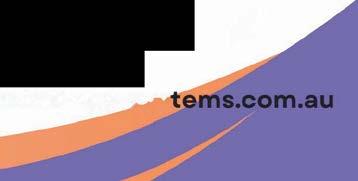

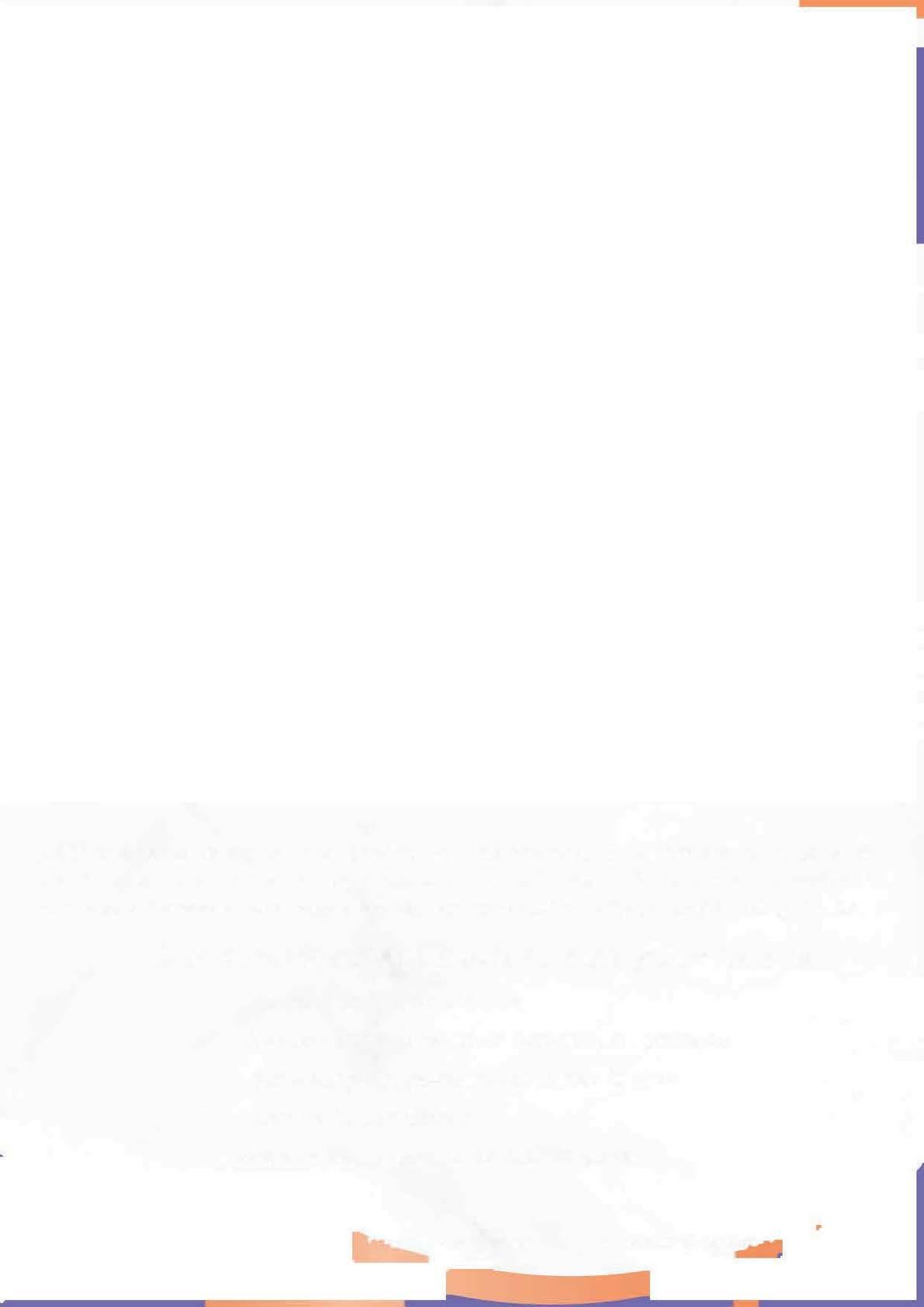
GEOCON’S SETTING NEW STANDARDS FOR MIXED-USE DEVELOPMENTS
FORMER CHANNEL 9 STUDIOS REIMAGINED KINGS
CELEBRATING CONCRETE CRAFTSMANSHIP, INNOVATION, AND INDUSTRY-LEADING SOLUTIONS
Find out more about how Cordell Connect and Cordell Estimator Platinum can help your business grow
Vicinity Centres (Vicinity), working closely with its committed and collaborative tenant Officeworks, has transformed an office space in suburban Melbourne into an internationally celebrated model for zero carbon development.
Chadstone Place has proudly become the first Australian building to receive the prestigious Zero Carbon Certification from the International Living Future Institute (ILFI). This landmark achievement underscores Vicinity and Officeworks’ commitment to sustainability and innovation, setting a new global benchmark for environmentally conscious development.
The ILFI’s Zero Carbon Certification is the world’s only performance-based standard for buildings that addresses both operational and embodied carbon emissions.
Alongside the ILFI Zero Carbon Certification, Chadstone Place has also achieved a 6-Star Green Star – Design and a 6-Star Green Star Design & As Built certification, plus committed to a 5.5 NABERS Energy rating.
Chadstone Place is a reference case for Australia’s property industry. By retrofitting, rather than rebuilding, Vicinity and Officeworks have made an 85% embodied carbon saving, electrified and future proofed the asset, and created a workplace that reflects the Officeworks team values.
Vicinity’s National Head of Design, David Waldren said, “Chadstone Place is a sustainability showcase that demonstrates the possibilities when an owner and tenant partner to create a net zero workplace. Importantly, it also highlights that the greenest buildings can be the ones that already exist.
“Chadstone Place is now fully electric, futureready and helping Officeworks meet its net zero ambitions. This project is a bricks-andmortar example of a building that meets the Paris Agreement goals of net zero emissions and moves us closer to the United Nations' Sustainable Development Goals, embracing
circular economy principles and delivers exceptional places for people.
“In addition to the outstanding sustainability, health and wellbeing benefits Chadstone Place provides, the Officeworks team also have access to the unparalleled amenity of working above Australia’s largest retail, dining and entertainment precinct at Chadstone –The Fashion Capital.”
Scan to read the full article.
We offer unique, cost effective and high quality professional aerial and site time lapse photography, along with video from drone, plane and helicopter for the construction and property industry.
SKYview has been in business for more than 20 years servicing the construction industry, with over 25 years of onsite construction experience.
We can service everything from small residential projects to the largest of government projects, throughout NSW and ACT. We are unconditionally certified, insured and operate from planes, helicopters and drones as required.
The construction industry is a key driver of economic growth, contributing 20% to Australia’s GDP. However, this sector often faces significant challenges, such as delays, cost overruns, and stagnant productivity, particularly in medium and large-scale projects.
These issues can substantially undermine project success. To address these challenges, we have developed an innovative decision support system that leverages machine learning to evaluate the feasibility of construction projects with remarkable accuracy.
By analysing key success factors and criteria, this system provides precise forecasts of project outcomes, reducing much of the uncertainty traditionally involved in construction planning.
Success in construction goes beyond merely completing a project; it involves meeting
criteria such as stakeholder satisfaction, business profitability, and public benefits.
Our system provides a strategic advantage by analysing the interactions of success factors, offering insights for timely interventions and informed decision-making.
Achieving success in construction is crucial. Successful projects lead to satisfied clients, enhanced reputations, and increased profitability.
By accurately forecasting project success, our decision support system empowers sponsors and managers to manage current projects effectively and plan strategically for the future.
This innovation marks a significant advancement for the industry, paving the way for more successful and efficient construction projects worldwide.
The construction industry is poised for an era of greater innovation, improved efficiency, and unparalleled success. The potential transformation is immense, and the tools are now within reach to make this vision a reality.
Development at Bradfield City Centre continues to forge ahead with works progressing on site. Covering approximately 38 hectares of land, the works will deliver new master planned roads, streetscapes, and services for almost 35% of the new city by mid-2025.
This will enable the private development of Superlot land parcels at Bradfield City Centre and accelerate growth of the city.
Over 150,000m3 of material, enough to fill 60 Olympic swimming pools, will be cut and filled in this stage. This will create:
• 4km of new roadways
• 8km of dedicated cycle and pedestrian paths
• On-street parking for 178 cars
• Four kiss and ride points, 3 taxi and 2 bus bays adjacent to Bradfield Metro Station
• Streetscapes lined with 600 trees
• In-ground services including potable, recycled and wastewater, electrical and fibre network communications, supporting development in future
Superlot land releases
• Provision for 132kv electrical transmission supply
With world-class sustainability underpinning Bradfield’s development, a more sustainable solution for road construction will be achieved using an innovative recycled asphalt product containing salvaged waste products diverted from landfill, while all in-situ concrete elements will be constructed with green concrete.
The works are being delivered by local civil business Western Earth Moving (WEM
Civil), highlighting the economic benefits an urban development project of this size can bring to the region from day one.
Bradfield Development Authority CEO, Ken Morrison said: “This is another exciting step showing the momentum underway at Bradfield City Centre. With the First Building near completion, the high-tech Second Building and Central Park progressing, and the first land release underway, these enabling works will help to fast-track further growth of the future city and drive economic outcomes in the region.”
Gold Medal Award Winner: Australia's Best Retail Sign Package - ecept (Flinder's University Health and Medical Research Building)
“At Ecept we are dedicated to delivering the highest quality solotuions in every project
DISCOVER MORE ABOUT FLINDERS HEALTH AND MEDICAL RESEARCH BUILDING PROJECT
The HMRB will house over 600 researchers, clinicians and support staff. The 10-storey building will provide state-of-the-art facilities for collaborative research, aiming to make a significant impact on the health and wellbeing of people worldwide.
Scan to read more.
My name is Emma and I work full time as a Services Manager (Assistant) in the construction industry, and I wrote and illustrated ‘This Girl Built That’.
‘This Girl Built That’ is a children’s story book aimed at exposing and inspiring primary school aged children (particularly girls) to the breadth of job opportunities available in the construction industry.
The book depicts a diverse and representative workforce through bright and bold illustrations.
In my own words, a spark is an inspiration. I hope to inspire a little girl to work in construction, to show a little boy that girls can do it too or challenge an adult on who they expect to see on a construction site.
Since its publication in February 2024, the book has made its way to every State and
we undertake. We are truly honoured to be recognised for our exceptional work both within the industry and by our peers.
“A special thank you to Hansen Yuncken for the oppertunity, and to everyone who collaborated with us throughout this exciting project.” - Ian Widdop (ecept Director)
Territory in Australia, to 8 countries around the world, but most importantly, into the hands of many little people to be read with their mums and dads.
For projects like this, it can be tricky to measure the impact, however, the anecdotal evidence speaks for itself:
• After reading ‘This Girl Built That’, a little girl was drawing princess builders.
• I have had numerous messages from women speaking with pride for the book which depicts their job role.
• Fathers have contacted me saying that they have ordered a copy of ‘This Girl Built That’ to read to their daughters
‘This Girl Built That’ was written to create a spark.
And I think it has done just that.
Get your copy here.
In recent years, the construction industry has experienced a rapid surge in the adoption of new sustainable construction technologies According to forecasts released by the Australian Construction Industry Forum (ACIF) reveal that the Australian building and construction market is bouncing back with a market size of $186.5 billion in 2023 and experiencing an AAGR of more than 2% from 2025 – 2028.
One such trend that’s picking pace is timber construction which is sustainable and also boasts a proven track record of profitability within the construction industry. The fact is supported by an article from Research Nester which states that the cross laminated timber market size is anticipated to expand at a CAGR of 14% from 2024 to 2036, reaching a revenue of USD 7 billion by
end of 2036, more than triple from 2023. The Australian government even launched the USD300 million Timber Building Program, to promote mass timber construction in the property sector. These initiatives have driven the completion of impressive projects such as the T3 Collingwood in Melbourne by Hines.
As Sydney grapples with rapid population growth projected to reach over 6 million by 2036 and urbanisation, TOD (Transit Oriented Developments) presents a strategic approach to integrate high-quality public transportation systems with mixed-use residential, commercial, and recreational spaces. The New South Wales government has committed over AUD 55 billion to public transport projects over the next decade, including the Sydney Metro and Light Rail extensions. Sydney's commitment
Your Subscription to the Australian National Construction Review ensures you receive our premium hard copy publication, featuring stunning Project Showcases, Case Studies, Product Information and Commentary from within the industry and associated disciplines.
OR if digital is more your speed, subscribe to our e-newsletter, released monthly for a snapshot of new products, innovations and services that can benefit your next project.
to TOD is evident in its ambitious projects and investments aimed at revitalizing urban spaces around major transit hubs.
Attending the THT Summit will provide access to top-notch case studies and projects presented by distinguished industry experts, connecting attendees with industry leaders, government officials, and key stakeholders to forge partnerships and explore collaborative opportunities in Australia’s diverse and rapidly developing construction industry.
Gain insights into the latest innovations and opportunities in Timber Construction, High Rise & Vertical Construction and TODs.
Scan to learn more about the Timber Construction High-Rise Summit, Sydney 2024
Scan the QR code to Subscribe
What will be the world’s tallest hybrid-timber commercial tower, Atlassian Central, has reached the halfway point of its four-year construction timeline, with the project on track for completion in late 2026. Once complete, Atlassian Central will be the new Australian headquarters for Atlassian.
The 39 level Premium grade office tower will anchor Australia’s largest innovation and technology precinct, Tech Central.
A new partnership between the Australian Institute of Health and Safety (AIHS) and the Working at Height Association (WAHA) will work on delivering more specialised training to improve workplace safety across construction and other industries.
The Memorandum of Understanding (MOU) outlines plans for the two organisations to connect subject matter experts; share expertise, resources and best practice in safe design; and develop projects to strengthen the knowledge and skills of safety professionals.
It is a significant milestone in the advancement of falls prevention and a major step towards safer workplaces.
AIHS CEO, Julia Whitford, said AIHS and WAHA will work together to create training material on working at heights, which will be applicable to a range of industries.
“Too many lives are lost due to falls in the workplace, and we are proud of this new partnership which gives us the opportunity to drive change by sharing knowledge and resources,” Ms Whitford said.
With industry leading energy efficiency, Q-ton can drastically reduce operating costs by reducing energy usage.
Q-ton produces 74% fewer emissions than an electric water heater and 76% fewer emissions than a gas boiler offering huge reductions in carbon emissions.
Q-ton can integrate with building management systems to provide advanced monitoring and control of water and energy usage data.
LEADING AUSTRALIA’S NET ZERO FUTURE: HOW THE CONSTRUCTION INDUSTRY CAN DRIVE SUSTAINABILITY
The construction industry delivers projects that will last well into the next century and should lead the way in net zero design and delivery.
While new technologies are already leading the next wave of innovation, more needs to be done to drive Australia's sustainable growth from a construction and development standpoint. Specifically, the construction industry needs to improve on three aspects: green electricity, green vehicles, and green materials. Incorporating solar and renewable energy into major developments will be key to achieving this goal.
The electric grid is becoming greener, and we must support its evolution to a clean, emissions-free grid at the lowest possible cost. Similarly, electric vehicles, whether fully electric or plug-in hybrids, will offer a wider range of utility-class options in the next five
years. Workers and technicians are already adopting electric tools, and adding a battery to their utility vehicles will be a valuable addition to their toolkit.
The construction and development sectors specifically also need access to green materials to reduce the embodied emissions of the things they build. Technologies for green steel, green cement, and other building products are already available.
However, Australia's small market means manufacturers need a steady demand to invest confidently in these new processes. Government procurement support is essential to create the demand, and consequently the supply, of these materials for the broader market.
By embracing these advancements and fostering a collaborative effort, the
construction sector can not only meet but exceed sustainability goals, ensuring a greener future for Australia.
BESIX Watpac has been appointed design and construction contractor to deliver one of the largest construction projects ever undertaken by Renewal SA, the Deep Maintenance and Modification Facility (DMMF) adjacent the Royal Australian Air Force Edinburgh base in northern Adelaide.
The BESIX Watpac team has taken possession of the 16-hectare project area where the new 2.1-hectare purpose-built facility will be built.
Construction works have now commenced on the mammoth four bay hangar that will support the maintenance and modification of 737-sized aircraft following sod turning and smoking ceremonies on 5 September.
BESIX Watpac CEO Mark Baker said the project marked an important milestone for the company in South Australia.
“We are thrilled to be partnering with Renewal SA for the first time to deliver the DMMF project – drawing on our extensive
experience in delivering aviation and defence projects in South Australia,” Mr Baker said.
“BESIX Watpac is committed to building the best projects together with our people and partners and we look forward to delivering another complex infrastructure project.”
BESIX Watpac is leading the construction of the hangar that will be used to maintain
and modify military aircraft operated by the Commonwealth Department of Defence.
The works will occur on land owned by Renewal SA (main building and ancillary works) and connected to land owned by Defence, which includes a tow-way for the aircraft to access the new hangar. Construction works will deliver the aircraft hangar, offices, workshops, stores, amenities areas and plant rooms.
Australasian real asset manager Dexus has turned the first sod on a premium eight-unit industrial estate that will provide more than 47,000m2 of gross lettable area in Marsden Park in Sydney’s Northwest Priority Growth Area.
Dexus will deliver the build-to-lease estate called Vertex at 311 South Street on behalf Dexus Australian Logistics Trust. The target completion date is mid 2025
Vertex at 311 South Street aims to meet the demand for flexible industrial rental units with strong sustainability features, which are not currently available in the rapidly growing area.
Each warehouse will have a future proof design, with adjustable inter-tenancy walls, units of differing sizes and the ability to combine tenancies. They will also have commercial-grade storage batteries linked to 800kW rooftop solar panels.
Veolia’s Taylors Road Resource Recovery Precinct, at Dandenong South will soon be home to EarthSure’s new $15 million contaminated soil washing technology facility, a joint venture between Veolia and Ventia that will see 160,000 tonnes of contaminated soils and aggregates cleaned and reused every year.
The facility has also been supported by a $1.15 million grant from Sustainability Victoria as part of its Circular Economy Infrastructure Fund ― Hazardous Waste Stream and is the latest addition to the precinct, which has seen it transform from a landfill to a resource recovery park.
The existing EarthSure thermal facility can already treat highly contaminated waste (Category A & B) through its direct fired thermal desorption process. Category A and B materials include commonly produced soils and waste resulting from key industrial processes, chemical storage and service stations.
RESTORING CONFIDENCE AND CONTINUITY IN AUSTRALIA’S INFRASTRUCTURE
The confidence of businesses designing and delivering Australia’s infrastructure depends on our ability to see what’s on the horizon.
But three quarters of the respondents to Consult Australia’s 2024 membership survey are operating in a higher risk environment that is harder to predict than just 12 months ago.
Australia’s infrastructure industry has spent the last four years buffeted by pandemic lockdowns and supply chain bottlenecks, labour shortages, cost escalation and record rates of insolvencies. Local businesses have dealt with the consequences of international conflicts and global inflation.
Yet Consult Australia members tell us the most unpredictable aspects of running their businesses are the creeping or sudden uncertainties in the pipeline of projects, ‘death by a thousand cuts’ through increasing regulation and red tape, unaffordable insurance and unfair contracts. Some of
these uncertainties are outside of our control; but many of these issues sit well within our governments’ sphere of influence.
In 12 months, we’ve witnessed a shift from most businesses saying they had “too much work” to most saying they have capacity; and 77% of respondents across almost all sectors expect to have capacity within the next 12 months.
Having some capacity gives businesses the breathing room to bid on new work; but this can become a concern when the continuity of work is not assured. Pipeline changes mean that almost half (46%) of consulting businesses have made resource cuts
Consult Australia’s team continues to champion greater infrastructure pipeline transparency and certainty in every roundtable, forum and committee meeting we host. It’s a message that we carry throughout the halls of power in every meeting with ministers and
However, less contaminated soils (Category C), which most commonly come from underground excavations and construction sites, require a separate treatment process.
The new soil washing facility under construction provides a solution for these lower contaminated soils and aggregates, enabling them to be reused. It uses advanced treatment processes to clean materials such as organic and inorganic contaminants including oils, fuel, debris, organic compounds, polycyclic aromatic hydrocarbons, and heavy metals.
This is an environmentally effective, bulk solution for the Category C contaminated soils, which when combined with the thermal facility will divert 100% of this category soil from landfill, and close the circular economy loop by making the cleaned product available for reuse.
Scan to read the full article.
JONATHAN CARTLEDGE Chief Executive Officer Consult Australia
policymakers. We know restoring confidence and continuity in Australia’s infrastructure sector requires a concerted effort from us all. With fairer contract practices, fewer regulatory burdens and greater pipeline certainty, we can look to the future together.
Public art has the power to transform the built environment. Expressing culture and identity, it also improves liveability, creating destinations in urban landscapes that engage and inspire. Reflecting local history, nature and people, public art can foster community connections, creating a true sense of place.
Integrating public art into new developments offers economic benefits too. Creating jobs in the creative industry, it can also boost tourism. Often contributing to safer public spaces, it can increase property values, and promote retail investment.
Private developers have the opportunity to shape public spaces by engaging artists and designers to harness the creative possibilities of facades, entrances, and pathways bordering the public domain.
Involving the whole project at the point of commission — developers, architects, landscape architects and industrial designers
— helps to deliver public art that creates more unique and culturally diverse cities.
At Tilt, we take a holistic approach to ensure seamless integration of art installations into architectural designs and local contexts.
Our multi-disciplinary team creates artistled outcomes that combine art, play, architecture, and landscape elements. Community engagement is central to our process, involving feedback sessions and codesign opportunities.
Technological advancements are revolutionising our field. New design tools, particularly design software, are influencing how cities evolve, allowing us to visualize projects before construction to ensure they're functional, inclusive, and tailored to their communities.
Tilt's expertise in design, advanced manufacturing, and modern materials
positions us at the forefront of innovation. We support artists to deliver a range of public art briefs — exploring various mediums, from kinetic and multi-media installations to computational design and mechatronics, as well as artisanal approaches — to deliver functional and design-driven outcomes that enhance the built environment.
Barangaroo’s sustainability plan has hit a major milestone with construction starting at the first two regional solar farms in Hay and Moama as part of a commitment to the precinct remaining carbon neutral well into the future.
The Hay and Moama Solar Farms are two of at least four regional solar farms to be delivered through the NSW Government’s $45 million green energy commitment to offset carbon emissions at Barangaroo over 25 years, the first long term agreement of its kind.
The agreement consolidates Barangaroo’s leadership in sustainable development while providing around $20 million in construction activity in regional NSW, boosting the local economy, creating around 130 jobs through construction and ensuring ongoing jobs once operational.
Until this agreement, green power has been purchased from the market at unpredictable varying rates, however, this new commitment will ensure Barangaroo’s sustainable energy
future is guaranteed long-term and at a consistent price.
Construction of the Hay and Moama solar farms are expected to take about six months to build, with two more solar farms to be completed in 2025.
The agreement for delivery and operation is with an Australian-owned and operated
renewable energy company, CleanPeak Energy and funding for the agreement is sourced from levies collected from Barangaroo's tenants under the Barangaroo Estate Levy.
The Green Product Purchase Agreement is the latest initiative in Barangaroo’s sustainability ambitions to be a reference to the world, and Barangaroo is the first large scale Carbon Neutral Precinct in Australia.
Specifying the best glass for noise reduction
The ability to control external sounds in our homes, workplaces, hospitals and schools has gained importance due to modern lifestyles and the close proximity of these buildings to highways, airports, construction sites and industry. Among the many building materials and products that make up a structure, windows and doors have a big impact on how well the home or building is insulated from outside noise. With the wide range of glazing solutions available, understanding the differences between singleglazing, multi-layered glazing, laminated glass and high-performance acoustic glazing is essential.
Understanding Acoustic Glazing: Specifying the best glass for noise reduction explores the role of glazing in acoustic design and how different types of glazing products compare in terms of sound reduction performance. We highlight what makes acoustic glass a high-performance solution distinct from other forms of glazing. We also look at common misconceptions surrounding acoustic glass.
Australia’s leading brand of acoustic glass, Genuine Hush™ is highly specified and made exclusively by Oceania Glass™ Genuine Hush™ offers a range of quality performance acoustic glass that has been tested and certified. The Genuine Hush™ acoustic performance range comprises of QLam Hush™ and ComfortHush™ –two distinct yet complementary products suited to a wide range of applications and available in a choice of colours.
Download this whitepaper and learn why acoustic glass stands above the rest when it comes to sound reduction.
www.oceaniaglass.com.au/resources/white-papers/
Wireless infrastructure presents a powerful opportunity for ANZ contractors, offering enhanced connectivity, scalability, cost savings and remote monitoring.
Enhanced connectivity solutions allow contractors to tie all project aspects together, whether the information is coming from the accounting side or the project delivery side.
Further, wireless infrastructure solutions are ‘future-proof’, an ideal option for evolving building projects where the scope or equipment needed is subject to change.
Since wireless infrastructure eliminates the need for extensive cabling, contractors can realise measurable cost savings, yet still reap the benefits of remote project monitoring capabilities. Project stakeholders located offsite can still gauge project performance, inventory levels and environmental conditions, thanks to a proper wireless infrastructure.
Contractors should partner with a trusted technology vendor willing to work
within their specific objectives and safely connect the data dots for the client. If not adequately secured, wireless infrastructure can be vulnerable to cyber threats. Many contractors think they’re secure enough when they’re really not. They don’t realise how vulnerable networks are nowadays as construction is one of the most heavily targeted industries for cyber-attacks.
There are numerous security measures to mitigate cybercrime, and reputable technology vendors will incorporate these measures and advise contractors on safe practices to follow. Training and education of all project stakeholders is key to reducing the risk of a cyber-attack.
Wireless infrastructures can be powerful, reliable, scalable, cost-effective and a safe option for ANZ contractors who want to increase project efficiencies, improve profit margins and remain competitive in the construction market.
ANDREW
Senior Product Manager Trimble
Andrew Tucker is a Product Manager for Trimble APAC. He helps construction professionals deliver their projects with superior productivity, quality, transparency, safety and sustainability. Trimble develops technology, software and services that drive the digital transformation of construction with solutions that span the entire architecture, engineering and construction (AEC) industry.
International engineering, design and advisory company, Aurecon, is part of a design alliance that has proposed an innovative reimagining of Brisbane’s Northshore. The vibrant new precinct will support housing, business, recreation, education, health and wellbeing, tourism and a Games-ready sports and entertainment stadium under a transformative scheme entitled ‘Northshore Vision 2050’.
The bold vision comes as Australia celebrates its stellar performance at Paris 2024 and looks ahead to the Brisbane 2032 Games. Since its release, the scheme has gained widespread support amongst the people of Brisbane, business and sporting groups, investors and individuals.
The brainchild of the Brisbane Design Alliance, a team of specialist designers in
architecture, engineering and planning, uniting the local and global expertise of Aurecon, with architects Buchan, HKS, NRA Collaborative and Nikken Sekkei.
Aurecon Managing Director, Community and Place, Tim Spies, said Aurecon was committed to supporting the development of sustainable urban neighbourhoods that provide long-term legacy for communities.
“Given the anticipated population, business, trade and tourism growth in Brisbane and Southeast Queensland over the next decade and beyond, Northshore provides a once-ina-generation opportunity to create a liveable city and region that celebrates our unique history, climate and lifestyle,” he said. “This is an opportunity to create legacy infrastructure including important transport connectivity well beyond the 2032 Games.”
Aurecon has provided engineering and advisory services to most of the sports and entertainment precincts across Australia, and many internationally, over the past few decades. The company is also the pre-eminent engineers for mass-engineered timber buildings in Australia, widely considered vital to meet the sustainability aspirations of Games infrastructure.
HKS director Andrew Colling said 'Northshore Vision 2050' leveraged underutilised industrial land to realise the potential of the Brisbane River and deliver a valuable social and economic legacy for Southeast Queensland – one that gives back to the community.
PROJECT : Warrigal Aged Care
LOCATION : Wollongong, NSW
COMPLETION DATE : August 2024
CONTRACTOR : Eymael Plumbing
Systems Installed
4 X ESA30EH2-25 Q-TON SYSTEMS
8 X 1,000L STAINLESS STEEL TANKS
Warrigal Aged Care, a leading provider of aged care services in the Illawarra region, is committed to enhancing the living standards of its residents. The Wollongong facility, one of Warrigal’s flagship locations with 155 rooms, offers a range of services including residential care, respite care, and specialised dementia care.
To maintain their high standard of care, Warrigal sought an innovative and sustainable hot water solution to meet the needs of their large residential population while reducing operational costs and minimising their carbon footprint.
Facing the challenge of maintaining a reliable and energy-efficient hot water supply, Warrigal’s existing natural gas system had become increasingly expensive to operate and maintain. The facility required a system capable of meeting high daily demand while being energy efficient and environmentally friendly. The challenge was compounded by the need to retrofit the new system into the existing infrastructure with minimal disruption to the facility’s operations.
After thorough consultation with facility management and Eymael Plumbing, the installing contractor, Mitsubishi Heavy Industries Air-Conditioners Australia (MHIAA) provided the perfect solution: the Q-ton air-to-water heat pump system.
Renowned for its high efficiency and environmental benefits, the Q-ton uses CO2 as a refrigerant—a natural, eco-friendly alternative to traditional refrigerants. This allows the system to deliver reliable hot water between 60°C to 90°C even in temperatures as low as -25°C.
“Warrigal has been transitioning away from fossil fuels, so this is another important step for the company.” Says Penelope Morton, Sustainability
Officer at Warrigal Aged Care. “Whilst being more sustainable and allowing for more of our energy needs to be offset by renewables, these Q-ton systems have also been a much more reliable source of hot water for the facility, significantly reducing system breakdowns and hot water outages for our residents.”
Paul from Eymael plumbing also highlighted the system’s flexibility with regards to installation. “Even with the system having to be retrofitted, it was easy to install and setup.” One standout feature of the Q-ton system which is highly relevant to the aged care industry, is its inbuilt legionella sanitary cycle, which heats the water to a temperature that effectively eliminates legionella bacteria—a key health concern in aged care facilities. This cycle not only ensures compliance with stringent health regulations but also provides peace of mind to the facility’s management and residents, knowing that the hot water system contributes to a safe and healthy environment.
Since the installation of four Q-ton systems and eight 1,000L stainless steel tanks, Warrigal Aged Care Wollongong has experienced several significant benefits:
Energy Efficiency: The facility has achieved notable reductions in energy consumption, leading to lower operational costs. The Q-ton’s high coefficient of performance (COP) of 4.3 during intermediate seasons translates into substantial energy savings, making it a costeffective solution for the long term.
Environmental Impact: By utilising CO2 as a refrigerant, the Q-ton system has substantially reduced Warrigal’s carbon emissions, aligning with the facility’s commitment to sustainability. This change not
only lowers the environmental footprint but also supports Warrigal’s broader goals of enhancing community and environmental health.
Reliability: The Q-ton system has proven to be reliable, delivering a consistent hot water supply even during peak demand periods. This reliability is crucial for maintaining the high standard of care expected at Warrigal Aged Care.
Cost Savings: The combination of energy efficiency and reduced maintenance needs has resulted in significant cost savings, allowing the facility to allocate resources to other areas of resident care and facility improvements.
By prioritising sustainability, efficiency, and resident safety, MHIAA and Warrigal Aged Care have set a new benchmark for hot water solutions in the aged care sector. This partnership not only enhances the quality of life for residents but also supports a greener and more cost-effective future for the facility.
For more information contact Mitsubishi Heavy Industries Air-Conditioning Australia, Pty Ltd., phone 02 8774 7500, mhiaa.com.au Scan the QR code to learn more about Q-ton
When it comes to the safety and comfort of residents in retirement communities, security is paramount. At Cumberland Gardens, an over-55s retirement village developed by RPF Building, Wallsgate, NSW, this priority was clear from the start.
With 40 residential villas, an indoor swimming pool, a community centre, and a bowling green, this project required robust, high-quality solutions for security and aesthetics.
That’s where Darley Aluminium’s KlassicView and ScreenGuard systems came into play, transforming the village into a safe and comfortable haven for its residents.
RPF Building turned to Space Windows & Doors to fabricate and install all the windows, doors, and security screening systems for the development, who in turn recommended Darley’s KlassicView residential systems and ScreenGuard security screening systems to meet the high standards required for this project.
One of the critical requirements from the developer was to install a security screening system that met the latest Australian security standards and was bushfire-rated to BAL40. After evaluating multiple options, ScreenGuard emerged as the perfect choice, ticking all the boxes.
ScreenGuard is a high-tensile security screening system made from a high-quality aluminium frame and 316 marine-grade stainless steel mesh. It has been tested and certified to meet the latest Australian Standard AS5039-2023 for security doors and window screens.
Updates to the AS5039-2023 standard includes an increase in the energy rating from 100 joules (SL100) to 200 joules (SL200) during Dynamic impact testing. This test is mandatory under the Australian Standard and is used to evaluate the performance of security doors
and simulates human impact against the door. ScreenGuard not only successfully tested to this newer and higher energy level of 200 joules but was one of the first security screening systems in Australia to achieve this rating.
ScreenGuard is also BAL40 Bushfire rated and provides protection against increasing levels of ember attack and burning debris. BAL stands for Bushire Fire Rating Level and BAL40 is the second highest bushfire rating.
Space Windows & Doors installed ScreenGuard hinged doors, sliding doors, and window grilles in each villa. These were paired with Darley’s KlassicView sliding doors, KlassicView 76mm sliding windows, and CityView 40mm commercial doors. The compatibility of Darley’s systems allowed for seamless integration, providing both security and visual appeal throughout the community.
The ScreenGuard security screens provided more than just a barrier against potential intruders—they offered peace of mind to the residents of Cumberland Gardens, with residents knowing that their security is safeguarded by a top-of-the-line system designed to withstand significant impact.
While security was the primary concern, ScreenGuard also delivered several other key benefits to the residents of Cumberland Gardens.
Privacy: The angle and thickness of the 316 marine-grade stainless steel mesh makes it difficult for people outside to see into the home,
providing enhanced privacy for residents while still allowing clear views from inside.
Energy Efficiency: ScreenGuard helps reduce UV light and solar heat from entering the home. By limiting the amount of heat entering the villas, residents can enjoy cooler interiors during warmer months, potentially reducing the need for air conditioning.
Improved Ventilation: The stainless steel mesh allows for excellent airflow while keeping insects out. This means that homes can stay naturally ventilated without sacrificing comfort or security.
Aesthetic Appeal: ScreenGuard systems are not only functional but also enhance the visual appeal of the homes. The 316 marinegrade stainless steel mesh and high-quality aluminium frame can be powder-coated in a variety of finishes from Dulux or Interpon, allowing the system to complement the design of each villa seamlessly.
The installation of Darley’s KlassicView and ScreenGuard systems at Cumberland Gardens is a prime example of how high-quality security solutions can enhance both the safety and comfort of a retirement community. Residents can enjoy their homes in peace, knowing they are protected by industry-leading security systems that also provide privacy, energy efficiency, and aesthetic benefits.
Scan the QR codes to learn more about how Darley Aluminium’s ScreenGuard can enhance the security and comfort of your next project
Strength in Every Layer
CPS Concrete Group
Laying the Foundations for Concrete Solutions
OZZ CRETE
Landmark Projects and Innovations in Precast Concrete
SVC Products
Eifers Uses Low-Carbon Concrete at Melbourne Airport’s Uber Terminal
Eifers Civil
A Legacy of Excellence in Civil Construction
GBG Concrete & Construction
Revolutionising Construction with Cutting-Edge Technology Azzurri Concrete
Locally owned and operated CPS Concrete Group has been in operation for over 40 years, growing excellent working relationships with many large builders in Canberra across commercial, large scale, and high profile developments.
CPS Concrete Group evolved from the family run business, CPS Concreters, established in 1990. Managing Director, Tony Costanzo and his family have grown alongside the company with Director Joe Bencich who manages the concrete pumping side of the business.
“The CPS Concrete Group is Canberra’s leading structure specialist. Offering concrete, reinforcement and post tension services in house, CPS Concrete, deliver complete packages to builders throughout Canberra and New South Wales,” Tony said. “We have been involved in numerous high-profile projects, fostering strong relationships with leading builders, including being involved in most of Canberra’s tallest buildings.”
CPS Concrete Group stands out for its unwavering commitment to delivering top-tier concrete products and services, backed by a highly skilled and experienced workforce. Known for tackling complex design challenges with innovative solutions, the company consistently exceeds expectations in both commercial and residential projects. By strategically expanding its team with professionals who possess
local expertise and specialised skills, CPS Concrete Group ensures that every project is completed to the highest standards. Equipped with state-of-the-art machinery, they are fully prepared to handle tasks of any scale, reinforcing their reputation as a trusted leader in the industry.
“We maintain a comprehensive range of equipment, ensuring that all machinery is serviced to manufacturer specifications and meets all relevant legislative standards. Our operators are fully trained to safely and efficiently use our equipment, with a strong emphasis on safety protocols,” added Tony.
Expanding CPS Concrete Group’s services has enabled the company to manage projects from start to finish, including reinforcement installation, concrete placement, and post tensioning services. “From tying steel of the first pad footing to final stress of suspended slabs, CPS can find a solution that works for all of our clients” said Tony.
For more information, contact CPS Concrete Group, 7/63-65 Wollongong Street, Fyshwick ACT 2609. phone 02 6228 1552, email info@cpscg.com.au, website www.cpscg.com.au
Since 2009, OZZ CRETE has firmly positioned itself as a trusted leader in concrete construction throughout southeast Queensland. For over 15 years, this Australian family-owned company has delivered a dynamic range of concrete solutions tailored to meet the diverse needs of residential, commercial, industrial, and civil projects.
Whether it’s a bespoke high-end residential build or a large-scale civil infrastructure project, OZZ CRETE’s commitment to quality, flexibility, and client collaboration ensures every job is executed with precision and excellence.
OZZ CRETE’s comprehensive service model sets it apart in the industry. By offering a one-stop-shop for concrete solutions, including all aspects Steel fixing, formwork and concreting, the company streamlines the construction process from design and procurement to project handover.
Managing Director Joe O’Brien, emphasises the importance of this approach, stating, “Our clients value the peace of mind that comes with knowing they have a single point of contact throughout the entire project lifecycle. This not only simplifies communication but also ensures consistency in quality and delivery.”
The company’s expertise spans various concrete applications, including residential concrete footpaths and driveways, commercial road pavements, and intricate civil stormwater and drainage structures.
OZZ CRETE’s portfolio is diverse, encompassing everything from the construction of cast in-situ concrete retaining walls and gully pits to the installation of large reinforced concrete box culverts and decorative finishes that elevate the aesthetic appeal of any project.
At the core of OZZ CRETE’s operations is its ability to adapt to the unique requirements of each project.
“No job is too big or small for us. We work closely with our clients to understand their specific needs and deliver concrete solutions that not only meet but exceed their expectations. Whether it’s high-flow or low-flow concrete, our team ensures the right mix is used to achieve the best results,” explained Operations Manager, Tanu Wulf.
This flexibility is particularly evident in OZZ CRETE’s work across southeast Queensland, including projects in the Northern Rivers, Toowoomba, and the Noosa Sunshine Coast Hinterland. The company’s ability to deliver high-end architectural finishes and custom concrete structures has earned it a reputation for excellence in the region’s most demanding construction environments.
With over 15 years of industry experience, OZZ CRETE has cultivated a team of highly skilled professionals, including formwork carpenters, steel fixers, and in-house engineers.
“Our team’s collective experience and dedication are what make us stand out. Each member brings a wealth of knowledge to the table, ensuring that every project is completed to the highest
standard, on time, and within budget,” highlighted Project Manager, Jake O’Brien.
OZZ CRETE’s commitment to excellence is further reinforced by its proactive approach to customer satisfaction. Regular communication with clients is a cornerstone of the company’s operations, with senior management personally overseeing each project to ensure superior quality and a seamless construction experience.
Beyond its technical capabilities, OZZ CRETE is deeply committed to fostering long-lasting relationships with its clients. The company’s collaborative approach has led to ongoing partnerships across various sectors, from residential developments to large-scale civil infrastructure projects. “Our success is built on the trust and loyalty of our clients. We don’t just complete projects; we build relationships that last,” said engineer, Andre De Villiers.
OZZ CRETE’s dedication to client satisfaction is reflected in the company’s impressive track record of delivering projects on time and within budget. This reliability, combined with a dynamic and agile operational model, positions OZZ CRETE as a leader in the concrete construction industry.
For more information contact OZZ CRETE, phone 0422 591 721, OZZCRETE.com.au
Trusted Structural Reinforcing Solutions. #AvoidKnockoffs Accept No Substitute.
ReidBar™ Couplers
ReidBar™ Rebate Inserts
Once the system is compromised or replaced with knockoffs, it is no longer compliant. The Genuine ReidBar™ Structural Reinforcing System components are meticulously designed, manufactured, tested, and supplied with the highest quality assurance and structural performance standards. There is no substitute.
ReidBar™ Threaded Inserts
Operating since 1948, SVC Products is an ISO-accredited Victorian manufacturer of high quality, industry-compliant precast concrete products made to suit multiple applications across civil and landscape construction.
SVC’s unique approach to precast concrete was recently showcased in Mirvac’s Liv Aston building project in Melbourne’s Northbank precinct. The team manufactured and supplied 78 large-format precast concrete planters for the building’s façade, each weighing about 5 tonnes. This project, which amounted to 390 tonnes of precast concrete, is yet another demonstration of their expertise in handling large-scale projects.
The manufacturing process for these planters began in late 2022, with deliveries completed by mid-2023. SVC faced significant challenges, including labour shortages due to COVID-19 and necessary design adjustments to meet weight constraints. Despite these hurdles, SVC re-engineered the planters to be lighter, with each floor featuring three smaller units installed side-by-side.
This project highlights SVC’s capability to innovate and adapt. Despite the complexity and typical use of precast products at ground
level, SVC successfully produced precast units that were feasible for installation on a high-rise building, demonstrating their proficiency in precast concrete fabrication.
Beyond Liv Aston, SVC’s portfolio includes high-rise projects like the Aurora Melbourne Central and Shadow Play apartment towers. SVC supports various infrastructure projects, and are currently working on bespoke signage for ANZAC Station, outdoor furniture for Parkdale Secondary College, and bollards for Luna Park and the Shrine of Remembrance.
SVC is a leader in precast concrete manufacturing and is committed to delivering high-quality, innovative solutions. Specialising in precast concrete fabrication, SVC offers both standard and custommade products tailored to meet unique project requirements. Their experienced team provides dedicated customer support throughout the design-to-delivery process, ensuring final product solutions satisfy all project criteria for quality, performance and durability.
For more information contact SVC Products Pty Ltd, 38 Japaddy Street, Mordialloc VIC 3195, phone 1300 287 782, email sales@svc.com.au, website www.svc.com.au
Eifers, the family-owned time-critical civil construction company, continues to cement its reputation as a premier contractor at Melbourne Airport with its latest project: the construction of the Uber Terminal at Terminal 4.
Eifers delivered a range of critical tasks, including canopy and foundation installation, guttering and downpipes, footpath and ramp design and construction, mechanical ventilation HDPE pipe installation, public lighting installation, bollard installation, and the relocation of hydrants, water meters, and fire hose reels. Additionally, landscaping works are being undertaken to enhance the aesthetic appeal of the site.
One of the most impactful features of this project is the installation of 472m2 of footpath and canopy. The project, which commenced in May 2024 and is expected to be completed by August 2024, involves 12 key staff members from Eifers.
Despite the challenges posed by the area’s high visibility, passenger traffic, and the relocation of numerous in-ground services, Eifers has managed to maintain progress thanks to innovative methods and products.
The offsite prefabricated structure from Stoddart Infrastructure has accelerated the construction program for Eifers, while the use of Adbri’s low-carbon concrete Futurecrete has reduced CO2 emissions by 23.8 tonnes.
Eifers’ ongoing projects also include maintenance and repairs at Melbourne Airport, Werribee River Park, and the Frankston Flinders Road widening. With a proven track record of delivering time-critical works using High Early Strength Concrete, Eifers is recognised as the go-to concrete contractor for Melbourne Airport.
Eifers is a family-owned Australian company with an agile and innovative approach to civil construction. Founded by the Eifermann family in 2003 as a small business, Eifers has grown to be a leading and trusted name within the civil construction and critical infrastructure works spaces.
For more information contact Eifers Civil Pty Ltd, 13 Newmarket Lane, Epping VIC 3076, phone 03 9357 6360, email admin@eifers. com.au, website www.eifers.com.au
In the heart of Victoria, GBG Concrete & Construction stands as a beacon of excellence, carrying forward a rich 70-year legacy. As a family-owned and operated business, GBG has transformed from its roots in domestic and commercial concrete works into a leader in civil construction, in-situ and precast concrete products. Their transformation has enabled them to undertake large-scale in-situ and precast projects throughout Victoria.
The company’s commitment to quality and innovation is showcased in its state-of-the-art facilities in Sale. These include a sprawling precast factory measuring 230m in length and 20m in width, which ensures uninterrupted operations regardless of weather conditions.
GBG Concrete & Construction prides itself on producing a diverse range of precast concrete products. From pits, sleepers, and footings to barriers, wall panels, and columns, their offerings are delivered across Victoria and beyond. The company specialises in coloured, polished, and exposed aggregate finishes, ensuring that every project is completed to the highest standards.
Their comprehensive service includes supplying and installing all precast elements, covering design, detailing, fabrication, transport,
and erection. This holistic approach eliminates the need for additional subcontractors, ensuring projects are completed on time and within budget.
GBG’s fleet of prime movers, trailers, transport frames, and a super layover frame capable of transporting panels up to 4.6m wide provides exceptional flexibility and control over deliveries. This capability allows the company to reliably meet project schedules, no matter the scale or complexity.
Specialising in civil and concrete construction services for commercial and industrial projects on both greenfield and brownfield sites, GBG boasts extensive experience in live major hazard facilities. Their highly skilled workforce, including carpenters, plant operators, steel fixers, and labourers, brings a wealth of industry expertise to every project. This dedication to craftsmanship and safety ensures that GBG not only meets but exceeds client expectations.
For more information contact GBG Concrete & Construction, 339 Raglan Street, Sale VIC 3850, phone 03 5144 2913, email info@gbg.com.au, website www.gbg.com.au
In the dynamic construction world, Azzurri Concrete stands as a leader in the concrete industry, exemplifying precision and excellence.
Azzurri played a crucial role in the construction of a $1 billion warehouse precinct by Fraser Property Industrial, Aware Super, and Altis Partners. They contributed their expertise to the impressive 110,000m² single-floor plate, the largest of its kind in New South Wales.
Azzurri was responsible for supplying, placing, and pumping all the concrete, tasks that required precise execution and a partnership with Western Suburbs Concrete for specialised mix designs.
Additionally, Azzurri handled pad footing excavation, reinforcement, sand, structural steel hold-down bolt installation, and fire tank piling works, demonstrating their versatility and industry leadership.
The project’s technical demands, particularly the requirement for an exceptionally flat floor, were met with Azzurri’s innovative approach and investment in advanced equipment. They strategically added state-of-the-art machinery to their fleet, including Riding Trowels from Allen in the USA, and Boom Laser Screeds from Somero Enterprises.
This cutting-edge equipment, combined with the expertise of their highly skilled team, ensured remarkable flatness results without the need for corrective grinding across the entire 110,000m2 of slabs.
Despite the heavy season of rainfall and COVID-19 challenges, Azzurri’s team demonstrated resilience and efficiency, completing their work by July 2023. This project is a testament to Azzurri’s capability to navigate adversities while maintaining high standards of quality and efficiency.
At the project’s peak, Azzurri had 120 staff and 70 subcontractors on site, working tirelessly to meet deadlines and deliver superior results. Their innovative approach, commitment to excellence, and strategic management have set a new benchmark in construction.
Scan here to watch Azzurri Concrete's timelapse of the entire slab pour at TTI, Kemps Creek!
For more information contact Azzurri Concrete, 5 Frank Street, Wetherill Park NSW 2164, phone 1300 299 877, email info@azzurriconcrete.com.au, website www.azzurriconcrete.com.au
MAIN CONSTRUCTION COMPANY : Geocon
ARCHITECT : Fender Katsalidis
PROJECT VALUE : $200 million
Positioned in the old Woden Town Centre and just a short drive from Canberra’s City Centre, WOVA blends residential, commercial, and lifestyle amenities into one stunning precinct. With 802 apartments, 22 commercial spaces, and 54 hotel rooms, WOVA stands as the largest single-staged development of its kind.
Geocon, the largest residential builder/ developer in the nation’s capital, continues to redefine urban living with its latest landmark project, WOVA. Positioned within the multi-billion-dollar regeneration of the old Woden Town Centre, WOVA is set to transform the area with its blend of residential, commercial, and lifestyle amenities.
“WOVA is the largest mixed-use development delivered at one time by Geocon, encompassing four buildings, 802 apartments, 22 commercial tenancies, and 54 hotel rooms. It’s an urban precinct that delivers on Geocon’s commitment to creating vibrant, contemporary communities,” explained Damian Rumball, Geocon’s General Manager – Construction.
Geocon’s role in WOVA extends beyond traditional property development. From site acquisition to design, construction, and sales, Geocon managed every aspect of the process, offering a seamless experience for buyers and investors alike. This end-to-end approach, coupled with Geocon’s focus on innovation and customer-centric design, ensured that WOVA not only met but exceeded the expectations of its residents and the broader community.
WOVA is more than just a collection of buildings; it’s a vision for the future of urban
living. The development features stunning amenities that cater to modern lifestyles, including a state-of-the-art indoor lap pool, sauna, fitness studio, co-working spaces, private cinema, rooftop barbecue terrace, and beautifully landscaped gardens.
Residents will soon enjoy the convenience of dining and retail options on the ground floor, creating a lively precinct that embodies the essence of community living.
“WOVA is designed to offer a lifestyle that balances convenience, luxury, and community. With hundreds of cafes and eateries surrounding the precinct and extensive onsite amenities, residents have everything they need,” said Damian. “The integration of co-working spaces, entertainment areas, and landscaped gardens reflects our commitment to providing a holistic living experience.”
The scale and complexity of WOVA presented unique challenges that required innovative solutions.
“The size and scale of WOVA demanded a unique materials handling strategy,” said Damian.
“We implemented LEAN construction methods and utilised custom-made man and materials hoists to manage the flow of high volumes of prefabricated materials. This
allowed us to maintain efficiency and meet the project’s demanding timeline.”
Prefabricated elements played a crucial role in the project’s success, including the installation of 984 prefabricated pod bathrooms, 14,419 façade pieces, and a 25m prefabricated indoor swimming pool. These components not only accelerated the construction process but also ensured high-quality finishes throughout the development.
The scale of WOVA also brought significant logistical challenges, particularly in materials handling and construction sequencing. Geocon’s innovative approach, which included the use of Stross custom-designed hoists and concept hoists for formwork, enabled the team to maintain momentum.
“The custom hoists were critical in facilitating vertical movement of heavy materials, such as the prefabricated bathroom pods and façade elements,” said Damian. “This not only improved efficiency but also reduced reliance on traditional tower cranes.”
The WOVA development is a testament to Geocon’s vision and expertise in delivering large-scale urban precincts that enhance the community and redefine contemporary living.
With its prime location, extensive amenities, and innovative construction, WOVA is set to become a vibrant hub within Woden Valley, reflecting Geocon’s commitment to creating homes, wealth, and urban spaces for everyone.
“WOVA is not just a development; it’s a new era for Woden Valley,” said Damian. “Geocon is proud to play a leading role in this transformation, setting new standards for mixed-use developments and shaping the skyline of Canberra.”
For more information contact Geocon, Level 6, 82 Northbourne Avenue, Braddon ACT 2612, phone 1300 979 757, website www.geocon.com.au
Goldenlight Pty Ltd has quickly become a key player in Canberra’s construction industry, known for its expertise in steel reinforcement and commitment to quality.
Since starting operations in early 2019, the company has made important contributions to many high-profile projects in the region, including the WOVA development. Specialising in the installation of reinforcement for various structural elements, Goldenlight ensures the safety and stability of complex construction projects.
Safety is a core value at Goldenlight. The company is committed to providing a safe working environment for all employees. It follows strict safety protocols and offers ongoing training to help team members manage risks effectively. Goldenlight is proud to have achieved great feedback reflecting its strong focus on safety.
“Our main responsibilities on the WOVA project involve the installation of reinforcement for lift pits, footings, slabs on grade, columns, walls, cores, stairs, and other general reinforcement needs,” said Gombosuren Lhamsuren, Operations Manager at Goldenlight. This technical and precise work highlights Goldenlight’s expertise in steel reinforcement, reflecting the company’s growing reputation in Canberra’s construction sector.
“The WOVA project is one of the most significant developments in Canberra for 2024,” Gombosuren said. “It’s a golden opportunity
rich in high-end amenities, abundant transport options, and once-in-a-generation value.”
WOVA had a number of unique parameters that provided an opportunity for collaboration across all trades. “Whenever a challenge arose, we prioritised thorough discussions with the builders and other tradespeople involved. Through collaborative problem-solving and a concerted effort to address issues promptly, we worked diligently to ensure that each task was completed within the scheduled time frame.”
This team-oriented approach helped Goldenlight manage the project smoothly, keeping a strong focus on efficiency and coordination.
“We managed the project with an average of 25 to 35 workers onsite each day, executing multiple tasks concurrently to ensure efficient progress,” said Senior Supervisor, Paanaa Ayurzana.
Each team operated under the guidance of experienced team leaders, supported by detailed schedules that outlined daily tasks. This structured approach, coupled with enhanced communication between teams and regular collaboration with other companies, streamlined operations and addressed any issues promptly.
Founded in 2018 and operating in Canberra since 2019, Goldenlight has quickly established itself as a cornerstone in the local construction industry. Specialising in steel reinforcement, the company’s commitment to quality, innovation, and industry standards is evidenced by its
membership in both the CFMEU and Master Builders Australia (MBA) in 2023. This dedication to excellence has made Goldenlight a reputable partner in Canberra’s most ambitious projects, including WOVA.
“Our unwavering commitment to quality, reliability, safety and innovation has set us apart, making us a trusted name in the Canberra construction landscape,” said company director Alex Tumurbaatar. The company’s role in WOVA not only demonstrates its technical expertise but also its ability to adapt, collaborate, and contribute to landmark developments that shape the region’s future.
“We’ve recently introduced four different reinforcement installation packages, including the supply of accessories, the supply and installation of reinforcements, and the post-tension service for all kinds of sizes of projects. Our team continuously seeks innovative changes to alleviate our clients’ concerns and ensure our projects succeed,” explained Alex Tumurbaatar.
As Goldenlight continues to play a vital role in Canberra’s growth, its contributions to projects like WOVA highlight the company’s core mission: to build enduring structures that serve and inspire communities for generations to come.
For more information contact Goldenlight, 490 Northbourne Avenue, Dickson ACT 2602, phone 0421 548 469, email alex@goldenlightcivil. com.au, website goldenlightcivil.com.au
Below ABE Consulting ensured WOVA complied with
and
ABE Consulting, a specialist consulting firm dedicated to creating accessible built environments, provided expert accessibility consulting services. Known for their outcome-based professional advice, ABE Consulting works with project managers, architects, and building certifiers to ensure compliance and accessibility for all end users.
“Our brief required a detailed review of the architectural plans to ensure compliance with key standards, including AS4299 for adaptable apartments, accessible hotel units, and the Disability Discrimination Act (DDA) requirements,” explained Managing Director Abe Strbik.
“We were involved from the detailed design phase right through to the Certificate of Occupancy to ensure compliance.”
One of the unique challenges faced on this project was addressing the street gradient interfacing pedestrian entries at the allotment boundary, which required careful alignment with building entries, pathways, and shopfronts.
“We addressed some of these site constraints via a Performance Solution report, which allowed us to navigate accessibility challenges and maintain compliance,” Abe said. Additionally, design changes
during construction had flow-on effects that required real-time adjustments to the accessibility design.
Since its establishment in 2013, ABE Consulting has been the preferred access consultant for thousands of projects across residential, commercial, education, healthcare, and retail sectors in New South Wales and the Australian Capital Territory. Their expertise spans all stages of design and construction, including site audits to identify and overcome access barriers.
With an impressive portfolio that includes Sydney’s Royal Prince Alfred Hospital, Meriton’s 180 George Street in Parramatta, and the Sydney Swans HQ, ABE Consulting continues to set the standard for accessible design.
Their involvement in WOVA demonstrates their commitment to ensuring inclusive environments that cater to the needs of all users, reinforcing their role as leaders in accessibility consulting.
For more information contact ABE Consulting, Level 1, 280 Norton Street, Leichhardt NSW 2040, phone 02 8065 0400, email info@abeconsulting.com.au, website www.abeconsulting.com.au
Below Capital Veneering delivers innovative, bespoke joinery for WOVA, with precision, quality craftsmanship, and expertise.
Capital Veneering, renowned for its motto ‘Innovation in Joinery’, has showcased their expertise in producing bespoke joinery solutions for the WOVA development. With nearly 25 years in the industry, Capital Veneering has evolved from a small workshop to a multi-award-winning company with over 70 staff, delivering high-quality craftsmanship to both residential and commercial projects.
“Our team was responsible for manufacturing and installing kitchens, laundries, storage units, and wardrobes across the entire WOVA project,” said Ben Stevens. “This included unit kitchens in residential Towers 1, 2, 3, and 4, as well as bespoke joinery in the penthouse units, such as wardrobes and vanities.”
Capital Veneering’s scope extended to the Hotel Tower 1, where they fitted unit kitchens and luggage storage on Levels 1 and 2, and in the common area of Tower 2, where they installed a communal kitchen on Level 4. Despite the scale of the project, their commitment to quality and precision remained uncompromised.
However, the WOVA development did present unique challenges. “Due to unforeseen site delays, one of our biggest challenges was managing storage capacity,” Ben said. “We had to secure over
3,100m² of off-site storage space to accommodate more than 400 units of joinery until site access was available. Our ability to adapt and manage these logistical challenges was key to our success on this project.”
Beyond WOVA, Capital Veneering is engaged in other significant projects, such as the Woden Green Apartments and Melrose Apartments in the Australian Capital Territory.
Capital Veneering’s dedication to excellence is reflected in every aspect of their work, from the use of state-of-the-art machinery to the expertise of their craftsmen. Their passion for unique designs, quality output, and outstanding customer service has solidified their reputation as leaders in the joinery industry.
For more information contact Capital Veneering, 67-71 Bayldon Road, Queanbeyan NSW 2620, phone 02 6299 1557, email info@ capitalveneering.com.au, website www.capitalveneering.com.au
Established in 1980, IC Formwork is a leading commercial formwork company with over 40 years of experience, providing innovative solutions across Canberra and Newcastle. Renowned for their proactive approach, commitment to safety, and high-quality outcomes, IC Formwork has played a crucial role in the development of WOVA.
IC Formwork Services were responsible for the design and delivery of all formwork systems at the WOVA inclusive of the jump form, perimeter screens, formwork hoists, prefabricated stairs, slab, column, wall and landscape formwork.
A company that prides itself on providing win-win solutions for builders, IC Formwork Services brought to WOVA its trademark commitment to ensuring clients receive the best possible formwork systems.
In the early stages of the project IC Formwork Services worked closely with GEOCON to ensure the formwork systems would be safe and efficient during the construction phase of the project. The results speak for themselves with the WOVA structure being delivered safely, within programme and to the highest quality standard.
IC Formwork Services’ extensive range of formwork systems for soffit, lift shaft, column, wall and stair formation systems include table and panel systems, hydraulic lift shaft systems, pre-fabricated wall and column systems, pre-fabricated metal decking systems and pre-fabricated stair systems.
For more information contact IC Formwork, 1 Couranga Crescent, Hume ACT 2620, phone 02 6260 1260, email icf@icformwork.com.au, website www.icformwork.com.au
MAIN CONSTRUCTION COMPANY : Mirvac Design
ARCHITECT : Mirvac Design
CONCEPT ARCHITECT : CHROFI
INTERIOR DESIGN : MIM Designs
LANDSCAPE ARCHITECT : McGregor Coxall
CIVIL / STRUCTURAL ENGINEER : ADG
PROJECT VALUE : $800 million
NINE by Mirvac is a boutique collection of 1, 2, and 3-bedroom residences and penthouses, with breathtaking views, timeless interior finishings, and approximately 6,500m2 of open space. The development also includes lush parks, gardens, a lawn for active play, sheltered BBQ areas and a children’s playground.
Once the home of Channel 9, the site has been transformed into an exceptional new residential community, marking another Mirvac legacy development.
NINE by Mirvac is more than just a residential development; it’s a testament to Mirvac’s commitment to creating vibrant, sustainable communities. “This project is a significant milestone for Mirvac, reflecting our dedication to excellence and innovation in urban living,” notes Warwick Bible, General Manager, Residential Development NSW & QLD.
NINE by Mirvac features 442 apartments, with spacious 1, 2, and 3-bedroom residences and penthouses, many capturing spectacular views. Meandering through the boutique collection of buildings is 6,500m2 of public open space.
The project stands out with its impressive specifics: 41,570m2 of concrete, 'more than 37,000 plants and trees, and more than 360,014 bricks laid. The build incorporates innovative construction methods, with 760 prefabricated bathrooms craned into each apartment, ensuring the highest quality and control standards.
NINE by Mirvac also comprises a retail offering; two retail tenancies providing food
and beverage options to the residents an local community. Parabol Playground, a children’s playground, that celebrates the history of television with a unique centrepiece: a section of the former transmission tower that broadcasts Channel 9 to millions of homes.
Serving as the front door to NINE by Mirvac and the parkland beyond, The Gateway Hub is a versatile space designed for residents and the local community to host meetings, celebrations, and events. This open-air pavilion, featuring a green roof, outdoor terrace seating and servery facilities delivers on the community values central to NINE by Mirvac. Additionally, the ground floor will house two workshops for bike repair, maintenance, and hobbies, along with a meeting room.
“NINE by Mirvac has been designed to seamlessly fit into the landscape with a purposeful approach. We’ve implemented lower impact, shorter buildings on the periphery, and placed taller structures in the middle, ensuring a harmonious balance with the surrounding environment,” said Warwick.
Residents and the broader community will benefit from approximately 6,500m2 of open space, thoughtfully designed by internationally renowned landscaper McGregor Coxall. This expansive area features parks, gardens, a lawn
for active play, sheltered barbecues, and a children’s playground, all set against the breathtaking panorama of Sydney.
The residential community occupies the 3.2ha site of the former Channel Nine television studios in Willoughby, just 6km north of the Sydney CBD. The development of the TX tower commenced in 2021 after the significant demolition of the old Channel 9 headquarters. At its peak, the site employed 40 Mirvac staff, 15 support staff, and up to 470 workers on-site, managing multiple work fronts across ten different buildings.
Despite challenges like inclement weather, COVID-19 restrictions, and market conditions affecting subcontractor availability and materials, the project reached practical completion in mid-June 2024. Two buildings feature glass-reinforced concrete for aesthetic appeal, and the extensive green spaces foster a sense of community and well-being.
Founded in 1972, Mirvac has contributed positively to our cities and the urban landscape for over 50 years through connected communities, exceptional workplaces, and thriving shopping centres. Mirvac’s purpose is to reimagine urban life, inspire innovative and bold solutions and create extraordinary places and experiences that enrich people’s lives.
Mirvac continues to work on other notable projects, including Highforest at West Pennant Hills, Harbourside at Darling Harbour, and the commercial project at 55 Pitt Street, demonstrating its ongoing impact on Australia’s urban landscape.
For more information contact Mirvac, Level 28, 200 George Street, Sydney NSW 2000, Australia, phone 02 9080 8000, website www.mirvac.com
AllPrep Flooring Specialists, renowned for its expertise in floor preparation, levelling, and concrete repair, applied innovative techniques to create perfectly flat floors within the 10 buildings of NINE by Mirvac project.
With over 30 years of experience, AllPrep has extensive expertise in preparing subfloors and can refurbish, and level both old and new concrete surfaces. For NINE by Mirvac, AllPrep Flooring utilised the Laticrete Supercap Pump Truck System, a methodology with over 15 years of global application success.
As the only fleet of its kind in Australia, the ALLPREP LATICRETE® SUPERCAP® system has earned a world-class reputation for its versatility and speed. It is also praised as a major advancement in occupational health and safety for floor-levelling workers and other trades nearby.
With all product mixing and pumping done in the Mobile Blending Unit (MBU), the ALLPREP LATICRETE® SUPERCAP® system eliminates the need for manual handling and unloading of heavy product bags—often hundreds of 20kg bags per job. It also prevents exposure to dangerous silica dust, a common hazard with traditional manual mixing inside buildings.
The ALLPREP LATICRETE® SUPERCAP® system lays a self-levelling compound 50% faster than other products in the
market and sets in only four hours, allowing further construction developments to take place in record time.
Tasked with completing comprehensive floor preparation works across all 10 buildings of the NINE by Mirvac site, AllPrep undertook concrete rectification using the advanced SUPERCAP® SC500 self-levelling underlayment to 445 Apartments.
AllPrep’s innovative approach to pouring the self-levelling cement involves pumping it from the self-contained truck at street level directly into the building. This not only enhances efficiency and ensures a quality finish but significantly reduces the environmental footprint by minimising silica dust exposure within the building.
When it comes to floor prep, levelling, and all things concrete repair, coatings, and polished concrete, AllPrep Flooring places quality first. For large projects, they start by inspecting the floor, then a team of skilled surveyors determine the rectifications required – an essential step for concrete rectification works.
AllPrep prides itself on delivering high-quality results on the first try.
“We have the expertise to provide the best solutions for almost any application. Getting it right the first time is crucial,” said David Kealy, AllPrep Flooring Managing Director. “We’re always raising the bar for our customers and clients. We’ve worked with Australia’s
top construction companies and, as our results show, we’ve met and exceeded their expectations,” David adds.
The AllPrep site team of 10 commenced work on the NINE by Mirvac site in November 2023 and completed their last pour in July 2024. Currently, the AllPrep team are utilising this system on the prestigious One Sydney Harbour Project, pumping self-levelling materials up to 70 floors in a single application from street level.
Through innovative techniques, a steadfast commitment to quality, and an unwavering focus on environmental and health standards, AllPrep continues to exceed industry expectations. Their reputation for delivering first-time excellence is well-earned, with a wealth of industry knowledge informing every aspect of their operations. From the initial floor inspection by experienced surveyors to the final installation of self-smoothing products, AllPrep’s meticulous approach guarantees optimal results, meeting even the tightest project requirements.
Recently completed and milestone projects include LendLease –One Sydney Harbour, Mirvac – Nine, Richard Crookes – Sirius, Toga – Wicks Place.
For more information contact AllPrep Flooring Specialists, PO Box 184, Round Corner NSW 2158, mobile (David) 0419 289 152, email david@allprepflooring.com.au, website www.allprepflooring.com.au
SYNC, an industry leader in prefabricated construction, has once again raised the bar with its latest project: the fabrication of 769 bathroom pods for Mirvac’s luxury residential development, NINE by Mirvac. This landmark project highlights SYNC’s commitment to innovation, quality, and sustainability, revolutionising how bathrooms are integrated into high-rise structures.
At the heart of SYNC’s approach is its state-of-the-art manufacturing facility in Laverton, Victoria, where each bathroom pod was meticulously crafted. The pods feature bespoke designs with premium fixtures, natural stone-clad walls, and advanced feature lighting. Integrating 28 unique pod types highlights SYNC’s customised, high-quality prefabrication capacity.
“Our focus on prefabrication allows us to deliver high-quality, bespoke bathroom solutions while significantly reducing waste and improving efficiency,” said Chris Ong, Managing Director of SYNC.
By employing Design for Manufacture and Assembly (DfMA) principles, SYNC significantly reduced waste and improved recycling rates. A remarkable 99% of materials were recycled within the factory, showcasing a true commitment to environmental stewardship.
“Innovative construction methods and a commitment to sustainability are at the core of what we do at SYNC. This project exemplifies how we can deliver exceptional results while maintaining our environmental and social responsibilities,” added Chris.
SYNC’s off-site fabrication of the bathroom pods not only streamlined the construction process but also significantly enhanced site safety and efficiency. SYNC effectively mitigated significant risks associated with traditional construction methods by reducing the number of trades required on-site and utilising specialised machinery for material handling.
“By building prototypes and manufacturing off-site, we can control quality and safety to a higher degree, ensuring that each pod meets our stringent standards before reaching the site,” Chris emphasised.
This project is yet another testament to SYNC’s mastery of integrated modular solutions, reinforcing its reputation as a premier contractor in the prefabricated construction industry.
For more information contact SYNC, phone 03 8329 4111, email info@sync.industries, website sync.industries.
Future Form, concrete and formwork solutions specialists have made significant strides in the construction industry with their role in the NINE by Mirvac project. This high-profile project saw Future Form applying its expertise in creating and installing advanced formwork systems essential for constructing luxury residences.
One of the standout features of this project is the use of bespoke formwork moulds. These custom moulds allowed for precise and
innovative concrete shaping, contributing to the NINE by Mirvac residences’ unique architectural features and high-quality finishes. “Our bespoke formwork solutions ensured both aesthetic excellence and structural integrity,” says Ibrahim Hafza, Construction Manager at Future Form.
The project involved a substantial workforce. At its peak, the Future Form team reached over 100 members, showcasing the company’s capability to scale its operations to meet the demands of large construction sites. This manpower ensured efficient project completion despite the challenges posed by COVID-19 restrictions and strict timelines.
Future Form’s commitment to safety and innovation has been a key factor in overcoming these hurdles. The company’s emphasis on these principles has allowed them to maintain progress and deliver high-quality results, even in the face of adversity.
“Managing COVID-19 restrictions and coordinating various trades were significant challenges, but our team's adaptability was crucial in overcoming these hurdles,” adds Ibrahim.
In addition to the NINE by Mirvac project, Future Form is engaged in other significant developments, such as the construction of 55 Pitt Street Sydney, Waterloo Over Station Development, and the Australian War Memorial in the ACT. These projects further solidify Future Form’s reputation as a leader in concrete and formwork solutions.
For more information contact Future Form, Suite 302, 45 Lime Street, King Street Wharf Sydney NSW 2000, phone 02 8376 6950, email enquiries@futureform.com.au, website www.futureform.com.au
Formerly the site of Channel 9’s headquarters, the new residential community, NINE by Mirvac, has been built on the solid foundations poured by Azzurri Concrete.
Initially engaged for the early works package with the civil contractor, Azzurri was later contracted to supply, pump, and place all the concrete for Stage 1, with Stage 2 as an optional extension. The team also handled temporary works engineering designs for the concrete tower placing boom and oversaw concrete mix designs.
Azzurri delivered a two-level carpark and 10 new buildings comprising 445 apartments in a controlled residential area. This included supplying, pumping, and placing 40,000m3 of concrete using four tower placing booms and a stationary boom.
“One of the standout aspects of this project was our environmentally efficient water washout system. It not only minimised wastage but also showcased our commitment to sustainable construction practices," said Bernie Orbell, Area Manager.
Work commenced with the early works pour in October 2022 and continued until February 2023. The first major ground slab pour and first major suspended slab took place in November 2021, while the final major suspended slab, Building H Level 7, was poured in July 2023, using 225m3 of concrete.
At peak times, Azzurri had up to 30 team members on-site, increasing to 40 for double pours, with a total of 240 personnel inducted over the project’s duration. The project faced significant challenges, including managing COVID-19 restrictions and unprecedented rain disruptions, but the team overcame these hurdles through dedicated efforts and strategic planning.
Established in 2004 by a team of seasoned professionals in Sydney’s west, Azzurri Concrete consistently enhances and expands its practices to meet and exceed the rising demand for world-class quality and service within the concrete construction industry.
For more information contact Azzurri Concrete, 5 Frank Street, Wetherill Park NSW 2164, phone 1300 299 877, email info@azzurriconcrete.com.au, website www.azzurriconcrete.com.au
Carparkking has solidified its reputation as the industry leader in comprehensive carpark solutions, showcasing its expertise in delivering a seamless carpark package for the NINE by Mirvac project.
“We provided a one-stop-shop, making project management easy for the builder – it’s what we do,” says Luke Hudson, owner of Carparkking. “Our versatile and experienced crew, 75 years’ collective experience in line-marking and other associated works, handled all aspects of the carpark development.”
The team began by thoroughly cleaning and sealing 27,000m² of concrete in the basement, incorporating acid treatment to enhance the slip rating. Precision line marking for approximately 6km of lines, over 4,950 numbered parking spaces, and 500m of kerbing was executed using high-quality materials, ensuring long-lasting results. Installing essential carpark furniture such as bollards, wheel stops, and signage further enhanced functionality and safety.
“This project is unique due to its strong emphasis on sustainability,” Luke highlights. Carparkking used Viroseal, a 6-star green rating sealer known for its low VOC content and minimal environmental impact. Additionally, vulcanised wheelstops from recycled materials underscored their commitment to environmentally sustainable solutions.
Commencing in May 2023 and completed in June 2024, the project saw a peak deployment of over 14 employees, ensuring timely and efficient progress. Despite the challenge of increasing the slip rating, Carparkking’s innovative approach and expert execution seamlessly met the specified standards.
“Each project is special to us, reflecting our commitment to excellence, and our low employee turnover demonstrates the pride and dedication of our crew,” added Luke.
Carparkking’s current portfolio includes over 100 projects, ranging from simple strata projects to large-scale Tier One Landmark projects. Notable completions include Barangaroo, Liverpool Hospital, Woolooware Bay, and Coronation at Merrylands, collectively exceeding $3 million in works.
For more information, contact Carparkking Pty Ltd, 7 Yalgar Road, Kirrawee NSW 2232, phone 02 8539 7367, email info@carparkking. com.au, website www.carparkking.com.au
MAIN CONSTRUCTION COMPANY : Deicorp
ARCHITECT : Architectus, MHNDU and BVN
Downtown Zetland is a striking array of 1, 2, and 3-bedroom residences, crafted to reflect Zetland's vibrant urban vibe. Featuring top-tier craftsmanship, these homes offer open floor plans, indoor/outdoor entertainment spaces, premium European appliances, and designer bathrooms.
Downtown Zetland represents the evolving landscape of architectural practice and offers a glimpse into the future of collaborative building design.
Australian property development and construction group Deicorp, recognises that architecture is not solely the result of creative impulses but also stems from sustained teamwork among architects, interior designers, landscape designers, and engineers.
Downtown Zetland, an architecturallydesigned urban oasis of four uniquely designed buildings, embodies this ethos, reimagining modern city living from conception to launch.
To make this vision a reality, Deicorp has partnered with leading Australian firms Architectus, MHNDU, and BVN, bringing together the best architectural minds to realise their shared vision of premium contemporary living in the vibrant inner-city suburb of Zetland, News South Wales.
Each of the four bespoke buildings has been uniquely designed in the signature style of each architect, coming to life under a shared vision in the true spirit of architectural collaboration not previously seen in Sydney.
This innovative approach reflects Deicorp’s commitment to fostering a collaborative environment where creativity and practicality converge to create outstanding living spaces.
Downtown Zetland:
Zetland is a lively and connected suburb, constantly evolving and reflecting its vibrant heart. Downtown Zetland showcases the highest quality craftsmanship to create contemporary, liveable spaces.
These residences are designed with spacious layouts and open floor plans, synonymous with sophistication. Offering a stunning
collection of one, two, and three-bedroom residences, Downtown Zetland echoes the suburb’s cool, urban energy. Select residences benefit from street-level access, a rarity in apartment living.
Downtown Zetland will be the final stage of the long-awaited Victoria Park precinct. The apartments are the largest in the area and are conveniently located on the cusp of the city, surrounded by acres of green spaces, with close proximity to East Village Shopping Centre, Green Square Train Station, and Sydney Airport.
The Arches: The Final Piece
Deicorp has released the final units within the mixed-use development, with The Arches completing the 546 apartments at Epsom Road. The Arches is characterised by an iconic archway entrance that transitions to peaceful inner courtyard spaces.
Designed by architectural giants MHNDU and BVN, The Arches offers open floor plans with generous balconies, allowing ample natural light and surrounding views.
Deicorp’s role in the development of Downtown Zetland exemplifies the future of collaborative building design. Through partnerships with leading architectural firms and a commitment to high standards,
Deicorp has created a modern urban oasis that redefines city living.
The success of Downtown Zetland respresents what collaborative, high-quality development can achieve in reshaping urban living spaces.
Deicorp: A Pillar in Property Development
Founded in 1999, Deicorp is a privatelyowned Australian property development and construction group with expertise in residential, commercial, and retail property.
Recognised as Sydney’s leading builder of modern, transport-connected developments, Deicorp is committed to ensuring that every buyer feels confident in their investment.
“The Deicorp team is committed to delivering the highest standards in everything we do. From site selection to design and construction, sales and customer care, we give every buyer peace of mind that they’ve made a smart choice,” explained Fouad Deiri OAM, Founder and Chairman of Deicorp.
For more information contact Deicorp, Level 2, 161 Redfern Street, Redfern NSW 2016, phone 02 8665 4100, email admin@ deicorp.com.au, website www.deicorp.com.au
DEVELOPER : CBD Development
MAIN CONSTRUCTION COMPANY : Hickory
ARCHITECT : Plus Architecture
PROJECT MANAGER : Pomeroy Pacific
ENGINEER : Rincovitch
Trio Box Hill is a striking development featuring three towers rising above a 6-level podium, offering 488 modern apartments, 87 luxurious hotel rooms, a childcare facility. This architectural marvel also includes a 4-level basement carpark and 3-levels of office spaces.
For over 30 years, Hickory has been a leader in advancing the capabilities of the built environment across Melbourne and Sydney. Through continuous investment in digital platforms, people, and products, Hickory has established itself as one of Australia’s most diverse property companies, spanning construction, development, manufacturing, and data centre segments.
This commitment to innovation and excellence is exemplified in the development of Trio in Box Hill, a premier mixed-use project that showcases Hickory’s expertise in delivering complex, high-quality urban environments.
Located at 851 Whitehorse Road, Trio is a striking addition to Box Hill’s skyline, featuring three towers rising above a sixlevel podium. The development includes 488 apartments, with two towers dedicated to residential living and the third housing independent living apartments along with a two-level childcare facility. Beyond its residential offerings, Trio integrates a wealth of retail, dining, and entertainment options, an eight-level car park, 126 hotel rooms, and sophisticated office and function spaces, creating a vibrant community hub.
The design of Trio, led by Plus Architecture and supported by key consultants like Detail 3 and Pomeroy Pacific, emphasises both
aesthetic appeal and functional excellence. Each of Trio’s three towers has a distinct façade treatment that contributes to the development’s iconic appearance. Tower 1 features a window wall system with rendered slab edges, Tower 2 incorporates aluminium fins to add dynamic visual elements, and Tower 3 stands out with its curtain wall system and curved spandrel panels that create a flowing, contemporary silhouette.
Hickory’s role in the Trio project extends beyond traditional construction. By leveraging its innovative construction methodologies, Hickory was able to significantly streamline the building process, offering the client earlier handover dates without compromising quality. A key aspect of this efficiency was the redesign of the building cores using precast core panels, which accelerated the construction timeline and improved overall productivity. This approach not only fasttracked the construction program but also set new benchmarks for efficiency in high-rise development.
Residents of Trio will benefit from an impressive array of amenities, including communal gardens, a gymnasium, pool, sauna, and steam room, offering a luxurious lifestyle within a bustling urban setting. The thoughtful design of these shared spaces reflects Hickory’s dedication to creating environments that not only meet the needs of
today but also anticipate the future demands of urban living.
The successful delivery of Trio speaks to Hickory’s ability to manage complex, large-scale projects from conception to completion. By applying its documented “Hickory Way” methodology, the company consistently mitigates risks on high-rise projects, ensuring exceptional outcomes for clients. Hickory’s approach blends meticulous planning, innovative construction techniques, and a deep understanding of client needs, resulting in projects that set new standards in the property industry.
Trio stands as a showcase of Hickory’s forward-thinking approach to urban development. This landmark project not only enhances the skyline of Box Hill but also enriches the community with a blend of residential, commercial, and recreational spaces designed for modern living.
Hickory’s role in this development cements its reputation as a leader in the construction industry, driven by a commitment to innovation, excellence, and the creation of better places for future communities.
For more information contact Hickory, Level 5, 68 Clarke Street, Southbank VIC 3006, phone 03 9429 7411, website www.hickory.com.au
Detail 3, leaders in the field of architectural documentation and support services, was asked to oversee the project through its documentation and construction phases of the Trio Box Hill project. This role involved the meticulous preparation of architectural construction documentation across a multi-staged permit process.
“Taking over the post-design stage from Plus Architects, our role was crucial in coordinating the consultant team, ensuring seamless collaboration among all stakeholders involved,” said Detail 3’s, Andrew Russo.
Working under a novated agreement, Detail 3 collaborated closely with Hickory to manage the architectural aspects of the project throughout the construction program. “Our goal was to ensure that the design intent was translated and maintained throughout the complexities of construction,” said Andrew. “Fook Hoong Chiang, Senior Architect, was tasked with leading the coordination of the consultant team, guaranteeing that every detail was accounted for and executed to the highest standards.”
One of the significant challenges faced during the project was managing client and marketing changes at the late stages of the podium levels.
“The podium has a carpark in the middle with a perimeter of Sole Occupancy Units, and the levels were different from the outside of the podium to the central carpark,” said Andrew. “Any changes to these areas had big implications where the two different levels came together and required coordination.”
The construction phase was delivered in the Revit BIM environment, with models collaborating on the cloud and sub-contractors providing clash detection analysis and reporting floor-by-floor. This advanced technological approach allowed Detail 3 to navigate the project’s complexities efficiently and effectively.
Detail 3’s unique business model is divided into three main services: consult, hire, and draw. This structure enables them to deliver unparalleled expertise and ensure that projects are documented and delivered to the highest standards in different ways to suit the needs of our clients. “We pride ourselves on our commitment to excellence and innovation, supporting the construction industry with high-quality, reliable documentation and support services,” said Andrew.
For more information contact Detail 3, phone 03 8415 1588, website www.detail3.com
Below Citywide Precast provided the distinctive architectural concrete balustrades for the residential towers at Trio Box Hill, starting from Level 7.
Specialising in a range of precast products, Citywide Precast has built a reputation for exceptional quality and innovative solutions for almost 40 years in business.
Citywide Precast was responsible for manufacturing and delivering the feature architectural balustrades from Level 7 to the roof, for the Trio Box Hill project. This task required planning and precision, along with a high level of craftsmanship to meet the project’s aesthetic and structural requirements. “Our team pride themselves on taking an innovative, flexible, and professional approach in order to provide the best service for all of our clients, ensuring that the whole operation runs smoothly from start to finish,” said Sebastian Marchese.
“We cater for a variety of projects; ranging from low-rise to high-rise developments, residential projects, offices, warehouses, apartments, schools, hospitals, and feature elements that a project may require. Our extensive experience includes producing Reckli lined/feature panels, curved panels, thermomass panels, columns, and bricksnaps, as well as using concrete additives like colour.”
Founded in 1985 by Phillip Marchese, Citywide Precast was built on a vision of utilising precast concrete panels as the most efficient and
effective construction method. “Back then, my father saw the future where precast concrete panels would dominate both high-end, multistory developments, and low-rise residential homes,” Sebastian said. “Fast forward 39 years, and today, you see precast panels everywhere in large-scale construction.”
Citywide Precast’s central operations plant is located in Hallam, southeast of Melbourne, but their reach extends across Australia. The company offers a complete professional service from estimating, drafting, and manufacturing to the transportation of finished precast panels to the site. “Our team take pride in their work, ensuring our manufacturing is quality controlled to provide a high standard product that is delivered on time for all our clients. Treating every job as if they'd be our own,” said Sebastian.
Working together with Hickory, Citywide Precast’s involvement in the Trio Box Hill project highlights their ability to deliver top-tier precast solutions, contributing to the project’s success and ensuring that architectural visions are brought to life with precision and excellence.
For more information contact Citywide Precast, phone 03 9702 4726, email estimating@citywideprecast.com, website citywideprecast.com
CLIENT : Homes Victoria
MAIN CONSTRUCTION COMPANY : Hansen Yuncken
ARCHITECT : Hayball
The Homes Victoria Bills Street redevelopment project features six multi-level buildings ranging from 3-storeys to 7-storeys, and includes 103 social and 103 affordable homes, offering a mix of 1, 2, and 3-bedroom units. The project is enhanced by various recreational and social communal spaces and includes both civil and external landscaping within the site boundary.
The Bills Street Project is the latest of the Victorian Government’s $5.3 billion Big Housing Build, the largest social and affordable building program in the state’s history.
Hansen Yuncken (HY) was awarded the design and construction contract for the multi-staged delivery of 206 new comfortable, modern and energy-efficient social and affordable dwellings for Victorians experiencing family violence, mental illness, disability or who are unable to secure a safe, affordable place to call home.
The project consists of a 50/50 blend of 103 social and 103 affordable homes, including homes designed specifically for disability access. Basement car parking will contain 165 spaces. The complex will be enhanced by a range of recreational and social communal spaces, including civil and external landscape works within the site boundary and landscaping works beyond the site boundary.
The environmentally efficient design is targeting a 5 Star Green Star rating and a 7 Star NatHERS average rating.
“The site was quite large, 10,000m2,” said Project Manager. “We had significant bulk excavation in the initial stages, which uncovered soil contamination that needed to be well managed in what is a residential area.”
With six individual buildings to construct, if stacked end-to-end equals 35 floors of construction, the construction program was particularly intricate in design.
“Our intention was we would start at one point and follow the snakes around all six buildings. However, the discovery of contaminated soil as well as some inground authority challenges, meant that we had to redesign the construction program many times over.”
The project management team was required to react quickly to the changing nature of the construction industry at large over the last 24 months, with challenges with supply chains and subcontractor availability. The team at Hansen Yuncken rose to the occasion and completion is forecast for mid 2024.
“We had some excellent contractors on this project. Our structural subcontractors, Oceania, EuroPrecast, Earth Electrical, Roar Fire, Croft Mechanical, Insight Fixing, Highbury Plumbing, Cranmore Carpentry, Express Interiors, Deca, Landscape Plus and General Cranes to name a few.”
A standout feature of the project is the façades of the buildings.
“Each building has its own unique façade. We used over 1,200 precast panels to achieve the individual looks.”
The Bills Street social housing project is one of the largest build in the first wave of projects being rolled out by the Homes Victoria, the Victorian Government's social and affordable housing agency.
“It is really fulfilling to be working on a project where there are tangible benefits for the community. At Hansen Yuncken we are proud to be part of creating homes for vulnerable and disadvantaged Victorians.”
At Hansen Yuncken, innovation is deeply rooted in their history. In 1929, they pioneered a suspended scaffold to renovate Melbourne’s State Library dome. In 1985, they transformed Adelaide Railway Station into a casino while trains continued to run beneath. In 2011, they etched the iconic MONA - Museum of Old and New Art - into a Tasmanian peninsula by the Derwent River.
Hansen Yuncken’s foundation lies in fair collaborations, industryleading talent and timely projects. Innovation is in their DNA, always seeking better ways. Their projects encompass various delivery methods, adapting to unique challenges. Hansen Yuncken isn’t just about construction; it’s about building sustainable solutions for the future.
For more information contact Hansen Yuncken, Level 10, 412 St Kilda Road, Melbourne VIC 3004, phone 03 9831 6500, email melbourne@ hansenyuncken.com.au, website www.hansenyuncken.com.au
The Axiom Group stands as Australia’s foremost balustrade consultants and suppliers of cutting-edge architectural glazing systems, serving as trusted partners to leading architects, installers, and builders across the industry.
A testament to their expertise, Axiom was contracted to helm the design, engineering, supply, and certification of all balustrades for the Bills Street Social Housing Project.
“Our involvement commenced during the project’s design phase, where we dedicated a full year to its successful realisation,” said General Manager, Harvey McAlpine.
“Our primary role revolved around delivering an engineered, customised solution,” said Harvey. “This particular endeavor featured an intricately detailed façade that required our designs to breathe life into it.”
Harvey attributed the project’s success to the outstanding efforts of Axiom’s accomplished design team, highlighting their dedication and creativity in meeting the project’s requirements.
Recognising the importance of efficiency and innovation in modern construction, Axiom Group actively sought opportunities to leverage offsite modular construction, reducing on-site time and streamlining the entire process.
The Axiom Group, with a rich history spanning over a decade, has consistently delivered top-tier architectural glazing systems to the glass and construction industry. Their commitment to excellence and ability to provide tailored solutions continue to set Axiom apart as industry leaders.
For more information contact The Axiom Group, 56 Lock Avenue, Werribee VIC 3030, phone 1300 652 336. email enquiries@ axiomgroup.com.au, website www.axiomgroup.com.au
With their extensive experience and commitment to excellence, Combined Steel Solutions played an important role in bringing the Bills Street Social Housing project to fruition.
“At Combined Steel Solutions, we take immense pride in our work and the impact it has on communities,” says Mick Trueman, Director of Combined Steel Solutions. “For the Bills Street project, we focused on delivering top-notch steel fabrication and installation services, ensuring every aspect met the highest quality standards.”
Combined Steel Solutions was responsible for a comprehensive scope of works that included the structural steel package. This encompassed the steel structure for residential components, steel erection, mechanical platforms and structures, rectification works, and temporary support steel for demolition works. Their meticulous approach and dedication ensured the project’s success without any complications.
“We believe in using Australian-made steel, sourced from local suppliers. It’s not just about quality but also about supporting the local economy and reducing our carbon footprint,” Mick said. “Sourcing recycled materials and utilising local businesses are integral to our operations. It’s our way of contributing to a sustainable future.”
One of the standout features of Combined Steel Solutions’ contribution was the architectural steelwork, which included architectural screening,
and handrails. These elements not only added to the aesthetic appeal of the housing units but also ensured durability and safety.
“Our directors, Ross McBride and Mick Trueman, bring together over 40 years of experience, having worked on some of Melbourne’s largest projects. This project, while straightforward, was an opportunity to showcase our ability to meet and exceed program requirements,” said Mick.
“We thrive on delivering the highest quality standards to our customers and solving any challenges that arise during the project. Meeting project timelines and delivering impeccable results are paramount to us,” said Mick. “We’re proud to have been part of a project that not only provides essential housing but also supports the local economy and environment.”
For more information contact Combined Steel Solutions, phone 03 5959 1050, email admin@combinedss.com.au, website www.combinedsteelsolutions.com.au
For over 12 years, Cranmore Carpentry, under the leadership of Director Thomas Murray has been a stalwart in serving the metropolitan Melbourne region, specialising in an array of services, ranging from fixed carpentry to façade works.
Cranmore Carpentry worked as the carpentry contractor on the Bills Street Social Housing Project, which comprised of 206 apartments across five buildings. “We completed the 2nd fix carpentry package,” said Thomas. “This was accomplished on time and within budget “
Cranmore Carpentry’s commitment to quality and precision is unwavering, regardless of the project’s scale. The teams dedication to delivering excellence remains a hallmark of their work.
Looking ahead, Cranmore Carpentry has its sights set on the horizon, anticipating a surge in social housing projects across Melbourne in the coming years. Their desire to contribute to the community and make a positive impact underscores their commitment to their craft.
With over a decade of experience under their belt, Cranmore Carpentry has a rich portfolio that spans high-rise apartments, educational
institutions, social housing, hospitals and more. Their expertise shines through in every aspect of their work, including façade work involving high-rise glass and side cladding, as well as intricate timber work for feature foyers.
Cranmore Carpentry has solidified its place as one of Melbourne’s leading carpentry companies. Their dedication to quality has positioned them as trusted partners in the construction industry.
Behind Cranmore’s success is a team of 60 to 80 staff, many who have been with the company over 10 years and share a common passion for their craft. Their collective expertise is the driving force behind the company’s ability to consistently deliver outstanding results.
Cranmore Carpentry’s recent projects include: Spotwoods Yard, Assemble BSB, Merri Northcote, Liberty 1 in Footscray, Ivanhoe Gardens Stage 2, GTV9 Retirement Village, and 2B2 Serviced Apartments.
For more information contact Cranmore Carpentry, phone 0404 895 735, email thomas@cranmorecarpentry.com.au
DEVELOPER : Little Projects
MAIN CONSTRUCTION COMPANY : Hickory
ARCHITECT : DKO ARCHITECTS
STRUCTURAL ENGINEER : Webber Design
BUILDNG SERVICES ENGINEER : WSP
CONSTRUCTION VALUE : $200 million
The state-of-the-art Dover House offers a modern and sustainable approach to office environments. Featuring an inviting communal rooftop terrace and luxurious end-of-trip facilities, this impressive structure seamlessly integrates vibrant ground floor retail spaces, two expansive basement parking levels, and seven sleek commercial floors, all within one cohesive building.
Situated on Fitzgibbon Street in Cremorne, Dover House sets a new standard for corporate offices, seamlessly blending modern aesthetics, sustainability, and functionality. As a carbon-neutral building, it reflects Hickory’s vision of creating better places for future communities.
The building features eight commercial levels with large open floorplates, maximising natural light throughout the workspace. The communal rooftop terrace offers an additional space for relaxation and collaboration, further reinforcing the idea of work-life balance.
Dover House is designed to cater to the needs of forward-thinking businesses. With over 8,000m2 of office space spread across the development, the space provided allows flexible and dynamic working environment. The building’s 92m2 food and beverage area adds to the appeal, providing tenants with on-site dining options that enhance convenience and comfort.
Hickory aimed to deliver a workspace for change makers, businesses and people who are leading the way for the future. Every detail of Dover House has been crafted to reflect this vision.
Dover House reflects the industrial charm of Cremorne while introducing a luxuriously modern feel. The recreated brick warehouse facade, combined with a striking curtain wall, pays homage to the area’s heritage while pushing architectural boundaries. The building's optimised façade not only
enhances its aesthetic appeal but also reduces heating and cooling costs, minimising its environmental impact.
Dover House stands as a beacon of modern architecture and sustainable design. Boasting a 5-Star Green Star rating, this building is designed with longevity and environmental responsibility in mind. Its impressive NABERS rating highlights its commitment to energy, water, and waste efficiency. Features like rainwater harvesting, optimised facades for reducing heat, and electric car charging stations further contribute to its eco-friendly profile.
Dover House boasts a 92% walk score, making it highly accessible in Cremorne. It offers 86 bicycle parks, promoting eco-friendly commuting, and premium end-of-trip facilities like showers and secure bike storage.
More than a workplace, Dover House is a community hub. Its design encourages collaboration within the offices and connection to the surrounding Cremorne area. With street frontages and ground floor retail spaces, Dover House is seamlessly integrated into the local community.
Completed in Q3 of 2024, Dover House has already become an iconic part of Cremorne’s landscape, providing a space that is not only beautiful and functional but also sustainable.
For more information contact Hickory, Level 5, 68 Clarke Street, Southbank VIC 3006, phone 03 9429 7411, website www.hickory.com.au
The Dover House project stands as a testament to architectural excellence, highlighted by the stunning contributions of Sara Stone, a company renowned for its high-end stone supply.
Involved from the early procurement stages in 2022, Sara Stone played a pivotal role in bringing the project’s unique vision to life by supplying exquisite natural stone and porcelain tiles and pavers.
“We’re proud to have sourced beautiful limestone from Europe for this project. The lift lobby walls, ground floor foyer benches, and all amenities vanity tops have been crafted using this exceptional material,” says Maulik Joshi, Director at Sara Stone. This careful selection process ensured that each block of stone met the project’s exacting standards, showcasing the team’s commitment to quality control.
One of the standout features of Dover House is the seamless integration of natural and porcelain materials. “The cut-to-size stone wall cladding was custom-made in Europe, reflecting the project’s dedication to precision and bespoke design elements,” adds Joshi. Complementing this are the Bluestone-look 20mm porcelain pavers used throughout the external areas, enhancing both functionality and aesthetic appeal.
Sara Stone’s involvement extends beyond just the material supply. The company’s close attention to detail ensured that each tile and stone was perfectly matched to the interiors. “Our goal was to create a harmonious, luxurious environment using top-tier materials that elevate the space,” said Mosh Chowdhury, Director at Sara Stone.
Sara Stone and Tiles has been providing homes and businesses with an excellent range of granite, marble, and stone products and services for the past 16 years. With the supply completed in mid-2024, Dover House is not just another project – it’s a symbol of Sara Stone’s ongoing commitment to craftsmanship and innovation in the field of architectural design.
For more information contact Sara Stone, 2 Kirkdale Street, Brunswick East VIC 3057, phone 03 9457 7489, email info@sarastone.com.au, website www.sarastone.com.au
Below Tormax Australia installed 4m-high automatic doors at Dover House, ensuring DDA compliance and seamless accessibility.
As part of the prestigious Dover House project, Tormax Australia played a key role in ensuring seamless and state-of-theart accessibility. Their contribution involved the supply, installation, and commissioning of oversized main entry automatic doors. These doors, powered by the Tormax 2401 Heavy Duty Operator, stand an impressive 4m high and 2m wide, making them one of the tallest automatic doors ever installed in a commercial building.
“The sheer size and weight of these doors made this project particularly unique,” said Aaron Cannata, Sales Manager at Tormax Australia. “We had to bring in specialist lifting equipment to handle the weight during installation, but the final result is a testament to the strength and engineering behind the Tormax imotion 2401 operator.”
Designed to comply with Australian Disability Discrimination Act (DDA) standards, these doors blend aesthetics with functionality. The automation of manual sliding door systems, initially sourced from overseas, required engineering precision to meet local compliance standards.
“The panels’ size showcases the reliability of our operator systems, while also adding a touch of grandeur to the building’s entrance,”
Aaron added. “These doors will provide smooth, long-term service for the many visitors who pass through them.”
All work on the Dover House project was completed in-house by Tormax’s trained technicians, ensuring the highest levels of craftsmanship and consistency.
Tormax’s involvement at Dover House is just one of many projects they are proud to highlight, along with other notable installations, including Seafarers Docklands and Ryton Girls School’s auditorium.
With its head office in Melbourne and branches in Adelaide, Brisbane, Canberra, Hobart, Launceston, and Sydney, Tormax has been operating in Australia since 1982 and is supported by a strong network of distributors across the country.
For more information contact Tormax, 13 Lillee Crescent, Tullamarine VIC 3043, phone 1800 60 8000, email info@tormax.com.au, website www.tormax.com.au
DEVELOPER : Hesperia and Aegis Health
MAIN CONSTRUCTION COMPANY : Multiplex
ARCHITECT : Hassell
BUILDING CERTIFIER : Resolve Group
SURVEYOR : MNG
Murdoch Square is an integrated, mixed-use development within a major healthcare precinct. It includes 182 aged care beds, a private hospital, 6,700m2 of medical suites, 6,100m2 commercial office, ground level retail and hospitality uses, as well as the 150-room Courtyard by Marriott, Murdoch hotel, 27 residential apartments and Western Australia's first Medihotel.
Murdoch Square seamlessly integrates healthcare, office space, and community living into a singular, transformative project. Located within the Murdoch Health and Knowledge Precinct, this ambitious development spearheaded by Hesperia and Aegis Health, and constructed by Multiplex, has redefined the concept of a mixed-use precinct in Western Australia.
The project’s scope is immense, encompassing five distinct buildings with a combined gross floor area exceeding 80,000m², all unified by a three-level underground carpark and landscaped public plaza. This architectural feat was achieved despite the complexities of developing multiple typologies — ranging from residential and commercial spaces to a medi-hotel and aged care facility — within a single stage, during the COVID-19 pandemic. Hesperia’s ability to deliver these diverse structures concurrently, while maintaining a cohesive design and functional unity, is nothing short of extraordinary.
“At Hesperia, we always aim to create developments that leave a lasting and, positive impact on the community,” said Ian Smyth, Director of Healthcare at Hesperia. “Murdoch Square is a prime example of this vision, bringing together a variety of uses into one cohesive space that not only meets the needs of the present but also anticipates the demands of the future.”
The project is centred around a landscaped public plaza, designed to promote community collaboration and interaction. Surrounding this plaza are diverse amenities, including dining venues, retail spaces, and relaxation areas, transforming the precinct into a vibrant town centre that extends beyond its traditional healthcare focus.
One of the most impressive aspects of Murdoch Square is the simultaneous construction of five buildings, each with its own distinct identity and function. Coordinating such a complex undertaking required meticulous planning and execution.
“The sheer scale of developing five buildings concurrently, all anchored by a three-level underground carpark, presented significant challenges,” Smyth said. “Each building had its own design requirements and functional needs, but they all had to work together as part of a larger, integrated precinct. This required a high level of collaboration between our team, the architects at Hassell, and our construction partners, Multiplex.”
The underground carpark itself is a critical component, not just in terms of providing ample parking space but also in unifying the entire development at the ground plane. “The carpark essentially serves as the foundation for the entire precinct, connecting the buildings both physically and functionally,” said Smyth. “Designing and constructing
it to accommodate the needs of all five buildings, while ensuring ease of access and flow for users, was a major achievement.”
Building five diverse structures at once is no small feat, especially when each building must maintain its own identity while contributing to the overall cohesion of the precinct. According to Smyth, one of the key challenges was managing the complexities of different building typologies within the same development.
“For example, the medihotel has very different design requirements compared to the aged care facility or the residential apartments,” he notes. “Each building needed to meet specific regulatory standards and functional needs, which required a flexible yet cohesive design and delivery approach. This is where our collaboration with Hassell and Multiplex was crucial. Their ability to understand and bring to life our vision for a unified yet diverse precinct was instrumental in the project’s success.”
One of the most complex aspects of the design was the integration of the buildings’ façades. Each building’s façade had to reflect its unique
function while maintaining a visual harmony with the rest of the precinct. “We didn’t want to replicate the same façade system across the project,” Smyth said. “Instead, we aimed to create distinct identities for each building, with subtle design elements that tie them together.”
The design review process played a crucial role in ensuring that these diverse elements came together seamlessly. “The design review panel was rigorous, which is exactly what was needed for a project of this scale and complexity,” Smyth added. “We had to balance creative flair with budget constraints while also adhering to strict design guidelines. The end result is a precinct where each building contributes to a cohesive whole while standing out in its own right.”
Murdoch Square’s strategic location adjacent to two of Western Australia’s largest tertiary hospitals, Fiona Stanley Hospital and St John of God Murdoch Hospital, enhances its role as a critical hub for healthcare and research. The precinct is also well-connected, with major bus, road, and rail networks nearby, ensuring easy access for residents, workers, and visitors.
Sustainability was a key consideration throughout the development process. Murdoch Square has been awarded a 5 Star Green Star - Design & As Built v1.2 certification from the Green Building Council Australia, reflecting Hesperia’s commitment to sustainability. The precinct is designed to achieve Net Zero Carbon status for both construction and operations, with three of the five buildings operating on 100% renewable energy sourced from solar PV.
“Environmental sustainability is at the core of everything we do at Hesperia,” Smyth emphasised. “For Murdoch Square, we wanted to go beyond the minimum standards and set a benchmark for sustainable development. The use of renewable energy, combined with our commitment to reducing carbon emissions, ensures that Murdoch Square is not just a great place to live and work today, but also a model for future developments.”
Murdoch Square is more than just a development; it is a landmark that exemplifies Hesperia’s vision for building Western Australia’s future. The project’s successful delivery, despite the challenges posed
by concurrent construction and complex design requirements, is a testament to the expertise and dedication of the entire team.
“Murdoch Square represents the culmination of years of planning, collaboration, and hard work,” said Smyth. “It’s a project that we are incredibly proud of, and one that we believe will have a lasting impact on the region. From the integration of diverse uses to the focus on sustainability, Murdoch Square is a development that truly reflects Hesperia’s commitment to creating spaces that benefit the community.”
As Murdoch Square opens its doors to residents, workers, and visitors, it stands as a shining example of what can be achieved when vision, expertise, and collaboration come together. With its strategic location, diverse offerings, and commitment to sustainability, Murdoch Square is poised to become a key destination in Western Australia, setting a new standard for integrated mixed-use developments.
For more information contact Hesperia, phone 08 9381 8301, email info@hesperia.com.au, website www.hesperia.com.au
Speciality Curtains and Blinds are established leaders in the design, supply and installation of commercial window furnishing solutions. The company’s role on the Murdoch Health and Knowledge Precinct was to supply all of the curtains and blinds in the Marriott Hotel, Aegis Aged Care, Medi Hotel and Mental Health facilities.
“There were a number of specialised products required in this project,” said Project Manager, Christine O’Sullivan. “These included custom printed fabrics with antimicrobial treatments as well as antiligature solutions for the mental health facility.”
Antimicrobial curtains and blinds are made from fabrics that are infused with antimicrobial technology during the manufacturing process, providing continuous protection against bacteria, mould, viruses and mildew. Antimicrobial solutions are designed to destroy or inhibit the growth of pathogenic microorganisms.
Established in 1965, Specialty Curtains and Blinds specialise in commercial window furnishing solutions. Their team of estimators, draftsman, installers and project consultants have the technology to assist at any stage of your project.
scbgroup.com.au, website www.scbgroup.com.au Below Specialty Curtains and Blinds provided custom solutions for window furnishings across the project.
Agenda Bold - AaBbCcDd 012345 Agenda Light - AaBbCcDd 012345
“We are the only choice to achieve your vision on time and on budget,” said Christine. “There is no project too large, small, remote or technical for our team.”
Specialty Curtains and Blinds are also working on the Wellington Street Student Accommodation project. For more information contact Specialty Curtains & Blinds,
Below Glen Esk designed and installed timber doors, skirting, picture rails, dado rails, and oak panels for Murdoch Health and Knowledge Precinct.
At Glen Esk Construction, excellence is not just a goal; it’s a commitment backed by a combined 40 years of experience in the building and construction industry.
For the Murdoch Health and Knowledge Precinct, Glen Esk was responsible for the design and installation of feature timber doors, 12km of paint-grade skirting, 5km of picture rails and dado rails, Tasmanian oak timber feature panelling, timber feature laminate for the hotel room entries and the supply and install of a ribbon art wall.
“When we saw the design intent for Lot 3 Tenancy doors we were concerned for the reality of the door sets and we really had to figure out to the millimetre how these doors were going to operate to ensure they were going to work with the specified hardware,” said Director, Simon Procter. “We worked closely with the Design Manager, William Sulaiman, for an uncountable amount of hours until we found a solution that all stakeholders were happy with”
Another significant aspect of the Murdoch project was the TM-03 Ribbon Wall, a substantial logistical mission due to the size and weight of each panel. With the challenging task of engineering and design by
Multiplex, Glen Esk Construction were able to successfully complete the installation with the help of their suppliers and partners.
“The TM-05 Tasmanian Oak wall lining in the corridors and the tenancy door sets along with working with a great team of people from Multiplex were the highlights of the project,” Simon said.
Glen Esk Construction focuses on maintaining honesty, quality, and reliability throughout all their work, consistently delivering projects that surpass client expectations. With a local team based in Perth, Western Australia, and surrounding areas, they possess the expertise to manage intricate construction projects for both residential and commercial clients from the initial design phase through to project completion.
Their commitment to delivering builds of exceptional standards, promptly, within budget, and to the utmost satisfaction of their clients, solidifies Glen Esk Construction's position as a leader in the industry.
For more information contact Glen Esk Construction, phone 0408 990 196, email info@glenesk.com.au, website www.glenesk.com.au
AIR CONDITIONING
(HVAC, REFRIGERATION & MECHANICAL SERVICES)
Mitsubushi Heavy Industries
Air-Conditioning Australia, Pty. Ltd.,
Page 8, 14| 1300 130 007 | mhiaa.com.au
AERIAL PHOTOGRAPHY
Skyview Aerial Photography
Page 4 | 0431 931 910
BALUSTRADES AND SCREENS
The Axiom Group
Page 60 | 1300 652 336
BATHROOMS (PREFAB/MODULAR)
SYNC
Page 44 | 03 8329 4111
CARPARKS (POLISHING, LINE MARKING)
Carparkking
Page 47 | 02 8539 7367
CARPENTARY & BUILDING SERVICES
Cranmore Carpentry
Page 63 | 0404 895 735
CONCRETE (CONSTRUCTION AND CIVIL)
OZZ CRETE
Page 20 | 0422 591 721
CONCRETE (PRECAST)
Citywide Precast
Page 55 | 03 9702 4726
GBG Concrete & Construction
Page 26 | 03 5144 2913
SVC Products
Page 24 | 1300 287 782
CONCRETE (PUMPING, SUPPLY)
Azzurri Concrete
Page 27 | 1300 299 877
CPS Concrete Group
Page 19 | 02 6228 1552
Eifers Civil Pty Ltd
Page 25 | 03 9357 6360
CONCRETE (STRUCTURAL REINFORCING)
Goldenlight
Page 30 | 0421 548 469
Reid
Page 22 | 1300 780 250
CONCRETE SERVICES
(COLOURING, CUTTING, POLISHING)
Azzurri Concrete
Page 46 | 1300 299 877
CONSTRUCTION COMPANIES & ALLIANCES
Deicorp
Page 48 | 02 8665 4100
Geocon
Page 28| 1300 979 757
Hansen Yuncken (VIC)
Page 58 | 03 9831 6500
Hickory
Page 66 | 03 9429 7411
Mirvac
Page 38 | 02 9080 8000
CONSTRUCTION SOFTWARE / DOCUMENT/PERSONNEL MANAGEMENT
CoreLogic
Page 1 | 1300 734 318
CONSULTANT (DOCUMENTATION)
Detail3
Page 54 | 03 8415 1588
DEVELOPERS
Hesperia
Page 72 | 08 9381 8301
DISABILITY ACCESS CONSULTANTS
ABE Consulting Page 34 | 02 8065 0400
DOORS
Glen Esk Construction Page 77 | 0408 990 196
DOORS (AUTOMATIC)
Tormax
Page 69 | 1800 60 8000
FLOORING
(ADHESIVES, COATINGS, LEVELLING)
AllPrep Flooring Specialists
Page 42 | www.allprepflooring.com.au
FORMWORK
IC Formwork
Page 37 | 02 6260 1260
Future Form
Page 45 | 02 8376 6950
GLASS & GLAZING
Oceania Glass
Page 12, 81| www.oceaniaglass.com.au
JOINERY & FITOUTS
Capital Veneering
Page 35 | 02 6299 1557
STEEL (STRUCTURAL/FABRICATION)
Combined Steel
Page 61 | 03 5959 1050
STONE AND TILE (NATURAL)
Sara Stone
Page 68 | 03 9457 7489
WINDOWS AND DOORS (ALUMINIUM)
Darley Aluminium
Page 16 | darleyaluminium.com.au
WINDOW FURNISHINGS
Speciality Curtains & Blinds
Page 76 | 08 9362 3588
in
and loading docks.
AGO Systems designs, manufactures, distributes, and installs products for Traffic Management Systems, ensuring the safe and efficient flow of traffic in car parks for residential apartments, commercial properties, and loading docks. Our solutions are built to suit your needs