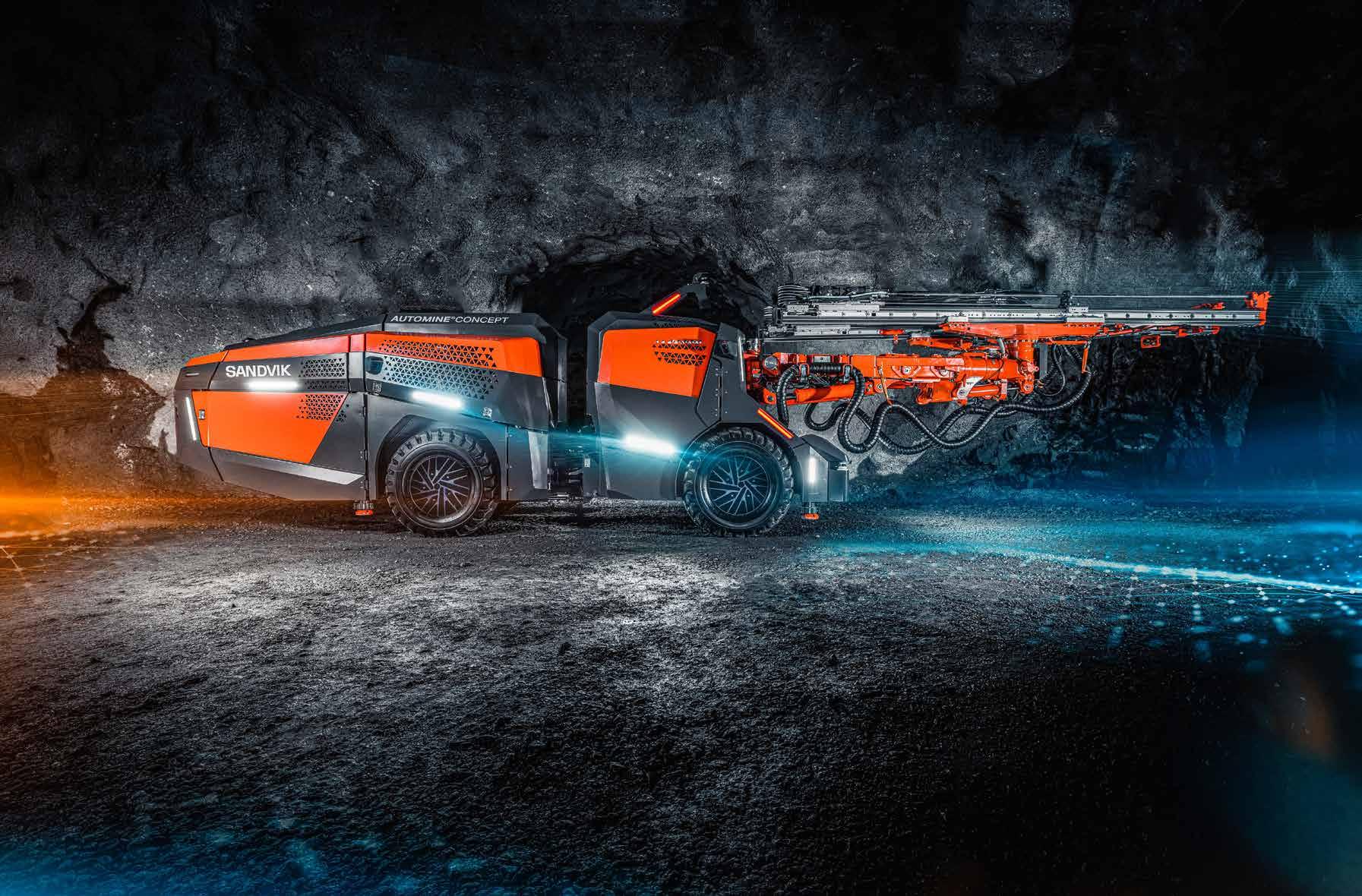
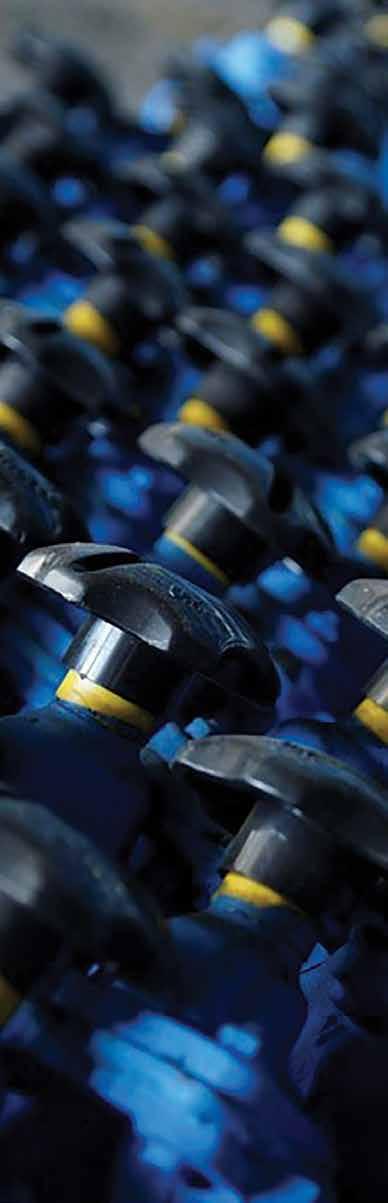
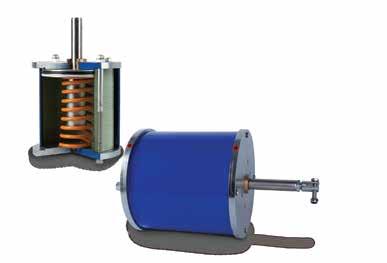
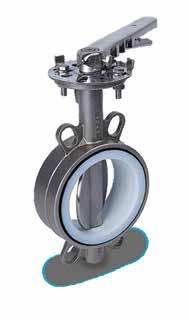
Augustine Ombwa austin@arobia.co.ke
COUNTRY WRITER: Lindsay Wagner
WRITERS: Delilah Aisu, Matimu Mahundla
COUNTRY LIAISON Thuthukile Klaas
South Africa: Shepherd Mthethwa, Rachel Molapo Jacqui Nyangabyaki, Tshegofatso Mokonyama
Nigeria: Seni Bello
East Africa: William Mutama
Published by Mining & Construction News Network (MCN) Ltd
African Mining Brief is published four times a year and is circulated to members of relevant associations, governmental bodies and other personnel in the mining industry as well as suppliers of equipment, materials and services in Africa, the Middle and Far East. The editor welcomes articles and photographs for consideration. Material may not be reproduced without prior permission from the publisher.
The publisher does not accept responsibility for the accuracy or authenticity of advertisements or contributions contained in the journal. Views expressed by contributors are not necessarily those of the publisher.
© All rights reserved.
The 27th UN Climate Change Conference of Parties (COP27) was held in Egypt recently, raising some interesting questions about the relevancy of sustainable business to African organizations and communities.
Many companies view sustainability as an exported Western and European problem, created elsewhere but unfairly burdening Africa, which has contributed far less to climate change. Specific to countries in the Southern African Development Community (SADC), mining is among the leading industries grappling with immediate problems such as infrastructure gaps, unskilled workers, crime, and social equity. Compared to these, rising environmental regulations is of little concern.
However, Environmental, Social and Governance (ESG) measures are quite key for investors, policymakers and other important stakeholders. It is a way to uphold businesses from future risks and ensure economic success and growth. Furthermore, the framework facilitates top-line growth in the long run, attracts competent staff, decreases costs and creates a sense of trust among consumers and stakeholders.
Mining companies need to set regular targets, have transparent progress reports and continuously refine their approach. Furthermore, they must demonstrate that they not only understand risks and opportunities of ESG but also display a commitment to addressing them in their day-to-day operations.
South Africa
MCN Network (Pty)Ltd
14 Ballyclare Dr, Bryanston,Sandton,2191 +27 (0)11 875 4328
E-mail: info@mcnnetwork.co.za
Kenya Office
Vinodeep Towers, 3rd floor, Baricho Road, Nairobi Tel:+254722525326/+254208000307. P.O Box 10109-00100. Nairobi Kenya.
The gold industry has come together, convened by LBMA and World Gold Council, to sign a Declaration of Responsibility and Sustainability Principles which formally expresses a shared commitment to operating in a responsible and sustainable way based on clear set of shared goals. The Declaration was announced at the LBMA/ LPPM Global Precious Metals Conference, Lisbon on 18th October.
Signatories to the Declaration are LBMA, World Gold Council (WGC), Singapore Bullion Market Association (SBMA), China Gold Association, Swiss Association of Precious Metals Producers and Traders, London Metal Exchange (LME), Dubai Multi Commodities Centre (DMCC), Indian Gold Policy Centre (IGPC), Indian Bullion and Jewellery Association (IBJA), Indian International Bullion Exchange (IIBX) and World Jewellery Confederation (CIBJO), Artisanal Gold Council (AGC), Responsible Jewellery Council (RJC), and the Watch and Jewellery Initiative 2030.
In all, this group has agreed ten key sustainability objectives, including commitments to responsible sourcing standards, respect for Human Rights, the advancement of the UN SDGs, and action and disclosures on climate change.
Gold industry participants understand that environmental and social concerns are increasingly important in shaping investment and policy decisions, as well as wider consumer and societal expectations. Whilst there has been significant progress in addressing many issues through industry-led initiatives and performance standards, it is important and timely that the gold sector adopts a clear collective statement of awareness and intent.
TOMRA Mining has published a new eBook to help mines enhance efficiencies and profitability by using information gathered by sorting machines. The easyto-read, 21-page booklet, titled ‘When Sorters Become Data Generating Machines’, explains how businesses can “connect to possibilities” with the TOMRA Insight data platform, and the competitive advantages this gives.
The eBook starts by reminding us that sensors in sorting machines can do a lot more than identify whether products or materials on a line should be accepted or rejected. As the book says: “They collect and store every piece of information about what they see. And this information can tell you a lot about how your machine is performing, about the products that pass through it, and your process.”
The eBook makes the encouraging point that turning TOMRA’s sorters into connected devices isn’t difficult, and businesses can benefit from digital sorting data with minimal impact – all that’s needed is wiring and a stable internet connection. The data solution’s software stores and processes the data coming from sorters and presents this in near real-time in a dashboard-style monitoring and reporting system.
Close monitoring is the basis for keeping vibrating screens productive and achieving the lowest cost of ownership, says Kenny Mayhew-Ridgers, chief operating officer of leading South African vibrating screen specialist Kwatani. Moving from paper systems to digital solutions is a vital step towards this goal.
“Where machine data recording – combined with periodic inspections and regular maintenance – can be captured in the digital sphere, you can generate a complete picture of the equipment’s lifecycle,” says Mayhew-Ridgers. “Real-time data monitoring is a game changer for screen reliability and performance.”
Wherever there are operational deviations from the prescribed norm, sensor-generated data can quickly alert the right people on the mine – giving them the ability to react timeously, he says. Importantly, this technology also allows patterns to be detected in the relationship between component life and throughput.
Hitachi Energy, a global technology leader that is advancing a sustainable energy future for all, today announced it has signed a long-term service agreement with Société Nationale d’Electricité (SNEL), the national electricity company of the Democratic Republic of Congo, to secure power supply in the country’s most important power transmission asset: the Inga-Kolwezi high-voltage direct current (HVDC) link.
The link supplies up to 1,000 megawatts of emissionfree electricity from the Inga Falls hydropower plant in the far west of the country to the Kolwezi mining region in the south. With a length of 1,700 kilometers, it is the longest HVDC link in Africa. It also enables the Democratic Republic of Congo to export surplus power to the member countries of the Southern African Power Pool.
The agreement continues the close collaboration between SNEL and Hitachi Energy over the past 40 years to ensure the link operates at maximum availability and reliability over its long operating life. Hitachi Energy supplied the two converter stations at either end of the link in 1982 and has subsequently upgraded them and doubled transmission capacity.
As part of the agreement, Hitachi Energy will assess the precise service needs of the converter stations and develop a preventive maintenance program and supervise its implementation over the next five years. The agreement includes training, knowledge sharing and expertise enhancement of SNEL service personnel.
Gold Industry Commits to Declaration of Responsibility and Sustainability Principles
Hitachi Energy to Secure Power Supply in Africa’s Longest HVDC Link
Tomra Mining Publishes New E-Book to Help Mines Turn Data from Sorting Machines into Greater Profitability
The GeoGroup comprises of a group of companies that provide a range of services to the Geotechnical, Civil, Exploration, and Mining industries.
Geomechanics and Geomech Africa have extensive experience in delivering Geotechnical and Exploration services at the highest standards in quality and safety in the following areas: Geotechnical services for railways, tunnels, dams, bridges, buildings, excavations, box cuts, roads, power stations, borrow materials, tailings facilities, void filling, and tunnel and dam grouting.
They are also equipped for Mineral Exploration core drilling up to 2000m deep.
The group owns a significant fleet of geotechnical and exploration drilling machines, supported by highly trained experienced operators & maintenance staff. They also have a staff count of over 200 employees.
Their Capabilities:
• Sonic drilling and coring
• Geotechnical & exploration rotary core drilling with:
• Double Tube: TBW, TNW, T2-101, T6-131, T6-146 and ZWF
• Split Double Tube: NWD4
• Wireline Drilling: BQ, NQ, NQ3 HQ, HQ3, PQ and PQ3
• Conventional air percussion drilling (Optional Jean Lutz)
• Sonic Coring
• 6 “x 8” system
• 3.75” x 4.75”system
• CPTu and SCPTu testing
• DPSH testing
• In-situ testing: SPT, Vane Shear, PMT, Lugeon and Goodman Jack
• Geotechnical instrumentation, monitoring and testing
• Drilling and grouting
• Hydro power projects
• Sub-horizontal holes for drainage of tailings dams and mine pit walls
They also offer the following fleet for support:
• 3 x Long-haul trucks
• 50 x LDV Vehicles
• 13 x Support trucks
With 33 years of experience, the team has an extensive fleet to services these industries.
One of the Group’s sister companies, Terra Monitoring, have successfully been delivering Geotechnical instrumentation, monitoring and in-situ testing services to the Civil Engineering, Mining, Railway and Road Infrastructure industries since 1980.
Terra Monitoring offers a turnkey solution, specifically aimed at assisting the mining industry with the automation of tailings facility readouts. Terra Monitoring specialises in installing Vibrating Wire Piezometers and slimline VWP’s connected to remote data loggers with a comprehensive list of additions to manage your facility.
Terra Monitoring has consistently and progressively expanded its Geotechnical Instrumentation and In-situ testing equipment portfolio by associating with world-leading manufacturers, to meet the growing demand in the market. Their broad and long-term experience translate into their sales and installation teams being able to provide clients with the best possible advice, technical support, and aftercare service.
Their sister companies, Geomechanics and Geomech Africa, offer a wide range of services that service the tailings divisions including sonic drilling for quality core recovery, CPTu testing, seismic testing, Mostap sampling, and standard standpipe piezometer installations. Working hand-inhand with Terra Monitoring, they can offer a turnkey solution for tailings facilities.
In-situ Testing Services
• Vibrating wire piezometers & slimline piezometers
• Standpipe piezometers
• Permeability tests: Falling head, constant head, rising head, and Lugeon testing using both conventional and wireline packers in all sizes (double and single packers)
• Goodman jack testing
• Plate bearing testing
• In-situ stress measurements
• Vane shear
• Pressuremeter testing & recycle tests
• Vibrating wire borehole stressmeters
• Norwegian hydro fracture
• Water sampling and pumping in small diameter boreholes
READ MORE: www.ambriefonline.com
SlurryFlo Control Valves excel in abrasive and corrosive mining applications, or any process where service life and performance are critical - helping clients save downtime as well as replacement costs. A case study of a recent project in Southern Africa, where SlurryFlo supplied its flagship control valve, illustrated this point.
There is a rule of the thumb in the mining specific slurry pumps: When you get a wrong valve for application in slurry pipes conveying corrosive and abrasive materials, you should expect to spend more on replacement costs, and worse still, to experience long intervals of equipment downtime resulting in loss of potential revenue. That is why it is always advisable to consult slurry valve specialists with a credible track record for informed views on the selection of mining-specific slurry control valves.
SlurryFlo, a company that provides slurry valve solutions to industries in Africa, has been solving complex slurry valve application problems for clients, saving them millions in replacement costs in addition to downtime. The company has been successfully replacing faulty control valves with its rugged SlurryFlo Control Valves for clients.
A problem for an African client
Recently, the team’s Application Engineering Team successfully installed a SlurryFlo valve for a mining client in a country neighbouring South Africa.
The client approached SlurryFlo for a solution to a severe application problem they were experiencing that was costing them dearly due to failure of a 20inch T. This valve would fail after 1 month in service.
Frank Olsen, the local representative for Slurryflo explains how the Engineering Team, approached the major problems the client had encountered, “The application was venting steam vapour from flash vessels. Due to the vapour containing acids and fine particles, the Titanium Butterfly valves would be removed after failure of 1 month and assessed for repair or replacement. This caused lost production due to repeated downtime and high cost of replacement of the valve.” (fig. 1)
Fig. 1
The valves in-line butterfly disc would also accelerate the abrasive fluid towards the downstream pipe walls. This caused premature failure of the client’s titanium pipe. (Fig. 2) further increasing the clients costs due to downtime, repair costs and lost production.
As the gate opens, it exposes two small ceramic orifices to vent steam (see Fig 4). Once the flash vessel has been vented, the gate can be retracted further if additional flow is required (see Fig 5). Note that flow is centred within the pipe in both scenarios.
In order to address this problem, the Team’s mandate was to design a solution to prevent the client from replacing their highperformance modulating control Butterfly. With an analysis of the process conditions and modulating history, SlurryFlo’ s engineering team developed a unique ‘dual purpose’ trim (see Fig 3).
The benefit of replacing Titanium Butterfly valve with SlurryFlo valves was realised earlier than the client had expected. “Upon replacing their Titanium butterfly valves with SlurryFlo control valve, the client quickly realised a return on investment. During the first inspection (1 month post installation), the maintenance team observed minimal erosion on the wear components,” Olsen narrates.
“As the downstream piping also remained in excellent condition, it was decided to operate the valves for several months between inspections. After 12 months of continuous service, the valve trims are replaced, and the valves are reinstalled,” he adds.
Fig. 5
Fig. 3
Without question, one area where the benefit of replacing Titanium Butterfly valve with SlurryFlow can be seen is in financial gains.
The financial benefits to the client have been calculated over a period of 5 years - doing a comparative cost of the new engineered Slurryflo Control valve against the Titanium Butterfly valve that was failing prematurely under the severe conditions. Costs for refurbishing the valve and replacement of the butterfly valve based on the history of the plant were taken into account. It was demonstrated that had the client continued with their existing Butterfly Valves, a total cost of $66 million would have been spent.
The SlurryFlo Titanium Control valve over the same period would cost the client $2,1 Million for the initial purchase of new valves and ongoing replacement trims on a 12-month basis. This gives the client a total saving of $63,9 Million over a 5-year period (calculations based on a quantity of 6 valves).
1 Month of Service
As illustrated above, SlurryFlo’s patented design centre’s flow like no other control valve, centered orifice design keeps abrasive flow away from pipe walls, flow is directed through the center of the valve, protecting the valve’s body and downstream pipe. In general, SlurryFlo control valves excel in abrasive mining applications, or any process where service life and performance are critical.
“The variable orifice technology will outlast all control valves in severe slurry service, giving the client a quantum leap in service life, lasting three to ten times longer than any other “Severe Service” control valve. After a long service life, a simple trim replacement resets the clock,” Olsen guarantees on SlurryFlow’s performance.
SlurryFlo’s engineers tailor a design for the client’s application which is Custom trim Geometry, Client application specific.
SlurryFlo control valves are available for 2” to 60” pipe diameters, and are manufactured to CWP, ANSI 150, ANSI 300 and ANSI 600 standards, provide Class IV shut-off when new, and deep into their service life. SlurryFlo’s unique seating surfaces maintain Class IV, even after substantial wear.
All valves are designed and manufactured in house in North America. SlurryFlo’s African customers are supported locally by Coral Valves based in South Africa.
The world is a global entity that requires constant evolution to supply the demands of its citizens.
In that case, we’d more clearly understand how important it is to provide sustainable solutions within the mining industry. This is because mining remains one of the largest contributors to its Gross Domestic Product (GDP) regarding gold, platinum, base metals and coal companies.
According to Stats SA, after two consecutive quarters of positive growth, GDP decreased by 0.7% in the second quarter of 2022 (Q2:2022). Floods and load shedding contributed to the decline and weakened and fragile economy. Mining, in particular, furnace technology, can positively impact the GDP and alleviate the electricity crises. To understand how it is vital to know precisely how furnace technology serves the mining community and how it factors into the economy’s growth.
Global demand and relative growth
Mining investments in terms of exploration and development indicate the future
sustainability of the mining sector. Mining companies with roots in South Africa are increasingly reducing their operations in South Africa and expanding to other parts of the continent and the globe.
For this reason, within South Africa itself, the need for technology to advance is required to ensure the country runs at its optimal best - and that investors remain interested in what South Africa has to offer. Even though Covid has impacted mining production, according to Netbank Economic Insights, the sector has performed better than the average growth levels during September 2017, 2018 and 2019, indicative of the relatively higher commodity prices and global demand.
What is the furnacing process?
Furnaces enhance and improve the mining process. Consider that once Ore has been extracted, it needs to be processed into usable materials, which can be turned into products for construction and engineering. As a result, furnaces are commonly used in the mining industry. The furnace has
undergone several technological evolutions over the millennia, and the need for highquality ore processing has necessitated this With technology constantly evolving, there is much to look forward to in the near and distant future. David Roelof De Wet, Managing Director and Founder of Therm Tech South Africa, a thermal equipment provider in South Africa, explains, “Furnace Technology Equipment in the mining sector involves the following equipment, Gold Mining, Plant Boilers, and Thermal Oil Heaters are all used in the elution heating system”.
What types of furnaces are available?
Furnaces offer various levels of capability. The furnace you choose is wholly dependent on your needs and overall objectives, with a strong focus on green mining. Modern-day furnacing technology is tuned to developing furnacing options that positively affect the environment, protecting the environment and repairing existing damage.
In addition, new technologies improve energy efficiency and align benefits between
miners and the environment. However, the three main furnaces to consider are Bloomery, Blast, Mechanical Furnaces and Induction furnaces.
Bloomery Furnaces are one of the earliest types of furnaces. It is capable of smelting Iron. It produces a bloom, a porous mass of iron and slag, and can be worked into wrought iron. It consists of a heat-resistant chimney made of clay, stone, or earth and pipes called tuyeres.
Blast Furnaces are single-chamber furnaces that produce iron. In addition, it can smelt lead and copper. Ore, Limestone, and Coke are fed into the top of the furnace. Preheated air is blown into the bottom of the furnace. Some modern Blast Furnaces can process tons of ore and metal.
Mechanical Furnaces are split into four classes, namely Stationary Health Furnaces, Rotating-Bed Furnaces, Rotating Cylindrical Furnaces and Shaft Furnaces. These types of furnaces are used in many mining industries across the world. Reverberatory furnaces isolate the material and prevent it from coming into contact with the fuel - although it does have the potential to come into contact with combustion gasses.
Induction Furnaces are highly-efficient, modern electrical furnaces that don’t require fuel to melt the desired substance. Instead, they are utilized induction coils to heat the ore. They also have an electric power supply and are water-cooled. Traditional furnaces can be significantly energy-intensive. They may require large amounts of fuel to operate. At times it may produce unwanted products, including smoke, dust and other pollutants.
De Wet elaborates by saying that Furnace technology also plays a significant role in roasting plants to expose the gold taped in sulphide. Plant kilns reactivate the carbon in the Gold Process plant system. Gold Melting furnaces melt the gold and produce Gold Bar’s. Boilers and Waste heat Boilers are used to increase the chemical reaction and
production in the Copper Mining sector and where Cobalt is a byproduct to dry Cobalt for transportation.
What advancements are there?
As the industry requires, technology has advanced. These are the most basic types of furnaces available, but consider that significant advancements have been made.
For example, consider Hybro Heat furnace technology, developed by the SMS Group Division, which combines the advantages of cost-effective preheating of log materials in a gas furnace and precise temperature setting by means of induction technology before extruding the billet. De Wet shares his thoughts on the advancements within the industry, “With IIOT technology, mines situated in remote and isolated locations can be provided with remote assistance from a service provider, ultimately reducing downtime.” “Modernday technology has advanced so much that electronic systems can be upgraded to link fewer controls. As a result, the furnace will operate within the optimized air-fuel ratio, with precise combustion control. This results in higher efficiency, less fuel and reduced CO2 emissions,” says De Wet.
How can furnaces alleviate the electricity crisis in South Africa? With the significant electricity crisis in South Africa, how does furnace technology alleviate the problem? According to De Wet, if systems are rebuilt with the right technology, the equipment can operate efficiently, particularly regarding the electricity crisis in South Africa. Therefore, he says he advises that electrical furnaces be converted to Combustion furnaces. “The result would be a high relief on the national grid. Also, the CO2 emission impact will be minimal as most of South Africa’s electricity is produced by fossil fuels,” concludes De Wet.
Sources: Therm Tech SA www.azomining. com/
Zijin Mining is a large multinational mining group. It is engaged in the exploration and development of copper, gold, zinc and battery metals worldwide, as well as the research of engineering technology.
The group has mining projects in 15 provincial-level regions in China and 13 other countries. It operates major projects in China, such as the Julong Copper Mine in Tibet, the Duobaoshan Copper Mine in Heilongjiang, the Zijinshan Gold and Copper Mine in Fujian, the Ashele Copper Mine in Xinjiang, Shanxi Zijin, Guizhou Zijin, and Longnan Zijin. Its main overseas mines include the Čukaru Peki Copper and Gold Mine and the Bor Copper Mine in Serbia, the Kamoa Copper Mine and the Kolwezi Copper Mine in the DRC, and the Buriticá Gold Mine in Colombia.
Zijin controls 62.77 million tonnes of copper resources, of which 20.33 million tonnes are reserves; 2,373 tonnes of gold resources, of which 792 tonnes are reserves; and 9.618 million tonnes of zinc resources,
of which 4.554 million tonnes are reserves.
Zijin Mining ranks No.324 in the 2022 Forbes Global 2000 List, No.1 among global gold companies, No.8 among metal miners; and No.486 in the 2021 Fortune 500 List.
Zijin’s core competitiveness lies in innovation, especially technological innovation. It has a wealth of experience in geological exploration; hydrometallurgy; the processing of low-grade, refractory ores; and large-scale engineering projects.
It is also accelerating its development in the field of renewable energy and advanced materials. It has added 7.63 million tonnes of lithium carbonate resources through the acquisition of the high-grade Tres Quebradas lithium project in Argentina. Its overseas copper and gold operations account for more than half of the group’s total reserves, production, and earnings.
It has developed the “Five-pronged” Mining Engineering Model and founded the State Key Laboratory of Comprehensive Utilisation of Low-Grade Refractory Gold Ores.
Its in-house technologies and engineering capabilities cover the full spectrum of exploration, mining, processing, smelting and environmental protection. Powered by its technological strength, Zijin Mining has been successful in the development of many mining projects across the world, and has fostered its own competitiveness in the global mining industry.
Zijin is building its ESG system on the basis of international standards, and it is committed to developing green, ecofriendly mines to high standards. Zijin’s vision is “Mining for a Better Society”. It stands by the values of “Harmony Brings about Wealth” and “Balanced Development of the Company, its Employees and the Wider Society”.
As an important player in the global mining industry, Zijin strives to become a “green, high-tech, leading global mining company”. It contributes to economic growth in China and the rest of the world by supplying high-quality minerals.
In Africa, the group has mining projects in the Democratic Republic of Congo (DRC), Eritrea and South Africa. The Kolwezi Copper Mine in the DRC was the first copper mine constructed by Zijin and put into operation abroad. Kolwezi has produced over 70,000 tonnes of copper, providing more than 1,000 jobs for local people.
Another DRC mine, the Kamoa-Kakula Mining Complex or known as “Kamoa Copper”, is a joint venture between Zijin Mining, Ivanhoe Mines, Crystal River Global Limited, and the DRC Government, and is the world’s fastest growing major copper mine. The mine strives to produce the world’s “greenest copper”. Following “carbon peak and carbon neutrality” initiatives, Kamoa Copper has implemented the Sustainable Livelihoods Program and set a net-zero GHG emission target for operation. Kamoa Copper is powered by clean and renewable energy with its main power source coming from the Mwadingusha hydropower plant and the Inga II hydropower facility. The project’s GHG emission per tonne of copper produced will continue to drop when Inga II hydroelectric refurbishment is accomplished. A 2020 independent audit of Kamoa-Kakula’s GHG intensity metrics performed by Hatch Ltd. of Mississauga, Canada, confirmed that the project will be foremost among the world’s lowest GHG emitters per unit of copper produced.
The Bisha Zinc-copper Mine is the largest producing zinc mine in the State of Eritrea in Africa. The mining and stripping capacity of the project is 32 million tonnes
per year, and its designed processing capacity is 2.4 million tonnes per year.
In South Africa, Zijin’s wholly owned subsidiary Nkwe Platinum Limited holds a 74% undivided share in the Mining Right in respect of the Zijin Garatau Platinum Mine.
The Zijin Garatau Platinum Mine is located on the Eastern Limb of the Bushveld Complex, about 25 km northwest of Steelpoort and 30 km west-northwest of Burgersfort in Limpopo Province, South Africa. The Mine is currently in the construction phase but is anticipated to average 3.6 million tonnes of ore per annum once full capacity is achieved in a few years’ time.
To date, Nkwe Platinum Limited has spent over R45 million on its Social and Labour Plan. The investment included the upgrading of the Garatau Community Access Road, as well as adult training and education, bursaries, learnerships, internships, traditional leadership training and excavator operations, which have benefited the surrounding mine communities of the Zijin Garatau Platinum Mine.
In June 2020, Nkwe Platinum Limited launched its first solar powered water supply system for the Ga Mpuru Village in the Garatau community, situated next to the Zijin Garatau Platinum Mine.
The pumps installed on the water borehole and storage tanks are powered by a complete solar system. In addition to providing round the clock water for the members of the community, the solar system also powers a security electric fence for the water supply infrastructure,
making it a self-sustaining unit. The community now has access to over 55,000 litres (continuous flow) of clean water from a pipeline, which spans over 2 kilometres within the community. Taps and water troughs are stationed at various strategic points along the pipeline to cater for both the community and livestock.
This solar-powered water system forms part of Nkwe Platinum’s second generation Social and Labour Plan, which enables Local Economic Development (‘LED’) projects in the form of clean water supply to the local mine communities over the next few years.
Nkwe Platinum Limited believes the development of enterprises is closely related to the sustainable development of its surrounding communities. Through, education, medical treatment, industrial support, infrastructure construction and disaster relief, it is committed to developing and working together in a mutually beneficial and harmonious way for the benefit of all.
“The mine strives to produce the world’s “greenest copper”. Following “carbon peak and carbon neutrality” initiatives, Kamoa Copper has implemented the Sustainable Livelihoods Program and set a net-zero GHG emission target for operation”.
management or remedial procedures may be carried out. A slope monitoring program should detect instabilities timeously in order to prepare mining operations for potential threats, by providing an early warning. The consequences of an uncontrolled instability or slope failure can result in: disruption of operations, loss of equipment, injury and worst of all loss of life, all of which ultimately could result in drop in market share. A comprehensive slope stability monitoring program is thus vital to support the safe recovery of ore.
Real-time monitoring is the viewing of continuously updated or streamed information. This occurs through the implementation of applications and tools that constantly track and record the overall pit performance, and provide continuous updates. It essentially means that one is able to have eyes on the slope at any given time. This permits the user to determine the current state of the slope and enables the team to identify, detect, diagnose, report and respond rapidly, when an incident occurs.
Reutech’s real-time slope stability monitoring products.
Slope stability is an important consideration in the management of various types of mining operations or geotechnical engineering projects. By definition, slope stability is a measure of how resistant a man-made or natural slope is to failure, due to collapse or sliding. Slope pit designs aim to provide a safe and stable slope for open pits mines, while still optimising excavation capabilities.
Increasing the pit wall steepness enables maximised ore recovery and minimised waste stripping. This implies that the quantity of excavated material is reduced, thereby considerably decreasing mine running costs and improving financial returns. This increased wall steepness does, however, increase in the depth of the pit, causing a decrease in the factor of safety in the pit slope design.
The primary purpose of a slope monitoring program is to assess the stability of the pit walls during operations and to detect any signs of instability, after which
Reutech Mining is a proudly South African company dedicated to developing, manufacturing and distributing innovative technologies for the management of safety within the mining industry. After being approached by industry leaders in the mining sector, requesting advanced geotechnical monitoring solutions, Reutech has been at the forefront of technological innovation for mining safety for more than 15 years. The demand for real-time geotechnical monitoring has led to the rapid advancement of monitoring technology.
The application of ground-based radar technology has been used in mines, across the world, since the early 2000’s. Reutech Mining is focused on providing and improving real-time mine safety for surface and underground applications, as well as, contributing towards a noteworthy increase in production for a large number of mines in Africa and around the world.
The Movement and Surveying Radar (MSR) is the world’s most advanced slope monitoring radar, used for assessing the
stability of mine pit walls, tailings dams and natural hazards. With the unique ability to extract multiple data points from a single antenna beam footprint. The MSR Modular delivers a high resolution three-dimensional (3D) point cloud and provides data in range, azimuth and elevation, without relying on any other external mechanisms. This implies that the most accurate slope stability insights is provided at all times. MSR Modular is capable of covering broad areas quickly, making it the ultimate tool for simultaneously performing strategic and critical monitoring on any scale.
The combination of radar data together with movement vectors from prisms and extensometers can be displayed on the same interface, allowing for the integration of data from various instruments. This integrated interface allows for a more holistic approach may be applied, in identifying areas of movement on the slope, and subsequently making more informed decisions. . The MSR Modular allows for various mounting options such as fully autonomous trailer or vehicle mounting or fixed installations.
MSRIV Esprit®, is the fourth generation of the MSR range, developed specifically for repeatability of measurement, increased scan speed, advanced atmospheric reduction and minimised mechanical wear. MSRIV Esprit® is a staring radar which scans a fixed area using the concept of Multiple Input and Multiple Output (MIMO) radar technology. The advantage of using a MIMO architecture instead of scanning single points or sweeping over the slope, is that the system scans the entire area instantaneously and constantly. This system produces superior real-time movement data with an exceptionally accurate 3D point cloud, and a full 2D area scan update in less than two seconds. With a scan speed of less than two seconds, fast moving slopes are effortlessly detected and the phenomena of phase wrapping (ambiguity) is reduced drastically.
The rapid scan time and reduction in phase ambiguity reduces the effects of rapidly changing atmospherics, almost completely, and accumulates only true movement. This radar is the fastest scanning radar on the market making it the ideal solution for mines with rapidly changing atmospherics and fast moving slopes. Smaller movement measurements are detected much faster and with greater accuracy, resulting in the early identification of potential slope failures. The Esprit system is fully autonomous and include solar panels to reduce the carbon footprint of the system.
How does the MSR Modular and MSRIV Esprit® aid slope stability monitoring in real-time?
• The data from both the MSR Modular and MSRIV Esprit® is captured automatically, reliably and updated in real-time, which boosts the confidence of mining personnel in solving slope stability concerns.
• The MSR systems aid in enabling risk management procedures and life-ofmine plans, which limit personnel exposure to geotechnical hazards. This subsequently increases productivity and allows for pit slope optimisation through design calibration.
• Teams are encouraged to include radar alarms for detected slope movement in their hazard planning and Trigger Action Response Plans (TARP).
• Warning and evacuation orders can be issued once the stability of the slope approaches a dangerous threshold level, in keeping with the protocol and the monitoring program implemented by the team on site.
• By identifying areas of continuous movement from the radar data, teams can get more proactive with their response methods and operational plans.
• Different scan region areas can be selected allowing the client to focus on areas of high importance, without wasting scan time on areas of no interest.
• The system is configured to perform the above tasks 24/7, in adverse weather conditions, therefore providing the client continuous safety critical monitoring throughout the day and night.
• Both systems have the ability to send immediate automatic alerts and notifications to geotechnical teams via email and telecommunications, should an alarm be triggered.
• The MSR Modular and MSRIV Esprit® systems can also be viewed remotely through MSR Connect (Reutech’s state
of the art web based software - allowing multiple users and viewers access to the MSR data via any platform from anywhere in the world, on condition that they have access to the mine’s network).
• The MSR Modular and MSRIV Esprit® systems can also be connected to the Reutech Slope Vision camera system to provide video or still photographs of the problematic areas.
Reutech’s radar products provide the key instrumentation required for informed and effective slope monitoring programmes. The primary goal is to significantly increase safety and productivity at mining operations, therefore Reutech’s highly complex radar technology has been developed to simply do what you need it to do, all of the time. The result is real time slope stability monitoring radars that have got what it takes to get you there. That’s the power of safety and productivity through accuracy and reliability.
The world is gradually becoming connected by millions of sensors and devices. IoT (Internet of Things) devices are already used for better and smarter living, saving costs and improving the quality of life.
The market demand for smart devices and their applications is experiencing dynamic growth as more consumers are looking to leverage the comfort, energy efficiency, and security benefits of smart technology.
In the scope of IoT systems and applications, a radar sensor is capable of sensing and potentially tracking one or more objects. In contrast to other Radio Frequency (RF) based passive or active wireless sensor systems, radar sensors are active, as they can send out pulses and receive their echoes. Radar technology makes it possible to estimate the target’s speed, direction, and range (i.e., distance from the radar transmitter or receiver). Likewise, there are radar sensors that can detect small movements and even the presence of humans due to their high sensitivity towards smallest motions.
Characteristically, radar technology is: Contactless: The radar detection measuring principle involves no contact at all. The sensor doesn’t have to have direct contact with a material or object being detected. Radar reliably measures and detects even at a long distance.
Anonymous: Radar sensors are used for industrial and automotive applications and do not produce images. They merely form a sort of cloud of dots, which gives a rough indication of objects’ contours and the
infrastructure of the surroundings. Contrary to a camera, people are not identifiable.
Comprehensive data: Radar sensors detect movements and stationary objects. After signal processing, the data received through the reflection provides a variety of information about the detected objects or persons. Data such as direction of movement, speed, distance, and angular position in relation to the sensor are available.
Multi-dimensional detection: Depending on its modulation, radar collects extensive data about its environment. This enables sensors to also record the environment in three dimensions, like a human eye.
Wide range variability: Radar waves spread freely in space or in the air.
Material penetration: The electromagnetic waves of radar sensors penetrate various materials. Plastics, in particular, are very well-suited for covering or designing a radome – a dome-shaped protective casing for the antenna. It allows the sensors to be integrated discreetly into a product design.
The Inxpect Radar Safety Scanner comes with multiple benefits, including:
Safe protection zone monitoring in rugged conditions; the safe radar sensor PSENradar, in conjunction with the Pilz Safety Relay or PLC system offers a safe and complete solution for protection zone monitoring – including conformity assessment for the plant or machine.
Safe radar sensors are used where optoelectronic sensors reach their limits, including rugged environments, such as mining, outdoors or in material processing.
They can be monitored safely using PSENradar because radar technology
FMCW (Frequency Modulated Continuous Wave) ensures high availability even where there are external influences such as dust, dirt, rain, light, sparks or vibrations.
In application, the underlying volumetric monitoring with a frequency of 24 - 24.25 GHz can be used up to SIL 2, PL d and Category 3, which is often a requirement in robot applications. The complete solution also has additional interfaces, such as Ethernet and Profisafe, making it easy to use the safety radar sensor in retrofit applications.
For rapid commissioning, the sensors are selected and configured simply via the appropriate configurator. Depending on the application, the safe radar sensor solution includes up to six radar sensors, one control unit and the appropriate Pilz Safety Relay.
The appropriate protection zone can be defined for each sensor, based on the size of the area to be monitored. This depends on the positioning, installation height and inclination of the sensor. A warning zone can also be configured in addition to the protection zone. In the event that a person violates the warning zone, this may be beckoned by an optical signal. This way, productivity of the plant can always be kept at a high level.
Read more: www.Ambriefonline.Com
Waste generation is an inevitable part of the mining process and can have detrimental effects on the environment if not managed responsibly.
As a result, the waste management sector has a huge role to play in the disposal of this waste. Although the mining sector has been a key driver for growth and development of the country’s economy, unfortunately, mining produces a significant amount of waste which has a large impact on the environment and communities across the country.
Some of these impacts range from water pollution, negative effects on the country’s biodiversity and human health. Hence the importance for mines to mitigate risks by conducting comprehensive Environment Impact Assessments (EIAs) and implementing sustainable solutions for the full lifecycle of the mine.
Mining companies have to gain insight into the stringent environmental legislation, standards as well as guidelines applicable to waste management within their business and mining concerns. This is to ensure that the impact of the waste is managed correctly and is not detrimental to the environment and more importantly, can be reduced to meet the rising need for sustainable solutions within the sector.
Linked to this, the global trends of zero waste to landfill and circular economies are challenging the status quo of how mines
work, with leading mines shifting to zero waste to landfill strategies, having already begun to separate their waste streams, and finding alternative use for them.
However, while welcome, this trend has encouraged a mindset of avoiding waste, as opposed to minimising it, recycling, reducing, recovering and as a last option, disposing waste to landfill. The Polokwane Declaration sets targets of zero waste to landfills by 2022 although the set target of zero waste to landfill was revised to ensure 70% waste diverted from landfills by 2022.
Moreover, Zero Waste to Landfill (ZW2L) has been adopted by mining giants, with vested interests and operations locally in support of their existing commitments to sustainable development, and to ensure compliance with the regulatory framework, i.e. National Environmental Management Act (NEMA, Act 107 of 1998) and the Waste Act, 2008 (Act 59 of 2008) all of which is encouraging.
According to Jason McNeil, Chief Operating Officer, Interwaste, given this ongoing commitment, it would actually eventually lead to eliminating unnecessary wastage and waste generation, which we know traditionally ends up at a landfill. “Of course, more will be needed if we want to make a real impact. Therefore, taking a longterm view to optimising resource efficiency through innovations like sustainable product designs, recovery, reuse and recycling of
products, or energy production through the systematic application of the waste hierarchy still needs to be a priority,” states McNeil.
In fact, with this change in mindset and legislation adoption, it will mean eliminating unnecessary wastage, and waste generation, which would eventually be disposed at a landfill. This can be further achieved by optimising resource efficiency through sustainable product designs, recovery, reuse and recycling of products, or energy production by utilizing the systematic application of the waste hierarchy and implementing strategies (to minimise this impact as well as reduce the impact going forward), such as the positive results of remediating, removing and repurposing dormant mine dumps are now considered a de factor standard for operations.
The waste management in mining is however evolving with new sustainable and innovative solutions coming into play. As a result, mining waste management companies need to create tailored waste management services, which range from analysing and classifying waste streams; aligning the processing thereof to current and future legislation, and then designing and implementing solutions that meet the mine’s goals.
These solutions must incorporate a key focus on safety, environmental, social and economic benefits. Examples of some solutions within the waste management
industry that are available to mining companies include:
• On-site bioremediation of hydrocarbon contaminated soils to compost for use on mine
• Oily rag, hydrocarbon contaminated PPE – laundry on or offsite – enables the cleaning and re-use of these materials back into workshops and old PPE cut into rags for reuse.
• Garden and wooden pallet processing onsite for potential bioremediation or alternative energy use
• On or off-site Anaerobic digesters for canteen and food waste – eliminates waste which can then be used to
generate energy such as steam or gas for other processing plants
• Collaborating on investing in central transfer stations involving communities to leverage economies of scale and minimize transport costs e.g. bulk recycling processing or consolidating loads to transport to alternative treatment facilities.
• Local waste opportunities such as the pyrolysis of general waste tailings, rubber or plastic products.
Going forward, it is going to become ever more business critical that a mining business incorporates its environmental impact into its business processes from inception and
throughout the lifecycle of the mine.
From the sourcing of various raw materials, to the production and final consumption/route to market, companies need to understand the generation of waste in each process to ensure the long-term commercial and environmental viability of the business.
Mining companies are becoming more receptive to the effective waste management solutions and programmes which are being offered and are actively investing in these solutions in recognising that effective waste management is not only fundamental to the sustainability and legal compliance for a mine, but it also has economic benefits.
Stack sampling and reporting is one of the main requirements for environmental compliance with Atmospheric Emission Licence (AEL) conditions, renewals and new applications.
Thereby, mining and associated operations which fall under National Environmental Management: Air Quality Act, 2004 (Act 39 of 2004) NEM: AQA Section 21 List of Activities which result in Atmospheric Emissions – Category 4 – Metallurgical Industry are required to conduct stack emission testing at least annually and report as required by their respective AEL.
The most common emissions testing requirement are for Particulate Matter (PM), Sulphur Dioxide (SO2), Oxides of Nitrogen (NOx) and Acid Gases.
All Holders of AEL’s in South Africa are required by law to conduct emission testing by accredited emission testing companies ISO/IEC 17025:2017 (Stack Emission) – or equivalent in accordance with the standard sampling and analysis methods listed in the regulations.
Principally, isokinetic sampling was developed for the determination of particulate (dust) emitted from stationary sources. One of the first standards to be
developed was BS 893, first published in 1940 for the determination of dust from coalfired power stations and later BS3405, for monitoring of small coal-fired installations.
These standards encompassed the basic principles of sampling, which have been carried through into modern-day standards and methods such as US EPA and ISO.
Over the years, the requirement to monitor and control particulate emissions from industrial processes using Continuous Emission Monitoring Systems (CEMS) has significantly increased.
Current legislation requires calibration against the Standard Reference Method
(SRM) using isokinetic sampling and gravimetric analysis in controlled conditions. Isokinetic sampling is therefore used for the determination of particulate and other pollutants that exist in aerosols or droplet phases and can be combined with gas phase components.
Over time, isokinetic stack sampling has been one of the main measures for determining the particulate matter (PM) load in a stack, often for environmental compliance with Atmospheric Emission Licences (AEL), new applications and renewals. Normally, the licensing authority requires more than just the PM load in the stack.
Notably, government legislation requires different gas measurements in a stack for different processes as per Section 21 NEMAQA, scheduled processes: a typical and often common example is for the stack measurement of furnaces, process plant, reactors, milling and crushing plants, boilers etc.
VREC understands that these requirements by licencing authorities are not a top priority by small to medium size companies and can seem overwhelming even though it is a requirement by law. That
less complicated.
As an Emission Testing Company with the unique Accreditation Number of T0767 indicating a SANAS Accredited Emission Testing and Analysis ISO/IEC 17025:2017 (Stack Emission) - Testing Laboratory – it is committed to providing quality environmental services that meet the requirements of industries and businesses alike.
VR Environmental Consultants (VREC)
offers isokinetic stack sampling services for stack flue gas emission measurement and reporting on small to medium-scale boilers and other industrial processes requiring stack emission measurement and monitoring.
VREC conducts stack sampling using ISO, EPA and NIOSH methods as prescribed by section 21 NEMAQA, scheduled processes: schedule a, methods for stack sampling and analysis.
VREC works closely with laboratories which have ISO/IEC: 17025:2017 and ISO 9001 accreditation service providers with independent world-class analytical chemistry testing facilities.
Beyond the complexities of isokinetic stack sampling services, VREC also offers stack sampling for other chemicals such as CO2 CO, SO2, NOx, HCl, HF, NH3, VOC, Heavy Metals, Dioxins and Furans, Lab analysis – Water and Effluent, AEL applications and Renewals and Online Emission Monitor Verification.
Real time conveyed quality measurement provides unique opportunities to improve process control. A number of proven technologies are used throughout the resources sector that provide significant improvements to existing processes by better measuring and managing bulk material quality.
Composition measurement can be performed using high specification Prompt Gamma Neutron Activation Analysis (PGNAA) for coal analysis in coke-making, sinter analysis in iron-making as well as scrap steel analysis in steel-making. Moisture can also be measured in coal and sinter using microwave transmission and in coke, sinter, magnetite concentrate, and scrap steel using fast neutron and gamma transmission.
All these technologies measure continuously through the full conveyed depth and provide results in real time directly to the plant control system and all analysis data is owned by the client. Remote access ensures onsite time is minimised and support is readily available if needed. All analysers can be installed during planned shutdowns and no interruptions to operations are anticipated throughout the life of the analysers which have no contact with conveyed flows and no wear components or consumable spare parts.
Material quality variability is a key challenge in process control. Despite mining, beneficiation and concentration processes, materials handling and blending there is still considerable variability when materials reach the next stage in the process. Iron ore, coal and scrap steel are typically received from multiple sources, each utilising their own quality control systems. Despite certificates of analysis there is usually significant quality variability within and between shipments received. Where bulk materials are sold on tonnage the risk is that moisture content has been added to increase weight.
Quality variability is well accepted as having a major impact on process performance and managing quality requires appropriate high quality measurement systems, preferably those that minimise sampling error. Rather than taking more samples and not reducing sampling error, the smarter solution has been to measure quality continuous using representative technologies. Real time measurement is an obvious method to achieve this, with typically short paybacks, sometimes a few months and normally much quicker.
Conveyed flows represent the best opportunity to measure continuously as flow rates can be relatively consistent and material presentation to the measurement
technology is ideal for penetrative analysis. High specification analysis systems are customised to each application to optimise the quality of the measurement data produced for the process control needs. Measurement of materials in stockpiles, hoppers, chutes or trucks is problematic for a number of reasons, mostly that no technologies will penetrate sufficiently to provide representative analysis and some systems interfere with material flow and can cause plant downtime so these are best avoided. Surface analysis technologies are appropriate for homogenised materials but these are rare in the resources sector. Coal, coke, iron ore, sinter and scrap steel will contain variable composition that is not reflected by the composition at a particular location on the surface of a stockpile or flow of material.
Representative sampling of bulk materials can prove unreliable due to segregation of materials by particle size, layering, or density variations and the required sample size and frequency to minimise sampling errors. Effective sampling is still required for analyser calibration and therefore a suitable sampling protocol should be developed to address these issues. Online analysers require calibration checks every six months so any sampling required can be made manageable through good planning and implementation and need not interfere
with normal production.
HAVER & BOECKER is one of the leading companies that provides innovative systems for particle shape and particle size analysis that set standards in function, precision and reliability. One of their renowned technology is the HAVER CPA, which is a versatile application for CPA Online measuring devices.
The HAVER CPA Online technology is the optimum basis for a versatile, flexible and reliable solution when it comes to
Dynamic image analysis (DIA) in the production process. The modules of the particle analyzer are compactly designed and can be integrated almost everywhere. It is also always possible to retrofit it to existing processes. Moreover, standard distances of up to 100 meters are possible for the connection between the PC system and the measurement instrument.
The modules are resistant against harsh surrounding conditions. This is achieved by its robust construction in stainless steel and
automatic pneumatic cleaning of camera and light scource.
The HAVER CpaServ software offers support for the common communication standard via Modbus TCP with plant PLC system. Thus a connection is a mere formality.
Moreover, the software also offers diverse evaluation tools and transfer components, e.g. TXT/CSV-Export. Together with the possible direct control of possibly already existing sample taking systems, the HAVER CPA Online can be operated as an independent system. In this case no process control system or PLC connection is necessary.
Underground mining exposes workers and equipment to some of the harshest working environments imaginable. The deepest mines for instance bottom out at over 3km with temperatures reaching 45 degrees centrigrade. However, the advancement of technology is slowly improving the working conditions in these hostile environments. Several mining equipment manufacturing companies are investing in state-of-the art equipment that meet various needs in underground mining.
Each type of mining equipment comes with its own set of mining activities. The most common types of mining equipment vary depending whether the work is being carried out above or below ground or mining for gold, metals, coal or crude oil. From drilling machines to excavators, crushing and grinding equipment – the mining industry comes complete with all the right tools.
Underground mining is carried out when rocks or minerals are located at a fair distance beneath the ground. But then they need to be brought to the surface.
Underground specialized mining equipment such as trucks, loaders, diggers etc. are used to excavate the material and are normally hauled to the surface with skips or lifts for further processing. Underground mining techniques have progressed significantly over the past years.
Apart from cost per ton ratio and durability, emissions levels are also a huge factor when deciding on underground machinery. Moreover, recent changes in regulation obligate mining companies to reduce greenhouse gas emissions and improve working conditions in underground environments in which they have operations. Conveniently, advances in electric vehicle technology have made converting a fleet of vehicles from diesel driven to electric to achieve these two critical objectives an attractive proposition.
Companies like Sandvik and Schar, have invested in the manufacturing of battery electric vehicles (BEVs) which promise to be a big part of the future of underground mining. BEVs are poised to play a leading role in improving health and safety, boosting
efficiencies and achieving sustainability goals. According to Deon Lambert, business line manager for load and haul at Sandvik Mining and Rock Solutions, the introduction of BEVs in Southern African mines has placed the industry in a vantage point in terms of sustainability.
“For mines who are working towards carbon neutrality, there are options to combine on-mine renewable energy generation with BEVs,” says Lambert. “In countries where grid power is unreliable, this strategy also holds the promise of more streamlined and uninterrupted operations,” he adds.
Scharf’s Managing Director, Shaun Amos, mentions that that BEV’s have emerged as capable alternatives to conventional diesel-powered vehicles in terms of performance and environmental compliance (reducing greenhouse emissions) due to the following features:
• Battery equipment does not emit greenhouse gasses during operation;
• BEV’s have better performance capabilities due to the advantageous
torque curves of electrical motors, which allows for improved tractive effort;
• Battery-electrical motor systems are far more energy efficient than fuel/ ICE systems, reducing the generated heat within confined mining spaces. This drastically reduces the ventilation requirements;
• BEV’s have less vibration and noise, which improves operator comfort; and
• BEV’s incorporate energy regeneration brake systems to charge the batteries when driving down declines.
He further advises mine operators to take a long-term view when considering adopting battery-powered vehicles as part of their fleet in the underground mining environments. “The ventilation cost saving is the largest benefit when migrating to a battery powered fleet. Ever increasing diesel emission regulations result in more expensive mine ventilation requirements, an issue that BEV’s can completely solve,” he add
With a solid reference base of its batterypowered LHDs and trucks already operating in the field, Sandvik Mining and Rock Solutions has made considerable progress in introducing BEV technology into mines. From 4 t LHDs in 2 to 3 m tunnels to 65 t trucks in 5 to 6 m tunnels, the BEV proposition is well-proven. Mr. Lambert says the key is to ensure that there is the right level of site readiness before bringing any innovation into an existing process.
“For instance, it is clear that BEVs cannot on their own improve on the carbon footprint of an older, cable-trailing fleet if the mine’s source of electricity is still a coal-fired power grid,” he notes. Key to the enabling infrastructure for a productive BEV fleet is the necessary expertise for maintaining and servicing all technical aspects to achieve the expected performance levels.
According to Mr. Scharf, in order to survive in the current mining sector, mines and mining houses need to constantly evolve together with the latest technology to improve productivity, reduce costs and
improve mine safety. Excessive conservative mining companies have the large risk of falling behind in terms of productivity and Environmental, Social and Governance (ESG) requirements.
“BEV’s offer the same traditional familiar functionality and flexibility as its conservative diesel counterparts, but with many added benefits. Without a doubt, BEV’s are an avenue which can enable mine operators to be environmentally compliant, safe, and, most importantly, remain profitable businesses,” he affirms.
Eriez Flotation technologies are rapidly changing mineral processors’ separation and recovery operations to deliver unprecedented economic and environmental impact. Eriez invented the revolutionary equipment enabling Coarse Particle Recovery. Eriez HydroFloat® Separator can float base metal sulphide and industrial mineral particles beyond the 150 micron norm to as much as 850 microns with very high recovery.
Now is the time to act, leap forward into new technologies for unprecedented economic and environmental impact. Visit EriezFlotation.com
>600µm particles recovered using HydroFloat CPF