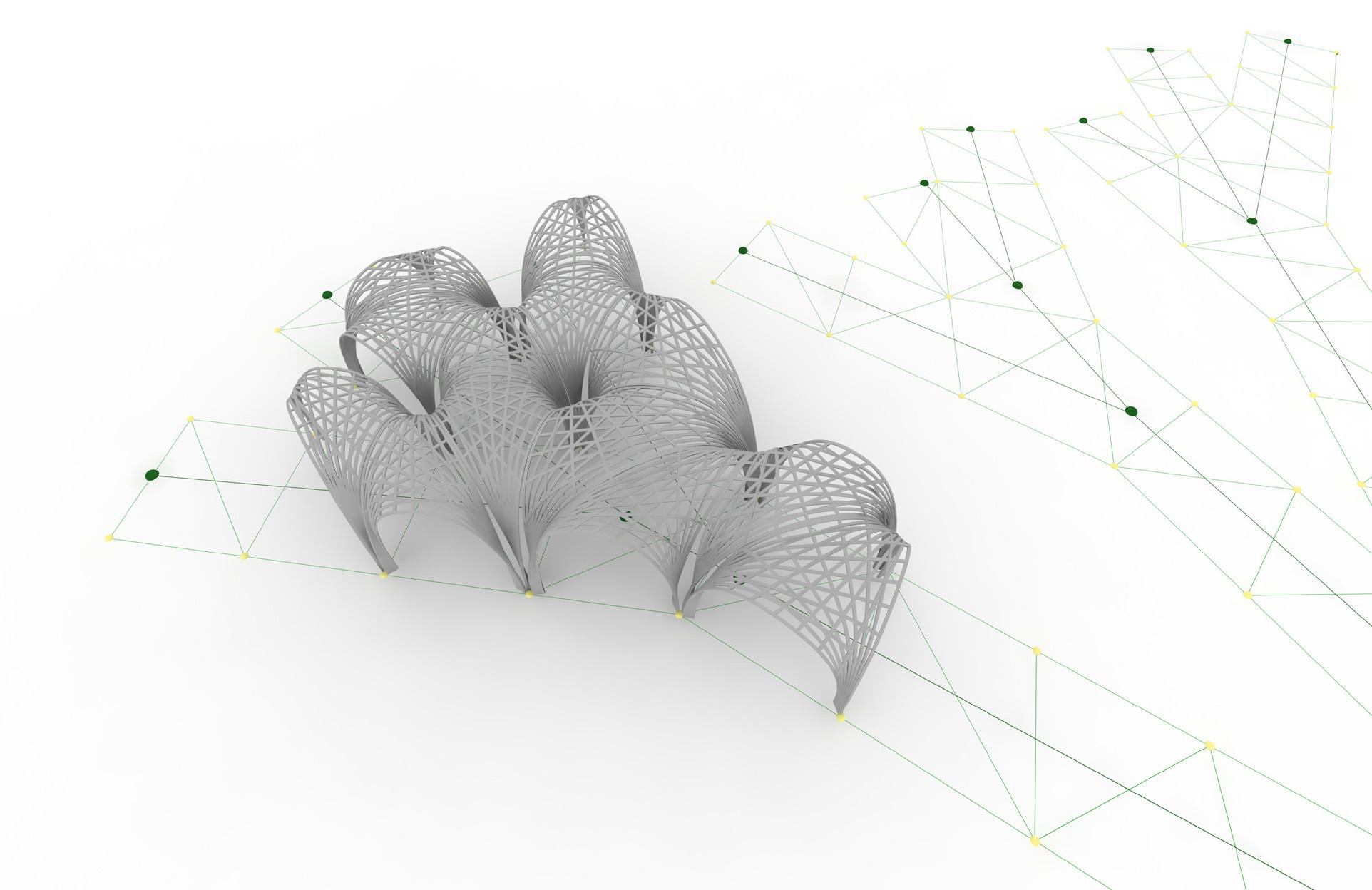
Acknowledgments
I would like to devote this thesis to miss Katerina Juraskova.
The author is very grateful to his advisors Michael Weinstock, Michael Hensel and Achim Menges for their guidance opening mind and also encouragement during the preparation of this thesis.
Contribution from Martin Hemberg, Nikolaos Stathopoulos, Chris Williams and Wolf Mangelsdorf was much appreciated. Thanks also to Guillem Baraut for fruitful discussions.
The research for this book was supported by grants from the Czech Architectural Foundation and company Ce Wood. The author would like to express his genuine gratitude to Ladislav Tucek and his Reprograficke stredisko for collaboration and support.
I would like to thank my family and friends for their love and support during this difficult and yet rewarding year.
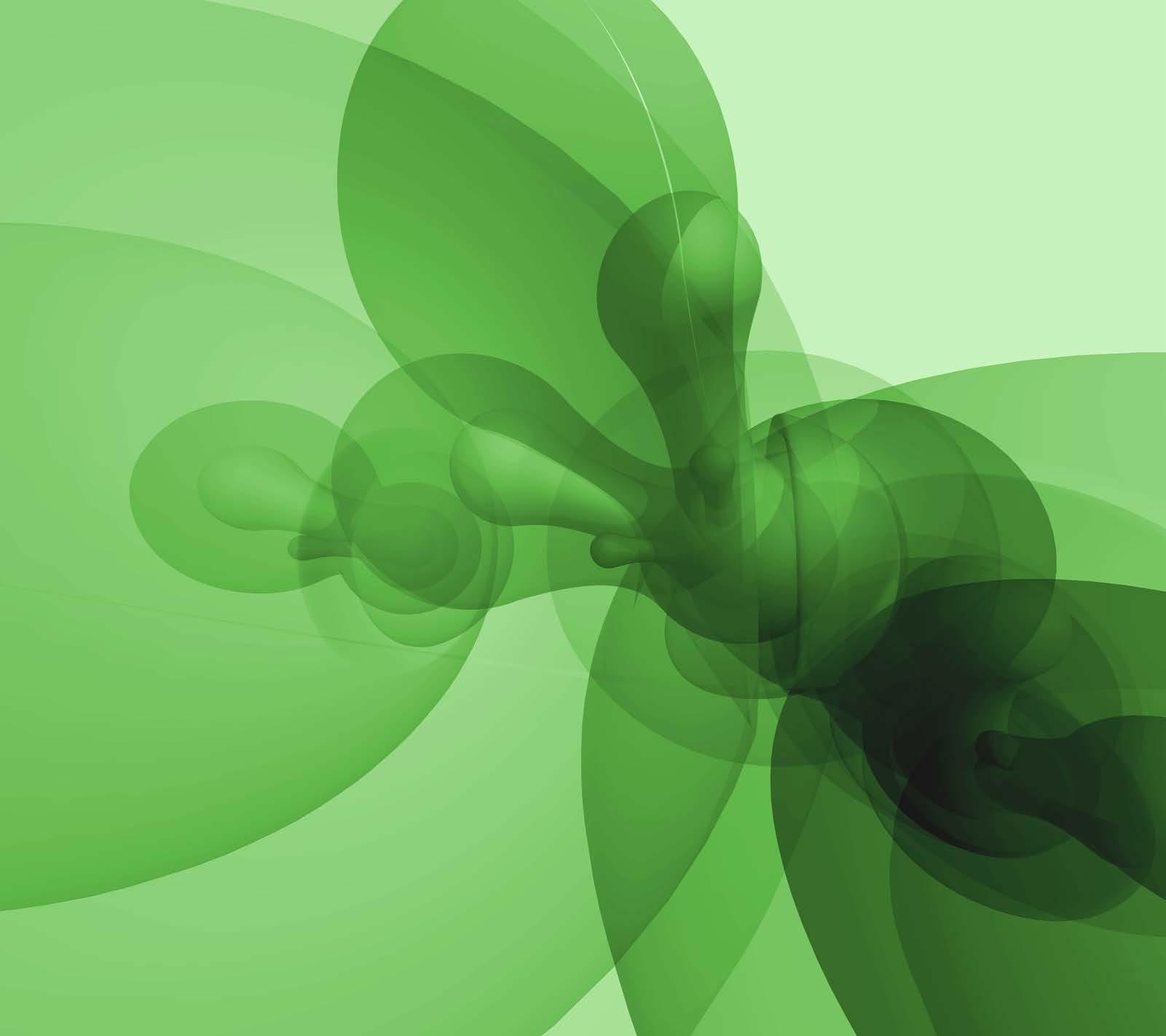
Recently, there have been introduced digital tools that allow for a simulation of the growth into architectural design. The research in the past decades have placed geometric design representations almost exclusively into the digital design environment without constraints of traditional materials and their fabrication.
In this research it is argued that the generative process driven by growth algorithm could be informed by the behaviour of a material and its production logic. The thesis explores the methodology for the bidirectional approach which links a digitally generated geometry with tectonic articulation. The bidirectional approach is understood as an alternative to the traditional analytical uni-directional approach for the articulation of digital geometry. The proposed methodology therefore takes advantage of form-finding - the behaviour and selfform of material under stress and links it directly to the generated geometry.
The work explores the capacities of laminated wood and its integration into the design in the structural paradigm. The structural scheme is the branching system developed into the complex adaptive system [].
A key contribution of this thesis is the use of parametric computation techniques in the convergence of structural scheme of branched structures and sensitive growth. The limits of proliferated geometry and behaviour of laminated timber were achieved. Abstract
Aim and Scope
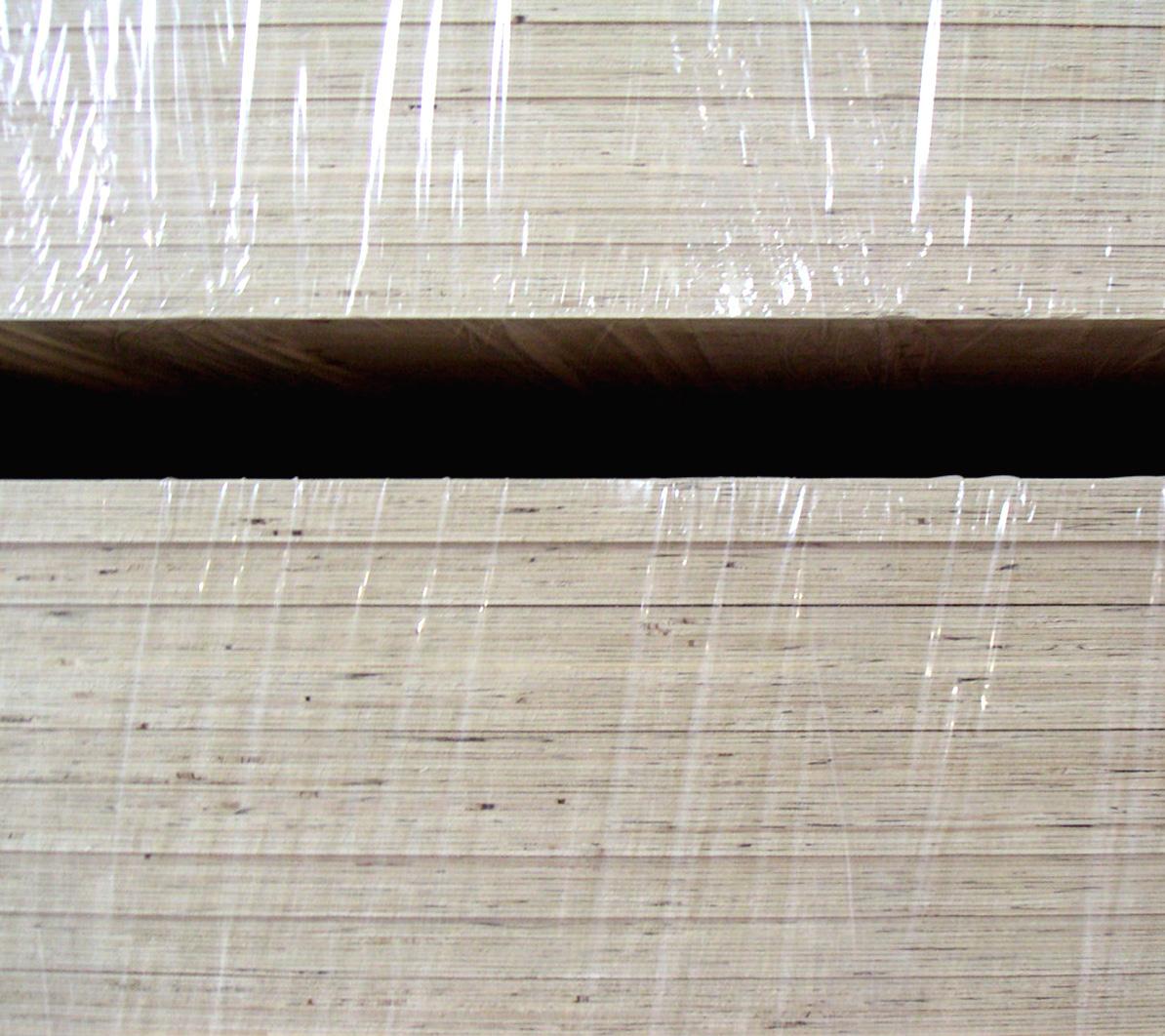
Having a system allowing for adaptation in diverse structural criteria is advantageous for maintaining the same structural scheme in different geometries. These geometries are produced by the growth algorithm L-system which responds to the requirements of the site through the spread of inputs that are base points for the proliferated branched geometry. The complex branched structure is investigated in terms of structural performance.
The aim of the research is focused on the relationship between vector active branched system and surface active system evolved from branches. The vector active system is explored in physical formfinding models based on dehiscence of water.
The research explores capacities of laminated timber in the structural scheme of branched geometry. Gained knowledge is then instrumentalized by a development of a material system which leads to the evaluation on the scale of the permanent pavilion.
Thesis is based on the research commenced in the institute of Lightweight Structures where related systems were studied and methodology for experiments with branching was outlined.
The scope of the research is divided into two parts.
The first is the generation of form in digital space according to rules gained from physical form-finding of branched structures. This part leads to the self-organisation in the digital environment with a possibility of growth.
The second part is devoted to the integration of self-form of laminated timber and generated branched system. The transition between bending and direct paths is examined and leads to an associative model of the material system.
Hypothesis
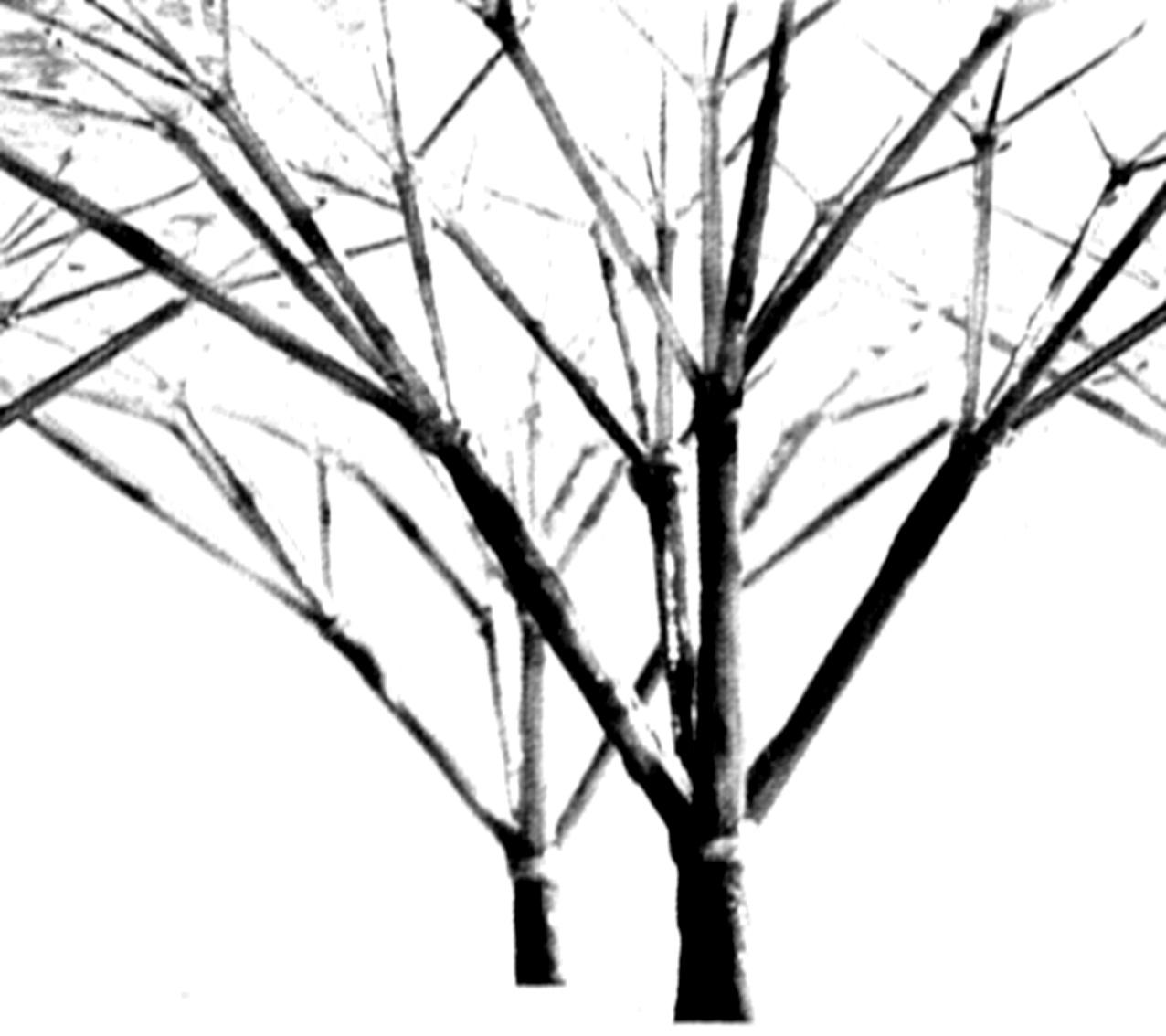
The research is based on a premise that complex branched system could perform structurally and compose a self-supporting structure made from laminated wood respecting fibre directionality of the composite.
Timber planks of certain sections could be laminated in order to achieve D geometry and then fit into the structural scheme where vector-active system prevails.
A complex system with a structural capacity is achieved by the convergence of computational techniques and inherent material properties.
The material system has extrinsic and intrinsic constrains that are implemented into the system by set of parameters that tune the behaviour of the whole and also provide necessary boundaries. These parameters together with associative parametric modelling provide a base for emergent structure.
Extrinsic constraints: morphology of site, fabrication, loads
Intrinsic constraints: structural capacities of geometry, capacities of material, self-load
Methods of Research
Experiments - Overall analysis and evaluation - page 28
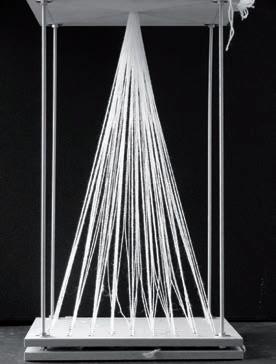
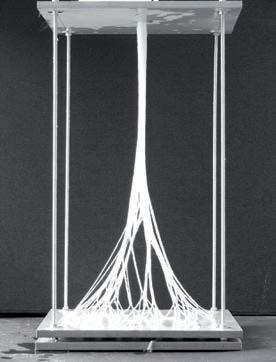

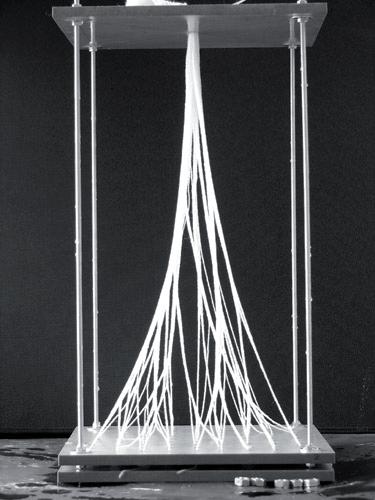
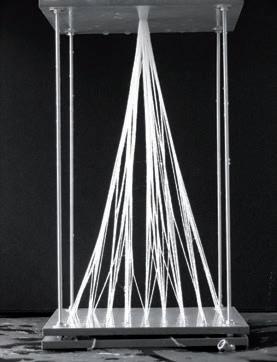
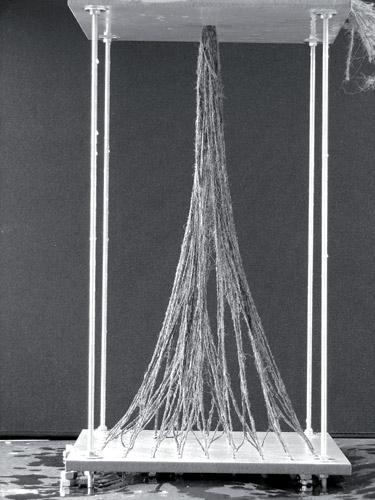
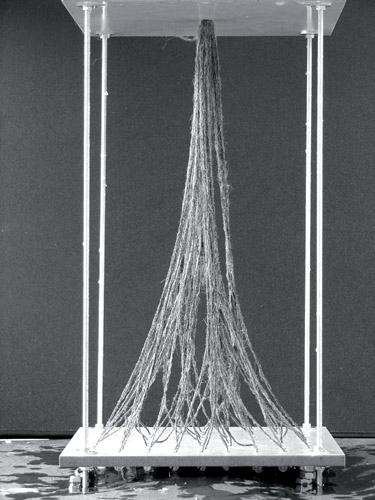
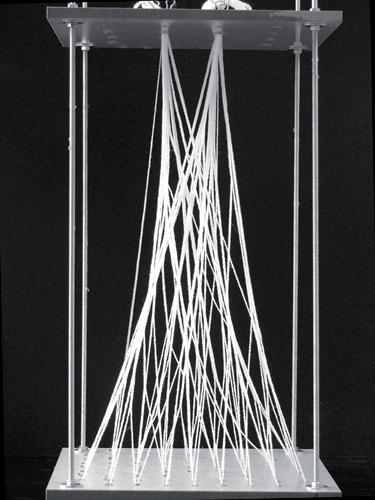
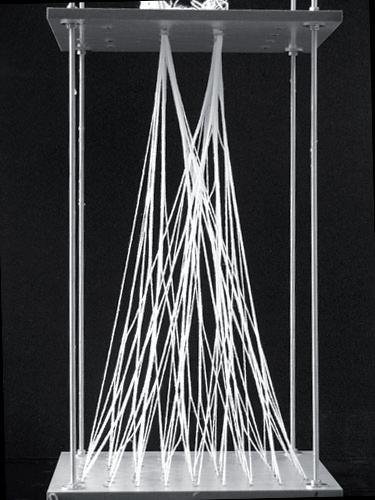
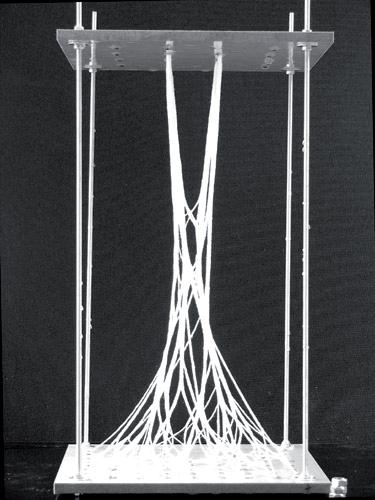
fig. 11, ex 06, threads with configuration of ex 05, II. degree
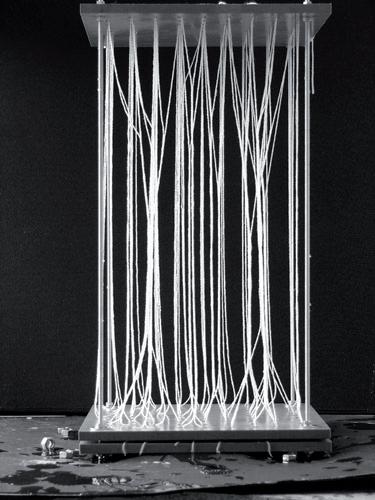
fig. 13, ex 07, 2 ply threads, co-joining of threads, bases oppposite each others, front view
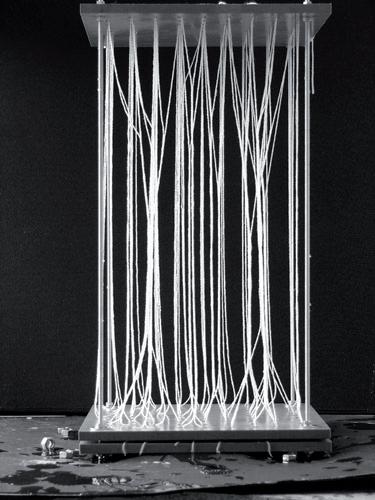
fig. 14, ex 07, 2 ply threads, co- joining threads, bases opposite each others, left view
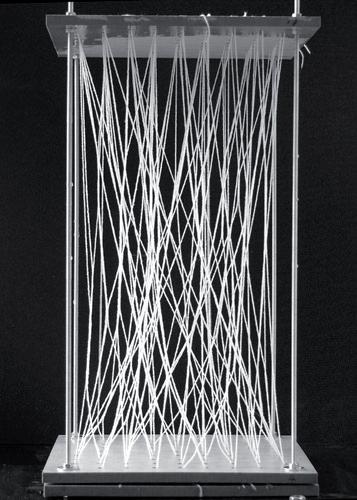
fig. 15, ex 08, threads dipped into water, bases connected according the random function run in excel, front view
Experiments from Nested Form-Finding module 05 - Hladik, Porras, Rabagliati - see appendix of the thesis.
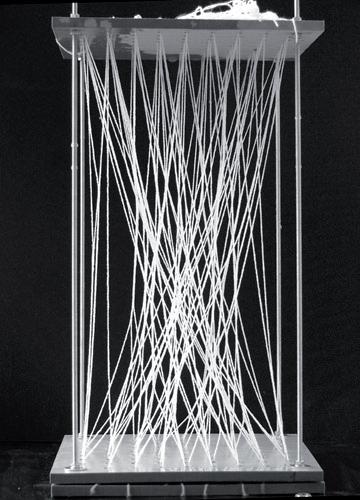
fig. 16, ex 08, threads dipped into water, bases connected according the random function run in excel, left view
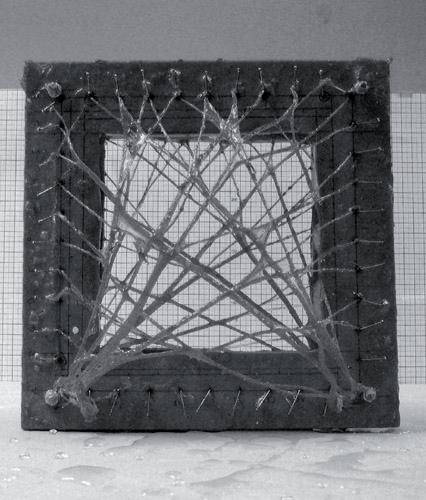
fig. 17, ex 09, threads dipped into latex, threads in two layers, 2. layer orinted - fig 02 page 14, top view
The methods of research involves the formulation of hypothesis which pertains to set of ideas based on certain initial assumptions. The key points of the research are deployed and evaluated in chapters of the thesis. These approaches are implemented through specific means which include physical and digital experiments.
Structural Scheme
The first and the most important method is the physical form-finding technique which examines the three-dimensional branching pattern that comes out from experiments with threads immersed into liquid. The threads are affected by surface tension of water and create the structure in tension. The inverted structure therefore act purely in compression without bending moments. The experiments result into models that were studied by architect Frei Otto and his Institute of Lightweight Structures in Stuttgart in 970’s and 980’s of the 20th century. The basic research commenced at the IL was considered as the starting point of the thesis.
The experiments of Frei Otto group were extended by variety of input geometry. Rules and pattern of emerged branching were studied. The distance of branching points and also number of threads bundled together were analysed and prepared for the digital model. The setup for the digital self-organisation was achieved by carefully prepared parameters.
Material Model
The second experiment introduced the behaviour of building material into the complex geometry. The material represents the natural composite and was chosen in order to achieve the branched structure according to the biomimetic studies. This knowledge gained by observation of material distribution in natural models was then abstracted into the assembly. The direction of fibres was the most important constraint in the material model. The curvature, flexibility and geometry under stress was studied in form-finding experiments with laminated wood.
Material System
The previously described physical experiments converge into the associative digital model that keep structural scheme of branched system and also the behaviour of laminated timber. It results into the material system with its limits of fabrication and structural performance. The digital form-finding of tree-structures within limits of D lamination represents the complex geometry that was later evaluated by procedures of finite elements methods. The actual behaviour and flexibility of the structure was studied on physical mod-
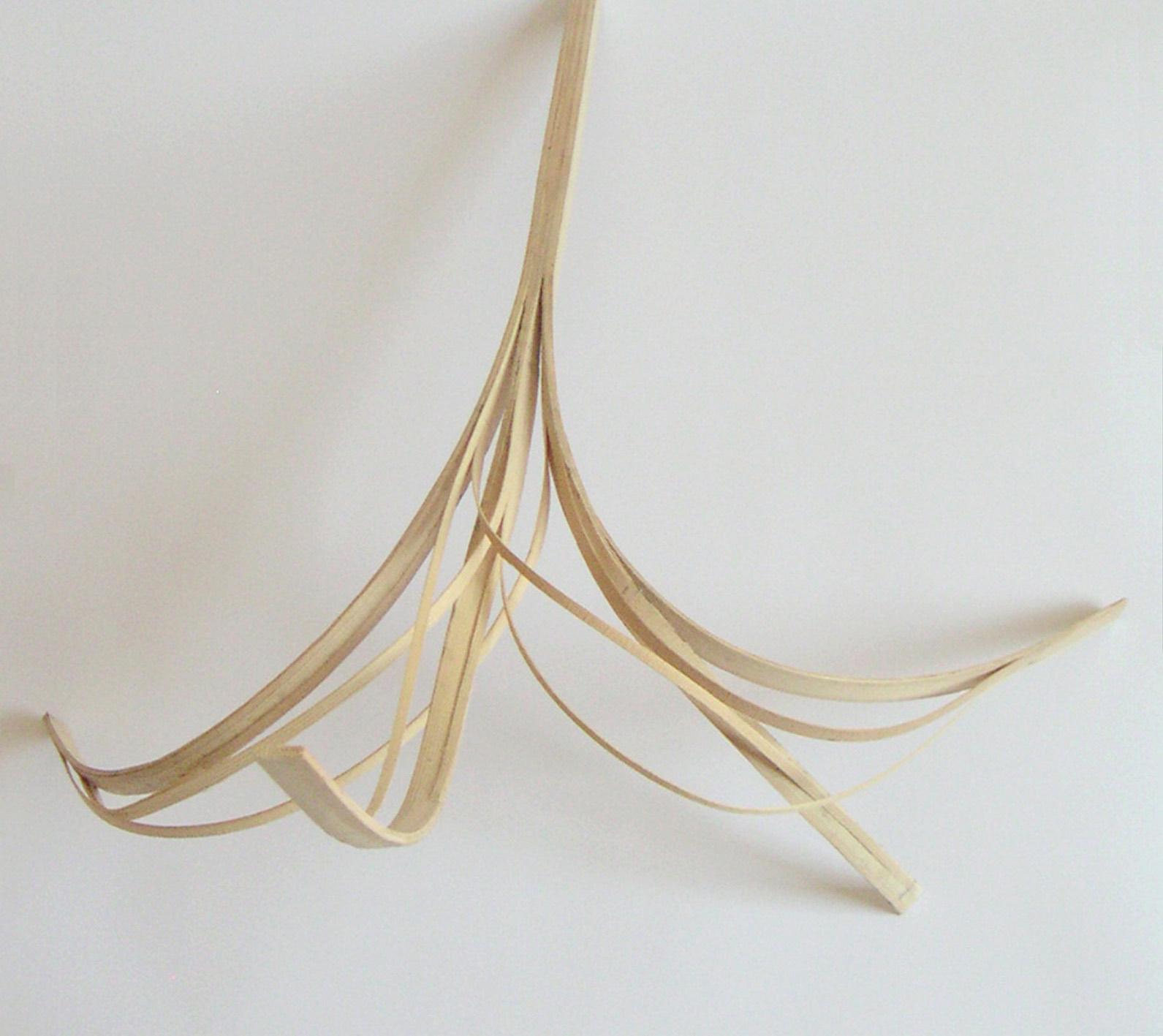
els of laminated plywood. The FEA was chosen in order to see the performance of the whole assembly not only of its parts. Manufacturing possibilities of wooden components learned when visiting these companies are considered as important feedback to the research.
Evaluation
The evaluation of the material system is provided both by physical tests and consequently by finite elements analysis (FEA). This provides the feedback to the research. The curvature, deflection and behaviour of the structure was studied. The behaviour of components (laminated planks) and also macrocomponents (branching supports incorporated into a surface) was tested in order to examine the transition between vector-active and surface-active systems. The assumption which drove experiments of physical form-finding of threads and liquid was evaluated digitally FEA in Ansys. Ansys software was also used for the design of dimensions of laminated branches.
Case Studies
Case studies is an essential part of the thesis and provided the feedback at all stages of the research. It aims to review examples of passed and prospective relations between production and conception to discuss relations between particular manufacture paradigms and their associations to related design processes. The architecture that has designed and been built provide the opportunity to gain knowledge from other teams that dealt with complex curvatures of wooden structures and branched supports.
Scheme of vertical supports in Stuttgart Airport Terminal by Von Gerkan, Marg + Partner feature branched columns that support steel grid of the roof. The branched structure represent merely as a widened head of columns.
Bordeaux Law Court by Richard Rogers Partnership is one of building where the thin shell was introduced as the main structural scheme. Although the structure was build separately as ribs covered by stressed skin the CAD methods developed by the project operte within limits of the material - wooden boards.
ExpoRoof by Thomas Herzog deals with a complex curvature and succesfully introduces the form-finding into the manufacturing process. Although the structural components of the shell are not laminated, the manufacturer (FinnforestMerck) is able to use the similar technique for D lamination.
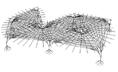

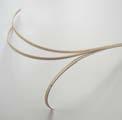
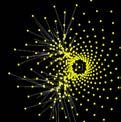
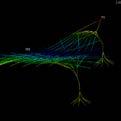
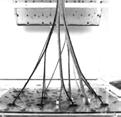
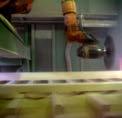
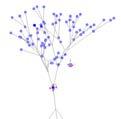
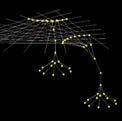
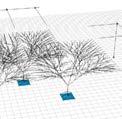
Diagram of the Work
. Growth and Branching
Concept of Sensitive Growth derived from natural systems. The explanation of the concept and relation to the research.
2. Physical Form-Finding 0
Research into more complex branched structures that went beyond executed experiments of IL and myself in previous research (viz appendix).
. Mathematical Model
The abstract model of branched structures and its possibility for digital form-finding.
4. Applied Model of Branching
Setting rules gained from results of actual Form-Finding and its emergent behaviour.
5. Physical Form-Finding 02
Behaviour of laminated timber and its inherent forces and parameters.
6. Production Logic
Available CAM technologies in correspondence with developed CAD.
7. Digital Form-Finding
Edge-rewritting L-system and IF statements that drive the model of the complex system. The generic process is informed by capacities of D lamination.
8. Proliferation Methods
Set of rules embedded in the digital system controlled by variables.
9. Model of Material System
Set of rules and variables that control the performance of continuously laminated wood. Size, thickness, strength and variability of the researched component assembly.
0.Performative Criteria
Set of constraints that evaluates the final assembly of the material system. The performative criteria are mainly structural.
.Manufacturing Constraints
Strategies for building the larger scale proliferation. The effectiveness within the constraints of performative criteria.
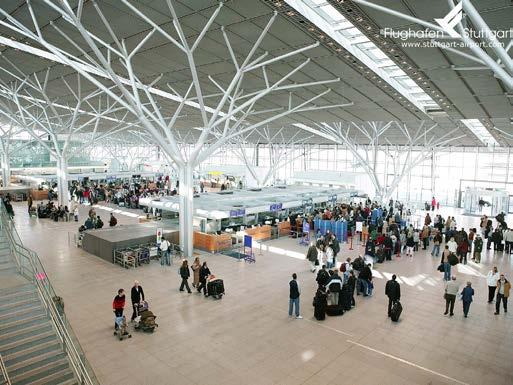
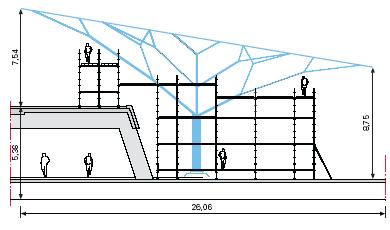

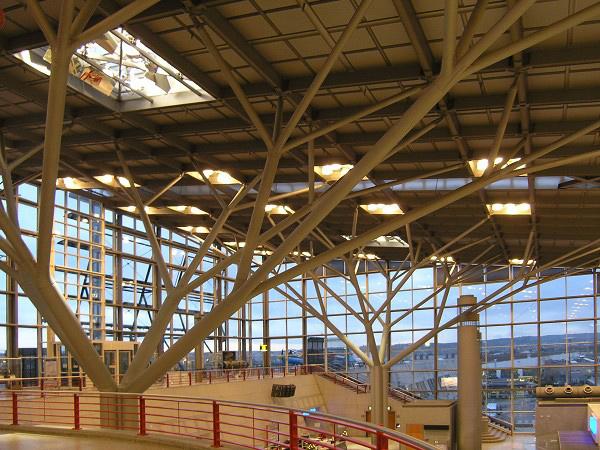
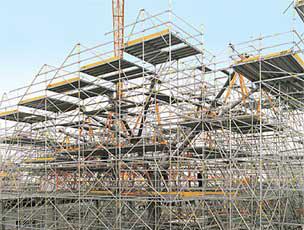


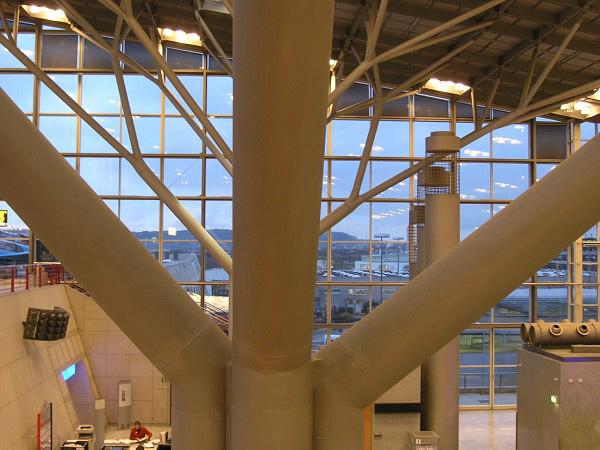

Von Gerkan, Marg + Partner
Structural Engineer Weidleplan Consulting
The characteristic design features of the Terminal , which has received several awards – the tree-shaped columns of the loadbearing structure and the dike-shaped building bar orientated towards the apron – were continued throughout the extension. The roof of Terminal was however dissolved into single shed areas, in order to maintain the tree structure with an identical roof incline but a reduced building height. A total of 8 steel trees support the stepped roof (Terminal : 2 trees).
All trees are the same construction and size, they vary in trunk length only. The inclination of the roof is also constant.
On the street side, the arrival hall connects Terminal and as a „mall“ over a length of 260 m. The simple and obvious positioning of the access elements and voids allowing vertical visual links guarantee an immediate orientation in the new „Terminal of Clarity“.
width 05 m
height max. 0 m
length 40 m
building volume ca. 270 000m
glazed surface ca. 7 00 m2
number of piers 2
gross floor space 8 000 m2
roof truss structural steel ca. 650 t columns structural steel ca. 205 t
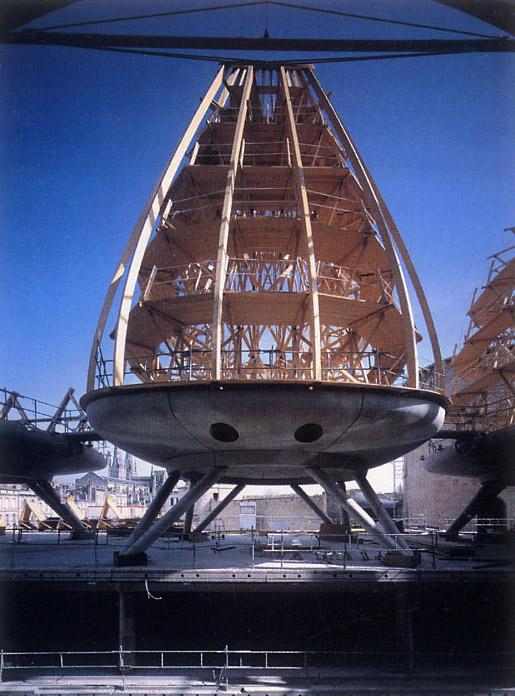
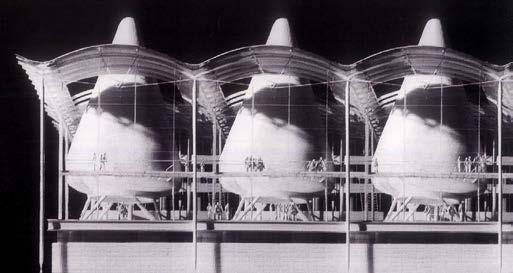
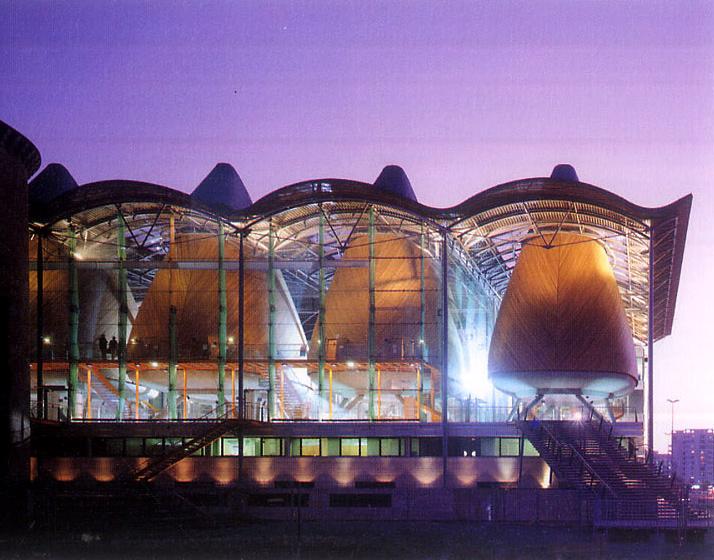
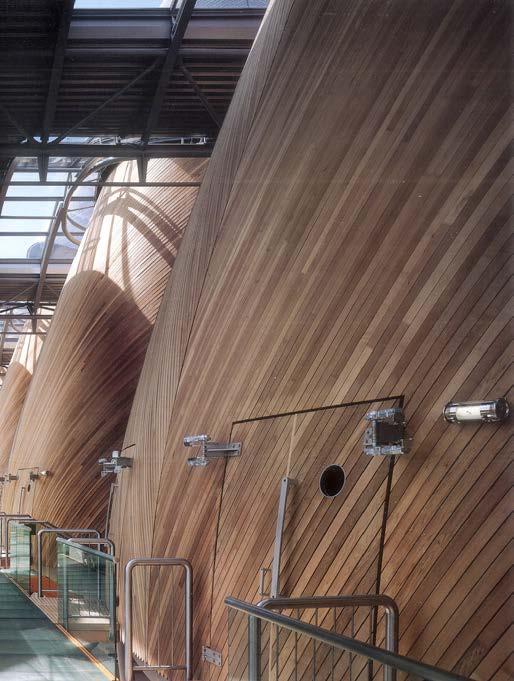
Richard Rogers Partnerships, 992 - 998
Design of Geometry: Arup
The individual courtrooms are enclosed within this frame in seven clearly identifiable volumes, tapering in section and rounded in plan.
The courtroom elements were originally conceived as exposed ferrocement structures. The design team has since explored the potential of stressed-skin systems that offer greater flexibility of construction and greater durability, including a lightweight aluminium honeycomb sheet structure (usually employed in the aircraft industry) with a painted epoxy resin finish, which can be prefabricated under factory conditions and easily assembled on site in individual onion like segments.
The technique used for this building was innovative in terms of structural purpose of the skin as a thin shell and its fabrication. In fact the entire volume and manufacturing was controlled by computer. However the process of the fabrication feature the great loss of the material which could be decreased by following rules of the material properties.
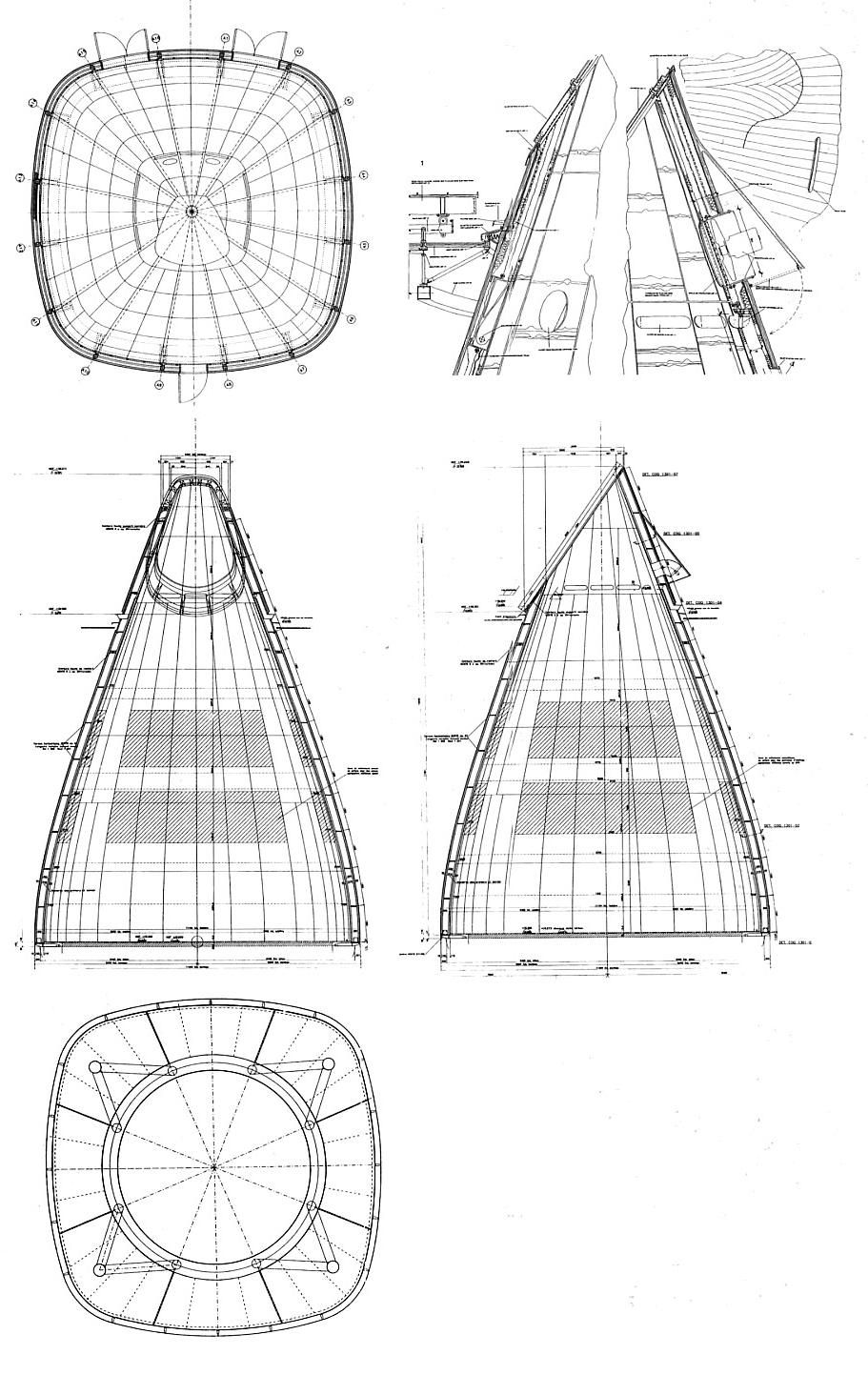
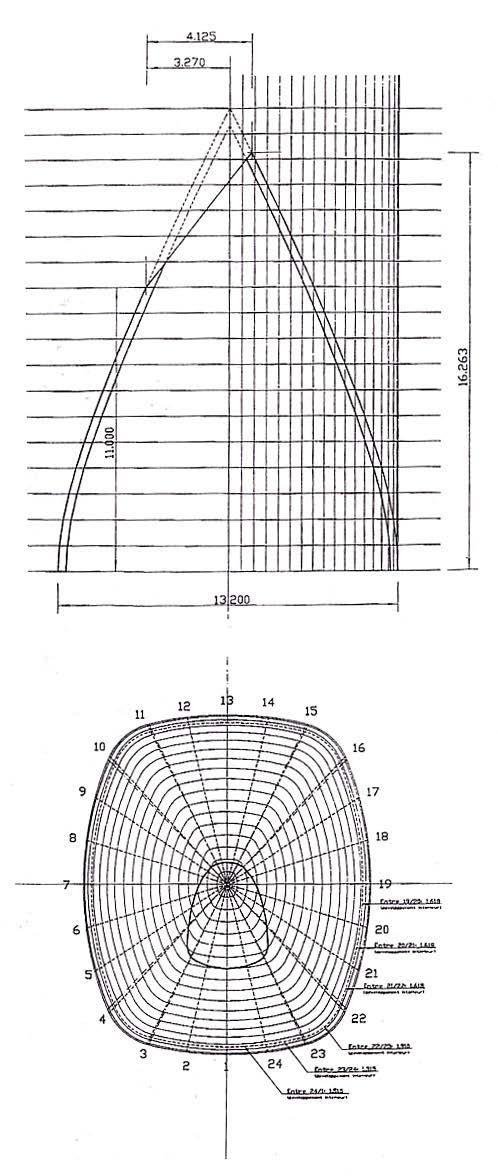
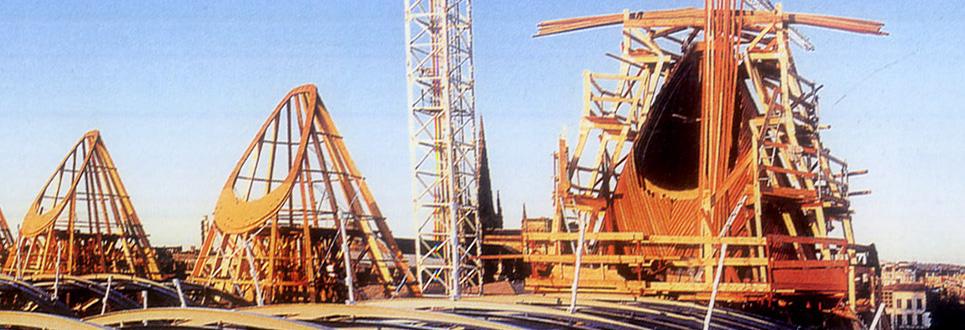
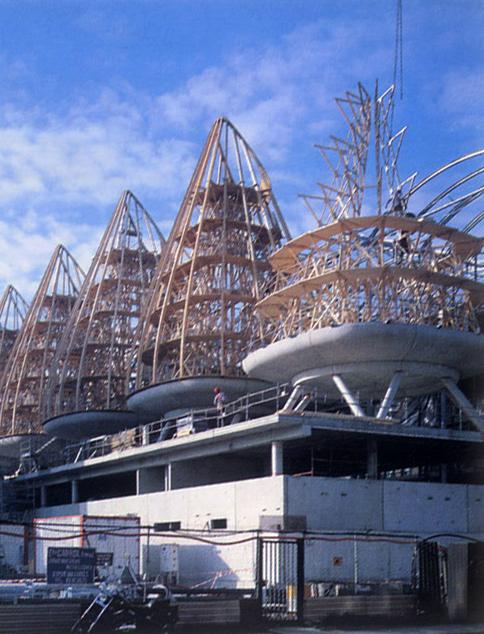
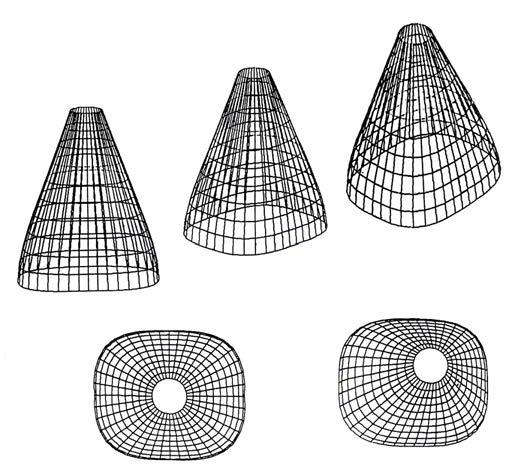
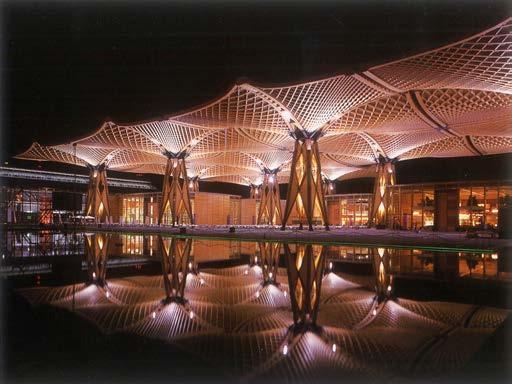
0. Court Covered by shell structure
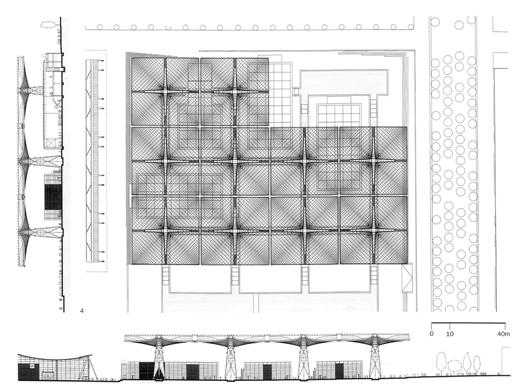
02. Plan of the expo square. The image shows the connection of components - supports with shells.
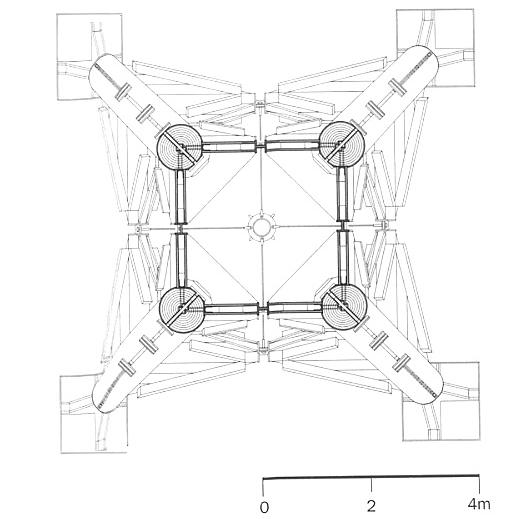
0. Horizontal section of tree-column.
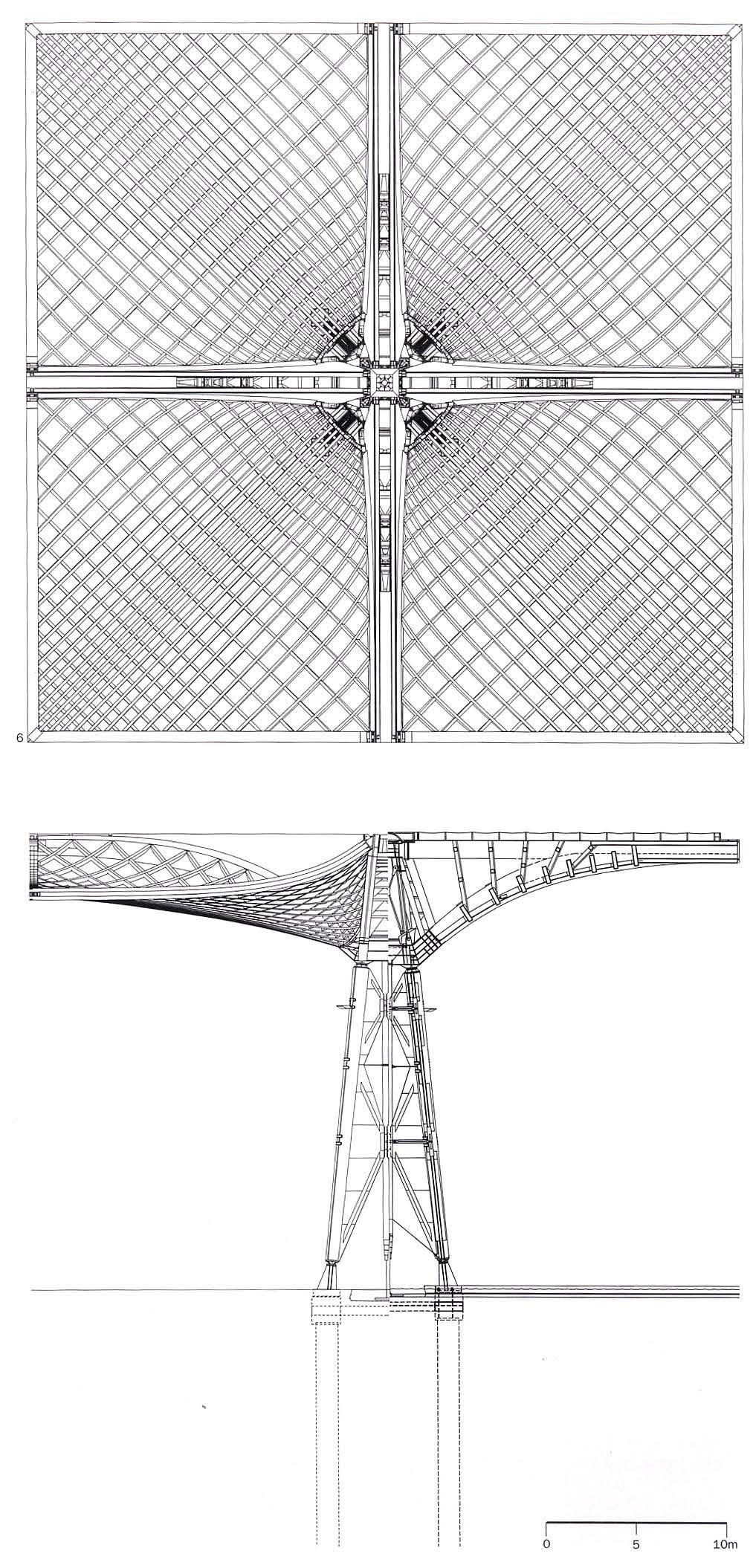
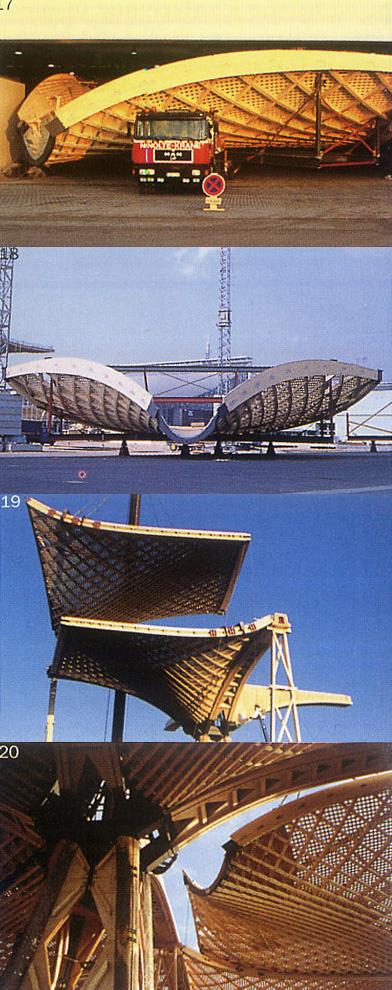
Herzog Studio, 2000
Fabrication: Finnforest - Merck

Each of the 0 upturned umbrellas, over 20m high, consists of a central four-legged tapering pylon of timber and steel supporting a 40 x 40m square crown, which is further divided into four identical square leaves. At the base of each pylon, steel feet are anchored in a 5m deep concrete ring foundation. The leaves of the crown are double curved surfaces made up of a skeletal net of laminated timber struts clad in a weatherproof membrane. Precipitation is conducted to the centre of each umbrella, down a rainwater pipe in the centre of each pylon, and feeds into a grid of 5m wide canals on the piazza which complement the roof geometry. The illusion is of pontoons and pavilions, floating on water, under a substantial billowing cloud. Changing daylight, the aspect of the sun and sky colour, is filtered through the millimetre thin translucent roofing membrane which is fireproof, self cleaning and, if necessary, recyclable.
The timber originated in the Black Forest, in south-west Germany. Here grows the biggest concentration of ancient white oaks in western Europe. Used for centuries as ships’ masts, the standard girth of the oaks chosen for the Expo-Roof columns was .4m, and some were up to 250 years old. For a forest, the culling of these older trees, up to 50m high, is essential for new growth. Suitable trees were selected using ultrasonic equipment to reveal any internal structural weaknesses.
The structure uses advantage of steel joints that provide necessary strength of the structure. The combination of form-found timber planks on a mathematical geometry presents an effective combination of CAD and CAM.

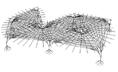

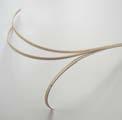
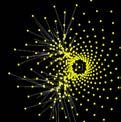
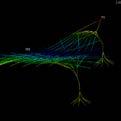
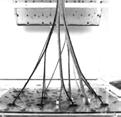
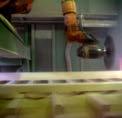
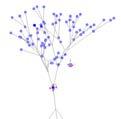
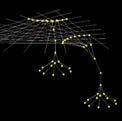
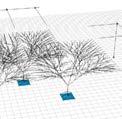
Sub-hypothesis:
If woollen threads are immersed into a liquid the branched structure is achieved and this geometry could be analysed and consequently used in digital environment. The result could be used as a model of self-organised tension structure later (inverted) acts in compression.
Different geometry is produced by connecting points from tilted planes than from horizontal ones. By tuning certain parameters could by achieved complex emergent system. Parameters could be summarized and control in digital models as well as in physical experiments.
Gained logic allows for proliferation and differentiation of nested hierarchies in digital environment. Careful observation could also lead to the digital self-organisation [].
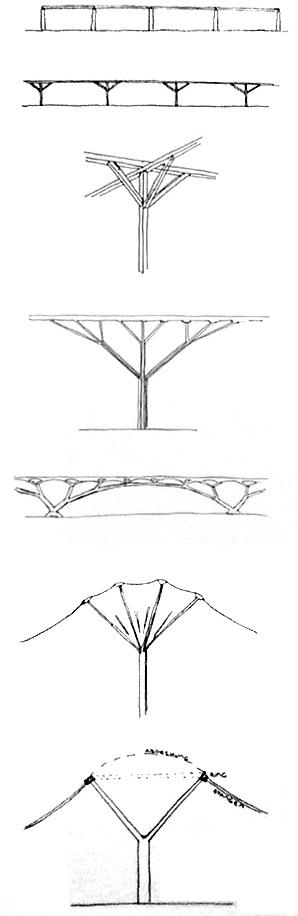


The methodology of understanding the structural concept of material system explores two levels of experiments - physical and digital form-finding. Form-finding is based on the behaviour of material under stress - self-organisation.
The structural scheme chosen for the material system was branched system that came out from experiments described by Institute of Lightweight Structures in Stuttgart under supervision of Frei Otto [2].
Branched structures are three-dimensional supporting systems used in various materials for buildings. They are ancient and derive from early pole building. Figure 0 shows different supporting systems - column-beam, traditional wooden braces and tree structures, stone structures in bridges. Images 0 f, g shows the recent thinking about supports in tents and suspended roofs - there is a connection of elements in tension and in compression. This way of the scheme is later deployed in this thesis in a way that branched supports are incorporated into the surface where its redundant structure is able to resist both tension and compression forces. Tree-shape supports are not bionic constructions, as the branches of a tree support nothing heavier than leaves and thus have a lower load-bearing function than the tree-like support structure of shown examples. Threads immersed in liquid are models of constructions that eliminate bending. The structure is not stiffened by any diagonal members. Schemes presented on images 02 b and d deals with branched supports and try to get closer to bionic structures. Branches are interconnected by additional members that stiffen the structure and in terms of topology it creates the closed branching system. Branches are still considered as straight members connected by specially designed nodes similar to that build in columns for Stuttgart airport.
Images on the figure 0 explains the relationship between distances of branches in different conditions. On the figure 0 a there is the direct paths system in a fan structure whereas on the figure 0 f there is a scheme of the minimal path system.
Transition stages between 0 a and 0 f could be studied on physical model of threads immersed in liquid. Bundling of threads in a certain density and distance result in the emergent structure which depends on the surface tension of used liquid. The setup of parameters and the background is widely described in the appendix of this thesis. It was commenced by the author and his colleagues in EmTech Phase as a Nested Form-Finding Module. In the previous work there was also suggested to explore parameters that control the system. Distances between connected points are constant and so parameter tuning the geometry sketched on fig 0 is the length of threads. 0. Schemes
0. Schemes of the experiment. The initial state represents the distance between points and a base point always as direct paths.

0. Studies for the design of an exhibition hall.
plane - tension and compression forces points on the plane branches
angle of branches - emergent bridge due to surface forces of water
branch (or trunk) base point
C 0
Horizontal plane. Square array of points.
C 04
Horizontal plane. Square array of points. Bundled threads.
C 02
Horizontal plane. Points on a square boundary.
C 0 Inclined plane. Square array of points.
In order to understand tree structures and prepare input for the digital models the setup for experiments with liquid and threads was established. Planes with an arrangement of points connected to one base point by threads were studied. There were studied different boundary conditions - planes are not always horizontal and they have different number of points. The other set of experiments is represented by a change of liquid type and the geometrical scheme: from direct paths systems to hanging models with branched supports.
Parameters that influence the structure are:
length of threads arrangement of points
Results gained from experiments are:
length between points
C 05
Horizontal plane. Points on a square boundary. Base point in the middle.
C 06
Vertical arrangement of points and a base point in a plane.
02. Different boundary conditions as an input for the form-finding experiments.
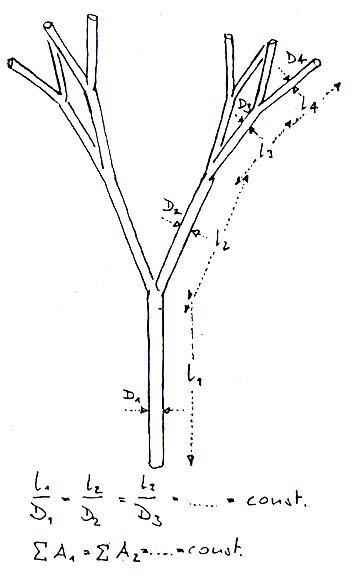
04. Open branching. Diagram shows structural relationships of members.
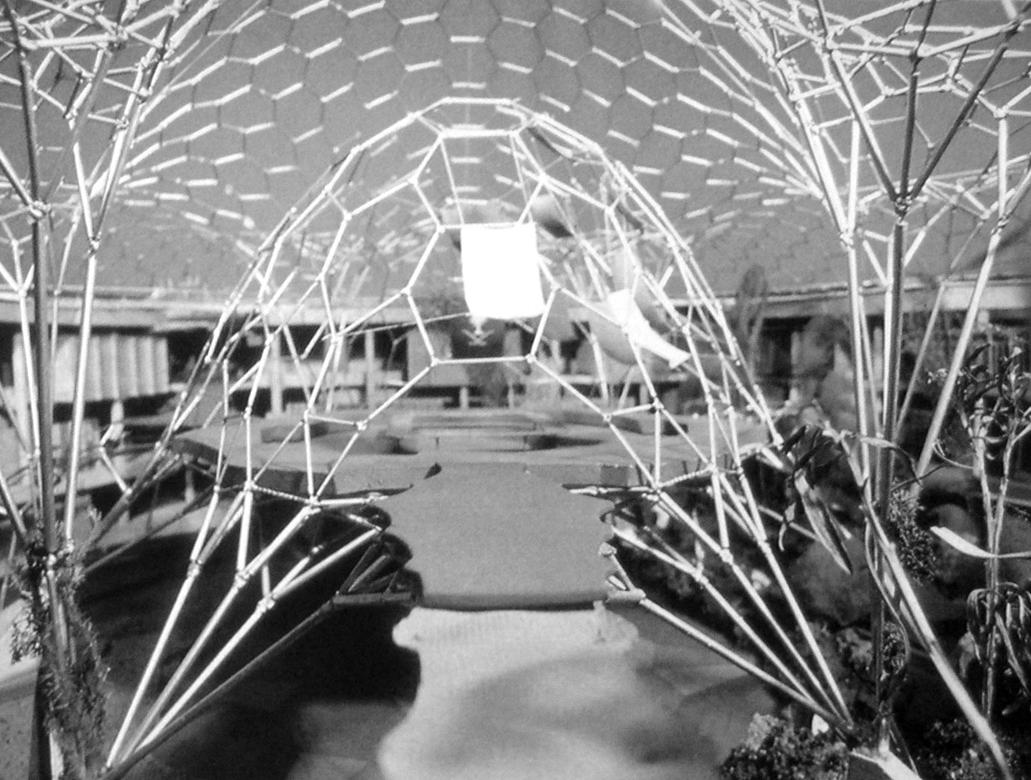
05. K0COMMAS Riyadh - branched columns and lattice shell roof in one structure.
number of bundled threads
inclination and curvature of trunk and branches
Frei Otto designed interesting project which goes beyod the scope of the pure vector acting system of branched structure.
The great KOCOMMAS (King’s Office, Council of Ministers, Majilis al Shura) complex in Riyadh, Saudi Arabia, consists of several lattice shells, rope constructions and some solid multi-storey buildings.
The lattice shell cover reception and meeting rooms and inner courtyards. The lattice have a hexagonal mesh with equal-length bars in welded tubular steel and are covered with glass. Specialaluminium umbrellas were developed as shade elements. The three-dimensional form of these bars constructions was arrived at in a suspended model, and the nodal points were also fixed in the suspended position.
The form of the branched supports was itself developed by self-forming processes. The great beuaty of the structure rests on the harmonious combination of two constructions that emerged by self-formation. The project was designed down to the last detail but could not be completed because of political developments. [4]
The hybrid system of surface active system and vector active supports was observed on hanging branched structures.

0. Axial tree - explanation of the L-system algorithm and its basic entities. All Images from [9].
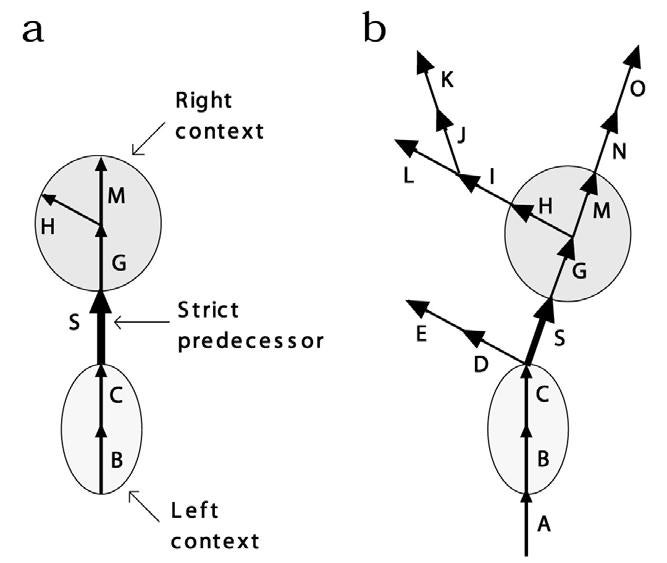
0. Context-sensitive L-systems. The predecessor of a tree production (a) matches adge S (b).
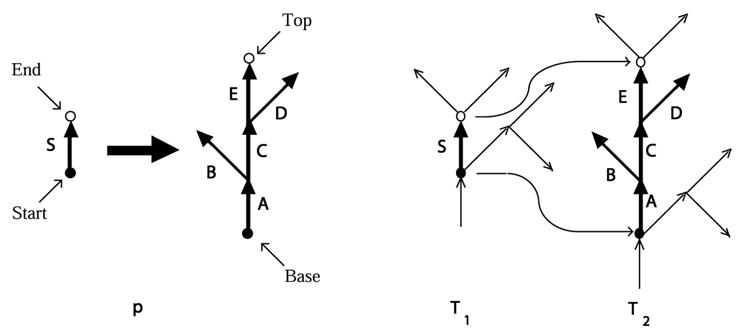
Digital experiments took advantage of the associative models that allows for algorithmic generation. In my particular case it was Generative Components - feature modelling and scripting. The geometry was later postprocessed by other software that allows for complex nurbs geometry (Rhino), 2D drawings (AutoCad, Microstation), data sorting (Excel), rendering (Max).
As an input for the digital generation data were used rules gained from physical form-finding with threads and liquid. Rules put into a model of features allow later algorithmic generation. Simple model of a feature with conditional statements was proliferated according to rules of edge-rewriting L-system. L-system was introduced in 968 by Lindenmayer as a theoretical framework for studying the development of simple multicellular organisms, and subsequently applied to investigate higher plants and plants organs [9].
The stochastic L-system used for modelling of trees was introduced and served as a scaffolding for further examination.
02. Explanation of the edge-rewriting L-system.
The possibility of a growing associative model opens an idea of selforganisation in digital environment. Then just by keeping the rules expressed parametrically the geometry could fit into different input criteria and constraints. Criteria are tuned by parameters until it reaches the crital values and cannot later maintain the form and features of branched system. It is one of important moments in the “life” of complex adaptive system. Constraints are understood as an input coordinates (arrangement) of points and base point (described on the previous page).

02. Different boundary conditions as an input for the form-finding experiments.
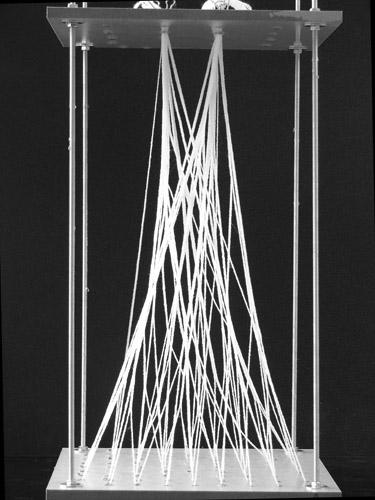
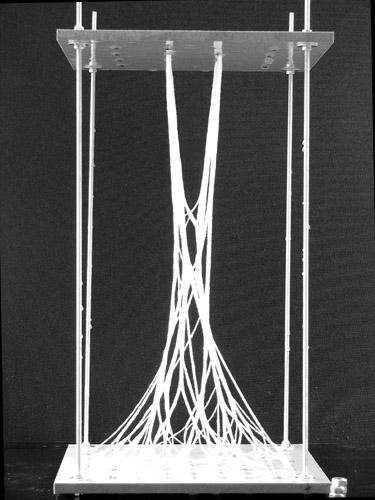
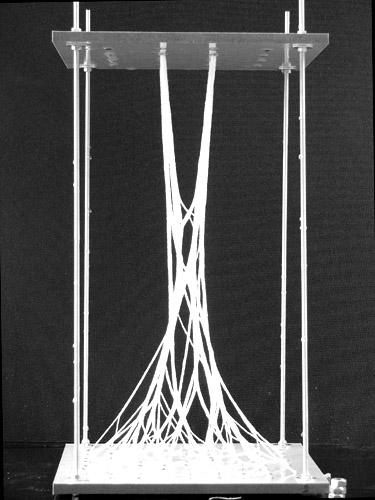
The aim of this experiment was to document and descirbe the behaviour of threads with different amount of slack. Threads interconnect points and base points when they are crossing each other. Because of this arrangement threads bundle easier.
On figures 0-0 there are three degrees of slack. It is 0%, 20 % and 0% of the direct length. Branched geometry is very complex and difficult to trace. The pattern of D branches is emergent and it varies with every dipp into the liquid.
Experiment 01
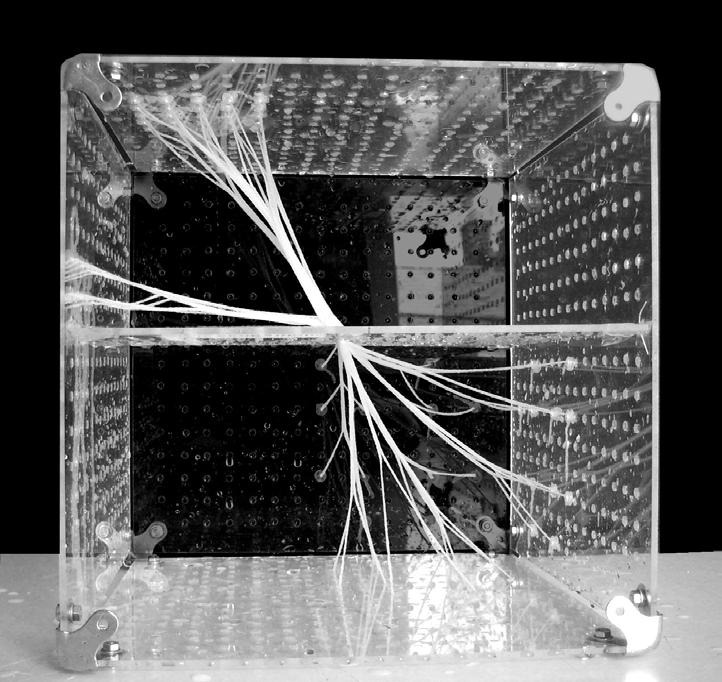
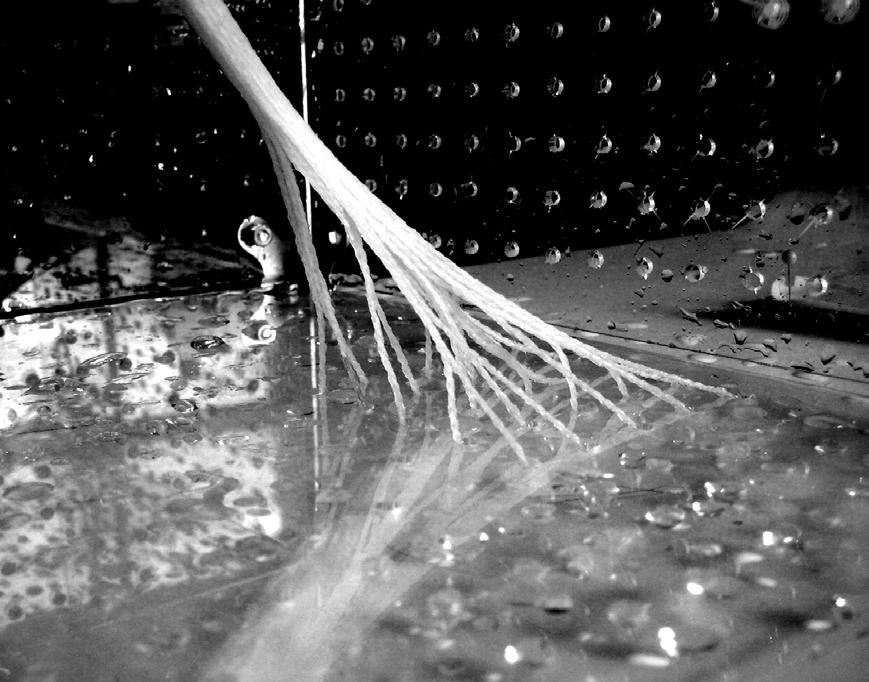
0. The image shows the number of bundled threads: 2, and occaisonelly 4 02. Detail of s-o structure. The typical end of the trunk is for inclined plane connected to a base point.
The first experiment examines inclined planes with points. In order to see distances of branching nodes the precise digital model in cartesian coordinate system was built.
Experiments unvail the behaviour of branching system affected by geometrical constraints.There is a certain logic in distances between branching nodes, distances of points and also the length of threads.
0. The geometry of the boundary conditions: The cube 250 mm. In the middle corner of the cube there was selected a start of the coordinate system.
trunk bifurcated at the base - 90° angle of point bases
Experiment 02
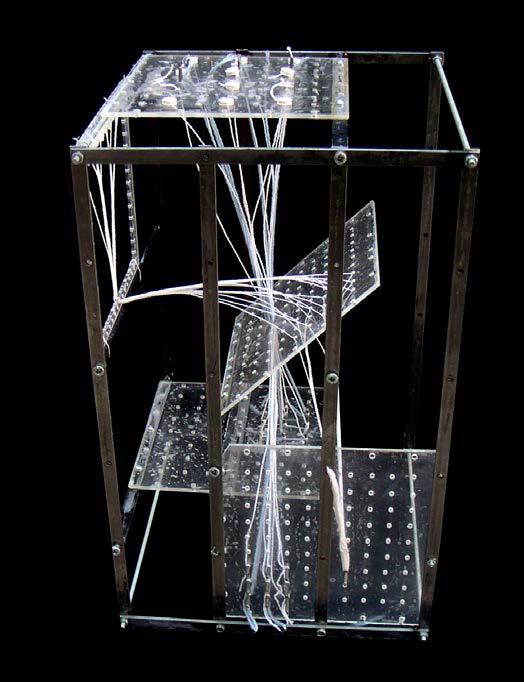
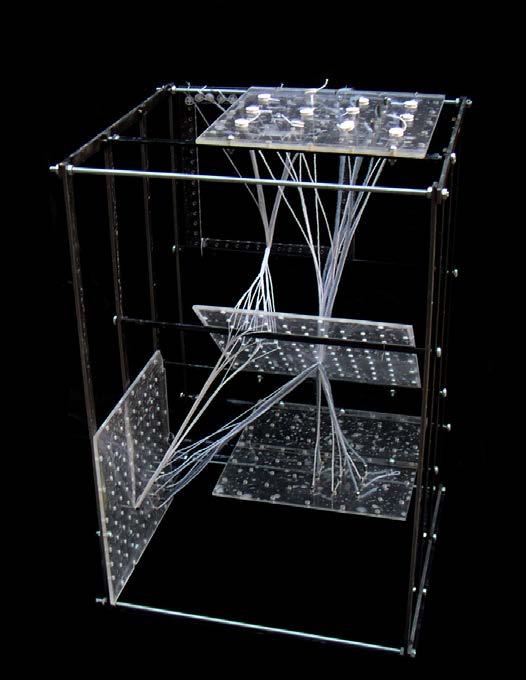
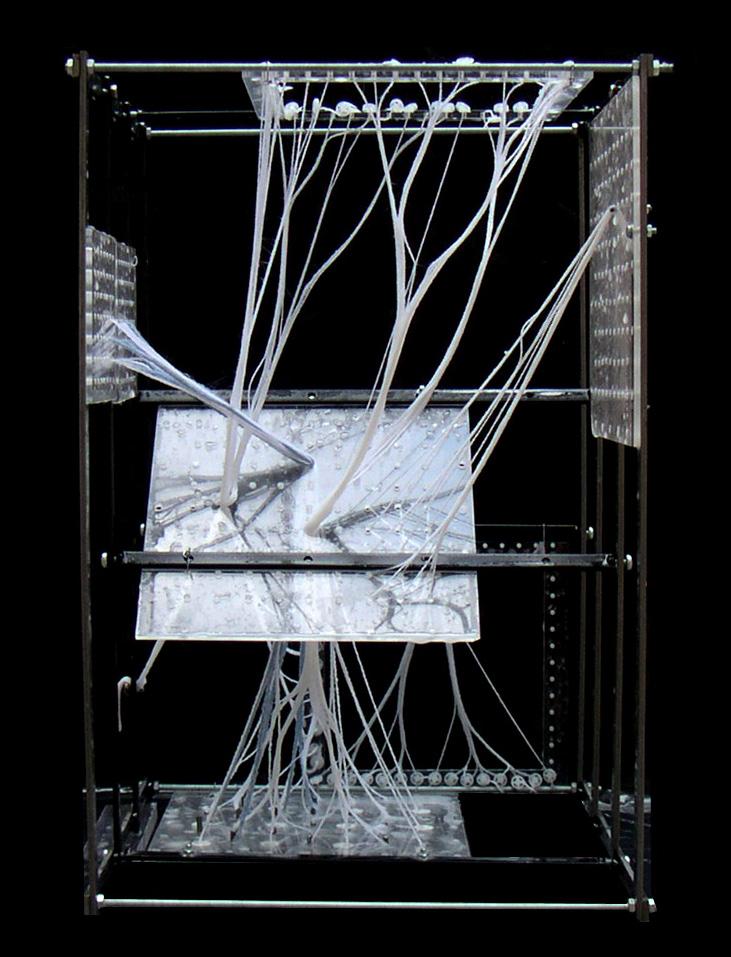
The second experiment with inclined planes explored the behaviour of trees when they affect each other and compose more complex geometry. The special steel “cage” enabling reconfiguration of planes was constructed.
Threads were immersed in liquid - in water and later in water with PVA glue in order to maintain its branching geometry. There was introduced also a hierarchy in the system by adding different thickness of threads. The results were expected according to the research made in Nested Form-Finding Module (see appendix of the thesis).
D pattern of branches now became clearer.
Points in cartesian coordinate system were later reconstructed digitally.
Planes with points are in these angles: 0°, 90°, 45°.
Experiment 03
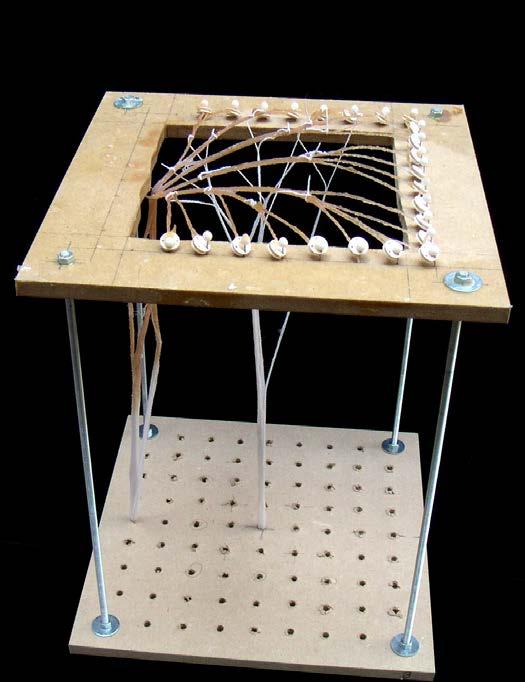
0 Branched hanging model. Branches result into a surface that forms a catenoid. The second tree is connected to branching nodes of the first geometry.
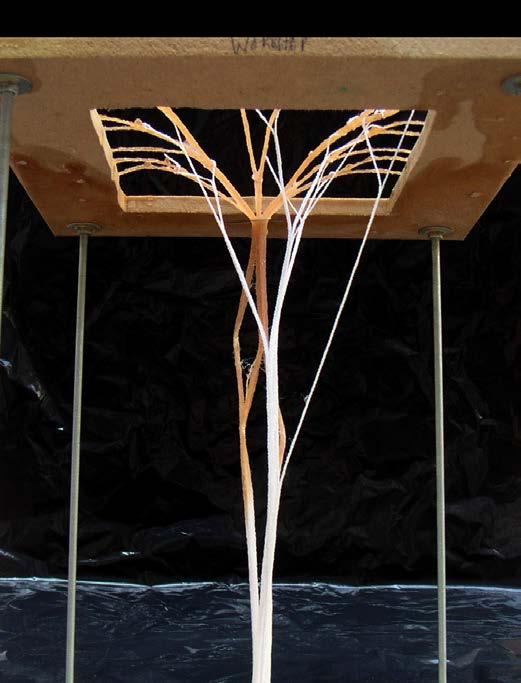
02. Image shows the connection of trees.
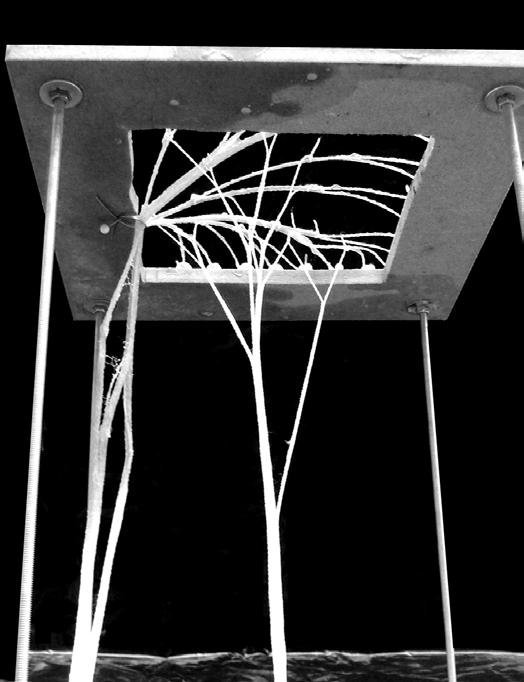
0 The tree structure reacts on the distances and geometry of the other tree.
The Experiment 0 explores the idea of branched hanging model. There was one branched model nested on the other structure.
Threads are dipped into latex and after solidifying the other tree structure is produced by threads connected to branching nodes of previous branched model.
This approach was not later deployed but it opens an interesting way how to connect two important structural concepts in architecture. The work of IL institute on this topic is documented in the design of KOCOMMAS Riyadh. The vector-active and surface-active systems could be in more equal ratio.
04. Boundary conditions for the nested tree structure.
Experiment 04
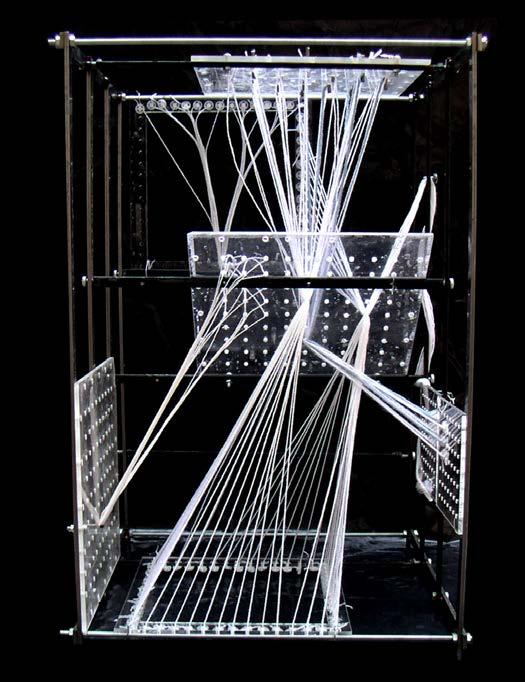
0a. Different boundary conditions and branched structures.
0b
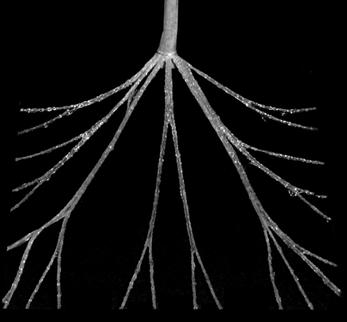
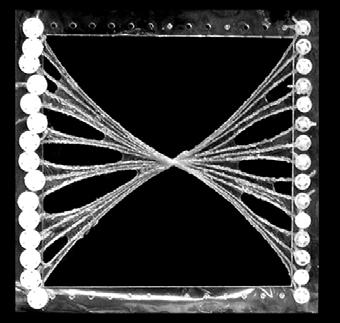

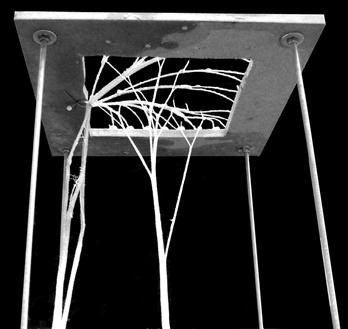
0c.
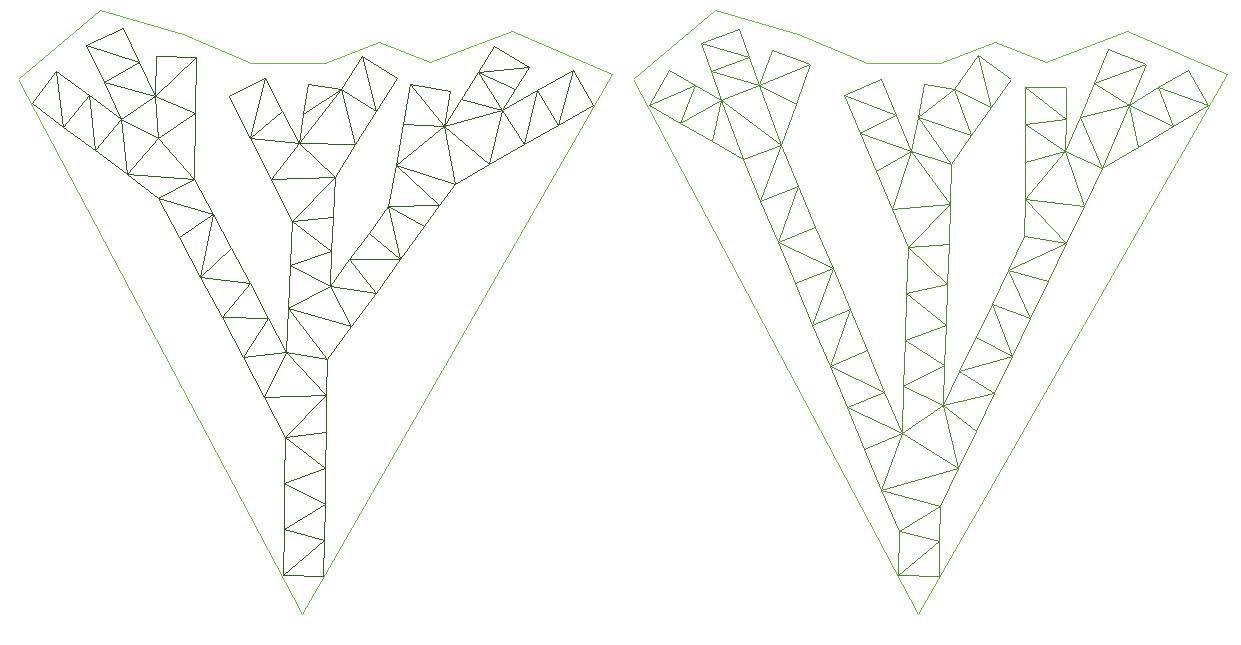
02. Two plans of the pavilion with the same input. Change of parameters of the branched structure in 2D cause the reconfiguration of the building. This has an impact on a built area of the site and also on the pavilion itself.
There were executed several experiments that were aimed to study the impact of surface tension of water as a form-finding method for minimal paths between points. Important issue was to study different boundary conditions for branched threads.
These experiments were later used for proliferation of the branched structure on plane an it could be later extended to morphology of a given site. It drives the layout of the pavilion. Presented set of pictures opens a discussion for further development of this strategy. The outlined strategy goes far beyond of this thesis but deserves further development. The sensitive growth algorithmicaly driven by algorithm L-system that is constraint by rules of minimal paths has been seen as a very innovative and powerful approach for designing.
In this thesis there is a framed possibility to control a spread of a pavilion structure on a given planar site. Later in the chapter Form Generation there are explained my design strategies.
Figures 0a-0c are photographs focused on the theme of minimal paths and different boundary conditions. There are structures in 2D as well as in D. On figures 02a and 02b there are two plans (examples of variations) of the plan of designed pavilion. The branched structure of the building itself is dependent on the triangulated geometry of an area. It comes out from points connected according to rules explained in the chapter Analysis and Evaluation. The self-organised model of minimal paths could have bigger impact and could also influence the environment. At this point it is possible to define and control the notion of nesting and hierarchy in designing.
base - water, variation
[0.0,0.0,0.0]
Preface Concept Material Properties Form Generation Evaluation
txt file: coordinates
2.5,7.5,-.0
2.5,4.5,-.0
[2.5,7.5,-.0]
2.5,0.5,-6.0]
[2.5,4.5,-.0]
2.5,7.5,-6.0]
2.5,0.5,-9.0]
[2.5,4.5,-6.0]
2.5,7.5,-9.0]
[2.5,.5,-6.0]
[2.5,4.5,-9.0]
2.5,7.5,-2.0]
[2.5,4.5,-2.0]
[2.5,.5,-9.0]
2.5,0.5,-6.0
2.5,7.5,-6.0
2.5,4.5,-6.0
2.5,.5,-6.0
2.5,0.5,-9.0
2.5,7.5,-9.0
2.5,4.5,-9.0
2.5,.5,-9.0
2.5,7.5,-2.0
2.5,4.5,-2.0
0 txt file with coordinates as an input to the GC associative model.
2.5,4.5,-.0]
0 Direct paths. The geometry of threads before dipping into water. Cartesian coordinates of points form external txt file.
2.5,7.5,-.0]
2.5,.5,-6.0]
centroid 0
2.5,4.5,-6.0]
centroid 02 L l l2 l2 l2
[0.0,0.0,0.0]
Analysis - Experiment 01
Experiments were analysed and carefully reproduced (fig. 0 direct paths, fig. 02 minimal paths) in order to understand emergent features. The dipped threads pulled out from water had always different geometry but after repeating of these experiments rules were abstracted.
Rules that later drove digital experiments were based on relationships of bundled threads. Images show digital reproduction of physical experiments. There are direct paths in red colour on figure 04 which analyse the tree structure with inclined plane of 90° from the horizontal plane. The distance (l) of branching node “centroid 02” is studied as a variable dependent on distances between points “”.
The exact mathematical formulae are on consequent pages.
L ... distance centroid of points last level, point first level l... distance of branching node
2.5,7.5,-.0]
[2.5,0.5,-6.0]
2.5,7.5,-6.0]
2.5,0.5,-9.0]
2.5,7.5,-9.0]
[0.0,0.0,0.0]
[2.5,4.5,-.0]
2.5,7.5,-6.0]
2.5,0.5,-6.0]
2.5,.5,-9.0]
2.5,4.5,-9.0]
2.5,7.5,-9.0]
2.5,4.5,-6.0]
2.5,.5,-6.0]
[2.5,4.5,-9.0]
2.5,7.5,-2.0]
2.5,.5,-9.0]
2.5,4.5,-2.0]
2.5,4.5,-2.0]
2.5,0.5,-9.0]
2.5,7.5,-2.0]
A > L > B l... range (L/2, 2L/) centroid 0 centroid 0 geometric center geometric center
05. Analysis of geometry as it is modelled in GC. The centroid of points in plane always shows the projection of the line onto this plane. On the hand the geometric center is the center of the circle which goes through all points.
02. Minimal paths. The geometry dipped into water.
04. Reconstruction of the physical model.
Analysis Experiment 02B
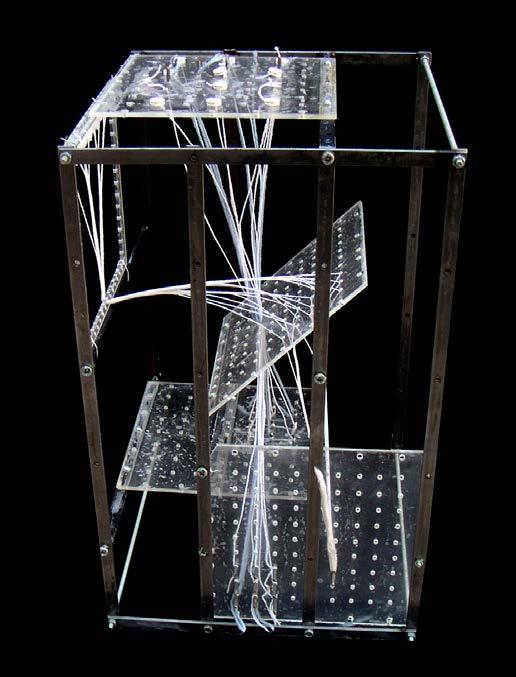
0. Picture of the experiment. There are two structures composed of three trees. One of them was analysed as an experiment 02B.
02. Scheme of the experiment: two prisms and a triangle. 0. Analysed model of the experiment 02B. The important feature of this model is the change of geometry in central part of the structure. The tree is almost horizontal and therefore all centroids are affected by gravity (c,c2).
Aim of the experiment was to observe the behaviour of threads in 2D and also in horizontal arrangement of base point and plane with points. The 2D plan was later used for summarizing of rules for branched structure in a plane as rules for minimal paths. The horizontal tree is affected by gravity and could be included into a group of hybrid structures of catenaries and linear branching.
The frame for the experiment of branching in 2D was arranged horizontally in the metal scaffolding so branches were form-found as a by pure tension. This part of the experiment is directly related to the basic research in minimal paths commenced in Institute of Lightweight Structures in Stuttgart. There were significant differences in geometry from experiments in D. The regular arrangement of points results in an irregular geometry. There were set parameters that were later used for tuning the plan of the pavilion structure. These parameters drove the complex system consisting of end points of branches with the entrance point of the structure in the plane (base point in my experiments).
The horizontal tree structure affected by gravity results in a very complex geometry that were not later analysed. But curvature introduced into the model could lead to a consequent structural performance where the curvature is beneficial. The feature of the system is documented in a shift of the centroid from c to c2.

0. Picture of the experiment. The experiment 02B is still present in the model.
02. Scheme of the experiment: complex system of threads abstracted into prisms that intersect each other.
0. Model of branched structure with hierarchy. The hierarchy was achieved by threads with different amount of slack and emphasised by various thicknesses of threads. Prisms are distinguished by different colours.
This experiment was made in order to understand the complexity of nested hierarchical structure. The differentiation of branches was observed. It came out from the experiment and analysis of the Frei Otto group which set dependances of thickness and lenght of branches in columns loaded in compression.
There were two independent base points and points in plane that were shared by threads from two bases. The basic ply woollen threads (white on figure 0) were mixed with ply threads (blue in figure 0). White threads had bigger slack and due to thickness and slack were nested on blue threads. This fact could have very important impact on the structure if this was considered. The research of Frei Otto confirmed that thicker elements have bigger loadbearing capacity.
The thickness and nesting in the digital model requires advanced skills in modelling and analysing of generated structure. This direction of research could be deployed later as a further area of research. It could result in the model where differentiation plays significant structural role.
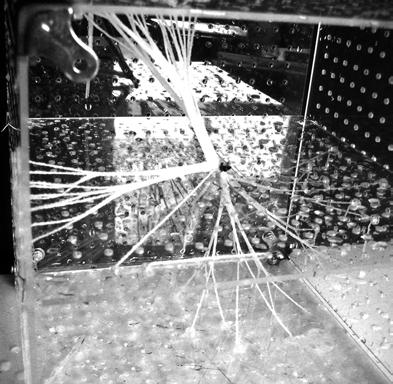

Branching pattern could be described by a simple equation that serves as an input into a parametric digital model. The most important is a parameter d which helps to define a distance of a branching node from the previous branching point (or obviously from a centroid of points P).
The experiment unveil that three threads are bundled together and create a branching form. From observation occurred two possibilities of a branching node: dividing into three branches in a single node or node with two branches and the last one is connected to the main branch in a certain distance.
The geometry of the first example is presented here the second s elaborated on consequent pages.
definition of a geometry:
defining of distances: (d+d2+d)
defining a branching point: L
additional constants:
S .... amount of slack
a .... angle of a plate
m ... material of threads
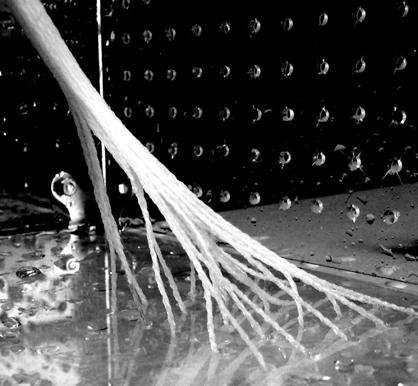
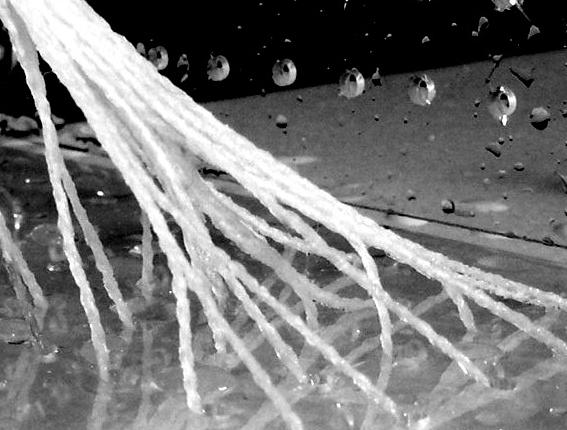
Emergent properties of the pattern feature a change of the distance of the node from the previous branching node. These distances (L and L’) vary according to the distances between points (P, P2,P).
Dependencies are described by if statements included in a digital model.
-
-
definition of a branching node:
d = (d+d2+d)
if (d+d2+d) [ (d+d/4)
then
L = L/(d+)
L’ = L
if (d+d2+d) [/ (d+d/4)
then
L = L/(d+)
L’ = L/(((d2+d)/2)+)
equation with parameters:
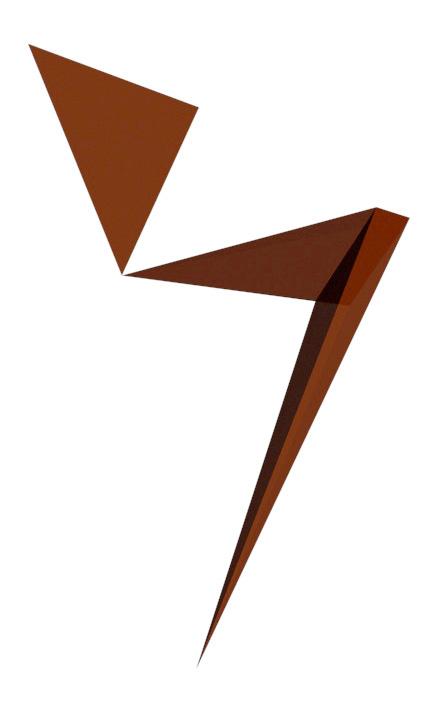
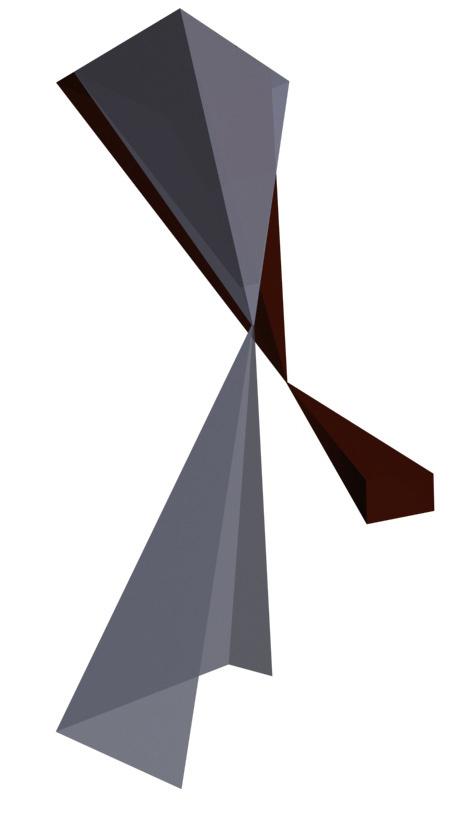

Prisms of threads represent the influence of branched structure. It is defined by points in plane and a base point. These pyramids could lead to these ideas:
_prisms as self-supporting structures
_prisms as a vector-active system that supports a slab
_prisms as a structure that fluently dissolve into any other type of structural scheme
Each prism is an unique structure according to its position to the main node. These structures could be then used in a space with its type of position.
The inner geometry of prisms (branched pattern) probably does not match with a pattern that could be produced by real building material. Wooden stripes in this case. The next part of research will be devoted to this problem and try to find out what is the range of this difference. Then could be set a criteria (parameters) that allows for fabrication of these branched structures.
given points in a plane
given points in a plane
02. Equilibrium of prisms concentrated into one point.
given point in a “trunk”
0. Equilibrium of prisms, “tree” structure is generated according to rules obtained from physical model and given planes.
known base plane
0. Base - plane that cause structure more stable against dynamic load - changing of forces G and G2.
Geometry of prisms and their equilibrium are studied in this analysis. The position could be balanced only on one point in a distance d0 from a vertical axis. Figure 0 shows a vertical axis arbitrarily chosen on a plane. The model is simplified if we consider a vertical axis in a position of one force.
moment equilibrium:
Gd+G2d2 = d0(G+G2)
d0 = (Gd + G2d2)/(G+G2)
equilibrium in one point:
d0 = (G2d2/(G+G2)
d0 .... length from a point of action G
The length of a base of the lower pyramid could vary between two critical numbers. It could be closed to 0 - ideal stable state (fig 02) or it could extend to a distance from forces G, G2 to E (fig. 0). This will cause more stable structure and provide a range for changing G and G2. The structure is therefore more stable under dynamic loads. The base pyramid could be divided into two parts when points of actions of G, G2 are too far from each other.
This approach could be extended by knowledge from biomimetic lessons, especially from building structure of trees. The reaction of wood on a sloping terrain with densifying fibers leads to a conclusion about a branched structure of the pyramid.
The shape of prisms (for easy understanding now represented as triangles) is informed by consequent series of form-finding. The experiments with laminated wood and possibilities of bending timber between fixed points cause the possible shape of pyramids.
Analysis and Evaluation
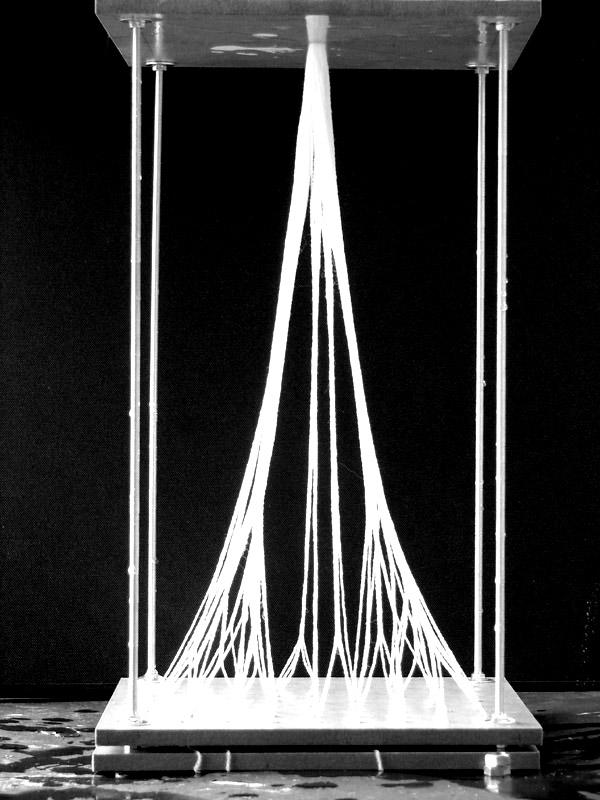
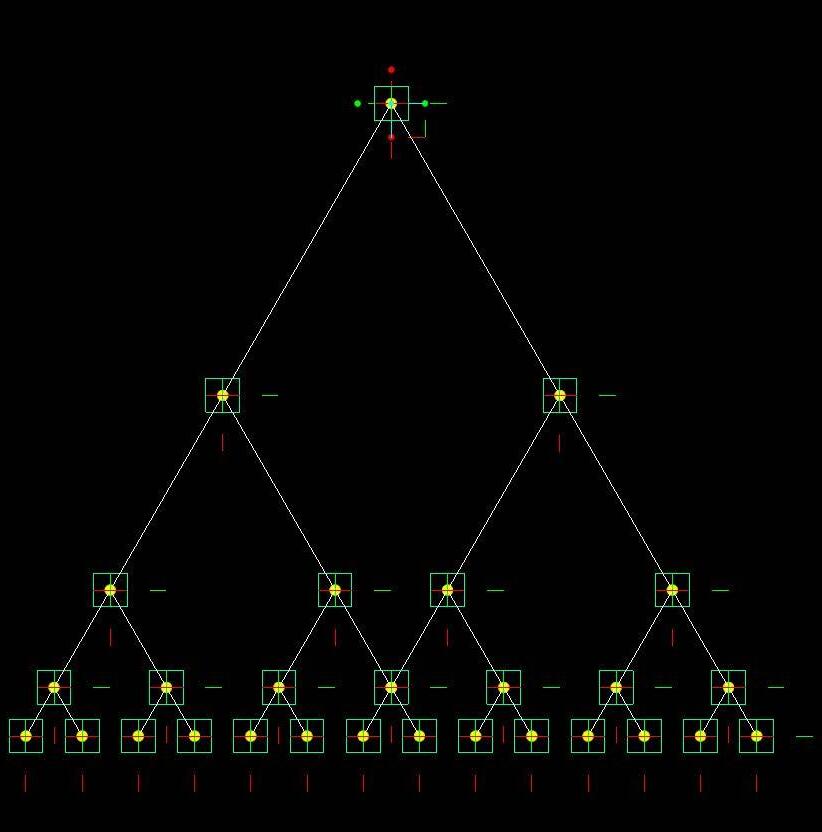
0. Geometry from physical models (example of the most simple one) 02. Geometry produced by L-system. The combination of parameters could achieve geometry that is extended beyond physical models. But rules remain the same.
Physical form-finding showed possible configuration of D branching pattern. This pattern could be assumed as a pyramidal shape that is made according to position of a plate and a base point. The internal organisation of these pyramidal shapes are unique and could be collected and described and stored to a data set for a consequent proliferation.
The approach of GC modelling by using logic of L-system could achieve pyramids with nodes that could mutate according to certain parameters. These parameters are obtained from physical models and could be extended with if statements. Than this models have emergent properties.
GC modelling L-system - node rewriting
parameters:
angle - position of final points
angle2 - amount of slack
thickness - number of threads
length - length o threads, amount of slack
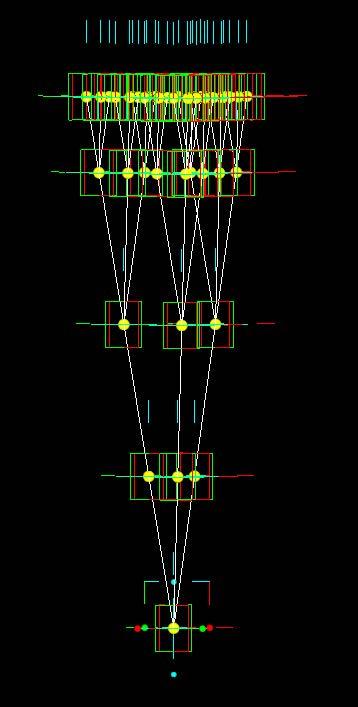
branching into lines
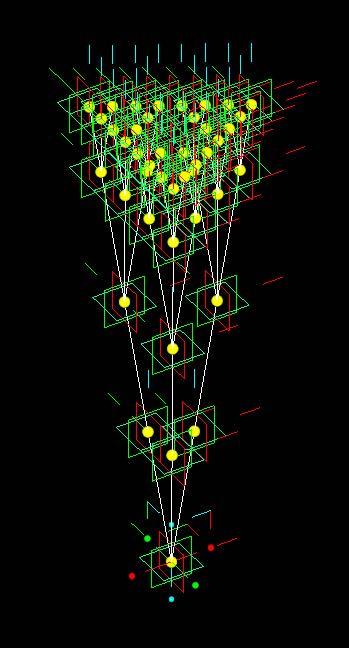
04. D L-system branching. Different “angle”, “angle2” could be introduced.
05. Rewriting rule creates a pyramidal geometry with a triangular base.
mutation: branching into 4 lines
0. Geometry of pyramids - these pyramids according to rules and parameters from physical form-finding make together a catalogue. This geometry will later serve as a basic row fro proliferation on certain space.
distance from a reference point
06. Possible strategy for a deviation from a three-branches node. This is a possible strategy for a non-triangular base of a pyramid.
Bifurcation
The act of splitting into two branches.
Branching
The subdivision of offshooting of a structure, developing or diverge from: into a number of elements. In computing: A programming structure that evaluates a condition and then takes one of two actions based on the outcome of condition evaluation.
Dichotomous
Branching into two equal structures (stem, veins, etc.) leading to „Y“.
Fork
A bifurcation or separation of two or more branches.
Fuse
To mix together as if by melting.
Hierarchy
A hierarchy is a systém of ranking, categorising, grading or organizing elements of a group or series.
Junction
The place where to entities (lines, planes, etc) come together at a connection point.
Merging
Act of combining two entities into more.
Nested
A material systém, process or activity self-contained within a larger entity, that retains its identity and characteristics. Each nested systém, process or activity can be embedded sequentially within any number of others.
Surface Tension
The elastic-like force in a body, especially a liquid, tending to minimize, or constrict, the area of the surface. It is the effect that allows insects (such as the water strider) to walk on water, and causes capillary action. Surface tension is caused by the attraction between the molecules of the liquid, due to various intermolecular forces, which exists in the surface film of all liquids that tends to draw the surface molecules into the bulk of the liquid and causes the contained volume to have a shape of the least surface area.
Tree
A path system in which does not contain a closed loop, that is one cannot go in a circle within the system.
st Iteration
2nd Iteration
rd Iteration
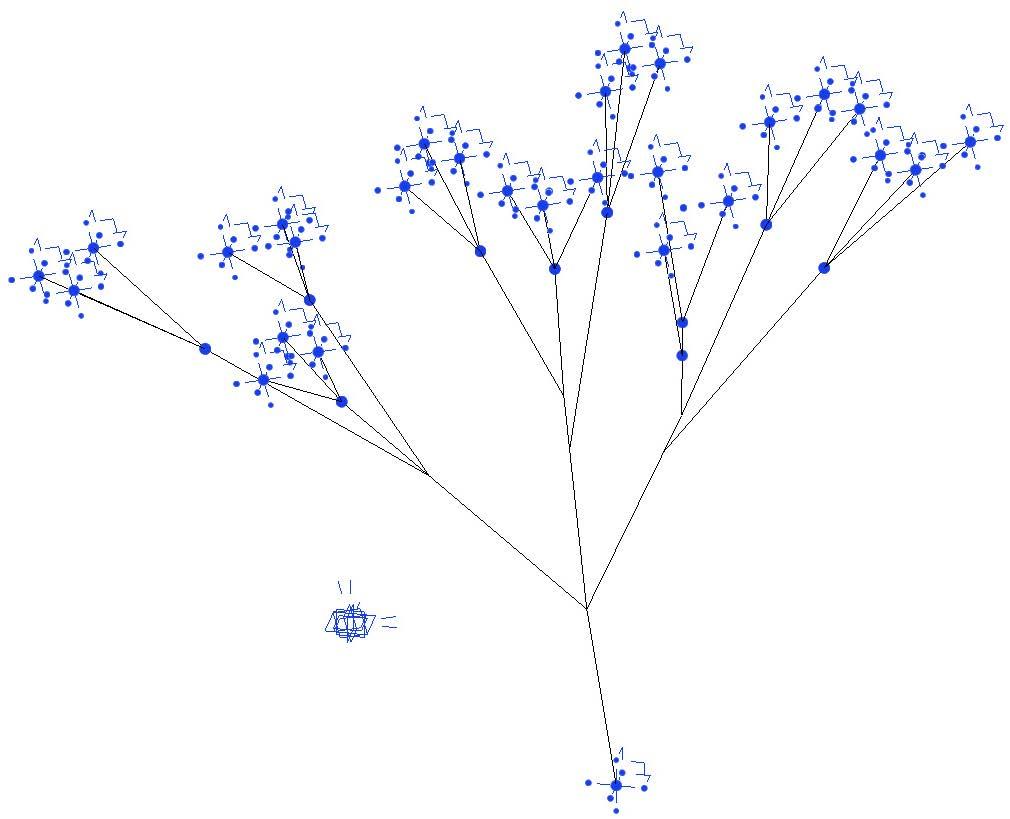
Aim of these experiments was to find the most efficient way for modelling branched structures in parametricaly controlled environment.
Associative model is based on a given array of points and one base point. The geometry is generic due to setup of relationship between lines and points and operative rules from L-system algorithm. Edge-rewriting method is used for the model. On Figure 0 there are three iterations of the algorithm. Each iteration looks for the central point of arrays of points that are multiplied by three until it ends in points itselfs. When it reaches an input point the algorizhm is terminated.
The model is tuned by parameters that control the distance of branching points and a base point. Parameters are explained on the following page. 0. Tree structure

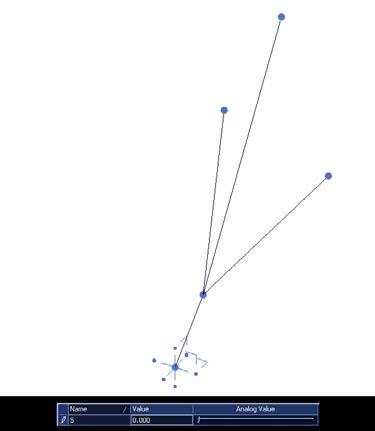
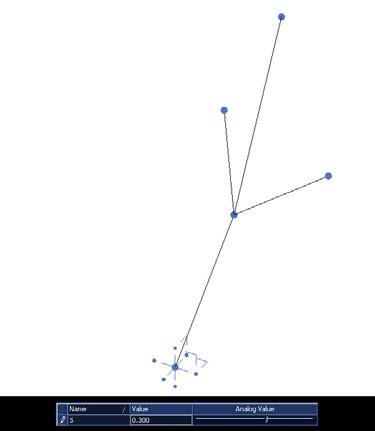
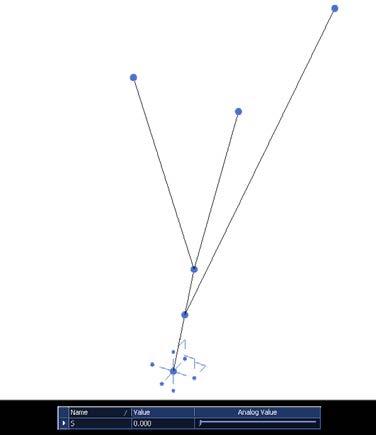


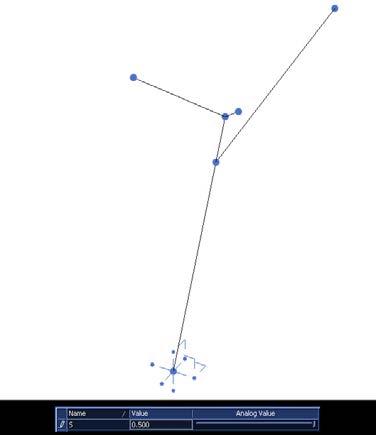
Presented structure was digitally modelled in order to be physically fabricated as a representative sample of the branched structure. The model represents generation of structure using edge rewriting L-system algorithm. The algorithm include IF statements with variables gained from the physical models of woollen threads immersed into liquid. Components with coded information replace previous branch of the structure. The change of parameters allows for control the lengths of branches and therefore density of the final outcome. Configuration of initial points determine the geometry of branches. The branching node and its position is dependant on the distance of connected points. The technique is developed for the further application with material. The curvature, twist and possibility to bend wood is very closely related to the length of branches.
The executed experiment is considered as a base for further digital experiments. The geometry of points and lines will serve as a scaffolding for the digital form-finding of laminated wooden material. The choice of the right parameters and its application would serve as an informed model of the branched structure.
Although the geometry does not have any concrete structural application it is considered as a starting point for the self-supporting branched structure. The flow of forces and connection to a plate that connects points are later elaborated in the research.
The configuration of points allows for further examination of the emergent structure where the connection of points forms the complex structure of interrelated points and lines. If the boundary condition is changed the geometry of the whole is changed. The physical model opens and deploy the question of actual size and dimension of the final structure.
Emergent Structure: Physical Model
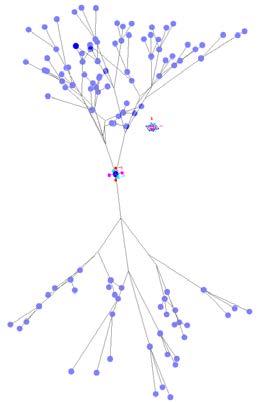
0. Generated Branched Structure by edge rewriting L-system.
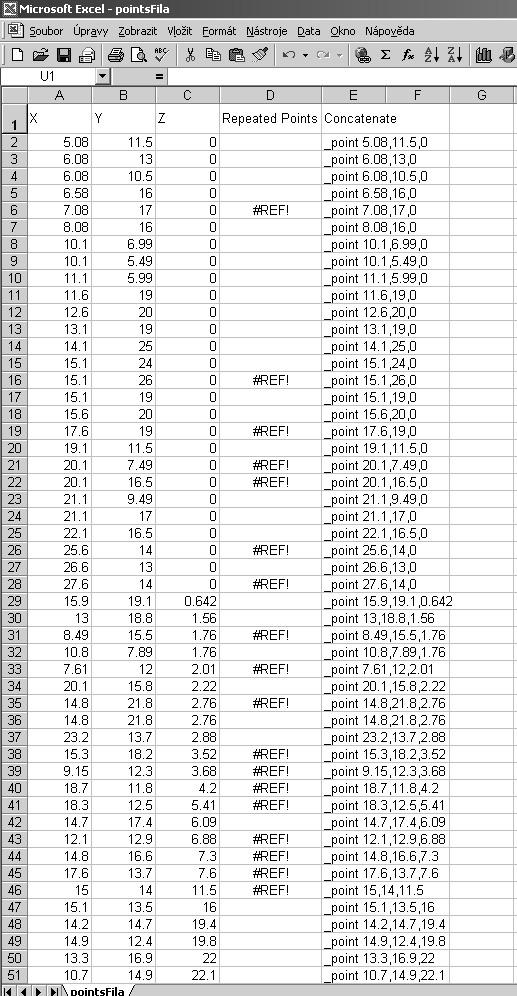
02. Excel spread sheet exported from GC. There are x, y, z coordinates in columns A, B, C. Column D is prepared for export to AutoCad.
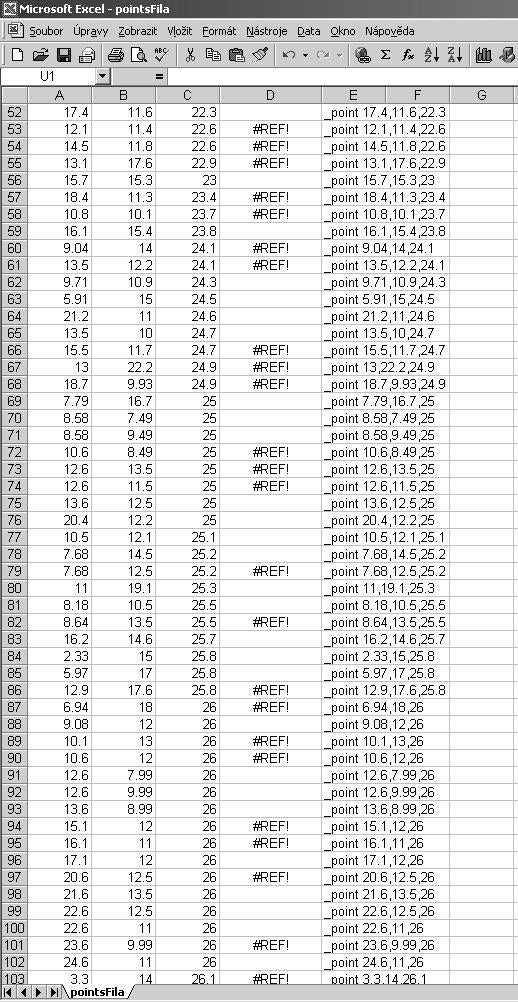

The digital self-organisation described on previous pages (fig 0) was intended to model physically. The intention was to built physically the relationships between branches, nodes and input points. There were also explored possibilities of communication between different programes.
The model in scale was important for the next steps in research because it showed the actual dimensions and from that could be estimated also capacity to modulate the environment in structure. That means dimension of branches and possible manufacturing techniques. The model was build as a cube with a side 00 mm.
The procedure starts with strategicaly placed points into the parametric software Generative Components. Strategicaly is understood as a top-down decission or a decission that comes out from other input. The second case was later explored in the thesis. Generated branching points are then sorted according to Zcoordinates in Excel spread sheet and imported to AutoCad.
There were several possibilities of constructing trees but for my purpose seemed to be the most accurate threads going through plexiglass plates. Plates were laser cut according to plans drawn in AutoCad.
Emergent Structure: Physical Model
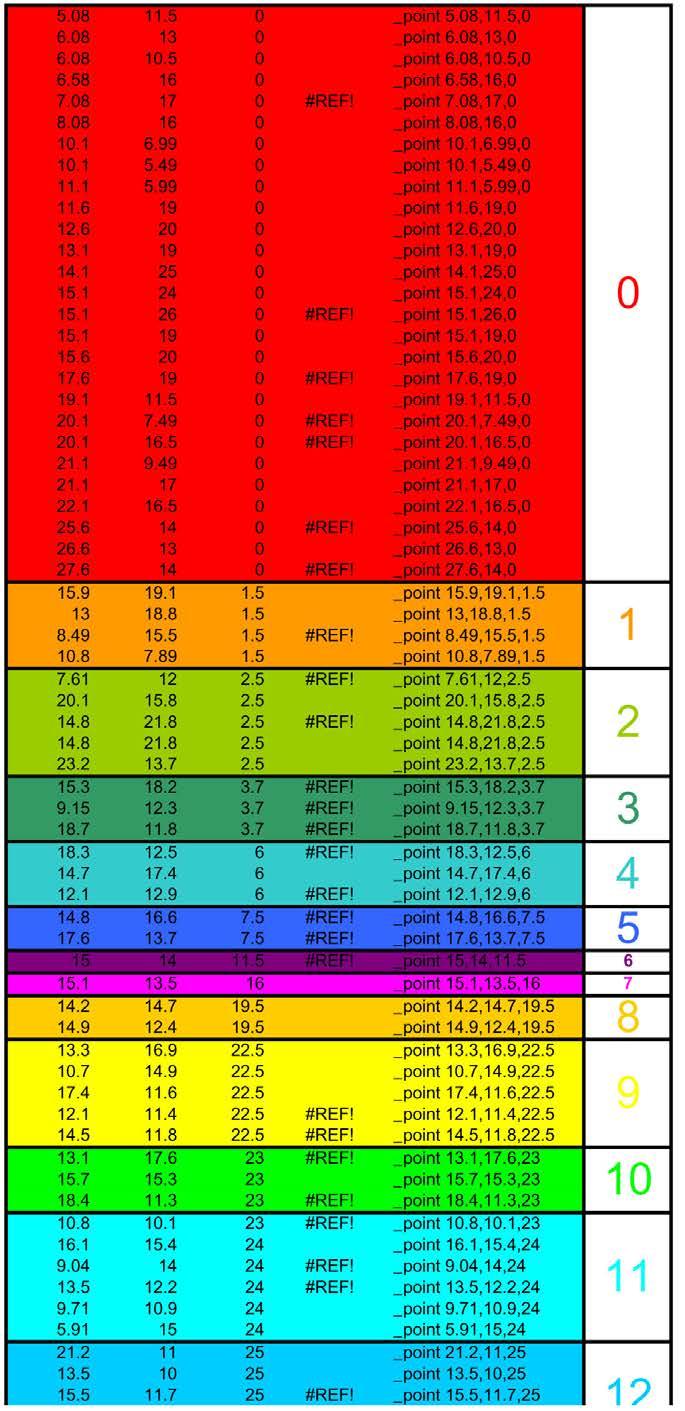
0. Adjusted excel spread sheet. Colours represents plexiglass slabs - points with the same value of the z coordinate. There are x, y, z coordinates in columns A, B, C. Column D is prepared for export to AutoCad.
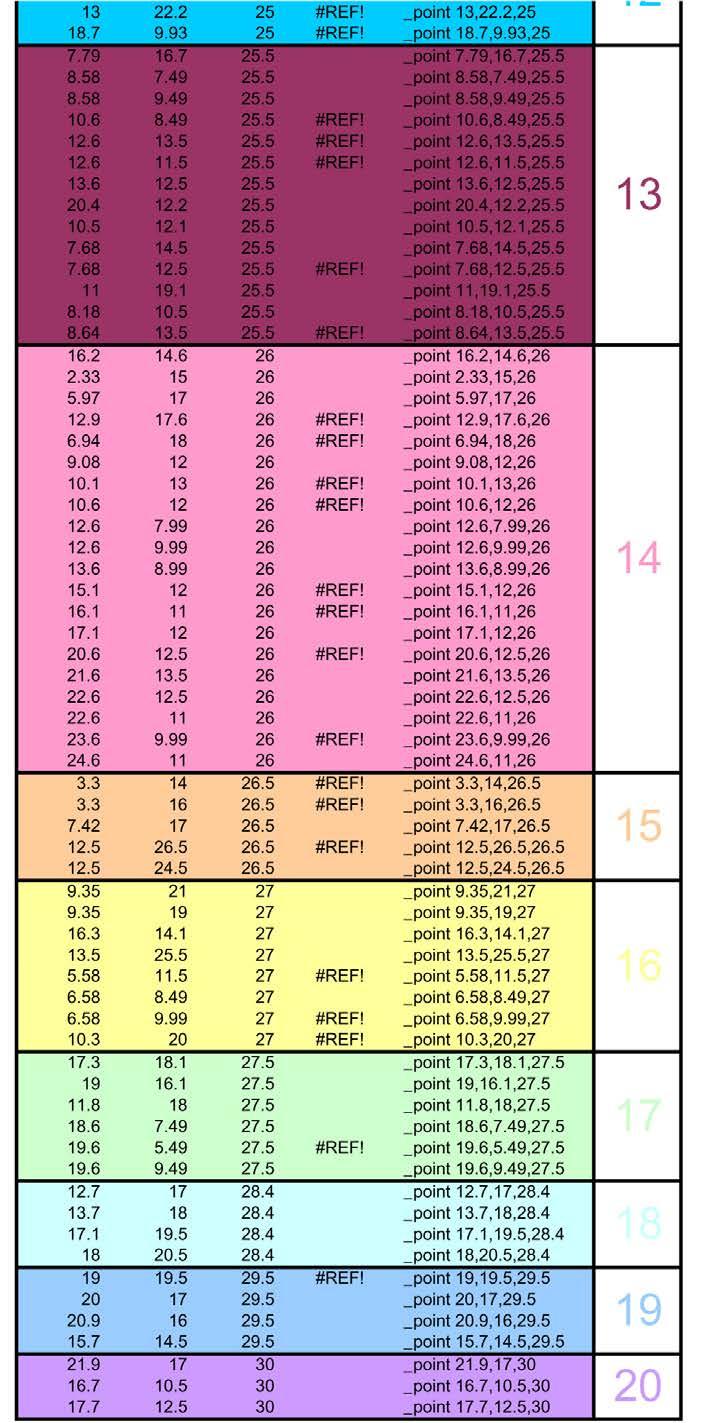
Points were concatenated according to their Z-coordinates. Values that varied in an interval of 5mm were interpolated into one plate. Figure 0 shows the excel spread sheet with 2 plates and coordinates of branching points. There was another sheet with points where branches go through plates as straight lines.
Preface Concept Material Properties Form Generation Evaluation

0. Elevation, Axonometry and Plan of the Tree Structure. Model is ready for manufacturing.
02. Nested plans ready for laser cutting.
Emergent Structure: Physical Model
AutoCad model of fabrication plans for the laser cutter. Every level (fig. 0) with circle openings had its own plan that was nested on a plane and prepared for laser-cutting.
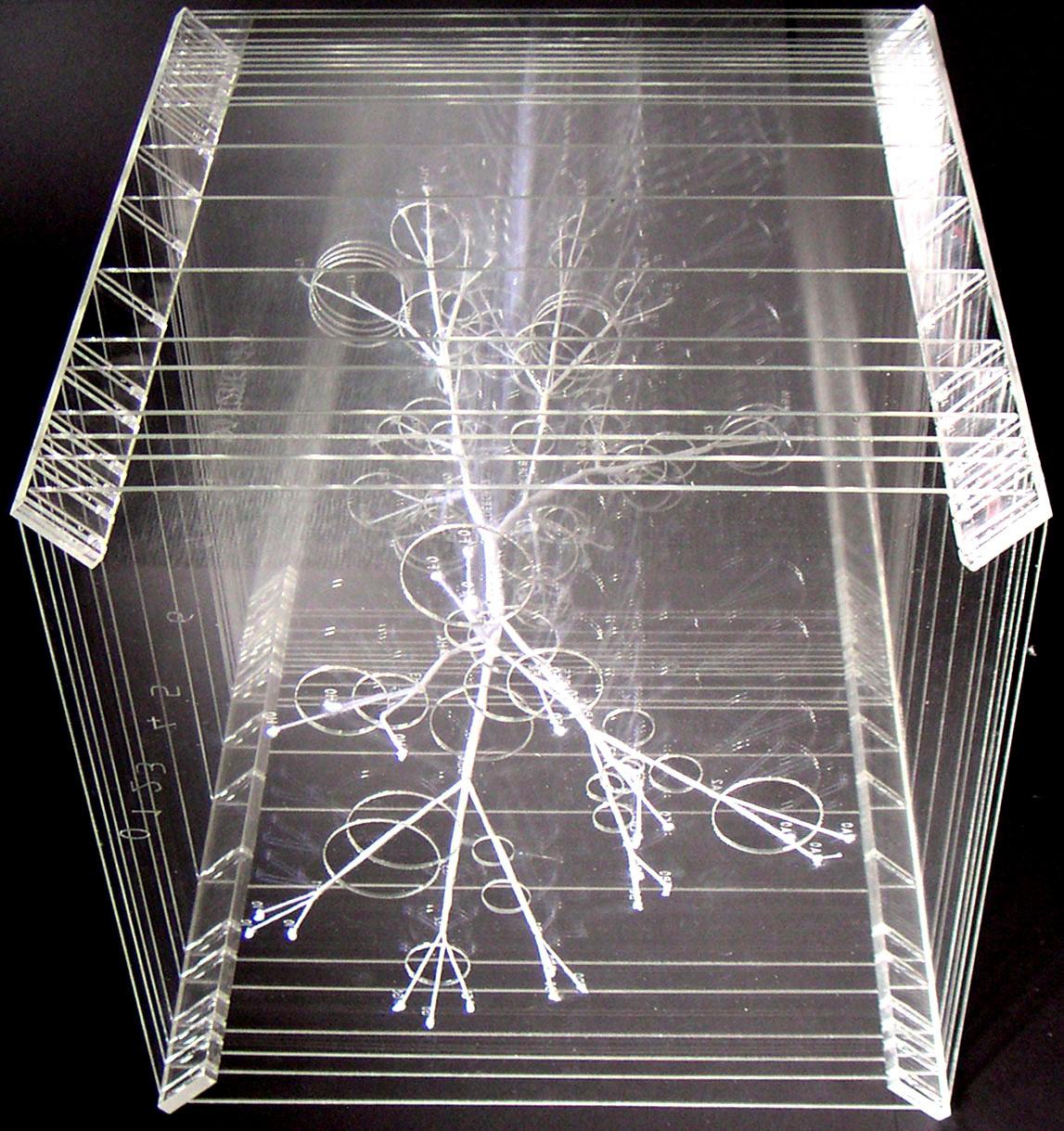
Finished model shows the arrangement of tree structures with 27 and 54 branches.
The manufacturing technique did consider the fiber continuity of material but is not very efficient when scaled up. But the idea of fixing control points could lead to succesful results when is chosen a material that is flexible enough and self-organise itselfs into the required position. This technique was later explored in chapter material properties with D lamination of plywood.
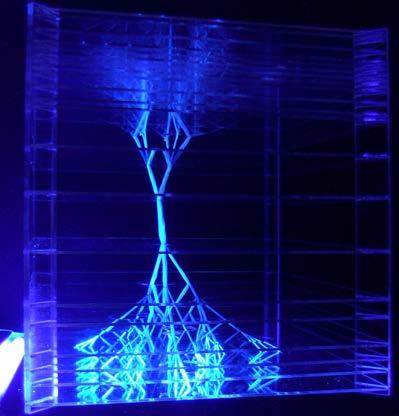

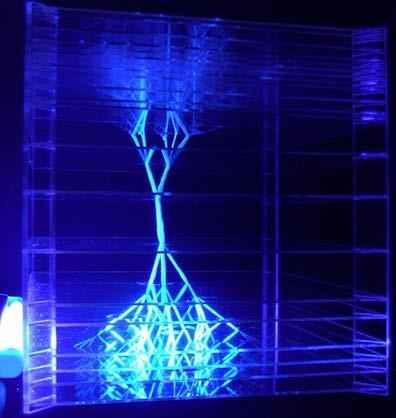
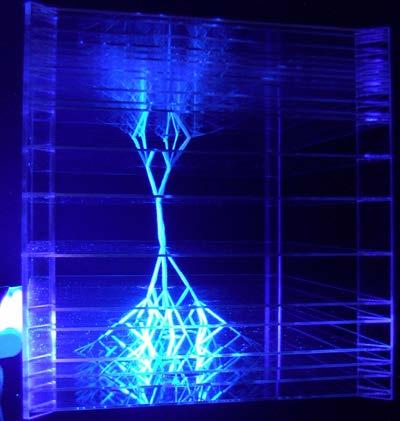
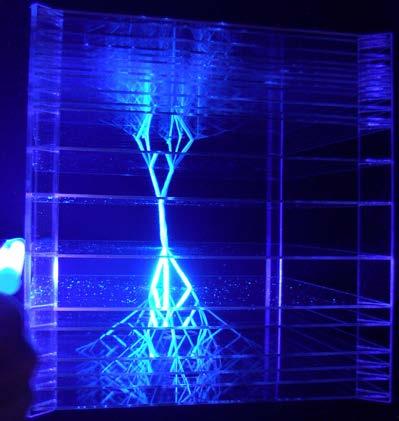

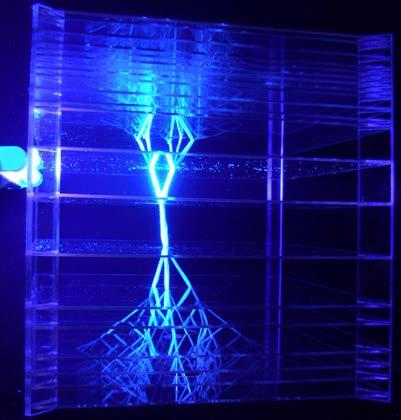
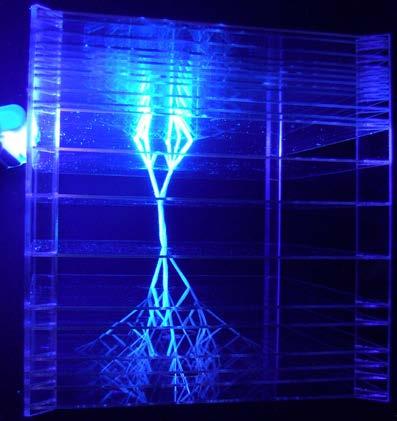
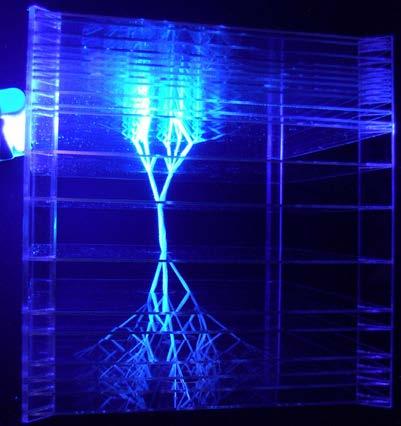

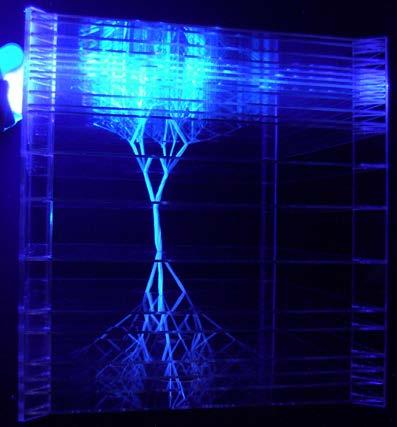
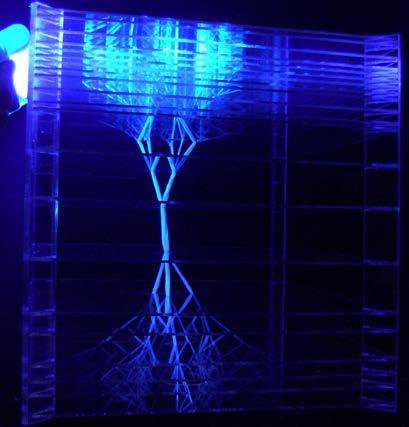
Branches got thinner when they were branched out from the base point. It was due to the material - woollen threads and also also there was mainatined a biomimetic approach of continuos fibers.
Analysis and Evaluation
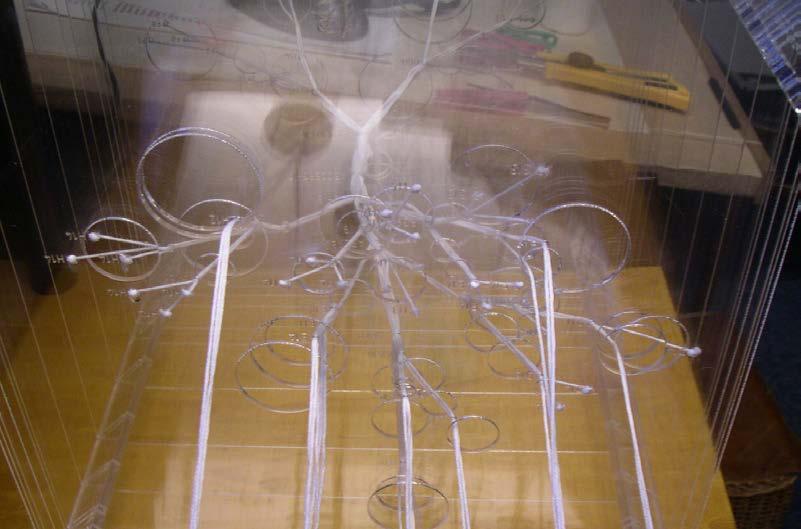
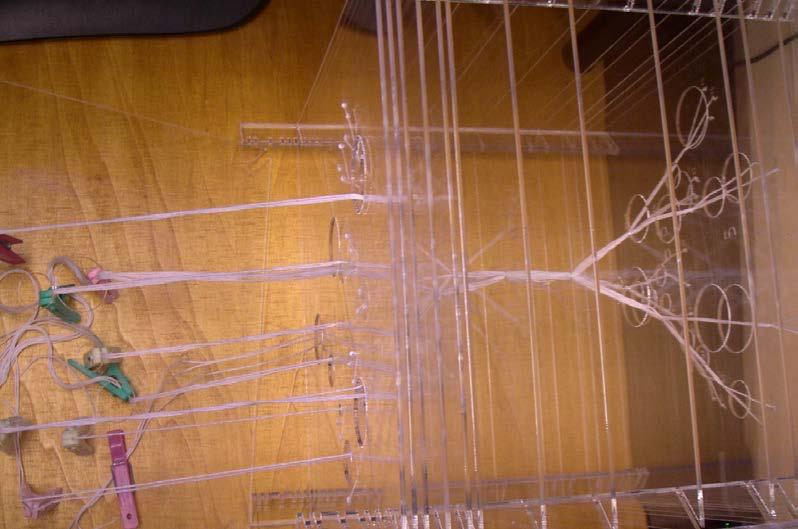
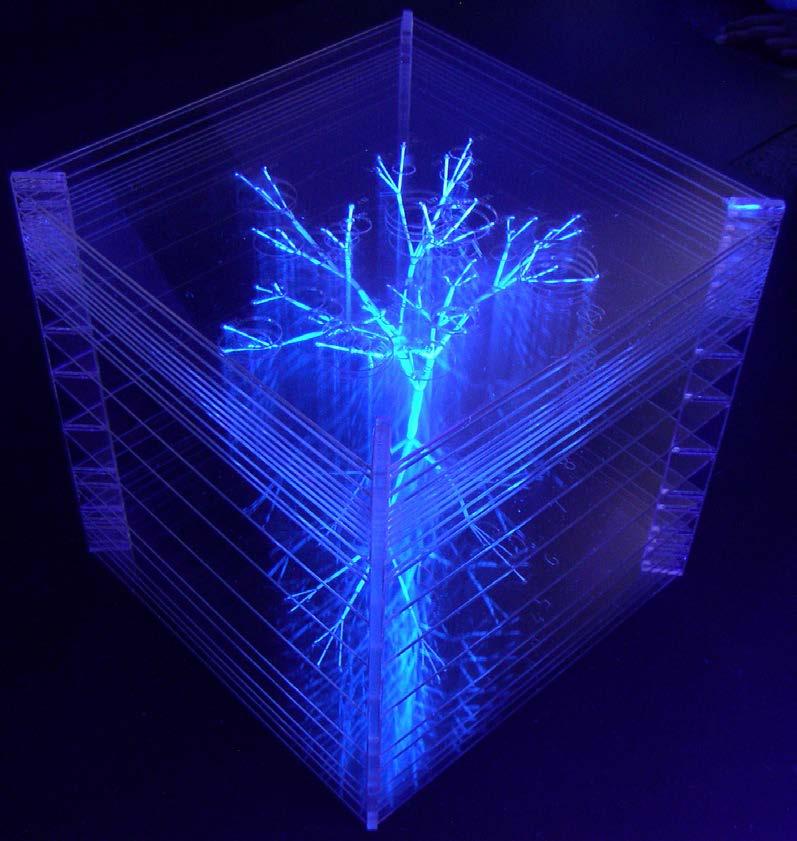
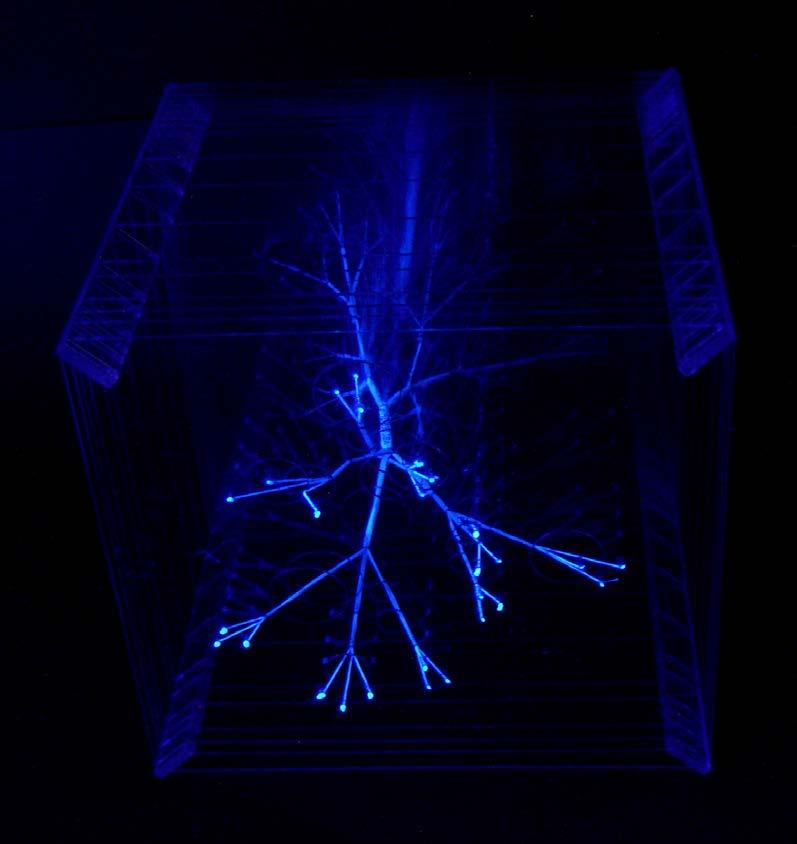
Manufacturing process is different from that used for building the Terminal in Stuttgart Airport. There was a scaffolding but the tree structures were made from isotropic material and then piece by piece welded together. Approach outlined in this research takes benefit from the anisotropic natural material - wood. Wooden planks are form-found and clamped in a position of branching nodes. Then the structure could be constrained by dimensions of manufacturing halls and also by transport means.
The smal cube of 0 cm was not built just for the demonstration of available techniques but it also represented.
Preface Concept Material Properties Form Generation Evaluation Branched Structures
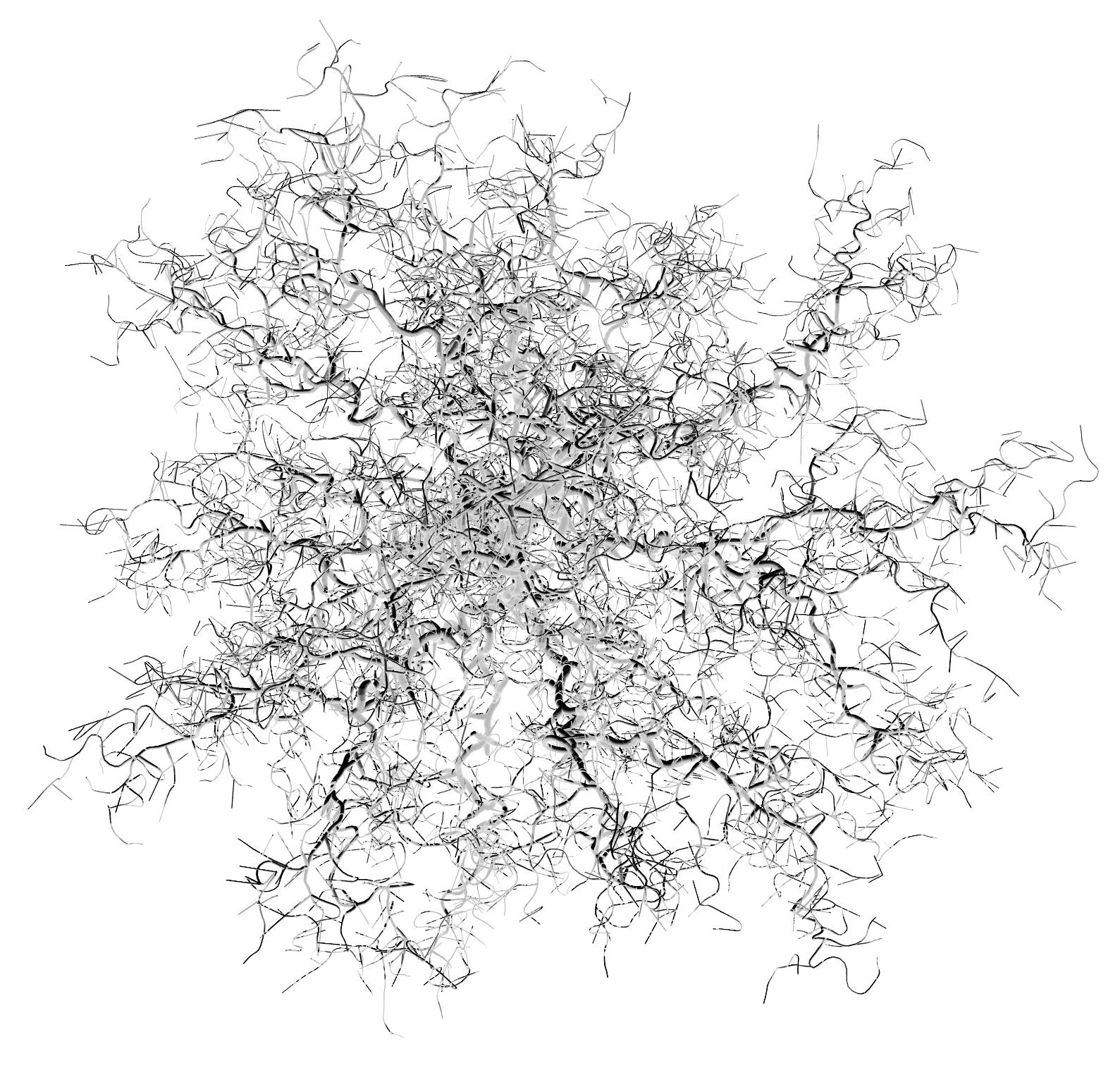
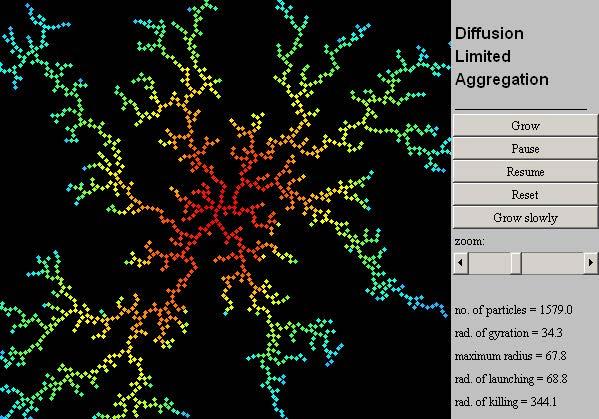
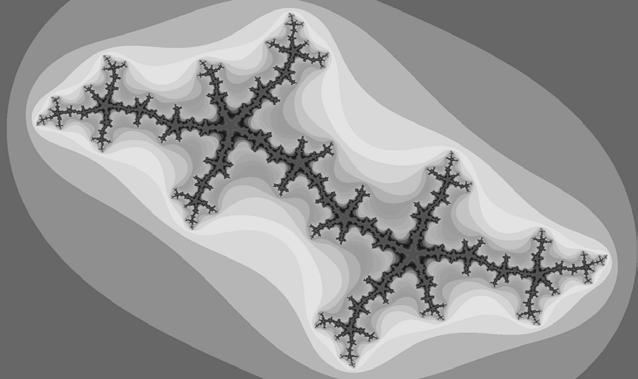
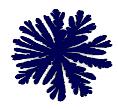
Many attractive images and life-like structures can be generated using models of physical processes from areas of chemistry and physics. One such example is diffusion limited aggregation or DLA which describes, among other things, the diffusion and aggregation of zinc ions in an electrolytic solution onto electrodes. “Diffusion” because the particles forming the structure wander around randomly before attaching themselves (“Aggregating”) to the structure. “Diffusion-limited” because the particles are considered to be in low concentrations so they don’t come in contact with each other and the structure grows one particle at a time rather then by chunks of particles. Other examples can be found in coral growth, the path taken by lightning, coalescing of dust or smoke particles, and the growth of some crystals. Perhaps the first serious study of such processes was made by Witten, T.A. and Sander, L. M. and published by them in 98, titled: “Diffusion limited aggregation, a kinetic critical phenomena” in Physical Review Letters.
New points are introduced at the borders and randomly (approximation of Brownian motion) walk until they are close enough to stick to an existing black pixel. If a point, during its random walk, approaches an edge of the image there are two strategies. The point either bounces off the edge or the image is toroidally bound (a point moving off the left edge enters on the right, a point moving off the right edge enters on the left, similarly for top and bottom). In general new points can be seeded anywhere in the image area, not just around the border without any significant visual difference.
Branched Structures
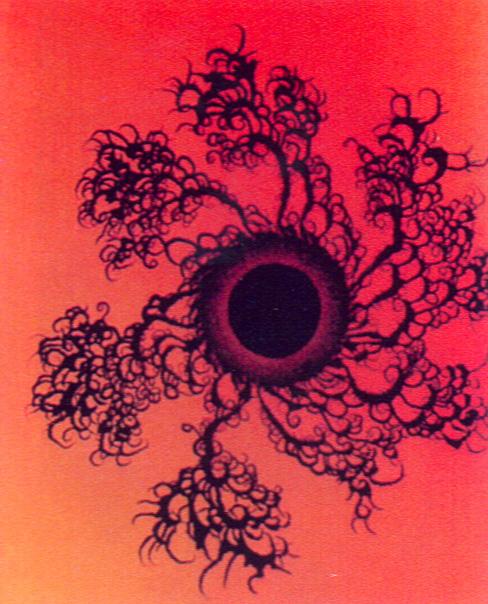

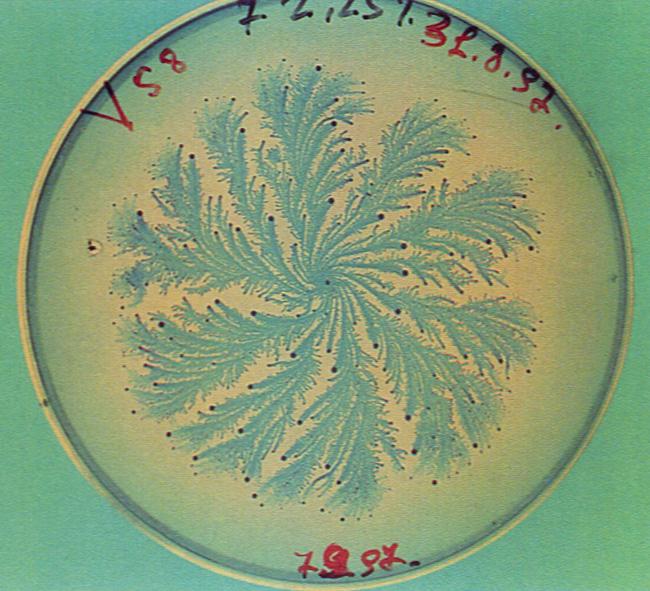
Fractal branching could be found both in living and also non-living nature. The experiments with colonies of bacteria have shown complex branching pattern tuned by amount of food (examples of colonies of different species are on fig. 0, 02).
The Interesting comparison with other concepts of branching is that of veins in bodies. The branching angle is dependent on a flow of energy. The topic was observed and worked up by D’Arcy Thompson in On Growth and Form.
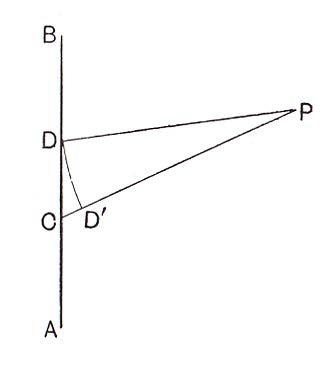

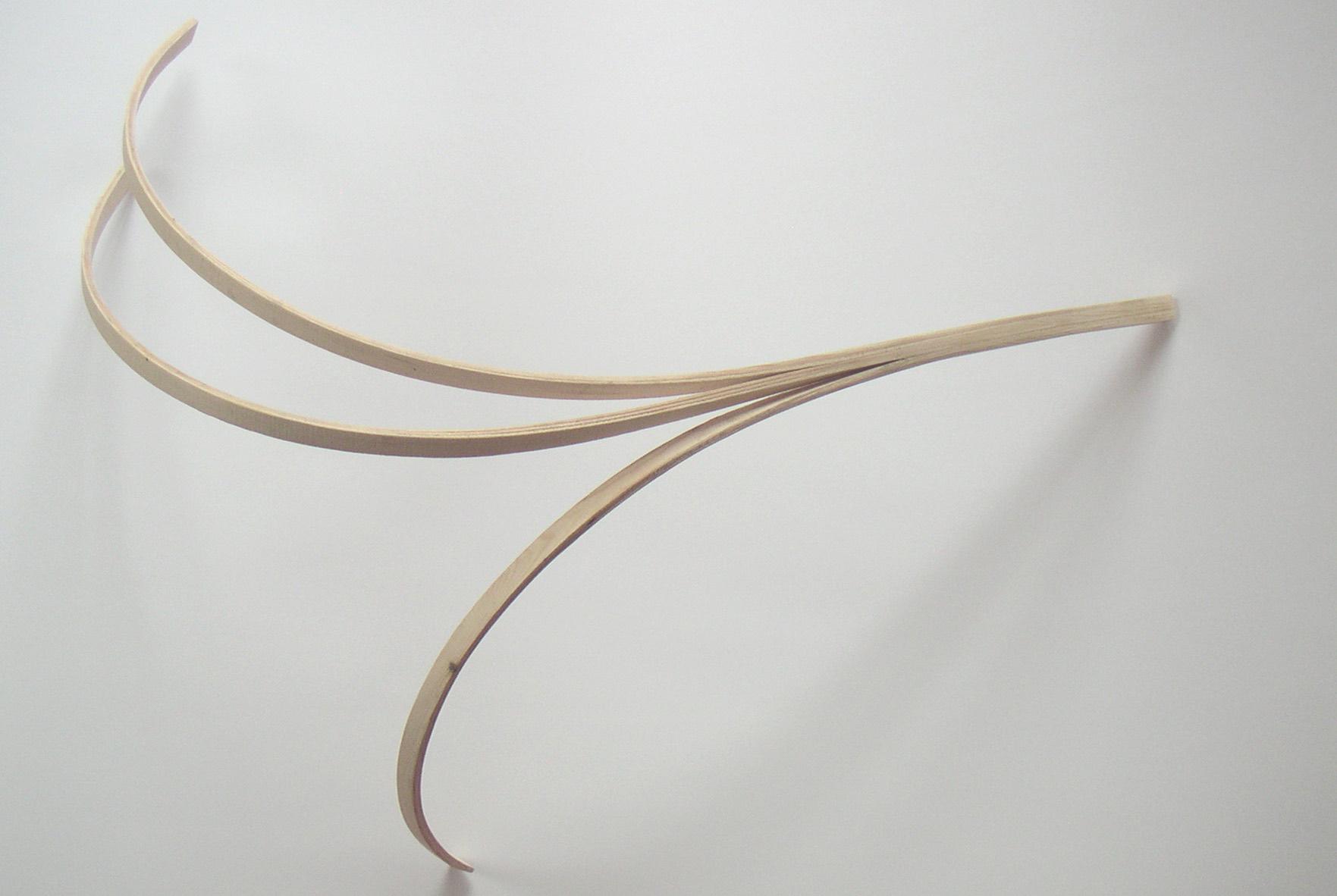
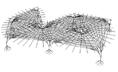

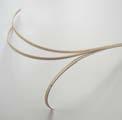
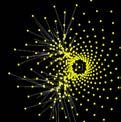
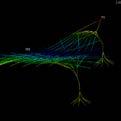
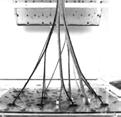
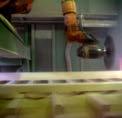
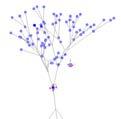
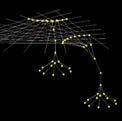
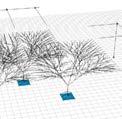
Suitable technique of wood-working helps to find a self-organised structure that follows rules similar (or the same) from those obtained experiments from threads-liquid experiments.
Lamination of wooden layers can record a self-organised curvature of a strip of a certain length between two points. This technique could fulfil task of branched system.
Nodes of branched structure could be bundled into one point and this point have higher structural capacity then a single branch or a straight member of a structure (e.g. column).
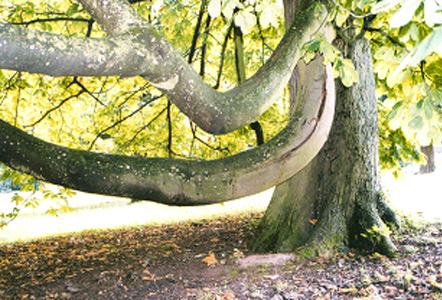
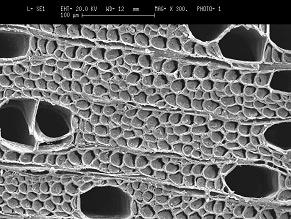
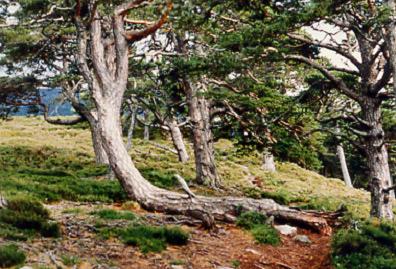
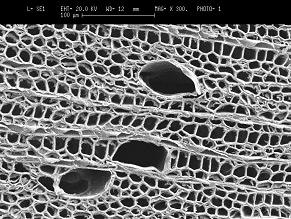
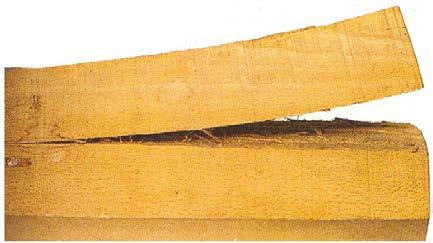
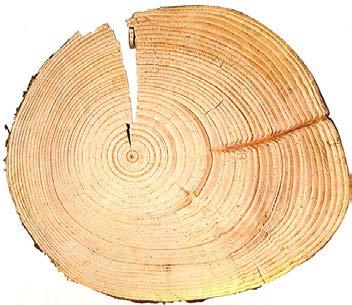
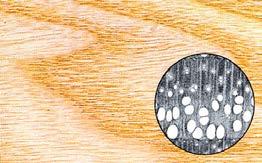
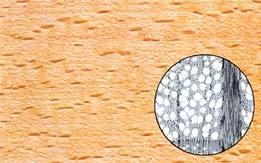
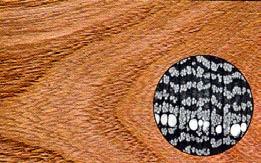
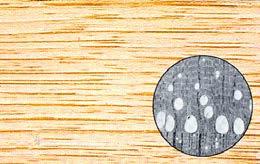
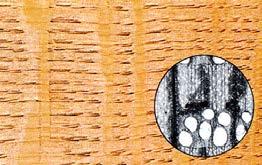
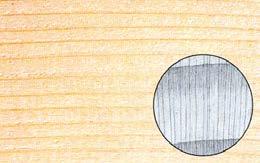
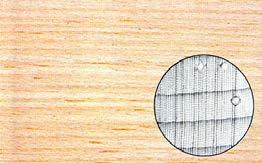
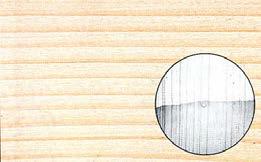
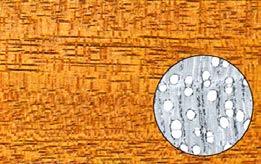
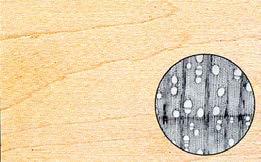

The methodology of the research into material behaviour starts with exploring properties of wood. There are several types of wood dependent on types of trees. It is also possible to distinguish two groups of wood according to the inner distribution of material (fig. 07, fig. 08). In furniture industry there is used a group on fig. 07 because it allows for severe curvature. In building industry the most common wooden material for lamination is from a group on fig. 08.
A tree itself has its own inner structure which differs according to the function of particular parts of the tree. The structure is distinguished into Reaction wood. Reaction wood is used by trees to modulate shape of a trunk and branches (gravitropism/phototropism). Tension wood is located on the uphill side of trees and compensate inclination of deciduous species. If it is drying it could split along grain. This effect is used by some sculpture-making techniques. Compression wood in coniferous trees (fig. 04) allows for upright position and seeking light.
For initial experiments with wooden components were selected species that are used for lamination of beams in wooden industry. They belong to a group of trees that have soft wood and are widely available in European forests. To this group belong pine, russian redwood and fir.
Although the usual manufacturing technique is the lamination in a plane it is possible to glue wood in D. The next step was to create a set-up for from-finding experiments where the curvature of laminated wood plays important role. Form-finding experiments started with exploring bending and twisting capacities of wooden stripes. These stripes were bent and twisted and documented. Information from these exercises was used for the set-up of consequent physical experiments with laminated stripes. Firstly a lamination was made in 2D and then a possibility of more complex lamination in D was explored.
In order to measure these experiments and input them to the associative model there was made a scaffolding with a fixed position of clamping points in a cartesian coordinate system. The input for the system was a position of clamping points and also the length of stripes - layers of lamination.
Executed experiments were then compared with gained information from visits to companies that work with fiber material. Consultantions with experts from the company Finnforest-Merk were very fruitful and led to better understanding of connection between CAD and CAM. Also problematic of work with wooden composites in products developed in 20th century was also explored. The famous wooden airplanes were studied and analysed as component based products.
Preface Concept Material Properties Form Generation Evaluation Scheme of the work
Geometry
Form-finding Geometry
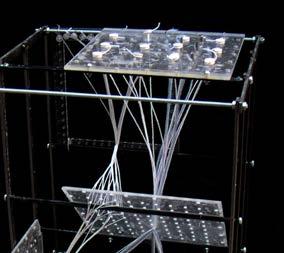
Form-finding
Methods:
Modelling
Scripting
Methods of Proliferation Material
concept of geometry and structural scheme - branching
form-finding experiments - lamination
Form-finding Material Form-finding Limits of Wooden Strips
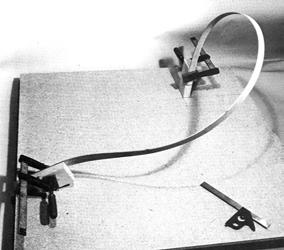
Parameters for Digital Experiments
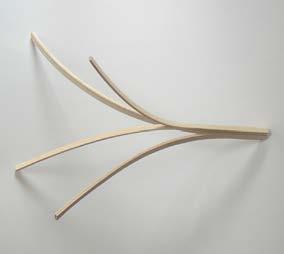
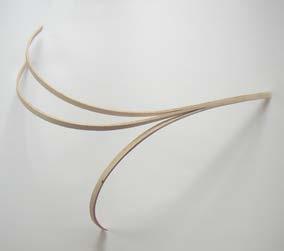
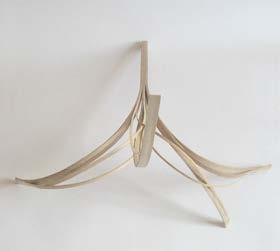
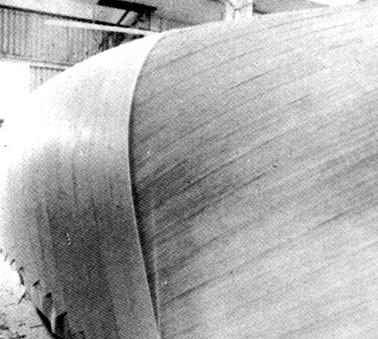
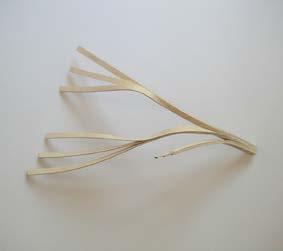
concept of branching informed by behaviour of wooden lamination constraints of material
Proliferation
Digital Modelling
Nesting of Pyramid
Extrinsic Influences
Loading Capacities
Bearing Capacities
Proliferation
Digital Modelling
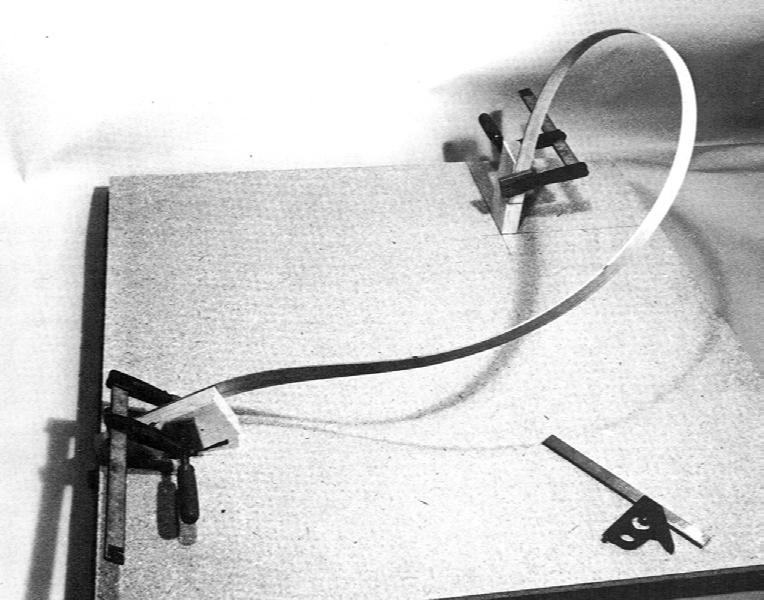
0. Form-finding with anisotropic wooden strip. The curvature is achieved by location of two points and length of stripe.
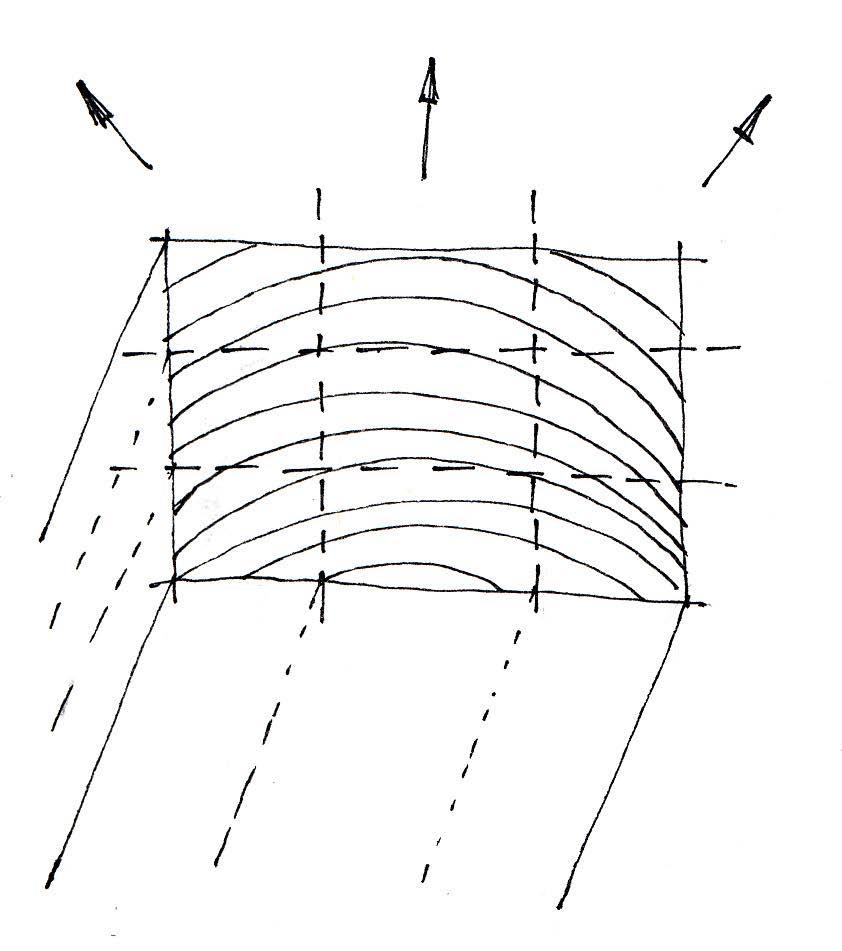
0. Splitting of tension wood. There must be chosen special timber that have specific direction of grain.
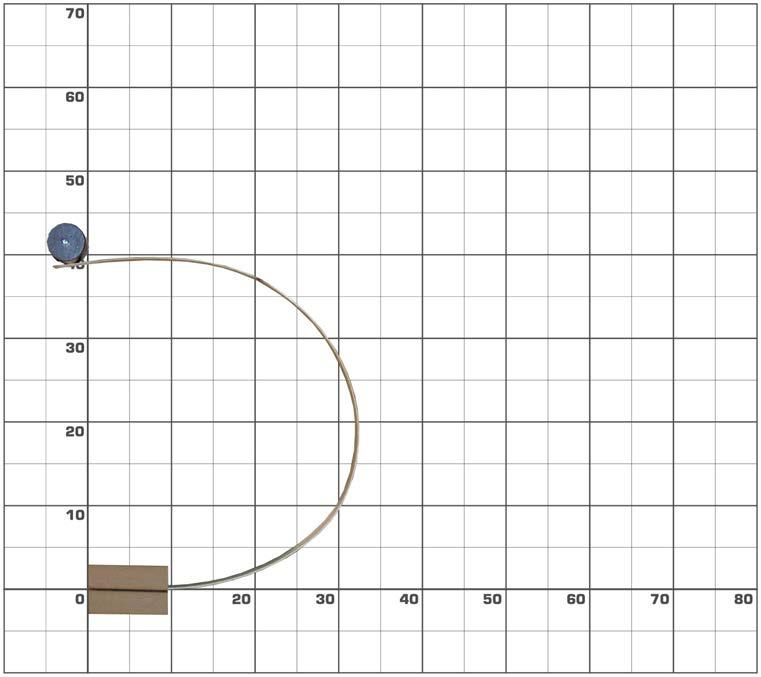
02. Form-finding with anisotropic wooden strip in 2D. This is the first set of experiments that inform physical and consequently digital models with its parameters.
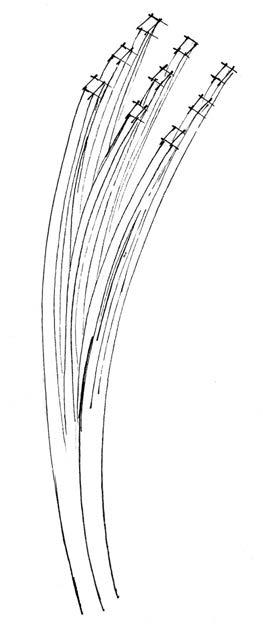
04. Piece of hardwood is split along grain. There could be hardly predict nodes of splitting and distance of split branches.
Thera are two suitable strategies of form-finding that could be used to fulfill the task of a branched contruction. The first is bending of wooden stripes and later laminate them, the other is splitting of wood. The aim was to achieve desirable structure without any other joining material than glue. This process maintained the fiber directionality of the composite.
Lamination represents one of techniques that allow for bending of wooden components. There is an impact on the curvature by thickness and width of wooden stripes.
Bending of wood
Furniture making method which is based on natural curvature of wooden stripes that are laminated in a form-finded position. The executed form-finding was made without any treatment of wood (steam, water, etc.) The composite is made of stripes of wood of different thickness and therefore adaptability to shapes (fig. 0).
Parameters of the composite are type of wood, length, thicknes, width. The curvature is dependent also on the distance and rotation of axis of clamping points. According to the visit to factories that work with wooden components it is possible to introduce complex curvature to the model.
top view bending top view torsion + bending
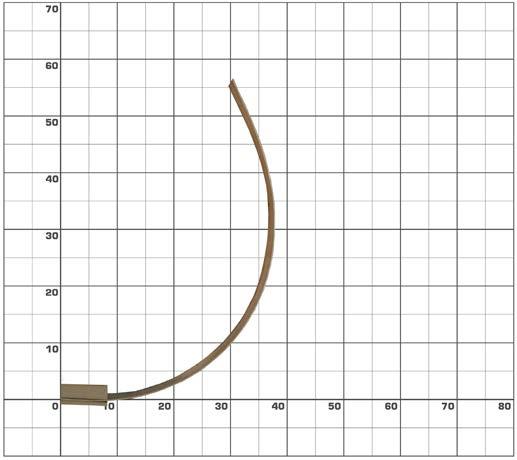
thickness: mm, width: 0 mm, length: 800 mm
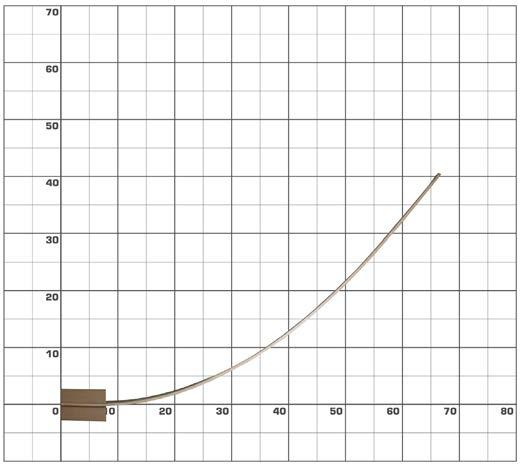
thickness: 4 mm, width: 0 mm, length: 800 mm
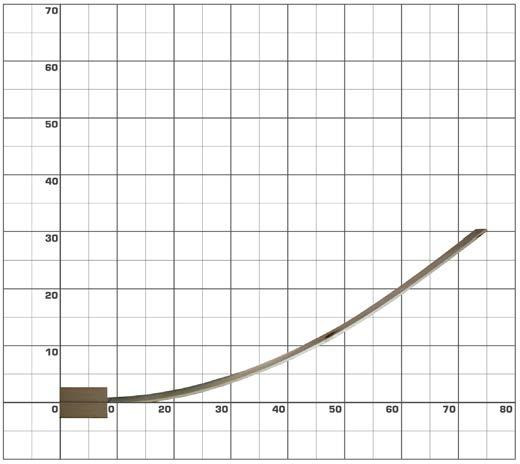
thickness: 4 mm, width: 40 mm, length: 800 mm
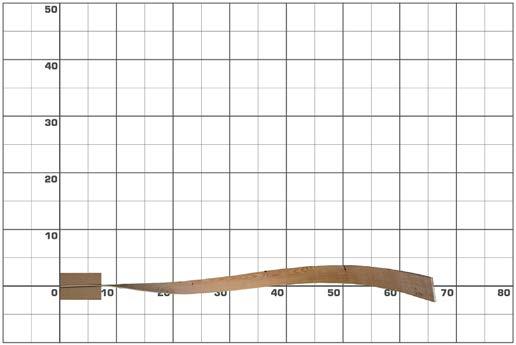
side view torsion + bending
Form-finding Experiments I
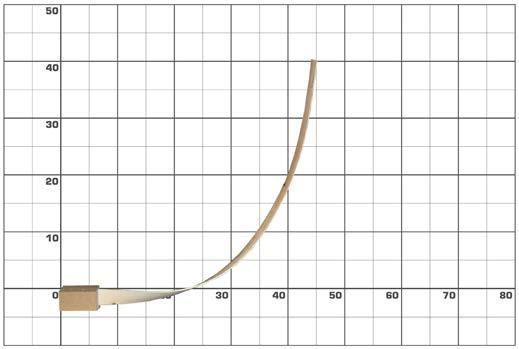

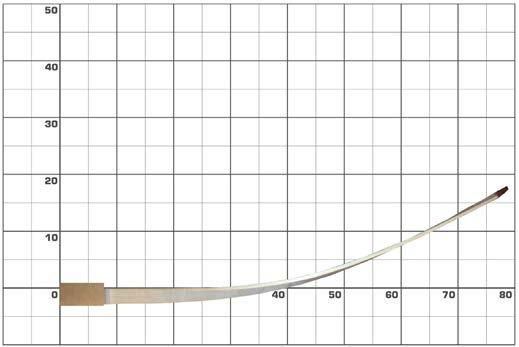
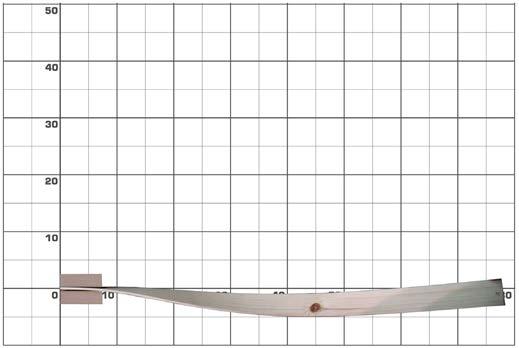
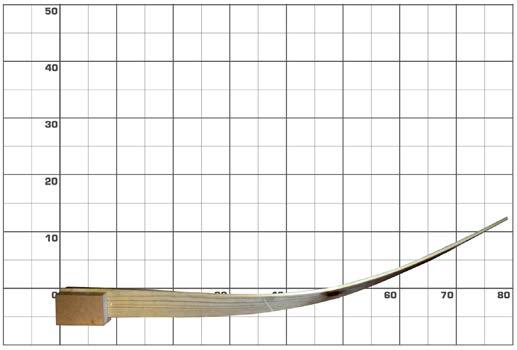
Form-finding experiments with wooden stripes of pine. The experiment was made with material of these size:
thickness: mm, 4 mm
width: 0 mm, 40 mm
The conclusion is that it is possible to achieve severe curvature with thinner material. There has to be take into acconut also the loss of material for milling and assembling and glueing time. These parameters were explored in consequent studies of laminated form-finding.
C [0,4]
C2 [9,4]
C5 [2,] 45° 90° 5°
C [6,7.5]
C4 6,0]
A - min. path
B - optimal path
C - max. path
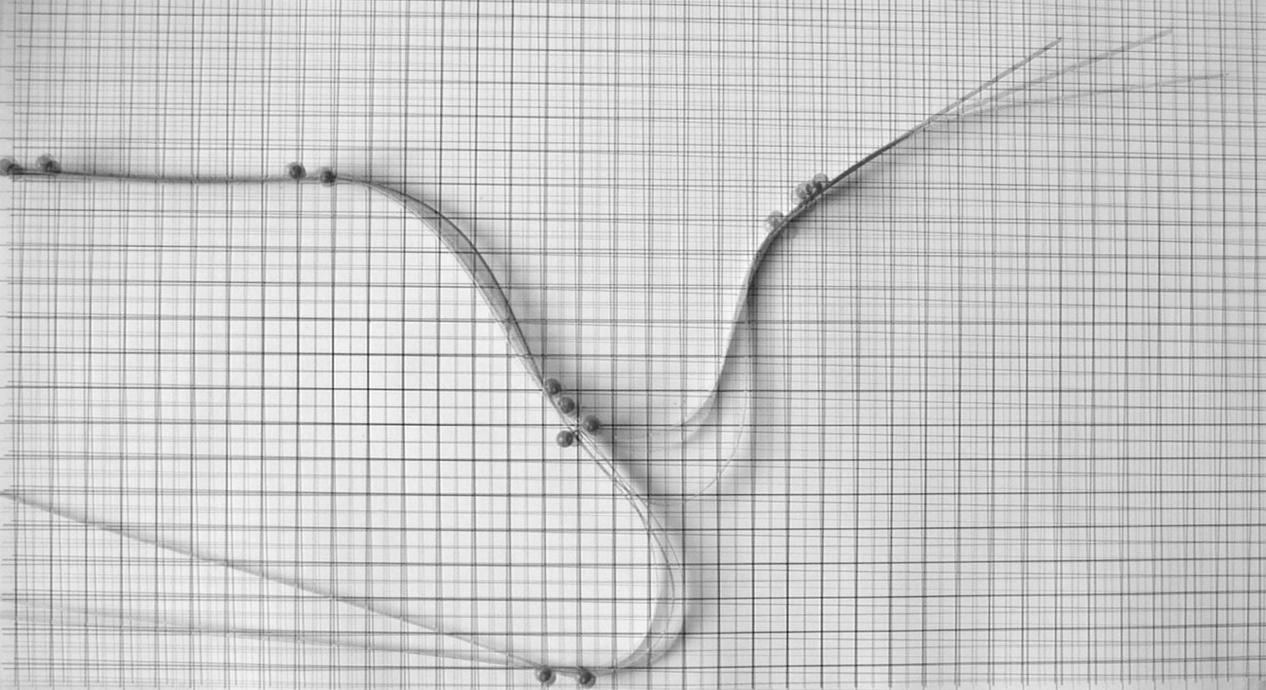
0 Composite image of the experiment.
02 - TLength 456

A: Minimal path for a strip of veneer.

C: Maximal path for a strip of veneer.
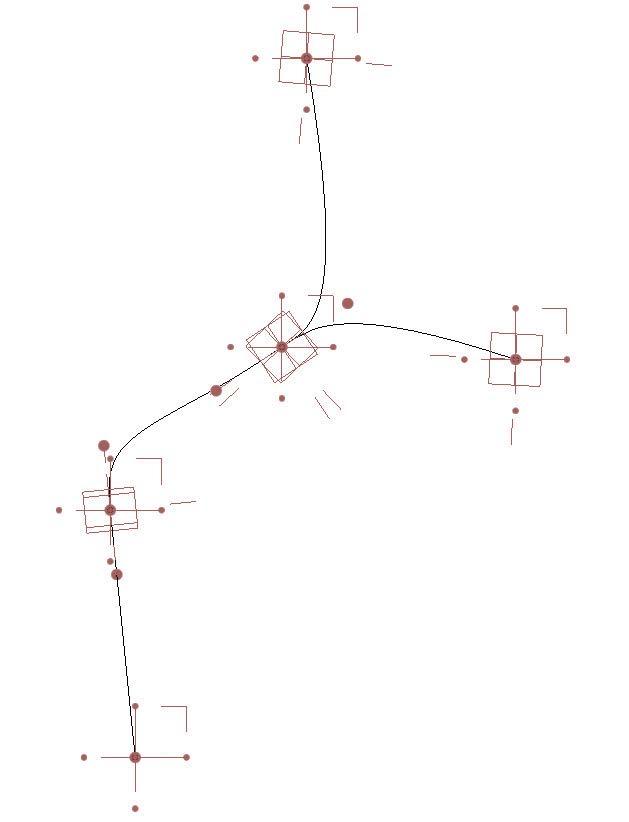

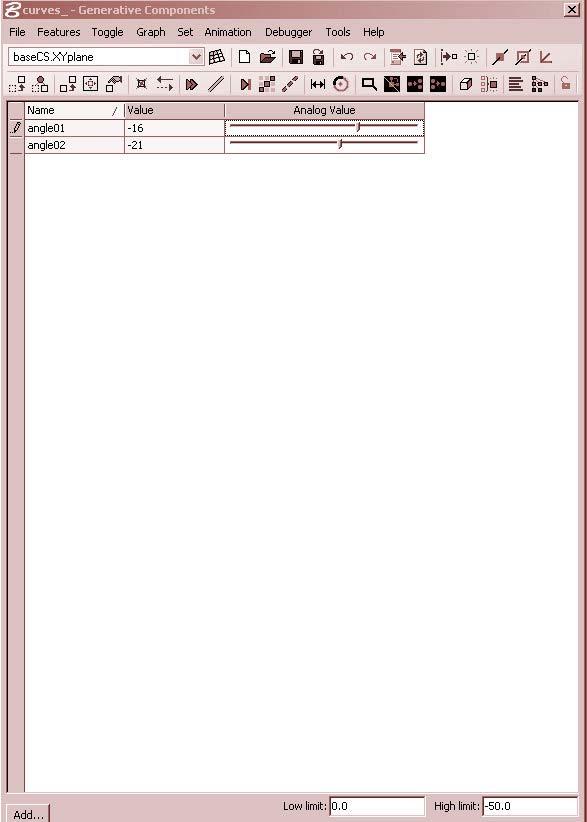
02. Control of BSplines, degree 0. Change of geometry by changing parameters - rotation of tangents. 04. Parameters of tangents controlling BSpline Curves.
The digital experiments started with the translation of informtion from physical model to the digital environment. The simple 2D curves were used to understand this logic.
Experiment examined two stripes of veneer (of length 50 and 456 mm) that were clamped between 5 points. Figure O shows the set-up of this experiment: angles of 45°, 90°, and 5°. There were studied three modes of the bent stripe: minimal path, maximal path and optimal path in which the stripe self-organise itself according to the given geometry. Optimal path is a state where one edge of the stripe (fig. 0, C [0,4]) is fixed to the position and the other end is left without any fixation.
Digital form-finding was done in parametric model in GC. Curves were controlled by rotation of tangency points. Points were on the X-axis of a coordinate system that aimed to the next clamping point. The angle of rotation was observed from the physical model and then limits of angle were set (fig 04).
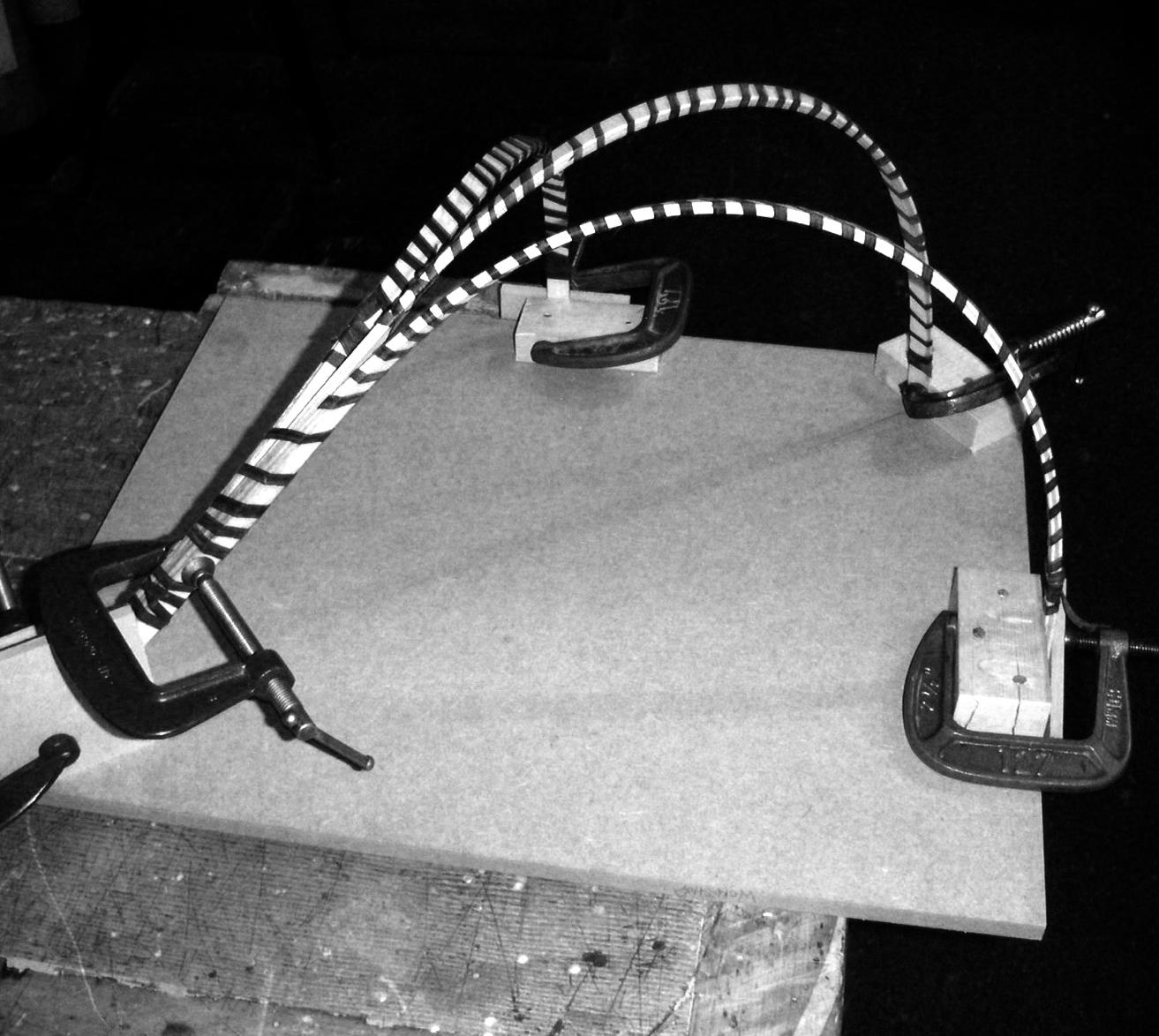
The aim of described experiments was to test the possibility to glue wooden stripes and later test them. The features of natural composite were observed - flexibility and also shape memory after hardening the glue.
The important issue was to solve branching nodes and alternatives for curved laminated planks. All described experiments xamine form-finding with four given points in space and given parameters. There is internal force that cause the form - it is a property of the material - natural anisotropic material. The form-finding process involves curvature continuity of geometry.
Curvature of stripes is formed according to certain parameters:
position of points - distance between each other position of branching point
length of wooden stripes
thickness of wooden stripes number of wooden layers

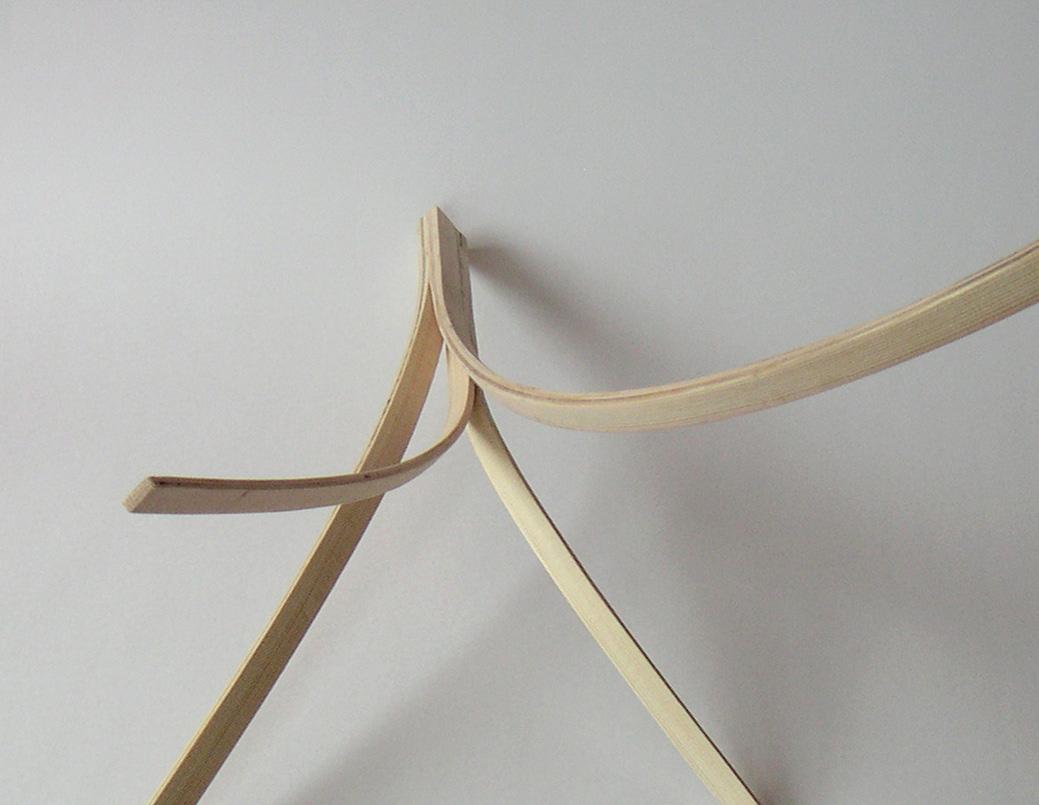
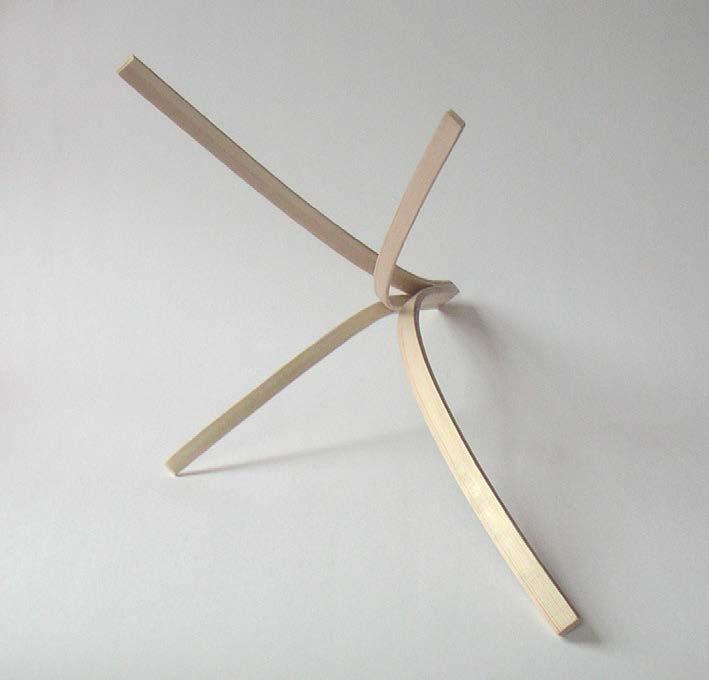
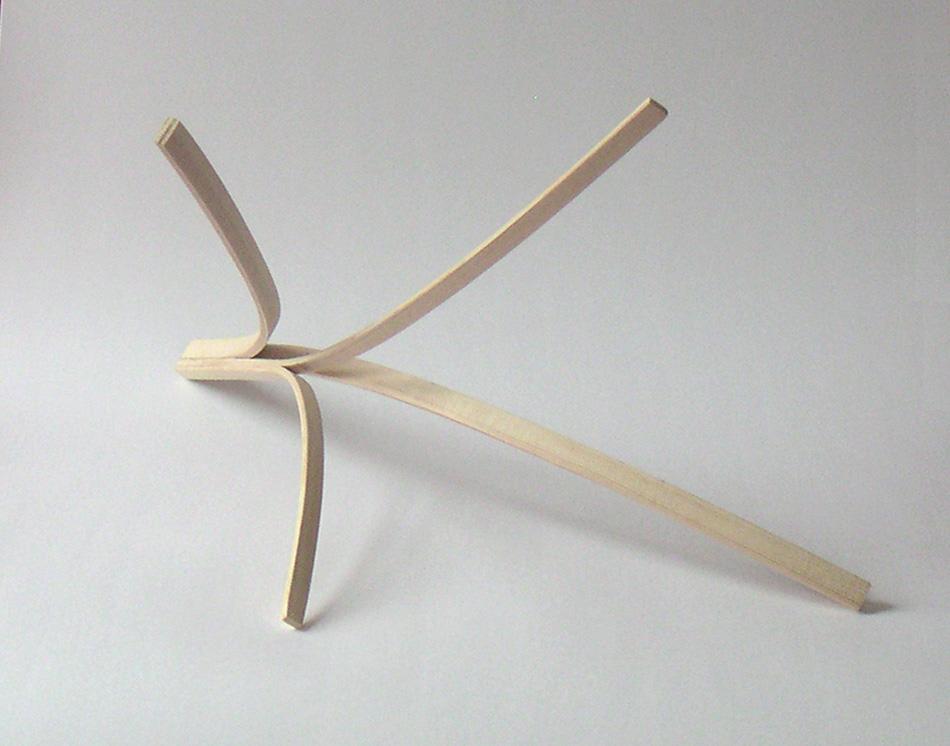
4 layers of russian redwood thickness: .5 mm width: 5 mm
The layers are bent in two directions - curves follow a plane. 4 layers of Russian redwood are used to produce this geometry. The possibility for sending and treatment after laminating are broader because of easily approachable machinery.
The branching node is glued from two parts and there is a higher probability that this glued joint fails. The other disadvantage is gluing two pieces together - it is suitable only in assembly of 90° without additional material.
The ability to retain its shape after lamination is higher then in D lamination.

0a.
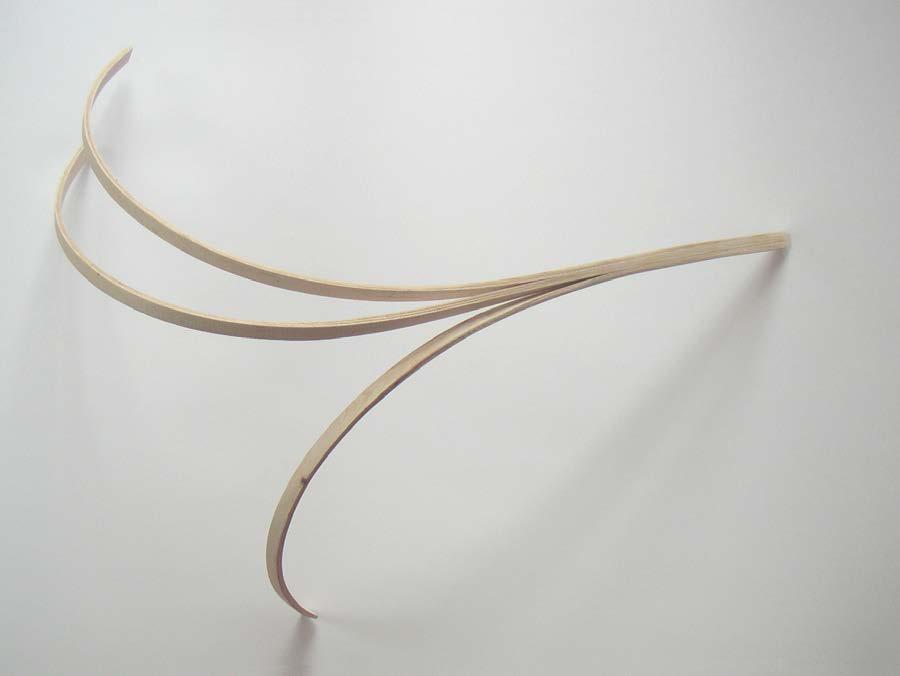
0b.
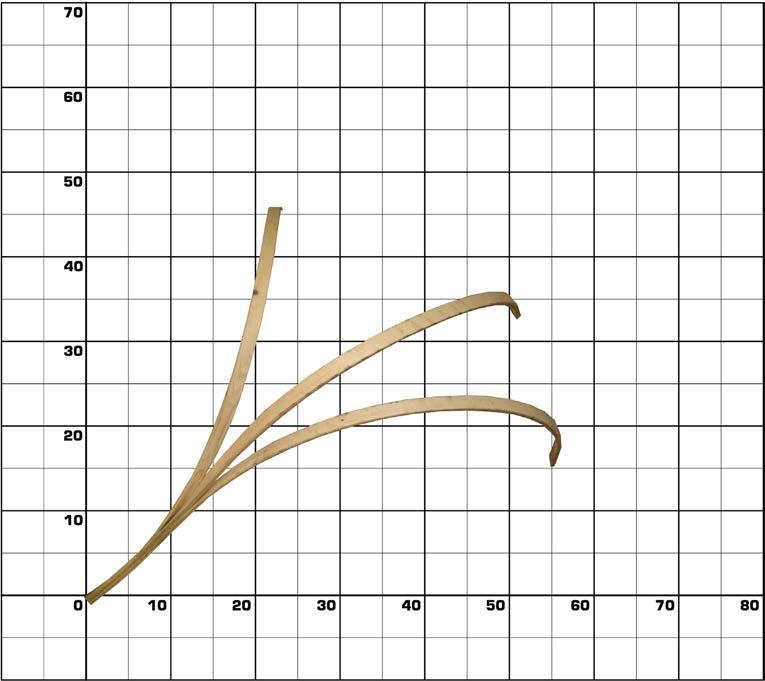
02.
layers of pine (bad quality wood) thickness: .5 mm width: 5 mm
The layers are bent in three directions and therefore there is also twisting introduced into the geometry. Branching node of three branches is not in the same position (fig. 0c). This was solved in the digital model by writing an IF statement in the script generated the BSplines geometry. This statement takes into account the distances between end points of curves branched out from the node. The process is very similar to that explored in the form-finding with woollen threads dipped into a liquid where a branching node emerged in dependance on the distance between points on planes.
The ability to retain its shape after lamination is poor. The central branch relocate itself and tends to get closer to side branch. Figure 0c shows detail images of the lamination. There is also visible delamination that happened when the structure was loaded.

0c.

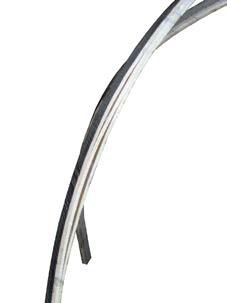
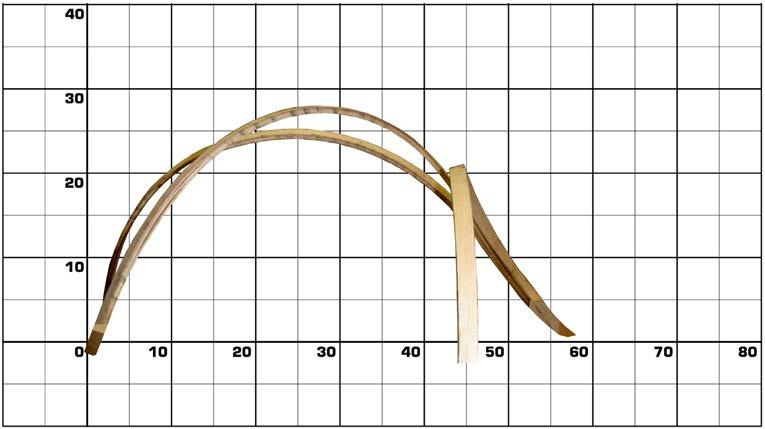
0.

0a. Curvature and twisting of branches - most significant is the middle branch which is twisted by 90°.
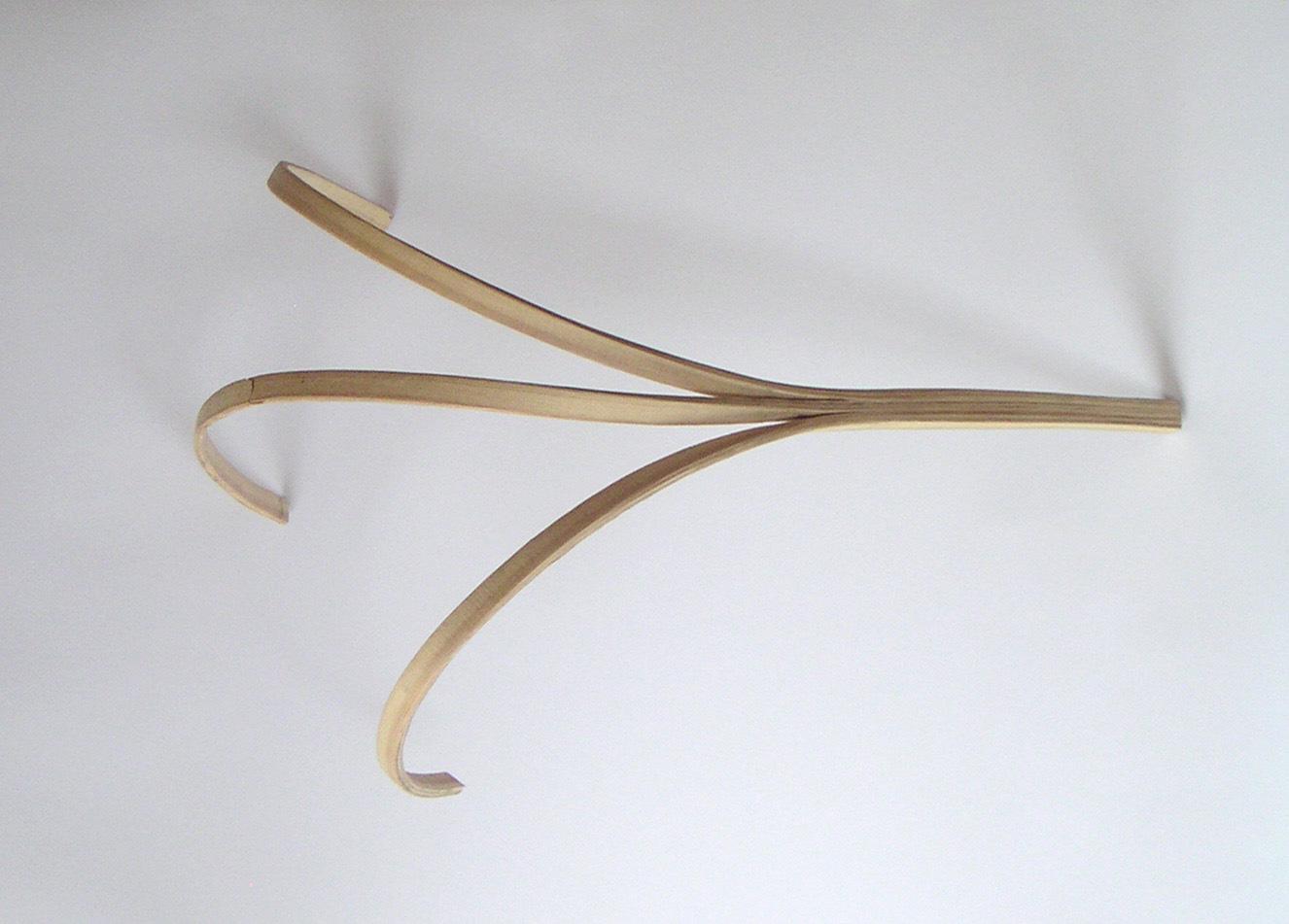
0b. Curvature and twisting of branches.

02a. Top view: geometry of a node (cm).
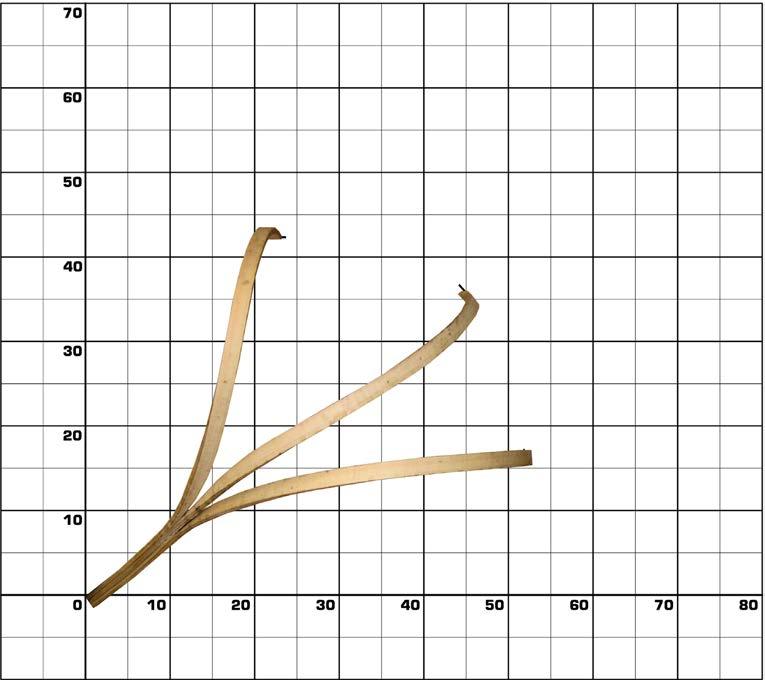
02b. Top view: geometry of a node (cm).
5 layers of russian redwood thickness: .5 mm width: 5 mm
The Eperiment 0C is different from the previous one in the bigger number of layers.
Legend:
black points - fixation points red points - actual points after lamination blue points - maximum value of Z coordinates, branching nodes
Parameters:
p - length between branching point and base point A
l - length of stripes
t - thickness of a branch (stripes have constant thickness t=k*n, n- number of layers)
h - height of the highest point of branches
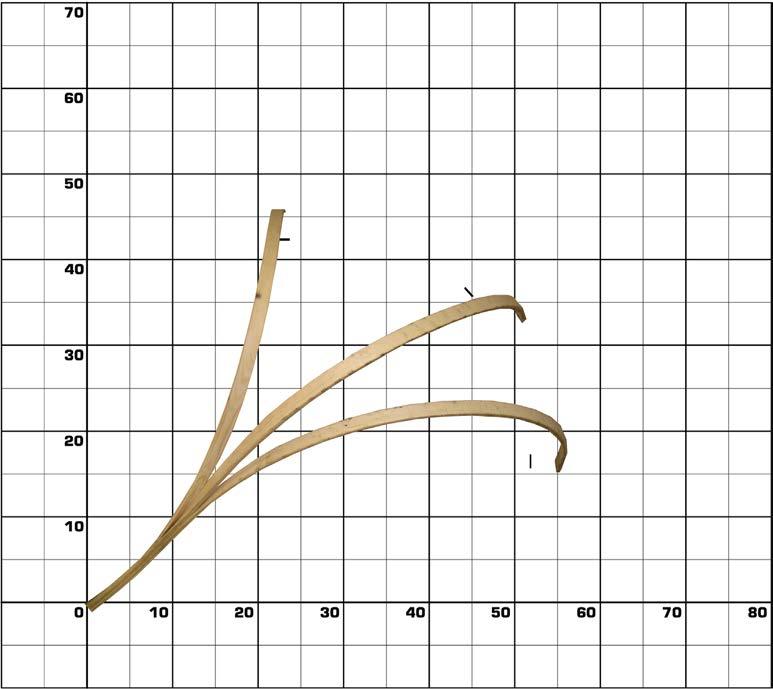
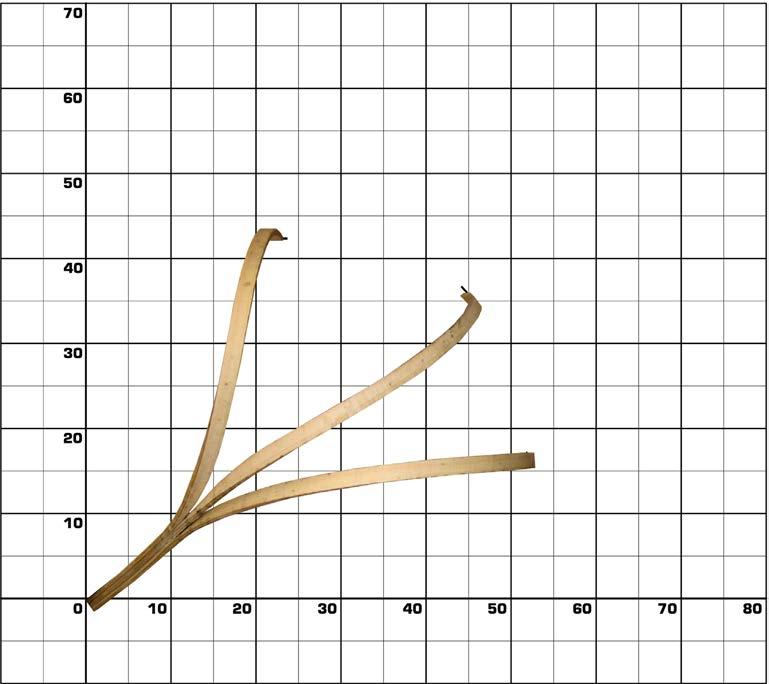
layers of pine (bad quality wood)
thickness: .5 mm
width: 5 mm
black points - fixation points red points - actual points after lamination blue points - maximum value of Z coordinates
p= 70 mm
p2= 20 mm
h= 200 mm
h2= 220 mm
h= 70 mm
l= 785 mm
l2= 790 mm
l= 670 mm
5 layers of russian redwood
thickness: .5 mm
width: 5 mm
black points - fixation points red points - actual points after lamination blue points - maximum value of Z coordinates, branching nodes
p= 90 mm
p2= 90 mm
h= 250 mm
h2= 25 mm
h= 224 mm
l= 770 mm
l2= 780 mm
l= 75 mm
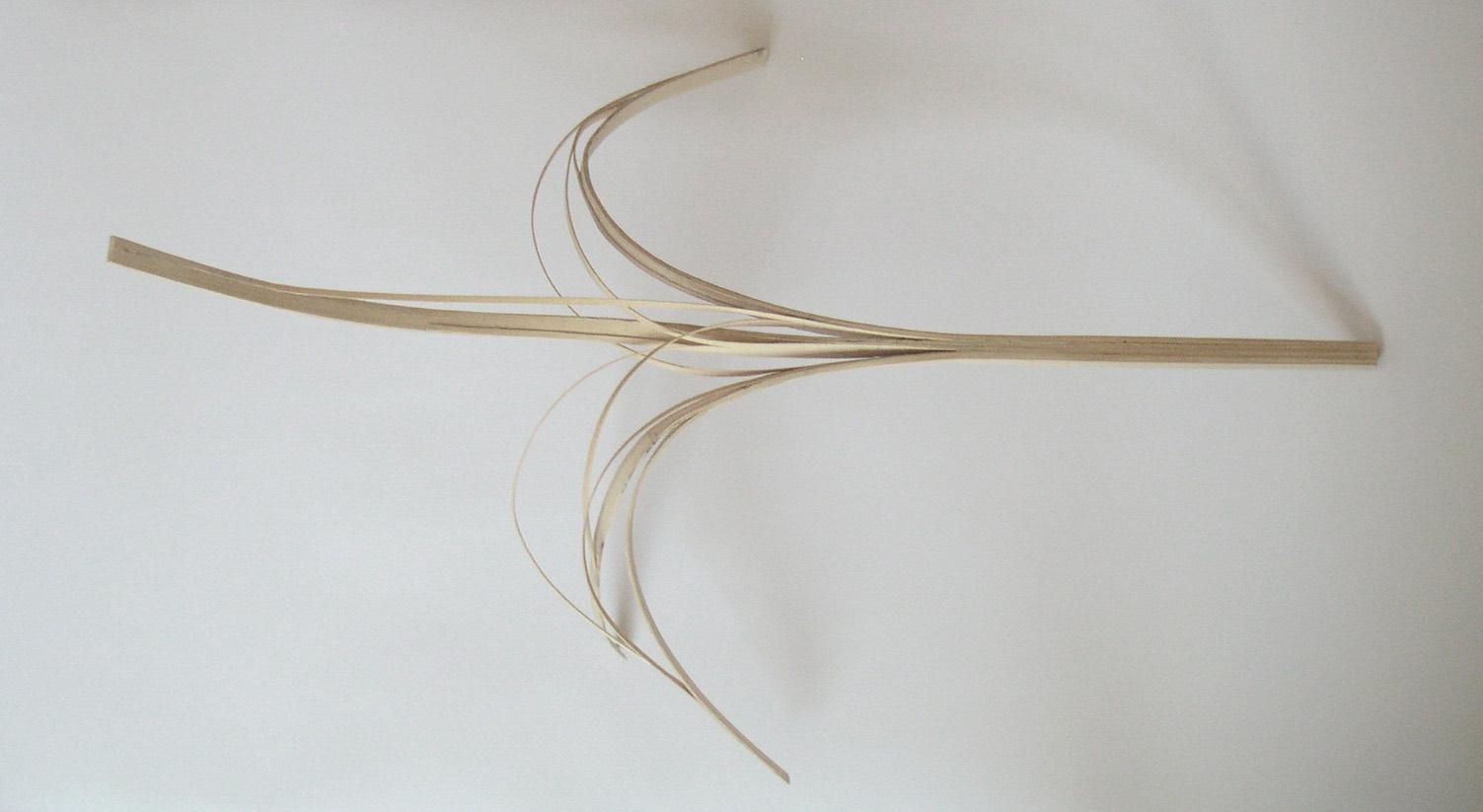
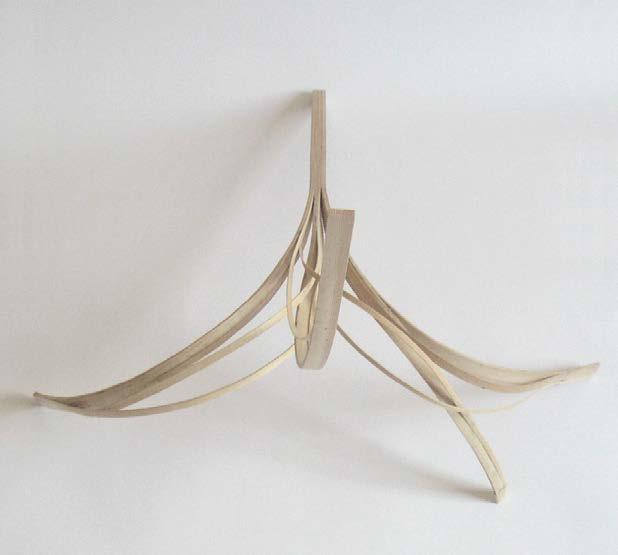
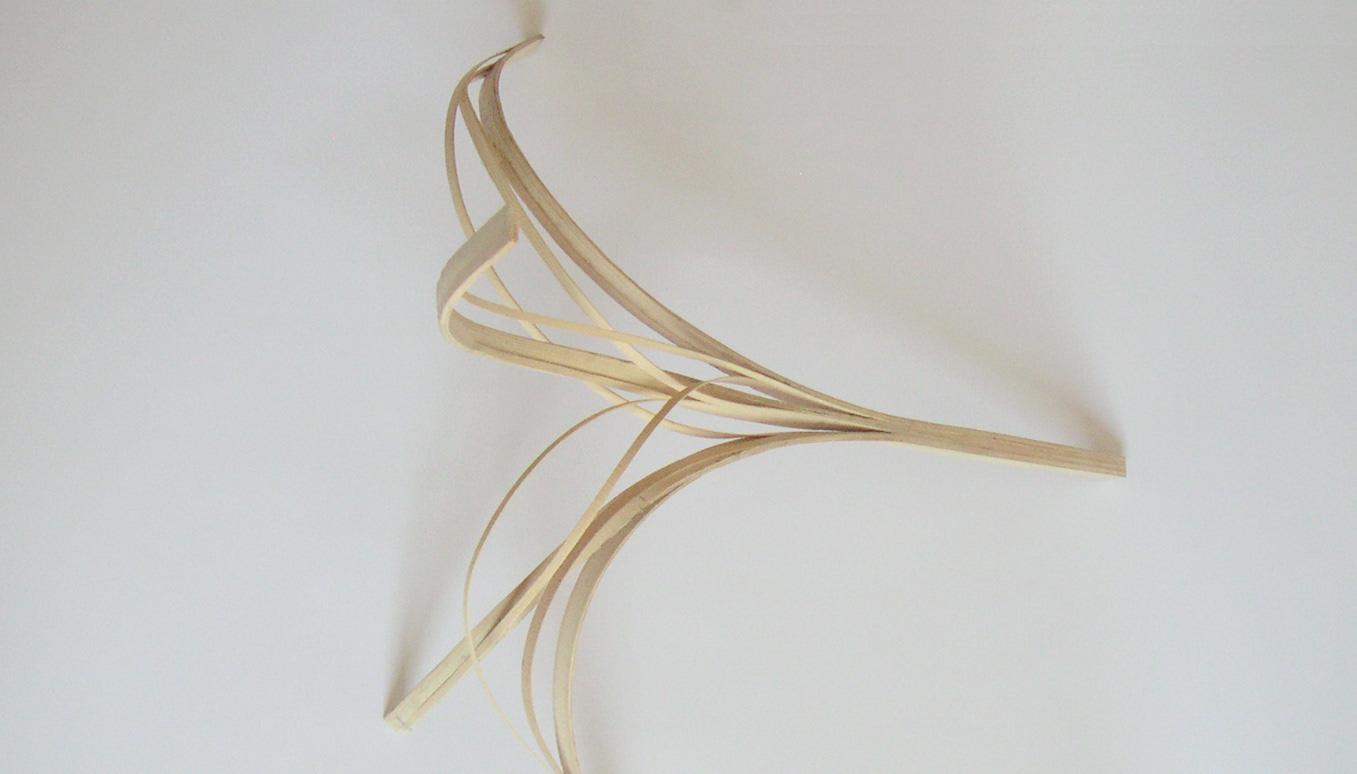
layers of russian redwood that go in the full distance of a branch
thickness: .5 mm
width: 5 mm
There are splits of an outer layer and these stripes go from this point (located arbitrarily on branches) to other branches. For the geometry analysis is important that these stripes follow curvature of full laminated layers.
This model was made as a result of the negotiation of all involved stripes in branch. This model also proved that there is a similarity in logic of nesting woollen threads. A thread with bigger thickness determine the shape and direction of a system.
Bundling of splitt stripes and layered main branches caused that shape was more stable than simple branched pattern. The logic of this geometry should follow the self-organised pattern of bridges that occur in the model of threads dipped into latex.
This claim will be also proofed by testing this node by different loads.
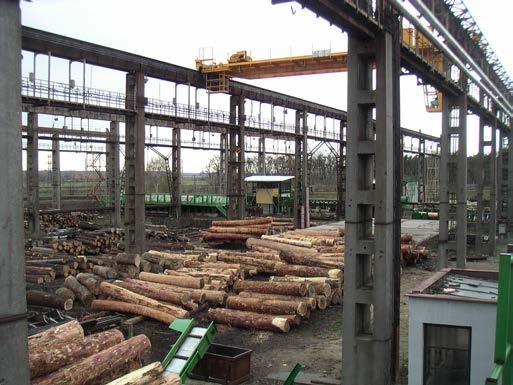
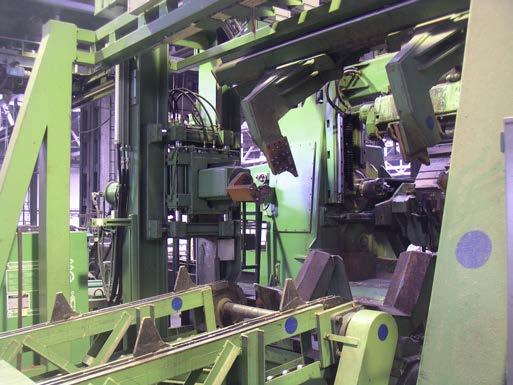
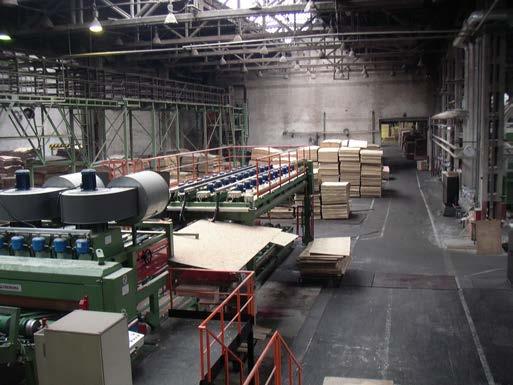
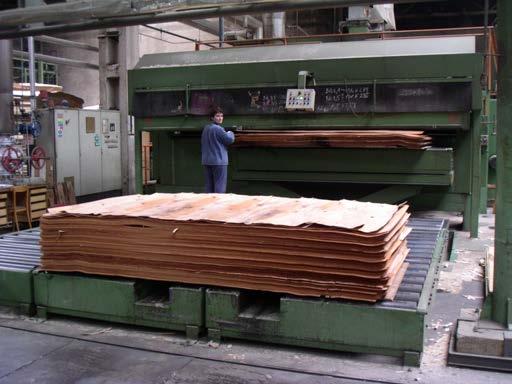

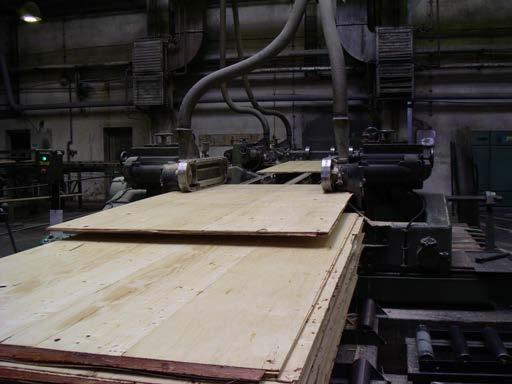
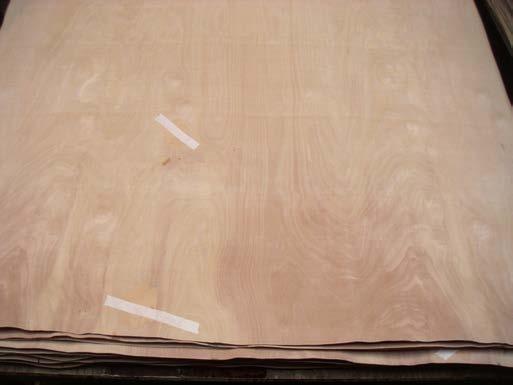

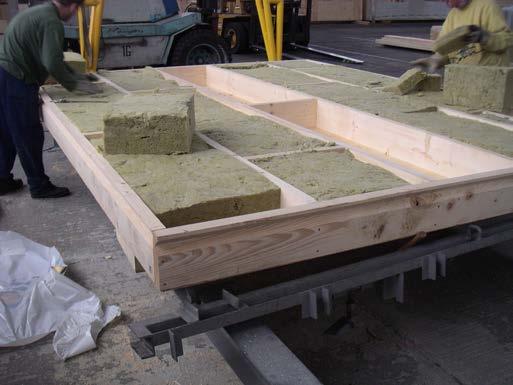
Ploma, Hodonin
Wooden industry degraded wood into a mass production because there was a strong idea that wooden composites would be replaced by synthetic materials. These automated procedures does not require any additional thinking about fabrication of components like CNC. But it leads to simple wooden components that later limits its use in building industry. Final products are then boards made of plywood that very often does not respect important feature of natural product - anisotropy.
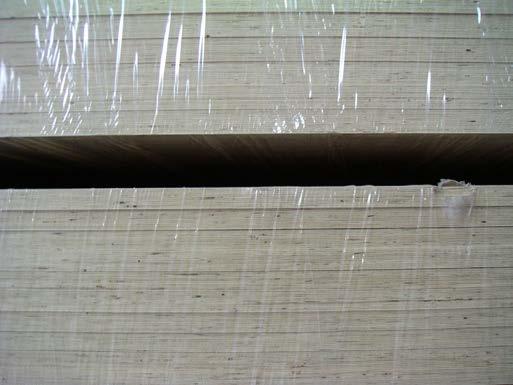

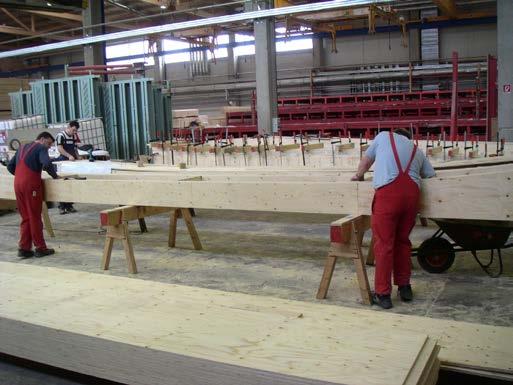
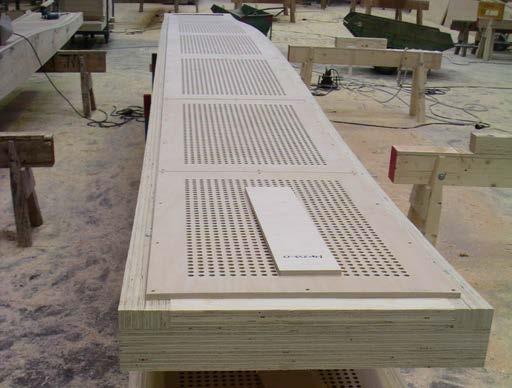

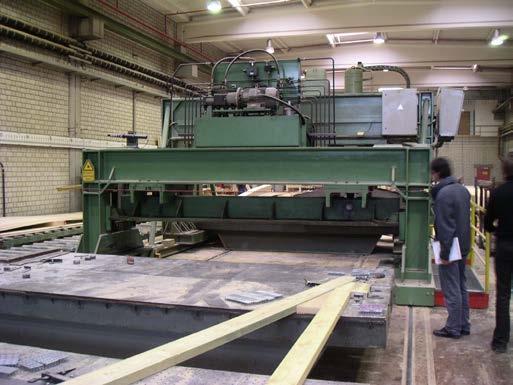
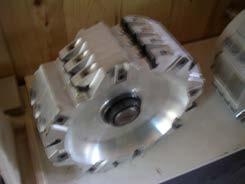
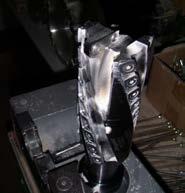
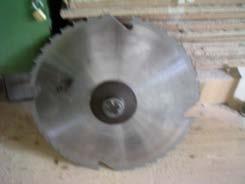
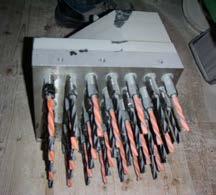
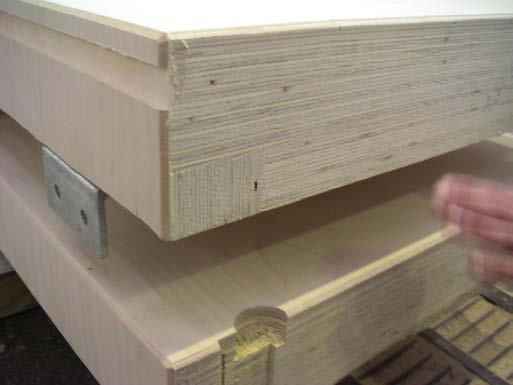
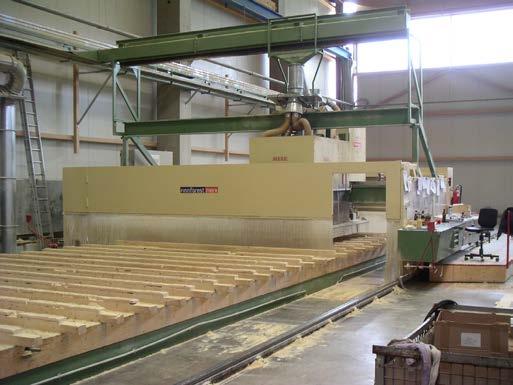
FinnforestMerk, Aichach
The post-fabrication of wooden products - plywood. The plywood are in two categories - 90°angle and parallel grain. These products are delivered from a similar factory like described in previous analysis but this time from Finland. The analysed fabrication is from company FinnforestMerk.
The company creates components that are used for special architectural application. Fig. 0, 02, 04, 05, 06 show procedures of manufacturing of ceiling and wall components for a theatre to Russia that have to fulfil acoustic and aesthetic requirements of the interior of the auditorium.
Plywood board are treated in a state of flat sheets and boards. Than they are glued and screwed together in order to achieve curved components of single curvature. There are at least two interesting robotic units that can CNC cut and mill wooden components. All the assembly are made by hands.
There is a machinery available to create a flat components in size of one storey walls - fig. 09. There is also a procedure for gluing together timber boards.
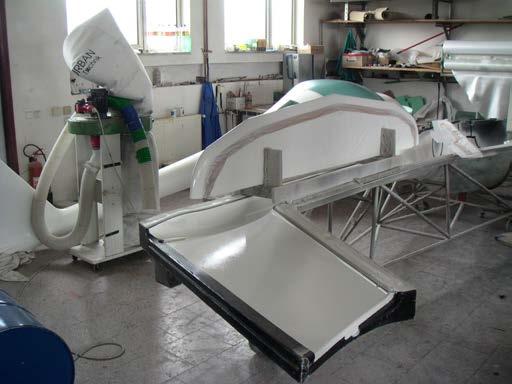
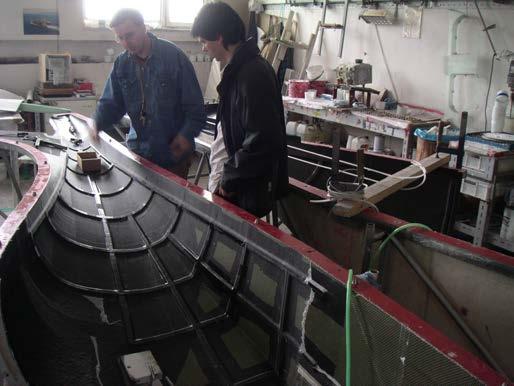
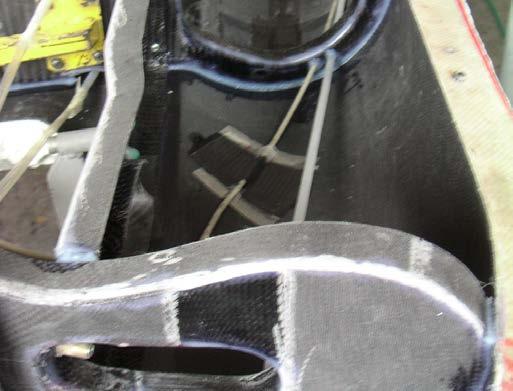
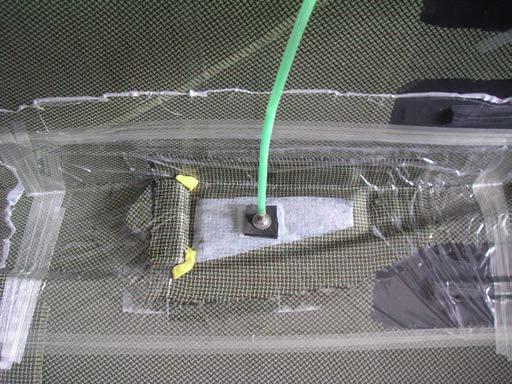
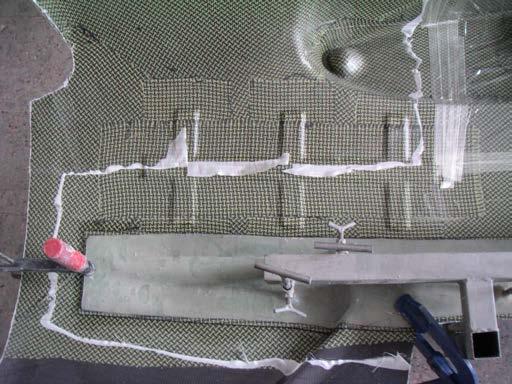

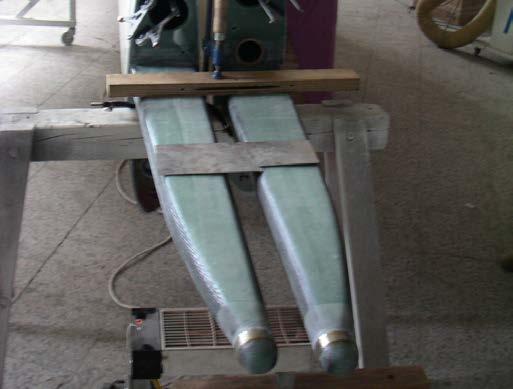
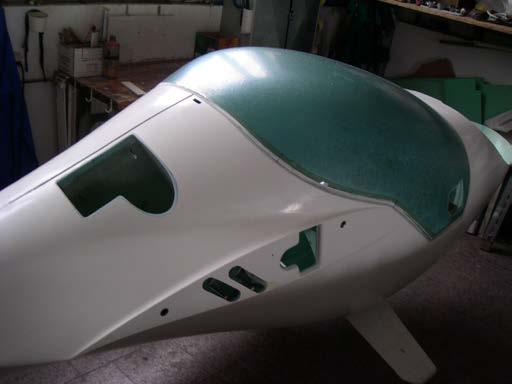
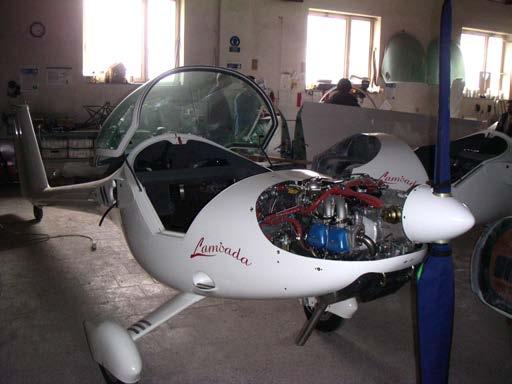
Composite aircraft from synthetic materials follow similar rules as aircraft made form wooden components. The analysed aircraft are designed by structural and mechanical engineers who use FEM (Nastran) to analyse the aircraft and locate parts with high strain. Composite aircraft is made by a company which create wings and fuselage on its own and incorporate engine and glass lid of a cabin only.
The procedure of the aircraft making is shown on pictures. Dimensions and weight are constrained by requirements and transport. That is why wings are always constructed for better dismounting and making-up on an airport.
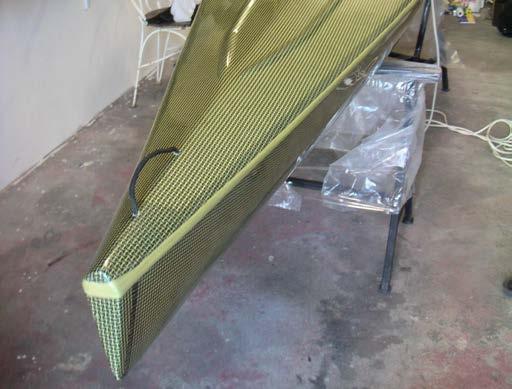
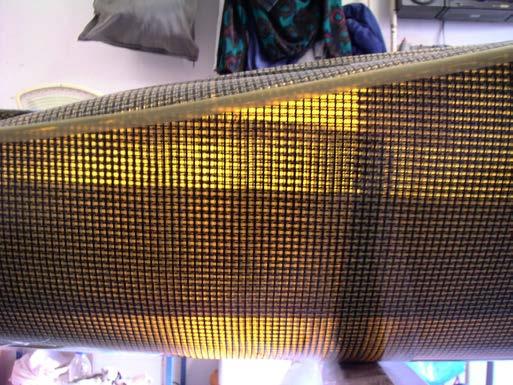
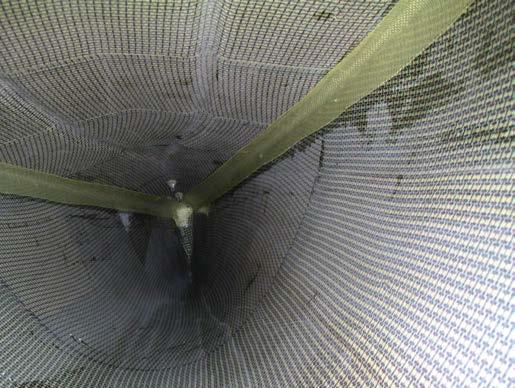
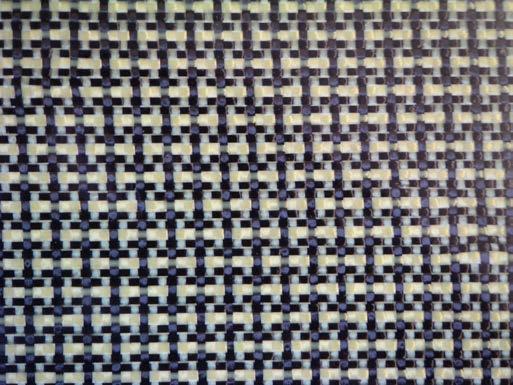
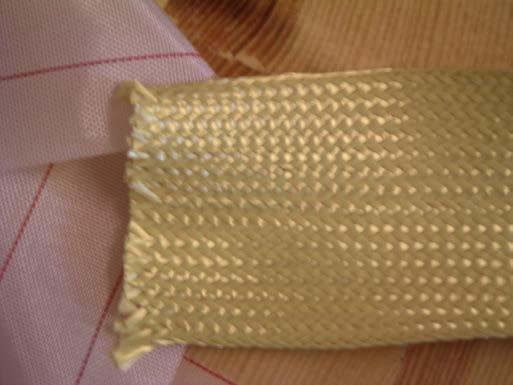
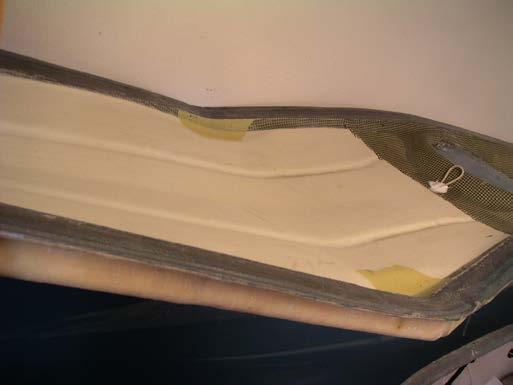

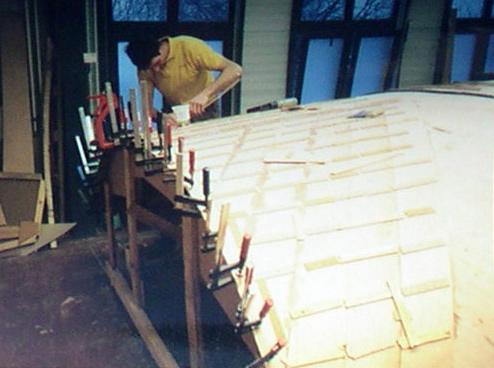

Bohemia Yacht, Hluboka nad Vltavou
There are requirements for individual boat production because forms change every year and they could be changed even three times a year. Hand manufacturing is nowadays the most suitable and cheapest solution on a demand from racing teams.
The hull of racing kayaks are monocoque structure and consists of two parts - top and a “belly”. The final assembly is similar to an aircraft technique but requires more fine work. The skin in general consists of several layers (usually up to 6) of fabric that is separated by additional foam divisions. The foam divisions cause higher profile and therefore better structural performance. This approach follows the successful technique used in Mosquito bomber which was made of wood.
Fabrication of replicas of wooden yachts and repairing of wooden yachts consists of layering of plywood and veneer in an angle of 45°. These layers could be permanently fixed to wooden ribs of the hull or could remain without ribs as a pure monocoque structure. This structure then requires further stiffening partitions.
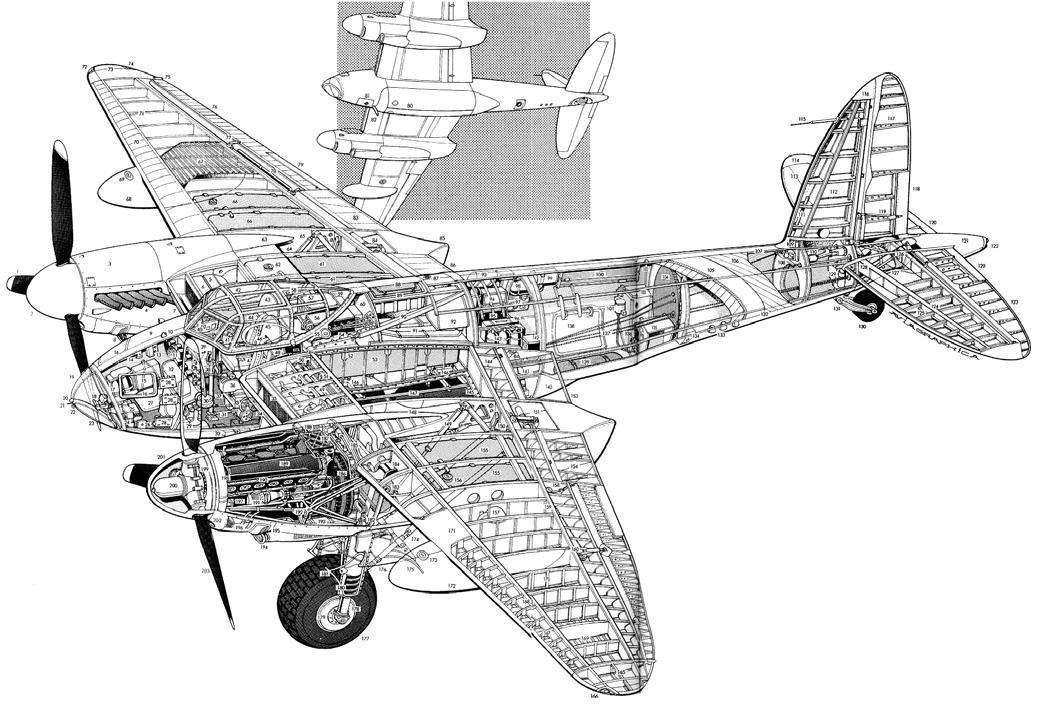

fig 02. fig 02. Comparison of forces and moments of the wing. More convenient is a wing that is supported by a rod. But the aircraft pays for worse aerodynamic and additional force into fusselage.
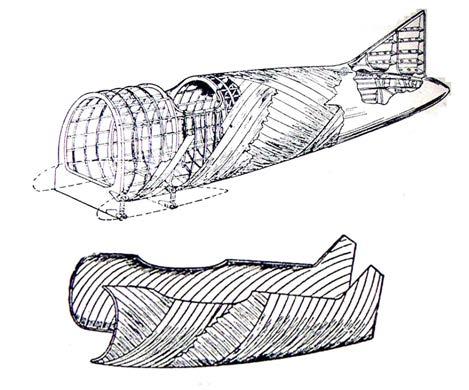
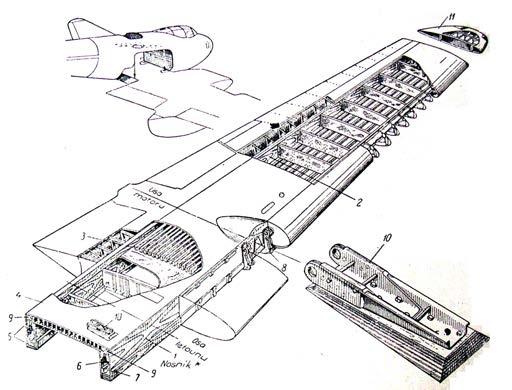
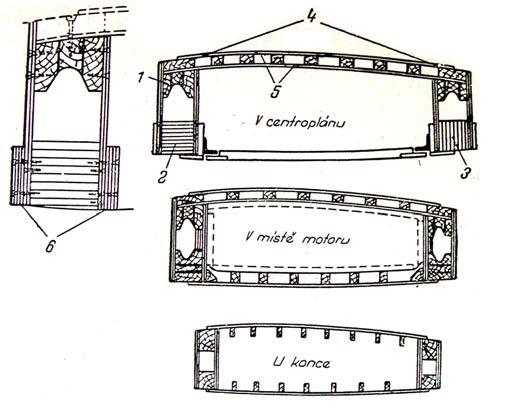
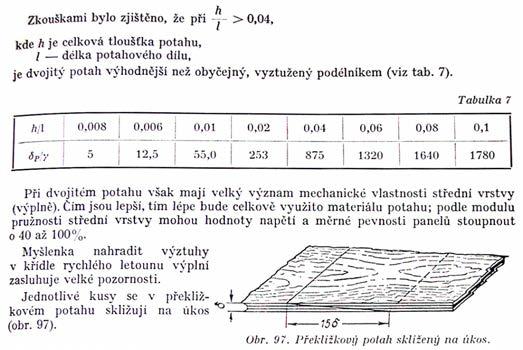
fig 06. Explanation of the equation of the thickness of the board of the wing. Picture shows a veneer connection in a wing board. Czech language is beautiful.
The most succesfull composite aircraft is made of wood. This aircraft combines th euse of moulded plywood with balsa cored macro composite components. The balso wood core was produced by Baltek Corporation company which still supplying balsa cores for the construction of boats, planes and buiůlding components. End grain balsa with its elongated vertical cell structure provides very high compressive stiffness and resistance to crushing. It has a great capacity for handling cyclkic loads and it is possible to obtain very strong skin to core bonds. These panels have the ability to handle excessive dynamic loads with high resistance to fatigue.
Mosquito fusselage is made from two halves that are connected together by steel linking material. An inner skin of a fusselage is applied onto a mould then the other layers are gloued onto it. The shapoe is then carefully lifted off the mould and connected to the other half.
Each part of the aircraft deserves deeper examination. The fusselage and wings construction represented the cutting edge technologies of its age. Nowadays the indusrty is mainly focused on synthetic materials - carbon, kevlar composites. But there is also possibility to taka into account to combine these techniques and create a hybrid structures that gain advantiges from both sides. The example could be very good ratio of wood in bending performance and ability of connection of synthetic fabrics.

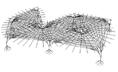

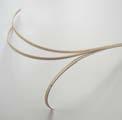
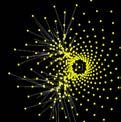
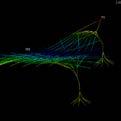
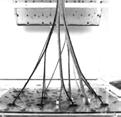
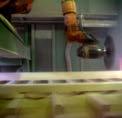
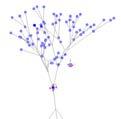
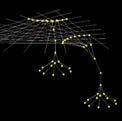
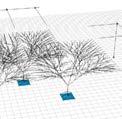
Experiment 0 Experiment 02
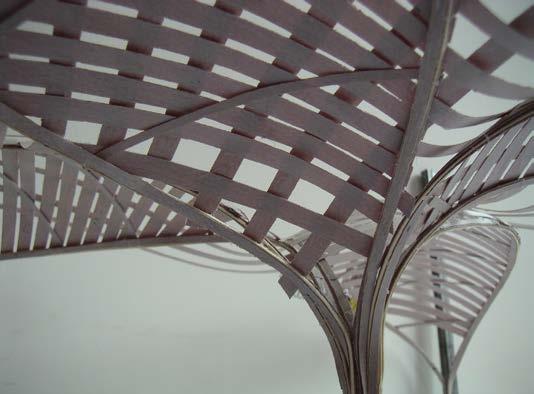
0a. Foto of the model. Surface is predominat in the assembly.

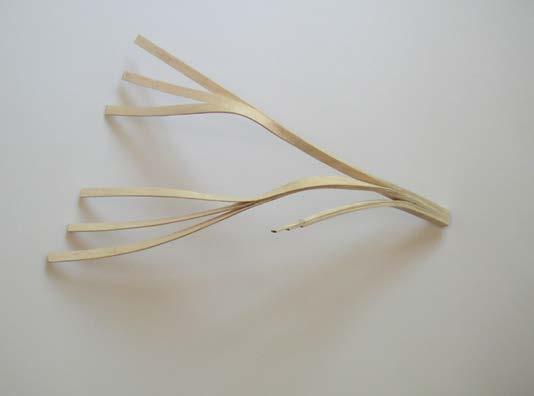
0b. D lamination of branches.
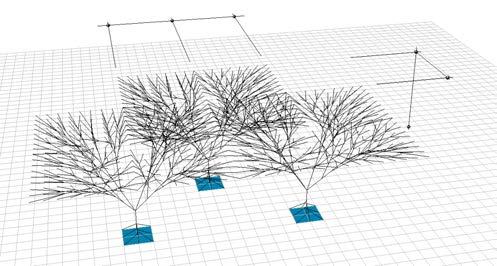
Experiment 0
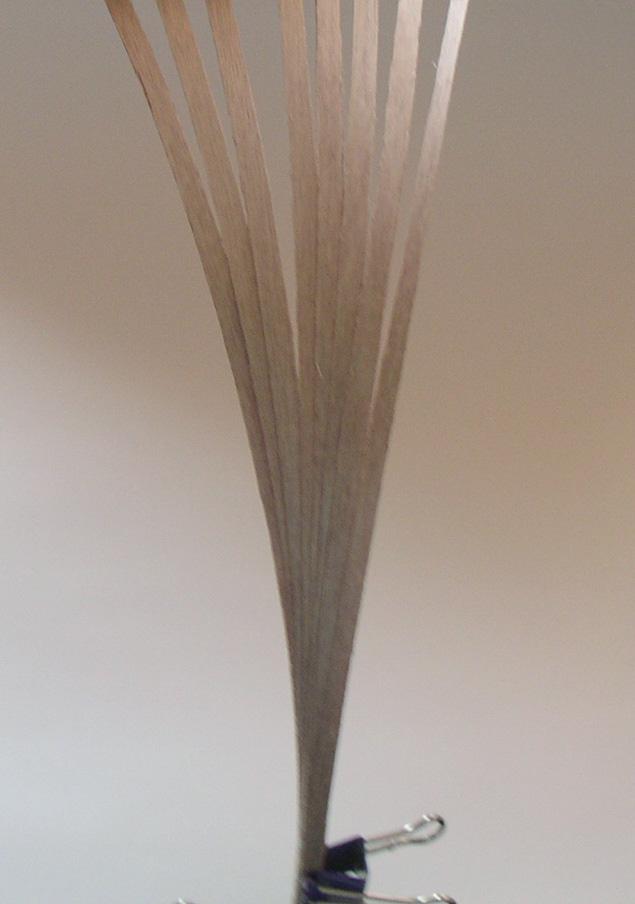
0c. Surface + Supports.
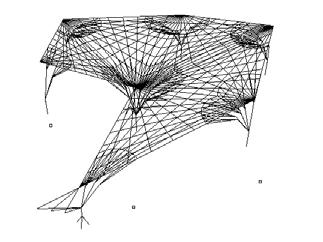
H 02a. Surfaces based on catenary curves from branched supports. 02b. Selfsupporting branches. 02c. Surface + Supports.
0a. Scheme - hybrid structure of arch, beam and shell.
0b. Branches are supporting each other.
0c. Supports are incorporated into the surface.
Methodology
The research in the form that leads to the tectonic articulation had been divided into three strategies that are documented in three experiments. Each experiment has its own setup and procedure which had been documented. All three experiments start with digital form-finding that results in the material system.
The first experiment feature surface that is dominant in the structure. The branched supports and a “shell” compose a hybrid structural scheme - mix of arch, beam and shell (fig. 0a - 0a).
The second experiment deploys the possibility of self-supporting branches. The structural stability is based on a hypothesis that components branched out from different bases could interact and support each other (fig. 0b - 0b).
The experiment 0 represents incorporated branches into a surface that can act both in tension and in compression. This had been seen as the most efficient connection scheme (fig. 0c - 0c).
The branched supports could be incorporated to the surface which span longer distances. By dependance on the distance different hight of the structure is achieved and the structural performance is the same.
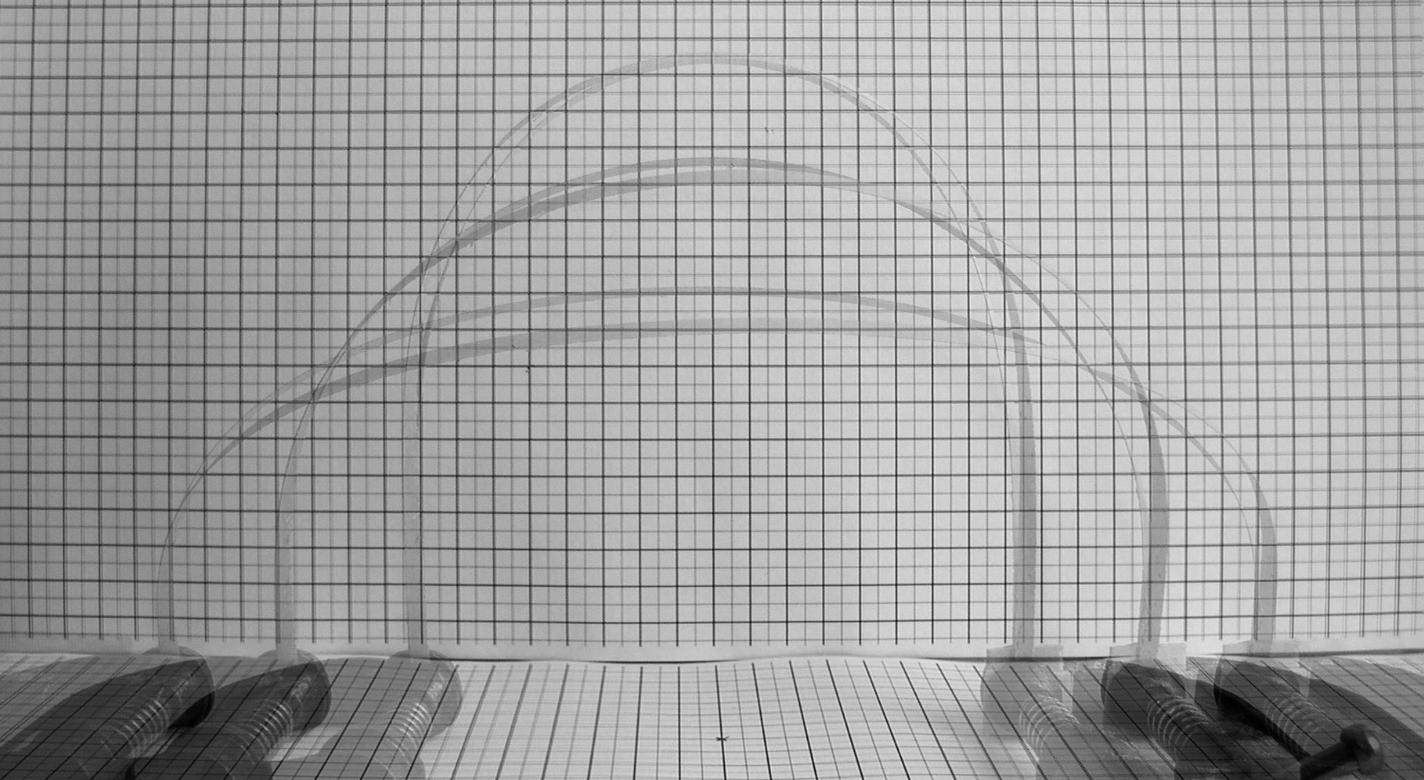
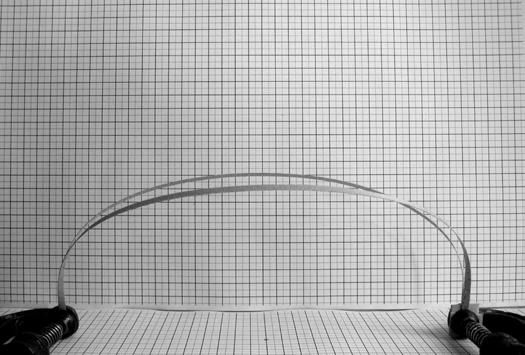
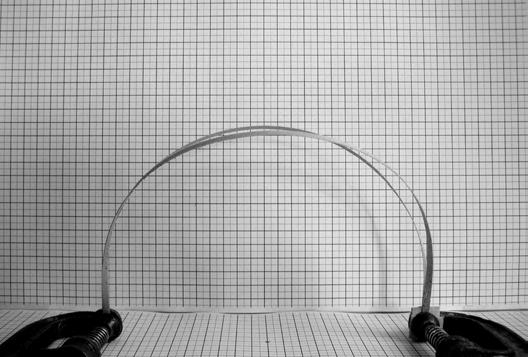
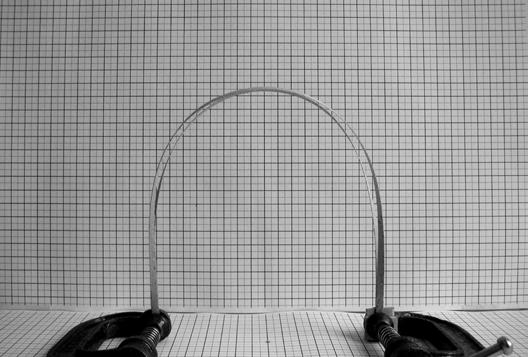
The first experiment started with form-finding of veneer stripe and its behaviour. These experiments document the interest in systems where vector-active system is incorporated into the surface-active system. The model on figure 0 shows heights of the stripe in dependance on the distance between vertical supports. The structure was then compared to the digital model of catenary and chosen geometry that was the closest to the catenoid.
Branched supports featured complex curvature and then they were continuously used as parts of the shell.
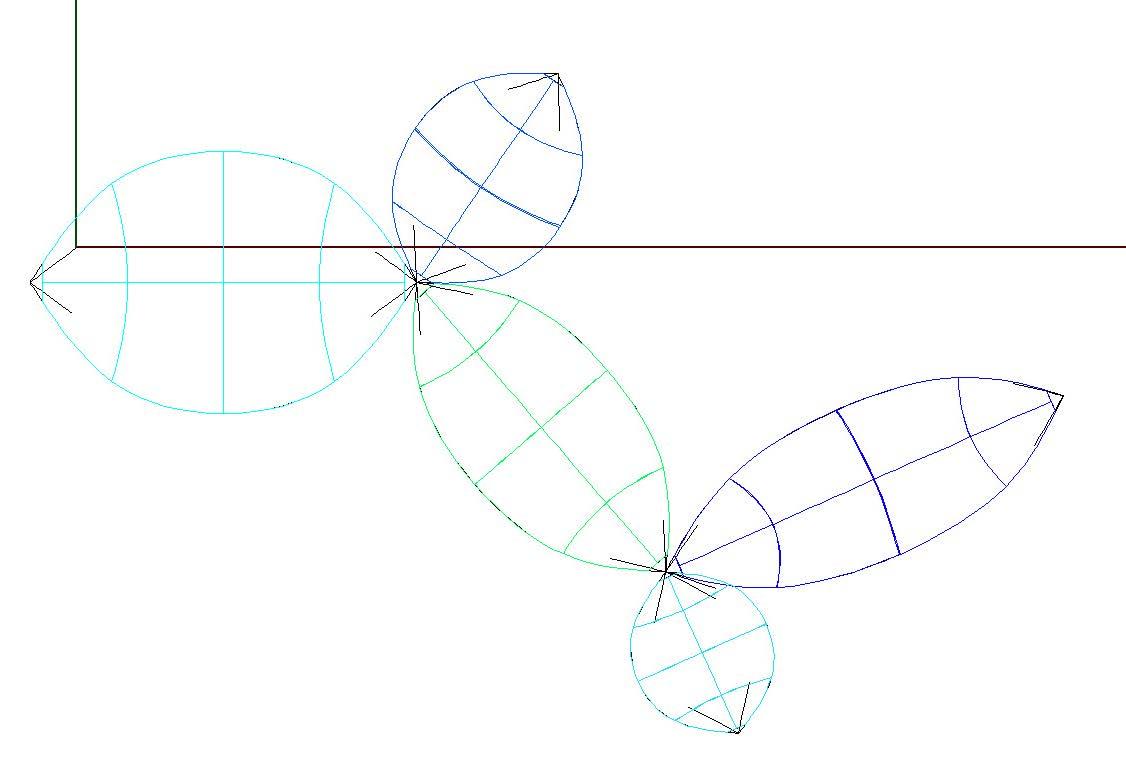
0. Points proliferated on a site by an L-system algorithm. Roof is generated according to these criteria: Top curve as catenary with a length: Distance(point,point2)* , Boundary curves are formfound. catenary curve
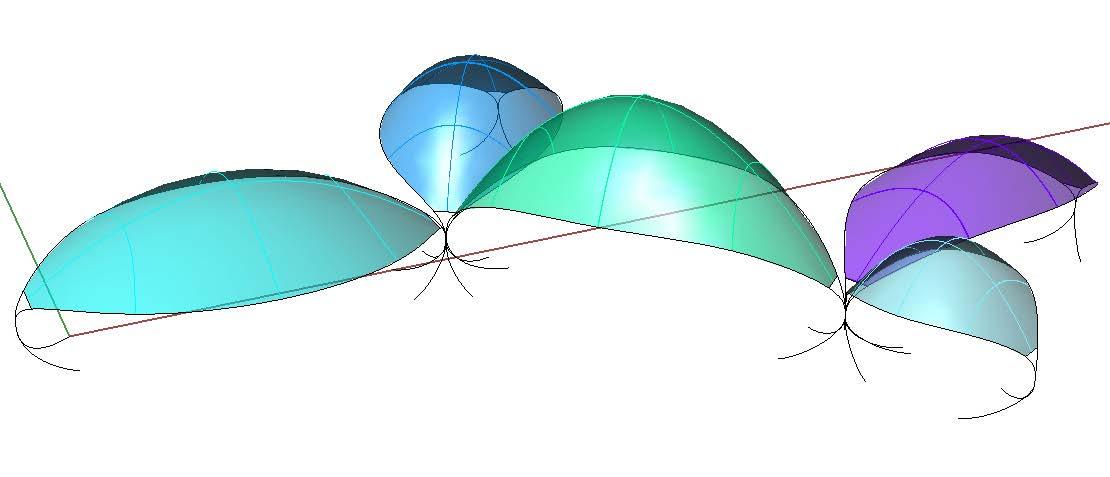

The model of catenaries had been evolved from set of points generated by L-system algorthm. The algorithm was chosen arbitrarily to test the structure and its proliferation. The structure is generated on figure 0, and 02 is based on the catenary model - fig. 0.
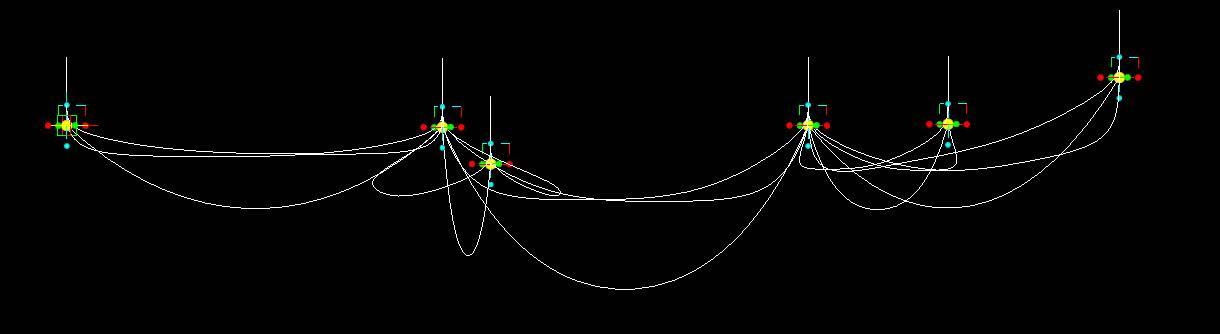
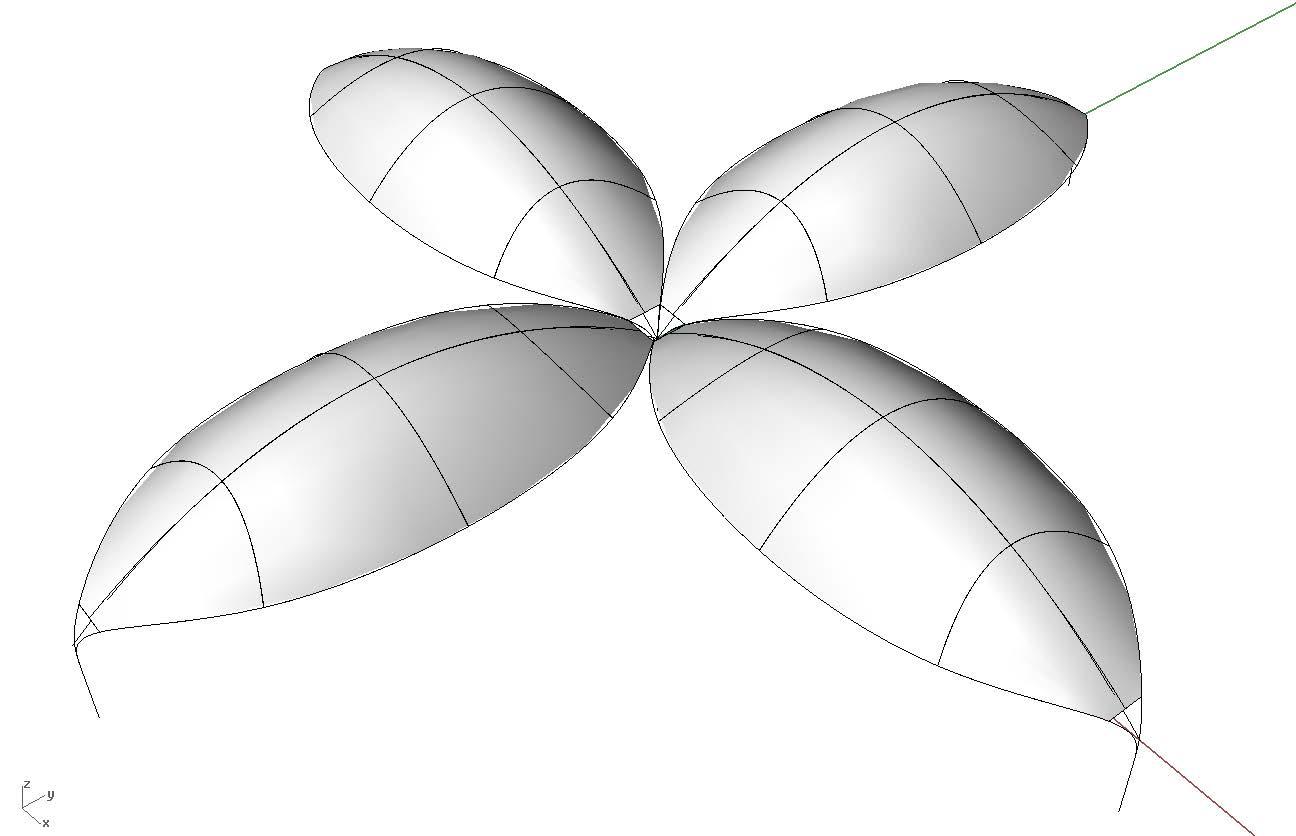
0. Test Model. One part of the system was tested - chenge of length and width under applied load. The test was also focused on the movement and deflection of the central support.
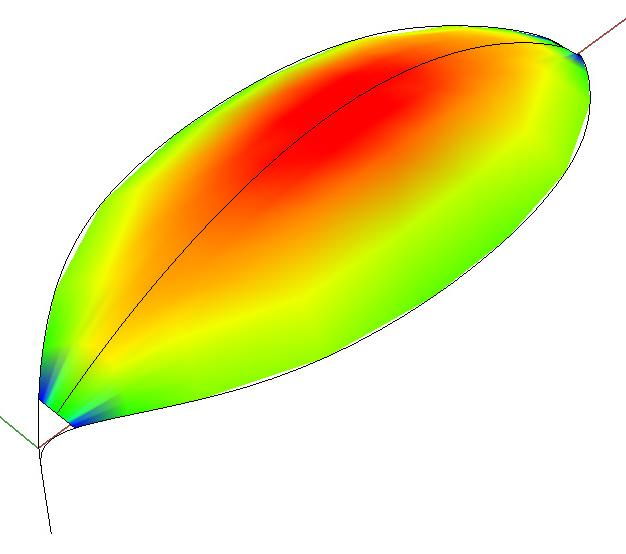
Digital data for the physical test model. Model was prepared for structural test of the branching support (red rectangle on the fig. 0). The boundary supports were fixed in space in order to do not allow any horizontal movement (black dots on fig. 0). Then there were studied deflections and flexibility of the structure.
0. Scheme of the structure.
section by a surface that follows the angle of f-f edge
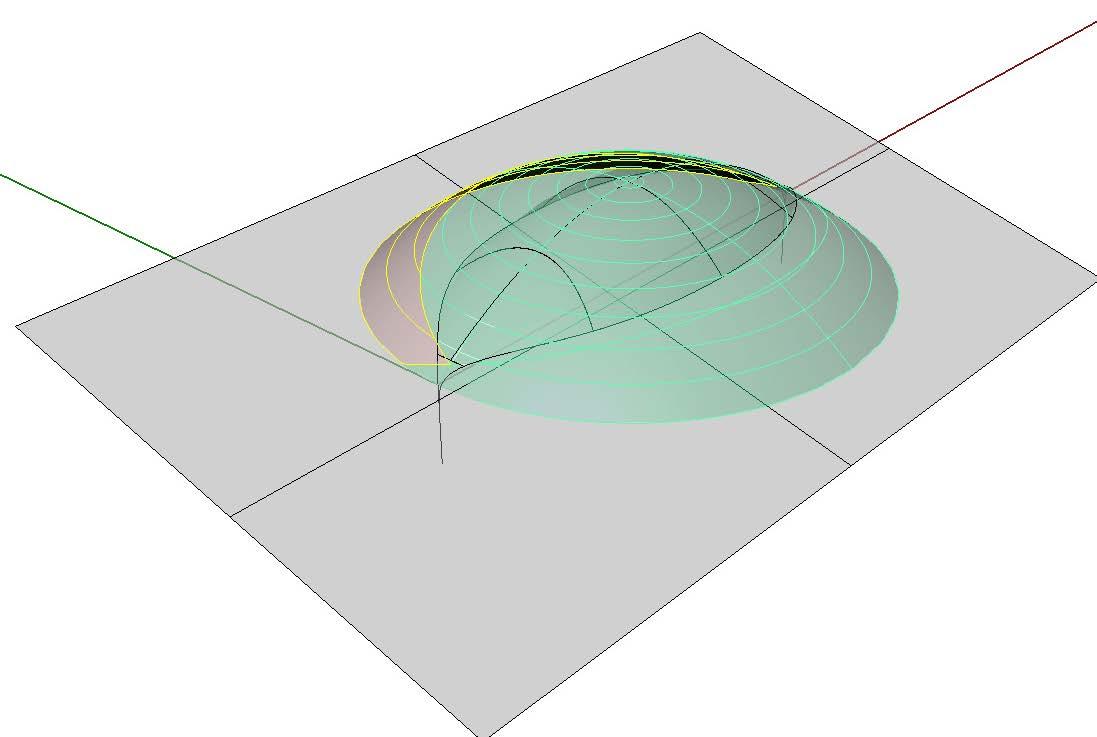
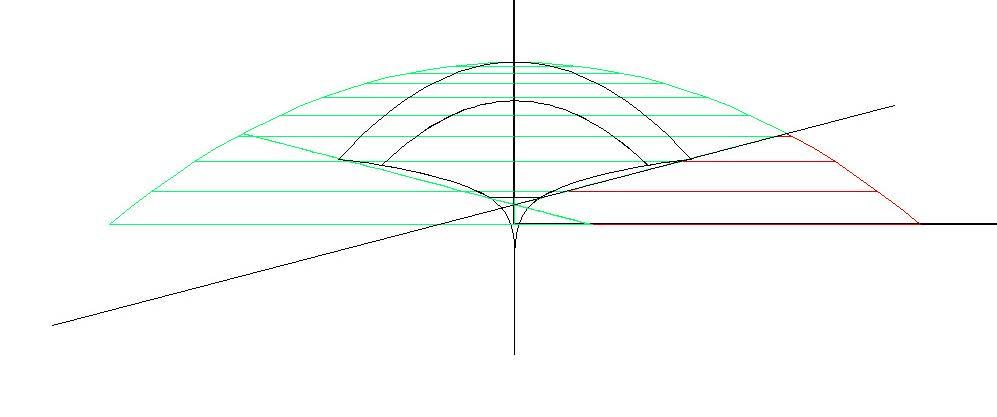
02. Elevation of the comparison f-f structure with catenoid
0. Elevation 2 of the comparison f-f structure with catenoid catenoid
Test Model of the Macro Component
form-found structure
catenoid
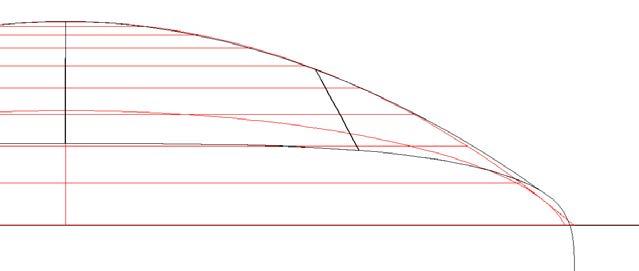
Analysis of the digital model explores the structural schemes in detail. Comparison of the surface with catenoid and direct branching paths of the support. There are certain gaps between ideal form-found structure and possible form made by fabrication constraints.
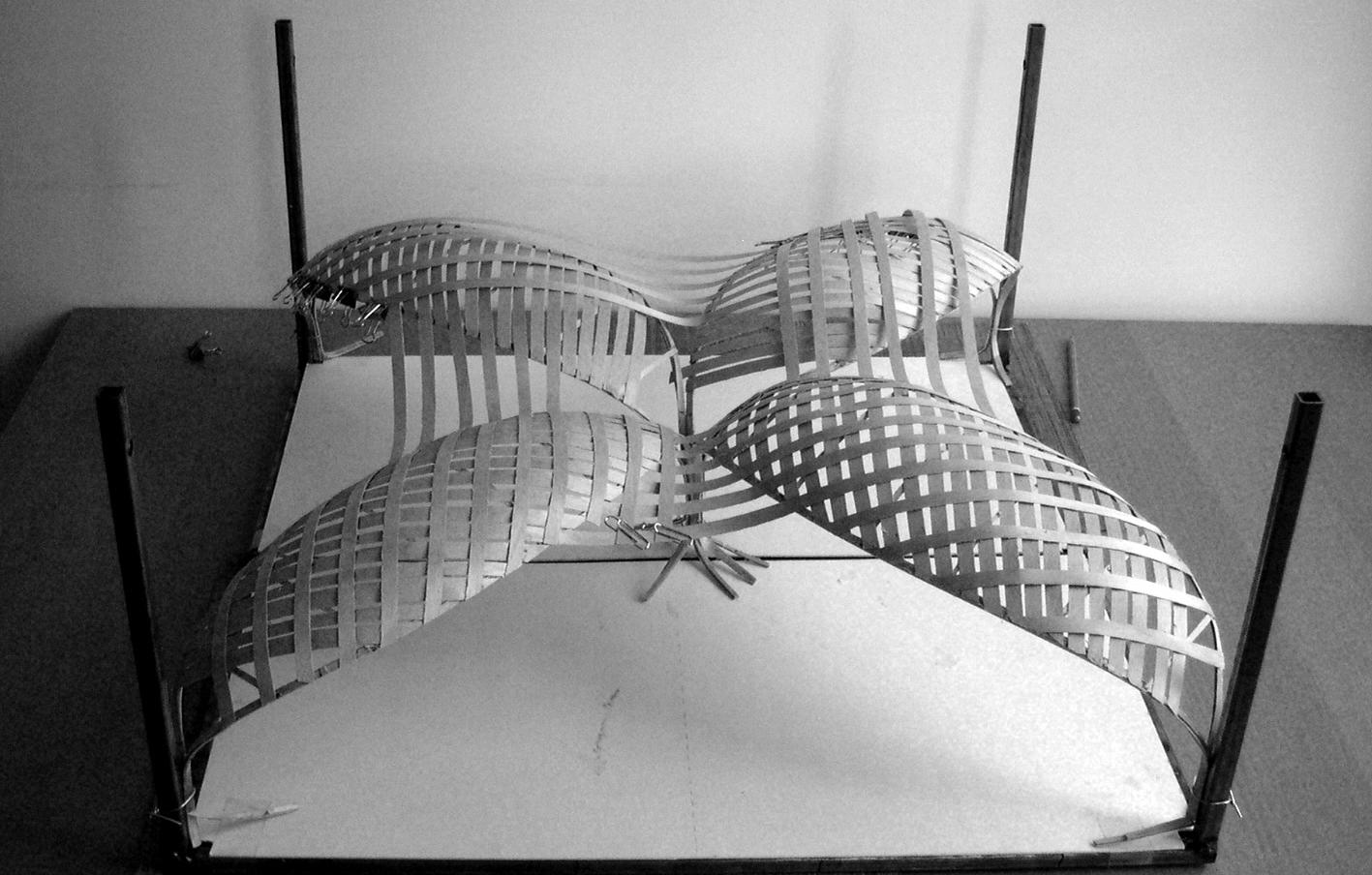
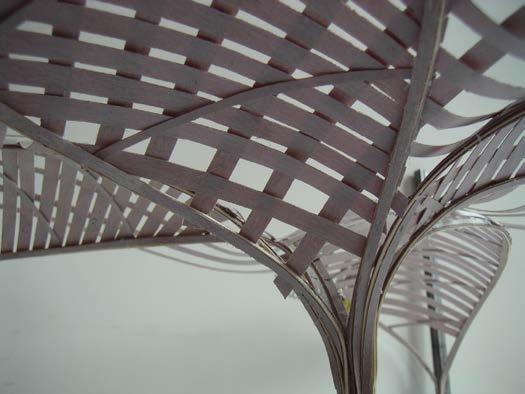
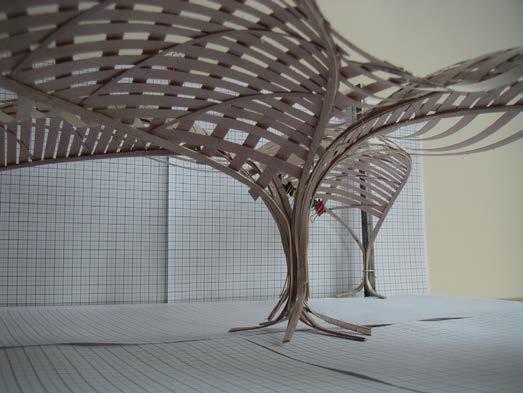
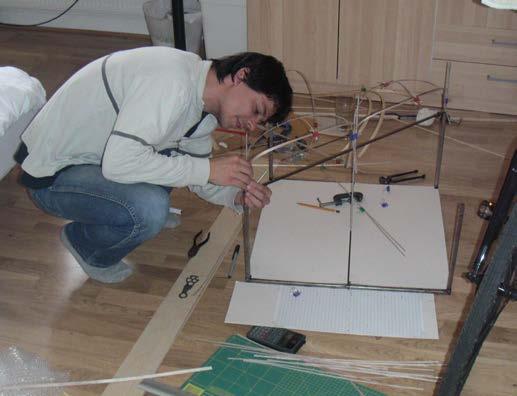
Model was built step by step on the metal scaffolding that held laminated bent beams. The bending form-finding was the most prevailing and also determinant concept that form the shape.
Bent form-found guides were glued (PVA glue) from 7 layers of veneer and fixed on the metal scaffolding. Than layers of veneer stripes were laid on ribs that were in perpendicular direction to the guides. Veneer stipes were laid in two layers. It was sufficient to whitstand loads applied to this test model.
Wooden shell structures were inspired by the boat manufacturing and also by wooden aircrafts that were succesfull in the beginning of the 20 th century. Today, wooden composites are still used in the these fields: marine, car industry, aerospace, wind energy. The famous aircraft Mosquito was made by companies that later fused into the corporation Alcan.
Alcan Composites Core Materials offers you many decades of broad experience not only from one company, but from two leading companies in the composite business. Alcan Airex, Switzerland and Alcan Baltek, U.S.A. are companies that provide support and technical advice.
Baltek is the manufacturer of the core materials based on the balsa wood.
www.alcanbaltek.com
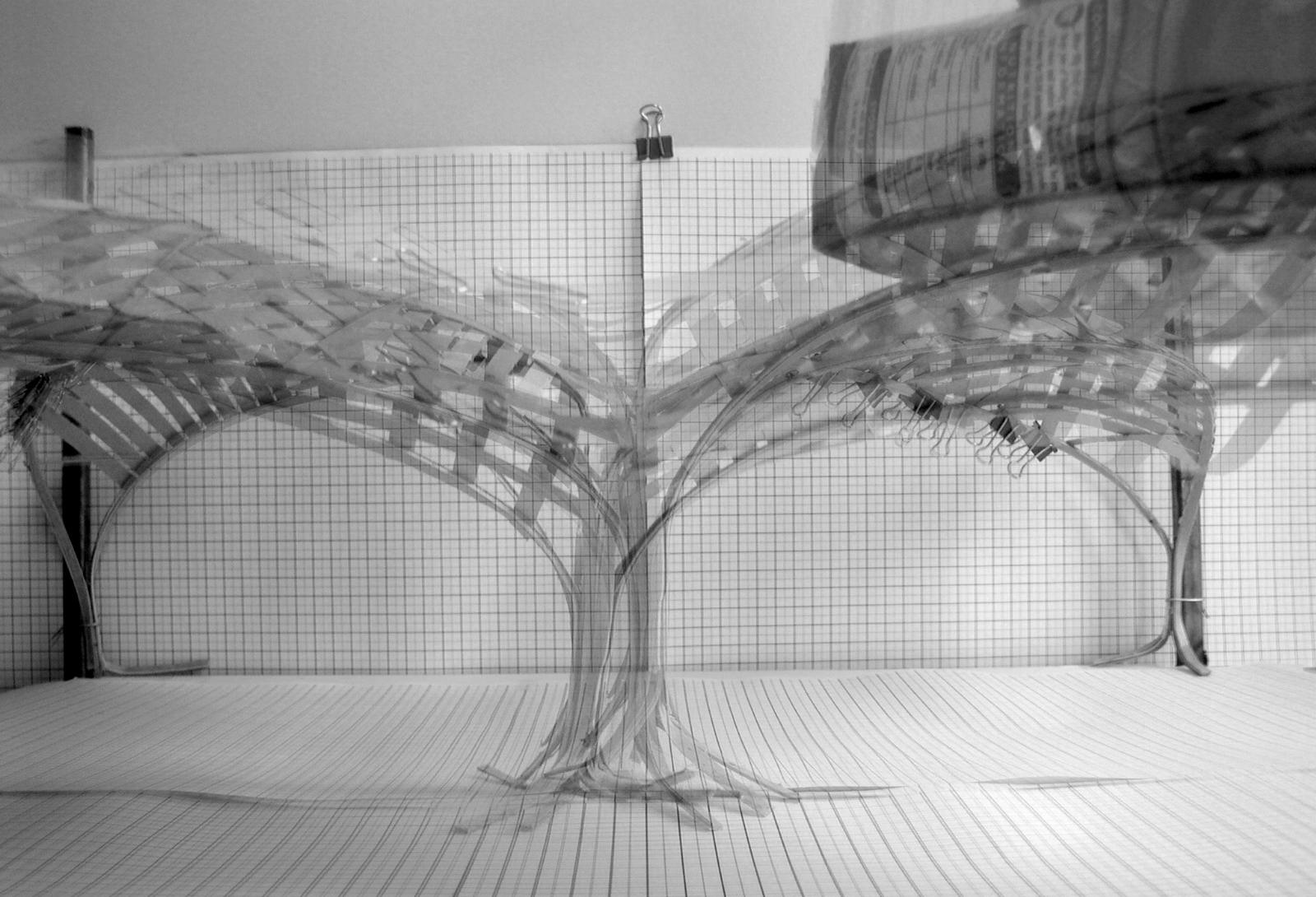
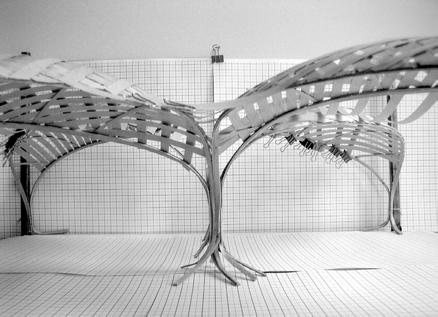
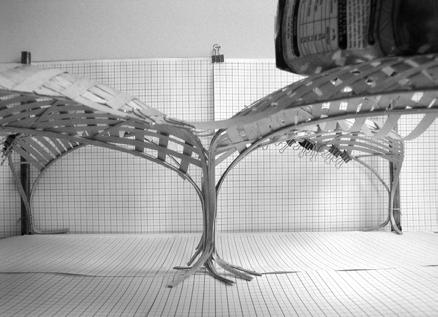

Test Model Analysis
Test 0 - Side View
Model was loaded by and then 2 kg and then observed deflections and displacement of the central support which was left free.
Model
:5
h= 7.5 cm
d= 6 cm (width of the shell)
f (distance the center of the support from the initial position)
l= 4 cm
l2= 56 cm
Load Case 0
h´= 2 cm
d´= cm
f = .5 cm
Load Case 02
h´= .5 cm
d´= 2cm
f = 4 cm
Height was smaller but the width was bigger than in the initial position without loads.
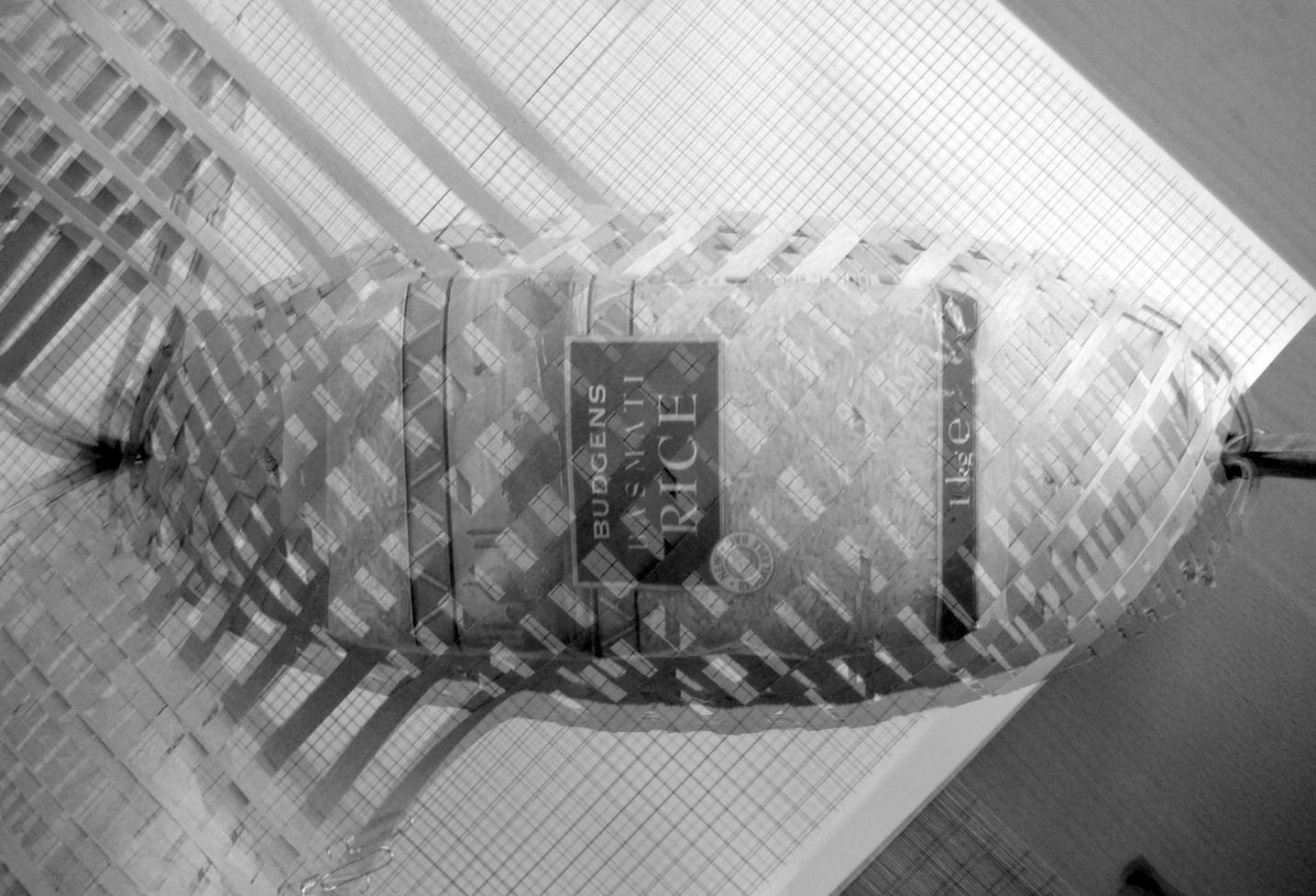
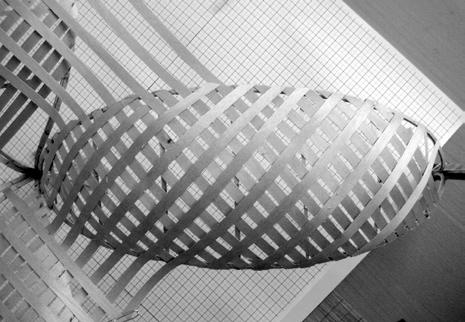
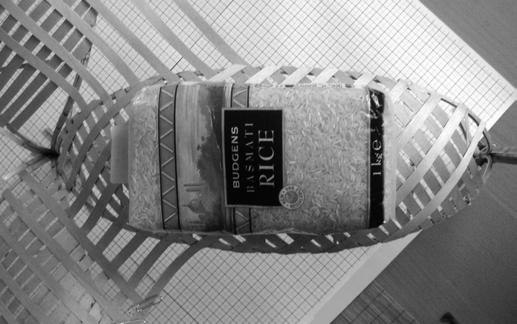
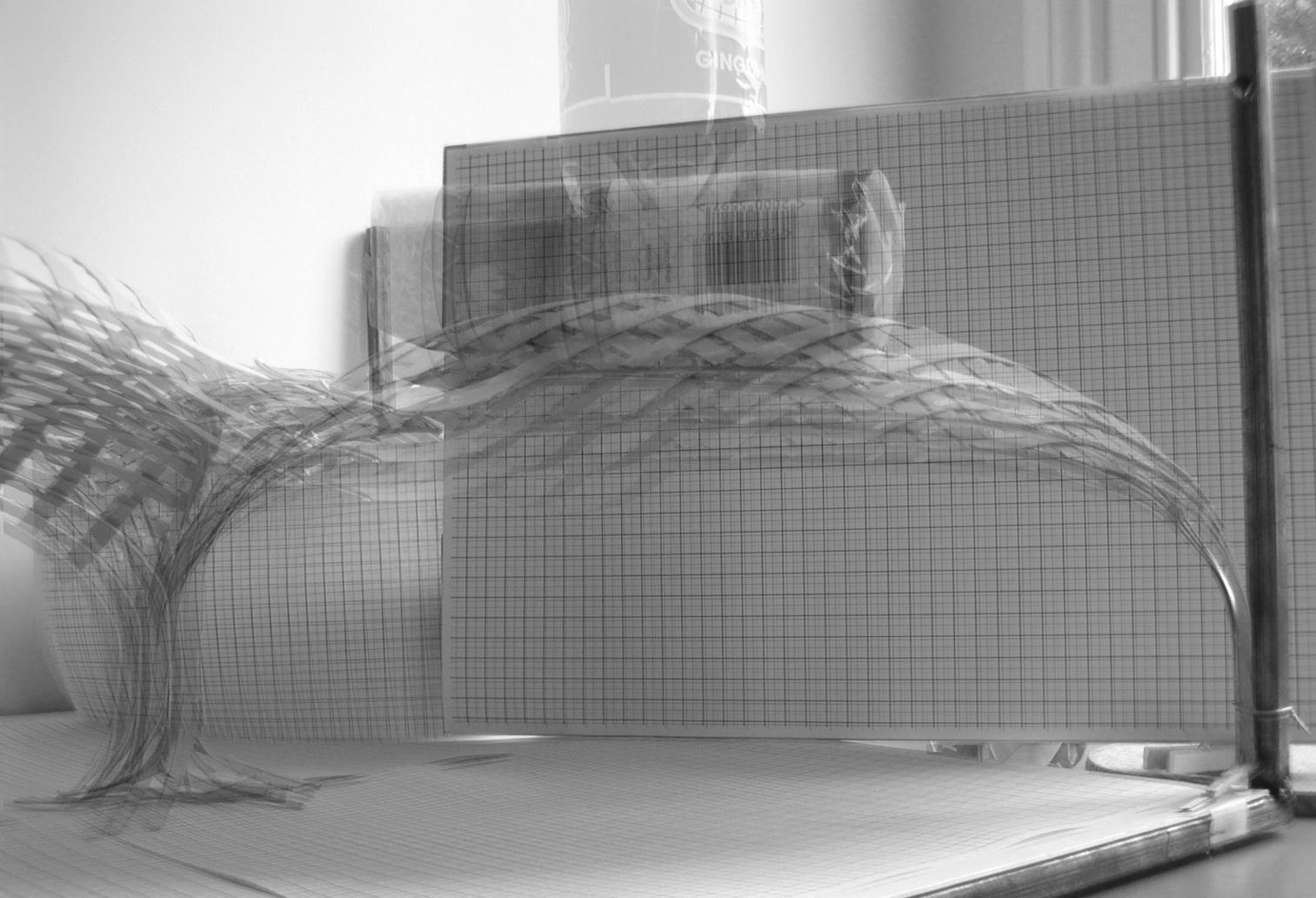
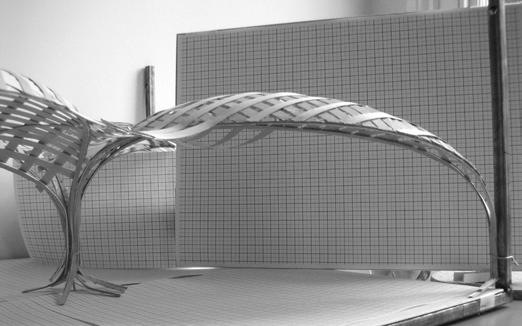
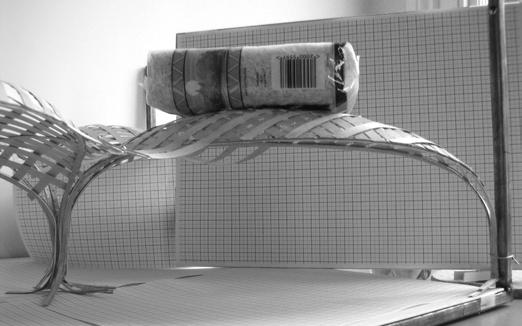
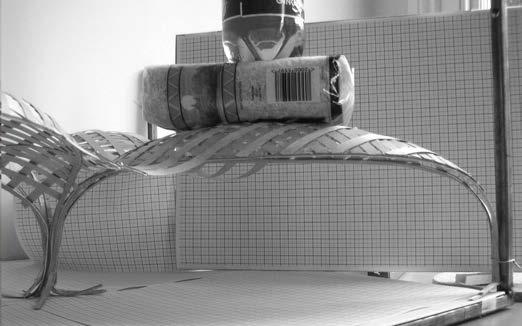
Conclusion
Building and testing of this model proved that the vector-active system of the branching did not perform as the main structural scheme. It was not coherent with the aim of this dissertetion and therefore this way outlined by this experiment is not considered as a desirable path for the further research. The complicated structural scheme of the model together with forcing material to desirable shapes did not satisfied set tasks of this research.
The methods of building this material system could be used for ideas about fabrication of the continuous lamination. The main beams branched out from supports clamped in key positions selforganise to the desirable shape and then were used as guides for other structural layers. All together compose a robust redundant (in biological terminology) structure of natural fiber composite
The work with porosity of the surface affected by structural scheme was followed by the experiments that followed these sets of models.
The branched structure could be self-supporting and by converging branching could achieve stable volume that respond to environment by modulating space in and under the structure. (The branched D laminated wood follows the conncept of trees in forest - research by Frei Otto and IL institute.)
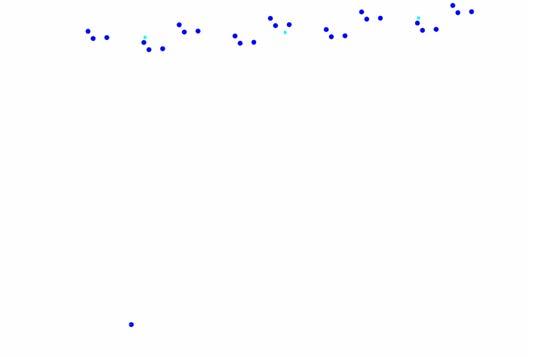
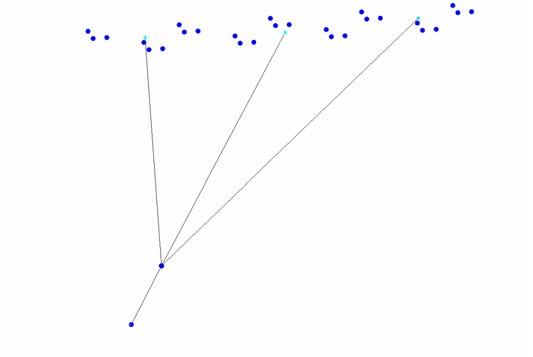
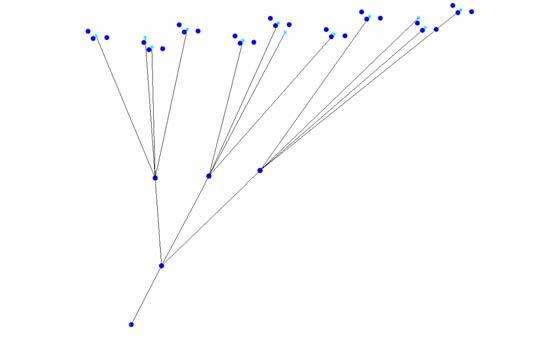
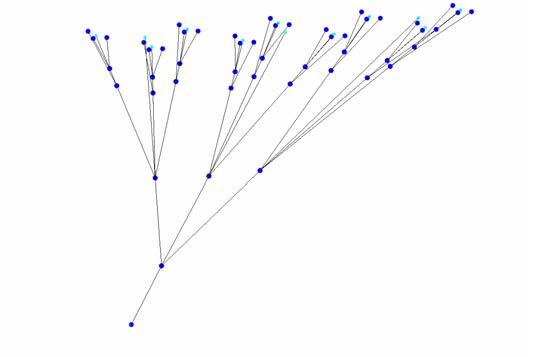
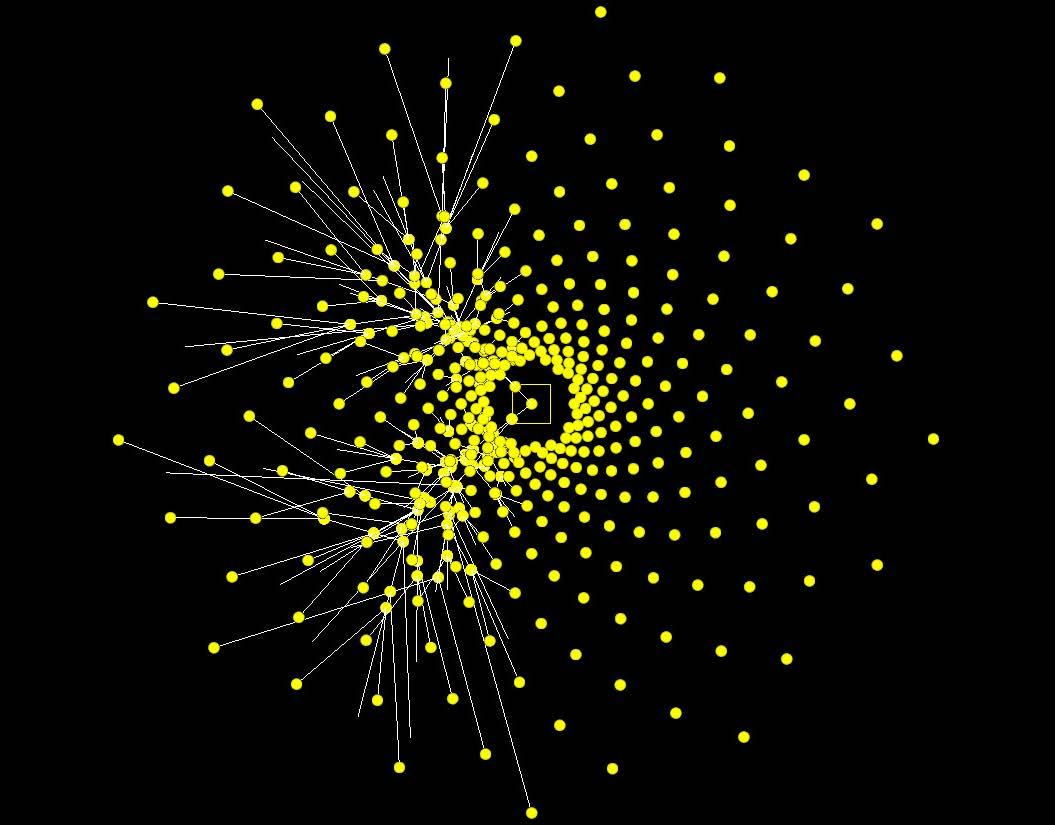
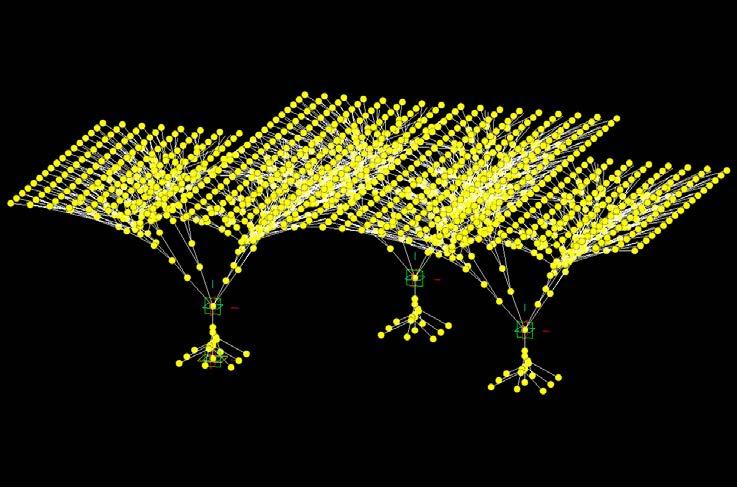
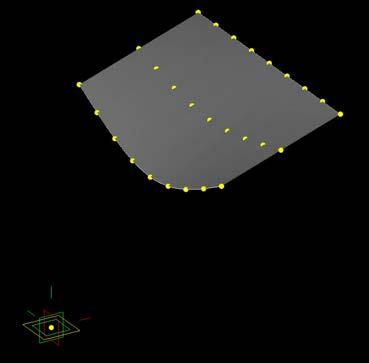
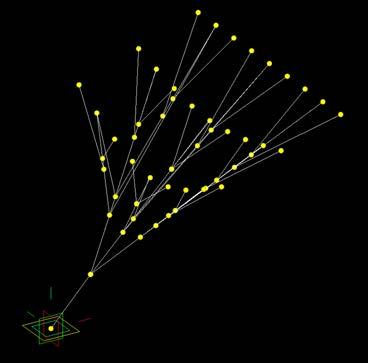
The research was directly linked to the form-finding described in the chpter Concept in this thesis. It is branching of threads dipped into water. The digital form-finding took advantage from the associative environment of GC and due to parameters it was possible to define limiting distances between branching nodes. These distances had to fulfill the requirements for the minimal length where the curvature of lamination took place. It was then constrained by the possibility of fabrication. The structural performance was guaranteed by following the rules from form-finding of woollen threads.
The complex branched system is achieved by input x,y,z coordinates of points that are later interconnected by lines. The geometry of input data drove the performance of the final structure.
Methodology
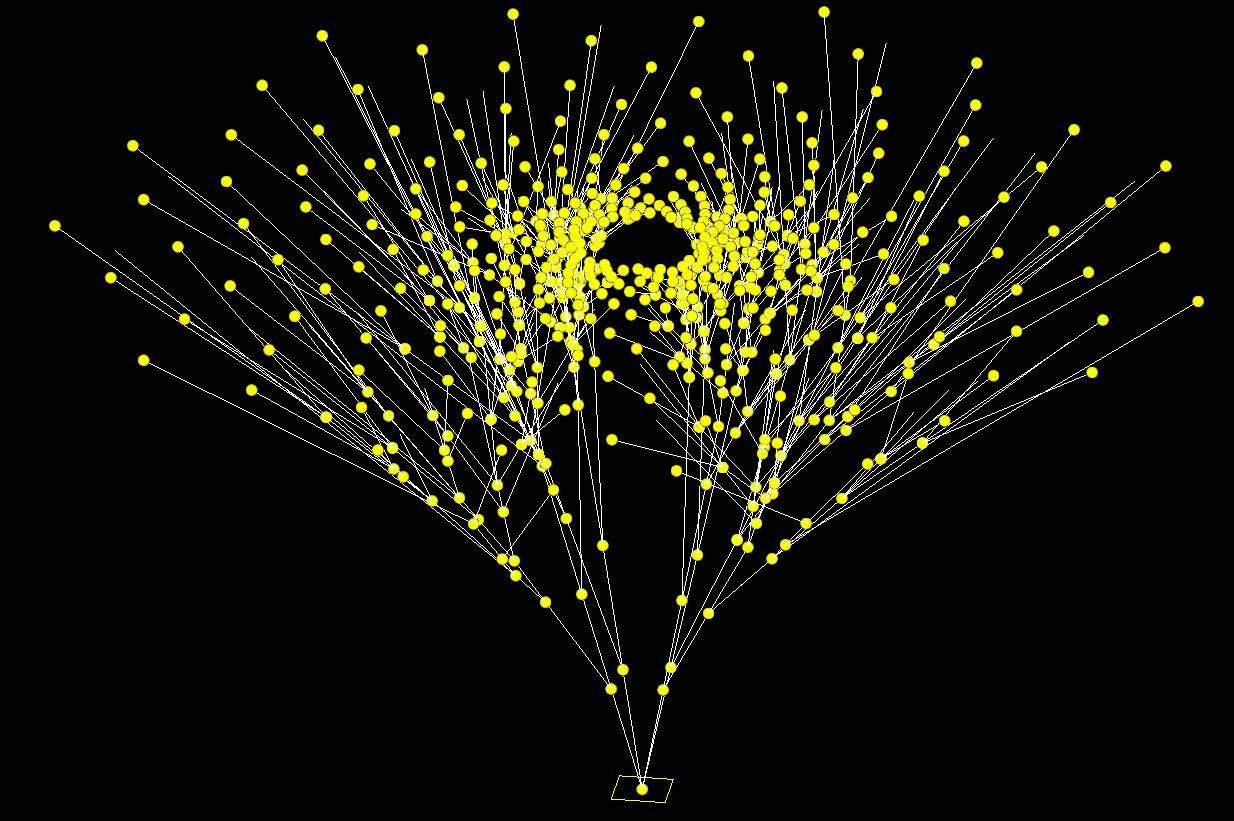

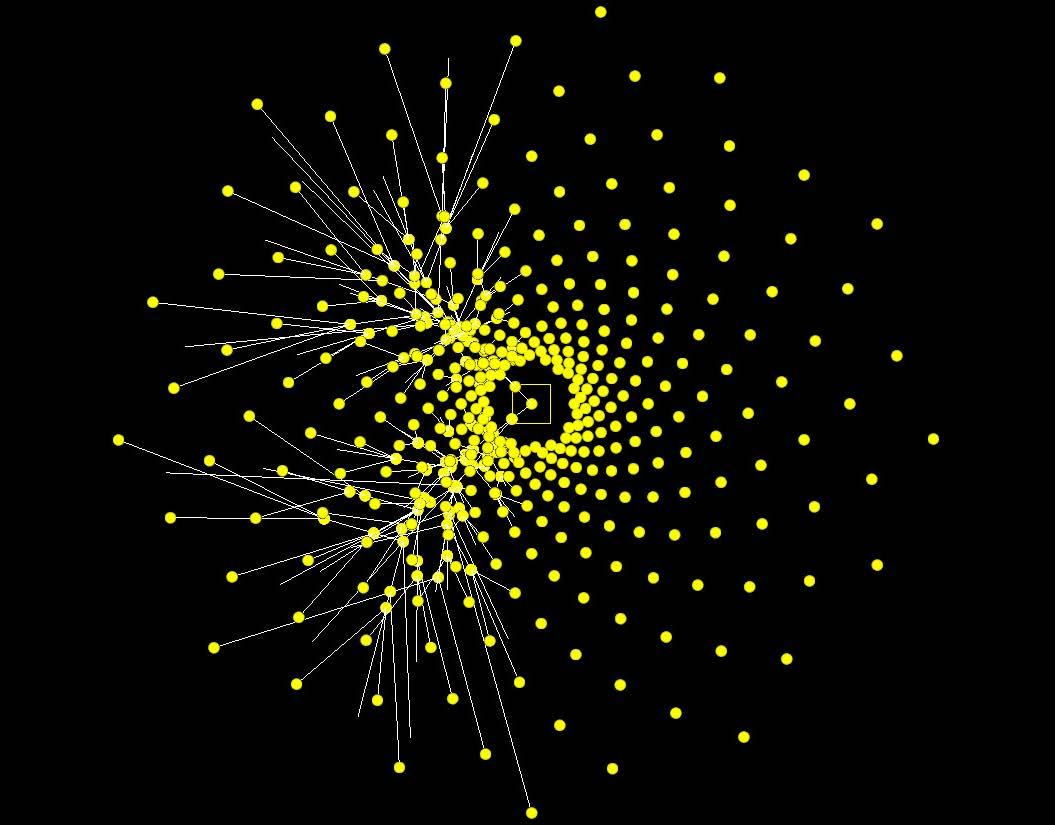
The process of dealing with input data. In this case points generated by spiral phyllotaxis. The spiral phyllotaxis was chosen in order to explore complex pattern. This pattern did not have even distribution of points but it features wider spread with bigger distance from the centre of the distribution.
The process starts with the pattern of points in GC that was later post processed in excel and put back to GC. The excel VBA script divide the x, y, z coordinates of D pattern into four quadrants where the number of points was 8. The consequent branched pattern generated by L-system connected points in quadrants with lines. These lines were later materialized by digital setup for the wooden lamination. It was done by digital form-finding based on principles gained from chapter Material Properties. The exact process of the digital procedure is described in the following part - Experiment 0. It was there used for the test model of branches interwoven together.
8 points distances
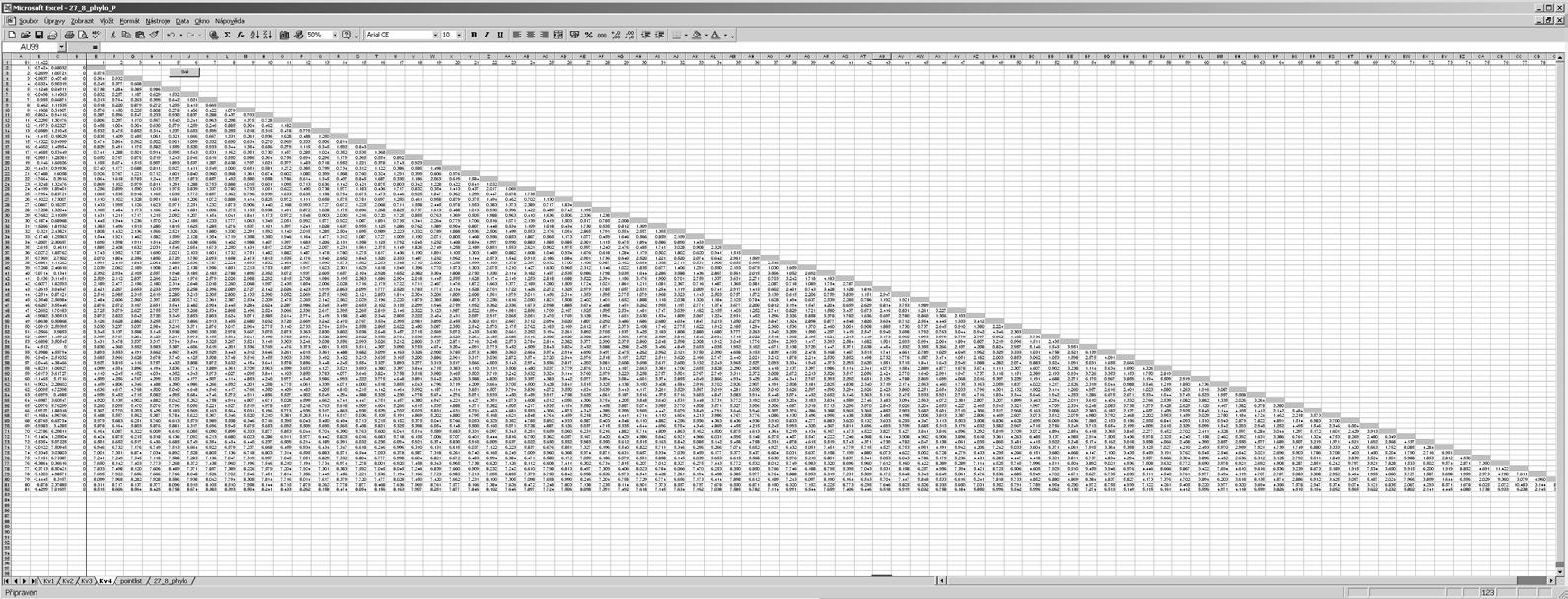
0 Excel spred sheet with 8 points generated according to the spiral phyllotaxis. The 4th quadrant. Distances between points are compared and then sorted.
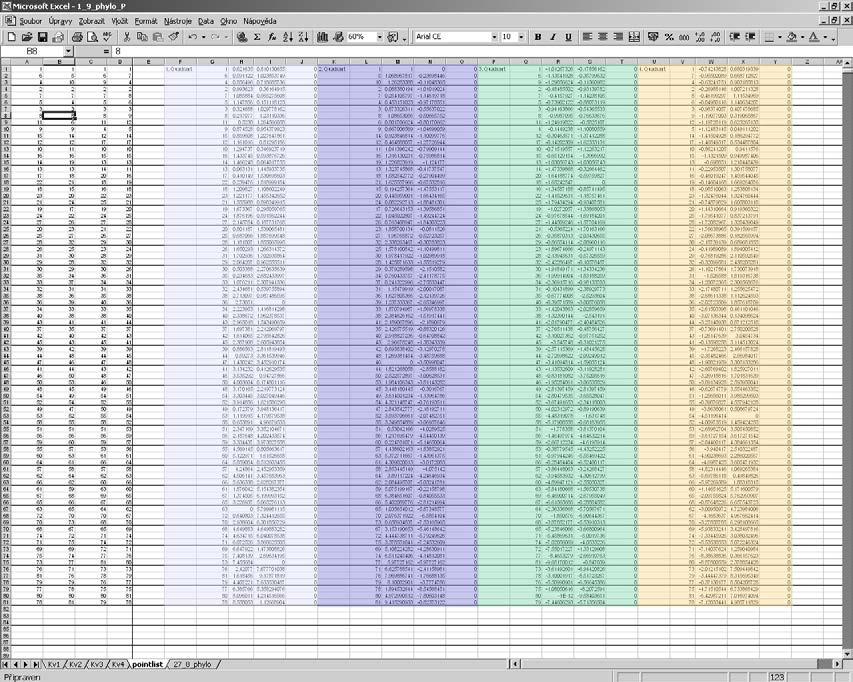
02. Excel spred sheet with 8x4 = 24 points. Colured are Quadrants of 8 points. In columns - x, y, z coordinates.
0 Diagram of 4 Quadrants. Points are divided into these Quadrants. QUADRANT I
Methodology
The process of dealing with input data. In this case points generated by spiral phyllotaxis. Explanation of the process of dealing with input data.
Methodology
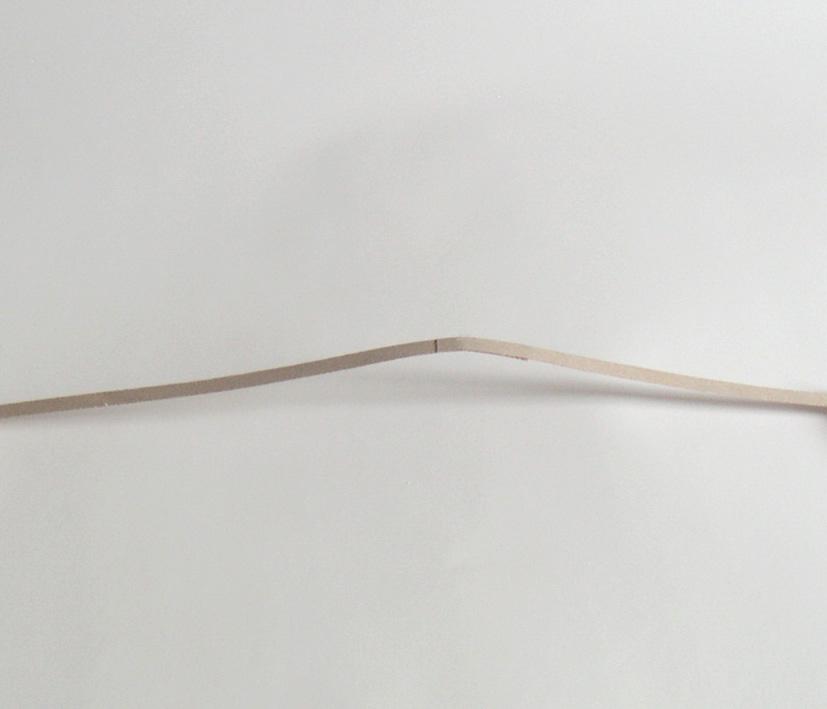
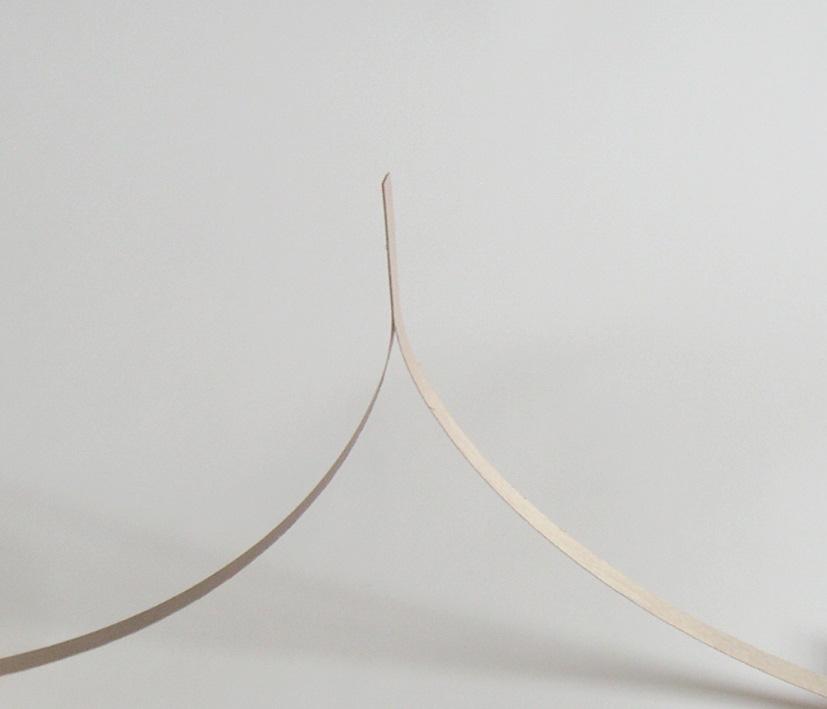
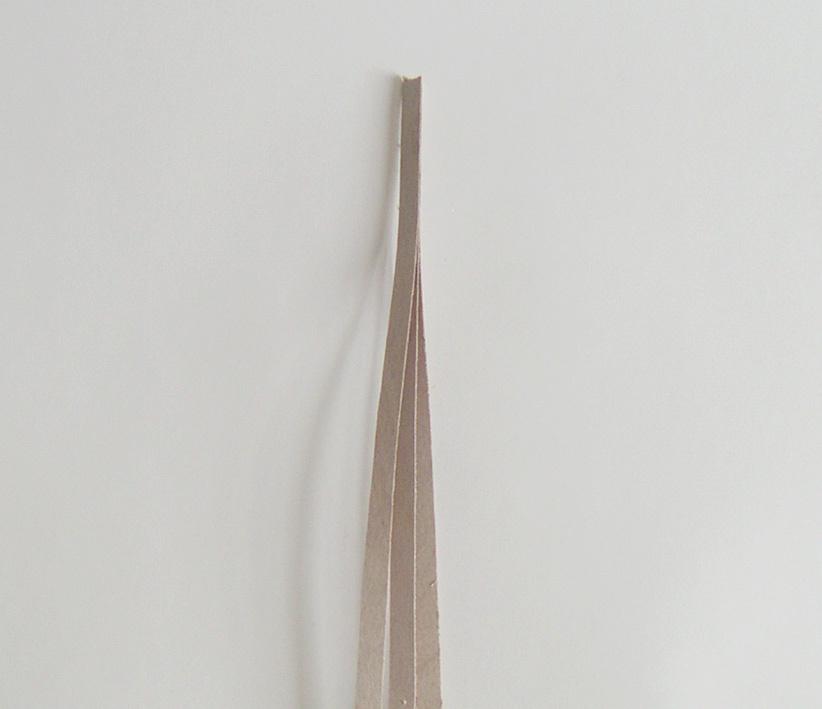
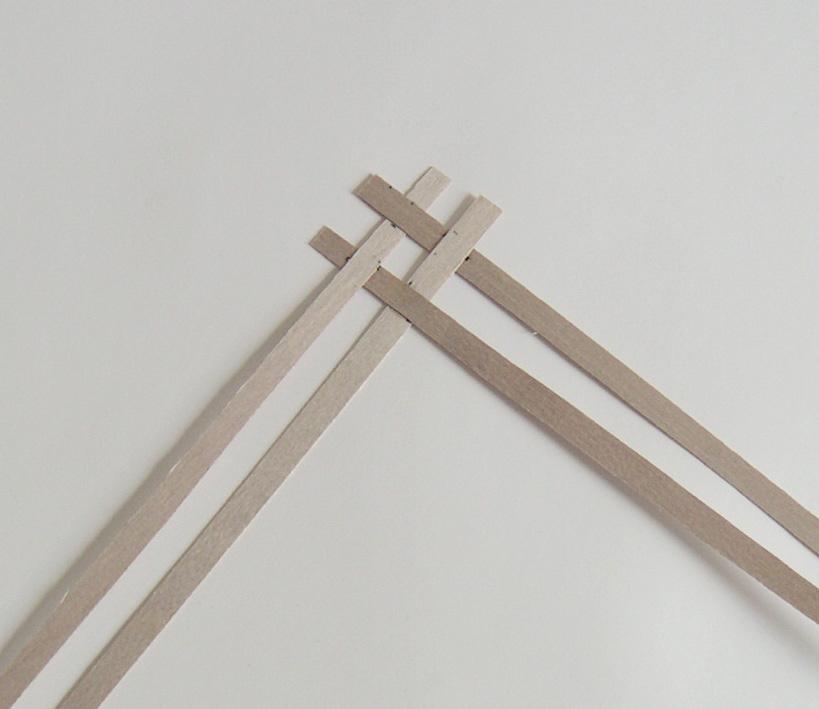
Physical models of possible connection between branches. It seemed to be tho most appropriate for this test to converge branches to one point.
The figure 04 shows the interweaving of stripes. This approach was followed in the last experiment. Branches there reached certain level and then bacame the surface.
7 m

0 Three trees sharing the array of 8 points. Dimensions are in m.
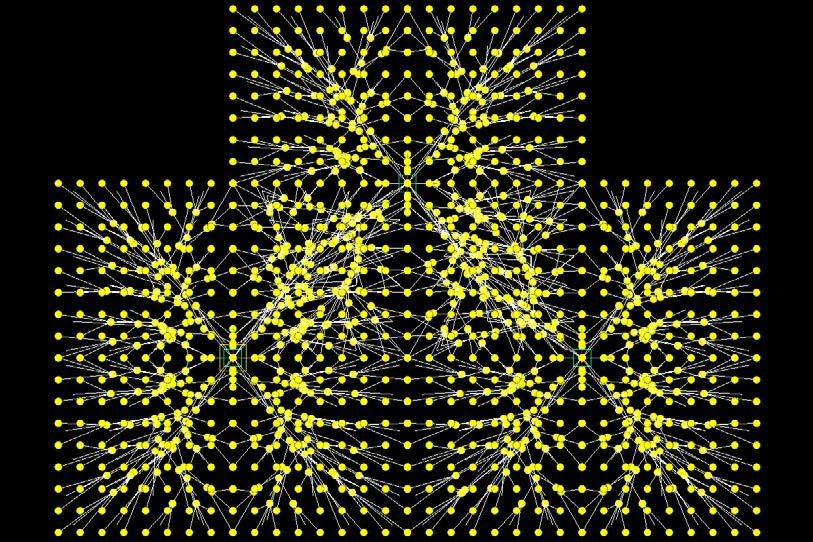
02. Top view. One base point is connected to 4 arrays of points.
750 mm
750 mm
04. Plan of the tip of the tree. Spacing between points 750 mm, top of branches 0 mm plank ply.
Top Points
0.0045
0.05
0.0405
0.25
0.645
0.645
0.25
0.25
Base Point
The process of dealing with input data. In this case points generated in a square array of 8 points.
Points have the constant Z coordinate and constant spacing. They form an array of size 6m by 6m.
Bottom Points
05. Schematic section of the structure in m. Numbers represents sections of branches in particular heights.
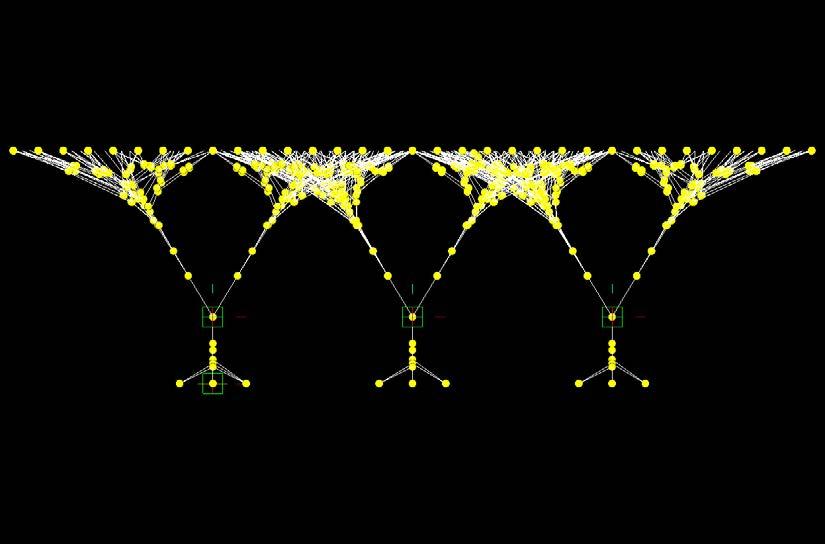
0. Elevation shows the position of starting branches from the base point.

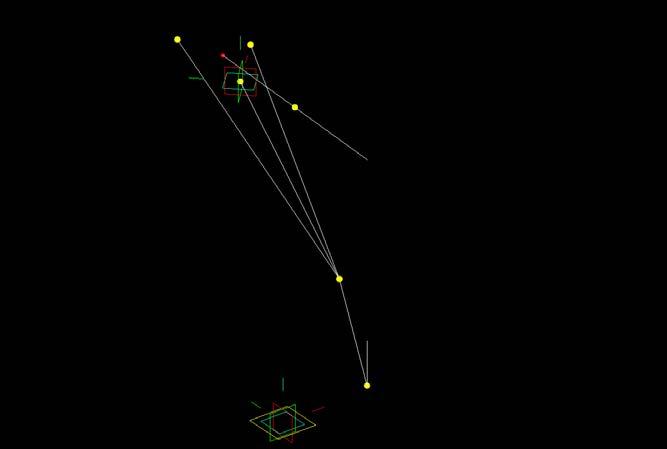
02. Geometry of the Component 02 - The component is informed by the behavior of the laminated wood.
0 Geometry of the Component 0 - The component follows the logic of the direct path system. centroid of points direction of the branching node point on the line (centroid-proj.bp) direction of the branching node branching points plane line - plane intersection distance between points
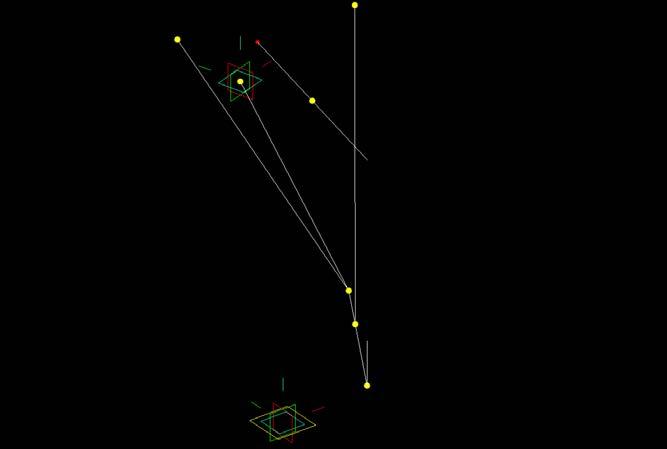
0 Geometry of the Component 02a - Distance between points is not even and therefore there are two branching points.
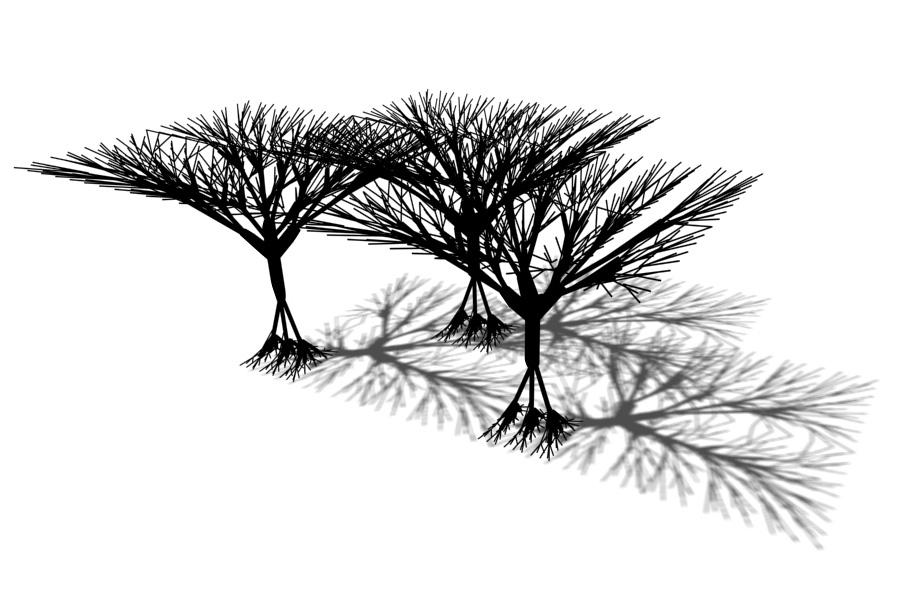
0a. Result of the L-system by rewriting of the component 0
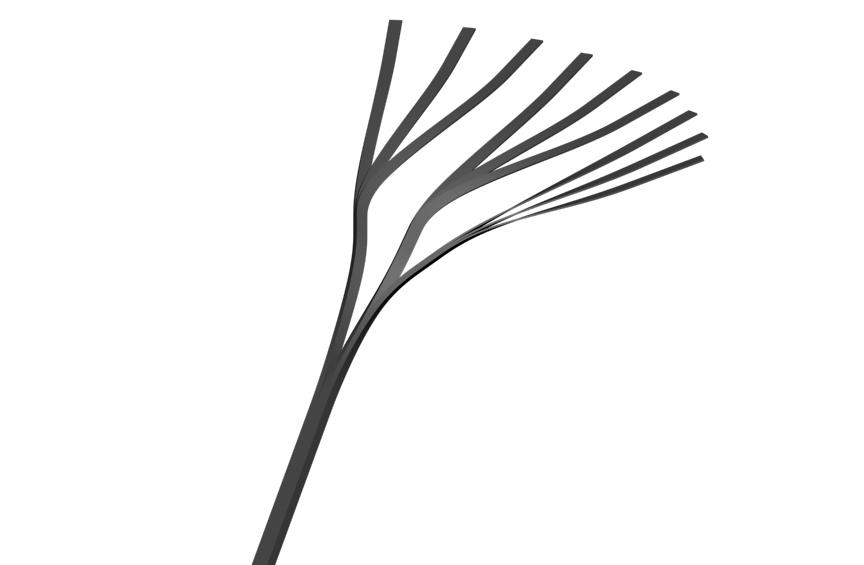
02a. Result of the L-system by rewriting of the component 02.
In the beginning of the parametric setup was obvious that concept of pure tension in threads-liquid experiment cannot be directly materialized by laminated wood. It could follow the technique of design and fabrication used in the Stuttgart Terminal but it was not the aim of this thesis. Geometry and therefore parameters suitable for associative model does not match and should be revised.
Presented pictures show the way how to understand and prepare digital models for fabrication - laser cutting (or saw cutting) of flat wooden material.
One part of the overall hypothesis driving this project was continuity of fibres. These fibres are parallel to cutting lines of an assembly.
Zhe length of fibres could be derived from the digital model of GC.
Subhypothesis:
The branched D pattern could modulate environment by controling positions of branching nodes. Wooden branches smoothly transmit into the surface. This surface has the smaller ratio in comparisson with direct paths of branching. The negotiation between surface and vectors could be explored.
It is possible to achieve complex design by adapting features of paths systems in 2D and D and introducing them to generic Lsystem. The L-system algorithm responds to needs of the site and has impact on the structural scheme as wel on the environment.

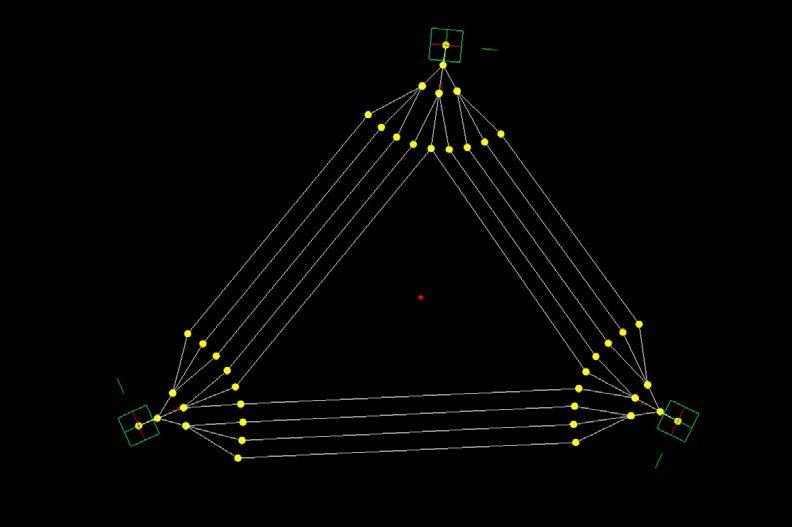
The aim was to create generic model of a digital macrocomponent from the self-supporting structure attached to the ground on three or four points. The branching described and analysed in the chapter Concept was always stable due to the attaching to the plexiglass plate. In Experiment 0 the interwoven branches acted as a surface. Later is shown and deployed the strategy for controlling the porosity and manufacturing.
The L-system algorithm drove the whole process of tectonics. Simple parameters and positions of input points and one base point directed the output that result in the macrocomponent with three supports attached to the ground. Figures 0-04 illustrate the possibilities of attaching branched supports to the structure.
Described macrocomponent was then proliferated on a site on a plan generated by other scaffolding of L-system. The L-system that drove these experiments had evolved from the previous studies. Firstly it was branching pattern informed by the behaviour of wooden laminated planks. The other method was used from studies of branching in 2D - see chapter Concept.

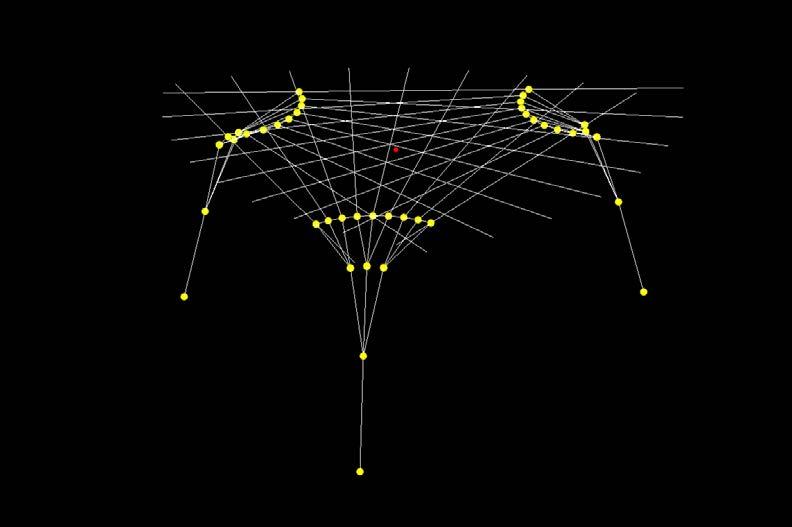
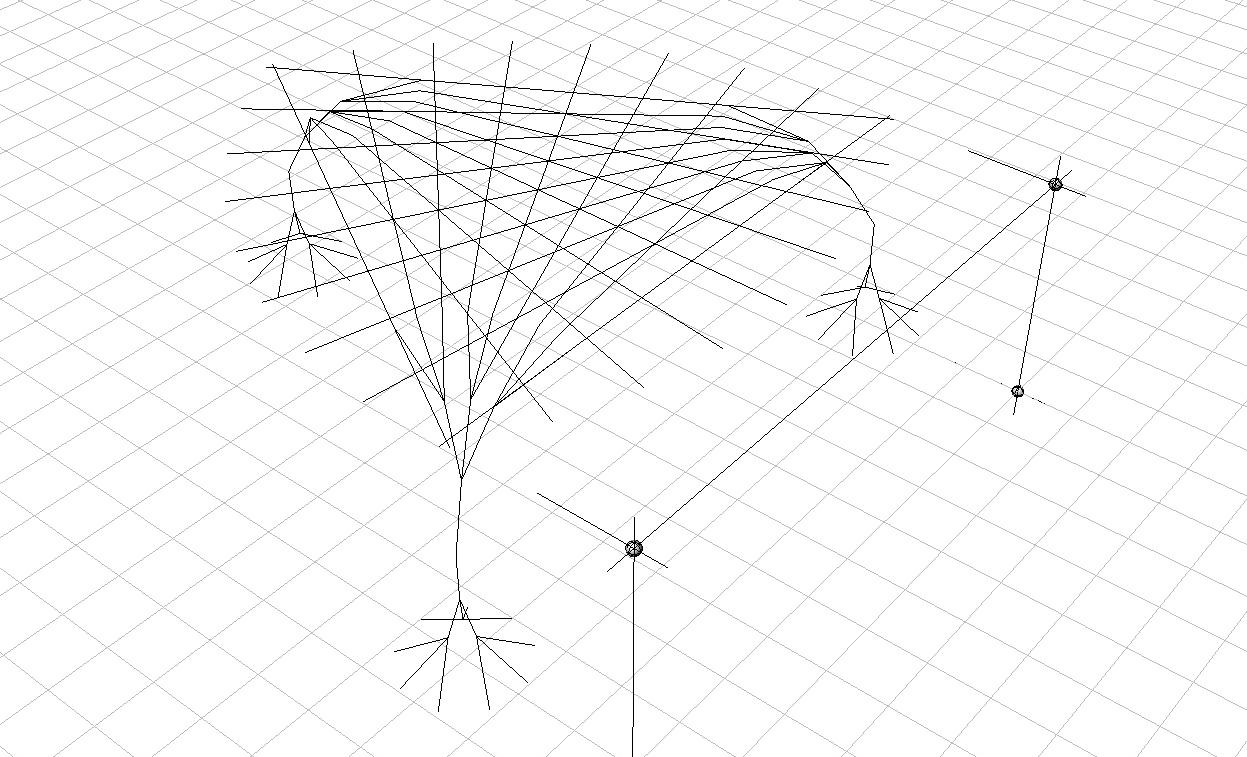
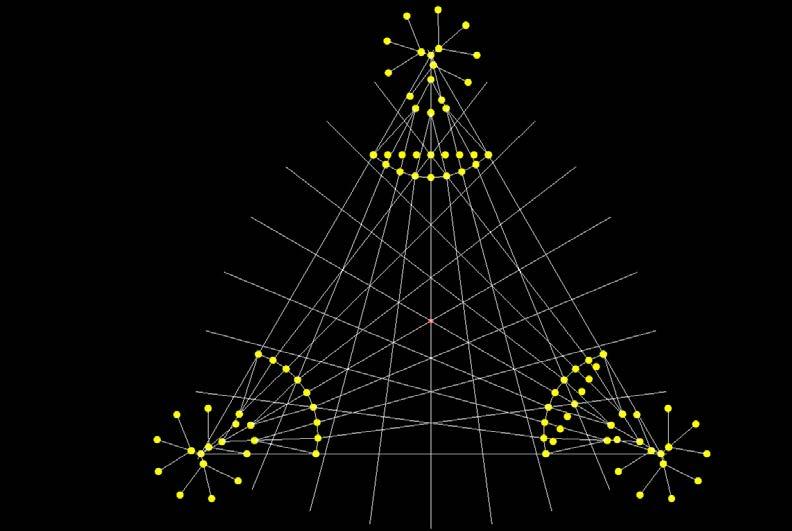
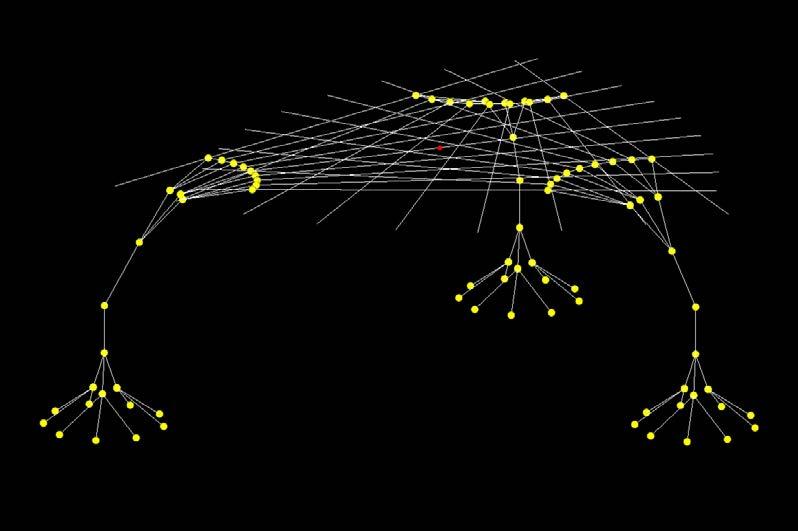
This experiment followed the logic of a plane and branched supports that have tangency continuity to the plane surface. This surface was a porous surface from laminated planks. These planks were continuous on the surface and cover like a slab the whole area of proliferated geometry. Because of the continuity the whole assembly was very stable against vertical loads. But there was a possibility to asses this structure as a slab and columns. Similar scheme was used in the roof of the Stuttgart Terminal
The advantage of this approach was the possible manufacturing. It was meant to made the surface off-site and then attach it on-site by laminating support tree.
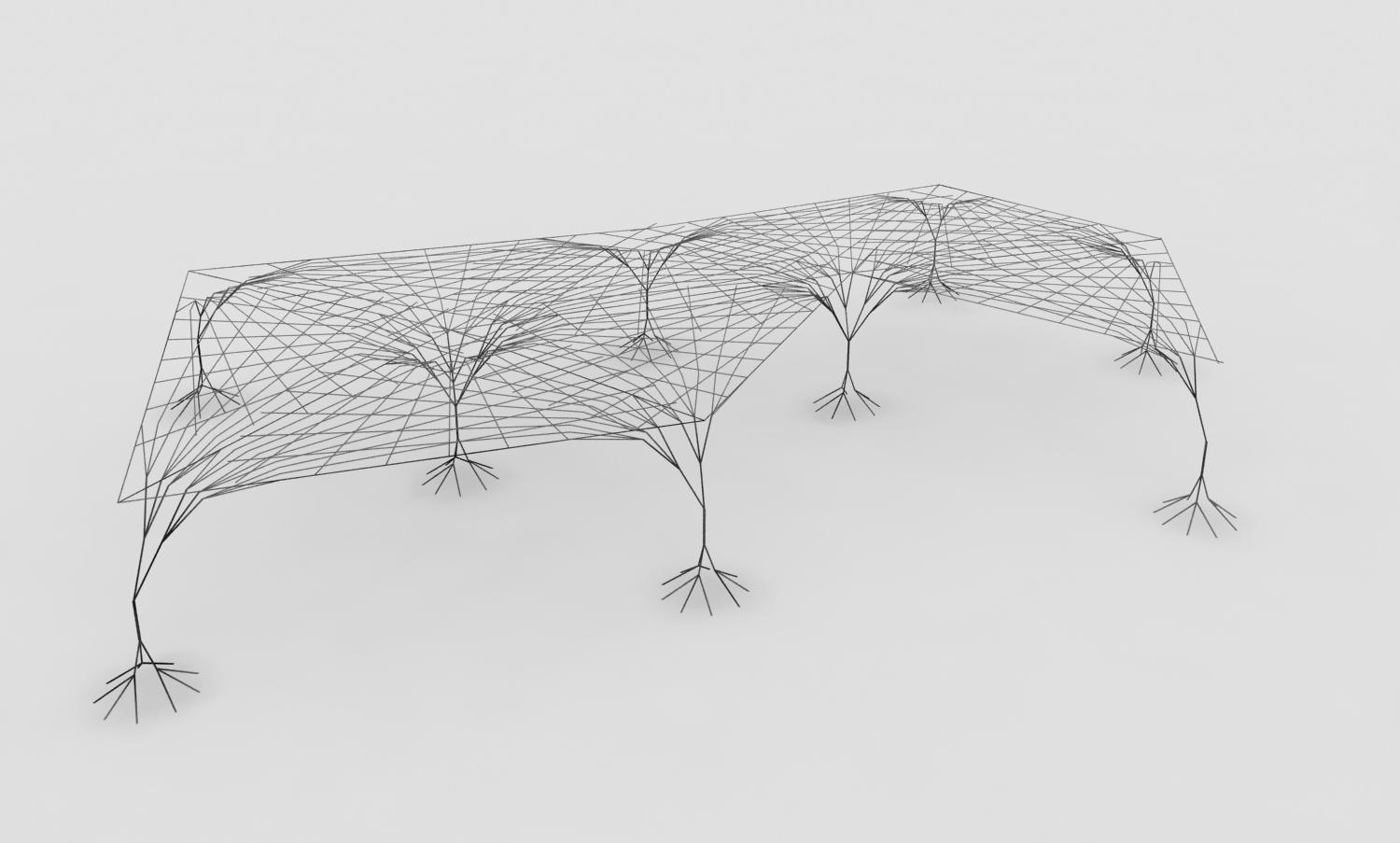
0 Proliferation of macrocomponents - Bird view
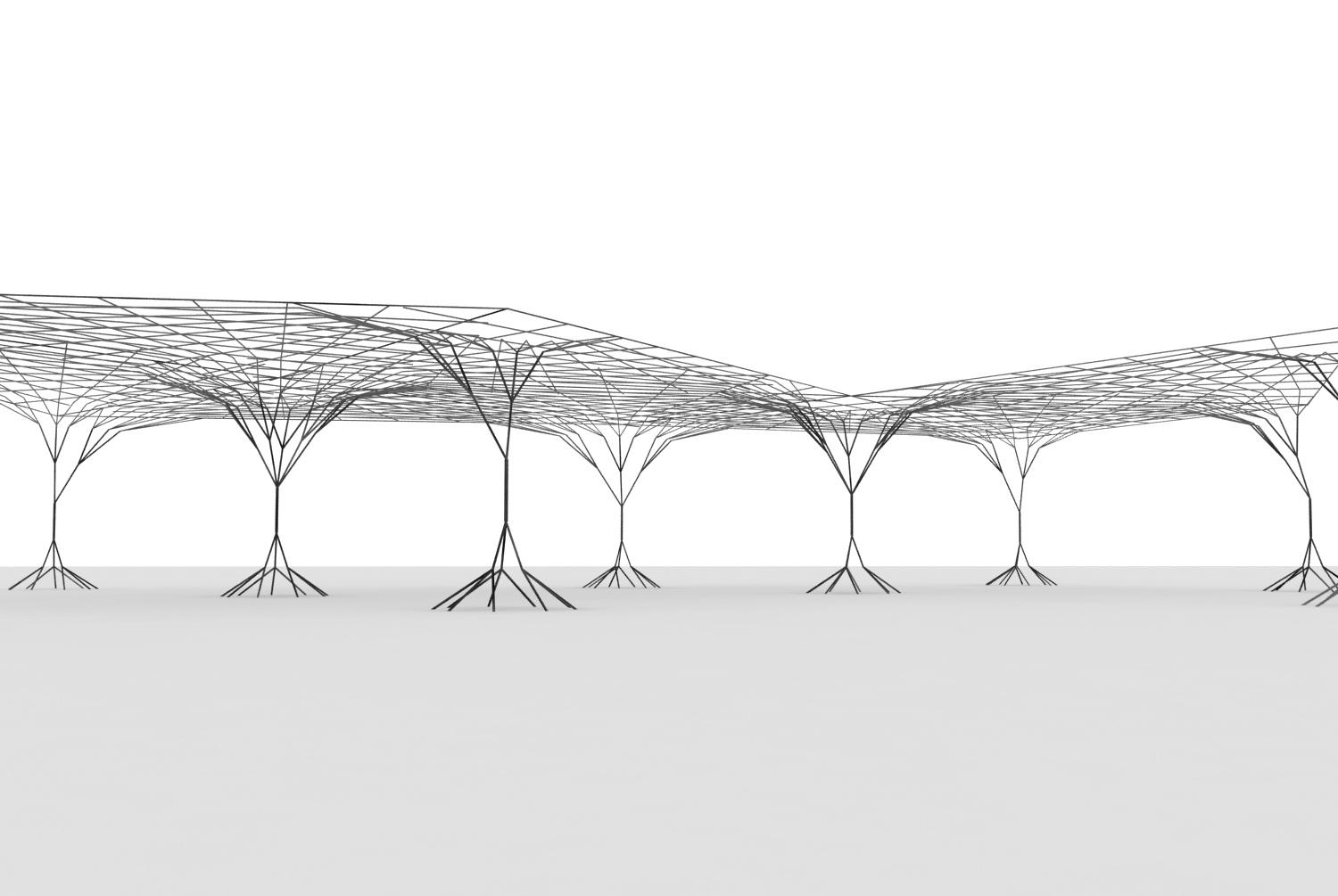
02. Proliferation of macrocomponents - Perspective
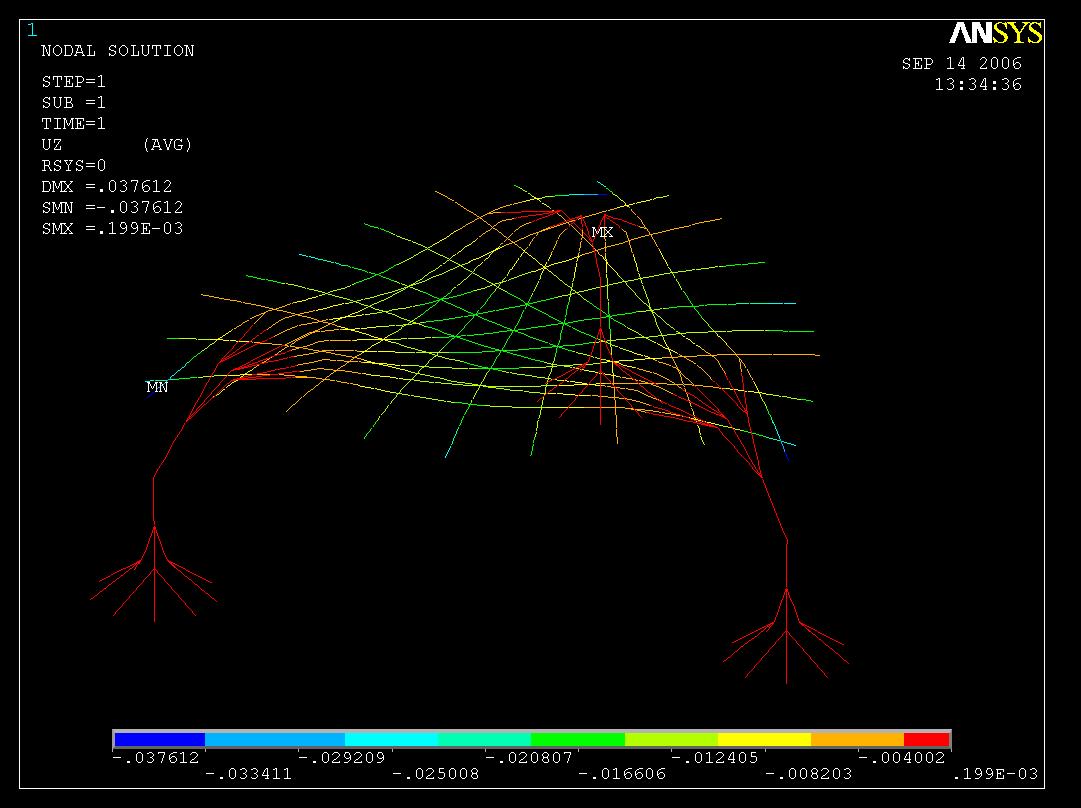
0. Structural evaluation of the Macrocomponent
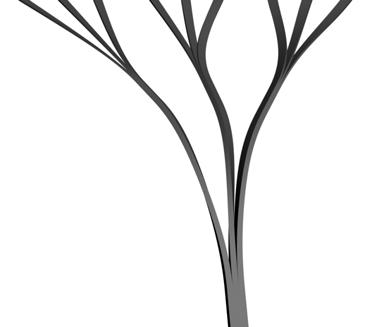
04. Geometry of the branched structure - digital for-finding of laminated timber.
The geometry is constrained by the structural capacity of the macrocomponent. The branched structure supports the layer evaluated by the FEA method.
The L-system as a scaffolding for the lamination controlled the porosity of the surface. The distance between points determined distances of branches and then distrubution of horizontal planks. This had a direct impact on the light, air and water permeability. Within certain limits the structural scheme was the same. The analysis of the finite elements method was set as a feedback for the structural scheme. The deflection of the surface of the macrocomponent in was critical in certain dimensions and distances of supports. These values were also cnfirmed by the physical teset with laminated timber planks.
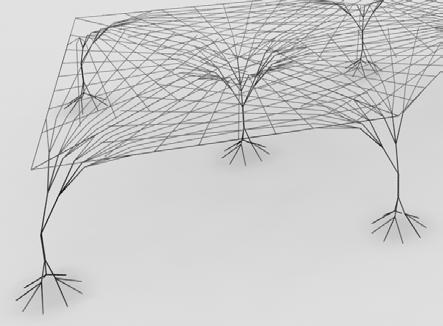
points - L-system in plan points L-system in supports
05. Detail of the macrocomponent - the porosity of the structure is controlled by two levels of L-system. The first level is the distribution of points on the plane and therefore the geometry of final branching points. The second level is the branching itself. By varying of the distance between branches the porosity of the surface is also afected. Strategy for the planar distribution is later explained.
P [0] = P[]
P [0]
CS [0]
P [0]
P []
CS []
P []
CS [b]
0 Branching node. Branches split under the influence of the distance of the next branching nodes. The control of the curvature is provided by manipulation of arrays of points.
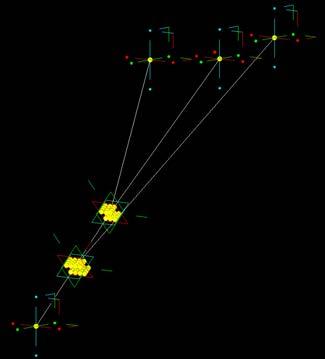
0 Array of points as tangency points for the volume of branches. Branches behaves according to set rules. c c c / a a a c c c / a a c c c / a a a
02. Details of three possibilities of branching points. The array of points in D serves for the cointinuity of BSpline curves determining the volume of laminated wood.
a = thickness of layers - number of layers
b = constant width of timber
c = distance of points in an array - curvature of BSplines
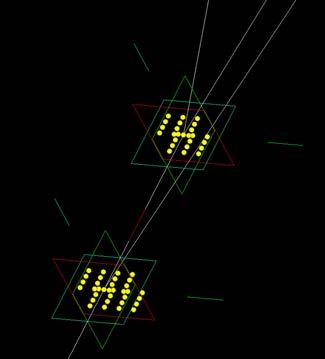
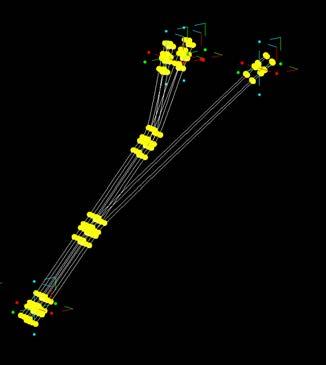
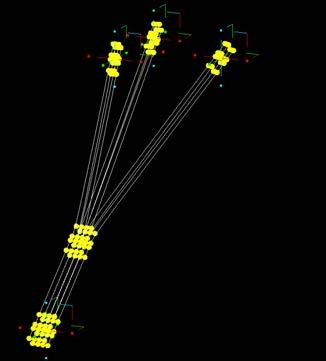
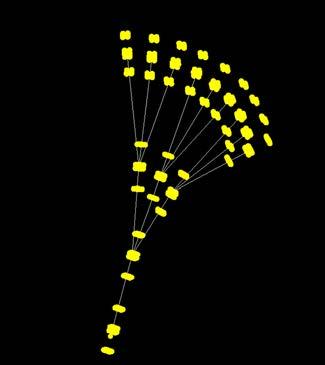
The dialog between surface-active and vector-active systems is deployed into detail by digital form-finding of laminated wood. This experiment ended up with the physical model and outlined the procedure for the manufacturing of larger pieces.
The digital model of lines and points were extended by adding sets of points that controlled the curvature of BSpline curves. Points were generated on coordinate systems placed on branching nodes. These coordinate systems were rotated according to the distance and position of the next branching node. Nodes from digital formfinding were then used as nodes in physical model as an area of first clamps. Fig 0 and 02 illustrate the strategy for control of BSplines. In fact it was nesting of additional scripts on the script of branching explored early in the thesis.
Digital Form-Finding
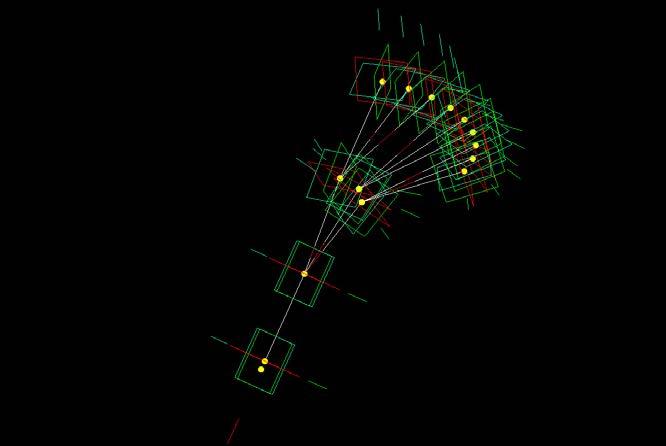
0 Brancehd structure proliferated by coordinate systems.

02. Arrays of points on branching nodes. The tangency continuity is maintained - clamping points.

0 BSplines Curves through arrays of points.
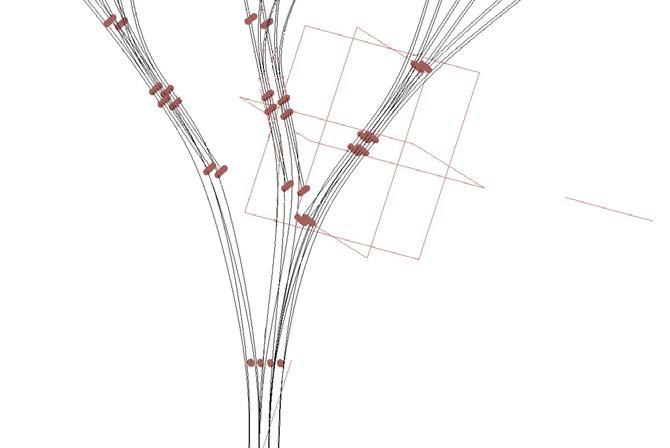
04. Detail of the branching node with one coordinate system0

05. Coordinate system02 rotated around coordinate system0 around X axis. Angle 45°.
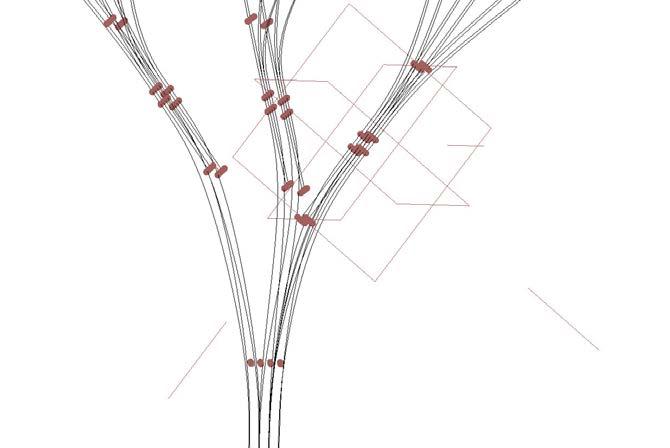
06. Final coordinate system - rotation around coordinate system02 around Z axis. Angle 20°.
The digital set-up for the geometry and volume control of laminated wood. Images on this page illustrate step by step how to get and control the geometry for the fabrication. The model was generic and so it could be used in the any branched pattern that came with certain constraints - dimensions - space for later BSplines.
This strategy is based on the premise that a plank board of wood of certain length achieve complex D curve by fixing its points. This curvature could be repeated consequently with the same type of wood and dimensions. This board could be then glued together, fixed by clamps and later milled by advanced CAM.

0 Model for prepared for the fabrication. The upper branch is made separately and then glued together.
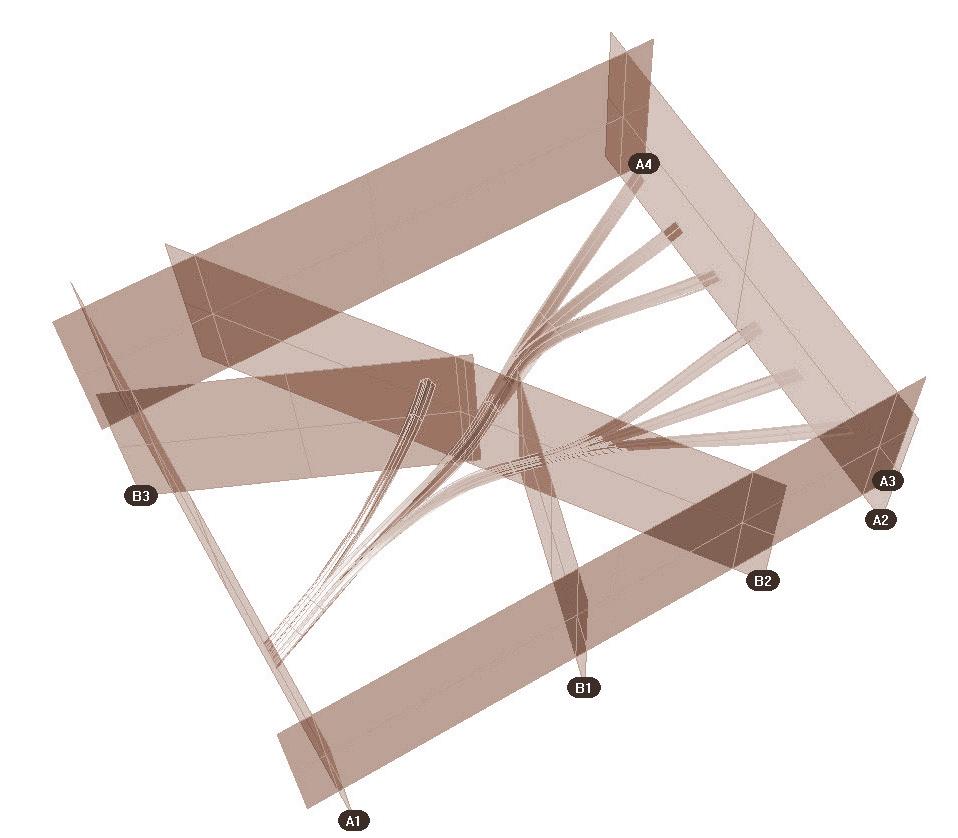
02. Model for prepared for the fabrication.
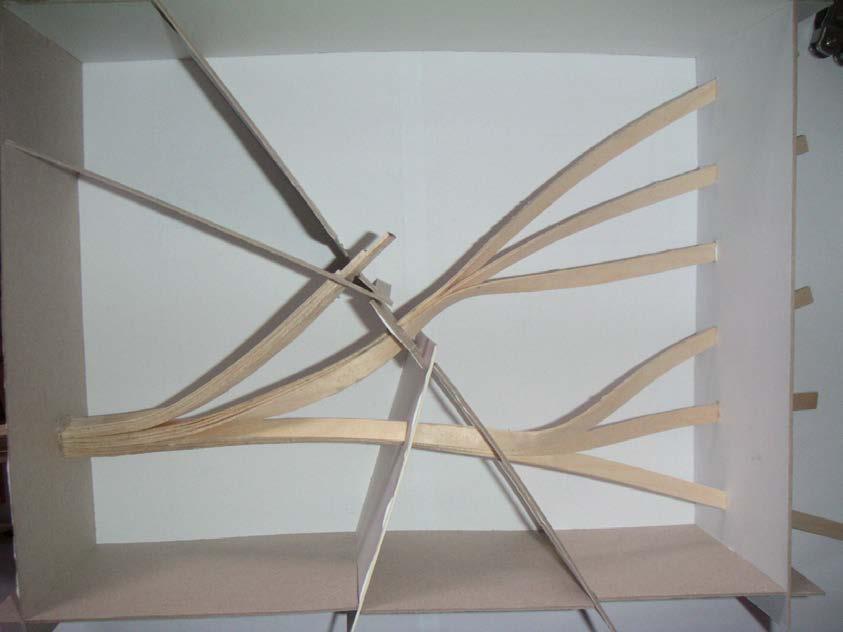
0.
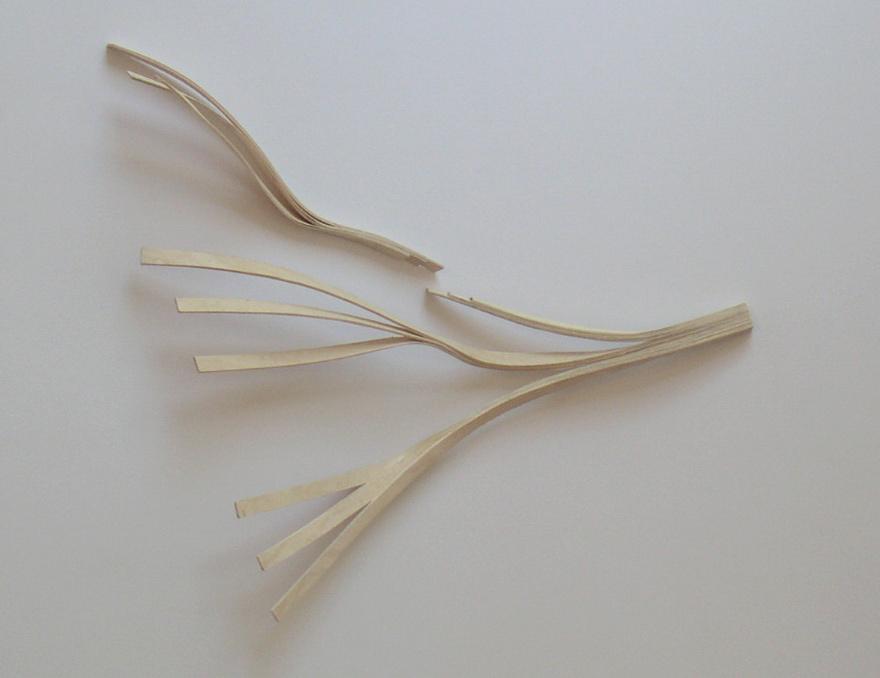
04.
The model of D branches was made in order to understand the limits of this technique. The model was built in scale :20. It was made of layers of veneer. This model could be scaled up because it is a model made by a composite material but it should be also teste don the bigger scale.
There were 9 clamping points and one base point of the tested model. The two images O, O2 showed the digital model of the structure with planes that determine clamping points. The figures 0, 04 have shown the finished model and scaffolding that held clamping points. The scarf joint was made because of the space requirements. These joints were also inteded to use in the assembly of pieces for buildings.

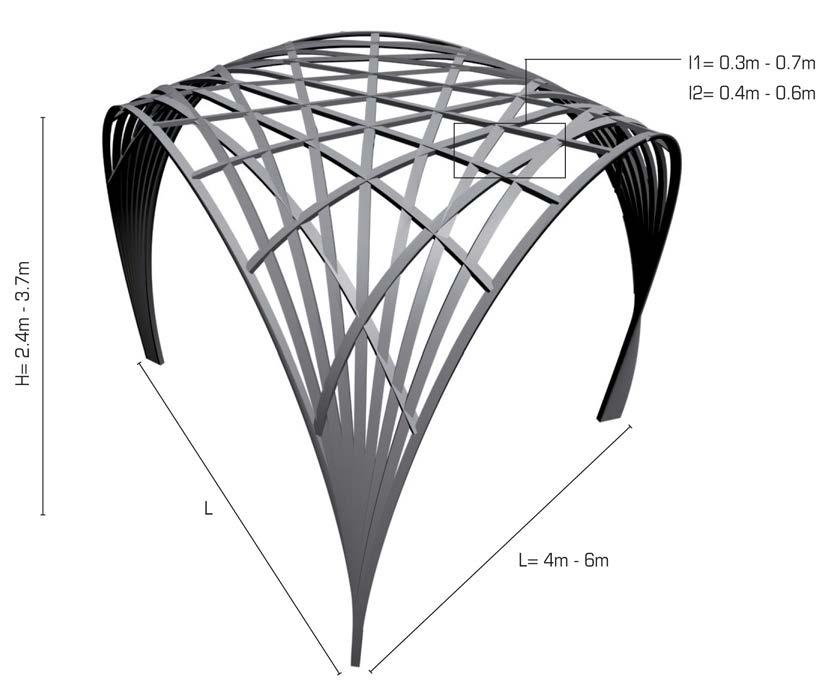
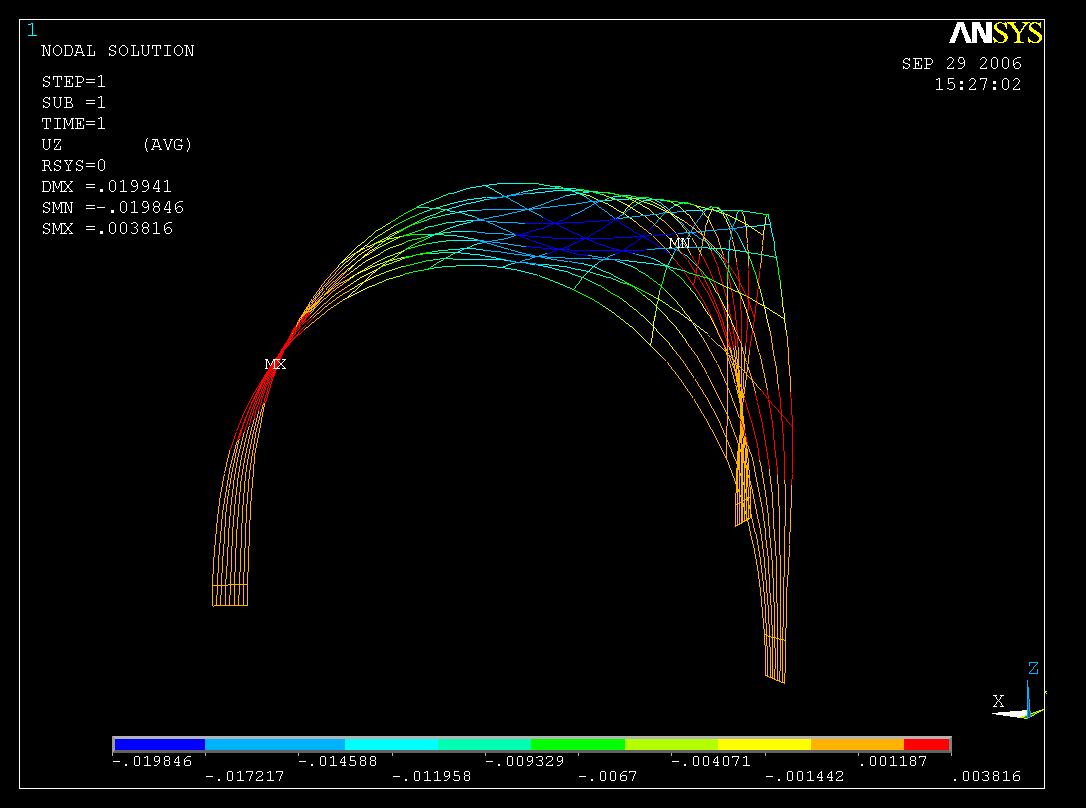
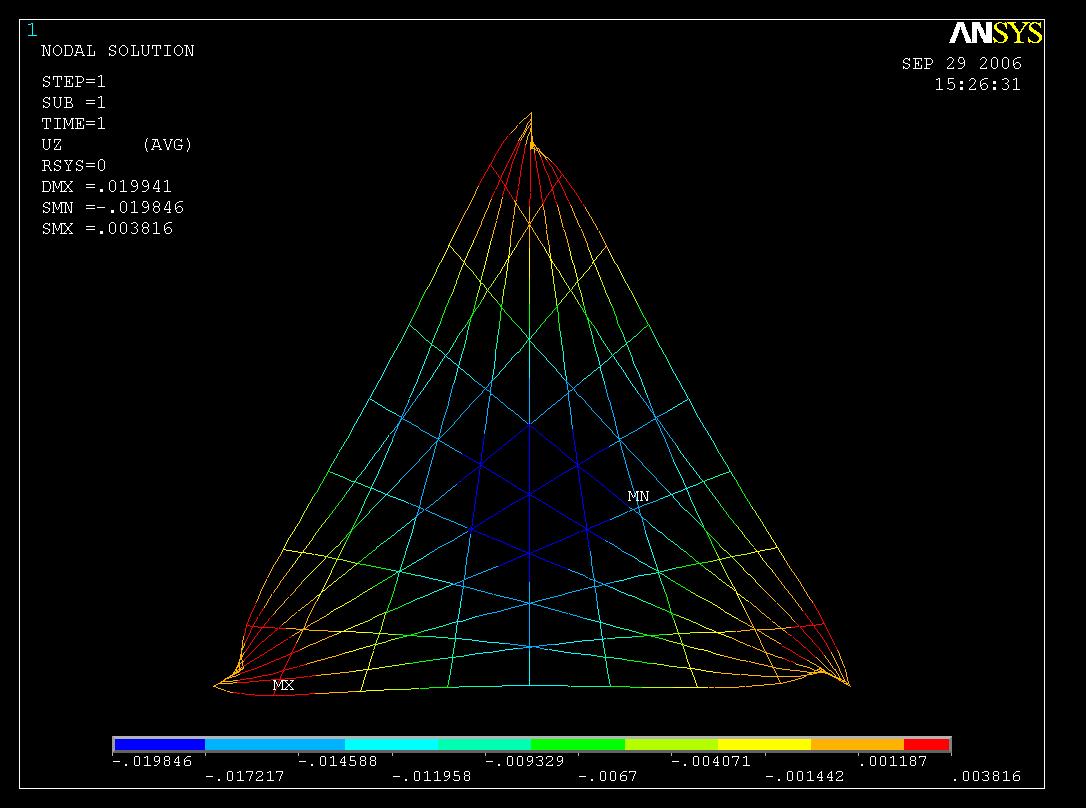
The second path of the Experiment 0 was assesed as the most successful. Here, the boundary between surface and support was blurred. Laminated timber branched out from the ground point and form an intervowen surface that can resist both tension and compression.
The design of macrocomponent was similar to the Experiment 0a. Here, there is not a plane that acts as a slab but there are only control points that determine the shape and also theporosity of the surface. 0
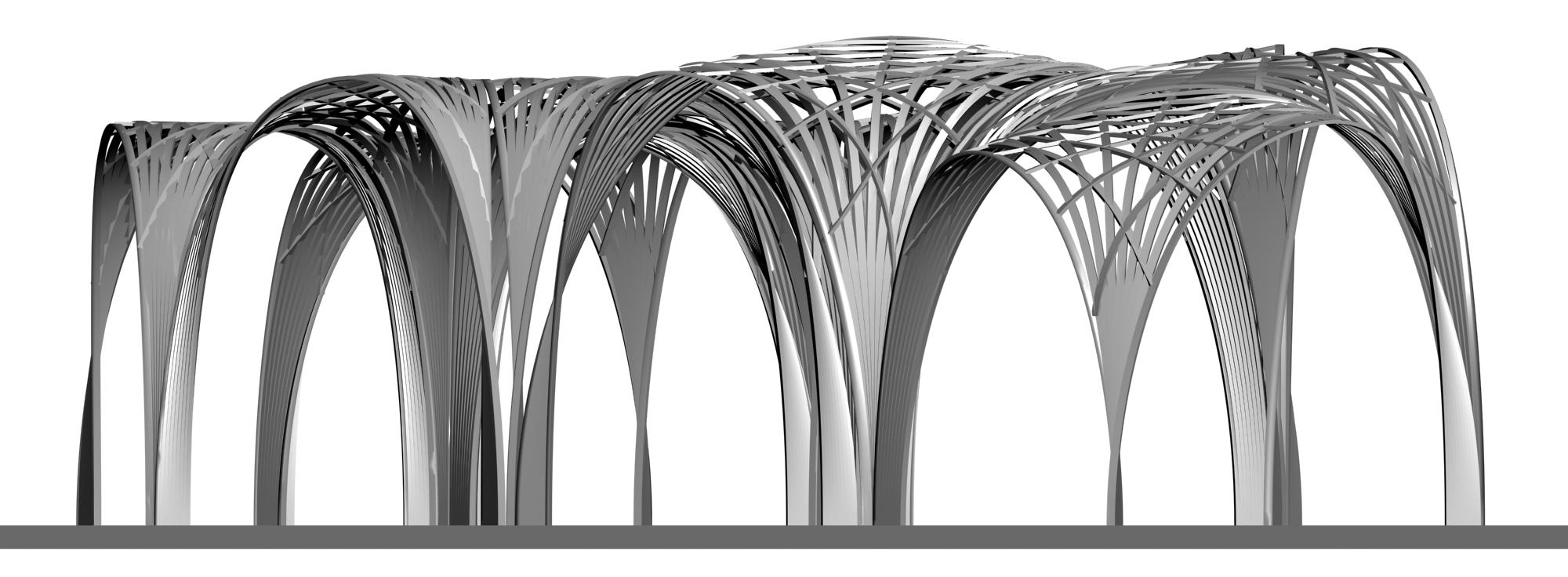
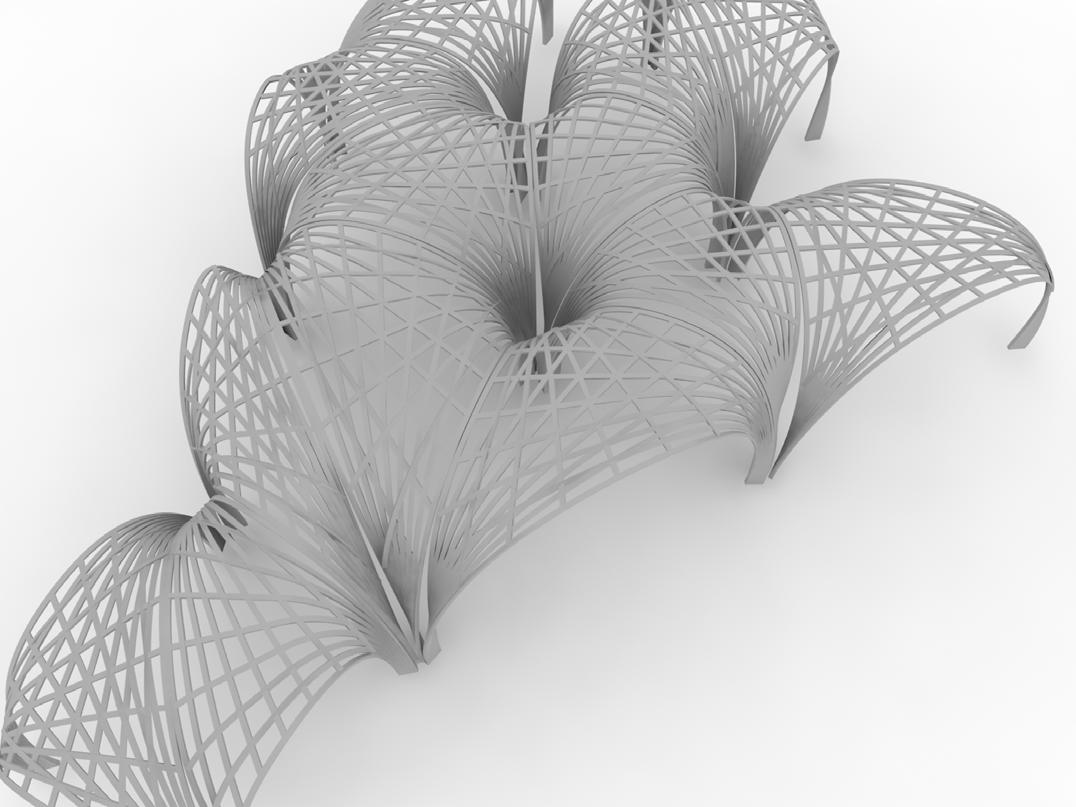
There was made the test design in which to examine the potential of L-system proliferation.
The significant architectural control is achieved by mastering parameters that determine the proliferation of the structure. This issue consists of the triangulation of the site and also the manipulation and number of control points (also clamp points) in the laminated structure. The triangulation of the site is important for the height of macrocomponent and also for the density of branches.
The material process followed the logic from previous experiments. The idea was to assemble large pieces off-site and then connect them on-site. The connecting could be made by gluing ends in the vacuum sleeve. The space required for the sleeve was also one of constraints of the design.
Structural performance of the pavilion was tested on the macrocomponents and also on a part of the proliferated geometry. The combination of the FEA and physical test gave necessary feedback for the design. The framework outlined in this thesis is open for the high variety of parameters and could be later extended.
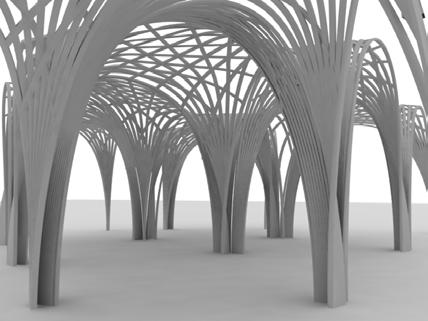
0. Site for the pavilion - given constraints by program and by configuration of the site.
02. Proliferaton strategy 0. Chosen starting point and geometry influenced by program constraints. Change in angle an length.
0. Proliferaton strategy 02. Main path (blue) influences smaller branches and bind other branches.
border of the site 00m
area of proliferation
The proliferation strategy of the geometry comes from requirements of the site and a program of the pavilion. The logic of the component is also informed by material, manufacturing technique and branched structure.
Branching nodes represent places where the “tree” structure is placed. These structures have certain properties and tectonics that are in direct influence with proliferated “map”. The behaviour could be a self-organisation with emergent properties.
The surface of an assembly is evolved from a branched geometry and follows two main structural constraints: span and density of branches. The “tree” structures could be also overcome without any porous openings in the area of other trees. As reference could be mentioned branches of mangrove supported by other small trees that emerge from heavy, long span branches.
border of the site 250m
angle- input from the site program constraints
R, R2 Reference points of the influence. The distance from these points influence the proliferated “map” on a site. The distance between branching points is different and therefore span of the final structure varies. Also the angle of the branching node is changing according to the distance from reference points.
S Starting point of the proliferation. Designer choose the location according to the “top - down” strategy of the design. There could be several starting points on the site.
Algorithm responds to the borders of site and to the points that are generated by this algorithm. The Start point and end points were as an input. Then paths of branches could not be crossed.
Input for the proliferation:
Topography + Obstacles
Spans of the structure
Distances of the support
Opening for the natural light and air
The role of the designer is in choice of the parameters and affection of the proliferated geometry by further strategical steps. One of these strategies is introducing higher degree of attracting paths gained from the nested form-finding. In experiments with threads of various thickness dipped into a liquid is observed that thicker threads bind more threads together and rapidly change the direction of paths.
In case the designer is not satisfied with generated model, it is possible just change values of parameters and run routine again
In this thesis there was the simplest mode explored. It meant Start and End points of the site as “entrance” points.
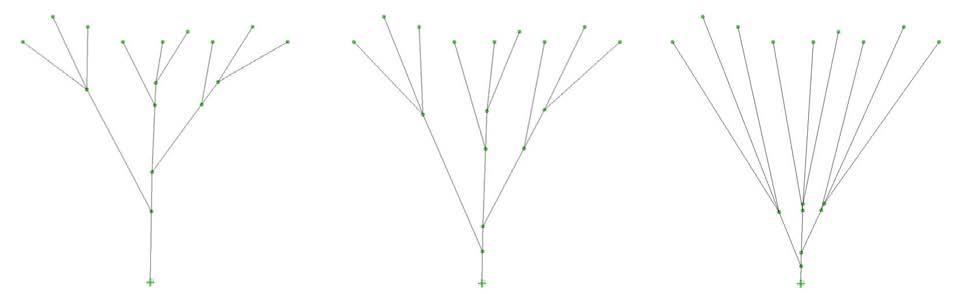
0. Various tree structures connecting points with a base point.
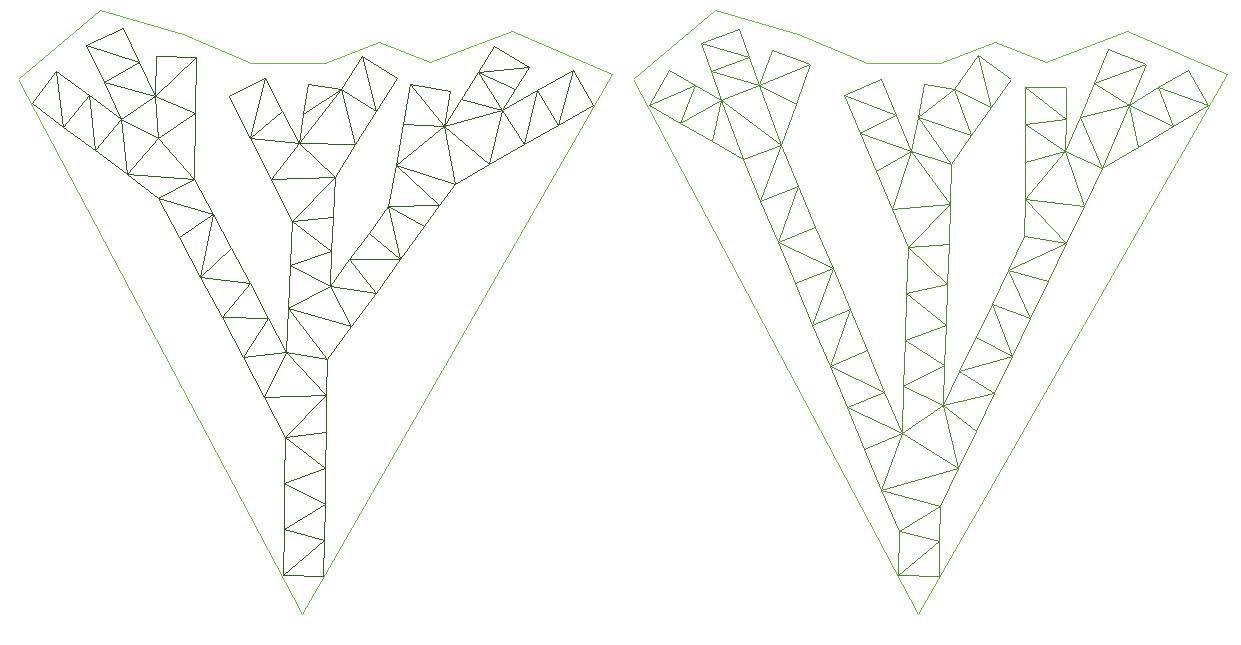
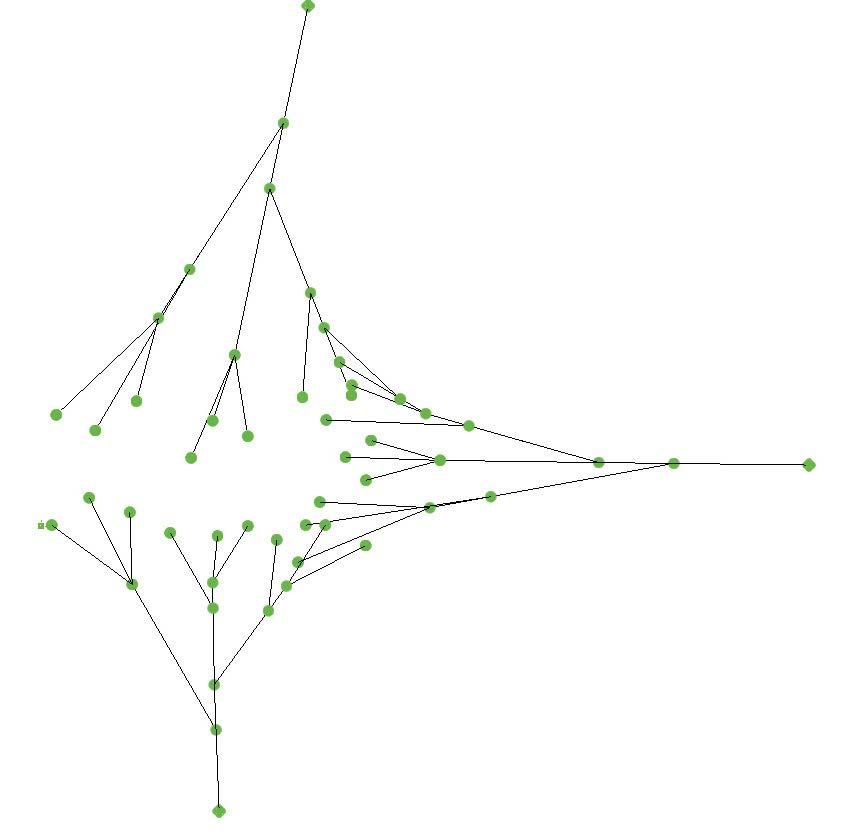
04. Strategy for the approach from the Start points “S” to the reference point “R”.
Example of the proliferation. Fig. 0 represents variety of paths leading from base point to points of branches. The branching lines traced the pavilion area. This area was then meshed into triangles which determined locations of supports. Fig. 0 explains the dependencies of the building on the site.
The design strategy shown on figures 04, 05 explains the aim for the whole pavilion. The site with entrance points S, S2, S and growth of pavilion towards the point R.
02. Triangular site... 70 m2. Area of pavilions: S- 704 m2, S2- 764m2.

0. Strategy for the proliferation: the grid of “map” (green points) and heights of the macrocomponent.
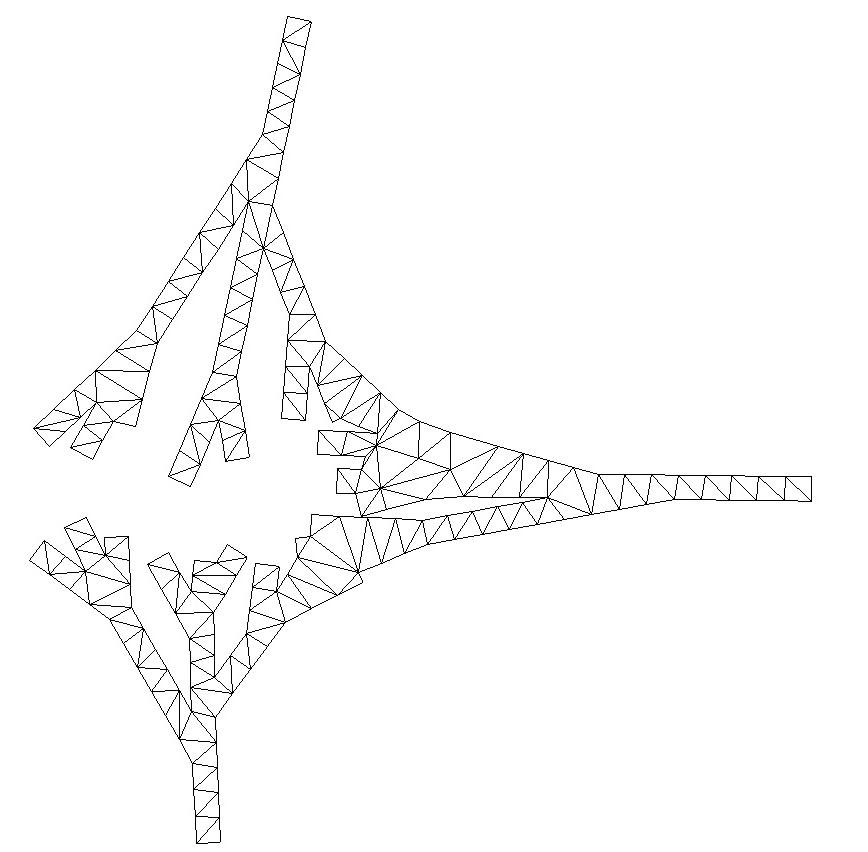
05. Meshed plan of the pavilion.
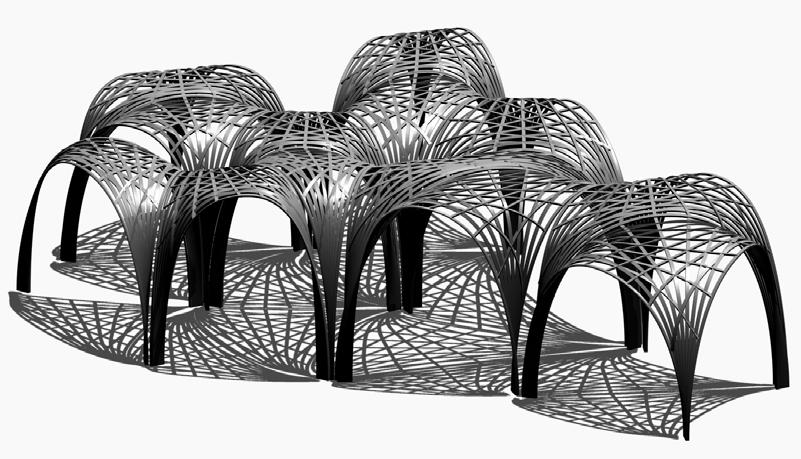

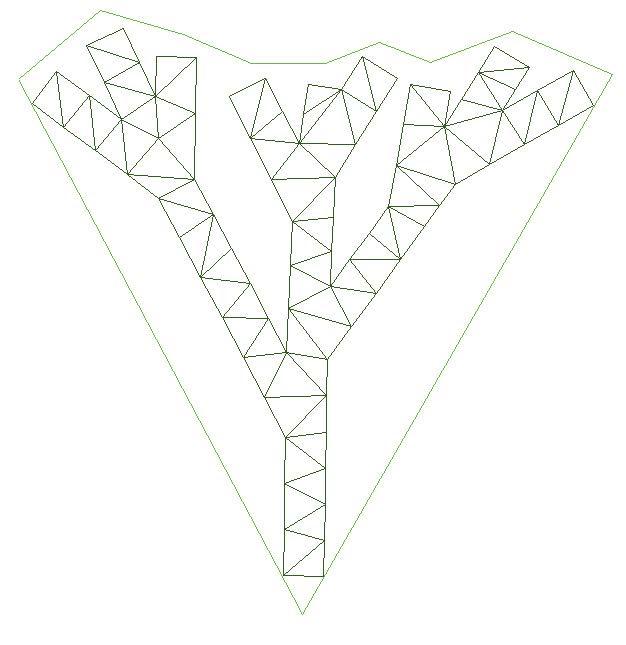
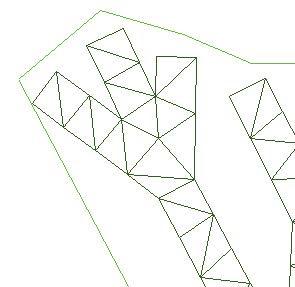
Dimensions of triangles determine the size of the macrocomponent. Macrocomponents consist of laminated planks in certain grid. The size of the grid varied in boundaries constrained by the space for manufacturing and also by the structural performance. The light studies shows that the impact on environment must be considered and the grid could modulate significantly light under the structure. The more control and more blurred shadows could be achieved by adding more layers and created then multi stored pavilion. The structure could be strong enough to bear the movement of people and could then branch into next level and get the input from the experiments described in chapter Concept.
Manufacturing Process
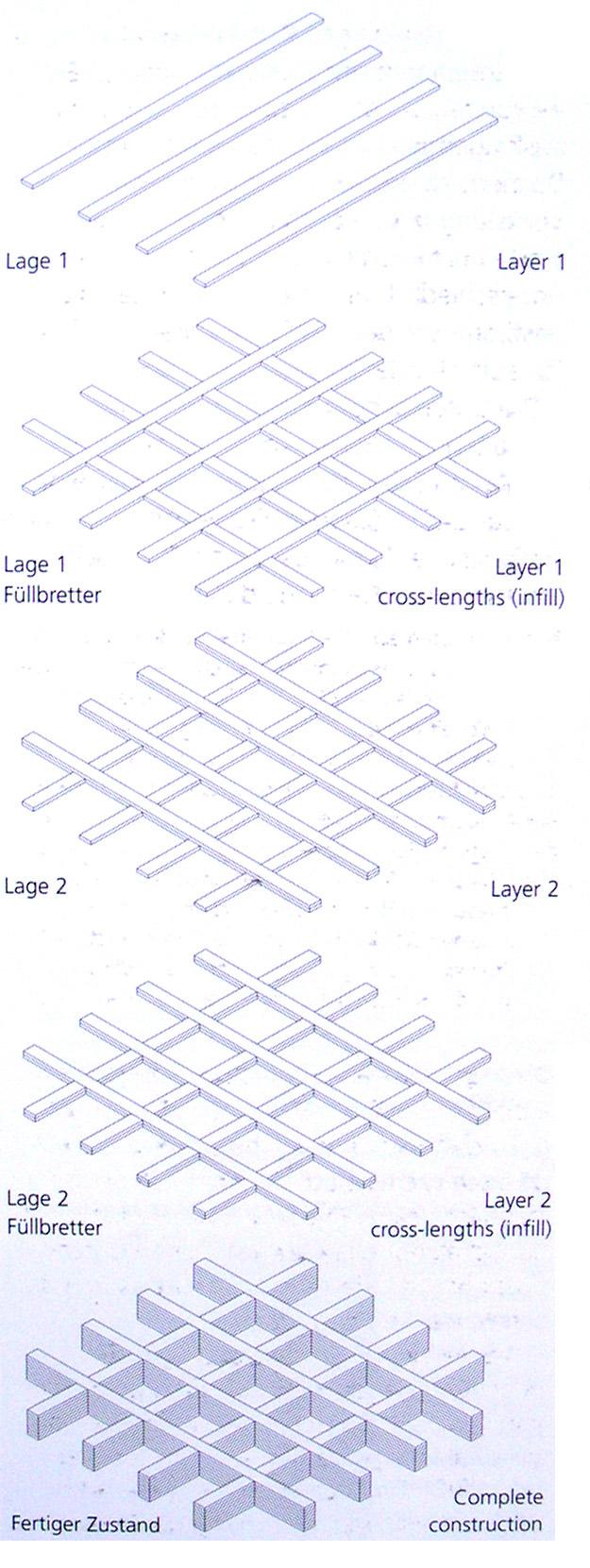
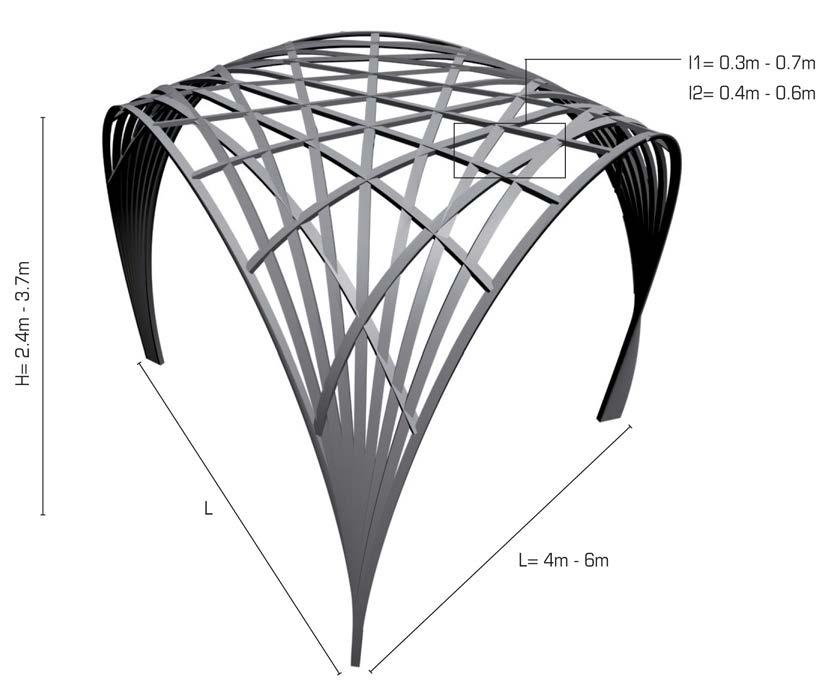
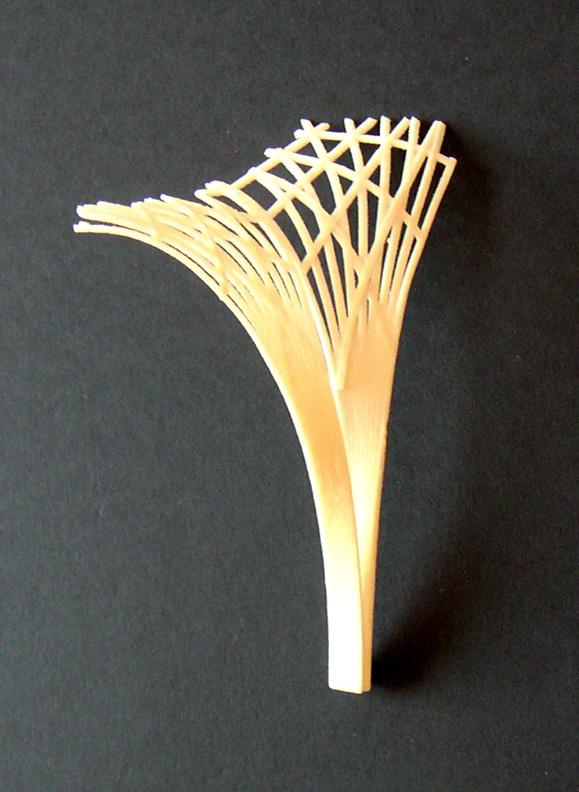
The pavilion was designed as an asembly from macrocomponents. Each macrocomponent consists of 4 pieces (fig. 02 - P, P2, P, P4). These pieces were intended to build off-site according to the transportation possibilities and then gleud together on-site in vacuum sleeve. Timber boards have its own length and dimensions and therefore they could be prefabricated by methods of form-finding- clamped on certain points and then glued together. The Expo Roof by Thomas Herzog is shown in detail on fig. 0. The process of dealing with timber lattice shell made in the company Finnforest Merk was used as the direct reference for this procedure.
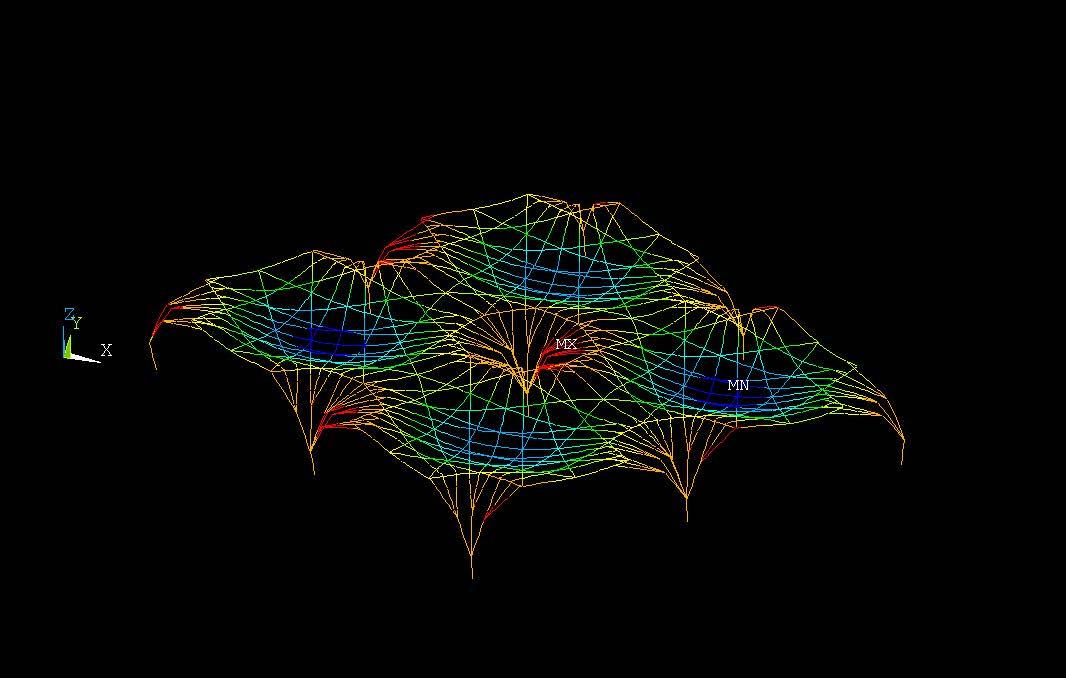
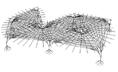

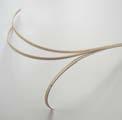
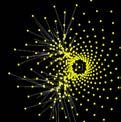
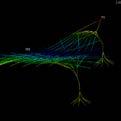
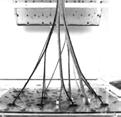
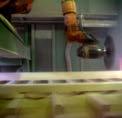
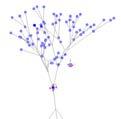
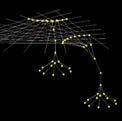
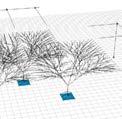
If physical tests with laminated planks preshaped and glued together are executed the important feedback for the relevant structural analysis could be set. The triangle between form, digital geometry and actual physical behaviour could be established.

The dissertation is mainly focused on the structural performance of developed material system. The feedback loop of the design is closed by evaluation methods that are presented in this part of the thesis. It is physical and digital structural analysis. The physical models provide information for the digital tools in terms of actual behaviour of selected components.
There were made tests with laminated timber. These tests studied the strength of lamination, flexibility and limiting curvature. This information were then compared to deflections of structure plot in FEA analysis of this complex structure. The first test was made in order to explore the flexibility of a single laminated “beam” and its limits the second two experiments represented two laminated pre-shaped beams. The laminations were made from the same type of wood - layered ply where the grain was crossed in 90°.
Material for the physical tests:
layers of birch ply (.5 mm thick - layers) glued together width: 0 mm
length: 000 mm
PVA glue
Digital analysis was made in engineering programe ansys - the tool for the finite elements method. Modeled geometry was imported to the program and then studied the deflection of the structure and compared to the results from physical tests. Although the normative values for buildings made of timber does not allow such high flexibility as were achieved in the physical modelling the interesting results could be made when one considers the flexibiity of the structure as an advantage of the design. The structural scheme presented here is the scheme for the pavilion loaded by snow and wind.
Values for the digital analysis:
snow: 0.6 kN/m2
wind: 0.5 kN/m2
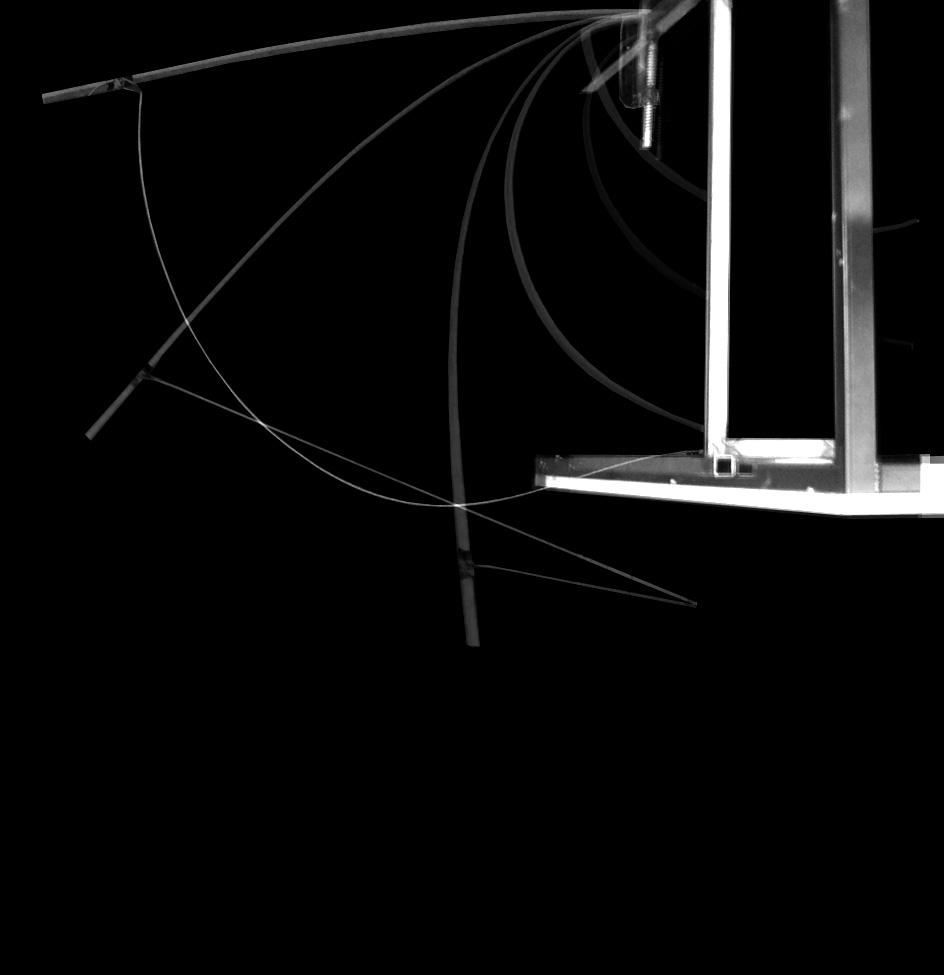
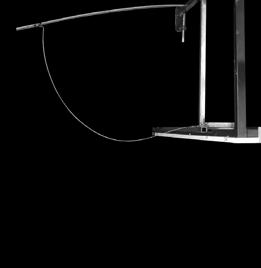
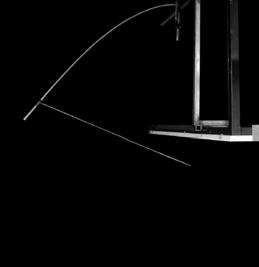

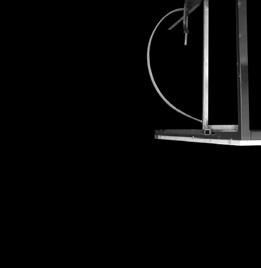
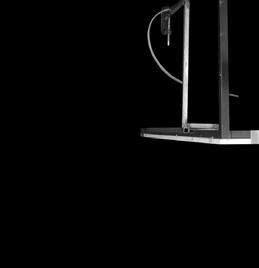
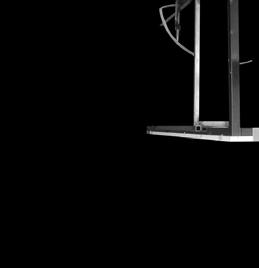
Material:
layers of birch ply (.5 mm thick - layers) glued together
width: 0 mm
length: 000 mm
PVA glue
The component was broken when there was applied force from the side of the testing model. The flexibility of the single beam was enormous. The interesting comparison would be when these single beams would be touching each other when load is applied. This scheme is not dissimilar from that in trees in forest. Branches of trees touch each other and that cause the complex whole that from the “distance” could be regarded as one piece. The emergent behaviour is significant.
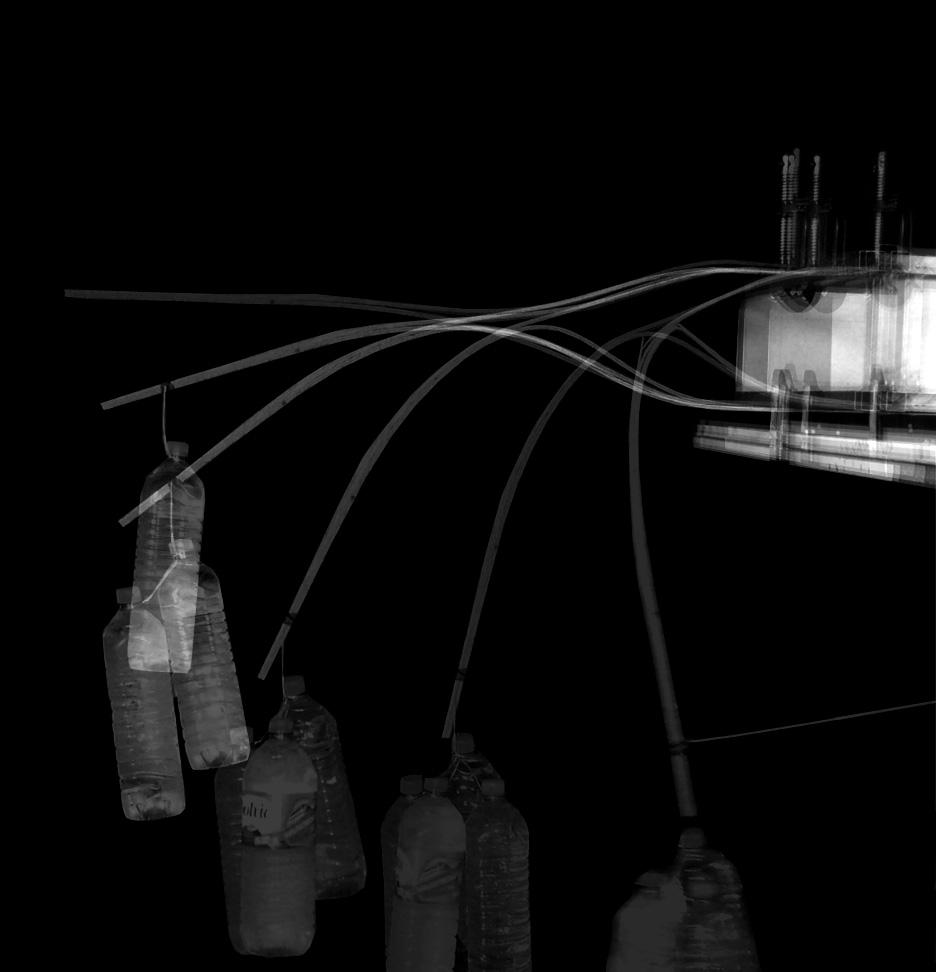
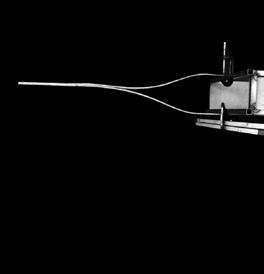
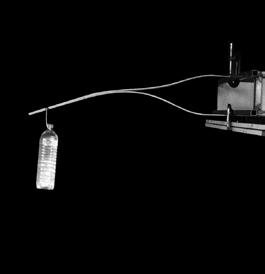
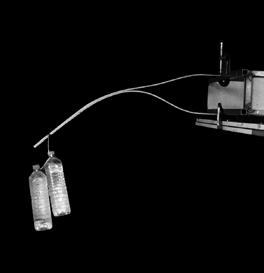
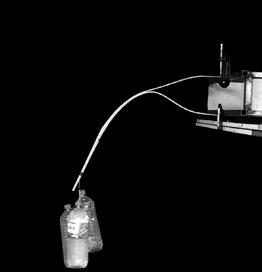
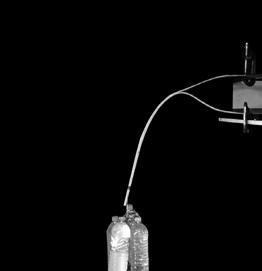
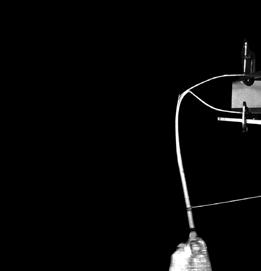
length: 000 mm PVA glue
Distance: 80 mm


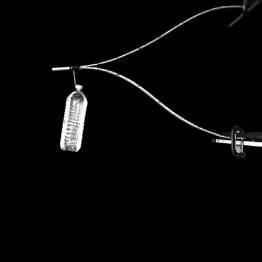
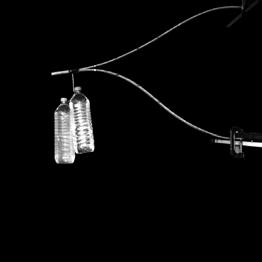
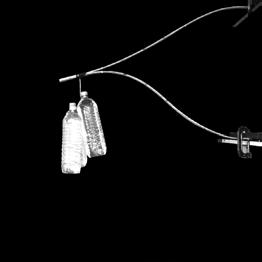

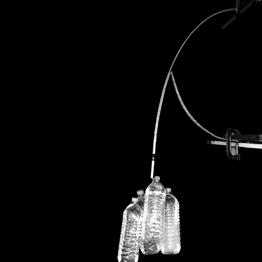
length: 000 mm PVA glue Distance: 600 mm
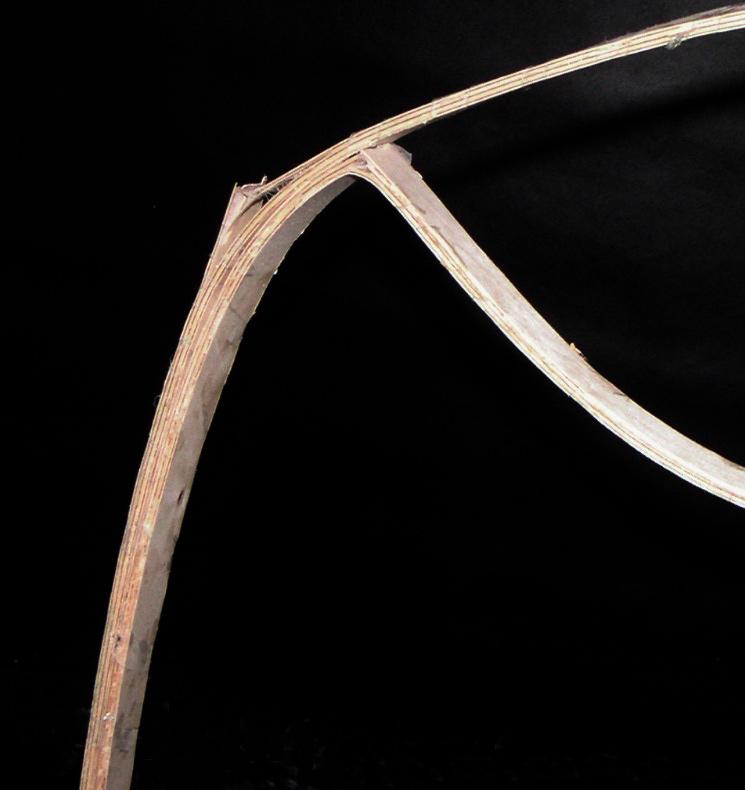
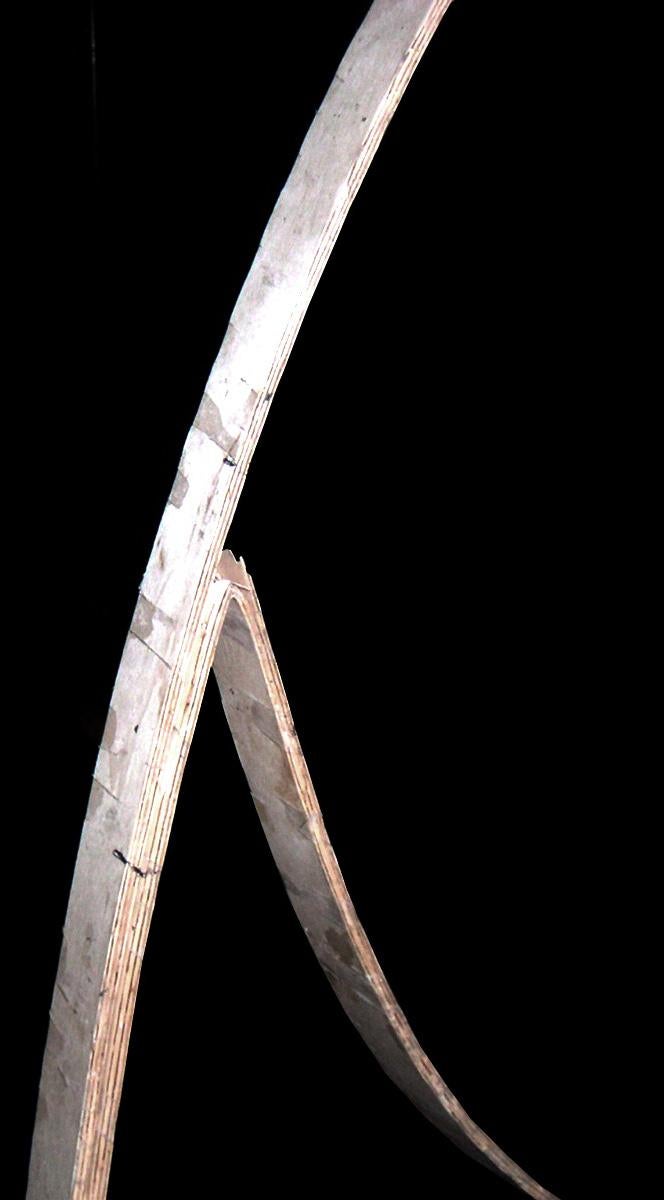
The physical test proved that laminated timber is highly flexible and can withstand forces that caused deflection that is not allowed in ordinary timber buildings. It was also obvious that dimensions of tested components could be used only as a porous surface of the “roof” of the pavilion not as a floor platform loaded by loads for floors in buildings.
Fig. 0 and fig. 02 presented details of cracks in the laminated timber. The Experiment 02 (fig. 0) had distance between laminated timber beams 8 cm and by applying force 60 N the structure was still flexible. After introducing side force the component broke. The detail showed that there were torn fibres that acted in tension (upper side of the component) and also in compression (lower part of the component). The other image with a distance of 60 cm was loaded by 60 N and lower part of the component was broken. These tests presented the potential application of connected branches. And also gave the idea about constraints of distance between branches and attaching them. The structural analysis is based on the premise that glue has the same structural capacity as wood. In reality this has to be reformulated and restated but it is possible to use that for the initial exercises and tests.


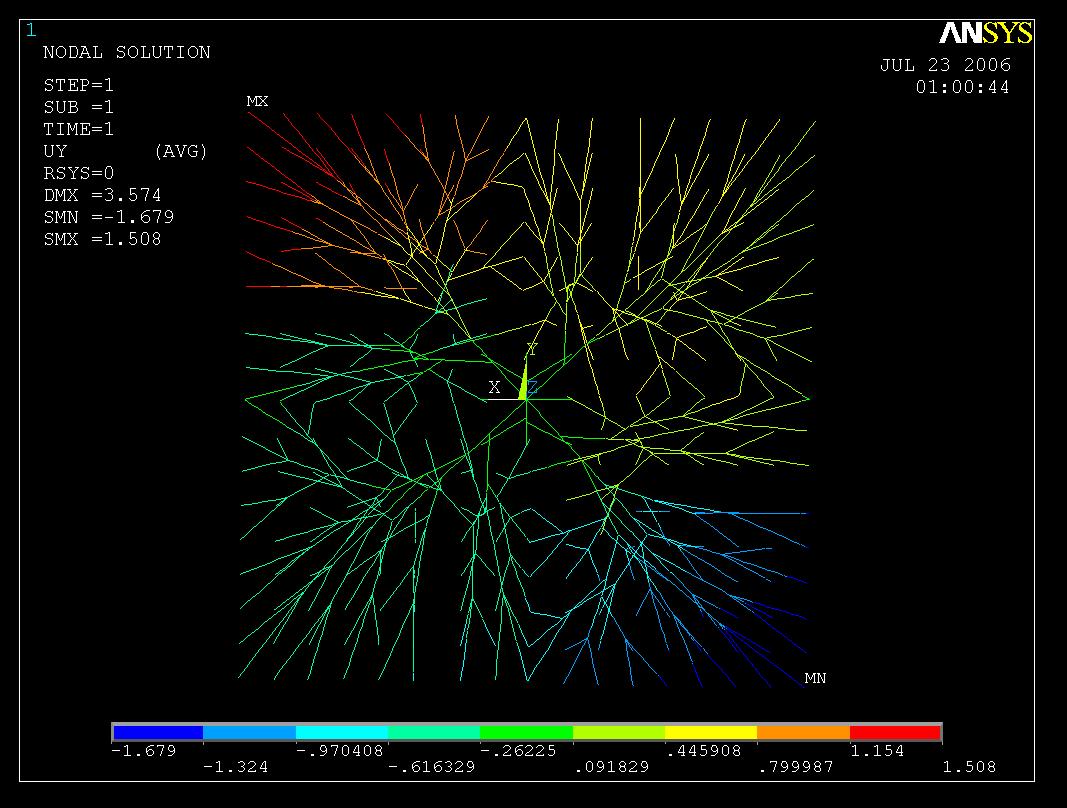
Digital experiments 0 and 02 were devoted to the models of material system described in the chapter Form Generation in Experiment 02. These experiemnts had their own hypothesis and were assesed as single beams that branched out from a “trunk”.
The images on the left - fig. 0, 02, 0 were analysed under self-load only. The deflection of branches in direction of the Z-axis was enormous. A possibility was to join one tree system to other trees. This assembly was then able to bear itself.
On the following page there are dimensions of sections used for the analysis of the experiment 02a. Experiment 02b was adjusted according to the values gained from enalysis 02a. Branches were shortened to values that were able to bear themselves.
Displacement under the self-load analysed by FEM.
E = 7e9 N*m2
v x,y = 0.2
dens: 800 kg*m
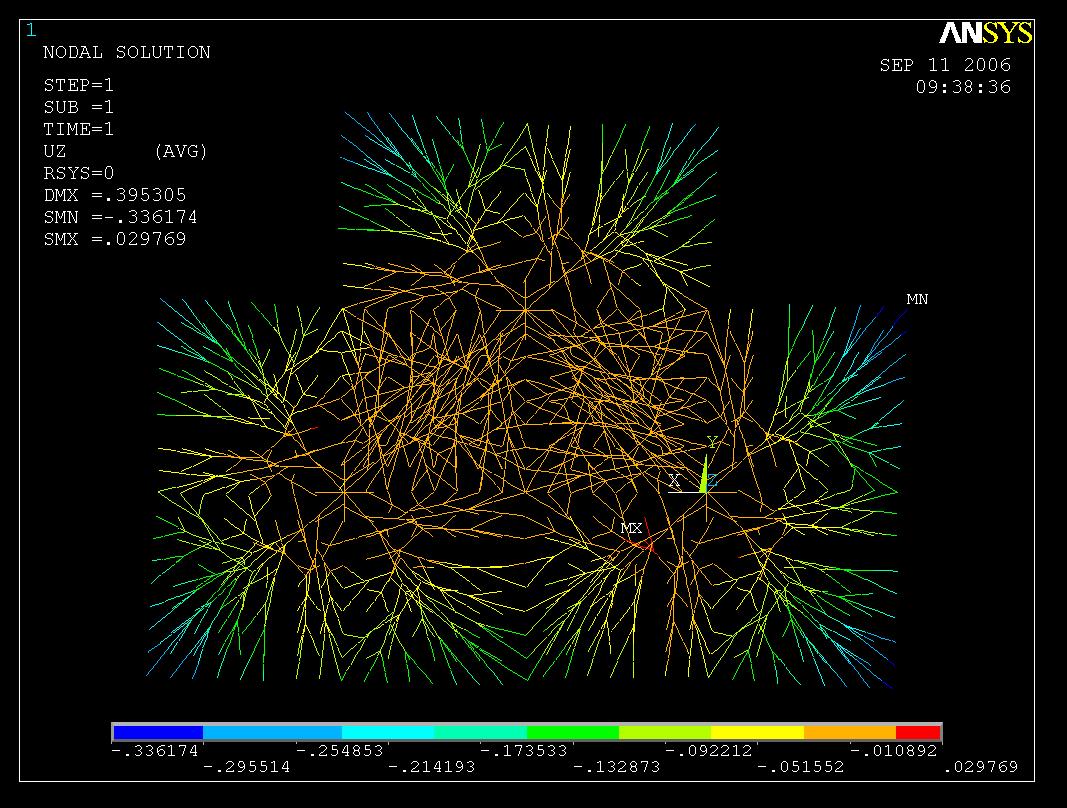
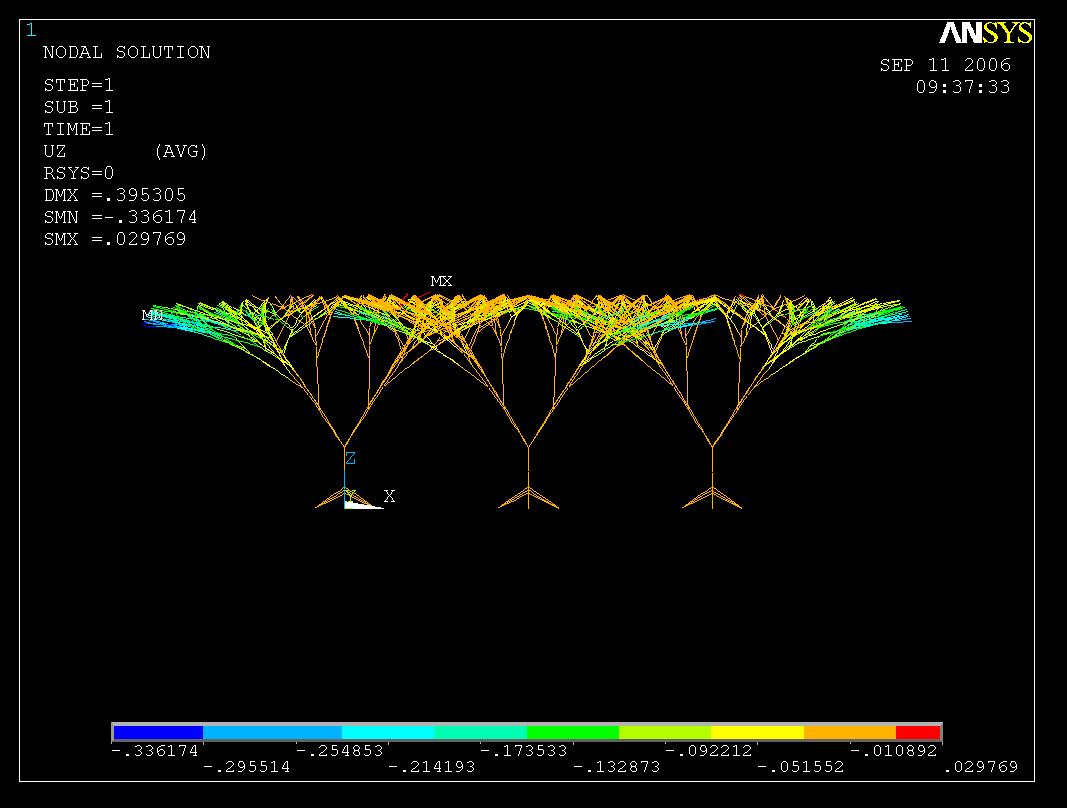
Digital Experiment 02
Displacement under the self-load analysed by FEM.
E = 7e9 N*m2
v x,y = 0.2
dens: 800 kg*m
Sections:
0... 0.06 x 0.06 m
02... 0.2 x 0.2 m
0... 0.54 x 0.54 m
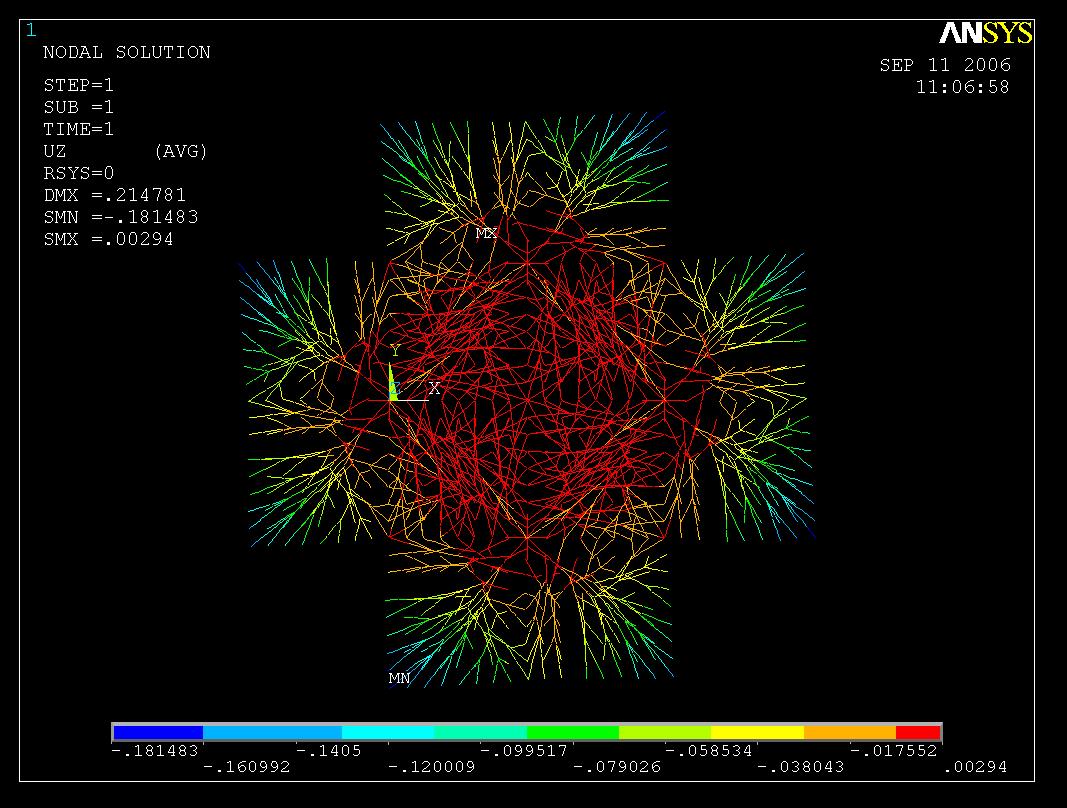
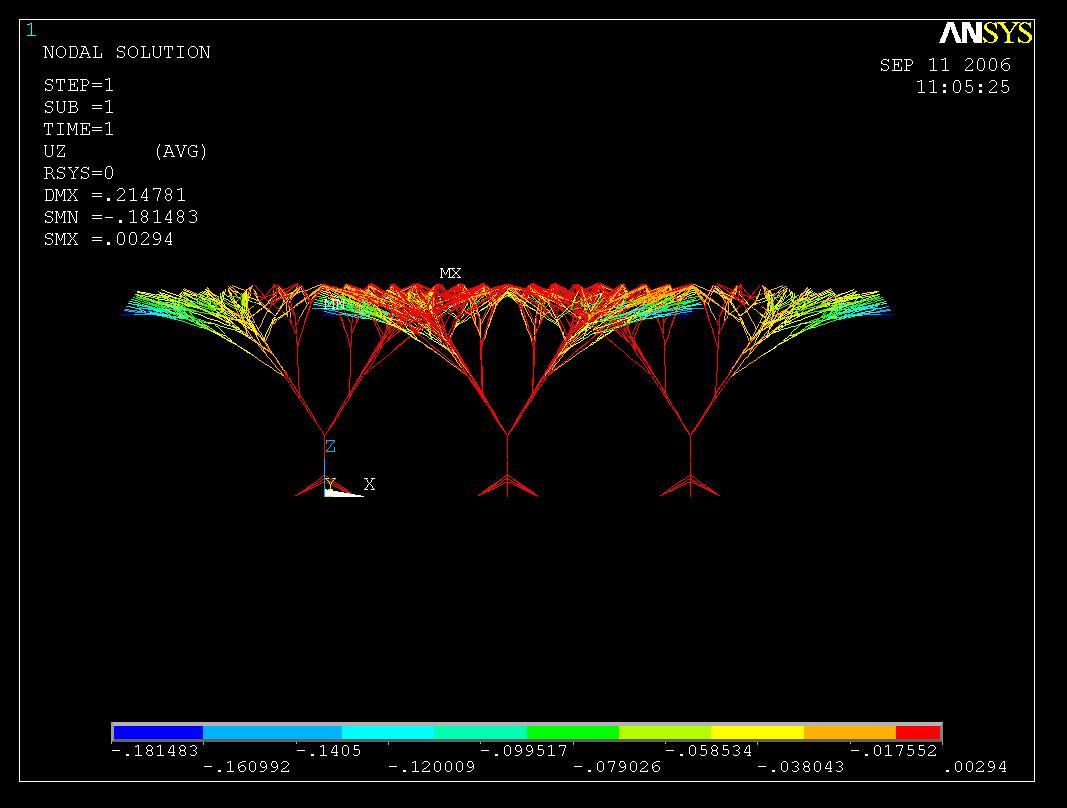


Digital Experiment 02a
Displacement under the self-load analysed by FEM.
E = 7e9 N*m2
v x,y = 0.2
dens: 800 kg*m
Sections:
0... 0.06 x 0.06 m
02... 0.2 x 0.2 m
0... 0.54 x 0.54 m

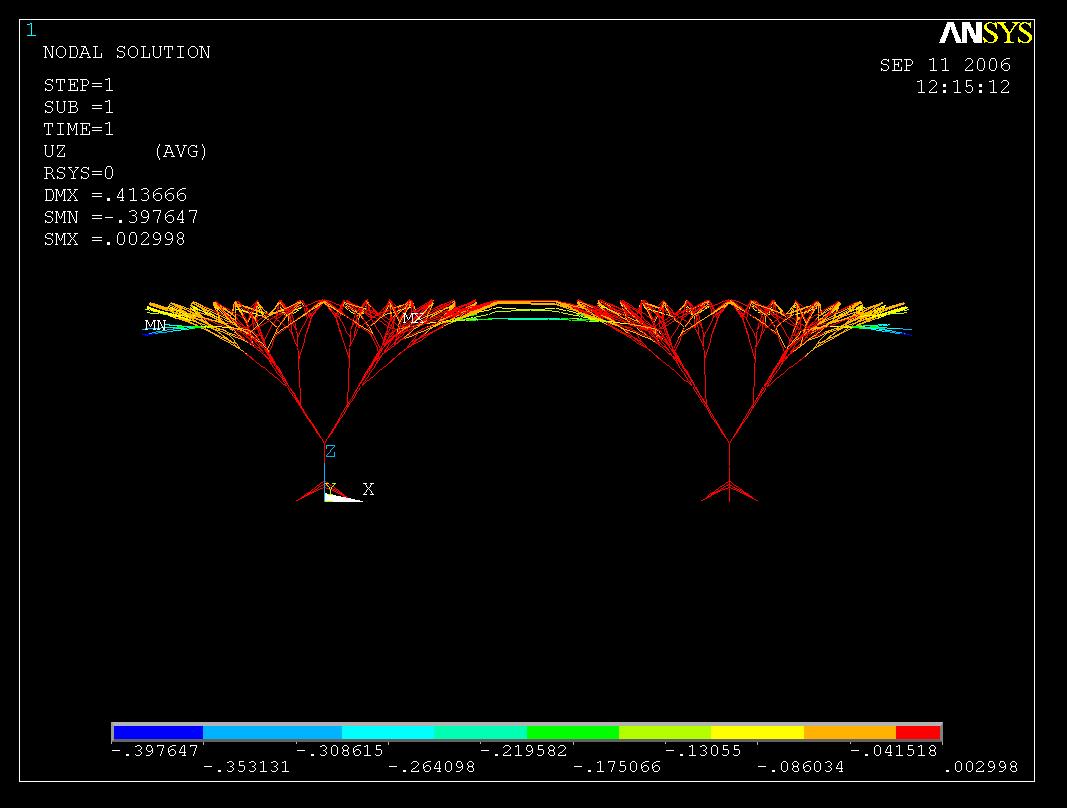
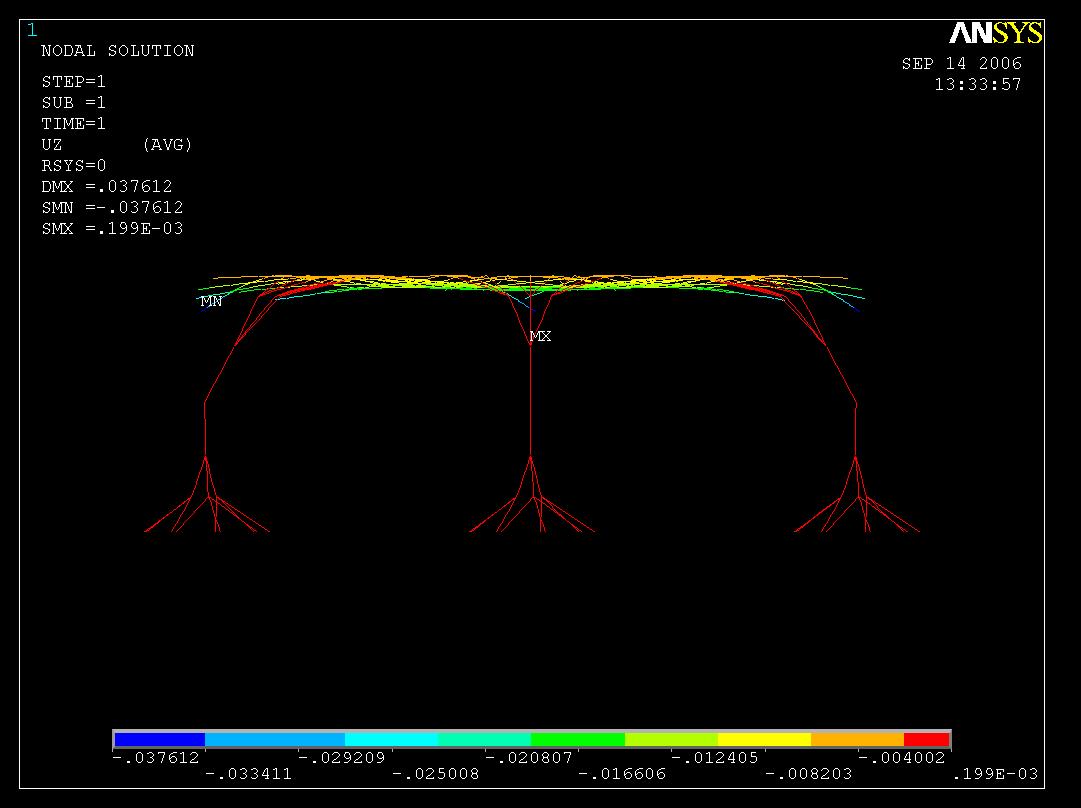
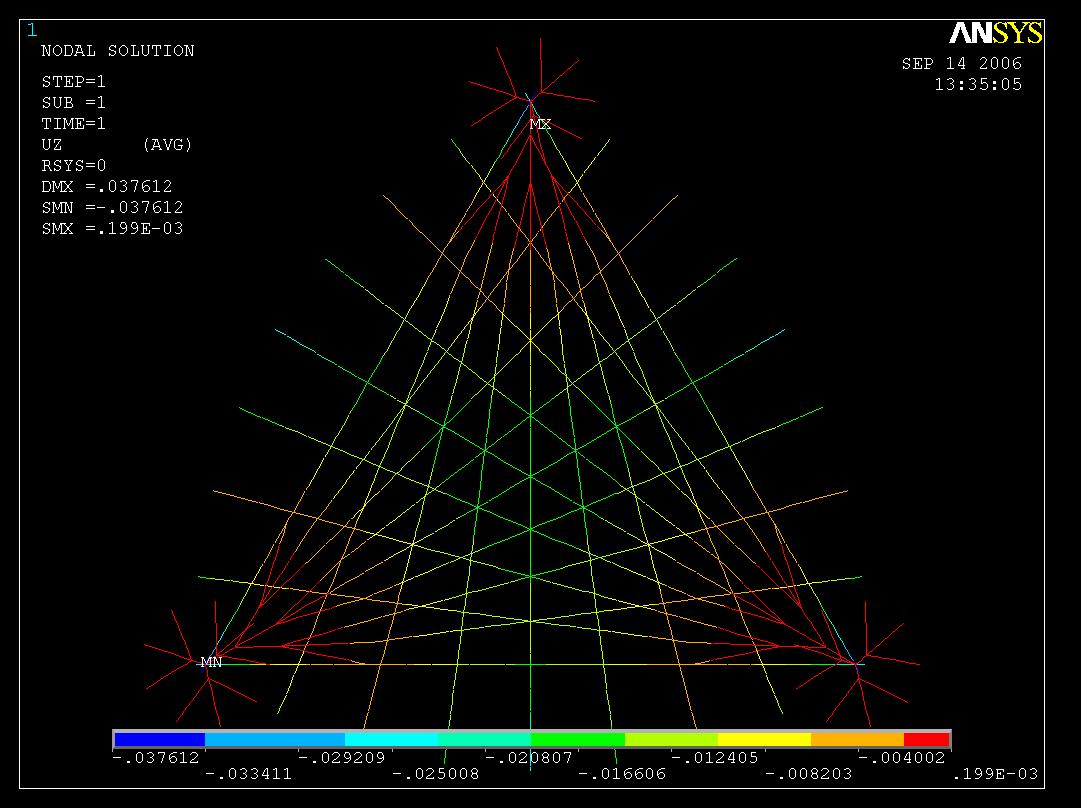
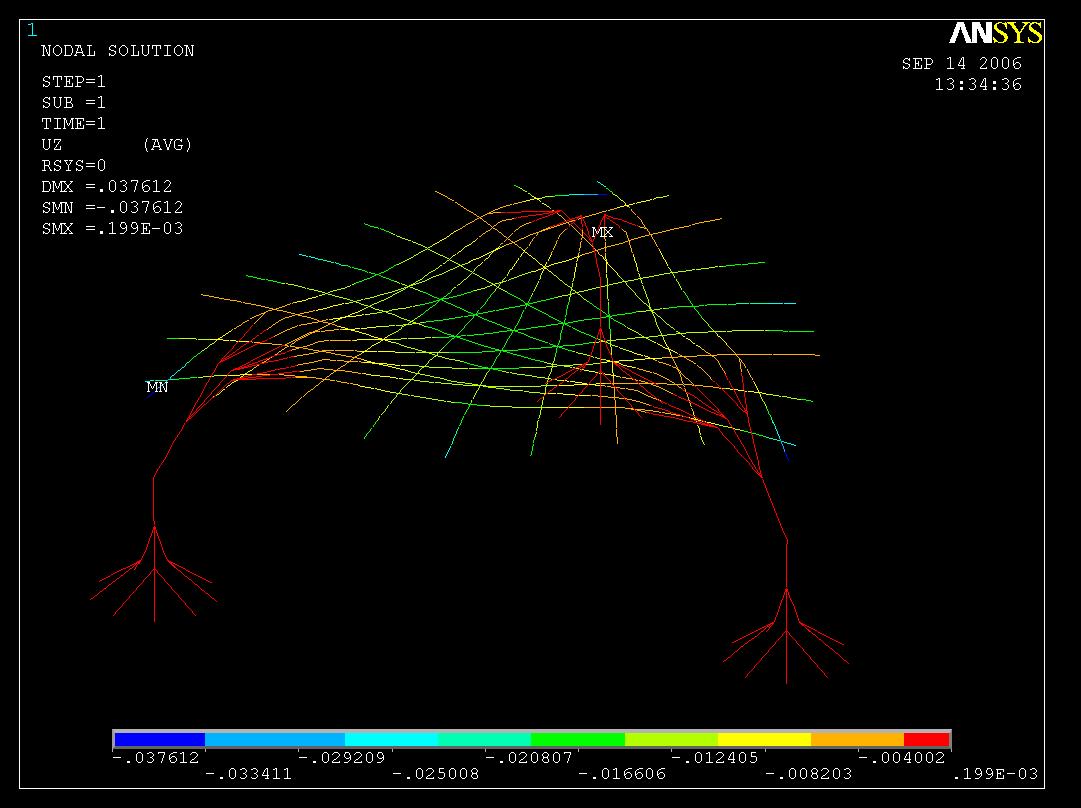
The Experiments 0 were executed in order to get precise dimensions for the Experiment 0 in chapter Form Generation. This material system that was found as the most succesful was expressed and analysed as beams that were interconnected. The aim was to create continuous porous surface that is more vector-active than surface-active and these digital experiments proved that it is possible to constraint developed macrocomponent by dimensions. The difference between experiment 0a and Experiment 0b is in the distances between supports in plan. The consequent development of the macrocomponent was made as the dependance between hight of the structure and distances in plan. It maintained the same scheme with the same sections. Due to the complex connections of laminated planks was achieved a redundant structure (redundant in biological terms) this was also proven by FEA.
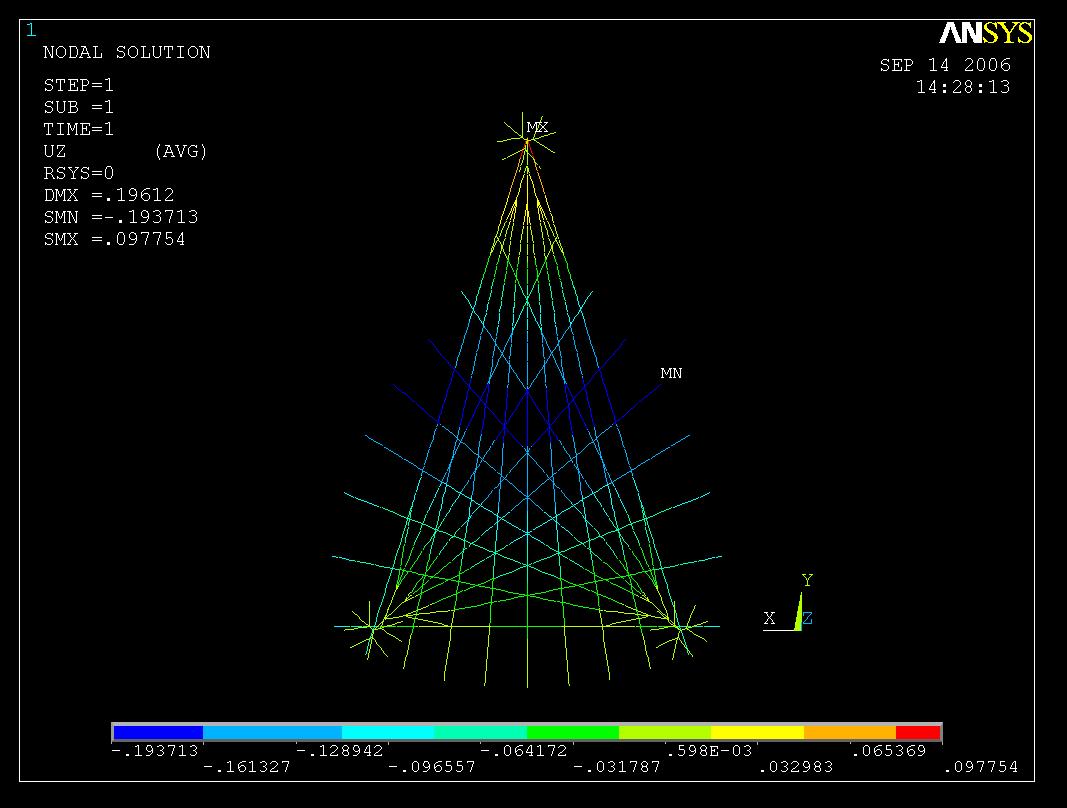
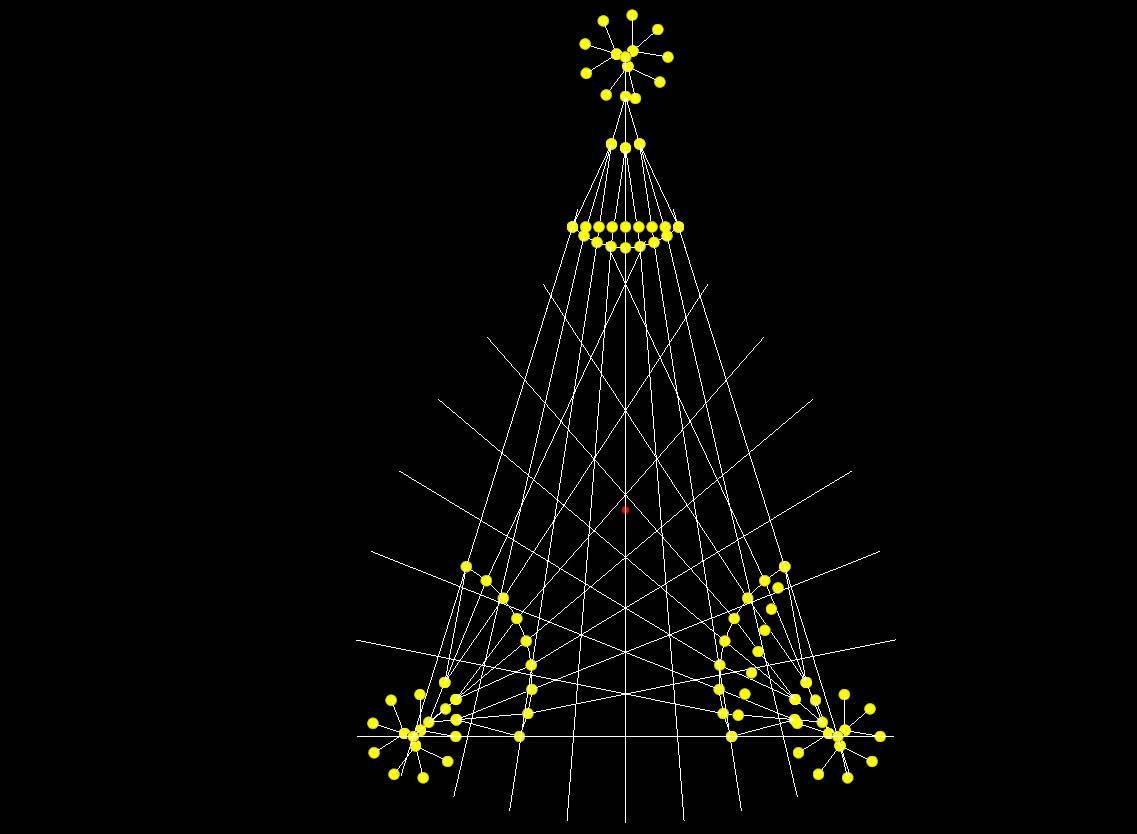
Limiting plan dimensions for the macrocomponent. The blue colour and the deflection in the surface between supports is dangerous for the structure and has to be avoid (fig. 0, 0, 04).

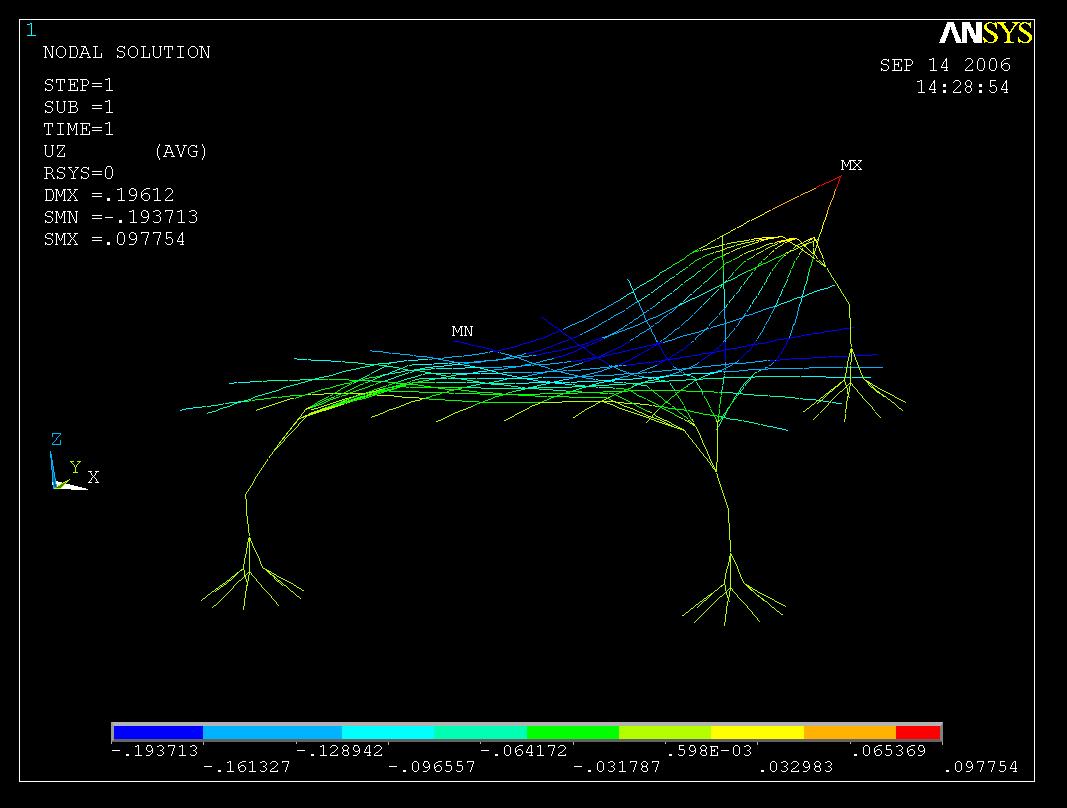
Digital Experiment 03c
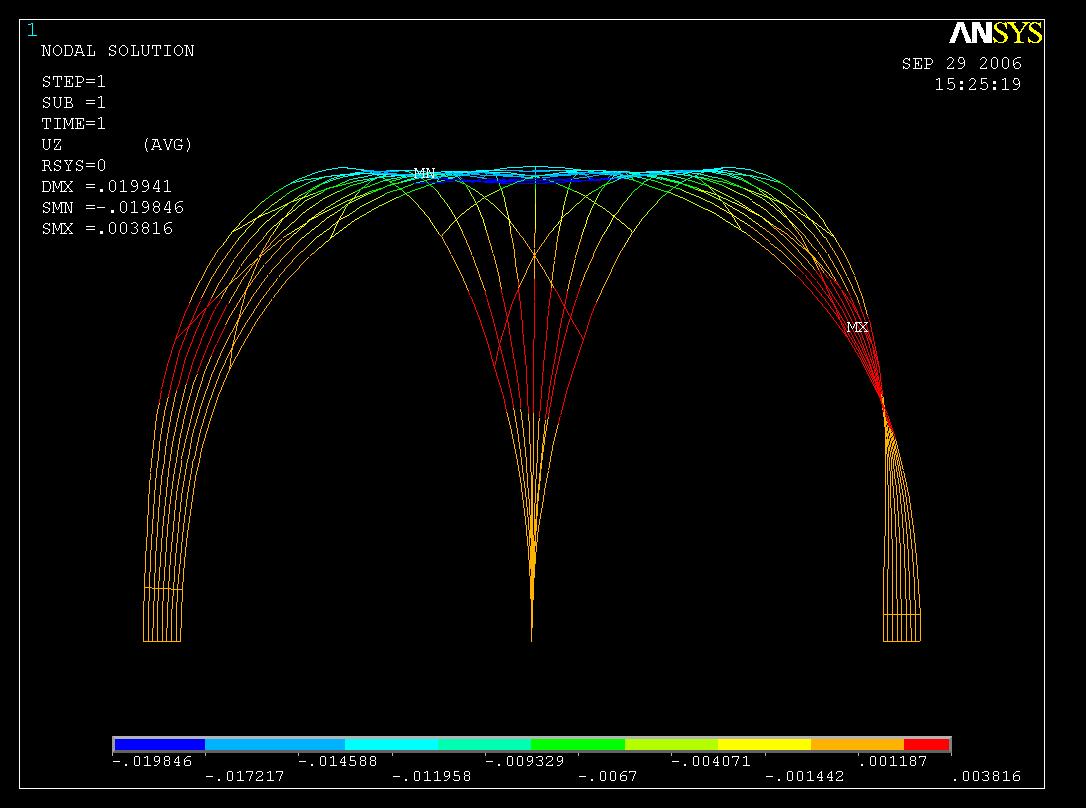
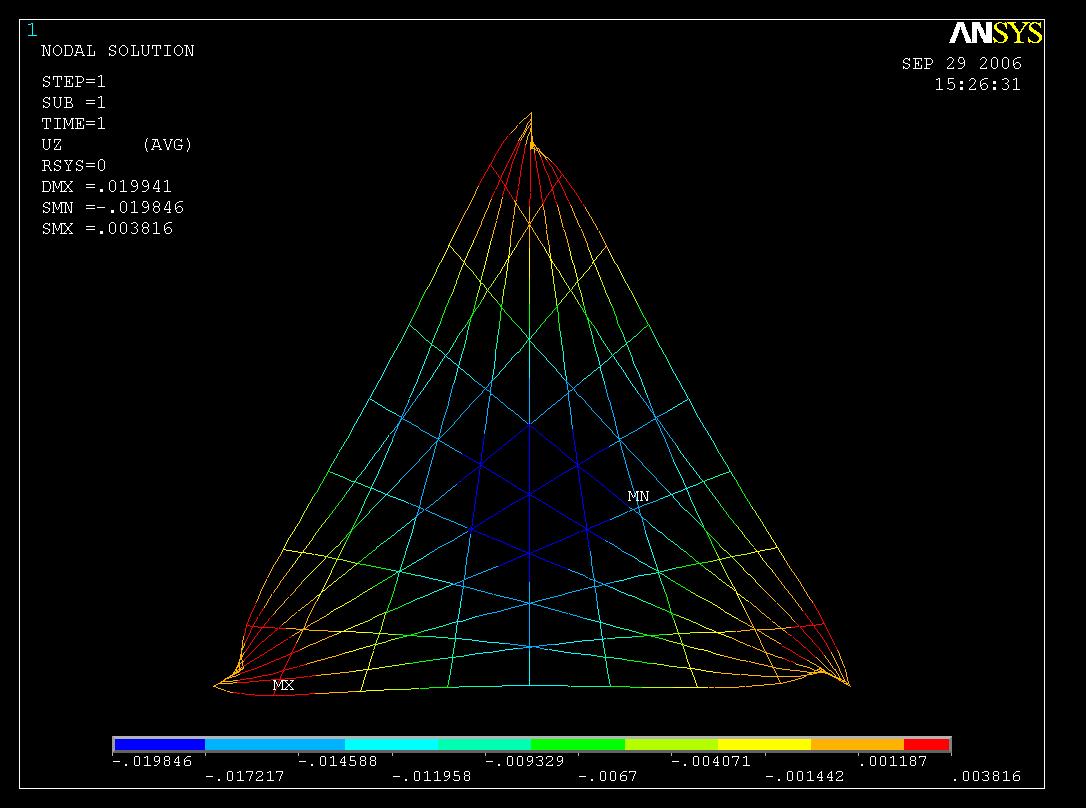
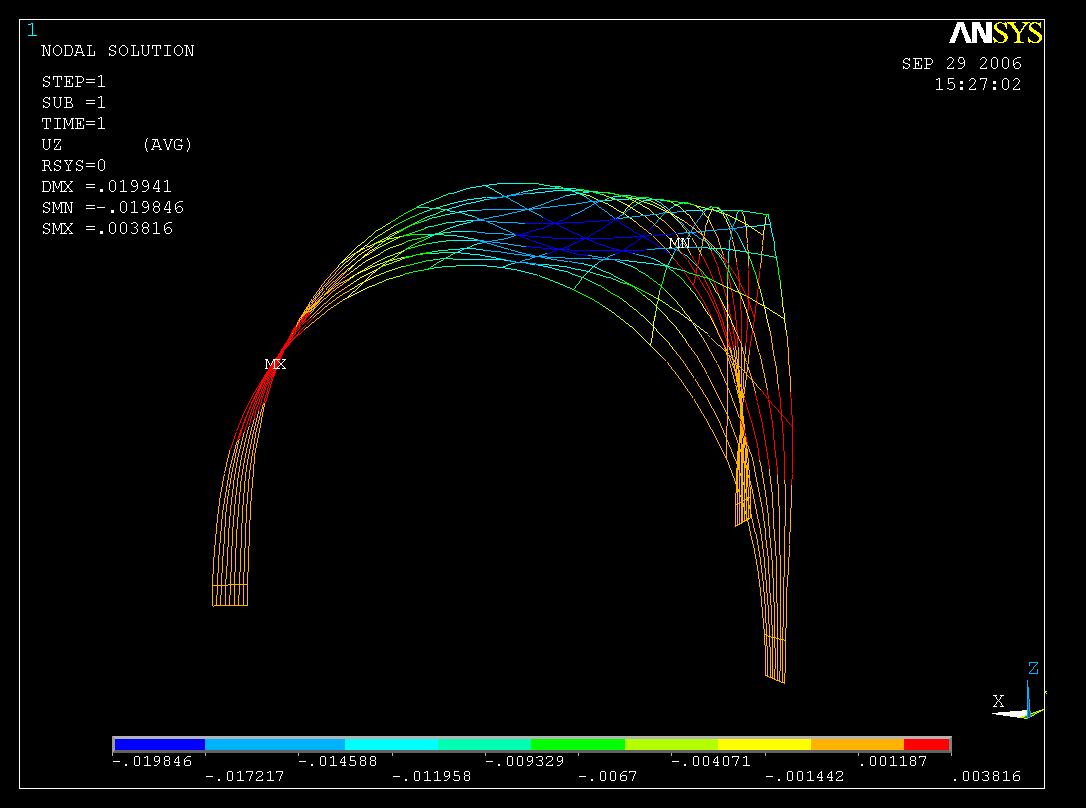
THe macrocomponent of the dimension (page 94, fig. 0):
L = 4 - 6 m
H = 2.4 - .7 m
The deflections and moments showed that the structure had high quality structural performance iven when asambled from small sections: laminated wood of thickness 4 cm and width of 0 cm.
Conclusion The presented research into the design methods and material behaviour presented powerful tools for architects. The convergence of computation methods and self-form of materials led to the and unique emergent structure. The self-form was explored in extensive use of form-finding and then used as an input data for algorithmic expressions of structure and proliferation on given site.
The potential of L-system proliferation was evaluated on the architectural - structural level and opened other areas which had not been explored (see chapter Further Areas of Research). The L-system was used as a tool for the significant control of space in plan and also in the form generation of components and macrocomponents. The achieved differentiated structure reacted on the site by associative geometry resulting in the successful structural performance. The structure followed the biomimetic approach of fibre directionality and redundancy. The redundancy in structure caused that the complex system was able to withstand dynamic forces in relatively small dimensions of components. The dialog between vector-active and surface-active systems was researched and instrumentalized.
The part Concept introduced important aspects in geometry and n structural scheme. Thanks to the generative parametric software GC very complex hierarchical structure could be developed. This complexity goes beyond physical modelling.
Digital form-finding could be than use directly to the fabrication. This procedure was successful deployed in the chapter Material Properties and Form Generation. The d laminated components were assembled to the macrocomponent and used as an unit for the proliferation. The dimensions of macrocomponent were constrained by specific requirement on a structure and on a site.
The methods of generation of the pavilion on the site was explored in the Experiment 0 in the chapter Form Generation. This test design evolved into one storey of pavilion that had a surface intended for the modulation of the environment only. The possibilities and developed skills and tools in the chapters Concept, Materia Properties and Form Generation could lead also to the multi level branched structure. That means that there is a potential also for branching into dimensions.
There was achieved a porous self-supporting surface responding to the plan of the pavilion. The plan was arbitrarily chosen from the wide interval of possibilities that offered parameters of developed algorithm. The surface could be also informed by other aspects that are related to the environment. Architectural concept then could get another layer of complexity to its design procedure.
Areas of Furter Research
It is possible to outline further areas of research on the findings of this research. There are issues developed in the thesis that could be used both in multidisciplinar research fields and also in the architectural praxis. The research is regarded as a generic process into methodology that can later evolve in several fields of interest.
Material Level
The research into the materials outlined in the thesis could continue with a hypothesis based on combining materials of different qualities into composites. It is possible to pre-stress a curved laminated beams by adding layer with different reaction on the glue. Glue used for lamination dissolves in water and therefore wood could shrink and pre-stress the curved beam. The structural capacity of this component could be later tested and evaluated.
Geometry
The work with complex curvature in wooden components has certain limits. Also the manufacturing techniques for continuous lamination have to be revised and match with limits of D lamination. The fibre directionality and continuity is an issue that requires further studies and examples form nature and biomimetic approach. The whole issue represents the attaching structure to the ground. In order to maintain the clarity of the structure (timber and glue) these joints are considered with a high degree of importance.
Environment Impact
The environment impact was not fully developed in the thesis but it is inseparable feature of the con temporal architectural development. Parameters modulating environment in the structure could be introduced into the material system and requirements on the surface of a pavilion could be stated in the beginning of the design. The evaluation methods for these issues would consists of digital software and also physical models.
Algorithmic Proliferation
The L-system proliferation could be developed into more complex design method by introducing simple statements. The algorithm deployed in the thesis would then serve as a scaffolding for the generic tool for architectural designing. By adding conditions could be achieved powerful emergent generations. The thesis proved that bottom-up approach constrained by material behaviour led to the effective architectural tool.
Complexity, Metaphors, Models and Reality, G. A. Cowan, D. Pines, D. Meltzer
2. Thread model, natural-spontanious formation of branches, Marek Kolodziejczyk, In Natural Structure, volume 7, pages 7-42, Stuttgart, 99. Universität Stuttgart, Sonderforschungsbereich 20
On Growth and Form, D´Arcy W. Thompson, 942
4. Finding Form, F. Otto, 995
5. Il 25 - Experiments, 990
6. Il 28 - Diatoms I,
7. Il 5 -
8. The Science of Structures and Materials, J. E. Gordon, 988
9. Algorithmic Beauty of Plants, P. Prusinkiewicz, E. Lindenmayer, 2004
0. NOX, L. Spuyerbrook, 2005
Parsimonious Universe : Shape And Form In The Natural World, S. Hildebrandt, A. Tromba, 995
2. What is mathematics?, R. Courat and H. Robbins, 967
Euclidean Steiner Minimum Trees in an Hour, Winter, Zachariasen, Large, 997
4. Experimental and Theoretical Static of Liquids Subject to Molecular Forces Only, J. Plateau, 87
5. Artefacts and Instruments, M. Weinstock, 998
6. The Experimental Determination of Minimal Nets, Institute for Lightweight Structures, 97
7. Emergence and Self-Organisation, T. De Wolf, T. Holvoet, 2005
8. Frei Otto, Complete Works, W. Nerdinger, 2005
9. Techniques and Technologies in Morphogenetic Design, AD Vol. 76, No 2, 2006
20. Creating Synthesis Partners, AD Vol. 72 No , K. Shea, 2002
2 Fine Woodworking – Bending Wood, 985
22. The International Book of Wood, M. Beazley, 992
2. The Self-made Tapestry: Pattern Formation in Nature, P. Ball, 2002
24. Atlas Of Novel Tectonics, Reiser + Umemoto, 2006
25. ExpoDach, Thomas Herzog, 2000
Pavel Hladik EmTech 2005 / 2006
Truss
The structural schemes presented on this page does not match with the structural scheme of the material system presented in the thesis but it is relevant as a comparison. The difference of achieved structural performance of material system and traditional schemes presented on this page is enormous. The required dimensions for single laminated arch are uncomperable to values presented in this thesis. Principles of laminated timber structures
Two-pinned frame
Three-pinned frame
Two-pinned arch
Three-pinned arch