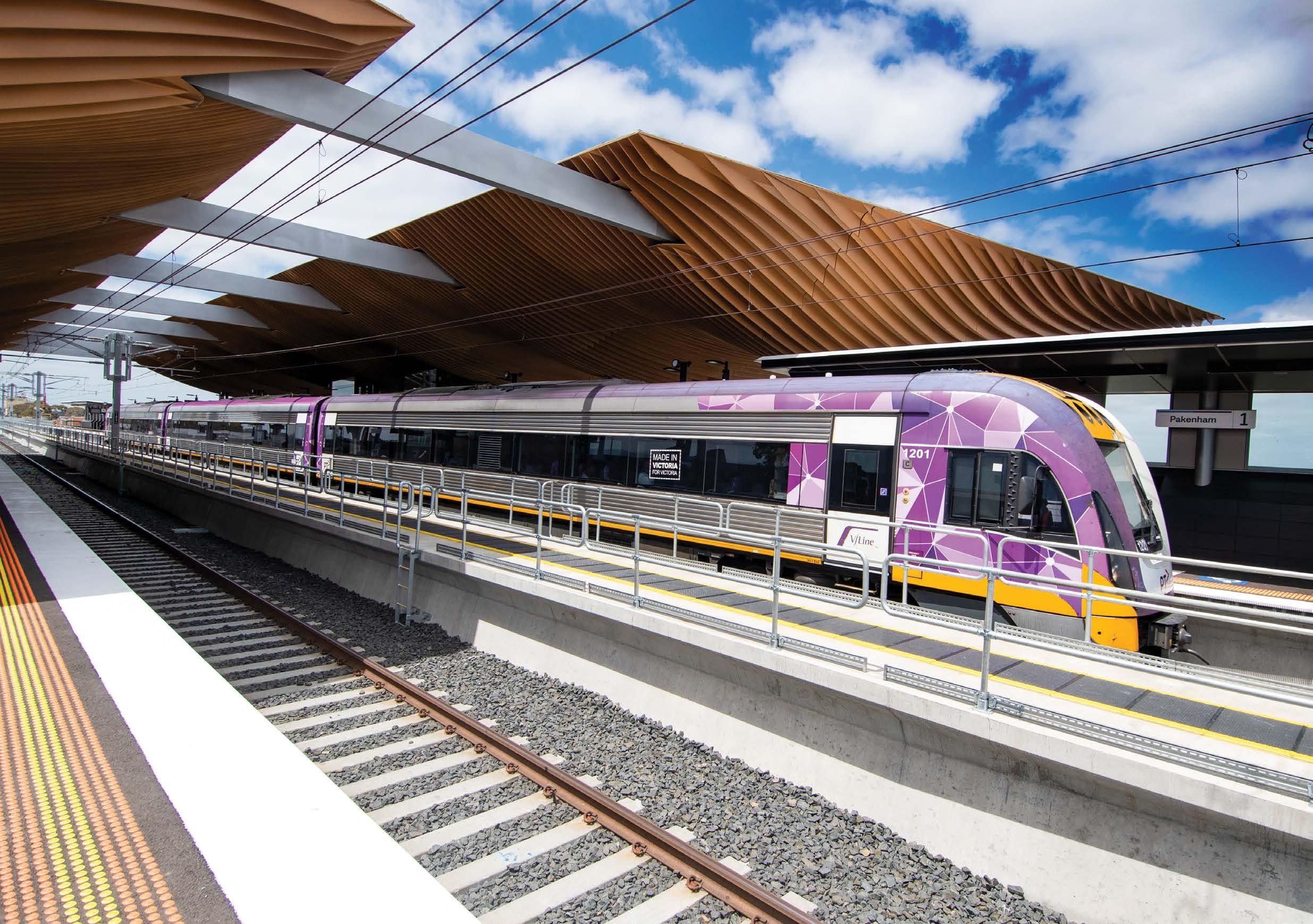
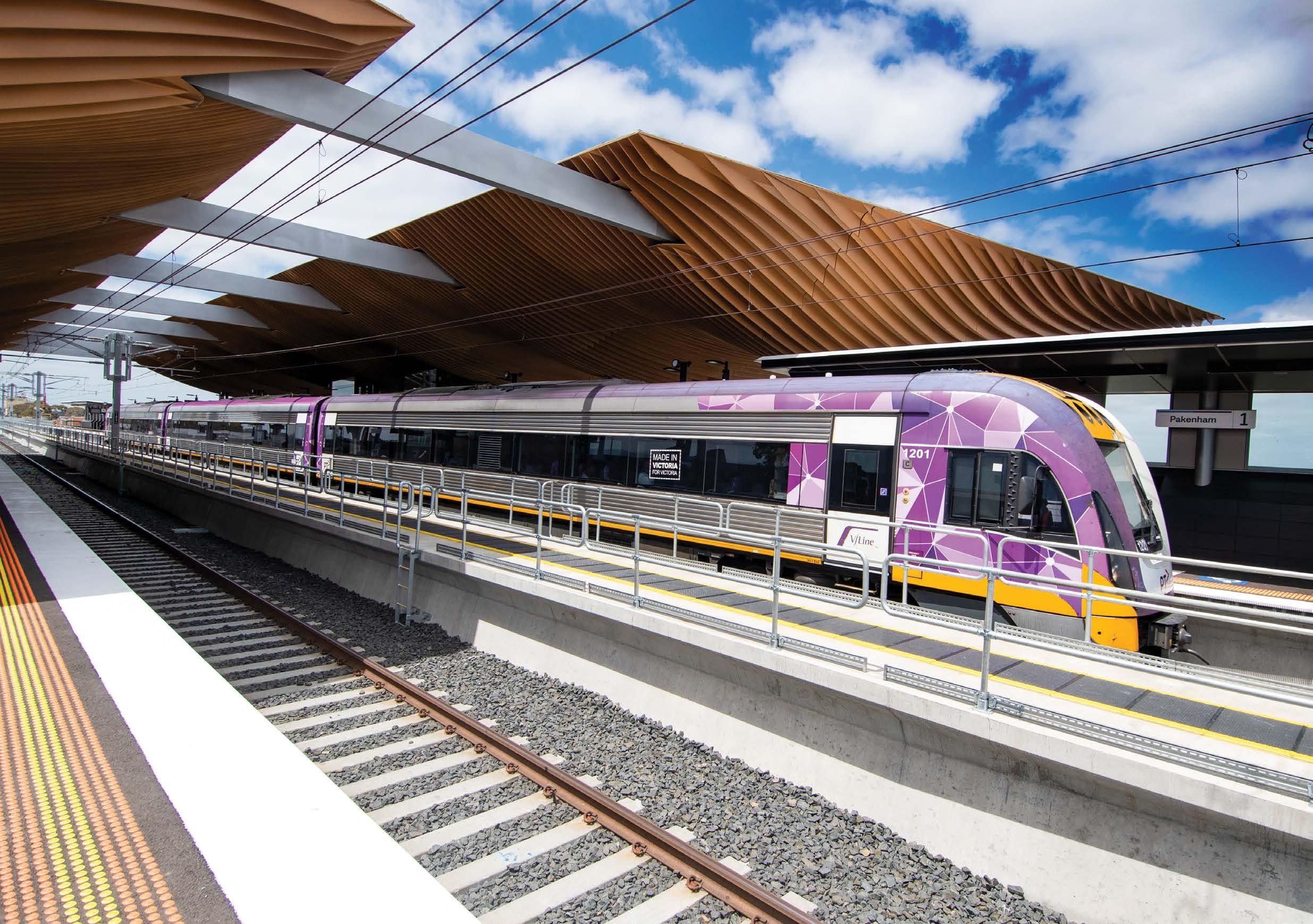
CONSTRUC TION
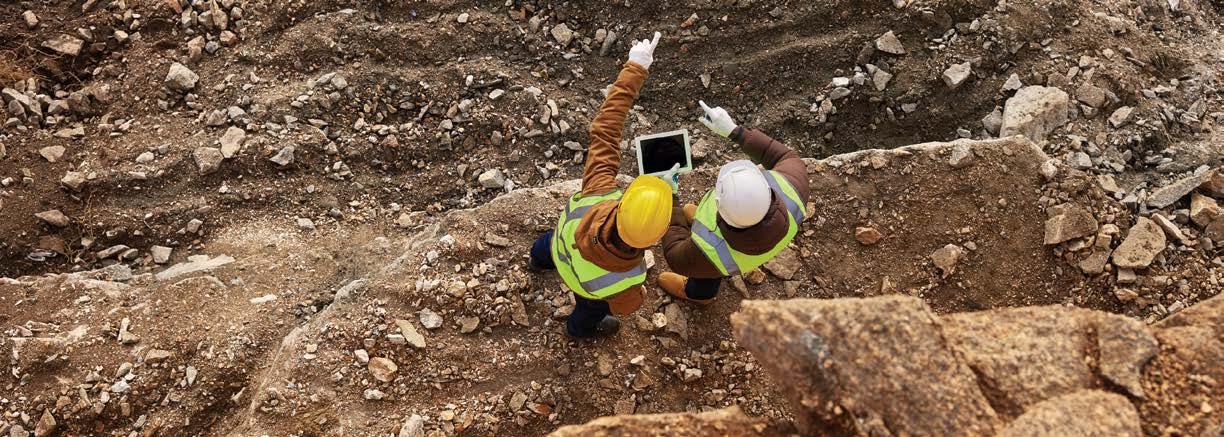
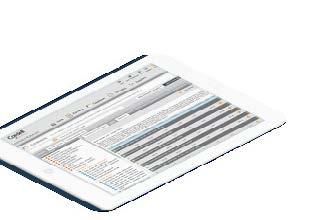
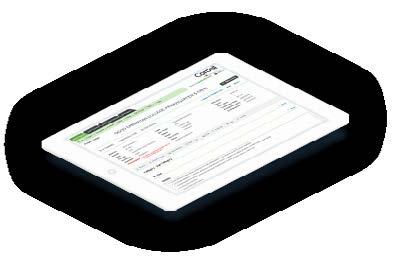
Find out more about how Cordell Connect and Cordell Estimator Platinum can help your business grow
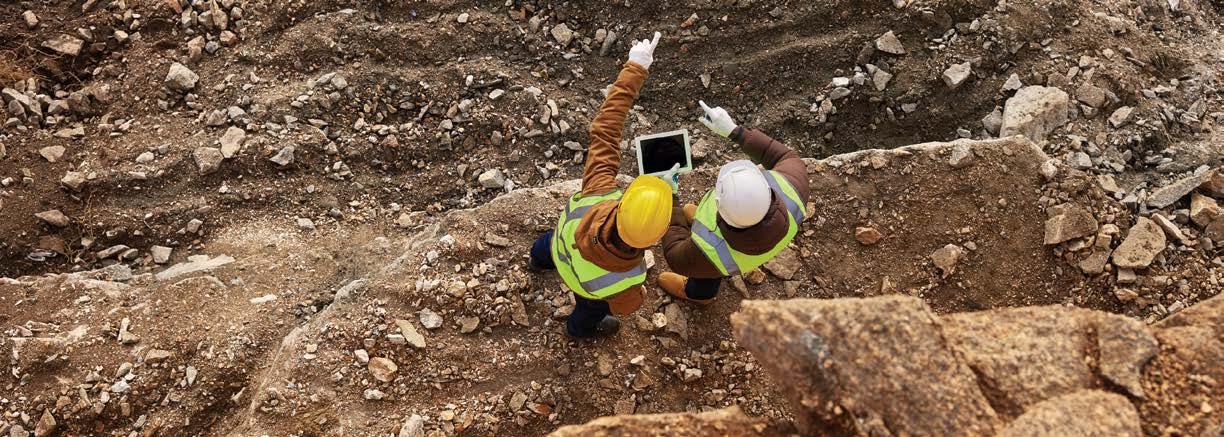
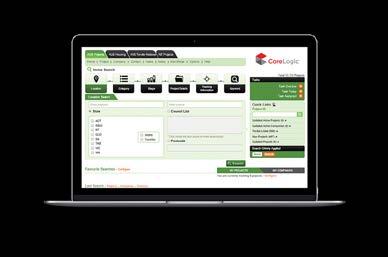
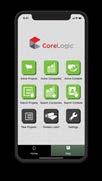
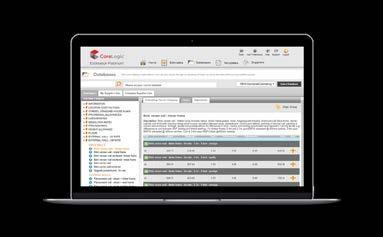
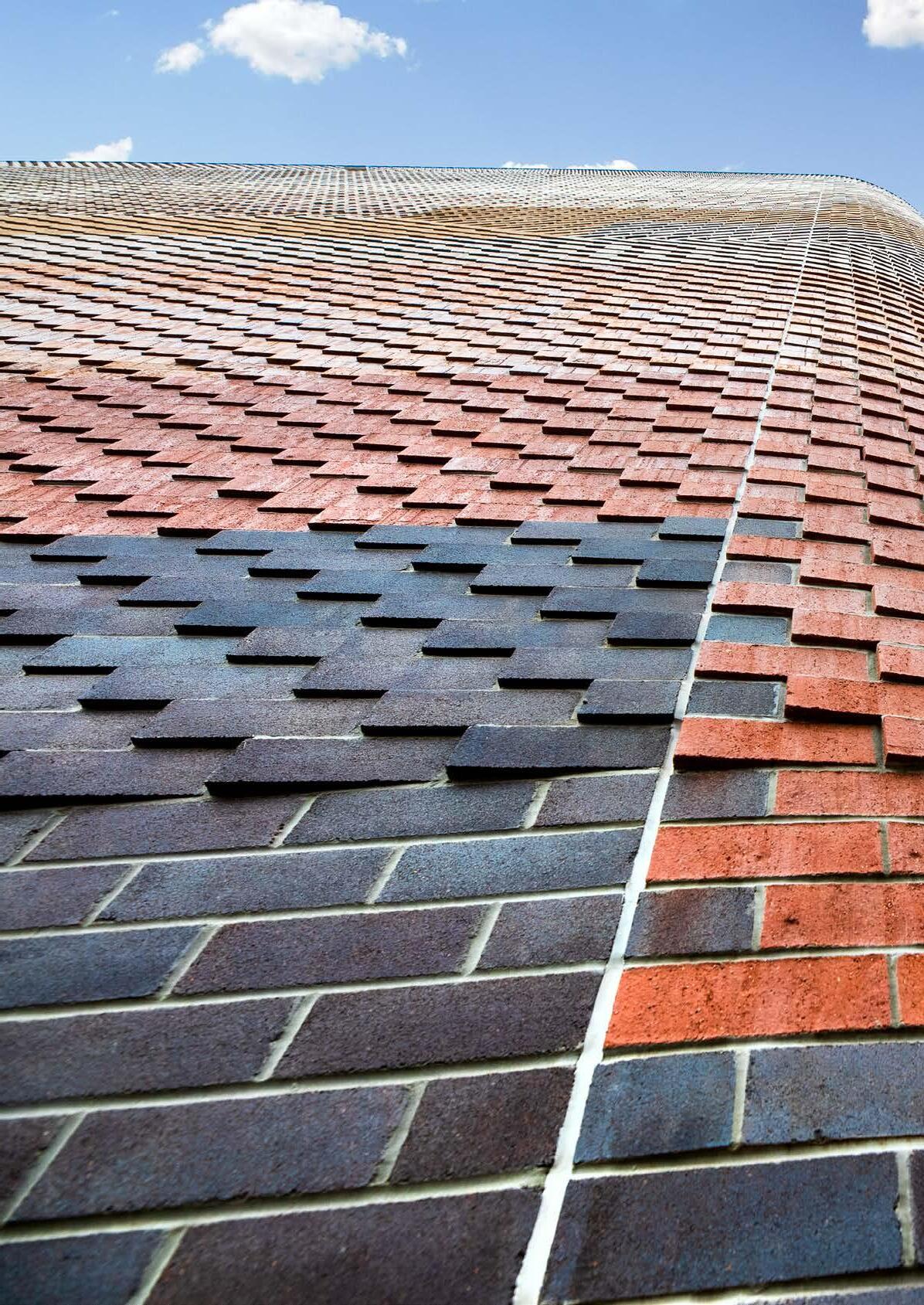
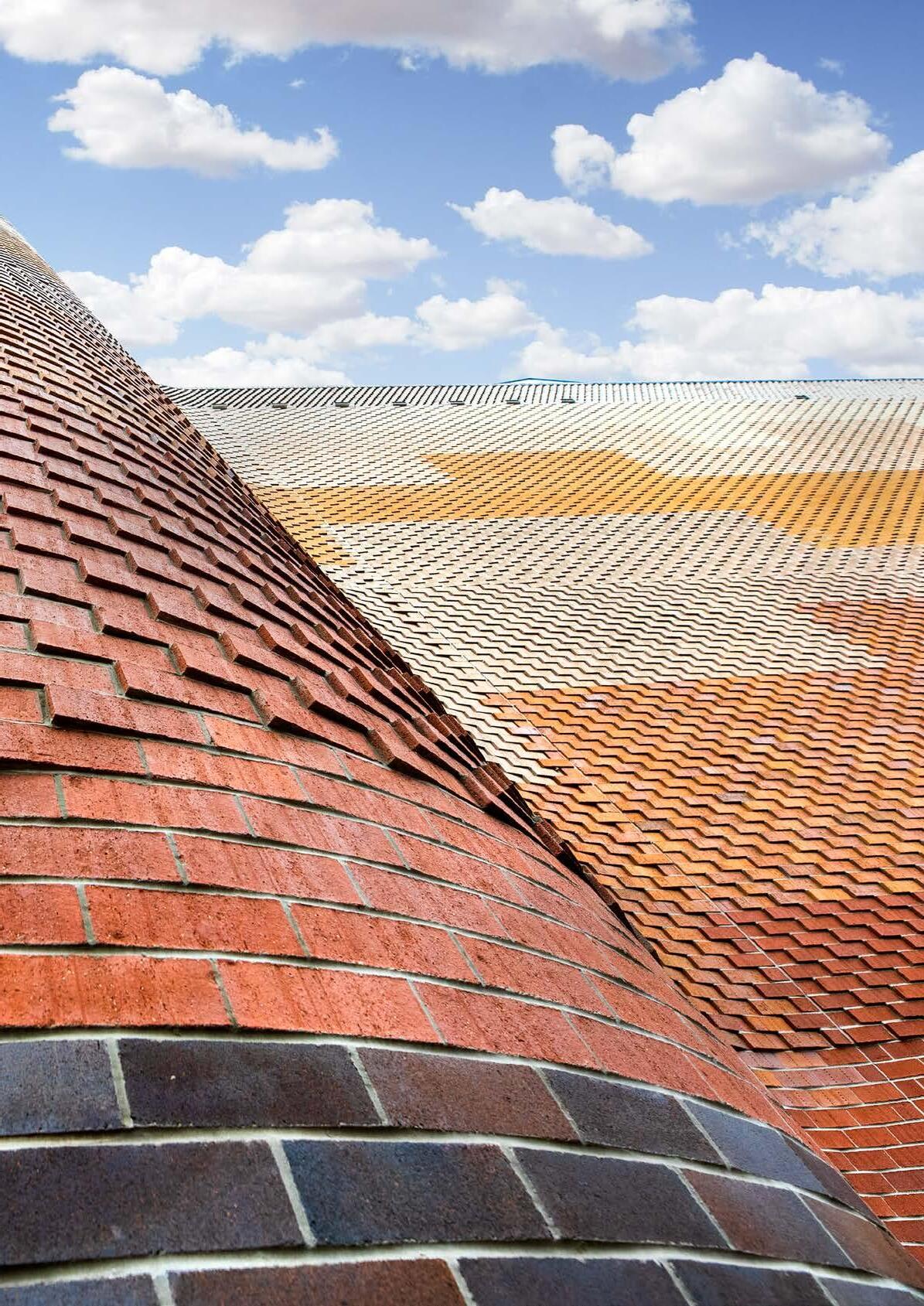
BORAL’S UPGRADED
CARBON-REDUCING TECHNOLOGY
AT ITS BERRIMA CEMENT WORKS
Boral Limited’s (Boral) upgraded carbonreducing technology at its Berrima Cement Works was officially opened, signifying a significant step in Boral’s move to net zero. Federal Minister for Climate Change and Energy, the Hon Chris Bowen MP was on-site to officially open the upgraded facility.
Located in the Southern Highlands region of New South Wales (NSW), Boral’s Berrima Cement Works is responsible for supplying 40% of cement in NSW and the Australian Capital Territory (ACT). The upgraded facility is a significant milestone in the company’s decarbonisation efforts and transition from its reliance on emissionsintensive fuels.
A key part of its upgraded facility, the Chlorine Bypass (which reduces the buildup of chlorides and other alternative fuel by-products), will enable alternative fuel usage to reach 60% over the next three years at the site. To date, Boral has already achieved 30 per cent coal substitution.
As part of Boral’s integrated operations in the NSW Southern Highlands, Berrima Cement Works is strategically significant for the company and to Australia’s manufacturing capability. It is also an important regional employer, with a workforce of around 115 people in operational and administrative roles, contributing to the approximately 350 people employed across integrated sites in the Southern Highlands.
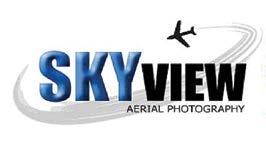

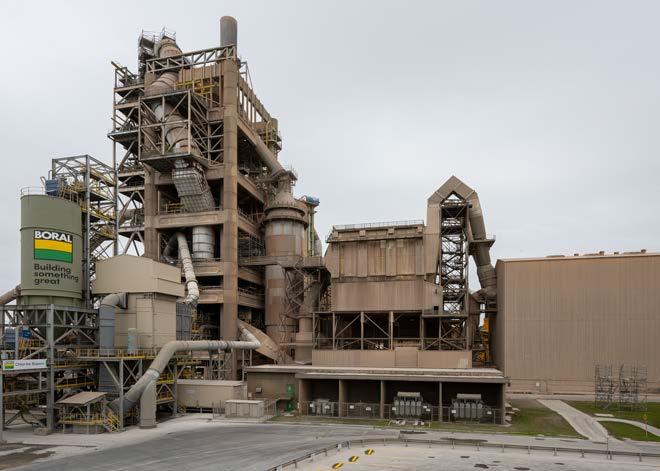
The site also indirectly supports local jobs associated with logistics, contractors, and suppliers. To this end, it is one of the largest employers within the Wingecarribee Local Government Area.
On the opening, Vik Bansal, CEO of Boral, said: “From our Federal Highways to the Sydney Opera House and Parliament House in Canberra, for almost a century, the Berrima Cement Works have helped to build and shape Australia.
“We all understand that though cement is vital to construction and building our
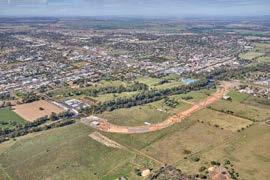
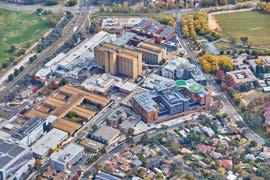
nation, it is carbon-intensive. Boral takes its responsibility to decarbonise our operations and comply with the Safeguard Mechanism obligations seriously. The Chlorine Bypass Facility reaffirms this commitment and moves our vital cement manufacturing infrastructure and Southern Highlands operations into a new era - one with less impact on the planet.
“We thank both the Federal government and NSW Government for their respective investment in this facility and remain committed to decarbonising our operations, in line with our net zero commitment.”
SKYview
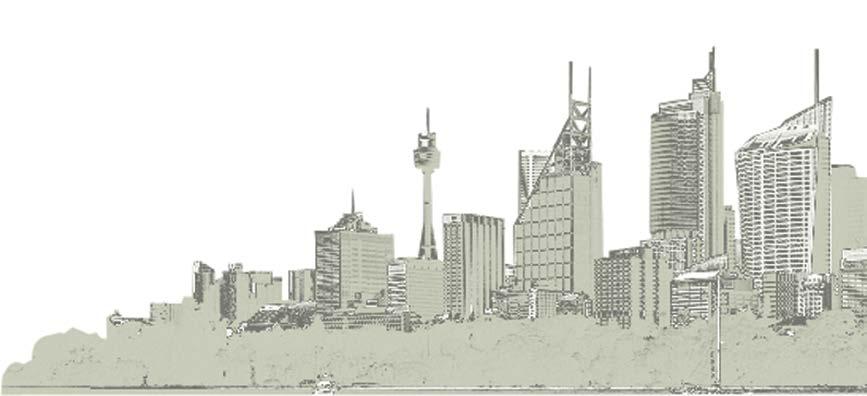
Boral’s Berrima Cement Works, photographer Paul Robbins
HEALTHY MINDS, SAFE SITES: NSW GOVERNMENT WORKING TO IMPROVE PSYCHOLOGICAL WELLBEING IN CONSTRUCTION
The Minns Labor Government is undertaking a campaign across New South Wales construction sites to improve psychological health and safety at work.
Known as the ‘Healthy Minds, Safer Sites’ campaign, inspectors are providing advice and resources to manage psychosocial hazards. These include aspects of work and situations that may cause a stress response, which in turn can lead to psychological, and sometimes physical harm.
The initiative forms part of the New South Wales Government’s Psychological Health and Safety Strategy 2024-2026 plan which is backed by $5.6 million over the next two years to deliver workplace mental health programs.
Some of the common psychosocial hazards in the construction industry are harassment (including sexual or racial), bullying, work pressure, exposure to a traumatic event and violence, and hazardous physical working environments.
Workplace mental ill health is estimated to cost Australian businesses up to $39 billion each year, due to lost participation and productivity. In addition, the rise in psychological injury is leading to an increase
in workers compensation claims which in turn is pushing up premiums. An investment in preventing psychological injury will also save money.
The NSW construction industry employs over 400,000 people. Data shows that psychosocial hazards are increasing, with the cost and time off work typically three times higher than that of physical claims. Between 2019 and 2024 there were almost 900 major workers compensation mental stress claims in construction, with work related harassment and/or bullying the most common reason.
SafeWork NSW Inspectors have found most employers are aware that poor mental health is an issue, with around half reporting that they have assisted a worker or colleague with mental health issues. They will continue their visits to construction sites until the end of March 2025.
One business working to achieve a psychologically healthy and safe workplace is Western Earthmoving Works Pty Ltd. They have a vision of mentally healthy workplaces by listening to their people and designing workplaces where people can thrive.
Preventing psychological harm, supporting
recovery, and promoting mental health are critical components of a mentally healthy workplace.
All employers can achieve psychologically healthy and safe workplaces by taking these steps:
• identify the things that could cause harm and consider the potential risks,
• consult with their workers on things that could cause harm and ways to manage risks,
• implement control measures to eliminate and minimise risks,
• monitor worker safety to ensure control measures are working, and
• review the controls regularly.
For more information on how to manage psychosocial risks and for further resources, visit the SafeWork NSW website

Need help? Reach out to your GP or access free help 24/7 by calling the following:
Lifeline Australia 13 11 14
Beyond Blue 1300 224 636
MensLine Australia 1300 789 978
Suicide Call Back Service 1300 659 467 Mates in Construction 1300 642 111
CHARTER HALL EXECUTES $3.35 BILLION GREEN LOAN TRANSACTION, ONE OF THE LARGEST IN THE SECTOR
Charter Hall Group (Charter Hall or the Group) has executed a fully underwritten $3.35 billion of Green Loan facilities on behalf of one of its funds, marking the completion of one of the largest Green Loan transactions in the Australian real estate sector.
Led by CBA, WBC, ANZ, HSBC and SMBC as Mandated Lead Arrangers, Underwriters and Bookrunners (MLAUBs), the transaction is part of a strategic capital management initiative for its $8.6 billion flagship office fund, Charter Hall Prime Office Fund (CPOF or the Fund).
The strategic capital management initiative has enabled the Fund to leverage its market-leading sustainability credentials and implement a best-in-class finance platform
providing significant financial and operating flexibility. This will facilitate the delivery of CPOF’s premium grade development pipeline and strategic objective of providing long term outperformance for its investors.
This transaction grows Charter Hall’s platform-wide sustainable finance to more than $9.0 billion, 100% of which is in the Office sector, reflecting its continued progress toward integrating sustainability
into its operating assets. Further, the Green Loan facilities secured in this transaction have been certified by the Climate Bond Initiative and independently verified by DNV and KPMG, ensuring a thorough and transparent approach.
Do you have a project, media release, product or news item you would like to feature with the Australian National Construction Review?
Get in touch with our submissions team by scanning the code or at submissions@ancr.com.au to find out more.
Scan to read the full article.

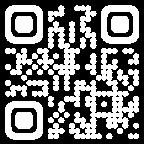
ARDEX AUSTRALIA OFFICIALLY OPENS OCEANIA HQ AT THE YARDS ESTATE, NSW
ARDEX Australia has officially opened its Oceania HQ at The YARDS Estate in Kemps Creek, NSW, a joint venture between Frasers Property Industrial and Aware Real Estate.
The new $140 million facility is targeting a 6 Green Star rating from the GBCA. The new manufacturing regional headquarters features a world-class 35m-high powder manufacturing tower, a 20m silo tower, onsite production and manufacturing, research labs, warehouse storage, training rooms and has been built to enhance employee wellbeing with an onsite gym, multiple cafes areas for staff, a rooftop terrace and highend interior designed offices by IA spanning over 3,000m2
ARDEX Australia, a global company that specialises in the development and manufacturing of high-performance building materials, is expanding its footprint in NSW and created their state-of-art flagship facility in Australia.
Fabian Morgan, Regional Managing Director for ARDEX Oceania and Member of the Global Management Committee, said:
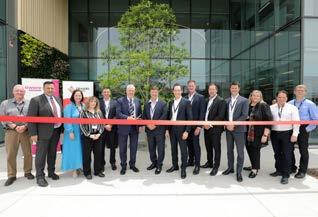

“ARDEX has built its reputation on quality performance and a relentless commitment to meeting the evolving needs of the building and construction industry.
Today, the facility enhances our ability to deliver on that commitment. We’re not just increasing production capacity, we’re embracing our future, we’re embracing innovation, sustainability and aspirational excellence. Thank you to Frasers Property Industrial and Aware Real Estate for your partnership in developing the site. The professionalism, vision and collaborative spirit across all teams has been critical in bringing this project to fruition.”
The new HQ location at The YARDS is strategic for an optimal national logistics network for the warehouse, located nearby the 24/7 Western Sydney International Airport and future Southern Link Road in
SUBSCRIBE NOW
Your Subscription to the Australian National Construction Review ensures you receive our premium hard copy publication, featuring stunning Project Showcases, Case Studies, Product Information and Commentary from within the industry and associated disciplines.
OR if digital is more your speed, subscribe to our e-newsletter, released monthly for a snapshot of new products, innovations and services that can benefit your next project. Scan the QR code to Subscribe
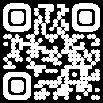
the Western Sydney Aerotropolis, close to the M4 and M7, and within Greater Western Sydney’s sought-after industrial zone.
The opening ceremony was attended by Mayor of Penrith, Councillor Todd Carney and Member for Badgerys Creek and Shadow Assistant Minister for Jobs and Small Business Tanya Davies MP, along with the teams at Frasers Property Industrial, Aware Real Estate, Barings and ARDEX Australia.
The YARDS, an expansive 77 ha estate in the Mamre Road Precinct, is undergoing significant construction with five additional buildings scheduled for completion in 2024. The estate is now 75 per cent leased, with a limited number of remaining available lots.
Currently available is Lot 6 and is planned for completion in early 2025.

SHORT-TERM PIPELINE UNCERTAINTY UNDERMINES LONG-TERM INFRASTRUCTURE DELIVERY
The release of Infrastructure Australia’s Infrastructure Market Capacity 2024 Report high-lights the urgent need for greater certainty and confidence to support Australia’s $213 billion five-year pipeline of major public infrastructure.
Consult Australia has welcomed the report’s insights while raising concerns about the shortterm volatility in the infrastructure pipeline, which continues to undermine business confidence, investment and workforce planning.
Jonathan Cartledge, Chief Executive of Consult Australia, says: “The report’s findings will come as no surprise to the industry. Businesses are grappling with a challenging environment where changes to previously committed projects are forcing firms to restructure and make redundancies. This volatility is particularly alarming in areas where we already face long-term skills and capability gaps, such as engineering and professional services.”
Now in its fourth year, the Infrastructure Market Capacity 2024 Report shows an 8% decline in the value of previously committed projects compared with projections from the same period last year.
Transport infrastructure remains the largest expenditure category, accounting for 59% of the major public infrastructure pipeline, but with a significant $32 billion reduction compared to the previous year’s forecast.
“The reduction in transport infrastructure investment, particularly in Victoria and New South Wales, is creating a ‘two-speed economy,’ with regional areas and northern Australia seeing greater growth while metropolitan areas bear the brunt of project delays and cost changes,” Mr Cart-ledge says.
Infrastructure Australia’s report notes that these delays and project reviews have shifted projected investment peaks further into the
future. While the report suggests the market may be struggling to deliver an overly ambitious pipeline, the issue lies with governments’ inability to deliver confidence and certainty, Mr Cartledge adds.
“Businesses need pipeline continuity to invest in capability, skills and workforce development. Without it, we risk further undermining Australia’s long-term capacity to deliver the infrastructure we need.”
The report also underscores the critical importance of improving construction productivity, pointing to the need for better risk allocation in contracts and a more collaborative approach to project delivery.
“We welcome Infrastructure Australia’s focus on construction productivity and look forward to working across government to support reforms through the National Construction Strategy.”
ALPHA HPA REACHES CONTRACTUAL CLOSE FOR $400 MILLION TO DELIVER AUSTRALIA'S FIRST LARGE-SCALE HIGH-PURITY
ALUMINA PLANT
Alpha HPA announced that it has reached Contractual Close with Export Finance Australia (EFA) and the Northern Australia Infrastructure Facility (NAIF), securing pivotal debt funding for Stage Two of its High Purity Alumina (HPA) First Project in Gladstone, Queensland.
The company has executed binding documentation for $400 million in senior debt financing which includes a $320 million construction facility, and an $80 million cost overrun facility, with competitive interest rates and an 11-year tenor from Financial Close.
Alpha HPA’s Managing Director Rimas Kairaitis, describes the milestone as a major achievement for the company.
“The Australian Government’s support underscores confidence in our innovative technology, sustainable production processes, and our role in the global critical minerals supply chain,” Mr Kairaitis said.
“This milestone consolidates the funding commitment and builds further on our
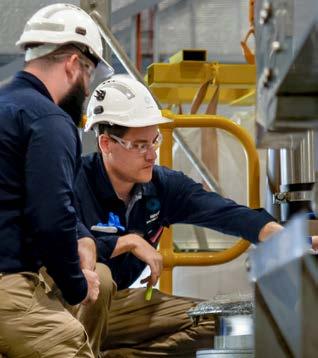
confidence in establishing the world’s largest, single site high purity aluminium materials facility manufacturing the high-tech materials essential for the global energy transition.”
EFA’s Managing Director and CEO, John Hopkins said today marks a key milestone with the Contractual Close of Alpha HPA’s Stage Two HPA First Project.
“We’re proud to support the delivery of Australia’s first high-purity alumina
processing facility in Gladstone, Queensland, reinforcing our commitment to the sector.” Mr Hopkins said.
Alpha HPA’s proprietary processing technology offers a low-carbon, near-zero waste solution to produce high-purity aluminium materials. Compared to traditional processes, Alpha HPA’s technology results in up to 70 percent lower carbon emissions, while recycling nearly 100 percent of its reagents. The facility will also operate on 100 percent renewable energy, further minimising its environmental impact.
These innovations place Alpha HPA at the forefront of sustainable manufacturing, supporting industries such as semiconductors, lithium-ion batteries, Direct Lithium Extraction (DLE) technology, synthetic sapphire and LED lighting.
This milestone cements Alpha HPA’s role as a cornerstone of Australia’s critical minerals strategy and showcases the transformative potential of innovative, sustainable manufacturing in supporting the global clean energy future.
© AlphaHPA
BREAKING GROUND AND BUILDING FUTURES:
2024 NAWIC NSW Awards Celebrate Excellence
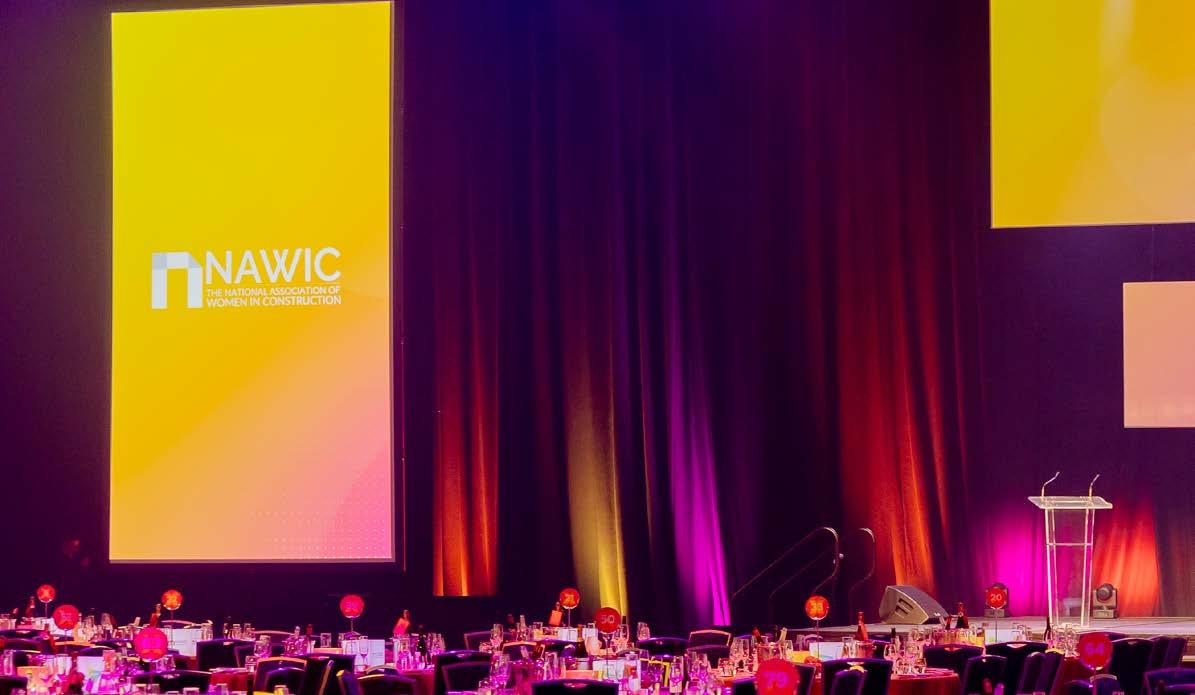
Trailblazing leaders, innovative projects and transformative workplace policies have been rewarded at the 2024 NAWIC NSW Awards for Excellence.
Hosted by the National Association of Women in Construction (NAWIC) NSW Chapter, the event attracted a record 153 nominations across 13 categories, drawing 1,100-plus industry professionals to Sydney’s ICC Ballroom to celebrate.
“This is more than an awards night – it is a call to action,” said Georgia Coulston, NAWIC NSW Chapter President. “The NAWIC NSW Awards for Excellence spotlight exceptional leadership and challenge the status quo. Together, we have the power to dismantle barriers, lead with empathy and lay the foundations for a future where every contribution builds lasting impact.”
Highlighting the critical need for change, Ms Coulston noted that women comprise just
12% of the construction workforce and only 2% of trades – a figure stagnant for over four decades.
“This isn’t just a gender challenge; it’s an industry-wide opportunity. Elevating women’s participation is essential to solving labour shortages, boosting productivity and securing Australia’s future.”
Award highlights
Lendlease Crystal Vision Award: Natalie Haydon of Multiplex, affectionately known as ‘Hard Hat Nat,’ was recognised for creating the Jump Start Juniors – Multiplex | LEGO® Australia Learn to Build program. Through engaging workshops, Natalie inspires primary school students to explore careers in construction while championing female leadership.
Richard Crookes Business Woman of the Year Award: Sianne Bennett, Head of

Human Resources at Gamuda Australia, was recognised for her transformative leadership. Under her guidance, Gamuda grew from 10 employees to more than 750 in just five years. Sianne’s focus on diversity has driven a 30% female workforce and a 65% female graduate participation rate.
ADCO Champion of Change Award: Greg Anderson, Alliance Manager for the Mulgoa Road Upgrade Alliance, achieved 31% female representation on his project through a holistic approach to diversity and mentorship. “We encourage more men in the industry to take Greg’s lead to innovate, advocate and take risks to create change,” Ms. Coulston said.
All finalists show how a diverse construction industry can deliver profound benefits for Australia, Ms Coulston concludes. “Each of us holds the power to address the challenges ahead. But only by working together can we build an industry where everyone thrives.”
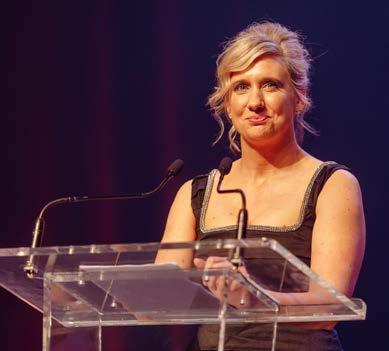
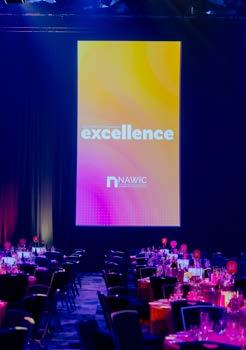
Photography © Nicholas Smith

AWARD RECIPIENTS
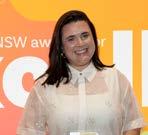
Lendlease Crystal Vision Award
Winner: Natalie Haydon
Affectionately known as ‘Hard Hat Nat,’ Natalie Haydon developed the Jump Start Juniors – Multiplex | LEGO Australia Learn to Build program, inspiring primary school students to explore careers in construction while promoting female leadership through LEGO© and role modelling. During her 13 years with Multiplex, Natalie has balanced site-based roles and parenting. As Design Manager on the $1.9 billion Western Sydney International Airport project, Natalie is committed to fostering an inclusive environment for women to thrive.
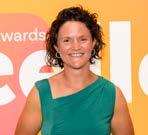
Richard Crookes Business Woman of the Year Award
Winner: Sianne Bennett
As Head of Human Resources at Gamuda Australia, Sianne Bennett has expanded the team from 10 to over 750 employees, achieving a remarkable $1.2 billion in revenue within five years. Her dedication to diversity and inclusion has resulted in a 30% female workforce and a 65% female graduate participation rate. Sianne played a key role in acquiring DT Infrastructure, diversifying the business and enhancing the company’s renewable energy capabilities.
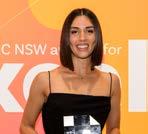
MPA Award for Achievement in Construction, Refurbishment and Fitout
Winner: Brie Ranchhod
Design Manager with Kane Constructions, Brie Ranchhod led refurbishment works at the Children’s Hospital at Westmead. By managing multiple design
teams and concurrent milestones, Brie accelerated the program and minimised disruptions. Her meticulous safety and design management ensured timely issue resolution and seamless project execution within a live hospital environment. As a leader of NSW Kane’s Women in Construction team, Brie actively mentors female colleagues and champions diversity within the construction industry.
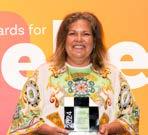
CPB Contractors Award for Contribution to Sustainability Winner: Robyn Simpson
As the National Manager – Environment and Sustainability at Coates, Robyn Simpson is spearheading strategies that minimise emissions and embodied carbon. Among Robyn’s achievements, she led the implementation of data visibility systems across 145 Coates branches, enabling trend analysis to pinpoint sustainability priorities. With this insight, solar panels were installed across 26 branches, and Coates uses almost 70% of the solar energy generated. Robyn’s hands-on leadership has inspired a movement towards sustainable practices at Coates.
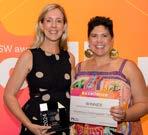
Scentre Group Award for Team Innovation
Winner: Lendlease Workforce Participation Team
The Lendlease Female Apprentice Development and Peer Networking Program was developed to increase engagement and trade completion rates, and to build a robust network for future female tradespeople. Designed by apprentices for apprentices, the program offers coaching and professional development typically reserved leaders, alongside access to a growing peer network. Lendlease has expanded the initiative to industry
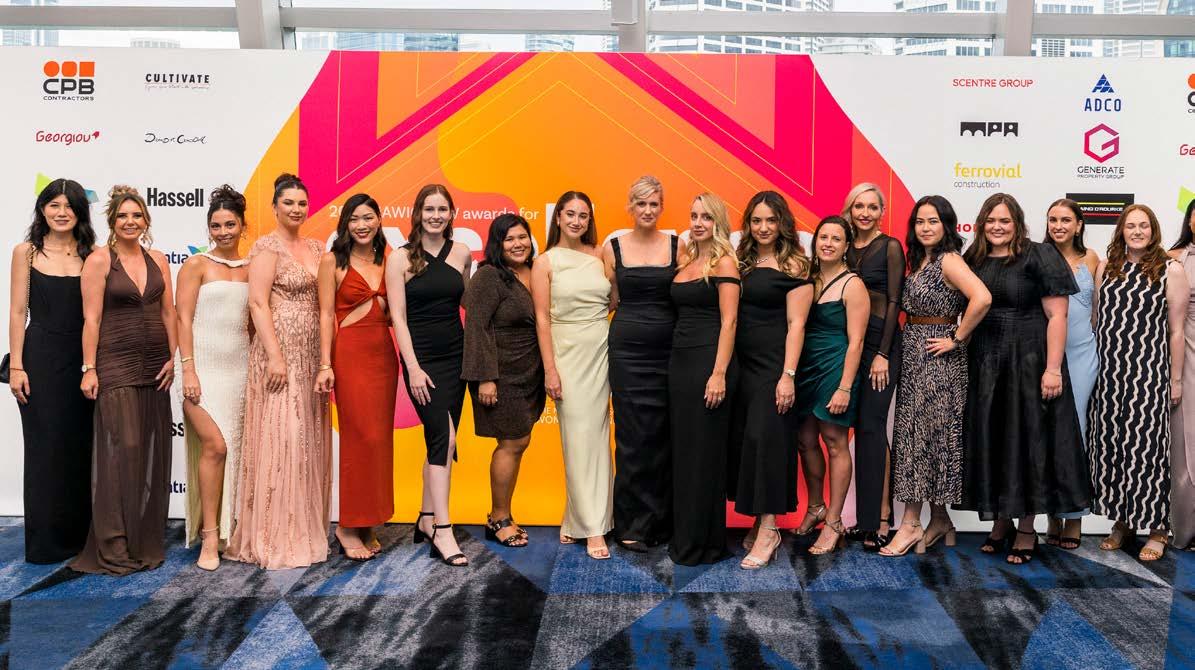
partners, and will soon include male apprentices, fostering allies and creating a more inclusive site culture.
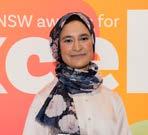
Hassell Award for Innovation in Design Winner: Afrida Salma
To minimise disruption during construction of the Warringah Freeway Upgrade, CIMIC Group’s CPB Contractors Design Engineer Afrida Salma developed an innovative slotted drain system that improved drainage while reducing excavation and construction time. Collaborating with principal designers, the construction team and Transport for New South Wales, Afrida created a solution that lowered the project’s carbon footprint, improved performance and enhanced air quality, benefitting both workers and nearby residents.
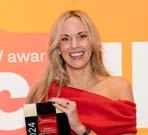
Ferrovial Project Manager of the Year Award
Winner: Melanie Bowden
As Project Director of the Mindyarra Maintenance Centre project in Dubbo, CPB Contractors’ Melanie Bowden has fostered a welcoming workplace for women, surpassing the national average for female representation in construction and exceeding NSW Aboriginal Procurement Policy targets. Through effective communication and team restructuring, Melanie reduced turnover and significantly improved morale. Under her guidance, the project achieved a ‘Leading’ Design rating from the Infrastructure Sustainability Council, demonstrating the real-world impact of Melanie’s leadership.
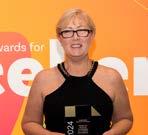
Roberts Co Award for Contribution to a Project’s Development
Winner: Carinne Watson
Leveraging her clinical background, CPB Contractors’ Health Facility Planner Carinne
Watson proposed an alternative staging strategy for the Royal Prince Alfred hospital redevelopment. Carinne’s approach reduced clinical decants – where patients are temporarily moved during construction activities – from eight to one, saving 12 months on the program and $10 million in costs, while ensuring uninterrupted patient care. Carinne’s innovative approach also minimised concurrent work sites, enhancing safety and reducing staff fatigue.
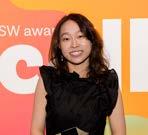
Laing O’Rourke Future Leader Scholarship Winner: Lufeng Zhang
A chartered civil and environmental engineer, Lufeng Zhang has demonstrated ingenuity and technical acumen in her work for Laing O’Rourke on Sydney Metro projects. Lufeng also helped to redesign procurement processes to enable greater local supplier participation in bushfire recovery construction. A mentor and role model for young women in construction, particularly from culturally and linguistically diverse backgrounds, Lufeng has delivered engaging sessions on digital innovation and STEM to high school students.
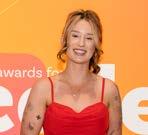
Transport for NSW Tradesperson Scholarship Winner: Jordyn Allan
Her family’s construction business and a love of tools led her to a carpentry apprenticeship, but Jordyn Allan's career took a turn when she discovered Gamuda’s Tunnelling Pre-Employment Program. Relocating from Goulburn to Sydney, Jordyn was the youngest in her cohort. Inspired by the program’s personalised support, Jordyn is now pursuing a Certificate III in Electrotechnology, confidently paving her way in the electrical trade and inspiring other women to follow.
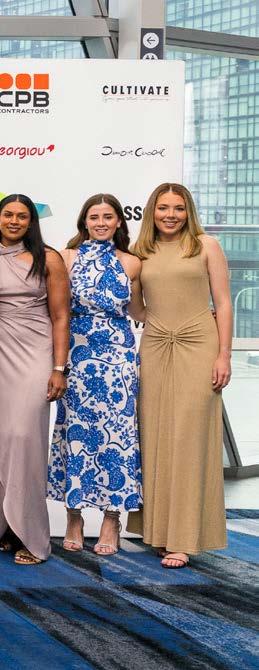
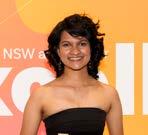
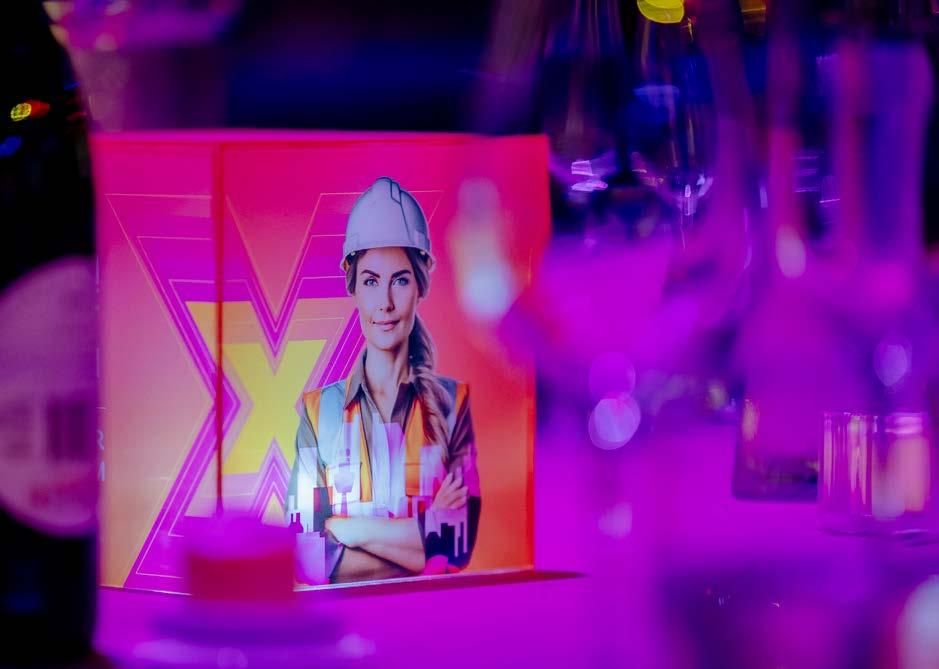
John Holland University Scholarship Winner: Imandee Jayawardena
Exemplifying determination and tenacity, Imandee Jayawardena overcame cultural and gender barriers in Sri Lanka and Australia to forge a rewarding construction career. After 45 unsuccessful job applications to Australian construction companies, Imandee boldly visited a potential employer’s head office to showcase her commitment. Her perseverance paid off, and Imandee is now an Assistant Quantity Surveyor with MBM while pursuing a Bachelor of Construction Management at Western Sydney University.
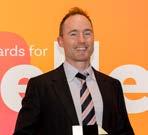
ADCO Champion of Change Winner: Greg Anderson
As Alliance Manager on the Mulgoa Road Upgrade Alliance, Greg Anderson achieved 31% female representation by embracing a holistic and authentic approach to diversity and inclusion. Greg piloted the Construction Industry Cultural Standard, prioritising flexibility, wellbeing and diversity, and created the ‘My Time’ flexible work program, now being embedded into all Seymour Whyte
About NAWIC
Established in 1995, the National Association of Women in Construction (NAWIC) champions and empowers women in the construction and related industries to reach their full potential. NAWIC’s vision is an equitable industry within which women fully participate, and it values are: Courage, In-clusion, Resilience, Integrity, Safety & Wellbeing. See: www.nawic.com.au
projects. Greg mentors women and actively engages high school students to inspire the next generation of female leaders and create lasting change.

NAWIC Regional Woman of the Year Award
Winner: Eliza Blight
As ADCO’s Project Engineer on the Griffith Base Hospital, Eliza Blight led the successful delivery of the façade package. Eliza expertly managed design clashes and material delays, ensuring the building was sealed and watertight so other trades could progress swiftly and recover lost time. Eliza’s expertise contributed to the building’s aesthetic appeal and long-term functionality. With an enduring commitment to her industry, Eliza also actively mentors other rising stars and inspires schoolgirls to embrace construction careers.
About NAWIC NSW Chapter
The NAWIC NSW Chapter is a passionate group of women who volunteer their time and expertise to host and deliver a range of events aimed at furthering women in the construction industry.
The committee and NAWIC members work in a variety of fields within the construction industry and the Chapter’s activities are designed to address the diversity of these
groups. NAWIC NSW’s goal is to celebrate the achievements of female colleagues in the construction industry as well as to inform, educate and provide networking opportunities.
Photography © Nicholas Smith
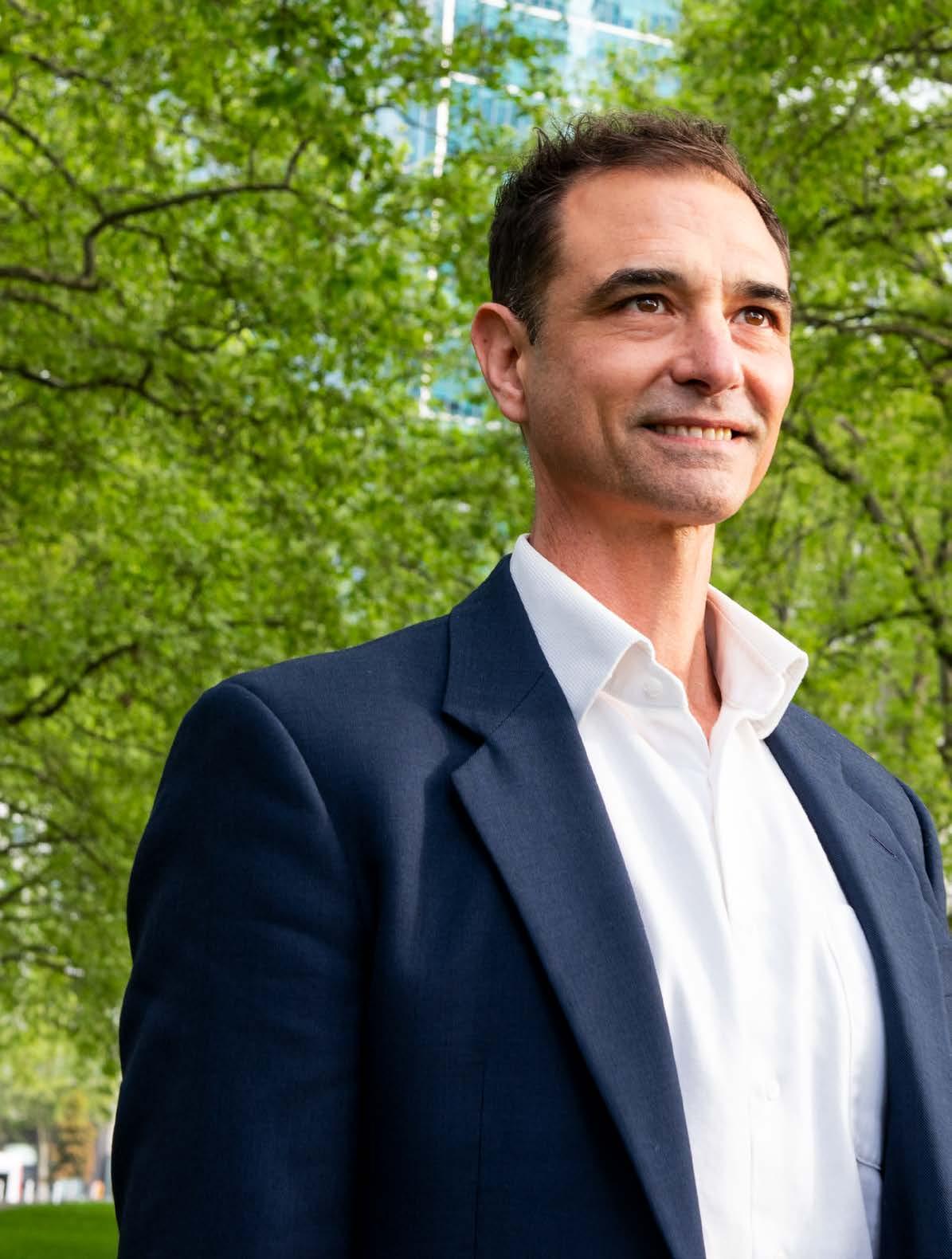
TOBY KENT
CHIEF EXECUTIVE OFFICER
Toby Kent, a renowned leader in sustainability and resilience, was recently appointed as the Chief Executive Officer of the Infrastructure Sustainability Council (ISC).
With over 25 years of experience across public and private sectors, Toby Kent brings a wealth of knowledge in sustainable development, energy transition, and infrastructure planning. Known for his innovative, collaborative approach, Toby is set to lead the Infrastructure Sustainability Council (ISC) toward a future of more sustainable and resilient infrastructure across Australia and New Zealand
What is your vision for the ISC?
My vision for the ISC is to be a critical part of every infrastructure decision across Australia, and New Zealand, and perhaps in coming years, the Asia-Pacific. Infrastructure is inherently multi-generational, and we need to transform our approach to ensure sustainable impacts for future generations.
This requires whole of sector change, not just those projects that are currently seeking to be certified ‘sustainable’.
What are the key priorities you plan to focus on during your tenure?
It’s still early in my tenure, but I’ve identified several priorities. First, our membership base is strong, but we need to connect more broadly outside of the current circle.
We also offer fantastic training programs that go beyond our membership, and there’s potential to expand these.
Our IS Ratings tools provide benchmarks for what sustainable infrastructure looks like, but we need to streamline some of the processes and make them easier to use, while retaining the rigour of our tools.
We also need to broaden the number of sectors that are using the tools. For example, we have some fabulous water and energy projects using IS ratings but we are not yet fully embedded across those sectors.
As demands for financiers to communicate the sustainability impacts of their lending and investments grows, we offer a clear solution to that and I expect us to be much more active in that space.
Some of this talks to the final point, which is that ISC has strong support among a core group of users. We need to expand this group, make it easier for people to engage with us.
Ultimately, the goal is to achieve greater transformation in how infrastructure is developed and to drive more significant sustainable impact.
How does your experience in resilience and sustainability shape your approach to leading the ISC?
In my role as Chief Resilience Officer for Melbourne, I often heard the question, ‘Isn’t resilience just another name for sustainability?’
There is lots of cross-over, but resilience thinking acknowledges that while pursuing sustainabile development, things will still go wrong along the way. The question becomes: ‘How do we plan for that?’
My experience has taught me to recognise the strengths of an organisation and amplify those to create real impact. Whether it’s for infrastructure or entire communities, it’s about preparing for the stresses and shocks that will inevitably come, and designing systems that can survive and ultimately thrive despite them.
Achieving Net Zero in construction is a major goal for the industry. How close are we, and what challenges do you see ahead?
We’re still quite far from achieving Net Zero, but national commitments in Australia and New Zealand provide a helpful framework. Collaboration across the private and public sectors is critical, and we’re seeing more of this now than ever.
Tools like IS Ratings are helping guide projects toward sustainability goals, both in terms of mitigation and adaptation. Over the past six years, projects certified under IS As Built Ratings have avoided more than 23 million tonnes of carbon emissions and in FY24 alone, projects diverted almost 35 million tonnes of resources from landfill. The challenge from a net zero perspective is that we’re moving forward with initiatives now that should have been implemented 20 years ago.
What role does innovation play in reaching sustainability targets within the infrastructure sector?
Innovation is essential. We’re seeing improvements in resource management, with
more materials being reused and recycled, reducing landfill waste. The use of renewable energy and energy-efficient practices is becoming more mainstream, which is encouraging. However, we still have work to do in preparing infrastructure that looks generations ahead, rather than focusing on short-term needs.
Integrating Internet of Things (IoT) technology, AI, and other smart infrastructure solutions will allow us to build systems that can evolve as technology does. We need to design infrastructure that isn’t just built for today but for decades into the future.
This means thinking about connected infrastructure – the aggregated opportunities that come from different infrastructure elements connecting effectively, as well as their interdependencies and consequent inter-vulnerabilities.
How does the ISC measure the impact of its work?
We’ve been fortunate to have an independent assessment that found for every dollar invested in IS Ratings, the return was $1.6$2.4 across the lifestyle of any given asset.
We’re also continuously refining how we articulate the financial and environmental benefits of our ratings tools. The numbers are clear—through IS Ratings last year alone projects have saved over half a million tonnes of asphalt.
Continues over page
We need to design infrastructure that isn’t just built for today but for decades into the future.
Toby
Kent,
CEO, Infrastructure Sustainability Council
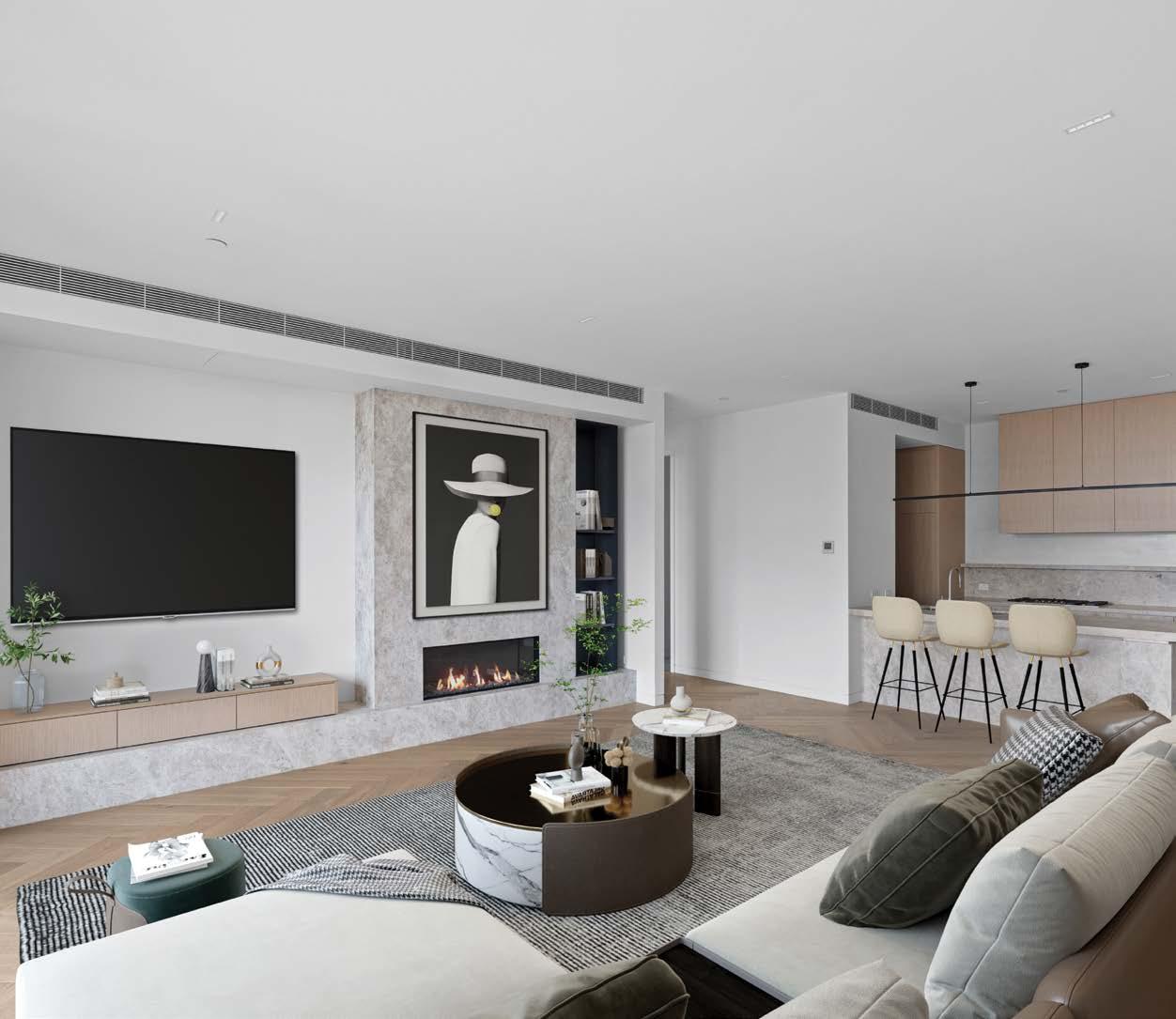
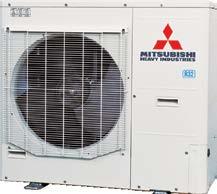
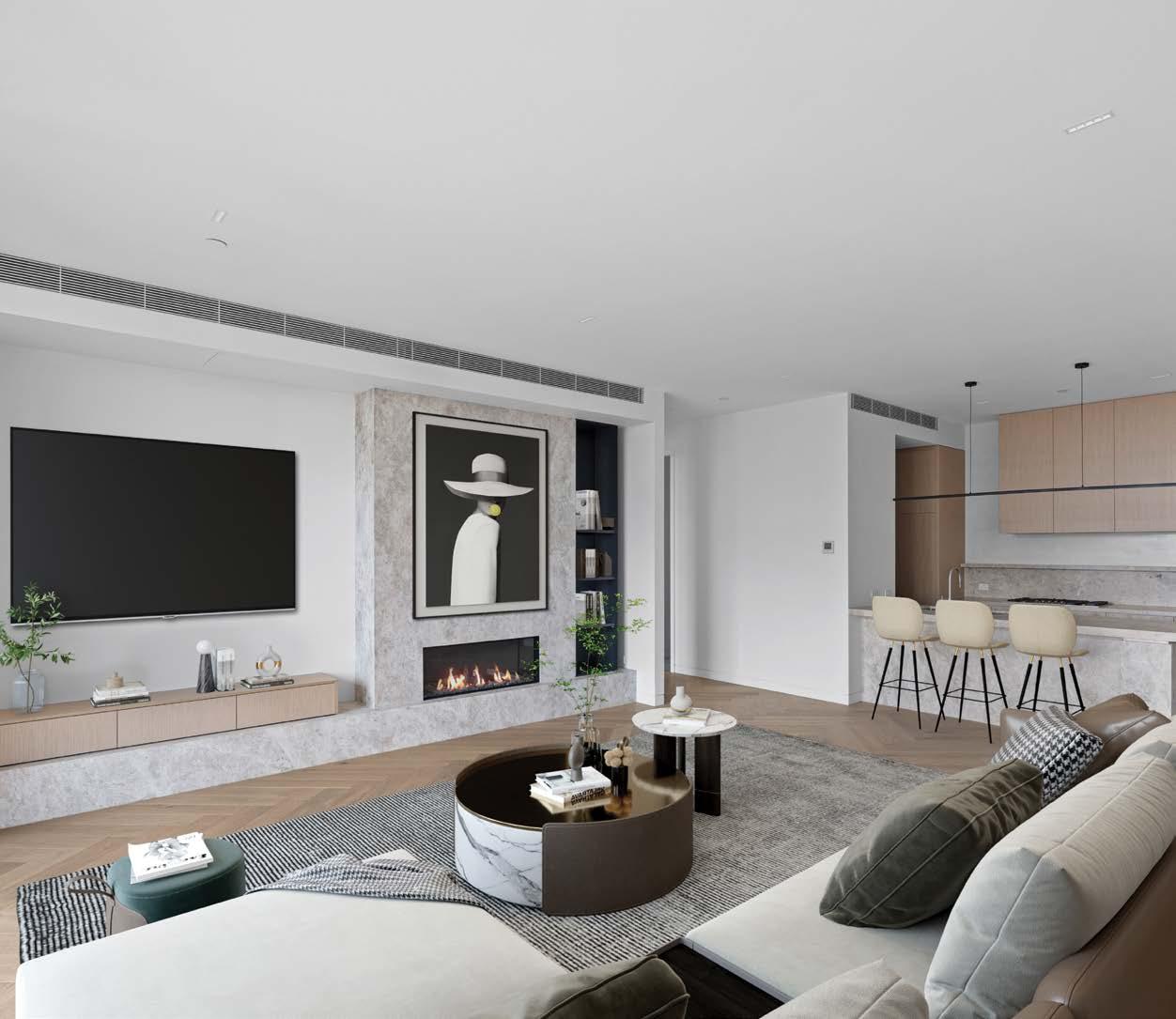
Also, the ISC provided training to over 1,700 professionals in sustainability and leadership. We produce an annual impact report that captures all such information.
Again, we need to communicate these impacts ever more effectively to demonstrate the value we bring to the industry.
Looking forward, what initiatives or projects at the ISC excite you the most?
I’m particularly excited about the new IS Essentials Design & As Built tool, which is designed for projects between $5 million and $100 million. This allows smaller projects to benefit from sustainability standards without compromising on quality.
Additionally, IS 2.1 ratings, which are now fully in the market, are receiving good feedback and we have significant work program in
place to make the tool more effective for users, supporting better outcomes.
These tools are helping the industry not only meet immediate needs but also set the stage for long-term sustainable infrastructure development.
Our new Sustainability Academy and enhanced membership model, both to be rolled out this year, are both important developments that will see us offer more benefits to the market and improve sustainability practices.
What legacy do you hope to leave at the ISC, and what impact do you want to have on the infrastructure sector?
My goal is to ensure that the standards we develop become the norm for preparing for and achieving infrastructure outcomes across Australia and New Zealand and, potentially,
the Asia-Pacific.
I want the ISC to be a well-resourced organisation that can be an employer of choice and afford to invest in more inclusivity and innovation ourselves. I see us driving sustainability outcomes for decades to come.
Ultimately, I hope to leave a legacy where infrastructure is inherently sustainable, resilient, and prepared for the future, serving communities in the long term and not just in the immediate.
Scan to read the IS Council's Impact Report 2024
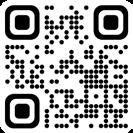
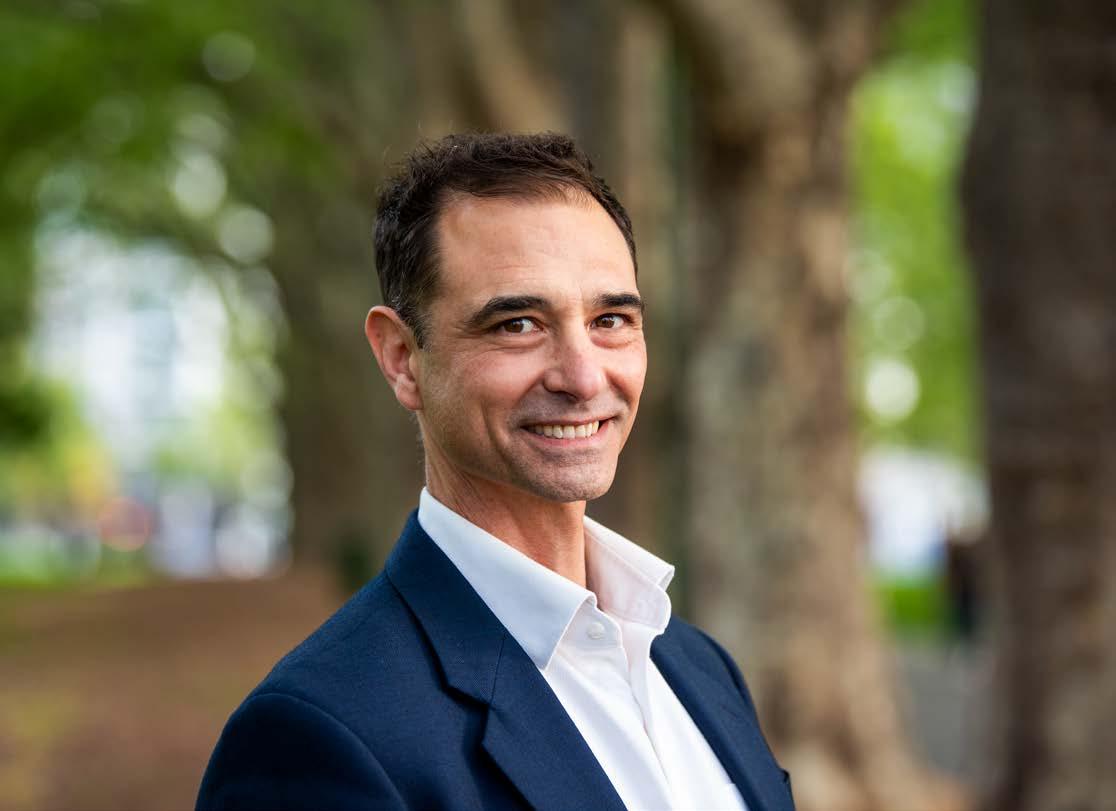
My goal is to ensure that the standards we develop become the norm for preparing for and achieving infrastructure outcomes.
Toby Kent, CEO, Infrastructure Sustainability Council
INNOVATIVE CLIMATE CONTROL SOLUTIONS POWERING LUXURY AT THE FELLOWSHIP
PROJECT : The Fellowship
LOCATION : Kew, VIC
COMPLETION DATE : October 2024
CONTRACTOR : DP Heating and Cooling
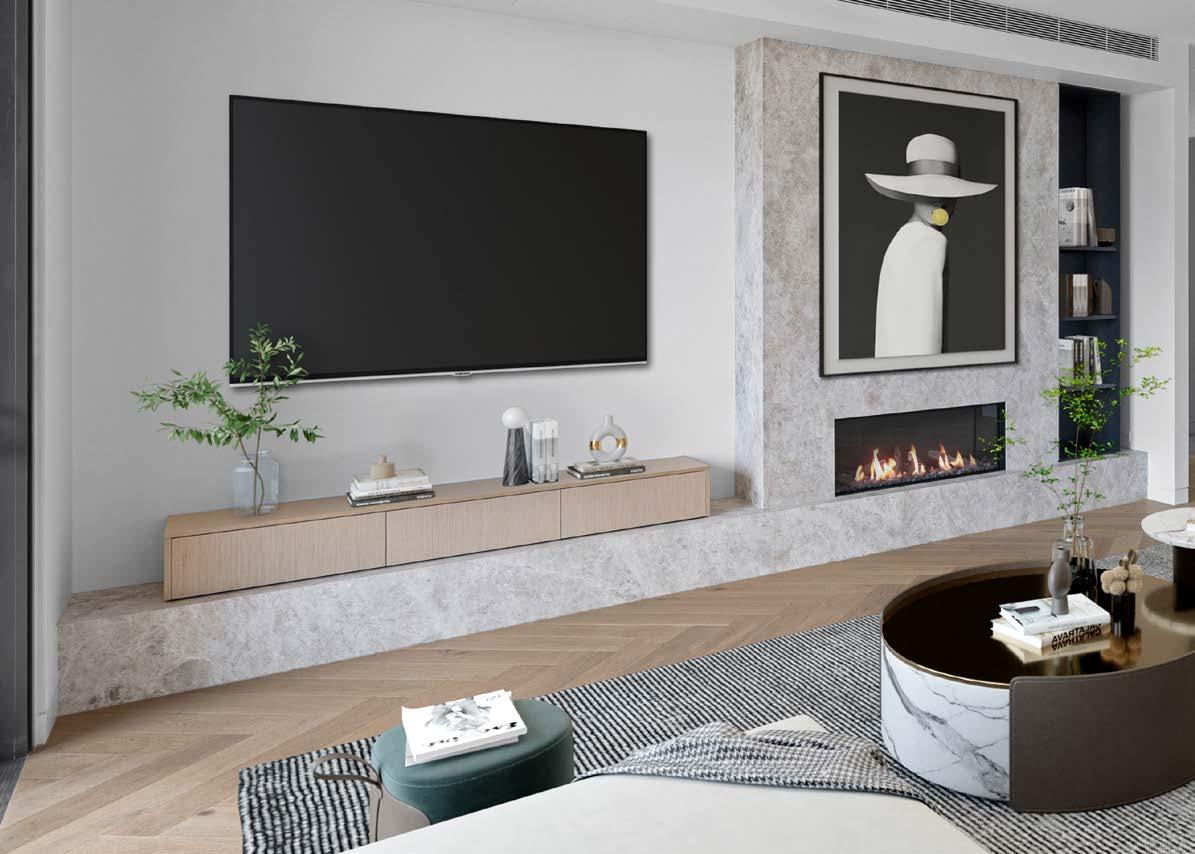
Nestled in the exclusive suburb of Kew, Victoria, The Fellowship redefines contemporary luxury living with its mid-century-inspired design, premium finishes, and seamless integration of modern amenities.
Comprised of 20 high-end residences designed by CHT Architects, Sora Interiors, and Jack Merlo Landscaping, this prestigious development required an advanced climate control solution that matched its aesthetic sophistication and operational demands.
Mitsubishi Heavy Industries Air-Conditioning Australia (MHIAA), in collaboration with DP Heating and Cooling, rose to the challenge with a tailored approach that exceeded expectations.
High-Performance Systems for a High-End Development
For a project of this calibre, the heating and cooling systems needed to blend functionality with elegance, providing comfort without disrupting the architectural integrity or tranquility of the residences.
MHIAA deployed a mix of state-of-the-art systems, including 96 FDUT**KX slimline ducted units, 41 compact VRF systems from
the KX Micro Series, and medium-static FDUM ducted units, all designed to deliver outstanding performance and energy efficiency.
“The KX Micro Series was a game-changer for this project,” said Nick Bennet from MHIAA. “These outdoor VRF units, with their compact size and long pipe run capabilities, are ideal for the constrained rooftop spaces while still delivering exceptional heating and cooling performance.”
Slimline FDUT ducted units were strategically installed in areas with limited ceiling space, ensuring a seamless fit into the design without compromising functionality. For larger, more open areas, FDUM units offered robust air distribution, paired with sleek metal linear grilles to maintain the luxurious aesthetic.
Overcoming Challenges with Tailored Solutions
Space constraints on the rooftops posed a significant challenge, requiring compact outdoor units that could operate efficiently without overcrowding the area. MHIAA's solutions, including the adaptable KX Micro VRF systems, turned these challenges into opportunities for innovation.
Another hurdle was the evolving project design, with adjustments being made even during construction. “The project demanded flexibility, and our collaboration with DP Heating and Cooling allowed us to adapt quickly,” Bennet said. “This ensured the system
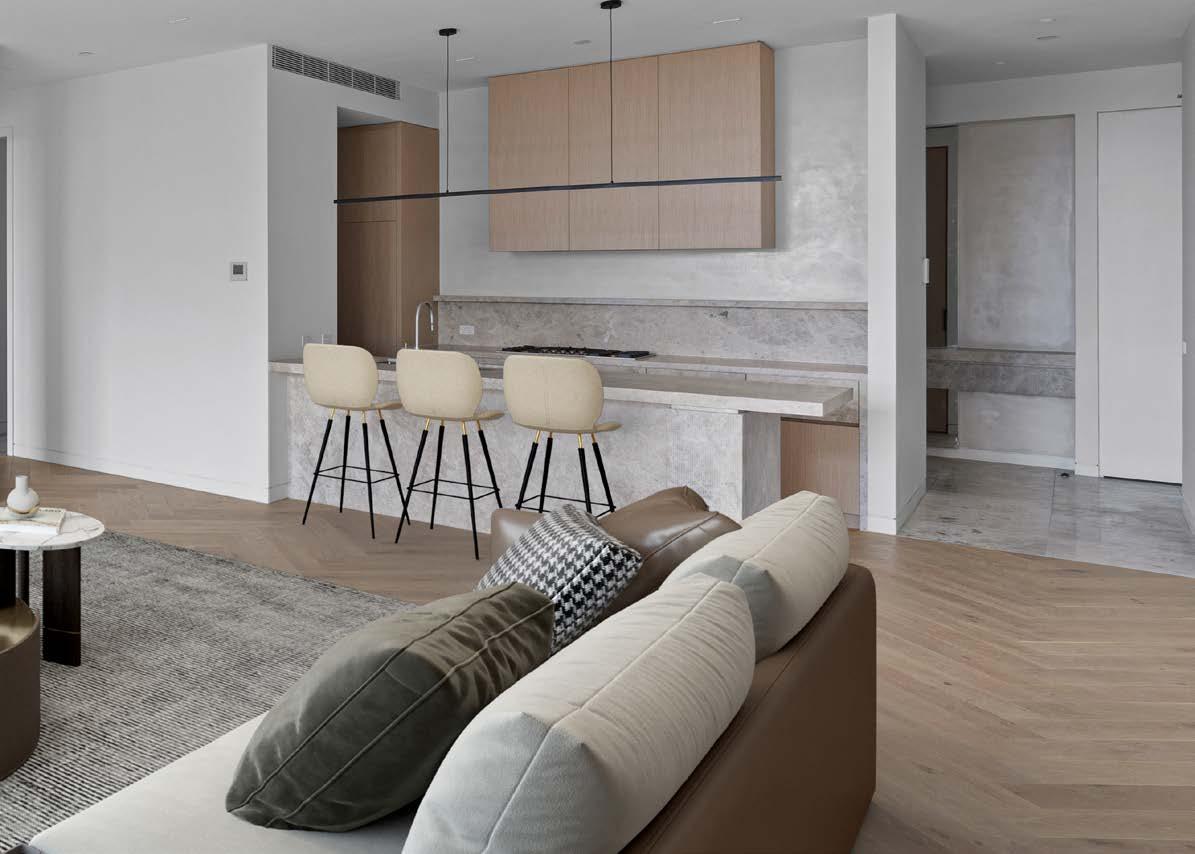
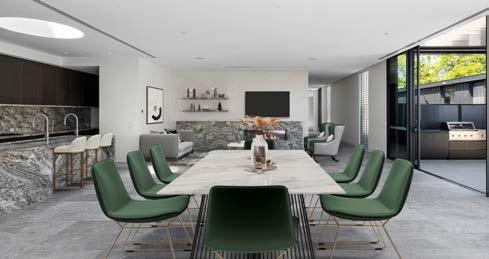
met the changing needs of the residences without delaying the project timeline.”
Modern, Sustainable Living with User-Centric Design
MHIAA systems prioritise user convenience and efficiency. All ducted systems are equipped with intuitive RC-EZX3A wallmounted controllers, offering streamlined operation for each resident. These systems allow for centralised management, ensuring optimal comfort while minimising energy consumption.
By addressing both technical challenges and design requirements, MHIAA delivered a comprehensive climate control solution that perfectly complemented the high-end nature of The Fellowship.
Beyond aesthetics and performance, sustainability was a guiding principle throughout the design and system selection process. Every choice was made with an emphasis on reducing environmental impact while maintaining exceptional efficiency. The KX Micro VRF systems were carefully selected for their superior energy efficiency thanks to the use of R32 refrigerant.
These innovative systems reflect MHIAA’s unwavering commitment to sustainable solutions by delivering outstanding heating and
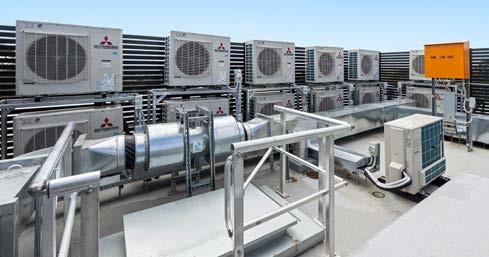
cooling capabilities with minimal energy consumption and ultra-quiet operation. This ensures not only comfort and performance but also a responsible approach to preserving the planet for future generations.
Setting a Benchmark for Excellence
The Fellowship stands as a testament to MHIAA’s ability to deliver bespoke climate control solutions for complex and high-profile projects. From innovative system design to seamless integration, the partnership with DP Heating and Cooling and The Fellowship’s design team has set a new benchmark for residential luxury in Melbourne.
As urban developments continue to raise the bar for comfort, sustainability, and design, MHIAA remains at the forefront, delivering solutions that enhance the living experience while maintaining environmental responsibility.
Understanding Acoustic Glazing
Specifying the best glass for noise reduction
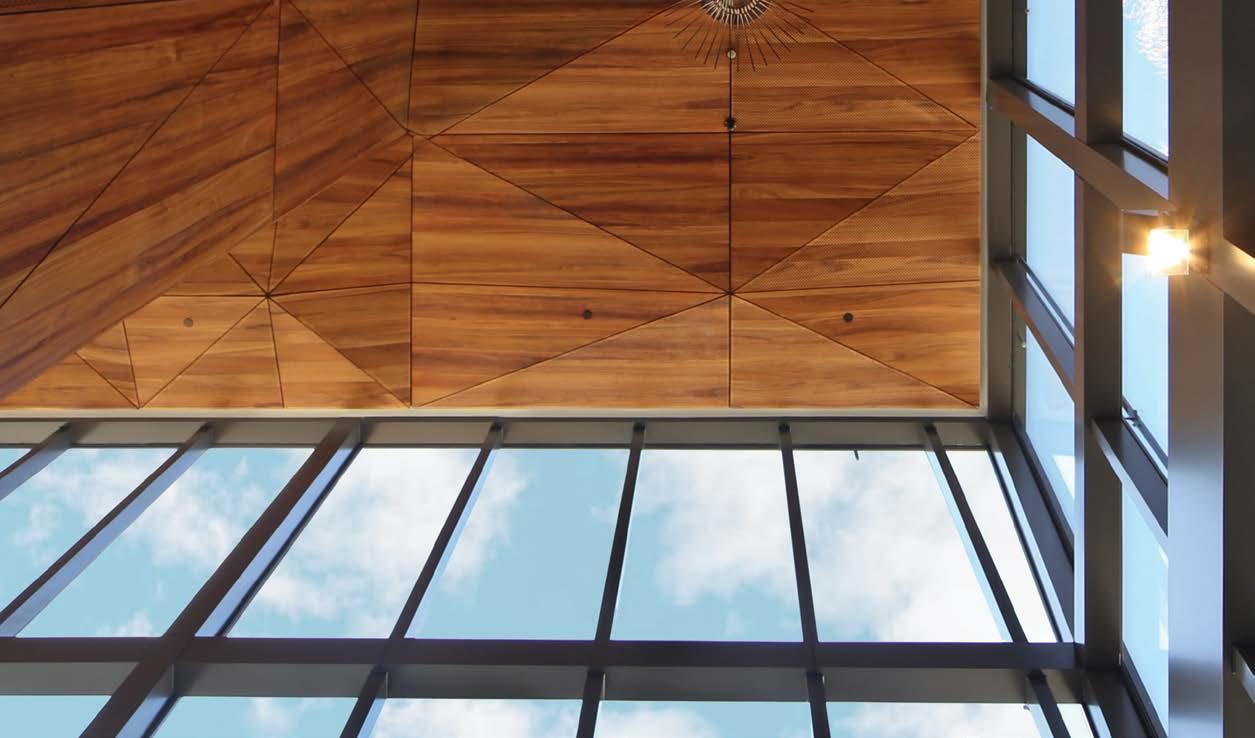
The ability to control external sounds in our homes, workplaces, hospitals and schools has gained importance due to modern lifestyles and the close proximity of these buildings to highways, airports, construction sites and industry. Among the many building materials and products that make up a structure, windows and doors have a big impact on how well the home or building is insulated from outside noise. With the wide range of glazing solutions available, understanding the differences between singleglazing, multi-layered glazing, laminated glass and high-performance acoustic glazing is essential.
Understanding Acoustic Glazing: Specifying the best glass for noise reduction explores the role of glazing in acoustic design and how different types of glazing products compare in terms of sound reduction performance. We highlight what makes acoustic glass a high-performance solution distinct from other forms of glazing. We also look at common misconceptions surrounding acoustic glass.
Australia’s leading brand of acoustic glass, Genuine Hush™ is highly specified and made exclusively by Oceania Glass™ Genuine Hush™ offers a range of quality performance acoustic glass that has been tested and certified. The Genuine Hush™ acoustic performance range comprises of QLam Hush™ and ComfortHush™ –two distinct yet complementary products suited to a wide range of applications and available in a choice of colours.
Download this whitepaper and learn why acoustic glass stands above the rest when it comes to sound reduction.
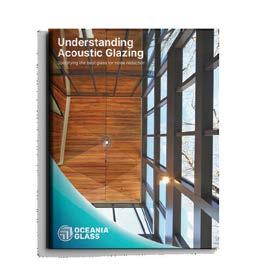
www.oceaniaglass.com.au/resources/white-papers/
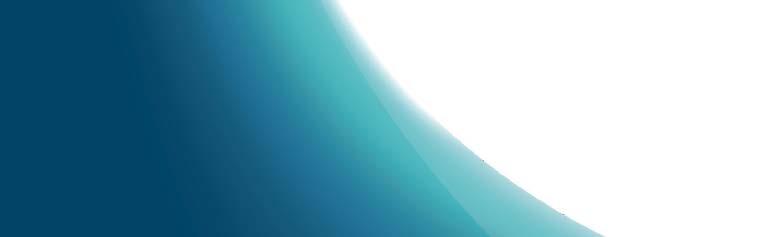
Our Range of Acoustic Glass is Made In Australia by Oceania Glass
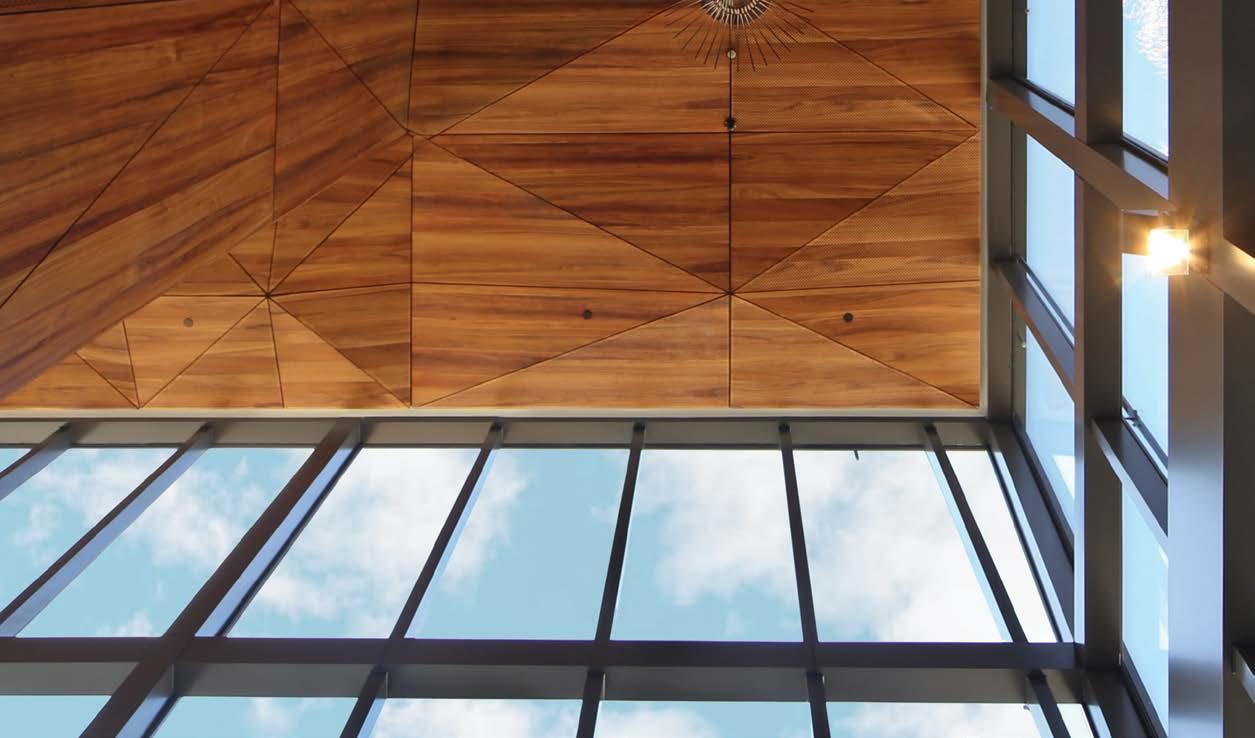
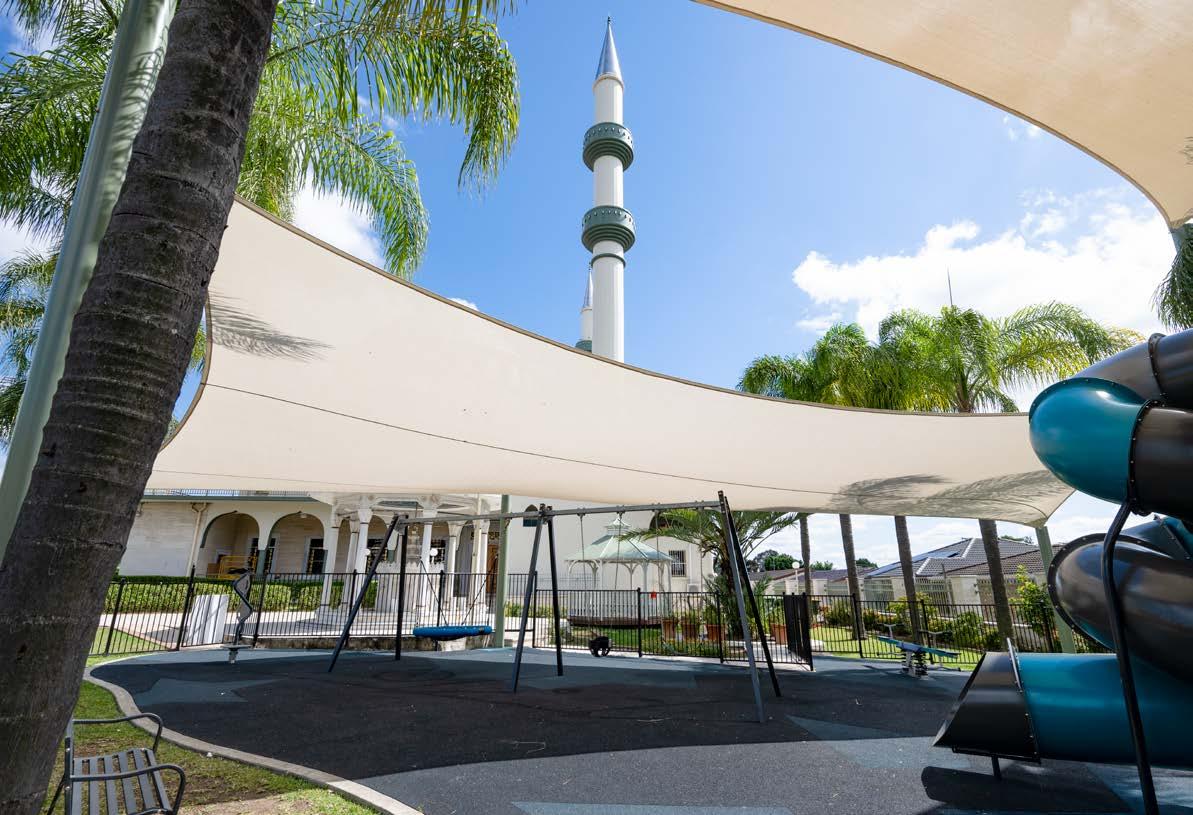
A COOL SOLUTION FOR THE AUBURN MOSQUE PLAYGROUND
Sydney Shade Sails recently completed an innovative shade sail installation at the Auburn Gallipoli Mosque, enhancing the children’s playground with a functional yet aesthetically pleasing design. The project, spearheaded by Managing Director Leonard Collins, is a testament to the company’s commitment to quality, customer service, and creating community-oriented solutions.
“The client needed to revamp the playground but didn’t have a clear vision of what they wanted,” Collins explained. “Our team designed a layered sail structure that not only provides vital shade but also complements the surrounding palm trees and environment.”
The playground, used daily by children, presented unique challenges. Softfall areas could reach over 50 degrees on hot days, posing safety risks. The solution involved strategically placed sails to ensure full coverage and UV protection, keeping the area cool and safe. “We considered design, height, and aesthetics to ensure the structure blended seamlessly with the mosque’s architecture,” Collins said, highlighting the pale eucalypt columns and cream sails chosen to harmonise with the outdoor aesthetic of the mosque.
The installation process was equally complex, requiring meticulous planning. “Accessing the site was a challenge,” Collins noted. “We had to lift columns over fences and navigate between palm trees without damaging tiles or other works. Safety and minimising disruption were


paramount, especially in this community space where prayer times and WHS risks had to be carefully managed.”
One standout feature was Sydney Shade Sails’ dedication to ensuring a complete process for the client. Although repair after cutting through existing softfall wasn’t part of their standard service, they coordinated with specialists to seamlessly restore the playground surface.
With this project, Sydney Shade Sails showcased its 25 years of industry expertise, delivering a durable, visually striking shade structure that serves the mosque’s vibrant community while embodying the company’s ethos of excellence and care.
For more information contact Sydney Shade Sails (NSW) Pty Ltd, 23 – 25 Norman Street, Peakhurst, NSW 2210, phone 02 9592 0401, email enquiries@shadesailsydney.net.au, website shadesailsydney.net.au
SETTING NEW STANDARDS IN CIVIL & CONSTRUCTION REINFORCEMENT SERVICES
Goldenlight Pty Ltd has firmly established itself as an innovator in Canberra’s construction industry, renowned for its mastery in reinforcement installation and dedication to sustainable practices. Among its standout achievements is the Woden Green development – a transformative project redefining urban living in the Woden Town Centre.
Hindmarsh Woden Green encompasses three architecturally stunning residential towers, housing 419 meticulously designed apartments, all harmonised with 3,000m² of lush green communal spaces.
The project exemplifies Goldenlight's unwavering commitment to quality, innovation, and environmental stewardship, setting a new standard for excellence in the region.
Goldenlight was responsible for overseeing reinforcement installation for critical structural components, including lift pits, footings, slabs, walls, columns, and stair cores. Their meticulous approach combined advanced techniques and a skilled workforce to ensure high-quality outcomes.
“We used specialised equipment and tools to tie, cut and bend reinforcement bars with precision, adhering strictly to engineering specifications,” said Alex Tumurbaatar, Goldenlight Director.
Regular inspections throughout the project allowed for immediate resolution of any discrepancies, maintaining the highest quality standards. This level of care not only secured the safety and durability of the structures but also elevated the overall execution of the Woden Green project,
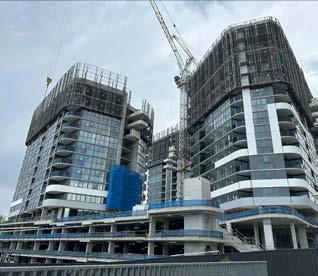
setting a benchmark for future developments in Canberra.
One of the standout achievements of Goldenlight’s involvement was the completion of their scope of work two months ahead of schedule. This remarkable milestone was attributed to efficient planning, task sequencing, and strong communication with subcontractors.
“By adopting lean construction principles and maximising productivity through concurrent tasks, we streamlined operations and minimised delays,” said Alex. “Our experienced team, led by skilled supervisors, ensured that the project progressed smoothly and met its deadlines.”
The early completion not only underscored Goldenlight’s reputation for reliability but also provided significant cost savings and allowed other project phases to advance ahead of time.
“Reinforcement installation remains primarily a labor-intensive task, we are committed to leveraging technological advancements and continuous skill development to optimise efficiency and quality,” said Alex. “By incorporating innovative tools and techniques, we aim to improve worker safety, and increase productivity.”
This ongoing focus on training and development ensures that their workforce stays updated with the latest industry practices, empowering them to deliver exceptional results.
Goldenlight focuses on minimising construction waste, including integrating accessory provisions into their services, such as bar caps, tie wires and spacers, to eliminate inefficiencies. Materials were carefully managed, and any spoil was repurposed for beneficial reuse, aligning with the company’s commitment to a circular economy.
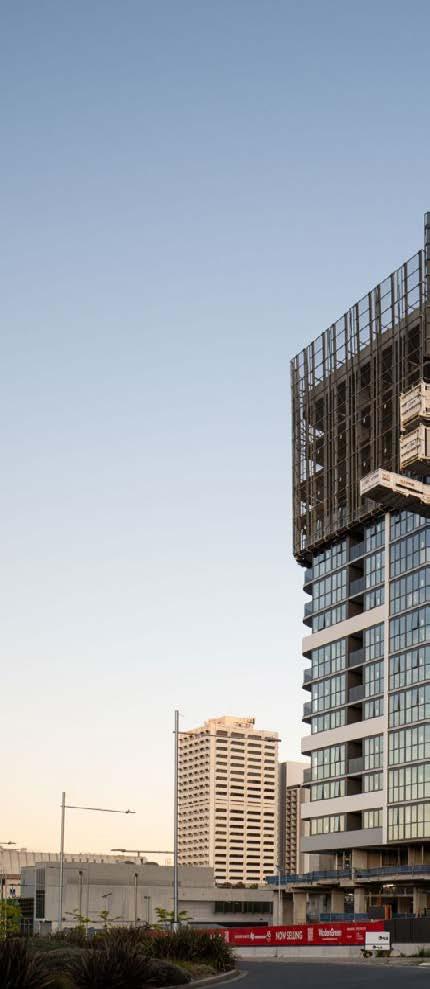
Their new package services, which supply and install their accessories, save lots of money and eliminate accessory wastage for their clients. Build369 Heather apartment project has already liked their packages.
Goldenlight consistently stays ahead of industry standards by incorporating cuttingedge tools and techniques. For the Woden Green project, they employed data-driven decision-making to track performance and optimise resource allocation. Additionally, their focus on workforce training ensures that team members remain well-versed in the latest industry practices.
“Our dedication to continuous improvement allows us to adapt to the unique challenges of each project,” Alex explained.
“By blending traditional methods with innovative approaches, we deliver solutions that are both practical and forward-thinking.” Goldenlight’s work on the Woden Green project is a testament to their expertise

and vision. As they continue to contribute to projects like the Heather Apartments in Dickson, they remain focused on quality, sustainability, and efficiency. Their innovative reinforcement services and eco-conscious practices position them as a trusted partner for contractors and developers across Canberra and beyond.
Through projects like Woden Green, Goldenlight Pty Ltd is shaping the future of Canberra’s construction landscape, delivering structural excellence while supporting a greener, more sustainable environment.
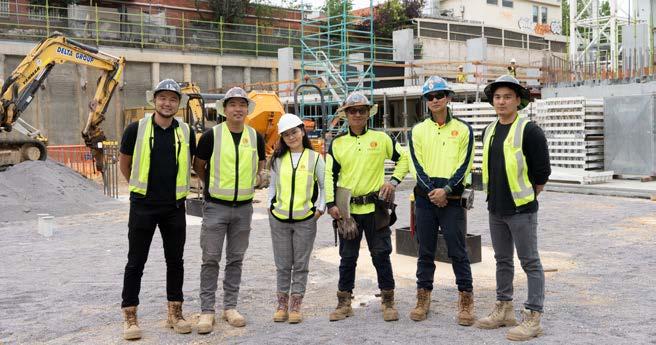
For more information contact Goldenlight, 490 Northbourne Avenue, Dickson ACT 2602, phone 0421 548 469, email alex@goldenlightcivil.com.au, website www.goldenlight.com.au.
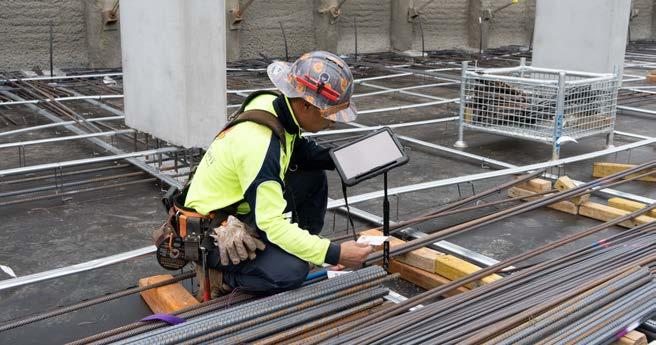
PAKENHAM’S TRANSFORMATION TO SMARTER TRANSPORT
The Pakenham Level Crossing Removal Project features a modernised Pakenham Station and the newly built East Pakenham Station, complemented by a 2.5km rail bridge. The upgrade includes an enhanced station forecourt, a bus interchange, dedicated pick-up and drop-off zones, street-level lifts, and a climate-controlled waiting room. Additional improvements expanded walking and cycling paths along the rail line, creating a seamless and sustainable transport experience.
The Pakenham Level Crossing Removal Project (LXRP) marked a significant achievement in improving transport infrastructure and safety in Victoria. As part of a broader initiative removing 110 level crossings by 2030, with 84 already gone, the Pakenham LXRP transformed the local community by reducing travel times and enhancing safety for pedestrians and drivers.
The $864 million project delivered a modernised Pakenham Station and a brand-new East Pakenham Station. It also involved the construction of a 2.5km rail bridge, an upgraded station forecourt, a bus interchange, and additional pick-up and drop-off zones. Alongside these improvements, the project created 450 new car parking spaces, secure bike storage, and new walking and cycling paths, providing a comprehensive upgrade to the area’s transport network.
“The rail bridge design and new stations improve safety, reduce road congestion, and create more than six MCGs of new open space for the Pakenham community to enjoy,” said an LXRP spokesperson.
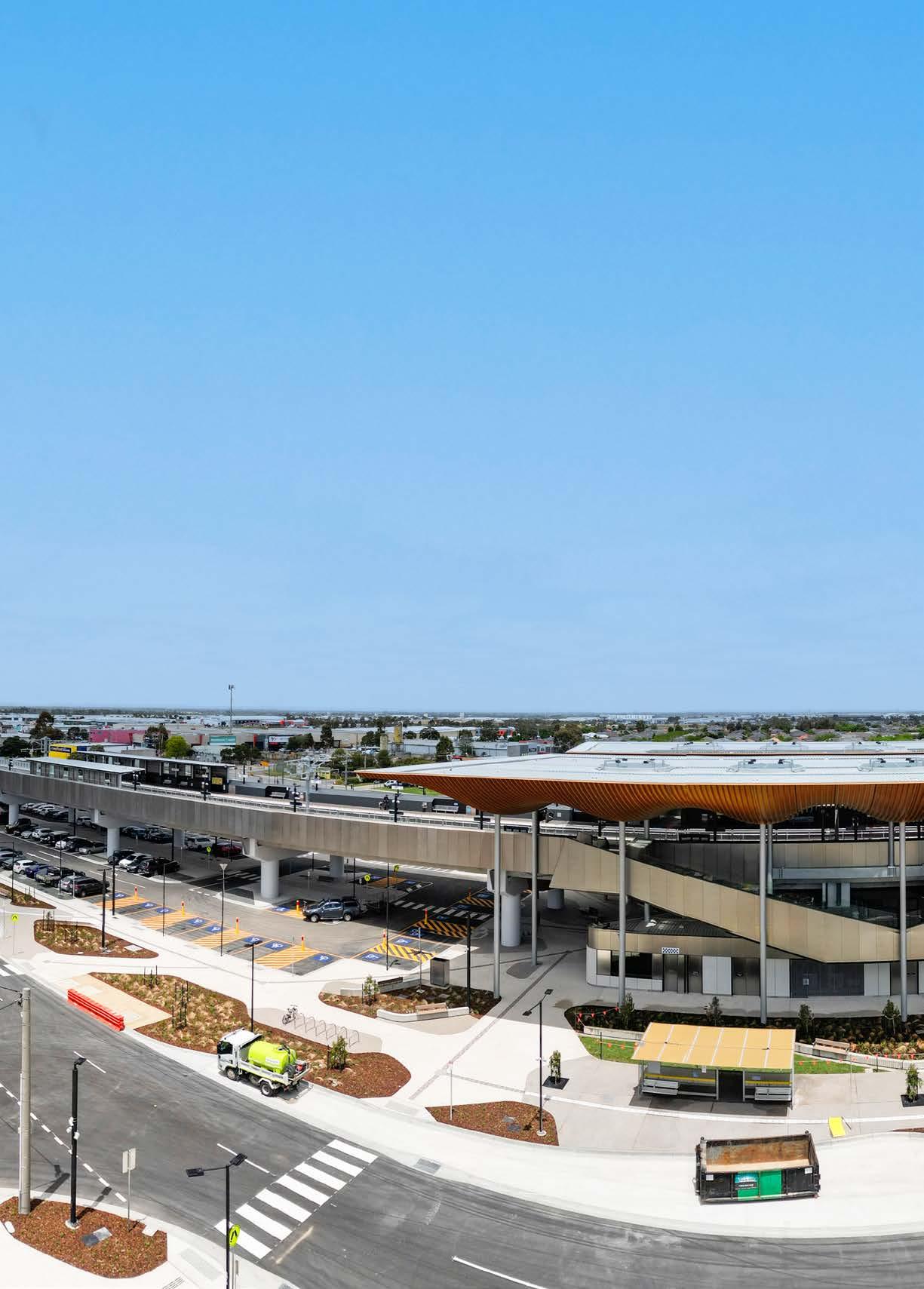
“The Pakenham LXRP was about more than just removing level crossings; it was about future-proofing the community by enhancing accessibility and safety,” said an LXRP spokesperson. “By upgrading the stations and improving infrastructure, we ensured that the area could support growth and provide a better commuting experience for everyone.”
The construction phase of the Pakenham LXRP focused on minimising disruption to commuters and residents. The centrepiece of the project was the 2.5km rail bridge, which elevated train tracks, allowing traffic to move freely underneath. This was complemented by the modernised Pakenham Station, which had been redesigned to accommodate growing passenger numbers and provide a more pleasant and accessible experience.
“One of our main goals was to ensure that the local community could continue with their daily routines with minimal impact during the construction period,” a LXRP spokesperson said. “We implemented
detailed planning and careful coordination with local authorities to manage traffic flow and ensure safety around the work sites.”
The community was invited to engage with the project throughout the construction period with opportunities to attend site tours, participate in information and online sessions, so residents could be involved at every stage.
Sustainability was a cornerstone of the Pakenham LXRP. The iconic roof of Pakenham Station exemplifies industry-leading innovation, integrating digital fabrication technology to reduce raw material use and incorporating an energy-efficient 27.6 kWh solar panel system. These panels save 37 tonnes of carbon emissions annually.
“At East Pakenham, we went a step further by using recycled-rubber kerbs in the station car park, capturing rainwater for reuse, and planting over 330,000 trees and shrubs across the project site,” said a LXRP spokesperson.
Like many large infrastructure projects, the Pakenham LXRP faced challenges, particularly in terms of coordinating the removal of multiple level crossings while ensuring that train services and road traffic could continue to operate smoothly.
The team worked closely with local businesses, residents, and other stakeholders to address concerns and keep the community informed
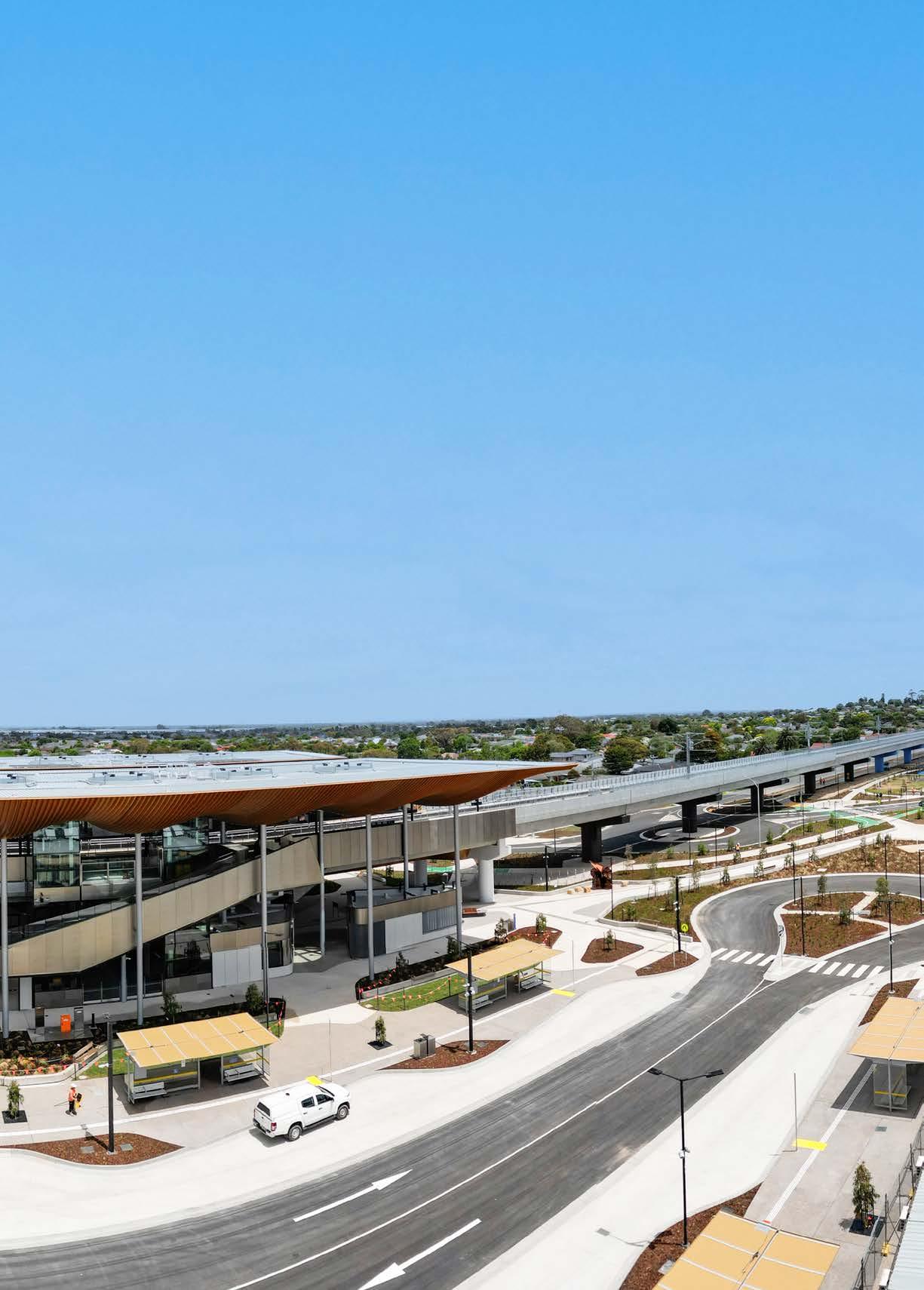
throughout the process. “Coordinating such a large project, especially in an area as busy as Pakenham, required us to be adaptable and responsive to changes,” a LXRP spokesperson noted. “The feedback from the community was invaluable, and it helped us make adjustments that kept the project on track.”
Now that the Pakenham LXRP is complete, the community is already reaping the rewards of this extensive upgrade. The removal of level crossings has significantly reduced congestion, cut travel times, and improved safety for pedestrians and drivers. The new and modernised stations, along with the added infrastructure, serve as a transport hub, supporting the area’s future growth and development.
The Pakenham LXRP was just one part of a wider effort to improve Melbourne’s transport network, but it stood out as a shining example of what could be achieved through thoughtful planning, innovation, and strong community collaboration.
“We’re proud of what’s been accomplished here,” said a LXRP spokesperson. “The Pakenham project left a lasting legacy that will benefit the local area for years to come.”
For more information contact Level Crossing Removal Project, website www.levelcrossings.vic.gov.au
CIRCULAR ECONOMY LEADERSHIP: SUSTAINABLE SOLUTIONS FOR
PAKENHAM LXRP
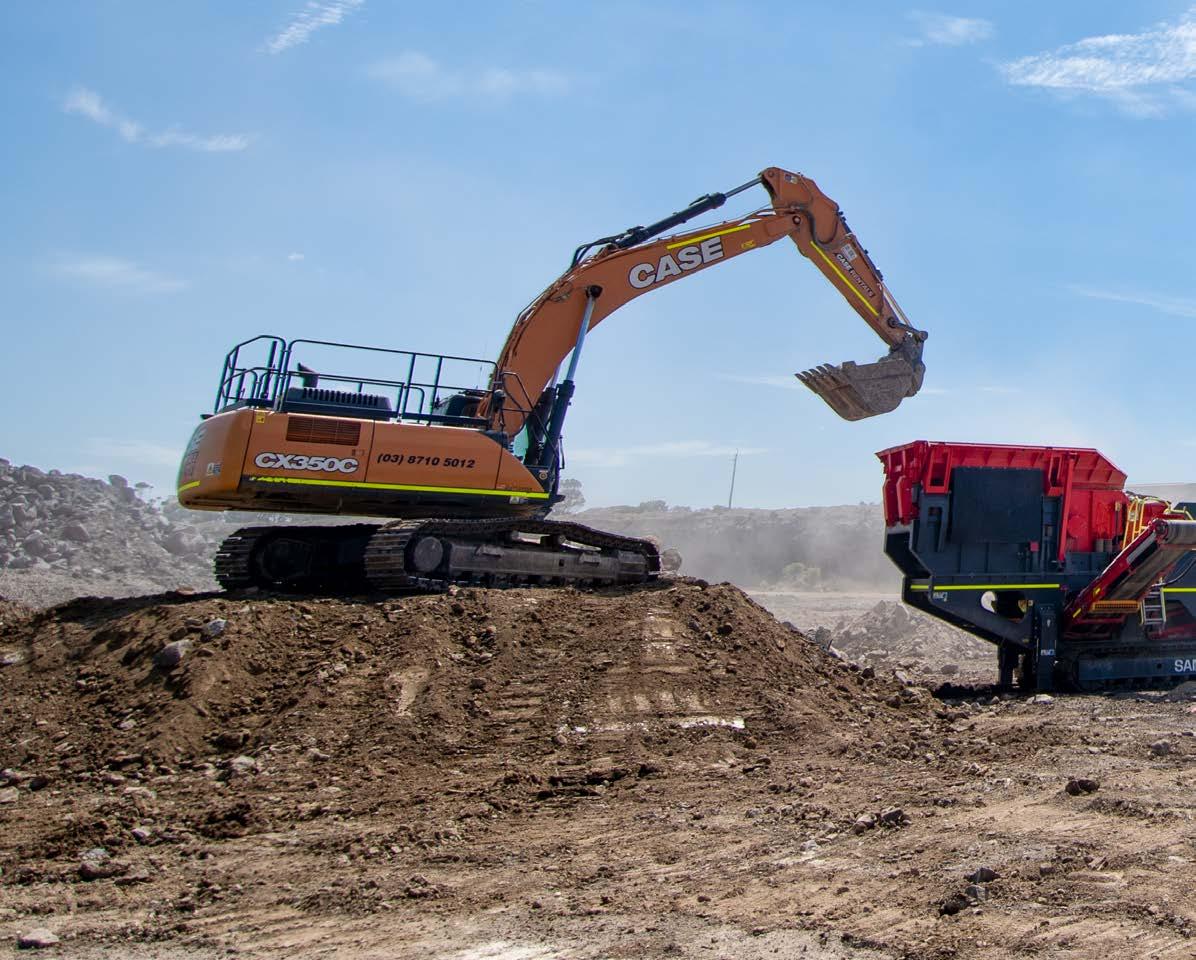
Lantrak, a leader in material management and plant hire, served as John Holland’s primary subcontractor on the Pakenham Level Crossing Removal Project (LXRP) for material disposal and truck hire. With decades of experience and a strong commitment to sustainability, Lantrak’s expertise was essential to the project’s success.
“Our goal was to ensure that every aspect of the bulk earthworks scope was handled efficiently, on schedule, and with minimal environmental impact,” said Rhys Tomlins, Lantrak’s Sales Manager.
Lantrak’s contributions included a comprehensive range of services essential to the project’s earthworks scope. These included onsite truck hire, haulage and disposal services, and material supply sourced from local quarries.
“Our involvement in this project speaks to the core of what Lantrak does best,” said Rhys. “By providing reliable and sustainable material and transport solutions, we were able to meet the project’s needs while upholding our environmental commitments.”
One of the primary challenges for Lantrak was providing a reliable disposal solution that could withstand Melbourne’s unpredictable weather. Lantrak leveraged its partnership with Barro Group, utilising their Nyora Quarry site as an all-weather disposal location. “This site was essential for maintaining the project’s timeline,” Rhys explains.
“The all-weather capabilities at Nyora ensured that material disposal could continue uninterrupted, even after heavy rainfall.”
Lantrak successfully navigated the challenge of the industry-wide truck shortage, which arose due to multiple large-scale infrastructure projects happening across Victoria.
“We made a conscious decision to avoid overextending our commitments to ensure that our fleet could meet the demands of the Pakenham project,” says Rhys. “This meant we were able to provide reliable, daily support without compromising quality or delivery.”
The scale of Lantrak’s involvement was significant, particularly during peak periods of the project. The company utilised a fleet of fully compliant rail-specified Tandem Tippers, alongside 3- and 4-axle PBS Truck and Trailer combinations. At peak, Lantrak supplied over 40 truck and trailer units, along with 25 tandems, each day.
“This level of deployment was crucial to maintaining the pace of the project,” said Rhys.
Lantrak’s role in the Pakenham LXRP aligns with its broader commitment to sustainability and material reuse. Through its Circular Economy initiative, Lantrak diverts materials from landfills, repurposing them for beneficial projects.
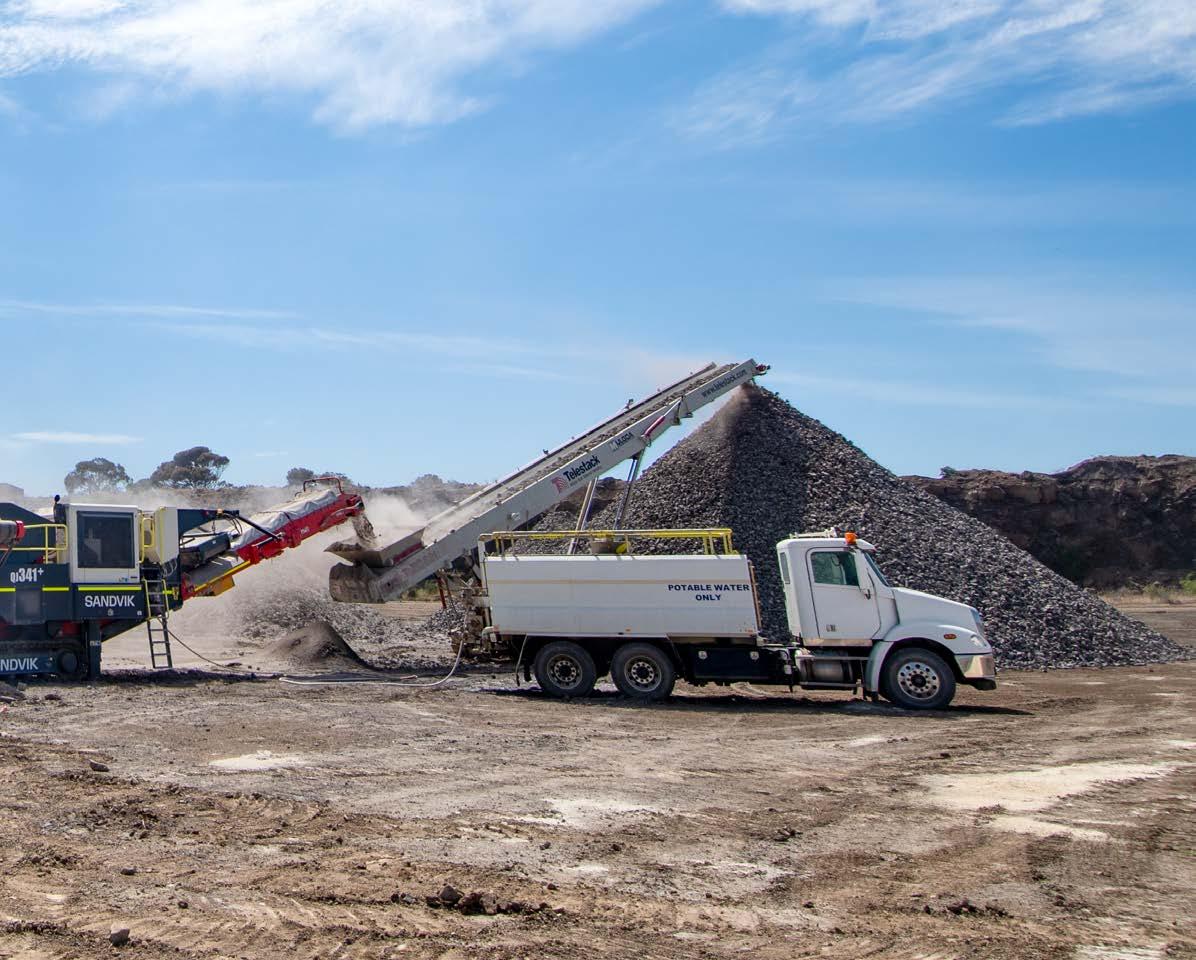
“We’re leaders in the reuse of raw materials, and we repurpose spoil from various infrastructure projects across Melbourne,” explained Rhys. The spoil from the Pakenham project, for example, contributed to the rehabilitation of an exhausted quarry hole at Nyora Quarry.
“Our disposal solution at Nyora serves a dual purpose. It enables us to assist in large-scale infrastructure while also supporting land rehabilitation, which is a key component of our sustainability efforts.”
Lantrak’s dedication to innovation is further exemplified by its Lantrak 360 initiative, launched at the Lysterfield Transfer Station during the Pakenham LXRP. This facility accepts mixed fill and inert waste materials, which are then sorted, screened, and recycled. This approach not only minimises waste but also contributes to a more sustainable model of material management, aligning with the company’s commitment to environmental responsibility.
Since its establishment as a transport cooperative in 1959, Lantrak has supported some of Australia’s most iconic infrastructure projects, including the Snowy Mountain Scheme, Homebush Bay Olympic Stadium, and the New Royal Children’s Hospital. With a history that spans more than six decades, Lantrak has grown into one of Australia’s largest material management and plant hire businesses, annually moving over 20 million cubic metres of clean and structural fill.

“Lantrak has an unrivalled reputation for delivering material and plant hire solutions that prioritise sustainability and efficiency,” says Rhys. “We’re proud to continue that legacy with projects like the Pakenham LXRP.”
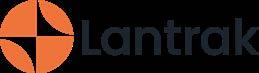
For more information contact Lantrak, 18 Dansu Court, Hallam VIC, phone 13 9666, email info@lantrak.com.au, website www.lantrak.com.au
Below Lantrak a trusted material management and plant hire expert, delivering sustainable solutions for Pakenham LXRP bulk earthworks success.
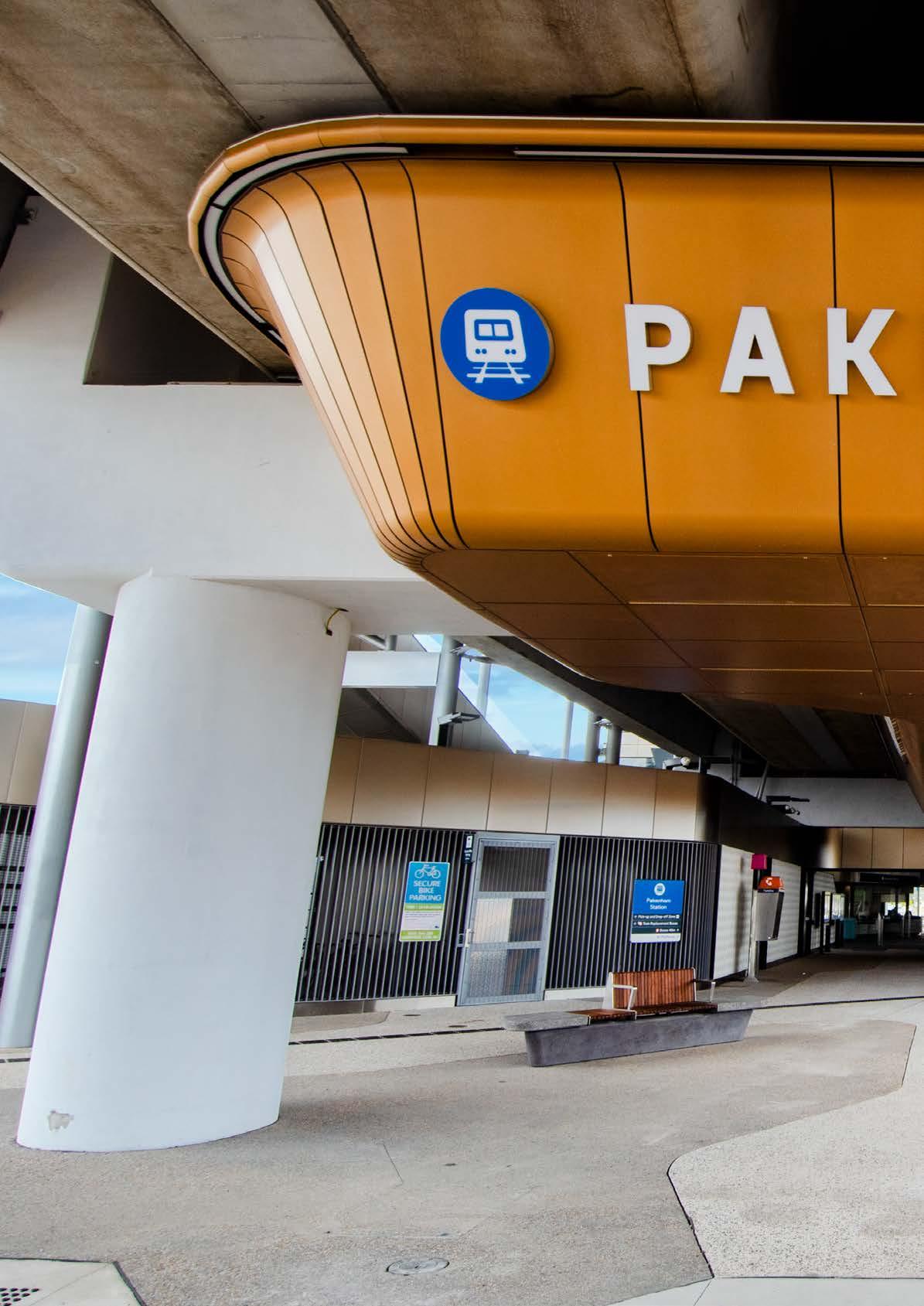

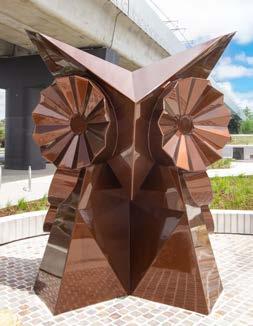

Below Daly’s Constructions provides expert design, civil works, cable installation, jointing, and terminating services for energy infrastructure projects.
WATT IT TAKES: FROM DEISGN TO DELIVERY
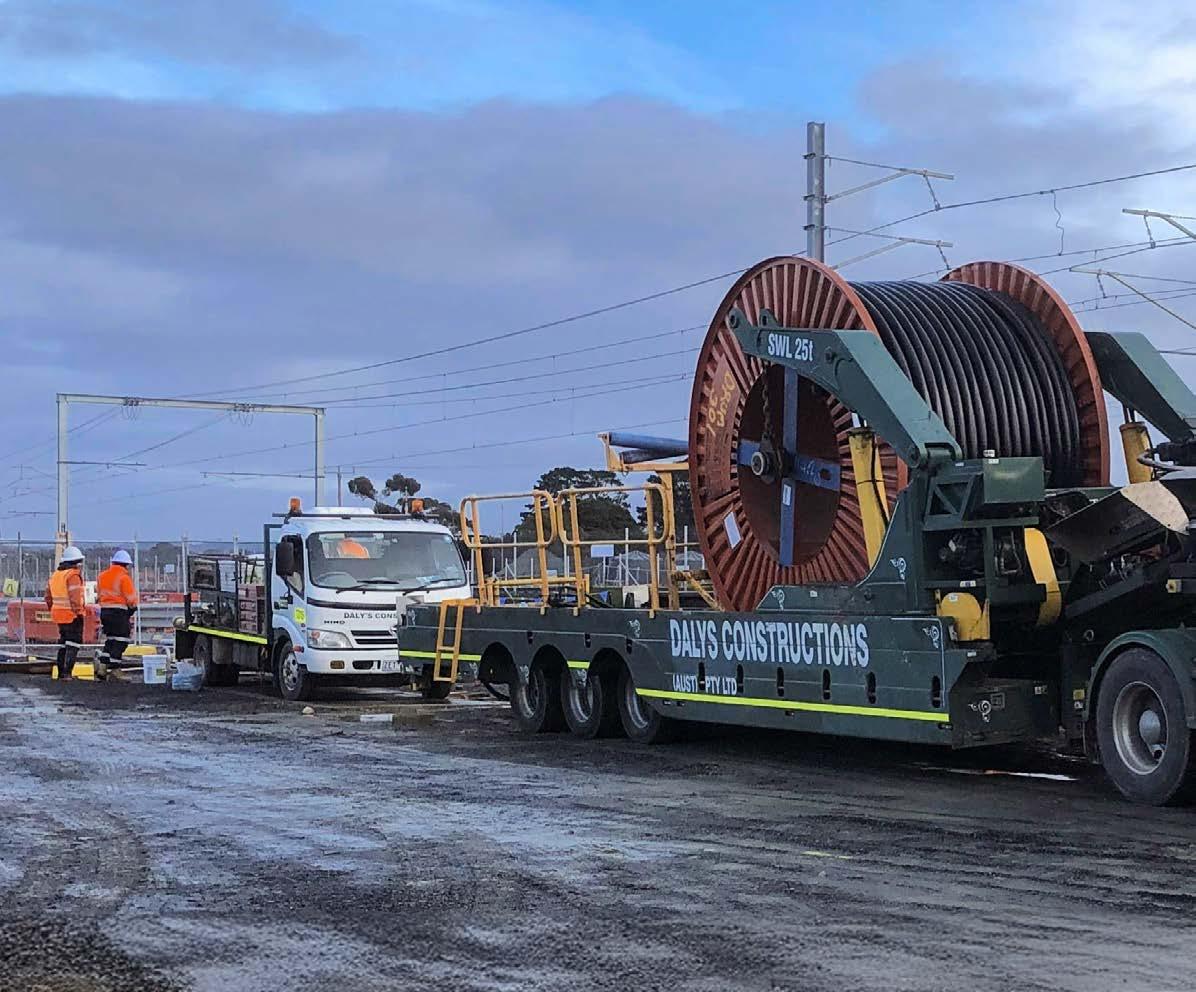
Daly’s Constructions, a family-owned and operated business with a 52-year legacy in the energy infrastructure industry. Daly’s expertise proved invaluable in navigating the complexities of the Pakenham Level Crossing Removal Project (LXRP)
“We provide specialist design, civil works, cable installation, jointing and terminating services to the energy infrastructure industry across Australia and New Zealand, specialising in major sub-transmission and transmission design and construct underground projects,”
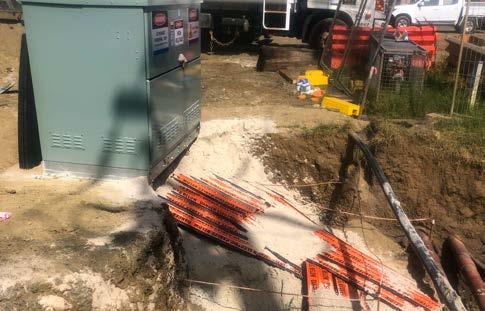
said Alex Anderson, Operations Manager at Daly’s Constructions.
The Pakenham LXRP demanded meticulous planning and execution to ensure minimal disruption to existing infrastructure and services. Daly’s Constructions rose to the occasion, contributing a team of 20 skilled professionals from their overall workforce of 100.
Their specific tasks included the crucial relocation of electrical assets.
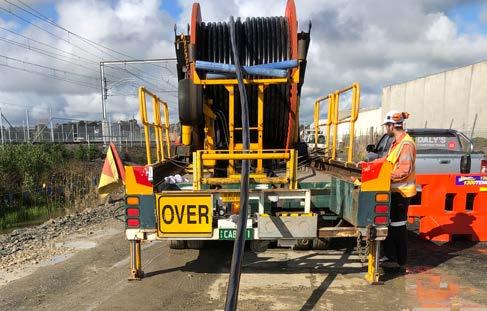
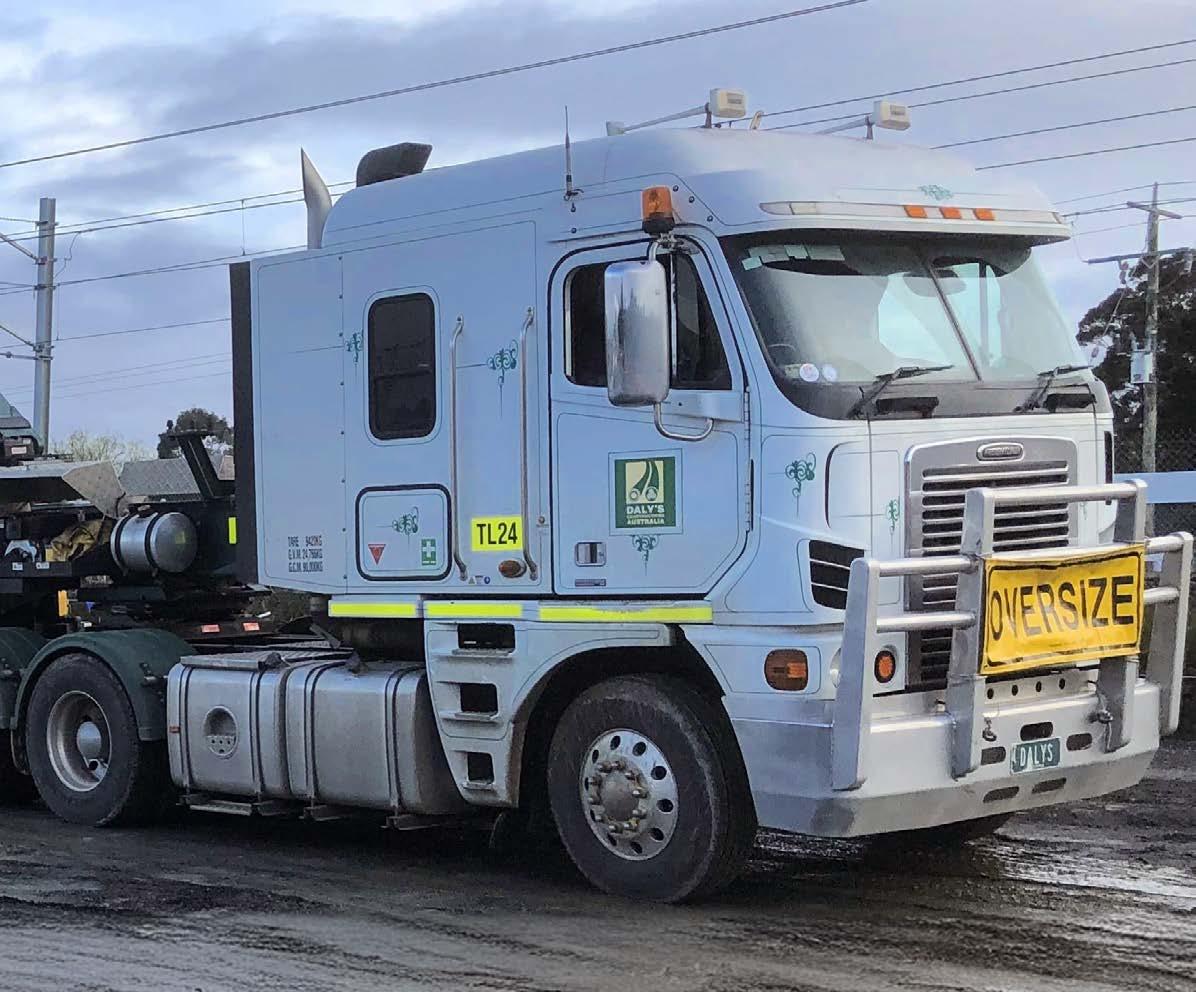
“We relocated high voltage and low voltage AusNet Services electrical assets to enable the LXRP and corresponding rail works to proceed,” Alex said.
Further demonstrating their comprehensive capabilities, Daly’s Constructions also undertook an upgrade of the rail corridor’s high-voltage underground cables. This involved not only replacing outdated infrastructure but ensuring its seamless integration with the broader LXRP network. “Multiple crews had to be coordinated across various work fronts in close cooperation with NWPA and AusNet Services,” Alex said, emphasising the collaborative nature of the undertaking.
While Daly’s Constructions didn’t deploy any entirely new products on this project, their success lay in their adept application of existing technologies and their commitment to safety and quality. Their long-standing reputation is built upon a strong value system prioritising these element.
“Our company has a strong value system based on principles that include commitment to safety, quality of service, integrity in our relationships and client satisfaction,” Alex said. This commitment has translated into a record of consistent, high-quality workmanship.
The Pakenham LXRP is just one example of Daly’s Constructions’ broad portfolio of significant projects across Australia and New Zealand. Their expertise is currently contributing to a wide range of initiatives, reflecting their leading position in the industry.
“We’re currently working on the North East Link (NEL), Suburban Rail Loop (SRL), West Gate Tunnel Project (WGTP), other LXRP projects, the Melton Renewable Energy Hub, and design and construction of sub-transmission supplies to power new Data Centres,” Alex said, highlighting the scope and diversity of their involvement in shaping critical infrastructure across the country.
Daly’s Constructions’ contribution to the Pakenham LXRP showcases their ability to successfully manage complex, large-scale projects. Their expertise in underground electrical infrastructure, combined with their unwavering commitment to safety, quality, and client satisfaction, solidifies their reputation as a reliable and capable partner for future major infrastructure projects.
For more information contact Daly’s Constructions, 20-26 Cyanamid Street, Laverton North VIC 3026, phone 03 9360 9485, email cable@daly.net.au, website www.dalysconstructions.com.au
BREAKING GROUND, NOT PIPES: NDD IS A GAME-CHANGER FOR COMPLEX PROJECTS
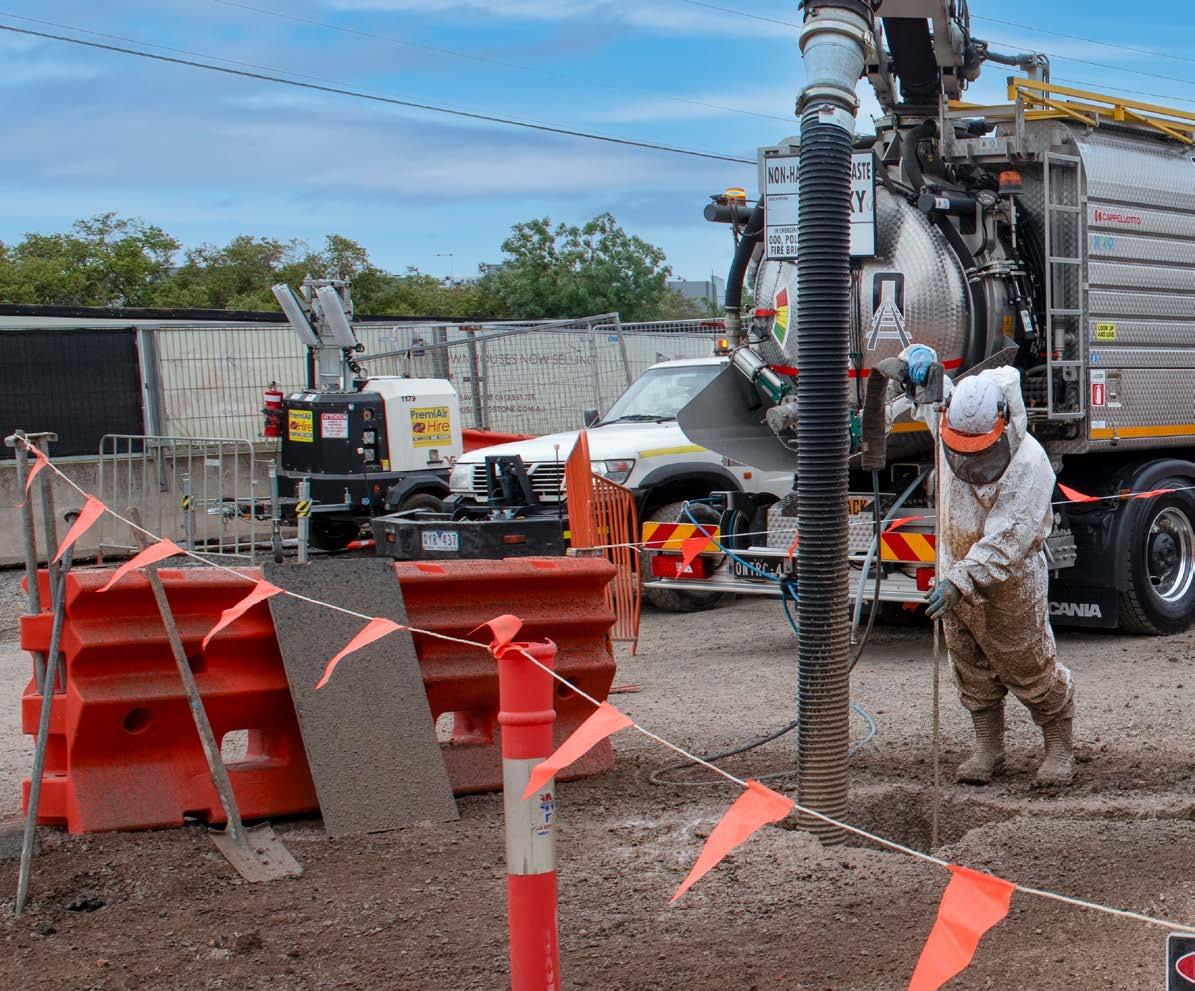
Enhancing project efficiency and safety, Ontrack Excavation Group has become a vital partner in the Pakenham Level Crossing Removal Project (LXRP) through its expertise in Non-Destructive Digging (NDD) and excavation services.
The family-owned, company has over three years of industry experience and is known for delivering customer-focused solutions using cutting-edge technology, reliability and safety. Ontrack Excavation Group’s commitment to excellence makes them a top choice for complex infrastructure projects across Australia
For Ontrack Excavation Group, one of the primary tasks was navigating the complex network of underground utilities while ensuring that all services were preserved during excavation. Their use of NDD was pivotal in overcoming these challenges, enabling them to carry out the work without the need for extensive manual digging, thus reducing the risk of accidental damage and project delays.
“With our state-of-the-art vacuum trucks, we were able to carry out the job without disturbing the critical services already in place. It’s what makes NDD such a game-changer for projects like Pakenham,” said Hasan Yalcin, Director of Ontrack Excavation Group.
The efficiency of their operations also contributed to the overall project timeline, allowing other contractors to proceed with construction activities promptly. By providing clear service identification and drain cleaning, Ontrack Excavation Group helped streamline the integration of new installations, including utilities, transport infrastructure, and public amenities.
“Working on a project like Pakenham requires precision and teamwork. We knew that every day our efficiency was helping to keep the project moving forward,” added Hasan.
With a team of 15 skilled professionals, including 12 who were directly involved in the Pakenham project, Ontrack Excavation Group successfully delivered services that met the project’s stringent safety and operational standards. “Our team’s expertise, paired with the best equipment, allows us to tackle complex projects with confidence. We’ve always been committed to investing in the latest technology to ensure the job gets done right,” explained Hasan.
Safety and efficiency are at the core of Ontrack Excavation Group’s operations. Throughout the Pakenham project, the team adhered to strict safety protocols, ensuring that all work was performed with
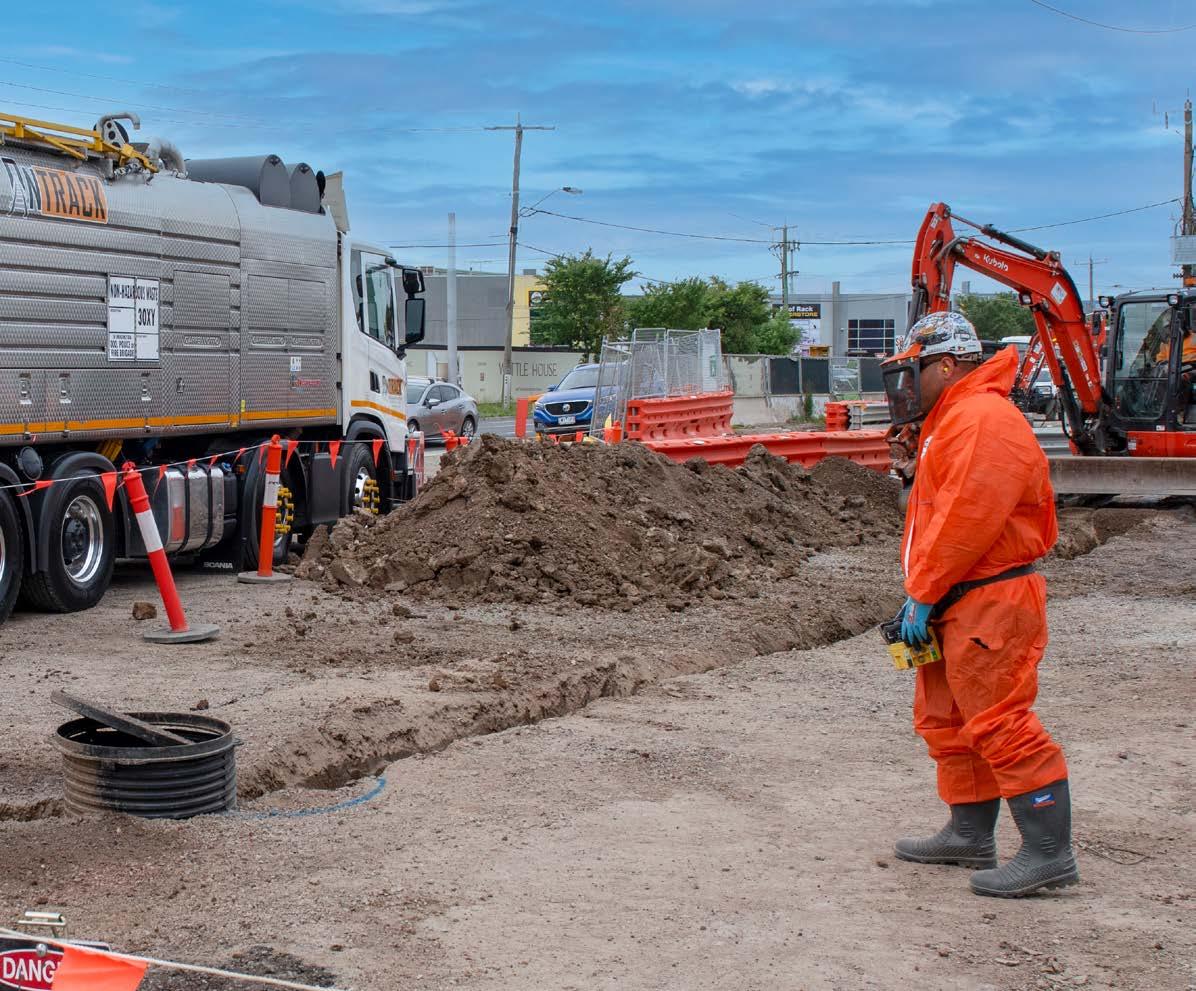
minimal risk to the public, their workers, and the environment. Their specialised fleet of vacuum trucks enabled precise, clean excavations, which was critical in maintaining the safety and cleanliness of the site, especially in areas with high foot and vehicle traffic.
The success of Ontrack Excavation Group’s involvement in the Pakenham LXRP underscores their capabilities in managing large infrastructure projects. Their recent projects, including the Tram Maintenance Facility (TMF) in Maidstone and the Suburban Rail Loop (SRL), demonstrate a continued expansion in scope and capability, reinforcing their position as a leader in the industrial services sector.
“We’re proud of the work we’ve done at Pakenham, and we look forward to bringing our expertise to future projects. Our mission is to keep pushing boundaries, always striving to deliver the best,” said Hasan.
For more information contact Ontrack Excavation Group Pty Ltd, phone 0499 654 865, email info@ontrackexc.com.au, website www.ontrackexc.com.au
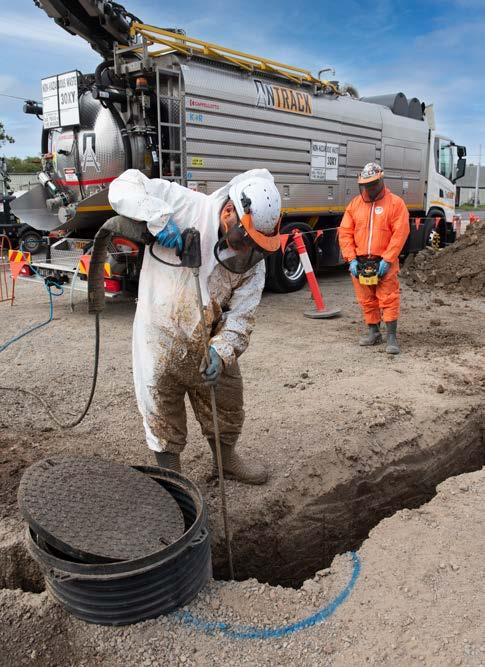
Below Ontrack Excavation Group excels in NonDestructive Digging, enhancing safety and efficiency in Australian infrastructure projects.
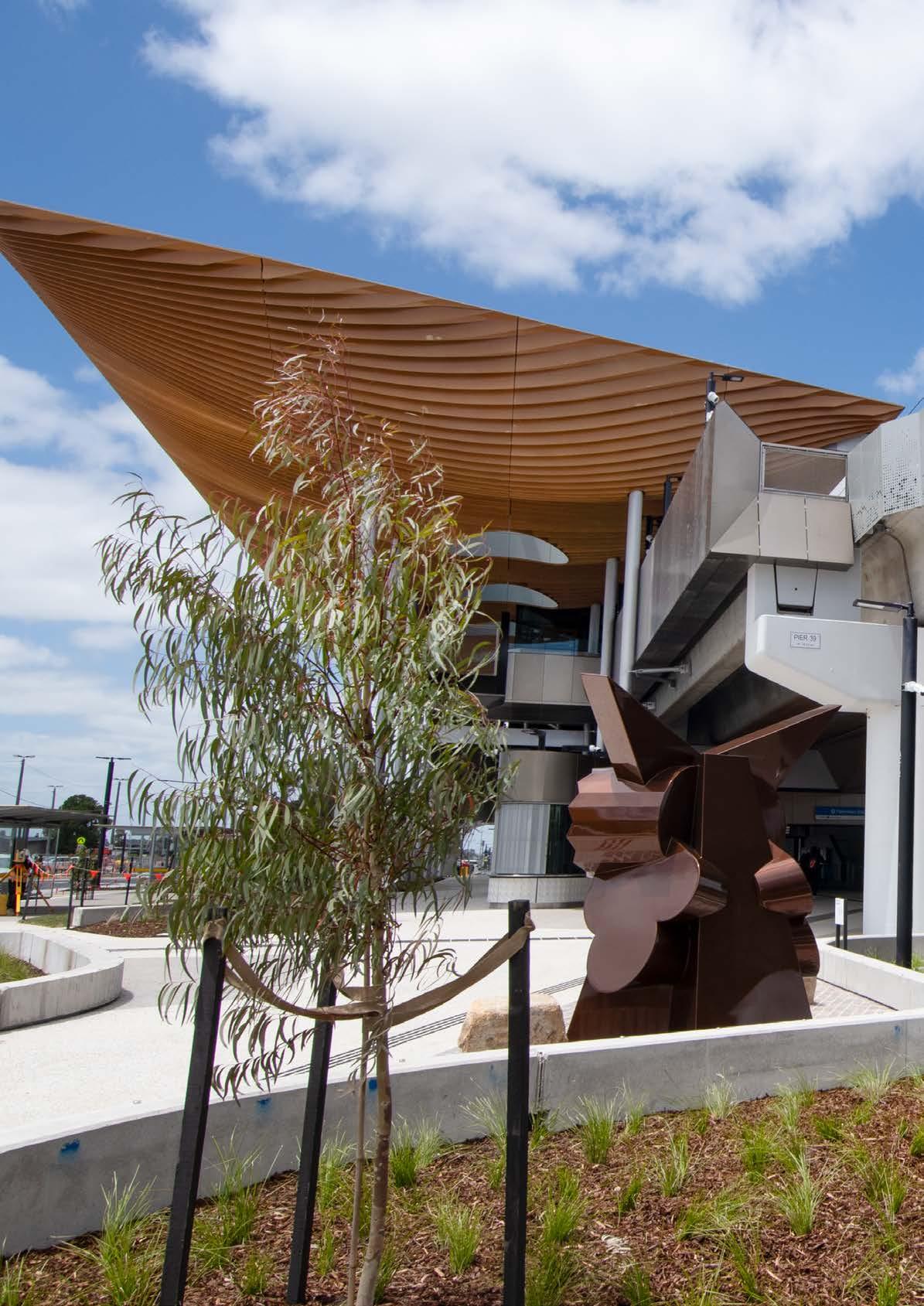
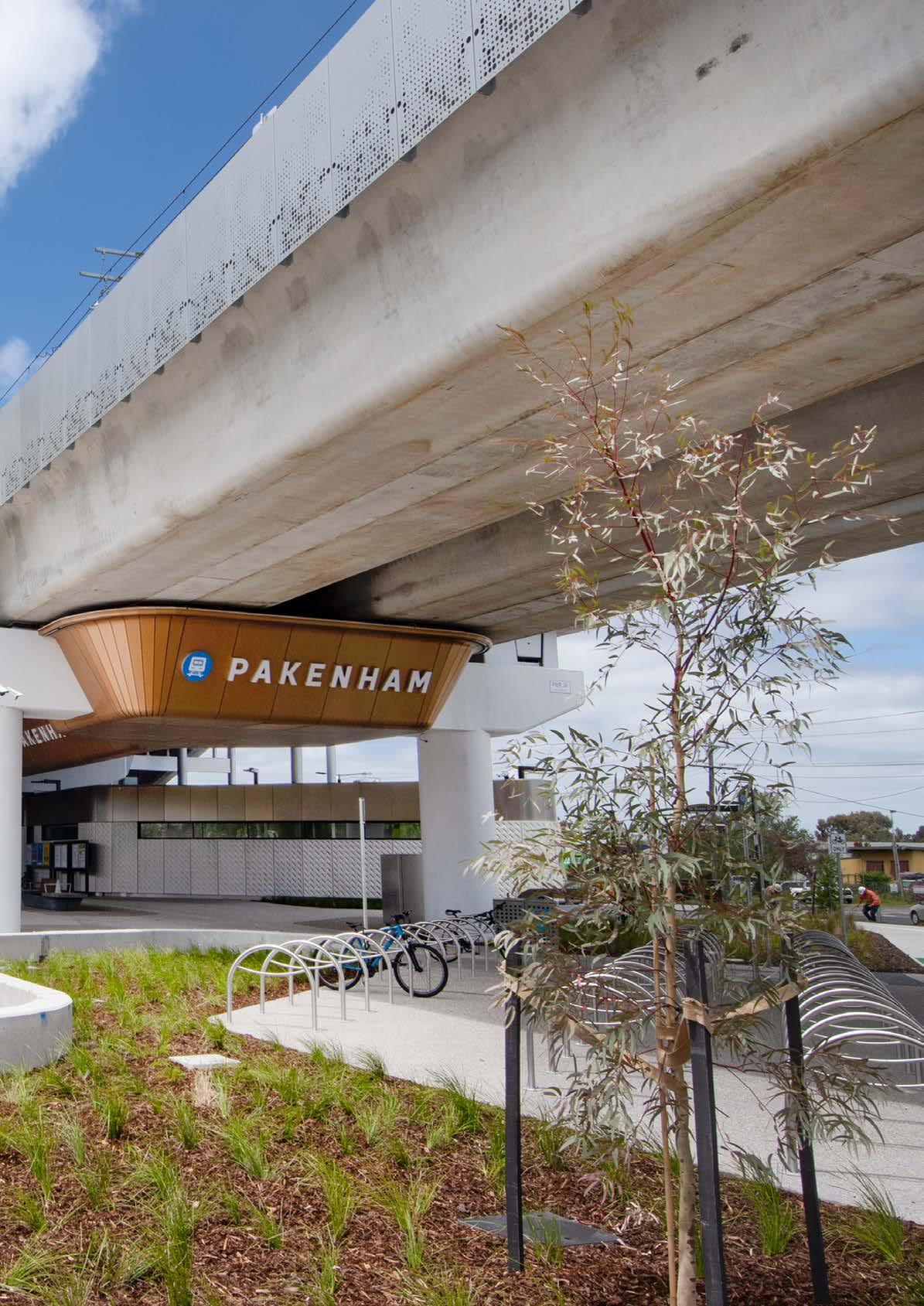
A FRESH PERSPECTIVE ON RETIREMENT LIVING
The Bert Newton Retirement Village in Highett, Victoria, offers luxurious living for 250 residents. With independent apartments, assisted living, and a care center, it provides seamless aged care. Amenities include a café, bar, pool, and cinema. Developed by Ryman Healthcare, it reflects innovation, quality, and a holistic approach to care.
Ryman Healthcare, a leader in retirement living and aged care, has successfully completed construction of its prestigious Bert Newton Retirement Village in Highett, Victoria.
This luxurious development showcases Ryman’s commitment to innovative design, exceptional resident services, and a holistic approach to aged care, offering a continuum of care within a single, vibrant community. The project highlights not only Ryman’s dedication to quality but also its resilience in navigating unforeseen challenges.
The Bert Newton Village provides a diverse range of accommodation options, catering to individual needs and preferences. From fully independent apartments to serviced apartments offering assisted living, and a 79-bed care centre providing low care, high care, and specialist dementia care, residents can seamlessly transition within the village as their needs evolve. This ‘continuum of care’ model is a cornerstone of Ryman’s philosophy, ensuring residents can age in place with dignity and support.

“From assisted living services and specialist care to fully independent apartments and resort-style amenities, the Ryman model empowers residents to design their own retirement experience and ensures no one is left behind,” said Andrew Moulding, Design Practice Lead Australia.
This philosophy is reflected in the village’s extensive amenities, creating a self-contained hub for recreation, relaxation, and social interaction. Residents enjoy access to a café, bar, shop, hair and beauty salon, workshop, craft room, billiard room, library, swimming pool, spa, and gym.
For aged care residents, dedicated lounge and dining areas and tranquil outdoor spaces provide comfortable and supportive environments. The inclusion of specialised dementia care further underscores Ryman’s commitment to providing comprehensive, tailored services.
Commencing in mid-2020, the onset of the COVID-19 pandemic introduced unforeseen logistical hurdles. Ryman and its construction
teams swiftly adapted by implementing rigorous safety protocols and revising project timelines to address labor shortages and evolving trade contractor availability. Adding to the complexity, Ryman also had to navigate unpredictable weather conditions.
The project team leveraged the versatility of precast concrete, incorporating textured form liners to introduced intricate patterns and visual depth to the surfaces, while satin finishes provided a sleek and refined aesthetic, without the need of additional materials or trades. The result is a visually striking and cost-effective solution.
The final development comprises 209 residential units: 85 independent apartments, 45 serviced apartments, and a 79-bed care centre. The design seamlessly blends luxury with practicality, providing residents with spacious, comfortable accommodations and access to a full range of amenities within a beautifully landscaped setting.
Ryman’s origins are rooted in a commitment to raising the standards of aged care. In 1983, co-founder Kevin Hickman envisioned a different model of care. His experience, coupled with his business partnership
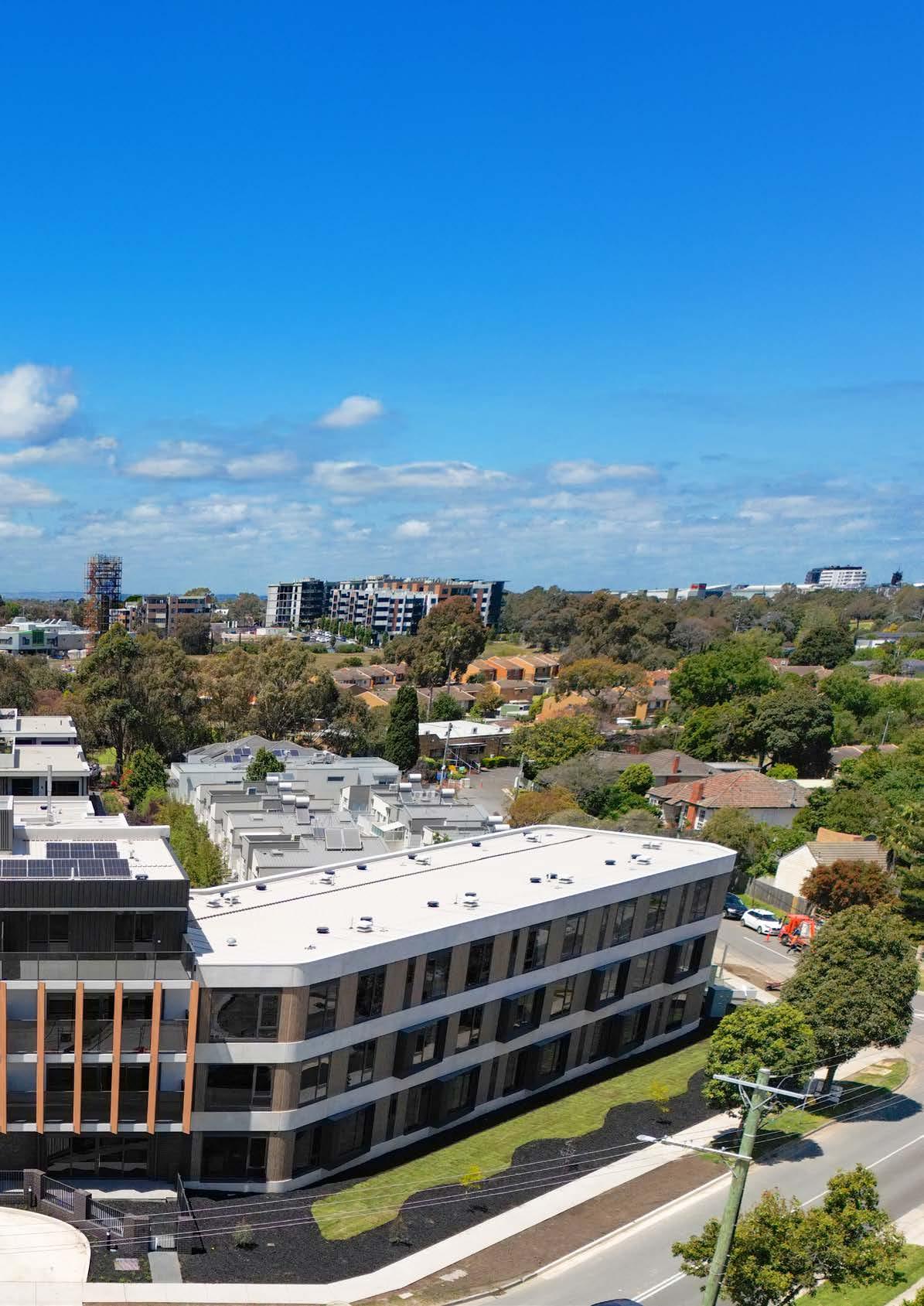
with John Ryder, led to the creation of Ryman Healthcare, built upon the philosophy of providing ‘single rooms with ensuites’, and a higher standard of living.
The Ryman recipe, established decades ago, remains effective: prime locations, meticulous design and construction, and an unwavering dedication to excellence. Today, Ryman Healthcare operates 49 retirement villages across Australia and New Zealand, providing exceptional care and support to over 14,000 residents.
The Bert Newton Retirement Village stands as a testament to this legacy, exemplifying the company’s commitment to creating thriving communities where residents can enjoy a fulfilling lifestyle, complete with peace of mind and security.
Construction of additional apartment blocks continues, further expanding the village's capacity and solidifying Ryman Healthcare’s position as a leader in the aged care sector.
For more information contact Ryman Healthcare, phone 1800 288 299, website www.rymanhealthcare.com.au
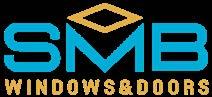
A LEGACY OF EXCELLENCE IN THE CONSTRUCTION INDUSTRY
SMB Windows, a fourth-generation family business, has been a cornerstone of the glass and window industry. With roots deeply embedded in craftsmanship and innovation, the company began its Melbourne operations in 2016. Since then, SMB Windows has successfully delivered over 500 projects across Australia’s commercial and residential construction sectors.
Notable projects include the Quarantine Centers in Melbourne, Brisbane, and Perth for Multiplex, Modscape, and Ausco for the Health Sector, Melbourne University’s B63 refurbishment with Shape for the Education Sector, and the Munro Library upgrades with Buildcorp, also the for the Education Sector. Additional highlights include AOD Rehabilitation Centers across regional Victoria and the prestigious Bert Newton Retirement Village for Ryman Healthcare.
Specialising in:
• Aluminium thermally broken and non-thermally broken windows and doors
• Skylights
• Glass and aluminium louvers
• Glass balustrades
• Aluminium and metal shrouds
• Frameless glass shower screens
A recent milestone, the Bert Newton Retirement Village, exemplifies SMB Windows’ commitment to enhancing Australian communities with cutting-edge and sustainable living solutions.
The Bert Newton Retirement Village is a large-scale project consisting of a commercial building and three residential buildings. With over 230 apartments and more than 1,000 windows and doors, SMB Windows’ involvement spanned two years, during which they provided a high degree of customisation to meet specific design, environmental and energy standards.
SMB prides itself on using innovative designs to meet project needs. For the Bert Newton Retirement Village, they provided AWS (Architectural Window Systems) thermally broken windows and doors equipped with double-glazed LowE glass (AGG Insulglass LowE Plus® - Grey), ensuring excellent thermal performance and energy efficiency. The doors also included automatic sliding systems, enhancing accessibility and ease of use for residents.
“Our windows and doors are fabricated locally, which not only supports the local economy but also ensures quality control and sustainability,” said Dawoodjee.
The use of LowE glass in combination with thermally broken frames allows for reduced heat transfer, maintaining comfortable indoor temperatures without excessive energy use.
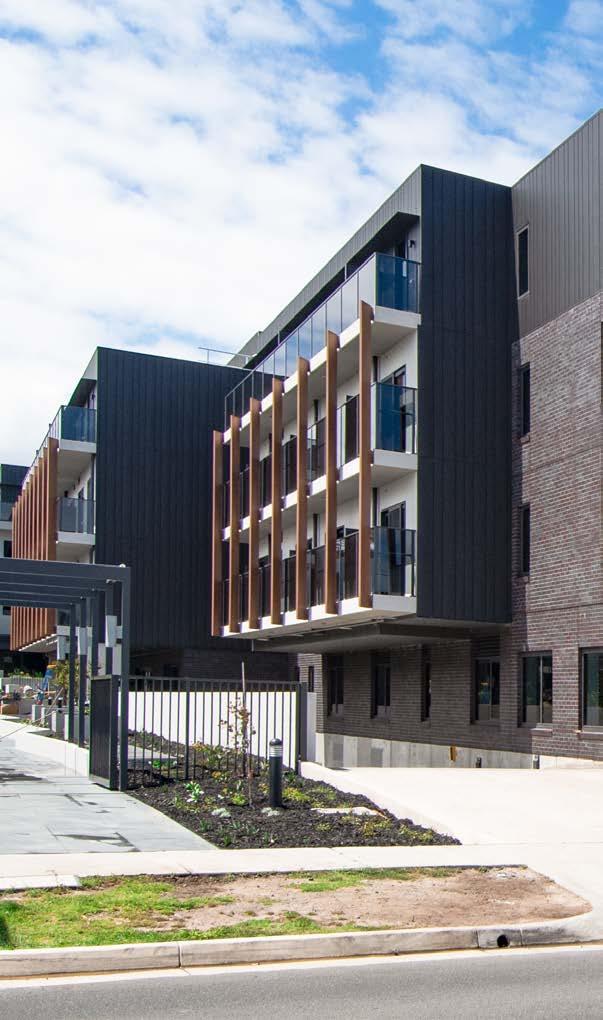
“Our highly efficient 100mm Residential suite has one of the best thermal values on the market for standard windows and doors. It’s perfectly suited to ensure that residents enjoy optimal indoor temperatures while reducing energy costs,” explained Juzer Dawoodjee, Sales and Project Director at SMB Windows.
In the commercial building, the company installed thermally broken windows, chosen to enhance energy efficiency and align with the architect’s design intent, and accommodating diverse wall cladding types.
“To ensure that the installation of windows and doors aligned perfectly with the architectural plans, we engaged in regular design meetings with the project architect and Ryman’s design team,” said Juzer. This close collaboration helped prevent delays, allowing SMB Windows to integrate their products smoothly.
One of the unique design challenges for SMB Windows, was the installation of a glass sky light that connects two of the buildings.
“The glass canopy not only gives the building a distinctive look but also allows ample natural light to reach pedestrians underneath, providing shelter from the rain and other elements,” said Juzer. SMB’s design incorporated these functional requirements without sacrificing
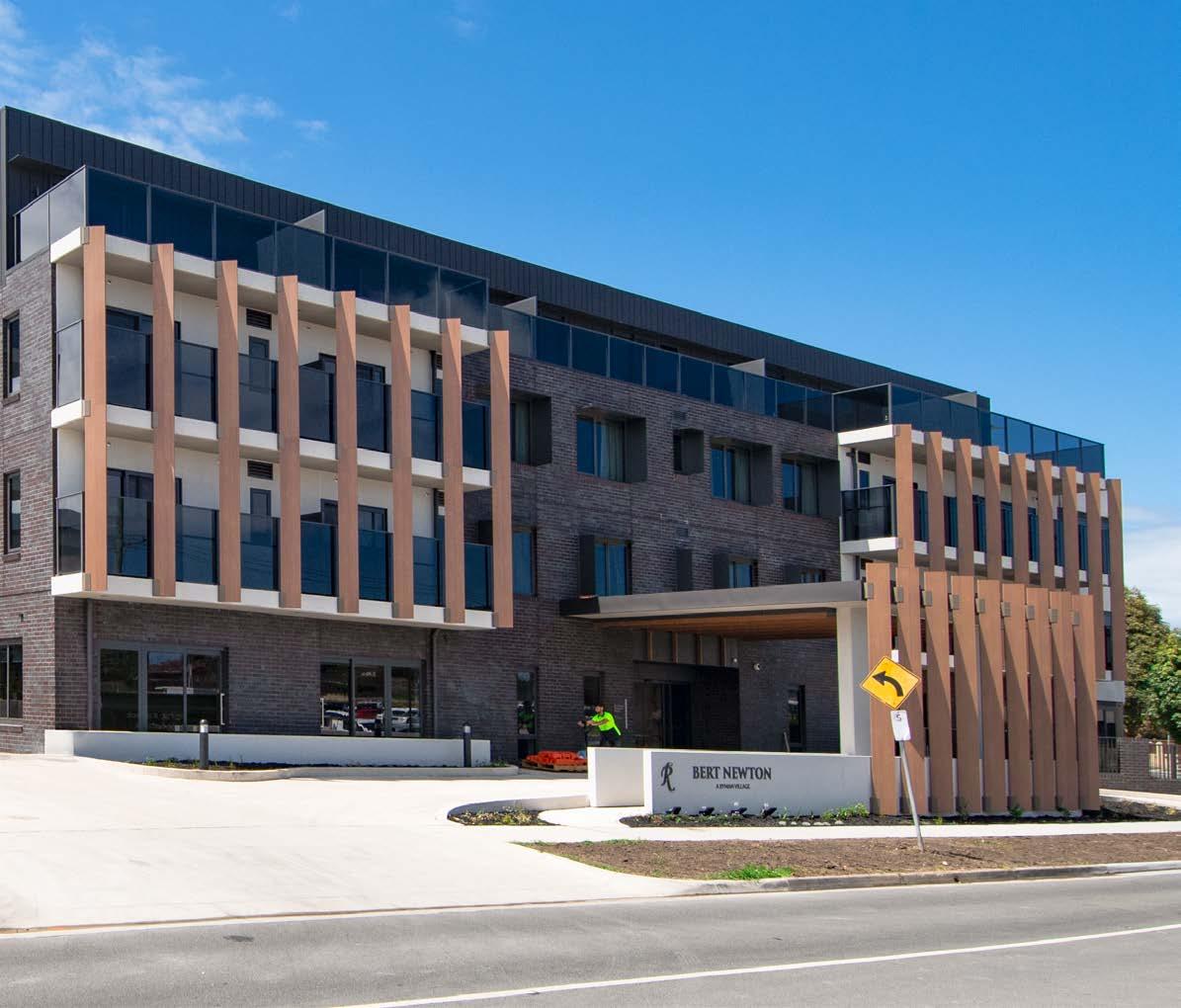
aesthetic appeal, ensuring the canopy contributed to both the form and function of the development.
Through careful design, collaboration, and an emphasis on highquality, energy-efficient materials, SMB Windows has made a substantial contribution to the Bert Newton Retirement Village. Their expertise in creating tailored window and door solutions has helped ensure that residents will enjoy a comfortable, energy-efficient living environment.
“This development truly showcases our commitment to quality, sustainability, and innovation. We’re proud to have contributed to such a meaningful project,” said Juzer.
For more information contact SMB Windows, 21-23 Zilla Court, Dandenong South VIC 3175, phone 03 9703 3106, email admin@smbwindows.com.au, website www.smbwindows.com.au
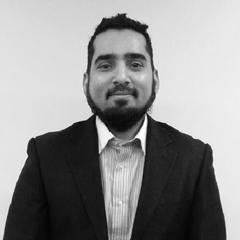

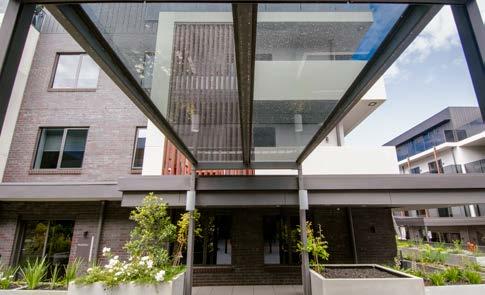
Right: Juzer Dawoodjee Commercial Sales & Project Director SMB Glass Windows & Doors


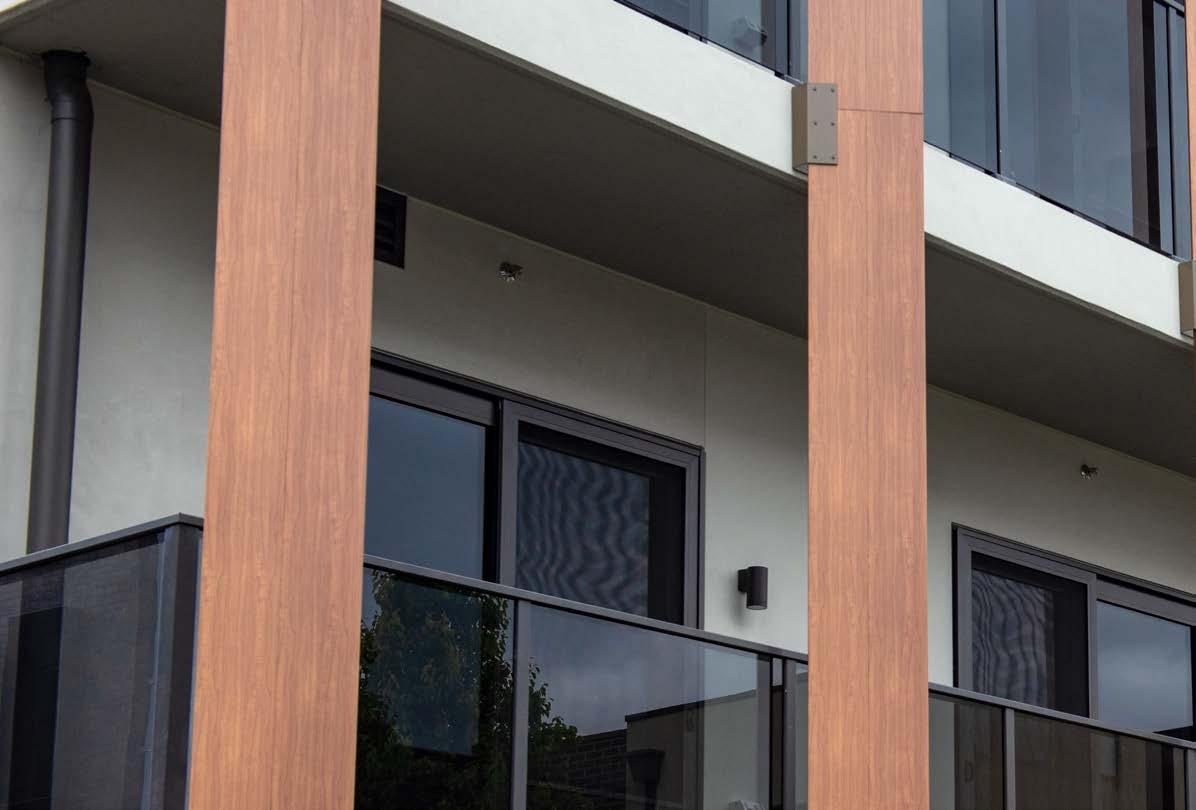
Vamp Cranes made a significant impact on the Bert Newton Retirement Village project, providing specialised crane and rigging services that ensured efficient and safe operations. Vamp Cranes handled mobile cranage, tower crane crew labour and rigging for the project.
“Our practice spans from general lifts to environmental retrofits of existing buildings and beyond,” said Valerie Patragoulas, Business Development Manager. “With our extensive range of mobile crane hire and highly trained staff, we strive to achieve continued excellence in quality.”
With a fleet that ranges from a 2.85-tonne to a 450-tonne mobile crane, Vamp Cranes has built a strong reputation for versatility. Their expertise spans precast erection, civil work, steel erection, and general crane hire. “No job is too big or too small,” said Patragoulas. “Taking on jobs of all sizes throughout Melbourne and its extended regions, our team is ready to tackle any challenge with over 50 years of combined experience.”
Vamp Cranes, based in Coburg North, Melbourne, employs a team of 115 professionals, who have earned a reputation for reliability
and safety. “Our goal is to be established as an industry leader in the delivery of crane and rigging services to Victorian construction and industrial sectors,” Patragoulas said. Their current projects include the Footscray Hospital, along with a growing portfolio of tier-one projects across Victoria.
Looking forward, Vamp Cranes has expanded beyond Victoria, entering the South Australian market and aspiring to enter the Queensland market. “We’re committed to building strong partnerships with businesses and communities,” Patragoulas said. With a dedication to innovation, safety, and quality, Vamp Cranes is poised to become a leader in crane and rigging services across Australia, ready to take on both large-scale and community-driven projects.
For more information contact Vamp Cranes, 14-22 Gaffney Street, Coburg North VIC 3058, phone 03 8652 8635, email operations@ vampcranes.com.au, website www.vampcranes.com
Below Vamp Cranes enhanced the Bert Newton Retirement Village project with specialised crane services, prioritising efficiency and safety.
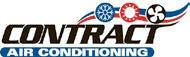
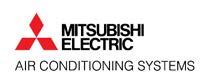


Below Contract Air Conditioning transformed comfort at Bert Newton Retirement Village with efficient, specialised air conditioning solutions.
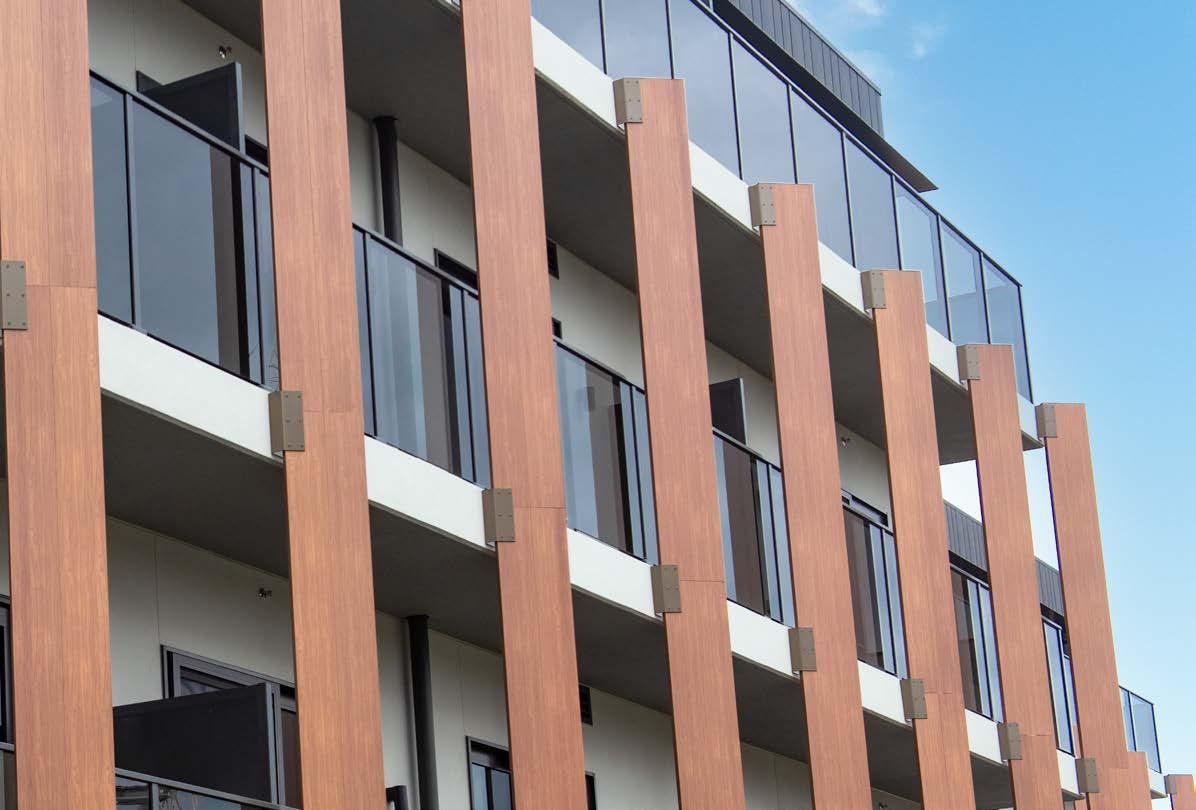
Contract Air Conditioning made a significant impact on comfort and energy efficiency at the Bert Newton Retirement Village by installing advanced, state-of-the-art Mitsubishi Electric air conditioning systems across the entire facility. Their expert team designed and implemented solutions tailored to meet the needs of residents, ensuring reliable temperature control, energy savings, and a comfortable living environment year-round.
Established in 2010, Contract Air Conditioning has built a strong reputation across Melbourne for delivering high-quality commercial air conditioning and mechanical services, making them the perfect choice for this project.
“Our approach was to design a system that not only provided reliable comfort for residents but was also energy-efficient and easy to maintain,” said Robert Baker, Project Manager Contract Air Conditioning. “We understand how important it is for a facility like this to have a system that works seamlessly, especially given the diverse needs of residents.”
The project required careful planning, from initial design to final installation, ensuring the air conditioning systems were integrated effectively with the architectural layout of the village. Contract
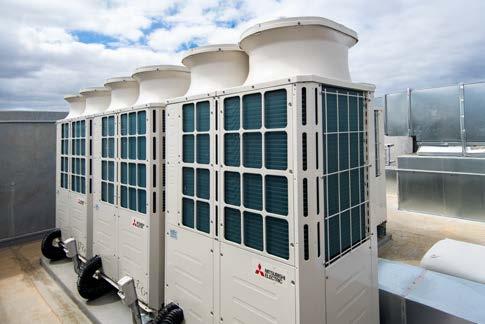
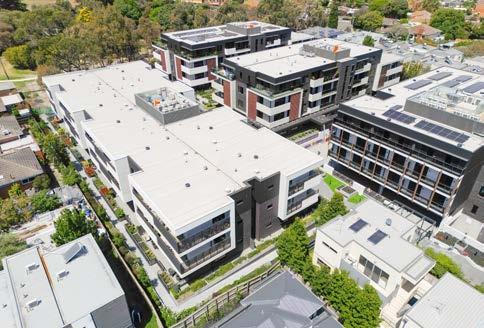
Air’s skilled team, based in Keysborough, Melbourne, brought their extensive expertise to ensure the systems were installed on time and within budget.
“We focused on selecting solutions that offered long-term performance without compromising on energy efficiency. Sustainability was a key consideration for us,” Robert noted. “With the assistance of Mitsubishi Electric Design Team, the systems we installed are designed to reduce energy consumption while ensuring the comfort of residents year-round.”
Contract Air’s team worked closely with the project’s developers to address any challenges and ensure the installation was completed to the highest standards. Their dedication and technical expertise have left the Bert Newton Retirement Village with a reliable, modern air conditioning system that meets the needs of its residents. “Our focus has always been on providing quality service and innovative solutions, and this project is a testament to those values,” Michael Eade, Director.
For more information contact Contract Air Conditioning, phone 03 9701 5411, email airconinfo@contractair.com.au, website www.contractair.com.au
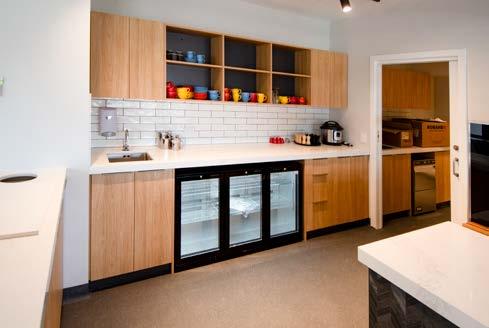
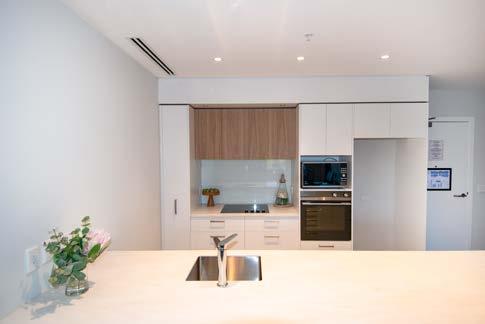
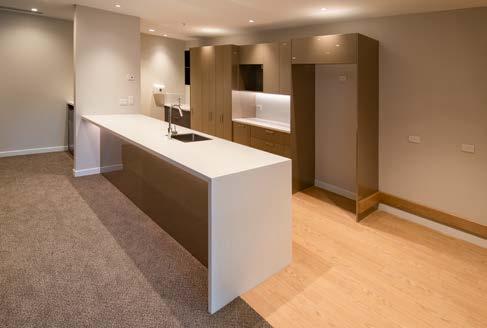
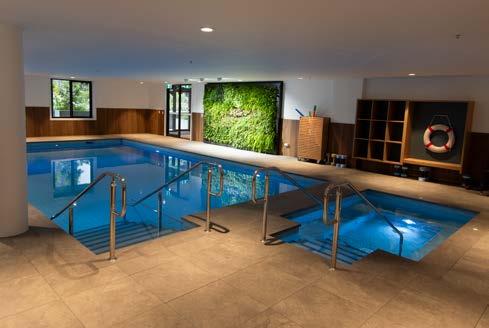
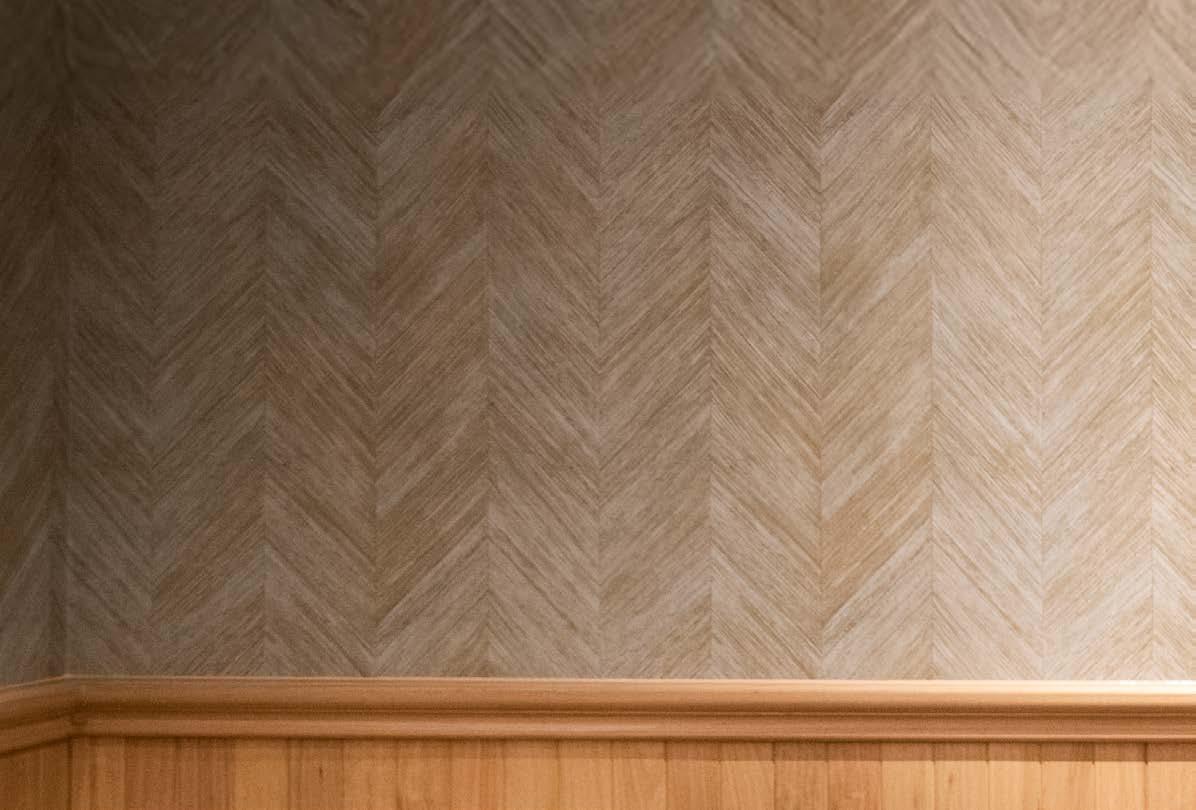
Cabinet Solutions contributed to the Bert Newton Retirement Village by providing high-quality, custom joinery that seamlessly integrates with the building’s architecture. Led by Director Aaron Rovers, the team designed and installed joinery elements tailored to enhance both the aesthetic and functional needs of the retirement community.
“Our focus was on creating joinery that was not only visually appealing but also practical and accessible for the residents,” said Aaron. “Each piece needed to complement the overall design of the village while standing up to daily use.”
Cabinet Solutions was responsible for a variety of fixed joinery installations, including kitchens, bar, library and reception areas. Using durable, high-quality materials and precise joinery techniques, they created elements that are both long-lasting and easy to maintain.
“Every aspect was crafted with the residents’ needs in mind, combining ease of use with a modern, welcoming style,” Aaron explained.
One unique feature of this project was Cabinet Solutions’ ability to customise joinery to fit specific architectural requirements and meet the varied needs of residents. The company’s custom designs allowed
them to integrate seamlessly into different spaces, providing both functional storage and visual continuity. “Each area required a tailored approach, so we worked to ensure our joinery would fit cohesively within the village’s environment,” said Aaron.
This project demonstrates Cabinet Solutions’ commitment to craftsmanship and attention to detail. Their custom joinery has contributed to the functionality and aesthetics of the Bert Newton Retirement Village, creating a comfortable, accessible environment that aligns with the village’s vision of a modern and welcoming community.
Aaron Rovers has supplied Ryman Healthcare for over 20 years and Cabinet Solutions are currently working on a number of Ryman Healthcare’s villages.
For more information contact Cabinet Solutions, 23-42 Mickle Street, Dandenong South VIC 3175, phone 0498 521 981
Below Cabinet Solutions crafted bespoke, durable joinery for Bert Newton Retirement Village, blending functionality with architectural elegance.
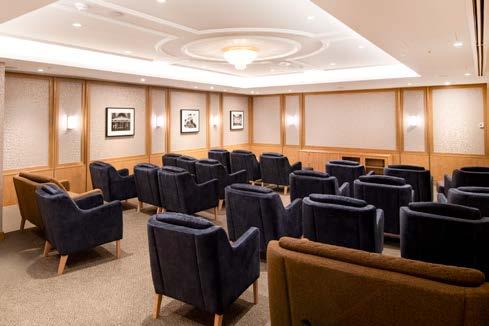
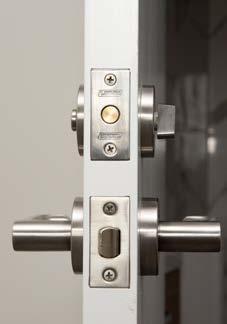
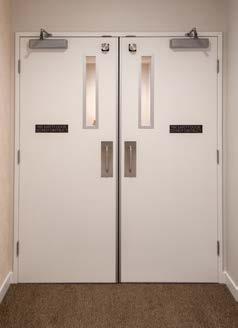
Below Koolie Building & Construction provided expert carpentry for Bert Newton Retirement Village, enhancing function and aesthetics.
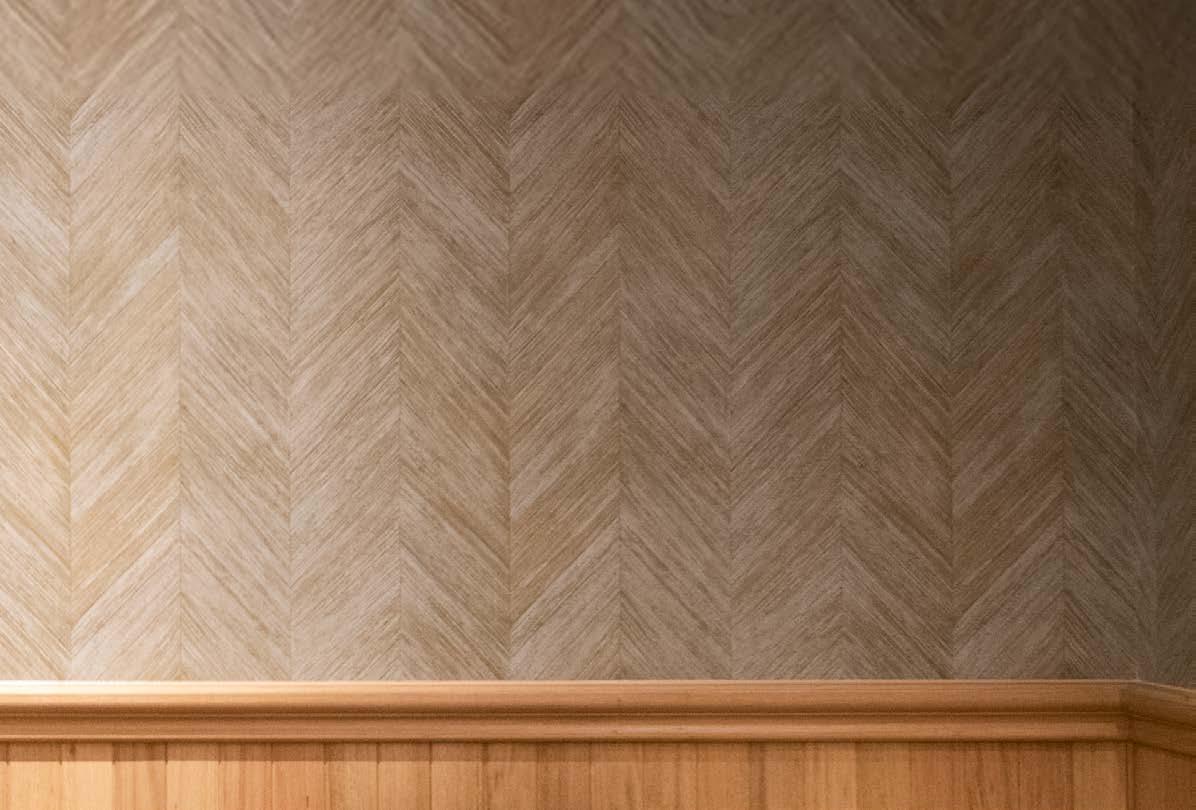
Koolie Building & Construction contributed their carpentry expertise to enhance both the functionality and aesthetics of the Bert Newton Retirement Village. Over a span of approximately three years, Koolie’s team provided a complete carpentry supply and installation package that included internal doors, sliders, fire doors, arcade joinery, and various fixtures such as skirting, architraves, and dado rails.
“Our focus was on providing a reliable and high-quality carpentry solution that would stand up to the unique demands of a retirement community,” said Hayden Johnson, Company Director of Koolie Building & Construction.
A key challenge arose toward the end of the project when limited on-site storage became an issue. To address this, Koolie leveraged their Lilydale warehouse, where doors and architraves were prepped, precut, and stored until installation. “By preparing materials offsite, we streamlined the process and reduced on-site waste and dust, which also meant fewer exclusion zones were needed,” said Johnson.
Koolie also implemented an innovative approach to the carpentry fix process, temporarily hanging doors with reusable painted hinges
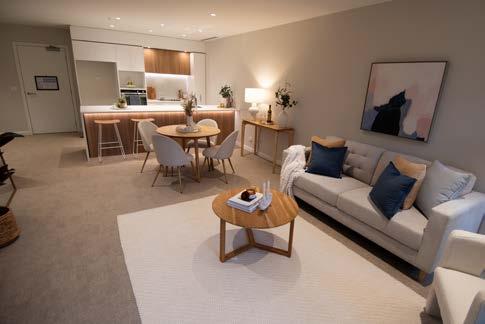
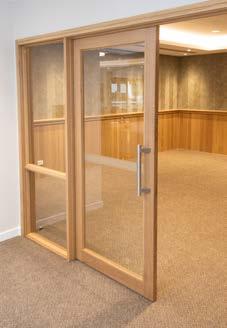
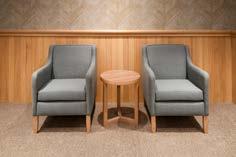
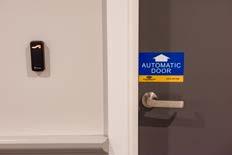
to allow painters to spray apartments freely. “This system saved the painters a lot of time, and our final product was neat and tidy,” Johnson said. For durability, Koolie painted the tops and bottoms of doors before installation, ensuring immediate sealing against wear and moisture.
Utilising their in-house Biesse Rover A 5 Axis CNC Router, Koolie manufactured many of the village’s custom doors, including lightweight, semi-solid doors designed to withstand frequent use.
“Our ability to make doors to order and machine custom timber products allowed us to meet Ryman’s exact specifications,” said Johnson.
This meticulous craftsmanship underscores Koolie’s dedication to quality and innovative solutions that enhance the longevity and aesthetics of the Bert Newton Retirement Village.
For more information contact Koolie Building & Construction, 31 Hightech Place, Lilydale VIC 3140, phone 0418 336 962
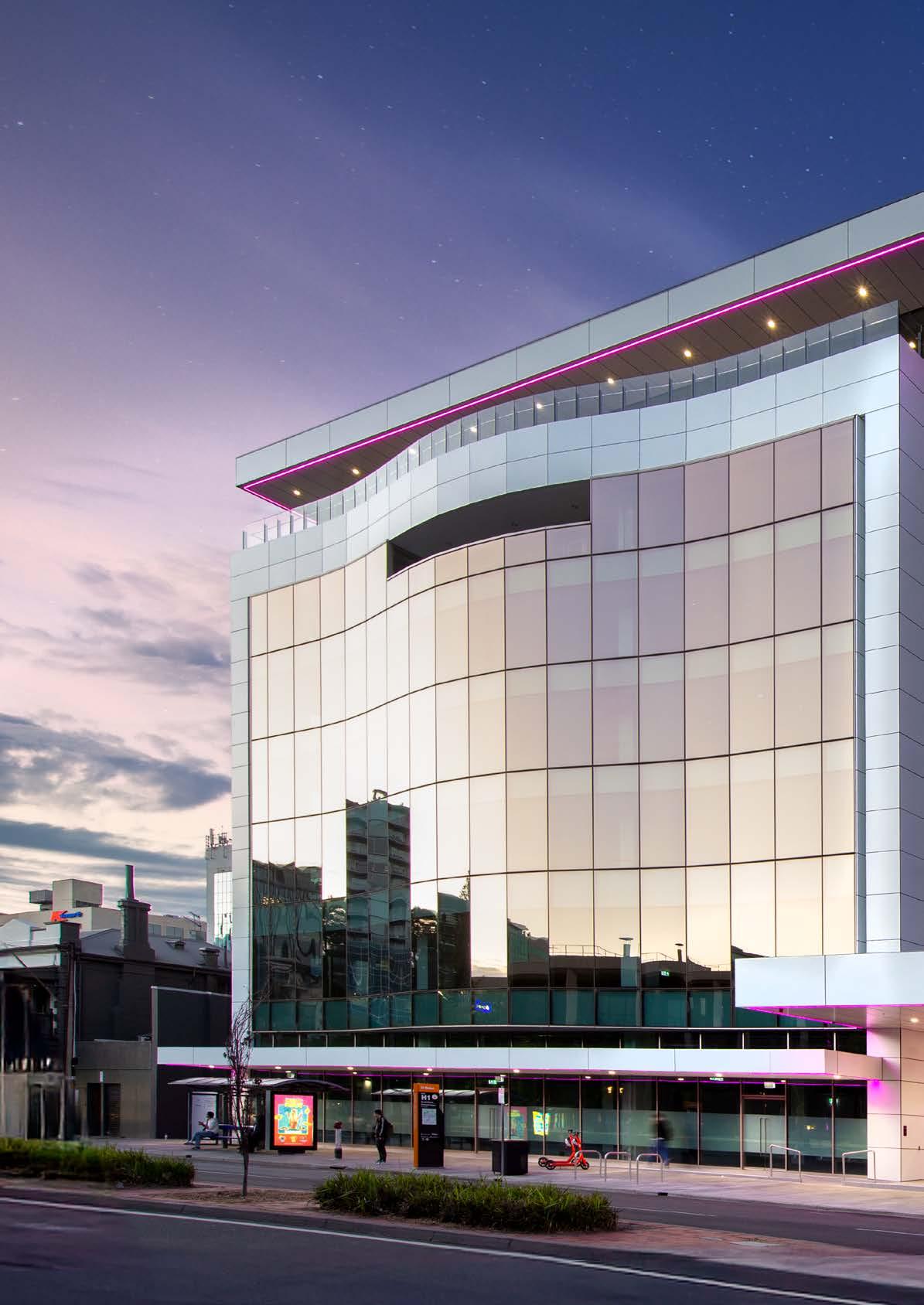
UNITY IN DESIGN
The 150 Grenfell project took two aging office buildings and reimagined them into a single exemplar of sustainability and adaptive re-use. A unified floor plate was created, a new sixth floor added with a centralised plant level above, and market leading innovations introduced. Destined to be Adelaide’s first Carbon Neutral certified office in construction and operation, 6-star Greenstar, Platinum WELL and 5.5 star NABERS ratings are also targeted. Key upgrades include efficient glazing, a new lift lobby with oversized video screens and luxury end-of-trip facilities.
DEVELOPER & OWNER : Kambitsis Group
MAIN CONSTRUCTION COMPANY : Built Environs
ARCHITECT : Cheesman
STRUCTURAL ENGINEER : MLEI
SERVICES : BESTEC
ESD CONSULTANT : dsquared Consulting
COST CONSULTANT : RLB
CONSTRUCTION VALUE : $40 million
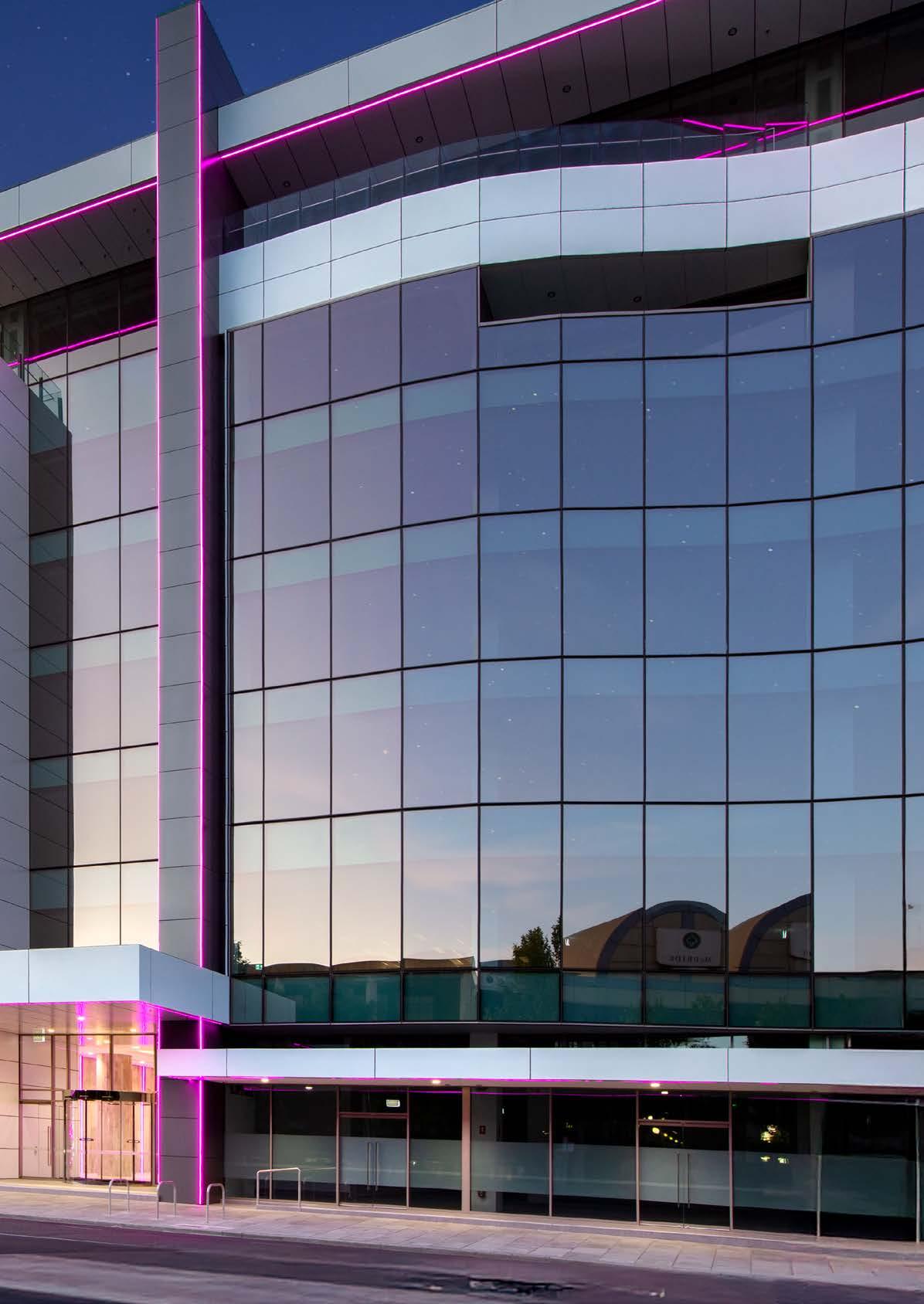
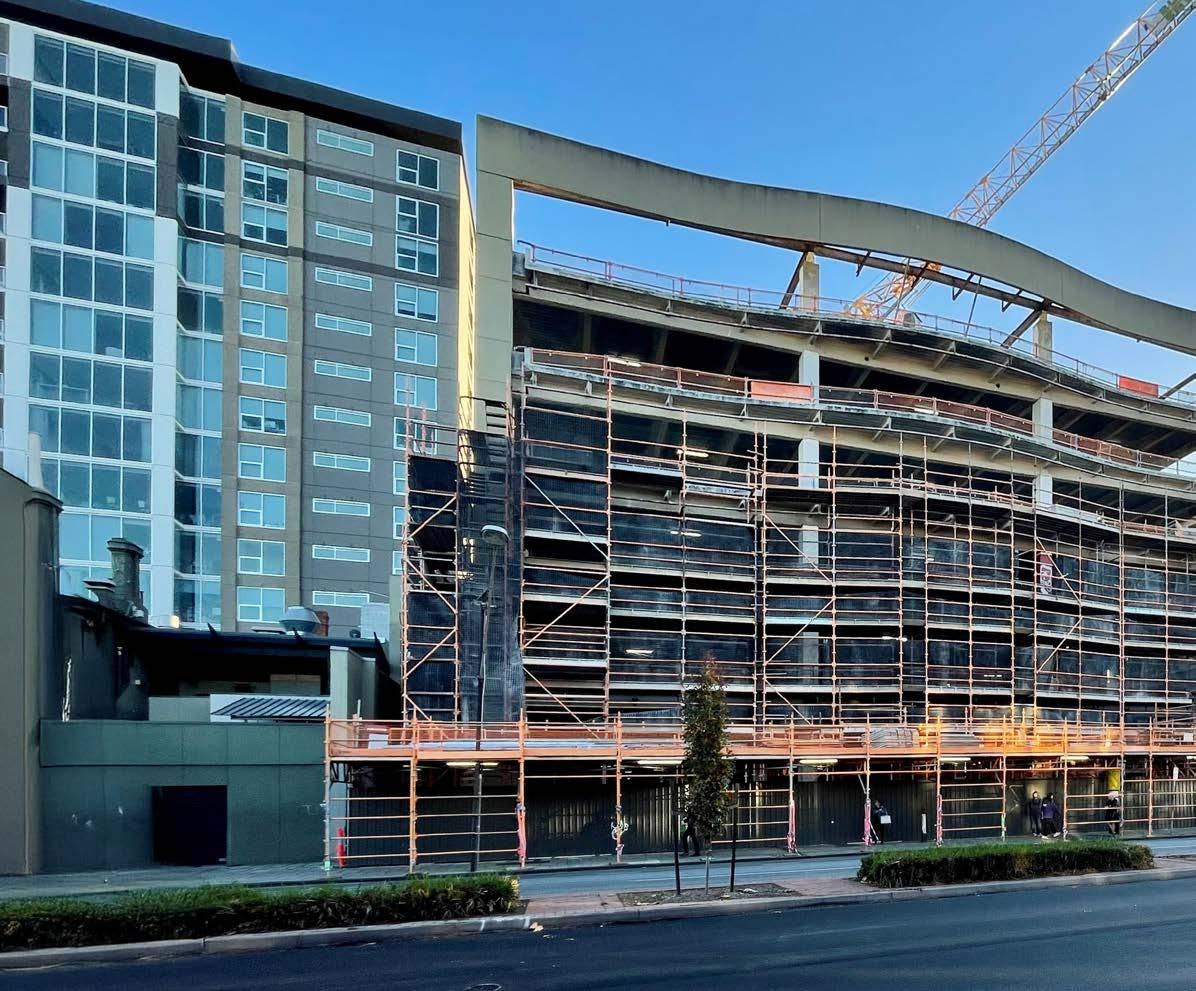
The revitalisation of 150 Grenfell Street in Adelaide stands as a testament to Built Environs’ expertise in complex construction projects. This significant development involved the complete reconstruction and expansion of two existing five-story office buildings, showcasing Kambitsis Group and Built Environs’ ability to seamlessly integrate innovative design, sustainable practices, and efficient project management.
Built Environs’ involvement in the project was multifaceted, engaged under a Construct Only delivery model for the primary building elements, while simultaneously taking on a Design and Construct responsibility for the new curtain wall façade. This dual role underscores their holistic approach, integrating design and construction expertise for optimal results.
“The existing services, fit-out and façade were removed and the structural framing modified to accommodate the new design. This included filling in previous lift shafts, creating a single floor plate across the two buildings, and constructing a further sixth floor and all new roof plant,” said Eddie Bampton, Project Manager at Built Environs.
Boosted to premium grade, the building now boasts a new ground floor lift lobby, enhanced end-of-trip facilities, upgraded amenities,
and redesigned tenancy lease spaces. A striking new high-performance glazed façade completes the transformation.
This project’s complexity demanded exceptional planning and flawless execution from the outset. One standout challenge was the installation of the tower crane base and footing, which required precision engineering within a highly constrained and intricate setup.
Overcoming this hurdle showcased the team’s expertise in navigating logistical challenges, setting the tone for a project defined by innovation and meticulous attention to detail.
The project’s sustainable design is targeting a 6-Star Green Star Design Review certification and a 5.5-Star NABERS rating. “The sustainable design is market-leading and this type of delivery is likely to become commonplace in the future,” Eddie said, in relation to the project’s contribution to a more environmentally responsible construction industry.
The development, in comparison to a traditional demolish and re-build saved approx 7621 tonnes of carbon (76% reduction compared to a new build and yielding an 85% decrease in energy consumption) and is seeking to be South Australia’s first upfront carbon neutral certified office building.

The 150 Grenfell Street project resulted in approximately 9,300m2 of lettable space, significantly expanding the building’s capacity and enhancing its appeal to prospective tenants, with the development securing a whole building tenant (Royal Automobile Association) on a long term lease. The project’s success reflects Built Environs’ broader capabilities and commitment to innovative construction practices.
“Built Environs has a long and proud history of designing and constructing significant buildings across Australia and New Zealand. Our experience is diverse and complexity is our forté – delivering projects that demand innovation and creativity for success,” said Eddie. Their success is built upon a foundation of investing in talented personnel, employing innovative methods, and leveraging smart technologies.
“We believe in relationships not transactions, developing trusted partnerships with our customers, consultants, subcontractors and suppliers that are built on honesty and integrity – one of our core values,” said Eddie.
The transformation of 150 Grenfell Street showcases Built Environs’ capacity to deliver high-quality, sustainable buildings that meet
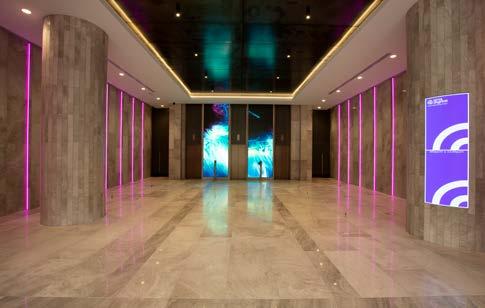
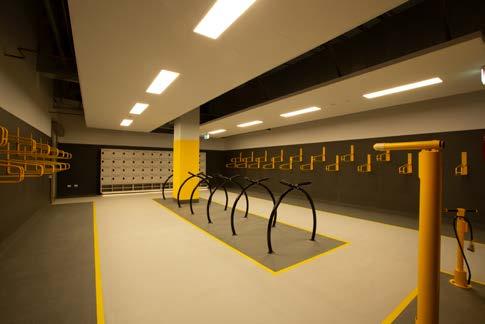
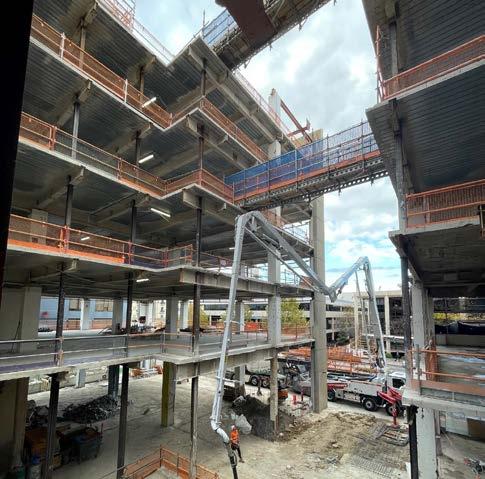
the demands of modern development. Their ability to seamlessly manage complex projects, coupled with their dedication to innovative design and sustainable practices, establishes them as a leading force in the Australian construction industry. Their commitment to client satisfaction, partnered with an emphasis on long-term relationships, is evident in their successful completion of the 150 Grenfell Street development project, a project designed to enhance the way people work and experience Adelaide's city centre.
For more information contact Built Environs, Level 12, 99 Gawler Place, Adelaide 5000 SA, phone 08 8232 1882, email be@builtenvirons.com.au, website www.builtenvirons.com.au
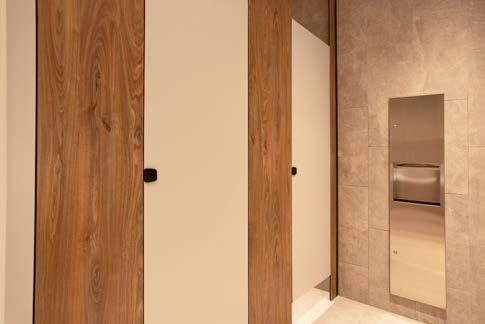

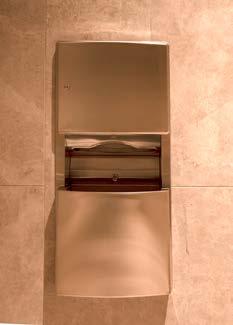
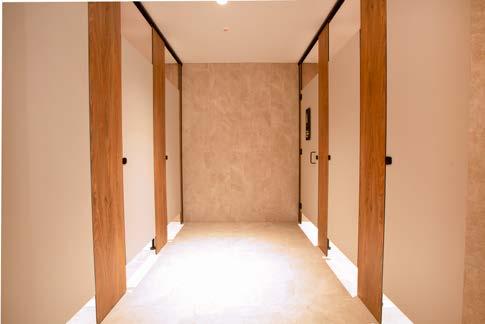

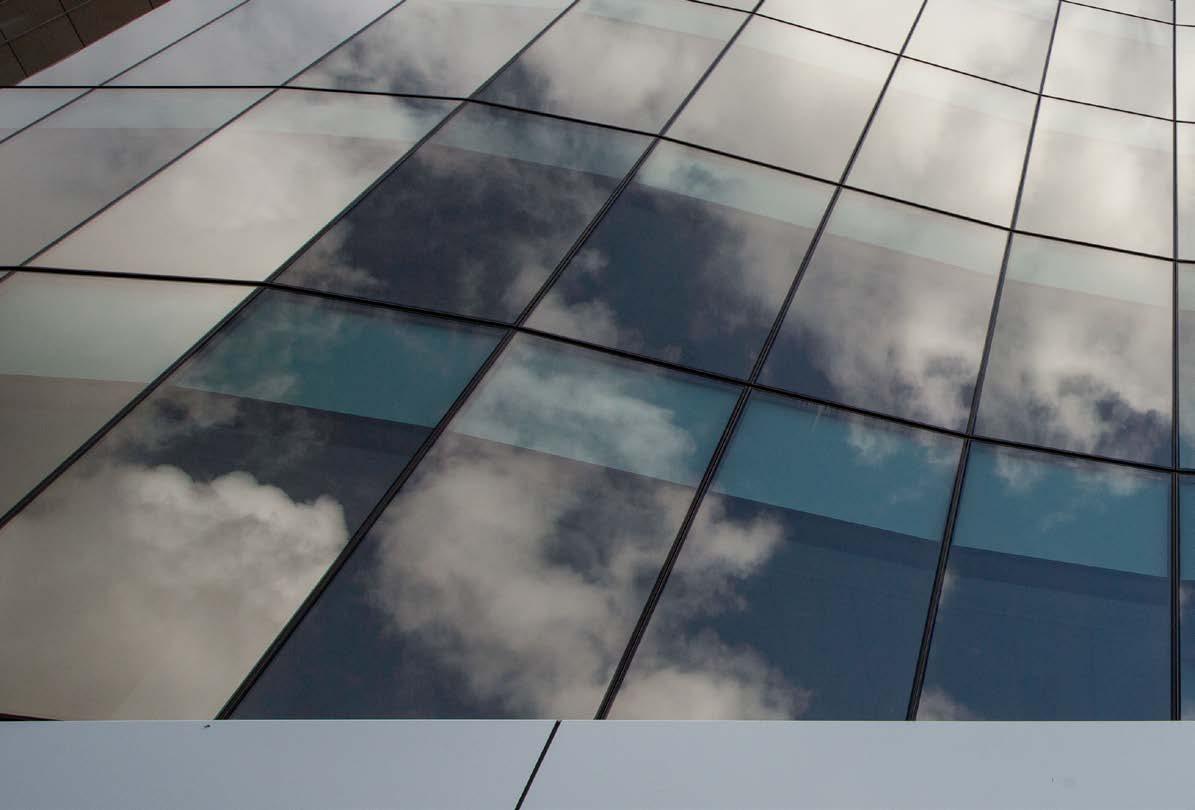
ASI JD MacDonald provide high-quality washroom and hygiene solutions that combine functionality with sleek, modern design. Known for their innovative and durable products, ASI JD MacDonald has helped transform 150 Grenfell Street’s amenities, offering a comfortable and stylish experience for occupants.
“Our goal was to provide products that not only function efficiently but also enhance the overall aesthetic of the building. We believe that high-traffic areas like washrooms should reflect the same standard of quality as the rest of the facility,” said Marketing Manager Rob Shackles.
The company supplied a range of products, including the Turbo Slim High-Speed Hand Dryer, which features a sleek satin stainless-steel finish, providing a fast and efficient drying solution, floor-to-ceiling toilet partitions from the Tranquility Collection, which offer both privacy and a contemporary design, as well as recessed paper towel dispensers from the Roval and Simplicity collections, designed to keep washrooms clutter-free.
“Our Tranquility Collection partitions are designed to provide privacy while maintaining a stylish appearance. We understand that these
spaces require durability and easy maintenance, and that’s exactly what we deliver,” added Rob.
ASI JD MacDonald’s contribution to 150 Grenfell Street demonstrates their commitment to quality, innovation, and customer satisfaction. Their expertise in delivering high-performance, aesthetically pleasing products has helped set a new standard for commercial washroom facilities in modern buildings. “We’re proud to be part of projects like this, where our products can truly make a difference,” Rob said.
For more information contact ASI JD MacDonald, 13-17 Naxos Way, Keysborough VIC 3173, phone 1800 023 441, email enquiry@asijdmacdonald.com.au, website www.jdmacdonald.com.au
Below ASI JD MacDonald delivers innovative, durable washroom solutions blending functionality and style, transforming 150 Grenfell Street’s amenities.
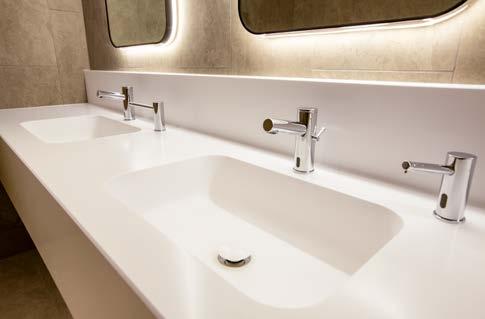

Below CASF Australia redefined 150 Grenfell Street amenities with Corian® materials, delivering seamless, modern, durable, and hygienic designs.
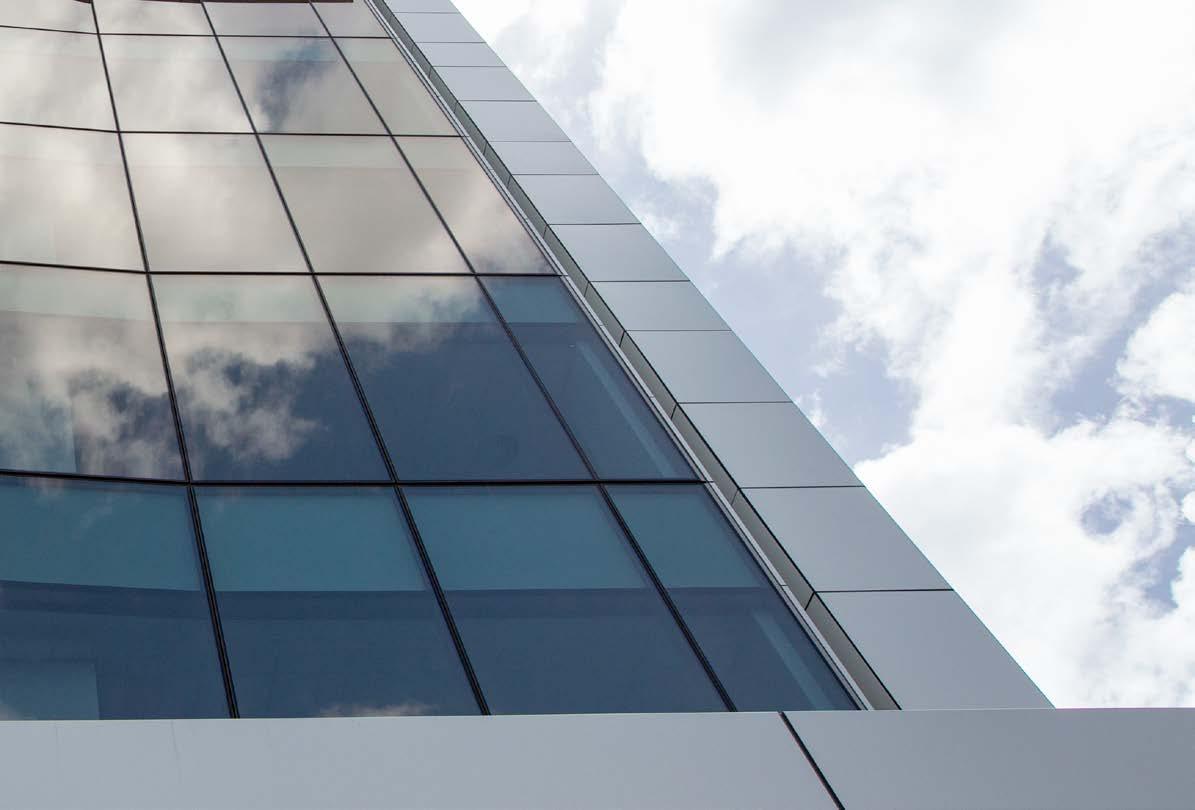
CASF Australia has elevated the design and functionality of the 150 Grenfell Street redevelopment through its high-quality Corian® materials, bringing a refined, modern aesthetic to the building’s amenities.
By supplying Corian® vanities and basins for all male, female, and staff restrooms, CASF Australia helped transform these spaces into sleek, durable, and hygienic environments.
“Our Corian® Solid Surface material provided the perfect solution for a seamless and sophisticated look,” said Emily Camongol, Marketing Coordinator at CASF Australia. This project highlights CASF’s commitment to combining innovative design with practical functionality, creating an experience that aligns with contemporary architectural standards.
The Corian® Solid Surface material blends effortlessly into the space and offers a clean, contemporary look. Known for its durability and low-maintenance, the non-porous surface resists stains and bacteria, making it a hygienic and practical choice for high-traffic areas. “The versatility of Corian® allowed for seamless integration, giving the bathrooms a sophisticated, functional aesthetic,” Emily said.
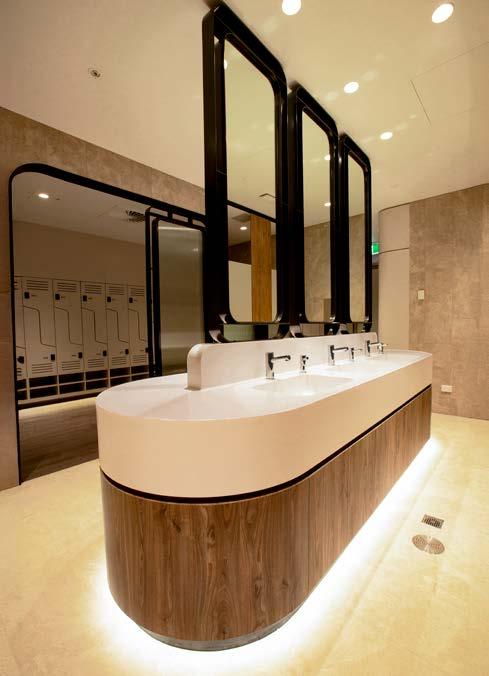
“Our South Australian team partnered with Cheesman Architects to deliver tailored solutions that complemented the overall design concept,” said Emily. The result: a stunning Glacier White Corian® vanity that seamlessly blends beauty and functionality, becoming a centerpiece in the building's restrooms.
CASF Australia streamlined logistics to ensure all materials were delivered to SA Solid Fabricators within just six weeks. “This quick turnaround enabled SA Solid Fabricators to maintain their workflow and complete the project on schedule, streamlining the entire process,” said Emily. The strong collaboration between CASF Australia and SA Solid Fabricators exemplified the importance of reliable partnerships in achieving timely project outcomes.
With its seamless design, low-maintenance features, and Greenguard certification, Corian® was the ideal choice for this project, embodying the balance of form and function.
For more information contact CASF Australia, Unit 3, 208 Walters Road Arndell Park NSW, phone 1300 795 044, email info@casf.com.au, website www.casf.com.au
Below Interior fit-out specialists Sakar Constructions completed bespoke carpentry throughout the project including feature foyer, timber fire doors, and wet area accessories.

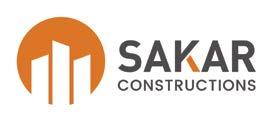
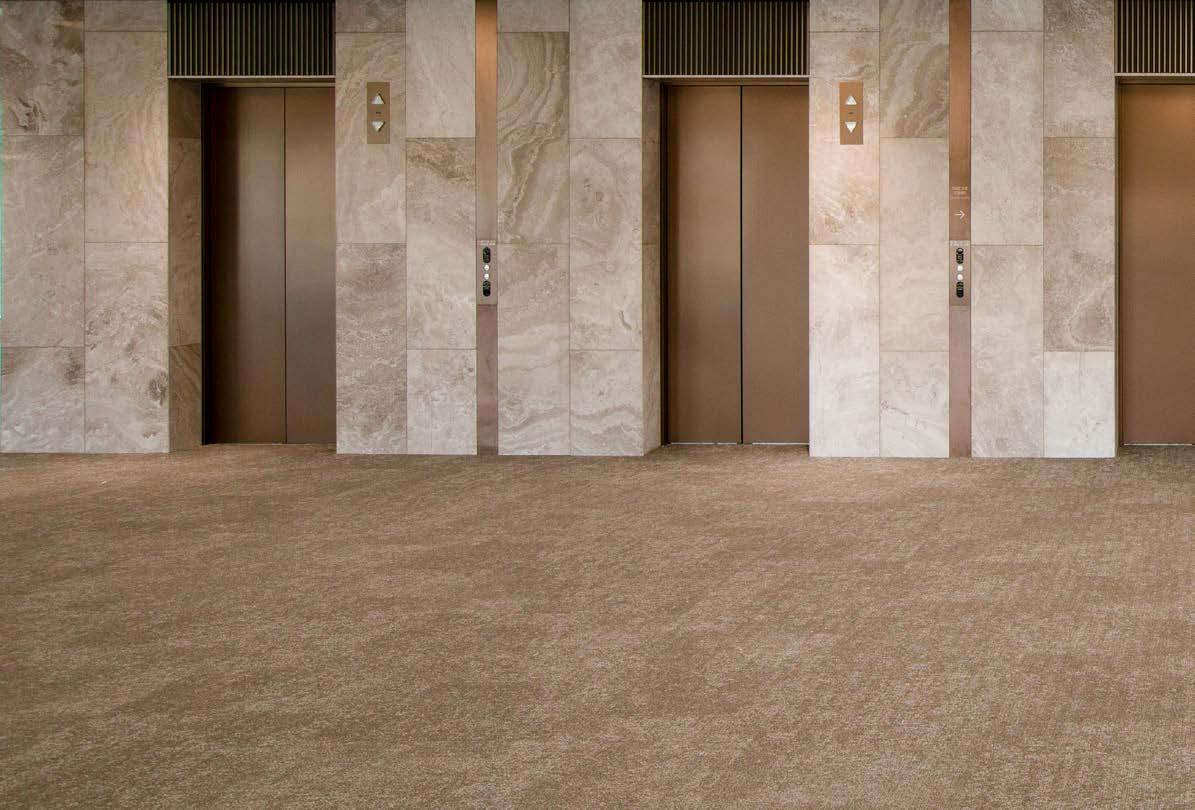
Established in 2015, Sakar Constructions, is a South Australian carpentry and interiors specialist. The company has rapidly gained a reputation for its commitment to quality and client satisfaction.
“Our scope of works included the subframing for the feature foyer, the timber and fire doors throughout the building, structural carpentry works and wet area accessories,” said Darius Hashemi, Managing Director of Sakar Constructions. This encompassed a significant portion of the interior fit-out, requiring precision carpentry and meticulous attention to detail.
“Timeframes were a challenge, especially for the foyer, which required a lot of coordination and precise layout for the framing. Coordination with Built Environs and other trades was also crucial for successful project delivery,” said Darius. These logistical complexities demanded efficient planning and excellent communication across all project stakeholders.
Sakar Constructions overcame the complex task of addressing compliance issues with existing fire doors, a critical aspect of ensuring fire safety in the building. To bring the doors up to code, they conducted a thorough assessment to identify deficiencies and
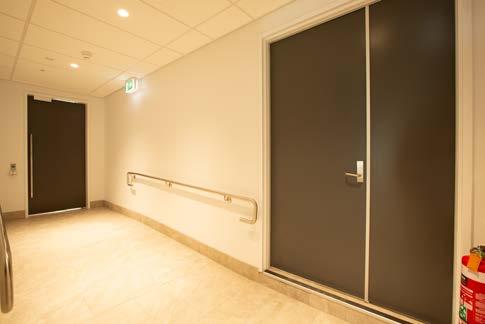
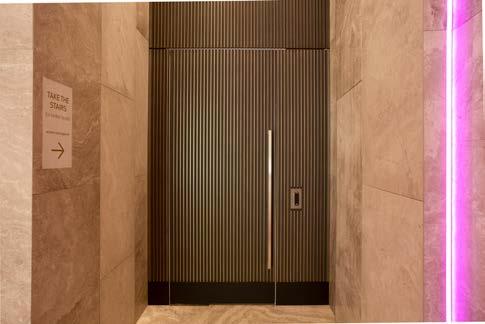
implemented tailored solutions working closely with local suppliers to meet compliance. This resulted in them completing the project ahead of programme and within the budget constraints.
Sakar Constructions’ work at 150 Grenfell Street demonstrates their capacity to successfully execute complex interior fit-out projects within demanding timeframes. Their expertise in commercial carpentry and architectural interiors has been instrumental in delivering high-quality results for a range of clients across various sectors. Their commitment to precision, attention to detail, and seamless collaboration with other trades ensures the successful completion of projects.
Dedication to quality, coupled with their innovative approach, has firmly established Sakar Constructions as a respected player in the South Australian construction industry. As well as having a management team with over 20 years of experience, Sakar Constructions has a large workforce of carpenters who share the companies dedication to quality and client satisfaction on each project.
For more information contact Sakar Constructions, phone 0425 788 241, email info@sakarconstructions.com, website www.sakarconstructions.com.au
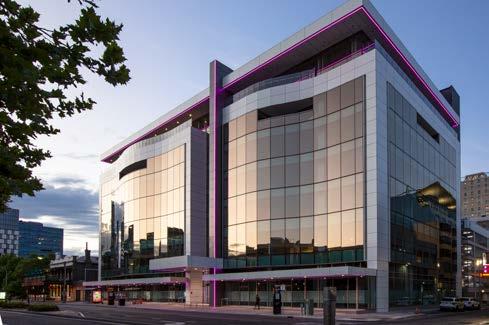

Below Swart Plastering Services completed 150 Grenfell Street's exterior with durable Dulux Acratex® coatings, ensuring quality results.
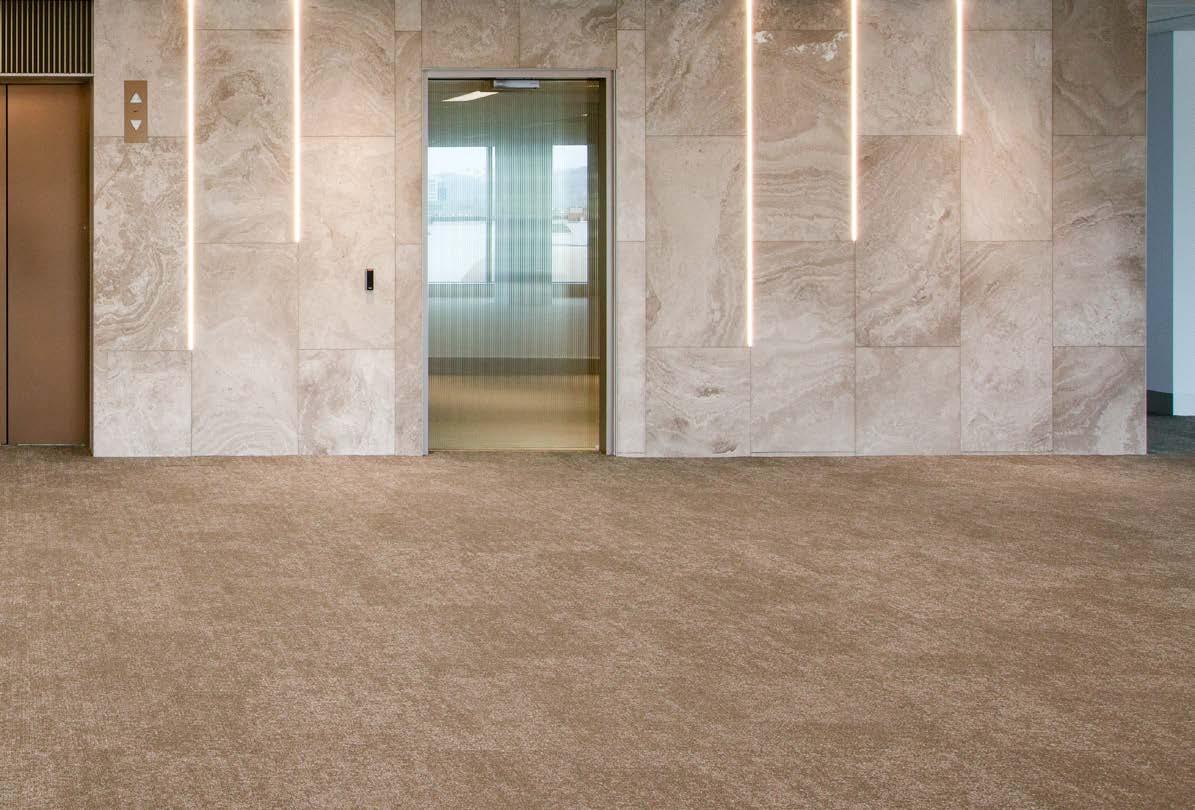
Swart Plastering Services, a South Australian institution with a rich history spanning over 70 years, completed the exterior render and texture coating in the recent refurbishment of 150 Grenfell Street. Conrad Swart, representing the latest generation of a family legacy in plastering, oversaw the project, bringing decades of experience and a commitment to quality to the landmark redevelopment.
“The scope of work was render and texture coating of the whole exterior,” said Conrad. “We used Dulux Acratex® products to help us to achieve our finish.” Dulux Acratex® coatings is a range of products providing comprehensive solutions for building remediation, repainting, and refurbishment. The choice of Acratex® reflects Swart Plastering’s dedication to utilising high-performance, durable materials.
The Grenfell Street project was straightforward, with elevated works being a familiar task for the team. Swart Plastering’s proficiency in handling complex and demanding projects, ensures consistently high-quality finish they provided.
Beyond the technical aspects, the project held a special significance for Swart Plastering. “It’s nice to give an old building a new lease on
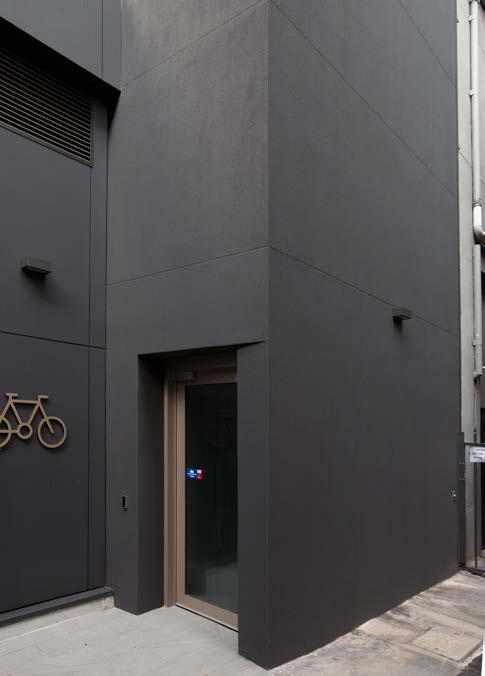
life,” Swart said, expressing a sense of pride in contributing to the preservation and enhancement of Adelaide’s built heritage.
Swart Plastering’s work on 150 Grenfell Street is in keeping with their long-standing reputation for reliable and quality plastering services. The company’s experience extends across a broad range of projects, encompassing commercial, industrial, domestic, housing, and architectural applications. Their ability to effectively manage complex projects, utilise high-quality materials, and meet tight deadlines has earned them a strong reputation within the industry.
Looking ahead, Swart Plastering Services continues to maintain its prominent position in the South Australian construction industry, with various projects currently underway across the state. The company’s legacy, built on generations of experience and a steadfast commitment to quality, ensures they remain a vital contributor to the region's building landscape for many years to come.
For more information contact Swart Plastering, 280 Gilbert Street, Adelaide SA 5000, email admin@swartplastering.com.au, phone 0418 833 367, website www.swartplastering.com.au
PLANTING THE SEEDS OF INNOVATION
CLIENT : The University of Queensland (UQ)
MAIN CONSTRUCTION COMPANY : Hansen Yuncken
ARCHITECT : m3 Architecture
CERTIFIER / DDA : Certis
ENGINEER : Bligh Tanner
The University of Queensland’s Plant Futures Facility is a cutting-edge innovation in plant science and the development of sustainable ecosystems with global impact. Located on the St Lucia Campus, this state-of-the-art facility is set to position UQ as a leader in plant research in the Southern Hemisphere and establish it among the most sophisticated controlled environment facilities in Australia.
Hansen Yuncken, a leading construction company renowned for its expertise in delivering highly technical projects, has played an instrumental role in bringing this ambitious vision to reality.
The scope of the project included the demolition of existing buildings, constructing two floors of Controlled Environment Growth Rooms, support spaces, and a basement. Additionally, the project involved intricate landscaping and a rooftop deck housing building services equipment and glasshouses.
“The University of Queensland’s Plant Futures Facility is exclusively a researchintensive building designed to simulate precise environmental conditions such as temperature, humidity, lighting, and CO2,” said Krystel Lawrence, Senior Contract Administrator at Hansen Yuncken.
“Our team has integrated highly controlled, flexible interior grow rooms and laboratory spaces to cater to a wide range of plant science research, particularly focusing on high-temperature research."
What sets the Plant Futures Facility apart is its commitment to sustainability and advanced architectural detail. The building adheres to Physical Containment Level 2 Laboratory (PC2) requirements under the Office of the Gene Technology Regulator (OGTR) and Approved Arrangements (AA) for a 5.2 Biosecurity Containment Level 2 (BC2) bio-containment facility, underscoring its role in addressing global food, fibre, fuel, and sustainable production systems.
From a construction perspective, the project presented multiple challenges. One notable complexity was the intricate detailed façade made of face brick, which took over 12 months to complete.
“The glasshouses, located on the rooftop, provided unique challenges in terms of their erection methodology,” Krystel said. “Service Coordination and reticulation through congested plant rooms required meticulous planning and the significant use of BIM (Building Information Modeling) to coordinate and resolve these challenges, ensuring adequate maintenance access for the future.”
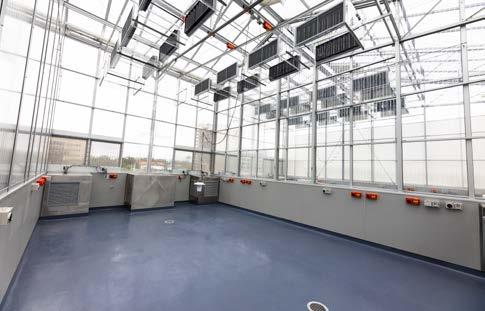
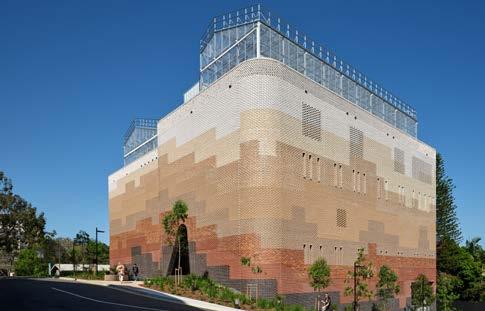
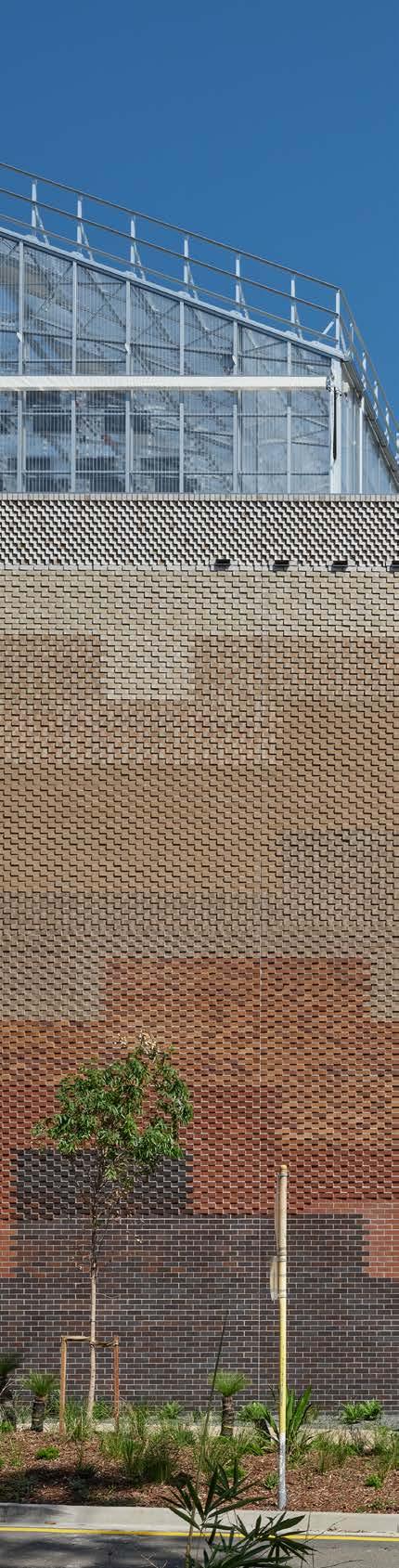
Image © Christopher Frederick Jones
Image © Christopher Frederick Jones
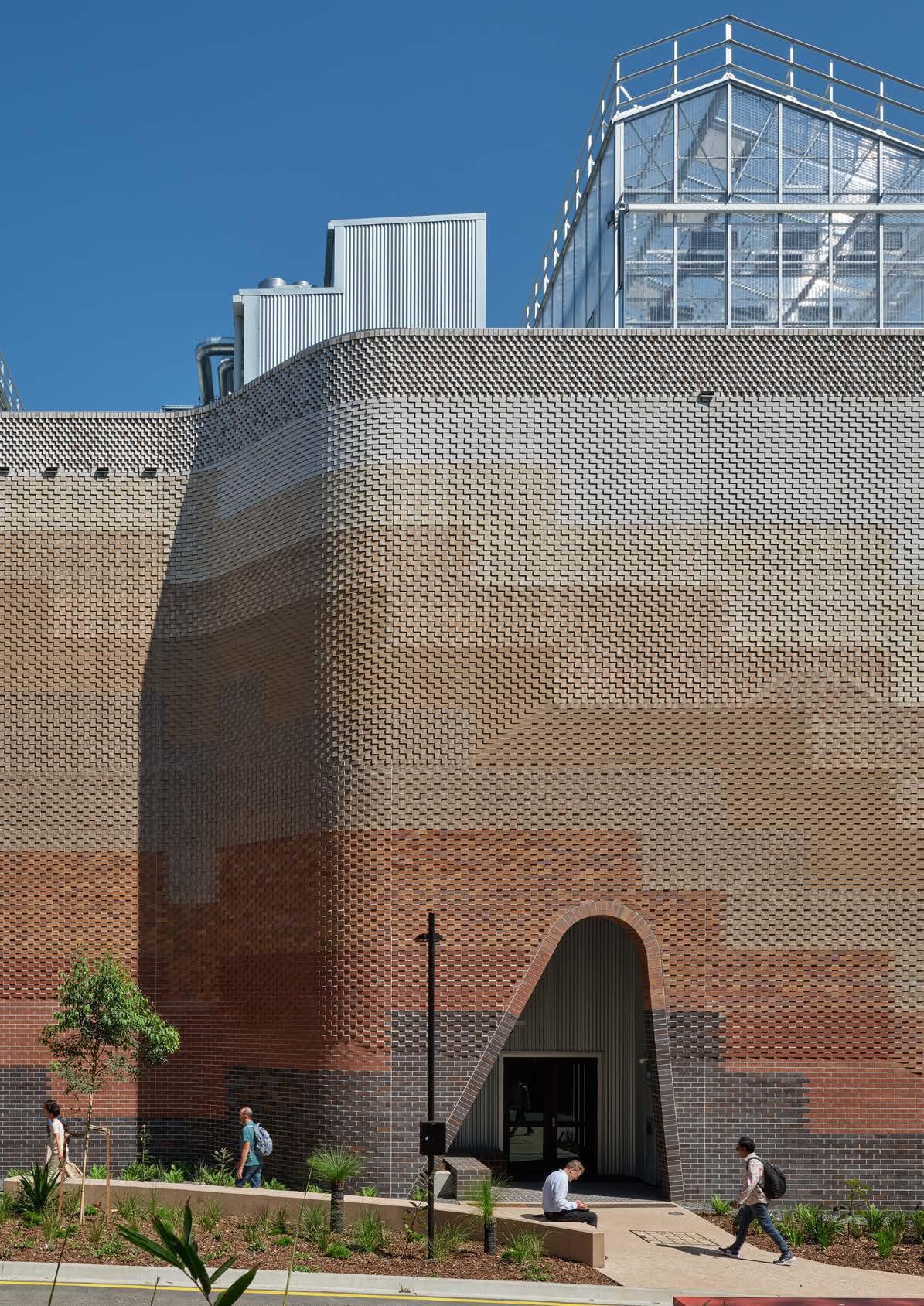
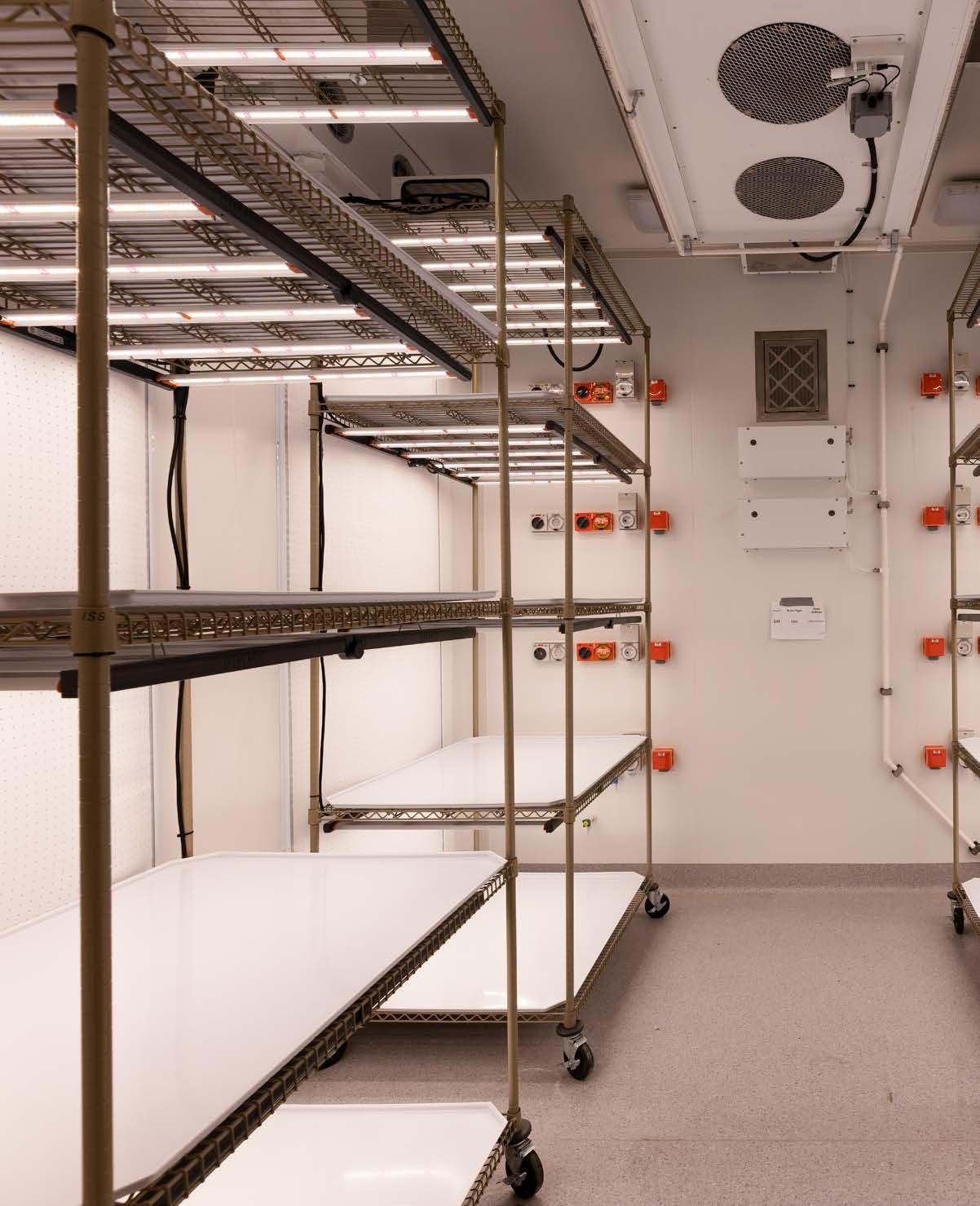
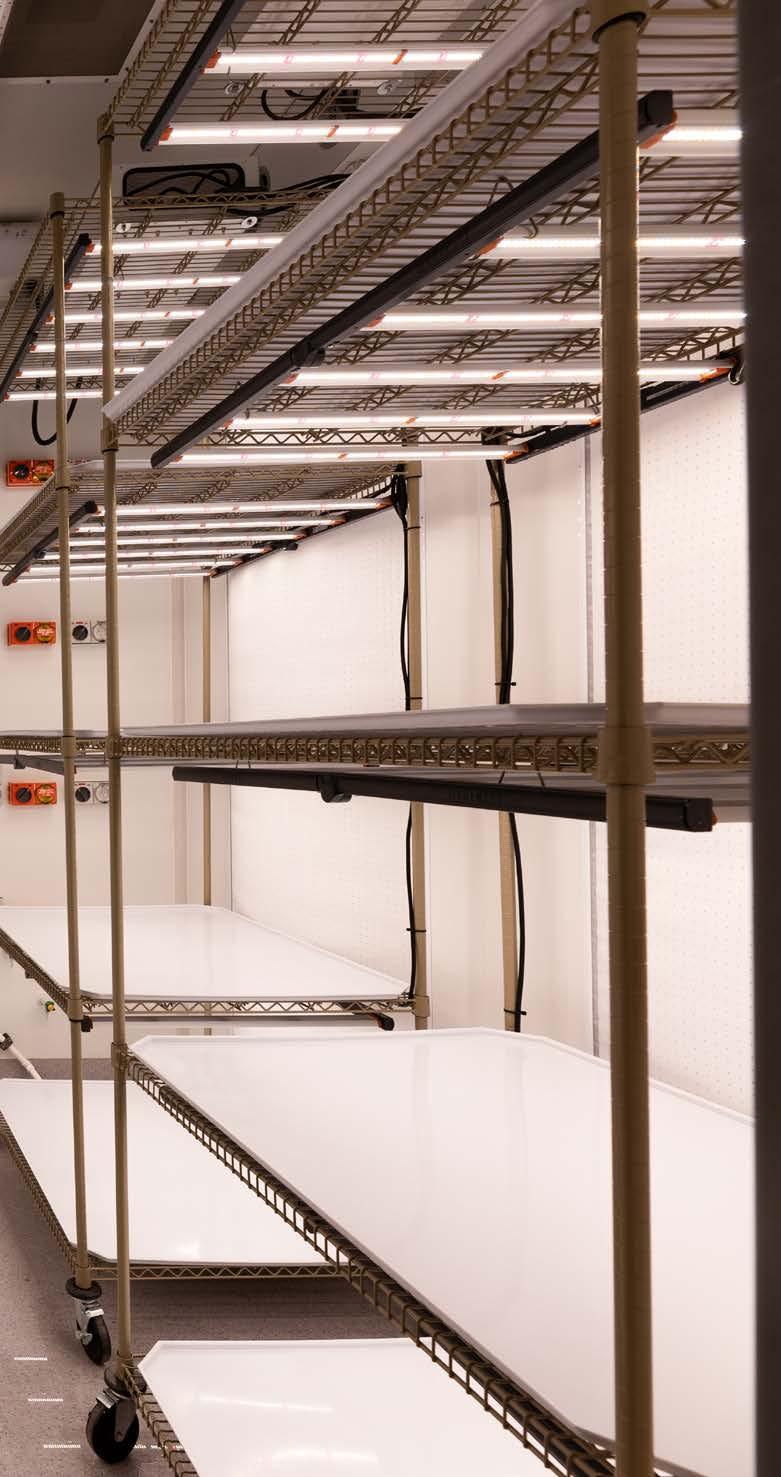
Hansen Yuncken commenced work on the Plant Futures Facility site in late November 2021, with make-safe and demolition operations starting in December 2021.
The first slab was successfully poured on May 4, 2022. At the peak of construction, the project team comprised 14 key members, with over 65 subcontractors engaged. On any given day, up to 130 workers were diligently working on-site to meet project milestones and deliver high-quality results.
Hansen Yuncken Queensland Manager, Michael Vicenzino reflected on the overall project; “The University of Queensland Plant Futures Facility has been one of the most complex research projects we’ve undertaken. The interface between numerous specialist contractors, some from the northern hemisphere and services contractors to deliver the specialist controlled environments with programming that enables multiple variants of atmospheric growing conditions in the grow rooms and glasshouses has been both a challenging and interesting learning experience. The exceptional quality of this building is a testament to our team’s ability to handle highly technical and serviced facilities, furthering our expertise in the education and research sectors.”
Hansen Yuncken’s precision engineering and commitment to excellence will leave a lasting impact on UQ's research capabilities and global contributions to sustainable ecosystems.
Proudly Australian, privately owned and controlled, Hansen Yuncken’s enduring success is shaped by experience and thirst for innovation. They are one of the nation’s largest commercial building contractors, employing over 600 team members across New South Wales, Northern Territory, Queensland, South Australia, Tasmania, and Victoria.
For more information contact Hansen Yuncken, Level 1, 639 Wickham Street Fortitude Valley QLD 4006, phone 07 3872 4000, brisbane@hansenyuncken. com.au, website www.hansenyuncken.com.au
Below Kerslake & Associates leveraged decades of expertise, to translate scientific needs into infrastructure requirements

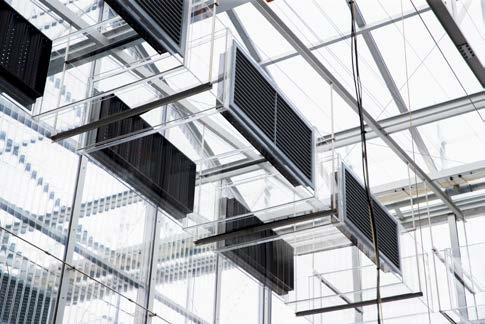
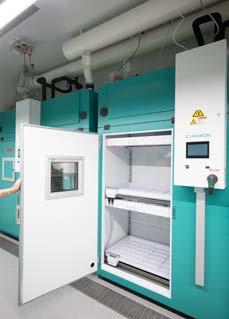
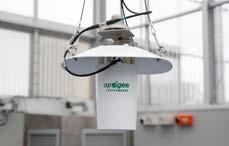

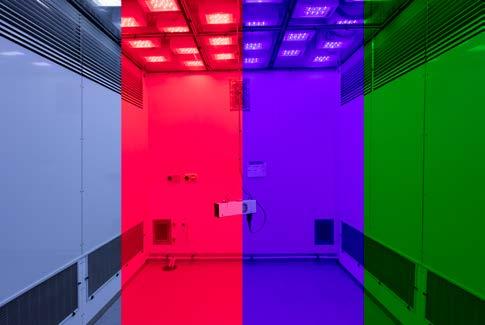
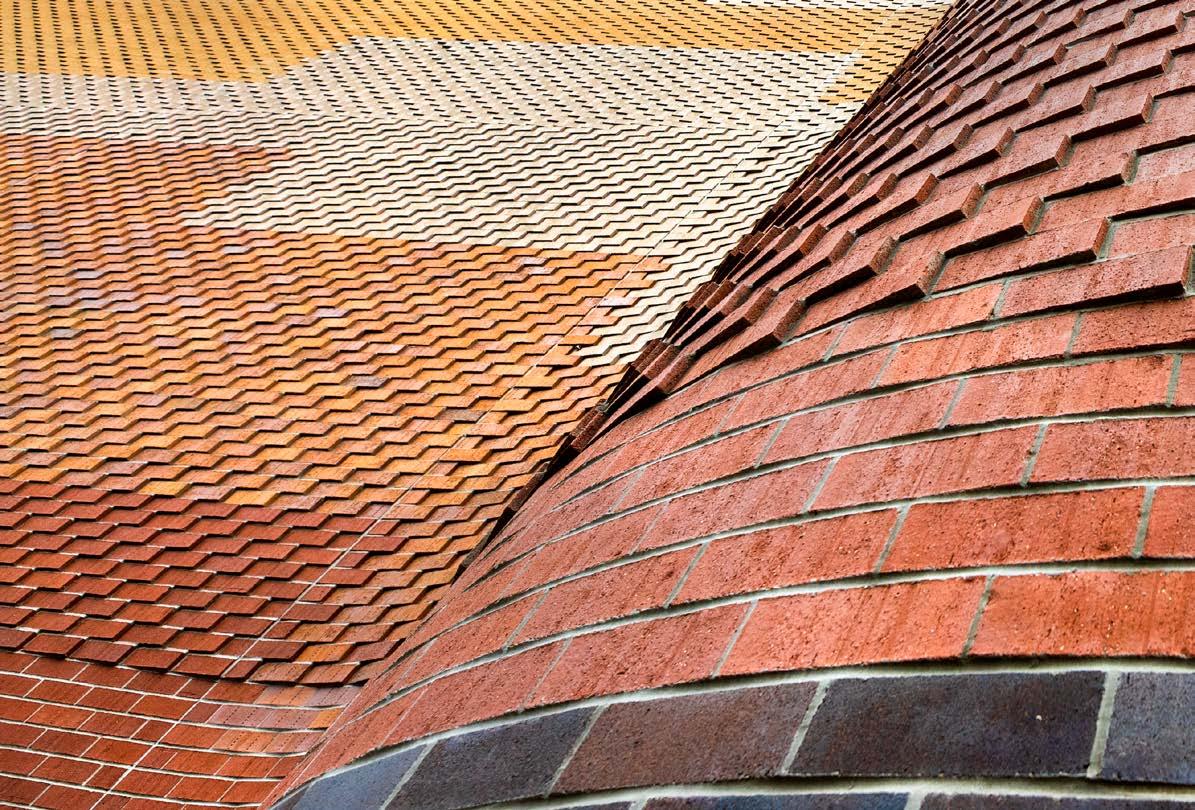
Kerslake & Associates have played a pivotal role in the development of the University of Queensland’s (UQ) Plant Futures Facility. Spearheaded by Director, Rob Kerslake, an internationally recognised specialist in research laboratories, glasshouses, and controlled environment facilities, the firm brings over three decades of expertise to this ambitious project.
Kerslake’s extensive experience, gained primarily through his work with the CSIRO in Brisbane, has positioned him as a vital contributor to the UQ project. His unique ability to translate scientific needs into infrastructure requirements was key to the successful development of the Plant Futures Facility. “My detailed knowledge of plant physiology and environmental requirements relating to plant growth within glasshouse and artificial environments, particularly in the tropics and sub-tropics, was crucial for this project,” said Rob.
“I provide a unique service to both the scientific community and infrastructure consultants. I can translate scientific needs into infrastructure requirements using an understanding of the different cultures of science and construction, thereby providing an interface between the scientific community and consultant teams for infrastructure development.”
There were a significant number of teams conducting research into a wide variety of crops that required a large range of experimental environmental conditions. The temperatures varied from a low of 8°C to 45°C in artificially lit cabinets and walk-in rooms and naturally lit rooftop greenhouses. “The facility will provide University of Queensland researchers with a world-class facility now and well into the future,” said Rob.
Kerslake has also lent his expertise to the design of Level 3 Quarantine insect laboratories and glasshouses in Brisbane and Melbourne, demonstrating his ability to handle complex and highstakes projects. His role as the controlled environment and glasshouse specialist consultant for the UQ Plant Futures Facility underscores his significance in the field.
With Kerslake & Associates’ involvement, the UQ Plant Futures Facility is set to become a benchmark in research infrastructure, offering unparalleled support for scientific advancements in plant growth and physiology.
For more information contact Kerslake & Associates, mobile (Rob) 0418 722 904, email rob@kerslake.com.au
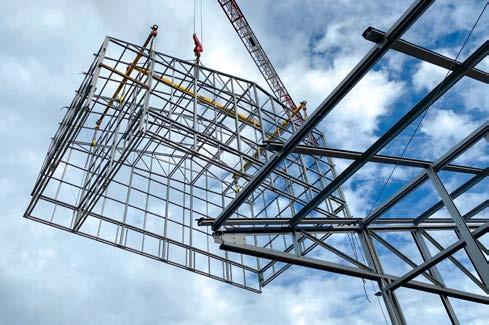
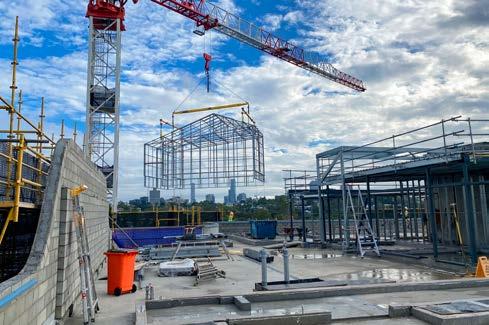
Below KUSCH designed and certified UQ’ s Plant Futures Facility, ensuring structural integrity for cool rooms, glasshouses, and façades.
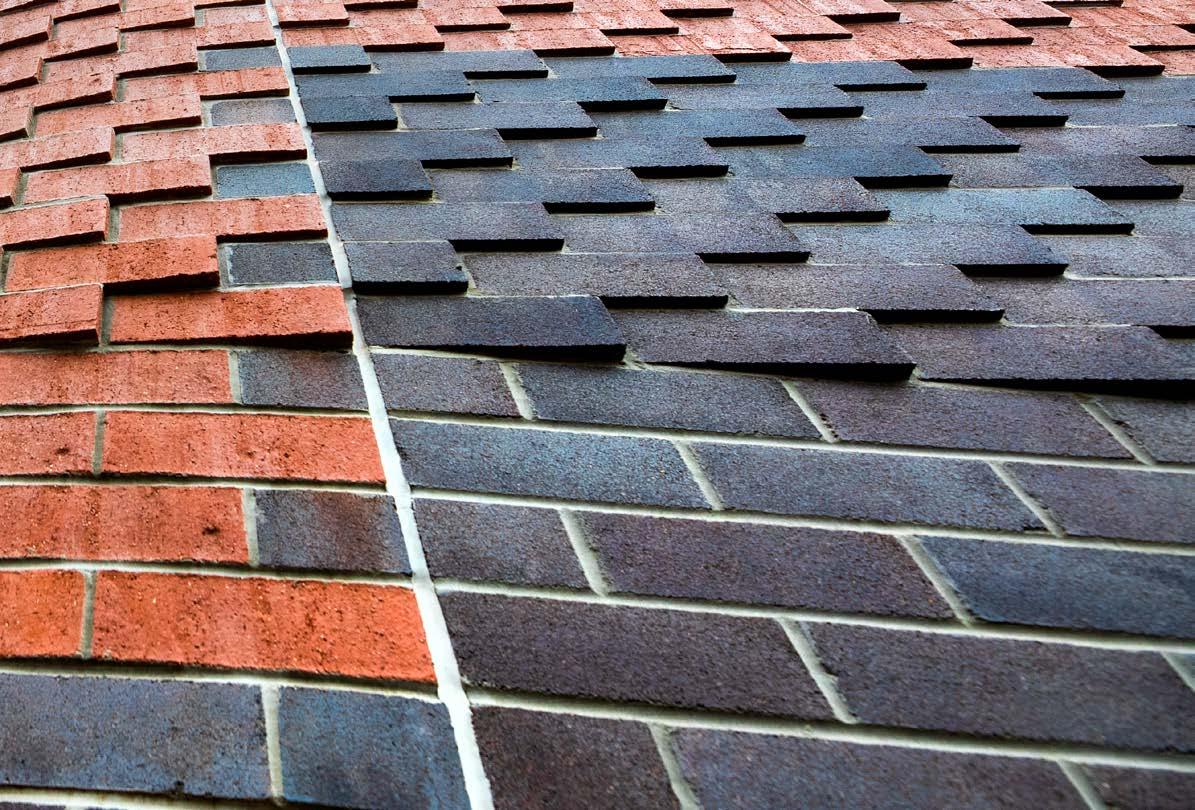
KUSCH provided the structural design and certification for the cool room panels, glasshouse frames, and the architectural masonry façade at the University of Queensland’s new Plant Futures Facility. Their design ensured these components could endure seismic loads, the weight of suspended services, and live loads from construction and maintenance personnel.
The cool rooms were designed to serve as trafficable platforms, supporting both construction and operational activities. The installation of mechanical and lighting services above and below the panel ceilings of the coolrooms created complex buildability challenges. KUSCH’s structural modelling enabled the panel ceilings to be rated for both personnel and equipment loads. This simplification of the installation process ensured safe and efficient access for maintenance in these congested areas.
Detailed modelling and analysis of the panel system allowed KUSCH to eliminate additional seismic bracing typically installed with laboratory cool rooms. “By bracing FCUs to the cool room panels rather than the overhead structure, we resolved personnel access issues, reduced material and labour costs, and mitigated differential movement problems,” said Jarrod.
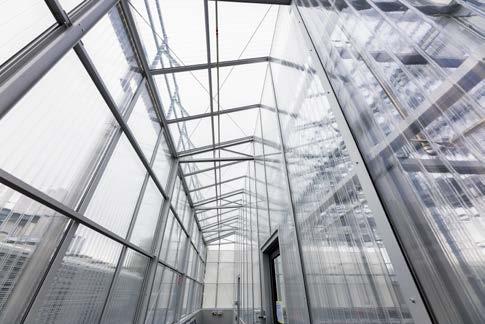

“One of the significant challenges of the project was the construction of the glasshouses on the roof of the 6-storey building. The builders faced difficulties in determining a safe and economical method for this task,” said Business Manager, Jarrod Vanderree.
KUSCH developed a methodology which saw the construction of the glasshouse frames at ground level, followed by lifting the completed frames onto the roof using the onsite tower crane. “This not only improved safety but also proved to be cost-effective. KUSCH’s detailed structural analysis and certification ensured the success of this lift operation,” explained Jarrod.
Additionally, KUSCH managed the structural design and certification of the architectural masonry façade. This included accommodating gravity, wind, and seismic loads, as well as building movement and brick expansion and contraction. Their detailed analysis and design certification addressed these complex factors, ensuring the durability and stability of the multi-storey masonry façade.
For more information contact KUSCH Engineering, 333 Ann Street, Brisbane QLD 4000, phone 1300 10 22 30, email design@kusch.com.au, website www.kusch.com.au
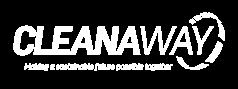
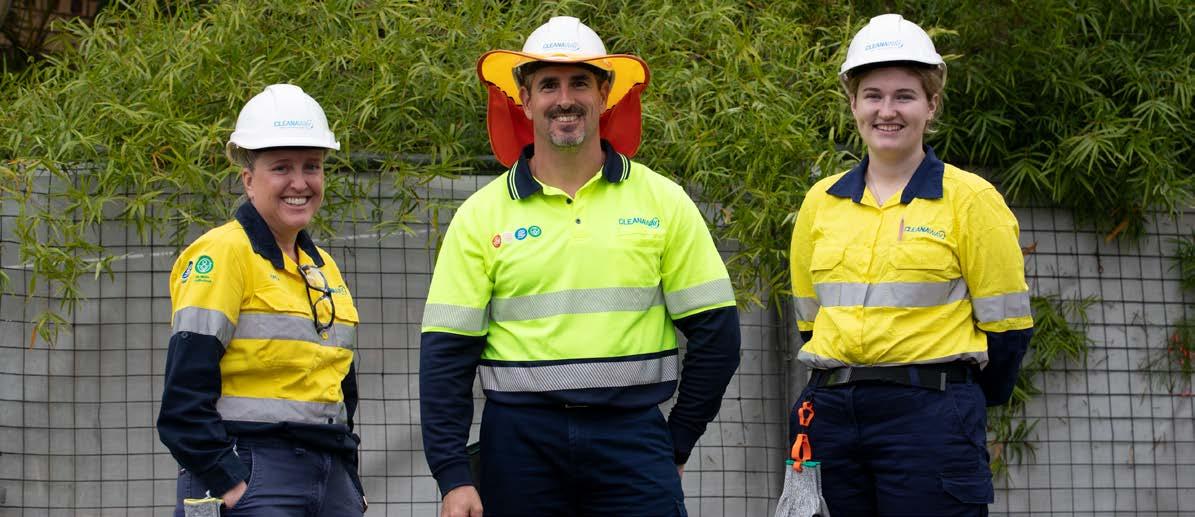
SUSTAINABLE WASTE MANAGEMENT DURING THE CONSTRUCTION OF UQ'S PLANT FUTURES FACILITY
Cleanaway’s involvement in the construction of the University of Queensland Plant Futures Facility underscores the significance of effective waste management solutions in large-scale projects.
With a steadfast focus on sustainability, resource recovery, regulatory compliance, and environmental standards, Cleanaway is the leading waste management company in Australia.
“Our dedicated staff are extensively trained in both construction and demolition waste management. This expertise allows us to handle diverse waste streams with precision and efficiency, ensuring a seamless waste collection and processing,” said Felicity Willmett, Cleanaway’s National Operational Performance Manager.
“Over 60 staff members from our Brisbane office, including frontline driver operators and customer call centre specialists, collaborated seamlessly to ensure smooth waste collection, processing, and recycling for more than 150 services for this project. The team’s dedication to customer service, exceptional work ethic, and commitment to the community was exemplary.”
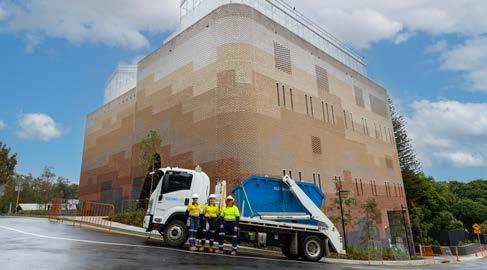
Throughout the project, Regional Manager Tiffany Paffey played a crucial role in overseeing the site and project, ensuring that waste management operations ran safely, smoothly and efficiently. Tiffany’s leadership and strategic oversight were instrumental in coordinating logistics, optimising waste removal processes, and maintaining timely service delivery, contributing to the overall success of the project and ensuring the safety of both the Cleanaway and site teams.
“Our waste management services operate on an ad hoc basis, where clients can simply call us when the need arises. We pride ourselves on being highly responsive and agile, ensuring that we can promptly address construction site requirements,” said Felicity.
“The waste bin plays a crucial role in site operations and must be serviced within the requested timeframe. We understand the intricacies of the industry, and work closely with our construction partners to navigate the challenges and complexities of project logistics, ensuring a seamless coordination of all the moving parts.”
Cleanaway prioritise high resource recovery rates and implement eco-friendly practices to not only facilitate effective waste disposal but also contribute to environmental conservation efforts. Their goal is to ensure that every aspect of their waste management services aligns with the principles of sustainability and environmental responsibility.
Through communication and collaboration, Cleanaway can get the best outcomes for customers.
For more information contact your local Cleanaway branch by calling 13 13 59, www.cleanaway.com.au

Below Maintek Roofing installed essential roofing, acoustic walls, and cladding for UQ’s Plant Futures Facility, ensuring innovation and quality

Known for their innovation and customer satisfaction, Maintek Roofing were contracted to provide and install critical roofing components in the University of Queensland Plant Futures Facility.
Maintek’s scope of work included installing acoustic walls and ceilings, roof sheeting, and stainless cappings that met the stringent requirements of a high-tech research environment. To ensure maximum efficiency and aesthetic results for the project’s façade, Maintek utilised a dual product system, combining Vulcan Acoustic Insulation and Aluminum Perforated Cladding.
Aluminium Perforated Cladding is designed to maximise airflow and enhance natural lighting while providing protection from harsh weather conditions. “These architectural products not only serve as a striking façade but also function as paneling and screening for both internal and external applications,” said Ryan Rahurahu, Project Manager.
Vulcan Acoustic Insulation is a high-density, rigid insulation made from mineral rock fibre stonewool. “It’s a non-combustible material suitable for both external and internal applications, known for its
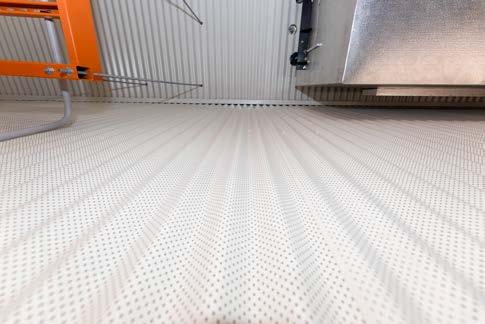
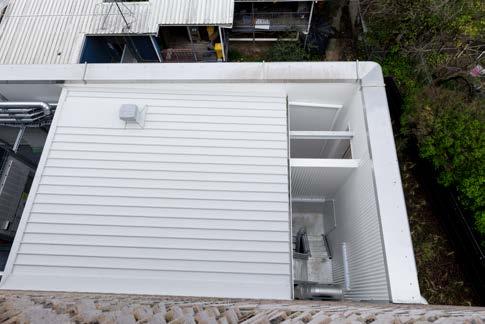
water-shedding characteristics. “This insulation is particularly effective in ventilated rainscreen façades and other thermal and acoustic wall, roof, floor, and ceiling applications.” Ryan said.
The complexity and importance of this project demanded the best, and Maintek Roofing delivered. Our role in ensuring the facility’s roofing meets the highest standards of durability, insulation, and acoustics has been a significant achievement for our team,” said Ryan.
Maintek’s other notable projects include Brisbane Metro Bus Depot, Palm Beach Aquatic Centre, and Collingwood State School. Maintek’s portfolio includes government projects, airport installations, and architectural commercial ventures, all of which speak to their capability and reliability.
For more information contact Maintek Roofing Pty Ltd, 75 Waterway Drive, Coomera QLD 4209, phone 07 5580 4697, email ryan@maintekroofing.com.au, website www.maintekroofing.com.au

Below Epcon Contracting offers eco-friendly, non-toxic epoxy flooring solutions for commercial, residential, and industrial projects.
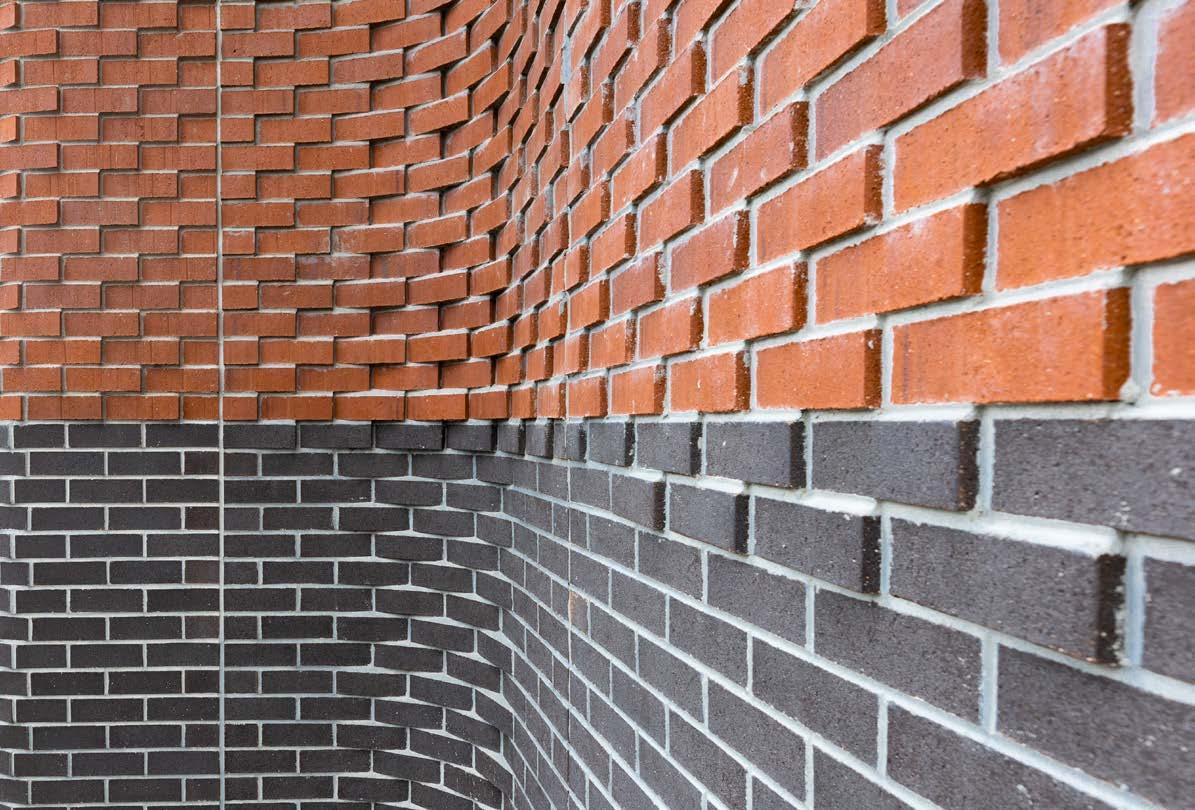
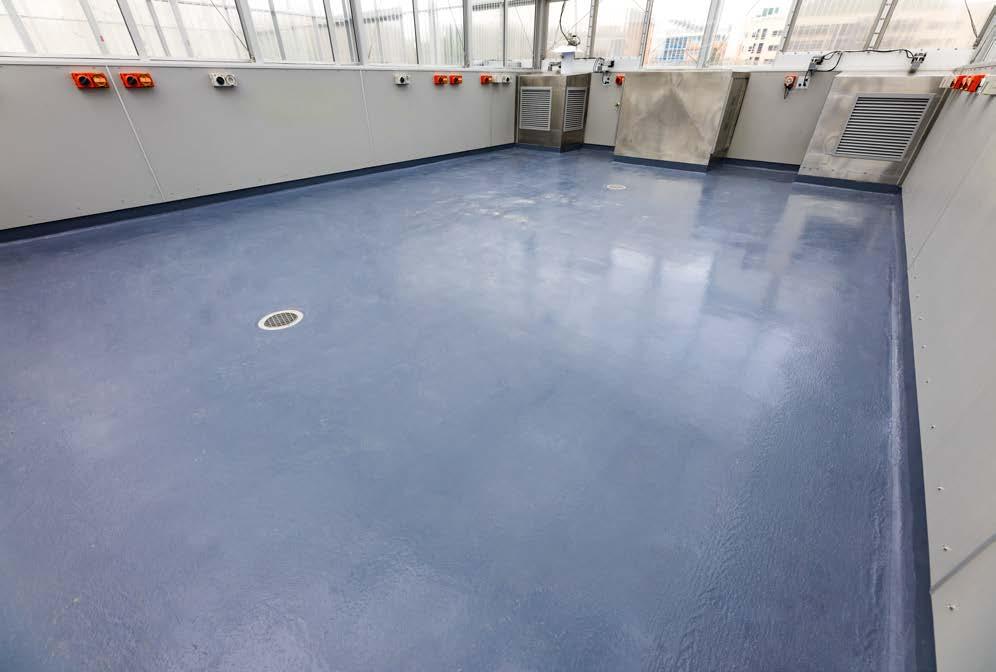
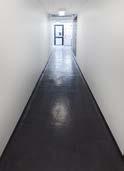


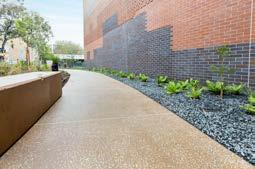
With years of experience in the flooring industry and a solid reputation among builders and construction companies across Australia, Epcon Contracting has proven itself as a leader in epoxy flooring solutions, and a clear choice for the University of Queensland (UQ) Plant Futures Facility project.
“At Epcon Contracting, we pride ourselves on being an independent, commercial, residential, and industrial floor contractor, specialising in epoxy flooring systems,” said Kirk Rome, Director of Epcon Contracting. “We promote and use only the most reliable components and materials, ensuring our services are non-toxic, safe, and environmentally friendly.”
Epcon Contracting’s involvement in the UQ Plant Futures Facility was comprehensive, encompassing a range of flooring solutions tailored to the facility’s unique requirements. The scope of work included applying epoxy resin to the staircase, using 2pac epoxy on Levels 2, 3 and 4 and concrete sealer on Levels 1-2 and Levels 4-6, maintaining slip resistant finish for compliant safety. Resin supplied by Sika Australia, with slip resistance verified by Slip Test Australia.
Additionally, they utilised epoxy resin mortar in the basement to
correct the concrete and applied Sika 263SL followed by Sika 264 Epoxy rollcoats incorporating aluminum oxide.
For the Level 6 greenhouses, Epcon’s team, installed the Tremco Alphaguard waterproof membrane, supplied by Tremco Australia, and for the external footpaths, a spray-applied Streetscape Concrete Sealer was utilised from Concrete Colour Systems.
“Our team had to coordinate closely with other trades to gain access to spaces, which extended our timeline to July,” Kirk explains. “Despite the challenges, we ensured that every aspect of our work met the highest standards of quality and performance.”
As a family-run business, Epcon Contracting operates with a personal touch and a commitment to excellence. “Our aim is to provide our clients with strong and great-looking floors at competitive prices and within budget,” Kirk said. “We install epoxy flooring that performs in harmony with the architecture of the building and the type of business carried out at the facility.”
For more information contact Epcon Contracting, phone 0431 083 575, website www.epconcontracting.com.au.
LUXURY, INNOVATION & HERITAGE IN ONE PRECINCT
DEVELOPER : TOGA Development
MAIN CONSTRUCTION COMPANY : TOGA Constructions NSW
ARCHITECT : SJB Architect
CIVIL / STRUCTURAL ENGINEER : Robert Bird Group
QUANTITY SURVEYOR : WT Partnership
PROJECT VALUE : $250 million

TOGA Constructions’ Surry Hills Village redefines modern urban living in Sydney, blending heritage with innovation. Spanning 10,500m², it features luxury residences, a five-star hotel, retail, and hospitality spaces. Key highlights include a 7-storey CLT commercial building, curved brick façades, sustainable materials, and green communal spaces.
Surry Hills Village stands as TOGA Constructions’ largest and most ambitious project to date. With a construction value of $250 million, this mixed-use precinct redefines modern urban living and innovation, setting a new standard for integrated design in the heart of Sydney.
Developed by TOGA Developments and delivered by TOGA Constructions NSW, the project encompasses an impressive 10,500m² footprint, featuring a harmonious blend of residential, commercial, retail, and hospitality spaces.
“Surry Hills Village is a testament to TOGA’s commitment to delivering world-class precincts that blend heritage and innovation seamlessly,” said James Nickeas, Project Manager at TOGA Constructions. “This project showcases our team’s expertise in
managing complex developments with multiple classifications and delivering a transformative urban experience.”
Surry Hills Village seamlessly integrates residential luxury, commercial vibrancy, and community-focused spaces. The development includes 122 high-end apartments, penthouses, and terraces designed to redefine urban living. These residences are complemented by a 102 room five-star hotel, the new ‘Eve’ Hotel, with vaulted ceilings and polished plaster finishes, offering guests an unparalleled experience. The rooftop pool and bar, further enhances the precinct’s appeal.
Retail and hospitality offerings include Harris Farm, Coles, and an array of food and beverage outlets within the thoughtfully curated Wunderlich Lane. The precinct’s two levels of basement parking ensure convenience for residents, workers, and visitors alike. “Surry
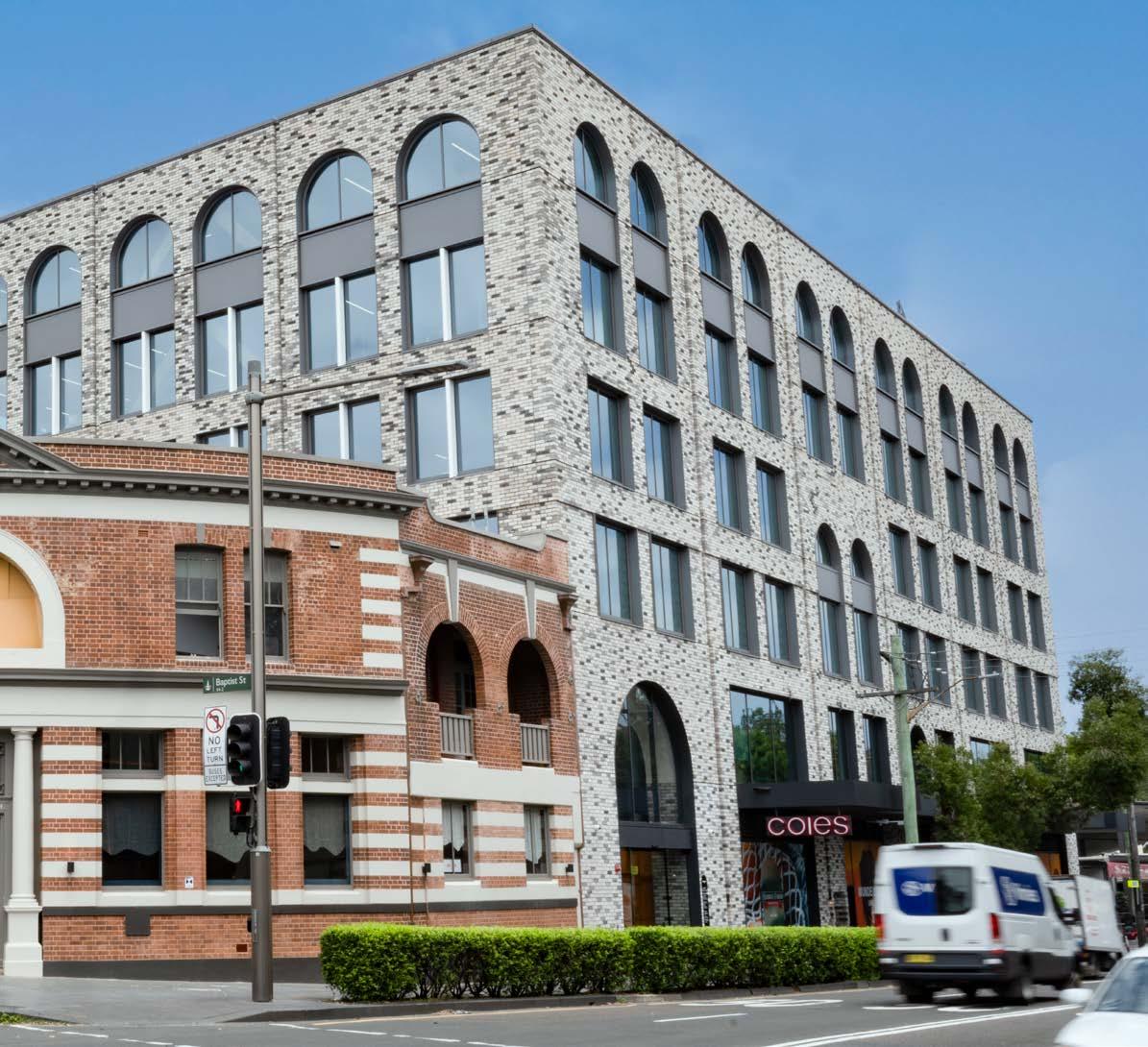
Hills Village embodies a true mixed-use precinct,” said James. “It’s a vibrant community in itself.”
Surry Hills Village boasts striking architectural features, including a 7-storey CLT (Cross Laminated Timber) commercial building – a first for TOGA Constructions, and one million bricks is across the precinct, which includes Empire double-groove bricks. The project has a distinctive signature look and the soffit detailing, adds a timeless charm to the podium façades.
The precinct’s sustainability initiatives further underscore its uniqueness. “From CLT timber to energy-efficient glazing systems, we’ve integrated cutting-edge materials and technologies to enhance environmental performance,” said Nickeas. The project incorporates over 7,500m² of glazing, two operable glazed roofs (210m² over Olympus restaurant and 120m² over Lottie, the hotel rooftop bar), and over 4,000m² of landscaping that softens the urban footprint while creating green communal spaces.
A hallmark of the project is its thoughtful preservation and celebration
of the site’s heritage. The intricate curved façades and brickwork pay homage to Surry Hills’ historic character while introducing a bold, modern aesthetic. The integration of heritage elements into the design ensures the precinct remains rooted in its cultural context while embracing innovation.
At peak, the site accommodated 400 workers daily, representing 70 subcontractors and a total workforce of over 6,200 inducted personnel. The collaboration of industry leaders, including civil and structural engineers, was instrumental in overcoming these challenges.
Surry Hills Village positions TOGA Constructions at the forefront of urban development, showcasing their ability to deliver projects that transcend functionality to enrich the community fabric. “This precinct is more than a development; it’s a destination that will serve as a model for future urban projects,” James concluded.
For more information contact TOGA Constructions NSW, Level 5/45 Jones Street, Ultimo NSW 2007, phone 02 9356 1000, email info@toga.com.au, website www.toga.com.au
ECO-FRIENDLY, ELEGANT, AND BUILT TO LAST
Orion Mechanical Services has successfully completed a comprehensive mechanical ventilation and air conditioning systems installation at Surry Hills Village. Orion’s work has elevated the precinct’s residential, commercial, and hospitality spaces with cutting-edge climate control solutions, setting new benchmarks for comfort, control and energy efficiency.
“Our involvement spanned from design finalisation to supply and installation of all mechanical ventilation and AC systems across this multi-faceted project,” shared Justin Phillips, Managing Director of Orion Mechanical Services.
The scope encompassed two levels of basement car parks, four residential buildings with 128 apartments, a luxury 103-room hotel with lobby and pool bars, and a 6-level commercial building with an event space. Additionally, Orion provided provisional base building mechanical services for all retail tenancies including COLES, plus complete HVAC fitout for prominent names such as Harris Farm Markets, Blooms
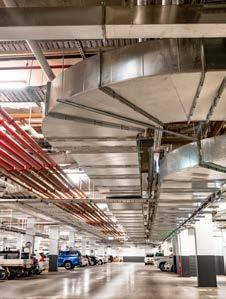
the Chemist, Raita Noda Omakase and Olympus Dining.
Orion employed a mix of independent air cooled and water cooled systems to address the diverse needs of the precinct. Each residential apartment is served by its own independent Fujitsu air cooled VRV AC system with remote condensers placed on the roof for premium amenity & silent operation. Meanwhile, the hotel, commercial, and retail spaces benefit from a shared central condenser water system supported by rooftop cooling towers and gas condensing boilers. A BMS monitors all thermal and electrical energy meters easily accessed by the Building Managers via the site wide ICN.
“The project’s complexity demanded thoughtful engineering and flexibility for future uncertainty,” Justin explained. “For the commercial and hotel areas, we chose Mitsubishi Electric Water-Cooled Heat Recovery VRF systems, which are also featured in some of the larger retail spaces like Harris Farm and Olympus. These system’s robust design and adaptability make

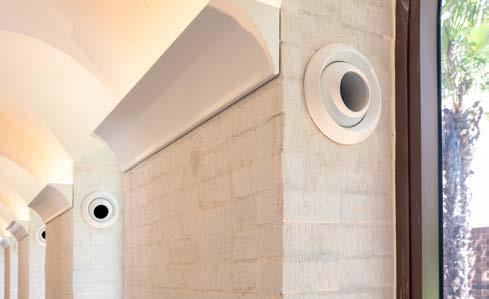
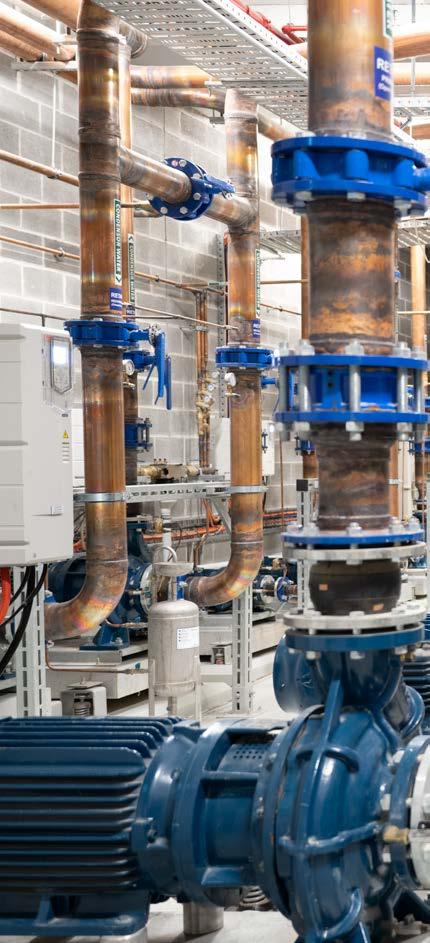
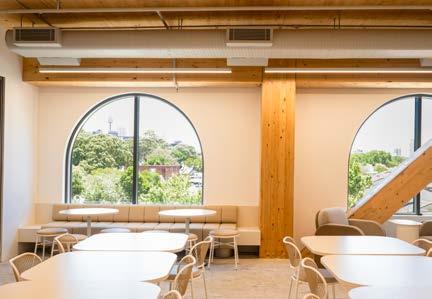
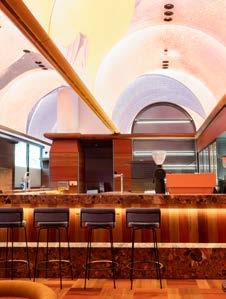
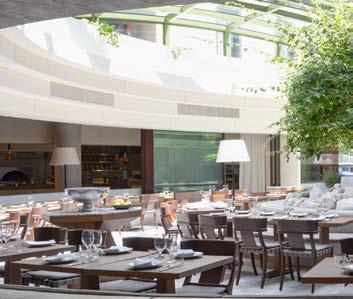
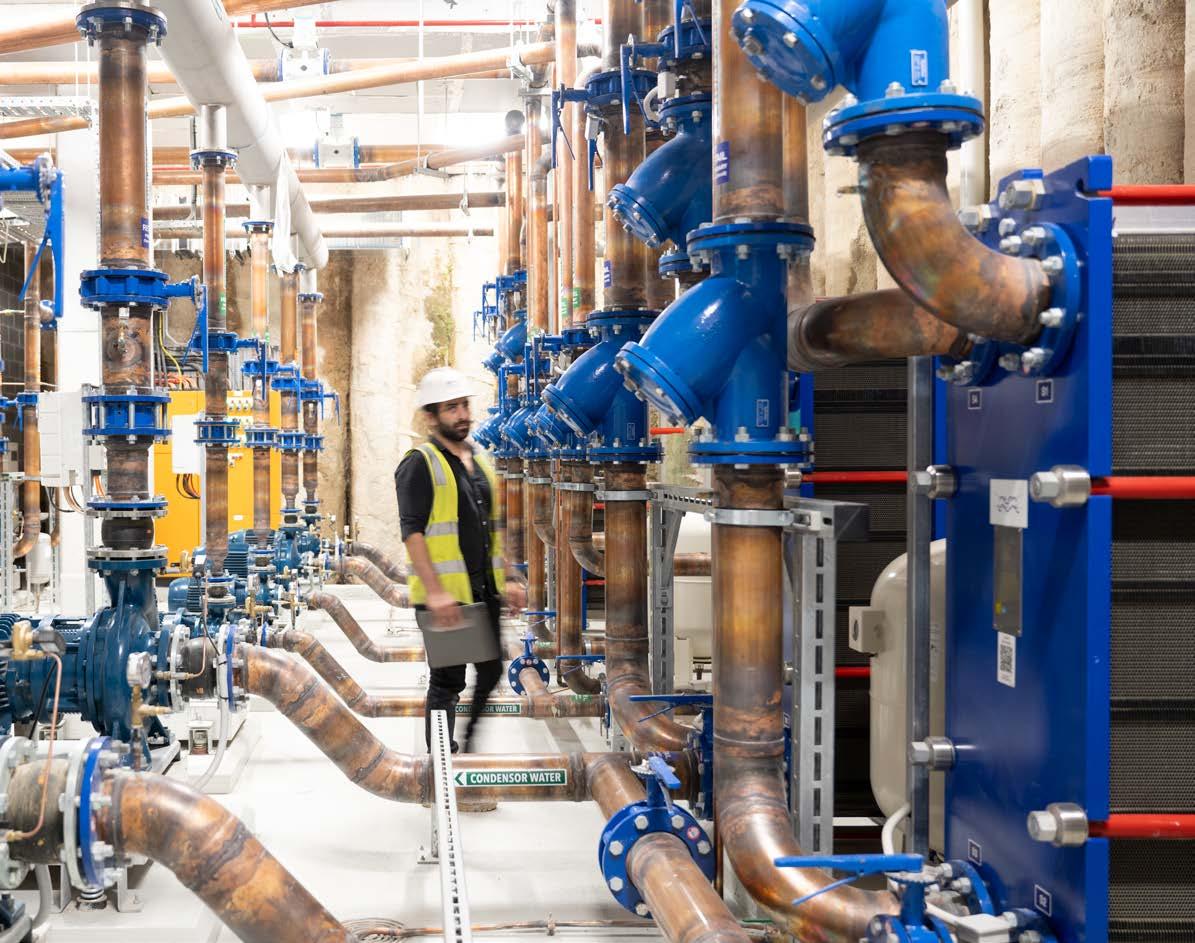
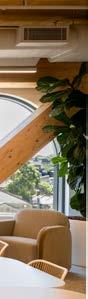
it a premium choice for larger tenancies with multiple thermal zones.”
One standout feature is the central condenser water system which consists of three closed circuit secondary side systems, serving each main stratum, each thermally connected via dual plate heat exchangers to the common open circuit primary.
This system not only supports the precinct’s HVAC needs but also shares heat between
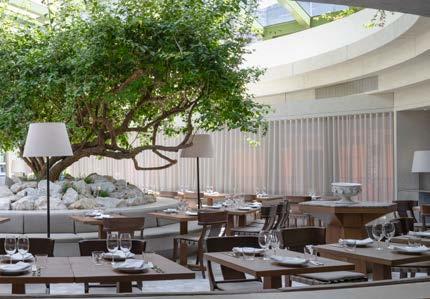
circuits, including delivering free heat to the domestic hot water plant in the commercial building via water-cooled heat pumps. Orion worked closely with TOGA to ensure all water-cooled plant & equipment are housed internally within the building, thus maximising the lifecycle longevity and efficiency of the central plant. The only external plant are the cooling towers, stainless steel pipework and boilers.
At peak, Orion deployed 12 direct employees and engaged five subcontractors, with a maximum workforce of 25 on-site daily.
“Through a collaborative design review process with stakeholders, we ensured the chosen systems were not only efficient but also aligned with the project’s architectural and sustainability goals,” noted Orion’s full time site based Project Manager, Mr Sajid Safadi.
Surry Hills Village reflects Orion’s commitment to quality and innovation. From initial engagement in December 2021 to the completion of base building works in
October 2024, the company has consistently prioritised simplicity, longevity, and performance. Even as tenancy fit-out works continue, the impact of Orion’s contributions is evident across the precinct.
“This is one of the largest and most complex projects we’ve worked on,” Justin stated.
“The integration of sustainable systems and meticulous attention to detail exemplifies our approach to delivering exceptional results.”
Orion Mechanical Services is proud to have been a part of this transformative project, enhancing the functionality and sustainability of Surry Hills Village. With a reputation for excellence in mechanical solutions, the company continues to set industry benchmarks across a diverse portfolio of projects.
For more information, contact Orion Mechanical Services, phone 0414 877 516, email info@orionmechanical.com.au, website www.orionmechanical.com.au
Below Orion Mechanical delivered sustainable HVAC systems for Surry Hills Village, setting new benchmarks in energy efficiency and innovation
Below Facade Concepts installed 7,500m² of glazing and 100 tonnes of aluminium across the Surry Hills Village’s seven buildings.


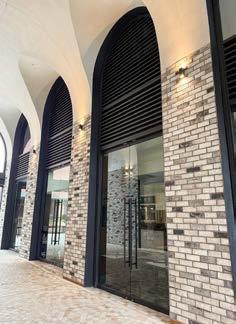
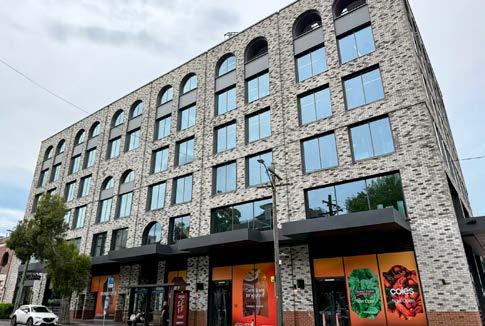

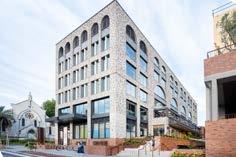

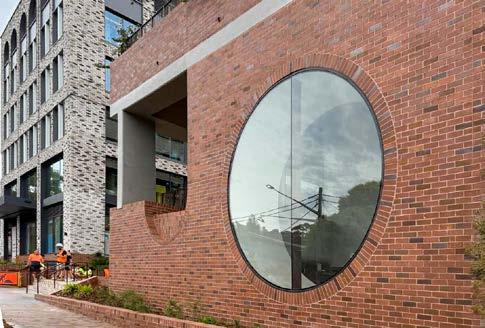
The Surry Hills Village project, a complex and ambitious mixed-use development, has been brought to life with Façade Concept’s unparalleled craftsmanship and innovative solutions.
Façade Concept was engaged in designing, fabricating, and installing the entire glass and aluminium windows and doors package, delivering a standout façade for this transformative project.
Spanning seven unique mixed-use buildings, the project demanded an impressive 7,500m² of glazing and 100 tonnes of aluminium, including curved and round windows, wood grain finish bifold doors, and deluxe custom powder-coated sunshades and hoods.
“This project epitomises complexity,” shared Director of Façade Concept, Jordan Moyle. “Unlike a single high-rise structure, integrating distinct functionalities across multiple buildings required meticulous planning and execution. The diversity in purpose and the unique designs of each structure added layers of complexity to the project.”
The advanced thermal performance features, such as sunshades and hoods, combined with the architectural innovation of curved glazing, set this project apart. “The custom powder coat colours were
a particular challenge, requiring large minimum order quantities that needed to be perfect,” Jordan added. Despite these challenges, Façade Concept’s dedication to quality ensured flawless execution.
Work commenced on site in December 2022, with Façade Concept deploying a peak workforce of 22 employees, averaging 8-12 personnel daily. While the original scope has been completed, Façade Concept continues to accommodate client variations and adjustments. “The scale and diversity of this project highlights our capability to deliver on large, multifaceted developments,” Jordan said.
Façade Concept’s commitment to innovation and excellence has positioned Surry Hills Village as a landmark in urban design and sustainability.
Current projects include Loreto Boarding House in Normanhurst, New South Wales
For more information contact Façade Concept, 4/1-13 Atkinson Road, Taren Point NSW, phone 02 9525 5446, email sales@facadeconcept.com.au, website www.facadeconcept.com.au.
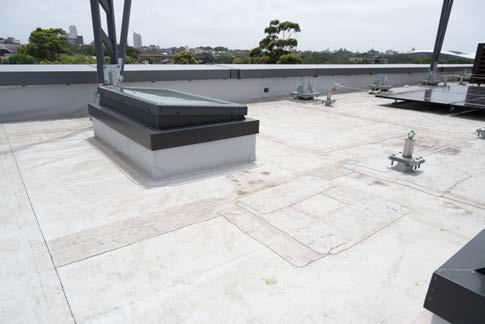

Below Sure Projects Australia delivers innovative, high-performance waterproofing solutions for Surry Hills Village, ensuring durability and sustainability.
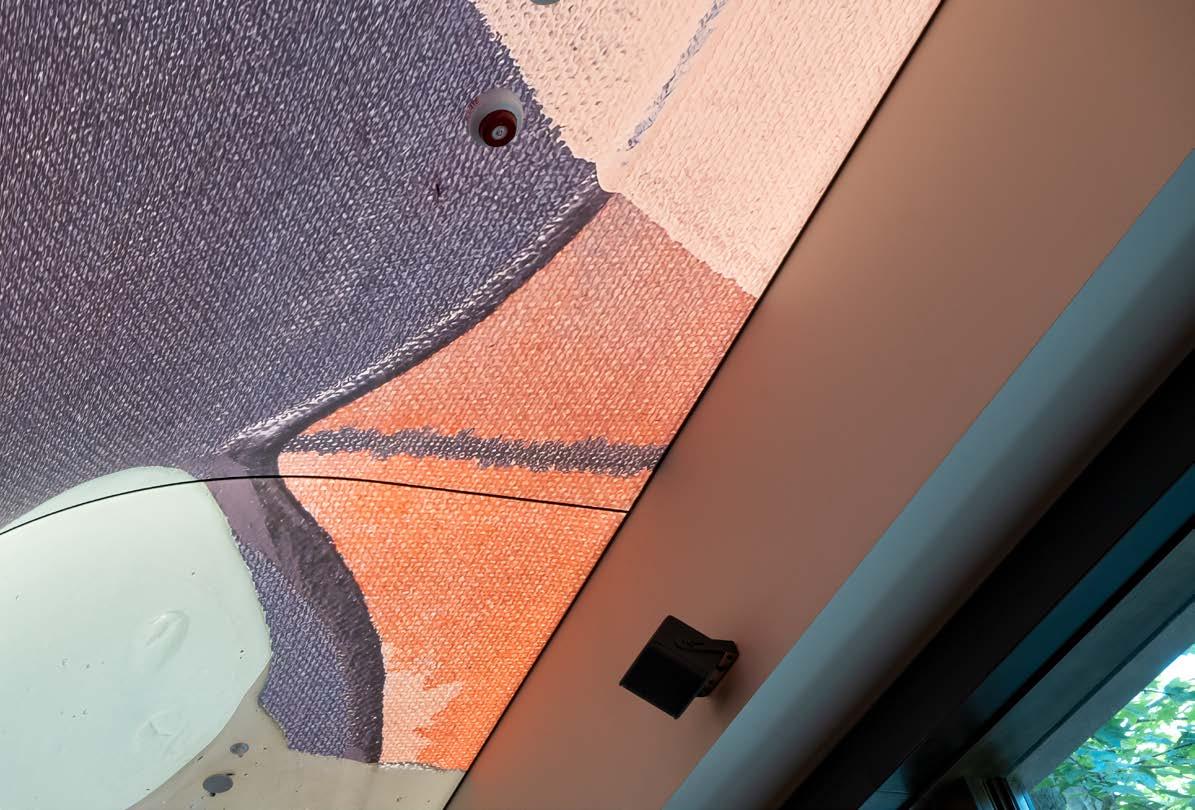
Sure Projects Australia Pty Ltd (SPA) has brought its 20 years of expertise to the ambitious Surry Hills Village redevelopment, delivering resilient, high-performance waterproofing systems across this extensive residential and commercial project.
Contracted for the design, consultation, supply, and installation of all waterproofing and epoxy coatings, SPA’s contributions have fortified every external and trafficable surface across this large-scale, multifaceted project. “Our approach centres on quality and innovation, setting the benchmark for waterproofing solutions across diverse, complex environments,” said Samire Fakhri, Managing Director of Sure Projects Australia.
Key installations on this project include 2,750m² of rooftop waterproofing, 11,150m² of podium areas, and 12,850m² of planter boxes. SPA’s meticulous approach extended across various challenging structures, including balconies, terraces, and retaining walls, ensuring seamless, high-standard finishes on every surface.
A particular standout of the Surry Hills project is Building G, a cross-laminated timber (CLT) structure where SPA pioneered the use of Fatra PVC sheet membranes, enhancing longevity and durability.
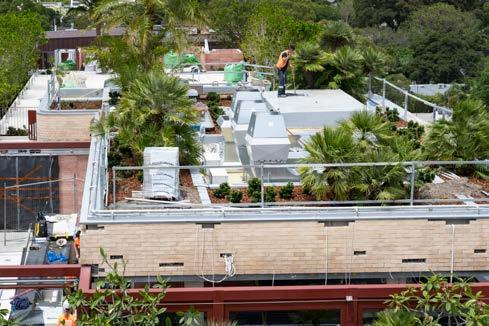
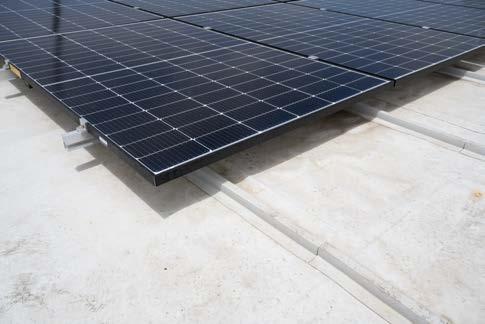
“This was the first CLT building in Australia to utilise such an advanced waterproofing system, and we’re proud to have navigated the complex detailing and integration needed to make it flawless,” added George Fakhri, Construction Manager at SPA. These achievements showcase SPA’s capability to navigate intricate project challenges, such as interfacing around solar panels, davit arm base plates, and service protrusions.
In addition to the CLT rooftop, SPA employed industry-leading Polyurea spray-applied membrane systems across podiums, planter boxes, and detention tanks. The project, which began with early waterproofing work in February 2022 and was completed in October 2024, consistently maintained SPA’s high standards for quality and durability.
Current projects include Multiplex’s New Sydney Fish Markets, Western Sydney Airport, and John Holland’s Sydney Children’s Hospital.
For more information contact Sure Projects Australia, phone Sam Fakhri 0405 976 417, email sam@sureprojectsaustralia.com.au, website www.sureprojectsaustralia.com.au
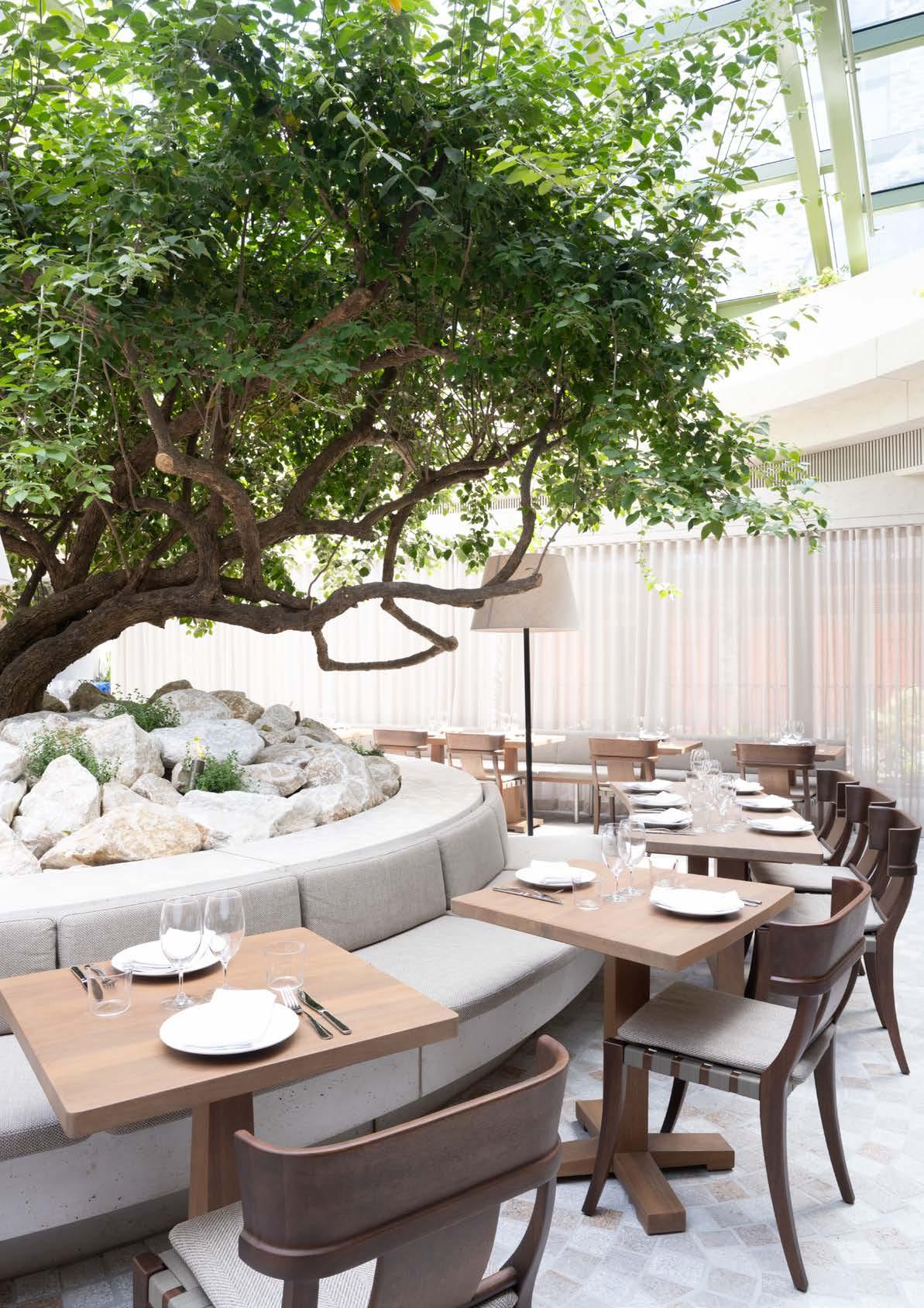
Below Auswide Corp completed intricate scaffolding for Surry Hill's seven-building project, installing 20,000m2 of scaffolding.
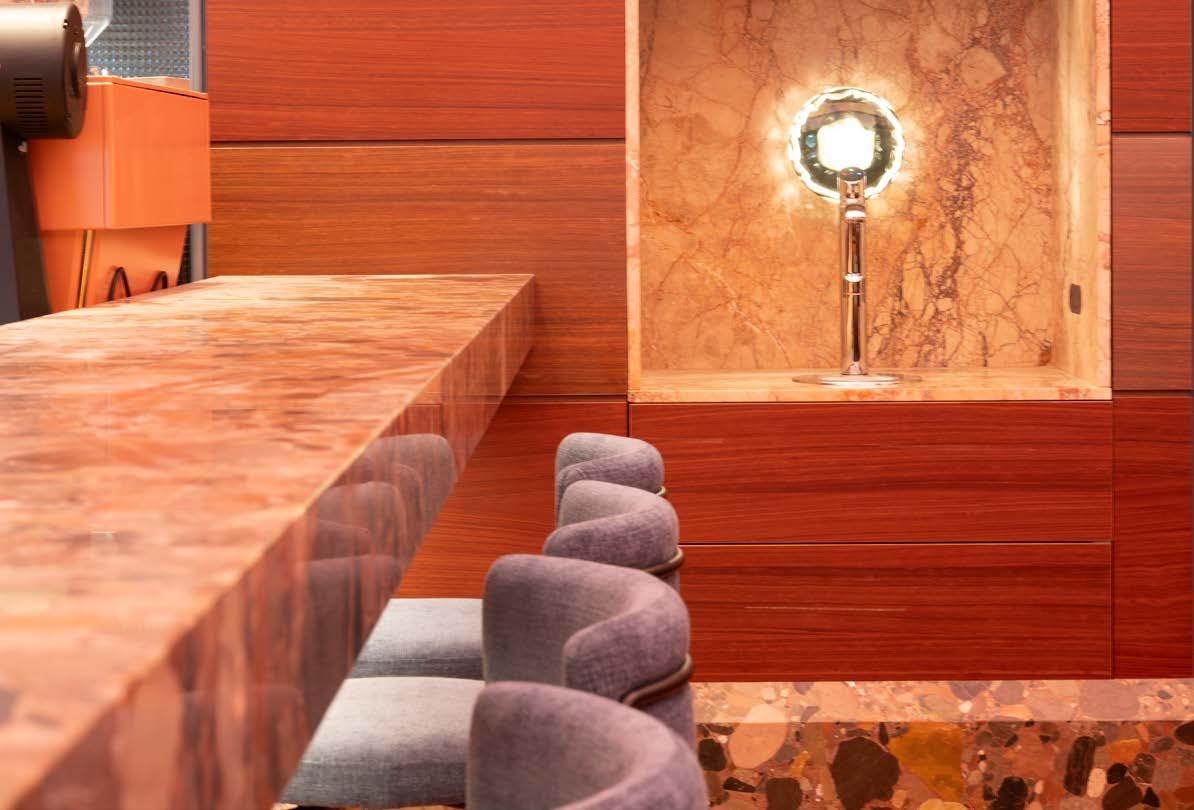
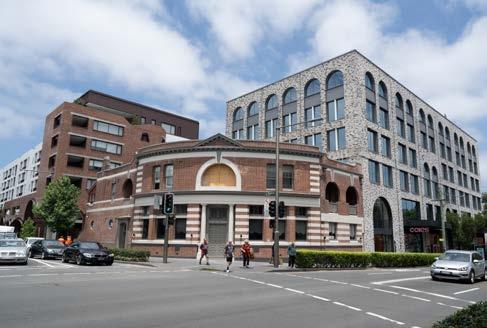
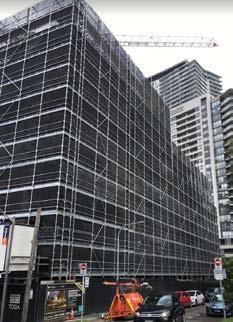
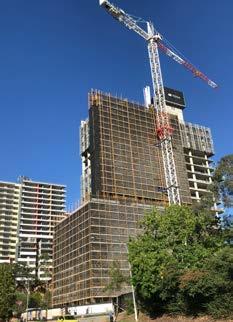
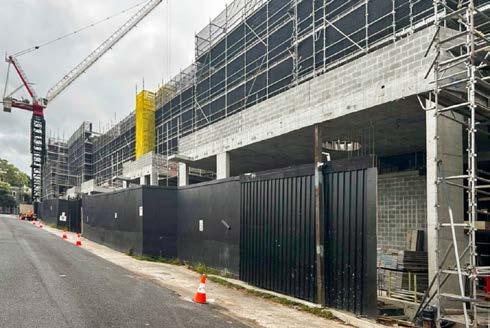

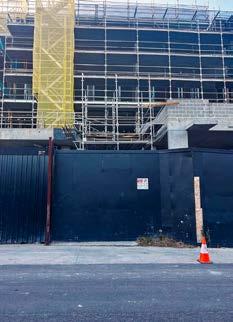
Auswide Corp has successfully completed intricate scaffolding for the Surry Hill Project, a multi-building development that demanded precision, innovation, and teamwork to ensure a seamless delivery.
The project included seven distinct buildings on a single site, and required a combination of perimeter scaffolding works, crane-assisted loading platforms, and advanced safety measures.
“This wasn’t the largest project we’ve worked on, but it was certainly one of the most intricate. The challenges of material handling, tight site access, and the sheer scale of the work required exceptional planning and execution,” said Michael Cohen of Auswide Corp.
Auswide Corp installed 20,000m2 of scaffolding, wrapping each building in perimeter safety chain, shade, and client advertising banners. Stretcher stairs and alloy stair access were strategically placed on all seven buildings, ensuring optimal site safety and accessibility for workers.
Auswide Corp’s retractable loading platforms deployed on the site, played a critical role in streamlining operations on-site, allowing
for materials to be delivered efficiently to each structure via crane, ensuring seamless workflows and significantly reducing downtime.
The project commenced in January 2020 and reached finalisation in April 2024. At peak, Auswide Corp deployed a dedicated crew of 30 skilled workers, reinforcing their reputation as a reliable, EBA-compliant scaffolding provider.
The importance of Auswide’s back-office team in overcoming the project’s complexities was immeasurable. Planning and design work were critical in enabling the site team to execute flawlessly. The collaboration between the back office and on-site leadership along with selecting the right team for the job ensured a smooth operation from start to finish.
With 35 active projects and a strong pipeline extending over the next 18 months, Auswide Corp continues to lead the way in scaffolding solutions across New South Wales.
For more information, contact Auswide Corp, 6.11, 55 Miller Street, Pyrmont, phone 02 8880 1020 or visit www.auswidecorp.com.
Marrickville, TOGA Macquarie Park, TOGA
NEWCASTLE EAST END
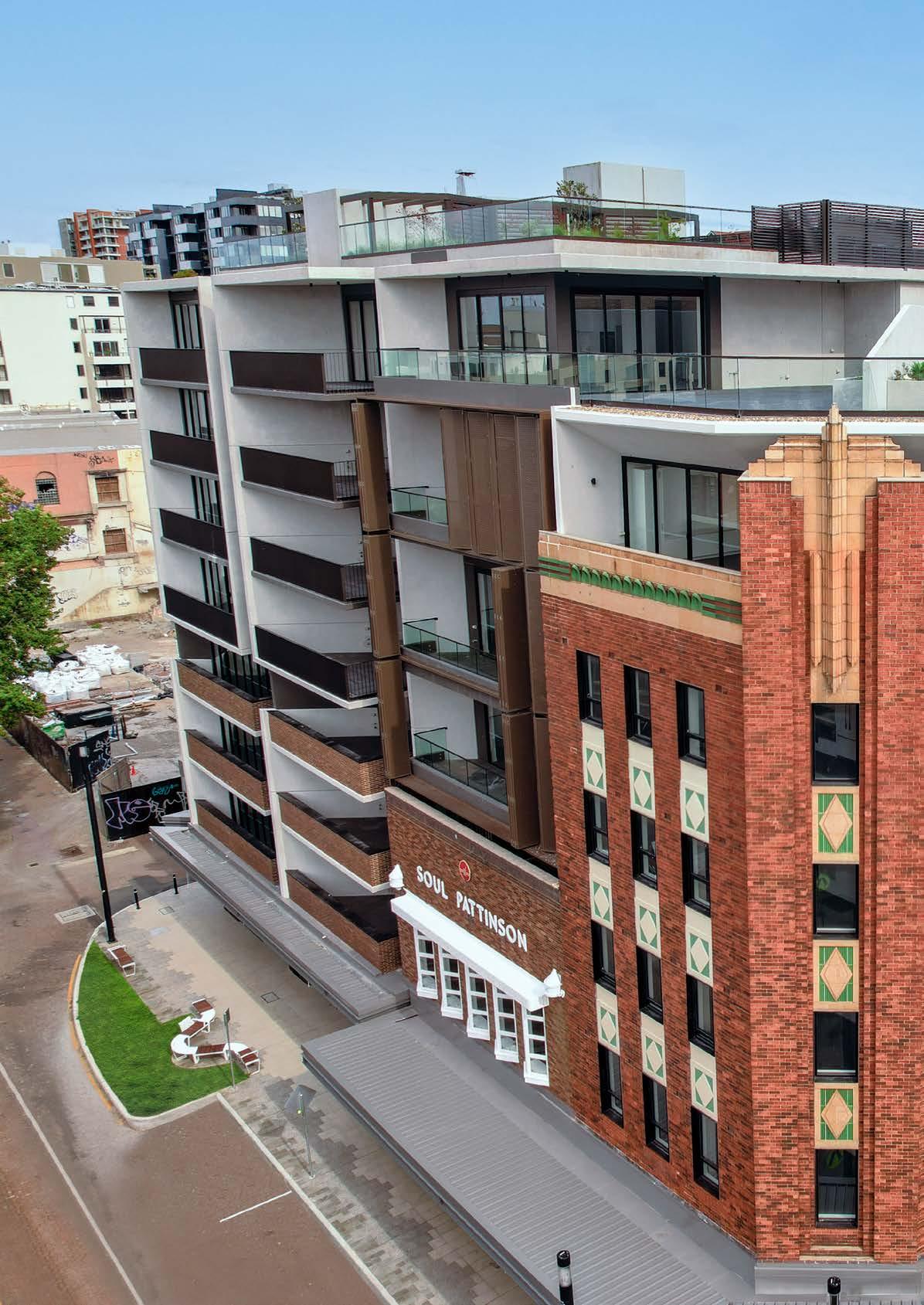


BREATHING NEW LIFE INTO NEWCASTLE’S EAST END
TQM Design & Construct’s Newcastle East End project masterfully blends heritage preservation with modern design, and marks a significant step in Newcastle's transformation, merging legacy with innovation. The $150 million development includes 116 apartments, heritage refurbishments, and adaptive reuse of historic buildings already on the site.
TQM Design & Construct’s latest project at Newcastle East End is a stunning fusion of modern architecture and heritage restoration. This ambitious $150 million development forms Stage 2 of the Newcastle East End precinct upgrade, an essential milestone in revitalising the city’s iconic urban landscape.
“Our team was entrusted with a project that merges engineering excellence with historical preservation,” stated Project Manager Joe Taouk “This project required precision in both design and construction to ensure that the new elements seamlessly complemented the heritage façades.”
The Newcastle East End development is definitive part of the city’s legacy, with the Lyric Theatre, Soul Pattinson Building, and King Street Terraces, thoughtfully preserved and integrated into the precinct. “This level of heritage integration is rare in modern construction,” Joe shared. “It presented a unique opportunity to respect Newcastle’s architectural history while elevating it with a contemporary approach.”
TQM’s work stands out for its innovative precast concrete system, thoughtfully crafted to complement heritage façades. This system incorporates floating concrete balustrades that enhance the existing architecture, with each element carefully designed to preserve Newcastle’s historic character while seamlessly integrating with new structures.
The project had a high degree of complexity due to the heritage elements and the multiple frontages. To meet these challenges, TQM conducted precise millimetre surveys on each heritage interface, ensuring a flawless connection between the precast panels and the historical façades.
The project began with extensive demolition and careful façade retention in September 2019, laying the groundwork for the subsequent construction stages, including the first basement slab, which was poured in January 2022.
Like many in the industry, TQM encountered delays caused by COVID-19 lockdowns and inflation-driven cost increases. The
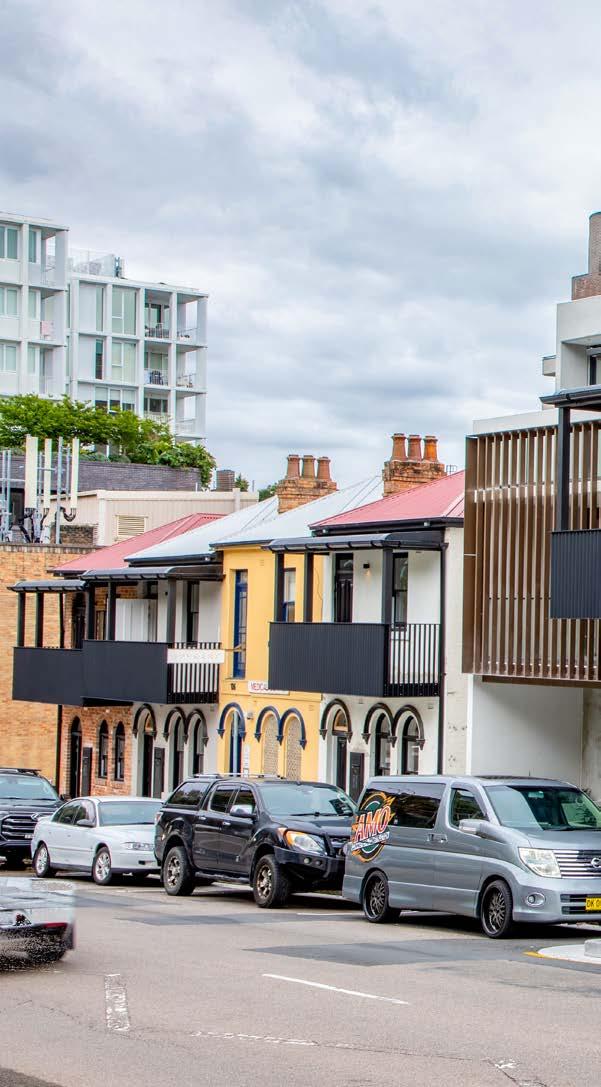
construction process was also complicated by 2022, one of the wettest years on record.
“Managing water was critical on this site as the basement sits well below the water table. We used state-of-the-art pumping technology to remove water during excavation and then treated it to meet environmental standards,” said Joe.
In addition, TQM engaged archaeologists to inspect and preserve any Indigenous artifacts discovered during excavation. “Excavation work included hand-sifting large soil stockpiles, an arduous process but essential in ensuring respect for the land’s historical significance,” Joe explained.
The commitment to sustainability was also evident in TQM’s choice of materials. In an environmentally conscious move, bricks from demolished heritage walls were repurposed to create planter boxes and other internal structures. A specialised HDPE Bentonite blanket was installed under the basement slab to waterproof the foundation and protect it from groundwater ingress.
Image: Newcastle East End's King Street Terraces
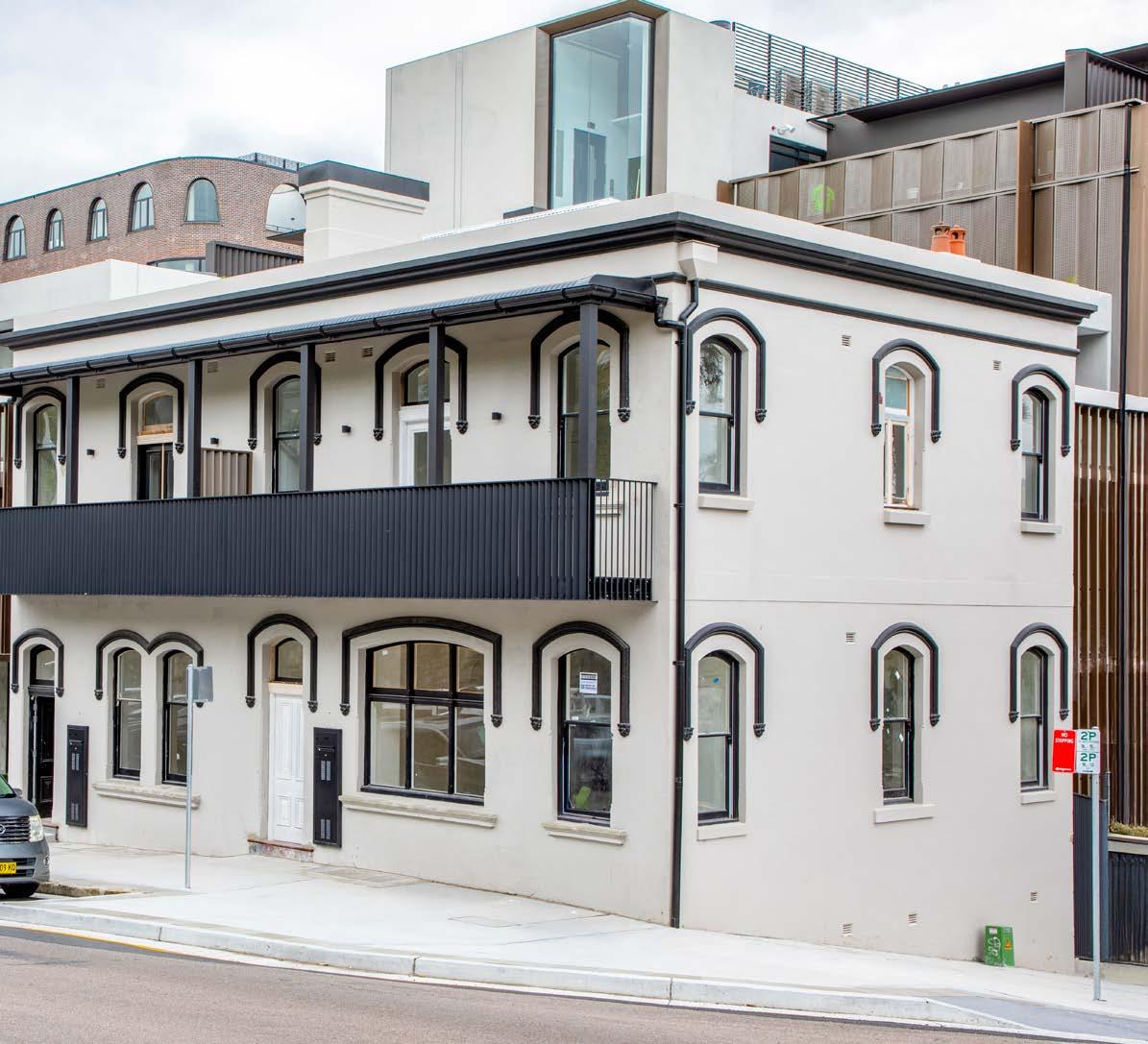
“Each step we took was driven by a commitment to preserving Newcastle’s architectural heritage and enhancing it with sustainable building practices,” Joe noted.
The Newcastle East End project has already positively impacted the community, created hundreds of jobs and revitalising one of the city’s most treasured districts. At peak, the site saw a workforce of approximately 190 employees, a blend of TQM’s own team and subcontractors.
“This is more than just a construction project,” Joe reflected. “It’s a way to honour Newcastle’s past while paving the way for its future.”
Founded in 1999, TQM blends family values with industry expertise. Their hands-on approach and focus on quality, innovation, and loyalty have built lasting client relationships, enabling TQM to deliver highquality projects on time and budget as a trusted market leader.
For more information contact TQM Design & Construct, phone 02 9556 1046, email info@tqmdc.com.au, website www.tqmdc.com.au
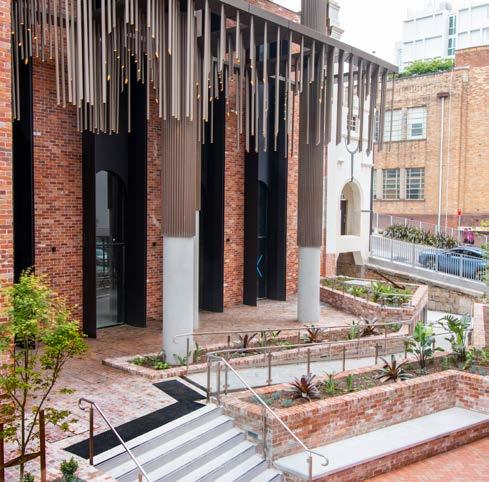
CONSTRUCTION
DIRECTOR
Michael Matthews
ART DIRECTOR/DESIGN
Jessica Mills
PUBLISHED BY
InBuild Media Group Pty Ltd ACN 667 363 779 p. 02 4322 1200 www.ancr.com.au
ancrmagazine
ausconstruction_review
The Australian National Construction Review Australian National Construction Review
WRITERS
Tanya Nellestein, Lexi Gugger
PHOTOGRAPHERS
Benjamin Halcomb, Bruce Robinson, Jim Young, Joe Sabljak, Leah Follett, David Castro, Christopher Millen, Cameron Longshaw, Steve Lock, Brad Chilby
COPYRIGHT
All material in this publication is copyrighted to the publisher and/or its advertisers and contributors. No material or portion of this publication may be reproduced in whole or part without the express written permission of the publisher.
DISCLAIMER
The Australian National Construction Major Project Review and the publisher InBuild Media Group Pty Ltd reserve the right to alter or omit any advertisement, editorial, or advertorial.
The Australian National Construction Major Project Review and the publisher are not liable for inaccuracy in any advertisement or editorial and do not accept responsibility for any claims made by advertisers/ contributors, or losses as a result of acting on the information provided with the publication.
Opinions published in The Australian National Construction Major Project Review are not necessarily those of the publisher or staff of The Australian National Construction Major Project Review.
The Australian National Construction Major Project Review is not related to any other publication.
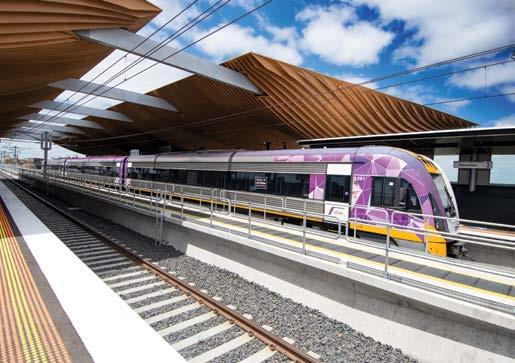
The Directory
AIR CONDITIONING, (HVAC, REFRIGERATION & MECHANICAL SERVICES)
Contract Air Conditioning
Page 39 | 03 9701 5411
Mitsubushi Heavy Industries Air-Conditioning Australia, Pty. Ltd.
Page 14, 16 |1300 130 007
Orion Mechanical Services
Page 62 | 0414 877 516
AERIAL PHOTOGRAPHY
Skyview Aerial Photography
Page 4 | 0431 931 910
BATHROOM PRODUCTS/EQUIPMENT
ASI JD MacDonald
Page 46 | 1800 023 441
BUILDING MATERIALS SUPPLIER
CASF Australia
Page 47 | 1300 795 044
CARPENTRY
Koolie Building & Construction
Page 41 | 0418 336 962
Sakar Constructions
Page 48 | 0425 788 241
CONCRETE (STRUCTURAL REINFORCING)
Goldenlight
Page 21 | 0421 548 469
CONSTRUCTION COMPANIES & ALLIANCES
Built Environs
Page 42 | 08 8232 1882
Hansen Yuncken (QLD)
Page 50 | 07 3872 4000
TQM Group
Page 68 | 02 9556 1046
Toga
Page 60 | 02 9356 1000
CONSTRUCTION SOFTWARE / DOCUMENT/PERSONNEL MANAGEMENT
CoreLogic
Page 1 | 1300 734 318
CONSULTANT (SCIENTIFIC/LABORATORY)
Kerslake & Associates
Page 54 | 0418 722 904
CRANES/HOISTS & RIGGING (ALL CRANE
PRODUCTS & SERVICES)
Vamp Cranes
Page 38 | 03 8652 8635
ELECTRICAL INFRASTRUCTURE (CIVIL AND CONSTRUCTION)
Daly’s Constructions
Page 28 | 03 9360 9485
ENGINEERS (STRUCTURAL)
KUSCH Engineering
Page 55 | 1300 10 22 30
EXCAVATION (NON DESTRUCTIVE DIGGING)
Ontrack Excavation Group Pty Ltd
Page 30 | 0499 654 865
FAÇADES
Façade Concepts
Page 64 | 02 9525 5446
FLOORING (EPOXY)
Epcon Contracting
Page 59 | 0431 083 575
GLASS & GLAZING
Oceania Glass
Page 18 | www.oceaniaglass.com.au
GOVERNMENT DEPARTMENTS & COUNCILS
Level Crossing Removal Project
Page 22 | www.levelcrossings.vic.gov.au
HEALTHCARE PROVIDERS (AGED CARE)
Ryman Healthcare
Page 34| 1800 288 299
JOINERY & FITOUTS
Cabinet Solutions
Page 40 | 0498 521 981
MATERIALS MANAGEMENT
Lantrak
Page 24 | 13 9666
RENDERING
Swart Plastering
Page 49 |0418 833 367
ROOFING
Maintek Roofing
Page 57 | 07 5580 4697
SCAFFOLDING
Auswide Corp
Page 67 | 02 8880 1020
SHADE SAILS
Sydney Shade Sails
Page 19 | 02 9592 0401
WASTE MANAGEMENT SERVICES
Cleanaway
Page 56 | 13 13 59
WATERPROOFING
Sure Projects Australia
Page 65 | 0405 976 417
WINDOWS, BLINDS, FRAMING & GLASS
FACADES
SMB Windows
Page 36 | 03 9703 3106
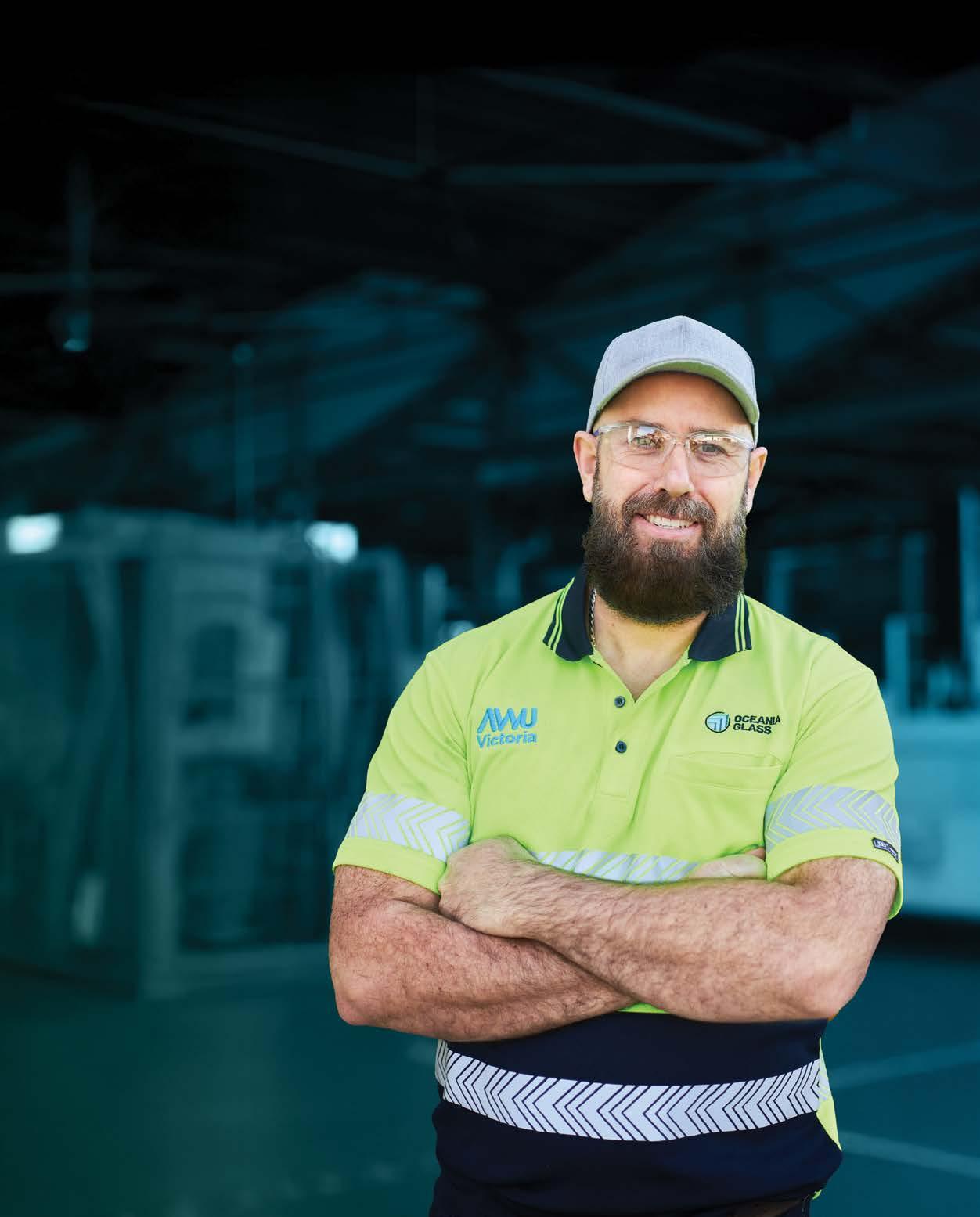
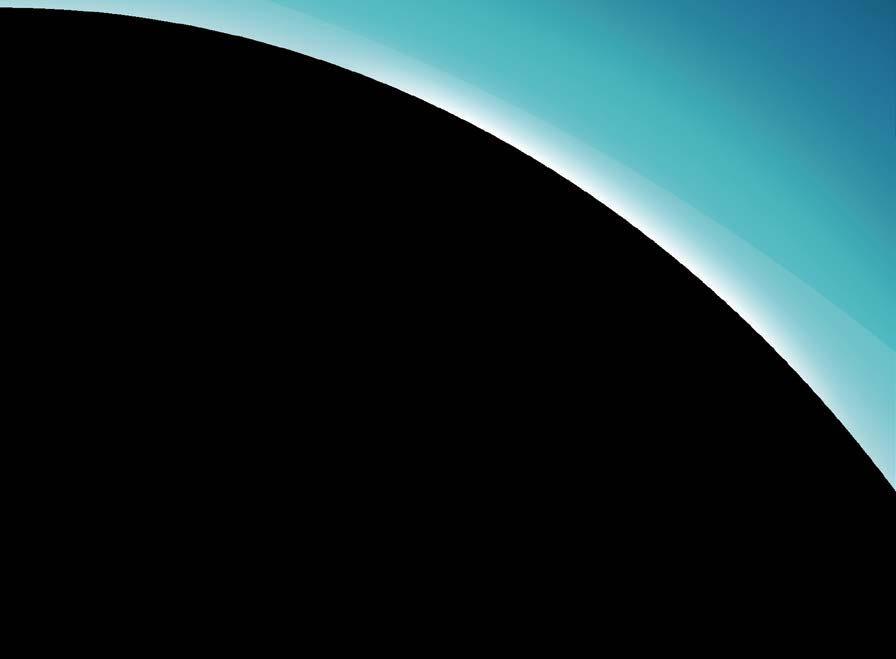
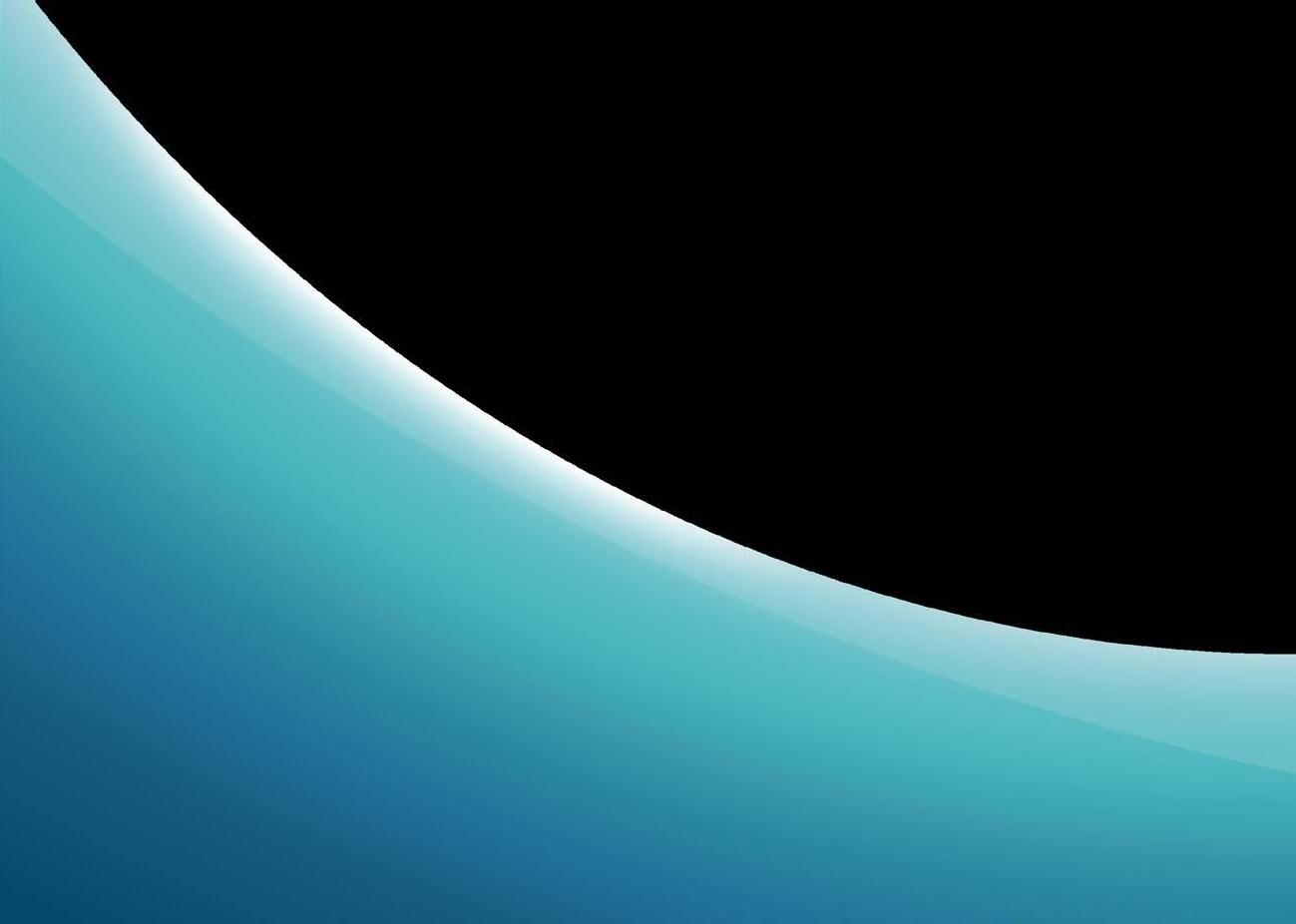
AUSTRALIAN MADE FLOAT GLASS
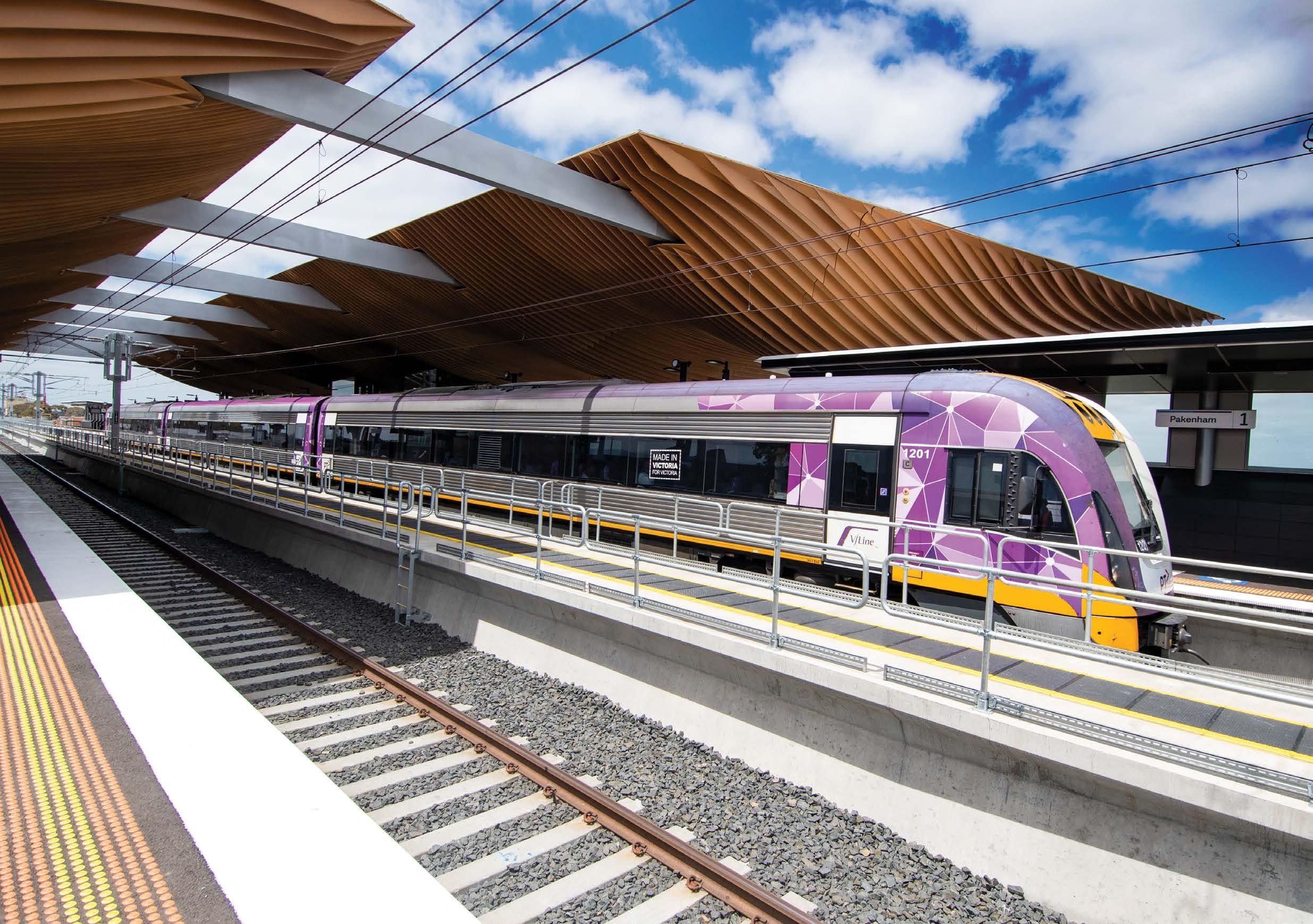