function, allows for control and experimentation of possible walking paths. It was found, as shown in Figure 31, that this point density leaves gaps between extruded members (with a radius of 3 cm each), and therefore cannot function as a proper walking surface. By reorganizing point density and placement, a configuration with 20-point rings is tested next. In each of the 20 rings, the bottom half contains 40 points evenly distributed, while the top contains 20. While the global morphology approaches one similar to the pneus in which the braider works around, and can be spatially more interesting, the walking path generated, although sufficient and without gaps, is rather large. Considering the control available over the braiding pattern, a narrower footpath is desired, thus lightening the structure. Figure 32 shows this configuration.
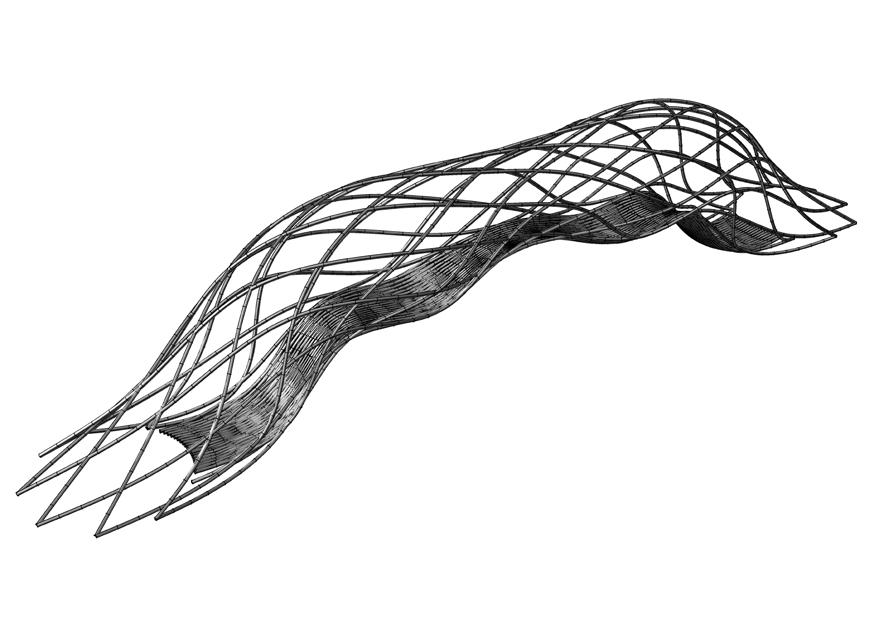
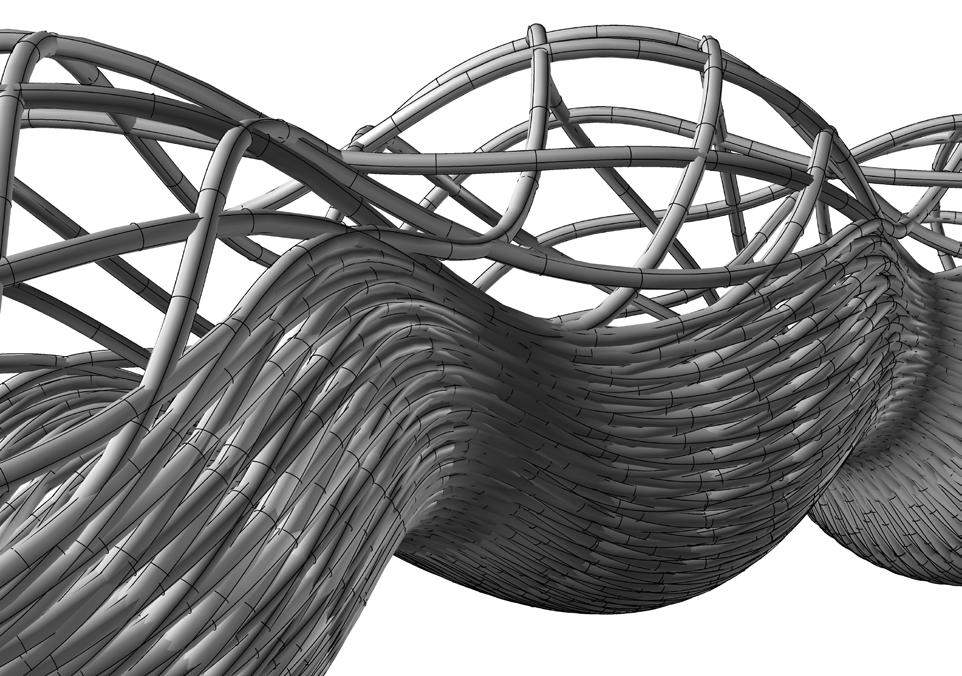
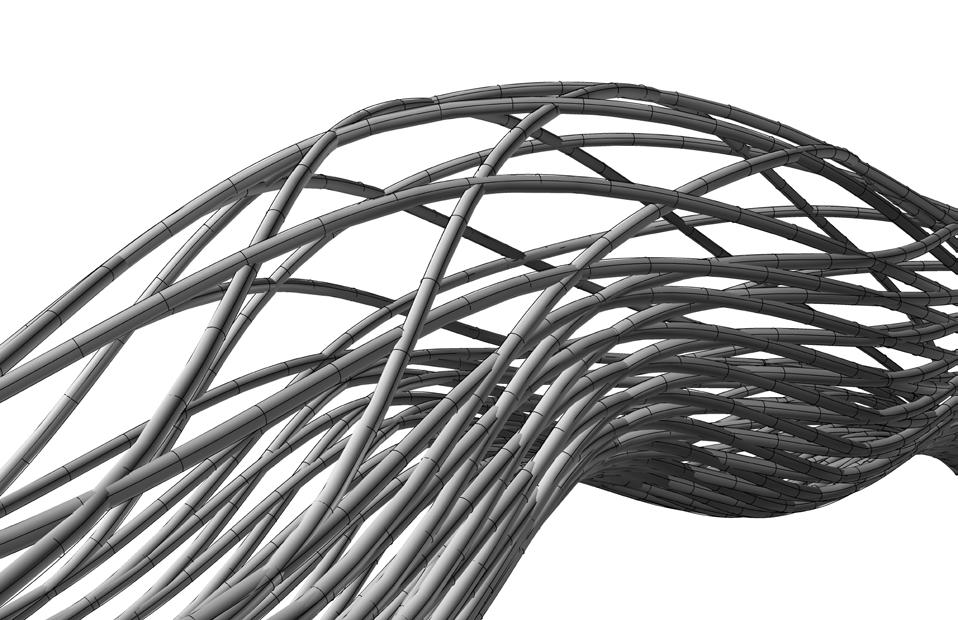
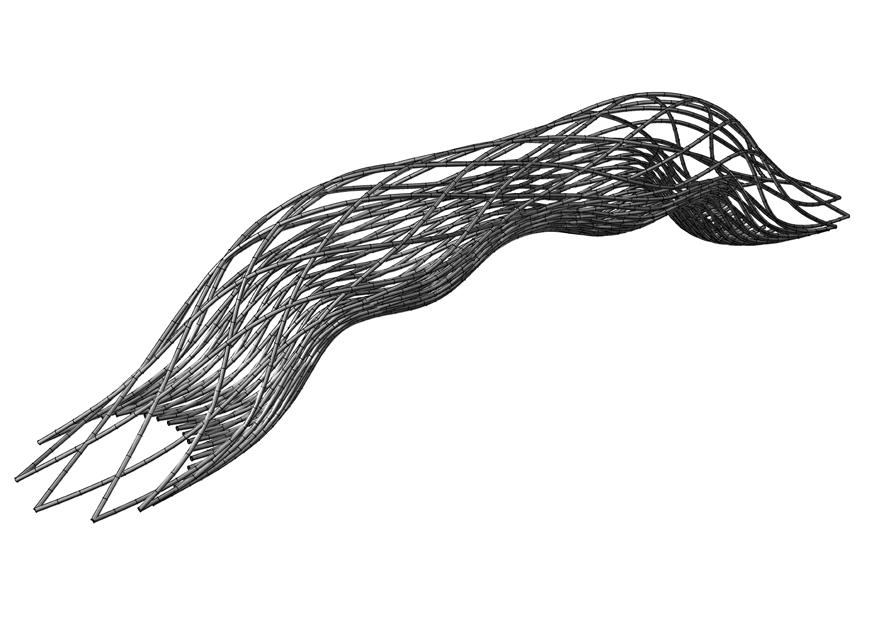
CHAPTER 11 - CASE STUDIES AND DESIGN EXPERIMENTS .0 DESIGN EXPERIMENT: PATAGONIA FOOTBRIDGE

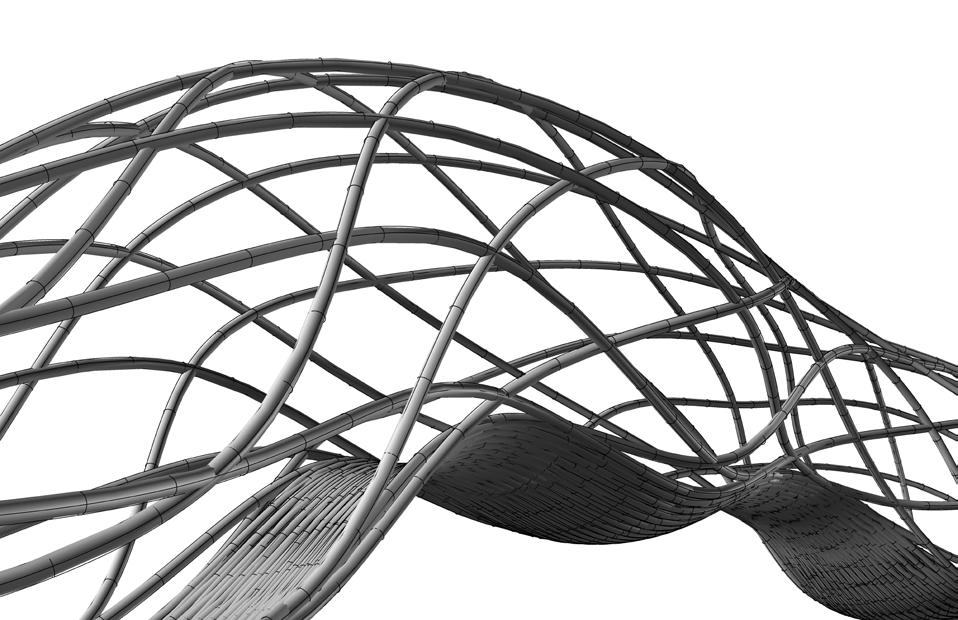
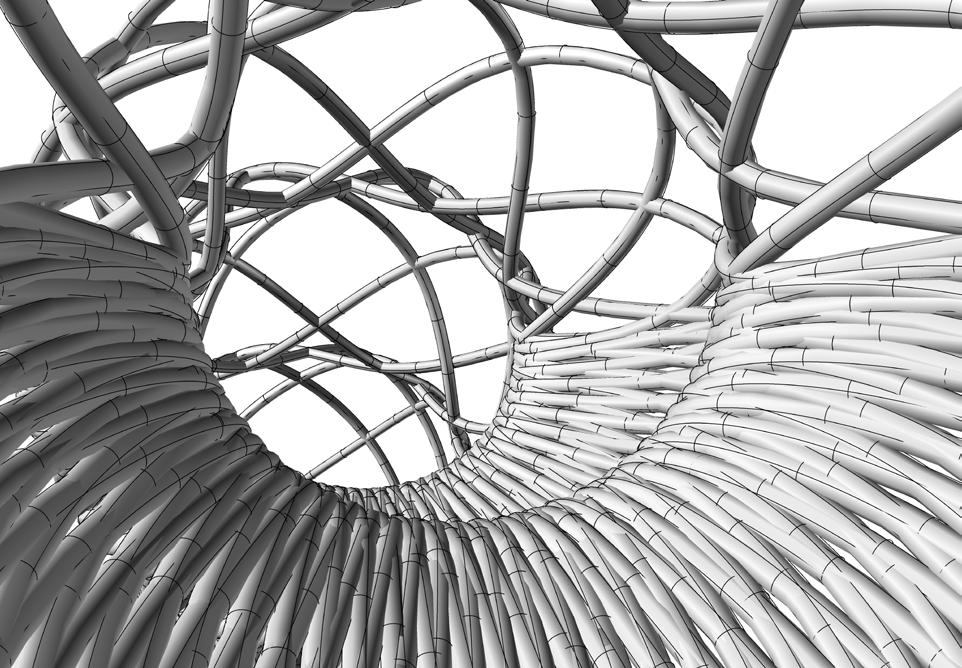
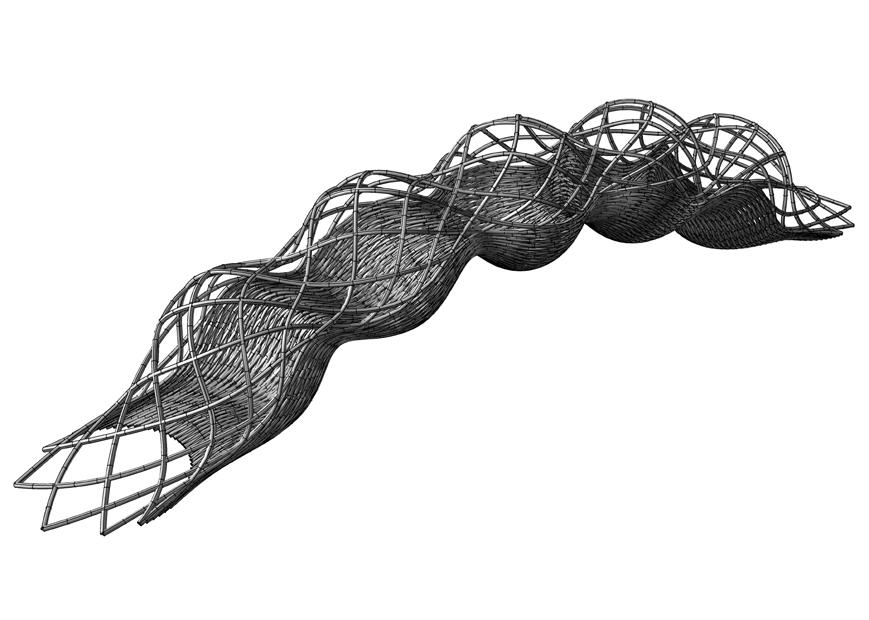
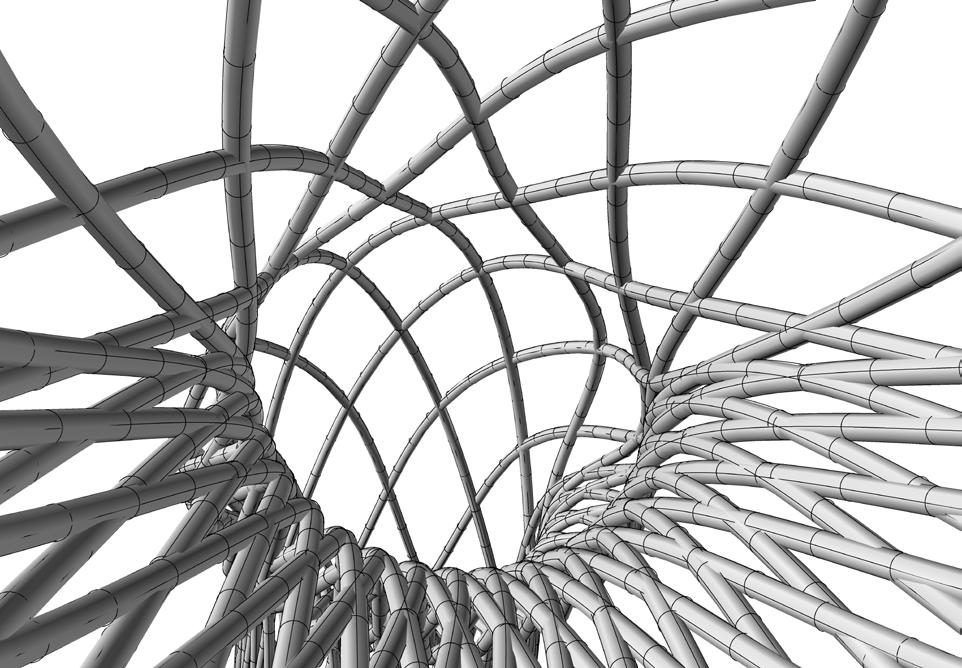
entry condition ground condition
Figure 33, diagram, pointing out two local conditions posing crucial design problems. While braiding density configuration - and therefore morphology - is solved on the global scale, both the entry condition and ground condition are two local instances that must be investigated, and will in turn affect the global condition.
LOCAL CONDITIONS
It is important to mention the local conditions that exist when investigating the construction of a new structure. For this footbridge case study, the two conditions most prevalent are how the structure meets the ground and how the bridge is entered and exited (Figure 33).
ENTRY CONDITION
The entry condition is a special condition where the local braid pattern must be changed to accommodate an opening large enough through which to walk. This local braid change, while successfully creating a suitable entry condition, will have repercussions on morphology.
By skipping the two innermost nodes on the second ring of braiding points (Figure 34), but continuing the regular braid pattern logic executed throughout the entire structure (see Figure 35), an entry to the bridge can be achieved. However, this entry condition creates another local condition which must be observed. As Figure 36 details, four rods converge at one node. While this condition is possible to control using the pulbraiding technique, it must be considered that a local change in dimension will occur, due to the complexity of the over-under-over condition. This geometric complexity is explored on the following page.
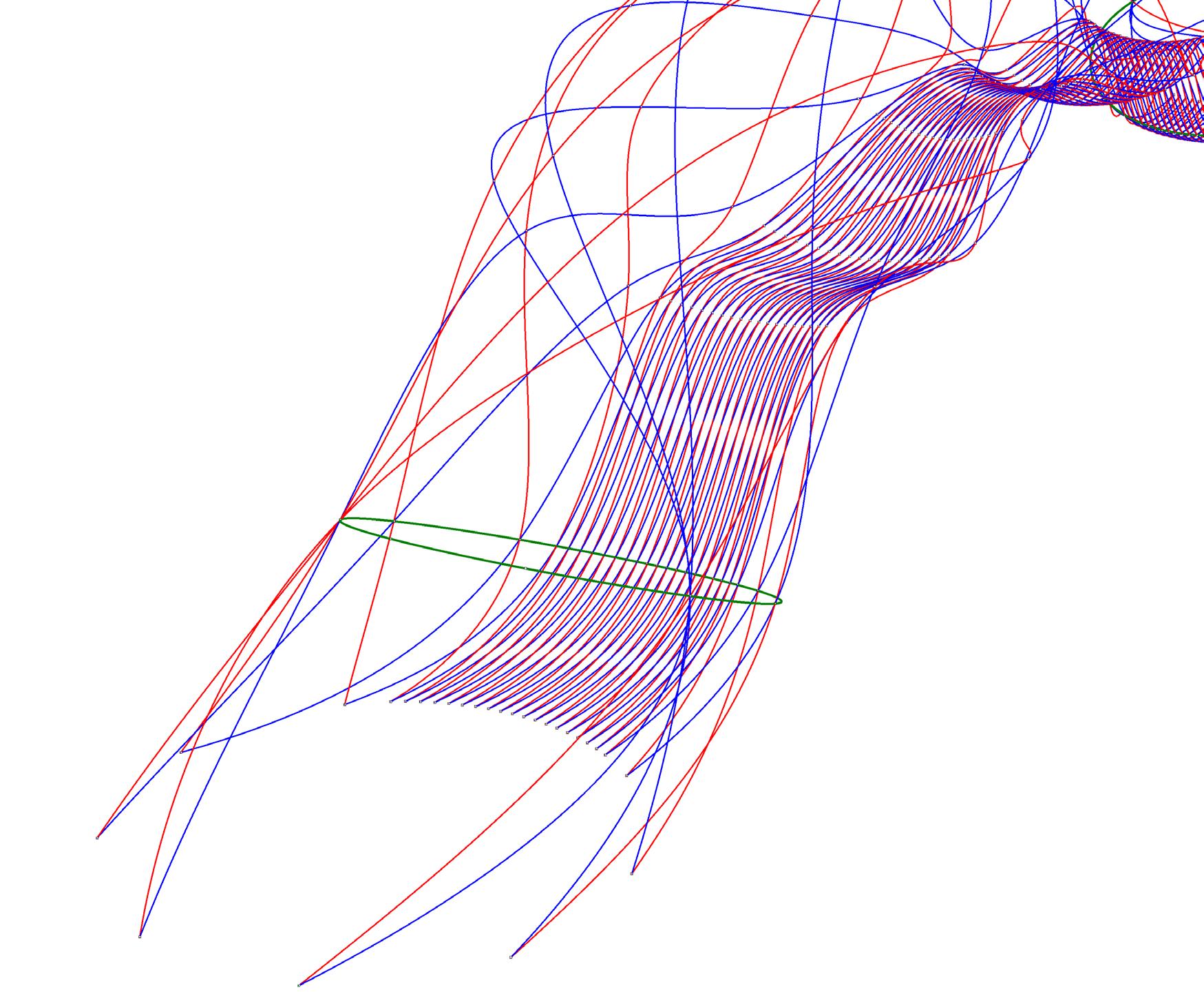
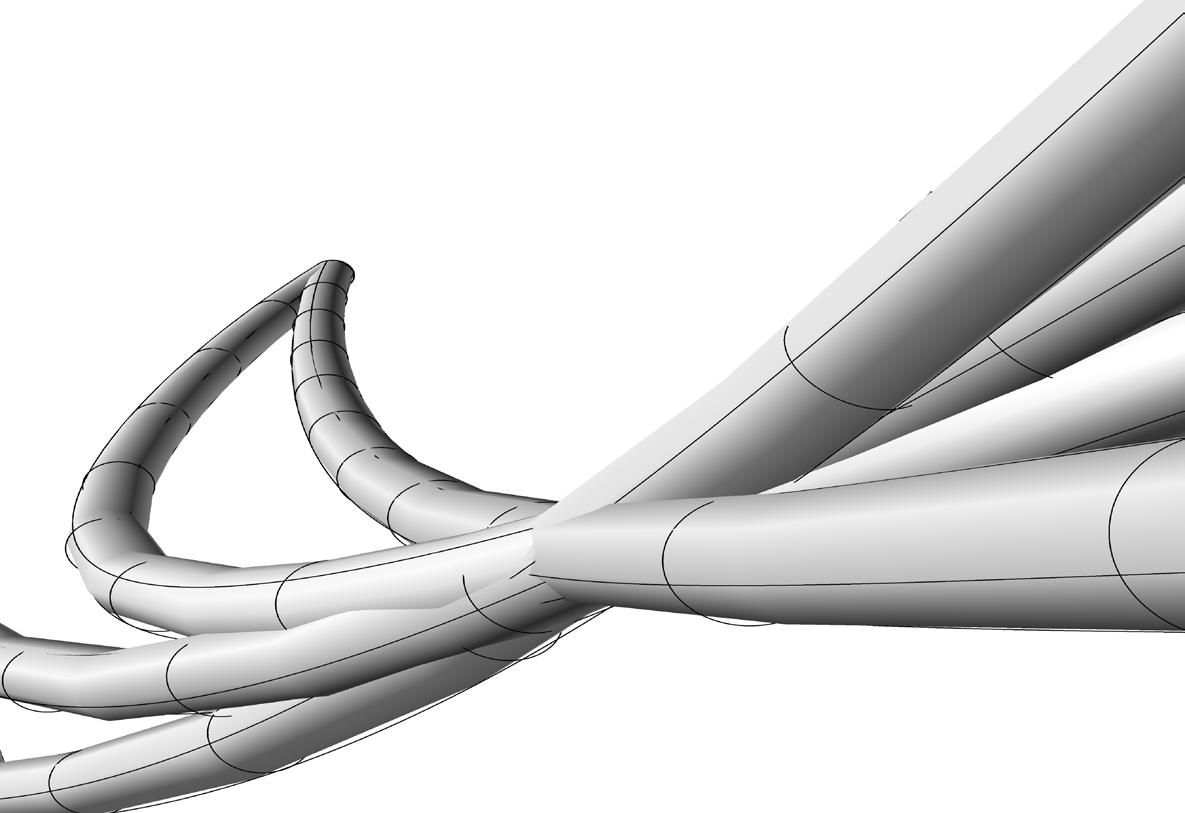
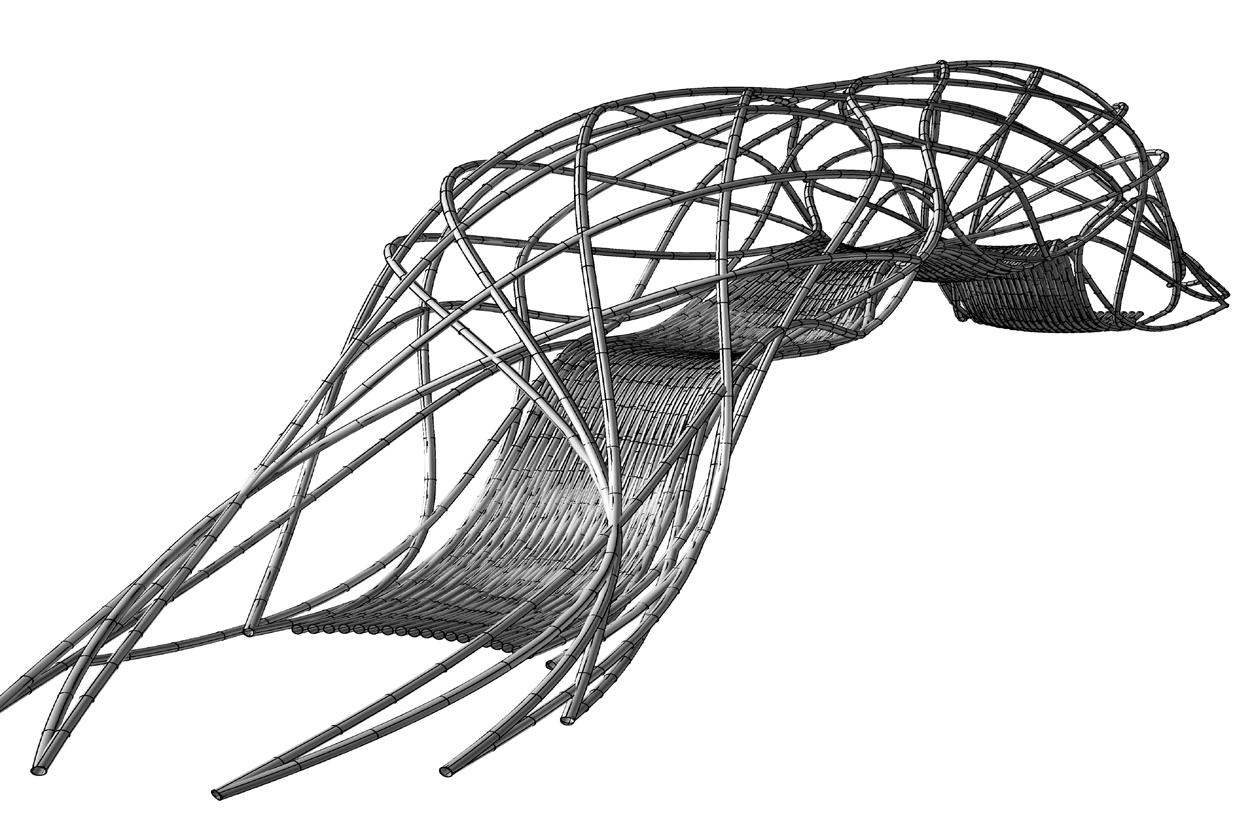
CHAPTER
11
- CASE STUDIES AND DESIGN EXPERIMENTS
.0 DESIGN EXPERIMENT: PATAGONIA FOOTBRIDGE
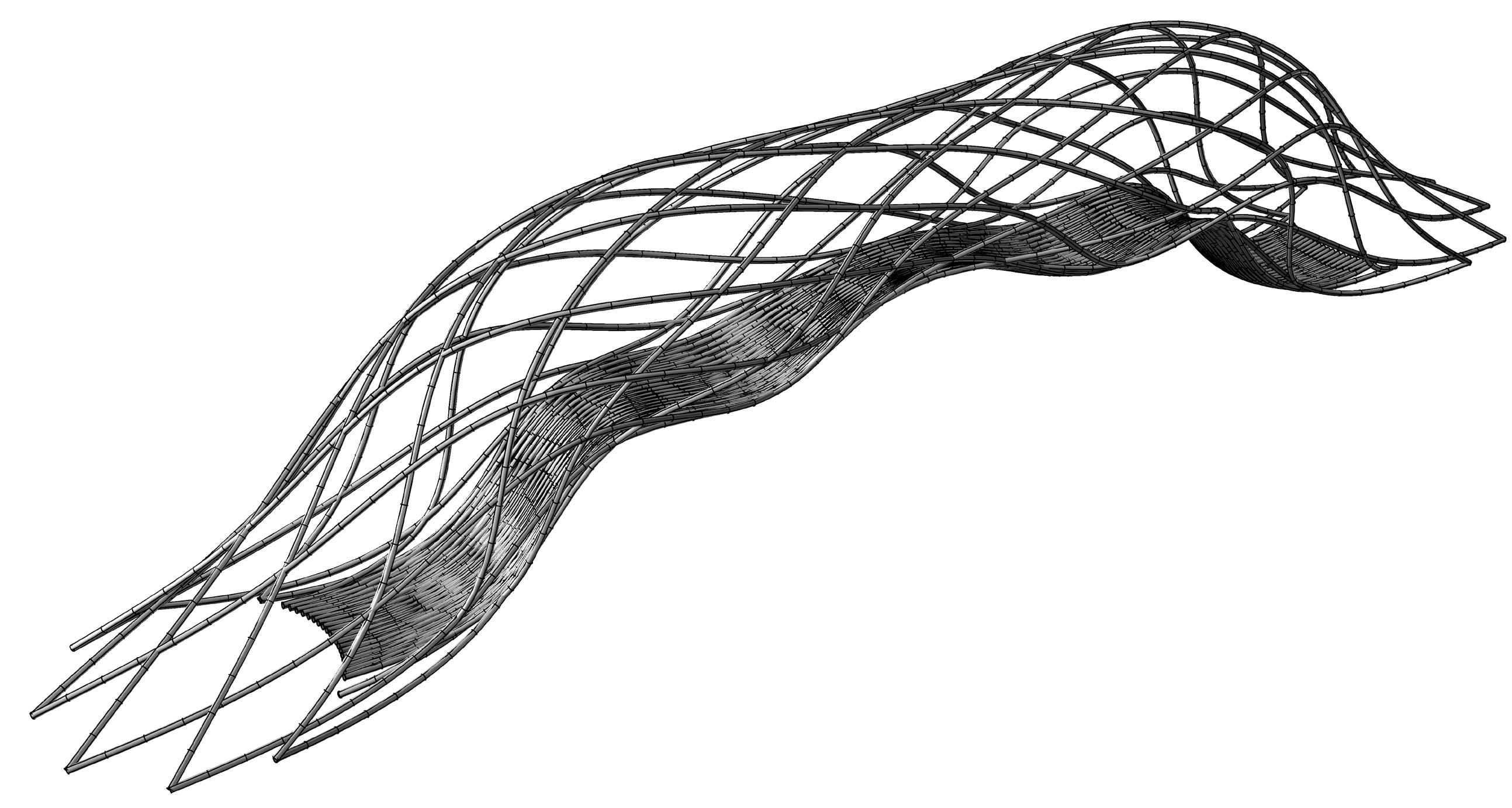
HIERARCHIES EXPLAINED
The complex fiber path resulting from multiple rods meeting at common nodes causes an interesting junction. The joint diagrammed in Figure 37, for example, describes the joint that occurs when four different braided strands converge as a result of the entry created. The configuration clearly illustrates the hierarchies involved in the pulbraided structure; each colored rod in Figure 37 represents a braided strand that is then braided with other strands in an over-under-over fashion.
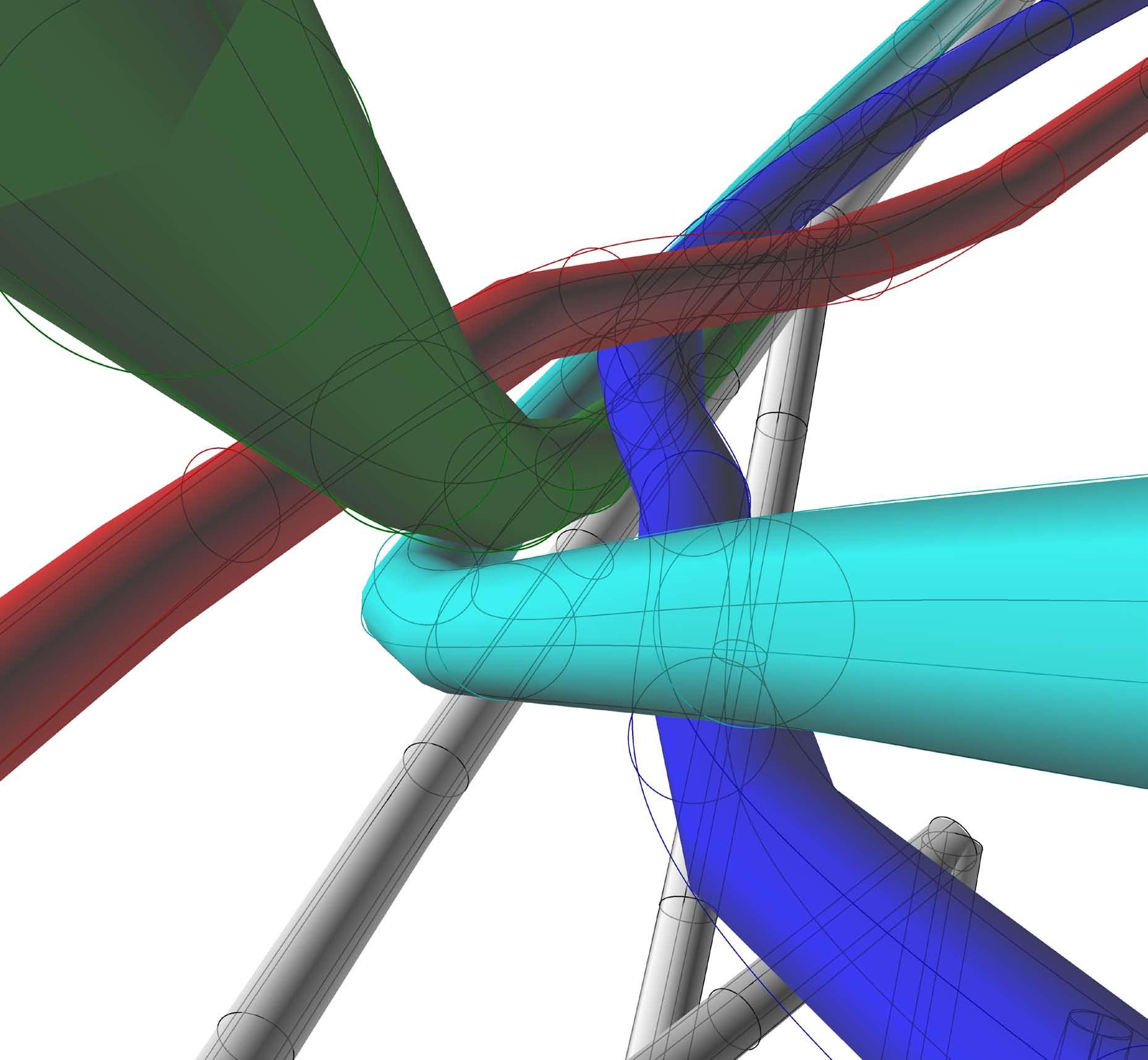
CHAPTER 11 - CASE STUDIES AND DESIGN EXPERIMENTS
.0 DESIGN EXPERIMENT: PATAGONIA FOOTBRIDGE
absorbing
GROUND CONDITION
A common area of negligence in the design and construction of fiber composite structures is its connection to the existing structure or ground (see section 3.01 for a description of the connection conditions for Testa’s Carbon Tower and Doumpioti’s Adaptive Growth of Fiber Composite Structures). It is often an afterthought of the design, and not integrated into the logic from the start. However, with the advantages of control in the thermopastic radial pulbraiding process, it may be possible to integrate this condition into the design.
In typical steel bridge construction, twisted steel cables break ground and are embedded in a concrete matrix (Figures 38-40). While this is an effective solution, it requires construction details that are external to the global logic of the bridge’s material system, and therefore is not the most efficient. While this anchoring solution actually is a composite - steel cables in a concrete matrix - this solution would not be viable for a radially overbraided glass fiber composite structure. Creating a single braid, without a hollow core, is not possible with the fabrication technique proposed. A 3D braiding machine would be necessary to create a solid braid. Since this is outside the scope of this research, an alternative solution must be explored.
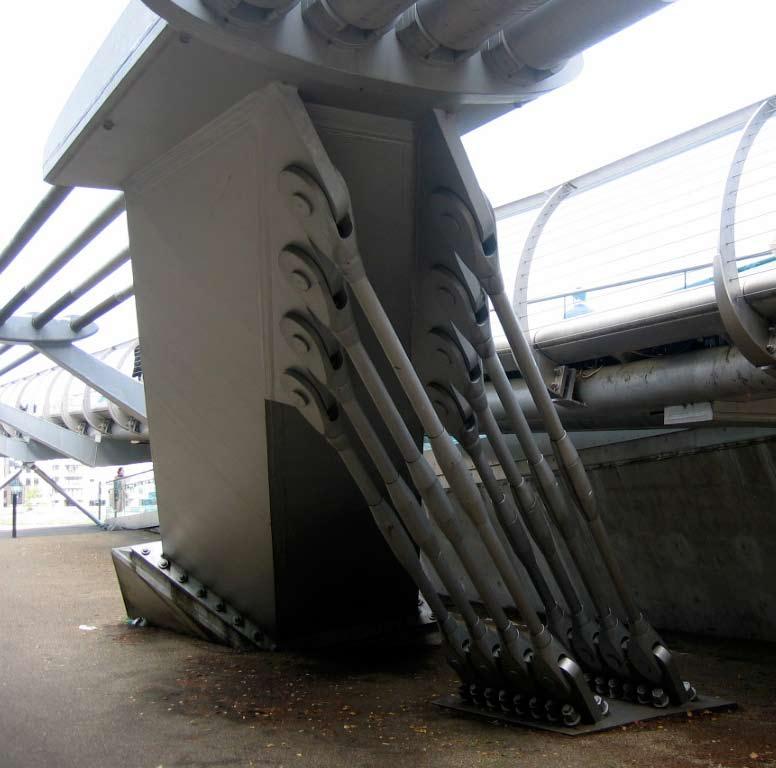
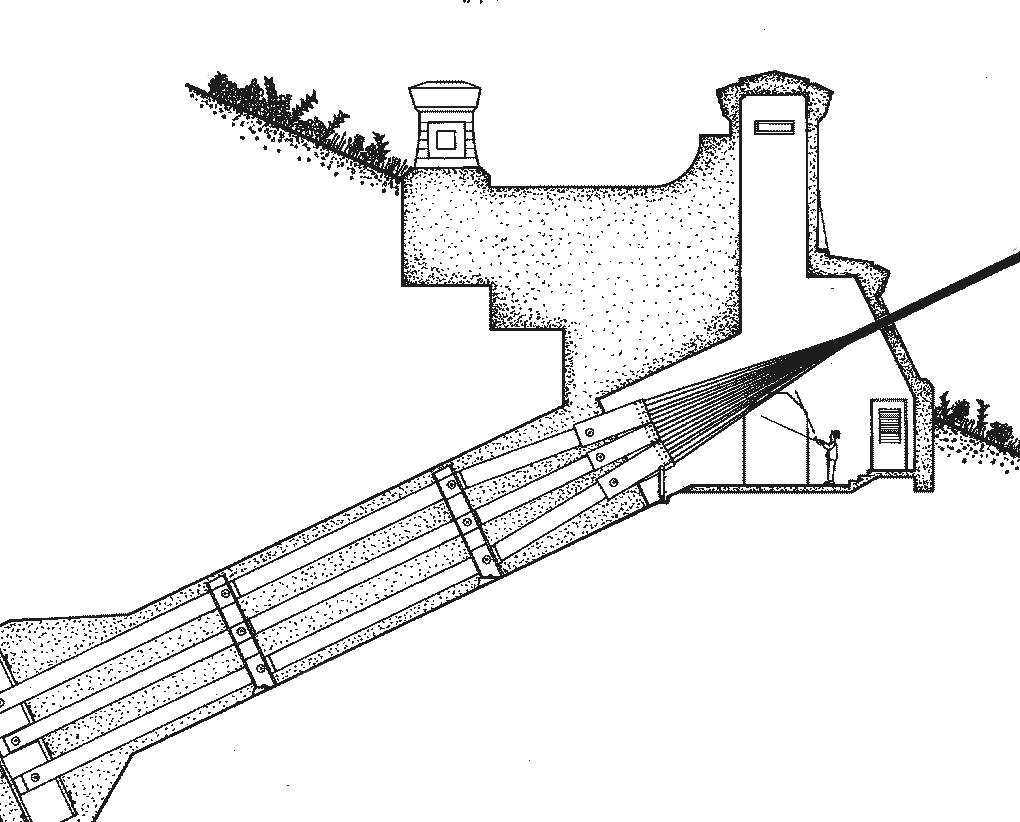
Because there is a clear hierarchy of braids in the global structure, it is hypothesized that by breaking down larger braids into their components, a branching structure can be designed to anchor the structure into the ground. It is crucial to understand branching patterns in order to integrate this logic into the design of a fiber composite structure. Branching patterns in trees can accurately explain this logic, and give insight into its use in this specific design problem.
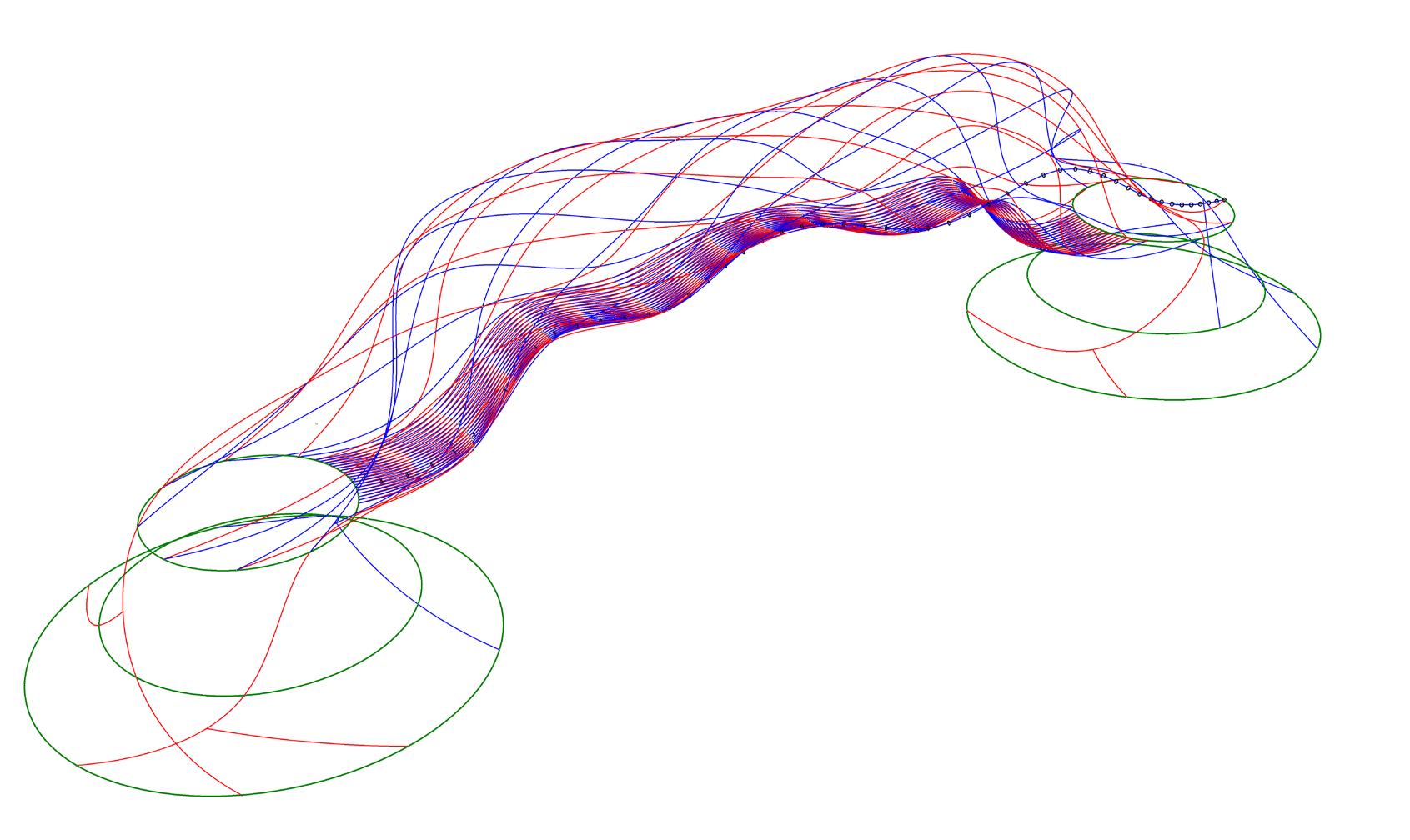
BRANCHING PATTERNS IN TREES
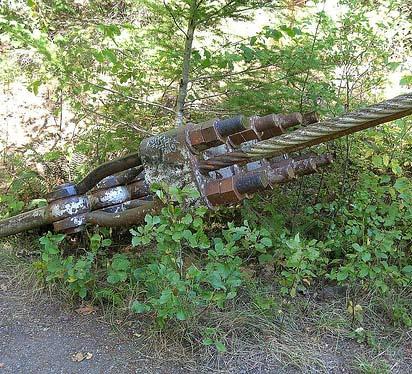
Trees branch in order to optimize sun exposure for their leaves, thus maximizing energy consumption. Similarly, roots branch in order to maximize water intake to allow for the process of photosynthesis. Although mathematical logics can be used to explain much of the patterns that emerge in tree branching patterns, the important logic to note in order to incorporate branching patterns into the footbridge being investigated is Murray’s Law. Murray’s Law states that the sum of the cubes of the radii of “daughter” branches equals that of the cube of the radius of the “parent” branch (Sherman, 1981). This can also be applied to root branching systems (Figure 41).
An interesting comparison, however, reveals that root branching continues to a much finer degree (because structural support of other roots is not an issue). These finer roots, then, are not used to ground the tree in the dirt, but rather only for the transportation of water into the tree. These roots lie within the first meter of ground, and more often, within the first 25 centimeters. It is then understood that only a small number of large roots are used to stabilize the tree into the ground. These roots grow further down into the soil, as well as outward in order to anchor the tree into the ground (Tree
CHAPTER 11 - CASE STUDIES AND DESIGN EXPERIMENTS
.0
DESIGN EXPERIMENT: PATAGONIA FOOTBRIDGE
A PROPOSED ANCHORING SYSTEM
It must be noted that a root system (Figure 45) will only anchor the structure if the soil conditions are suitable. The proposed site, in Hacienda Quitralco in Chilean Patagonia, has a thin layer of soil, roughly 25 centimeters thick, with a mixture of large rocks and soil below. The Emergent Technologies and Design Program at the AA School of Architecture constructed a form-found footbridge on this same proposed site, and used a low-tech anchoring system which holds in the ground’s soil, with the addition of rock. Figure 43 explains the anchoring system used.
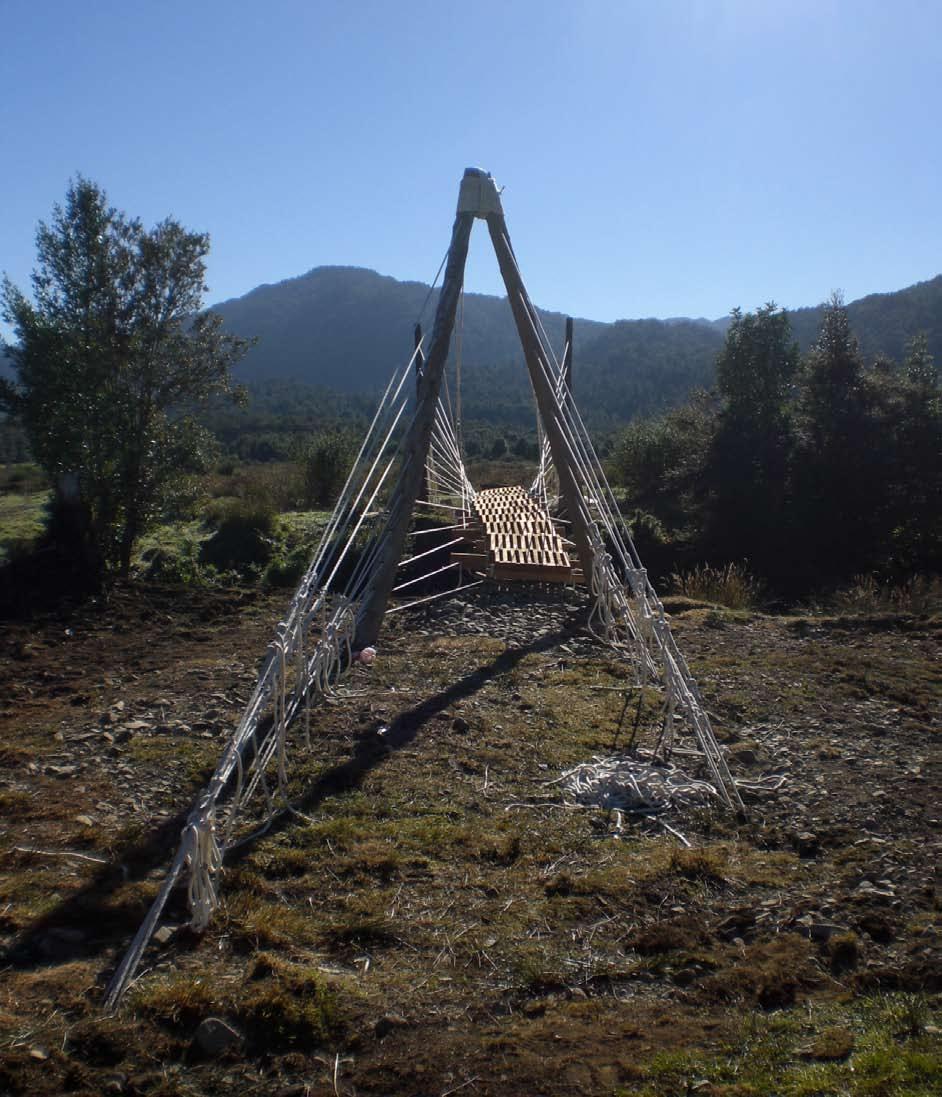
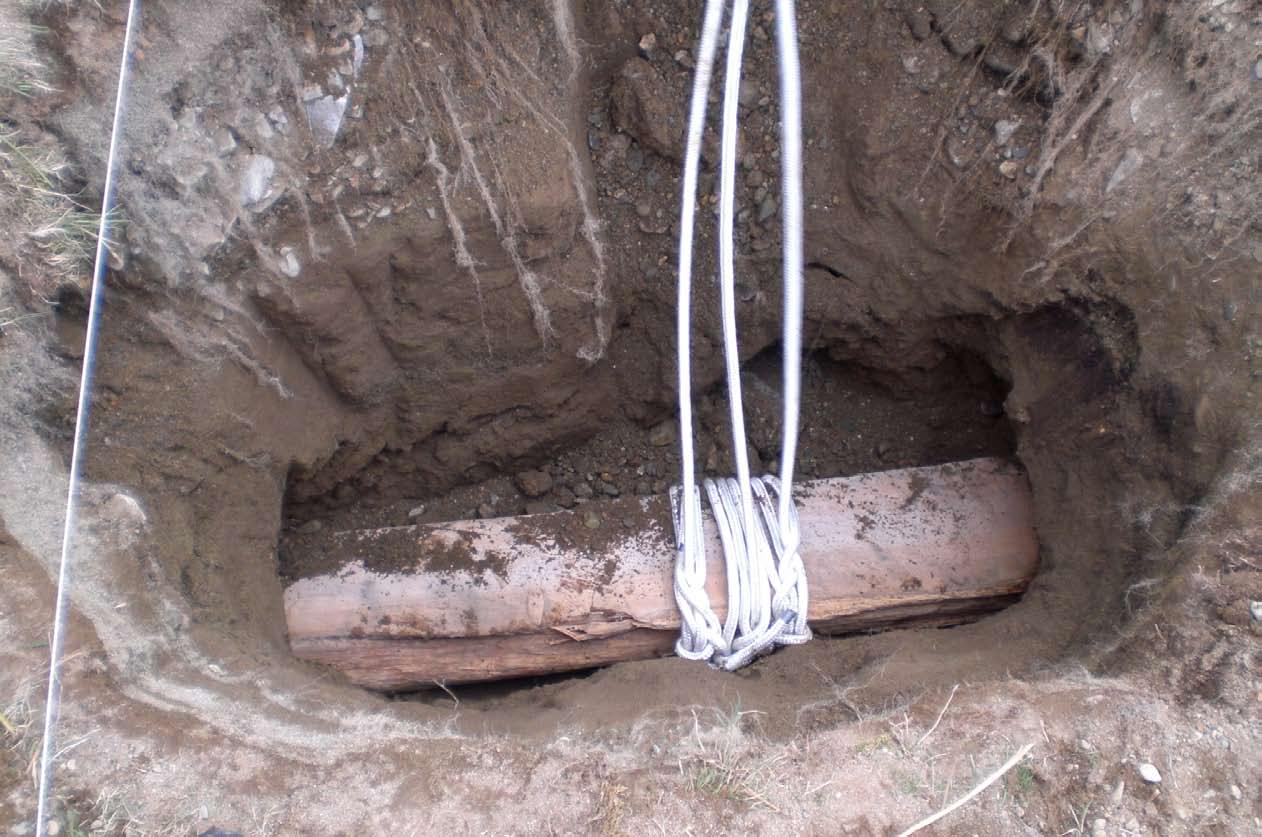
Although a root anchoring system is different than the one used (Figure 44), it is the soil makeup which is important to this study. The earth contains a large enough amount of rock for a root anchoring system to seem viable. Therefore, a minimal branching root system (Figure 45) is proposed.
CONCLUSIONS: FABRICATION POSSIBILITIES
This design experiment clearly exposes the viability of a novel fabrication technique to respond to necessary changes in braid density, braid angle, and global morphology. With the control of bobbins regulating glass and resin fiber organization on a thermoplastic radial pulbraider, this experiment is possible.
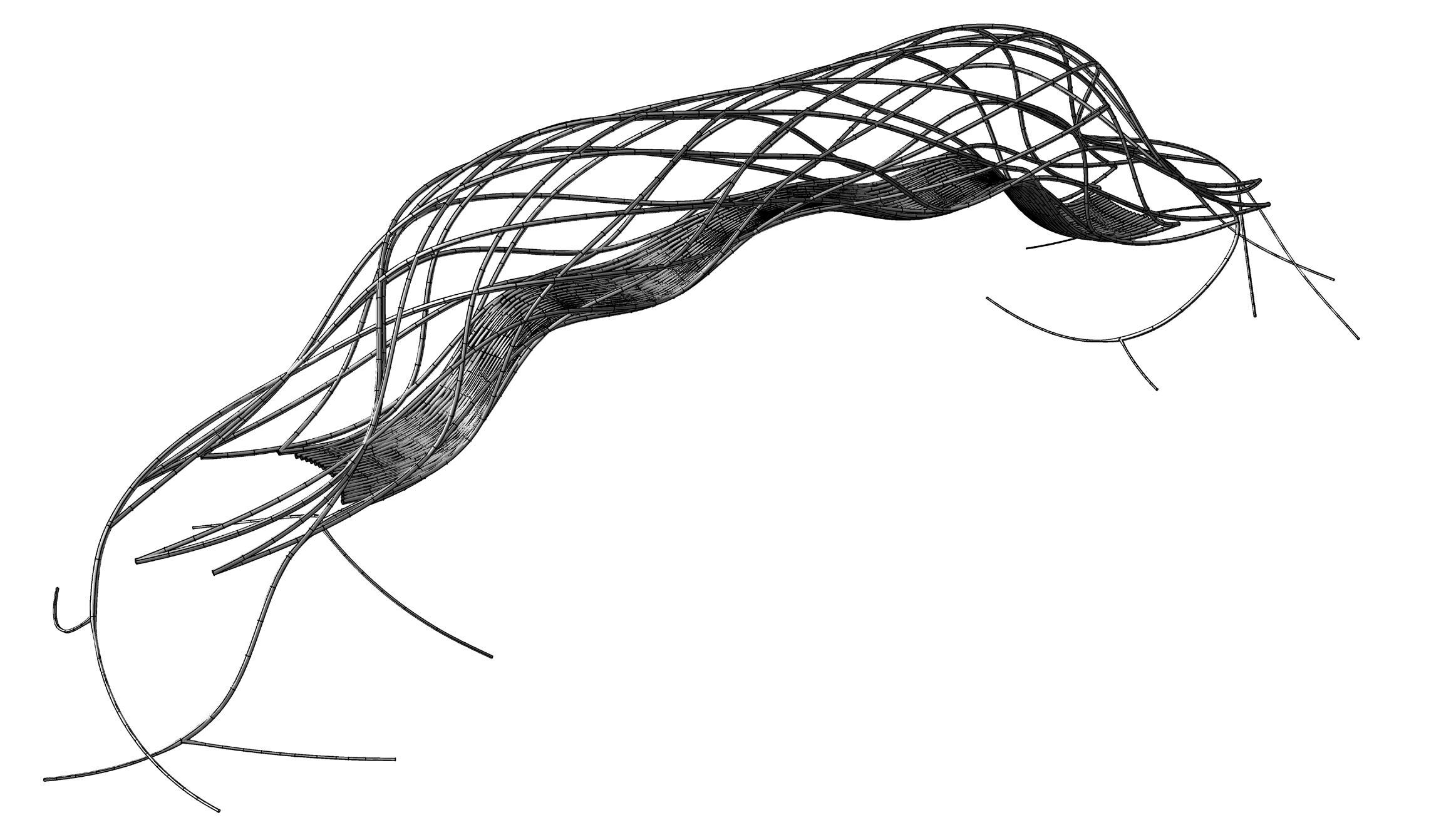
The issue of anchoring becomes an interesting area to investigate as well, considering the constraints of a novel technique. SImilar to the pencil tower experiment, the necessity for a braiding formwork poses a design problem for the tooling of the technique. However, in keeping with the aim of synthesizing the construction process, an alternative branching system is proposed, which is possible given the process constraints.
While this design experiment does not include structural analysis, it is important to reiterate the inclusion of structure within the fabrication technique. This experiment does, however, advance the viability of a material organization to become an architectural artifact. The ability to control this material through the tooling process is the direct cause of the end-result structure, therefore strengthening the argument that a synthesized fabrication technique exists, and can perform effectively.
CHAPTER 11 - CASE STUDIES AND DESIGN EXPERIMENTS
A SLENDER MUTLI-STRESS DRIVEN STRUCTURE
Guillem Baraut and Mattia Gambardella investigated the performance of a fiber composite bridge structure in their Emergent Technologies and Design Program Master Dissertation titled, Slender Multistress Driven Structures The aim of the dissertation was to define a design methodology by combining stressdriven form-finding with fiber distribution in structures in order to achieve a coherent design framework (Baraut & Gambardella, 2006). Within this research was the explanation of their proposed methodology realized in the design of a pedestrian footbridge (Figure 46).
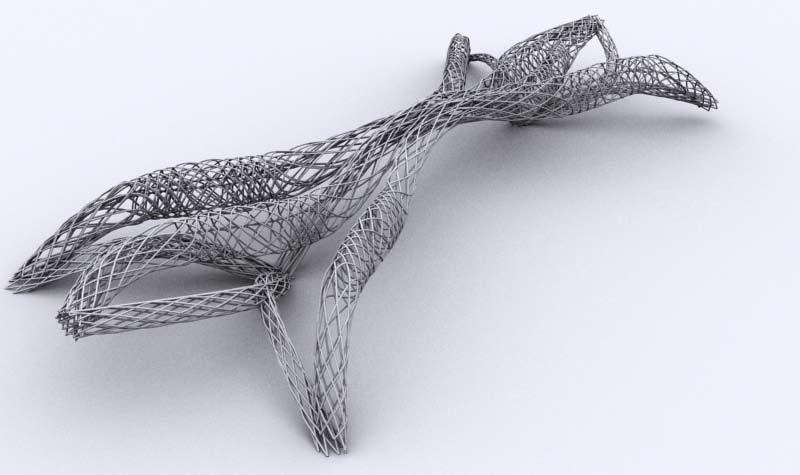
PROJECT SCOPE
The scope of this project included a series of physical and digital form-finding experiments to generate a stress-driven design method. While this design method is one possible solution in designing with structural performance in mind, it is not within the scope of this case study. This case study looks to critically analyze the manufacturing methods proposed as well as their viability in construction.
FIBER LAY-UP AND FOAM MOLDS
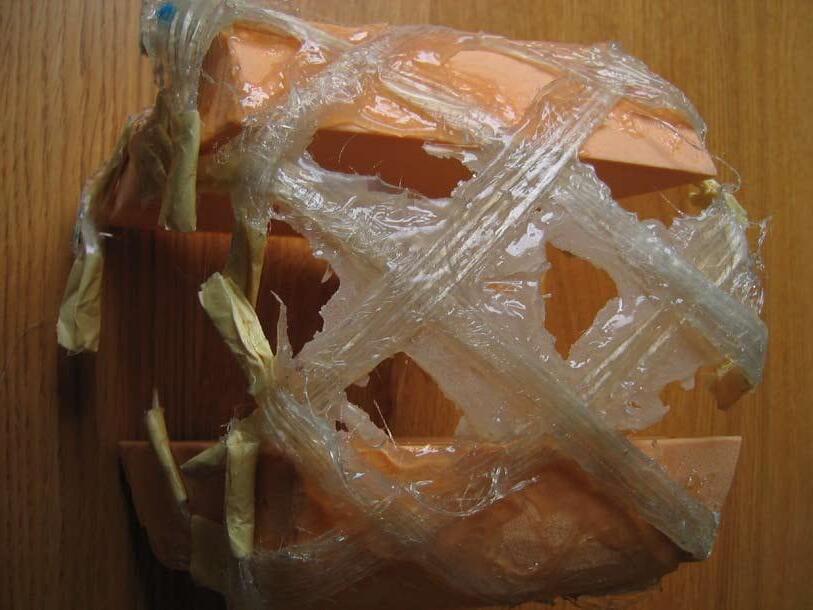
Much like most fiber composite structures, Baraut and Gambardella propose a foam mold generation method over which to lay glass fibers (Baraut & Gambardella, 2006). While the anisotropy of the material is respected, this fabrication method is not efficient. The project employs a foam mold where a “standard” rectangular section of foam is used as a core, while specialized mold sections are added to this to create a somewhat circular mold with paths for fibers to follow (Figure 47). While this may be a viable option at a small scale (Figure 48), it is difficult to conceive this as a viable large-scale option. This fabrication process brings up a series of manufacturing questions. Firstly, the size of each “standard” section is not mentioned; because the bridge design is so complex and sections are incredibly differentiated, it is unclear as to how small the “standard” section must be in order to accomodate these smallest areas of the bridge. Thus, if the easily reproduced section is only a fraction of the entire mold, the process becomes inefficient (Figure 49).
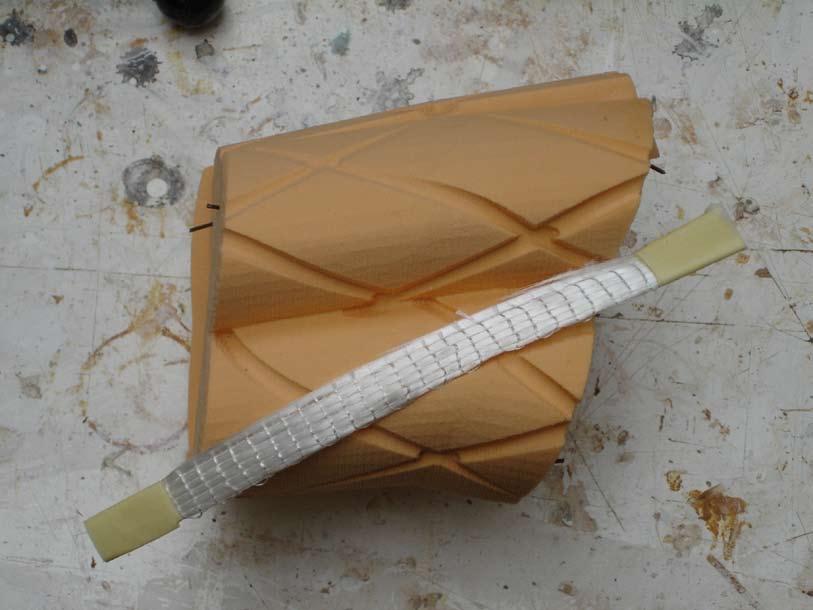
Secondly, this work references structural connectivity so that walking paths which cross internally are connected creating a more equal distribution of applied loads (Baraut & Gambardella, 2006). However, it is unclear as to how this complexity (Figure 50) can be manufactured. It does not appear possible that intertangled fibers can be laid upon a mold without serious problems arising.
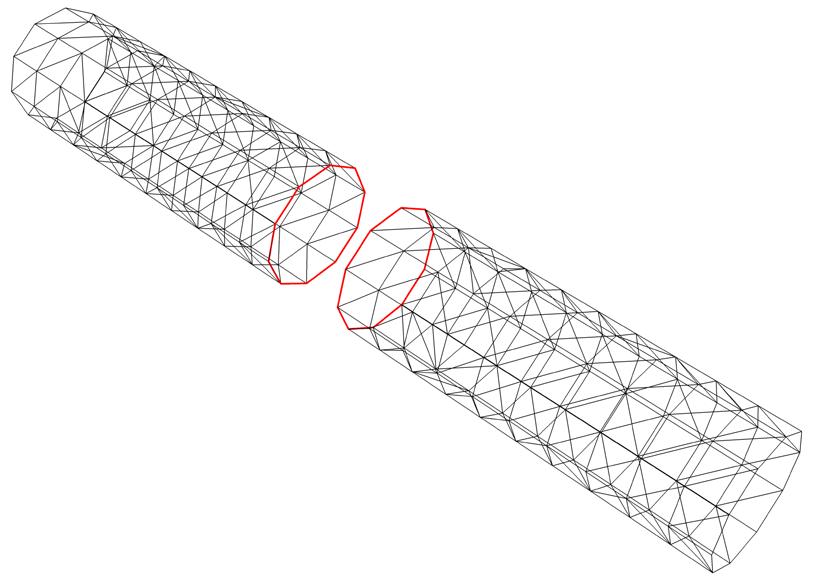
The next manufacturing question regards full-scale construction of the bridge. The research proposes off-site fiber lay-up on a mold with transportation to the site. This dissertation has already uncovered the major problematic aspects of transportation as well as the conceptual problem of connecting fiber composite parts - a material system that provides the opportunity for connectivity. Baraut and Gambardella propose a piece-by-piece assembly of the bridge without commenting on jointing methods or matrix options. Therefore, the structural connectivity issues previously mentioned become a greater concern without the investigation of how two bridge pieces come together, either consecutively (Figure 51) or through interconnectivity (Figure 52).
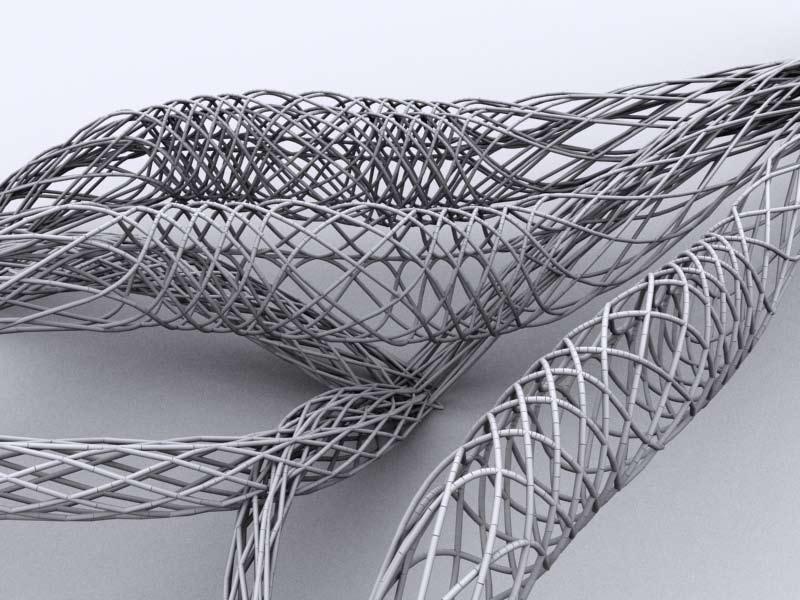
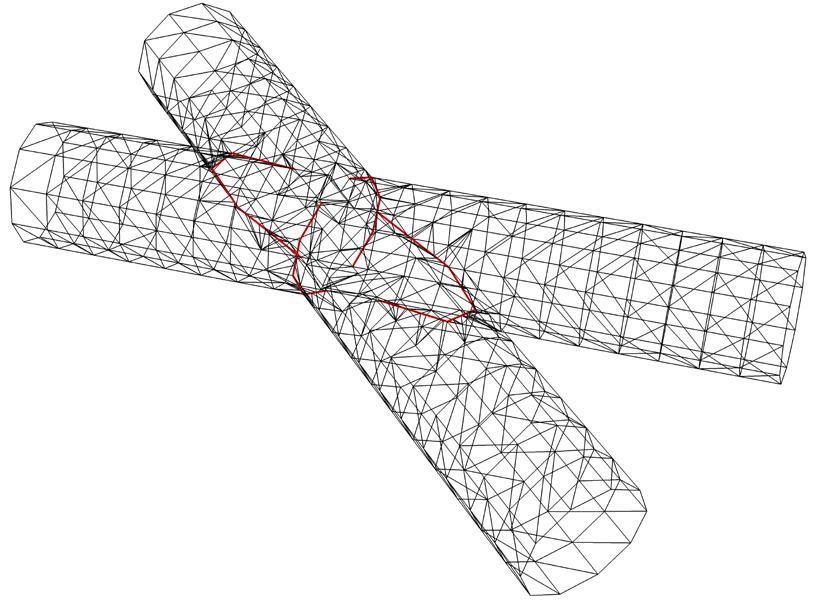
CHAPTER 11 - CASE STUDIES AND DESIGN EXPERIMENTS
11.05 CASE STUDY: BARAUT/GAMBARDELLA FOOTBRIDGE
COMPARING TWO FOOTBRIDGES
Baraut and Gambardella’s footbridge proposal is evaluated through two different analyses - spatial and structural. A comparative analysis between their footbridge proposal and the Patagonia footbridge design experiment undertaken in this body of research will uncover potential performative capabilities between two similar-looking structures with quite different fabrication techniques.
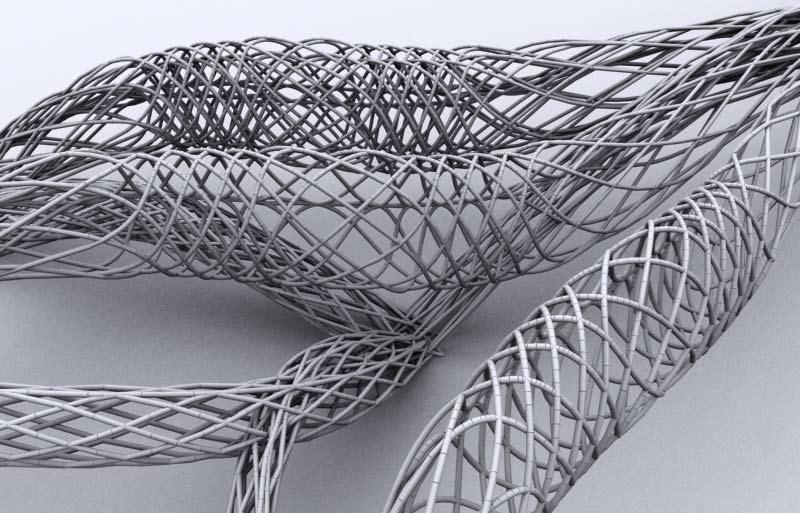
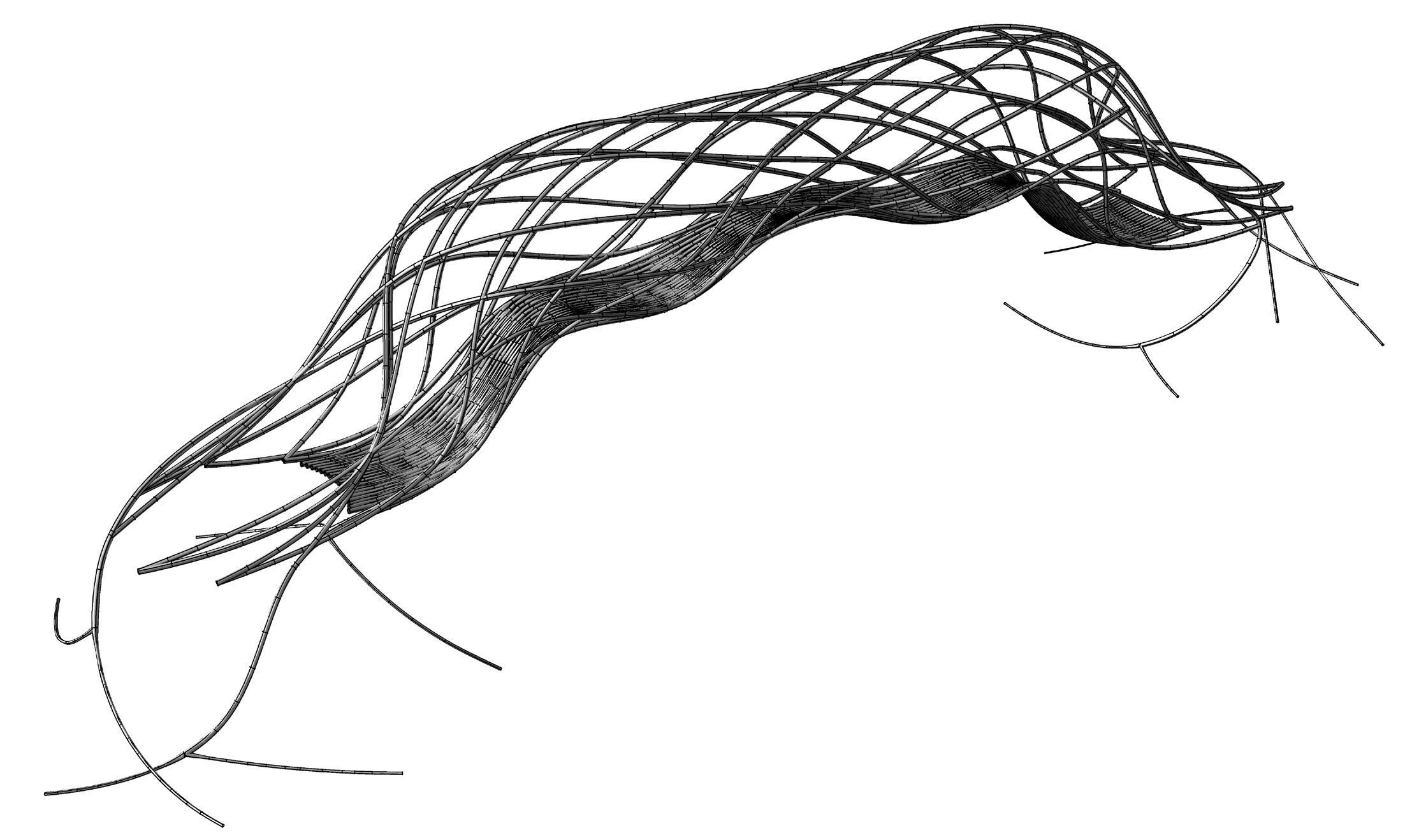
SPATIAL COMPARISON
The spatial analysis undertaken looks at minimal paths and the ability to enter, occupy, and exit the structure. However, no attempt is made at designing a walking path through the bridge. It is unclear how one may access the bridge without this design element. With this realization aside, it is clear that the spatial complexity at which Baraut and Gambardella’s bridge design arrives is a direct result of the computational design process (Figure 53). In addition, with the mandrel geometry generation proposed in this dissertation, thermoplastic radial pulbraiding cannot currently achieve this complexity (due to the lack of research in branching patterns). However, spatial complexity may be achieved through the change in density of braid nodes (Figure 54). While branches are not possible, visual complexity can still be achieved.
CHAPTER 11 - CASE STUDIES AND DESIGN EXPERIMENTS
11.06 PATAGONIA FOOTBRIDGE REVISITED: COMPARATIVE ANALYSIS
Figure 54, model, showing the walking path acheived with the control over braid nodes in the Patagonia footbridge proposal. Figure 53, model detail, showing complexity of the proposed bridge achieved through computation.STRUCTURAL COMPARISON
This spatial complexity is an interesting factor when considering the structural performance of both bridges. Baraut and Gambardella’s proposal considers the performance variables of fiber distribution and connectivity. Fiber distribution was tested as either regular or irregular, while connectivity studied the structural interconnectivity between different spacial branches. Fiber distribution is only tested in an unconnected state, which creates a difficult comparison point to the Patagonia footbridge design experiment, considering the thermoplastic radial pulbraiding technique creates an inherently interconnected structure. However, some comparisons can be made.
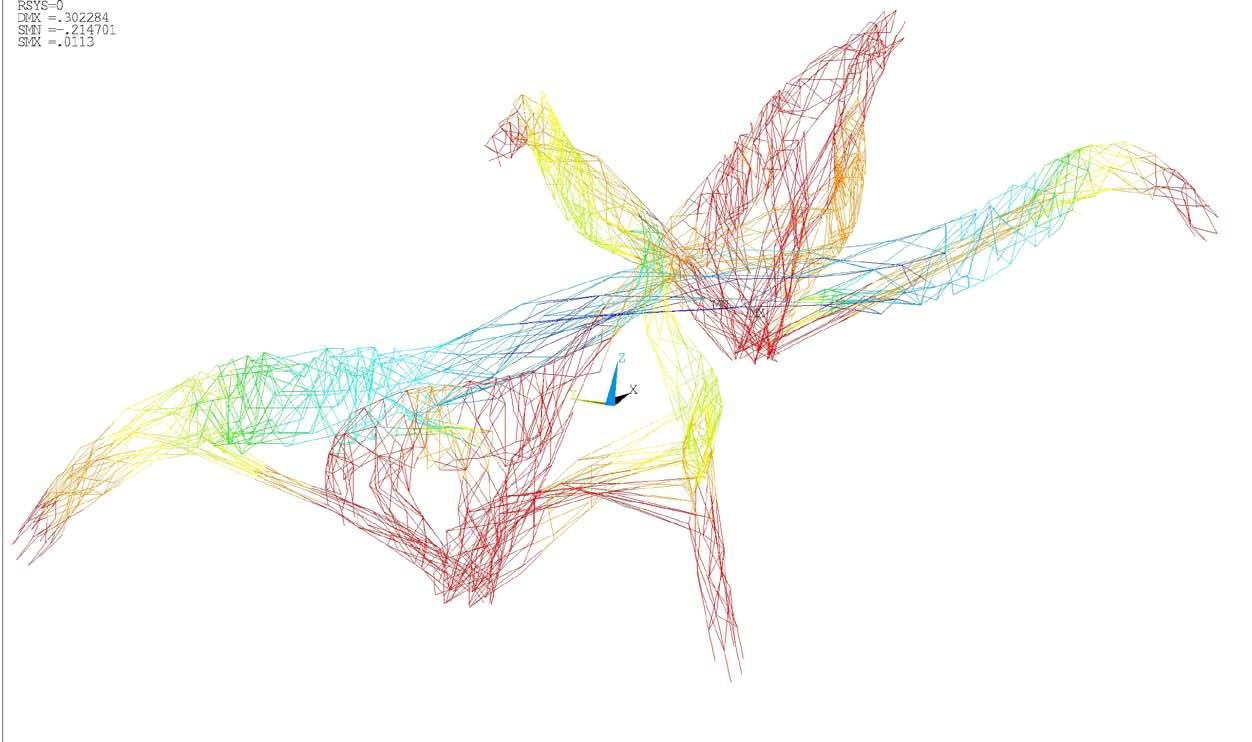
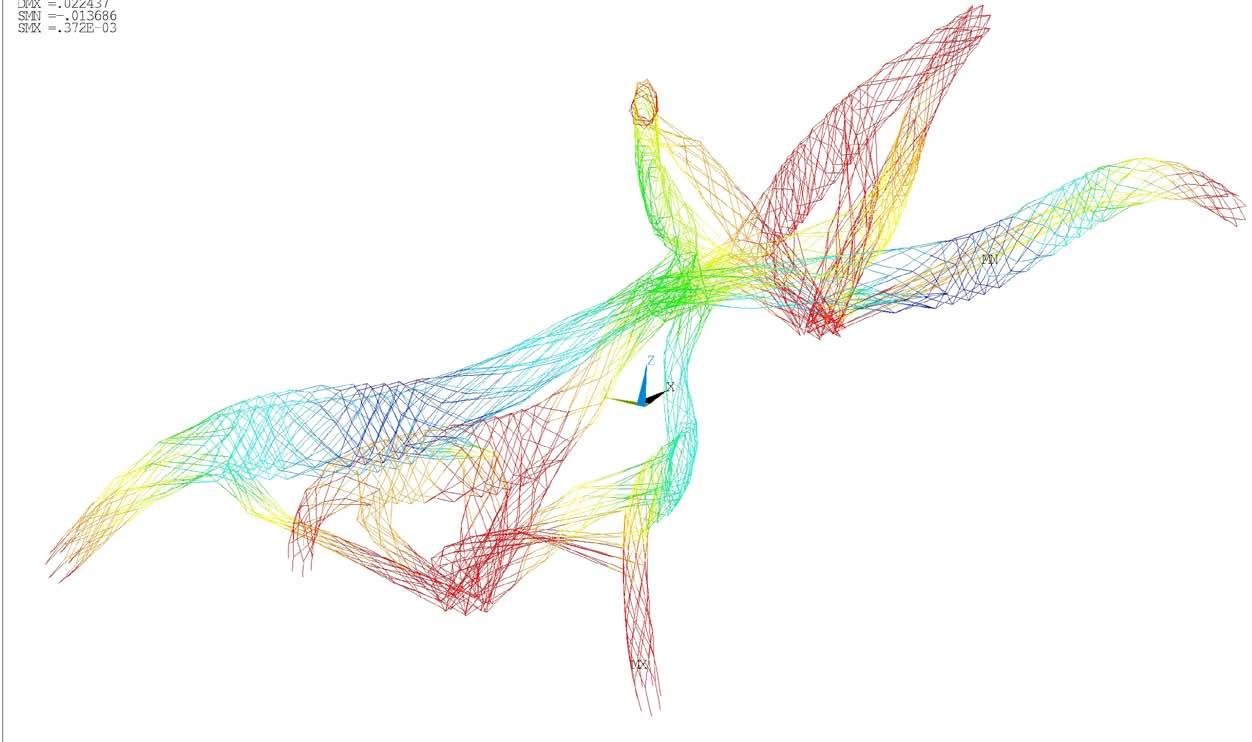
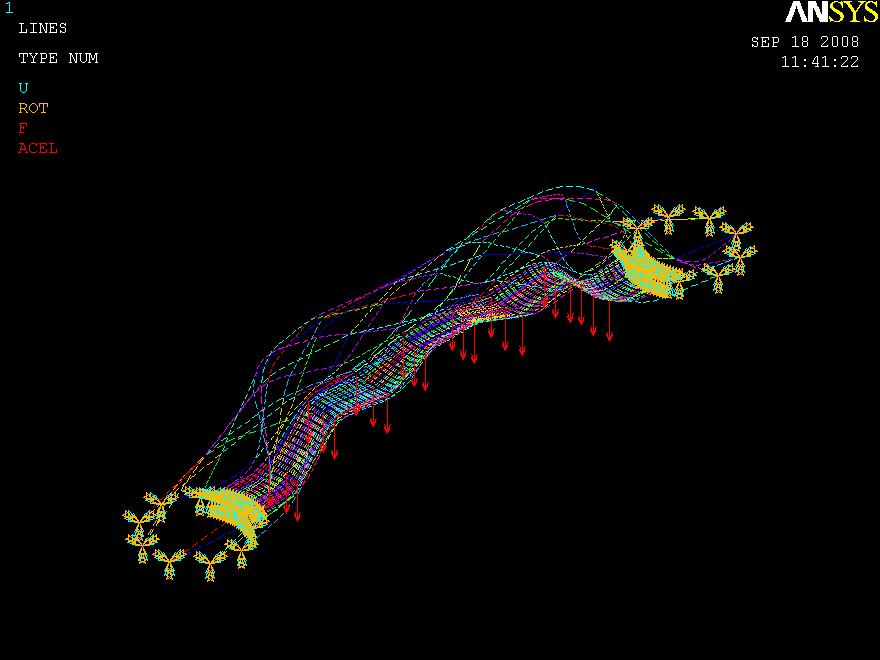
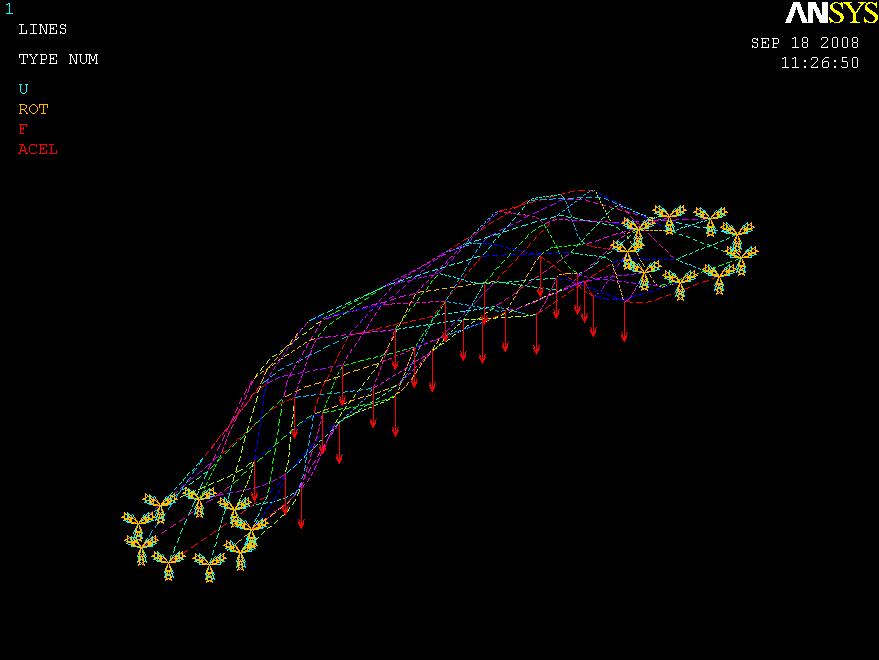
In Baraut and Gambardella’s bridge, it was proven that an irregular fiber distribution performed worse than a bridge with a regular fiber distribution. Vertical displacement for an unconnected but regularly distributed fiber placement strategy was -.169m (Figure 55, left), while displacement in the irregularly distributed case was -.215m (Figure 55, right) (Baraut & Gambardella, 2006). These results, showing lesser structural performance for irregluarly distributed fiber paths makes it difficult to consider the bridge with the addition of a walking path, which would require an irregular fiber distribution strategy. The Patagonia footbridge design experiment was thus analyzed using Finite Element Analysis software in order to compare vertical displacement in a regular and irregular pulbraiding pattern. A distributed load of 500N was applied to the bottom of the bridge (where a walking path would be on both configurations (Figure 56). After the loading condition was analyzed, it was found that maximum vertical displacement in the regular pulbraided pattern was -.073m (Figure 57, top), while the irregular pattern (with a walking path) resulted in a vertical displacement of -.019m (Figure 57, bottom). From this analysis, it is clear that the irregular pattern is of benefit to the bridge designed and fabricated using thermoplastic radial pulbraiding.
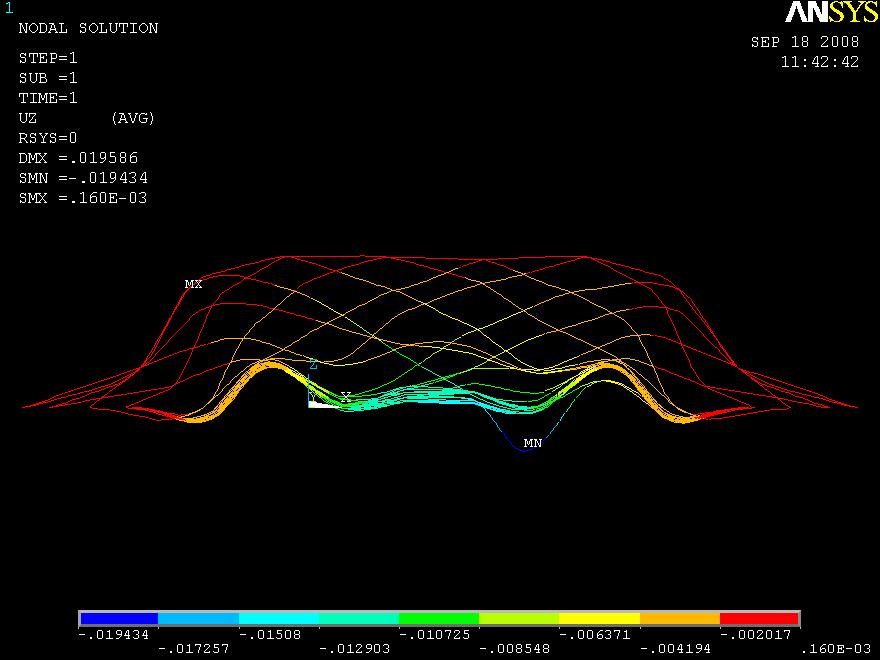
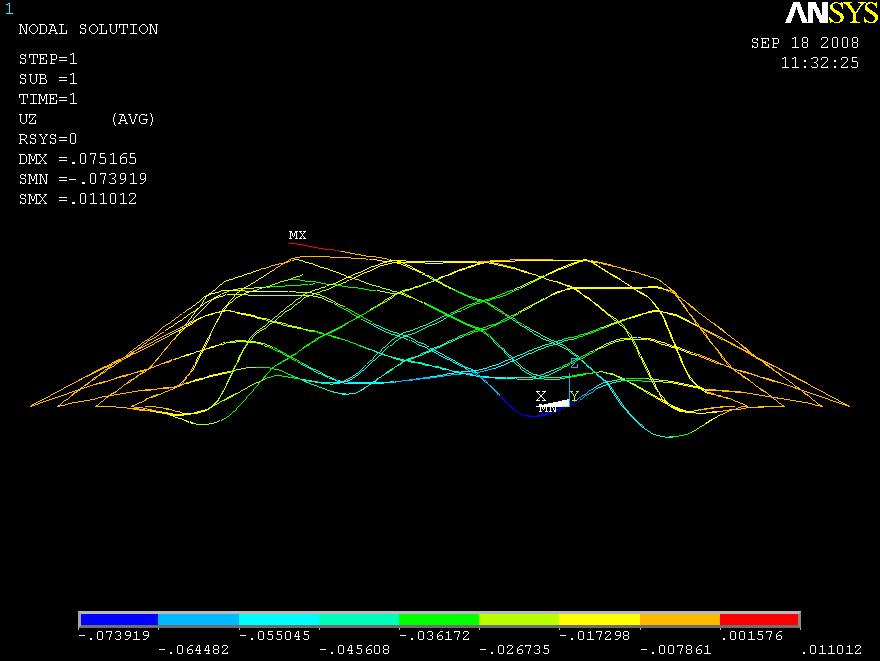
EVALUATION CONSIDERATIONS AND CONCLUSIONS
As mentioned, the comparison is a difficult one with the lack of an equal testing ground. The material properties used in Baraut and Gambardella’s analysis are unknown, and therefore an accurate comparison based on empirical data is impossible. In addition, the irregular pattern tested in the their work is not explained completely, and it is unknown if this irregular pattern contains the same number of fiber strands in a different organization. Although a true data comparison is not possible, it is clear from this analysis that the addition of a walking path, created directly by irregular fiber distribution, performs better than a regular pulbraiding pattern.
CHAPTER 11 - CASE STUDIES AND DESIGN EXPERIMENTS
Figure 56, model, showing the loading condition for both a regular pulbraiding pattern (top) and an irregular pattern (bottom). Figure 57, model, comparing the vertical displacement found from a Finite Element Analysis of the applied loading condition in both a regularly pulbraided bridge (top) and an irregular configuration (bottom). Figure 55, model, comparing the Finite Element analysis of Baraut and Gambardella’s bridge proposal with regularly distributed (left) and irregularly distributed fibers).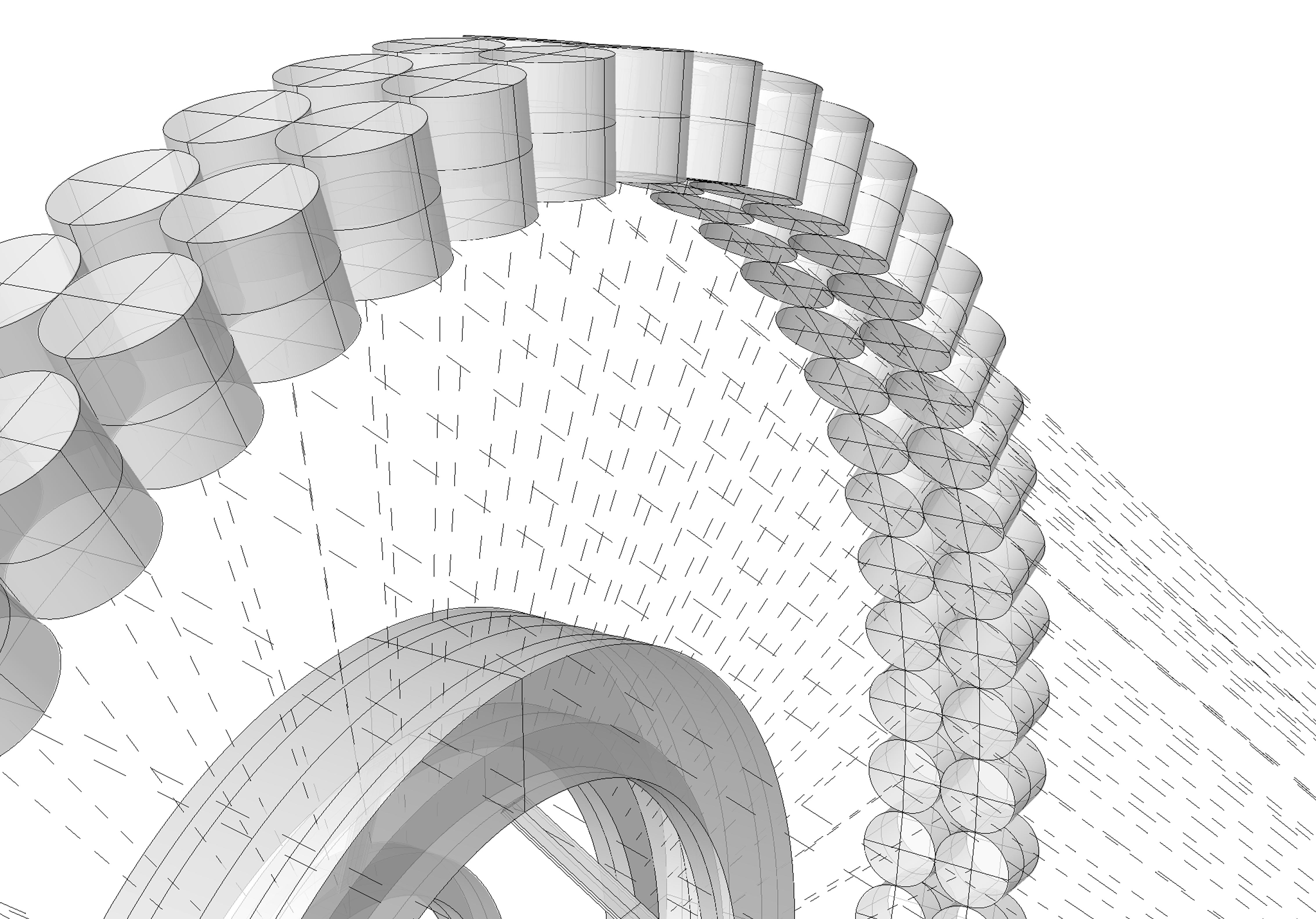
CONCLUSIONS
Through a critical investigation of glass fibers and their possible organizations at the material level, the tooling process involved to organize these fibers, and the potential structures that the process produces, the viability of a synthesized construction process becomes a solution for a novel thermoplastic radial pulbraiding fabrication technique.
The combination of three traditionally separate entities - material, tooling, and structure - is possible only through the exploration of existing techniques and technologies; in proposing a novel fabrication technique, the knowledge of current industrial braiding processes as well as current pulbraiding possibilities is crucial. By adapting these contemporary techniques, along with the inherent advantageous characteristics of glass fibers and thermoplastic resin, a new technique synthesizes the material, tooling, and structure into one cohesive fabrication process.
Both design experiments – the Hong Kong pencil tower and the Patagonia footbridge – successfully find possibilities in fabrication using the novel technique proposed. Through these two explorations, it has been found that thermoplastic radial pulbraiding is a viable technique for the fabrication of a pulbraided glass fiber structure of varying fiber volumes and fiber densities, allowing for the design of a differentiated structure responding to specific buckling stiffness and programmatic requirements through the synthesis of material, tooling, and structure. Furthermore, the proposal of a form-active tension system employed as an adaptable, on-site mandrel supports the existence of in-situ construction.
This dissertation begins to acknowledge all three areas of contextualization in which the necessity for a novel technique is based. Relative to Peter Testa’s Carbon Tower, thermoplastic radial pulbraiding brings a viable fabrication technique to the highly speculative and extremely imaginative technique proposed in Testa’s work. By revisiting the Carbon Tower with a new fabrication approach, an increased understanding and attainability in construction is made possible.
Thermoplastic radial pulbraiding also provides a contrast and great potential in comparison to Doumpioti’s work. While Doumpioti proposes tow-steering over a foam mold, this work eliminates the necessity for a pre-designed formwork, and allows for in-situ construction. In addition, pulbraiding addresses the delamination issues faced in tow-steering multiple laminae. The iterative process of layering various directional laminae is eliminated in this pulbraiding technique. It is important to note, however, that while thermoplastic radial pulbraiding may help alleviate many of these problems associated with Doumpioti’s proposed fabrication technique, the inherent tubular forms generated are less complex morphologically than what can be achieved through tow-steering.
The synthesis of material, tooling and structure taking place in thermoplastic radial pulbraiding is now clear; it is imperative to return to the issues that continuous construction achieves through this process. Unlike timber and steel construction, jointing is fully eliminated through the novel implementation of a heated pultrusion die and the incorporation of commingled fibers. The elimination of the necessity to joint material has huge architectural implications; just like in biological systems, the absence of mechanical joints has serious effects on structural performance. Joints are commonly where structures fail, and by elminating these problem areas, a higher-performance structure is viable.
Finally, each problematic element identified in Ville Hara’s Korkeassaari Zoo Tower has been addressed with the use of this novel fabrication technique. Through the two design experiments carried out in this work, it has been found that platform connections, openings, ground connection, jointing, and a curvilinear geometry are all possible to achieve through constructing with thermoplastic radial pulbraiding.
By concluding this work relative to the areas of context which provide the need for this investigation, it becomes clear as to what contributions to architecture this research can provide.
CONTRIBUTIONS
The work of this dissertation furthers the crucial discussion of how fabrication takes advantage of the inherent qualities of the material and tooling that takes place in the creation of a pulbraided fiber composite structure. For a number of years, research into fiber composites has pushed the knowledge of the material’s performative qualities; it is widely understood that fiber composite structures are a direct result of their material makeups. However, this process has never been synthesized through a fabrication technique. Rather than investigating a coherent fabrication technique, as this dissertation does, current fiber composite fabrication techniques at the building scale continue to work in the realm of construction techniques from early industrialization – namely the jointing or bonding of separate composite parts.
This research brings that neglect to the forefront of architectural fabrication, questioning the disconnect between material potential and subsequent structure. By beginning the investigation of a novel technique, responding directly to the disjointed fabrication processes currently in place today, this work advances the possibilities of large-scale design and construction of fiber composites in an architectural context.
FURTHER RESEARCH
While thermoplastic radial pulbraiding has been found to be a process combining material, tooling, and structure, there are limitations to the current proposed technique that must be mentioned. Most importantly, thermoplastic radial pulbraiding cannot be considered as a serious option in the design and construction of an architectural tower without the ability to construct platforms. Without platforms, a pulbraided envelope is merely that – and cannot perform as an architectural work. As mentioned, this is due largely in part to the necessity for a mandrel geometry during the radial pulbraiding process. However, this is an area that is open to further investigation. By solving the problem of interference with the mandrel, the proposed technique can be greatly advanced. One speculation on this topic is the fluxuation of the heated pultrusion die ring. While overbraiding currently requires a formwork to braid over, there is the possibilty of adjusting this ring, much like an aperture, to control the exact radius of the form created. By creating variation in this manner, a mandrel geometry may eventually be eliminated. Additionally, this dissertation provides the capacity to manufacture the tooling proposed based on existing technology. A standard 3D radial overbraider can be designed to meet the proposal herein this dissertation, and a structure can be fabricated to physically test this work. Computational simulation, of course, is necessary before this step, and the research put forward in this work provides a strong basis for the simulation of the design process. Current software exists where the design of fiber volume and braiding angles can be simulated, and by incorporating the principles set forth in this work within the simulation software, greater potential can be realized.
Now that the groundwork has been set in developing a novel fabrication technique, further work can focus on structural performance as a design driver. By further investigating the ability of a pulbraided structure to perform under certain conditions, architects can better understand the technique’s capacity. An architectural application can explore, in greater depth, the full potential of thermoplastic radial pulbraiding, as well as address additional constraints. While this work has considered current limitations of the technique, an architectural project can fully address these limitations by including them in the design process. This will ultimately advance the novel technique researched, and refine it to the point where prototyping may be possible.
Finally, radial overbraiding fabrication - and therefore thermoplastic radial pulbraiding - currently produces a cylindrical structure. Because the braiding process is radial, and fibers are braided around formwork, there is little variation in the basic form of a resulting structure. This dissertation has shown that the specific shape of the mandrel directly affects the shape of the structure; this structure is always cylindrical. Further investigation could begin to explore other modifications to industrial braiding techniques which may achieve greater complexity and variation in form.
SCALE, MATERIAL, AND DESIGN APPLICATION
Within the larger scope of this work, three areas of further research must be rethought. First, this research is limited to a specific scale of architecture; design experiments look at a footbridge and a pencil tower - both large-scale relative to current braided filber composite structures, but modestly scaled in relation to works of architecture. This research can theoretically be applied at any scale, considering the technical adaptability of industrial braiding. In addition, by investigating different scales, new potentials and limitations may become apparent.
In continuing the research of structural performance, this research can provide a basis for the investigation into different materials used. Although glass fibers commingled with thermoplastic resin fibers is proposed here, alternative fibers and matrices can provide different performative characteristics, thus uncovering new areas of research that may affect the fabrication of a composite structure. Design application is a broad area in which this research can be taken further. While this dissertation already does focus on the architecture industry - one that current fiber composites are not often applied to at the building-scale - this research can be furthered through a number of different applications. Architectural scales can be investigated further; while this work does question the synthesized fabrication of platforms, other necessary local conditions like stairs and opening details can be investigated. By continuing on the path of this work - realizing a fabrication technique which synthesizes material, tooling, and structure - the new construction paradigm contributed to here can be furthered still, where architects can address the lingering problem of creating structure from material through an innovative fabrication technique.
Part VI: References
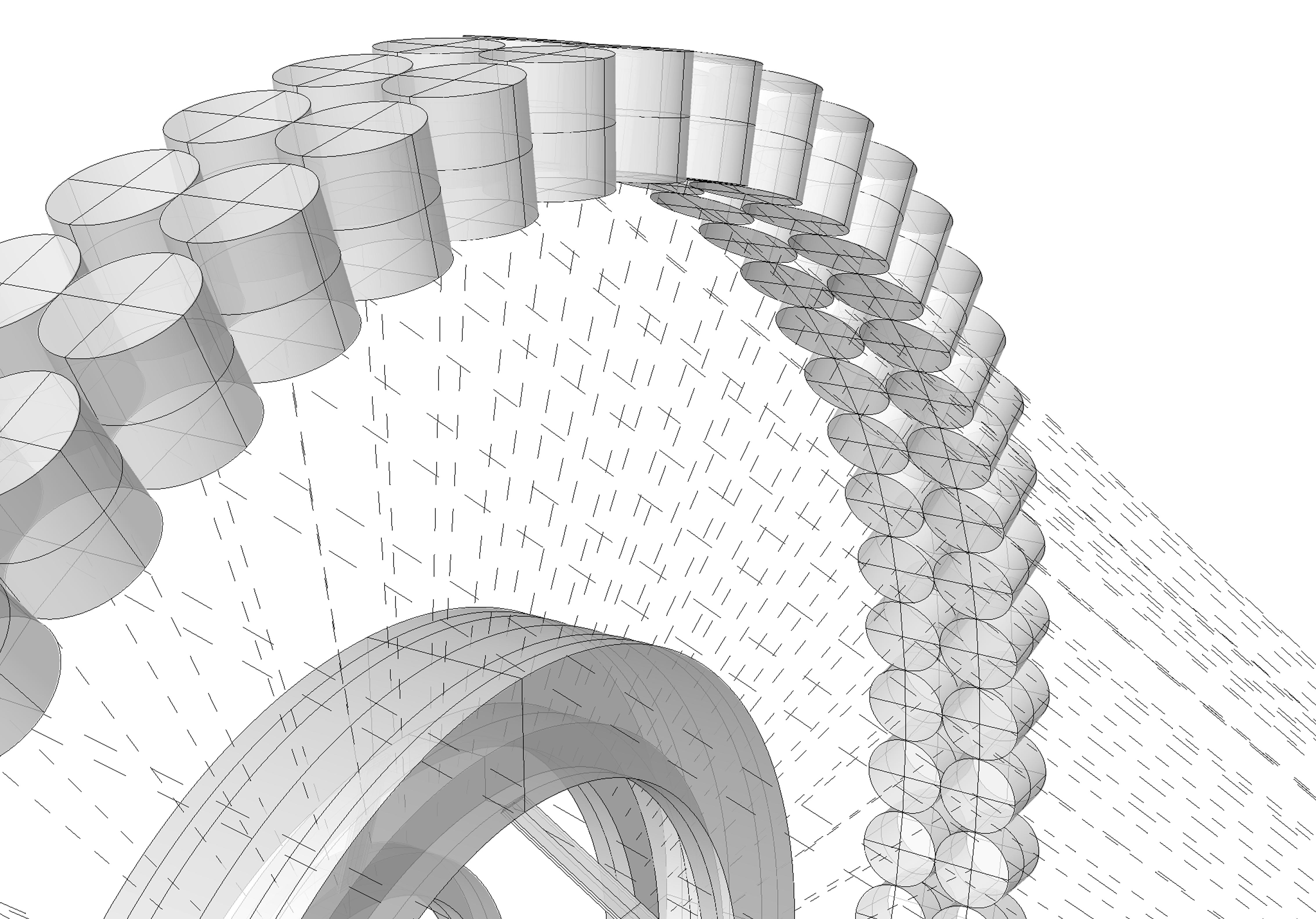
GLOSSARY
anticlastic: a surface geometry with negative Gaussian curvature; surface curves are in opposing directions, where on is positive and one is negative
buckle: to bend or kink under external compressive load
buckling stiffness: resistance to buckling
effectiveness: the capability of a system to produce an observable effect, regardless of whether it conforms to the desired standards
efficiency: the ratio of the effective output to the total input in a system
fiber: a material with a length many times longer than its diameter (from Gary E. Freger, Braiding Pultrusion Technology. 2004)
out-of-surface action: a force exerted on a thin-shell structure is transferred out of the thickness of the material
mandrel: a mold used as formwork in the fabrication of tubular braids
novel: of a new kind of nature
(from The Oxford English Dictionary)
pneu: pneumatic structure
specific stiffness: ratio of stiffness to weight (from Forbes Aird, Fiberglass and Other Composite Materials. 2006)
specific strength: ratio of strength to weight (from Forbes Aird, Fiberglass and Other Composite Materials. 2006)
strength: the tensile stress acting on a material necessary to for that material to break (kg/sq. m) (from Forbes Aird, Fiberglass and Other Composite Materials. 2006)
stiffness: resistance to deflection (from Forbes Aird, Fiberglass and Other Composite Materials. 2006)
strand: bundle of untwisted glass fibers (from Gary E. Freger, Braiding Pultrusion Technology. 2004)
synclastic: a surface geometry with positive Gaussian curvature; surface curves are in the same direction, where either both are positive or negative
I would like to thank my tutors, Mike Weinstock, Achim Menges, and Michael Hensel for their invaluable guidance and critical input throughout the entire Emergent Technologies and Design Program course. I would also like to to thank George Jeronimidis for his generosity and continued support throughout this research. I am grateful to my Emtech colleagues for the knowledge I have gained from them and their constant encouragement. would like to acknowledge David Carlton at Sedace, Ltd. and Eurocarbon BV for providing braided glass fiber sleeving samples for the benefit of this academic work. Finally I would like to thank my father, for it is his passion for construction and how things work that has influenced my enthusiastic interest in fabrication.
CHAPTER 14 - ACKNOWLEDGEMENTS AND CREDITS .0 ACKNOWLEDGEMENTS
All figures by Evan Greenberg unless otherwise noted.
CHAPTER 2
Figures 01 & 03 from McQuaid, Matilda, 2005. Extreme Textiles London: Thames & Hudson.
Figure 02 from Schilperoord, Paul, 2006. Future Tech: Innovations in Transportation. London: Black Dog.
CHAPTER 3
Figures 01-02 from McQuaid, Matilda, 2005. Extreme Textiles London: Thames & Hudson.
Figure 03 from Hales, Linda, Washington Post Online, 2005. When Textiles Go To Extremes. [Online] Available at: http://www.washingtonpost.com/wp-dyn/articles/A56477-2005Apr15.html [Accessed 10 March 2008].
Figures 04-06 from Doumpioti, Christina, 2008. Adaptive Growth of Fibre Composite Structures. MArch. London: AA School of Architecture.
Figure 07 from Davey, Peter, Ed, 2003. Timber Lookout Tower. The Architectural Review. CCXIV (1279), p. 43.
Figures 08-11 by Michael Hensel.
Figure 13 by Kyle Sturgeon.
Figure 14 from MattressInside.com, 2006-2007. Selecting Case Goods. Wood. Wood Joinery Methods. [Online] Available at http://www.mattressinside.com/casewood.html [Accessed 13 August 2008].
Figure 16 from Anon, 199?. SAC Database of Steel MRF Connection Tests. [Online] Available at http:// www.sacsteel.org/connections/AppA.html [Accessed 13 August 2008].
CHAPTER 5
Figure 01 from Weinstock, Michael, 2006, from Hensel, Michael, Menges, Achim, & Weinstock, Michael, Eds. Self-Organization and the Structural Dynamics of Plants. Chichester: Wiley Academy.
Figures 02-03 from Dinwoodie, J.M., 2000. Timber: Its Nature and Behavior. London: Spon Press.
Figures 04-05 from Otto, Frei, 1995. IL 5: Pneu and Bone. Stuttgart: Institut fur Leichte Flachentragwerke.
CHAPTER 6
Figures 01-02 from Ko, Dr. Frank, Pastore, Dr. Christopher M., & Head, Andrew A., 1989. Atkins and Pearce Handbook on Industrial Braiding. Covington (KY): Atkins and Pearce.
CHAPTER 7
Figures 01-03 from Ko, Dr. Frank, Pastore, Dr. Christopher M., & Head, Andrew A., 1989. Atkins and Pearce Handbook on Industrial Braiding. Covington (KY): Atkins and Pearce.
Figure 06 from Beukers, Adriaan & Van Hinte, Ed, 2005. Flying Lightness: Promises for Structural Elegance. Amsterdam: 010 Publishers.
Figures 09-10 from Milwich, M., Burgert, I., Seidl, R., Speck, T., Speck, O., & Planck, H., 2008. Plant Stems as Role Models for Composite Profiles. In Biological Approaches for Engineering Conference Southampton 17-19 March 2008. s.l., s.n.
Figures 12-13 from Weijenberg, Camiel, 2004-2005. Large scale variable section concrete casting. Diploma. London: AA School of Architecture.
CHAPTER 8
Figures 04-09 from Gass, Siegfried, 1990. IL 25: Experiments. Stuttgart: Stuttgart University.
CHAPTER 9
Figure 31 from August Herzog, 2008. Radialbraider. [Online] Available at http://www.herzog-online.com/ conpresso4/en_rubric/index.php?rubric=[EN]+Research [Accessed 1 October 2008].
CHAPTER 11
Figure 01 by Robert Cortright.
Figures 02-03 from Anon, 200?. Hong Kong: The Denscity. [Online] Available at http://home.hetnet. nl/~hongkongphotopage/ [Accessed 7 August 2008].
Figure 38 by The National Parks Service.
Figure 40 by Stephen Rees.
Figure 41 from Evans, Erv, 2000. Tree Anatomy. [Online] Available at: http://www.ces.ncsu.edu/depts/ hort/consumer/factsheets/trees-new/text/tree_anatomy.html [Accessed 5 September 2008].
Figures 46-48, 50, 53, & 55 from Baraut, Guillem & Gambardella, Mattia, 2006. Slender Multistress Driven Structures. MArch. London: AA School of Architecture.
CHAPTER 15
Figure 09 from Universitat Stuttgart, Institut fur Leichte Flachentragwerke, 1975. IL : Nets in Nature and Technics. Stuttgart: Stuttgart University.
Figure 11 from Otto, Frei, 1995. IL 5: Pneu and Bone. Stuttgart: Institut fur Leichte Flachentragwerke.
Figure 12 from Bach, Klaus, 2004. IL : Diatoms II : shells in nature and technics III. Stuttgart: Stuttgart University.
Figure 14 from Gass, Siegfried, 1990. IL 25: Experiments. Stuttgart: Stuttgart University.
Figures 25-27 from Pearman, Hugh, 2003. Architecture of Eden. London: Transworld Publishers.
Figure 28 from Gass, Siegfried, 1990. IL 25: Experiments. Stuttgart: Stuttgart University.
CHAPTER 14 - ACKNOWLEDGEMENTS AND CREDITS .0 IMAGE CREDITS
BIBLIOGRAPHY
Agarwal, Bhagwan D. & Broutman, Lawrence J., 2006. Analysis and Performance of Fiber Composites. Hoboken (NJ): Wiley.
Aird, Forbes, 1996. Fiberglass and Composite Materials: An Enthusiast’s Guide to High Performance Nonmetallic Materials for Automotive Racing and Marine Use. New York: HP Books.
Bach, Klaus, 2004. IL : Diatoms II : shells in nature and technics III. Stuttgart: Stuttgart University.
Baraut, Guillem & Gambardella, Mattia, 2006. Slender Multistress Driven Structures. MArch. London: AA School of Architecture.
Beukers, Adriaan & Van Hinte, Ed, 2005. Flying Lightness: Promises for Structural Elegance. Amsterdam: 010 Publishers.
Braley, Mike & Dingeldein, Molly, 199?. Advancements in Braided Materials Technology. Cincinnati (OH): A & P Technology, Inc.
Campbell, F. C., 2004. Manufacturing Processes for Advanced Composites. Oxford: Elsevier Advanced Technology.
Davey, Peter, Ed, 2003. Timber Lookout Tower. The Architectural Review. CCXIV (1279), p. 43.
Day, Ken W., 1995. Concrete Mix Design, Quality Control, and Specification. London: E and FN Spon.
Dinwoodie, J.M., 2000. Timber: Its Nature and Behavior. London: Spon Press.
Doumpioti, Christina, 2008. Adaptive Growth of Fibre Composite Structures. MArch. London: AA School of Architecture.
Elices, M, Ed., 2000. Structural Biological Materials. Amsterdam & Oxford: Pergamon.
Engel, Heino, 1997. Structure Systems. Osfildern-Ruit: Gerd Hatje Publishers.
Evans, Erv, 2000. Tree Anatomy. [Online] Available at: http://www.ces.ncsu.edu/depts/hort/consumer/ factsheets/trees-new/text/tree_anatomy.html [Accessed 5 September 2008].
Freger, Garry E., 2004. Braiding Pultrusion Technology: For Advanced Structural Composites. New York and London: McGraw Hill.
Garcia, Mark, Ed., 2006. Textiles in Architecture, from Garcia, Mark, Ed. Architectextiles. Chichester: Wiley Academy.
Gass, Siegfried, 1990. IL 25: Experiments. Stuttgart: Stuttgart University.
Harvey, William J., 1993. A Reinforced Plastic Footbridge, Aberfeldy, UK. Structural Engineering International. 4(3), pp. 229-232.
Hensel, Michael, Menges, Achim, & Weinstock, Michael, 2004. Fit Fabric: Versatility Through Redundancy and Differentiation, from Hensel, Michael, Menges, Michael, & Weinstock, Michael, Eds. Emergence: Morphogenetic Design Strategies. Chichester: Wiley Academy.
Jeronimidis, George, 2004. Biodynamics, from Hensel, Michael, Menges, Achim, & Weinstock, Michael, Eds. Emergence: Morphogenetic Design Strategies. Chichester: Wiley Academy.
Jeronimidis, George, 16 March 2006. Geometry, Materials, Modeling and Simulation for Morphogenetic Design. Lecture. London: AA School of Architecture.
Ko, Dr. Frank, Pastore, Dr. Christopher M., & Head, Andrew A., 1989. Atkins and Pearce Handbook on Industrial Braiding. Covington (KY): Atkins and Pearce.
Leubkeman, Chris H., 1996. Pencil Towers. [Online] Available at: http://darkwing.uoregon.edu/~struct/ courseware/hk1/hk1_pencil/pencil.html [Accessed 7 August 2008].
Lewis, W.J., 2003. Tension Structures: Form and Behaviour. London: Thomas Telford.
Mallick, P. K., Ed., 1997. Composites Engineering Handbook. New York: Marcel Dekker. 1997.
McQuaid, Matilda, 2005. Extreme Textiles London: Thames & Hudson.
Milwich, M., Burgert, I., Seidl, R., Speck, T., Speck, O., & Planck, H., 2008. Plant Stems as Role Models for Composite Profiles. In Biological Approaches for Engineering Conference. Southampton 17-19 March 2008. s.l., s.n.
Rudd, C.D., 1997. Liquid Moulding Technologies. Cambridge: Woodhead Publishing.
Shames, Irving H. & Dym, Clive L., 1985. Energy and Finite Element Methods in Structural Mechanics New York: McGraw-Hill.
Sherman, T.F., 1981. On Connecting Large Vessels to Small: The Meaning of Murray’s Law. The Journal of General Physiology. 78, pp. 431-53.
Shuster, John W., 1997. Structural Steel Fabrication Practices. New York: McGraw Hill.
Starr, Trevor F., 2000. Pultrusion for Engineers. Cambridge: Woodhead Publishing.
Wallenberger, Frederick T., Watson, James C., & Li, Hong, 200?. Glass Fibers. Materials Park (OH): ASM International.
Weijenberg, Camiel, 2004-2005. Large scale variable section concrete casting. Diploma. London: AA School of Architecture.
Weinstock, Michael, 2006, from Hensel, Michael, Menges, Achim, & Weinstock, Michael, Eds. SelfOrganization and the Structural Dynamics of Plants. Chichester: Wiley Academy.
Zhongshan Pulwell Composites Co., Ltd., 2002. Pulwell Technology. [Online] Available at: http://www. pulwellpultrusions.com/applications.htm [Accessed 17 June 2008].
CHAPTER 14 - ACKNOWLEDGEMENTS AND CREDITS
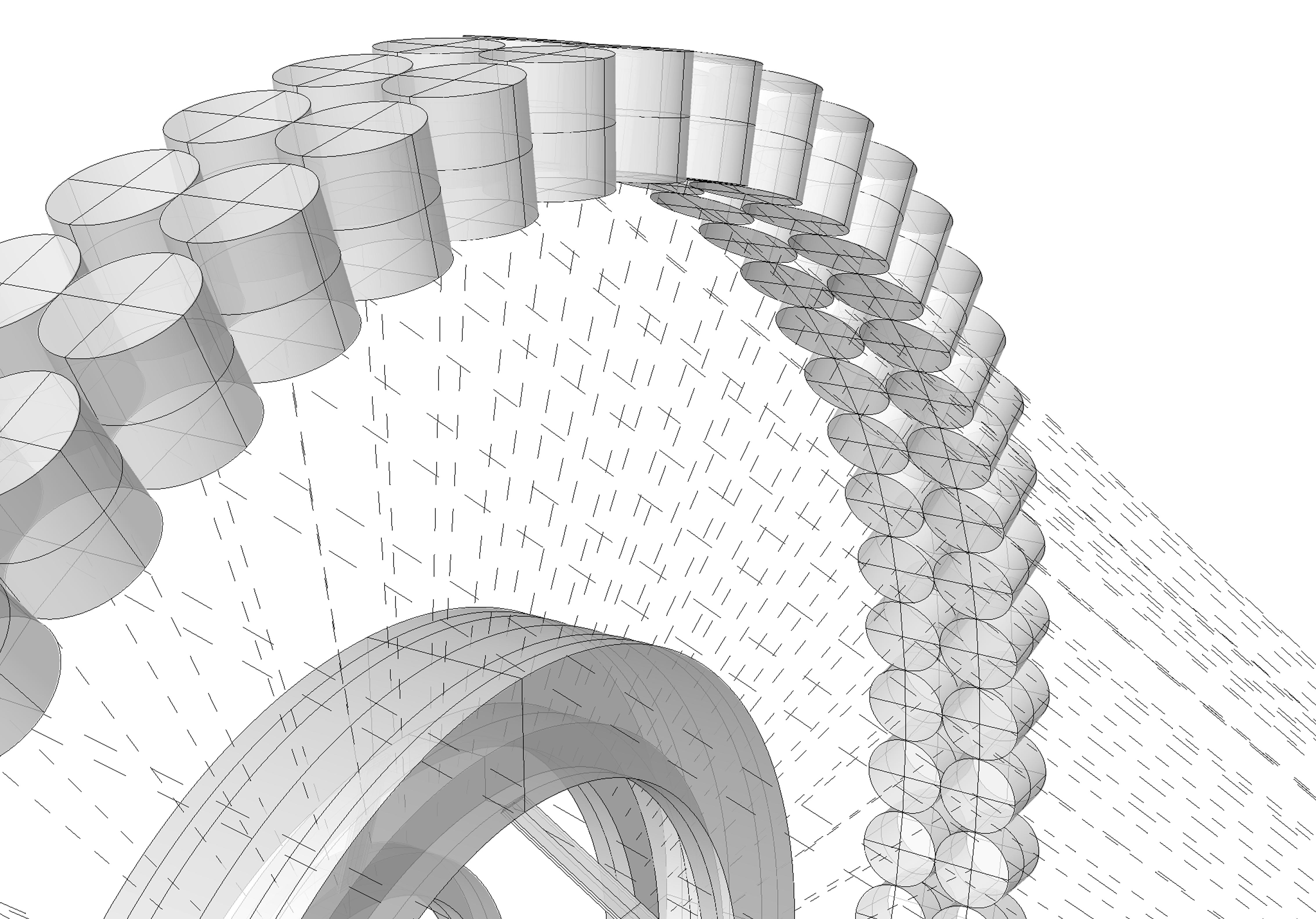
EXPLORING A SOLUTION FOR STABILITY
This experiment aims to stiffen the cable net externally, so that the pneus can be eliminated and a rigidified cable net can be overbraided. Braided nylon fishnet stockings covering balloons are tested using various stiffening materials - PVA glue (Figure 01), fabric stiffener spray (Figure 03), liquid starch spray, liquid starch powder mixture, a sugar and water mixture, and polyurethane resin (Figure 02). Each of these various strategies fail to rigidify the net in such a way that the pneus could be removed. The application of PVA glue fails due to the adhesion of the stocking to the balloon itself. Because the glue creates a bond between the two materials, the deflation of the balloon causes the net to take its shape. The stiffness of the material cannot overcome its adhesion to the balloon, and therefore remains stuck to it. With the remaining implemented methods, it is believed that the thinness of the material, as well as its porosity are the causes for its inability to stiffen. Each application attempted could not create an adequate bond between stiffener and material, and thus could not prevent the elastic material from returning to its original shape upon deflation of the pneus. Due to the failures observed in this experiment, it is hypothesized that global stability of the form-active tension system can be achieved without net rigidity. If the hybrid system is treated as a whole mold geometry, stiffness is not necessary. Therefore, the form-finding method can be exploited for one of its major advantages, and if geometry can be controlled, material organization can create performative stability.
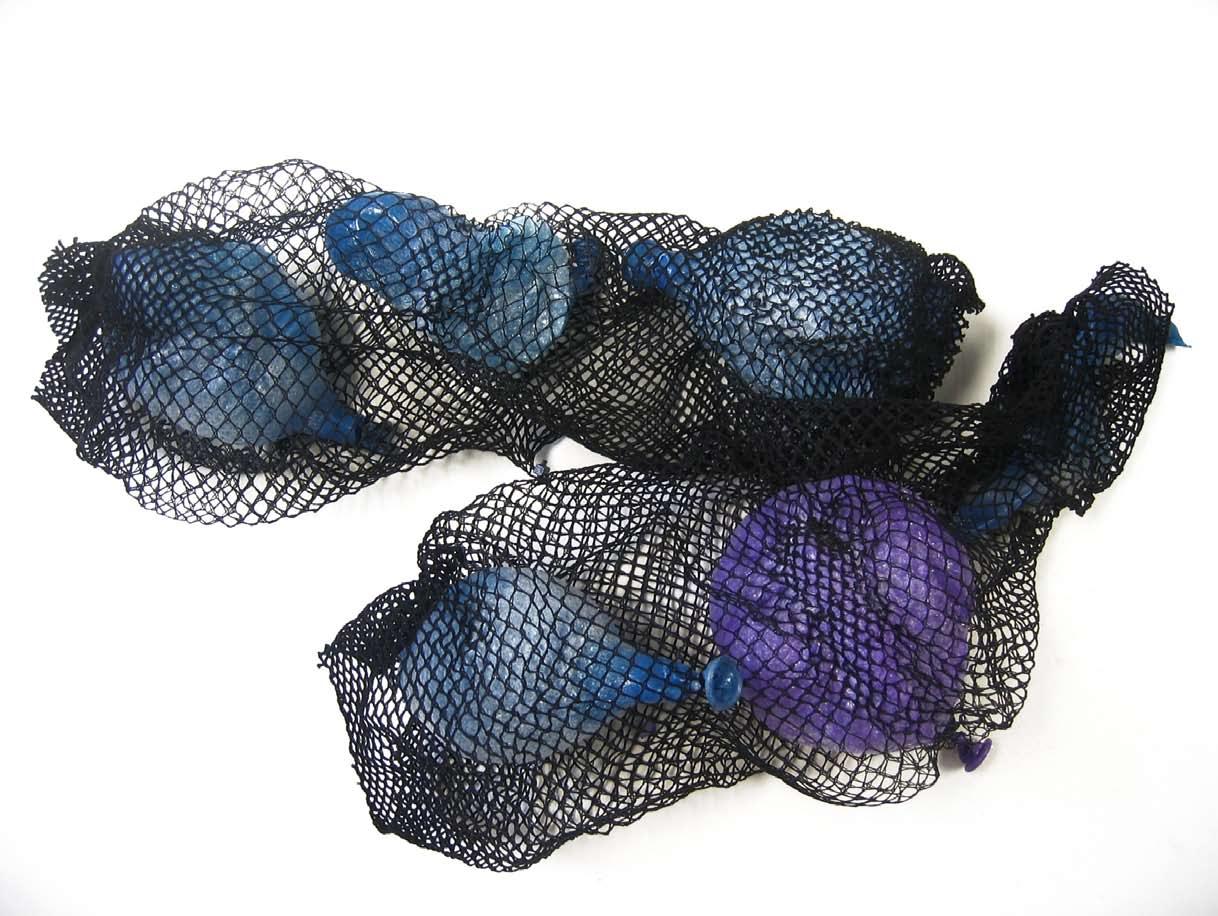
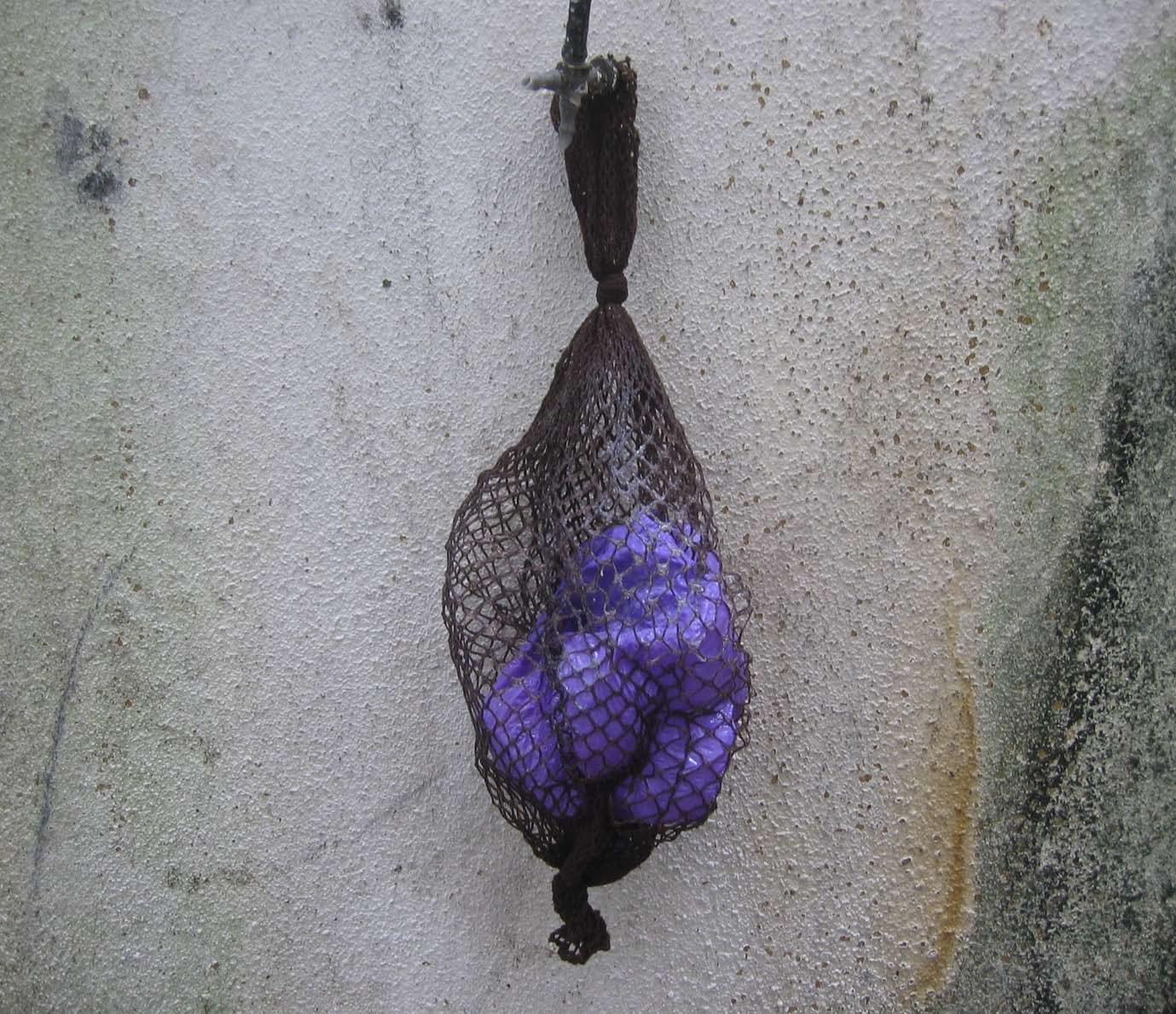
CHAPTER 15 - APPENDIX A 5.0 STIFFENING EXPERIMENTS
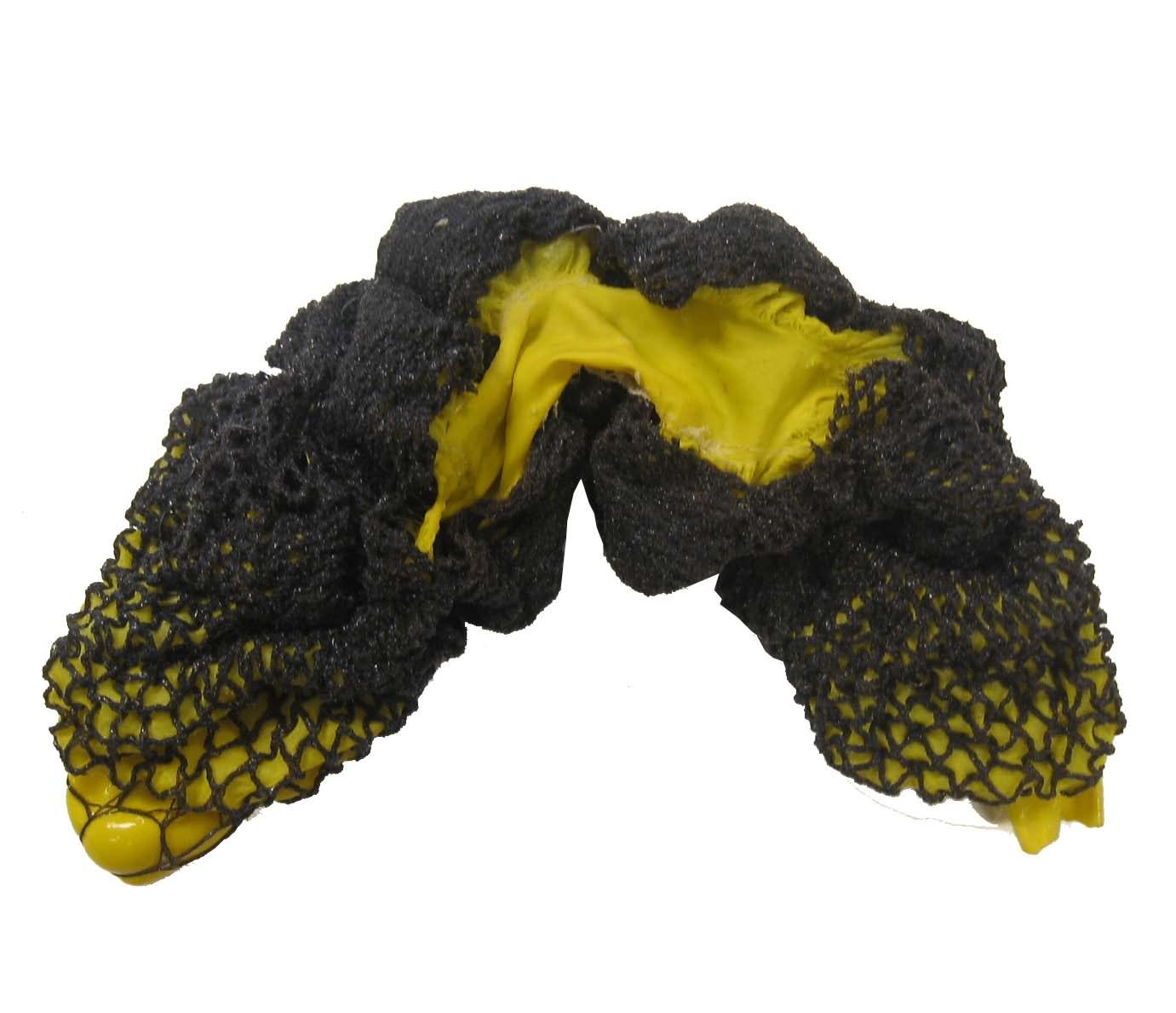
OVERALL form-found pneu-cable net system
INTERMEDIATE cable net of braided nylon strands
MICRO-SCALE thin/elastic nylon fiber
THREE
The material system developed using a pneu-cable net form-active tension system behaves according to the specific material properties of the cable net used (Figure 04). The nylon braided stocking takes an overall global morphology based on both the positional configuration of the pneus inflated within as well as the inherent material properties of the nylon net at the intermediate and micro-scales. The braided cable net, in turn, self-organizes based on the properties of the fibers that are braided to make up the net as a whole. At the micro-scale, the nylon fibers are extremely thin and elastic. These material properties contribute to the self-organization of the stocking as a material, as well as the morphology of the pneu-cable net configuration as a system. It is due to this thinness and elasticity at the micro-scale that out-of-surface action occurs. Although braiding the fibers creates thicker strands of fibers, they are not thick enough to overcome the elasticity of the fibers, and therefore do not successfully transfer load through the material’s surface without external intervention.
CHAPTER 15 - APPENDIX A 5.0 OUT-OF-SURFACE
SCALES OF MATERIAL BEHAVIOR Figure 04, diagram, showing the three material scales of the pneu-cable net form-active tension system. The cable net behaves according to its material properties on the global, intermediate, and microscales.OUT-OF-SURFACE ACTION IN A VERTICAL CONFIGURATION
To experiment with possible solutions to out-of-surface action that occurs in vertical configurations (Figure 05), two pneu-cable net tubes are inflated, and connected to each other at synclastic geometric peaks (Figure 06). This connection allows the flow of force vectors to continue through the net material of the adjacent tube (Figure 08). In order to secure the nets to each other, without creating a local peak, which is experienced in configurations undertaken during the first two experiments, the cable used to tie the nets together is brought down to the cable tie connecting the tubes to the model base (Figure 07). This cable does introduce a new force vector into the system, and plays a role in changing the global force vectors acting on the system. However, its role in connecting the two nets together is a vital one, and can be attributed to a possible solution of out-of-surface action. The configuration tested in this experiment behaves in a more stable way.
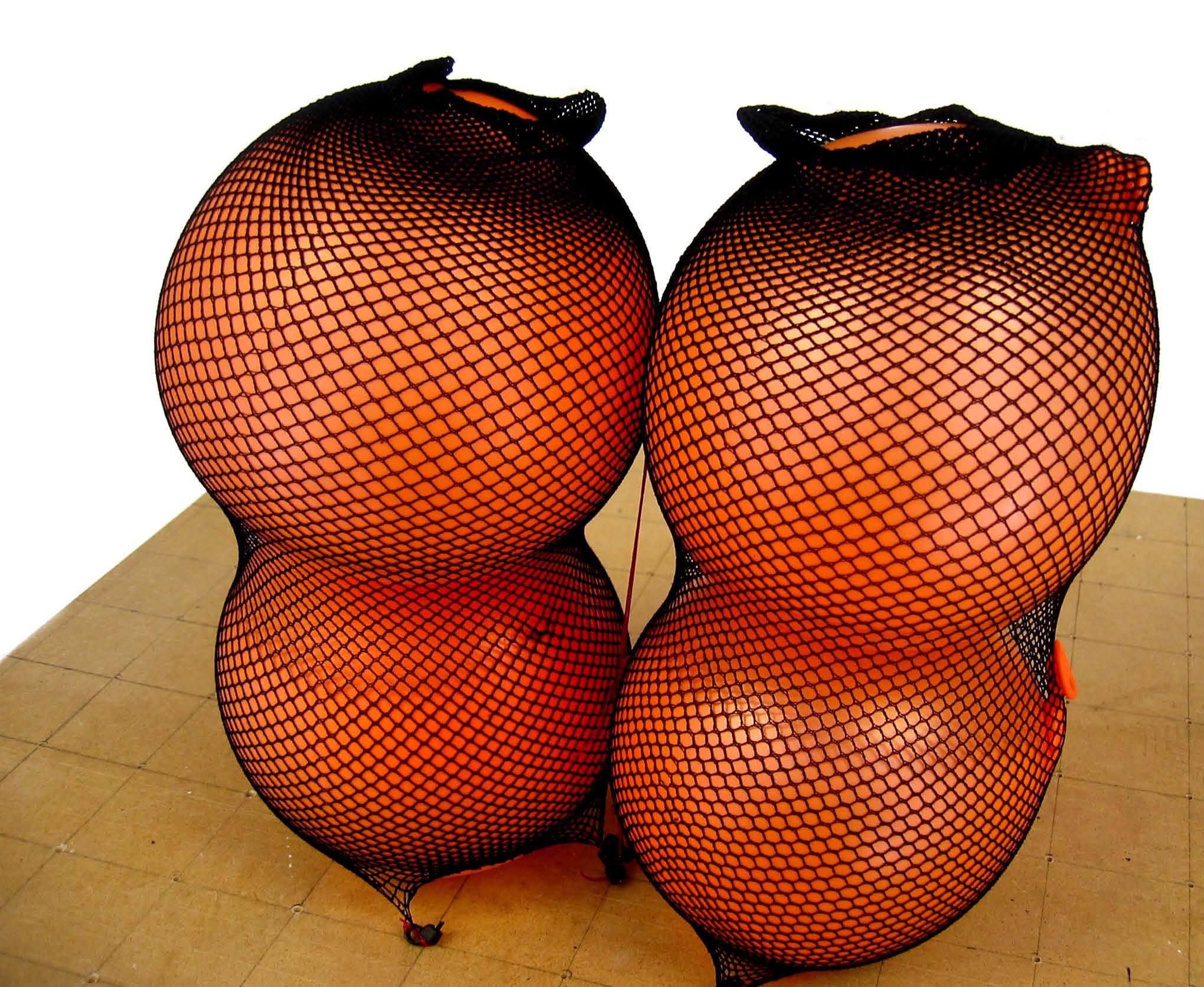
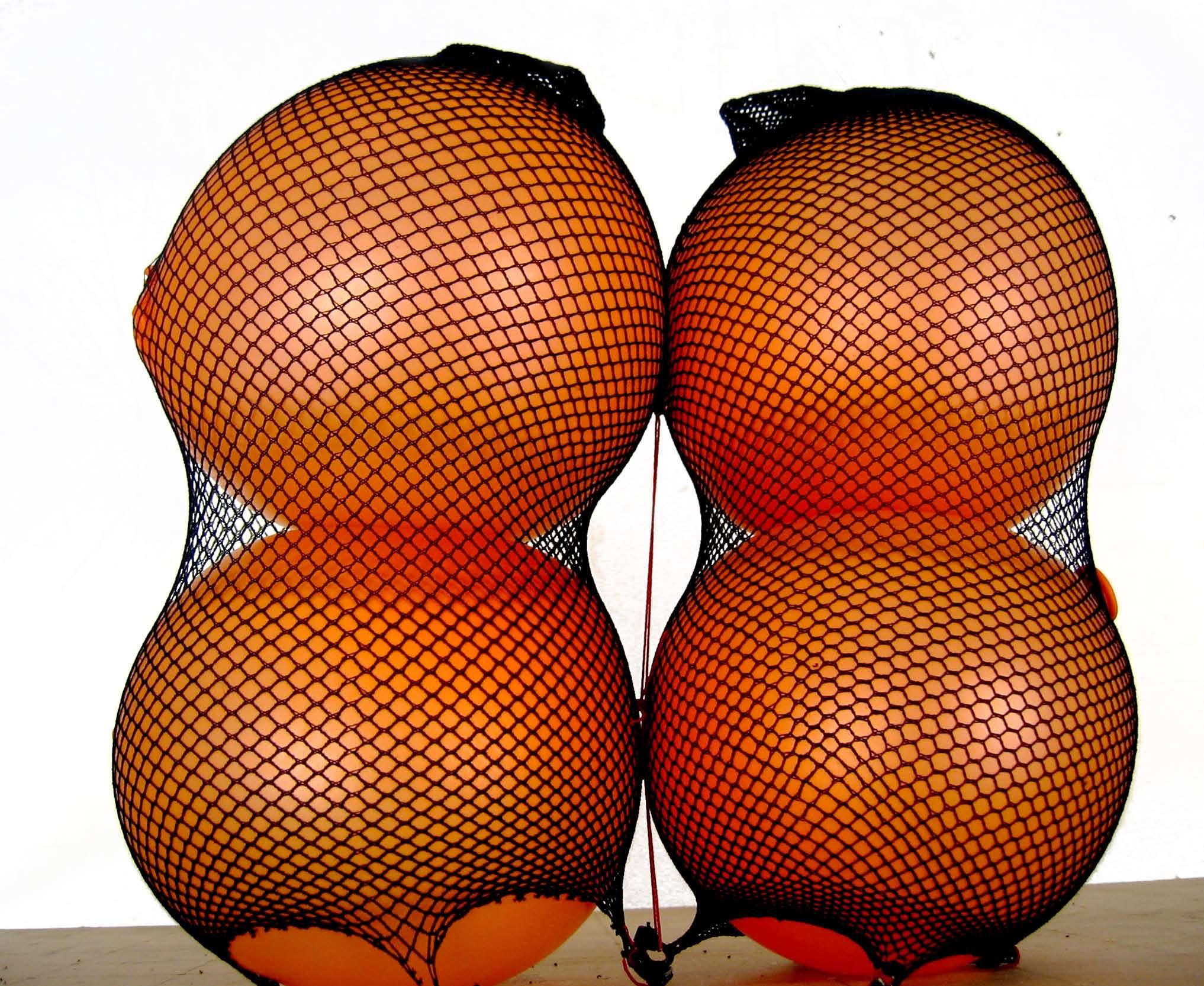
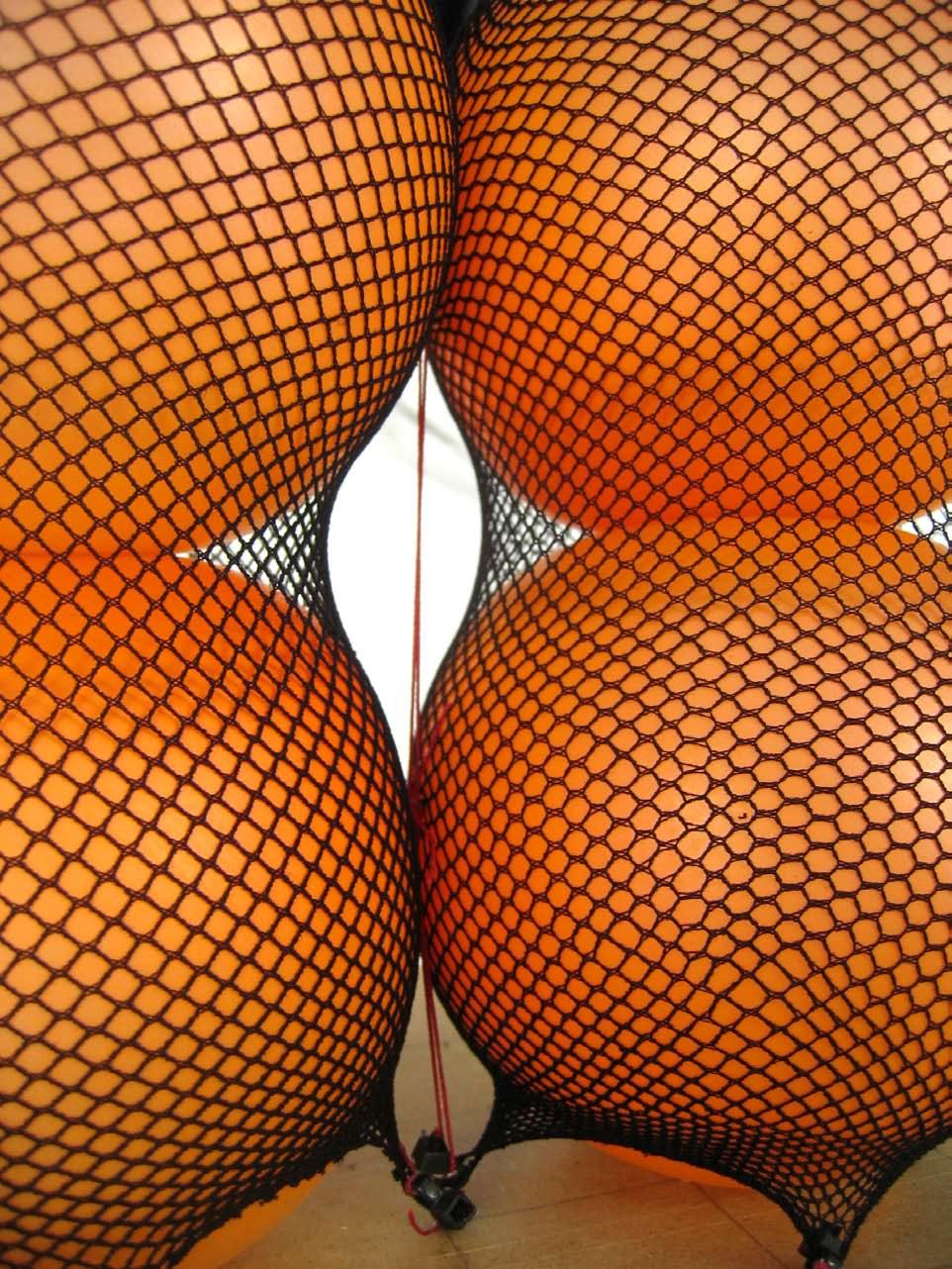
CHAPTER 15 - APPENDIX A
5.0 OUT-OF-SURFACE ACTION
CHAPTER 15 - APPENDIX A
5.0 OUT-OF-SURFACE ACTION
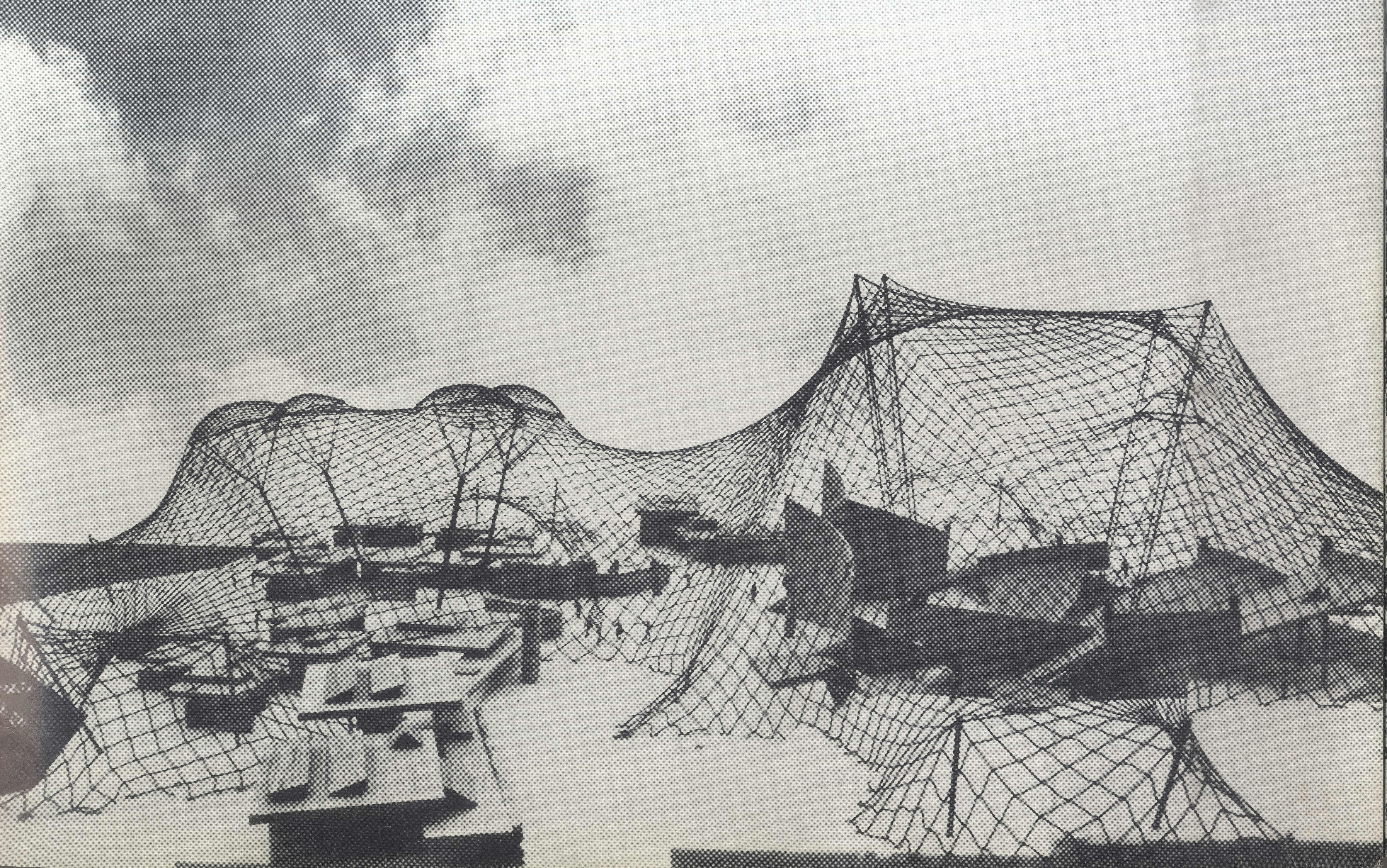
SURFACE STRUCTURES IN NATURE
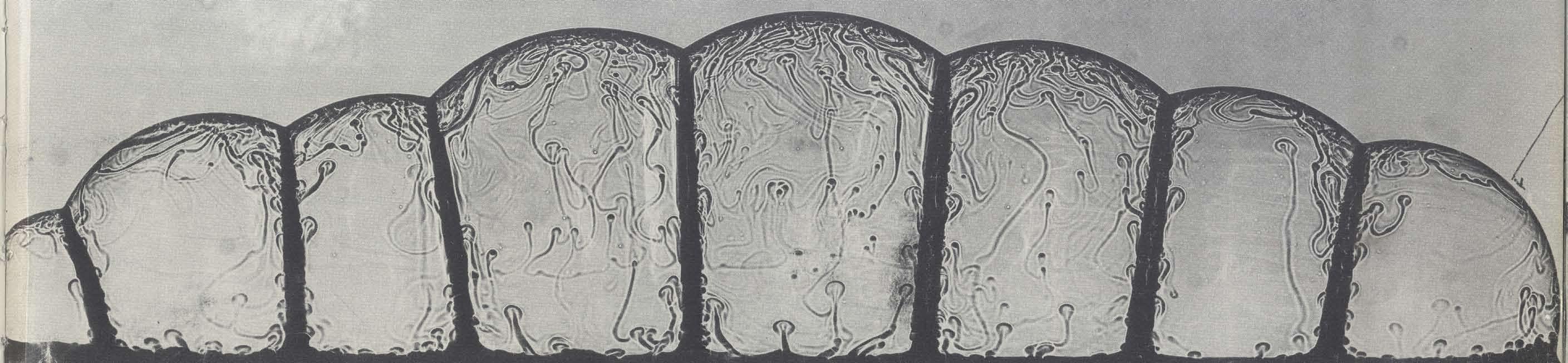
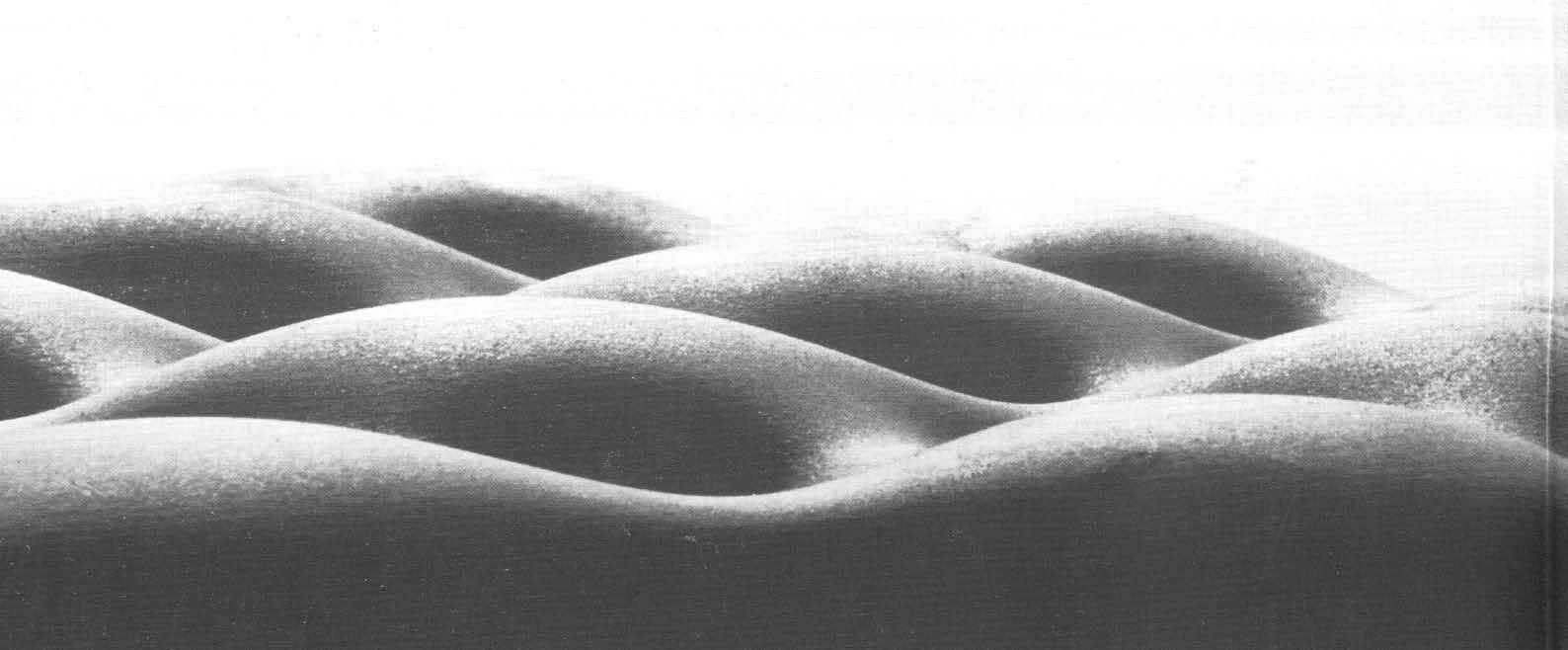
In nature, there are numerous surface structures, like the shell of the Biddulphia tuomeyi shown in Figure 12 that are generated by pneumatic stresses. In shells, differences in shell thickness often exist that create different morphologies. When pressure is exerted on the membrane, the thinner areas bulge, while the thicker areas form pre-stressed braces preventing uniform bulging. The differentiation in membrane makeup accounts for a crucial structural occurrence (Bach, 2004); the braces not only stabilize the shell, but prevent anticlastic surfaces to emerge. This in turn eliminates out-of-surface action. In addition, in soap bubble experiments carried out at the Institute for Lightweight Structures, it is shown that soap film self-organizing into a minimal surface creates partitions, or bracing as well (Figure 14). Although these partitions occur due to surface tension, they are essential to the structural system in supporting self-weight (Bach, 2004). Separate spherical pneus come together at these braces and eliminate interfaces between anticlastic and synclastic surface geometries. Another strategy to structure surfaces with both anticlastic and synclastic geometries is to create interstitial anchor points, as shown in Figure 11.
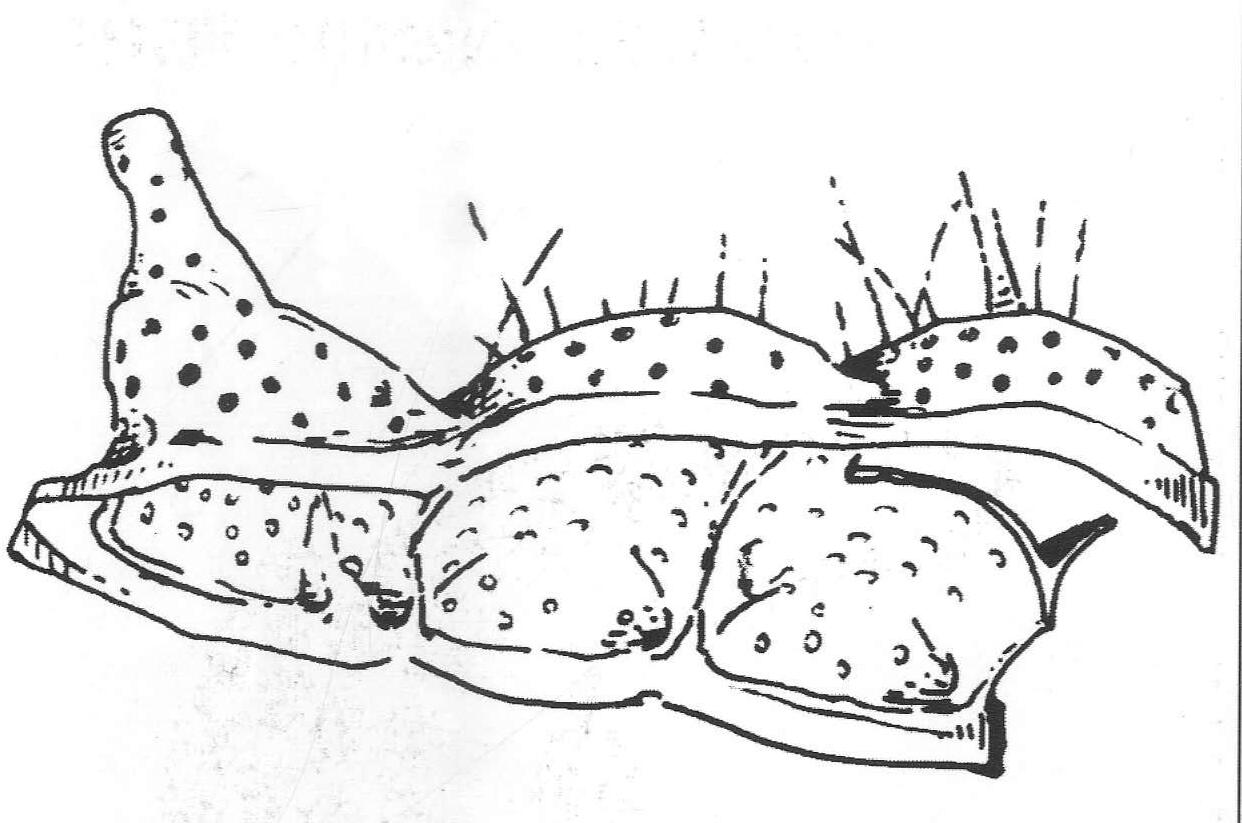
OUT-OF-SURFACE ACTION IN A HORIZONTAL CONFIGURATION
This experiment aims to eliminate these problematic interfaces in a horizontal setup (where the cable net is above the pneus (Figure 13) by redistributing loads to avoid out-of-surface action (Figure 10). The setup is conducted using a flat MDF board 25 cm x 60 cm as the base, a flat sheet nylon stocking measuring 15 cm x 30 cm, and 6 cable ties. Each corner of the nylon sheet is secured to the base with cable ties, so that the sheet is tied down but not stressed. The center of each long side of the sheet is then secured down to the base. Two balloons, centered on each half of the sheet, are fed through the MDF base and inflated with a pressure of 10 psi. The experiment has three different configurations, with all other parameters remaining unchanged. Each configuration explores a possible
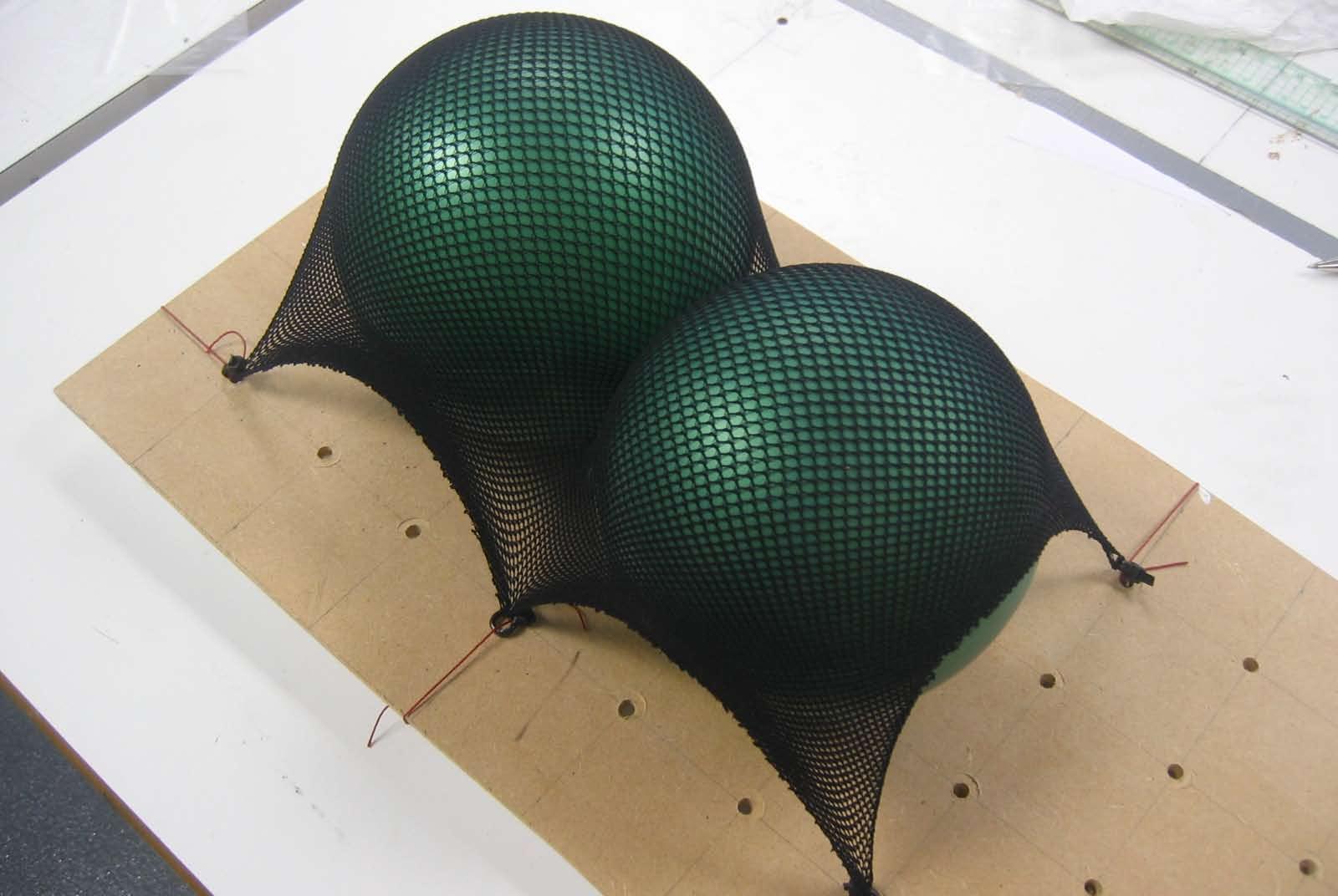
solution:
CHAPTER 15 - APPENDIX A
5.0 OUT-OF-SURFACE ACTION
bracing vertical cable bracing, vertical sheet bracing, and longitudinal cable bracing. Figure 10, diagram, describing out-of-shell action on a horizontal pneu-cable net system. Stresses are being transferred through the material out to the anchor points (shown in red), however the force vectors bring the forces out of the material at the inflection points between anticlastic and synclastic surfaces. Figure 12, sketch, showing a natural shell created by biological pneus. the shell has vertical ribs stabilizing the structure at the junction between synclastic surfaces, eliminating anticlastic geometries. Figure 11, photograph, showing a complex geometry surface created by a pneumatic system. Forces are transferred between anticlastic and synclastic surfaces by surface points being pulled down to the ground to act as anchor points. Figure 14, soap bubble model, showing a pneumatic system self-organizing into a minimal surface. Synclastic geometries merge to form ribs that transfer tensile stresses to the anchor points of the system. Figure 13, model, describing the behavior of two pneus infalted beneath a flat cable net. This configuration does not address the issues of out-of-surface action experienced in earlier experiments, but acts as the control configuration in this experiment.THE ADDITION OF CENTRAL VERTICAL CABLES AND NETS
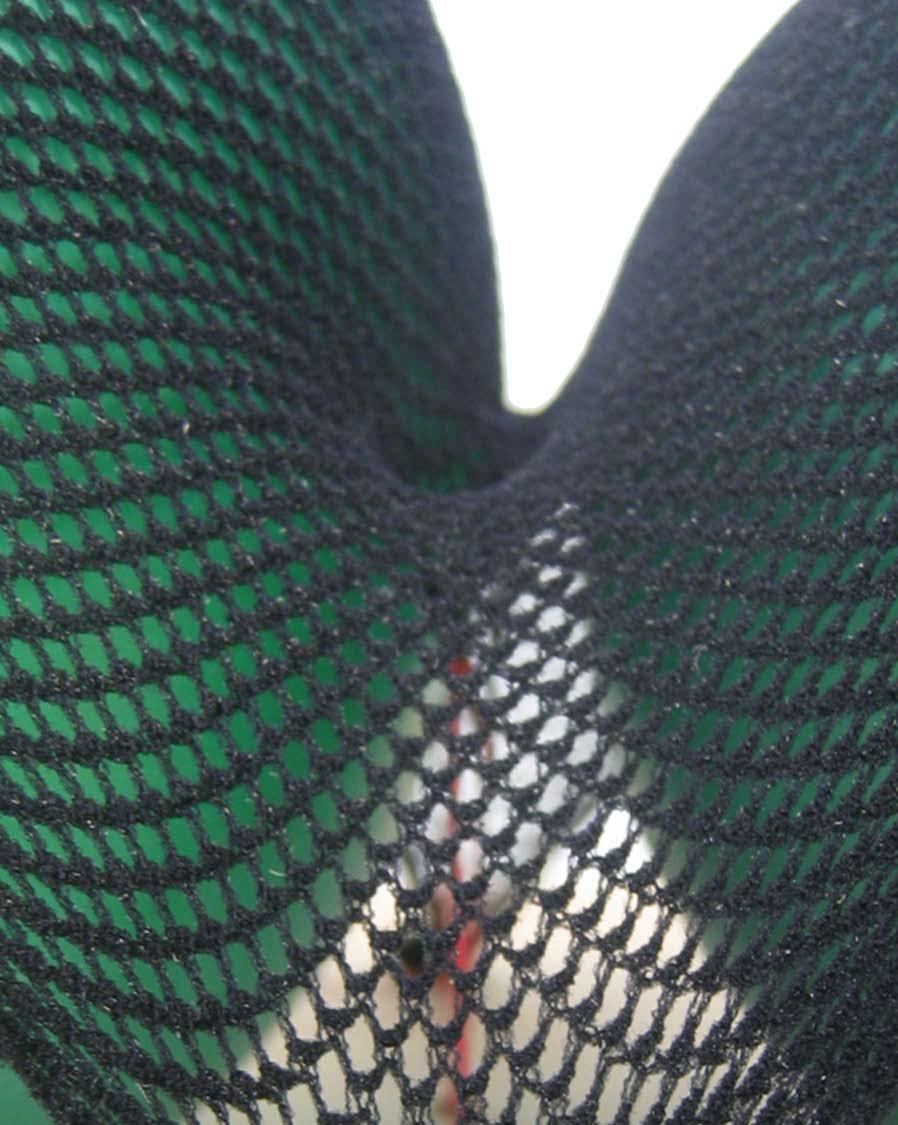
Taking references from biological structures as well as minimal surface soap bubble experiments by the team at the Institute for Lightweight Structures, this experiment aims to eliminate out-of-surface action by bracing synclastic geometric surfaces to provide stability through a force vector shift. It is hypothesized that the addition of bracing at the peak of the synclastic curve on the cable net can eliminate these surfaces, eliminating out-of-surface action, and therefore stabilize the material system. This would thus allow the system to resist compressive loads. In the first test, individual cables of 8 cm in length are used to connect the cable net to the base (as shown in Figures 15 and 17). These cables, when tensioned by the tensioning of the net itself, create a force vector downward to the base (Figure 20). While these downward cables create synclastic funnels (Figure 21) which provide local stiffness, they create further areas of anticlasticism, and expand the number of interfaces between anticlastic and synclastic geometries.
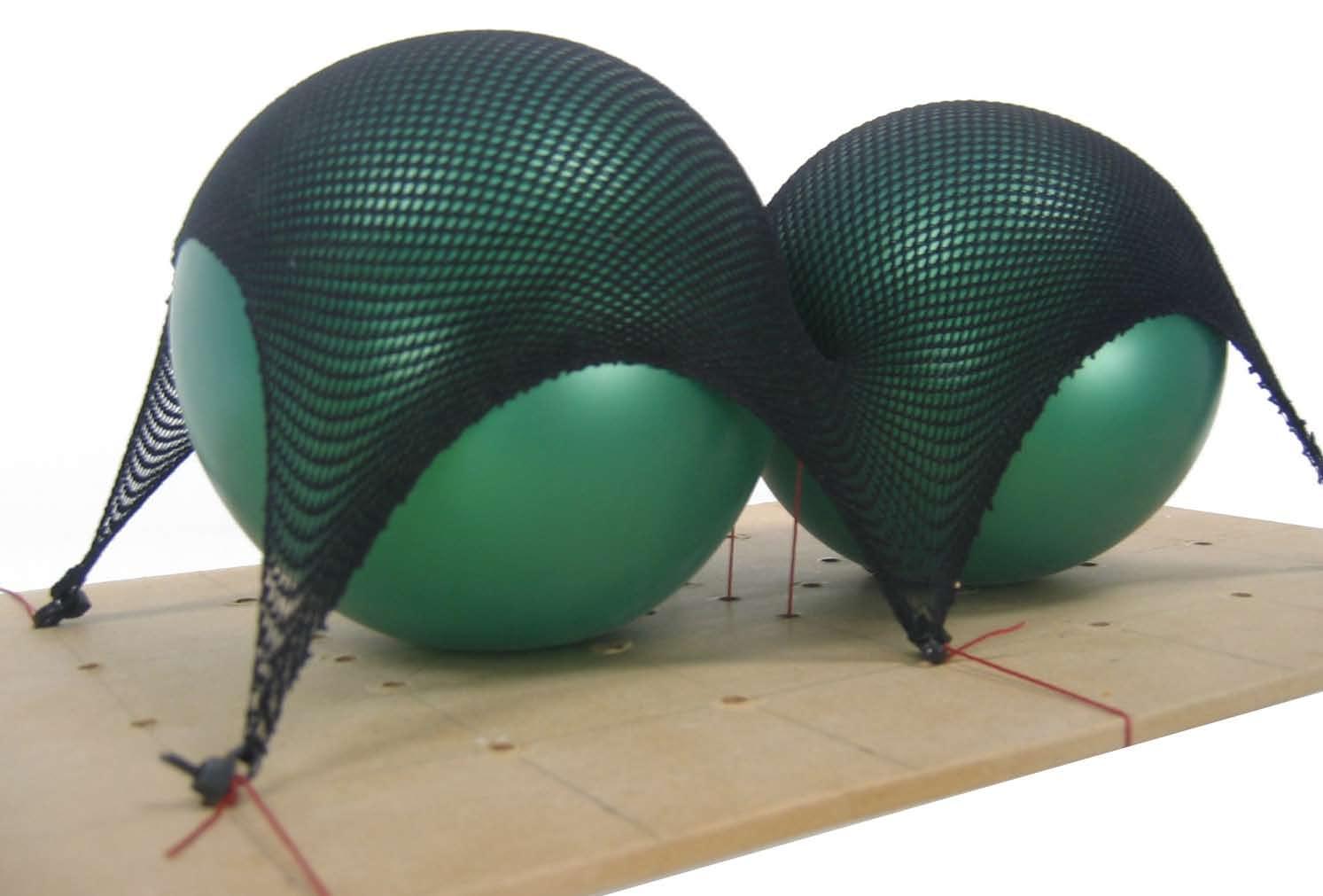
A net is also implemented to transfer stresses and eliminate out-of-surface action (Figure 18). However, while local stiffness is created through arches at the bottom of the vertical net (Figure 19), the placement of the net is incorrect according to the principals of out-of-surface action. The proper location of the net is noted as red points in Figure 16.
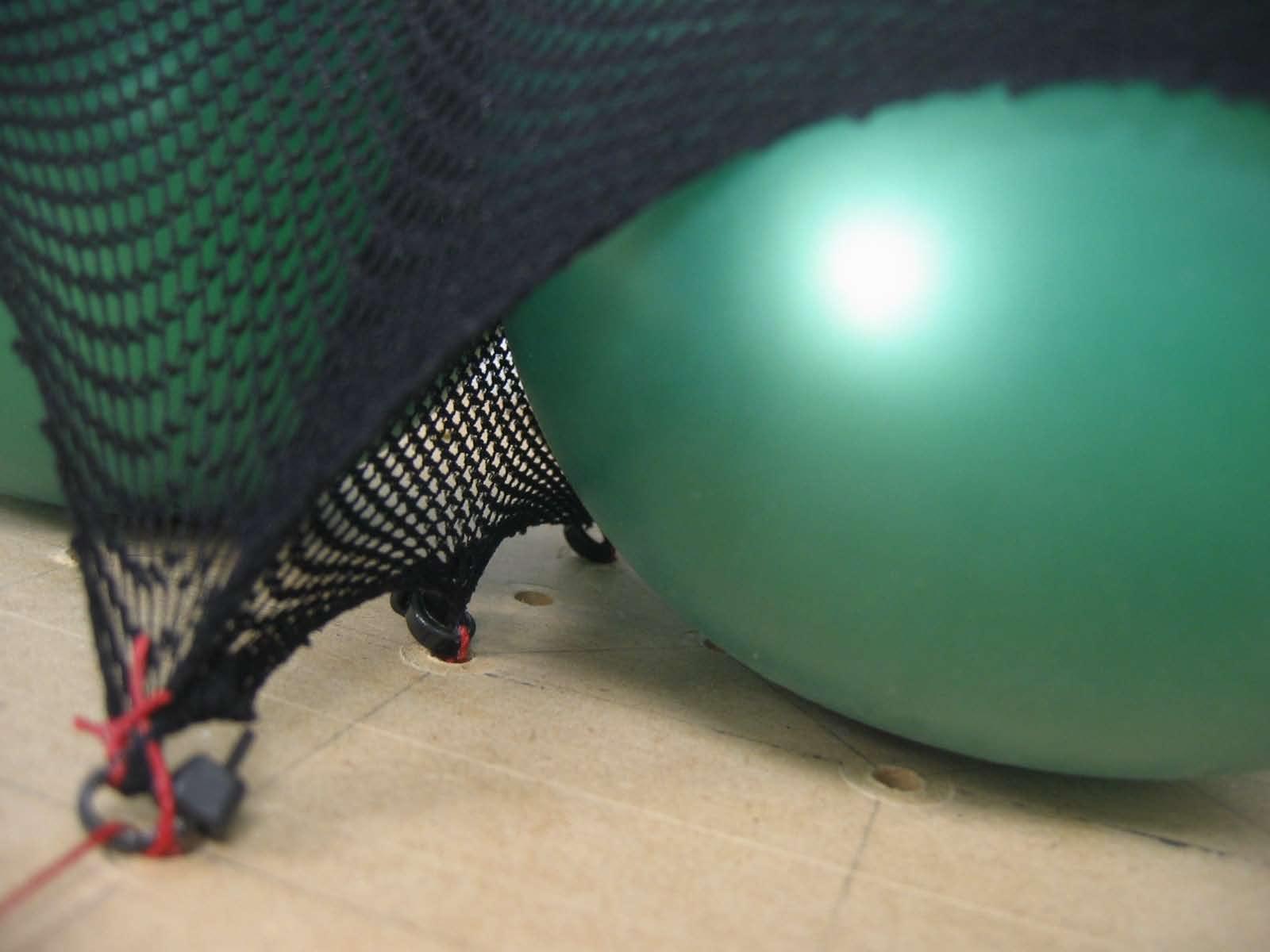
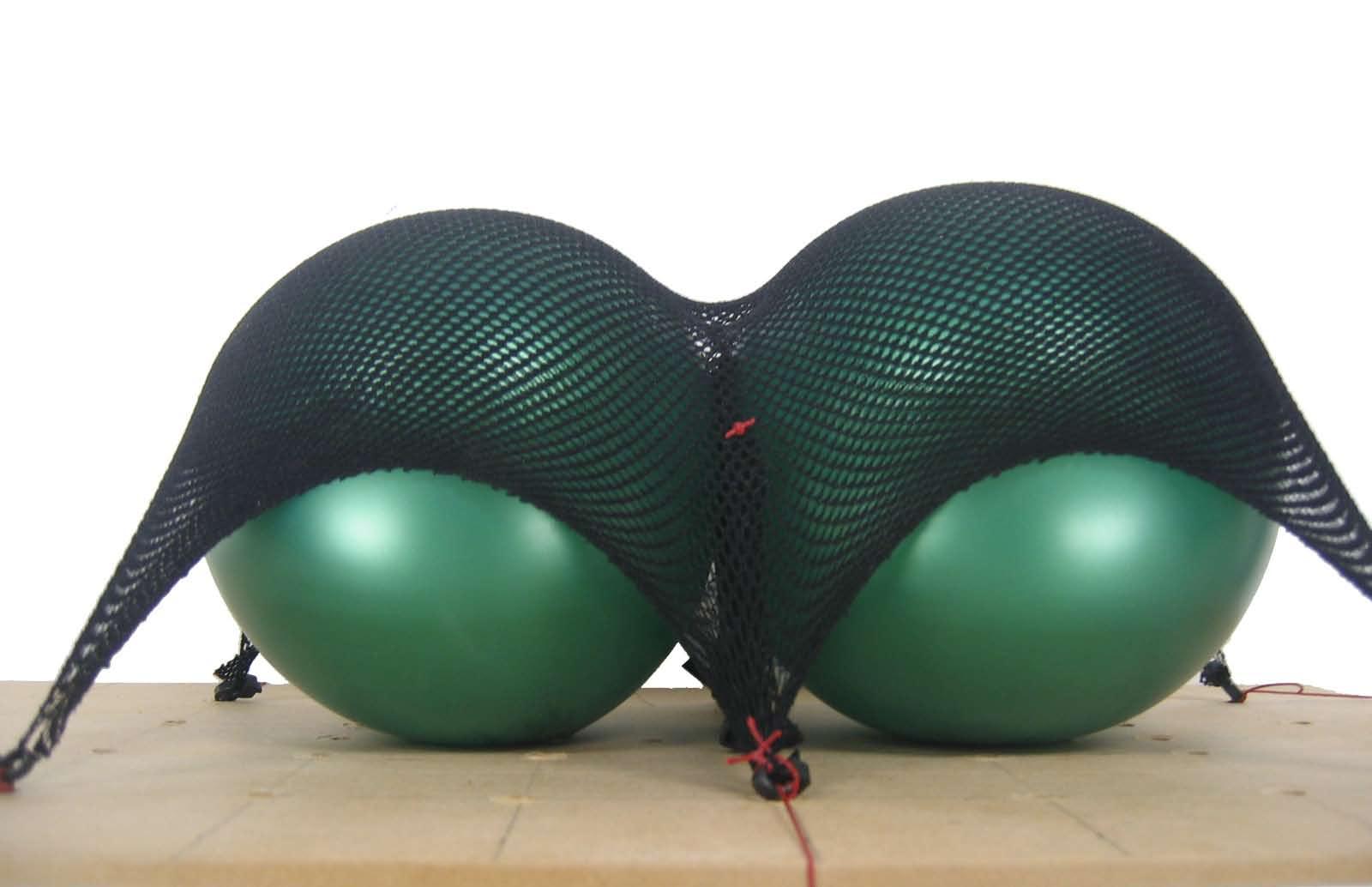
CHAPTER 15 - APPENDIX A 5.0 OUT-OF-SURFACE ACTION
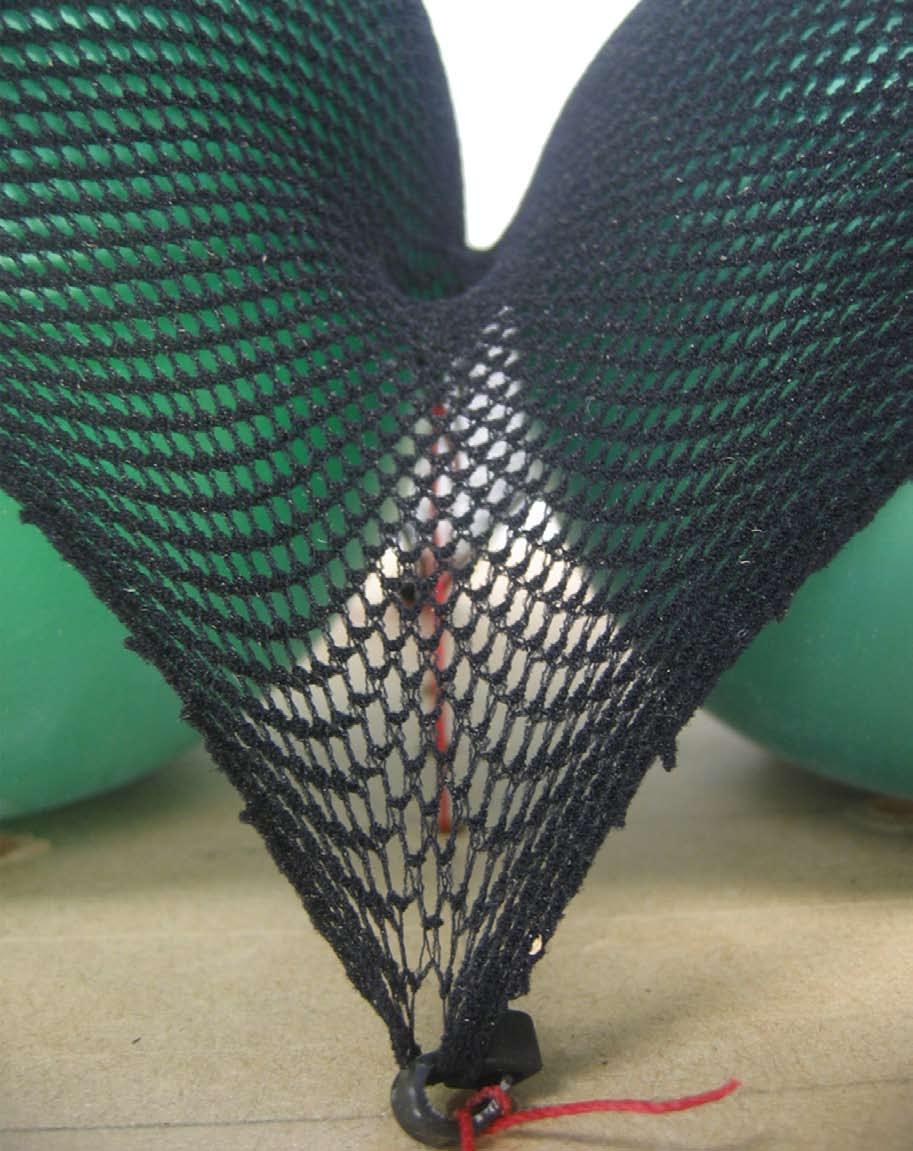
showing bracing formed by surface tension between two soap bubbles. The bracing eliminates out-of-surface action by eliminating anticlastic surfaces entirely, however creates a pinch condition, as seen in the experiment configuration shown in Figures and
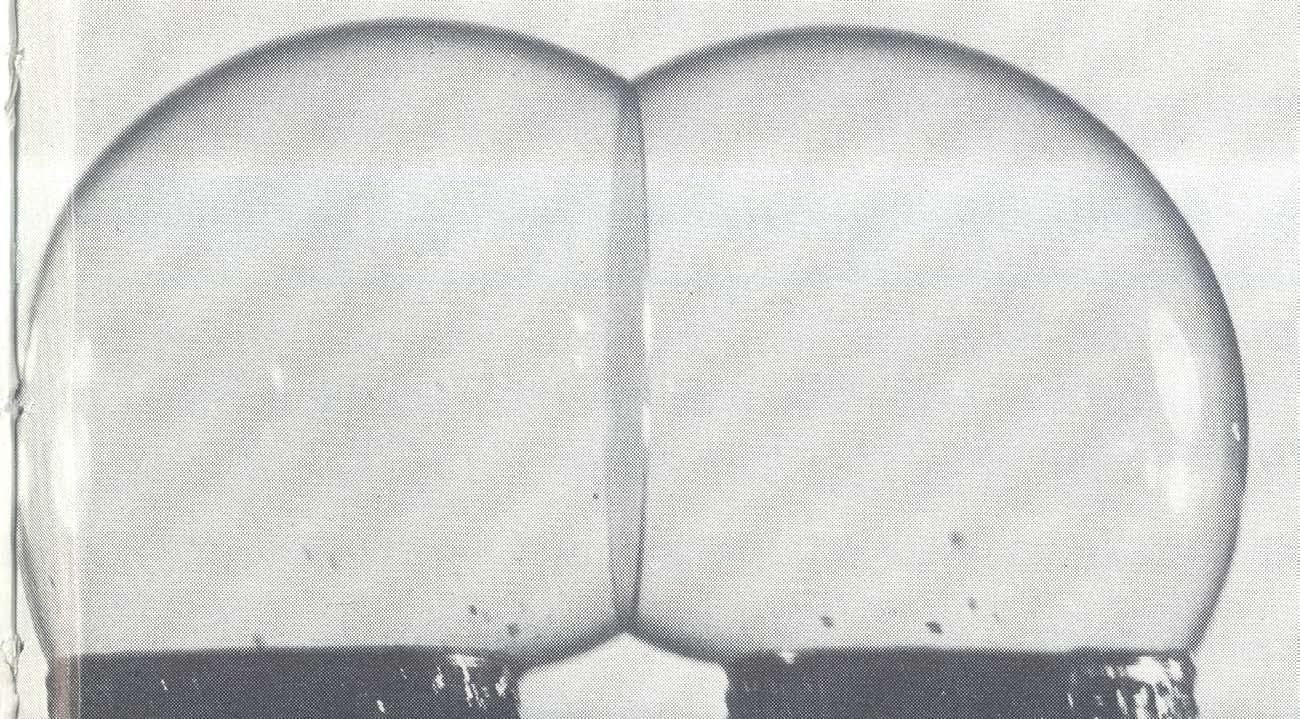
THE ‘PINCH’
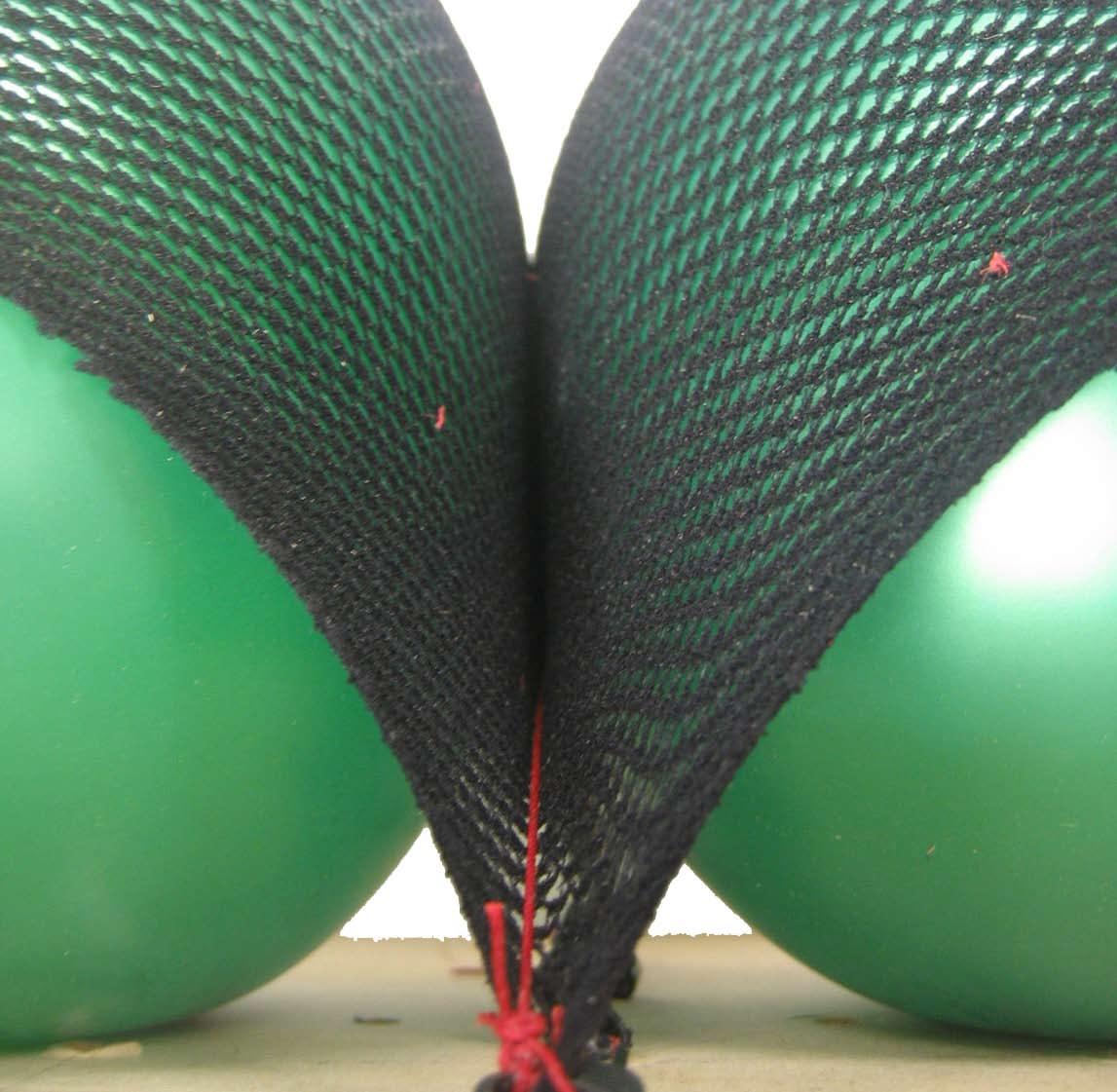
By adding a longitudinal cable as bracing in the configuration diagrammed in Figure 22, the deployed material system is devoid of problematic interfaces, and thus does not experience out-ofsurface action. Although formally dissimilar, the configuration achieved (Figure 23) acts structurally like the soap bubble experiment shown in Figure 28 undertaken at the Institute for Lightweight Structures, where bracing (internal or external) provides structural stability while eliminating the anticlastic area between two synclastic surfaces. However, the elimination of anticlastic surface geometries brings certain repercussions. The cable bracing creates a local pinch (Figure 24) in the material system. Although this pinch solves the local structural weakness, it creates problems of equal global stress distribution. The cable net in tension is no longer able to distribute forces equally to the anchor points; it is important to note the large amount of tension present at the local phenomenon this body of work has defined as a “pinch.”
THE EDEN PROJECT: A STRUCTURAL REFERENCE
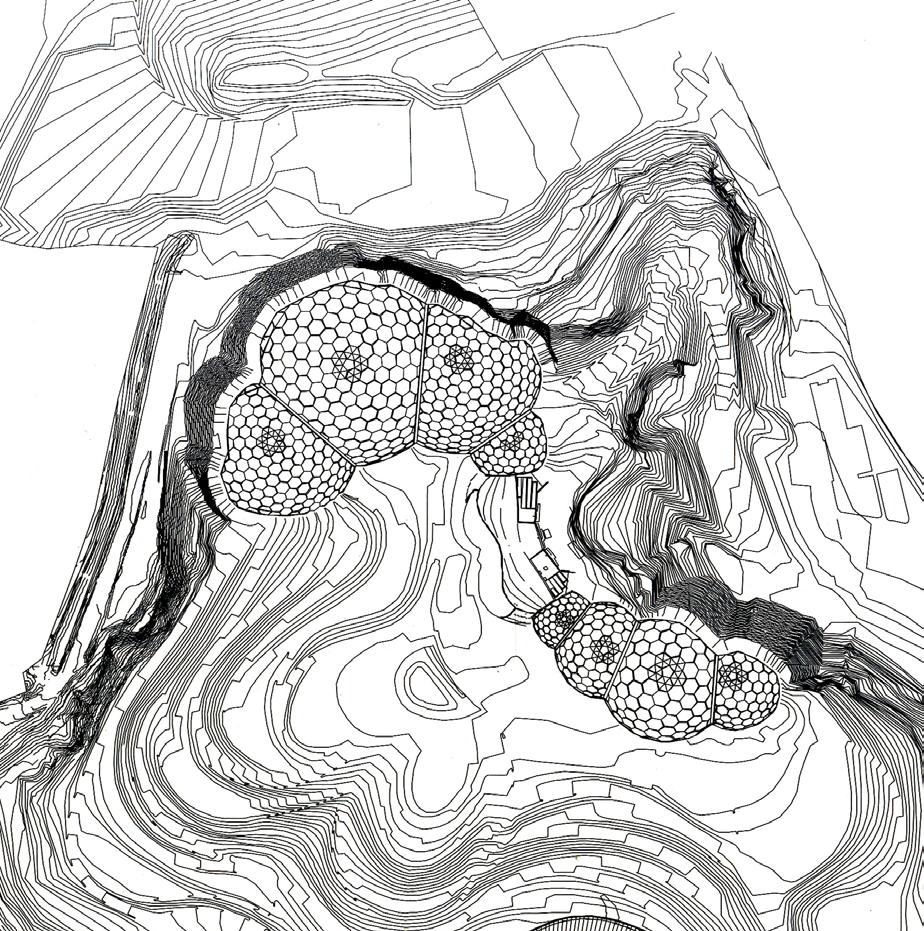
This pinch is referenced in Nicholas Grimshaw and Partners’ The Eden Project, where ETFE spheres converge (Figure 25). To overcome the uneven distribution of stresses that this pinch creates, steel trusses are constructed along the pinch, as seen in Figures 26 and 27. This truss transfers the concentrated load down the length of the arch and to the ground (Figure 27).
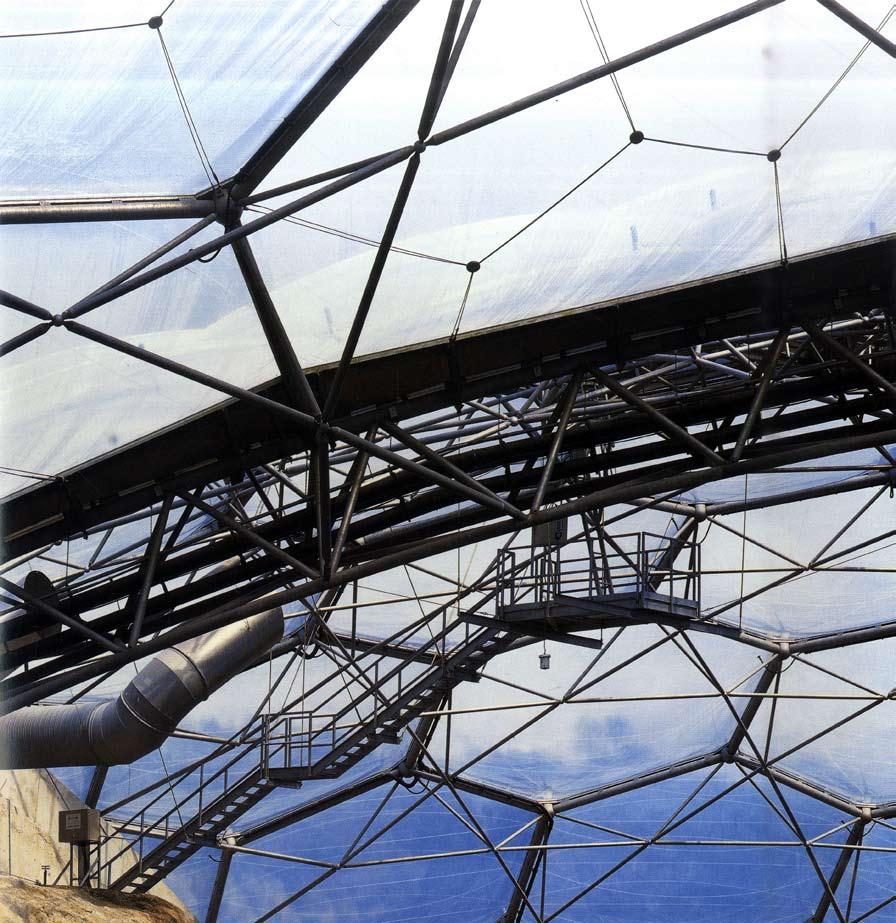
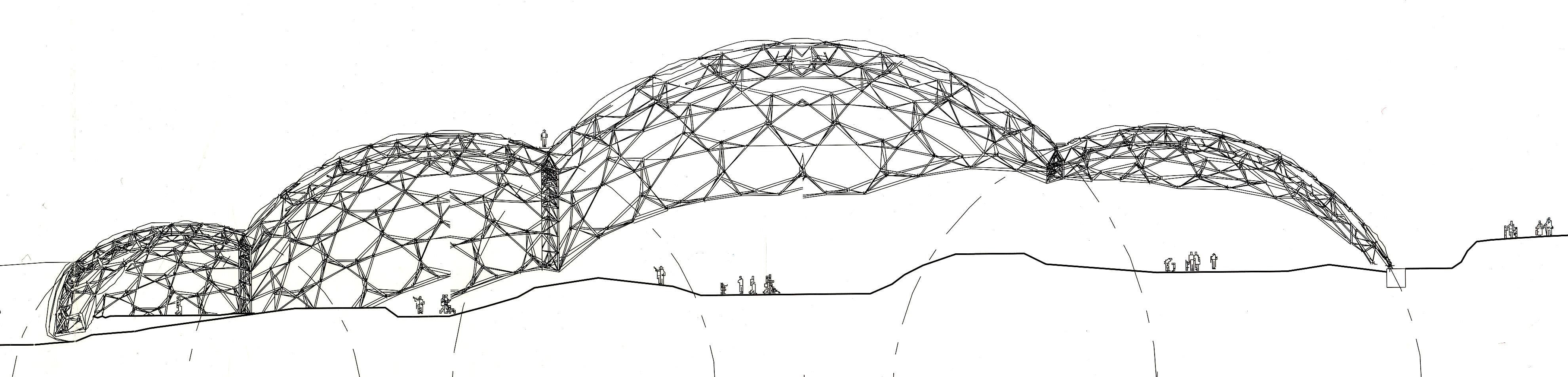
CHAPTER 15 - APPENDIX A
5.0 OUT-OF-SURFACE ACTION
Figure 22, diagram, describing an experimental solution to out-of-surface action. A cable is tied to the base spanning the area of expected anticlastic geometry to introduce new force vectors to the system. Figure 23, model, showing the introduction of a spanning cable and the behavior of the pneu-cable net system when deployed. The cable eliminates the anticlastic geometries, and therefore out-of-surface action. However, this elimination creates a pinch, whose structural implications are described throughout this chapter in further detail. Figure 27, section, The Eden Project, Nicholas Grimshaw and Partners, showing the arch system used at the convergence of two spheres, and the resulting pinch that occurs. Figure 28, model, Figure 25, diagram, The Eden Project, Nicholas Grimshaw and Partners, showing the overall geometric intersections of the ETFE bubble domes. The spheres intersect at a pinch, similar to the condition observed in Figure Figure 26, arch detail, The Eden Project, Nicholas Grimshaw and Partners, showing an arch spanning along the pinch that occurs between two intersecting spheres. This arch is the structural solution chosen to disperse converging forces caused by the pinch geometry. Figure 24, diagram, describing the flow of forces in the investigated configuration. The pinch created in the membrane between the two pneus keeps the forces within the surface material, but creates a concentration of forces at the pinch.THREADING CABLES
In another experiment to eliminate out-of-surface action, two individual cables are added to an existing pneu-cable net configuration (Figures 29 and 30). To avoid the cables from slipping into the valley between each pneu, they are weaved through the net along the line of curvature (Figure 32) created between the anticlastic and synclastic surface geometries. After activating the system by inflating the two balloons, it is observed that while an anticlastic surface geometry exists between two synclastic surfaces (Figure 31), there is a greater amount of global stabilization than in the configuration where these additional cables are not present. This configuration can provide a possible solution in a situation where anticlastic surface geometry is necessary and cannot be compromised, with little to no interference with local configuration conditions.
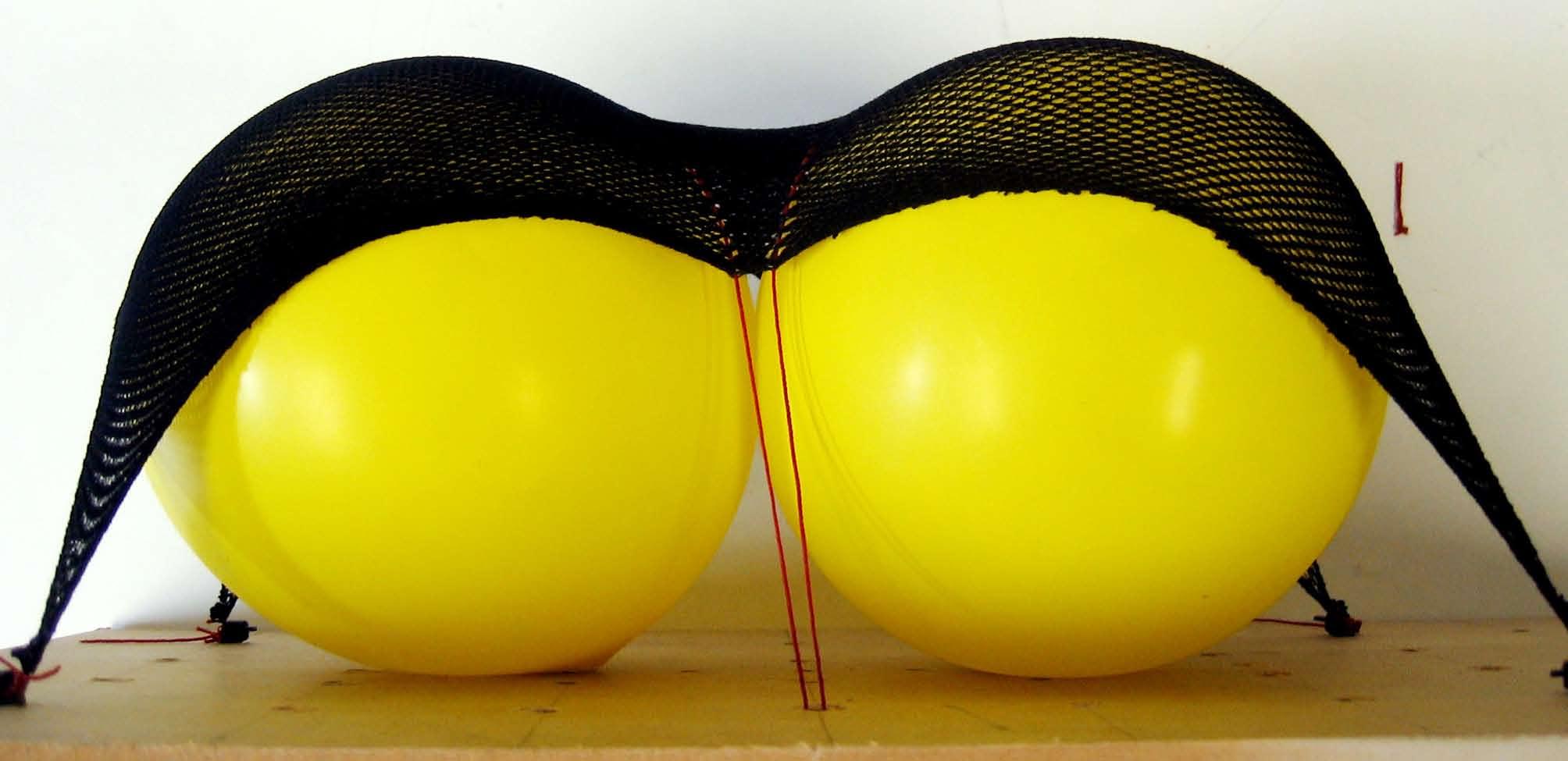
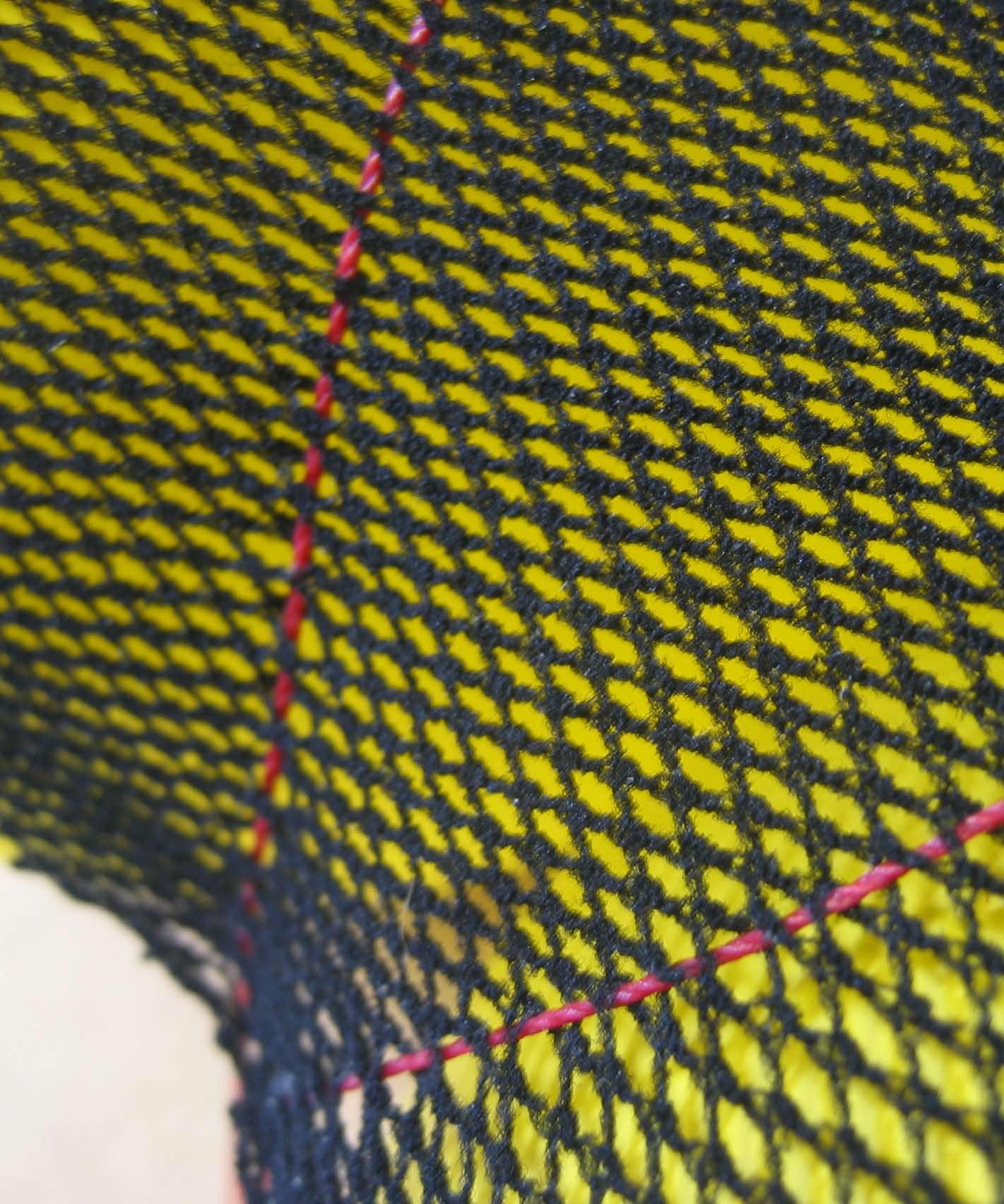
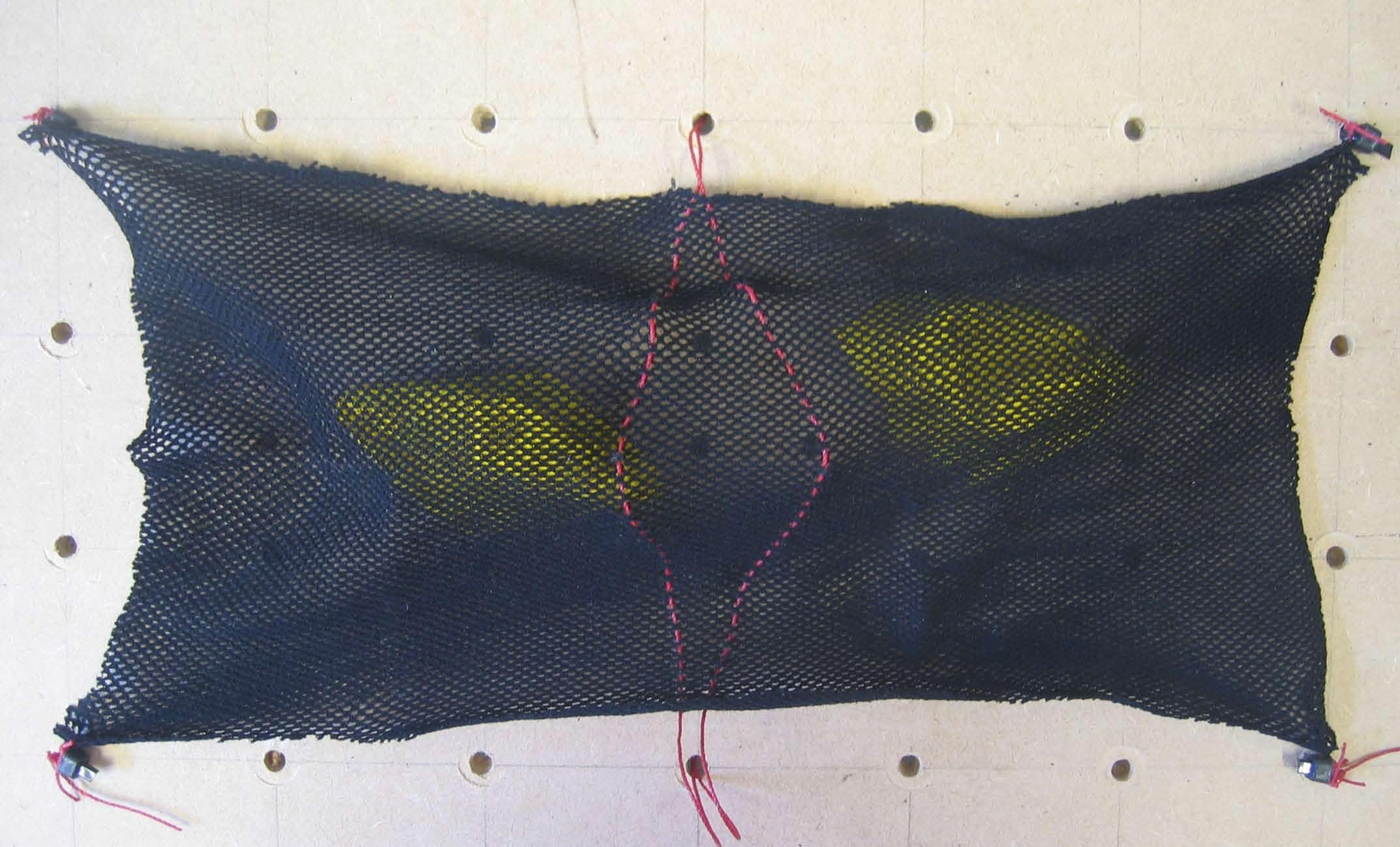
CHAPTER 15 - APPENDIX A
5.0 OUT-OF-SURFACE ACTION
THE EMERGENCE OF FLAT-SHEET GEOMETRIES
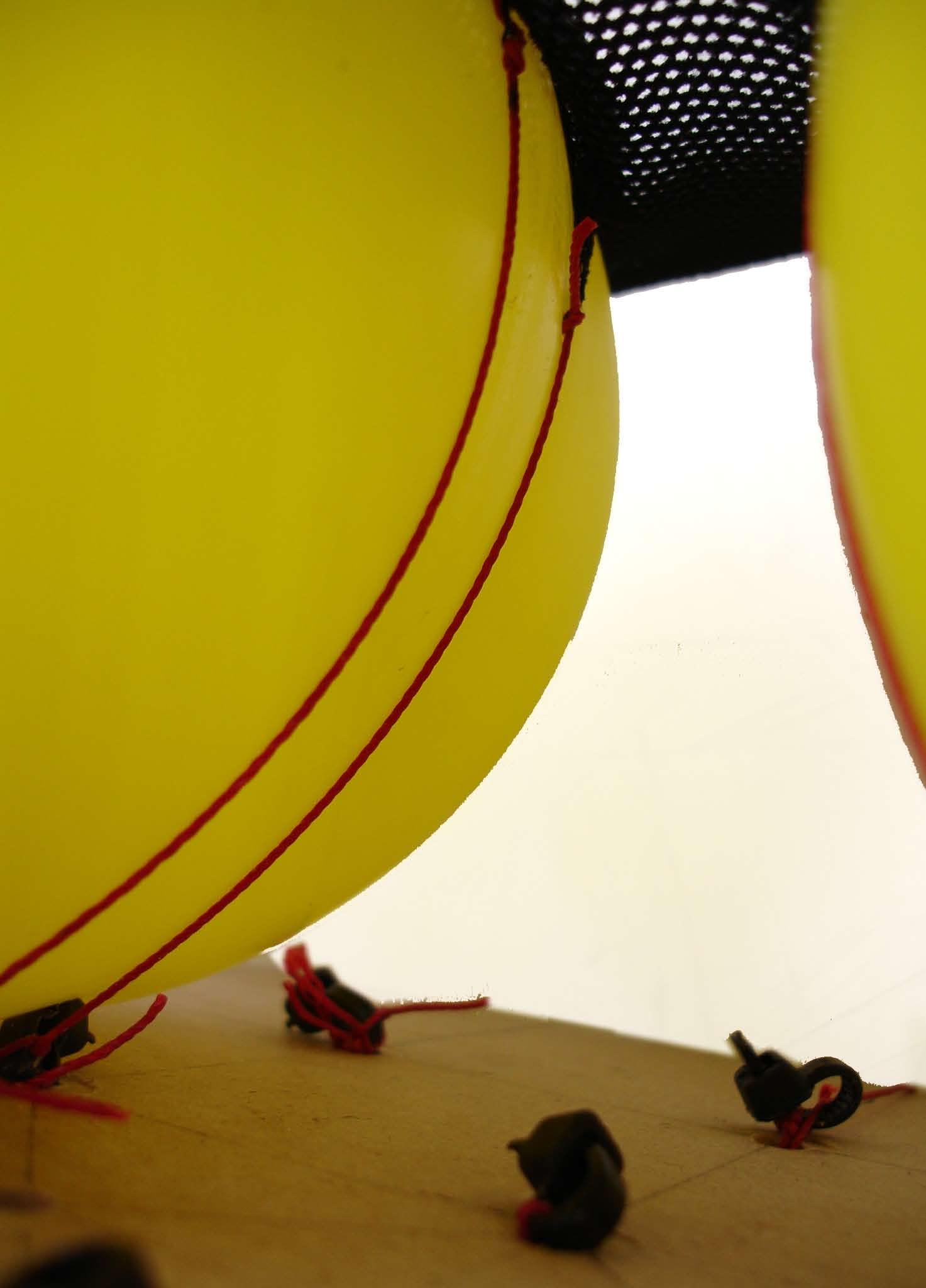
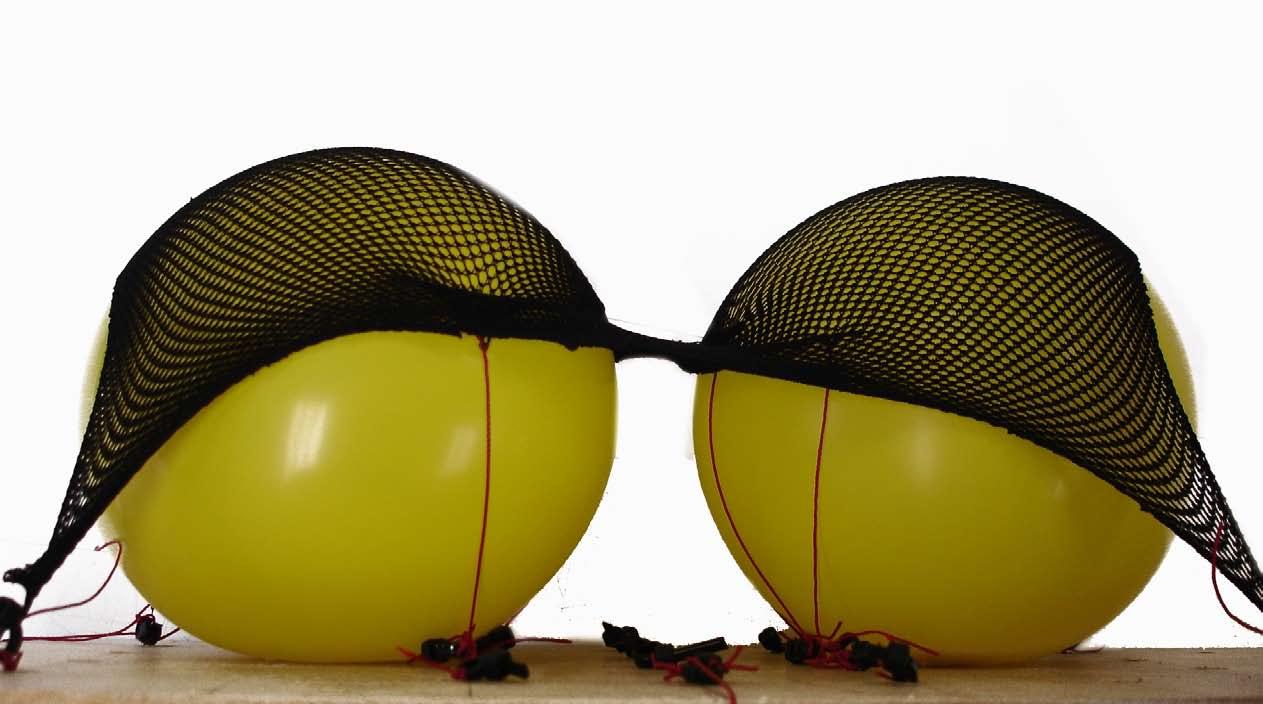
In this configuration shown in Figure 33, individual cables are placed at inflection points between anticlastic and synclastic surfaces. Two sets of three cables are attached to the net and run vertically to the base of the model. Upon deployment of the pneus, it is observed that rather than transferring the force vector down to the board, the cables are distorted by the pneus (Figure 36). This distortion, where the cables are no longer running vertically but instead take the shape of the pneu surface in which they interact (Figure 35), creates an area of the cable net where no curvature is present (Figures 34 and 37). The absence of curvature creates a structural problem in transferring load to the anchor points.
WRINKLING
The cables that pull the net down toward the board create a geometry that, when converging with the flat-sheet geometry created, forms a series of wrinkles (Figure 37). Materially, the cable net is not working in full tension when wrinkles are present. This is of importance to note in order to classify these experiments as structurally effective. Although this configuration allows flat surfaces to emerge, it also poses specific repercussions to the configuration’s setup.
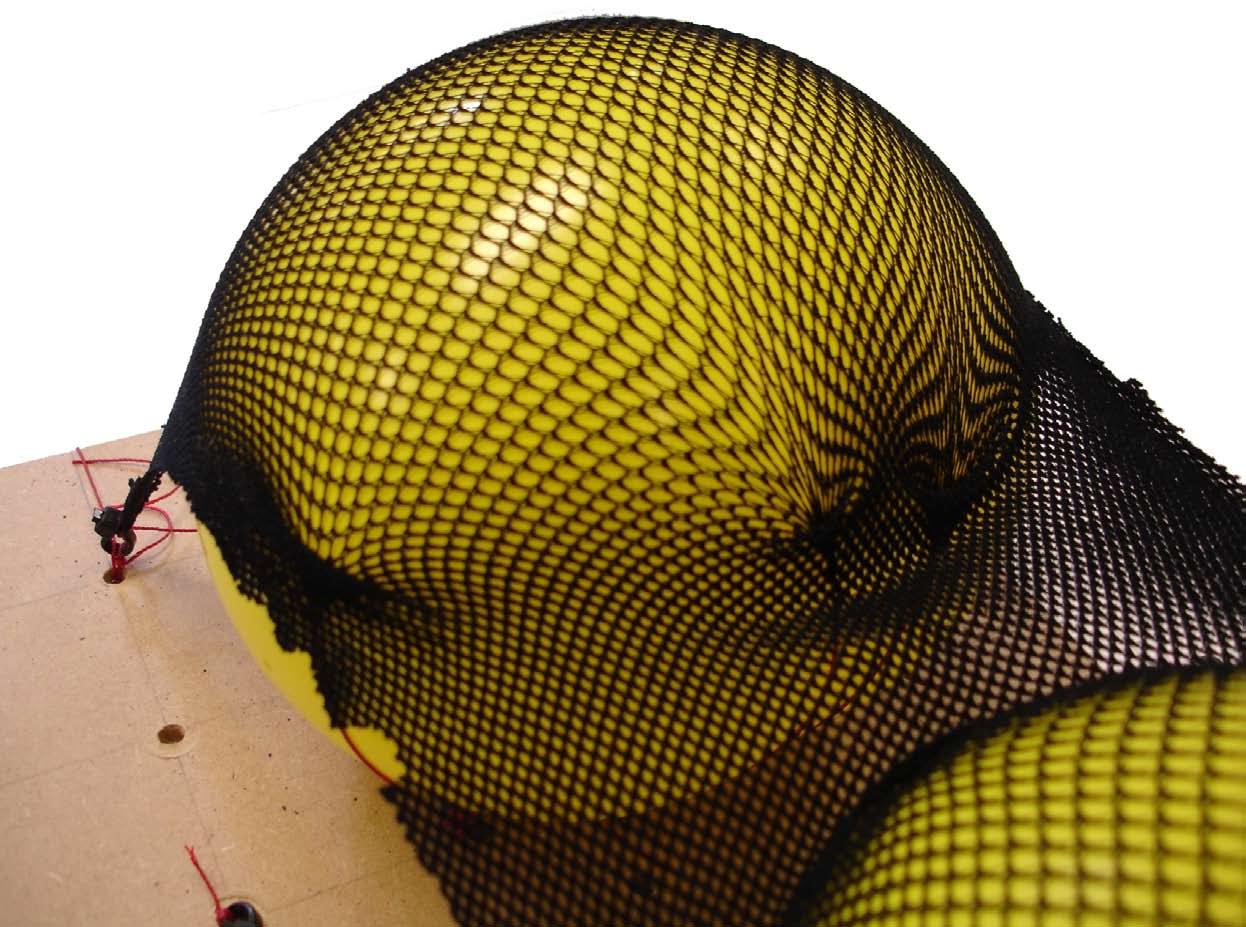
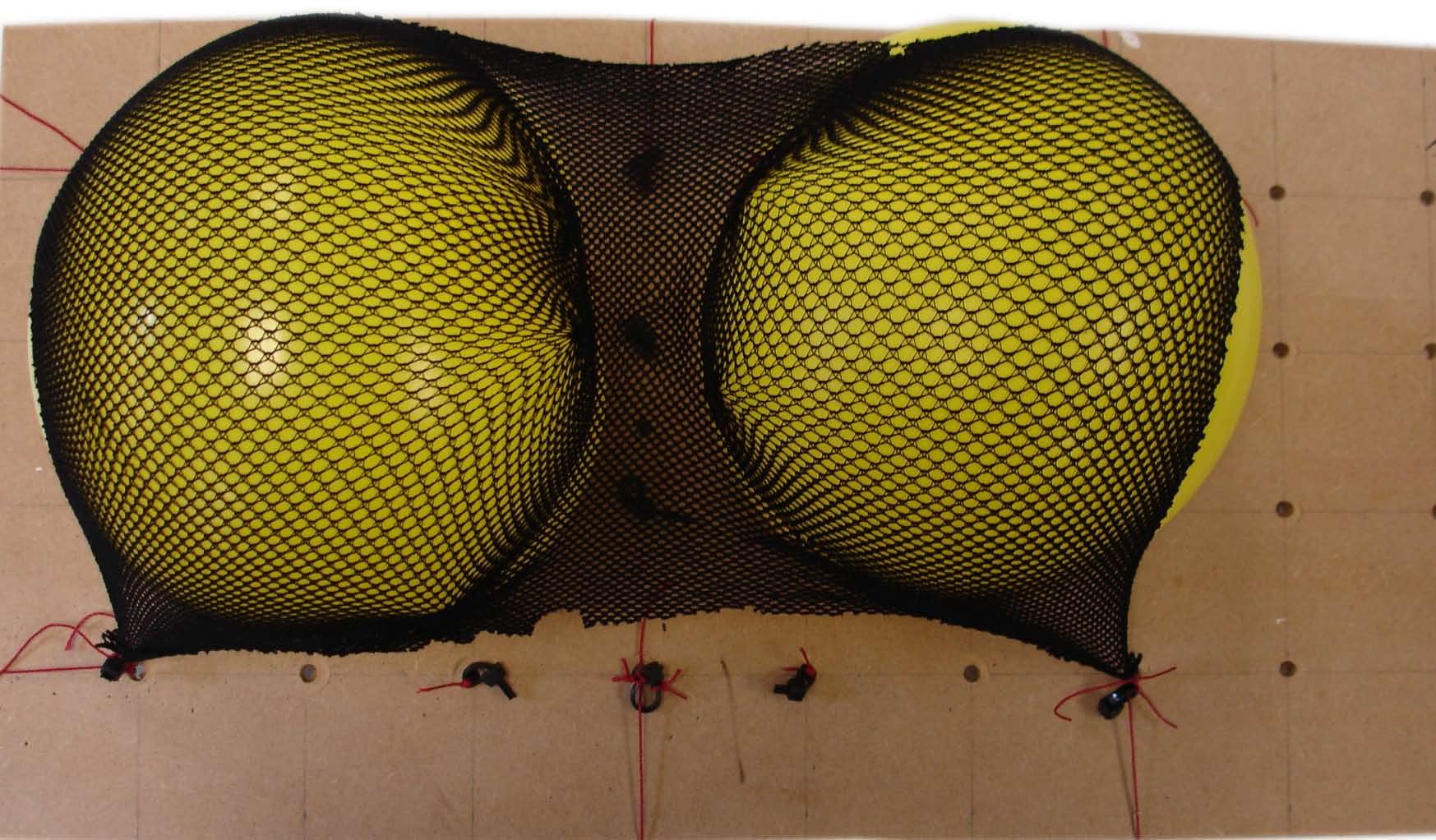
CHAPTER 15 - APPENDIX A
5.0 OUT-OF-SURFACE ACTION
Figure 33, diagram, describing an experimental solution to out-of-surface action. A cable is tied to the base spanning the area of expected anticlastic geometry to introduce new force vectors to the system. Figure 34, model. A plan view of the configuration in Figure 33 shows the synclastic curvature of the net directly influenced by the pneus, while a flat surface is present between them. Figure 35, model, showing the curvature that the cables take when influenced by the pneus. The cables are no longer vertical and follow the balloon’s curvature. Figure 36, model. Elevational view of the configuration diagrammed in Figure 33 showing synclastic surfaces on either side of a flat surface. The cables that are connected vertically take the curvature of the pneus. Figure 37, model. Detail describing the flat net geometry created between the synclastic surfaces.VERTICAL NETS
This configuration (Figure 38) explores the addition of two vertical nets at points of inflection on the cable net surface. While the vertical nets do not remain vertical and take the geometry of the pneus pushing on them (Figure 40), there is enough surface area in the vertical nets to achieve downward force distribution. While the location of these vertical nets is the same as the vertical cables used earlier in this section, a new global geometry emerges. The inclusion of vertical nets at points of inflection completely eliminates anticlastic geometry, and between the two synclastic surfaces where pneus are directly interacting with the cable net, there exists a single curvature barrel geometry, as shown in Figure 41. These findings provide interesting insight into the manipulation and possible control of pneu-cable net systems in a horizontal configuration.
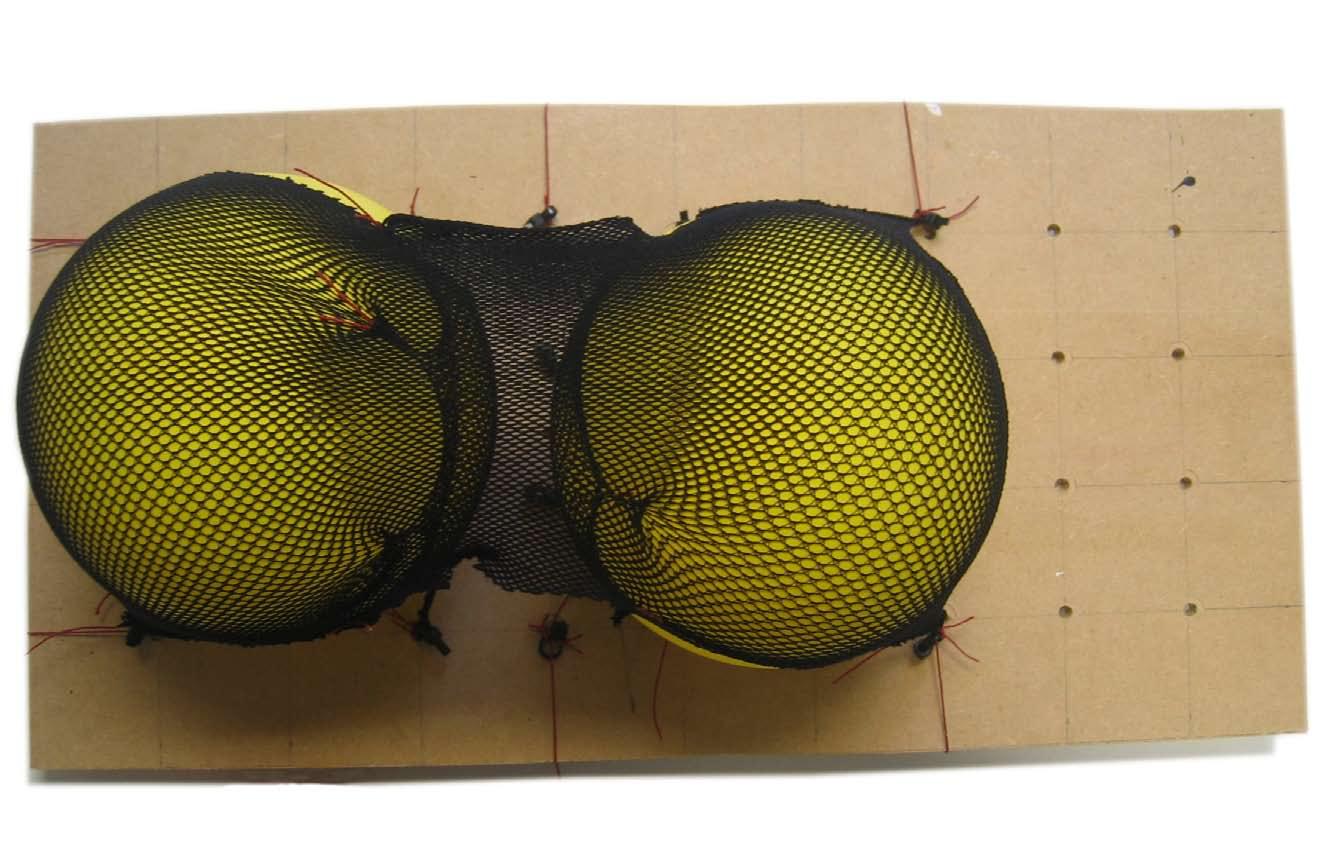
A SINGLE-CURVATURE SURFACE
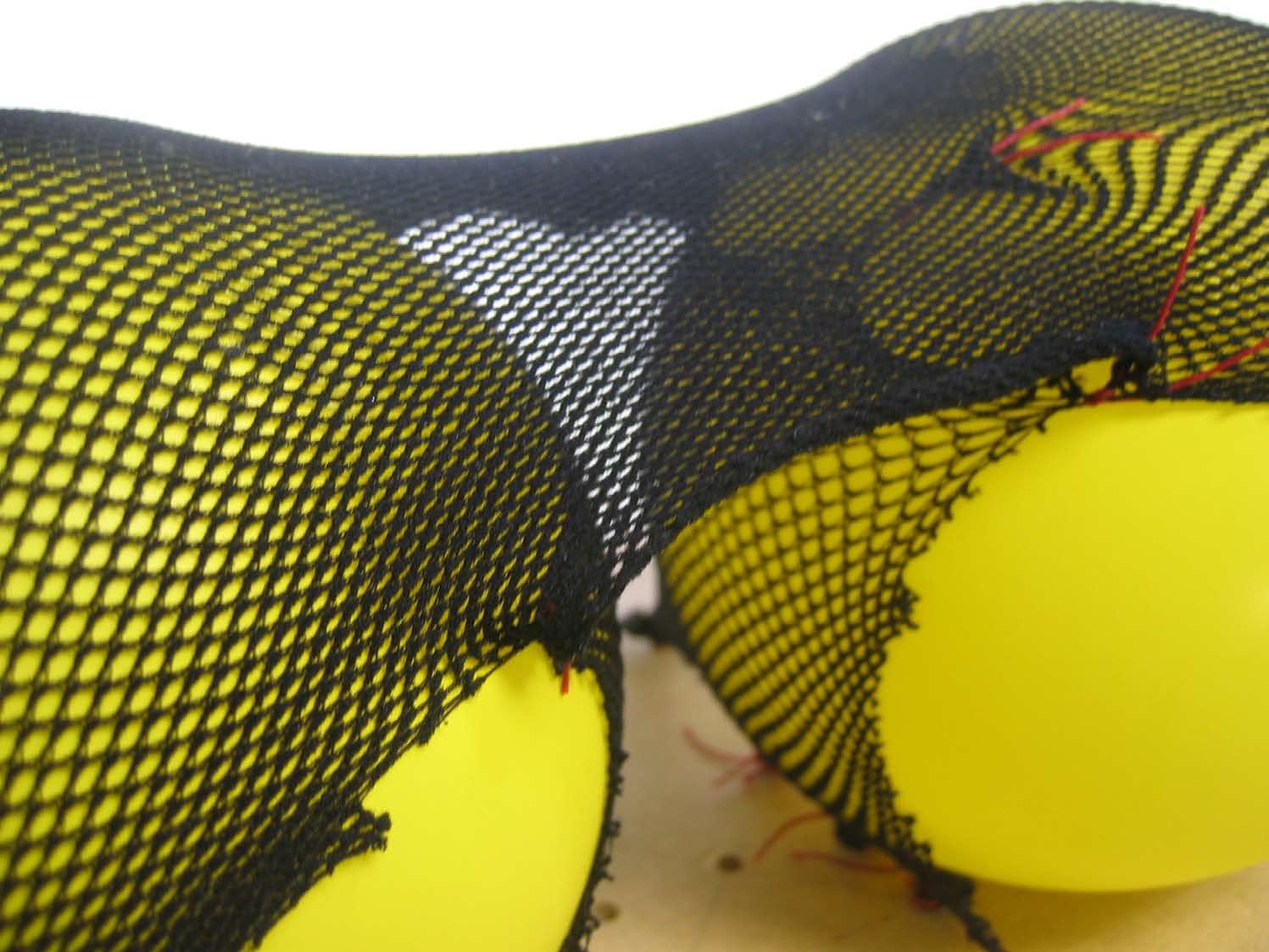
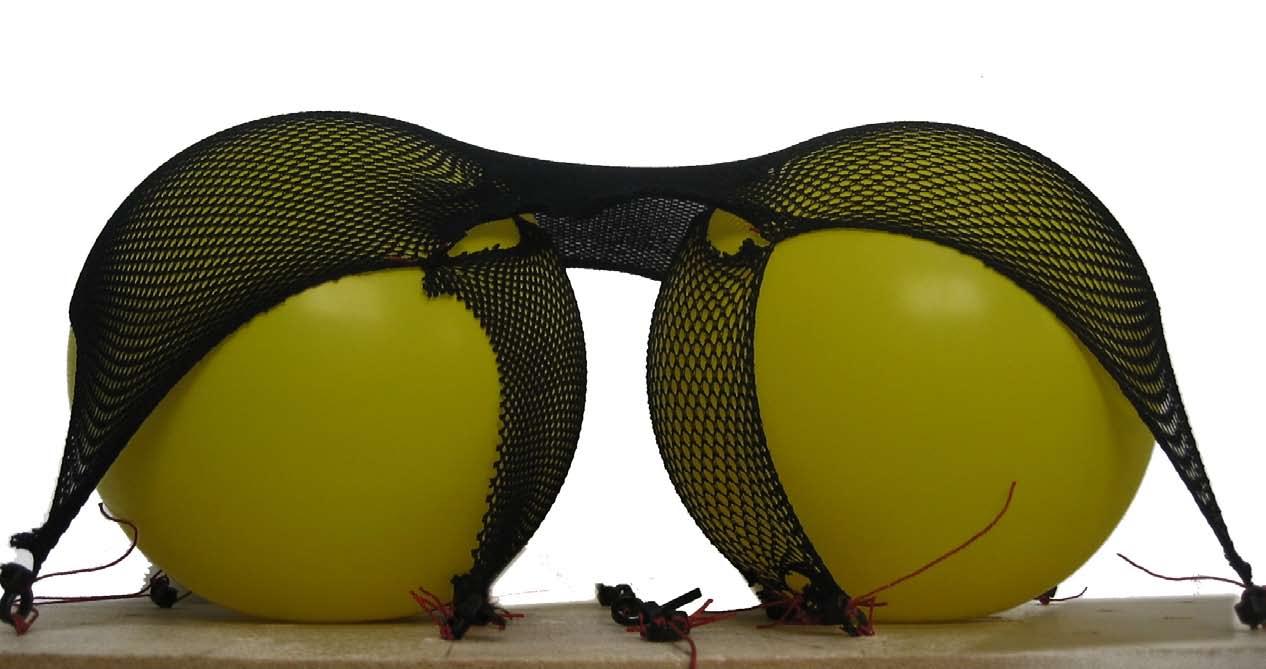
By an additive process, out-of-surface action has been solved. Although this is a step forward in the control of a form-found tensile mandrel geometry working structurally in compression, this experiment poses further questions that must be investigated. While synclastic geometry has been eliminated, the system is not in full tension, as exhibited by wrinkling shown in Figure 39. This problem is crucial, in that the membrane is no longer structurally active to the fullest extent, and forces are not being distributed evenly throughout the surface.
CHAPTER 15 - APPENDIX A 5.0 OUT-OF-SURFACE ACTION
Figure 38, diagram, describing an experimental solution to out-of-surface action. A cable is tied to the base spanning the area of expected anticlastic geometry to introduce new force vectors to the system. Figure 39, model. Plan view of a model set up to satisfy the configuration drawn in Figure 38, showing wrinkling of the material at the net edges. Figure 40, model. Elevational view showing how the vertical nets take the shape of the pneus stressing them. The self-organization of the cable net results in a singly curved barrel surface between the two anticlastic surfaces. Figure 41, model. In this configuration, stressing the system creates a single curvature barrel surface spanning the synclastic surfaces sitting directily on the balloons.