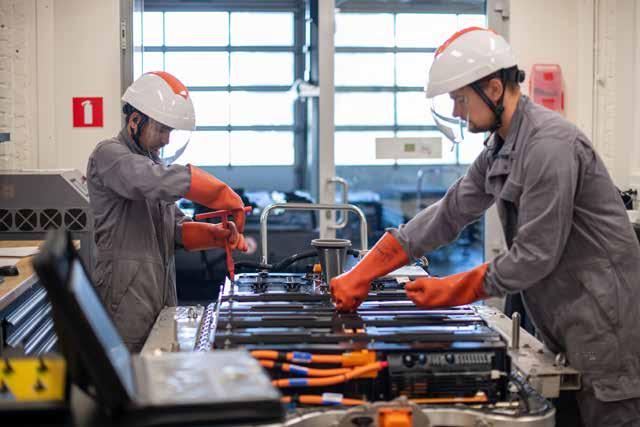
4 minute read
Battery Repair Center
from FLEET 137 NL
Herstellingen (z)onder hoogspanning
Battery Repair Center
Batterijen van elektrische auto’s worden steeds betrouwbaarder. Maar wanneer ze toch een defect hebben, is de expertise om ze te herstellen dun gezaaid. Daarom werd al in 2019 het Battery Repair Center opgericht in Asse door Valanfort, wat een 50/50 joint venture is tussen Valckenier in Vlaanderen en RMGA in Wallonië. We spraken met verantwoordelijke Tony Deruyter over het hoe en waarom van dit center.
Philip De Paepe philip.depaepe@effectivemedia.be
Het herstelproces is eigenlijk een vervangproces, waarbij modules met defecte cellen vervangen worden. (foto: Doof Vlaanderen)
“We zijn op het idee gekomen omdat er bij Renault Frankrijk een grote achterstand was bij de herstelling van batterijen”, opent Tony Deruyter. “Zij herstelden de batterijen in de fabriek zelf. Maar omdat de productiecapaciteit altijd omhoog moest, was er eigenlijk weinig tijd om defecte batterijen te herstellen. Er waren toen wel al enkele gespecialiseerde herstelcenters maar in landen zoals Noorwegen, niet meteen in de buurt. Wij zagen daar een opportuniteit in om hier lokaal een dedicated herstelcenter op te starten. In eerste instantie hebben we dus de achterstand van de fabriek in Frankrijk weggewerkt en gaandeweg zijn daar de herstellingen voor de Belgische markt bijgekomen. In een eerste fase zijn het dus louter batterijen van Renaultproducten die we herstellen, maar we hebben ook contacten met andere merken om hen dezelfde service te bieden.”
Investeren in materiaal en mensen
Net omdat batterijen zo betrouwbaar zijn, loont het voor individuele
dealers niet de moeite om zelf te investeren in materiaal en mensen voor die paar keer dat er toch een defect is. Voor een apparaat om batterijmodules te balanceren, samen met het speciale gereedschap voor werkzaamheden onder hoge spanning, tel je al snel ettelijke tienduizenden euro’s neer. Daarbij komt dan ook nog de investering in continue opleidingen. Het is dus niet rendabel voor individuele concessies om daarin te investeren. Dat is ook de reden waarom het idee van een dedicated repair center twee jaar geleden al concreet werd. Er werken nu twee medewerkers full time en nog eens twee andere zijn ook opgeleid om bij te springen wanneer de workload te hoog is.
Het proces
In het Battery Repair Center worden de volledige voertuigen met een defecte batterij afgeleverd. Daar is ook een goede reden voor. Indien de concessiehouder de batterij zelf zou demonteren, valt het transport daarvan onder ADR-vervoer. Daarvoor moet een receptionist van de concessie een certifi cering hebben. Opnieuw een investering die de moeite niet loont, gezien het lage aantal defecten. Eens het voertuig arriveert in het Battery Repair Center, wordt het gedemonteerd met een speciale heftafel en paspennen. Die heftafel is nodig omdat batterijen al snel tussen de 300 en 400 kg wegen. De paspennen zorgen voor de precisie en verankering die nodig is om de batterij gecontroleerd uit de auto te laten zakken. Voor men aan de herstelling begint, wordt de batterij in verschillende fases veilig gemaakt om aan te werken (zie kaderstuk). Het herstelproces zelf is eigenlijk een vervangproces. Individuele cellen die defect zijn, worden niet vervangen. Die vormen samen in serie geschakelde modules van 8, 16 of 32 cellen. Wanneer men de module gevonden heeft waarin de defecte cel(len) zich bevinden, wordt de volledige module vervangen.
Snelle doorlooptijden
Bij het Battery Repair Center gaan ze er prat op dat ze de klanten een snelle doorlooptijd kunnen bieden. Samen met het transport van en naar de concessie neemt een herstelling tussen de 3 en 4 dagen in beslag. Zolang de batterij onder garantie is, moet de klant ook niets betalen en neemt de constructeur de kosten op zich.
Tony Deruyter ziet de toekomst positief tegemoet, zeker nu met de toenemende elektrifi catie bij de verschillende merken: “Defecten van batterijen blijven zeldzaam, maar wij hebben er op twee jaar tijd toch al een 800-tal hersteld. In eerste instantie waren dat dus batterijen vanuit Frankrijk en later zijn die van de Belgische markt erbij gekomen. Nu EV’s mainstream beginnen te worden gaat het aantal defecten niet proportioneel mee de hoogte in. Dat is alleen maar goed voor de klanten en voor het imago van de elektrische auto. Maar als het dan toch fout loopt, zijn wij er om snel en effi ciënt een service te bieden die tot op heden uniek is in België.”
Net omdat batterijen zo betrouwbaar zijn, loont het voor afzonderlijke dealers niet de moeite om zelf te investeren in materiaal en mensen voor die paar keer dat er toch een defect is.
Tony Deruyter: “In eerste instantie hebben we de achterstand van de fabriek in Frankrijk weggewerkt en gaandeweg zijn daar de herstellingen voor de Belgische markt bijgekomen.” Investeren in veiligheid is een topprioriteit. Daarvoor worden ook opleidingen gevolgd door de medewerkers van het Battery Repair Center. (foto: Doof Vlaanderen)
OPLEIDING: SAFETY FIRST!
Verschillende instanties, waaronder Educam, bieden ondertussen opleidingen aan om te kunnen werken aan elektrische voertuigen en batterijen. Ze geven daarbij ook een eigen certifi cering, want van overheidswege is er momenteel eigenlijk geen wettelijk kader. Vanzelfsprekend ligt daarbij veel nadruk op veiligheid.
Tony Deruyter: “Het eerst niveau is basic. Zoals bijvoorbeeld: een oranje kabel, daar blijf je af. Het tweede niveau is iemand leren hoe je een auto zonder spanning zet door de batterij veilig te scheiden van de auto. Het derde niveau zijn technici die aan de batterij die onder spanning staat, mogen werken. En dat zijn de mensen die voor ons werken.”
Naast het veiligheidsaspect is er ook de know how rond het product zelf. Die opleidingen gebeuren door de fabrikanten en veelal op afstand met technologie zoals hololensen. Daarbij kan de instructeur in het beeld van een virtuele bril zaken aanduiden.