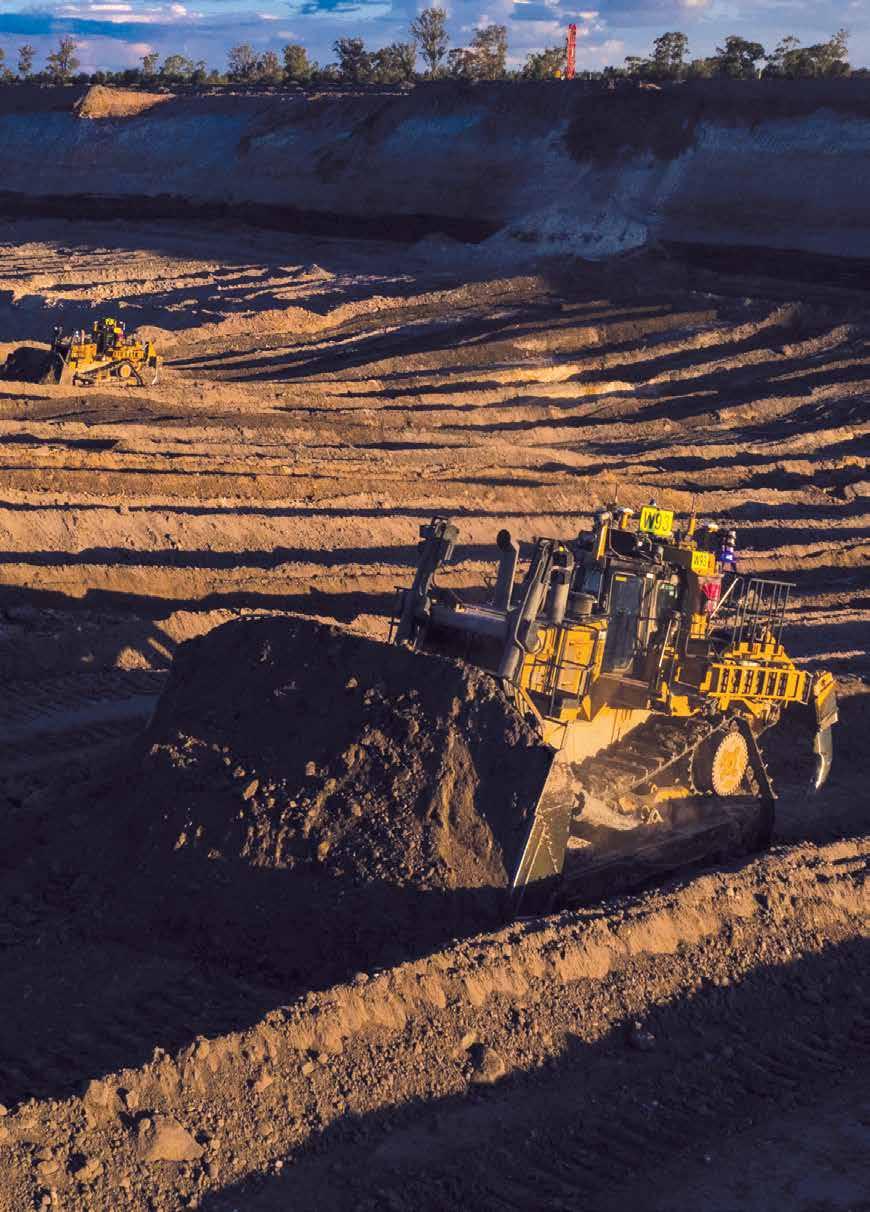
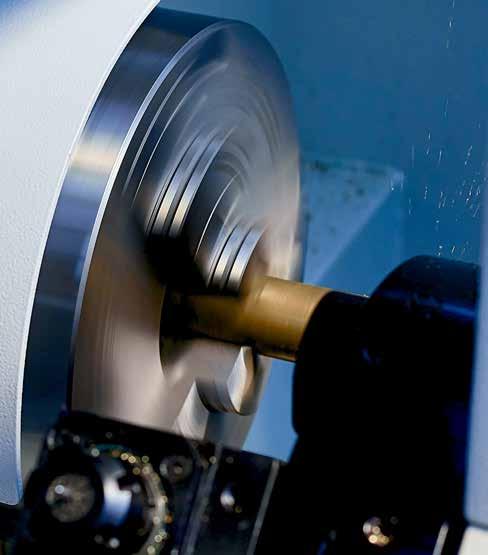
600 Machine Tools has a world-class reputation in the manufacture and distribution of high-quality machine tools. Customer support and service is the number one priority to ensure a machine tool is best suited to your exact needs.
Highly flexible combination CNC lathes, utilising the renowned, easy to use ALPHA operating system. Large capacity working envelopes ideal for ‘one offs’ and small batch size production.
A wide range of versatile, rugged, precision lathes designed to give years of lasting performance. Ideal for industrial and education applications.
An impressive and versatile range of high performance, heavy duty, rigid Vertical Machining Centres with increased accuracy and precision.
A flexible range of compact, heavy duty CNC turning centres including 2 axis, driven tool, Y axis and sub-spindle machines.
National Group: Unstoppable earthmoving 40
Stochastic scheduling with Spry & daedalus 42
Clean Critical Minerals mining 44
EnduroCo4x4 Conversions 45
ANSTO and Lithium Australia 46
Mathematics of Manufacturing 48 Resources Tally 50
SEA Electric aviation refueller 51
INDUSTRY 4.0
Integra smarter country 52 SoftIron HyperCloud 54
TIBCO 56
Laser shock peening 57
A better working culture 58
SAF Technology 62
‘Repair not produce’ with Chiron Additive 63
Micro Additive Manufacturing 64
AM solutions increases the efficiency of 3D printing 67
Component Cleanliness 68
Tackling corrosion at NSW Ports 71
ZoneRV 76 Technofast 78
Work for QLD 80
SOFTWARE Software as a Coworker 84
Garman Facility 85 Mathworks 86 DigiPart 87
Skills Shortage 90
Facteon SMC 92
Kemppi Master MIG 93
Iscar Multi Master 96 THK Rhythm 98
Micro Moulding 102
Cube Precision Engineering 103
WISE Woman 104
Firing Bricks 105
From The Editor 8
From The CEO 10
From The Ministry 12
From The Industry 14
From The Union 16
INDUSTRY NEWS 20
VOICEBOX 26
TECH NEWS 32
PRODUCT NEWS 34
ONE ON ONE Dr Hermione Parsons 74
COMPANY FOCUS Remsense Virtual desktop 82
FORUMS 108
AMTIL INSIDE: The latest news from AMTIL 112
INDUSTRY CALENDAR 116
MANUFACTURING HISTORY: A look back in time 118
National Group has supplied end-to-end mining services to the world’s largest resource companies for more than 20 years.
Integra Systems looks at the many Smarter ways of doing business in manufacturing.
Dr Hermione Parsons is the CEO at the Australian Logistics Council and has worked in the supply chain and freight logistics industry for over 30 years. She speaks to AMT.
COMPANY FOCUS Resense is a WA technology firm using imagining technology to build lifelike representations of far-flung assets.
Innovative technology, quality manufacturing and comprehensive service and support define the Okuma experience.
We offer the leading edge of ‘full service’ distribution and lifetime support for Okuma CNC machines. Solution focussed, our team work with our customers to provide machining realities, with exceptional results.
Our team gives you immediate access to decades of industry experience and a network of local and global machine tool experts. We partner with you from the very first meeting, guide you through project planning and support you through implementation, training and after sales care.
A collection of thoughts, while digging through the badlands of Industry Policy in the lead up to the Australian Jobs & Skills Summit.
I get it. The manufacturing industry uses a lot of energy. Whether that is diesel, gas, petrol, electricity or unicorn sweat, the supply cannot be allowed to run out, or the whole wheelhouse stops rolling. But think about this at a personal level. How did you feel after you last paid your gas and power bill? Hold that thought.
The Australian Workers’ Union passed an emergency resolution recently calling on the Australian Government to urgently expedite its review of the Australian Domestic Gas Security Mechanism (ADGSM), to activate a price trigger mechanism to at least give certainty to the Australian manufacturing industry. The Secretary General of the United Nations Antonio Guterres, called out the obscene profits announced last month by the world’s gas, petroleum and oil companies world-wide as, ‘grotesque greed’. $100bn in just three months. There’s another thought for you to hold.
Like what Kevin Rudd called for on the local mining companies here during his time as PM, the UN chief has called for taxation on windfall profits of oil and gas companies. This might just ease the impact of the global energy crisis on the most vulnerable people. The resolution comes in the wake of a damning ACCC analysis that forecasts a 56 petajoule shortfall in east coast gas supply for 2023, despite Australia producing abundant quantities of the stuff. The ACCC calls this figure a “significant risk to energy security” and accuses gas exporters of not supplying the domestic market in the spirit of the 'gentleman’s agreement' brokered by the former government between the major players.
Delegates from the heavy manufacturing sector supporting the AWU resolution at the Union’s National Conference cited gas bills rising up to $700,000 per month at a glass manufacturer in Melbourne and $1m a month at a steel manufacturer in Newcastle.
“The previous government left us all an unholy mess to clean up and we'll have to move decisively to avoid disaster,” the AWU National Secretary Daniel Walton said. “The ACCC analysis confirms what the AWU has been saying for a decade — you cannot trust multinational gas exporters with Australia’s energy security. Falling for their ‘trust us’ routine leads inevitably to the destruction of the Australian manufacturing sector. The writing has been on the wall since the very beginning. So much of the manufacturing sector relies on gas and those costs have risen astronomically this year. They just can't afford to go on. If they shut we will see thousands upon thousands of workers lose their jobs. This will have far-reaching flow-on effects for families and whole communities.”
Australian manufacturing companies have previously struggled to compete with offshore competitors working to razor-thin profit margins. But a unique combination of factors including the ongoing Ukraine conflict, supply chain delays, the effects of COVID-19 dealing out skills and local personnel shortage, now has been added to by those gas exporters selling our fuel overseas at premium prices, while risking us not having enough to heat our homes or power our production facilities. Instead of green-lighting more coal and gas projects, what we have to do is fast track the transition to renewable-generated electricity. If government can help the manufacturing sector get onboard renewables and storage power, that would ensure more reliable power overall, cheaper home-grown products, and power prices would come down very quickly. It would cost less.
But, try as they might, the regulators have struggled to find any evidence of gaming the gas price systems, just of perfectly legal “re-bidding”. The industry has even evolved its own vocabulary – opportunistic cost, for instance – to assign some sort of economic rationale, if not moral justification, for the exploitation of consumers. Which doesn’t instill much comfort. The east coast gas market has all the features of a cartel, in that just a few companies control 90% of the supply. They’ve been reported to be using anti-competitive practices, even of forcing prices up above international levels. Remember only a month ago, they went too far and the Australian Energy Market Operator suspended the market, proving that you can’t just ask these fuel suppliers to play nicely.
I’ll just add that thought to the others you’re holding.
Editor
Paul Hellard phellard@amtil.com.au
Contributors
Carole Goldsmith
Drew Turney
Sales Manager
Nicholas Raftopoulos nraftopoulos@amtil.com.au
Publications Co-ordinator
Gabriele Richter grichter@amtil.com.au
Publisher Shane Infanti sinfanti@amtil.com.au
Designer Franco Schena fschena@amtil.com.au
Prepress & Print
Printgraphics Australia
AMT Magazine is printed in Australia under ISO140001
Environmental Certification using FSC® Mix certified paper sourced using sustainable tree farming practices.
Contact Details
AMT Magazine
AMTIL Suite 10, 5 Corporate Boulevard Bayswater VIC 3153 AUSTRALIA
T 03 9800 3666
F 03 9800 3436 E info@amtil.com.au W www.amtil.com.au
Copyright © Australian Manufacturing Technology (AMT). All rights reserved. AMT Magazine may not be copied or reproduced in whole or part thereof without written permission from the publisher. Contained specifications and claims are those supplied by the manufacturer (contributor).
The opinions expressed within AMT Magazine from editorial staff, contributors or advertisers are not necessarily those of AMTIL. The publisher reserves the right to amend the listed editorial features published in the AMT Magazine Media Kit for content or production purposes.
AMT Magazine is dedicated to Australia’s machining, tooling and sheet-metal working industries and is published bi-monthly.
Subscription to AMT Magazine (and other benefits) is available through AMTIL Associate Membership at $185.00 (ex GST) per annum. Contact AMTIL on 03 9800 3666 for further information.
AMTIL, along with a number of our international association colleagues, commission Oxford Economics to conduct a six-monthly report of global machine tool sales and forecasts, along with key industry drivers and economic outlooks. It is a major piece of work that give us a really good picture of the world of machine tools and markets.
The full Oxford Economics report has so much detail in it, I found it hard to know where to start in giving you some information that may be of interest. So what I have done is pull out four graphs that may give some context to the overall report and highlight some high level activity that is apparently on the global stage.
You can see from the first image, the most recent survey data points to weaker manufacturing activity in the quarter from JulySeptember 2022. The lower right quadrant shows a manufacturing sector still expanding, but in most cases surveys have weakened significantly over the last three months. The lower left corner is consistent both with shrinking manufacturing output and worsening over the last three months. Of the major economies shown in this graph, only India and Indonesia are still seeing an expansion which appears to be strengthening.
Interestingly, the Australian PMI dropped 3.2 points to 49.3 points in August 2022, indicating a slight contraction (seasonally adjusted). This is the first time the index has contracted since January 2022 following the Omicron outbreak during the summer break. This would put us on the graph around the same area as China over the past three months.
The second image (Fig 2) shows the significant supply chain pressures in late 2021 through to early 2022 – from semiconductor shortages, labour shortages, to shipping backlogs, raw material issues, to supply constraints due to the war in Ukraine – that have held back production, most notably in car production. Global supply chains have been easing over the past six months and have now fallen to the lowest level in more than 18 months. While pressures remain above normal, the momentum in this indicator is clearly down, although it is worth noting that some of the easing is likely related to weakening demand.
The past seven years of machine tools sales, using 2015 as a baseline and following the global trough in Q2 of 2020, orders are back at pre-pandemic levels signalling the strength in demand over the past two years.
CECIMO 8 is the combined major eight European countries and, along with the US, have tapered somewhat in the past quarter. However, despite some small signs of weakening, machine tool sales are still the highest they’ve been over the past seven years, highlighting a remarkable achievement given the COVID crisis and the impact it has had on so many aspects of our lives.
A number of industry sectors have experienced some volatility over the past year or two. The big ‘winner’ from COVID, if that can be said, was the electronics and electrical engineering sector with 15.1% growth in 2021 and a forecast of 7% growth in 2022. It is expected that this industry will cool off over the coming few years. The strongest growth forecasts are in the sectors with pent up demand – aerospace and automotive – although both these sectors are vulnerable to an inventory led swing if demand slows significantly. From 2023 through to 2026, global forecasts have industry production and GDP growth around the 2.5 – 3.0% per annum and reasonably stable. Overall, industry sector growth will continue to push machine tools sales over the coming few years and some stability in production and growth figures point to a relatively healthy outlook.
The Oxford Economics Global Machine Tool Report is available to all AMTIL members on request. Please contact Shane Infanti on sinfanti@amtil.com.au for a copy.
For more information on AMTIL membership please visit amtil. com.au/join-amtil
Best choice.
Cutting. Bending. Automation.
Discover the latest generation of bending. The Xpert Pro from Bystronic fulfils your demands for highest process speed and flexibility. To enable a wide spectrum of bending applications, the press brake offers an extensive range of performance options. In addition, intelligent assistance functions ensure precision from the very first bent part.
The development of technology and tech skills are the keys to building an economy that is globally competitive.
I was greatly encouraged by the spirit of cooperation among participants at September’s Jobs and Skills Summit and pleased at the outcomes. We were united by a simple proposition: a belief in the power of our ideas, brought to life by skill, can contribute to national wellbeing.
There was a shared understanding that stronger businesses backed by a skilled workforce with secure jobs and better wages can provide more opportunity for Australia in the global economy.
Digital skills in particular were well understood to underpin the development of a modern workforce, particularly in the tech area.
These goals were supported by the Summit outcomes, including the agreement between the Australian Government, States and Territories to accelerate the delivery of 465,000 additional fee-free TAFE places, with 180,000 to be provided next year.
A Digital and Tech Skills compact was agreed at the Summit between the Government, Unions and technology employers.
This is designed to ensure the development of skilled, digitally adept workers across all industries. The Government will develop a model pilot scheme under the compact to help workers enter the techrelated jobs. They will be supported by a blend of employment and training. My colleague the Minister for Skills and Training Brendan O’Connor and I have convened a working group with stakeholder representatives to develop proposals, including for the White Paper process established by the Summit.
This compact builds on work from the ACTU and the Tech Council of Australia and is an important step towards achieving the Government’s target of 1.2 million tech-related jobs by 2030.
To help ease critical skills shortages, the Government has also increased the permanent migration program planning level by 35,000 in 2022-23, and moved to accelerate visa processing and relaxed work restrictions.
This move supplements the efforts being made to increase the skills level through education and training. Enterprise bargaining is also being made easier so that workers and businesses have flexible options for reaching agreements.
The measures undertaken will unburden businesses from unnecessary restrictions while supporting wages growth. There was also agreement that people who have been underrepresented in skilled areas be given better opportunities to participate and contribute. Providing better, more inclusive pathways for women, First Nations people, migrants, mature workers and those living with disability is an equity priority for the Government and increases available skills.
As part of this we are moving to widen the pipeline of talent in the science and technology sectors. This makes good business sense.
There will be a review of existing programs to support diversity in Science, Technology, Engineering and Mathematics (STEM), particularly those designed to encourage more women and girls to get involved.
The review will consider what is working and what is not, build on strengths and develop concrete measures to attract, promote and retain diverse groups in the STEM workforce.
As present, only 16% of those with STEM qualifications are women and only half a percent of First Nations people hold university-level STEM qualifications.
The benefits of an advanced economy have to be spread more evenly across the population. Giving more Australians from all corners of our community the opportunity to be trained in STEM skills is part of maximising the human potential of our nation.
All of us - in government and the private sector - need to be ready to invest in our people to support the jobs of the future. The Government is committed to providing more support for industry.
Our flagship program the $15 billion National Reconstruction Fund (NRF) is a co-investment platform that will help transform and strengthen industries, create jobs and support long-term growth for the economy. Within it, a Critical Technology Fund will focus on support for emerging industries such as AI, robotics and quantum technology, making sure investments retain value for Australian industry and national wellbeing.
To make the NRF work, we need the private sector to support its roll out so we can return to creating world-class products here, build on our strengths and broaden our industrial base.
Our Buy Australian Plan will open government contracts to strengthen industry capability, growing small and medium-sized enterprises. The Government is also assisting small and mediumsize enterprises by introducing tax incentives to encourage digital technology adoption and boost skills and training.
It all comes back to skills and training. And the Jobs and Skills Summit was the first step of a journey in which we need to work together to maximise the potential of our industries.
All of us need to be ready to invest in our people to lay the foundations for a skilled, inclusive and resilient workforce.
Ensuring the transformation of our nation into a high-value, highwage modern economy needs to be a collaborative effort, involving governments, businesses, unions, the research sector and other industry stakeholders.
I want Australia to be known as a nation that makes things, a nation that has faith in its own ideas, its know-how and ability to get the job done. A smart nation that is a maker, not just a taker, of high-value products.
Working together we can get the best results for our economy, our businesses, our workers and the nation.
industry.gov.au
The Capral online store makes viewing and ordering aluminium, extrusion, sheet and plate a breeze. Available 24/7 at the click of a button, select from the Capral standard offering or custom exclusive sections for your business. Find what you want, when you want it.
Online orders can be delivered to your door or collected from one of our national network of regional distribution and Aluminium Centres. Convenient online ordering, Capral Can Do.
Ai Group represented our members’ interests at the recent Jobs and Skills Summit in Canberra and will continue to do so during the Employment White Paper process that now follows.
A golden thread that ran through all of the Summit’s discussion – around the jobs of the future, around gender equality, around workplace relations – was the need for skills, a proper skills base and a proper program for skills development.
The reality is that our future depends on a highly skilled workforce. We have no option but to focus on skills in a significant and focused way. Another reality is that there are significant pay increases occurring right now within workplaces, and they are primarily focused on the skilled component of those workforces – those who are highly sought after, highly contributive and seen as highly valuable.
On the Summit’s first day, UTS Chancellor Catherine Livingstone reflected on the 2020 Summit of 2008 and talked about a ‘groundhog day’. My reference point is a little more recent than that.
In 2016, with others, I stood in front of the then Prime Minister and the Premiers at a COAG meeting and talked then of the skill shortages that industry was experiencing and of the crisis that was unfolding before us, and yet here we are: we still have crippling labour and skill shortages with no relief in sight. And to be blunt, there is no more important issue for employers.
We need urgent and wholehearted action that makes a significant down payment on developing a pipeline of skilled workers for at least the next decade. Enough of the excuses.
This plan must deliver bold, generational reform. A history of tepid reform has left us unprepared and wasted precious time and money. It now seems that our teenagers would rather be influencers than engineers.
We are now at a critical juncture, with no option but to step up to the challenge.
As I see it, there are seven priority areas for reform and I will touch on them quickly:
1) The first is new entrants. Reinvigorating our apprenticeship system, evolving it to a model that embraces higher and degree apprenticeships, traineeships and cadetships across more occupations is crucial. It must become a system that people are keen to join, keen to complete and is the primary skill development pathway for industry.
2) For existing workers, we need to focus on the skills of those currently in the workforce, to ensure their skills remain contemporary. This will involve developing a lifelong learning framework that builds skilling options for existing workers and mature age people seeking employment. A particular focus is on developing a range of ‘industry endorsed’ micro-credentials enabling shorter and sharper and targeted upskilling and reskilling. Careers are no longer linear and predictable, and every worker – young and old – needs to be flexible, adaptable and capable of rethinking how best to use and grow their skills and their capabilities.
3) The high paying, high skilled jobs of now and the future are digital. We need a national strategy that includes digital capability standards and a framework that supports the digital transformation and enablement of our economy. Nobody should be left behind. We need to provide the skills to power our companies, large and small. Industry knows this, but the education and training system is just catching up.
4) The fourth point is foundational Skills – without a successful foundation you can’t build something that you are proud of. Without language, literacy, numeracy and digital skills we will not have successful participation in employment and the necessary capacity to upskill.
5) If we are really serious about focussing our education and training sector on our future needs we need a coherent and connected tertiary sector – a sector that equally values vocational and higher education in a fluid, seamless and dynamic way. Full implementation of the Noonan Review of the Australian Qualifications Framework is an essential first step. We also need a tertiary system that consistently provides high quality, trusted education and training, worthy of our investment. This means lifting our game on funding and regulation to ensure that every dollar invested – public or private – delivers for us all.
6) Pathways from schooling are crucial – our nation’s skills will better match those that industry needs where young people move into careers that are right for them. Our systems of careers advice, from an early age, still need great improvement.
7) Funding – None of these actions will be possible without adequate funding of our tertiary education and training sector. The announcement at the Summit of an additional 180,000 fee-free TAFE places in 2023 was fantastic. But as Mary Faraone, Chair of TAFE Directors Australia alluded to, more will be needed. We need urgent action which restores investment levels in Vocational Education and Training, remedying longterm declines. We need federal and state governments to be together and working off the same page.
Six years ago we told the Prime Minister and the Premiers that building our skills base was the great national challenge and it still is.
This is an edited version of the Statement delivered by Innes Willox to the first session of the Jobs and Skills Summit on Friday 2 September: Skills and Training for the future labour market.
After the Jobs and Skills Summit, we all have to move with the times or be left by the roadside, again.
At the federal government’s Jobs and Skills Summit earlier this month, Tesla chair Robyn Denholm said she was optimistic that “most of our problems, as a society, can be cured by technology”.
For the chair of a company that has suppressed reports on workers’ injuries at its US gigafactories, paid contractors as little as US$5 an hour, illegally sabotaged efforts by its workers to unionise and faced multiple lawsuits alleging widespread racial and gender discrimination, that’s a pretty optimistic belief.
Thankfully, this assumption that technological change will magically solve all of society’s problems by itself is increasingly seen as outdated thinking. I was at the Jobs Summit too, and at the Electric Vehicles Summit two weeks earlier. Nearly everyone I spoke with at both events recognised that the upcoming transition to EVs can’t just be left to the tech giants and venture capitalists. To live up to its potential, it will need unions, government, and employers to work together, and it will need to give manufacturing workers agency and power over their futures.
Too often, governments and employers present economic and technological change to workers as something that happens to them, not with them. That’s what happened at the Hazelwood coal-fired power plant in regional Victoria, and to our car industry in Adelaide. As technological and other circumstances changed, employers moved on, government was caught flat-footed, workers lost their jobs, and their communities suffered. The EV transition cannot repeat those mistakes.
To be clear, the transition to EVs is a massive opportunity. It’s another way Australia can contribute to the fight against global heating. It's a chance to rebuild our sovereign capability in vehicle manufacturing. And it’s a chance to create thousands of high skilled, well paid, secure jobs.
But if we just leave the transition up to private capital, none of that will happen. Industry won’t move up the value chain from exporting raw minerals to manufacturing lithium batteries, let alone get back to building cars again. Local small and medium businesses won’t get a chance to get a foothold in the new supply chains. Workers in legacy industries and the communities they live in won’t benefit. And many EV workers won’t get the skills and training they need to move between employers and other emerging industries – they'll be tied to an employer, their skills will degrade until the technology moves on again, and they’ll be left behind.
Realising these opportunities requires coordination, direction, and consistency. That’s why I, on behalf of the Australian Manufacturing Workers’ Union, have called on the federal government to establish a National Innovation Council (NIC) to shape a domestic EV industry that puts workers front and centre. The NIC would comprise representatives from government, industry and the unions covering workers in EV industry supply chains, and would be tasked with overseeing a rapid transition of our industries, workforces and markets to EV-driven growth.
It would steer industry policy to give Australia a competitive advantage in EVs by developing the supply chain capabilities of SMEs, value-add our mineral exports and speed up the rollout of national EV infrastructure. It would provide a just transition for workers in fossil fuel industries by providing well-paid, secure jobs in legacy mining and energy communities.
It would facilitate the massive and rapid upskilling of workers that will be required to support the manufacturing and maintenance of EVs domestically – similar to what the Victorian Government, unions, employers and TAFE are working together on to upskill workers in the state’s bus network. And it would recommend smart regulation to keep Australia’s EV industry aligned with international benchmarks. None of this will be easy. It will require ambition from the federal government, commitment from industry, and a willingness from all parties to work together. We’ve already lost a decade of opportunity under the previous government, which decimated our local car industry, created the climate culture war, and claimed that introducing EVs would kill off our beloved utes.
However, after so many years of inaction and delay, there is a real desire from key stakeholders to come together and make progress.
No one wants Australia to become the dumping ground for old petrol-powered cars while the rest of the world moves to better, cleaner technology.
If we pull this off, we can solve a lot of problems. But it won’t happen without workers. A National Innovation Council is the way to get this transition moving, and to get it right. amwu.org.au
STEVE MURPHY – National Secretary Australian Manufacturing Workers UnionThe Australian Government celebrated the work of our scientists this National Science Week, working to close the gender gap and inspire the next generation to be part of the highly skilled STEM sector.
Minister for Industry and Science Ed Husic made the comments at Parliament House as he marked this year’s National Science Week, which ran from 13-21 August.
“Australia is home to some of the best and brightest scientists and researchers – and it’s an incredible talent pool that we want to grow,” Minister Husic said. “The Government is determined to address the gender gap in our science and research sectors, to ensure that girls and women can see a place in that STEM talent pool and then to take a deep breath and dive in.”
National Science Week is a key part of the Government’s approach to science engagement and inspiring Australians to pursue a career in STEM. “As the new science minister I want to assure you that science is back in government. Science and the scientific community will play a vital role in guiding evidence-based policy for the Albanese government,” Minister Husic said.
National Science Week features more than 1,000 talks and activities around Australia, by universities, schools, research institutions, libraries, museums and science centres.
In 2022, the Australian Government is supporting 35 National Science Week projects across Australia with $500,000 of funding.
“National Science Week is an incredible opportunity to celebrate the remarkable achievements of our scientists who are making
our world a better place,” Minister Husic said. “At the launch event for National Science Week today we heard from three outstanding First Nations scientists, and I acknowledge the unique perspective and knowledge that Indigenous STEM experts bring to Australian science.
“The Government is committed to ensuring that everyone has equal opportunities to learn, work and succeed in STEM, especially here in Australia, and I’m very much looking forward to exploring how we can achieve this commitment at the Jobs and Skills Summit next month.
“Our Government is also committed to providing opportunities to grow the research sector, such as through our $1bn commitment to develop and commercialise critical technologies in areas like quantum via the Critical Technology Fund.
“This is in addition to the $4m we are providing for up to 20 PhDs in quantum research and to support universities to establish a national research and education partnership between universities.
“Initiatives like these will help achieve our vision of a ‘brain regain’ for Australia, encouraging talented STEM researchers to stay here or return from overseas, and provide the fuel that powers the nation’s high-tech industries.” scienceweek.net.au
$4.45m to be invested into developing advanced manufacturing skills and technology in the Northern Territory.
The Northern Territory Government partners through investment from the Advanced Manufacturing Ecosystem Fund (AMEF) to lift automation capability and advanced technology deployment across the Territory.
The partnership includes a collaborative program between Diverseco and Charles Darwin University (CDU) to develop and deliver bespoke microcredential qualifications and support services to boost local businesses adoption of advanced manufacturing technology. The $4.45m project is the second to receive co-investment via the Territory’s $7.5m AMEF initiative, administered by the Advanced Manufacturing Growth Centre (AMGC).
Territory based manufacturers will soon gain access to a multimillion-dollar advanced manufacturing facility. The facility will house robotic and bespoke automation products and services to support the implementation of technology such as robotic welders, automated pick and pack systems and product inspection services.
“This exciting collaboration will support the advancement of the NT’s manufacturing industry by leveraging its manufacturing capabilities in the defence, transport, logistics, agriculture, mining and waste industries,” Minister for Advanced Manufacturing, Nicole Manison said. “Growing the Territory’s advanced manufacturing industry is a key part of our strategy to grow the economy to 40 billion by 2030 and create more jobs.”
The project will see Diverseco and Charles Darwin University (CDU) work closely to develop four new robotic and automation micro
credential qualifications tailored to the region and boost local skills and knowledge in advanced processes and machinery for the industry.
The commitment also enables Diverseco to expand its support services to local manufacturers wishing to advance their operations and improve staff capability by supporting them with access to the latest technology, training programs, design services, equipment implementation, and operations and maintenance activities.
Diverseco and its project partners will provide on-site technical support and training services to local businesses seeking to adopt advanced technologies in their operations and support these businesses to upskill their staff. The facility will also be available to local business to demonstrate these technologies and develop tailored automated solutions for their individual business needs.
The AMEF will provide almost $500,000 towards this initiative, giving industry the ability to test the latest in automation technology with the total project representing $4.45m investment in the NT’s manufacturing ecosystem.
“This exciting partnership between CDU and Diverseco will support course expansion into new robotic and automation qualifications tailored to the region,” Charles Darwin University, Vice Chancellor, Professor Scott Bowman AO said. “This investment into advanced manufacturing skills and technology is a welcome addition to the Northern Territory and offers new and exciting opportunities for our students.” cdu.edu.au
The Australian Research Council commits $5m to establish UOW centre for training and research into the future of mining equipment.
Minster for Education, The Hon Jason Clare has announced that the Australian Research Centre will fund the establishment of the ARC Training Centre for Innovative Composites for the Future of Sustainable Mining Equipment at the University of Wollongong (UOW).
UOW Vice-Chancellor Professor Patricia Davidson said the Illawarra is the perfect setting for a centre focussed on sustainable mining.
“Wollongong has deeply held roots in mining and manufacturing, and this training centre will be the perfect launch pad for global collaboration and innovation,” Professor Davidson said. “Our state of the art engineering and technology hubs will offer the perfect environment to train the future minds of mining and to find solutions to revolutionise an industry that contributes 15 percent of Australian GDP.”
In Australia the Mining Equipment, Technology and Service (METS) sector is estimated to add more than $50bn and 80,000 new jobs to the Australian economy by 2030. The transformation of the sector towards more efficient, cost-effective, innovative, sustainable and digital operations will require safer machinery and equipment, which is able to operate in deeper mines and harsh environments.
Over the next five years, the ARC Training Centre for Innovative Composites for the Future of Sustainable Mining Equipment will train and produce engineering graduates to be highly qualified professionals who are empowered to take on future challenges in the METS sector. Director of the new Centre, Distinguished Professor Zhengyi Jiang of UOW’s School of Mechanical, Materials,
Mechatronic and Biomedical Engineering, said the Centre will bring together a team of world-class researchers and industry leaders to train a workforce to meet the future skills demand.
“This Centre, by working with industry, will improve and streamline the research and development process, building a solid national network to address the needs of the mining equipment manufacturing, enhancing sustainability, and making a safer mining environment,” Professor Jiang said. “The Centre will support Australian industry to maintain its position as a world leading innovator in the METS sector.” The Centre’s program of industry integrated research focussing on innovative steel composites, coupled with work integrated learning, will empower graduates to develop unique solutions, incorporating into valueadded technologies and products into the Australian METS sector. The Centre aims to train industry-focused researchers in advanced manufacturing of new-generation mining equipment and sustainable mining technology, through close collaborations among key universities and mining and manufacturing companies.
ARC Training Centre for Innovative Composites for the Future of Sustainable Mining Equipment will be established with industry partners Roobuck, Bisalloy Steels, SNS Unicorp, HBIS Group, Baosteel Company, Komatsu Australia, Top Iron, Australia L&Y Mine Equipment Manufacturing, and University Partners University of Queensland, Deakin University, University of Adelaide, Western Sydney University, University of New South Wales, and Curtin University. uow.edu.au
Innovation technologies funding a welcome boost for Queensland.
Australia’s peak industry representative body for innovative technology, the Australian Information Industry Association (AIIA), welcomes the $142m Advance Queensland – Innovation for a Future Economy 2022-2032 roadmap announced by the Palaszczuk Government.
The funding will support Advance Queensland programs, Queensland Innovation Precincts, Innovation Action Plan and funding supporting industry-science centres of excellence and partnerships, accelerating university commercialisation through the Department of Environment and Science.
With the University of Queensland finding that 80,000 new jobs can be created in the next decade, along with a $11bn-a-year boost to the economy, the funding to boost innovation hubs offers significant potential for Queensland.
“The AIIA is pleased that the Queensland Government realises the potential of a digital led strategy in strengthening its economy through this investment,” AIIA CEO, Ron Gauci said. “The funding announcement by the Queensland Government is encouraging for Queensland’s innovative technologies sector. This is a sector that will generate significant growth for the economy for years to
come. South East Queensland is seeing notable expansion in the innovation and ICT sectors, showing the high demand for these services and the skills to deliver them.”
“Seeing the investment flow into the sector is most important. From supporting commercialisation to growing the skills of Queenslanders, it is vital the funding makes its way to support developing technologies. Support of commercialisation will ensure brilliant Australian innovations remain Australian, creating jobs and ensuring Australia retains the economic benefits for years to come.
“There is incredible demand for skilled workers across the ICT sector Australia-wide; our industry could easily be employing over 1.2m skilled workers today given the vacancies. We need to continue to work with governments to develop job-ready and relevant skills, from tailored microcredential courses to tertiary qualifications. This is a promising announcement for Queensland that we look forward to seeing the innovative technologies sector continue to grow and support other economic sectors,” Gauci said.
AIIA is a not-for-profit organisation aimed at supporting and advocating for Australia’s future social and economic prosperity through technology innovation. qld.gov.au
Henkel embarks on local production of Loctite PUR adhesives in Australia.
Henkel is slated to produce Loctite polyurethane (PUR) adhesives in Australia from the first half of 2023. The adhesives will be manufactured in Kilsyth, Victoria, to serve the engineered wood industry across Australia and New Zealand.
“Purbond adhesives are used globally and have long been the benchmark for innovation and reliability in the engineered wood industry. Producing Purbond locally is an exciting endeavor that opens many opportunities for us to help our customers in Australia and New Zealand to grow,” said Brad Simpson, Sales Manager and Business Unit Manager, Adhesives Technologies, Engineered Wood, Furniture and Building Components.
Henkel’s adhesive experts at its Innovation and Application Labs in Sydney and Auckland, help customers explore ways to expedite the time to market and optimise their own production processes for the development of engineered wood solutions. With the production of Purbond in Australia, adhesives production can be customised for specific performance requirements such as fire resistance and for use with modified timbers. “By localising the production of Purbond adhesives, our customers will benefit from reduced lead times from order to delivery, as well as greater supply chain security. This reflects our commitment to putting our customers at the centre of what we do,” said Warren Grigsby, Business Development Specialist, New Zealand.
Purbond adhesives for engineered wood construction With a growing environmental awareness surrounding construction and material use, engineered wood has become an increasingly popular design choice for load-bearing mass timber and high-tech structural engineering applications.
Approved for use in all major engineered wood construction markets, Loctite Purbond adhesives make it possible to manufacture glued wood components that are free from harmful industrial solvents and formaldehyde. In addition, they can be specifically engineered and controlled to enable the use of engineered wood in ever-new ways. Henkel holds leading positions in many markets and categories around the world. Founded in 1876, Henkel looks back on more than 140 years of success. In 2021, Henkel reported sales of more than 20bn euros and an adjusted operating profit of about 2.7bn euros. The company employs more than 52,000 people globally – a passionate and highly diverse team, united by a strong company culture, a common purpose, and shared values. henkel.com
Manufacturing the advanced future in Dandenong with Nissan Casting Australia, BWX, Spee3D and more.
The Andrews Labor Government is backing advanced manufacturers in Dandenong to expand, shaping the south-east Melbourne region into a hub for production excellence and a magnet for investment and high-skill jobs.
A growing list of leading companies are choosing to expand or base their global operations in Dandenong, including automotive component producer Nissan Casting Australia, 3D printing manufacturer Spee3D and skincare giant BWX and many others.
With support from the Labor Government, these advanced manufacturers are injecting a combined investment of more than $150 million into the region and creating 230 new local jobs.
Dandenong hosts almost 1,400 manufacturing businesses and more than 21,000 workers. They transform a range of advanced materials into new products, creating high value components for the next generation of space, aerospace, defence, mobility and medical technologies.
The highly skilled jobs that have been created in the region include engineering, production and technical roles in mechanical, mechatronics, electrical and digital technologies.
Nissan Casting Australia has invested $15.5m to expand its Dandenong South facility, which produces aluminium die-cast components used in Nissan’s electric vehicle models sold around the world.
“With nearly 40 years of operations in Melbourne’s south-east, this will help us to expand our production of Australian-made electric vehicle components to the global market,” says Peter Jones, Nissan Casting Australia Plant Managing Director.
The investment will create 41 local jobs in engineering, management, and production and allow the company to boost its automation and robotic operations, building Victoria's skills base.
The locally made parts will be used at assembly plants around the world, including in Japan, Thailand, and the USA.
Nissan Casting Australia's Dandenong South facility produces aluminium die cast components used in Nissan's electric vehicle models sold around the world, including the LEAF.
Greater Dandenong is located approximately 35kms from Melbourne’s CBD and is the most culturally diverse community in Victoria with residents from over 160 birthplaces around the world.
Victoria is the manufacturing state of the nation. The industry is worth around $30bn to the Victorian economy each year, providing more than 27% to the nation’s manufacturing output.
The Government is helping the state’s advanced manufacturers to grow, innovate and stimulate job creation through initiatives including the $2bn Breakthrough Victoria Fund and the $40m Victorian Industry Investment Fund, which was included in the 2022/23 Budget.
“We support advanced manufacturers in Dandenong and around the state so they can expand and create secure jobs for Victorians,” the Minister for Industry Support and Recovery Ben Carroll said. “Dandenong is a success story of innovation and good investment – and we will continue to back the region so it can fulfil its cement itself as one of the key advanced manufacturing precincts in Australia.” djpr.vic.gov.au
Manufacturing is the answer to improving Australia’s falling complexity ranking.
Australia’s Economic Complexity Index (ECI) ranking has fallen to 91st on the global index, the lowest of any OECD nation. Manufacturing is the answer to address Australia’s declining ECI ranking by helping transition the economy from raw commodities trade to valueadd manufacturing. The Advanced Manufacturing Growth Centre (AMGC) advocates for greater focus on helping local manufacturers to transform and scale, to increase global competitiveness, and secure the nation’s future prosperity. The latest data released by the globally respected Harvard Business School reveals that Australia’s Economic Complexity Index (ECI) rating has slid to 91st, down eight positions in the last ten years. The Harvard index systematically ranks 133 countries by their ability to manufacture and export diverse and complex things and has been a global benchmark of a nation’s global impact since 1995, when Australia ranked 55 on the index. The result places Australia in the bottom third of monitored nations for complexity, between Kenya and Namibia, and also means Australia is the lowest ranked OECD country despite its high level of wealth.
The Index brings into sharp focus Australia’s economic reliance on exporting items of low complexity in the form of commodities, and highlights the immense opportunity the nation has to improve the complexity of the items it exports, by adding value to its abundant natural resources or making more complex items in areas of relative strength. The report states that: “Australia is less complex than expected for its income level" and goes on to say that: “Australia has seen a troubling pattern of export growth, with the largest contribution to export growth coming from low and moderate complexity products, particularly Ores, slag and ash and ICT products.” Since its inception in 2016, the Advanced Manufacturing Growth Centre
(AMGC) has advocated and demonstrated the potential of Australia to grow the complexity of its exports through co-investing in local manufacturing excellence. AMGC’s Managing Director Dr. Jens Goennemann said, “The latest ECI rankings are a damning reflection of Australia’s reliance on raw commodities trade – or luck. If these ECI results were reflected in the elite sporting world, we would be mortified.” “Why is it that we accept such a poor result in our global complexity ratings when it is directly tied to our future prosperity?
At some point the ‘Lucky Country’ will run out of luck; now is the time for us to act and begin to increase the complexity of the things we manufacture and export,” said Goennemann. The Harvard report goes on to state that: “Australia has not yet started the traditional process of structural transformation. A key source of economic growth, this process reallocates economic activity from low to high productivity sectors. It broadly moves activities out of agriculture into textiles, followed by electronics and/or machinery manufacturing.”
Raising the nation’s manufacturing profile requires long-term policy and co-investment from the government as well as private sources. Multiple micro-investments matched dollar-for-dollar by industry participants incentivises Australia’s largely SME-based manufacturing companies to innovate and scale. To meet this national challenge, AMGC has successfully managed over $57m in co-investments directly to Australia’s manufacturing industry and encouraged manufacturers to scale and export. AMGC’s targeted co-investments into 141 projects, are expected to generate 4,000 new, highly skilled, and well-paid roles and on completion will return $1.6bn to the economy. atlas.cid.harvard.edu/countries/14 amgc.org.au/projects/
When fast, precise and synchronised linear motion is required, our Lifgo rack and pinion gear units have proven to be reliable in many industry sectors around the world.
Smart and robust modular units offer designers the opportunity to tailor projects to meet unique needs at low cost.
Lifgo enables rapid design and ease of system development for complex projects. Offers reliability and capabilities that transcend traditional product designs and boundaries, securing a competitive advantage.
Industry
Replace awkward ballscrews with Lifgo innovative gear units and precision racksMaximising operational efficiencies and unlimited combinations for various applications.
Harnessing power from ocean waves is a complicated endeavour into which a South Australian-Chinese research team is diving deep to take into a new direction.
A prototype system designed by Flinders University researchers delivers a robust generator made from recycled material that promises to help address small-scale local energy requirements and environmental pollution issues with further R&D.
The ‘green machine’, designed around a wave-driven triboelectric nanogenerator (WD-TENG for short) model, integrates two small generators inside a recyclable tube to make cost-effective electricity in water from continuous immersion in waves.
A new study published in the journal Nano Energy, by researchers at Flinders University and Beibu Gulf University in China, evaluated the low-frequency energy output of the TENG unit under various ocean wave conditions.
“The experimental testing result indicates the WD-TENG can almost reach the rated output at Hz with 1.05 W/m2 power density,” says Flinders University College of Science and Engineering PhD candidate Mr Yunzhong (Steven) Wang.
“Our modelling indicates that the new WD-TENG has decent durability and robustness under continuous operation and has potential to provide electricity to remote or rural properties close to the coastline, or on islands.”
The experiment also showed the WD-TENG can sustainably charge a 47 μF capacitor to 0.496 V in a minute. The exchange charge density of the used triboelectric materials arising from the triboelectric charge exchange is 19.81 nC.
The R&D will expand with support from the State Government’s Green Industries SA via a ‘circular economy’ student award for the research into ‘a wave-driven generator constructed from recycled materials’ presented last week. Lead researcher, Flinders University Professor Youhong Tang, says the team will now test the design in a watertank system, which integrates a self-designed wave creator to simulate actual ocean conditions as much as possible before the devices are tested at local metropolitan beaches.
“This study shows the potential speculation approach to estimate an approximately best response wave amplitude to determine the suitable ocean state to obtain the optimised output performance of the wave-driven triboelectric nanogenerator,” says Professor Tang. “The 3D printing technology provides a cost-effective and relatively convenient approach to fabricate multi-shape triboelectric nanogenerators to satisfy the different ocean wave states,” adds co-author Mr Anh Tran Tam Pham.
Associate Professor Xiangxi Han, from the College of Mechanical and Marine Engineering at Beibu Gulf University, says ocean engineering and technology have great potential in creating clean energy from wave power, or ‘blue energy’.
China and other countries have been looking at various TENGs to convert the irregular kenetic energy of waves into electrical energy, including to electrochemical water splitting to produce zeroemission hydrogen. flinders.edu.au
Leussink has been appointed the sole distributor for Omega Sinto Foundry Machinery for Australia and New Zealand.
Omega Sinto is a global manufacturer of chemically bonded sand equipment used in the foundry/metal casting industry. Originally established in the UK, Omega Sinto now operates around the world offering a wide range of products which includes sand mixers, mould handling equipment, core making machines, shakeouts, sand reclamation plants, coating plants, and more.
Leussink Sales and Marketing Manager, Stuart Ward, says that the partnership with Omega Sinto takes Leussink into a new area of Australian manufacturing. “Under our new partnership, we will supply Omega Sinto’s equipment off-the-shelf, but provide installation and modifications where required,” he said. “After joining Leussink last year I began to look at new business opportunities and approached Omega Sinto. My professional background is in the foundry industry so it made sense for me to look at that area.”
“At the time I began speaking with them about fabrication and engineering work, the local business manager they had in place had decided to retire so they needed new representation in Australia and New Zealand. It fell into place from there,” added Ward.
Omega Sinto has almost 40 years of experience in the foundry equipment manufacturing industry, specialising in chemically bonded mould production equipment.
The Australian metal casting/foundry industry produces iron, steel, and non-ferrous product for every major industry, including rail, defence, mining, construction, manufacturing, agriculture, water, automotive, health and energy.
“At Leussink we don’t just sell products and walk away. We work with our clients to make sure the equipment we provide works for them by tailoring a solution to their needs and providing onsite visits and training sessions.
“With the Omega Sinto products added to our range will work with clients to make recommendations about which item will suit their needs, as well as undertake modifications in our Illawarra state-ofthe-art workshop,” Ward said. leussink.com.au
Australia’s largest clean energy event returns to Melbourne this October.
All-Energy Australia, Australia’s largest clean energy event, is taking place this October in Melbourne to continue supporting the industry’s growth and to help accelerate Australia’s transition to a renewable energy future. This is a free-to-attend exhibition and conference from 2627 October 2022 at the Melbourne Convention and Exhibition Centre.
With energy being at the forefront of many discussions with the government’s ambitious climate change bill being pushed through at the moment and countries across the globe realising that they can no longer rely on fossil fuels for their energy needs, it will be a welcome return for All-Energy Australia.
All-Energy Australia is the country's largest and most anticipated clean energy event in Australia, which opens up a world of opportunities for industry suppliers and experts as well as those involved in renewable energy and energy storage sectors to expand business networks. All Energy Australia is organised in partnership with the Clean Energy Council and is where renewable energy professionals can get exclusive access to the latest technologies and trends and discuss the opportunities and challenges facing the sector. As the industry’s largest all-encompassing clean energy event, the expo floor will feature over 290 leading companies including Enphase, Fronius, GoodWe, Growatt, Nextracker, Sungrow, Longi, TrinaSolar, Shoals & More.
And for the first time, there will be a dedicated Energy Management Zone within the All-Energy Australia exhibition. This dedicated zone will host its own theatre with sessions running throughout both days on sustainable solutions that facilitate improved energy management and increased cost savings.
Clean Energy Council Chief Executive, Kane Thornton said, “Our industry stands ready to electrify Australia and establish our nation as a global clean energy superpower. We are on our way into the electric age, an age where Australia can be proud and powerful. It’s an incredible time of change and opportunity for our industry. All-Energy brings us together.”
These sessions will also highlight innovative energy management technologies and services that support the reduction of energy bills and emissions. Session topics will be in agriculture, food and beverage manufacturing, metals and other materials manufacturing, residential buildings, commercial buildings and Government operations.
“The 2022 event takes place at a crucial time in our country where Australia’s clean energy transition is more important than ever,” noted Robby Clark, Portfolio Director at All-Energy Australia. “AllEnergy Australia provides a platform for the industry to connect visitors with leading suppliers on our exhibition floor and drive conversations about the future of renewables at our multi-stream conference.”
With the conference agenda to be announced in September, this year’s program will have more than 200 expert speakers discussing the latest in solar energy, energy storage, hydrogen energy, electric vehicles, bioenergy, distributed energy resources and more. Registrations are now open. The Exhibition and conference is colocated with Waste Expo, forming the largest gathering for waste and recycling management, clean and renewable energy and energy storage professionals in the country. all-energy.com.au
Founded in 1985 and acquired in 2004 by Phil Wicks and his son Ray Wicks, Kingsway Confectionery has cemented its reputation as a supplier of quality wholesale and retail confectionery products along with being a prominent co-packing partner for branded and private label products in the confectionery and snack food industries.
In 2016 the business relocated to their current premises in Melbourne’s bayside suburb of Seaford. This move facilitated the immediate expansion of the operation and provided the necessary scope for further growth opportunities. In 2020 the need for additional capacity became apparent and the installation of their third production line was commissioned.
Ray Wicks has taken over the mantle of General Manager from his now semi-retired father overseeing the day-to-day operations. Ray is supported by partners Jason Keegan (Production & Warehousing), Niki Totton (Sales & Development) and what they all agree are amazing and committed production and warehousing crew. “While our recognisable expertise is packaging goods, behind the scenes we are problem solvers and a valuable knowledge centre. We pride
ourselves on being a trusted and agile business partner, and we are absolutely committed to the longterm growth and success of our customers’ products and brands,”
Ray said.
“We operate on an ethos of safety, quality, honesty, reliability, performance, innovation, cost competitiveness & efficiency. As Enmin’s values are aligned with ours, they have been awarded our new equipment contracts,” he added.
Kingsway Confectionery’s association with Enmin commenced 15 years ago when a top cross feeder was installed to an existing production line. This was rapidly followed by an order for a hopper feeder to further modernise the line.
“This installation was crucial and extremely time sensitive to our business and any delay would have created significant issues. For them to have got our new line up and running on time and on budget in the middle of the Covid lockdown last year, is testament to their abilities,” Ray concluded. enmin.com.au confecpackaging.com.au
Enmin’s quality, service and support the key ingredients for Kingsway Confectionery.
The Clean Energy Finance Corporation, Kiko Ventures, IP Group Australia, Vestas Ventures, and Hostplus are among the top-tier investors supporting Hysata’s capillary-fed electrolyser.
Australian company Hysata’s world-leading hydrogen electrolyser technology has been supported by renowned global investors, as the organisation closes its oversubscribed Series A funding round of $42.5m. Virescent Ventures led the funding round on behalf of the Clean Energy Finance Corporation (CEFC), with participation from Kiko Ventures, IP Group Australia, Vestas Ventures (Denmark), Hostplus and BlueScope.
Assembling such a high profile and high impact list of investors underlines the significance of the transformation that Hysata is bringing to the green hydrogen industry. The Hysata electrolyser operates at 95% system efficiency (41.5kWh/kg), delivering a giant leap in performance and cost over incumbent technologies, which typically operate at 75% or less. This high efficiency, coupled with the simple approach to mass manufacturing and low supply chain risk puts the company on a path to delivering the world’s lowest cost green hydrogen.
“Our mission is to redefine the economics of green hydrogen production through our innovative proprietary electrolyser technology. The support of this international syndicate of clean energy practitioners and investors validates our core technology and our approach to scaling and mass manufacture,” said Paul Barrett, CEO of Hysata.
“Green hydrogen is a vital energy vector on the world’s path to net zero, critical to decarbonising the hard-to-abate, yet vital, sectors of our economy such as steelmaking, heavy transport, and the chemical industry. The extensive end use cases for green hydrogen translate to a greater than trillion-dollar market opportunity.
“Over the last 12-18 months, Hysata has been interacting with dozens of major customers globally. The impact our efficiency and system simplicity delivers to customers’ project economics truly moves the needle. We look forward to continuing to work with our shareholders and customers to bring this much needed technology to market as soon as possible.”
The CEFC invested $10m into the Series A funding round, building on its initial $750,000 investment in the early commercial development of Hysata’s research. CEFC CEO Ian Learmonth said that backing a company like Hysata and its cutting-edge electrolyser technology is vital in helping to grow Australia’s clean technology ecosystem.
“The CEFC is proud to continue our support for Hysata, which is set to be a major player in the global electrolyser industry. Green hydrogen will be essential to addressing the hardest to abate sources of emissions, and we’re excited to see Australian ingenuity providing the technology solutions that will help this industry reach scale. The CEFC has a strong focus on hydrogen related investments through both our Innovation and Advancing Hydrogen Funds and we are delighted to see Hysata continue to advance hydrogen to help meet future energy needs and reduce emissions in more sectors of the Australian economy,” Learmonth said.
The CEFC investment is via its specialist Clean Energy Innovation Fund, which is managed by Virescent Ventures. “Hysata continues to make rapid progress and we are pleased to support such an innovative company with an outstanding team,” Virescent Ventures Partner Blair Pritchard said. “The continued growth of Hysata is an important pointer to the enormous potential of hydrogen to our net zero future.”
Kiko Ventures’ Founding Partner, Robert Trezona, said Hysata has real potential to become a major global clean technology player.
“Having assessed scores of electrolyser technologies in my 20 years in cleantech, Hysata’s technology stands out as a true breakthrough. The company has redefined the core cell architecture for alkaline electrolysis, producing a practical and scalable solution with game-changing efficiency. Hysata has the potential to be a globally significant company in the hydrogen economy and we look forward to supporting its growth, especially here in Europe,” Dr Trezona said.
BlueScopeX’s General Partner, Michael Quinn, agreed that Hysata’s technology could play a significant role in the development of commercially viable hydrogen production.
“BlueScopeX is pleased to be investing in Australian technologies coming out of our local communities, with Hysata being born in the Illawarra. Our industry requires smart, affordable technologies like Hysata’s to help progress the broader goal of decarbonisation, and we are excited to be supporting them on their path to commercialisation,” he said. hysata.com virescent.vc bluescope.com
IperionX successfully develops low carbon titanium enrichment process.
IperionX has successfully developed an innovative low carbon titanium mineral enrichment technology that upgrades lower content titanium dioxide ilmenite minerals into a high titanium synthetic rutile product.
The company’s synthetic rutile product has been tested and evaluated by customers, which has confirmed the potential for a high-quality, high grade titanium feedstock with scope to be a superior and more sustainable product than other upgraded titanium feedstocks, including titanium slag.
IperionX’s low carbon process eliminates the use of carbon reductants, including coal, which are typically used to upgrade low grade titanium feedstocks into high value, high grade titanium feedstocks. The low carbon synthetic rutile production process is the result of exhaustive R&D by Dr. Zak Fang and his team at the University of Utah on upgrading and purification methods for titanium feedstocks to produce titanium metal.
Patent applications have been filed for this innovative synthetic rutile process technology, adding to IperionX’s valuable patent portfolio. Co-products of IperionX’s synthetic rutile process include a purified iron powder for potential sales into lithium iron phosphate (LFP) battery applications.
IperionX intends to commercialise this low carbon, high grade titanium synthetic rutile product and has commenced feasibility studies for a synthetic rutile production pilot plant at the Titan Project in Tennessee.
IperionX Limited has successfully developed high quality, low carbon titanium mineral enrichment technologies, having upgraded ilmenite titanium minerals from the Titan Project in Tennessee into a high-grade titanium synthetic rutile product.
High grade titanium dioxide (+80% TiO2) feedstocks include natural rutile, synthetic rutile and titanium slag, and are primarily used in creating inputs for titanium metal in the form of titanium tetrachloride and paint and pigments in the form of purified TiO2.
Natural rutile is a mineral with TiO2 content of 92%-95%, while synthetic rutile and titanium slag are upgraded high grade TiO2 feedstocks produced from ilmenite, with a TiO2 content of 88%95% and ~80% respectively. Given their relative scarcity and value in use, high grade TiO2 feedstocks are higher priced products than the more commonly found lower grade ilmenite.
Importantly, the global supply of natural rutile is in significant decline, with other high grade titanium feedstocks including synthetic rutile and titanium slag expected to fill the widening supply gap. Synthetic rutile commands a price 4-5x that of ilmenite, which has a typical TiO2 content of 45%-65%. Long term price forecasts for synthetic rutile are ~$1,000-$1,200 per ton, compared to ilmenite with a long-term price forecast of ~$200-$300 per ton. This price multiple allows for the potential to significantly increase the value of the Titan Project resource base through upgrading of ilmenite to low carbon synthetic rutile.
The majority of global synthetic rutile production occurs in Western Australia by the world’s largest titanium mineral companies, Iluka and Tronox, via processes based upon the Becher Process. The Becher Process consists of roasting low-grade ilmenite using coal in a rotary kiln at temperatures of more than 1,100°C to convert the iron oxide in the ilmenite to metallic iron, and then ‘rusting’ the kiln product in an aerated salt solution to remove most of the metallic iron.
Titanium slag is a widely adopted method to produce high grade titanium feedstocks, which occurs via open arc AC or DC smelting of ilmenite with electricity, using a carbon reactant in the form of coal, to produce titanium slag and pig iron products.
The development of IperionX’s low carbon synthetic rutile is the product of exhaustive R&D by Dr. Zak Fang and his team at the University of Utah, which originated around development of purification methods for titanium feedstocks for use in HAMR titanium metal production. Over the last year, Dr. Fang, his team, and IperionX’s R&D division have worked closely together to adapt the titanium purification methods to produce a low carbon, standalone synthetic rutile product.
Anastasios (Taso) Arima, IperionX’s Managing Director and CEO said: “We are delighted that Dr. Fang’s research and development, in collaboration with IperionX’s engineers, has successfully delivered an innovative process technology to produce a high quality, low carbon synthetic rutile product. This patented technology has the potential to significantly enhance the value of the Titan project by manufacturing a low carbon, high grade titanium feedstock for a market that is increasingly demanding a low carbon supply chain.” iperionx.com
IperionX Titan Project ilmenite (LHS) prior to conversion to low carbon, high grade synthetic rutile (RHS) (Photo: Business Wire)Climate change narratives often overlook the need for more sustainable manufacturing and waste management practices. UNSW SMaRT Centre Director and 2022 NSW Australian of the Year Professor Veena Sahajwalla wastes no time.
Manufacturing that aligns with innovative waste management, recycling and materials circularity are central to helping address the globe’s biggest challenges. A combination of new science, technical innovation, strong industry collaboration and supportive government priorities will deliver the solutions needed for a more sustainable future in Australia, and the world.
In the sustainability space, the big challenges are clear. Reduce harmful atmospheric emissions, deliver greater renewable energy, readdress the growing waste crisis, enhance our manufacturing and sovereign capability, and reduce the reliance upon polluting global supply chains.
There is growing appetite in industry and society to tackle these issues more swiftly.
Australia has world-leading scientific research and development institutions and leaders, but many feel progress on delivering practical outcomes to our big sustainability challenges is lacking. It is understandable people feel this way. We have record amounts of waste going into landfill and stockpiles. We are burying, burning, and polluting our oceans with many highly valuable “waste” materials.
Collaboration through co-investing and nurturing pathways to innovation and economic success must be our focus if we want to realise that “waste is a resource” that can be used in so many new, innovative ways.
I see very bright future because there are many examples that Australia is actually making progress across these areas to create a circular economy. Central to this observation is the notion of “materials circularity”, where waste is seen as a resource of raw materials.
Sustainability needs to be at the heart of design, production and materials usage, so it is vital to ensure waste is used as a source of raw materials for manufacturing.
As we develop new and transformative approaches to what needs to be a new era of ‘green manufacturing’, we need to build new and localised supply chains that are laterally integrated.
The lateral integration of supply chains of green materials and products is needed to ensure we connect different sectors across our regions.
This integration would build interconnectivity between and across markets, sectors and logistics networks, enabling decentralised, localised and regional pathways to new national and global opportunities. This can be done for micro to macro materials and manufacturing opportunities, eventually leading to mega solutions, depending on the volumes and values associated with the materials concerned.
Such an approach will boost our sustainability and sovereign capacity. So, materials needed for a sustainable future can and must not only come from mining, but also from our waste resources.
We do need more momentum, but we also need to celebrate our successes in this challenge. Collaborations between industry and our world class researchers are resulting in many breakthroughs but getting them “industrialised” is key. A recent important breakthrough comes from the UNSW Sustainable Materials and Research (SMaRT) Centre, where hydrogen from various wastes can improve the efficiency of steel making.
This represents the next generation of our home grown, patented Green Steel® Polymer Injection Technology® with our steel industrial partner, Molycop, which started out as the Commonwealth Steel Company. Our first 1.0 generation of Green Steel® is well known for using millions of waste rubber tyres destined for landfill as an alternative source for partial replacement coke and coal in electric arc furnace steel making.
Moving into the next generation of our Green Steel, our research now shows waste coffee grounds which contain hydrogen can be used as a sustainable alternative to coking coal. A report by environmental and social purpose not for profit business Planet Ark shows 921 cafes in Sydney city produced more than 3,000 tonnes of coffee grounds a year with 93% ending up in landfill and just 7% used for composting.
There are other technologies emerging that can reform many wastes, especially problematic wastes not subject to traditional forms of recycling, into new value-added products and manufacturing feedstock, and our various SMaRT Centre-designed MICROfactorie® modules attest to this.
With the right will, society can find a purpose for most of our waste by understanding the elemental value inherent in it. This can only be done through rigorous scientific analysis and active collaboration with industry, the community and governments to ensure innovations are taken up and used.
Many of the commodities and critical materials needed for global electrification can come from waste, and metals can be recovered and used many times over.
Even many plastics can be used multiple times, or used in completely new ways, such as being reformed into plastic filaments for 3D printing to save on having to create so much original plastic. Batteries and electronic waste items are typically recycled in smelters, however that requires long-distance transport which is expensive, causes high emissions and can create fire risks. Microrecycling is an innovative approach to recycling waste by reforming the waste’s constituent materials through thermal isolation of targeted elements, like copper, nickel and cobalt.
By better valuing our waste materials and creating circularity for their reuse, we can help the world be more sustainable and tackle our big global challenges. unsw.edu.au
Onshoring your manufacturing back to Australia. Ray Keefe is the Managing Director of Successful Endeavours. He describes the Onshoring Framework.
The Onshoring Framework looks at the product Total Cost of Ownership and not just at individual transactional costs. This is especially important because not all costs are tracked and the real cost of a line item can be a lot more than its transactional cost.
The areas to consider for Total Cost of Ownership:
• Quality, reliability, confidence
• Remove unnecessary labour
• Automate everything including production, customer support, field support
• Know your customers
• And your value proposition to them
This is the generic process for a product that is made, sold and supported through its lifecycle.
This shows the order the costs are incurred in. By the end of Product Development all the important decisions have been made. Once in Production, it is hard to alter anything. The design is done, tooling made, processes defined, labour requirements set and the supply chain engaged.
Let’s briefly look at each of these areas.
This sets up the rest of the project for success. Successful products meet the needs of every stakeholder. The key thing we focus on is understanding what every stakeholder needs. Commonly forgotten stakeholders are production, sales and field support. Sometimes even the end customer.
If the design has been done well, the tooling designed and built well, then you are in a good position to buy components and do your pilot production run. Generally mechanical tooling is much more expensive than PCB tooling and how much you spend on automation is a function of the production volume you want to achieve.
At this point you don’t have a lot of levers to pull. The development has already set the stage for most of this. You are buying the parts, doing the process and hopefully packing and shipping units without any rework.
This affects the total business case so we have always had this as part of our design thinking. The field support and service areas are often not considered enough in design briefs. We have always built remote configuration and firmware updates into our communicating products. Phones, computers and smart appliances do this. It significantly reduces Total Cost of Ownership.
Because products can still keep costing you after you have shipped them.
By the time you know your real Total Cost of Ownership for the product, all of the design and process decisions have been made and there are almost no variables to play with.
If it is designed in Asia for Asian business practices, then the design is probably not ideal for Australian manufacturing. It is necessary to address this before you start making the product here.
But you can have an acceptable cost of manufacture if you go about this the right way. Local minima generally don’t lead to overall system minima unless they are the cost bottleneck (theory of constraints).
Focusing on BOM cost generally gives you a more expensive product overall. The right level of tooling reduces costs in a lot of areas including product assembly, parts costs and inventory.
Spending the right amount on design is where you have the highest profit leverage. So don’t shortcut that part of the process. Use the design team to the full. It is your investment after all. Software is usually one of the higher R&D expenses but you can reduce hardware by doing more in software. Which can reduce both BOM Cost and Process Cost. In one project, increasing the software budget by $50,000 delivered $1,500,000 in extra profit to the manufacturer.
The existing design was done by a Chinese factory for free; the tooling is also free. The PCB costs $70 a unit. The rest of the product is built and assembled locally. PCBs fail within two years, most inside the warranty period. The factory can’t offer a fix. The Australian business approaches us to design a replacement. Has to be dropin replaceable as they need to retrofit to existing units. A PCB that works is $200 per PCB. Since they are already losing money, they don’t see how they can afford to pay more for the PCB.
After reviewing the design and also the manufacturing process they identify $1200 in savings per system by making the PCB smarter so they don’t have to do as much to configure each system. They aren’t tracking the cost of replacing PCBs in the field nor the potential loss of business. The $200 PCB is at least $1070 cheaper than the $70 PCB when you calculate the Total Cost of Ownership. They gave us the go ahead and have been selling their product with confidence ever since.
I am confident that great products, designed to meet the total value proposition, can be profitably Made in Australia. Australian manufacturing has been growing steadily since 2016 and the recent pandemic has shown us that local jobs matter to us all. I am also keen to bring as much manufacturing back to Australia as we can. Hopefully this article has provided some insight in how to go about this so you can do this profitably.
successful.com.au
AMT OCT 2022 027VOICE BOX Rework is waste. There are many potential sources. You must identify faults, rectify or scrap units and use labour, facilities and materials to do this. Keep rework as low as you can. There are tradeoffs in effort level to get to 0% rework so this also needs to be a business case driven outcome.
How businesses can confidently accelerate performance with precision. Mark Velthius is President at Jedox Asia Pacific. He also has over 20 years of diverse business experience in the IT industry and working in Asia. While responsible for driving growth for the region, he builds growth strategies, partnerships, and development of new markets.
Businesses today are being empowered by artificial intelligence (AI) to grow in ways that they could only dream of just a few years prior. The data on increasing use of AI demonstrates that turning to such automated solutions is, arguably, the equivalent of taking your vitamins – those making the strongest impact have already begun investing in a complete digital transformation journey. As global business becomes increasingly more complex, we must adapt to keep the health of our businesses at peak performance. Much like a routine medical check-up, assessing the health of your business processes will inform you on how best to nurture it in its entirety.
Speed and precision are among the top concerns for companies looking to streamline and extract value from mountains of data that contribute to overcomplexity and unpredictability. How can you be precise if don’t have the full picture? McKinsey’s survey on post-pandemic strategies points to the starkly apparent trend of developing stronger digital strategies to make room for better analysis, creative decision-making and input from new talent. The highest-performing companies are the ones making the boldest decisions to support their digital transformation journey so they can harness stronger production and performance capabilities. Doing so freed up their time and resources to strengthen their team, one of the many benefits of mobilising your business and planning at a quicker, sharper pace.
Companies that utilise adaptable modeling can enable turnkey solutions for finance, sales, and workforce planning. Through machine learning predictions, your business can improve the quality and speed of human decision-making, especially as your business grows and develops over time. Growth can come with additional responsibilities and creative tasks that machine learning can thankfully make available to your team, which can leave you with more room and resources to explore new business pursuits.
What does better adaptability through automation in strategic planning look like out in the wild? We can observe the success of the Dubai-based Shelf Drilling, which has been enabled to spend more time on significant business and financial operations by introducing an adaptable solution that reduced their wait time for the transferring and consolidation of data by an impressive 98%. No one needs to question whether or not they have access to the latest version of data, which empowers them to formulate and execute faster and more effective business strategies.
Employing new technological solutions throughout the digital transformation of your business does not mean ditching what is familiar. In fact, striking the right balance between incorporating modern tech solutions while preserving simplicity has the advantage of enhancing user experience, and thereby making the implementation process not only easier, but more likely to have a long-lasting impact on business performance. The reason? Many who do not envision what the user experience will be when using new solutions may overlook the negative impact it can have on the speed and precision of their planning and operations.
Tap into your strengths. Taking inventory of the existing skill sets of your workforce is necessary on the road to digital transformation. Businesses can leverage their expertise in programs already in use like Excel to design, implement, and manage a solution that can efficiently forecast and plan initiatives at scale. Heiniger, a leading Swiss manufacturer of animal shearing equipment, sought out a
flexible solution to navigate ever-increasing analysis requirements, which began to affect the accessibility of key information in crucial tasks. However, a key priority for them in their digital transformation was to keep processes user-friendly and capable of integrating with existing systems. By looking into ways in which they could integrate data without sacrificing ease-of-use, Heiniger has been able to profit with their powerful yet simplified planning. Placing emphasis on a smooth implementation and user experience can re-energise operations that have begun to feel unwieldy.
Through effective integration of diverse, complex systems, you can also gain more control and security over your business’ data by containing it within a modeling engine that is highly scalable and available around the clock. Amidst the global pandemic, businesses have been seeking out more modern digital architecture to weather the storms of supply-chain disruptions and other persistent issues that affect speed and precision. Minimising unpredictability to combat the chaos is one of the surest ways that we can free ourselves to spend more time on significant and value-add tasks with more confidence and decisiveness in business performance.
Cases like those of Shelf Drilling and Heiniger are not unique. AIbased solutions are mobilising countless businesses around the world to tame the beast of unpredictability while also bolstering speed and precision to keep in lock-step pace with their competitors. Indeed, automation in financial planning and beyond will be a top strategy to improve performance for the manufacturing sector.
Gone are the days of scattered data. Disconnected, humanmanaged digital architecture no longer has to shape your company’s outcomes. The statistics encourage us to take the next step in the digitalization process. Given the technology available today, implementation is not the slow-moving behemoth it once was. By empowering the sector to automate, adapt and react in real-time to change, we can confidently accelerate performance with muchneeded precision. jedox.com/en
Australia needs a people-led digital backbone to accelerate supply-leader ambitions. Warren Zietsman, is the Managing Director of IFS Australia and New Zealand.
Australian manufacturing is at a pivotal juncture. The nation so accustomed to mining, and then immediately exporting, has a very real opportunity on the horizon as the impacts of the world’s energy transition and global supply chain constraints are laid bare.
For far too long, Australia has sought the assistance of global supply chains to do the heavy lifting for its manufacturing needs. The COVID-19 pandemic has put supply chains into sharp focus, leading manufacturers to reconsider their reliance on global networks.
Australia could be much more than just another country that manufactures onshore. Australia could be a supply-leader, and has all the tools at its disposal to invest in projects such as onshore battery production due to its mineral-rich resources. This is exemplified by the recent news that mining companies are looking to extend the value of lithium before exporting it.
For this to be the case – and if Australia is to venture down the path of reshoring manufacturing – this time it needs to be different. This time, it needs to be digitally enhanced to supercharge its capabilities to compete globally.
One could be forgiven for thinking terms such as ‘business agility’, ‘digital transformation’ and ‘robust supply chains’ are merely industry doublespeak designed to sell the dream of unrealised efficiencies. This might be because the advances in technology underpinning these such as IoT, AI and the cloud, in isolation, are not anything new.
But the synthesis of these advancements brings about something truly special for companies seeking to improve productivity and operational efficiencies, particularly in manufacturing. For Australia to compete with the rest of the world on the manufacturing front, it needs widespread digital adoption to realise this goal.
The right implementation of digital technology, via a companywide digital transformation, can allow manufacturing companies to recognise the strong link between digital tools and increased productivity, efficiency, operational resilience, and a wealth of sustainability benefits.
The recent IDC MarketScape: Worldwide Manufacturing Field Service Management Applications 2021-2022 Vendor Assessment confirmed this notion, by stating that digital technologies, such as AI and IoT, were key drivers for delivering service effectively.
Now, it’s important to note there’s certainly no dearth of advancements in technology – and this certainly contributes to the overwhelming, and in some cases, saturated space of enterprise technology.
But the key here is to ensure technology is not being adopted without first targeting a specific problem to solve. For technology to make meaningful change to an organisation, it must be adopted wholeheartedly across the entire business. It must have a transformative effect.
Technology can do wonderful, transformative things. Its impact is exciting and alluring, but a transformative effect is impossible without the common denominator: people.
Australia has one of the lowest uptakes of technology across the world. So, while technology plays a critical role in digital transformation, it’s on the people using it to fully harness its power. It’s vital to get the buy-in of people within an organisation by understanding the benefits that new, company-wide technologies bring to the table. Not solely by the misnomer of “new is better”, but by communicating the tangible problems that can be solved by innovative technology.
A digital backbone is essential for Australia to realise its supplyleader ambitions as it embarks on reshoring manufacturing. Getting the fundamentals right with buy-in from its people, is pivotal to building that backbone.
So before Australian manufacturing contends on the global scale, it must first digitally transform with the commitment of its most important component: our people. ifs.com.au
Conversations with senior executives require a completely different approach and skill set compared to buyers at other levels of an organisation,” explained Martin Noonan, Learning and Development Consultant and Facilitator at Innovate Learn, a Melbourne-based training company.
Sales professionals today have a multitude of communication mediums to choose from when reaching out to prospective customers: email, text, phone and LinkedIn are all methods that can be utilised to their advantage. But establishing contact with C-Suite executives requires a higher level of strategic thinking.
Martin Noonan has been a learning consultant, facilitator and coach for over 20 years and the most satisfying part of his role is watching adult learners move from resistance to willingness to change. Many sales professionals find it particularly challenging to get time with C-Suite executives. According to Martin, getting to this point takes patience and research. “The best way to overcome this hurdle is to start by understanding the levels of hierarchy within their client’s organisation.”
“Firstly, the decision-making roadmap needs to be explored. When a sales proposal is presented at a lower level of a client organisation, what journey does it take to get to the C-Suite? What happens after that? It’s a matter of uncovering and working through the different critical success factors at every level of the company,” he added.
Once a pathway has been mapped, Martin recommended attending the company’s Annual General Meeting (AGM) and talking to a board member or executive who has been with the company for a long time to gain more insight into the longer-term vision of the company.
‘What’s in it for me?’
“A key part of engaging at the C-Suite is the ability to position yourself as someone who is not trying to sell something, but rather to find out exactly how you can add value to their organisation. For example, a critical success factor a salesperson might uncover is that the organisation has brought forward its sustainability targets by three years,” Noonan explained.
This sort of information gives the sales professional direction as to where to take the conversations and find the opportunities that will contribute to achieving that objective.
To move their sales strategy from a conversation to a partnership, sales professionals must draw on the research they did on the company’s decision-making processes. “At the lower levels, sales conversations generally focus on customer wants and needs, sometimes price negotiation and then the productivity gains they want to achieve. As conversations progress through the higher levels of the organisation themes such as innovation, sustainability and long-term growth and profitability emerge,” said Noonan.
Therefore, it is critical that the salesperson understands the direct connection between their own company’s offering and how it could contribute to their client company’s profitability and revenue growth. This comes back to the sales professional’s need to answer the question ‘What’s in it for me?’ (from the client’s perspective) at every level.
“If a sales professional wants to engage with the C-Suite at a major corporation, they must expect to have multiple preliminary conversations and understand that the customer’s vision will evolve at every touch point as they reach higher within the company. The whole process will probably take about 18 months” he adds.
At the C-Suite level, it’s typical for executives to have 40-50 people (internal and external) wanting direction and input on any one day. “As the different levels of the company are navigated, the bandwidth of attention narrows dramatically so all conversations must be relevant and engaging,” stated Noonan.
Martin Noonan’s other tips for effective selling to the C-Suite include:
• Do your research and design your approach to your audience. Determine the C-Suite executives’ personal decision-making style, how they prefer to process information and the company culture before you even consider trying to engage with them.”
• Send a preview of the meeting agenda. “Send a sample of the type of questions you want to ask to show your clear intention. Tailor these to the company’s vision and goals, which you can usually find in their Annual Report.”
• Give a little to gain a lot. Executives may test your credibility so be prepared to share insights you have gained from your research and examples of what you have helped similar organisations to achieve.
• Develop a call to action. “At the end of your meeting, propose a specific call to action that moves the conversation forward and gain the executive’s agreement.
• Build a relationship with administrative assistants. “They are the gatekeepers, and you won’t get access without them. Be friendly, business-like and relevant.
• Ask low-level questions. “Time with C-Suite executives is precious, and you have one shot to convince them of the value you can add.”
• Focus on the short-term. “Your questions must be targeted at their horizon – what is their vision for the future?”
• Advocate solutions. You are not there to make a sale; you are there to conduct a strategic business conversation.
“And finally, you may only get one chance to meet with someone at this level, so ensure you have done your research and prepared for all contingencies,” he concluded.
innovatelearn.com.au
There is a disconnect in the latest business and people management software apps, says Daniel West, Chief Sales and Support Officer at MYOB.
Australia’s small and medium sized enterprises (SMEs) are collectively investing $2.2bn each year on digital solutions to help improve business operations, however three in five are finding some of these tools are in fact hindering them, according to new research from business management platform MYOB.
In a survey of 1,500 Australian SMEs, 59% say they are currently experiencing ‘bad digitisation’ - where their business and people management software apps and tools run in silos, rather than seamlessly integrating with each other. This was true of 62% of the 137 construction businesses surveyed.
While SMEs are increasingly embracing digital tools for jobs such as managing people, tax, project management and cashflow, the new research unveils that a lack of integration between applications businesses have invested in is costing them time, money and resources, and posing a strategic risk. To put it in perspective, Australian households spend around $660 each year on streaming subscriptions like Netflix and Kayo, while our data shows the average SME spends 25% more than this on software subscriptions.
The main difference is the streaming services we use as consumers do what we expect of them, they connect seamlessly with our smart devices. The digital systems that businesses use however, are not integrating together properly and it’s costing businesses dearly. With rising inflation rates, minimum wage increase pressures and ABS data showing over a third of businesses expect to increase their prices over the coming months, businesses need to be smart with their spending. They cannot afford to waste money on services that are not truly helping them.
More than a quarter (27%) of the SMEs surveyed have experienced costs blowing out because of disconnected digital tools, and across Australian businesses approximately $1.4bn is being wasted each year on unused digital tools.
Almost one in two businesses (42%) admit they have given up using some digital business solutions due to their inefficiencies, but are still paying for them. When asked why they still pay despite no longer using these tools, the top reasons included that it was too much hassle to change, or because there is a lack of better alternatives to switch to.
It’s subscription overload for businesses. Many consumers are cancelling subscriptions amidst rising cost of living pressures, and it’s an optimum time for businesses to also assess their subscription overheads, especially if some are sitting there unused. Choosing tools that offer multiple services in the one place or ensuring they only pay for the features they really need, could help businesses alleviate the financial and productivity costs they’re facing.
One in ten businesses polled (12%) believe getting rid of software applications they seldom use could save them between $100 and $200 each month, and a similar proportion (9%) estimate it could be a $200 to $400 monthly saving.
The research revealed Australian construction businesses are currently wasting the equivalent of one working day each week (seven hours) on average carrying out tasks caused by a lack of integration between their digital tools. This was aligned with the Australian SME average.
Nine in ten (91%) businesses are wasting valuable time on manual tasks or having to duplicate jobs. For construction businesses, this
includes manually entering information from one system to another (34%), checking for consistency across the platforms (38%), and editing or fixing errors after information is transferred between systems (22%).
Disconnection issues also pose a strategic risk. The MYOB survey revealed that seven in ten Australian SMEs say they find it difficult to get a full picture of business performance based on the intel from across their various systems or find themselves making operational decisions without full visibility of their business. A third (34%) also say it is making it difficult to add capabilities to their team and services or adapt the business as they need to – a challenge ultimately stifling growth and risking opportunities for success.
As an industry, software companies like ours need to take this ‘bad digitisation’ burden off businesses and work on creating better connected systems. Nothing should hold back ambitious businesses, and we recognise we need to do something about it. Our deep, direct integration with MYOB’s payroll and workforce management services lets businesses onboard an employee via Flare, without the need to log into another app, and is included in the subscription cost for MYOB users. This saves time for both the new starter and employer, ensures the business remains compliant, and provides a smooth and secure experience for the employee.
There are six core business processes around managing jobs, employees, suppliers, cashflow, finances and generating revenue, that when digitised can make a phenomenal difference to a SME's chance of survival and success. But what’s become evident from our research is that local SMEs are really struggling to find systems that truly integrate with each other, or the one solution that offers all the capabilities they need all in the one place. That is why we are particularly passionate about building a cohesive business management platform and investing in the strategic partnerships and acquisitions that will help us deliver this for SMEs. Their productivity and growth depends on it. myob.com.au
Engineers have created a way to 3D print large and complex parts at a fraction of the cost. Known as Multiplexed Fused Filament Fabrication (MF3). The technique will change how thermo-plastic printing is done. MF3 uses a single gantry to print individual or multiple parts simultaneously. By programming a prototype to move in efficient patterns, and by using a series of small nozzles rather than a single large nozzle, printing resolution and size were increased and printing time significantly decreased. The industry has struggled with the speed at which 3D printers deposit material vs the resolution. Larger-diameter nozzles are faster than smaller ones but generate more ridges and contours that must be smoothed out, adding significant costs. By contrast, smaller nozzles deposit material with greater resolution, but current methods are too slow to be cost-effective. The hardware can be purchased off-the-shelf and the nozzles can be turned on and off independently.
Rutgers University
Rolls-Royce has begun the final phase of manufacturing its demonstrator UltraFan, the world’s largest aero engine. This powerplant will offer a set of technologies that will ensure the industry’s sustainability for decades. The demonstration unit mounts a 355cm diameter fan and will use 100% sustainable aviation fuel with a 25% improvement in fuel consumption compared to the first-generation Trent engine. A new engine architecture, fan system technology, new materials and a power gearbox all create a very high bypass ratio engine, meaning greater efficiency and sustainability. It offers 40% less NOx and 35% less noise and almost zero nvPM particulates at cruise. Those technologies are scalable, capable of being developed to create an engine with a thrust range of 25,000lb to more than 100,000lb, for narrowbody or widebody aircraft that may be developed from the 2030s. Its first run will take place towards the end of the year
Rolls Royce/Aviacionline
Researchers have made a major breakthrough in renewable energy technology by producing electricity from so-called ‘night-time’ solar power. A semiconductor device called a thermoradiative diode, composed of materials found in night-vision goggles, was used to generate power from the emission of infrared light. Although the amount of power generated at this stage is very small – around 100,000 times less than that supplied by a solar panel – the researchers believe the result can be improved in the future. The process harnesses solar power in the form of sunlight during the day. At night, this same energy radiates back into outer space in the form of infrared light with the thermoradiative diode now proven to be able to generate electricity by taking advantage of this process. The breakthrough is an exciting confirmation of a previously theoretical process and is the first step in making specialised, and much more efficient, devices that could one day capture the energy at much larger scale.
((cap)) A thermal imaging camera highlights the amount of heat radiating from Sydney Harbour and its surroundings back into the atmosphere at night UNSW
Scientists have proposed a novel method of multilayer coating to improve the corrosion resistance of steel. The coating comprises three layers fabricated using PVD. A Zn-Mg layer is sandwiched between two Zn layers. The top Zn layer protects the Zn-Mg layer from being in contact with the corrosive environment. The last line of defense is the bottom Zn layer. This multilayer coating on steel makes it highly stable, economical, and durable, affording an ideal choice for use in harsh environments. It will have far-reaching applications in infrastructure and construction where long-lasting steel is an essential requirement.
Korea Maritime & Ocean University
Researchers have developed a new non-flammable electrolyte material for use in sodium batteries, providing a safer and cheaper alternative to lithium-ion. Electrolytes in traditional lithium and sodium batteries are commonly flammable, so this breakthrough paves the way for a new critical material for safer batteries. A solid polymer electrolyte material has been developed which can
replace the flammable liquid solvents currently used. The different approach uses reactive sodium metal as an anode to increase battery capacity and in the process, safer electrolytes. Known as a fluorine-containing polymer and originally used for biological application, this is the first time this class of polymer has been used in solid-state sodium batteries. One of the main benefits is its low production cost. One drawback of sodium is shorter life compared to lithium. However, in pairing with the new polymer electrolytes, they offer close to 1000 cycles, comparable to lithium.
Deakin
There may soon be a new weapon in our centuries-old battle against germs: the first durable coating that can quickly kill bacteria and viruses and keep on killing them for months at a time. Polyurethane locks in the antimicrobial power of tea tree and cinnamon oils; the new technology could start making public spaces safer within a year. The coating proved deadly to SARS-CoV-2, E. coli, MRSA and a variety of other pathogens. It killed 99.9% of microbes even after months of repeated cleaning, abrasion and other punishment on real-world surfaces like keyboards, cell phone screens and cutting boards. Disinfectant cleaners can kill germs in only a minute or two but they dissipate quickly and leave surfaces vulnerable to reinfection. Metals like copper and zinc are available, but they take hours to kill bacteria. This coating offers the best of both worlds. The coating, which is clear and can be brushed or sprayed on, gets its durability and germ-killing power by combining tried-and-true ingredients in a new way. It uses antimicrobial molecules derived from tea tree oil and cinnamon oil. The coating's durability comes from polyurethane, a tough, varnish-like sealer that's commonly used on surfaces like floors and furniture. The antimicrobials are regarded as safe by the FDA.
University of Michigan
Norway-based firm WorldWideWind is developing a new type of floating, vertical-axis wind turbine (VAWT) that it believes is a significant improvement. Their VAWTs employ two sets of counter-rotating turbines tilted with the wind with no nacelle. It is claimed to produce double the output of today's biggest turbines. It is scalable up to 40MW and 400m in height. There is reduced wake effect and increased turbine density. There will also be less impact on wildlife. The design should allow more turbines into a given area. The company aims for a working 40-MW model by 2029.
Interesting Engineering/WorldWideWind
HongKong: Converting 3D-printed polymer to 100x stronger, carbon microlattice
Developing a lightweight material that is both strong and highly ductile has been regarded as a long-desired goal in the field of structural materials. Researchers recently discovered a low-cost, direct method to turn commonly used 3D printable polymers into lightweight, ultra-tough, biocompatible hybrid carbon microlattices, which can be in any shape or size, and are 100 times stronger than the original polymers. They discovered that by carefully controlling the heating rate, temperature, duration and gas environment, it is possible to simultaneously enhance the stiffness, strength and
ductility of a 3D-printed polymer microlattice drastically in a single step. The ratio of polymer to carbon fragments is also crucial to obtaining optimal strength and ductility. If there are too many carbon fragments, the material becomes brittle, and if there are too few, the material lacks strength. During the experiments, the team successfully created an optimally carbonized polymer lattice that was over 100 times stronger and over two times more ductile than the original polymer lattice.
City University of Hong Kong
New materials with unique properties that can be used for 3D printing are constantly being devised, but determining how to print with these materials can be a complex, costly exercise. Parameters include printing speed and how much material the printer deposits. MIT researchers have now used artificial intelligence to streamline this procedure by training a machine-learning model to monitor and adjust the 3D printing process in real-time (a machine-learning system that uses computer vision to watch the manufacturing process and then correct errors in how it handles the material in real-time). They used simulations to teach a neural network how to adjust printing parameters to minimise error, and then applied that controller to a real 3D printer. Their system printed objects more accurately than all the other 3D printing controllers they compared it to. The work avoids the prohibitively expensive process of printing thousands or millions of real objects to train the neural network. And it could enable engineers to more easily incorporate novel materials into their prints, which could help them develop objects with special electrical or chemical properties. It could also help technicians make adjustments to the printing process on-thefly if material or environmental conditions change unexpectedly.
Techxplore/MIT
"Bushmasters are actually saving lives in Ukraine," - Vasyl Myroshnychenko - Ukraine's ambassador to Australia during a visit to Bendigo's Thales factory where he thanked Australia for its donations so far, including 60 Bushmaster armoured vehicles made in Bendigo. Bushmasters have become synonymous with Australia in Ukraine: “Australia is the biggest ally outside of NATO for us. "Australia is punching above its weight”
“We have several Bushmasters which are operating as ambulances, so they're used to deliver wounded from the battlefield to the military hospital where they get the treatment," he said.
"Because of the scale of this war we could benefit from more, definitely — we could make use of another 40, make it 100."
Conflux Technology scalable, configurable, ultra-high performing water charge air cooler.
Conflux Technology releases its first product - an ultra-high performing Water Charge Air Cooler (WCAC). Conflux Technology has used their rich and extensive knowledge in additive manufactured (AM) heat exchangers to deliver a premium WCAC product that rivals and out-performs other leading WCACs, applicable to motorsport and high-end automotive markets.
As AM technology advances, the industry leaders are recognising the complementary power of digital inventory and mass customisation. “The Conflux WCAC embodies how we deliver what motorsport and elite auto makers ask for – a definitive performance advantage. A product is rapidly configured to our customer’s prioritisation of performance, size, and packaging requirements. AM lets us supply the WCAC with low lead time and competitively priced.” says Dan Woodford, Chief Product Officer at Conflux.
This technologically advanced product has already made an impact in European motorsport circles as the superior WCAC; consistently eliciting demonstrable enthusiasm from leaders in the field over its fine features, incredible geometry and highly competitive pricing. Conflux Products deliver industry-leading performance; are scalable and configurable to unique boundary conditions, performance and packaging requirements. "I am really excited about the product roadmap for Conflux Technology's AM heat exchangers. The team has made significant strides developing in-house tools that deliver very high performance without compromising quality. I am really proud of everyone at Conflux for launching the next phase of our business with the WCAC product line." says Dan Woodford, Conflux’s new Chief Product Officer. “Conflux has aggregated our expertise in first principles calculations, core engineering design and AM into a set of tools that can rapidly inform a solution.”
Conflux Technology is a world-leading AM company pioneering thermal and fluid applications through expert engineering and production. Conflux began in the world of F1 engineering, where founder & CEO Michael Fuller, transformed heat exchanger designs and performance outcomes. Today, Conflux is a well-established, senior-by-design team leading the advancement of AM applications. Its revolutionary heat exchange technology has transformed product and system performance across aerospace, automotive, motorsports, micro-electronics, industrial and energy industries.
With vertically integrated, advanced manufacturing operations, Conflux encompass all aspects of the engineering process – from design and CFD analysis through to in-house AM serial production, post-processing and independent validation. Conflux consistently pushes AM technology to the cutting edge, deriving groundbreaking outcomes for its customers. confluxtechnology.com
Tiny smart bed sensors embedded in hospital mattresses could put an end to painful and potentially life-threatening pressure sores, thanks to new technology developed by the University of South Australia.
UniSA scientists have designed minute optical fibre sensors, which can be attached to the upper surface of a mattress to monitor movement and record heart and respiratory rates.
The unobtrusive sensors can detect when a hospital patient turns over, leaves a bed, or just remains motionless, picking up their breathing. Nurses can therefore be remotely alerted if a patient has not moved within a couple of hours, prompting them to adjust the patient’s position.
Lead researcher Dr Stephen Warren-Smith says the technology could “significantly relieve” the burden on hospital staff having to constantly monitor patients for pressure sores. “Each year, thousands of older Australians in hospitals and nursing homes experience pressure injuries, or ulcers, which take a long time to heal and can be fatal,” Dr Warren-Smith says.
“At the very least these injuries can cause severe pain, disrupt sleep, affect their mood as well as their rehabilitation, mobility and quality of life.” Unlike the sensors that many people wear on their wrists to monitor physical activity and physiological signs, the optical fibre sensors are embedded in the same space as a person, but not on them physically. Hospitals currently use weight-based sensors or cameras installed in the room to monitor patients, but both have limitations, Dr Warren-Smith says.
“Existing weight-based hospital sensors cannot predict when a patient leaves the bed until their feet touch the floor, leaving little time for nursing staff to respond in the event of a fall. Also, there are privacy issues with camera-based technology.”
The optical fibre sensors are sensitive enough to record heart and respiration rates and can detect whether a person is in the bed, even if they remain stationary for long periods.
“Respiration rates are often the first sign that a patient is deteriorating. This normally requires devices to be attached to the patient, either on the chest, as a mask on the face, or ventilator. These can be restrictive and sometimes inappropriate in an aged care setting.
“Monitoring vital signs continuously, unobtrusively and cheaply via the mattress-embedded sensors is a far better solution for both patient and nurse,” Dr Warren-Smith says.
The technology is explained in a recent paper published in the Journal of Biomedical Optics. unisa.edu.au
New generation Enmin drives designed to energise production lines.
Leading materials handling manufacturer Enmin are manufacturing electromagnetic drives in Australia. These drives offer a unique handling method for controlling the flow of food products, ingredients and bulk material. Products can be screened, sized, or accurately metered to ensure a smooth, uniform and fully variable flow.
With minimal moving parts, next to no on-going maintenance and low energy consumption it’s a reliable, low-cost method of product handling. The drives are designed and constructed to meet the rigorous requirements of the food and pharmaceutical industries such as maximum hygiene, ease of cleaning and continuous 24/7 operation. The cyclic operation is controlled from a range of electronic controllers that will vary the feeding rate in a manner to suit the specific application enabling high-speed filling coupled with pinpoint accuracy. The controllers are available in different enclosures or as standalone for incorporation into central panels.
As production lines evolve and other components are updated to achieve higher throughput, older and less efficient drives cannot match the required capacity increase. “Fitting one of our new generation drives will ensure that a higher conveying speed can be achieved to match the performance of other production line components. New drives also offer reduced energy consumption and of course less likelihood of stoppages and production disruptions due to breakdowns,” said Enmin Group Sales Manager, Harley Over. “Installing new drives is relatively easy and straightforward; given the improved efficiencies of the new drives the ROI is quickly realised. The longevity of our drives has been well proven so it’s a smart longterm investment,” Mr Over went on to say.
A wide range of drives are available to suit most requirements and applications. The drives are available with either an epoxy or a recently introduced Teflon coating. The Teflon coating provides greater cathodic protection thereby eliminating surface rust making it the ideal surface finish for a food environment. The Teflon is fully FDA approved; its 40-micron surface coating means that it does not suffer from the chipping that can occur on painted models. This makes it ideal
for use on mobile equipment that is susceptible to knocks and bangs as it is moved around the workplace. “For harsh cleaning and washdown environments within the food industry our new Teflon coated drives are the perfect solution,” Mr Over said.
In addition to the food industry, virtually any industry that handles dry bulk material, processed products or parts can employ the use of an electromagnetic drive. Enmin’s drives have been successfully utilised in the metals, ceramics, chemical and plastics industries in an extensive array of applications. “For companies looking to increase the conveying speed of an existing production line, installing new drives is a cost-efficient way to achieve that. Quite simply, new drives will transform the performance of existing lines,” Mr Over concluded. enmin.com.au
Book a FREE demo to see how we can support your business.
Minimise inventory issues and accurately manage order processing & reporting seamlessly through our fully integrated software system.
The new NT Smart Cube included in Nakamura JX-200.
Taking its industry-leading turning technology to a new level, Nakamura-Tome has now introduced the new JX-200 multi-tasking mill/turn centre. The JX-200 incorporates Nakamura’s new NT Smart Cube - the world’s shortest tool spindle in its class. This provides a compact footprint with a spacious work area and unrivalled kinematics that drastically improve machining performance.
Nakamura has recognised the increased need of industry to manufacture smaller batch sizes with higher flexibility. With customers wanting ‘more flexible machining’ and ‘higher part production’ rates with a single machine, the JX-200 is the solution. This new machine can accommodate a larger number of tools and this delivers unrivalled flexibility for handling multiple types of lowquantity production.
The impressive new JX-220 is a twin-spindle machine with an upper tool spindle that swivels +/-95 degrees to provide exceptional flexibility. This unit has an impressive 15/11kW power output and a 12,000rpm spindle with an 18,000rpm spindle as an option. The upper tool spindle has an 80-position tool carousel as standard with 40 or 120 tools as optional extras.
On the lower tooling turret as standard is milling capability and also Y-axis machining. The lower turret provides a 6,000rpm milling spindle with 8,000rpm optional and both upper and lower milling capability is extremely rigid and robust for heavy-duty material removal applications.
In combination with the upper tool spindle and the lower turret, the new JX-200 machine is perfect for a multitude of different machining methods such as simultaneous machining with both left and right spindles, engaging both upper and lower tool positions simultaneously, and even machining with centre support mounted on the lower turret. Whatever your application, the JX-200 is the
epitome of flexibility for your machining tasks. With the facility for operations such as turning, milling, drilling and gear cutting, this ‘All in One’ machine will appeal to manufacturers in an extremely wide variety of industry sectors.
This flexibility is underpinned by a new heavy-duty column structure that has now been introduced to the JX-200. To create the most stable and robust platform for machining all material and component types, the new design has an optimised centre of gravity design that gives unparalleled strength and stability against loads from any direction.
The machine has a 65mm bar capacity with 51 and 80mm diameter options. The 65mm machine has a maximum turning diameter of 325/255mm with a maximum turning length of 1058mm. All this is crammed into a compact floor area of 2.9m by 5.2m. With the Nakamura-Tome JX-200, ETG can change the impossible to possible. engtechgroup.com
Concrete using recycled tyre rubber hits the road to a circular economy.
Engineers have discovered a way to replace 100% of conventional aggregates in concrete – such as gravel and crushed rock – with rubber from discarded tyres that meets building codes, promising a boost for the circular economy.
The team from RMIT University says the new greener and lighter concrete also promises to reduce manufacturing and transportation costs significantly.
Small amounts of rubber particles from tyres are already used to replace these concrete aggregates, but efforts to replace all of the aggregates with rubber have produced weak concretes that failed to meet the required standards – until now.
The study published in the Resources, Conservation & Recycling journal reveals a manufacturing process for structural lightweight concrete where the traditional coarse aggregates in the mix were completely replaced by rubber from used car tyres.
Lead author and PhD researcher from RMIT University’s School of Engineering, Mohammad Momeen Ul Islam, said the findings debunked a popular theory on what could be achieved with recycled rubber particles in concrete.
“We have demonstrated with our precise casting method that this decades-old perceived limitation on using large amounts of coarse
rubber particles in concrete can now be overcome,” Islam said.
“The technique involves using newly designed casting moulds to compress the coarse rubber aggregate in fresh concrete that enhances the building material’s performance.”
Study co-author and team leader, Professor Jie Li, said this manufacturing process will unlock environmental and economic benefits. “As a major portion of typical concrete is coarse aggregate, replacing all of this with used tyre rubber can significantly reduce the consumption of natural resources and also address the major environmental challenge of what to do with used tyres,” Jie said. Used tyres in Australia cannot be exported, making new methods for recycling and reprocessing them locally increasingly important. About 1.2bn waste tyres will be disposed of annually worldwide by 2030.
“The greener and lighter concrete could also greatly reduce manufacturing and transportation costs,” Jie said.
“This would benefit a range of developments including low-cost housing projects in rural and remote parts of Australia and other countries around the world. rmit.edu.au
A specialist supplier of steel tube and pipe, Austube Mills, part of the InfraBuild Group, is benefitting from a low-maintenance, timesaving, and safe hydraulic clamping solution for its steel slitters at its Acacia Ridge plant in Queensland.
Austube Mills Acacia Ridge, which has been manufacturing and producing steel solutions since 1984, installed Technofast EziTite clamp nuts, which provide reliable and precisely repeatable force, on its steel slitters to allow the rotating slitter blades to cut through kilometres of black steel. Once the steel is cut to width, it is shaped into rectangular, square or round tubes on tube rolling mills, which are subsequently used in a huge range of applications in industries such as construction, manufacturing, mining, transport, and agriculture.
“The Technofast solution is not just more reliable – it’s safer, too,” says Austube Mills Manufacturing Superintendent, Michael Thomasson, who has been working with the company for more than 30 years, starting as a fitter, and holding roles such as maintenance planner, maintenance superintendent and manufacturing superintendent. He has a Mechanical Engineering Diploma and Graduate Diploma in Maintenance Management.
“I remember the old days when workers would use a C spanner and whack the nut with as much force as possible, which came with a much higher risk of hand injuries. Plus, it wasn’t easy to get the same clamp load each time when using manual force,” says Thomasson. EziTite Hydraulic Nuts and Bolts are rapidly applied by being installed on bolt studs then hydraulically actuated, stretching the bolt to the precise tension required and then locking it in place mechanically with a locking device. The reverse procedure permits equally rapid disassembly when it is eventually required for maintenance.
“The globally available technology – which is proven in more than 30 years’ service in slitter applications – also curbs damage caused by slitter blade movement during operation,” says Technofast Founder and CEO, John Bucknell. “Without sufficient clamping force, the
slitter blade is subject to move during the cutting process, which can damage the product and reduce output.”
Thomasson adds that a steel plant is a particularly harsh environment, so rugged technologies are required. “We’re cutting black steel, so there’s always mill scale puffing off and settling on any surface it can find. The Technofast clamp nuts have been so reliable, however, that there’s been no maintenance required for the past 12 years,” said Thomasson. “Additionally, we need to change the slitter blade configuration typically four times a shift, so rapid disassembly and re-assembly is a major advantage. With the Technofast solution, this can be done in about half the time, and with fewer personnel, compared to previous methods with the C spanner.”
“Austube Mills has a very strong safety ethos, so having technologies in place to minimise injury risk was a good fit for us.”
Such safety benefits are also true of many applications. EziTite hydraulic nuts are ideal for tensioning all of the studs on a flange, joint, or cover simultaneously, loading 100% of the fasteners at once. technofast.com
Bonfiglioli’s range of hoist drive units deliver on safety and reliability.
Bonfiglioli recently added the HF series to its robust portfolio of gear motors. Getting to grips with real-world applications and the needs of its customers, this range of high-quality hoist drive units was designed following a detailed study on operating equipment in realtime. The series features three units: the HF40, HF60 and HF125, designed to carry 4, 6 and 12.5 tons respectively. Martin Broglia, Managing Director of Bonfiglioli Australia explains that these units are specifically designed for hoist applications in material handling cranes. “Our international team worked closely with several prominent crane manufacturers to better understand the operating challenges that they faced. Our range was designed to combat these demands.”
In addition, the range was designed for higher FEM and ISO classes to ensure the highest levels of safety and reliability. “In addition, the higher input to output offset and the higher space between the motor and drum install provides an advantage for OEMs to choose from a wide range of drum sizes available to the market.”
With the commercial construction activity that Australia is currently experiencing, Martin believes that there is no better time to bring the HF series to market. He outlines the added benefits as follows:
• Rugged structural design and high load carrying capacity: “This series features a high radial load carrying capacity - a key requirement for hoists/ cranes.”
• High centre and offset distance: “OEMs can select from a wide range of drum sizes and motor frame size combinations.”
• Wide range of output connections: “This provides added design flexibility for OEMs.”
• High performance gears and bearings: “Gear profiles are optimised and designed for high power density and to satisfy a wide range of FEM/ ISO mechanism classes. It also offers superior bearings to support higher loads.”
Adding to this, the HF series offers an array of gearbox mounting options and the option to include an external brake solution for additional safety.
To conclude, Martin says that that series will be a welcomed addition to its portfolio. “As heavy-duty specialists, we are so pleased to bring this series to market. Our customers trust us to bring reliable solutions for the most demanding applications to market. We are excited to see their response to the HF series.”
Bonfiglioli is a worldwide designer, manufacturer and distributor of a complete range of gearmotors, drive systems, planetary gearboxes and inverters, which satisfy the most challenging and demanding needs in industrial automation, mobile machinery and renewable energy. bonfiglioli.com/australia/en
Time-saving clamp nuts safely deliver repeatable force for Austube Mills’ steel slitters. Steel being cut to length by a steel slitter at Austube Mills’ Queensland plantLatest ZeoMed spill kits combat potential blood-borne virus infection outbreaks threatening workplaces and supply chains.
Workplace spill kits and body fluid clean-up kits announced by Clean Stream Technologies provide rapid response to blood-borne biohazards with the potential to spread disease within production and distribution plants already coping with COVID and flu.
The ZeoMed kits’ 100% natural mineral and ecologically safe ZeoLite aluminosilicate is a fast-acting natural absorbent of liquids and odours, including toxic and noxious odours. “The inert and non-toxic absorbent is highly effective against the types of body fluid spills most typical in workplaces and public domains, including vomit, blood, faeces and urine,” says Clean Stream Technologies General Manager, Scott Whittaker.
Applications of the quick-access ZeoMed kits include chemicals, cytotoxic hazards (associated with drugs that can be absorbed through skin contact), multiple biohazards, blood-borne pathogens (such as Human Immunodeficiency Virus HIV, hepatitis B virus (HBV), and hepatitis C virus (HCV)), as well as a broad range of infectious diseases and general clean-up applications.
“These latest ZeoMed spill kits have been designed to comply with Department of Health regulations in the handling of bloodborne pathogens in the workplace,” says Whittaker. “They provide a hygienic handling and disposal system for spills commonly encountered in workplaces, public, and recreational areas, protecting both employees and visitors as part of a comprehensive risk management programme.”
ZeoMed body fluid clean-up kits can be hung next to fire extinguishers or placed in first aid kits for quick recognition. The kits – part of a broader range of individual products – include protection required by Safe Work Australia
“Spills are a hazard that employers want to clean up quickly. Quite apart from their unsightly appearance, or foul smell, they can cause a slip hazard on hard floors, or they can transmit bloodborne diseases,” he added.
“It is now a legal requirement for all employers to have controls in place to protect staff from potential infection from body spills. The legal requirements extend across a broad range of industry, commerce and public institutions, ranging from manufacturing and technology plants, laboratories, hospitality and entertainment venues, to retail, transport, distribution and medical and laboratory facilities,” says Whittaker.
Customised kits can also be produced to suit the particular needs of individual sites, including manufacturing technology sites where employers are taking every step to protect their valued employees against disease and downtime. The main kits include:
• Body Fluid Spill Kit: designed for in-field use with portable first aid kits for quick access by employees;
• Biohazard Spill Kit: ideal for corporate, hospitality and public domains, located near first aid stations or cleaning trolleys;
• Cytotoxic Body Fluid Spill Kit: provides additional protection for clean-up of body fluids from patients who have been treated with cytotoxic drugs;
• Laboratory Spill Kit: configured for laboratory and similar applications where spills may be body fluid or other liquids, such as chemicals;
• Multipurpose Spill Kit: for venues such as supermarkets, variety stores, shopping centres, restaurants, hospitality and transport terminals where staff or the public may be at risk from biohazard and chemical hazards as well as slip and fall hazards;
• Sharps Kit: ideal for safely disposing of needles and syringes.
The kits – which include employer instructions – complement Clean Stream Technologies’ protection against airborne viruses, its EnviroKlenz Air System Plus which kills viruses multiple times smaller than the COVID-19 virus, such as SARS-COV-2. EnviroKlenz Air System Plus, which combines medically proven ultraviolet UVC germicidal irradiation with safe and effective earth mineral technology.
“Like ZeoMed kits, EnviroKlenz Air System Plus is highly effective. In this case, it goes much further than standard mass-market purifiers by combining medically proven ultraviolet UVC germicidal irradiation with safe and effective earth mineral technology originally developed for the US military and still used today to destroy chemical warfare agents and toxic industrial chemicals,” says Whittaker. cleanstreamtechnologies.com
For more than two decades, National Group has supplied heavyearthmoving equipment and end-to-end mining services to the world’s largest resource companies. Their machinery is used at flagship Australian mines to dig up iron-ore, coal, gold, nickel and other commodities. Led by founder Mark Ackroyd, National Group owns one of this country’s largest and most advanced fleets of mining equipment.
“National Group continues to grow and diversify its NSW operations,” says Ackroyd. “We have significant long-term contracts in coal and gold, and a strong pipeline of opportunities for sustained growth in NSW. National Group has created well over 100 regional jobs in NSW in the past two years. We intend to create plenty more.”
By his own account, Mark Ackroyd was born and bred into this industry. He learned all about the machinery by working on roadworks at a very, very young age. “Like eight to 10 years old, I was going to work,” he says. Ackroyd was clearly not scared of a risk,or playing the long game. He worked his way up from owning one bullbozer, into someone running this immense company, servicing a massive industry with deep relationships with the major mining companies like Fortescue, BHP, Rio Tinto and others.
“I always backed myself and it’s also important to have good customer support. You must work with your customers and gather their trust as well,” he says. “This is a big part of doing business. You must find the trust within your customers and be able to deliver a service that’s valuable for everyone.”
The Yancoal Moolarben project is a contract mining job, but in this case, National supplies the personnel as well, supervisors, project managers, and they’re there to shift the earth at the back of the pit. “We do that with large equipment, huge dump trucks, a large excavator, and staff as well. So that’s very different to just them hiring out the gear,” he explains. “We run the whole job and it’s a 24/7 operation. This is a blue-chip mine at Moolarben Coal, and a threeyear contract initially, with a two-year extension.”
Ackroyd says the Moolarben contract diversifies National Group in other ways. “Our company is best known as a leading supplier of heavy-earthmoving equipment to the large miners. The Moolarben contract expands our work in mining services and further strengthens National Group’s unique end-to-end offering and its operational diversification.” National Mining Services is well-positioned to take on more work in mining services by providing mining and infrastructure
services to National Group’s major open-cut mining clients. The business has extensive capabilities in large-scale mining projects, meeting production requirements in excess of 15 Mbcm per year of waste and coal.
Ackroyd says National Mining Services’ position within the National Group is a competitive advantage. “Through National Group, National Mining Services has access to one of the country’s most advanced mining fleets, a large supply of experienced labour, and access to capital. Most of all, National Mining Services has a great team.”
National Mining Services will use National Group’s ultra-class mining equipment on the contract, including Liebherr R9800 excavators, Liebherr T282 dump trucks and other ancillary equipment. The contract will create 75 jobs. A large-scale excavator can cost up to $20m, and weight up to 800-tonne. It can also take 18 months to manufacture one of these offshore and a bit more obviously now. National Group owns over 300 vehicles, covering the Caterpillar, Komatsu, Liebherr and Hitachi brands. Ackroyd details that they range from bulldozers, and to smaller to larger dump trucks. “While we have some of those, we also have smaller trucks at $15m to $2m each, and we’re always looking to widen the range.”
Global political and environmental pressures are known to be gaining on the mining of fossil fuels. National Group has been working in the background to expand their work, while there are still calls for the ‘black rock’. Commodity diversification is a strategic goal of National Group. “Whilst we remain positive on the long-term outlook for coal and have a significant pipeline of work in the sector,” says Ackroyd, “National Group continues to increase its exposure to other commodities.”
For example, National Group has won significant contracts in the gold sector in recent years. They are continuing to expand in Western Australia, increasing exposure to iron ore. The services businesses within National Group, for example National Heavy Haulage, continue to grow, further diversifying its business. “Longer term,” explains Ackroyd, “our goal is to do more work in commodities exposed to the boom in electric vehicles and renewables, for example lithium, nickel and copper.”
“In fact, our long-term sustainability strategy is built on three main foundations. First, we continue to increase diversity within
National Group, particularly with respect to gender and culture. More employment of women and First Nations peoples at National Group is a focus. Our new apprenticeship program aids National Group’s diversity goals by attracting young people, including women.
“Second, National Group is expanding its corporate social responsibility program. For many years, we have supported sporting and industry associations, often in regional areas where our employees live and work. We are expanding that program, particularly in areas such as mental health and other healthrelated charities. This work is central to National Group’s long-term sustainability and our organisational culture,” he said.
“And third, National Group continues to invest in state-of-the-art equipment. The latest machinery from the world’s top manufacturers typically has higher environmental performance and safeguards,” Ackroyd adds “By industry standards, we have a relatively young, modern fleet. In addition, National Group continues to collaborate with its customers to understand their sustainability goals and ensure we help achieve them.”
Wolff Mining is one of National Group’s newer companies, purchased three years ago, complete with its fleet of autonomous tractor systems, the CAT D11T. The drivers can operate the dozers from a comfortable office equipped with multiple screens and controls. “It’s also the first in Australia to do this,” quips Ackroyd. “In fact, that’s the main reason that prompted me to buy it.”
“We could look at a scan of a site, from which they could then do remote-dozing of the area. Looking at this from more of a safety aspect for the operator, where they can't be too close to high walls and other dangerous situations, this is way of the future for mine sites,” says Ackroyd. “The days we can dig out a site completely remotely.” Now this has been another success for the company as well. A very good add-on to National’s existing business. nationalgroup.co
There are many obstacles to scheduling and supply chain logistics, none moreso than right now. Kurt Lawrence is a mining and software engineer. He presents the Stochastic scheduling framework using Spry and daedalus.
Production schedules for mine sites are notoriously sensitive to input assumptions. Generally these assumptions are constructed using average historical values, with forward looking scalars about performance improvement/degradation applied. Assumptions such as equipment availability, utilisation and production rates all have large impacts on monthly or annual material movements.
A set of assumptions carries risk; if an availability assumption was overzealous for a month, the production target will not be reached, and the schedule becomes invalidated. It is important to note that these risks are not independent; missing a target can have causal effects on the remainder of the schedule. A common practice is to run three schedule simulations, varying the input assumptions above and below the headline value. These schedules are considered as ‘worst, likely, best’ (nomenclature varies). This practice is useful to understand sequencing bottlenecks as productivity increases or decreases, but is lacking in data points to identity risks. There are now three schedules which become invalidated as reality sets in. This is where stochastic scheduling is applicable. Productivity assumptions are defined according to a distribution, and by running a Monte Carlo simulation, a range of production outputs can be collected which describe the distribution of production values. A Monte Carlo method is most useful for the scheduling problem due to the numerous coupled degrees of freedom a scheduling system has. This is where the performance of one equipment will have direct impacts on the performance or path of another. With sites with more than three resources interacting with one another, a more systematic simulation approach would quickly run into a combinatorial explosion problem. Constructing a stochastic scheduler in the Spry scheduling software package uses a Monte Carlo simulation method at its core.
The three main productivity drivers in the Spry scheduling software package are availability, utilisation, and rate. All three combine to give an effective consumption/calendar hour, however, the framework will split out each as a separate input assumption. It would be possible to simulate using a single distribution for the consumption, but this method does not lend itself to ergonomic reporting. For instance, a typical report would chart an equipments operating hours across the simulations, so granularity into the operating hours inputs (availability and utilisation) are required. The framework requires a productivity distribution per input. This means the availability, utilisation, and rate would all be defined using a distribution, per equipment. The framework utilises fields within the calendar table to define a distribution.
The framework supports various distributions, here the inputs are defined using a PERT distribution, where a, b, c represent the minimum, most likely, maximum values, defining the shape of the distribution. Two other constraints are required, Lower Clamp and Upper Clamp. These values bound the sampled value, since sampled values could end up being invalid, such as negative rates or availabilities greater than 100%. The distributions are defining a factor, not an absolute value. This is intentionally done as it is common to define different rates for different processes and to alter inputs over time as machines undergo major overhauls or replacements. So the framework will generate a sample using the defined distribution, apply the sample as a factor against the scheduled input value, and bound the result using the clamps.
Simply setting up the productivity inputs as continuous distributions yields the below distributions for the example Cat6040 equipment. These distributions were achieved with 100 simulations, each observation is a productive step in the schedules.
Equipment productivity is not the only driver to total material movement. Delays such as weather events, unexpected mechanical breakdowns, or manning issues can all negatively impact a schedule. The industry approach is to forecast expected delays and build these delays into the schedule. If these forecasts are too optimistic, production targets will not be achieved, whilst if the forecasts are too pessimistic, under-budgeting can occur (this is especially true for manning). The stochastic scheduling framework accounts for these risk using the notion of Discrete Randomised Events (DRE) where a particular event (e.g. rain) has a likelihood of occurring and a defined impact. The impact is defined as a distribution of delay hours. The framework supports events which can impact equipment or areas, for example a mechanical breakdown would be modelled for the equipment, but a weather event will impact the whole site. DREs can also supplement forecast models to provide insight as to how sensitive a schedule is to changes in the forecasts.
Simply put, the more, the better. The framework hooks into the Spry scheduling engine and runs a specified number of simulations. For each simulation, the input values and DREs are precomputed rather than computing on the fly. This helps separate out the stochastic logic from Spry's scheduling logic. The framework also optimises the scheduling runs, trying to reduce the amount of work Spry has to do if it is not going to change per schedule run. For each scheduling run, a collection of outputs are gathered. These outputs are collated into a large tabular output, aggregating the results from the run on a specified period of time (month, year), and separating out the result for each run.
Choosing an adequate number of simulations is a tradeoff between processing time and the output validity. The total processing time is linearly proportional to the number simulations which are to be run, and is directly impacted by how long a single schedule takes to run. Whether the outputs are well distributed depends on the number of degrees of freedom in the model. A model with two excavators and no DREs will only require a small number of simulations (say 100), whilst more complex models will require thousands of simulations to produce well shaped outputs.
It is important to understand how sensitive schedules are to varying inputs. If long tails are present, or secondary humps in the overall output, there may be degenerate schedules. A degenerate schedule typically comes from equipment and dependency interaction. A dragline which must follow a specific path would have to wait until material has been blasted and ready to dig, or slight delays in one area of a pit might have ramifications for another. Running the stochastic scheduler highlights the input schedule's sensitivities to these risks, but it also goes one step further. Each simulation is deterministic, and can be replicated given the same seeding value. So a scheduling engineer has the power to run specific stochastic schedules and visually check how the schedule performs. This can assist the scheduler to identify what particular paths or dependencies in a schedule are causing schedules to fall over so readily.
The output of the stochastic scheduler is a large table as a CSV. This data must be post-processed to visualise the output distributions. As an example of some outputs that can be constructed from the framework, a demonstration model was constructed and 300 simulations run. The post-processing and charting is done with daedalus.report.
First, overall movement of material shows the underlying distribution that the simulations exhibit.
Equipment operating hours are also particularly useful to see if equipment are not being full utilised.
Finally, temporal distributions can be used to look at the spread of production over time.
The above charts are just a few examples of outputs that can be constructed, typically each site would want to track and gain insight into metrics specific to the site's operating constraints.
The stochastic scheduling framework for Spry is a fantastic adjunct to the regular scheduling models employed by the mining industry. The framework takes very little to set up and start running simulations. Most sites already track equipment performance, this data can be used to form the continuous distributions for input into the framework. Leveraging daedalus.report's ability to richly visualise the output data, and to post process the results in a fast, automated fashion, a powerful process is presented for conducting stochastic analysis of schedules, repeatedly.
kurtlawrence.info
Kurt LawrenceAustralian – Indian research cooperation is crucial for rare earth manufacturing.
With the increasing demand for high technology equipment (e.g., catalytic convertors) and a transition to green energy economies, rare earth minerals (e.g., Cerium and Lanthanum) are critical. In recent years, significant commitments have been made by the Australian and Indian governments, consitent with transitioning to a net zero economy by 2050. The projected demand for rare earth minerals in India presents a unique opportunity to increase coorperation with Australia which has abundant resources and world-class expertise.
InnovEco Australia has developed and patented two technologiesresin in pulp (RIP), and resin in moist mix (RIMM) with a high target metal extraction performance from fine particles in an eco-friendly manner. “Our company has been developing a novel metal recovery technology since 2012 when we first identified a key issue in heap leaching process – the process of fine fractions in copper ore,” said Gennadiy Sukhinin, Managing Director at InnovEco Australia. Particularly, the technology has been successful in copper recovery resulting in 96 – 98 wt.% yields compared to 70 wt.% for conventional heap leaching technology. The technologies have received funding for development from the AusIndustry’s Accelerating Commercialisation grant and two Mobility grants at the University of South Australia as part of the Future Industries Accelerator Program sponsored by the South Australia State Government.
“Our research will apply new technologies to evaluate their capabilities to both extract minerals from low grade process and mineral tailings streams, together with recyclable spent batteries and magnets,” said Dr Richmond Asamoah of UniSA. “Accumulated mining wastes, from a range of primary commodities, are becoming an increasingly valuable source of metals, but there is often a lack of viable extraction technologies.”
In this project, advanced beneficiation and extraction (RIMM) methods will be further developed for battery metals (cobalt, nickel, lithium and manganese) and Rare Earth Elements (REE), which is relevant to Australia and India. Fundamental and applied studies will be undertaken together with the development of prototype equipment for pilot studies. “The new technologies to be developed will build upon over three decades of research and development activities at UniSA,” said Professor William Skinner: FII Research Leader – Minerals Processing.
A stable critical mineral supply stream for key manufacturing areas was hampered during the COVID-19 pandemic. The Australian government is currently seeking an alternative to the non-renewable sources of the material supply to ensure the nation’s resilience in the face of global supply chain disruptions. Those might be induced by external threats, including scarcity of geological resources, geopolitical issues hindering their extraction, processing and shipment.
The Australia-India Strategic Research Fund (AISRF) that supports this project is a strategic initiative of the Australian Department of Industry, Science, Energy and Resources, and the Government of India’s Department of Science and Technology (DST) and Department of Biotechnology (DBT) to increase the uptake of leading science and technology by supporting strategic collaboration and alliance between Australian and Indian researchers and technology companies.
The Advanced recovery of the battery materials and REE from ores and wastes project falls under one of the recent priority areas for AISRF, focussing on developing novel solutions to improve downstream processing, recycling and tailings reclamation of critical minerals. Particularly, the project aims to develop advanced ecoefficient critical mineral extraction technologies for Australian and Indian resources.
“Achieving global goals for climate change mitigation requires switching from fossil fuel based energy supply and demand towards low carbon technologies and practices,” said Dr Kali Sanjay, CSIR–IMMT. “The low-carbon transition needs adaption of renewable power technologies and electric vehicles. Metals like Ni, Co, Li, Mn, REEs, etc., are essential for pursuing these goals for a sustainable growth. CSIR-IMMT has expertise in non-ferrous extractive metallurgy while KIIT will be contributing in the process optimisation and IIT Bhubaneswar to produce the functional materials. The expertise of the Indian and Australian partner institutes and technology companies combined with the geologically and compositionally diverse resources targeted, provides this IndoAustralian collaboration a strong potential for developing technically advanced and commercially viable technologies that can benefit both the countries.”
“Eco-efficiency of new technologies for critical metals extraction are very important,” said Joseph Mifsud, Managing Directoro of COOE. “A technology that can also address challenges at legacy and abandoned mines will be of great benefit.”
Several potential projects have been identified where this technology could be used for the recovery of critical minerals and major metals. The identified mining companies and deposit owners in South Australia and other states will be approached in regard to obtaining mineral samples for the tests. This project will foster a synergetic and multidisciplinary collaboration between the Australian and Indian research groups in the field of critical minerals recovery from mineral ores and wastes. The expected project outcomes include economic, scientific, environmental, as well as cross-cultural links. unisa.edu.au innoveco.com.au immet.res.in cooe.com.au
Vehicles used in mining and remote area transport are subjected to some of the harshest conditions and usage imaginable. They need to be built extra tough, have improved ground clearance, improved gross vehicle mass (GVM) and be super reliable to meet the extraordinary off-road demands of remote and difficult terrain travel.
Based in Carrum Downs Victoria, EnduroCo provides 4x4 conversions for the Toyota Hiace and Toyota Coaster buses and vans. These vehicles offer the perfect 4x4 mini bus or van transport solution for mining sites with the ability to traverse all harsh and difficult to navigate terrain in absolute safety and confidence.
From the outback to sand and beach environments, whether it be for passenger transport, tourism, off road ambulance, disaster recovery, search and rescue or even law enforcement vehicles, the EnduroCo 4x4 conversions provide the build quality, reliability, comfort and affordability which has been tried, tested and manufactured to withstand the harshest Australian conditions.
EnduroCo’s impressive customer list includes mining operators such as BHP, BMA, Golding, Harmony Gold PNG, Glencore and Thiess.
All the components for the EnduroCo 4x4 conversions have been designed locally by EnduroCo and manufactured in a collaborative partnership with Alfred Lewis Engineering. This partnership enabled the design, R&D development, manufacture of a diverse range of components, component testing and Federal Government approval of EnduroCo’s 4x4 conversions and products in record breaking time. Established in 1966, Alfred Lewis Engineering has built its business through a commitment to quality, service and partnering with clients across markets as diverse as low-pressure gas distribution hot tap fittings, medical instruments, industrial process equipment, transport components, mining and packaging equipment and the automotive aftermarket.
Alfred Lewis purchased their first Mazak CNC machine from John Hart in 1981, a Mazak Quick Turn 10 which was only just replaced in 2021 with a new Mazak Quick Turn 250, coinciding with the 40th birthday of the Mazak Quick Turn series and the introduction of the world’s first conversational CNC system for lathes – the MAZATROL T-1. Fittingly many years of reliable service from this first and subsequent Mazak CNC machines as well as the longterm partnership with John Hart and Mazak, parallels the reliability and endurance designed and manufactured into the EnduroCo 4x4 conversions. The company’s world class manufacturing facility, located in Braeside Victoria, boasts 17 state-of-the-art Mazak CNC machines including the following three most recent new Mazak investments.
A Mazak HCN-6800 optioned with a 6 pallet changer for unmanned operation over extended periods, delivering unsurpassed performance, precision, reliability and production value for highvolume large heavy part operations with a maximum workpiece diameter of 1,050mm, a height of 1,300mm and a maximum load on pallet of 1,500kg.
A Mazak Quick Turn 250 which is a high output, high rigidity machine designed to meet a wide range of production requirements, combining productivity, accuracy, and reliability, while providing excellent performance and unsurpassed production value.
A Mazak Integrex i-400 advanced multi-tasking machine delivering maximum versatility, high precision and throughput for medium to large complex parts. The machine combines the capabilities of a high-powered turning center and a full-function machining center to produce parts in single set-ups.
Alfred Lewis is a quality endorsed company and relies heavily on a proven quality system combined with state-of-the-art Mazak CNC machinery to deliver on time quality products such as cast iron
differentials and C-end weldments to suit, cast iron steer knuckles for both vehicle conversions, cast iron brake calliper brackets, heavy duty dual flange, dual bearing serviceable ABS wheel hubs for both vehicle conversions, torque arms, Panhard rods, tie rods and shock mounts, just to mention a few parts required for the EnduroCo 4x4 conversion kits.
John Ellis, the Managing Director of Alfred Lewis Engineering, cited a number of critical challenging factors that many Australian manufacturers would identify with, however the most important is the ability to deliver quality components and to deliver on time.
“Aside from the performance, precision and reliability, Mazak’s own Mazatrol programming language together with expanded tool magazines is a significant aid to expediting production of small batch lots and assists enormously in simplifying team member operator and programming training,” said Ellis.
“The Mazaks were purchased for their ease of programming, setting and prove-out features,” Ellis continued. “We considered other brands but the ease of operation and the programming language made the choice simple.”
The successful partnership between EnduroCo 4x4, Alfred Lewis Engineering and John Hart is behind the creation of a world class transport solution for mining sites. The partnership will continue to benefit from the leading edge technology provided by Mazak and the strong training and ongoing support from John Hart.
enduroco.com alfredlewis.com.au johnhart.com.au
These vehicles offer the perfect 4x4 mini bus or van transport solution for mining sites with the ability to traverse all harsh and difficult to navigate terrain in absolute safety and confidence. Alfred Lewis is a quality endorsed company and relies heavily on a proven quality system combined with state-of-the-art Mazak CNC machinery to deliver on time quality products.Maximising Lithium Australia with ANSTO and LieNA.
Scientists at ANSTO together with Lithium Australia Limited (LIT) have developed a world-first technology to extract more lithium from lithium mining waste, in a game-changer for Australian lithium industry.
Lithium demand is being driven by the ever-expanding lithium-ion battery market – the leading technology for portable electronics and electric vehicles, which has revolutionised our lives over the last 30 years.
Australia supplies about 60% of the world’s lithium in the form of a mineral concentrate called spodumene. With an abundance of ‘hard rock’ lithium, we are amongst the countries with the largest lithium deposits globally.
The conventional way of extracting lithium from spodumene is in a rotary kiln, which requires very high temperatures (>1000°C) and can only be applied to spodumene of a certain type and size.
This process is highly energy intensive, and the constraints placed on the feed applicable to this process, results in a large proportion of the lithium in these hard rock deposits to be wasted.
The issue scientists at ANSTO together with LIT have been working to address, is that these current techniques only recover between about 50 to 70% lithium from the original ore.
The two organisations developed a process called LieNA®, which removes the need for high temperature processing and is ideally suited to processing of the waste, and realising the majority of the (lithium) value from Australia’s hard rock deposits.
Patented by Lithium Australia, the LieNA® technology involves an initial treatment of the waste spodumene with caustic under autoclave conditions to form a synthetic lithium sodalite which can be easily recovered.
Lithium is then easily extracted and purified in relatively straightforward, hydrometallurgical processing steps and finally isolated as lithium phosphate, which can be directly used in manufacture of lithium ferro-phosphate batteries.’
The new technology enables the majority (>95%) of the lithium value to be realised, with vastly reduced energy inputs as compared to conventional processing.
Drive costs down, and get more from your rocks
Dr Chris Griffith, Senior Process Chemist at ANSTO, explained that not only would the new technology improve the overall extraction, it avoids the energy intensive, high temperature step of conventional spodumene processing, and increases the sustainability of lithium operations world-wide.
“Until now, it has been quite accepted by industry that a large amount of lithium is ‘lost’ during processing. We’re the first in the world to achieve such an efficient level of extraction,” Dr Griffith said. “This technology really has huge potential for an industry which is integral to our transition to the electrification of transport, and ultimately to a cleaner and greener future.”
In early 2020, Lithium Australia Limited was awarded $1.3m from the Federal Government’s Department of Industry, Science and Technology CRC-P Round 8 program. The overall objective of the CRC-P program is to progress the development of LieNA® to a Feasibility Study level and eventual commercialisation of the LieNA® technology.
“ANSTO has been pleased to work with Lithium Australia Limited on processing technology development since 2015, and it is sensational to see the LieNA technology reach this stage,” Dr Griffith said.
An industry partnership with huge potential for the Australian economy
Stuart Tarrant, Chief Financial Officer at Lithium Australia, said "Partnering with ANSTO to develop the LieNA® technology has been highly beneficial to Lithium Australia.
“Upcoming ESG regulations are forcing the industry to consider ways to improve recoveries and shorten supply chains.
“If commercialised, LieNA® has the potential to achieve both and as an outcome we have experienced higher interest from lithium concentrate producers.”
Demand for lithium has reached record level highs and the amount of metal used has almost quadrupled in the last decade.
“The possibilities here are tremendous – some estimates are that the global lithium-ion battery market size will grow from $60bn in 2021 to $171.5bn by 2030,” Dr Griffith said.
“Innovation like this puts Australia in a good position to move away from simply supplying a mineral concentrate to overseas converters as quickly as possible,” he said. “It provides another avenue for Australia to maximise the value from our valuable critical and energy mineral resources and allows us to conduct more value-adding downstream processing here in Australia.” Compared to lead-acid batteries, lithium-ion batteries lose less charge when not in use, and almost all lithium-ion battery components can be recovered and reused.
ANSTO has more than a 40-year track record of partnership with the mining and minerals industries, and a team of more than 60 dedicated professionals and technicians working in the Minerals business unit. ansto.gov.au
Automation technology for sustainability. Here John Young, APAC sales director at automation parts supplier EU Automation, considers some of the technologies that will help mining companies work towards a sustainable future.
New products require new materials, and the rapid advancement and uptake in the electric vehicle (EV) and green energy industries means that demand for rare earth metals, for use in batteries and other components, is only set to increase. In order to meet global emissions targets, the industry must quickly embrace change and find ways to reduce its carbon footprint.
Legislation and guidance around sustainability is having a profound impact on all industries, not least of which is mining. For example, the International Council of Mining & Metals has introduced Mining Principles that have been designed to help realise the United Nations’ 17 Sustainable Development Goals. Mining nations around the world are beginning to implement measures towards this end, as exemplified by Australia's recent pledge to invest $1.5bn to establish Pilbara — Australia's mining powerhouse — as a hub for low-emissions industries, including manufacturing and metals and iron ore production.
According to recent analysis from McKinsey & Company, efforts towards zero-carbon mines are likely to involve significant shifts in operations and infrastructure, such as a switch to sustainable fuels and green electricity. However, there are many current and upcoming technologies that will also be important for the decarbonisation of the industry. These technologies can further boost companies’ efforts or act as an interim solution before larger-scale measures can be tested and adopted.
AngloAmerican's vision of FutureSmart Mining involves the use of various technologies and digitalisation methods that will each contribute to improving the sustainability of mining operations.
Precision mining technologies will include coarse particle recovery, bulk sorting and ultrafine recovery to reduce energy, water consumption and waste production while increasing head grade. Furthermore, the use of sensors, artificial intelligence (AI), digital twins and data analytics will facilitate process optimisation and automation to further improve efficiency, which will ultimately mean lower energy and resource input.
Autonomous vehicles have seen increased use in mining in recent years as they offer a way to increase productivity while improving worker safety and reducing cost. It is fortunate then that they also have the potential to benefit the environment, a benefit shared with many other forms of automation. Examples of technologies include autonomous trucks and long-distance trains that can make journeys more efficiently than human drivers to reduce fuel consumption, and automated drilling and tunnel-boring systems that can drill more precisely, thereby reducing drilling time and waste. Automated ventilation systems can also eliminate the need for continuous ventilation, which can further reduce energy wastage.
A benefit of automation technology is that it can often be retrofitted to existing equipment and avoids the need for an entirely new investment. Furthermore, with the field of automation advancing so rapidly, the price of automation technologies is constantly coming down. A reliable parts supplier like EU Automation can ensure that access to spare parts, whether new or obsolete, is not an issue. euautomation.com
Full range of industry standard measuring equipment with many popular sizes supplied with calibration certificates.
Mathematics is the accurate measurement of the state of manufacturing. Mathematician and Logistics expert Adrian Stephan steps through the process.
Since the beginning of time civilisations have made things to provide for their needs and growth; the necessities of life as Adam Smith describes in ‘The Wealth of Nations’. Manufacturing involves processes and practices to convert the raw materials by hand or by machinery into the outcome according to an organised plan. These processes, practices and plans are collectively known as. What is to be made, how many are to be made, where they are to be made, and costs are some of the basis of the manufacturing ability to supply the outcome to meet demand. The ratio of input to outcome is the productivity of a process, a manufacturing organisation or a nation. Setting and measuring productivity is a significant analysis. Words alone are unable to describe the analysis, and a numeric description is needed to explain patterns, trends, values, and other measures. This analysis is not as easy as it seems and requires a fluency with numbers as well as words. Fluency has a deeper meaning than literacy and provides greater insight into the mathematics and manufacturing relationship than literacy. Unfortunately, mathematics is believed to be too difficult. That might be the case, but maybe the need is for mathematics fluency programs to explain the mathematics practices differently to the learner.
Over time the understanding of different branches of mathematics needs to be refreshed. Following are the main branches.
Arithmetic: Arithmetic is the branch of mathematics that deals with the study of numbers using various operations on them
Algebra: Algebra is the study of mathematics with rules, equations and variables.
Geometry: Geometry is the branch of mathematics concerned with the properties and relations of points, lines, surfaces, solids, and higher dimensional analogues.
Mensuration: Mensuration is the branch of geometry that deals with the measurement of area, length, or volume in 2D and 3D shapes.
Trigonometry: Trigonometry deals with triangles and their measurements.
Probability: Probability is how likely something is to happen. Many events can't be predicted with total certainty. The best we can say is how likely they are to happen.
Statistics: Statistics is the practice or science of collecting and analysing numerical data in large quantities, especially for the purpose of inferring proportions in a whole from those in a representative sample.
Calculus: Calculus is the branch of mathematics that deals with the finding and properties of derivatives and integrals of functions, by methods originally based on the summation of infinitesimal differences.
Financial: Financial Mathematics is the application of mathematical methods to financial situations.
Discipline Specialist Branches (e.g. Finite Element Analysis)
In a manufacturing business the quality of production is measured using methods generally known as Statistical Process Control. Over recent years this has been named six sigma ( ) referring to the six standard deviations in a normal distribution.
Six Sigma is a set of methods used for process improvement. A six sigma process is one in which 99.99966% of products are
statistically expected to be free of defects. It can be expressed s 2.4 defects per million operations. There are different views on how to calculate it; but, for our purposes just be aware of these methods to measure process performance.
This table shows the relationship between processes and whether or not they are under statistical control.
Process is centered Cp Pp
Process not centered Cpk Ppk
Process Capability Process Performance Cp
This table provides a guide to the extent processes are under control.
Evaluation Assessment Cp > 1.33 Good Meets Specification
1.3 >= 1.0 Acceptable Incomplete 1.0 >= Cp Inadequate Inadequate
The graphic shows the relationship between accuracy and precision.
Precision is how close measure values are to each other, basically how many decimal places are at the end of a given measurement. Precision does matter.
Accuracy is how close a measure value is to the true value. Accuracy matters too, but its best when measurements are both precise and accurate.
The pump manfacture shop makes pump shafts to manufacturer specifications. However, the pump shafts are not achieving the required performance level, so you decide to measure their diameter.
The results of the sample are as follows:
Shaft dimension specifications: 86.000 +/- 0.018mm
Upper specification: 86.000 + 0.018 = 86.018 mm
Lower specification: 86.000 – 0.018 = 85.982 mm
Sample measurements: 86.004 +/- 0.005 mm
Sample upper: 86.009 mm
Sample lower: 85.999 mm
The sample dimensions suggests the repair is within specification
Cp= (0.036)/(6 x 0.006) = 1.00 Inadequate control
It is necessary to understand the result and not just look at it. A small change in variation changes the state of the product.
In this case of the pump shaft the strength is a function of the area of the shaft. It is necessary to determine area as a function of diameter. The following table describes the method.
Cpk is a measure of “centredness”
Cpk = either (USL-Mean)/(3 x sigma) or (Mean-LSL)/(3 x sigma) whichever is the smaller Activity
Consider the standard deviation of 0.005.
Now, what if there is a variation and the true value is 0.006? This is a change of 0.001
The objective of this very synoptic description of manufacturing and mathematics is to propose that emphasis should be placed on fluency will it be possible on being fluent in their relationship. Only by fluency will it be possible to make mathematics interesting and solve the manufacturing and other civilisation problems of the future. Manufacturing facilities should put fluency programs in place as they are essential to the ability to meet productivity goals. logistics.com.au
Resources lead Australia’s exports medal tally. Tania Constable, Chief Executive Officer of the Minerals Council of Australia navigates the balance with Climate Bill.
For a sixth consecutive financial year, Australia’s resources have set a new export revenue record with $413bn in FY22, up an extraordinary 37% from the previous period, according to trade data released by the Australian Bureau of Statistics.
Resources contributed 69% of Australia’s total export revenue and were the main driver of our highest ever trade surplus recorded – $136bn. New records were recorded for coal ($112.8bn – up 188% from FY21), aluminium, alumina and bauxite ($14.4bn – up 20% from FY21) and copper ($12.5bn – up 8% from FY21). Iron ore and gold export revenue were down but still recorded significant trade figures – $133.9bn (down 12% from FY21) and $25.8bn (down 9% from FY21) respectively. This incredible record growth again demonstrates the importance of Australia’s mining industry to the nation. It is the backbone of the Australian economy. And it has delivered at a time when it mattered most during the pandemic.
The industry in Australia continues to pay the highest wages on average, approximately 30% out of total company tax, delivers the most export revenue and is critical to supporting regions and communities – providing 1.1 million jobs in the mining industry, the mining equipment, technology and services sector and their supply chains. The record exports come
after a record tax contribution in 2020-21 with a combined $43.2bn in company tax and royalties, a 16% increase from the $37.3bn in the previous period.
This export and tax performance should not be taken for granted. Ongoing success for the industry and the community will heavily depend on a comprehensive policy environment that supports all businesses. However, achievement of both the 2030 target and the 2050 net zero target in the Climate Change Bill 2022 will require close consultation and collaboration with all stakeholders. Federal, state and territory governments need to develop more consistent approaches to climate and energy policy if the country is to transition to net zero in an orderly manner.
It is vital that as the country seeks to achieve these challenging targets, that Australia’s export industries continue to thrive and remain internationally competitive. Mining supports the escalation of renewable energy into the Australian electricity sector to reduce the emissions intensity of our electricity.
Mining is investing heavily in R&D and new low emissions technology development and deployment. Many such technologies relevant for mining are at various stages of readiness and maturity. We must manage this transition in a manner which reflects
technology readiness and cost. We can’t have policy reform that drives businesses to reduced production or closure due to an inability to compete with competitor countries who are not implementing strict emissions constraints on their export industries.
This would just shift emissions overseas to jurisdictions without strict emissions requirements. It would be neither sustainable nor real emissions reduction. The objective must be to develop the policy reforms in a manner which keeps our industries strong and sustainably puts us on a course of emissions reduction through the development and deployment of low emissions technologies and processes. The pathway will not be linear for all industries but great progress is being made across mining.
More needs to be done to attract investment needed for new projects to meet the growing demand for minerals for everyday living and to drive the energy transition to net zero emissions.
Globally competitive tax rates, workplace flexibility and increased government funding for pre-competitive exploration programs are all essential to mining’s longterm future. And when the mining industry is strong, all Australians benefit.
minerals.org.au
The first all-electric aviation refueller in Australia was put into operation this week – a SEA Electric SEA 500 EV which has been designed and engineered in Australia.
Built in conjunction with global aviation fuel products and service supplier Air bp and leading aviation specialists Refuel International in Melbourne, the vehicle will be based at Brisbane Airport, uplifting Jet-A1 for business and general aircraft at the busy international airport.
The refueller can carry approximately 16,000 litres of aviation fuel, with all onboard pumps and functions fully electrified, with the management of the systems provided by the proprietary SEA-Drive® power-system.
This system has previously been adapted to electrify a wide range of ancillary functions, such as the hydraulic systems found on refuse vehicles, elevated work platforms, tippers and tilt trays, or the cooling units found in refrigerated delivery trucks. This latest adaptation sees the bulk of the energy for the truck devoted to the fuel delivery task, rather than propulsion for the vehicle.
“SEA Electric is proud to be partnering with Air bp on this world-leading project, which sets the standard for environmental credentials and performance, all while showcasing the possibilities of EV technology,” said Tony Fairweather, SEA Electric’s CEO and Founder.
“Working airside on the tarmac has its own special suite of conditions when contrasted to a delivery truck on the open road, with the energy demands of the vehicle vastly different to the norm, however, leading criteria such as safety and reliability remain imperative.”
“Of course, there are environmental benefits of converting to EV, with CO2 and other exhaust particulates eliminated, which makes for a healthier work environment at airports.
“Furthermore, this is the first step towards an airport becoming a Virtual Power Plant (VPP). Imagine the near future whereby every Brisbane airport vehicle is battery electric and networked to both renewable sources of energy for charging (such as roof-mounted solar) and also to the grid itself to deploy excess energy when the grid requires it. This is just around the corner.
“Transport makes up a significant portion of total emissions, with the adoption of pioneering EV technology, such as this aircraft refuelling truck, showing a great level of social responsibility,” Mr Fairweather said. The project is proof that Australian ingenuity and manufacturing is alive and well.
“Air bp has been collaborating with SEA and Refuel International for two years on the custom-designed and specialised electric refueller to meet exacting performance and safety requirements. We are delighted to launch the refueller at Brisbane Airport where we are responsible for fuelling 30 airlines and approximately 100 flights daily,” said Daniel Tyzack, Managing Director, Air bp Asia Pacific.
“Our work reflects bp’s ambition to become a net zero company by 2050 or sooner and to help the world get to net zero by working with our customers to help decarbonise.”
For Refuel International, the vehicle is the latest in a long line of projects working with Air bp. “Refuel International are very proud to have developed Australia’s first electric aviation refueller in partnership with Air bp and SEA Electric,” said Geoff Pinner, General Manager for Refuel International. sea-electric.com
How digitisation is reinvigorating Australian manufacturing.
Since opening their doors in 1991, the people at Integra Systems have seen many radical changes occur within Australia’s manufacturing sector. They’ve seen the era of offshoring, and they’ve seen the massive transformation that’s accompanied the shutdown of large-scale manufacturing, particularly in terms of the motor vehicle industry.
“All through, we've tried to lead the way with a range of different adjustments,” admits Erika Hughes, Commercial Director at Integra Systems. “Now, we're part of the era of digitisation. We see ourselves as pioneering the digitisation movement with Industry 4.0, and pioneering the circular economy movement in manufacturing.”
As she bluntly assesses, “Technology and digitisation is Australia’s opportunity to supercharge its manufacturing capability.”
The concept of circularity in manufacturing has been around for some time; however it’s a movement that’s yet to fully take hold here in Australia. At Integra, not only is circularity seen as servicing a need to take urgent action against the harmful effects of climate change, but it’s also a necessary element for the ongoing growth of Australia’s manufacturing capabilities.
The push for Integra to create a factory paperless environment – along with their highly successful transformation to a lowvolume, high variability manufacturing model – has been the key driver behind the business and the way they work with their clients. It has also forced them to be smarter about how they attack designing and manufacturing, positioning them perfectly to embrace circularity.
“We call it ‘design for manufacture’,” explains Erika. “We design for the ease of deployment of transportation. All of those design cores, which we've been involved in – as well as our innovative use of our machinery – have been the key driver behind who we are and what we are, and how we've been able to very, very quickly move into new eras without having to go through enormous change.”
“From a supercharging point of view, we know that digitisation and technology, and embracing smarter ways of designing and manufacturing to reduce environmental damage, are the next logical steps in how the industry has transformed itself over a long period of time,” Erika continues. “But, as well as Industry 4.0, digitisation and circular economies, there'll be a bunch of other actions that are going to take place with manufacturers, that are going to stimulate more smarter forms
of manufacturing rather than the oldfashioned churn-and-burn approach.”
Having adapted and overcome numerous challenges over the years, Integra Systems sees this ‘happy collision’ of technology and sustainability in manufacturing as a major opportunity. As well as driving more efficient factories, this creates strong employment growth opportunities. With the right investment, argues Paul Hughes, CoFounder and Managing Director of Integra Systems, the transformation doesn’t need to be the widespread replacement of people with artificial intelligence and robots. "You've got to be throwing money at hightech,” Paul remarks. “You have to invest in smart design, high-tech, automated manufacture where possible but upskilling your people at the same time is the way we've got to go. When you get smarter with your automation, it actually leads to hiring more staff."
Investment in tech-savvy youth is another way in which technology and digitisation is benefiting Australian manufacturing. Part of Integra’s success comes from backing quality education and training for the emerging generation of engineers and designers. It’s also about understanding that today’s workforce has a stronger, more comfortable relationship with technology, making digitisation easier to embrace.
“We have some of the best education facilities in the world here in Australia,” says Paul. “There is the capacity here to build up the skills required to drive the manufacturing market where it needs to go. So, you've got opportunities for employment at all levels, if you can be smart about how you do it.”
“New employees don't need to be shown how to use a computer,” adds Erika. “Some organisations and industries are almost scared of Industry 4.0 and digitisation and turning everything paperless, but today’s workforce are already trained in digitisation because they use digital technology all day, every day. To deploy that throughout your manufacturing facility — whether it be a touchscreen, facial recognition or gesture control, or whatever it is — is to create a digital environment where people can monitor things in a digital format. They're used to it already, even if they are unskilled."
Erika attributes the development of a strong, young workforce within Integra as being a strategic pillar within the business. She and Paul say that effectively tapping into the know-how of young workers has helped them remain agile, as well as drive the business in the right direction.
An important element of the company’s integration of design into their manufacturing processes can be attributed to the fact that all of Integra’s designers have worked in the manufacturing plant.
“We’re not just talking a two month or three month cadetship,” Erika clarifies. “We’re talking about a couple of years in the facility.”
The reasons for this underscore Integra’s approach to the next frontier of manufacturing. They believe that time spent at the coalface enables their designers to better understand how to design for manufacture more intuitively through the hands-on experience with clients.
“A client knows what they want,” Erika continues. “They know their customer base better than we ever will. So, by giving designers manufacturing know-how as well, they know we're honestly committed to their professional development.”
“They say that you can’t put old heads on young shoulders, and there's a massive place for experience, but experience may need to be in the form of commercial knowhow or entrepreneurialism, or processdriven, because I think that a lot of this new stuff that's coming through is going to be driven by the younger workforce.”
“Not only will you see buying behaviours change as these generations come through,” says Erika. “You're also going to see the way they expect their employer to be performing, and what their employer offers them in terms of life-long learning and career progression. If they're in an environment that offers them some fun forms of interaction – and, often, digitally is the way that's done – you'll start to see
higher employee engagement, because they're enjoying their employment more, because they can see their employers are relevant and, as employees, they’re empowered and valued for what they do because they can see their contribution is making a big difference."
As Paul sees it, “We believe that if employers in manufacturing can start thinking along those lines, as well as investing in machinery that is high-tech –because the higher tech machinery you get, the lower cost of production you can gain – then you start to see the ripple effect and it helps build resilience."
“It's the way we've chosen our people,” says Erika. “It's the way we work with governments, and the way we work with universities and the way we handpick people who match our values. Our people are the change. Our people make the change. The management team can create the strategic direction but the guys that work with us are the real drivers behind how we go about it.”
“And if you put the right tools into their hands,” concludes Paul, “then they'll push those tools to the limits and really get good results.” integrasystems.com.au
A turnkey, fully-integrated Intelligent Cloud Fabric which enables deployment and operation of private and hybrid clouds.
SoftIron, the leader in purpose-built and performance-optimised data centre solutions – which will soon open the first-ever baselevel computer manufacturing facility on Australian soil – proudly announces its newest flagship offering, HyperCloud – the world’s first fully turnkey, totally integrated and supported, Intelligent Cloud Fabric.
Designed and manufactured from the ground up by SoftIron in its own factories, HyperCloud is a fully-integrated platform that removes the complexity of integrating the many independent hardware and software layers needed to build and run a unified private or hybrid cloud. Using pre-integrated building blocks, HyperCloud fully automates the provisioning of storage, compute, networking and infrastructure services, providing a fully functioning, multi-tenant cloud that can be deployed in as little as half a day and less than half a rack and scale almost infinitely.
“When we founded SoftIron in 2012, we did it recognising that the industry’s path for manufacturing IT solutions was fundamentally broken for the requirements of the future, both in the core data centre and especially at the edge,” said Phil Straw, CEO and cofounder of SoftIron.
“In essence, SoftIron has completely reinvented and modernised how data infrastructure is designed, manufactured and delivered in virtually every regard. The results are solutions that are superior in virtually every way possible, from power draw and heat emissions, to density, and to eliminating vendor lock-in through our use of open source - the list goes on. We’ve designed a platform for IT solutions that is centred around the modern needs of our customers, enabling them to flexibly scale their IT solution wherever it is needed without the constraints and limitations of traditional commodity hardwarebased solutions,” added Straw.
The goal of an intelligent cloud fabric is to dramatically reduce the complexity of operating a resilient, multi-site hybrid cloud by providing stateless building blocks holistically designed and pre-integrated for assimilation by a distributed cloud orchestration control plane. Using these building blocks - the addition of more storage and/
or compute resources becomes simply “plug and play.” The result radically simplifies the architecting of a cloud, enabling operations teams to quickly empower application owners and data users to consume and manage services seamlessly across private and public resources.
"Opening the first factory on Australian soil to build the hardware needed to build secure, sovereign, resilient clouds is an honour,” said SoftIron COO, Jason Van der Schyff. “We're seeing huge demand in the region for the cloud platform that we're about to start manufacturing here, but at the same time we regularly hear concerns about supply chain resilience from the more traditional vendors. Our unique ‘Edge manufacturing’ approach - using leading edge, super flexible production lines, coupled with digital twinning techniques to enable us to execute in region, but plan across our facilities efficiently, really is the way forward we believe in how the IT industry should operate - building long term, resilient capability in the markets we serve. Australia is at the leading edge of nations really taking sovereign capability in IT seriously. In other parts of the world we see a focus on chip manufacture with multi-billion dollar investments in building domestic capability - but that's only part of the challenge. If we're not also building the economy and skills required to utilise that capability we’re at risk of just shipping those chips back into the same supply chain that exists today! What we're doing here at SoftIron is, we believe, a model for others to emulate - building not only manufacturing infrastructure, but also the associated skills to design, develop and support IT products right here”.
SoftIron Chief Operating Officer Jason Van der SchyffIndependent of all public cloud vendors, HyperCloud enables IT generalists to build and operate highly sophisticated hybrid and/ or multi-cloud infrastructures that operate with a level of reliability, availability, elasticity and serviceability previously available only to hyperscale cloud builders with specialist skills and access to large engineering teams. HyperCloud’s modular nature, combined with the simplicity with which new compute and storage resources can be added, and the out-of-the-box secure multi-tenancy capabilities mean that the cloud fabric can be scaled up or down just in time, eliminating needless over-provisioning and reducing financial outlay.
“Building and running clouds today is overly complex as engineers battle to integrate disparate layers of technology into a resilient, performant and scalable solution,” said Kenny Van Alstyne, CTO for SoftIron.
“It was time to take a step back and architect an entire platform, from the ground up, with the single task of making cloud consumable. HyperCloud removes the complexity of integrating the many independent hardware and software layers needed to build a cloud into a unified purpose-built fabric. With HyperCloud, you can deploy virtualised and containerised workloads across federated on-premises zones and public clouds, with support for secure multi tenancy, full programmability, and full lifecycle automation all ‘out of the box.’ We’re giving organisations sophisticated control of their cloud architecture, eliminating the need for complex integrations between multiple vendors and technologies while providing the ability to scale limitlessly as workloads demand, incrementally adding resource services as needed,” added Van Alstyne.
“Public Cloud is popular because it creates a consumption-based experience hiding the complexity of operating a resilient, elastic infrastructure, and the sheer brute force of engineering that is needed to accomplish it - historically, that’s only been possible at hyperscale,” added Phil Straw. “It’s a useful utility in your IT tool belt, but most organisations today want a hybrid model. Creating a complexity breakthrough required a totally new approach to deliver the first and only complete technology to be used specifically for building clouds. After a decade of innovation, HyperCloud realises that goal and will forever change expectations of how clouds can and should be built.”
“In today's highly competitive infrastructure market, we believe the team at SoftIron is developing and delivering innovative solutions
to solve cloud complexity across the stack,” said Daniel Newman, Principal Analyst and CEO of Futurum Research. “Leveraging its trusted supply chain hardware model, coupled with its comprehensive consumption-based offerings, we see a robust long-term growth trajectory for SoftIron as it focuses on meeting the rapidly shifting demands of enterprise IT.”
“We see many of our larger customers embarking on data repatriation projects, tired of the unpredictable egress fees being charged resulting from hosting their apps and data in the public cloud,” commented Dev Tyagi, CSMO at SoftIron+Co channel partner, Boston Limited. ”We’re excited by HyperCloud from SoftIron and its ability to make these hybrid clouds a reality in what promises to be a fraction of the time and with a fraction of the skills needed.”
HyperCloud is available immediately from SoftIron and its partners in the SoftIron + Co. channel program. It is delivered fully capable with no additional licensing required to access any features, compute or storage capacity.
softiron.com/hypercloud/intelligent-cloud-fabric
The processes used to manufacture goods have changed beyond recognition in the past 200 years, through a series of steps characterised as four ‘industrial revolutions’ often referred to as industry 1.0, 2.0. 3.0 and 4.0. Alessandro Chimera, TIBCO’s Director of Digitalisation Strategy explains.
First came the use of energy sources— water then steam—to power manufacturing processes, which required a consolidation around these energy sources. Then came the great efficiency gains from the streamlining of manufacturing processes— the assembly line—followed by automation and control, thanks to the development and deployment of digital technologies.
The latest revolution, industry 4.0, takes that one step further by turning the flow of digital information into a two-way street: data is used to control the manufacturing process, and is collected and analysed to improve efficiency and detect problems.
There is one common denominator to all four phases. The operators of manufacturing systems and processes strive to anticipate and if possible, prevent any malfunction of production machinery that will compromise product quality or interrupt production. It’s not good to discover a machine has been producing malformed widgets after it has created a few hundred.
In industry 1.0 and 2.0, the ability to do this was limited and processes largely empirical: an engineer attuned to the sound of the machinery might detect a subtle change indicating a malfunction, for example. In Industry 3.0, monitoring many operational parameters enabled a one-to-one correlation between a malfunction and an alert: a light coming on to indicate a specific fault.
In Industry 4.0, masses of data are generated from all components of a machine and all stages of a process. Massive computing power is now available to employ machine learning and artificial intelligence techniques to detect anomalies long before they become apparent to a human observer or before they interrupt production or compromise product quality. In today’s large-scale, high throughput, and extremely complex manufacturing processes, such techniques are becoming essential for the early detection of anomalies and performance degradations that can quickly have large-scale and costly impacts on the outputs of manufacturing processes.
Real-time data from a machine or process can now be analysed to predict the likelihood of an anomaly occurring. Anticipating an event before it impacts product quality of operations can produce considerable savings in costs and time.
However, extracting maximum value from available data to detect anomalies early before they have a significant impact is challenging, even with the power of AI and ML. The datasets produced by manufacturing processes are massive and exist in multiple silos scattered across numerous systems. So, the first stage in applying AI and ML to anomaly detection is to bring together data from these disparate sources. The next stage is to employ technologies designed specifically to extract meaning from these disparate datasets, which can be achieved using an autoencoder. A good description of an autoencoder is “an unsupervised artificial neural network that learns how to efficiently compress and encode data then learns how to reconstruct the data back from the reduced encoded representation to a representation that is as close to the original input as possible.”
United States semiconductor manufacturer Hemlock Semiconductor (HSC) has successfully used anomaly detection to boost the efficiency of its semiconductor manufacturing.
Anomaly detection enables HSC employees to compare key parameters against predefined thresholds and optimal patterns developed by gathering a wide range of operating data and applying machine learning and AI. As soon as the parameters for critical indicators for a process breach predetermined thresholds determined by this analysis, an alert is raised enabling staff to determine exactly what has caused the alert and take remedial action, in many cases pre-empting any impact on production and product quality.
Over time the use of anomaly detection will lead to more energy and resource efficient manufacturing and to more reliable and better-quality end products, all of which will be good for the planet.
In Australia, not-for profits like the ARM (advanced robotics for manufacturing) Hub, are assisting manufacturers in embracing AI to overcome the present skills shortage. It provides expert advice on AI solutions and scientific and technical expertise. During its first year of operations, it reported it had worked with over 200 companies in this capacity, seeking ways to maintain and grow their digital capabilities.
Two successful instances are Verton Pty Ltd and Australian Droid and Robot (ADR) Pty Ltd. With its world-first range of remote-controlled, load-management systems, Verton reinvented heavy-lifting operations, delivering “safer, faster and smarter crane operations”, but now with the addition of its AI capabilities it is forming international joint ventures and looking for big data opportunities. This reach into AI was its response to the industry 4.0 call for digital capabilities to aid and improve manufacturing processes, particularly in the integration of advanced robotics and artificial intelligence.
ADR, on the other hand, does not lift cargo; instead, it drives and flies them. It has applied robotics and automation to industries including emergency search and rescue, where it developed a highly specialised drone and automated vehicles in mining.
Overall, the ARM Hub is delivering some exciting AI initiatives across many industries – from mass manufacture of construction solutions using platform technology, to the use of computer vision and ML algorithms to detect disease in ginger root stock. It is increasingly successful in demonstrating how AI and machine learning technology may assist Australian manufacturers in increasing productivity and efficiencies. tibco.com/solutions/anomaly-detection
Harnessing the energy from pulsed lasers provides a new tool to improve the reliability and lifetime of metal parts. Laser shock peening offers significantly deeper residual compressive stresses (RCS) than traditional shot peening methods. With the introduction of THEIA, a diode-pumped Nd:YAG laser, Thales enters a new sector, that of laser shock peening, shifting metal fatigue prevention to a higher plane.
History indicates ‘shot peening’ (SP) has been used over the past five decades in surface modification to metals and alloys, for the purpose of changing the surface integrity, obtaining superior mechanical properties, preventing metal fatigue, or surface cracking and in so doing improve the service life of parts. The result is a dimpling effect. Following the impact, the recovery process induces residual compressive stresses (RCS) on the surface of the substrate making it stronger and resistant to surface cracking. Shot peening is widely used on various metals and alloys across industrial, aerospace, medical, and the automobile sector.
Recently laser shock peening (LSP) has been adopted as a more suitable
process in critical industries such as nuclear, biomedical and aerospace. In the aerospace industry, LSP is used in passenger and military aircraft to enhance the fatigue performance of the compressor blade, landing gears, shafts, valves, discs, and complex forming of wing surfaces. In the United States, laser shock peening is now being used on F-35B’s short take-off aircraft used by the U.S. Marine Corps. Following months of testing and accreditation, laser shock peening is being applied to strengthen the materials in the aircraft’s bulkhead and airframe subjected to excessive performance stresses of landing in small spaces or aircraft carrier decks. The aim is to enable the aircraft to reach its full structural life limit. Aircraft
components are subject to critical life limits and require scheduled maintenance procedures, laser shock peening provides a new improved solution. LSP has been shown to enhance cracking resistance up to ten times deeper than shot peening for fatigue prevention and part performance. What is important for the F-35Bs, is that this maintenance process doesn’t add any additional weight nor does it reduce the fuel or weapons carrying capacity.
LSP techniques can be applied to strengthen turbine fan blades with testing of fatigue strength demonstrating it is two times more effective than with traditional shot peening processes. Recent research has shown that LSP can be successfully applied to thin wall welds of Ti6A14V, used to strengthen components of aircraft engines. While residual stress profiles vary based on part thickness and material properties, LSP consistently produces residual compressive stresses many times deeper than those produced with SP. As a result, laser shock peening is being heralded as the ultimate fatigue enhancement solution. raymax.com.au
How Industry 4.0 can improve manufacturers’ shop floor working culture, and the bottom line.
Big data and the Industrial Internet of Things (IIoT) grant employees easier and more centralised, control and access to data. But do these technologies improve the working culture on the shop floor? That question was put to the test by OSI Precision when it installed software by Sandvik Coromant, to help with its Industry 4.0 roll-out.
OSI Precision, a general engineering manufacturer of complex parts based in Quebec in Canada, has a long-running relationship with Sandvik Coromant and uses the latter’s hard-wearing machining tools in several CNC machining lathes, and a milling machine on its shop floor.
This time, OSI wanted to take this partnership in a new direction - machine monitoring. The company wanted to better connect nine CNC machines on the shop floor, but in practice, Sandvik Coromant needed to help OSI consolidate the control and performance analysis for all of these machines, quickly and securely, and in a way that would benefit the organisation’s cultural shift towards Industry 4.0.
The machines came from different manufacturers — DMG, Mazak, Correa and Parpas — and were both old and new which presented additional connectivity challenges. Furthermore, each machine was very costly to run, so the control solution that OSI decided upon would have a real impact on financial gains.
The customer began research into software in early-2019, before signing a final agreement in May. Sandvik Coromant started gathering data on most machines that summer, and an initial pilot project was fully up-and-running by the Autumn of that year. “Before choosing, we took a few months to properly research all the tools available, and to select the right partner for this project,” explains Hubert Breton, operational efficiency and digital technology manager at OSI Precision.
“In fact, we had up to 15 criteria. They included that the control and monitoring system had to be versatile, configurable, and easily adapt to all our different types of machine. We also needed it to integrate with our other digital systems — databases and so on — and also required an easy-touse interface for our operators.”
In the end, OSI opted for Sandvik Coromant’s CoroPlus MachiningInsights platform, a modern cloud-based machine monitoring solution. The main reason was for its trusted partnership and support.
“We have worked with Sandvik Coromant for our cutting tools for many years,” he explains. “The support from the company
and from our contact person there has been very good over the years,” says Breton.
Bijal Patel worked closely with OSI Precision on the project as Senior Digital Machining Specialist at Sandvik Coromant. “Having data is really the first step in deriving the best performance and profitability from these machines, and to be able to measure this ourselves,” says Patel. “That is where Sandvik Coromant comes in.”
OSI Precision was also won over by Sandvik Coromant’s plans to develop the CoroPlus MachiningInsights platform further into the future. “We really liked what we saw there, including the ability to integrate with the machine tools themselves. This was also a big factor in our decision.”
OSI Precision agreed to become an early adopter of CoroPlus® MachiningInsights. Not only does the platform give manufacturers greater visibility of their CNC machine tools and machining processes, but it also provides the tools needed to analyse, identify and eliminate common sources of downtime and inefficiency.
“MachiningInsights automates the processes of data collection and analysis,” explains Patel. “The software’s end goal, to provide machine shops with complete transparency about how their machine tools are be utilised, seemed to perfectly suit OSI Precision’s Industry 4.0 digital shift — and to offer a solution that could be easily adopted by their workforce.”
The parameters and data managed by the operators relate to tool and part changes, breakages, and machine failures. The data yielded by the machine monitoring solution can prove especially helpful in drilling down to the causes of machine stoppages. Sandvik Coromant was also fully aware of the importance of a working culture within OSI Precision.
“I think it all boils down to how people treat one another, and that includes through the use of data, data management and sharing and better reporting — and, therefore, better communication — within the plant,” says Patel.
OSI Precision first implemented CoroPlus MachiningInsights as a pilot project: three machine operators ran the equipment following internal training, which Breton supervised internally. At the same time, he explained the pilot project. The second part of training was a lot more hands-on, covering how the system can be controlled from an iPad.
“The implementation was very important to ensure that everyone got on board and worked towards the same goal,” adds Breton. “It was vital to involve people directly in the project, rather than develop it in a silo away from everyone.”
Highly customisable
For the pilot project, OSI’s workers had to get accustomed to using all-new software.
Fortunately, the CoroPlus MachiningInsights platform is easy to get up and running and to use, with a simple login and menu interface.
The platform is also highly customisable, whether it is accessed from operator channels on iPads, or from dashboards.
“In fact, OSI has customised dashboards with all the information that we thought was pertinent, as a modified version of the interface supplied by Sandvik Coromant,” says Hubert.
Patel adds: “Through remote iPad access, operators can not only see the current state of machines, but also how they have performed since the day they were connected. The operators can access empirical data about every part ever produced, every tool used, every shift they ever worked and even how operators impact operations.”
Nevertheless, there as some trepidation from OSI’s operators at the beginning of the project — not least because the data from CoroPlus MachiningInsights would measure performance and activities.
“It was really important that people realised that it is not a surveillance system. Instead, MachiningInsights fuels our continuous improvements, to be more competitive, so that everyone can be better at their job, and use data to drive those improvement efforts.
“We’re very careful in how we share our data internally, so everyone is on board
with the fact that this is to fuel continuous improvement efforts. Customised reporting was crucial for this,” argues Breton.
With Sandvik Coromant’s support, the company was soon able to demonstrate the advantages of the new, digitalised approach in a way that made sense — specifically, being able to demonstrate the advantages of the system through data.
Before long, OSI’s operators were fully onboard with the new project.
One challenge arose when OSI Precision had to work with vendors of different machines to install adaptors that would translate each machine’s data to make it compatible with the CoroPlus MachiningInsights platform.
All signals and data form the machines are translated into one machine language, and then put together for analysis by OPS.
“For the first adaptors, Sandvik Coromant was present at the plant, which was very helpful for the hands-on installation by the machine manufacturers. There was also a compatibility issue with one of the adaptors, but Sandvik Coromant was able to quickly solve the problem online, by connecting us with the right people,” says Hubert.
In fact, 95% of Sandvik Coromant’s support for the project was offered remotely. OSI and Sandvik Coromant communicated
regularly through Zoom and TeamViewer meetings, and the installation and configuration of the machine monitoring solution was also remote. OSI Precision plans to use data from the pilot project for future improvements, and to roll the system out to the rest of its 15 to 20 operators.
The pilot project has been a success, says Hubert: “We have worked well together so far, and the system has been really easy to use. We have also been able to integrate this data with other software, using the Sandvik Coromant Application Programming Interface (API), with which we had excellent support from Germany.
“The system has never broken down and nothing has ever been offline. It has been super reliable so far and our operators have been using it 90% of the time, as expected. Going forward, OSI Precision predicts that the system will prove how competitive it can be and how fast the company delivers complex and bespoke machined components to customers.
“Moreover, the new technology has made OSI’s operators more efficient. We are on the right track to changing our working culture for the better,” concludes Hubert.
sandvik.coromant.com
SPEE3D has announced the launch of the Phaser, a new ultra high energy nozzle designed to work with a wider range of hard phase materials.
The new SPEE3D Phaser nozzle uses compressed air or nitrogen to deposit material four times faster than the speed of sound at a much higher energy. This process achieves high particle velocity to enable more deformation of particles during the deposition process. As a result, harder materials can be made including stainless steel, titanium, high strength aluminium and nickel based carbides. These materials are in addition to our existing various copper, aluminium bronze and aluminium materials.
“The SPEE3D PHASER nozzle is revolutionary because anyone can print what’s considered ‘hardier’ materials, and without having to rely on helium to cold spray these materials like other nozzles,” said CTO Steven Camilleri. “With supply chain issues continuing to delay parts for industries such as space, defense, auto racing and maritime, the Phaser nozzle can create these parts in just minutes to withstand severe conditions, high stress, immense shock loads and abrasive environments.”
SPEE3D’s cold spray metal 3D printers are the world’s fastest, most robust, deployable additive solution to manufacture full-density, solid metal parts in just minutes. Our cold spray process is highspeed, consistent, and able to produce high quality applications every time. The technology is used world-wide and proven reliable by customers including the Australian Army, EWI, Penn State Applied Research Laboratory, and other global organizations that require fabricating parts in harsh expeditionary field environments.
With the Australian Army, SPEE3D has tested and validated metal 3D printing as a military capability with the latest field trial being the longest and toughest to date taking place in remote Northern Territory, alongside exercise Koolendong.
SPEE3D's cold spray metal 3D printers are already the world's fastest, most robust, deployable additive solution to manufacture full-density, solid metal parts in just minutes.
The Phaser nozzle is a new ultra-high-energy nozzle that has been designed to work with a wider range of hard phase materials. The high particle velocity achieved with the Phaser nozzle means more deformation of the particles during the deposition process, which allows harder, tougher materials to be made.
As with its predecessor, with Phaser you don't need to rely on Nitrogen and Helium to cold spray these materials.
Using compressed air, the PHASER nozzle can effectively deposit material four times faster than the speed of sound at much hotter temperatures, up to 800-degrees C. You can also use nitrogen if you choose, but it isn't required.
Industries such as defense, auto racing, maritime and space can create parts with these harder materials in minutes that can withstand severe conditions, high stress and immense shock loads.
SPEE3D has already been working with customers including the Australian Army, which has tested and validated their printer in harsh expeditionary field environments. spee3d.com
Wayland Additive is ready to show off the new NeuBeam technology for powder-bed fusion
Developed in-house from the ground up by a team of physicists that have worked for many decades with electron beam technology and industrial systems in the semi-conductor industry, Wayland Additive’s NeuBeam technology is a ground-breaking, reliable system for powder-bed fusion (PBF). The science, combined with extensive expertise and experience has allowed Wayland Additive to develop a very capable and reliable system rather than imitating existing systems or adapting off-the-shelf components and repurposing them.
The NeuBeam process offers a completely new approach to eBeam powder bed fusion (PBF). This is metal AM technology that represents a big step forward compared with existing PBF systems. The technology overcomes the compromises that most companies have to contend with when using the PBF fusion process with either lasers or eBeams for metal materials. As a result, design engineers can revisit applications that were previously seen as troublesome or impossible and/or begin development projects with a clearer view of the process and the possibilities that can now be realised. Neubeam effectively neutralises the charge accumulation generated by an electron beam. This offers greater flexibility than laser PBF while overcoming the stability issues of eBeam PBF. In addition, this means that the NeuBeam process enables metallurgical requirements to be tailored to application requirements rather to maintain the print process within the narrow bounds permitted by the process. These process capabilities, along with the greatly improved ease of process development, also opens up the use of a much wider range of metal materials.
“We are all excited by what the Calibur3 opens up for industry through the use of metal AM for production,” says Peter Hansford, Business Development Director at Wayland. NeuBeam is a hot part process rather than a hot bed process. This efficiently creates parts that are free of residual stresses because the high temperatures are only applied to the part and not the bed, ensuring free-flowing powder post-build (no sinter cake) and stress-free parts with reduced energy consumption. Furthermore, the process overcomes many of the limitations for manufacturing large components – no residual thermal stresses, no gas cross-flow, and a much simpler powder removal process than existing eBeam systems. With Neubeam there is no need for structural supports (or the use of EDM to remove them), or specific build plates, meaning time and money spent on post-processing is vastly reduced. There are also faster warm-up and shorter cool-down times meaning improved productivity. waylandadditive.com
The Extreme Dynamics of KIMLA’s POWERcut series reduce production cycle times while maintaining the highest accuracy. With a wide range of flexible material handling and working areas means KIMLA can provide the right solution for your needs.
The Toughest just
The new SLAGHOG™ Version 3 has 50% more torque making slat cleaning even faster and easier! Built tough in the USA the SlagHog laser slat cleaner is the most powerful and fastest slat cleaner in the world. Increased ROI through fast and efficient cleaning of steel or copper slats on CO2 or Fiber laser cutting machine. Watch your productivity SOAR.
The Rhino Hammer makes removing tabbed parts much easier. This innovative tool uses shop air to create impact vibration that breaks tabs loose. The long-lasting polyurethane tip leaves finished parts in perfect condition. Your guys will thank you for getting them this tool.
Transforming industrial machinery production through reliability, consistency, cost efficiency and expedited time to market.
When it comes to manufacturing industrial equipment – be it scientific instruments, factory equipment or power tools, to name just a few – a multitude of different intricate parts are needed to ensure the product functions as intended.
For industrial manufacturers of such equipment, there is a clear and common need for parts, however complex they may be, to deliver the robustness, consistency, accuracy, and repeatability to uphold the performance expectations and functionality of the product faithfully. Failure to ensure this could result in malfunction, which in turn could lead to extra costs and damage to the brand’s image.
But the challenge for industrial machinery manufacturers doesn’t end there; the need for such parts to also be produced both timely and cost-effectively will always be an equally inherent objective.
With traditional manufacturing techniques, there is an immediate and accepted recognition that long lead times and high costs will typically be part and parcel of the process. Therefore, traditional manufacturing options often hinder the industrial equipment manufacturers’ quest to streamline efficiencies across their production operations.
The Stratasys’ industrial-grade SAF technology is a new form of powder-based additive manufacturing (AM) technology and the culmination of over a decade of R&D.
Using a single pass print-and-fuse process, industrial equipment manufacturers finally can produce robust end-use parts with the level of control, accuracy and repeatability expected from injection moulding. Better still, SAF also achieves a ‘Holy Grail’ in its ability to enable the 3D printing of tens of thousands of consistent functional production parts – and with a cost-per-part that frequently renders injection moulding or CNC machining uncompetitive. When you add to the mix that those ten thousand parts can all be completely unique and customised, then for manufacturers the business case cannot be ignored.
Additionally, with SAF technology, industrial equipment manufacturers can access the inherent benefits of a technology that delivers the production resiliency and agility increasingly demanded within a sector that continues to evolve and where adaptability is key.
Stratasys has delivered its SAF technology via the H350 3D printer, engineered to deliver the accuracy, repeatability and process control demanded by industrial
equipment manufacturers to meet their need for production consistency and competitive part costs.
Just like the manufacturing requirements of Stratasys’ own customers, the development and production of the H350 itself demanded consistent end-use parts with a superior level of accuracy and consistency to ensure the 3D printer was fit-for-purpose.
Since each printer must operate in a uniform manner, it was critical that all these parts function at the same high level, with a high degree of consistency. If one of these industrial components was out of tolerance, the H350’s wouldn’t perform properly. This would negatively impact the printer’s ability to achieve high production throughput and repeatability build-tobuild and reproducibility printer to printer.
In addition to part quality, a short turnaround for these industrial components was a significant factor so pressing deadlines could be met.
Taking this into account, and perfectly underscoring Stratasys’ utmost belief and confidence in the attributes of SAF technology, the H350 proudly incorporates a range of different industrial machine components that are created, and 3D printed by the company using the H350.
In total, every H350 3D printer comprises of thirty production-grade PA11 parts, each of which exhibits repeatability, excellent mechanical properties, and exact consistency. Currently, these internally produced components are added to each new printer. This demonstrates the confidence in the H350’s high-yield end-use parts since they are accurate, repeatable, and durable.
Printing with the H350 enabled a faster time to market and saved unnecessary production and transport fees. As compared to days or even weeks with traditional manufacturing, accurate enduse parts for the H350 were produced and ready for implementation within hours.
In addition to producing parts on-demand, it was essential that they exhibited consistency, accuracy, and repeatability. This was successfully achieved with the H350. The unwavering confidence in the strength and durability of these parts is exemplified by their implementation in every H350 3D printer.
objective3d.com.au
‘Repair not produce’ with automated Chiron Additive Solution.
In terms of economic and ecological sustainability, the call to repair rather than ‘produce new’ is correct and forwardlooking. When it comes to repairing moulds and other components instead of producing new ones, laser metal deposition (LMD) is a proven key technology - with a growing potential for new areas of application.
It's actually like machining, only LMD works the other way around. Instead of removing material, it is applied. Using powder or wire, or both in combination. What is feed and depth of cut for one is deposit rate and layer thickness for the other. Where one cools his workpiece, the other heats it. Either way, the component has to be produced with the required quality and cost-effectiveness with the additional criteria of being energyefficient and resource-saving.
LMD was represented at the CHIRON Group's ‘reFORM’ workshop in Tuttlingen (Germany) where Cedric Bardenhagen, Key Account Manager at Siemens AG, gave a very clear picture of the motivation to face this challenge in his lecture. He discussed a newly produced gear wheel with a diameter of 500mm and a weight of 230kg that requires almost 2,000kW/h throughout its production chain. That's 90% of the energy for steel production and forging the mould, and the remaining 10% for machining and post-processing.
In comparison, a gear wheel made from recycled steel uses ‘only’ 39% of the manufacturing energy. If you now repair such a wheel with an automated LMD process, you only need 17% of the energy of a new wheel, or 42% of a recycled one to get a wind turbine running with these components. In short, repairing with additive manufacturing is highly positive for climate balance.
Heat-resistant chrome steels are generally used for moulds and tools. The stresses to which a forming tool is subjected can vary greatly. Whether it's a forging tool for the production of a generator shaft with a dead weight of 250 tons or a cone roller for the production of seamless rings, the loads that occur are fundamentally different.
What is important when manufacturing new tools, but also when repairing them is the breakouts and worn punching surfaces. In terms of material and process technology, it is a science in itself.
However, this is the only way to achieve a good form and tool quality with long service life as the result. At best, these even surpass those of unwelded new dies. This finding represents indispensable knowledge for the successful implementation of automated LMD processes.
The CHIRON Group additive manufacturing team used this highly specialist knowledge of material properties in welding processes to develop the AM Cube. With today's very large variety of materials, the flexibility of the system is an important criterion for an automated LMD process. With so many shapes and contours and so many materials used in daily practice, it makes sense that the system can be changed easily and quickly. Powder is the preferred welding material on the one hand, and wire on the other – the user has all the options.
Dominik Hipp, Head of Toolmaking at Hammerwerk Fridingen GmbH, is one such user, responsible for the production of dies and tools with a daily tonnage of around 200 tons. Together with the CHIRON Group, he works on several projects, including the repair of cutting rings. “Automated welding on the AM Cube meets our quality requirements and increases service life by a factor of 2.5 to 3,” reports Hipp in his presentation. “The decisive factor in automating the LMD repair was also the fact that there are hardly any skilled workers left for manual welding. Now that the automated process is in place, it is important to introduce
employees to the automated LMD process and get them enthusiastic about it.”
Till Oeschger, Project Manager AM Cube at the CHIRON Group says: “Process control and data effectiveness are a must for automated LMD solutions.”
What the workshop participants recognised in the lecture was the complexity of the topic, from the physical, chemical and mechanical requirements for tools and materials to build-up welding for graded alloys. A lot of factors come together and ultimately, parameters and data must be used to construct the component to make automated LMD processes safe and reproducible.
This data is valuable on several levels. An error-free and already optimised program can be transferred 1:1 to the system. Data also plays an important role during machining. All relevant process data is recorded via two new digital systems from the CHIRON Group. The Via DataLine AM permits all relevant process data to be continuously displayed live, recorded and documented in a compact quality report. Product and process quality can thus be reliably assessed. The VisioLine AM system visualises and saves video files that are captured by multiple camera systems. Once parameters and tolerances have been entered, they serve as a reference and in the event of deviations, you can take immediate, targeted action. chiron-group.com
How Micro AM is impacting time-to-market for precision plastic parts. Christopher Hunt, additive manufacturing Manager at Accumold takes up the story.
Some 30 years ago now, additive manufacturing (AM), which used to be known as rapid prototyping, disrupted the prototyping stage of product development. The ability to print parts in three dimensions from CAD solid models facilitated concurrent engineering, as within days of a design being complete, all relevant product development departments could sit together analysing an accurate prototype, and designs could be easily re-iterated to overcome potential downstream manufacturing issues. For a tooling manager to be able to initiate changes in product designs to streamline the tooling process a few days into the development of a product knocked weeks if not months off product development cycles.
Move on 25 years, and AM began disrupting the traditional manufacturing paradigm once again, this time in the area of production. In general terms, AM technologies have become increasingly sophisticated over time, and the precision and accuracy of builds in a variety of materials means that AM is now challenging legacy manufacturing processes in terms of speed, cost, and tolerance attainment.
This history of AM over the last 30 years, however, is only really accurate when looking at the production of macro-sized parts and components. It is only in the last few years that AM has been able to disrupt the area of micro manufacturing, as it is only in the last few years that innovators have managed to refine the AM process to achieve the micron level tolerances and surface features that have been the preserve of legacy production processes such as micro moulding for decades.
Today, however, micro AM processes like the Fabrica 2.0 from Nano Dimension that we use at Accumold can now additively build parts and components only previously possible through the use of micro moulding, and can do so in a way that allows manufacturers to completely re-imagine the way that precision micro parts and components are made, and which changes the basic economics of manufacturing.
The Fabrica 2.0 can attain 1.9-micron resolution in X and Y, and the technology builds “additively” in 1-5 micron layers. With this breakthrough, the path to the creation of innovative miniaturized parts at amazing speed and reduced cost is open for all industry sectors.
The Fabrica 2.0 micro AM platform promotes innovation, and stimulates cost and time-to-market reductions. But in general terms, success through the use of the Fabrica 2.0 is measured in microns and hours. Micron-level detail can be achieved without the need
to fabricate tools, and this means that you can have intricate and geometrically complex prototypes in a matter of hours. There is a limit to the ability to create complicated parts using traditional micro tooling. With increased complexity comes increased cost, but not when using the Fabrica 2.0 micro AM technology. The absence of the requirement for a physical tool lifts the lid for design engineers to think outside the box and attain design goals previously unimaginable. This design freedom coupled with the inherent manufacturing agility that is a core characteristic of AM require a root and branch reassessment of all aspects of the product development process, a disruption that is a spur to the stimulation of future product successes and enhanced market-share and profitability.
Through the use of the Fabrica 2.0, you can also optimize workflow, the technology producing less scrap and fewer tools than conventional manufacturing processes. It also promotes the reduction of iterative process, assembly, and inventory. This means that significant operational cost benefits are now attainable at the micro manufacturing level.
Through a combination of design optimisation and improvements in materials, we are able to additively manufacture Direct Rapid Soft Tooling (DRST) which we can use to injection mould real parts. This unlocks new business possibilities for mould makers and manufacturers who up until this point have been restricted to the use of long lead time and expensive traditionally manufactured mould tools for the achievement of any volume of moulding, from prototype runs all the way through to mass manufacture. The business case for a process chain that includes DRST, with dramatically shorter lead times at reduced cost is obviously compelling.
At Accumold, we use micro AM as a tool to reduce the time from initial design to market. When looking at a conventional prototyping scenario, prototype tooling needs to be fabricated at often considerable cost, and also taking upwards of six weeks, meaning that initial testing cannot take place until at least week seven of a product development process. The time involved when using conventional tooling is only exacerbated if (as is often the case) design changes are required, and tooling needs to be modified.
When using micro AM, by week seven a design can have been refined numerous times as the process requires no traditional tooling, just DRST. This means that time and focus in this early stage of product development can be spent on design optimisation, and so micro AM not only saves time and cost in product development, but it also stimulates innovation.
The theoretical case for the use of micro AM in precision plastics part and component development is seemingly therefore extremely compelling. However, Accumold now has significant experience in using the technology for customers, and so we are able to illustrate the way in which micro AM has benefitted OEMs in real time.
Due to confidentiality issues related to the case studies discussed below, we are unable to include pictures of the products discussed. Pictures used in this article are non-related part shots that show the precision and resolution that can be achieved using the Fabrica 2.0 technology.
Case Study 1 – Intraocular Implant: Our first example is a medical OEM customer making an intraocular implant that measured 1.6x2.9x0.7mm. The customer was up against a looming FDA submission deadline. The part design included a small gap on one side of the part. While the rest of the part design was pretty much frozen, the customer needed to determine what size gap would be optimal for the part considering that in its final assembly it would need to be accurately handled and safely implanted inside the eye.
Due to the micro size of this part, using the Fabrica 2.0 we could print a lot of samples in the 50mm x 50mm x 100mm print envelope of the machine. We successfully printed multiple samples of six different designs for the customer to test. This took less than 24 hours to design, print, post process, package, and ship out to the customer, which was able to complete their testing in about two weeks. Their tests proved one of the designs superior to all others, and this was the design the company froze and submitted for FDA approval. Had we not been able to provide multiple part iterations for testing at one time the customer would have had to delay their FDA submission or choose a design without adequate test data. Once the customer is satisfied with their test performance Accumold can start to design and build the production tool so that we can qualify the tool and scale up to meet production volumes.
Case Study 2 – Implant Tip: Another one of our medical device customers needed to finalise an implant tip design measuring 1.5 x 3.0 x 2.5mm before the design freeze date. The customer needed a frozen design so that they could kick off tooling and not push out their overall project timeline. Using the Fabrica 2.0 we were able to print 16 different tip designs for the customer to evaluate. Again, we
could print a lot of parts in the Fabrica 2.0 print envelope, and our first print included ten samples of each of the 16 design iterations. It took less than 24 hours to design, print, post process, package, and ship the parts to the customer, which completed its testing in a few weeks and came back with six different modified designs for another round of testing. Our second print was turned around in about one day so the customer could quickly resume testing.
Once all testing was completed, the customer shared with us their frozen design. With that, we kicked off our mould manufacturing process with a DFM session to ensure the moulded thermoplastic part would meet the quality and functional requirements defined by the customer. With project work starting a couple months prior, we already had an established line of communication with the customer so we could quickly design the production tool and production process understanding all the criteria that needed to be met.
Case Study 3 – Valve Assembly: The last example comes from another medical customer that was trying to finalise the design of a valve assembly measuring 9.0 x 9.0 x 10.7mm. This valve was comprised of a softer material overmoulded on top of a harder machined part. The valve needed to maintain a seal while being rotated within the final assembly.
Our first round of samples was molded in DRST with the Versaflex material. Testing found that we had a few dimensions out so the insert CAD models were updated, and new inserts printed a day later. The second round of samples worked better but we found the Versaflex was too rigid when rotating it in the test assembly. We then used the same printed inserts to mould parts in Sarlink. The Sarlink parts performed better in the test assembly, but some leakage was observed. Sources of the leak were identified, the CAD models were modified, and another set of inserts were printed. This final set of inserts produced valves that could be easily rotated in the assembly and did not leak.
From start to finish we were able to test three different DRST mould designs and two materials in about two weeks. The customer was extremely pleased with the results and was excited by how much we learned in such a short period of time.
All of the successful case studies discussed would not have happened without the Fabrica 2.0 micro AM technology being used as a central tool in the product development process. Fundamental to the success of the Fabrica 2.0 is that it brings the benefits of AM to micro manufacturers for the first time, including previously impossible part complexity (enhancing design and functionality), no tooling costs, minimal set up costs, the ability to mass customise and personalise products, and the ability to produce DRST. As a versatile technology appropriate for prototyping, small batches, and potentially even mass manufacturing, the technology is now stimulating innovation in the micro manufacturing sector, and is truly changing the economics of manufacturing. accu-mold.com
Figure 1. The Nano Dimension Fabrica 2.0 machine Figure 2. Micro gears made using the Nano-Dimension Fabrica 2.0 micro AM machine. The smallest gears shown have 20 teeth contained on a wheel diameter of 1.25 mm, each tooth measuring 100 microns.Konica Minolta chosen to provide 3D printing solution to underpin Australian innovation for space and defence.
Fleet Space, Australia’s only commercial small satellite manufacturer, has partnered with Konica Minolta to implement 3D printers from 3D Systems to support Fleet Space’s groundbreaking innovation, which aims to bring manufacturing for the space, strategic, and mineral exploration industries back onshore. The 3D printer will also scale up Fleet Space’s manufacturing of small satellites for low Earth orbit to connect billions of devices.
Fleet Space is leading the way in innovative manufacturing for the space, strategic, and mineral exploration industries. With production in Australia co-funded by the South Australian Government, Fleet Space focuses on using cutting edge communications and space technologies to enable the next giant leap in human civilisation. The small satellites from Fleet Space incorporate the world’s first 3D-printed, all-metal patch antenna, which delivers 10 times more throughput per kilogram of spacecraft. The 3D printing of these antennae was outsourced to an offshore provider; however, significant scale-up efficiencies can be found in bringing production to Australia. Fleet Space has been contracted to scale its operations significantly in 2022 and 2023 and needed a more efficient way to 3D print these antennae at scale.
“Fleet Space is one of Australia’s most innovative companies, pushing the boundaries of what’s possible,” said Matthew Hunter, National Manager, Emerging Technology, Konica Minolta. “However, this level of innovation often comes at a significant cost. Fleet Space is harnessing the efficiencies that can be found by deploying a smart, in-house 3D printing solution.”
“Konica Minolta reached out to Fleet Space to start a discussion and begin a proof of concept to prove that the 3D Systems DMP350 Flex metal 3D printing solution could deliver the outcomes Fleet Space required.”
Konica Minolta and 3D Systems then worked with Fleet Space to develop a build strategy, first proving that the DMP350 was capable of printing the quality of aluminium part and in the volume required
for Fleet Space to keep up with demand. This process was key in Fleet Space’s decision to implement the DMP350 metal printer. “Fleet Space has a mission to unlock the power of global connectivity to effect true change for our critical industries,” said Flavia Tata Nardini, CEO and co-founder, Fleet Space. “For example, we are making critical energy transition mineral exploration faster, more sustainable, and less expensive. This is not possible without the very best technical partners. We are delighted to work with Konica Minolta to deliver an entirely new constellation of fully 3D-printed satellites at scale and to the very highest technical specifications.”
“This is a highly technical environment with precise specifications,” Hunter continued. “Konica Minolta was able to prove that the 3D Systems metal printers include market-leading technology that lets users 3D print with aluminium in a precise, repeated, and scalable method. This made Fleet Space both more productive and cost effective for its volume manufacturing offices and provides ongoing capacity for important research and development, keeping the organisation at the cutting edge. The consultative approach taken by Konica Minolta and 3D Systems means that Fleet Space will be able to go straight into volume manufacturing as soon as the device arrives.”
Fleet Space initially plans to use the 3D printer to scale up manufacturing of the metal antennae. However, the efficiencies provided by this new device will let Fleet Space ramp up innovation at the same time, using it to develop prototypes and new parts during downtime from manufacturing the antennae.
One of the key criteria for Fleet Space was that the 3D printer could deliver a repeatable process to avoid any variation between parts. The Konica Minolta printer has a closed-loop architecture, which guarantees an accurate and repeatable process. The machine also has the lowest oxygen content on the market, which delivers a pure part without defects, something that is very important when it comes to aerospace applications. konicaminolta.com.au
Prototec partially automates its post processing operations with a S1 system from AM Solutions – 3D post processing technology.
To streamline its post processing operations, Prototec, a company specialising in 3D printing, purchased the new S1 system from AM Solutions. The General Manager was impressed by the operational flexibility and excellent cleaning performance of this machine.
Prototec is known as one of the first and oldest 3D printing companies in Germany. With different printing systems, the company provides tailormade, high-end solutions for customers from many industrial sectors ranging from prototyping, concept, design and functional models to printing small to medium batches of plastic and metal components. Especially the production of larger product batches is rapidly gaining in importance. “3D printing has established itself as a technology for rapid prototyping,” Prototec General Manager, Torsten Wolschendorf explains. “But now it is definitely trending towards volume production. To provide cost-effective solutions to our customers in this field, at the moment we are investing in several new 3D printing and post processing systems. Especially the post processing in the SLS field offers a great potential and contributes significantly to a higher quality and cost-efficiency of our products. With AM Solutions we found a partner who can offer excellent technological and economical solutions.”
For this reason, since July 2021 Prototec has been using a S1 system from AM Solutions for cleaning and surface finishing of products printed with the SLS method. “I have carefully studied the offers of numerous suppliers. But in the end I decided to purchase the S1, because it offered the highest operational flexibility,” says Wolschendorf. In fact, the machine’s smart plug-and-play concept is setting new standards in the field of post processing components printed with powder-bed based polymer printing systems. Especially impressive is that the de-powdering, cleaning and surface finishing functions can all be handled in one single machine. As needed, the blast media can be easily and quickly exchanged. This operation just takes a few minutes. The 2-in-1 concept saves not only the expenditures but also the space requirements for an additional machine. Whenever special single components must be processed, the integrated machine controls allow a simple switch to manual operation. Time-consuming retooling, as required with other machines, is no longer necessary.
The machine controls with a full color display panel offer an intuitive navigation through the menu and allow the callup of up to 30 processing programs.
The S1 permits the effective, automated removal of residual powder from the components after the printing operation. Wolschendorf continues: “Actually, the cleaning performance of the S1 is so good that we are saving a lot of time with the preceding unpacking operation.” In this context the effective blast media cleaning and recycling system is particularly advantageous. It separates the usable blast media from broken down media and the loose powder removed from the components. This guarantees not only consistent blast results but also a longer uptime of the dust collector cartridges.
The components are processed in a tiltable rotary basket. The rotation causes the work pieces to gently tumble over each other. This ensures excellent, consistent all-around blasting results. Wolschendorf is particularly pleased with the time savings. “The S1 significantly reduced the time required for post processing,” he says. “Previously manual blasting of a full load of midsize components required about five to eight hours. Today we only need about one hour for the same process, including unpacking.”
Customer-specific design yields optimal results In various details the S1 design was adapted to the specific technical requirements of Prototec. “I am impressed by the open and cooperative atmosphere at AM Solutions,” Wolschendorf concludes. “My comments and requests were openly received, their feasibility was examined, and together we found an optimal solution.” Because of the in-house engineering and manufacturing capabilities such a flexibility comes easy for AM Solutions. As a matter of fact, it is specially promoted. Compared to other suppliers, this is an invaluable advantage. In the end both parties benefit from the mutual information exchange. This results in well-engineered, practical solutions with a significant added value for the customers. solutions-for-am.com rosler.com
Ensuring quality through optimal cleaning processes.
Today, component cleanliness is just as much a quality criterion as dimensional accuracy. It is defined by given particulate - and increasingly also thin-film - cleanliness specifications. Meeting these reliably can be quite a task. For operations to be cost-effective, it is becoming ever-more important to design cleaning processes in line with user requirements and for reproducible cleaning results.
Regardless what industry sector, parts cleaning today has become one of critical processes in manufacturing. For one, parts must be sufficiently clean for subsequent processing steps like coating, printing, heat treatment and assembly. For another, product quality and functionality are crucially dependent on clean components.
In recent years, the focus has been on removing particulate contamination, including chips produced in machining and forming processes, but also burrs and particles generated from abrasion. Meanwhile, thin-film contamination has also taken on a more prominent role. This is because the tiniest residues of machining oils and emulsions, cleaning media, drawing, forming and release agents, etc., can impair the quality of the joints in joining processes such as laser welding, soldering and bonding. When it comes to thin-film contamination, cleanliness specifications are often defined in terms of surface energy or surface tension (mN/m = milli-newtons per meter). Compliance can be checked comparatively easily with test inks and by measuring contact angles.
For the vast majority of parts, specifications regarding particulate and/or filmic cleanliness can be met using wet chemical cleaning processes. The parts are generally cleaned in batches, either in bulk or arranged in part carriers. However, a stable and reproducible process quality and consistently good results can only be attained if the cleaning chemicals as well as the system engineering and process technology are optimally tailored to the cleaning task. Choosing the right cleaning medium for the contamination
When selecting the cleaning medium, the chemical principle of “like solves like” can serve as a guideline. This means: polar contaminants such as:
cooling emulsions, polishing pastes, salts, particles from abrasion and other solids are normally removed using water as a polar cleaning medium in conjunction with pH-neutral, acidic or alkaline cleaners. For mineral oil-based (organic, non-polar) contaminants such as machining oils, greases and waxes, solvents like non-halogenated hydrocarbons or chlorinated hydrocarbons are generally used. Modified alcohols (3-butoxy-2-propanols) have lipophilic and hydrophilic properties and are therefore capable of removing both non-polar and polar contaminants to a certain extent.
To determine exactly which cleaning medium is best for effectively removing the contaminants adhering to the respective parts, cleaning trials with original contaminated parts are recommended. In its technology centres around the world, Ecoclean GmbH disposes of a variety of cleaning systems for all types of media. They are used to conduct tests on parts made of metallic materials, plastics, ceramic materials, glass and combinations thereof. In addition to the achievable cleaning result, the team also checks that the materials of the components to be cleaned are compatible with the cleaning media used.
The faster and more effectively the predefined cleanliness specifications are met in the cleaning process, the lower the proportion of costs that are incurred for each cleaned part. The cleaning effect of the medium is therefore enhanced by various
Component cleanliness is a quality criterion that contributes to customer satisfaction and thus to a high level of competitiveness.
physical process technologies such as spraying, vapor degreasing, dipping, ultrasonics and injection flood washing, as well as highpressure cleaning, which is used to deburr the parts at the same time. During spray cleaning, the kinetic energy of the jet boosts the effect of the cleaning chemicals used and removes impurities from the component surface. Pressures between 2 and 20 bars are applied to all or specific areas, for example boreholes and blind holes. Especially with pinpointed spray cleaning, the cleaning result depends on how the nozzles are directed at the surface to be cleaned. The result can be improved if the part is moved relative to the spray nozzle or vice versa. Where particulate cleanliness requirements are high, spray cleaning can also be used as a final cleaning step to remove any small particles still adhering to the surface.
During vapour degreasing, which is carried out in the closed working chamber of a solvent cleaning system, the cleaning medium is heated to boiling point and the resulting solvent vapours are directed at the components to be cleaned. The temperature difference between the hot vapours and the cooler component causes the solvent to condense on the surface of the workpiece so that the solvent condensate has a rinsing effect. Steam degreasing is used to remove contaminants such as oils, greases and emulsions from lightly soiled parts.
In immersion cleaning, which can be carried out with water-based media and solvents, contaminants are primarily removed by the chemical action of the medium. This effect can be enhanced by swiveling and rotating the parts. The process is mostly used for parts with complex geometries, such as blind holes or undercuts, and frequently combined with injection flood washing (IFW) and/or ultrasonic cleaning.
Injection flood washing is used in almost all cleaning processes involving components that are heavily contaminated with chips and oil or emulsion. The parts are subjected to pressures between three and 15 bars in an immersion bath. Since this is done below the level of the liquid, high volume flows are generated which can easily penetrate the cavities even of very complex workpieces.
The cleaning effect of ultrasonic units is based on cavitation: the electrical signals generated at a specific frequency by an ultrasonic generator are transmitted by a transducer as sound waves to the cleaning liquid. This results in an interplay of negative and positive pressure, with microscopic cavities forming in the negative pressure
When starting out with water-based cleaning, the EcoCcube is an ideal system that features compact dimensions, low weight, two standard flood tanks optimally matched in size, and simple operation.
phases, which collapse (implode) in the ensuing positive pressure phase. This creates microcurrents in the liquid, which virtually ‘blast’ and wash away any particulate and thin-film contamination adhering to the parts. For the cleaning effect, the following applies: the lower the frequency, the larger the cavitation bubbles and the higher the energy released.
The use of water jetting at high pressure, usually in the range of 300 to 1,000 bars but sometimes higher or lower depending on the application, makes it possible to reliably remove machininggenerated feather burrs from parts and clean them at the same
Ultrasonic cleaning meets the highest cleanliness requirements in very short cleaning times. Photo: EcoCvelox
time. High-pressure cleaning is also used to remove sand residues from castings and stubborn soils from part surfaces, including welding residues and scale. The pressures used depend on the type and level contamination as well as on the test results obtained in Ecoclean’s Technology Centres.
In addition to the cleaning medium and the system technology, the personnel operating the cleaning system influence the quality of the process. Knowledge of the interrelationships and processes of the parts cleaning step in manufacturing is therefore crucial in order to meet cleanliness requirements reproducibly and cost-effectively. ecoclean-group.net
M.T.I. Qualos Pty. Ltd. are leaders in the manufacturing and service of Industrial Transparent Flexible Doors, Insulated Traffic Doors, and Roll-Fast Doors. We produce to the highest quality standard within a full range of industrial doors to suit any door application.
NEW
When NSW Ports embarked on a twoyear program to rehabilitate the structures and combat corrosion levels at its Bulk Liquid Berth 1 (BLB1), it commissioned Melbourne-based consultancy Infracorr to deliver a bespoke cathodic protection (CP) system. Designing the system presented several challenges because BLB1 houses hazardous gas, petroleum and chemical pipelines that could be at risk of ignition if exposed to unsafe levels of voltages and currents. To safely deliver the system, the consulting firm engaged cathodic protection specialist Omniflex to support the hazardous area and remote monitoring aspects of the CP system design.
Over the last decade, reports have established that chlorine-induced corrosion is affecting some of the major structures at NSW Ports, including Sydney Harbour and Port Botany, Australia’s largest container port.
NSW Ports commissioned Infracorr to design a CP system for use at BLB1, which is located at Port Botany and houses hazardous gas pipelines. The project also included the repair of defective concrete structures, which were suffering from the effects of corrosion and concrete spalling in the many pre-stressed beams and headstocks of the various bridges and catwalks at the port.
“The system needed to be designed to allow for tight control of the currents and voltages used across the site for two key reasons,” explained the project consultant.
“First, Port Botany is NSW’s main bulk liquid and gas port and BLB1 is a key part of this facility, playing an active role in loading and unloading volatile liquids and gases. These hazardous materials are present in the environment on an ongoing basis, meaning that any stray sparks caused by excess voltages and currents could become an ignition source for a major fire or explosion.
“Secondly, because many of the structures present are constructed using pre-stressed concrete, it was extremely important that all electrical currents applied were carefully controlled to avoid structural damage caused by over protection.”
“To control corrosion in steel it is necessary to give it a more negative electric potential than its environment by 800mV. However, if the charge applied results in the steel being more than 1V negative than its environment, hydrogen embrittlement can occur, leading to failure of the steel and long-term structural damage that is not easily repaired,” concluded the consultant.
“One of the big technical challenges for the project was that there is no off-the-shelf CP system available that has certification for use in zone 1 classified hazardous areas,” explained Ashley Rangott, Asset Manager at NSW Ports. “This meant that we had to go through the process of designing a bespoke system that met the cathodic protection objectives, including dealing with the challenge of prestressed concrete, and a system that could be certified to meet the necessary requirements under AS60079 regulations.”
The system designed for use at BLB1 by Ian Godson, Director at Infracorr, was a hybrid CP system that combines the properties of both passive galvanic and impressed current cathodic protection (ICCP). It works by inserting specially designed anodes directly into the structure in a matrix. A voltage is applied to force salt migration
from the steel to the anode and passivate the zone. When the zone is sufficiently charged, the power source is disconnected and the sacrificial anodes are left to operate galvanically, providing passive protection to the structure.
“The decision to go with a hybrid CP system was jointly made between NSW Ports and the project consultants. The hybrid system reduces the ongoing risk of hydrogen embrittlement on prestressed concrete elements that a standard ICCP system presents,” added Rangott.
The system uses remote monitoring technology to provide asset managers with ongoing reassurance that systems are operating as intended and corrosion levels are under control. To deliver this, Godson requested the assistance of Omniflex to advise on the hazardous area and remote monitoring aspects of the design.
Intrinsically safe cathodic protection systems for hazardous environments in one of Australia’s key ports.“Because of the low currents required to meet the prestressed steel and hazardous area limitations, the hybrid CP system required an initial power-up phase of three to four months before the external power source was disconnected and the system left to operate galvanically,” explained David Celine, Managing Director of Omniflex.
“The system comprises of nearly 35,000 embedded hybrid anodes that were installed in the structures at BLB1 and is designed to control corrosion for up to 50 years. Because of BLB1’s ongoing operational nature, extra controls were put in place to manage activities across the site during the system installation phase.
“Because this was the first large scale implementation of hybrid CP used in a working hazardous area anywhere in the world, some components needed certification for the design to meet the requirements of AS60079 as an intrinsically safe certified system. Most countries
have their own certification process so it can be costly and time consuming to get installations like this one certified as being intrinsically safe,” added Celine.
“In this case, the hybrid anodes were sourced from CP Technologies in the UK, Omniflex’s technology is manufactured in South Africa and the project is in Australia, so navigating certifying bodies was challenging. However, the design was approved and certified as being intrinsically safe for use in areas classified as zone 1 hazardous for gas group IIB in the BLB1 project, where there is the potential for exposure to volatile, flammable substances,” continued Celine.
“System performance and corrosion levels are continuously monitored 24/7 using 24 remote monitoring units that are situated throughout the site, each with the capacity to monitor 16 structures. Crucially, these works ensure that the integrity of BLB1 is maintained, and the berth remains reliable and available to handle NSW’s growing bulk
liquid trade volumes for the next 50 years,” concluded Celine.
“There were no major issues obtaining the required IEC/AS60079 approvals for the system because there was a competent team of people and companies involved in the project,” added Rangott. “Because the approval process was completed outside of Australia, this slightly increased lead time but was not a major issue. Communication and business dealings across countries through various companies and suppliers did not present a challenge.
“Omniflex’s systems are all high quality, suited to our unique harsh marine environment, and have met our quality expectations for this high-end system. The knowledge that Omniflex brought to the project ensured that the monitoring and control system was procured and operated to a high level and to our expectations,” concluded Rangott.
omniflex.com
Food processing and food packaging are uniquely fast-paced environments, where the margin for error is slim to none. Particularly in the tightly-regulated world of food and beverage production, a breakdown in the production line can result in a whole batch of products being discarded.
Manufacturers looking to avoid food waste and costly production disruptions have looked to machinery data and predictive maintenance tools as a way to gain greater insight into what is happening on the factory floor, perform essential maintenance when it is required and anticipate and prevent breakages before it is too late.
“Once you give manufacturers involved in food and beverage manufacturing the ability to visualise data, everything changes,” says Jim Wallace, Sales Manager at Balluff Australia and member of Industry 4.0 advocacy group Open IIoT. “It gives them greater control over the production process, and once that data visualisation is paired with predictive maintenance, efficiency and revenue gains are realised.”
This proactive approach uses innovative diagnostic and sensing technologies to monitor the condition of equipment and predict when maintenance should be performed. Predictive maintenance tools such as infrared thermography (detecting high temperatures), acoustic monitoring (detecting leaks), vibration analysis and oil analysis alert manufacturers of potential failures.
“Essentially, predictive maintenance uses data to estimate when a machine might fail (causing costly disruptions) so that maintenance can be scheduled before the point of failure, to reduce downtime,” says Wallace. “Another benefit is that it gives manufacturers the ability to schedule maintenance when it is most cost-effective and does not interfere with production, as well as helping to extend the equipment’s lifespan.”
As food and beverage manufacturing is a tightly regulated industry, the strictest hygiene and sanitation standards must be upheld. The need for heightened cleanliness can create a wet environment, which can easily damage important equipment. “Add on the fact that machines deployed in the food processing industry are highly complex and challenging to maintain due to the connected system of conveyors, electronic and electrical equipment, and the heightened risk of machinery breakdown becomes abundantly clear,” Wallace explains.
Poor maintenance results in unexpected breakages, and even worse – if a machine has missed multiple maintenance cycles due to a lack of monitoring, it may be broken beyond the point of repair. The Wall Street Journal estimates that unexpected downtime costs manufacturers an estimated $50bn annually and reduces plant productivity by between 5-20%.
In the food industry, these consequences are magnified. Food processing equipment is working with delicate products which have a variety of time requirements to ensure health and safety standards are met. Any delays in the production process may result in spoiled goods. Broken machines are unsafe and carry the threat of contaminating food and beverages or damaging food packaging. If any contamination or damage occurs, manufacturers will need to dispose of the goods and restart the production process from scratch leading to food waste, missed deadlines and additional costs incurred.
“While predictive maintenance is key to predicting and ultimately avoiding these obstacles, manufactures in this industry will realise
additional benefits when these technologies are combined with data visualisation tools,” says Wallace.
Data visualisation refers to presenting data in a visual context such as a chart or graph so that it can be more easily understood. In food and beverage production, this is made possible by adding sensors to machinery to monitor what is going on on the factory floor. By using IoT connectivity, this information is shared as data that manufacturers can access in real-time and use to make decisions.
“Using sensors to transmit real-time data can alert employees when equipment malfunctions so that they can make the necessary adjustments to avoid goods from becoming contaminated or destroyed. Data insights allow employees to adjust equipment in real-time to get it back to normal functionality, reducing the need to shut down production completely,” says Richard Roberts, Industry 4.0 Operations Manager at ZI-Argus and fellow member of Open IIoT.
In the food and beverage industry, where contamination is always a risk, data-driven insights have further advantages. If there are reports of consumers getting sick from products, manufacturers can check machinery data to trace back the food production line and determine the source of the contaminants. This gives them the facts necessary to decide whether or not a product should be recalled. Combining predictive maintenance with data visualisation helps to boost equipment reliability, quality standards and production.
With all of these benefits, why is predictive maintenance not more widely adopted by food and beverage manufacturers?
“Compared to other manufacturing industries, the food and beverage sector has historically been a late adopter of digital trends. This is often because of the complex manufacturing processes needed to comply with the strict safety and hygiene standards of this industry, which may result in manufacturers being more hesitant to adopt new solutions,” explains Roberts.
The initial cost of implementing predictive maintenance and related Industry 4.0 technologies on the factory floor is a factor, but Roberts reassures manufacturers that these tools have not only become much more affordable in recent years, but that they will soon pay for themselves in gains realised. “Predictive maintenance is a cost-effective strategy as it reduces downtime and helps prevent food waste.”
“Smart connected systems give food and beverage manufacturers a competitive advantage, boost product quality and safety, increase efficiencies and increase productivity – there is very little to lose by implementing them,” he concludes. openiiot.com.au
im Wallace, Sales Manager at Balluff Australia Richard Roberts, Industry 4.0 Operations Manager at ZI-ArgusCustomised oil tank cleaning system leaves no drop wasted.
Oil is a valuable resource and in Kenya, a relatively new oil producing nation, every drop is precious. That’s why they were looking for a tank cleaning system that:
• Didn’t waste a drop of oil by extracting any residual oil from each transport tank
• Allowed them to reuse the water utilised in the cleaning process
• Was very easy for local workers to use
• Require little maintenance and was designed to be extremely robust
• Was portable so the system could be used in every oil transport tank
Tecpro Australia was asked to assist in developing an oil tank cleaning system that met all these criteria.
It was a challenging brief that took many months to solve. However, the client is so happy with the results, they immediately ordered another tank cleaning unit and there are more orders to come.
How the tank cleaning system works
In Kenya, each oil transport tanker must be thoroughly cleaned after every shipment to extract any residual oil. The Tecpro solution cleans the tanks onsite using rotating cleaning heads inserted into each tank. Once the water is drained away, it is treated using a separator so the water can be re-used. The residual oil is also reused.
The client gave Tecpro Australia the transport tank specifications and asked them to design a cleaning system.
They started the process by sourcing the best type of cleaning head for the job. Then they collaborated with a local pump supplier to build a suitable high-pressure pump station.
The customer is delighted with the results obtained by the tank cleaning system. It’s producing good quality oil that would normally be considered waste by other nations. It’s also proving to be simple to use with a robust design. In fact, this custom set-up achieved all criteria set by the client. That’s why a second tank cleaning system was ordered almost immediately.
Since 1982, Tecpro Australia has specialised in providing reliable technical solutions to solve challenging problems, like this one. tecpro.com.au
AMT: You started as CEO at the Australian Logistics Council (ALC) this July. Tell me a little about your career journey until now. Dr Hermione Parsons: My career focus has been on end-toend supply chain strategy and complexity, planning multimodal infrastructure and solving freight logistics in metropolitan, regional and international markets. Multimodal infrastructure involves two or more types of transport.
AMT: To help others wanting to move into supply chain management, what did you study?
HP: I completed a Masters of Urban Planning – Intermodal Freight Systems, specialising in integrated port freight logistics at the University of Melbourne. Then I did a PhD at Monash University in end-to-end supply chain in the fresh produce and retail industry. I am also a graduate of the Australian Institute of Company Directors. On-the-job training in corporate and government roles related to supply chain has also helped me to gain extensive industry knowledge.
AMT: Tell me a little about ALC?
HP: ALC represents the major Australian supply-chain customers, providers, infrastructure owners and suppliers. Our members span the entire supply chain sector incorporating road, rail, air, sea ports and intermodal ports. ALC was established in 2002 to work with all levels of government to transform the freight and logistics industry. Our organisation focuses on advocacy efforts on the following three areas to improve supply chain efficiency, safety, improved productivity and to help achieve sustainability. I've been a strong supporter of ALC, because it is the strong, single voice of the industry and has the most extraordinary end-to-end supply chain representation by the major companies.
AMT: What are the challenges facing the supply chain sector?
HP: First, let’s talk about the greater awareness today of the supply chain and logistics sector compared to pre-COVID19 pandemic. Very few people in the community or government really understood the sector, as we were a hidden enabler and the impacts of the pandemic helped to raise our profile. Today, supply chain and freight logistics are spoken about at every family table. That presents a whole new set of opportunities about working towards supply chain resilience and supporting Australia's future in a very different world. The current challenges facing ALC members include the rising costs of transport, fuel and containers. We have also seen a severe shortage of AdBlue diesel exhaust fluid, used for diesel engine vehicles to reduce emissions.
There’s also been shortages of containers, pallets and workers and a massive cost increase in doing business because of the pandemic. So, the lingering issues of skills and labour training is significant, along with the changing consumer demand for on time delivery, and the rapid growth in e-commerce during COVID. So, these are all main challenges that the industry is dealing with. We work closely with the members to support them on these and a range of other issues.
AMT: Could you explain why Australian businesses are experiencing supply chain disruptions?
HP: Before COVID19 our western society depended on complex global supply chains. Many manufacturing businesses rely on components from several countries. For example, a German car manufacturer may require a component from South Korea or elsewhere in Europe. The equipment is received and put together
at different locations and then final assembly at another location. So, our country and the world have become very reliant on global supply chains. A year after COVID19 hit Australia, supply line capacity was significantly reduced as airlines stopped flying and Australian borders closed. People often think it's about the equipment, the penalties, but it's fundamentally about relationships between different people and companies in supply chains. When the pandemic hit, our aviation industry was severely impacted and that meant that the air freight to and from Australia couldn't move. Our high value agricultural and fishery products couldn't get out and critical componentry, spare parts, medical equipment, vaccines and testing kits were not reaching Australia.
The maritime industry supply chain was also hit badly over the same period. Ships would be out at sea and their crews would not be allowed to get off the ship, some for 18 months because of COVID cases on-board. The global shipping companies’ transport prices increased dramatically. The Australian Industry Group reported that 30% of Australian businesses experienced supply chain disruptions in April 2021, with container freight rates rising from $1500 to $5000 per container. It's been the Australian supply chain and freight logistics’ workers and operations teams that have been the heroes. For two years, there’s been major blockages, delays and it’s still taking time to return to normal.
AMT: How are Australian manufacturers affected by the supply chain challenges?
HP: Manufacturers rely on components to make their products and on the data that allows them to forecast demand and plan supply. Delays in components and equipment arriving at their plant, means delays in final production. Manufacturers are now far more aware of their reliance on end-to-end supply chains than previously.
Everyone in the freight and supply chain industry is necessary to keep products moving. The transport operators, the truck or train drivers, the maritime sector, air cargo pilots, stevedores, intermodal workers, logistics planners and shelf stackers are all important in manufacturers’ production.
AMT: What is the National Freight and Supply Chain Strategy (NFSCS) and how is the ALC involved in it?
HP: The NFSCS provides a national approach to Australia’s freight and supply chains and all levels of government are involved in it. ALC participated in the formation of the NFSCS and has been involved in every aspect of it since its inception. We participated in the COAG Transport and Infrastructure Council (TIC) meeting in Adelaide on 2 August 2019, where Ministers representing all jurisdictions agreed to the release of the NFSCS.
The Department of Infrastructure, Transport, Communications, Regional Development and the Arts manages the strategy and reports on implementation. This Department coordinates with the states and local government. The strategy commits to action in four key areas: Smarter and targeted infrastructure; improved supply chain efficiency; better planning, coordination & regulation plus better freight location and performance data.
ALC has been a strong proponent of the NFSCS and has worked closely with our members across the end-to-end supply chain to inform and develop the strategy with government.
The NFSCS’s 2020 – 2021 (latest) annual report advises that work continues on the government’s $110bn Infrastructure Investment Program to cut congestion, better connect our regions, improve safety on our roads and meet national freight challenges. The National Freight Data Hub also enters a new phase, with the Australian
Dr Hermione Parsons is the CEO at the Australian Logistics Council and has worked in the supply chain and freight logistics industry for over 30 years. She spoke to Carole Goldsmith.
Government’s additional commitment of $16.5m over four years. The Hub will enhance the collection and access to freight data across all modes.
ALC has been in constant partnership with the government for the further development and the improvement of the strategy. It’s a work in progress to improve productivity, safety and intermodal logistics opportunities.
AMT: What are the latest advanced technologies used in supply chain and logistics?
HP: There is a massive investment in electric vehicles and in green hydrogen as fuel for trucks. There is so much activity by supply chain companies on how they can improve sustainability.
Two of the world’s largest truck manufacturers Volvo and Daimler have formed a partnership in Europe to explore the use of green Hydrogen and they are normally competitors.
Many Australian logistics companies are investing in electric vehicles as there is a strong commitment to improving our country’s supply chain and environment. Our sector is looking at strategic inventory management, planning systems and adopting new technologies like Artificial Intelligence (AI) for supply chain automation.
Digital twins are used increasingly in the Australian supply chain industry. A digital twin is a virtual representative of a physical system or process. If you have staff shortages, then through AI, you can create the digital twin of the worker’s process. That artificial twin will then feed information as the worker needs it. Leveraging technology and data is fundamental to every successful supply chain.
AMT: What is the best part of your job?
HP: Working with very skilled and talented people in the supply chain and freight logistics industry. I am very excited to continue to have a wonderful career in this industry at ALC. austlogistics.com.au
Queensland manufacturer Zone RV has made a major investment in its production capability with the purchase of the largest 3D printing system in the southern hemisphere, supplied by CNC Design.
Established in 2016, Zone RV offers a range of Australian-made off-road caravans that combine lightweight composite bodies with class-leading components. Headquartered in Coolum Beach, QLD, the company employs technologies from sectors such as aerospace and maritime to manufacture off-road caravans that are lighter, stronger and safer. The Zone RV team boasts more than a quarter-century of experience in true composite manufacturing across the marine, aeronautical and civil construction industries.
In its ongoing pursuit of improved processes at its production facility, Zone RV recently turned to additive manufacturing as a means of expanding capability and raising productivity. In particular it was keen to streamline its mould-making operations through the adoption of 3D printing. Following extensive research, the company opted for a VSF122 large-area gantrybased machine from CNC Design, a hybrid additive-subtractive system capable of both 3D printing and machining in composite materials.
“At Zone RV we’re always looking for new ways to deliver a better product more efficiently,” Dave Biggar from Zone RV said, “and the new 3D printer from CNC Design will undoubtedly help us achieve that goal. It will give us greater flexibility in how we design and manufacture, while delivering big gains in productivity. I think the fact that this will be the biggest 3D printer in the southern hemisphere demonstrates Zone RV’s ambition to be a true innovation leader in our sector and across Australian manufacturing.”
The new system has been installed at Zone RV’s manufacturing facility, and is being used for trimming and polishing moulds and printing of blanks for mould production. CNC Design will work closely with the team at Zone RV in the development of new processes for directly printing large moulds. The Large Area Gantry system is able to combine five-axis milling and three-axis printing in a single machine. It features a single-bridge gantry with a volume of 22m x 5m x 1.6m, and is equipped with a Siemens SINUMERIK ONE, one of the most advanced CNC systems on the market today. Five-axis milling is undertaken with a 10kW, 20,000rpm milling spindle from HSD Mechatronics, complete with swarf extraction. Three-axis 3D printing is performed using a CNC Design Model 30 print head, featuring a vacuum pellet drying and conveying system, enabling printing
rates of up to 30 kilograms per hour. The system also features five-axis orbital sanding, with a tool rack and print head calibration unit built in.
“Zone RV is a terrifically exciting advanced manufacturing business, and investing in this new machine will give them even more of an edge over their competitors,” John Croft, Development Manager – additive manufacturing at CNC Design said. “CNC Design is looking forward to working with them to ensure they get the most out of the new machine, and helping them to demonstrate the enormous potential this technology has to offer.”
The VSF122 machine is part of CNC Design’s Virtual Smart Factory (VSF) concept: a versatile gantry-based additive manufacturing system designed for the production of large components in the construction industries, mining,
entertainment, aerospace and defence. VSF printers can produce parts in a growing range of materials, including composites, plastics, concrete and wax. CNC Design has supplied some of the largest additive manufacturing machines in the world, making parts up to 30m in length. cncdesign.com.au virtualsmartfactory.com zonerv.com.au
New Touch Industries (NTI) is a progressive company with locations in Bayswater and Clayton South.
Our dynamic, rapidly expanding business provides high quality services in metal laser cutting, bending/ folding, welding and fabrication, delivering customers with precise streamlined project management with minimal margin for error.
This is achieved by our philosophy regarding the importance of teamwork and investing in staff. We pride ourselves on offering ‘pay for schooling’ and ‘promote from within’ policies, providing our staff with an environment to thrive. We are continuously striving to better serve our staff and become an employer of choice
Come and join a company where we believe happy staff are great staff!
Learn more at newtouchind.com.au, or contact us today.
Reach out to our team
Technofast Founder and CEO John Bucknell began innovating with farming technology, before applying similar principles to create Technofast’s hydraulic tensioning technology now used globally by mining, sugar, cement, food processing, quarrying and other applications.
Another Australian farmer is following in the footsteps of the inventors of the stumpjump plough by achieving international renown for his ingenuity for down-to-earth solutions for problems encountered by producers globally.
Queensland farmer John Bucknell’s hydraulic bolts are now used around the world in applications such as nuclear reactors, boilers, turbines and mining and energy equipment where speed, accuracy and even, precise fastening of multiple sets of bolts is required.
The idea originally stemmed from his desire to find a quicker and more secure way to fasten bolts used to tighten gang bolts on large disc ploughs on his family’s property near Nindigully, Queensland (about 500km west of Brisbane).
Just like brothers Richard and Clarence Smith of Yorke Peninsula who invented the stump jump plough in 1876 to allow farmers to cultivate land without removing rocks and stumps, John used his disc plough to break in new country, ready for production, after his father converted the property from grazing to agricultural production, predominantly wheat.
At the time, disc ploughs used scalloped discs mounted in gangs turning in order to chop up the ground. But these were prone to breaking if they encountered a stone, stump, or other obstacle. To replace them involved using a sledgehammer to loosen and tighten the large nut of the centre shaft of the gang. The whole gang had to be taken to replace broken discs, then the whole assembly had to be rebuilt once it was fixed… only for the plough to hit another obstacle 100 metres on, and the time-consuming process had to start again.
Frustrated by this laborious process, he developed sets of hydraulic nuts and bolts to do the job of fastening and unfastening disc assemblies simultaneously, far faster and more securely than the old way of twisting individual bolts on and off using sledgehammers and brute force.
Hydraulic nuts had existed since the 1930s, but nothing that could lock without losing the induced force. This is where John came up with the original idea for what is
now the EziTite Hydraulic Nut, which had a non-deflecting thread form, and an in-built locking ring to lock the force mechanically after hydraulic pressure was removed.
John modestly admits that there were other producers around of hydraulic fasteners around before him, but he turned the principle into an industrial reality that today is sold around the world, including Australasia, the Asia-Pacific, Europe, Africa and the Americas.
After his father sold the rural property, with the hydraulic nut idea in motion, John moved to Brisbane to start his business.
John worked with the University of Queensland and used Finite Element Analysis (FEA) to check and further refine the technology, including the nondeflecting thread pattern crucial to the nut’s performance. By the early 1980s, he had registered a patent for the technology – his first of many.
“There were doubters – probably include me initially – that we could produce an international technology success in Australia. But success built on success, because we focussed on quality and applications that were too hard for others sometimes. It is a never-ending story of continuing product development and improvement,” said John Bucknell, who in recent years has opened a purpose-built manufacturing facility in Brisbane and a branch office in the US.
In between innovating, John studied engineering at the Queensland University
of Technology, where he focused on metallurgy and tribology, which he describes as “essential principles needed to make innovations work”. He then went on to do a BA at Griffith University and a Masters in Innovation and Entrepreneurship at Adelaide University.
“We keep finding new uses for the technology – one day we are supplying mines or sugar mills in North Queensland, then the next we have an inquiry from wind tower energy producers in Europe or the US. Every application is different, and that’s where our particular expertise has led to success in the market,” said Mr Bucknell, who recently had his enterprise recognised with an Australian Manufacturing Growth Centre grant, to commercialise Technofast’s EziTite Hydraulic Head Nut technology globally. “I think one of our big advantages was that we went into this decades ago without any preconceived notions about the best way to do a job. Like many DIY inventors in Australia and New Zealand, we had to use what we had and a bit of brain power to figure out the best way on a clean sheet of paper. It has really been a fantastic journey,” said Mr Bucknell.
After refining and patenting the technology, John received the backing of some friends, formed parent company TechNovus, and received his first order for a tube mill application, where the technology is still in use today.
“Naturally, there has been a bit of wear since the 1980s, but we’ve been able to perform simple service and maintenance on
Farmer John stumps the doubters with his international technology success. Technofast’s EziTite Hydraulic Head Nut being installed on a gyratory crusherthe hydraulic nuts and bolts to keep them operating reliably,” said Mr Bucknell.
“At that stage, we didn’t even have a workshop – I was working on a lathe in my garage! But once we received some interest from BHP (now BMA), we knew the technology had strong potential, and we bought our first commercial lathe, which is still in use today – with the same operator, who has more than 30 years’ service to the company!”
Of all the patents registered by John Bucknell, it was clear that the hydraulic tensioning technology had the strongest commercialisation potential, with its clear benefits to user safety and uptime. By the early 1990s, orders had grown to the point that John created Technofast Industries
as a separate entity, dedicated to this particular product line. John bought a factory in Richlands, Queensland, to scale up the company.
The Australian Government – at all levels –encouraged the development of Technofast as an innovative local manufacturer. In 2002, Technofast developed its first solution for the nuclear industry in USA, and in 2004 won a power industry award – Platts Award for Commercial Product of the Year – for its high temperature hydraulic nut.
By 2011, Technofast was ready to introduce a new product line. The company was receiving increasing enquiries for demanding applications, such as nuclear,
power generation, mining, quarrying and other harsh environments.
In 2015, Technofast’s current facility in Crestmead, Queensland, was built, and a new chapter in the company had begun with the development of the EziTite Hydraulic Head Nut for gyratory crushers which are the backbone of many mining, quarrying, and crushing operations.
Reflecting on his journey, John says it was a difficult but highly rewarding path. “With new innovations, no one has been there before, so there’s no template or guide. It’s a bit daunting at first, and it means you have to rigorously test the new product, but once you’ve developed a solution, it’s an immensely satisfying feeling,” he said.
Technofast has now grown to a team of 18 people in Australia, and two representatives in the US, and is looking to grow even further. With the latest grant, and mining operations already responding positively to the Hydraulic Head Nut – which saves significant time, while also enhancing safety – John is looking to future expansion.
“We’ve built up a great base now, particularly in mining, heavy equipment, power generation, and sugar industries, and as these new innovations become even more widely used, I see potential for Technofast to grow from an SME (small-tomedium enterprise) into a larger business, where it can provide time and labour-saving benefits to more operations nationwide, and across the globe,” he says. technofast.com
You can apply for opportunities to supply to, or work on, Queensland Government transport and infrastructure services projects. Work is managed through a tender process and various construction and maintenance contract arrangements with the Department of Transport and Main Roads (TMR).
The first thing you need to do is register as a supplier. You can register as a supplier for tender opportunities for some transport and infrastructure services projects on a couple of sites, QTenders, and QBuild eTender.
Tenders are generally called for construction projects. In general, tenders will only be considered for major works using the Transport Infrastructure Contract (TIC) document if the tenderer is currently prequalified. The prequalification level of the tenderer must be equal to or greater than the advertised requalification level for the works.
If your business has experience in building civil type infrastructure, you may be eligible for prequalification with TMR by following the framework in the Transport Infrastructure Project Delivery System (TIPDS), Volume 3A. The TIPDS is for those who have the responsibility for obtaining value for money in the delivery of a project. The aim of TIPDS is to provide guidance for the procurement of works including:
• Developing the best delivery strategy;
• How tenders should be called, compiled and assessed;
• Who should be eligible to tender.
To become a specialised registered supplier for certain products related to infrastructure type works, follow the framework in the TIPDS, Volume 3B.
This document, the National Prequalification System (NPS) consolidates all the various jurisdiction-specific prequalification schemes previously in place to create a seamless, harmonised framework for applications, assessments and reviews. The main objectives of the National Prequalification System are to:
• Enable Participating Authorities to assess the capabilities of contractors and identify those with the requisite technical, managerial and financial capacity to efficiently deliver road and bridge construction contracts in accordance with their specific requirements;
• Minimise the contractual risks associated with constructing roads and structures;
• Minimise the costs of the tendering process for both Participating Authorities and industry;
• Promote best practice in the road and bridge construction industry;
• Ensure robust, consistent, transparent and objective processes across all Participating Authorities.
The Department of Transport and Main Roads provides a forward program of works indicator for when projects are proposed to be advertised across Queensland. This information is provided based on projects valued at $1m and above to be procured over the next year. The report is updated quarterly for infrastructure contracts.
Business is awarded using the:
• Queensland transport and roads investment program (QTRIP) which sets out capital works and maintenance proposals;
• Transport Infrastructure Project Delivery System (TIPDS) which determines the delivery options for major works and projects.
QTenders lists business awarded by the department for:
• Awarded contracts and standing offer arrangements of $10,000 and over;
• Additional details of contracts and standing offer arrangements of $10m and over.
business.qld.gov.au
The University of Southern Queensland has been named one of Australia’s Trailblazer universities to accelerate growth in space manufacturing and lead a new research hub of national priority.
The University of Southern Queensland is a successful recipient under the Australian Government’s $362m Trailblazer Universities initiative, giving the greenlight to the University of Southern Queenslandled ‘Innovative Launch, Automation, Novel Materials, Communications and Hypersonics (iLAuNCH) Hub’.
In a giant step for the Australian space sector, the University of Southern Queensland leads Australia’s effort to boost commercialisation and national capability in the space sector thanks to $50m in funding from the Federal Government’s inaugural Trailblazer Universities Program. ViceChancellor Professor Geraldine Mackenzie said along with university partners the Australian National University (ANU) and the University of South Australia (UniSA), and industry partners, the University would lead Australian breakthroughs in an area of critical national manufacturing priority.
“The University of Southern Queensland is already a leader in space manufacturing with expertise in hypersonic propulsion systems, advanced materials, and astrophysics,” Professor Mackenzie said.
“iLAuNCH Hub will improve Australia’s skills in the space sector, providing new jobs and boosting the economy, and also help ensure our country’s space expertise grows well into the future.” It is anticipated that the new hub will generate over $3.65bn in economic benefits across the region and Australia.
University of Southern Queensland’s Institute for Advanced Engineering and Space Sciences Executive Director Professor Peter Schubel said the hub would support industry to address sovereign space manufacturing. “iLaunch will operate as a national space commercialisation Hub with three nodes – the University of Southern Queensland, ANU in the Australian Capital Territory, and UniSA in South Australia,” Professor Schubel said.
“Our industry partners have identified $3.65bn in economic benefits associated with the 18 core iLaunch commercialisation projects, which will accelerate Australian
IP to market, and the development of a Space Engineering Degree that will create a pipeline of skilled, job ready engineers into this exciting high-value, high-growth sector.
“The program will provide critical research, equipment and infrastructure in support of rocket manufacturing, rocket launch and in-space hardware such as satellites, communications and sensors.”
The Hub will support its industry partners to develop a space manufacturing precinct in regional Queensland for rocket manufacturing and associated supply chain development, servicing civil and defence requirements. Director of the ANU Institute for Space Professor Anna Moore said Australia had breathtaking capability to offer the global space industry.
“Key to success is working with each other across states to offer our best efforts in a focused and purposeful way,” Professor Moore said.
“That’s what makes this project so special. That’s what it takes to create sovereign capability and to educate our next generation of Australians who will be excited and proud to grow our space industry.”
UniSA Industry Associate Professor Colin Hall will lead the UniSA team, developing components, antennas and optics for small satellites and creating optical coatings for high-powered lasers.
“This is a wonderful opportunity for us, and our industry partners, to commercialise technology to grow Australia’s space manufacturing capability. Together with the University of Southern Queensland and ANU we will cement Australia’s reputation as a major player on the global space stage,” Professor Hall said.
The University of Southern Queensland’s Institute for Advanced Engineering and Space Sciences is renowned for its research to deliver cutting-edge technologies, industry solutions and knowledge at the forefront of discovery, with worldclass facilities including the Mount Kent Observatory in a dark-sky site, just outside of Toowoomba.
The University of Southern Queensland’s Mount Kent Observatory, Queensland’s only professional astronomical research facility.
Whether you’re a solo engineer looking for mechanical CAD only, or a high tech manufacturing facility looking to explore the world of industry 4.0, TopSolid has modules to suit your needs, all wrapped up in a PDM system to manage your data securely and efficiently.
• Kinematic Simulation
• Dynamic Simulation
• Bills of Materials
• Steel Structures
• Realistic Rendering
• Mould Tool Design
• 2.5/3-axis Milling
• 4/5-axis Milling
• Accurate Kinematic Simulation
• Impeller/Blade Machining
• Cylinder Head Porting
• Lead/Timing Screw Machining
• Multifunction Mill/Turn
• Swiss Turn
• G-code Verification
A few of our customers who are already benefitting from working with TopSolid and IDW CAD/CAM:
Contact us for more information 1300 439 223 info@idwcadcam.com.au idwcadcam.com.au
A WA technology firm is using imaging technology to build lifelike representations of far-flung assets, as Drew Turney learns.
You've landed back home after visiting your offshore oil rig when you realise you need to set up a meeting with that drilling rig assessor. Her email address is written on a Post-It Note and stuck to the PC monitor... back on the rig.
Wouldn't it be handy to call up a remote view, virtually walking right up to your desk to read the Post-It Note just like you’re walking a through a videogame environment?
That's exactly what Perth company RemSense can deliver. After starting in 2012 as a drone operator for Western Australian resources clients, a decade of technical experience has opened the door to opportunities with a range of clients across industries from mining to airports and everything in between.
That's why founder and CEO Steve Brown describes RemSense as a technology development company more than just an imaging business (more below).
But giving customers the best possible access to remote facilities is still a cornerstone of what he and his team do. Using magnetospheric or multispectral readings, LIDAR (light detection and ranging – a way of measuring distance by the time it takes a laser to reflect from a surface to a receiver) and photographic data, RemSense can capture and assemble a representation of a facility or property as large as hundreds of square kilometres right down to millimetre accuracy.
Drones are still a critical part of the puzzle, like they were in a recent operation when water samples were required from the bottom of a disused mine pit. Instead of sending watercraft and crews to the remote (and expensive) site, an operator piloted a drone with an attached sampling probe across the water, a sensor reporting when it had reached the floor and could collect the sample.
But RemSense uses a comprehensive suite of sensing technologies to produce results including plenty of ground-based technologies as well.
Embracing whatever imaging tools are available – and being ready to adopt new ones that offer an advantage – has put Brown in a unique position to appreciate how the field has advanced.
“The resolution and the size of the sensor,” is how he responds when asked what he's seen change the most in his time in the field.
“Your new iPhone has as good a camera in it as you'd have found in a professional camera a few years ago. There have always been very high resolution sensors and imaging cameras available, but they've traditionally been quite large.”
But innovation in the field has bought the size of imaging sensors down, so they're far more versatile and – therefore – much more portable in a wider variety of applications.
In one example, the company used a specialised confinedspaces drone to inspect car dumpers on mine sites (the mechanism that rotates both the rail car and section of track together to unload the contents), reducing the need for human inspectors in such hazardous environments. In a previous era it would have been the job of an extremely safety-conscious human operator with heavy photographic equipment.
But a corresponding increase in resolution size and decrease in physical footprint has meant a steep rise in data quality. You can now capture a higher number of data points for less cost, and we've crossed the threshold where a digital representation of a remote asset can be seen as clearly as is it in real life.
It's all led to one of RemSense's most compelling products, Virtual Plant – a 360º, high resolution walkthrough of every inch of your far-flung facility, delivered to and viewable right on your laptop or device screen.
It's not a 3D model like the type you see in the area of Building Information Management (BIM), it's a completely photo-real digital twin, in full colour and detailed down to the very last rivet.
Virtual Plant was born from RemSense's history with a Woodside/ BHP partnership. When combined, the two resources giants had one of the most widely-spaced asset bases in Australian business history with plants, mine sites, refineries and transport hubs all under management.
“They wanted a system that allowed anyone in the company – from the receptionist to the CEO – be able to visit their assets anytime, any place on any approved advice,” Brown remembers.
On the surface, the benefits of such a system seem obvious. You’ll save the plane fare and two lost days just to retrieve a Post-It Note from your faraway computer screen (or even the 15 wasted minutes asking the plant manager to leave his/her duties and go over to your office to read it to you).
Steve BrownThen there's safety. For obvious reasons, only approved staff can have access to mechanised or industrial environments, and the accreditations and training needed to onboard them are costly and time-consuming.
But Virtual Plant lets anyone ‘fly’ right through a facility – right there among the pipes, trucks, dust and chemicals – on a screen in front of them from the comfort of their office. Most of all there’s a deeper, more philosophical and less tangible benefit Brown calls ‘holistic’.
“The more your staff understand about your business, the better the business is.”
But he happily admits Virtual Plant's a bit like the iPhone in that users are coming up with behaviours even RemSense hadn't thought of.
One example is integration with Woodside's asset management system, an IBM product called Maximo which Brown says isn't the easiest to navigate despite commanding around 30% of the market.
“Virtual Plant works so well with [asset management platforms] because again, we're visual animals,” he says. “When you're going through a plant visually you can zero in on one particular asset and say ‘I want all the maintenance data on that’. You click the image and it takes you straight to the relevant section in your asset maintenance data.”
Where doing so in ages past would mean switching back and forth between applications (or worse, a site worker on the phone trying to describe what he/she's looking at), today it's achievable through Virtual Plant's connectivity with other platforms. What's more, you don't need the same investment in training for staff to navigate their way around a complex asset management system.
Because – and at the risk of being too repetitive – we're not talking about a 3D wireframe model or even the characteristic alien-looking haze of a point cloud taken from LIDAR data. The Virtual Plant visual representation of your factory, marshalling yard or freight terminal is all built using high resolution, 4K photographic data.
“In a lot of cases you have to know what you're looking at to know how to interpret it,” Brown says of many other imaging technology outputs. “But if you look at the same thing on a high resolution photograph, you're going to know this is a gauge where you take a reading or that's a valve where you turn it one way or another – even if you're not mechanical.”
RemSense's other major market presence is as a technology partner, or what Brown describes as innovation through engineering. It's quite telling that at one point in the conversation Brown says he doesn't generally talk about the software, he talks about the application. “We're focused on creating a solution that solves a problem,” he adds.
All of which means that no matter how cool Virtual Plant (or any of its other tools) are, RemSense has an eye on the bigger prize – making their customers’ lives easier through whatever expertise they can offer.
Still, we're talking about industries where the decision makers and leaders are quite used to heavy industry and logistical assets. Surely they're fairly up to date with automation and engineering tools and trends?
“If people from an oil and gas company sit down to discuss a problem, they're all from oil and gas,” Brown says. “They don't know anything about aviation or ports. They'll look for a solution from oil and gas, and there might not always be one.”
The engineering and technology development team at RemSense have come from automotive, subsea, telecommunications and beyond. Such varied backgrounds means the team isn't constrained by what they 'know', bringing solutions from countless other fields to the table to find the best way forward. “We have the right culture, and I think it combines with the experience of the people to become critical for an innovation company,” Brown says.
When RemSense attacks a technology problem for a client, the workflow is quite structured, but Brown says that actually gives the team more freedom to discover what does and doesn't work in close collaboration with the client.
Often, they arrive at the solution not through reinventing the wheel but repurposing something that already exists – engineering as systems management, rather than just invention.
“We pivot during development quite often and come to an entirely different solution than we imagined because there was a better way of doing it all along,” Brown reports. “In a lot of cases there's already a solution out there in a different form or another industry. If we can find something we can apply to a client need off the shelf that's exactly what we do.”
Delivering a seamless, high resolution representation of your assets and helping you make them better through engineering innovation are the twin pillars keeping RemSense at the top of their game, and both their technology and practices are ensuring this decade-old player has a bright future yet.
It’s time to start viewing technology as a valuable co-worker. An opinion piece by Andrew Mamonitis, VP of APAC Manufacturing Division at ECI Software Solutions.
The supply and labour constraints afflicting the Australian economy continue to create challenges for the manufacturing sector. According to the Australian Industry Group (AIG), the Australian Performance of Manufacturing Index (PMI) dropped by 1.5 points to 52.5 in July.
With production and employment both falling, it’s clear that manufacturers are struggling with the impact of chronic labour shortages and supply chain interruptions, leading many to reevaluate their processes to drive efficiency.
While many might have hoped for a more positive year, 2022 continues to challenge manufacturers. In fact, business groups across Australia have raised concerns about a shortfall of skilled workers across a number of critical industries such as health, trades, manufacturing and tech, amid historically low unemployment rates. In August the NSW skills minister, Alister Henskens, went as far as describing the critical workforce shortages as a “handbrake” on the state’s economy.
Against this backdrop, a growing number of manufacturers are considering implementing specialist technology, not only to minimise downtime but to also prevent their existing workforce from being completely overwhelmed.
Keeping costs low and production cycles short needs to be a top priority, and achieving this relies on all departments working together. No matter how hard they try, those reliant on disintegrated systems will struggle to streamline communication between departments, chasing seemingly endless paper trails or running around the building speaking to different colleagues.
Specialist EPR systems can act as a valuable co-worker, designed to seamlessly link all departments across the business and avoid disjointed processes. Armed with a single source of truth, the entire business can access key information on the status of every order, meaning that the sales team no longer need to bother the schedulers or planners when a new order comes in, or vice versa.
With margins tight, manufacturers need to be able to offer customers accurate cost and delivery estimates - even when managing complex, multi-phase projects, as well as providing updates on the status of every order.
With complete visibility, sales representatives can easily calculate the time and resources required to fulfil a certain order, before quickly adding new orders to the planning schedule. Should a customer request an update on their order status, anyone in the business can simply log-in and immediately relay the information required. In such a competitive marketplace, being able to offer this level of service will help improve customer satisfaction and enable future growth.
The ability to manage larger inventories or raw materials has become increasingly important, especially as the needs of custom manufacturers have continued to evolve. This task is hugely labour intensive without the right technology in place.
Through the implementation of a specialist ERP, the entire inventory management process can be streamlined. With employees able to view the material supply and demand information on screen and, if required, drill into the details. Similarly, teams can view the material-on-hand balance for each project to avoid material shortages and prevent costly order delays.
Alongside the efficiency gains, a more accurate inventory management system will minimise unnecessary overspend or guesswork - something that few businesses can afford during such uncertain economic times.
As those reliant on manual processes or an array of disintegrated systems will appreciate, when resources are strained the entire business will struggle to run efficiently. Small errors and oversights start to creep in and over time this can have a detrimental impact on the businesses overall reputation. As soon as a piece of information is entered into an ERP, it’s saved on the system. Not only will this help to improve data accuracy, it will significantly minimise the duplication of work and time spent on data input - a huge benefit for those struggling to cope with the current labour shortages.
Overcoming the challenges manufacturers are currently facing is no easy task, however technology can act as a much needed ally, working alongside existing employees to reduce their administrative burden and drive efficiency.
ecisoftware.com.au
Global tech company Garmin doubles its footprint in Australia with new Sydney DC.
Garmin, a leading global provider of GPSenabled products across diverse markets, has signed a ten-year lease for a purpose built distribution facility (DC) in Marsden Park, Sydney.
The $45m facility at Sydney Business Park will be partially operational from September 2022 and expected to be fully operational from early 2023. The facility features 12,036sqm of warehouse space and 1,320sqm of corporate office space.
Founded in 1989 and with its global operational headquarters in Olathe, Kansas, USA, Garmin employs more than 19,000 associates across 34 countries worldwide and its GPS and wearable technology products are sold all over the world. The new facility will initially employ 101 Garmin associates with a potential headcount of 142 employees supporting the company’s wider team in Australasia.
With strong demand for lifestyle and fitness products throughout the pandemic, in March this year Garmin reported 2021 total revenue of $4.98bn, with all five business segments posting double-digit growth over the prior year.
This new facility at Marsden Park will see the global tech manufacturer double its footprint in Australia, as it expands its retail and e-commerce and fulfilment operation from a 6,000sqm facility in Eastern Creek, Sydney and represents Garmin’s commitment to long-term growth in Australasia.
The purpose-built DC at Sydney Business Park will serve as Garmin’s online fulfilment centre as well as service its traditional bricks and mortar retail partners in Australia.
“We’ve been on a very steep growth trajectory since the pandemic prompted a technology-driven fitness revolution and people around the world found creative and safe ways to keep moving,”
Matthew Thomas, Managing Director at Garmin Australasia says. “By expanding our footprint in Australia, this new facility at Sydney Business Park will allow us to focus on continuing to meet the growing demand for our products and services throughout the country. Our staff have been a key consideration in choice of
location, and we looked to provide a more comfortable and pleasant workplace as well as proximity to amenities such as food and shopping. Sustainability was an important consideration also and to that end significant solar capability and energy saving initiatives have been incorporated into the design.”
Home to Linfox, Dulux, IKEA, Bunnings and ASICS, the award-winning Sydney Business Park is located in Sydney’s rapidly growing North West Region and features a wide range of amenities including supermarket, child care, medical centre, gymnasium, cafes and eateries, and the 90,000sqm homemaker and trade centre.
AMT OCT 2022 085SOFTWARE Garmin partnered with business transformation consultancy TMX on procuring this pre-lease site. TMX will now project manage the delivery of the development on behalf of Garmin and alongside Sydney Business Park. garmin.com
With close proximity to the M7 motorway and convenient and efficient access to Sydney’s road, rail and port network as well as public transport connectivity, Sydney Business Park is located in Marsden Park, which is only 35 minutes from the Sydney CBD.
Our ‘make it right first time’ approach is the key to quality production and customer satisfaction
SPRINGS
PARTS
COATINGS
Explainable AI is a set of tools that can help engineers better understand how Machine Learning models arrive at predictions and exercise transparency when it comes to instilling confidence in the results of these complex models.
“Explainable AI is a set of tools and techniques that help us to understand model decisions and uncover problems like bias,” says Stephane Marouani, the Country Manager at MathWorks Australia. “Explainability can help those working with AI understand how machine learning models arrive at predictions, which can be as simple as understanding which features drive model decisions but more difficult when explaining complex models.”
AI is transforming nearly every industry and application area. With that comes requirements for highly accurate AI models. These AI models can often be more accurate than traditional methods, yet this can sometimes come at a price. Most advanced AI models are “black boxes” by nature of the underlying neural network techniques where results are hard to trace and it’s difficult to understand the line of reasoning.
This is never truer than today in the face of the world’s race to electrify everything and the ubiquitous integration of AI, which are two separate but interconnected megatrends. AI is being deployed into heavy construction vehicles that are connected to both the cloud and each other within the fleet of vehicles, which are themselves being electrified to move to zero emissions.
For all the positives about moving to more complex AI models with larger data sets including decision accuracy and predictability, the ability to understand what is happening inside the model becomes increasingly challenging. In general, more powerful models tend to be less explainable so engineers will need new approaches to maintain confidence in their AI models as predictive power increases.
There are two Explainable methods. Firstly, global methods provide an overview of the most influential variables in the model based on input data and predicted output. Global methods include feature ranking, which sorts features by their impact on model predictions, and partial dependence plots, which hone in on one specific feature’s impact on model predictions across the whole range of its values.
Local methods explain a single prediction result. The most popular local methods are:
• LIME for machine and deep learning: Local Interpretable, Model-agnostic Explanation (LIME) can be used in both traditional machine learning and deep neural network debugging. The idea is to approximate a complex model with a simple, explainable model in the vicinity of a point of interest and thus determine which predictors most influenced the decision.
• Shapely values: The Shapley value of a feature for a query point explains the deviation of the prediction from the average prediction due to the feature. Use the Shapley values to demonstrate the contribution of individual features of a prediction at the specified query point.
Visualisations are one of the best ways to assess explainability when building models for image processing or computer vision applications. Local methods like Grad-CAM and occlusion sensitivity can identify locations in images and text that most strongly influenced the model’s prediction.
Explainability is important when facing regulatory requirements. For example, in 2018, the European Union introduced a right to explanation in the General Data Protection Right (GDPR). As AI models become more pervasive and more complex, applications that are safety critical are good candidates for explainable AI.
Explainability can be included in verification and validation processes to ensure that minimum standards are met and engineers’ can have confidence in the reliability and robustness of the system against data bias or adversarial attacks
“The more complex the AI model is, the harder it is to explain the results,” states Marouani. “This set an obvious challenge for engineers. How do we create complex AI models to tackle large data sets and increase decision accuracy while demonstrating transparency in the model? As explainability methods continue to be developed, engineers will need to make sure AI tools provide transparency; however, they also must be able to demonstrate results and transparency of their models to end users from the beginning.”
“I started my career in the 90s working with decision-making software based on truth maintenance systems techniques such as rule or inference engines,” explains Marouani. “Such systems were popular and until now as it is easy to demonstrate the line of reasoning from facts to conclusions. Neural network techniques, which are the basis of machine learning models, were not as popular with businesses because the decisions and associated bias were harder to detect and explain.
In the last 20 years, with the strong investment in AI, explainability techniques have been an important development to reduce the angst linked to AI based automated decisions amongst business users.
As AI becomes more complex and pervasive across many different industries, I foresee an increased pressure from the business users as well as regulation for AI explainability. Engineers will need to integrate explainability in the development cycle of their systems.”
mathworks.com.au
Spare Parts 3D has developed DigiPART, an AI-based software solution to facilitate the creation of digital inventory and enable adoption of AM in industries.
Spare Parts 3D (SP3D), with offices in Paris (HQ) and Singapore, has been helping companies adopt Additive Manufacturing (AM) in their supply chains as part of the solutions to address spare parts problems: spare parts obsolescence, long lead time, high cost of inventory, MOQ etc.
AM adoption brings up multiple obstacles that can be overwhelming: incomplete part data (lack of dimensions, materials, drawings), lack of in-house AM knowledge, picking which part to print, estimating how much savings can be achieved, dealing with limited manpower, etc.
Spare Parts 3D has developed DigiPART, a powerful AI-based software solution to facilitate the creation of Digital Inventory and enable the adoption of AM in industries. DigiPART identifies the parts that are technically 3D printable and those that make business sense, thus getting tangible results faster and creating value for your company and supply chain. It sifts through very large inventories, does not require drawings, and has been designed to operate with partial data set. Results are fully transparent and traceable.
In last two years, conventional supply chains have been challenged with COVID, the Suez blockage, the Russian war in Ukraine and the China lockdown. The new keywords are Agility and Resilience, and additive manufacturing and digital inventory have brought in innovative solutions to these challenges.
Adoption of Additive Manufacturing does not happen overnight. It is a journey that involves external parties (OEM, end user, Service Bureaus) and internal stakeholders (Engineering, Supply Chain, Procurement, Legal, QHSE, Field Operation team) that need to be convinced of the value of Additive Manufacturing.
We would like to share with you how two of our customers have started their journey to adoption of Additive Manufacturing and how our funnel approach helped them focus quickly on the right parts.
First customer is Ocyan, a company specialised in the offshore oil and gas industry in Brazil and abroad. Ocyan wanted to investigate whether it was possible to reduce parts lead time and inventory cost and get quick wins to on-board management and operational teams. In eleven weeks, DigiPART enabled the project team to analyse 17,000 spare parts from Ocyan’s inventory (with no 3D files). Various supply chain issues were looked at (lead time reduction, minimum order quantity optimisation, simple cost reduction, etc), and the number of viable AM parts totaled up to 11% of the total parts analysed.
The Ocyan team took the results from the analysis and used DigiPART to focus first on parts with cost reduction potential and low criticality. This gave way to the first additively manufactured part in the company’s history. What was also achieved by the Ocyan team, beyond the actual building of a part, was the creation of a common framework to develop an AM adoption roadmap for spare parts. Ocyan had started its AM journey.
The company now plans to focus on metal parts with a strong lead time reduction business case and with materials the company is comfortable with, such as 316L. It also plans to look at more innovative solutions, such as replacing metal parts with high-end polymers, which could bring significant savings.
Second customer is a National Oil Company in the Middle East for whom we recently completed a spare parts catalogue analysis of 150,000 references. It had clear objectives and KPI when it came to savings in inventory cost and capital spare, and percentage of digitalisation. We completed analysis of its 150,000 SKUs in six months. Although 80% of the data was missing, (dimension, weight or material for example), DigiPart was able to operate with partial
data and narrow it down to a first opportunity list of 200 parts.
DigiPart was able to identify which printing technology could cover most of the printable parts and based on quantity, deciphered whether printing should be considered in-house or outsourced.
According to our customer, the cost of a ‘hit and miss’ approach was too high and slowed down the progress too much. They confirmed this analysis sped up their AM deployment by two years.
To this date, DigiPart has over 3,300 solutions (printing technology, raw material) and has analysed over one million lines.
Our funnel approach increases efficiency going from large to more manageable catalogue. DigiPART makes the identification process fast and automated, frees up resources and palliates to lack of inhouse AM expert on customer side.
In both cases, Spare Parts 3D was both an enabler and accelerator of adoption of Additive Manufacturing, greatly reducing time to perform Inventory Analysis and quickly pointing out parts that were matching these companies’ business cases.
These companies made the leap and started their journey to AM adoption. What are you waiting for? sp3d.co
CAM Software technology keeps pace with aerospace challenges. Alan Levine, Managing Director at Open Mind USA brings his deep industry knowledge into play.
Advancements in materials and engine efficiency have created clear benefits for replacing a surplus of older aircraft equipment. The advancements cover both the engine and structural components. The demand is so significant that machine tool manufacturers are challenged to supply the equipment fast enough. Since OEMs and suppliers already operate at a high utilisation rate, there has been growth at existing facilities and an increasing number of new certified vendors. The high demand is expected to continue for many years. This challenge can be met by increasing the number of spindles or also by increasing the productivity of tooling, work holding and CAM software solutions. Enhancements to these support technologies can increase the productivity of existing equipment.
There are many CAM software products available and most of these have targeted capabilities. The focus may be on a process such as 5-axis milling, mill/turn, or wire EDM. Or the CAM software may be optimal for applications such as mould and die or aerospace applications.
Not many aerospace machining companies, especially tiered vendors, machine all types of aerospace components. However, some do and certainly, aerospace OEM companies tend to machine a wide array of aerospace parts, even if only for development components.
Therefore, the ideal CAM software for aerospace manufacturers has to excel at high material removal rates and the machining of aluminium structures whilst working well with high precision requirements of compressors and turbines that are often machined with long slender tools.
Machining of aerospace components requires excellence by the manufacturer to adopt and carefully follow procedures to ensure quality, repeatability and traceability. The components required in this industry have very stringent and varying requirements. Structural components must be lightweight, generally made from aluminium or composites (may have moulds from aluminium). Engine components and landing gear are generally made of titanium, steel or nickel-based superalloys. These materials focus on strength and temperature resistance. For engine components, titanium is used where possible as the material density is nearly half that of steel or superalloys. It also helps to control weight.
High-performance roughing is necessary to bring aluminium blocks or plates to a near-net shape. Up to 90% or more of the block weight may be removed during roughing processes. Not only is this important in typical 3-axis structural components, but it is equally crucial in 5-axis components. Many CAM software programs have a high-performance roughing module. Here, Open Mind offers its hyperMILL MAXX Machining roughing module. This machining approach is based on Celeritive’s Volumill kernel but has been extended by Open Mind to have an application for 5-axis roughing. In cases of shaped structural components (some wing segments for example or doors), a 5-axis roughing process provides a huge benefit to subsequent machining processes. Following highperformance roughing operations, innovative finishing techniques can have a big impact on results.
The surfaces of standard structural parts are machined with a swarf milling operation, with the side of the cutter aligned to the side of the part. This process enables very good performance, but it is limited to ‘short’ wall surfaces typically up to 50mm in height. For larger wall surfaces, the swarf milling operation may lead to vibration in
the cutter or the wall surface, or multiple steps with overlap and inconsistent deflection patterns. In these cases or other cases that do not have ruled surface walls, the next best option is point milling in many passes by using the tip of a ball-nose endmill with a small step-over. This point milling method increases cutting time dramatically.
Recent innovations include applying barrel cutter geometry to these surfaces. Open Mind’s hyperMILL MAXX Machining finishing approach uses a conical barrel cutter to enable a barrel contact radius of 1000mm or more, thereby producing a wider step-down of 10- to 15-times compared to that of a ball-nose endmill. This enables the cutting time for these surfaces to be reduced by 90% or more. The conical barrel cutter has a large barrel radius ground on a tapered feature, compared to a traditional barrel cutter where the large radius blend is at a tangent to the cutter shank. HyperMILL MAXX Machining and conical barrel cutters enable a large contact radius and clearance from wall surfaces.
The benefit of having the taper angle is that the tool axis can be pulled away from the surface being cut. The result is a shorter and stiffer set-up without interference from the cutter holder. The machining benefits far outweigh the increased cost of conical barrel cutters, especially in aerospace production applications. Though the tangent barrel cutter provides some benefits, the conical barrel cutter is generally superior to enabling a larger barrel radius and allowing shorter cutters without interference from the cutter holder.
cutters. The CAM software must possess robust collision detection and avoidance techniques to find a solution to the close spacing between blades.
Engine components are generally classified into two categories – multi-blade and single-blade. The difference is that multi-blade components are produced as a monolithic shape from one stock while single-blade components are machined as individual airfoils with mechanical attachment features. These are then mechanically assembled to make engine components. Engine components face high temperatures and stresses and potential impact, so materials like titanium, steel and superalloys are used.
An assembled turbine or compressor from machined single blades and a hub disk weighs more than a one-piece compressor or turbine blisk (bladed disk). As engine performance is directly related to its weight, blisks have become more common than single blades in recent generations of engines.
Single-blade machining can start from a rectangular block, cylindrical stock, or near-net forgings. Roughing as always is a critical task to control costs, and also to set up for finishing operations. Due to various starting stock shapes and irregular finishing shapes, stock tracking is essential during roughing operations to avoid wasteful air cuts. As blades can also be twisted, multiple cutting orientations should be used during roughing to leave minimal stock for the finish.
Single-blade finishing is historically performed with ball nose endmills, especially on twisted surfaces and near attachment platforms. Open areas of the blade surface are often cut with a tilted bull-nose cutter. This cutting style gives a large effective radius of curvature and can produce a fine surface finish with fewer passes compared to a ball-nose endmill. As with structural components, recent developments with conical barrel cutters further extend the benefits of using a large contact radius with a stable and controlled machining process.
Finishing of multi-blade components raises additional challenges due to tight blade spacing and requirements for high aspect ratio
Due to the small cutter radius that is allowed based on blade spacing and fillet geometry and the fine surface finishes required to meet design specifications, hundreds of passes around the blade may be required to attain the needed surface finish using a ball-nose endmill. Applying these long path lengths against hard metals is time-consuming and leads to cutter wear and concerns for manufacturing consistency. Some engine manufacturers change a cutter for each subsequent blade surface to assure consistency of wear and reduced imbalance of the resulting machined part.
Twisted multi-blade surfaces typically do not allow the use of swarf milling process. Conical barrel cutter solutions are also being applied to achieve cycle time and quality improvements. The larger step-over for conical barrel cutter processes means less overall path length and tool wear compared to ball nose endmills.
Both single-blade and multi-blade components can be classified with feature-based and family-of-parts (macro) programming. In both cases, there are repeated geometry selections of curves and surfaces. These are more complex than typical holes and pockets but can equally be represented by feature definitions. Re-using best practices for materials and tooling including feed rate and spindle speed, holders, step-down, step-over and more, can be useful when programming multiple parts. By having a comprehensive family-of-parts strategy, the programming effort can be reduced over many parts while achieving high productivity results.
CAM software has a large influence over machine tool performance, so users can gain benefits by selecting the proper CAM software for the application at hand. The most advantageous CAM software is continually evolving with each new version release to offer enhancements and innovations which keep up with the requirements of aerospace manufacturing.
openmind-tech.com
Australian fabricators are turning down work due to skill shortages.
The results of the Weld Australia 2022 Member Survey demonstrate that significant concerns remain for Australia’s welding industry. In particular, Australia’s fabricators are being forced to turn down work due to a severe shortage of skilled welders.
“Distributed in June 2022 and completed by approximately 140 companies, our 2022 Member Survey indicates that skills shortages, local content and sustainability remain high on the agenda for the welding industry,” says Geoff Crittenden, the CEO of Weld Australia.
“When asked what they are most concerned about, 64% of senior managers cited lack of skilled staff in an extremely constrained recruitment market. This comes as little surprise, with Australia facing a looming shortage of skilled welders—70,000 additional welders will be needed by the end of the decade.”
“With a considerable volume of work being onshored in the wake of international supply chain disruptions, most Australian fabrication companies are so strapped for skilled welders that they are working at anywhere between 30% and 50% of their full capacity. They are being forced to turn down jobs because they simply don’t have the manpower to complete the work. This is having a major impact on production and causing delays throughout downstream industries including building and construction, mining, oil and gas, and manufacturing,” said Crittenden.
It is little wonder that almost half (47%) of survey respondents have a pipeline of work that extends for six months or longer— this protracted pipeline is necessary in the face of these ongoing skills shortages. By way of context, this is a marked increase on Weld Australia’s 2020 member survey results. In the wake of the COVID-19 pandemic, the most common answers were a pipeline of work that extended less than one month (at 28%), one month (19%), and two months (16%).
Given the concern over Australia’s looming skills crisis, it makes sense that 95% of respondents support the concept of free TAFE, increased funding to upgrade TAFE facilities, or both initiatives. Clearly, the welding industry is looking to the government to help increase the supply of skilled labour over the coming years.
“Our members are also investing in their own welder training programs. BHP, Komatsu, JRS Manufacturing, Maxi-Trans and Precision Manufacturing Group have all established their own schools. While industry appreciates the roll-out of governmentfunded TAFE places, it remains to be seen whether this initiative will translate into high completion rates. Moreover, while encouraging more students into TAFE is always a positive, government spending also needs to focus on resources for TAFEs, teachers and equipment—TAFEs need the right tools to teach this sudden influx of students,” said Crittenden.
Industry is also investing in advanced welding technology to help overcome skills shortages. Over 28% of respondents indicated that their company or the company they work for has purchased robots or cobots, and 25% has invested in Industry 4.0 capabilities. A range of other types of technology were also mentioned, from drones and automated welders, through to various software solutions.
Despite the skills shortages, local procurement and content targets remain top of mind for the welding industry. 100% of respondents confirmed that they would support Federal and State Government policies to increase Australia’s share of fabricated steel product to at least 75% as part of a joint government-industry plan to grow the manufacturing industry.
“Importantly, whether it is imported or locally manufactured, all fabricated steel erected in Australia must comply with Australian Standards. Weld Australia is committed to ensuring that no
Australian lives are lost through an accident caused by noncompliant welding, without causing undue regulatory burden on industry. We firmly believe in quality welding for structural safety,” said Crittenden.
Inflation and rising costs were also of concern for approximately 23% of respondents, followed by weak international supply chains (9%) and reliability and affordability of power supply (4%).
Environmental sustainability and corporate responsibility
Australia is rapidly moving from carbon-fuelled power generation to a renewable energy system. In June 2022, Prime Minister Anthony Albanese announced more ambitious climate targets. Albanese pledged to cut carbon emissions by 43% from 2005 levels by 2030, up from the previous government’s target of between 26% and 28%. Given these targets, private companies will play a key role, making sustainability a priority for many businesses. As such, our 2022 member survey asked a series of environmental sustainability focused questions.
Welders are environmentally responsible. 30% of respondents support the target of zero emissions before 2050; 20% prefer cutting emissions by 35% by 2030; and another 17% support cutting emissions by 43% by 2030. In addition, 74% of respondents would support a Federal Government package to help employees transfer from carbon intensive to carbon free industries. Clearly, Australia’s welding industry is already taking steps to reduce its carbon emissions. While 41% of respondents have already installed solar panels to supplement power supply, another 53% have installed LED or sensor lighting, 46% have waste reduction programs in place, 46% operate recycling, up-cycling or repurposing programs, and 13% have a net zero carbon plan in place. When asked if an electric or hybrid UTE was available in Australia at a competitive price would you buy them for your company or employees as fleet cars, 50% of respondents answered in the affirmative. Interestingly, 63% of respondents would buy an electric or hybrid UTE for themselves.
Corporate responsibility remains a growing area of focus for the welding industry. Over 63% of respondents indicated that they have initiatives aimed at improving opportunities for women; 63% promote opportunities for apprentices and trainees; 63% have diversity and inclusion initiatives in place; 59% have mental health and fitness initiatives in place; and 31% have a Reconciliation Action Plan.
weldaustralia.com.au
A real-time flow meter manifold from SMC seals the deal.
Facteon have spent the past four decades crafting factory automation and proprietary welding solutions and have grown to become international specialists in factory solutions, smart manufacturing and IIoT technologies.
The company’s welding solutions focus on developing technologies that deliver on weld strength, alignment, and a superior cosmetic finish, as Warren Collenette, Senior Design Engineer from Facteon explains. “We are focused on customer confidence; we want our customers to be confident in each and every solution that we supply.”
Facteon provides robust welding solutions to some of the world’s largest appliance manufacturers and their welding technology can be used to process aluminum, mild steel, and multiple grades of stainless steel. “Irrespective of the industry, consistency and repeatability are key,” Collenette says.
Naturally, finding the right automation partner is central to the success of any manufacturer and Collenette says that Facteon looks to SMC Corporation Australia New Zealand for many of its unique automation requirements. “We started working with SMC more than 25 years. The initial relationship was between Fisher and Paykel, who at the time owned Facteon, and SMC,” he says.
“We have a great working relationship with SMC,” explains Collenette. “We are happy with their wide product range and commonly make use of their ISO cylinders. They’re always ahead of the curve, reengineering and developing new products, and we are satisfied with their sales and after sales support.”
SMC’s solution offers seven times the benefit
Collenette says that receiving feedback from manifolds have become pertinent to Facteon’s processes. “We use manifolds for spot welding machinery, that have water circuits running through them at a specified flow rate,” he adds. “The manufacturer stipulates the flow rate and if we don’t adhere to these parameters, then things can go wrong, and the customer may no longer be protected by their warranty. This is one of the reasons for feedback manifolds.”
Detailing SMC’s involvement, Collenette explains the application required a multistation flow meter manifold. “Rather than having many flow meters, each with their own configuration, we wanted to make use of one tidy solution.”
Facteon needed a solution where water flow could be controlled across multiple water-cooling circuits within a machine. “In addition, we wanted to monitor flow rates in real-time.”
This is where the 7-station flow meter manifold (PF3WB07B-W720P-04-LTN-M) with IO link capability from SMC comes into play. Compared to its predecessor the PF2W, this series offers a refreshed design. It also features 40% smaller volume, enabling shorter entry piping with flexibility. The display is rotatable and has a 3-colour distinct display as well as temperature monitoring. “The solution has been used in both SPOT welding and MIG welding applications. The first one that we developed was a 7-station unit in 2020 but this year it’s a 2-station unit. It’s a modular solution that can be adapted as needed,” says Shyam Suresh, Global Accounts Manager for SMC in New Zealand.
He adds that this customised solution from SMC is pre-configured and comes as a plug-and-play solution from its head office in Japan. “The customer only needs one part number and it’s configured to their exact specifications. It also features an IO link display for remote monitoring and to demonstrate flow rates.” According to Shyam the delivery time on these units is quick with turnaround times in six to seven weeks, and some units arriving even sooner. In addition, it features individual shut off valves for safety purposes and optional flow control valves, to adjust the flow rate for each circuit as required.
The manifold needed to be tested within the confines of Facteon’s premises during machinery commissioning. “We needed to get enough water flow through all the circuits, however, we were struggling with
this due to our inadequate water supply inhouse. Ultimately, the maximum flow rate through each valve is 12 liters per minute per output, so it shouldn’t be a problem onsite,” explains Warren.
While the team was sure that it would work, based on the initial in-house testing, the solution could only truly be put to the test at the customers’ factories in China and the USA.
Speaking to the safety requirements of this application, Warren adds that they made sure that the manifold was positioned away from any direct line of sparks or danger. “We could also put covers on them if required, and others were mounted to service towers - some meters away from the applications.”
IO link flow sensors are big draw cards for its customers, as Warren explains: “We changed all our equipment to IO link capability where possible due to customer feedback and demand.”
He adds that the demand for smart manufacturing and remote monitoring remains top of Facteon’s priority list. “Today, customers are asking for a lot more feedback from their processes to ensure tighter quality controls. In addition, it gives them the option to monitor their processes remotely which is of major benefit when you think about the cost of labour.”
It also helps with routine and preventative maintenance. “In the case where welding guns are overheating, faults and/or water leaks, customers can instantly shut down the machine and plan ahead.”
Warren concludes saying that the success of this project can be underpinned by collaboration and forward-thinking.
“Together with SMC, we are so pleased that both these projects turned out to be a resounding success.” smcanz.com
Kemppi releases new MasterMig range to elevate industrial welding performance and quality.
Leading international welding equipment manufacturer, Kemppi, has released its new MIG/MAG MasterMig welding machine models 353 and 355. Designed in conjunction with professional welders, the new MasterMig range delivers a range of features to help enhance industrial welding productivity and quality. The 358 model is scheduled for release later this year.
The new, compact and powerful Kemppi MasterMig range comes with Weld Assist as standard. This feature lets users set-up welding parameters quickly and easily to save time and improve productivity levels. By simply selecting the joint type, welding position and material thickness, users are ready to weld.
Equipped with memory channels, the MasterMig range also lets users save chosen parameters for fast retrieval. The ability to save customised settings means welders do not have to go through an initial setup for every job. At the turn of a knob, they can highlight the desired setting and proceed to weld. Highly convenient, this feature saves precious time, while helping to increase productivity.
For greater welding productivity and control, the MasterMig 355 and 358 models can switch on the new MAX arc performance welding processes. MAX Cool, MAX Position and MAX Speed are new Kemppi welding processes that offer solutions for challenging steel, stainless steel and aluminium welding applications by increasing productivity, minimising spatter and speeding up welding without compromising quality. The MAX software options easily integrate with the MasterMig 355 and 358 models.
Suitable for use on site or at the workshop, the MasterMig range delivers real choice. It
includes the 353, 355 and 358 models in the compact MIG welding category. These are available as manual, synergic (Auto), and pulse (Auto Pulse) welding options. Users can also choose to weld with gascooled guns or the optional MasterMig cooling system for an integrated liquidcooled package that maximises the 350A 40% ED welding power and enables more extended welding periods. The new MasterMigs also come with a range of convenient, optional transport units.
Equipped with integrated and self-charging LED work lights, the new MasterMig range helps improve worksite safety, efficiency and convenience. The LED lights operate with and without mains power to help enhance productivity in low light conditions. The new MasterMig range can be combined with the compact sub-feeder SuperSnake GTX to extend the reach of your welding gun. This provides greater convenience when working on hard to reach welding sites. The SuperSnake GTX includes digital metering, a safetylock ON/OFF switch and a strong protective frame.
Integrated digital connectivity lets users examine their welding data. The MasterMig 358 can be easily connected to Kemppi WeldEye ArcVision. This software solution lets you track and record arc-on time and welding parameters for better insight into welding production. Raw data is collected digitally from connected welding stations and processed, and it can be viewed directly from your laptop.
Designed and made in Finland, and strong and robust, the MasterMig range has been built to last. The new MasterMigs feature an injection-molded reinforced plastic casing that absorbs knocks, and ensures the machines can withstand challenging environments. kemppi.com
stop online shop for engineering plastics
In conjunction with Weld Australia, Langi Kal Kal Prison recently hosted a Welding Employment Expo to help facilitate connections between prisoners and prospective employees.
Given the proven success of VET programs for prisoner rehabilitation, in 2022 Corrections Victoria expanded the VET Centre of Excellence model to deliver Fusion Welding to ISO 9606 certification standard to complement their Metal Fabrication industry at HM Prison Langi Kal Kal. Federation University delivers the training program with the support of Weld Australia and on-site prison industry staff.
“Australia’s prison population is rapidly expanding, and is increasingly comprised of younger people and reoffenders,” according to Geoff Crittenden, the CEO of Weld Australia. “This gives rise to the need for practical rehabilitation and vocational education and training (VET) programs that can help alleviate recidivism.”
“A recent study confirmed that participation in VET whilst incarcerated helps prisoners to remain custody-free post-release. In fact, prisoners who successfully completed VET were 59.96% more likely to remain custody-free at two years post-release; and 78.23% more likely to remain custody-free at five years postrelease.”
As part of the program, augmented reality training was introduced to expand the welding skills of the prisoner learners to meet international standards. A welding workshop sits alongside the augmented reality training room so that participants can work on projects to use and practice their welding skills in the physical as well as virtual environments.
To participate in the program, prisoners are invited to submit an Expression of Interest and then selected through an interview process. Up to eight participants can be accommodated in the intensive 14-week program.
“I wanted to take part in this course to not only further my knowledge and experience of welding but to be able to give myself the ability to provide a positive, reliable, and sustainable future for my family,” student *Daine said. “When I am released, I am keen to find as much work as possible in the engineering trade working in the railways, or similar areas that require good welders. I don’t see my life revolving around prison and I want to have real work opportunities in the community when I’m released.”
The VET Centre of Excellence model links participating prisoners with prospective employers and pre and post-release support service providers. These connections provide prisoners with sustainable pathways to employment and support to reintegrate to society post-release.
The Welding Employment Expo was attended by several Weld Australia members, including Jeff Wanliss (Engineering and Business Development Manager, Keppel Prince). Based in Portland, Victoria, Keppel Prince specialises in the construction, fabrication and maintenance of industrial structures and equipment, ranging from wind farms to bridges.
“I didn’t really know what to expect from the Employment Expo, but the experience was a big eye-opener for me,” said Wanliss. “During the tour of the facilities, one of the prisoners produced an industry standard vertical up weld — one of the hardest welds to do. We would have accepted that weld in our workshop. It can be difficult to find potential employees with the skills and experience needed in our workshop. I’d definitely consider employing any of the guys based on the standard of welding they’re doing.”
“These types of training and rehabilitation programs are so important. They help give prisoners purpose. Many of the prisoners have obviously faced challenges in the past, but, this is a delineation point—it’s like drawing a line in the sand and saying ‘the past is the past’. VET and training programs like this one equip prisoners with knowledge and give them practical skills that they can use on release. It is an essential step to ensuring that their future is successful,” said Wanliss.
“Australia is facing a looming shortage of skilled welders — 70,000 additional welders will be needed in the next 10 years. VET training and employment pathways as part of prisoner rehabilitation could help alleviate some of these skills shortages,” said Crittenden. “However, this will require commitment and collaboration from industry and government — not only to fund VET training in Australia’s prisoners — but to help provide secure employment opportunities post-release.”
*
weldaustralia.com.au
withheld
Welding technology showcase inspires Mackay manufacturing.
Leading gas and engineering company BOC, a Linde company, together with Weld Australia and Diverseco celebrated the launch of Weld Australia’s newly formed Mackay Committee with a technology showcase at BOC Mackay’s Gas and Welding store.
The event was attended by Geoff Crittenden, CEO of Weld Australia, and a panel of welding industry experts who delivered interactive and engaging demonstrations featuring a welding cobot, EWM welders, EWM Xnet welding quality management software and Soldamatic augmented reality welding simulators.
Kyle Scott, Head of Product Management and Manufacturing Applications at BOC South Pacific said regional events that showcase welding automation and technology solutions were critical as Australian manufacturers struggle with the skilled labour shortage and focus on boosting productivity and quality.
“BOC has been supporting the manufacturing industry in Mackay for over 50 years and believes industry collaboration can help drive growth in the region, supporting the objectives of the Queensland Government’s Mackay Manufacturing Hub.”
Tony Newnham, Head of Welding at BOC South Pacific said customers with specialised needs are focused on implementing automation and new digital welding technology solutions. “New technologies have a critical role to play and our partnership with automation specialist Diverseco is delivering welding collaborative robot (cobot) solutions across Australia. “Our BOC welding specialists are working closely with customers to implement new gas and welding technologies and as the exclusive distributor of German manufactured EWM products, BOC can help customers enter the world of Industry 4.0 with EWM’s welding quality management software Xnet. “We congratulate Weld Australia on the launch of the Mackay Committee which will increase engagement with the welding community and nurture the next generation of skilled welders.”
Geoff Crittenden, CEO of Weld Australia said manufacturing contributes $20bn a year to Queensland's economy and regional areas have a key role to play in expanding this contribution.
"We are excited to be launching our new Mackay regional committee that will help support businesses and advocate for their interests. Mackay is already home to many first-class, innovative fabricators that service global markets."
Jason Rowe, Managing Director at Engineering Industries Australia said local manufacturers need to collaborate with industry to solve welding and fabrication challenges.
“BOC has given excellent technical advice on welding procedures, welding machines and consumables, and correct gas mixtures. This has helped us increase welding efficiencies and quality of output.”
The event followed an announcement by the Queensland Government that $500,000 in grants had been awarded to local businesses in the manufacturing industry, funding which was encouraged by the work of the Mackay Manufacturing Hub. boc-limited.com.au weldaustralia.com.au
Pemamek introduces Skyhook Pro intelligent positioner for assembly, arc-welding, and post-weld finishing operations.
Pemamek Oy and Pemamek LLC have introduced the Skyhook Pro Intelligent Positioners building upon their proven Skymaster Pro positioning technology. Controlled by a RC32H-wired remote control and intelligent software, the Skyhook Pro positioners can work with heavy loads up to 15 tons. The ability to pre-program and modify movements as needed has eliminated the need for clamping and increased productivity by 70%. They can also be rotated +/-180 degrees for optimal positioning. Additionally, because the programs are generated ahead of time by more experienced welders, those new to the trade can continue operations for optimal working cycles using just the remote control and a pedal. This also provides for safer operation.
The Skyhook Pro positioners require virtually no installation, requiring just a few fasteners and cables. Inside an electrical cabinet on the backside of the positioner contains a proprietary communication system connected by Wi-Fi technology to mobile phones, tablets and laptops for programming, diagnostics, and maintenance schedules, providing a vehicle for importing or exporting work cycle information to other Skyhook machines. They are easily integrated with Pema Column and Booms and are ideal for assembly, Arcwelding and post-weld finishing operations.
“The Skyhook Pro Intelligent Positioner expands upon the capabilities of our Skymaster Pro positioning technology to handle the heavy loads often found in Heavy Industry, oil and gas
manufacturing, HD Trucking, and other similar heavy-duty welding applications. The ability to pre-program and modify those programs as needed provides great flexibility from a positioning, operational and welding personnel standpoint. We’re excited to provide weld shops with another solution to their heavy-duty welding and employee challenges, saving them significant time and at the same time increasing throughput immensely,” said Michael Bell, Director of Sales, Pemamek USA. pemamek.com
ISCAR's invention of the Multi-Master tool line has had a significant impact on the world of cutting tools at the turn of the last century.
The three-pronged principle of the Multi-Master family was based on the face contact between a carbide head and tool, centring the head by use of a short taper, and securing the head in the tool body by use of a threaded connection. It was the last of these three elements that benchmarked the connection of carbide heads in assembled tools. The successful design of the thread, made of hard brittle carbide, enabled fast and simple head replacements, and created the easy-to-use tool that features ISCAR's no setup time phenomenon. The threaded connection quickly found its way into various tool assembly systems with exchangeable carbide heads, now an industry standard.
At first, the Multi-Master line was intended specifically for milling in the Die and Mold industry. Soon after, the automotive, aerospace, and general machinery industries adopted ISCAR's Multi-Master in their production processes. Milling remains the focus of the MultiMaster line, which now lends itself to drilling applications as well. The Multi-Master line has greatly expanded, and now covers a broad range of applications that include drilling, countersinking, and chamfering hole edges. When looking back more than two decades, it is apparent that the Multi-Master line found its way into the holemaking sector of applications by providing highly effective solutions.
There are two types of heads which create the cutting section of the Multi-Master tool. The first type is similar in its shape to a multiflute solid carbide tool but differs in the overall and cutting-edge lengths. Increasing the number of flutes on the cutting head makes cutting more stable and productive. The heads of the first type are produced from stepped cylindrical blanks by use of a grinding operation. The heads of the second type are shaped beforehand by pressing and sintering with a minimal oversize. Additional grinding defines the final shape of the Multi-Master head and its accuracy. The heads of this type have only two flutes characterised by high strength. This facilitates increased feeds per tooth in comparison with the heads of the first type. Pressing technology enables the production of diverse complicated Multi-Master geometric shapes. The head is mounted on a holder that may be an integral body (shank) or an assembly comprised of a shank, extension, and reducer. The holder is a rotating solid tool with cylindrical and conical sections without flutes that allow the evacuation of chips. Multi-Master drilling heads are suitable for relatively shallow holes. This may pose a limit in holemaking applications, yet for short-hole drilling when the shape of a part or a work-holding fixture requires high tool overhang, a Multi-Master long-reach tool is more rigid compared to a typical drill with flutes.
MM HCD two-flute heads stand tall above other Multi-Master hole making products. These extremely versatile heads are made with various point angles - 60, 80, 90, 100 and 120-degrees which ensure a wide range of applications such as centre drilling, spot drilling, hole chamfering and countersinking. They enable conical holes for countersunk screws, bolts, and rivets according to ISO/ DIN/ANSI standards in solid material. If the workpiece is pre-drilled, countersinking efficiency can be improved by using multi-flute MM EDF heads that increase productivity in chamfering operations. When chamfering or deburring the back side of a hole, Multi-Master double-sided chamfering heads are the solution.
Centre drilling is one of the most common holemaking operations. Typical tools that perform this task are called centre drills. Highspeed steel double sided centre drills have been the common tools used over the past years to achieve low cost solutions. ISCAR's MultiMaster new centre drilling heads have won undeniable popularity by
Versatile MM EDF head effectively performs as a backside chamfering tool.
Multi-Master heads facilitate both spot drilling and chamfering.
Multi-Master flat bottom drilling heads are also suitable for drilling holes on slanted surfaces.
providing increased tool life and productivity, even under strenuous cutting conditions. NC spot drills are also commonly used tools. Characterised by their small cutting depth of cut, these tools are primarily used on CNC machines for creating pre-holes that allow precise drilling without the use of guide bushings. For machining shallow holes, the Multi-Master line has great advantages with NC spot drilling heads. A thin web at the head point prevents 'drill walking' during the machining operations. In addition, as a result of the 90-degree point angle the heads can be applied to hole chamfering.
Flat bottom holes are commonly created in many applications. Such holes are needed for seats of springs, sockets of screw heads or the ports of washers. The simple way to produce these holes is by drilling with flat bottom drills. If the drilling depth does not exceed 1.2 times the length of a hole diameter, Multi-Master provides two-flute heads. The heads are suitable for drilling holes on slanted surfaces, featuring versatile cutting geometry, which allows machining most engineering materials.
Over recent decades, Multi-Master has quickly expanded its field of use and established itself as an effective tool for holemaking as well. ISCAR's engineering design concept that features over 40,000 tool options has anchored itself to become much more than a milling tool line. It now features many more options for drilling with ISCAR's ‘No Setup time’ phenomenon to assure fast indexing and minimum machine downtime. iscar.com.au
Tillsonburg has come a long way since Canadian country music legend, Stompin’ Tom Connors thrust the small Ontario town and its tobacco fields into the spotlight with its namesake song. Today, Tillsonburg is part of a thriving automotive region, home to the THK Rhythm automotive plant that serves global manufacturers including BMW, Ford and Daimler Mercedes Benz. A tough, competitive landscape meant THK Rhythm needed to make its offering stand apart from competitors. To give its products the edge, the company enlisted the support of Sandvik Coromant and its new steel turning grades. The THK Rhythm automotive plant specialises in suspension components found in vehicles worldwide, along with ball joints and ball studs for these components. Being a global automotive player demands stringent quality and cost-optimisation measures, which is evident in the THK facility.
THK’s quality policy, which is prominently displayed at the plant’s entrance, reads: “Right the first time, right every time, continually improve”. And it’s more than just a catchy mantra. Several manufacturing improvement practises evidence this policy, including Kaizen, Japanese for continuous improvement, which focuses on optimising efficiency, productivity and overall equipment effectiveness (OEE).
Despite THK’s crystal clear efficiency goals, reaching productivity targets and controlling cost was a challenge when producing the front lower tension arm, a component that goes into the suspension assembly of a car. “The front lower tension arm requires the removal of a lot of material during several steps including drilling, roughing and finishing a bore,” explained Adrian Dabrowski, a process engineer at THK Rhythm.
The component is made of a forged ISO P steel that is particularly abrasive, with a high tensile strength. Machining this part requires a specialist tool with a number of inserts that are staggered or stepped — meaning they are not all of the same diameter. The original machining process for the front lower tension arm was designed to make 140 parts per tool, however, THK could only produce about 92 pieces on average before one of the inserts on the largest diameter failed, which caused the entire tool to fail.
Frequent failure meant operators had to change tools far too often. The machines in the THK Rhythm workshop are set up in a way that if one tool breaks, a spare tool is brought in automatically so that machines can keep running. With frequent tool failures, however, there were not enough spare tools to keep production flowing. Chip control, a vital consideration for any steel turning operation, was also a concern. “When the tool failed, chips would often get wrapped around it; so, we had to physically take the tool out and remove the chips,” revealed Gary Martin, a machine operator at THK. “These chips were sharp and could cause finger cuts and injuries.”
Dabrowski further highlighted the pains of tool failure: “We were running the machines with just a single tool and when that tool broke, the operators had to physically take it out, manually change all the inserts and put it back in the machine. That equates to around five-to-six minutes of downtime per machine, which quickly adds up.” On average, operators oversee three machines. So, if one machine is down, in essence all three are down. “On good days, we had just one breakage per shift,” continued Dabrowski. “On these days, downtimes were as frequent as three-to-four times per shift per machine.”
Using the previous inserts there was a lot of downtime, which made meeting daily productivity targets difficult.
In search for the right solution, THK tried to adjust the machines on a daily basis, fine-tuning feed rates and revolutions per minute (RPM). The team also tried out different inserts and geometries from a couple of tool suppliers, but nothing hit the mark. That was until THK turned to Sandvik Coromant.
Sandvik Coromant added two high performing carbide insert grades, GC4415 and GC4425, to its existing range at the end of 2020. The inserts have a broad range of applications and are recommended for both continuous and interrupted cuts. While GC4425 delivers improved wear resistance, heat resistance and toughness, GC4415 complements GC4425 where enhanced performance and better heat resistance is needed. For THK Rhythm, GC4415 was a fitting addition to its machining process.
Both grades contain the second generation Inveio coating technology. “What makes this tool coating particularly unique is that it can be examined at the microscopic level,” explained Rolf Olofsson, Product Manager at Sandvik Coromant. The material’s surface has a uni-directional crystal orientation. Each crystal linesup towards the cutting edge, creating a strong barrier that improves crater and flank wear resistance. Heat is also lead away from the cutting zone more quickly, which keeps the cutting edge in shape for longer time in cut.
“GC4415 and GC4425 can machine a larger number of pieces, while contributing towards extended tool life, eliminating sudden breakages and reducing reworking and scrap. For THK, the GC4415 insert is the remedy to its turning troubles,” continued Olofsson.
Since introducing GC4415 to its machining operations, THK has seen shop floor productivity change for the better. In fact, because it runs at higher cutting rates, THK witnessed an 11% increase in productivity as soon as operators started using the insert.
During the first four months of 2021, THK used roughly 3,800 inserts of their previously-favoured grade. When the GC4415 grade was introduced in May 2021, the workshop used just 3,000 of the new inserts in the same timeframe — an 18% decrease in the number of inserts used, dramatically improving overall cost-per-part.
Change isn’t just about numbers. “On the shop floor, our operators are happier as they can focus on loading parts and not having to worry about frequent tool changes or chip jams,” concluded Dabrowski. “The new grade has helped save 194 hours of production time per year. Thanks to GC4415, the THK Rhythm workshop now experiences far less downtime, and more reliable production.”
Following the success of the GC4415 insert grade in machining vehicle front lower tension arms, THK Rhythm now plans to test and introduce the grade in other parts of its production line, such as ball studs and ball joints.
thk-rhythm-auto.com sandvik.coromant.com
Sandvik Coromant’s new steel turning insert grade helps THK Rhythm take control of its machining process.
ANCA and CSIRO developing novel 3D printing technology to manufacture cutting tools.
Australian industry will soon have access to an innovative cutting tool manufacturing platform, thanks to a research collaboration between leading tool manufacturer ANCA and Australia’s national science agency CSIRO.
The nine-month project costing just under $1m, which is supported by the Innovative Manufacturing Cooperative Research Centre (IMCRC), is developing a new additive manufacturing (3D printing) process for tungsten-carbide tools.
The additive manufacturing technology will enable affordable, high-performance tools to be manufactured using one platform, replacing the current production process of mould pressing, sintering, brazing and grinding.
Now in the advanced phase, the research is focused on refining the additive manufacturing technology ahead of ANCA taking the hybrid manufacturing platform to market.
Dean McBain, Research & Technology Manager at ANCA, said the project had the potential to transform the way tungsten-carbide brazed insert tools were made in Australia and across the world.
“ANCA’s collaboration with IMCRC and CSIRO has accelerated the development of an innovative additive manufacturing technology which we believe has the potential to disrupt the $2.2bn global cutting tool market,” he said.
“Successful completion of this project will allow ANCA to commercialise the new hybrid additive manufacturing machine platform, grow our workforce and revenue and fill a significant gap in the global tooling market.” Dr Kathie McGregor, Research Director for Advanced Materials and Processes at CSIRO, said the project would make metallic additive manufacturing technologies more accessible to Australian industry. “In keeping with CSIRO’s role of providing high-end research and development (R&D) support
Tungaloy introduces new PCD line for high-speed milling.
With the global launch of the new ADDFORCE brand from Tungaloy, the cutting tool manufacturer has introduced its new TungRec DX110 Series of PCD insert grades for machining aluminium alloy components.
The Tungaloy TungRec milling range has long been an exceptional performer with its innovative tool bodies and insert geometries, but now, this line is set to take aluminium machining to a new level with the new DX110 PCD insert grade. Developed for the finish machining of ISO N materials, the new DX110 grade incorporates an ultrafine micrograin structure that provides outstanding surface finishes and component quality whilst demonstrating exceptional cutting edge integrity. This ability to maintain edge sharpness over a prolonged period ensures that end-users benefit from impressive tool life and extended periods of unmanned running with the economical benefit of reduced insert consumption.
The new DX110 inserts are the first PCD solution to be incorporated into the TungRec line, offering existing TungRec users the facility to enhance aluminium machining capabilities with existing tool bodies. At present, the PCD inserts are available for TungRec 11 size toolholders, offering the facility for improving small diameter milling tools where vibration and excessive tool overhang are commonplace. Furthermore, the insert geometry and composition reduce cutting forces to generate a particularly smooth cutting action that rapidly removes chips from the work area whilst further reducing vibration and improving surface finishes.
to the Australian industry using state-of-the-art equipment and world class know-how, we have collaborated with ANCA to further develop a unique technology,” she said.
“We expect the outcomes may enable ANCA to diversify and grow its business and provide a boost to the local economy in terms of additional job opportunities and export income.”
Dr Matthew Young, IMCRC’s Manufacturing Innovation Manager, said IMCRC was pleased to be supporting ANCA’s innovation, and in turn, contributing to the growth of Australia’s advanced manufacturing ecosystem.
“As ANCA and CSIRO’s R&D partnership demonstrates, additive manufacturing can generate significant benefits for Australian manufacturers, reducing costs and improving speed to market,” he said.
“Once developed, this revolutionary technology can be applied to a range of cutting applications, creating significant global export opportunities and furthering ANCA’s position as a market-leading manufacturer of cutting tools and equipment.” imcrc.org csiro.au machines.anca.com
TungRec DX110 Series of PCD insert grades.
Perfect for the machining of aluminium components in the aerospace, automotive and general subcontract sectors, the DX110 insert grade and the TungRec toolholders for insert size 11 provide manufacturers with an indexable cutting tool solution from as small as 12mm diameter. With tool diameter bodies extending up to 100mm diameter, this new arrival to the TungRec range perfectly complements the existing TungSpeed-Mill PCD Series where the smallest diameter tool body is 50mm. tungaloy.com
When working with metal, a poor choice of tool or machining strategy can be the difference between success and failure. Waste material, poor productivity and scrap components are all signs of an inadequate machining process. They’re also signs of unsustainable machining.
With the right tools and processes in place, many sustainability gains can be made when cutting metal. But lots of machine shops aren’t realising these advantages. Here, Matilda Gynnerstedt, Head of Product Management for Turning at Sandvik Coromant, explores the tools and technologies that drive productivity, reduce waste and improve the sustainability of metal cutting.
Metals are the backbone of today’s industrialised world. From steel in our buildings and aluminium in our cars, to titanium in modern aircraft and the copper found in electronics, metals are important building blocks in our economy. And their prevalence isn’t going to dwindle. As governments across the world implement plans to decarbonise, demand for renewable technologies will see our reliance on metals continue to soar. In fact, The International Energy Agency (IEA) Steel and Iron Technology Roadmap reports that global demand for steel will increase by more than a third between now and 2050.
But, as metal demand increases, so too will expectations on how metals are sourced, produced are used in manufacturing.
Producing metals has long been considered a carbon-intensive process. While it’s true that steelmaking produces a lot of emissions, industry has made successful strides towards reducing its impact. Green steels, for example, replace coking coal, traditionally needed for ore-based steelmaking, with renewable electricity and hydrogen. This can drastically reduce carbon emissions during the metal production process.
While recent innovations, like green steel, could bring a more sustainable future for the metal industry, there are several other technologies that can make metalworking processes more sustainable. Manufacturers must become more aware of these methods if they are to tackle tomorrow’s sustainability challenges.
For machine shops tasked with cutting difficult-to-machine metals into desired forms, with tight tolerances and the utmost surface quality, the right tools and expertise are essential. Specifically, the tool should aid more efficient and less wasteful machining process, and support major sustainability benefits.
Scrapping components is a factor that prevents a workshop from achieving top performance. Common situations that lead to scrapping include using the wrong tools, human errors in machine programming and undetected variations in the raw material that cause unpredictable machining issues. Moreover, waste has a serious impact on the environment if it isn’t recycled. In fact, World Bank estimates that waste produced by industry, on a global scale, is 18-times more than solid waste produced by municipalities around the world.
If machine shops are to reduce scrap, they must implement the right tooling set-up and cutting data. Failure to secure these factors can result in irregular tool wear and unpredictable insert tool life — this leads to component rejections and, in turn, scrap.
Tool choice is especially integral to reducing waste in turning, a common lathe machining operation. Efficient steel turning can be achieved by reducing scrap and component rejections, as part of an effective strategy to bring down the cost of production within an existing machining set-up. The strategy might include maximising machine use or selecting more reliable tooling solutions, like the insert, to reduce cost per part.
But what are the characteristics of a more reliable tool? Turning grades that provide long and predictable tool life, with good chip control, should be considered for secure and productive machining. Selecting a tool with longer life, combined with greater wear and heat resistance, can yield tangible benefits like minimising unplanned stops, or reducing material waste from the workpiece material or from the carbide insert itself. These are all necessary preconditions for sustainable machining. Sandvik Coromant’s dedication to using recycled materials in our turning grades is also an important factor that make our customers’ own manufacturing more sustainable. One of the criteria in our development project is to increase the use of recycled material in our tools, as well as to reduce waste. Smoothing out the pain points
While awareness of sustainability is gaining momentum across virtually all industries, so too is digital transformation. In a survey of more than 400 global manufacturing companies, 94% of respondents indicated that Industry 4.0 has helped keep their operations running during the pandemic. The challenges of COVID-19 have also served as a wake-up call to manufacturers that are lagging behind in implementing Industry 4.0 strategies.
A good place to start in any sustainability strategy is to conduct an audit of a plant’s current status with data-led insights. This approach can identify several areas of inefficiency that might impede a machine shop’s productivity and sustainability. For instance, if a facility is experiencing premature tool wear, subpar surface finishes or high machine downtime, then data gathered through sensors can help operators make informed improvements to their machining process in ways that help reduce waste and increase energy efficiency.
The CoroPlus Productivity Improvement Programme (PIP) is one solution to these pain points. The PIP is a proven, structured process that can be performed on a single machine, a process chain, or across the whole plant. To begin the process, Sandvik Coromant experts identify inefficiencies in production and, for there, Sandvik Coromant installs machine monitoring solutions that give data insights in real-time. This data can be accessed remotely to provide an in-depth analysis of a complete production cell, right down to the cutting tool.
A few misinformed decisions can be the difference between productive, sustainable metal cutting and a wasteful machining process. However, as we become more aware of the impact of metalworking on the environment, innovations are being realised that can significantly improve industry’s credentials. That includes finding more sustainable ways of not just producing, but also machining metals for people, planet and profit.
sandvik.coromant.com
Finding and investing in the best laser cutting metals manufacturing machinery is often just the first step in a sound purchase in this rapidly expanding, competitive business.
The even more important process afterwards is making the purchase pay by expanding your business using it, ideally by freeing up the time of skilled staff to produce more work for it by producing quotes faster and better tailored to customer needs –thus improving service and response to customer needs.
This was the situation in which Melbourne sheet metal building product manufacturer Jonda found itself after buying a top-line laser cutting machine that enabled it to do the job of cutting material more speedily and accurately – but then finding that was only part of the solution to expanding their business in custom flashing and rainwater goods.
“After purchasing a fibre laser machine, we quickly ran into the issue of not being able to get quotes back to our customers in a timely manner. The manual quoting process was just too time-consuming, which slowed down productivity,” says Jonda Manager, Jake Nikolopoulos.
Jonda’s solution was the online quotation software, ToolBox, from ipCompute (which includes Tempus Tools and ipLaser), which replaces the painfully slow process of manual inputting of data. ToolBox was developed by laser industry professionals who have a combined 100 years of experience in the laser industry, extending from hands-on work on the cutting floor through to international commercialisation of their technology.
To meet the needs of their global industry, ipCompute's CEO and Co-Founder, Ivan Cooper, and Product Executive, Bruce Thomas,
designed ToolBox to more than halve the time and manual input currently required by laser cutting companies to prepare and deliver precise estimates to their own customers.
The Australian-developed laser cutting and fabrication quoting software ToolBox is used by laser cutting and metal manufacturing companies throughout Australia, Europe and the USA to save job shops’ time, and keep quotes accurate and consistent, no matter who is preparing them.
“Getting the fastest and best machine is only half the equation,” says Cooper. “If you just buy the best machine and stop there, you have only improved half the business. If you let the old manual quotation output method continue to plod along at the same slow pace, you are doing only half the job of growing the business, or less.”
Jake Nikolopoulos agrees 100% – “Using ToolBox, we’re now able to get a personalised and professional looking quote to our customers within minutes, not days,” he says.
“Having our material database and secondary processes like folding, welding, powder coating, electro plating and more all integrated within ToolBox is super-efficient. The whole process from importing drawings to exporting the finished quotes is absolutely effortless.”
“ToolBox has brought our company to a new level of professionalism and efficiency,” says Nikolopoulos, "whose customer response comments reflect the benefits and service the online technology has brought to them." iplaser.com. ipcompute.com
Validation and quality control: optimising micro moulding outcomes. Dave O’Leary is Quality Director at Accumold, which has a 130,000 square foot fortified facility with over 350 staff at its Ankeny plant in Indiana, USA.
You will have heard it discussed on many occasions that specialist micro moulders need to be vertically integrated to optimise outcomes for customers. Of the various stages involved in taking a product design to volume micro-manufacturing, some of the steps that should be accessible under the one roof are obvious. Design and material experts need to be on hand, micro tooling must be undertaken in-house, so too micro-moulding (obviously) and automated assembly.
But there is one aspect of a micro moulding project that is often overlooked, especially when customers are assessing the in-house capabilities of a micro moulding partner, and that is validation and quality control. You will no doubt have heard the phrase, “if you cannot measure it, you cannot make it,” and in micro-manufacturing this is fundamental, as when assessing the conformity to design of parts often difficult to even see with the naked eye, an understanding of the importance of validation and measurement is vital.
Measurement development time, and Gage R&R are vital and extremely valuable when undertaking a micro-moulding project, and micro-moulders should work closely with their customers on model and print interpretation and Design for Micro Moulding (DfMM) — during the product development process.
The measurement processes must be assessed and validated as the moulding process is qualified. Very often, with measurement taking this central role, it moves from being seen as a necessary evil to a set of technologies that can help improve designs, re-dimension prints, and better use Geometric Dimensioning & Tolerancing (GD&T) so that the part design is easier to mould, easier to measure, and it performs better for the end user. As so often in product development of micro plastic parts, it is the influence of all departments early in the design stage that leads to optimal outcomes, and an interrogation of your chosen micro moulder’s view of metrology and its central role in manufacturing success should be prominent in any discussions before embarking on your project.
When looking at advanced manufacturing settings, there is a balance between the use of metrology in the lab and its use in-situ in the production facility. A key driver in all scenarios is to get meaningful data as quickly as possible, and that this data allows you to make decisions that help to optimise results.
The first step is to assess the metrology requirements for a specific application in terms of the number of critical features/dimensions, tolerance requirements, part geometry, measurement systems available (lab and in-process), estimated part volume/run rate, cost of parts, and potential for scrap if measurements are delayed. With some projects it is important to work with a customer to identify critical features/dimensions, develop a measurement process on a OGP machine, prove the measurement method utilising a fixture and programs as repeatable and reproducible, buy duplicate OGP machines and deploy the machines, fixture, and programs and trained production personnel to operate the machines and collect data in the production room.
Accumold prefers to perform measurements as close to production (in-process) as practical with a metrology system that is repeatable and reproducible. However, sometimes project details require measurements to be done in a lab environment, and when these are required, it is important to establish processes for part handling and delivery, prioritisation of part measurements, measurement method, data collection, and reporting of results to production. All metrology requirements are included in part specific control plans.
Undertaking measurements in a micro-moulding project throws up numerous challenges, not least the part size which can be extremely small, part-fixturing (for in-lab validation), print tolerances, and surface roughness.
The part size is the constant battle, and with parts as small as the ones we routinely micro mould at Accumold, the only viable metrology tools are non-contact, typically using a light source to measure instead of a physical probe. We overcome fixturing problems by building plastic or steel custom fixtures which allow the measurement of all the relevant features on a particular part.
Surface roughness is another critical metrology challenge because of the small size and critical finish requirements. Non-contact metrology tools are vital for such applications, tactile tools having the potential to compromise surface integrity.
Choosing a micro moulder with an extensive suite of best-in-class metrology options and the expertise to use them effectively is not just important in terms of the securing of relevant data and therefore having the tools to optimise manufacturing outcomes. When used properly, metrology tools provide invaluable insight concerning the demanding micro size tooling and parts required to meet customer needs. Metrology equipment and skills are used to measure steel details in the mould, part features/dimensions to ensure the parts meet print tolerance, and to ensure we have a capable process. Intense design of experiments, stress runs, operational qualification and production qualification runs are undertaken to assess dimensional capability to our internal or customer Cp, Cpk, Pp and Ppk requirements to values of 1.0, 1.33 and 1.67 as required for the project. Using the metrology equipment and expertise in house at Accumold, we can provide data and immediate feedback that help determine if steel in the mould is acceptable or if adjustments are required.
Metrology technology is constantly evolving, and it is important to actively assess new technology. The expertise and experience in our design, mould and automation build, production/process, and quality assurance personnel is critical to success.
accu-mold.com
As a company that specialises in press tooling and subcontract machining, the throughput of work at Cube Precision Engineering can be as diverse as it is challenging.
When the Rowley Regis based subcontract manufacturer was tasked with drilling 55,600 holes in a 3m by 2m press tool recently, it turned to the cutting tool experts from Industrial Tooling Corporation (ITC) and its industry-leading drilling lines.
The Black Country manufacturer produces anything from small to large volume batches as well as bespoke tooling, stamping dies and more from an equally wide range of materials. To ensure the 37-employee toolmaking business can facilitate the production of large tooling projects, the company has a large bed Hurco DCX32i machining centre with a 3.2m by 2.1m bed – the perfect work envelope to accommodate the latest press tool that demands drilling over 55,000 holes in one 25mm thick plate and also a second 50mm thick EN8 steel plate.
With 13 CNC machining centres on the shop floor and a range of additional machining technology, the West Midlands company that works in the aerospace and automotive industries among others has witnessed a significant upturn in business since the pandemic. Discussing this, Cube Precision Tools, Managing Director Mr Neil Clifton says: “The pandemic was a difficult time for most businesses in the manufacturing sector, but we were proud to retain all of our highly skilled staff and exit the period with a strong forward order book. Our expertise in the toolmaking arena has now seen our business win significant levels of new business from both existing and new customers. One new customer is a ceiling tile manufacturer, and it was the recent design and production of a press tool for ceiling tiles that required the support of ITC.”
The press tool for ceiling tiles for offices is an onshoring project with the work being brought from the US to the UK, a factor that brought another challenge with Cube Precision having to work to imperial drawings and dimensions. The 3 by 2m press tool that can press 6 tiles simultaneously has one punch plate accommodating 55,000 pins and a corresponding base plate for the pins to enter after punching through the ceiling tile material – the company needed to drill a colossal 111,000 holes.
With the daunting prospect of drilling 111,000 holes, Cube Precision turned to its long-term tooling supplier for a solution. The West Midlands company has worked closely with ITC for more than seven years and now has a complete consignment stock of cutting tools from the UK’s leading cutting tool manufacturer. Despite having an ITC vending machine with consignment stock of upwards of 60 different product lines that includes everything from end mills, taps, drills, indexable inserts, thread mills and more - the challenge of 111,000 holes in EN8 steel plate required something different.
On this extremely precise press tool, the holes being drilled had to meet tolerances of +/-1thou (0.025mm) to ensure the punching pins would locate in the base plate. The project required a solution that was the epitome of precision, concentricity and runout. The first step for Simon Yeomans, the ITC Application Engineer tasked to find a solution, was to enhance the working environment and particularly the concentricity and run-out of the tools. Luckily for Cube Precision, its preferred cutting tool partner is also the UK’s primary BIG KAISER solution provider. Prior to trialling any drill, the ITC expert set about improving the toolholding environment for the subsequent drill by maximising process stability. This involved the installation of the BIG KAISER New Baby Chuck NBS13, an extremely high-precision through coolant collet chuck that demonstrates unparalleled accuracy, stability and run-out to within just a few microns.
With the drilling environment optimised, the next step was to select the optimal drill. The challenge for the ITC engineer was to introduce a drill with an effective chipbreaker to break the swarf of the medium tensile and strong steel that inherently creates chipping challenges – especially when tasked with drilling 111,000 holes. Drilling the 1/8inch (3.175mm) holes, ITC’s Simon Yeomans trialled one or two drills with different cutting data. However, it was the performance of the ITC Widia VDS403 drills that stood out. The solid carbide 8XD 30 degree helix drill with through coolant facility performed like a dream, evacuating the swarf with ease.
On this challenging project, the VDS403 drill from ITC processed more than 1200 holes before swarf control proved difficult – a sign that the drill needed re-sharpening. Thankfully for the West Midlands manufacturer, as a fellow UK manufacturer, ITC has the facility to regrind cutting tools to reduce tooling costs and waste for customers. Concluding the project, Neil Clifton adds: “As always, Simon from ITC has been at our side throughout this project, supporting our engineers with the right solution for the job. The ITC Widia drills have performed impeccably and we are delighted with the results. The speed, precision, concentricity and surface finish within the holes has enabled us to comfortably meet our deadlines and exceed the customers’ quality expectations. Furthermore, the tool life has been extremely impressive and this has contributed to reducing our costs on the project.” widia.com
As her kids fly the nest, Keri goes back to school to start a new chapter.
For the past 30 years, Keri dedicated all her time, love and energy to raising her kids. But at 53-years-old, her kids no longer needed constant care and she was looking to get back into the workforce to try something new.
Through a recommendation from Centrelink, Keri was encouraged to go to WISE Employment to help find her the perfect job. Employment Consultant and Business Manager of WISE Women, Lisa Ryan, realised upon meeting Keri that this was a customer who needed to think outside the box when it comes to her skill set for the next phase of her life. Keri was very keen to work and roll her sleeves up, but was at a bit of a loss as to what to do. She was also dealing with some things in her personal life that were impacting her career decisions.
Together they touched up her resume and started applying for a variety of positions. “I didn’t want to offer her a normal administrative or service-type role, encouraging her to have a go at learning a trade. I reassured Keri if it didn’t work out, at least we had a crack at it,” explains Lisa.
A position came available via AMTIL, as a Computer Numerical Control (CNC) operator training at Chisholm Institute in Dandenong. The course teaches students how to operate and maintain a numerically controlled computer, which follows a program to cut and shape metal. The course teaches engineering skills such as basic engineering measurement, inspection and workshop safety.
Keri always had an interest in auto mechanics and fixing cars, so she thought a hands-on, practical skill would be a good start. “I’m not a girly girl in the slightest,” says Keri. “If Lisa had suggested something like hairdressing I would’ve said that’s not going to work,” she chuckles.
Keri fell in love with the course straight away, learning how to use hand tools, chisels, saws, and filing, while exploring metrology and maths. “I suck at maths, but it’s an important part of the course, so I made sure I put my hand up and asked for extra help when I needed it,” says Keri.
Russell Morrison, teacher of Mechanical Engineering at Chisholm Institute Dandenong, noticed quite quickly that Keri was a standout student. “She showed up every day and had a willingness to go above and beyond – asking the ‘why’ questions and wanting to learn more outside the course curriculum,” says Russell.
Keri also toured the factories and the workshop environments, which solidified her love for the industry even more. “It gets me so excited – I’m even getting my kids to look into it. I’ve met highranking people in this field and can see with my own eyes that you can work your way up from the bottom to the top. All you have to have is an open mind and a willingness to learn,” she adds.
Given engineering is such a male-dominated industry, Keri is also humbled to be a part of the wave of women taking over the field. “When I was in my 20s and 30s, I couldn’t even be in a workshop with men, now look at me!” she laughs.
While Keri is sad the course is over, she is thrilled to have already found employment thanks to the help of WISE Women, AMTIL and Chisholm Institute Dandenong. “I’m not going to stop at one machine, I want to learn how they all operate and hopefully in time I’ll even be programming the machine myself!” she says. wiseemployment.com.au
Firing bricks and making mortar and cement is very costly, but organic chemists at Flinders University are working on more sustainable alternatives – focusing on building materials made from waste products.
In another move into the circular economy, researchers from the Flinders Chalker Lab have used low-cost feedstocks to make lightweight but durable polymer building blocks which can be bonded together with an adhesive-free chemical reaction.
Their latest study tested the strength of these materials and explored ways they can be reinforced in construction. Matthew Flinders Professor of Chemistry, Justin Chalker, says the need to develop sustainable building materials is increasingly important, with cement, iron and steel production accounting for more than 15% of global CO2 emissions each year.
“In this study, we tested a new type of brick we can make from waste cooking oil, mixed with sulfur and dicyclopentadiene (DCPD). Both sulfur and DCPD are byproducts of petroleum refining,” says project leader Professor Chalker. “The bricks bond together without mortar upon application of a trace amount of amine catalyst. All the starting materials are plentiful and can be classified as industrial waste. This research is part of a larger effort to move towards a sustainable built environment.”
The Chalker Lab's new polymer research team at Flinders University's College of Science and Engineering is collaborating with Clean Earth Technologies for further development. scale-up and possible commercialisation.
The latest study, published as a cover feature in a special issue on Sustainability in the journal Macromolecular Chemistry and Physics, expanded the research to test the new bricks’ mechanical properties and look at ways to reinforce them in construction, including with carbon fibre fillers. Chalker Lab research associate Dr Maximilian Mann says as well as repurposing waste materials
into value-added construction materials, the polymer bricks’ sulfursulfur bond means they can be bound together without mortar like traditional building method.
“The bonding in this novel catalytic process is very strong, producing a sustainable construction material with its own mortar which will potentially streamline construction,” Dr Mann says. First author Paris Pauling says the research is an excellent example of new scientific developments in sustainable materials science.
The paper, ‘Chemically Activated S-S Metathesis for Adhesive-Free Bonding of Polysulfide Surfaces (2022)’ by M Mann, PJ Pauling, SJ Tonkin, JA Campbell and JM Chalker is the lead article in the Sustainability edition of the journal Macromolecular Chemistry and Physics. chalkerlab.com
The Surftest SJ-210 is a user-friendly surface roughness measurement instrument designed as a handheld tool that can be carried with you and used on-site
• 2.4-inch colour graphic LCD with backlight
• Simple key layout
The Surftest SJ-210 can be operated easily using the keys on the front of the unit and under the sliding cover.
• Advanced data storage capabilities
• Optional memory card
• Password protection
• Multilingual support
• Stylus alarm
An alarm warns you when the cumulative measurement distance exceeds a preset limit.
Contact MTI Qualos today to learn more about the SJ-210 Series.
• Complies with many industry standards
The Surftest SJ-210 complies with the following standards: JIS (JISB0601- 2001, JIS-B0601-1994, JIS B0601-1982), VDA, ISO-1997, and ANSI.
• Displays assessed profiles and graphical data
In addition to calculation results, the Surftest SJ-210 can display sectional calculation results and assessed profiles, load curves, and amplitude distribution curves.
M.T.I. Qualos Pty. Ltd. 1300 135 539 or email sales@mtiqualos.com.au www.mtiqualos.com.au
Professor Justin Chalker. Photo: Randy Larcombe, 2021 SA Science Innovation and Excellence Awards (SA Government)Dwarf planet diamonds could hold the key to stronger machine parts.
Strange diamonds from an ancient dwarf planet in our solar system could lead to the production of ultra-hard machine parts, according to scientists.
This is a cool astronomical story with practical implications for the manufacturing industries of tomorrow. Researchers found the diamond in samples of ureleite meteorites. The meteorite had broken out of the interior of a destroyed dwarf planet. A dwarf planet (like Pluto or a large asteroid) is smaller than a regular planet like Earth or Mars. The diamond appears to have formed from a catastrophic collision. As temperatures and pressures decreased afterwards, the lonsdaleite replaced existing graphite crystals.
Strong fabrication begins with creating tough bonds at the polymer-level. Durable machine parts are today created in synethic production lines. CSIRO scientist Mr Colin MacRae said the discovery could have enormous implications for industries like mining. “If something that’s harder than diamond can be manufactured readily, that’s something industry would want to know about,” MacRae said.
A team of researchers, including those from Australia’s national science agency, CSIRO, has confirmed the existence of lonsdaleite in ureilite meteorites from the dwarf planet’s mantle.
Lonsdaleite is a rare, hexagonal-shaped diamond believed to be much stronger and harder than its more typical cubic cousin. Research led by Monash University, in collaboration with CSIRO, RMIT University, the Australian Synchrotron, and Plymouth University, was published today in the Proceedings of the National Academy of Sciences (PNAS).
The study provides clear evidence of lonsdaleite’s formation in nature, offering clues to synthetic production that could make more durable machine parts.
Lonsdaleite is named in honour of pioneering British crystallographer Dame Kathleen Lonsdale, though its existence has been a controversial topic.
This study, using a range of cutting-edge science techniques on the largest sample of ureleite meteorites to date, provides clear evidence of its existence.
At CSIRO, an electron probe microanalyser (EPMA) was used to quickly map the relative distribution of graphite, diamond, and lonsdaleite in the samples.
This flagship instrument, together with highresolution transmission electron microscopy (TEM) at RMIT University, helped identify the
largest lonsdaleite crystallites to date—up to one micron in size. CSIRO’s Dr Nick Wilson said this collaboration of technology and expertise allowed the team to confirm the lonsdaleite with confidence.
“Individually, each of these techniques give us a good idea of what this material is, but taken together—that’s really the gold standard,” Dr Wilson said.
The study, which was led by geologist Professor Andy Tomkins from Monash University, reveals a novel process in which the lonsdaleite is created, replacing graphite crystals in the dwarf planet’s mantle facilitated by a super-hot fluid as it cools and decompresses. “We propose that lonsdaleite in the meteorites formed from a supercritical fluid at high temperature
and moderate pressures, almost perfectly preserving the textures of the pre-existing graphite,” Professor Tomkins said. “Later, lonsdaleite was partially replaced by diamond as the environment cooled and the pressure decreased,” he said.
Typically containing large abundances of diamond, ureilite meteorites are arguably the only major suite of samples available from the mantle of a dwarf planet.
The parent asteroid was catastrophically disrupted by a giant impact while the mantle was still very hot, creating the ideal conditions for lonsdaleite then diamond growth as the pressure and temperature decreased in a fluid and gas-rich environment csiro.au
It could be the most profitable hour you spend on your business.
Many business owners, CEOs and Managing Directors find themselves spending a large percentage of time working on day to day tasks which, while critical, don't necessarily improve performance, business value or contribute towards the business strategy.
The William Buck Hour is designed to assess your current business position, realign thinking and maximise potential We'll guide you through a detailed discussion on a range of fundamentals including: Financial management Funding Regulatory requirements, and Succession planning
Following the session, our advisors will use commercial insights, professional experience and best practice standards to conduct an analysis of your business and present you with a personalised written report.
Contact us today to book your complimentary William Buck Hour
Ian Cattanach Director Business Advisory Ph: 03 8823 6975
ian cattanach@williambuck com
Jeremy Raniti Senior Manager Business Advisory Ph: 03 8823 6838 jeremy raniti@williambuck com
Tamara Cardan provides a reminder to businesses to review their contractor and employee arrangements in light of State Revenue Office payroll tax compliance investigations.
More recently, we have observed an increase in State Revenue Office (SRO) investigations regarding payroll tax compliance.
The current focus of the SRO provides a timely reminder for businesses to review their arrangements with contractors and employees and to ensure they are meeting their payroll tax obligations.
The payroll tax legislation contains exemptions and other forms of relief for businesses.
Relevantly for those who work with or as transport and delivery services in the manufacturing industry, this article examines:
• the payroll tax exemption for owner-drivers; and
• the lower payroll tax rates applicable to ‘regional employers’.
Payroll tax is a state-based tax imposed on employers and calculated on wages paid to employees. Victorian employers who pay wages which exceed the monthly threshold of $58,333 (or the annual threshold of $700,000) will be liable to pay monthly payroll tax at the rate of 4.85%.
To assess an employer’s payroll tax liability, it is necessary to distinguish between employees and contractors. Typically, a worker who is engaged via a company or trust would not be considered an employee and may instead be a contractor.
However, even if you only engage contractors to perform services for your business, you may still have a payroll tax liability on payments made to these contractors if the arrangement constitutes a ‘relevant contract’.
Under the Victorian payroll tax regime, any amounts paid to contractors pursuant to a ‘relevant contract’ are deemed to be taxable wages on which payroll tax is imposed, with the business engaging the contractor deemed to be an employer.
This is the case irrespective of whether the contractor provides their services via a company, trust, partnership or as a sole trader.
However, certain types of contracts are specifically exempt from this treatment. Where an exemption applies, there will be no payroll tax liability on payments made to contractors.
If your business engages owner-drivers for the provision of transport and delivery services, you may be eligible for an exemption on this basis.
Payments made to owner-drivers who provide transport and delivery services will be exempt from payroll tax if:
• the vehicle provided by the contractor is not owned or leased by the principal;
• the principal makes no contribution to the capital or running expenses of the vehicle; and
• the main purpose of the contractor’s work is the transportation and delivery of goods.
To qualify for the exemption, it is not necessary that the contractor own the vehicle outright; the vehicle may be leased to, or hired by, the contractor.
If, however, the owner-drivers convey goods for the purpose of installation at the point of delivery, or for use in connection with
repair, maintenance or servicing work, the SRO considers the ‘main purpose’ of the contract is not the actual conveyance of the goods but rather the installation or repair/maintenance work.
If your business currently claims this exemption, we recommend that your entitlement to this exemption be reviewed with respect to your contractor arrangements, given the current SRO compliance focus.
A lower payroll tax rate applies to taxable wages paid by ‘regional employers’ to their ‘regional employees’. For wages paid from 1 July 2021, the rate is 1.2125% (as opposed to the general rate of 4.85%).
A ‘regional employer’ is an employer that pays at least 85% of their Victorian taxable wages to regional employees. A ‘regional employee’ is an employee who performs more than 50% of their services in regional Victoria during the month.
For example, if the majority of your employees regularly travel to regional Victoria when providing transport and delivery services, and spend the majority of their time in regional Victoria, you may wish to review your entitlement to access reduced payroll tax rates.
Previously, it was also necessary that the ‘regional employer’ was based in regional Victoria. This is no longer the case – a ‘regional employer’ can be physically based in metropolitan Melbourne – with the sole focus being on the location of the services performed by its employees.
Rigby Cooke Lawyers’ Tax team can assist you with reviewing your payroll tax obligations, including entitlement to the ownerdriver exemption, or whether you may be eligible to access the reduced rates applicable to regional employers.
Tamara Cardan
Tax Counsel
T: +61 3 9321 7862
E: TCardan@rigbycooke.com.au
Tamara Cardan is a Tax Counsel at Rigby Cooke Lawyers with over 12 years of tax expertise.
We have observed an increase in State Revenue Office (SRO) investigations regarding payroll tax compliance
Alan Girle, Special Counsel at Macpherson Kelley, provides a qualified view of workplace safety laws and prosecutions, including mines, quarries and other worksites.
Since 1 July 2018, businesses and their Executives have been bound by the industrial manslaughter laws. The industrial manslaughter laws attract significant penalties of up to 20 years imprisonment and fines up to $10m if the employer is to be seen as at fault.
This being said, the laws are significantly different from the remainder of the provisions in the Work Health and Safety Act 2011 and can be viewed in isolation. Under the industrial manslaughter laws, an employer commits an offence if:
(1) a worker dies from injuries suffered at work; and (2) the employer’s conduct causes the death; and (3) the employer is negligent.
A similar offence exists for a Senior Officer of the corporation.
With either offence, it does not matter that the person charged did not intend the death and they may still be liable even though the person’s conduct was not the sole cause of the death. More importantly, by “imputation”, the conduct of another person can be held to be the conduct of the business. Even the actions of a person not employed by the business, can be relied on by the prosecutor if their actions appear to have the authority of the business charged.
A charge of industrial manslaughter is classified as a “crime”. This means a person can be arrested before being charged, may be held in custody until trial, or alternatively, may be compelled to surrender their passport as a condition of bail. Employers may not realise the culpability of running a high safety risk environment and indeed that the conduct of their employees may result in their arrest and custody as they await to be tried in a criminal trial.
The process of investigating and prosecuting a person for industrial manslaughter is a long one. In the recent prosecution of Jeffrey Owen, it was approximately three years from the date of the offence until the date he was sentenced to five years imprisonment. Owen has appealed the decision, so it may be significantly longer before the case is finally resolved. In the prosecution of Owen, he was granted bail prior to hearing, but had he not been granted bail, it would have been a long wait in prison.
When considering the potential for an industrial manslaughter charge, it is important to note that for other offences under the Act, if the prosecution is unsuccessful the WHS Prosecutor may be ordered to pay the defendant’s legal costs. For industrial manslaughter prosecutions, if the jury finds the defendant not guilty, the defendant will be unlikely to recover any legal costs. In addition, in industrial manslaughter prosecutions, the reasons for the jury making findings of fact are often never known. Consequently, there is insignificant risk of a statement about whether the WHS Prosecutor failed to prove specific facts. In other words, both from a cost and reputational perspective, a prosecution for industrial manslaughter is a less risky form of prosecution for the WHS Prosecutor.
The existence of the industrial manslaughter provisions does not mean that businesses and their Executives will necessarily be charged with an industrial manslaughter offence. From a statistical perspective, charges are more frequent under the other provisions of the Act and an industrial manslaughter charge can only occur where there has been a death. That being said, the risk should be taken seriously enough to elicit the implementation and review of risk management strategies on a regular basis.
To further reduce the risk of industrial manslaughter charges, businesses should:
1. Ensure that a risk assessment of the businesses operations has been undertaken to identify those activities that could potentially cause a death.
2. Start thinking about how the business and of the Executive Officers, could demonstrate the exercise of reasonable precautions and proper diligence.
3. Where a death occurs:
a. take the incident extremely seriously; b. secure the scene and render it safe; c. immediately get professional help; and d. notify in accordance with obligations.
In the fog of emotion that comes with a fatality, applying these simple steps can be difficult. It can be useful to take early steps to protect yourself and the business against the risk of prosecution be reviewing and potentially modifying the:
• role of the person recognised as the ‘operator’ under the legislation;
• role of anyone who funds or controls the operations of the site;
• safety and health management system;
• management structure; and
• standard terms of engagement of contractors.
Industrial manslaughter offences are not unique to the Work Health and Safety Act 2011. They appear in many other Queensland statutes and across Australia and are a common feature of modern regulatory frameworks. As such, it is important for businesses and Executives, to understand their risk profile and to develop mechanisms to eliminate or where not possible minimise the risk. Worksites are no exception to this legislative burden and the time has come to proactively manage those risks.
Macpherson Kelley is a full service commercial law firm on the East Coast of Australia, committed to helping its clients succeed. Our lawyers take the time to get to know each client’s business and to understand the commercial drivers behind every matter. Our firm is pragmatic in the advice we give and bold in our recommendations. This considered approach enables our lawyers to develop practical and innovative solutions – every time.
info@mk.com.au
Alan.girle@mk.com.au 07 3235 0409
Brisbane: 07 3235 0400; Melbourne: 03 8615 9900 Sydney: 02 8298 9533 mk.com.au
Manufacturers and distributors closing the Industry 4.0 skills gap using digital transformation. Rob Stummer explains.
In an ideal world, manufacturers and distributors would all be embracing Industry 4.0. Machines and business functions would have the right technologies in place to be interconnected to autonomously manage production, improve efficiencies and improve the customer experience. But the reality is that the true benefits of Industry 4.0 cannot be realised if employee skills sets are not matching the rate of digital growth due to staff working with legacy systems and investment in skills development and training to enable a digital workforce.
An employee on a 1.0 level operates on a manual or paper-based legacy system, whilst a 2.0 employee is a digital explorer that may use some technology on a project basis. Employee 3.0 has access to optimised machinery and devices but may not have a full picture of what is happening across the business. The ideal level, employee 4.0 thinks and behaves around real-time data and they apply these skills to the workplace.
The Federal Government’s Senate Economics References Committee 2022 report into the Australian manufacturing industry states that Australia's manufacturing sector has the advantage of a highly skilled workforce, which positions local businesses well for a transition towards high value add products and advanced manufacturing. However, there are skills shortages that the Committee recommends addressing through the development and implementation of a national action plan that will include improving skills and training quality and delivery, responsiveness and collaboration with industry; address skills shortages; and ensure that VET courses, particularly in occupations with current or forecast skills shortages, are accessible and affordable. Manufacturers and distributors need to realise for the industry to capitalise on digital transformation, a corresponding transformation within the workforce is required to ensure emerging skills can reach a 4.0 level. Preparing for the future of work should become an integral part of every organisation’s digital strategy as technology alters the way the work is done.
The digital transformation of a business requires an increase in human centric skills for it to function properly. Research shows that the top jobs for the next 10 years will rely heavily on human characteristics such as communication, creativity, flexibility, critical thinking and innovation. To identify the workplace skills that manufacturers and distributors need as their business embraces Industry 4.0, an analysis of employee skills and their skills gap can help identify whether staff require upskilling or reskilling.
When investing in improving the digital skills of a workplace, manufacturers and distributors should take into account the required ‘human’ skills to balance the digital skills investment into technical needs like data-driven tools for analytics and planning.
Building the foundations of the future smart factory workforce
A common issue among manufacturers and distributors is that they embark on digital transformation without assessing their inhouse resources and fail to invest the appropriate time and money in employee training and upskilling opportunities.
SYSPRO’s latest global research report ‘Realigning the links of the disconnected supply chain’ reveals only 38% of manufacturers and distributors have upskilled their staff to use new systems to improve business operations during any disruptions. The study also shows that 61% of businesses had no intention of building long terms skills training programs to enable a digital workforce.
Technology itself can be used to assist an employee 1.0 in becoming skilled to operate in Industry 4.0. Organisations can do this by encouraging the use of digital tools like low code to support innovation. Low code tools are software application design tools that can connect to an Enterprise Resource Planning (ERP) system to make it easy for employees to build, design and launch applications without the need for an in-house coding specialist. These tools can be used to improve operations across the business by transforming processes and improving efficiency.
As more millennials and Gen Zs enter the workplace, their experience of being raised in the digital age, could be harnessed to provide practical leadership to those less digitally skilled employees in the workplace.
Like any aspect of company culture, fostering a digital-savvy mindset will take time to accomplish. The first step is to get leadership and the C-suite to not only drive digital transformation but to ensure that the workforce is also digitally transforming in the same direction. Technology such as ERP systems can help ease employee stress and make it easier for employees to reach 4.0 where they can manage and leverage the data that’s coming in from their factories, inventories, and raw materials, and from signals along the supply chain. Consequently, this will remove the risks of human error as there will not be a need to track operations via spreadsheets.
Manufacturers and distributors simply cannot avoid the rise of Industry 4.0 as it will help them remain globally competitive. However it’s vital that the workplace has the right skills and technologies to fully leverage the commercial and industry benefits of Industry 4.0. This may take time for a sustained investment but with the right strategies and easing the transition to support employees, manufacturers and distributors can reap the rewards over the long-term.
Rob Stummer is Chief Executive Officer, SYSPRO APAC. With SYSPRO Enterprise Resource Planning business software, a full view of all business activities is gained, including financial, warehouse and inventory management, across supply chains and business operations, specialising in the manufacturing and distribution sectors.
au.syspro.com
Early identification of business distress indicators can give a business a chance of turning things around and prevent Directors potentially becoming personally liable for the debts incurred by the business. Garth O’Connor-Price explains.
Below, we focus on the indicators to look for to assess business distress and how to discuss these issues with your trusted advisors.
Trading losses are not always an indicator of insolvency, however if not addressed, will erode a business’ liquidity and potentially pose a threat to solvency. Where trading losses are apparent, you need to identify who is funding the losses. Is a company director or related party funding the losses? If so, is this sustainable and is the funding being made with a deliberate strategy or is it just making the hole bigger? Is the business not paying certain creditors? This is not a long-term strategy and if creditor management is required in the short term, it is important to assess a creditor’s will and skill to affect the business and manage the relationship accordingly.
Is third party finance being used or needed? Does the funding provide enough runway to turn things around? If not, question whether the funding is doing more harm than good.
A profitable business on paper may still be burning cash. If it is, you need to determine whether you’re facing a temporary lack of liquidity or an endemic shortage of working capital.
When discussing cash flows, the focus should be on:
1. Whether poor debtor collections are a result of lack of focus / effort in collection process, customer credit issues or low product or service quality?
2. How quickly is inventory turned over and whether any redundant stock exists that can be liquidated?
3. What is the tipping point for enforcement action by a creditor not being paid on time and what actions are available to creditors?
4. Is there any capex that can be deferred or non-core assets that can be sold?
5. Do the current financing facilities align with current funding needs or were facilities structured at a time when the company was in a more stable position?
Hope is not a strategy and chasing revenue just to ‘feed the beast’ could impact margins and profitability and exacerbate financial distress. Margin, working capital requirements and capacity should be given equal weighting with top line revenue in assessing new work in times of distress.
‘Strategic’ contracts that offer longer term benefits at the expense of the short term should be avoided and nothing erodes liquidity quicker than delayed payments, withheld having retentions and getting bogged down in contractual disputes.
Inability to produce timely and accurate financial information
Bad data leads to bad decisions. If a business is unable to produce timely data on its financial position, rarely is the prognosis going to be better than expected. Most companies experiencing financial distress won’t be able to completely revamp their financial reporting systems. This means that in the short-term, cash flow reporting should be the focus rather than profit and loss. Directors should take control of this reporting and not delegate the responsibility.
This will allow them to closely guard cash outflows and pull the right levers to increase cash inflow. Measuring actual performance to forecasts will create accountability within the business.
The physical appearance of and morale within a business may decline as a business slips into financial distress. Maintenance and firm culture may move down the priority list as the directors fight fires elsewhere in the business. This decline is likely to be a gradual process but be obvious to stakeholders that only visit occasionally. The confidence of stakeholders, such as customers and suppliers, will have a bearing on the prospects of the business.
A company’s solvency is not limited to the cash resources immediately available to pay debts. Hence, understanding what money can raised by way of debt or equity injections is a key consideration in assessing solvency.
In terms of funding and finance, red flags that could trigger a conversation about the risk of insolvency include:
• Inability to seek further funding from current financier.
• Rejection of request to rollover a facility.
• Unable to refinance with alternative financier.
• Funding obtained with costs well in excess of market rates, and
• Due diligence by investor raises concern about business model or that balance sheet is beyond repair.
As cash flow dries up, decisions may need to be made on which creditors are paid. A supplier’s behaviour can have a greater bearing on the company’s ability to trade in the short term and therefore the squeakiest wheel often gets the oil first.
Inevitably this means that when taxes become due, payment is moved down the priority list. The first instance of deferring statutory debts is something to look for when assessing solvency and this should give Directors pause to think about the long-term viability of their business.
Legal action will be the last step in creditor disputes and often, due to commercial considerations, disputes will not escalate beyond informal demands and negotiations. Insolvency is likely in play well before formal legal action is taken by creditors.
Suspicions of insolvency should be raised upon the occurrence of:
• Significant aged creditor ledger
• Creditors stopping of supply or implementing cash upon delivery terms
• Material changes of terms and rates to recoup losses, and
• Special payment arrangements with creditors.
Garth O’Connor-Price is a Director, Restructuring and Insolvency at William Buck. William Buck is a leading firm of accountants and advisors.
Ph: 03 9824 8555
williambuck.com
IMTS in Chicago is one of the major machine tool/manufacturing technology exhibitions in the world and this year, along with our AMTIL stand and delegation, we had two companies exhibiting and showcasing their products to the world.
ANCA and Agile Robotic Systems are two great Australian companies. ANCA have been manufacturing CNC tool and cutter grinders since 1975 and have established themselves as the global leader of these products. So to see them again represented at an international exhibition and performing so well was no surprise.
Agile Robotic Systems are a relative newcomer, albeit with a strong backing. They are an American headquartered company which develops, builds, sells and supports CNC Machine Tool Loading Systems and Robotic Automation Systems. A wholly owned subsidiary of John Hart Australia, they are able to draw upon John Hart’s heritage of over 70 years in machine tools, and close to 40 years in automation and robotics.
112 AMTIL INSIDE AMT OCT 2022 The AGILE FLEX Systems can be rapidly deployed, and are easy to program. Compact and affordable, they have developed a niche market as automation and robotics becomes a more critical part of the production cycle.
AMTIL once again had a stand in the International Association Pavilion and spent the week catching up with our international colleagues, attending meetings and answering the questions from delegates visiting the stand. Our booth always doubles as a base for the 20-odd Australian delegates who attended the show this year. The overall feedback from the exhibition was that, whilst visitor numbers were slightly down on expectations, the quality of delegates was high and the outlook was positive.
13 Oct, 2022 AMTIL’s AGM (Melbourne) & Guest Speaker @ Riversdale Golf Club, Mt Waverley, Victoria
19 Oct, 2022 AMTIL (Brisbane) Australian Manufacturing Network event @ Belle Epoque, Emporium Hotel, South Bank, Brisbane
20 Oct, 2022 AMTIL (Sydney) Australian Manufacturing Network event @ Bar30, Parkroyal Parramatta
3 Nov, 2022 Women in Manufacturing Oaks Day Lunch in Melbourne @ Left Bank, Southbank
The Ambrose event will once again be hosted at the amazing Riversdale Golf Club in Mt Waverley, Victoria.
There will be a morning tee off followed by lunch and some presentations. All abilities are welcome to play. You can be placed in a team by the organisers or gather a team of four of your own. Placed are limited and preference will be given to AMTIL members if demand exceeds availability.
Winner, Winner, Chicken Dinner! Big congrats goes out to Tungaloy Australia who has taken the chocolates in AMTIL's 2022 Footy Tipping comp… by one point! This one point thing has gone a tad nuts… Collingwood denies Carlton a spot in the finals by one point, Collingwood loses their preliminary final by one point, Patrick Cripps secures his first Brownlow Medal, by (you guessed it) – one vote! The AFL Finals have been a cracker so far with many a tight game and now hope the Grand Final lives up to the expectations of the two best teams who have both been undefeated for some months now, to deliver one for the ages… then the silly (trade) season starts. Has Grundy played his last game as a Magpie? The exits from Freo havebeen extraordinary given their successful season, can the Tiggies march back up the ladder with so many trades nominating them as their preferred club? – We'll see in 2023. Till next time… Sanchez
AMTIL found some great venues for members to gather for our Networking events in Sydney, Brisbane, Adelaide, Perth and then Melbourne.
These AMTIL State Networking events get better and better. Melbourne turned it on for us with some great weather and a ready crowd of manufacturers, coming together finally to catch up after such an unsure couple of years. The Melbourne AMTIL
event was staged at the Boatbuilders Yard on the Yarra riverfront and there was a steady stream of food and drinks to help the conversation along. So great to see so many faces and hear stories of new projects coming together. Some new names and
some other established members guiding the way. It was marvellous to hear many of these companies haven’t slowed down at all, and this means there’s a better year ahead.
Melbourne AMTIL crowd at the Boatbuilders Yard on the Yarra.Due to the ongoing Coronavirus pandemic, many industry events world-wide have been postponed, rescheduled or cancelled. Readers are advised to check with all event organisers for the latest information. For the latest international travel advice, please visit health. gov.au/health-topics/novel-coronavirus-2019-ncov – For more events, please visit amtil.com.au/events
BI-MU Italy, Milan 12-15 October 2022 bimu.it
IMT Taiwan, Kaohsiung 19-21 October 2022 imttaiwan.com
METAL MADRID 2022
Spain, Madrid 19-20 October 2022 metalmadrid.com/en
INAWELDING Indonesia, Jakarta 19-21 October 2022 inawelding-exhibition.net
EUROBLECH 2022 Germany, Hanover 25-28 October 2022 euroblech.com
CEMAT China, Shanghai 1-4 November 2022 International trade fair for materials handling, automation, transport and logistics, cemat-asia.com
ADVANCED MANUFACTURING
USA, Minneapolis 2-3 November 2022 advancedmanufacturingminneapolis.com
WARSAW INDUSTRY WEEK Poland, Warsaw 7-9 November 2022 industryweek.pl
FABTECH EXPO
USA, Atlanta 8-10 November 2022 fabtechexpo.com
JIMTOF Japan, Tokyo 8-13 November 2022 jimtof.org
ADM Canada, Montreal 9-10 November 2022 admmontreal.com
DMP GREATER BAY AREA
INDUSTRY FAIR China, Shenzhen 9-12 November 2022 dmpsz.com
CINCE 2022 India, Gujarat 11-13 November 2022 kdclglobal.com/cince-2022.html
FORMNEXT Germany, Frankfurt 15-18 November 2022 formnext.mesago.com
METALEX
Thailand, Bangkok 16-19 November 2022 metalex.co.th
METEC INDIA India, Mumbai 23-25 November 2022 metec-india.com
POWDER METALLURGY Germany, Hagen 24-25 November 2022 pulvermetallurgie.com
MANUFACTURING INDONESIA Indonesia, Jakarta 30 November-3 December 2022 manufacturingindonesia.com
ALUCAST India, Chennai 1-3 December 2023 alucastexpo.com
CHINA COAT China, Guangzhou 6-8 December 2023 Coating technology exhibition chinacoat.net
STEELFAB UAE, Sharjah 9-12 January 2023 steelfabme.com
IMTEX India, Bangalore 19-25 January 2023 imtex.in
ASIAMOLD China, Guangzhou 1-3 March 2023 asiamold-china.cn.messefrankfurt.com
ALL ABOUT AUTOMATION Germany, Friedrichshafen 7-8 March 2023 automation-friedrichshafen.com
INTERMOLD Japan, Tokyo 12-15 April 2023 intermold.jp
HANNOVER MESSE Germany, Hannover 17-21 April 2023 hannovermesse.de
KOREA MAT Korea, Goyang 17-21 April 2023 Exhibition for the logistics industry koreamat.org
TAIWAN INTERNATIONAL FASTENER SHOW Taiwan 3-5 May 2023 fastenertaiwan.com.tw
AISTECH 2023 USA, Michigan 8-11 May 2023 iron and steel technology conference/ exposition aist.org
STAINLESS Czech Republic 10-11 May 2023 bvv.cz/de/stainless
INTERMACH & MTA ASIA Thailand, Bangkok 10-13 May 2023 intermachshow.com/2022
EASTEC USA, Springfield 16-18 May 2023 Ieasteconline.com
MACH-TECH Hungary, Budapest 16-19 May 2023 Parnapjai.hu/en
WIN EURASIA Turkey, Istanbul 7-10 June 2023 win-eurasia.com/tr
METEC Germany, Dusseldorf 12-16 June 2023 Metec.de
THERMPROCESS Germany, Dusseldorf 12-16 June 2023 thermprocess.de
MOULDING EXPO STUTTGART Germany, Stuttgart 13-16 June 2023 messe-stuttgart.de
MANUFACTURING EXPO Thailand, Bangkok 21-24 June 2023 manufacturing-expo.com
MTA VIETNAM Vietnam, Ho Chi Minh 4-7 July 2023 www.mtavietnam.com
WA MINING PERTH CONVENTION & EXHIBITION CENTRE
10-12 OCTOBER 2022
Exhibition will showcase the technical and digital innovation across the entire mining value chain, while illustrating the economic importance of WA. waminingexpo.com.au
SYDNEY ICC
23-25 OCTOBER 2022
Discover over 450 exhibitors showcasing the latest food, drink and equipment. foodserviceaustralia.com.au
AUSTRALIA
MELBOURNE, MECC
26-27 OCTOBER 2022
Co-located with All-Energy Australia, offers waste management, sustainability, clean energy and energy management information. wasteexpoaustralia.com.au
PERTH CONVENTION & EXHIBITION CENTRE
26-28 OCTOBER 2022
Australia’s biotech industry is world leading. Local and international speakers in biotechnology and life sciences.Themes have included regenerative medicine, cell and gene therapies, investing, IP, precision medicine, clinical trials, digital health, medical technology, and agri-biotechnology. ausbiotechnc.org
IMARC ICC SYDNEY
2-4 NOVEMBER 2022
The International Mining and Resources Conference. From ground-breaking technology, world-class content, to a vivid showcase of all the elements. imarcglobal.com
PERTH CONVENTION CENTRE
29-30 NOVEMBER 2022
Construction managers, project directors, consultants and investors learning about what projects are in the pipeline across WA. Waconference.com.au
BRISBANE CONVENTION & EXHIBITION CENTRE
5-7 DECEMBER 2022
Premier rail industry event in Australasia, bring industry together. Ausrail2022.com
AVALON AIR SHOW GEELONG, AVALON AIRPORT, VIC 28 FEBRUARY – 23 MARCH 2023 Airshow.com.au/airshow2023
SYDNEY BUILD EXPO
SYDNEY ICC 6-7 MARCH 2023
Australia's construction, architecture, engineering and infrastructure industries. Contractors, architects, engineers, housebuilders, developers, government and construction professionals. sydneybuildexpo.com
ICC SYDNEY
9-11 MAY 2023
Bringing together Australia’s architecture, building, construction and design communities. Co-locating with Total Facilities and The Built Environment Summit. Bringing brands, products and innovations from conception to construction and beyond. Includes the new Digital Building Zone. designbuildexpo.com.au
Advertiser Index
600 Machine Tools 1
Air Liquide 17
Applied Machinery 15
Aurarum 55
BJC Machine Tools 53
Bystronic 11 Capral 13
CNC Design 59
Complete Machine Tools 39
D&D Barry 114
Development WA 49 Die Mould Equipment 21 ECI 35
Epicor 114
EPOL 93 Hare & Forbes 4-5
HiTech Metrology 43 IDW Cadcam 81 IMTS 9
Integra 67
Jim's machines and Accessories 57
Laser Machines 119 Laser Things 61 LRQA 73 M Gamer 47
Machinery Forum 120 Marsh Alliance 85 MTI Qualos 69, 105
New Touch Industries 77
Okuma 7
OPEN IIoT 114
Rigby Cooke 115 Romheld 114 Sandvik 91 Seerpharma 51 Sterna 101
Sutton 97
William Buck 107 Markforged Insert Industrial Laser Insert
There has never been a more important time to ensure you are well marketed to industry and ready when opportunities open up. Reach out to 31,500 targeted readers and 63% decision-makers.
I would be delighted to have a non-obligatory chat on how we can help.
Nicholas Raftopoulos: 0431 753 381
AGRICULTURE,
STATE SPOTLIGHT:
PLASTICS
ROBOTICS
BUSINESS
WORKHOLDING
CUTTING TOOLS
FORMING
SOUTH WALES
FABRICATION
MATERIAL REMOVAL
In London I linked up with LieutenantColonel G. C. Rowe, an Australian from the Munitions Department; who was in England to put forward Australia's case for the supply of equipment. Rowe arranged for me to meet senior officers in the many technical branches of the British Army at the War Office in Whitehall.
There were about forty officers - generals, brigadiers and colonels - representing all branches of the Army, waiting for me in one of the very large planning rooms at the War Office. A general introduced me, and I spoke for nearly an hour on military equipment in the Pacific and its maintenance, and on our munitions production. As in America, I tried to be as informative as possible. I got into technical matters immediately and, with these technical men, had a most attentive audience. Many of them had notebooks and they scribbled furiously.
I emphasized that in New Guinea, in particular, with its jungle conditions of high humidity and temperature, fungus growth on equipment was almost as tough an opponent as the Japanese. "Radio and electrical equipment coming from England isn't worth a tinker's cuss unless it has been thoroughly tropic-proofed beforehand," I said. This was elementary stuff to Australians, but the British had had little occasion to do research on anti-fungus protection, and they were very interested.
I told them, "It's almost impossible to reproduce jungle conditions in England by artificial means. You won't get the same effect by subjecting material to steamboxes, for example. Fungus is a living thing. The best place I can think of for testing your material here would be the tropical house at Kew Gardens. I'm sure you'd find conditions there ideal for stimulating fungus growth."
A few days later one of the generals rang me and said, "Oh, Hartnett, you've really started something. Most of the chaps who heard your talk the other day have been sending truck-loads of equipment to Kew Gardens to be hung up among the orchids for a week or so. The Kew Gardens people are screaming mad. They don't know who suggested it, but they'd like to wring his neck."
In the UK, the courtesies, the hospitality and, in particular, the real desire to help, were overwhelming. The good old British Navy took the lead. From the first day, a Rear-Admiral Engineer Perring was specially assigned to take me around, and he did this very thoroughly. We covered every aspect
After the entry of Japan into the war, materiel was quickly transported by the Allies to East Asia, Africa, The Mediterranean and The Middle East. The hot, humid conditions there were very different from those of Europe or North Africa and were ideal for the growth of fungal infections on equipment. While military masterminds were mapping the Battle for Normandy, scientists were working on classified experiments to protect army supplies (telecommunications, boots, parachutes etc,) from the ravages of rot and mould. Radio sets, for example, failed completely and in the confusion of the resulting breakdown of communications, advanced parties became lost.
On another occasion Allied troops attempted to attack the Japanese with hand grenades, only to find the grenades fail completely. An equally disastrous experience occurred with mine detectors. Optical instruments, even though sealed, were liable to internal fungal damage and well-assembled instruments sometimes lasted only a few weeks before becoming inoperable.
In February 1944, the UK Ministry of Supply convened a secret conference on the prevention of mould growth. The secrecy demonstrated the sensitive nature of the work and was intended to provide the Allies with an advantage over hostile forces. Australia’s help proved vital.
of torpedo-manufacture whether it was at Peterborough, Rochester or Scotland.
I recall a vivid character: Colonel Shepherd, the man responsible for the Sten Gun, and later the Polsten. Shepherd knew rifles - he had been at the Small Arms Factory at Enfield -but he had the courage to throw aside all the normal methods of manufacture so that large quantities of submachine-guns could be made a quicker and easier way. It was Colonel Shepherd whom Churchill summoned after Dunkirk to get more rifles somehow, and in the corner of Shepherd's office was the original bayonet bound on to a broom-handle as a souvenir of all there was then available at that time.
The "S" of the Sten Gun is for "Shepherd"; the "en" for "Enfield". The "Pol" of "Polsten" comes from the fact that Shepherd had several competing teams of designers
and draftsmen at the Council Buildings at Walthamstow, including a team of Polish fellows, and the Poles won that round for a low-cost, easy-to-make twenty-millimetre fast-firing gun.
The Minister of Production, Mr. Oliver Lyttleton, impressed me by his knowledge and appreciation of what Australia was doing in munitions production. It was he who caused the optical and instrument sections to follow in detail how we had been able to produce such a wide range of excellent optics and gun-sights in so short a time. The volume-production of Dial Sight 9A used on the twenty-five-pounder gun had certainly made a name for Australia.
After five weeks with plenty of enemy blitz, I flew back to the U.S.A. and then back to Australia by air from San Francisco.
To be continued…
This is an extract from ‘Big Wheels & Little Wheels’, by Sir Laurence Hartnett as told to John Veitch, 1964. © Deirdre Barnett.
Laurence’s overseas adventures during the hectic days of WW2 continue. Next stop: London where a novel method of testing military equipment for tropical fungus-protection is proposed by Laurence. PART 51 Big wheels & little wheels – the story of UK-born Australian Sir Laurence John Hartnett (1898 – 1986) Australia’s “Father of the Holden” and much more