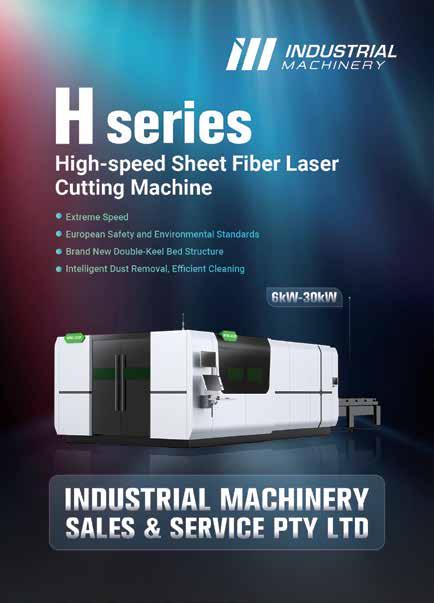
POWER SHIFT
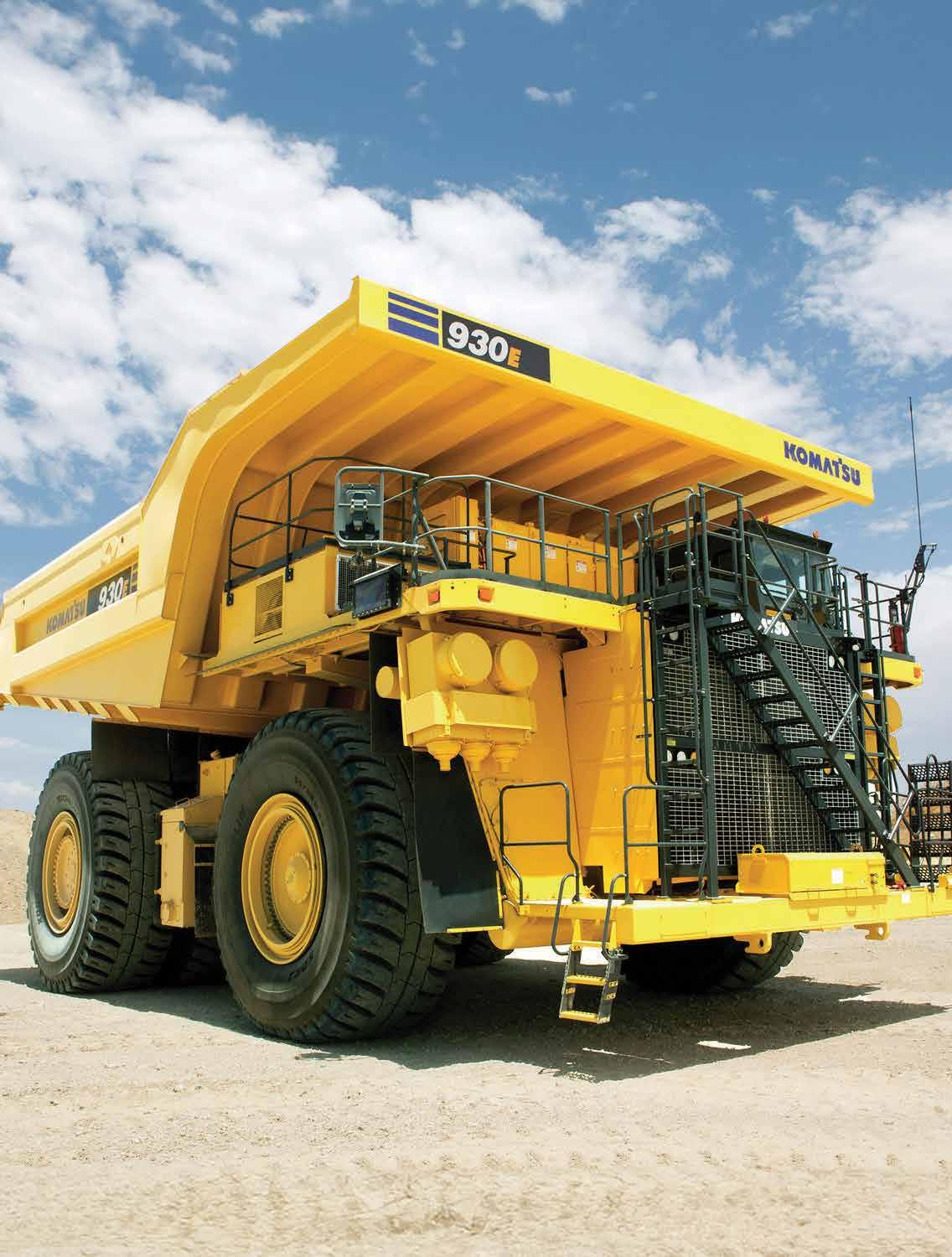
MINING & RESOURCES
Transport & Logistics
State Spotlight: Queensland
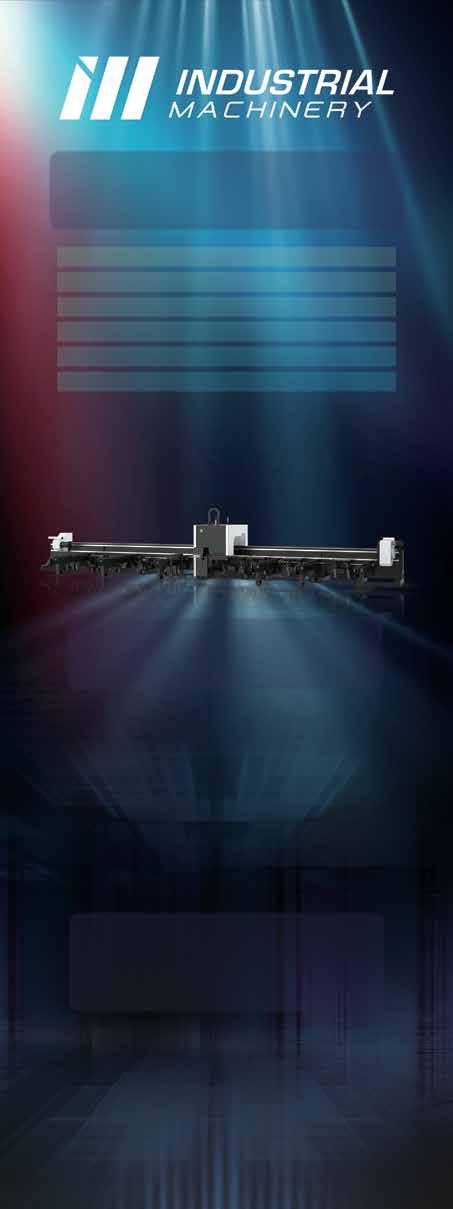
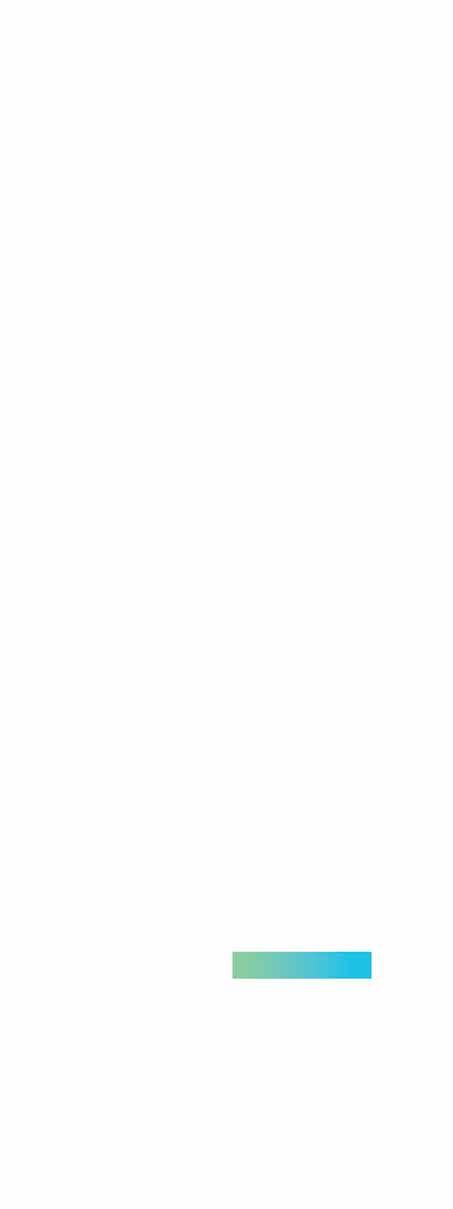
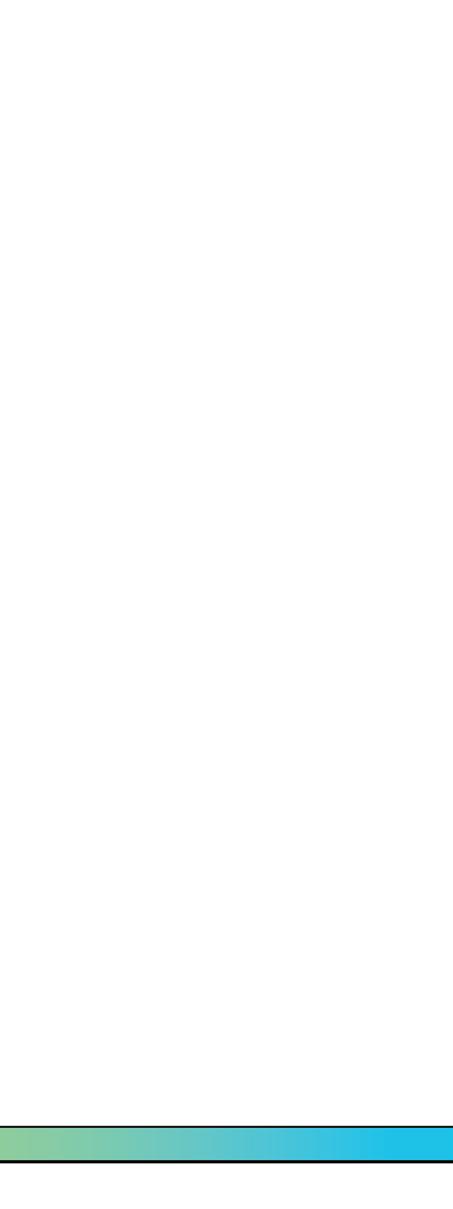
POWER SHIFT
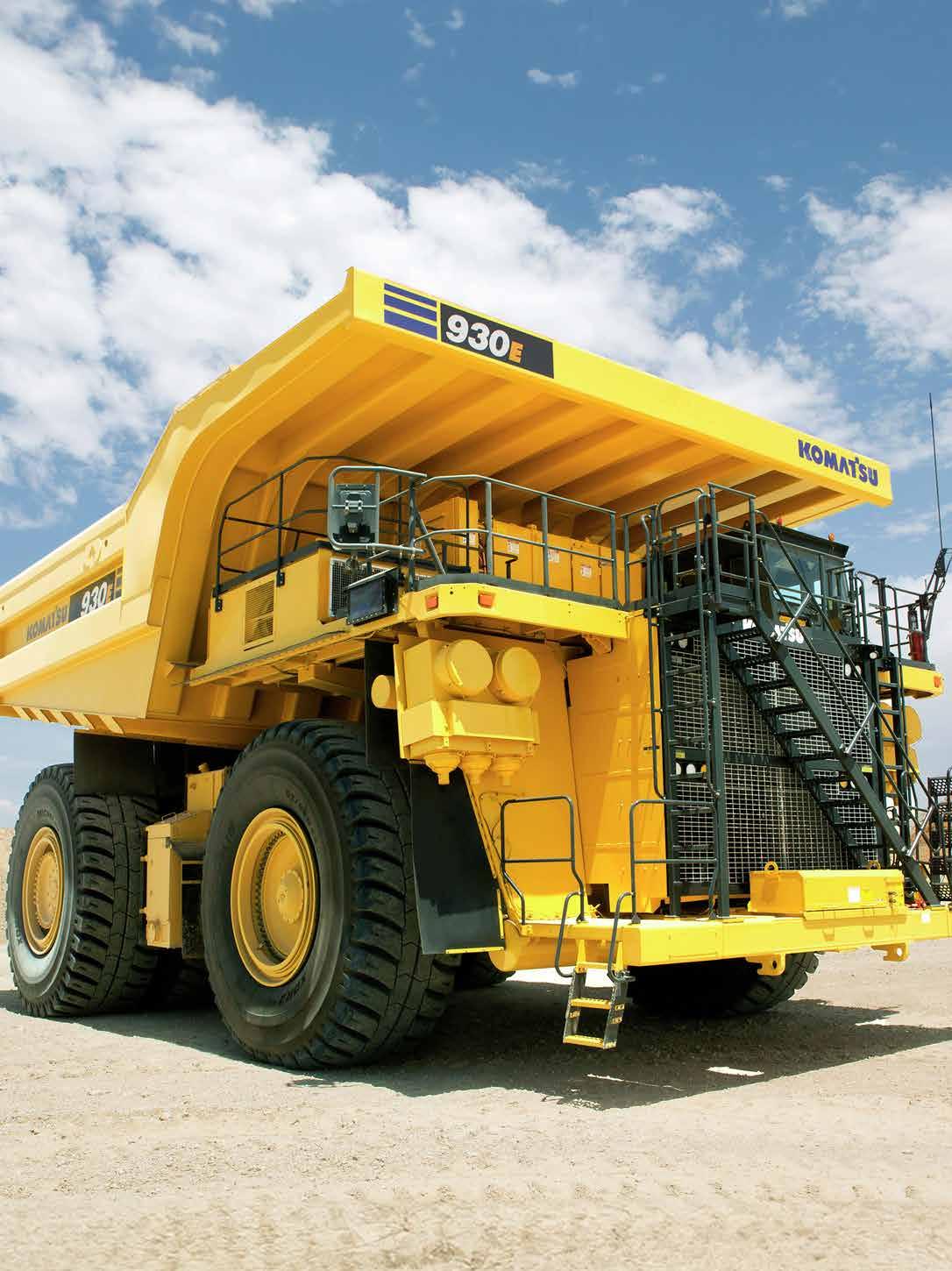
MINING & RESOURCES
Transport & Logistics
State Spotlight: Queensland



Transport & Logistics
State Spotlight: Queensland
Transport & Logistics
State Spotlight: Queensland
SCAN HERE to find out more about the range
The Swift-Jet Pro has been designed by a skilled team of engineers to provide an all-encompassing waterjet cutting solution with industry-leading features as standard. Packed with technology while remaining userfriendly, the Swift-Jet boasts built-in material databases, High and Low-pressure control for piercing brittle materials, an auto garnet delivery system, and an adjustable water level for submerged cutting.
WITH
ONLY OR WATER AND ABRASIVE CUTTING
• 3048 x 1524mm capacity
• Cuts up to 100mm - (Material Dependant)
• Submerged cutting system reduces noise and mess
• German direct drive pump produces 3400 bar/ 50000psi at 100% duty cycle
• CNC touch screen combines IGEMS CAD/CAM and SwiftCNC software, specifically designed for waterjet applications
View and purchase these items online: www.machineryhouse.com.au/AMT2410
Bodor’s compact i Series has been specially designed to increase productivity, using as little ßoor space as possible. The completely enclosed design leads to more economical processing and faster performance, with a much lower power consumption.
• Working area ranges from 1000mm x 1500mm to 3048mm x 1524mm
• Lasers ranger from 3kw to 12kw
• Maximum Acceleration = 1.5G
• 91m / minute maximum linkage speed
AUSTRALIA’S PREMIER MANUFACTURING SOLUTIONS EVENT
6-9 MAY, 2025 • MELBOURNE CONVENTION & EXHIBITION CENTRE
16 BAYS • 24,000 SQM • OVER 400 EXHIBITORS
Our customers can be confident when they deal with Okuma they are dealing with professionals who have a comprehensive knowledge of the industry and understand the importance of commercial outcomes.
Okuma built CNC machine and OSP control
100% Okuma Japan owned
Locally delivered Okuma genuine parts
Outstanding field service and support
Local factory trained service engineers
Repair facilities in Melbourne and Sydney
Excellent machine delivery record
National full service facilities
PUT ALL THE PIECES TOGETHER, OKUMA JUST MAKES SENSE
Free unlimited training support for all new machine installations (first 12 months)
PAUL HELLARD
Mining is a complex business with many moving parts. External factors like skilled labour shortages and extreme weather events suggest that fully autonomous exploration may be the answer.
Mining can be highly mechanised and often occurs in remote locations with vulnerable supply chains. But these days, more elements in mining don’t need to ‘get their hands dirty’. Remote visualisation technology, deep spectral analysis of test sites, fully autonomous exploration and extraction of rare earth minerals are all part of the future of mining. However, according to FM Global’s 2024 Mining Loss Report, grand promises of profits come with more significant risks and barriers to overcome.
One must remember that the mining and processing of the ore is the source of the steel our industry forms and fabricates. It is our raw material to manufacture.
The complexity of the mining industry can lead to a significant risk of business disruption, costing companies millions or even billions of dollars due to lost market share, missed growth opportunities, and negative investor sentiment.
External factors, such as the increasing frequency of extreme weather events and skilled labour shortages, heighten the risk of disruption. Mining companies understand these risks and aggravating factors well. The comprehensive financial impacts due to the downstream effect of disruption on the entire business need to be better understood.
An operational disruption impacts an entire operation. Beyond the direct cost of repairs are the opportunity costs: lost time, business, and work hours. Corporate reputation can suffer. Market share can be lost. Stock prices can fall, reducing investor confidence and even capital flight.
A report by Pentland Analytics measured over 20 years showed that a reputational crisis's average share price impact is -5% across the post-event year, significantly reducing a company’s market capitalisation.
In this environment, you can’t afford not to be prepared. Only through a thorough evaluation of your operations can you develop a holistic view of how risks might impact your business. This will allow you to plan for and adequately mitigate the effects of a catastrophic event or disruption. Through risk mitigation, you can help your enterprise become resilient and prepare for future threats.
In the Canadian context, with labour disruptions, infrastructure interruptions, and extreme weather events becoming more common, this type of holistic analysis is more necessary than ever. By adopting robotics and AI and having workers operate machinery remotely, these risks can be prioritised, and investment in resiliency can be justified and secured.
Operations and facilities in some areas of Canada were shuttered, and underground mining activities across the country were suspended during the major fires in northern Spring/Summer 2023. These wildfires are estimated to have cost Canada’s mining sector millions of dollars in direct costs and millions more in losses due to the disruption of value chains.
Mining companies may need help mitigating these risks using internal resources. Many companies try to control costs in a capital-intensive business, leaving few resources to invest in risk mitigation. For example, companies often keep very little excess inventory on hand and are reluctant to spend the money required to keep spare equipment in storage — meaning a disruption in operations can quickly snowball, leading to missed deliveries and lost market share.
The threat of disruption will only increase, with wildfires, floods and other extreme weather events on the rise. Investing in resilience is not just insuring against loss. It is about investing in the future and bolstering your competitive position for decades.
Editor Paul Hellard phellard@amtil.com.au
Contributors
Paul Hellard
Drew Turney
Sales Manager
Pavla Thomas pthomas@amtil.com.au
Publications Co-ordinator
Caroline Robinson publications@amtil.com.au
Publisher AMTIL info@amtil.com.au
Visual Communications Manager
Franco Schena fschena@amtil.com.au
Prepress & Print
Printgraphics Australia
AMT Magazine is printed in Australia under ISO140001
Environmental Certification using FSC® Mix certified paper sourced using sustainable tree farming practices.
Contact Details
AMT Magazine
AMTIL
Suite 10, 5 Corporate Boulevard Bayswater VIC 3153
AUSTRALIA
T 03 9800 3666
E info@amtil.com.au
W amtil.com.au
Copyright © Australian Manufacturing Technology (AMT). All rights reserved. AMT Magazine may not be copied or reproduced in whole or part thereof without written permission from the publisher. Contained specifications and claims are those supplied by the manufacturer (contributor).
Disclaimer
The opinions expressed within AMT Magazine from editorial staff, contributors or advertisers are not necessarily those of AMTIL.
The publisher reserves the right to amend the listed editorial features published in the AMT Magazine Media Kit for content or production purposes.
AMT Magazine is dedicated to Australia’s machining, tooling and sheet-metal working industries and is published bi-monthly. Subscription to AMT Magazine (and other benefits) is available through AMTIL Associate Membership at $210.00 (ex GST) per annum. Contact AMTIL on 03 9800 3666 for further information.
Need to build trust in AI if manufacturing is to benefit.
It’s nearly impossible to think about manufacturing technologies such as robotics and automation without considering artificial intelligence (AI), but our thoughts are often polarised to the opportunity or the threat. The opportunity is by all accounts mindblowing and the potential threat perplexing and worrying, but a lack of trust – or the unknown - is at the centre of both.
The flow-on is that if we are to seize the opportunity and protect from the threat, we will need to build understanding and regulation – the combination of which will build trust.
While business is often averse to regulation, especially that referred to as red tape, a Federal Government consultation in 2023 with the general public and industry about AI resulted in a resounding push for stronger regulation—and businesses asked for clarity on that regulation so they could confidently seize the opportunities that it presents. The World Economic Forum (WEF), earlier this year, said:
“The global AI in manufacturing market is valued at $3.2bn in 2023 and is poised to grow to $20.8bn by 2028.”
“Yet, despite these possibilities and significant investments, manufacturers are not harnessing the full potential of AI.
“Once manufacturers address the key challenges in AI deployment, they can transform every aspect of their business for the better.”
The WEF’s December 2022 white paper, ‘Unlocking Value from Artificial Intelligence in Manufacturing,’ identified six barriers to AI adoption in manufacturing, including a lack of explainable AI models that undermine trust.
Their consultations showed that globally leading manufacturers have successfully overcome challenges to implement “a variety of AI applications and achieving a positive impact on operational performance, sustainability and workforce engagement, mainly
in six areas: health and safety, quality, maintenance, production processes, the supply chain, and energy management.”
WEF asserts that organisations are looking for a common framework that outlines how to implement AI solutions and ensure a successful return on investment.
The September release of the Australian Government’s Proposals Paper for Introducing Mandatory Guardrails for AI in High-Risk Settings is not specific to manufacturing but is highly relevant. In its release, Minister for Industry and Science Ed Husic said: “We need more people to use AI and to do that we need to build trust.”
The Paper, includes:
• A proposed definition of high-risk AI.
• Ten proposed mandatory guardrails.
• Three regulatory options to mandate these guardrails. The three regulatory approaches could be:
• Adopting the guardrails within existing regulatory frameworks as needed
• Introducing new framework legislation to adapt existing regulatory frameworks across the economy.
• Introducing a new cross-economy AI-specific law (for example, an Australian AI Act).
The Minster also released a new Voluntary AI Safety Standard with immediate effect. The standard provides practical guidance for businesses using AI at high risk. It is available at industry.gov.au/ VAISS.
Consultation on the Proposals Paper will likely be closed by the time you read this (close 4 October 2024) but can be found at: consult.industry.gov.au/ai-regulatory-guardrails.
The upcoming round of applications for the Export Market Development Grant (EMDG) program will open on 12 November 2024. Your business may qualify for financial support, strategic guidance, and market entry opportunities to enhance its international presence.
With recent adjustments to grant amounts and increased support for market diversification, the EMDG program offers even more opportunities to boost your exports and strengthen your global footprint.
How can William Buck help?
We offer a complimentary consultation to assess your businesses opportunity to secure R&D Tax Incentive and grant claims.
As part of this consultation we can assist with:
Understanding your business’ strategic plans and identifying any relevant tax incentive or grant funding programs
Assessing eligibility for the R&D Tax Incentive program, EMDG program, and other relevant government grants
Exploring opportunities to mitigate compliance risks with past and future R&D claims
Berrin Daricili
Principal, R&D Tax Incentives & Grants
Berrin Daricili@williambuck com
Scan for a complimentary consultation with Berrin Daricili
From a simple statement, a plan to turbo-charge Australian science and technology research, for the country’s sake.
Thirty-five years ago, Prime Minister Bob Hawke put science and technology at the centre of actions by the Australian government to build a more internationally competitive economy. In a National Science Statement to Parliament, he set up the Prime Minister’s Science Council and named Ralph Slatyer as Australia’s first Chief Scientist. The council was tasked with setting national science and technology priorities, while Professor Slatyer analysed developments in Australian science and technology and advised the PM’s Office on policy development.
In the Statement, Mr Hawke said, “we are showing our determination that Australia will be a full participant in the exciting and vital processes of scientific discovery, innovation and adaptation.”
Backing words with actions, his government set up the Cooperative Research Centre program in 1991 to drive industry-led collaborative research in manufacturing, agriculture, mining, and other important sectors of the economy. Since then, developments in advanced materials, smart robots, and sensors have flowed from our CRCs, universities, and national science agency, the CSIRO, and have transformed Australian manufacturing. Our R&D expertise, bolstered by the growth in computer processing power, means those breakthroughs will keep coming.
Last month [August], I released a new National Science Statement so we can continue to benefit from having science strategically placed at the centre of Australian industry. The statement is anchored by five overarching objectives, including developing a diverse, skilled workforce to underpin the translation of sciences like quantum computing into new industries.
To complement the refreshed statement, we have updated our National Science and Research Priorities to better reflect accelerating climate change impacts and rapidly emerging new technologies.The five priorities that will guide future government, university and private sector efforts include:
• Transitioning to a net zero future by developing and adopting next-generation technologies, particularly in clean energy and storage, advanced materials, AI, quantum and robotics;
• Supporting healthy and thriving communities so more Australians can enjoy healthier lives from birth well into old age;
• Elevating and investing in Aboriginal and Torres Strait Islanders’ knowledge and knowledge systems so First Nations people are empowered to take a leadership role in advancing research that affects them;
• Protecting and restoring Australia’s environment to mitigate the impacts of climate change and protect our biodiversity, diverse landscapes and ecosystems, and;
• Building a secure and resilient nation.
Fittingly, our current and ninth Chief Scientist, Dr. Cathy Foley, led the national conversation and consultation process to decide the new priorities.
Nearly 500 written submissions were received during that process, reflecting enormous interest in the important role science plays in economic development at the local and national levels. Refreshing the National Science Statement and Science priorities is about promoting sovereign capabilities – a key plank of our Future Made in Australia agenda.
The $470m the Australian Government recently invested in PsiQuantum – an amount matched by the Queensland Government – is part of that strategy. Founded by two Australian researchers in 2016, PsiQuantum is well advanced in its plans to build the world's first commercially useful quantum computer.
Being able to access processing power that is many orders of magnitude greater than that offered by classical computing will supercharge the development of new industries here in Australia.
Over the next twenty years, Australia’s manufacturing industry must embrace more complex, value-adding opportunities and the new statement and priorities provide further clarity on how the Government will do that. industry.gov.au
The belated but clear signs that the Federal and key state governments have recognised they need to reverse course to avert a debilitating major gas shortfall are welcome first steps to inject realism into our energy debate.
There are signs of welcome pragmatism emerging from many quarters. That newly found pragmatism must continue to trump ideology if we are to keep the industry competitive during the energy transition. Victoria approved gas exploration and took steps in September to expand gas storage while focusing on its gas substitution roadmap better. This welcome shift comes after years of refusal to engage meaningfully on the supply side of gas policy. The Federal Government is developing sectoral transition plans to answer some of the demand shift questions posed by its Future Gas Strategy.
NSW is retooling its hydrogen scheme, which may also incentivise biogas. Stakeholders call for a major national push to upgrade and electrify buildings but also increasingly acknowledge the need to shore up supply along the way. That practicality is welcome but well overdue. We are now playing catch-up to secure our energy future after years of failing to recognise the need to keep local industry competitive. The reality is three overlapping gas challenges demand urgent action.
Supply adequacy is threatened as soon as 2027, with expected supply declining faster than expected demand. Shortfalls should not be possible, but they are. They can be avoided but might not be. If shortfalls ensue they will mean serious disruption either to Australia’s trade relationships, or to industry and power systems in the depths of winter. Some mix of supply increase and demand transition is needed to maintain balance.
Gas prices are much lower than during the crisis of 2022, but much higher than before it. The Federal Government has sought to keep a lid on prices with the Mandatory Gas Code of Conduct. But fundamentals of production cost and pipeline distance mean that future Eastern Australian gas prices will be challenging for industrial and residential investments made back when gas was cheap.
National, state and corporate emissions reduction goals also imply much lower overall gas consumption over time. However, gas plays many different roles, and some uses will last a long time – or even increase – within that overall decline. Peaking and backup gas power generation is a small but vital component of the Integrated System Plan through 2050.
The broad outline of a package of solutions is becoming more apparent. Boosting efficiency, electrification, biogas, and hydrogen will make sense for different gas users, but mass upgrades will take time and substantial support. That work needs to happen now if it is to pay off later. And since electrification is likely a large part of the overall solution, we must ensure that the costs of a declining gas network over time do not fall disproportionately on hard-pressed industries or vulnerable households.
New gas production and pipeline capacity will be needed to bring it to demand. Reinvesting in existing basins and expanding existing pipelines will often make more sense than building new assets that face stranding within their technical lives. But these, too, will take time to deliver. Unfortunately, one or more Liquefied Natural Gas import terminals appear increasingly necessary to provide near-term breathing space. It is crazy that they are needed, but confirmed that they can be quick to deliver, highly flexible and lock in little capital. As policymakers and stakeholders square up to that reality, we need firm reassurance that such terminals will neither push off better long-term solutions nor send local gas prices permanently to import parity levels.
Simple stories that pretend there are black-or-white solutions to our problems won’t take us far. Not everything can be electrified, and renovating millions of buildings is hard work. The cheap gas that sustained the industry for decades is not returning, though the cost can always worsen. Gas produces emissions, though some uses support emissions cuts.
Gas usage over time will decline, but every use case is different and will have its solutions and pace of transition.
The gas debate is starting to move beyond simple stories, which is good. However, we need more time. 2027 shortfalls are close. Nor are emissions goals for 2030 and 2035.
Business competitiveness and even viability are challenged every day right now by high prices and policy-induced uncertainty. We can solve these problems if governments, industry, and other stakeholders are hard-headed and clear-sighted. aigroup.com.au
The need for national consistency and safety in training for our EV workers.
There are some big discussions going on across the country with the economic and industrial shift to a less carbon-intensive economy. One of the real experiences is vehicle electrification, where AMWU members play a significant role in a manufacturingled response. Replacing and upgrading our bus fleets from diesel engines to electric has been motoring along for several years across the country.
The AMWU represents thousands of workers across the vehicle industry in various parts of the supply chain. We represent workers still designing and making suspension and driveline components, workers who service your car, and workers who come to your aid when your car breaks down on the side of the road.
We also represent workers in every state and territory working in the maintenance and manufacturing of electric bus fleets. The AMWU has been pushing for national consistency in skills, training, and safety for workers transitioning from internal combustion engines to high-voltage electric vehicles.
For example, in Victoria the AMWU leads the way in delivering the upskilling and training of our members in the maintenance and safety of electric buses and heavy vehicles. With the support of the Victorian State Government, the AMWU together with industry and TAFE partners, has for the last two years been developing and trialling a training skillset with courses in depowering, inspection, diagnostics, maintenance, repair, and safety.
We stand with a great opportunity here to deliver a nationally transportable skill. Australia has the skills, infrastructure, and natural resources to build and sustain a domestic electric vehicle (EV) manufacturing industry. But our members report a lack of
consistency, with training providers in some states offering a skill set or accredited qualification. In contrast, in other states, a certificate of attainment but that means the qualification can’t be used elsewhere. There’s also significant inconsistency in the framework for upskilling.
There are also issues with the quality of training. Some of our delegates felt they received surface-level training, particularly on safety. A number of safety concerns arise when workers don’t feel confident working on and around the dangerous levels of energy stored. But across the board, we are seeing disparate EV rollouts, with some states reporting a significant number of EVs in their fleets while others are still in the early stages.
There are some solutions the AMWU is keen to see implemented to bridge these gaps. We’re pushing for a national consistency with either licensing or accreditation that lends itself to the portability of workers’ skills. We want to see national standardised training, through TAFE, when it comes to obtaining an EV licence.
When it comes to a specific heavy vehicle and high voltage qualification, the skillset should be transferrable nationally and eventually internationally, and replicate what we already have with existing heavy vehicle licensing and qualifications.
The development of the EV market, in the global context of a carbonconstrained future, is also an opportunity to secure Australia’s place in a growing market.
If we make them here, our local manufacturing industry can provide high-skill, high-wage jobs now and into the future. The global race to secure these jobs is already underway. amwu.org.au
PRIMA POWER OFFERS THE WIDEST SELECTION OF SEMI-AUTOMATIC AND AUTOMATIC PANEL BENDERS, ALL EQUIPPED WITH SERVO ELECTRIC TECHNOLOGY. WHICH ONE SUITS YOUR NEEDS BEST?
BCe Smart - Semi automatic panel bender
EBe Express Bend - With automatic loading
EBe Express Bend with direct connection to Shear Genius and Combo Tower Complete Flexible Manufacturing System for 24/7 production
Solutions for Australia to maximise its $124bn manufacturing industry.
The Manufacturing Industry Skills Alliance (Manufacturing Alliance) Jobs and Skills Council has released the 2024 Manufacturing Workforce Plan, highlighting the numerous opportunities the multibillion-dollar industry presents to job seekers and the country.
The plan is a roadmap outlining the key skills and emerging workforce needs for the industry. With projected employment growth indicating a likely increase equivalent to around 120,000 additional workers (16.8%) by the year 2033, the plan is designed to turn challenges into solutions and begin building the capacity of the manufacturing workforce in Australia.
The plan also highlights sectors with the greatest opportunities for growth, development, and expansion, including defence, clean energy, medical, and space sectors and the urgent need for skilled workers.
"The 2024 Workforce Plan is a step forward in addressing the pressing workforce shortages in Australia's manufacturing industry. Our aim is to not only fill the existing gaps but to build a resilient and skilled workforce that can drive the industry forward,” said Manufacturing Alliance CEO Sharon Robertson.
Ms. Robertson continued, "We are committed to delivering tangible solutions that address the skills and workforce challenges faced by the manufacturing industry. By focusing on practical, actionable strategies, we are building priority actions that can offer solutions to supply-side skill shortages.”
The plan was developed through extensive consultation (conducted in 2024) with industry, unions, Australian state and territory governments, training organisations including TAFEs, Dual Sectors, universities and registered training organisations and other key industry stakeholders. manufacturingalliance.org.au
Breakthrough Victoria invests in groundbreaking technology that reduces livestock methane emissions.
Breakthrough Victoria is investing $1.7m in Number 8 Bio, a leading innovator in sustainable agriculture technologies, joining a round led by Main Sequence Ventures and including The March Group. This investment marks a significant step forward in the fight against climate change and the drive toward more efficient food production. Methane is a potent greenhouse gas and a significant contributor to global warming, with livestock responsible for up to 15% of global greenhouse gas emissions.
"Our $1.7m investment in Number 8 Bio reflects our commitment to sustainable innovation,” Breakthrough Victoria CEO, Grant Dooley said. “Their 'Performance Digestion' technology tackles the critical challenge of reducing livestock methane emissions while boosting productivity. We're excited to support this groundbreaking solution, alongside Main Sequence, The March Group, and others, as we drive toward a more efficient and sustainable future in food production."
These emissions from ruminants, such as cattle and sheep, are particularly concerning. Over a 20-year period, they are 80 times more effective at trapping heat in the atmosphere than carbon dioxide.
“By investing in sustainable agriculture, we are creating more jobs in regional Victoria while also reducing our emissions,” said Victoria’s Minister for Economic Growth, Tim Pallas. “We know that by supporting innovation in sectors like sustainable agriculture, we create more jobs in the regions - not just the inner city.”
To combat this, Number 8 Bio has developed a groundbreaking technology known as "Performance Digestion". Number 8 Bio's BetterFeed products are feed additives for cattle that reduce methane emissions by up to 90% while improving feed efficiency. In addition to reducing methane emissions, Performance Digestion also increases livestock productivity. The feed supplements will contain productivity modifiers that redirect the animal’s metabolic pathways towards growth-promoting compounds. This dual-action approach helps the environment and optimises the animal’s energy use, leading to increased production of meat, milk, and wool.
As the global population grows, the demand for meat and dairy products is expected to rise, further straining our planet’s resources. Number 8 Bio is leading the way in making livestock farming more sustainable. Alongside the production of methane-inhibiting feed additives, the company is also exploring ways to expand its core technology to enhance the profitability of fermentation processes. They are testing how to replicate the low-methane fermentation process that occurs inside a cow's stomach in anaerobic digesters, making fermentation significantly cheaper and producing a range of carbon-negative food ingredients.
As part of Breakthrough Victoria's investment, Number 8 Bio plans to run trials with Agriculture Victoria at Ellinbank SmartFarm and has committed to a research collaboration with Monash University. A proposed regional Victorian manufacturing facility post-Series A funding is anticipated to create over eight skilled FTEs by 2026. breakthroughvictoria.com number8.bio
AAAA urges the Government to unlock manufacturing funds to secure the automotive industry’s future.
The Australian Automotive Aftermarket Association (AAAA) is urging the government to act on manufacturing funding commitments, which are essential to the growth and competitiveness of the automotive manufacturing industry.
The AAAA, the peak body for the automotive aftermarket industry was encouraged by last year’s announcement of the $15bn National Reconstruction Fund and the more recent $22.7bn Future Made in Australia Fund, which sparked optimism within the industry. However, the lack of clear guidance and access to these funds has frustrated and made many automotive manufacturers uncertain.
“Our manufacturing industry needs clear action now to ensure we can continue to innovate and compete on the global stage,” said Stuart Charity, CEO of the AAAA.
“It’s been over a year since the funds were announced, and the industry is still waiting for details on accessing this critical support.
The lack of progress is not only frustrating but is also putting our industry at a disadvantage.”
The government’s announcements without follow-through could exacerbate existing challenges in the sector, including global supply chain disruptions, technological advancements in ADAS and EVs, and increasingly harsh regulations.
“Our industry is navigating complex challenges, and the promised funding could provide crucial support in adapting to these changes. However, without clear guidance and timely allocation, these opportunities remain out of reach,” said Charity.
The automotive manufacturing industry is particularly concerned about the complexity of eligibility requirements, often excluding small and medium-sized businesses with innovative ideas.
“The government aims for a guaranteed 10-times return on investment, but this expectation is unrealistic for many in our sector. Instead of fostering innovation, these funds are being made inaccessible to the very businesses that could drive growth.”
“The Honourable Tim Ayres, who is the new Assistant Minister for a Future Made in Australia has a chance to advocate for the automotive manufacturing industry, which contributes so much to Australia’s economy.
Gino Ricciuti, Chair of the Australian Automotive Products Manufacturers and Exporters Council (APMEC) has echoed the AAAA’s call for funding commitments.
“Our industry is ready to evolve into the EV space, producing global quality products as we have always done, but we need a plan to ensure that the government and industry are on the same page. If we want manufacturing to continue to thrive, it is vital that a clear automotive manufacturing roadmap is developed in partnership with the federal government,” said Ricciuti.
The AAAA has written to the new minister seeking action regarding the Future Made in Australia Fund, and will continue to campaign on behalf of its manufacturing members. aaaa.com.au
The Federal Minister for Industry and Science approves the progression of six applications to Stage 2 of CRC grants.
The Hon. Ed Husic MP, Federal Minister for Industry and Science, has approved the progression of six applications to Stage 2 of CRC Grants Round 25, including the Additive Manufacturing Cooperative Research Centre (AMCRC).
CRC Grants provide funding for medium to long-term, industryled research collaborations. The CRC Program supports industry, research and the community in two ways.
CRC Grants support medium to long-term industry-led collaborative research for up to ten years. CRC Projects (CRC-P) grants – support short-term, industry-led collaborative research for up to three years.
CRC Grants provide funding for collaborations to solve industryidentified problems. They must be medium—to long-term industryled collaborative research programs that aim to solve industryidentified issues and improve Australian industries’ competitiveness, productivity, and sustainability.
The CRC Grants include an industry-focused education and training program, including a PhD program that builds capability and capacity; they increase research and development (R&D) capacity in small to medium enterprises (SMEs) and encourage industry take-up of research. business.gov.au
All aboard as two major Pilbara rail projects are on track to deliver.
The Cook Government is right on track in driving advanced manufacturing in the Pilbara with its multimillion-dollar investment into two major rail projects. The WA Government has awarded nearly $8m from the Local Manufacturing Investment Fund to open the CORE Innovation Hub's new Rail Collaboration Centre. Gemco's new iron ore railcar manufacturing facility in Karratha is now on track to open later this year.
Minister Assisting the Minister for State and Industry Development Stephen Dawson said almost $8m was being invested under the Government's Local Manufacturing Investment Fund (LMIF).
The funding towards both projects will establish an iron ore railcar manufacturing production line and a centre of excellence in Karratha. The LMIF is part of the State Government's 2021 election commitment to support local companies to develop manufacturing opportunities and create more jobs as part of its ongoing Diversify WA program. The Minister recently opened CORE Innovation Hub's Rail Collaboration Centre (RCC), which will provide a platform for world-class testing, research, and development to support iron ore railcar manufacturing. The State Government provided CORE with almost $1m under the LMIF to help boost design, manufacture,
decarbonisation, and employment training opportunities in WA. The new centre in Karratha and hubs located in Newman and Perth will help boost these opportunities. The centre, established with strong support from Rio Tinto, fills a strategic gap as an innovative and collaborative platform for assessing the development of new rolling stock, infrastructure, technology, and ideas.
Gemco Rail was awarded almost $7m under the LMIF to establish an iron ore railcar manufacturing facility in Karratha. The facility will manufacture 100 wagons for Rio Tinto and repair and refurbish key wagon componentry.
The Karratha facility will enable the WAbased company to manufacture iron ore railcar wagons and refurbish rail bearings for Pilbara-based miners. Since its establishment in 2021, the LMIF has awarded more than $13.5m to several Western Australian companies. "The opening of this new Rail Collaboration Centre in the Pilbara is another major step towards building an exciting new industry specialising in manufacturing world-class iron ore railcars,” said Minister Assisting the State and Industry Development, Jobs and Trade Minister Stephen Dawson. "Our resources sector relies heavily on railcars, and it makes perfect sense to invest in developing
a local industry that will manufacture, test and conduct research on delivering a stateof-the-art iron ore railcar.
"Creating and investing in local manufacturing opportunities is a priority for the Cook Government and the LMIF continues to boost our local companies, provide job security and support businesses to maintain a competitive edge in an evolving market."
"As the Member for Pilbara, I'm excited to see that the Pilbara region is advancing with key rail infrastructure projects,” added Pilbara MLA Kevin Michel. "The new Rail Collaboration Centre by CORE Innovation Hub, supported by nearly $1m from our Government's LMIF, will drive cutting-edge research and local manufacturing for iron ore railcars.
"Additionally, Gemco Rail's upcoming new facility in Karratha, funded with nearly $7m from the LMIF, will produce and refurbish railcars, creating jobs and boosting our local economy. These initiatives align with the Cook Government's Diversify WA program, which is investing in our region's future and strengthening our manufacturing sector. It's great that the LMIF has invested over $13.5m in supporting local WA businesses and continues to underscore our commitment to economic growth and job creation in the Pilbara. wa.gov.au
Pfizer's Melbourne plant upgrade to become one of Australia's most advanced pharmaceutical production facilities.
The Melbourne manufacturing site is one of Australia's most advanced pharmaceutical production facilities for treatments aiming to help address rising levels of antimicrobial resistance – one of the biggest threats to global health. This Australian investment strengthens Pfizer’s capability to produce and supply critical medicines for people worldwide.
Robotics and AI-powered technologies will further the site’s highly specialised manufacturing capabilities. Pfizer has invested A$150m to offer advanced pharmaceutical production facilities in Australia for new antimicrobial treatments to help address rising levels of antimicrobial resistance, considered one of the biggest threats to global health.
The Hon. Natalie Hutchins MP, Victorian Minister for Jobs and Industry, visited the site to mark the milestone installation of key technology known as lyophilisers and witness the site’s highly specialised capabilities, including productivity
enhancements, such as robotics.
Antimicrobial resistance (AMR) has been described as ‘the silent pandemic’ and is considered by the World Health Organization to be a top ten area of public health concern. AMR makes infections more complex to treat, increasing the risk of disease spread, severe illness and death, with annual deaths from AMR predicted to rise to 10 million by 2050. Without intervention, it is estimated that by the same year, 10,000 Australians will die each year from drug-resistant infections.
“We are thrilled to reach this important milestone in our investment to support the development and delivery of new antimicrobials at our Melbourne site, and to be investing in Australia’s advanced manufacturing capabilities,” said Anne Harris, Pfizer Australia & New Zealand Managing Director.
“A key strategic pillar of Pfizer’s product innovation work is our effort to help slow the spread of antimicrobial resistance,
one of the biggest global health threats of our time. We are also pleased to provide 500 advanced manufacturing jobs at our Melbourne site,” Harris said.
Investment in the Melbourne site has included the construction of a new separate facility that hosts two newly installed freezedrying machines, known as lyophilisers, used in the antimicrobial manufacturing process. The site has also been selected for a trial of Artificial Intelligence (AI) technology designed to support key site processes. The site upgrades are on track to complete installation work and be operational by mid-2025, with commercial manufacture commencing in 2026.
Medicines currently manufactured at the Melbourne site – which include those for the treatment of cancer as well as antimicrobials, anaesthetics, anti-inflammatory and other medicines – are exported to more than 60 countries worldwide and treat up to 15 million patients each year. pfizer.com
A new Hexagon Manufacturing Intelligence division release combines laser tracking and non-contact measurement, slashing large-scale manufacturing processes from hours to minutes.
The new Leica Absolute Tracker ATS800 accurately measures critical features from a distance, using direct scanning to meet the demands of low-tolerance inspection and alignment in aerospace and other largescale manufacturing sectors.
Hexagon’s Manufacturing Intelligence division has announced a new technology to reduce quality inspection delays in large-scale manufacturing operations. Combining laser tracking with laser radar functionality enables manufacturers to measure detailed features and meet tight assembly tolerances from tens of metres away. Built on established measurement and positioning technology, the Leica Absolute Tracker ATS800 offers significant productivity improvements in largescale part manufacturing and assembly operations by safely and rapidly measuring critical features and minimising common production bottlenecks.
The new system enables manufacturers to accurately measure fine edges and features across large volumes with unparalleled measurement process productivity from a convenient standoff distance. Whether used to inspect large aerospace or automotive structures, ship sections, or wind turbine components, operators or robots need not be in close proximity to the part being measured. This avoids unreliable measurements and safety issues and provides significant time savings.
The new system replaces two pieces of hardware with a single device by combining direct scanning and reflector tracking capabilities. Using Hexagon’s patented PowerLock technology, the ATS800 automatically and immediately “locks on” to a fixed reflector and tracks its movements in real-time, providing an absolute position reference. The ability to measure target reflectors also greatly simplifies robotic automation processes, providing precise position referencing within a wider coordinate system when the tracker is mounted on a linear rail or an autonomous mobile robot (AMR).
The ATS800 can perform high-precision measurements of intricate geometries and complex surfaces from a safe distance, making it a versatile measurement tool for rapid inspection in various industries and applications.
• An aircraft fuselage can be quickly inspected alongside production without bringing target reflectors to the part, reducing total inspection time from hours to minutes. Several
fuselage sections or panels can be batch inspected overnight using multiple devices or an AMR, reducing inspection time and avoiding disruption during shifts.
• Guided assembly processes that require up-to-date digital measurements during 3D assembly and mating operations will be streamlined using the ATS800’s unique simultaneous tracking capability. It provides metrology-grade guidance with accuracy to help experts align and troubleshoot issues in real-time without stopping recalibrating and remeasuring.
• The device’s accurate high-speed measurement of holes, fastenings, and edges can keep up with highvolume automotive production by automatically inspecting critical features within seconds without interruption or the risk of robot collision.
• Many inaccessible features, such as the holes that make up the bolt pattern – critical for the alignment and fastening of huge wind turbine sections or industrial pipework – can be measured reliably and safely in the factory.
“Industries like aerospace and shipbuilding make large structures where scale and detail are equally important,” said Pirmin Bitzi, General Manager for Portable
Measuring Devices at Hexagon. “We’re excited to offer manufacturers a system that delivers leading-edge capabilities to measure intricate features with less disruption at the heart of production and throughout the critical stages of assembly.” Until recently, robotic automation has been limited by the supporting cabling and large control cabinets that prevent AMR use and complicate robot deployment in large-scale manufacturing. The ATS800 is IP54 rated, can be operated wirelessly, and is highly portable. It integrates all systems and electronics into a single lightweight tracker unit with a small control box that can be securely mounted to and integrated with standard robotic control systems.
This new technology is based on Hexagon’s established Absolute Trackers platform, extending its successful ATS family, which now includes both the existing ATS600 and the new ATS800. As their needs change, customers can interchange accessories like batteries, tripods, and reflectors as required across their existing install base. Designed to plug into customers’ existing workflows, the ATS family supports Hexagon’s comprehensive software development kits, providing open support for integration within third-party manual and automated solutions. go.manufacturing.hexagon.com/ats800imts/ hexagon.com
Funding from the Industry Growth Program spans batteries to blueberries.
The Federal Government has released a funding round for Industry Growth, which includes grants for battery manufacturing and robot design. This is just part of the $392m Industry Growth Program stipulated last month.
This offering is designed to assist small to medium businesses in overcoming barriers associated with scaling up. The program focuses on growing manufacturing capabilities, creating stronger supply chains, and delivering more secure, well-paid jobs.
Lithium metal foil is used for the anode of both lithium sulphur and lithium metal batteries, but the current imported supply is limited in quality and needs to be optimised for Li-S cells. In addition to supplying foil for its own cell production, Li-S Energy intends to market the foils to both domestic and international customers.
Li-S Energy hosted the Hon. Ed Husic MP, Federal Minister for Industry and Science, to officially open the Li-S Energy 2MWh Battery Cell Production Facility in Geelong, Victoria. During the event, the Minister announced that Li-S Energy had been awarded an Industry Growth Program (IGP) Commercialisation and Growth Grant of $1.7m to develop Australia’s first lithium foil production facility. The new state-of-the-art Li-S Energy pouch cell production facility in Geelong is the largest of its kind in Australia and is installed inside Australia’s largest battery dry room.
Built at a cost of over $10m, the facility spans the entire production process from creating and coating cathode powders to final cell fabrication and testing.
With the support of the IGP Grant announced by Minister Husic, Li-S Energy plans to extend beyond its cell manufacturing capability to produce high-quality lithium foils and laminates from lithium metal ingots. Lithium metal foil is used as the anode for both lithium sulphur and lithium metal batteries, but the current imported supply is limited in quality and not optimised for Li-S cells.
This will be a new sovereign manufacturing capability for Australia, reducing supply chain risk and increasing the value of Australia’s advanced battery material exports. Beyond using the lithium foil in its batteries, the Company intends to export the foils internationally as an additional revenue stream to capitalise on this growing market.
“Australia currently produces 52% of the world’s lithium ore, yet much of this is exported without adding additional value,” said Dr Lee Finniear, CEO of Li-S Energy. “With global demand for lithium metal foil forecast to reach nearly $80bn by 2032, Australia has a unique opportunity to capitalise on this emerging market to produce lithium foils here, adding value here, before exporting this high-value product to global markets.”
Forager Automation is the company behind the development of a robotic blueberry picking device, tackling labour costs and increasing farmers' yield efficiency. Forager has received $157,943 to assist their venture. industry.gov.au
Hare & Forbes launches new store in Adelaide, South Australia.
Hare & Forbes Machinery House has expanded its footprint, opening a new store in Adelaide, South Australia. This exciting development marks a significant milestone for the family-owned Australian business as it seeks to serve its customer base in the region better.
The new store, boasting over 4,300sqm, will offer a wide range of machinery and equipment catering to various industries, including metalworking, woodworking, automotive, and fabrication. This is the fifth Hare & Forbes Machinery House store, with existing branches in Sydney, Perth, Melbourne and Brisbane.
“We’re really pleased to be trading in Adelaide finally,” said Rick Foster, General Manager. “This project has been in the plans for almost five years. It’s really exciting for us to invest in a brick-andmortar store in a new location.”
The new store's launch underscores Hare & Forbes' dedication to innovation and growth and its ongoing commitment to providing industry-leading solutions to its customers, as it has done for over 90 years. Through its extensive product offerings, knowledgeable staff, and dedication to customer service, Hare & Forbes aims to become the go-to destination for engineering machinery and accessories.
Store Manager Jim Burton brings a wealth of experience and will look after the almost dozen full-time staff, which includes a CNC specialist and aftersales support. "After running my own machinery business for over 20 years, it was an easy decision and a great opportunity to join the team. The interest we’ve had already from the public and my old customers has been incredible,” said Burton.
As Hare & Forbes continues to expand its reach across Australia, opening the new store in Adelaide signals a bright future for the company and its commitment to serving the needs of the engineering and manufacturing communities nationwide.
The new store is at 11/20 Cheltenham Parade Woodville, South Australia. machineryhouse.com.au
Australia’s best and brightest student engineers on show in Victoria.
Formula SAE-A is a university competition where students design, build and validate their Formula-style open-wheeled race car.
Students participating in Formula SAE-A are highly sought-after candidates for many businesses and organisations, especially those in the transport technologies industry sector. Not only do they participate in a real-life project utilising their engineering knowledge and skills, but students also have the opportunity to build on their leadership, management and teamwork capabilities in a highly pressured and Agile project management environment.
With an electric-dominated field, driverless car demonstrations and powerful backing from Australia’s mobility engineering sector, over 800 Formula SAE-A students will gather at the annual event, which is now held at Calder Park Raceway in under three months.
Over 30 Australian and International University teams will soon display their year’s work and pit themselves against some very professional teams, all vying for that coveted prize, the best team overall award. But it’s not all about winning. All teams and team members benefit from the experience. They will gain priceless skills and key learnings from over 100 technical experts from the transport and mobility engineering sector who volunteer their time to help all students learn from their vast knowledge and experience.
Run by the Society of Automotive Engineers – Australasia (SAE-A), the event is the last phase of a year-long program for students from Universities around Australia, New Zealand, Asia and beyond.
Teams compete in events such as Business Presentation, Cost and Design before taking their vehicles to the track. Cars are subjected to two days of dynamic assessment on the Calder Park racetrack, including straight-line acceleration, a skid pad (to assess suspension design), and an autocross sprint event, finishing with a demanding endurance event incorporating fuel efficiency. All are real-world events that are closely aligned to Automotive company test regimes. “We welcome people to come and see the achievements of our brightest and best young automotive engineers Australia has to offer,” SAE-A’s CEO Adrian Feeney said.
“There is no entry charge, and spectators are welcome to witness the competition, especially the on-track action throughout the weekend. Formula SAE-A is the perfect recruitment tool for any organisation wanting to employ the best students available in several disciplines. With a great lineup of sponsors in 2024 such as Caterpillar, PACCAR Australia, Thales, Toyota, Ford and Tesla, ADF Careers, Supacat, Henkel, Leap Ansys, Victorian Government and Altair, Formula SAE-A is a collective showcase of what we can do with the best we have.
We appreciate our mobility engineering industry getting behind what has been Australia’s best kept secret (until now)….
Dates: 5-8 December 2024
Where: Calder Park Raceway, 377 Calder Hwy, Calder Park sae-a.com.au/formulasae-a
With the retirement of Okuma’s highly respected New Zealand General Manager, Fred de Jong, the company has appointed Karl Medley as his replacement.
Karl Medley’s appointment will further expand Okuma CNC machines' already strong business development in the New Zealand manufacturing sector, with many customers becoming internationally competitive, resulting in strong export growth.
To continue this strong market presence Karl Medley joined the New Zealand Okuma team in May this year. Karl who hails from the UK, and comes with an extensive background and a wealth of experience in precision machine applications with major manufacturers within medical, military, aerospace and general engineering industries.
With responsibilities for Okuma New Zealand’s overall management, focusing on sales and managing service, Karl is a qualified mechanical engineer trained in CNC and CAD/CAM programming. Previously, from hands-on engineering experience to production and management, Karl was ultimately responsible for CNC machine sales throughout Northern England.
Further strengthening technical and service support for its customers, Okuma New Zealand has also announced the appointment of an additional Service Engineer, Rodel Estoya to the New Zealand team
based in Auckland. Rodel has an extensive service background and knowledge of many CNC machine tool brands, including Okuma, which will further benefit New Zealand customers.
On his appointment, Karl commented, “My role will be to continue providing unparalleled service to Okuma customers and new customers New Zealand-wide with the Okuma brand. With exports so important to the industry, I see the accuracy, durability, automation, and robotics of the Okuma machines providing strong economic benefits for engineering manufacturers in ultimate precision, power, and performance,” he said.
Dean McCarroll, Managing Director, Okuma Australia and New Zealand, said, “We are delighted to welcome Karl Medley, who has a strong skill set to lead the New Zealand team into a new phase. He is supported by a very strong and experienced team: Ian Cox, South Island Manager responsible for service, applications, and new machines; Terry Barber, customer liaison officer with almost 20 years of service within Okuma in administration, shipping, and accounts; and the recent addition of an experienced Service Engineer in Rodel.” okumaaustralia.com.au okuma.nz
Dr. Phillip Toner and Emeritus Professor Roy Green from the UTS, summarise the last forty years of the Industry Capability Network.
The origins of ICN lie in the 1960s with international responses of nation-states seeking to maximise the gains to their domestic economies from large, one-off and non-renewable resource projects. In adapting to Australian circumstances, ICN differed in some essential respects from these original models.
For the first few decades, ICN was primarily focused on the import substitution of manufacturers, aligning with the policy concerns of the time as Australia reduced tariffs and macroeconomic decisionmaking was centred on reducing trade deficits. However, over the past two decades, in response to shifting economic policy and changes to government procurement programs, ICN has shifted its focus towards maximising ‘local content’ inputs from any domestic industry, showcasing its adaptability and current orientation.
Arguably, the most remarkable aspect of ICN’s history is its very survival. ICN stands alone in Australia’s barren industry policy landscape, remaining intact through four decades of changing governments, shifting public sector budgetary priorities, and large swings in dominant economic ideas. This longevity and success can be attributed to multiple causes. The most compelling is that ICN meets real-world market needs by remediating fundamental problems in public and private sector procurement and capabilities of local firms, thereby supporting economic growth.
Over the decades, ICN has evolved services and products to remediate these barriers to participation by acting as an intermediary between local suppliers and purchasers. Key to this intermediary role is ICN’s engagement in state and federal government procurement programs that require public and private sector project proponents of projects above a threshold value to provide full, fair and reasonable bidding opportunities to local firms. From the beginning, this engagement has been crucial to ICN facilitating the development of supply chains and delivering its services.
ICN has three core functions:
• It develops and operates the Gateway software system, which connects over 100,000 local suppliers with project proponents.
• It works with project proponents to structure their procurement process to maximise the participation of all domestic firms, particularly SMEs.
• It cooperates with SMEs to enhance their capability to ensure they understand. It can satisfy the rigorous information requirements, accreditations and technologies demanded by major private-sector project proponents and the government. More recently, ICN has developed other products, such as supply chain mapping, which is used to identify local capability and capability gaps and inform policy development to remediate these gaps. The study finds that the level of ICN resourcing needs to be improved. It constrains and distorts its capacity to deliver certain current services. Current funding and staff levels limits ICN in activities such as:
• helping SMEs form consortia to bid for larger projects.
• allowing ICN staff to specialise and develop greater expertise in particular industries and technologies.
• promoting ICN services to more suppliers and purchasers. Limited resources also require ICN to focus on major projects to the disadvantage of small projects. Funding restricts ICN from developing novel products and services such as new software to meet industry need and embedding staff specialists full-time in
major projects such as defence, health and agri-food companies. In the past, dedicated Australian Government funding was provided for this activity under the Supplier Access to Major Projects (SAMP) program and proved highly successful. ICN officers also report they are constrained in assisting firms looking to invest in research and development (R&D) and commercialisation by cooperating with universities and government innovation promotion programs.
Since ICN’s inception in 1984, there has been over $54bn in project ‘wins’ for local firms assisted by ICN. Using national ICN data for 2022-23, The main findings are that in 2022-23 ICN assisted firms with $2.7bn of project ‘wins’ nationally, of which $756m, or 28%, was transferred from the state in which the project originated to supplier firms in other states. This demonstrates the large interstate flow of project funds across the states and establishes that ICN operates as an integrated national network, transferring work to the most efficient supplier, regardless of their location. In the case of the Northern Territory and Western Australia, 53.5% and 35.1%, respectively, of work generated within the state was won by firms in other states.
ICN data also provides insights into the industry distribution of projects. ICN activity is concentrated in just four industries − transport, manufacturing, mining and construction − with these accounting for 93% of total ICN activity in 2022-23.
Construction represents well over half (56.3%) of total ICN projects. Reliance on just one data point, 2022-23, could distort these results. This industry concentration is primarily attributed to the fact that most projects involving ICN are classified as investment rather than consumption expenditures, and the former is, by definition, comprised of two principal elements: built structures and equipment.
The preponderance of construction is also a function of the shift some two decades ago in government procurement programs to be ‘agnostic’ regarding the industries supplying ‘local content’. icn.org.au
How can the Export Market Development Grant help my business? By Berrin Daricili, Principal, R&D Incentives & Grants at William Buck.
The highly anticipated next round of the Export Market Development Grant (EMDG) program is set to open for applications in November 2024. There have been a few notable changes since the last funding round. This article will summarise the key changes and important things to consider regarding the application process.
The EMDG program provides critical financial support to Australian SMEs, helping them with costs associated with exporting products and services, such as producing promotional materials, overseas travel, and providing free samples. As businesses face the challenges of entering and competing in international markets, this program serves as a vital resource to boost their global presence and has, therefore, seen unprecedented demand since its relaunch as a grant program in 2021. The upcoming funding round, therefore, introduces several important changes aimed at enhancing the program’s effectiveness and addressing ever-increasing demand.
The EMDG program still offers funding across three tiers, each designed to support businesses at different stages of their export journey as follows:
• Tier 1: Ready to export: Aimed at first-time exporters.
• Tier 2: Expanding: For businesses already exporting and looking to expand their activities.
• Tier 3: Expanding and strategic shift: Targeted at businesses making a strategic shift, such as entering new markets or reaching new customer segments.
What’s new in Round 4?
Designed to provide businesses with greater planning certainty, support successful exporters at various stages of their journey, encourage market diversification, and enhance accountability and compliance across the program, the key changes to the program are as follows:
1. First-come, first-served funding allocation: Applications will now be assessed and grants awarded in the order that applications are received until all funds are fully allocated. Unlike previous rounds, not all eligible applicants will receive funding, allowing successful applicants to receive a more meaningful grant amount.
2. Larger grant amounts and greater clarity: Maximum grant amounts will be set at a meaningful level and will be clearly outlined for each tier:
• Tier 1: This tier provides up to $30,000 per financial year for two years.
• Tier 2: Tier 2 offers up to $50,000 per financial year for up to four years.
• Tier 3: Tier 3 provides up to $80,000 per financial year for up to four years.
3. Enhanced eligibility criteria for SMEs: The EMDG program eligibility criteria have been adjusted to better reflect successful exporters' characteristics. In addition to the requirement to have a turnover of less than $20m in the previous financial year and be exporting or ready to export eligible goods, services, events, IP, know-how, or software of substantial Australian origin (which remain unchanged from the last round), applicants must also:
Be an Australian entity (e.g., sole trader, trust, partnership, company) that has held the same ABN for at least two years.
Meet minimum turnover requirements for the 2023-24 financial year:
• Tier 1: Over $100,000
• Tier 2: Over $500,000
• Tier 3: Over $1m
Demonstrate capacity to spend at least $20,000 on marketing and promotional activities per financial year, exclusive of the grant amount.
4. Focused support for market diversification: Tier 3 grants are now tailored to encourage experienced exporters to target key international markets and pursue broader opportunities for market diversification. With input from businesses, Austrade has identified 27 key markets for these applicants, helping them strategically expand their global reach.
Austrade has said these markets represent exporters’ diversification interests and preferences. They also prioritise Southeast Asian countries as recommended in Invested: Australia’s Southeast Asia Economic Strategy to 2040.
5. Improved support for representative bodies: Industry associations and other representative bodies can access grants of up to $50,000 per financial year to support their SME members. These funds can be used for training and promotional activities that directly benefit SMEs, particularly those with a turnover under $20m. To qualify, representative bodies must submit detailed plans demonstrating how their initiatives will help members and deliver clear outcomes.
6. Stronger compliance measures: To maintain the program’s integrity, stricter compliance requirements have been introduced, including enhanced tax compliance and ethical business practices. The definition of ‘eligible export product’ has also been revised to ensure that goods are of substantial Australian origin.
Given these changes, it’s important you speak to an advisor who can help you determine whether your business is eligible and if so, how to submit an application that covers all requirements.
Applications for the EMDG program must be submitted online, accompanied by supporting documents that verify the applicant’s identity, eligibility, and export marketing intentions. The required documents vary based on the grant tier, the nature of the export activities, and whether the applicant is an SME or a representative body.
• Representative body applications: Open 6 November 2024.
• Tier 1-3 Applications: Open 12 November 2024.
• Application close: Once all funding has been allocated. Don’t miss out on this opportunity to take your business to the global stage.
If you need assistance determining your business’s eligibility or applying for the Export Market Development Grant, contact your local William Buck advisor. williambuck.com
Mines doing things differently to reduce carbon emissions. By Tom Cawley, Executive Chair and Interim CEO, MaxMine. optimising diesel trucks, the average open pit mine could cut 5–15% of its on-site emissions, reducing its carbon footprint by about 30,000 tonnes of CO2. Combining best practices and current commercialised technologies, including electric excavators, mines could target emission reduction of up to 40% in the near term.
According to McKinsey, the mining sector is responsible for 4% to 7% of greenhouse gas emissions globally. Yet, the world’s demand for mining is greater than ever to meet the 2050 Net Zero goals. The International Energy Agency (IEA) observes that clean energy technologies “generally require more minerals to build than their fossil fuel-based counterparts”. The transition away from fossil fuel, needing conversion of large-scale energy systems to electrical power, will require mining two times more copper over the next decade, from 25 million metric tons today to about 50 million metric tons by 2035, according to S&P Global.
Mine operators face a triple challenge. They need to increase output while simultaneously decreasing their emissions. At the same time, they battle rising costs, from energy costs to rapidly falling ore grades that require more material to be moved and more rock to be crushed. To be more sustainable, productive and cost-efficient, it’s clear that mining needs to be done differently in future.
Other sectors facing these challenges have adopted a range of pathways. For example, the power sector has shifted towards renewable energy and energy storage solutions. There’s been a focus on waste reduction and resource efficiency with product lifecycle management in manufacturing.
The most relevant innovations for mining stem from the electric vehicle and tech sectors. In the immediate term, advances in cloud computing and artificial intelligence (AI) have the potential to significantly reduce emissions in mining by optimising operations to deliver maximum output without additional costs, reducing fuel burn, and extending the life of consumables (such as tyres). Major equipment changes, in the form of electrification of mobile machinery, are still years away from commercialisation.
Dealing with the diesel dilemma
Diesel-powered equipment is a major contributor to mining emissions. The average mine site has a fleet of around forty trucks and excavators, generating around 150,000 tonnes of carbon a year. Reducing these diesel emissions is critical to meeting net zero goals, but we have yet to see zero or even low-emissions machines gain traction in commercial operations.
Some companies such as Fortescue and Anglo-American are conducting battery and hydrogen-powered mining haul truck trials. However, these technologies still need to be proven and remain far from mainstream adoption. Another barrier that will slow adoption is the higher capital cost of electric vehicles than their diesel counterparts.
One option that could make a significant difference now is unlocking the power of data with AI. Using existing data analytics technology, mine fleets could be operated more efficiently, with maximised payloads, reduced downtime, and safer and more efficient driving— leading to an increase in sustainability. Data collected from mobile mining equipment can be augmented and analysed to contextualise what the asset was doing at every moment, providing crystal clear visibility of load and haul productivity across the entire operation. Insights can then be generated to determine the best optimisations to make to improve operational efficiency and reduce diesel use: from the right gear choice to optimise truck efficiency, the best speed on each road section to safely optimise cycle times and tonnes moved, and improving fill factor to maximise payloads without damaging trucks. It’s similar to the feedback a Formula One race driver receives on every lap of the course. Simply by
NRW Civil & Mining, one of Australia’s leading contractors, is partnering with MaxMine to reduce greenhouse gas emissions at the Karara Iron Ore project, the largest mining operation in Western Australia’s Mid-West region. NRW is responsible for extracting ore and waste, managing haulage, and loading trains.
NRW wanted to deploy an intelligent technology solution at Karara to harness data-driven insights to refine operator behaviours, improve performance, and establish tangible carbon emissions reduction strategies. Unlike traditional fleet management solutions, MaxMine’s platform offers granular details of what every piece of mining equipment is doing at any given moment.
MaxMine Improvement Coaches and data scientists work closely with Karara staff, using data pulled into MaxMine’s software that comes from MaxMine’s proprietary hardware installed directly on the asset, to optimise efficiency and promote environmentally sustainable practices. MaxMine also provides tailored reports that are sent to production management and Mine Control every day, as well as screens for the front line teams to provide them with near real-time insights about performance. Additionally, operators are able to see how they are travelling through the phone-based application that displays individual performance vs. agreed targets to encourage self-learning and improvement.
NRW’s main objective was to enhance operator behaviour and ensure each operator maintained optimal travel speeds to maximise safety and productivity while reducing road degradation and overall carbon footprint.
Initially, ramp, zone, and corner speeds were targeted. Expectations were set and crews were coached on how to meet them. The solution also provided personalised performance feedback to individual operators, displayed as a league table to encourage healthy competition. Every day, operators could refine their practices based on near-real-time data.
This improved NRW’s overall operator performance scores from a baseline of 72% to 96%, ensuring that all operators are consistently meeting clearly defined operating standards. The average fill factor also increased to three extra tons per load. With approximately 17,000 loads monthly, this translates to an additional 612,000 tons of material being moved annually without incurring any extra costs.
Advanced technologies such as AI hold huge potential for the mining sector, but industry collaboration is key to achieving net zero. MaxMine’s #first40 initiative collaborates with mining companies to reduce emissions on mine sites by 40 percent using data and analytics, and the integration of existing technologies such as electric hydraulic phase shovels and low-carbon diesels.
The mining industry’s role in enabling a net zero future is undeniable, but its practices must evolve to sustainably meet the growing demand for minerals. By embracing advanced technologies, alongside industry-wide collaboration, and a commitment to reducing emissions, mining can become not only more productive but also a significant player in the global effort to combat climate change. maxmine.com.au
The Government’s ‘Future Made in Australia’ package – worth $22.7bn – provides both incentives to keep expertise on shore, but also direction (particularly towards renewables and sustainability) and some level of certainty for large swathes of the manufacturing sector. Yet challenges remain. What makes Australia “the lucky country” is both its apparent imperviousness to recession compared to global peers and its high-salaried workforce, making the nation one of the highest-cost environments in the world. Combine this with a need to decarbonise, which can be expensive (though necessary), and it’s clear the sector needs to find ways to increase efficiency and reduce costs.
This makes the emergence of Industry 5.0—the next phase in the evolution of manufacturing where humans work alongside intelligent machines—so important. If leveraged correctly, the “smart factory” can unlock numerous benefits that can help manufacturers establish competitive advantages regardless of economic conditions, while reducing their carbon footprint in the process and ultimately enabling a net zero business.
In a smart factory, digital technologies connect machinery, production systems and devices to provide end-to-end visibility of the entire manufacturing process. With a real-time view of the value chain—from raw materials to finished product—manufacturers can predict demand fluctuations, and make informed decisions about resource allocation, scheduling, and capacity planning.
This is happening now, including just over the Timor Sea in Indonesia. A factory in Batam, Indonesia, produces power and industrial automation products, and the team there wanted to improve oversight of the plant’s operational performance and efficiency. Management, meanwhile, wished to develop more detailed data on equipment failures to pinpoint how to tackle them. Leveraging asset performance management (APM) and manufacturing execution system (MES) solutions, and a Lean Management solution developed specifically for Batam, the factory was able to digitise lean manufacturing practices, reduce downtime and maintenance cost through managing asset performance, and could now aggregate and visualise real-time performance data in the cloud. This led to 44% less downtime, a 40% increase in ontime delivery for customers, and energy savings of 21%.
The site has since been recognised as a Fourth Industrial Revolution (4IR) Lighthouse by the World Economic Forum.
But to replicate this model among its other factories across the globe, it will need to rely on another kind of technology that is already commonplace for most enterprises, including one manufacturer in Australia which has seen efficiency skyrocket.
The latest connected digital solutions leverage the cloud to run application services and share data across distributed manufacturing sites.
Think of it as Industrial Intelligence as a Service (IIaaS)—the idea is to create an intelligent network where a single view of activity is available to all stakeholders, and even authorised external partners. This single-source-of-truth technology can remove guesswork, enable the standardisation of production practices and processes across the breadth of sites across the globe, identify and share trends, and—importantly—ensure that improvements made at one site can quickly be shared across the network.
Over the longer term, IIaaS platforms, together with artificial intelligence and machine learning applications, support proactive approaches to planning. By facilitating scenario modelling and what-if analysis, manufacturers can simulate various production scenarios and assess their potential impact on operations to capitalise on emerging opportunities, anticipate and mitigate risks, and maintain visibility over energy consumption across sites to help find efficiencies and reduce emissions.
Borg Manufacturing is a leading privately-owned Australian melamine and joinery manufacturer, that wanted to increase batch flexibility on products while accelerating high-quality, consistent production and keeping their next-day-delivery commercial promise. However, it was experiencing disparate processes across multiple manufacturing sites, manual stock-picking processes were proving unsustainable, and manual reporting was hindering access to key data metrics.
It installed an integrated MES and Warehousing IIaaS solution which standardised operations from order through to shipment across the 20 sites, allowing them to ramp up order picking from 2,000 in 12 hours, to 3,000 in four hours. It’s reduced injuries on-site to virtually zero, and wastage from 5% to 2%. All told, they estimate an efficiency gain of 400%, and it’s ensured they could scale orders while continuing to deliver on time as promised the next day – a huge differentiator.
Ultimately, what will protect Australian businesses while also enabling decarbonisation is improving efficiency and productivity, which will lead to reduced costs, energy consumption and carbon footprint, and a more competitive overall offering.
The answer to doing so lies in both the people and the technology—connected information and insights are already helping manufacturers build more nimble, robust, and sustainable operations in incredibly fragmented and uncertain economic conditions. aveva.com
An air taxi has completed the first flight of a hydrogen-fueled aircraft capable of vertical takeoff and landing, breaking a distance record with no emissions other than water.
A mixture of electricity and a tank of hydrogen fuels this air taxi, the latest vertical take-off and landing vehicle from a ban of prototypes in Joby Aviation’s hangars. The flight took place on June 24. Previous tests required a runway and with smaller vehicles. The flight, three times further than the distance records set by electric air vehicles from the same developer, "demonstrates the potential for hydrogen to unlock emissions-free, regional journeys," according to Joby Aviation.
The vehicle has been modified from a fully electric aircraft and has six rotors that can be used in a rural setting. While the original build of the craft did over 40,000kms of testing, the company’s engineers converted this by adding a 40-kilogram tank for hydrogen.
The fuel cells convert hydrogen into electricity, water and heat in the presence of oxygen. According to the statement, the electricity then powers the aircraft's rotors, while the water is released as a waste product. The aircraft also carries a reduced number of batteries at all times, providing extra power during takeoff and landing.
In a world first, scientists are closer to giving the next generation of solar cells a powerful boost by integrating a process that could make the technology more efficient by breaking particles of light –photons – into small chunks.
Researchers are unravelling the scientific understanding of what happens when light particles split—a process called singlet fission—and its underlying workings.
Lead researcher Professor Tim Schmidt from UNSW Sydney’s School of Chemistry has studied singlet fission for over a decade. He says the process could be invoked and applied to improve silicon solar cell technologies.
“Today’s solar cells work by absorbing photons which are then sucked away to the electrodes to do the work,” Prof. Schmidt says. “But as part of this process, much of this light is lost as heat. Which is why solar panels don’t run at full efficiency.”
Almost all photovoltaic solar panels on the market today are made from silicon, says Co-author Professor Ned Ekins-Daukes from UNSW’s School of Photovoltaics & Renewable Energy Engineering. Although the technology is now cheap, it is also nearing its fundamental limits in terms of performance.
Prof. Ekins-Daukes says, “The efficiency of a solar panel represents the fraction of energy supplied by the sun that can be converted into electricity.”
“Our industrial collaborator, LONGi, set the highest efficiency earlier this year, opens in a new window. They demonstrated a 27.3% efficient silicon solar cell,” he says. “The absolute limit is 29.4%.”
Prof. Schmidt says scientists were still trying to understand how the molecular process of singlet fission worked. Specifically, how does one become two? He says the process is complex and detailed.
Last year, the Australian Renewable Energy Agency (ARENA) selected UNSW’s singlet fission project for their Ultra Low Cost Solar program. The program aims to develop technologies capable of achieving greater than 30% efficiency at a cost below 30 cents per watt by 2030.
The team used a single-wavelength laser to excite the singlet fission material. Then, they used an electromagnet to apply magnetic fields, which reduced the speed of the singlet fission process, making it easier to observe.
“From this firm scientific understanding of singlet fission, we can now make a prototype of an improved silicon solar cell and then work with our industrial partners to commercialise the technology,” Prof. Ekins-Daukes says.
“We’re confident we can get silicon solar cells to an efficiency above 30%,” Prof. Schmidt says.
Nature Chemistry
A fleet of foiling, electric ships is set to be deployed on the Red Sea. In a landmark deal, the Candela P-12, the world's first electric hydrofoil ship, will service the planned water network in NEOM, the gigantic, sustainable development in Northwest Saudi Arabia. NEOM has procured an initial batch of 8 of the foiling, electric shuttle ships, making it the largest announced order in Candela’s history.
"The P-12 is designed to create zero-emission water transport systems that are significantly improved over traditional water commuting,” says Gustav Hasselskog, CEO and founder of Candela.
“Unlike legacy systems with large, slow, and energy-inefficient conventional ferries, the Candela P-12 is a smaller and faster unit, allowing much more frequent departures and quicker journeys for passengers. All daily necessities and services will be just a short boat commute away.”
Candela P-12 was launched last year and is set to debut in Stockholm’s public transport during fall 2024. Technology News
A team of US and Korean researchers has developed a 3D-printing ink that makes structures easy to recycle without needing heat or light. The polymer ink dries on contact with salt and dissolves back into reusable ink when it contacts fresh water. The researchers say their ink could be useful for disposable electronics, robotic components, and prototyping.
The researchers’ method uses poly(N-isopropyl acrylamide) or PNIPAM. The pharmaceutical industry uses this non-toxic substance for drug delivery systems. PNIPAM dissolves in water to make a liquid, but it solidifies when it comes into contact with a salty calcium chloride solution.
The researchers used a commercial healthcare-grade 3D printer to pump PNIPAM into calcium chloride and water mixtures. It solidified into neat structures immediately.
“This is all done under ambient conditions, with no need for additional steps, specialised equipment, toxic chemicals, heat or pressure,” says senior author Professor Jinhye Bae, a researcher at the University of California – San Diego, USA.
Researchers at TMOS, the ARC Centre of Excellence for Transformative Meta-Optical Systems, and their collaborators at RMIT University have developed a new 2D quantum sensing chip using hexagonal boron nitride (hBN) that can simultaneously detect temperature anomalies and magnetic field in any direction in a new, groundbreaking thin-film format.
They detail a sensor significantly thinner than current quantum technology for magnetometry, paving the way for cheaper, more versatile quantum sensors.
To date, quantum sensing chips have been made from diamonds, a very robust platform. The limitation of diamond-based sensors, though, is that they can only detect magnetic fields when aligned
in the direction of the field. If unaligned, they have large blind spots. As a result, magnetometers made of diamond must contain multiple sensors at varying degrees of alignment. This increases the difficulty of operation and, as a result, the versatility of different applications. In addition, the rigid and three-dimensional nature of the quantum sensor means that its ability to get close to perfectly smooth samples is restricted.
TMOS Associate Investigator Jean-Philippe Tetienne (RMIT University) and Chief Investigator Igor Aharonovich (University of Technology Sydney) and their teams are pioneering a new quantum sensing platform using hBN. These hBN crystals are made up of layers of atomically thick sheets and are flexible, which allows the sensing chips to conform to the shape of the sample being studied, getting far closer to the sample than a diamond can.
Different defects exist in the hBN that produce different optical phenomena. A recently discovered carbon-based defect, the atomic structure of which remains unidentified, detects magnetic fields in any direction but has not been used for magnetic imaging until now.
Nature Communications
Space Machines Company, an Australian-Indian in-space servicing firm, has forged strategic partnerships with two industry leaders: Ananth Technologies, India’s premier aerospace and defence manufacturer, and Digantara, the leading full-stack space infrastructure company easing space operations and space traffic management. These collaborations mark a significant milestone in Space Machines Company’s mission to revolutionise space operations and traffic management.
The partnerships will play a pivotal role in the upcoming Space MAITRI (Mission for Australia-India’s Technology, Research and Innovation) mission and the launch of Space Machines Company’s second Optimus satellite. Scheduled for 2026, the satellite will be deployed aboard NewSpace India Limited’s (NSIL) cutting-edge Small Satellite Launch Vehicle (SSLV).
Space Machines Company’s CEO and Co-Founder, Rajat Kulshrestha, formally announced and signed the two key agreements at the Bengaluru Space Expo (BSX) 2024 in Bengaluru, India.
Space Machines
The Emerson AVENTICS XV pneumatic valves provide greater automation flexibility and optimised flow.
Emerson has launched its AVENTICS™ Series XV pneumatic valves. These valves are designed with interoperability in mind to provide machine builders across multiple industries and factory automation applications with a flexible and costeffective valve platform. The new valves are ideal for global machine builders and end users, with universal threads and other features supporting regional standards and global availability.
Series XV valves provide higher flow rates in a compact valve package, enabling more efficient and flexible pneumatic system performance for factory automation, automotive and tyre, and food and packaging applications. This helps manufacturers boost productivity and allows them to offer products customised for specific markets and customer preferences.
“In all industries, manufacturers need high-performance technology that gives them the agility and flexibility to stay ahead of rapidly changing market demands,” said Wolf Gerecke, director of product marketing for Emerson´s machine automation business. “The new AVENTICS Series XV pneumatic valves deliver that performance with optimised flow, a wide range of valves and an extensive portfolio of accessories.”
Drying the air on the factory floor is not negotiable.
It’s no secret that the key benefit of air dryers on the factory floor is quality-prepared air. These compact but powerful units help remove moisture in compressed air systems for complete peace of mind.
And while it’s ‘that easy’, Product Specialist for SMC Corporation
ANZ Robert Taylor said that the integral benefits of a refrigerated air dryer are often overlooked. “Refrigerated air dryers are not new to our range and should, in fact, be sold as complementary products across the board,” he shared.
However, perhaps the lesser-addressed benefit of air dryers is the potential savings that they can produce on the factory floor. “By removing the moisture out of the compressed air system, you are protecting your pneumatic components and ensuring a long life span—saving you on downtime and replacement costs.”
“No longer a nice-to-have, dryers are now a must-have essential on the factory floor,” stated Taylor. Designed to meet dew points as low as -60°C ( Membrane Air Dryer IDG series) and flow range up to 1340m3/h (for the Refrigerated Air Dryer - IDFA series), SMC’s broad range of air dryers answers the call of various applications and industries – and has proved to be particularly popular in the local meat processing sector among others.
“The series is designed to perform in demanding environments and delivers dry compressed air, ideally suited for meat processing plants which are currently experiencing an uptick in demand.”
Regarding development prospects, Taylor noted that “as it stands, our range is up-to-date and comprehensive. At this stage, we don’t require any new R&D developments on this product because we have the right solution to meet every customer requirement.”
When it comes to spec’ing an air dryer, Taylor cautioned that it’s not a ‘one-size-fits-all’ approach. “Conversely, we work with customers to determine their exact requirements.”
Taylor broke down the various considerations to spec an air dryer as follows:
Series XV valves include the XV03, which provides flow volumes of up to 350 litres per minute in normal conditions (NL/min), and the XV05, which is scheduled for release in October 2024 and provides up to 880 NL/min. All valves in the Series XV line use proven AVENTICS core technology and include metal threads, parallel wiring, aluminum base plates and compact dimensions to make it easier to integrate into production system designs.
Series XV valves use consistent interfaces with wide connectivity from single wiring over parallel connections such as D-SUB connectors. They also support leading fieldbus protocols, including PROFINET®, Ethernet/IP, EtherCAT, Powerlink, Modbus TCP, IOLink, AS-I, to simplify integration into machine control networks.
Series XV valves are also easy to commission. The AVENTICS online configurator supports system layout and provides helpful information, while easy-to-understand system documentation in the design phase helps speed up machine development.
emerson.com
1. What dew point does your equipment require?
2. What is the flow rate required?
3. What is the inlet temperature to the dryer at its warmest peak?
4. What are the ambient temperature conditions?
“While we work with our customers to determine these considerations, we also offer an easy-to-use online Refrigerated Air Dryer Model Selection Software,” he added.
IDFA series - Refrigerated Air Dryer
“The IDFA series remains a firm favourite for the food, beverage and processing sectors. It’s designed to improve flow ratings and features an auto drain and standard dust filter for years of reliable service.”
Key benefits include:
• Applicable for the high-temperature environments
• Ambient temperature: Max. 45°C
• Inlet air temperature: Max. 65°C
• Increased air flow capacity
• Power supply voltage: Single-phase 230 VAC (50 Hz)
IDG-D series - Modular Connection Type Membrane Air Dryer
Key benefits include:
• Compatible with various ISO water quality classes, Modular connection is possible.
• Non-fluorocarbon
• Power supply not required
• No vibration or heat discharge
• Contributes to energy-saving
• Pressure drop: Reduced by up to 61%
• Outlet air flow rate: Max. 25% increase
• Purge ratio: Approx. 14% smcanz.com
Enmin expands into the inspection market with Antares Vision Group’s combination metal detector & check weigher.
Enmin is Australia’s leading materials handling and vibratory equipment manufacturer and is the exclusive Australian representative for Antares Vision Group’s solutions to the food industry.
The European-based manufacturer has an extensive portfolio of inspection equipment designed specifically for the food and allied industries.
Enmin will be responsible for marketing the complete Antares Vision Group’s food industry product range, which covers metal detection, check weighing, X-ray inspection, in-line leak detection and seal, label, and code inspection.
Expected to be one of the most popular models is the innovative and compact ‘2-in-1’ metal detector and check weigher, which is designed to ensure any metal contaminants are removed and weight correctness is confirmed. The machine has all the advantages of two single units but offers a reduced cost and smaller footprint compared to two separate machines.
Designed specifically for the food industry, its hygienic construction features quick-removal conveyors and a completely washable structure. A double rejection system keeps contaminated products separated from those with out-of-tolerance weight.
A wide range of models is available. The compact series offers metal detection and weight control up to 3.2kg for small and medium-sized products.
For medium and large products, the maxi-series offers metal detection and weight control up to 12kg—something no other machine on the Australian market can offer. Both units allow flexibility for different configurations, sensitivity, and line speeds. The two systems work together in total synchronisation, but if required,
the metal detection and check weigher can work independently without affecting the line's functionality. The machine features the latest inspection technology and high-quality components. It is designed to be simple to operate and manage. The check weigher operator interface, coupled with a 30cm touch screen, allows simultaneous format change-over for both units. The main support structure is constructed of stainless steel, while the moving aluminium parts are coated with hard nickel and anodised for maximum durability. The unit is specifically designed for use in the most demanding environments.
The metal detector is impervious to electrical interference and sensitive enough to detect products with uneven physical characteristics and light-metallised wrappers. It guarantees that any metal contaminants are removed, which is crucial in the food sector.The weighing unit features the latest load cell technology. It is designed to operate with the utmost precision and impressive accuracy of plus or minus 0.2g (subject to operating environment).
Phillip Garro has recently joined Enmin as Sales Manager (Inspection & Packaging) and will be responsible for the sales and customer support of the Antares Vision Group brand. He has a wealth of industry knowledge, having spent the last twenty years working in the specialised inspection market.
“The combination metal detector and check weigher offers outstanding performance and the latest technology along with a
“It takes quality control to the next level and provides an added level of security and reassurance. Additionally, you get the space benefit that only a single machine with a small footprint can offer,”
“Given Antares Vision Group’s extensive range and successful track record in Europe, we are confident the products will prove popular in Australia with a diverse range of food manufacturers,” Garro said.
Every major mining company has a decarbonisation project, and a large part of it is moving from diesel to electrical energy, as Drew Turney reports.
Electric cars are becoming increasingly common on Australian roads, and industrial players are investigating their use in commercial fleets, with one recent study from the University of Michigan finding electric trucks can reduce air pollution and greenhouse gas emissions by between 13% and 35%
Research firm IDTechEx expects electric trucks to become a US$15bn industry. Could the same change transform mining? If so, we're a long way off—a 2022 study said only 1% of industry power came from electricity—but plans are accelerating.
Several Australian industry players and their supply chain partners are members of the Electric Mine Consortium, a think tank driven by the mission to accelerate progress towards a fully electrified zeroCO2 and zero-particulates mine.
As a spokesperson from automation technology provider Rockwell Automation told us, mine site tools are fertile ground for adopting wide-scale electric power. “Most mines are in places with lots of renewable energy, and many are a long way from the grid and have to run generators,” he said. “It's not just more sustainable; it's more affordable to capture energy on-site rather than shipping fuel to a remote location.”
In many ways, it's not just an opportunity but the response to an urgent problem as power needs at mine sites increase. In just one example, BHP operates two major locations in Chilé. The power needs of both, which were seven terawatt-hours per year in 2022, are set to increase to 12TWh/y by 2033, an increase of 70%. Without electrification, there would be a lot more diesel carbon emissions.
The company's June 2023 decarbonisation report said the diesel displacement in the Chilean sites' cathode operation boilers would mean 1,000 fewer round trips by diesel trucks every year.
The report said that the 2020s would be characterised by mine electrification challenges thanks to further increases in power consumption. BHP intended to meet these tasks by exploring solar generation and storage and power purchase agreements from renewable sources. As the report said, 'Our preferred pathway to eliminate diesel is via electrification.'
Continued next page
Continued from previous page
The mining giant has already announced a partnership with heavy industry manufacturer Caterpillar to replace the diesel fleet at one Chilean site completely, bought four battery-powered locomotives for its WA iron ore operations, and announced a partnership with Rio Tinto to conduct trials of battery-electric haul trucks in both companies' Pilbara, WA operations.
As the above makes clear, most of the activity around electrification so far is in vehicles. IDTechEx reports that the mining industry produces 2-3% of the world's CO2 emissions, with around half of that total coming from diesel vehicles.
However, the Australian mining and resources industry needs about two gigawatts of off-grid power. Some support operations can come from small-scale solar (think of the technology behind those remote highway solar-powered emergency phones powering the rec area barbecue), but offloading the burning of diesel to generators that provide electric power for heavier use will only move the problem, not solve it.
So there are plenty of other areas where electrification can make a difference like conveyor belts, hoist systems, grinding machinery, etc. “The first thing that comes to mind is, of course, battery electric vehicles to reduce diesel,” says Thomas Steigler, research engineer of energy solutions provider Ampcontrol. “They not only reduce CO2 emissions, they eliminate diesel particulates and generate less heat, so reduced underground ventilation saves energy.”
Steigler calls Ampcontrol, a 55-year-old energy industry provider based in Newcastle, one of the primary suppliers of electrical equipment to the resource industry. The company also services the energy and infrastructure industries and has recently made inroads into electric vehicles with the Driftex battery electric personnel carrier and BEV chargers.
"It's the first battery electric vehicle certified for use in explosive atmospheres, which is required in underground coal applications," he says.
One of the biggest challenges to overcome in electric vehicles is range—batteries don't power a big mine truck as long as an onboard tank of diesel fuel—which is why much of the industry is concentrating on the surrounding infrastructure first, either as a proof of concept or because it's an easier market to develop.
So what's driving all this – will it save money or the planet? Happily, both those aims can advance in lockstep. One WA gold mine hopes to get most of its power from an on-site solar and wind farm (more below), which will save a lot of diesel, not to mention the costs of purchasing and transporting fuel.
The industry has also undertaken modelling to compare diesel against electrified mine operations, with illuminating findings.
The research finds that while CapEx for electrified mines is higher than that of diesel mines, OpEx is lower. The net result is that electrified mines and already economically viable when compared to diesel operations. The savings in smaller scale operations were more marginal depending on the operation, but in a bigger mine, the net result was clearly positive.
Depending on variables such as what the operation was extracting, commodity prices, etc., the study found that the costs of electrification would pay for themselves within eight to twenty years. "Estimates vary," agrees Pranav Jaswani, Technology Analyst at IDTechEx, "but broadly speaking, electric machines have shown they'll cost 40-80% less to operate than equivalent diesel ones."
In fact he's even more optimistic, saying most electric surface mining vehicles will pay for themselves in saved fuel and maintenance within two to four years – one to two years in underground operations. Identifying and managing those costs is a whole other ball game. You don't just buy an EV and scrap an existing truck.
One is training. Jaswani says there'll be a period of adjustment, just like you or I would need when going from a petrol to an electric car. Still, mine vehicles have far more intensive license and training requirements, so most drivers and operators will pivot quickly.
“It's a similar story with maintenance workers, who'll need some training to provide proper care for an electric machine,” he says. “But so far, members of the equipment manufacturer’s teams have helped train mining company staff so they can monitor and maintain the equipment thoroughly.”
The real learning curve will be imposed on mine managers, engineers, and planners. “They'll need to understand the intricacies and nuances of operating an electric fleet, understanding all the different levers you can use to make improvements,” says Steigler. “Where do you put your chargers? How fast do you charge? What data measurements do you take to optimise operations?”
But where will the energy come from to recharge batteries and power the electric mine? As mentioned above, a gold mine in Leinster, around 1,000km northeast of Perth, has its own solar and wind farms, operated by sustainable distributed energy system provider EDL.
The Agnew Hybrid Renewable Microgrid is intended to power the mine using 50-60% renewable energy over the long term, the equivalent of the power needs of around 16,000 homes every year. Solar, wind, battery, and gas engines produce over 14,000kW of power without a single drop of diesel.
But it's much harder than throwing up a paddock full of panels or windmills. “Charging and power infrastructure is one of the biggest challenges for electric mining,” says Jaswani.
“Current infrastructure can vary widely. Renewables like solar and wind are already popular and expected to become even more widely used. Some companies also set up microgrids – smaller and entirely self-contained grid systems using local energy generation, transmission, and storage. Some shorter-term solutions are diesel or hydrogen-powered mobile charger units, but they're both more expensive and less energy efficient.”
This means the Australian mine is going electric by hook or by crook, and the race is on to find the most cost- and energy-efficient way to do it. With the price and demand for energy not heading down any time soon and the climate changing on a seemingly yearly rather than a generational basis, can we afford not to?
rockwellautomation.com ampcontrolgroup.com
RUC Mining and Rockwell Automation use the gravity potential of underground mine hoists utilising Rockwell Automation PowerFlex drive systems.
Underground mining hoists, or winders, are powerful machines used to raise and lower minerals and materials in a mine shaft. They allow efficient vertical transport of materials, which would otherwise require larger machinery and further extraction cost from the mine. While travelling upward, a large amount of power is required, but this is different on the way down. It’s the downward trip that sparked an innovative idea by underground mine hoist specialists, RUC Mining: what if energy generated on the way down could be stored, then used to power the upward journey?
The sustainability implications and broader contribution to the electric mine of the future were huge, but first, a technically complex and challenging task had to be figured out.
RUC electrical manager Greg Bell, believed this was more than an idea, and began working on how to make it a reality. He and the RUC team chose strategic partners, Rockwell Automation, and Energy Power Systems Australia (EPSA), to create a fully integrated solution that could be rolled out to hoists across the globe.
Collaborating with these partners, the RUC team created what they believe to be the world’s first regenerative energy storage solution for underground mine winders, allowing these machines to run totally on their own stored energy, rather than requiring a separate diesel generator.
In its first application in an Australian mine, RUC installed its RUCShaw 512 singledrum winder, which is powered by 710 kW drives, has a hoist capacity of five metres per second, with 12-tonne line pull, and operates with a design depth of 1,600m.
A technically complex sustainability solution
Electric motors consume energy when hoisting a load up a mine shaft. But when travelling downwards, they have the potential to become generators.
“Most mine hoists use a brake resistor pack with a cooling fan to deal with the heat generated. But these packs create a single point of failure, and are application-specific, so they need recalculation if a variation in brake power is required,” explained Bell.
“Instead, we proposed for the generating power to be supplied back onto the incoming supply bus, to be absorbed by system loads,” he added.
To make this solution a reality, Rockwell Automation, the world’s largest company dedicated to industrial automation and digital transformation, provided Active-
Front-End (AFE) Powerflex® 755TR regenerative variable speed drives, Low Voltage Motor Control Centres, and GuardLogix® controllers as well as ThinManager® software for application management, FactoryTalk® View Site Edition software for a complete real-time overview of HMI operations, network and security services, and product and technical support.
The battery selected to store regenerative energy was a Cat® PGS 1260 Battery Energy Storage System (BESS), supplied by EPSA, which provided added redundancy through its parallel inverter and battery stack architecture.
“We have one operational project where we have implemented this solution with two hoist drives, and we are looking into
incorporating this into future projects. We also see potential for this solution to be rolled out internationally on new and existing mine shafts,” said Bell.
Significant environmental gains are achievable with the regenerative energy storage solution in place by reducing the amount of diesel power generation. RUC has estimated that in their initial installation, over two years, the regenerative energy storage solution will achieve an estimated reduction in diesel consumption of 1.427 megalitres (costing about two million dollars); a reduction of 3.85 tonnes of CO2 output (that’s approximately equal to travelling 12,700km in a petrol car); and an approximate 42% reduction in greenhouse gas emissions from power generation.
“In addition to these strong sustainability benefits, the regenerative energy storage solution also reduces daily operating costs, reduces plant operating hours and maintenance requirements, and provides additional redundancy to the power system that was unavailable in passive components such as load banks,” said Bell.
Rockwell Automation regional director— South Pacific, Anthony Wong, added, “Sustainability is a key focus for Rockwell, and when RUC came to us with this forwardthinking project, we were enthusiastic to work with them to turn it into a reality and to help deliver reliability and performance with our hardware and software solutions.”
“While this solution was designed and built in Australia, it will apply to mines worldwide. It’s a small but significant step towards a more sustainable mining industry and the dream of fully electric mines. We commend RUC for its ingenuity and vision in conceiving this truly innovative solution,” he said.
Not only was there a complex integration of technologies, but the regenerative storage project involved a lot of industry firsts, so there was no existing template to follow.
“Some companies dislike being the first to do something, because there’s no guarantee it will work. But Rockwell was supportive from the start. They helped us select the right drives for powering our hoists, and worked to integrate this seamlessly to achieve regeneration coordination with the battery,” said Bell.
While not an initial goal of the regenerative energy storage project, the new solution is delivering “bump-less” performance
and an additional level of redundancy within the battery. “Faults happen when you lose power, and hydraulic braking is aggressive. With the regenerative energy storage solution, we can split the battery with two inverters, so we have an added layer of redundancy. This means if we lose power, the winder does not stop, which delivers smooth, bump-less performance,” said Bell.
“Because power goes straight back to the battery with no heat loss, this solution could readily be scaled down to any energy application – even elevators. We believe
this is the only successful gravity kinetic energy storage system using a hoist in the world, and we are proud to introduce it here in Australia.
“We have plans to use this technology more widely because if you think about the electric mine of the future, vertical haulage delivers the most affordable, operable, and achievable solution for transporting material out of the mine. The technology has great export potential, too, so we can showcase Australian innovation globally.
ruc.com.au
rockwellautomation.com.au
Ensuring reliable long-distance critical signal delivery in mining applications.
The mining industry is the backbone of modern civilisation, providing the raw materials essential for everything from buildings and infrastructure to electronics and medicine. The global coal mining industry has grown by nearly 20% on average for each of the last five years, meaning conveyors are carrying more coal than ever. However, these mining operations often occur in remote and challenging environments where reliable communication is paramount.
Coal-carrying conveyor belts can be up to 20km long. If they break and do not immediately stop, cargo can be spilled everywhere and cause a major safety risk. Conveyors usually come equipped with contacts that indicate problems like breakages, but with the extreme distances involved, these can be unreliable. Ian Loudon, international sales manager at remote monitoring specialist Omniflex, explains why new fibre optic modules are game changers in mining applications in terms of reducing downtime and improving safety.
Modern mining conveyor belts can extend for tens of kilometres, carrying tonnes of material daily. These mammoth systems are crucial for transporting extracted resources from the mine to processing facilities or stockpiles. Therefore, ensuring efficient and uninterrupted operation is vital for maintaining production quotas. However, conveyor belt safety is an equally important consideration. Belt breakages can have catastrophic consequences – causing damage to infrastructure, environmental spills and even worker injuries or fatalities.
Wireless telemetry systems play a vital role in ensuring conveyor belts' smooth and safe operation. These systems continuously monitor belt tension, speed and alignment and can detect anomalies that could indicate potential problems. Real-time data transmission allows for early intervention, preventing minor issues from escalating into catastrophic failures. In the unfortunate event of a belt breakage, sensors can trigger emergency shut-off mechanisms immediately, minimising damage and potential injuries.
Getting switch contact signals point-to-point can be a matter of life and death. When an operator hits the conveyor’s emergency stop button, they must be confident that the system will shut down as intended. If someone is in danger in a mining environment, the risk of signal failure must be mitigated to an acceptable level.
However, maintaining reliable long-distance signal delivery in mining environments can be challenging for several reasons. First, signal strength can be limited in any underground operations where rock formations hamper radio wave transmissions.
Next, mining activities can generate significant electromagnetic interference (EMI), which can interfere with wireless signals.
Furthermore, mining applications often take place in harsh environments where temperature, humidity and dust levels can place excessive strain in communication equipment.
Finally, the distances involved are also a big hurdle to overcome for many transmission options. Copper wiring is extremely costly and, when required to run over many kilometres, the costs are often prohibitive. Furthermore, copper systems do not even guarantee reliable transmission over those distances. For example, standard communication links on copper wires like RS485 are generally limited to about a kilometre of reliable transmission.
Therefore, to overcome all these challenges and ensure ongoing worker safety, the mining industry must source signal transceiver modules that can operate reliably even in the harshest of environments.
Omniflex’s new FCX module is a bidirectional transceiver, meaning it combines both transmission and reception capabilities into one device. This eliminates the need for separate modules, halving the number of modules required in any given setting and dramatically reducing costs for purchasing and installation. Costs are reduced further because fibre optic cabling is much cheaper than copper, so the cost per module is lower, and fewer modules are needed.
To set the units up, users should place one module at either end of a duplex fibre optic link. When the contact on the first is closed, the other module is energised, replicating the contact signal.
The transceiver is compatible with either 850nm multi-mode or 1310nm single-mode fibre optic cabling; the latter can send switch contact signals up to 20km of range. The FCX is powered from a 10-30Vdc power supply and can operate from 0-60C.
The FCX can also be used in nuclear and radiological safety warning signals and monitoring and controlled shutdown of electrical substations. It is certified for use in SIL-2 applications, meaning system designers can trust that the risk associated with transmitting switch contact signals over long distances can be limited to appropriate levels using the module.
With many years of experience providing SIL-rated safety systems across mission-critical industries, Omniflex is well placed to identify and provide the most suitable solution for any given application. Omniflex designs and manufactures electronic products and systems worldwide for the automation, control and cathodic protection industry, specialising in remote monitoring. This includes industrial networking, remote I/O systems, utilities monitoring, process automation systems, signal conditioning, and alarm and event management. omniflex.com
Australian manufacturers leverage cosmic rays and hyperspectral imaging in mining operations.
Two Australian manufacturers are leveraging spaceborne particles and hyperspectral imaging to boost the safety and productivity of mining operations both locally and abroad.
EQ Resources has commercialised a system to detect and extract tungsten from previously unviable mining waste, supported by a co-investment from the Australian Manufacturing Growth Centre (AMGC). mDetect has commercialised a system to manage tailings dams in mining better.
It sounds like something out of Star Wars, yet cosmic rays and hyperspectral imaging are a central feature in two mining technology projects backed by the Advanced Manufacturing Growth Centre, with major implications for safety and access to strategically important materials.
mDetect is a Swinburne University spinout specialising in astrophysics research into muons, a type of subatomic particle that results from the Earth’s atmosphere being hit by cosmic rays, which fall harmlessly and constantly down on us1. They are sometimes described as the heavy cousin of electrons, with their mass helping them pass deep into objects; much further, for example, than ground penetrating radar.
The company has commercialised telescopic devices and software in a system that uses muon behaviour to monitor and map tailings dams, providing real-time information on stability of the critical infrastructure in mining operations.
Assisted by $248,191 in co-funding from AMGC’s Commercialisation Fund, mDetect has trialled its muography-based imaging system at Oz Minerals (now part of BHP), and leveraged key partner Swinburne to assist with development, documentation, design for manufacture, production automation and other input ahead of scale manufacture.
Co-Founder of mDetect, Dr Jerome Donovan said, "Thanks to AMGC, we've gone from idea to impact, developing our product for commercial sales, securing key agreements, and developing our design for scaling manufacturing – it has by far been our best government-funded program experience. With high-profile partnerships secured, mDetect is set to revolutionise global industries and enhance mining safety."
“Taking highly-technical IP – and which has heritage in dark matter research, no less – and delivering a market-ready product is never easy. But we are very nearly there thanks to the support from AMGC.”
The project is expected to lead to $7.7m in revenues in the fifth year after completion, resulting in new jobs at the growing company.
AMGC Managing Director, Dr Jens Goennemann said: "An Australian manufacturer harnesses the power of space to protect lives on Earth. That’s Australian manufacturing at its best – globally relevant, collaborative, and highly complex. mDetect is truly a leader in their field, poised to make a global impact."
From utilising space particles to leveraging electromagnetic imaging, EQ Resources, the owner of the formerly dormant Mount Carbine Tungsten Mine in North Queensland, has innovatively
devised a method to identify and extract tungsten from waste sources, following its discovery at the site in the year 1895. Today tungsten is recognised in the EU, US and elsewhere as a critical mineral2. It is used to toughen steels for the space, defence and renewable energy sectors and is found in many products such as lighting and heating elements. An estimated 85 per cent of global supply is currently derived from China3.
AMGC supported EQ Resources (EQR) through $600,000 in coinvestment to support a project to recover tungsten from a mine waste stockpile and low-grade deposits, incorporating high-tech hyperspectral imaging sensors on a front-end loader, AI-assisted decision-making, and X-ray sorting technology.
The project linked EQR with Mt Carbine Quarrying Operations, Plotlogic, Tomra, Cronimet, and the University of Queensland. Since its completion, it has created an extra 20 jobs, upskilled 30 employees, and helped deliver an additional $3.6m in revenues.
Kevin MacNeill, CEO of EQ Resources, said, “Early co-investment from AMGC allowed EQ Resources to accelerate the commercial development of our technology. Furthermore it gave us the credibility to apply for follow-on programs and secure a $6 million grant from the Critical Minerals Accelerator Initiative to move from pilot to operational scale.”
“EQ Resources’ hyperspectral imaging technology demonstrates that there is still significant life in historical mines where waste piles are mountains of opportunity – in this case, 130-year-old piles of tungsten-containing waste.”
eqresources.com.au mdetect.com.au
The impact of OMAX water jet technology in remote areas.
Small businesses in remote and isolated areas in Australia encounter unique challenges when sourcing specialised materials and components for their manufacturing operations. One obstacle is the difficulty in accurately cutting steel plates that exceed a certain thickness. These robust metal plates are crucial for various industrial applications, such as mining equipment, construction projects, and heavy machinery repairs. BEZ Engineering connected with Headland Technology at AMTIL’s Australian Manufacturing Week, and their experts understood the challenges and presented the OMAX Maxiem 1530 water jet machine as a technology solution. Andrew Smith, Managing Director of BEZ Engineering, oversees all business operations and financial aspects.
Bez Engineering is a family-owned and operated business in the Pilbara since 2000. The company was initially opened to service the Oil & Gas, Mining and Marine industries in the Pilbara region. The business has undergone many transitions, with a change of directors in 2023. The vision of the business follows Henry Ford’s saying, “Quality means doing the right thing when no one is looking”. This mindset allowed Bez Engineering to be a leader in manufacturing quality products for fabrication, machining, design & engineering, coded welding & mechanical repairs in the Pilbara region. With 30 dedicated employees, the business has consistently prioritised quality, upholding the highest standards and ensuring exceptional client outcomes.
BEZ Engineering is in a small, remote city in WA, servicing the oil & gas, construction, government, marine & mining sectors. Their options to source accurately cut steel plates thicker than 20mm were limited, especially after their supplier, a local plate cutter, closed in mid-2023. Consequently, 90% of their CNC cut parts had to be sourced from Perth, 1,600 km away. This led to significant delays and increased costs for their projects. The vast distances and limited infrastructure in these remote regions create significant logistical obstacles, often resulting in delays, inaccuracies, or compromised quality in delivering these critical materials. This situation can severely impact small businesses like BEZ, impacting their productivity, timelines, and overall profitability.
The OMAX Maxiem 1530 water jet cutting machine proved to be a game-changing technology solution that addressed several challenges faced by their business and the broader Pilbara region. The OMAX water jet offered a comprehensive solution that filled a significant void in the regional market, providing exceptional cutting capabilities and versatility. The Maxiem 1530 displayed unparalleled cutting power and precision, allowing for the precise cutting of materials up to 200mm thick. The Maxiem 1530 water jet cutting machine tackles challenges such as power supply, precision, extreme temperatures, and dust mitigation, making it ideal for operations in remote areas like the Pilbara region and opening up new business growth opportunities by effectively addressing geographical and environmental constraints.
“We have had a great experience working with the Headland team from initial contact right through to after-sales support.”
Andrew Smith, BEZ Engineering.
The integration of the new OMAX Maxiem water jet cutting machine into BEZ Engineering’s existing operations was seamless. The company already had a small CNC plasma cutter in operation, and introducing the waterjet technology aligned well with their established workflows.
With the opening of Headland Technology’s new office in Balcatta, Western Australia, led by Jacques Strauss and his service team, we have become a valuable asset for this area and our customers.
The water jet machine expanded BEZ’s cutting capabilities by a factor of 10, virtually eliminating any previous limitations. With the plasma and water jet cutter operating in tandem, the company can now take on a much wider array of jobs that require precise cutting of diverse materials. Bez Engineering are very agile now and can promptly cut through various challenging materials like a 100mm thick GR 350 lugs, 40mm Bisalloy wear plates, and
10mm Teflon packers with high quality using the OMAX Maxiem 1530. Without this technology, the alternatives would have been less desirable – manual labour taking twice as long with lower quality or outsourcing to Perth with a substantial 5–7-day delay and cost involved.
Adopting the new technology allowed them to produce 90% of the needed cut parts. This makes them an industry leader and innovator, giving BEZ a competitive advantage by transforming them into a one-stop shop for CNC cutting services in the Pilbara region. Many customers value the local capabilities and choose BEZ for all their cutting needs.
“We are letting BEZ offer more competitive pricing since they no longer have to outsource this part of the manufacturing process. Adding self-service cutting capabilities that provide convenience and flexibility. Andrew also emphasised the significance of reliable support from technology partners, especially when
operating a geographically remote manufacturing business. “Headland Technology has delivered exceptional aftermarket support, ensuring our machines operate at peak capacity,” said Smith. “Their dedication to service has been indispensable in maintaining seamless operations, and we are grateful for their commitment to our continued success.”
“Over the next five years, I envision substantial growth and expansion for our business. Headland’s expertise and services could play a pivotal role in helping us achieve this vision. With our current waterjet machine operating at nearly full capacity, acquiring a second waterjet cutting system is a distinct possibility to meet the increasing demand. Headland’s guidance in evaluating the feasibility, timing, and implementation strategies for such an investment would be invaluable as we chart our course for the future.”
bezengineering.com.au headland.au
MaxMine enables NRW Mining to enhance fleet efficiencies and curb emissions.
NRW Civil & Mining (NRW) is one of Australia’s leading contractors, able to deliver a complete suite of civil and mining services at numerous locations Nationwide. It is part of the NRW Holdings Group, an ASX-listed entity offering diverse contract services to the resources and infrastructure sectors throughout Australia.
After securing the mining, train loading, and miscellaneous services contract with Karara Mining Ltd, NRW began reducing GHG emissions at the Karara Iron Ore project, the largest mining operation in the Mid-West Region.
With a track record of excellence in managing the environmental implications of mining and civil projects, NRW doesn't just stop at ensuring compliance with legislative mandates. They go beyond partnering with clients to refine best practices and find innovative ways to reduce the carbon footprint of their operations.
NRW planned to introduce an intelligent technology solution at Karara, to harness data-driven insights to refine operator behaviours, improve performance, and establish tangible carbon emissions reduction strategies.
NRW partnered with MaxMine to achieve these objectives, building on their successful collaboration at the Dalgaranga project.
The MaxMine intelligent technology platform is designed to help mining operations collect and collate data, in good time and in granular detail. “We engaged MaxMine at our Dalgaranga project, and it is on that project that NRW saw the benefits of the MaxMine solution and improvement in operator behaviour and resultant efficiency and productivity improvement,” said Brendan Shamrock, NRW’s Alternate Project Manager at Karara. “Unlike traditional fleet management systems, our technology provides a view of what each piece of mobile mining equipment is doing at every moment, through every shift. Our data scientists and partnership coaches then work closely with clients to decipher the insights and meet their goals.”
NRW’s main objective was to enhance operator behaviour, initially focusing on the truck fleet. The goal was to ensure each operator maintained optimal travel speeds to maximise safety and productivity while reducing road degradation and the overall carbon footprint of its operations.
“Initially we targeted ramp, zone and corner speeds. By setting expectations and coaching our crews, we have improved our overall score from a baseline of 76%, to 96%,” notes Shamrock.
The MaxMine solution monitored speeds and was flexible enough to be configured to specific speed rules, providing personalised performance feedback to operators. The feedback was made accessible in a designated area and displayed as a league table to ensure the visibility of results and encourage healthy competition between operators. Every day, operators had an opportunity to refine their practices based on real-time data.
NRW has also implemented a MaxMine Pulse solution, which gives them a near-live snapshot of operation and production. Supervisors can review fleets and look at trucks in circuit, queuing and cycle times.
One notable achievement was an average fill factor improvement of three extra tons per load. With approximately 17,000 loads monthly, this translates to an additional 612,000 tons of material being moved annually without incurring any extra costs.
“This optimisation in productivity directly translates to reduced fuel consumption and minimised tyre wear, and ultimately leads to savings in CO2 emissions,” Brendan adds.
Shamrock notes two components that have proven to be instrumental in achieving positive outcomes: the availability of quality data and the support of the solution by the site team.
The availability of high-quality data forms the foundation for any successful technology implementation. The accuracy and reliability of the data collected by MaxMine enabled accurate analysis, benchmarking, and informed decision-making. By leveraging this quality data, NRW gained valuable insights into our operational workflows, identified areas for improvement, and established ambitious targets to drive performance enhancements. This datadriven approach empowered our teams to make informed decisions that lead to positive carbon reduction outcomes.
Equally important was the way operators on site have embraced the system. It has become a talking point amongst the crews on what they must do to improve their overall scores. Technology implementation requires collaboration, coordination and effective communication among team members. When the entire site team fully embraces the solution, the likelihood of success increases exponentially. By fostering a culture of openness and receptiveness to change, team members have maximised the benefits of MaxMine and effectively leveraged its capabilities to drive operational efficiency. maxmine.com.au
Critical minerals’ part in global carbonisation flags a copper future. John Fennell speaks about the Roadmap to Zero.
The urgent global focus on decarbonisation and clean energy is driving the unprecedented emergence of new technologies, creating a new era of demand and development for a wide range of minerals, including copper. Copper continues to have a foundational role in modern society and its diverse applications are integral to the transition to a clean energy future.
The International Energy Agency (IEA) reported that the global capacity for renewable energy saw an unprecedented 50% increase in 2023, the fastest growth in two decades. With the acceleration of technological advancements and electrification, copper demand remains strong and resilient. Predictions are that 115% more copper must be mined in the next 30 years than has ever been mined historically. Exploration and discovery are crucial to expand or develop mines and provide the primary copper supply. Despite growing investment in copper exploration, the industry faces various challenges. The discovery rate for all economic deposits globally has halved in the last decade, and the average cost of discovery is now four times higher than 20 years ago. Recent discoveries are relatively small and of lower grade when compared to historic exploration success. Further, the lead time to progress to mine development is now almost 18 years. Today is exploration focuses on greenfield and brownfield exploration, including new search spaces and expanding current operations. This is occurring amidst increased government regulation and rising environmental and social considerations. The challenges and costs for traditional exploration are encouraging
alternative sourcing of copper, including reprocessing, recovery, and recycling as well as opportunities for novel sourcing. Many exploration processes have remained relatively unchanged compared to the technological innovations in other parts of the mining chain. However, very recent advances, including the use of artificial intelligence (AI), machine learning (ML), data analytics, data management, as well as a new range of sensors and geophysical techniques and real-time data capture, indicate that the industry is on the cusp of a new frontier that will bring lower impact exploration, reduce investment risk, and allow fast-track discovery.
Innovation in exploration must target both incremental and stepchange technologies to enable more effective and efficient exploration practices. Advancing the adoption of new technologies is also important due to the lengthy delays in new technology becoming standard industry techniques. The importance of alternative business models and collaboration between industry, government, Mining Equipment, Technology and Service (METS), and research organisations cannot be overstated in advancing the innovation effort.
Discovery provides detailed insight into the rising global demand for copper and the industry's challenges in meeting this demand. It also emphasises the importance of new thinking, innovation and technology to drive exploration and discovery to deliver on the essential elements to support our Roadmap to Zero.
copper.com.au
Australia’s national security demands reliable steel manufacturing. A senior Australian Strategic Policy Institute fellow, David Uren speaks about our steel.
Risks to the future of the Whyalla steel mill should prompt the federal government to develop contingency plans to ensure Australia’s continued capacity to manufacture basic steel products.
The Whyalla mill is Australia’s only producer of ‘long’ steel products, such as steel beams for construction and rails, and is an essential supplier of reinforcing bars and steel plates.
Basic steel-making capacity is essential to metal manufacturing in Australia and should be seen as a national security priority, similar to the national capacity to produce diesel fuel.
The Whyalla blast furnace is slowly coming back into commission after what was supposed to be a 48-hour maintenance shutdown turned into a three-month closure, during which customers had to turn to imports.
However, concerns linger about the financial stability of the ultimate corporate owner, GFG Alliance, headed by entrepreneur Sanjeev Gupta, in the wake of the 2021 collapse of its chief financier, Greensill Capital.
Although the Australian operations report healthy profits, the overall group has faced challenges refinancing its debts while criminal authorities in Britain and France investigate the group’s relationship with Greensill. GFG denies any wrongdoing and has managed to stave off direct threats to its solvency in the three years since Greensill collapsed.
However, the recent decision to delay for two years the purchase of a $500m arc furnace from Italy intended to speed Whyalla’s transition from coal has added to concerns of a cash squeeze. After difficulties over payments, the Italian manufacturer suspended a contract to deliver a furnace similar to another GFG steel mill in the Czech Republic.
The federal and South Australian governments have offered $110m for the arc furnace and an associated plant using hydrogen to produce iron. Both tiers of government have justified their offers of support as advancing their climate change agendas, but the preservation of basic industrial capacity should be a priority.
Amid uncertainty about the security of the supply of basic products from Whyalla, steel insiders say more fully fabricated steel products are being imported. Although large quantities of steel are already imported, domestic supply problems undermine downstream customers' ability to compete.
This dynamic can be seen in the plastics and chemicals industry following the decision to shut down Australia’s last manufacturer of ethylene, Qenos. Industry analysts expect the closure of the Singapore-owned Indorama Ventures, which processed ethylene from Qenos into 100,000 tonnes a year of specialty chemicals, including brake fluid, anti-freeze, and ‘surfactants’, which enable the mixing of oil and water, including detergents and foams. It is based at the same Botany Bay site as the Qenos petrochemicals plant, which is expected to be repurposed as container storage. Other companies immediately impacted by the Qenos closure include the Australian Solvents and Chemicals Company, which distributed products based on Qenos ethylene and the packaging company Pact, which purchased its resin from Qenos.
Qenos only ever had half the Australian market for ethylene. Still, with imports now expected to provide the entire market, there will be further downstream closures as distributors find it more costcompetitive to import finished products.
Australia loses its ability to respond in an emergency if the foundations of its manufacturing industry have been removed. The industry has
become a lot more specialised since the Second World War, but the experience then was that Australia speedily developed a host of new manufacturing capabilities, ranging from the manufacture of aircraft in South Australia to radios, trains, clothing, and the supply troops, tinned food.
Much of the required manufacturing equipment came from the United States under its Lend-Lease program and was transferred to Australian ownership at the end of the war. However, Australia's ability to respond depended on its own industries in steel, chemicals, textiles, and electrical goods.
The Defence Industry Development Strategy, released earlier this year, identified seven highly specialised capabilities as sovereign industrial priorities, including the commitment to continuous shipbuilding, the domestic manufacture of guided weapons, explosive ordnance and munitions, the development and integration of autonomous systems, the maintenance and repair of aircraft, the manufacture of vehicles and small arms for the army and the technologies required to manage battles, including sensors, communications and software.
Each of these priorities demands highly sophisticated skills, technologies, and equipment. None will devel an industrial structure that supplies the essential inputs and skilled personnel. National sovereignty is only gained if the Australian contribution is essentially reduced to the assembly of imported parts.
Australia’s manufacturing sector has been contracting since 2007, with new investments failing to match the depreciation of existing assets. Australian manufacturers lack the scale to match Asian competitors and are penalised by their distance from both export markets and suppliers.
It is beyond the federal government's budget to reverse this trend, but there is a case for the government to review what basic industrial capabilities are important for our national security and what strategies would ensure their preservation.
This article appeared in The Strategist magazine in mid-June 2024, and is being republished with kind permission from the Australian Strategic Policy Institute. aspistrategist.org.au
Brave new virtual world fast becoming a reality in the mining sector.
According to one of the country's leading geologists and immersive technology experts, a virtual and robotic revolution in Australia’s mining industry could end fly-in-fly-out (FIFO) workers within decades.
Virtual and augmented reality, along with automation, are transforming the mining sector, says UniSA Professor Tom Raimondo, allowing more work to be done remotely, saving time, money and removing many of the risks and travel for workers.
Professor Raimondo, Dean of Programs for Information Technology and Mathematics at the University of South Australia, is developing VR and AR platforms to enhance core logging with machine learning, create fully digital reconstructions of mining operations, and even simulate the drilling process.
MinEx CRC, the world’s largest mineral exploration collaboration, has facilitated this innovative work. It includes projects such as the RoXplorer digital twin, an ultra-realistic simulation of the drill site of the future, and the Exploration Metaverse, a collection of immersive AR and VR platforms for collaboratively viewing and analysing complex mining data with colleagues and experts from across the world in real time.
“Globally, it is becoming more difficult and more expensive to discover new mineral deposits because they are deeper than ever,” says Prof Raimondo.
“It is also more difficult to extract and process minerals. VR and AR platforms give us a better way to visualise and interpret highly complex data and spatial information and make good decisions about where we should be targeting our exploration efforts.”
The RoXplorer digital twin, replicating a drill site and its operations, enables industry workers to run repeated drilling simulations safely and efficiently with zero environmental impact.
“In terms of training workers, it also removes the hazards. Mining is inherently a dangerous activity, so the more we can transition to autonomous systems, the better off the mining industry will be.” His Project LIVE team in collaboration with UniSA’s Australian Research Centre for Interactive and Virtual Environments (IVE) is also exploring the potential of digital twins for other industries that involve hazardous processes, including forestry, construction and fire management services.
Prof Raimondo explains that these technologies will enable ZeroEntry Mining, where all operations are done remotely. The miners of the future will interact with digital twins and autonomous robots rather than rock cuts and blast sites.
“This technology is improving all the time. If you remember even ten years ago, we almost exclusively relied on desktop computers or even pen and paper to interpret data. It was often clunky, slow, and done out of context. Now we’re integrating VR headsets, mobile phones and wearable technology like AR goggles to do this analysis much more rapidly and in situ, with data informing our decisions every step of the way.
“Instead of being constrained to a small desktop display, keyboard and mouse, we now have the full 360 degrees of our surrounding environment to interpret things more accurately and intuitively, freeing up our hands, giving us space to think, and engaging our brain differently. It’s a very exciting future.”
csiro.au unisa.edu.au
Some might argue that WA State Minister for Mines and Petroleum, Ports and Road Safety David Michael has one of the most important jobs in the country: setting and shepherding government policy for one of Australia's most consistently high-performance industries. In WA for AMT, Drew Turney asked David Michael about the present and future and what part the WA government has to play in it all.
AMT: Thank you for your time. First up, I’d like to hear about your background.
David Michael MP: I grew up in Tuart Hill, went to school there and have lived locally my whole life. I studied Economics at the University of Western Australia and while there I joined both the Australian Labor Party and the Australian Republican Movement.
AMT: How did this lead you to head up the department responsible for such an important industry?
DM: I'm dedicated to serving the community. At 25, I became the youngest Councillor the City of Stirling has ever had. I held that role for 12 years, including two years as Deputy Mayor, before being elected to State Parliament as the Member for Balcatta in March 2017. In 2021, I was appointed as the Cabinet Secretary and Parliamentary Secretary to the Premier after previously serving as the Government Whip in the Legislative Assembly for his first term of Parliament.
Then, in June 2023, I was appointed as Minister for Ports, Local Government, Road Safety and Minister Assisting the Minister for Transport. In December, I was handed the portfolio of Mines and Petroleum and relinquished Local Government.
In 2017, the former McGowan Labor Government announced a process of amalgamation and abolition to reduce the number of government agencies from 41 to 25, delivering on a pre-election commitment to deliver services more efficiently and effectively. The decision to merge the Department of Mines and Petroleum into the Department of Energy, Mines, Industrial Regulation and Safety created synergies between overlapping government policy areas.
AMT: How's the financial health of investment in the sector?
DM: Outside of smelting or refining, more than $27bn was invested in WA's mining and petroleum sector in 2022/23. That's an increase from the previous year and represented the highest level of investment since 2015/16.
Although investment was still less than a third of the highs it reached during the investment boom between 2011 and 2015, mining investment has increased for 16 consecutive quarters after adjusting for seasonal variability.
This result was largely driven by new and expanding lithium projects such as Covalent Lithium's Mount Holland and Albemarle Corporation's Kemerton, iron ore projects such as Fortescue's Iron Bridge, which is now in production, Mineral Resources' Onslow, Rio Tinto's Western Range, and the Scarborough project.
Investment right now probably also reflects the cost of inflation, but WA's share of national mining and petroleum investment is fairly stable at 58%, around its 10-year average. The resources sector was again a key contributor to total new capital expenditure growth in Western Australia, 71%, although that's still lower than the over80% share during the investment boom.
AMT: What are the major projects on the table at the moment?
DM: As of September last year, the major developments supporting investment spending in WA include Woodside Energy's Pluto LNG expansion and Scarborough gas, Chevron's Jansz-Io compression project, Shell's Crux gas, Mineral Resources' Onslow iron ore, Rio Tinto's Western Range iron ore, Covalent Lithium's Mt Holland lithium, Albermarle Corporation's Kemerton lithium, hydroxide plant Trains 3 and V, BHP's West Musgrave nickel and copper, Iluka Resources' Eneabba rare earth refinery, BCI Minerals' Mardie salt and Lynas Corporation's Mt Weld rare earth mine expansion and Kalgoorlie cracking and leaching plant.
AMT: How is the government involved in them, or other large projects like them?
DM: In the 2023/24 State Budget, we announced $136m for projects to increase port capacity and diversify exports. Part of that is technology investments at the Southern Ports, expansion of wharf facilities in Broome to support the export of mineral sands and improving safety and reducing the risk of shutdowns.
Probably the two most significant projects in the Ports portfolio getting significant government investment are the multi-billion dollar Westport container project south of Perth and the Lumsden Point project at Port Hedland.
AMT: It's no secret that mining can damage the environment, and the state government is interested in providing cleaner energy infrastructure and protecting wildernesses against exploration. How do you balance the two?
DM: We're investing $3bn in new spending to take action on climate change and achieve net zero emissions by 2050. That includes $2.8bn to deliver on our plan to decarbonise the State's main electricity grid and replace state-owned coal-fired power stations with renewables by 2030.
Part of that is $2.7bn for [power provider] Synergy to build a massive 700 megawatts of battery storage capacity in Collie and Kwinana and to develop up to 210 megawatts of wind generation capacity, including the King Rocks Wind Farm. There's also $126m for network upgrades, including planning and ordering long leadtime items that will enable the industry to decarbonise and drive growth opportunities in new industries like hydrogen and critical minerals.
The 2023/24 budget also provided $196m of new climate initiatives, including $65m for Perth's third desalination plant, plus $39m for a range of climate adaptation initiatives. This funding builds on preexisting commitments to initiatives like the Electric Vehicle Highway, ending native logging, our Climate Action Fund, and METRONET, the biggest investment in public transport in State history.
AMT: Electric cars are taking off, and more Teslas are showing up on Perth roads all the time. Talk a bit more about the Electric Vehicle Highway.
DM: Synergy and Horizon Power are working with the government to create Australia's longest Electric Vehicle (EV) charging network – the WA EV Network. Once it's completed, EV drivers will have access to 98 EV charging stations across 49 locations from Eucla at the South Australian border to Kununurra in the far north.
In November, the State Government launched round two of our Charge Up Electric Vehicle grant program, offering $12.5m in grants to make EV chargers more affordable for businesses, not-for-profits and Local Governments. WA residents buying EVs are also entitled to a $3,500 rebate. The scheme offers a rebate on up to 10,000 new EV vehicles or until 10 May 2025, whichever comes first.
AMT: The sector is always at the mercy of international economics. We've recently seen a lot of nickel operations close as the price has plummeted. What can the government do to protect the industry against such shocks?
DM: The Cook Government is offering royalty relief to WA's crucial nickel industry to support thousands of local jobs and the state's vision of becoming a global battery minerals processing hub. Local nickel producers are being offered a 50% royalty rebate starting from the March quarter 2024. It will be available over 18 months through a new Nickel Financial Assistance Program.
The rebate will be provided if the average price of nickel in concentrate is below US$20,000 per tonne for a given quarter and will then be repayable by recipients in equal quarterly instalments over the following 24 months. The Federal Government also recently announced that nickel would be added to its list of critical minerals, making the industry eligible for billions of dollars in Federal funding.
AMT: The Barnett government was criticised for being too freewheeling with treasury funds from the boom that left the state $40bn in debt when it ended. How is the Cook government being more responsible with resources and income?
DM: WA has the strongest economy in the country thanks to good economic management from the WA Labor Government. Our state has around 10% of the nation's population, but we account for nearly half of its exports!
Our budget remains surplus, and we're paying down the debt legacy left by the previous Liberal National Government. Since the last budget, we have regained the state's AAA credit rating, which the last Liberal National Government lost in 2013.
We'll always protect our fair share of the GST, build METRONET across our suburbs, grow our tourism industry to put WA on the map and upgrade local roads and our schools. Instead of just shipping our resources overseas, we want to make things here, and we also want to WA into a renewable energy powerhouse. wa.gov.au
So many vital elements must come together for Tasty Fresh Food Co. to succeed —it’s not just the Tasty Trucks. Paul Hellard goes back for more.
There’s a lot of heart and soul in the Tasty Fresh Food Company. There’s the staff, the food and the trucks, and the interface can be the entire community. Since opening in 1979, this little food truck company has expanded from Melbourne into NSW, QLD, and Perth.
A proud people person, CEO Colin Lear leaps around the headquarters, from accounts to the boardroom, from the kitchens to the vast hangar where vans shoot in and out, and from the large workshop and garage where eastern Victoria’s Tasty vans are fitted out and gassed up. Colin knows practically everyone in the Ferntree Gully HQ by name.
Highly organised chaos greets us as the vans return from a busy day out. Then there’s the setup for tonight’s production.
Tasty Trucks has a fully-fitted bakery in the headquarters here as well. “We make all our fresh products here ready to stock our vans tomorrow morning, and we do that in four states,” explains Lear. “We've got tomorrow’s production right here. What's happening here is that a day crew comes in and sets up for the night team of 50 employees, who come in to line up on the conveyor belts to assemble all the products for the Melbourne fleet of 70 vans. This includes sandwiches, wraps, sushi, salads, hot meals, burritos and other items bought to stack the vans to complete the spread.
“And that surprises most people: we manufacture most of it ourselves,” adds Lear. “As far as food manufacturing goes, we are HACCP certified which involves a great deal of international food safety regulations which we take very seriously.”
Tasty Trucks operate 24 hours on business days. While they handle a 24-hour cycle, they only operate on the 243 business days of the year. “On each of those days, we have a very, very narrow window of retail opportunity, from about seven in the morning out to one o'clock in the afternoon. That's the typical time our Tasty Trucks are out there.”
An important key to the Tasty Fresh Food Co. business is the crew of Tasty Trucks Van Sales Managers who merchandise the product in the trucks before heading out in droves to provide morning tea and lunches to employees at their place of work. “They develop a happy relationship with the customers and make sure the fresh food product is well presented for the express Grab n Go experience, which is the culmination of a mighty Tasty Team effort,” says Lear.
Colin has managed to engage family members who remain heavily involved in the business. As we head back to the boardroom, he introduces me to his daughter Katherine Pereira. Katherine is clearly engaged with the team at the head office and working closely alongside Colin. “My son, Matt, works on the Tasty MicroMarkets, too. This is another arm of the business specialising in food vending machines, which has great promise.”
Tasty Fresh Food Co. is a registered vehicle builder specialising in managing the production of its uniquely designed Tasty Fresh Lunch Vans. At its FTG HQ and Fleet Facility, Tasty has manufactured and fitted out approximately 200 Tasty Mk.II vans since 2010, utilising the Toyota Hi-Ace van as the base model. Local fabricator, New Touch Industries has produced the stainless steel ovens and shelving in kit form ready for the Tasty Fresh Fleet Team to incorporate into the fibreglass catering body produced by highly valued longterm local partners Kings Fibreglass. On average, the company has been capable of producing a dozen new vans per year, with each van taking approximately three months to complete. However, since significant design changes in 2019 rendered the Hi-Ace Van no longer fit for purpose, Tasty Fresh Food Co. has joined forces with the Monash Innovation Labs to
develop the next-generation Tasty Mk.III van. This van will feature a catering box mounted on a Hino 300 cab chassis and offer many enhanced capabilities.
Colin works with talented local mechanics and mechanics recruited through TPRC, a Philippino recruitment company. Three engineering students from Monash Innovation Labs were brought on to help simulate an open-face delivery system on the side of the delivery vehicles. Since then, one of the students has stayed as a parttime employee during the final stages of his degree.
“The big task that we challenged the Monash team was to remove all barriers (doors, etc.) for the customer while choosing their favourite product and still maintaining a five-degree food-safe temperature,” explained Lear. “And that's what the Monash guys came up with by redesigning the refrigeration system and incorporating customised air curtains to keep the product fresh no matter the external ambient temperature.”
Tasty Fresh Food Company Mk II vans all began their lives as a very empty, raw version of a Toyota Hi-Ace van. The next version will be an even lighter HINO van with a fibreglass body to complete that signature Tasty Truck shape. It will weigh the same, but it will have more power, which can be used in the improved refrigeration system. “These vans are so dependable that after
15 years of service, we decommission them as a lunch van to protect our unique IP and sell them off as a tradie van.”
The Tasty Fresh Food Company has an exciting future ahead. Many innovations and great initiatives are happening throughout the whole business, which is fantastic. The Tasty team is ready to go with enthusiasm for working in this dynamic environment, and the energy for progress is thriving. tastyfresh.com.au
MaxiTRANS announces partnership with Freighter, Triple Eight and Red Bull Ampol Racing.
MaxiTRANS is announcing its partnership with Triple Eight Race Engineering/ Red Bull Ampol Racing, one of the most successful teams in Australian motorsport. Promoting the company’s Freighter brand, this partnership marks a significant milestone in MaxiTRANS’ commitment to promoting excellence, durability and quality as it continues through the exciting transformation of its trailer manufacturing business.
“We are excited to join forces with Red Bull Ampol Racing,” said Greg L’Estrange, MaxiTRANS Executive Chairman. “This partnership brings together two brands that both reflect a shared dedication and commitment to high performance, innovation and delivering excellence. Particularly at a time as the MaxiTRANS business is forging ahead with its plans to transform the trailer manufacturing industry in Australia.”
“We are certainly thrilled to be part of supporting a high-performing team, collaborating and working towards achieving great things together, said Greg.”
“We couldn’t be prouder to announce Triple Eight’s partnership with the team at MaxiTRANS, representing their Freighter brand for the remainder of the season and into next year,” said Jamie Whincup— Managing Director of Triple Eight Race Engineering.
“Their focus and drive towards strong, durable, and top-tier equipment is a quality we love at Triple Eight.”
“There is no doubt in my mind our partnership with Freighter is a brilliant chance to merge our thinking and processes moving forward, and I can’t wait to see what the future holds between our two brands.”
MaxiTRANS is the largest supplier of locally manufactured, heavy-duty road transport trailer solutions, including trailer repairs and service, in Australia.
Synonymous with road transport in Australia through market-leading brands Freighter, Maxi-CUBE, Lusty EMS, Hamelex White, Trout River, and AZMEB, MaxiTRANS is the leading supplier of road transport equipment for general freight, temperature-controlled freight, and bulk transport market sectors.
maxitrans.com
The new financial year marks Tyre Stewardship Australia's 10th anniversary of operation, and more rubber product recycling opportunities are opening up across the country than ever before.
As Australia’s Tyre Product Stewardship Scheme reaches its ten-year milestone, Tyre Stewardship Australia (TSA) has reported unprecedented growth in rubber product recycling opportunities across the country.
Industry case studies show rubber product users and recyclers in metro, regional, rural, and remote areas are defying challenging economic times to gain value from tyre recycling.
“As Australia’s tyre product steward, we provide focused and practical pathways for government, business, and consumers to take action. And they are. They are putting in the hard yards to take us into the future,” Tyre Stewardship Australia (TSA)
CEO Lina Goodman says.
“We’re seeing more innovation than ever before, and it’s all down to the stamina, staying power and will to do the right thing of those who have invested dollars, time and energy into building Australia’s circular tyre economy,” says Goodman.
Currently, 16 tyre and auto brands are investing in circular tyre economy outcomes for Australia through their support of TSA.
Eight tyre brands—Bridgestone, Continental, Goodyear Dunlop, Kumho, Michelin, Pirelli, Toyo, and Yokohama—have been doing so since the early years. Now, joining them in paying a levy on every tyre they sell in Australia are Ascenso, Bearcat, Hankook, Kal Tire, Mercedes Benz, Porsche, TyreConnect, and Get A Grip Tyres.
afford to compromise sustainability – Australia must become the custodian of its waste, or we risk having no choices. “In addition to regulating the Tyre Product Stewardship Scheme, a practical and effective choice that can be implemented now is mandating government procurement.
Those contributors have made it possible for TSA to inject over $10m directly into developing markets for tyre-derived materials and research into solutions for end-of-life tyres. These projects are critical to achieving the growth of the tyre recycling sector and across the entire value chain.
Together with market development funding, TSA spends around 40% of its budget each year directly on boosting the recycling sector by stimulating and expanding markets for tyre-derived material and facilitating collaboration between industry entities and the government.
“We are not going to take our foot off the pedal in seeking regulation that requires every tyre importer and auto brand to follow the strong leadership of the existing 16 tyre and auto brands which voluntarily contribute for the products they import and sell – and putting a stop to free riders in the Australian market.
“The need for an all-in scheme is amplified as we move closer to the global and domestic environment target dates Australia has signed up to, including the pathway to net zero by 2050.
“With only 57% of tyre importers and only 3% of auto brands contributing, Australia’s circular tyre economy has grown from just a few pioneers driving change in 2014 to more mainstream innovation in 2024. Just imagine what we could do with 100% contributing to an all-in scheme,” says Goodman.
On reflecting on the past decade, Goodman says: “We can all acknowledge that it is not easy, or always possible, to do the right thing every time. Particularly now when the cost of living is reducing household and business budgets and, ultimately, our choices.
“However, this means the choices we can and do make become more important. The lessons we have learned tell us we cannot
“We know that countries gaining the most value from the recovery of end-of-life tyres have regulatory systems in place, but also use the weight of government procurement.
“Procurement mandates that look beyond short-term tender budgets to long-term cost savings and sustainability will increase local manufacturing, jobs, and markets, and reduce environmental and social harm,” says Goodman.
The demand for circular choices is gaining momentum, but this could come to an abrupt halt if government is slow to act. By continuing to focus on the collection and processing, we are treating used tyre waste as the starting point – thwarting circular economy solutions.
We need to focus on the entire value chain with a pathway towards circular economy outcomes, and that begins with better design and manufacturing, retreading, repairing, and using recovered rubber back into value-added products, including back into tyres.
“Developing new, higher value end markets for tyre-derived materials will open choices for investors looking to strengthen Australia’s circular economy businesses, manufacturing, and jobs.
“For 10 years we have persevered under a voluntary tyre stewardship arrangement, and it has delivered on the back of the innovation and commitment of the industries, importers, recyclers, retailers, and manufacturers committed to the cause. But it has delivered all it can,” says Goodman.
A few steps forward by the government will take Australia leaps and bounds into the circular economy – with an all-in scheme and mandated procurement policies; TSA is ready to support the necessary steps. tyrestewardship.org.au
Adelaide tram overhaul details reveal a contract for CIMIC Group is on track.
The Federal and South Australian governments have selected CIMIC Group CPB Contractors to deliver the Tram Grade Separation Projects in an Alliance with McConnell Dowell, Mott MacDonald, ARUP, and Aurecon.Designed to improve transport safety, efficiency, and reliability, the Tram Grade Separation Projects will also enhance amenity, connectivity, and liveability along the existing tram line from Adelaide’s CBD to Glenelg.
Modifications to the existing overpass at South Road are key to this project, which are required to facilitate the construction of the highly anticipated River Torrens to Darlington Project.CIMIC said in a news release that the Tram Grade Separation Project will generate revenue of approximately $212.8m for CPB Contractors.
“These upgrades will be critical to supporting economic growth in South Australia and reducing travel times for motorists, buses, freight, and airport traffic while promoting sustainable urban growth and low-emission, healthy transport choices for commuters,” said CIMIC Group Chairman Juan Santamaria.
“On completion, these works will foster a stronger sense of community between the suburbs of Adelaide, providing better, safer, and more accessible tram stops with improved open spaces for the local people and visitors to enjoy,” he added.
CPB Contractors Managing Director Jason Spears expressed his enthusiasm for the project, stating, “CPB Contractors looks forward to further growing our partnership with South Australia’s Department for Infrastructure and Transport to safely deliver this important piece of infrastructure on time and on budget for the city of Adelaide.”
“With over 40 years’ experience delivering city and region-shaping infrastructure in South Australia, we look forward to furthering our legacy in providing local employment and training opportunities, focusing on diversity.”
Spears continued, “Our expert team will continue our commitment to ensuring that social and economic benefits are maximised for the communities in which we work by prioritising the engagement of local businesses and suppliers, including Indigenous-owned businesses and social enterprises.”
The scope of work for the Tram Grade Separation Projects includes efforts at three main locations along the Glenelg Tram Line, works along the tram corridor, modifications of the existing tram overpass at South Road, replacement of the level crossings at Marion Road, Cross Road, and Morphett Road with tram overpasses, intersection upgrades, tram depot upgrades at Glengowrie, and a temporary tram maintenance depot on Peacock Road on the edge of the CBD.
The project will also include installing signalling upgrades along the tram corridor and creating new public spaces for local communities.
Site investigations to inform planning are underway, with major construction set to start in late 2024 and the removal of level crossings expected by the end of 2025. cimic.com.au
DB Schenker signs commitment to significant Sustainable Aviation Fuel (SAF) volume on flights from Cathay.
DB Schenker has officially announced its participation in Cathay's Corporate Sustainable Aviation Fuel (SAF) Programme. The programme aims to advance sustainability in the logistics industry by partnering to reduce emissions in cargo shipments.
Cathay established a Corporate SAF Programme in 2022 to fight climate change. It enables members to purchase SAF for uplift on Cathay Pacific and Cathay Cargo flights from Hong Kong and other ports on the network. By joining and committing to buy 878 metric tons of SAF (the equivalent of 290,000 US gallons), DB Schenker has become one of the biggest contributors to the scheme to date, which demonstrates its commitment to sustainable logistics.
"By partnering with Cathay on SAF, we are reinforcing our sustainability commitment and leadership in the skies,” said Thorsten Meincke, Global Board Member for Air and Ocean Freight at DB Schenker. “The collaboration underlines our environmental stewardship in air cargo and supports the global push for SAF by increasing demand for it across more regions, ultimately contributing to a more sustainable future."
"We are delighted to welcome DB Schenker as the newest member of the Cathay Corporate SAF Programme – and one of the biggest contributors to date,” said Tom Owen, Cathay’s Director of Cargo. “It is great to have this level of support from an important player in the air cargo industry to work with us in decarbonising aviation. By replacing conventional jet fuel with sustainable aviation fuel, DB Schenker's commitment is the equivalent of saving more than 2,600 tonnes in CO2 emissions. This powerfully conveys the message that there is real and growing demand for SAF, and this partnership is a testament to the collaborative ethos of Greener Together as we move one step closer to the goal of a more sustainable air cargo industry."
Warehousing, packaging, and transportation consume large amounts of energy and generate significant greenhouse gases (GHG) in the logistics sector. Optimising energy consumption to reduce carbon emissions is a pressing issue for logistics companies.
Back in 2020, DB Schenker became the first company in the logistics industry to cover a commercial full charter round trip flight with SAF. As of spring 2021, all direct emissions of a weekly charter rotation between Frankfurt and Shanghai onboard Lufthansa Cargo were avoided by fully covering the fuel consumption with SAF. Since then, the global logistics service provider continued to push the boundaries of sustainability in air freight. The new collaboration with Cathay further expands DB Schenker’s network of biofuel partners.
In total, DB Schenker's SAF program is available globally for all flights on all airlines and has attracted a wide range of customers including Lenovo and Nokia.
The Australian government has committed to a Net Zero Plan, which will guide the country’s transition to a legislated target of net zero greenhouse gas emissions by 2050. New Zealand has a similar 2050 Net Zero target. Daniel Andersen, Director of air Freight at DB Schenker Australia & New Zealand Cluster, says the industry's focus on reducing greenhouse gases is integral and requires collaboration between airlines, logistics companies, and their customers.
“This major partnership with Cathay on SAF opens the door to more sustainability collaboration in the region. SAF is available throughout Australia and New Zealand on DB Schenker air freight for customers looking to elevate their contributions to a more sustainable aviation industry,” said Andersen.
DB Schenker is one of the world's leading logistics service providers with around 72,700 employees at more than 1,850 locations in over 130 countries. The company operates land, air, and ocean transportation services and offers comprehensive logistics and global supply chain management solutions from a single source. Aiming for a sustainable future in the logistics industry, DB Schenker continuously invests in innovative transport solutions, renewable energies, and low-emission products for its customers.
dbschenker.com
Four key things for SMEs to align to create sustainable business growth through automation.
Small and medium-sized enterprises (SMEs) should align their organisations' business, technical, operational, and commercial aspects to create a clear case for automation and generate business growth, according to a panel of industry experts assembled by global intralogistics solutions specialist Kardex at CeMAT Australia 2024.
Is automation the key to mastering business growth for SMEs? This question was asked during a round table event organised by global intelligent automation specialist partner Kardex at CeMAT Australia 2024 on 25 July. Leading logistics consultants Francis MeierExecutive Director of Trios Consulting (with more than 40 years’ experience in the intralogistics industry) and Arthur Dardoumbas, Executive Director of ThreeSixty Supply Chain Group (with more than 25 years’ industry experience) discussed the steps growing SMEs need to take when considering automation solutions.
Speaking with Grant Smith, Director of Business Development AutoStore, ANZ Kardex, Arthur Dardoumbas advocated balancing four key aspects of their operations—business, technical, operational, and commercial—to help companies “make the right decision” regarding automation.
In turn, Francis Meier emphasised the importance of SMEs fully understanding their own organisation and having a clear picture of where they are and where they need to go before starting their automation journey. “The right level of automation is driven by your data, what you want to achieve, what your growth rate is going to be,” he explained.
Meier and Dardoumbas identified property, labour shortages and safety as the key drivers for businesses choosing automation, with the latter pointing out that in some areas of Australia, costs have doubled in the past five years. “One of the key drivers to reduce footprint is via automation,” he added. With fewer people choosing logistics as a career path, in part because of safety concerns, Meier explained that automation provides a means to make careers safer and more attractive to recruits, in addition to enhancing efficiency and reducing headcount.
Finding the right level of automation for
Dardoumbas and Meier explained SMEs do not have to automate everything and can instead find the “right level of automation for the business” with automation evolving to become increasingly adaptable and solutions more standardised for easier integration both with one another and with manual operations, reducing lead and ramp-up times.
According to both experts, it is important to explore all options concerning business objectives, growth projections and return on investment over time to reach the correct decision about whether and what to automate as “automation may not be for everyone”. However, it can offer huge benefits when implemented appropriately, with the right planning and dedicated resources, in the form of project management, training, change management and preparation in the transition.
A video case study presented during the round table event showed one company ideally placed to benefit from automation. New Zealand pharmaceutical company Douglas - exporting to over 50 countries and selling its products through various channels (distribution partners, pharmacies, and direct-to-consumers online) - has chosen the AutoStore™ systems empowered by Kardex. Douglas Group General Manager of the Consumer Business,
Katherine Douglas, emphasised the company needed a solution that could handle increased sales and orders, ranging from large pallets to single SKUs. This new setup is designed to support growth and enhance operational efficiency, particularly in handling increased sales and complex order fulfilment.
Ryan Gibbs, Douglas Pharmaceuticals Warehouse Operations Manager, said the two key challenges the company was facing were “space and efficiency”. Douglas had looked at options ranging from extending its warehouse to using a third-party company, finally choosing Kardex for their AutoStore implementation to deliver increased capacity and throughput.
“One of the greatest things about automation is the scalability that it provides,” Ryan Gibbs noted, adding, “When starting your automation journey, it’s really important to understand your data and your business. It’s a great opportunity to evaluate your processes and understand where the growth is taking you.”
Commenting on the success of the round table event at CeMAT Australia 2024, Grant Smith, ANZ Kardex Director of Business Development AutoStore, concluded, “The lively and engaging round table discussion highlighted how SMEs can prepare for and successfully integrate automation into their operations through careful planning and a deep understanding of their strategic business needs.
“Kardex FulfillX Software (an innovative warehouse execution system designed specifically for AutoStore empowered by Kardex systems) and the Intuitive Picking Assistant (IPA), a user-friendly picking display responding to movements and enabling ergonomic, fast and error-free picking, were on display at CeMAT Australia, demonstrating how they deliver increased capacity, higher efficiency, scalability, safer working and enhanced accuracy to businesses of all sizes. For companies looking for the best ways to manage their business growth, automation can provide the answer and SMEs can follow the steps outlined to create a strong roadmap to success.” kardex.com
Markforged introduces the world’s first metal and advanced composite industrial 3D printer.
Markforged has unveiled the FX10 Metal Kit, a print engine that makes the FX10 capable of metal printing. With this kit, the FX10 becomes the world’s first industrial 3D printer to print metal filaments and composites with continuous fibre reinforcement. The new metal printing capability for the FX10 will accelerate adoption on the factory floor.
“Customers no longer have to choose between a metal and a composite printer. Years of R&D investment and field experience have come together to provide an all-in-one solution for 3D printing to provide immediate return on investment once installed on a factory floor,” said Shai Terem, CEO of Markforged. “The FX10 supercharges other equipment on the factory floor to be better utilised and run more efficiently, increasing productivity and reducing potential line down events.”
The FX10, released in November 2023 as a composite-only printer, was designed to be the most versatile tool on the factory floor and has received tremendous feedback from early customers. With its modular architecture, upgrades like the Metal Kit enable FX10 customers to gain additional value from the machine after purchase.
Markforged also announced a new 316L stainless steel metal filament for the FX10 Metal Kit. Users can also print in 17-4PH with additional support for other Markforged metal filaments.
“We designed the FX10 to be a modular platform so that we are able to release new innovations and upgrades without customers having to purchase a new printer every year,” said Terem. “Along with new software capabilities we release regularly, the FX10 Metal Kit is poised to provide continuously growing value on factory floors for years to come.”
The FX10 Metal Kit comprises a swappable print engine with a metal-specific print head, material feed tubes, routing back, and dual preextruders. An FX10 can be swapped between metal and composite as often as needed, which takes about 15 minutes.
Similar to the fifth Generation Continuous Fiber Reinforcement (CFR) print system in the FX10 that prints nearly twice as fast as previous composite printers, the second Generation Metal FFF engine, built on years of Markforged’s experience printing metal, prints significantly faster than previous Markforged metal systems. FX10 combines faster print speed with a print volume twice as large as Markforged’s prior industrial metal printers.
Metal prints are built from the metal filament and a ceramic release filament. The ceramic release is extruded as an interface between the part and supports for easy separation and removal. Once metal prints are complete, they must be washed and sintered in Markforged’s Wash-1 and Sinter-2 solutions. Eiger, Markforged’s slicer and print management software automates the process, including scaling parts to account for shrinkage during sinter.
The Digital Forge is the additive manufacturing platform that enables every aspect of the FX10 and is purpose-built to integrate into existing manufacturing ecosystems. With the Digital Forge, users can share parts across their organisation and monitor fleet performance from a central location.
Markforged showcased the FX10 Metal Kit at the International Manufacturing Technology Show in Chicago, Illinois, from September 9 to 14, at booth 432305. It will print in both continuous fibre-reinforced composites and metal. markforged.com
3D printing with sub-micron resolution. Dr Cameron Chai from AXT takes us on this fantastic journey.
In the October/November issue of AMT last year, we described Projection Micro Stereolithography (PµSL), which has allowed 3D printing resolution to go beyond the limits of ~300µm of FDM techniques, using resin-based printing technology. Using PµSL it is possible to achieve resolutions of just 2µm. But what if you want to print features in the nanometer range? The solution here lies in two-photon polymerisation (2PP), another resin-based printing technology that uses light curing or polymerisation.
In microfabrication, systems like the NanoOne from UpNano set the standard, and printing features down to 170nm. The NanoOne is ideal for fabricating parts with complex geometries for academic research and industrial applications as engineers continue to push the bounds of miniaturisation. Contrary to popular belief, 2PP is a fast printing process, and producing parts using 2PP can also be done at a reasonable price.
2PP printing technology takes advantage of the spatial selectivity of 2-photon absorption (2PA), i.e. inducing polymerisation at the point where the two photons converge, enabling 3D structures to be directly created in a predetermined volume with a spatial resolution better than 1µm. The higher spatial resolution is possible because 2PA significantly reduces beyond the focus point. This minimises the fluorescence volume, culminating in higher spatial resolution. The benefit becomes obvious when single and multi-photon beam paths are compared using fluorescent microscopy. As can be seen in the figure, 2PA only occurs at the focal point of the beam, meaning that monomer crosslinking takes place in this plane. Conversely, in the case of single-photon absorption (per other techniques such as stereolithography), the emitted light is absorbed along the whole beam, leading to a reduction in resolution.
This method allows printing directly within the resin volume. As such it avoids the need for repeated material coating that is required for SLA (stereolithography) processes. These processes can induce stresses on fine structures during the printing process.
The UpNano NanoOne takes things further using a patented process that adapts the printing resolution to cater for the
required resolution. The software compensates and adapts the voxel size accordingly by classifying the required resolution as high or low. The system automatically enlarges the laser focal spot for low-resolution regions, thus increasing the print speed. Conversely, it reduces the focal spot size for high-resolution areas, allowing it to achieve resolutions in the nanometer size range. In either case, there is no effect on mechanical properties.
Materials
There are now many resins compatible with 2PP 3D printers that are optimised for properties such as resolution, optical transparency (for optical and microfluidic applications), biocompatible formulations for biomedical research, high-performance formulations for ultimate strength or temperature capabilities, and even silica ceramic formulations for producing fused quartz micro components.
Applications
2PP is ideally suited to the microfabrication of high precision parts that incorporate features in the sub-micron realm. Systems like the NanoOne can print at >450mm3/hr, producing components up to 42x42x42mm with a surface finish that rivals injection moulding. While the output is limited only by the operator’s imagination examples of what can be produced include:
• Extracellular matrices
• Optoelectronics
• Micro needles
• Micromechanical devices
• Microlenses axt.com.au
• Lab-on-chip devices
• Photonic devices
• Filter elements
• Microfluidic devices
Additive Industries and Additive Assurance partner to enhance L-PBF monitoring.
Additive Industries and Additive Assurance partner to provide in situ process monitoring with Additive Industries’ MetalFab portfolio of laser powder bed fusion (L-PBF) machines. This collaboration will leverage both companies' complementary strengths to improve the process monitoring of additively manufactured parts in highperformance applications.
Additive Industries is one of the significant manufacturers of metal L-PBF machines globally and has been serving production-oriented customers for over a decade. Additive Industries’ MetalFab printers offer class-leading automation, scalability, and capability. Their product portfolio has recently been updated with their newest machine, the MetalFab 300 Flex. It is the only metal printer on the market that offers a unique on-demand platform size, providing flexibility for manufacturers and making metal AM more accessible than ever.
As AM printers increase build rates and productivity, the requirement for in-process monitoring and quality assurance is becoming essential in many industries to ensure repeatability and generate high production yields. Additive Industries has identified the market gap and is leading the charge with offering this extended capability to its customers.
Australian start-up Additive Assurance was spun out of Monash University and backed by IP Group three years ago. The partnership with Volkswagen exposed the company to industrial-scale requirements, and they appear to have excelled. Additive Assurance Co-Founder Marten Jurg said, “Metal additive manufacturing is taking the world by storm, but quality is still not at the level it needs for important applications. We see a huge opportunity for Additive Manufacturing and are thrilled to be working with a leading company like Volkswagen to transform how they develop their products.” AMiRIS® allows additive manufacturers to inspect quality during production. This can accelerate the quality validation process and ultimately lead to higher yield and production consistency of L-PBF manufactured parts. AMiRIS® is a logical extension to the MetalFab series, addressing the QA challenge with state-of-the-art in situ monitoring. It enables manufacturers to detect and address quality problems during production. By providing real-time insights into the build process, AMiRIS® strengthens certification and quality assurance efforts, ultimately leading to shorter production cycles and higher confidence in the final product's quality.
"Our partnership with Additive Assurance aligns perfectly with our commitment to advancing metal additive manufacturing capabilities. By integrating AMiRIS® with our MetalFab portfolio, including our new MetalFab 300 Flex, we're enhancing real-time quality assurance, offering our customers greater flexibility, and setting new standards in production consistency and reliability,” said Mark Massey, CEO at Additive Industries. "We are delighted to be working with Additive Industries to add value to their customer’s experience and to push the boundaries of what is possible with L-PBF AM," added Marten Jurg, CEO of Additive Assurance. The partnership between Additive Industries and Additive Assurance is expected to result in a broader deployment of in situ monitoring for MetalFab portfolio users and, ultimately, a broader adoption of L-PBF's maturing manufacturing process.
Additive Industries is a pioneer in industrial metal 3D printers, offering cutting-edge technology that enables customers to industrialise and accelerate their manufacturing processes. As a company, it helps to solve the challenges of the most forward-thinking industry leaders in highly demanding sectors, including aerospace, automotive, high tech, and energy. Offering customised automation, modularity and unique calibration options, the company delivers smart and highly
scalable solutions focusing on productivity, safety, and sustainability to meet rapidly changing customer demand. Headquartered in Eindhoven (The Netherlands), Additive Industries also has a service and support centre in the USA.
Additive Assurance is a quality assurance leader in metal additive manufacturing. The company’s AMiRIS® in situ quality assurance system allows manufacturers to identify defects rapidly, produce repeatable quality metal additive-manufactured products, and increase productivity. additiveassurance.com
Sevaan Group unveils new additive manufacturing service.
Sevaan Group has announced that it has expanded its manufacturing services to include additive manufacturing (AM).
The addition of 3D printing capability will provide greater choice for customers regarding parts manufacturing, and the opportunity to attain tangible benefits that can help improve their productivity and revenue. Sevaan already provides a unique integrated capability, an end-to-end workflow from design, prototyping and testing through to the production, assembly and finishing of precisely manufactured metal parts, for its customers.
The inclusion of AM into its service mix brings further key customer deliverables. “They will now benefit from more choice when purchasing manufactured parts,” explained David Green, Chief Executive Officer, Sevaan Group. “Our customers can choose to have their required parts manufactured via either traditional processes or 3D industrial printing.
“For certain components and production runs, 3D printing can offer specific benefits including rapid prototyping, a faster production turnaround, enhanced quality and cost savings, making it a desirable manufacturing option.
“Thanks to AM, customers who only require a small number of parts or perhaps longer-lasting components now no longer need to wait for parts to come in from overseas while experiencing downtime and can explore hardier and more cost-effective part options.”
Sevaan’s AM service includes parts inventory auditing to identify components suitable for 3D printing, reverse engineering if required, parts design, prototyping and testing, and production. To ensure high-quality 3D printing of components, Sevaan uses the
Sevaan’s Markforged X7 carbon fibre 3D printer produces industrial grade parts.
latest advanced 3D industrial printing technologies. This and its experienced design and production team, helps secure the delivery of precise components produced in plastics, composites and continuous fibres. “These flexible materials are surprisingly robust, strong, and lightweight, and can be optimised to create parts in great detail and complexity, to the required tolerance and with minimal waste and a small carbon footprint. In the case of low-quantity production runs, AM is indeed a value proposition,” says Green. The insertion of AM into Sevaan’s service offering also further cements the firm’s commitment to providing a one-stop shop for its customers. “This step is a perfect example of our ongoing determination to continue to offer our customers what they need under the one roof to help further simplify supply chains, reduce lead times and costs, and deliver peace of mind,” said David. The company is also using its new capability to manufacture tools for its own inhouse needs.
“We are very excited about our 3D printing service and the benefits it will provide to our customers. We will continue to embrace innovation and creativity to keep driving our customers and Sevaan into the future,” concluded David. sevaangroup.com.au
3D printing brings immediate cost- and time-savings to MHM Automation.
New Zealand-based MHM Automation, which services clients globally in the design and manufacture of automated reverse packaging and product handling systems for the food processing industry, is turning to 3D printing for the manufacture of a wide range of components and is recording substantial cost and time savings through the adoption of Markforged additive manufacturing technology.
The company purchased a Markforged X7™ industrial printer in 2023. It is well advanced in its planned transition to inhouse additive manufacturing of a wide range of previously outsourced parts using traditional manufacturing methods.
The decision to commit to additive manufacturing followed studies that predicted the technology could yield substantial savings over contracting the work out to local machine shops or fabricating components in-house.
Operations Manager Graeme Lincoln said initial returns on the investment in additive manufacturing more than justified the move.
“We’re currently undertaking short runs of a selected range of components, with very encouraging results,” said Lincoln.
“Across the board, we’re consistently seeing savings in the order of 75% on the items we’re producing, which is directly in line with the results Markforged had forecast. We’ve identified many components that lend themselves to being printed, so the potential is enormous. Our preference as we head forward is to use printed parts over outsourcing wherever applicable.”
“We’re not yet using the X7™ to its full capacity, but I anticipate we'll continue to expand our 3D printer fleet in due course and also to adopt other Markforged materials such as the food-grade Nylon. I want to go down the metal printing route at some stage,” he said.
He said MHM was developing a strategy for the long-term integration of 3D printing into its manufacturing processes for various reasons. “Although cost is probably the main consideration in our assessment of 3D printing, we’re also very aware of the time factor benefits. When you outsource, you lose control of the timeline, and this can lead to serious supply chain problems. Printing a wide range of parts in-house means we can react quickly to client ‘on demand’ requests without holding a large inventory of spares.
“The challenge facing our designers right now is to adjust their thinking to the new technology. It takes a different mindset to
design for printing instead of fabrication, and the online Markforged University is an invaluable aid in that process.
“A good example of the new thinking in action is the design of a de-boxer vacuum manifold that, until now, had been fabricated in seven parts that needed to be assembled to form the finished component. Using 3D printing, we can now produce this as a single unit, and the cost saving is a massive 93%; compared to the outsourcing process, I estimate it’s saving us 32 days in production time from release to manufacture to arrival in the store as a completed item,” Lincoln added.
“Additive manufacturing is presenting us with a whole range of benefits. While these are primarily in cost savings and production speed, the lightness of Markforged’s Onyx material is another big plus – the weight saving over aluminium without any loss of
strength allows us to increase the payload of our robotic equipment. “Perhaps the keyword in our transition from outsourcing to in-house printing is ‘flexibility’. We can react quickly to a client’s specific challenges by designing, testing and producing new parts within a tight time frame, giving us a real customer service edge,” he said.
Graeme Lincoln said the X7™ was also an asset to the company’s R&D programme. Prototype parts were designed, printed, and tested within a very tight time frame, avoiding the lengthy delays and relatively high costs incurred in outsourcing the work. As a result, the company has been able to pursue ideas that would previously have been cost-prohibitive to outsource. And, because the overall development period was substantially reduced, more R&D work could be fitted into the time available. mhmautomation.com markforged.com
Bringing some tactile designs into reality, Bilby3D creates 3D models for Group GSA.
Group GSA, a renowned design firm with offices in Sydney, Melbourne, Brisbane, Perth, Beijing, Shanghai, and Ho Chi Minh City, has successfully integrated Raise3D 3D printers from Bilby3D into its operations. Known for its innovative designs, such as the award-winning North Fitzroy Library and Community Hub, Group GSA offers multidisciplinary services in Architectural Design, Interior Design, urban design, Landscape Architecture, and Graphics.
Challenges faced
Prior to adopting in-house 3D printing technology, Group GSA relied on CGI flythroughs and occasionally outsourced 3D prints for final display pieces. This process was time-consuming and costly, with each outsourced model taking one to two weeks to produce. The lack of rapid prototyping capability hindered their ability to develop and visualise design concepts efficiently and iteratively.
To overcome these challenges, Group GSA adopted the Raise3D Pro2 Plus, provided by Bilby3D. This decision was driven by the need to enhance their design process, allowing for quick and cost-effective production of 3D models. The Raise3D Pro2 Plus has significantly reduced the time required to produce models, from weeks to mere hours, enabling more frequent and detailed client interactions.
Practical applications
“Clients find it much easier to visualise how the design fits into the surrounds,” explains Mauricio Fuentes, an architect at Group GSA. “They can touch and see the design, providing another level of interaction. They get excited about the project because they can see and touch a representation of it.” The tactile nature of 3D models offers clients a clearer understanding of the design concepts, leading to more informed feedback and decisions.
The integration of 3D printing into their design process has expanded the scope of what Group GSA can achieve internally.
Rohit Broka, National BIM/Digital Design Manager, explains that 3D printing has become an integral part of their workflow, allowing them to quickly produce sample models of design options. This capability has been positively received by clients, who appreciate the ability to visualise design concepts more concretely.
Efficiency and Cost Savings: By bringing 3D printing in-house, Group GSA has significantly reduced the time and cost associated with model production. Models
that took weeks to outsource are now created in approximately two days. This rapid turnaround speeds up the design process and reduces costs, allowing the firm to allocate resources more effectively.
Conclusion
The adoption of the Raise3D Pro2 Plus by Group GSA has revolutionised their design process, enhancing their ability to develop and present designs to clients. The speed, reliability, and versatility of the 3D printer have allowed them to produce
detailed models in-house, facilitating better client interactions and more efficient project development. Bilby3D's support has been instrumental in this transition, providing the necessary training and parts to ensure the long-term success of Group GSA's 3D printing capabilities. With the Raise3D Pro2 Plus, Group GSA is well equipped to continue delivering innovative and awardwinning designs, with 3D printing now an essential tool in their arsenal.
b3d.com.au groupgsa.com
Advanced wheel and chassis washing system for a fertiliser plant.
Tecpro distributes all kinds of spray nozzles, tank cleaning equipment, ergonomic guns, Stainless steel hose reels, odour control systems, fogging nozzles and fog makers for dust suppression and evaporative cooling.
A new fertiliser plant in Western Australia needed an effective solution to clean trucks' wheels and chassis, preventing the contamination of surrounding areas. Tecpro was asked to design and supply a comprehensive washing system.
The primary challenge was preventing contamination: ensuring that trucks and other vehicles from the fertiliser plant left the site without residue. Also, efficiency: The system needed to handle a high volume of trucks with minimal downtime and minimal water usage. Automation: Reducing manual intervention to ensure consistent cleaning, reduce time per clean and reduce labour costs. Tecpro provided a tailored solution using its Italian-made washing technology, which included rotating nozzles and a high-pressure, automated pump skid.
The system was designed as a fixed-location, drive-through wash to accommodate different vehicle types and sizes. Construction drawings were developed to assist the construction company in seamlessly integrating the system into the plant's new infrastructure.
High-Pressure Wash Heads: Four high-pressure rotating wash heads were installed, each capable of delivering powerful jets to remove stubborn dirt and residues from the wheels and undercarriage.
High-Pressure Pump Set: A robust 150 L/min, 110 bar highpressure pump set was selected to ensure thorough cleaning with each cycle, capable of handling large trucks and ensuring minimal water wastage.
Automation with Ultrasonic Sensors: Ultrasonic sensors were integrated into the system to detect vehicle presence. These sensors activated the pump when a vehicle approached and shut it off once the vehicle passed through, ensuring optimal water and energy use.
Water Management: The system featured disposable and recycled water options, aligning with environmental and operational needs. This flexibility allowed the plant to choose the most sustainable and cost-effective water management approach.
The installation of Tecpro's wheel and chassis washing system was a huge success, resulting in:
Environmental Compliance: The plant significantly reduced the risk of contaminating surrounding areas, ensuring compliance with environmental regulations.
Operational Efficiency: The automated system minimised manual intervention, reducing labour costs and water usage and improving vehicle turnaround times.
Enhanced Safety and Cleanliness: The thorough cleaning process enhanced the safety and cleanliness of vehicles, benefiting both the plant and the community.
Conclusion: Our innovative washing system, leveraging their partners washing technology, provided an effective solution for the fertiliser plant, addressing all key concerns and delivering long-term benefits.
For more information or help in designing a wheel or truck wash solution, call Tecpro on 02 9634 3370 or email sales@tecpro.com.au tecpro.com.au
ALIO Industries leads the way in air-bearing technology.
ALIO Industries stands at the forefront of air-bearing stage technology, providing market-leading solutions with their patented 6D Nano Positioning® systems.
Air bearings are crucial components in ultra-precise motion control systems. They offer frictionless operation by suspending components on a thin film of air. This eliminates mechanical contact, reducing wear and vibration while achieving unparalleled accuracy and smooth motion. They are essential in semiconductor manufacturing, metrology, and photonics, where even minute inaccuracies can lead to significant issues.
ALIO's air-bearing stages, such as their planar XY, linear X, and rotational air-bearing systems, are designed to deliver exceptional precision and repeatability down to nanometer-level accuracy. These systems are built to handle demanding applications, offering high payload capacities, smooth motion over long travel distances, and high-speed capabilities without compromising precision.
“One of ALIO's standout offerings is the Planar XY Air Bearing Stage, which achieves sub-micron accuracy and bi-directional repeatability of +/- 100nm,” explains Bill Hennessey, President of ALIO Industries. “This stage is ideal for ultra-precise positioning applications, such as semiconductor inspection and metrology. A granite base ensures minimal thermal expansion and maximum stability, essential for maintaining high precision over extended periods and varying environmental conditions.” ALIO’s Nano Z® stages use dual voice coil motors and air bearings to overcome limitations in vertical motion, providing exceptional stability and
accuracy in the Z-axis. This design is particularly beneficial in applications like wafer inspection and photonics, where vertical precision is critical.
ALIO’s commitment to innovation and quality is further demonstrated by its custom solutions, which cater to specific industry needs and ensure that each motion control system is optimized for its intended application. The company’s air bearing stages are renowned for their precision, robustness, and reliability, making them a preferred choice for high-precision industries worldwide.
By leveraging advanced materials, innovative design, and rigorous testing methods, ALIO continues to set the standard in nanoprecision motion control. ALIO’s air-bearing systems are a testament to its leadership in the field, providing unmatched performance and reliability that meet the exacting demands of cutting-edge technology sectors. alioindustries.com
Reliable identification of delivered goods directly at the loading gate.
The SICK Ident Gate System automatically identifies inbound goods directly at the loading dock based on shipping labels. The trackand-trace system detects the shipping labels when the worker drives through the gate—without stopping—with a loaded pallet. The acquired data are compared with the available order details thanks to the direct ERP connection. A visual loading and status check indicates to the personnel whether the data matches.
The Ident Gate System has a modular structure and can be individually adapted. To round off the concept, selected identification technologies such as RFID, 1D and 2D, or even hybrid approaches can be combined with functions for measuring or classifying the containers. In the rapidly evolving world of logistics, where “over $400bn worth of goods are sold based on a measurement,” in Australia alone, efficiency is crucial. As the industry propels towards heightened efficiency, SICK presents technologies that meet these crucial needs, thereby revolutionising the logistics landscape.
The Ident Gate System automatically identifies delivered goods based on shipping labels during loading and unloading directly at the loading gate. The data is transmitted to a high-level system and is always available to check against the delivery order. This allows for the seamless and transparent traceability of the goods.
SICK always steps in with a comprehensive track-and-trace solution. Their portfolio includes static and dynamic dimensioning and weighing systems for reading labels, dimensions and weight of cuboid and irregular objects, thereby aligning with evolving customer demands. These systems ensure that volume measurement rates remain highly accurate regardless of “the sorter system” used. As a result, logistics companies have seen an increase in revenue due to validated freight costs.
But it’s not just about dimensioning. SICK offers “fast and reliable identification solutions for 1D barcodes and 2D matrix codes”, ensuring precise tracking and analysis of all parcels, regardless of their colour or reflectivity. These systems come with enhanced features for object verification, such as determining whether an item is a bag or box, identifying hazardous labels, or recognising multiple items as they pass through the system.
SICK modular designs integrate time-saving, automatic shipping label recording, seamless, transparent traceability of goods, and higher throughput through an automated loading process. Thanks to the modular solution approach, these are cost-effective solutions that are easy to commission. Also, there is simple integration into the customer’s existing ERP or WMS systems.
Combined RFID and camera technologies, there is a direct ERP connection for bi-directional data exchange with a higher-level customer system and visual feedback to compare the pallet load with the delivery order. sick.com.au
Antares Vision Group's ‘all-in-one’ system eliminates the need for multiple inspection machines.
A new generation system from European-based inspection equipment manufacturer Antares Vision Group allows customers to select individual inspection modules and integrate them into one machine.
Food manufacturers can select what they need to suit their specific production line. Modules include X-ray, check weigher, leak detection, seal, code, and label inspection.
All the modules are designed specifically for the food industry. The machine’s hygienic construction features quick-removal conveyors and a completely washable structure.
“Antares Vision Group’s ‘ALL-IN-ONE’ inspection machine is a game changer for the food industry,” said Phillip Garro, Enmin’s Sales Manager (Inspection & Packaging). “Multiple processes can be combined into a single machine providing a solution that fully guarantees the product’s compliance in an extremely reduced footprint,” he added. “Plus, all the modules can be controlled through a single control screen for maximum convenience and efficiency.”
A popular combination of modules is X-ray, checkweigher and leak detection. This configuration provides a comprehensive product inspection by these three powerful modules.
Firstly, the innovative LDS module checks the package's correct sealing, detecting micro-leaks. Then, a state-of-the-art X-ray inspection system ensures the absence of foreign bodies.
At the same time, the weighing unit identifies packages out-ofweight tolerance. The weighing unit features the latest load cell technology. It is designed to operate with the utmost precision and impressive accuracy of plus or minus 0.2g (subject to operating environment). A double rejection system completes the solution.
“The ‘ALL-IN-ONE’ system takes flexibility and productivity to the next level. Now food processors need one machine to carry out all of their end-of-line inspections,” Garro added.
Enmin is the exclusive Australian representative for Antares Vision Group’s extensive portfolio of inspection equipment designed specifically for food and allied industries.
“In the short period since we launched Antares Vision Group into the Australian market, we’ve had a very positive reception to the company’s range of machines. The equipment offers cutting-edge design and the latest technology at a competitive price point,” he added.
“And of course, customers can expect the same outstanding service, back up and support that Enmin has built its reputation on for the last 40 years,” Garro said. enmin.com.au
"ReBels on Wheels" makes driverless transport systems affordable thanks to modern plastic technology.
Mobile robotic systems are being used in more and more work areas, from e-commerce warehouses to modern restaurants. However, widespread use is often unaffordable for small and medium-sized companies due to the high prices. igus wants to change this with new low-cost robotics offerings and presents a series of low-cost mobile plastic robots.
The market for automated guided vehicles (AGV) and autonomous mobile robots (AMR) is booming: the global market for mobile robotics, including service robotics, currently totals around $20.3bn, and experts expect this figure to almost double by 2028. Mobile robots are ubiquitous in material handling and industrial applications. And these smart helpers are even increasingly making their rounds in catering and hospitals. The plastics experts at motion plastics specialist igus have also been successfully testing AGVs in-house for four years - driverless shelves that deliver mail and shipments to offices and mobile robots in production that move transports and rotary stacking containers. The experience gained flows directly into developing a new Low-Cost Automation product line, the "ReBeL on Wheels". The goal is to pave the way for small and mediumsized enterprises (SMEs) to cost-effective mobile robotics. The goal of all these developments is the lighthouse project, a mobile robot with integrated HMI and vision that could even tidy up an office on its own. "With this project, we are pursuing a bottomto-top strategy in which certain components such as safety laser
scanners are not included in the basic package to keep the price low," explained Alexander Mühlens, Vice President and Head of the Low-Cost Automation Business Unit at igus. "Nevertheless, the solution can be retrofitted for industrial requirements." This year, igus will present an affordable gripper with a large stroke and travel that offers a high degree of flexibility when gripping different geometries, among other things. Says Mühlens: "The areas of application for this planned low-cost AMR are extremely diverse and go far beyond simple transport tasks. They cover many use cases in different areas of life, such as cleaning tasks or serving coffee directly at the workplace." treotham.com.au
How the Swiss Army knife of monitoring promotes safe and effective plant functionality in Australasia.
Plant managers often have a deep understanding of all the critical operational challenges facing their facility and a broad knowledge of the instrumentation that can help solve them. However, they might only sometimes be aware of the latest innovations that can make their lives easier. For instance, multifunctional monitoring instrumentation simplifies all plant measurement and control processes. Ian Loudon is an international sales and marketing manager at Omniflex, a remote monitoring specialist.
Streamlining technology is one of the most effective ways to innovate. In almost every industry, a business will likely opt for a single solution with multiple functionalities over a selection of specialised products—provided it doesn’t compromise on quality.
Signal conditioning is no different. Signal conditioning converts physical qualities into readable data that computer systems can process. Often, applications are complex, with multiple specialised components configured to measure an individual physical property, such as line linearisation in tanks. This method quickly becomes impractical across all industries with signal conditioning applications because multiple physical processes require 24/7 monitoring.
In an industrial plant environment, physical processes must work and are measured accurately. They act as catalysts for each other, constantly propelling an efficient plant operation, which is why signal conditioning is an integral interface in plant management.
Tank monitoring involves measuring the volume of liquid in storage tanks and detecting issues like overflows and leaks before they cause major structural and environmental damage and safety incidents. While this can often be a straightforward process, it becomes trickier if the tank is uneven or awkwardly shaped. This can make levels harder to read, as it requires additional mathematical computations on top of simply reading the analogue signals.
A classic example of this would be in petrochemical applications where spherical tanks are commonplace, such as the 30 million-
litre fuel storage facility at Port Melville, Melville Island. Here, liquid levels inside the tank don’t rise linearly with liquid volumes, and mathematical calculations are required to work out liquid volumes from the readable tank level.
This is where Omniflex’s TFX module shines, acting as a ‘one-stop shop’ for signal conditioning. Its ability to manipulate analogue signals and configure the appropriate mathematical functions means it can simultaneously measure multiple physical properties. Additionally, its SIL-1 rating makes the module suitable for use in harsh and hazardous environments where safety is a key consideration. This is critical in petrochemical applications where the potential for combustion and explosion must be factored into all operational considerations.
When applied to the challenges in tank monitoring, the module provides an easy solution that mitigates them. The TFX works out the volume of conical or spherical tanks to differentiate tank shapes without needing an additional kit.
Tanks can also deform due to pressure or temperature changes over time. They could have minor denting that is not severe enough to warrant a replacement; however, the shape of the tank has still changed, and the original linearisation data is obsolete. This can be mitigated easily by using the TFX module to monitor linearisation because it can calibrate itself to adjust to the subtle deformations. Thanks to the device’s multifunctionality, the risk of the tank leaking is significantly reduced. The TFX’s ability to adapt means that the data collected is accurate even with unconventional physical properties. Any tank issues will likely be resolved quickly, and the chances of significant errors—like leaking—will dramatically decrease.
Finding the right signal conditioning application is critical for plant operations. Multifunctional modules like the TFX are smoothing out the monitoring process, maintaining the accuracy needed for successful data monitoring. omniflex.com/sigcond
How can heavy industrial manufacturing mitigate rising interest rates and inflation by enhancing operational efficiency? James Robinson, the Head of Services for Asia Pacific at SYSPRO, has an answer.
The current economic climate in Australia, marked by escalating interest rates and inflation, challenges heavy industrial manufacturers. This is particularly true for those in the fabricated metals and Industrial and Machinery Equipment (IME) manufacturing sectors. Companies in these sectors must adopt a strategic response to sustain profitability and competitiveness. A key strategy to alleviate economic pressures in these challenging times is to enhance operational efficiency by adopting Enterprise Resource Planning (ERP) and Manufacturing Operations Management (MOM) systems. When designed explicitly for the manufacturing sector, these systems can be the key to effectively addressing these economic challenges and unlocking new opportunities.
The impact of rising interest rates and inflation
Interest rates in Australia have been on an upward trajectory, driven by the Reserve Bank of Australia’s efforts to curb inflation. This has led to higher borrowing costs, affecting capital expenditure and operational costs. Conversely, inflation erodes purchasing power, raises the cost of raw materials, and increases wage pressures. These economic conditions can squeeze margins and hinder growth for heavy industrial manufacturers, particularly the fabricated metals and IME sectors.
The role of ERP and MOM systems in enhancing operational efficiency
ERP and MOM systems are pivotal in addressing these economic challenges. They provide comprehensive solutions to streamline operations, reduce costs and improve productivity. Here’s how these systems can specifically benefit the fabricated metals and IME sectors:
1. Streamlining supply chain management
Supply chain inefficiencies can be a significant cost burden, exacerbated by inflation and interest rate hikes. An ERP system offers robust tools for supply chain management, enabling fabricated metals and IME manufacturers to:
Optimise inventory levels: ERP systems are adept at maintaining optimal inventory levels using real-time data and predictive analytics. This reduces holding costs and mitigates the risk of overproduction or stockouts, making them a practical solution for manufacturers in the fabricated metals and IME sectors.
Enhance supplier relationships: ERP systems facilitate better supplier communication and collaboration, ensuring timely deliveries and favourable terms. This can lead to cost savings and improved cash flow management.
Implement Just-in-Time (JIT) practices: MOM systems support JIT manufacturing, reducing inventory carrying costs and waste. This approach is particularly beneficial in a high-interest-rate environment where capital efficiency is crucial.
2. Improving production efficiency
In the fabricated metals and IME sectors, efficient production processes are vital. MOM systems, integrated with ERP, can significantly enhance production efficiency through: Advanced scheduling and planning: MOM systems provide sophisticated scheduling tools that optimise production schedules, minimise downtime, and ensure optimal resource utilisation.
Quality Management (QM): Ensuring high product quality reduces rework and scrap rates, directly impacting profitability. MOM systems integrate quality management processes, ensuring compliance with standards and reducing defect rates.
3. Enhancing financial management
Effective financial management is essential in navigating economic uncertainties. ERP systems offer comprehensive financial management modules that help manufacturers:
Optimise cash flow: ERP systems enhance cash flow management by improving accounts receivable and payable processes, which is crucial in a high-interest-rate environment.
Budgeting and forecasting: ERP systems provide powerful tools for budgeting and forecasting, enabling manufacturers to make informed financial decisions and prepare for economic fluctuations.
Cost control: Detailed cost analysis and reporting capabilities help identify areas for cost reduction, improving overall financial health.
4. Driving continuous improvement
Continuous improvement is at the heart of operational efficiency. ERP and MOM systems support a culture of continuous improvement through:
Data-driven decision-making: These systems provide realtime data and analytics, empowering decision-makers to identify inefficiencies and swiftly implement corrective actions.
Lean manufacturing practices: ERP and MOM systems facilitate lean manufacturing practices, reducing waste, improving workflow, and increasing customer value.
Employee empowerment: These systems empower employees by providing them with the tools and information they need, enhancing productivity and job satisfaction and fostering a culture of continuous improvement.
Rising interest rates and inflation present formidable challenges to heavy industrial manufacturers in Australia. However, by leveraging the capabilities of ERP and MOM systems, manufacturers can enhance operational efficiency, reduce costs, and improve profitability. These systems provide the tools to streamline supply chain management, improve production efficiency, enhance financial management, and drive continuous improvement.
For manufacturers in the fabricated metals and IME sectors, adopting ERP and MOM systems is not just a response to economic pressures but a proactive strategy to thrive in a competitive landscape. By embracing these technologies, manufacturers can mitigate the impact of economic fluctuations and secure a sustainable future. syspro.com.au
How unified observability powers smarter manufacturing. Richard Gerdis is the VP of APAC at LogicMonitor.
Manufacturing today depends on efficient software performance to keep production running smoothly and minimise costly interruptions. However, traditional monitoring systems often need more complete visibility manufacturers need, which leads to inefficiencies and delayed problem-solving. Unified observability addresses these issues by gathering data from software, hardware, and networks into a comprehensive view. This approach helps manufacturers pinpoint potential issues early to prevent them from growing into larger problems.
Some of the greatest benefits of unified observability include:
1. Gain full visibility across IT and operational systems to optimise production
Traditional monitoring tools often operate in silos, providing visibility only within specific systems, which leads to slow problem resolution and production inefficiencies. Unified observability breaks down these silos, integrating IT and operational data into a single, cohesive view. This full visibility empowers manufacturers to detect issues early and identify the root causes of recurring inefficiencies, whether in software performance or operational workflows. For example, slow response times in machinery may be traced back to misaligned IT systems, which, with this level of observability, could be noticed.
By bridging the gap between IT and operations, manufacturers can proactively prevent minor issues from escalating into production halts. This level of integration also provides valuable insights into where automation can be implemented to enhance productivity further and reduce manual interventions.
2. Reduce downtime with real-time insights and predictive maintenance
Unplanned downtime from emergency repairs or damaged equipment results in lost production time and delayed schedules for manufacturers. Unified observability goes beyond traditional monitoring by leveraging artificial intelligence (AI)-driven analytics to provide real-time insights into both software and equipment performance. This means that teams aren’t just reacting to problems; they can predict and address issues proactively. With predictive maintenance, real-time data from sensors and equipment empowers manufacturers to forecast when machines are likely to fail. For example, minor fluctuations in temperature or vibration might signal that a component is close to breaking down, which would otherwise be missed by routine maintenance checks. These early warnings allow maintenance teams to address issues during planned downtime and significantly reduce the chance of unexpected breakdowns that halt production. This proactive approach also extends the life of expensive machinery and reduces maintenance costs.
3. Strengthen security and ensure compliance with full oversight
Manufacturers face significant risks regarding system security, particularly as operational systems become more integrated with IT networks. A cyberattack or vulnerability in software systems can lead to operational shutdowns, data breaches, and regulatory violations. Unified observability enhances security by providing realtime alerts on any anomalies across the entire software environment, including operational technologies. It helps manufacturers detect vulnerabilities such as outdated software patches or unusual network traffic, which could indicate a breach. This is particularly crucial as manufacturing systems often operate with legacy software that may be more vulnerable to attacks.
With the growing number of compliance regulations across industries, observability platforms also streamline the process by logging and reporting all system activities automatically. This ensures compliance and provides an auditable trail to reduce the need for manual oversight during audits and significantly lower the risk of non-compliance fines.
4. Achieve 360-degree visibility across the supply chain
Supply chain disruptions are among manufacturers' costliest challenges, especially in global production environments where delays or shortages can have a ripple effect across the entire operation. Unified observability extends beyond the manufacturing floor, integrating data from the entire supply chain to provide a comprehensive view of inventory levels, logistics, and supplier performance. This helps manufacturers pinpoint potential bottlenecks or delays in real time. For example, manufacturers can quickly adjust production schedules to avoid running short of necessary materials if a key raw material shipment is delayed.
Observability also supports smarter inventory management as manufacturers can track usage rates and trends to ensure that stock levels remain optimised to avoid both excess and shortages. This real-time visibility across the supply chain lets manufacturers better manage risks, reduce costs, and maintain smooth production even in the face of external disruptions, such as global supply chain crises or localised issues.
A cloud-based infrastructure monitoring platform provides manufacturers with unified observability to transform how they manage software systems. By offering real-time, comprehensive visibility across IT and operational systems, manufacturers can bridge the gap between the two for more streamlined production. Manufacturers can prevent issues before they escalate with AIpowered insights and predictive capabilities, reducing downtime and enhancing system reliability. This unified observability empowers manufacturers to maintain high-performance systems so they stay one step ahead of their competitors. Scalability and automation mean IT teams can focus on strategic tasks while keeping infrastructure optimised and business continuity intact. logicmonitor.com
Unlock competitive advantages with ERP software. Aaron Crees is the Director of Sales and Marketing at Jobman.
In today’s rapidly evolving manufacturing landscape, staying ahead of the competition requires more than producing quality products.
Streamlined processes, optimised resource allocation, and datadriven decision-making are where Enterprise Resource Planning (ERP) software emerges as a transformative tool. Manufacturers can unlock significant competitive advantages when implementing this type of technology. The size of the business is unimportant; whether you are a two-person operation or have 100 staff, a competitive edge will always be essential.
As businesses evolve, efficient management of various functions like quoting, scheduling, inventory, and purchasing becomes crucial. Enterprise Resource Planning (ERP) systems step in to simplify these complexities by offering a comprehensive platform to aggregate and analyse data from different business facets.
Understanding ERP software
ERP software integrates core business processes such as production planning, inventory management, supply chain operations, lead management, and more into a centralised system. It provides real-time visibility into various facets of operations, allowing manufacturers to make informed, data-driven decisions swiftly. The advantage of ERP Solutions is that they present many benefits tailored for diverse industries, fostering centralised access to cloud resources, bolstering productivity, and driving automation, among others.
So, here below is an overview of those advantages:
Centralised information and processes
ERP systems streamline data collection and storage, replacing multiple systems with a unified platform. This centralised approach enhances operational efficiency, reduces errors and promotes uniformity across the organisation.
Cloud-based ERP solutions enable remote access to data, facilitating swift decision-making and flexibility, even outside traditional office settings.
Centralising data and offering cloud accessibility software accelerates task completion and frees time for more strategic endeavours. Enhanced automation further boosts productivity, alleviating workforce stress and improving output quality.
Reduced overhead costs
The streamlined processes of ERP systems reduce overheads, from labour costs to inventory optimisation. Moreover, improved forecasting capabilities minimise wastage and aid in prudent financial planning.
Better inventory tracking
ERP solutions offer enhanced transparency and accuracy in inventory management, curbing losses and enabling leaner inventory practices, ultimately translating to substantial cost savings.
Automated business processes
ERP platforms automate routine tasks, paving the way for increased operational efficiency. This automation, coupled with advanced data analysis fosters predictive capabilities, optimises resource allocation and drives strategic decision-making.
Improved cross-department collaboration
A good system fosters seamless collaboration across departments, facilitates cohesive workflows, and enables effective communication for customers, suppliers, and staff.
Through comprehensive data insights, ERP software optimises supply chain processes, from demand forecasting to inventory management, reducing costs and enhancing profitability.
ERP solutions are robust data repositories, simplifying analytics, reporting, and strategic planning. They provide holistic insights for informed decision-making by consolidating information from various departments.
ERP systems enhance quality control mechanisms, ensuring adherence to standards and minimising errors throughout the production cycle. Thus, they bolster customer satisfaction and brand reputation.
With built-in security features, ERP systems safeguard sensitive data, mitigating the risks associated with data breaches and ensuring regulatory compliance.
ERP software minimises human errors inherent in manual data entry, enhancing data accuracy and reliability, thereby instilling confidence in decision-making processes.
The cumulative effect of ERP benefits results in a superior customer experience, characterised by streamlined processes, improved product quality and cost efficiencies passed on to consumers.
Challenges associated with ERP Software despite the manifold benefits, implementing ERP software poses specific challenges, including the need for executive buy-in, upfront costs, customisation requirements, onboarding, and time to realise the return on investment (ROI).
The key considerations for ERP Implementation to determine the suitability for your business, are:
• Is your company experiencing growth?
• Do you need to streamline business processes?
• Are you aiming to reduce operational costs?
• Do you require access to accurate business data?
• Are your business systems integrated?
• Can you provide the best customer experience?
In an increasingly competitive manufacturing landscape, ERP software emerges as a strategic enabler for organisations seeking to gain a competitive edge. By streamlining operations, enhancing inventory management, providing real-time insights, facilitating supply chain integration, ensuring regulatory compliance, and fostering scalability, ERP solutions empower manufacturers to optimise efficiency, reduce costs, and drive sustainable growth. As technology advances, leveraging ERP software will be indispensable for manufacturers aiming to thrive in the digital age. jobman.com
Every manufacturer needs a reliable data backup, by Matt Caffrey, Senior Solutions Architect ANZ at Barracuda Networks.
Over the last decade, the manufacturing sector has increasingly relied on advanced digital technologies to meet evolving customer and operational needs. While this shift has drastically improved productivity and efficiency, it has also exposed the sector to greater cyber risk. In 2023, Barracuda Networks research showed that around two-thirds of manufacturing companies had experienced an email security breach (66%) or ransomware incident (68%) in the previous 12 months.
The repercussions of these cyber incidents can be severe, including downtime and business disruption (cited by 53% of the manufacturing companies surveyed), the loss of sensitive data (37%), reputational damage (42%), and substantial financial costs associated with recovery. On average, Australian organisations reported an annual cost of $4.2m to respond to security compromises. Furthermore, the fallout from a successful attack can disrupt the rest of the supply chain, not just the manufacturer that was initially targeted.
Defending against cyber threats targeting digital infrastructure requires multi-layered, defence-in-depth security solutions that can help to prevent, detect, contain and neutralise attacks. A fundamental component of this approach is a reliable backup for digital assets and data. Backups can be on-premises, in the cloud, or a hybrid of both. Here, we will explore some of the main cybersecurity challenges facing manufacturing and how a robust backup can help to mitigate risks.
Manufacturing’s technology ecosystem can make it particularly vulnerable to attacks. IDC expects manufacturing to account for 18% of all digital transformation investment over the next five years, with some of the top use cases including robotics, automation, inventory intelligence and smart warehousing. Each of these will further extend the potential attack surface and will create, process, store and transmit vast amounts of data. All that data needs to be securely backed up to be easily recovered and restored following an incident.
Many manufacturing companies also hold considerable intellectual property (IP). If their IP is stolen or exposed, manufacturers may lose their competitive advantage, which could devastate their bottom line. Australian manufacturing companies have been actively targeted by nation-state hackers looking for trade secrets.
Ransomware attacks are a particular menace for data security in manufacturing as they focus on encrypting, deleting, and removing files. Recent ransomware incidents involving Australian manufacturing, production, and distribution companies include an alleged attack by PLAY ransomware against a Sydney-based engineering firm and one targeting an international Australian logistics company that transports 40% of Australia’s container traffic.
Cyber resilience is about effectively responding to and recovering from a security breach, minimising the impact on customers, suppliers, and operations.
Reliable backups are central to cyber resilience, but not just any old backup. Attackers will hunt down, target, wipe, or otherwise disable any exposed or accessible backup. For effective data protection, companies need a robust, access-restricted, network-segmented, offline, immutable backup. A backup that attackers can’t easily access and, even if they do, can’t tamper with. If you can, keep this backup in the cloud, where it can back up and restore your cloudbased workloads and communications.
Offline, segmented, immutable, cloud-based backups: A manufacturing necessity
Your backup is your go-to if data is encrypted, damaged, deleted or lost. Some of the key benefits include:
• Extra defence against determined attackers: Even with strong security measures in place, attackers can still find ways to compromise manufacturing systems. An effective backup will allow you to can roll back any unwelcome changes and restore operations quickly.
• Ransomware mitigation: In a ransomware attack, these backups ensure that a clean, unaltered copy of the data is available for restoration, reducing the need to pay the ransom.
• Protection from accidental data corruption: Data corruption can occur due to hardware failures, software bugs, or simply human error. Robust, immutable cloud-based backups provide a reliable, unmodifiable point-in-time copy of the data, enabling consistent and accurate data restoration.
• Compliance and regulatory requirements: Certain industries and regulatory frameworks mandate the use of immutable backups for data retention and compliance. These backups guarantee the integrity and authenticity of the data, helping manufacturers meet such requirements.
The manufacturing sector’s increasing reliance on digital technologies has heightened its attack vulnerability. With this steady increase in cyber risk, a robust and resilient cybersecurity strategy is increasingly essential. Your rock-solid backup should underpin everything. barracuda.com
Proud Queensland family company is a crucial specialist engineering supplier to rail authorities.
A second-generation family business based in Narangba, Queensland, Steelrod Pty Ltd is a leading specialist engineering supplier to rail authorities and mining companies throughout Australasia and selected export regions.
Founded in 1974 by Doug Veneris and celebrating its 50th Anniversary this year, the company continues to expand and is now run by sons Damian and Shawn Veneris as joint Managing Directors.
Damian is a qualified boiler maker, and Shawn specialises in the commercial side of the business. Today, the company employs a highly skilled team of more than 55 experienced personnel.
Based on the strongest foundations built on quality engineering excellence and delivery performance across a diverse range of engineering capabilities and complex industrial projects, Steelrod has continued to invest in modern state-of-the-art highend machining centres and has kept abreast of cutting-edge technological developments.
In 2008, Steelrod commissioned its first Okuma Double Column machining centre, replacing an older alternate machine. In June this year, it commissioned a second Okuma Double Column machining centre, MCR-A5CII 20x40 with OSP P300MA Control, based on the earlier machine's performance and reliability, the factory service backup, user-friendly controls and training provided, and the speed and increased capabilities of the new model. These sophisticated machines cater to large rail components such as rail point machines, chassis for train bogies, and large mining components.
“The new Okuma Double Column machine has reduced our machining time due to its very high speed, amazing accuracy and universal three heads which has resulted in much improved set up times and flexibility and was the brand of choice for us,” said General Manager & Director, Damian Veneris. “We generally buy one of more machines a year to keep abreast of technology developments, and this has a direct impact on the company’s performance and our ability to attract and retain apprentices and skilled operators who seek to work on the latest machines to advance their skills and keep abreast of advances in technology,” he said.
As a specialist, the company offers a comprehensive range of engineering services that meet the highest level of industry standards in Track and Signal engineering, CNC machining, and fabrication. The extensive operations include welding, fabrication, assembly, hard chroming, heat treatment and painting for Track & Signal equipment for Rail Authorities throughout Australia, Mining Equipment and Construction including Bridges and Wharf infrastructure, plus Aftermarket Automotive Products.
Apprenticeship technical training plays an important part of the company’s strategic planning. Six to eight apprentices are under training at any one time, and the company achieves a high retention rate after such training is completed.
As can be expected in such a quality manufacturer, the company is fully accredited to ISO 9001:2015 and has a continuous improvement policy in quality systems, with the customers central to all it does. It is also committed to implementing a comprehensive OHS & S Management System.
Today, the company’s markets cover Rail and Rail Infrastructure, Mining, Automotive, and General Engineering, with the bulk of work coming from long-standing clients and word-of-mouth referrals. In general terms, Steelrod's markets are Queensland (30%), Mainland Australia (60%), and export (10%).
The company has several new projects coming up, particularly in the Queensland infrastructure areas, where some are scheduled to commence in the coming months.
Looking to cater to increased demand and free up space for additional machining centres and equipment in the future, the factory has just completed an 800-square-metre extension.
Steelrod Pty Ltd is a company celebrating 50 years and looking positively ahead to the next 50 years through sound business practices and investments in people and advanced technology.
“It is always a pleasure to work with Steelrod,” said Okuma Queensland Branch Manager John Baker. “With the Queensland Okuma team completing the installation of the second Double Column machine to the company’s facility, this has further strengthened our relationship,” he said.
okumaaustralia.com.au steelrod.com.au
Transitioning the world’s biggest companies to net zero.
A new $60m Biosustainability Hub at The University of Queensland will use synthetic biology to help the world’s biggest businesses transition to net zero.
Funded by government, industry, and UQ, the Biosustainability Hub aims to be a one-stop shop for big companies to transform their production practices and create carbon-neutral, economically viable products and materials.
Hub director Professor Esteban Marcellin from UQ’s Australian Institute for Bioengineering and Nanotechnology said the facility is the first in Australia and co-locates research groups and industries that share a vision to transition society to net zero. Professor Marcellin is a synthetic biologist who uses carbon monoxide, CO2 and methane to feed microbes in biomanufacturing to produce products.
“The Hub brings together cutting-edge research projects and some of the world’s biggest companies to find solutions to challenges like climate change, biodiversity, mining sustainability and future food production,” Professor Marcellin said.
“We will be using the process of synthetic biology, which develops new materials, fuels, foods, chemicals, or medicines from waste using biological processes.
“By changing production practices from those dependent on fossil fuels to biomanufacturing, we are changing the game for our planet.
“To address climate change, we need to help big businesses find alternative solutions that are better for the environment.”
The Hub is set to become the home of translational biomanufacturing in Australia, with industry partnerships already underway at UQ including:
• Working to turn greenhouse gas into a feedstock for sustainable aviation fuel with carbon capture company LanzaTech;
• Using gas fermentation to create new products with global energy company Woodside Energy;
• Reducing pollution and recovering resources needed to achieve global net zero carbon with global mining group Rio Tinto;
• Creating future ingredients as part of the Food and Beverage Accelerator (FaBA).
Woodside Energy VP Energy Solutions, Technical and Energy Development, Jason Crusan, said biological solutions could contribute to decarbonising efforts.
“At Woodside Energy, we have set obvious emissions reduction targets, and we believe that biological solutions could be an important part of the solutions to help us achieve our emissions reductions,” he said.
LanzaTech co-founder Dr Sean Simpson said the carbon capture company had successfully pioneered the commercial production of sustainable fuels and chemicals from large-volume, low-cost waste streams worldwide.
“We are excited to bring our knowledge and experience to the UQ Biosustainability Hub to help accelerate the industrial transition to net zero,” Dr Simpson said.
Professor Marcellin said the UQ Biosustainability Hub was the convergence of engineering, biology and industry into a unique model that would aim to enable real and lasting change.
“This is an exciting opportunity to model a new way of working with industry leaders, not only for society but also to create economically viable solutions and opportunities for our partners to help them transition their production practices,” he said.
The hub will be located at UQ’s Andrew N. Liveris Building and is open to industry, researchers and governments in Australia and overseas. uq.edu.au
Making the renewable energy revolution a reality, all industries at a time.
Building on the momentum of the 2023 National Manufacturing Summit, which focused on Renewable Energy: Challenges and Opportunities, the 2024 Summit embarked on an ambitious journey with its theme: Pathways to Success…Making the Renewable Energy Revolution a Reality.
Geoff Crittenden opened proceedings at the Amora Hotel in Brisbane. He promised an even more in-depth and important event than in previous years, and Crittenden delivered. “The hope is that Australia can take the opportunity to start making what we need here at home,” he said. The 2024 Summit began by delving into the practical aspects of manufacturing within the renewable energy sector, highlighting the essential components driving Australia’s transition to a sustainable future. The Queensland Premier Steven Miles was there to open the conference, and the newly titled Assistant Minister for the Future Made in Australia, Tim Ayres, lent his presence as a call to action for the room of manufacturers, movers and shakers. “We stand at the crossroads of two futures,” said Ayres. “The only resource we don’t have is time.”
The Australian Government’s commitment to reducing emissions by 43% by 2030 and achieving net zero by 2050, as outlined in the Climate Change Act 2022, sets the stage for a transformative era in renewable energy.
With an anticipated growth in renewable energy generation from 64GW to over 218GW by 2050, the manufacturing sector is at the forefront of this change, with unparalleled opportunities and significant challenges.
From the Centre for Future Work, Charlie Joyce touched on the state of the global energy transition and implications for manufacturing, where Australia stands in the emerging renewable energy economy, and spoke about our pathway to success. Charlie’s co-presenter, Emeritus Professor David Peetz, loudly mentioned our position in the Harvard Growth Centre’s calculations of export system complexity. He said, “Pakistan, Uganda and Namibia have more complex export systems than Australia.” Joyce underscored Australia’s unique position to capitalise on the renewable energy sector due to its skilled labour, strong innovation capacity, and rich mineral resources critical for renewable technologies. However, he also pointed out the risk of Australia missing these opportunities due to its current role in the global value chain and low investment in manufacturing R&D. According to Joyce, “Australia has the opportunity to rebuild our value-added manufacturing sector, drive emissions reduction, and create thousands of good jobs. But our governments are pursuing a contradictory industrial strategy of supporting renewable energy industries while presiding over and subsidising expanded fossil fuel production.”
He noted Australia’s subsidies to fossil fuel producers and major users totalled $14.5bn in 2023–2024, an increase of 31% on the previous year. Fossil fuel production and export compete with renewable energy for investment and skilled workforce. “Australia needs a coherent clean energy industrial strategy that phases out fossil fuel production and consumption and focuses on the renewable energy revolution.”
Simon Kuestenmacher, from The Demographics Group, mapped out a future where Australia can capitalise on its demographic and natural advantages to foster a robust manufacturing sector aligned with global renewable energy demands, advocating for strategic policy frameworks to make this transition viable.
The presentation addressed global primary energy consumption trends from 1965-2023, with a continuing dominance of coal, oil, and gas. “You cannot have a green revolution without also having a lot of holes in the ground,” he said. However, he emphasised the
critical need to shift this energy base towards renewables to meet climate targets and global demand, mainly driven by the urban Asian middle class. Global energy demand will continue to grow for a decade or two. Ensuring renewables cover this additional demand is crucial in reaching climate targets. Australia can play a vital role in this transition.
“Contrary to popular belief, the demise of Australian manufacturing has been greatly exaggerated,” said Kuestenmacher. Data from 1984 to 2021 shows fluctuations but not a steep decline in manufacturing jobs, which suggests a resilient sector capable of adaption. His analysis showed Australia’s ongoing transformation into a knowledge economy with evolving skill levels in the workforce from 1987 to 2023. This shift supports the narrative that Australia can develop a robust renewable energy manufacturing base due to its skilled labour force.
Elizabeth Thurbon, a Professor of International Political Economy at the University of NSW, described this polycrisis as a situation where governments face various challenges. At the same time as scaling down fossil fuels, governments need to scale up renewables, all while navigating changes in the geo-strategic landscape, including a growing rivalry between China and the US. This poly-crisis is causing countries like Korea, China and Japan to rethink their energy policies and embrace a state-led energy approach. This approach is Green Energy Statecraft – using green energy policies to address economic, energy, environmental, and military security challenges. This new kind of statecraft in Southeast Asia is helping to speed up the benefits of a green energy economy. Green Energy Statecraft is a policy approach that Australia may also benefit from. Koen De Backer, an International Expert in Public Policy, spoke about green energy policy from a global perspective. According to Koen, the discussion is changing beyond the old and tired policy
debates – from whether industry policy is needed to how to design and implement a green industry policy. The government has an active role, but a green industry policy isn’t easy. Industry policy works better in theory than practice – the devil is in the detail. In Australia, there are calls for strategic autonomy, supply chain resilience and sovereign manufacturing capabilities because of national or economic security. However, Koen noted how important it is that both government and industry focus beyond the small Australian market and look towards exports. Australia also needs to have realistic expectations, particularly for a manufacturing revival. Australia cannot be suitable for all (green) industries. Georges Antoun, the Chief Commercial Officer at First Solar, provided an overview of the experience in the United States, particularly in light of the Inflation Reduction Act. Antoun highlighted how the IRA introduces expanded tax credits for renewable energy projects, which are pivotal for companies like First Solar. He discussed the surge in investments following the IRA's enactment, the favourable economic conditions created by the IRA, and the growth in job creation and technological innovation within the solar energy sector.
Professor Cori Stewart, the Founder and CEO of Advanced Robotics for Manufacturing (ARMHub), provided a highly engaging
overview of ARMHub's work in robotics and how manufacturers can use their data and AI.
“AI and automation are estimated to increase Australia’s productivity by 50% to 150% - if we can adopt it at a mid- to fast-pace,” said Stewart. “Everyone is ready for AI, except your data.” Stewart cited the number of active robots in the Australian industry but flagged a 150% acceleration requirement to succeed in the transition. The 700 autonomous trucks on QLD mining sites are just the beginning. “The next frontier in scaling deep technology innovation and modernising manufacturing is the smart use of data and AI. We are harnessing opportunities to collaborate with our partners to embed Australian deep tech companies and manufacturing businesses in high-value global supply chains.”
At the end of the proceedings, Weld Australia staged a practical demonstration where participants had the chance to workshop the steps considered during the Summit. To refine an action plan for government, industry, unions and the community for a successful renewable energy revolution. weldaustralia.com.au
Cutting the ‘monotonous’ out of handheld laser welding. Give the job to a robot.
Cobots, or collaborative robots, are designed to work with and around humans. Like any robot, cobots enable repetitive tasks to be completed more efficiently and precisely.
If you are considering a cobot to increase welding productivity and safety in your operation, read on to learn everything you need to know to get started with a laser welding cobot solution.
What is a welding cobot?
While cobots are used for various tasks, they have experienced a surge of adoption in manufacturing and fabrication applications like welding. Cobots for welding combine a multi-axis robotic arm with a welding torch and power source and are capable of performing many welding operations. Cobot arms can be mounted in various ways, but welding cobots are typically mounted to a table or cart with a surface for fixturing workpieces.
Welding cobots can use the same handheld welding methods as human welders, including laser welding, MIG and TIG, ultrasonic, plasma, and spot welding. Choosing the ideal welding method is critical when selecting a cobot welding system, as many of the advantages and disadvantages of each technique persist regardless of the level of welding automation.
What are the advantages of laser welding?
Laser welding involves transferring a laser beam’s energy in the form of heat to fuse or join parts. It offers several significant advantages, whether handheld, fully automated, or integrated with a cobot.
Laser welding is exact and offers consistent results after each weld. Laser welding experiences virtually no degradation in weld quality over time as a non-contact process. The precision of laser welding pairs excellently with cobots because the process and motion are highly controlled and repeatable.
Laser welding directs heat precisely and generates significantly smaller heat-affected zones than alternative welding methods. Since laser welding transmits minimal heat to the surrounding material and dramatically reduces workpiece distortion, it is an excellent choice for sensitive features and thinner materials.
Laser welding can be performed with and without shielding gas and in various materials and thicknesses. Steels, stainless steel, aluminium, copper, titanium, nickel, brass, and dissimilar materials are all excellent candidates for laser welding.
For many applications, laser welding is significantly faster than alternative welding methods. This advantage is most pronounced in fully automated systems, but the higher welding speeds carry over to handheld and cobot applications. Laser welding has experienced widespread adoption mainly because it is up to four times faster than alternative methods like TIG.
Laser welding creates exceptionally high-quality joints with excellent visual finish and mechanical properties. Depending on how laser parameters are set, lasers can create narrow and wide weld seams and can be used with wire feeders to create larger weld beads and fill wider gaps. Laser welded seams often require no or minimal finishing beyond a quick pass with a brush, further reducing tedious manual labour and increasing productivity.
Lasers are used for various tasks in fabrication and materials processing beyond welding. Laser cleaning is an application that has surged in popularity due to its speed and flexibility. Some laser welding systems offer pre-weld cleaning to minimise porosity in the
weld joint due to contaminants while post-weld cleaning functionality reduces or eliminates the need for slower weld cleaning methods like blasting, pickling paste, and grinding. These laser cleaning functions are powered by the same laser as the welding functions and are accessed easily by changing the torch nozzle.
What applications are a good fit for welding cobots?
Choosing between a handheld laser welder, fully automated laser welding, or something in between is a big decision, particularly for smaller fabricators and shops. While there are several factors to consider, one of the most critical is what kind of applications, projects, and parts you expect to encounter.
Ultimately, laser welding cobots are a form of automation. While they bridge the gap between human welders and traditional robotic systems, automation is most effective when handling repeat tasks.
The two primary benefits a cobot offers are productivity and consistency. Once a welding cobot is taught how to make a weld, it can do so virtually perfectly (and quickly) repeatedly. Whether the cobot has been taught ten welding tasks or 100 is true. Welding cobots truly shine when handling repetitive welds in High-Mix, LowVolume manufacturing environments.
Repetitive welds can come in many forms. On one end, a large volume of small parts requiring a single weld is a good fit for a welding cobot, as multiple can be fixtured to a weld surface and addressed as part of a single program. Conversely, larger parts that require numerous welds, such as vehicle seats, are also often excellent candidates for welding cobots. The flexibility and ease of programming mean that welding cobots can handle one project one day and seamlessly pivot to a different project the next day.
The same is true, of course, of human welders. However, no amount of welding skill or experience can eliminate mistakes, imperfections, and inconsistencies. A welding cobot can be the answer if a weld must be made to an exacting spec, and imprecision means extra finishing steps, rework, or scrap.
Despite being a form of welding automation, it is important to understand that welding cobots are not intended as a replacement for skilled human welders. The opposite is true—by definition, collaborative robots rely on humans to teach and work alongside them. Even if that were not the case, welding cobots are not a perfect fit for every application, such as when parts have inconsistent fit-up or require particular attention or care.
However, welding cobots offer a surprisingly affordable and easyto-integrate way to increase welding throughput and productivity. The speed and consistency achievable with a cobot empower skilled welders to get more done while reducing fatigue and letting them focus on higher-skill tasks rather than repetitive jobs. By increasing welder productivity and decreasing the time spent on mundane work, welding cobots help fabricators stay competitive and make welding a more attractive profession.
Human welders interact with a welding cobot by programming it to perform welding operations. Programming is a key differentiator between cobots and traditional industrial robots. Traditional robots typically require workers with robotic programming experience— even then, the process is usually complex and time-consuming. By comparison, welding cobots can be programmed by operators with no programming experience in as little as a few minutes.
Although cobots can be programmed using traditional g-code, this is usually unnecessary. The most common method of programming
a welding cobot is teach-by-touch. Teach-by-touch manually guides the robotic arm through the welding job steps before saving the program. Creating the weld move profile this way involves setting waypoints like weld start and weld stop points. Welding cobots can be manually programmed by physically moving the arm by hand or by using a controller pendant to jog the arm.
Programming a welding cobot does involve more than just going through the motions, however. Most welding cobots include software accessed on a controller that allows operators to define weld parameters. In the case of the LightWELD® Cobot System, parameters like laser power, seam width, type of weld, and material are defined, and exact welding steps are specified using a visual programming language.
Once a job has been taught, operators typically run the cobot through the program with laser power off to confirm that it is behaving as intended before running the actual job. Laser welding cobots can store many programs and parameter presets that can be recalled once the operator is happy with the results.
Safety is a primary concern for both welding cobot and laser welding solutions. Ensuring the safety of both operators and bystanders is easier than you might expect but still requires PPE and integration considerations.
Let’s start with the cobots themselves. Cobots are usually equipped with various safety features, such as robots that work close to human workers. Unlike traditional robots, which often require a cage to ensure they do not come into contact with obstructions, cobots are power and force-limited, meaning they do not move quickly enough to cause injury. In a collision with an obstruction, a
welding cobot will immediately stop moving and shut off welding power. Cobots are also typically designed with rounded geometry and no pinch points.
Laser welding requires safety measures like any other type of welding. Welder PPE is necessary and should include heat-resistant gloves and clothing and eye protection. When laser welding is in progress, laser safety goggles with an Optical Density (OD) rating greater than six at 1070nm are the minimum requirement for anyone with a line of sight to the welding torch. A laser safety welding helmet is also required for welders that are closer to the weld. Fumes must also be considered, and adequate fume extraction may need a dedicated fume extractor and respiratory protective equipment if the welding area does not have sufficient ventilation.
The location where the laser welding cobot is installed must also be considered. Some laser welding cobots include interlocked enclosures that can be shut when the laser is on—this option allows the system to be installed virtually anywhere. Laser welding cobots without integrated enclosures must be installed in a closed environment with laser-safe walls, interlocked doors, and safety signs. When integrating any laser solution, a designated employee should serve as the Laser Safety Officer (LSO) who ensures that laser safety best practices are upheld.
Getting started with a laser welding cobot solution
Implementing a laser welding cobot solution can seem intimidating, particularly for those without automation or laser welding experience. Fortunately, the laser welding experts at IPG are ready to help. Go to our site, below, and click through to one of our global application labs. ipgphotonics.com
Novarc Technologies computer vision system to produce X-ray quality welds with zero operator intervention.
In the pipe welding industry, advancements in automation continue to provide solutions to the labour gap caused by an acute shortage of skilled welders. Novarc Technologies Inc., a full-stack robotics company specialising in designing and manufacturing cobots and computer vision AI for automated welding applications, has been a pioneer in welding automation since 2013, providing a solution to the welding labour shortage.
Weld Australia predicts a shortage of nearly 70,000 skilled welding operators in Australia by 2030. With an aging welder workforce and a need for uptake of the welder trade, there are no simple solutions to the welder demographic.
According to Geoff Crittenden (CEO, Weld Australia), a member survey conducted in 2023 found that “labour shortages, and the rising cost of materials, energy and labour remain high on the agenda for the welding industry. Without funding and support from governments at all levels, these challenges will make it nearly impossible for industry to deliver the necessary manufacturing capability required for the Federal Government’s ambitious renewable energy revolution.”
Novarc Technologies Inc.'s flagship product is the Spool Welding Robot (SWR™), the world’s first collaborative welding robot that automates the pipe welding process. The SWR works alongside a human welder to increase productivity, weld quality, and consistency, potentially recovering capital investment within six to 18 months.
Novarc recently launched a new computer vision and image processing system that fully automates the pipe welding process, called NovEye™ Autonomy (Gen 2).
With NovEye Autonomy (Gen 2), the SWR is armed with gamechanging software developed using years of Novarc’s data collection and deep learning. The software is embedded in the SWR's control system and controls the weld in exactly the same way a human welder would, allowing the boring, repetitive welds to be delegated to the robot.
NovEye Autonomy (Gen 2) delivers X-ray quality welds with zero operator intervention, maximising productivity and minimising errors. The autonomous welding process continuously improves through a terabyte-scale library of welding videos, ensuring unmatched precision and reliability.
NovEye Autonomy (Gen 2) uses live-stream video from the camera mounted on the SWR’s torch to analyse the scene and detect welding states. The AI then adjusts welding and motion parameters in real-time based on these detected states.
“This marks the beginning of a new era as we have developed the intelligence to automate the welding process fully,” says Soroush Karimzadeh, CEO of Novarc. “This accomplishment has resulted from years of data collected through machine learning, and we are extremely excited to be able to offer this solution to the industry.”
Novarc has been developing NovEye Autonomy (Gen 2) for several years, performing extensive internal and external tests to ensure all features perform properly and the weld quality meets ASME standards. The technology delivers a perfect root pass by controlling the weld and motion parameters against gaps, hi-lo, tacks, and outof-round pipe changes.
This development will have a positive impact on fabricators and contract manufacturers in Australia and New Zealand. They are held to strict standards to provide sophisticated welds for industries such as mining, energy, utilities, and manufacturing. All of these industries stand to benefit from the consistent, X-ray-quality welds that result from the engineering features and advanced AI provided by NovEye Autonomy (Gen 2).
NovEye Autonomy (Gen 2) can easily integrate into customers' existing manufacturing processes across a range of industries. The Spool Welding Robot with NovEye Autonomy (Gen 2) is designed with a very small footprint but a very long reach, enabling it to fit in almost all fabrication shops and ease the adoption of automation.
NovEye Autonomy (Gen 2) also dramatically reduces human exposure to all welding hazards, as it positions the operator several metres away from the welding arc and fumes. Operators can program the weld and observe the weld away from the arc, reducing the risk of exposure to dangerous fumes and radiant heat. Muscle fatigue is also reduced as the welding process is fully automated: ultimately, a win-win for the health/safety and job satisfaction of the welder and the productivity of the fabrication shop.
“NovEye Autonomy is truly hands-free welding. It can change welding parameters and torch manipulation in real-time, all based on the current joint geometry,” says Karimzadeh.
This is helping to solve the labour issue in the welding industry, as the prospect of working with a cobot attracts more young people into the profession and does not require the high level of skill that is currently mandatory.
“NovEye Autonomy (Gen 2) does not require the operator to be a highly skilled welder. After some basic training on how to operate the SWR, an operator can oversee equipment that can make X-ray quality welds in a fraction of the time, at a fraction of the cost to the fabrication shop,” said Karimzadeh.
Novarc’s technology solves the labour gap, which is particularly ominous in the welding industry. It allows less skilled welders to do more sophisticated welds, making welding more attractive to young people considering the profession.
“The welder just has to get the pipe fitted and on positioner, hit weld, and NovEye handles the rest,” adds Karimzadeh.
Novarc’s SWR is sold in Australia, New Zealand, North America, Europe, and the Middle East. novarchtech.com
Kemppi launches lightweight welding helmets with maximum breathing protection.
Leading international welding equipment manufacturer Kemppi has released its new Zeta Fresh Air welding and grinding helmets. The brand-new lightweight helmets have a respirator for maximum breathing protection, complete eye and face safety, and various additional features.
The Zeta Fresh Air helmets have a respirator for TH3-level breathing protection. The synergy between the helmet and powerful certified respirator stops 99.8% of harmful fumes, gases and particles to help keep the user safe. The helmets also deliver comprehensive face protection. Both the grinding and welding helmets are certified to AS/NZS 1716:2012. The best-in-class auto-darkening welding filter (ADF) provides maximum eye protection.
Although tough and robust, the new Zeta Fresh Air range of helmets is remarkably lightweight. The helmets’ lightweight design delivers maximum comfort and reduces neck fatigue. Plus, the helmets' narrow shape makes it easier to move around on-site or in the workshop.
All welding helmets in the Zeta Fresh Air series provide enhanced visibility. The welding models come with VISION+ technology for
an accurate view of the environment and a best-in-class autodarkening filter – a 2.5 DIN shade makes it easier to see bright colours and details when the arc is turned off. There are also grinding and surface-finishing Fresh Air helmets with a 200mm high viewing area and 180° viewing angle.
Each model in the Fresh Air range is specifically designed for onehand use. Well-placed buttons and controls are easy to reach and operate with one hand, allowing for no-nonsense usage.
The Zeta Fresh Air W201x helmet features integrated LED lights. These built-in automatic work lights increase safety while providing the best visibility for the task at hand. The blowing unit powers the lights and automatically turns off or on based on the ambient light. Alternatively, they can be easily controlled manually.
Users can choose from six helmet models within the range of welding and grinding helmets. For more information on the new Kemppi Zeta Fresh Air helmets, call Kemppi Australia on 02 8785 2000 or email sales.au@kemppi.com kemppi.com
Jason Allen sets the direction for ISCAR’s strategy in the coming years.
The latest ISCAR LOGIQUICK campaign has unveiled various new cutting tools, effectively replenishing the company's portfolio. ISCAR is known for prioritising innovation, so it comes as no surprise that these new products have piqued the interest of the metalworking community, including machine shops and other cutting tool manufacturers. The innovations span all aspects of the company's range, including turning, parting, hole-making, milling, threading, and tool holding. Along with these new developments, the campaign also introduces additional designs that improve and expand the existing families. There is also a particular emphasis on the digital component, which has become an integral part of tools for modern smart manufacturing.
In fact, LOGIQUICK sets the direction for ISCAR's strategy in the coming years. Our brief review aims to explore the benefits of some recently introduced products and reveal how they can boost the profitability of machining operations. At times, a newcomer might appear insignificant. However, even a seemingly minor change is strategically directed towards enhancing cutting performance to improve cost-effectiveness. According to ISCAR, this aspect is the heart, the essence of the entire product development process.
Following the market demands, the set of product families has been expanded using a traditional approach. For example, the SUMOCHAM self-centring drilling heads family, which falls within the diameter range of 4.0 to 32.9mm, has been enriched by introducing 0.1mm diameter increment sizes in addition to the initial 0.5mm increment. The cutting geometry of these heads is optimised for drilling steel and cast iron (ISO P and ISO K groups of application). This means that one head can replace two other types, reducing stock.
Another example is the CHATTERFREE solid carbide end mills (SCEM) family. These versatile tools are designed for machining steel, stainless steel, and hardened steel (ISO P, ISO M, and ISO H groups of application). They have been expanded with a variety of new corner radii.
Additionally, the T-SLOT family, a popular range of slot milling cutters with exchangeable solid carbide heads, has been expanded to include a new head diameter of 25mm. This upgrade lowers the minimum limit of the T-SLOT head diameter range. It is designed to accommodate a broader range of widths, making the heads highly efficient for milling narrow slots and grooves in various workpiece materials. (See Fig 1)
New developments in thread milling
ISCAR has expanded its family of solid carbide thread endmills by introducing new tools with an increased number of flutes (up to eight), significantly reducing machining time. A few words are worth mentioning about the new QUICK-M-THREAD family of milling cutters with triangular inserts (Fig.1) in the range of indexable threading products. These incorporate a step-release design concept that substantially reduces cutting forces, minimises bending load, and improves dynamic stability, thereby enhancing productivity. The new tools, both solid and indexable, are also equipped with an internal coolant supply option, which not only increases the cooling effect and lubricity during thread milling but also contributes to better chip flow and surface finish.
MULTI-MASTER's Headline
The MULTI-MASTER family of tools with exchangeable cutting heads has been ISCAR's flagship product for almost a quarter of a century. Despite its “considerable enough” age, innovation never stops within this versatile product line. The launch of the
LOGIQUICK campaign has introduced new developments, further expanding the popular family's application range. (See Fig 2)
One of the new products is a series of six-flute solid carbide heads intended for quick metal removal in roughing using the high feed milling (HFM) method (Fig.2). These heads have ramping and slotting capabilities and are suitable for machining hard steel and cast iron (up to HRC 65). They are available in diameters ranging from eight to 25mm. Another addition is represented by new three-flute heads designed explicitly for shallow drilling operations (with a depth of up to one head diameter). The heads seamlessly combine the highly efficient cutting geometry of LOGIQ-3-CHAM, another popular company product, with the MULTI-MASTER concept's exceptional robustness. This combination produces a highly productive drilling tool, primarily when using materials that produce short chips.
A new double-sided design featuring two pockets in one shank offers cost-effectiveness and sustainable utilisation of the shank material. The steel shank includes a central trough hole for internal coolant supply.
The concept of an “all-in-one” compact 90-degree indexable cutter suitable for various milling operations - for example, milling square shoulder, slot or complex contour, and drilling capabilities – is not new. Such a cutter excels in many machining applications, eliminating the need for specialised tools. However, the QUICK-DMILL (Fig.3), a new family of these cutters, features an innovative design that undoubtedly provides additional customer benefits. The family includes double-toothed right-hand cutters with two rectangular-shaped indexable carbide inserts. (See Fig 3)
Each insert has four cutting edges, and the QUICK-D-MILL design enables the insert to be used for central and peripheral cutting. This optimises insert utilisation, reduces the frequency of insert replacements, and lowers costs. The insert pocket's robust design incorporates a dovetail clamping mechanism, enhancing process reliability. While the cutter is characterised by one effective tooth during drilling, it boasts two effective teeth during milling, offering
a significant functional advantage. The new cutters are produced in an endmill design with a 16-25mm diameter range. The MULTIMASTER head configuration is also available within the same range, featuring an option for a pinpointed internal high-pressure coolant supply. Elevating the well-known to a higher level by infusing it with new quality - this phrase perfectly summarises the essence of the QUICK-D-MILL family.
The NEOITA - ISCAR Tool Adviser, a “hybrid expert” that suggests optimal tooling solutions for specific machining applications, has improved its online features. Regarding drilling processes, the recently introduced editing and comparison functions make it easier to challenge the NEOITA. This is done by adjusting the suggested cutting data and considering machine characteristics, batch sizes, and adaptation limitations. Consequently, this empowers engineers to choose the most suitable machining parameters. By simulating drilling cycles, customers can achieve the desired commercial result.
Also, NEOITA has been enhanced with a new smart AI feature, which allows NEOITA users to search for and access detailed material specifications, including metallurgical composition and common uses. The search results can then be incorporated into the NEOITA material library database or the customer's personal libraries if needed.
An attentive reader may have noticed that the core of our review pertains to rotating tools. Does this imply that turning, grooving, and parting applications are not included in the LOGIQUICK campaign? The answer is a resounding no. We will revisit ISCAR's innovations in the non-rotating cutting tool field (and tool holding, too), which warrants a separate analysis shortly. iscar.com
Mill materials yourself instead of buying expensive steel blanks.
A 130% price increase for a cast steel blank is a challenge for the Albstadt-based security engineers of Assa Abloy. The solution? Do it yourself—with a new machining strategy and tools from Gühring. The result? A 50% cost saving per component is not the only benefit for the company.
Whether it’s a cucumber in the supermarket or a steel component in an industrial company, war and a pandemic have made shopping expensive. Assa Abloy, a security technology manufacturer in Albstadt, also felt this. The company usually purchases the housing for its electric strikes from a steel precision casting manufacturer. But about three years ago, it increased its prices by 130%. “Suddenly, it was no longer economical for us to offer these products,” recalled Patrick Matysiak, Deputy Product Cell Manager at Assa Abloy. An alternative needed to be found. Can we reduce prices with cheaper injection moulding from China? Patrick Matysiak had a better idea: “I had a thought: Why don't we switch to free-cutting steel and machine the entire component in-house?"
The plan is clear: A new machining centre will be purchased, and a new machining strategy will be developed. “And, of course, I needed the right tools for this,” said Matysiak.
The fact that we were in very close contact with this customer for many years meant that it landed on my desk,” recalled Jürgen Knorr, a Gühring sales representative who advises Assa Abloy. "So, we looked together: What solutions can Gühring offer here?"
The considerations resulted in a complete offer with 24 different Gühring tools. Patrick Matysiak created the programming using a mix of CAD/CAM and a unique macro program. In this way, up to 346 components can be manufactured automatically without personnel, representing a runtime of around 92 hours. The offer is rounded off by quality monitoring using a 3D probe and a tool breakage check, which involves measuring the components during production, adjusting dimensions fully automatically and replacing worn-out tools with new sister tools. The concept was technically adapted on-site, and a sample component was produced. “We knew straight away that our solution was vastly less expensive –even compared to a cheap steel precision cast component from China,” confirmed Matysiak. “Of course, that made our decision easy.”
Gühring has access to an extensive range of standard tools for tool selection. “We put together the best tools for a process that works,” sums up Jürgen Knorr. Different solid carbide drills are used for pre-drilling, for instance, From the Gühring classic RT 100 U to a range of NC spotting drills and pilot drills to the ExclusiveLine micro-precision drill with a diameter of 1.8 mm. When it came to milling, the challenge was to cut the high machining volume as quickly as possible. This is no simple task, as the housing has several radii, which calls for a semi-wrap or even full wrap of the milling cutter. Due to thin-walled areas, clamping of the component is also tricky. This leads to vibrations during milling, which must be absorbed by the tool. The RF 100 Diver has proven particularly successful for applications that require a high degree of flexibility. The solid carbide milling cutter covers five operations with a single tool: Drilling, ramping, slotting, roughing and finishing. The RF 100 Diver scores points with a high metal removal rate and guarantees running smoothness and process stability despite high feed rates. And thanks to its special geometry, it even impresses under unstable conditions. This is because the unequal pitch reduces power consumption compared to conventional milling cutters and thus lowers vibrations.
With these high chip volumes, it is also important that chips are cut as short as possible and transported away safely. This is precisely where the strengths of the Gühring HR 500 high-performance reamer lie. It enables perfect reaming in all diameters from 1.97 to 150mm. It ensures absolute process reliability, significantly reduced process time and maximum tool lives. But a solution was also quickly found for work steps for which Gühring cannot provide a practical standard solution. The cross holes that needed to be drilled into the housing presented the machining experts with a challenge. Jürgen Knorr remembers: “Together, we had to tinker a little on an axis hole because this required a tool that met the high standards of tolerance and dimensional accuracy of the holes.” But here, too, a customer-specific special tool ensures a reliable process.
As the customer now mills the component from solid material, it is around 50% less expensive than buying in steel precision cast housing, including any rework. Regarding quality, the machined component is the clear leader, especially regarding surface precision, the product's dimensional accuracy, the holes' tolerances and, ultimately, product functionality. For the customer, this means that significantly fewer products are rejected during quality control. “We are better all around – not only in terms of costs but also in terms of quality,” concluded Matysiak.
The new solution is also better for the environment: The component no longer needs to be transported and shipped, as in-house production enables short transport routes. The Albstadt-based company is also independent of foreign markets and their pricing policies. “And in the event of changes, we can immediately intervene in the process and react flexibly,” said Matysiak. These successes also motivated the company to switch to machining for two other types of electric strike housing. At the moment, these are still made of metal powder injection moulding, but the chips will soon be flying on a second new machine. Gühring tools have already been ordered for this. guhring.com.au assaabloy.com
As ANCA celebrates 50 years of advancing tool manufacturing technology, Edmund Boland, General Manager of ANCA CNC Machines (Bayswater North, Australia), looks ahead five to ten years.
Just a person and a dog?
The old story about the factory of the future being populated by one human and a dog—the human’s role is limited to feeding the dog, while the dog is charged with keeping the person away from the machinery—will be close to reality for tool grinding.
At a minimum, said Boland, the entire production process will be linked digitally, “from the intake of the raw material to palletising, laser etching, and blank preparation…to the tool and cutter grinding, edge prep, coating, and right through to shipping the finished goods.” For example, when a particular job transitions from OD prep to the 5-axis grinders, the machines will automatically call up the correct program to finish grinding the tools. Everything will also be linked to a company’s ERP and MES system, providing “very good data analytics to help make the right decisions and improve your processes.”
Individual processes, such as OD grinding or stream finishing, are often highly automated once they’re set up. So, what will differ among thriving companies, as Boland sees it, is the degree to which those processes have been automated and the degree to which the transfer of material between stations has also been automated.
“A small to medium shop will probably have a person who’s physically moving and scanning, let’s say, a pallet from the OD machine to the five-axis machine. But digitally, the five-axis machine receives a file that says it’s getting these blanks, and it’s all tied in with the ERP system. The same thing would happen if they’re subcontracting the coating. Digitally, they’re sending that information to the coater, but somebody is manually moving tools from the five-axis to the shipping department. In a large shop, a robotised cart would make the physical moves.” That’s the case with ANCA’s Integrated Manufacturing Systems (AIMS).
Boland says the more automation a shop achieves, the more consistent its output quality and the more its workers can concentrate on solving isolated problems and improving the entire process, aided by AI. “Invariably, there will be tools that are out of tolerance. And someone will need to ask, ‘Why? What do we need to tweak? Is there an issue with one of the production steps? Is the program wrong?’”
Competitive companies will rely on relatively few highly skilled problem solvers. These people will, in turn, rely on the advanced training available at the ANCA Academy.
Boland also envisions a continuing role for skilled people to set up machines, though changes are also coming. “For example, technology like steady rests will have sensors and the ability to make automatic adjustments.”
“Automatic compensation to correct errors detected in-process is already a reality, and this capability will only improve,” Boland adds. For example, with today’s technology, if the machine loads a blank askew, the probe detects the error, and the grinding problem automatically adjusts to produce a satisfactory tool. But, “you still need to manually check the first piece, especially if it’s a new type of tool. After that, the system can take over. ‘First tool right’ is already our big mantra. You should be able to measure the first tool, and if wrong, be able to compensate.”
One contributing factor is the ever-increasing capability of internal measurement devices. Boland observes that their new generation lasers can measure in coolant mist and even some residual oil on the tool itself. Vision systems still require manual placement and removal after use, but “that will change.
Continued next page
Continued previous page
Camera systems require better ventilation than lasers, but there are solutions. A robot can blow out the debris from the environment within the machine right after grinding. Or you could use a robot to bring the camera into the machine from an external location.”
At the same time, the list of features that can be measured internally and automatically compensated will grow. Today, it’s “things like OD, tool profile, and flute depth. In a short time, we’ll be able to do more. The threads within a thread mill or a tap, for example. A K-land. Or the gash. It can be compensated as long as measured within the system.”
Boland doesn’t think we’ll eliminate the need for stand-alone measuring machines like the ZOLLER Genius, especially when measuring complex features. But he foresees improvements in the interplay between such systems and tool grinders.
The key, he explains, is the establishment of standardised measurement protocols for specific geometric features. “Until these measurement protocols are created, no tool grinder can compensate for a measured deviation. Currently, ANCA has a standard set of measurements available for simpler end mills and drills. But as we install AIMS throughout our customer base, we’re also working with these customers to expand the range of measurements we can compensate. We’re getting into quite complex profile tools, and complex end mills, for example.”
It’s no secret that tolerances are getting tighter. Boland says achieving micron, and even sub-micron, levels of precision will be the key to capturing many future applications. Demand for such accuracy “will grow because of the benefits of these cutting tools, whether it’s the surface finish of the workpiece that’s being machined, tool life, or other factors. Removing all the small inaccuracies within the cutting tool lifts its performance significantly.”
This is also why the market is moving toward solid round tools versus indexable cutters. “Customers want the rigidity of a solid round tool and the advantages of pushing the tool while achieving
an excellent surface finish,” reports Boland. Maintaining higher levels of precision will take more than the highly functioning automation, in-process measuring, and closed-loop compensation functions covered earlier. “Simple, though expensive, things like air conditioning,” lists Boland. “The coolant systems. The types of wheels you buy… It’s not just the tool and cutter grinder. It’s the whole system around it.
“Eliminating vibration is going to be critical. No longer will you be able to attach a mist extractor directly under the canopy. The air conditioning unit within a machine tool will become very important. Because if it vibrates, it will cause problems.” Thus, a central coolant system and central mist extraction are required.
Although Boland predicts a growing demand for ever more accurate tools, he also thinks there will continue to be demand for lowercost tools. That, plus the inherent cost and difficulty of meeting the tightest tolerances, will limit the adoption of the discussed improvements.
According to Boland, Carbide continues to be the dominant cutting tool material, but PCD use is growing faster. Thus, PCD may reach 30% of the market in 10 years. Ceramics are also getting more interest, but remain a small part.
Likewise, the need for material removal technologies other than grinding will grow. Boland says that wire and rotary EDM are now predominant for PCD, but laser ablation bears watching. “It is definitely an emerging technology. Customers with early machines are using them not only for PCD but also for carbide. In particular, micro tools are now seen as having the potential for laser ablation, and tool makers are getting interesting results.
“In terms of PCD, laser ablation has its advantages over erosion. It doesn't require coolant or consumable copper electrodes.” So, though the machines might remain 40-50% more expensive than competing technology, they might save money over time due to lower consumable costs. Laser ablation also can produce shapes
that can’t be created with erosion, including surface features. Conversely, it doesn’t make sense for fluting larger diameter tools. Boland remains uncertain of laser ablation’s near-term future being more than a niche solution.
Similarly, additive machining is not likely to replace more than a few material removal applications in the industry. And its applicability to the production of cutting tools appears to be limited. “I don’t see it becoming efficient enough in ten years. But potentially, it has a place in producing special tools, with otherwise impossible internal coolant channels and those kinds of things. It might also have a role in creating big, expensive, cutting tools. But even if it does take off, I don’t believe it will be accurate enough to eliminate the need for finish grinding.”
Other market considerations
Given the production efficiencies Boland envisions, you might expect regrinding to die. But not only will the automation solutions discussed earlier also apply to regrinding, Boland surmises that sustainability concerns will continue to make it a viable business. At the same time, the greater efficiencies achieved by forward leaning tool producers will create expectations in the market for faster turnaround times, even for small quantities of special tools. Boland said, “the ability to easily produce optimised special tools for a specific job is what will be important to our customers.”
Unsurprisingly, the move to electric vehicles reduces cutting tool demand in the automotive sector by as much as 50%. This varies around the globe, with the US lagging in EV adoption. There are also “growing applications outside of the EV area which might be compensating,” Boland states, though the total impact of EVs will undeniably be large.
“And then there’s the question of where the technology will land.
But it’s almost a philosophical discussion rather than a factual one. Will hydrogen take over? Will ultraclean fuel return and give the combustion engine
Boland predicts that AI will “be a huge productivity improvement mechanism for the future,” partly because it contributes to accurate warning of component failures in advance. It can even automatically order the replacement part. Thus, preventative maintenance becomes targeted and efficient while ensuring nearly seamless uptime.
Conversely, Boland points out that multi-machine automation makes any downtime intolerable. “Customers can live without a single machine for a day or two. But if a fully automated system is not up within a few hours, that’s a big problem. So, responding rapidly and around the clock will be important. Different technologies will allow that.” This includes remote and predictive diagnostics “to reduce the necessity of having a service person on site.”
Whatever the future holds, it’s sure to be interesting. And if Boland turns out to be wrong about anything, you can always count on your dog. anca.com
Precise manufacturing in the construction industry: A journey to efficiency, quality, and safety with TRUMPF Technology.
Blade Pile, a top supplier of screw piles for Australia’s residential construction, began in 2007 in Southeast Queensland, producing locally at their Burleigh Heads factory and have since grown steadily. The management team realised that their traditional fabrication processes incurred high costs and challenged their competitive advantage. In 2022, Blade Pile recognised the opportunity to automate its production processes in its new purpose-built Yatala site using a TRUMPF TruLaser Tube 5000, automated material handling, and robotic welding.
The Blade Pile Group manufactures, supplies, and installs a wide array of steel piles and piling accessories for the construction industry throughout Australia and New Zealand. Blade Pile is recognised as a leader in residential piling products and foundation systems. Our technical innovation and inventive approach to piling has provided our customers with a range of industry-leading products alongside our network of engineering and installation support services.
Blade Pile encountered a pressing challenge: to differentiate their product in the market and control costs. Robotic welding was part of the solution. Robotic welding provides consistent welding results with a consistent throughput and little risk, thus reducing production costs. However, it has tighter tolerance requirements than manual welding, which cannot be achieved with a traditional bandsaw pipe-cutting process. Also, bandsaw and notching machines do not give the flexibility to continually optimise product design or differentiate them in the market via product labelling or marking. The final challenge was to minimise materials handling costs. An integrated materials handling solution was needed.
In summary, Blade Pile needed to solve the following challenges:
• Cut pipe to length within the tight tolerances needed by robotic welding.
• Have a flexible solution that can enable continuous product development.
• Mark and label their parts to make them visually differentiated in the market.
• Develop an integrated materials handling solution.
The solution
Zak identified tube laser cutting as the solution to his main challenge of cutting the pipe to the required tolerance. He had observed that the international brands he admires have invested in TRUMPF technologies. He felt that if TRUMPF was their partner of choice, TRUMPF would not let BladePile down. He found Headland Technology to be TRUMPF’s exclusive agent in Australia. Subsequently, Zak connected with Tim Stoddard, the Queensland sales manager based in the Brisbane office. The consultation process narrowed down to a TRUMPF TruLaser Tube 5000 (Fiber) as the suitable technology solution. Headland also collaborated with AMM Engineering and AKA Electrical & Automation to develop an automated unloading solution and configured the machine to provide the required control signals to the unloading robot.
Tim coordinated a visit to a valued customer who had already invested in a TRUMPF TruLaser Tube 5000 (Fiber) and achieved significant success with it. Witnessing the customer’s production first-hand, Zak knew he had selected the right machine technology and a brand that perfectly suited Blade Pile’s needs.
The installation of the TruLaser 5000 (Fiber) at Blade Pile was a smooth process organised by Headland’s project management office with expert service provided by Headland and TRUMPF technicians. The technicians installed and commissioned the machine and provided the necessary operator and software training. Headland and TRUMPF continued to support Blade Pile through the commissioning process for the unloading robot. This solution was innovative, and the team worked to establish communication between the laser and the robot. The communication proved to make ongoing programming and optimisation of the robot unloading system very straightforward.
Zak Plotkin enthusiastically shares that Blade Pile has witnessed remarkable improvements across various fronts giving them a competitive advantage in their industry. The streamlined process
has significantly boosted productivity and efficiency and will enable Blade Pile to scale easily with future increases in demand. Furthermore, employee satisfaction and engagement levels have soared, reflecting a positive work environment. Notably, the quality of their output has experienced a substantial enhancement, impressing visitors, potential clients, and their staff alike.
A visible sense of excitement resonates among the team members as they eagerly embrace the opportunity to work in a world-class fabrication process. Safety has also undergone a transformative shift, thanks to the robust safety features embedded in the TRUMPF TruLaser 5000 (Fiber), which provides a profound sense of peace of mind. Compared to operating the old band saws.
Their investments in technology have enabled Blade Pile to secure a contract with a prominent National account with stringent regulatory requirements. The repeatable quality that automated processes enable gave this customer that Blade Pile is the partner they could trust. While the construction industry remains largely traditional, Blade Pile now stands out by using cutting-edge machinery such as the TRUMPF TruLaser 5000 (Fiber) and modern automation.
Blade Pile’s investment in technology enabled them to overcome their challenges with the following outcomes successfully:
• Accurate cutting of tube to within +/-0.1mm in length.
• Ability to continuously improve their design using powerful offline programming software.
• Mark the parts with Blade Pile branding and individual part information.
• Automatically unload the machine with a robot and pack finished parts into stillages prepared for robotic welding.
“My experience with Headland Technology has been great,” said Zak Plotkin. “They have deep expertise and are committed to promptly solving any issues. Working with them feels like getting top-notch service directly from the manufacturer. I am very happy with Headland’s support, which ensures smooth operation and handles any challenges with professionalism and skill.”
Regarding Blade Pile’s future, Zak stated that they aim to expand from their current eight to 12-hour production schedule to a roundthe-clock operation within the next five years and may add another TRUMPF machine. bladepile.com.au headland.au
First was coal and steam power, then secondly came electricity, and followed by digital automation. We now approach Industry 4.0, the era of increased human-to-machine interaction, intelligent computers, and AI. By Jovia Prem.
Each such industrial revolution symbolised a significant development in the manufacturing world. Industry 1.0 represented the introduction of machinery usage in the manufacturing industry. This allowed for faster, more efficient production. Next was Industry 2.0, extending upon machine use, now utilising electric features. Industry 3.0, also known as the digital revolution, started delving into a more widespread use of digital logic. The third revolution introduced computers, microprocessors, and the Internet to manufacturing. Now, Industry 4.0 is extending on the findings of Industry 3.0, except now entering the realm of artificial intelligence. 4IR has extended on the Third Industrial Revolution in four main ways – connectivity and computational power, advanced engineering, human-machine interaction, and analytics and intelligence. By combining the enhancement of these four aspects, Industry 4.0 thrived beyond what was previously imaginable.
There are nine key pillars of Industry 4.0 technology. Big Data and analytics, horizontal and vertical integration, cloud computing, augmented reality, Industrial Internet of Things (IIoT), additive manufacturing 3D printing, autonomous robots, simulation or digital twins and cybersecurity.
These main pillars support Industry 4.0, and implementing even one of them in your company can be a game-changer in the efficiency of your work, the energy you use, and the quality of your services. Industry 4.0 itself is the way to go.
Unfortunately, as often happens with major changes, many companies have struggled to grasp the full potential of Industry 4.0. To lead the way in adapting to this new development in manufacturing, the Global Lighthouse Network was launched in 2018. This network identified companies already well-acquainted with the concepts and advances in 4IR and then displayed these sites as a benchmark for Industry 4.0 implementors. These lighthouses were also preferred by companies that run sustainable practices. Many lighthouses aim to mix competition in the business world with sustainable practices. This aim to be sustainable typically stems from the understanding of waste and other harm formed in production; however, the outcome of this realisation can look very different across different companies. While some companies may still be getting to a point where they can mix sustainability with outcomes, certain companies have already been practising forms of sustainability. More than half of the lighthouses consider sustainability one of their main reasons for incorporating 4IR.
4IR has many advantages of its own. Industry 4.0 allows for easier access for businesses, consumers, and any other stakeholders. Especially in this period of post-pandemic recovery, the ability to work without much physical contact would be very beneficial.
As of December 2023, the Global Lighthouse Networks consists of 153 lighthouses spread out globally. Unfortunately, none of these lighthouses are from Australia. With the right support from the Government and an aspiration to be the leader in manufacturing, any business can be admitted to this prestigious global network. For your business to be considered informed enough about 4IR to be reckoned as a potential lighthouse, you would have had a significant, radical change in your company's innovation, considering the level of advancement of the industry or company. This means you have had a recognisable shift to 4IRpredominant technologies that prove your company is now in line with Industry 4.0.
Next, your business should find the best methods to employ when using enablers such as a clear 4IR strategy, capability-building, IIoT usage throughout your company, and agile use case development.
The final criterion is that your business should use Industry 4.0 platforms that utilise different 4IR technologies. The previous factors were requirements to become an ordinary lighthouse. However, if you aim to become a sustainability lighthouse, there are some more criteria you must also be concerned about.
Your business should have sustainability practised in multiple 4IR cases. This ensures that you are making a change in many places rather than a minor change in just one situation.
The technical application process.
Submit your application. Go to the Global Lighthouse Network Application and submit your application. If you are considered to have the potential to be a lighthouse, the next stage will be a site visit. The Global Lighthouse Network team will contact you to schedule a date for a full-day site visit, whether physically or virtually. This will allow them to see your integration of 4IR at work. During the site visit, interviews will also be held with key staff.
After the site visit, the Global Lighthouse Network team will refine the list of nominees. The finalised new lighthouses of the year will be announced at a World Economic Forum event.
Becoming a lighthouse can give your business a serious boost. Not only would you be recognised as one of the few lighthouses in the world, but you would be one of, if not the only, lighthouses from Australia. Furthermore, implementing 4IR technologies will generally enhance the efficiency and quality of your company, making tasks and productivity much easier to achieve.
If you are interested in submitting your business to become a lighthouse, be prepared for Wave 14, which will be held in December 2024. The applications will open on the website [Become a Lighthouse | Global Lighthouse Network [weforum.org]].
Results may take six months.
astonprecision.com weforum.org
Another inspirational success in design, development and manufacturing.
Auckland-based KANDO Innovation, headed by Keith Blenkinsopp, is a New Zealand manufacturing company that inspires innovation and success through world-leading design and technology. This has led to major export sales in the competitive international markets of America and Europe.
KANDO Innovation began with the drive and objective of making New Zealand and international markets safer, more efficient, and more confident, leading to a safer workplace by developing and implementing the latest technology. Leveraging the latest in engineering, automation, machining, vision technologies and more, the idea was to maximise competitive advantage whilst meeting the challenges of safety, skilled labour shortages and minimising downtime and wastage in the industry.
Advanced Okuma CNC machines and robotics today play an essential part in this strategy, with the first Okuma machine purchased in 2019 and now with an additional four machines following the Okuma Monozukuri philosophy in “The Art of Making Things Better”. KANDO’s Managing Director Keith Blenkinsopp commented, “The investment in Okuma is always the first we look at due to design, unparalleled service, robustness, precision and user-friendly programming.”
KANDO Innovation is the home of the Guardian Bandsaw and the world’s first and only automated mussel opener, each developed with engineers working closely with industry leaders on innovative ways to automate and improve repetitive manual and potentially dangerous processes. The Guardian Bandsaws are manufactured in various sizes to meet the market demand in the meat industry and supermarket butcheries. These machines incorporate worldleading safety technology to keep workers safe.
Today, the company employs more than eighty personnel, plus ten in the USA, and has an in-house design team of twenty covering disciplines such as software, mechanical, electrical, and industrial design. KANDO has a positive approach to training, with five apprentices under training in machining, fabrication, and assembly operations.
The latest innovation from the KANDO design team is a meat membrane skinner designed for the meat industry. It incorporates world-leading safety vision technology and is about to be released. The industry will welcome this advanced machine due to its safety features and innovative technology.
With exports already a significant part of its manufacturing output, KANDO Innovation is poised for further major expansion. It has geared up to be ready for the rapid uptake of its tested and proven Guardian Brand Bandsaws and the latest membrane skinner machine, with advanced orders from the USA and new markets opening up in Europe.
“Once we build and install the systems and technologies for our clients, the same team that was first engaged with the customer to capture and incorporate the lessons for success are involved in the installation, training and ongoing service and support,” said Keith Blenkinsopp.
Newly appointed Okuma New Zealand Manager Karl Medley said, “This is a proud and innovative Okuma machining shop that will be a pleasure to work closely with in further developments following the amazing work of my predecessor.”
okumaaustralia.com.au okuma.nz kandoinnovation.com
Australia’s most versatile saw and knife manufacturing company.
Henry Bros Saws Australia started out very small, with the family company name dating back to the 1950s.
In 1964, the Henry family started a hardware store in Vineyard, NSW. They also built a small sawmill named Henry Bros & Co. to supply Vineyard Hardware with its structural and fencing timbers. As time went on, the sawmill expanded its operations into joinery and window manufacturing. This included the production of mouldings, architraves, axe, pick, and shovel handles, steam-bent chair backs, and sulky/gig shafts for the trotting industry.
As timber production grew, the need for in-house sharpening and the manufacture of specialised tooling became apparent. In 1978, the first piece of machinery was purchased to service their 60-inch recut bandsaw.
In 1982, Henry Bros & Co started taking on contract bandsaw sharpening for other timber yards in Sydney. Over time, the saw shop expanded its capacity to tungsten carbide circular saws, knife grinding, and profile grinding, which led to even more outside sharpening from joinery/cabinet makers, frame and truss manufacturers, pallet makers, box and crate manufacturers, etc. Eventually, Henry Bros & Co. took over the timber production side of the business due to the need for log supply issues.
In 1998, Henry Bros & Co. started a new company called Henry Bros Saws to reflect the nature of its business more accurately, but it still retained the connection to the family name.
In the 2000s, Henry Bros expanded into state-of-the-art CNC machinery for sharpening satellite-tipped bandsaws, TCT circular saws, knives and router bits.
Henry Bros was the first company to purchase and introduce Stellite tipping equipment to produce stellite bandsaws to the timber industry, dramatically improving their performance and efficiency.
Due to the demand from the industry, they expanded even further into the metal industry with the supply of specialised bi-metal and TCT bandsaws, HSS circular saws, and annular cutters, to name a few products.
Since 2000, in the last eight years, they upgraded their equipment to the latest CNC machines available worldwide, all from Germany, Italy, France and Switzerland. They now service and manufacture saws and machine knives for timber, metal, plastic, food and textile industries. See more detail below:
We supply and service carbon, bi-metal, carbide tipped, and stellite tipped bandsaws up to 260mm wide, TCT circular saws, router bits, compression and spiral bits, planner blade knives, profile knives and profile heads to your design, square chisel and chain mortise equipment, Insertable TCT turnover tips for spiral heads and routers.
Bi-metal and carbide-tipped bandsaws, HSS circular saws, annular cutters, drills, up to 4500mt knife grinding capacity for the manufacture and servicing of metal guillotine knives, granulator knives, chipper knives, surface grinding, aluminium cutting and dry cut metal cutting saws.
Specialised TCT circular saws, band knives, including straight, wavy, and scalloped-edge bandsaws, circular slitting knives for plastic, foam, and food, hydraulic hose cutters, mincing heads and knives, and meat and fish bandsaws.
Henry Bros Saws Australia is a worldwide known and respected company in the saw and knife industry for its innovations and design of products with the ability to step outside the square and develop new products with the help of its international partners. All of them are happy to work with us to create new cutting systems, especially with many new man-made and recycled products on the market, which in some cases are proving to be a challenge to cut. henrybrossaws.com.au
Structural steel has several advantages in construction, so it is increasingly used in the industry.
The first step is to finalise the design and architecture, which must align. This involves analysing the height, shape, layout, spacing, loads, forces, weight and resistance, including dead loads, live loads, wind resistance, water resistance and others. The design and architecture should withstand these forces without compromising the structure’s stability and safety.
Structural steel fabrication begins with good surface preparation. This includes thorough inspection for any existing defects, removal of existing coatings and rust, cleaning and more to ensure it is ready for the next step of fabrication.
The next step is to cut and shape steel into the desired shape using different types of saws, shears, cutters, plasma torches, and punches. You may also need custom machining if you require custom components for a project.
Bending involves deforming steel to create the desired shape. In contrast, drilling creates holes of specific diameters to accommodate the attachment of different components using screws, bolts and other types of fasteners.
The material is now ready for welding and assembly. Everything is re-checked once again to make sure it fits together. Welding then joins different components as they are assembled into one or multiple structures.
Metal finishes will depend on the nature of the project, but some options include powder coating, galvanising, painting and priming. Factors influencing the finish include weather conditions, budget, aesthetics, and project specs.
Quality control measures in metal fabrication ensure all fabricated components meet project specifications and industry standards. It includes inspections, testing, safety processes and more to guarantee the structural integrity of the final product.
Once everything meets quality control checks, the components will be prepared for shipping and transportation to the final site. This is done swiftly and effectively, making it easy to finish assembling onsite.
The construction crew then assembles the finished product where prefabricated structures and components are joined together in alignment with the project requirements.
Prioritising safety is crucial to reduce the risk of injuries and accidents, not just to create a safe work environment but also to ensure structural integrity for those using the final product.
Only professionals with proper training and qualifications can do the job to ensure that structural steel components are strong and durable. A proper understanding of compliance requirements and regulations is crucial to ensure the safety of workers onsite and future users. Modern innovations defy the boundaries of what’s possible in structural steel fabrication.
Conclusion
Whether you’re commissioning a construction project or an engineer planning the design, it’s important to consider who can help you with structural steel fabrication in Sydney. At Prime Fabrication, we’ll work with you to ensure your project sees a successful outcome. primefabrication.com.au
Advancing the Triad of AI, Data, and Simulation.
In the dynamic realm of aerospace and defence- where precision, reliability, and innovation reign supreme - the convergence of cutting-edge technologies is redefining the landscape. Among these technologies, 3D printing is a transformative force that revolutionises how complex components are created. However, the true potential of 3D printing is unleashed when it is coupled with AI, data analytics, and simulation. This triad is propelling these industries into a new era of efficiency and adaptability.
The evolution of 3D printing: From novelty to precision crafting
The journey of 3D printing from being a mere novelty item creator to a powerful tool for crafting intricate aerospace and defence components has been remarkable. With the advent of Industry 4.0 and the digitisation of manufacturing processes, 3D printing has transformed into a data-driven phenomenon. This transformation has empowered 3D printers to gather extensive information about the fabrication process, creating a wealth of data that becomes the bedrock for further innovation.
The crucial role of data in data-driven 3D printing
At the heart of data-driven 3D printing lies the immense treasure trove of information that is collected during the fabrication process. Smart 3D printers, interlinked with digital repositories of existing components, can discern the ideal candidates for additive manufacturing techniques. By analysing historical data and patterns, these printers can not only optimise the manufacturing process but also predict potential pitfalls.
In the aerospace and defence industry, where precision and reliability are non-negotiable, the ability to ensure the quality of each printed component is paramount. AI algorithms, fed with the wealth of data gathered during fabrication, become vigilant sentinels. They meticulously inspect components as they materialise, identifying anomalies and ensuring the highest quality standards. The synergy of data and AI expedites production and serves as an insurance against faulty parts, contributing to the industry's uncompromising safety standards.
AI's empowering touch on 3D printing
Artificial intelligence adds a layer of intelligence to 3D printing that extends beyond quality assurance. It empowers 3D printers to make autonomous decisions, optimising the manufacturing process for performance, cost, and time constraints. These AIdriven decisions are not merely reactive but proactive, adapting to real-time challenges and dynamically adjusting printing parameters to ensure optimal outcomes.
Simulation: The virtual playground for innovation
Simulation is the bridge that connects data and AI in 3D printing. It enables engineers and designers to virtually test their creations in a controlled environment, making informed decisions before physical production even begins. In the aerospace and defence industry, where precision and reliability are typically tested repeatedly through many different iterations, simulation is a game-changer.
Simulation is particularly impactful in the context of composite materials, which play a crucial role in aerospace and defence applications due to their lightweight and durable nature. It allows designers to experiment with various composite material combinations, structures, and manufacturing methods, predicting how these variations will affect performance under different conditions. By optimising the design through simulation, engineers can avoid costly iterations and streamline the path from concept to reality.
The unprecedented benefits for aerospace and defence
The amalgamation of AI, data analytics, and simulation catapults 3D printing to new heights in the aerospace and defence industries.
The ability to predict and prevent defects through data analysis, coupled with AI-driven decision-making, minimises risks and ensures consistency in production. Conversely, simulation paves the way for innovation, allowing designers to push the boundaries of what's possible while maintaining rigorous quality standards.
This triad of technologies presents a silver lining for aerospace and defence supply chains, notorious for their vulnerability to disruptions. Real-time data acquisition and analysis ensure that supply chains can swiftly adapt to unforeseen disruptions, offering a buffer against the unpredictability that often plagues these industries. With the capability to simulate and optimise designs, engineers can accelerate the development of new components and adapt existing ones to changing requirements, facilitating agile responses to emerging challenges.
The future: Navigating uncharted skies with confidence
As the aerospace and defence industries continue their relentless pursuit of innovation and efficiency, the role of AI, data, and simulation in 3D printing is set to be a cornerstone of progress. From designing intricate components to ensuring their quality and performance, these technologies form a symbiotic ecosystem that enhances every facet of the manufacturing process.
The future envisions aerospace and defence manufacturers harnessing the power of AI to make data-informed decisions while simulation acts as a virtual playground for testing and refining designs. As this convergence gathers momentum, the aerospace and defence sectors will be well-equipped to navigate the challenges of an ever-evolving landscape, confident in their ability to create, adapt, and excel. Through the fusion of AI, data, and simulation, 3D printing emerges not just as a manufacturing technique, but as a catalyst for innovation, resilience, and progress in the aerospace and defense industries. alfex.com.au
iLAuNCH Trailblazer space camera takes a quantum leap.
The Australian defence and space industry is set to gain onshore manufacturing of new eye-in-the-sky technology. This space camera can provide images back to Earth at high speed to aid in disaster resilience operations, land management, and defence.
This multi-sensor Earth observation camera is now being developed with Leonardo, Spiral Blue, Nominal Systems and The Australian National University (ANU), brought together under an iLAuNCH Trailblazer project.
“This partnership will bring first mover advantage to Australian industry and ANU, which is set to deliver a commercially viable product for future satellites,” said iLAuNCH Trailblazer Executive Director, Darin Lovett.
“iLAuNCH is bringing together best-in-class technology that will help detect environmental changes, with translation opportunities to defence, including space domain awareness and missile guidance, and establishing an export market in partnership with Leonardo UK.”
• Leonardo has developed susceptible detectors for shortwave infrared, which can show heat on an image and see the earth's surface through clouds. However, this shortwave infrared technology has yet to be integrated into a full camera system for space applications.
• ANU has been developing its Rosella processor, the computer behind the detector that reads in the images and makes them available for other processing.
• Spiral Blue has developed an in-space computer tailored for edge processing AI and will integrate it against the ANU processor to capture and process imagery through refining AI, which enables more advanced processing capabilities.
• Nominal Systems helps make the integration of this space camera into a full satellite bus seamless by bringing their satellite hardware into the loop design tools. At the completion of the project, they can offer a fully integrated plug-and-play space camera.
• ANU will further qualify the hardware for spaceflight readiness and develop an optics assembly to create a ‘ready to fly’ space camera/telescope.
“This program is a great example of technology developed for a particular astronomy focused, problem which we can transition
to a wider market,” said ANU Professor Robert Sharp, Advanced Instrumentation Technology Centre.
The development and application of these technologies create a pathway to commercialisation for a space solution capable of remote imaging and high-speed data communication. Using AI software and laser communications support will increase the efficiency and accuracy of satellite imaging, leading to more excellent space observation capabilities.”
Once the project is in full production, the space-ready Rosella controller will operate Leonardo UK’s mercury-cadmium-telluride (MCT) shortwave infrared (SWIR) detectors on commercial satellites. Space qualification opens doors to a $4bn satellite Earth Observation (EO) market by 2025 and $2bn in space astronomy missions.
Directly interfacing Rosella with GPU-based AI platforms, such as Spiral Blue’s SpaceEdge hardware, enables automated processing and downlink of critical data at high speed in a low-bandwidth environment.
“Demonstrating the Spiral Blue product as part of a fully integrated turn-key sensor and data management system builds on existing commercial capability and fills a current gap in the market for small form factor value-added AI-assisted data product delivery,” said Spiral Blue, Founder Taofiq Huq.
The Rosella will also gain access to a global market and end-user base for an advanced space infrared detector package through Nominal System’s online vendor marketplace and digital twin platform for space missions.
“This program provides an opportunity to demonstrate Nominal Systems operational support and modelling framework within a powerful mission framework that is underrepresented internationally and unprecedented in Australia,” said Nominal Systems, Chief Technology Officer Brenton Smith.
Working on this industry-directed project will enable PhD graduates to transition directly into skilled jobs. This provides the optimal opportunity for exchanging and translating university research to industry through a direct pipeline. ilaunch.space anu.edu space.leonardo.com
Making smart manufacturing cyber secure. A thought-piece by industrial cybersecurity expert Leon Poggioli, ANZ Regional Director of cybersecurity firm Claroty.
The fourth industrial revolution, aka Industry 4.0, completely transformed the manufacturing industry by giving rise to highly sophisticated technologies and digital systems that have enabled manufacturers to enhance their productivity and reduce costs.
The result is ‘smart manufacturing,’ which brings enormous benefits in terms of increased automation, production efficiency, proactive maintenance, and the integration of administrative processes such as sales and inventory control with production processes.
But with increased connectivity comes increased risk. As manufacturers have connected their formerly isolated factory systems with their IT networks, it has become increasingly difficult for organisations to protect their systems against cyber-attacks.
Given that manufacturers have grown so highly dependent on digital technologies to meet their tight production deadlines, the risk of disruption and financial loss from a successful cyber-attack is massive. This, in turn, makes smart manufacturing facilities of every kind attractive and potentially lucrative targets for attackers.
It has been estimated that in 2023, there were 13 cyber-attacks every second on critical infrastructure worldwide, a 30% increase from 2022. These attacks can take many forms, with ransomware being one of the most common. KPMG expects to see a 15% year-on-year increase in ransomware attacks on Australian critical infrastructure providers over the next five years.
A ransomware attack on a manufacturing facility can cause financial and reputational damage, damage to the facility, and disruption to its processes, which can have serious safety consequences. Also, no manufacturing facility is truly isolated: it is one link in a long supply chain, relying on a steady flow of components and materials and, in many cases, supplying its output to other manufacturers. An attack on any link can disrupt the entire chain and potentially corrupt products further down the chain.
However, there are several challenges when creating and maintaining robust protection against cyber-attacks.
The challenge with protecting smart manufacturing systems
Firstly, cyber-physical systems (CPS) often use proprietary protocols and legacy operating systems incompatible with IT security tools. Cyber-physical systems rarely follow standard patching regimes in IT because these critical systems can’t afford the necessary downtime. In many cases, there is simply no patch available anyway.
There are also several organisational challenges: operational technology (OT), which includes cyber-physical systems, and IT, which are often managed by different teams with different skill sets and priorities. Security policies developed for IT systems are often inapplicable to OT systems, which, until recently, were largely isolated from the Internet. Fortunately, tools are available to integrate IT and OT security solutions. Their deployment can, in turn, lead to more effective collaboration between IT and OT teams, which can help improve the overall security of cyber-physical systems.
Below are some key steps manufacturers should take to improve security across their facilities:
1. Maintain a strong inventory of all connected
You can’t protect what you can’t see. Therefore, it is essential to maintain a complete inventory of all cyber-physical systems and ensure visibility over every individual component at any given time.
This can present a significant challenge, but one that can be made much easier by deploying a cyber-physical system protection platform. They can be tailored to suit the particular needs of individual organisations.
A strong vulnerability and risk management program is an essential part of any cybersecurity program. A good plan must first consider the security weaknesses of all components of a smart manufacturing system and then estimate the likelihood of these being compromised and, most importantly, the potential business impact of any compromise.
3. Segment the network
Proper OT network segmentation can stop attackers from moving laterally throughout the network. Manufacturers should only connect different components and subsystems of their facility if strictly required. By isolating networks where possible, manufacturers can greatly reduce the potential for adversaries to attack other parts of the network.
4. Automate threat detection
Every smart manufacturing system should be equipped with comprehensive threat detection technology capable of recognising cyber-attacks and neutralising them before damage can be done. Automated technologies can identify threats much faster than humans, reducing the likelihood of a successful attack and the reputational/financial damage that comes with it.
Remote access is essential for almost every smart manufacturing system, enabling the rapid response and remediation of operational issues. But it also comes with the risk of an authorised user, deliberately or accidentally, initiating a change that disrupts normal operations. So, all manufacturers should limit remote access to those needing it and review these permissions regularly.
Smart manufacturing holds a crucial position in the global economy, driving technological progress, streamlining supply chains, and improving product quality, among other benefits. With Industry 4.0 leading the charge, the extensive advantages of digital transformation have become apparent. However, these benefits are increasingly overshadowed by cybersecurity risks, as cybercriminals continue to exploit the expanding attack surface. To overcome this, organisations in manufacturing and the wider critical infrastructure sector must understand the full extent of the challenges they face and adhere to best practices to maintain a resilient cybersecurity strategy. claroty.com
MathWorks accelerates the development of software-defined workflows in MedTech with NVIDIA.
MathWorks has announced an integration that makes MATLAB® available in the NVIDIA Holoscan platform. Medical device engineers can now accelerate the development and deployment of streaming data analysis and visualisation applications by wrapping existing MATLAB algorithms and functions into GPU-accelerated NVIDIA Holoscan operators for real-time data processing and inference. Medical device engineers must navigate complex, ever-evolving global regulations while keeping pace with rapid technological innovation using cutting-edge materials and electronics. These conflicting forces caused many devices to be near-obsolete shortly after reaching the market and fueled the emergence of Software as a Medical Device (SaMD). The International Medical Device Regulators Forum defines SaMD as “software intended to be used for one or more medical purposes that perform those purposes without being part of a hardware medical device.” To stay competitive in the market after deployment, the SaMD products require the capability to integrate additional software feature functionality over time, necessitating engineers to develop a software-defined workflow for their development.
“The medical technology industry is being transformed by artificial intelligence,” said David Niewolny, Director of Business Development for MedTech at NVIDIA. "By providing a seamless development experience for the growing MATLAB development community within NVIDIA’s medical-grade Holoscan platform, NVIDIA and Mathworks are accelerating AI-powered innovation in med tech.”
NVIDIA Holoscan is a sensor processing platform that streamlines the development and deployment of AI and high-performance computing applications for real-time insights. The platform helps bring the latest AI applications into clinical settings by providing fullstack infrastructure for scalable, software-defined streaming data processing at the edge. The MATLAB integration into Holoscan will help medical device engineers use existing built-in matrix operations and complex toolbox functions for image and signal processing, filtering, transforms, and deep learning algorithms. Implementing a Holoscan pipeline with MATLAB requires four steps: creating a MATLAB function, generating accelerated CUDA code using GPU Coder™, creating a Holoscan operator wrapper, and re-building the Holoscan application with a new MATLAB operator. This allows the creation of a completely functional, software-defined workflow for medical devices. Additional integrated verification and validation capabilities in MATLAB and Holoscan allow developed software-defined workflows to comply with industry regulations and standards, including IEC 62304.
“Engineers can now write MATLAB functions and execute them thousands of times faster with NVIDIA Holoscan,” said MathWorks’ Director of Product Marketing David Rich. “Our collaborations with industry leaders like NVIDIA are set to drive medical device innovation as millions of our customers seek to design, develop, and test their products while complying with industry regulations and standards.” mathworks.com
OnRobot and DCISIV Technologies bring off-the-shelf collaborative palletiser to Australia.
OnRobot, a world-leading turnkey provider for collaborative applications, has partnered with Queensland-based robotics and machine company DCISIV Technologies to introduce an off-theshelf collaborative palletised for SMEs in Australia. This industry-first solution offers same-day installation, requires no programming, and can be re-deployed within minutes. DCISIV Technologies is situated in Toowoomba, inland from Brisbane.
“OnRobot has successfully introduced end-of-arm tooling and sensors for robotic automation to the market by ensuring seamless integration with all major robot brands and providing a simplified and consistent user experience,” said James Taylor, Chief Commercial Officer for OnRobot. “With D:PLOY, we are taking the next logical step in simplifying the overall application rather than just focusing on individual components within the robot cell.”
Founded in 2018 in Denmark – more than two decades after the first collaborative robot (cobot) came onto the scene - OnRobot identified a need for quality cobot hardware. “With so many cobot manufacturers coming onto the scene, we recognised a need for a reputable manufacturer that could provide all the complementary physical hardware required.”
From two- and three-finger grippers to sanders, vacuums, polishers, vision sensors, and more, OnRobot provides solutions for various applications and tasks. “No matter the application or task, we have a solution.”
OnRobot continues to evolve with the market's ever-changing needs. “Our vision is to be the worldwide leader in collaborative applications,” added Taylor.
“And while we remain ever committed to developing and enhancing OnRobot’s hardware, our sights are set on transcending the norm to deliver a total solution. More than that, we want to make it simple for all producers or manufacturers to use robots by removing the barriers to entry: cost, complexity and inflexibility.”
The missing piece of the puzzle is D:PLOY by OnRobot, the industry’s first automated software platform for building, running, monitoring, and re-deploying collaborative applications.
“Our goal is to ensure that no matter what robots customers choose to use, they will always have a consistent OnRobot experience,” Taylor added. “We recognise the fact that the end-user has a desired outcome. They aren’t necessarily focused on the branding but rather on the required output. Their challenges are centred around time and cost –specifically when changing box sizes.”
According to Taylor, the ultimate peace of mind lies in D:PLOY’s same-day installation, changing an application or box size within minutes and the quick changeover of a production line. “This enables manufacturers to automate applications with robots that they have not been able to in the past due to the cost and time needed for production changeovers.”
“Today, for example, most palletising is done manually due to the high mix nature of production lines with one line often changing productions or box sizes. With D:PLOY, changeover can now be reduced to only a few minutes, which means automating tasks with robots is now achievable and affordable since the application cell can automate multiple palletising tasks.”
Other differentiators include its transparent, competitive pricing –which James Taylor believes hasn’t been seen in the market before. So, why Australia?
Regarding OnRobot’s investment in Australia, Taylor shares that many small to medium-sized manufacturers face workforce challenges and require a cost-effective solution for high-mix palletising applications.
“Australia is privy to high labour costs as well as labour shortages. As a developed country, the majority of the workforce isn’t interested in undertaking menial, strenuous labour tasks associated with palletising, and this is why a high-value proposition like that of D:PLOY will be well-received by the market.”
He shares that OnRobot’s partnership with DCISIV delivers a unique advantage to the local market. “We partner with local companies who can best serve the local market—this is our tried-and-trusted global model. DCISIV are the industry experts, and we are there to support them and their customer offering, which includes a flexible, quick-to-deploy, always available solution.”
Ben Leamon is Director of DCISIV. He believes the launch of PalletProX, in conjunction with OnRobot’s D:PLOY will reduce the barriers to entry – particularly for SMEs.
“We want automation to be accessible to companies of all sizes. The PalletProX is an entry-level system intended to help SMEs automate their palletising and protect their people by reducing the risk of back injuries,” he explained. “The system is designed with functionality and ease of installation, service and maintenance in mind. We’ve additionally made it flexible to accommodate multiple pallet sizes.”
Regarding the partnership, Leamon explains that OnRobot's support will ensure easy configuration, lowering the total cost of ownership by reducing the need for ongoing engineering support. “OnRobot has the resources to maintain and continually improve the software, and the customer is empowered to use the system flexibly.”
The PalletProX is an OMRON TM25 equipped with an OnRobot VGP20 gripper, OR:Base Controller and D:PLOY software license which will be sold at an introductory price of $114,540. It comes with a 12-month warranty, DCISIV Palletiser Base Dual Pallet with robot pedestal, training, installation and set-up.
“We are pleased to partner with DCISIV to bring cutting-edge, easily accessible technology to Australia. We believe it will be well received and is set to shake up the market as we know it, offering the first truly off-the-shelf cobot palletising solution for the region,” Taylor said.
OnRobot was founded in 2018 to break down automation barriers and bring the benefits of robotic automation to manufacturers of all sizes. As a leading provider of robotic end-of-arm tooling and solutions, they enhance automation with innovative no-code platforms, grippers, sensors, and tool changers. Their solutions and products integrate seamlessly with collaborative and light industrial robots, boosting flexibility and efficiency. They aim to simplify automation for all businesses, enabling quick deployment in assembly, material handling, packaging, and CNC machine tending, screw-driving, sanding and much more.
dcisiv.com.au onrobot.com
Preparing for mandatory climate-related financial reporting. Brendan Herriott is a Director of Sustainability at Commonwealth Bank.
Following other jurisdictions such as the UK and Singapore, the Australian Government has set out its proposed rollout of mandatory climate-related financial reporting. To help businesses navigate what's coming, we look at the requirements of the proposed reporting framework.
What needs to be reported?
Businesses will be required to make detailed disclosures regarding their governance, strategy, risk management, metrics and targets related to climate change, including but not limited to for example: Scope 1 and 2 emissions, expanding to Scope 3 (supply-chain) from the second year of reporting. The current and anticipated effects of climate-related risks and opportunities on the entity's financial position, financial performance, and cash flows.
Scenario analysis for the reporting entity, which is used to inform an assessment of the resilience of the entity's strategy and business model to climate-related changes. Assurance requirements will be phased in over time.
Where will it be reported?
Companies will need to include a sustainability report together with their financial report and both will need to be lodged with ASIC at the same time. Depending on the type of entity, the sustainability report may also need to be publicly available on an entity's website.
According to Nicky Landsbergen (Co-lead of the EY Sustainability Disclosure Hub) the proposed regulatory changes will extend to a significant number of Australian businesses across the economy. Nicky says that while many are implementing environmental, social and governance initiatives, far fewer have the reporting capabilities the mandatory regime will require.
"Australian businesses have been focussed on developing and implementing sustainability actions, but many lack the governance, risk management and reporting capabilities to support the reporting and assurance to comply with the upcoming
requirements," Nicky says. "An important first step for many businesses will be to conduct a gap assessment against the upcoming requirements in both internal processes and external disclosures across governance, strategy, risk management and metrics and targets. They will then need to develop an action plan to address gaps, which considers responsibilities and time horizons for reporting."
A driver of the new reporting requirements is the need for markets to efficiently allocate capital and invest in initiatives that support climate-related goals, according to Chris Williams, Executive General Manager Major Client Group, CBA.
He says CommBank has a range of sustainable finance products to support businesses, including the Business Green Loan, Green Building Tool for commercial property, and structured, sustainable finance products such as Sustainability-Linked Loans (SLL), which link the cost of borrowing to the client's performance against predefined sustainability targets.
"Customers see there is alignment between sustainable finance requirements and the basic foundations of the upcoming reporting requirements. We are working with clients on sustainable finance structures that support their business case for developing reporting capability early," Williams says. commbank.com.au
This article is intended to provide general information only and must not be relied upon as financial product advice. You should consider seeking independent advice before making any decision based on this information. The information in this article and any opinions, conclusions or recommendations are reasonably held or made, based on the information available at the time of its publication but no representation or warranty, either expressed or implied, is made or provided as to the accuracy, reliability or completeness of any statement made in this article.
This is not an exhaustive outline of the requirements under the Treasury Laws Amendment (Financial Market Infrastructure and Other Measures) Bill 2024, and there are also exemptions. The requirements may change before being passed into law. You should seek independent advice on how these requirements impact your business.
Credit provided by the Commonwealth Bank of Australia. SLL are only available to approved business customers and for business purposes only. Applications for finance are subject to the Bank’s eligibility and suitability criteria and normal credit
approval processes. T&Cs, rates, fees and charges are included in the loan offer and are subject to change.
EY Disclaimer: This communication provides general information which is current at the time of production. The information contained in this communication does not constitute advice and should not be relied on as such. Professional advice should be sought prior to any action being taken in reliance on any of the information. Ernst & Young disclaims all responsibility and liability (including, without limitation, for any direct or indirect or consequential costs, loss or damage or loss of profits) arising from anything done or omitted to be done by any party in reliance, whether wholly or partially, on any of the information. Any party that relies on the information does so at its own risk. Liability limited by a scheme approved under Professional Standards Legislation
© 2024 Commonwealth Bank of Australia
ABN 48 123 123 124 AFSL and Australian credit licence
234945
The quiet cost of borrowing. By Sharon
Grice and Nicholas Mirarchi at William Buck.
The Australian Government has legislated changes that tightened restrictions under the thin capitalisation provisions. In this article, we explore what this could mean for Australian manufacturers.
What is thin capitalisation?
Thin capitalisation rules aim to limit Australian debt deductions, such as loan interest, line fees or other borrowing costs. The overarching policy intends to avoid profit shifting by multinational entities through excess debt deductions in Australia.
For manufacturers, we see that these companies constantly grapple with thin capitalisation:
• Australian manufacturing companies that are expanding and have overseas subsidiaries
• Australian manufacturing companies that are foreign-owned and growing in the Australian market, or
• a combination of the above.
The thin capitalisation provisions are commonly triggered when one of the above entities has total debt deductions exceeding $2m in a tax year. If the total debt deductions of the company and all its associates for that year are below $2m, these rules do not apply.
Before the recent changes, our experience was that many Australian manufacturers relied upon a ‘safe harbour’ ratio test. This broadly allowed debt deductions to be deducted when the debt-to-equity ratio was 1.5:1 (60% of the entity’s Australian assets).
What changes were made to thin capitalisation?
From 1 July 2023, if that entity has debt deductions exceeding $2m, it can choose to apply one of the new threshold tests below to calculate the amount, if any, of the denied debt deduction.
1. The Fixed Ratio Test
2. The Group Ratio Test
3. The Third-Party Test
The changes also include the addition of a new integrity rule, which will apply to income years on or after 1 July 2024 if the debt finance arrangement was in place before 22 June 2023. Broadly, debt deductions must be directly linked to income-producing assets or activities; otherwise, the integrity rule will prevent the deduction of interest on non-income-producing debt.
The thin capitalisation rules now shift the focus for manufacturers to an earnings-based analysis, intended to replace the previous ‘safe harbour’ test.
For manufacturers using this test, we calculate 30% of their tax earnings (i.e., taxable income) before interest, taxes, depreciation, and amortisation (EBITDA). Any debt deductions exceeding this calculated limit are disallowed, with the option to carry forward denied debt deductions for up to 15 years.
While this new test may be clear and straightforward, we have found that manufacturers with slim margins or loss-makers have had debt deductions denied in full under this test. This is particularly so for manufacturers scaling up or using debt funding to expand new operations.
The group ratio test considers a multinational corporation's worldwide financial position. It limits net debt deductions by calculating a ratio of the worldwide group's net interest expense and tax EBITDA above, as found in the group's financial statements.
Unlike the fixed ratio test, denied debt deductions cannot be carried forward as part of this test. However, this test is a viable alternative to the Fixed Ratio Test for Australian manufacturers that are subsidiaries of large and sophisticated global groups. For example, if there is a high reliance on inputs or raw materials from related parties, that could impact margins and EBITDA.
This final test distinguishes between third-party and related-party debt. Under this test, only debt deductions attributable to external debt are allowed, while deductions associated with related-party debt are denied. For Australian manufacturers that are largely reliant upon external third-party debt finance, as opposed to related party finance, we find that this test would be most applicable if the thirdparty finance is secured against Australian real property or assets and is exclusively being used to fund the Australian business and ongoing investment. Ordinarily, even if third-party debt gives rise to debt deductions exceeding AU$2 million, the thin capitalisation provisions may still deny a deduction.
Under this test, there is also no provision for carrying forward denied debt deductions in this test. The application of the third-party debt test can become technical and requires expert input, as there are strict conditions to be met when analysing financing arrangements.
Manufacturing businesses demand a significant level of upfront capital investment in things such as plants, equipment and research and development. Critically, many manufacturers rely on debt finance as opposed to capital raising. For example, foreignowned manufacturers may depend upon the global financing of their overseas parent, whereas Australian manufacturers expanding overseas may rely upon a mix of third-party or related-party debt finance.
Characteristics of proactive debt funding strategies we see are:
1. Constantly reviewing whether it is aligned with the strategies and goals of the entity.
2. A sound understanding of how thin capitalisation applies to the optimum level of debt deductions.
3. An application of transfer pricing in relation to related party debt (inbound or outbound).
Proactively understanding the impact, if any, of thin capitalisation is also a great example of effective governance within your business. If you have a manufacturing business that relies on debt funding, consideration of thin capitalisation should be a part of your financial strategy and modelling. William Buck’s advisory team can discuss what thin capitalisation may mean for your business and work with you to add value to your strategic and financial decisions. williambuck.com
The largest and longest-running industrial trade show in the Western Hemisphere returned to Chicago, and AMTIL was there.
The International Manufacturing Technology Show (IMTS) in Chicago’s McCormick Place is one of the world’s largest tool/ manufacturing technology exhibitions, staged in September every two years. AMTIL’s new CEO, Lorraine Maxwell, flew across to hoist the Australian flag and support the large contingent of Australian exhibitors, accompanied by Anne Samuelsson, our Head of Sales. AMTIL had their stand in the International Association Pavilion. Our two travellers spent the week catching up with our many international colleagues, attending meetings and answering questions from worldwide delegates visiting the stand.
The AMTIL booth doubled as a base for the Australian delegates participating in the show each year and DIMAC, ANCA, John Hart (Agile Robotic Systems) and The Execution Factor were represented, among many others. “It’s so hard to describe the sheer scale of 100,000 people in one place with robotics, machine tools and technologies,” said Maxwell. “The logistics are mindblowing! Four exhibition halls and kilometres of exhibition space.”
Speaking with Ed Christopher, VP of Global Services at AMT (the Association for Manufacturing Technology), Lorraine reports there were 56kms of carpet laid for the show. That’s big.
AMTIL attended the International Associations meeting and the Global Statistics Managers meeting. Notable information provided by AMT - The Association For Manufacturing Technology included the points below:
Three separate agencies' 2024 GDP forecasts for the USA, predict growth rather than recession. The US Federal Reserve forecasts 2.1%, Oxford Economics predicts 2.6%, and ITR Economics predicts 1.1%.
The USA continues to see a growth trend for ‘personal consumption expenditure for durable goods’, while ‘durable manufacturing industrial production’ has softened and is sitting on a plateau. Employment related to both measures is flatlined. A survey of the value of US machinery, orders, and capability utilisation for durable goods manufacturing shows a downward trend.
COVID-related shutdowns and supply disruptions have shown the value of production close to the location of use, and we’re seeing environmental and political issues continue to highlight the importance of sovereign capability. In terms of government and private investment, three massive bills in the USA have provided direct funds to manufacturing. As a result, investment in data centres and factory construction have accelerated.
Since the pandemic, manufacturing technology uptake has increased massively, but 2024 has seen a slow start to investment. Labor issues, technological advancements, and costs have made automation more attractive. Interestingly, trade organisations worldwide are interested in the trends around Additive Manufacturing, which currently accounts for about a tenth of the global manufacturing market and is on a firm market growth trajectory.
Monash Innovation Labs opened its doors for another AMTIL ‘AI in Manufacturing’ event.
Many manufacturing projects involve artificial intelligence (AI), and AMTIL collaborated with Monash Innovation Labs once again recently. They invited AMTIL members to tour the facilities and network with the best minds in the business.
Prof. Adrian Neild, Director of the Monash Innovation Labs, presented on industry partnership opportunities. There were guided tours of the Makerspace, the Monash Deep Neuron display, Monash Automation, and Monash Smart Manufacturing with the digital twin systems, as demonstrated by Dr Keenan Granland.
To bookend the tours, there was a panel on the critical theme of the evening, ‘AI in Manufacturing, ’ moderated by Monash’s Michelle Willis, with Dr Yunlong Tang from Monash University, Dr Juxi Leitner of LYRO Robotics and Dr Ziejue Chen from CSIRO. Up for discussion were the current developments in AI that are most impactful to the Australian manufacturing sector.
Dr Ziejue Chen from CSIRO addressed the security concerns about the data being collected for the AI engine. “The collection can be from just one camera and collected on just one PC, which doesn’t have to be connected to the internet,” she described. “The data is the most important, and you don’t always have to push it to the Cloud.”
Dr Chen continued: “AI in manufacturing is considered quite different from pure computer science. Each project has various products to follow, and unique sensors are tracked to varying speeds in many situations,” she said, “and the AI algorithm should be seen as just a tool.”
In many Australian companies, the final inspection of a high number of tools being manufactured is a crucial step that must be completed on time. But the human eye and brain can become tired and miss blemishes. An audience member asked how an AI system can check 100,000 tools to ensure inspection is entirely correct at
the end of their manufacturing process. Once again, Dr Ziejue Chen had the answer. She said that Deep Learning is the application field of Computer Vision, and this scenario would be the perfect case with a fairly simple answer. Bringing computer vision (i.e., a camera) into this process saves all the angles from which a human would check the tools. The job would involve saving the best visuals of the tool from each angle. Dr Juxi Leitner is the roboticist in the room. He builds the robotics and installs and tests the AI API.
At the end of the tour, the panel, and the vibrant Q&A session, attendees had the chance to enjoy refreshments from not only the Secret Garden Eatery but also Monash’s own BrewLab, where samples of craft beers were available. monash.edu.au amtil.com.au
AMTIL’s corporate partners offer a selection of products and services that will benefit our members in their business. For any enquiries about our Corporate Partnerships, and how they can benefit you, contact Greg Chalker on 03 9800 3666 or email gchalker@amtil.com.au Our Partners. Our Members. Your Benefits.
AMTIL brought together around 250 members to celebrate the association’s 25th year, at a party up on the 89th floor of the Eureka Tower in Melbourne.
AMTIL’s 25th birthday was always going to be a big event. A party everyone would remember for a long time—one for the record books. Organised over several months, the occasion brought together AMTIL members to acknowledge the opportunities and business milestones of the last quarter century.
With an unrivalled view of the sun setting over the entire city of Melbourne, AMTIL members were served an array of beautifully presented hors d'oeuvres by a small army of impeccably dressed staff. The venue boasted floor-to-ceiling windows offering a breathtaking panoramic view of the city skyline, illuminated by a billion or so lights as night fell. Drinks flowed throughout the evening, and the live music provided by Rita Satch and her band, added to the party atmosphere. The main event of the evening was the awarding of trophies to
companies that had been members of AMTIL since the association's foundation. Many attendees flew in from interstate. Brigitte Stavar, the president of AMTIL, handed 22 representatives their large chrome medals.
On the occasion of his retirement, Shane Infanti gave his deep thanks and congratulations to the AMTIL team for such a great event and spoke of the association’s long history and his love for the people in the industry. “I was humbled by the attention and opportunity to see so many members in an excellent venue,” he said later. “It was a great evening.”
Incoming CEO Lorraine Maxwell was equally enthusiastic. “It was such a pleasure to meet so many of the legends of AMTIL, and I loved the warmth in the room and enthusiasm at coming together,” she said. amtil.com.au
AMTIL's founding members were recognised for being an active part of the association since its beginning in 1999.
They are as follows:
ACRA MACHINERY
ALFEX CNC AUSTRALIA
ANCA
APPLIED MACHINERY AUSTRALIA
BENSON MACHINES
DIMAC TOOLING
DMG MORI AUSTRALIA
GWB MACHINE TOOLS
HARE & FORBES
HEADLAND TECHNOLOGY
HG FARLEY LASERLAB AUSTRALIA
HI-TECH METROLOGY
IMTS MACHINERY
ISCAR AUSTRALIA
JOHN HART
KENNAMETAL AUSTRALIA
LASER 3D
LOVITT TECHNOLOGIES
MACHINERY FORUM (NSW)
MODERN TOOLS (VIC)
MTI QUALOS
MULTICAM SYSTEMS
NICHOL INDUSTRIES
OKUMA AUSTRALIA
POWER MACHINERY AUSTRALIA
PRECISION SPECIALTY TOOLING
RENISHAW OCEANIA
ROMHELD AUTOMATION
RON MACK MACHINERY
SANDVIK COROMANT
SECO TOOLS AUSTRALIA
SHEETMETAL MACHINERY AUSTRALIA
SUTTON TOOLS
TECHNI WATERJET
AMTIL would like to welcome the following companies who have signed up as new members of our association.
ANKA ENGINEERING & AUTOMATION
3/19 McLean Street BRUNSWICK WEST, VIC 3055 ankaeng.com.au
BAI COMMUNICATIONS
Level 10, Tower A, 799 Pacific Highway CHATSWOOD, NSW 2067 baicommunications.com
CORRECTIVE SERVICES NSW
Francis Greenway Correctional Complex
2 The Northern Road BERKSHIRE PARK, NSW 2765 dcj.nsw.gov.au
EXCISION PTY LTD
35 Peck Street
HAMILTON, VIC 3300 excision.com.au
GREEN ENERGY & CARBON MANAGEMENT
G2/109 Burwood Road HAWTHORN, VIC 3122 gecm.com.au
IGNITE HR & EMPLOYMENT LAW 58 Ferodale Road MEDOWIE, NSW 2318 ignitehr.com.au
MECHIO PTY LTD
P.O BOX 179
BURLEIGH HEADS, QLD 4220 mechio.com.au
NORD DRIVESYSTEMS
18 Stoney Way DERRIMUT, VIC 3026 nord.com
NOVARC TECHNOLOGIES
Unit 6, 1225 Keith Road East NT VANCOUVER, BC V7J1J3 CANADA novarctech.com
NVMS PTY LTD
Level 38, 71 Eagle Street, Riparian Plaza BRISBANE, QLD 4000 nvms.com.au
OSAAP AUSTRALIA 17 Jaybel Street
SALISBURY, QLD 4107 osaapaustralia.com.au
OPENIIOT 14-18 Hudson Avenue CASTLE HILL, NSW 2154 openiiot.com.au
SALVAGNINI AUSTRALIA PTY LTD 11A 29/31 Clarice Road BOX HILL SOUTH, VIC 3128 salvagninigroup.com
SEDIN TECHNOLOGIES PTY LTD
Level 19, 15 William Street MELBOURNE, VIC 3000 sedintechnologies.com
People we have a winner!! After a mad finish, it was fitting that Mad-Hawker is crowned AMTIL Footy Tipping Champion for season 2024… cue the exploding confetti cannons and balloons. One point separated WRXGuru from the top prize, with Tungaloy Australia rounding off in third place. There have been many highlights this season and for the most part some exciting footy was played. The Pies missed out on finals altogether after posting 13 wins, the Blues scraped in and the Hawks were super exciting and the team to watcgh in 2025. The semi finals dished out two thrillers (ol' boy Hinkley dished out some of his own as well). Thanks to all who participated, at the time of printing, we weren't sure who was going to the 'big dance', let's hope it lives up to the cracker of 2023 – good luck to both teans. Till next time… Sanchez
During the COVID-19 pandemic, many industry events world-wide were postponed, rescheduled or cancelled. Readers are advised to check with all event organisers for the latest information. For the latest international travel advice, please visit smartraveller.gov.au For more events, please visit amtil.com.au/events
EUROBLECH 2024
GERMANY, Hanover 22-25 October 2024 euroblech.com
WARSAW INDUSTRY WEEK
POLAND, Ptak 5-7 November 2024 industryweek.pl
JIMTOF 2024
JAPAN, Tokyo
5-10 November 2024 jimtof.org
ADVANCED DESIGN & MANUFACTURING EXPO
CANADA, Montreal
13-14 November 2024 admmontreal.com
FORMNEXT 2024
GERMANY, Frankfurt 19-22 November 2024 formnext.mesago.com/Frankfurt/
METAL MADRID
SPAIN, Madrid
20-21 November 2024 advancedmanufacturingmadrid.com
AI EXPO TOKYO – AUTUMN
JAPAN, Makuhari Messe 20-22 November 2024 nextech-week.jp
METALEX
THAILAND, Bangkok 20-25 November 2024 metalex.co.th
METEC INDIA
INDIA, Maharashtra 27-29 November 2024 metec-india.com
MANFACTURING INDONESIA
INDONESIA, Kemayoran 4-7 December 2024 manufacturingindonesia.com
SEMICON JAPAN
JAPAN, Tokyo
11-13 December 2024 expo.semi.org/japan2024/
STEELFAB
UAE, Sharjah
13-16 January 2025 steelfabme.com
SMART FACTORY EXPO
JAPAN, Tokyo
22-24 January 2025 cantonfair.net/event/13734-smart-factoryexpo
ATX WEST
USA, Anaheim 4-6 February 2025 imengineeringwest.com/en/show/showbrands/atx-west.html
METEF
ITALY, Bolgna 5-7 March 2025 metef.com
PLAST IMAGEN
MEXICO, Mexico City 11-14 March 2025 plastimagen.com.mx
MACHINEERING
BELGIUM, Brussels 26-28 March 2025 machineering.eu
ADVANCED ENGINEERING
SWEDEN, Goteborg 2-3 April 2025 advancedengineeringgbg.se
STAINLESS
CZECH REPUBLIC, Prague 2-3 April 2025 stainless2025.com
INTERMOLD ASIA
JAPAN, Osaka 16-18 April 2025 intermold.jp
MADE IN STEEL
ITALY, Milan 9-11 May 2025 radonexhibition.eu/trade-shows/made-insteel/
EASTEC
USA, West Springfield 13-15 May 2025 easteconline.com
SCHWEISSEN & SCHNEIDEN ESSEN
GERMANY, Rhine-Westphalia 15-19 September 2025 schweissen-schneiden.com/joining-cuttingsurfacing/
EMO HANNOVER
GERMANY, Hannover 22-27 September 2025 emo-hannover.de
CMTS CA CANADA, Toronto 29 Sept – 2 Oct 2025 cmts.ca
ADVANCED DESIGN & MANUFACTURING EXPO
CANADA, Toronto 21-23 October 2025 admtoronto.com
2026
EUROGUSS
GERMANY, Nuremberg 13-15 January 2026 euroguss.de
KONEPAJA
FINLAND, Tampere 17-19 March 2026 konepajamessut.fi
INTERTOOL
AUSTRIA, Vienna April 2026 intertool.at
INTERPLAS
UK, Birmingham 2-4 June 2026 interplasuk.com
2027
NEWCAST
GERMANY, Dusseldorf 21-25 June 2027 newcast.de
WASTE EXPO AUSTRALIA
MELBOURNE CONVENTION & EXHIBITION CENTRE
23-24 OCTOBER 2024
Advancing best practices in waste management and making a positive difference to the environment and community. Opportunities to explore innovative material usage, enhance recovery processes, and minimise landfill waste. wasteexpoaustralia.com.au
INTERNATIONAL MINING & RESOURCES CONFERENCE & EXPO (IMARC)
ICC, SYDNEY
29-31 OCTOBER 2024
Delivering ideas, inspiration and serving as a meeting ground for mining leaders. Seven concurrent conferences with a program covering the entire mining value chain. Networking events, 20,000m2 expo show floor featuring 500+ leading companies. imarcglobal.com
AUSBIOTECH
MELBOURNE CONVENTION & EXHIBITION CENTRE
30 OCTOBER – 1 NOVEMBER 2024
For over 38 years, the AusBiotech conference has served as the leading international meeting place for the Australian life science community. Biotechnology continues to unlock vast potential for improving human life. Join us at AusBiotech 2024 in Melbourne for in-person networking, cutting edge programming and to advance our industry. It’s time to bring Australian life sciences to the world stage - exploring what’s possible across biotechnology, medical devices and agri-tech to heal and feed the world. ausbiotechnc.org
AUSRAIL
GOLD COAST CONVENTION & EXHIBITION CENTRE
25-27 NOVEMBER 2024
Connect with industry leaders and strengthen your brand position in the Australian and New Zealand Rail industry. ausrail.com/about-ausrail-2024/
WA MAJOR PROJECTS CONFERENCE PERTH CONVENTION & EXHIBITION CENTRE
19-20 MARCH 2025
The 14th Annual WA Major Projects Conference will take place on March 19 and 20, 2025 at the Perth Convention and Exhibition Centre. Attracting 250 delegates, the State’s premier major projects and infrastructure conference will provide a highlevel platform to discuss key projects and topics centred on WA’s infrastructure pipeline. expotradeglobal.com/events/ wamajorprojects
AVALON AIR SHOW
GEELONG, AVALON AIRPORT
INDUSTRY: 25-28 MARCH 2025
General Public: 28-30 March 2025
The major international event comprises of two sides:
AVALON – The Australian International Aerospace & Defence Exposition – a major trade exposition for Australia’s aviation, aerospace and defence industries.
AIRSHOW – The International Airshow – a three-day, action-packed public spectacular with breathtaking public flying displays and an amazing array of static aircraft to view up close. Together they form one of the most exciting attractions on the Australia tourism calendar.
airshow.com.au
Early in January 1947, I flew to New York. It was a ghastly trip in every way. I was flattened by nine years of solid work without a break, physically and mentally exhausted.
Iknew what I was going to tell Riley, but I wanted to hear what he had to say first. The plan trip across the Pacific was a nightmare. Shocking weather most of the way, and then engine trouble between Honolulu and Los Angeles forced us to turn back to Honolulu to get another plane. It was just as bad on the last hop. Los Angeles was fogged in, and we landed away at Palm Springs. The hotels were booked out, and to make matters worse, I had a skin complaint caused by a wog I'd picked up on that previous island-hopping trip across the Pacific.
Eventually, and almost as a cot case, I arrived in New York. And immediately I detected the first touch of acid. On every precious visit, there had been two or three senior people waiting to greet me; this time no one turned up.
Riley put the situation to me as soon as I saw him. "Larry," he said, "you've done a great job in Australia, there's no question of that, and we're grateful to you for it. But you have grown away from us and from our way of looking at things and doing things.
''General Motors has changed a lot in the time you've been in Australia, and you haven't been close enough to us to keep in tune with the changing set-up here. You've been in a top war job with a socialist government down there for six years and, we all agree, you've become too Australian in your thinking. We don't want that. We want you to get back into the General Motors team. We want you to come over here and work with us in New York." He reminded me that on my previous visit in 1944, when I had put forward the case
for the Australian car, he had suggested that I should work alongside him in the New York office. I had refused the offer then for two reasons: my war job was far from finished, and I didn't want to take my family away from Australia. (He had even suggested that I should leave my wife and children in Australia and go home to visit them once a year. That, of course, was totally unacceptable.)
"If you come back now you'll have a wonderful job here. You'll be right alongside me, and you'II be virtually the assistant general manager of GM Overseas Operations.''
"I can't do it, Ed," I told him. "I can't come to work in America without moving my family here, and I won't do that. I don't want to live in America. My home's in Australia. Another thing: you're forgetting that, as an Australian, I could get a visa to stay here only for six months."
"We could fix that," Riley said. "Why, you'd be taking your first papers out in a few months. You'd be an American citizen before you knew it." That did it! "That's the last thing I'd want to be, an American," I said.
"You people took me on in the first place because I was British. Now, because you reckon you've won the war, everybody's got to be an American. Well, include me out!"
I was as steamed up as I've ever been.
It was I who suggested we should part. "Look, Ed," I said, "there's only one way out of this, and that's for me to resign. To get right out of the whole show.''
"Well, that's a great pity, Larry. Say, you're tired and upset now. Why don't you sleep on it? We'll have another talk tomorrow.
We'll forget what's been said today and start afresh when you're feeling less tired and less het up. But I must tell you this, Larry: we can't have you out in Australia running things your own way and getting into fights with us here over things.”
"We know we've let you run things on your own for a long time. We've let you negotiate the whole of this car deal with the Australian Government, and you've done a terrific job towards making it a success. But that's as far as it goes. If you stay with us, you come to New York. And we can't shift from that."
I wouldn't shift either, so I resigned of my own free will.
Each night during my stay in New York, I telephoned Gladys, in Melbourne, to tell her of the day's developments. On the second night I asked her what she thought about the situation. ''Darling,'' she replied, ''Douglas Galbraith, your doctor, has been trying to tell you that you've gone beyond your point of endurance. You've taken a physical beating for the past six years, and so have I. If you went to work in New York you'd be dead within a year.Just let us go on living the way we should, the way we want to.
"We've got three girls at school, two of them just finishing. And just look at the GM men, and how they live-rushing all over the world all the time and when they go back to America, they are going home. But we are being asked to live permanently in a foreign land.''
If had had any doubts about my decision to resign, Glady's thoughts would have dispelled them.
To be continued…
As a market leader we are proud to support a professional organisation such as AMTIL and the AMT magazine. They have excellent reach and recognition in our industry and it provides a strong channel to our customers and our industry stakeholders.
DEAN McCARROLL, MANAGING DIRECTOR OKUMA AUSTRALIA + NEW ZEALAND
Turnkey machine integrations including delivery, commissioning, operator training & lifetime support.
Robust fabrication machines and spare parts that are designed to withstand harsh mining conditions.
Advanced machines with integrated safety features that comply with industry regulations and legislation.
Cutting-edge technology and efficient machines that will optimise production and improve quality control.
Reliable sourcing & inventory management to ensure a steady supply of machines, parts and consumables.